Автоматическая вибродуговая наплавка — Энциклопедия по машиностроению XXL
Вибродуговая наплавка. Автоматическую вибродуговую наплавку широко применяют для наплавки цилиндрических деталей небольшого размера, особенно при ремонте деталей станочного оборудования (оси, валы, шпиндели, шлицевые валки и т. п.). [c.548]Автоматическая вибродуговая наплавка [c.188]
Автоматическая вибродуговая наплавка широко применяется для наплавки цилиндрических деталей небольшого размера, осо- [c.107]
АППАРАТЫ ДЛЯ АВТОМАТИЧЕСКОЙ ВИБРОДУГОВОЙ НАПЛАВКИ [c.73]
Аппараты для автоматической вибродуговой наплавки устанавливаются на станках вибродуговых установок. Конструкции станков зависят от формы наплавляемых деталей и их изнашивающихся поверхностей. В случае наплавки деталей с цилиндрическими поверхностями конструкции станков обеспечивают крепление детали и ее вращение вокруг своей оси с линейной скоростью точек поверхности детали, равной скорости наплавки, а также перемещение вибродугового аппарата вдоль оси детали со скоростью, соответствующей шагу наплавки.

Оценивая автоматическую вибродуговую наплавку как способ восстановления изношенных поверхностей деталей, можно отметить следующие ее достоинства небольшой нагрев деталей, не оказывающий влияние на их термообработку небольшая зона термического влияния достаточно высокая производительность процесса, которая по площади покрытия составляет 8—10 см /мин. [c.156]
АВТОМАТИЧЕСКАЯ ВИБРОДУГОВАЯ НАПЛАВКА [c.106]
Автоматическая вибродуговая наплавка в струе защитной (охлаждающей) жидкости (рис. 236) применяется при восстановлении изношенных деталей машин. Способ состоит в том, что к вращающейся детали подается электродная проволока, подключенная к источнику питания. [c.363]
Для наплавки цилиндрических деталей небольшого диаметра за последнее время стала применяться автоматическая вибродуговая наплавка. Автоматическая вибродуговая наплавка в струе охлаждающей жидкости является новым методом восстановления изношенных деталей машин и механизмов. Основные преимущества вибродуговой наплавки
[c.574]
Автоматическая вибродуговая наплавка. Наплавка деталей вибрирующим электродом с применением охлаждающей жидкости получила наиболее широкое применение. Основным преимуществом этого процесса наплавки является небольшой нагрев деталей (около 100° С), малая зона термического влияния и возможность получения наплавленного металла с требуемой твердостью и износостойкостью без дополнительной термической обработки.
Автоматическая вибродуговая наплавка в струе защитной (охлаждающей) жидкости (рис. 238) применяется при восстановлении изношенных деталей машин. Способ состоит в том, что к вра- [c.358]
Изношенные боковые поверхности шлицев 1 цапфы 2 (рис.
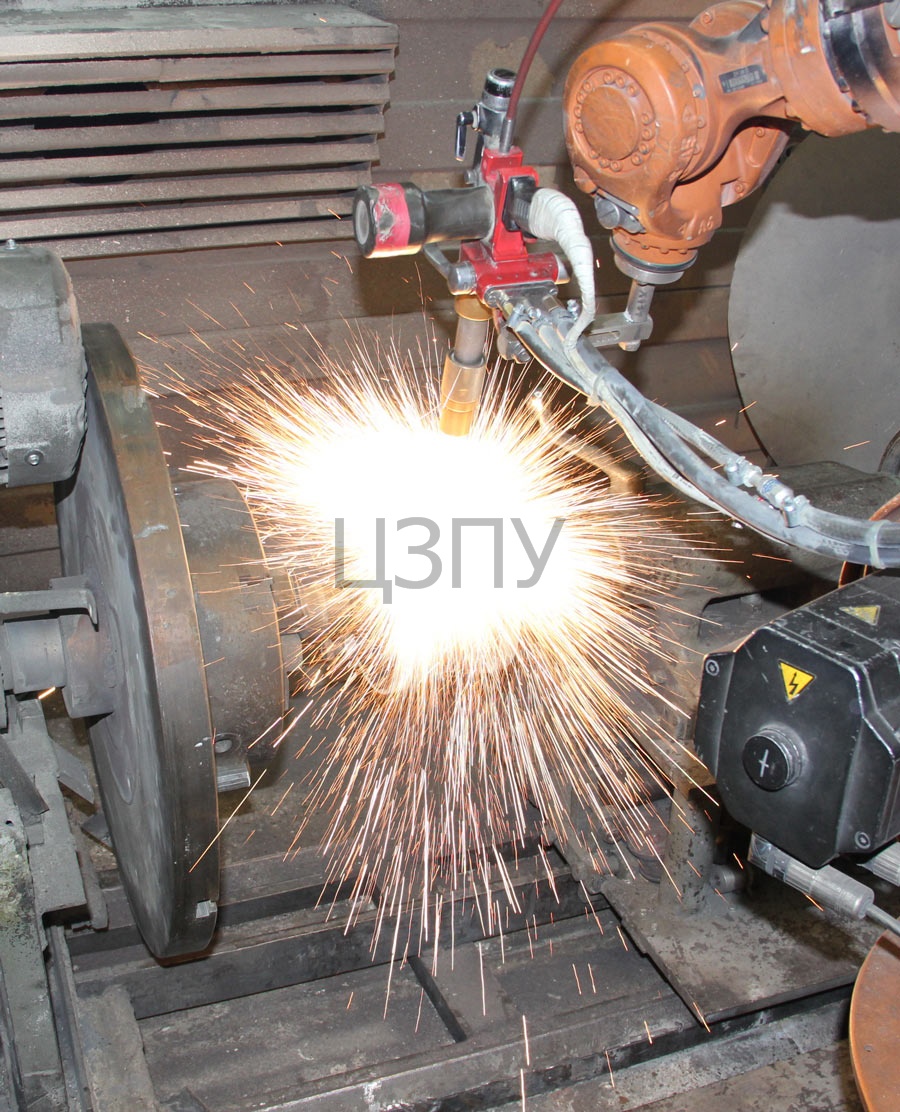
Ремонт (восстановление) изношенных деталей методом автоматической вибродуговой наплавки. [c.345]
Автоматическая вибродуговая наплавка отличается следующими преимуществами небольшим нагревом деталей, не влияющим на их термообработку небольшой зоной термического влияния достаточно высокой производительностью процесса, которая по площади покрытия составляет 8. .. 10 см мин. [c.179]
Автоматическую вибродуговую наплавку широко применяют для восстановления цилиндрических деталей небольшого размера, особенно при ремонте деталей автомобилей и тракторов, станочного оборудования (оси, валы, шпиндели, шлицевые валы и т. п.). Напряжение источника тока 14—24 В, диаметр электродной проволоки 1,6—2,5 мм, сила сварочного тока 100—250 А. Деталь, зажатая в центрах или патроне станка, равномерно вращается с необходимой скоростью, сварочная (вибродуговая) головка перемещается вдоль наплавляемой детали.
В последнее время изношенные зубья валов начинают восстанавливать электровибрационной (вибродуговой) наплавкой. Процесс наплавки зубьев ведут при неподвижной установке наплавляемой детали и продольном перемещении автоматической головки. [c.411]
Материалы для восстановления автомобильных деталей механизированными (автоматическими и полуавтоматическими) видами наращивания поверхностей. При восстановлении автомобильных деталей механизированными видами наращивания изношенных поверхностей наибольшее применение нашли автоматическая наплавка под слоем флюса, электроимпульсная (вибродуговая) наплавка, наплавка в среде углекислого газа, металлизация напылением и электроискровое наращивание.
Для нанесения металлических покрытий на изношенные поверхности деталей наиболее широкое применение получили следующие механизированные способы наплавки автоматическая электродуговая наплавка под слоем флюса, наплавка в среде углекислого газа, вибродуговая, плазменная и электроконтактная наплавки. [c.139]
Оборудование для вибродуговой наплавки состоит из станка для вращения детали или ее продольного перемещения при наплавке на плоскость и автоматической сварочной головки, которая подает проволоку к изделию и сообщает ей вибрационные колебания. [c.377]
Вибродуговая наплавка — разновидность автоматической наплавки под слоем флюса и в защитных газах. Она отличается тем, что сварку ведут проволочным электродом с частотой [c.90]
Сварочные головки принципиально устроены так же, как и автоматические сварочные головки, но в отличие от последних не имеют бункера для флюса и снабжены вибратором. На ремонтных предприятиях в основном применяют наплавочные головки с механическим вибратором ОКС-1252, ОКС-6569, ВГ-4, ВГ-5 и ВГ-8М. Последняя предназначена для вибродуговой наплавки в среде углекислого газа.
[c.91]
Изложите сущность аргонно-дуговой сварки и ее преимущества. 5. Какие источники питания дуги током применяют при электросварке 6. Каковы особенности сварки и наплавки стальных деталей 7. Чем обусловлены трудности при сварке чугунных деталей 8. Изложите приемы горячей сварки чугунных деталей. 9. Изложите приемы холодной сварки чугунных деталей. 10. Каковы особенности и приемы сварки деталей из меди и ее сплавов II. Каковы особенности и приемы сварки деталей из алюминия и его сплавов 12. Изложите сущность газопламенной сварки. Назовите ее преимущества и недостатки по сравнению с ручной электродуговой сваркой. 13. Расскажите о процессе автоматической наплавки под слоем флюса, его преимуществах и недостатках. 14. В чем заключаются особенности и преимущества автоматической сварки в защитных газах 15.
Восстановление наплавкой. Этим способом лучше восстанавливать изношенную резьбу уменьшенного размера или номинальную на валу (оси). Резьбу диаметром менее 40 мм наплавляют вибродуговой наплавкой без применения охлаждающей жидкости, используя проволоку Нп-30 диаметром 1,2,..1,6 мм или автоматической наплавкой в среде углекислого газа с этой же проволокой. Успешно наплавляют изношенную резьбу плазменной струёй с применением порошков и колебателя, обеспечивающего наплавку за один проход и один оборот детали. Перед наплавкой поврежденную резьбу зачищают стальной щеткой до блеска или протачивают. После наплавки деталь протачивают и нарезают резьбу номинального размера.
Разновидностью дуговой наплавки является вибродуговая наплавка (рис. 9.3). Наплавка при этом способе осуществляется вибрирующим электродом с помощью автоматической головки с применением охлаждающей жидкости. Процесс протекает при слабом нагреве восстанавливаемой детали, отсутствии деформации, незначительной величине зоны термического влияния, в результате чего химический состав и физико-механические свойства детали почти не изменяются.
[c.106]
Восстановление изношенных деталей автоматической вибродуговой наплавкой, Сб. статей, Челябгиз, 1956. [c.576]
С. Нагревают при помощи ацетилено-кислородных горелок, паяльных ламп. При ремонте валов и осей могут быть использованы автоматическая наплавка под слоем флюса, автоматическая вибродуговая наплавка, металлизация, хромирование, обработка на ремонтный размер и другие методы. [c.325]
Изношенные ручьи блоков, входящих в конструкции грузовых ПКД, конвейеров, экскаваторов и т. д., разрешается восстанавливать автоматической наплавкой под слоем флюса или автоматической вибродуговой наплавкой. Наплавка производится проволокой Св-08А или Св-08ГА, флюсы применяются марки ОЦС-45 или АН-348А.
[c.328]
Автоматическая вибродуговая наплавка была впервые предложена в 1948 г. советским инженером Г. П. Клековкиным.
Установки для автоматической вибродуговой наплавки обычно монтируются на базе токарных или токарно-винторезных станков, на суппорте которых устанавливается Бибродуговая головка. Станок оснащается источником питания дуги и устройством подачи охлаждающего раствора. [c.218]
Многими заводами изготовляются установки для вибродуговой напла вки. Установка для вибродуговой наплавки состоит из сле-дуюш,их узлов автоматической головки, имеющей механизм подачи электродной проволоки в зону дуги, механизма вибрации проволоки и устройства для подвода охлаждающей жидкости станка для вращения детали и перемещения сварочной головки источника питания. [c.108]
Аппараты для автоматической вибродуго-вой наплавки (автоматические вибродуговые аппараты) являются основной частью наплавочных вибродуговых установок и служат для подачи к месту наплавки электродной проволоки и вибрации конца проволоки с заданной частотой и размахом.
[c.73]
Действующие технические условия на ремонт автомобилей даже при их полном соблюдении не обеспечивают одинакового качества ремонта автомобилей и агрегатов. Это можно подтвердить следующими примерами. Коленчатый вал двигателя можно восстановить способом ремонтных размеров, автоматической наплавкой под слоем флюса, вибродуговой наплавкой. При этом, если в каждом отдельном случае будут соблюдены все требования технических условий, качество его ремонта все же будет разным. У автомобиля (агрегата, узла или детали) есть параметры, которые оказывают решающее влияние на его характеристики и надежность. Такие параметры необходимо оценивать не только определенным миниму- [c.58]
Вибродуговая наплавка. Сущность способа состоит в том, что к вращающейся детали автоматической головкой подводится проволока, конец которой совершает продольно-осевые колебательные движения, прикасаясь к детали и отходя от нее на заданную величину. Благодаря таким колебаниям между вращающимся изделием и проволокой периодически зажигается дуга, которая угасает в момент короткого замыкания проволоки с изделием и вновь возбуждается при удалении от изделия. В момент короткого замыкания расплавленный металл проволоки приваривается к детали. Для уменьшения разогрева детали дуговой промежуток и деталь охлаждаются водяной имульсией, содержащей 50—60 г кальцинированной соды и 10—15 г технического мыла на 1 л воды.
[c.376]
Шлицы (наружные), изношенные по толщине, наплавляют ручной или автоматической сваркой, а также заменяют изношенную шлицевую часть новой, соединяемой обычно сваркой. Шлицевые канавки валов диаметром менее 50 мм заваривают и нарезают шлицы номинального размера. При заварке канавок ручной или вибродуговой наплавкой валики накладывают вдоль шлицев поочередно в шлицевые канавки с диаметрально противоположных сторон, чтобы избежать коробления вала. При ручной наплавке применяют электроды ОЗН-ЗООУ, ОЗН-350У и другие типа Э42А и Э46А с качественными покрытиями, а при вибродуговой наплавке — проволоку Нп-30 и охлаждающую жидкость. [c.169]
Восстановление изношенных деталей автоматической вибродуговой наплавкой
Категория:
Ремонт машин с гидравлическим приводом
Публикация:
Восстановление изношенных деталей автоматической вибродуговой наплавкой
Читать далее:
Восстановление изношенных деталей автоматической вибродуговой наплавкой
Вибродуговая наплавка в настоящее время — один из наиболее распространенных способов восстановления изношенных деталей — имеет ряд существенных преимуществ перед другими способами восстановления деталей. В процессе вибродуговой наплавки деталь нагревается незначительно, поэтому деформации восстановленных деталей малы и править их после наплавки обычно не нужно. Благодаря малому нагреву не нару-. шается термическая обработка. Другое важное преимущество вибродуговой наплавки заключается в том, что восстановленные этим методом детали не нуждаются в последующей термической обработке, так как непосредственно в процессе наплавки под действием охлаждающей жидкости происходит закалка наплавленного слоя, твердость которого может доходить до 60—62 HRC. Толщину слоя при вибродуговой наплавке можно регулировать в пределах 0,5…3,5 мм на сторону. Изменение количества охлаждающей жидкости и
Рис. 42. Схема установки вибродуговой наплавки металла
1 — дроссель; 2 — генератор; 3 — канал для подачи жидкости; 4 — ролик подающего механизма; 5 — кассета для электродной проволоки; 6 — вибратор; 7 — пружина; 8 — насос; 9 — вибрирующий мундштук; 10 — электрод; 11 — наплавляемая деталь; 12 — фильтр-отстойник
Рекламные предложения на основе ваших интересов:
условии ее подачи на деталь позволяет в широких пределах регулировать твердость слоя, наплавленного одним и тем же материалом. Кроме того, вибродуговую автоматическую наплавку изношенных деталей осуществляют под слоем флюса и в среде защитных газов.
В процессе наплавки электродная проволока непрерывно подается в зону наплавки к вращающейся детали под углом (рис. 42). Под действием электромагнитного вибратора конец электродной проволоки вибрирует. Периодически происходят замыкания и размыкания электрода с деталью. В зону наплавки через канал подается охлаждающая жидкость. К электродной проволоке и детали подводится электрический ток низкого напряжения от генератора. Сила тока наплавки опре-, деляется диаметром электродной проволоки и скоро-, стью ее подачи при наплавке. При установленном режиме во время импульсного разряда она также зависит от частоты вибрации электрода, сопротивления в цепи и напряжения на, электродах. Ток для наплавки можно определять по величине его плотности, которая принимается равной 60…75 А/мм2. При ускоренной подаче электродной проволоки необходимо повышать плотность тока.
Скорость подачи электродной проволоки, скорость наплавки и частоту вращения наплавляемой детали определяют по следующим формулам.
Для вибродуговой наплавки широко применяют следующие наплавочные головки: ГМВК-1, ГМВК-2, КУМА-5, КУМА-5М, УНЖ, ВГ-2 и ВГ-4.
Рекламные предложения:
Читать далее: Восстановление изношенных деталей газотермическим напылением
Категория: — Ремонт машин с гидравлическим приводом
Главная → Справочник → Статьи → Форум
Вибродуговая наплавка
Категория:
Прогрессивные методы ремонта
Публикация:
Вибродуговая наплавка
Читать далее:
Вибродуговая наплавка
Вибродуговая наплавка разработана в ЧИМЭСХ под руководством докт. техн. наук И. Е. Ульмана. Сущность процесса заключается в периодическом замыкании и размыкании находящейся под током электродной проволоки, которая в процессе плавления вибрирует с частотой 40…50 кол/с и больше. Наплавленный валик интенсивно охлаждается за счет теплоотвода в деталь и охлаждающую жидкость и получает закалку.
Вибродуговая наплавка по сравнению с ручной электродуговой увеличивает производительность труда в 2…4 раза. В процессе наплавки деталь нагревается не более чем на 100 °С, благодаря чему удается избежать коробления. Кроме того, исключена возможность изменения структуры металла детали, так как зона термического влияния при этом способе невелика. Не требуется дефицитных электродных материалов и дорогого оборудования. Эта наплавка дает возможность получить слой высокой твердости без последующей обработки и восстанавливать детали диаметром 10 мм и более.
Однако вибродуговая наплавка имеет и некоторые недостатки. Так, например, наплавленный слой имеет неоднородную твердость, значительное количество пор, высокие внутренние растягивающие напряжения, что ограничивает область применения этого способа для деталей, работающих в условиях тяжелых, знакопеременных и ударных нагрузок.
Рекламные предложения на основе ваших интересов:
Цикл вибродуговой наплавки состоит из трех периодов: короткого замыкания, дугового разряда и холостого хода.
ВиброДуговая наплавка производится с помощью автоматической головки, которая устанавливается на суппорте токарного станка вместо резцедержателя. Основание головки изолируется от плиты суппорта станка- текстолитовыми прокладками и втулками. Станок заземляется. Наплавляемая деталь, закрепленная в патроне или в центрах станка, вращается с определенной скоростью. Сварочный ток к обрабатываемой детали подводится токоподводящим устройством. Для этой цели на шпиндель токарного станка напрессовывается медное кольцо; к станине привинчивается траверса со щеткодержателем и щеткой. Рекомендуется обратная полярность тока (на детали «минус»), так как при ней уменьшаются термические воздействия на деталь с включением в цепь регулируемого индуктивного сопротивления.
Автоматическая вибродуговая головка предназначена для подачи электродной проволоки и отрыва ее от детали. Проволока из кассеты 6 подается механизмом, который состоит из роликов, редуктора и электродвигателя. Вибрирует электрод с помощью электромагнитного или механического вибратора. Охлаждающая жидкость в зону наплавки подается насосом.
Лучшими источниками питания для вибродуговой наплавки являются агрегаты типа АНД. Они состоят из электродвигателя и генератора НД с жесткой внешней характеристикой, имеющего два коллектора и шунто-вую обмотку с самовозбуждением. Генераторы снабжены шунтовыми регуляторами напряжения типа РШН-1.
Рис. 1. Принципиальная схема вибродуговой наплавки:
1 — электродвигатель; 2 — цасос; 3 — наплавляемая деталь; 4 — вибрирующий мундштук; 5—механизм подачи проволоки; 6 — кассета; 7 — вибратор; 8 — индуктивное сопротивление; 9 — бак для жидкости.
Агрегат АНД-500/250 используют для питания одной головки при диаметре электродной проволоки до 2 мм и скорости подачи не более 2м/мин. Более мощные агрегаты АНД-1000/500 и АНД-1500/750 позволяют наплавлять либо одновременно двумя-тремя наплавочными головками, либо проволокой большего диаметра, либо ленточным электродом. При вибродуговой наплавке можно также применять селеновые выпрямители марок ВС-600, ВДГ-301 и сварочные преобразователи ПСГ-300, ПСГ-500.
Для перечисленных типов источников тока в сварочную цепь необходимо включить регулируемое реактивное сопротивление в целях настраивания сварочной цепи на оптимальные переходные процессы наплавки. Для этого -используют дроссели РСТЭ-34, РСТЭ-24. Индуктивность сварочной цепи должна быть 300…400 мГ, что соответствует 8… 12 виткам реактивной катушки дросселя РСТЭ-34.
Вибродуговым способом наплавляют различные детали тел вращения по внутреннему и наружному диаметру, изготовленные из стали и чугуна. Технологический процесс восстановления деталей включает следующие операции: подготовку к наплавке, наплавку, последующую обработку наплавленного слоя, контроль качества покрытия.
Детали перед наплавкой очищаются от ржавчины, масла и нагара химическим или механическим способом. Если неравномерность износа детали превышает 0,3… 0,5 мм, ее подвергают механической обработке до полного устранения искажений геометрической формы. Имеющиеся на наплавляемой поверхности отверстия, пазы, канавки, которые нужно сохранить, заделывают графитовыми, медными или стальными вставками.
Качество и толщина наплавленного вибродуговым способом металла зависят от электродной проволоки и режима наплавки. Поэтому марку проволоки выбирают исходя из требований, предъявляемых к наплавленному слою. Следует иметь в виду, что необходимую твердость наплавленного слоя можно получить за счет применения проволоки соответствующего химического состава. При наплавке высокоуглеродистой проволокой Нп-65Г (0,65 % С) диаметром 1,6…1,8 мм твердость наплавленного металла достигает 46, 5…59 HRC3.
Если требуются низкие твердости, можно наплавлять проволокой марки Св-08, которая дает твердость НВ 200…275, или проволокой марки Нп-ЗОХГСА для получения средней твердости 32…41,5 HRC3. Можно использовать также стальную ленту.
Для вибродуговой наплавки перспективно применение порошковых проволок ПП-25Х5ФМС-0, ПП-ЗХ5Г2М-0, ПП-1Х14Т-0 и др.
Порошковой проволокой можно восстанавливать детали ходовой части гусеничных тракторов, поворотные цапфы тракторов МТЗ, крестовины карданных валов тракторов К-700, К-701, ступицы вариаторов зерноуборочных комбайнов и др.
Режим наплавки характеризуется величиной тока, скоростью подачи электродной проволоки, шагом наплавки, расходом охлаждающей жидкости, частотой вибрации электрода и т. д.
Напряжение дуги при вибродуговой наплавке целесообразно регулировать в пределах 16…24 В. При более низких напряжениях уменьшается производительность труда, а при повышении напряжения (более 25 В) увеличивается интенсивность выгорания легирующих элементов. Сила тока должна быть в пределах 130… 180 А и более.
Оптимальные значения скорости наплавки, обеспечивающие хорошее формирование наплавленного слоя, находятся в пределах 18…120 м/ч. Скорость подачи проволоки может изменяться в пределах 50…110 м/ч. Следует отметить, что низкая скорость приводит к образованию пропусков на наплавленной поверхности. При очень большой скорости не вся проволока расплавляется.
Шаг наплавки зависит от диаметра электрода, напряжения дуги и скорости подачи проволоки. Практика показывает, что шаг наплавки должен быть в 1…3 раза больше диаметра электродной проволоки. При малом обработка в момент кристаллизации наплавленного слоя благоприятно скажется на уменьшении пор и трещин и на увеличении усталостной прочности деталей. Работы в этом направлении проведены Э. Л. Левиным и В. С. Ибрагимовым в Башкирском сельскохозяйственном институте.
Рекламные предложения:
Читать далее: Автоматическая наплавка под флюсом
Категория: — Прогрессивные методы ремонта
Главная → Справочник → Статьи → Форум
Вибродуговая наплавка
При этом способе электродуговая наплавка поверхности детали осуществляется вибрирующим электродом при помощи наплавочной головки в струе жидкости или защитных газов. Электрокинематическая схема установки представлена на рис. 17.5.[ …]
Деталь, как и при наплавке под слоем флюса, закрепляется в патроне или центрах токарного станка, а на суппорте монтируется наплавочная головка с механизмом подачи проволоки, вибратором и мундштуком. Вследствие вибрации конца электродной проволоки происходит замыкание и размыкание сварочной цепи, а следовательно, возбуждение и прерывание электрической дуги между проволокой и деталью, В связи с разрывом дуги происходит мелкокапельный переход металла с электрода на деталь. [ …]
Мундштук получает колебания от вибратора с частотой 50-100 кол/с. Внутренний диаметр трубки мундштука должен быть больше диаметра проволоки на 0,5 мм.[ …]
В зону наплавки подается охлаждающая жидкость: 3- 4 %-ный раствор кальцинированной соды или 15-25 %-ный раствор технического глицерина. Жидкость защищает расплавленный металл от окисления, предохраняет деталь от деформации, способствует качественному протеканию процесса и закаляет наплавленный слой.[ …]
Вибродуговая наплавка производится на постоянном и на переменном токе. Лучшие результаты получаются при наплавке на постоянном токе при обратной полярности. Восстановление деталей обычно ведется при напряжении 18-22 В и силе тока 80-300 А. В качестве источника тока используют низковольтные генераторы НД 1000/500, НД 500/250 или сварочные генераторы СУГ-26, ПС-300.[ …]
Нп-80, Нп-65Г, Нп-ЗОХГСА диаметром 1-3 мм, который выбирают в зависимости от толщины наплавляемого слоя и мощности источника тока. Так, для наплавки слоя толщиной до 1 мм принимают проволоку диаметром 1-1,6 мм, толщиной 2 мм — диаметром 2,5 мм, более 2 мм — диаметром 2-3 мм. [ …]
Вибродуговая наплавка в струе охлаждающей жидкости имеет следующие преимущества перед другими способами.[ …]
Основным недостатком вибродуговой наплавки в струе охлаждающей жидкости в силу особенностей технологического процесса является возникновение в наплавленном слое микротрещин, что снижает усталостную прочность восстановленных деталей по сравнению с новыми. Для устранения этого недостатка разработаны способы вибродуговой наплавки в среде защитных газов, газожидкостной среде, в среде пара и др.[ …]
Вибродуговая наплавка вгазозащитной среде производится постоянным током с обратной полярностью. В качестве защитной среды используют смесь кислорода с небольшим (0,3 л/г) количеством воды. Присадочным материалом служит проволока с повышенным содержанием кремния, марганца и углерода диаметром 1,6-1,8 мм.[ …]
Рисунки к данной главе:
Вернуться к оглавлениюСхема вибродуговой наплавки
Вибродуговая наплавка имеет отличия от обычных сварочных процессов наличием колебаний электрода с частотой 50-100 Гц и низким напряжением источника сварочного тока. Перенос металла электродной проволоки на деталь происходит благодаря чередованию электрических разрядов и коротких замыканий цепи. Устойчивость процесса и хорошее формирование наплавленного металла возможны только при определенном значении индуктивности сварочной цепи. Расплавленный металл можно защищать флюсом, газом или жидкостью.
Наибольшее распространение получила вибродуговая наплавка в среде жидкости. Регулируя отвод тепла количеством и местом поступления охлаждающей жидкости, можно в широких пределах изменять механические свойства наплавленного металла. Правда чрезмерное снижение усталостной прочности дает ограничения на применение вибродуговой наплавки. Использовать вибродуговую наплавку и схемы вибродуговой наплавки для восстановления деталей, разрушение которых может привести к аварии не разрешается.
Схема установки для вибродуговой наплавкиСхема вибродуговой наплавки деталей приведена на рисунке. Восстанавливаемая деталь помещается в центры токарного станка, а сварочную головку закрепляют на суппорте станка.
Электродная проволока из кассеты 5 роликами подающего механизма 4 через мундштук 12 вибратора подается в зону горения дуги. В результате вибраций электрода происходит чередование электрических разрядов и коротких замыканий цепи и, следовательно, контакт между электродом и деталью. В период разряда происходит оплавление конца электрода, в период короткого замыкания – перенос металла на деталь. Жидкость, поступая через шланг 3 в зону горения дуги, оказывает двоякое действие. С одной стороны, пары ее, оттесняя воздух из зоны горения дуги, защищают расплавленный металл, с другой стороны, охлаждая расплавленный металл, жидкость сокращает пребывание металла в жидком состоянии. Ввиду быстрого перехода металла из жидкого состояния в твердое состояние содержащиеся в нем газы не успевают выделиться и в наплавленном слое образуют поры. Быстрое охлаждение металла вызывает резкую его закалку, вследствие чего возникают значительные по величине внутренние растягивающие напряжения, вызывающие трещины в наплавленном слое. Количество пор и трещин в наплавленном слое металла можно сократить, применяя для наплавки соответствующие проволоки и замедляя скорость охлаждения расплавленного металла.
Вибродуговая наплавка
Автоматическую
вибродуговую наплавку широко применяют
для восстановления преимущественно
деталей типа вала диаметром более
20 мм, а также для восстановления отверстий
диаметром более 40 мм и глубиной до
100 мм. Процесс наплавки осуществляют
при вибрации электродной проволоки с
подачей охлаждающей жидкости на
наплавленную поверхность. В качестве
охлаждающей жидкости применяют 2,5…6%-й
водный раствор кальцинированной соды
или 10…20%-й водный раствор глицерина.
Образующийся пар защищает расплавленный
металл от воздействия кислорода и
азота воздуха и охлаждает наплавляемую
деталь, чем способствует получению
валика с более высокими механическими
свойствами.
Сущность способа вибродуговой наплавки деталей состоит в том, что электродная проволока подается из кассеты к наплавляемой поверхности специальным механизмом, который одновременно с подачей проволоки вниз, к детали, придает ей колебательные движения с определенной частотой (50… 110 Гц) и амплитудой (до 4 мм).
К детали и электродной проволоке подводится ток 80…300 А при напряжении 12…20 В. В место соприкосновения проволоки с деталью подаются охлаждающая жидкость, защитный газ или флюс. Процесс может вестись и без защиты дуги.
Цикл наплавки включает в себя короткое замыкание (в момент касания электродом детали), горение дуги (во время отрыва электрода от детали) и холостой ход (от момента, когда дуга погасла, до следующего короткого замыкания).
При включении в цепь тока индуктивности нарастание и падение импульсов тока сглаживаются, длительность и устойчивость горения дуги возрастают.
Принципиальная
схема вибродуговой установки с
электромеханическим вибратором
показана на рисунке 6. Деталь 3, подлежащую
наплавке, устанавливают в патроне или
центрах токарного станка. На суппорте
станка монтируют наплавочную головку,
состоящую из механизма подачи 5 проволоки
с кассетой 6, электромагнитного
вибратора 7 с мундштуком 4. Вибратор
создает колебания конца электрода с
частотой 110 Гц и амплитудой колебания
до 4 мм, обеспечивая размыкание и замыкание
сварочной цепи. При периодическом
замыкании электродной проволоки и
детали происходит перенос металла с
электрода на деталь. Вибрация электрода
во время наплавки обеспечивает
стабильность процесса за счет частых
возбуждений дуговых разрядов и
способствует подаче электродной
проволоки небольшими порциями, что
обеспечивает лучшее формирование
наплавленных валиков.
Электроснабжение
установки осуществляется от источника
тока напряжением 24 В. Последовательно
с ним включен дроссель 9 низкой
частоты, который стабилизирует силу
сварочного тока. Реостат 8 служит
для регулировки силы тока в цепи. В зону
наплавки при помощи насоса 1 из
бака 2 подается
охлаждающая жидкость (4…6%-й раствор
кальцинированной соды в воде), которая
защищает металл от окисления.
Качество соединения наплавленного металла с основным зависит от полярности тока, шага наплавки (подача суппорта станка на один оборот детали), угла подвода электрода к детали, качества очистки и подготовки поверхности, подлежащей наплавлению, толщины слоя наплавки и др.
Высокое
качество наплавки получают при токе
обратной полярности («+» на электроде,
«—» на детали), шаге наплавки 1,5…3,5
мм/об. и угле подвода проволоки к детали
15…30°. Твердость наплавленного слоя
зависит от химического состава электродной
проволоки, условия подачи охлаждающей
жидкости, взаимного перекрытия валиками
друг друга. Для вибродуговой наплавки
применяют преимущественно углеродистую
проволоку с содержанием углерода до
0,9% (Св-08, Нп-65Г, Нп-ЗОХГСА, У-7, ПК-1, Нп-30,
Нп-50). Диаметр проволоки 1…3 мм. Следует
учитывать, что с увеличением диаметра
проволоки существенно возрастает
производительность наплавки: при
использовании проволоки диаметром 2 и
2,5 мм увеличивается производительность
соответственно в 2 и 3 раза по сравнению
с применением проволоки диаметром 1,4
мм, но при этом снижается твердость слоя
на 5…8 единиц.
Толщина наплавляемого слоя зависит от диаметра проволоки, соотношения скорости подачи проволоки и скорости наплавки. Ниже даны рекомендуемые диаметры проволоки в зависимости от толщины наплавляемого слоя.
Достоинства способа: незначительная по глубине зона термического влияния; незначительная деформация деталей после наплавки; высокая твердость и износостойкость покрытия; высокая производительность процесса; возможность получения покрытия различной толщины и механических свойств.
Недостатки
способа: снижение усталостной прочности
до 60 % из-за образования закалочных
структур в материале, вызывающих
«стягивающие напряжения и неоднородность
твердости ;наличие пор в покрытии по
причине быстрого перехода металла из
жидкого состояния в твердое.
ВИБРОДУГОВАЯ НАПЛАВКА | Инструмент, проверенный временем
Этот метод основан на использовании тепла кратковременной дуги, которая возникает в момент разрыва цепи между вибрирующим электродом и наплавляемой поверхностью. Особенность этого способа: -получение малой толщины наплавляемого слоя, -прерывистый характер процесса -непрерывное охлаждение поверхности наплавки. |
Вибродуговая наплавка применяется для цилиндрических деталей небольшого размера, особенно при ремонте деталей автомобилей и тракторов, станочного оборудования (оси, валы, шпиндели, шлицевые валики). За счет вибрации электродной проволоки (амплитуда — 0,5-3,0 мм) обеспечивается чередование кратковременной дуги, коротких замыканий и холостого хода Деталь, закрепленная в центрах или в патроне станка, равномерно вращается с необходимой скоростью. Для получения наплавленного слоя по ее длине сварочная (вибродуговая) головка перемещается вдоль наплавляемой детали. Электрод и деталь оплавляются за счет дугового разряда. Перенос металла, образующегося в виде капли на конце электрода в период горения дуги, происходит преимущественно во время короткого замыкания. Перенос металла небольшими каплями облегчает формирование ровных плотных слоев наплавленного металла.
При этом процессе горения дуги достигается хорошее формирование, наплавленных валиков, обеспечивается возможность наплавки тонких валиков, площадь сечения которых близка к площади сечения проволоки. При необходимости время горения дуги может быть увеличено включением в сварочную цепь дросселя или уменьшено включением конденсатора параллельно разрядному промежутку. Для улучшения условий горения дуги в зону наплавки подается охлаждающая жидкость, которая содержит соли; в ее состав вводятся ионизирующие элементы. В качестве охлаждающей жидкости чаще всего применяют водный раствор кальцинированной соды или 20% — ный водный раствор глицерина.
Применение флюса обеспечивает спокойное горение дуги и замедленное остывание металла, что предотвращает образование трещин. В этом случае наплавочная установка дополнительно оснащается устройством для удержания флюса. Так как при вибродуговом способе происходит быстрое охлаждение маленьких порций расплавленного металла, то возникает возможность наплавки деталей малых диаметров.
Вибродуговая наплавка особенно эффективна при восстановлении изношенных деталей, у которых допускаемый износ составляет менее 1 мм. Вибродуговой наплавкой восстанавливают стальные и чугунные детали, на которых необходимо нанести равномерный тонкий слой наплавки при их минимальной деформации, допускающей отдельные незначительные дефекты наплавки.
Преимущества вибродуговой наплавки:
-незначительный нагрев деталей;
-малая деформация детали в процессе наплавки;
-получение твердой поверхности без термообработки;
-несложное оборудования;
— высокая производительность;
-получение равномерного слоя наплавленного металла.
Недостаток вибродугового способа наплавки: — непрерывное охлаждение и прерыви — стый характер процесса способствует образованию мелких газовых пор, которые вызывают неравномерную твердость наплавленного слоя.
Кроме того развиваются новые технологические направления модификации. К ним следует отнести наплавку в среде углекислого газа, водяного пара, в потоке воздуха и т. д. Разработаны и внедряются также методы механической, термической, термомеханической и ультразвуковой обработки металла, наплавленного вибродуговым способом.
Также применяется способ двухэлектродной вибродуговой наплавки, в отличие от одноэлектродной имеет более высокую производительность (до двух раз) и меньший расход электроэнергии на единицу наплавленного металла (на 2025%).
Существенной особенностью двухэлектродной вибродуговой наплавки является то, что электроды вибрируют со смещением фазы амплитуд на 180°, т. е. во время замыкания одного электрода на сварочную ванну, второй находится на наибольшем расстоянии от нее.
Рекомендуемые ориентировочные режимы вибродуговой наплавки, а также диаметры проволоки (в зависимости от толщины наплавляемого слоя) выбираются по табличным данным.
Твердость наплавленного слоя зависит от марки электродной проволоки и режимов наплавки.
Вибродуговую наплавку характеризуют следующие показатели:
— потери электродного металла на угар и разбрызгивание
11-30%;
— коэффициент наплавки ан= 8-11 г/А • ч;
— коэффициент перехода из проволоки в наплавленный металл
для углерода 0,40-0,50, для марганца — 0,50-0,60;
— стоимость восстановления деталей в большинстве случаев
10-30% стоимости новой детали;
— коэффициент расплавления порошковой проволоки ар и потерь |/, ширина b и высота hH, глубина проплавления h;
— кроющая способность шлака E=Sm/Sb, где Sm и Sb — площади
поверхности наплавленного валика.
При обычно применяемых режимах вибродуговой наплавки коэффициент расплавления составляет 9-12 г/А • ч, коэффициент наплавки 8-10 г/А • ч, потери электродного материала на угар и разбрызгивание 11-15%, количество наплавленного металла 1,2-1,5 кг/ч, коэффициент перехода углерода в наплавленный металл 0,45-0,55, марганца 0,45-0,60.
Пример. Толкатели клапанов двигателей наплавляют вибродуговой наплавкой на переоборудованном токарном станке наплавочной головкой, смонтированной на суппорте.
Толкатель обезжиривают и устанавливают в патрон токарного станка, где наплавляемую поверхность зачищают до металлического блеска.
Режим наплавки:
сила тока, А
120-160
напряжение на дуге, В 14-16
Наплавку начинают с кромки цилиндрической поверхности от тарелки в сторону стержня. Толкатели клапанов двигателей
ГАЗ-51 наплавляют на длину 24 и 15,5 мм, двигателей ЗИЛ-120
на всю длину до диаметра 17,0 мм.
Для лучшей механической обработки наплавленный металл,
подвергают отпуску токами высокой частоты. Затем наплавленную часть толкателя обтачивают на станке и подвергают
поверхностной закалке токами высокой частоты до 51,0 HRC
после чего шлифуют.
Исследование влияния механической вибрации на сварочную ванну из низкоуглеродистой стали
Производство Rev. 6 , 21 (2019)Исследовательская статья
Исследование влияния механической вибрации в сварочной ванне из низкоуглеродистой стали
Кафедра машиностроения и автоматизации, Университет AMITY, Ранчи, Индия
* электронная почта: pravinsingh. [email protected]
Поступило:
17
Май
2019 г.
Принято:
27
июль
2019 г.
Аннотация
В этом исследовании представлена новая концепция вибрационной сварочной установки, которая может передавать механические колебания в зоне сварного шва во время процесса дуговой сварки защищенным металлом (SMAW), а также может создавать резонансную частоту 300 Гц.В настоящем исследовании пластины из мягкой стали толщиной 6 мм свариваются встык с использованием как обычных, так и вибрационных режимов сварки. Проведена оценка микроструктуры и механических свойств стыковых сварных соединений, результаты сопоставлены. Кроме того, для оптимизации параметров процесса вибрационной сварки были приняты методы Тагучи и дисперсионного анализа (ANOVA). Для анализа учитываются следующие характеристики: твердость, предел прочности при растяжении (UTS) и ударная вязкость.Результат исследования показывает, что за счет применения вибрационной обработки в процессе сварки механические свойства, такие как твердость, предел прочности и ударная вязкость, были улучшены. Наконец, полученные результаты коррелируют с результатами прошлых исследований.
Ключевые слова: Вибрационная сварка / SMAW / анализ Тагучи / ANOVA / отношение сигнал / шум / предел прочности / твердость
© П.К. Сингх, опубликовано EDP Sciences 2019
Это статья в открытом доступе, распространяемая в соответствии с условиями лицензии Creative Commons Attribution License (http: // creativecommons.org / licenses / by / 4.0), что разрешает неограниченное использование, распространение и воспроизведение на любом носителе при условии правильного цитирования оригинальной работы.
1 Введение
Сварка — это однородное соединение двух или более металлических деталей, при котором прочность сварного соединения превышает прочность основных металлических деталей. Некоторые из наиболее распространенных процессов дуговой сварки: FCAW (порошковая сварка), SMAW (дуговая сварка защищенного металла), SAW (дуговая сварка под флюсом), PAW (плазменно-дуговая сварка), GMAW (газовая дуговая сварка металла), GTAW ( Газовая вольфрамовая дуговая сварка) и др. Микроструктура сварного соединения имеет большое значение, поскольку от нее зависят механические свойства [1]. Поэтому существует острая необходимость в улучшении механических свойств сварных соединений.
В настоящем исследовании механические свойства сварных соединений были улучшены за счет улучшения их микроструктуры с помощью процесса вибрационной сварки. Метод вибрационной сварки — это процесс передачи вибраций расплавленной сварочной ванне с помощью различных режимов вибрационной установки.Для улучшения микроструктуры и механических свойств сварных соединений были проведены различные исследования методов вибросварки [2]. При дуговой сварке вибрацию можно применять как во время процесса, так и после него. Техника вибрации после сварки называется методом снятия вибрационного напряжения (VSR); это метод снятия стресса. Продолжая поиски более высокой производительности, исследователи теперь прилагают усилия для разработки процесса дуговой сварки при вибрации, т.е.Сварка с применением вибрации (VAW), которая может сократить большую часть расходов, связанных с вибрациями после сварки или термообработкой. Срок изготовления может быть значительно сокращен за счет параллельной обработки вибрацией и сваркой [3]. Кроме того, VAW приводит к улучшенной микроструктуре и лучшим механическим свойствам. Мелкозернистая структура, связанная с превосходными механическими свойствами, является конечной целью процесса затвердевания. Принято считать, что измельчение зерна вызвано фрагментацией дендритов.Исследования, проведенные исследователями в прошлом, также доказали, что механические свойства любых сварных соединений в основном определяются его зеренной структурой и режимом затвердевания [4–7]. В аналогичном контексте в настоящем исследовании было доказано, что по сравнению с крупнозернистыми структурами мелкие структуры обладают высокой прочностью и меньшей вероятностью образования горячих трещин. Многие исследователи провели исследования по совершенствованию вибрационной установки и изучили их влияние на сварочные конструкции [8,9].Поэтому краткое описание вибрационных методов, используемых различными исследователями для улучшения различных сварочных процессов, обсуждено в таблице 1.
В последние годы высокочастотное механическое воздействие (HFMI) используется в качестве одного из самых последних методов отделки для улучшения сопротивление усталости [10]. Некоторые авторы также исследовали влияние магнитного поля и ультразвукового воздействия на процесс затвердевания [11–15].
Из вышеупомянутого обзора литературы можно сделать вывод, что не существует работ по использованию наведенных вспомогательных механических колебаний в сварочной ванне, когда она находится в расплавленном состоянии.Исследователи выбрали вибрацию в качестве основного металла или присадочного металла, тем не менее, ни одна область не объявила публично о возникновении дополнительных механических колебаний в зоне расплавленного сварного шва во время операции сварки.
В данной экспериментальной работе устройство было спроектировано таким образом, что образец закреплен на рабочем столе, а вибрационная установка передает вибрации только расплавленному сварному шву, следовательно, передавая максимальную энергию зоне сварки во время сварочный процесс. Эта экспериментальная установка, разработанная в данном исследовании, намного экономична по сравнению с применением электромагнитных, ультразвуковых и ультразвуковых методов во время сварки. Кроме того, было замечено, что оптимизация параметров процесса вибрационной сварки не обсуждалась в литературе. Следовательно, чтобы заполнить этот пробел, в настоящем исследовании был использован метод Тагучи для определения оптимальных уровней технологических параметров вибрационной сварки. Метод Тагучи обеспечивает систематическую и эффективную методологию процесса оптимизации [31–34].
Микроструктура и механические свойства сварных соединений также зависят от скорости охлаждения сварочных конструкций. Правин и др. [35] провели исследование по изучению влияния вибрации на характеристики охлаждения сварочной ванны. Кривая охлаждения показывает, что приложение вибрации увеличивает тепловой градиент во время операции сварки. Сравнительно более быстрое охлаждение было обнаружено во время вибрационной сварки.
Сравнительное исследование различных методов вибросварки и экспериментальной установки, использованной в настоящей работе.
2 Методика эксперимента
2.1 Устройство вибрационной установки
С целью улучшения механических свойств стыкового сварного соединения в настоящем исследовании была спроектирована и разработана вибрационная установка, как показано на рисунке 1. Основная функция разработанной вибрационной установки заключается в том, что она способна перемешивать расплавленная сварочная лужа до того, как она затвердеет. Наконечник стержня вибрационной установки погружается в зону расплавленного сварного шва, вибрация передается через неплавящийся стержень в зону расплавленного сварного шва и сотрясает расплавленный металл сварного шва до его затвердевания.В настоящем эксперименте процесс вибрационной сварки поддерживает квазистационарное состояние, при котором наблюдатель обнаруживает, что в любой момент времени по всей длине сварного шва вибрационный наконечник погружается в сварочную ванну и передает колебания расплавленному металлу до его затвердевания. Вибрационная установка постоянно движется в одном направлении с той же скоростью, что и скорость сварки, поддерживаемая сварщиком. Примерное значение углов между стержнем и заготовкой и другие измеренные углы показаны на рисунке 1.Фактический рисунок вибрационной установки и процесса вибрационной сварки представлен на рис. 2a – d. Вибрирующий стержень изготовлен из сплава торий-цирконий-вольфрам, что позволяет ему выдерживать очень высокие температуры. Стержень диаметром 3 мм имеет коническую форму с одной стороны стержня. Другой конец стержня прикреплен к непроводящему держателю, используемому для захвата вибрационной установки во время операции сварки.
Электродвигатель массы с эксцентриковым вращением (ERM) используется для создания вибрации во время процесса сварки.Электродвигатель ERM прикреплен к середине стержня из тория-циркония-вольфрама. Это важнейшее устройство вибрационной установки, работающее по принципу вращения неуравновешенной массы. Двигатель ERM — это стандартный двигатель постоянного тока со смещенной от центра нагрузкой на валу. В настоящем исследовании использовались два двигателя ERM. Технические характеристики двигателей представлены в Таблице 2. Чтобы предотвратить перегрев двигателя ERM во время сварки, керамические трубы и кусок стекла были покрыты вокруг двигателя ERM.Поскольку размер двигателя небольшой, генерируемая амплитуда относительно меньше. С помощью акселерометра, сбора данных и анализа сигналов была определена частота этой вибрационной установки. Во избежание сильного нагрева вибрационной установки во время сварки двигатель ERM покрыт керамическими трубками и стеклом.
рисунок 1 (а) Принципиальная блок-схема вибрационной установки с указанием углов и положений вибрационной установки.(b) Схема вибрационной установки, вид сверху. |
Рис. 2 (а) и (б) Фотография реальной вибрационной установки. (c) и (d) Процесс вибрационной сварки, использованный в настоящем исследовании. |
Спецификация двигателя ERM.
2.2 Подготовка образцов
Для стыкового соединения пластин из мягкой стали размером 200 × 100 × 6 мм использовалась операция дуговой сварки защищенным металлом (SMAW). Присадочный металл (E-3106) использовался в качестве электрода для процесса SMAW.Основным металлом, использованным в настоящем эксперименте, была мягкая сталь, состоящая из 0,16–0,18% углерода, 0,40% кремния, 0,7–0,9% марганца, 0,04% фосфора и 0,04% серы. В настоящем исследовании во избежание каких-либо дефектов все ограничения, такие как аккуратный и чистый образец без ржавчины, электрод с флюсовым покрытием не содержал влаги любого типа, сохранялась надлежащая структура сварного шва, на задней стороне пластин использовались сварочные приспособления для избежать искажения и т. д. были рассмотрены. В то же время перемешивание сварочной ванны способствует выделению растворенных газов из расплавленного металла, в результате чего валик сварного шва не имеет дефектов пористости. В результате мер предосторожности, предпринятых во время сварки, структура сварного шва была однородной и без дефектов.
Разработан комплекс экспериментальных работ по методу Тагучи. Требуемые ответы зависят от расположения входных параметров во время каждого эксперимента. Эти типы показателей называются ортогональным массивом. Значения параметров процесса на разных уровнях указаны в таблице 3, были выбраны такие параметры, которые оказывают большее влияние на желаемый результат.Эксперименты проводились на трех уровнях частот [300 Гц, 150 Гц и 0 Гц (обычные условия)], трех уровнях тока (60, 80 и 100 ампер) и трех уровнях скорости (6, 8 и 10 см / мин. ). Подходящий ортогональный массив описывает план эксперимента на основе степеней свободы.
В этом эксперименте отношение сигнал / шум использовалось для изучения влияния каждого фактора на конкретный отклик. Сигналы показывают влияние каждого фактора на отклик, тогда как шум является мерой влияния на отклонение от среднего отклика. Отношение сигнал / шум основано на критериях: чем меньше, тем лучше, больше — тем лучше и номинально: тем лучше. Отношение сигнал / шум основано на предыдущих знаниях и опыте, поэтому его следует выбирать тщательно [32,33]. В этом исследовании ответы связаны с прочностью сварного соединения, которая должна быть как можно более высокой, поэтому был выбран критерий «чем больше, тем лучше». Прочность сварного соединения, которая обычно считается высокой, проверяется уравнением (1).
(1) где n = количество измерений; y i = значение отклика для каждого коэффициента шума; i = количество проектных параметров в этом исследовании OA имеет 9 экспериментов (L9).
Ортогональный массив рассчитан на 9 экспериментов, поэтому его общая степень свободы будет 9−1 = 8. Для изучения влияния каждого параметра на значение отклика использовался метод дисперсионного анализа (ANOVA). ANOVA утверждает, что общая сумма квадратов отклонения равна сумме квадратов стандартного отклонения, вызванного каждым входным фактором [34].
Входные параметры и уровни.
2.3 Металлургическое исследование образца
Для изучения влияния дополнительных колебаний, индуцированных в зоне сварного шва, и их последующего влияния на соответствующую микроструктуру, металлографические исследования были проведены на различных образцах сварных швов.Эти поверхности подвергаются электролитическому травлению в следующих условиях: — Используемый электролит: щавелевая кислота (10 г) + дистиллированная вода (100 мл), напряжение ячейки — 6 В, время травления — 1 мин.
2.4 Механические испытания
Образец, сваренный встык, изначально был рассчитан и вырезан таким образом, чтобы можно было взять образец для испытаний на удар, растяжение и исследования микроструктуры. Образцы на растяжение были подготовлены в соответствии со стандартами ASTM E-08. Образцы на растяжение были испытаны на универсальной испытательной машине (производитель: FIE, нагрузка: 600 кН).Скорость перемещения составляла 0,5 мм / мин [36]. Испытание на ударную вязкость по Шарпи с V-образным надрезом проводилось при комнатной температуре. В соответствии с ASTM E-23 были приготовлены три образца размером (6 мм × 10 мм × 55 мм) с надрезом под 45 ° глубиной 2 мм и радиусом 0,25 мм. Испытания проводились на аппарате Шарпи фирмы Zwick-Rowell мощностью 450 Дж. Тестер микротвердости (производитель: Omnitech, вместимость: 1000 грамм) использовался для измерения микротвердости в различных зонах интереса в различных сварных деталях.В этих исследованиях использовалась нагрузка 500 грамм и время выдержки 20 секунд. Значение твердости измерялось вдоль центральной линии и средней толщины сварного шва, каждая точка измерялась три раза, чтобы узнать ее среднее значение.
3 Результат и обсуждения
Сварные швы были подготовлены при различных частотах ( f ), сварочном токе ( I ) и скорости сварки ( S ) и подверглись механическим испытаниям. Из различных параметров процесса сварки были выбраны ток и скорость сварки, поскольку эти параметры являются наиболее основными и очень эффективными для механических свойств стыковых сварных соединений.
Предел прочности на разрыв (UTS), микротвердость ( H ) и ударная вязкость ( J ) были выбраны в качестве значения отклика. В таблице 4 описаны результаты испытаний на растяжение, твердость и удар при различных условиях сварки. Влияние взаимодействия между параметрами сварки не учитывается. Во втором, третьем и четвертом столбцах ортогональная матрица (OA) L 9 представлена в кодированной форме. Фактическое значение сварочного тока ( I ), скорости сварки ( S ) и приложенной частоты ( f ) указано в столбцах 5, 6 и 7 соответственно.Значения твердости ( H ), ударной вязкости ( J ) и прочности на разрыв (UTS) указаны в столбцах 8, 9 и 10 соответственно. План эксперимента был подготовлен с помощью MINITAB 17.
Таблица 4Результаты испытаний на твердость, удар и растяжение для L 9 OA.
3.1 Анализ микротвердости
Таблица отклика и график отношения сигнал / шум для значений твердости приведены в Таблице 5 и на Рисунке 3 соответственно. Оптимальные коэффициенты получены при скорости сварки 20 см / мин (уровень 3), частоте 300 Гц (уровень 3), и никакого влияния сварочного тока на значение твердости не обнаружено. Из рисунка 3 видно, что при увеличении частоты и скорости сварки значение отклика (твердость) увеличивается, тогда как для сварочного тока была найдена прямая линия, которая показывает небольшое влияние сварочного тока на значение отклика. Таблица 6 показывает ранг входных параметров. Частота имеет 1-й разряд, скорость — 2-й, а ток — 3-й разряд, что указывает на то, что на большее значение влияет частота, чем скорость сварки и, наконец, сварочный ток.Для проверки отчета Тагучи был применен метод дисперсионного анализа (ANOVA), и процентное влияние [34,37,38] каждого параметра процесса на значение твердости рассчитано с помощью уравнения (2). (2) SS d = сумма квадратов отклонений; SS T = сумма квадратов общей суммы.
В таблице 6 показан дисперсионный анализ (ANOVA) для одного из значений отклика, то есть твердости. Результаты ANOVA показали, что частота является наиболее значимым фактором, имеющим 94.Вклад 5%, за которым следует скорость сварки. Второй влияющий фактор — скорость сварки. При увеличении скорости сварки с 10 до 20 см / мин микротвердость сварного соединения улучшается. Теоретические знания говорят о том, что при высокой скорости сварки наименьшее количество тепла передается в зону сварного шва, что приводит к увеличению скорости затвердевания зоны сварного шва, что приводит к мелкой структуре и высоким значениям твердости. Скорость сварки является основным и неэлектрическим параметром, который влияет на тепловложение на единицу длины сварного шва и, следовательно, влияет на микротвердость сварных швов в настоящей работе.
Исследование Balasubramanian и Balusamy [17] показало, что твердость сварного шва значительно увеличивается с увеличением частоты вибрации. На графике основного эффекта (см. Рис. 3) результат отражает то же состояние, поскольку частота увеличивает одновременно повышенное значение твердости. Ye et al. [26] представили свое исследование электроимпульсной ультразвуковой обработки и пришли к выводу, что ультразвуковые колебания повышают микротвердость сварного соединения.В последней исследовательской статье Фулади и Аббаси [39] обсуждали влияние вибрации на сварку трением с перемешиванием и пришли к выводу, что вибрация, возникающая при сварке трением с перемешиванием, увеличивает твердость образца сварного шва. В настоящем исследовании частота является основной причиной повышения значения твердости вибросварных соединений.
Таблица отклика для отношения S / N твердости L 9 OA.
Рис. 3 График основного эффекта отношения сигнал / шум значений твердости для L 9 OA. |
Дисперсионный анализ твердости L 9 OA.
3.2 Анализ ударной вязкости L
9 OA Отношение сигнал / шум и график основного эффекта для ударной вязкости указаны в Таблице 7 и Рисунке 4 соответственно. Наиболее благоприятные факторы обнаруживаются при сварочном токе 80 А (уровень 2), скорости сварки 10 см / мин (уровень 1) и частоте 150 Гц (уровень 2). Таблица 8 показывает дисперсионный анализ (ANOVA) для ударной вязкости.Таблица ANOVA показывает, что наиболее значимым фактором является частота, имеющая 92% вклада (PI) в значение отклика (сила удара). Как показано на Рисунке 4 (т.е. график основного эффекта отношения сигнал / шум для ударной вязкости для L 9 OA), сварные образцы были улучшены до определенного диапазона частот (150 Гц), но когда частота была еще больше увеличиваясь до своего резонансного значения (300 Гц), величина удара уменьшается. Дальнейшие результаты показали, что соединения, сваренные с использованием низкого сварочного тока (80 А), показали более высокую способность поглощать энергию удара, чем соединения, сваренные с использованием высокого сварочного тока (100 А), и более высокая ударная вязкость обнаружена при самой низкой скорости сварки (10 см / мин).
В этом случае частота является наиболее влиятельным фактором при 150 Гц (2-й уровень).
Предыдущие исследования показали, что влияние вибрации на механику ударных свойств является сложным [2,3,14,18,40]. Лу [3] и Пуко [14] изучили влияние вибрации на ударную вязкость и обнаружили неравномерные изменения ударных свойств вибрационной сварочной ванны. Jose et al. В [2] сказано, что виброобработка не оказывает значительного влияния на ударную вязкость. Rao et al. [18] сообщили, что ударная вязкость сварного соединения была улучшена за счет приложения вибрации во время сварки до определенного диапазона приложенных вибраций.Итак, на основе вышеупомянутой литературы и результатов, полученных в результате настоящего исследования, было замечено, что необходимы дальнейшие исследования, чтобы лучше понять это явление.
Таблица 7Таблица отклика для отношения сигнал / шум для ударной вязкости L 9 OA.
Рис. 4 График основного эффекта отношения сигнал / шум для ударной вязкости для L 9 OA. |
Дисперсионный анализ ударной вязкости L 9 OA.
3.3 Предел прочности при растяжении L
9 OA Анализ отношения сигнал / шум для прочности на разрыв показан в таблице 9. Применяемая вибрация значительно повысила предел прочности на разрыв (UTS) стыковых сварных соединений. Частота имеет наивысшее значение дельты, то есть 0,84, и имеет ранг 1, что указывает на то, что наибольшее влияние на предел прочности на растяжение оказывает частота, за которой следуют сварочный ток (ранг 2) и скорость сварки (ранг 3). График отношения сигнал / шум / график основного эффекта для прочности на разрыв показан на рисунке 5.Значимые факторы для наивысшего значения UTS были обнаружены при сварочном токе 100 А (уровень 3), скорости сварки 15 см / мин (уровень 2) и частоте на его резонансном уровне, равном 300 Гц (уровень 3). Результат ANOVA показывает (табл.10), что наиболее влияющим фактором является частота, имеющая 97% вклада ( P U ) о желаемом ответе. Кроме того, было замечено, что образцы, сваренные с использованием низкого подводимого тепла (то есть при низком сварочном токе 60 А), не претерпели таких заметных изменений, поскольку сварочная ванна, образованная с использованием низкого сварочного тока, не подвергалась значительному влиянию условий вибрации.При высоком сварочном токе температура сварочной ванны высока, из-за чего плотность металла сварного шва относительно меньше по сравнению с плотностью металла сварочной ванны, сформированной при более низком сварочном токе. Эта разница в плотности между сварочными ваннами при разных температурах по-разному реагировала на вспомогательные колебания, то есть при низкой температуре металл шва медленно реагировал на вызываемые в нем колебания.
Различные исследователи проявили интерес к изучению влияния вибрации на свойства при растяжении сварных соединений и нашли положительный отклик от своих исследований.Мостафапур и Голизаде [21] сообщили, что при увеличении частоты от нуля до резонансной частоты механические свойства улучшаются. В настоящем исследовании свойство растяжения демонстрирует ту же характеристику; предел прочности при растяжении минимален на нулевой частоте и максимален на уровне резонансной частоты (300 Гц). Амини и Амири [22] изучали влияние вибрации на сварку трением с перемешиванием и обнаружили, что предел прочности на растяжение был увеличен за счет применения вибрации. Рахми и Аббаси [27] модифицировали новую версию сварки трением с перемешиванием (FSW) и называли ее процессом вибрационной сварки трением с перемешиванием.Прочность вибрационного сварного шва сравнивалась с соединениями, полученными в соответствии с конвенцией FSW, и был сделан вывод о том, что сварные образцы с вибрацией более прочны, чем обычные FSW. После предыдущих исследований было замечено, что вибрационная установка, использованная в настоящем исследовании, способна улучшить механические свойства сварных соединений.
Чтобы оценить эффективность соединения образца вибросварки, были проведены дальнейшие эксперименты с наилучшими найденными оптимальными параметрами вибросварки. Эффективность соединения [35] сварных соединений может быть рассчитана по уравнению (3)
(3)
Расчетное значение UTS основного металла составляет 520 МПа. Оптимальные параметры сварки для максимальной прочности на разрыв: ток = 100 А, частота = 300 Гц и скорость = 15 см / мин.
Эффективность соединения вибросварного шва указана в таблице 11.
Таблица 9Таблица отклика для отношения сигнал / шум UTS L 9 OA.
Рис. 5 График основного эффекта отношения сигнал / шум UTS для L 9 OA. |
Дисперсионный анализ для ЕТС L 9 OA.
Таблица 11Совместная эффективность вибросварных соединений.
3.3.1
R -тест Анализ эффективности моделей для определения твердости, ударной вязкости и прочности на разрыв, выполненных с помощью R 2 (коэффициент детерминации, R 2 ) значения. R 2 (Коэффициент детерминации) используется для проверки качества модели; он определяет, насколько близки предсказанные значения к экспериментальным значениям [36,41–44].Когда R 2 приближается к значению 1, подразумевая, что модели отклика очень похожи на фактические (экспериментальные) данные. Он показывает, что существует хорошее согласие между предсказанными значениями и экспериментальными значениями. Значения R 2 значение твердости (Табл.6) R -sq = 99,88% и R -sq (прил.) = 99,51%, для ударной вязкости (Табл.8) R -sq = 96,48% и R -кв (прил.) = 85,91% и для прочности на разрыв (Табл.10) R -sq = 99,12% и R -sq (прил.) = 96,49%. Эти значения указывают на качество разработанной модели и доказывают, что разработанная модель действительна.
Краткий вывод результатов, полученных в настоящем эксперименте, представлен в Таблице 12.
Таблица 12 Завершенные результаты эксперимента Тагучи и описание наиболее значимых значений методом ANOVA.
3.4 Характеристика микроструктуры
Исследованы металлографические свойства сварного соединения, полученного в наилучших оптимальных условиях ( I = 100 А, S = 15 м / с и f = 300 Гц).Один комплект сварных швов был подготовлен в обычных условиях, то есть без использования вибрации при сварке сваркой. Сообщается о сравнительном исследовании микроструктур. Микрофотографии различных сварных деталей и поперечных сечений макрошлоков / профилей сварных швов (для стыковых сварных соединений) представлены на рисунке 6. На рисунках 6a и b показаны макроструктура и микроструктура стыкового соединения, сваренного обычным способом, соответственно. Рис. 6в представляет собой макроснимок вибросварного стыкового соединения, полученного при частоте 150 Гц.Соответствующая микроструктура представлена на рисунке 6d. Макроснимок образца стыкового соединения, полученного при частоте 300 Гц, показан на рисунке 6e, а его соответствующая микроструктура представлена на рисунке 6f. Сравнительное исследование микроструктуры показывает, что сварка в условиях вибрации (150 и 300 Гц) имеет мелкозернистую структуру по сравнению с обычным режимом.
Вибрация, создаваемая во время процесса сварки, вызывает следующие эффекты [25–27,39,45,46]:
ломает растущие дендриты,
увеличивает скорость охлаждения,
предотвращает повторное плавление ядра новорожденного,
увеличивает количество зерен и
обеспечивает мелкозернистую структуру.
Характеристики микроструктуры можно понять по тому факту, что вибрация, возникающая в расплавленной сварочной ванне, вызывает некоторые возмущения во время затвердевания [28–30,37,40,47,48]. Растущий кончик дендрита фрагментируется и превращается в дендриты небольшого размера. Фрагментированный дендрит служит новой системой зародышеобразования, если это крошечное ядро поддерживается при более высокой температуре, тогда оно будет расти в форме нового зерна.
Микроструктура и механические свойства сварных соединений также зависят от скорости охлаждения сварочных конструкций.Правин и др. [38] провели исследование по изучению влияния вибрации на характеристики охлаждения сварочной ванны. Кривая охлаждения показывает, что приложение вибрации увеличивает тепловой градиент во время операции сварки. Сравнительно более быстрое охлаждение было обнаружено во время вибрационной сварки. Устойчивость новорожденного ядра зависит от температуры переохлаждения затвердевающей структуры, которая обеспечивает критический радиус для новорожденного ядра. Возникающая во время сварки вибрация перемешивает расплавленный металл до его затвердевания, это прерывание увеличивает скорость охлаждения расплавленной зоны сварного шва и помогает достичь температуры переохлаждения.Итак, для мелкозернистой структуры важна как фрагментация дендритов, так и высокая скорость охлаждения
Рис. 6 (a) Макрограф обычного SMAW. |
4 Выводы
Разработка вибрационной установки и экспериментальные исследования с использованием установки заключаются в следующем:
, представленная здесь работа показала и доказала, что можно улучшить механические свойства сварных соединений, если в сварочную ванну вызвать благоприятные механические колебания. Таким образом, настоящая попытка исследования предоставила альтернативу измельчению зерна сварных деталей. Эффективность вибрационной установки, разработанной и использованной в настоящей работе, была признана удовлетворительной с точки зрения обеспечения лучших свойств сварного шва.
, важные параметры процесса вибрационной сварки, а именно сварочный ток ( I ), скорость сварки ( S ) и частота ( f ) были оптимизированы с использованием анализа Тагучи. График основных эффектов показывает, что твердость и предел прочности в основном зависят от частоты. Из результатов ANOVA очевидно, что частота является наиболее влиятельным фактором для изменения механических свойств сварных соединений.
ударные свойства сварных соединений демонстрируют неравномерное поведение, из-за чего ударная вязкость увеличивается до частоты 150 Гц, а затем уменьшается на резонансной частоте 300 Гц.Для понимания сложности значений воздействия необходимы дальнейшие исследования.
- Исследования микроструктуры сварных соединений
показали, что за счет дополнительного перемешивания сварочной ванны в режиме вибрационной сварки устанавливаются более крутые температурные градиенты и получаются более мелкозернистые структуры.
Список литературы
- Коу С., Ле Й. Механизм зародышеобразования и измельчение зерна металла шва // Сварка.65 (1986) 63–70 [Google ученый]
- М.Дж. Хосе, С.С. Кумар, А. Шарма, Сварочные процессы с использованием вибрации и их влияние на качество сварных швов, Науки. Technol. Сварка. Присоединиться. 22 (2015) 243–258 [Google ученый]
- В.Лу, Л. Чен, К. Ни, Повышение качества сварных клапанов за счет кондиционирования шва с помощью вибрации, Mater. Sci. Англ. А 457 (2007) 246–253 [CrossRef] [Google ученый]
- Л.Цинхуа, Ч. Лигун, Н. Чуньчжэнь, Влияние вибрационной обработки шва на свойства сварной арматуры. Мех. Материал 40 (2008) 565–574 [CrossRef] [Google ученый]
- С.-C. Hsieh, C.-H. Лай, В. Ву, Влияние вибрации на микроструктуру и механические свойства GTA-сварных швов из нержавеющей стали 304, Met. Mater. Int. 19 (2013) 835–844. [CrossRef] [Google ученый]
- М.Малиновски-Бродницка, Г. Ден, У. Дж. Винк, Влияние магнитных полей на сварные швы GTA аустенитной нержавеющей стали, Weld. Res. Дополнение 52-е (1990) 52–59 [Google ученый]
- К. Вивес, Влияние электромагнитной вибрации на микроструктуру непрерывнолитых сплавов, Матер.Sci. Англ. А 173 (1993) 169–172 [CrossRef] [Google ученый]
- W.Ву, Влияние частоты вибрации на затвердевание сварных деталей, Scr. Дело 42 (2000) 661–665 [CrossRef] [Google ученый]
- А.S.M.Y. Мунси, А.Дж. Уодделл, К.А. Уокер, Влияние вибрационного напряжения на сварочную микроструктуру и распределение остаточных напряжений, J. Mater. Des. Appl. 215 (2001) 99–111 [Google ученый]
- М. Сун, Ю. Сун, Р. Ван, Снятие вибрационных напряжений сварных листовых сталей из низколегированной высокопрочной стали, Матер.Lett. 58 (2004) 1396–1399 [CrossRef] [Google ученый]
- Д.Рао, Д. Ван, Л. Чен, Оценка эффективности снятия вибрационного напряжения из нержавеющей стали 314L с помощью динамического напряжения, Int. J. Fatig. 29 (2007) 192–196 [CrossRef] [Google ученый]
- ИКС.Цзицзинь, Ч. Лигун, Н. Чунчжэнь, Влияние кондиционирования вибрационных сварных швов на остаточное напряжение и деформацию в многопроходных трубах, сваренных встык с кольцевой сваркой, Междунар. J. Press. Судно Пип. 84 (2007) 298–303 [CrossRef] [Google ученый]
- Ю.Цуй, К. X, Влияние ультразвуковой вибрации на образование несмешанной зоны. Scr. Материал 55 (2006) 957–958 [Google ученый]
- Б. Пуцко, В. Глиха, Вязкость по Шарпи вибрирующей микроструктуры. Оригинальная научная статья-Изворны знаний Рад, Металлургия 44 (2005) 103–106 [Google ученый]
- Ю.Лей, З. Ван, Х. Чен, Влияние ультразвука на микроструктуру и механические свойства сварных соединений плазменно-дуговой сварки SiCp / Al MMC, Trans. Цветные металлы Soc. Китай 21 (2011) 272–277 [CrossRef] [Google ученый]
- Р.Дехмолаи, М. Шаманян, А. Керманпур, Влияние электромагнитной вибрации на образование несмешанной зоны в жаропрочной стали 25 Cr-35Ni / разнородные сварные швы сплава 800, Матер. Персонаж. 59 (2008) 1814–1817 [CrossRef] [Google ученый]
- К.Баласубраманян, В. Балусамыкешаван, Исследования влияния вибрации на образование горячих трещин и размер зерна при сварке алюминиевого сплава AA7075, Междунар. J. Eng. Sci. Technol. 3 (2011) 1 [Google ученый]
- П. Говинд Рао, П. Шриниваса Рао, А.Гопала Кришна, Улучшение механических свойств сварных деталей с помощью системы вибросварки. Inst. Мех. Англ. — J. Eng. Manuf. В 229 (2014) 776–784 [Google ученый]
- А. Краевский, В. Влосинский, Т. Хмелевский, П. Колодзейчак, Ультразвуковая вибрационная дуговая сварка алюминиевых сплавов.Бык. Польский акад. Sci. Tech. Sci. 4 (2012) 841–852 [Google ученый]
- J.S. Wang, C. Hsieh, C.M. Линь, Чен Э.С., Куо К.В., Ву В. Влияние релаксации остаточных напряжений с помощью метода снятия вибрационного напряжения на текстуры зерен в алюминиевом сплаве AA 6061, Mater.Sci. Англ. А 605 (2014) 98–107 [CrossRef] [Google ученый]
- А.Мостафапур, В. Голизаде, Экспериментальное исследование влияния вибрации на механические свойства сварных деталей из нержавеющей стали 304, Int. J. Adv. Manuf. Technol. 70 (2014) 1113–1124 [CrossRef] [Google ученый]
- С.Амини, М. Амири, Исследование влияния ультразвуковой вибрации на сварку трением с перемешиванием, Int. J. Adv. Производство. Technol. 73 (2014) 127–135 [CrossRef] [Google ученый]
- С.Се, П. Ван, Дж. Ван, В. Ву, Эволюция микроструктуры и остаточное напряжение при различных режимах вибрации в сварных швах из нержавеющей стали 304, Sci. Мир J. (2014) DOI: 10.1155 / 2014/895790 [Google ученый]
- Т. Вэнь, С.Ю. Лю, С. Че, Л.Лю, К. Ян, Влияние высокочастотной вибрации на микроструктуру и механические свойства сварных соединений TIG магниевого сплава AZ31, Пер. Цветные металлы Soc. Китай 25 (2015) 397–404 [CrossRef] [Google ученый]
- Дж.Ван, К. Сан, Л. Ву и др., Влияние ультразвуковой вибрации на эволюцию микроструктуры и механические свойства подводного сварного соединения мокрым способом, J. Mater. Процесс. Technol. 246 (2017) 185–197 [CrossRef] [Google ученый]
- Ю.Е, X. Ли, Дж. Куанг, Ю. Гэн, Г. Тан, Влияние электроимпульсной ультразвуковой обработки на сварные детали, Mater. Sci. Technol. 31 (2015) 1583–1588 [CrossRef] [Google ученый]
- М.Рахми, М. Аббаси, Процесс сварки трением с перемешиванием и вибрационной сваркой: модифицированная версия процесса сварки трением с перемешиванием, Int. J. Adv. Производство. Technol. (2016) DOI: 10.1007 / s00170-016-9383-9 [Google ученый]
- Тивари С.П., Шанкер А. Влияние продольной вибрации на механические свойства сварных деталей из низкоуглеродистой стали.Proc. Inst Mech. Англ. B: J. Eng. Manuf. 207 (1993) 173–177 [CrossRef] [Google ученый]
- С.Кумар, К.С. Ву, Г.К. Padhy, W. Ding, Применение ультразвуковых колебаний в сварке и обработке металлов: обзор состояния, J. Manufact. Процесс. 26 (2017) 295–322 [CrossRef] [Google ученый]
- П.К. Сингх, Д. Патель, С. Б. Прасад, Исследование влияния вспомогательных колебаний на микроструктуру и механические свойства стыковых сварных соединений SMAW, Indian J. Eng. Mater. Sci. NISCAIR 25 (2018) 155–162 [Google ученый]
- Л.Ши, К. Вуй, Х. Лю, Моделирование эффектов ультразвуковой вибрации на сварку трением с перемешиванием, J. Mater. Процесс. Technol. 36 (2015) 25–262 [Google ученый]
- С. Раджакумар, К. Муралидхаран, В. Баласубраманян, Оптимизация процесса сварки трением с перемешиванием и параметров инструмента для достижения максимальной прочности на разрыв алюминиевого сплава AA7075-T6, Proc.Inst. Мех. Англ. Часть B J. Eng. Manuf. 224 (2010) 1175–1191. [CrossRef] [Google ученый]
- П.Баманкар, С. Савант, Исследование влияния параметров процесса на глубину проплавления и ширину валика в процессе SAW, Int. J. Adv. Англ. Res. Stud. 2 (2013) 8–10 [Google ученый]
- Y.H.P. Манурунг, М.А.Мохамед, А.З. Абидин, Повышение стойкости конструкции при сварке трением с перемешиванием AA6061 с оптимизированным процессом и параметрами HFMI / PIT, Int.J. Adv. Производство. Technol. (2016) DOI: 10.1007 / s00170-016-9697-7 [Google ученый]
- С. Кумар, А.С. Шахи, Влияние тепловложения на микроструктуру и механические свойства соединений из нержавеющей стали AISI 304, сваренных дугой вольфрамовым газом, Матер.Des. 32 (2011) 3617–3623 [CrossRef] [Google ученый]
- С.Махаджан, Н. Бирадар, Р. Раман, С. Мишра, Влияние механических колебаний дуги на структуру зерна сварочного металла из низкоуглеродистой стали, Пер. Индийский институт Металлы 65 (2012) 171–177 [CrossRef] [Google ученый]
- Рахул, Х.К. Арья, Р.К. Саксена, Влияние скорости охлаждения на микроструктуру листа из низкоуглеродистой стали, сваренного SAW (марка C 25 согласно IS 1570), Int. J. Mod. Англ. Res. 4 (2014) 222 [Google ученый]
- П. Сингх, Д. Патель, С. Б. Прасад, Исследование влияния вибраций на характеристики охлаждения и механические свойства стыковых сварных соединений методом SMAW, Наука.Бык. Сер. D (2017) 79. [Google ученый]
- С. Фулади, М. Аббаси, Влияние процесса сварки трением с перемешиванием и вибрацией на характеристики соединения SiO 2 , J. Mater. Процесс. Technol. 243 (2017) 23–30 [CrossRef] [Google ученый]
- Ф.Лефевр, К. Пейрак, Г. Эльбель, HFMI: понимание механизмов повышения усталостной долговечности и ремонта сварных конструкций, Weld World (2017) DOI: 10.1007 / s40194-017-0455-8 [Google ученый]
- А.К. Патак, Г.Л. Датта, Трехмерный анализ методом конечных элементов для прогнозирования различных зон микроструктуры при сварке под флюсом, Proc.Inst. Мех. Англ. J. Eng. Manuf. В 218 (2003) 269–280 [CrossRef] [Google ученый]
- С.Шанживи, С. Сатиш Кумар, П. Сатья, Многоцелевая оптимизация параметров сварки трением в соединениях из аустенитной нержавеющей стали и меди AISI 304L, Proc. Inst. Мех. Англ. J. Eng. Manuf. В 230 (2016) 449–457 [CrossRef] [Google ученый]
- П.Mondal, D. Bose, M. Tech, Оптимизация параметров процесса для сварки MIG сварки AISI 304 и 1079 с использованием метода нечеткой логики, Int. Res. J. Eng. Technol. 2 (2015) 483–488 [Google ученый]
- П.К. Сингх, Д. Патель, С.Б. Прасад, Разработка техники вибрационной сварки и исследование свойств при растяжении сварных соединений экранированной металлической дугой, Индиан Дж.Sci. Technol. 9 (2016) DOI: 10.17485 / ijst / 2016 / v9i35 / 92846 [Google ученый]
- К.Н.Х. Ямамото, С. Харада и др., Благоприятное влияние низкочастотной импульсной сварки MIG на измельчение зерна металла шва и улучшение склонности алюминиевых сплавов к растрескиванию при затвердевании, Weld.Int. 7 (1993) 456–461 [CrossRef] [Google ученый]
- ИКС.Лян, Ю. Ван, Ч. Чжан, Б. Чжан, Х. Мэн, Комплексная оценка качества сварки встык с помощью дуговой вибрационной сварки CO 2 , Int. J. Adv. Производство. Technol. 90 (2016) 1911–1920. [CrossRef] [Google ученый]
- Ю.Б. Чжун, К.С. Ву, Г.К. Padhy, Влияние ультразвуковой вибрации на сварочную нагрузку, температуру и поток материала при сварке трением с перемешиванием, J. Mater. Процесс. Technol. 239 (2017) 273–283 [CrossRef] [Google ученый]
- П.Кумар Сингх, С. Дипак Кумар, Д. Патель, С.Б. Прасад, Оптимизация параметров процесса вибрационной сварки с использованием методологии поверхности отклика, J. Mech. Sci. Technol. 31 (2017) 2487–2495 [CrossRef] [Google ученый]
Цитируйте эту статью как : Правин Кумар Сингх, Исследование влияния механической вибрации в сварочной ванне из низкоуглеродистой стали, Manufacturing Rev. 6 , 21 (2019)
Все таблицы
Таблица 1Сравнительное исследование различных методов вибросварки и экспериментальной установки, использованной в настоящей работе.
Таблица 2Спецификация двигателя ERM.
Таблица 3Входные параметры и уровни.
Таблица 4Результаты испытаний на твердость, удар и растяжение для L 9 OA.
Таблица 5Таблица отклика для отношения S / N твердости L 9 OA.
Таблица 6Дисперсионный анализ твердости L 9 OA.
Таблица 7Таблица отклика для отношения сигнал / шум для ударной вязкости L 9 OA.
Таблица 8Дисперсионный анализ ударной вязкости L 9 OA.
Таблица 9Таблица отклика для отношения сигнал / шум UTS L 9 OA.
Таблица 10Дисперсионный анализ для ЕТС L 9 OA.
Таблица 11Совместная эффективность вибросварных соединений.
Таблица 12Завершенные результаты эксперимента Тагучи и описание наиболее значимых значений методом ANOVA.
Все фигуры
рисунок 1 (а) Принципиальная блок-схема вибрационной установки с указанием углов и положений вибрационной установки. (b) Схема вибрационной установки, вид сверху. | |
По тексту |
Рис. 2 (а) и (б) Фотография реальной вибрационной установки.(c) и (d) Процесс вибрационной сварки, использованный в настоящем исследовании. | |
По тексту |
Рис. 6 (a) Макрограф обычного SMAW. (б) Анализ микроструктуры обычного SMAW в условиях отсутствия вибрации. (c) Макрограф вибрационной SMAW. (d) Анализ микроструктуры вибрационной SMAW при частоте 150 Гц. (e) Макрограф вибрационной SMAW. (f) Анализ микроструктуры вибрационной SMAW при частоте 300 Гц.Стерео увеличенные (10 X) изображения, показывающие поперечное сечение профиля сварного шва и микрофотографию (100 X) стыкового сварного шва зоны сварного шва при обычном и вибрационном SMAW. | |
По тексту |
— Принцип работы, детали, преимущества и недостатки применения — The Welding Master
Что такое ультразвуковая сваркаУльтразвуковая сварка (USW) — это метод сварки, в котором для сварки двух частей вместе используются ультразвуковые колебания высокой частоты.Чаще всего он используется для сварки термопластов и разнородных материалов. Металл с тонким сечением также можно сваривать с помощью USW.
Принцип работыВысокочастотная (от 20 кГц до 40 кГц) ультразвуковая вибрация используется для соединения двух пластиковых деталей. Высокочастотная вибрация генерирует тепловую энергию на границе раздела двух частей и плавит материал. Расплавленный материал сплавился друг с другом, образуя прочный сварной шов при охлаждении и затвердевании.
Типичная используемая частота — 15, 20, 30, 35 или 40 кГц.
Основные деталиРазличные основные части или компоненты ультразвуковой сварки:
- A Пресс: Он используется для приложения давления на две соединяемые пластмассовые детали. Может быть с пневматическим или электрическим приводом.
- Гнездо, опора или приспособление: Это зажимное устройство, которое используется для удержания и зажима двух пластиковых деталей вместе.Это позволяет направлять высокочастотную вибрацию на поверхность раздела двух частей.
- Ультразвуковой стек : Он состоит из трех компонентов: преобразователя или пьезоэлектрического преобразователя, усилителя и рупора или сонотрода. Эти три элемента настроены для работы на резонансной частоте 15 кГц, 20 кГц, 30 кГц, 35 кГц или 40 кГц.
- Преобразователь: Преобразует электрические сигналы в высокочастотную механическую вибрацию. И это происходит за счет пьезоэлектрического эффекта.
- Booster: Механически изменяет амплитуду вибрации. В некоторых стандартных системах он используется для зажима стопки в прессе.
- Рупор или сонотрод: Он вибрирует с высокой частотой и передает механическую вибрацию на две свариваемые детали. Он также механически изменяет амплитуду. Он принимает форму детали. Рупор изготовлен из титана или алюминия.
- Ультразвуковой генератор: Он генерирует и доставляет высокочастотные электрические сигналы, соответствующие резонансной частоте пакета.
- Контроллер: Он используется для управления движением пресса и подачи ультразвуковой энергии.
Также читают:
Рабочий процесс ультразвуковой сварки- Две соединяемые пластмассовые детали собираются в гнезде (опоре или приспособлении)
- Рупор обеспечивает контакт в верхней части детали.
- К двум деталям прилагается давление, прижимающееся к приспособлению.Давление прикладывают через пресс с пневматическим или электрическим приводом.
- Рупор колеблется вертикально с очень высокой частотой (от 20 кГц до 40 кГц), передает механическую вибрацию на две пластмассовые детали. Это генерирует тепловую энергию на контактном наконечнике двух поверхностей и плавит их.
- К двум деталям прикладывают зажимное усилие в течение заданного времени, чтобы сплавить их вместе и сформировать прочный сварной шов при охлаждении и затвердевании.
- После затвердевания зажимное усилие снимается и рог втягивается.Сварная пластиковая деталь вынимается из приспособления как одно целое.
Для лучшего понимания посмотрите видео, представленное ниже:
Приложение
Он в основном используется в компьютерной и электротехнической, аэрокосмической и автомобильной, медицинской и упаковочной промышленности.
- Компьютерная и электротехническая промышленность: Здесь он используется для соединения проводных соединений и создания соединений в небольших чувствительных цепях.
- Аэрокосмическая и автомобильная промышленность
В автомобильной промышленности он используется для сборки крупных пластиковых и электрических компонентов, таких как дверные панели, приборные панели, воздуховоды, лампы, рулевые колеса, а также детали обивки и двигателя.
В аэрокосмической отрасли он используется для соединения тонких листов толщиной и легких материалов, таких как алюминий.
- Медицинская промышленность
Не вызывает загрязнений или разрушения сварного шва.Именно поэтому его используют в медицинской промышленности.
Такие изделия, как анестезиологические фильтры, артериальные фильтры, фильтры для крови, диализные трубки, пипетки, фильтры для крови / газов, резервуары для кардиометрии и т. Д., Могут быть изготовлены с использованием метода ультразвуковой сварки.
4 . Упаковочная промышленность
Применяется для упаковки различных материалов в пищевой промышленности.
Используется для упаковки опасных материалов, таких как взрывчатые вещества, фейерверки и химикаты.
Также читают:
Преимущества- Это быстрый процесс сварки.
- Имеет быстрое время высыхания, т.е. изделия не остаются в течение длительного времени в приспособлениях для высыхания
- Это легко автоматизировать.
- Обеспечивает чистый и точный стык.
- Он демонстрирует чистые места сварки и не требует подкраски.
- Обладает низким тепловым воздействием на материалы.
- Его нельзя использовать для изготовления швов большого размера (более 250 x 300 мм).
- Он требует специально разработанных соединений, чтобы он мог касаться наконечника в процессе сварки.
- Высокая стоимость оснастки для приспособлений.
- Ультразвуковая сварка ограничивается стыками внахлест.
Наши журналы | ||||||
Как крупный международный издатель академических и исследовательских журналов Science Alert издает и разрабатывает названия в сотрудничестве с самыми престижные научные общества и издатели.Наша цель заключается в том, чтобы максимально широко использовать качественные исследования аудитория. | ||||||
Для авторов | ||||||
Мы прилагаем все усилия, чтобы поддержать исследователей которые публикуют в наших журналах. Есть масса информации здесь, чтобы помочь вам публиковаться вместе с нами, а также ценные услуги для авторов, которые уже публиковались у нас. | ||||||
Подписчикам | ||||||
2021 цены уже доступны. Ты может получить личную / институциональную подписку перечисленных журналы прямо из Science Alert. В качестве альтернативы вы возможно, пожелает связаться с выбранным вами агентством по подписке. Направляйте заказы, платежи и запросы в службу поддержки. в службу поддержки клиентов журнала в Science Alert. | ||||||
Для обществ | ||||||
Science Alert гордится своей тесные и прозрачные отношения с обществом. В качестве некоммерческий издатель, мы стремимся к самым широким возможное распространение публикуемых нами материалов и на предоставление услуг высочайшего качества нашим издательские партнеры. | ||||||
Справочный центр | ||||||
Здесь вы найдете ответы на наиболее часто задаваемые вопросы (FAQ), которые мы получили по электронной почте или через контактную форму в Интернете. В зависимости от характера вопросов мы разделили часто задаваемые вопросы на различные категории. | ||||||
База данных ASCI | ||||||
Азиатский индекс научного цитирования (ASCI) стремится предоставить авторитетный, надежный и значимая информация по освещению наиболее важных и влиятельные журналы для удовлетворения потребностей мировых научное сообщество.База данных ASCI также предоставляет ссылку к полнотекстовым статьям до более чем 25000 записей с ссылка на цитированные ссылки. | ||||||
Исследование механических свойств соединения дуговой сварки с помощью вибрации
Wu, W. (2005, февраль) «Механическое поведение прецизионного компонента после синхронного вибрационного соединения» В Micro- and Nanotechnology: Materials, Processes, Packaging, and Systems II (Vol.5650, с. 438-446). Международное общество оптики и фотоники.
Тевари, С. П. (1999) «Влияние поперечных колебаний на свойства растяжения сварных конструкций из мягкой стали» ISIJ international, 39 (6), 570-574.
Tewari, SP, & Shanker, A. (1993) «Влияние продольной вибрации на механические свойства сварных конструкций из низкоуглеродистой стали» Труды Института инженеров-механиков, Часть B: Журнал Engineering Manufacture, 207 (3), 173- 177.
Джу Дж., Суга Ю. и Огава К. (2002, январь) «Контроль проникновения путем мониторинга колебаний ванны расплава при дуговой сварке TIG» В Двенадцатой Международной конференции по морской и полярной инженерии. Международное общество морских и полярных инженеров.
Munsi, A. S. M. Y., Waddell, A. J., & Walker, C. A. (1999) «Вибрационное кондиционирование сварного шва — эффект вибрации движения твердого тела во время сварки» Strain, 35 (4), 139-143.
Тевари, С.П. (2009) «Влияние продольных колебаний на свойства растяжения сварных швов из среднеуглеродистой стали различной толщины» Наука и технологии, Азия, 14 (4), 17-27.
Мацуда, Ф., Накагава, Х., Наката, К., и Аяни, Р. (1978) «Влияние электромагнитного перемешивания на структуру затвердевания сварных швов алюминиевых сплавов (отчет I): исследование металла шва GTA на тонких листах» Труды JWRI, 7 (1), 111-127.
Wu, C. S., Chen, M. A., & Li, S.К. (2004) «Анализ возбужденных колебаний и отрыва капли при активном управлении переносом металла» Вычислительное материаловедение, 31 (1-2), 147-154.
Чен, М. А., Ву, С. С., Ли, С. К., и Чжан, Ю. М. (2007) «Анализ активного контроля переноса металла в модифицированном импульсном GMAW» Наука и технология сварки и соединения, 12 (1), 10-14.
Гриль, А. (1981) «Влияние колебаний дуги на распределение температуры и микроструктуру в сварных швах из тантала GTA» Metallurgical Transactions B, 12 (4), 667-674.
孙清洁, 林 三宝, 杨春利, 范 阳阳, & 赵国庆. (2008) «Характеристика дуги при ультразвуковой сварке TIG» 中国 焊接: 英文 Version, 17 (4), 52-57.
• Аэрокосмическая техника | • Антропология | • Агротехника |
• Агротехника | • Астрофизика | • Автоматизация и робототехника |
• Архитектура и региональное планирование | • Биология | • Биоинженерия |
• Автомобильная техника | • Ботаника | • Биоинформатика |
• Химическая инженерия | • Химия | • Биотехнологии |
• Гражданское строительство | • Компьютерные науки | • Строительные технологии |
• Коммуникационная техника | • Вычислительная математика | • Пищевая наука и технологии |
• Компьютерная инженерия | • Науки о Земле | • Генная инженерия |
• Электротехника и электроника | • Науки об окружающей среде | • Геномика и протеомика |
• Электроника и коммуникационная техника | • Геология | • Обработка изображений |
• Геотехническая инженерия | • Генетика | • Иммунология |
• Промышленное проектирование | • Медицинские науки | • Информационные технологии |
• Материалы и производство | • Науки о жизни | • Приборостроение |
• Машиностроение | • Математика | • Металлургические технологии |
• Оптическая инженерия | • Физика | • Молекулярная биология |
• Технологический процесс | • Физиология | • Микробиология |
• Строительное проектирование | • Космические науки | • Нанотехнологии |
• Теплотехника | • Зоология | • Фармацевтические технологии |
Влияние частоты вибрации на затвердевание сварных деталей (Журнальная статья)
Ву, В. Влияние частоты вибрации на затвердевание сварных деталей . США: Н. п., 2000.
Интернет. DOI: 10.1016 / S1359-6462 (99) 00416-9.
Ву В. Влияние частоты вибрации на затвердевание сварных деталей . Соединенные Штаты. https://doi.org/10.1016/S1359-6462(99)00416-9
Ву, В.Пт.
«Влияние частоты вибрации на затвердевание сварных деталей». Соединенные Штаты. https://doi.org/10.1016/S1359-6462(99)00416-9.
@article {osti_20050493,
title = {Влияние частоты вибрации на затвердевание сварных деталей},
author = {Wu, W},
abstractNote = {Вибрационные методы для улучшения свойств литых металлов известны уже много лет.Бойл и др. облучал расплавленный металл ультразвуковыми волнами, определив, что ультразвуковые колебания эффективно дегазируют легкие металлы. Позже был разработан процесс обработки расплавленных металлов высокочастотными механическими колебаниями. Было обнаружено, что газовые включения, окалина и шлак выносились на поверхность технологическим путем. Это позволило получить однородные мелкозернистые отливки и повысить ударную вязкость, предел прочности на разрыв и предел текучести литого материала. При сварке, когда в процессе сварки применяется вибрация, это влияет на затвердевание сварочной ванны.По мере затвердевания сварочной ванны дендриты могут разрушиться до того, как станут слишком большими. Следовательно, зерна не только ограничены в размере, но и ограничиваются дендриты, растущие перпендикулярно линии сплавления. Эффект этих явлений заключается в частичном случайном изменении направления роста зерен и предотвращении сегрегации на пути сварки. Эта более мелкая микроструктура может обеспечить лучшие механические свойства и устранить чувствительность сварного шва к образованию горячих трещин. При вибрационной сварке внутреннее напряжение распределяется по мере его образования.Кроме того, на микроструктуру металла шва влияют возмущения сварочной ванны во время затвердевания. В идеале остаточное напряжение всей сварной детали снимается, в то же время улучшается ее микроструктура.},
doi = {10.1016 / S1359-6462 (99) 00416-9},
url = {https://www.osti.gov/biblio/20050493},
journal = {Scripta Materialia},
issn = {1359-6462},
число = 7,
объем = 42,
place = {United States},
год = {2000},
месяц = {3}
}
Сварка
Сварка
Применение сварки широко распространено в современном мире.В
новые газопроводы протяженностью 6.000 км, используемые для транспортировки природного газа с другой стороны
Уральских гор в Западную Европу, гигантские военные корабли, великие
мосты и большие алюминиевые резервуары для хранения сжиженного газа — это лишь некоторые из
более впечатляющие примеры. Сварка не менее важна при
изготовление деталей меньшего размера, например, гипордемических игл,
электрические выключатели, части компьютеров
Для изготовления этих сварных швов используется широкий спектр материалов. детали и конструкции.Эта шкала охватывает не только металлы из алюминий в цирконий, но и значительное количество пластика.
По материалам и размерам очень разные сварные детали требуют широкого выбора сварочных процессов. В настоящее время больше более ста сварочных процессов или технологических переменных используются в упражняться.
В несмотря на это, сварка — самый эффективный метод соединения материалы.У него есть некоторые ограничения, так как в процессе создания Сварка практически всех видов металлургических явлений. Обычно сварка связана с плавлением, затвердеванием, газометаллический и реакции шлак-металл, поверхностные явления и другое твердое состояние реакции. Не только большое разнообразие металлургических реакций очень сложно, но эти реакции происходят очень быстро при сварке, в отличие от других областей металлургии, таких как производство стали, литье или нагрев лечение.
Все сварочные процессы требуют приложения тепла и / или давления для получения подходящая связь. Тепловые, механические и электрические процессы связаны с сварочные процедуры.
Металлический соединительный элемент методы обычно группируются по механизму связывания:
прилипание,
пайка и пайка,
сварка.
В приклеенное соединение, силы притяжения, которые существуют между клеем и основной материал имеют физический характер. Два основных взаимодействия, которые способствуют адгезии, — это связь Ван-дер-Уоллса и постоянные дипольные связи — как они хорошо известны — относительно слабы.
Во время пайки и пайки коалесценция материалов осуществляется с помощью присадочного металла, находящегося в температура ликвидуса ниже солидуса основного материала.Наполнитель металл в жидком состоянии распределяется между плотно прилегающими друг к другу поверхности стыка за счет капиллярного действия. Связь между наполнителем металла и основного металла обычно происходит из-за некоторой диффузии присадить металл в горячий основной металл в горячий основной металл и решить поверхностное легирование металлов. В этом отношении пайка и пайка находятся между прилипанием и сваркой. Разница между пайкой а пайка — только при температуре плавления нанесенного присадочного металла.Когда температура плавления присадочного металла выше 450 o C температура процесс называется пайкой.
Прочность сварного соединения составляет на основе металлической связки. Напротив ван дер Валлса или постоянного диполя облигации, металлическая связь является первичной связью. Структура кристаллической линии построены хорошо расположенными металлическими положительными ионами. Каждый ион окружен не менее двенадцати соседей.Считается, что валентные электроны обладают полной подвижностью и могут свободно перемещаться между ионами. Каждый атом вносит свой валентный электрон в это «электронное облако» и там нет способа связать данный электрон с конкретным ионом. Держатель облигаций структура вместе вызвана притяжением отрицательно заряженные электроны к положительно заряженным ионам. Эта металлическая связь очень сильный.
Условие союза двух ранее разделенные металлические части таковы, что расстояние между поверхностными ионами из двух частей не должно быть больше некоторого таймера их решетки параметры.Это желаемое расстояние составляет не более половины нанометра.
В нормальных условиях вся поверхность или металлические части покрыты адсорбированными молекулами газа. Этот слой молекул имеет толщину несколько манометров и затрудняет соединения между ионами металлов. Есть возможность уменьшить количество адсорбированных газов уменьшением давления газа или повышением температуры. Должен быть отметил, что при более высокой температуре оксидные пленки образование выше.Оксидные пленки или другие подобные загрязнения на поверхности мешают контакту металла с металлом и должны быть удалены, чтобы получить металлическую связь.
В полном вакууме, где слой газа не препятствует ионному соединению двух металлических частей, размещаемых на каждой другие сваривать не буду. Шершавость поверхности объясняет это явление, так как при обычных условиях только каждая стотысячная — миллионная ионная пара поверхности выступов и впадин находятся в подходящей близости.Сжатие металлические детали на относительно небольшой площади соприкосновения, давление достигает предела текучести при сжатии и часть поверхности металла течет пластически. При пластическом течении металла количество адсорбированного газов уменьшается, при этом образуется все больше и больше металлических связей.
Те сварочные процессы, в которых давление используется при комнатной температуре для коалесценции металлов с значительная деформация сварного шва создает первый основной класс сварка и классифицируются как сварка холодным давлением .
Основное условие для удовлетворительная сварка холодным давлением состоит в том, что хотя бы один из металлов быть соединенным очень пластично и не проявляет чрезмерного деформационного упрочнения сила. Металлы, успешно прошедшие холодную сварку давлением, имеют гранецентрированная кубическая структура решетки, такая как алюминий, медь, свинец, никель, золото, серебро и платина.
Чрезвычайно высокая мощность, которая требуется для пластических потоков металла ограничивает применение холода сварка давлением.Необходимая мощность определяется площадью сустава и пределом текучести металла при сжатии.
Есть возможность уменьшить предел текучести при сжатии и, таким образом, требуемая мощность давления сварка повышением температуры. Когда температура сварки выше температура рекристаллизации, падение предела текучести и деформационное охрупчивание не происходит. Коалесценция в зоне сварного шва достигается путем нагревания и приложения давления.Эти сварочные процессы которые объединяют давление и тепло, сгруппированы во второй основной класс по телефону процессы сварки горячим давлением . В большинстве из них процессы сварные швы выполняются без расплавления заготовки или, по крайней мере, с очень небольшим плавлением. Горячая деформация, результаты ковки в более мелкозернистой структуре сварного шва разрушает и диспергирует поверхность газовая или оксидная пленка. Сварка горячим давлением имеет высокую эффективность и процесс сварки очень быстрый.В этих процессах особенно Сопротивление и сварка трением, тепло обычно получается в площадь шва от электрического сопротивления заготовки до прохождения электрический ток или от теплового сигнала до трения.
Нагреваемые поверхности — в горячем состоянии. процессы сварки давлением — связаны друг с другом и исключены из атмосферы, поэтому они защищены от окисления.
Третий основной класс сварки Процессы сварки плавлением. В процессов сварки плавлением основные металлы плавятся, и во многих случаях добавляется присадочный металл. В расплавленный металл, выходящий из основного и присадочного металлов, образует общий сварной шов бассейн. Сварочная ванна зарождается твердыми основными металлами. Жидкий металл окруженный кристаллами основного металла начинает затвердевать, растущие дендритные зерна в области контакта с более холодным основным металлом.Это общие зерна обеих частей сварного шва. Общее затвердевание приводит к металлической связи между основными металлами.
Все сварочные процессы требуют приложение энергии для создания подходящей связи. Сварочные процессы сгруппированы по этим четырем категориям источников энергии: механические, химические, лучистые и электрические источники.
Наиболее распространенные прикладные процессы сгруппированы по источнику энергии.
Энергия сварки | Сварочные процессы |
Механический | Трение Ультразвуковой Взрыв |
Химическая промышленность | Газ Термит |
Сияющий | Лазерный луч Электронный пучок |
Сопротивление | Электрошлак Место сопротивления Сопротивление приклада |
Электрическая дуга | Газовая вольфрамовая дуга Плазменная дуга Газовая металлическая дуга Экранированная металлическая дуга Подводная дуга |
Механическая энергия используется для изготовления металлической связки при трении, ультразвуке и взрыве. сварка.
В сварка трением а связь создается между неподвижным и вращающимся элементом с помощью тепло трения, возникающее между ними, при воздействии высоких нормальных силы на интерфейсе. На рис.2 показаны основные стадии трения. сварка.
Трение сварные швы выполняются удерживанием невращающейся заготовки в контакте с вращение заготовки под постоянным или постепенно увеличивающимся давлением до тех пор, пока поверхность раздела достигает температуры сварки, а затем вращение останавливается формирование сварного шва.Теплота трения быстро развивалась на границе раздела. повышает температуру заготовок на очень коротком осевом расстоянии до значений приближающихся, но ниже температуры солидуса. Сварка происходит под действием давления, которое прикладывается, пока нагретая зона металлургически достигается за счет диффузии, а не плавления.
Из-за этого процесс превосходно подходит для соединения разнородных металлов, особенно тех, которые претерпевают нежелательные фазы при объединении в процессе плавления.Заявление этого процесса требует, чтобы вращающийся элемент был по существу симметричный относительно оси вращения, а другой может быть любого геометрия.
Ультразвуковая сварка с производятся путем введения высокочастотных (15-75 кГц) вибрационных энергия в зону сварки соединяемых металлов. Заготовки зажаты между двумя наконечниками, и энергия вибрации передается через один или оба наконечника, которые колеблются в плоскости, параллельной сварному шву интерфейс.Это колебательное движение нарушает оксидную пленку на поверхности. металлических поверхностей, очищает слой адсорбированного газа и позволяет контакт металл-металл. Осциллирующее напряжение сдвига, возникающее во время движение приводит к электрическому гистерезису, локальному скольжению и пластичности деформация соприкасающихся поверхностей. Упругие и пластические деформации вызывают очень локализованное и кратковременное повышение температуры в сварном шве интерфейс. При надлежащих условиях зажимного усилия и вибрационной мощности, достигнутая температура обычно составляет половину абсолютной точки плавления металлы соединились.По этой причине ультразвуковая сварка считается как процесс холодной или твердотельной сварки давлением.
Потому что нет слияния, это Метод дал хорошие результаты с разнородными металлами. Обычно используется для выполнения точечных, прямых и кольцевых швов между заготовками толщиной листа или фольги не более 2 мм.
В сварка взрывом , деформация взрывчатого вещества используется для ускорения одного из детали до высокой скорости, прежде чем они столкнутся с неподвижным компонент.В момент удара кинетическая энергия летчика равна высвобождается как волна сжимающего напряжения на поверхности. Уровень давления этих волн напряжения значительно превышает предел текучести пластины материал. Существенной особенностью процесса является то, что два соединяемые поверхности встречаются под небольшим углом, так что «склеиваемый фронт» установлен, который перемещается по интерфейсу. Поверхностные пленки выбрасываются границы раздела за счет деформирующего воздействия фронта склеивания на идеально чистая, без окислов и газов поверхность.Межатомная сила создает металлическая связь.
Результат этого процесса — насморк. прессованный шов без зоны термического влияния. Сварка взрывом обычно используется для изготовления облицовочной плиты, но подходит для сварки стержней. Удовлетворительные сварные швы могут быть выполнены между медью и сталью, а также между различными металлы, такие как золото, серебро, никель и титан.
Химическая энергия хранящиеся в самых разных формах, могут быть преобразованы в полезное тепло.В температура и скорость реакции окисления — два основных характеристики, которые определяют применение различной энергии источники для сварки.
Вовлеченное тепло химического реакция используется для плавления исходных материалов в газе и термите сварка. По этой причине эти процессы считаются термоядерными. сварка.
В газовой сварке , отработанные топливные газы обладают двумя важными характеристиками.Первый важный Характерной чертой пламени является его химическая активность. Вариация пламени характеристики — окислительные, нейтральные или восстанавливающие — достигаются изменение пропорций топливного газа и кислорода или воздуха. Нейтральный пламя является наиболее часто используемым, поскольку нейтральная атмосфера, окружающая расплавленный металл предотвращает загрязнение сварного шва до затвердевания.
С точки зрения сварки, второй важной характеристикой пламени является его температура, так как это в значительной степени определяет скорость горения, с которой можно продолжать сварку.Пламя более горячее, если топливный газ сжигается в чистом кислороде, чем на воздухе. В присутствие в пламени азота, который тоже нагревается, но не принимает участия при горении снижает температуру пламени. Максимум температуры, пламя имеет окислительный характер и обычно не подходит для сварки из-за образования оксидов в металле шва.
Ацетилен и кислород ниже умеренное давление при смешивании и сжигании в ручной сварочной горелке.В пламя направляется на рабочую поверхность и обеспечивает сплавление деталей путем плавление соприкасающихся металлов.
Газовая сварка может применяться к широкий спектр металлов и используется не только для сварки, но и для пайка тоже.
Сварка термитом использует тепло экзотермической реакции. Ряд оксидов металлов может быть восстанавливается реакцией с мелкодисперсным алюминием с высвобождением значительного тепла, так что продукты реакции расплавляются.В реакция с оксидом железа дает 2450 o C температура. Из загрузки 1000 г оксида и алюминия получается 476 г шлак 524 г железа и 0,76 МДж энергии.
Расплавленное, перегретое железо, произведенное в таким образом можно заливать в полость между двумя частями стыка произвести сварку. Шлак всплывает на поверхность, а расплавленный материал нагревается до расплавления обеих сторон основного металла.Когда присадочный металл остывший, можно удалить весь нежелательный излишек материала. Термитная сварка — это также используется для сварки меди, никеля и их сплавов.
Наиболее широко используемое использование Сварка термитом предназначена для соединения рельсов, арматурных стержней, для ремонт и сварка тяжелых конструкций с зарядами до 3 тн.
Лазерная и электронно-лучевая сварка использовать энергию в виде лучистой энергии .
Методы сварки лучистым излучением уникальна, потому что энергия сварки должна быть сосредоточена на объекте, который будет сварены, и тепло выделяется только там, где сфокусированный луч падает на заготовка. В отличие от других источников энергии, работа не приводится в контакт с любой нагретой средой, газом или парами металла, и процессы обычно могут проводиться в системах низкого давления, где максимальная чистота может быть достигнут.
Лазерный луч фокусируется различные конфигурации линз, а также электронный луч за счет электростатического или магнитным путем. Сфокусированный луч дает высокую плотность мощности до 100 кВт / мм 2 , что в несколько тысяч раз превышает удельную мощность газовой сварки. С помощью лучистой энергии сварка может производиться обычным способом с ограниченной проводимостью и методом замочной скважины. В При сварке с ограниченной проводимостью луч падает и поглощается металлическая поверхность.Внутренняя часть материала полностью нагревается за счет проводимость с поверхности.
В этом режиме сварки интенсивный Концентрация энергии на поверхности детали вызывает локальное испарение. Паровая полость, окруженная расплавленным металлом, образуется, когда луч начинает двигаться. двигаться по суставу. Полость поддерживается против гидродинамики силы окружающего его жидкого металла давлением испаренного металл.Металл постепенно плавится на передней кромке подвижного расплавленной ванны и обтекает глубокую полость проникновения к задней части бассейн, где он застывает. В режиме замочной скважины проникновение не ограничивается температуропроводностью материала, поскольку энергия пучка проникает прямо в полость.
Многие металлы могут быть удовлетворительно сварены методами сварки лучистым излучением. Медь, никель, железо, цирконий, алюминий, титан, магний, вольфрам, молибден и их сплавы свариваются с помощью этого процесса.
Поскольку оборудование для лучистой сварки стоит дороже, чем обычные системы эквивалентной мощности, выбор приложения должны основываться на уникальных технологических возможностях. Что-нибудь из этого возможности, которые могут быть использованы в качестве ориентира для выбора, следующие:
то удельная энергия, подводимая к заготовке, очень мала
то высокая удельная мощность может использоваться для сварки или разнородных металлов с очень разные физические свойства или большие различия в массе и размеры
точность сварка может выполняться с четко определенной сфокусированной точкой
то окружение сварки очень чистое
Oни идеально подходят для автоматизации.
Электронно-лучевая сварка это процесс, который вызывает коалесценцию металлов за счет тепла, полученного от концентрированный пучок высокоскоростных электронов, падающих на поверхности быть присоединенным. Пучок электронов создается и ускоряется электронно-лучевая пушка.
Электроны генерируются при нагревании отрицательно заряженный излучающий материал до температуры его тепловыделения классифицировать.Электроны выкипают из этого эмиттера и ускоряются и направляются их притяжением к положительно заряженному аноду. Точно настроенный окружающий эмиттер электрод электростатически формирует выбрасываемый электрод в пучок.
Система электронно-лучевой сварки способна получения мощности пучка до 100 кВт и сверхнормативной мощности 100 кВт / мм. 2 штук.
В лазерная сварка источник энергии — лазер.С инженерной точки зрения лазер может рассматриваться как устройство преобразования энергии, в котором энергия от первичная форма (электрическая, химическая, тепловая, оптическая, ядерная) превращается в пучок когерентного электромагнитного излучения на ультрафиолетовая, видимая или инфракрасная частота. Лазерный «свет» монохроматический (одна длина волны) и когерентный (все волны синфазны). Поскольку лазерные лучи когерентны, они могут сильно концентрироваться передающая или отражающая оптика для обеспечения высокой плотности энергии требуется для сварки и резки.
Наиболее часто применяемая сварка процессы используют электроэнергии . Электроэнергия может преобразовываться в тепло при сопротивлении или в электрической дуге. Способ преобразования энергии дают классификацию или электросварку процессов, а именно контактной и дуговой сварки.
Сварка сопротивлением процессы — кроме электрошлаковой сварки — используют комбинацию силы и тепла для создания сварного шва между деталями. Сопротивление нагрев происходит при прохождении электрического тока через детали.
В электрошлаковой сварке , электрод, такой как проволока, пропускается через электропроводящую ванну расплавленного шлака.Тепло генерируется сопротивлением, оказываемым на ток при его прохождении из электродной проволоки через шлак в сварочные бассейны. Это тепло плавит не только проволоку, но и основные металлы. Металл сварного шва осаждается через расплавленный шлак, который очищает некоторые загрязнений и защищает сварочную ванну от воздействия атмосферы.
Металл сварного шва затвердевает вверх как тепло отводится окружающей сварной конструкцией и вмещающей обувью.Электрошлаковая сварка — это, прежде всего, метод сварки больших толщин металла. сталь в вертикальном или почти вертикальном положении.
В точечная контактная сварка две детали для точечной сварки помещаются между медные сварочные электроды с водяным охлаждением. Однако тепло для сварки требуется только на границе раздела основного металла, а тепло, выделяемое при любом другие места должны быть сведены к минимуму.На практике с момента величайшего сопротивление находится на границе раздела, при этом наиболее быстро выделяется тепло место расположения. Тепло на границе раздела основного металла рассеивается намного медленнее в основной металл. Следовательно, поскольку сварочный ток продолжает течь, скорость повышения температуры будет быстрее, чем в других точках. В хорошо контролируемый сварной шов, температура сварки сначала будет достигнута при многочисленные точки соприкосновения с интерфейсом, которые быстро превратились в самородок со временем.
Во время точечной сварки заготовки сжимаются электродами. На интерфейсе контакт сопротивление между деталями уменьшается, и, таким образом, генерируемые тепло увеличивается при увеличении сжатия. Сварочный ток имеет большее влияние на выделение тепла, чем сопротивление или время.Следовательно, это важная переменная, которую необходимо контролировать. Это типично для точечная сварка с высоким сварочным током до 100 кА и сварка время очень короткое, несколько сотых секунд.
Сварка сопротивлением это особый вид точечной контактной сварки. Этот процесс использует вращение колесные электроды, которые зажимают два металлических предмета и управляют Импульсы тока сваривают непрерывную точечную серию, шов внахлест точечная сварка.Точечная и шовная сварка сопротивлением применяется для сварки тонкие кусочки до 3 мм.
Сварка контактная стыковая это процесс, который производит коалесценцию одновременно по всей площадь двух стыкуемых поверхностей. Этот процесс сварки в основном выполняется твердое состояние. Металл на стыке нагревается до температуры, при которой рекристаллизация может происходить быстро по соприкасающимся поверхностям.А сила приложена к сварке, чтобы привести поверхности в близкое контакта и во время нагрева, чтобы осесть, материал имеет тенденцию очищать соединение окисленного металла.
Этот процесс сварки используется для изготовление довольно широкого ассортимента изделий из прутка, катанки, проволоки, ленты и труба.
Особенно привлекательная особенность точечный шов и процесс стыковой сварки: высокая скорость эксплуатации, высокая производительность, простота механизации, устранение окисление за счет закрытия нагретых поверхностей и отсутствия кромки заготовка или присадочный металл.
Второй основной способ изменить электрическая энергия в тепло — это применение электрической дуги . Дуга — это непрерывный электрический разряд между двумя твердыми или жидкими электроды, проходящие через частично или полностью ионизированный газ, известен как «плазма». Дуга, как источник тепла, используется во многих важные сварочные процессы, потому что он производит высокую интенсивность тепла и его легко контролировать с помощью электрических средств.
В нормальных условиях газы изоляторы. Ионы и свободные электроны, являющиеся носителями тока, являются производится тепловыми средствами и автоэмиссией для газовой среды. В установление состояния плазмы происходит за счет столкновительных процессов высокой энергии частицы. Частицы сварочной плазмы, ионы, электроны, нейтральные или возбужденные газовые атомы и молекулы получают свою высокую энергию при нагревании или электрическое поле.
Когда газ нагревается, индивидуум молекулы или атомы получают больше энергии. При низких температурах эта энергия в основном поступательный, связанный со скоростью движения. На более высоком температуры двухатомные молекулы, такие как азот (N 2 ), поглощают энергия, во-первых, вращением, а во-вторых, вибрацией ( движение двух атомов относительно друг друга).
Когда энергия вибрации достигает на достаточно высоком уровне, это может привести к разрыву валентных связей, удерживающих два атомы вместе, заставляя их диссоциировать в одноатомное состояние.
При более высоких температурах часть энергия поглощается внешней электронной связью отдельных атомов, и в конечном итоге вызывает отрыв одного из внешних электронов. Во время этого В процессе атом ионизируется на один электрон и положительно заряженный ион.
Уровни энергии для ионизации: существенно выше, чем для диссоциации. Следовательно, ионизация становится имеет значение, когда газ в основном одноатомный и две реакции могут рассматривать отдельно.
Нагретый газ сварочной дуги достигает максимального диапазона температур от 5000 до 30 000 К, в зависимости от типа газа и силы проводимого им тока. Газ, который находится между электродами, состоит из защитного газа или воздуха и пары основного металла и шлака.
Только часть самого высокого уровня энергии катода излучает электрон.Эта часть называется катодным пятном.
Самый большой и самый важный область в сварочной дуге — столб дуги. В большинстве дуговых колонн передача энергии в газе происходит в результате взаимодействия частиц из которых он состоит. Эти отдельные частицы находятся в состоянии или непрерывное случайное движение, и энергия передается от одной частицы к другой при столкновениях. Такие столкновения называются упругими, если суммарное кинетическая энергия участвующих частиц остается неизменной, и только движение изменяются параметры столкнувшихся частиц.Если энергия столкновения детали поглощается внутренне — например, возбуждением, диссоциацией или ионизация — тогда столкновение называется неупругим. Увеличивая При температуре газа неупругие столкновения будут преобладать.
При рекомбинации возбужденных диссоциированные или ионизированные частицы, они излучают дискретный квант энергии в природе ультрафиолетовые, видимые и инфракрасные волны. Этот сияющий энергия поддерживает высокую температуру дуги и состояние плазмы.
На практике плазма сварки дуга считается сильно ионизированной. В высокоионизированной плазме далеко встречи между электронами, ионами и атомами — основной способ взаимодействие между частицами.
Хотя анод играет жизненно важную роль в играть в сохранение непрерывности тока, получая поток электронов, он имеет меньшее влияние на дугу во многих отношениях, чем катод.Проникая в анод пучком электронов и отрицательных ионов, они переносят ему их кинетическая энергия и энергия конденсации. Инцидент частицы создают давление на поверхности на анодное пятно, создавая проникновение в сварочную ванну.
С точки зрения приложения, сварочные процессы бывают двух основных типов в зависимости от того, электрод расплавляется. Если электрод тугоплавкий — значит, если он сделан из углерода или вольфрама — он не плавится в процессе дугой и не расходуется.Когда электрод — например, присадочный материал расплав и капли расплава могут отделяться и перемещаться по дуге зазор с заготовками быстро движущейся плазменной струей, электрод расходный материал. Любой процесс дуговой сварки, при котором электрод оплавляется. чтобы стать частью сварного шва, описывается как « металлическая дуга ».
С неплавящимся электродом, тепло попадает в работу электронными или ионными процессами, которые происходят на границе столба дуги с работой — это самый большой источник тепла — а также за счет подключения горячей плазмы струи и рекомбинации любых частиц, диссоциировавших в дуге столбец.
Тепло теряется из-за присутствующих флюсов в дуге, а также в ограниченной степени. Лишь несколько процентов теряются излучения и газов, покидающих дуговое пространство. Дополнительно тепло генерируется теряется из-за проводимости электрода.
Если электрод расходный и передается в сварочную ванну, это тепло снова доступно в ванне. Поскольку электрод является частью электрического сопротивления, прохождение ток по электроду к дуге может вызвать резистивный нагрев в заметная степень.
Во время дуговой сварки сварной шов бассейн нагревается значительно выше температуры плавления основных материалов а температура капель близка к температуре кипения. На это температура окисления и других подобных химических реакций очень быстро. Следовательно, тогда должен быть какой-то способ исключить воздушную атмосферу. пока идет процесс. Шлак или защитный газ используется для защиты горячий металл.Шлак может образоваться при плавлении электродного покрытия или сварочный флюс. Те сварочные процессы, в которых используется защита шлак, обозначаются как « дуговая сварка в защитном флюсе »
Если флюс не используется, экранирование может обеспечивается за счет газовой подушки или газа, не образующего огнеупор соединения с основным металлом. Сварка неплавящимся электродом процессы в каждом случае используют инертный газ для защиты металлической дуги можно применять как активный газ, так и.
Защитный газ имеет четыре функции:
- ионизирует газ и действует как проводник для электронов.
- газовые щиты сварочная ванна от окружающего воздуха, предотвращает окисление
- г. на стабильность дуги влияет защитный газ при низком и высоком токи.
- жара дуга и, следовательно, проникновение также определяются газом.
Аргон, диоксид углерода, гелий, кислород и их смесь используются наиболее часто.
Аргон — наиболее часто используемый защитный газ для сварка. Это относительно дешево и дает стабильную дугу, которую можно запустить. с легкостью. С чистым аргоном можно сваривать все металлы.
Гелий интересен высоким напряжением дуги. что обеспечивает более глубокое проникновение.Это положительно сказывается на скорость сварки. Поскольку газ очень легкий, требуется больше газа для сварка. Дуга менее устойчива, чем с аргоном. Газ относительно дорогой. Чистый гелий используется для сварки меди, алюминия и их сплавы.
Газовая вольфрамовая дуговая сварка (GTAW) — это процесс, в котором коалесценция металлов производится путем нагрева их с дугой между дугой вольфрамового (неплавящегося) электрода защищен от атмосферы подачей инертного газа (Ar, He) через газовое сопло.Кроме того, существует смесь Ar / H 2 . также сделано с аргоном и небольшим процентом водорода, потому что это уменьшение и дает более чистый результат.
Сварной шов выполняется дугой. так что стыкуемые детали расплавляются и соединяются вместе как сварной шов металл затвердевает. Присадочный металл можно добавлять, а можно и не добавлять. Присадочный металл сварочный стержень держат вручную или проволоку подают механически.
GTAW можно адаптировать как к ручному и автоматический режим. Этот процесс используется при сварочных токах от 1 От А до 700 А и является одним из самых универсальных методов сварки в отношении материала. Хотя высокие сварочные токи позволяют сваривать возможны толстые металлы, GTAW — это в первую очередь процесс сварки листа металл или мелкие детали. Поскольку GTAW — это металлургически чистый процесс и обеспечивает высокое качество сварных швов, точность процесса значительно увеличивается сварка в авиастроении, атомной энергетике и приборостроении.
Плазменная сварка (PAW) — это процесс дуговой сварки, при котором нагрев происходит с сжатая дуга между вольфрамовым электродом и деталью (перенесенная дуга) или между электродом и сужающим соплом (неперенесенная дуга). Сужение дуги обычно достигается прохождение дуги через медное отверстие с водяным охлаждением. Цель сужение предназначено для контроля и увеличения плотности энергии дуги транслировать.Экранирование обычно обеспечивается выходящим горячим ионизированным газом. от отверстия сужающего сопла. Защитный газ может быть инертным. газ или смесь инертных газов. Газ через отверстие — это газ, направляется через горелку, чтобы окружить электрод. Он становится ионизированным в дуге для образования плазмы и выходит из отверстия в горелке сопло как плазменная струя. Аргон, гелий и водород применяются в качестве отверстие для газа.Присадочный металл можно добавлять, а можно и не добавлять.
Суженная дуга, используемая в плазменно-дуговая сварка имеет ряд преимуществ перед дугой без сужения. используется в GTAW:
- концентрация энергии больше,
- дуги повышена стабильность, особенно на низких уровнях тока,
- твердый подкладка не требуется для получения полного проплавления, потому что Можно использовать технику замочной скважины.
Применяются процессы плазменной дуги. не только для сварки, но и для резки и наплавки металлов. Заявление PAW похож на GTAW.
Газовая дуговая сварка металлом (GMAW) — это процесс электродуговой сварки, при котором происходит слияние металлов, нагревая их дугой между непрерывно подаваемыми присадочная металлическая (расходная) проволока и работа.Экранирование дуги и расплавленная сварочная ванна полностью получается из внешнего газа или газовая смесь. Аргон, диоксид углерода, гелий, кислород и их смесь являются наиболее часто используется для GMAW. Хотя Ar и He используются для газового металла Дуговая сварка большинства металлов, CO 2 получила широкое распространение (наряду с смесью Ar-CO 2 ) для сварки мягких сталей.
GMAW — это эксплуатируется в полуавтоматическом и автоматическом режимах.Это используется особенно при высокопроизводительных сварочных операциях. Все коммерчески важные металлы, такие как углеродистая сталь, нержавеющая сталь, алюминий и медь можно сваривать этим способом во всех положениях, выбрав соответствующий защитный газ, проволока и условия сварки.
Экранированная металлическая дуга сварка — это процесс ручной сварки, при котором тепло для сварка производится дугой между покрытыми флюсом расходный электрод и работа.Наконечник электрода, сварочная ванна, дуга и прилегающие участки заготовки защищены от атмосферного воздействия загрязнение газовой защитой, полученной в результате сгорания и разложение флюсового покрытия. Дополнительное экранирование предусмотрено для расплавленный металл путем покрытия расплавленным флюсом, шлаком.
Присадочный металл подается сердечником расходуемого электрода и, в некоторых электродах, из металлического порошка смешивается с электродным покрытием.
SMAW — один из наиболее широко используемых сварочный процесс для соединения металлических деталей, в основном из-за универсальность. Кроме того, оборудование менее сложное, более портативное и менее сложное. дороже, чем другие процессы дуговой сварки.
Использование сварки не ограничивается процессом, но типом и размером электрода. Суставов практически в любом положении, доступном электродом, можно сварной.Углеродистые и низколегированные стали, нержавеющие стали, жаропрочные сплавы, медь и никель и их сплавы — металлы, легче свариваемые по процессу SMAW. Чугун, высокопрочные и закаливаемые. стали также можно сваривать этим способом, но дополнительные процедуры которые включают предварительный или последующий нагрев, или и то, и другое. Низкий плавящиеся металлы, такие как свинец, олово, цинк и их сплавы, не свариваются с SMAW, потому что интенсивный нагрев дуги для них слишком высок.Также химически активные металлы, такие как титан, цирконий, магний и алюминиевые сплавы не сваривают покрытыми электродами. Эти металлы очень чувствителен к загрязнению кислородом и обеспечивает защиту покрытый электрод для них не подходит.
Сварка под флюсом (SAW) — это процесс дуговой сварки, при котором тепло для сварки подается дугой (или дугами), возникающей между непрерывно подаваемым и расходным материалом сварочная проволока (или проволока) и заготовка.Дуга экранирована слоем гранулированного и легкоплавкого флюса, который покрывает расплавленный металл шва и неблагородный металл от атмосферного загрязнения. Пока процесс выполняет присадочный материал, проволока продвигается в направлении сварки и механически подается в дугу при постоянном добавлении флюса.
Плавленая основа и присадочный металл. сливаются вместе, образуя поверхность сварочной ванны и защитную крышку плиты.Нерасплавленный флюс утилизируется для повторного использования. Флюсы для SAW легированных сталей могут содержат легирующие ингредиенты, которые изменяют состав сварного шва металл.
Есть три общих метода какой процесс может быть применен: полуавтоматический, автоматический и машинный сварка.
Пила может использоваться в широком диапазоне или промышленное применение. Высокое качество сварных швов, высокая наплавка скорость, глубокое проникновение и приспособляемость к автоматической работе делают процесс особенно подходящим для изготовления больших и тяжелых сварные детали.Широко применяется в судостроении, вагоностроении. изготовление, изготовление труб и изготовление конструктивных элементов там, где требуются длинные сварные швы.
Процесс можно использовать для сварки материалы от листов толщиной 3 мм до очень толстых и тяжелых сварных деталей. SAW подходит не для всех металлов и сплавов. Он широко используется для сварка углеродистых сталей, низколегированных конструкционных сталей и нержавеющих сталей.Сварку под флюсом можно использовать только в горизонтальном положении.
При дуговой сварке подача электроэнергии от сети. В сварочном аппарате электричество преобразуется в напряжение. и ток, пригодный для сварки. Машина подключена к электросети. питание, обычно 415 В и три фазы. С этой машиной возможно для сварки двумя типами тока: постоянным и переменным током.При сварке постоянным током сначала подается напряжение 415 В от сети. преобразовано в более низкое напряжение, а затем выпрямлено. Выпрямитель преобразует переменный ток в постоянный с помощью диодов. Диоды — это полупроводники, пропускающие только положительный или отрицательный часть переменного тока. В результате получается постоянный ток с высокой силу тока и низкое напряжение менее 120 В. При сварке с переменный ток (AC), напряжение преобразуется в безопасное низкое значение менее 50 В.Напряжение сети преобразуется в безопасный низкий уровень. сварочное напряжение для сварки.
Наибольшее тепловыделение приходится на положительный полюс. Тепло дуги в первую очередь приводит к плавлению металла. В то же время тепло способствует лучшей ионизации газа; проводимость улучшенный.
При дуговой сварке металлическим газом и под флюсом Сварка дуги начинается с простого короткого замыкания.Некоторые кратковременные короткое замыкание приводит к искрообразованию. Это приводит к ионизации газа. который становится проводящим, и может образовываться сварочная дуга.
При дуговой сварке в защитном металле прикосновение зажигание дуги используется, когда кончик электрода опирается на заготовку. После этого электрод поднимается медленно (метод подъема) или быстро (метод царапины) из заготовки; при малейшем зазоре между электродом и деталью a передается искра и зажигается дуга.
Такое касание дуги — не лучший способ для газа вольфрамовая дуговая сварка. Это может привести к загрязнению сварочной ванны или вольфрамовый электрод. Поэтому источники питания для дуговой сварки газом вольфрамом есть электронное устройство для зажигания дуги.
При зажигании используется высокочастотный генератор.Это выдает высокочастотные импульсы тока от 2000 до 10000 В при частота 150 кГц .. Результатом этого является избыток электронов на минусовой полюс и недостаток электронов на плюсовом полюсе, что приводит к искрение. Когда зажигается сварочная дуга, напряжение холостого хода меняется на меньшее напряжение, необходимое для поддержания сварочной дуги: это так называется сварочным напряжением, которое необходимо для преодоления сопротивления в полный сварочный контур, включая сварочную дугу.
Электродуговую сварку обычно проводят прямым Текущий. Это хорошо подходит для сварки стали и ее сплавов. В течение сварка легких металлов, таких как алюминий или магний, явление происходит, что приводит к нарушению этого процесса. Оксидный слой формируется на поверхности заготовки и в сварочной ванне. Этот керамический слой препятствие для металлического соединения. Решение — профилактика или устранение оксидного слоя на легком сплаве.Алюминий может быть правильно сварены при использовании переменного тока.
При сварке переменным током (AC) дуга должна воспламеняться снова и снова. Дополнительная проблема — так называемый выпрямитель. эффект. Когда поток электронов поворачивается, и они бегут от заготовки к электрод, оксидный слой разрушается под воздействием ионов, и условия сварного шва улучшают.
Сварщик GMAW не всегда использует присадочный металл, но дуговая сварка металла возможна без использования присадочного материала.это материал, который по каплям подается в сварочную ванну и заполняется сустав. Выбор присадочного металла должен быть таким, чтобы создается прочное плавление с основным материалом. Обычно наполнитель металл имеет тот же состав, что и основной материал. Неудивительно, что есть много видов. В спецификации процедуры сварки вы найдете указание правильного состава присадочного металла.
Есть несколько вещей, которые могут пойти не так во время сварка. Дефекты сварного шва классифицируются в стандарт EN 26520 в шести основных группах:
- трещины,
- пористость,
- твердый включения,
- отсутствие сварка / недостаточное проникновение,
- геометрический отклонения,
- другое отклонения.
Трещины может возникнуть из-за остывания или напряжения. Их можно рассматривать как продольные или поперечные трещины внутри сварного шва или внутри нагрева пораженная зона.
В сварном шве может образоваться пористость например, из-за отсутствия или прерывания экранирования. Иногда это может видел это на поверхности.Пористость на рентгеновском снимке видна как темная, круглая пятна. Они газовые дыры. Пористость также существует в виде газовых каналов.
Цельный включения встречаются во многих вариациях. На На рентгеновских лучах можно увидеть частицы вольфрама в виде белых пятен неправильной формы. Они возникают при соприкосновении электрода со сварочной ванной.
Отсутствие сварка / недостаточное проникновение в основном вызвано недостаточной квалификацией сварщика.На рентгеновском снимке мы признать местное недостаточное проникновение. Острые края V-образного шва не плавятся и хорошо видны в виде серой линии.
Известное геометрическое отклонение является нестандартное позиционирование деталей. Обычно это называется high-low. В отклонение обычно вызвано навыками сварщика. На рентгеновском снимке мы увидеть черно-белые различия между одной и другой стороной сварка.
Отклонения, которые не могли быть помещены в другой группы упомянуты в « прочие отклонения ». В нашем примере показываем брызги.
При визуальном осмотре сварной шов проверены на отклонения, такие как правильное значение a, поднутрение, выпуклость, избыточный металл шва и т. д.Приведены допустимые отклонения для сталей. в стандарте EN 25817.
При исследовании дефектов поверхностного растрескивания a Различают магнитный и краситель проникающий . При магнитном исследовании жидкость, содержащая порошок железа, распыляется на сварка. При приложении сильного магнитного поля становятся видны трещины. потому что магнитные силовые линии нарушаются трещиной и заставляют виден железным порошком.Таким образом, трещины под поверхностью также могут быть видимым. При исследовании пенетранта красителя применяется красная жидкость, проникает в трещину. Это становится видно разработчику.
Основной материал и сварной шов исследуются с помощью Рентгеновские лучи. Результат записывается на материале, чувствительном к этому радиация. Другими словами, это рентгенография : а фотографическое изображение выполнено на основе рентгеновских лучей.С некоторой практикой вы может распознать всевозможные недостатки, такие как пористость, включения, неровности. Это один из самых известных и полезных способов изучения сварка во всех аспектах качества (EN 1435).
В УЗИ сварной шов исследованы с помощью высокочастотных направленных звуковых волн. Работает с излучатель-приемник, в котором приемник регистрирует эхо, с которым он можно четко распознать шлаковые включения, неплавление.С этим технику можно очень точно определить дефект в сварном шве и определить его размеры. (EN 1714)
Для разрушающего контроля деталей заготовки и сварной шов необходимо подготовить. Образцы снимаются со сварного шва и обработанный. В некоторых случаях эти образцы дополнительно готовятся путем изготовления местное уменьшенное сечение, насечка или полировка поверхности. Специальный Методика разрушающего контроля предполагает разрушение сварной детали на очень низкая температура.
Испытание на излом в основном применяется для угловые швы. Это быстрая проверка, которая показывает, имеет ли угловой сварной шов хорошее проникновение и нет ли проплавления. Приговор требует некоторого опыта. (EN 1320)
Для производства необходима тщательная подготовка. Макрос поперечного сечения шва .После необходимой распиловки и На шов наносится полировка, травитель. Через некоторое время вы увидите что сварной шов становится видимым относительно основного материала. Со временем становятся видны неровности, такие как пористость, недостаточная проплавление, отсутствие проплавления угловых швов и отсутствие плавления.
Это измерение должно дать некоторую информацию о пластичность сустава.На эту пластичность отрицательно влияет когда твердость сварного шва слишком высока. Максимум твердость сварного шва для определенного материала предписана и указана в «HV», твердость по Виккерсу. Процедура измерения также указывается в точный способ измерения твердости в месте сварного шва. (EN 1043-1)
Для стыкового шва соединение сварного шва с основанием Материал можно проверить и измерить с помощью поперечного испытания на растяжение .Перед испытанием точно снимают размеры образца. Наконец, нагрузка на разрушение и местоположение разрушения зарегистрирован. Это также критерий принятия или отклонения сварка. (EN 895)
испытание на изгиб выполняется на правильно подготовленном образце, взятом из стыкового шва. Это дает в основном информацию об удлинении сварного шва и наличие неплавких дефектов сварного шва.
Испытание на удар дает информацию о пластичности сварного соединение. Образец для испытаний может быть взят из разных частей образец; его можно снимать со сварного шва и зоны термического влияния. В На этом образце фрезеруется выемка, которая будет или не будет перелома. Этот тест можно проводить при разных температурах, потому что температура также влияет на пластичность.
Сварочные позиции шт.