Температура плавления металла при сварке
пер.Каштановый 8/14 51100 пгт.Магдалиновка

Nikolaenko Dmitrij
Температура плавления металла при сварке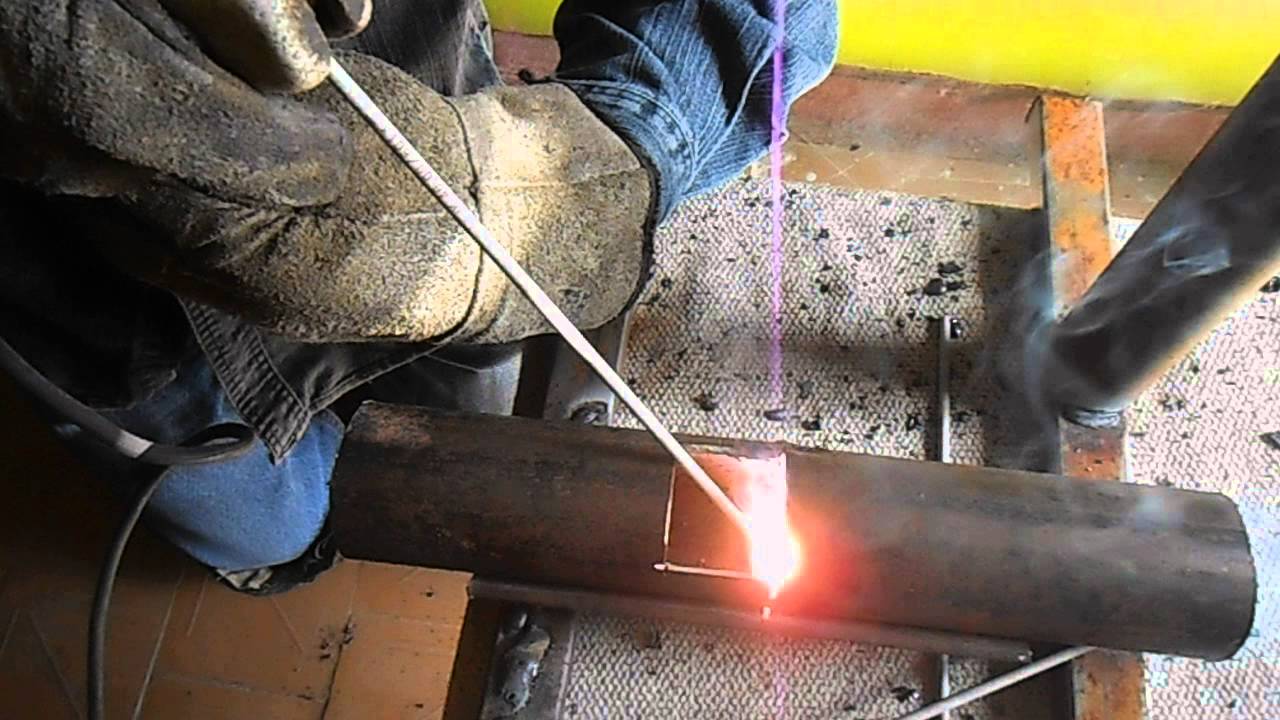
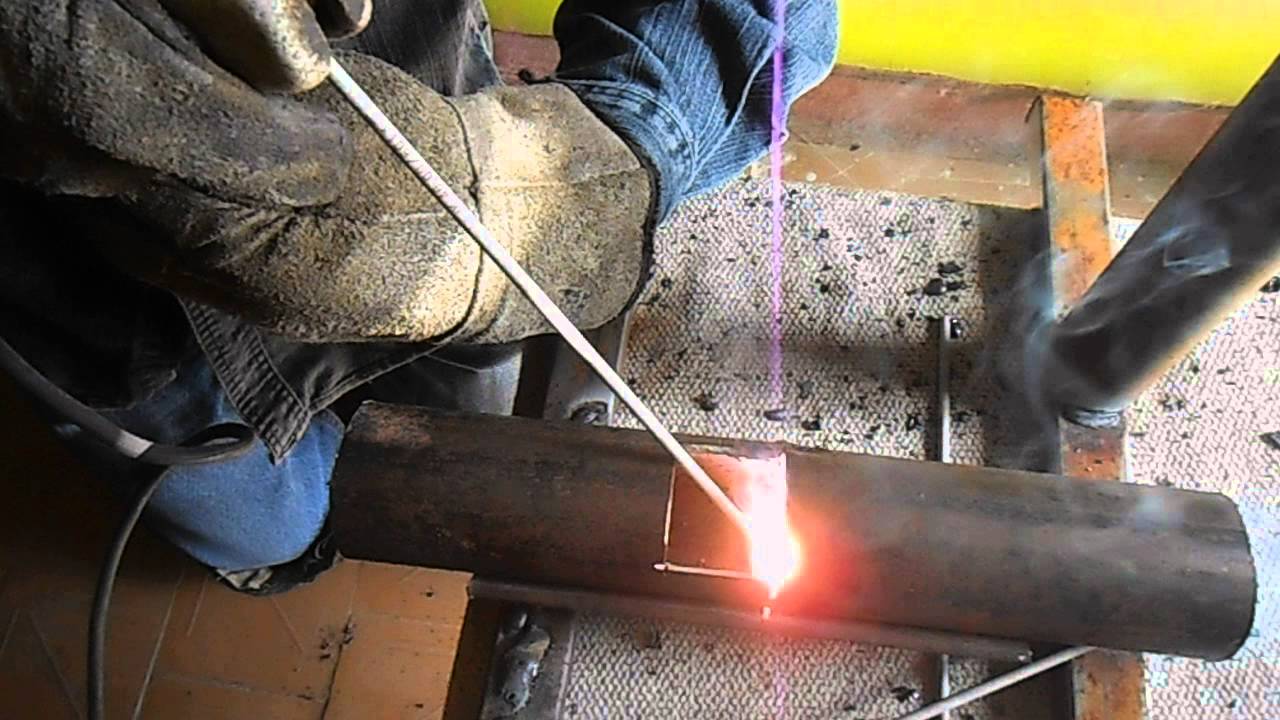
- 5
- 4
- 3
- 2
- 1
- Газовая сварка. Используемый горючий газ — ацетилен, кислород. Каждый из газов способен нагреть и расплавить любой металл.
- Дуговая сварка. Источником энергии при этой сварке служит электрический дуговой разряд, который появляется при соприкосновении свариваемых деталей к одному полюсу источника тока, а электрода к другому полюсу. При этом, движение совершает электрод с дуговым разрядом, необходимо использовать присадочный материал для образования прочного соединения.
- Аргонодуговая сварка. Прогрессивная сварка для цветных металлов. Применяют плавящийся электрод-проволоку, который подходит по составу со свариваемым металлом или используют неплавящийся вольфрамовый электрод, его в основном применяют для ответственных конструкций, а сбоку подают присадочный металл. Особенно хорошо использовать этот вид сварки для титана и его сплавов.
Температура плавления при сварке титана 16680 С, а аргонодуговой сварки 20000 С. Дело в том, что титан при температуре 5000С начинает активно реагировать с окружающей средой, и он начинает окисляться, а при такой сварке аргон исполняет роль защиты от атмосферы и титан не реагирует на нее. Плавление сплава происходит равномерно, и шов получается ровный и чистый. Это только некоторые виды сварки плавлением. Существуют средства, которые содействуют плавлению, метала — это флюсы, роль которых растворять окислы при повышенных температурах и способствовать равному шву. Также имеются еще такие средства как шлаки, защитные газы, которые вдуваются в зону сварки.
Температура сварки дуговой, плазменной, в инертной газовой среде
Сегодня нет ни одной отрасли промышленности или хозяйствования, в которой не применялась бы сварка. Самым старым, но до сих пор самым востребованным остается ручная дуговая сварка, которая осуществляется при помощи электрода, сделанного из металла. Температура сварки такого типа может колебаться от 6000 до 12000 градусов. С ее помощью можно сваривать элементы в помещении и на открытом воздухе, добираться в труднодоступные места.
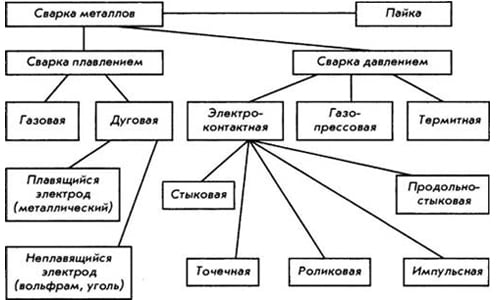
Классификация основных видов сварки.
Механизм сваривания заключается в том, что металл разогревается под действием газа, давления либо тока до начала плавления. Расплавленные кромки перемешиваются с таким же электродом, а потом остывают и твердеют, создавая качественный (или некачественный) шов.
Но как выбрать температуру для конкретного случая? Нужно просто вспомнить школьные знания. В старших классах на уроках химии школьники узнают, что каждый металл имеет собственную температуру плавления. Рассуждая логично, можно сделать вывод, что и температура для их сварки должна быть разной. Это подтверждает практика. Алюминий коробится, если его сваривать при температуре, необходимой чугуну, а температура, необходимая для сварки чугуна, абсолютно не подходит для стальных конструкций и элементов.
По этим причинам перед сварочными работами нужно сначала изучить особенности материала, с которым придется контактировать, выбрать подходящий вид сварки.
Температура и особенности дуговой сварки
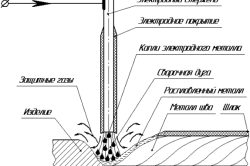
Рисунок 1. Схема ручной дуговой сварки.
Электродуговая сварка – самый распространенный процесс, предназначенный для получения цельных деталей, неразъемных на уровне атомных связей. Именно электродуговая сварка позволяет достичь максимально высоких температурных показателей. Минимальный нагрев составляет не меньше 6 тысяч градусов, но при необходимости при помощи электрической дуги можно разогреть стык металла и электрода до 12 тысяч градусов.
Электрическая дуга получила свое название из-за внешнего вида. При сварке в газовой среде образуется электроразряд, который характеризуется высокой плотностью тока, температурой и газовым давлением. Нагретый газ начинает светиться и изгибаться, образуя известную сварщикам дугу, которая горит между краем свариваемого металла и электродом. На рис.1 наглядно показан процесс, который имеет место при дуговой сварке.
Когда между деталью и электродом возникает раскаленная дуга, они начинают расплавляться, образуя сварочную ванну. Через дугу в эту ванну попадает расплавленный металл с электрода. Покрытие, плавящееся одновременно с электродом, образует шлак на поверхности горячего металла и газовую среду вокруг дуги. По мере того как сварщик продвигает дугу вперед, металл затвердевает, образуя сварочный шов, покрытый коркой из шлака. После остывания шва она ликвидируется.
Чаще всего электродуговая сварка применяется для соединения очень толстых деталей или элементов, выполненных из углеродистых сталей, имеющих высокую тугоплавкость.
Сварка в газовой среде
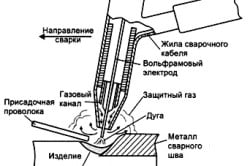
Рисунок 2. Схема сварки в инертном газе.
Наиболее известное название такой сварки – аргонно-дуговая, или АДС. Однако это не точное название, потому что для создания инертной газовой среды может использоваться не только аргон, но и азот, гелий, различные газовые смеси. Сварка в газовой среде проводится при помощи неплавящегося электрода и используется там, где требуется температура, не превышающая 6 тысяч градусов.
Неплавящиеся электроды изготавливают из вольфрама. Сварка с его применением в инертной аргоновой или гелиевой среде позволяет разогревать металл при помощи тепла. Оно выделяется, когда между разогретым металлом и неплавящимся электродом загорается электродуга. Инертный газ не просто предохраняет стык от любого окисления, но и полностью изгоняет кислород из сварного шва, поэтому последний образуется только из металлических расплавленных кромок.
Иногда, чтобы уплотнить шов, используют присадочную проволоку из материала, идентичного свариваемому элементу, которую вручную подводят к месту сварки. На рис.2 показан механизм работы с неплавящимся электродом.
Вольфрам закрепляется в специальной горелке с токопроводящим устройством, к ней при помощи шлангов подводится газ и провод, по которому течет ток. Струя инертного газа, выделяющегося из сопки, одновременно защищает от окисления или попадания азота и сварочную ванну, и шов, и электрод, и дугу.
Преимущество такой сварки заключается в том, что с ее помощью можно на атомном уровне соединять большое количество однородных металлов (например, золото, бронзу, титан, любые магниевые сплавы). Технология также позволяет сваривать разные металлы, например низкоуглеродную и нержавеющую сталь, медь и бронзу и т.п.
Плазменная сварка
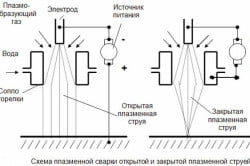
Схема плазменной сварки открытой и закрытой плазменной струей.
Если требуется получить температуру свыше 30 тысяч градусов, используют плазменную сварку.
В этом случае на поверхность металла подается не инертный, а ионизированный газ, который состоит из незаряженных атомов и молекул, заряженных электронов и ионов.
Плазменная дуга от обычной отличается по многим параметрам:
- Дуга имеет форму цилиндра, а не конуса и значительно меньший диаметр.
- Плазменная дуга имеет значительно более высокую температуру.
- Ее давление на металл в 6-10 раз выше, чем у обычной дуги.
- Плазменный процесс может поддерживаться на токах 0,2-30 А.
Плазма является более универсальным источником тепла, необходимого для нагрева. Она позволяет проплавлять металл на большую глубину, одновременно обеспечивая меньший диаметр проплавления.
Цилиндрообразная форма дуги позволяет работать в максимально труднодоступных местах или там, где колеблется расстояние между горелкой и деталью.
Процесс плазменной сварки заключается в том, что в дугу принудительно вдувают ионизированный газ. При помощи плазмотрона дуга сжимается, увеличивается ее мощность, а температура может достигнуть 30 тысяч градусов.
Самый распространенный вид плазменной сварки – микроплазменный. Такой метод позволяет соединять тонкостенные трубы, фольгу и т.п. не прожигая их, но добиваясь глубокого соединения.
Другие виды сварки

Таблица температур при сварке.
- Варить металл можно не только снаружи, но и внутри сварочной камеры. Так. при диффузной сварке у элементов, которые нужно соединить, зачищают кромки, а сами детали помещают в камеру с заранее заданным давлением. Кромки разогреваются до 600-700°C, детали сдавливаются и свариваются. Такой метод лег в основу соединения пропиленовых изделий. При сварке полипропилена обычно достаточно 260°C.
- При электрошлаковой сварке температуры в сварочной ванне могут достигать 1700°C, поэтому она не подходит для соединения деталей из тугоплавких металлов. Механизм работы заключается в том, что ток подогревает и поддерживает на одном уровне температуру в шлаковой ванне, в которой расплавляются металлические кромки. Если температура в ванне ниже, чем точка плавления рабочего металла, то процесс становится невозможным.
- Электронно-лучевая сварка, при которой для нагрева используют пучок электронов, позволяет получать температуру около 6 тысяч градусов.
- В ультразвуковой сварке температура зависит от самого металла. На его концы воздействуют ультразвуковыми волнами, от микроколебаний кромки раскаляются и начинают плавиться, а потом свариваются. Процесс для разных металлов происходит при разных температурах. Так, для меди необходимо достичь 500°C, а для алюминия достаточно 400°C.
- Холодная сварка не нуждается в разогреве деталей, но не может проводиться при температуре окружающего воздуха ниже +5°C. Это не сварочный процесс, а процесс образования клея из двух составляющих.
- Лазерная сварка позволяет получить температуру в 25 тысяч градусов. Для соединения деталей на кромки направляют лазерный луч и подносят специальную присадку. Метод позволяет сваривать самые тугоплавкие металлы.
Для получения качественного шва мало знать температуру плавления нужного металла и температуру самой сварки. Необходимо учитывать температуру окружающей среды и тщательно подготовить детали, предназначенные для сварки.
Металлургические процессы в зоне сварки плавлением
Применение при сварке мощных высококонцентрированных и высокотемпературных источников теплоты приводит к расплавлению кромок свариваемого изделия, электродного (или присадочного) материала и покрытия или флюса. При этом образуется сварочная ванна расплавленного металла, окруженная относительно холодным металлом, иногда значительной толщины, и покрытая слоем расплавленного шлака.
Нагрев основного и присадочного металлов до расплавления с последующим охлаждением и затвердеванием сопровождается фазовыми переходами в веществе. При сварке плавлением происходит взаимодействие расплавленного металла со шлаком, а также с выделяющимися газами и воздухом. Это взаимодействие начинается с момента образования капель металла и продолжается до полного охлаждения наплавленного металла шва. Основными особенностями металлургических процессов, протекающих при сварке, являются:
- высокая температура процесса;
- небольшой объем ванны расплавленного металла;
- большие скорости нагрева и охлаждения;
- отвод теплоты в окружающий ванну основной металл;
- интенсивное взаимодействие расплавляемого металла с газами и шлаками в зоне интенсивного нагрева;
- быстрая кристаллизация сварочной ванны.
Все это усложняет получение сварного шва с заданными физико-механическими свойствами, которые предопределяются химическим составом металла шва и его структурой.Химический состав металла шва и его свойства зависят от состава и доли участия в формировании шва основного и присадочного металлов, покрытия и флюсов, степени защиты от воздуха, приемов ведения и режимов сварки. Металл шва образуется в результате перемешивания в сварочной ванне основного и присадочного металлов и реакций взаимодействия нагретого металла с газами атмосферы и защитной средой.
Высокая температура источника тепла ускоряет физико-химические процессы, происходящие при плавлении металла. Она вызывает также диссоциацию (распад) молекул кислорода, азота и паров воды. В атомарном состоянии газы, обладая высокой химической активностью, интенсивно взаимодействуют с расплавленным металлом шва. Поэтому одной из серьезных задач при сварке плавлением является защита сварочной ванны от вредного воздействия воздуха и предотвращение попадания в металл шва вредных веществ (влаги, ржавчины, минеральных масел и т. п.). Кроме того, высокая температура способствует выгоранию примесей и тем самым изменяет химический состав свариваемого металла.
Небольшой объем ванны расплавленного металла (при ручной сварке -0,5-1,5 см3, при автоматической сварке — 24-300 см3) и интенсивный отвод теплоты в окружающий ванну металл не дают возможности полностью завершиться всем реакциям взаимодействия между жидким металлом, газами и расплавленным шлаком. Большие скорости нагрева и охлаждения значительно ускоряют процесс кристаллизации и, соответственно, приводят к образованию закалочных структур, трещин и других дефектов. Под воздействием теплоты происходят структурные изменения в металле околошовной зоны, которые приводят к ослаблению сварного шва.
Рассмотрим взаимодействие расплавленного металла сварного шва с газовой средой, которая состоит главным образом из кислорода, азота и водорода. Кислород, поступающий в зону сварки из воздуха и покрытия электродов, является наиболее вредной примесью, и его повышенное содержание в сварном шве приводит к понижению прочности, пластичности, вязкости и антикоррозионных свойств шва.
С железом кислород образует три вида оксидов: FeO, Fe203, Fe304. Наиболее отрицательное воздействие оказывает FeO, который хорошо растворяется в расплавленном металле шва, но растворимость его зависит от содержания углерода в стали и температуры. С ростом температуры растворимость повышается. Поэтому при охлаждении стали происходит выпадение его из раствора. При высоких скоростях охлаждения сварного шва часть оксидов FeO остается в растворе, образуя шлаковые прослойки между зернами металла, при этом повышая порог хладноломкости, т. е. температуру, при которой металл теряет пластичность. Для швов с повышенным содержанием FeO этот порог составляет -10…-15 °С.
Азот в зону сварки попадает из воздуха и в зоне сварки находится как в молекулярном, так и в атомарном состоянии. Атомарный азот более активно растворяется в расплавленном металле сварочной ванны, чем молекулярный, образуя при этом нитриды железа (Fe2N, Fe4N), марганца (MnN) и кремния (SiN), которые, в свою очередь, снижают пластичность и повышают твердость наплавленного металла. На степень насыщения металла шва азотом оказывают влияние режимы сварки и охлаждения. Медленное охлаждение шва способствует удалению из него газообразною азота. При больших скоростях охлаждения азот не успевает полностью выделиться и составляет с металлом перенасыщенный твердый раствор. Такой азот со временем становится причиной старения металла шва и снижения его механических свойств.
Водород в зоне сварки образуется во время диссоциации водяных паров при высокой температуре дуги. Водяные пары поступают в зону сварки из атмосферной влаги, а также из влаги, содержащейся в покрытии электродов, флюсах, ржавчине на кромках заготовок и т. п. Молекулярный водород при дуговой сварке распадается на атомарный, который хорошо растворяется в расплавленном металле. Атомарный водород, растворяясь в жидком металле, может оставаться в таком состоянии до тех пор, пока температура не опустится примерно до 200 °С. При дальнейшем понижении температуры водород из атомарного состояния переходит в молекулярное, вызывая при этом значительные внутренние напряжения и, как следствие, образование флокенов. Гидриды и флокены снижают прочность и пластичность металла шва, что, в свою очередь, приводит к водородной хрупкости и образованию трещин Для уменьшения содержания в сварном шве водорода пользуются рядом практических приемов:
- электроды и флюсы перед сваркой тщательно прокаливают;
- кромки свариваемых заготовок и сварочную проволоку очищают от влаги, грязи и ржавчины;
- швы выполняют с минимальным числом проходов, так как при наложении последующего шва предыдущий шов в момент вторичного расплавления насыщается водородом;
- при выполнении сварочных работ на открытой площадке обеспечивают защиту зоны сварки от атмосферных осадков;
- сварку ответственных конструкций выполняют только при положительных температурах.
МЕТАЛЛУРГИЧЕСКИЕ ПРОЦЕССЫ В ЗОНЕ СВАРКИ ПЛАВЛЕНИЕМ. КРИСТАЛЛИЗАЦИЯ МЕТАЛЛА СВАРОЧНОЙ ВАННЫ
В процессе сварки по мере перемещения источника тепла вслед за ним перемещается и сварочная ванна. При этом в задней части ванны расплавленный металл охлаждается и, затвердевая, образует сварной шов. Кристаллизация металла сварочной ванны начинается у границы с нерасплавившимся основным металлом в зоне сплавления. Различают кристаллизацию первичную и вторичную. Первичной кристаллизацией называют процесс перехода металлов и сплавов из расплавленного состояния в твердое. Первичная кристаллизация металла сварочной ванны начинается от частично оплавленных зерен основного или ранее наплавленного металла и продолжается по нормали от линии расплавления.
Первичная кристаллизация металла сварочной ванны протекает периодически, так как периодически ухудшается теплообмен, периодически выделяется скрытая теплота кристаллизации. Это приводит к слоистому строению металла шва и к появлению ликвации. Толщина закристаллизовавшихся слоев зависит от объема сварочной ванны и скорости охлаждения металла и колеблется от долей миллиметра до нескольких миллиметров.
Ликвация — это отделение легкоплавкой составляющей сплава от остальных, встречается в сплавах, имеющих широкий интервал температур плавления. Зональная (слоистая) ликвация проявляется в неоднородности химического состава металла шва в периферийной и центральной зонах. Это является следствием того, что металл периферийных зон затвердевает раньше и поэтому содержит меньше примесей, чем металл центральных зон. Большое влияние на величину ликвации оказывает температурный интервал кристаллизации. Чем меньше температурный интервал кристаллизации, тем ниже уровень ликвации. Например, в низкоуглеродистых сталях, имеющих интервал кристаллизации 25-35 °С, ликвация незначительна. С увеличением содержания в стали углерода температурный интервал кристаллизации возрастает, и степень ликвации повышается.
Вторичная кристаллизация происходит после завершения первичной и характеризуется сменой кристаллических решеток и изменением структуры, т.е при вторичной кристаллизации металла происходит изменение форм зерен. Вторичная кристаллизация характерна только для металлов, испытывающие полиморфные превращения (железо, кобальт, титан, марганец и некоторые другие), и в значительной степени зависит от химического состава металла, скорости охлаждения, а также ряда других факторов. Теплота, выделяемая при сварке, распространяется в основной металл. При этом по мере удаления от границы сплавления скорость и максимальная темпера тура нагрева металла снижаются. Вследствие этого в зоне основного металла про исходят фазовые и структурные изменения, которые влияют на прочность сварного соединения. Зону основного металла, прилегающую к сварочной ванне, называют зоной термического влияния. Температура нагрева в зоне сварки колеблете! от температуры точки плавления до начальной температуры основного металл.
Строение структуры металла в зоне термического влияния и размеры этой зоны зависят от химического состава, толщины основного металла, способа и режима сварки, а также от термического цикла сварки и других факторов. Зона сплавления расположена рядом с металлом шва и является важным участком зоны. Этот участок формируется из жидкой и твердой фаз, и в нем происходит сращивание основного и наплавленного металлов, протекают диффузионные процессы, развивается химическая неоднородность и происходит образование общих кристаллов. Участок представляет собой узкую полосу, измеряемую десятыми, а иногда и сотыми долями миллиметра в зависимости от способа сварки. Свойства участка зоны сплавления часто оказывают решающее влияние на прочность и работоспособность наплавленного слоя. На этом участке обычно образуются трещины, ножевая коррозия, усталостные разрушения и т. п. Поэтому правильное его формирование имеет большое значение.
Участок перегрева включает в себя металл, нагреваемый до температуры, близкой к температуре плавления. Этот участок характеризуется крупнозернистой структурой. Металл на этом участке претерпевает аллотропические превращения: а-железо переходит в у-железо, и в результате значительного перегрева происходит рост зерна. Эта часть зоны термического влияния — наиболее слабое место. Она приобретает большую хрупкость и низкую прочность по сравнению с основным металлом. Перегрев снижает прочность и пластичность металла и особенно опасен для сталей, склонных к образованию закалочных структур. Выбор рациональной технологии сварки сводится, в первую очередь, к обеспечению наименьшего ухудшения свойств металла в этой части.
Участок перекристаллизации или нормализации характеризуется наиболее мелкозернистой структурой, образующейся при температуре 900- 1100°С. При нагреве и охлаждении металла на этом участке происходит перекристаллизация и значительное измельчение зерна. Метал участка приобретает высокие механические свойства и имеет наилучшую прочность и пластичность. Участок неполной перекристаллизации характеризуется температурой 720-880 °С. Этой температуры оказывается недостаточно, чтобы полностью изменить структуру основного металла в мелкозернистую. Поэтому в этой зоне наряду с зернами основного металла имеются зерна, образующиеся при перекристаллизации. Этот участок имеет достаточную прочность и мало влияет на прочность сварного соединения. Участок рекристаллизации формируется в пределах температур 500-700 °С, при которых происходит восстановление формы и размера зерен, разрушенных или деформированных при обработке давлением основного металла. В металле, не подвергавшемся деформации, структурных изменений в этой зоне не происходит.
Участок синеломкости, нагреваемый до температуры 500 °С и ниже, структурным изменениям не подвергается. Металл данного участка по структуре не отличается от основного. Однако металл участка имеет несколько пониженные пластичность и вязкость и повышенную склонность к образованию трещин. При сварке низкоуглеродистых сталей с повышенным содержанием газов возможно резкое падение ударной вязкости, которое можно объяснить старением металла после холодной деформации. Структурные изменения основного металла в зоне термического влияния мало отражаются на механических свойствах низкоуглеродистой стали при сварке ее любыми способами. Однако при сварке некоторых конструкционных сталей в зоне термического влияния может происходить образование закалочных структур, которые резко снижают пластические свойства сварных соединений и часто являются причиной образования трещин.
СВАРИВАЕМОСТЬ МЕТАЛЛОВ И СПЛАВОВ
Под свариваемостью понимают способность металлов образовывать соединения, механические и другие эксплуатационные свойства которых находятся на уровне основного металла. Свариваемость может быть оценена конкретными количественными характеристиками. В зависимости от назначения и условий эксплуатации конструкции определяют:
- склонность к образованию горячих и холодных трещин в металле шва и зоне термического влияния;
- склонность к образованию пор;
- механические свойства;
- коррозионную стойкость;
- химический состав и другие свойства.
Свариваемость определяется не только свойствами металла — она зависит от способа и режима сварки, состава сварочных материалов, конструктивного оформления сварного узла, условий эксплуатации изделий. Различают физическую, технологическую и эксплуатационную свариваемость. Физическая свариваемость определяется процессами, происходящими на границе соприкосновения свариваемых изделий при различных физико-химических методах соединения металлов (физический контакт, химическое взаимодействие, рекристаллизация и т. п.). Под технологической свариваемостью понимают возможность получения сварного соединения определенным способом сварки. Технологическая свариваемость влияет на выбор параметров режима сварки и технологическую последовательность выполнения работ. Под эксплуатационной свариваемостью понимают условия допустимого применения материалов в сварных конструкциях и сварных изделиях.
Нагрев и плавление металла при сварке
Нагрев и плавление металла при сварке создают внутренние напряжения в металле и его деформацию, вызываемые следующими причинами [c.189]НАГРЕВ И ПЛАВЛЕНИЕ МЕТАЛЛА ПРИ СВАРКЕ [c.455]
При электрической дуговой сварке нагрев и плавление металла осуществляются энергией, выделяемой дуговым разрядом. При электрошлаковой сварке необходимая для сварки теплота получается при прохождении тока через шлаковую ванну, образуемую при расплавлении флюса. Нагрев и плавление металла при электроннолучевой сварке достигаются за счет интенсивной бомбардировки свариваемого металла быстродвижущимися электронами. При лазерной сварке необходимая для плавления металла теплота выделяется световым пучком, являющимся весьма концентрированным источником теплоты. [c.13]
Наиболее распространена лазерная сварка импульсных излучением в электронной и электротехнической промышленности, где сваривают угловые, нахлесточные и стыковые соединения тонкостенных деталей. Хорошее качество соединений обеспечивается сваркой лазерным лучом тонких деталей (0,05…0,5 мм) с массивными. В этом случае, если свариваемые детали значительно отличаются по толщине, в процессе сварки луч смещают на массивную деталь, чем выравнивают температурное поле и достигают равномерного проплавления обеих деталей. Чтобы снизить разницу в условиях нагрева и плавления таких деталей, толщину массивной детали в месте стыка уменьшают, делая на ней бурт, технологическую отбортовку или выточку (рис. 123). При лазерной сварке нагрев и плавление металла происходят так быстро, что деформация тонкой кромки может не успеть произойти до того, как металл затвердеет. Это позволяет сваривать тонкую деталь с массивной внахлестку. Для этого надо, чтобы при плавлении тонкой кромки и участка массивной детали под ней образовалась общая сварочная ванна. Это можно сделать, производя сварку по кромке отверстия в тонкой детали или по ее периметру. [c.238]
В последнее время в сварочной практике находят применение оптические квантовые генераторы (ОКГ), так называемые лозе/)ы. При лазерной сварке нагрев и плавление металла осуществляются мощным световым лучом, получаемым от специальных твердых или газовых излучателей. Для управления сформированным излучателем лучом служат специальные оптические системы. Вакуум при сварке лазером не нужен, и сварка может осуществляться на воздухе даже на значительном расстоянии от генератора. [c.429]
При интенсивной бомбардировке металла или какого-либо другого материала ускоренными электронами в высоком вакууме около 99% их кинетической энергии переходит в теплов /ю, расходуемую на нагрев. Температура в месте бомбардировки достигает 5000—6000° С, что достаточно для плавления металла при сварке и для тепловой обработки материалов (плавления, испарения, резки, сверления и др.). [c.371]
При электрической сварке плавлением источником нагрева служит электрическая энергия. Электрическая сварка плавлением подразделяется на дуговую] при этом способе нагрев и плавление осуществляются за счет энергии, выделяемой дуговым разрядом электро-шлаковую, при которой нагрев и плавление металла осуществляются за счет термической энергии, выделяемой током, проходящим через расплавленный флюс (шлаковую ванну) электроннолучевую сварку при которой энергия, расходуемая на нагрев и плавление металла, получается за счет интенсивной бомбардировки основного металла в месте соединения быстродвижущимися в вакууме электронами сварку лазером — источником нагрева является световой луч, получаемый в специальном оптическом квантовом генераторе . сварка дуг.овой плазмой — источником нагрева является струя ионизированного газа. При химической сварке плавлением в качестве источника нагрева используется экзотермическая реакция горения газов газовая сварка) и порошкообразной горючей смеси термитная сварка). Приведем классификацию основных методов сварки металлов по физическим признакам [c.438]
При электроннолучевой сварке энергия, необходимая для расплавления металла, подводится к детали электронным лучом. Благодаря бомбардировке поверхности изделия электронами и переходу их кинетической энергии в тепловую происходит местный нагрев и плавление материала. При перемещении кромок свариваемых деталей под лучом образуется сварной шов. Можно перемещать луч вдоль неподвижных прямолинейных или криволинейных кромок. [c.460]
Электрошлаковая сварка, разработанная институтом электросварки им. Е. О. Патона, имеет принципиальное отличие от описанных выше способов сварки плавлением. При этой сварке тепловая энергия, расходуемая на нагрев и плавление металлов изделия [c.213]
Принцип электродуговой сварки заключается в следующем. Свариваемая деталь соединяется с одним из полюсов сварочного агрегата постоянного или переменного тока (рис. 126), второй полюс соединяется с держателем электрода. При соприкосновении электрода с деталью происходят сильный нагрев и плавление металла. Если в это время не отвести электрод, то он приварится к основному металлу. При отводе электрода на 2—3 мм от детали расплавленный конец электрода излучает электроны, которые расщепляют атомы окружающего воздуха на ионы при этом ионизированный воздух обеспечивает получение устойчивой электрической дуги, температура которой достигает 3000—3500°. [c.201]
При электрической сварке плавлением источником теплоты служит электрический ток. Электрическую сварку плавлением подразделяют на дуговую, при которой нагрев и плавление осуществляют за счет энергии, выделяемой дуговым разрядом электрошлако-вую, при которой нагрев и плавление металла осуществляются за счет термической энергии, выделяемой током, проходящим через расплавленный флюс (шлаковую ванну) электроннолучевую, при которой энергия, расходуемая на нагрев и плавление металла в месте соединения, получается за счет интенсивной бомбардировки быстродвижущимися в вакууме электронами плазменную, при которой источником теплоты является струя ионизированного газа. Особое место занимает сварка лучом оптического квантового генератора (лазера), при которой нагрев и плавление металла осуществляются мощным световым лучом. При хи- [c.597]
Электрошлаковая сварка, разработанная в Институте электросварки им Е. О. Патона, имеет принципиальное отличие от описанных выше способов сварки плавлением. При этой сварке тепловая энергия, расходуемая на нагрев и плавление металлов изделия и электрода, получается за счет теплоты, выделяемой в объеме расплавленного флюса (шлаковой ванны) при прохождении через него преимущественно переменного тока (рис. 28.12). Шлаковая ванна не только нагревает металл изделия и электрода, но и надежно защищает расплавленный металл от вредного действия воздуха. [c.273]
Электрическая дуговая сварка. При электрической дуговой сварке, или коротко-дуговой сварке, нагрев и плавление металла осуществляется дуговым разрядом, возникающим между электродами. Энергию, необходимую для образования и поддержания дугового разряда, получают от источников питания постоянного или переменного тока. Широкое практическое применение находит дуга прямого действия (рис. 1-3, а), горящая между свариваемым металлом и специальным стержнем-электродом. Для сварки используется теплота, выделяемая в столбе дуги и на электродах. [c.14]
Лазерная сварка. В последнее время в сварочной практике находят применение оптические квантовые генераторы, так называемые лазеры. При лазерной сварке нагрев и плавление металла осуществляются мощным световым лучом, получаемым от специальных твердых или газовых излучателей. Для управления сформированного излучателем луча служат специальные опти- [c.23]
Источники теплоты при сварке. Нагрев и плавление металла происходят за счет выделения теплоты на электрических сопротивлениях при прохождении через них электрического тока. Полное количество теплоты (0ээ), генерируемое между электродами за время сварки ( св), определяется законом Джоуля — Ленца [c.130]
Это ориентировочное значение силы тока, его корректируют в зависимости от свариваемого материала или особенностей соединения. Например, при сварке высоколегированных сталей для уменьшения перегрева металла силу тока уменьшают на 20…30 %. Минимальный ток должен обеспечивать нагрев и плавление торца электрода, максимальный ток не должен перегревать электрод по всей длине и вызывать осыпание покрытия. [c.120]
Нагрев свариваемого металла, в особенности до температур, близких к температуре кипения металла, при сварке плавлением увеличивает его способность окисляться. Для уменьшения окисления и изоляции от окружающей атмосферы металла шва расплавляемый при сварке металл (при некоторых видах производства сварных труб) окружается специальными шлаками, получаемыми в результате плавления флюсов. [c.284]
При сварке основной металл нагревается в зоне плавления до температуры более высокой, чем температура металла, окружающего сварочную ванну и удаленного от нее. Неравномерный нагрев металла, вызванный.сваркой, приводит к появлению сжимающих сил в зоне металла, прилегающей ко шву, и растягивающих сил вдали от сварного шва. В результате происходит коробление сварного соединения. Кроме того, затвердевание и охлаждение металла шва приводят к его усадке и деформации свариваемого изделия. Структурные напряжения связаны с изменением размеров кристаллов и их взаимного расположения и сопровождаются изменением объема тела, вызывающим внутренние напряжения. Внутренние силы, возникающие в металле при сварке, могут быть достаточными, чтобы привести к образованию трещин в швах или рядо.м с ними. [c.116]
Нагрев и охлаждение металла в околошовных участках отличаются от обычной термообработки металлов н сплавов кратковременностью теплового воздействия и нагревом металла до высоких температур вплоть до температуры плавления. Такая своеобразная термическая обработка при сварке вызывает различные структурные изменения металлов и сплавов, оказывая серьезное влияние на свойства металла в околошовных участках. [c.24]
Характеристики дуги. Дуга — весьма эффективный источник тепла при сварке. Сварочная дуга с плавящимся металлическим электродом в различных случаях эффективно отдает на нагрев и плавление основного металла 60 —80% энергии, полученной от источника тока. Потери энергии идут на излучение дуги в окружающее пространство, на теплопроводность металла, уносятся вместе с брызгами металла. [c.78]
Структура сварного соединения в зависимости от исходной структуры металла определяется скоростью его нагрева и степенью деформации при сварке, а также скоростью охлаждения после нее. Для стыковой сварки характерен быстрый и концентрированный нагрев ограниченного объема металла в диапазоне температур от комнатной до сварочной, часто равной температуре плавления. [c.33]
При сварке сопротивлением детали прижимают с большим усилием (2…5 кгс/мм ). Сварочный ток нагревает детали до температуры 0,8.,.0,9 от температуры плавления. В стыке происходит пластическая деформация, соединение образуется без расплавления металла. Этим способом не всегда удается обеспечить равномерный нагрев деталей большого сечения по всей площади и достаточно полно удалить из стыка деталей окисные пленки. Поэтому стыковую сварку сопротивлением применяют только для соединения деталей малого сечения (до [c.283]
Титан обладает весьма высокой температурой плавления (1668 °С) и кипения (3260 °С). Коэффициент теплопроводности у Ti в 4 раза меньше, чем у Fe, и в 13 раз меньше, чем у А1, поэтому при сварке Ti происходит весьма концентрированный нагрев при значительном градиенте температур. Необходимо также отметить высокое электрическое сопротивление Ti. В химическом отношении титан весьма активный металл при высоких температурах, особенно в расплавленном состоянии. При комнатной температуре он устойчив к окислению и обладает высоким сопротивлением коррозии во многих агрессивных средах. [c.272]
При сварке плавлением скорость нагрева в интервале температур A i — Асз и длительность пребывания металла околошовной зоны при температуре выше Асз оказывают существенное влияние на процесс гомогенизации аустенита и рост зерна. Существует два возможных варианта развития процесса. Первый вариант, когда высокая температура нагрева металла околошовной зоны способствует росту зерна, особенно при большой длительности пребывания металла при температуре выше Асз и одновременно увеличивает устойчивость аустенита. Второй вариант, когда быстрый нагрев и малая длительность пребывания металла выше температуры Асз понижают степень гомогенизации и устойчивость аустенита. [c.285]
Электронно-лучевая сварка. Нагрев металла при этом способе осуществляется потоком лучей быстродвижущих-ся электронов, ускоряемых электрическим полем. Падая на поверхность изделия, электроны отдают свою кинетическую энергию, превращающуюся в тепловую и нагревают металл до температуры 5000-6000 °С, что достаточно для плавления металлов при сварке и для их тепловой обработки (резки, сверления, испарения). Процесс обычно ведется в герметически закрытой камере с высоким вакуумом, необходимым для свободного движения электронов и обеспечения чистоты наплавленного металла. [c.334]
Сварка — один из наиболее распространенных технологических процессов получения неразъемных соединений. Сварное соединение характеризуется непрерывной структурной связью и монолитностью строения, достигаемыми за счет образования атомномолекулярных связей между элементарными частицами свариваемых деталей. При электрической дуговой сварке покрытым или вольфрамовым электродом нагрев и плавление металла производится дуговым разрядом, возникающим между электродом и свариваемым изделием. Энергию для образования и поддержания дугового разряда получают от источников питания постоянного и переменного тока. Электрод закрепляется в электрододержате-ле, который с источником питания соединяется сварочным проводом. Для получения электрического разряда необходимо наличие электрической цепи. Поэтому источник питания кроме электрододержателя соединен еще со свариваемым изделием. Практически это оформляется в виде сварочного поста, в который входит источник питания, электрические провода, электрододержатель, устройства для присоединения сварочного провода к источнику питания и свариваемому изделию, устройства для соединения между собой отрезков сварочного провода, щиток и инструмент сварщика, сбо-рочно-сварочные приспособления (рис. 3). Сварочный пост может быть стационарным или передвижным. При сварке на строительно-монтажной площадке или при сварке крупногабаритных изделий в цеховых условиях используются передвижные посты. [c.21]
При производстве труб широкое применение находят различные методы дуговой сварки, при которых нагрев и плавление металла происходят за счет энергии, выделяемой дуговым разрядом. При электронно-лучевой сварке энергия, расходуемая на нагрев и плавление металла, образуется в результате интенсивной бомбар- [c.284]
Электрош лаковая сварка. При электрошлаковом процессе основная часть энергии, расходуемая на нагрев и плавление металла, обеспечивается за счет теплоты, выделяемой в замкнутом объеме расплавленного шлака — шлаковой ванне при прохождении через нее тока. Шлаковая ванна 1 образуется (наводится) путем расплавления флюса, заполняющего пространство между кромками основного металла 2 и специальными охлаждаемыми водой приспособлениями—ползунами 3, плотно прижатыми к поверхности свариваемых де- [c.21]
Когда испытания по методу Gleeble только начинались, проводили много опытов, в которых вьшолняли и нагрев, и охлаждение. Конечно, при нагреве полезную информацию извлекали, однако самый большой спад пластичности и прочности происходил в условиях охлаждения от максимальной температуры, близкой к температуре плавления. Чтобы эти явления не пропустить, испытания теперь проводят, как правило, в режиме охлаждения. Этот подход, по-видимому, и полнее соответствует механизму растрескивания при сварке. Представляется, что трещины в подлинной зоне термического влияния возникают в процессе охлаждения, а в зоне смешения растрескивание тем более должно совершаться в процессе охлаждения, ибо в противном случае они были бы залечены при расплавлении металла в этой области. [c.271]
Тепло, выделяющееся при протекании реакций (82) п (83), по приближенным расчетам [22] составляет около 12% всего тепла, затрачиваемого на нагрев и плавление стержня эле рода, что, по-видимому, и обеспечивает, наряду с вос-ста ювлеиием железа по реакции (82), высокий коэффициент наплавки при сварке этими электродами (10—11 г/а-ч). Незначительная часть марганца ферромарганца непосредственно переходит в металл шва, несколько повышая в нем концентрацию этого элемента. [c.121]
Нагрев металла при сварке может производиться не только электрическим током но и, например, за счет экзотермических химических реакций, идущих с большим выделением тепла. Примером подобной сварки может служить газовая сварка. Обычная газовая, или газоплавильная, сварка относится к группе сварки плавлением. [c.9]
Стыковая сварка. При этом виде сварки детали подключаются ко вторичной обмйтке сварочного трансформатора с по-У мощью специальных держателей. Место соединения деталей нагре-вается током до температуры плавления металлов, при сдавливании деталей образуется сварной шов. Для получения высокого качества сварного шва необходим одинаковый нагрев обеих деталей в месте соединения. Площади поперечных сечений деталей Б этом месте должны быть одинаковьши. Сварка встык применяется для соединения трубчатых деталей и стержней. [c.51]
Выравнивание химического состава наплавленного металла производится перемешиванием жидкого металла и диффузией на границе сплавления это выравнивание про-исходит главным образом за счет диф- фузии и осуществляется в меньшей степени, чем у жидкого металла. Поэтому на границе сплавления концентрируется большее количество элементов, пе- реходящих из основного металла в на- плавленный или наоборот, по сравнению со средними участками шва или наплав- ленного валика. При этом необходимо иметь в виду, что при сварке или на- плавке нагрев и охлаждение металла происходят быстро. Это в значительной степени затрудняет выравнивание химического состава металла шва. [c.15]
Сварные швы. Наиболее ачабые места в аппаратуре — сварные швы и прилегающие к ним зоны, в которых при сварке возникают термические напряжения. Как известно, в процессе сварки металл нагревается неравномерно. В зоне сварного шва достигается температура плавления металла, а в прилегающих зонах температура металла намного ниже. На рис. 1-1Х схематически показано изменение температуры металла при сварке и указаны температурные интервалы на упрощенной диаграмме состояния железо — углерод. На участке 1—2 происходят плавление металла, на участке 2—3 — частичное оплавление со значительным ростом зерна участок 3—4 соответствует процессу нормализации структуры с измельчением зереи на участке 4—5 происходит частичная перекристаллизация, на участке 5—6—рекристаллизация зерен на участке 6—7 температура снижается с 400 до 200° С — в этом интервале температур наблюдается синеломкость у сталей, склонных к старению. Здесь по границам зерен скапливаются нитриды и карбиды и пластичность стали снижается. Нагрев до температур ниже 200 С ие вызывает изменения структуры и свойств стали. Следует отметить, что рассматриваемая схема является условной она использована для пояснения темперного влияния на структуру металла в процессе сварки. [c.131]
В связи с опасностями такого рода при стыковой контактной сварке всегда рационально обеспечивать осадку, не выключая сварочного тока. Вокруг всякого дефекта, концентрирующего механические напряжения, электрический ток и его магнитный поток создают также свои собственные концентрации. Если концентрация механического сдвига усиливает разрушение, то электромагнитное поле своей концентрацией может противостоять этим действиям. И концентрация тока, и магнитный поток вызывают значительный и мгновенный нагрев в зоне концентрации. Нагревы могут доводить металл до мгновенного плавления, когда не только залечиваются микротрещины, но и ргезко меняется структурная картина со всеми ее бывшими микродефектами. Влияние электромагнитных полей на трещинообразование при сварке полезно иметь в виду и исследователям прочностных свойств соединений при дуговой сварке. Оказывается совершенно небезразлично, как подводился сварочный ток к сварным образцам, с какой именно стороны и в каком направлении. И сварочный ток, и магнитное поле при сварке могут быть и не быть полезными концентраторами. [c.155]
При затвердевании расплавленного материала слабые адге знойные связи заменяются прочными химическими связями, соответствующими природе соединяемых материалов и типу их кристаллической решетки. При сварке плавлением вводимая энергия (обычно тепловая) должна обеспечивать расплавление основного и присадочного материалов, оплавление стыка, нагрев кромки и т. д. При этом происходит усиленная диффузия компонентов в расплавленном и твердом материалах, их взаимное растворение. Эти процессы, а также кристаллизация расплавленного металла сварочной ванны (или припоя) обеспечивают объемное строение зоны сварки, что обычно повышает прочность сварного соединения. [c.13]
Ele trosiag welding — Электрошлаковая сварка. Процесс сварки плавлением, в котором нагрев при сварке производится пропусканием электрического тока через расплавленный проводящий шлак (флюс), содержащийся в шлаковой ванне, образованной охлаждаемыми водой преградами, которые соединяют промежуток между свариваемыми элементами. Нагретый сопротивлением шлак не только расплавляет электроды присадочного металла, поскольку они находятся в слое шлака, но также и обеспечивает защиту для массивной сварной ванны, характерной для этого процесса. [c.949]
Плавление основного металла
ТЕОРИЯ сварочных процессов
ФОРМЫ СВАРОЧНОЙ ВАННЫ ПРИ РАЗЛИЧНЫХ СПОСОБАХ СВАРКИ
Плавление основного металла при сварке осуществляется с целью соединения между собой свариваемых деталей. Идеальным в отношении затрат теплоты представляется такое тепловыделение в источнике, при котором обеспечивалась бы минимальная глубина проплавления сопрягаемых поверхностей, а присадочный металл не требовался бы вовсе или входил в соединение в минимальном объеме. Если не рассматривать диффузионную сварку и пайку, при которых детали нагреваются полностью, и сварку трением, при которой полного плавления металла не достигается, наиболее близко этому требованию отвечает высокочастотная сварка и некоторые виды контактной сварки (точечная, шовная, рельефная). В перечисленных способах сварки существенная роль в образовании соединения принадлежит давлению, что позволяет плавить основной металл незначительно. Ограничимся рассмотрением случаев плавления основного металла в способах сварки без применения давления.
При электронно-лучевой сварке удается получить минимальное проплавление основного металла при сварке встык вплоть до толщин, измеряемых сотнями миллиметров. Сварочная ванна в поперечном сечении имеет форму, близкую к конусу (см. рис. 5.14, д), а в плоскостях, перпендикулярных лучу, — близкую к эллипсу.
При электрошлаковой сварке также можно получить минимальное проплавление основного металла (см. рис. 5.14, в), но для ведения шлакового процесса с целью получения достаточного выделения теплоты необходим зазор, который затем должен заполняться присадочным металлом. Сварочная ванна может быть мелкой или глубокой в зависимости от скорости сварки
и мощности источника. Форма ванны при электрошлаковой сварке зависит от соотношения между количествами теплоты, поступающими в основной металл непосредственно от шлака и от опускающегося в металлическую ванну перегретого электродного металла.
При использовании дуговых, плазменных и газопламенных источников теплоты при сварке встык металла небольшой толщины форма ванны близка к форме изотермической линии температуры плавления, рассчитанной для движущегося линейного источника теплоты в пластине. С ростом толщины металла разница в размерах ванны на верхней и нижней поверхностях листа становится все более значительной, а при некоторой толщине полное проплавление уже не достигается, как показано на рис. 7.19. Для увеличения проплавляющей возможности указанных источников используют разделку кромок. Особенности различных источников нагрева в части их проплавляющей способ-
Рис. 7.19 Формы сварочной ванны при дуговой сварке: а — поверхностная дуга; 6 — погруженная дуга; в — дуга под флюсом |
В
ности обычно оценивают экспериментальным путем, расплавляя поверхность массивного тела или толстой пластины (рис. 7.19).
Ванну характеризуют следующими параметрами: L — длина ванны, В — ее ширина, Н — глубина проплавлення, Нк — глубина кратера. Очертание зоны проплавления характеризуют относительной глубиной проплавления Н/В или обратной ей величиной — коэффициентом формы проплавления Ф =В/Н, а также коэффициентом полноты проплавления ц„р= гп?/{НВ), где Fa? — площадь проплавления. Значения р обычно находятся в пределах 0,6…0,8. Для дуговой сварки под флюсом характерно большое Н/В, но при дуговых способах сварки оно все же не превышает 3. Очертание зоны наплавки характеризуют коэффициент формы валика А>в = В/А, а также коэффициент полноты валика iB = FJ(AB), где А — высота шва, FH—площадь наплавки.
Расчеты позволяют лишь приближенно оценить размеры ванны при дуговых способах сварки. При наплавке на поверхность массивного тела длину ванны L можно получить из уравнения (6.42), приняв г = 0, а АТ=ТП, — ТН и использовав при этом соотношение tu=L:
2лк(Тш-Т„) ‘ (7-44)
Формула (7.44) показывает, что длина ванны на поверхности массивного тела от скорости сварки не зависит. Опытные данные в целом указывают на справедливость этой формулы, хотя и обнаруживают некоторую зависимость длины ванны от скорости. Аналогично можно оценить и ширину ванны.
При заполнении разделки в случае многослойной сварки форма ванны имеет меньшее значение. Более существенно полное сплавление наплавляемого металла с ранее уложенными слоями и отсутствие шлаковых включений.
Форма и размеры ванны при прочих равных условиях (мощности источника и скорости сварки) существенно зависят от характера подачи и температуры присадочного металла. При подаче в ванну холодной непрерывной или рубленной на мелкие части проволоки ванна становится короче. Поэтому оценка L по формуле (7.44) справедлива лишь для идеализированных условий.
ТЕМПЕРАТУРА СВАРОЧНОЙ ВАННЫ
Температуры жидкого металла в различных точках сварочной ванны могут сильно различаться между собой. У границы с твердым металлом температура жидкого металла близка к температуре его плавления (табл. 7.2). Она может быть как несколько ниже Тпл вследствие кристаллизационного переохлаждения, так и выше при больших скоростях движения жидкого металла вдоль твердой границы. Как следует из рис. 7.19, расплавляю-
Таблица 7.2. Температуры плавления и кипения различных металлов, К, при атмосферном давлении
|
щийся на передней кромке ванны жидкий металл поступает в ее заднюю часть, проходя вдоль боковых поверхностей и дна ванны. При этом скорости движения металла могут превышать скорость сварки в 1,5…10 раз. Максимальные температуры жидкого металла существенно зависят от источника теплоты. При лучевых способах сварки, особенно при значительной концентрации энергии в пятне нагрева, металл может достигать температуры кипения (см. табл. 7.2).
Дуговые и плазменные источники энергии также способны создавать на поверхности металла довольно высокие температуры, например у сталей до 2300 К. При электрошлаковом процессе температура жидкого присадочного металла, проходящего через активную зону шлаковой ванны, где выделяется теплота, достигает температуры шлака, которая в средней по высоте части шлаковой ванны составляет 2100…2200 К, а на поверхности шлака около 2000 К-
При способах сварки плавлением, особенно с использованием дуги, происходит интенсивное перемешивание жидкого металла как вследствие его движения из передней части ванны в заднюю, так и под влиянием других воздействий источника теплоты на жидкий металл. Происходит интенсивный теплообмен между отдельными порциями различно нагретого жидкого металла, а также вследствие теплоотвода в твердый металл. По этой причине энергетическое состояние ванны целесообразно характеризовать не только возможными максимальными и минимальными температурами, но и средней температурой жидкого металла. Она зависит от режима сварки (тока, напряжения, скорости сварки), характера подачи присадочного металла, устойчивости дуги и положения ее активного пятна. Например, средняя температура ванны при аргонно-дуговой сварке алюминиевого сплава АМгб может изменяться от 920 до 1050 К при возрастании тока от 300 до 450 А при (/д= 14 В и от 1070 до 1200 К при 1/д= 8 В, в то время как температура плавления сплава АМгб составляет около 890 К.
Во многих случаях, в особенности при сварке легированных сталей и различных сплавов, требуется прежде всего получение определенных механических свойств и структуры металла околошовной зоны и шва, которые зависят от длительности пребывания металла выше определенной температуры, скорости охлаждения в необходимом интервале температур, повторного нагрева и многих других особенностей термического цикла сварки (см. разд. IV). Поэтому оценка эффективности процесса сварки по энергетическим критериям часто оказывается второстепенной. Однако для сталей, мало чувствительных к воздействию термического цикла сварки, оценка эффективности различных режимов сварки по энергетическим затратам необходима. Следует различать сварные соединения двух основных крайних типов: соединения, в которых преобладает наплавленный металл (заштрихованные участки на рис. 7.20, вверху), и соединения, образуемые преимущественно в результате расплавления основного металла (рис. 7.20, внизу). Для последнего типа соединений, например
стыкового, тепловую эффективность процесса целесообразно ха
рактеризовать удельной затратой количества теплоты на единицу площади свариваемой поверхности:
г— UI/F СВ), (7.45)
где Ссв1 — площадь соединения, свариваемая за 1 с; для однопроходной сварки встык, например Ссв| = иб; UI—полная тепловая мощность сварочного источника.
Эффективность использования тепловой энергии движущихся источников теплоты характеризуют также так называемым термическим к. п. д. процесса проплавления основного металла:
4t=vFupphaJq. (7.46)
Коэффициент т)/ выражает отношение условного теплосодержания vFn;phn„ проплавленного за единицу времени основного металла к эффективной тепловой мощности источника теплоты. Величина теплосодержания в единице массы металла /гпл включает в себя также скрытую теплоту плавления, затрачиваемую на
ут
-4А
без присадки
Рис. 7.20. Поперечные сечения сварных соединений (штриховыми линиями показаны границы расплавления)
переход металла из твердого в жидкое состояние. Здесь принято, что лишь теплота, истраченная на плавление металла, израсходована полезно, а остальная часть, ушедшая на подогрев металла, окружающего ванну, истрачена бесполезно. Расчетное определение тр для точечного и линейного источников теплоты соответственно в полубесконечном массивном теле и в пластине проводят по формулам (6.22) и (6.26). По ним определяют площадь F„р в выражении (7.46), ограниченную изотермой ДТ =Т„А — Тп. Для точечного источника т]( возрастает с ростом безразмерного критерия ез —qv/(a2phm), т. е. термический к. п. д. выше у мощных дуг, движущихся с высокой скоростью. Однако при вз —оо не может быть выше 1/0 = 0,368.
Соответственно для линейного источника теплоты в пластине т], возрастает с ростом безразмерного критерия е2= q/(8aphnJ, но не может быть более У2/(ле) = 0,484 в случае предельно мощных линейных источников теплоты, т. е. при q/8-voo.
Полный тепловой к. п. д. проплавления т)пр выражает отношение vFBpph„„ ко всей (полной) тепловой мощности сварочного источника теплоты VI. Источники теплоты, когда они используются для соединений, формирование которых происходит в основном в результате наплавки металла (см. рис. 7.20, вверху), целесообразно оценивать по полному тепловому к. п. д. наплавки
4H=vFuph„J{UI), (7.47)
где F„ — площадь наплавки.
Чтобы решить дифференциальное уравнение теплопроводности, необходимо задать распределение температур в начальный момент времени (начальное условие) и условия взаимодействия тела с окружающей средой на его границах (граничные условия). Начальное условие определяется …
На современном уровне развития математики аналитическое решение уравнения теплопроводности в общем виде (5.21) еще не найдено, однако при введении некоторых допущений и упрощений можно получить пригодные для практического использования частные …
Сложный процесс изменения температуры точек тела с координатами jc, у, z во времени t описывается дифференциальным уравнением теплопроводности. Для вывода этого уравнения необходимо рассмотреть баланс теплоты в некотором элементарном объеме …
Сварка плавлением.
Сварка плавлением — это процесс соединения двух деталей или заготовок в результате кристаллизации общей сварочной ванны, полученной расплавлением соединяемых кромок. Этот процесс наиболее распространен в сварочной технике.
Нагреть металл соединяемых кромок изделия выше температуры плавления для образования сварочной ванны можно только в том случае, если источником энергии вводится в зону сварки теплоты гораздо больше, чем отводится за это же время процессами охлаждения.
Основная часть теплоты уходит на нагрев холодного изделия, так как теплопроводность металлов очень высокая. Кроме того, большое количество теплоты теряется излучением в окружающую среду.
Поэтому источник энергии при сварке плавлением должен быть большой мощности, высокой сосредоточенности, т. е. концентрировать выделяющуюся энергию на малой площади сварочной ванны и успевать расплавлять все новые и новые порции металла, обеспечивая этим определенную скорость сварки.
Из всех источников энергии, применяемых при сварке плавлением, наибольшей плотностью энергии обладает электронный луч (109 Вт/см2).
Однако наиболее широкое применение в качестве источников энергии для сварки плавлением получил дуговой электрический разряд, или электрическая дуга. Это связано с тем, что для возбуждения электронного луча требуется вакуум 10-4—10-5 мм рт. ст.; кроме этого, применение электронного луча для сварки связано с разработкой специальной аппаратуры, высоким напряжением (~20 кВ) и с необходимостью защиты обслуживающего персонала от опасного рентгеновского излучения.
Поэтому его используют для специальных целей, главным образом для сварки тугоплавких и химически активных металлов.
Пламя ацетилено-кислородной горелки находит более ограниченное применение, главным образом при ремонтных работах.
Итак, процесс сварки плавлением осуществляется источником энергии, движущимся по свариваемым кромкам с заданной скоростью (рис. 7).
Рис. 7. Схема сварки плавлением.
Если бы он был неподвижным, то форма сварочной ванны была бы симметричной, а ее сечение круглым. Так как источник энергии движется, то форма сварочной ванны оказывается несимметричной и имеет вид вытянутого овала. Размеры и форма сварочной ванны зависят от мощности источника и от скорости его перемещения, а также от теплофизических свойств металла.
При сварке листовых конструкций из пластически деформированного металла (проката) зона сварки существенно отличается по структуре и свойствам от основного металла. Наличие неоднородностей металла вызывает, в свою очередь, деформацию при короблении сварного соединения.
Введение большого количества энергии при сварке для образования сварного шва вызывает существенную неоднородность в металле сварного соединения — как результат воздействия теплового поля.
Рис. 8. Структура металла шва и околошовной зоны после сварки плавлением.
В сварном соединении резко различаются три области (рис. 8):
а) основной металл, имеющий в результате прокатки и термической обработки однородную мелкозернистую кристаллическую структуру;
б) зона термического влияния (околошовная зона), в которой металл находился некоторое время при высокой температуре, доходящей на линии сплавления до температуры плавления металла; в этих условиях может резко изменяться структура металла, особенно структура заливающихся сталей; увеличивается размер кристаллических зерен, прорастающих в процессе кристаллизации ванны за линию сплавления; по ширине зоны термического влияния структура металла тоже неоднородна в соответствии с температурным полем при сварке;
в) сварной шов — металл шва представляет собой литую структуру, но имеет характерные особенности.
Кристаллизация сварочной ванны начинается от поверхности сплавления, состоящей из оплавленных кристаллов, которые прорастают в еще жидкую сварочную ванну, как только ее температура достигнет точки плавления. Такая встречная кристаллизация с двух поверхностей сплавления (оплавленные кромки) оттесняет примеси в центр сварочной ванны, создавая неоднородность состава металла шва. Правда, эта неоднородность сглаживается в результате диффузии, идущей при высоких температурах с большой скоростью; в целом структура металла шва оказывается неблагоприятной.
Однако, регулируя процесс кристаллизации изменением скорости охлаждения и направлением отвода теплоты, можно значительно улучшить литую структуру металла шва. Академик Н. Н. Рыкалин создал стройную теорию тепловых процессов при сварке, позволяющую заранее определить оптимальные режимы сварки изделий и регулировать процессы кристаллизации в зоне сварки.
Нагрев металла при сварке до температур, превышающих температуру его плавления, вызывает окисление металла шва и изменение его химического состава. Как будет показано при рассмотрении отдельных способов сварки, существуют два основных пути сохранения требуемого качества металла шва и защиты его от окисления:
1) защита металла сварочной ванны шлаком и введение в процессе сварки легирующих компонентов, повышающих качество металла шва и предохраняющих его от окисления;
2) защита зоны сварки от воздушной атмосферы путем создания защитной атмосферы из инертных газов (аргона, гелия) или из активных газов, таких, как углекислый газ (С02), а также путем создания вакуума.
Нагрев и плавление металла при сварке — КиберПедия
Эффективность использования теплоты, выделяемой источником нагрева, характеризуется э ф ф е к т и в н о й т е п л о в о й м о щ н о с т ь ю – количеством теплоты, введенным в изделие в процессе его нагрева за единицу времени qи. Отношение qи к скорости сварки vсв характеризует количество теплоты, вводимое на единицу длины шва, и называется п о г о н н о й э н е р г и е й сварки. Для обозначения погонной энергии сварки часто используют символ .
Рассмотрим ряд сварочных T- процессов.
В ходе дуговой сварки подводимая к сварочной дуге энергия источника питания расходуется на нагрев электрода и основного металла, а также отдается окружающей среде путем конвективной и радиационной теплоотдачи, светового излучения, звуковых колебаний, вместе с брызгами электродного металла и т.д. (рис.2.17).
Рис. 2.17. Тепловой баланс ручной дуговой сварки покрытыми электродами |
При дуговой сварке qи связана со сварочным током Iсв, напряжением дуги Uд и эффективным коэффициентом полезного действия (КПД) нагрева металла сварочной дугой hи соотношением .
Коэффициент hи уменьшается с увеличением длины дуги и повышается с увеличением скорости сварки и углублением дуги в сварочную ванну и имеет различные значения в зависимости от способа сварки (табл.2.4).
Таблица 2.4
Значения hи для различных сварочных дуг
Способ сварки | hи |
Покрытыми электродами | 0,70 – 0.85 |
Под флюсом | 0,80 – 0,95 |
В углекислом газе | 0,58 – 0,72 |
В аргоне неплавящимся электродом | 0,60 – 0,80 |
В аргоне плавящимся электродом | 0,70 – 0,80 |
Плазменная с аргоном в качестве плазмообразующего газа | 0,3 – 0,75 |
Для дуг, мало погруженных в металл, , а для сильно погруженных – , где DUст – часть падения напряжения в столбе дуги. Однако при сварке на постоянном токе эффективность нагрева изделия зависит также от полярности. В дугах при плавящемся электроде большее количество тепла выделяется на катоде, а в дугах при неплавящемся электроде, как правило, – на аноде. Поэтому сварку неплавящимся (вольфрамовым) электродом наиболее часто ведут на прямой полярности.
Наплавочные работы, выполняемые плавящимся электродом, с целью повышения производительности ведут на прямой полярности, а сварочные работы, требующие глубокого проплавления изделия, – на обратной полярности.
В дуге переменного тока расположение анодных и катодных областей на электроде и изделии чередуется с частотой питающей сети. По этой причине интенсивность тепловыделения на электроде и изделии в дуге переменного тока занимает промежуточное положение по отношению к дугам постоянного тока прямой и обратной полярности.
При электронно-лучевой сварке энергия электронного луча затрачивается на нагрев изделия, а также на испарение металла и отражение излучения в окружающую среду, на вторичную термоэлектронную эмиссию электронов и электромагнитное излучение.
Эффективный КПД нагрева зависит от атомного номера свариваемого металла и составляет 70 – 90 %.
Для лазерной сварки применяют импульсные и непрерывно действующие лазеры.
В лазерах до 94 % энергии теряется в системе накачки. Около 3 % энергетических потерь приходится на оптическую систему и ~1 % – на испарение металла и отражение лазерного излучения от изделия.
Эффективный КПД нагрева во многом зависит от степени заглубления лазерного луча в металл и может лежать в пределах от ~6 % (сварка алюминия) или ~10 % (сварка стали) до ~90 % (сварка стальных или алюминиевых конструкций).
Распространение теплоты в изделии осуществляется теплопроводностью, а в сварочной ванне – конвективным теплообменом и теплопроводностью.
Распределение температуры в изделии в конкретный момент времени представляет собой т е м п е р а т у р н о е п о л е.
Температурное поле в изделии при сварке обычно анализируют в системе пространственных координат, перемещающихся с источником нагрева.
Процесс распространения теплоты в изделии при сварке разделяют на три стадии:
– теплонасыщение, когда в температурном поле, перемещаемом вместе с источником тепла, температура нарастает;
– предельное квазистационарное состояние, когда подвижное температурное поле практически устанавливается;
– выравнивание температуры после окончания сварки.
Если тепловые процессы анализировать путем наблюдения за температурой в некоторой точке изделия, то изменение температуры в данной точке при сварке называют т е р м и ч е с к и м ц и к л о м.
При однопроходной сварке (наплавке) термический цикл простой (рис.2.18, а). Такой цикл характеризуется максимальной температурой Tmax, скоростью нагрева и скоростью охлаждения, а также длительностью tп пребывания материала при температуре выше заданной температуры Tз.
При многопроходной сварке термический цикл сложный. Например, при трехпроходной сварке без расхолаживания изделия после каждого прохода максимум температуры в рассматриваемой точке достигается несколько раз (рис.2.18, б).
а | б |
Рис. 2.18. Простой (а) и сложный (б) сварочные термические циклы
Температурное поле в каждый момент времени часто представляют в виде совокупности и з о т е р м – линий на поверхности или в сечении тела, соединяющих точки с одинаковой температурой (рис.2.19).
Рис. 2.19. Изотермы температурного поля на поверхности изделия
из стали 12Х18Н10Т толщиной 3 мм, свариваемого аргонодуговой сваркой
неплавящимся (вольфрамовым) электродом диаметром 5 мм;
Iсв = 470 А, lд = 2,5 мм (Uд = 11 В), Vсв = 90 м/ч
Изотерма температуры солидуса определяет собой профиль сварочной ванны, например, на рис.2.19 это 1403 оС.
Сварочная ванна при дуговой сваркехарактеризуется длиной L и шириной e, практически равной ш и р и н е ш в а (рис.2.20). Глубина сварочной ванны, отсчитываемая от поверхности основного металла, определяет г л у б и н у п р о п л а в л е н и я H. Выступающая над поверхностью основного металла часть сварного шва высотой g называется у с и л е н и е м ш в а.
Рассмотрим характеристики сварного соединения в поперечном сечении (рис. 2.20).
Рис. 2.20. Основные параметры сварочной ванны и сварного шва |
Площадь основного металла Fпр, переплавленного при сварке, называется п л о щ а д ь ю п р о п л а в л е н и я. Форму зоны проплавления оценивают коэффициентом формы провара , а также коэффициентом полноты проплавления . Для Т-процессов в зависимости от способа сварки (наплавки) mпр изменяется от 0,05 до 20.
Площадь сварного шва Fн, образованная путем расплавления электродного металла, называется п л о щ а д ь ю н а п л а в к и. Очертания зоны наплавки характеризуются коэфициентом формы валика и коэфициентом полноты валика . Для плоского шва (не имеющего усиления) . Для швов стандартных соединений, выполненных луговой сваркой, .
Объем сварочной ванны в зависимости от способа и режима сварки плавлением составляет от 0,1 до 10 мл.
Максимальное время пребывания металла в сварочной ванне для разных случаев составляет до 30 – 40 с.
Сварочная ванна нагревается неоднородно. Г о л о в н а я ч а с т ь сварочной ванны (abc – на рис.2.20) перегрета, в ней идет плавление основного и электродного металла. Х в о с т о в а я ч а с т ь сварочной ванны (cda) более холодная. В хвостовой части ванны идет охлаждение расплава и его кристаллизация.
Средняя температура металла Tср в сварочной ванне определяется источником нагрева, теплофизическими свойствами свариваемого материала и параметрами теплоотвода с наружной и внутренней поверхностей ванны. Например, при дуговой сварке низкоуглеродистых и низколегированных сталей оС.
Сварочная ванна образуется смешением расплавленных основного и электродного металла.
Доля основного металла в шве . Доля электродного металла составляет 1 – q.
Давление столба сварочной дуги,возникающее вследствие давления газов, электродинамических усилий и упругих ударов заряженных частиц о поверхность металла, оттесняет жидкий металл от основания дуги (см. рис.2.20).
Величина прослойки жидкого металла под сварочной дугой во многом определяет глубину проплавления H (см. рис.2.20, сечение А – А). Это обусловлено тем, что жидкий металл, обладая меньшей теплопроводностью, чем твердый, затрудняет процесс распространения теплоты источника нагрева в глубину изделия.
Чем больше давление дуги, оказываемое на поверхность расплавленного металла, тем больше глубина погружения дуги в его толщу, меньше прослойка жидкого металла под сварочной дугой и больше H. Давление дуги растет с увеличением силы и плотности сварочного тока.
Плавление электрода происходит в основном за счет тепловой энергии дуги. Скорость плавления зависит от состава сварочной проволоки, покрытия, флюса, защитного газа, плотности и полярности тока и других параметров режима сварки.
Технологические характеристики плавления электрода определяются экспериментально и используются для оценки производительности процесса сварки. К таким характеристикам в первую очередь относят производительность расплавления и производительность наплавки.
Производительность наплавки оценивается количеством металла с плотностью r, наплавленного на изделие в единицу времени: . Количество наплавленного электродного металла всегда меньше, чем расплавленного, на величину коэффициента потерь на угар и разбрызгивание kп (под угаром понимаются потери металла на испарение и окисление). По этой причине производительность расплавления .
Вклад разбрызгивания в величину kп зависит от типа переноса электродного металла через дуговой промежуток.
Удельные производительности расплавления и наплавки оцениваются коэффициентами расплавления и наплавки , причем . Для ряда способов дуговой сварки коэффициенты aр и kп приведены в табл.2.5.
Перенос электродного металла через дуговой промежуток осуществляется, как правило, каплями. Различают крупнокапельный с замыканиями дугового промежутка, мелкокапельный и струйный перенос металла.
Таблица 2.5
Характеристики процесса плавления электрода
Способ дуговой сварки | aр, г/(А×ч) | kп |
Покрытыми электродами | 8 – 14 | 0,05 – 0,3(с учетом огарков) |
В углекислом газе | 15 – 25 | 0,05 – 0,14 |
Под флюсом | 14 – 23 | 0,01 – 0,02 |
Мелкокапельный перенос может осуществляться с замыканиями дугового промежутка и без замыканий (рис.2.21, а).
С т р у й н ы й п е р е н о с представляет собой поток быстро следующих друг за другом капель электродного металла, производящий внешнее впечатление струи расплавленного металла (рис.2.21, б).
Рис. 2.21. Мелкокапельный без замыкания дугового промежутка (а) и струйный (б) перенос электродного металла | ||
а | б |
Характер переноса электродного металла зависит от соотношения сил, действующих на каплю при ее образовании и перемещении через дуговой промежуток. Основные из них: сила тяжести, сила поверхностного натяжения, электромагнитная сила, электростатическая сила, электродинамическая сила, сила реактивного давления паров и нейтрализовавшихся на катоде ионов и аэродинамическая сила. Направление и величина равнодействующей данных сил зависит от параметров режима сварки, состава электродного металла и газовой среды, наличия поверхностно-активных веществ на торце сварочной проволоки и ее диаметра.
Лучшее формирование и качество шва обеспечиваются при струйном переносе, а также при принудительном направленном переносе металла. Последний случай достигается при импульсно-дуговой сварке. Электродинамические силы пропорциональны квадрату тока, поэтому с помощью периодических кратковременных импульсов сварочного тока достигается направленный мелкокапельный перенос металла порциями с частотой воздействия импульсов. В наиболее оптимальном случае реализуется режим «одна капля за один импульс сварочного тока» (рис.2.22). Вертикальными линиями на осциллограммах сварочного тока (см. рис.2.22) указаны моменты времени, для которых представлены кадры скоростной киносъемки переноса.
Время пролета капель через дуговой промежуток для различных типов переноса составляет 10-3 – 10-1 с. За это время металл капель сильно перегревается.
Рис. 2.22. Плавление электрода (а), формирование капли (б) и ее перенос
через дуговой промежуток (в) при импульсно-дуговой сварке
в режиме «одна капля за один импульс сварочного тока»
Например, средняя температура стальных капель при различных способах дуговой сварки составляет 2100 – 3200 оС. Такая высокая температура обусловливает интенсивное протекание химических реакций металла капли с окружающей средой.
Вопросы для самоконтроля
1. Дайте определение погонной энергии сварки.
2. Какие составляющие определяют тепловой баланс при дуговой сварке и как различаются эффективные коэффициенты полезного действия нагрева металла при различных дуговых и лучевых способах сварки плавлением?
3. Охарактеризуйте стадии процесса распространения теплоты в изделии при сварке.
4. Представьте примеры различных термических циклов сварки.
5. Приведите показатели, характеризующие сварочную ванну, и укажите основные параметры сварного шва (в поперечном сечении).
6. Какими показателями определяются технологические характеристики плавления электрода?
7. Сравните между собой различные типы переноса электродного металла через дуговой промежуток.
Точка плавления стали — Science Struck
Точка плавления стали
Понравилось? Поделись!

Если вы пытаетесь узнать, какова температура плавления стали, вы попали на нужную страницу. Читайте дальше, чтобы узнать больше по этой теме.

Сталь — это сплав железа. Почти 90% стали, производимой во всем мире, — это углеродистая сталь, то есть сплав железа и углерода с различным процентным содержанием углерода (0.От 2 до 2,1% по весу). Чистое железо очень мягкое и вызывает коррозию, и его нельзя использовать в активной среде, где железо может химически реагировать с образованием оксидов или сульфидов. Добавление углерода решает эту проблему, делая сталь менее реактивной и, таким образом, предотвращая ее окисление, сохраняя при этом желаемые качества железа. Точка плавления определяется как температура, при которой состояние любого вещества меняется с твердого на жидкое. Например, температура плавления льда составляет 0 ° C или 32 ° F, когда он меняет свое состояние с твердого льда на жидкую воду.Знание температуры плавления стального сплава важно для его изготовления в полезной форме.
Точка плавления стали
Хотели бы вы написать нам? Что ж, мы ищем хороших писателей, которые хотят распространять информацию. Свяжитесь с нами, и мы поговорим …
Давайте работать вместе!
Температура плавления стали зависит от ее типа. Большинство типов этого сплава имеют следы других элементов (в том числе металлов), добавленных к нему для повышения его коррозионной стойкости, простоты изготовления и прочности.Их температура плавления зависит от процентного содержания в них других элементов. Как правило, температура плавления стали составляет около 1370 ° C (2500 ° F). Давайте больше узнаем о типах стальных сплавов и их соответствующих температурах плавления. Выделяют пять основных марок стали:
- Углеродистая сталь:
Сталь с содержанием углерода от 0,05 до 0,15% по массе называется мягкой или низкоуглеродистой сталью. Она также известна как простая углеродистая сталь. Помимо углерода, он также содержит следы меди (0.6%), марганец (1,65%) и кремний (0,6%). Температура плавления низкоуглеродистой стали составляет 1410 ° C (2570 ° F). Этот тип далее подразделяется на среднеуглеродистую сталь, высокоуглеродистую сталь и сверхвысокоуглеродистую сталь с температурами плавления в диапазоне 1425-1540 ° C (2600-2800 ° F). Сталь с содержанием углерода от 0,3 до 1,7% называется высокоуглеродистой сталью. - Нержавеющая сталь:
Это самый популярный стальной сплав, который в основном используется для изготовления кухонных столовых приборов. Она также известна как нержавеющая сталь или просто нержавеющая сталь и легирована 10.От 5% до 11% хрома по весу. Существует пять типов нержавеющей стали, а именно аустенитная, ферритная, мартенситная, дисперсионно-твердеющая мартенситная и дуплексная нержавеющая сталь. Температура плавления нержавеющей стали составляет 1510 ° C (2750 ° F). - Мартенситностареющая сталь:
Этот тип в основном представляет собой низкоуглеродистый сплав железа с никелем в качестве основного легирующего элемента (от 15 до 25% по весу). Его температура плавления составляет 1413 ° C (2575 ° F). Это в основном используется для изготовления велосипедных рам, лезвий для фехтования и головок клюшек для гольфа. - Легированная сталь:
Сталь, легированная количеством элементов от 1 до 50% по весу, называется легированной сталью. Они делятся на две группы, а именно, низколегированные стали и высоколегированные стали, причем первая из двух является наиболее часто используемой. Температура плавления низколегированной стали составляет 1432 ° C (2610 ° F), а для высоколегированной стали — 1415 ° C (2600 ° F). - Инструментальная сталь:
Как следует из названия, этот тип в основном используется для изготовления инструментов, так как это самая твердая разновидность стали.Это более твердая версия углеродистой и легированной стали с процентным содержанием углерода от 0,7 до 1,4%. Марганец, хром, никель, вольфрам, молибден, фосфор и сера — это некоторые из элементов, добавляемых в различных пропорциях для изготовления других типов инструментальной стали. Температура плавления этого типа варьируется в диапазоне от 1400 до 1425 ° C (от 2550 до 2600 ° F).
Значение стали известно всем. Одним из основных достоинств стали является простота переработки без потери физических свойств в процессе.
Похожие сообщения
- Свойства низкоуглеродистой стали
Цель этой статьи — объяснить, что такое низкоуглеродистую сталь, и представить некоторые из наиболее важных фактов, связанных с ней. Знать различные свойства низкоуглеродистой стали и понимать роль…
- Физические свойства стали
Сталь, сплав углерода и железа, имеет много значительных преимуществ с точки зрения долговечности и универсальности. В этой статье рассматриваются компоненты стали и ее физические свойства.
- Использование оцинкованной стали
Прочтите следующую статью, чтобы получить дополнительную информацию о оцинкованной стали и ее различных применениях.
Получайте обновления прямо на ваш почтовый ящик
Подпишитесь, чтобы получать самые свежие и лучшие статьи с нашего сайта автоматически каждую неделю (плюс-минус) … прямо на ваш почтовый ящик. ,Сравнение сварки алюминия и стали
Во многих случаях сварка алюминия требует соблюдения некоторых специальных процедур. Одним из ключевых факторов является выбор правильного присадочного металла для основного материала и требований к области применения.
Сварка алюминия представляет некоторые уникальные проблемы по сравнению со сваркой стали или других распространенных материалов, особенно с точки зрения химического состава и чувствительности к трещинам.
Во многих случаях сварка алюминия требует соблюдения некоторых специальных процедур.Важные факторы при сварке материала: выбор правильного присадочного металла; правильное хранение и тщательная очистка основного материала; и правильные методы сварки.
Вот некоторые общие проблемы при сварке алюминия и основные передовые методы их решения.
Характеристики алюминия
Надежная сварка — это все о химии, восстановлении углеводородов и правильной технике. Характеристики алюминия несколько отличаются от стали. Температура плавления алюминия намного ниже, чем у стали — 1221 градус по Фаренгейту у алюминия по сравнению с 2500 градусами у стали.Алюминий также имеет оксидный слой, который плавится примерно при 3700 градусах. Этот оксидный слой намного тверже алюминия и помогает материалу противостоять коррозии и истиранию. Однако он также действует как изолятор, который может создавать проблемы во время сварки.
Поскольку прочность алюминия имеет тенденцию к увеличению при понижении рабочей температуры — в отличие от стали, которая становится более хрупкой при понижении рабочих температур, — алюминий обычно используется в холодных температурах, таких как криогенная техника и транспортировка сжиженного природного газа.
В то время как железо является основным сплавом стали, алюминиевые материалы — это в основном алюминий с добавлением множества элементов.
Деформируемые сплавы, такие как алюминий серии 1ххх, представляют собой чистый алюминий без намеренно добавленных легирующих элементов. Основными легирующими элементами в других типах алюминия являются медь в серии 2ххх, марганец в серии 3ххх, кремний в серии 4ххх, магний в серии 5ххх, магний и кремний в серии 6ххх, цинк в серии 7ххх и другие элементы в серии 8ххх.
Проблемы сварки алюминия
Различные характеристики алюминия проявляются в процессе сварки. Теплопроводность и проблемы с пористостью — это два самых больших отличия сварки алюминия от стали.
Водород хорошо растворяется в жидком алюминии. Поскольку присадочный материал и основной металл алюминия становятся жидкими в процессе сварки, они поглощают водород и могут удерживать его в растворе. Когда расплавленный материал начинает затвердевать, он больше не может удерживать водород в гомогенной смеси.Водород образует пузырьки, которые застревают в металле, что приводит к пористости.
Смесь защитного газа гелий / аргон может использоваться для борьбы с проблемами пористости, если испробованы все другие варианты. Имейте в виду, что с гелиевой смесью необходимо увеличить напряжение, чтобы преодолеть более высокий потенциал ионизации этого газа по сравнению с аргоном. Повышенное напряжение вызовет более высокое тепловложение и дополнительное проникновение, поэтому эта смесь используется для более толстых алюминиевых базовых материалов.
Тщательно очистите основной материал перед сваркой от масла, грязи, остатков и влаги.Это помогает обеспечить наилучшие результаты и снижает вероятность пористости.
В отличие от стали, присутствие водорода не вызывает трещин в сварных швах алюминия. Однако горячее растрескивание, которое может возникнуть при затвердевании сварного шва, представляет угрозу для алюминия. Решением этой проблемы является химия. Если возникает проблема с горячим растрескиванием, обратитесь к таблице выбора алюминиевого присадочного металла, чтобы найти присадочный металл, который наилучшим образом решает эту проблему.
Основной металл из алюминия 6061 представляет собой пример материала, который имеет максимальную склонность к растрескиванию при его нынешнем химическом составе, что очень затрудняет автогенную сварку или сварку с присадочным материалом аналогичного химического состава.Использование наплавочного металла с такими элементами, как магний (ER5XXX) или кремний (ER4XXX), может помочь вытолкнуть материал за пределы диапазона восприимчивости к трещинам.
Другая проблема алюминия заключается в том, что он в пять раз более теплопроводен, чем сталь. Холодные участки основного металла пытаются отвести тепло от сварочной ванны, что может вызвать непровар в сварном шве. Из-за этой разницы в теплопроводности алюминий требует гораздо более высоких тепловложений, чем сталь во время сварки.
Выбор присадочного металла
Очень важно использовать таблицу выбора при выборе присадочного металла для алюминия. Для каждой комбинации обозначений алюминия есть рекомендуемые варианты присадочного металла в зависимости от характеристик сварного шва, требуемых для конкретного применения.
Таблица выбора включает восемь характеристик, которые важны для различных сварочных работ: чувствительность к трещинам, прочность, пластичность, коррозионная стойкость, работа при повышенных температурах, соответствие цвета после анодирования, термообработка после сварки и ударная вязкость.Анализируя потребности конечного компонента, можно определить, какие свойства наиболее важны для конкретного применения, и выбрать присадочный металл, который наилучшим образом соответствует требуемым характеристикам. Важно отметить, что повышенная рабочая температура алюминия составляет от 150 до 350 градусов по Фаренгейту. Это и другие определения характеристик можно найти в таблице выбора алюминия.
Другой вариант — использовать приложение для выбора присадочного металла, подобное этому.В приложении можно найти ту же информацию, что и в полной таблице выбора, но он показывает присадочный металл только для выбранных основных материалов.
Правильный выбор присадочного металла всегда является ключевым моментом. Например, если основным свариваемым материалом является алюминий 6061, хорошие варианты присадочного металла включают 4043, 4943 и 5356. Проволока для газовой дуговой сварки (GMAW) 4043/4943 или пруток для газовой вольфрамовой дуговой сварки могут уменьшить пористость и обеспечить лучшую свариваемость. и увеличенная текучесть лужи, в то время как продукт 5356 обеспечивает большую вязкость и прочность.
Передовой опыт
Наряду с выбором присадочного металла, наиболее подходящего для данной области применения, следование некоторым основным передовым методам также может помочь в достижении успеха при сварке алюминия.
- Не плести. Хотя для сварки стали обычно используется метод переплетения, его нельзя использовать с алюминием. Вместо этого используйте стрингер, который помогает обеспечить правильное проникновение и сплавление. Для алюминия GMAW обязательно используйте более высокие тепловыделения и высокую скорость движения, чтобы оставаться перед лужей.
- Очистите металл. Тщательно очистите основной материал перед сваркой от масла, грязи, остатков и влаги. Это помогает обеспечить наилучшие результаты и снижает вероятность пористости. Ацетон или очиститель алюминия хорошо подходят для удаления углеводородов, которые могут быть на поверхности материала. При подготовке сварных швов не продувайте их сжатым воздухом, так как это может привести к загрязнению из-за влаги и масел при использовании инструментов в мастерской.
- Удалить оксидный слой. После очистки используйте щетку из нержавеющей стали — новую или использовавшуюся только для алюминия — для удаления слоя оксида алюминия перед сваркой. Как упоминалось ранее, оксид алюминия имеет гораздо более высокую температуру плавления, чем алюминий. Он действует как изолятор, который может вызвать проблемы с зажиганием дуги, и для сварки через оксидный слой требуется очень высокий нагрев. Это может вызвать прожог материала основы и пористость, так как оксидный слой имеет тенденцию удерживать влагу.
- Храните правильно. Правила хранения основных материалов и присадочных металлов также играют роль в предотвращении пористости. По возможности храните листы алюминия внутри. Если они должны храниться на открытом воздухе, ставьте листы вертикально, а не друг на друга, чтобы предотвратить задержку воды, которая будет способствовать образованию более толстого слоя гидратированного оксида алюминия. Материалы и присадочные металлы, хранящиеся снаружи или в кондиционируемой части здания, приносите их в цех перед сваркой — желательно накануне — чтобы температура металла стабилизировалась и не допустила конденсации влаги в воздухе алюминий.
- Проверьте расходные материалы. Некоторые проблемы со сваркой алюминия, особенно при использовании GMAW, могут быть связаны с расходными материалами. Чтобы снизить риск образования пористости, используйте новые или в хорошем состоянии газовые линии и шланги и убедитесь, что все соединения шлангов плотно затянуты, чтобы воздух не попадал в линию.
Также важно использовать подходящие футеровки и приводные ролики. Пластиковые вкладыши и входные направляющие могут обеспечить преимущества по сравнению со стальными вкладышами при сварке алюминия, поскольку металлические или латунные входные направляющие и стальные вкладыши могут истирать более мягкую алюминиевую проволоку, когда она проходит через систему привода и гильзу.Это может привести к попаданию стружки, которая забивает лайнер и вызывает проблемы с подачей. Точно так же приводные ролики с U-образной канавкой являются стандартными для алюминиевых приложений, поскольку другие типы приводных роликов могут разбить или деформировать проволоку.
- Следите за температурой. Обратитесь к руководству по алюминиевому присадочному металлу или нормативам, чтобы определить соответствующие диапазоны температур предварительного нагрева и промежуточного прохода. Предварительный нагрев можно использовать для уменьшения теплового воздействия на размер секции при сварке толстых основных металлов или материалов разной толщины, но при сварке алюминия поддерживайте предварительный нагрев до минимума.
Термически обрабатываемые недрагоценные металлы и недрагоценные металлы серии 5xxx, содержащие более 3 процентов магния, не должны подвергаться предварительному нагреву или температурам между проходами выше 250 градусов по Фаренгейту в течение более 15 минут. Время, проведенное при повышенных температурах, может снизить прочность материала и способствовать растрескиванию.
Достижение успеха
Решение проблем сварки алюминия часто сводится к химии. Правильное соответствие основного материала и присадочного металла имеет большое значение для достижения успеха и минимизации проблем.Также важно следовать рекомендуемым передовым методам сварки алюминия. И помните, что методы и передовые методы сварки алюминия сильно отличаются от методов сварки стали.
.Температура плавления меди — Science Struck
Медь — это металл красновато-коричневого цвета, используемый для различных целей. Если вы ищете информацию о температуре плавления меди, прочтите следующую статью.
Свойства меди
Этот металл мягче железа, но тверже цинка. Его можно полировать для придания более яркого покрытия. Он помещен в группу 11 периодической таблицы с серебром и золотом. Он имеет очень низкую химическую активность и растворяется в горячей концентрированной соляной или серной кислоте.Он разъедает соленую воду и образует хлорид.
Хотите написать для нас? Что ж, мы ищем хороших писателей, которые хотят распространять информацию. Свяжитесь с нами, и мы поговорим …
Давайте работать вместе!
Древний металл, такой как медь, использовался для изготовления украшений, монет, посуды, статуй и т. Д. Он пластичен и обладает высокой теплопроводностью и электропроводностью. Обозначается символом «Cu». Он использовался более тысячи лет и был впервые добыт в Кире в римскую эпоху.Отсюда и название «Киприум», которое также называют «кипрским металлом». Он был обнаружен в древние времена в естественной форме, что положило начало «медному веку» после «каменного века».
Медь и ее точка плавления
Температура плавления этого элемента составляет 1357,77 ° K, 1084,62 ° C или 1984,32 ° F. Чистая медь и сплавы с высоким содержанием меди очень трудно плавятся. Он также подвержен газообразованию. Когда медь-хром плавится, это приводит к потере «Cr». Эта проблема решается путем плавления этого соединения под плавающим флюсом, который предотвращает окисление, а также поглощает водород из атмосферы.Когда расплавленный металл достигает 1260 ° C, борид кальция или литий погружается в ванну расплава, что способствует его раскислению.
Карбонат меди
Это соединение встречается в выветрившейся латуни, меди и бронзе. Его легко узнать по ярко-синему или зеленому цвету. Во влажном воздухе медь окисляется до тускло-зеленого цвета, и поэтому архитекторы используют ее для создания интересных деталей на зданиях. Температура плавления карбоната меди составляет 200 ° C. При высокой температуре карбонат меди разлагается на диоксид углерода и оксид меди (II).
CuCO 3 (твердый) → CuO (твердый) + CO 2 (газ)
Медные сплавы
Они делятся на три группы в зависимости от диапазона их замораживания. Отверждение этих сплавов происходит, когда температура опускается ниже ликвидуса (температура, при которой металлы начинают замерзать), и завершается до того, как температура достигает солидуса (температуры, при которой металл полностью замерзает). Металлические зеркала и бронза — это некоторые сплавы меди и олова, температура плавления которых составляет 1900 — 1950 ° F.Латунь представляет собой сплав меди и цинка с температурой плавления 900–940 ° C.
Таким образом, все свойства меди, описанные выше, особенно в отношении ее температуры плавления, очень важны в различных областях химии и металлургии.
,% PDF-1.4 % 5847 0 obj> endobj Xref 5847 89 0000000016 00000 н. 0000006263 00000 п. 0000002122 00000 н. 0000006584 00000 н. 0000006726 00000 н. 0000007117 00000 н. 0000007379 00000 н. 0000007546 00000 н. 0000007713 00000 н. 0000007880 00000 н. 0000008047 00000 н. 0000008214 00000 н. 0000008381 00000 п. 0000008546 00000 н. 0000008713 00000 н. 0000008880 00000 н. 0000009048 00000 н. 0000009216 00000 н. 0000009384 00000 п. 0000009552 00000 н. 0000009720 00000 н. 0000009887 00000 н. 0000010054 00000 п. 0000010222 00000 п. 0000010390 00000 п. 0000010557 00000 п. 0000010725 00000 п. 0000010893 00000 п. 0000011061 00000 п. 0000011229 00000 п. 0000011397 00000 п. 0000011565 00000 п. 0000011733 00000 п. 0000011899 00000 п. 0000012133 00000 п. 0000012585 00000 п. 0000012873 00000 п. 0000012999 00000 н. 0000013077 00000 п. 0000013213 00000 п. 0000013442 00000 п. 0000013488 00000 п. 0000013865 00000 п. 0000014114 00000 п. 0000014275 00000 п. 0000014516 00000 п. 0000015247 00000 п. 0000015936 00000 п. 0000016492 00000 п. 0000017032 00000 п. 0000017608 00000 п. 0000018167 00000 п. 0000018737 00000 п. 0000019282 00000 п. 0000019928 00000 п. 0000019992 00000 п. 0000020078 00000 п. 0000020150 00000 п. 0000020246 00000 п. 0000053684 00000 п. 0000053744 00000 п. 0000053864 00000 п. 0000053918 00000 п. 0000053982 00000 п. 0000054040 00000 п. 0000054110 00000 п. 0000054166 00000 п. 0000054234 00000 п. 0000054296 00000 п. 0000054368 00000 п. 0000054422 00000 п. 0000054474 00000 п. 0000054522 00000 п. 0000054580 00000 п. 0000054662 00000 п. 0000054734 00000 п. 0000054784 00000 п. 0000054972 00000 п. 0000055024 00000 п. 0000055257 00000 п. 0000055331 00000 п. 0000062403 00000 п. 0000062477 00000 п. 0000062549 00000 п. 0000062746 00000 п. 0000062804 00000 п. 0000063047 00000 п. 0000063119 00000 п. 0000006014 00000 н. прицеп ] >> startxref 0 %% EOF 5849 0 obj> поток x ڼ Xy3ȒDeO0: 94Yc -! Ei Չ H, Rz; I3dy> 3}} z
.