Сварочная дуга и ее свойства
Сварочная дуга и ее свойства
Категория:
Сварочные работы
Сварочная дуга и ее свойства
Мощным концентрированным источником тепла для расплавления металла при дуговой сварке является электрическая сварочная дуга, которая представляет собой длительный электрический разряд, происходящий в газовой среде между двумя электродами.
В процессе горения дуги в ней развивается высокая температура, достигающая в центре столба дуги 6000—7000 °С.
Электрическая энергия, потребляемая дугой, в основном превращается в тепловую.
В процессе сварки не все тепло, выделяемое дугой, переходит в шов; часть тепла бесполезно расходуется на нагрев окружающего воздуха или защитного газа, на плавление покрытия флюса, угар, разбрызгивание и др.
Образование металла шва происходит вследствие расплавления основного и присадочного металлов. Расплавление присадочного металла характеризуется коэффициентом расплавления, т.
Сварочная дуга является гибким газовым проводником между концом электрода и сварочной ванной. В процессе сварки вокруг электрода, дуги и в свариваемом металле возникают магнитные поля. Если эти поля расположены вокруг дуги несимметрично, то они могут отклонять дугу и тем самым затруднять процесс сварки. Это явление называется магнитным дутьем и особенно заметно при сварке постоянным током большой величины (более 300— 400 А). Чтобы уменьшить магнитное дутье, сварку следует выполнять возможно более короткой дугой, подводить ток к изделию на максимально близкое расстояние к дуге, соответственно изменять угол наклона электрода и т. д.
Металл переходит с конца электрода в сварочную ванну в виде отдельных капель. С электрода в секунду стекает от 20 до 50 капель примерно одинакового размера. Отрыв и перенос капель в дуге происходят под действием электромагнитных сил, силы тяжести и силы поверхностного натяжения.
Сварочная дуга, горящая под слоем флюса, имеет ряд особенностей по сравнению с открытой дугой. В процессе горения ее одновременно плавятся сварочная проволока основной металл и флюс. Расплавленный флюс образует вокруг дуги газовый пузырь, заполненный газами и парами металла. Дуга под флюсом дает меньшие тепловые потери на излучение и является более сосредоточенным источником тепла, чем открытая дуга. Сварочные токи при сварке под флюсом можно применять значительно большие, чем при ручной сварке, что обусловлено более близким токоподводом к дуге.
Реклама:
Читать далее:
Особенности металлургических процессов при сварке под флюсом и в среде углекислого газа
Статьи по теме:
Cварочная дуга и её свойства
1.

оборудование (МДК.01.01)
Тема: Основы технологии сварки
2. Природа сварочной дуги
• Электрическая дуга представляет собой один из видовэлектрических разрядов в газах, при котором наблюдается
прохождение электрического тока через газовый
промежуток под воздействием электрического поля.
Прохождение электрического тока через газ возможно
только при наличии в нем заряженных частиц — электронов и
ионов.
• Возникновение заряженных частиц в дуговом промежутке
обусловливается эмиссией (испусканием) электронов с
поверхности отрицательного электрода (катода) и
ионизацией находящихся в промежутке газов и паров.
Электрическую дугу, используемую для сварки металлов,
называют сварочной дугой.
3. Сварочная дуга
Сварочная дуга представляет собой электрическийдуговой разряд в ионизированной смеси не только газов,
но и паров металла и компонентов, входящих в состав
электродных покрытий, флюсов и т.

Если ионизированный воздушный промежуток находится
в электрическом поле, то подвижные газовые ионы
приходят в движение и создают электрический ток.
Как только прекращается действие ионизирующих
факторов, исчезает электропроводность и ток
прекращается.
Дуга является частью электрической сварочной
цепи. При сварке на постоянном токе электрод,
подсоединенный к положительному полюсу
источника питания дуги, называют анодом, а к
отрицательному — катодом.
Если сварку ведут на переменном токе, то
каждый из электродов является попеременно
анодом или катодом.
областью дугового разряда, или дуговым
промежутком; длину дугового промежутка —
длиной дуги.
5. Области дугового промежутка:
Дуговойпромежуток
подразделяется
на три основные
области:
-катодную Lk;
-анодную La;
— столб дуги Lc.
6. Области дугового промежутка:
Катодное пятно является источником потока свободныхэлектронов.

достигает 2400-2600 °С. В катодном пятне выделяется около
38% общей теплоты дуги.
7. Области дугового промежутка:
Анодное пятно является местом входа и нейтрализациисвободных электронов. Оно имеет примерно такую же
температуру, как и катодное пятно, но в результате
бомбардировки электронами на нем выделяется больше
теплоты, чем на катодном (примерно 42%).
8. Области дугового промежутка:
Столб дуги представляет собой проводник электрическоготока. В нем свободные электроны и отрицательно заряженные ионы
движутся к аноду, а положительно заряженные ионы — к катоду. В
целом столб дуги не имеет заряда. Он нейтрален, так как в каждом
сечении столба одновременно находятся равные количества
противоположно заряженных частиц.
9. Возбуждение дуги
При коротком замыкании электрода и детали в местахкасания их поверхности разогреваются. При
размыкании электродов с нагретой поверхности катода
происходит испускание электронов — электронная
эмиссия.

Выход электронов в первую очередь связывают с
термическим эффектом (термоэлектронная эмиссия) и
наличием электрического поля высокой напряженности
(автоэлектронная эмиссия).
Наличие электронной эмиссии с поверхности катода
считают непременным условием существования
дугового разряда.
10. Зажигание дуги
Зажигание дуги при сварке плавящимсяэлектродом также начинается с короткого
замыкания. Из-за шероховатости поверхностей
касание электрода с основным металлом
происходит отдельными выступающими
участками, которые мгновенно расплавляются
под действием выделяющейся теплоты,
образуя жидкую перемычку между основным
металлом и электродом.
11. Области дугового промежутка
По длине дугового промежутка можно выделить три области :катодную, анодную и находящийся между ними столб дуги.
Катодная область включает в себя нагретую поверхность катода,
называемую катодным пятном, и часть дугового промежутка,
примыкающую к ней.

Температура катодного пятна на стальных электродах достигает
2400… 2700С. В катодном пятне выделяется до 38% общей теплоты
дуги. Основным физическим процессом в этой области является
разгон электронов.
Падение напряжения в катодной области UK составляет 10…20 В.
Анодная область состоит из анодного пятна на поверхности анода и
части дугового промежутка, примыкающего к нему. Анодное пятно
— имеет примерно такую же температуру, как и катодное пятно, но
в результате бомбардировки электронами на нем выделяется
больше теплоты, чем на катоде. Для дуг с плавящимся электродом
анодное падение напряжения составляет 2…6 В.
Столб дуги, расположенный между катодной и анодной областями,
имеет наибольшую протяженность в дуговом промежутке.
12. Классификация сварочной дуги
• по применяемым электродам — с плавящимся инеплавящимся;
• по степени сжатия дуги —свободная и сжатая;
• по схеме подвода сварочного тока — прямого и косвенного
действия.

• по роду тока — постоянного и переменного (однофазного
или трехфазного) тока;
• по полярности постоянного тока — прямой и обратной
• Дугу называют короткой, если длина ее составляет 2…4 мм.
Длина нормальной дуги составляет 4…6 мм. Дугу длиной
более 6 мм называют длинной.
13. Сварочную дугу классифицируют:
14. Сварочную дугу классифицируют:
15. Сварочную дугу классифицируют:
16. Сварочную дугу классифицируют:
17. Сварочную дугу классифицируют:
Сварочная дуга
Сварочная дуга
Сварочная дуга представляет собой электрический дуговой разряд в ионизированной смеси газов, паров металлов и компонентов, входящих в состав электродных покрытий, флюсов и других средств.
Физические и электрические свойства сварочной дугиДля возникновения электрического разряда газовый промежуток между электродами должен быть ионизирован. Процесс ионизации протекает в следующем порядке. При соприкосновении торца электрода и свариваемого изделия выступы шероховатых поверхностей мгновенно разогреваются током до температуры плавления и испарения вследствие большого омического сопротивления контакта. После отрыва электрода от изделия разогретый торец электрода (отрицательный полюс) начинает испускать электроны, устремляющиеся к аноду под действием разности потенциалов между электродами. При столкновении с электродными частицами металлов, которые в виде паров имеются в межэлектродном промежутке, электроны ионизируют их. Ионизация мгновенно охватывает весь межэлектродный промежуток, и он становится электропроводным. В процессе горения дуги ионизация поддерживается благодаря высокой температуре.
Напряжение на дуге равно сумме падений напряжений в трех ее основных (рис. 1) областях:
Uд=Uк+ Uc+ Ua =f(Iд),
где Uд — напряжение на дуге, В; UK — падение напряжения на катоде, В; Uс-падение напряжения в столбе дуги, В; Uа — падение напряжения на аноде, В; Iд — сила тока в дуге.
Рис.1. Распределение падения напряжения в дуге
Зависимость напряжения дуги от силы сварочного тока называют статической (вольтамперной) характеристикой дуги.
В общем виде статическая характеристика дуги показана на рис. 2. При малых значениях силы тока в электроде (область 1) статическая характеристика дуги падающая. При средних значениях силы тока (при ручной и автоматической дуговой сварке под флюсом) напряжение на дуге не зависит от силы тока (область 2, жесткая характеристика). В этом случае с достаточной точностью статическая характеристика может быть выражена уравнением
Uд= a+ blд,
где lд — длина дуги, мм; а, b — постоянные коэффициенты, зависящие от материала электродов, давления и свойств газовой среды.
Рис. 2. Общий вид статической характеристики дуги
Из этого уравнения следует, что напряжение на дуге, при всея прочих равных условиях, будет зависеть от длины столба дуги.
Возрастающая статическая характеристика дуги (область 3, см. рис. 2) получается при большой силе тока (при автоматической сварке под флюсом или при сварке в среде защитных газов).
Сварочная дуга переменного токаВследствие того, что мгновенные значения переменного тока 100 раз в секунду переходят через нуль, причем меняет также свое местонахождение катодное пятно, являющееся источником вылета электронов, ионизация дугового промежутка получается менее стабильной и сварочная дуга менее устойчива, при прочих равных условиях, по сравнению с дугой постоянного тока.
Если дуга включена в цепь переменного тока последовательно с активным сопротивлением, то мгновенные значения напряжения источника и сварочного тока совпадают по фазе. В каждый полупериод дуга угасает и вновь зажигается (восстанавливается) через некоторый промежуток времени, пока напряжение источника тока поднимается до некоторой величины, называемой напряжением повторного зажигания.
Зажигание, дуги характеризуется началом прохождения тока в сварочной цепи. В каждый полупериод имеется перерыв в прохождении тока при угасаниях дуги. Эти перерывы называют временами угасания дуги. Момент угасания происходит при несколько меньшем мгновенном значении напряжения источника, чем в момент зажигания, для которого требуются более высокие значения для получения ионизации остывшего промежутка. Время угасания дуги зависит от максимального значення напряжения зажигания дуги и частоты переменного тока.
Время восстановления дуги снижается при повышении напряжения холостого хода и при использовании повышенных частот. Это время уменьшается также и при снижении напряжения зажигания. Из указанных мер повышения устойчивости горения дуги наиболее распространено снижение напряжения зажигания, чего достигают применением электродов с ионизирующими обмазками.
Величина напряжения зажигания зависит от целого ряда факторов, в первую очередь от величины силы тока дуги. С увеличением силы сварочного тока напряжение зажигания дуги снижается.
Для сварки открытой дугой напряжение зажигания Uз и напряжение горения дуги Uд имеют следующую зависимость:
Uз = (1,3 – 2,5) Uд
При сварке на больших силах тока под флюсом напряжение зажигания почти равно напряжению горения дуги.
Повышение напряжения холостого хода источника питания ограничено правилами техники безопасности, а использование высоких частот требует применения специальной аппаратуры. Общепринятой мерой повышения стабильности сварочной дуги переменного тока является включение в сварочную цепь катушек со стальным сердечником (дросселей), которые позволяют вести сварочные работы металлическими электродами при напряжении сварочного трансформатора порядка 60 — 65В и стандартной частоте. При этом в обмазке электродов должно быть достаточное количество ионизирующих компонентов.
Электрическая дуга и ее свойства Билет5 Сварочная
Электрическая дуга и ее свойства Билет5
Сварочная дуга представляет собой концентрированный электрический разряд, который протекает только в среде специального газа, предназначенного для ведения работ.
При этом сварочная дуга характеризуется двумя основными свойствами, а именно: при работе с дугой выделяется большое количество тепла, а также, сварка производится с выделением световой энергии. При выполнении работы температура дуги может достигать 6000 градусов.
Свет электрической дуги невероятно яркий, поэтому нашел свое применение в различных осветительных приборах, в том числе во всем известной лампе накаливания. Кроме световой энергии, сварочная дуга выделяет инфракрасное и ультрафиолетовое излучение, оно особенно опасно для глаз и кожи человека. Это опасное излучение может вызвать воспаление глаз, а также ожог роговицы, вследствие чего может произойти полная или частичная потеря зрения. На коже ультрафиолетовые лучи могут оставить серьезные ожоги: именно для того, чтобы избежать столь серьезных последствий, сварщиками применяются специальные щитки и маски, которые защищают глаза, а также одежду, защищающую от негативного воздействия сварочной дуги.
Среда дугового разряда. Итак, электрическая сварочная дуга различается по среде, в которой происходит ее горение, а именно: Дуга может гореть в обычном воздухе. Ее принято называть открытой. Газовую среду в зоне сварки составляет воздух с небольшой примесью испарений металлов, которые участвуют в процессе сварки. Кроме этого, в примесях присутствуют материалы самих электродов для сварки. Другой тип дуги принято называть закрытым, так как горит она под специальным слоем флюса. При этом зону сварки составляют пары материала, который сваривается при помощи дуги, а также флюса и электрода.
И последний вид — это дуга, которая горит с применением специальных газов, защищающих ее от попадания воздуха. В зону сварки подается углекислый газ, аргон и другие.
Питание дуги. Питание сварочной дуги происходит от специальных источников, которые создают переменный или постоянный ток. Для нормальной работы со сварочной дугой необходимо дополнительное оборудование, например, трансформатор, выпрямитель тока. Эти приборы довольно габаритные и тяжелые, правда сейчас появилась возможность заменить все громоздкие и неудобные аппараты на один сварочный инвертор, вес которого составляет всего несколько килограмм. Однако питание дуги от инвертора имеет и свои минусы, например, длина проводов не должна превышать 2, 5 метров, что не очень удобно, но вполне можно привыкнуть.
Напряжение сварочной дуги. Напряжение сварочной дуги может изменяться и оно напрямую зависит от такого важного показателя, как плотность тока. Как показывает практика, напряжение дуги имеет обратно пропорциональное отношение к силе тока. Современный инвертор как раз основан на этом принципе. После прохождения всех преобразований, ток попадает в трансформатор, там его напряжение понижается, за счет чего и увеличивается сила тока. Обычно напряжение на выходе составляет около 70 Вольт, а сила тока — примерно 200 ампер, что вполне достаточно для выполнения процесса сварки.
Возникновение сварочной дуги. Дуга сварки обычно возникает при касании поверхности свариваемого материала концом электрода. При этом происходит быстрое замыкание, и ток в точке своего соприкосновения имеет невероятно большую плотность. В результате чего почти мгновенно металл расплавляется, а между электродом и свариваемым материалом возникает небольшая полоска из расплавившегося металла.
Далее сварщик просто отводит электрод, в результате чего возникает шейка в жидком металле, которая быстро разрушается под действием тока высокой плотности. Испарившиеся при разрушении газы ионизируются и именно в результате этого процесса возникает сварочная дуга.
Выбор параметров сварки билет4(2)
1. Род и полярность тока 2. Диаметр электродной проволоки 3. Сварочный ток 4. Напряжение на дуге 5. Скорость подачи электродной проволоки 6. Скорость сварки 7. Расход защитного газа 8. Вылет электрода
Род и полярность тока Сварку обычно выполняют на постоянном токе обратной полярности. Иногда возможна сварка на переменном токе. При прямой полярности скорость расплавления в 1, 4 -1, 6 раз выше, чем при обратной, однако дуга горит менее стабильно, с интенсивным разбрызгиванием. Прямая полярность «–» на электрод.
Диаметр электродной проволоки Выбирают в пределах 0, 5 -3, 0 мм при полуавтоматической сварке. в зависимости от толщины свариваемого материала и положения шва в пространстве при ручной Больший диаметр проволоки требует увеличения сварочного тока.
Сварочный ток Устанавливают в зависимости от диаметра электрода и толщины свариваемого металла. Сила тока определяет глубину проплавления и производительность процесса в целом. Сила сварочного тока при ручной сварке находится по формуле академика Хренова I = K X d
Напряжение на дуге С ростом напряжения на дуге глубина проплавления уменьшается, а ширина шва и разбрызгивание увеличиваются. Ухудшается газовая защита, образуются поры. Напряжение на дуге устанавливают в зависимости от выбранного сварочного тока и регулируют положением вольт-амперной характеристики. При сварке электродами 2 мм и менше нужно применять оциляторы.
Скорость сварки Устанавливают в зависимости от толщины свариваемого металла с учетом качественного формирования шва. Металл большой толщины лучше сваривать узкими швами на высокой скорости. Медленная сварка способствует разрастанию сварочной ванны и повышает вероятность образования пор в металле
1. Что представляет собой электрическая дуга. 2. Строение электрической дуги 3. Виды дуг. 4. Свойства электрической дуги. 5. Среда дугового разряда. 6. Питание дуги. 7. Возникновение дуги. 8. Перечислить параметры сварки. 9. Выбор диаметра электрода. 10. Выбор сварочного тока. 11. Выбор ширины валика. 12. Выбор разделки кромок металла. 13. Скорость сварки
Определение сварочной дуги, ее строение, условия зажигания и горения. Сварка
Определение сварочной дуги, ее строение, условия зажигания и горения
Электрической сварочной дугой называют устойчивый электрический разряд в сильно ионизированной смеси газов и паров материалов, происходящий при давлении, близком к атмосферному, используемом при сварке, и характеризуемый высокой плотностью тока и высокой температурой.
Температура в столбе сварочной дуги достигает 5 000–12000 °C и зависит от плотности тока, состава газовой среды дуги, материала и диаметра электрода. А потому сварочная дуга является мощным концентрированным источником теплоты. Электрическая энергия, потребляемая дугой, в основном превращается в тепловую энергию.
В столбе сварочной дуги протекают следующие процессы:
1. Столб дуги заполнен заряженными частицами – электронами и ионами. В нем присутствуют также и нейтральные частицы – атомы и даже молекулы паров веществ, из которых сделаны электроды. Под действием электродинамических сил частицы перемещаются. Скорость их перемещения различна. Быстрее всего перемещаются электроны. Они легко разгоняются и, сталкиваясь с атомами и ионами, передают им свою энергию. Столкновения электронов с атомами могут быть упругими и неупругими. При упругих столкновениях атомы начинают двигаться быстрее – увеличивается их кинетическая энергия. В результате повышается температура плазмы дуги.
2. Электрон, который в электрическом поле приобрел достаточно большую энергию, является источником неупругих столкновений. Столкнувшись с атомом, он возбуждает его, а когда удар достаточно силен, то и выбивает из атома его собственные электроны.
Энергию, которая должна быть сообщена электрону для ионизации какого-либо атома, выражают в электронвольтах (эВ) и называют потенциалом ионизации. Величина потенциала ионизации зависит от строения атома. Чем меньше номер группы и больше номер периода в таблице элементов Менделеева, тем меньше энергии необходимо затратить для ионизации. Наименьшим потенциалом ионизации (3,9 эВ) обладает атом цезия, поскольку он самый тяжелый из всех щелочных металлов. Самый легкий из инертных газов – элемент последней, нулевой группы – гелий обладает наивысшим потенциалом ионизации (24,5 эВ).
Энергия, расходуемая на диссоциацию (разделение) различных молекул, также различна. Так, например, для диссоциации молекулы водорода необходимо затратить 4,48 эВ, фтора – 1,6 эВ, а углекислого газа – 9,7 эВ. Эти величины имеют для сварщиков особое значение. При разработке электродных покрытий, флюсов и проволок приходится учитывать, молекулы каких веществ диссоциируют раньше, а каких – позже, какие элементы ионизируются легче, а какие – труднее, и сколько для этого потребуется энергии.
В зависимости от числа электродов и способов включения электродов и свариваемой детали в электрическую цепь различают следующие виды сварочных дуг (рис. 46):
1. Прямого действия, когда дуга горит между электродом и изделием.
2. Косвенного действия, когда дуга горит между двумя электродами, а свариваемое изделие не включено в электрическую цепь.
3. Трехфазную дугу, возбуждаемую между двумя электродами, а также между каждым электродом и основным металлом.
Рис. 46.
Виды сварочных дуг:
а – прямого; б – косвенного; в – комбинированного действия (трехфазная)
По роду тока различают дуги, питаемые переменным и постоянным током. При использовании постоянного тока различают сварку на прямой и обратной полярности.
При прямой полярности электрод подключается к отрицательному полюсу и служит катодом, а изделие – к положительному полюсу и служит анодом.
При обратной полярности электрод подключается к положительному полюсу и служит анодом, а изделие – к отрицательному и служит катодом.
В зависимости от материала электрода различают дуги между неплавящимися электродами (угольными, вольфрамовыми) и плавящимися металлическими электродами.
Сварочная дуга обладает рядом физических и технологических свойств, от которых зависит эффективность использования дуги при сварке.
К физическим свойствам относятся электрические, электромагнитные, кинетические, температурные, световые.
К технологическим свойствам относятся мощность дуги, пространственная устойчивость, саморегулирование.
Электрическим разрядом в газе называют электрический ток, проходящий через газовую среду благодаря наличию в ней свободных электронов, а также отрицательных и положительных ионов, способных перемещаться между электродами под действием приложенного электрического поля (разности потенциалов между электродами.
Сварка дугой переменного тока имеет некоторые особенности. Вследствие того, что мгновенные значения тока переходят через нуль 100 раз в 1 с, меняет свое положение катодное пятно, являющееся источником электронов, ионизация дугового промежутка менее стабильна и сварочная дуга менее устойчива по сравнению с дугой постоянного тока.
Общепринятой мерой повышения стабилизации сварочной дуги переменного тока является включение в сварочную цепь последовательно с дугой индуктивного сопротивления. Последовательное включение в сварочную цепь катушек со стальным сердечником (дросселей) позволяет вести сварочные работы металлическими электродами на переменном токе при напряжении сварочного трансформатора 60–65 В.
Процесс, при котором из нейтральных атомов и молекул образуются положительные и отрицательные ионы, называют ионизацией. При обычных температурах ионизацию можно вызвать, если уже имеющимся в газе электронам и ионам сообщить при помощи электрического поля большие скорости. Обладая большой энергией, эти частицы могут разбивать нейтральные атомы и молекулы на ионы. Кроме того, ионизацию можно вызвать световыми, ультрафиолетовыми, рентгеновскими лучами, а также излучением радиоактивных веществ.
В обычных условиях воздух, как и все газы, обладает весьма слабой электропроводностью. Это объясняется малой концентрацией свободных электронов и ионов в газах. Поэтому, чтобы вызвать в газе мощный электрический ток, т. е. образовать электрическую дугу, необходимо ионизировать воздушный промежуток (или другую газообразную среду) между электродами.
Ионизацию можно произвести, если приложить к электродам достаточно высокое напряжение, тогда имеющиеся в газе свободные электроны и ионы будут разгоняться электрическим полем и, получив энергию, смогут разбить нейтральные молекулы на ионы.
Однако при сварке, исходя из правил техники безопасности, нельзя пользоваться высокими напряжениями. Поэтому применяют другой способ. Так как в металлах имеется большая концентрация свободных электронов, то надо извлечь эти электроны из объема металла в газовую среду и затем использовать для ионизации молекул газа.
Существует несколько способов извлечения электронов из металлов. Из них для процесса сварки имеют значения два: термоэлектронная и автоэлектронная эмиссии.
Во время термоэлектронной эмиссии происходит «испарение» свободных электронов с поверхности металла благодаря высокой температуре. Чем выше температура металла, тем большее число свободных электронов приобретают энергии, достаточные для преодоления «потенциального барьера» в поверхностном слое и выхода из металла.
Во время автоэлектронной эмиссии извлечение электронов из металла производится при помощи внешнего электрического поля, которое несколько изменяет потенциальный барьер у поверхности металла и облегчает выход тех электронов, которые внутри металла имеют достаточно большую энергию и могут преодолеть этот барьер.
Ионизацию, вызванную в некотором объеме газовой среды, принято называть объемной.
Объемная ионизация, полученная благодаря нагреванию газа до очень высоких температур, называется термической. При высоких температурах значительная часть молекул газа обладает достаточной энергией для того, чтобы при столкновениях могло произойти разбиение нейтральных молекул на ионы. Кроме того, с повышением температуры увеличивается общее число столкновений между молекулами газа. При очень высоких температурах в процессе ионизации начинает также играть заметную роль излучение газа и раскаленных электродов.
Ионизация газовой среды характеризуется степенью ионизации, т. е. отношением числа заряженных частиц в данном объеме к первоначальному числу частиц (до начала ионизации). При полной ионизации степень ионизации будет равна единице.
При температуре 6000–8000 °C такие вещества, как калий, натрий, кальций, обладают достаточно высокой степенью ионизации. Пары этих элементов, находясь в дуговом промежутке, обеспечивают легкость возбуждения и устойчивое горение дуги. Это свойство щелочных металлов объясняется тем, что атомы этих металлов обладают малым потенциалом ионизации. Поэтому для повышения устойчивости горения электрической дуги эти вещества вводят в зону дуги в виде электродных покрытий или флюсов.
Электрическая дуга постоянного тока возбуждается при соприкосновении торца электрода и кромок свариваемой детали. Контакт в начальный момент осуществляется между микровыступами поверхностей электрода и свариваемой детали. Высокая плотность тока способствует мгновенному расплавлению этих выступов и образованию пленки жидкого металла, которая замыкает сварочную цепь на участке «электрод – свариваемая деталь». При последующем отводе электрода от поверхности детали на 2–4 мм пленка жидкого металла растягивается, а сечение уменьшается, вследствие чего возрастает плотность тока и повышается температура металла.
Эти явления приводят к разрыву пленки и испарению вскипевшего металла. Возникшие при высокой температуре интенсивные термоэлектронная и автоэлектронная эмиссии обеспечивают ионизацию паров металла и газов межэлектродного промежутка. В образовавшейся ионизированной среде возникает электрическая сварочная дуга. Процесс возбуждения дуги кратковременен и осуществляется в течение долей секунды.
В установившейся сварочной дуге различают три зоны: катодную, анодную и столба дуги.
Катодная зона начинается с раскаленного торца катода, на котором расположено так называемое катодное пятно. Отсюда вылетает поток свободных электронов, осуществляющих ионизацию дугового промежутка. Плотность тока на катодном пятне достигает 60–70 А/мм2 к катоду устремляются потоки положительных ионов, которые бомбардируют и отдают ему свою энергию, вызывая нагрев до температуры 2500–3000 °C.
Анодная зона расположена у торца положительного электрода, в котором выделяется небольшой участок, называемый анодным пятном. К анодному пятну устремляются и отдают свою энергию потоки электронов, разогревая его до температуры 2500–4000 °C.
Столб дуги, расположенный между катодной и анодной зонами, состоит из раскаленных ионизированных частиц. Температура в этой зоне достигает 6000–7000 °C в зависимости от плотности сварочного тока.
Для возбуждения дуги в начальный момент необходимо несколько большее напряжение, чем при ее последующем горении. Это объясняется тем, что при возбуждении дуги воздушный зазор недостаточно нагрет, степень ионизации недостаточно высокая и необходимо большее напряжение, способное сообщить свободным электронам достаточно большую энергию, чтобы при их столкновении с атомами газового промежутка могла произойти ионизация.
Увеличение концентрации свободных электронов в объеме дуги приводит к интенсивной ионизации дугового промежутка, а отсюда к повышению его электропроводности. Вследствие этого напряжение тока падает до значения, которое необходимо для устойчивого горения дуги. Зависимость напряжения дуги от тока в сварочной цепи называют статической вольт-амперной характеристикой дуги.
Вольт-амперная характеристика дуги имеет три области: падающую, жесткую и возрастающую.
В первой (до 100 А) с увеличением тока напряжение значительно уменьшается. Это происходит в связи с тем, что при повышении тока увеличивается поперечное сечение, а следовательно, и проводимость столба дуги.
Во второй области (100–1000 А) при увеличении тока напряжение сохраняется постоянным, так как сечение столба дуги и площади анодного и катодного пятен увеличиваются пропорционально току. Область характеризуется постоянством плотности тока.
В третьей области увеличение тока вызывает возрастание напряжения вследствие того, что увеличение плотности тока выше определенного значения не сопровождается увеличением катодного пятна ввиду ограниченности сечения электрода.
Дуга первой области горит неустойчиво и поэтому имеет ограниченное применение. Дуга второй области горит устойчиво и обеспечивает нормальный процесс сварки.
Необходимое напряжение для возбуждения дуги зависит от рода тока (постоянный или переменный), материала электрода и свариваемых кромок, дугового промежутка, покрытия электродов и ряда других факторов. Значения напряжений, обеспечивающих возникновение дуги в дуговых промежутках, равных 2–4 мм, находятся в пределах 40–70 В.
Напряжение для установившейся сварочной дуги определяется по формуле:
U= a + b ? l,
где: а – коэффициент, по своей физической сущности составляющий сумму падений напряжений в зонах катода и анода, В;
b – коэффициент, выражающий среднее падение напряжения на единицу длины дуги, В/мм;
1 – длина дуги, мм.
Рис. 47.
Схема сварочной дуги и падения напряжений в ней:
1 – электрод; 2 – изделие; 3 – анодное пятно;
4 – анодная область дуги; 5 – столб дуги;
6 – катодная область дуги; 7 – катодное пятно
Длиной дуги называется расстояние между торцом электрода и поверхностью сварочной ванны. Короткой дугой называют дугу длиной 2–4 мм. Длина нормальной дуги составляет 4–6 мм. Дугу длиной более 6 мм называют длинной.
Оптимальный режим сварки обеспечивается при короткой дуге. При длинной дуге процесс протекает неравномерно, дуга горит неустойчиво – металл, проходя через дуговой промежуток, больше окисляется и азотируется, увеличиваются угар и разбрызгивание металла.
При помощи магнитных полей, создаваемых вокруг дуги и в свариваемой детали, электрическая сварочная дуга может быть отклонена от своего нормального положения. Эти поля действуют на движущиеся заряженные частицы и тем самым оказывают воздействие на всю дугу. Такое явление называют магнитным дутьем. Воздействие магнитных полей на дугу прямо пропорционально квадрату силы тока и достигает заметного значения при сварочных токах более 300 А.
Магнитные поля оказывают отклоняющее действие на дугу при неравномерном и несимметричном расположении поля относительно дуги. Наличие вблизи сварочной дуги значительных ферромагнитных масс нарушает симметричность магнитного поля дуги и вызывает отклонение дуги в сторону этих масс.
В некоторых случаях магнитное дутье затрудняет процесс сварки, и поэтому принимаются меры по снижению его действия на дугу. К таким мерам относятся:
• сварка короткой дугой;
• подвод сварочного тока в точке, максимально близкой к дуге;
• наклон электрода в сторону действия магнитного дутья;
• размещение у места сварки ферромагнитных масс.
При использовании переменного тока анодное и катодное пятна меняются местами с частотой, равной частоте тока. С течением времени напряжение и ток периодически изменяются от нулевого значения до наибольшего. При переходе значения тока через нуль и перемене полярности в начале и в конце каждого полупериода дуга гаснет, температура активных пятен и дугового промежутка снижается. Вследствие этого происходят деионизация газов и уменьшение электропроводности столба дуги. Интенсивнее падает температура активного пятна, расположенного на поверхности сварочной ванны, в связи с отводом теплоты в массу основного металла.
Повторное зажигание дуги в начале каждого полупериода возможно только при повышенном напряжении, называемом пиком зажигания. При этом установлено, что пик зажигания несколько выше, когда катодное пятно находится на основном металле.
Для облегчения повторного зажигания, снижения пика зажигания дуги и повышения устойчивости ее горения применяют меры, позволяющие снизить эффективный потенциал ионизации газов в дуге. В этом случае электропроводность дуги после ее угасания сохраняется дольше, пик зажигания снижается, дуга легче возбуждается и горит устойчивее.
Применение различных стабилизирующих элементов (калий, натрий, кальций и др.), вводимых в зону дуги в виде электродных покрытий или в виде флюсов, относится к этим мерам.
Данный текст является ознакомительным фрагментом.
Продолжение на ЛитРесОтклонение сварочной дуги
Отклонение дуги во время сварки может вызывать множество проблем, в том числе чрезмерное разбрызгивание, недостаточную глубину проплавления, пористость и низкое качество сварных швов. Что это такое и как его можно избежать? В этой статье мы рассмотрим явление отклонения сварочной дуги и несколько способов его устранения для повышения качества сварки.Отклонение дуги возникает при сварке на постоянном токе, когда дуга следует не кратчайшему пути от электрода к рабочему изделию, а отклоняется вперед, назад или, реже, в сторону по отношению к направлению сварки.
Сначала давайте дадим определения некоторым понятиям, связанным с отклонением дуги. Обратное отклонение происходит при сварке по направлению к рабочему соединению, в конце шва или при угловой сварке. Переднее отклонение происходит при сварке по направлению от рабочего соединения или в начале шва. Переднее отклонение может вызвать особенно много проблем при сварке защищенной дугой металлопрошковыми или другими типами электродов с обильным образованием шлака, когда тяжелый шлак или кратер приходится перемещать вперед под дугу.
Магнитное отклонение дуги
Магнитное отклонение происходит из-за искажений магнитного поля вокруг сварочной дуги. Эти искажения возникают из-за того, что в большинстве случаев дуга оказывается на большем расстоянии от одного конца соединения, чем от другого, и непостоянного расстояния от рабочей клеммы. Дисбаланс также может быть вызван постоянными изменениями направления тока в цепи между электродом, дугой и рабочим изделием.
Визуализация магнитного поля
Чтобы понять, почему происходит отклонение дуги, нужно представить себе магнитное поле. На Рисунке 3-37 показан проводник (который может представлять собой электрод или поток плазмы между электродом и сварным соединением), через который проходит постоянный ток. Проводник при этом окружает магнитное поле, которое можно изобразить в виде концентрических силовых линий на плоскости под прямым углом к направлению тока. Интенсивность магнитного поля уменьшается по мере удаления от проводника.
Концентрические линии магнитного поля будут сохранять форму круга только в том случае, если среда вокруг них достаточно велика для того, чтобы вместить все эти линии, пока их интенсивность не станет равна практически нулю. Но если эта среда неоднородна, например, если линии переходят из стальной пластины в воздух, они исказятся и окажутся более сконцентрированы в металле, где им приходится преодолевать меньшее сопротивление. На границе между стальной пластиной и воздухом магнитные силовые линии сужаются и теряют свою круглую форму. Такое сужение приводит к повышению интенсивности магнитного поля позади или перед сварочной дугой. Из-за этого дуга смещается в направлении, которое уменьшило бы концентрацию и восстановило баланс магнитного поля. Другими словами, дуга смещается в сторону, противоположную зоне повышенной концентрации магнитного поля. Это смещение и называется отклонением дуги.
На Рисунке 3-38 изображено вытягивание и искажение магнитного поля в начале и конце сварного соединения. В начале сварки силовые линии магнитного поля оказываются сконцентрированы позади электрода. Дуга пытается скомпенсировать этот дисбаланс и смещается вперед. По мере приближения электрода к концу шва повышенная концентрация перемещается в пространство перед дугой, из-за чего дуга смещается назад. В середине шва, на одинаковом расстоянии от концов соединения, магнитное поле симметрично и переднего или обратного смещения дуги обычно не возникает. Однако, если материал с одной стороны соединения шире, а с другой – уже, даже в середине шва возникнет боковое смещение.
Влияние тока в рабочем изделии
«»Вытягивание» » также может возникать из-за электрического тока внутри рабочего изделия. Как показано на Рисунке 3-39, этот ток, который проходит через все изделие к клемме, также образует магнитное поле. Жирная линия означает путь сварочного тока, тонкая – созданное этим током магнитное поле. Так как ток меняет направление, то есть делает поворот в точке между дугой и рабочим изделием, в точке X возникает повышенная концентрация магнитного поля, которая вызывает смещение сварочной дуги в сторону от рабочего изделия, как это показано на рисунке.
Смещение дуги из-за этого эффекта накладывается на смещение, вызванное вышеописанным воздействием сконцентрированного магнитного поля. Таким образом влияние тока в изделии может снизить или еще больше увеличить смещение дуги из-за магнитного поля. Но если обратный ток научиться контролировать, его можно использовать как способ регулировать смещение дуги, который особенно хорошо подходит для автоматических процессов сварки.
На Рисунке 3-40(a), рабочий кабель подключен к начальной точке шва, а магнитное поле, вызванное током внутри изделия, направлено назад от дуги. При этом возникает переднее смещение дуги. Однако у конца шва общее смещение будет минимальным, так как это переднее смещение компенсирует обратное смещение, вызванное высокой концентрацией магнитного поля при приближении дуги к краю рабочего изделия – см. Рисунок 3-41(a). На Рисунке 3-40(b), рабочий кабель подключен к конечной точке шва, что приводит к обратному смещению. В таком случае в конце сварного шва это приводит к еще большему обратному смещению из-за магнитного поля дуги.
Подобное «»наложение»» магнитных полей показано на Рисунке 3-41(b). Однако рабочее соединение со стороны конца шва может помочь снизить переднее смещение дуги в начале сварки.
Так как воздействие тока в рабочем изделии менее заметно, чем сконцентрированного магнитного поля вокруг дуги, расположение рабочего соединения позволяет регулировать смещение дуги лишь в какой-то степени. Для полного устранения смещения дуги во время сварки также нужно использовать и другие способы.
Другие проблемные зоны
Угловые и стыковые соединения с глубоким V-образным зазором
В каких еще случаях может происходить смещение дуги? Оно часто наблюдается при угловой сварке и в сварных соединениях, для которых требуется глубокий сварной шов. Причина этому точно такая же, как и в предыдущем случае – высокая концентрация силовых линий магнитного поля и смещение дуги для снижения этой концентрации. На Рисунках 3-42 и 3-43 показаны ситуации, в которых при использовании постоянного тока высока вероятность отклонения дуги.
Высокая сила тока
При низкой силе тока отклонение дуги ниже, чем при высокой. Почему? Потому что интенсивность магнитного поля на заданном расстоянии от проводника электрического тока пропорциональна квадрату силы сварочного тока. При ручной сварке на постоянном токе серьезные проблемы с отклонением дуги обычно возникают только при силе тока выше 250 ампер (это не точная цифра, так как на отклонение дуги также сильно влияют тип и геометрия соединения).
Постоянный ток
Переход на переменный ток часто приводит к значительному снижению отклонения дуги. Из-за постоянных смен полярности ток в металле основы начинает двигаться в форме вихрей. Для таких вихревых потоков характерно довольно слабое магнитное поле, которое не оказывает на дугу значительного влияния.
Чувствительные к магнитному воздействию материалы
Некоторые материалы, например, 9-процентные никелевые сплавы, очень чувствительны к магнитному воздействию и очень легко намагничиваются внешними магнитными полями, например, от кабелей питания и т. п. При сварке таких материалов могут возникнуть большие сложности в связи с отклонением дуги из-за намагниченного материала. Такие поля можно легко выявить и измерить недорогими ручными измерителями магнитной индукции. Интенсивности поля более 20 Гс обычно достаточно для того, чтобы оно могло вызвать сложности со сваркой.
Термическое отклонение дуги
Мы уже рассмотрели самый распространенный тип отклонения сварочной дуги – магнитный, но с чем еще может столкнуться сварщик? Второй тип – это термическое отклонение дуги. По законам физики ток между электродом и рабочей пластиной проходит между самыми горячими точками на их поверхности. Во время перемещения электрода дуга обычно от него несколько отстает. Это отставание вызвано «нежеланием» дуги сдвигаться на более холодное место. Пространство между кончиком электрода и горячей поверхностью расплавленного металла ионизируется и поэтому имеет более высокую электропроводимость, чем возле более холодных участков пластины. При ручной сварке небольшое термическое обратное отклонение из-за отставания дуги не принесет большого вреда, но оно может стать серьезной проблемой при высокоскоростной автоматической сварке или если термическое обратное отклонение накладывается на магнитное обратное отклонение.»»
Отклонение при многодуговой сварке
В новейших системах сварки для повышения производительности применяется метод многодуговой сварки. Такой процесс тоже может приводить к отклонению дуг. В частности, когда две дуги работают в непосредственной близости друг от друга, их магнитные поля начинают взаимодействовать, что приводит к отклонению обеих дуг.
Если рядом находятся две дуги разной полярности, как показано на Рисунке 3-44(a), магнитные поля между дугами заставят их отклониться друг от друга. Если дуги имеют одну полярность, как показано на Рисунке 3-44(b), магнитные поля будут ослаблять друг друга, из-за чего дуги станут притягиваться.
Обычно при использовании двух дуг для одной дуги рекомендуется использовать постоянный ток, а другой – переменный, как это показано на Рисунке 3-44(c). В таком случае магнитное поле дуги с переменным током каждый цикл будет меняться на противоположное и благодаря этому оказывать минимальное воздействие на поле постоянного тока. В результате взаимодействие дуг станет пренебрежимо малым.
Также часто используется конфигурация с двумя дугами на переменном токе. В таком случае помехи между дугами большей частью минимизируются сдвигом фазы тока в одной из дуг на 80-90 градусов по отношению к другой. Для этого используется так называемое автоматическое соединение «»Scott»». Благодаря сдвигу фазы ток и магнитное поле одной дуги достигают максимума в тот момент, когда ток и магнитное поле другой дуги находятся практически в минимуме. Это позволяет свести отклонение к минимуму.
Способы снижения отклонения дуги
Отклонение дуги – не всегда неблагоприятное явление. Более того, в разумных пределах оно помогает создавать швы правильной формы, лучше контролировать расплавленный шлак и глубину проплавления. Но если отклонение дуги вызывает или усиливает такие дефекты, как подрезание, непостоянную глубину проплавления, неровность швов, неравномерную глубину швов, пористость, волнистые швы и избыточное разбрызгивание, с ним нужно бороться.
Возможные способы решения:
Если для сварки в защитных газах используется постоянный ток – особенно силой более 250 ампер – возможно, проблемы можно устранить переходом на переменный ток
Сохраняйте минимальную длину дуги, чтобы ее давление компенсировало отклонение
Уменьшите силу сварочного тока – что может потребовать снижения скорости сварки
Наклоняйте электрод в противоположном направлении от отклонения дуги, как это показано на Рисунке 3-45
С обоих концов шва сделайте широкие прихваточные швы и создавайте прихваточные швы вдоль всей длины шва – особенно при некачественной подготовке соединения
Ведите сварку по направлению к широкому прихваточному шву или уже завершенному сварному шву
Используйте обратно-ступенчатую технику сварки, как показано на Рисунке 3-46
Для снижения обратного отклонения ведите сварку по направлению от рабочего соединения, для снижения переднего отклонения – по направлению к рабочему соединению
В случае процессов с обильным образованием шлака может понадобиться умеренное обратное отклонение дуги. Для этого сварку нужно вести по направлению к рабочему соединению
Оберните рабочий кабель вокруг рабочего изделия, чтобы магнитное поле тока, поступающего обратно в источник питания,
компенсировало магнитное поле, вызывающее отклонение дуги
Отклонение дуги хорошо заметно при сварке открытой дугой, но в случае сварки под флюсом его выявление может оказаться достаточно сложным. В таком случае оно диагностируется по дефектам сварки.
Для обратного отклонения характерны:
Сильное разбрызгивание
Подрезание, будь то постоянное или перемежающееся
Узкие, высокие сварные швы, часто с подрезанием
Большая глубина проплавления
Пористость поверхности в конце сварного шва на листовом металле
Для переднего отклонения характерны:
Широкий сварной шов с неравномерной шириной
Волнообразная форма шва
Подрезание, обычно перемежающееся
Меньшая глубина проплавления
Влияние креплений на отклонение дуги

При этом нужно учесть следующее:
Конструкция креплений для сварки продольных швов цилиндров (см. Рисунок 3-47) должна предполагать расстояние между опорной балкой и рабочим изделием как минимум 2,5 см.
Зажимы, которые удерживают рабочее изделие, должны быть немагнитными. Рабочий кабель нельзя подключать к медной подкладке –
по возможности соединение должно быть расположено на рабочем изделии.
Крепление должно быть изготовлено из низкоуглеродистой стали. Это позволит избежать накапливания постоянных магнитных свойств.
Сварка по направлению к закрытому концу «»рогообразных»» креплений также помогает снизить обратное отклонение дуги.
Крепление должно быть достаточно длинным для того, чтобы при необходимости можно было использовать конечные опоры.
Не используйте в качестве подкладки медные полосы на стальных балках, как показано на Рисунке 3-48. Стальная часть подкладки лишь усилит отклонение дуги.
Расстояние между зажимами должно быть минимальным. Большие промежутки могут привести к
образованию зазоров и отклонению дуги.
Не используйте системы фиксации с крупными стальными деталями только с одной стороны шва. Сбалансируйте их аналогичной конструкцией с другой стороны.
Понимание причин отклонения дуги и способов его диагностики позволит операторам полностью его контролировать и создавать сварные швы без связанных с ним дефектов.
Сварочная дуга — Cварочные работы
Сварочная дуга
Условия горения дуги. Газы и пары при обычных температуре и давлении не проводят электрический ток. Электропроводными они становятся при наличии в них частиц, несущих электрические заряды (положительные и отрицательные). В обычном состоянии в воздухе имеется только незначительное число ионов и электронов. В отличие от воздуха в металлах всегда есть некоторое число свободных электронов, переносящих электрическую энергию и делающих их электропроводными
Сварочная дуга представляет собой мощный и длительный электрический разряд в газовой среде между электродом и свариваемым изделием (между двумя электродами), сопровождающийся выделением большого количества тепла и световым излучением. Для возникновения электрического разряда газовый промежуток между электродом и свариваемым изделием должен быть ионизирован. В результате ионизации в газе возникают свободные носители заряда и газ становится электропроводным. Процесс ионизации воздушного промежутка протекает следующим образом.
Сварочная дуга возбуждается при касании концом электрода свариваемого изделия и последующем отрыве электрода от изделия. Вследствие большого омического сопротивления в месте контакта свариваемое изделие и промежуток между ними сильно разогреваются. В металле электрода имеются отрицательно заряженные свободные электроны, а в свариваемом металле — положительно заряженные ионы. Под действием нагрева (термоэлектронная эмиссия), энергии излучаемого света (фотоэлектронная эмиссия), электрического поля, появляющегося при соединении электрода с источником электрического тока (автоэлектронная эмиссия), притяжения положительно заряженных ионов свариваемого металла электроны с конца электрода устремляются к свариваемому изделию. В воздушном промежутке электроны, сталкиваясь с атомами и молекулами воздуха и паров металла, выбивают из них электроны, образуя ионы и свободные электроны. Воздух между электродом и свариваемым изделием становится проводником электрического тока, т. е. ионизируется. В результате удара кинетическая энергия электронов и ионов превращается в тепловую и поддерживает высокую температуру электрода и свариваемого изделия. Этот процесс будет продолжаться до тех пор, пока горит дуга.
Возбуждение дуги и перенос металла. При касании электрода и свариваемого изделия происходит короткое замыкание сварочной цепи. Вследствие того, что электрод и свариваемое изделие не имеют идеально ровных поверхностей, они соприкасаются отдельными выступами. Благодаря высокой плотности тока в этом месте выделяется большое количество тепла и выступы плавятся, образуя тонкую прослойку жидкого металла. Последующий отвод электрода от изделия способствует образованию в жидком металле шейки. Плотность тока и температура еще более возрастают. Расплавленный металл шейки испаряется, она разрывается, образуя сварочную дугу.
Под действием сварочной дуга электрод плавится, расплавленный металл стекает в сварочную ванну в виде капель. При ручной сварке покрытыми электродами в сварочную ванну переносится 90% электродного металла, 10% уходит на брызги и пары. Электрод длиной 450 мм расплавляется в течение 1,5—2 мин. В секунду с электрода переносится 20—50 капель металла. Чем больше сварочный ток и чем толще электродное покрытие, тем больше металла переносится в виде потока мелких’ капель. У электродов с тонким покрытием, а также при сварке на ‘малых токах перенос металла крупнокапельный.
Строение, свойства и виды сварочной дуги. Электрод, присоединенный к положительному полюсу источника питания сварочной дуги, называют анодом, а к отрицательному полюсу — катодом. При сварке на постоянном токе катодам может быть свариваемое изделие и электрод, т. е. сварочная дуга может иметь прямую и обратную полярность. При прямой полярности электрод соединен с минусом, а свариваемое изделие — с плюсом источника питания дуги. При обратной полярности это соединение выполнено наоборот. С помощью сварочной дуги обратной полярности уменьшают выделение тепла на свариваемом изделии (тонколистовой и легкоплавкий металл; легированные стали, чувствительные к перегреву) .
Сварочная дуга (рис. 9) состоит из катодной, анодной областей и столба дуги. Катодная область расположена у катода и является источником электронов, ионизирующих дуговой промежуток. Предполагают, что длина катодной области равна длине свободного пробега электрона в газе. Анодная область расположена у анода и концентрирует электроны. Пространство, ограниченное катодной и анодной областями, называется столбом дуги. Столб дуги нейтрален — суммы зарядов отрицательных и положительных частиц равны. Температура катодной области достигает 3200°С, а анодной — 3400°С. Разница температур обусловлена тем, что катодом выбрасывается больше заряженных частиц, которые сильно бомбардируют анод, в результате чего выделяется большое количество тепла. В столбе дуги температура колеблется в пределах 5000—8000 °С. При сварке на постоянном токе на аноде выделяется 43% тепла сварочной дуги, на катоде — 36%, в столбе дуги — 21%. Длина дуги равна расстоянию между торцом электрода и поверхностью расплавленного металла. У покрытых электродов 0 4—5 мм длина устойчиво горящей нормальной дуги составляет 5—6 мм. Такая дуга считается короткой. Дуга длиной более 6 мм называется длинной. Горит она неустойчиво, металл электрода плавится неравномерно, капли металла больше подвергаются воздействию кислорода и азота воздуха, наплавленный металл пористый с неровной поверхностью.
Рис. 9. Схема сварочной дуги
1,3 — анодное и катодное пятна; 2, 4 — анодная и катодная области; 5 — столб дуги
Под действием тепла дуги металл свариваемого изделия расплавляется на определенную глубину, которая называется глубиной проплавления или проваром, а жидкий расплавленный металл — сварочной ванной. Давление газов сварочной дуги отбрасывает расплавленный металл со дна ванны на боковую ее поверхность. При этом образуется углубление — кратер. В конце сварки необходимо с помощью специальных технологических приемов заделать кратер, так как в нем, как правило, обнаруживаются усадочные рыхлости, часто переходящие в трещины.
Сварочные дуги подразделяются на прямые, косвенные и комбинированные. Прямой считается дуга, которая горит между электродом и свариваемым изделием. Дугу, горящую между двумя электродами над свариваемым изделием, называют косвенной. Комбинированная сочетает в себе прямую и косвенную дуги.
Дуга переменного и постоянного тока. Сварочная дуга может питаться постоянным и переменным током. В первом и во втором случаях имеются свои преимущества и недостатки.
При сварке дугой переменного тока промышленной оягтоты катодные и анодные пятна меняются местами 100 раз в 1 с. В процессе перехода тока через нулевое -значение и при изменении полярности в начале и конце каждого полупериода дуга гаснет, что приводит к снижению температуры дугового промежутка. Одновременно с этим падает температура активных пятен, и особенно на активном пятне сварочной ванны следствие отвода тепла в изделие. Повысить устойчивость горения дуги переменного тока можно увеличением частоты его с помощью специальных генераторов и осцилляторов Кроме того, для повышения устойчивости горения дуги -в покрытие электродов вводят элементы с низким потенциалом ионизации (калий, натрий, кальций), которые облегчают возбуждение дуги.
Дуга постоянного тока горит значительно устойчивее. Однако она имеет существенный недостаток — магнитное дутье. Сварочную дугу можно рассматривать как газовый проводник электрического тока, который под действием электромагнитных сил может отклониться от своего нормального положения. Ток, проходя но сварочным проводам, электроду и дуге, создает вокруг дуги и в свариваемом металле магнитные поля. Когда эти поля расположены несимметрично относительно оси дуги, они могут отклонять дугу как гибкий проводник тока. А это затрудняет сварку и даже может привести к обрыву дуги. При сварке на переменном токе явление магнитного дутья значительно слабее. К преимуществам источников переменого тока можно отнести меньшую их стоимость и простоту в эксплуатации.
Меры борьбы с магнитным дутьем. Сила магнитного поля при сварке пропорциональна квадрату тока. Вследствие этого магнитное дутье особенно заметно при сварке на больших токах (300—400А). Однако причиной образования магнитного дутья служит только неравномерное расположение магнитного поля относительно сварочной дуги. Распределение магнитного поля в сварочном контуре зависит от места подвода тока к свариваемому изделию, его конфигурации и наличия зазоров в свариваемом стыке (рис. 10).
В случае присоединения обратного провода сварочной цепи в непосредственной близости от места сварки появление магнитного дутья исключается, так как образуется симметричное магнитное поле. При удалении места присоединения от места сварки образуется несимметричное магнитное поле. Важным фактором образования несимметричного магнитного поля являются большие ферромагнитные массы, расположенные рядом со сварочной ванной (массивные металлические изделия). Массивные ферромагнитные изделия имеют большую магнитную проницаемость по сравнению с воздухом и поэтому магнитные силовые линии устремляются в среду с меньшим сопротивлением, отклоняя при этом сварочную дугу.
Рис. 10. Места подвода тока относительно сварочной дуги
а — ток подведен к изделию слева от дуги; 6 — ось подведенного тока совпадает с осью сварочной дуги; в — ток подведен к изделию справа от дуги
Ослабить действие магнитных полей можно, изменив, угол наклона электрода таким образом, чтобы нижний конец электрода был направлен в сторону действия магнитного дутья, или применяя сварку короткой дугой, так как чем короче дуга, тем меньше возможность ее отклонения.
Статическая вольт-амперная характеристика дуги.
Для горения дуги на электроде и свариваемом изделии должно поддерживаться напряжение (напряжение на дуге), которое прямо пропорционально длине дуги. Напряжение на дуге равно сумме падений напряжения в катодной, анодной областях и столбе дуги. Для возбуждения дуги необходимо более высокое напряжение по сравнению с напряжением, установившимся в процессе сварки. Это требуется для ионизации воздушного промежутка, который еще недостаточно нагрет, и для придания электронам большой скорости.
Для обеспечения устойчивого горения дуги ток и напряжение ее должны находиться в определенной зависимости, называемой статической вольт-амперной характеристикой (рис. 11).
Повышение силы тока в дуге до 100А вызывает резко? увеличение площади сечения столба дуги, что при-чнт ‘К возрастанию его электропроводности и уменьшению напряжения. В этом случае характеристика дуги нязпвается падающей. При дальнейшем повышении си-лы тока до 1000А площадь сечения столба дуги увеличивается пропорционально силе тока, поэтому плотность
Рис. 11. Статическая вольт-амперная характеристика дуги
его и падение напряжения на всех участках столба дуги сохраняются постоянными. Такая характеристика именуется жесткой. Повышение силы тока в дуге свыше 1000А приводит к резкому возрастанию напряжения: увеличение плотности тока выше определенного значения уже не может увеличить сечение столба дуги. Поэтому напряжение на дуге повышается. Характеристику называют возрастающей.
—
Сварочная дуга —это мощный и длительный разряд электричества в газовой среде, сопровождающийся выделением большого количества тепла и световым излучением. При нормальной температуре и давлении газы, в том числе и воздух, не проводят электрический ток. Сварочная дуга возбуждается при соприкасании электрода с изделием. Большое омическое сопротивление приводит к тому, что электрод и воздушный промежуток, в месте контакта сильно нагреваются. Под действием тепла электроны из электрода (или свариваемого изделия), присоединенного к отрицательному полюсу источника питания, вырываются в воздушный промежуток, где сталкиваясь с атомами и молекулами воздуха, выбивают из них электроны и образует ионы и свободные электроны. Воздух между электродом и свариваемым изделием становится проводником электричества. Этот процесс продолжается до тех пор пока горит дуга. Электрод (свариваемое изделие), присоединенный к положительному полюсу источника питания сварочной дуги, называют анодом, а к отрицательному полюсу—катодом. Поверхность катода, из которой вылетают электроны, называют катодным пятном. При сварке на постоянном токе катодом может быть как электрод, так и свариваемое изделие. Сварочная дуга в данном случае может быть прямой и обратной полярности. При прямой полярности электрод присоединен к «минусу», а свариваемое изделие — к «плюсу» источника питания. При обратной полярности — наоборот. Сварочный ток обратной полярности применяют, когда нужно уменьшить выделение тепла на свариваемом изделии или при использовании электродов некоторых марок. На аноде выделяется 43% тепла, на катоде — 36%, в столбе дуги —21%.
Рис. 8. Схема строения сварочной дуги
рис. 9. Статическая вольт-амперная характеристика дуги
Сварочная дуга (рис. 8) состоит из катодной и анодной областей, столба дуги. Катодной областью называют пространство, расположенное у катода, анодной— у анода. Пространство между катодной и анодной областями называется столбом дуги. Расстояние между конечной точкой электрода и нижней точкой поверхности расплавленного металла свариваемого изделия составляет длину дуги. Дуга бывает короткая (3—6 мм) и длинная (более 6 мм). Плавление электрода при длинной дуге протекает неравномерно, увеличивается разбрызгивание, понижается производительность, капли расплавленного металла более подвержены окислению, дуга горит неустойчиво. На свариваемом изделии в ванне расплавленного металла под действием струи газов дуги образуется углубление, называемое кратером. Под действием тепла дуги металл свариваемого изделия расплавляется на определенную глубину, которая называется глубиной проплавления или проваром, а жидкий расплавленный металл — сварочной ванной.
Сварочная дуга может питаться переменным и постоянным током. При сварке на переменном токе промышленной частоты катодные и анодные пятна меняются местами 100 раз в 1 с. В процессе перехода тока через нулевое значение и при изменении полярности в начале и конце каждого полупериода дуга гаснет, что приводит к снижению температуры дугового промежутка. Одновременно с этим падает температура активных пятен, и особенно пятна сварочной ванны вследствие отвода тепла в изделие. Все это приводит к неустойчивому горению дуги. Дуга постоянного тока горит значительно устойчивее. Однако она имеет свой недостаток— магнитное дутье. Ток, проходя по сварочным проводам, электроду и дуге создает вокруг дуги и в свариваемом металле магнитные поля. Когда эти поля расположены несимметрично относительно оси дуги, они могут отклонять дугу как гибкий проводник тока, что не только затрудняет сварку, но и может привести к обрыву дуги. Распределение магнитного поля в сварочном контуре зависит также от места присоединения обратного провода сварочной цепи к свариваемому изделию, от конфигурации изделия и наличия зазоров в свариваемом стыке.
Присоединение обратного провода в непосредственной близости от места сварки исключает появление магнитного дутья. Образование несимметричных магнитных полей вызывают большие ферромагнитные массы (массивные металлические изделия), расположенные рядом со сварочной ванной. Ослабить действие магнитных полей можно путем изменения наклона электрода таким образом, чтобы нижний конец электрода был направлен в сторону действия магнитного дутья, или применяя сварку короткой дугой, имеющий меньшую возможность для отклонения.
Для обеспечения устойчивого горения дуги ток и напряжение должны находиться в определенной зависимости, называемой статической вольт-амперной характеристикой дуги (рис. 9). Увеличение тока в дуге до 100 А вызывает резкое увеличение площади сечения столба дуги, что приводит к увеличению его электропроводности и уменьшению напряжения. Такую форму характеристики дуги называют падающей. При увеличении тока от 100 до 1000 А площадь сечения столба дуги увеличивается пропорционально току, поэтому плотность тока и падение напряжения на всех участках столба дуги сохраняются постоянными. Характеристику тогда называют жесткой. Значение тока в дуге свыше 1000 А приводит к резкому увеличению напряжения: повышение тока выше определенного значения уже не может увеличить сечение столба дуги. Поэтому напряжение на дуге растет. Характеристика называется возрастающей.
Читать далее:
Сварочные флюсы
Сварочные электроды
Общие сведения о сварке арматуры
Противопожарные мероприятия при сварке
Безопасность труда при сварке технологических трубопроводов
Безопасность труда при сварке строительных металлических и железобетонных конструкций
Защита от поражения электрическим током при сварке
Техника безопасности и производственная санитария при сварке
Управление качеством сварки
Статистический метод контроля
Сварочная дуга: определение, структура и типы
Прочитав эту статью, вы узнаете: — 1. Определение сварочной дуги 2. Структура и характеристики сварочной дуги 3. Типы 4. Роль полярности электродов.
Дуга — это электрический разряд между двумя электродами, который возникает в электропроводящем горячем ионизированном газе, известном как плазма. Электрическая дуга, используемая для сварки, называется сварочной дугой и обычно возникает между тонким стержнем (или проволокой) и пластиной, поэтому она имеет форму колокола, как показано на рис.3.1 (а).
Структура и характеристики сварочной дуги :Сварочная дуга — это сильноточный электрический разряд низкого напряжения, действующий обычно в диапазоне от 10 до 2000 ампер и от 10 до 50 вольт. В сварочной цепи дуга действует как нагрузочный резистор.
Вообще говоря, сварочная дуга состоит из механизма испускания электронов из катода, которые после прохождения через ионизированный горячий газ сливаются с анодом.Для анализа сварочную дугу обычно делят на пять частей, а именно. катодное пятно, зона катодного падения, столб дуги, зоны анодного падения и анодное пятно. Падение напряжения на катоде и зонах падения напряжения на аноде довольно крутое, в то время как падение напряжения на столбе дуги более плавное, как показано на рис. 3.1 (b). Из рисунка видно, что напряжение дуги (V) складывается из катодного падения (Vc), падения столбца (Vp) и анодного падения (Va).
Таким образом, это можно выразить как:
В = Vc + Vp + Va …….(3-1)
Хотя сварочная дуга обычно имеет форму колокола, могут иметь место значительные колебания ее формы в тех сварочных процессах, где стержневой электрод (называемый просто электродом в остальной части текста) является расходуемым, например, при дуговой сварке в среде защитного металла и газовая дуговая сварка металлов. Чтобы получить исчерпывающие сведения о поведении сварочной дуги, необходимо знать характеристики ее различных зон.
Катодное пятно :
Это та часть отрицательного электрода, из которой испускаются электроны. Наблюдались три типа режимов катодного пятна.
Это:
(а) Режим подвижного катодного пятна,
(б) Режим термоэмиссионного катодного пятна и
(c) Нормальный режим.
В подвижном катоде в режиме пятен одно или несколько очень маленьких катодных пятен появляются на поверхности катода и перемещаются с высокой скоростью от 5 до 10 м / с и обычно оставляют после себя видимый след. Поведение подвижного катодного пятна зависит от материала, на котором оно образуется.Например, на алюминии наблюдаются множественные пятна, которые образуют сложную серию разветвленных дорожек, в то время как на меди оставленный след обычно одиночный без каких-либо ответвлений, как показано на рис. 3.2.
Оксидная пленка на поверхности металла ослабляется движением подвижного катодного пятна, а иногда также теряется слой металла. Эта характеристика делает подвижный катод очень важным для использования в промышленности, особенно для сварки алюминия и магния. Плотность тока в таком катодном пятне составляет порядка от 10 2 до 10 3 А / мм 2 .
В термоэлектронном режиме катодное пятно образуется на конце остроконечного стержня из вольфрама или торированного вольфрама, используемого с защитой из аргона. Катодное пятно остается на месте и имеет плотность тока порядка 10 2 А / мм 2 . Он виден либо как яркое пятно, либо может быть обнаружен по схождению столба дуги к точке на поверхности катода.
В нормальном режиме катодное пятно не образует четко очерченного пятна. Например, в случае стального электрода с низкоуглеродистым покрытием катодное пятно покрывает весь расплавленный наконечник электрода. Подобный тип катодного пятна наблюдается при дуговой сварке вольфрамовым электродом в газе с использованием вольфрамового электрода с закругленным концом, экранированного аргоном, как показано на рис. 3.3.
Вольфрамовая дуга, экранированная аргоном, работает либо с четко определенным катодным пятном второго типа, либо с плохо определенным катодным пятном третьего типа, и вольт-амперные характеристики в двух случаях различаются.
Механизмы эмиссии электронов :
Эмиссия электронов с катода может происходить посредством любого из нескольких механизмов, таких как термоэлектронная эмиссия, автоэлектронная или автоэлектронная эмиссия, фотоэлектрическая эмиссия и вторичная эмиссия.
а. Термионная эмиссия:
Он включает освобождение электронов от нагретых электродов. По мере повышения температуры электрода кинетическая энергия свободных электронов увеличивается до точки, в которой они могут уйти с поверхности отрицательного электрода в катодном пятне в свободное от поля пространство снаружи, несмотря на притяжение положительным электродом. ионы, оставленные на катоде.
Считается, что эмиссия электронов из углеродных и вольфрамовых катодов имеет термоэмиссионный характер, но большинство других металлов кипят при температурах значительно ниже температуры, необходимой для термоэлектронной эмиссии.
г. Автоэлектронная эмиссия:
Этот тип электронной эмиссии создается достаточно сильным электрическим полем, то есть когда напряжение на электродах настолько велико (порядка 10 4 вольт), что воздух между ними ионизируется под его влиянием и электрическим разрядом. происходит с эмиссией электронов с поверхности катода.
г. Фотоэлектрическое излучение:
Это происходит, когда энергия в форме луча света падает на поверхность катода и приводит к увеличению кинетической энергии электронов и, таким образом, к их испусканию с катода в вакуум или другой материал. Такой механизм электронной эмиссии используется при генерации рентгеновских лучей.
г. Вторичные выбросы:
Относится к испусканию электронов под действием быстро движущихся ионов.Когда скорость падающих ионов превышает орбитальные скорости электронов в атомах материала катода, это приводит к изгнанию (или испусканию) электронов.
В сварочных процессах электронная эмиссия является либо термоэмиссионной, например при газовой вольфрамовой дуговой сварке, плазменно-дуговой сварке и дуговой сварке угольным газом, либо она является автоэмиссионной в сочетании со вспомогательными средствами ионизации воздушного зазора между электродами. и заготовки, например для дуговой сварки в защитном металлическом корпусе, дуговой сварки под флюсом и дуговой сварки металлическим электродом в газе.
Эмиссия электронов из катодного пятна зависит от энергии возбуждения или работы выхода материала, которая определяется как энергия, необходимая в электрон-вольтах (эВ) или джоулях, чтобы высвободить один электрон с поверхности материал к окружающему пространству. Потенциал ионизации, который определяется как энергия на единицу заряда в вольтах, необходимая для удаления электрона от атома на бесконечное расстояние, также играет важную роль в поддержании электрического разряда.Оба параметра для большинства материалов, участвующих в сварке, приведены в таблице 3.1.
Зона катодного падения :
Это газовая область, непосредственно примыкающая к катоду, в которой происходит резкое падение напряжения. Совокупный размер зоны катодной капли и зоны анодной капли составляет порядка 10 2 мм, что почти равно длине свободного пробега электронов. Было обнаружено, что падение напряжения в зоне катодного падения для вольфрамового электрода, экранированного аргоном, составляет около 8 вольт при 100 амперах и увеличивается с уменьшением тока.
Колонна Arc:
Это яркая видимая часть дуги, имеющая высокую температуру и низкий градиент потенциала. Температура столба дуги зависит от присутствующих в нем газов и величины сварочного тока, протекающего в цепи. Обычно температура колонки варьируется от 6000 ° C для паров железа до примерно 20000 ° C для вольфрамовой дуги, защищенной аргоном. При такой высокой температуре все молекулярные газы, присутствующие в колонке, расщепляются на атомарную форму, а сами атомы далее диссоциируют на электроны и ионы.Однако количество электронов и ионов в любом заданном объеме дуги остается неизменным, что сохраняет дугу электрически нейтральной.
Так как средний ион примерно в тысячу раз тяжелее электрона, электроны гораздо более подвижны и, следовательно, переносят большую часть тока через столб дуги. Градиент потенциала в столбе ниже, чем градиент потенциала в зоне катодного падения или в зоне падения анода, и обычно он колеблется от 0-5 до 5 вольт / мм для вольфрамовых дуг, экранированных аргоном, тогда как для дуговой сварки экранированным металлом он обычно составляет около 1 вольт. / мм.
Сварочная дуга почти всегда возникает между стержнем или проволочным электродом и плоской или широкой заготовкой. Это, независимо от полярности электрода, приводит к возникновению дуги в форме раструба или конуса с вершиной конуса на кончике стержневого электрода или рядом с ним. Из-за этого сужения дуги возле стержневого электрода она имеет самую высокую плотность энергии там, но из-за охлаждающего эффекта из-за близости электрода максимальная температура находится в центре столба.
Область, в которой суженный столбик встречается с электродом, называется корнем дуги.Распределение температуры в столбе дуги для вольфрамовой дуги, экранированной аргоном 200 ампер, показано на рис. 3.4.
Рис. 3.4 Распределение температуры в столбе дуги
Прохождение тока в столбе дуги вызывает развитие электромагнитных сил. Также хорошо известно, что два параллельных проводника, по которым проходит ток в одном направлении, притягиваются друг к другу.
Если ток проходит через газовый цилиндр, его можно рассматривать как состоящий из большого количества кольцевых цилиндрических проводников, следовательно, существует взаимное притяжение между различными газовыми цилиндрами, причем все силы действуют внутрь из-за высокой плотности тока в сердечнике цилиндра. дирижер.
Эти сжимающие силы уравновешиваются градиентом статического давления, установленным в газопроводе с нулевым давлением на внешней периферии и максимальным по оси.
Однако в данном случае из-за конической формы дуги действующие на нее электромагнитные силы имеют две составляющие, причем статическое давление имеет две противоположные составляющие, одна из которых расположена вдоль оси дуги и является причиной образования плазмы. струя, которая течет со скоростью около 10 4 см / сек по направлению к заготовке.Осевая скорость плазмы уменьшается по мере приближения к периферии дуги, как показано на рис. 3.5.
В установившемся режиме плазменная струя имеет обтекаемый поток, скорость которого приблизительно пропорциональна сварочному току. На рис. 3.6 показан рисунок линий газового потока и линий скорости в угольной дуге 200А. Считается, что значительное количество тепловой энергии передается к изделию за счет конвективных потоков плазменной струи.
Фиг.3.6 Линии потока газа и линии скорости плазмы при сварке угольной дугой
Когда ток в дуге не симметричен, возникают магнитные силы, которые отклоняют столб дуги. Если это происходит в сварочной дуге, это называется дуговым разрядом и часто приводит к некорректным и неправильным сварным швам.
Зона анода и падения анода:
Достигнув анода, электроны теряют свою теплоту конденсации. Однако, в отличие от катодного пятна, редко можно увидеть четко очерченное анодное пятно, а плотность тока также мала, как показано на рис.3.7 для вольфрамового катода, экранированного аргоном, на 200 А и анода из медной пластины. Токопроводящая площадь анода немного меньше самого широкого распространения дуги на конце анода, а средняя плотность тока также довольно мала.
Падение напряжения в зоне анодного падения дуги этого типа составляет b6 от 1 до 3 вольт. Глубина анодной зоны падения составляет от 10 -2 до 10 -1 мм. Когда стержневой электрод действует как анод, он занимает нижнюю полусферу расплавленной капли на кончике электрода.Однако в случае струи плазмы низкого давления анод, кажется, окружает расплавленную каплю.
Общее тепловложение на аноде происходит из-за конденсации электронов, а также проводимости и конвекции из-за плазменной струи. В дуге постоянного тока с неплавящимся электродом, например, из вольфрама или углерода, тепло анода больше, чем тепло высвобождается на катоде, как показано на рис. 3.8.
С увеличением длины сварочной дуги напряжение на дуге увеличивается и, следовательно, для тока выше примерно 100 А тепловложение увеличивается с увеличением столба дуги, особенно для режима катодного пятна, как показано на рис.3.9. Однако с увеличением длины столбца ширина столбца также увеличивается, что приводит к еще более низкой плотности тока на аноде и, таким образом, анод становится более рассеянным.
КПД дуги:
Из описания характеристик различных частей сварочной дуги можно определить КПД дуги, математическая обработка которого следующая:
Итак, общая тепловая энергия, выделяемая на аноде, q a , определяется суммой энергии, полученной через электроны, и энергии, полученной при прохождении через зону падения анода, т.е.е.,
Задача 1:
Найдите коэффициент полезного действия дуги для процесса GTAW, если сварочный ток составляет 150 ампер, а напряжение дуги 20 вольт. Предположим, что катодное падение составляет 8 вольт, а анодное падение — 3 вольта, при этом 30% энергии столба дуги передается аноду. Возьмем температуру дуги как 15000 К. Работа выхода, 0 для вольфрама = 4,5 эВ и постоянной Больцмана = 8,62 x 10 -5 эВ / К.
Решение:
Задача 2:
При дуговой сварке вольфрамовым электродом в среде аргона катодное падение составило 10 вольт при сварочном токе 120 вольт и напряжении дуги 18 вольт. Определите (а) длину дуги, если КПД дуги составляет 55% при температуре дуги 10000 Кельвинов.
Предположим, что падение напряжения на колонке составляет 1,2 В на 1 мм, и что 20% тепла колонки передается аноду.
(b) Эффективность дуги, если те же параметры процесса применимы к процессу GMAW и проволочный электрод выполнен в качестве анода.
Возьмем работу выхода для вольфрама при OK = 4,5 эВ и постоянную Больцмана. К ’= 8-60 x10 -5 эВИК
Решение:
Типы сварочных дуг :
С точки зрения сварки дуги бывают двух типов:, неподвижная, или стационарная, или фиксированная дуга, и подвижная, или движущаяся, или бегущая дуга. Фиксированная дуга образуется между неплавящимся электродом и заготовкой. Дуга может использоваться с наполнителем или без него. В первом случае отдельная проволока вводится в столб дуги и, таким образом, расплавляется для передачи в сварочную ванну под совместным действием силы тяжести, электромагнитных сил и механической силы, действующей на плазменную струю, в неподвижной дуге большая часть тепла уходит. к неплавящемуся электроду остается неиспользованным, и его, возможно, придется отводить охлаждающей водой или защитным газом.Таким образом, тепловой КПД такой дуги невелик и может составлять от 45 до 60%. Этот тип дуги наблюдается при сварке угольной дугой, газовой вольфрамовой дугой и плазменной дугой.
Подвижная дуга образуется между плавящимся электродом и заготовкой. По мере плавления присадочной проволоки расплавленный металл на кончике электрода отделяется под действием силы тяжести, электромагнитных сил, силы плазменной струи и пинч-эффекта. Однако удерживающая сила из-за поверхностного натяжения также действует на каплю.По мере плавления электрода дуга продолжает двигаться вверх по электроду. Подвижная дуга связана с такими процессами, как дуговая сварка в защитном металлическом корпусе, дуговая сварка металлическим электродом в газовой среде и дуговая сварка под флюсом.
Дуга, при которой расплавленный металл от кончика электрода проходит через него и становится частью сварочной ванны, называется «металлической дугой». Подвижная дуга — это металлическая дуга.
Большая часть тепла, поступающего на электрод в подвижной дуге, используется для плавления металла и, таким образом, используется эффективно.Таким образом, термический КПД процесса с использованием подвижной дуги высок и обычно составляет от 75 до 90%. Следовательно, сварочные процессы с использованием подвижной дуги термически более эффективны, чем процессы с использованием неподвижной или фиксированной дуги.
Роль полярности электродов в дуговой сварке:Дуговая сварка может выполняться на переменном или постоянном токе. Если используется переменный ток, полярность электродов не возникает, поскольку она меняется каждые полцикла. Однако, если используется постоянный ток, можно сделать электрод либо отрицательным, либо положительным.
На аноде выделяется больше тепла, поэтому во всех процессах, в которых используются неплавящиеся электроды, лучше подключать электрод к отрицательной клемме, чтобы минимизировать тепловые потери. Однако это может быть не всегда возможно, потому что иногда необходимо использовать очищающее действие подвижного катодного пятна для отделения прочного тугоплавкого оксидного слоя от металла, например, при сварке алюминия и магния.
В таких случаях предпочтительно использовать переменный ток, чтобы найти компромисс между термической эффективностью и очищающим действием.Таким образом, в процессах дуговой сварки вольфрамовым электродом и угольной дуговой сварки обычно используются источники переменного тока, когда обязательно требуется опора на обрабатываемую деталь. Когда такого принуждения нет, можно использовать dcen.
Однако для дуговой сварки экранированным металлом сварочный трансформатор переменного тока довольно популярен, и в то же время при тех же технических характеристиках он намного дешевле, чем сварочный электродвигатель-генератор постоянного тока или набор трансформатора с выпрямителем, необходимый для получения питания постоянного тока. Также при сварке на постоянном токе есть устройство смены дуги, которое может привести к неприглядному зигзагообразному сварному шву низкого качества.
Из-за регулярного прерывания дуги переменного тока не рекомендуется использовать неизолированную проволоку, например, при дуговой сварке металлическим электродом в газе. Однако для дуговой сварки защищенным металлом были разработаны соответствующие электродные покрытия, которые облегчают инициирование и поддержание сварочной дуги.
При использовании расходуемого электрода перенос металла от проволочного электрода к обрабатываемой детали является более равномерным, частым и более направленным, если электрод выполнен положительным. Поэтому DCEP или обратная полярность является популярной для GMAW, который также обеспечивает необходимое очищающее действие на металлах с прочным оксидным слоем, таких как алюминий.
Урок 1 — Основы дуговой сварки
Урок 1 — Основы дуговой сварки © АВТОРСКИЕ ПРАВА 1999 УРОК ГРУППЫ ЭСАБ, ИНК. I, ЧАСТЬ B 1.9 ПОСТОЯННАЯ ТОК ИЛИ ПОСТОЯННОЕ НАПРЯЖЕНИЕ Сварка Источники питания имеют разные размеры и формы. Они могут поставлять либо AC или DC, или оба, и они могут иметь различные средства контроля их напряжения и силы тока вывод.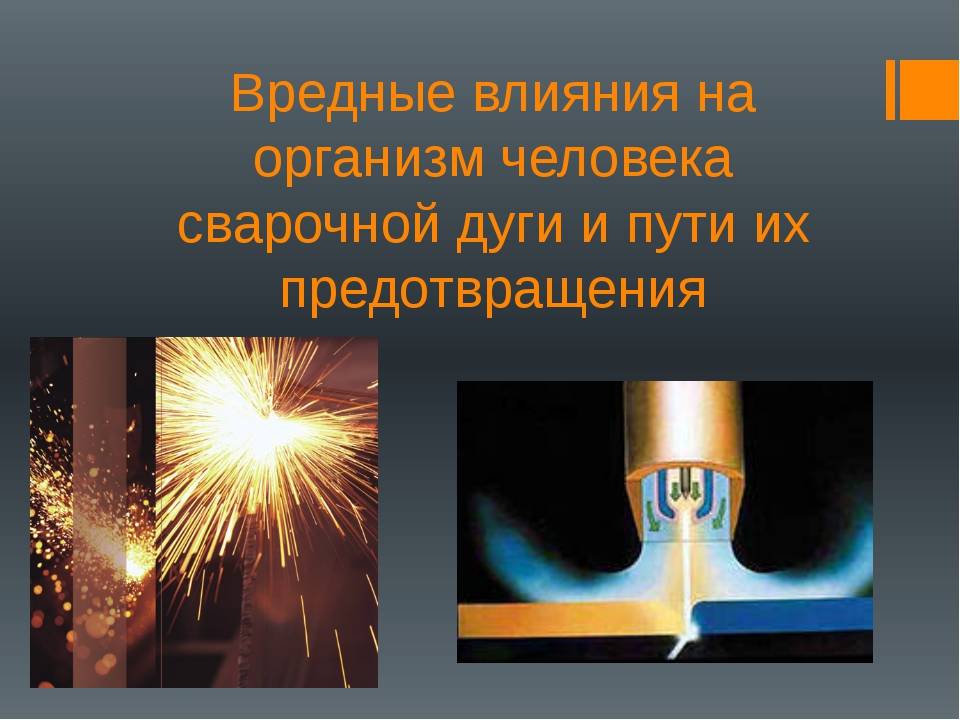
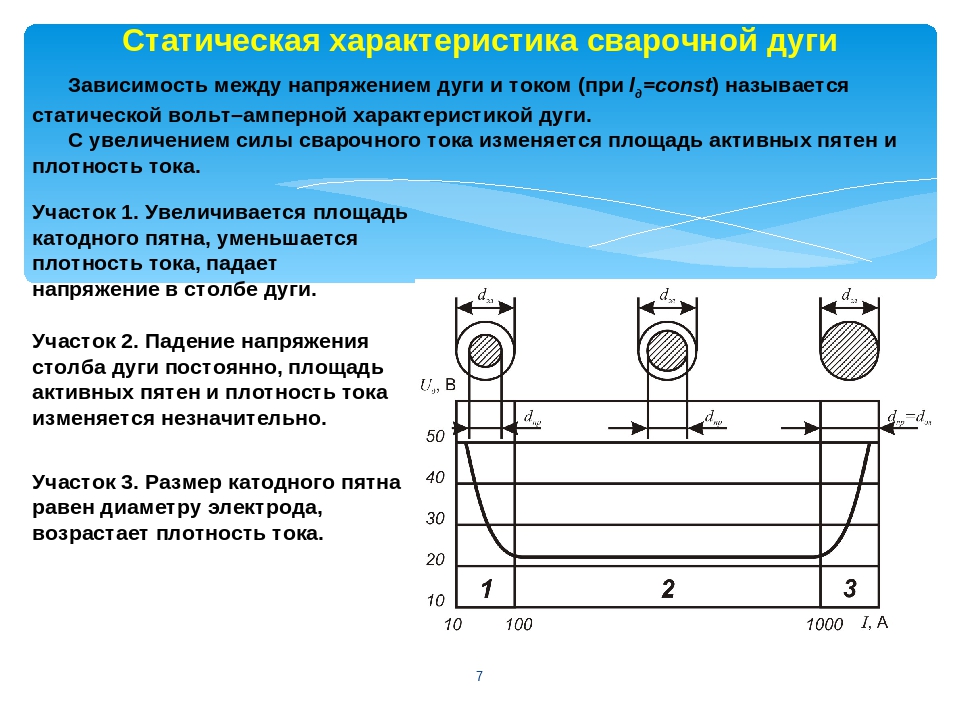
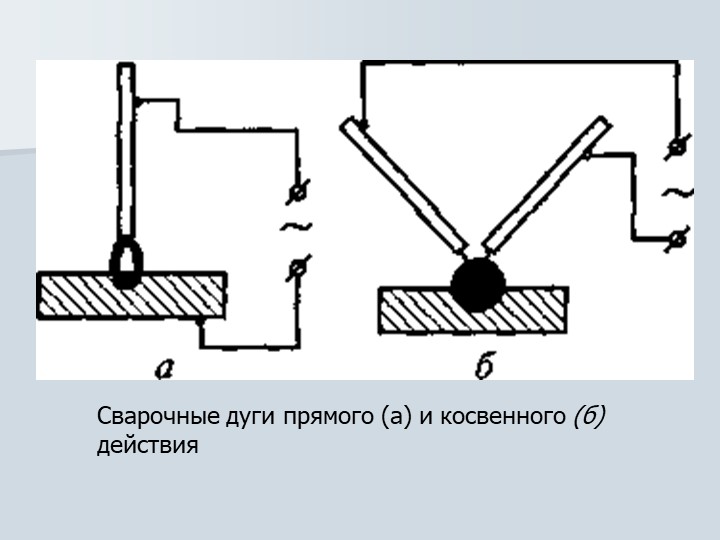
Arc Voltage — обзор
6.03.3.6 Взаимосвязь напряжения дуги и длины дуги
Термины «напряжение дуги» и «длина дуги» часто используются как синонимы. Однако эти термины имеют разные коннотации, даже если они напрямую связаны. При использовании GMAW длина дуги является критически важной переменной, которую необходимо тщательно контролировать. Например, в режиме переноса металла методом струйной дуги (обсуждается ниже) с защитой аргоном слишком короткая дуга вызывает кратковременное короткое замыкание. Эти короткие замыкания вызывают колебания давления, нагнетая воздух в поток дуги, создавая пористость или охрупчивание из-за абсорбированного азота.При слишком короткой дуге наконечник электрода закорачивает сварочную ванну, вызывая нестабильность.
При слишком длинной дуге она имеет тенденцию колебаться и блуждать; влияет как на глубину проплавления, так и на профили поверхностных валиков и нарушает газовую защиту. В случае заглубленной дуги с экраном из углекислого газа длинная дуга приводит к незаглубленному состоянию и вызывает чрезмерное разбрызгивание и пористость.
AV зависит от длины дуги, состава и размеров электрода, защитного газа, техники сварки, удлинения электрода и даже длины сварочного кабеля, поскольку AV часто измеряется на источнике питания, а также от многих других переменные.Как показано на рисунке 13, AV представляет собой приблизительное средство выражения физической длины дуги в электрических единицах, даже несмотря на то, что измеренная AV также включает в себя падение напряжения на удлинении электрода за пределами контактного наконечника. Если все переменные остаются постоянными, AV напрямую зависит от длины дуги. Несмотря на то, что длина дуги является переменной и ее необходимо контролировать, напряжение легче контролировать. Поскольку в процедуре сварки требуется указать AV, обычно используется термин AV.
Рисунок 13.Номенклатура пистолетов для дуговой сварки.
Воспроизведено из Справочника по сварке, Том. 2, Часть-1, 9-е изд., Сварочные процессы, Американское сварочное общество (AWS), 2001. Настройки AV различаются в зависимости от материала, защитного газа и режима переноса. Необходимы пробные запуски, чтобы отрегулировать AV для получения наиболее благоприятных характеристик дуги и внешнего вида сварного шва. Испытания необходимы, поскольку оптимальная AV зависит от толщины металла, типа соединения, положения сварки, размера электрода, состава защитного газа, типа сварного шва, а также ряда других факторов.При любом конкретном значении AV увеличение напряжения приводит к сглаживанию сварного шва и увеличению ширины зоны плавления. Чрезмерно высокое напряжение может вызвать пористость, разбрызгивание и подрезку. Снижение напряжения приводит к получению более узкого сварного шва с более высоким гребнем и более глубоким проплавлением. Чрезмерно низкое напряжение может привести к заглушке электрода, при котором электрод погружается в сварочную ванну, а затем затвердевает на месте из-за отсутствия тока короткого замыкания.От любого конкретного значения AV увеличение имеет тенденцию к сглаживанию сварного шва и увеличению ширины зоны плавления. Чрезмерно высокое напряжение может вызвать пористость, разбрызгивание и поднутрение. Снижение напряжения приводит к получению более узкого сварного шва с более высоким гребнем.
GMAW широко используется в производственных процессах на заводах для сварки различных черных и цветных металлов. Поскольку в нем используется сварочная проволока с непрерывной присадкой, а не сварочные стержни, он имеет значительное преимущество перед MMAW с точки зрения времени дуги при выполнении вручную. По той же причине он также поддается автоматизации дуговой сварки. Штыри электрода, оставшиеся после сварки штангой, также становятся отходами присадочного металла, поэтому использование электродного материала выше при GMAW. Другие особенности GMAW включают отсутствие необходимости в удалении шлака (поскольку в GMAW не используется флюс), поэтому можно достичь более высоких скоростей наплавки, чем SMAW, с хорошей универсальностью.
Электрическая дуга образуется в защитном газе между непрерывно подаваемым металлическим проволочным электродом и заготовкой, при этом ток подается на электрод, когда он проходит через медную контактную трубку.Детали горелки и области дуги для GMAW показаны на рисунке 13. В процессе GMAW диаметры электродов значительно меньше, чем в MMAW, так что энергия дуги очень сконцентрирована около оси, что дает характеристику глубокого проникновения. Его можно использовать как ручную, так и механизированную технику в ряде приложений, в зависимости от типа материала, толщины и положения сварки. Как правило, высокие скорости наплавки могут быть достигнуты за счет механизированной операции, при которой расходуемый электрод непрерывно подается в сварочную дугу.Состав защитного газа оказывает значительное влияние на характеристики процесса, форму сварных швов, разбрызгивание и механические свойства металла шва. GMAW с защитным газом CO 2 широко используется для сварки низкоуглеродистых сталей общего назначения, где требуются хороший внешний вид поверхности, улучшенная устойчивость к изменению параметров сварки и хорошие характеристики ударной вязкости. При использовании смесей Ar / CO 2 или Ar / CO 2 / O 2 увеличение стоимости компенсируется улучшенным внешним видом сварного шва.
Возможность использования типов дуги в промышленной сварке
Введение
Дуговая сварка — ключевой процесс в промышленном производстве (Naidu et al.2003), а газовая дуговая сварка (GMAW) обычно используется во многих обрабатывающих отраслях из-за своей основные преимущества, такие как регулируемые профили проплавления, гладкий валик, малое разбрызгивание и высокая скорость сварки (Kah et al. 2009). За последние два десятилетия GMAW стала основной технологией в индустрии роботизированной сварки (Chen and Wu 2009).Тип дуги является важным фактором во многих приложениях; однако явление дуги полностью не объяснено и проявляет неизвестные свойства и поведение.
Использование дуги соответствующего типа при сварке различных материалов с разной толщиной обеспечивает экономию средств, сокращает время производства и улучшает качество. В последнее время важной проблемой стало соединение тонких материалов и материалов, чувствительных к нагреванию. Лучшее понимание явлений дуги может помочь разработать и усовершенствовать интегрированный дизайн промышленных сварочных систем (Iordachescu and Quintino 2008).В связи с растущим разнообразием соединяемых материалов и множеством различных процессов дуговой сварки потребность в понимании различных типов процессов дуговой сварки становится как никогда актуальной. Кроме того, при управлении и изменении процесса сварки знание явления дуги упростит получение улучшенного качества сварных швов и надежных соединений (Eagar 1990a, b).
Это исследование дает краткое введение в характеристики дуги, обсуждает классификацию сварочных дуг, представляет сравнение дуг и обсуждает преимущества и недостатки различных дуг.Наконец, рассматриваются типы сварочных дуг и их роль в промышленном применении.
Характеристики дуги
Сварочную дугу можно рассматривать как проводник газа, который преобразует электрическую энергию в тепловую (Найду и др., 2003). В исследовании Ланкастера (1984) сварочная дуга рассматривается как газообразное тело цилиндрической формы, ограниченное температурным градиентом. Одна из проблем, с которой обычно сталкивается сварочная промышленность, — это плохая стабильность дуги. Стабильность дуги и длина дуги влияют на характер переноса металла (Pal et al.2010). При стабильной дуге перенос металла происходит равномерно, а количество брызг минимально (Hermans and Ouden 1999). В ситуации стабильной дуги можно найти взаимосвязь между напряжением и током, показанную на Рисунке 1 (Ибрагим Хан 2007). График показывает, что дуга не подчиняется закону Ома. Кроме того, уменьшающаяся часть характеристики дуги является частью Айртона и характеризуется нестабильной дугой, в то время как часть Ома, увеличивающаяся область, применяется при сварке. Другие факторы, такие как атмосфера дуги, длина дуги и металлы, также влияют на наклон кривой.
Рисунок 1Типичная характеристика дуги по сравнению с законом Ома (Ибрагим Хан 2007 г. ).
Дуговая плазма
Дуговая плазма представляет собой ионизированное состояние сварочного газа и представляет собой смесь почти равных количеств электронов и ионов. Плазма переносит ток дуги. Большую часть тока проводят электроны. В случае дуговой сварки электродом обычно считается катод, а заготовка — анод.Электроны выходят из электрода (т. Е. Отрицательного вывода) и направляются в заготовку (т. Е. Положительный вывод) (Найду и др., 2003). Чтобы определить влияние дуговой плазмы на сварочную ванну, необходимо учитывать четыре фактора: (i) тепловой поток, (ii) плотность тока, (iii) напряжение сдвига и (iv) давление дуги.
Существует прямая зависимость между увеличением теплового потока и плотности тока и глубиной сварочной ванны. Увеличение напряжения сдвига в расплавленной ванне способствует протеканию наружу потока в верхней части сварочной ванны, а увеличение давления дуги может привести к более вогнутой поверхности сварочной ванны (Мерфи и др.2009 г.). Однако давление дуги не влияет на плоскостность поверхности сварочной ванны при токе менее 200 А (Лин и Игар, 1985; Ван и Цай, 2001).
Температура дуги
Первоначально считалось, что температура сварочной дуги состоит из тепла плазмы дуги, но Кобайн и Бургер (1955) показали, что большая часть тепла, передаваемого на изделие от электрода, происходит от потока ток в металл. Позже это понимание было расширено Куигли и др.(1973), которые отметили, что только 20% тепла переносится за счет теплопроводности горячих газов, а 80% остается в электрическом токе. В зависимости от точной природы плазмы и силы тока, протекающего через нее, температура сварочной дуги варьируется от 5 000 до 30 000 К (Найду и др., 2003; Роберт и Месслер, 2004). В некоторых случаях мощность чрезвычайно высока, а температура может подниматься до 50 000 К (Найду и др. 2003).
На температуру плазмы влияют два важных фактора: конкретная плазма и ее плотность (Роберт и Месслер, 2004).При дуговой сварке однокомпонентным газом, которая используется в некоторых сварочных процессах, температура в GMAW ниже, поскольку расплавленные капли, пар и ионы металлов более концентрированы. На рис. 2 показано распределение температуры дуги при сварке алюминия методом GMA при 250 А. Как видно, центральная сердцевина дуги имеет самую высокую температуру, которая изменяется в зависимости от используемого защитного газа (Роберт и Месслер, 2004).
Рисунок 2Распределение температуры дуги при сварке GMA алюминия при 250 А (Smårs and Acinger 1968 г. ).
Ток дуги
На процесс сварки влияет несколько факторов, таких как ток дуги, напряжение дуги, скорость перемещения горелки, присадочная проволока и частота вращения (Лу и др. 2009; Мун и др. 2006). При выборе этих параметров следует учитывать количество подводимого тепла и желаемое плавление (Мин и др. 2011). На режим дуги и, следовательно, на качество сварки сильно влияет сила тока (Ху и Цай, 2006). На глубину проплавления также существенно влияет ток дуги.При дуговой сварке металлическим газом увеличение тока дуги увеличивает проплавление шва. Однако повышенное проникновение в стык также увеличивает вероятность прожога и растрескивания при затвердевании. Эксперименты, проведенные Ху и Цай (2006), показали, что более высокий ток приводит к более высокой электромагнитной силе, которая заставляет каплю отделяться от электрода к сварочной ванне. Кроме того, при более высоком токе размер расплавленной капли меньше и частота появления капель выше.
Напряжение дуги
Напряжение дуги пропорционально длине дуги.Следовательно, напряжением дуги можно управлять, изменяя длину дуги (Найду и др., 2003). На рис. 3 показаны кривые напряжения дуги типичного источника питания на диаграмме сварочного тока и напряжения. Видно, что небольшое изменение напряжения приводит к очень большому изменению сварочного тока. Как следствие взаимосвязи между сварочным током и напряжением дуги, свойства и геометрия сварного шва могут быть предсказаны (Shoeb et al.2013): сварка высоким напряжением дает очень широкий валик с возможными поднутрениями и вогнутой формой, а сварка тоже низкое напряжение приводит к низкому качеству сварного шва.
Рисунок 3Саморегулирование напряжения дуги (Найду и др. 2003 г. ).
Как видно из рисунка 3, напряжение значительно изменяется при небольшом изменении длины дуги, в то время как изменение тока незначительно. Следовательно, длина дуги больше влияет на напряжение, чем на сварочный ток. Длина дуги на этой диаграмме разделена на три части: длинную, среднюю и малую, которые представляют собой так называемые кривые источника напряжения.Соединение кривых CC и CV с кривой источника напряжения называется рабочей точкой источника питания и может изменяться в процессе сварки (Найду и др., 2003).
Проникновение дуги
Чтобы определить проникновение дуги, необходимо знать положение дуги, которое рассчитывается на основе таких параметров, как сварочное напряжение, сварочный ток и скорость подачи проволоки. Положение дуги определяется как сумма удлинения проволоки и длины дуги. На рисунке 4 эти параметры показаны для GMAW как L и L a , соответственно.Расстояние между сварочной горелкой и заготовкой составляет H , а параметр P отображает глубину проплавления (Ивата и др. 2009a, b).
Рисунок 4Параметры для прогнозирования положения дуги (Ивата и др. 2009a , б ).
На рис. 5 показана взаимосвязь между положением дуги и проплавлением при сварке плоских листов под флюсом.Подгоночная линия на графике показывает, что значения глубины проникновения дуги и положения дуги очень близки. Таким образом, связь такая, как и ожидалось (Ивата и др. 2009a, b).
Рисунок 5Сравнение прогнозируемой и фактической глубины проникновения для ПАВ (Ивата и др. 2009a , б ).
Эффективность дуги
Эффективность дуги является важным фактором в процессах дуговой сварки и обычно объясняется как вклад тепла в металл, деленный на общую тепловую энергию дуги (Eagar 1990a).Другими словами, эффективность дуги измеряется как количество энергии дуги, подводимой к подложке (Дюпон и Мардер, 1995). Эффективность дуги влияет на скорость сварки и может варьироваться от 60% до 99% для различных сварочных процессов (Eagar 1990b). Важно знать эффективность дуги, чтобы измерить эффективность плавления, как экспериментально, так и с помощью моделей теплового потока (Dupont and Marder 1995). Параметры сварки (например, ток и напряжение) мало влияют на эффективность дуги для данного процесса, а эффективность процессов сварки неплавящимся электродом считается немного ниже, чем у процессов с плавящимися электродами (Kou 1987; Lancaster 1984).Подвод тепла можно рассчитать с использованием эффективности дуги по формуле, показанной в уравнении 1 (Gunaraj and Murugan, 2002):
$$ \ mathrm {Heat} \; \ mathrm {input} \ left (\ frac {\ mathrm {kJ}} {\ mathrm {cm}} \ right) = \ frac {\ mathrm {Arc} \; \ mathrm {Voltage} \ times \ mathrm {Arc} \; \ mathrm {current}} {\ mathrm {Welding} \; \ mathrm {скорость} \ times 1000} \ times \ mathrm {Arc} \; \ mathrm {эффективность} $$
(1)
Стабильность дуги
Стабильность дуги — еще одна важная характеристика дуговой сварки.На стабильность дуги влияют такие параметры, как мощность дуги, режим переноса металла и регулярность режима переноса металла (Ghosh et al. 2006). Брызги во время сварки — главный отрицательный результат плохой стабильности дуги; разбрызгивание приводит к потерям материала, увеличивает время очистки и снижает качество сварного шва (Suban and Tusek 2003).
Свойства идеальной и стабильной сварочной дуги следующие (Suban and Tusek 2003): (i) форма всего переносимого материала постоянна, (ii) длина дуги постоянна, и (iii) существует небольшое количество брызг или их полное отсутствие.
При сварке плавящимся электродом, например GMAW, стабильность дуги зависит от поведения корня дуги (Коста и др., 2010). Еще одним фактором стабильности дуги является смесь защитного газа. Стабильность дуги ниже в газовой смеси с повышенным содержанием углекислого газа (CO 2 ). На рисунке 6 показано, что большая длина дуги и более тонкое изотермическое распределение — две характеристики смеси с низким содержанием диоксида углерода (Pires et al. 2007).
Рисунок 6Распределение температуры для смесей: высокое (слева) и низкое (справа) содержание диоксида углерода. Для того же тока и напряжения I 1 выше, чем I 2 (Pires et al. 2007)
Дуговый разряд
Дуговый разряд — это явление, при котором дуга имеет тенденцию отделяться от точка сварки, как если бы дул сильный ветер (Найду и др., 2003). Причиной возникновения дуги является дисбаланс магнитного поля, окружающего заготовку (Gerbec 2009). Обычно это явление возникает в трех ситуациях: (i) направление тока изменяется, (ii) вокруг сварочной дуги есть магнитные материалы, и (iii) магнитные материалы находятся рядом с краем пластины (Naidu et al.2003 г.). Дуговая дуга обычно наблюдается только при высоких сварочных токах постоянного тока. Этого можно избежать, снизив уровень тока, используя сварочный ток переменного тока и размагничивая приспособление (Gerbec 2009). Напряжение дуги влияет на отклонение дуги, так что дуга с более низким напряжением короче и жестче и имеет лучшее сопротивление отклонению, чем дуга с более высоким напряжением дуги.
Как упоминалось ранее, тепловая энергия дуги создается за счет электрических реакций между анодом и катодом внутри плазмы.2 $$
(2)
В данной формуле и α , и β являются константами, l s — удельное сопротивление электрода, α ω — это площадь поперечного сечения проволоки, а I — сварочный ток (Найду и др., 2003).
Пинч-эффект
Дуга во всех проводниках, по которым проходит ток, окружена магнитным полем (Luksa 2006).При дуговой сварке площадь поперечного сечения плавящегося электрода меняется, а направление электромагнитной силы зависит от направления потока сварочного тока. Магнитное поле имеет силу, направленную к центру дуги, так называемую силу Лоренца. С увеличением силы тока увеличивается сила тока и радиальное сужение дуги из-за большей магнитной силы. Этот процесс называется пинч-эффектом (Дзельницки, 2000; Роберт, Месслер, 2004). Величина сжимающего усилия напрямую зависит от сварочного тока и диаметра проволоки и влияет на отрыв капли от сварного шва (Kasikci 2003).Пинч-эффект показан на Рисунке 7 (Надзам, 2006).
Рисунок 7Пинч-эффект при КЗ (Надзам 2006 г. ).
Когда площадь поперечного сечения электрода увеличивается, сила Лоренца действует в том же направлении, что и ток. Уменьшение площади поперечного сечения электрода заставляет силу Лоренца действовать в направлении, обратном току.Сила Лоренца может действовать двумя способами, отделяя капли от наконечника электрода до сварочной ванны. Во-первых, если электрод положительный и размер капли больше диаметра проволочного электрода, магнитная сила разделяет каплю. Во-вторых, есть сужение или сужение. В этом случае магнитная сила действует в обоих направлениях от точки сужения (Роберт и Месслер, 2004).
Типы дуги
После первой классификации типов дуги в 1976 г. (Lancaster 1984) было предложено несколько дополнительных классификаций.Короткая дуга, шаровидная дуга и дуга со струйным переносом являются тремя основными классификациями типов дуги Американским сварочным обществом (AWS) (Iordachescu and Quintino 2008). Международный институт сварки (IIW) в 1984 г. разделил типы дуги струйного распыления на три категории: (i) капельное или спроецированное распыление, (ii) вращающееся распыление и (iii) струящееся распыление (Iordachescu and Quintino 2008; Lancaster 1986). ). Норриш (2003), а затем Пономарев и др. (2003) изменили эту категоризацию. Использование цифрового управления источниками питания привело ко многим улучшениям в управлении дугой, особенно при сварке короткими и импульсными дугами.Цифровое управление увеличивает скорость реакции инвертора источника питания, а использование сложного программного обеспечения позволяет напрямую влиять на дугу (Weman 2003; Iordachescu and Quintino 2008).
В таблице 1 обобщена попытка классификации переноса металла. Использование цифрового управления источниками питания привело ко многим улучшениям в управлении дугой, особенно при сварке короткими и импульсными дугами. Цифровое управление увеличивает скорость реакции инвертора источника питания, а использование сложного программного обеспечения позволяет напрямую влиять на дугу (Weman 2003; Iordachescu and Quintino 2008).Текущая классификация дуги IIW показана в таблице 2. Таблица также включает пример процесса сварки и доминирующую силу для каждого типа режима переноса (Iordachescu and Quintino 2008; Robert and Messler 2004).
Таблица 1 Сводная информация об эволюции режима переноса металла Таблица 2 IIW классификация режимов переноса металла и примеры сварочных процессов aРазличные факторы побудили усилия по классификации дуги и переноса металла, в том числе необходимость лучшего понимания процесса, чтобы иметь возможность лучше исследовать и контролировать его.Лучшая классификация позволила различить дугу по капельному переносу. Таким образом, в зависимости от стабильности дуги может происходить желательный (например, перемычка, распыление) или нежелательный (например, отталкивающийся, взрывной) перенос металла.
При мостовом переносе расплавленный металл растет, пока не коснется сварочной ванны. Возникает короткое замыкание и повышается ток; таким образом, сужение и разрыв отделяют каплю. При переносе в полете нет контакта между электродной проволокой и сварочной ванной (Li and Zhang 2007).Если размер капель, оторвавшихся от электрода до расплавленной сварочной ванны, меньше диаметра электродной проволоки, то в дуговом режиме проецируется режим распыления. Если расплавленный металл от электрода вращается, это называется вращающейся струей дуги. Спроецированное распыление в основном называется распылительной дугой для упрощения терминологии (Роберт и Месслер, 2004). Характеристики, которые обычно типичны для проецируемой струйной дуги, — это устойчивый отрыв, малое разбрызгивание, постоянный размер капли и прямой перенос капель. Следовательно, этот режим дуги предпочтителен при обычном GMAW (Li and Zhang 2007).
Режимы дуги связаны с напряжением дуги и уровнем тока. Изменяя эти два параметра, можно изменять режимы дуги. При небольшом токе капля не образуется, пока не коснется сварочной ванны; этот режим дуги представляет собой так называемую короткую дугу. Режим дуги меняется на шаровую дугу, когда ток увеличивается так, что создается небольшая электромагнитная сила (Wang et al. 2004). В шаровой дуге диаметр капли больше, чем у электрода, и капля образуется под действием силы тяжести.При дальнейшем увеличении тока тип дуги меняется на спроецированную дугу с разбрызгиванием, затем на струящуюся дугу и, наконец, на вращающуюся дугу (Li and Zhang 2007). Различные типы дуг могут быть показаны на диаграммах напряжения и тока дуги.
В качестве иллюстрации влияния тока, напряжения и состава защитного газа Иордакеску и Кинтино на заседании Международного института электротехники в 2003 г. классифицировали типы дуги на основе «естественных режимов переноса». Однако сегодня из-за использования более развитых контроллеров естественные режимы передачи уже не используются так часто (Iordachescu and Quintino 2008).На рисунке 8 из исследования Пономарева показан тип дуги в зависимости от тока, напряжения и защитного газа (Пономарев и др., 2003).
Рисунок 8IIW классификация переноса металла, отображаемая на диаграмме напряжения дуги и сварочного тока (Пономарев и др. 2003 г. ).
Переходный ток был важной темой в типе дуги при сварке GMA.Он устанавливает предел между шаровой дугой и дугой со струйным переносом и определяет рабочие условия процесса сварки, как было предложено Пономаревым и др. (2003) на рисунке 8. Согласно Иордакеску и Квинтино (2008), может быть второй ток перехода между короткой дугой и шаровидной дугой, как показано на рисунке 9. Цель предложения — охватить как обычную, так и проецируемую струю. .
Рисунок 9Основные режимы передачи. Диаграмма U (I) на основе классификации Иордакеску и Кинтино (2008).
В дополнение ко второй линии переходного тока исследование Иордакеску и Квинтино (2008) предложило новую классификацию режима переноса дуги в GMAW в зависимости от тока, напряжения и защитного газа: короткое замыкание, глобулярная капля, шаровидный отталкивающий, капельный, струйный и вращающийся режимы переноса. Рисунок 9 иллюстрирует эту классификацию дуг в GMAW (Иордакеску и Квинтино, 2008). На рисунке показаны контролируемый, основной и переходный режимы на той же диаграмме, и каждая часть разделена зонами переходного тока.Первый переходный ток разделяет контролируемую и основную моды, а второй переходный ток разделяет области спрея и глобулярной основной группы. Кроме того, режим дуги меняется с увеличением сварочного тока и напряжения дуги. На рисунке показано, что электрический ток при переносе короткой дуги ниже, чем в других типах дуг, и что вращающийся перенос требует большого тока.
В таблице 3 показан режим переноса типа дуги из классификации стандартов DIN для сварки GMA (Iordachescu and Quintino 2008).Размер капель и режим переноса металла также названы для каждого типа дуги. Знание типа дуги и соответствующего режима переноса уменьшается, если игнорировать их соответствующее применение. Важность соответствующих приложений возрастает с разработкой нового термочувствительного металла (Matusiak and Pfeifer 2011).
Таблица 3 Классификация переноса металла при сварке GMA в соответствии со стандартами DIN (Iordachescu and Quintino 2008 г. )Сравнение различных типов дуги: преимущества и недостатки
В этом разделе дается сравнение типов сварочной дуги.Список сварочной дуги состоит из естественного и контролируемого типов. В таблице 4 представлена сравнительная таблица основных свойств типов дуги. В зависимости от типа дуги и свойств дуги в таблице указаны характеристики для промышленного применения. Можно заметить, что традиционная управляющая дуга демонстрирует более низкую стабильность дуги и, как следствие, низкую производительность с точки зрения качества сварки. Кроме того, работа невозможна во всех положениях, кроме короткой дуги. Управляемая дуга обеспечивает более высокую скорость наплавки и лучшую стабильность.Вследствие повышения устойчивости увеличивается производительность. Экономия самая высокая, но оборудование немного дороже. Уровень разбрызгивания выше при неконтролируемой шаровидной дуге; однако регулируемая короткая дуга может обеспечить сварку практически без брызг. Подвод тепла сводится к минимуму с помощью регулируемой короткой дуги, но дуга с более высокой скоростью наплавки требует достаточного подводимого тепла. Управление нацелено на ограничение неожиданного короткого замыкания дуги, работа стабильна, а затраты на экономию значительно улучшаются.Слабость шаровой дуги может быть успешно уменьшена за счет управления скрытой дугой, проплавление увеличивается, а разбрызгивание подавляется. Импульсное управление — наиболее стабильная дуга с большим диапазоном тока; следовательно, можно сваривать более толстый профиль и более широкий диапазон металла.
Таблица 4 Сравнение различных сварочных дуг aПрименение различных типов дуги
Правильный выбор типа дуги может снизить риск появления дефектов сварки и повысить производительность.В этом разделе обсуждаются применения дугового типа. Обсуждение начинается с естественной дуги, затем следует управляемая дуга. Обсуждение основано на сравнительной характеристике из таблицы 4 относительно их применения, а в таблице 5 представлены типы дуги и их применения.
Таблица 5 Сварочная дуга и ее применениеКороткая дуга
Короткая дуга подходит для приложений, требующих низкого тепловложения, и позволяет соединять тонкие материалы и листы в любом положении.Это хороший выбор, когда необходимо минимизировать деформацию конструкции. Он подходит для сварных швов с канавками в качестве корневого прохода или для заполнения зазоров стыков, а также для корневого прохода сварных швов с открытыми канавками и сварных швов с плоскими кромками. Режим короткой дуги широко используется в трубной промышленности и очень применим для корневых швов труб. Его можно использовать с углеродистой сталью со 100% защитным газом из двуокиси углерода или смесью максимум 25% CO 2 и остальным аргоном. Режим короткой дуги также применим к низкоуглеродистой стали, низколегированной стали и нержавеющей стали с толщиной от 0.5 и 2,6 мм. Однако он не может выполнять сварку алюминия (Deruntz 2003). Хотя обычная короткая дуга используется во многих приложениях, ее использование ограничено из-за высокого потенциального чрезмерного образования брызг, образования дыма, отсутствия плавления, меньшей перекрываемости зазора и нестабильности дуги (Hermans and Ouden 1999; Jenkins et al. 2005). Плохая производительность обычной короткой дуги является результатом ограниченной способности источника питания управлять каждой последовательностью режима короткого замыкания металла (Lyttle and Praxair 1990; Althouse et al.2004; Laren 2004; Goecke 2005a, b; Джеффус и Бауэр 2010). Вследствие этого ограничения обычная короткая дуга постепенно заменяется управляемой короткой дугой при корневом проходе при сварке листового металла.
Шаровая дуга
Режим шаровидной дуги имеет мало применений из-за множества недостатков. Из-за размера капли (больше диаметра электрода) она может неожиданно коснуться сварочной ванны и вызвать короткое замыкание. Корень дуги очень подвижен, поэтому силы дуги имеют тенденцию перемещать каплю неравномерно, что вызывает высокий уровень разбрызгивания и нестабильность сварного шва.Кроме того, расплавленный металл не ускоряется по направлению к сварочной ванне, что приводит к неглубокому и широкому сварному шву. Крупные капли отделяются на низких частотах (<10 Гц), что снижает производительность. Следовательно, режим глобальной дуги ограничивается сварными соединениями низкого качества, сваренными в плоском положении сварки или вертикальном положении вниз (Kou 2003; Xu and Wu 2007). Наиболее подходящее применение для шаровидной дуги - это сварка тонких материалов при очень малых токах. Хотя его также можно использовать с более высоким током, это неэффективно.Он подходит для GMAW стали (Althouse et al. 2004; Jeffus and Bower 2010).
Распылительная дуга
Распылительная дуга требуется для более толстого сечения, чем короткая дуга. Он очень подходит, когда требуется высокая скорость наплавки и когда требуется глубокое проплавление для сварки массивных основных материалов, которые могут выдерживать большое количество тепла. Большая сварочная ванна затрудняет сварку в вертикальном или потолочном положении, особенно в случае простой углеродистой стали и нержавеющей стали. При соединении сталей ток перехода можно варьировать в большей степени, чем при сварке алюминиевых сплавов.Распылительная дуга может использоваться практически со всеми распространенными сплавами, содержащими алюминий, а также с никелевыми сплавами, медными сплавами, нержавеющими сталями, магнием и углеродистыми сталями (Lyttle and Praxair 1990; Althouse et al. 2004; Robert and Messler 2004; Goecke 2005a, b). ; Джеффус и Бауэр 2010). Несмотря на преимущества традиционной струйной дуги, нестабильность дуги и неупорядоченный перенос металла ограничивают ее применение. В режиме струйной дуги ток и напряжение почти постоянны, что приводит к случайному размеру и частоте капель (Hutt and Lucas 1982).Следовательно, образуется большое количество дыма, брызг и тепла. Недостаточный контроль может отрицательно сказаться на качестве сварки. Следует также отметить, что защитный газ на основе аргона, используемый для создания дуги с распылением, дороже, чем CO 2 . Ввиду этих недостатков струйная дуга не подходит для алюминия, конструкционной стали, стали с покрытием и высокопрочных сталей.
Управляемая дуга короткого замыкания
Эти типы дуги относятся к категории режимов с управляемой формой волны.Отделение капель во время короткого замыкания контролируется таким образом, чтобы уменьшить образование брызг и дыма и повысить производительность (Stava 1993; Goecke 2005a, b; Huisman 2000). Эти дуги продаются на коммерческом рынке под разными торговыми названиями: перенос холодного металла (CMT): (FRONIUS International GmbH), ColdArc: (EWM Hightec Welding GmbH), перенос поверхностного натяжения (STT): (Lincoln Electric), холодный процесс (CP). : (CLOOS), FastRoot (KEMPPI), Регулируемое осаждение металлов (RMD): (Miller Electric Mfg) и т. Д.Pépe et al. (2011) исследовали эффективность управляемого GMAW. Результаты показали, что для STT, Fast root и CMT эффективность составляет около 85%. Управляемая короткая дуга может использоваться практически во всех положениях сварки, с почти всеми видами металлических материалов и с разной толщиной. Контролируемая короткая дуга применяется для соединения тонких листов, соединения металлических листов из нержавеющей стали с цинковым и непокрытым покрытием, а также соединения алюминиевых сплавов. Также возможна сварка очень тонких металлических листов из углеродистой стали, высоколегированной стали, низколегированной стали и алюминия (Deruntz 2003).В настоящее время толщина материалов, используемых в автомобильной промышленности, становится ниже 0,3 мм, и процесс GMAW с короткой дугой больше не подходит. Другими применениями управляемой короткой дуги являются роботизированная сварка GMAW и пайка листов сверхлегкой толщины как в ручном, так и в автоматическом режимах в любом положении. Можно сваривать разнородные материалы, такие как алюминий и сталь, сталь и магний, а также магниевые сплавы (Rosado et al. 2008; Srinivasan and Balasubramanian 2011; Matusiak and Pfeifer 2011).Хотя управление короткой дугой обеспечивает большую гибкость приложений, для этого требуются усовершенствованный источник питания, а иногда и специальные горелки.
Управляемая шаровая дуга
В этом режиме дуга используется в диапазоне тока шаровидной дуги, но с короткой длиной дуги. Это позволяет дуге работать под поверхностью сварочной ванны (так называемая «скрытая дуга») и использовать давление дуги экранированного CO 2 для улавливания брызг. По данным Nishiguchi et al.(1975), метод сварки в скрытой дуге позволяет достичь более высоких скоростей сварки и скорости осаждения присадочного металла, чем шаровая дуга. Скорость сварки может достигать 2540 мм / мин, а очистка минимальна (Lienert et al. 2011). Stol et al. (2006) изучали использование GMAW с заглубленной дугой для сварных швов. Подход со скрытой дугой имеет большой потенциал для использования в автомобильной, железнодорожной и морской отраслях для сварки узлов. Примером применения является сварка краев и сторон алюминиевых деталей в качестве альтернативы GMAW.Режим управляемой шаровидной дуги можно использовать для угловых или шовных сварных швов внахлестку, тройников и стыковых соединений с квадратной канавкой. Он подходит для механизированной сварки тонких материалов на высоких скоростях и может использоваться при полностью механизированной или автоматической газовой дуговой сварке металла. Он также используется при сварке цилиндров из труб. Скрытая дуга может использоваться в автомобилях при стыковой сварке кузова и полуавтоматической сварке рамы и кузова (Kielhorn et al. 2001; Aoki et al. 2003; Kah et al. 2013).
Управляемая струйная дуга
Для управления подводом тепла и уменьшения образования брызг и дыма были разработаны источники питания, способные выпускать одну каплю в течение последовательности дуги и импульсов. В дуге используется постоянный ток (например, импульсный GMAW) или переменный ток (например, AC-GMAW) с различными формами волны тока. Импульсная дуга может использоваться во всех положениях сварки и с любой толщиной основного материала как в ручных, так и в автоматических сварочных системах. Сварка вне положения также возможна из-за уровня тока ниже среднего.Из-за низкого тепловложения этот режим подходит для заполнения зазоров. Он широко используется в GMAW алюминия (Kah et al. 2012). Этот метод подходит для сварки всех стандартных и высокоэффективных марок нержавеющей стали, когда используются присадочные металлы на основе никеля или нержавеющей стали. Высоколегированные стали также можно сваривать импульсной дугой. Супераустенитная нержавеющая сталь демонстрирует лучшие механические и металлургические свойства с оптимизированными параметрами при сварке GMA по сравнению с традиционной напылением (Sathiya et al.2012). Импульсная дуговая сварка находит применение в судостроении, например, при сварке вне положения высокопрочных низколегированных базовых материалов при изготовлении корпусов судов. Преимущества импульсной дуги в судостроении заключаются в том, что ее электродный КПД выше по сравнению с дуговой сваркой с флюсовым сердечником (FCAW), и она может обеспечивать меньшее количество водородных отложений при сварке швов (Lyttle and Praxair 1990; Knopp and Lorenz 2002; Althouse et al. 2004; Ларен 2004; Уэяма и др. 2005; Лебедев 2010; Торбати и др. 2011; Ка и др.2013).
Дуга повышенной мощности
Перенос металла потоком и вращением происходит в более высоких диапазонах мощности. Вращение расплавленного металла является результатом более длинного вылета электрода (от 25 до 35 мм) и более высоких значений тока и напряжения, из-за которых струя металла отклоняется от оси симметрии и начинает вращаться под действием магнитных сил. Хотя стыковая сварка является наиболее типичным применением сварки в режиме вращающейся дуги, вращающуюся дугу также можно использовать при сварке в узкий зазор. Этим методом можно сваривать толстые толстые листы.Благодаря гибкости, эффективности и производительности этого режима, его можно использовать при производстве больших и тяжелых конструктивных деталей (Church and Imaizumi 1990). Хотя Черч и Имаидзуми (1990) сообщают, что этот процесс требует четвертичной защиты (He-Ni-CO 2 и O 2 ), что допускает очень ограниченные допуски, Субан и Тусек (2003) указали, что двоичный защитный газ (аргон и CO 2 ) может дать удовлетворительные результаты при оптимальных параметрах сварки.Полное использование его потенциала происходит в полностью механизированных процедурах (Masseti 2010). Крупномасштабные детали мостов, тяжелое машиностроение, судостроение и тяжелые цилиндрические конструкции — вот лишь некоторые примеры его применения. Новая разработка вращающейся дуги, вращение которой происходит не за счет магнитного эффекта, а благодаря специальным маленьким вращающимся горелкам, позволяет применять режим вращающейся дуги для угловой сварки в судостроении, на мостах и т.д. Пластины из углеродистой стали (Ивата и др.2009а, б; Ян и др. 2009; Christensen et al. 2005).
Том XXII: Процессы дуговой сварки
СОСУДЫ ДЛЯ ДАВЛЕНИЯ ASME
Цель данной презентации — представить основную информацию и понимание правил ASME для проектирования сосудов под давлением для химической и перерабатывающей промышленности, применимых в Соединенных Штатах и большей части Северной и Южной Америки.
Процессы дуговой сварки
Основы дуговой сварки
Дуговая сварка — это один из нескольких способов соединения металлов плавлением.Под воздействием сильного тепла металл на стыке между двумя частями расплавляется и смешивается — непосредственно или, что более часто, с промежуточным расплавленным присадочным металлом. После охлаждения и затвердевания образуется металлургическая связь. Поскольку соединение происходит путем смешивания вещества одной части с веществом другой части, с промежуточным соединением из аналогичного вещества или без него, окончательная сварка может продемонстрировать на стыке те же прочностные свойства, что и металл деталей. .
При дуговой сварке сильное тепло, необходимое для плавления металла, вырабатывается электрической дугой. Дуга образуется между свариваемым изделием и электродом, который вручную или механически перемещают вдоль стыка (или изделие может перемещаться под неподвижным электродом). Электродом может быть углеродный или вольфрамовый стержень, единственная цель которого — проводить ток и поддерживать электрическую дугу между его наконечником и заготовкой. Или это может быть специально подготовленный стержень или проволока, которая не только проводит ток и поддерживает дугу, но также плавит и подает присадочный металл к стыку.Если электрод представляет собой углеродный или вольфрамовый стержень и в соединение требуется добавленный присадочный металл для заполнения, этот металл подается с помощью отдельно нанесенного стержня или проволоки из присадочного металла. Однако большая часть сварки при производстве стальных изделий, где требуется присадочный металл, выполняется с использованием электродов второго типа — тех, которые подают присадочный металл, а также обеспечивают проводник для электрического тока.
Базовая сварочная цепь
Базовая схема дуговой сварки показана на рисунке 1.Источник переменного или постоянного тока подключается заземляющим кабелем к заготовке и «горячим» кабелем к электрододержателю того же типа, который обеспечивает электрический контакт со сварочным электродом. Когда цепь находится под напряжением и кончик электрода касается заземленной заготовки, а затем извлекается и удерживается близко к пятну контакта, в зазоре возникает дуга. Дуга создает температуру около 6500oF (3600oC) на кончике электрода, температуру более чем достаточную для плавления большинства металлов.Вырабатываемое тепло плавит основной металл вблизи дуги и любой присадочный металл, подаваемый электродом или отдельно введенным стержнем или проволокой. Образуется обычная лужа расплавленного металла, называемая «кратером». Этот кратер затвердевает за электродом по мере его перемещения по свариваемому стыку. В результате получается соединение плавлением и металлургическая унификация деталей.
Дуговое экранирование
Однако использование тепла электрической дуги для соединения металлов требует большего, чем просто перемещение электрода относительно сварного шва.Металлы при высоких температурах химически реагируют с основными составляющими воздуха — кислородом и азотом. Если металл в ванне расплава вступит в контакт с воздухом, будут образовываться оксиды и нитриды, которые после затвердевания ванны расплава будут нарушать прочностные свойства сварного соединения. По этой причине различные процессы дуговой сварки предоставляют некоторые средства для покрытия дуги и ванны расплава защитным экраном из газа, пара или шлака. Это называется защитой от дуги, и такая защита может быть достигнута с помощью различных технологий, таких как парогенерирующее покрытие на электродах из присадочного металла, покрытие дуги и ванны расплава отдельно подаваемым инертным газом или гранулированный флюс или использование материалов в сердечнике трубчатых электродов, которые генерируют защитные пары.
На рис. 2 показана защита сварочной дуги и сварочной ванны с помощью покрытого «стержневого» электрода — типа электрода, используемого в большинстве случаев ручной дуговой сварки. Экструдированное покрытие стержня присадочного металла под воздействием тепла дуги создает газовый экран, который предотвращает контакт воздуха с расплавленным металлом. Он также поставляет ингредиенты, которые вступают в реакцию с вредными веществами на металлах, такими как оксиды и соли, и химически связывает эти вещества в шлак, который, будучи легче металла сварного шва, поднимается в верхнюю часть ванны и покрывает новую корку. затвердевший металл.Этот шлак даже после застывания выполняет защитную функцию; он сводит к минимуму контакт очень горячего затвердевшего металла с воздухом до тех пор, пока температура не снизится до точки, при которой реакция металла с воздухом уменьшится.
Проектирование дуговой сварки
Проектирование сварных соединений
Нагрузки в сварной стальной конструкции передаются от одного элемента к другому через сварные швы, расположенные в сварных соединениях. И тип соединения, и тип сварного шва определяет проектировщик.
На рисунках 3 и 4 показаны типы соединений и сварных швов. Указание соединения само по себе не описывает тип используемого сварного шва. Таким образом, для выполнения стыкового соединения показано десять типов сварных швов. Хотя здесь все сварные швы, кроме двух, показаны с стыковыми соединениями, некоторые из них могут использоваться с другими типами соединений. Таким образом, сварной шов с одной кромкой можно также использовать в Т- или угловом соединении, а сварной шов с одной V-образной кромкой можно использовать в угловом, Т-образном или стыковом соединении.
Соединения угловым сварным швом
Угловой шов, не требующий подготовки канавки, является одним из наиболее часто используемых сварных швов при проектировании машин.Различные угловые сварные швы показаны на рисунке 5.
Угловое соединение, как в (A), сложно собрать, потому что ни одна пластина не может опираться на другую. Необходимо использовать небольшой электрод с низким сварочным током, чтобы не прожечь первый сварочный проход. Стык требует большого количества металла.
Угловое соединение, показанное на (B), легко монтируется, не прогорает и требует вдвое меньше сварочного металла, чем соединение на (A). Однако, используя половину размера сварного шва, но размещая два сварных шва, один снаружи, а другой внутри, как в (C), можно получить такую же общую ширину сварного шва, как и при первом сварном шве.Необходимо использовать только половину сварочного металла.
Для толстых пластин часто используется соединение с пазом с частичным проплавлением, как в (D). Это требует снятия фаски. Для более глубокого стыка можно использовать J-образную препарировку, как в (E), а не скос.
Угловой шов в (E) не виден и создает аккуратный и экономичный угол.
Размер сварных швов всегда должен определяться с учетом размера более тонкого элемента. Соединение невозможно сделать более прочным, используя более толстый элемент, соответствующий размеру сварного шва, и потребуется гораздо больше металла сварного шва.
Комбинация канавки и галтели
Для многих соединений используется комбинация сварного шва с частичным проплавлением и углового шва. Угловые швы легко накладываются и не требуют специальной подготовки листа. Их можно изготавливать с использованием электродов большого диаметра с высокими сварочными токами и, как следствие, высокой скоростью наплавки. Стоимость сварных швов увеличивается пропорционально квадрату размера ноги.
Для сравнения, сварной шов с двойной косой кромкой имеет примерно половину площади сварного шва, чем угловой шов.Однако это требует дополнительной подготовки и использования электродов меньшего диаметра с меньшими сварочными токами, чтобы выполнить начальный проход без прожига. По мере увеличения толщины пластины эта начальная область низкого осаждения становится менее важным фактором, а более высокий фактор стоимости уменьшается.
Соединения с пазами
На рис. 6 показано, что корневое отверстие — это разделение между соединяемыми элементами. Корневое отверстие используется для доступа электрода к основанию или корню сустава.Чем меньше угол скоса, тем больше должно быть отверстие в корне, чтобы обеспечить хорошее соединение в корне. Если отверстие в корне слишком мало, сплавление корня получить труднее, и необходимо использовать электроды меньшего размера, что замедляет процесс сварки. Если корневое отверстие слишком велико, качество сварного шва не ухудшается, но требуется больше металла сварного шва; это увеличивает стоимость сварки и ведет к увеличению деформации.
Использование соединения с двумя пазами вместо соединения с одним пазом сокращает объем сварки вдвое.Это уменьшает деформацию и делает возможным чередование сварных швов на каждой стороне соединения, что опять же снижает деформацию. Опорные полосы используются на больших корневых отверстиях и являются обычным явлением, когда все сварочные работы должны выполняться с одной стороны или когда корневое отверстие слишком велико. Иногда подпорные планки остаются на месте и становятся неотъемлемой частью стыка.
Материал опорной полосы должен соответствовать основному металлу. Следует использовать короткие прерывистые прихваточные швы, чтобы удерживать опорную полосу на месте, и их желательно расположить в шахматном порядке, чтобы уменьшить любое первоначальное ограничение соединения.Опорная полоса должна плотно прилегать к обоим краям пластины, чтобы избежать захвата шлака у основания.
Для стыкового соединения номинальное усиление сварного шва (примерно на 1/16 дюйма выше заподлицо) — это все, что необходимо, как показано на рисунке. Дополнительный нарост не имеет смысла и увеличивает стоимость сварного шва. Следует следить за тем, чтобы ширина и высота арматуры были минимальными. См. Рисунок 7.
Коды и спецификации
Общественная безопасность участвует в проектировании и изготовлении трубопроводов и сосудов под давлением, и для минимизации опасности катастрофического отказа или даже преждевременного отказа разработаны документы, регулирующие их проектирование и строительство.Эти документы называются спецификациями, кодами, стандартами и правилами. Иногда термины используются как синонимы.
Коды и спецификации обычно разрабатываются промышленными группами, торговыми или профессиональными организациями или правительственными бюро, и каждый код или спецификация касается приложений, относящихся конкретно к интересам органа-автора. Крупные производственные организации могут подготовить свои собственные спецификации для удовлетворения своих конкретных потребностей. Среди основных национальных организаций, составляющих кодексы, связанные с дуговой сваркой, можно выделить следующие:
- Американское общество сварки (AWS)
- Американский институт стальных конструкций (AISC)
- Американское общество по испытанию материалов (ASTM)
- Американское общество инженеров-механиков (ASME)
- Американский институт нефти (API)
Конструкция сварных котлов и сосудов под давлением регулируется нормами и спецификациями, которые, среди прочего, описывают допустимые материалы, размер, конфигурацию, эксплуатационные ограничения, требования к изготовлению, термообработке, проверкам и испытаниям.Эти правила также определяют требования к квалификации сварщиков и операторов. Многочисленные государственные, городские и местные правительственные учреждения также издают правила, регулирующие сосуды под давлением. Обычно применяемые коды:
- Код ASME для котлов и сосудов под давлением Коды API
- • Общие технические условия для постройки военно-морских судов
- Морские инженерные правила и спецификации материалов
- Правила ABS для строительства и классификации стальных судов
- Стандарты TEMA
- Правила и положения Ллойда
Расходные материалы и оборудование
Электроды
Электроды для дуговой сварки имеют маркировку A.Система нумерации W.S (Американское сварочное общество), размеры от 1/16 «до 5/16». Примером может служить сварочный стержень, обозначенный как электрод E6011 1/8 дюйма. Диаметр электрода составляет 1/8 дюйма. Буква «E» обозначает электрод для дуговой сварки. Затем на электроде будет выбито 4- или 5-значное число. Первые два числа из 4-значного числа и первые 3 цифры из 5-значного числа указывают минимальную прочность на растяжение (в тысячах фунтов на квадратный дюйм) сварного шва, которую будет производить стержень без напряжения.Примеры будут следующими:
E60xx будет иметь предел прочности на разрыв 60 000 фунтов на квадратный дюйм. E110XX будет иметь предел прочности на разрыв 110 000 фунтов на квадратный дюйм. Предпоследняя цифра указывает положение, в котором можно использовать электрод.
- EXX1X для использования во всех положениях
- EXX2X предназначен для использования в горизонтальном и горизонтальном положениях
- EXX3X для плоской сварки
Последние две цифры вместе указывают тип покрытия на электроде и сварочный ток, при котором электрод может использоваться.Например, прямой постоянный ток, (DC -) постоянный ток, обратный (DC +) или переменный ток.Чем толще свариваемый материал, тем выше требуемый ток и тем больше требуется электрод.
Сварочное оборудование
Поскольку существует несколько основных процессов дуговой сварки и различные этапы механизации в каждом, сварочное оборудование, помимо источника питания, включает в себя множество механизмов и устройств, облегчающих укладку сварного шва. На рисунке 1 проиллюстрирована основная сварочная схема.В этой схеме находится источник питания, от которого идут кабели в одном направлении к работе, а в другом — к электроду, на конце которого зажигается дуга. По обе стороны от источника питания — вплоть до рабочего места или электрода, подающего дугу, — расположены другие элементы оборудования, необходимые для выполнения сварки. Это оборудование будет отличаться в зависимости от процесса сварки и степени его механизации. Основное оборудование:
- Сварочный кабель
- Держатель электрода
- Заземление
- Полуавтоматический пистолет и устройство подачи проволоки
- Механизированные передвижные блоки
- Головки для полуавтоматической сварки
- Оборудование для дугового нагрева
- Защитное снаряжение
Дуговый процесс под флюсом
Дуговая сварка под флюсом (SAW) — это высокопроизводительный автоматический метод сварки, при котором дуга зажигается под покровным слоем флюса.Это повышает качество дуги, поскольку загрязняющие вещества в атмосфере блокируются флюсом. Шлак, образующийся на сварном шве, обычно снимается сам по себе, и в сочетании с использованием непрерывной подачи проволоки скорость наплавки высока. Рабочие условия значительно улучшаются по сравнению с другими процессами дуговой сварки, поскольку флюс скрывает дугу и не образуется дыма. Этот процесс обычно используется в промышленности, особенно для крупногабаритных изделий. Поскольку дуга не видна, требуется полная автоматизация. Сварка в рабочем положении невозможна с помощью SAW.
Процесс газовой дуговой сварки металлов
Газовая дуговая сварка металла (GMAW) — это полуавтоматический или автоматический процесс сварки, в котором используется непрерывная подача проволоки в качестве электрода и инертный или полуинертный защитный газ для защиты сварного шва от загрязнения. Использование инертного газа в качестве защиты называется сваркой в среде инертного газа (MIG). Источник постоянного напряжения постоянного тока чаще всего используется с GMAW, но могут использоваться системы постоянного тока, а также переменного тока.Скорость сварки GMAW относительно высока из-за автоматической подачи непрерывного электрода, но она менее универсальна, поскольку требует большего количества оборудования, чем более простой процесс SMAW. Первоначально разработанный для сварки алюминия и других цветных металлов в 1940-х годах, GMAW вскоре стал применяться для стали, поскольку он позволял сократить время сварки по сравнению с другими сварочными процессами. Сегодня GMAW широко используется в таких отраслях, как автомобильная промышленность, где его предпочитают из-за своей универсальности и скорости.Однако, поскольку в нем используется защитный газ, он редко используется на открытом воздухе или в местах с нестабильностью воздуха.
Рисунок 10: Газовая дуговая сварка металла (GMAW)Процесс порошковой порошковой самозащиты
В процессе, связанном с GMAW, дуговой сваркой порошковой проволокой (FCAW) используется аналогичное оборудование, но с использованием проволоки, состоящей из стальной электродной трубки, окружающей порошковый наполнитель. Эта порошковая проволока дороже стандартной сплошной проволоки и выделяет дополнительный защитный газ и / или шлак, но обеспечивает более высокую скорость сварки и большее проникновение металла.
Рисунок 11: Сварка порошковой проволокой
Процессы газо-вольфрамовой дуговой сварки
Газовая дуговая сварка тунстена (GTAW) или сварка вольфрамовым инертным газом (TIG) — это процесс ручной сварки, в котором используется неплавящийся электрод, сделанный из тунстена, смеси инертного или полуинертного газа и отдельного присадочного материала. Этот метод особенно полезен для сварки тонких материалов, он характеризуется стабильной дугой и высококачественными сварными швами, но требует значительных навыков оператора и может выполняться только на относительно низких скоростях.Его можно использовать практически для всех свариваемых металлов, хотя чаще всего применяется для нержавеющей стали и легких металлов. Его часто используют, когда качество сварных швов чрезвычайно важно, например, в велосипедах, самолетах и на море. В родственном процессе, плазменной сварке, также используется вольфрамовый электрод, но для создания дуги используется плазменный газ. Дуга более концентрированная, чем дуга GTAW, что делает поперечный контроль более критичным и, таким образом, в целом ограничивает технику механизированным процессом. Благодаря стабильному току этот метод может использоваться для материалов с более широким диапазоном толщины, чем процесс GTAW, и работает намного быстрее.Его можно применять ко всем тем же материалам, что и GTAW, за исключением магния; Автоматическая сварка нержавеющей стали — одно из важных применений этого процесса. Разновидностью процесса является плазменная резка, эффективный процесс резки стали.
Контроль качества
Качество сварки
В производственной сварке термин «качество сварного шва» является относительным. Как правило, любой сварной шов является хорошим сварным швом, если он соответствует требованиям к внешнему виду и будет бесконечно долго выполнять свою работу, для которой был предназначен.
Первым шагом в обеспечении качества сварки является определение степени, требуемой приложением. Стандарт должен быть установлен на основе потребностей в обслуживании. Технические характеристики будут основным фактором при разработке стандарта, но внешний вид также может иметь значение. В стандарт обязательно должен быть включен коэффициент безопасности, но он должен быть разумным. После того, как стандарт установлен, ответственность за его соблюдение возлагается на всех, кто занимается работой.
Что касается низкого качества, то предопределенный стандарт качества никогда не должен нарушаться. С другой стороны, нет никаких возражений против дополнительного качества, при условии, что оно было получено без штрафных санкций. Если испытания неоднократно показывают, что качество сварных швов намного выше, чем требуется стандартом, возможно снижение затрат за счет изменения конструкции или процедур сварки.
Часто стандарты предварительно устанавливаются действующими спецификациями или инженерными и юридическими кодексами.Иногда такие стандарты ультраконсервативны, но когда они применяются, их необходимо соблюдать. Инженер может оказать своей компании или заказчику услугу, указав нереалистичные спецификации и возможности экономии средств, но спецификации должны строго соблюдаться до тех пор, пока они не будут пересмотрены.
Пять P, обеспечивающих качество
Если уделить внимание пяти «П», качество сварных швов будет обеспечиваться почти автоматически, что сводит последующий контроль к проверке маршрута и контролю.Пять P:
- Выбор процесса — процесс должен подходить для работы
- Подготовка — конфигурация стыка должна быть правильной и совместимой с процессом сварки
- Процедуры — для обеспечения однородных результатов процедура должна быть подробно описана и строго соблюдаться во время сварки
- Предварительные испытания — с помощью полномасштабных макетов или смоделированных образцов доказано, что процесс и процедуры обеспечивают требуемый стандарт качества
- Персонал — на работу должны быть назначены квалифицированные специалисты
Инспекция и испытания
Визуальный осмотр в процессе работы
Визуальный осмотр следует начинать до зажигания первой дуги.Необходимо проверить материал, чтобы убедиться, что он соответствует требованиям по качеству, типу, размеру, чистоте и отсутствию дефектов. Следует удалить посторонние предметы, которые могут повредить сварной шов. Соединяемые детали необходимо проверить на прямолинейность, плоскостность и размеры. Выравнивание и сборка деталей и приспособлений должны быть тщательно проверены. Следует проверить совместную подготовку. Осмотр перед сваркой также должен включать в себя проверку того, что используются правильный процесс и процедуры.
Если предварительные требования в порядке, наиболее продуктивный контроль будет проводиться во время изготовления сварной детали. Осмотр сварного шва и кратера на конце может выявить недостатки качества, такие как трещины, недостаточное проплавление, газовые и шлаковые включения, перед компетентным инспектором. В случае простых сварных швов, осмотр образца в начале операции и периодически по мере выполнения работы может быть адекватным. Однако, когда наносится более одного слоя присадочного металла, может быть желательно проверить каждый слой перед нанесением следующего слоя.
Визуальный контроль после сварки
Визуальный осмотр после завершения сварки также полезен для оценки качества, даже если будут использоваться радиографические, ультразвуковые или другие методы. Здесь могут быть обнаружены дефекты поверхности, такие как трещины, пористость и незаполненные кратеры, которые могут иметь такие последствия, что потребуется ремонт или работа будет отклонена без использования последующих процедур проверки.
На этом этапе визуально обнаруживаются отклонения размеров от допусков, коробление и дефекты.Протяженность и непрерывность сварного шва, его размер и длину сегментов прерывистых сварных швов можно легко измерить или отметить.
Сварные швы необходимо очистить от шлака, чтобы можно было проверить наличие поверхностных дефектов. Стекло с увеличением до 10 диаметров помогает обнаружить мелкие трещины и другие дефекты. При подготовке сварного шва к проверке не следует использовать дробеструйную очистку, так как упрочнение может закрыть мелкие трещины и сделать их невидимыми.
Другие методы проверки кратко описаны ниже:
УЛЬТРАЗВУКОВОЙ ОСМОТР
Может быть ручным или механизированным.На зонд подается импульс электрической энергии, в котором пьезоэлектрический кристалл преобразует его в механические колебания с ультразвуковой частотой. Вибрации передаются (через слой смазки, чтобы исключить воздух) через работу. Если они сталкиваются с дефектом, некоторые из них отражаются обратно в зонд, где они регенерируют электрический сигнал. Трасса электронно-лучевой трубки, запускаемая при отправке исходного сигнала, отображает отраженный сигнал дефекта, и по нему можно рассчитать время, указывающее расстояние от зонда, и амплитуду, указывающее размер дефекта.
Ультразвуковой контроль можно использовать для большинства металлов, за исключением тех, которые имеют крупнозернистую или изменяющуюся зернистую структуру. Типичные сварочные работы — это сварка швов в толстостенных сосудах и сварка с доступом только с одной стороны.
Преимущества ультразвукового контроля:
- Немедленное представление результатов.
- Нет необходимости в эвакуации персонала.
- Может работать от аккумулятора.
- Глубина дефекта.
Ограничения ультразвукового контроля:
- Требуется обученный и опытный оператор.
- Нет записи с изображениями.
ИНСПЕКЦИЯ МАГНИТНЫХ ЧАСТИЦ
Может быть ручным или механизированным. Работа намагничивается либо путем пропускания тока через нее, либо через окружающую ее катушку. Дефекты на поверхности или рядом с ней нарушают магнитное поле (если они не параллельны ему). Применяется жидкая суспензия магнитных частиц, которая концентрируется вокруг дефектов. Работа просматривается либо непосредственно, либо в ультрафиолетовом свете с использованием флуоресцирующего красителя — i.е. излучает видимый свет (это необходимо делать при приглушенном обычном освещении). После тестирования при необходимости работу можно размагнитить.
Магнитопорошковый контроль может использоваться только для магнитных материалов, включая ферритные стали и некоторые никелевые сплавы. Типичные области применения сварки — это быстрый контроль сварных деталей конструкции и контроль производительности мелких компонентов.
Преимущества магнитопорошкового контроля:
- Прямая индикация места дефекта.
- Первичный осмотр неквалифицированной рабочей силой.
- Некоторое указание на подповерхностные дефекты, но с низкой чувствительностью.
- Критически не зависит от состояния поверхности.
Ограничения магнитопорошкового контроля:
- Не используется для немагнитных материалов.
- Обнаружение дефектов критически зависит от выравнивания по магнитному полю.
- Подземные дефекты требуют специальных процедур.
ГАММА-РАДИОГРАФИЯ
Гамма-лучи, похожие на рентгеновские лучи, но с меньшей длиной волны, непрерывно испускаются изотопом.Его нельзя «выключить», поэтому, когда он не используется, он хранится в тяжелом контейнере для хранения, который поглощает радиацию. Они проходят через работу для проверки. Части работы, представляющие меньшее препятствие для гамма-излучения, такие как полости или включения, позволяют увеличить экспозицию пленки. Пленка проявляется так, чтобы сформировать рентгенограмму с полостями или включениями, обозначенными более темными изображениями. Увеличение толщины сечения (например, сварного шва) выглядит как менее плотное изображение.
Большинство свариваемых материалов можно проверить с помощью гамма-радиографии.Типичные сварочные работы — это инспекция на месте и панорамная съемка для небольших работ.
Преимущества, ограничения, расходные материалы и безопасность как при рентгенографии.
РЕНТГЕНОВСКАЯ РАДИОГРАФИЯ
Рентгеновские лучи излучаются из трубки и проходят через исследуемый объект. Части работы, представляющие меньшее препятствие для рентгеновских лучей, такие как полости или включения, позволяют увеличить экспонирование пленки. Пленка проявляется так, чтобы сформировать рентгенограмму с полостями или включениями, обозначенными более темными изображениями.Увеличение толщины сечения (например, под сварным швом) выглядит как менее плотное изображение.
Можно проверить большинство свариваемых материалов. Типичными сварочными операциями являются трубопроводы и сосуды под давлением.
Преимущества рентгенографии:
- Точное графическое представление результатов.
- Рентгенограммы могут храниться постоянно.
- Не ограничивается сварными швами.
Ограничения рентгенографии:
- Персонал не должен находиться в зоне воздействия во время воздействия.
- Трещины, параллельные пленке, могут не проявляться.
- Пленка дорогая.
ПРОВЕРКА КРАСИТЕЛЯ
Может быть ручным или механизированным. На поверхность исследуемого изделия наносится специальный краситель. Подходящий временной интервал позволяет ему впитаться в любые дефекты поверхности. Затем поверхность освобождается от излишков красителя, и краситель в трещине выявляется либо путем нанесения белого порошкового проявителя, в который впитывается краситель с получением цветовой индикации, либо путем освещения ультрафиолетовым светом, под которым краситель флуоресцирует, то есть , излучает видимый свет.Это необходимо делать там, где обычное освещение приглушено.
Контроль проникновения красителя может проводиться на любом непористом материале. Типичные сварочные работы — это корневые участки в стыковых швах труб и пути утечки в контейнерах.
Преимущества дефектоскопии красителя:
- Низкая стоимость.
- Прямая индикация местоположения дефекта.
- Первичный осмотр неквалифицированным работником.
Ограничения проверки на проникновение красителя:
- Обнаружены только дефекты поверхности.
- Дефекты не могут быть легко устранены из-за захваченного красителя.
- Черновые сварные швы дают ложные показания.
Источники:
1. Руководство по дуговой сварке — Lincoln Electric Company
Эта статья представлена вам как услуга от компании BOARDMAN, LLC, расположенной в Оклахома-Сити, штат Оклахома.
С 1910 года Boardman является уважаемым производителем нестандартных изделий. Мы гордимся своей способностью выполнять самые строгие спецификации и требования, чтобы предоставить нашим клиентам высококачественные решения.Имея более 75 лет инженерного опыта ASME Section VIII, Division I, мы обладаем уникальной способностью предоставлять индивидуальные решения нашим клиентам.
Сфабрикованные проекты включают:
- Башни и колонны с лотками
- Сосуды под давлением ASME
- Молекулярные сита
- Ротационные сушилки и печи
- Цистерны API
- Кислотные отстойники
- Стопы, скрубберы
- Термические окислители
- Аккумуляторы, конденсаторы
- Кристаллизаторы
- Воздуховоды
- Бункеры
- Трубопровод большого диаметра
Размеры этих проектов составляют до 200 футов в длину, 350 тонн, 16 футов в диаметре и 4 дюйма в толщину.
BOARDMAN, LLC доступен для посещения магазинов и классов по изготовлению сосудов высокого давления и статического оборудования.
Пожалуйста, свяжитесь с: John W. Smith, P.E.
Технический менеджер
405-601-3367
нажмите здесь, чтобы Запросить цитату
(PDF) Влияние состава защитного газа на свойства дуги при сварке TIG
Влияние состава защитного газа на свойства дуги
при сварке TIG
M.Tanaka *
1
, S. Tashiro
1
, T. Satoh
2
, AB Murphy
3
и JJ Lowke
3
Влияние состава защитного газа на свойства дугового газа включая температуру, напряжение, тепло
, поток и напряжение сдвига на аноде, а также глубину сварного шва, на которую указывает максимальная температура
анода с водяным охлаждением. Установлено, что добавление гелия, водорода
и азота к аргону увеличивает температуру дуги и анода.Для гелия это
из-за более низкой электропроводности; в других случаях это связано с более высокой удельной теплоемкостью.
Ключевые слова: дуговая сварка, коэффициенты переноса, газовые смеси, моделирование, термическая плазма
Введение
Свойства сварочной дуги вольфрамовым инертным газом (TIG)
и сварных швов, выполненных с использованием дуги, значительно
зависит от выбора защитного газа. В то время как аргон
остается наиболее широко используемым газом из-за его инертности
и относительно низкой стоимости, тепловой поток к аноду в аргоновых дугах невелик
.По этой причине также используются гелий и смеси аргона
с гелием, водородом и азотом.
Недавно было предложено использование экранированной дуги CO
2
.
1,2
В то время как дуговая сварка моделировалась в течение многих лет,
в большинстве ранних работ обрабатывалась только дуга
3,4
или только сварной шов
бассейн
5,6
. Унифицированные модели дуги и электродов
ибыли разработаны сравнительно недавно.
7–11
Разработана двумерная численная модель
сварки TIG,
, включая электроды. В частности, в
учитываются плавление и потоки жидкости в заготовке
(анод при сварке TIG),
позволяет рассчитать глубину сварного шва.
12
Авторы
также разработали компьютерный код и базу данных, которые
позволяют рассчитывать термодинамические свойства
и транспортные коэффициенты всех стандартных сварочных газов
и любых смесей этих газов.
13
В данной статье авторы используют эти возможности
для исследования влияния состава защитного газа
на свойства дуги при сварке TIG,
, включая напряжение дуги, температуру и поля потока, и
Плотность теплового потока, напряжение сдвига и температура на заготовке
. Они сравнивают эти свойства для дуг в
аргоне, гелии, азоте, водороде и смесях
аргона с водородом, гелием и азотом, а
исследуют, какие термодинамические свойства и портовые коэффициенты трансмиссии
ответственны за изменения в arc и
параметров детали для разных газов.
Методы
Расчет термодинамических и транспортных
свойств плазмы требует знания состава
. Это было вычислено в предположении локального термодинамического равновесия (LTE) с использованием метода минимизации
свободной энергии Гиббса. Требуемые термодинамические данные
были рассчитаны на основе спектроскопических данных
, например, данных, приведенных в таблице Мура,
14
или взятых
из таблиц JANAF.
15
Были рассмотрены следующие разновидности
: Ar, Ar
z
, Ar
2z
и Ar
3z
для аргона; N
2
,
N
2
z
, N, N
—
, N
z
, N
2z
для азотаи N
; H2
, H
2
z
,
H, H
—
и H
z
для водорода; и He, He
z
и He
2z
для гелия, а также электрон во всех случаях.Состав плазмы
определялся методом минимизации свободной энергии Гиббса
.
16
Термодинамические свойства, такие как энтальпия и удельная теплоемкость
, были рассчитаны с использованием стандартных методов.
16
Коэффициенты переноса были рассчитаны с использованием метода
Чепмена – Энскога решения уравнения Больцмана
.
17,18
Вязкость была рассчитана до первого уровня приближения
(где уровень приближения
— это количество членов, используемых в конечном полиномиальном разложении Sonine
, которое является основой метода Чепмена). —
метод Энскога).Теплопроводность была записана как
как сумма трех компонентов, то есть поступательной,
,внутренней и реакционной теплопроводности соответственно.
Поступательная теплопроводность из-за переноса поступательной энергии
делится на
вкладов тяжелых частиц (ионов, атомов и
молекул) и электронов. Первый рассчитывается до
второго уровня приближения, а второй — до
третьего порядка, используя метод разделения тяжелых
частиц и электронов, разработанный Devoto.
19
Внутренняя теплопроводность
, обусловленная переносом
внутренней энергии, рассчитывается на втором уровне приближения
, а теплопроводность реакции
, обусловленная высвобождением энтальпии реакции, когда частицы
рекомбинируют после диффузии из области с более высокой температурой
в более низкую, рассчитывается с использованием выражений
Батлера и Брокоу.
20,21
Электропроводность
была рассчитана в третьем порядке приближения,
без учета вклада ионов, как описано в
Devoto.
19
Расчет транспортных коэффициентов
потребовал определения интегралов столкновений для
взаимодействий между всеми видами, перечисленными выше.
22–25
1
JWRI Осакский университет, Осака, Япония
2
Taiyo Nippon Sanso Corp., Яманаси, Япония
3
CSIRO Industrial Physics, Сидней, Австралия Электронная почта для корреспонденции
Автор для корреспонденции [email protected]
ß
2008 Институт материалов, минералов и горного дела
Опубликовано Мани от имени института
Получено 11 августа 2007 г .; принята к печати 5 декабря 2007 г.
DOI 1 0.1179 / 174329308X283929
Наука и технология сварки и соединения 2008 VOL 13 NO 3 225
Электрическая дуга — свойства дуги — газ, ионы, ток и электроны
Электрическая дуга была впервые обнаружена в 1808 году британским химиком Хамфри Дэви. Он увидел яркое светящееся пламя, когда два стержня из углерода , проводящие ток, были разделены, и конвекционный ток горячего газа отклонил его в форме дуги. Типичные характеристики дуги включают относительно низкий градиент потенциала между электродами (менее нескольких десятков вольт) и высокую плотность тока (от 0.От 1 ампер до тысяч ампер или выше). В проводящем канале существуют высокие температуры газа (несколько тысяч или десятков тысяч градусов Кельвина), особенно при высоких давлениях газа. Испарение электродов также является обычным явлением, и газ содержит молекулы материала электродов. В некоторых случаях может быть слышен шипящий звук, заставляющий дугу «петь». Градиент потенциала между электродами неоднороден. В большинстве случаев можно различить три различных области: область, близкую к положительному электроду, называемая катодным падением ; область, близкая к отрицательному электроду, или анодный подъем ; и тело основной дуги.Внутри корпуса дуги имеется равномерный градиент напряжения. Эта область электрически нейтральна, где кумулятивная ионизация приводит к тому, что количество положительных ионов равно количеству электронов или отрицательных ионов. Ионизация происходит в основном за счет возбуждения молекул и повышения температуры.
Область катодного падения составляет около 0,01 мм с разностью потенциалов менее 10 вольт. Часто на катоде достигается термоэлектронная эмиссия. Электроды в этом случае изготовлены из преломляющих материалов, таких как вольфрам и углерод, а область содержит избыток положительных ионов и большой электрический ток .На катоде происходит переход от металлического проводника, в котором ток переносится электронами, к газу, в котором проводимость осуществляется как электронами, так и отрицательными ионами и положительными ионами. Газообразные положительные ионы могут свободно достигать катода и образовывать потенциальный барьер. Электроны, вылетающие из катода, должны преодолеть этот барьер, чтобы войти в газ.
На аноде происходит переход от газа, в котором и электроны, и положительные ионы проводят ток, к металлическому проводнику, в котором ток переносится только электронами.За некоторыми исключениями, положительные ионы не попадают в газ из металла , металла . Электроны ускоряются по направлению к аноду и обеспечивают за счет ионизации запас ионов для колонки.