Термическая обработка сварных конструкций |
В машиностроении широко применяют сварнолитые и сварнокованые конструкции. Сварнолитые конструкции, состоящие из нескольких отливок, свариваемых между собой или с заготовками из проката и поковок, особенно целесообразно применять в тех случаях, когда невозможно отлить детали целиком, в частности, из-за недостаточной мощности металлургических печей или грузоподъемности кранов литейного цеха.
Применение сварнокованых конструкций упрощает технологический процесс горячей обработки. Сварную конструкцию получают путем сварки отдельных частей из одной или разных сталей.
В обоих случаях следует обращать особое внимание на термическую обработку сварных конструкций, четко назначать режим термической обработки. Для этого необходимо знать, какие структурные участки образуются в зоне сварки и чем характеризуется каждый участок. Схема строения сварного шва, когда свариваемые части конструкции изготовлены из низкоуглеродистой стали, приведены на рис.
В связи с неоднородностью структуры неоднородны также и механические свойства различных участков. Участок перегрева обладает пониженными механическими свойствами, а участок нормализации, наоборот, имеет высокие механические свойства, иногда даже превышающие свойства основного металла.
Структуры зоны термического влияния легированных сталей, закаливающихся при быстром охлаждении после сварки, отличаются от структур, образующихся в низкоуглеродистой стали. Вместо участков перегрева и нормализации образуется участок полной закалки со структурой мартенсита, а вместо участка неполной перекристаллизации – участок неполной закалки со структурой мартенсита и феррита.
Для изготовления сварных конструкций применяют многие марки углеродистых и легированных сталей. Из углеродистых сталей обыкновенного качества используют стали Ст2, СтЗ, Ст4 из низколегированных конструкционных сталей 10ХСНД, 15ХСНД, 18Г2С, 25Г2С, 15ГФ, lбГС, 14ХГС, а также углеродистые котельные стали l5K, 20К и 25К. Сталь, предназначенная для сварных конструкций, должна дополнительно раскисляться алюминием, титаном и т. п.; при толщине проката более 25 мм должна поставляться в термически обработанном состоянии (отожженная или нормализованная).
Устранение внутренних напряжений, возникающих при сварке, и изменение структуры и свойств наплавленного и основного металлов в зоне термического влияния достигается последующей после сварки термической обработкой. Внутренние напряжения снимают общим или местным высокотемпературным отпуском при 600-650 °С. Общий отпуск сварных конструкций производят в печи. Нагрев при местном отпуске (например, трубопроводов) осуществляется переносными термическими печами, специальными высокочастотными индукторами. Местный отпуск не устраняет полностью напряжений, вызываемых сваркой.
Новым методом термической обработки сварных соединений является локальный импульсный отпуск, при котором сокращается длительность процесса, снижается твердость, понижается температура хладноломкости и получается однородная структура, не отличающаяся от структуры основного металла. При таком методе зона термического влияния сварного соединения помещается в зазоре между медными зажимами сварочной машины, охлаждаемыми водой. На зажимы подается импульс сварочного тока для нагрева зоны термического влияния до температуры Ас3 + (30-40 °С). Далее подаются импульсы тока с таким расчетом, чтобы обеспечивалось медленное равномерное охлаждение зоны термического влияния со скоростью ниже критической при переходе точки Ar3 . При температуре на 30-40 °С ниже точки Ar3 прекращают подачу тока; общая длительность составляет 10- 11 с. В большинстве случаев в сварных конструкциях из низкоуглеродистых сталей внутренние напряжения снимать не требуется, так как они существенно не влияют на прочность конструкций. Повышение прочности при переменных нагрузках сварных конструкций из низкоуглеродистых сталей достигается обкаткой роликами или обдувкой дробью. После такой обработки в поверхностных слоях металла в результате пластической деформации возникают наклеп и напряжения сжатия. Высокий отпуск при 600-650 °С не повышает предела выносливости, а иногда даже понижает его.
Сварка конструкций из легированных сталей сопровождается структурными изменениями в зоне термического влияния (образование мартенсита), в результате которых резко снижается пластичность, возникают значительные напряжения, в связи с чем как в сварном шве, так и в основном металле могут появиться трещины. Поэтому при сварке конструкций из легированных сталей применяют предварительную термическую обработку, термическую обработку в процессе сварки и последующую после сварки (окончательную) термическую обработку.
Предварительная термическая обработка заключается в отжиге (полном, изотермическом или низкотемпературном – смягчающем) и применяется в том случае, если сварке подвергают неоднородный металл, имеющий внутренние напряжения. Сопутствующая сварке термическая обработка заключается в подогреве, осуществляемом до сварки, во время сварки и после сварки (выравнивающий нагрев) с последующим замедленным охлаждением. Последующая после сварки (окончательная) термическая обработка проводится для улучшения структуры сварного шва и зоны термического влияния и получения необходимых механических свойств.
Для снижения твердости и возможности обработки сварного шва на металлорежущих станках производят высокотемпературный отпуск при 550-650 °С.
Термообработка после сварки — Справочник химика 21
Термообработка после сварки [c.279] Термическую обработку в заводских условиях можно выполнять по следующим режимам закалка с отпуском и термообработка после сварки нормализация с отпуском и термообработка после сварки только термообработка после сварки Очевидно, что риск неполучения желаемых свойств является наибольшим при первом и наименьшим при последнем режиме термообработки.
При термообработке после сварки имеют место следующие проблемы. Так, для получения наилучших характеристик ударной вязкости металла сварного шва температура термообработки должна соответствовать ее верхнему пределу. С другой стороны, слишком высокая температура (или очень длительный нагрев) будет снижать предел текучести и длительную прочность стали
Основной металл Метод сварки Сварочный материал Вид термообработки после сварки Ф. [c.86]
При соединении частей вала требуется его термообработка после сварки и проточка наставки после удлинения. [c. 161]
Наиболее опасны разрывы трубопроводов или их элементов с низкой ударной вязкостью или не прошедших необходимую-термообработку после сварки, так как при этом может произойти полный разрыв трубопровода по окружности, сопровождаемый интенсивным истечением газов. [c.66]
Эти статьи служат примером важности проблемы свариваемости сталей и обеспечением механических свойств, связанных со сварными соединениями, которые не подвергаются термообработке после сварки. [c.281]
Сварной образец поперечный стыковой шов сварка методом Т16 с использованием электрода. Повторная термообработка после сварки до состояния Тб. Образец анодированный Часть одного образца отсутствовала. 5 С образца сошло 80 % плакировки. Сошло 10 % плакировки. Плакировка толщиной 0,078 мм. Сошло 15 % плакировки. Образец после сварки методом Т и старения. Сварной поперечный стыковой шов сварка с использованием проволоки 7039. » Плакировка толщиной 0,061 мм. [c.386]
Значительное влияние на выбор металла оказывает характер агрессивной среды [189]. Для ряда сред выбор соответствующего им металла является совершенно обязательным условием для создания работоспособной конструкции. Нередко необходима термообработка после сварки. [c.18]
Перлитные стали могут подвергаться охрупчиванию около концов сварочных трещин в том случае, когда термообработка после сварки проводилась при слишком низкой температуре. В одном широко известном случае [53] охрупчивание такого вида (главным образом в металле шва) привело к хрупкому разрушению сосуда при гидравлич еском испытании. При уровне наших знаний на сегодняшний день еще нельзя достаточно точно обосновать выбор для сосудов стали из различных имеющихся в нашем распоряжении высокопрочных легированных сталей. Однако стали, требующие более высоких температур отпуска, предпочтительнее, поскольку допускают большую свободу выбора температуры термической обработки после сварки.
Исключение образования трещин в результате релаксации остаточных напряжений для толстостенных сосудов высокого давления стало проблемой возрастающей важности и первейшей необходимости. В сосудах давления из перлитной стали образование трещин обычно происходит в процессе термообработки для снятия остаточных напряжений. Не исключена также возможность образования трещин в толстостенных сосудах во время их эксплуатации при высокой температуре, так как для жестких сварных соединений некоторых легированных сталей температура термообработки после сварки в интервале 600— 650° С недостаточна для полной релаксации напряжений. В случае аустенитных сталей основная проблема связана с исключением образования трещин в стыковых швах толстостенных трубопроводов в результате взаимодействия приложенных и остаточных напряжений в процессе эксплуатации при высокой температуре. [c.221]
В процессе производства сосудов давления опасность возникновения таких чешуйчатых трещин появляется во время приварки к толстостенным обечайкам несквозных штуцеров или других деталей.
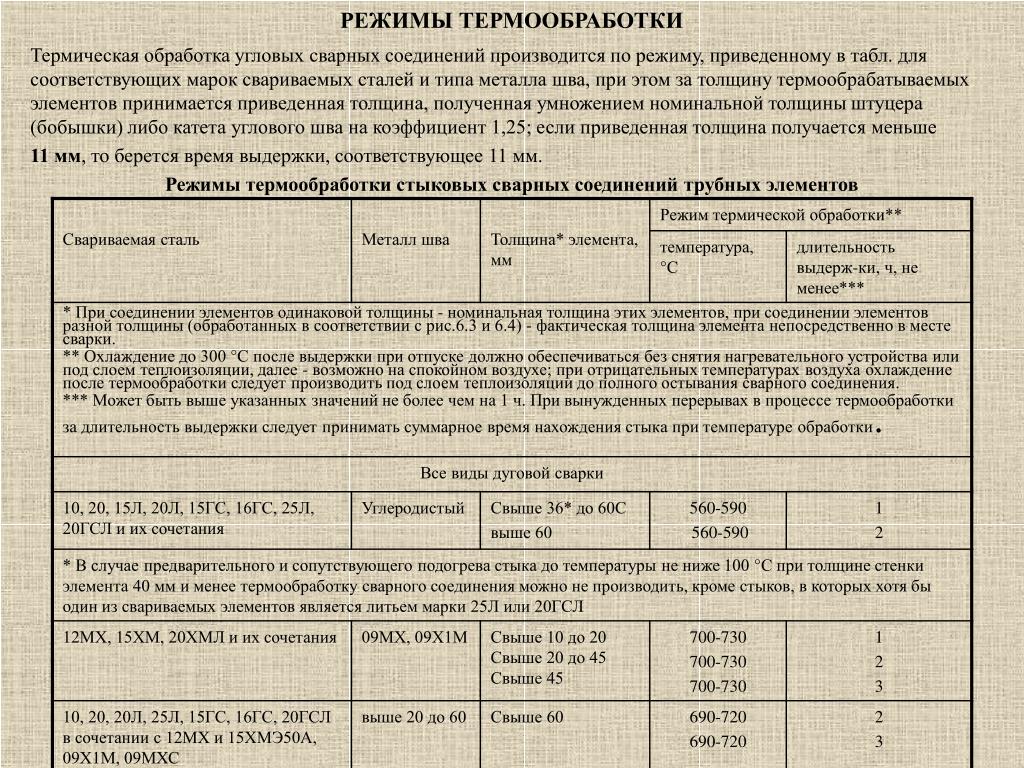
С одной стороны, термообработка после сварки не только снимает напряжения, но и может уменьшить максимальные значения твердости в зоне термического влияния сварки и неблагоприятное влияние сварки на механические свойства основного материала. С другой стороны, неправильно назначенный режим термообработки может ухудшить свойства стали. В случае аустенитных сталей, где важна коррозионная стойкость, соответствующая термообработка может восстановить способность стали сопротивляться таким видам коррозии, как общая, точечная, и коррозии под напряжением. В то же время выбор неправильной температуры термообработки может привести к выделению карбидов и другим эффектам, снижающим механические свойства, а также коррозионную стойкость. [c.280]
Термообработка до сварки Вид сварки Термообработка после сварки и механические свойства Покрытие Среднее время до разрушения, сутки [c.134]
На коррозионную стойкость хромоникелевых сталей большое влияние оказывают условия термообработки. Наивысшая коррозионная стойкость достигается при закалке на твердый раствор с быстрым переходом зоны температур 500—800° С. При медленном охлаждении или повторном нагреве в интервале указанных температур пересыщенный твердый раствор частично распадается с выделением по границам зерен карбидов хрома. В результате коррозионная стойкость металла резко снижается. Поэтому сварные швы и околошовные зоны аппаратов из нержавеющей стали, не прошедших повторную термообработку после сварки, наиболее подвержены коррозии. [c.171]
Часть испытания по согласованию с заказчиком может быть снята. Технологические вопросы, касающиеся режимов термообработки, свариваемости, термообработки после сварки и др. , решаются в зависимости от выбранной марки стали, условий изготовления трубопровода и режима эксплуатации. В этом случае необходимые рекомендации могут быть получены в специальной литературе 127], [42], [57]. [c.259]
Необходимость термообработки после сварки элементов из вновь вводимых марок легированной стали устанавливается при согласовании применения указанных марок сталей. [c.989]
Акустико-эмиссионная (АЭ) диагностика в настоящее время широко применяется при диагностировании и проведении испытаний оболочковых конструкций. АЭ проводится при нагружении объектов со скоростью, при которой не возникают помехи, Нагружение проводится ступенями 50, 65, 85 и 100 % от максимального испытательного давления. Время выдержки на каждом из уровней составляет 10 мин, конечная выдержка -30 мин. При испытании новых сосудов, не прошедших термообработку после сварки, возможна регистрация АЭ, вызванная выравниванием напряжений и не связанная с развитием дефектов. Поэтому при первом нагружении принимают во внимание только сигналы большой амплитуды и сигналы, регистрируемые в течение выдержки. Если при первом нагружении вы- [c.136]
Были проведены теоретические и экспериментальные исследования по вварке штуцеров в рулонированные сосуды, проведен анализ переходных термических напряжений, срока службы в условиях меняющихся давлений и температур, а также методов термообработки после сварки. Таким образом рулонированные сосуды по конструкции и по качеству изготовления пригодны для применения в любых рабочих условиях. [c.23]
Предварительный контроль предусматривает проверку качества сварочных материалов, состояния сварочного оборудования. Пооперационный контроль включает проверку качества подготовки и сборки деталей под сварку, соблюдения режимов предварительного подогрева, режимов сварки и порядка выполнения многослойных швов, проведения термообработки после сварки. Контролю внешним осмотром подвергают сварной шов и прилегающую к нему зону шириной 20 мм по обе стороны от шва по всей протяженности сварного соединения. При внешнем осмотре проверяют качество поверхности сварных соединений. В сварных швах не допускаются следующие виды наружных дефектов трещины, подрезы и резкие переходы от основного металла к металлу шва, прожоги, наплавы, незаплав- [c.238]
В деталях сечением более 20 мм, сваренных из аустенитных сталей (за исключением молибденсодержащей стали 316 по стандарту AJSJ и сплава инкаллой с 32% Ni и 22% Сг), существует опасность возникновения трещин в результате релаксации напряжений в процессе термообработки после сварки или в течение эксплуатации при определенном уровне приложенных напряжений [32]. Оптимальным выбором материала для толстостенных изделий была бы сталь типа 316, однако при температурах выше 650° С она подвержена ускоренному окислению [33]. Такое катастрофическое окисление обычно связывают с условиями застойной окружающей среды или с контактом с изоляционными материалами, содержащими силикаты натрия или подобные им легкоплавкие вещества. В данных неблагоприятных условиях рекомендуется применять сплав с 32% Ni и 22% Сг, не подверженный окислению в результате наличия обоих вышеуказанных факторов. Проблемы релаксации напряжений и трещинообразования при повторных нагреваниях будут рассмотрены далее. [c.210]
С другой стороны, охрупчивание вследствие деформационного старения может быть устранено или существенно уменьшено термической обработкой после сварки. Это, в свою очередь, значительно снижает риск хрупкого разрушения спокойной раскисленной кремнием и полуспокойной углеродистой и углеродистомарганцевой сталей. Исходя из сказанного, в стандарте В5 1515 для сосудов, подвергающихся после сварки термической обработке, допускаются более низкие рабочие температуры, чем для сосудов, не подвергающихся термообработке после сварки. [c.220]
Поэтому компромиссным решением является использование стали 304 (стандарт ASTM), содержащей 0,08% С (не более). Эта сталь имеет приемлемую коррозионную стойкость во многих окислительных средах. Однако в некоторых европейских стандартах не разрешается применение других материалов, кроме особо низкоуглеродистых и стабилизированных аустенитных сталей. Кроме того, сталь 304 непригодна для использования в плакированных нержавеющей сталью сосудах, подвергающихся термообработке после сварки, так как при этом в нержавеющей стали будет иметь место интенсивное выделение карбидов. [c.224]
Однако использование стабилизирован 1ых сталей оказывается необходимым в любом случае, в том числе и для плакированного листа, если сосуд подвергается термообработке после сварки в обычном интервале температур, поскольку при этом в нестаби-лизированной стали с 18% Сг и 8% N1 происходит выделение карбидов. Стабилизированные стали также предпочитают при выборе материала для службы при высокой температуре вследствие более [c.241]
В другой методике используется принцип автофреттажа, применяемый ранее для изготовления стволов пушек. Этот принцип заключается в изготовлении нескольких цилиндров, надеваемых один на другой с натягом. Первый цилиндр (внутренний) имеет точно определенные размеры. Его сваривают, а сварные швы контролируют обычными неразрушающими методами. Затем таким же образом изготавливают эторой цилиндр, причем его внутренний диаметр точно устанавливают равным внешнему диаметру внутреннего цилиндра с соответствующим допуском, гарантирующим расчетный натяг. Второй цилиндр затем нагревают до температуры, не превышающей температуры термообработки после сварки, и насаживают на первый цилиндр. Операция, несомненно, требует тщательности и соблюдения допусков на диаметры. Эту операцию можно повторять до тех пор, пока не будет получена требуемая толщина стенки сосуда. При расчете общая толщина стенки определяется таким же образом, как в случае однослойной стенки. [c.279]
Дакворс [15] составил перечень закаленных и отпущенных сталей разных марок, производящихся в 1966 г., и отметил, что многие из них имеют одинаковые свойства. В Японии, в частности, большое внимание уделяют свариваемости этих сталей, так как во многих случаях сварка будет проводиться на месте монтажа без термообработки после сварки. [c.281]
Эффект смягчения можно наглядно наблюдать на образцах, у которьЕК термообработка после сварки выровняла микроструктуру твердого металла. При растяжении таких образцов вслед за мягкой прослойкой в определенный момент в пластическую стадию вступают приконтактные участки твердого металла, в то время, как вдали от прослойки этот металл продолжает работать упруго. При дальнейшем нагружении, если аг основной металл на всей длине образца. Однако, локализация деформаций в прикон-гактной области твердого металла остается хорошо заметной (рис. 3.5). [c.58]
Химический состав и механические свойства термически улучшенной никелевой стали 12NU9, вязкой при низких температурах, приведены в табл. 240. Сталь I2Nil9 сваривается применяется газовая, электродуговая сварка, а также электродуговая сварка в атмосфере защитного газа. При толщине свариваемой стенки более 10 мм сталь предварительно нагревают до 100—130°С. Термообработка после сварки не допускается. При обработке стали применяется ковка и отпуск при температуре от 1100 до 850°С. [c.443]
Термическая обработка после сварки — Энциклопедия по машиностроению XXL
Сплав рекомендуется для изготовления деталей, работающих при повышенных температурах (до 400° С) для изготовления деталей, требующих сварки допускающих по своим габаритам термическую обработку после сварки для изготовления крепежных деталей.
Определены механические свойства и чувствительность к надрезу при температуре вплоть до 4 К сварных соединений 22 сочетаний деформируемых и литейных алюминиевых сплавов и различных их состояний, разных видов полуфабрикатов, марок присадочной проволоки и термической обработки после сварки. [c.189]
Общий уровень прочности сварных соединений, выполненных ЭЛС и ДЭС, сравним с термообработанным основным металлом. При 297 К пределы текучести и прочности сварных соединений без термообработки после сварки 75 % значений этих характеристик основного материала и возрастают до 90 % при 4,2 К. В случае полной термической обработки после сварки (закалка и двухступенчатое старение) прочность сварных соединений (как для ЭЛС, так и для ДЭС составляет 95—110 % от значений для основного материала в интервале температур от 297 до 4,2 К. [c.318]
Повторная термическая обработка после сварки до состояния Тб.
[c.380]
Термическая обработка после сварки — отпуск 600—620° С, но не выше температуры последнего отпуска, предшествующего сварке. Повторные отпуски при сварке (промежуточные и окончательные) не влияют на стабильность свойств сварных соединений. [c.141]
Способ сварки Электроды, проволока Термическая обработка после сварки а а в кГ/мм- а н в кГ/см- нв [c.142]
Сталь хорошо сваривается автоматической и ручной аргонодуговой, точечной и роликовой сваркой как в мягком, так и в упрочненном состоянии, образуя при этом вязкие сварные швы, не требующие обязательной термической обработки после сварки (табл. 12). [c.141]
В последнем случае приходится разрабатывать специальную технологию изготовления деталей при помощи сварки, подбирать оптимальные составы присадочного материала и применять- дополнительные режимы термической обработки после сварки для повышения прочностных свойств сварных соединений.
[c.228]
Применение термической обработки после сварки. [c.115]
Длительность цикла естественного старения крупных деталей обыкновенно ограничивается 20 сутками, но иногда этот срок уменьшается или увеличивается в несколько раз в зависимости от конфигурации и назначения детали. При обработке металлоконструкций также возникает необходимость в снятии напряжений сварных швов. Металлоконструкции, изготовленные из сталей, обладающих плохой, ограниченной и удовлетворительной свариваемостью, подвергаются термической обработке по режиму стали до и после сварки. При хорошей свариваемости материала металлоконструкции, работающие в условиях статиче ской нагрузки, термической обработке не подвергаются. При динамической нагрузке проводится термическая обработка после сварки по режиму стали. Борьба с внутренними напряжениями заготовок ведется главным образом путем улучшения технологичности конструкций деталей и введением операций старения.
[c. 398]
Термическая обработка после сварки [c.118]
Термической обработке после сварки должны в обязательном порядке подвергаться сварные соединения труб и фасонные сварные детали, изготовленные из углеродистой стали при толщине стенки более 35 мм. Сварные соединения труб и фасонных литых и кованых частей из перлитных жаропрочных сталей подвергают обязательной термической обработке независимо от толщины стенки. [c.205]
Как правило, возможность появления трещин в сварном соединении и степень изменения свойств отдельных участков зоны термического влияния с увеличением легированности стали повышаются. Поэтому наиболее широко применяемые в энергомашиностроении легированные стали требуют при сварке соблюдения ряда технологических ограничений, связанных с введением подогрева изделия и термической обработки после сварки, жестко регламентированных сварочных режимов и т. д. При этом для каждой марки стали, намеченной к использованию в сварной конструкции, необходимо проведение большого объема исследования, связанного с выбором сварочных материалов и оценкой работоспособности сварных соединений в условиях работы конструкции.
[c.20]
Отличительной особенностью изготовления сварных узлов арматуры, и в первую очередь паровой арматуры высокого давления из литых и кованых элементов, является необходимость сварки деталей с большой толщиной стенок. При выполнении последних из перлитных теплоустойчивых сталей необходимо применение высокого подогрева и, в ряде случаев, немедленного отпуска после сварки. При сварке узлов из аустенитных сталей подогрева не требуется, но термическая обработка после сварки является обязательной. [c.183]
Необходимость в термической обработке после сварки сталей I и II групп определяется назначением конструкции [c.24]
Электрошлаковая сварка. . Термическая обработка после сварки. ……….. [c.531]
Разработаны многочисленные способы конструктивного и технологического характера, позволяющие повысить прочность термическая обработка после сварки, искусственное утолщение сечений элементов в зоне сварных соединений, различные виды последующей механической обработки и др.
[c.132]
Коэффициент прочности стыковых сварных соединений, выполненных любым допущенным способом автоматической, полуавтоматической или ручной сварки, обеспечивающим полный провар по всей толщине стыкуемых элементов, при условии проведения в необходимых случаях термической обработки после сварки и контроля качества шва по всей его длине неразрушающими методами принимается следующим [c.139]
При изготовлении труб из стали иных марок необходимость термической обработки после сварки и гибки указывается в чертеже. [c.386]
При дуговой сварке для предупреждения межкристаллитной коррозии сварных соединений рекомендуется сварка на малых погонных энергиях (q/V e, Дж/см) с применением теплоотводящих медных подкладок в целях получения жестких термических циклов и уменьшения времени пребывания металла при высоких температурах термическая обработка после сварки нагрев до температуры 1100 «С и закалка в воду. При нагреве происходит растворение карбидов, и закалка фиксирует чисто аустенитную структуру.
[c.277]
При применении в связи с эксплуатационной необходимостью металлов с пониженной свариваемостью проектировать конструкции следует с учетом этого свойства. Для сведения к минимуму неблагоприятных изменений свойств металла сварного соединения и исключения в нем дефектов необходимо применять виды и режимы сварки, оказывающие минимальное термическое и другие воздействия на металл, и проводить технологические мероприятия (подогрев, искусственное охлаждение и др.), снижающие влияние на него сварочных воздействий. Термическая обработка после сварки (нормализация, закалка с отпуском и др.) может в значительной степени устранять неоднородность свойств в сварных заготовках. Прочность зоны сварного соединения может быть повышена механической обработкой после сварки прокаткой, проковкой и др. [c.288]
Таким образом, на стадиях проектирования, изготовления и монтажа сварных конструкций необходимо принимать меры по уменьшению влияния сварочных напряжений и деформаций.
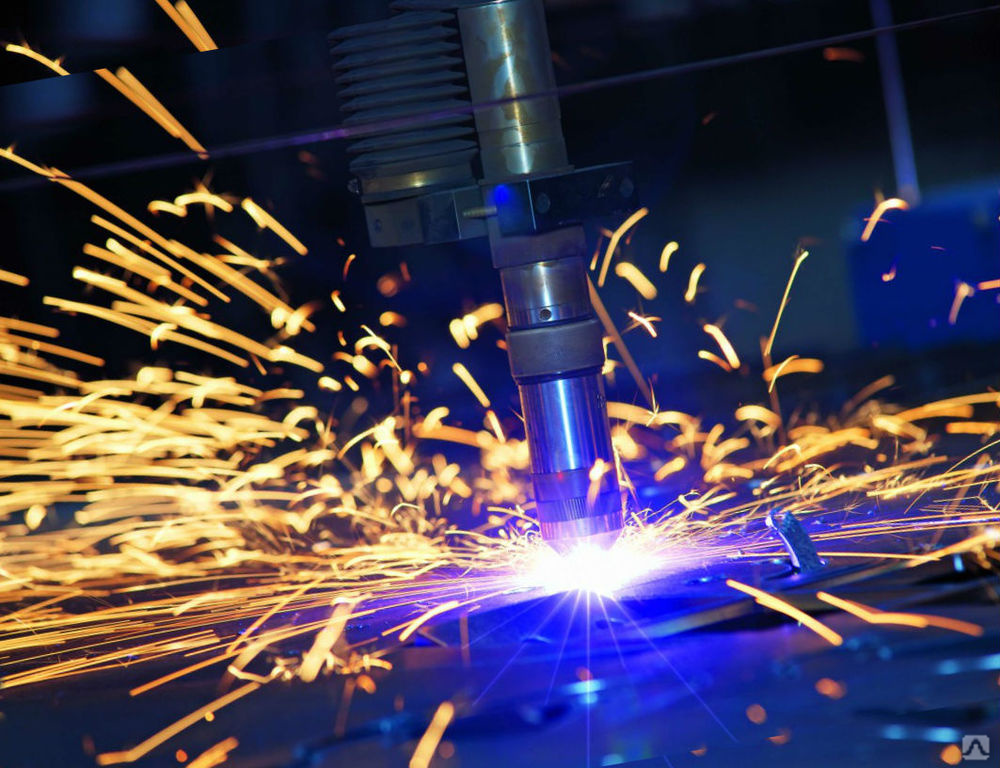

Ко второй группе материалов относятся титан и его сплавы. Если сплавы после изготовления деталей пройти прокопку и отжиг, то термической обработке после сварки они не подвергаются. Если сплавы прошли ранее упрочняющую термическую обработку (закалку и старение), то перед сваркой металл закаливают или отжигают, а после сварки подвергают закалке и старению. К этой группе относятся сплавы с (а + Р)-структурой. [c.244]
Как показано в п. 6, более высокая прочность сварных щвов по сравнению со сталью аналогичного состава с повышением температуры и длительности испытания становится менее выраженной, а при предельных для того или иного состава их значениях шов может даже стать менее прочным, чем основной металл. Эта зависимость, в наибольшей степени проявляющаяся в швах, не подвергавшихся термической обработке после сварки, связана, очевидно, с развитием процессов разупрочнения. Она может быть прослежена с известной степенью приближения по показанным на рис. 102 кривым изменения твердости металла шва при длительном старении. Для швов типа Э-50А (рис. 102, а), обладающих
[c.181]
Положение шва Термическая обработка после сварки в- кгс/мм- Место разрыва [c.207]
Еще более важное значение имеют эти вопросы при сварке среднелегированных и высоколегированных сталей. Удовлетворительного качества соединений в этом случае можно достигнуть применением специальных электродов при узких пределах режима сварки, предварительным или сопутствующ,им подогревом и термической обработкой после сварки. [c.252]
Термическая обработка Без термической обработки после сварки 1 U 1 и о 3″ ю 5 СМ 1 и о а ГТ X 1 1 S8 Ч ю [c.251]
Для повышения прочности сварных соединений в узлах и конструкциях, которые не могут подвергаться термической обработке после сварки, рекомендуется применять усиливающие накладки, приваренные к основному материалу точечной сваркой. Такой же метод конструктивного упрочнения сварного соединения можно применять и при роликовой сварке.
[c.255]
Кольцевые швы между обечайками, а также между обечайкой и днищем или фланцем выполняют многослойными. Кромки монолитных днищ и фланцев из сталей 22ХЗМ или 20Х2МА также подвергают предварительной наплавке с целью исключения необходимости термической обработки после сварки кольцевых швов. Сварочные напряжения в этих швах в значительной степени снимаются при обязательном приемочном испытании готового сосуда в результате нагружения внутренним давлспн1 м, превышающим рабочее. [c.294]
Таким образом, стабильность иикельхромомолибденового твердого раствора сплава Х15Н55М16В, а-следовательно, и сопротивляемость его МКК, может быть существенно повышена за счет повышения его чистоты по содержанию углерода, железа и особенно кремния. Этот вывод справедлив и для сплава системы № — 15%, Мо — 25% Сг [М. С учетом этих положений создан спл ав ХН65МВ (ЭП-567), содержание углерода, кремния и железа в котором ограничено соответственно 0,03%, 0,15% и 1,0% [135, 123]. Сварные соединения такого сплава (G — 0,03%, Si — 0,11%, Fe — 0,3%) при толщине листа до 10 мм не подвержены МКК и не требуют термической обработки после сварки. При больших толщинах рекомендуется использовать сплав с еще более низким содержанием углерода (0,01%) и кремния (0,06%) [87].
[c.151]
Расчетный коэффициент прочности цилиндрического элемента ф принимается равным наименьшей из следующих величин фев, фц фа, Фк-Коэффициенты прочности сварных соединений, выполненных любым допущенным способом, обеспечивающим полный провар по толщине, при условии проведения в необходимых случаях термической обработки после сварки и контроля качества шва по всей длине неразрущающими методами принимаются [c.248]
Монтажные стыки трубопроводов нагревают в процессе термической обработки после сварки при помощи переносных муфельных печей сопротивления, индукторов или иропан-бутановых горелок. Наиболее совершенный из всех применяющихся способов нагрева стыков — индукционный. Частота тока низкая, поэтому прогрев получается сплошным. Термическую обработку сварных стыков поверхностей нагрева производят при помощи газовых горелок. На рис. 5-14,г сварной стык обозначен цифрой I. Рядом с ним располагают асбестовый манжет, под который направляют пламя газовой горелк . Манжет обеспечивает более равномерный нагрев сварного стыка.
[c.209]
В практике изготовления конструкций могут встречаться сварные соединения различных 12-процентных хромистых сталей между собой. В этих случаях целесообразно применять сварочные материалы, предназначенные для менее легированной стали. Так, например, в сварном соединении сталей 1X13 и 15Х12ВМФ между собой могут использоваться электроды типа ЭФ-13, предназначенные для сварки стали 1X13. Режим термической обработки после сварки обычно выбирается по более легированной составляющей. [c.32]
Для сварки изделий, работающих в контакте с агрессивной средой при температуре до + 360°С и пе подвергающихся термической обработке после сварки. Для сварки второго слоя шва облицовки двухслойной стали и наплавки поверхностей фланцев, люков и т. п. для второго и последующих слоев, работающих при температуре до + 360°С при наличии требования по стойкости металла шва к межкристаллитпой коррозии.
[c.359]
Сварки конструкций из сталей 08Х17Н13М2Т, 10Х17Н13МЗТ и др., работающих в агрессивных средах при температуре до 360 °С и не подвергающихся термической обработке после сварки [c.122]
Монтажные стыки трубопроводов нагревают в процессе термической обработки после сварки при помощи переносных муфельных печей сопротивления, индукторов или пропано-бутано-вых горелок. Наиболее совершенный ив всех применяющихся способов нагрева стыков—индукционный. Принцип индукционного нагрева сварных стыков такой же, как и при нагреве стали в случае индукционной поверхностной закалки. Но частота применяемого тока низкая, поэтому лрогрев получается сплошным. На рис. 127, а показан индуктор, применяемый для термической об работки стыков паропроводов. Схема питания индуктора представлена на рис. 127, б.
[c.263]
Выбор аустенитных сталей для сварных высокотемпературных конструкций определяется условиями их изготовления и эксплуатации. Для изделий, работающих до 500° С, в которых данные стали применяются как нержавеющие (например, в атомных и химических установках, регенераторах газовых турбин и т. д.), ограничений в выборе состава нет. Наиболее целесообразным является для них использование стали марки Х18Н10Т. Изделия указанного типа термической обработке после сварки, как правило, не подвергаются. В целях уменьшения веса конструкции можно использовать для работы до 500° С и более прочные стали на базе 18-8, дополнительно легированные ванадием, азотом и другими элементами, а также феррито-аустенитные стали повышенной прочности. [c.216]
Термообработка при сварке металла | Сварка своими руками
Печь для термообработки
Термическая обработка (ТО) – процесс нагрева металлических изделий до критической точки по превышению которой меняется микроструктура и характеристики металла; выдержка и последующее резкое или медленное охлаждение.
Часто задают вопрос, можно ли варить термообработанную сталь? Термообработка не влияет на свариваемость. Можно варить как закаленную, так и «сырую» сталь, либо отоженную сталь.
ТО допускается до, во время и после проведения сварочных работ.
Часто используемые виды термообработки для стали
Отжиг – снимает напряжения, улучшает пластичность, формирует мелкое зерно. Температура (650±10) оС. Время выдержки рассчитывается в зависимости от максимальной толщины детали и усредненно составляет 2,5 мин. На 1 мм толщины. При отжиге детали всегда охлаждаются вместе с печью.
При полном отжиге детали нагревают до 800-900 оС. Происходит рекристаллизация и упрочнение сварного шва. Время выдержки и условия охлаждения, как и в предыдущем случае.
Данные приведенные здесь являются ознакомительными, точные данные можно почерпнуть из справочника.
Нормализация – процесс очень похожий на отжиг, с одним только отличием – охлаждение делают на воздухе (самоотпуск).
Отдых проводится на низких температурах 200 … 300 оС в течении 2…3 ч. Такая процедура понижает содержание диффузионного водорода и снижает величину внутреннего напряжения.
Все виды ТО проводят в печах с нагревом электросопротивлением в воздушной атмосфере.
Термообработка алюминия
Предварительный подогрев алюминия необходим в следствии его высокой теплопроводности. Образование нормальной сварочной ванны и формирование сварного шва будет затруднено из-за недостатка температуры, которую постоянно «отнимает» тело алюминиевого сплава. Если речь идет о деталях небольших размеров, отсутствие подогрева не будет катастрофичным, но когда имеешь дело, например, с подваркой дефектов крупного литейного корпуса, тогда трудности станут очевидны даже человеку, не посвященному в тонкости сварочного искусства. Подогревать можно как все изделие целиком, так и выполнять местный (локальный подогрев) подвариваемого места ацетилено-кислородными, пропановыми и другими горелками. Так же, возможен подогрев непосредственно во время выполнения сварочной операции при условии, что это осуществимо технически.
Предварительный подогрев применяется так же для некоторых видов сталей, склонных к трещинообразованию (например, 30ХГСА).
Послесварочная термообработка для алюминия представляет собой закалку + старение. Правда подобная ТО чревата большими короблениями. Если ремонтируемые изделия имеют уже готовые чертежные размеры, проведение такой процедуры становится невозможной. В таком случае придется обойтись совсем без ТО, либо применить полумеры: нагрев до температуры старения и выдержка в течение определенного времени (режим подбирается исходя из марки алюминиевого сплава). На что влияет подобная мера вопрос спорный, но это лучше, чем вообще ничего не предпринимать.
Если после сварки нужно повысить пластичность и снизить твердость, целесообразно выполнить неполный или полный отжиг.
Так же нужно понимать, что если вы варите термообработанный алюминий, шов даже при последующей полной ТО, будет мягкий (существенно отличаться от твердости основного металла). Пишите в комментариях, если есть присадочные прутки, которые могут испытывать полиморфные превращения.
ТЕРМИЧЕСКАЯ ОБРАБОТКА СВАРНЫХ СОЕДИНЕНИЙ АУСТЕНИТНЫХ СТАЛЕЙ
Высоколегированные хромоникелевые стали даже при отсутствии дополнительного легирования малыми количествами карбидообразующих элементов (молибден, титан, ниобий и др.) чаще всего не являются однородными аустенитными, а после горячей или холодной прокатки содержат в различных количествах феррит и карбиды. Эти фазы аустенитной стали могут присутствовать одновременно. Наличие феррита и карбидов в аустенитной стали заметно сказывается на свойствах. Часто эти фазовые составляющие снижают коррозионную стойкость сталей, а также отрицательно сказываются на ее пластичности и ударной вязкости. Для получения однофазного аустенитного состояния стали подвергают аустенитизации.
Изменение фазового состояния аустенитной стали, определяющее изменение ее свойств, может быть проиллюстрировано диаграммой на рис. 8. 9. Линия S—Е на этой диаграмме характеризует условия растворения карбидов в аустените при нагреве или выделение их из аустенита при охлаждении. Для аустенитизации сталей с содержанием углерода до 0,1 % нужен нагрев от 750
до 950 °С в равновесных условиях (длительный нагрев). 11ри наличии в стали карбидообразующих элементов интервал температур будет увеличиваться. Поэтому практически при термической обработке температура аустенитизации составляет 1050—• 1150 °С. С другой стороны, при наличии до 1 % С встали типаХ18Н10, закаленной на аустенит, при нагреве до 650 С будут выделяться карбиды, а при недостаточной устойчивости аустенита — емфаза.
Последующий нагрев закаленной аустенитной стали также приводит к фазовым изменениям. Нагрев до температуры 500 °С приводит к выделению из закаленного аустенита карбидов. Это вызывает повышение прочности стали, понижение ее пластичности (табл. 8.1), ударной вязкости и коррозионной стойкости. При более высоком нагреве (850—900 °С) процесс растворения карбидов идет очень медленно, а в стали с активными карбидообразующими элементами растворения вообще не происходит, наоборот, может начаться медленное их выделение. При таком протекании процессов повышение прочности стали и снижение ее пластичности будет меньшим, чем при нагреве до 750 °С. Коррозионная стойкость стали при нагреве до 900 °С повышается и приближается к коррозионной стойкости закаленной стали.
При сварке аустенитных сталей распределение температур в ЗТВ приводит к тому, что в ней создаются участки различного фазового состава. Если учесть, что продолжительность пребывания металла при высокой температуре в ЗТВ невелика, то рассмотренные выше процессы изменения фазового состояния аустенитных сталей при сварке сдвинутся в сторону более высоких температур. Так, чисто аустенитной зоной будет зона, нагревавшаяся при сварке выше температуры 1100 °С. В зоне, нагревавшейся приблизительно в интервале 900—1000 °С, могут остаться частицы нерастворившихся карбидов. Однако эта зона будет близка к чисго аустенитной и по сравнению с более высоко нагревавшейся зоной будет иметь более мелкие зерна аустенита. По свойствам в состоянии после сварки без дополнительного нагрева эти зоны будут характеризоваться повышенной вязкостью и коррозионной стойкостью. Однако, если при эксплуатации эти участки будут подвергаться дополнительному нагреву в интервале 500—650 °С, то в них начнется процесс выделения карбидов из 166
раствора, даже в том случае, если в стали содержатся активные карбидообразующие элементы (титан или ниобий). Правда, при наличии этих элементов потребуется больше времени, но если количество этих элементов близко к нижнему’ пределу, процесс выделения карбидов будет заметным.
Причиной понижения кор
Рис. 8.10 Межкристаллитная коррозия в ЗТВ аустенитной стали |
ных соединений аустенитных сталей, эксплуатирующихся в коррозионно-активных средах при повышенных температурах, их следует подвергать термической обработке, заключающейся в продолжительном (3—5 ч) нагреве при 900 °С. Такой нагрев одновременно с выделением карбидов из аустенита приводит к развитию диффузионных процессов внутри аустенитных зерен и к обогащению хромом приграничных участков зерна, откуда хром перешел в карбиды.
Для таких сварных соединений закалка или нормализация с высоких температур (1000—1150 °С) недопустима, поскольку они приводят к аустенитизации, выделению карбидов и понижению стойкости, к межкристаллитной коррозии в околошовной зоне при 500—650 °С.
Например, сварные соединения стали 08Х18Н10Т, склонные после сварки к межкристаллитной коррозии при эксплуатационных нагревах 650 °С, после стабилизирующего отжига при 875 °С в течение 3 ч при последующем эксплуатационном нагреве при 500 °С в течение 10 000 ч склонности к межкристаллитной коррозии не обнаруживают.
Нагрев до 600 °С приводит к снижению стойкости не только к межкристаллитной коррозии, но и стойкости к коррозионному растрескиванию. Как известно, причиной понижения стойкости к коррозионному растрескиванию изделий из аустенитных и неаустенитных сталей, работающих в коррозионно-активных средах при статических нагрузках ниже предела текучести, является сегрегация атомов водорода.
Для сварных соединений, которые эксплуатируются в коррозионно-активных средах без нагрева (температура до 300 °С), закалка или нормализация с высокой температуры является допустимой.
В зоне сварного соединения, нагретой до 900 °С, можно ожидать некоторое повышение прочности и снижение пластичности, а также коррозионной стойкости металла в результате выделения из раствора карбидов. Для этой зоны послесварочная закалка с температуры 1050—1150 °С будет полезна в целях восстановления свойств. В зоне сварного соединения, нагревающейся до 700 °С, процессы карбидообразования также будут протекать достаточно активно и скажутся на изменении свойств, поэтому для этой зоны закалка также будет полезна.
В остальных зонах сварных соединений аустенитных сталей существенных изменений фазового состояния и свойств не происходит, хотя длительная эксплуатация при температуре 400— 500 °С может вызвать выделение карбидной фазы в дисперсном виде, кратковременный нагрев на эту же температуру при сварке к таким изменениям фазового состояния не приводит.
В заключение можно отметить, что закалка сварных соединений высоколегированных аустенитных сталей является рациональной операцией, если сварные соединения не эксплуатируются 168
Работа разрушения ЗТВ сварных соединений аустенитных сталей при низкой температуре
1 Малопроходиая. 8 Многопроходная. |
Условные обозначения видов сварки: РДС — ручная дуговая; АДС — аргонодуговая; АФС — автоматическая под флюсом.
в коррозионно-активных средах при температуре 500—•
650 °С.
Аустенитные стали целесообразно применять для конструкций, работающих при низких температурах, так как они обладают высокой хладостойкостью и сохраняют ударную вязкость. Наиболее высокую вязкость аустенитных сталей при гомогенном состоянии и их сварных соединений можно достичь аустенитизацией — закалкой с 1050—1150 °С. Аустенитизация сварных соединений хладостойких конструкций рациональна и по другой причине. При недостаточной стабильности аустенита в стали, определяемой ее составом, глубокое охлаждение может привести к распаду аустенита с образованием мартенсита и снижением вязкости. Наличие в отдельных участках ЗТВ сварки карбидных выделений приводит к обеднению аустенита в этих участках легирующими элементами и, соответственно, к понижению его устойчивости. Для повышения устойчивости аустенита в этих участках и, соответственно, повышения (восстановления) их хладостойкости следует проводить закалку на аустенит, при которой выделившиеся карбиды растворяются.
Об изменении ударной вязкости в ЗТВ сварных соединений разных аустенитных хромоникелевых сталей можно судить по данным табл. 8.2.
Если принять, что на расстоянии 12,7 мм от линии сплавления ударная вязкость соответствует ударной вязкости основного металла (см. табл. 8.2), то можно отметить, что на расстоянии 1,6 мм уже имеет место нагрев, снижающий ударную вязкость стали.
О роли термической обработки в изменении ударной вязкости в ЗТВ сварных соединений аустенитной стали типа Х16Н6 можно судить по данным табл. 8.3. Термическая обработка заключалась в закалке в воде с 1000 °С, обработка холодом при —70 °С и отпуск при 250 °С в течение 1 ч. Термическая обработка улучшает хладостойкость ЗТВ сварных соединений. Необходимо отметить очень высокую вязкость и хладостойкость участка сплавления. По-видимому, это связано о высокой температурой нагрева около — шовной зоны, в результате нагрева сталь подвергалась аустенитизации и приобрела высокую вязкость.
Аустенитный металл шва при одинаковом либо отличающемся химическом составе металла шва и основного металла, как правило, имеет более низкую вязкость и хладостойкость, чем свариваемая сталь. Это связано с особенностями кристаллического строения металла шва. В связи с отсутствием перекристаллизации при охлаждении после сварки металл шва имеет сравнительно крупнокристаллическое транскристаллитное строение. Однако аустенитизация, повышая гомогенность металла шва, несколько повышает его ударную вязкость и хладостойкость (табл. 8.4). В то же время высокий отпуск (*~650 °С), проводившийся для
Таблица 8.3 Ударная вязкость, МДж/м®, сварных соединений стали типа Х16Н6
Примечание. |
Таблица 8.4 Работа’разрушения металла шва аустенитных сталей
Примечание. В числителе приведены данные, полученные сразу после сварки, в знаменателе — после термообработки. |
снятия напряжений, а также стабилизирующий отжиг с нагревом до 850 °С ухудшают ударную вязкость и хладостойкость.
Таким образом, для сварных конструкций из аустенитных сталей, работающих при отрицательных температурах, термической обработкой, улучшающей вязкость и хладостойкость, является аустенитизация с нагревом до 1150 °С.
Использование аустенитной стали как жаропрочного материала имеет место в конструкциях, работающих при температурах до 650 °С. В них наряду с хромоникелевой или хромоникелевомарганцевой основой содержится значительное количество элементов (молибдена, ванадия, ниобия и др.), образующих карбидную или интерметаллидную упрочняющую фазу. В целях образования карбидной упрочняющей фазы и для стабилизации аустенита в эти стали иногда вводят повышенное количество углерода (до 0,4 %).
Присутствие в стали карбидов титана, ниобия, циркония, дающих устойчивые труднорастворимые карбиды для гомогенизации аустенита при термической обработке, требуют более высокого нагрева, чем коррозионно-стойкие и хладостойкие аустенитные стали. Чаще всего для аустенитизации жаропрочных аустенитных сталей требуется нагрев до 1200 °С, который может и не обеспечивать полного растворения карбидов. Другой особенностью аустенитных жаропрочных сталей, имеющей значение при термической обработке, является высокая температура (700—800 °С) нагрева — старения, необходимая для выделения упрочняющей фазы. Кроме того, эксплуатация таких сталей при 620—650 °С связана с возможностью выделения упрочняющих фаз из аусте-
нита и изменения в процессе эксплуатации свойств стали. Для того чтобы при эксплуатации жаропрочные аустенитные стали находились в стабильном состоянии и претерпевали минимальные изменения свойств, предэксплуатационной термической обработкой должен быть продолжительный нагрев до температуры несколько выше (на 100—150 °С) температуры эксплуатации. Эффективным является проведение двойного старения — первого при более низкой температуре, близкой к температуре эксплуатации (650 °С), и второго — при 800 °С.
В закаленном состоянии жаропрочная аустенитная сталь имеет наибольшую ударную вязкость, жаропрочность ее также не низкая, что обусловлено высокой степенью легирования аустенита и наличием нерастворившихся стойких карбидов. Однако при старении имеет место существенное повышение жаропрочности благодаря выпадению дисперсной упрочняющей фазы. Вязкость при этом снижается. Двойное старение позволяет получить более высокую вязкость, чем однократное старение. Проведение старения в две стадии при наличии в стали карбидов различной природы приводит к тому, что в объеме стали создаются локальные неупрочненные карбидами зоны. При нагружении эти зоны становятся зонами релаксации напряжений, что приводит к повышению пластичности и ударной вязкости стали.
Термическая обработка сварных соединений жаропрочных аустенитных сталей имеет и некоторые особенности. В сварных соединениях жаропрочных сталей металл шва, как правило, по составу заметно отличается от состава свариваемой стали (табл. 8.5). В металле шва часто содержится значительно меньше углерода, чем в свариваемой стали. В ЗТВ имеются участки, где по-разному прошли процессы растворения и выделения карбидных и интерметаллидных фаз. Все это приводит к тому, что при последующем длительном эксплуатационном нагреве процессы
Таблица 8. Свойства сварного соединения стали 4Х14Н14В2М с металлом шва типа 09Х19Н11ГЗМ2Ф
|
фазовых превращений и связанные с этим объемные изменения и изменения свойств разных участков могут протекать по-разному. Описанное выше приводит иногда к локальным разрушениям по одному из участков ЗТВ. Для получения однородных свойств сварного соединения следует прибегать к высокому нагреву (1150—1180 °С) для аустенитизации. Столь высокий нагрев сварной конструкции практически осуществить трудно, поэтому для аустенитизации проводится более низкий нагрев (1050—1100 или 1075—1125 °С). При 1075—1125 °С обеспечивается более полное растворение карбидов, большая стабильность аустенита, высокие пластичность и ударная вязкость, более равномерные свойства зон сварного соединения, а следовательно, и большая устойчивость к локальным разрушениям.
Повышение стабильности свойств при длительных эксплуатационных нагревах может быть достигнуто в результате старения при 750—800 °С в течение 3—10 ч, проводимого после стабилизации. Правда, в этом случае наблюдается некоторая потеря пластичности и ударной вязкости (табл. 8.6).
Некоторую стабилизацию свойств может дать старение при 650—950 °С в течение 3—5 ч без предварительной аустенитизации (табл. 8.7 и 8.8). Однако в этом случае сохраняется неоднородность свойств сварного соединения и не гарантируется отсутствие локальных разрушений при эксплуатации.
Таблица 8.7 Влияние температуры отжига иа ударную вязкость сварных швов типа 18-8
|
Влияние нагрева на ударную вязкость / аустенитных сварных швов
|
Сварные соединения жаропрочных аустенитных сталей иа неответственных конструкциях и конструкциях с большим запасом прочности можно эксплуатировать без всякой термической обработки после сварки. Естественно, при этом не будут использованы все возможности жаропрочных аустенитных сталей как по уровню свойств, так и по их стабильности при эксплуатации и однородности в зоне сварки.
8.2. ТЕРМИЧЕСКАЯ ОБРАБОТКА СВАРНЫХ СОЕДИНЕНИЙ НИЗКОУГЛЕРОДИСТЫХ СТАЛЕЙ
Низкоуглеродистые нелегированиые стали термической обработке не подвергаются. В некоторых случаях в целях измельчения зерна, снятия следов наклепа, улучшения обрабатываемости резанием эти стали подвергают нормализации. При нормализации также улучшается их хладостойкость. Вопрос о термической обработке сварных соединений этих сталей является более сложным. Рациональной термической обработкой для них является нормализация и высокий отпуск. Назначение того или иного вида термической обработки или отказ от нее определяются многими условиями — толщиной свариваемых элементов, условиями сварки, назначением и условиями работы изделия.
Нормализация сварных соединений может обеспечить некоторое улучшение свойств вследствие перекристаллизации и измельчения зерна, поэтому термообработка рациональна при однослойной сварке под флюсом металла большой толщины, при 174
элекгрошлаковой сварке, при ручной дуговой сварке электродами со стержнем диаметром 5—-6 мм. Нормализация улучшает микроструктуру металла шва и ЗТВ, повышает вязкость металла этих вон и их хладостойкость. Нормализация рациональна при нагреце всего изделия. Локальный нагрев для нормализации толькб зоны сварного соединения может привести к созданию остаточных напряжений растяжения в этой зоне, не меньших остаточных напряжений, возникающих после сварки. Уменьшать скорость охлаждения при нормализации нерационально, так как это не позволяет обеспечивать требуемый эффект — измельчение зерна.
Высокий отпуск сварных соединений низкоуглеродистых сталей не изменяет структурного состояния металла. Его назначение состоит в снижении уровня остаточных сварочных напряжений, которые при эксплуатации могут оказать отрицательное влияние на работоспособность конструкции. Высокий отпуск может быть как локальным, так и общим, скорость охлаждения после локального отпуска желательно ограничить, чтобы снизить величину остаточных напряжений, связанных с локальностью нагрева.
Одним из важнейших условий, определяющих необходимость проведения термической обработки сварных соединений из низкоуглеродистых сталей, является контактирование их со средами, способными вызвать коррозионное растрескивание (щелочи, наво — дораживающие среды). Склонность к коррозионному растрескиванию сварных соединений низкоуглеродистых незакаливающихся сталей определяет наличие упругих или пластических деформаций металла, вызванных внешними или внутренними напряжениями, а чаще их суммой. Внешние напряжения можно изменять, регулируя нагрузку на изделие, а внутренние — технологией сварки либо отпуском после сварки.
Роль технологии сварки может быть различной. Подогрев перед сваркой или в процессе сварки уменьшает градиент температур между зоной сварного соединения и основным металлом и тем самым понижает величину остаточных сварочных напряжений. Многослойная сварка небольшими валиками будет способствовать снижению уровня остаточных напряжений, потому что при сварке каждого последующего слоя будет происходить нагрев предыдущих и соответственно снижение остаточных напряжений. Важно также, при какой температуре окружающего воздуха осуществлялась сварка — низкая температура будет приводить к увеличению температурного градиента и росту остаточных напряжений. тка
До 25
Любая
Любая
Отсутствует
Не требуетеsj
25—45
Многослойная с валиками высотой до 4 мм
Выше —15
Отсутствует
То же
Ниже —15
Отсутствует
Отпуск при 550 °С
100
Не требуется
Автоматическая под флюсом со слоями более 8 мм, электро — шлаковая
Выше —15
Отсутствует
То же
Ниже —15
Отсутствует
Отпуск при 600 °С
100
Не требуется
Более
45
Многослойная с валиками высотой до 4 мм
Выше —10
Отсутствует
Отпуск при 550 °С
150
Не требуется
Ниже —10
Отсутствует
Отпуск при 650 °С
200
Не требуется
Автоматическая под флюсом со слоями более 8 мм
Выше —10
Отсутствует
Отпуск при 600 °С
150
Не требуется
Ниже —10
Отсутствует:
Отпуск при 600 °С
200
Не требуется
Электрошлаковая
Любая
Отсутствует
Нормализация
Таблица 8. 10
Режимы термической обработки сварных соединений из стали 10, работающих в средах, вызывающих коррозионное растрескивание
|
Толщина сварива емого металла, мм | Вид сварки | | Температура, °С | Термообработка | |
| воздуха при сварке | подогрева | |||
Ї4—2б 1 | Автоматическая под флюсом в 1— 2 слоя | Выше —5 | Отсутствует | Отпуск при 550 °С |
100 | Не требуется | |||
Ниже —5 | Отсутствует | Отпуск при 550 °С | ||
100 | Не требуется | |||
26—40 | Многослойная с валиками высотой до 4 мм | Выше —5 | Отсутствует | Отпуск при 550 °С |
100 | Не требуется | |||
Ниже — | Отсутствует | Отпуск при 550 °С | ||
150 | Не требуется | ||||
Автоматическая под флюсом со слоями 8 мм и более | Выше —Б | Отсутствует | Отпуск при 550 °С | ||
150 | Не требуется | ||||
Ниже —5 | Отсутствует) Отпуск при 650 °С | |||
150 | Отпуск при 550 °С | ||||
Более 40 | Многослойная с валиками высотой до 4 мм | Выше 0 | Отсутствует) Отпуск при 550°С | |
200 ) Не требуется | ||||
Ниже 0 | Отсутствует) Отпуск при 650°С | |||
200 | Отпуск при 550 =С | ||||
Автоматическая под флюсом со слоями 8 мм и более | Выше 0 | Отсутствует) | Огоуск при 550 °С | |
200 | Не требуется | ||||
Ниже 0 | Отсутствует! Отпуск при 650 «С | |||
200 | Отпуск при 550° |
Режимы термической обработки сварных соединений
из стали 20 и СтЗсп, работающих вие сред,
вызывающих коррозионное растрескивание
Толщина сварива емого металла, мм | Вид сварки | Температура, °С | Термообработка | |
воздуха при сварке | подогрева | |||
До 20 | Любая | Любая | Отсутствует | Не требуется |
Многослойная с валиками высотой до 4 мм | Выше —10 | Отсутствует | Отпуск при 550 СС | |
150 | Не требуется | |||
—4U | Ниже —10 | Отсутствует | Отпуск при 650 °С | |
200 | Не требуется |
Толщина сварива емого металла, мм | Вид сварки | Температура, °С | ———————— — р ~г | |
воздуха при сварке | подогрева | |||
20—40 | Автоматическая под флюсом со слоями более 8 мм | Выше —10 | Отсутствует | Отпуск при 5$0 °С |
150 | 1 Не требуется 1 | |||
Ниже —10 | Отсутствует | Отпуск при бЬ0°С | ||
200 | Не требуется | |||
Более 40 | Многослойная с валиками высотой до 4 мм | Выше —10 | Отсутствует | Отпуск при 550 «С |
250 | Не требуется | |||
Ниже —10 | Отсутствует | Отпуск при 650 °С | ||
250 | Не требуется | |||
Автоматическая под флюсом со слоями более 8 мм | Выше —10 | Отсутствует | Отпуск при 650 °С | |
250 | Не требуется | ||||
Ниже —10 | Отсутствует] Отпуск при 650 °С | |||
250 | Отпуск при 550 °С |
Режимы термической обработки сварных соединений из стали 20 и СтЗсп, работающих в средах, вызывающих коррозионное растрескивание
|
Толщина сварива емого металла, мм | Вид сварки | Температура, °С | ||
воздуха при сварке | подогрева | Т ермообработка | ||
13—20 | Любая в 1—2 слоя | Выше 0 | Отсутствует | Отпуск при 650 °С |
150 | Не требуется | |||
Ниже 0 | Отсутствует j Отпуск при 600 °С | |||
200 | Не требуется | ||||
21—35 | Многослойная с валиками высотой до 4 мм | Выше 0 | Отсутствует | Отпуск при 600 °С |
200 | Не требуется | |||
Ниже 0 | Отсутствует | Отпуск при 600 °С | ||
200 | Отпуск при 550 °С | |||
Любая в 1—4 слоя | Выше 0 | Отсутствует | Отпуск при 650 °С | |
200 j Отпуск при 550 °С | ||||
Ниже 0 | Отсутствует | Отпуск при 650 °С | |||
250 Отпуск при 550 °С | ||||
Более 35 | Многослойная G валиками высотой до 4 мм. | Выше 5 | Отсутствует | Отпуск при 600 °С | |
250 | Отпуск при 550 °С | ||||
Ниже 5 | Отсутствует | Отпуск при 650 °С | |||
250 | Отпуск при 550 °С | ||||
Слоями более 7 мм | Выше 5 | Отсутствует) Отпуск при 650 °С | ||
300 | Отпуск при 600 °С | ||||
Ниже 5 | Отсутствует | Отпуск при 650 °С | |||
300 | Отпуск при 600 °С |
Определенное значение для назначения термической обработки имеет содержание углерода в свариваемой стали. У более низкоуглеродистых сталей (сталь 10) предел текучести существенно ниже, чем у стали с более высоким содержанием углерода (сталь 20, СтЗ). В первом случае он составляет 180 МПа, во втором — 240 МПа. Такая разница приводит к тому, что и рабочие, и остаточные напряжения в сварной конструкции из стали 10 будут ниже, чем в конструкции из стали 20, и условия, влияющие на проведение термической обработки сварных соединений, будут разными.
Надо учитывать и толщину свариваемого металла, так как с ее увеличением растет величина остаточных напряжений и соответственно увеличивается необходимость проведения отпуска после сварки.
На основании перечисленных факторов, влияющих на величину сварочных остаточных напряжений, в табл. 8.9—8.12 приведены ориентировочные режимы термической обработки сварных соединений сталей 10 и 20.
Обработка сварного шва после сварки: термическая, механическая, антикоррозийная
Нержавеющие стали активно используются в промышленности для изготовления емкостей и трубопроводов под агрессивные жидкости. В быту из этого металла изготавливают кухонные принадлежности и красивые полотенцесушители. Зеркальная поверхность имеет привлекательный вид, а изделие способно служить очень долго. Но чтобы добиться такого эффекта на готовой конструкции требуется правильно обработать сварные швы нержавейки. Если этого не сделать, то места сварки будут иметь желтый и черный цвет, или они могут даже поржаветь.

Основные способы обработки сварных соединений
Наиболее распространенными стали следующие методы обработки сварного шва:
- Термическая. Применяется для ликвидации внутренних остаточных напряжений. Проводится путем локального или общего прогрева.
- Механическая. Зачистка сварных швов после сварки удаляет шлаки и окалину с поверхности соединения.
- Химическая. Состоит из обезжиривания и покрытия защитным слоем. Препятствует возникновению коррозионных очагов. Метод используют для обработки материалов, подверженных коррозии, которым предстоит работать в активных средах.
Способ воздействия выбирают, применяясь к техническим требованиям к конструкции и условиям ее эксплуатации. Часто применяют последовательно все три метода.
Шлифовка механического характера
Нержавеющая сталь характеризуется присутствием высокого уровня коррозийных свойств, которые обуславливают ее активное применение в той среде, где зачастую применяются жидкости. Хотя изделия из подобного материала активно соприкасаются с водой и подвергаются предварительному проведению сварочных работ, со временем их внешний вид существенно не изменяется. Данная особенность прослеживается в результате задействования определенных принципов обработки.
Среди основных вариантов обработки принято выделять механическую шлифовку нержавейки после сварки. В ходе данного процесса устраняется верхний слой оксидной составляющей, образующийся на месте сварки и представляющий собой слабое место во всей конструкции. Также подвергаются устранению различимые переходы цвета и присутствующие неровности в соединении сварки.
Для данного процесса характерна следующая очередность:
- устранение волн в области металлического шва посредством применения толстого шлифовального круга и болгарки, а также нивелирование присутствующих выпуклостей;
- задействование лепестковых кругов для функционирования болгарки; основная цель подобных элементов — более аккуратное проведение работ наряду с большей длительностью процесса и расходованием материалов, что особо актуально для значительных масштабов выполнения работ;
- использование специально разработанного оборудного комплекса в виде шлифовальной машины, в результате работы которой создается одноцветное матовое покрытие;
- обязательное применение респиратора для снижения риска попадания в дыхательные пути абразивной пыли и металлических частиц, которые находятся в воздушном пространстве в течение выполнения работ.
Термообработка
Термическая обработка сварных соединений обязательно проводится после сварки тонкостенных изделий, особо подверженных деформациям под воздействием внутренних напряжений. К таким конструкциям относятся трубопроводы, различные емкости, сосуды давления.
Термическая обработка сварного шва
Проводится термообработка и для большинства ответственных конструкций, таких, как корпуса атомных и химических реакторов.
Заключается термообработка в нагреве детали и ее последующем охлаждении по строго заданному температурному графику.
Зачем нужна
В ходе сварки нагревается небольшая область детали в районе шва. Неравномерный прогрев и приводит к возникновению внутренних напряжений, способных деформировать или даже разрушить деталь. Кроме того, в зоне неравномерного нагрева изменяется структура кристаллической решетки металла, что приводит к ухудшению его физико-механических и химических свойств.
Рядом со сварным швом зона закалки, в которой прочность повышена, а упругость, наоборот, понижена. Ее окружает зона разупрочнения, в которой пластичность сохраняется, а прочность становится ниже, чем была до сваривания.
Термическая обработка сварных соединений призвана восстановить внутреннее строение металла и его свойства, вернуть характеристики прочности, пластичности и коррозионной устойчивости к проектным значениям.
Особенности проведения
Обработка осуществляется при высоких температурных значениях, в диапазоне 600- 1000 °С. Это позволяет преодолеть негативные последствия неравномерного нагрева и приблизить структуру шва и околошовной зоны к структуре самой детали.
Обработка проходит в три стадии:
- Нагревается область рядом со швом.
- Конструкция выдерживается некоторое время в нагретом состоянии.
- Изделие охлаждается в соответствии с графиком обработки.
Процесс термообработки швов на трубопроводе
Существует несколько видов обработки сварного шва. Выбор зависит от конфигурации конструкции, толщины детали и цели, которую собираются достигнуть.
Для каждого вида обработки применяется свой специфический график нагрева, выдержки и охлаждения.
Достоинства и недостатки
К достоинствам обработки нагревом относят:
- Восстановление целевых характеристик прочности и пластичности;
- Снятие внутренних напряжений, обеспечение долговечности шва и всей конструкции;
- Улучшение, при необходимости, этих показателей.
Отрицательные моменты при проведении обработки нагревом следующие:
- Высокие требования к квалификации работников.
- Необратимость процессов. В случае несоблюдения графика термообработки сварных швов исправить брак практически невозможно.
- Требуется дорогостоящее и громоздкое оборудование
- Высокое энергопотребление, низкая экологичность.
В большинстве случаев преимущества перевешивают недостатки.
Что подвергают обработке
Термообработке подвергают сварные швы в ответственных конструкциях. Сюда входят
- магистральные трубопроводы
- сварные конструкции различных механизмов и станков, испытывающих высокие нагрузки
- изделия, которым предстоит работать в сложных условиях эксплуатации.
При термообработке сравнительно небольших изделий используют муфельные печи.
Самодельная муфельная печь
Для обработки нагревом габаритных конструкций применяют нагрев пламенем газовых горелок или индукционный способ. В отдельных случаях применяют радиационный метод.
Термообработку для повышения коррозионной стойкости следует проводить по возможности скорее по окончании сварки.
Параметры проведения процесса
Продолжительность процесса во многом определяется маркой сплава и толщиной заготовки. Для хром-молибденовых сплавов применяют индукционный или радиационный способы нагрева. С увеличением толщины типовая продолжительность нагрева (в минутах) растет:
Толщина детали, см | Радиационный | Индукционный |
2,0 | 40 | 25 |
2,0-2,5 | 70 | 40 |
2,5-3,0 | 100 | 40 |
3,0-3,5 | 120 | 60 |
3,5-4,5 | 140 | 70 |
4,5-6,0 | 150 | 90 |
6,0-8,0 | 160 | 110 |
Индукционный способ требует меньшего времени на обработку, но отличается большими энергозатратами. Перед обработкой следует обязательно выполнить зачистку сварочного шва.
Используемое оборудование
Термообработка сварных швов выполняется с использованием нескольких основных способов, каждый требует своего набора оборудования:
- Индукционный. Требует генератора высокочастотного переменного тока большой мощности. Нагревательным элементом является катушка индуктивности, намотанная поверх участка детали, подлежащего нагреву.
- Радиационный. Используется инфракрасное излучение от нагретой нихромовой проволоки, через которую пропускается сильный электрический ток. Требует мощных источников тока. Может применяться для прогрева материалов со слабыми электромагнитными свойствами.
- Газовый. Наиболее экономичный по энергозатратам способ. Используется специальная горелка. Факел пламени формируется так, чтобы равномерно прогневать зону термообработки.
Выбор метода нагрева проводят, сопоставляя цель обработки, толщину конструкций, характеристики материала и экономические соображения.
Зачистить краску болгаркой
Зачистка металлической поверхности от старой краски невозможна без наличия специальной оснастки. Кроме болгарки, понадобятся специальные насадки, такие как металлические щетки. Щетки делятся на:
По типу крепления различают:
- насадки с резьбовым креплением;
- насадки с фиксирующей шайбой.
Если предполагается удаление старого, многослойного покрытия, подойдут жесткие щетки. Насадки сделаны из витой металлической проволоки и без труда снимают слой старой краски.
Читать также: Чертеж ножа из дерева с размерами
Для обработки поверхности в щадящем режиме выбирайте оснастку из мягкой витой проволоки.
Чтобы снять тонкий слой краски, можно также использовать лепестковый наждачный круг для УШМ. Эта оснастка предназначена чтобы шлифовать деревянные поверхности, но краску она снимет бережно и без проблем.
Также подойдут наждачные круги для болгарок или фибровые диски. Все зависит от площади обрабатываемой поверхности, возраста покрытия, количества слоев и пр.
Зачистить ржавчину болгаркой
Удаление ржавчины с металлических поверхностей болгаркой трудоемкая работа. Кроме УШМ, нужно обзавестись специальной насадкой — жесткой щеткой из витой проволоки. Отметим, что при помощи такой насадки возможно только зачистка. Шлифовать щеткой нельзя, так как на поверхности остаются царапины.
После того как завершена очистка, воспользуйтесь крупнозернистой наждачной бумагой для финишной обработки.
Зачистить сварочные швы болгаркой
Зачистка сварных швов — работа, требующая ответственного подхода. Чтобы не повредить шов, а поверхность выглядела гладкой и аккуратной, нужно сточить его болгаркой.
В процессе зачистки, помните о том, что после процесса обработки должно остаться как можно больше металла на сварном шве. Правильная зачистка сварочных швов возможна при наличии диска толщиной не меньше, чем 3 мм. В противном случае, диск может лопнуть и нанести вред окружающим предметам и здоровью оператора болгарки.
После проведения сварки двух металлических элементов, в пределах 2-3 см от шва остаются окалины и шлак, которые нужно шлифовать. Делать это нужно сразу, ведь когда поверхность покроется краской она должна быть гладкой. А если не зачистить эти места, останутся выпуклости и вид будет испорчен.
Там где трудно или невозможно достать болгаркой, используйте плоское зубило.
Удалить ржавчину с кузова автомобиля
Коррозия — болезнь многих авто, особенно бюджетного сегмента. Запущенные пораженные участки кузова не подлежат восстановлению. Но своевременные действия помогут избежать катастрофических последствий.
Инструмент, который понадобится:
- Болгарка. Для очистки поверхности от ржавчины в гаражных условиях не обязательно нужен профессиональный инструмент. Достаточно и бытовой УШМ.
- Специальная оснастка для УШМ. Щетки чашечного типа с проволокой разной по жесткости, шлифовальные круги.
- Инструмент для ручной очистки.
Действия! Поверхность нужно зачистить от ржавчины при помощи болгарки до голого металла. При этом, старайтесь снять как можно меньше “живого” металла.
Если коррозия образовалась на номере кузова — снимайте ржавчину только вручную, чтобы не повредить номер.
Если коррозионные повреждения кузова не слишком глубокие — обработайте эти места болгаркой до металла и выровняйте поверхность шпатлевкой.
Если на местах поражения после зачистки не осталось сильных углублений, покройте их грунтовкой и подготовьте к покраске.
Как зачистить гаражные ворота от ржавчины
В этом процессе понадобится болгарки и чашечная щетка. С их помощью удаляется ржавчина и поверхность готовится к покраске. Не забывайте про средства защиты: респиратор, защитные очки, перчатки.
Зачистные работы очень трудоемкий процесс, требующий ответственного подхода. От того, как они выполняются зависит вид и прочность изделия, поэтому мы рекомендуем использовать только проверенные болгарки и насадки для них.
Работая с УШМ, не забывайте о технике безопасности. Надевайте защитные очки, шумоизоляционные наушники и защитные перчатки. Работайте в закрытой обуви и одежде. Это убережет от получения травм и нанесения вреда здоровью.
Если необходимы расходные материалы на болгарку: круги, диски и пр. приглашаем посетить сайт ukrabraziv.com.ua. Там вы найдете широкий ассортимент оснастки по доступным ценам. Для заказа воспользуйтесь сайтом или звоните по указанным телефонам.
Надеемся наша статья внесла ясность в процесс зачистки металлических изделий при помощи болгарки. Если остались вопросы, обращайтесь!
Виды термической обработки
Виды термообработки сварных швов различаются по своей цели. Специалисты отличают следующие процессы:
- Отдых. Конструкцию доводят до 300 °С и выдерживают полтора — два часа. Снижает механические напряжения и снижает содержание водорода в материале шва.
- Отпуск. Состоит в нагреве до 700 °С и трехчасовой выдержке. Практически полностью снимает напряжения, дает возможность повысить пластичность.
- Нормализация. Всю конструкцию, включая шов, нагревают до 800 °С и выдерживают 30-40 минут.
Позволяет достичь однородности и мелкозернистости структуры металла. Используется на изделиях малой толщины.
- Аустенизация. Изделие нагревают до 1100 °С и выдерживают 120 минут. Охлаждение проводят при комнатной температуре. Повышает пластичность высоколегированных сплавов за счет преобразования их кристаллической структуры.
- Отжиг. Нагрев до 960 °С, трехчасовая выдержка и остывание при комнатной температуре. Используется для высоколегированных сплавов для повышения коррозионной стойкости.
Индукционный отпуск сварного шва
Подготовка труб к нормализации сварного шва
Как правило, перед термообработкой проводится зачистка сварного соединения.
Полировка нержавеющей стали после сварочных работ
Следующим шагом в комплексе обработки, осуществляемой по отношению к области проведения сварочных работ, является полировка нержавейки после сварки. Следует отметить, что подобному процессу подвергается не только отдельные области изделия, но и вся поверхность изделия в целом, что гарантирует получение блеска окончательного вида.
Полировка обеспечивает еще больший уровень зачистки обрабатываемой поверхности за счет получения цельного и ровного участка, что впоследствии имеет результатом способность противостоять внешнему влиянию жидкостей агрессивного характера.
Поначалу область сварных швов подвергается воздействию диска с вулканитом, цель которого заключается в придании шву необходимой формы и глубины за счет формирования структуры вогнутого образца.
Следующим этапом принято считать нанесение специальной пасты, предназначенной для осуществления полировки. В большинстве случаев применяется паста ГОИ. Основная задача полировочного процесса состоит в достижении зеркальной поверхности с одномоментным отсутствием ранее присутствовавших матовых пятен.
Контроль температуры
При проведении термообработки ключевое значение имеет температура нагрева конструкции. Для контроля температуры применяют:
- Термокарандаш и термокраска. Представляют собой химическое соединение, меняющее цвет по мере изменения температуры.
Наносятся на поверхность изделия.
- Тепловизоры и пирометры. Электронные устройства, дистанционно измеряющие температуру.
Термокарандаши и термокраска – традиционные средства, достаточно трудоемкие в применения и требующие постоянного визуального контроля со стороны оператора и его оперативного вмешательства в случае выхода параметров за пределы допустимых значений.
Пирометр
Тепловизоры и пирометры обладают большей точностью и могут быть встроены в автоматическую систему поддержания постоянной температуры.
Травление кислотами
Максимальный эффект травления нержавеющей стали кислотами достигается при последовательном взаимодействии поверхности нержавеющей стали в ваннах с двумя типами кислот – серной и азотной. Очередность стадий следующая
- Обезжиривание, удаление крупных зацепок, окалины
- Травление в сернокислотной ванне (концентрация 10-12%) или сернокислотной ванне (8% серной кислоты, 4% соляной).
При этом происходит разъедание окалины и шероховатостей на поверхности. Идеальная температура протекания процесса находится между 60 и 80 градусов Цельсия. Контроль этого параметра важен для управления процессом. Продолжительность обработки зависит от марки стали, наличия контролируемого соотношения, концентрации кислот. В случае истощения ванны возможны проявления точечной коррозии. Для примера, сталь с 18% Cr, 8% Ni требует от 23 до 45 минут травления в сернокислой ванне. Сокращения времени обработки в два раза можно добиться, если проводить эту операцию в среде контролируемой атмосферы.
- Промывка в большом количестве проточной воды
- Погружение обрабатываемой детали в ванну, наполненную раствором азотной кислоты и плавиковой (10 – 20, 1-2 весовых процентов, соответственно). При температуре ванны 60 – 70 градусов время обработки 7 – 15 минут.
- Повторная промывка большим объемом водой
Представленный способ является базовым и имеет множество вариаций. Травление в одной азотнокислой ванне, с примесью кислоты плавиковой, увеличивает время травления до 30 минут. Заменителем плавиковой кислоты может выступать фтористый натрий. Увеличение концентрации плавиковой кислоты до 10% позволяет проводить процесс при низких температурных показателях, позволяя избежать предварительного опускания в серную кислоту.
Сокращение времени травления в серной кислоте можно добиться, добавив не более 5% хлористого натрия. Такой ход дает необходимый эффект за 15 минут, но при той же температуре, порядка 80 градусов Цельсия.
Будьте осторожны: если необходимо произвести процедуру, в помещении с недостаточной аспирацией, замените компоненты второго этапа травления. Кислоты выделяют вредные пары при травлении. Предлагается для замены раствор сернокислого железа (7%) и плавиковой кислоты (2%).
Для правильного выбора метода кислотного травления нужно знать, учитывать состояние окисной пленки на поверхности нержавеющей стали. Внешний вид может подсказать о составе пленки. Зеленый цвет окалины говорит о высоком содержании окислов хрома. Соответственно действие кислотных сред будет затруднено и потребует большего времени.
Рекомендуется промежуточная механическая очистка между двумя ваннами, если снятие окалины затруднено.
Другие виды обработки
Кроме термообработки, широко используются также механические и химические виды очистки сварных швов.
Механическая
Проводится с использование проволочных щеток или абразивных дисков. В промышленных условиях щетка, диск или лепестковая абразивная насадка закрепляет в угловой шлифовальной машинке (в быту называемой «болгарка»)
Способом механической зачистки с поверхности соединения удаляют шлаки, окалину, брызги застывшего металла и оксидную пленку.
Механическая обработка сварного шва
Зачистка сварного шва после сварки применяется перед термообработкой или покраской.
Щелочное травление
Обработка поверхности нержавеющей стали расплавом каустической соды называется щелочным травлением. Следует отметить, что при этом процессе происходит разрушение окисной пленки, при этом химикалии не реагируют с металлом. Повышение температуры способствует разъеданию оксидной пленки, улучшая качество обрабатываемой поверхности. Резкое охлаждение в жидкости также способствует улучшению обрабатываемой поверхности.
Добиться 100% результата при этом типе обработки практически невозможно. На металле возможны остаточные плены от окислов хрома, окислов никеля и железа. Среди рекомендаций по окончательной доводке таких дефектов значится кратковременная обработка в азотнокислой ванне.
Методы щелочного травления
Различают следующие методы
- Выдержка в соде. Содержание нитрата натрия должно колебаться в пределах 20-40%, разогретого до температуры 460-500 градусов Цельсия. Травление в такой среде длится в течение 15 минут. Некоторые аустенитные марки нержавеющей стали запрещено нагревать выше 450 градусов. Это может привести к межкристаллитной коррозии. Далее следует этап промывки в большом количестве воды, затем следует 5-минутное опускание в сернокислотную ванну и до 10 минут в азотнокислой.
- Известный в Англии, с первой половины 19 века метод травления, в комплексе с пропусканием электрического тока через протравливаемую деталь. При плотности тока 11 А/м2 достаточно 15 секунд. Данная скорость протекания реакции связана с процессом электролиза. Выделение на катоде натрия и водорода способствуют восстановлению окислов. Восстановленный металл осаждается на поверхности. Данный вид травления позволяет получить обезжиренный металл, характеризующийся чистотой и однородностью. При таком способе используют соду. Возможны вариации с составом и добавлением хлористого кальция. Применяется такой метод для травления плоских, стержневых заготовок, волоченых изделий.
- Обработка гидридами натрия основано на восстановлении воздействием на металл натрием и водородом. Наличие гидрида натрия добиваются взаимодействием водорода и натрия, находящегося в расплавленном состоянии. В расплавленную каустическую соду помещают цилиндр без нижней плоскости. Верхняя плоскость имеет отверстие.
Натрий всыпают в это отверстие, он реагирует на поверхности ванны. Через пятно натрия на каустической соде пропускают струю водорода. Происходит образование гидрида и диффундирование его в объеме ванны. Достижение необходимой концентрации 1-2 % гидрида натрия происходит в контролируемых пороговых значениях. При отсутствии продукта разделения воздуха применяют диссоциированный аммиак. Детали разогревают в такой ванне до 400 градусов Цельсия. Нержавеющие стали показывают хорошие результаты травления при такой методике и продолжительности 4-17 минут. После травления рекомендуется тщательно промыть детали. В случае необходимости произвести дополнительную обработку в азотнокислой ванне. При высокой себестоимости такого метода очевидным его преимуществом является тот факт, что металл не взаимодействует с травителем. Потери металла минимальны. Более низкая температура процесса позволяет сократить расходы на теплоноситель и безопасность проведения операций.
Существуют определенные правила, выполнение которых обязательно для любого из представленных способов. Среди них приоритетные обработка поверхности металла перед травлением, удаление окисной пленки, обезжиривание. Процесс травления не менее важен.
Термическая обработка
«УЗДТ» предоставляет услуги по термической обработке соединительных деталей трубопроводов и деталей различного технического назначения с применением современных технологий. Предприятие оснащено оборудованием, позволяющим оказывать услуги по термообработке деталей из углеродистых, низколегированных и коррозионностойких сталей аустенитного класса.
Отжиг Отжиг — термическая обработка металла, при которой производится нагревание металла, а затем медленное охлаждение. В процессе отжига достигается однородная зернистая микроструктура материала, происходит растворение микровключений, при охлаждении образуется неравновесная структура мартенситного типа.
Твердость металла снижается, растут пластичность и ударная вязкость, снимается наклеп. При отжиге происходят процессы гомогенизации, отдыха металла и рекристаллизации.
Закалка Закалка — термическая обработка стали (сплавов), основанная на перекристаллизации стали (сплавов) при нагреве до температуры выше критической; после достаточной выдержки при критической температуре для завершения термической обработки следует быстрое охлаждение.
Нагрев и охлаждение осуществляется с повышенной скоростью в воде, масле или других жидкостях. Происходит увеличение твердости и прочности, ударная вязкость снижается.
Отпуск Отпуск — термическая обработка стали (сплавов), повышающая вязкость, уменьшающая твердость и хрупкость металла, проводимая после закалки для уменьшения или снятия остаточных напряжений в стали и сплавах или для снижения напряжений после сварки в сварных швах деталей.
В зависимости от требований к изделиям, отпуск проводят при различных температурах:
Низкий отпуск (150÷200 °С) Применяется для инструментальных сталей, деталей, работающих на истирание, структура – отпущенный мартенсит.
Средний отпуск (300÷500 °С) Применяется для рессор, пружин, штампов, пил и сверл по дереву, структура – тростит отпуска.
Высокий отпуск (500÷680 °С) или улучшение Применяется для сварных соединительных деталей трубопроводов и деталей из нержавеющих и прочих легированных сталей для оптимального соотношения прочности и ударной вязкости.
Нормализация Нормализация — термическая обработка, при которой материал нагревают до температуры закалки, выдерживают при этой температуре, а потом охлаждают на воздухе. Сталь в итоге получается более мелкозернистая, а ударная вязкость, прочность и твердость выше, чем при отжиге.
Завод гарантирует соблюдение технологической дисциплины, а также проверку качества проведенных операций термообработки путем обеспечения температурного режима, что подтверждается диаграммами термообработки.
Предприятие обладает следующими термическими мощностями:
Комплекс «Cooperheat 16050»
для локальной термообработки сварных соединений с применением гибких керамических электронагревателей. Рабочие температуры до 1200°С. Проводятся операции отпуска кольцевых стыковых сварных соединений деталей трубопроводов диаметрами от 219 мм до 530 мм и толщиной до 35 мм.
Что такое термическая обработка после сварки (PWHT)?
Что означает термическая обработка после сварки (PWHT)?
Термическая обработка после сварки — это процесс, включающий повышение температуры материала или материалов после процесса сварки. Термическая обработка после сварки выполняется для снятия остаточных напряжений, повышения прочности, увеличения или уменьшения твердости и снижения риска образования трещин. Для проведения термообработки после сварки можно использовать множество процессов нагрева.
Corrosionpedia объясняет термическую обработку после сварки (PWHT)
Термическая обработка после сварки имеет решающее значение для дисперсионно-упрочненных сплавов, которые были сварены, потому что они полагаются на выделения, блокирующие дислокации в кристаллической структуре металла для повышения их прочности и твердости. Эти осадки формируются до нужного размера с помощью процесса термической обработки, известного как искусственное старение. Когда дисперсионно-твердеющий металл подвергается воздействию тепла от сварки, выделения в зоне термического влияния этого металла, вероятно, изменились и стали менее эффективными.Таким образом, важно проводить термообработку этих материалов после сварки, чтобы выделения имели правильный размер и чтобы снизить риск образования более слабого материала вблизи зоны сварки.
Термическая обработка после сварки используется для уменьшения остаточных напряжений после процесса сварки. Сварка, особенно в толстых участках материалов, которые сильно ограничены, вызывает образование остаточных напряжений из-за локального нагрева и быстрого охлаждения во время затвердевания сварочной ванны. Остаточные напряжения, оставшиеся после сварки, могут создать возможность для образования водородных трещин.Для предотвращения этого эти остаточные напряжения должны быть сняты.
Не только остаточное напряжение может вызвать водородное растрескивание, но и чувствительная микроструктура, особенно хрупкая микроструктура, такая как мартенсит или бейнит. Когда сварка выполняется на стали с высоким содержанием углерода, быстрый нагрев и охлаждение в процессе сварки могут привести к образованию этих твердых, хрупких микроструктур. Эти микроструктуры более подвержены водородному растрескиванию, чем феррит или перлит.Чтобы снизить риск водородного растрескивания, используется термообработка после сварки для нагрева стали и медленного охлаждения, чтобы уменьшить количество хрупкой микроструктуры в стали, тем самым снижая риск водородного растрескивания. Это также может повысить пластичность стали.
Что такое термическая обработка после сварки (PWHT)?
Слышали ли вы о термической обработке после сварки (PWHT)? Конечно, есть. Если вы занимаетесь сваркой, вы наверняка слышали этот термин.Но что такое ПХВТ? Когда требуется PWHT? При какой температуре следует проводить PWHT? Термическая обработка материалов может быть очень сложной темой, но когда дело доходит до термической обработки после сварки, она сводится к простой концепции: PWHT проводится для сохранения или улучшения прочности и механических свойств материала, а также для снятия остаточных напряжений. В производстве стали наиболее распространенными процедурами PWHT являются последующий нагрев и снятие напряжения.
При сварке мы подводим достаточно тепла, чтобы расплавить основной материал.Эта повышенная температура вызывает микроструктурные изменения в основном материале, которые могут изменить очень важные свойства материала, такие как прочность на растяжение, твердость, пластичность и ударная вязкость. Степень влияния на эти свойства зависит от химического состава основного материала и скорости охлаждения после сварки. Требования к обработке PWHT обычно диктуются нормами и стандартами, а также любыми особыми требованиями, обусловленными условиями эксплуатации сварной конструкции.
Использование PWHT для производства стали обусловлено необходимостью сопротивления хрупкому разрушению за счет последующего нагрева и снижения остаточных напряжений за счет снятия напряжения.
Последующий нагрев в первую очередь проводится для предотвращения водородного растрескивания (HIC), также известного как холодный крекинг и водородный крекинг (HAC). Для возникновения HIC должны присутствовать три вещи:
- Восприимчивая микроструктура основного материала (обычно из-за высокого содержания углерода)
- Пороговый уровень водорода
- Повышенный уровень стресса (внутренний или внешний)
Для получения более подробной информации по этой теме вы можете прочитать Факторы, влияющие на водородное растрескивание.
Если вы устраните один из трех вышеперечисленных факторов, растрескивания, вызванного водородом, не произойдет. Последующий нагрев позволяет водороду диффундировать из сварного шва и зоны термического влияния (ЗТВ), тем самым уменьшая количество диффундирующего водорода ниже порогового уровня. Для получения дополнительной информации о предотвращении HIC прочитайте Предотвращение водородного растрескивания.
Сварной шов не должен охлаждаться до комнатной температуры до последующего нагрева. HIC произойдет, как только температура материала упадет ниже 200F. Прежде чем это произойдет, деталь должна быть нагрета до определенной температуры и выдержана в течение определенного времени, которое зависит от типа и толщины материала. Это позволяет водороду диффундировать из сварного шва и предотвращает образование холодных трещин при достижении комнатной температуры.
Коды и стандарты определяют температуру и время выдержки. Как правило, вы должны нагревать деталь достаточно сильно, чтобы позволить водороду диффундировать из сварного шва и ЗТВ, но недостаточно сильно, чтобы вызвать какие-либо микроструктурные изменения. Как правило, эта процедура прогрева выполняется при температуре от 300°F до 600°F [149°C – 316°C]. Эта температура поддерживается не менее 1 часа на каждый дюйм [25 мм] толщины материала.Всегда консультируйтесь с кодом, с которым вы работаете, или с ответственным инженером, прежде чем разрабатывать собственную процедуру последующего нагрева.
Графики, показывающие температуры и время выдержки после нагрева и PWHT, должны быть включены во все WPS. Пример такого типа диаграммы показан ниже.
Образец диаграммы PWHT для стали P91. Фактическая температура и время выдержки определяются составом и толщиной материала.
Снятие стресса Другая распространенная цель применения PWHT.Снятие напряжения осуществляется при гораздо более высокой температуре и обычно в течение более длительного периода времени, чем последующее нагревание. Напряжения могут развиваться в сварных соединениях из-за высоких уровней удерживающих и усадочных сил. Эти напряжения могут не привести к мгновенному растрескиванию детали, но значительно снизить усталостную долговечность сварной конструкции или компонента.
Снятие напряжения уменьшит эти остаточные напряжения, которые присутствуют после сварки, тщательно контролируя нагрев детали до определенной температуры, выдерживая ее в течение определенного периода времени, а затем контролируя скорость охлаждения.В отличие от последующего нагрева, температуры для снятия напряжения намного выше. Для большинства углеродистых сталей снятие напряжения производится при температуре 1000–1400 °F [538–760 °C].
Помимо снятия напряжений, PWHT обеспечивает другие преимущества: отпуск, удаление водорода, повышенную пластичность, ударную вязкость и коррозионную стойкость. Однако имейте в виду, что PWHT также может иметь разрушительные последствия, если она выполняется неправильно или на материалах, которые не должны подвергаться термообработке после сварки.
Превышение температуры снятия напряжения может снизить предел прочности при растяжении, уменьшить сопротивление ползучести и уменьшить ударную вязкость.Кроме того, некоторые стали не должны подвергаться термообработке после сварки или, по крайней мере, не рекомендуется. В стандарте AWS D1.1 по сварке конструкций (сталь) указано, что снятие напряжения со следующих распространенных конструкционных сталей не рекомендуется:
- ASTM A514 (обычно называемая сталью T-1 – торговая марка Arcelor Mittal)
- АСТМ А517
- ASTM A709 Класс HPS 100 Вт
- АСТМ А710
Стоит еще раз подчеркнуть, что любая PWHT должна выполняться в соответствии со специальными нормами или стандартами, регулирующими изготовление конструкции или компонента.Несмотря на то, что PWHT выполняется после сварки, он является частью спецификации процедуры сварки (WPS), и в этом документе должны быть приведены четкие инструкции о том, как выполнять PWHT.
Каталожные номера:
Металлы и способы их сварки — Теодор Джефферсон, Горхэм Вудс
Сварка Металлургия и свариваемость Джона К. Липпольда
AWS D1.1/D1.1M:2015 Нормы сварки конструкций – сталь
Литейный цех из нержавеющей стали
Карбиды хрома образуются в нержавеющих сталях по обеим сторонам сварного шва.Эти карбиды образуются там, где металл находится в диапазоне температур примерно 1100–1500 F. Поскольку температура сварочной ванны намного выше этой температуры, а основной металл ниже ее, всегда есть часть свариваемой детали, которая находилась в этом диапазоне температур. . Количество образующихся карбидов зависит от нескольких факторов, включая время пребывания в критическом температурном диапазоне и концентрации углерода и хрома. Поскольку нержавеющие стали по определению содержат большое количество хрома, уровень хрома не является контролируемым фактором.
Карбиды хрома нежелательны, потому что хром в сочетании с углеродом больше не обеспечивает коррозионную стойкость. Результатом является «ножевая» атака вдоль сварных швов. Для сквозных сварных швов атака может проникнуть через стену. Обратите внимание, что «ножевая» коррозия представляет собой особую форму межкристаллитной коррозии, которая возникает в нержавеющих сталях, которые не были должным образом термообработаны (в том числе после сварки). Межкристаллитная коррозия вызывает большую озабоченность в одних агрессивных средах, чем в других.
Выпадения карбида в осадок и связанной с этим подверженности коррозии можно избежать, используя одно или несколько из следующих средств:
- Повторная термообработка сварной детали для растворения карбидов хрома и восстановления максимальной коррозионной стойкости. Эта термическая обработка обычно аналогична термической обработке исходного раствора. Термическая обработка с полным раствором обычно искажает размеры с жесткими допусками и часто ухудшает чистоту поверхности, в зависимости от атмосферы в печи и используемой техники закалки.
- Использование сверхнизких уровней содержания углерода, обычно ниже 0,03 процента.
Теория состоит в том, что карбиды не будут образовываться, если уровень углерода ниже некоторого критического значения. На самом деле, некоторые карбиды образуются даже при низком уровне углерода и в должным образом термообработанном материале, но их очень мало.
- Использование углеродных стабилизирующих элементов, таких как колумбий (ниобий) или титан. Сплавы с добавлением этих элементов подвергаются специальной термообработке с образованием карбидов колумбия (или титана). Таким образом, углерод больше не может образовывать карбиды хрома, оставляя хром свободным для обеспечения коррозионной стойкости.Добавки титана не используются в литых сплавах из-за образования оксидов титана. Оксиды являются нежелательными включениями в металле. Кроме того, титан становится недоступным для образования карбидов, что делает металл «нестабилизированным». Марки подшипников из колумбийского сплава, такие как CF8C, склонны к горячему разрыву, что снижает литейные свойства металла.
- Длительная выдержка в диапазоне температур образования карбида хрома.
Теория состоит в том, что хром будет диффундировать в области с низким содержанием хрома, оставшиеся после образования карбида, тем самым восстанавливая коррозионную стойкость.Этот метод очень редко используется и, возможно, не доказал свою эффективность.
- Использование методов сварки с низким подводом тепла. Эти методы сводят к минимуму время осаждения карбидов, тем самым сводя к минимуму количество переноса хрома в карбиды. Этот подход часто используется, когда обработка раствора после сварки нецелесообразна, например, когда речь идет об обработанных поверхностях.
- Конструкция сварного соединения такова, что околошовная зона не подвергается воздействию агрессивной среды.
Дополнительные пункты, которые следует упомянуть, включают:
- Некоторые считают, что марки со сверхнизким содержанием углерода вообще не нуждаются в термической обработке, что их можно использовать в литом состоянии. Мы категорически не согласны с этим утверждением, поскольку первоначальная термообработка выполняет важные функции, помимо растворения карбидов хрома.
- Некоторые люди отмечают, что стабилизированные марки не могут быть невосприимчивы к межкристаллитной коррозии, поскольку операция сварки может растворять карбиды колумбия, таким образом обеспечивая углерод для образования карбида хрома.Мы согласны с тем, что это возможно, но не видели работ, подтверждающих или опровергающих это.
- Многие тонны как литых, так и кованых нержавеющих сталей были введены в эксплуатацию без PWHT и работали удовлетворительно. Вероятно, это связано с удачным совпадением хороших технологий сварки (минимальная погонная энергия), небольших сварных швов и воздействия сред, не вызывающих межкристаллитную коррозию. Другими словами, обстоятельства не всегда требуют предельной композиции и практики.
Анализ микроструктуры околошовной зоны стали Р92 после сварки и послесварочной термообработки
Khalaj G, Pouraliakbar H, Jandaghi MR, Gholami A (2017) Сварные швы микролегированных сталей методом HF-ERW: новые циклы PWHT, эволюция микроструктуры и улучшение механических свойств. Int J Press Vessel Pip 152: 15–26. https://doi.org/10.1016/j.ijpvp.2017.04.003
Артикул Google Scholar
Ширан М.К.Г., Халадж Г., Поуралиакбар Х., Джандаги М., Бахтиари Х., Ширази М. (2017) Влияние термической обработки на интерметаллические соединения и механические свойства интерфейса сварки взрывом из нержавеющей стали 321–алюминий 1230.Int J Min Met Mater 24 (11): 1267–1277. https://doi.org/10.1007/s12613-017-1519-x
Артикул Google Scholar
Ennis PJ, Czyrska-Filemonowicz A (2003) Последние достижения в области жаростойких сталей для применения на электростанциях. Садхана 28 (3-4): 709–730. https://doi.org/10.1007/BF02706455
Артикул Google Scholar
Хесам Пуралякбар, Мохсен Хамеди, Амир Хоссейн Кокаби, Али Назари, «Проектирование разнородных сварных швов из углеродистой стали CK45 и нержавеющей стали AISI 304», Mater Res, 17 (2014) 1, 106–114, https://doi. org/ 10.1590/С1516-14392013005000170
Артикул Google Scholar
Эннис П.Дж. (2006) Поведение на разрыв при ползучести и сопротивление паровому окислению сварных изделий P92. Материалы при высоких температурах 23(3-4):187–193.https://doi.org/10.1179/mht.2006.013
Vaillant JC, Vandenberghe B, Hahn B, Heuser H, Jochum C (2008) T/P23, 24, 911 и 92: Новые марки для современных угольных электростанций – свойства и опыт. Int J Pres Ves Pip 85 (1-2): 38–46. https://doi.org/10.1016/j.ijpvp.2007.06.011
Артикул Google Scholar
Вухерер Т., Дунджер М., Милович Л.Я., Зрилич М., Самарджич И. (2013) Микроструктурное исследование зоны термического влияния моделируемого сварного соединения стали Р91.Металлургия 52(3):317–320
Google Scholar

Richardot D, Vaillant JC, Arbab A, Bendick W (2000) The T92/P92 Book, трубки Vallourec-Mannesmann
Yatomi M, Fuji A, Tabuchi M, Hasegawa Y, Kobayashi KI , Yokobori T, Yokobori T, Yokobori T (2010)Оценка скорости роста трещин ползучести сварных швов P92 с использованием параметров механики разрушения. J Press Vessel Technol 132 (4): 132–140. https://doi.org/10.1115/1.4001522
Артикул Google Scholar
Yin L, Wang J, Chen X, Liu C, Siddiquee AN, Wang G, Yao Z (2018) Микроструктуры и их распределение в ЗТВ трубопроводной стали X80, сваренной с использованием гибридной лазерной сварки MIG. Мир сварки 62 (4): 721–727. https://doi.org/10.1007/s40194-018-0582-x
Артикул Google Scholar
Фотоввати Б., Уэйн С.Ф., Льюис Г., Асади Э. (2018) Обзор характеристик ванны расплава при лазерной сварке металлов. Adv Mater Sci Eng 2018: 18–18.https://doi.org/10.1155/2018/4920718
Артикул Google Scholar
Пуралиакбар Х., Халадж М.Дж., Назерфахари М., Халадж Г. (2015) Искусственные нейронные сети для прогнозирования твердости ЗТВ с химическим составом и испытанием на растяжение трубных сталей X70. J Iron Steel Res Int 22 (5): 446–450. https://doi.org/10.1016/S1006-706X(15)30025-X
Артикул Google Scholar
Аллен Д.Дж., Харви Б., Бретт С.Дж. (2007) FOURCRACK — Исследование характеристик ползучести сварных швов из усовершенствованной высоколегированной стали. Int J Pres Ves Pip 84 (1/2): 104–113. https://doi.org/10.1016/j.ijpvp.2006.09.010
Артикул Google Scholar
Абэ Ф., Табучи М., Цукамото С., Ширане Т. (2010) Эволюция микроструктуры в ЗТВ и подавление разрушения типа IV в передовых ферритных сталях для электростанций. Int J Pres Ves Pip 87 (11): 598–604. https://doi.org/10.1016/j.ijpvp.2010.08.005
Артикул Google Scholar
Chen X, Chen X, Xu H, Madigan B (2015) Моделирование Монте-Карло и экспериментальные измерения роста зерна в зоне термического влияния нержавеющей стали 304 во время многопроходной сварки. Int J Adv Manuf Technol 80 (5-8): 1197–1211. https://doi.org/10.1007/s00170-015-7024-3
Артикул Google Scholar
Хоррами М.С., Мостафаи М.А., Пуралиакбар Х., Кокаби А.Х. (2014) Исследование микроструктуры и механических характеристик соединений из низкоуглеродистой стали и ферритной нержавеющей стали. Mater Sci Eng A 608: 35–45. https://doi.org/10.1016/j.msea.2014.04.065
Артикул Google Scholar
Shirana MKG, Khalajb G, Pouraliakbarc H, Jandaghic MR, Dehnavia AS, Haimd Bakhtiar (2018) Многослойные сварные соединения Cu/Al/Cu взрывом: характеристика влияния термической обработки на микроструктуру интерфейса и механические свойства. J Manuf Process 35:657–663. https://doi.org/10.1016/j.jmapro.2018.09.014
Артикул Google Scholar
Pouraliakbar H, Jandaghi MR (2018) Механистическое понимание роли интенсивной пластической деформации и последеформационного отжига в поведении при разрушении сплава Al-Mn-Si. Мех Матер 122: 145–158. https://doi.org/10.1016/j.mechmat.2018.04.002
Артикул Google Scholar
Поуралиакбар Х., Джандаги М.Р., Хейдарзаде А., Джандаги М.М. (2018) Прессование в канавках с ограничениями, холодная прокатка и изотермический отжиг после деформации: последствия их синергии для поведения материала. Mater Chem Phys 206: 85–93. https://doi.org/10.1016/j.matchemphys.2017.12.010
Артикул Google Scholar
Бертрам Л.А. (1996) Цифровая функция Рыкалина для сварки. Отчет № SAND-97-8225.Альбукерке и Ливермор — Sandia National Labs, Ливермор, Калифорния, США
Книга Google Scholar
Рыкалин Н.Н. (1952) Die Wärmegrundlagen des Schweissvorganges, Verlag Technik (Pohl H. ed), Берлин, Германия
Tabuchi M, Kondo M, Watanabe T, Hongo H, Yin F, Abe F (2004) Улучшение стойкости к растрескиванию типа IV сварного шва из жаропрочной стали 9Cr за счет добавления бора. Acta Metall Sin 17(4):331–337
Google Scholar
Albert SK, Kondo M, Tabuchi M, Yin FX, Sawada K, Abe F (2005) Улучшение ползучести сталей 9Cr-3 W-3Co-NbV и их сварных соединений путем добавления бора. Metal Mater Trans A 36(2):333–343
Артикул Google Scholar
Кимура М., Ямагути К., Хаякава М., Кобаяши К., Канадзава К. (2006) Микроструктуры ползучести 9-12% Cr ферритных жаропрочных сталей. Int J Усталость 28: 300–308. https://doi.org/10.1016/j.ijfatigue.2005.04.013
Артикул Google Scholar
Зачем нужна термообработка после сварки
Из-за того, что стальная труба, транспортирующая газ или жидкость, должна выдерживать определенное давление, внутреннее напряжение, возникающее в процессе холодной прокатки, должно быть устранено. Процесс сварки, поскольку локальный перегрев вызовет деформацию трубы и усадочное напряжение, поэтому стальная труба возвращается к термической обработке после сварки для устранения внутреннего напряжения.
PWHT основан на твердости стали, толщине свариваемых деталей, жесткости конструкции, методах сварки и условиях использования. Общие характеристики сварки углеродистой стали хорошие, сварка может быть без предварительного нагрева и термической обработки. Но для высокого содержания углерода и высокой жесткости свариваемых деталей требуется предварительный нагрев и термическая обработка, например, для трубы из углеродистой стали толщиной 30 мм.
Метод PWHT
Метод ПТО – электронагрев.Гусеничный электронагреватель и линейный электронагреватель должны быть закреплены на частях, необходимых для ПТО; они соединяются с автоматическим контроллером через кабель. А термопара должна быть закреплена на частях, необходимых для ПТО через компенсирующий проводник. Он соединяется с автоматическим контроллером компьютера. Затем контроллер будет работать автоматически в соответствии с параметром процесса, который вводится в контроллер.
Общие правила для PWHT
- При коррозии сварного шва под напряжением следует проводить послесварочную термическую обработку.
- При сварке стали, склонной к замедленному растрескиванию, следует своевременно проводить термообработку после сварки. Когда термообработка несвоевременна, ее следует нагреть до 200 ℃ ~ 300 ℃ сразу после сварки, а для сохранения тепла и медленного охлаждения диапазон нагрева должен быть таким же, как у PWHT.
- После термической обработки сварки и перед испытанием давлением необходимо провести внешний осмотр и неразрушающий контроль.
- Детали, соответствующие требованиям PWHT, не должны подвергаться сварочным работам, в противном случае они должны подвергаться повторной термообработке.
- Инспектор по сварке должен пройти профессиональную подготовку, а персонал по термической обработке сварки должен соответствовать нормам и инструкциям по сварочным работам для проведения термической обработки.
- При проведении термообработки температура должна быть измерена и записана, положение и количество точек измерения температуры должны быть разумными, а прибор для измерения температуры должен быть квалифицированным и эффективным.
Условия процесса предварительного нагрева и термообработки после сварки обычной трубы
Сталь марки | Предварительный подогрев перед сваркой | Термическая обработка после сварки | ||
---|---|---|---|---|
Толщина стенки (мм) | Температура (℃) | Толщина стенки (мм) | Температура (℃) | |
С | ≥26 | 100~200 | >30 | 600~650 |
C-Mn | ≥15 | 150~200 | >20 | |
Мн-В | 560~590 | |||
С-0.![]() | 600~650 | |||
0,5Cr-0,5Mo | 650~700 | |||
1Cr-0,5Mo | ≥10 | 150~250 | >10 | |
1Cr-0,5Mo-V | ≥6 | 200~300 | >6 | 700~750 |
1.5Cr-1Mo-V | ||||
2.25Cr-1Mo | ||||
5Cr-1Mo | 250~350 | |||
9Cr-1Mo | 750~780 | |||
2Cr-0,5Mo-WV | ||||
3Cr-1Mo-VTi | ||||
12Cr-1Mo-V |
Процесс обработки головки после сварки
Полная термообработка
Сборка труб, которая должна быть обработана после сварки головки в печи для термообработки, насколько это возможно, но компонент не должен быть сварен с клапаном и другими компонентами.
Подраздел термической обработки
Когда к сварным компонентам трубопровода нельзя добавить печь для термообработки, термообработка позволяет сегментировать. В подразделе термической обработки длина повторного нагрева составляет не менее 300 мм, при этом необходимо защитить внешнюю часть печи, чтобы предотвратить вредный температурный градиент.
Местная термообработка
При применении местной термической обработки сварные швы, кольцевой пояс спускной трубы и, где применимо, ответвления должны нагреваться до тех пор, пока заданный температурный диапазон не будет достигнут по всему сечению трубы, постепенно уменьшаясь за пределы пояса, включающего сварной шов или изогнутой или сформированной секции и не менее чем на 25 мм за ее концы.
Правила безопасности PWHT
- Предупреждающая линия безопасности должна быть установлена для предотвращения входа постороннего персонала в процесс термической обработки.
- Оператор должен пройти обучение по термообработке, ознакомившись с техникой работы.
- Легковоспламеняющиеся материалы с дальностью термообработки 30 м подлежат обезвреживанию.
- Обслуживающий персонал должен быть обеспечен средствами индивидуальной защиты, такими как хлопчатобумажные перчатки, темные очки и т.п.
Как восстановить жесткость алюминиевой пластины после сварки?
Как вернуть жесткость алюминиевой пластине после сварки?
В: Когда я привариваю алюминиевый лист от 3/16″ до 1/4″ для кузовов грузовиков, он теряет свою жесткость. То же самое происходит и при изготовлении панелей для кузовов автомобилей. Если я нагрею панели примерно до 400 или 500 градусов и дам им остыть, они станут очень гибкими, и я смогу очень легко сформировать пластины. Как я могу вернуть пластинам жесткость после того, как я закончу их формирование?
A: Алюминиевые сплавы обычно приобретаются в определенном состоянии.В случае сплавов, не подвергающихся термической обработке, это состояние -H, которое относится к упрочненному состоянию материала. В случае термообрабатываемых сплавов это -T Temper, который отражает термическую обработку, которой подвергался материал во время производства. Оба эти метода отпуска используются для придания прочности основному материалу. На упрочняющие характеристики сплавов -H и -T может существенно повлиять нагрев основного материала.
Например, после дуговой сварки наблюдается снижение прочности, а также увеличение пластичности в локализованной области, прилегающей к сварному шву.Эта область была нагрета во время операции сварки до температуры, достаточной в течение времени, достаточного для отжига или частичного отжига основного материала. Тот же эффект будет иметь место при нагреве всей панели. Операция нагрева начнет удалять часть упрочнения, которое было введено операциями отпуска, и снизит предел прочности на растяжение и повысит пластичность материала (формируемость). Чем выше температура и чем дольше время при температуре, тем более выражено воздействие на материал.
К сожалению, нет практического способа восстановить жесткость основного материала готовой детали после того, как он был уменьшен путем нагревания. Теоретически можно упрочнить обработанный материал деформационным упрочнением или термической обработкой, однако из-за процедур, необходимых для выполнения этих операций, это обычно не подходит. Деформационное упрочнение достигается за счет контролируемой физической деформации основного материала, которая обычно включает уменьшение площади поперечного сечения.Термическая обработка для улучшения механических свойств обычно включает нагрев до очень высокой температуры с последующей закалкой в воде, а затем контролируемый повторный нагрев в течение дополнительного периода времени. Послесварочная термообработка алюминиевых сплавов используется в некоторых специализированных приложениях, однако существует ряд важных соображений, таких как деформация изготовленной детали при ее нагреве и охлаждении в очень широком диапазоне температур, практичность физического нагрева и охлаждения. весь компонент и стоимость, связанная с этой сложной процедурой.
В: У меня есть клиент, у которого возникли проблемы с прохождением управляемых испытаний на изгиб на основном материале 5083. Какой присадочный сплав он должен использовать и почему не проходят испытания на изгиб.
A: Основной материал 5083 можно успешно сваривать с 5356, 5183 и/или 5556. Все три из этих присадочных сплавов могут подходить для сварки этого основного материала, однако выбор одного из этих присадочных сплавов зависит от области применения. и требования к обслуживанию свариваемого компонента.Базовый материал 5083 может использоваться в различных областях, включая судостроение, криогенные резервуары, военную технику и строительные конструкции. С точки зрения конструкции, учитывая угловые сварные швы, типичные значения прочности на поперечный сдвиг для этих трех присадочных сплавов составляют 26Ksi, 28Ksi и 30Ksi для 5356, 5183 и 5556 соответственно. Принимая во внимание поперечную прочность на растяжение сварного шва с разделкой кромок, присадочный сплав 5356 обычно используется только на основном материале 5083, когда нет требований к квалификации процедуры сварки с разделочной сваркой.Присадочный сплав 5356 может не всегда обеспечивать минимальные требования к прочности на растяжение, установленные нормами (40ksi – 275 МПа) для испытаний на поперечное растяжение сварного шва с разделкой кромок основного материала 5083.
Присадочный материал 5183, разработанный специально для сварки основного материала 5083, будет соответствовать требованиям к механическим свойствам для аттестации процедуры разделочной сварки. Основной сплав 5556 имеет несколько более высокие механические свойства по сравнению со сплавом 5183 и может использоваться для сварки чуть более прочного основного материала 5456, но также будет соответствовать минимальным требованиям к прочности на растяжение для основного материала 5083.Основной материал 5083 не следует сваривать с присадочным сплавом 4043 или 4047. Не рекомендуется сваривать любой основной материал серии 5xxx с содержанием магния более 2,5% с присадочным сплавом серии 4xxx.
Неудачная проверка управляемого изгиба может быть вызвана рядом причин:
- Наиболее очевидная причина заключается в том, что в сварном шве имеется какая-либо несплошность, которая вызвала разрыв, обычно непровар. Чтобы определить наличие каких-либо существенных неоднородностей, которые могли вызвать отказ, необходимо проверить образец, вышедший из строя.
- Правильно ли проведен тест? Образцы могли быть неправильно подготовлены перед изгибом или, возможно, они были согнуты по неправильному радиусу. Исследование неудавшихся образцов необходимо для подтверждения того, что они были подготовлены в соответствии с соответствующей спецификацией. Процедура испытаний должна быть оценена для определения ее правильности.
- Какой метод тестирования использовался? Метод испытания на управляемый изгиб с закруглением является предпочтительным методом испытания алюминиевых сварных соединений из-за значительных различий в механических свойствах некоторых алюминиевых сплавов после сварки.Метод плунжерных испытаний не рекомендуется для более прочных алюминиевых сплавов, подобных тем, которые вы испытываете.
- Использование неподходящего присадочного сплава, такого как серия 4ххх, используемого для этого основного материала, может привести к получению сварного шва с низкой пластичностью и, следовательно, склонности к разрушению.
Термическая обработка после сварки (PWHT)
Intertek предлагает термообработку после сварки (PWHT) для улучшения микроструктуры сварного шва и снижения остаточных напряжений, возникающих во время сварки.
Intertek специализируется на выполнении PWHT для сталелитейной и металлообрабатывающей промышленности, включая строительство сосудов под давлением, напорных трубопроводов, резервуаров для хранения, зданий, мостов, морских платформ, электростанций, нефте- и газоперерабатывающих заводов и нефтехимических заводов.
Часто существует обязательное требование для PWHT из-за соответствия нормам и спецификациям сварки для определенных материалов, включая, помимо прочего, углеродистую сталь, нержавеющую/высоколегированную сталь и закаленную сталь.Также могут быть требования к PWHT, основанные на толщине стенки свариваемых деталей.
PWHT уменьшает или перераспределяет остаточное напряжение, возникающее в процессе сварки, с помощью метода, который включает нагрев, пропитку и охлаждение свариваемой/обработанной поверхности до контролируемых температур. Это улучшает свойства свариваемой/обработанной поверхности. Другие преимущества PWHT включают:
- Улучшенная пластичность материала
- Повышенная или сниженная твердость
- Снижение риска хрупкого разрушения
- Расслабленное тепловое напряжение
- Закаленный металл
- Удаление диффузионного водорода (
- )
- Улучшенная металлургическая структура
Intertek может выполнять PWHT как на собственных площадях, так и на объектах наших клиентов.Наши локальные объекты включают в себя большие печи, где мы можем размещать многочисленные сварные детали/обработанные поверхности для PWHT. Кроме того, мы предоставляем услуги самовывоза и доставки. Intertek может выполнять PWHT на объектах наших клиентов в любом морском и наземном местоположении, используя наше портативное оборудование.
Наша команда высококвалифицированных и обученных техников PWHT гарантирует, что все сварные детали/обработанные поверхности, предназначенные для обработки, будут соответствовать указанным требованиям правил сварки и соответствовать назначению.
Сотрудничая с Intertek для PWHT, вы также получите выгоду от наших глобальных услуг и опыта. Мы можем обеспечить неразрушающий контроль, который обычно требуется после завершения PWHT, включая испытание на твердость, магнитопорошковый контроль и рентгенографию после стресса. Наши металлургические лаборатории и опытные инженеры с металлургическим опытом дополняют богатство знаний и опыта, необходимых для выполнения любой критической PWHT, обеспечивая при этом полную гарантию качества.
Отправьте нам запросНужна помощь или есть вопрос? +61 (0) 2 8039 8111
.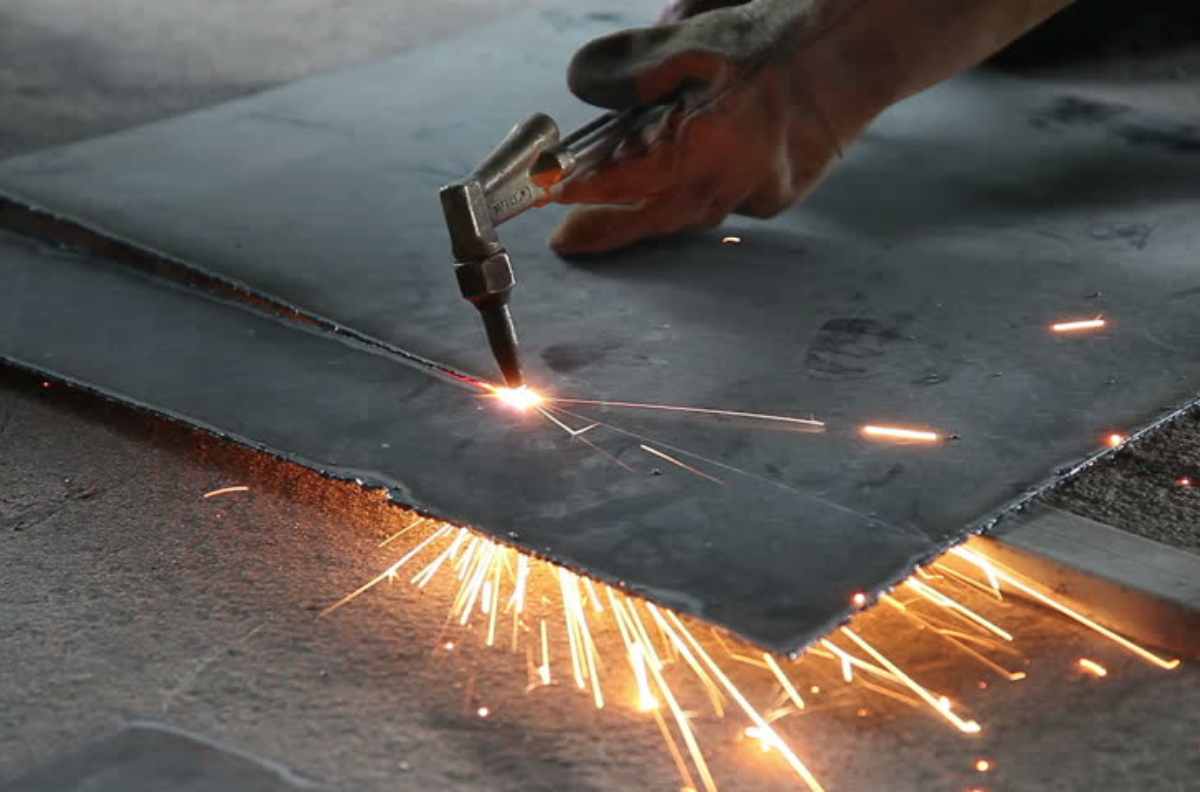