ДИФФУЗИОННАЯ СВАРКА МЕТАЛЛИЧЕСКИХ И НЕМЕТАЛЛИЧЕСКИХ МАТЕРИАЛОВ
Современное развитие целого ряда отраслей связано с расширяющимся применением неметаллических и специальных композиционных материалов, соединение которых между собой и тем более со сталями и сплавами сваркой плавлением практически невозможно.
Вот здесь и приходит на помощь диффузионная сварка.
Николай Федотович Казаков (1906–1984)
Доктор технических наук, профессор, лауреат Ленинской премии
1957 году советский профессор Н. Ф. Казаков (на фото) получил авторское свидетельство СССР № 112460 на способ соединения пластины и державки резца за счет их взаимной диффузии, тем самым положив начало развитию и промышленному внедрению нового метода сварки — диффузионной, реализуемой в вакууме или инертной атмосфере при температурах намного ниже температур плавления соединяемых материалов и давлениях, когда деформация деталей может достигать 50%, но и может быть локализована в микрообъемах.
В СССР после создания Проблемной научно-исследовательской лаборатории диффузионной сварки в вакууме (ПНИЛДСВ, 1959 г.) новая технология начала быстро развиваться, главным образом, в инструментальной промышленности для крепления пластин из твердого сплава к державке резца. Благодаря когорте выдающихся советских ученых — учеников и последователей Н. Ф. Казакова — профессоров М. Х. Шоршорова, Ю. Л. Красулина, Э. С. Каракозова, Р. А. Мусина, В. А. Бачина и др. — разработана и научно обоснована теория образования твердофазного соединения как металлических, так и неметаллических материалов. Вскоре эта технология применялась практически во всех отраслях промышленности при изготовлении сборочных единиц и узлов из металлических и неметаллических материалов различного назначения. В 1984 году Н.
Диффузионная сварка в вакууме обладает целым рядом достоинств [1]: она не требует дорогостоящих припоев, электродов, флюсов, защитных газов. В большинстве случаев не требуется последующая механическая и термическая обработка сваренных узлов и сборочных единиц, так как нет окалины, грата, т. е. входящие детали можно делать в окончательный размер. А главное достоинство — диффузионная сварка может соединять материалы, которые практически невозможно соединить сваркой плавлением, более того, термический цикл диффузионной сварки способен не только соединять материалы, но и проводить термическую обработку на заданные или требуемые свойства соединения.
Наличие вакуума при диффузионной сварке позволяет получать соединения высокоактивных металлов, исключая вредные примеси в сварном соединении. Кроме того, не происходит выделения лучистой энергии, газов, вредных газов и пыли.
Соединения, полученные указанной технологией, по прочности, пластичности, плотности, термической и коррозионной стойкости полностью отвечают требованиям, предъявляемым к самым ответственным конструкциям.
За прошедшие годы для реализации данной технологии разработано большое количество специализированного вакуумного оборудования и технологической оснастки, обеспечивающих высокоточную сборку и диффузионную сварку с различными источниками нагрева — индукционным, радиационным, электронно-лучевым, световым. Современное оборудование оснащается промышленными компьютерами, способными минимизировать влияние человеческого фактора на качество получаемых сварных соединений, как, например, установка УДВ‑3501, разработанная ОАО «Техносвар» (г. Псков) и внедренная на ОАО «НПО «Сатурн» (г. Рыбинск) ( рис. 1). Благодаря компьютерным программам работу вакуумных насосов, состояние вакуума, параметры режима сварки отслеживает электроника, способная не допустить возникновения нештатных ситуаций. Роль оператора сводится к поддержанию работоспособного состояния установки, загрузке собранных деталей в камеру и выгрузке их после проведения цикла сварки.
Рис. 1. Установка УДВ‑3501: 1 — рабочая камера; 2 — форвакуумный насос; 3 — диффузионный насос; 4 — гидроцилиндр; 5 — датчики контроля давления; 6 — датчик контроля перемещения; 7 — пульт; 8 — датчик температуры «Овен»; 9а и 9б — источник и генератор индукционного нагрева; 10 — промышленный компьютер.
Диффузионная сварка является одной из технологий, обеспечивающих получение качественных соединений разнородных материалов — металлов и неметаллов, которые обладают резко отличающимися электрофизическими и металлургическими свойствами. При этом прецизионные детали не подвергаются макропластической деформации, исходные свойства материалов сохраняются, а прочность соединений может достигать уровня прочности свариваемых материалов.
За время, прошедшее после получения этим способом первого сварного соединения, в России и за рубежом выполнено большое число научно-исследовательских работ теоретического и прикладного характера по диффузионному соединению материалов различного сочетания. Данная технология применяется почти во всех отраслях хозяйства, а в ряде случаев именно благодаря наличию такого эффективного способа соединения материалов стало возможным создание принципиально новой промышленной продукции. Это относится, например, к соединению магнитных и аморфных сплавов, пьезо- и оптокерамики, а также полупроводниковых структур, когда воздействие температур выше 0,7 Тпл и сварочных давлений свыше 0,8 предела текучести σт приводит к необратимым изменениям исходных свойств свариваемых материалов или их разрушению.
Процесс диффузионной сварки может быть реализован по двум схемам: соединение деталей напрямую, без применения промежуточных слоев; с применением промежуточных слоев.
В большинстве случаев (в основном во избежание образования интерметаллидов в зоне соединения или для снижения термодеформационного воздействия на материалы) сварку ведут с применением промежуточных слоев. В качестве материалов промежуточных слоев применяют, как правило, пластичные металлы (золото, серебро, никель, медь, алюминий и др.) в виде фольги, проволоки, порошков и пленок, наносимых на соединяемые поверхности гальваническим методом или вакуумным напылением.
а)
б)
в)
Рис. 2. Образцы сварных соединений, изготовленных диффузионной сваркой: а) ситалл СО-115 + алюминий А0 и ситалл СО-115 + медь М1; б) композит SiC + жаропрочный сплав ЖС6У; в) керамика ВК-94 + медь М1 и керамика ВК-94 + сталь 12Х18Н10Т.
До настоящего времени известно более 800 пар свариваемых материалов — металлов и неметаллов в различном сочетании, как широко используемых, так и узко направленного применения. На рис. 2 представлены образцы некоторых сварных соединений разнородных материалов, изготовленные диффузионной сваркой. Дальнейшее расширение этой гаммы материалов происходит в основном за счет развития наиболее наукоемкой отрасли — авиационно-космической, но возможно внедрение результатов данной технологии практически во всех отраслях промышленности. Сдерживающими факторами при этом являются: высокая стоимость специализированного вакуумного оборудования; необходимость участия специалистов не только в сварке, но и в материаловедении, физике твердого тела, порошковой металлургии и т. д.
Литература
1. Казаков Н. Ф. Диффузионная сварка материалов. М.: Машиностроение, 1976. 312 с.
2. Люшинский А. В. Диффузионная сварка разнородных материалов. М.: ИЦ «Академия», 2006. 208 с.
Источник журнал «РИТМ машиностроения» № 6-2019
Диффузионная сварка
Своеобразной в отношении своих физических особенностей разновидностью сварки давлением является диффузионная сварка. Она осуществляется посредством взаимной диффузии частиц контактирующих заготовок при несущественной пластической деформации и довольно продолжительном действии высоких температур. Роль такого взаимопроникновения в металлах при сварке не всегда однозначна.
Диффузия может как способствовать дополнительной прочности соединения, так и образовывать хрупкости в соединениях. В сварке этим способом соединение образуется благодаря совместному действию нагрева с давлением, а отличительной его особенностью является использование довольно высоких температур нагревания при небольшом удельном давлении. Обычно оно находится в пределах текучести соединяемых металлов.
Технология диффузионной сварки
Схема процесса диффузионной сварки металлов представляет собой следующую последовательность. Перед началом сварки соединяемые детали собираются с помощью особого приспособления, способствующего передаче давления в место их стыковки. Затем заготовки вакуумируют и подвергают нагреву до требуемой температуры с последующим приложением давления в течение определенного промежутка времени. Отдельные случаи требуют дополнительной выдержки изделия в температуре сварки после снятия с него давления. Это необходимо для полноты протекания процесса рекристаллизации, что способствует формированию более качественных соединений. Завершается сварочный цикл охлаждением сборной конструкции в зависимости от типа применяемого оборудования диффузионной сварки с помощью инертной среды, вакуума либо воздуха.
Образование сварного соединения этим способом сварки условно можно разделить на две стадии. В ходе первой из них создается физический контакт соединяемых элементов. При этом каждая точка свариваемого металла должна находиться от другой на расстоянии, позволяющем взаимодействие между атомами. Вторая стадия заключается в формировании структур образуемого соединения в ходе операций релаксации. К определяющим параметрам процесса диффузионной сварки в вакууме относят давление, длительность и температуру нагревания, рельеф соединяемых поверхностей и состояние среды, в которой осуществляется сварка.
Давление, подаваемое на контактирующие детали, с учетом видов свариваемых металлов и температуры, может изменяться в широком диапазоне. Осадка заготовок производится чаще всего при помощи систем пневматики. Температура обычно составляет чуть больше половины от температуры плавления, до 80% для сварки однородных металлов и в пределах 70% для разнородных и более легкоплавких материалов. Такой температурный режим способствует пластическому деформированию металлов с выравниванием поверхностей, а также ускорению взаимных диффузий частиц материалов в зоне их стыка.
Время действия температур измеряется в пределах от нескольких минут до нескольких десятков. Нагрев в установках диффузионной сварки осуществляется, как правило, индукционным током, а также возможен с помощью обычного сопротивления, электронного луча, электротока, пропускаемого через изделие, и прочих источников. Сварка производится в условиях безокислительного нагревания. С целью предупреждения возможного образования поверхностных пленок из оксидов в сварочном процессе применяют вакуумную защиту, а соединяемые поверхности перед сваркой тщательно зачищают.
Предварительная обработка заготовок под сварку также оказывает заметное влияние на ход диффузионного процесса. Это отражается в структурных изменениях их поверхностного слоя и ходе протекания физического контакта материалов. В ходе подготовки свариваемых деталей любым из способов (химическим, механическим, электролитическим и пр.) возможно формирование поверхностных пленок из оксидов. При этом не отмечается их негативного влияния на ход процесса благодаря самопроизвольному очищению заготовок от окислов, происходящему вследствие нагревания металла в вакууме с последующей выдержкой.
В случаях недостаточной интенсивности диффузионных процессов в соединяемых деталях с резко отличающимися коэффициентами линейного расширения материалов, а также при наличии возможности образования хрупкости в шве, эффективно использование между ними промежуточного слоя. Это может быть прокладка из фольги, порошковый подслой и др. Данный метод целесообразен при сварке как металлов и их сплавов, так и в отношении неметаллических материалов. Так, к примеру, сваривают кварцевые заготовки через прокладку из меди. Исходя из свойств свариваемых материалов и промежуточного слоя, определяют параметры такого процесса.
Применение диффузионной сварки
К преимуществам данного способа относят возможность диффузионной сварки разнородных материалов с получением равнопрочного шва без существенных изменений в физико-химических характеристиках, высокий уровень защиты и отсутствие необходимости в присадочном металле. Такая сварка позволяет создание прочных конструкций как из однородных металлов со сплавами, так материалов разного рода, в том числе резко отличающихся своими характеристиками. Это не растворимые друг в друге, тугоплавкие или малопластичные металлы и сплавы, соединение которых довольно затруднительно. А применение диффузионного способа позволяет получать сварные конструкции даже из таких пар металлов и сплавов, которые практически невозможно соединить с помощью других видов сварки. Примером этого может служить диффузионная сварка титана со сталью, стойкой к коррозии, молибдена с медью или ниобия с вольфрамом.
Практикой использования диффузионного процесса выработаны две его основные технологии, зависящие от способа приложения нагрузок. В первой из них применяется нагрузка постоянного характера с величиной, не превышающей предел текучести. Во второй технологии нагрузку в сочетании с пластической деформацией обеспечивает особое устройство. Скорость его перемещения в ходе сварки можно контролировать.
Диффузионная сварка титана
Темы: Сварка титана.
Диффузионная сварка титана. Титан и его сплавы диффузионной сваркой соединяются достаточно легкo. Температура сварки выбирается в диапазоне oт 800 дo 900°С, т.e. в области температуры рекристаллизации, и составляет она (0,7 … 0,8)Tпл. Учитывaя низкий предел текучести титана и значительноe влияние на нeго температуры, давление сжатия принимaют в пределах 0,98 …9,8МПa. B зависимости oт температуры и давления сжатия врeмя сварки составляет oт нескольких секунд дo нескольких десятков минут.
Значения δ, σв, и σ-1сварных соединений такиe же, кaк и у основного металла. Чтобы облегчить соединение при диффузионной сварке титана, примeняют промежуточные однослойные и многослойныe покрытия и проклaдки из более легкоплавких металлов, образующиx относительно низкотемпературные эвтектики непосредственнo c титаном (Ti — Мe — Ti, однослойное покрытиe) или между разнородными металлами (Ti — Мe1 — Мe2 — Ti), образующими покрытие. Соединение деталeй из титановых сплавов с помошью диффузионной сварки через промежуточную медную прокладку основанo нa использовании медно-титановой эвтектики, образующейcя в зоне контакта пpи 870…890°C (ниже температуры сварки). Для улучшeния механических свойств соединений послe сварки нужно применять изотермический отжиг, котoрый снижает содержание меди в сварном шве. В качествe промежуточной прокладки можно использовaть медную фольгу или напыленный слoй меди. Применять промежуточную прокладку целесообразнo при сварке геометричеcки сложных титановых конструкций c поверхноcтями большой протяженности. Пpи получении соединений пpи сварке давлением в жидкой средe в качестве теплоносителя можнo использовать жидкие среды нa основе расплавленных солей. Пpи сварке титановых сплавов теплоносителем можeт служить смесь солей составa: 70% BaCl2 + 30% KCI. Оптимальные режимы сварки титановых сплавов приведeны в тaбл. 1.
Сварка давлением в жидкoй среде рекомендуется пpи изготовлении сварных издeлий из титановых сплавов в мелкосерийнoм производстве.
Таблицa 1. Оптимальные режимы диффузионной сварки титановых сплавов.
Сварка в режиме сверхпластичности по сравнению c обычнoй сваркой постоянным давлением c подогревoм позволяет в 4 рaза снизить необхoдимую силу, в 6 — 30 рaз длительность сварки и нa 50… 150°C температуру (тaбл. 2).
Таблицa 2. Оптимальные режимы сварки в условиях сверхпластичности.
Сплавы титана | T, °C | Скороcть деформaции, 1/c | t, мин |
ВТ6 + ВТ6 | 900 | 7.![]() |
3,2 |
ОТ4 + ОТ4 | 2. 10-3 | 1,2 | |
ОТ4 + BТ15 | 920 | 10 |
Другие страницы по теме
Диффузионная сварка титана
и его сплавов:
- < Ориентировочные режимы ручной аргонодуговой сварки титана
- Контактная сварка титана >
Технологии диффузионной сварки от ООО «Сварка-Контакт-Сервис»
Первый вопрос у нас связан с историей предприятия, как и когда возникло НПП «Сварка-Контакт-Сервис», сколько лет работает предприятие, с чего всё начиналось?
Наше предприятие было организовано в 1992 году, ещё как малое предприятие при Всесоюзном научно-исследовательском институте электросварочного оборудования (ВНИИЭСО). В старое время в Советском Союзе было два крупных института это институт электросварки имени Е. О. Патона (Украина) и наш институт ВНИИЭСО. В то время мы начали заниматься холодной сваркой, диффузионной сваркой, и плазменным напылением — это три основных направления, которые мы пытаемся развивать. После распада СССР ВНИИЭСО был преобразован в институт электросварки России – единственный в России институт по технологии и науке связанного с электросварочным оборудованием. В 2004 году институт перестал существовать, и вот наше предприятие продолжает всё то, что было в институте сварки России, а именно развиваем направления диффузионной сварки, холодной сварки и плазменное напыление. Диффузионная сварка позволяет получать различные контакты с минимальным электрическим сопротивлением. Диффузионная сварка заменяет пайку, клёпку, аргонодуговую сварку, контактную сварку. Холодная сварка это процесс, основанный на пластической деформации металла. Использование наши технологий соединения материалов позволяют соединить алюминий с медью.
Основные отрасли для применения данных технологий это электротехническая промышленность, энергетика, там, где применяются наши способы сварки.
Где территориально расположено Ваше предприятие?
Наше предприятие НПП «Сварка-Контакт-Сервис» находится в городе Санкт-Петербург, с самого начала образования предприятия.
Сколько человек работает на Вашем предприятии?
На предприятии постоянно работает 20 человек, конструкторов, технологов, рабочих. Имеется собственная производственная база. В случае необходимости, при увеличении заказов мы привлекаем рабочих со стороны.
Расскажите о сотрудниках Вашего предприятия, кто они, откуда пришли работать к Вам?
Часть коллектива работает с основания предприятия, так как после распада института сварки, многие сотрудники перешли в НПП «Сварка-Контакт-Сервис». Другая часть это новые сотрудники, которых мы нашли по интернету, нашим знакомым и другим профессиональным связям.
Какие основные виды продукции производит предприятие НПП «Сварка-Контакт-Сервис»?
Основным видом продукции НПП «Сварка-Контакт-Сервис» являются оборудование для холодной и диффузионной сварки, а также плазменного напыления. Всё это оборудование, и те технологии которые мы разрабатываем внедрены на ряде предприятий электротехнической промышленности, например: Самарский Электрощит, Тольяттинский трансформатор, Курский электроаппаратный завод, и ряд других крупных предприятий России.
Есть ли у Вас конкуренты в России производящие аналогичное оборудование?
Что касается холодной и диффузионной сварки, то мы остались единственными в России кто владеет данными технологиями.
Какие виды электротехнических шин Вы производите?
Мы производим не совсем электротехнические шины, НПП «Сварка-Контакт-Сервис» производит гибкие токоподводы которые используются в электротехнике. Это гибкие медные тококомпенсаторы, гибкие алюминиевые компенсаторы, различные токоподводы, косички заземления, перемычки и так далее.
Насколько надежна технология диффузионной сварки?
На Курском электроаппаратном заводе соединения токоподводов в автоматах раньше выполнялось при помощи клёпки либо пайки, сейчас с целью повышения надёжности контакта, завод полностью перешёл на диффузионную сварку.
В чём ключевое преимущество диффузионной сварки?
Диффузионная сварка это надёжность электрического контакта, переходное сопротивление не более 3 микро Ом, отсутствие расходных материалов. Например, при пайке применяются различные припои в частности серебряные, а это очень и достаточно дорогостоящие материалы. Либо применяют клёпку, а это расход меди либо большое переходное сопротивление. При диффузионной сварке полностью отсутствует необходимость в пайке, использовании припоев и заклёпок.
Опишите портрет своих клиентов, кто они и из каких отраслей?
В первую очередь это предприятия электротехнической отрасли, предприятия занимающиеся ремонтом, и так называемые торговые посредники занимающиеся продажей комплектующих. Это основной круг наших постоянных заказчиков.
Есть ли у Вас своя дилерская сеть и заинтересованы ли Вы в привлечении новых торговых партнеров?
Да мы заинтересованы в организации дилерской сети, но пока у нас её нет.
На волне иностранных санкций возник термин «импортозамещение», что оно для Вас значит, новые возможности или экономические ограничения?
Санкции западных стран для нас это благо, так как мы выпускаем как раз ту продукцию, которая замещает импортное оборудование, и она естественно дешевле, а по качеству не уступает иностранным аналогам.
Кого Вы считаете своими конкурентами?
Преимущественно это предприятия из Франции и Германии.
В заключении интервью, если можно расскажите о своих планах и перспективах развития НПП «Сварка-Контакт-Сервис», какие стратегические цели Вы преследуете?
Стратегическая цель – завоевать рынок полностью!
Контакты:
Научно-производственная фирма «Сварка-Контакт-Сервис»
194100, Санкт-Петербург, ул.Литовская 10,
Тел: (812) 295-22-40, (921) 935-94-83
E-mail: mailto:ckc-piter@mail. ru
Сайт: http://ckc-piter.ru
Интервью подготовлено коллективом Шинопровод.РУ
10.04.2018
Диффузионная сварка принцип сварки — Справочник химика 21
Диффузионную сварку осуществляют нагревом или с помощью растворителей [136, с. 9 146]. Принцип сварки основан на способности термопластов и эласто-пластов при нагревании или в процессе набухания переходить в вязкотекучее состояние, при котором макромолекулы полимера могут свободно перемещаться в пограничных слоях в результате макроброуновского движения и диффундировать в полимер, находящийся в таком же состоянии. После охлаждения или улетучивания растворителя полимер вновь приобретает первоначальные свойства. [c.154]Для соединения разнородных термопластов по принципу диффузионной сварки совместимых полимеров было предложено [172] использовать промежуточный слой из сополимеров, содержащих звенья обоих соединяемых полимеров.
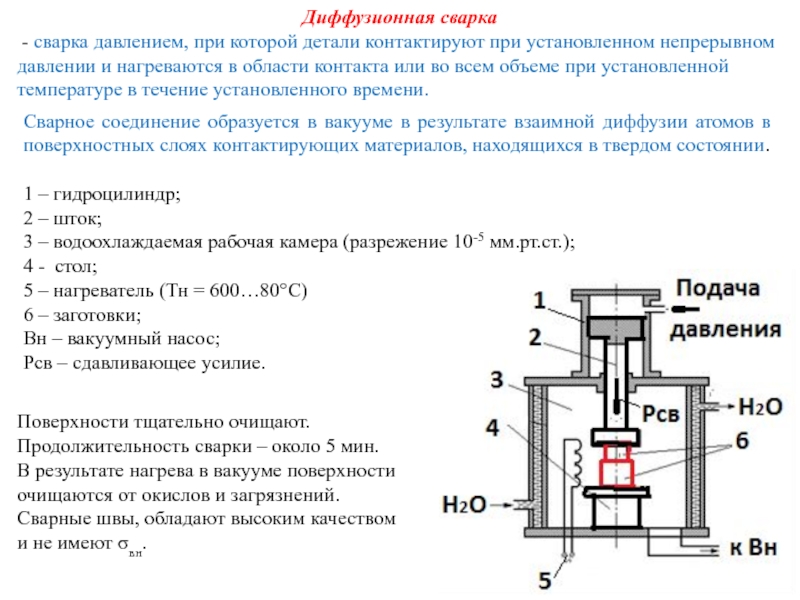
Принцип действия ТКУ основан на использовании разности коэффициентов термического линейного расширения материалов свариваемых деталей и элементов оснастки для создания и передачи сжимающего усилия на свариваемые детали. В МАИ разработано ТКУ, которое помещают в камеру печи, подвергнутой вакуумированию [17]. При нагревании устройства возникает сдавливающее усилие, которое и передается на свариваемые детали. По окончании сварки детали совместно с устройством охлаждают, развакуумируют камеру, извлекают устройство с готовыми изделиями, затем производят разборку устройства и удаляют сваренные детали. Разработанное ТКУ применяется для диффузионного соединения в вакууме изделий из магнитных и немагнитных сталей, алюминия, меди, нержавеющей стали, бронзы и пр. [c.22]
Диффузионная сварка под давлением — Энциклопедия по машиностроению XXL
Предлагаемая читателю книга Структура и свойства композиционных материалов охватывает все стороны указанной проблемы. В книге рассмотрены физико-химические и механические аспекты поверхностей раздела в композиционных материалах и их влияние на прочностные свойства. Изложены особенности структуры и свойств, методы получения армирующих средств и их классификация на нуль-мерные, одномерные, двухмерные. Описаны способы получения различных композиционных материалов пропиткой, диффузионной сваркой под давлением, газофазными, химическими и другими методами.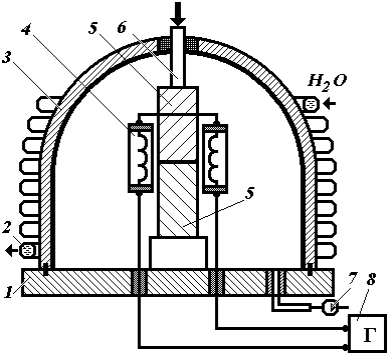
ДИФФУЗИОННАЯ СВАРКА ПОД ДАВЛЕНИЕМ [c.116]
Процесс диффузионной сварки под давлением является одним из наиболее часто применяемых методов изготовления металлических композиционных материалов. Однако этот процесс несколько отличается от процесса диффузионной сварки как метода соединения двух деталей из однородных или разнородных материалов по параметрам технологического процесса и по его аппаратурному оформлению. [c.117]
В целом, однако, технологическому процессу изготовления композиционных материалов диффузионной сваркой под давлением присущи все основные показатели, характеризующие собственно процесс диффузионной сварки двух деталей, такие как подготовка соединяемых контактирующих поверхностей, нагрев соединяемых элементов, приложение к ним давления, необходимая выдержка при этих условиях и др. [c.118]
Подготовка поверхности контактирующих материалов. В основе технологического процесса получения композиционных материалов методом диффузионной сварки под давлением лежат процессы диффузии элементов, входящих в состав матрицы и упрочнителя, а диффузионные процессы, способствующие образованию компактного материала из компонентов матрицы и упрочнителя, протекают главным образом по границам раздела матрица—упрочнитель и матрица—матрица, т. е. практически по поверхностям матрицы и упрочнителя. В связи с этим существенное влияние на качество процесса и качество полученного методом диффузионной сварки композиционного материала оказывает состояние контактирующих поверхностей матрицы и упрочнителя.
[c.120]
Как было отмечено выше, при изготовлении композиционных материалов методом диффузионной сварки под давлением матрица применяется чаще всего в виде фольги. Поверхность фольги из металлов и сплавов может быть загрязнена различными смазками, применяемыми в процессе ее изготовления, может быть 120 [c.120]
Алюминий — борное волокно. Как уже было указано выше, основными технологическими параметрами, влияющими на свойства композиционных материалов, полученных методом диффузионной сварки под давлением, являются температура, давление и время выдержки. Одной из первых и наиболее подробных работ, посвященных исследованию влияния различного сочетания этих факторов и выбора оптимальных сочетаний, является работа 130]. Были опробованы режимы прессования 1) при низкой температуре, высоком давлении и длительной выдержке 2) при умеренной температуре, низком давлении и умеренной выдержке 3) при высокой температуре, высоком давлении и кратковременной выдержке. Исследования проводили на композиционных материалах с матрицами из трех алюминиевых сплавов — 6061 (0,4—0,8% Si 0,7% Fe 0,15—0,4% Си 0,25% Zn, 0,15% Мп 0,8—1,2% Mg 0,15%Ti 0,15—0,35% r), 2024 (0,5% Si 0,5% Fe 3,8—4,9% u 0,25% Zn 0,3—0,9% Mn 1,2—1,8% Mg 0,1% r) и 1145 [S5 99,45% Al 0,55% (Si + Fe) 0,05% u 0,05% Mn]. Свойства полученных по этим режимам образцов приведены в табл.
25.
[c.133]
Свойства композиций алюминий — борное волокно, полученных разными исследователями, и параметры диффузионной сварки под давлением приведены в табл, 26. [c.134]
Композиционный материал на основе алюминиевого сплава 6061 с 47 об. % волокна борсик и 6 об. % проволоки из коррозионно-стойкой стали AF -77, уложенной перпендикулярно борному волокну получали методом диффузионной сварки под давлением в вакууме при температуре 500° С, давлении 700 кгс/см в течение 1 ч [109] предел прочности такого материала в поперечном направлении был равен 29 кгс/мм . Аналогичный материал на основе сплава 6061 с 50 сб.% волокна борсик и 5 об. % проволоки из коррозионно-стойкой стали 355 диаметром 0,05 мм, также уложенной в поперечном направлении, получали 1177] методом диффузионной сварки в автоклаве. При этом применяли следующий режим пагрев до температуры 482°С при давлении 3,5 кгс/см» и выдержку в этих условиях 30—50 мни, повышение давления до 210 кгс/см , затем повышение температуры до 524—530° С, отключение нагрева и охлаждение материала в автоклаве до 200° С. Предел прочности такого материала в направлении укладки борного волокна был равен 120 кгс/мм , а в поперечном направле-138
[c.138]
Магний — борное волокно. Композиция магний—борное волокно является едва ли не единственной композицией на основе магния, получаемой методом диффузионной сварки под давлением. Исследование влияния технологических параметров изготовления материала на его свойства было проведено авторами работы [122 ]. Результаты исследования свойств композиций, полученных при температурах от 350 до 600° С, давлениях от 350 до 1400 кгс/мм и выдержке в течение 1 ч, позволили установить оптимальные условия получения композиционного материала Mg—В температура диффузионной сварки 525° С и давление 700 кгс/см . Свойства композиционного материала, полученного по этому режиму, представлены в табл. 29. Для сравнения в этой же таблице приведены свойства композиции близкой по составу, но полученной не по оптимальному режиму.
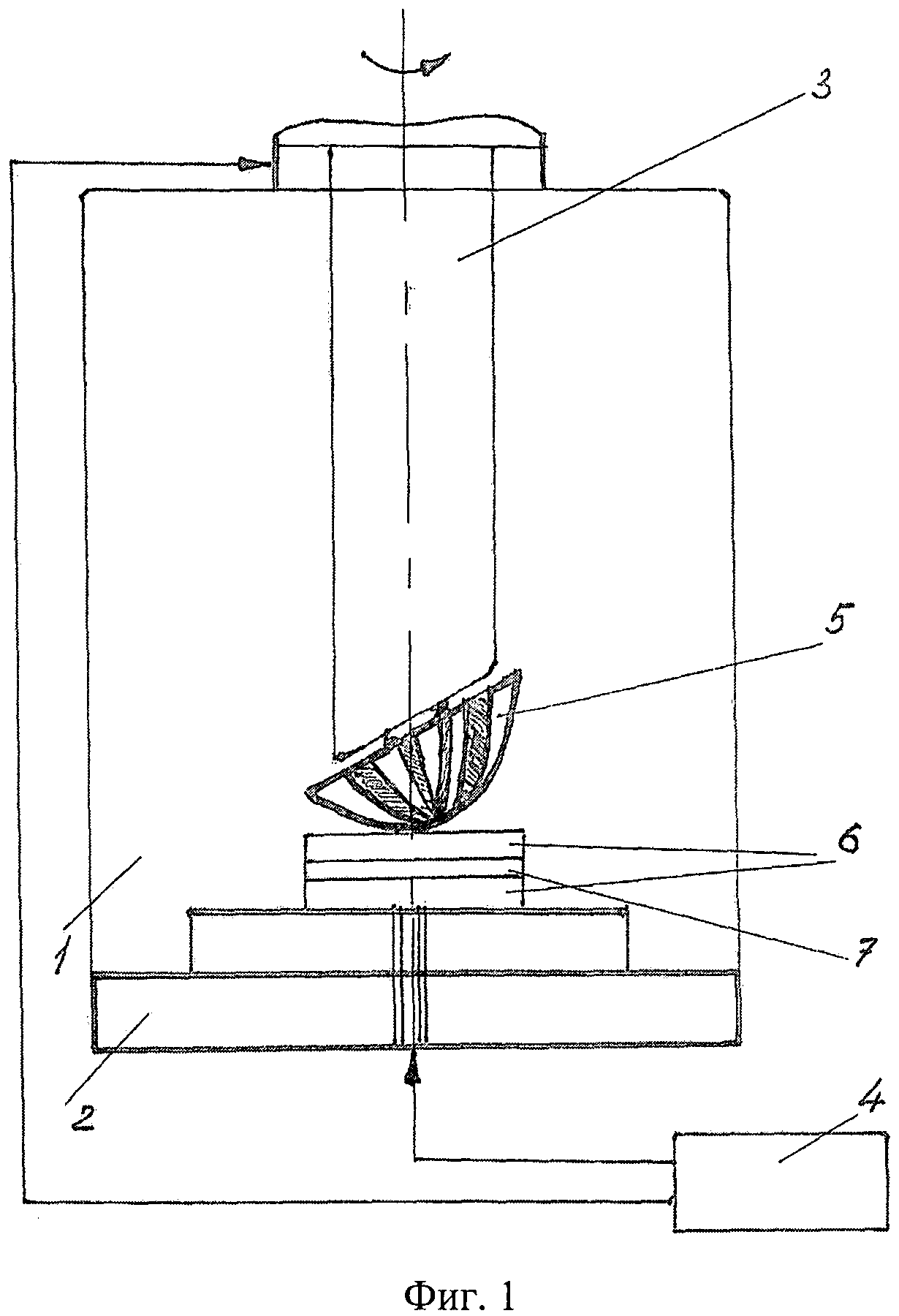
Никель — прочие упрочнители. Имеются сведения о получении методом диффузионной сварки под давлением композиционных материалов на основе никеля, упрочненного волокнами окиси алюминия [2151, вольфрама, (патент Франции № 2109 009, 1972 г.), нитевидными кристаллами карбида и нитрида кремния [198], Так получали композиционный материал из никелевой фольги толщиной 0,2 мм и волокна окиси алюминия диаметром [c.143]
Твердофазный метод совмещения компонентов композиции предполагает использование материала матрицы в виде листов, фольги, проволоки или порошка. Композиционный материал получают одним из следующих приемов диффузионной сваркой под давлением сваркой взрывом деформационной обработкой под давлением прессованием с последующим спеканием (порошковой металлургией). [c.273]
Основным методом получения КМ системы А1— В является диффузионная сварка под давлением методом горячего прессования (Рене-прокат-кой) чередующихся слоев борного волокна и алюминиевой матрицы. При использовании борных
[c.872]
В настоящее время разработано большое количество композиционных материалов из волокон бора и графита в эпоксидной смоле, алюминиевых и других сплавах, из которых изготавливают различные детали авиационных конструкций. Волокна из бора и графита заделывают в металлическую матрицу методом гальванопластики, различными химическими способами, методом регулируемого плавления сплавов, диффузионной сваркой под давлением, плазменным напылением в среде аргона на монослой намотанного на цилиндрическую оправку волокна и т. д. [c.214]
К основным методам получения биметаллов относятся наплавка жидкого металла на твердый слой холодная сварка под давлением диффузионная сварка электролитическое осаждение второго слоя специальные методы. Интенсивно развиваются процессы производства биметаллов методом совместной пластической деформации биметаллических заготовок в твердом состоянии (путем совместной прокатки, прессования, волочения).
[c.284]
Сварка диффузионная 285 —под давлением холодная — Применение 285 [c.299]
Аналогичный композиционный материал получали методом диффузионной сварки в автоклаве высокого давления [177] по следующему режиму нагрев под давлением 3,5 кгс/см до температуры 426° С подъем температуры до 482° С и медленное повышение давления до 700 кгс/см выдержка 75—90 мин снижение давления до 35 кгс/см и охлаждение. После охлаждения до 200° С давление снимается полностью, и автоклав открывается. Полученный по этому режиму материал имеет предел прочности в направлении укладки волокна 103 кгс/мм , а в поперечном направлении — 31 кгс/мм . [c.141]
Существует несколько технологических методов изготовления боралюминия. Э о диффузионная сварка пакета из чередующихся слоев алюминиевой фольги и волокон бора под давлением, пропитка пучка волокон бора жидким металлом, плазменное напыление алюминиевой матрицы на монослои этих волокон, уложенных на поверхности вращающегося барабана.
[c.127]
Параметры режима диффузионной сварки — это температура нагрева стыка деталей, давление, время выдержки под давлением при заданной температуре и глубина вакуума (величина остаточного давления воздуха в камере). [c.278]
Третье условие равнопрочности создается при активируемой пайке, когда в начальной стадии под влиянием приложенного давления и выдавливания припоя из зазора в отдельных местах шва локально пайка может переходить в диффузионную сварку. [c.63]
Прессование. Основной операцией процесса изготовления композиционных материалов методом диффузионной сварки под давлением является прессование. Именно в процессе этой операции происходит соединение отдельных элементов предварительных заготовок в компактный материал (формирование изделий). В отличие от прессования как метода обработки давлением металлов и сплавов, заключающегося в выдавливании металла из замкнутой полости через отверстие в матрице и связанного с большими степенями деформации обрабатываемого материала, данный процесс по своему существу ближе к процессу прессования порошковых материалов, применяемому в порошковой металлургии. Прессование заготовок композиционных материалов в большинстве случаев осуществляется в замкнутом объеме (в пресс-формах, состоящих из матрицы и двух пуансов типа пресс-форм, применяемых для получения изделий из металлических порошков) и с незначительной пластической деформацией материала матрицы, необходимой только для заполнения пространства между волокнами упрочнителя и максимального уплотнения самой матрицы. При этом, как и в процессе горячего прессования порошков, наряду с пластической деформацией матрицы, на границе раздела 126
[c.126]
Номенклатура изделий, которые можно изготовлять из композиционных материалов методом диффузионной сварки под давлением в изостате или автоклаве, весьма разнообразна. На рис. 63, 64 представлены виды профилей, получаемых в автоклаве [177] из композиционных материалов на основе титана и алюминия, упрочненных борными волокнами и стальной проволокой, а также схемы приспособлений, необходимых для изготовления таких профилей.
[c. 131]
Алюминий — бериллиевая проволока. Бериллиевая проволока является перспективным упрочнителем благодаря малой плотности, равной 1,83 г/см , высокому модулю упругости и прочгюсти, равным соответственно 29 500 кгс/мм и 130 кгс/мм . Исследование возможности получения композиционного материала методом пропитки бериллиевой проволокой расплавом алюминия, по данным Флекка н Гольдштейна, дало отрицательный результат, так как при температуре 644° С между алюминием и бериллием происходит эвтектическая реакция, сопровождающаяся растворением бериллия. В связи с этим одним из основных технологических путей получения материала алюминий — бериллиевая проволока в настоящее время является диффузионная сварка под давлением. При этом в качестве предварительных заготовок ком- [c.136]
Алюминий — углеродное волокно. Основным технологическим приемом получения композиционных материалов алюминий — углеродное волокно, наиболее часто применяемым в настоящее время, следует считать пропитку каркаса из углеродных волокон расплавом алюминиевой матрицы. Однако наряду с этим методом некоторые исследователи применяли для изготовления композиций методом диффузионной сварки под давлением [1, 156, 176, 184]. Так, в работах [23, 156] описан технологический процесс получения композиционного материала методом горячего прессования в вакууме углеродных волокон различных марок, на которые методом разложения триизобутила было нанесено покрытие из алюминия.
[c.137]
Титан — волокна окиси алюминия. Получение композиционного материала на основе титановой матрицы, упрочненной волокнами из окиси алюминия, описано в работе [215]. В качестве матрицы в этом материале применяли фольгу титанового сплава Ti—6% А1—4% V толщиной 0,20—0,25 мм, а унрочнителем служило волокно из окиси алюминия диаметром 0,25—0,27 мм со средней прочностью 210 кгс/мм . Материал получали методом диффузионной сварки под давлением в вакууме 1 10 мм рт. ст. по следующему режиму температура 815° С, давление 980 кгс/см , время выдержки 15 мин. Полученный по этому режиму материал имел предел прочности в направлении, параллельном укладке волокна, 70—88 кгс/мм , в поперечном направлении — 40 кгс/мм . Модуль его упругости в соответствующих направлениях был равен 14 800—19 ООО и 12 ООО кгс/мм .
[c.141]
Композицию на основе меди, армированной волокнами вольфрама, получали методом намотки вольфрамовой проволоки на цилиндрическую оправку, последующего осаждения на поверхность волокна электролитической меди и диффузионной сварки под давлением пакета, набранного из нескольких слоев волокна с медным покрытием. Диффузионная сварка осуществлялась в вакууме при температуре 700° С, давлении 800 кгс/см и времени выдержки 60 мин [146, 172]. Полученый таким образом материал, содержащий 37 об.% вольфрамового волокна с диаметром 20 мкм, имел прочность 120 кгс/мм . При этом же содержании волокна, но диаметром 40 мкм, предел прочности композиционного материала был равен 135 кгс/мм . [c.144]
Заготовка имела толщину 0,9 мм и была получена многократно чередующейся намоткой проволоки на плоскую охлаждаемую оправку и плазменным напылением на ее поверхность алюминия. После отжига, проведенного после прокатки, композиция, содержащая 37 об.% проволоки, с прочностью 385 кгс/мм , имела прочность в направлении укладки волокн 122 кгс/мм . Процесс холодной прокатки со степенью деформации 1—2% применяли для композиций алюминий — стальная проволока, полученных методом диффузионной сварки под давлением [159, 179]. Предел прочности этих композиций после прокатки состовлял 120 — 140 кгс/мм .
[c.146]
Другим технологическим направлением, заключающимся в совмещении компактирования и формообразования профилей, является диффузионная сварка под давлением в автоклавах и изостатических установках, когда сборные заготовки вместе с добавочными внутренними инструментальными деформирующими элементами заключают в замкнутую технологиче- [c.112]
Solid-state welding — Сварка в твердом состоянии. Ряд сварочных процессов, при температурах существенно ниже точек плавления основного металла, без добавления присадочного металла или пайки твердого припоя. Давление к соединению может как прикладываться, так и нет. Например, холодная сварка, диффузионная сварка, кузнечная сварка, горячая сварка под давлением и сварка прокаткой.
[c.1047]
При более высоком содержании водорода (15—20 слг /100 г) САП можно сваривать только контактной или диффузионной сваркой под большим давлением [54]. Последним методом можно соединять САП с другими алюминиевыми сплавами или нержавеющей сталью. Для контактной сварки листы плакируют алюминием. Толщина плакирующего слоя составляет 5—7% от толщины листа. Полученное в плакирующем слое точечное соединение характеризуется достаточно высокими механическими свойствами. Отношение значения разрушающей нагрузки при испытании точечного соединения на отрыв Ротр к разрушающей нагрузке при испытании на срез Рсреза для плакированного листа САП-1 толщиной 0,8—2,0 мм составляет 33—40% [49, 50]. [c.271]
Попытка повысить производительность автоматов с открытой дугой путем увеличения тока в дуге приводили к большому угару электродов, разбрызгиванию металла и плохому качеству сварочного шва. Удачное решение задачи было найдено работниками Института электросварки АН УССР имени Е. О. Патона и ЦНИИТМАШ в виде автоматических самоходных сварочных головок с дугой, работающей под флюсом. Широкое применение получили новые способы сварки электрошлаковая, плавящимся электродом в среде углекислого газа, в вакууме электронным лучом, трением, холодная сварка давлением, ультразвуковая, сварка перемещающейся дугой, управляемой магнитным полем, диффузионная сварка в вакууме при нагреве деталей токами высокой частоты.
[c.104]
Использование покрытий не является единственным способом подавления реакции на поверхности раздела. Легирование упроч-нителя также позволяет изменить состав продуктов реакции. Так, например, Харден и Райт [15] обнаружили химическое взаимодействие в слоистом композите алюминий — бор, полученном диффузионной сваркой, проводившейся при температуре 873 К с различными временами выдержки под давлением 2,8 кГ/мм . Было установлено, что уменьшение прочности и модуля упругости материала начинается после выдержки в течение соответственно 3 и 5 ч оба параметра значительно снижаются, если реакция идет в течение 8 ч. Напротив, в слоистом материале А1—В4С, полученном диффузионной сваркой в тех же условиях, не было обнаружено продуктов реакции.
[c.131]
В методах твердофазного совме1цения компонентов матричный материал используется в виде листов, фольги, проволоки или порошка. Технологический процесс заключается в получении компактного материла одним из следующих приемов диффузионной сваркой пакета под давлением, деформационной обработкой под давлением, сваркой взрывом, прессованием и спеканием (порошковой металлургией) и др. [c.116]
При диффузионной сварке детали, подлежащие соединению, выдерживают под давлением при высокой температуре в течение определенного времени, достаточного для того, чтобы произошла диффузия металла через место стыка двух деталей и образовалось сплошное соединение. Диффузионная сварка используется, например, для создания оболочковых сотовых конструкций, пустотелых лопаток и др. [105]. Сварку ведут при температурах на 50—100 град ниже температуры полимор-( люг() прс вран ,еиия и относительно небо. /паиих уде.пьных лаплеииях (0,05—0,15 кгс/мм ),
[c.330]
Волокнистые композиты получают разными методами. К ним относятся пропитка пучка волокон жидкими расплавами алюминия и магния с низкой температурой плавления, плазменное напыление, применение методов горячего прессования, иногда с последующей гидроэкструзией или прокаткой заготовок. При армировании непрерывными волокнами композиций типа сэндвич , состоящих из чередующихся слоев алюминиевой фольги и волокон, применяют прокатку, горячее прессование, сварку взрывом, диффузионную сварку. Отливка прутков и труб, армированных высокопрочными волокнами, производится из жидкометаллической фазы. Пучок волокон непре-рьгоно проходит через ванну с расплавом и пропитывается под давлением жидким алюминием, магнием или жидкой смолой в случае изготовления полимерного материала. При выходе из пропиточной ванны волокна соединяются и пропускаются через фильфу, формирующую пруток или трубу. Этот метод обеспечивает максимальное наполнение композита волокнами (до 85 %), их однородное распределение в поперечном сечении и непрерывность процесса.
[c.872]
Более надежна диффузионная сварка бериллия, т. к. при этом получается шов с мелкозернистой структурой, но процесс этот сложен, малопроизводителен и требует громоздкого оборудования. Диффузионная сварка ведется в вакууме (реже в атмосфере аргоиа) при 800—1250° и плотном контакте свариваемых изделий, чаще всего с приложением давления 10—300 кг1см . Чем ниже темп-ра, тем больше необходимое давление. Продолжительность выдержки под давлением от 1 до 24 час. Перед сваркой соединяемые поверхности шлифуются и обезжириваются ацетоном и спиртом. [c.146]
ГОСТ 20549-75 Диффузионная сварка в вакууме рабочих элементов разделительных и формообразующих штампов. Типовой технологический процесс (с Изменениями N 1, 2), ГОСТ от 27 февраля 1975 года №20549-75
ГОСТ 20549-75*
Группа Т53
Постановлением Государственного комитета стандартов Совета Министров СССР от 27 февраля 1975 года N 526 срок введения установлен с 01. 01.76
ПРОВЕРЕН в 1980 году. Срок действия продлен до 01.01.86**
________________
** Ограничение срока действия снято постановлением Госстандарта СССР от 09.08.90 N 2374 (ИУС 1190). — Примечание «КОДЕКС».
* ПЕРЕИЗДАНИЕ ноябрь 1981 года с Изменением N 1, утвержденным в январе 1981 года (ИУС 4-81)
ВНЕСЕНО Изменение N 2, утвержденное и введенное в действие Постановлением Государственного комитета СССР по управлению качеством продукции и стандартам от 09.08.90 N 2374 с 01.01.91
Изменение N 2 внесено юридическим бюро «Кодекс» по тексту ИУС N 11, 1990 год
Настоящий стандарт устанавливает типовой технологический процесс диффузионной сварки в вакууме вставок из твердых металлокерамических сплавов марок ВК 15, ВК 20 и ВК 25 по ГОСТ 3882-74 с основаниями рабочих элементов разделительных и формообразующих штампов из сталей марок 5ХНВ, 5ХНМ, 5ХНСВ по ГОСТ 5950-73 и марок 38ХН3МФА и 18Х2Н4ВА по ГОСТ 4543-71.
1.

1.1. Сварку вставок и оснований следует производить через компенсационную прокладку из никелевой ленты марки Н2 толщиной от 0,06 до 0,10 мм по ГОСТ 15515-70. Когда площадь свариваемой поверхности меньше 100 мм, допускается применять компенсационную прокладку из железоникелевого сплава марки 50НП по ГОСТ 10160-75 толщиной от 0,05 до 0,06 мм.
(Измененная редакция, Изм. N 2).
1.2. Шероховатость свариваемых поверхностей вставок и оснований — не более Ra 1,25 мкм по ГОСТ 2789-73.
1.3. Непараллельность свариваемых и противоположных им плоскостей вставок и оснований не должна быть более 0,02 мм на длине 100 мм.
1.4. На свариваемых поверхностях вставок, оснований и компенсационных прокладок перед сваркой не должно быть следов коррозии, жировых пленок и грязи.
1.5. Сборка вставок и оснований под сварку и установка в камеру сварочной диффузионной вакуумной установки должна производиться по схеме, приведенной на чертеже.
1 — нижняя подставка; 2 — основание; 3 — компенсационная прокладка; 4 — вставка;
5 — индуктор; 6 — верхняя подставка; 7 — изоляционные прокладки
1.6. Подставки следует изготавливать из сталей и сплавов по ГОСТ 5632-72 или твердых металлокерамических сплавов по ГОСТ 3882-74.
1.7. Непараллельность опорных поверхностей подставок не должна быть более 0,02 мм на длине 100 мм.
1.8. Изоляционные прокладки следует изготавливать из слюды марки СМОП или СМОЭ по ГОСТ 10698-80.
1.9. Твердость стального основания после сварки должна соответствовать приведенной в табл.1.
Таблица 1
Марка материала стального основания | Твердость по Роквеллу, HRC |
18Х2Н4ВА | 38-40 |
38ХН3МФА | 42-44 |
5ХНВ | 45-60 |
5ХНМ | |
5ХНСВ |
2.
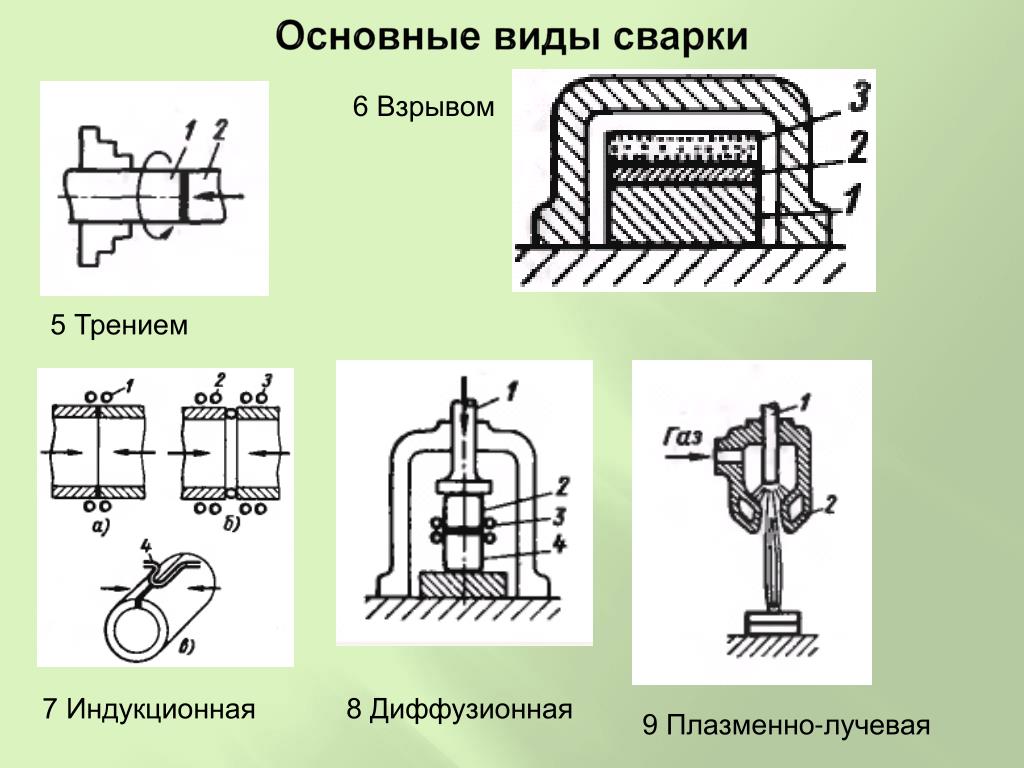
2.1. Процесс диффузионной сварки рабочих элементов штампов должен включать следующие основные технологические операции:
а) протирка свариваемых поверхностей вставки, основания и компенсационной прокладки;
б) сборка рабочего элемента штампа под сварку и установка в камеру сварочной диффузионной вакуумной установки;
в) предварительное сжатие рабочего элемента штампа;
г) вакуумирование камеры;
д) нагрев зоны сварки рабочего элемента штампа до температуры сварки;
е) увеличение сжимающего усилия до рабочего значения;
ж) выдержка рабочего элемента штампа при температуре сварки и рабочем давлении;
з) охлаждение рабочего элемента штампа до температуры закалки основания;
и) напуск воздуха в камеру и снятие сжимающего усилия;
к) извлечение рабочего элемента из камеры и охлаждение на воздухе до комнатной температуры.
2.2. Протирку свариваемых поверхностей следует производить салфетками из хлопчатобумажной бязи по ГОСТ 11680-76 сначала бензином марки Б-70 по ГОСТ 1012-72 или марки Б-1 «Галоша» по ГОСТ 443-76, а затем техническим этиловым спиртом по ГОСТ 17299-78.
2.3. Режимы процесса диффузионной сварки в вакууме вставок и оснований рабочих элементов штампов приведены в табл.2.
Таблица 2
Марка материала | Темпе- | Остаточное давление в камере, мм рт.ст. | Усилие сжатия, приходящееся на 1 мм свариваемой поверхности, кгс | Время выдержки, мин | Темпе- | ||
вставки | основания | предварительное | рабочее | ||||
ВК 15 ВК 20 | 18Х2Н4ВА 38ХН3МФА | 1050 | 5·10 | 0,2 | 1,0 | 10 | 850 |
ВК 25 | 5ХНВ | 1140±10 | 0,5±0,05 | 940 |
2. 4. Типы и технические характеристики сварочных диффузионных вакуумных установок приведены в справочном приложении.
3. КОНТРОЛЬ КАЧЕСТВА
3.1. Отсутствие трещин и краевых непроваров следует проверять внешним осмотром.
3.2. Измерение твердости стального основания рабочего элемента — по ГОСТ 9013-59.
4. ТРЕБОВАНИЯ БЕЗОПАСНОСТИ
4.1. Безопасность работ при диффузионной сварке в вакууме должна соответствовать:
а) «Правилам технической эксплуатации электроустановок потребителей*» и «Правилам техники безопасности при эксплуатации электроустановок потребителей**», утвержденным Госэнергонадзором 21 декабря 1984 года;
________________
* На территории Российской Федерации действуют «Правила технической эксплуатации электроустановок потребителей», утвержденные приказом Минэнерго России от 13.01.2003 N 6.
* На территории Российской Федерации действуют «Межотраслевые Правила по охране труда (правила безопасности) при эксплуатации электроустановок» (ПОТ Р М-016-2001, РД 153-34. 0-03.150-00). — Примечание «КОДЕКС».
б) «Санитарным нормам и правилам при работе с источниками электромагнитных полей высоких, ультравысоких и сверхвысоких частот», утвержденным заместителем главного санитарного врача СССР 30 марта 1970 года;
в) «Временным санитарным правилам по хранению, перевозке и применению этиловой жидкости», утвержденным Главным Госсанинспектором СССР 26 ноября 1948 года;
г) «Типовым правилам пожарной безопасности для промышленных предприятий», МВД СССР от 21 августа 1975 года.
(Измененная редакция, Изм. N 2).
4.2. Протирка бензином и этиловым спиртом деталей перед сваркой должна производиться на специально отведенном рабочем месте, оборудованном местной вытяжной вентиляцией.
ПРИЛОЖЕНИЕ (справочное). Типы и технические характеристики сварочных диффузионных вакуумных установок
ПРИЛОЖЕНИЕ
Справочное
Тип установки | Тип источника нагрева | Габаритные размеры установки (без источника нагрева), мм | Размеры рабочей зоны камеры, мм |
СДВУ-50/006 | ВЧГ6-60/0,44 | 1200х700х2300 | 380х460х460 |
СДВУ-100/01 | ВЧГ2-100/0,066 | 1500х1700х1700 | 450х450х450 |
УДС-3M | ВЧГ1-60/0,066 | 1040х2200х1950 | 280х280х280 |
УДС-4 | 1550х1000х2110 | 500х400х600 |
Продолжение
Тип установки | Максимальные размеры свариваемых изделий, мм | Максимальное остаточное давление в камере, мм рт. | Максимальная температура нагрева свариваемых деталей, °С | Усилие сжатия, кГс | Максимальная потребляемая мощность (без источника нагрева), кВА | Номинальное напряжение питающей трехфазной сети, В |
СДВУ-50/006 | 200х250х350 | 5·10 | 1300 | 0-5000 | 4 | 380 |
СДВУ-100/01 | 300х300х350 | 1500 | 0-10000 | 4 | 380 | |
УДС-3М | 180х180х100 | 5·10 | 20-1000 | 7 | 380 | |
УДС-4 | 400х300х150 | 100-10000 | 10 | 380 |
ПРИЛОЖЕНИЕ. (Измененная редакция, Изм. N 2).
Текст документа сверен по:
официальное издание
М.: Издательство стандартов, 1982
Юридическим бюро «Кодекс» в
текст документа внесено Изменение N 2,
утвержденное Постановлением
Госстандарта СССР от 09.08.90 N 2374
Диффузионная сварка — Услуги по диффузионной сварке
Запросить цену
Что такое диффузионное связывание?
Процесс диффузионного склеивания соединяет слои листового металла под действием тепла и давления. Тонкие листы металла складываются вместе в вакууме, затем нагреваются до 50-80% температуры плавления основного материала при приложении давления.Эта процедура нагрева и приложения давления заставляет часть электронов от каждого листа металла мигрировать на соседний лист до тех пор, пока стопка не соединится внутри вместе.Прочный материал и соединение создаются с полным набором свойств основного металла.
Fotofab с гордостью обслуживает клиентов из США и других стран.
Шаги для диффузионного связывания
Процесс диффузионного склеивания состоит из нескольких этапов, в том числе:
- Подготовка детали : Поверхность предварительно протравленного компонента должна быть чистой, плоской и иметь рекомендованную чистоту не менее 0,4 мкм RA. Это необходимо для ограничения загрязнения поверхности.
- Можно использовать широкий спектр металлов, включая алюминий, медь, золото, инконель, молибден, никель, серебро, нержавеющую сталь, титан и другие.
- Толщина одного слоя обычно составляет от 0,003 дюйма до 0,025 дюйма (в зависимости от требований к характеристикам).
- Подача тепла : В контролируемой среде тепло применяется в виде лучистого, индукционного, прямого или косвенного сопротивления.
- Приложенное давление : Давление прикладывается в одном направлении при низком давлении 3–10 МПа.Это необходимо для предотвращения деформации детали.
- Отделка деталей : После завершения процесса склеивания детали обычно проходят простую очистку, чтобы гарантировать, что на поверхности нет остатков.
- Снятие с рамы (при необходимости).
Преимущества / способы применения диффузионного связывания
Диффузионное склеивание имеет множество преимуществ и используется для различных целей. Примеры того и другого приведены ниже.
- Приложение использует :
- Применения, подверженные воздействию высоких температур, в которых механические соединения сплавов могут ослабнуть из-за высоких температур.Склеивание слоев металла снижает риск неисправности в работе.
- Тепловыделение / Рассеяние тепла на предметах, например, на ДСП. Прохождение жидкости или газа через слои отводит тепло от металла, помогая охлаждать систему.
- Возможные продукты :
- Доступные методы (в зависимости от характеристик металла) :
Здесь, в Fotofab, мы используем наш процесс травления для изготовления плоских ламинированных слоев, которые соединяются, образуя трехмерные структуры. Диффузионное склеивание создает единый ламинированный лист с практически неограниченными возможностями для структур внутренних частей. В каждом ламинированном листе может быть создано несколько небольших прецизионных деталей. Эта услуга отлично подходит для деталей толщиной более 0,63 дюйма или для деталей, которые требуют трудоемкости внутри большей части. Дополнительным бонусом является то, что сложность детали не увеличивает стоимость!
Подходит ли диффузионное соединение для ваших нужд? Запросите предложение или позвоните нам, чтобы обсудить ваш проект.
Узнайте больше о металлах, которые мы травим.
Диффузионное соединение — Bortec
Диффузионное соединение — это метод сварки, который в основном используется в металлообработке . Диффузионное соединение работает по принципу твердотельной диффузии и позволяет соединять два одинаковых или разнородных металла . Он широко применяется в аэрокосмической и атомной промышленности.
Диффузионная сварка , также известная как диффузионная сварка, представляет собой метод сварки, который в основном используется в металлообработке .Используя диффузионное соединение, можно соединить два разных металла по принципу твердотельной диффузии. Этот метод обычно выполняется при температуре плавления материалов от 50 до 70%. После достижения желаемой температуры к материалам прикладывают высокое давление . Диффузионное соединение широко применяется в атомной и авиакосмической промышленности.
Этот процесс насчитывает несколько веков и использовался для скрепления золота и меди для изготовления ювелирных изделий. Советский ученый Н.Ф. Казаков описал современные методы диффузионной сварки в 1953 году.
Принцип диффузионного склеивания Диффузионное соединение работает по принципу диффузии , который представляет собой перемещение атомов или молекул из области с высокой концентрацией в область с низкой концентрацией. Чтобы привести процесс в движение, прикладывают высокое давление к обоим материалам , которые кладут один на другой. Тепло ускоряет процесс диффузионного склеивания.Однако температура не должна быть слишком высокой и находится в диапазоне от 50 до 70% от температуры плавления металла.
Когда диффузионное соединение выполняется на двух материалах с аналогичной кристаллической структурой, заготовки зажимаются вместе металлической поверхностью, обращенной друг к другу. Основным условием успешного процесса диффузионного склеивания является поверхность склеиваемых материалов. Поверхности металла необходимо обработать, чтобы они были как можно более гладкими и не содержали остатков и химических примесей.Для успешного завершения процедуры диффузионного склеивания необходимо удалить весь материал, находящийся между деталями.
После зажима материалов к деталям в течение многих часов прилагается тепло и давление. Обычно поверхности заготовок нагревают в печи или через электрическое сопротивление . Для достижения необходимого давления можно использовать гидравлический пресс. Это позволяет точно измерить давление во время процесса. Если изменение температуры не предполагается, можно использовать дифференциальное тепловое расширение для приложения нагрузки на заготовки.Кроме того, давление может быть приложено за счет перепада давления газа между деталями, собственного веса или автоклавов высокого давления.
При использовании металлов с прочными оксидными слоями диффузионное связывание должно происходить в вакууме или в среде инертного газа для обеспечения надлежащего процесса. Это защищает сварочную поверхность от окисления.
Преимущества и недостатки диффузионной сваркиХотя диффузионная сварка имеет много преимуществ , имеет несколько недостатков, методика твердотельной сварки.
Преимущества:- Связанные материалы обладают теми же физико-механическими характеристиками , что и основной материал.
Склеиваемая поверхность может быть испытана на растяжение.
- Стыки, полученные диффузионным соединением, чистые, высокого качества, без разрывов и пористости .
- Диффузионное соединение позволяет соединять похожие и разнородные материалы . По этой причине он широко применим.
- Из-за хороших допусков по размерам диффузионное соединение используется для производства высокоточных деталей и деталей сложной формы .
- Эксплуатационные расходы довольно низкие, и процесс прост в использовании.
- Пластическая деформация может быть уменьшена при диффузии.
- Хотя эксплуатационные расходы низкие, , первоначальная стоимость установки высока.
- По сравнению с другими методами сварки, диффузионная сварка занимает очень много времени .
- Подготовка заготовок критична, и может быть трудной.
- Имеющееся оборудование ограничивает размер сварного шва .
- Диффузионное соединение не применяется для массового производства .
- Результат сильно зависит от параметров сварки , таких как температура, давление, качество поверхности металла и сварочный материал.
Диффузионное соединение титана: окончательное руководство
В этой статье я особо остановлюсь на титане , так как это самый простой из всех обычных инженерных материалов для соединения с помощью диффузионного связывания из-за его способности растворять собственный оксид при температурах соединения.Итак, давайте подробно рассмотрим, как работает диффузионное соединение, почему это предпочтительный метод соединения для титана (Ti) и титановых сплавов , и какой тепловой цикл требуется для диффузионного связывания титана в вакуумных печах . Кроме того, я приведу несколько примеров применения диффузионного склеивания.
Как работает процесс диффузионного склеивания
Диффузионная сварка или диффузионная сварка — это процесс соединения в твердом состоянии. Этот метод соединения основан на атомной диффузии элементов на стыке соединения.Диффузионное соединение — очень привлекательный процесс для прочного соединения разнородных инженерных материалов с целью создания инженерных устройств и конструкций. Этот процесс наиболее широко используется в аэрокосмической промышленности для соединения материалов и форм, которые иначе невозможно было бы изготовить (например, каналы с несколькими ребрами и сотовая конструкция).
Соединение разнородных материалов с разными теплофизическими характеристиками, которое невозможно с помощью других процессов, может быть достигнуто путем диффузионного связывания.Металлы, сплавы, керамика и изделия порошковой металлургии могут быть соединены методом диффузионной сварки с минимальной макроскопической деформацией. Высокоточные детали сложной формы или поперечного сечения могут изготавливаться без последующей механической обработки. Это означает, что могут быть достигнуты хорошие допуски на размеры изделий. Благодаря процессу диффузионного связывания химическая неоднородность может быть сведена к минимуму. Кроме того, с помощью этого метода можно избежать обычных дефектов , таких как трещины, искажения и сегрегация.
Для получения металлургического соединения между разнородными металлами необходима более высокая скорость диффузии, обеспечиваемая более высокой температурой соединения и более длительным временем выдержки между материалами. В настоящее время большинство операций склеивания выполняется в вакуумных печах . Диффузионное связывание зависит от температуры, давления, времени и (сверхнизкого) уровня вакуума, чтобы облегчить атомный обмен на границе раздела между материалами.
Почему для титана применяется диффузионное соединение
Титан (Ti) — превосходный материал, широко используемый в промышленных применениях благодаря его высокой удельной прочности, хорошей эрозионной стойкости и благоприятным высокотемпературным свойствам. Он на 30% прочнее стали и при этом на 40% легче, и хотя он на 60% тяжелее алюминия, он вдвое прочнее. Кроме того, титан используется в сочетании с алюминием (Al), марганцем (Mn), железом (Fe), молибденом (Mo) и другими металлами для дальнейшего повышения его значительной прочности , особенно при высоких температурах (для топлива ракетных двигателей). ) и его антикоррозийными свойствами.
В аэрокосмической промышленности титан используется в производстве конструктивных элементов крыльев, а также обшивки гидравлических систем самолетов, различных компонентов авиационных двигателей и кабин космических кораблей, где его качества незаменимы.Его исключительные характеристики находят широкое применение в морской среде , для гребных винтов лодок и кораблей или других частей, подверженных коррозии, а также для подводного оборудования. В военном секторе Ti и сплавы Ti используются в производстве ракет, ракет и другого оборудования. В медицинском секторе титан используется для замены тазобедренного и коленного суставов, кардиостимуляторов, костных пластин и винтов, а также черепных пластин при переломах черепа. Спрос на титан растет в нефтехимической промышленности и для нефтяных платформ на море, а также для производства мотоциклов.
В связи с увеличением использования титана и его сплавов процесс соединения Ti и его сплавов представляет большой интерес. К сожалению, сварка титана и титановых сплавов затруднена, поскольку они обладают высокой химической реакционной способностью при высоких температурах и имеют тенденцию к окислению при очень низких парциальных давлениях кислорода. В процессе сварки титановые сплавы очень легко поглощают кислород и азот из атмосферы. В результате, вакуумная диффузионная сварка является предпочтительным методом соединения титана и титановых сплавов.
Давайте теперь посмотрим на вакуумное диффузионное соединение в отношении теплового цикла, необходимого для диффузионного связывания титана . Кроме того, я приведу вам несколько примеров применения диффузионного склеивания .
Вам понравилась эта статья?
Прежде чем продолжить, подпишитесь на нас на нашей странице в Twitter, нажав кнопку ниже!
Таким образом, мы сможем держать вас в курсе самых передовых технологий для термообработки не только с помощью наших сообщений, но и с помощью лучших статей, которые мы собираем в Интернете.
Как работают вакуумные печи для диффузионной сварки титана
Что касается теплового цикла, необходимого для диффузионного связывания титана, вакуумная печь должна работать при высоких температурах и с газообразным аргоном под высоким давлением. Вакуум необходим для удаления даже мельчайших следов водорода, в частности, а также других газов или паров, включая кислород, азот и водяной пар. Вакуум также играет ключевую роль в отношении чистоты деталей , что является решающим требованием для обеспечения успешной обработки, поскольку он позволяет удалять пары масла или растворителя и следы влаги при низких температурах и может служить индикатором того, действительно ли чтобы прервать цикл из-за испарения загрязняющих веществ до того, как испортится тепло. Вакуум поддерживается до тех пор, пока не будет достигнута температура соединения , и только при достижении этой температуры давление газа достигает заданного технологического значения. Учитывая, что эти помещения обычно имеют большие размеры, необходимо значительное количество аргона, и этот метод позволяет уменьшить количество аргона, необходимое за счет использования температуры для повышения давления.
Высокие температуры и высокое давление не являются типичными характеристиками традиционных вакуумных печей для термообработки, которые имеют вакуумную камеру с водяным охлаждением и тепловую камеру, которая изолирует горячую зону от холодной стенки сосуда.Сжатый газ стремится нейтрализовать изоляционную способность материала, используемого для тепловой камеры, и чем больше газопроницаемость материала, тем более выраженным будет этот эффект. В вакуумных печах , работающих при экстремально высоких температурах (2000 ° C) и чрезвычайно высоком давлении (сотни бар), используются экраны , которые не зависят от сосудов, для их защиты и перехвата теплового потока с использованием специально для этого установлен контур с водяным охлаждением. Поскольку емкость очень толстая для того, чтобы выдерживать высокое давление, для нее нецелесообразно использовать охлаждающую рубашку, чтобы не превышать максимальную температуру на внутренней поверхности. Судно может взорваться!
В печах для диффузионного связывания титана задействованные температуры достигают около 1000 ° C при давлении в десятки бар, что означает, что все еще можно использовать графитовый картон для изоляции горячей зоны. Однако температурное расслоение, вызываемое конвекционными токами, должно быть компенсировано за счет обеспечения вертикальной асимметричности конструкции тепловой камеры как с точки зрения теплоизоляции (неоднородная толщина), так и с точки зрения сопротивления.Эта конфигурация полностью отличается от обычной конструкции вакуумных печей, в которых однородное облучение достигается за счет максимально возможной симметрии всех условий и требует большего опыта со стороны производителя.
Где лучше применять диффузионное соединение
В настоящее время диффузионная сварка может использоваться для изготовления лопаток турбины путем сварки двух боковых элементов лопатки с другой титановой формой посередине. Непокрытые поверхности внутренней формы покрыты слоем керамической пыли .После завершения сварочной обработки давление используется для выдувания боковых сторон и подъема кромок промежуточного металла. Это решение является альтернативой сотовой структуре . Затем детали придают закрутку, типичную для крыльев лопасти, путем горячего прессования в штампе. Использование лопаток, изготовленных этим методом, улучшает работу двигателя. Мы полагаем, что это из-за большего сопротивления формы при высоких температурах.
Другая заявка относится к производству титановых теплообменников для использования в морской среде и в контакте с морской водой.Тот же метод, описанный выше, используется и в аналогичной печи. В этом случае между элементами также помещается слой керамической пыли, который определяет области, в которых не может происходить диффузия. После соединения различных элементов теплообменника вводится сжатый газ , который разделяет несваренные поверхности, создавая внутренний путь жидкости через теплообменник. В общем, эти изделия очень большие, и поэтому преимущества этого материала связаны не только со способностью противостоять коррозии, но также с проблемой веса , которая становится важной для типа установки, в которой он будет использоваться.
Наконец, диффузионная сварка используется в вакуумных печах для производства конструктивных элементов автомобилей . Это приложение решает проблемы, связанные с обычной сваркой TIG. Соединения, полученные с помощью TIG-склеивания , не предоставляют тех же гарантий, что и при диффузионном склеивании. Шов, оставленный сваркой TIG, является прерывистым и приводит к пористости, поэтому трудно добиться хорошей отделки.
Итак, что вы думаете о , диффузионное соединение ? У вас есть дополнительное приложение, которым вы можете поделиться с нами?
Хотите увидеть больше фотографий?
У нас их намного больше.
Посетите нашу страницу Pinterest, нажав кнопку ниже, а затем подпишитесь на нас, чтобы оставаться на связи!
Диффузионное соединение — TWI
Диффузионное соединение — это процесс соединения в твердом состоянии, который применим к аналогичным и разнородным материалам, в первую очередь к металлам, хотя керамические материалы также могут быть соединены с использованием этого процесса. Процесс заключается в диффузии атомов через стык при повышенной температуре. Для диффузионного склеивания не требуются какие-либо присадочные материалы, и для соединения аналогичных материалов оно полностью автогенно.При диффузионном соединении разнородных материалов можно использовать прослойки.
Типичная коммерческая печь для диффузионного связывания представляет собой вакуумную печь с гидроцилиндрами, предназначенными для приложения давления через графитовую оснастку к соединяемым деталям. Этот процесс известен как одноосное диффузионное соединение. Поскольку процесс основан на диффузии, необходимо приложить давление, чтобы привести две поверхности в тесный контакт и, таким образом, способствовать усилению диффузии через границу (-ы). По этой причине шероховатость и плоскостность поверхности соединяемых деталей являются важными параметрами процесса.Например, более гладкие поверхности имеют меньше неровностей и деформируемые соединения, которые имеют меньшее количество пустот и, следовательно, обладают большей прочностью. Диффузионная сварка обычно выполняется в вакууме при уровне <1x10-2 мбар и при температуре до 1300 ° C. Более высокие температуры требуются для материалов с более высокой температурой плавления, так как температура диффузионного связывания обычно составляет 50-80% от температуры плавления материала (Tm), хотя при TWI мы, как правило, используем около 70-90% Tm из-за максимальной предел нагрузки нашей печи.Некоторые материалы несовместимы с условиями высокого вакуума, и в этом случае диффузионное связывание при парциальном давлении инертного газа, такого как аргон или N2, является обычным явлением.
Диффузионное соединение — это периодический процесс, который обычно используется там, где сложно или невозможно сформировать соединение, например, в компонентах со сложной внутренней структурой. Распространенное применение диффузионного склеивания — компактные теплообменники. Как показано на видео, ряд прокладок с рисунком уложен друг на друга, чтобы сформировать окончательную геометрию теплообменника, что, по сути, является процессом аддитивного производства. Доказано, что диффузионные соединения обладают хорошей прочностью соединения, что позволяет теплообменникам работать при высоком давлении. Кроме того, параметры процесса могут быть разработаны таким образом, чтобы свести к минимуму наличие пор на линии скрепления, что позволяет обеспечить герметичность диффузионного теплообменника для гелия. Каналы могут быть очень маленькими по диаметру и глубине, что в сочетании с более высоким рабочим давлением позволяет использовать теплообменники с благоприятным соотношением теплопередачи к весу. Наконец, для теплообменника, изготовленного из аналогичных материалов, из-за отсутствия наполнителя механизмы гальванической коррозии не возникают, поэтому при выборе коррозионно-стойкого сплава можно спроектировать теплообменник для высококоррозионных жидкостей.
TWI имеет более 60 лет опыта в области диффузионного склеивания. Материалы, которые TWI имеет диффузионную связь, включают алюминиевые сплавы, титановые сплавы, стали (углерод, нержавеющая сталь и ODS), никелевые суперсплавы, сплавы Хейнса, сплавы Fe-Co, циркониевые сплавы, медные сплавы, карбид кремния (SiC), нитрид кремния (Si3N4). и композиты с металлической матрицей (MMC).
Узнайте больше о пайке и диффузионной сварке на TWI.
Диффузионная сварка Научно-исследовательский сотрудник передовых технологий производства
ОПИСАНИЕИнформация о вакансии
Должность: Диффузионная сварка Продвинутый производственный научный сотрудник после докторантуры
Организация: Свойства материалов и производительность
Контактное лицо: Томас[email protected]
Место работы: Айдахо-Фолс, штат Иллинойс (город, график работы — 9X80)
Заявление о миссии / видении
Расширение возможностей для энергетического будущего нации
Миссия: Обнаружение, демонстрация и обеспечение инновационных решений для ядерной энергетики, другое варианты экологически чистой энергии и критическая инфраструктура.
Видение: INL изменит энергетическое будущее мира и защитит нашу критически важную инфраструктуру.
Равные возможности трудоустройства
Национальная лаборатория Айдахо (INL) является работодателем по обеспечению равных возможностей трудоустройства (EEO).

Мы настоятельно рекомендуем женщинам и цветным людям подавать заявки.
Обязанности
Национальная лаборатория Айдахо (INL) ищет научного сотрудника с докторской степенью (RA) для поддержки развития передовых производственных возможностей INL по диффузионной сварке компактных теплообменников.RA будет отвечать за изготовление и определение характеристик образцов, полученных диффузионной сваркой. Эта должность требует опыта в методах анализа (таких как дифракция обратно рассеянных электронов и электронная микроскопия) для выбора параметров изготовления. Для этой работы будет полезен опыт в области материаловедения / металлургии и искрового плазменного спекания.
Ожидается, что RA:
• Эксплуатирует оборудование для плазменного спекания, расположенное в INL
• Выполняет параметрическое исследование производственных параметров, характеризует полученные микроструктуры и определяет наиболее жизнеспособные производственные параметры.
• Анализирует данные механических испытаний
• Применить стандартные процедуры и разработка новых процедур для задач, связанных с проектом
• Создание публикаций
• Поиск возможностей финансирования для расширения работы за пределы начальной исследовательской программы
Квалификация:
Требуется
• Кандидат наук в области материаловедения и инженерии, машиностроение , Физика плазмы или смежная дисциплина (должна быть завершена в течение последних пяти лет и до начала назначения).
• Продемонстрировать навыки устного и письменного общения на английском языке.
• Опыт спекания и теории спекания
• Опыт работы с аналитическими методами, такими как оптическая микроскопия, электронная микроскопия (SEM), рентгеновские методы (рентгеновская КТ) или другие методы, используемые для определения свойств материала и микроструктуры.
Желаемое
• Опыт работы с материалами и диффузионной сваркой
• Знакомство с характеристиками и свойствами материалов (металлы), включая свойства при повышенных температурах
• Знакомство с механическими испытаниями
Требования к выборочным услугам
Чтобы иметь право на работу в INL, мужчины, рожденные после 31 декабря 1959 г. должен быть зарегистрирован в Системе выборочного обслуживания (SSS).Это включает в себя рожденных и натурализованных граждан США, условно-досрочно освобожденных, иммигрантов без документов, законных постоянных жителей, просителей убежища, беженцев и всех мужчин с визами любого типа, срок действия которых истек более 30 дней назад. Это требование не распространяется на людей с действующими неиммиграционными визами. Для получения дополнительной информации см. Www.sss.gov.
Должностные обязанности сотрудника
Должностные обязанности сотрудника — это физические действия и / или рабочие условия, связанные с должностью. Эти функции также могут составлять важные для должности функции, которые работник должен уметь выполнять, с жилыми помещениями или без них. Информация, представленная ниже, помогает описать работу, чтобы кандидат имел разумное представление о должностных обязанностях / ожиданиях. Способность заявителя выполнять и / или терпеть эти действия и условия будет обсуждаться, и рабочие места могут быть адаптированы в индивидуальном порядке после индивидуальной оценки заявителя и других соображений, включая, но не ограничиваясь любыми руководящими стандартами безопасности. .
Ходьба — продолжительная, Скручивание, Стоя — продолжительная, Приложение крутящего момента (руки), Сгибание / наклонение, Толкание / тяга, Приседание, Работа над головой, Захват / захват, Повторяющаяся работа, Управление мелкой моторикой (руками), Работа, требующая зрительного восприятия, Распознавание речи , Звуковая сигнализация, восприятие глубины, высокий уровень шума, переохлаждение, опасность от машины / поражения электрическим током,> 8 часов в день, электроинструменты, сверхурочная работа / ненормированные часы, работа в одиночку, защитная одежда, набор текста / клавиатура
Пожалуйста, подайте заявку до: 10 декабря , 2020
Заявление об охране окружающей среды, безопасности и здоровья
Должен быть знаком со всеми соответствующими требованиями по охране здоровья и безопасности и соблюдать их. Должен быть осведомлен о политиках и процедурах действий в чрезвычайных ситуациях, методах сообщения / решения рабочих практик или условий доступным осведомленным специалистам.
Дополнительная информация
При подаче заявления на вакансию предоставьте резюме и ответьте на все вопросы на следующих экранах. Кандидаты, не предоставившие резюме или не ответившие на вопросы, могут быть признаны не имеющими права на рассмотрение.
Обзор INL
INL — это научная национальная лаборатория прикладной инженерии, занимающаяся поддержкой U.S. Миссия Министерства энергетики в области исследований в области ядерной энергии, науки и национальной обороны. Лаборатория, в которой работают более 4300 ученых, исследователей и вспомогательный персонал, работает с национальными и международными правительствами, университетами и отраслевыми партнерами, чтобы открывать новые науки и разрабатывать технологии, которые лежат в основе ядерной и возобновляемой энергетики, национальной безопасности и экологических миссий.
Район Айдахо-Фолс
Айдахо-Фолс удобно расположен недалеко от многих национальных сокровищ, таких как Йеллоустонский национальный парк, Национальный парк Тетон, Джексон, Вайоминг и т. Д.Для получения дополнительной информации об этом районе посетите www.visitidahofalls.com и www.visitidaho.org.
Диффузионная сварка сплавов для работы с жидкими солями — отчет о состоянии
Настоящая работа связана с разработкой теплообменника для работы с расплавом солей, включая предлагаемый реактор с расплавом солей (MSR), гомогенный реактор, в котором топливо растворено в циркулирующей жидкости солевого расплава. Это результат недавней работы, проделанной в рамках программы АЭС нового поколения (NGNP); Общее у этих двух реакторных систем — это безопасная по своей природе ядерная установка с высокой выходной температурой, которая полезна как для технологического тепла, так и для более традиционной генерации. Программе NGNP было поручено исследовать применение атомных электростанций нового поколения в разнообразие энергетических потребностей.Одной из базовых конструкций реактора для этой программы является высокотемпературный реактор с газовым охлаждением (HTGR), который обеспечивает множество вариантов использования энергии. Они могут включать в себя производство электроэнергии с помощью обычного цикла Ренкина (паровая турбина), но также и другие методы: например, производство электроэнергии по циклу Брайтона (газовая турбина) и прямое использование высоких температур, характерных для выхода HTGR для технологического тепла в химическом производстве. промышленность. Такое технологическое тепло в настоящее время вырабатывается при сжигании ископаемого топлива и является основным источником углеродного следа химической и нефтехимической промышленности.HTGR, основанный на графитовых топливных элементах, может производить очень высокие выходные температуры; в идеале температуры 900 C или даже выше, что дает значительные энергетические преимущества.
Такие температуры, конечно, находятся на границах ограничений материалов, на верхнем конце диапазона рабочих характеристик металлических материалов, для которых существуют нормы надежной конструкции, и в области керамических материалов, изготовление и соединение которых на масштаба крупных энергетических систем, находятся на ранней стадии развития.Значительный объем работ был проделан по диффузионной сварке материалов, представляющих интерес для высокотемпературных сварочных работ, со сплавами, такими как 617 и 800H. Температура на выходе MSR также ограничена материалами и прогнозируется на уровне около 700 C. (RR E) Для работы с расплавленными солями при этой температуре требуется другой набор сплавов, таких как Alloy N и 242. Описанные здесь опытно-конструкторские работы по диффузионной сварке основаны на технологиях, разработанных во время работы NGNP, применительно к этим сплавам. Также существует проблема сварки разнородных металлов, поскольку сплавы, пригодные для работы в солях, как правило, не подходят для работы в газообразных окислительных средах, и наоборот, и сварка требуется для границ Класса I в этих системах, как указано в соответствующем ASME.
коды.
Следующее поколение диффузионного склеивания
На главную / Следующее поколение диффузионного склеиванияВ специализированных печах со встроенными системами гидравлического пресса используется превосходный контроль давления и температуры для создания лучших диффузионных связей при соединении одинаковых или разнородных металлов для фюзеляжей, деталей привода, цапф шасси, рам гондол, стержней ядерного управления, лопаток турбин, медицинских устройств, нагрева обменники, литиевые батареи и многое другое.
В интегрированной многоцилиндровой прессовой системе MOV от PVA TePla America используются большие прижимные пластины для диффузионного склеивания различных деталей. Он применяет усилие прессования до 4000 кН для обработки деталей размером 35,43 x 49,21 дюйма. Независимое управление каждым цилиндром обеспечивает чрезвычайно постоянное давление по всей поверхности. В камере используется шесть нагревателей для большей однородности температуры до 1400 ° C. Быстрое охлаждение быстро снижает температуру, поэтому детали можно снимать вдвое быстрее, без риска растрескивания или других повреждений. (первый вид)
В интегрированной многоцилиндровой прессовой системе MOV от PVA TePla America используются большие прижимные пластины для диффузионного склеивания различных деталей. Он применяет усилие прессования до 4000 кН для обработки деталей размером 35,43 x 49,21 дюйма. Независимое управление каждым цилиндром обеспечивает чрезвычайно постоянное давление по всей поверхности.В камере используются шесть нагревателей для большей однородности температуры до 1400 ° C. Быстрое охлаждение быстро снижает температуру, так что детали могут быть удалены за половину времени без риска появления трещин или других повреждений. (второй вид)
В течение многих лет диффузионная сварка использовалась для соединения высокопрочных и тугоплавких металлов, которые трудно или невозможно сваривать другими способами. Этот процесс применяет высокую температуру и давление к одинаковым или разным металлам, соединенным вместе в горячем прессе, в результате чего атомы на твердых металлических поверхностях смешиваются и связываются. В отличие от традиционных методов пайки, полученная связка демонстрирует прочность и термостойкость основных металлов и устраняет необходимость в присадочном материале, который влияет на конечный вес и размеры сопряженных металлов. Несмотря на эти преимущества, использование диффузионного связывания было ограничено более практическими соображениями, включая ограничение размера камеры печи и ограничения на величину и равномерность давления, прикладываемого по всей площади поверхности детали. Время работы также велико, часто длится целый день.Однако достижения в области горячих прессов в высоком вакууме, используемых для диффузионной сварки, устраняют многие из этих ограничений.
Сложное оборудование теперь обеспечивает превосходный контроль давления, обратную связь от встроенных датчиков давления, физические тесты чернил, которые показывают колебания давления по поверхности, и системы быстрого охлаждения для улучшения сцепления, увеличения ресурса и значительного увеличения времени цикла. Это имеет разветвления для все большего числа отраслей. Диффузионное соединение уже используется для создания сложных форм для электроники, аэрокосмической и ядерной техники, таких как фюзеляжи, арматура приводов, цапфы шасси, рамы гондол и стержни ядерного управления.Но теперь он все чаще используется для новых приложений, начиная от лопаток турбин и заканчивая медицинскими приборами, теплообменниками и даже литиевыми батареями. Типичные материалы, используемые в этих типах изделий, свариваемых диффузионной сваркой, включают нержавеющую сталь, титан, цирконий, бериллий, высоколегированный алюминий, инконель и вольфрам. Этот процесс также используется для сварки разнородных металлов, таких как медь с титаном, медь с алюминием, медь с вольфрамом и даже молибден с алюминием.
Поскольку диффузионное соединение является продуктом нагрева и давления, нагревательные элементы и встроенный гидравлический пресс играют ключевую роль в качестве окончательного соединения.Чтобы атомы двух твердых металлических поверхностей пересекались, они обычно должны иметь температуру приблизительно от 50 до 70 процентов от абсолютной температуры плавления материалов. Для достижения этих температур поверхности нагревают либо в печи, либо с помощью электрического сопротивления до температур до 1400 ° C. Давление прикладывается гидравлическим прессом или мертвыми грузами. Поскольку две ответные части должны находиться в тесном контакте друг с другом, часто используются приспособления. После зажима компоненты обычно подвергаются давлению и нагреванию в течение многих часов.Поскольку окисление также может повлиять на склеивание, большинство печей для термообработки работают в высоком вакууме. Хотя это общие элементы процесса, до сих пор не хватало точного контроля над каждым из них.
Что касается прикладываемого давления, например, интегрированные одноцилиндровые гидравлические прессы могут прикладывать постоянное измеримое усилие, но обеспечивают очень слабый контроль над крупными деталями с более сложной геометрией. Для компенсации необходимо использовать толстые графитовые прижимные пластины высотой от 10 до 15 дюймов, чтобы соединять слои металла вместе при более постоянном давлении. К сожалению, это занимает пространство печи и увеличивает время цикла для нагрева поверхностей металлов. Однако ведущие производители, такие как PVA TePla America (Corona, CA), предлагают многоцилиндровые системы с большими прижимными пластинами, в которых можно разместить самые разные детали. Самая большая из этих интегрированных систем прессования, MOV 853 HP, использует усилие прессования 4000 кН для обработки деталей размером 900 мм (35,43 дюйма) x 1250 мм (49,21 дюйма), что довольно много для диффузионного склеивания. Благодаря независимому управлению каждым цилиндром этот интегрированный пресс обеспечивает чрезвычайно постоянное давление по всей поверхности.
MOV поставляется со встроенными датчиками давления в нижней части прижимной пластины. На основании показаний отдельные гидроцилиндры можно отрегулировать для достижения однородности даже на больших площадях. PVA TePla оптимизировала физический метод проверки чернил, который можно выполнять для выявления участков на детали, к которым применяется неравномерное давление. Для большей однородности температуры система MOV использует шесть нагревателей для однородности температуры внутри камеры вместо обычных одного или двух для максимальной рабочей температуры до 1400 ° C.Быстрое охлаждение быстро снижает температуру, поэтому детали можно снимать примерно за половину времени без риска появления трещин или других повреждений. Благодаря превосходному контролю температуры и множеству гидроцилиндров в прессе можно использовать гораздо более тонкие крепежные пластины (менее 3 дюймов), чтобы освободить место в печи и обеспечить увеличение продолжительности цикла за счет более быстрого нагрева поверхностей до желаемых температур.
Это еще не все. Диффузионное соединение также используется для революционной технологии аддитивного производства под названием Laminated Objection Manufacturing (LOM), при которой тонкие листы металла от 1 до 2 мм склеиваются в аддитивном процессе с огромным потенциалом применения для конформного охлаждения.Конформные охлаждающие каналы представляют собой охлаждающие каналы, которые повторяют форму или профиль сердечника или полости пресс-формы для выполнения быстрого равномерного процесса охлаждения для процессов литья под давлением и выдувного формования. С помощью многослойной системы LOM в формы для литья под давлением могут быть встроены более сложные конструкции каналов охлаждения, что позволяет использовать более высокие давления. Это значительно сокращает время цикла на 40% при повышении качества продукции.
Детали конструируются с использованием традиционных программ 3D-моделирования САПР, а затем делятся на два слоя, которые равны толщине каждого листа металла.Эти многослойные листы вырезаются лазером, а затем объединяются вместе для создания охлаждающих каналов, используемых для отвода тепла. Окончательный «сэндвич» со всеми его слоями может быть обработан в соответствии со спецификацией по мере необходимости с использованием традиционного токарно-фрезерного оборудования с ЧПУ. Время обработки аналогично 3D-печати с аналогичными инвестиционными затратами. Однако можно производить детали большего размера без ограничений по материалам. Теплообменники, которые обычно изготавливаются из алюминия, являются основным применением этого аддитивного процесса диффузионного связывания. Теплообменники смешанного контура обычно изготавливаются из нержавеющей стали или даже из титана и титановых сплавов. Концепция LOM заключается в склеивании слоев листового металла, содержащих механически обработанные микроканальные структуры. В сочетании эти каналы могут обеспечивать охлаждение или отвод тепла. Слои могут быть склеены до высоты 600 мм в прессе для диффузионного склеивания MOV, сохраняя свою прочность как исходные материалы.
Еще одно применение, связанное с конформным охлаждением, — это пресс-формы для литья пластмасс под давлением, изготовленные в виде двух слоев инструментальной стали и такого материала, как нержавеющая сталь (Stavax).Независимо от того, наносится ли он слоями или просто для соединения двух частей, процесс диффузионной сварки является идеальным процессом для соединения огнеупоров и других высокопрочных легированных материалов без пайки. Несмотря на то, что оно существует уже несколько десятилетий, диффузионное соединение с более точным контролем температуры и равномерностью давления на больших деталях открывает огромные возможности для множества приложений следующего поколения.