технология, приспособления, операционная технологическая карта на работы по сборке и ручной дуговой – Определенных деталей и элементов на Svarka.guru

Соединения
За период существования сварочной технологии было разработано множество методов соединения. Основным параметром, на который обращают внимание, является взаимное расположение свариваемых элементов после окончания работ. Встречаются следующие виды соединений металлоконструкций:
- встык;
- внахлест;
- тавровое;


Помимо типа соединения, важными факторами являются применяемое сварочное оборудование, толщина элементов, а также вид основного металла.

Узлы
Сварные металлоконструкции используются гораздо чаще, чем металлопрокат на болтовом крепеже. К ним предъявляются требования, согласно СНиПов, которые действуют на конкретном производственном участке. Например, надежность узла при строительстве мостов должна быть более высокой, чем при монтажных работах на печной трубе котельной.
На стадии разработки плана организации работ, инженеры составляют технологическую карту на сварочные работы металлоконструкций, в котором указан оптимальный способ стыковки отдельных элементов. При этом необходимо руководствоваться требованиями ГОСТов. В смету заносится уже чистовой вариант. Идеальными условиями для сварки являются следующие факторы:
- Подавляющее большинство швов выполняются в горизонтальном положении.
- Сварка выполняется специальными роботами с функцией контроля рабочих параметров. Процент выполнения ручных работ минимален.
- При соединении отдельных элементов преобладает стыковой или угловой методы сварки.
Вспомогательное оборудование
Сварить конструкции значительных габаритов невозможно без использования вспомогательных приспособлений, с помощью которых выполняют фиксацию сборочных элементов, а также их подачу к месту монтажа.

- Кондуктор. Обеспечивает неподвижное положение металлопроката при его монтаже. Существуют различные способы исполнения данных приспособлений. Как правило, их внешний вид напоминает стенд или станину. Простейшая конструкция для домашних работ представляет собой устройство для стыковки свариваемых элементов под прямым углом.
- Стапель. Представляет собой грузоподъемное приспособление, выполняющее роль опорного механизма в строительно-монтажных работах. Применение стапелей позволяет увеличить производительность работы со сборными конструкциями.
Требования
К рассматриваемым работам допускают только профессиональных сварщиков. Их уровень квалификации регулируется требованиям нормативно-правовых документов, в зависимости от сложности объекта.
Качество применяемых материалов должно соответствовать ГОСТу 27772-88. В данном межгосударственном стандарте классифицирован стальной прокат, который разрешено использовать при монтажных работах.
На сварочных чертежах металлоконструкций необходимо выполнять полную расшифровку, которая включает в себя:
- тип применяемого металла;
- габаритные размеры;
- способ стыковки элементов;
- применяемое сварочное оборудование


Согласно действующему законодательству, сборка металлоконструкций на всех объектах выполняется под контролем государственных органов технического надзора.
Виды сварки для сборки
Сталь – основной материал для металлоконструкций. Как правило, при монтаже используются обычные марки. Нержавеющую сталь применяют только в случае особых требований технологического процесса, например, на объектах пищевой промышленности.
На конечный результат решающее влияние оказывает режим сварки.
На крупных сборочных предприятиях используют автоматические установки для работы под слоем флюса или защитным газом. В последнем случае используют аргон, азот, гелий и прочие технические газы, а также смеси на их основе. Специфика использования флюса заключается в том, что работы невозможно выполнять под углом. Например, сборку и сварку конструкций из листового и профильного металла можно выполнять с использованием сварочного флюса, а при работе с круглым профилем необходимо использовать защитный газ.
При незначительных объемах работ целесообразнее использовать ручной труд с применением полуавтоматов и прочих аппаратов для ручной дуговой сварки.
Температурный режим процесса
Опытные сварщики знают, какое влияние на рабочий процесс оказывает температура окружающей среды. При отрицательных показателях зону соединения подвергают дополнительной термообработке, для облегчения работ.
При сварке разнородных материалов обрабатывается только термостойкий элемент.
Классические методы для конструкций из металла
Независимо от метода соединения проката существует три режима выполнения работ:
- автоматический;
- полуавтоматический;
- ручной.
Рассмотрим их подробнее.
Автоматический

Данный метод сводит участие человека в процессе к минимуму. Функция оператора заключается в контроле над производственным процессом, а также корректировке вводных параметров, в случае возникновения необходимости. Применяется на крупносерийных предприятиях.
Полуавтоматический
Задачей сварщика является определение оптимальной скорости движения дуги, а также регулировка направления. Подача присадочного материала осуществляется в автоматическом режиме, согласно предварительно настроенных параметров.
Ручной
В этом случае все операции выполняются руками сварщика. При этом существует несколько способов создания неразъемного соединения. Помимо электросварки, в ручном режиме можно выполнить пайку металла, а также работать газосварочным оборудованием.
Инновационные технологии
Времена, когда сварную конструкцию из металла изготавливали исключительно классическим способом позади. Инновационное оборудование прошло этап испытания прототипов и сейчас активно используется на передовых предприятиях.
К современным методам соединения относят:
- трением;
- лазерный;
- ультразвуковой;
- взрывом;
- термитный;
- плазменный.

Наибольший интерес представляет последний способ. Его особенность – использование ионизированного газа, который выполняет функции электрической дуги
. При этом рабочие параметры плазменного генератора гораздо выше.В случае необходимости, простой настройкой можно переориентировать сварочный аппарат под функции резака для металла.
Как обеспечить правильную сборку конструкции
Для получения надежной конструкции необходимо соблюдать следующие правила:
- при выборе проката запрещено отступать от требований проекта;
- необходимо соблюдать очередность монтажных работ;
- каждый элемент должен находиться на месте, предусмотренным чертежом;
- четко соблюдайте величину зазоров и рабочий угол стыковки;
- перед проведением сварочных работ необходимо выполнить подготовительные процедуры, предусмотренные технической документацией.
Заключение
Сварка металлических конструкций относится к категории ответственных работ, которые контролируются органами технологического надзора. На крупных предприятиях сварочные операции выполняются на роботизированных установках, с автоматической регулировкой всех параметров. При небольших объемах работы выполняются вручную.


Технология сварки металлоконструкций
Наиболее известным способом соединения металлических деталей является электросварка. Открыта она была в начале девятнадцатого века В. В. Петровым. Он впервые предложил использовать электрическую дугу для пайки металлов.
Электросварка — один из видов сварки, в процессе которого для расплавления металла используется электрическая дуга. Температура этой дуги достигает 7000 °С, что превышает температуру плавления любого металла.
Описание ручной электросварки
Процесс сваривания металлов между собой достаточно сложный и заниматься им могут только обученные специалисты. В основе процесса лежит действие теплоты электрической дуги. Для электросварки необходимо:
- электрод
- свариваемое изделие (основной металл)
- сварочный трансформатор
- источник электропитания
К свариваемому металлу и электроду подводится электроэнергия от сварочного трансформатора. Под действием температуры электрической дуги основной металл и электрод расплавляются, образую сварочную ванну. Некоторое время она находится в жидком состоянии. Металл электрода смешивается с основным, а образующийся при этом шлак всплывает на поверхность, что создает защитную плёнку. После затвердения металла образуется сварной шов. Для поддержания электрической дуги необходима значительная энергия, которую получают от источников постоянного либо переменного тока.
По степени механизации процесса электросварка разделяется на:
- ручную дуговую
- полуавтоматическую дуговую
- автоматическую
Зависит этот параметр от того, как выполнено зажигание и как поддерживается длина дуги, а также каким образом производятся манипуляции электродом для придания шву необходимой формы. В данной статье рассмотрим ручную дуговую электросварку. Все операции при данном методе выполняются специалистом вручную (без применения механизмов).
Разновидности инверторов
Инвертор— приспособление для электросварки, значительно упрощающее работу с металлом. Это современный вид трансформаторов. С появлением инверторов стало возможным выполнять соединения, для которых раньше потребовались бы громоздкие и сложные агрегаты. Электроэнергия, необходимая для его работы направляется исключительно на поддержание дуги. Так как инвертор является электронным сварочным аппаратом, то основная нагрузка приходится на электрическую сеть (напряжением от 220 до 380 Вт). Принцип его работы в сдвиге фазы напряжения и увеличении сдвига тока и частоты. Сначала инвертор изменяет переменный ток на постоянный, потом он делает из него вновь переменный, но уже с уменьшенным напряжением и увеличенной силой тока и частотой. Как же выбрать инвертор начинающему электросварщику?
Хороший инвертор отличает наличие вентилятора. Конечно, это помогает охлаждать прибор и защищает от перегрева. Но минусом является прилипание пыли. Так что не стоит покупать инверторы с самыми мощными вентиляторами. Они будут накапливать большое количество пыли внутри. В любом случае необходимо иногда очищать инвертор.
Так как принцип работы устройства основан на преобразовании электрического тока и удерживании его в нужном диапазоне, то важным показателем при выборе будет встроенный элемент, защищающий от скачков напряжения. Оптимальным будет уровень защиты 10-15%. Также стоит обратить внимание на температурный диапазон использования. Если планируется только бытовая эксплуатация, то нет смысла переплачивать за европейский стандарт EN 60974-1, позволяющий эксплуатацию при температуре от -150 до +150°С. Обычный инвертор будет приспособлен для работы в пределах от 0 до +30°С.
Еще одним показателем работы инвертора является его время бесперебойной работы. Так, например, бытовой агрегат способен сваривать полчаса с последующим часовым перерывом. Промышленные устройства рассчитаны на многочасовую смену с небольшими перерывами.
Также внимание при выборе инвертора стоит обратить на диапазон напряжения. Он должен быть не слишком большой. Лучший вариант, если указано, что аппарат будет работать при 220 — 230 В. Если нижняя граница меньше, то это свидетельствует о малой производительности при низком напряжении.
Какие бывают типы электродов
Электродом для сварки называется металлический или неметаллический стержень, подводящий ток к свариваемому изделию. Существует более двухсот марок, половина из которых предназначена для расплавки при ручном дуговом сваривании.
Электроды бывают металлические и неметаллические (всегда неплавящиеся). Металлические подразделяются на:
- неплавящиеся (из тугоплавких металлов типа вольфрама)
- плавящиеся (из сварочной проволоки).
В соответствии с ГОСТ, электроды плавящиеся для ручной дуговой сварки классифицируются по многим показателям, таким как:
- наиболее распространенная класификация сварочных электродов — по назначению (для сварки низколегированных и углеродистых сталей (обозначаются буквой У), для легированных конструкционных сталей (буква Л), для легированных теплоустойчивых сталей (Т), для высоколегированных сталей (В), для наплавки поверхностных слоёв с особенными свойствами (Н))
- по толщине покрытия (тонкое, среднее, толстое, особо-толстое)
- по типу покрытия (кислое, основное, целлюлозное, рутиловое, смешанное и прочие виды)
- по допустимому положению сварки
- по полярности и роду сварочного тока
Следует помнить, что не бывает универсальных электродов. Их необходимо подбирать каждый раз, исходя из материалов и конкретных условий работы!
Марки электродов можно посмотреть тут. Маркировки электродов написаны на упаковочной коробке.
Как правильно сваривать металлические конструкции сваркой
Перед началом работ свариваемый участок очищается шкуркой либо болгаркой. Далее нужно хорошо закрепить заготовку (привариваемую деталь).
Приступая к работе, первым делом необходимо подобрать электроды и установить силу тока. Диаметр электродов обычно 3,2 — 4 мм. Нужно замерить толщину заготовки. Для сварки заготовки из тонкого металла толщиной до 3 мм применяется электрод 3,2 мм и сила тока 90 А. Если заготовка от 3 до 4 мм, берется электрод 4 мм и устанавливается сила тока 120 А.
Начало сварочных работ — это формирование дуги между электродом и поверхностью привариваемой детали. Для этого держателем проводят по поверхности заготовки под углом около 60 градусов до появления характерных искр. После чего, электрод поднимается над поверхностью на 5 мм. В месте между электродом и свариваемой деталью должна образоваться электрическая дуга. Она должна поддерживаться на протяжении всего процесса и не изменяться в размерах. В процессе работ плавящийся электрод с покрытием под действием электрической дуги сам плавиться, таким образом расстояние между концом электрода и поверхностью заготовки увеличивается, сварочный ток падает и дуга пропадает. Чтобы дуга не пропадала, электрод нужно постоянно подводить с равной скоростью в зону плавки, при этом нельзя уменьшать 5мм зазор между электродом и свариваемой поверхностью.
Следующий этап — это формирование сварочного шва. Образовавшаяся дуга направляется к участку начала работ и расплавляет металл. Сварочный шов образуется путём медленного равномерного передвижения электрода по линии сварки. В зависимости от способа перемещения электродов швы разделяются на:
При формировании правильного шва, электрод нужно направлять под углом 70-80 градусов к поверхности изделия в направлении сварочной линии и строго под углом 90 градусов в направлении от неё.
Достоинства и недостатки электросварки, альтернативы
Рассмотрим явные преимущества ручной дуговой электросварки:
- сваривание во всех положениях пространства
- возможность сваривания в местах с ограниченным доступом
- относительно быстрая смена свариваемых материалов
- благодаря широкому выбору электродов, возможно сваривание различных сталей
- простота технологии.
Однако, у такого вида работ есть и недостатки:
- вредные условия при процессе
- качество швов сильно зависит от квалификации работника
- низкая производительность
Альтернативой электросварке может служить ковка. Однако, это кропотливый процесс, требующий большого мастерства. Также используют разъёмные соединения (болты, шурупы). Если необходимо соединить металл, а сварка невозможна, то прибегают к заклёпочному соединению. Оно также является неразъёмным.
Для соединения разнородных металлов используют газовые паяльные лампы. Метод пайки пламенем отличается от сварки тем, что при нём основной металл не расплавляется, а только нагревается до очень высокой температуры. Это даёт определённые плюсы: возможность многократного разъединения материалов без нарушения их свойств. Также плюсом будет то, что можно соединять более мелкие детали, чем при сварке.
Эффект коробления при сварке
В результате неравномерного прогревания, охлаждения и усадки металла при сваривании в нём возникают напряжения. Эти напряжения могут приводить к деформациям и снижениям прочностных характеристик шва. Для уменьшения такого эффекта в процессе сваривания под место предполагаемого шва подкладывают медную пластину. Она служит для отвода чрезмерного тепла. Чтобы уменьшить эффект коробления металла после сваривания еще применяют метод, когда сваривают участки таким образом, чтобы деформации были примерно равны по величине но противоположны по направлению.
Мероприятия для уменьшения деформаций при сварке:
- рационализация сварного узла
- припуск на усадку по форме и размерам изделия
- рационализация сборки и подготовки к сварке
- правильный выбор способа сваривания
- подогрев изделия на всех стадиях работы
- проковка зоны сварного шва
- механическая правка
- термическая правка
- общая термическая обработка
Высокая эффективность в борьбе с коррозиями достигается путём отпуска стальных изделий (вид специальной термической обработки стали).
Итак, мы убедились, что ручная дуговая сварка — эффективный и очень популярный метод соединения металлических деталей. Зная все нюансы выбора инвертора и электрода, вы сможете реализовать любой сварной шов. Конечно, нужна практика и профессионализм для того, чтобы выполнить его качественно.
Сварка металлоконструкций своими руками
Профессиональные сварщики подтвердят, что современный мастер должен уметь изготавливать любые типы металлических конструкций. При этом типов поистине много, предприятия и частные лица часто заказывают изготовление толстостенных конструкций. Поэтому любой уважающий себя сварщик должен знать, как происходит изготовление сварных конструкций.


В этой статье мы кратко расскажем, какие бывают сварные металлические конструкции, какова технология сварки металлоконструкций и какие особенности стоит учесть, чтобы вашу работу оценили по достоинству.
Содержание статьи
Виды металлоконструкций
Существуют различные виды сварных конструкций. Самые популярные — балки. Именно сварка двутавровых балок является самой часто запрашиваемой услугой. Запомните, что балки должны быть жестко соединены между собой. Это основное требование.


Второй тип — колонны. Колонны должны хорошо переносить сжатие. В целом, сварка колонн — это такая же популярная услуга, как и сварка двутавровых балок. Еще существуют решетчатые металлоконструкции. Для сварки решетчатых конструкций нужно убедиться, что они смогут выдержать существенное растяжение. К такому типу относится сетка из арматуры, металлический каркас или ферма.
Дополнительно выделяют оболочковые металлоконструкции. Зачастую это трубопроводы и различные емкости. Главное к ним требование — абсолютная герметичность и устойчивость к повышенному давлению. Не забывайте и о корпусных металлоконструкциях. К ним относятся составы поездов и кузова авто. Главное требование — устойчивость к перманентным динамическим нагрузкам.
Как вы понимаете, к каждому типу есть свои требования. Их обязательно нужно учитывать. Нельзя выполнять работу «наобум», основываясь лишь на своих соображениях. Нужно принимать во внимание среду, в которой будет эксплуатироваться металлоконструкция, и нагрузки, которые она должна выдерживать.
Технология сварки металлоконструкций
Технологичность сварных конструкций не так уж сложна. Здесь все просто: технология соединения деталей для той или иной металлоконструкции зависит от выбранного вами метода сварки. Например, вам предстоит сварка металлоконструкций полуавтоматом. Для этого вам необходим полуавтомат, защитный газ в баллонах, присадочная проволока и электроды.


Такой подход уместен вне зависимости от того, какая сварка конструкций вам необходима. Вам может быть поручена сварка двутавровых балок или коробчатых конструкций. В любом случае опирайтесь на особенности выбранного вами метода сварки. Впрочем, есть некоторые советы, которые подходят к любому типу сварки металлоконструкций. Далее мы подробно поделимся ими.
Выбор метода сварки
Теперь, когда вам известна классификация сварных конструкций, вам будет проще выбрать тип сварки. Может с уверенностью сказать, что сборка металлоконструкций может осуществляться с помощью любого оборудования. Например, сварка строительных конструкций часто производится с помощью полуавтомата. Это не удивительно, ведь сварка металлоконструкций полуавтоматом проста и удобна, она экономит время и ресурсы. Мы рекомендуем выбирать метод сварки исходя из ваших умений, условий работы и предъявленных требований по качеству.
Выбор режима сварки
Чтобы правильно сварить конструкции из металла нужно настроить свой сварочный аппарат. Проще говоря, выбрать режим сварки. Здесь рекомендация одна: постарайтесь соблюдать золотую середину. Не нужно устанавливать завышенное значение тока в надежде выполнить работу быстрее. И не нужно варить на малом токе просто из страха испортить шов.


Сварка ответственных металлоконструкций (например, балок двутаврового сечения) требует от вас максимальной концентрации и опыта. Поэтому полагайтесь на свои силы и устанавливайте настройки, рекомендуемые ГОСТами для каждого метода сварки. Что касается скорости, то постарайтесь варить примерно 20 метров шва в час. Это усредненное значение.
Выбор температурного режима
Сварка конструкций должна производится при температуре металла не менее 17 градусов по Цельсию. Это особенно важно, если планируется изготовление сварных конструкций с повышенными требованиями к качеству швов (к примеру, упомянутая выше сварка балок). Прогрейте место будущего шва до 20 градусов перед началом работ.
Выбор типа сварного соединения
В большинстве случаев, для сварки металлических конструкций выбирают стыковое и угловое соединение. О каждом из них поговорим подробнее.
Стыковой шов должен равномерно провариваться по всей длине и толщине металла. Это оптимальный метод. Также можно сварить шов на одной стороне, а затем с обратной стороны проварить корень шва. Это особенно актуально, если предстоит сборка и сварка решетчатых конструкций.
С угловыми швами все сложнее. Они больше подвержены деформациям, чем стыковые, поскольку не способны выдерживать такие большие нагрузки. Если у вас есть возможность заменить угловой шов на тавровый, то лучше сделайте это. Также запрещено использовать односторонний угловой шов при соединении толстостенных конструкций. Двусторонний шов обязателен.
Сборка и сварка металлоконструкций также требует понимания, каким нагрузкам будет подвержено изделие. Если будет много статической нагрузки, то разделывайте кромки к-образно.
Особенности сварки
Во-первых, перед работой у вас на руках обязательно должны быть чертежи сварных конструкций. Еще лучше, если будет полноценный пакет с технической документацией. Специалисты должны определить, какой тип сварки лучше подходит, и подобрать оптимальные типы сварных соединений.
Металлоконструкции сварные содержат множество узлов, и к каждому предъявляются свои требования. Например, при сварке стыков металлоконструкций расстояние между швами должно быть не более 10-ти кратной толщины самого металлического профиля. Это особенно важно при соединении балочных конструкций.
Есть еще одна особенность. Профессионалы часто используют термины «местная прочность» и «непрочность». Местная прочность — это узлы, к которым были приварены ребра жесткости, например. А непрочность — это отверстия в металлических профилях, непроваренные швы, большие зазоры между деталями и так далее. Считается, что если у конструкции замечено оба этих недостатка, то изделие уже нельзя называть долговечным.
Поэтому, если вам предстоит изготовление сварных конструкций постарайтесь избегать упомянутых выше «болячек». Даже если вы решили, что на неответственном участке можно сделать менее качественный шов, то вы ошибаетесь. В конечном итоге именно эта ошибка приведет к разрушению всей конструкции. Сварка конструкций не прощает даже мелких недочетов.
Вместо заключения
Технологичность сварных конструкций заключается лишь в разнообразии способов сварки. Непосредственный процесс сварки (он же технологический процесс) и изготовление сварных металлоконструкций — это не так сложно, как может показаться на первый взгляд.
Да, вам придется выбрать оптимальный метод соединения металлов, правильно настроить оборудование и соблюдать технологию. И многим новичкам все это кажется сложным просто из-за большого разнообразия способов сварки. Но поверьте, стоит вам однажды выполнить работу подобного рода, и вы уже без проблем будете варить любые другие конструкции из металла. Обязательно поделитесь своим опытом в комментариях. Желаем удачи в работе!
[Всего голосов: 1 Средний: 5/5]Особенности сварки металлоконструкций
Сварка металлоконструкций открыла много возможностей для конструкторов. Можно включать в проект более рациональные сечения материала. Это позволяет значительно уменьшить металлоемкость.

Схема сварки металла.
Когда создаются сварные конструкции, имеется возможность проверить на практике свариваемость сталей, убедиться в правильности методов расчетов металлических конструкций при использовании сварных соединений.
Сварка металлоконструкций позволяет практическим путем определить необходимые материалы и оборудование для монтажа металлических конструкций. Кроме того, перед разработчиками открывается много возможностей разработки новейших конструкций и продления срока их эксплуатации.
Стандартные способы сварки
Уже давно сварку конструкций выполняют несколькими способами. При этом используется два вида энергии:
- газовое пламя;
- электрическая дуга.

Расположения сварных швов металлоконструкций.
Эти виды сварки подразделяются на:
- ручную;
- полуавтоматическую;
- автоматическую.
При ручной сварке сварочный шов образуется вручную. Все управление сварочным процессом, его настройки, подача присадочного материала или электрода делаются только руками.
Когда используется ручной режим, применяется технология сварки металлоконструкций, которая подразумевает:
- сварку под флюсом;
- сварку газосварочным аппаратом;
- газовую пайку.
Такой режим больше всего применяется в бытовых условиях.
Вернуться к оглавлению
Основные характеристики
Вернуться к оглавлению
Автоматическая сварка

Схема автоматической дуговой сварки под флюсом.
В данном случае технология сварки металлоконструкций предусматривает получение шва без человеческого участия. Все нужные настройки и другие операции производит специальный механизм, запрограммированный на определенный вид операции.
Конечно, перечень таких операций небезграничен. Его ограничивает функциональность устройства. Однако на сварку металлоконструкций это очень сильно влияет. Снижается стоимость работ, такую сварку стали широко применять при крупносерийном производстве.
Используя «автоматический» режим, стало возможным применять:
- контактную сварку;
- электрошлаковую сварку;
- сварочный робот.
Вернуться к оглавлению
Полуавтоматическая сварка
При таком способе наложение шва делается только руками, однако подача присадочного материала или электродов происходит автоматически.Применение такого метода позволяет значительно увеличить производительность сварочных работ.
Технология сварки с использованием полуавтоматического режима предусматривает применение:
- газового флюса;
- неплавких электродов;
- сварочной проволоки.
Вернуться к оглавлению
Новейшие открытия и технологии
Сегодня в сварочном мире появилось несколько новых видов сварки. На смену электрической дуге сварку конструкций выполняют:

Схема плазменной сварки открытой и закрытой плазменной струей.
- лазером;
- ультразвуком;
- силой трения;
- направленным движением электронов.
Иными словами, технология сварки конструкций стремительно движется вперед. Каждый год в технологическом процессе появляются новые способы. Среди самых новых технологических новинок особо выделяется:
- термитный метод;
- плазменный способ;
- электронная сварка.
- Термитная технология. Применяется для монтажа металлоконструкций, когда свариваемые детали расплавляются особой смесью, которая подается в зону сварки. С помощью термита появилась возможность заделывать трещины в уже собранной металлоконструкции, необходимо просто сделать «наплыв» термита.
- Плазменная сварка. Для такого метода необходим ионизированный газ, который подается в зазор между парой электродов. В основном этот газ заменяет электрическую дугу. Но эффект, который дает плазменная струя, в несколько раз больше классической сварки. Перегретый газ позволяет осуществлять плавку металла, независимо от его толщины. Газ легко режет заготовку.
- Электронная технология. С открытием такого вида сварочного процесса стало возможно заваривать очень глубокие швы, величина которых превышает 20 сантиметров. Причем глубина погружения луча не более одного сантиметра. Но в данном случае негативной стороной стала возможность работать таким генератором электронных лучей только в полном вакууме. Создать такие условия на обычном производстве очень сложно, поэтому данная технология нашла применение в решении особых задач.
Вернуться к оглавлению
Дефекты в сварочных швах

Дефекты сварочных швов.
Когда создается металлоконструкция, для удобства и получения более точных размеров применяется кондуктор. Однако во время сварки металлоконструкций очень часто возникают определенные дефекты:
- наплывы;
- прожог;
- непровар;
- трещина;
- пористость;
- пережог;
- подрез;
- шлакоотложение;
- возникновение кратера.
Появление наплывов происходит из-за натекания расплавленного металла на торцы плохо прогретого металла. В большинстве случаев такой дефект имеет место при получении горизонтальных швов. Получившиеся наплывы удаляют молотком, а затем проверяют наличие непровара.
Под прожогом понимается сквозное проплавление, когда на обратной стороне появляются натеки жидкого металла. Причиной такого дефекта является:
- увеличенный зазор;
- плохая обработка кромок;
- увеличенная мощность пламени;
- низкая скорость.
Такие прожоги исправляется вырубкой и последующей заваркой.
Под непроваром понимается несплавление деталей между собой.
Причиной появления такого дефекта считаются:
- плохие кромки деталей.
- низкая сила пламени;
- большая скорость;
- наличие окалины;
- наличие ржавчины;
- оставшаяся грязь.
Непровары – это самый опасный дефект, влияющий на прочность и надежность сварочного соединения. Все непроваренные участки полностью вырубают, все заново зачищают и снова заваривают.

Схема полуавтомата для сварки в защитных газах.
Возникновение трещин возможно не только при сварке. Наличие трещины может обнаружиться и после окончания сварочной операции. Причиной возникновения трещин считается:
- невыполнение требований технологии;
- неправильный сварочный режим;
- неверное расположение швов.
Заметим, что швы, неправильно расположенные в металлоконструкции, становятся концентраторами напряжения, которые постепенно разрушают всю конструкцию. Очень большие значения напряжений наблюдаются там, где не соблюдается очередность наложения швов.
Трещины, образовавшиеся на поверхности сварочных швов, полностью удаляют и затем заваривают. Для ограничения распространения трещины по шву на ее концах делаются отверстия.
Иногда сварочные швы становятся пористыми. Причина этого явления – газы, которые находятся в расплавленном металле. Они просто не успевают покинуть шов до его затвердевания. Появившиеся поры снижают прочность сварочного шва. Причиной образования пор являются:
- плохо зачищенные свариваемые кромки;
- грязная присадочная проволока;
- наличие ржавчины;
- масло;
- много углерода в основной детали;
- большая скорость;
- марка проволоки;
- выбор силы сварочного пламени.
В некоторых случаях поры появляются прямо на поверхности, возникают свищи. Такие места вырубаются и снова завариваются.
Когда происходит пережог, начинают образовываться окисленные зерна, у которых очень низкая сцепляемость, так как их поверхность закрыта окисной пленкой. Пережженный металл очень хрупок, его нельзя исправить.
Сварка металлоконструкций
Соединение металлоконструкций с помощью сварки
Металлоконструкции сами по себе применяются очень широко и в различных отраслях, но чаще, всё-таки, в строительстве. Кроме того, видов металлоконструкций также много, так как металл, применяемый при их создании, может иметь различный профиль, толщину и состав.
Единственно, что может объединять их, это способ создания металлоконструкций –применение сварки для их создания. Причем способ сварки в зависимости от профиля проката также разнообразен. Это сварка встык, внахлёст, угловая, торцевая, под определённым углом, для сталей с разным составом.
Металлоконструкции это ответственные элементы, которые должны иметь определённые характеристики и выдерживать заданные нагрузки и сварка должна давать эти характеристики. Она соединяет металл в виде труб, уголков, листов, профиля различного сечения в единое целое, любая точка которого должна соответствовать тем нагрузкам, которые будет выдерживать и вся конструкция.
Естественно, делать расчет на изгиб или разрыв для каждой конструкции абсолютно из ряда фантастики, поэтому приняты ГОСТы на сварку металлоконструкций. В них оговариваются и качество, и состав металла, то есть марку стали, применяемой для возведения этих конструкций, и размеры заготовок, и вид сварки и её режимы, и закладные материалы, и тому подобные важные детали.
Технология выполнения сварки металлоконструкций
Как оговаривалось, сварка металлоконструкций должна проводиться согласно ГОСТам, например ГОСТ 5264 – 80, ГОСТ 14771 – 76.
ГОСТ 5264-80, регламентирующий сварку металлоконструкций ручной дуговой сваркой, учитывает как типы и элементы конструкций, так и их размеры, а также материал, из которого они изготовлены. В ГОСТе отмечается и то, что этот стандарт не может быть использован для сварки трубопроводов из стали.
Соединение при ручной дуговой сварке допускается:
- стыковое (в основном),
- угловое (также наиболее применяемое),
- нахлёсточное (применяется реже)
- тавровое.
ГОСТ 14771 – 76 устанавливает правила для работы по сварке металлоконструкций, которая производится дуговой сваркой под прикрытием защитного газа.
Также в данном документе указано, что этот стандарт не может быть использован при сварке стальных трубопроводов, на который есть свой ГОСТ.
Сварка с среде защитного газа может быть четырёх типов:
- ИН – сварка в среде инертного газа, при применении неплавящегося электрода и без применения присадочной проволоки;
- ИНп – сварка в среде инертного газа, при применении неплавящегося электрода и с применением присадочной проволоки;
- ИП – сварка в среде комбинированного газа, то есть инертный газ , углекислый газ с кислородом с применением плавящегося электрода;
- УП – сварка в среде углекислого газа и кислородно – углекислой смеси с применением плавящегося электрода.
Большое внимание уделено в ГОСТе подготовке кромок к свариванию и геометрическим размерам выполненного сварного шва.
Перед началом работ по сварке металлоконструкций согласно технологии нужно разработать технологическую карту.
Это официальный документ, в котором проработан весь процесс сварки и его технология, а также указаны все параметры. Дело в том, что качество шва зависит от многих условий, в том числе и от квалификации сварщика.
Составление технологической карты сварки металлоконструкций
При составлении карты инженерные службы делают расчеты, которые помогают выбрать режим сварки, способы сварки металлоконструкций, размеры сварочного шва и остальные необходимые параметры. При расчетах, которые производятся при помощи данных, взятых из справочников и с тех условий работы, в каких будет находиться конструкция в готовом виде.
В карте должны быть указаны все операции, от подготовительных до контроля качества полученного шва, а также разработаны чертежи с пояснениями к ним в виде спецификаций. Составление такой карты – работа очень ответственная, так как любая неточность или ошибка может привести к серьезным последствиям.
Начинается составление карты с того, что указывается, какие металлоконструкции можно варить при помощи указанного технологического процесса, схема с полными геометрическими данными соединяемых деталей с указанием углов и расстояний между деталями этой конструкции.
Пример составления технологической картыТакже указывается место и условия работы. Это может быть и сварка в производственном помещении, сварка на открытом воздухе или сварка непосредственно на месте, а также температура проводимых работ (Сварка обычно не должна проводиться при температуре ниже -18 градусов, но бывают технические исключения проведения работ при -30 градусах).
Обязательно должны быть учтены в карте условия для соблюдения техники безопасности и пожарной безопасности работающих в соответствии СНиП III-4-80 и ГОСТ 12.3.003. При этом должны в обязательном порядке быть указаны наиболее безопасные способы и приемы выполнения работ для обеспечения максимально полной безопасности при проведении таких работ. Должен быть указан и ответственный за их соблюдением.
При проведении работ при помощи дуговой сварки в среде защитного газа, обязательно учесть подводку кислорода и углекислого газа к месту работы. Все подводки и необходимость его использования должны иметь расчёты.
Далее указываются подготовительные работы и поэтапный их перечень. К подготовительным работам относится заготовка металла для сварки. Металл должен иметь сертификат от завода – изготовителя. Также должен быть включен в перечень и визуальный осмотр на предмет выявления брака и испытание образцов – так называемый входной контроль качества металла.
Следующим пунктом будет вид применяемых сварочных работ с указанием применяемого оборудования, марки электродов, проволоки и защитного газа.
При этом описывается процесс сварочных операций с указанием, в какой очередности наносятся швы, общее направление проведения сварки, сколько и какой длины устанавливаются прихватки. Прихватки должны быть указаны на чертежах с дополнительными указаниями в пояснительной записке. Если должна будет устанавливаться приварка строповочных элементов, она также указывается в чертеже и в пояснительной записке. Если после окончания работ эти элементы должны будут удалены, это также помечают. Удаляют их обычно или механически специальным оборудованием или при помощи газопламенной резки.
Также в технологической карте указывается нормативное время, которое должно быть потрачено на проведение каждой операции, и в итоге суммарное время на весь цикл работ.
В конце в спецификации указывается количество расходных материалов. Если расчетная технологическая карта не будет устраивать одну из сторон, её можно изменить до начала проведения работ.
Контроль за работами по сварке металлоконструкций обычно возлагается на мастера участка.
Как производится контроль качества сварочных работ
Контроль качества сварки металлоконструкций, который проводится при сдаче работ, имеет очень важную роль. Он фактически отвечает за то, что работы, в основном ответственные, проведены правильно, соответствуют технологической карте и выдержат нагрузку, которую рассчитала инженерная служба.
Контроль делится на три части.
- Проверка квалификации сварщика, которая осуществляется проверкой документов рабочего на предмет квалификации, наличия допуска к сварочным работам и документа о прохождении обязательного инструктажа по технике безопасности а также по противопожарной защите. В удостоверении, которое предъявляется рабочим, должны быть также перечислены группы сталей, с которыми он может работать. Также должен быть получен образец сварочного шва, идентичный тому, который будет выполняться при монтаже при той же температуре, что и будут производиться работы. Если сварка будет производиться при температуре -30 градусов, образец не должен быть сварен при температуре, превышающей рабочую.
- Контроль за качеством деталей, которые подлежат сварке. Все детали должны иметь сопровождающие документы, с которых указывается марка металла, из которого они изготовлены. Эти вопросы урегулированы РД 34.15.132-96 и СНиПом.
- Внешний осмотр и механическое испытание сварных соединений. Производится после очистки шва от шлака и брызг металла. Внешний визуальный осмотр помогает выявить до 50% брака перед тем, как отправить шов на испытание. Для этого не нужно разрушать шов, давно существует оборудование по его выявлению. Дефекты, которые обнаруживаются при помощи дефектоскопа, это непровары различных зон, внутренние трещины шва, прожоги.
При выявлении таких дефектов швы или переделываются или, при большой длине, вырезаются в месте дефекта.
Один из методов проверки качества металлоконструкции- при помощи ультразвукаКонтроль при помощи ультразвука относится к наиболее точным для определения внутренних дефектов шва.
Для того, что бы правильно оценивать и контролировать качество сварочных работ, существует рабочий документ от 1996 года РД 34.15.132-96.
Этот документ разработан как для работ с ручной дуговой сваркой металлоконструкций, так и для сварки полуавтоматами и автоматами в среде защитных газов, порошковой проволокой и сваркой под флюсом.
Нормативы, все расчеты, разъяснения в документе позволяют обеспечить полный контроль по организации работ, за её проведением, а также контроль качества готовых изделий.
Вконтакте
Google+
Внимание покупателей подшипников Уважаемые покупатели, отправляйте ваши вопросы и заявки по приобретению подшипников и комплектующих на почту или звоните сейчас: +7(499)403 39 91
Доставка подшипников по РФ и зарубежью. Каталог подшипников на сайте themechanic.ru
|
Внимание покупателей подшипников
Уважаемые покупатели, отправляйте ваши вопросы и заявки по приобретению подшипников и комплектующих на почту или звоните сейчас:
tel:+7 (495) 646 00 12
[email protected]
Доставка подшипников по РФ и зарубежью.
Каталог подшипников на сайте
Внимание покупателей подшипников
Уважаемые покупатели, отправляйте ваши вопросы и заявки по приобретению подшипников и комплектующих на почту или звоните сейчас:
tel:+7 (495) 646 00 12
[email protected]
Доставка подшипников по РФ и зарубежью.
Каталог подшипников на сайте
Сварка металлоконструкций: технология и особенности
Одним из наиболее часто применяемых в производстве массовых и мелкосерийных изделий способов соединения деталей является сварка. С ее помощью можно собрать практически любое сопряжение элементов – тавровое, угловое, торцевое и нахлесточное. С течением времени технологические приемы, при помощи которых осуществляется сварка металлоконструкций, улучшаются, становясь более эффективными.
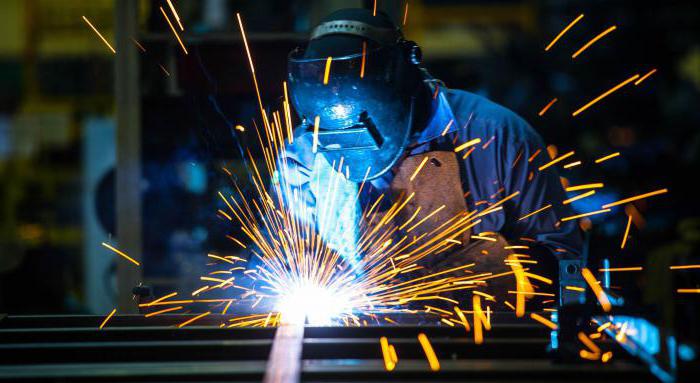
Классические способы сварки
Стандартные способы сварки металлических элементов подразумевают под собой использование двух основных источников энергии: газового пламени либо электрической дуги.
Газовая и дуговая сварка может быть автоматической, полуавтоматической и полностью ручной. Последний вариант подразумевает формирование сварочного шва только собственными руками мастера. Помимо этого, ручная дуговая (РД) сварка металлоконструкций включает в себя и ручное управление процессами подачи электрода, или присадочной проволоки, и самим процессом сваривания деталей.
Ручной режим наиболее эффективен только в бытовых условиях. При его использовании применяют в основном технологии сварки под флюсом, пайки газосварочным аппаратом или классический способ электродуговой сварки.
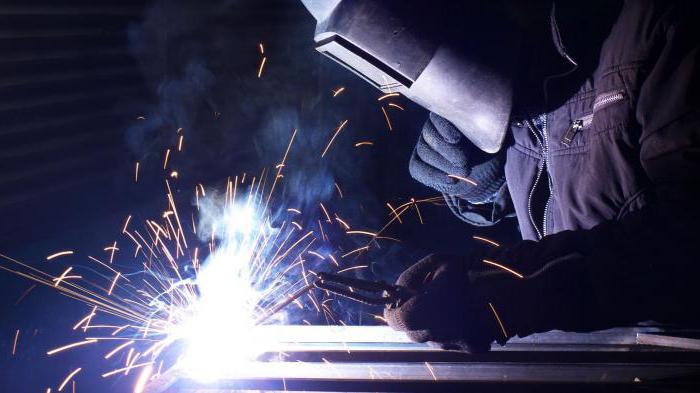
В основе первого варианта – автоматической сварки – лежит процесс наложения на участок шва без прямого участия человека. Всей работой занимается специальный механизм, который предварительно настраивается. Естественно, что у данного агрегата спектр функций весьма ограничен, однако это значительно снижает стоимость готовых изделий, благодаря чему в крупносерийном производстве она становится весьма популярной.
Сборка металлоконструкций, сварка в автоматическом режиме позволяет применять контактную технологию, включающую нагрев и опрессовку элементов, электрошоковую сварку и прочие «ручные» способы. Единственная разница – всем заправляет не мастер, а специально созданный и запрограммированный робот.
Полуавтоматический режим подразумевает наложение сварочного шва мастером, однако электроды либо проволока в зону работы подаются автоматически, что значительно увеличивает производительность работ на участке.
В таком режиме используется практически любая технология сварки металлоконструкций, применяющая неплавкие электроды, газовые флюсы и автоматизированную подачу в зону нагрева присадочной проволоки. В быту и мелкосерийном производстве полуавтоматическая сварка металлоконструкций является наиболее выгодным и эффективным вариантом технического процесса.
Технологические новинки
В современной сварке для соединения металлических деталей применяют не только пламя перегретого газа и электрическую дугу, но и тепловой эффект трения, лазерную энергию, ультразвук и даже силу пучков электронов.
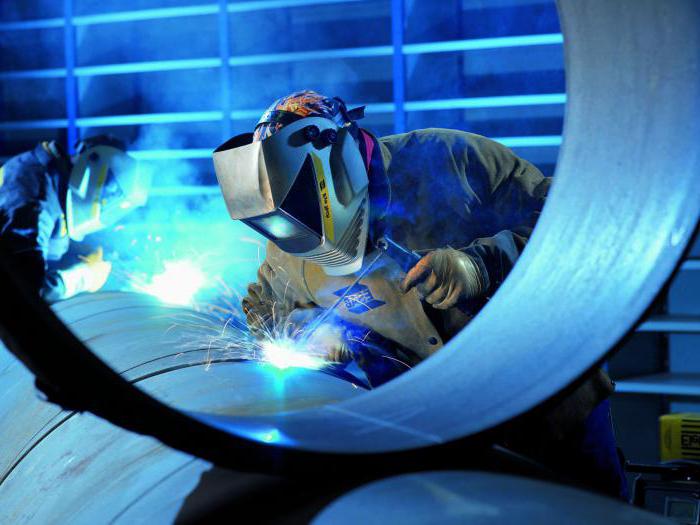
Проще говоря, сама технология сварки постоянно совершенствуется. Достаточно регулярно изобретаются новые способы реализации данного технического процесса. К числу таких новинок можно отнести следующие виды сварки – плазменную, термитную и электронно-лучевую.
Посредством термитной технологии осуществляется сварка ответственных металлоконструкций, составляющие которых по шву расплавляются во время горения специальной смеси, вводимой в место соединения. Термит также используется для устранения дефектов и трещин в уже готовых металлоконструкциях путем «наплыва» металла.
Плазменная сварка осуществляется в условиях пропускания через два электрода ионизированного газа. Последний выступает в качестве электрической дуги, но при этом эффективность ее значительно выше. Перегретый газ используют не только для сварки металла, но и для его резки, благодаря чему вокруг плазменного генератора можно создать автоматическую и многофункциональную сварочную систему.
При помощи электронно-лучевых технологий производят сварку глубоких швов до 20 сантиметров, при этом ширина такого шва не будет превышать одного сантиметра. Единственным минусом такого генератора является то, что работать с ним можно только в полном вакууме. Соответственно, подобную технологию используют только в узкоспециализированных областях.
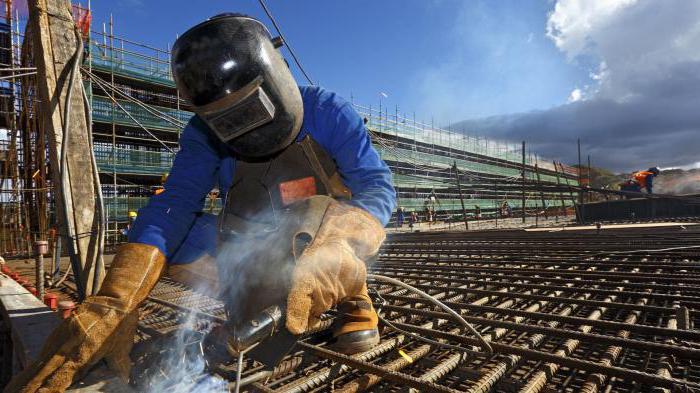
Для сборки небольших по размеру металлоконструкций эффективнее всего использовать газовую либо электродуговую ручную сварку. Полуавтоматический аппарат окупается при осуществлении работ с мелкосерийными объектами. Современные технологии сварки, соответственно, применяются только в серийном производстве.
Сварка металлоконструкций: особенности
Технология сварки применяется не только при работе с металлом, но и с различными полимерами. Весь процесс представляет собой нагрев и деформацию поверхностей, которые затем соединяются в одно целое.
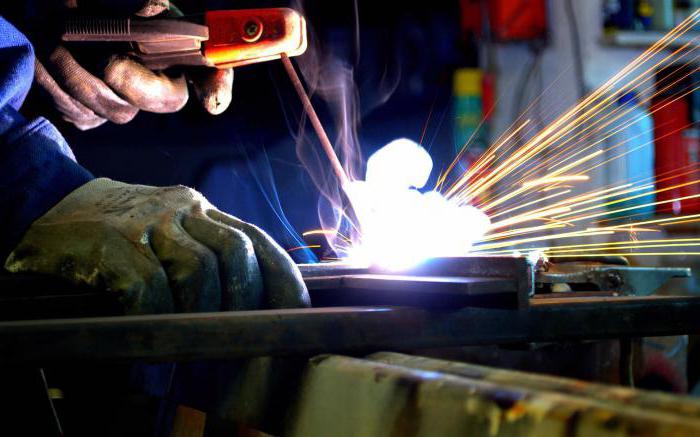
Все сварочные работы состоят из двух основных этапов: сборки и соединения.
Самым трудоемким и сложным является первый этап. Надежность и прочность конструкции во многом зависит от соблюдения всех требований. Больше половины всего времени приходится именно на сборку составляющих.
Обеспечение правильной сборки металлоконструкций
Высокое качество, прочность и надежность конечного результата обеспечивается соблюдением определенных требований.
- При выборе деталей необходимо строго придерживаться заложенных в проекте размеров.
- Зазоры должны быть определенного размера – при их увеличении прочность готового изделия значительно снизится.
- Углы измеряются и контролируются при помощи специальных инструментов. Важно, чтобы они полностью соответствовали указанным в проекте, иначе появится риск обрушения всей конструкции.
Преимущества сварки
Помимо того, что сварка металлоконструкций значительно экономит время проведения всех работ, а шов получается качественным, процесс обладает и другими характеристиками:
- Масса готовой спайки не изменяется, поскольку используются только две основных детали, что позволяет сэкономить материал.
- Отсутствие ограничений по толщине металла.
- Возможность контроля и корректировки форм металлоконструкций.
- Доступность сварочного оборудования.
- Возможность применять сварку для ремонта и реконструкции.
- Высокая герметичность и прочность стыков.
Дополнительные моменты
Для того чтобы полученная конструкция была качественной и надежной, необходимо соблюдать все технологические требования.
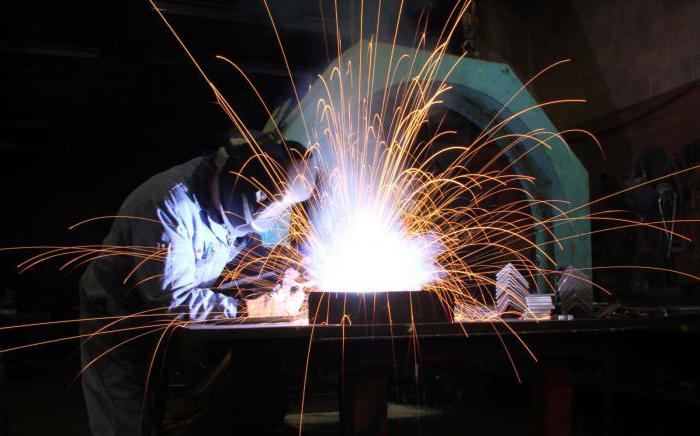
Правильно подобранные материалы, комплектующие и оборудование позволяют получить швы высокого качества. В противном случае готовая конструкция не только теряет товарный вид, но и свои эксплуатационные характеристики.
Дефекты сварочных швов
Для получения точных размеров и упрощения работы при создании металлоконструкции применяют кондуктор. Несмотря на это, РД сварка металлоконструкций, кранов может обернуться во время процесса определенными дефектами – наплывами, трещинами, прожогами, пористостью, пережогами, подрезами и прочими.
Причины появления дефектов
Наплывы формируются на металлоконструкциях в результате натекания расплавленного металла. Чаще всего такой дефект характерен для проведения работ по созданию горизонтальных швов. Удаляют их молотком, после чего проверяют изделие на наличие непроваров.
Причинами появления прожога может быть некачественная обработка кромок конструкций, увеличение зазора, низкая скорость проведения работ и малая мощность пламени. Устраняют его путем вырубки и заварки шва.
Самым опасным видом дефекта считается непровар, поскольку он отрицательно сказывается на надежности и прочности сварочного шва. Такие участки устраняются полностью, металлоконструкции зачищаются и заново завариваются.
виды, способы и возможные дефекты.
Заказать проект
Оформите заявку на сайте. Наш менеджер свяжется с вами для уточнения деталей.
При возведении зданий и сооружений широко используются металлические конструкции. Их собирают при помощи сварки. Такой способ монтажа металлокаркаса относительно прост и дешев. Также применение сварки позволяет снизить металлоемкость за счет уменьшения требований к параметрам заготовок.
Виды сварки
- Газовая. Источником энергии служит смесь кислорода с горючим газом, в роли которого чаще выступает ацетилен. Из-за медленного нагревания металла снижается скорость обработки деталей. Также метод не позволяет применять автоматизацию процессов. По этим причинам им редко пользуются для выполнения масштабных работ.
- Электродуговая. Выполняется при помощи низковольтного источника тока большой силы. В результате одновременной подачи напряжения на электрод и заготовку образуется дуга, расплавляющая края деталей. Для предотвращения окисления сварка металлоконструкций может выполняться в среде углекислого газа, аргона или гелия. Этот способ остается самым распространенным.
- Термитная. Относительно новая разработка, основанная на покрытии деталей специальным составом, который расплавляет края заготовок. Метод удобен для ремонта трещин в готовой металлической конструкции.
- Плазменная. Напоминает классическую сварку. В отличие от нее в промежуток между двумя электродами поступает ионизированный газ. Плазменная струя мощнее электрической дуги, поэтому подходит для плавки металла любой толщины.
- Электронная технология сварки. Позволяет заваривать швы глубиной более 20 см. При этом луч погружается не более чем на 1 см. Для выполнения работ требуется создание вакуума. По этой причине на производстве метод используется редко.
Способы сварки металлоконструкций
- Ручной. Все операции выполняются самостоятельно, без использования вспомогательных механизмов. Это увеличивает срок обработки каждой детали, поэтому метод чаще применяется в быту. Возможно использование газового аппарата или газовой пайки, а также флюса. На качество соединений, выполненных в таком режиме, большое влияние оказывает мастерство сварщика.
- Полуавтоматический. Руками накладывается только шов, а вот электроды или необходимые присадки подаются автоматически. Такой подход повышает скорость работ, что позволяет использовать его на производстве. Таким способом чаще применяют для вертикальных, угловых и потолочных швов. Для режима могут использоваться сварочная проволока, газовый флюс или неплавкие электроды.
- Автоматический. Человеческое участие во время самого процесса сварки не требуется. Специальный механизм программируется на выполнении конкретного типа операции. Далее настройки и все манипуляции по сварке металлоконструкций производятся автоматически. Такой режим позволяет пользоваться сварочным роботом контактной или электрошлаковой сварки. Последний вариант постепенно выходит из употребления. Новейшие исследования подтвердили, что полученные таким способом швы становятся менее прочными при низких температурах. Способ используют для сварки нижних положений.
Температурный режим
Надежность монтажа металлоконструкций во многом зависит от внешней температуры. Работы нельзя выполнять, если заготовка холоднее –18 градусов. Показания измеряют в месте стыка деталей. Если температура неудовлетворительна, то металл подогревают. Делают это не со всей деталью, а только на 7,6 см по всем сторонам. В других случаях достаточно прогрева на размер толщины заготовки от ее края.
При соединении сталей разных марок выбирается температура самой прочной. Также нагрев зависит и от размера стенки заготовки, которую нужно обработать. Деталь из стали марки А514 с толщиной 3,8 см достаточно нагреть до +205 ⁰С. Более крупные варианты требуется греть уже до 230 градусов.
Разновидности соединений
- Тавровое. Край заготовки прислонен концом к торцу другой.
- Внахлест. Детали располагаются так, чтобы их края перекрывались.
- Встык. Детали расположены в одной плоскости, их края соприкасаются.
- Угловое.
На практике чаще всего встречаются два последних типа соединений. С их помощью фиксируют балки, стойки и фермы. При стыковом монтаже шов варится по всей толщине детали. Также возможно применение технологии сварки со специальными подкладками, устанавливаемые возле кромок заготовок. При полуавтоматическом режиме оставляют расстояние между деталями 1,6 см, при ручном — 0,7 см. Если нужно соединить заготовки с разными размерами, то выполняют проточку в большей детали.
Нагрузка на угловые соединения выше, чем на стыковые. Это накладывает ряд требований на сварку металлоконструкций с такими вариантами:
- Нагружаемые каркасы не могут иметь односторонний стык. Требуется шов с двух сторон, который сокращает концентрацию напряжений в верхней доле.
- В случае невозможности выполнения шва с обеих сторон стараются сократить объем наплавляемого металла. В этом случае кромки не разделываются.
- При статической нагрузке конструкции накладывается неполный шов с разделкой кромок обеих заготовок.
- Рекомендуется заменять угловые стыки на тавровые соединения, где это возможно.
Сварные узлы
Это основные соединения, от надежности которых зависит качество монтажа металлоконструкций. Поэтому благоприятные параметры для сварки стараются задать на стадии проектирования. Для этого выбирается нижнее расположение швов, оптимальное стыковочное соединение и рекомендуется исключить ручную работу. Последнее условие не всегда выполнимо, потому что с наклонными и вертикальными швами нельзя работать в автоматическом режиме.
У каждого сварного узла есть свои требования. В балках швы размещают сначала на полках, а затем на стенках. Расстояние между швами выбирается по профилю с самой большой толщиной в узле. Части фермы сваривают от середины к опоре. Первыми работают со стыковыми, далее переходят к угловым швам. Двигаются от большего сечения швов к меньшему. Длина каждого шва — 30-40 мм. Если соединения располагаются близко, то их выполняют только после остывания участка основного металла. Это необходимо для снижения пластических деформаций и перегрева металла. Продольный шов заходит на торец закрепляемого элемента на 20 мм.
Прочность конструкции определяется наличием следующих моментов:
- местной прочности — ребер жесткости и различных накладок;
- непрочности — отверстий, непроваров и незапроектированных зазоров в швах.
Если в металлическом каркасе присутствуют оба параметра, то его считают непрочным. По физическим законам наибольшее напряжение появляется в месте с самым хорошо проваренным швом. В результате он принимает на себя большую нагрузку и становится самым опасным местом. Поэтому при монтаже металлокаркаса важно оценить качество всех соединений: дефект в одном может привести к негодности всю конструкцию.
Определение качества сварных швов
- Визуальный осмотр. Швы очищаются и проверяются невооруженным глазом или при помощи лупы.
- Просвечивание рентгеновскими лучами. Применяется на части стыков, что отмечено в СНИП II 23-81. Если обнаруживаются дефекты, то число проверяемых соединений удваивают.
- Ультразвук. Места контроля обрабатывают маслом, чтобы уловить звуковые колебания от металла. Метод позволяет определить пустоты в шве.
Проблемные участки помечаются мелом для их последующего исправления.
Возможные дефекты
- Наплывы. Появляются в случае протекания металла на плохо прогретые торцы заготовки. Часто встречаются на горизонтальных швах. Удаляются при помощи молотка, затем соединения проверяются на целостность.
- Прожог. Деталь проплавлена насквозь, на обратной стороне есть потеки металла. Причинами дефекта могут стать низкая скорость или плохая обработка кромок, слишком большая мощность пламени и увеличенный зазор. Исправляются вырубкой и последующим заполнением.
- Непровар. Очень опасная ситуация, которую обязательно надо устранить при монтаже металлоконструкций. Причиной могут стать наличие грязи, окалины или ржавчины, а также неправильно подобранная сила пламени. Все испорченные участки вырубаются и заново завариваются.
- Трещины. Образуются из-за неверного расположения швов или неправильного режима. Ошибки в расположении стыков дестабилизируют всю конструкцию, создавая излишние напряжения, что приводит к разрушению. Трещины полностью вычищают и переваривают. Чтобы трещина не распространялась, на ее концах делают отверстия.
- Пористость. Появляется, если газы не успели выйти из металла до его остывания. Это снижает надежность шва. Причиной могут стать плохая обработка кромок, наличие любых загрязнений в месте обработки и неверный выбор силы пламени. Такие швы полностью устраняются и перекрываются.
- Пережог. Из-за появления окисленных зерен качество таких швов низкое. Появившаяся пленка препятствует надежному сцеплению. Дефект не подлежит исправлению, потому что такой металл очень хрупок.
При соблюдении требований проекта и технологии работы с типом металла сварные соединения отличаются высокой прочностью. При этом полученные конструкции гораздо легче, чем литые или изготовленные с помощью заклепочного монтажа. Способ соединения позволяет экономить до 20 % материала по сравнению с другими способами. Также сварка позволяет работать с любыми материалами, контролируя или корректируя формы законченных конструкций в случае необходимости.