Материал — Википедия
Материал из Википедии — свободной энциклопедии
Материа́л — вещество или смесь веществ, из которых изготавливается продукция, которые способствуют процессу труда, либо придают изготовленной продукции определенные свойства.
В традиции советской и российской экономической науки под материалами понимают только продукты, прошедшие предварительную обработку на промышленных предприятиях (в отличие от сырья). Материалы делят на основные и вспомогательные. Основными считают материалы, входящие в состав готовой продукции в виде его главной субстанции (например, мука при производстве хлебобулочных изделий). Вспомогательными называют материалы, которые потребляются в процессе труда для придания продукту новых свойств (соль, красители), либо способствуют нормальному протеканию производственного процесса. Материалом не являются пища, энергия, топливо и лекарства, поскольку в процессе использования они вступают в химические реакции и постепенно почти полностью исчезают
Изучением физико-химических свойств материалов занимается междисциплинарный раздел науки — материаловедение.
Продукты сельского хозяйства, добывающей промышленности, в значительной степени сохранившие свои природные свойства, но предназначенные для дальнейшей промышленной обработки (древесина, хлопок, руда), называют сырьём[3].
Материалы для возведения зданий и сооружений — строительные материалы.
В бытовом смысле, материал — ткань для изготовления одежды.
Расходный материал, облегчающий механическое движение — смазка.
Вспомогательные материалы — чистящие средства, порошки, ветошь.
Материалы, ускоряющие/замедляющие химические реакции — катализаторы/ингибиторы.
Информационный материал, сведения — набор данных, имеющих определённое значение.
Механические свойства физических материалов[править | править код]
Механические свойства физических материалов, такие как прочность, сопротивление разрушению, твёрдость и др. являются во многих случаях определяющими для принятия решения о применении материала.
Методы проверки механических свойств[править | править код]
Следует отметить следующие основные методы проверки механических свойств:
Важным фактором является влияние термической обработки на механические свойства. Механические свойства должны рассматриваться в комплексе, с учётом конструкции, технологии и условий нагружения.
Существуют ещё параметры материала, связанные с изменением механических свойств при изменении температуры:
- М. Л. Бернштейн, В. А. Займовский. Механические свойства металлов. — 2-е изд.. — М.: Металлургия, 1979.
- Я. Б. Фридман. Механические свойства металлов. — Изд. 3, в 2-х частях. — М.: Машиностроение, 1974.
- Ходаков Ю. В., Эпштейн Д. А., Глориозов П. А. и др. Преподавание неорганической химии в средней школе. Методическое пособие для учителей. —
- Бакланов Г.И. и др. Статистика промышленности:Учебник. — М.: Финансы и статистика, 1982. — 439 с.
Вики-разметка — Википедия
Материал из Википедии — свободной энциклопедии
- О вики-разметке в Википедии смотрите страницу Википедия:Вики-разметка.
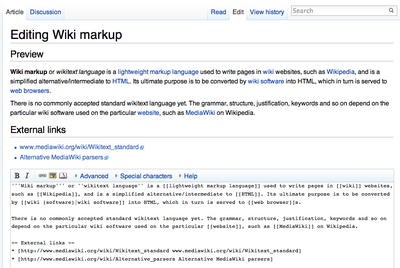
Вики-разметка — язык разметки, который используется для оформления текста на веб-сайтах (как правило, относящихся к классу вики-проектов) и позволяет упростить доступ к возможностям языка HTML. Страницы, оформленные с применением вики-разметки, предварительно преобразуются в HTML для просмотра в веб-браузере, преобразование реализует специальное программное обеспечение — вики-движок (англ. wiki engine).
На данный момент нет общепринятого стандарта для вики-разметки. Существуют различные языки вики-разметки, несовместимые между собой. Грамматика, структура, правила применения, ключевые слова и прочие детали зависят от конкретной реализации для конкретной вики-системы. Например, языки вики-разметки позволяют делать перекрёстные ссылки на другие страницы, но используют свой синтаксис. Многие вики, особенно ранние реализации, используют соглашение CamelCase для разметки слов, по которым нужно сформировать перекрёстные ссылки.
В Медиавики необходимо использовать конструкцию [[…]] для создания перекрёстных ссылок, такие ссылки называются «free links».
Разные вики-программы поддерживают разные наборы HTML-элементов в правилах разметки вики-текста. В некоторых случаях доступные HTML-элементы могут иметь индивидуальное оформление в едином стиле с веб-сайтом. Медиавики поддерживают множество стандартных HTML-элементов.
Creole — это попытка «использовать общие правила вики-разметки на разных вики-сайтах»
материал — Викисловарь
Морфологические и синтаксические свойства[править]
падеж | ед. ч. | мн. ч. |
---|---|---|
Им. | материа́л | материа́лы |
Р. | материа́ла | материа́лов |
Д. | материа́лу | материа́лам |
В. | материа́л | материа́лы |
Тв. | материа́лом | материа́лами |
Пр. | материа́ле | материа́лах |
ма-те-ри-а́л
Существительное, неодушевлённое, мужской род, 2-е склонение (тип склонения 1a по классификации А. А. Зализняка).
Корень: -материал- [Тихонов, 1996].
Произношение[править]
- МФА: ед. ч. [mətʲɪˈrʲjaɫ] мн. ч. [mətʲɪˈrʲjaɫɨ]
Семантические свойства[править]
Значение[править]
- вещество, служащее для изготовления чего-либо ◆ Строительный материал. ◆ Полимерные материалы.
- текст. вид или сорт ткани ◆ В магазине продают сатин и другие материалы.
- перен., обычно мн. ч. документы и прочие данные, используемые в качестве фактологической основы для создания художественного произведения, ведения исследования или расследования и т. п. ◆ Фильм снят по материалам кинохроник. ◆ На материале городских архивов строится сюжет пьесы. ◆ Прокурор ознакомился с материалами следствия.
- перен. информация, как правило, структурированная и дозированная, используемая в процессе обучения ◆ В этом семестре материала осталось на две лекции. ◆ Материал подаётся в несколько этапов: от простого к сложному. Каждый этап сопровождается наглядными пособиями и подробными объяснениями педагога. «Отчёт о практике», 2003 г. (цитата из Национального корпуса русского языка, см. Список литературы)
Синонимы[править]
- вещество, сырьё
- материя
- источник, документ
- —
Антонимы[править]
- —
- —
- —
- —
Гиперонимы[править]
- материя
- —
- —
- —
Гипонимы[править]
- металл, щебёнка, песок, дерево; стройматериал, пиломатериал, наноматериал, биоматериал, виноматериал, пеноматериал
- —
- —
- —
Родственные слова[править]
Этимология[править]
Происходит от лат. māteriālis, далее из māteria «первичное вещество, материя», далее из mater «мать», далее из праиндоевр. *mater- «мать». Русск. материал — начиная с Уст. морск. 1720 г., также в 1718 г. Заимств. через нидерл. mаtеriааl или нов.-в.-нем. Маtеriаl (с ХVI в.) из лат. Использованы данные словаря М. Фасмера. См. Список литературы.
Фразеологизмы и устойчивые сочетания[править]
Перевод[править]
![]() | Для улучшения этой статьи желательно:
|
Вики — Википедия
Материал из Википедии — свободной энциклопедии
Ви́ки (англ. wiki) — веб-сайт, содержимое которого пользователи могут самостоятельно изменять с помощью инструментов, предоставляемых самим сайтом. Форматирование текста и вставка различных объектов в текст производится с использованием вики-разметки. В частности, на базе этих принципов построена Википедия и другие проекты Фонда Викимедиа
История
Впервые термин «вики» для описания веб-сайта был использован в 1995 году Уордом Каннингемом, разработчиком первой вики-системы WikiWikiWeb, «Портлендского хранилища образцов» программного кода[2], созданной 25 марта 1995 года, который заимствовал слово гавайского языка, означающее «быстрый»[3][4]. Каннингем объяснил выбор названия движка тем, что он вспомнил работника международного аэропорта Гонолулу, посоветовавшего ему воспользоваться вики-вики шаттлом — небольшим автобусом, курсировавшим между терминалами аэропорта. Каннингем же планировал сделать движок, позволявший пользователям максимально быстро редактировать и создавать статьи. Каннингем первоначально описал вики как «простейшую онлайн-базу данных, которая может функционировать»[5]. Позже этому слову был придуман английский бэкроним «What I Know Is…» («то, что я знаю, это…»)[6]
.Сущность концепции вики

Уорд Каннингем и его соавтор Бо Леуф в их книге The Wiki Way: Quick Collaboration on the Web описали сущность концепции вики следующим образом:
- Вики предлагает всем пользователям редактировать любую страницу или создавать новые страницы на вики-сайте, используя обычный веб-браузер без каких-либо его расширений.
- Вики поддерживает связи между разными страницами за счёт почти интуитивно понятного создания ссылок на другие страницы и отображения того, существуют данные страницы или нет.
- Вики не является тщательно изготовленным сайтом для случайных посетителей. Напротив, Вики стремится привлечь посетителей к непрерывному процессу создания и сотрудничества, который постоянно меняет вид сайта.
Определяющие свойства
Вики характеризуется такими признаками:
- Возможность многократно править текст
- Особый язык разметки — так называемая вики-разметка, которая позволяет легко и быстро размечать в тексте структурные элементы и гиперссылки; форматировать и оформлять отдельные элементы[7].
- Учёт изменений (версий) страниц: возможность сравнения редакций и восстановления ранних.
- Проявление изменений сразу после их внесения.
- Разделение содержимого на именованные страницы.
- Гипертекст: связь страниц и подразделов сайта через контекстные гиперссылки.
- Множество авторов. Некоторые вики могут править все посетители сайта.
Техническая основа
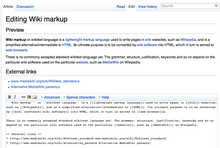
Для создания вики-среды необходимо особое ПО — движок вики. Это частный вид систем управления сайтом, довольно простой в своём устройстве и функциональности, поскольку почти все действия по структурированию и обработке содержимого делаются пользователями вручную.
Работа Википедии и других сайтов Фонда Викимедиа основана на движке MediaWiki.
Особенности
Язык вики поддерживает гиперссылки для создания ссылок между вики-страницами и является более наглядным, чем HTML, и более безопасным, поскольку использование JavaScript и каскадных таблиц стилей ограничено.
Вандализм
Многие вики позволяют изменять их содержимое всем желающим, а не только зарегистрированным пользователям. Подобно тому, как стены зданий и заборы исписывают непристойными надписями и украшают рисунками граффити, в таких вики иногда портят содержимое или добавляют что-то неуместное. Но, в отличие от стен и заборов, в вики легко вернуть содержимое к ранней версии: исправлять легче, чем портить. Если же кто-либо настойчиво и намеренно стремится навредить пользователям вики-сайта, можно закрыть ему возможность вносить правки.
См. также
Примечания
Ссылки
- WikiMatrix — сайт-энциклопедия о вики движках, на английском языке.
Композитный материал — Википедия
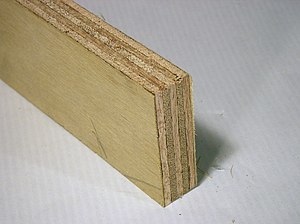
Композитный материа́л (КМ), компози́т — многокомпонентные материалы, состоящие, как правило, из пластичной основы (матрицы), армированной наполнителями, обладающими высокой прочностью, жёсткостью и т. д. Сочетание разнородных веществ приводит к созданию нового материала, свойства которого количественно и качественно отличаются от свойств каждого из его составляющих. Варьируя состав матрицы и наполнителя, их соотношение, ориентацию наполнителя, получают широкий спектр материалов с требуемым набором свойств. Многие композиты превосходят традиционные материалы и сплавы по своим механическим свойствам и в то же время они легче. Использование композитов обычно позволяет уменьшить массу конструкции при сохранении или улучшении её механических характеристик.
По структуре композиты делятся на несколько основных классов: волокнистые,стекловолокниты , дисперсноупрочненные, упрочнённые частицами и нанокомпозиты. Волокнистые композиты армированы волокнами или нитевидными кристаллами — кирпичи с соломой и папье-маше можно отнести как раз к этому классу композитов. Уже небольшое содержание наполнителя в композитах такого типа приводит к появлению качественно новых механических свойств материала. Широко варьировать свойства материала позволяет также изменение ориентации размера и концентрации волокон. Кроме того, армирование волокнами придаёт материалу анизотропию свойств (различие свойств в разных направлениях), а за счёт добавки волокон проводников можно придать материалу электропроводность вдоль заданной оси.
В слоистых композиционных материалах матрица и наполнитель расположены слоями, как, например, в особо прочном стекле, армированном несколькими слоями полимерных плёнок.
Микроструктура остальных классов композиционных материалов характеризуется тем, что матрицу наполняют частицами армирующего вещества, а различаются они размерами частиц. В композитах, упрочнённых частицами, их размер больше 1 мкм, а содержание составляет 20—25 % (по объёму), тогда как дисперсноупрочненные композиты включают в себя от 1 до 15 % (по объёму) частиц размером от 0,01 до 0,1 мкм. Размеры частиц, входящих в состав нанокомпозитов — нового класса композиционных материалов — ещё меньше и составляют 10—100 нм.
Полимерные композитные материалы (ПКМ)[править | править код]
Композиты, в которых матрицей служит полимерный материал, являются одним из самых многочисленных и разнообразных видов материалов. Их применение в различных областях даёт значительный экономический эффект. Например, использование ПКМ при производстве космической и авиационной техники позволяет сэкономить от 5 до 30 % веса летательного аппарата. А снижение веса, например, искусственного спутника на околоземной орбите на 1 кг приводит к экономии 1000$. В качестве наполнителей ПКМ используется множество различных веществ.
А) Стеклопластики — полимерные композиционные материалы, армированные стеклянными волокнами, которые формируют из расплавленного неорганического стекла. В качестве матрицы чаще всего применяют как термореактивные синтетические смолы (фенольные, эпоксидные, полиэфирные и т. д.), так и термопластичные полимеры (полиамиды, полиэтилен, полистирол и т. д.). Эти материалы обладают достаточно высокой прочностью, низкой теплопроводностью, высокими электроизоляционными свойствами, кроме того, они прозрачны для радиоволн. Использование стеклопластиков началось в конце Второй мировой войны для изготовления антенных обтекателей — куполообразных конструкций, в которых размещается антенна локатора. В первых армированных стеклопластиках количество волокон было небольшим, волокно вводилось, главным образом, чтобы нейтрализовать грубые дефекты хрупкой матрицы. Однако со временем назначение матрицы изменилось — она стала служить только для склеивания прочных волокон между собой, содержание волокон во многих стеклопластиках достигает 80 % по массе. Слоистый материал, в котором в качестве наполнителя применяется ткань, плетённая из стеклянных волокон, называется стеклотекстолитом.
Стеклопластики — достаточно дешёвые материалы, их широко используют в строительстве, судостроении, радиоэлектронике, производстве бытовых предметов, спортивного инвентаря, оконных рам для современных стеклопакетов и т. п.
Б) Углепластики — наполнителем в этих полимерных композитах служат углеродные волокна. Углеродные волокна получают из синтетических и природных волокон на основе целлюлозы, сополимеров акрилонитрила, нефтяных и каменноугольных пеков и т. д. Термическая обработка волокна проводится, как правило, в три этапа (окисление — 220° С, карбонизация — 1000—1500° С и графитизация — 1800—3000° С) и приводит к образованию волокон, характеризующихся высоким содержанием (до 99,5 % по массе) углерода. В зависимости от режима обработки и исходного сырья полученное углеволокно имеет различную структуру. Для изготовления углепластиков используются те же матрицы, что и для стеклопластиков — чаще всего — термореактивные и термопластичные полимеры. Основными преимуществами углепластиков по сравнению со стеклопластиками является их низкая плотность и более высокий модуль упругости, углепластики — очень лёгкие и, в то же время, прочные материалы. Углеродные волокна и углепластики имеют практически нулевой коэффициент линейного расширения. Все углепластики хорошо проводят электричество, чёрного цвета, что несколько ограничивает области их применения. Углепластики используются в авиации, ракетостроении, машиностроении, производстве космической техники, медтехники, протезов, при изготовлении лёгких велосипедов и другого спортивного инвентаря.
На основе углеродных волокон и углеродной матрицы создают композитные углеграфитовые материалы — наиболее термостойкие композитные материалы (углепластики), способные долго выдерживать в инертных или восстановительных средах температуры до 3000° С. Существует несколько способов производства подобных материалов. По одному из них углеродные волокна пропитывают фенолформальдегидной смолой, подвергая затем действию высоких температур (2000° С), при этом происходит пиролиз органических веществ и образуется углерод. Чтобы материал был менее пористым и более плотным, операцию повторяют несколько раз. Другой способ получения углеродного материала состоит в прокаливании обычного графита при высоких температурах в атмосфере метана. Мелкодисперсный углерод, образующийся при пиролизе метана, закрывает все поры в структуре графита. Плотность такого материала увеличивается по сравнению с плотностью графита в полтора раза. Из углепластиков делают высокотемпературные узлы ракетной техники и скоростных самолётов, тормозные колодки и диски для скоростных самолётов и многоразовых космических кораблей, электротермическое оборудование.
В) Боропластики — композитные материалы, содержащие в качестве наполнителя борные волокна, внедрённые в термореактивную полимерную матрицу, при этом волокна могут быть как в виде мононитей, так и в виде жгутов, оплетённых вспомогательной стеклянной нитью или лентой, в которых борные нити переплетены с другими нитями. Благодаря большой твёрдости нитей, получающийся материал обладает высокими механическими свойствами (борные волокна имеют наибольшую прочность при сжатии по сравнению с волокнами из других материалов) и большой стойкостью к агрессивным условиям, но высокая хрупкость материала затрудняет их обработку и накладывает ограничения на форму изделий из боропластиков. Кроме того, стоимость борных волокон очень высока (порядка 400 $/кг) в связи с особенностями технологии их получения (бор осаждают из хлорида на вольфрамовую подложку, стоимость которой может достигать до 30 % стоимости волокна). Термические свойства боропластиков определяются термостойкостью матрицы, поэтому рабочие температуры, как правило, невелики.
Применение боропластиков ограничивается высокой стоимостью производства борных волокон, поэтому они используются главным образом в авиационной и космической технике в деталях, подвергающихся длительным нагрузкам в условиях агрессивной среды.
Г) Органопластики — композиты, в которых наполнителями служат органические синтетические, реже — природные и искусственные волокна в виде жгутов, нитей, тканей, бумаги и т. д. В термореактивных органопластиках матрицей служат, как правило, эпоксидные, полиэфирные и фенольные смолы, а также полиимиды. Материал содержит 40—70 % наполнителя. Содержание наполнителя в органопластиках на основе термопластичных полимеров — полиэтилена, ПВХ, полиуретана и т. п. — варьируется в значительно больших пределах — от 2 до 70 %. Органопластики обладают низкой плотностью, они легче стекло- и углепластиков, относительно высокой прочностью при растяжении; высоким сопротивлением удару и динамическим нагрузкам, но, в то же время, низкой прочностью при сжатии и изгибе.
Важную роль в улучшении механических характеристик органопластика играет степень ориентации макромолекул наполнителя. Макромолекулы жесткоцепных полимеров, таких, как полипарафенилтерефталамид (кевлар) в основном ориентированы в направлении оси полотна и поэтому обладают высокой прочностью при растяжении вдоль волокон. Из материалов, армированных кевларом, изготавливают пулезащитные бронежилеты.
Органопластики находят широкое применение в авто-, судо-, машиностроении, авиа- и космической технике, радиоэлектронике, химическом машиностроении, производстве спортивного инвентаря и т. д.
Д) Полимеры, наполненные порошками. Известно более 10000 марок наполненных полимеров. Наполнители используются как для снижения стоимости материала, так и для придания ему специальных свойств. Впервые наполненный полимер начал производить доктор Бейкеленд (Leo H.Baekeland, США), открывший в начале 20 в. способ синтеза фенолформальдегидной (бакелитовой) смолы. Сама по себе эта смола — вещество хрупкое, обладающее невысокой прочностью. Бейкеленд обнаружил, что добавка волокон, в частности, древесной муки к смоле до её затвердевания, увеличивает её прочность. Созданный им материал — бакелит — приобрёл большую популярность. Технология его приготовления проста: смесь частично отверждённого полимера и наполнителя — пресс-порошок — под давлением необратимо затвердевает в форме. Первое серийное изделие произведено по данной технологии в 1916, это — ручка переключателя скоростей автомобиля «Роллс-Ройс». Наполненные термореактивные полимеры широко используются по сей день.
Сейчас применяются разнообразные наполнители как термореактивных, так и термопластичных полимеров. Карбонат кальция и каолин (белая глина) дёшевы, запасы их практически неограничены, белый цвет даёт возможность окрашивать материал. Применяют для изготовления жёстких и эластичных поливинилхлоридных материалов для производства труб, электроизоляции, облицовочных плиток и т. д., полиэфирных стеклопластиков, наполнения полиэтилена и полипропилена. Добавление талька в полипропилен существенно увеличивает модуль упругости и теплостойкость данного полимера. Сажа больше всего используется в качестве наполнителя резин, но вводится и в полиэтилен, полипропилен, полистирол и т. п. По-прежнему широко применяют органические наполнители — древесную муку, молотую скорлупу орехов, растительные и синтетические волокна. Большую популярность приобрел полимерно-песчаный композит на основе полиэтиленов с наполнителем из речного песка. Для создания биоразлагающихся композитов в качестве наполнителя используют крахмал.
Е) Текстолиты — слоистые пластики, армированные тканями из различных волокон. Технология получения текстолитов была разработана в 1920-х на основе фенолформальдегидной смолы. Полотна ткани пропитывали смолой, затем прессовали при повышенной температуре, получая текстолитовые пластины. Роль одного из первых применений текстолитов — покрытия для кухонных столов — трудно переоценить.
Основные принципы получения текстолитов сохранились, но сейчас из них формуют не только пластины, но и фигурные изделия. И, конечно, расширился круг исходных материалов. Связующими в текстолитах является широкий круг термореактивных и термопластичных полимеров, иногда даже применяются и неорганические связующие — на основе силикатов и фосфатов. В качестве наполнителя используются ткани из самых разнообразных волокон — хлопковых, синтетических, стеклянных, углеродных, асбестовых, базальтовых и т. д. Соответственно разнообразны свойства и применение текстолитов.
Композитные материалы с металлической матрицей[править | править код]
При создании композитов на основе металлов в качестве матрицы применяют алюминий, магний, никель, медь и т. д. Наполнителем служат или высокопрочные волокна, или тугоплавкие, не растворяющиеся в основном металле частицы различной дисперсности.
Свойства дисперсноупрочненных металлических композитов изотропны — одинаковы во всех направлениях. Добавление 5-10% армирующих наполнителей (тугоплавких оксидов, нитридов, боридов, карбидов) приводит к повышению сопротивляемости матрицы нагрузкам. Эффект увеличения прочности сравнительно невелик, однако ценно увеличение жаропрочности композита по сравнению с исходной матрицей. Так, введение в жаропрочный хромоникелевый сплав тонкодисперсных порошков оксида тория или оксида циркония позволяет увеличить температуру, при которой изделия из этого сплава способны к длительной работе, с 1000° С до 1200° С. Дисперсноупрочненные металлические композиты получают, вводя порошок наполнителя в расплавленный металл, или методами порошковой металлургии.
Армирование металлов волокнами, нитевидными кристаллами, проволокой значительно повышает как прочность, так и жаростойкость металла. Например, сплавы алюминия, армированные волокнами бора, можно эксплуатировать при температурах до 450—500° С, вместо 250—300° С. Применяют оксидные, боридные, карбидные, нитридные металлические наполнители, углеродные волокна. Керамические и оксидные волокна из-за своей хрупкости не допускают пластическую деформацию материала, что создаёт значительные технологические трудности при изготовлении изделий, тогда как использование более пластичных металлических наполнителей позволяет переформование. Получают такие композиты пропитыванием пучков волокон расплавами металлов, электроосаждением, смешением с порошком металла и последующим спеканием и т. д.
В 1970-х появились первые материалы, армированные нитевидными монокристаллами («усами»). Нитевидные кристаллы получают, протягивая расплав через фильеры. Используются «усы» оксида алюминия, оксида бериллия, карбидов бора и кремния, нитридов алюминия и кремния и т. д. длиной 0,3-15 мм и диаметром 1-30 мкм. Армирование «усами» позволяет значительно увеличить прочность материала и повысить его жаростойкость. Например, предел текучести композита из серебра, содержащего 24% «усов» оксида алюминия, в 30 раз превышает предел текучести серебра и в 2 раза — других композиционных материалов на основе серебра. Армирование «усами» оксида алюминия материалов на основе вольфрама и молибдена вдвое увеличило их прочность при температуре 1650° С, что позволяет использовать эти материалы для изготовления сопел ракет.
Композитные материалы на основе керамики[править | править код]
Армирование керамических материалов волокнами, а также металлическими и керамическими дисперсными частицами позволяет получать высокопрочные композиты, однако, ассортимент волокон, пригодных для армирования керамики, ограничен свойствами исходного материала. Часто используют металлические волокна. Сопротивление растяжению растёт незначительно, но зато повышается сопротивление тепловым ударам — материал меньше растрескивается при нагревании, но возможны случаи, когда прочность материала падает. Это зависит от соотношения коэффициентов термического расширения матрицы и наполнителя.
Армирование керамики дисперсными металлическими частицами приводит к новым материалам (керметам) с повышенной стойкостью, устойчивостью относительно тепловых ударов, с повышенной теплопроводностью. Из высокотемпературных керметов делают детали для газовых турбин, арматуру электропечей, детали для ракетной и реактивной техники. Твёрдые износостойкие керметы используют для изготовления режущих инструментов и деталей. Кроме того, керметы применяют в специальных областях техники — это тепловыделяющие элементы атомных реакторов на основе оксида урана, фрикционные материалы для тормозных устройств и т. д.
Керамические композитные материалы получают методами горячего прессования (таблетирование с последующим спеканием под давлением) или методом шликерного литья (волокна заливаются суспензией матричного материала, которая после сушки также подвергается спеканию).
- Кербер М. Л., Полимерные композиционные материалы. Структура. Свойства. Технологии. — СПб.: Профессия, 2008. — 560 с.
- Васильев В. В., Механика конструкций из композиционных материалов. — М.: Машиностроение, 1988. — 272 с.
- Карпинос Д. М., Композиционные материалы. Справочник. — Киев, Наукова думка
- СП 164.1325800.2014 Усиление железобетонных конструкций композитными материалами. Правила проектирования.
- Техническое заключение по результатам лабораторных испытаний арматурных выпусков из стеклопластика, установленных в монолитный бетон, на действие продольных относительно оси выпуска усилий // Tekhnicheskoe zaklyuchenie po rezul’tatam laboratornyh ispytaniy armaturnyh vypuskov iz stekloplastika, ustanovlennyh v monolitnyy beton, na deystvie prodol’nyh otnositel’no osi vypuska usiliy
- Высокопрочные системы усиления ITECWRAP/ITECRESIN. Екатеринбург: ООО НИИ Высокопрочные системы усиления ИНТЕР/ТЭК, 2010. 69 с. // Vysokoprochnye sistemy usileniya ITECWRAP/ITECRESIN. Yekaterinburg: OOO NII Vysokoprochnye sistemy usileniya INTER/TEK, 2010. 69.
- Коршунов, Я. Бурейская ГЭС: сверхпроектные работы/ Я. Коршунов // Газета «Вестник РусГидро».№ 4 — 2014. С.8. // Korshunov, Ya. Bureyskaya GES: sverhproektnye raboty/Ya. Korshunov//Gazeta «Vestnik RusGidro» #4-2014. P.8
- Усиление железобетонных конструкций (Пособие П 1-98 к СНиП 2.03.01-84*). Минск, 1998. // Usilenie zhelezobetonnyh konstrukciy (Posobie P 1-98 k SNiP 2.03.01-84*). Minsk, 1998.
- Хозин В. Г., Пискунов А. А., Гиздатуллин А. Р., Куклин А. Н.//Сцепление полимеркомпозитной арматуры с цементным бетоном / Известия КГАСУ № 1(23) — 2013. С.1-8
- Хозин В. Г., Пискунов А. А., Гиздатуллин А. Р., Куклин А. Н.//Сцепление полимеркомпозитной арматуры с цементным бетоном / Известия КГАСУ № 1(23) — 2013. С. 1-9
Отделочные материалы — Википедия
Отделочные материалы — класс строительных материалов для декоративного оформления зданий и сооружений, защиты их от вредного воздействия окружающей среды, улучшения гигиенических и эксплуатационных свойств[1].
По назначению отделочные материалы делятся на[2]:
Обои[править | править код]
Обои широко используются при отделке стен и потолков в жилых и служебных помещениях. Основные виды обоев:
- Бумажные.
- Виниловые (виниловые обои на бумажной основе).
- Флизелиновые (виниловые обои на флизелиновой основе).
- Флизелиновые обои под покраску — в основном используются для отделки потолков.
- Стеклотканевые обои под покраску — в основном используются для отделки стен офисных помещений.
Панели ПВХ[править | править код]
Пластиковые панели — сравнительно новый материал и используется он во внутренней и реже наружной отделки стен.
Изготавливается из ПВХ (поливинилхлорида) методом экструзии. Основные типоразмеры:
Толщина пластиковых панелей 5, 8, 9, 10 мм. По толщине пластиковые панели по сути делятся на два основных размера — 5 и 8-9-10 мм. Размеры от 8 до 10 мм считаются как один размер, так как под них идут молдинги стандартного размера.
Стандартная длина пластиковых панелей: вагонка (10 см) — 3 м; широкая панель (от 20 до 37 см) — 2,6, 2,7 и 3 м.
Ширина пластиковых панелей:
- Вагонка
Ширина 10 см бывают двух видов — обычная, с широким замком (европейка), и более редкая, с узким замком (полька).
Ширина 12,5 см — малораспространённая, панель имеет двойной профиль.
Вагонка выпускается в основном белого цвета, гораздо меньше выпускают цветную вагонку, окрашенную в массе в однотонные цвета, такие, как жёлтый, синий, зелёный, коричневый и т. д. Совсем редко делают вагонку с расцветками с помощью термопереноса.
- Панель
Главное отличие панели от вагонки — в отсутствии шва при соединении. При монтаже панелей (при условии качественной панели) шов между панелями не заметен ни зрительно, ни на ощупь. Ширина панели может быть от 15 см до 40-50 см. Фактически самая распространённая ширина пластиковых панелей составляет 25 см.
По цветам панель делится на несколько видов по способу нанесения цветового покрытия. Белая панель — на панель не наносилось никакое покрытие. Лакированная — на панель нанесён слой лака для придания блеска в основном белого цвета. Термоперенос — на панель нанесён рисунок с помощью термоплёнки. Способ, когда с плёнки с помощью горячего вала изображение и цвет переносится на панель, — самый распространённый вариант окрашивания панели в силу дешевизны и простоты, а также широкого выбора расцветок. Печатный способ — рисунок на панели оставляет вал с изображением наподобие типографской печати. Используется для создания рисунков под мрамор.
- Лист
Ширина обычно от 800 до 2030 мм, длина — от 1500 до 4050 мм, толщина от 1 до 30 мм, зависит от марки материала и фирмы-производителя. Наиболее распространены листы вспенённого ПВХ, при этом поверхность может быть гладкой и ударопрочной. Листы из свободно вспенённого ПВХ отличаются небольшим весом и лёгкостью обработки, благодаря чему из них часто делают вывески и указатели. Листовой ПВХ ещё называют ПВХ-плитами.
Керамическая плитка используется для облицовки стен и пола внутри помещений и фасадов зданий. В жилых помещениях часто применяется для облицовки ванных комнат и кухонь.
Облицовочный камень используется для отделки стен внутри помещений и фасадов зданий.
Красочные составы состоят из пигмента, придающего им цвет; наполнителя, экономящего пигмент, улучшающего механические свойства и увеличивающего долговечность окраски; связующего, соединяющего частицы пигмента и наполнителя между собой и с окрашиваемой поверхностью. После высыхания красочные составы образуют тонкую плёнку. Кроме основных компонентов, при необходимости в красочные составы вводят разбавители, загустители и другие добавки.
Пигменты[править | править код]
Пигменты — это тонко измельчённые цветные порошки, не растворимые в воде и органических растворителях, но способные равномерно смешиваться с ними, передавая красочному составу свой цвет.
Белые пигменты. К ним относят мел, воздушную строительную известь. Мел используют в виде тонко измельчённого порошка, из которого приготавливают различные водоразбавляемые (водные) красочные составы, грунтовки, шпатлёвки и пасты.
Известь воздушную строительную используют в качестве пигмента и связующего материала для приготовления красочных составов, шпатлёвок и мастик.
Чёрные пигменты. К ним относят сажу газовую канальную, двуокись марганца, чернь.
Сажа газовая канальная образуется при сжигании различных масел, нефти, смолы при ограниченном доступе воздуха. Используют её для приготовления неводных красочных составов.
Двуокись марганца встречается в природе в виде минерала и пиролюзита. Используют её для приготовления водных и неводных красочных составов.
Чернь получают при прокаливании без доступа воздуха ореховой скорлупы, древесины, торфа.
Серые пигменты. К ним относят графит и цинковую пыль.
Графит — природный материал серовато-чёрного цвета с жирным металлическим блеском. Его используют для приготовления красочных составов и натирки поверхности железных предметов, подвергающихся нагреванию, отчего она получает вид полированной.
Цинковая пыль — механическая смесь окиси цинка с металлическим цинком. Её используют для приготовления неводных красочных составов.
Красные пигменты. К ним относят сурик железный сухой, мумию природную и искус.
Сурик железный сухой получают из железной руды, содержащей окись железа. Это очень прочный пигмент с высокими антикоррозионными свойствами и светостойкостью. Выпускают его в виде тонко измельчённого порошка кирпично-красного цвета и используют для приготовления клеевых составов, эмалей и масляных красок.
Мумия природная — тонко измельчённая глина, окрашенная окислами железа в коричнево-красный цвет различных оттенков. Используют для приготовления водных и неводных красочных составов.
Мумия искусственная — тонко измельчённый порошок керамического изделия ярко-красного цвета.
Жёлтые пигменты. К ним относят охру сухую, крон свинцовый сухой и сиену природную.
Охру сухую получают из глины, окрашенной окислами железа. Используют для приготовления всех видов красок, применяемых при окрашивании деревянных и металлических поверхностей.
Сиену природную получают из глины, содержащей большое количество окиси железа (70 %) и кремнезёма.
Зелёные, синие, коричневые и др. пигменты.
Олифы и эмульсии[править | править код]
Олифу натуральную льняную и конопляную получают соответственно из льняного и конопляного сырого масла путём варки его при 200—300 °C и обработки воздухом с введением ускорителя высыхания (сиккатива). Используют её для приготовления красочных составов, грунтовок и в качестве самостоятельного материала для малярных работ при наружной и внутренней окраске деревянных и металлических конструкций.
Эмульсия ВМ состоит из натуральной олифы, бензола, животного плиточного клея, известкового 50%-го теста и воды. Используют её для разведения густотёртых красок.
Эмульсия МВ приготавливают из смеси 10%-го раствора животного клея, щёлочи (соды, буры, поташа) и натуральной олифы. Применяют её при окрашивании внутри помещений штукатурки, древесины.
Лакокрасочные составы[править | править код]
Масляные краски — различные белила и цветные красочные составы, приготовленные на натуральных или комбинированных олифах с различными добавками, доведённые до малярной консистенции. Лакокрасочные составы применяются для защиты строительных конструкций от коррозии и негативного воздействия внешних факторов, в том числе для окраски металлоконструкций, технологического оборудования, техники, стен, пола (см.: Наливные полы) и других элементов, требующих защиты.
Виды лакокрасочных материалов (составов)[править | править код]
- Органорастворимые
- Воднодисперсионные
Органорастворимые (на основе растворителя) лакокрасочные материалы чаще всего применяются для наружных работ, так как лучше выдерживают атмосферные воздействия, воздействия внешней среды. Воднодисперсионные материалы (на основе воды) применяют внутри помещений, для окраски мебели и предметов интерьера, оконных рам и т. п.
Нетканые текстильные материалы — Википедия
Нетканые текстильные материалы — материалы из волокон или нитей, соединённых между собой без применения методов ткачества.
История развития отрасли нетканых материалов[править | править код]
С древнейших времён известны два вида нетканых материалов: ватин и войлок.
Началом эпохи современных нетканых материалов считаются 1930-е годы[1]. Первые образцы были созданы в Европе. Это были полотна из вискозных волокон, скреплённых между собой химическими связующими. Несколько позже были освоены и другие способы их получения, различающиеся как по виду сырья, так и по способу скрепления.
Классификация[править | править код]
Нетканые материалы в зависимости от методов скрепления подразделяются на четыре класса[2]:
- скреплённые механическим способом;
- скреплённые физико-химическим способом;
- скреплённые комбинированным способом
- скреплённые термическим способом (термоскрепление).
Нетканые материалы вырабатываются как из натуральных (хлопковых, льняных, шерстяных), так и из химических волокон (например, вискозных, полиэфирных, полиамидных, полиакрилонитрильных, полипропиленовых), а также вторичного волокнистого сырья (волокна, регенерированные из лоскута и тряпья) и коротко-волокнистых отходов химической и других отраслей промышленности.
Основные технологические операции получения нетканых материалов[3][4]:
- Подготовка сырья (рыхление, очистка от примесей и смешивание волокон, перемотка пряжи и нитей, приготовление связующих, растворов химикатов и т. д.).
- Формирование волокнистой основы.
- Скрепление волокнистой основы (непосредственно получение нетканого материала).
- Отделка нетканого материала.
Способы получения нетканого материала[править | править код]
Основной стадией получения нетканых материалов является стадия скрепления волокнистой основы, получаемой одним из способов: механическим, аэродинамическим, гидравлическим, электростатическим или волокнообразующим.
Способы скрепления нетканых материалов:
- Химическое или адгезионное скрепление (клеевой способ) — сформованное полотно пропитывается, покрывается или орошается связующим компонентом, нанесение которого может быть сплошным или фрагментированным. Связующий компонент, как правило, применяются в виде водных растворов, в некоторых случаях используют органические растворители.
- Термическое скрепление — в этом способе используются термопластичные свойства некоторых синтетических волокон. Иногда используются волокна, из которых состоит нетканый материал, но в большинстве случаев в нетканый материал еще на стадии формования специально добавляют небольшое количество волокон с низкой температурой плавления («бикомпонент»).
Механическое (фрикционное) скрепление:
- иглопробивный способ.
- вязально-прошивной способ.
- гидроструйный способ (технология Спанлейс).
Технология Спанлейс[править | править код]
Технология Спанлейс[5] появилась в 1960-х годах, но впервые была официально представлена фирмой DuPont в 1973 году (материал Сонтара®) и была результатом напряжённой работы, проделанной фирмами DuPont и Chicopee. В 1990-х годах струйная технология значительно шагнула вперёд и стала более производительной[6] и доступной для многих производителей нетканых материалов.
Технология гидросплетения основана на переплетении волокон материала высокоскоростными струями воды под высоким давлением. Обычно полотно скрепляется на перфорированном барабане с помощью струй воды, бьющих под высоким давлением из форсуночных балок. За счёт этих струй волокна холста связываются между собой.
Лидером и новатором в области технологии спанлейс является фирма «Rieter».
Иглопробивные материалы[править | править код]
При данной технологии холст формируется из нарезанного («штапельного») волокна либо из непрерывных нитей («филаментов»), полученных из расплава полимера. Волокна формуются из полимера фильерно-раздувным способом и практически одновременно укладываются в холст. Единичные волокна конечной длины («штапельки») в чесальной машине ориентируются преимущественно в горизонтальном направлении и формируются в холст («ватку»).
Впоследствии уложенный холст проходит процедуру скрепления механическим способом путём пробивания полотна иглами специальной конструкции треугольного сечения, с одной либо двух сторон. Целью иглопробивания является уплотнение уложенных филаментов («штапелек») и спутывание их между собой. На данном этапе технологического процесса полотно приобретает свои прочностные свойства, которые могут варьироваться в зависимости от характера дальнейшего применения иглопробивных полотен. При необходимости пробитый холст проходит процедуру дополнительного термоскрепления при помощи каландра. Также для иглопробивных полотен используемых в качестве основы для полимерных покрытий (линолеум, искусственная кожа, кабельная продукция), применяется дополнительное прогревание в промышленных печах, так называемая «усадка».
Иглопробивная технология очень популярна, поскольку полученный по такому способу производства продукт имеет уникальное сочетание прочностных и потребительских характеристик.
Отрасли применения иглопробивных нетканых полотен: геотекстиль, фильтры, линолеум, ковровые покрытия, автомобилестроение, мягкая мебель, искусственная кожа, одежда, обувная промышленность, галантерея.

Технология Спанджет[править | править код]
Технология, при которой окончательная фиксация происходит с помощью водных струй под высоким давлением. Прочность готового материала несравнимо выше, чем у нетканого полотна, скреплённого любыми иными способами.
Технология Термоскрепления[править | править код]
Суть технологии — воздействие высоких температур (до 180°C) на легкоплавкие полиэфирные волокна в смеси с другими химическими волокнами, посредством многосекционных печей, в которых рубашка лекгоплавких волокон подплавляется и скрепляется с другими волокнами бесклеевым способом.
Технология Струтто[править | править код]
«Strutto» обозначает вертикальную укладку волокон при производстве нетканых материалов.
Технология AirLay[править | править код]
Технология AirLay — это система образования волокон, готовых для иглопробивания и термофиксации. Данная технология предназначена как замена устаревшим кардочесальным машинам и холстоукладчикам. Производительность такой линии позволяет производить около 1500 кг готовой продукции в час. Грамматура производимого материала варьируется от 150 г/м² до 3500 г/м². Использование технологии AirLay разнообразно. Например, автомобильная промышленность, сельское хозяйство, мягкая мебель, строительство, одежда и упаковка.
Технология Айрлайд[править | править код]
Айрлайд — тип нетканых материалов, получивший своё название от способа его производства — воздушная (air) укладка (laid). Представляет собой нетканое полотно из природной целлюлозы хвойных пород древесины, бикомпонентного штапельного волокна и добавок. В отличие от обычного процесса изготовления волокна, Айрлайд не использует воду в качестве среды для производства волокна.
Технология Аэродинамика[править | править код]
При аэродинамическом способе расчёсанные волокна увлекаются потоком воздуха и переносятся по каналу (диффузору) на сетчатый барабан или транспортёр, где укладываются с образованием холста бесслойной структуры (неориентированное расположение волокон).
- ↑ Нетканые материалы: вчера, сегодня, завтра (неопр.) (недоступная ссылка). Дата обращения 25 октября 2018. Архивировано 27 декабря 2014 года.
- ↑ Структура нетканых материалов (неопр.) (недоступная ссылка). Дата обращения 11 ноября 2009. Архивировано 7 января 2010 года.
- ↑ Производство нетканых материалов (неопр.) (недоступная ссылка). Дата обращения 11 ноября 2009. Архивировано 27 октября 2009 года.
- ↑ А.Ф. Плеханов, Е.И. Битус, Н.А. Виноградова, С.А. Першукова, Ю. В. Братченя. Инновационные технологии нетканых материалов (RU) // Полимерные материалы. — 2019. — № 2. — С. 30-34.
- ↑ СПАНЛЕЙС: технология, свойства, применение
- ↑ Преимущества технологии спанлейс
- ↑ Müller Werner W, Saathoff Fokke. Geosynthetics in geoenvironmental engineering // Science and Technology of Advanced Materials. — 2015. — 20 июня (т. 16, № 3). — С. 034605. — ISSN 1468-6996. — doi:10.1088/1468-6996/16/3/034605. [исправить]