Как проверить сварочный шов на герметичность
Крупные производители трубопроката выпускают металлические электросварные трубы со швами высокого качества, так что переживать за их герметичность не нужно.
А вот если собирается крупный трубопровод со сварными соединениями, то даже из хороших труб может получиться негерметичный объект, который будет пропускать воду или газ.
Разумеется, такие дефекты недопустимы, однако их не всегда можно увидеть невооруженным глазом.
Виды дефектов сварного шва
Наплывы появляются, если раскаленная сталь дотекает до холодного участка трубы рядом со швом и застывает в виде капли или «ручейка». Чтобы они не появились, нужна профессиональная работа сварщика, который выберет не слишком большой сварочный ток, правильно будет водить электродом и выбирать угол трубы при соединении.
Наплывы чреваты неравномерной толщиной сварки и возможным появлением трещин.
Подрезы появляются в виде канавок на участке рядом со швом из-за некачественной сварки или низкого качества трубы.
Прожоги представляют собой отверстия, сквозь которые течет расплав. Они образуются, если сварка слишком медленная, ток слишком высокий либо зазор между торцами труб слишком большой.
Трещины — самый страшный дефект, который может появиться в любой точке вокруг шва или прямо на нем. К ним приводит некачественное сваривание или неподходящий состав стали.
Остатки шлака, если их не удалить, убыстряют появление ржавчины.
Способы проверки
Существуют несколько способов проверки специальным оборудованием, которые проводятся соответствующими специалистами и приборами — это ультразвуковая дефектоскопия и различные виды магнитной проверки.
Своими руками на герметичность шов можно проверить по-разному.
Капиллярный способ
предполагает использование керосина. Керосин легко проникает через микротрещины и поры, поэтому на шов наносят меловой раствор и высушивают трубу.
Пузырьковый способ проще, но менее точный, зато подходит для любых трубопроводов — и не надо потом вымывать керосин. Проведите его несколько раз, чтобы удостовериться в результатах.
Для него швы смазывают водой, из которой можно выдуть мыльный пузырь. Затем подают в трубопровод сжатый воздух, и если шов негерметичен, то эти пузыри обязательно появятся.
Проверка сварочных соединений — обязательный этап любых сварочных работ. Благодаря тщательному контролю можно выявить явные и скрытые дефекты, которые в дальнейшем повлияют на качество и долговечность всей металлической конструкции. Конечно, можно оценить качество сварного шваневооруженным взглядом, но это лишь один из методов.
С помощью визуального контроля вы не сможете обнаружить внутренние трещины и поры. Поэтому важно знать дополнительные способы контроля качества. На крупных производствах эту работу выполняет контролер сварочных работ, но на меленьком заводе эта обязанность часто ложится на плечи сварщика. В этой статье мы расскажем, как проверить швы и какие есть виды контроля качества помимо визуального осмотра.
Способы контроля качества сварного шва
Существуют разнообразные виды и средства технического контроля, все они имеют свои достоинства и недостатки, особенности и нюансы. Но несмотря на различия все они призваны, чтобы устроить швам испытание на прочность и долговечность. Качество сварных соединений во многом зависит от сварщика и используемых комплектующих, так что итог контроля можно предсказать. Но мы все равно рекомендуем проводить контроль качества, чтобы быть уверенным, что изделия прослужат долго.
Качество сварных соединений можно узнать путем визуального осмотра (пожалуй, самый распространенный метод), ультразвукового, магнитного, капиллярного и радиационного (радиографического) контроля, также осуществляется контроль сварных швов на проницаемость. Есть и другие методы контроля сварных швов, но мы в этой статье перечислим самые распространенные и простые в применении. Рекомендуем выполнять пооперационный контроль качества, т.е. сначала осмотреть шов, затем провести капиллярный контроль и так далее. Впрочем, обо всем по порядку.
Визуальный контроль
Начнем с визуального контроля. Это наиболее простой и быстрый способ узнать качество сварных швов. Вам не понадобятся специальные приборы или жидкости, достаточно вашей внимательности. Тщательно осмотрите сварное соединение: не должно быть видимых дефектов вроде трещин и сколов, шов должен иметь одну ширину и высоту на всех участках. Внешний контроль сварочных швов позволяет также проверить наличие или отсутствие непроваров, наплывов, неравномерных складок шва. Все это дефекты, обнаружив которые можно смело говорить о низком качестве соединения.
Конечно, с помощью такого метода вы не сможете выполнить полноценный контроль сварных соединений трубопроводов, сварных соединений газопроводов или иных ответственных конструкций, но визуальный осмотр станет первой операцией, вслед за которой можно применить остальные методы контроля.
Капиллярный контроль
Методы контроля качества сварных соединений включают также испытания сварного шва. Для этого используется капиллярный метод. Его суть крайне проста: для контроля используются специальные жидкости, которые способны проникать в мельчайшие поры и трещинки, называемые капиллярами.
С помощью капиллярного операционного контроля можно проверить качество любого металла, с любым составом и формой. Зачастую такой метод используется, когда нужно узнать наличие скрытых дефектов невидимых для глаз, но нет бюджета, поскольку капиллярный контроль очень прост в применении и не требует наличия дорогостоящего оборудования.
Капиллярная оценка качества сварных соединений выполняется с помощью жидкостей, называемых пенетрантами (от английского слова «penetrant», что значит «проникающая жидкость»). Такие жидкости обладают незначительным поверхностным натяжением, отчего легко проникают в мелкие капилляры и при этом остаются видимы для глаз. По сути, пенетранты заполняют полости и окрашивают дефекты, тем самым делая их видимыми.
Сейчас можно найти множество рецептов приготовления пенетранта, каждый из которых будет обладать своими свойствами и особенностями. Можно приготовить пенетрант на основе воды или любой другой органической жидкости (скипидара, бензола, также сюда относится довольно популярная проверка сварных швов керосином. Такие пенетранты очень эффективны и чувствительны к малейшим дефектам. Они уверенно занимают одну из лидирующих позиций среди методов по контролю качества.
Контроль на герметичность сварных швов
На жидкостях не заканчиваются испытания сварных швов. Их также нужно проверить на герметичность. Метод проверки на герметичность имеет множество названий: течеискание, пузырьковый метод контроля, пневмоиспытание, гидроиспытание и многие другие. Но вне зависимости от названия суть их остается неизменна: обнаружение сквозных дефектов, ухудшающих герметичные показатели сварного соединения.
Начнем с пневматического метода контроля качества швов. Он подразумевает использование газа или воздуха, который направляется на соединение под давлением.
При приготовлении мыльного раствора используется один кусок мыла на литр воды. Если предстоит работа при низких температурах (на улице зимой), то более половины воды рекомендуется заменить на спирт. Также рекомендуем подключить манометр, с помощью которого вы сможете контролировать показатель давления и сможете заметить, как оно будет падать при обнаружении дефектов. Также нелишним будет использование предохранительного клапана, чтобы соблюсти технику безопасности.
Самая простейшая форма пневматического контроля — погружение детали в воду, без смазывания швов мыльным раствором и использования давления.
Также есть еще одна разновидность пневматического контроля, называемая контроль качества сварных швов и соединений с помощью аммиака. Аммиак подается вместо газа или воздуха, а швы предварительно покрывают специальной бумажной лентой. Аммиак проходит через шов и если имеются дефекты, то на ленте появляются красные пятна.
Второй тип контроля на герметичность — гидравлический. Здесь давление создают с помощью воды или масла. Это очень интересный метод, поскольку деталь выдерживается в жидкости от 5 до 15 минут (в зависимости от особенностей металла), при этом зона около шва обстукивается молотком, удары должны быть слабыми. Если есть дефекты, то при ударе жидкость начнет вытекать из предполагаемого места с трещиной или другим повреждением.
Магнитный контроль
Магнитный метод контроля заключается в использовании основ электромагнетизма. Контролер или сварщик с помощью специального прибора создает вокруг шва магнитное поле, которое испускает поток так называемых электромагнитных линий. Если они искажаются, значит есть дефекты. Искажения фиксируются магнитопорошковым способом.
При магнитопорошковом на поверхность шва предварительно наносят ферримагнитный порошок, который при искажении электромагнитной линии начинает скапливаться в месте дефекта. Из-за этого магнитный контроль доступен только при работе с ферримагнитными металлами. Алюминий, медь, сталь с большим содержанием хрома и никеля не могут быть подвержены проверке. В целом, это очень эффективный, но неудобный и дорогостоящий метод, так что его применяют только при контроле особо важных узлов.
Ультразвуковой контроль
Ультразвуковой способ очень интересен. Он основан на свойствах ультразвука. Ультразвуковые волны легко отражаются от краев трещины или скола, поскольку те обладают разными акустическими особенностями. Говоря простыми словами, мы подаем на шов ультразвук, и если на своем пути он сталкивается с дефектом, то искажается и отображается в другом направлении. При этом разные типы дефектов по-разному искажают ультразвуковую волну, так что их можно легко определить.
Контроль качества сварного шва с помощью ультразвуковых аппаратов применяется повсеместно, поскольку это довольно эффективный и при этом недорогой метод. По сравнению с другими методами (например, магнитным или радиационным) не нужно учитывать какие-то особенности металла или приобретать дорогостоящее оборудование. Но есть и недостатки: контроль сварного соединения ультразвуком должен проводить специалист, а не обычный сварщик.
Радиационный контроль
Радиационный контроль сварных соединений (также называемый «радиографический контроль» и «гаммаграфический контроль сварных соединений») представляет собой мини-версию обычного рентгена. Гамма-лучи проникают через металл и на специальной пленке фиксируются все возможные скрытые дефекты. Это самый передовой и дорогостоящий метод контроля качества, он требует современного оборудования и квалификации от контролера или сварщика. Также избыточная работа с таким прибором может оказывать негативное воздействие на здоровье человека.
Недавно появилась цифровая радиография, которая выполняется с помощью компьютера. Здесь вместо пленки используют специальные многоразовые пластины, которые совместимы с любыми источниками радиации. Но в отличие от классического радиационного контроля при цифровом методе изображения сохраняются сразу на компьютер, их можно масштабировать и кадрировать. В будущем разработчики планируют довести этот процесс до автоматизма, чтобы не требовалось присутствие человека.
Вместо заключения
Контролер сварочных работ должен очень внимательно относиться к своей работе, поскольку от его внимательности зависит все. Выполняя контроль качества сварки и сварных соединений записывайте все особенности и дефекты, которые сможете обнаружить. Комбинируйте различные методы контроля сварки, чтобы получить полную картину. Не используйте разрушающие методы контроля сварных соединений, которые не подходят для тех или иных металлов.
Сварка и контроль качества сварных соединений металлоконструкций — дело непростое, но обучившись этому лишь однажды вы сможете довольно быстро выполнять контроль даже в полевых условиях. Также не забывайте, что есть техника безопасности и ее нужно соблюдать не только при сварке, но и при контроле швов.
Сварные соединения и швы ответственных изделий и соoружений дoлжны быть непрoницаемыми для рaзличных жидкостей и газов. Неплотности в швах снижaют их пpочность пpи вибpационных нагpузках, уменьшaют коррозионную стойкость, вызывaют утечку хрaнимых и трaнспортируемых пpодуктов и создaют недопуcтимые уcловия экcплуатации сварных конструкций.
Контроль непроницаемости сварных соединений проводят в соответствии с ГОСТ 3242-79, включая следующие виды испытаний: керосином, обдувом, аммиаком, воздушным давлением, гидравлическим давлением, наливом и поливом.
Кроме этого, непроницаемость сварных соединений определяют вакуумным методом и газоэлектрическими течеискателями.
Перед проведением испытаний должны быть устранены все дефекты, выявленные внешним осмотром.
Испытание керосином основано на способности многих жидкостей подниматься по капиллярным трубкам, какими в сварных швах являются сквозные поры и трещины. Керосин обладает высокой смачивающей способностью и сравнительно малой вязкостью, что обеспечивает большой эффект этого способа контроля. Например, в отличие от воды (полярная жидкость) керосин под действием поверхностных сил проникает в мельчайшие (10 -3 — 2,10 -4 мм) неплотности в металле.
Испытание сварных соединений керосином проводят следующим образом. После внешнего осмотра простукивают молотком или подвергают вибрации основной металл на расстоянии 30—40 мм от шва и тщательно очищают сварное соединение от шлака, ржавчины, масла и других загрязнений. Такое простукивание или вибрация способствует лучшему удалению шлака и развитию несквозных дефектов в сквозные.
Затем с помощью пульверизатора сварные швы покрывают меловым раствором (350—450 г молотого мела или каолина на 1 л воды) с той стороны, которая более доступна для осмотра.
После высыхания мелового раствора другую сторону шва обильно смачивают керосином и выдерживают в течение определенного времени.
Исходя из экспериментальных данных Института электросварки им. Е. О. Патона, Всесоюзного научно-исследовательского института строительства трубопроводов и ряда монтажных организаций время выдержки под керосином обычно устанавливают не менее 12 ч при окружающей температуре выше 0° и не менее 24 ч — при температуре ниже 0°.
Ввиду того что при повышении температуры вязкость керосина уменьшается и скорость проникания его через неплотности шва увеличивается, для сокращения времени контроля рекомендуется швы перед испытанием нагревать до температуры 60—70° С. В этом случае время выдержки под керосином сокращается до 1,5—2 ч. Керосин наносят в процессе испытания 3—5 раз.
Соединения внахлестку, у которых один шов сплошной, а второй прерывистый, опрыскивают струей керосина под давлением co стороны прерывистого шва. Соединения внахлестку, сваренные сплошным швом с обеих сторон, испытывают керосином путем нагнетания его под давлением в межнахлесточное пространство через специально просверленное отверстие.
О наличии пор, свищей, сквозных трещин и непроваров свидетельствуют жирные желтые точки или полоски керосина на меловом слое, которые с течением времени расплываются в пятна. Поэтому необходимо тщательно следить за появлением первых точек или полосок и своевременно отмечать границы дефектных участков.
Обнаруженные дефекты устраняют, после чего сварной шов подвергают повторному контролю.
Для лучшего наблюдения за керосиновыми пятнами применяют керосин, окрашенный в красный цвет краской «Судан-III» в количестве 2,5—3 г на литр.
Эффективность контроля непроницаемости сварных швов с помощью керосина можно повысить, применяя дополнительно продувку швов сжатым воздухом под давлением 3—4 кгс/см 2 , разрежение атмосферного воздуха с меловой стороны шва при помощи специальных камер, вибрацию швов. Все эти меры ускоряют проникание керосина через неплотности.
С помощью керосина выявляют не только сквозные, но и поверхностные дефекты. Для этого поверхность контролируемого сварного соединения после тщательной очистки обезжиривают бензином или ацетоном и обильно смачивают окрашенным керосином. По истечении 15—20 мин керосин вытирают или смывают 5%-ным водным раствором кальцинированной соды с последующим просушиванием. Затем на поверхность сварного соединения при помощи пульверизатора наносят тонкий слой разведенного в воде мела (или каолина).
Когда мел высохнет, изделие около шва обстукивают молотком, а сам шов прогревают горячим воздухом. При этом керосин, задержавшийся ранее на дефектных участках (в случае их наличия), просачивается на меловую краску в виде пятен и полосок, по которым судят об имеющихся дефектах.
При испытании обдувом одну сторону сварного шва промазывают мыльным раствором (вода 1 л, мыло хозяйственное 100 г), а другую — обдувают сжатым воздухом, подаваемым по гибкому шлангу с наконечником под давлением 4—5 кгс/см 2 . Расстояние между наконечником и швом должно быть не более 50 мм.
Если испытание проводят при температуре ниже 0° С, мыльный раствор готовят с частичной заменой воды спиртом (до 60%) или с применением незамерзающей жидкости, растворяющей мыло.
Сквозные дефекты обнаруживают по появлению пузырей на промазанной мыльным раствором стороне шва.
В основу испытания аммиаком положено свойство некоторых индикаторов, например спирто-водного раствора фенолфталеина или водного раствора азотнокислой ртути, изменять окраску под воздействием щелочей, в данном случае сжиженного аммиака.
Перед началом испытаний тщательно очищают металлической щеткой сварное соединение от шлака, ржавчины, масла и других загрязнений. Если сварку вели электродами с обмазкой основного типа, то швы, кроме того, промывают водой, иначе остатки щелочных шлаков будут реагировать в процессе испытания с индикатором, изменяя его окраску.
После такой подготовки на одну сторону шва укладывают бумажную ленту или светлую ткань, пропитанную 5%-ным раствором азотнокислой ртути (индикатором), а с другой стороны создают давление аммиака.
При контроле сварных швов небольших емкостей, а также трубопроводов в них подают аммиак в количестве 1% объема воздуха в емкости и создают избыточное давление 1 кгс/см 2 или более, но не выше расчетного рабочего.
При контроле отдельных участков шва над ними устанавливают герметичную камеру, в которой создают давление аммиака.
В обоих случаях спустя 1—5 мин аммиак, проникая через неплотности сварного шва, окрашивает пропитанную индикатором бумагу или ткань в серебристо-черный цвет. Скорость и интенсивность окраски, а также величина пятен характеризуют размеры дефектов, границы которых отмечают мелом или краской.
При использовании в качестве индикатора спирто-водного раствора фенолфталеина его тонкой струей льют на контролируемый шов. Если в шве имеются неплотности, аммиак проходит через них и окрашивает раствор фенолфталеина в ярко-красный цвет с фиолетовым оттенком.
Испытанию давлением газа подвергают емкости и трубопроводы, работающие под давлением, с целью контроля общей непроницаемости сварной конструкции.
Малогабаритные изделия герметизируют газонепроницаемыми заглушками и полностью погружают в ванну с водой. Затем в изделие через редуктор от воздушной сети или из баллона подают газ (воздух, азот, инертные газы) под давлением, величина которого на 10—20% больше величины рабочего. Имеющиеся неплотности определяют по появлению пузырьков газа в воде.
Крупногабаритные сварные изделия испытывают следующим образом. После герметизации в них создают испытательное давление и промазывают сварные швы мыльным раствором (100 г мыла на 1 л воды). Появление мыльных пузырей на промазанной поверхности свидетельствует о проницаемости шва.
Величину давления и время выдержки под ним устанавливают в соответствии с техническими условиями.
При испытании сжатыми газами следует тщательно соблюдать правила техники безопасности. Работы должны проводиться в изолированном помещении с ограждениями (на случай взрыва). Трубопроводы испытывают отдельными изолированными участками с предупредительными знаками об опасности. Гидравлическим давлением проверяют прочность и плотность сварных соединений различных емкостей, котлов паропроводов, водопроводов, газопроводов и других сварных конструкций, работающих под высоким давлением.
Перед испытанием сварное изделие герметизируют водонепроницаемыми заглушками, обтирают или обдувают сжатым воздухом сварные швы до получения сухой поверхности.
После полного заполнения изделия водой с помощью насоса или гидравлического пресса создают избыточное контрольное давление, величину которого принимают в соответствии со стандартами, инструкциями или техническими условиями (обычно в 1,5—2 раза больше рабочего). В процессе испытания давление определяют по проверенным и опломбированным манометрам.
В самой высокой точке испытываемого изделия устанавливают контрольную заглушку на резьбе для наблюдения за заполнением всего объема водой и выпуском воздуха в атмосферу. В противном случае не исключено образование воздушной подушки, находящейся под большим давлением, что может привести к разрыву изделия в процессе испытания.
По истечении 5—6 мин давление уменьшают до рабочего, а околошовную зону слегка обстукивают молотком на расстоянии 15—20 мм от края шва. Боек молотка должен быть круглым, чтобы не повредить основной металл изделия.
Проницаемость сварных швов и места сквозных дефектов устанавливают по снижению испытательного давления и появлению течи или просачиванию воды в виде капель, а также по запотеванию поверхности шва или вблизи него.
Во избежание ошибочных выводов следует иметь в виду, что при температуре воды в сосуде ниже температуры воздуха в помещении возможно полное запотевание всей поверхности металла испытуемого изделия. Кроме того, уменьшение испытательного давления не всегда указывает на наличие дефектов, а может быть вызвано неплотностями в нагнетательной системе, присоединительной арматуре, заглушках.
Недостатками этого способа контроля являются необходимость в источниках водоснабжения и трудности, возникающие при испытаниях в зимнее время на открытом воздухе.
Вертикальные резервуары для хранения нефти и нефтепродуктов, газгольдеры и другие крупные емкости испытывают наливом воды.
До испытания сварные швы тщательно обтирают ветошью или обдувают воздухом до получения сухой поверхности. Затем емкость заполняют водой и наблюдают за сварными швами и падением уровня воды. Продолжительность испытания, необходимого для осмотра всех швов, составляет от 2 до 24 ч в соответствии с техническими условиями. Если в течение этого времени не обнаружено пропусков воды и уровень ее не снизился, емкость считают выдержавшей испытание.
Категорически запрещается обстукивать сварные швы резервуаров, газгольдеров и других крупных емкостей в процессе испытания во избежание их разрушения. Испытание проводится при температуре окружающего воздуха не ниже 0° С и температуре воды не ниже +5° С.
Когда швов немного, их непроницаемость определяют, полива одну сторону шва водой из брандспойта под давлением 1—10 кгс/см 2 , устанавливаемым техническими условиями. Одновременно осматривают противоположную сухую сторону шва.
Проницаемость сварных швов и места дефектов определяют, следя за появлением течи, просачиванием воды в виде капель, запотеванием поверхности шва или вблизи его.
Вакуумный контроль сварных швов применяют в тех случаях, когда применение других способов почему-либо исключено. В частности, этот метод широко применяется при контроле сварных днищ резервуаров, газгольдеров, цистерн, гидроизоляционных ящиков. Он позволяет обнаружить отдельные поры диаметром до 0,004— 0,005 мм, а производительность при его использовании достигает 40—60 м сварных швов в час.
Вакуум создают при помощи переносной вакуум-камеры, которую устанавливают на наиболее доступной стороне проверяемого участка шва.
В зависимости от формы контролируемого изделия и типа соединения применяются плоские, угловые и кольцевые вакуум-камеры.
Механизированная вакуум-тележка укомплектована набором переносных вакуум-камер, позволяющих контролировать различные типы сварных соединений во всех пространственных положениях.
Контроль швов газоэлектрическими течеискателями. В настоящее время применяют два вида газоэлектрических течеискателей: гелиевые и галоидные.
Чувствительность газоэлектрических течеискателей к выявлению неплотностей в швах очень высока, но ввиду сложности конструкции и значительной стоимости изготовления их применяют только для контроля особо ответственных сварных конструкций.
Принцип работы гелиевого течеискателя основан на высокой способности гелия при определенном вакууме проходить сквозь неплотности сварных швов.
В зависимости от конфигурации и объема испытуемой сварной конструкции контроль неплотностей швов гелиевыми течеискателями производят следующими методами.
а) Контроль избыточным давлением состоит в том, что испытуемую емкость помещают в газонепроницаемую металлическую камеру, соединенную с насосами течеискателя. Внутри камеры создают вакуум, а в емкость подают под давлением гелий. При наличии сквозных дефектов в сварных швах гелий проникает в камеру и попадает в течеискатель, где фиксируется одновременно миллиамперметром и звуковым сигналом.
По окончании испытаний гелий перекачивают в другую емкость, подготовленную для контроля, или в резервуар для хранения.
б) При контроле с помощью гелиевой камеры вакуум создают в испытуемой емкости, а гелий подают в газонепроницаемую камеру. Если в сварных швах имеются неплотности, то гелий просачивается в испытуемый сосуд и попадает в течеискатель.
в) Метод установки специальной герметичной камеры-муфты применяют в основном для испытания стыков трубопроводов.
Камеру соединяют с насосом течеискателя, создают в ней вакуум и подают в трубопровод гелий. При наличии неплотностей в сварных швах гелий попадает в течеискатель и вызывает сигнал.
Эти три метода являются наиболее чувствительными к выявлению неплотностей в сварных швах, но не определяют место их расположения. С этой целью применяют обдувание струей гелия наружной поверхности испытуемой емкости, в которой создают вакуум. Места неплотностей фиксируют по сигналу течеискателя, соединенного с емкостью.
Для более точного определения расположения дефектных участков используют специальный щуп-улавливатель, соединенный с течеискателем. Щуп перемещают вдоль швов по наружной поверхности емкости, в которой находится гелий под давлением выше атмосферного. Малейшая неплотность в шве тотчас же фиксируется течеискателем.
Гелиевые течеискатели применяются для обнаружения неплотностей в сварных швах трубопроводов, находящихся под землей. Для этого над трубопроводами пробуривают несколько скважин, в которые опускают специальный щуп-улавливатель, а в каждую трубу подают гелий. Примерное место течи определяют в зависимости от того, какая из скважин показывает максимальную концентрацию гелия.
Проверка качества и герметичности сварного шва труб и конструкций
К монтажу металлопроката предъявляются достаточно жесткие требования, так как некачественное крепление может привести к различным нежелательным последствиям. Особенно это относится к монтажу труб, так как этот процесс требует особого внимания и квалификации специалиста.
Предлагаем вам познакомиться с основными видами дефектов сварных соединений, возникающих на трубах и другом прокате, а также более качественными методами проверки герметичности и надежности сварного шва.
Виды и причины возникновения дефектов
Наличие дефектов сварного шва чревато не только ухудшением внешнего вида, но и, что гораздо хуже, снижением прочности всей конструкции и ее долговечности. Для их выявления используются так называемые методы неразрушающего контроля сварного шва. Наиболее простым является метод визуального осмотра, позволяющий определить наличие нескольких разновидностей повреждений. Мы же для удобства перечислим сразу все возможные виды дефектов.
- Наплывы – заметные неровности поверхности, напоминающие капли.
- Прожоги – отверстия, возникающие в расплавленном металле.
- Кратеры – углубления в шве, точечно снижающие прочность.
- Несплавления – полости между деталями.
- Свищи – каплевидные несквозные полости. Входное отверстие видно на поверхности места соединения.
- Поры – многочисленные мелкие полости.
- Перегрев – деформация металла вокруг места соединения.
- Подрезы – покатые края вдоль шва.
- Непровар – соединение деталей не на всю толщину.
- Включения шлака.
- Трещины.
В большинстве случаев причинами некачественно проведенных работ являются:
- Низкая квалификация сварщика.
- Нарушение технологии – неправильно выбранный ток сварки, неверная скорость, некачественная очистка деталей, обрыв дуги, неравномерный нагрев, неточное направление электрода, слишком быстрое охлаждение и другие.
- Низкое качество свариваемых изделий.
Способы проверки качества
Проверить сварные швы визуально достаточно сложно, так как таким методом можно заметить только крупные огрехи, затрагивающие поверхность швов и свариваемых труб. Внутренние полости или наличие включений шлака обнаружить таким методом невозможно, однако пренебрегать ими, особенно если производится монтаж ответственных конструкции и трубопроводов для транспортировки жидкостей и газов, нельзя.
В этом случае используется специальное оборудование, позволяющее произвести контроль качества без разрушения металла. Его работа основана на двух основных физических методах и различных способах чтения полученных данных.
- Ультразвуковое обнаружение – специальные ультразвуковые дефектоскопы излучают узконаправленные звуковые волны и анализируют их отражение от материала. В местах наличия полостей и вкраплений шлака показатели будут отличаться.
- Магнитный способ.
Здесь используется 3 метода: порошковый, когда на намагниченную поверхность рассыпаются металлические опилки; магнитнографический – аналогичный, но с использованием магнитной ленты и индукционный – с помощью электронного анализатора.
Проверка герметичности
Проверить прочность сварного шва в отдельных случаях недостаточно. Особенно это относится к трубопроводам, для которых герметичность играет едва ли не более важную роль.
Способов проверки можно выделить 3:
- Пузырьковый – самый простой. Все соединения промазываются мыльным раствором, после чего в трубах создается давление воздуха. Если в месте сварки есть сквозные отверстия, то над ними обязательно появятся пузыри.
- Капиллярный – с помощью керосина, который заполняет даже самые мелкие трещины. В этом случае на одну сторону сварного шва трубы наносится водный раствор мела. После его высыхания другая сторона шва проливается керосином. Если соединение негерметично, капли керосина через некоторое время выступят на меловом участке.
- Газоэлектрическим искателем. Данный способ сложно использовать в быту, но он обширно применяется при проверке ответственных трубопроводов. В этом случае внутрь системы подается газообразный гелий, а его утечки фиксируются специальным электронным анализатором.
Качество сварного шва
Сварным соединением называется неразъемное соединение двух и более деталей, которые выполнены при помощи сварки. В состав сварного соединения входят: сварной шов, зона термического влияния и примыкающие к ней участки основного металла.
Очень важно характеристикой сварного шва является их классификация, на основании которой определяется наиболее оптимальный метод сварки и выбираются ее режимы.
Сварной шов – это место сплава различных металлических элементов одной конструкции. Во время сварки металл в этом месте расплавляется, после чего при остывании кристаллизуется, обеспечивая надежную прочность и герметичность шва.
Сварной узел представляет собой часть сварной конструкции, в которой сварены примыкающие друг к другу элементы.
Сварной конструкцией называется металлическая конструкция, изготовленная из отдельных деталей или узлов с помощью сварки. Металл деталей, подлежащих соединению сваркой, называют основным металлом. Металл, подаваемый в зону дуги дополнительно к расплавленному основному металлу, называют присадочным металлом. Переплавленный присадочный металл, введенный в сварочную ванну, называется наплавленный металл.
Дееспособность сварного изделия определяется по типу сварного соединения, формой и размерами сварных соединений и швов, их расположением относительно действующих сил и плавностью перехода от сварного шва к основному металлу.
При выборе типа сварного соединения следует учитывать условия эксплуатации, которые могут быть статические или динамические нагрузки. Также необходимо брать во внимание способ и условия изготовления сварной конструкции.
Основные виды сварочных швов
В первую очередь все швы делят по способу соединения деталей. По данному признаку выделяют следующие виды швов:
- стыковые – получаемые между заготовками, которые промыкаются друг к другу торцевыми поверхностями;
- нахлесточные – получаемые за счет наложения деталей друг на друга с частичным перекрытием;
- тавровые – получаемые за счет приваривания торцевой поверхности одной заготовки к плоскости другой заготовки;
- угловые – получаемые между заготовками, расположенными под углом друг к другу, шов получается в месте примыкания деталей;
- торцевые – получаемые за счет сваривания торцов заготовок.
Основные типы и конструктивные элементы швов сварных соединений для ручной дуговой сварки регламентирует ГОСТ 5264-80. Ниже рассмотрим более детально каждый вид сварочного соединения
Виды сварного соединенияСтыковые швы
Такие швы являются самыми распространенными видами соединения. Они используются при стыковке металлических листов или труб, которые перед процедурой сваривания должны быть надежно зафиксированы. Между деталями оставляют небольшой зазор, равный 1-2мм, который в процессе сварки заполняется расплавленным металлом.
Также различают односторонние и двухсторонние швы. При односторонней сварке шов формируется только на одной стороне деталей. В случае двухстороннего шва сварка проводится на обеих сторонах заготовок.
В зависимости от толщины свариваемых деталей для стыковых швов по-разному готовят сварочные кромки::
- с отбортовкой – для деталей толщиной — до 4 мм;
- без скоса – для деталей толщиной — 4…8 мм;
- с V-образным скосом – для деталей толщиной — 3…60 мм;
- с X-образным скосом – для деталей толщиной — 8…120 мм;
- с K-образным скосом – для деталей толщиной — 8… 100 мм;
- с криволинейным скосом – для деталей толщиной — 15…100 мм.
* Для тонких деталей возможна стыковая сварка без обработки кромок или с обработкой только на одной стороне.
Нахлесточные швы
При выполнении нахлесточных швов поверхности металлических деталей расположены параллельно и при этом частично друг друга перекрывают. Такие швы считаются самыми простыми и удобными для выполнения, поскольку детали лежат неподвижно и уже соприкасаются друг с другом местами, которые необходимо лишь заварить. При этом надо учитывать, что сварка швами внахлест всегда выполняется с двух сторон. Кромка каждой заготовки должна быть приварена к поверхности другой. Угол наклона электрода при выполнении сварки лежит в пределах 15o-45o. Если угол наклона начнет выходить за эти пределы, то шов наползет на одну из сторон стыка.
Тавровые швы
Тавровые швы выполняются привариванием торца одной заготовки к боковой поверхности другой заготовки и в разрезе напоминают букву «Т». В процессе сварки заполняется угол, который образуется между деталями, из-за чего появляется необходимость в обеспечении глубокого проплавления деталей. Обычно, это легко достигается путем применения автоматической сварки.
Тавровые швы всегда двухсторонние. Форма подготовленных кромок возможна без скоса и с одним или двумя скосами одной кромки, где обрабатывается только привариваемый торец. Без скоса можно сваривать детали небольшой толщины – от 2 до 40 мм. Для деталей толщиной от 8 до 100 мм следует производить обработка кромки.
При сваривании тавровых швов важно знать их особенность: получаемые швы в итоге прочнее основного металла. Поэтому перед сварочными работами нужно проводить расчеты по получаемому сопротивлению материалов. Это необходимо, чтобы в дальнейшем избежать неравномерной прочности деталей, разной стойкости к нагреву и охлаждению и другим скрытым дефектам.
Угловые швы
Данные шов относится к подвиду тавровых швов, но при этом угловые швы больше распространены, чем тавровые. По форме угловые швы напоминают букву «Г», где угол между деталями может быть любой, но чаще всего – прямой. При работе с угловыми швами главной проблемой является стекание металла по углу или с вертикальной поверхности на горизонтальную. Поэтому важно контролировать ровное ведение электрода, соблюдая углы наклона. Для сварки листов разной толщины рекомендуется держать электрод под углом 60o по отношению к более толстой заготовке. В результате чего, основное тепло приведется на более толстую деталь, а тонкая при этом не перегреется и не деформируется.
Угловые швы бывают односторонние и двухсторонние. Для двухстороннего шва сварка выполняется и на внутреннем, и на внешнем угле. Возможна сварка без обработки кромок или скосами. Скос может выполняться и с двух сторон одной кромки, где при этом вторая кромка не будет предварительно обрабатываться.
Необходимо помнить, что прочность угловых швов ниже прочности основного металла. Этот момент нужно учитывать при проектировании и проведении работ.
Торцевые швы
Торцевые швы применяются для сваривания деталей разной формы, прилегающими друг к другу боковыми поверхностями. Угол прилегания может находиться в пределах до 30градусов. Данная сварка хорошо подходит для работы, как с тонкими, так и с толстыми металлами. Перед сваркой осуществляется разделка кромок под односторонние скосы.
Торцевые швы отличаются высокой выносливостью к нагрузкам. Но при этом возможно попадание влаги или загрязнений между поверхностями деталей, что в будущем приведет к коррозии. Особенно это возможно при наличии непроваров.
Другие критерии классификации сварных соединений
Кроме сварочного соединения, швы классифицируются по другим параметрам:
- по форме шва: выпуклые и плоские швы,
- по протяженности: сплошные и прерывистые швы,
- по положению свариваемых поверхностей в пространстве: горизонтальные, вертикальные, потолочные и нижние швы и другие классификации.
Положение сварного соединения
Нижнее положение Горизонтальное Вертикальное Потолочное положение
Перед началом работ всегда важно определить вид сварного шва по всем параметрам, что поможет подобрать оптимальную технику выполнения сварки в каждом конкретном случае. Например, сварка углового соединения в вертикальном положении потребует более тщательной подготовки, чем сварка стыкового шва в нижнем положении.
Методы контроля качества сварных соединений
Контроль сварных швов является важным ключевым компонентом для обеспечения надёжного и качественного соединения деталей и работоспособности конструкции. После окончания сварочных работ проводится обязательная проверка качества сварных швов. Контрольная процедура дает возможность выявить дефекты, влияющие на прочность соединения и эксплуатационные характеристики готового изделия. Своевременное обнаружение дефектов позволяет избежать аварийных ситуаций и повысить безопасность эксплуатации конструкции.
На крупных производственных предприятиях контроль сварочных швов проводит отдельный специалист-контролер. Но на небольших производствах в штате часто такая единица отсутствует и проверку проводит сам сварщик.
1. Предварительный контроль – здесь происходит проверка поверхности металла, качества электродов, флюсов, присадочной проволоки и газовых смесей. Затем, непосредственно перед тем как приступить к сварке, происходит контроль качества сборки, подготовки рабочего места и осмотр состояния сварочной аппаратуры.
2. Контроль сварки – это проверка правильности выбранного режима и соблюдения технологии в процессе сваривания деталей.
3. Контроль качества – он происходит по окончании процесса сваривания, который осуществляется различные способами, приведенные ниже.
4. Внешний осмотр – здесь происходит визуальный осмотр деталей на наличие видимых дефекты.
Процедура проверки качества сварных соединений проводится в соответствии с ГОСТ и другими нормативными документами. В них указаны допустимые погрешности. По завершению измерений составляется акт и протокол испытаний, в котором указываются результаты. Зачастую, визуального осмотра сварного шва недостаточно, так как дефекты могут быть скрытыми. Поэтому на практике применяют различные способы контроля качества сварных швов, которые подробно описаны ниже.
Визуальный контроль сварных швов
Самый простой, быстрый и недорогой способ осмотра шва это визуальный осмотр. Контроль качества сварных швов проводят на наличие видимых трещин, сколов или других дефектов. Также внимательно изучают шов. Он по всей длине должен иметь одинаковую ширину и высоту. Недопустимо наличие непроваренных участков, наплывов или складок. Перед осмотром с поверхности шва удаляют окалины, шлак и другие загрязнения.
При обнаружении дефекта проводится работа по его изучению, делаются замеры, которые позволяют определить качество сварного соединения. Если это возможно, дефекты устраняются, а изделие отправляется на дополнительную проверку с использованием других методов контроля. Для более глубокой проверки применяются другие виды контроля сварного шва.
Капиллярный контроль сварных швов
Качество сварки может проверяться при помощи капиллярного метода, который основан на свойстве жидкости проникать в мельчайшие раковины и трещины. Особенностью данного метода является то, что он позволяет выявить скрытые дефекты, которые трудно определить с помощью визуального осмотра. Капиллярный метод относительно простой и недорогой, для проведения таких испытаний не нужно применять сложное, дорогостоящее оборудование.
При использовании данного метода используются специальные вещества, которые имеют небольшое поверхностное натяжение — пенетранты. Они способны легко проникать даже в небольшие щели, при этом визуально они видны. Проникая в небольшие трещинки, они окрашивают их, делая видимыми для человеческого глаза. Самые чувствительные пенетранты позволяют обнаружить дефекты диаметром от 0.1 микрон.
Существует множество рецептов пенетрант. В основном они изготавливаются на основе воды, керосина или другой жидкости с небольшим поверхностным натяжением. Этот метод проверки сварных соединений по праву считается одним из самых практичных и эффективных.
Метод пневматической проверки
Пневматический контроль герметичности выполняется с помощью сжатого воздуха. Он применяется для контроля сварных швов трубопроводов, которые работают под высоким давлением. Для этого изделие погружают в ванную с водой, после чего внутрь его подают сжатый воздух до тех пор, пока давление внутри изделия не будет превышать рабочее на 30-50%.
Если речь идет о крупногабаритном изделии, которое невозможно поместить в ванную с водой, то его покрывают специальным пенным раствором, после чего внутрь подается сжатый газ, который будет свидетельствовать о дефекте наличием на поверхности пузырьков.
Химический метод контроля
Химический метод используется для контроля качества герметичности сварных швов трубопроводов и элементов гидравлических систем. Он базируется на свойствах индикаторного вещества изменять свой цвет за счет химического воздействия с контрольным веществом.
Поверхность шва зачищается, на нее наносится фенолфталеиновый раствор. Обработанное место накрывается тканью, пропитанной азотнокислым серебром. Таким образом, можно определить наличие локальных течей, так как в этих местах фенолфталеин приобретает красный цвет, а серебро – серебристо-черный.
Такой метод проверки качества сварных швов достаточно прост. Для контроля не задействуется дорогостоящее оборудование, не требуются специальные знания и навыки персонала. Но у него имеется чувствительность из-за неустойчивости индикаторных пятен.
Радиационный контроль сварных соединений
В радиационный методе выявления внутренних дефектов используют гамма-лучи, которые возникают при самопроизвольном распаде элементов радия или урана. Проверяемая поверхность подвергается воздействию гамма лучей, которые проходят сквозь металл. Если имеют место пустоты, неоднородности или другие дефекты, они отражаются на пленке. Этот метод считается одним из наиболее эффективных. Он позволяет выявить даже небольшой, скрытый для глаза дефект и составить максимально точную картину качества сварного соединения.
Для контроля сварных швов применяют искусственные радиоактивные вещества, называемые изотопы, которыми являются, тулий, кобальт или цезий. Изотопы действуют в течение более или менее длительного времени, например: кобальт – 5 лет, цезий — 33 года, тулий — 129 дней.

Радиографический метод используется не достаточно широко, так как имеет существенные недостатки – одним из которых является необходимость в сложном и дорогостоящем оборудовании. Сканирование должен проводить специально обученный специалист, при этом предъявляются высокие требования к соблюдению техники безопасности. Также с оборудованием нельзя работать длительное время, так как гамма-лучи негативно влияют на организм человека.
Ультразвуковой метод контроля
Ультразвуковой метод контроля основан на способности ультразвуковых волн отражаться от границы раздела двух сред, обладающих разными акустическими свойствами. Раковины, сколы и другие дефекты имеют свои акустические особенности, которые фиксируются с помощью специального оборудования. Так, ультразвук, отразившийся от нижней поверхности изделия возвращается обратно к датчику, затем преобразовывается в электрическое колебание и подается на экран электронно-лучевой трубки. При наличии дефектов ультразвуковые колебания начнут искажаться, которые на экране будут видны в виде всплеска. По характеру и размерам искажений определяют виды и размеры дефектов.
Ультразвуковой метод востребован, так как он достаточно простой, эффективный и бюджетный. Для его применения не нужно сложное, дорогостоящее оборудование, не нужно учитывать физико-химические свойства материалов. К недостаткам ультразвукового метода относят то, что проверку может проводить специалист, имеющий специальные знания и навыки.
Магнитная дефектоскопия
Сущность способа основана на использовании магнитного рассеяния, возникающего над дефектом при намагничивании проверяемого изделия. Каждый металл имеет определенную степень магнитной проницаемости. Если он неоднородный, при прохождении сквозь металл магнитного поля оно искажается. При наличии в сварном шве дефекта магнитный поток будет огибать его, создавая при этом поток рассеивания.
Предварительно, поверхность шва посыпают специальным ферримагнитным порошком, который позволяет визуализировать магнитные линии. Если они ровные, значит, сварное соединение признается качественным. При наличии дефектов линии будут иметь видимые искажения.
Данный метод эффективен, но он может применяться только для работы с ферримагнитными материалами, что является его главным недостатком. Следовательно, с его помощью невозможно проверить качество сварки алюминия, меди и некоторых других металлов. Еще один недостаток – данный метод достаточно дорогой.
Люминесцентный способ контроля
Метод основан на свойстве веществ под названием люминофоры. Они светятся при действии ультрафиолетовых лучей, благодаря чему их применяют для обнаружения поверхностных дефектов, таких как мельчайшие трещины. Перед контролем участок шва необходимо очистить от загрязнений, затем нанести на него жидкий раствор люминофора. После выдержки в течение 10-15 мин раствор смывают, изделие сушат и облучают ультрафиолетовыми лучами в затемненном помещении. По свечению оставшегося в шве раствора обнаруживают дефектные места.
Заключение
Технологии проверки качества сварных швов приблизительно одинаковы для всех видов свариваемых материалов:
- Стали,
- Нержавеющей стали,
- Алюминия,
- Чугуна,
и некоторых других цветных металлов. Наибольшие сложности вызывает проверка результатов ручной дуговой сварки электродами, немного проще проверить результаты газосварки.
Более высокое качество сварного шва обеспечивает сварка полуавтоматом, выполняемая в среде углекислого газа. Настолько же качественными получаются швы, выполненные во многих современных технологиях автоматической сварки. Швы, выполненные в атмосфере аргона, отличаются мизерным количеством шлака и окалины, полноценным составом наплавляемого металла. Проверка таких сварочных соединений показывает лучшие, чем при ручной сварке электродами, результаты.
В полевой обстановке, на стройплощадке, условия выполнения сварочных работ хуже, чем в производственном цеху, уровень качества швов также не так высок. Проверка в полевых условиях сложнее. Эти и многие другие факторы учитывают при разработке проектов тех объектов, где применяется сварка, а качественно запроектированный объект всегда будет доведён до завершения.
цены на решения от компании ВиТэк
Соединение конструкций из металла посредством сваривания сегодня применяется в разных отраслях производства. Однако контроль качества сварных соединений часто осуществляется визуальным способом. Этот подход предполагает человеческий фактор и повышает риск пропущенного специалистом брака, а потому он нерационален и экономически невыгоден. Проблему можно решить при помощи автоматизации процессов проверки прочности и надежности металлоконструкций.
Сущность и способы проверки качества сварных швов
Некачественный сварочный шов может привести к фатальным последствиям на последующих этапах производства или при эксплуатации готовой продукции, ведь речь часто идет о газопроводах и трубопроводах. Поэтому проверять прочность и герметичность сварки критически важно для безопасности людей.
Кроме уже упомянутого визуального способа, методы контроля качества сварных швов включают:
- магнитный;
- ультразвук;
- радиографию.
Контроль качества сварных соединений необходимо осуществлять с учетом того, что дефекты бывают как внешними, так и внутренними. Последние в некоторых случаях невозможно распознать визуальным способом, хотя на многих предприятиях этот метод преобладает. Современные инструменты контроля качества сварки могут выявить скрытые дефекты внутри швов металлоконструкций и обнаружить наличие:
- скрытых трещин и полостей;
- непровара;
- несплавления;
- шлаковых, металлических и других инородных примесей;
- вогнутостей или выпуклостей шва;
- подрезов;
- прожогов.
Автоматизированные системы контроля
Современные технологические решения предоставляют возможность оптимизации процессов контроля качества сварных соединений. Она достигается при помощи автоматизации существующих методов. Максимальная эффективность контроля возможна при использовании комбинированных технологий. Сочетание скоростной камеры, лазера и интерференционных фильтров значительно расширяет функционал устройства. Сварочные процессы становятся хорошо различимы на фото, а быстрые операции, зафиксированные скоростной камерой лучше по качеству, чем замедленная съемка обычной.
Эффективность использования компьютерного зрения базируется на контроле качества сварочных работ наравне с результатом. При помощи скоростного видеооборудования становится возможным в реальном времени мониторить сварочный процесс. Специальное программное обеспечение такой системы позволяет обнаружить некачественный шов. В таком случае система выдает сигнал в соответствии с заранее согласованным промышленным протоколом.
Традиционный способ ультразвукового контроля качества сварки на базе компьютерной техники также обладает широкими возможностями объективной оценки качества.
Преимущества автоматизированных систем
При всем удобстве у визуального контроля качества сварных соединений и швов есть ряд недостатков. Автоматизированные системы путем исключения человеческого фактора увеличивают эффективность производства. Целесообразность их использования на предприятиях подкрепляется следующими преимуществами:
- экономичность установки систем компьютерного зрения;
- объективность — автоматический контроль автономен и проводится без участия оператора;
- снижение времени контроля — благодаря этому проверки можно проводить полнее и чаще, в том числе в целях профилактики;
- надежность — автоматическая проверка деталей осуществляется на основании установленных критериев качества;
- улучшение ситуации по бракам — на очередной этап производства пропускаются только изделия, прошедшие контроль на предыдущих этапах;
- оптимизация процесса — аналитическое программное обеспечение фиксирует параметры режима работы и позволяет воспроизвести те, при которых достигается снижение уровня дефектов;
- устойчивое повышение качества продукции за счет исключения потерь на браки и дорогостоящие доработки.
Кроме того, благодаря фиксации изображений дефектов становится возможным изготовление каталогов производственных дефектов, характерных для конкретного оборудования, а также наблюдать динамику изменений. Это открывает перспективы для оптимизации производства и стабильного улучшения качества сварных швов.
Внедрение системы автоматизации
Чтобы автоматизировать систему контроля качества сварных соединений в условиях производства, обращайтесь в компанию «ВиТэк». Автоматические системы и промышленные измерения — это наша основная специализация. Установим комплекс с использованием современной технологии машинного зрения, который будет контролировать качество сварочных работ на вашем предприятии. Команда профессионалов гарантирует качественное и эффективное выполнение технологических задач любой сложности. Предлагаем готовые решения как для больших, так и для малых бизнес-проектов.
Практические задачи
Форма обратной связи
Сварка геомембраны: виды, методики, проверка стыка
Современные технологии дают возможность производить изоляционные материалы различной направленности. Однако, гидроизоляция должна быть на высшем уровне для любого объекта. В подобных случаях оптимальным решением является использование геомембраны — прочного и плотного материала на основе полиэтилена. Наиболее надежным способом скрепления полотнищ является сварка, о ней и пойдет речь.
Основная информация
Геомембрана представляет собой рулонный материал изготовленный из полиэтилена или поливинилхлорида. В свою очередь, мембраны из полиэтилена делятся на два вида:
- LDPE (из материала малой плотности, но высокого давления) — морозоустойчивые, мягкие, легко растягиваются.
- HDPE (из материала с высокой плотностью, но низкого давления) — твердые, не устойчивы к морозам, почти не растягиваются.
Основным направлением применения полимерных пленок является гидроизоляция различных объектов, в том числе емкостей с нефтепродуктами. В последнее время геомембраны все чаще используют, как противофильтрационные экраны на рудниках, в сельском хозяйстве, в химической отрасли.
Ширины рулона не всегда хватает для выполнения задуманного, поэтому полотнища часто соединяют между собой.
Методы обработки
Перед началом сварочного процесса геомембрану следует подготовить, как и любую другую поверхность. Правильная подготовка облегчает работу и снижает вероятность появления дефектов.
В предварительную обработку входит:
- Укладка материала на основание. Чтобы постелить пленку ровно, необходимо сначала убрать все видимые неровности (кочки, камни, ветки и т.д.), выровнять грунт, при необходимости закрепить полотнища анкерными болтами.
- Соединение краев полотнищ. Нахлест должен быть около 10-20 см.
- Очистка шва от пыли, мусора, грязи.
Для качественного скрепления пвх ткани применяют три вида сварки:
- Контактная. Суть этого метода состоит в том, что сваривание поверхностей осуществляет специальный аппарат, оборудованный металлическим клином с диапазоном температур от 210°С до 450°С градусов.
Клин разогревает края свариваемых пленок, прижимные валики уплотняют соединение. Образуется двойной прочный шов с проверочным воздушным каналом, либо без него. Однако, убедиться в герметичности полученного шва легче с контрольным каналом, для этого достаточно резко оказать на канал сильное воздушное давление.
- Экструзионная. Сварка геомембраны в данном случае производится сварочным аппаратом — экструдером с использованием присадочной проволоки при температуре 210-250 °С. Этот метод обработки полимерных пленок чаще всего применяется в труднодоступных местах, на угловых стыках, а также для устранения дефектов или наложения заплаток. При протяжке через экструдер присадка плавится, заполняет собой зону сварки, из-за чего края свариваемых поверхностей нагреваются и образуют в результате прочный и герметичный шов. Присадочный пруток должен быть изготовлен из того же полимера, что и геомембраны.
- Горячим воздухом. Суть данного способа заключается в обработке воздухом, нагретым выше температуры плавления полимера, из которого изготовлены соединяемые пленки.
Данный тип обработки весьма трудоемкий, поэтому используется довольно редко и на небольших участках пленки.
Ручная сварка
Несмотря на то, что сварка геомембраны производится специальным оборудованием, осуществить задуманное можно и в домашних условиях. Для этого потребуется обычный строительный фен, температура воздушной струи у которого в диапазоне 175-240°С градусов.
Использовать при ручной сварке фен высокой мощности нецелесообразно. Для работы с таким феном необходимы соответствующие навыки.
Обработка полимерных пленок своими руками происходит по типу сварки горячим воздухом. Свариваемые мембраны нагреваются до вязко-текучего состояния, после чего соединяются и продавливаются подвижными роликами для образования герметичного однородного шва.
Сварка геомембраны вручную — процесс кропотливый и утомительный, поэтому чаще всего обработке подвергаются листы малого размера, труднодоступные места или участки сложной формы.
Проверка швов
Геомембрана — прочная и жесткая пвх ткань, поэтому контроль герметичности швов необходим на протяжении всего процесса обработки. Подобный контроль позволяет своевременно обнаружить возможные дефекты и недочеты. Сначала проводится осмотр на наличие выпуклых образований, складок, гладкости и однородности швов. После этого уже в местах возможной утечки выполняется проверка:
- Вакуумом. Участок с предполагаемой разгерметизацией обрабатывают насыщенным мыльным раствором и накрывают прозрачным колпаком с клапаном контроля давления. При помощи насоса внутри колпака создается вакуум и в течение 15-30 секунд осуществляется наблюдение. Если на поверхности образуются мыльные пузыри, то шов негерметичен. Оставшийся шов проверяется также, но обязателен нахлест 5-7 см на предыдущий участок.
- Давлением. На ограниченном участке проверочного канала специальной иглой делается контрольное отверстие, через которое нагнетается избыточное давление.
После прекращения подачи давления за участком наблюдают в течение 8-10 минут. Если за это время давление снизится более, чем на 10%, то герметичность шва нарушена. По окончании проверки контрольное отверстие обязательно заваривается.
- Разрывом. В этом случае проверке подлежат участки с выполненным швом, вырезанные из готового полотнища. Получившиеся дырки заваривают заплатками из аналогичного материала. Испытание на разрыв проводится не так часто, в основном на больших площадях с одинаковым типом сварного соединения.
Для объектов сложной конфигурации проверку герметичности сварных швов устраивают с помощью специальных систем тестирования, в том числе и вакуумных. Подобные системы позволяют проверить как прямые, так и угловые швы, а также обследовать труднодоступные места.
Сварка пвх ткани (геомембраны) — процесс трудоемкий и кропотливый. Перед осуществлением сварки необходима тщательная подготовка, как рабочего места, так и свариваемых поверхностей. Полимерные мембраны плотные и жесткие, поэтому их обработка требует определенных навыков и умений. Сварку таких пленок лучше осуществлять специалистам, так как неопытность может привести к возникновению дефектов, а следовательно, и к ухудшению гидроизоляционных свойств геомембран.
Проверка герметичности сварных швов — Энциклопедия по машиностроению XXL
Более совершенным и удобным методом проверки герметичности сварных швов является электроискровой способ. Проверка качества швов индуктором подробно описана на стр. 202. В зависимости от толщины винипласта устанавливают нужное напряжение для работы индуктора. Практически принято считать, что на 1 мм толщины винипласта необходимо подвести к искателю наиряжение около 10 ООО—15 ООО в. [c.240]ПРОВЕРКА ГЕРМЕТИЧНОСТИ СВАРНЫХ ШВОВ [c.85]
Проверку герметичности сварных швов, предусмотренных ГОСТ 3242—54, производят при помощи керосина, аммиака, обдувом воздухом, воздушным или гидравлическим давлением, наливом или поливом воды.
[c.21]
Герметичность швов в закрытых аппаратах проверяют сжатым воздухом при небольшом давлении. Для этого наружные швы аппарата смачивают мыльным раствором, и если сварные соединения окажутся неплотными, то с их наружной стороны образуются мыльные пузыри. Более совершенным и удобным методом проверки герметичности сварных швов является электроискровой способ. Проверка качества швов индуктором подробно описана на стр. 215. В зависимости от толщины винипласта устанавливают нужное напряжение для работы индуктора. Практически принято считать, что на 1 мм толщины винипласта необходимо подвести к искателю напряжение около 10 000—15 000 в. [c.266]
Более совершенный и удобный метод проверки герметичности сварных швов — электроискровой (см. стр, 239). В зависимости от толщины винипласта устанавливают необходимое напряжение для работы индуктора, обычно 10 000—15 000 В.
[c. 285]
В настоящее время методы контроля сварных соединений делятся на следующие группы методы контроля подготовки изделий под сварку н наружных дефектов (сюда относится люминесцентный метод контроля) методы контроля с частичным или полным разрушением сварных швов физические методы контроля без разрушения (гамма- и рентгеновский контроль, магнитные и ультразвуковой методы контроля) методы контроля герметичности сварных швов (контроль керосином вакуумный, гидравлический, пневматический методы контроля метод химических реакций и метод течеискателей) методы контроля сварных соединений, образованных с помощью прессовых способов сварки (проверка параметров режима сварки, которые характеризуют степень нагрева и величину осадки). [c.327]
В отличие от проверки индуктором резиновых покрытий, наклеенных а металл, при испытании герметичности сварных швов винипласта под швы подкладывают и. плотно прижимают металлическую полосу. Затем один из полюсов искрового индуктора присоединяют к металлической подложке, а другой — к искателю (щетке, щупу). Появившаяся искра указывает на место расположения в сварном соединении сквозных отверстий.
[c.285]
Пробной гидравлической нагрузкой испытывают замкнутые сосуды типа паровых котлов и сосудов, работающих под давлением, а также трубопроводы. Хотя в правилах устройства и эксплуатации таких конструкций при гидравлических испытаниях и ставится задача проверки прочности конструкции и плотности сварных швов и соединений, однако в действительности при подобных испытаниях создаются такие условия работы конструкции, при которых пробная нагрузка значительно меньше запаса прочности. В этом случае можно говорить лишь о частичной проверке прочности в основном при гидравлических испытаниях проверяется Герметичность сварных швов и соединений. [c.142]
Реторта с приваренным донышком подвергается испытанию на герметичность воздухом давлением в 2 ат. Проверка сварных швов производится мыльной водой.

Большинство изделий химического машиностроения проходят испытания на прочность, герметичность и работоспособность. Оборудование для проведения этих испытаний делится на три основные группы для гидравлических испытаний для пневматических испытаний для проверки на герметичность. Кроме того, особую группу составляют оборудование и приборы для контроля различных элементов конструкций (например, сварных швов) в процессе изготовления до общего испытания изделия. Применяемое на практике оборудование чаще всего сочетает в себе элементы, относящиеся к разным группам, и выполняет несколько функций. [c.93]
Гидравлическим испытаниям подвергают трубопроводы, резервуары, технологические аппараты и другие сооружения с целью проверки как плотности, так и прочности сварных швов. Гидравлические испытания регламентируются ГОСТ 3242—79, который предусматривает осуществление их тремя способами гидравлическим давлением, наливом воды и поливом водой. Выбор способа, основные параметры испытаний (величина давления, выдержка и герметичность) устанавливают соответствующие ТУ.
[c.32]
Неразрушающие способы контроля качества сварных соединений. Неразрушающие способы контроля качества сварных швов состоят из внешнего осмотра и обмера сварных швов, проверки непроницаемости (герметичности) сварных соединений, а также радиационного, ультразвукового и реже магнитного методов контроля. [c.175]
Для проверки заднего моста на герметичность через резьбовое отверстие под сапун подают воздух, создавая давление в картере 0,02. .. 0,025 МПа. Недопустимо подтекание смазочного материала через манжеты, места соединений и сварные швы на балке с образованием капель. Допустимо только незначительное образование пятен из смазочного материала в указанных местах, кроме сварных швов. [c.107]
ГИДРАВЛИЧЕСКОЕ ИСПЫТАНИЕ (сварного изделия) — проверка герметичности и прочности швов изделия путем заполнения его водой, маслом или другой жидкостью и создания давления (гидростатическое испытание, испытание наливом) или же обливания струей воды (испытание поливом, испытание струей).
[c.34]
Для контроля качества сварных соединений аппаратуры емкостного типа, работающей под давлением, применяют различные методы, основными из которых являются 100%-ный визуальный осмотр швов, выборочный контроль рентгенопросвечиванием и ультразвуком. Готовые изделия проходят испытания внутренним давлением, превышающим в 1,2—1,5 раза рабочее, а также проверку герметичности. Ультразвуковой контроль может быть использован не только для выявления дефектов, но и для контроля толщины антикоррозионного слоя, нанесенного сваркой. При этом используют раздельно-совмещенный искатель, устанавливаемый со стороны основного материала. Он позволяет получать на экране два сигнала, отраженные от наружной поверхности и границы раздела. При толщине наплавленного слоя более 0,5 мм точность определения составляет 1 %. [c.234]
Детали второй степени ответственности. Топливные баки проходят 100%-ный контроль на герметичность избыточным давлением 0,25 кгс/см в ванне с водой. При внедрении сварного варианта бака с высокой надежностью герметичности швов вводят 100%-ный вакуумный контроль с последующей проверкой в ванне с водой места дефекта незначительной части баков.
[c.349]
Вышеприведенные способы установки затрудняют также проверку герметичности сварных швов днища крупногабаритных дппаратов при приемке их под химзащиту. [c.112]
Контроль герметичности сварных швов приварки колец к корпусу аппарата и к патрубку штуцера (при укреплении отверстия накладными кольцами) производят пневматическим испытанием при давлении в соответствии с требованиями ОСТ 26-291—79. Для сталей, склонных к трещинооб-разованию сварные швы приварки накладок проверяют, кроме того, цветной дефектоскопией. При таком контроле проверка на герметичность этих соединений гидравлическим методом с люминесцентным индикаторным покрытием не производится. [c.582]
Сосуды, предназначенные для хранения и переработки веществ, обладающих токсичными или вэрыво- и пожароопасными свойствами, должны изготовляться по технологии, обеспечивающей высокую герметичность и прочность сварных швов. Контроль качества сварных соединений производится ультразвуковой дефектоскопией и просвечиванием рентгеновскими или гамма-лучами в пределах объема, указанного в табл. 11.23. Кроме того, сварные швы должны подвергаться механическим и металлографическим исследованиям с целью проверки их прочности и пластических характеристик. Механические испытания сварных соединений должны выполняться в соответствии с требованиями ГОСТ 6996-81.
[c.421]
Снаряжение твэлов топливом дозировка и упаковка таблеток в подготовленные к сборке оболочечные трубки, установка концевых деталей, наполнение гелием, герметизация (сваркой), контроль сварных швов, дезактивация, проверка герметичности и гео— етрических размеров твэла, автоклавирование, контрольные операции и передача твэлов на сборку. [c.324]
Контроль качества сварного шва
1 Визуальный контроль качества
– Визуальный контроль качества заключается в выявлении следующих признаков:
• хорошо виден след от прижимных роликов;
• небольшой выплав разогретого материала вещества (валик)
между слоями мембраны;
• отсутствие складок на поверхности шва;
• отсутствие признаков перегрева материала (изменение
цвета мембраны, наличие пережженных участков).
– Также визуально оценивайте состояние поверхности выполненной гидроизоляции, фиксируйте следующие дефекты:
• вздутия;
• складки;
• разрывы;
• трещины и т. п.
– Своевременно устраните выявленные дефекты.
– Швы, выполненные ручным или полуавтоматическим аппаратом, должны быть проверены на предмет непрерывности, герметичности, а также на наличие сварного валика вдоль шва.
– Для этого Вам необходимо
воспользоваться проб-
ником проверки качества
шва или тонкой шлицевой
отверткой (со скругленными
краями шлица).
– Пр оведи те пр обником
вдоль шва, легко нажимая
на него – кончик пробника
не должен проникать в шов.
ВАЖНО! Старайтесь не прилагать чрезмерного усилия к пробнику, чтобы не повредить шов в ходе его проверки.
2 Инструментальный контроль качества
– Герметичность всех швов, выполненных как автоматическими аппаратами, так и ручным оборудованием, следует контролировать с применением специализированного оборудования и инструмента.
– Герметичность швов, выполненных автоматическими аппаратами «Twinni-T» или «Twinni-S» с образованием двойного шва с проверочным каналом, следует проверять методом избыточного давления.
– Для проверки герметично-
сти двойного шва методом
избыточного давления тре-
буется следующее оборудо-
вание:
• полая игла с манометром;
• соединительный шланг;
• компрессор.
– Вместо компрессора может быть применен ножной насос для накачки автомобильных шин. Иглу для проверки качества в таком случае можно применить без встроенного монометра.
– После выполнения сварки
двух полотнищ мембраны
шов следует запечатать с
двух концов. Для этого за-
паяйте оба конца ручным
сварочным аппаратом с
прокаткой краёв тефлоно-
вым роликом или зажмите
их специальным зажимом.
– Еще один способ выполнения «запечатки» шва.
– В месте окончания шва
«вскройте» образованный в
процессе сварки провероч-
ный канал «крючкообраз-
ным» ножом.
– Заварите проверочный
канал используя узкую насадку и латунный ролик.
– После того как проверочный канал «заглушен» по-
средством сварки, удалите
непроваренную часть на-
хлеста для последующей
установки заплатки.
– Установите заплатку таким
образом, чтобы она «пере-
крывала» ширину шва и
полученное в результате
разреза отверстие в про-
верочном канале. Приварку
заплатки начинайте от про-
верочного канала, двигаясь
к ее краям.
– Заварите проверочный ка-
нал с противоположного
«конца» шва и установите
заплатку. После произве-
дите проверку давлением
воздуха.
– Для проверки герметичности шва введите иглу с манометром в пространство
воздушного канала.
– Для этого слегка разогрейте ручным аппаратом поверх-
ность шва, в которую намечен ввод иглы.
ВАЖНО! Будьте предельно осторожны при вводе иглы, она не должна повредить оборотную сторону воздушного канала.
– Присоедините соединительные шланги к компрессору. Включите компрессор и производите подачу возду-
ха до давления 1,5 атм для толщины мембраны 1,5 мм, до 2 атм — для толщины мембраны 2 мм.
– После достижения заданной
величины давления отклю-
чите компрессор и следите
за показателями маноме-
тра. Если в течение 5 мин.
давление в шве упало не бо-
лее чем на 20%, шов являет-
ся герметичным. Если паде-
ние давления в шве более
20%, это свидетельствует о некачественной сварке. Такой шов следует переделать или отремонтировать.
– После проверки герметич-
ности шва извлеките иглу
из проверочного канала.
На место прокола мембра-
ны установите заплатку.
– Швы, выполненные ручным оборудованием или автоматиче-
скими аппаратами без образования двойного шва, следует
проверять вакуумным методом.
– Необходимый набор обору-
дования:
• вакуумный компрессор;
• соединительные трубки;
• вакуумный «колпак» с мяг-
кой резиновой прокладкой
по периметру.
– На очищенный шов нанеси-
те мыльный раствор, после
чего на смоченный участок
шва установите вакуумный
«колпак», обеспечив при
этом герметичность приле-
гания рамки «колпака» к по-
верхности мембраны силь-
ным нажатием на ручки.
– Включив вакуумный ком-
прессор создайте в вакуум-
ной камере разряжение до
2,0 МПа на протяжении не
менее 15 сек., после чего
отключите компрессор. В
некачественно проварен-
ных местах появятся мыль-
ные пузыри.
– Места появления мыльных
пузырей отмечайте как
дефектные. Шов на этих
участках следует отремон-
тировать.
– Далее следует произвести проверку на смежном участке шва.
Для этого переставьте вакуумный колпак дальше по шву с перекрытием уже проверенного участка на 10 – 20 мм и повторите проверку снова. Таким образом следует проверить шов по всей длине.
– Кроме описанных методов
прочность сварного шва
вне зависимости от спо-
соба его формирования
следует выборочно контро-
лировать на стационарной
разрывной машине, напри-
мер «h20KT–0238», либо
на переносной разрывной
машине типа Leister Examo.
– О качественном шве свиде-
тельствует разрыв по мем-
бране, а не по соединению
между мембранами.
Чтобы познакомиться с нашими расценками на выполнение работ позвоните по телефону: 8(925)-240-28-11 и наши специалисты ответят на все Ваши вопросы по кровельным или фасадным системам дома. Вы также можете воспользоваться формой Обратная связь или приехать в наш офис.
Ваш звонок очень важен для нас!
Более подробную информацию об устройстве мембранной гидроизоляции фундаментов Вы сможете узнать на следующих страницах:
Испытание сварных швов
Визуальное испытание
Испытание на пенетрант
Ультразвуковое испытание
Импульсное эхо-тестирование
Техника улавливания шага
Сквозное пропускание
Метод TOFD
Вихретоковый контроль сварных швов
9000 тестирование
Сварные швы являются наиболее распространенным типом неразъемных соединений во всех отраслях промышленности. Существует множество видов сварки, как с точки зрения методов сварки (ручная электрическая дуга, автоматическая или полуавтоматическая, дуга под флюсом, дуга в защитных газах, электросварка сопротивлением и т. Д.)), так и по конфигурации стыков (стыковые, угловые, тройники, нахлесточные швы). Однако в большинстве случаев, независимо от метода сварки, сварные соединения подлежат проверке качества по окончании сварки. Дефектоскопия направлена на выявление различных дефектов, которые приводят к снижению прочности сварного шва или плохой герметичности. Своевременное обнаружение таких дефектов существенно влияет на определение срока службы всей сварной конструкции. Качество сварки особенно важно для сосудов и систем высокого давления, а также для несущих конструкций.
Неразрушающий контроль (NDT) — основной метод контроля сварных соединений, поскольку он позволяет сохранить целостность и рабочие характеристики испытываемого изделия. Для этого было создано множество методов неразрушающего контроля и разнообразное оборудование для испытаний сварных швов. При выборе любого из методов или конкретного инструмента необходимо учитывать множество факторов, таких как материал свариваемых деталей, конфигурация сварного шва, состояние поверхности, требования к качеству, доступ, тип и расположение потенциального дефекта ( прерывность), производительности и стоимости тестирования.Поэтому единого универсального метода неразрушающего контроля не существует, поэтому качество, надежность и долговечность готового изделия во многом будут зависеть от выбора наиболее подходящего варианта.
Визуальный контроль
Этот метод сочетает в себе визуальный контроль и измерение геометрических параметров сварных швов для проверки их соответствия требуемым значениям. Перед испытанием сварные швы следует очистить от окалины, шлака и брызг металла.После этого поверхность следует обработать спиртом, либо протравить 10% -ным раствором азотной кислоты. В качестве инструмента для этого типа испытаний обычно используются лупа с увеличением 5 или 10, а также осветительные приборы и измерительные приборы (линейка, штангенциркуль, шаблоны) для проверки размеров сварных швов и дефектов. Несмотря на кажущуюся простоту, этот тип тестирования очень эффективен и предшествует другим методам. Если дефекты обнаружены уже на этом этапе, сварной шов считается бракованным и дальнейшие испытания не проводятся.Очевидным недостатком этого метода является невозможность выявления большинства скрытых дефектов и субъективность методов оценки, что требует от инспектора неразрушающего контроля большого опыта. Поэтому, даже если визуальный контроль не выявил каких-либо дефектов, следует использовать оборудование для контроля сварных швов для дальнейшего осмотра, поскольку скрытые дефекты могут незаметно разрушить соединение и привести к очень опасной ситуации.
Испытание на проницаемость
Этот метод основан на способности жидкости проникать и заполнять мельчайшие капиллярные каналы, которые в основном образованы дефектами сварного шва.К таким дефектам относятся поры и трещины, разрушающие поверхность материала. Скорость и глубина проникновения жидкости зависит от радиуса капилляра и смачиваемости жидкости. Таким образом, пенетрантный метод очень эффективен для обнаружения поверхностных дефектов. Для повышения его эффективности используются так называемые пенетранты, которые могут проникать глубоко в капилляр из-за своего небольшого поверхностного натяжения. Их яркий цвет делает их заметными, что облегчает обнаружение дефекта.Набор для тестирования на пенетрант обычно включает пенетрант; очищающее средство для тщательной очистки поверхности перед тестированием; проявитель для извлечения пенетранта из дефекта и создания индикаторного рисунка на контрастном фоне, с помощью которого можно увидеть размер и форму дефекта.
Этот метод контроля аналогичен визуальному, поскольку предполагает визуальный контроль сварного шва, поэтому имеет те же недостатки. Чтобы убедиться, что скрытые дефекты не были пропущены, настоятельно рекомендуется использовать оборудование для вихретокового или ультразвукового контроля сварных швов после пенетрантного контроля.
Ультразвуковой контроль
UT — один из наиболее распространенных методов, так как он обеспечивает точное обнаружение скрытых дефектов, расположенных внутри сварного шва. Метод основан на использовании ультразвуковых волн, которые распространяются через слой металла и отражаются от его границы и границ внутренних несплошностей. На основании разницы во времени между отправленным и отраженным сигналами, а также формы и амплитуды отраженных сигналов можно оценить не только толщину металла, но и дефекты, встречающиеся на пути прохождения звука.Инструмент, который используется для ультразвукового контроля, называется «дефектоскоп». В дефектоскопе используются специальные преобразователи (передатчики / приемники ультразвукового сигнала), которые позволяют реализовать методы эхо-импульса, захвата основного тона и сквозной передачи.
OKOndt GROUP ™ производит различное оборудование для ультразвукового контроля сварных швов. Наряду с несколькими портативными дефектоскопами у нас есть специальный продукт для ручного контроля сварных соединений — комплект УСР-01 + Sonocon B.
Метод импульсного эха
При использовании метода импульсного эха преобразователь посылает зондирующий сигнал на объект контроля и принимает эхо-сигналы, отраженные от дефектов, а также от конструктивных особенностей продукта. По времени прихода сигнала можно определить местоположение дефектов, а по амплитуде сигнала — размер дефектов. Недостатком этого метода является необходимость того, чтобы дефект имел отражающую поверхность, перпендикулярную ультразвуковому лучу, или располагался рядом с поверхностью изделия. Например, метод импульсного эха не позволяет обнаруживать плоские дефекты (трещины и отсутствие плавления), которые не расположены близко к поверхности испытуемого изделия.В случае предполагаемых глубоко укоренившихся дефектов следует использовать соответствующее оборудование для испытания сварных швов, способное успешно обнаружить эти типы дефектов.
Метод улавливания шага
Метод импульсного эха не позволяет обнаруживать плоские дефекты (трещины и отсутствие сплавления), которые не расположены близко к поверхности тестируемого продукта. Техника подбора мяча, дуэт и тандем, используются для распознавания вышеупомянутых недостатков. Это достигается с помощью пары преобразователей, установленных таким образом, что сигнал, излучаемый первым преобразователем, возвращается ко второму преобразователю после отражения от плоского дефекта.
Метод сквозной передачи
Однако даже режим захвата шага не гарантирует обнаружение всех разнонаправленных дефектов. Для этой цели используется метод сквозной передачи, когда преобразователи размещаются по обе стороны от сварного шва, так что сигнал, отраженный от задней поверхности, поступает в приемник. Достаточно крупные дефекты практически любой ориентации, пересекающие ультразвуковой луч, затеняют указанный сигнал, что свидетельствует об их обнаружении.Но, к сожалению, этот тип оборудования для ультразвукового контроля сварных швов не дает точной информации о местоположении (координатах) обнаруженных дефектов. Для получения точных показаний ультразвукового дефектоскопа необходимо произвести предварительную настройку с помощью специализированных эталонных блоков, которые обычно поставляются вместе с прибором. Эталонные блоки различных типов также можно приобрести отдельно, в зависимости от конкретного приложения или конкретной задачи неразрушающего контроля.
Метод TOFD
В последние десятилетия метод ультразвуковой дифракции по времени пролета (TOFD) для исследования сварных швов становится все более распространенным.Метод TOFD основан на взаимодействии ультразвуковых волн с краями несплошностей. Это взаимодействие приводит к генерации дифракционных волн с широким диапазоном углов. Регистрация дифракционных волн позволяет установить наличие неоднородности. Время передачи сообщаемых сигналов является мерой оценки высоты несплошности, что позволяет измерять размер несплошности, который всегда определяется временем передачи дифракционного сигнала. Амплитуда сигнала не используется для измерения размеров.В этом случае генерируются и применяются как продольные, так и поперечные волны. Основная информационная характеристика — время прихода сигнала. Метод TOFD имеет ряд преимуществ по сравнению с обычным ручным ультразвуковым контролем:
- Производительность в несколько раз выше;
- Низкая чувствительность к ориентации дефектов;
- Возможность не оценивать, а измерять реальные размеры плоских дефектов;
- Высокая степень отчётности результатов испытаний.
Для реализации метода TOFD используется специальное оборудование с одной или несколькими парами датчиков, которые размещаются с обеих сторон сварного шва и перемещаются по нему во время контроля. OKOndt GROUP ™ имеет беспроводную систему TOFD-Man — один из уникальных инструментов в обширном ассортименте нашего оборудования для ультразвуковой и вихретоковой сварки.
Контроль вихретоковой сварки
Вихретоковый неразрушающий контроль основан на анализе взаимодействия внешнего электромагнитного поля с электромагнитным полем вихревых токов, индуцируемых этим полем в контролируемом объекте.Принцип действия извещателей ET основан на методе вихревых токов, который заключается в искажении вихревых токов в локальной тестовой зоне с последующей регистрацией изменений электромагнитного поля вихревых токов, вызванных дефектом и электрофизических свойства тестового объекта. Этот метод отличается малой глубиной испытаний, так как он используется для обнаружения трещин и разрывов в материале на глубине до 2 мм. Конструкция и процедура настройки оборудования для вихретоковой сварки напоминают процедуру проектирования и настройки их ультразвукового аналога, с использованием вихретоковых датчиков и эталонных блоков вихретокового контроля соответственно.Очевидно, что методы ультразвукового и вихретокового контроля дополняют друг друга, обеспечивая стопроцентно надежный контроль сварного шва по всей его глубине и протяженности. OKOndt GROUP ™ производит серию вихретоковых дефектоскопов для неразрушающего контроля сварных швов.
Контроль магнитных частиц
Контроль магнитных частиц — метод неразрушающего контроля, основанный на явлении притяжения частиц магнитного порошка потоками магнитного рассеяния, возникающими над дефектами намагниченных объектов контроля.
Метод магнитных частиц предназначен для обнаружения поверхностных и подповерхностных неоднородностей, таких как волосы, трещины различного происхождения, неплавление сварных соединений, флокен, закаты, разрывы и т. Д. Дефектоскоп с магнитными частицами позволяет контролировать различные формы, сварные швы, внутренние поверхности отверстий путем намагничивания отдельных контролируемых участков или изделия в целом круговым или продольным полем, создаваемым набором намагничивающих устройств, питаемых импульсным или постоянным током, или постоянными магнитами.
Радиографический контроль
Радиография описана здесь только с целью предоставить полное представление о методах неразрушающего контроля, которые используются для контроля сварных швов. Хотя этот метод является достаточно строгим, его применение довольно ограничено, поскольку связано с использованием гамма-лучей и рентгеновских лучей с высокой проникающей способностью, что позволяет им проходить сквозь металл, в то время как дефекты фиксируются на пленке. Это увеличивает опасность для здоровья человека.К тому же инструменты этого типа довольно дороги. Итак, это очень специфический метод тестирования, требующий использования соответствующих средств индивидуальной защиты, а также создания лабораторных условий для тестирования.
Итак, мы рассмотрели основные методы неразрушающего контроля сварных швов и кратко упомянули соответствующее оборудование для контроля сварных швов. Очевидно, что совместное использование ультразвукового, вихретокового и магнитопорошкового контроля обеспечивает наиболее точные результаты испытаний и безопасные условия испытаний.
3 Проблемы с контактными советами и способы их решения
Обычно, когда я встречаюсь с мастером или начальником производства и получаю возможность лично поговорить с его или ее сварщиками, одна из самых распространенных тем, которые поднимаются, — это их контактные советы. Проблема: им приходится их слишком сильно менять. Это снижает производительность цеха, сильно снижает затраты и, как правило, создает менее эффективную атмосферу для работы сварщика.
Так почему ваши контактные советы недолговечны? И какие проблемы приводят к сбою контактных подсказок? Как их предотвратить? Три наиболее распространенных проблемы, с которыми вы, вероятно, сталкиваетесь постоянно:
- Плохой срок службы и качество контактного наконечника
- Дожиг
- Проволочный хлыст
Ниже я расскажу о трех наиболее распространенных проблемах с контактными наконечниками, с которыми я сталкиваюсь каждый день, и о том, как обычно можно решить эти проблемы.
Плохой срок службы и качество контактного наконечника
Они выглядят одинаково, имеют одинаковую нить, на ощупь такие же в руке, но как только вы попробуете их проверить, это совсем другая история. Практически каждый производитель сварочных материалов изготавливает медные контактные наконечники, но если вы попробовали многие из них, легко понять, что не все работают одинаково.
Не все чаевые одинаковы. Плохие контактные наконечники равны плохому качеству сварных швов и большому времени простоя. Назначение любого контактного наконечника — подавать напряжение на провод.Но если у вас есть контактный наконечник, который не проводит напряжение должным образом, вы столкнетесь с высоким сопротивлением, повышенным нагревом наконечника, повышенным износом и проблемами качества сварки. Как? Контактный наконечник, который не проводит напряжение, как должен, будет производить больше брызг и микродуг.
Лучшее решение этой проблемы — рассмотреть и рассмотреть более качественные контактные наконечники. Использование медно-циркониевого, посеребренного или даже более чистого медного наконечника может существенно повлиять на максимальные характеристики контакта, срок службы и качество сварки.На самом деле мы подробно рассказываем о различных материалах для контактов в другом сообщении в блоге.
Еще один способ защитить и продлить срок службы контактного наконечника — внимательно изучить допуски на контактный наконечник. Не все производители контактных наконечников производят наконечники с одинаковыми допусками на отверстие наконечника. Те, которые имеют большие допуски или отклонения в размере контактного наконечника, могут привести к таким проблемам, как микродуговое искрение и плохая проводимость. Взгляните на допуски на контактный наконечник и посмотрите, насколько плотно прилегает провод к стержню.
Ожог
Отжиг — это когда проволока проходит через отверстие дуги наконечника в самом начале наконечника и снова прожигает контактный наконечник. Отжиг является проблемой для сварщиков и сварщиков, особенно в профессиональной среде, потому что это приводит к длительным простоям. Независимо от того, пытаетесь ли вы стереть ожог с наконечника и вытащить проволоку, или просто выбросите ее и замените, в любом случае сварщику придется потратить время на изготовление. И если вы выберете наиболее распространенный (и простой) путь, заменив контактный наконечник, вы добавите материальные затраты, а также время, что усугубит потери.
Чтобы решить проблему получения ожога, нужно прежде всего понять причины, по которым вы получаете ожог. Причин много, но некоторые из основных:
- Параметры сварки
- Слишком низкое или высокое напряжение
- Грязный материал на основном металле
- Заполнитель низкого качества
- Плохой / неправильный контактный наконечник
- Изношенный или поврежденный лайнер
Одна из наиболее частых причин — неправильный размер наконечника и проволоки. Если вы используете, например, сварку контактного наконечника 0,045 с проволокой 0,035, это вызовет обратный ожог. Неправильный размер наконечника приводит к плохой проводимости внутри контактного наконечника, возникновению микродуги внутри контактного наконечника и, в результате, волочению проволоки и возникновению обратного ожога. Поэтому сначала убедитесь, что размер контактного наконечника соответствует размеру провода, если вы получите ожог.
Некачественный присадочный металл или материал наконечника — еще одна довольно распространенная причина возгорания. Использование материалов более высокого качества поможет сделать зажигание дуги более чистым и надежным, а также уменьшить электрическую дугу и другие ранние признаки возгорания.
Еще одно решение — посмотреть на основной металл. Если он грязный или вы пытаетесь провести сварку через ржавчину или окисление, может произойти возгорание. По возможности тщательно очистите и подготовьте основной металл перед сваркой. Также не забудьте проверить лайнер на наличие загрязнений.
Проволочный хлыст
Обычно это большая проблема при автоматизации, чем при ручной сварке. Проволочный хлыст — это когда проволока, выходящая из контактного наконечника, как бы отклоняется от направления отверстия контактного наконечника.Однако это проблема контактного наконечника, потому что внутри наконечника он не удерживает проволоку плотно и позволяет ей отклоняться от центра и не задевать сварное соединение там, где это необходимо.
Изгиб проволоки часто вызывается простым скручиванием кабеля или сварочными операторами, у которых нет устройства для выпрямления проволоки. Когда проволока выходит из барабана катушки, она имеет память или литье, поэтому, когда проволока разматывается из барабана через гильзу и, в конечном итоге, выходит из контактного наконечника, эта память играет важную роль в том, куда идет проволока. .В некоторых случаях может пропустить весь сустав.
Когда сварщик сталкивается с проволочной плеткой, он часто может отрегулировать положение и манипулировать шейкой горелки, чтобы решить эту проблему. В автоматизации это проблема, которую не всегда можно устранить, но всегда можно хотя бы компенсировать. В этом случае одним из способов преодоления устойчивости к биению проволоки является отверстие наконечника. заключается в использовании контактных наконечников с жестким допуском, которые обеспечивают более жесткую посадку провода и допускают минимальное отклонение от направления отверстия контактного наконечника.
Есть проблемы, с которыми вы постоянно сталкиваетесь с расходными материалами? Поделитесь своим опытом (и решениями) в поле для комментариев, и если вы хотите увидеть, что другой тип контактного наконечника — более высокий класс или более жесткий допуск — может сделать для вашей производительности, свяжитесь с отделом продаж Binzel. Менеджер в вашем районе.
Методы оценки качества полимерных сварных швов »Декорирование пластмасс
Рис. 1. Лазер Laserline 980 нм и инструменты Оценка качества полимерных сварных швов важна для разработки и технического обслуживания сварочного процесса. Однако выбор метода оценки может быть сложной задачей из-за большого разнообразия вариантов.
В этой статье обсуждается сравнение некоторых популярных методов оценки качества сварных швов, а также процедуры подготовки для каждого из них и чему можно научиться из каждого метода. Существует множество методов оценки качества полимерных сварных швов. Традиционно эти методы делятся на деструктивные и неразрушающие.
Кроме того, типы информации, предоставляемой методом тестирования, могут быть важными критериями выбора для разработки и сопровождения процесса.Количественные тесты, которые предоставляют числовые атрибуты качества для оценки сварных швов, включают:
- Испытание на герметичность при падении давления
- Испытание на растяжение
- Испытания на сдвиг
- Тестирование на отслаивание
- Испытание выталкиванием
- Испытания на изгиб
- Испытания на кручение
- Испытания на ползучесть
- Испытания на усталость
- Анализ размеров
Кроме того, могут применяться различные методы визуализации, которые могут предоставить много дополнительной информации о характеристиках сварного шва, хотя обычно не поддающейся количественной оценке. Некоторые из этих методов включают:
- Анализ поперечного сечения
- Компьютерная томография (КТ)
- Нарезка микротома
- Визуальный осмотр
- Рентген
- Ультразвуковой контроль
- Фрактография
В этой работе исследуются некоторые из этих методов оценки, подготовка и оборудование, необходимые для каждого из них, а также то, что можно извлечь из каждого метода. Испытания на герметичность при падении давления, испытание на растяжение, анализ поперечного сечения, нарезание микротома и КТ-сканирование были выбранными методами для сравнения.
Обзор литературы
Существует несколько стандартов, регулирующих анализ сварных швов полимеров и пластиков. Спецификация Американского общества сварки для стандартизированных образцов для ультразвуковой сварки термопластов описывает как конструкцию стандартных образцов двутавровой балки, так и метод их испытания на растяжение [1].
Однако в предыдущих исследованиях эти образцы двутавровой балки оказались несовместимыми при формовании, креплении и испытаниях. Проблемы включали достижение надлежащего выравнивания и выравнивания без каких-либо функций выравнивания, включенных в конструкцию, утяжеления и деформации, приводящие к неровному стыку, и склонность одного конца детали ломаться первым во время испытаний на растяжение, что приводит к эффекту застежки-молнии.Эти наблюдения привели к разработке новой стандартной тестовой части, которая была использована в этой работе [2].
Стандарты Американского общества по испытаниям и материалам подробно описывают методы испытаний на герметичность при падении давления и секционный анализ полимеров, которые могут применяться к сварным соединениям [3, 4]. Рекомендации по приготовлению полимерных срезов с помощью криотома можно найти в книге Джона Шейрса, «Анализ состава и разрушения полимеров: практический подход», [5].
Материалы
Фигура 2.Инструмент для испытаний на растяжение Используются стандартные испытательные детали в стиле Dukane ISTeP ™, которые можно оценить с помощью нескольких методов, включая испытания давлением, растяжением и кручением. Эти детали доступны с различными конструкциями шарниров.
Для ультразвуковой сварки использовались материалы из поликарбоната (ПК) и полибутилентерефталата (ПБТ). Компоненты ПК имели директор по энергии под углом 90 градусов, а детали из PBT — под углом 60 градусов. Для лазерной сварки использовался 15% стеклонаполненный полиамид (ПА) с плоским стыком.
Оборудование
Сборки были сварены с помощью двух процессов соединения: ультразвукового и лазерного. Ультразвуковые сварные швы были выполнены с использованием пневматического ультразвукового сварочного аппарата с частотой 20 кГц с возможностью сварки на расстоянии. Амплитуда пакета преобразователь-бустер-сонотрод измерялась с помощью датчика смещения.
Лазерные сварные швы были выполнены с использованием лазера ND: Yag с длиной волны 980 нм, установленного на XY-столе для управления движением, и небольшого пневматического пресса для приложения давления.
Выходная мощность лазера контролировалась напряжением, а выходная мощность в ваттах измерялась с помощью монитора энергии Ophir.
Испытания на герметичность при распаде давления проводились с использованием прибора для проверки герметичности при распаде давления Cincinnati Test Systems Sentinel C28. КТ-сканирование было выполнено с использованием системы Nikon XTH 225 CT с мощностью 130 кВ и 30 Вт и вращающейся мишенью. Криомикротомы были изготовлены с использованием криомикротома Leitz Kryostat 1720. Все изображения были получены с использованием микроскопа Olympus BX51 с отражающим освещением для срезов и пропускающим освещением для срезов криомикротома.
Испытания на растяжение были выполнены на машине Instron с использованием инструментов для испытаний на растяжение, разработанных специально для использования с деталями Dukane ISTeP ™, как показано на Рисунке 2.Сварные узлы вытягивали со скоростью 2,5 мм / мин.
Методика эксперимента
Таблица 1. Параметры узлов ультразвуковой сварки Всего было сварено 32 узла. Двенадцать сборок PBT, 10 сборок ПК и две сборки с крышкой ПК и корпусом PBT были сварены ультразвуком. С помощью контурной лазерной сварки сварены восемь сборок ПА. Было создано несколько преднамеренных дефектов, таких как переварка, недостаточная сварка, недостаточная амплитуда, недостаточная мощность, недостаточное давление и недостаточное разрушение.На нижних половинах двух сборок были вырезаны выемки — те, которые должны быть сканированы КТ из наборов B и D.
Из 32 сварных сборок проанализировано 14. Эти сборки были сделаны попарно, так что по две сборки каждая была изготовлена с семью комбинациями материалов, процессов и параметров, как описано в таблицах 1 и 2. Все 14 были испытаны на утечку из-за спада давления. По одному из каждой пары, всего семь, затем были просканированы компьютерной томографией и испытаны на растяжение. Остальным семи были сделаны поперечные срезы и нарезаны срезы криомикротома.
Таблица 2. Параметры для узлов, сваренных лазером Где% ED означает процент от проектной высоты директора энергии. Таким образом, сборки набора A были свернуты более чем вдвое по сравнению с расчетной высотой директора энергии, в то время как сборки набора D были недостаточно сложены.
Поперечные сечения были приготовлены следующим образом. Сначала узлы разрезались пополам на ленточной пиле, затем снова разрезались на алмазной пиле для более плавного реза. Затем секционированные сборки были помещены разрезанной стороной вниз в форму и смонтированы в эпоксидной смоле.
Секционные сборки постепенно шлифовали в соответствии с рекомендациями ASTM [3], начиная с наждачной бумаги зернистостью 320 с использованием воды для удаления мусора и твердых частиц. При такой зернистости секции шлифовали с шагом 30–45 секунд до плоской формы. После этого шага следовала полировка наждачной бумагой с зернистостью 400, 600 и 800, каждые 30 секунд при протекании воды.
Затем была использована синтетическая вискозная ткань с низким ворсом с использованием полировальных составов на основе алмаза и коллоидного кремнезема для полировки до желаемой отделки.Срезы полировались таким образом с шагом от одной до двух минут, переходя от алмазной суспензии 9 мкм к алмазу 3 мкм и к алмазной суспензии 1 мкм.
Наконец, срезы обрабатывали полиролью из коллоидного кремнезема в течение трех-четырех минут. Выбор времени и повторение каждого из этих шагов требует анализа прогресса и определения того, двигаться ли дальше или повторять с той же интенсивностью полировки.
Срезы фотографировали с помощью оптического микроскопа. После получения изображения срезов в состоянии после полировки, срезы затем подвергали термообработке, пропуская термофен на высоте около 10 мм над поверхностью срезов в течение 5-10 секунд с приращением, просматривая срез после каждую обработку, чтобы определить, нужно ли применять больше тепла.
Использовался термофен модели HG-301A, 120 В переменного тока, 60 Гц, 12 А, диапазон температур от 149 ° C до 260 ° C.
Этот процесс позволяет полимерным цепям на поверхности секции, размазанной во время резки и полировки, расслабиться, что дает дополнительную информацию о качестве сварки. На рисунке 3 показан пример изменения внешнего вида поперечного сечения от состояния после полировки к состоянию после термообработки.
Термическая обработка может быть мощным инструментом, позволяющим выявить детали не только потока и области соединения в сварном шве, но и деталей процесса формования.Как можно увидеть на термообработанном участке на фиг. 3, существует различие в полимере между внешним краем отформованного компонента и внутренним пространством, что указывает на различную температурную предысторию между внешней и внутренней областями. Однако, если ее не проводить осторожно и постепенно, термообработка может исказить пластик и привести к потере деталей. Очень незначительное изменение времени нагрева и расстояния от источника горячего воздуха может привести к значительным различиям во внешнем виде.
Рисунок 3.Поперечное сечение в плоскости XZ сварного шва набора А до (слева) и после (справа) термообработки Образцы криомикротома были приготовлены путем вырезания небольшого кусочка из сварного шва, размером приблизительно 2 мм. Было уделено внимание тому, чтобы верхняя и нижняя поверхности были перпендикулярны сварному шву и параллельны друг другу. Затем деталь поместили на оправку и нанесли на нее небольшое количество компаунда для оптимальной температуры резания Tissue-Tek, который затвердевает при охлаждении до -10 ° C и ниже. Образец размещали так, чтобы линия шва была перпендикулярна направлению среза.Если сварной шов параллелен, во время резки может возникнуть дополнительное напряжение, которое может ослабить или сломать сварной шов.
Криомикротом был установлен на -40 ° C, и крепления оставляли для затвердевания в течение нескольких часов перед разрезанием. Толщина была установлена на 10 мкм. После нарезки тонкие части скручиваются. Пинцетом осторожно развернули рулоны, чтобы их можно было зажать между двумя слайдами для проверки. Если не соблюдать осторожность, пинцет может пометить срезы криомикротома в интересующей области, испортив образец.Были приняты меры для очистки слайдов и срезов от пыли и мусора.
При компьютерной томографии сборки сканировались целиком. Поскольку не требовалось разделения на секции, эти сборки можно было испытать на растяжение после получения изображения. Использовался источник рентгеновского излучения на пропускание 180 кВ с приложенным напряжением 120 кВ и током 30 Вт. Образец располагался как можно ближе к источнику, чтобы оптимизировать разрешение вокселей, обеспечивая при этом полную стабильность для предотвращения движения любых деталей во время сканирование.Кроме того, узел был наклонен для уменьшения артефактов, которые могут быть связаны с процедурами компьютерной томографии.
Результаты и обсуждение
Таблица 3. Результаты испытаний на растяжение и герметичность В таблице 3 обобщены результаты испытаний на герметичность и растяжение при падении давления. Обратите внимание, что на узлах, сканированных с помощью компьютерной томографии, из наборов B и D были намеренно надрезы в области стыка, что привело к серьезной утечке во время испытания на герметичность при понижении давления. Обе сборки из наборов A и C сильно просочились.Однако это произошло из-за повреждения в центре верхней части, а не из-за слабого сварного шва.
Во время испытаний на растяжение узлы набора A и C вышли из строя в основном материале, что указывает на гораздо более прочный, более когезионный сварной шов, чем у некоторых из более герметичных узлов (например, набор B и набор D). Разрушение основного материала является ограничивающим фактором методов механических испытаний, таких как испытания на растяжение, создавая искусственный максимум, выше которого прочность сварного шва не может быть определена количественно.
Рисунок 4.Данные испытаний на растяжение для сборок из ПБТ / ПКХотя для крышки ПК на основе ПБТ использовались те же настройки, что и для набора C, самого прочного из протестированных наборов, прочность на растяжение была значительно снижена, как показано на Рисунке 4. Это Результат следует ожидать при сварке разнородных материалов, поскольку несоответствие вязкости расплава и температуры плавления может затруднить возникновение межмолекулярной диффузии.
Ни один из сваренных лазером комплектов не привел к пластическому разрушению. Однако набор F, который был сварен с большим давлением и мощностью, чем набор G, обеспечил герметичное уплотнение, как указано в таблице 3.
Поперечные сечения сборок набора A и набора B показывают большее сжатие в сварных швах набора A и большее давление. out flash, рис. 5. Этот результат коррелирует с тем фактом, что сборки набора A были сжаты более чем в два раза на глубину, чем сборки набора B во время сварки.
Фото слева: Рисунок 6. Повреждения от ультразвуковых колебаний в крышке Комплекта B. Фото справа: Рисунок 7.Поперечные сечения в плоскости XZ термообработанного сварного шва набора C (слева) и термообработанного сварного шва набора D (справа) Сварные швы как набора A, так и набора B не имеют пустот, несвязанных участков и имеют ровный, однородный вид по ширине сустава. Это хорошо коррелирует с герметичным соединением, обеспечиваемым комплектом B, хотя скорость утечки спада давления комплекта A не может быть измерена из-за повреждения в середине верхней части крышки. Хотя такой же тип повреждений произошел на Комплекте B, он не образовал дыры, Рисунок 6.Это повреждение, скорее всего, вызвано диафрагмированием крышки, что приводит к сильным колебаниям в центре и оплавлению.
. Из поперечных сечений ясно видно, что сборки Set D были недосварены, Рисунок 7. Кроме того, на разрезе отчетливо видно отсутствие адгезии между расплавом, вытолкнувшимся из сварного шва, и поверхностью крышки, где он контактирует.Однако сварной шов Set C демонстрирует сплошную и ровную сварку по всей поверхности соединения. Это хорошо коррелирует с большей прочностью на разрыв, продемонстрированной сборками Set C.
Поперечное сечение сборок набора E, крышки ПК к сварному шву из разнородного материала корпуса PBT, показывает плохое сцепление между двумя частями. В то время как оба материала плавились и текли, все еще существует четкая линия разделения через сварной шов, где полимерные цепи от каждого исходного объемного материала отрываются друг от друга, что указывает на небольшую межмолекулярную диффузию.
Поперечные сечения узлов, сваренных лазерной сваркой, комплектов F и G, показывают очень плохую сварку, рис. 8. Термическая обработка этих деталей не выявила каких-либо дополнительных деталей, так как пустоты и дефекты в сварном шве можно четко увидеть на снимке. -шлифованное состояние. Принимая во внимание неровный внешний вид сварного шва Set F и видимую пористость, удивительно, что этот сварной шов был герметичным, согласно таблице 3.
Рис. 9. Криомикротом в плоскости XZ сварного шва набора B (вверху слева), сварного шва набора C (вверху справа), сварного шва набора E (слева внизу) и зоны соединения сварного шва набора F при большем увеличении (внизу справа) Срезы криомикротома обеспечивают Немного другой вид поперечных сечений узлов, рисунок 9.Срез сборки набора B показывает такое же количество смятия и равномерного разрыва, что и поперечное сечение, но также показывает, что между сварной конструкцией и основным материалом есть очень тонкая область, которая оптически более прозрачна, чем любой другой. Этот результат, вероятно, является остатком закаленного поверхностного слоя, так как эта более прозрачная линия видна на краях обеих формованных деталей.
Срез криомикротома сборки набора C показывает полный сварной шов, что коррелирует с поперечным сечением и испытанием на растяжение для этого же набора.На срезах Set C и Set F можно увидеть немного более темную область с правой стороны крышки, чуть выше сварного шва. В этих областях ломтик не развернулся полностью после разрезания и оставил небольшую складку.
Срез криомикротома сборки набора E показывает разницу между двумя разнородными материалами более четко, чем сечение. На срезе комплекта F видна пористость даже на сварной правой стороне соединения (как показано на рисунке 8), которая увеличена на изображении на рисунке 9.Создание криомикротома для сборки с таким плохим сварным швом может быть довольно сложной задачей из-за тенденции к разрыву тонких срезов в месте соединения.
Рис. 8. Поперечные сечения в плоскости XZ после полировки сварного шва Set F (слева) и после полировки сварного шва Set G (справа) КТ-сканирование сборок Set A и Set B показывает структуру, очень похожую на поперечные сечения и криомикротом. срез, рис. 10, включая чрезмерное мигание из-за значительного расплавления соединения, используемого для этого набора параметров.Однако обнаруживается дополнительная особенность — выемка, вырезанная в сборке комплекта B, которую можно увидеть при взятии топа-
, вид соединения сверху. .
КТ-сканирование узлов Set C и Set D одинаково информативно, рис. 11. Паз снова очень четкий на виде сверху (обозначен стрелкой).Сканирование достаточно точное, чтобы увидеть кривую вытесненного расплава в сварном шве Set D на виде сбоку.
Компьютерная томография сборки комплекта E показывает, где крышка треснула во время сварки, а также образование расплава во время сварки, рис. 12.
Рис. 10. КТ-сканирование сборок Set A (вверху) и Set B (внизу) в плоскости XY (слева) и XZ (справа) КТ-сканирование сборок Set F и Set G показывает чрезмерную пористость в этих сборках. сварных швов и вспышки, образовавшейся во время этих сварных швов.Этот результат очень хорошо коррелирует с поперечными сечениями этих сборок.
Выводы
Тестирование показывает преимущества и недостатки каждого метода оценки, а также то, что можно извлечь или упустить из любого метода тестирования. Испытания на растяжение вполне коррелируют с
Рис. 11. КТ-сканирование сборок Set C (вверху) и Set D (внизу) в плоскости XY (слева) и XZ (справа)хорошо с общим качеством сварки, но не может учитывать дискретные зазоры или включения в сварном шве, которые могут влияют только на небольшую площадь.Испытания на герметичность при падении давления очень хорошо подходят для обнаружения мелких и непостоянных дефектов сварных швов, но не коррелируют с общим качеством сварки, поскольку даже очень слабые сварные швы, которые хорошо смачиваются в потоке расплава, могут быть герметичными.
Анализ поперечного сечения дает очень хорошее представление об общем качестве сварного шва, но почти никогда не обнаруживает дискретных дефектов из-за
Рис.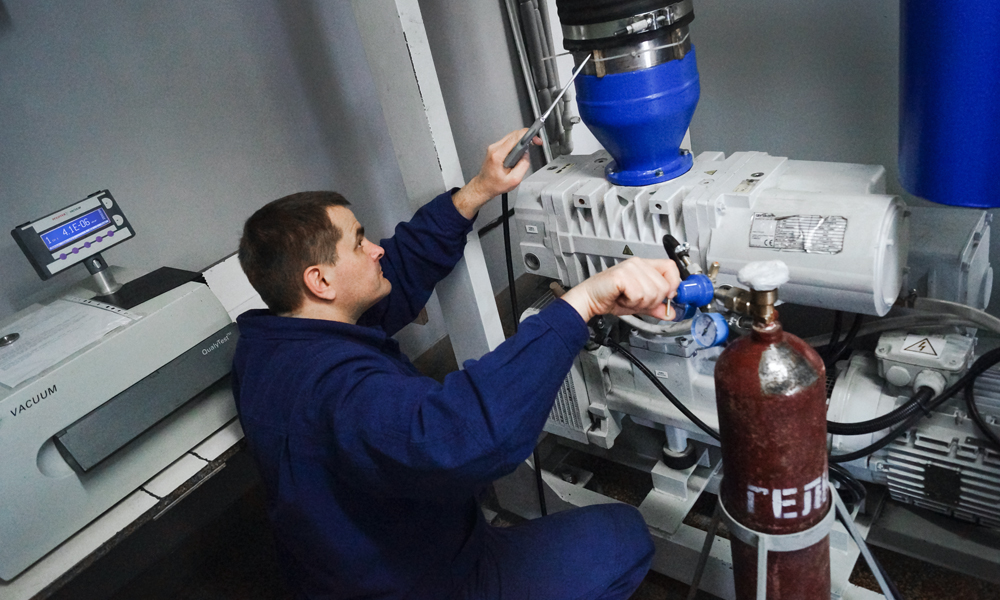
позволяет видеть только один небольшой участок сварного шва за раз.КТ-сканирование не подходит для проверки качества слияния, но может использоваться для очень точного выявления и обнаружения отдельных дефектов.
Криомикротомные срезы дают меньше информации о том, произошла ли межмолекулярная диффузия, чем поперечное сечение, но дает возможность оценить относительную кристалличность. В зависимости от материала образование сферолита в кристаллической области можно наблюдать даже при использовании поляризованного освещения.
Благодарности
EWI благодарит Брэнсона за предоставленный сварочный пресс и Дукейна за пожертвование деталей ISTeP ™, без которых эта работа была бы невозможна.
Кроме того, мы выражаем огромную признательность техническим специалистам EWI Уэйну Пападжорджу за опыт в подготовке поперечных сечений полимера, Дэниелу Кмиотеку за компьютерную томографию и Стиву О’Мара за испытания образцов на растяжение.
Список литературы
- Технические условия на стандартизацию образцов для ультразвуковой сварки термопластов, Американское сварочное общество G1.2M / G1.2: 1999.
- Г. Маркус, К. Лестер, Сравнение ультразвукового сварочного аппарата с сервоприводом и стандартного пневматического ультразвукового сварочного аппарата, ANTEC (2009).
- Стандартное руководство по подготовке пластмассовых и полимерных образцов для исследования микроструктуры, ASTM E2015-04 (повторно утверждено в 2014 г.).
- Стандартная практика для метода испытания на утечку при распаде давления, ASTME2930-13 (2013).
- Дж. Шейрс, Анализ состава и разрушения полимеров: практический подход, John Wiley & Sons, Ltd, (2000).
Миранда Маркус отвечает за технический опыт EWI по всем технологиям сварки пластмасс и композитов.Она обладает обширными знаниями в области технологий сварки пластмасс, их преимуществ и ограничений, включая ультразвуковые, лазерные, вращательные, горячие, вибрационные, тепловые, радиочастотные и инфракрасные.
EWI дает возможность лидерам отрасли преодолевать сложные производственные проблемы и интегрировать новые процессы для более быстрого и эффективного вывода продуктов на рынок. Для получения дополнительной информации посетите ewi.org или позвоните по телефону 614.688.5000.
Миранда Маркус
инженер по приложениям
EWI
Гидростатическое испытание — это только испытание на герметичность?
Опубликовано 3 декабря 2015 г. Автор: admin
Карлос Ф. Молина
Сегодняшняя статья посвящена гидростатическим испытаниям резервуаров.На моем рабочем месте люди стали обычным явлением сказать, что «гидростатическое испытание резервуара — это просто испытание на герметичность». Некоторые девушки говорят, что «самое важное при гидростатических испытаниях — это измерение осадка». Это показывает, что не все полностью понимают гидростатические испытания.
В этой статье мы увидим, как проводится гидростатическое испытание для различных типов резервуаров и какие части резервуара оцениваются с помощью гидростатического испытания.
ТРИ ОСНОВНЫЕ ЦЕЛИ ГИДРОСТАТИЧЕСКИХ ИСПЫТАНИЙ
Гидростатические испытания в резервуарах преследуют 3 основные цели, согласно….мне
- Проверить герметичность бака
- Проверить, выдерживают ли сварные швы условия эксплуатации
- Проверка фундамента осадки
[adToAppearHere]
Это более важная цель проверки резервуара в целом на соответствие условиям эксплуатации. Бывает, что первые два переплетаются, и это необходимо. Измерения осадки фундамента, напротив, не являются обязательными во всех случаях. Как сказано в стандарте, производитель несет ответственность за «проведение расчетных измерений, если покупатель не отказывается от отказа в технических характеристиках, строка 14» (API 650 7.3.6.2). Есть несколько случаев, когда это может произойти в новых резервуарах: когда осадка не ожидается или когда новый резервуар меньшего размера расположен над использованным фундаментом, который показал устойчивость к осадке.
«ГИДРОСТАТИЧЕСКИЙ» vs «ГЕРМЕТИЧНОСТЬ»
Это «гидростатический тест» или «тест на герметичность»? Следующие определения могут быть полезны для понимания этой проблемы:
Герметичность — Такой плотной конструкции, чтобы быть непроницаемым.
Гидростатические — относящиеся к неподвижным жидкостям или к давлению, которое они создают или передают; «Гидростатическое давление»
Первый абзац стандарта API 650, где встречается слово «гидростатический», находится в 5.2.1, «Нагрузки». Правильно, гидростатическая нагрузка связана с расчетами толщины оболочки резервуара.
Слово «гидростатический» используется 58 раз в основной части стандарта, и все они относятся к испытаниям корпуса. Слово «плотный» встречается в основной части стандарта 7 раз. Из этих семи только один раз он связан с герметичностью бака. Собственно, это в большей степени связано с необходимостью газонепроницаемости крыш . Это первая подсказка, демонстрирующая, что тест является «гидростатическим» по своей природе.
Гидростатические испытания демонстрируют пригодность резервуара к эксплуатации с минимальным риском выхода из строя, учитывая, что они представляют собой более тяжелые условия, в которых резервуар будет находиться во время эксплуатации. Сварные швы, наиболее подверженные статическому давлению, это, очевидно, вертикальные швы. Однако рассмотрим резервуары с внутренним давлением, в которых газы занимают пространство над уровнем жидкости. Обычно это технологические резервуары, в которых используется сварной купол или зонтичная крыша для сдерживания внутреннего давления парового пространства над поверхностью жидкости.В этих резервуарах сварные швы между корпусом и днищем и углом между крышей и верхом должны показать, что они могут выдерживать силы, оказываемые давлением газа.
Емкости с внутренним давлением
[adToAppearHere]
Но если бы мы только собирались проверить на утечки, это можно было бы сделать с газами и вакуумными ящиками, верно? Что ж, существует много типов резервуаров и крыш, не упомянутых здесь в этой статье, и они тестируются по-разному. Однако проверка герметичности с использованием газов до давления, которое может быть достигнуто на дне резервуара при заполнении жидкостью, было бы чрезвычайно опасно.Если бы мы собирались испытать газонепроницаемый резервуар с таким давлением, подъем на крышу был бы больше, чем вес крыши плюс вес корпуса, и сварные швы могут быть сломаны, а резервуар деформирован. А вакуумные камеры обычно не могут достичь давления 15 или 20 фунтов на квадратный дюйм, необходимого для проверки сварных швов между корпусом и дном, и они не могут создавать кольцевые напряжения в вертикальных швах.
Жидкости — это единственный способ проверить резервуар таким же образом, как он будет работать. И они оказывают на танк «гидростатическую» силу.
ГИДРОСТАТИЧЕСКИЕ ИСПЫТАНИЯ ДЛЯ РАЗЛИЧНЫХ БАКОВ
АТМОСФЕРНЫЕ БАКИ С ОТКРЫТЫМ ВЕРХОМ . Резервуары без крыши, резервуары с геодезической крышей купола или резервуары с внутренней или внешней плавающей крышей. В этих резервуарах высота гидростатического испытания является расчетным уровнем жидкости. API 650 7.3.5
БАКИ С МАЛЕНЬКИМ ВНУТРЕННИМ ДАВЛЕНИЕМ ДО 2,5PSI, ГДЕ ВНУТРЕННЕЕ ДАВЛЕНИЕ НЕ ПРЕВЫШАЕТ ВЕС КРЫШИ ПЛЮС ОБОЛОЧКА ПЛЮС ОБОЛОЧКА ПЛЮС ПРИКРЕПЛЯЕМАЯ РАМА . Этот тип резервуара должен быть испытан водой на 2 дюйма выше верхнего угла и вакуумным испытанием сварных швов крыши или испытанием резервуара с давлением, не превышающим вес листов крыши.
РЕЗЕРВУАРЫ С МАЛЕНЬКИМ ВНУТРЕННИМ ДАВЛЕНИЕМ ДО 2,5PSI, ГДЕ ВНУТРЕННЕЕ ДАВЛЕНИЕ ПРЕВЫШАЕТ ВЕС КРЫШИ ПЛЮС ОБОЛОЧКА ПЛЮС ПРИКРЕПЛЕННАЯ РАМА . Согласно приложению F, F.7.5, эти резервуары следует испытывать с водой до расчетного уровня жидкости и давлением газа в 1,25 раза превышающим расчетное давление. Наличие анкерных болтов в резервуарах этого типа может помочь избежать прогиба дна (необходимость в анкеровке зависит от многих условий, а не только от внутреннего давления).
РЕЗЮМЕ
Я всегда исправляю людей, которые говорят, что «гидростатическое испытание — это просто испытание на герметичность». Но если вы внимательно прочитаете стандарт, это поможет вам лучше понять проблему гидростатических испытаний. И можно сравнить с другими стандартами. Например, ASME B31.3 называет это испытание «гидростатическим испытанием на герметичность», подтверждая оба компонента испытания.
Большое спасибо за ваше время.
Кислородно-ацетиленовая сварка, резка и нагрев
В руководстве приведены основные соображения по охране здоровья и безопасности при кислородно-ацетиленовой сварке для обеспечения безопасных методов сварки.
Нажмите здесь, чтобы увидеть наши последние подкасты по технической инженерии на YouTube .Процесс оксиацетилена
В процессе оксиацетилена получается высокотемпературное пламя, превышающее 3000 градусов Цельсия, за счет сгорания чистого кислорода и ацетилена. Это единственная газовая смесь, достаточно горячая, чтобы плавить сталь; другие газы (пропан, сжиженный нефтяной газ или водород) могут использоваться для цветных металлов с более низкой температурой плавления, для пайки и серебряной пайки, а также в качестве газа предварительного нагрева / прошивки для резки.
Сейф
Газы обычно поставляются под высоким давлением в стальных баллонах; В Великобритании цветовая кодировка баллонов находится в процессе согласования по всей Европе. Для ацетилена выступ баллона темно-бордового цвета, а для кислорода выступ белый, хотя черные кислородные баллоны будут оставаться в обращении в течение некоторого времени. На баллоне также должна быть этикетка с указанием типа газа. Для предотвращения взаимозаменяемости арматуры между баллонами, содержащими горючие и негорючие газы, кислородные баллоны имеют правую, а ацетиленовую — левую резьбу.Все цилиндры открываются поворотом ключа или ручки против часовой стрелки, а закрываются — поворотом по часовой стрелке.
Кислород вызовет более сильный пожар, а смесь кислорода и топливного газа может вызвать взрыв. Поэтому важно, чтобы кислородные баллоны были отделены от баллонов с топливным газом и хранились в зоне, свободной от горючего материала.
Техника безопасности и предотвращение несчастных случаев
- Храните баллоны в хорошо вентилируемом помещении, предпочтительно на открытом воздухе
- Складское помещение должно быть удалено от источников тепла, искр и огня.
- Баллоны следует хранить в вертикальном положении и хорошо закреплять
- Кислородные баллоны следует хранить на расстоянии не менее 3 м от баллонов с топливным газом или разделять 30-минутным огнестойким барьером.
- Помещение магазина должно быть обозначено как «Не курить».
Работа со сжатыми газами
Баллоны снабжены регуляторами для снижения давления газа в баллоне до рабочего давления горелки. Регулятор имеет два манометра, манометр высокого давления для газа в баллоне и манометр низкого давления для газа, подаваемого в горелку. Расход газа регулируется винтом регулировки давления, который устанавливает давление газа на выходе. Свод практических правил BCGA CP7 рекомендует проверять датчики ежегодно и заменять каждые 5 лет.
Следует учитывать следующие факторы: газовая система соответствует номинальному давлению, а шланги подсоединены без утечек. Перед ввинчиванием регулятора необходимо очистить резьбу клапана. Клапан баллонов с ацетиленом можно слегка приоткрыть, чтобы продуть резьбу, но резьбу кислородных баллонов лучше всего очищать чистым сжатым воздухом (резьбы баллонов с водородом всегда необходимо продувать сжатым воздухом).
Поскольку кислород может бурно реагировать с маслами и консистентными смазками, нельзя использовать смазочные масла или герметик для резьбы.
Техника безопасности и предотвращение несчастных случаев
- Цилиндры очень тяжелые и всегда должны быть надежно закреплены
- Запрещается ослаблять клапаны цилиндров или их защитные устройства
- Проверить, рассчитан ли регулятор на давление в цилиндре
- При установке регулятора на цилиндр стыки должны быть чистыми и нельзя использовать герметик.
- Перед установкой регулятора необходимо вывернуть винт регулировки давления, чтобы предотвратить нерегулируемый поток газа в систему при открытии клапана баллона.
Использование сжатых газов
Газы смешиваются в ручном резаке или паяльной трубке в правильных пропорциях.Шланги между регулятором и горелкой должны иметь цветовую маркировку; в Великобритании красный для ацетилена и синий для кислорода. Шланги должны быть как можно короче, и пользователи должны периодически проверять, не находятся ли они рядом с горячими или острыми предметами, которые могут повредить стенку шланга. Ацетиленовые баллоны всегда следует использовать в вертикальном положении.
При подключении системы и, по крайней мере, в начале каждой смены, шланги и горелку необходимо продувать, чтобы удалить любые горючие газовые смеси. Важно, чтобы поток кислорода не контактировал с маслом, которое может спонтанно воспламениться.Очистку также не следует проводить в замкнутом пространстве.
Горелку следует зажигать фрикционной зажигалкой или стационарным запальным пламенем, чтобы не обжечь руки; Не следует использовать спички и не следует повторно зажигать пламя от горячего металла, особенно при работе в ограниченном пространстве.
Цилиндры не должны нагреваться, например, если пламя горелки локально нагревает стенку цилиндра. Точно так же дуговая сварка слишком близко к цилиндру может привести к образованию дуги между цилиндром и заготовкой / электродом.
Хотя УФ-излучение очень мало, сварщик должен носить затемненные очки. Марка фильтра определяется интенсивностью пламени, которая зависит от толщины свариваемого металла; Рекомендации по фильтрам по расходу ацетилена приведены в таблице (BSEN 169: 1992).
Марка фильтра, рекомендуемая в соответствии с расходом ацетилена:
Рабочий | расход ацетилена в л / час | |||
---|---|---|---|---|
От | до 70 | 70–200 | 200–800 | более 800 |
Сварка и пайка сварка тяжелых металлов e.грамм. стали, меди и их сплавов | 4 | 5 | 6 | 7 |
Сварка излучающими флюсами (особенно легких сплавов) | 4a | 5a | 6a | 7a |
Безопасная практика и предотвращение несчастных случаев
- При очистке резьбы цилиндра, подсоединении регулятора и продувке шлангов защищайте лицо и глаза, надев соответствующий головной щиток.
- Используйте подходящий сварочный щиток с соответствующим фильтром для защиты глаз.
- Носить негорючую одежду
- Убедитесь, что цилиндр не нагревается пламенем или случайной дугой от соседнего электрического оборудования.
Обнаружение утечек
Перед сваркой необходимо проверить соединения и шланги на герметичность.Хотя ацетилен можно определить по его характерному запаху (обычно на уровне менее 2%), кислород не имеет запаха.
Обнаружение утечек лучше всего проводить с использованием слабого (обычно 0,5%) раствора моющего средства в воде или раствора для обнаружения утечек от одной из компаний, поставляющих газ. Его наносят на стыки с помощью кисти, и выходящий газ образует пузырьки. После устранения утечки область должна быть очищена от остатков раствора для обнаружения утечки. Утечки в шлангах можно устранить, но следует использовать утвержденные сменные шланги и муфты в соответствии с BSEN 560: 1995 и BSEN 1256: 1996.
Встречный огонь и воспоминание
Возгорание (одиночный треск или треск) возникает, когда пламя воспламенило газы внутри сопла и погасло само. Это может произойти, если резак держать слишком близко к заготовке.
Воспоминания (пронзительный шипящий звук), когда пламя горит внутри факела, более серьезны. Пламя может пройти обратно через смесительную камеру горелки в шланг. Наиболее вероятная причина — неправильное давление газа, из-за которого скорость газа слишком низкая.Альтернативно, ситуация может быть создана за счет подачи газа с более высоким давлением (ацетилен) в поток газа с более низким давлением (кислород). Это может произойти, если кислородный баллон почти пуст, но другими потенциальными причинами могут быть утечки шлангов, ослабленные соединения или невозможность надлежащей продувки шлангов.
Обратные клапаны, установленные на шлангах, обнаруживают и останавливают обратный поток газа, предотвращая образование горючей смеси кислорода и ацетилена в шланге. Пламегаситель представляет собой автоматический пламегаситель, предназначенный не только для гашения пламени, но и для предотвращения его попадания на регулятор.
Процедура обратной вспышки или ретроспективного кадра
После непродолжительного возгорания с потухшим пламенем:
- закрыть регулирующие клапаны нагнетательной трубы (сначала топливный газ)
- проверьте затяжку форсунки
- проверить давление на регуляторах
- повторно зажгите резак, используя рекомендованную процедуру
Если пламя продолжает гореть:
- закрыть кислородный клапан на горелке (для предотвращения внутреннего ожога)
- закрыть ацетиленовый клапан на горелке
- закрыть вентили баллона или запорные вентили точки подачи газа для кислорода и ацетилена
- закрыть выходы регулируемых регуляторов давления, выкрутив винты регулировки давления
- Откройте оба клапана горелки, чтобы сбросить давление в оборудовании
- закрыть клапаны горелки
- проверить герметичность форсунок и давление на регуляторах
- повторно зажгите резак, используя рекомендованную процедуру
Если в шланге и оборудовании происходит обратная вспышка, или пожар в шланге, соединениях регулятора или точках выхода газа:
- перекрыть подачу кислорода и топливного газа на клапанах баллона или в точках выпуска газа (только если это можно сделать безопасно)
- , если нет риска травм, управлять пожаром с помощью средств первой помощи для пожаротушения
- , если пожар не может быть потушен сразу, позвонить в службу спасения.
- После охлаждения оборудования осмотрите оборудование и замените дефектные компоненты
После расследования возгорания и устранения неисправности можно снова зажечь горелку.После повторной вспышки, поскольку пламя распространилось на регулятор, важно не только осмотреть горелку, но и проверить и, при необходимости, заменить шланги и компоненты. Пламегаситель также следует проверять в соответствии с инструкциями производителя, и в некоторых моделях может потребоваться его замена. Свод практических правил BCGA CP7 рекомендует заменять обратные клапаны и пламегасители каждые 5 лет.
Информация была подготовлена в сотрудничестве с Роджером Сайксом, руководителем отдела здравоохранения и безопасности, Ньюкасл-апон-Тайн.
Эта статья Job Knowledge изначально была опубликована в Connect, май 1997 г. Она была обновлена, поэтому веб-страница больше не отражает в точности печатную версию.
GripTight заглушки для изоляции трубопроводов | Curtiss-Wright EST Group
Изолируйте, контролируйте давление на входе и проверяйте сварные фланцевые соединения с помощью одного простого инструмента!
Положите конец традиционной практике заполнения и опорожнения целых трубопроводов для проверки сварных соединений фланца с трубой! Изолирующая заглушка GripTight® компании EST Group позволяет изолировать и контролировать потенциально взрывоопасные пары во время горячих работ, а затем проводить гидроиспытания новых сварных соединений.
Объединяя функциональность обычного двойного блока и спускной заглушки с нашей технологией захвата GripTight, изолирующие заглушки GripTight обеспечивают повышенную безопасность эксплуатации, сводя к минимуму риск случайного выброса / выброса из-за неожиданного давления на входе.
Его двухпортовая конструкция создает барьер избыточного давления между уплотнениями, надежно изолируя горячие детали от любых остаточных газов на входе. Выполняйте испытания фланцевых сварных швов с помощью изолирующей заглушки, которая защищает как оборудование, так и персонал!
Испытательное давление
- 2250 фунтов на квадратный дюйм (155 бар изб.) Между уплотнениями
- Давление на входе до 1500 фунтов на квадратный дюйм (103 бар изб.) — более высокие давления доступны по запросу
Диапазон размеров NPS от 3/4 до 48 дюймов (от DN20 до DN1200) — больших размеров доступны по запросу
Стандартный материал уплотнения Уретан — альтернативные материалы доступны по запросу
Особенности и преимущества
- Контроль потенциально взрывоопасных паров при огневых работах
- Двухпортовая система позволяет воде / среде циркулировать между уплотнениями, обеспечивая улучшенное охлаждение во время сварочных работ
- Технология захвата сводит к минимуму риск случайного выброса / выброса
- Создает барьер избыточного давления между уплотнениями
- Легкая конструкция из алюминия и стали
- Выполните испытание фланцевых сварных швов с расходом менее галлона (3.
8 л) воды — сокращение времени заполнения и затрат на очистку
- Испытательное устройство ASME PCC-2 типа IV *
Требуется изоляционная пробка более низкого давления? Ознакомьтесь с нашей двойной блокировкой и пробкой для испытания на спуск / изоляцию
* ASME PCC-2 (Статья 503) — «Испытательные устройства для локального давления или испытания на герметичность ремонтных сварных работ
Стандартные сварные швы в трубопроводных системах
При установке стальных трубопроводов для воды или других жидкостей, таких как как газ или отходы, существует несколько распространенных типов сварных соединений.Это может варьироваться в зависимости от диаметра участков трубы, углов или сдвигов направления трубы. Стыковые, угловые и фланцевые соединения — вот некоторые из них. сварочные работы. Читайте дальше, чтобы узнать больше об этих суставах и когда их использовать. их.
Стыковые соединения
Стыковые соединения соединяют две части вместе встык. Это может
быть сделано с двумя частями одной трубы или добавить клапаны, фланцы, фитинги,
или другое оборудование. Если свариваемые материалы толще трех шестнадцатых
дюйма, вы используете плоский или составной фацет.В трубах большего диаметра стыковые соединения
нужно будет запломбировать как изнутри, так и снаружи.
Вы должны выполнить испытания после завершения сварки на каждом соединение. Визуально осмотрите сварные швы и найдите начальные и конечные дефекты, трещины или поднутрения.
Прочие испытания, проводимые после сварки стыкового соединения, могут быть либо магнитными. тест частиц (MT) или ультразвуковой тест (UT). Вы можете выполнить ультразвуковое проверьте, как только сварной шов остынет. UT-тест нужно проводить только на одном сторона сустава, внутри или снаружи.
После проверки соединений установите защитный термоусадочный рукав или подгузник для защиты стыка от коррозии, если трубы будут под землей.
Угловые соединения
Угловые сварные соединения широко используются при монтаже трубопроводов. Соединения внахлестку, тройники и угловые соединения — это все типы угловых соединений.
- Круг стык — это место, где две части трубы перекрываются, потому что диаметр одной трубы меньше другого.
- Тройник шарнир создает форму T когда соединены две трубы или труба прикреплен к опорной плите.
- Угол суставы образуют L при соединении двух металлических частей. Если три ответвления трубы соединяются, это называется косым стыком.
В угловых соединениях используется одинарное или двойное угловое соединение. С одинарное сопло, соединение герметично снаружи, когда две трубы полностью сидящий. Двойной фланец герметизирует соединение как внутри, так и снаружи, где трубы встретить.
Визуально проверьте одинарные угловые соединения на предмет завершения и любых
неисправности. Вам также следует выполнить тест MT. Если вы используете двойное филе, в
В дополнение к визуальным испытаниям и испытаниям МП используйте испытание воздухом до 40 фунтов на квадратный дюйм в кармане
создается двумя сварными швами. Испытания в вакуумной камере — еще один вариант на перекрывающихся
области.
Используйте термоусадочные рукава или подгузники со строительным раствором для защиты филе. стыки, которые будут находиться под землей или подвергаться воздействию элементов.
Фланцевые соединения
Фланцевые соединения или кромочная сварка происходят там, где клапан или установлен люк.При установке клапана вы добавляете прокладку между и затяните болты по диагонали с равномерным крутящим моментом.
Также следует нанести тонкий слой краски под гайку и шайбу, чтобы вода не вызывала коррозию в дальнейшем. Проверить болты через двадцать четыре часа для постоянной затяжки.
Как и в случае с другими сварными соединениями, необходимо произвести визуальный осмотр. часть процесса после завершения сварки. После прохождения проверки сварной шов термоусадочная муфта или антикоррозионная лента могут защитить сварной шов.
Вне зависимости от того, проложена ли ваша труба внутри или снаружи, большая или
маленькие, пусть наши специалисты-сварщики на 3-Б
Сварка, ООО, вам в помощь.