Записки начинающего сварщика, часть 1 — Страница 62 — Ручная дуговая сварка — ММA
СварщикРучник, доброго вечера, вот мой безотрыв на трубе уонями, история такова, исправляю я значит косяк ступеней, вот на данной подставке Чуть дальше можно увидеть некий «помошник в сборке ступеней» аля деревянный кондуктор, по завершению исправлений, уже смеркалось,дай думаю трубу в безотрыв лупану, а че энтузиазьм прет, глаза горят….ну и получилась дудка…Затем образовалась идея прихватить 2 обрезка трубы на прихватки и прихватить к подставке, затем поднять вертикально подставку типа изобразить неповоротный стык с элементами удобства, и получился некий патронодержатель (а че, обрезать потом косынку и готово, а когда надо, по месту куданить прихватить). Трубу прихватывал МР3 , прожег дыру, металл ржавый,пластина толстая около 2 мм, но вся в кратерах, рука дрогнула доли секунды придержал на одном месте — вот она «технологическая отверстия» .
И так действие первое — лень, напомню смеркалось, свариваемые обрезки не зачищал.

Универсальная глупость один — взял по ржавчине Уони
Действие второе взял уголок чтоб прожеч немного электрода, посушить,дугу подержать да уставку тока проверить (ставил 100А)
Универсальная глупость два — от электрода отвык,вернее ожидаешь шлак (рутиловый),а это металл плывет, на горизонтали шов прошел без залипаний и затуханий
Действие третье — поставил подставку в вертикальное положение, так чтоб начиная варить можно было опереться на колено ведя шов, начиная с 6:30, плавно выводя электрод к 12ти и продолжая (решил, а че в крутых видосах можно шпарить и сверху вниз)
Универсальная глупость три — излишняя самоуверенность и плохая подготовка под сварку… а еслиб срочно надо было трубу заварить, чтоб обеспечить водой пару домов да хотя бы себя.
Действие четвертое, лепнина пошла в районе 4х . из-за боязни прожеч отрываю электрод, тухнет, по привычке к легко зажигаемому рутилу тычу в надежде поймать дугу, но…вновь неудачный розжиг.
Универсальная глупость четыре — без коментариев, жопа она и в африке и в камбоже и в сварке бывает.
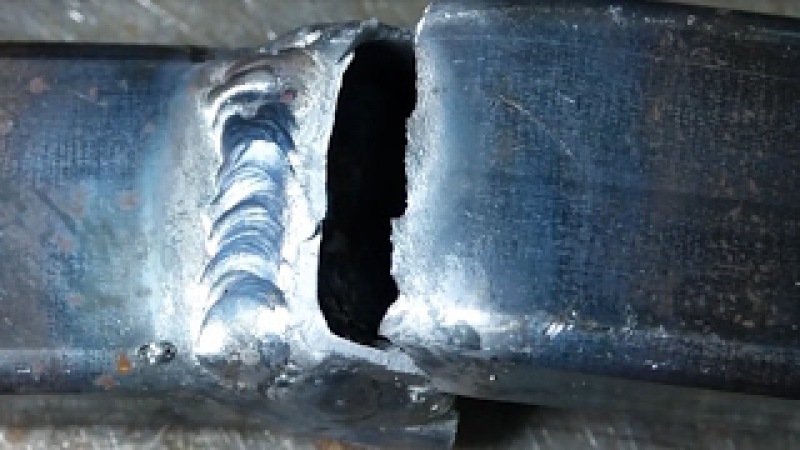
Действие пять как только вышел на 11:30, повернул электрод как рутил углом к поверхности 20град. и на обмазку, миновал 12 часов, ускорился.
Универсальная глупость пять — нефих торопиться, трубный процесс не понят, теория опережает практику, нет чувства процесса, знаю как , а не могу сделать.
Вывод — пьесса коротка и не продуктивна, неповоротный стык не дается, Уонями незя по каке, много тока и(или) вялые движения.
УОНИ Полярность прямая, ток 100А, в последствии снижен на 95А, МР3 прихватка трубы ток 105, полярность прямая, изначально варив МР3 полярность обратная ,однако переключив на прямую понравилось больше (субъективно) диаметры электрода тройка, жертва(трубы) 32ая.
Прочность — сварочный шов — Большая Энциклопедия Нефти и Газа, статья, страница 1
Прочность — сварочный шов
Cтраница 1
Прочность сварочного шва зависит от его размеров и от качества наплавленного металла. [1]
Лучшие результаты по прочности сварочного шва были получены при использовании ролика, когда резонансная частота колебательной системы равна собственной частоте концентратора и преобразователя ( технологические зависимости — прочность сварных соединений от параметров режима сварки рассмотрены в гл.
[2]
Отдельные поры практически не влияют на прочность сварочного шва, поэтому такой дефект исправляют путем вырубки и повторной заварки дефектного участка только в том случае, если шов должен быть не только прочным, но и герметичным. [3]
Несмотря на большие успехи сварки и достижения прочности сварочного шва, равной прочности основного металла изделия, заклепочные соединения еще широко применяются при изготовлении и монтаже технологических металлоконструкций, так как в отдельных случаях применение сварки затруднено. [4]
Непровары, особенно по кромкам и между слоями, являются самыми опасными, так как влияют на прочность сварочного шва. Обнаруженные участки с непроваром вырубают до основного металла, зачищают и заваривают вновь. [5]
Прочность на растяжение в сечении трубы, ослабленном проточкой под цементирующее кольцо, не проверяется, так как прочность этого сечения примерно на 10 % выше, чем прочность сварочного шва.
[6]
Прочность на растяжение в сечении трубы, ослабленном проточкой под центрирующее кольцо, не проверяется, так как прочность этого сечения примерно на 10 % выше, чем прочность сварочного шва. [7]
Подогревная лента остается в сварочном шве. Прочность сварочного шва на растяжение равна или даже больше прочности полиэтиленовой оболочки. [8]
Электроды для сварки обозначают буквой Э с двухцифровым числом через дефис. Число показывает прочность сварочного шва на растяжение. Электроды для наплавки обозначают буквами ЭН и числом, которое указывает гарантированную твердость наплавленного материала. Каждому типу электродов соответствует несколько их марок, различающихся видом и составом покрытий. Для сварки и наплавки деталей применяют электроды с покрытиями. [9]
Технологические особенности электродуговой наплавки используют в целях ослабления нежелательных сопутствующих явлений, таких как окисление металла, поглощение азота, выгорание легирующих примесей и нагрев материала детали выше температуры фазовых превращений. Эти явления приводят к снижению прочности сварочного шва, нарушению термообработки материала, объемным, структурным и фазовым изменениям и короблению детали. Перемешивание материалов основы и покрытия ухудшает его свойства.
[10]
На рис. 75 показано соединение винипластовых труб муфтой, приклеенной и приваренной по торцам. Сварка труб в стык не получила широкого распространения, так как прочность сварочного шва для винипласта составляет 65 — 85 % прочности основного материала. [12]

Взаимодействие расплавленного металла в столбе дуги и сварочной ванне с кислородом и азотом воздуха ухудшают химический состав металла. Неуправляемое охлаждение приводит к нежелательным объемным и структурным изменениям, что вызывает, в свою очередь, коробление детали, трещины, нарушение термообработки и снижение прочности сварочного шва. В жидких металлах растворяется водород, который приводит к хрупкости материала. [15]
Страницы: 1 2
Сварочный дефект — Welding defect
Дефект сварки является любой недостаток , который ставит под угрозу полезность сварной конструкции . Дефектов сварки великое множество . Дефекты сварки классифицируются в соответствии с ISO 6520, а их допустимые пределы указаны в ISO 5817 и ISO 10042.
Основные причины
По данным Американского общества инженеров-механиков (ASME), причины дефектов сварки можно разбить следующим образом: 41 процент плохих условий процесса, 32 процента ошибок оператора, 12 процентов неправильной техники, 10 процентов неправильных расходных материалов и 5 процентов плохих сварных канавок. .
Хрупкость водорода
Остаточные напряжения
Величину напряжения, которое может образоваться при сварке, можно приблизительно рассчитать, используя:
- E α Δ Т {\ Displaystyle E \ alpha \ Delta T}
Где E — модуль Юнга , α — коэффициент теплового расширения , а ΔT — изменение температуры. Для стали это примерно 3,5 ГПа (510 000 фунтов на квадратный дюйм).
Типы
Трещины
Дефекты, связанные с переломом .
Удары дуги
Дуговый разряд — это разрыв сплошности, возникающий в результате дуги, состоящей из любого локализованного переплавленного металла, металла, подвергшегося термическому воздействию, или изменения профиля поверхности любого металлического объекта. Удары дуги приводят к локальному нагреву основного металла и очень быстрому охлаждению. Находясь за пределами предполагаемой области сварного шва, они могут привести к упрочнению или локальному растрескиванию, а также могут служить потенциальными участками для инициирования разрушения. В статически нагруженных конструкциях искры дуги не нужно удалять, если только такое удаление не требуется в контрактных документах. Однако в конструкциях с циклической нагрузкой разряды дуги могут привести к концентрациям напряжений, которые могут отрицательно повлиять на работоспособность таких конструкций, и их следует отшлифовать до гладкой поверхности и осмотреть на предмет трещин.
Холодное растрескивание
Остаточные напряжения могут снизить прочность основного материала и привести к катастрофическому разрушению из-за холодного растрескивания. Холодное растрескивание ограничивается сталями и связано с образованием мартенсита по мере охлаждения сварного шва. Растрескивание происходит в зоне термического влияния основного материала. Чтобы уменьшить величину деформации и остаточных напряжений, количество подводимого тепла должно быть ограничено, а последовательность сварки должна быть не от одного конца непосредственно к другому, а, скорее, сегментами.
Холодное растрескивание происходит только при соблюдении всех следующих предварительных условий:
- чувствительная микроструктура ( например, мартенсит )
- водород, присутствующий в микроструктуре ( водородное охрупчивание )
- рабочая температура окружающей среды (нормальное атмосферное давление): от -100 до +100 ° F
- высокая сдержанность
Устранение любого из них устранит это состояние.
Кратерная трещина
Кратерные трещины возникают при разрыве сварочной дуги. Кратер образуется при наличии достаточного количества расплавленного металла для заполнения полости дуги.
Шляпа трещина
Трещины шляпки получили свое название от формы поперечного сечения сварного шва, потому что сварной шов расширяется на поверхности сварного шва. Трещина начинается на линии плавления и распространяется вверх по сварному шву. Обычно они вызваны слишком большим напряжением или недостаточной скоростью.
Горячее растрескивание
Горячее растрескивание, также известное как растрескивание при затвердевании, может происходить со всеми металлами и происходит в зоне плавления сварного шва. Чтобы уменьшить вероятность этого типа растрескивания, следует избегать чрезмерного удержания материала и использовать соответствующий наполнитель. К другим причинам относятся слишком высокий сварочный ток, плохая конструкция соединения, которое не рассеивает тепло, примеси (например, сера и фосфор ), предварительный нагрев, слишком высокая скорость и длинные дуги.
Трещина под бортом
Трещина под бортом, также известная как трещина зоны термического влияния (ЗТВ), представляет собой трещину, которая образуется на небольшом расстоянии от линии сплавления; это происходит в низколегированной и высоколегированной стали . Точные причины этого типа трещин до конца не изучены, но известно, что растворенный водород должен присутствовать. Другим фактором, влияющим на этот тип трещины, являются внутренние напряжения, возникающие из-за неравномерного усадки основного металла и металла шва, ограничения основного металла, напряжения от образования мартенсита и напряжения от выделения водорода из металла. .
Продольная трещина
Продольные трещины проходят по длине сварного шва. Есть три типа: проверка трещина , корневые трещины и полная осевая линию трещина . Проверьте, что трещины видны с поверхности и частично заходят в сварной шов. Обычно они вызваны высокими усадочными напряжениями , особенно при заключительных проходах, или механизмом горячего растрескивания. Корневые трещины начинаются у корня и частично доходят до сварного шва. Они являются наиболее распространенным типом продольных трещин из-за небольшого размера первого сварного шва. Если не устранить этот тип трещины, она обычно будет распространяться на последующие проходы сварного шва, как правило, именно так и образуются полные трещины (трещина от корня до поверхности).
Повторный нагрев крекинга
Растрескивание при повторном нагреве — это тип растрескивания, который возникает в стали HSLA , особенно в хромистых , молибденовых и ванадиевых сталях, во время последующего нагрева. Это явление также наблюдалось в аустенитных нержавеющих сталях. Это вызвано плохой пластичностью ползучести в зоне термического влияния. Любые имеющиеся дефекты или зазубрины усугубляют образование трещин. Вещи, которые помогают предотвратить растрескивание при повторном нагреве, включают термообработку сначала с выдержкой при низкой температуре, а затем с быстрым нагревом до высоких температур, шлифовку или упрочнение подошв сварных швов, а также использование техники двухслойной сварки для улучшения структуры зерен ЗТВ .
Трещины на корнях и пальцах ног
Корневая трещина — это трещина, образованная коротким валиком у основания (подготовки кромки) в начале сварки, слабым током в начале и из-за использования неподходящего присадочного материала. Основная причина трещин такого типа — водородная хрупкость. Эти типы дефектов можно устранить, используя высокий ток на старте и надлежащий присадочный материал. Трещина на носке возникает из-за содержания влаги в зоне сварки, она является частью поверхностной трещины, поэтому ее легко обнаружить. Предварительный нагрев и правильное формирование швов являются обязательными для устранения таких дефектов.
Поперечная трещина
Поперечные трещины перпендикулярны направлению шва. Как правило, это результат продольных усадочных напряжений, действующих на металл шва с низкой пластичностью. Кратерные трещины возникают в кратере при преждевременном прекращении сварочной дуги. Кратерные трещины обычно неглубокие, горячие трещины обычно образуют одиночные или звездчатые трещины. Эти трещины обычно начинаются у кратерной трубы и проходят продольно в кратере. Однако они могут перейти в продольные трещины сварного шва в остальной части шва.
Искажение
Методы сварки, предполагающие плавление металла в месте соединения, обязательно склонны к усадке по мере остывания нагретого металла. Затем усадка вызывает остаточные напряжения и деформацию. Искажение может стать серьезной проблемой, поскольку конечный продукт не имеет желаемой формы. Чтобы уменьшить некоторые виды деформации, заготовки можно смещать, чтобы после сварки изделие имело правильную форму. На следующих рисунках описаны различные типы сварочной деформации:
Поперечная усадка
Угловое искажение
Продольная усадка
Скругленное искажение
Искажение нейтральной оси
Включение газа
Газовые включения — это широкий спектр дефектов, в том числе пористость , выбоины и трубы (или червоточины ). Основной причиной газовых включений является улавливание газа в затвердевшем сварном шве. Образование газа может быть вызвано любой из следующих причин: высокое содержание серы в заготовке или электроде , чрезмерная влажность электрода или заготовки, слишком короткая дуга или неправильный сварочный ток или полярность .
Включения
Есть два типа включений: линейные включения и округлые включения . Включения могут быть как изолированными, так и кумулятивными . Линейные включения возникают, когда в сварном шве присутствует шлак или флюс . Шлак формы от использования потока, поэтому этот тип дефекта , как правило , происходит в процессах сварки , что использование потока, таких , как экранированные дуговой сварки металла , порошковая для дуговой сварки и дуговой сварки под флюсом , но она также может происходить в газе металлическая дуговая сварка . Этот дефект обычно возникает в сварных швах, которые требуют нескольких проходов и между сварными швами плохое перекрытие. Плохое перекрытие не позволяет шлаку от предыдущего сварного шва расплавиться и подняться до вершины нового сварного шва. Это также может произойти, если предыдущий сварной шов оставил поднутрение или неровный профиль поверхности. Для предотвращения включения шлака шлак следует очищать от валика сварного шва между проходами путем шлифования , чистки проволочной щеткой или сколов.
Изолированные включения возникают при наличии ржавчины или прокатной окалины на основном металле.
Отсутствие сплавления и неполное проникновение
Недостаток плавления — это плохая адгезия сварного шва к основному металлу; Неполный проплав — это сварной валик, который не начинается у основания сварной канавки. Неполное проплавление формирует каналы и щели в корне сварного шва, которые могут вызвать серьезные проблемы в трубах, поскольку в этих областях могут оседать коррозионные вещества. Такие дефекты возникают при несоблюдении сварочных процедур; возможные причины включают настройку тока, длину дуги, угол электрода и манипуляции с электродом. Дефекты можно классифицировать как критические и некритические. Пористость (пузырьки) в сварном шве обычно в определенной степени приемлема. Шлаковые включения, поднутрения и трещины обычно недопустимы. Некоторая пористость, трещины и включения шлака видны и могут не нуждаться в дополнительной проверке, чтобы потребовать их удаления. Подобные мелкие дефекты можно проверить с помощью теста на проницаемость жидкости (проверка красителя). Включения шлака и трещины прямо под поверхностью можно обнаружить с помощью магнитопорошковой инспекции. Более глубокие дефекты могут быть обнаружены с помощью методов рентгенологического (рентгеновское) и / или ультразвукового (звуковые волны) тестирования.
Ламеллярный разрыв
Пластинчатый разрыв — это тип сварочного дефекта, который возникает в прокатанных стальных листах, которые были сварены вместе из-за усилий усадки, перпендикулярных сторонам листов. С 1970-х годов изменения в производственной практике, ограничивающие количество используемой серы , значительно снизили частоту возникновения этой проблемы.
Пластинчатый разрыв вызван в основном включениями серы в материале. К другим причинам относится избыток водорода в сплаве. Этот дефект можно смягчить, если содержание серы в стальном сплаве будет ниже 0,005%. Добавление в сплав редкоземельных элементов , циркония или кальция для контроля конфигурации включений серы по всей металлической решетке также может смягчить проблему.
Изменение процесса строительства для использования литых или кованых деталей вместо сварных может устранить эту проблему, поскольку пластинчатый разрыв происходит только в сварных деталях.
Подрез
Подрезание — это когда сварной шов уменьшается толщина поперечного сечения основного металла, что снижает прочность сварного шва и деталей. Одной из причин этого типа дефекта является чрезмерный ток, вызывающий плавление краев стыка и просачивание в сварной шов; это оставляет желобчатое впечатление по длине сварного шва. Другая причина заключается в использовании некачественной техники, при которой не остается достаточного количества присадочного металла по краям сварного шва. Третья причина — использование неподходящего присадочного металла, поскольку это приведет к большему перепаду температур между центром сварного шва и краями. Другие причины включают слишком маленький угол наклона электрода, демпфированный электрод, чрезмерную длину дуги и низкую скорость.
Рекомендации
Библиография
- Кэри, Говард Б.; Хелцер, Скотт К. (2005), Современные сварочные технологии , Верхняя река Сэдл, Нью-Джерси : Pearson Education, ISBN 0-13-113029-3 .
- Радж, Балдев; Jayakumar, T .; Thavasimuthu, M. (2002), Практический неразрушающий контроль (2-е изд.), Woodhead Publishing, ISBN 978-1-85573-600-9 .
- Рампаул, Хубасар (2003), Процедуры сварки труб (2-е изд.), Industrial Press, ISBN 978-0-8311-3141-8 .
- Морено, Прето (2013), Дефекты сварки (1-е изд.), Aracne, ISBN 978-88-548-5854-1 .
- Weman, Klas (2003), Справочник по процессам сварки , Нью-Йорк, Нью-Йорк: CRC Press, ISBN 0-8493-1773-8 .
внешние ссылки
Как заполнить большой сварочный шов
При выполнении сварочных работ может понадобиться заполнить достаточно широкий шов.

Что потребуется:
- пара электродов;
- молоток;
- наждачная бумага;
- болгарка с зачистным диском.
Процесс заполнения больших швов
Чтобы при наложении плоскости расплавленный электрод не стекал, а соединяемые детали не прожигались, необходимо использовать дополнительный пруток. Легче всего работать очищенным сердечником электрода такого же сечения, как и у того которым выполняется сварки. Его нужно обстучать молотком и стереть остатки обмазки наждачной бумагой.
При заваривании отверстия необходимо прикладывать торец очищенного сердечника к его краю, образовывая зазор в пару миллиметров. Шов накладывается между прутком и стенкой отверстия.
Приставляемый сердечник отлично плавится, при этом горячий металл из него держится заданной плоскости. Дойдя до края, нужно на горячую оторвать прикладываемый пруток и приставить его снова чуть выше.

При необходимости наложить длинный широкий шов используется такая же техника. Сначала торец сердечника приставляется к началу шва, чтобы сцепить края сваркой. Затем пруток отрывается и располагается вдоль шва под острым углом. В результате большой зазор между свариваемыми деталями частично перекрывается сердечником и разбивается на 2 узких просвета. Далее выполняется заполнение поперечным движением электрода.
Данная техника выполнения сварки позволит заварить практически любое отверстие или зазор, конечно в разумных пределах. Поначалу до получения опыта сердечник будет прикипать к шву. Нужно стараться его смещать пока металл жидкий, и таких проблем не возникнет.
Смотрите видео
ANSI / AWS B4.

ANSI / AWS B4.0 подробно описывает требования к механическим испытаниям сварных швов. Часть этого стандарта описывает испытания сварных швов на растяжение. Испытание на растяжение можно проводить на образцах, вырезанных поперечно или продольно по отношению к центральной линии сварного шва. Желаемый результат обычно ограничивается пределом прочности на разрыв, поскольку эти образцы неоднородны. Испытания на растяжение также могут проводиться на основном металле и металле сварного шва для определения механических свойств этих материалов, и результаты могут включать в себя предел прочности на разрыв, предел текучести со смещением, предел текучести, полное удлинение и уменьшение площади.Испытания следует проводить в соответствии с требованиями ASTM E8.
Может потребоваться оборудование для обработки образцов как плоского, так и круглого типа. При испытании сварных труб или насосно-компрессорных труб в системе также может потребоваться возможность работы с полными круглыми образцами номинальным диаметром до 3 дюймов. По этим причинам мы обычно рекомендуем нашу машину Industrial Series HDX с двумя проемами со встроенными клиновыми захватами для тестирования плоских или круглых деталей. Конструкция с двумя пространствами также может удовлетворить любые требования к испытаниям на изгиб в нижней части испытательного пространства на сжатие.Вы также можете включить дополнительный канал кондиционера и экстензометр для измерения деформации. Пакеты программного обеспечения для испытаний материалов автоматически сгенерируют результаты необходимых расчетов, перечисленных выше.
Сварные образцы часто могут иметь изгиб по длине. Чтобы поддерживать осевое совмещение, машина должна быть прочной и обеспечивать достаточное усилие зажима для преодоления небольшого изгиба образцов. Вот почему мы предлагаем использовать модель HDX. Нагрузка на образец также измеряется непосредственно с использованием тензометрических датчиков веса, что позволяет герметизировать гидравлическую систему и защитить ее от загрязнения. Этот тип системы также лучше противостоит эффектам нецентральной нагрузки, создаваемой слегка изогнутыми образцами.
Как рассчитывается прочность сварки
Некоторые люди удивляются, узнав, что сварные детали компонентов из нержавеющей стали на самом деле могут быть прочнее основного металла. Как точно рассчитывается прочность сварного шва? Один из способов — это прочность на разрыв.
Прочность на растяжение — это метод разрушающих испытаний, который демонстрирует максимальное напряжение, которое выдерживает материал перед разрушением или разрушением.Вытягивая или растягивая материал до его предела прочности, можно рассчитать предел прочности на разрыв.
Существует также несколько методов неразрушающего контроля (NDT), которые регулярно используются техническими специалистами Axenics для проверки наилучших характеристик сварных деталей из нержавеющей стали (например, визуальный контроль, проверка утечки гелием и ультразвуковой контроль). Однако разрушающие испытания иногда требуются в таких отраслях, как науки о жизни, химическое производство, медицинские устройства и альтернативные источники энергии, которые транспортируют легколетучие химические вещества. Для этих отраслей мы выполняем орбитальную сварку в чистых помещениях на различных трубах из нержавеющей стали.
Обычно мы не проводим разрушающие испытания на месте, но для того, чтобы лучше обслуживать наших клиентов, мы выехали за пределы площадки, чтобы определить предел прочности стали на разрыв. Целью этого испытания было выяснить, как отсутствие проплавления сварного шва может в конечном итоге повлиять на предел прочности при растяжении. Цель состояла в том, чтобы определить ценность сварного шва с полным проплавлением по сравнению со сварным швом без проплавления.
Испытания на прочность при растяжении
Испытания на прочность на растяжение — отличный способ показать важность надлежащей практики сварки.Мы протестировали нержавеющую сталь 316L диаметром 1,00 ”. Трубка со стенкой х 0,065 дюйма, проведенная для равного отбора проб как сварных соединений с полным проплавлением, так и сварных соединений без проплавления.
Чтобы подготовить образец, разрежьте трубку пополам, а затем расплющите ее. Чтобы измерить прочность сварного шва, есть расчет, в котором общая площадь сварного шва определяется прочностью, необходимой для разрыва этого шва.
Постоянство размера сварного шва или трубы не имеет значения. Формула берет ширину образца сварного шва и измеряет высоту сварного шва.Это дает вам «площадь». Когда машина растягивает образец, величина приложенной силы измеряется фунтами. Когда образец в конечном итоге разобьется, прибор покажет вам размер в фунтах. В этой точке возьмите «площадь» и разделите на фунты силы. Это вычисляет количество фунтов на квадратный дюйм, необходимое для разрыва сварного шва.
Результаты показывают, что образцы с полным проникновением разрушаются при гораздо более высоком пределе прочности PSI, чем образцы с частичным проникновением. На всех испытанных образцах предел прочности сварных швов без проплавления находился на сварном шве.На полностью проплавленных образцах точка разрыва обычно располагалась за пределами самого сварного соединения, на участке термического влияния трубы.
Испытание демонстрирует необходимость выполнения сварных швов на самом высоком уровне качества, чтобы гарантировать, что система трубопровода не будет повреждена из-за отказа одной части трубки. Опять же, неразрушающий контроль обычно обеспечивает высочайшую производительность сварных соединений, но мы знаем, что мы готовы пройти весь путь до разрушающих испытаний, чтобы облегчить ваше мнение.
Лучший поставщик сварочных материалов в Китае
Около Qingdao Tensileweld Welding Consumables Co., Ltd. Основанная в 2012 году, расположена в Циндао, провинция Шаньдун, одном из экономически развитых прибрежных городов, рядом с портом Циндао, одним из самых важных портов Китая, с исключительно выгодным географическим положением и удобной транспортировкой. Обладает высококлассным передовым оборудованием. , строгий менеджмент и упорный труд наших сотрудников, мы специально производим высококачественную сварочную продукцию. Выпуск сварочной продукции составит более 80 000 метрических тонн в год.
Qingdao Tensileweld Welding Consumables Co., Ltd., производитель и поставщик сварочных установок, предлагает комплексные продукты для обработки сварочных материалов, такие как сварочная проволока / пруток (сварочная проволока с защитой от газа CO2, сварочная проволока из нержавеющей стали, алюминиевая сварочная проволока, сварочная проволока из медных сплавов, сварочная проволока из никелевых сплавов), сварочные электроды. (Электрод из углеродистой стали, Электрод из нержавеющей стали, Сварочный электрод из никелевого сплава, Сварочный электрод из медного сплава, Чугунный электрод), сварочная проволока с флюсовой сердцевиной, Углеродный стержень для строжки, силикат, проволока для дуговой сварки под флюсом, а также свинец и свинцовые сплавы. держать вас в курсе текущих новостей! Высокое качество и лучшая цена, своевременная доставка! Запросите цитату прямо сейчас!
Мы являемся профессиональным производителем сварочных электродов и сварочной проволоки.Между тем, сильные команды исследований и разработок, обеспечивающие различные потребности различных отраслей; ведущее в отрасли производственное оборудование, обеспечивающее стабильное качество продукции с момента ее создания.
Почему выбирают нас?
Под нашим брендом «Tensileweld» наши сварочные материалы широко использовались в сосудах высокого давления, мостах, кораблях, транспортных средствах, нефтяной и химической промышленности, тяжелой технике и т. Д. В стране и за рубежом. Основные продукты были одобрены Китайским классификационным обществом (CCS), Американским бюро судоходства (ABS), Bureau Veritas (BV), Germanischer Lloyd (GL), Регистром судоходства Ллойда (LR), Японскими промышленными стандартами (JIS).
Вся продукция произведена в соответствии с системой менеджмента качества ISO9001: 2015.
Искренние услуги, хорошая кредитоспособность и разумные цены — все это обеспечит вам уверенность и удовлетворение.
Одновременно наша продукция может найти широкое применение в различных отраслях промышленности, таких как нефтехимическая промышленность, сосуды высокого давления, судостроение, автомобили, велосипеды, алюминиевая опалубка и т. США, Великобритания, Италия, Польша, Испания, Чехия, Россия, Аргентина, Бразилия, Мексика, Южная Африка и более 40 стран и регионов.
В заключение, наша компания придерживается принципов «Целостность, инновации, сервис» в качестве нашей бизнес-философии и «Лучший бренд, лучшая репутация» в качестве маркетинговой концепции, которая обязуется предоставлять высококачественные продукты и лучший сервис для отечественных и зарубежных клиентов.
Кто мы?
*** В 1991 году г-н Сюй Чжункай, основатель компании, поступил на 3 года специалиста по сварке в Машиностроительный факультет Университета Цинхуа.
*** С 1994 по 2012 год работал техническим менеджером, начальником производства и заместителем генерального директора на заводе сварочных электродов Laiyang
.*** В 2012 г.Сюй Чжункай основал частное предприятие Laiyang Jinkaishun Special Welding Electrode Factory для производства сварочных электродов и совместного производства сварочной проволоки с Anqiu San Kin Yip Dengfeng Welding Material Co., Ltd.
. *** В 2015 году компания Qingdao Booster Welding Consumables Co. , Ltd. была зарегистрирована для экспорта сварочных материалов в более чем 40 стран мира
*** В 2017 году завод специальных сварочных электродов Laiyang Jinkaishun был преобразован в акционерное общество Shandong 7thSTEEL Welding Consumables Co., ООО
Что мы основной продукт?
*** Различные сварочные электроды.
*** Сварочная проволока для сварки MIG / MAG
*** Сплошная сварочная проволока и вольфрамовый электрод для сварки TIG
*** Порошковая сварочная проволока
*** Проволока и флюс для дуговой сварки под флюсом
*** Силикат
Оптимизация и прогноз предела прочности на разрыв при сварке металлов активным газом
Мы исследовали влияние параметров сварки на предел прочности на разрыв конструкционной стали ST37-2, сваренной сваркой металла активным газом.Дробный факторный план использовался для определения значимости шести параметров: скорости подачи проволоки, сварочного напряжения, скорости сварки, угла перемещения, расстояния от наконечника до рабочей поверхности и расхода защитного газа. Была разработана регрессионная модель для прогнозирования предела прочности на разрыв. Наконец, мы проверили оптимизацию параметров процесса экспериментально. Мы достигли оптимального предела прочности на разрыв (558 МПа) и скорости подачи проволоки 19 м / мин, что дало наибольший эффект, за которым следовало расстояние от наконечника до рабочей поверхности, 7 мм, скорость сварки, 200 мм / мин, сварочное напряжение, 30 В. , и угол хода 60 °.Скорость потока защитного газа, равная 10 л / мин, была немного лучше, но не имела большого эффекта в диапазоне 10–20 л / мин. Испытания показали, что наша регрессионная модель может предсказать предел прочности на разрыв в пределах 4%.
1. Введение
Процесс сварки металлоактивным газом (MAG), подтип газовой дуговой сварки (GMAW), используется в сварочной промышленности на протяжении многих десятилетий благодаря своим значительным преимуществам, включая высокую производительность, простой механизм, хорошее качество. качество и механические свойства сварного соединения, а также широкий спектр свариваемых материалов и присадочных металлов [1]. При сварке MAG между сплошным присадочным электродом и основным металлом образуется электрическая дуга постоянного тока. Вырабатывается тепло для плавления металла в области стыка. Активный защитный газ защищает расплавленную сварочную ванну и электродную проволоку от загрязнений в атмосфере [1, 2].
В любом процессе сварки параметры сварки играют важную роль в качестве продукции, поскольку они влияют на механические свойства и геометрию сварного соединения [1–4]. Однако выбор оптимальных параметров для соответствия требуемой спецификации затруднен, поскольку на качество сварки может влиять несколько переменных, таких как химический состав материала заготовки и проволочного электрода, защитный газ и любая термообработка [1, 5].Кроме того, экспериментальная оптимизация методом проб и ошибок очень трудоемка и затратна [3, 4, 6]. Следовательно, несколько методов и подходов, таких как план эксперимента (DoE) и статистические методы, были использованы для решения этой проблемы [1–3, 6]. Среди различных используемых методов дробный факторный план широко используется для определения важных параметров процесса и оптимизации качества продукции, поскольку он полезен для моделирования и анализа проблем, включающих несколько параметров [7]. Несколько исследований были сосредоточены на оптимизации геометрии сварного шва и механических свойств сварного соединения [1–6, 8].
В данной работе дробно-факторный расчет был использован для определения влияния параметров сварки MAG на предел прочности при растяжении (UTS) мягкой стали. Прочность на растяжение была выбрана для оценки качества сварного шва, поскольку это ключевое механическое свойство, которое может описывать характеристики сварного соединения [6]. UTS сварного соединения важен, потому что это оценка максимальной нагрузки, которую сварной шов может выдержать [5]. Также были рассмотрены оптимальные параметры для максимального UTS. Дисперсионный анализ (ANOVA) и регрессионный анализ использовались для определения значимых параметров и для разработки модели UTS.
2. Детали эксперимента
2.1. Подготовка и испытание образцов
Низкоуглеродистая сталь (ST37-2) толщиной 6 мм была основным металлом; он имеет предел текучести 340 МПа и предел прочности при растяжении 470 МПа: его химический состав показан в таблице 1. Образцы размером 125 мм × 100 мм были подготовлены и очищены щеткой для лучшего качества сварки. Стыковое соединение без зазора формировалось за один проход сваркой MAG; см. рисунок 1 (а). После сварки образцы для испытания на предел прочности на разрыв (UTS) были вырезаны в соответствии со стандартом ASME IX; см. рисунок 1 (b).УТС испытывали при комнатной температуре на универсальной испытательной машине грузоподъемностью 10 тонн.
|
2,2. Оборудование
Для сварки использовался сварочный аппарат WIM MIG 350SEF с источником постоянного напряжения и положительной полярностью электрода постоянного тока (DCEP). В качестве сварочного материала использовалась электродная проволока AWS A5.18 ER70S-6 с диаметром стержня 0,8 мм. Химический состав этого электрода приведен в таблице 1.Технический диоксид углерода (99,98% CO 2 ) использовался в качестве защитного газа для предотвращения химических реакций между горячей поверхностью детали и атмосферой.
2.3. Выбор параметров сварки и их уровней
Были исследованы шесть входных параметров с допустимыми диапазонами, рекомендованными руководством по сварке [9] и ограниченными возможностями аппарата. Два уровня используемых входных факторов показаны в таблице 2.
|
2.

В эксперименте использовался дробный факторный план 2 6-2 с 16 комбинациями. Для каждой комбинации было проведено два повтора, что дало всего 2 × 16 = 32 эксперимента. Схема эксперимента была создана с помощью программного обеспечения MINITAB [10], в котором систематическая ошибка была устранена путем случайного назначения параметров; см. Таблицу 3.
3.3. Модель для UTSМножественный регрессионный анализ для прогнозирования UTS был проведен на экспериментальных данных в таблице 3. Модель регрессии (некодированные единицы) в (1) была разработана путем расчета коэффициентов регрессии сокращенных членов модели: где UTS является окончательным предел прочности на разрыв (МПа), — скорость подачи проволоки (м / мин), — сварочное напряжение (вольт), — скорость сварки (мм / мин), — угол перемещения (градусы), — расстояние от наконечника до рабочей поверхности (мм), — расход защитного газа (л / мин). При проведении двухуровневого факторного эксперимента мы обычно используем модель первого порядка, которая включает только основные эффекты и условия взаимодействия [7]; см. (1). 3.4. UTS Оптимизация параметров сварки Максимальное значение UTS было единственной целью данного исследования. Чтобы выбрать оптимальные параметры сварки, было рассмотрено основное влияние каждого параметра на рисунке 3 (а). 3.5. Подтверждающий тестДля проверки модели множественной регрессии (1) и оптимизации параметров сварки в шести экспериментах использовались оптимальные условия сварки. UTS, полученные с помощью предсказанной модели и экспериментов, сравнивались, и процентные ошибки показаны в таблице 5. Прогнозируемая UTS хорошо согласовывалась с измеренной UTS. Отклонения составляли от -2% до 4%.
Примечательно, что максимальное значение UTS, полученное в результате эксперимента (558.В среднем 3 МПа) было больше, чем ОТС основного металла (470 МПа). Во время испытания на растяжение было замечено, что разрыв сварного образца происходил на сварном шве, а не на основном металле. 4. Выводы Мы применили дробно-факторный расчет для стыковой сварки мягкой стали без зазора с использованием MAG. Исследование было сосредоточено на влиянии параметров сварки на предел прочности при растяжении (UTS) сварного соединения и оптимальные условия сварки для максимального UTS.Мы пришли к следующему выводу: (1) Параметры процесса, которые показали наибольшее или наименьшее влияние на UTS сварного соединения, были следующими: скорость подачи при сварке, расстояние от наконечника до рабочей поверхности, скорость сварки, сварочное напряжение и угол перемещения. Было обнаружено, что расход защитного газа в выбранном диапазоне оказывает незначительное влияние. (2) UTS увеличивается с увеличением скорости подачи сварочного материала, сварочного напряжения и угла перемещения. Напротив, UTS увеличивалось с уменьшением скорости сварки и расстояния от наконечника до рабочей поверхности. Важно отметить, что модель, полученная в результате этого исследования, является моделью первого порядка, в которую включены только главный эффект и члены взаимодействия. Однако есть вероятность, что более подходящей является модель второго порядка или нелинейная модель. Поэтому мы планируем изучить методы поверхности отклика (RSM), чтобы исследовать оптимизацию процесса. Конфликт интересов Авторы заявляют об отсутствии конфликта интересов в связи с публикацией данной статьи. БлагодарностиАвторы благодарят Университет Махасаракхама и Технологический университет Раджамангала Исан, Таиланд, за вспомогательные материалы и оборудование. СВАРКА ВЫСОКОПРОЧНЫХ СТАЛЕЙ | Производство и металлообработкаСкорость имеет решающее значение в современном мире производства и изготовления. Компании стремятся зарабатывать больше с меньшими затратами? меньшая доступность квалифицированной рабочей силы и меньшие накладные расходы? при этом все еще идя в ногу с требованиями общества, жаждущего высоких технологий, и увеличивая прибыль. В этих условиях сварщики завтрашнего дня столкнутся с уникальным набором проблем, не последняя из которых — научиться сваривать больше и быстрее. Они также должны научиться сваривать различные материалы, в том числе высокопрочные стали, которые все чаще используются для удовлетворения более высоких производственных требований. Итак, что нужно для решения задач завтрашнего дня? В двух словах: знания, осторожность и время. ПОНИМАНИЕ ОСНОВАНИЯ. . . Как и любой другой материал, сварщики завтрашнего дня должны будут понимать химический и механический состав высокопрочной стали в качестве первого шага к успеху в сварке. Из-за повышенного отношения прочности к массе высокопрочные стали используются для изготовления изделий, которые несут больше, меньше весят и выдерживают экстремальные условия эксплуатации. Материалы, отвечающие этим требованиям, включают стали HSLA (высокопрочные низколегированные) и AHHS (усовершенствованные высокопрочные стали), а на горизонте появится еще больше и более прочных сталей. В частности, стали HSLA используются уже много лет, но они все чаще находят применение в новых отраслях промышленности из-за их долгосрочной рентабельности в высокопроизводительных приложениях. Они часто используются в производстве тяжелого оборудования и конструкционной стали в качестве средства для облегчения нагрузки? Эти стали позволяют производителям использовать более тонкие поперечные сечения материала (по сравнению, например, с A36) для таких применений, не жертвуя ударной вязкостью или прочностью.Другие области применения HSLA включают балки или рамы для прицепов, а также части мостов, крановые стрелы и мачты. В среднем эти материалы обеспечивают предел текучести до 85 ksi (586 МПа). AHHS также начали появляться в последние годы и предлагают даже более высокие механические свойства, чем HSLA? предел текучести до 140 тыс. фунтов на квадратный дюйм (965 МПа). Также есть сообщения о разработке AHSS, которые обеспечивают предел текучести до 160 тыс. Фунтов на квадратный дюйм или более (1103 МПа +). AHHS особенно полезны при производстве автомобильных компонентов, облегчая общий вес автомобиля, сохраняя при этом прочность, необходимую для безопасности. Высокопрочные стали приобретают свои механические свойства, в том числе за счет закалки и отпуска. Сначала материал закаливается, при этом сталь быстро охлаждается до комнатной температуры. Часто это делается с помощью водяного распылителя или специального нефтегазового метода. В процессе отпуска сталь нагревается до температуры чуть ниже ее точки плавления в течение определенного времени. Обычно температура отпуска варьируется от минимум 300 ° F (150 ° C) до 1600 ° F (871 ° C).Продолжительность отпуска зависит от толщины материала и желаемых свойств. Высокопрочные стали сохраняют химический состав, аналогичный стандартной мягкой (или низкоуглеродистой) стали на протяжении всего процесса закалки и отпуска, но вместе взятые процессы значительно повышают прочность этих сталей. Эта дополнительная прочность потребует от сварщиков завтрашнего дня особых мер предосторожности во время процесса сварки. УДАР. . . Высокопрочные стали более чувствительны к растрескиванию, чем мягкие стали, поэтому очень важно обеспечить хороший контроль нагрева до и во время процесса сварки. Во-первых, предварительный нагрев — лучший шаг к управлению температурным градиентом или диапазоном повышения и понижения температуры, происходящего во время сварки. Это особенно важно, так как сварка холодного изделия из высокопрочной стали приведет к слишком быстрому нагреву материала и, в свою очередь, слишком быстрому охлаждению. Такое быстрое охлаждение является основной причиной растрескивания, а предварительный нагрев помогает предотвратить его. Предварительный нагрев также помогает снизить уровень водорода и, в свою очередь, минимизировать вызванное водородом растрескивание.Правильная температура предварительного нагрева определяется точной маркой высокопрочной стали и ее толщиной. Сварщики должны следовать рекомендуемым процедурам сварки для конкретного применения, чтобы определить правильную температуру. Точно так же сварщикам необходимо поддерживать правильную температуру между проходами для данной толщины высокопрочной стали. Это предотвращает образование большей зоны термического влияния (HAZ) во время сварки. могут использовать контактные пирометры, Tempilstiks или другие термочувствительные устройства (включая инфракрасные) для отслеживания температуры между проходами, указанной для их конкретной процедуры сварки. Как и в любом сварочном процессе, контроль скорости хода и поддержание рекомендуемых параметров сварки (вольт, ампер) сводит к минимуму тепловложение при сварке высокопрочных сталей. ПРИНИМАЙТЕ ДВА НА НАПОЛНИТЕЛЯХ. . . При сварке высокопрочных сталей решающее значение имеет выбор присадочных металлов с наименьшим содержанием водорода, а также металлов с хорошей ударной вязкостью (высокими значениями ударной вязкости) и соответствующей прочностью. Как с точки зрения стоимости, так и с точки зрения дизайна, в некоторых случаях требуется соединение высокопрочных сталей со сталями с более низким пределом текучести. В зависимости от конструкции соединения и пути нагружения (область, которая будет нести основную нагрузку на готовое изделие) сварщикам часто необходимо согласовывать прочность присадочного металла с более низкопрочной сталью. В качестве примера, при сварке стали HSLA (предел текучести 85 тыс. Фунтов на квадратный дюйм) со сталью A36 (минимальный предел текучести 36 тыс. Фунтов на квадратный дюйм) сварщики выберут порошковую проволоку марки 70 или порошковую проволоку с пределом прочности на разрыв 70 тыс. Фунтов на квадратный дюйм. Примечание. Основной материал измеряется по пределу текучести, а присадочные металлы измеряются по UTS или пределу прочности на разрыв. Если сварщик сваривает друг с другом высокопрочные стали, то обычно присадочный металл будет соответствовать пределу текучести этих двух. Варианты присадочных металлов с таким пределом прочности на разрыв включают порошковую проволоку из низколегированных металлов или проволоку из низколегированных порошковых материалов. Также доступны сплошные проволочные и стержневые электроды. Проволока с металлическим сердечникомимеет преимущество более высокой скорости движения (по сравнению с сплошной проволокой или стержневыми электродами), что помогает минимизировать тепловложение и, как следствие, возможность растрескивания и деформации. Большинство низколегированных порошковых проволок также обладают превосходной прочностью и более эффективно перекрывают зазоры, чем другие присадочные металлы.У них также низкий уровень водорода. Порошковая проволока для низколегированных низколегированных проволок в защитном газе — это вариант для сварки высокопрочной стали между собой или с материалом с более низкой прочностью. Шлаки с базовой системой шлака Т-5 рекомендуются из-за их хороших механических свойств и прочности. Они также устойчивы к поглощению водорода и могут сваривать легкую ржавчину и прокатную окалину. Однако проволока с шлаковой системой Т-5 не так удобна для сварщиков, как проволока с рутиловой шлаковой системой Т-1. И наоборот, проволока со шлаковой системой Т-1 имеет хорошую стабильность дуги и свариваемость, но, как правило, не обладает такой хорошей пластичностью и вязкостью.Как и другие порошковые проволоки, обе образуют шлак, который необходимо удалять после сварки или между проходами. На сегодняшний день для сварки стали с пределом текучести более 120 тыс. Фунтов на квадратный дюйм доступна только сплошная проволока. Конечно, сварка высокопрочных сталей — это больше, чем просто наблюдение за подводом тепла и выбор присадочного металла. Но в будущем, когда сталелитейная промышленность продолжит расширять границы прочности и ударной вязкости с материалами, сварщикам завтрашнего дня придется продолжать обучение, тренировать и поддерживать более строгие параметры сварки, чем когда-либо прежде. Кейт Паккард — менеджер по продажам и маркетингу подразделения низколегированных трубных проводов компании Hobart Brothers, 101 Trade Square East, Troy, OH 45373, 937-332-4000, факс: 937-332-5224, [email protected], www.hobartbrothers.com. Урок 1 — Основы дуговой сваркиУрок 1 — Основы дуговой сварки © АВТОРСКИЕ ПРАВА 1999 ГРУППА ЭСАБ, ИНК. УРОК I, ЧАСТЬ A Удлиненный — Редукция Перелом Урожайность Прочность Ultimate Прочность 1.6.2 Урожай Прочность — когда металл находится в напряжении, он действует как резиновая лента.![]() ![]() ![]() Слишком низкая прочность на растяжение в ходе процедурных испытаний для 6061-T6?Q — У меня проблемы с прохождением квалификационного испытания процедуры GMAW для шва с разделкой кромок с основным материалом 6061-T6.Я не могу получить минимальную прочность на растяжение, требуемую правилами сварки. Мои тесты на управляемый изгиб, взятые из того же образца для испытаний сварного шва, проходят успешно, и, по-видимому, в образце не наблюдается каких-либо значительных разрывов сварного шва. Образцы для испытаний на поперечное растяжение разрушаются в зоне термического влияния, а не в сварном шве.![]() A — Это часто задаваемый вопрос. Наиболее частой причиной того, что сварной шов, выполненный из этого основного материала, который не имеет крупных неоднородностей, не соответствует минимальным требованиям к растяжению, является перегрев основного материала во время процесса сварки. Чтобы понять, почему может возникнуть эта проблема, мы должны сначала понять характеристики базовых материалов серии 6xxx. Эта серия алюминиевых сплавов является одной из серий, подвергающихся термообработке, которые приобретают свою прочность в процессе термической обработки.Их часто используют в состоянии -T6, что указывает на то, что они были подвергнуты термообработке на твердый раствор и искусственно состарены. Состояние -T6 достигается путем нагрева основного материала до температуры около 990 ° F. Когда мы рассматриваем контролируемую термообработку, которая проводилась с этими материалами перед сваркой, чтобы получить условие -T6, мы можем оценить их реакцию на процесс дуговой сварки, который нагревает материал до тех же температур в неконтролируемом манера. Чтобы соответствовать минимальным требованиям к пределу прочности при растяжении, установленным нормами, нам необходимо тщательно контролировать нашу процедуру сварки, чтобы предотвратить перегрев основного материала. Во-первых, необходимо учитывать размер свариваемых испытательных образцов.В кодексе указаны минимальные размеры испытательной пластины для сварки с разделкой кромок. Вы должны соблюдать это требование; фактически, если это возможно, используйте больший образец для испытаний, чем указано. Это обеспечит превосходный теплоотвод и снизит вероятность чрезмерного перегрева и продолжительного пребывания при температуре в зоне термического влияния. Во-вторых, соблюдайте требования норм к температуре предварительного нагрева и промежуточного прохода, которые для этого типа материала определяют максимальную температуру предварительного нагрева и промежуточного прохода 250 градусов по Фаренгейту.Также соблюдайте время выдержки при требуемой температуре, которое не должно превышать 15 минут. |