Электрическая дуговая сварка — Википедия. Что такое Электрическая дуговая сварка
Электродуговая ручная сварка покрытым электродомЭлектросварка — один из способов сварки, использующий для нагрева и расплавления металла электрическую дугу.
Температура электрической дуги (до 7000 °С) превосходит температуры плавления всех существующих металлов.
История электросварки
1802 год — В. В. Петров открыл явление вольтовой электрической дуги и указал, что появляющийся «белого цвета свет или пламя, от которого оные угли скорее или медлительнее загораются, и от которого тёмный покой довольно ясно освещён быть может».
1803 год — В. В. Петров опубликовал книгу «Известия о гальвани-вольтовых опытах…», где описал способы изготовления вольтова столба, явление электрической дуги и возможность её применения для электроосвещения, электросварки и электропайки металлов.
1882 год — Н. Н. Бенардос изобрёл электрическую сварку с применением угольных электродов, которую запатентовал в Германии, Франции, России, Италии, Англии, США и других странах, назвав свой метод «электрогефестом».
1888 год — Н. Г. Славянов впервые в мире применил на практике дуговую сварку металлическим (плавящимся) электродом под слоем флюса. В присутствии государственной комиссии он сварил коленчатый вал паровой машины.
1893 год — На Всемирной выставке в Чикаго Н. Г. Славянов получил золотую медаль за способ электросварки под слоем толчёного стекла.
1905 год — В. Ф. Миткевич впервые в мире предложил применять трёхфазную дугу для сварки металлов.
1932 год — К. К. Хреновым впервые в мире в Советском Союзе осуществлена дуговая сварка под водой[2].
1939 год — Е. О. Патоном разработаны технология автоматической сварки под флюсом, сварочные флюсы и головки для автоматической сварки, электросварные башни танков, электросварной мост.
Описание процесса
К электроду и свариваемому изделию для образования и поддержания электрической дуги от сварочного трансформатора (или сварочного агрегата, сварочного преобразователя, сварочного инвертора) подводится электроэнергия.
В процессе электросварки могут быть использованы плавящиеся и неплавящиеся электроды. В первом случае формирование сварного шва происходит при расплавлении самого электрода, во втором случае — при расплавлении присадочной проволоки (прутков и т. п.), которую вводят непосредственно в сварочную ванну.
Для защиты от окисления металла сварного шва применяются защитные газы (аргон, гелий, углекислый газ и их смеси), подающиеся из сварочной головки в процессе электросварки.
Для повышения устойчивости электрической дуги в электроды могут вводиться легко ионизируемые элементы (калий, натрий, кальций)[4]..
Различают электросварку переменным током и электросварку постоянным током. При сварке постоянным током шов получается с меньшим количеством брызг металла, поскольку нет перехода через ноль и смены полярности тока.
В аппаратах для электросварки постоянным током применяются выпрямители.
Возможно управление положением сварочной дуги при сварке постоянным током. Дуга является проводником тока и как обычный проводник отклоняется в магнитном поле в соответствии с законом Ампера.
Классификация
Классификация дуговой с
Электродуговая сварка, история изобретения
Лучший способ соединения металлов на сегодня – сварка. Сваривание появилось еще в глубокой древности. В прежние времена применялись различные виды обработки и соединения металлов. Однако они почти никогда не применялись для создания слишком сложных конструкций. Например, способы соединения частей металлических изделий пайкой и свариванием знали древние. Египетские пирамиды содержат в себе золотые детали с соединениями, паянными при помощи олова.
Когда еще не было электросварки, для сваривания свинцовых труб и кровельных листов из свинца часто применялась ковка. Подогревали тогда древесным углем. Такая кузнечная сварка выполнялась ударами молота. Очень популярной была в те времена и ремонтная сварка, восстанавливающая каретные оси.
Изобретение электросварки
В конце ХІХ века, благодаря усилиям русского инженера Н. Г. Славянова, была изобретена дуговая сварка. Именно он придумал метод соединения материала посредством плавящегося электрода, сделанного из металла. Этот метод сейчас применяется наиболее часто. Славянов обучил целый коллектив сварщиков, они исправляли дуговым свариванием брак в литье, приводили в порядок паровые механизмы и прочее крупное оборудование.
Развитие технологий
Кроме того, Славяновым был создан сварочный генератор, а также автоматический регулятор, определяющий длину дуги. Им разработаны флюсы, резко повышающие качество сварочного шва. Созданные этим ученым технологии соединения стали основой для нынешних методов электросварки металла. В ХХ веке известный строитель мостов академик Патон, предвидевший, что электросварка будет иметь славное будущее, резко поменял область своих научных исследований. Он создал в 1929 г. в Киеве лабораторию, а позже и первый НИИ электросварки. Он разработал и предложил множество эффективных технологических методов электросварки.
Современный подход
Сегодняшняя сварка получила наибольшее развитие благодаря работам ученых, новаторов и талантливых инженеров, работающих в данной области. Они создали много типов оборудования, разные марки электродов. Кроме того, они разработали современные сварочные технологии, включающие также автоматизированные способы. К середине прошлого столетия была освоена методика получения неразъемного соединения множества металлов, очень подробно и фундаментально разработана теория технологии ручной сварки.
Основные этапы развития сварки
⇐ ПредыдущаяСтр 3 из 4Следующая ⇒Развитие сварки в нашей стране можно условно разделить на 5 этапов.
Подготовка кадров (1918-1928) и начало развития науки. В 1925 г. академики В. П. Никитин и А. И. Вологдин организовали сварочные специальности в институтах Днепропетровска и Владивостока.
1929-1935 годы — бурное развитие сварки и резкое повышение ее качества. Сварка стала применяться как технический процесс для изготовления новых изделий в отдельных областях промышленности. В 1929 г. создан Автогенный комитет, который способствовал внедрению электродуговой сварки.
1935-1940 годы — курс на резкое повышение качества сварных конструкций и производительности труда сварщиков. В этот период сварку стали внедрять во всех отраслях промышленности. В 1936 г. началось применение качественных электродов вместо электродов с меловой обмазкой.
1941-1945 гг. — активное применение сварки, продиктованное условиями военного времени.
С 1946 г. — дальнейшее всестороннее развитие сварки и наплавки, появление новых видов и способов сварки, наплавки и резки, например, сварка трением, ультразвуковая сварка, взрывом, вибродуговая наплавка, плазменная, лазерная сварка и резка, сварка в защитных газах и другие.
Виды сварки
Дуговая сварка покрытыми электродами — один из наиболее распространенных способов, используемых при изготовлении сварных конструкций. При сварке покрытыми электродами покрытие расплавляется и образующиеся шлак и газы защищают расплавленный металл от воздуха. Покрытый электрод представляет собой металлический стержень с нанесенным на его поверхность покрытием (обмазкой). Покрытие электродов готовят из порошкообразной смеси различных компонентов. Его назначение — повысить устойчивость горения дуги, провести металлургическую обработку сварочной ванны, обеспечить защиту расплавленного металла от атмосферных газов и улучшить качество сварки.
При сварке в защитных газах струя газа через сопло непрерывно подается в зону дуги.
Газы изолируют расплавленный металл от воздуха. При этом используют как неплавящийся, так и плавящийся электроды. Процесс можно выполнять вручную, механизированным или автоматическим способом. При сварке неплавящимся электродом изделий большой толщины применяют присадочную проволоку. В качестве защитных газов применяют углекислый газ, аргон, гелий, иногда азот для сварки меди. Наиболее распространены смеси газов: аргон + кислород, аргон + гелий или аргон + углекислый газ + кислород. В процессе сварки защитные газы, подаваемые в зону горения дуги через сопло сварочной горелки, оттесняют атмосферные газы от электрода и сварочной ванны.
В плазменной сварке сварочным устройством является плазмотрон. Плазменной струей можно сваривать различные металлы, производить их резку и наплавлять на поверхность тугоплавкие покрытия. Процесс основан на пропускании под давлением потока газов через электрический разряд большой плотности. В результате получают высокотемпературный ионизированный газ с практически одинаковыми плотностями положительных и отрицательных зарядов, называемый плазмой. Температура плазменной струи достигает 30000 град. C. Плазменную сварку можно выполнять при изготовлении как тонкостенных изделий, так и деталей большой толщины из различных материалов. В качестве плазмообразующего газа чаще всего используют аргон, гелий или азот. Состав и расход плазмообразующего газа зависят от вида электрода и свариваемого материала.
Электрошлаковой сваркой можно соединять металлические части большой толщины. Источником теплоты служит шлаковая ванна, образуемая при расплавлении флюса. В отличие от дуговой сварки для расплавления основного и присадочного металлов используют теплоту, выделяющуюся при прохождении сварочного тока через расплавленный электропроводный шлак (флюс).
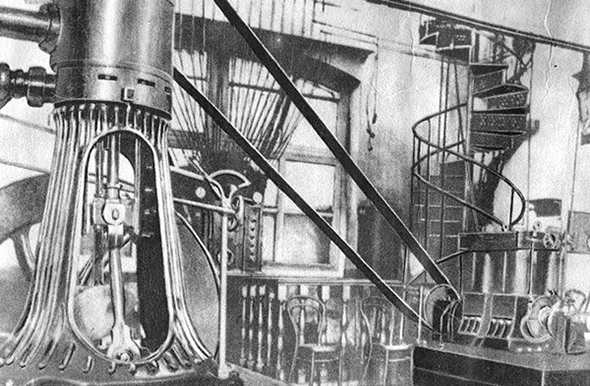
Электрошлаковую сварку различают:
— по виду электрода — проволочным, пластинчатым электродом и плавящимся мундштуком;
— по наличию колебаний электрода — без колебаний и с колебаниями электрода;
— по числу электродов — одно-, двух- и многоэлектродную. Обычно электрошлаковую сварку применяют для соединения деталей толщиной от 50 мм до нескольких метров. Электрошлаковый процесс используют также для переплавки отходов стали и получения отливок.
Электронно-лучевая сварка ведется в условиях вакуума. Электронный луч глубоко проплавляет металл.
В результате интенсивной бомбардировки места сварки быстродвижущимися электронами, излучаемыми нагретым вольфрамовым или металлокерамическим катодом, выделяется энергия, необходимая для нагрева и плавления металла. Ускорение движения электронов обусловлено постоянным высоким напряжением (до 100 кВ) между катодом и анодом (изделием). Поток электронов фокусируется в узкий луч и направляется в место соединения деталей.
Электронно-лучевую сварку можно выполнять без колебаний и с колебаниями электронного луча, остросфокусированным или расфокусированным лучом. Электронным лучом сваривают тугоплавкие и химически активные металлы, выполняют узкие и глубокие швы на деталях большой толщины (до 70 мм и более).
Поиск по сайту:
Новые технологии сварки металлов
Современная цивилизация многим обязана процессу сварки. Без сварочных элементов мы не получили бы транспорта, огромных строений, технологических конструкций, мобильных телефонов и пр. Несмотря на то, что этот физический процесс применяется много столетий, он не останавливает своего прогресса. Учёные многих стран продолжают исследовать и совершенствовать сварочные механизмы, применять новые приёмы и производить революционные открытия в этой сфере.
Новые технологии позволяют добиться более совершенного результата с использованием минимальных ресурсов. Разработки, появляющиеся ежегодно, делают возможным сварку тех материалов, которые раньше оставались за границами данной технологии.
Основные инновационные направления
Все разработки в данной области направлены на то, чтобы улучшить основные показатели процесса с наименьшими затратами:
- снижение коррозии и коробления металлов во время эксплуатации;
- повышение скорости выполнения сварочного процесса;
- облегчение зачистки мест соединения или обеспечение отсутствия такой необходимости;
- минимальный расход материалов;
- облегчённое и упрощенное управление процессом;
- способность соединения самых тонких листов металла различных марок.
Портативные аппараты
Такие типы сварочных аппаратов позволили вывести сварку на новый – бытовой — уровень. Если до изобретения портативных устройств подобные работы выполнялись преимущественно профессионалами с высокой квалификацией, то портативная техника позволила применять их и дома.
Современные сварочные аппараты
Во-первых, такие аппараты очень лёгкие по весу, в связи с чем их удобно транспортировать. Во-вторых, производители снабдили их полным готовым для использования комплектом, не забыв о системе подачи электродов (проволоки весом до 10 кг).
Главным усовершенствованием можно считать то, что в аппарат вмонтирована система цифрового управления. На дисплее каждый может указать основные параметры сварки: диаметр закладываемой проволоки, тип газа и т.д. На основании введённых данных портативный аппарат самостоятельно настраивается и выполняет сварку на достаточном для непроизводственных сварных швов уровне.
Усовершенствованные горелки
Самым примитивным звеном во время сварки считается газовая горелка, но даже небольшие изменения этого элемента позволили значительно улучшить качество выполняемой работы. Современные конструкции горелок производят не только из новых материалов, но имеют другой диаметр выходного отверстия, которое способно работать с нестандартными температурами и создавать необходимое давление.
Предлагаемые учёными газовые горелки стали безредукторными и высокодинамичными, при помощи их даже во время продолжительного процесса на самых высоких температурах можно получить идеально ровное пламя, в котором не будут появляться факелы, вспышки и хлопки. Из-за таких инноваций работа сварщика не требует частых остановок, что позволяет выполнить больший объём работ за то же самое время.
Разработаны агрегаты с многочисленными соплами, которые используются для соединения труб большого диаметра. Ширина пламени при использовании линейных горелок может достигать нескольких метров. Эта технология часто применяется для соединения деталей под водой или в воздухе, где существует острая необходимость в резком сокращении времени выполнения работ.
Гибридная лазерная технология
Такой способ был разработан для автомобилестроения, но нашёл применение и в других промышленных отраслях. Гибридный лазер используют для получения качественных швов при соединении тугоплавких сортов стали при совмещении с диоксидом углерода. Это позволяет получить идеальные сварные швы при точном управлении мощности лазерного излучения в пределах 1,5 – 4,0 кВт.
Ещё одной особенностью, присущей гибридной лазерной технологии, является высочайшая скорость плавящегося электрода и выполняемых работ – от 40 до 450 м/час. С такими же показателями можно обрабатывать тончайшие листы, изготовленные из автомобильной стали, что стало причиной финансовой поддержки и усовершенствования этой разработки ведущими автомобильными корпорациями.
Двухдуговая сварка
Такая методика была разработана для крупногабаритных конструкций, в изготовлении которых задействованы толстые листы закаливающейся стали таких марок как 30ХГСА. Способ основан на том, что при двухдуговом воздействии одномоментно применяются проволоки двух разных типов, имеющие в составе легирующие (сверхпрочные) компоненты. Диаметр таких электродов – 5 мм.
Для обеспечения устойчивого горения дуги при двухдуговой сварке необходим керамический флюс, созданный на основе керамики марки АНК-51А. Именно с керамическим флюсом данный способ показывает самый высокий результат и формирование идеальной сварной поверхности.
Щадящая методика
Для определённых работ была разработана новая щадящая технология, которая очень высокорезультативна, но отличается низкой себестоимостью. Во время процесса применяют специальные смеси защитных газов: диоксид углерода в соединении с аргоном или смесь аргона, диоксида углерода и кислорода. По сравнению с традиционным применением обособленного диоксида углерода, получаемый шов выходит более гладким и безупречным.
Ещё одним позитивным моментом является значительное удешевление сварочного процесса: на равный объём выполненных соединений расходуется меньшее количество проволочных электродов. Экономия составляет около 20%, что в промышленных масштабах представляет собой значительную сумму. Кроме того, во время сварочного процесса переход к деталям, поддающимся сварке, становится очень постепенным и плавным. Профессиональные сварщики, которые были задействованы в начальных тестах щадящей методики, подчеркнули, что разбрызгивание электродных металлов при многокомпонентной смеси газов значительно уменьшается.
Двухкомпонентная методика
Этот новый метод, который получил широкое распространение в развитых странах за короткий промежуток времени, обязан своим появлением запуску новых скоростных составов на железных дорогах. Двухкомпонентная технология является модифицированным вариантом литьевого способа. Она разрешила достичь результатов, которые раньше считались взаимоисключающими: обеспечить высочайшую пластичность шовного соединения, не ухудшив при этом износоустойчивость металла в месте сварного шва.
Технически двухкомпонентная методика выполняется сложно, поскольку требует особой подготовки: на месте проведения работ должна быть расплавленная сталь, которая аккуратно помещается в жидком виде в зазор между рельсами. Для того, чтобы придать соединению внушительную вязкость, применяется плавка с низколегированными компонентами. Износостойкость увеличивается посредством использования керамических флюсов, которые позволяют после заполнения сварного стыка вывести легирующие добавки из процесса. Керамика разрушается под действием высокой температуры, а добавки, укрепляющие соединение, застывают на поверхности, обеспечивая длительную эксплуатацию без трещин и деформаций.
Орбитальная аргонодуговая технология
Эта технология нашла применение в аэрокосмической отрасли, в автомобилестроении и полупроводниковой промышленности. Такая методика является высокоспецифичной и применяется для объектов со сложным конструктивным контуром. Впервые она была разработана 50 лет назад, но её значительно усовершенствовали, применив вольфрамовый электрод.
Главным преимуществом орбитальной аргонодуговой вольфрамовой сварки является то, что расход активирующего флюса при таком методе рекордно низкий: на 1 м сварного шва расходуется всего 1г флюса. Это делает возможным проводить процесс при пониженном токе, что уменьшает не только объём, но и вес сварочной ванны. При этом качество соединения регулируется в режиме реального времени посредством корректировки давления дуги.
Такой методикой успешно пользуются при необходимости соединить жаропрочные, высокопрочные сплавы, углеродистые стали, титан, медь и никель.
Технология СМТ
Эта методика основана на холодном переносе металлов. Когда говорят о холодном переносе, в виду не имеют реально низкую температуру, просто она значительно ниже, чем при классических вариантах.
Главное отличие заключается в том, что заготовки и зона будущего шва не прогреваются до максимальных значений, поэтому тепловложение в области обработки в разы уменьшается. Из-за того, что металл точечно не перегревается, не происходит сильная деформация. Работа электрода основана на контролируемом коротком замыкании, которое прекращается быстрым отодвиганием проволоки из зоны действия разряда и быстрого повторного его возвращения (до 70 раз в секунду).
Применение СМТ-сварки осуществляется через автоматизированные системы, которые дают очень однородные и качественные швы на местах соединения оцинкованных или стальных листов с алюминиевыми сплавами.
В данном случае сварка ведётся короткозамкнутой дугой с систематическими прерываниями. В результате такой системы шов атакуется горячими и холодными импульсами, что позволяет снизить давление в районе вхождения дуги. По такому же принципу снижается разбрызгивание при переносе металлов.
Таким образом, при помощи СМТ-сварки был достигнут стандарт, который ранее считался только теоретическим. Это стало возможным из-за контроля короткого замыкания и полного отсутствия разноса брызг, что резко снижает необходимость послесварочной механической обработки.
Плазменная сварка
Этот метод делает возможной сварку металлов разной толщины, начиная от самых тонких листов и заканчивая глубиной шва до 20 см. Плазменная технология позволяет одновременно с выполнением сварочных работ производить резку.
В основе плазменного метода находится ионизированный газ, который полностью заполняет пространство между двумя электродами. Именно через этот газ проходит электрическая дуга определённой мощности, обеспечивая очень сильный эффект.
Использование плазменного генератора представляет собой сложный процесс, требующий высокого профессионализма и профессиональных навыков, поэтому использовать его в бытовых целях не получится. Внутри генератора возникает многофункциональная сварочная система, которая может использоваться в узкоспециализированных сферах.
Технология компьютерного моделирования
Самое современное направление в сварочных технологиях по праву отводится компьютерному моделированию. Оно одинаково целесообразно для выполнения соединений самых мелких деталей со сложными контурами и для масштабных работ, где необходимо управление огромными площадями и множеством сварочных аппаратов.
Если раньше объёмные работы выполнялись при использовании многих аппаратов или целым сварочным комплексом, то компьютерное моделирование позволяет иметь одну функциональную единицу с разветвлённой периферией, оснащённой множеством горелок и насадок.
Полная автоматизация позволяет внедрять принципиально новые способы сварочных работ, которые недоступны для большинства сварщиков. Сами сварщики в таком случае функционально превращаются в операторов, задающих компьютеру все необходимые параметры, на основании которых программа задаёт оптимальные значения и контролирует процесс. Такой подход значительно повышает результат выполняемой работы.
Компьютерное моделирование сварочного процесса
Новые технологии вывели сварку на совершенно новый уровень, который позволяет выполнять сварочный процесс в рекордные сроки с минимальными трудозатратами и максимальным результатом. В то же время, прогресс не стоит на месте, поэтому вполне возможно, что в ближайшем будущем появятся системы, которые будут работать автономно, практически без участия людей. Разработки подобных проектов уже ведутся, и в том случае, если испытания увенчаются успехом, скоро человечество сможет получить новые масштабы и концепции сварочных производств.
Основные виды сварки
Технологические составляющие сварочного процесса были известны еще в 17 веке. Тогда они были представлены литьем и кузнечным делом. «Осовременивание» началось после открытия такого явления как электрическая дуга. Дополнительный толчок развитие сварочного дела получило с изобретением порошкового покрытия для электродов. А вот основной скачок выпал на конец 20-го века, когда стали доступны лазерные, ультразвуковые и плазменные технологии. Внедрение электроники позволило автоматизировать сварочный процесс, увеличить точность выполнения работ и производительность.
В настоящее время разделяется три вида сварки, которые отличаются между собой используемым для выполнения работ типом энергии:
- термический;
- механический;
- термомеханический.
Термическая сварка
Для выполнения сварочных работ потребуется тепло. Под воздействием высоких температур стыки соединяемых заготовок оплавляются и, остывая, скрепляются между собой, а впоследствии кристаллизируются. В качестве источника тепла служит пламя газовой горелки, электрическая дуга или поток плазмы.
Электродуговая контактная сварка
Наибольшее распространение получили именно аппараты электродуговой сварки. Для нагрева и плавки металла задействуется электрическая дуга, которая представляет собой разряд между катодом и анодом. При этом освобождается тепловая энергия большой мощности. Воздействуя на металлическую заготовку, она приводит к ее плавлению с последующим образованием сварочной ванны.
После угасания дуги немедленно начинается остывание и кристаллизация расплава. В результате образуется соединение по составу и прочности сопоставимое с металлами, которые сваривались. Существует несколько видов электродуговой сварки.
ММА – ручная дуговая сварка
Используется со штучными электродами, представляющими собой металлический стержень с обмазкой. Процесс протекает под воздействием постоянного или переменного тока. Покрытие расходников плавится, выделяя газы, которые образуют облако для защиты свариваемого металла от окисления. Помимо этого, в обмазку включаются разные химические соединения, которые служат в качестве добавки в сварочную ванну для изменения свойств сварочного шва и поддержки стабильного горения электрической дуги.
Аппараты – инвертеры, выпрямители, трансформаторы – позволяют выполнять работы в любом пространственном положении. Если подобрать расходные материалы правильно, то можно сваривать любые металлы: черные, цветные, легированные и т.п. Важно подчеркнуть, что держатели могут проникать в труднодоступные места, где использование другого вида сварки невозможно.
Сварка ММА подходит и для профессионалов, и для новичков. Она широко используется в строительстве, монтаже металлоконструкций, в разных отраслях тяжелой промышленности, в частном предпринимательстве. Она необходима для небольшой мастерской по изготовлению металлоконструкций, станции технического обслуживания автомобилей, большого машиностроительного завода. Она незаменима в хозяйстве, когда требуется сконструировать что-то из металла самостоятельно или отремонтировать прохудившийся металлический каркас.
Читайте также: Сварка ММА
Аргоновая сварка TIG
Применяются электроды вольфрамовые, неплавящиеся, графитовые, угольные. В качестве инертного газа используется аргон, азот, гелий или смесь из этих газов в зависимости от соединяемых металлов. Процесс характерен тем, что сварной шов состоит исключительно из металлов заготовок. Добавляется только присадка – металлический пруток или полоса, по своему составу идентична свариваемым металлам. Инертные газы необходимы для защиты рабочей зоны от атмосферного воздуха, чтобы исключить окисление металла и обеспечить стабильность горения электрической дуги.
В процессе выполнения сварочных работ используется переменный или постоянный ток. Сравнительно низкая производительность компенсируется за счет высокого качества сварного соединения. Процесс характеризуется высокой трудоемкостью и требует от специалиста большого практического опыта. Использование TIG оправдано в случаях, когда требуется наложить ответственный шов, который должен выдержать высокие нагрузки, или в случаях, когда большое внимание уделяется эстетической стороне вопроса.
Аргоновая сварка востребована для герметизации нефте- и газопроводов, резервуаров для пищевой промышленности, посуды; при изготовлении сосудов высокого давления или микросхем. Она незаменима для соединения тонкостенных заготовок и листовых материалов. Сварка позволяет работать с большим перечнем металлов: нержавеющая, углеродистая, легированная сталь; магний, титан, медь.
Читайте также: Сварка TIG
MAG –сварка полуавтоматом
В качестве присадочного материала используется проволока, которая подобно электроду плавится под воздействием высокой температуры. Проволока поступает в рабочую зону через горелку, куда параллельно подается инертный или активный газ. Состав защитного газа напрямую зависит от типа свариваемого металла. Работает исключительно с постоянным электрическим током. Во время применения активных газов образуется много брызг, а шов получается неаккуратным. Но это с лихвой компенсируется высокой производительностью установки.
Такого рода оборудование пользуется большой популярностью среди профессионалов и большой аудитории любителей. Отчасти из-за автоматической подачи расходного материала в зону сварки и возможности электронной регулировки настроек. Технология особенно популярна в европейских и североамериканских специалистов. Полуавтоматы сваривают широкий спектр металлов: сталь низколегированную и высоколегированную, большинство марок чугуна; марганец, медь, алюминий, никель, а также их сплавы. Оборудование позволяет выполнять самые сложные разнотипные соединения.
Сварка под флюсом
При сваривании металлических заготовок применяются разные флюсовые порошки. Они необходимы для того, чтобы обеспечить рабочую область защитным газом, который выделяется в процессе плавления. Благодаря наличию флюса не только защищается расплав, но и поддерживается стабильное горение электрической дуги. Подбором флюса специалисты добиваются нужных характеристик сварного шва.
Метод активно используется в промышленном производстве и характеризуется полной автоматизацией: от подачи флюса в зону горения до перемещения оборудования вдоль стыка. Технология применяется в процессе изготовления корпусов морских судов, фюзеляжей самолетов, локомотивов и вагонов, башенных кранов, модулей спутников и множества иного оборудования. На выходе получается очень качественный сварной шов, который легко выдержит самые сложные условия эксплуатации, включая экстремальные температуры и огромное давление.
Газоплазменная
В этом случае металл заготовок плавится под воздействием температуры открытого пламени. Оно образуется в результате горения кислорода с горючими газами – водородом, пропаном, бутаном, ацетиленом и другими. Самой эффективной считается МАФ – метилацетиленовая фракция. Она отличается высокой температурой пламени (2927 градусов) в кислороде и, соответственно, более высокой теплоотдачей. Соединение кислорода и МАФ уступает по токсичности дициану (температура горения 4500 градусов) и менее взрывоопасно по сравнению с ацетилендинитрилом (температура горения 5000 градусов).
Открытое пламя в качестве источника тепла для сварки имеет важное преимущество: оно независимо от энергоснабжения. Поэтому технология широко применяется в «полевых» условиях. Еще одно достоинство заключается в постепенном нагревании металла, что практично при работе с листовыми материалами. Метод непригоден для промышленного использования из-за невозможности автоматизации и низкой производительности. Для работы с такой сваркой от оператора требуется большой стаж сварочных работ.
Электрошлаковая
Кромки деталей плавятся за счет нагрева шлака от расплавленного под воздействием электроэнергии флюса, который предварительно насыпается между свариваемыми элементами. Во время процесса применяется проволока или присадочный пруток. Технология востребована для соединения деталей из чугуна, реже – для сварки цветных металлов.
Данный тип сварки востребован в промышленности для соединения крупногабаритных деталей с толстыми стенками (40-500 мм): роторные и турбинные валы, опоры, паровые котлы и т.д. Экономическая выгода от такого метода сварки тем выше, чем больше площадь свариваемой поверхности.
Плазменная
Плавит и соединяет кромки струя плазмы, которая генерируется в плазмотроне или между поверхностью заготовок и электродом. Метод отличается большой глубиной обработки деталей и высокой точностью сваривания. Она востребована для соединения как мелких и тонкостенных элементов электротехнических конструкций, так и крупных блоков для тяжелой промышленности. Плазма эффективно воздействует на все без исключения виды металлов.
Помимо рассмотренных к термическим видам сварки относится:
- лазерная;
- контактная стыковая с оплавлением;
- электролучевая;
- с закладными нагревателями.
Термомеханический класс сварки
Контактная сварка: метод характеризуется одновременным нагревом кромок соединяемых заготовок и их деформированием под давлением. Точечная сварка: выполняется при помощи специальных аппаратов или малогабаритными клещами. Обе детали закрепляются между анодом и катодом, через которые пропускается ток. В результате заготовки разогреваются в конкретном месте. После разогрева подача тока прекращается и усиливается давление электродов в месте температурного воздействия. Локальный расплав постепенно кристаллизуется и в результате получается прочное точечное соединение.
Точечная сварка может быть:
- односторонней – оба электрода располагаются по одну сторону заготовок;
- двухсторонней – электроды размещаются с разных сторон заготовок один напротив другого.
К недостаткам сварки специалисты относят то, что сваривание заготовок возможно только внахлест. Характеризуется высокой производительностью и возможностью автоматизации.
Точечная сварка широко применяется в автомобилестроении: конвейеры по всему миру используют именно данный тип соединения кузовных элементов. Клещи для точечной сварки отличаются компактностью и мобильностью. Они применяются в мелких мастерских и в домашних условиях. Однако они востребованы и на крупных СТО для выполнения разного рода кузовных работ.
К термомеханическому типу относятся также рельефная и стыковая сварки. Все остальные виды термомеханической сварки не стали популярными и не получили широкого распространения. Это:
- диффузная – соединение неоднородных металлов в условиях вакуума или в среде защитных газов;
- кузнечная – металлы соединяются в результате пластичной деформации;
- за счет высокочастотного тока;
- трением.
Определив особенности сварочного процесса, специалист легко сможет выбрать подходящий сварочный аппарат с учетом его технических показателей. Большинство сварочных процессов легко автоматизируются, дают возможность сформировать надежный и эстетичный сварочный шов, характеризуются невысокой себестоимостью и небольшими временными издержками.
История развития сварки. Роль сварки в современном мире
История развития сварки далеко до нашей эры. С тех пор, как люди научились добывать металл, они стремились создавать из него что-то полезное. Самый надежный способ соединения – горячим методом. Сейчас трудно представить, что два века назад русские ученые стояли у истоков современных сварочных аппаратов.
С тех пор началась новая страница жизни человечества. Сейчас существует несколько и видов сварочных технологий, применяемых на производстве и в быту. Современная история сварки – это изобретение новых агрегатов, методов соединения металлов, индивидуальных средств защиты нового поколения. Но по-прежнему популярной остается традиционная дуговая с помощью расплавляемых и тугоплавких электродов. Сварщики создают огромные металлоконструкции и миниатюрные произведения искусства.
- аргонодуговая технология позволяет получать все виды соединений: стыковые, угловые, тавровые, внахлест,
- газовая, с помощью нее создаются магистральные трубопроводы, пролегающие далеко от источников тока,
- полуавтоматическая позволяет ускорить процесс соединения элементов, обладает высокой точностью, снижает риск образования некачественного шва,
- всегда остается востребованной традиционная ручная электродуговая.
Меняются источники питания, усовершенствуются держатели, но принцип горячего соединения металлов не претерпевает изменений. Сварочный метод предпочтительнее других видов соединений из-за ряда преимуществ:
- из-за экономии металла,
- износостойкое оборудование имеет большой запас прочности, его применяют в любых условиях,
- образуются соединения на молекулярном уровне, обладающие высокой прочностью.
Первые упоминания сварки
Задолго до появления сварочных агрегатов существовали другие способы соединения металла. Найдены образцы соединений, созданных в VIII – VII веках до нашей эры. Самородное золото, кусочки меди и метеоритные сплавы использовали для бытовых целей, оружия. Их скрепляли при нагреве методом, сравнимым с ковкой.
Читайте также: Можно ли холодной сваркой заварить алюминий
Этап возникновения литья – следующая страница история сварочной технологии. Зазоры между частями металла заливали расплавами, получалось подобие швов. Когда были открыты легкоплавкие металлы, для соединяя металлов стали применять их, возникла пайка. Технологии пайки и ковки использовались до открытия метода электрической дуги, до конца XIX века.
Открытие электрической дуги
Василий Владимирович Петров
Физик и электротехник, академик Василий Петров открыл эффект электродуги в 1802 году. Во время опытов он пропускал электроток через металлический и угольный стержень и заметил, что возникает яркая вспышка – высокотемпературная дуга. В его трудах есть описание этого явления. Но до открытия сварочного аппарата были годы, пока развивалась электротехника. Для дуговой технологии нужны были мощные источники тока.
Николай Николаевич Бернадос
Русский изобретатель Николай Бенардос разработал электродуговую сварку только через 80 лет после открытия дуги. Начался новый этап истории развития сварки. Николай Николаевич применил дугу для резки и соединения металлических элементов. Через несколько лет Славянов Николай Гаврилович создал первый сварочный аппарат и электроды. Он официальный автор, признанный во всем мире. Впервые именно он, русский инженер изобрел сварку, запатентовал ее, только потом стали развиваться технологии в других странах. Славянов активно пропагандировал свой метод:
- исправлял брак, возникший при литье деталей,
- восстанавливал части паровых турбин,
- заваривал изношенные детали.
Славянов Николай Гаврилович
Он разработал флюсы, защищающие горячий шов от окисления, придумал сварочный генератор с регулируемой мощностью. Внедрение его изобретений занимались за рубежом. Сварка стала применяться повсеместно.
Развитие технологий в новое время
Следующий этап истории связан с фамилией Патон. Отец организовал первый институт сварки в 1929 году, под его руководством развивалась технология сварочных процессов. Во время Великой Отечественной войны новые методы применялись в оборонной промышленности. Разрабатывались новые виды флюсов, электроды для толстостенных изделий. Они применялись при производстве военной техники: танков, орудий, бомбардировщиков и их оснащения.
Евгений Патон
В киевском институте разработан метод порошковой, контактной и шлаковой сварки в жидкой и разряженной среде, для защиты шва стали применять инертные газы. Дело Евгения Патона продолжил его сын, Борис. Он возглавил институт сварки после ухода отца. Технологии космической лазерной сварки разработаны под его руководством. Стали шире применяться методы соединения металлов под водой. Эта технология используется в судоремонтных доках. Метод снижает сроки ремонта судов в 1,5 раза.
Читайте также: Вязать или варить арматуру для фундамента
Перспективы развития сварочного процесса
В настоящее время традиционные методы потеснили лазерные методы. Им предрекают большое будущее. Управлять процессом можно будет дистанционно. Роботы приходят на смену сварщикам. Разработано устройство для автоматической подачи присадочного материала в зону шва, с высокой точностью регулируется тонкий луч, расплавляющий металл.
Второе направление развития технологии высокотемпературного соединения металлов – использование оптико-волоконных материалов. Это позволит увеличивать КПД силового оборудования: генераторов, преобразователей. Постепенно будет повышаться мощность выходного тока, сейчас максимальная 6 кВт, ее планируется довести до 25 Квт и выше.
Постепенно лазерная технология вытеснит газовый метод сварки. Будут создаваться гибкие модули, использовать которые можно будет в любых погодных условиях. Будет снижаться трудоемкость технологических процессов, разрабатываться новые методы контроля качества высокотемпературного соединения металлов.
Загрузка…Историческое развитие компьютеров
Историческое развитие компьютеров
Мы живем в компьютерный век. На большую часть нашей повседневной работы влияет использование компьютеров. Его все чаще используют во всех сферах нашей жизни. В области науки и техники улучшения не могут быть достигнуты без использования компьютеров. Следовательно, возникла необходимость иметь базовые знания о компьютерах.
Строго говоря, компьютер — это вычислительное устройство, имеющее некоторые важные характеристики, такие как скорость, емкость памяти, точность и т. Д.Но в наши дни он используется для многих других приложений, помимо вычислений. Он стал незаменимым инструментом в области коммуникаций.
История компьютеров:
Историки начинают историю вычислений со счётов, деревянной рамки с шариками или бусинами, нанизанными на параллельные проволоки. Но, по сути, первая такая машина, имеющая принципы современных вычислительных машин, была разработана Чарльзом Бэббиджем в девятнадцатом веке. У него были определенные основные идеи о хранимых в машине компьютерных программах.Такая машина была изобретена Бэббиджем в 1822 году и получила название разностного двигателя. Он использовался для выполнения простых арифметических вычислений, необходимых для создания тригонометрических и логарифмических таблиц. В 1871 году он разработал и аналитический двигатель, который был прототипом компьютера.
Между тем важное теоретическое развитие произошло примерно в 1850 году, когда математик Жерог Буль разработал алгебраическую систему, которая сейчас называется булевой алгеброй. Эта булевская алгебраическая система используется для представления величин в виде двоичных чисел i.e 0 и 1, а также представляют и управляют логическими выражениями.
Значение булевой алгебры в то время не использовалось. В девятнадцатом веке, примерно в 1880 году, Холлерит разработал методы и машины, которые оказали значительное влияние на будущий дизайн компьютеров. Он сконструировал машину, в которой данные представлялись в виде отверстий на бумажных карточках. Эта машина могла работать с перфокартами и обрабатывать 50-80 перфокарт в минуту. Перфокарты содержали 80 столбцов и прямоугольные штампы.Эти машины назывались табуляторами. Эти машины также использовались для полуавтоматического отбора и сортировки карт. Он основал свою собственную компанию Computer Tabulating Recording Company, которая в конечном итоге стала International Business Machine Corporation (IBM). Сегодня IBM — одна из крупнейших компаний компьютерного мира.
Ранние компьютеры: В 1937 году Говард Алкен из Гарвардского университета сконструировал огромный механический калькулятор под названием MARK I с рядом переключателей, механических реле и плат.Размер был 15 х 2,4 х 0,6 м. Это был непосредственный предшественник автоматических электронных вычислительных машин. ENIAC (Электронный числовой интегратор и калькулятор), разработанный в 1946 году, был первым электронным калькулятором. Он занимал комнату размером 15 х 9 м и весил 30 тонн. Это была вода
с водяным охлаждением и намного быстрее, чем MARKXI.
Примерно в 1950 году был разработан компьютер EDVAC (Electronic Discrete Automatic Computer), основанный на идее Неймана. (Часто упоминается как отец современного компьютера) Он был первым, кто использовал концепцию хранимых программ в компьютерах.Емкость EDVAC составляла 1024 слова по 44 бита каждое. У него также было вспомогательное хранилище на 20 000 слов.
Компьютеры первого поколения (1946-55):
Компьютеры, произведенные в период с 1945 по 1945 годы, называются компьютерами первого поколения. Они были чрезвычайно большими по размеру, в их схемах были вакуумные лампы, которые выделяли значительное количество тепла. Следовательно, для отвода этого тепла требовались специальные устройства кондиционирования воздуха.
Они были чрезвычайно медленными, и их емкость для хранения была намного меньше, чем у современных компьютеров.В этих компьютерах перфокарты использовались для ввода данных в компьютер. Это были карты с прямоугольными отверстиями, в которых пробивались какие-то дыроколы. UNIVACI был первым коммерчески доступным компьютером, построенным в 1951 году компанией Remington Rand. Он имел емкость около 2000 слов. Они использовались в основном для расчета заработной платы, выставления счетов и некоторых математических вычислений.
Компьютеры второго поколения (1956-1965) :
Компьютеры, в которых вакуумные лампы были заменены полупроводниковыми транзисторами, назывались компьютерами второго поколения.Использование транзисторов уменьшило тепловыделение во время работы. Это также уменьшило размер и увеличило емкость хранилища. Для работы требовалось меньше энергии, и они были намного быстрее, чем компьютеры первого поколения. Магнитные носители использовались как вспомогательное хранилище данных. Эти компьютеры использовали языки высокого уровня для написания компьютерных программ. В качестве языков использовались ФОРТРАН и КОБОЛ.
Компьютеры третьего поколения (1966-1976):
Компьютеры третьего поколения появились в 1966 году с включения интегральных схем (ИС) в схемы.IC представляет собой монолитную схему, содержащую схему, эквивалентную десяткам транзисторов на одном полупроводниковом кристалле, имеющую небольшую площадь с несколькими выводами для подключения внешних схем. В компьютерах серии
IBM 360 этого поколения были предусмотрены функции разделения времени и мультипрограмм.
Это были небольшие по размеру и экономичные компьютеры по сравнению с компьютерами второго поколения. Объем памяти и скорость этих компьютеров были увеличены во много раз, включая удобные для пользователя пакетные программы, текстовый редактор и удаленные терминалы.Удаленные терминалы могут использовать центральное компьютерное оборудование и мгновенно получать результат.
Компьютеры четвертого поколения:
Компьютеры четвертого поколения были представлены после 1976 года, и в этих компьютерах электронные компоненты были дополнительно миниатюризированы с помощью методов крупномасштабной интеграции (БИС). В этих компьютерах используются микропроцессоры, которые представляют собой программируемые ИС, изготовленные с использованием техники БИС. Микрокомпьютеры были разработаны путем объединения микропроцессора с другими микросхемами LSI, с компактным размером, повышенной скоростью и увеличенной емкостью памяти.В последние дни ИС, изготовленные с использованием методов СБИС (очень крупномасштабная интеграция), используются в компьютерах. Благодаря этим методам емкость хранилища увеличивается во много раз. Мало того, скорость этих компьютеров также очень высока по сравнению с более ранними компьютерами.
В течение 1980-х годов на рынке были представлены некоторые компьютеры, называемые суперкомпьютерами. Эти компьютеры выполняют операции с исключительно высокой скоростью (около 100 миллионов операций в секунду). Эта скорость достигается за счет использования большого количества микропроцессоров, поэтому стоимость также очень высока.Обычно они используются в очень сложных приложениях, таких как искусственный интеллект и т. Д.
Историческое развитие мостов — древние и величайшие мосты
Мост — это конструкция, которая построена над некоторыми физическими препятствиями, такими как водоем, долина или дорога, и ее цель — обеспечить переход это препятствие. Он сконструирован таким образом, чтобы быть достаточно прочным, чтобы безопасно выдерживать собственный вес, а также вес всего, что должно пройти через него.Мосты были и может быть построен из разных материалов и в разной конструкции, в зависимости от предназначения, местности, на которой построен мост, материала использовались для его изготовления и свободные средства.
Первые мосты появились в природе сами по себе. Бревно могло упасть через ручей и образовать естественный мост, или камни могли упасть в реку из рядом скала. Когда люди начали строить мосты, они строили их в простой форме из обрезанных деревянных бревен или досок, камней с простой опорой и расположение перекладин, иногда с использованием сплетенных вместе натуральных волокон для удержания материалов.Один из старейших существующих арочных мостов — Аркадико. Мост на Пелопоннесе, Греция. Он датируется 13 веком до нашей эры.
Древние римляне были величайшими мостостроителями древних времен. Они построили арочные мосты и акведуки, некоторые из которых сохранились до наших дней. Они также использовали цемент, который состоял из воды, извести, песка и вулканической породы. Некоторые из их самых красивых мостов были построены через овраги, а другие — через реки, в которых нет скал или островов, выходящих из воды, чтобы нести пристань.
Индейцы также строили мосты, что задокументировано в их древнем тексте Арташастра, который был написан между 4 и 3 веками до нашей эры. Они использовали плетеные бамбук и железная цепь как материалы.
Самый старый из сохранившихся каменных мостов Китая — мост Чжаочжоу. Он был построен с 595 по 605 год нашей эры во времена династии Суй. Это также самый старый в мире каменный сегментарный арочный мост с открытыми пролетами.
Между 12 и 16 веками было построено много мостов с домами на них.Они были решением для ограниченного размещения в городах-крепостях и только во Франции. было аж 35.
Цивилизация инков использовала веревочные мосты, простой тип подвесного моста, в 16 веке. Ханс Ульрих, Йоханнес Грубенманн и другие улучшили мостостроение в 18 веке. В то же время Юбер Готье написал книгу по мостостроению.
Железный мост, построенный в Коулбрукдейле, Англия, в 1779 году, был одним из инженерных чудес того времени, потому что в нем впервые использовался чугун.
Промышленная революция 19 века принесла ферменные системы из кованого железа (железный сплав с очень низким содержанием углерода), но не имел прочности на растяжение. сила переносить большие веса. Включает сталь с ее более высокой прочностью на разрыв, которая заменяет железо и позволяет создавать мосты гораздо большего размера. Густав Эйфель со своими свежими идеями был одним из первых, кто использовал его.
Первый в мире сварной автомобильный мост был построен пионером сварки Стефаном Брылой в 1927 году.
С промышленной революцией появилось много разных типов мостов, которые стали возможными благодаря технологическому прогрессу.
Википедия — Википедия
Эта статья об онлайн-энциклопедии. Домашнюю страницу Википедии см. На главной странице. Для ознакомления посетителей с Википедией см. Википедия: О программе. Чтобы узнать о других значениях, см. Википедию (значения). «Бесплатная энциклопедия» перенаправляется сюда. Список других энциклопедий см. Списки энциклопедий.Бесплатная онлайн-энциклопедия, которую может редактировать каждый
Логотип Википедии, глобус с глифами из различных систем письма | ||
Скриншот Главная страница английской Википедии 23 июля 2018 г. | ||
Тип сайта | Интернет-энциклопедия | |
---|---|---|
Доступен на | 309 языках | |
Страна происхождения | Фонд Викимедиа | |
Создано | Джимми Уэльс Ларри Сэнгер [1] | |
Веб-сайт | www | |
Рейтинг Alexa | 10 (Глобальный, январь 2020 г. [обновление] ) [2] | |
Коммерческий | № | |
Регистрация | [необязательно] | |
Пользователи | > 315 147 активных пользователей [примечание 2] и> 85 634 144 зарегистрированных пользователя 1145 администраторов (английский) | |
Запущен | 15 января 2001 г .; 19 лет назад (2001-01-15) | |
Текущее состояние | Активно | |
Лицензия на контент | CC Attribution / Share-Alike 3.0 Большая часть текста также имеет двойную лицензию в рамках GFDL; лицензирование СМИ различается | |
Написано на | Платформа LAMP [3] | |
Номер OCLC | 52075003 |
Википедия /229- -ə или / ˌwɪkiˈpiːdiə / (
История железной дороги — Развитие железнодорожного транспорта
Современные перевозки пассажиров и грузов невозможно представить без поездов, транспортных средств, которые произвели революцию в нашей отрасли, человеческой экспансии, и то, как мы можем перемещаться из одного места в другое.Такое важное присутствие в нашей истории появилось немногим более 200 лет назад, но даже тогда оно было очевидным. что эта новая транспортная парадигма могла бы стать одной из величайших битв человечества, если бы технические препятствия ранней промышленной революции могли быть преодолен.
Все началось более 2000 лет назад в древних цивилизациях Египта, Вавилона и Греции. Перевозка людей и товаров в то время осуществлялась тележками. которые тащили животные (лошади или быки), и их инженеры быстро заметили, что животные будут тратить гораздо меньше энергии, если телега едет на заданный путь, без возможности поворота или передвижения по неровной местности.Чтобы использовать этот новый вид транспорта, они строят дороги из предварительно построенных ограничения для колес. Это были первые в мире железнодорожные пути, и их археологические остатки до сих пор можно найти в Италии и Греции. Большинство Знаменитый образец этих древних каменных «вагонных путей» можно найти на Коринфском перешейке в Греции.
Эти повозки вышли из употребления после падения Римской империи и смогли вернуться только после увеличения торговли и ранних промышленных усилий европейских стран. Ренессанс.К 18 веку каждая шахта в Великобритании имела собственную простую сеть железных дорог, по которой лошади тащили телеги от шахты к фабрикам. Изменения в Этот вид транспорта появился в 1774 году после того, как мир узнал о невероятном открытии Джеймса Ватта — стационарной паровой машине. Как он защищал свои патенты Поистине повсеместная работа над паровыми локомотивами началась только после того, как в 1800 году истек срок действия его патента. улучшение конструкции Ватта, в первую очередь разработка камер высокого давления без конденсации, которые позволили двигателю преобразовывать больше энергии пара в механическую. энергия.
Первые паровые машины начали работать по примитивным железнодорожным путям в 1804 году. Мэтью Мюррей первым сумел продемонстрировать свой простой локомотив, но Ричард Тревитик привлек больше внимания своим локомотивом «Penydarren», который во время первой поездки потянул за собой 25 тонн и 70 человек. Это событие оказалось Сообщество инженеров считает, что у паровых двигателей под давлением действительно достаточно мощности, чтобы они могли использоваться для перевозки грузов и людей.
Коммерческое появление сетей поездов произошло в конце 1820-х годов, и пионером в этой области был английский изобретатель Джордж Стефенсон, который вошел в конкурс, который хотел выяснить, какая конструкция паровоза была самой простой в использовании, самой надежной и мощной.Его «Ракета» выиграла ему это соревнование, продемонстрировать всему миру, что паровозам действительно суждено светлое будущее. Конструкции таких локомотивов вскоре отправились в США, где они начали свою быструю экспансию на недавно приобретенные земли и долгую попытку Америки «цивилизовать» западные границы.
По мере того как в течение первых нескольких десятилетий общественной работы технология поездов претерпевала огромные изменения, городские инженеры в Лондоне начали формулировать первые планы на будущее. междугородние железнодорожные пути и подземные тоннели.Первый участок знаменитого ныне «Лондонского метрополитена» начал свою работу в 1863 году, хотя и получил много жалоб из-за дыма в туннелях, он продолжал расти до 1890 года, когда весь лондонский железнодорожный парк начал использовать электрические двигатели. Этот ознаменовало начало новой эры городских систем скоростного транспорта, и подземные метро стали появляться по всему миру (слово «метро» пришло от названия системы парижского метро «Chemin de Fer Métropolitain», что означает «Метрополитен железная дорога»).
Еще одним очень важным моментом в истории поездов было внедрение дизельных двигателей, положившее конец эпохе паровозов. После Вторую мировую войну почти абсолютное большинство мира оставило позади пар и приняло намного более быстрые, простые в обслуживании и надежные дизельные двигатели. В виде Шло время, дизельные двигатели стали сочетаться с электрическими, что позволило поездам использовать лучшее из обоих миров.
Сегодня поезда представляют собой один из важнейших способов передвижения людей и товаров.Большие города не могут жить без полностью функционирующих систем подземного метро, которые ежедневно перевозят миллионы людей, а более тяжелые и прочные промышленные поезда перевозят более 40% мировых товаров между городами, странами и континенты.
Разработка транзисторов»Электроника
— после изобретения первого транзистора все еще требовалось много разработок, чтобы сделать его жизнеспособным устройством.
История клапана / трубки Включает:
История транзисторов Изобретение Развитие
После того, как были продемонстрированы первые транзисторы, стало очевидно, что это устройство нелегко в изготовлении и использовании.Потребовалась большая разработка транзисторов.
Чтобы транзистор стал жизнеспособным устройством, потребовалось разработать не только процессы, но и материалы.
Развитие транзисторов является такой же частью истории транзисторов, как и любые другие.
Развития переходного транзистора
Первые транзисторы с точечным контактом были очень ненадежными и непригодными для производства. Требовалось разработать более надежную и технологичную идею.
Осознавая эту проблему, Шокли сам разработал идею замены точечных контактов правильным p-n-переходом. Это была не мимолетная мысль, потому что вся теория, лежащая в основе работы переходного транзистора нового типа, была полностью определена расчетами. Вероятно, что более удивительно, так это то, что он разработал эту идею всего через несколько недель после того, как его команда изобрела первое устройство для точечного контакта.
Несмотря на то, что Шокли смог доказать возможность создания переходного транзистора, ему потребовалось несколько больше времени, чтобы сделать его в лаборатории.Первый был выпущен только в апреле 1949 года. Он сделал это, капнув расплавленный германий p-типа на горячий n-тип. Затем полученную каплю нужно было распилить посередине, чтобы образовались два p-n перехода. Используя эту очень грубую демонстрацию, он смог показать, что устройство имеет коэффициент усиления как по току, так и по мощности.
Разработка материалов
В 1950-е годы в разработке транзисторов произошли очень большие изменения. Во многом это стало возможным благодаря совершенствованию технологий производства и переработки сырья.
В 1950 году Тилу удалось использовать процесс Чокральского для изготовления кристаллов германия. Позже, в 1952 году, Pfann продемонстрировал процесс зонной очистки. В этом процессе индукционная катушка проходит вдоль кристалла. По мере того, как он движется вниз, он плавит материал, заставляя примеси переноситься до конца. Таким образом можно было производить полупроводники с гораздо меньшим содержанием примесей.
Ранние стадии этих разработок позволили Шокли производить кристаллы, в которые он мог легировать контролируемыми уровнями правильных примесей для образования p-n-перехода.На следующем этапе своей работы ему удалось создать полную n-p-n структуру на кристалле германия. Хотя транзистор работал, его характеристики не соответствовали стандартным ожиданиям Шокли. Требовалась дальнейшая материальная разработка.
По мере развития технологии материалов все больше компаний начали производить транзисторы. Первоначально Bell продавала сорта как с точечным контактом, так и с выращиванием на стыке. Вскоре после этого General Electric представила тип, который они назвали своим сплавным соединительным устройством.
До этого времени все транзисторы были сделаны из германия. Фактически, на конференции Института радиоинженеров в мае 1954 года ряд ораторов заявили, что кремниевые транзисторы далеки от того, чтобы стать реальностью. К их удивлению, Тил, который теперь перешел в малоизвестную компанию Texas Instruments, произвел работающее кремниевое устройство. Это дало Техасу лидерство в области транзисторов, сделав их крупным производителем полупроводников. Другим производителям потребовалось несколько лет, чтобы представить свои собственные разновидности кремниевых устройств.
В то время как Texas взяла на себя инициативу в разработке кремниевого транзистора, Bell и General Electric продолжили исследования в других направлениях. Процесс диффузии примесей в полупроводник был усовершенствован таким образом, чтобы можно было создавать требуемые структуры. В дополнение к этому еще одним важным улучшением была возможность наращивать оксидные слои на структурах. С помощью фотографических технологий это позволило более точно контролировать загрязненные участки.
С освоением диффузионных и фотографических технологий стало возможным производить множество транзисторов на одной пластине.Затем срез можно было разрезать, чтобы получить отдельные транзисторы. Таким образом, их можно было производить в достаточном количестве, чтобы снизить цены до уровней, на которых они были бы более конкурентоспособными по сравнению с клапанами.
Несмотря на улучшения, транзисторы все еще были относительно дорогими. К началу 1960-х годов обычный маркированный транзистор стоил около 1 10 шиллингов (1–50 фунтов стерлингов), но для тех, кто не был так озабочен спецификацией, можно было купить транзисторы с красным и белым пятном. Фактически это были отбракованные производителями, но во многих отношениях они идеальны для энтузиастов-любителей.Цвет обозначал частотную характеристику устройства, красное пятно — аудиоустройства, белое пятно — радиочастотное. приложений, но с частотной характеристикой, ограниченной в лучшем случае двумя или тремя мегагерцами. Эти устройства можно было купить гораздо дешевле, примерно по пять шиллингов (25 пенсов) за штуку.
В 1960-х годах цены на транзисторы резко упали по мере увеличения их использования. Кремний заменил германий, а также производительность улучшилась благодаря широкому использованию транзисторов, таких как BC107.
Дополнительная история:
Временная шкала истории радио
История радио
История радиолюбителей
Когерер
Хрустальное радио
Магнитный детектор
Датчик искры
Телеграф Морзе
История клапана / трубки
Транзистор
Интегральная схема
Кристаллы кварца
Вернуться в меню истории. . .
Краткая, но увлекательная история Tesla
Tesla Motors с момента своего основания в 2003 году штурмом захватила рынок электромобилей (EV) и аккумуляторных батарей.Под руководством Илона Маска компания неукоснительно следовала и завершила так называемый «Секретный мастер-план», чтобы навсегда изменить мир автомобилестроения.
Здесь мы исследуем некоторые ключевые вехи в истории Tesla. Мы также пытаемся ответить на некоторые из наиболее часто задаваемых вопросов о компании.
СВЯЗАННЫЕ С: КРАТКАЯ ИСТОРИЯ И ЭВОЛЮЦИЯ ЭЛЕКТРИЧЕСКИХ АВТОМОБИЛЕЙ
Почему Tesla названа в честь Николы Теслы?
Выбор имени Николы Теслы довольно очевиден — в конце концов, он был одним из главных пионеров в области электричества.Тесла также был гением, стоящим за разработкой электродвигателя переменного тока, который используется, помимо прочего, в автомобилях Тесла.
Но почему основатели компании выбрали именно его имя?
Источник: TeslaСогласно Business Insider , название было выбрано соучредителем Tesla Мартином Эберхардом. Обсуждая идею своего нового предприятия со своей тогдашней девушкой (а теперь и женой) Кэролайн, Эберхард решил, что это название идеально подходит его видению компании.
Выбирая название, Эберхард знал, что ему нужна сильная торговая марка для его новой компании, стартапа, который собирался создавать необычные электромобили.
Он хотел, чтобы компания изменила правила игры, а автомобили были спроектированы настолько хорошо, что они навсегда изменили представление всех об электромобилях. Но какое имя они могли использовать, чтобы передать это сообщение?
Он несколько месяцев предлагал своей девушке идеи названия компании. Но ничего не подходило.
Эберхард не был заинтересован в том, чтобы называть эту фирму чем-то слишком «зеленым».Имена, которые в первую очередь означали экологичность, просто не казались ему достаточно сильными.
Однажды, когда он сидел в ресторане Blue Bayou в Диснейленде, идея поразила его, как молния. Почему бы не назвать его в честь Николы Теслы?
Источник: Paopano / iStockВ конце концов, он изобрел асинхронный двигатель переменного тока, и его имя было легко запомнить.
Его подруга ответила: «Отлично! А теперь приступай к изготовлению машины».
Итак, 23 апреля 2003 года соучредитель Эберхарда Марк Тарпеннинг официально зарегистрировал доменное имя: Teslamotors.com. Теперь им просто нужно было построить несколько машин.
Как Илон Маск создал Tesla?
Короче, не стал. Tesla была основана Мартином Эберхардом и Марком Тарпеннингом в 2003 году.
Илон Маск присоединился к Tesla в 2004 году после инвестирования $ 6,3 миллиона в акции Tesla в ходе инвестиционного раунда серии A. Маск был назначен председателем совета директоров.
Почему была создана Тесла?
Tesla, первоначально Tesla Motors, начала свою деятельность в 2003 году, когда группа инженеров, увлеченных электромобилями, хотела показать людям, что им не нужно идти на компромисс при рассмотрении вопроса о покупке одного из них.
Они стремились разработать собственный модельный ряд автомобилей, которые, по словам компании, «лучше, быстрее и веселее в управлении, чем бензиновые автомобили».
Источник: Илон Маск / TwitterОдним из основных мотивов создания Tesla был недавний отказ от программы General Motors EV1. General Motors выполняла эту программу всего три года с 1996 по 1999 год и произвела ограниченный тираж автомобилей.
Машины никогда не выпускались для государственных закупок, но считались большим успехом с инженерной точки зрения.
Вдохновленные этим, инженеры-основатели Tesla Motors Мартин Эберхард и Марк Тарпеннинг основали компанию в июле 2003 года. Они стали генеральным директором и финансовым директором Tesla соответственно.
Пара самостоятельно финансировала стартап, пока компания не открылась для финансирования серии А от внешних инвесторов.
Маск в то время уже был успешным предпринимателем и заработал состояние, работая на PayPal. Он помог вести финансирование серии A и вложил миллионы собственных средств, став председателем компании.
В следующем году Lotus подписала контракт с Tesla на помощь в разработке шасси и кузова для первой модели Tesla, Roadster.
Источник: Роберт Вей / iStockВ рамках раунда финансирования серии B 2006 года основатели Google Сергей Брин и Ларри Пейдж также инвестировали в Tesla. В июле того же года миру был представлен первый прототип Roadster.
Вскоре после этого Tesla опубликовала свой «секретный» план для компании:
«Постройте спортивный автомобиль. Используйте эти деньги, чтобы построить доступный автомобиль.Используйте эти деньги, чтобы построить еще более доступный автомобиль. Выполняя вышеперечисленное, также предоставляйте варианты производства электроэнергии с нулевым уровнем выбросов ». — Илон Маск / Тесла.
Компания шла полным ходом к революционному развитию автомобильной промышленности.
Когда был выпущен первый автомобиль Tesla?
В 2006 году Tesla представила прототип своего первого предприятия на рынке электромобилей — Roadster. После еще нескольких лет разработки в 2008 году была запущена финальная серийная модель.
В это время оба основателя покинули компанию, и Микаэль Маркс занял пост временного генерального директора.Вскоре после этого в ноябре 2007 года Зеев Дрори занял место постоянной замены Эберхарда.
Дрори должен был вывести Roadster на рынок в следующем году.
2008 Tesla Roadster. Источник: Mariordo / Wikimedia CommonsЭтот зловещий спортивный автомобиль был оснащен новейшими аккумуляторными технологиями и полностью электрической трансмиссией. Автомобиль официально был запущен в производство в марте 2008 года.
Roadster стал не только выдающимся достижением для такой молодой компании, но и тем, что ни одна другая компания не смогла создать.Tesla произвела полностью электрический автомобиль с практическими характеристиками, который действительно мог удовлетворить потребности потребителей, хотя и по цене, которую немногие могли себе позволить.
Многие до них терпели неудачу, потому что, среди прочего, они не могли произвести аккумулятор с достаточной мощностью, чтобы быть практичным для повседневного вождения, или экономичный двигатель, способный вписаться в потребительский автомобиль и разгоняться до скоростей шоссе .