этапы, физические и механические методы
Содержание:
- Главные этапы
- Способы проверки
- Особенности визуального осмотра
- Особенности капиллярного метода
- Интересное видео
Сварочная технология должна проводиться правильно и с соблюдением необходимых требований, от которых зависит качество и прочность сварного шва. Независимо от типа свариваемого материала (металл, пластик, стекло) обязательно должны выполняться испытания сварных соединений. Если будет отмечаться хоть небольшое несоответствие заданным характеристикам швов, то это может привести к быстрому разрушению конструкций и изделий. По этой причине после работ обязательно должен проводиться контроль качества соединений.
Главные этапы
Испытание на прочность сварных швов требуется для того, чтобы удостовериться в высоком качестве швов. Это в дальнейшем сможет уберечь от разрушения конструкций ответственного значения. Благодаря данным манипуляциям подтверждается пригодность изделия к дальнейшему использованию.
Испытания состоят из основных этапов:
- сначала проверяется наличие квалификации сварщика;
- оценивание качественных характеристик сварных швов;
- проверка последовательности проведения технологии сварки;
- контролирование качества швов;
- проведение механических испытаний.
Стоит отметить! Во время начального этапа проверяются навыки и умения специалистов. Перед тем как выполнять работы, сварщик обязательно должен показать специальный паспорт, в котором указан допуск к сварочным работам. После он производит пробное соединение.
Пробные швы должны выполняться из того же материала и при помощи приборов, которые применяются при основных работах. Оценивание результатов производится визуальным осмотром. При необходимости могут быть проведены механические испытания.
Физические и механические испытания сварных швов должны проводиться последовательно. Все действия должны учитывать:
- сборка соединений должна быть правильной;
- соблюдение требуемых показателей сварочной технологии — ток, напряжение;
- способ формирования швов;
- очищение от окалин, шлаковых образований. Это должно выполняться предварительно, перед нанесением последующих слоев.
Способы проверки
Металлографические исследования сварных соединений могут быть разрушающего и неразрушающего типа. Первый метод применяется в выборочном порядке. Выполняется проверка одного или нескольких изделий из большой партии или части металлической конструкции.
Проверка производится с учетом необходимых показателей, которые указываются в специальных протоколах испытаний. В обязательном порядке применяются устройства или материалы, которые позволяют проконтролировать качественные характеристики швов с сохранением целостности изделия.
Выделяют следующие физические методы контроля сварных соединений:
- Визуальный.
- Капиллярный.
- Радиационный.
- Магнитный.
- Ультразвуковой.
Чтобы минимизировать дефекты соединений обязательно выполняется операционное контролирование сварочных работ. Регулярно проводится аттестация, на которой комиссия должна дать допуск на сваривание контрольных швов. После прохождения данного испытания выполняется проверка теоретических знаний сварщиков.
Многие способы производятся с использованием специальных приборов, которые оказывают радиационное, магнитное, ультразвуковое воздействие. Обычно они выполняются на производствах с соблюдением требуемых норм и выставленных параметров.
Особенности визуального осмотра
Физические методы контроля сварных швов включают визуальный осмотр изделия. При помощи данного исследования можно обнаружить внешние и внутренние дефекты. По этой причине данная диагностика считается наиболее точной.
Физический метод контроля сварных соединений — это диагностика, которая проводится с применением различных излучений (лазерное, рентгеновское), они взаимодействуют с объектами контроля. При осуществлении данных диагностик соединение никогда не разрушается, обычно оно визуально исследуется.
Частые обрывания дуги можно обнаружить при помощи нескольких характерных качеств — разная высота и ширина катета. По этой причине обязательно требуется проводить предварительное исследование материалов, правильность подключения рабочего оборудования, его готовность к проведению сварочных работ.
Перед тем как будут проводиться испытания, соединения требуется очистить от следующих ненужных элементов:
- окалины;
- шлаки;
- брызги от расплавленного металла;
- различные загрязнения.
Обратите внимание! Чтобы лучше выявить мелкие трещины, стыковую область можно обработать при помощи раствора с азотной кислотой. Это придаст поверхности матовость, сделает более подходящей для проведения визуальной диагностики.
Этот способ испытаний позволяет выявить целый ряд дефектов шва:
- внешние дефекты;
- поры;
- трещины;
- непровары;
- наплывы.
Для лучшей эффективности часто используют увеличительное стекло. Лупа оказывается незаменимым изделием, при помощи которого можно выявить незаметные дефекты.
Особенности капиллярного метода
Данное испытание на твердость сварных швов предполагает применение качества жидкости затягиваться в достаточно небольшие капилляры. Быстрота и степень проникновения во внутреннюю структуру материала связана с его смачиваемостью и размером диаметра капилляров.
Капиллярное исследование может применяться не только для металлических изделий, но и для элементов из керамики, стекла, пластмассы. Основное его назначение состоит в выявлении внешних изъянов, которые не получается обнаружить с первого взгляда. К примеру, при использовании керосина можно выявить сквозные дефекты.
К главным особенностям этого способа проверки качества шва относят:
- При капиллярном методе часто применяются пенетранты.
Данные компоненты обладают небольшим поверхностным натяжением и сильным цветовым контрастом.
- При проникновении в области дефектов, пенетрантов подсвечивают их, именно это позволяет быстро обнаружить изъяны сварочного процесса.
- Пенетранты с высокой чувствительностью могут выявить дефекты с размером от 0,1 микрона.
- Капиллярное исследование подходит для дефектов с размером ширины до 0,5 мм. При большем размере трещин этот метод не работает.
Механические испытания сварных соединений — обязательные манипуляции, которые должны проводиться во время сварочной технологии. Они могут выполняться при помощи разных разрушающих и неразрушающих методов. Если все будет соответствовать установленным нормам и правилам, то сварщик допускается к проведению дальнейших сварочных работ.
Интересное видео
Дефекты и способы испытания сварных швов
Государственное бюджетное профессиональное образовательное учреждение Воронежской области «ВОРОНЕЖСКИЙ ИНДУСТРИАЛЬНЫЙ КОЛЛЕДЖ»
По дисциплинам
МДК 04. 01 Дефекты и способы испытания
сварных швов
ОДБ. 06 Химия
Тема урока: Дефекты сварных швов и причины их возникновения
Разработали:
Преподаватель спецтехнологии
С.С. Гунькова
Преподаватель химии
С.С. Пикулина
Воронеж
2020 г.
Тема урока:
Дефекты сварных швов и причины их
возникновения
Тип урока: урок формирования новых знаний.
Цели урока:
- дать представление о дефектах сварных швов;
- ознакомить обучающихся с видами дефектов и причинами их возникновения;
- развивать умения анализировать, сопоставлять, выделять главное; организовать работу по усвоению обучающимися понятий, определений, научных фактов, предусмотренных учебной программой;
- показать важную и практическую значимость применения знаний по дисциплине.
- ПК 4.2. Определять причины дефектов сварочных швов и соединений.
- ПК 4.3. Предупреждать и устранять различные виды дефектов в сварных швах.
- ОК 1. Понимать сущность и социальную значимость своей будущей профессии, проявлять к ней устойчивый интерес.
- ОК 2. Организовывать
собственную деятельность, исходя из цели и способов ее достижения,
определенных руководителем.
- ОК З. Анализировать рабочую ситуацию, осуществлять текущий и итоговый контроль, оценку и коррекцию собственной деятельности, нести ответственность за результаты своей работы.
- ОК 4. Осуществлять поиск информации, необходимой для эффективного выполнения профессиональных задач.
- ОК 6. Работать в команде, эффективно общаться с коллегами, руководством, клиентами.
Оснащение урока:
- презентация «Дефекты сварных швов и причины их возникновения»,
- компьютер, мультимедийное оборудование, экран,
- образцы сварных швов,
- учебники,
- опорные конспекты,
- карточки-задания,
- тестовые задания.
Ход урока
Преподаватель: Здравствуйте! Садитесь, пожалуйста.
Тема сегодняшнего урока: «Дефекты
сварных швов и причины их возникновения».
Преподаватель ставит цель урока. Итак, сегодня вы должны познакомиться с определениями основных дефектов, главными причинами их возникновения и мерами предупреждающими возникновение дефектов.
Эта тема одна из самых важных для вашей профессии. Вы, как сварщики, должны выполнять свою работу качественно и профессионально, а для этого вам необходимо знать какие дефекты и почему могут появиться в процессе сварки и как с ними бороться. Вам уже в ближайшее время предстоит работать на производстве.
Преподаватель. Ребята, на прошлом уроке мы с вами познакомились с такими понятиями как, качество сварных соединений, дефекты сварных швов, выяснили какие дефекты относятся к наружным, а какие к внутренним, научились отличать качественные швы от швов с дефектами.
Поэтому, прежде чем приступить к изучению новой темы, давайте с вами повторим материал, изученный на предыдущих уроках.
1. Актуализация
знаний обучающихся.
Преподаватель обращает внимание обучающихся на слайд на экране: «Вопросы к повторению». На эти вопросы вам сейчас предстоит ответить. А некоторые ответят письменно на вопросы тестов и выполнят работу у доски.
Некоторым обучающимся одновременно раздаются тесты для письменного ответа.
Работа у доски. Задание: Вставить в текст пропущенные слова, чтобы получилась правильная фраза.
Задание 1. Качество – это ____________ свойств продукции, обусловливающих ее ___________ удовлетворять потребности в соответствии с ее _________________.
Задание 2. Контроль качества продукции — это ____________ соответствия показателей ____________ установленным __________________.
(На доске плакат «Дефекты сварных
соединений», на столе: образцы сварных соединений. )
Обучающиеся отвечают на поставленные вопросы.
После устных ответов обучающихся, преподаватели собирают на проверку письменные задания.
Подведение итогов работы у доски и переход к новой теме.
2. Изучение нового материала.
Преподаватель: Итак, мы с вами вспомнили и повторили основные понятия: качество сварных соединений, дефекты сварных швов, деформации и напряжения. (На доске: «Основные понятия»).
Преподаватель:
Изучать новый материал мы будем с помощью аудиторной самостоятельной работы. Вы в своей работе будете использовать опорный конспект, таблицы дефектов, образцы швов с дефектами и увидим результаты внеаудиторной самостоятельной работы. Сообщения самостоятельно подготовили: Левинченко Д., Студеникин Д., Подольский Д., Курганов А., Ефремов Д..
Производственная ситуация.
Во время изготовления сварной конструкции
были обнаружены дефекты сварных швов. Задание:
определить эти дефекты, выяснить причины образования дефектов и предложить
меры предотвращения дефектов.
Эту производственную ситуацию Вам предстоит решить в процессе изучения нового материала.
Ребята, на уроках производственного обучения вы уже научились выполнять сварные швы в различных сварных соединениях. И, наверное, обращали внимание, что по качеству сварные швы у вас получались разные.
Вопрос:
Скажите, а какие дефекты вы обнаруживали в своих работах чаще всего?
(Обучающиеся называют дефекты: прожоги, нарушение геометрической формы шва, непровары, подрезы, брызги металла).
Правильно!
Вопрос:
Скажите, должен сварщик знать определение этих дефектов и причины их возникновения?
[Да конечно].
Ответьте: А зачем?
[Чтобы не допускать возникновения дефектов
и качественно выполнять свою работу].
Правильно!
Поэтому тема урока так и называется:
«Дефекты сварных швов и причины их возникновения».
Запишите сегодняшнее число и тему урока.
Работать мы с вами будем по плану, который вы видите на экране.
Преподаватель: Итак, знания о дефектах и причинах их возникновения необходимы в вашей профессии, чтобы вы стали высококвалифицированными специалистами.
Для сварных соединений, выполняемых сваркой плавлением характерны 7 основных дефектов.
Ребята подготовили небольшие сообщения об этих дефектах, давайте внимательно послушаем эту информацию.
Преподаватель химии:
Водород поглощается в
процессе сварки металлом шва. Источником водорода в зоне сварки может служить
атмосферная влага, влага покрытия или флюса, влага ржавчины на поверхности
сварочной проволоки. Водород не образует в процессе сварки химических
соединений с железом, он растворяется в расплавленном металле. Повышенная
растворимость водорода в жидком металле приводит к пористости.
Вопрос: Каким образом можно добиться уменьшения содержания водорода в металле шва?
Ответ: Уменьшения содержания водорода в металле шва можно добиться путем предварительного прокаливания электродов.
Преподаватель химии:
Азот попадает в зону сварки из окружающего воздуха. В процессе охлаждения азот выпадает из раствора в виде соединений – нитридов Fe2N и Fe4N.
При насыщении металла азотом усиливается образование газовых пор.
Для снижения содержания азота в металле шва добавляют в металл шва химические элементы, связывающие азот в неметаллические включения.
Fe 2N + Al= 2Fe + Al N
Обучающиеся делают сообщения по слайдам. (Запись в тетрадях после каждого сообщения – виды дефектов).
Преподаватель химии: Трещины
являются самым опасным дефектом.
Вопрос: Как Вы думаете, почему?
Ответ: Трещины очень трудно обнаружить, как снаружи, так и внутри. Если в конструкции имеются трещины, то она очень быстро разрушается.
Преподаватель химии:
Кислород образует с железом следующие оксиды: Fe3O4, Fe2O3, FeO. Оксид железа FeO, растворимый в жидком металле оказывает наиболее неблагоприятное влияние на качество шва.
2Fe + 2О2= Fe3O4 (FeO Fe2O3)
Удаление кислорода из расплавленного металла достигается за счет введения в сварочную ванну таких элементов, как марганец и кремний.
2FeO + Si = 2Fe + SiO2
FeO + Mn = Fe + MnO
Преподаватель химии:
Сера – вредная примесь
в сталях. Особенно вреден сульфид железа FeS, хорошо растворимый в железе. Наличие в металле
сварного шва серы ухудшает его механические свойства и повышает склонность к
образованию трещин. Избавиться от появления такого дефекта можно с помощью
марганца и кальция, которые содержатся в сварочной проволоке и обмазке
электродов.
Преподаватель: Итак, мы рассмотрели определения основных дефектов.
Найдите в опорном конспекте причины образования дефектов: наплывов, подрезов и прожогов. (Обучающийся читает)
Преподаватель: откройте учебники на стр. 225 и найдите причины возникновения самых распространенных дефектов – непроваров.
(Обучающийся читает)
Преподаватель. Сравните эти причины
(Что общего и чем отличаются).
У наплывов, подрезов и прожогов — это
На образование дефектов большой ток, а у непроваров-
влияет величина сварочного
тока недостаточный сварочный ток.
Вопрос: Итак, какая же из всех причин самая распространенная?
(Неправильно выбрана сила сварочного тока и скорость сварки.)
Вопрос: А как ее (эту причину) устранить?
[Правильно подобрать силу тока, отрегулировать ее на источнике питания].
3.Закрепление материала.
Преподаватель: А сейчас вы попробуете применить полученные знания при выполнении небольшой практической работы, решая производственную ситуацию.
Во время изготовления сварной конструкции были обнаружены дефекты сварных швов.
Практическая работа. Нам на экспертизу принесли образцы, которые лежат у вас на столах. Вам необходимо сделать заключение о качестве этих образцов. Ваша задача с помощью таблицы определить вид дефекта и причины его возникновения.
Эти данные запишите в листы экспертного заключения, которые у вас на столах.
(Спросить несколько обучающихся, назвать
обнаруженные дефекты и что нужно сделать, чтобы этих дефектов не допускать).
Обучающиеся выполняют практические задания.
4. Итог урока.
Подведем итоги:
Ребята, скажите, с чем вы сегодня познакомились?
[Мы познакомились с определениями основных дефектов сварных швов и выяснили причины их возникновения и способы предотвращения этих дефектов].
Правильно, молодцы.
Преподаватель: Я думаю, что цель нашего урока достигнута. Вы теперь знаете определения дефектов сварных швов, причины их возникновения и меры предотвращения этих дефектов и свои знания примените на практике.
5.Домашнее задание.
Преподаватель: сообщает домашнее задание (на экране – слайд «Домашнее задание».)
Преподаватель: объясняет, как выполнять домашнее задание.
6. Оценки за урок.
Преподаватель: объясняет оценки учащихся за урок.
виды, способы контроля и устранения
Само название уже говорит за себя. На месте сварки и в свариваемых металлах по кромкам образуются отверстия. Причины:
Чаще всего этот вид дефектов получается, когда свариваются между собой тонкие листы металлов, или когда ведется многослойная сварка и наносится первый слой.
Это углубления в сварном шве. Обычно этот дефект образуется при обрыве дуги. Поэтому его опытные сварщики пытаются сразу же оплавить. Это самое простое устранение дефектов сварки. Когда сварка ведется автоматическим способом, то кратер обычно появляется на выходе из шва, то есть, на выходной планке.
Есть подвид кратеров, который называется усадочной раковиной. Она образуется под воздействием усадки металла в шве. Все дело в том, что металл при остывании уменьшается в объеме.
Причины появления дефектов
Каждый из всех встречающихся дефектов возникает вследствие конкретных факторов. При этом выделяют причины образования дефектов сварных соединений общего характера:
- использование некачественных расходных материалов для сваривания элементов;
- несоблюдение сварочных технологий;
- низкое качество металла, из которого создаются конструкции;
- некачественное или неисправное оборудование;
- неправильный режим сварки;
- технологические ошибки, вызванные низкой квалификацией сварщика.
Чтобы металлоконструкции получались качественными и выносливыми, следует строго соблюдать нормы сваривания и доверять работы профессиональным сварщикам.
Восемь советов для уменьшения вероятности образования подрезов в сварном шве
Ниже приведены рекомендации, которые помогут уменьшить вероятность образования подрезов при сварке изделий из труб, листов, швеллеров, уголков и т.д.
Правильное тепловложение
Одной из самых главных причин образования подрезов в сварных швах является большая величина нагрева при выполнении сварки вблизи свободных краев детали в результате чего происходит более глубокое проплавление одной из кромок, что приводит к образованию канавки, которая остается после затвердевания металла сварочной ванны. Это может привести к перегреву и расплавлению близлежащего основного металла или ранее наложенного металла шва. Для предотвращения необходимо следить за тепловложением при этом уменьшая сварочный ток при приближении к более тонким участкам детали или к свободному краю изделия.
Правильный угол электрода
Как известно угол электрода играет очень важную роль для предотвращения образования дефектов при сварке. Если выполнить сварку с неправильным углом, который будет направлять больше тепла к свободным кромкам изделия, вероятность образования подреза увеличивается в несколько раз. В связи с чем необходимо использовать правильный угол, чтобы направлять больше тепла на более толстую часть детали.
Правильная скорость сварки
Сварка с большой скоростью является еще одной причиной образования подрезов на сварных швах. При большой скорости некоторая часть основного метала переходит в расплавленный металл сварного шва и в результате быстрой кристаллизации остаются углубления (канавки) по краям. Поэтому рекомендуется производить сварку в умеренном темпе потому что слишком маленькая скорость сварки не дает удовлетворительных результатов. Таким образом, конкретным условиям сварки соответствует определенный диапазон скорости, в пределах которого возможно получение швов без подрезов.
Правильный выбор газовой защиты
При сварке полуавтоматом неправильный выбор защитных газов также является одной из основных причин подрезов при сварке. Сварщик должен быть уверен, что использует правильную сварочную смесь, которая подходит именно для сварки этого металла. Применение смесей углекислоты с инертными газами обеспечивает качественные результаты при сварке углеродистых сталей.
Правильная техника сварки
Причиной образования подрезов при сварке также является попытка сварщика выполнять сварку с чрезмерными поперечными колебаниями электрода. Рекомендуется выполнять сварку с минимальными поперечными колебаниями – так называемым «ниточным швом». Размер колебаний не должен превышать допустимых значений, потому что это значительно увеличивает вероятность образования подреза в сварном шве. Для предотвращения образования данного дефекта сварного шва необходимо либо уменьшить ширину поперечных колебаний электрода, либо выполнять многослойный шов вместо однослойного.
При ручной дуговой сварке покрытыми электродами рекомендуемый размах поперечных колебаний должен составлять не более 2-3 диаметров электрода.
Правильное пространственное положение при сварке
Сварка в горизонтальном или вертикальном положении в свою очередь увеличивает вероятность образования подреза шва. В данном случае, канавка образуется из-за недостаточного заполнения вдоль зоны сплавления шва. Если есть возможность, сварку необходимо выполнять в нижнем положении.
Использовать многослойную сварку
Это самый лучший вариант для предотвращения образования подрезов при сварке. Техника наложения многослойного шва подразумевает выполнение всех вышесказанных рекомендаций и помогает добиться качественных сварных соединений с гарантированными механическими свойствами.
Использование предварительного подогрева
Предварительный подогрев снижает скорость кристаллизации металла и улучшает смачиваемость за счет меньшей разности температур между сильно нагретым металлом сварочной ванны и слабо нагретым основным металлом.
Методы выявления дефектов
Выявление дефектов сварных соединений осуществляется следующими способами:
- визуальный осмотр и обмер стыковочных швов;
- испытания стыков на непроницаемость;
- определение дефекта сварного соединения специальными приборами;
- испытания образцов на прочность в лабораторных условиях.
Осмотр сварочного шва осуществляется только после очистки его от шлака, устранения застывших брызг металла и других типов загрязнений. Проверке подлежат размеры и правильность формы соединений, наличие или отсутствие прожогов, кратеров, трещин, свищей и других погрешностей.
Испытание непроницаемости позволяет выявить дефекты сварных соединений трубопроводов, например, поры, трещины, сквозные непровары. Проверяются конструкции несколькими способами:
- обдуванием или заполнением швов воздухом;
- поливом струей воды или наполнение отсеков водой под давлением;
- смазыванием швов керосином.
Если в ходе проверки обнаружен дефект, то деталь возвращается на дополнительную обработку.
Подрезы сварных швов, другие возможные дефекты и контроль качества
Организация рабочего процесса включает в себя множество факторов, включая и нормирование труда. Утверждение единых норм трудового процесса повышает эффективность и скорость производства, как при монтаже однотипных конструкции, так и совершенно разной продукции. Временные нормативы имеют ключевое значение.
Прихватки в сварке – важный технологический процесс, позволяющий произвести сборку сварной конструкции с максимальной точностью. Наложение прихваток предшествует ведению основных сварочных работ, а к их выполнению предъявляются определенные требования, которые зависят от типа металла и от вида сварной конструкции или узла.
Расскажем сегодня о правильной дуговой сварке. Дуговая сварка во многом строится на технике и правильном подборе материалов, от чего и зависит качество выполненных работ. Рассмотрим подробнее основную технику выполнения работ, а также правила сварки наиболее распространенных швов.
stalevarim.ru
Способы устранения дефектов
Любой сварочный процесс сопровождается образованием дефектов, вне зависимости выполняется он инвертором, полуавтоматом, трансформатором или другим оборудованием. При этом выделяют недопустимые и допустимые дефекты сварных соединений, по сложности которых определяется пригодность или непригодность конструкции к дальнейшей эксплуатации.
Способы устранения дефектов сварных соединений выбираются с учетом типа обнаруженного повреждения:
- прожоги исправляют тщательной зачисткой стыка с последующей его заваркой;
- для устранения подрезов выполняется наплавка тонкого соединения по всей линии дефекта;
- исправление трещины осуществляется методом ее полного рассверливания, вырубкой шва на проблемном участке, очисткой поверхностей и повторным завариванием с соблюдением сварочной технологии и действующих нормативов;
- непровары удаляются путем их вырезания и повторного сваривания;
- свищи и кратеры вырезаются до достижения основного металла, после чего по-новому завариваются;
- наплывы аккуратно срезаются, но при этом обязательно следует проверить срез на предмет наличия непровара;
- деформация при сварке устраняется термическим или термомеханическим способом;
- все типы дефектов с посторонними включениями устраняют вырезкой и завариванием.
Если в ходе обследования обнаружены технологические дефекты сварных соединений труб, то устранять их следует строго в соответствии нормативных требований одним из методов:
- механическим без последующей заварки;
- механическим с завариванием места выборки;
- вырезкой участка трубы, на котором присутствует дефект;
- полным удалением шовного соединения и выполнением нового.
При проверке на прочность и герметичность газораспределительных сетей разрешается исправлять дефекты сварных соединений газопроводов в случае, когда сварочный процесс выполнялся дуговой сваркой и не допускается при сваривании газовой сваркой.
Дефекты микроструктуры
К дефектам микроструктуры нужно отнести микроскопические трещины и поры, включения неметаллического типа (кислородные, нитридные), крупная зернистость структуры наплавленного металла с элементами перегревов и пережогов.
Самый опасный из всех перечисленных дефектов – пережог. При нем внутри шва появляются в большом количестве крупные зерна структуры металла, которые имеют минимальные прочностные связи между собой. Отсюда высокая хрупкость стыка. Причинами пережога являются присутствие кислорода в зоне сварки, а значит, изоляция ванны была плохой. Сюда же можно добавить высокую температуру сварочного процесса.
Методы контроля сварных соединений
Тот факт, что влияние дефектов на качество сварной металлоконструкции максимизирует риски разрушения изделий доказывать не нужно. Чтобы в процессе сваривания получать действительно надежные, прочные и выносливые конструкции, после завершения работ должен проводиться контроль качества сварных соединений.
Осуществляется контроль сварочных швов поэтапно:
- предварительный. Включает проверку марки металла, качества заготовок, кислорода, присадочной проволоки и других расходных материалов;
- контроль в ходе сварочных работ. Подразумевает постоянные проверки режима сварки, исправности оборудования, осмотр швов и измерение их специальными шаблонами. При выявлении отклонений от установленных стандартов сразу же можно провести удаление дефектов сварных соединений;
- контроль готовой конструкции.
Внешние дефекты можно увидеть при обычном осмотре. При необходимости стыки проверяются на плотность, а также подвергаются другим испытаниям.
Все методы контроля сварных соединений разделяются на две группы – разрушающие и неразрушающие. Как правило для выявления дефектов применяются неразрушающие методы, к которым принадлежат:
- внешний осмотр:
- ультразвуковая дефектоскопия;
- магнитный контроль;
- цветная дефектоскопия;
- радиационная дефектоскопия;
- капиллярная дефектоскопия;
- контроль стыков на проницаемость и другие методы обнаружения дефектов сварных соединений.
Методы разрушающего контроля подразумевают испытания отобранных образцов и применяются в основном при необходимости получить параметры сварного шва и зоны термического влияния. Контроль осуществляется химическим анализом, механическими и металлографическими испытаниями.
Причины образования подрезов при сварке
Причиной образования подреза при сварке является выполнение сварки либо на повышенных режимах или с большой скоростью. Также, результатом возникновения может служить выбор неправильного угла наклона к более тонкому краю детали, что в свою очередь вызывает ее перегрев.
Исследования показывают, что с уменьшением температуры твердой поверхности смачивание ее жидким металлом ухудшается и улучшается с повышением температуры. Следовательно, одним из основных факторов, влияющих на смачивание является температура. На горизонтальных плоскостях смачивание играет ключевую роль т.к. вследствие действия сил поверхностного натяжения, жидкий металл на холодной поверхности стремиться к сжиманию, сокращая свою площадь и поверхность, которую он занимает, что и приводит к образованию подреза в сварном шве. В вертикальной плоскости, т.е. при сварке угловых и горизонтальных швов, дополнительной причиной является стекания жидкого металла под действием силы тяжести.
Неправильное использование газовой защиты, неправильная техника сварки и положение при сварке являются дополнительными причинами образования подреза сварного шва.
Подрезы при сварке всегда были серьезной проблемой в сварочном производстве, поэтому в последние годы все больше производителей сварочного оборудования и материалов и предпринимают попытки решить данную проблему.
Наличие подрезов обусловливает существенную концентрацию напряжений вблизи данного дефекта и может вызвать локальное или общее разрушение конструкции. Продольные углубления снижают сечение основного металла в зоне термического влияния. В результате чего сварные швы плохо воспринимают динамическую нагрузку и в данных местах могут возникнуть трещины. При проведении испытаний сварных швов на растяжение и угол загиба разрушение металла начинается от подреза, при значительного заниженных механических показателях.
5 Методы неразрушающего контроля сварных швов
Материалы
Дипломированный инженер
Неразрушающий контроль сварных швов является важным процессом для определения структурной целостности сварных швов и обеспечения качественного сварного шва. Если ее не выполнить, некачественные сварные швы и дефекты сварных швов, такие как непровар боковых стенок и кратерные трещины, не будут выявлены и могут привести к преждевременному выходу из строя. Ниже мы рассмотрим 5 методов неразрушающего контроля сварных швов.
Визуальный контроль сварных швовВизуальный контроль является наиболее часто используемым неразрушающим методом контроля сварных швов. После того, как сварка завершена, первая предпринятая проверка – это визуальная проверка. Визуальный осмотр состоит из проверки неоднородностей поверхности глазом. Несмотря на простоту, визуальный осмотр может быстро дать информацию о качестве сварного шва.
Преимущества визуального контроля сварных швов- – дешево
- – Не требуется дорогостоящее оборудование
- – Быстрая идентификация поверхностных дефектов
- – Необходимо обучение – Требуется хорошее зрение
- – Необходимо заполнить отчет
После визуального контроля магнитопорошковый контроль (MPI) является следующим наиболее распространенным методом неразрушающего контроля сварных швов. Магнитопорошковая дефектоскопия используется в ряде отраслей, что подчеркивает ее популярность и надежность.
В отличие от визуального контроля магнитопорошковая дефектоскопия позволяет обнаруживать подповерхностные дефекты, однако они должны находиться вблизи поверхности. Использование контрастной краски позволяет легко визуализировать любые дефекты поверхности.
Преимущества MPI Testing Welds- – Визуальное выявление дефектов
- – Недорогой по сравнению с другими методами неразрушающего контроля.
- – Можно быстро проверить сварные швы.
- – Может обнаруживать поверхностные и приповерхностные дефекты
- — Поверхностная подготовка не требуется (или мало)
- — Требуется тренировка
- — Трудно тестировать сварки с Welds
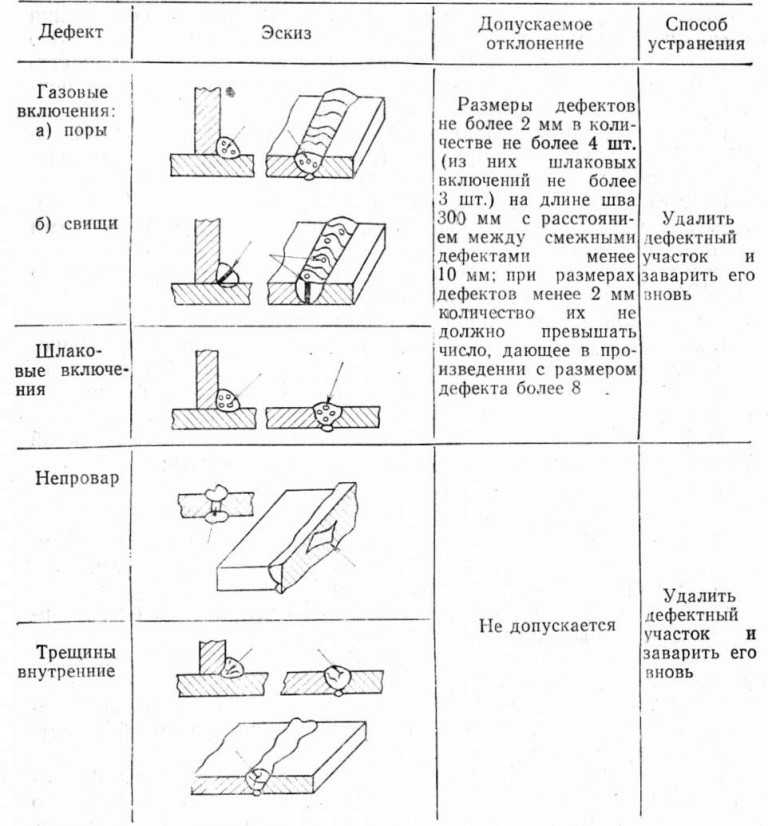
Вихревые токи создают свое магнитное поле, которое противодействует магнитному полю катушки и изменяет его. Изменения фазы и амплитуды, наблюдаемые в первичной катушке, затем определяют обнаружение любых дефектов в образце для испытаний.
Вихретоковый контроль не очень популярен для контроля сварных швов, но более популярен для контроля целых компонентов.
Визуализация индукции вихревых токов. Кредит: Стефан Трахе. Лицензия: CC BY-SA 4.0 Преимущества вихретокового контроля сварных швов:- – Может обнаруживать подповерхностные дефекты, а также поверхностные дефекты
- – Тестирование может проводиться на объектах сложной геометрии
- – Обеспечивает немедленную обратную связь
- – Оборудование маленькое и легкое
- – очень чувствительны к изменениям магнитной проницаемости, что затрудняет контроль сварных швов из ферромагнитных материалов
- – невозможно обнаружить дефекты, параллельные поверхности испытуемого образца
- – Непостоянная глубина проплавления
Как следует из названия, ультразвуковой контроль использует ультразвук для обнаружения дефектов. Пучок ультразвуковых волн вводится в образец для испытаний. Когда луч проходит через материал, он испытывает лишь незначительные потери. Луч отражается от поверхностей и возвращается к преобразователю в зонде. Когда луч сталкивается с дефектом, он отражает датчик. Изменение электрической энергии показывает обнаруживаемый дефект и выделяется аномальными всплесками на выходе графика.
- — Оборудование портативное
- — обеспечивает постоянные результаты
- — обнаружает поверхность и подземные сварки Defects
Капиллярная дефектоскопия также известна как капиллярная дефектоскопия и представляет собой метод неразрушающего контроля, который обычно используется для обнаружения поверхностных дефектов. .
Метод заключается в нанесении пенетранта (обычно яркого цвета) на испытуемую поверхность и выдерживании достаточного времени, чтобы пенетрант впитался в дефекты. Время этого процесса известно как время выдержки. Поскольку дефекты в сварных швах, как правило, меньше, требуется большее время выдержки.
По истечении времени выдержки излишки пенетранта удаляются с помощью растворителя. Однако в зависимости от пенетранта будут использоваться разные растворители. Когда излишки пенетранта удалены, на сварной шов наносится проявитель, чтобы вытянуть любой пенетрант в дефектах, давая видимые признаки.
Для осмотра сварного шва инспектор будет использовать либо свет подходящей интенсивности, либо ультрафиолетовый свет в зависимости от того, использовался ли видимый флуоресцентный пенетрант
Преимущества использования жидкого/красящего проникающего вещества для проверки сварных швов- – Тест можно провести быстро
- – Процесс тестирования дешевый
- – Можно тестировать сложные геометрические формы
- – Портативное оборудование
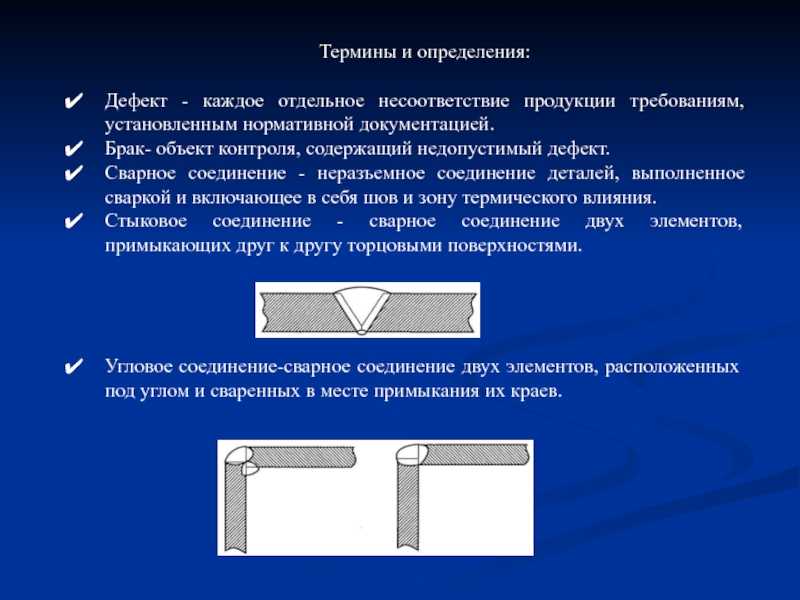
Как обнаружить дефекты сварных швов с помощью неразрушающего контроля
Неисправности сварных швов:
Что вызывает дефекты и как их обнаружить с помощью неразрушающего контроляОсознаете вы это или нет, но ваш бизнес или отрасль поддерживается где-то материалами, которые были сварены вместе. Сварка существует с бронзового века, создавая миллиарды инструментов и конструкций для людей на протяжении тысячелетий. С тех пор технология сварки прошла долгий путь и считается одним из наиболее эффективных способов соединения двух материалов.
В Британской Колумбии, Альберте и Саскачеване сварка часто используется в нефтяной и газовой промышленности. Металлические трубы обычно соединяют вместе, соединяя два куска металла в один сплошной трубопровод с применением сильного нагрева. Любая металлическая конструкция или инструмент, с которыми вы можете столкнуться на строительной площадке, вероятно, были сформированы с использованием по крайней мере одного сварного шва.
Нарушение сварки
Сварка — чрезвычайно эффективный метод соединения двух отдельных кусков металла в единое целое, однако существует небольшая вероятность того, что сварной шов может выйти из строя, что может привести к большим проблемам для вашего бизнеса или сотрудников. Неисправность сварного шва может привести к быстрой смене оборудования или материалов, что может привести к массовым травмам или смерти любых рабочих, которые могут находиться поблизости. Помимо проблем со здоровьем и безопасностью, неисправность сварного шва может также привести к остановке производства и стоить тысячи долларов упущенной выгоды или штрафов, особенно если вы имеете дело с нефтью.
Существует множество причин, по которым сварной шов может быть неисправен или выйти из строя во время работы. Если на вашем предприятии работают неопытные сварщики или сварка ведется в сложных условиях (сварка на открытом воздухе в плохую погоду, ненормированный рабочий день сотрудников и т. д.), вы можете чаще сталкиваться с дефектами сварки, чем другие предприятия.
Общие методы отказа
- Сварные соединения не нагреваются до достаточно высоких температур . Сварщик не может правильно приварить один горячий объект к другому холодному, оба должны быть теплыми одновременно. Невыполнение этого требования может привести к слабому сварному шву.
- Отсутствие отжига может привести к отжигу. Отжиг позволяет материалам медленно остывать, в отличие от быстрого охлаждения металла, которое может вызвать напряжение, необходимое для растрескивания.
- Окружающая область, затронутая сваркой. Иногда при сварке оператор может нагревать материалы или область вокруг сварного соединения. Это может вызвать деформацию, что может привести к неправильному выравниванию, создавая большую нагрузку на сварной шов, что может привести к дефектам.
- Слишком сильное окисление. При нагревании металлы могут окисляться, что приводит к неправильному сварному шву. Сварщики могут использовать защитный газ или флюс, чтобы предотвратить окисление.
- Коррозия или химическая деградация. Сварной участок более подвержен коррозии, чем несварной участок, и начнет разрушаться раньше остального оборудования или трубопровода. Химическое воздействие также может со временем ослабить сварной шов.
- Пузырьковые карманы или пустоты в сварных швах. Они вызваны образованием влаги или CO2 при смешивании углерода и кислорода. Эти пузырьки бывает трудно обнаружить, и они могут значительно ослабить прочность сварного шва.
- Грязные сварочные поверхности . Грязь и другой мусор могут вызвать пористость сварного шва, что нарушит однородность структуры и резко снизит ее общую прочность.
Проверка сварных швов
У каждой компании свои стандарты качества. Эти стандарты и системы качества (СМК) необходимо распространить на все сварочные работы, проводимые вашим предприятием. Независимо от того, насколько строги ваши стандарты качества, все сварные швы должны быть проверены . Простой визуальный осмотр — это первый шаг, но когда на карту поставлена безопасность ваших сотрудников и вы имеете дело с ценными ресурсами/оборудованием, необходимо принять дополнительные меры.
20/20 NDT Inc. Совет -> Визуальный осмотр сварного шва должен проводиться до, во время и после сварки оператором.
Неразрушающий контроль и контроль сварных швов
Из-за того, что сварной шов представляет собой сплав двух металлов, может быть очень трудно визуально обнаружить какие-либо дефекты внутри сварного шва. Именно здесь ценен неразрушающий контроль (НК), который дает вам представление о целостности ваших сварных швов, не повреждая какое-либо оборудование, а также обеспечивая бесперебойную работу.
Магнитопорошковая дефектоскопия
Электромагнитно-порошковая дефектоскопия является одним из лучших неразрушающих методов обнаружения поверхностных трещин, дефектов, которые слишком малы для человеческого глаза, и несплошностей, находящихся под поверхностью сварного шва. Этот стиль тестирования намагничивает рассматриваемый объект, а затем использует уникальное флуоресцентное решение, которое выделяет эти дефекты для документирования нашим инспектором. Этот процесс очень быстрый и оставляет ваше оборудование без маркировки.
Ультразвуковой контроль
Ультразвуковой контроль (УЗК) использует высокочастотные звуковые волны для исследования внешней и внутренней части твердых объектов. Этот тип проверки полезен не только для обнаружения трещин внутри и снаружи сварного шва, но и для точного определения места, где были обнаружены дефекты. Оборудование, которое мы используем в 20/20 NDT Inc, посылает высокочастотные лучи в объект, и когда они взаимодействуют с дефектом, они возвращаются к нашей машине, давая нам четкое представление о потенциальном дефекте и его точном местоположении. Это может быть чрезвычайно полезно, если есть небольшой сбой в большой площади оборудования. Точно определяя, где находится трещина или неисправность, проблема может быть быстро обнаружена и устранена, что сэкономит время вашей компании, а также оставит незатронутыми другие области.
Радиографический контроль
Радиографический контроль является одним из наиболее универсальных методов неразрушающего контроля, который чрезвычайно адаптируется к широкому спектру ситуаций. Этот метод контроля использует «рентгеновские лучи» или гамма-лучи, чтобы получить представление о внутренней части оборудования или, в данном случае, о сварном шве. Это проводится так же, как врач использует рентген, чтобы проверить, сломана кость или нет. Опять же, настройка выполняется быстро и просто, и наши технические специалисты могут гарантировать, что ваш трубопровод или оборудование не будут повреждены в результате этого процесса.
Если вас интересует целостность ваших сварных швов, обратитесь к нашей команде в 20/20 NDT. Звоните сегодня! Мы обслуживаем всю Западную Канаду и предоставим вам неразрушающий контроль. Позвольте нашим техническим специалистам помочь вам получить представление о целостности ваших операций и обеспечить безопасность ваших трудолюбивых сотрудников!
Испытание – производительность сварки
Неразрушающий контроль сварных швов (НК) – это процесс осмотра, испытаний и оценки сварных швов с целью определения наличия дефектов или изъянов без разрушения какой-либо части испытуемого образца. Во многих отраслях промышленности крайне важно подтвердить соответствие сварного шва стандартам сварки путем осмотра сварного шва и окружающего металла. NDT регулярно используется в производстве и изготовлении для обеспечения надежности систем и продуктов.
Некоторые методы неразрушающего контроля относительно просты, в то время как другие требуют специально разработанного оборудования. У различных методов есть свои плюсы и минусы, начиная от стоимости (некоторые дороже других) и заканчивая различными подходами, которые можно применять. Неудивительно, что различные методы могут быть направлены на выявление различных типов дефектов.
Во время визуального осмотра следует обращать внимание на недостаточное проникновение, подрезку и пористость. Видеть значит верить Визуальный контроль часто считается наиболее рентабельным методом неразрушающего контроля, поскольку он не требует никакого оборудования. На самом деле, визуальный осмотр требуется в качестве предварительного условия для других проверок неразрушающего контроля. Сварной шов с более очевидными дефектами можно легко оценить с помощью визуального осмотра, что избавляет от необходимости перемещать специальное оборудование на место, когда оно может не понадобиться.
Визуальный осмотр необходимо проводить до, во время и после сварки, чтобы убедиться в соблюдении стандартов сварки. Перед сваркой металлы должны быть тщательно осмотрены. Металл должен быть чистым и ровным, а размеры должны быть точными с правильным выравниванием.
Во время сварки следует проводить визуальный осмотр, наблюдая за валиком сварного шва. Недостаточное проникновение, подрезы и пористость — вот некоторые из дефектов, которые следует наблюдать. После сварки осмотрите поверхность сварного шва на наличие дефектов. К ним относятся все, от деформации металла, размера сварного шва и трещин до незаполненных кратеров и пористости.
Испытания на проникновение жидкого красителя включают в себя нанесение красителя, который часто поставляется в аэрозольном баллончике.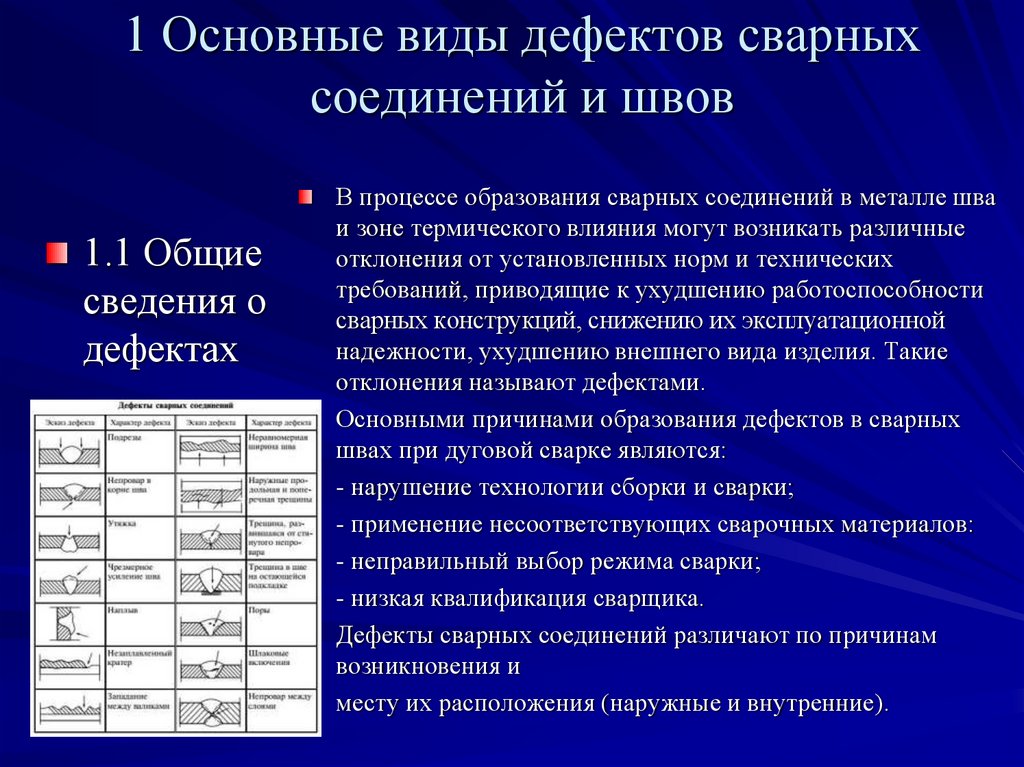
Пенетрант с жидким красителем представляет собой относительно простой метод неразрушающего контроля, который выделяет любые отверстия или трещины в сварном шве. Одним из преимуществ этого метода является то, что он не требует большого количества дорогостоящего оборудования. Для выполнения теста необходимо выполнить следующую процедуру.
1. Начните с очистки сварного шва, включая удаление кремнезема из сварного шва.
2. После очистки шва нанесите краску на сварной шов. Обычно это красный спрей в аэрозольном баллончике. Нанесите довольно много на сварной шов, чтобы обеспечить достаточное проникновение.
3. Оставьте краску примерно на полчаса, помня, что правильная шкала времени зависит от используемого оборудования. По истечении этого периода распылите очиститель вокруг сварного шва, чтобы удалить излишки краски.
4. Когда сварной шов будет чистым, распылите на сварной шов белый проявитель, чтобы вытянуть краску, впитавшуюся в дефекты сварного шва. Они отображаются как цвет на проявителе.
Это наиболее популярный метод определения пенетранта красителем, но в качестве альтернативы можно использовать флуоресцентный пенетрант вместо видимого пенетранта, что дает лучшие результаты. При использовании этого метода для воздействия на краситель необходим ультрафиолетовый свет, который светится при наличии дефекта.
Под поверхностью
Радиографический контроль — это тщательный и надежный метод контроля, который лучше всего подходит для обнаружения дефектов внутри сварного шва. Это выполняется путем размещения рентгеновской пленки с одной стороны сустава и рентгеновской трубки с другой стороны.
Для неразрушающего контроля также можно использовать флуоресцентный пенетрант, который светится при наличии дефекта в сварном шве. Во время радиографического контроля в стык попадают рентгеновские лучи, в результате чего на пленке появляется черно-белое изображение, подчеркивающее любые дефекты сварного шва. Дефекты могут включать в себя любые трещины, скрытые внутри сустава.
Человеческий глаз может определить эти дефекты на пленке, но существует также программное обеспечение для выделения дефектов, чтобы исключить те, которые могут быть упущены из-за человеческой ошибки. Важно знать, что этот тип неразрушающего контроля может быть дорогостоящим методом, особенно если рентгенографическое оборудование необходимо перемещать на место. Он в основном используется на оборудовании, где прочность сварного шва имеет решающее значение для безопасности.
Ультразвуковой контроль — это еще один метод неразрушающего контроля, который используется для обнаружения несплошностей внутри сварного шва. Он часто используется как средство проверки толстых секций металла, доступных только под одним углом.
Ультразвуковой контроль выполняется путем воздействия ультразвуковыми волнами на основной металл и сварной шов. Если в сварном шве есть разрыв, путь волны прерывается, и она возвращается к своему началу. Затем звуковые волны отображаются на экране и готовы к интерпретации.
Интерпретация этих результатов требует опыта, навыков и обучения для определения наличия дефектов в сварном шве.
Во время ультразвукового неразрушающего контроля ультразвуковые волны воздействуют на основной металл и сварные швы. Если в сварном шве есть разрыв, путь волны прерывается, и она возвращается к своему началу. Магнитное притяжениеМагнитопорошковая дефектоскопия используется для обнаружения дефектов в магнитных металлах. Он в основном используется для выявления поверхностных или незначительно подповерхностных дефектов, таких как трещины, которые слишком малы, чтобы их можно было увидеть человеческим глазом.
В этом процессе ферромагнитный материал необходимо намагнитить, пропуская через металл большую силу тока. При этом через шов создается магнитный поток, и если шов не имеет дефектов, то флюс остается внутри металла.
Однако, если в сварном шве есть трещина, магнитный поток будет просачиваться через дефект.