Установка контактной точечной сварки. 7,5кА. Предназначена для прецизионной контактной точечной сварки деталей толщиной от нескольких микрон до 1,2 мм из цветных металлов и сталей. Выпускается с механическим и пневматическим приводом. описание |
Установка контактной сварки кольцевых швов. 7,5кА. Предназначена для сварки мембран между собой, их приварки к корпусным деталям, а также приварки других тонкостенных деталей к корпусным деталям. Установка может быть использована для сварки толщин до 0,8 мм описание |
Установка контактной продольной роликовой сварки. ![]() Предназначена для сварки продольных швов деталей длиной до 200 мм, толщиной до 0,8мм. описание |
Установка контактной шовной сварки сильфонов и других тонкостенных
цилиндрических деталей. 7,5кА. Установка может быть использована для сварки толщин до 0,8 мм описание |
Источник контактной сварки инверторного типа. 7,5кА. Предназначен для контактной точечной сварки деталей малых толщин — до 1,2мм. описание |
Установка контактной точечной сварки.![]() Предназначена для прецизионной контактной точечной сварки деталей толщиной от нескольких микрон до 1,2 мм из цветных металлов и сталей. описание |
Сварка роликовая — Энциклопедия по машиностроению XXL
Для прочно-плотных нахлесточных соединений применяют шовную сварку роликовыми электро-да.ми 3 (эск. д). [c.162]Шовная сварка. Шовную сварку роликовыми электродами применяют для соединения тонких элементов общей толщиной 4…6 мм преимущественно при возможности расположения электродов с обеих сторон соединения. Перекрытие выбирают равным (5…6)s. Напряжение среза T = F/la, где f — сдвигающая сила 1,а — соответственно длина и ширина шва.
Кромки — Подготовка под сварку газовую — Виды 219 — Прибыли — Вес 21, 29 — Размеры — Допуски при выдавливании холодном 116 —Сварка роликовая — Прочность — Коэффициент 235, 236 — Твердость и прочность — Повышение после цементации 318 [c.

Рентабельность сварки 160, 167, 168 Ритм на автоматических линиях 719 Радиевые покрытия 408 Ролики — профили рабочие 614, 615 Роликовая сварка—см. Сварка роликовая Роликовые машины — Характеристики 232, 233 [c.456]
При конденсаторной сварке (роликовой, точечной, стыковой) обеспечивается точное дозирование электрической энергии на сварку каждой точки или стыка. За счет этого обеспечивается стабильный процесс сварки. [c.220]
Роликовая сварка. Роликовую, или шовную, сварку применяют для получения сплошного, прочного и плотного швов. На рис. 173 дана схема роликовой сварки. Свариваемые [c.323]
Роликовая сварка может быть непрерывной и прерывистой, при последней применяют прерыватели тока. Прерывистая сварка обеспечивает высокое качество сварного соединения, однако шов получается менее чистый, чем при непрерывной сварке. Роликовая сварка дает прочный шов и может быть использована при изготовлении силовых конструкций. Основное достоинство этого способа — получение плотного шва высокой прочности.
[c.324]
Контактная сварка имеет три разновидности стыковую, точечную и роликовую. Для сварки труб, штанг применяют стыковую сварку, а для сварки крыльев брызговиков, тонких стальных листов — точечную сварку. Роликовая сварка применяется преимущественно при изготовлении баков для масла и бензина, труб из листовой стали и т. п.
Иногда для повышения герметичности соединений применяют дополнительную сварку роликовыми швами, которые накладываются предварительно. Такие соединения могут удовлетворительно работать лишь при толщинах 2 мм. и выше. На меньших толщинах в связи со значительным нагревом роликового шва при последующей сварке плавлением металл роликового шва разрушается диффундирующим в микропустоты и микротрещины водородом (рис. 10). [c.131]
Роликовая сварка. Роликовую или линейную сварку роликовыми электродами применяют преимущественно для изготовления герметичных изделий из тонкого листового материала, например бензобаков, коробок противогазов и т.
Машина марки МСП-1 является первой машиной, разработанной для непрерывной сварки пленки. Для улучшения процесса сварки роликовая сварочная головка в ней заменена сварочным полозом. [c.119]
ШОВНАЯ СВАРКА, контактная шовная сварка, роликовая сварка — особый вид точечной сварки, при котором отдельные сварные точки. частично перекрывают друг друга, образуя сварной шов. Практически это достигается выполнением электрода в виде плоского ролика. [c.181]
Основные виды контактной сварки стыковая сварка оплавлением или сопротивлением, точечная сварка, рельефная сварка, роликовая сварка. [c.13]
Внахлестку Ручная дуговая сварка Точечная контактная сварка Роликовая контактная сварка Полуавтоматическая сварка под флюсом Сварка в среде защитных газов [c.18]
Роликовая сварка. При сварке роликовыми электродами получается непрерывный или (при включении тока кратковременными импульсами) прерывистый шов.
Кроме длинных цилиндрических сосудов или труб на этих установках могут свариваться изделия более сложной формы. На фиг. 153 показана приварка сферических днищ к узким обечайкам на роликовом стенде. Как видно из рисунка, сборка двух сферических днищ позволила использовать при сварке роликовый стенд.- [c.218]
Пятая позиция предусматривает правила нанесения обозначений для прерывистых швов, для одиночных сварных точек, для швов контактной сварки точечных или роликовых. Например, для прерывистых швов записывают размер длины провариваемого участка /, знак 2 или / и размер шага шва для шва контактной роликовой электросварки — размер расчетной ширины шва для шва контактной точечной электросварки — диаметр точки d, знак / или знак 2 и размер шага и т.
При производстве труб сваркой сопротивлением ленты или полосы свертывают в холодном состоянии в трубу в формовочных непрерывных станах (рис. 3.12). При выходе из формовочного стана трубная заготовка поступает на трубоэлектросварочный стан, где кромки трубы прижимаются друг к другу двумя парами вертикаль, ных валков и одновременно свариваются роликовыми электродами. После сварки трубу калибруют, разрезают на части. [c.69]
К неподвижным разъемным соединениям относят те, которые можно разобрать без повреждения соединяемых и скрепляющих их деталей (резьбовые, шпоночные, некоторые шлицевые, конические, а также соединения с переходными посадками) к неподвижным неразъемным — такие, разъединение которых связано с повреждением или полным разрушением деталей. Такие соединения получают посадкой с гарантированным натягом, развальцовкой и отбортовкой, сваркой, пайкой, клепкой, склеиванием.
Рис. 2.7. Соединения роликовой сваркой |
Точечная и роликовая сварки (цифры в скобках) [c.34]
При точечной и роликовой электросварке тонких изделий (толщиной менее 2. мм) диаметр точки и ширина шва должны быть в 2 — 3 раза больше толщины s наиболее тонкого свариваемого элемента. При сварке более толстых материалов диаметр точки и щирину щва выбирают из соотношения d = s + Ъ мм (рис. 188, а).
[c.181]
Тонкостенные трубы сваривают встык валиковым швом (вид 19) предпочтительно газовой сваркой с отбортовкой одной (вид 20) или двух (вид 21) кромок, а также роликовой сваркой (вид 22). Если диаметр и длина труб допускают введение внутрь электродов, применяют роликовую сварку по отбортованным кромкам (вид 23).
Точечную или роликовую сварку (вид 4) применяют при больших диаметрах втулок. [c.184]
Рис. 2. Контактная сварка с электронагревом и с давлением а — точечная, между двумя электродами б — роликовая, между двумя роликами. |
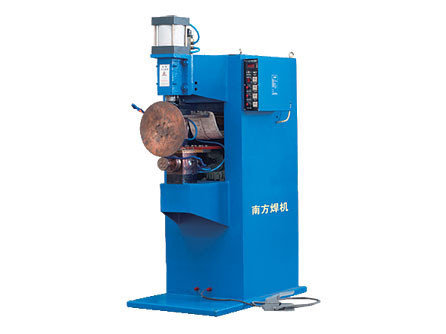
Для удобства выполнения тех или иных швов изделие приходится устанавливать в различные положения. Это осуществляется с помощью приспособлений — позиционеров, вращателей, кантователей, роликовых стендов, манипуляторов. Подобного рода приспособления (табл. 4) могут быть как установочные, предназначенные только для поворота изделия в положение, удобное для сварки того или иного шва, так и сварочные, обеспечивающие, кроме установки изделия, его вращения (перемещение) с заданной скоростью, равной скорости сварки. [c.141]
Роликовая сварка. Роликовая высокочастотнай сварочная установка показана на рис. 58. Рабочий конденсатор в этом случае выполняется в виде двух одновременно вращающихся роликов — электродов, между которыми зажимается, захватывается и непрерывно движется свариваемая пленка. При подаче на электроды высокочастотной энергии зажатая пленка будет нагреваться, при этом ролики создают также и необходимое при-сварке давление. Роликовую сварку можно применять лишь для соединения тонких пленок
[c.90]
В третьей позиции указывают способ выполнения сварки. Кроме ручной электродуговой сварки, все остальные швы имеют несколько способов исполнения, например А — автоматическая сварка под слоем флюса П — полуавтоматическая сварка под слоем флюса Кт — контактная точечная сварка Кр — контактная роликовая сварка Кс — контактная стыковая сварка и т. д. Сгюсобы выполнения сварки даны в стандартах на типы и конструктивные элементы сварных швов. [c.223]
Несколько изменена и структура осиовйого обозначения. Высоту катета наплавленного металла в швах угловых и тавровых соединений, а также величину диаметра точки точечного шва и ширину роликовых швов, выполняемых контактгсои сваркой, указывают перед условным графическим знаком шва. После графического знака во всех случаях указывают толщину и другие параметры шва сварного соединения (длина шва, длина npoBapnBaeNroro участка, шаг и количество рядов). Для более наглядного выделения швов, выполняемых по периметру,
[c.100]
Конструкции звездочек. Имеется большое количество конструктивных исполиепий звездочек [см, 13]. Для роликовых и втулочных цепей они могут изготовляться цельными (рис. 4.7, а) или состоящими из двух частей — диска с зубьями (ненца) и ступицы, соединенных болтами, заклепками, сваркой и т. д. (рис. 4.7,6). Иногда соединение диска со ступицей конструируется как предохранитель- [c.70]
Проволоки для продольных стержней / поступают с катушек 7 с помоп ью правильцо-подающего устройства 6 в направляющие кронштейны 5, расположенные в пазах неподвижной плангиайбы 4. Кронштейны 5 могут перемещаться вдоль пазов в радиальном направлении с помощью ходовых винтов 10. Вокруг планшайбы на специальной кольцевой направляющей перемещается машина 9 для контактной сварки, имеюпия сварочный трансформатор 3, роликовые электроды 2, в бухту 8 с проволокой для скрепляющей спирали. Один из роликовых электродов 2 имеет желоб, корректирующий положение очередного витка спирали, а второй контактирует только с продольным стержнем арматуры. Уста)ювка имеет универсальный характер все три движения— подача продольных
[c.238]
Соединения внахлестку сваривают нажатием пуансонами круиюю или прямоугольного сечения (точечная сварка, эск. б) или прокатыванием ро—чика.ми (роликовая сварка, зек. в). Детали из цветных метал.чов (контакты, седла) приваривают к аальным деталям путем запрессовки в конические 1иетда (зек. а) [c.164]
Соединение роликовой сваркой (вид 12) применяют, когда диаметр трубы позволяет ввести роликовый элекзрод внутрь трубы. [c.184]
Рис. 5. Примеры обозначений а — днустороНЕШЙ шов стыкового соединения со скосом одной кромки, выполняемый электроду говой ручной сваркой при монтаже 6 — односторонний шов стыкового соединения без скоса кромок, на остающейся подкладке, выполняемый сваркой нагретым газом с присадкой (для изделий из винипласта или полиэтилена) в — двусторонний шов таврового соединения без скоса кромок, прерывистый с шахматным расположением, выполняемый плектродуговой сваркой в защитных газах по замкнутой линии катет шва 6, / 50, t = 100 мм г — двусторонний шов углового соединения без скоса кромок, выполняемый автоматической сваркой под флюсом по замкнутой линии д — односторонний шов внахлестку, выполняемый дуговой сваркой алюминия по незамкнутой линии катет [пва 5 мм е — шов, выполняемый контактной роликовой электросваркой шаг шва 6 мм ж — шов соединения внахлестку с двумя электрозаклепками диаметром 11 мм.![]() |
Контактная сварка в Стерлитамаке от компании «ООО «ИНМАШ.ПРО»».
Контактной называется такой вид сварки, который относится к термомеханическому классу сварки и представляет собой сварное соединение, которое получается в результате нагрева подвергаемых нагреву сваркой изделий. Далее эти изделия сжимаются друг с другом. Выделяют несколько видов контактной сварки. Это стыковая, точечная и шовная, или роликовая сварка. Для этого типа сварки используется специальное оборудование, которое можно классифицировать по способу и возможности его переноса на: стационарное, передвижное и сварочные клещи, представляющие собой сварочные подвесные аппараты.
Любой аппарат, предназначенный для контактной сварки, состоит из следующих элементов: электрической части, главным элементом которого является сварочный силовой трансформатор и вторичный контур сварки. Также в конструкцию входит механическая часть, с помощью которой производится зажатие, а также пневматическая или гидросистема, с помощью которой производится регулирование притока воздуха к приводу. Есть в сварочных аппаратах также и система водяного охлаждения.
Одним из условий проведения успешной контактной сварки, помимо наличия качественного оборудования, является подготовка поверхностей, которые будут соединяться. Для этого нужно, чтобы поверхности были плоскими при их стыке, ровными и полностью совпадали друг с другом, между деталями и электродами нужно обеспечить минимальное электрическое сопротивление, между самими соединяемыми деталями сопротивление должно быть с одинаковой площадью контакта.
Сейчас контактная сварка представляет собой один из самых часто встречающихся способов сварки для получения неразъемных соединений. Если вы решили купить оборудование контактной сварки для труб, арматуры и аккумуляторов, добро пожаловать в наш магазин, который занимается продажей машины и аппаратов для конденсаторной сварки, и всех видов контактной сварки. Здесь вы можете купить конденсаторную, ручную машины для роликовой, шовной, стыковой контактной сварки и многое другое. Стоит отметить, что цена на электрическую машину односторонней, контактной, точечной сварки оплавлением являются одной из самых выгодных и низких.
Точечная сварка. Роликовая сварка. Рельефная сварка. История развития
Рекомендуем приобрести:
Установки для автоматической сварки продольных швов обечаек — в наличии на складе!
Высокая производительность, удобство, простота в управлении и надежность в эксплуатации.
Сварочные экраны и защитные шторки — в наличии на складе!
Защита от излучения при сварке и резке. Большой выбор.
Доставка по всей России!
Нагрев места стыка двух деталей проходящим через них электрическим током характерен для всех способов контактной сварки. Вторым существенным признаком этого вида сварки является обязательное приложение усилия сжатия контактируемых деталей. По характеру приложения такого усилия и типа соединения различают стыковую, точечную, шовную (роликовую) сварку и другие способы. Э. Томсон и его коллеги в США разрабатывали технологию стыковой контактной сварки и не пытались изменить характер приложения силы и форму соединения, несмотря на то, что прототипом нового способа контактной сварки мог послужить самый распространенный в XIX в. вид неразъемного соединения — клепка.
Неизвестно, когда и при каких обстоятельствах пришел Н. Н. Бенардос к принципу точечной контактной сварки. Первый в мире патент на этот способ (и «прибор» для его реализации) был выдан на его имя в Германии: № 46776—49 от 21.01.1888 г. В качестве электродов служили графитовые бруски, вставляемые в клещи, которые сжимали вручную (рис. 33).
В заявке на изобретение, поданной в России, Бенардос подробно описывает технологию и предлагает несколько устройств для точечной сварки. Так, один из «приборов» выполняли в виде стойки, на которой укрепляли изолированно друг от друга кронштейны: нижний жестко, а верхний — на шарнире (рис. 34).
На концах кронштейнов, к которым подавали напряжение, крепили электроды из угля или другого электропроводного «огнеупорного тела, соответственно для этого подготовленного» [20]. Свариваемые заготовки собирали встык или со скосом кромок и заводили между электродами. При этом верхний кронштейн поднимался. Перед началом сварки этот кронштейн с электродом прижимали грузом. По мере разогревания кромок до пластического состояния или до подплавления изделие передвигали, и вслед за нагревом производилось обжатие роликами.
Точечная сварка продолжала развиваться. Спустя 10 лет О. Кляйншмидт заменил угольные электроды в «приборах» Бенардоса медными электродами и усовершенствовал устройство для сварки, встроив трансформатор в клещи (рис. 35).
На разработку был выдан патент США № 616463 от 20.12.1898 г. С этого времени точечная сварка вышла из стадии лабораторных экспериментов, и началась работа над повышением производительности процесса. Бушайе разработал конструкции «дуплекс-электродов» для выполнения сразу двух сварных точек (пат. Франции № 330200 от 13.03.1903 г.). Верхний и нижний электродные узлы имели собственные трансформаторы. При параллельном подключении обмоток трансформаторов получается только одна точка, при последовательном включении — сразу две.
Оптимальную конструкцию электродов разработал Харматта (патент США № 1046066 от 3.12.1912 г.). Тейлор предложил перекрестный процесс нагрева места сварки таким образом (рис. 36), чтобы ток проходил по диагонали между двумя разделенными на части электродами (пат. США № 1243004 от 16.10.1917 г.).
Одновременно отрабатывали оптимальную конструкцию узлов, механические и электрические схемы машин для точечной сварки (рис. 37). Были разработаны машины с качающимся плечом-хоботом, мощные стационарные и легкие переносные машины, клещи разных конструкций.
В конце XIX в. точечную сварку использовали для приварки ручек к кастрюлям и сковородкам, для изготовления других неответственных изделий, заменяя клепку, а иногда — пайку. Однако это малозаметное применение убедительно доказало, что точечная сварка намного производительнее клепки и что пригодна она для соединения многих металлов. Точечную сварку начали широко использовать в США в 1914 г., когда в автомобильной промышленности клепка была заменена приваркой листовых элементов автомобилей (крыльев, обшивки кузова, деталей шасси). Мощность установок колебалась в пределах 5—35 кВ А. Установки имели ручное или ножное управление. К 1923 г. стационарные точечные машины позволяли сваривать до 200 точек в минуту. Использование новой технологии в массовом производстве создало возможность дальнейшего развития процесса сварки, совершенствования сварочного оборудования и даже создания новых способов сварки, таких как рельефная и роликовая. Идея рельефной сварки возникла благодаря многократному появлению «ошибочных» соединений, которые выполняли в спешке неквалифицированные рабочие. В 1918 г. Гамильтон и Оберег обратили внимание на преимущества приварки деталей сразу в нескольких местах на заранее отштампованных выступах и разработали промышленную технологию рельефной сварки.
В процессе изготовления изделий цилиндрической формы часто нижний опорный электрод выполняли в виде ролика, вращающегося вместе с изделием при установке в требуемое положение, а верхний — в виде короткого цилиндрического стержня. На таких машинах осуществляли точечные соединения, они же послужили прототипом машин для шовной сварки, когда свариваемые детали проходят между двумя роликами, нагреваются мощными импульсами тока, в результате чего образуется шов из отдельных перекрывающихся точек.
В 1905 г. Снурек и Гислер предложили схему многоэлектродной точечной сварки [110]. Однако только в 1924 г. была разработана конструкция соответствующих машин, которые были применены при сборке корпусов автомобилей на заводе Форда.
В 1910 г. Джевонсом был изобретен способ контактной сварки, заключающийся в том, что между свариваемыми кромками помещали небольшие пластинки (закладки), в которых и концентрировалась теплота. Эта технология была достаточно сложной. С целью ее упрощения как при точечной, так и при шовной сварке вместо закладок были предложены тонкие полоски (ленты), которые сматывали с катушек и подавали сверху и снизу изделия (рис. 38).
В 1930 г. на верфях Германии были внедрены машины с двумя электродами и двумя трансформаторами фирмы «Оттенземер Айзенверке». Затем в короткое время различными фирмами в США и Европе были разработаны схемы многоточечной сварки — с несколькими постепенно включаемыми электродами; с одновременным включением в симметричном и несимметричном исполнении; с трансформаторами, имеющими двойную вторичную обмотку; с трансформаторами, расположенными с противоположных сторон и др. Многоэлектродными машинами можно было одновременно или почти одновременно выполнять несколько сварных точек, полностью сваривать изделие (например, узел автомобиля), не перемещая элементы и электроды до окончания процесса [111, 112].
Для многоточечной сварки были разработаны два типа машин — многоцелевые машины и сварочные прессы [113, 114]. Первые были снабжены перемещающимся столом, их использовали для сварки различных изделий; вторые применяли для сварки строго определенных изделий, когда положение электродов и опорных поверхностей было фиксированным. В 30-е годы были решены многие технические проблемы; обоснованы расстояние между электродами и расположение трансформаторов, разработаны системы подвода тока, выбрано оптимальное количество одновременно свариваемых точек, установлена последовательность постановки точек и т. д. Особое внимание было уделено конструкции электродов и системам регулирования процесса сварки.
Кляйншмидт, заменив угольные электроды Бенардоса медными, обеспечил точечной сварке практическое применение. Электролитическая медь обладает большой тепло- и электропроводностью, а при механической обработке (протяжке) — удовлетворительной твердостью. Однако в результате нагрева в процессе эксплуатации прочность меди падает. Начиная с 1915 г., поиск материала для электродов велся в двух направлениях: электролитическую медь легировали с целью придания ей твердости, добиваясь при этом незначительного снижения электропроводности; повышали электро- и теплопроводность сплавов на другой основе, добавляя медь. В 1925 г. были разработаны «псевдосплавы», названные «элколит», «элмет», «моллори» и т. п., получаемые путем спекания при высоких давлениях и температурах порошков вольфрама, покрытых медью [115]. Поскольку проводимость этого материала была ниже, чем чистой меди, из него выполняли только наконечники, которые припаивали к охлаждаемому полому стержню. В машинах для шовной сварки вольфрам медную ленту припаивали в виде обода к торцу роликов, Однако паяная конструкция стоила дорого, и, кроме того, всегда существовала опасность плохого контакта в месте соединения из-за неточной сборки и дефектов пайки.
В результате поиска достаточно прочных материалов с хорошей электро- и теплопроводностью были подобраны элементы, способные образовывать твердый раствор с медью (кобальт, хром, кадмий, бериллий и молибден) при их содержании не более 1%. Из этих сплавов начали изготавливать цельнометаллические электроды и ролики.
Серьезным недостатком первых машин для контактной сварки, особенно шовных, являлся большой расход энергии — «лишний» нагрев зоны сварки происходил из-за длительного воздействия сравнительно небольшой силы тока. В 1920 г. было предложено осуществлять подачу токов большой силы, и в машинах установили реле времени. Роликам придавалось прерывистое вращательное движение через фрикционную муфту и стопорный механизм. Для уменьшения силы тока в период перемещения изделия во вторичный контур сварочного трансформатора включался элемент индуктивности. Сердечник индуктивной катушки был связан с роликами и перемещался при их движении, возвращаясь в исходное положение с помощью пружины. Однако вскоре обнаружили, что чем больше сила сварочного тока, тем меньше точность регулирования длительности импульса. Поэтому пришлось заниматься совершенствованием системы управления.
Регулирование параметров тока и длительности сварки являются важными составляющими технологии, а аппаратура управления — существенной частью сварочных машин. В аппаратах Томсона в первичной обмотке трансформаторов находились отводы, переключением которых регулировалось напряжение во вторичной обмотке, как правило, состоявшей из одного витка. Продолжительность прохождения сварочного тока контролировалась электромагнитной системой, содержащей конденсатор, питаемый от резистора и включенный параллельно обмотке соленоида. В 1924 г. в схему была включена неоновая лампа, благодаря чему ток мог проходить через систему только при напряжении строго определенного уровня.
В 1932 г. в США в контактных машинах появилась система управления, основанная на тиратронах. Эта система нашла применение на машинах средней мощности (до нескольких кВ А), однако при их эксплуатации обнаружились серьезные недостатки, в частности, плохо работали прерыватели.
В 1934 г., практически с момента появления в США игнитронно-ртутных вентилей со вспомогательным (поджигающим) электродом, управляющим зажиганием основного дугового разряда, их стали использовать в сварочных машинах. В последующие годы система управления контактными машинами, основанная на игнитронах, совершенствовалась. Были разработаны схемы управления игнитронами, в которых использовали достижения электронной техники и применяли вспомогательные элементы (стабилизаторы, усилители и т. д.), а также элементы защиты.
В 1930-х гг. продолжали работать над проблемой перегрузки сетей однофазными машинами, что вызывало колебания напряжения. Одно из решений этой проблемы было найдено в 1941 г. братьями Марио и Давидом Сиаки: оно основывалось на применении трехфазных источников с выпрямителями [116].
К концу 1930-х гг. конструкция (узлы, компоновка, архитектоника) контактных машин претерпела серьезные изменения по сравнению с исходными образцами. Первые машины часто выполняли, кроме прочих действий, проковку или обкатку, и в некоторых из них были предусмотрены механические командоаппараты в виде валов с кулачками. Производительность машин во многом зависела от быстродействия систем захвата и сжатия свариваемых деталей. В поисках оптимальных конструкций были опробованы гидравлические, пневматические и электромагнитные системы.
В конце XIX в. машины для стыковой сварки представляли собой сравнительно простое устройство с электрическим и механическим узлами, управление работой которых осуществляли педалью (рис. 39, а, б).
Первые устройства для точечной сварки имели вид клещей. Через два-три десятилетия были созданы несколько десятков различных по назначению универсальных и специализированных машин, а по размерам — от огромных формовочных станов для производства труб и изготовления автомобилей до подвесных и переносных клещей.
Серьезной проблемой в развитии контактной точечной сварки явилось создание клещей, отличающихся высокой маневренностью, легкостью и быстродействием. В первое десятилетие XX в. в таких подвижных сварочных постах генераторы тока конструктивно отделялись от механических, пневматических или гидравлических устройств для позиционирования и сжатия. Длина кабеляи шланга водяного охлаждения составляла 2—3 м, и, учитывая потери, приходилось повышать напряжение вторичной обмотки сварочного трансформатора, а следовательно, его мощность и габаритные размеры.
Следующим этапом было создание клещей с трансформатором, вмонтированным в подвижную конструкцию. Возникли новые проблемы — необходимость уменьшения габаритных размеров трансформатора, увеличения удельной мощности, минимизации потерь, С этой целью были применены трансформаторы с броневой магнитной системой, в которых первичная и вторичная обмотки были навиты и защищены магнитной цепью, выполненной из листов кремнистой стали с ориентированными кристаллами. Первичную обмотку выполняли из медной проволоки, а вторичную — из литой меди с припаянными трубками-каналами для охлаждающей воды. В подвесных трансформаторах первичные обмотки чередовались с витками вторичной обмотки, что увеличило удельную мощность до 0,7—1 кВА/кг [117].
Первая технология стыковой сварки труб, разработанная в 1902 г. Э. Томсоном и получившая название «прямошовный» метод, по способу приложения давления была сходна с кузнечно-прессовой сваркой. В цельносварных трубах были заинтересованы многие отрасли промышленности и строительства. Технология их изготовления и соответствующее оборудование продолжали совершенствоваться. За два десятка лет были предприняты попытки использовать для производства труб все известные способы контактной сварки. В 30-х гг. фирма «А. О. Смит» разработала технологию сварки оплавлением и внедрила ее в производство труб с толщиной стенки 5 мм и диаметром 500 мм, которые сваривались по всей длине (12 м) на машинах мощностью 5000 кВА.
В контактной сварке использовали ток промышленной частоты до тех пор, пока в 1939 г. фирма «Бабкок энд Вилько Ко» не применила ток частотой 200—350 Гц, Трубы из полосового проката сваривали машинами с вращающимся трансформатором. Однако это еще не был процесс, основанный на индукционном нагреве токами, открытыми Фуко, и теоретически исследованный в 1884 г, Хевисотдом. Впервые на практике это явление использовал в 1891 г. Э. Томсон, осуществивший индукционный нагрев листового железа. В 1900 г. была пущена в эксплуатацию индукционная плавильная печь Челлина. Началом развития процессов высокочастотной сварки считается разработка фирмой «Лоррен-Эско» в 1928 г. процесса (пат. Франции № 922431), в котором индуцированный ток концентрировался в зоне сварки ферритным сердечником. Однако основное развитие сварка токами высокой частоты получила после 1940-х гг.
Много общих существенных признаков с контактной сваркой имеет и конденсаторная сварка, идея которой возникла благодаря случаю. В 1905 г. сотрудник фирмы «Вестингауз Электрик» Л. В, Чабб, экспериментируя с электрическими конденсаторами, обнаружил, что проволока приваривается к алюминиевой пластине при прохождении через них разряда накопленного электричества [118]. Это наблюдение позволило сделать определенные выводы: разряд разрушил прочную оксидную пленку, затрудняющую пайку, и поэтому появилась возможность получить прочное соединение алюминиевых проводов. Конденсаторную сварку сразу же стали применять в электротехнике (приварка серебряных, вольфрамовых и других контактов, соединение алюминиевых и медных проводов), в ювелирном деле (приварка золотых и платиновых булавок и проволочек).
Как уже отмечалось, стыковая сварка нашла применение почти сразу после создания Томсоном первых образцов машин, Сначала это было изготовление проводов для электротехнических целей, затем — производство труб и различных стержней и, наконец, наиболее эффективное применение — производство вооружения в США, в частности, снарядов в годы Первой мировой войны. В Европе в это время наиболее активно развивала и внедряла контактную сварку немецкая фирма «Альгемайне Электрише Гаэельшафт» (АЭГ). Кроме «чисто» контактных машин, эта фирма в 1930-х гг. разрабатывала и выпускала машины для приварки шпилек.
Контактная сварка нашла применение в самолетостроении уже в 1908 г., вскоре после того, как в ряде стран было решено использовать для основных узлов самолетов металл. При изготовлении стальных ланжеронов, стоек, раскосов, элеронов и т. д, применяли точечную и роликовую сварку. В 1928 г. фирма «Форд Мотор» внедрила контактную сварку для ответственных узлов самолетов из дюралюминия. В начале 1930 г. были проведены статические и усталостные испытания на натурных образцах и моделях, подтвердившие возможность применения контактной сварки алюминиевых конструкций. В США с 1935 г. ее начали использовать фирмы «Боинг», «Дуглас» и «Сикорски», почти одновременно в Европе — фирмы «Фиат» вместе с «КантьериАэронавтика д’Италия», выпустившие первый металлический итальянский самолет [119, 120].
Особенно широкое применение все способы контактной сварки находят в автомобилестроении.
Г. Форду принадлежит особая роль в развитии контактной сварки. Его заказы были стимулом для усовершенствования технологии и оборудования. В свою очередь сварка обеспечила высокие темпы производства автомобилей. В первые годы на заводах Форда выпускали до 3000 автомобилей в год, а в 1909 г. их количество достигло 10 тыс. в основном благодаря применению стыковой и точечной сварки вместо клепки.
К началу 1928 г. на заводах компании «Форд Мотор» было 320 машин для сварки оплавлением, 540 машин для точечной сварки и 25 машин для роликовой сварки. В 1928 г. на автомобиле модели «Форд-А» насчитывалось около 1300 сварных точек, на модели 1932 г. их количество составило 2000 шт. Соединение всех штампованных деталей корпуса, крепящихся к шасси, осуществлялось точечной и роликовой сваркой. В следующем году технология была усовершенствована — днище и две боковые стенки сваривали за одну операцию на машинах с двумя трансформаторами (мощностью по 250 кВ А) менее чем за 60 с, причем чистое сварочное время составляло менее 10 с. В конечном итоге развитие оборудования для точечной сварки пошло по двум направлениям — создание клещей (подвижных сварочных постов) и создание многоточечных машин (контактных машин-прессов). Также были усовершенствованы и машины для роликовой сварки.
Развитие контактной сварки в СССР также стимулировалось интенсивным ростом автомобилестроения. Нижегородский (Горьковский) автомобильный завод был спроектирован и оснащен в основном оборудованием фирмы «Форд» и, в меньшей степени, установками нескольких германских фирм. Разнообразные машины для контактной сварки, поставленные Советскому Союзу из США, а также обученный американскими специалистами инженерно-технический персонал определили направления развития Контактной сварки в СССР [121].
Развитию и внедрению высоких технологий придавалось большое значение. С середины 1930-х гг. оборудование контактной сварки, разработанное и выпускаемое заводом «Электрик» им. А. К. Скороходова, применялось на уже работающих и строящихся заводах страны. Так, на стыковых машинах АСН —25 на строительстве Уралвагонзавода в месяц сваривалось до 500 т арматурной стали.
В 1934 г. на заводе «Электрик» были также разработаны машины АС—75 и АС—100 для стыковой сварки непрерывным оплавлением, специальные роликовые машины АШ—25 для сварки продольных швов, АШ—16 для сварки поперечных швов и фланцев, аппараты для точечной сварки AT-50—1, прессы для рельефной сварки.
Кроме производства автомобилей, с применением точечной контактной сварки для прикрепления обшивки к каркасу начали выпускать цельнометаллические пассажирские вагоны. Опыт, полученный при пуске первых автомобильных и тракторных заводов, послужил толчком к организации выпуска мощных отечественных контактных машин улучшенной конструкции и одновременно способствовал освоению ряда относительно новых технологических процессов — рельефной сварки при изготовлении тормозных колодок и колес, шовностыковой сварки труб из непрерывно сворачиваемой стальной ленты, точечной и шовной сварки стальных деталей с гальваническим покрытием и т. д.
С применением контактной сварки из коррозионно-стойкой стали были изготовлены самолеты, дирижабли, скульптурная группа В. И. Мухиной «Рабочий и колхозница». Основные работы были выполнены в лаборатории акционерного общества «Оргаметалл» (впоследствии ЦНИИТМАШ) Я. М. Глуховым, П. Н. Львовым, В. И. Коровиным, в Институте гражданского воздушного флота С. М. Поповым и др. В конце 30-х гг. в СССР было начато освоение стыковой сварки железнодорожных рельсов (ЦНИИТМАШ совместно с научно-исследовательскими организациями Наркомата путей сообщения и др.).
Контактная сварка
В связи с тем, что соединение при контактной сварке формируется за время, гораздо меньшее сварки плавлением, то это обеспечивает более высокую производительность и меньшее коробление детали, т.к. ЗТВ мала.
Т.к. процесс легко автоматизируется и более легко встраиваются поточные конвейеры, этот способ лучше применять при массовом и серийном производстве.
Этот способ нашел применение в автомобильной и авиакосмической промышленности.
Благодаря тому, что соединения, полученные контактной сваркой, обладают очень высокой прочностью и качество мало зависит от квалификации сварщика, то этот способ находит применение и в других отраслях.
Контактной сваркой сваривают толщины от сотых до десятых долей мм, а также до десятков мм. 2свRtu
2. Теплоотвод тепла из зоны сварки λ-теплопроводность
Т.е. в зоне между электродами действует тепло, выделяемое при прохождении тока и отводимое тепло в массу детали и электрода.
Т.к. Э. Томсон решил применить медные электроды, а λсu >> λстали, то форма литого ядра имеет благоприятную для сварного соединения чичевицеобразную форму.
Если увеличить Jсв и tсв, то начинает развиваться литое ядро.
Т.е. применение литых электродов и повышенный теплоотвод в них по сравнению с массой детали определяют развитие процесса плавления в литом ядре именно в массу детали, а не в сторону электрода.
В связи с этим снижается вероятность брака по причине плавления в ядре, т.е. прожег затруднителен, что определяет производительность точечной контактной сварки.
Рельефная сварка – ее можно отнести к одной из разновидностей точечной сварки.
Соединение при точечной сварке формируется при местном нагреве детали электрическим током и пластической деформацией в зоне соединения в счет усилия сжатия. 2R
— Qλ
Шовная контактная сварка (роликовая)
Кш – обозначение швов, детали сваривают перекрывающимися точками по линии качения роликов (электродов), сжатия детали р, подвода тока Jсв и перемещения детали со скоростью сварки Vсв – тоже с помощью этих роликов.
Применяется в тех случаях, когда нужно получить герметичное сварное соединение с помощью контактной сварки.
Герметичный шов – для сварки резервуаров, бензобаков, емкостей, полостей и др.
J = I / S – плотность тока
Jш – ток шунтирования
Процесс производится засчет выделения тепла и теплоотвода.
Шовная сварка разделяется на 3 процесса:
— непрерывная
При этом способе, когда ток протекает непрерывно, получаем сплошной шов без явно выраженных литых ядер, перекрывающих друг друга. Недостатком является повышенный нагрев электрода и необходимость их частой перезаточки.
— отдельными импульсами (прерывистая)
+ Q = J2св R tсв
— Q = f (λ) (tсв + tn)
Изменением тока Jсв по амплитуде, длительности его протекания — Jс, длительности его паузы — tn и скорости сварки — Uсв можно регулировать величину перекрытия литых ядер ln, обычно достаточно 25%, но не следует делать ln>50%.
Благодаря лучшему отводу от электродов стойкость их значительно повышается. При сварке жаропрочных сталей, обладающих низкой теплопроводностью и высокой стойкостью к деформациям при высокой t (жаростойкость) необходимо применять повышенные сварочные усилия, т.е. шаговую сварку.
Шаговая сварка – сварочный ток включают прерывисто, электроды останавливаются в момент пропускания сварочного тока.
Позволяет в момент остановки электродов и пропускания сварочного импульса осуществить более надежный контакт в зону протекания тока.
После выключения тока сварочные усилия в зоне контакта позволяют избежать горячих трещин.
Контактно – стыковая сварка
Существует несколько разновидностей контактно-стыковой сварки (Кс).
Рассмотрим способ контактной сварки сопротивлением, при этом детали сначала прижимают к электродам губками (призматические электроды) для обеспечения электрического контакта и невозможности проскальзывания детали между электродами.
Затем сжимают с усилием сварки Р нагрева, включают сварочный ток и детали в стыке нагреваются этим током Iсв. Затем прикладывают Росадки, в 1,5 – 2 раза меньше Рнагрева, потом включают ток и детали находятся под действием Р осадки.
В момент, когда деформируемое сопротивление наименьшее, прикладывают усилие осадки и выключают ток, при этом слои металла, нагретые до высокой пластичности, выдавливаются от центра стыка до периферии.
При этом из стыка выносятся остатки окисных пленок и град (металл на периферии зоны соединения).
Таким способом сваривают детали небольшого сечения, диаметром до 20-40 мм, соединение формируется в твердой фазе без расплавления металла в стыке. Нагретый пластичный металл выдавливается в град и в контакт вступают твердые нагретые частицы материала детали.
Недостатком является необходимость тщательной подготовки торцев под сварку и необходимость огромных мощностей установки для соединения больших сечений.
Второй способ – стыковая сварка оплавлением.
Технологически отличается от сварки сопротивлением тем, что напряжение на первичной обмотке трансформатора (и на вторичной) подается до момента контактирования свариваемых торцев.
Поэтому при сближении деталей в контактирование вступают отдельные микронеровности на торце, количество которых значительно меньше, чем в том случае, когда предварительно детали сдавили. Выступы сминаются и площадь контактирования возрастает. При первом контактировании возникает сварочный ток и он приходится на несколько микровыступов, отсюда плотность тока в контакте отдельных микровыступов настолько высока, что металл нагревается за тысячные доли секунды, а затем закипает. При этом происходит взрывное разрушение жидких перемычек контакта.
В контактирование вступают новые микровыступы и в зоне выступа появляются повышенные пары металлов, т.е. повышенное давление паров металлов в стыке защищает зону сварки, нагретую до tпл от взаимодействия с атмосферой.
При расплавлении торцев детали до такого состояния, когда на поверхности появляется тонкий слой жидкого металла, что гарантирует равномерный прогрев по всей площади стыка, к детали прикладывается усилие осадки. Жидкий слой с торцев выдавливается на периферию стыка – в град и под высоким давлением твердые части детали вступают в контакт, а т.к. tтв. ме вблизи жидкого слоя не намного ниже tпл и он был очень пластичный, то частично и твердый металл выдавливается в град и под давлением формируется прочное сварное соединение с минимальным количеством дефектов, т.к. продукты разложения и окисные пленки были выдавлены в град.
Стыковая сварка оплавлением обеспечивает более качественное соединение, т.к. металл на поверхности торцев, на которых могли быть загрязнения, удаляются при взрыве жидких перемычек в процессе оплавления.
Жидкий слой и часть пластичного металла также выдавливаются в град и в контакт вступает абсолютно чистые (молодые) поверхности.
Не требуется тщательной обработки свариваемых торцев как при сварке сопротивлением.
Более того, при сварке деталей с разным сечением делают специальный скос кромок, тогда площадь начального контактирования уменьшается и процесс оплавления эффективнее, а по мере процесса детали прогреваются и имеют нормальную форму.
Стыковая сварка прерывистым оплавлением или оплавлением с предварительным подогревом
При стыковой сварке крупногабаритных деталей: железнодорожных рельсов, труб, магистральных трубопроводов – для облегчения процесса начальной стадии оплавления применяют прием, заключающийся в том, что вначале детали медленно сводят до возникновения контакта и образования жидкости и паров металла. Затем разводят детали и тепло, выделившееся в зоне сплавления, распространяется в массу детали и они нагреваются.
Затем вновь создают контакт между торцами до тех пор, пока торцы не нагреются, что последующий процесс будет идти стабильно, без перерыва.
Контактная рельефная сварка (Кр)
Ее можно отнести к разновидностям точечной сварки. Применяется при сварке деталей, занимающих большое пространственное положение.
Обычно процесс по схеме 1 не получается, т.к. контактирование по всем участкам нашей детали не может быть одинаковым в связи с разницей в качестве подготовки, условиями деформирования, месторасположением контакта от токоподвода.
Данный процесс контактной рельефной сварки перекрещивающихся прутков происходит с формированием соединения в твердой фазе с выдавливанием жидкой фазы на периферию.
Для обеспечения равных условий контактирования и деформирования большого количества деталей нужно приложить сначала ковочное сварочное усилие (или усилие предварительного сжатия), которое отрихтует все прутки, обеспечит надежный контакт каждой детали с электродом и друг другом. Это должно обеспечить незначительную деформацию деталей в контакте.
Затем усилия снимаются до значения усилия сварки. Т.к. одинаковые условия контактирования всех деталей не гарантированы, но лучше сначала обеспечить импульс тока подогрева, при котором детали в контакте и под действием сварочного усилия разогреются.
Затем можно еще Jпод, после этого включают ток сварки.
Для снижения коробления прикладывается ковочное усилие и получаем многоточечное соединение с высоким качеством.
В начальный момент ток течет по вершинам, площадь мала и ток высокий, они начнут плавиться, а потом деформироваться от сварочных усилий. Получим литые ядра и незначительные следы без подгаров и пригаров.
За одну операцию контактной рельефной сварки получаем несколько сварных соединений. Но когда детали имеют защитное покрытие, которое должно остаться на поверхности после сварки, то следует применять только рельефную сварку, т.к. благодаря большой площади между электродом и деталью плотность тока будет мала и покрытие сохранится.
Физико-химические условия образования соединения Формирование сварного шва при контактной сварке. Нагрев металла сварочным током Нагревание и расплавление металлов в точке контакта энергией, выделяющейся при прохождении через него электрического тока. Шунтирование тока при точечной сварке Компенсация токов шунтирования при контактной сварке в нескольких точках. Свариваемость при контактной точечной и шовной сварке Факторы, влияющие на образование качественного сварного шва. Точечная сварка Точечные соединения при контактной сварке. Шовная сварка Соединения в виде шва из последовательных точек.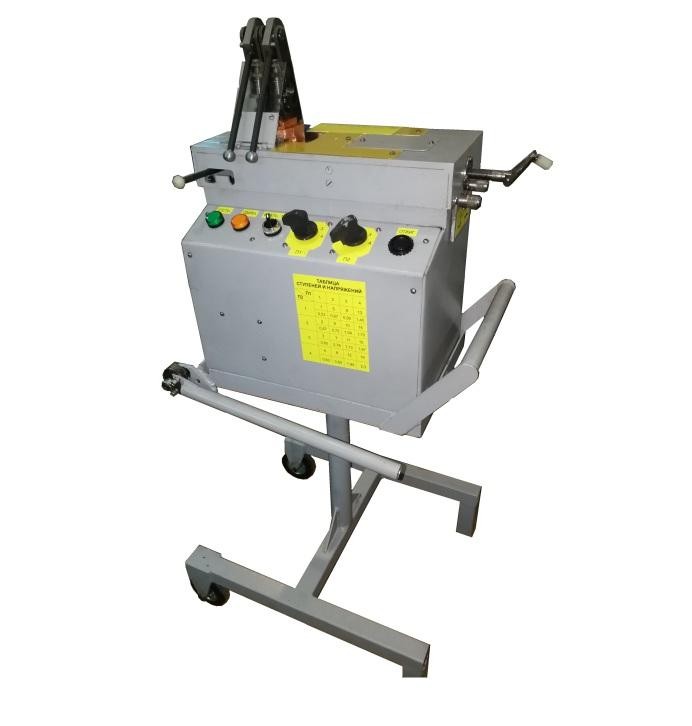
Также по теме:
Контактная сварка. Виды, типы, устройства и схемы контактной сварки.
Электрическая контактная сварка основана на принципе выделения тепла на участках электрической цепи, обладающих наибольшим сопротивлением, т. е. в месте стыка свариваемых деталей. Контактная сварка делится на стыковую, точечную и роликовую. На рис. 4.7 показаны разновидности контактной сварки.
Существуют два вида стыковой контактной сварки: сварка сопротивлением и сварка оплавлением. При стыковой сварке (рис. 4.7, а) свариваемые стержни 3 закрепляются в зажимах 2, которые являются электродами. Места соприкосновения свариваемых деталей имеют большое переходное сопротивление и при пропускании через них электрического тока нагреваются до температуры пластического состояния. Для повышения качества сварки, свариваемые детали прижимаются друг к другу силой F, благодаря перемещению подвижной плиты 4 со свариваемой деталью 3 к неподвижной плите 6. Ток получают от сварочного трансформатора 5. В месте сварки образуется шов 1.
Нагрев металла приводит к повышению его пластичности. В результате, под действием осевой силы происходит пластическая деформация. Микронеровности поверхности сминаются, пленки разрушаются, поверхностные атомы сближаются до расстояний, соизмеримых с параметром кристаллической решетки, что обеспечивает возможность образования межатомных связей.
Рис. 4.7. Виды контактной сварки: а – стыковая; б – точечная; в – роликовая; 1 – сварочный шов; 2 – электрод; 3 – свариваемые детали; 4 – подвижная плита с перемещаемой деталью; 5 – сварочный трансформатор; 6 – неподвижная плита
При сварке сопротивлением заготовки сначала сжимают усилием, обеспечивающим образование физического контакта свариваемых поверхностей, а затем пропускают сварочный ток. После разогрева места сварки происходит осадка и образуется соединение в твердой фазе. Для обеспечения равномерного нагрева по всему сечению поверхности заготовок тщательно готовят. Необходимость обеспечения равномерного нагрева ограничивает возможность применения сварки сопротивлением только для деталей небольшого (площадью до 200 мм2) и простого сечения (круг, квадрат).
При сварке оплавлением свариваемые заготовки сближают при включенном сварочном трансформаторе. Касание поверхностей происходит по отдельным выступам. При этом на соприкасающихся выступах плотность тока настолько велика, что происходит мгновенное оплавление металла с образованием жидких перемычек, которые под действием паров металла разрушаются. Часть металла в виде искр выбрасывается из стыка. Вместе с жидким металлом выбрасываются загрязнения, которые присутствуют на поверхности заготовок. Продолжающееся сближение заготовок приводит к образованию новых перемычек и их оплавлению. Непрерывное образование и разрушение контактов перемычек между торцами приводит к образованию на торцах слоя жидкого металла.
Точечная сварка (рис. 4.7, б) заключается в местном нагреве до расплавления электрическим током двух или нескольких листов металла3, предварительно сжатых между медными электродами 2сварочной установки силой F.
После прогрева свариваемых деталей и отключения тока, расплавленный металл охлаждается и кристаллизуется, образуя точечное сварное соединение. Усилие с электродов снимается, и свариваемый металл перемещается на некоторое расстояние (шаг сварки). Сваривание повторяется. Таким образом, получается сварной шов 1. Точечная сварка может быть односторонней и двухсторонней. Разновидностью точечной сварки является рельефная сварка. В этом случае один из свариваемых листов имеет отштампованные выступы. Эти выступы обеспечивают высокую плотность тока и концентрированный нагрев в месте контакта, который приводит к плавлению металла и образованию сварных точек.
При роликовой сварке (рис. 4.7, в) токоподвод к месту нагрева свариваемых листов металла 3 осуществляется медными вращающимися роликами2, являющимися электродами. В зависимости от скорости вращения роликов и времени включения и отключения тока образуется сварной шов1 с заданным шагом, состоящий из ряда сваренных точек. Можно получить непрерывный шов. Шовную сварку можно осуществлять при одностороннем и двустороннем положении электродов. Шовную сварку выполняют с непрерывным включением тока и с прерывистым включением тока. Очень редко применяют прерывистое вращение роликов с остановкой их в момент включения сварочного тока.
Установки для точечной и роликовой сварки состоят из трансформатора и прерывателя тока. Они имеют электродвигательный или педальный привод механизма сжатия.
Конденсаторная сварка представляет собой один из видов контактной сварки с использованием запасенной энергией. Энергия накапливается в конденсаторах при их зарядке от источника постоянного напряжения (выпрямителя), а затем в процессе разряда преобразуется в теплоту, используемую для сварки. Эта теплота выделяется в контакте между соединяемыми заготовками при протекании тока.
Существуют два вида конденсаторной сварки: бестрансформаторная и трансформаторная (рис. 4.8). При бестрансформаторной ударной сварке конденсатор подключен непосредственно к свариваемым заготовкам. Разряд конденсатора происходит в момент удара заготовки 3 по заготовке 4. Разряд оплавляет торцы заготовок, которые свариваются под действием усилия осадки.
При трансформаторной конденсаторной сварке конденсаторы С разряжаются на первичную обмотку сварочного трансформатора Т2, во вторичной цепи которого находятся предварительно сжатые между электродами заготовки. Бестрансформаторная сварка используется в основном для стыковой сварки, трансформаторная – для точечной и шовной.
Рис. 4.8. Схемы конденсаторной сварки: а – бестрансформаторная с разрядом на изделие; б – сразрядом на первичную обмотку трансформатора; 1 – пружина; 2 – защелка; 3 и 4 – заготовки; С – конденсатор; VD – выпрямитель; Т1, Т2 – трансформатор
Преимуществами конденсаторной сварки являются: точная дозировка энергии (за счет изменения емкости конденсаторов и напряжения зарядки), малое время протекания тока (0,001-0,0001 с) при высокой плотности тока, возможность сварки материалов очень малых толщин (от нескольких микрометров до 1 мм), невысокая потребляемая мощность (0,2-2 кВА).
Автоматическая и полуавтоматическая дуговая электросварка применяются в основном на промышленных предприятиях, в том числе на предприятиях строительной техники.
Электрическая контактная сварка — презентация онлайн
1. ЭЛЕКТРИЧЕСКАЯ КОНТАКТНАЯ СВАРКА
Цель работы: ознакомиться с физическимиосновами, изучить
технологию контактной сварки и области ее
применения, рассчитать
параметры сварки
Точечная сварка
Схемы точечной контактной сварки
а – двухсторонняя одноточечная;
б – односторонняя двухточечная;
в – двухсторонняя двухточечная
Стадии цикла и циклограммы точечной
сварки
а — без увеличения давления;
б — с увеличением давления при
проковке
Стыковая сварка
Циклограмма контактной
сварки сопротивлением
Циклограммы контактной
сварки оплавлением
Расчет параметров контактной сварки
Стыковая сварка сопротивлением
Основные параметры стыковой сварки сопротивлением:
— сила сварочного тока I,
— усилие осадки РОС,
— установочная длина LH.

— припуск на осадку СОС ,
— время нагрева tСВ
1.Сила сварочного тока I (A)
I=F⋅ j
где
F – площадь сечения свариваемого прутка, мм2;
j – плотность тока, А/мм2, (определяется по таблице 1 в зависимости от
площади сечения прутка)
Таблица 1 — Ориентировочные величины плотности тока и времени нагрева
прутка при стыковой сварке сопротивлением
Площадь сечения
Плотность тока,
прутка, мм2
А/мм2
Время нагрева, с
6
300
0,2…0,3
25
200
0,6…0,8
50
160
0,8…1,0
100
140
1,0…1,5
150
120
1,2…2,0
200
100
1,4…2,5
250
80
1,6…3,0
300
60
1,8…3,5
350
40
2,0…4,0
400
20
2,2…4,5
2.Величина усилия осадки POС, Н
РОС = р ⋅ F⋅10-4
При сварке малоуглеродистой стали удельное давление принимается равным (20…50) ⋅ 106 Па
3.Установочная длина LН (мм)
LН = (0,5…0,7) ⋅ d
где d – диаметр свариваемого прутка, мм
4.
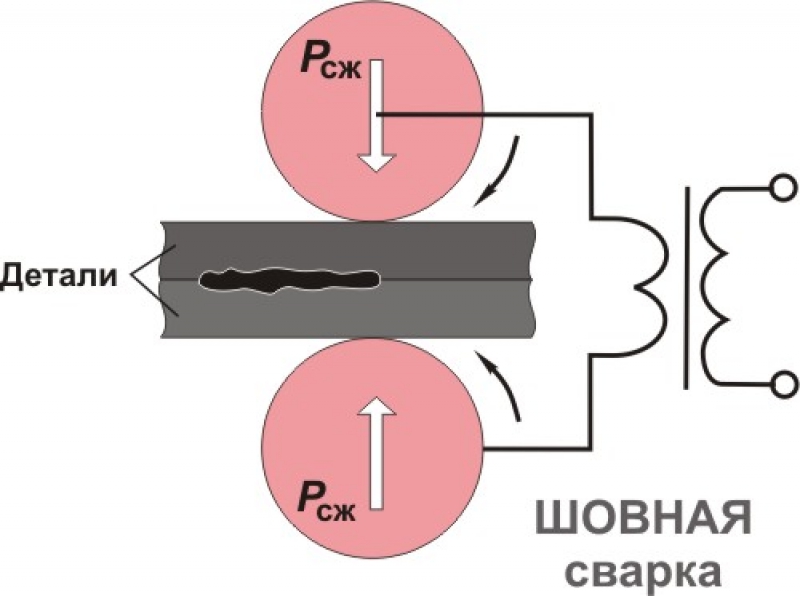
Сос 0,7 3 d 0,07 d
5.Время нагрева tсв (с) – время прохождения тока через заготовки зависит
от плотности тока и площади сечения свариваемого прутка (таблица 1)
Роликовая (шовная) сварка
Циклограммы шовной сварки
Расчет параметров роликовой сварки
1.
Диаметр отдельных точек dm (мм), зависящий от толщины свариваемых деталей:
2. dm = 2 ⋅ S + 2 ,
где S – толщина более тонкой из свариваемых деталей, мм.
2. Площадь контакта F, мм2:
F = π ⋅ d2m / 4.
3.
Сила сварочного тока I, (A)
I=F⋅ j.
Шаг точек (расстояние между центрами точек) а, мм
a = (0,5…0,7) ⋅ dm.
Примечание: Уравнение приведено для плотных швов; в не плотных швах точки могут не перекрываться
и для получения плотного шва расстояние между центрами сварных точек при больших скоростях сварки
берётся не более 2…3 мм (шаг точек).
4.
5. Скорость сварки Vсв (м/мин) определяется по формуле
Vсв = 2f ⋅ 60 ⋅ a / 1000 ,
где f = 50 – частота тока, Гц; а – шаг точек, мм.

6. Усилие сжатия Рсж (Н):
Рсж = р ⋅ F ,
где р – удельное, Па (при сварке малоуглеродистой стали толщиной до 3мм составляет (40…120)10 5Па.
7. Ширина рабочей контактной поверхности роликовых электродов Вэ (мм) зависит от толщины
свариваемого металла S (мм) и определяется по формуле
Вэ 5 S 2
Содержание отчета
1 Титульный лист
2 Цель работы
3 Схемы и циклограммы процессов контактной сварки с кратким их описанием.
4 Результаты расчетов параметров стыковой и роликовой контактной сварки (таблица 2 и 3)
5 Выводы
Контрольные вопросы для самопроверки
1. В чем заключается сущность контактной сварки?
2. Как определяется полное сопротивление сварочного контура?
3. Почему сопротивление сварочного контакта является наибольшим?
4. Перечислите основные виды контактной сварки?
5. В чем заключается сущность стыковой контактной сварки?
6. Какими способами осуществляется стыковая контактная сварка?
7. Чем отличается стыковая сварка оплавлением с подогревом от сварки непрерывным оплавлением?
8.

9. В чем заключается сущность точечной контактной сварки?
10. Какие детали свариваются точечной сваркой?
11. Сущность роликовой (шовной) контактной сварки.
12. Какие детали и материалы соединяются роликовой сваркой?
13. Перечислите основные параметры стыковой контактной сварки.
14. От чего зависит сила сварочного тока при контактной сварке?
15. Какие факторы влияют на скорость роликовой сварки?
Таблица 6 — Исходные данные для выполнения работы по контактной сварке
ПРОЧНАЯ СВАРКА РОЛИКАМИ | MUNDOLATAS
РЕЗЮМЕ
Основные принципы электросварки по точкам в металлургической промышленности и критерии хорошего формирования точки сварки.
Эта работа обобщает и дополняет работу, уже опубликованную на этой веб-странице под заголовком:
— Электросварка
Anuncios
ОПРЕДЕЛЕНИЕ
В металлических банках, сваренных посредством электросварки, точка сварки получается между двумя соединяемыми металлическими частями, без какого-либо внешнего воздействия, достаточно прохождения сильного тока через эти металлические части в зоне, считающейся придерживаться.
Тепло, необходимое для сварки, создается за счет сопротивления, которое материал оказывает прохождению этого тока в месте сварки.
Линия непрерывной сварки достигается за счет последовательности точек, которые образуются между двумя соединяемыми металлическими деталями, подвергаются давлению двух круглых электродов, по которым циркулирует электрический ток, вызываемый движением вращения в направление обратное. См. Рисунок № 1:
.Рисунок №: Формирование линии непрерывной сварки
ОСНОВНЫЕ ПРИНЦИПЫ
А.- Понятие об электрическом токе: Закон Ома
Сила тока, измеренная в амперах, в любой электрической цепи равна напряжению, измеренному в вольтах, на выводах цепи, деленному на сопротивление указанной цепи в Ом:
I = V / R
См. Рисунок № 2:
Рисунок № 2: Схема точки сварки
B.- Понятие тепла: закон Джоуля
Количество тепла, выделяемого в проводнике при прохождении электрического тока, зависит от:
— сила тока I
— сопротивление драйвера R
— из времени в обращении т
все связаны выражением:
2
Вт = 0.24 Р И т
C.- Сопротивления в сварочном оборудовании
В сварочной цепи присутствуют следующие резисторы:
— R1 = Сопротивление между верхним шкивом и медным проводом
— Re = Сопротивление между проводом и металлом
— Ri = Внутреннее сопротивление металла (1-я зона)
— Rc = Контактное сопротивление (интерфейсы)
— R’i = Внутреннее сопротивление металла (2-я зона)
— R’e = Сопротивление металла / медная проволока
— R2 = Сопротивление резьбы / нижний шкив
См. Рисунок № 3:
Рисунок № 3: Сопротивления в сварочной цепи
Сопротивления Re, Rc и R’e меняются в зависимости от:
— давление сварки между электродами (шкивами)
— состояние поверхности металлов
— форма и размеры электродов
— материал электродов
— состояние поверхности электродов.
Резисторы R1, Re, R’и R2 являются паразитными резисторами и вызывают следующие потери энергии:
Wp = W1 + We + W´e + W2
Резисторы Ri, Rc и R’i являются эффективными сопротивлениями для образования точки сварки и вызывают энергию:
Ср = Wi + Wc + W´i
Наблюдения:
a.- Энергия W1 и W2 увеличивается в зависимости от загрязнения и деформации канавок сварочных роликов.
b.- We и W’e нагревают поверхность металла и способствуют окислению сварного шва. Количество образующегося окисления зависит от времени и температуры.
D.- Энергетический баланс
Потребляемая энергия: Q = We + Wp
Количество тепла, необходимое для достижения температуры сварки, зависит от:
Anuncios
— объем металла. См. Рисунок № 4. Это том:
V = 2e x c x против .Быть против скорости сварки.
Рисунок № 4: Свариваемый объем
— удельная теплоемкость металла
— тепловые потери.
Эти тепловые потери составляют:
— По проводимости в электроде, в зависимости от:
o Поверхность электрода
o Контакт металла с электродом
o Погода
— По теплопроводности в свариваемом металле, в зависимости от:
o Теплопроводность
o Толщина металла
— По радиации
— Путем охлаждения валков холодной водой.
E.-Основные функции сварочного давления:
1.- Поддерживайте контакт с свариваемыми материалами
2.- Предотвращает попадание воздуха в зону сварки
3.- Заставляет электрический ток проходить между контактирующими поверхностями
4.- Поддерживает постоянное сопротивление контакта с воздухом.
5.- Вызывает деформацию кристаллов металла путем ковки.
6.- Предотвращает образование мешков и пористости в зоне сварки.
7.- Обеспечивает рекристаллизацию свариваемого металла при охлаждении.
8.- Предотвращает вытекание расплавленного металла во время сварки
9. — Допускает сопротивление вращающемуся шкиву
Вывод:
Идеальная сварочная цепь должна быть спроектирована таким образом, чтобы:
— Потери энергии — Wp — минимальные
— Количество образовавшегося окисления минимально
— Эффективная энергия — Мы — максимум
— Полученная структура однородная
ХАРАКТЕРИСТИКИ МЕТАЛЛА
Материалы, используемые в электросварных банках, изготовлены из низкоуглеродистой стали.Его содержание в C составляет <до 0,5% и <до 1% в других элементах.
Влияние различных элементов, которые входят в состав железа с образованием стали, вызывают различные эффекты, такие как:
Углерод : твердость поверхности стали увеличивается с увеличением содержания углерода. Не оказывает значительного влияния на сварку при C <0,2%.
Марганец : Повышает твердость и устойчивость к разрушению. Если Mn> 0,6%, то при высоком содержании углерода припой становится хрупким.Если Mn <0,3%, возникает пористость и сварной шов становится хрупким. Следовательно, Mn должен находиться в% между двумя предельными значениями.
Сера : Ее присутствие должно составлять 0,035%, если возможно, и никогда не превышать 0,05%, так как это может вызвать ослабление структуры сварного шва, особенно если углерод имеет тенденцию к увеличению.
Кремний : от 0,01% до 0,10% улучшает свариваемость.
Фосфор : Это примесь, которая должна присутствовать в минимально возможном количестве.Он не должен превышать 0,04%. Сварка становится хрупкой, вызывает трещины, снижает сопротивление ударам и усталость.
Влияние поверхностных покрытий:
Олово: Поверхностное олово или жесть снижает сопротивление на границе раздела, поэтому необходимо увеличивать сварочный ток в зависимости от содержания поверхностного олова, то есть его покрытия. Другой аспект заключается в том, что чем выше содержание олова, тем больше поверхностное загрязнение электродов.
Anuncios
Хром: Обработка на основе хрома и оксида хрома препятствует прохождению тока и не подходит для электросварки.
ФОРМИРОВАНИЕ ТОЧКИ СВАРКИ
A. — Изменение контактных сопротивлений (Re, Rc и R’e)
1º.- Функция давления:
— Если давление сварки увеличивается, это вызывает:
o Снижение паразитарной резистентности Re и R’e
o Уменьшение сопротивления интерфейса Rc
См. Рисунок № 5:
Рисунок № 5: Изменение сопротивлений в зависимости от давления сварки
— Это уменьшение зависит от:
o Характер поверхности
o Твердость материалов
o Его проводимость
2º.- Температурная функция:
— Под действием температуры T происходит размягчение неровностей поверхности, уменьшение Rc (контактное сопротивление) и увеличение Ri (внутреннее сопротивление металла)
См. Рисунок № 6:
Рисунок № 6: Изменение сопротивлений в зависимости от температуры
3º.- Эволюция в процессе сварки:
— 1) Во время начала сварки наиболее значительная потребляемая энергия обусловлена сопротивлением Rc .
— 2) Rc уменьшается до 0, до точки плавления
— 3) Ri увеличивается до точки плавления
— 4) После Ri уменьшается, когда объем точки увеличивается
График 7 показывает изменение общего R под действием Rc и Ri во время сварки острия.
Рисунок № 7: Изменение сопротивления в зависимости от времени сварки
Rc действует как катализатор в начале процесса сварки и позволяет увеличить Ri .
Re и R’e (сопротивление между металлом / медной проволокой) являются источником потерь энергии, значение которых невелико, но не меняется во время сварки, при условии, что электрод является хорошим проводником и достаточно охлажден.
B.- Сила сварочного тока — время сварки:
Для того, чтобы явления, описанные в пункте А, хорошо развились, необходимо:
— Высокая интенсивность I
— Время сварки Ц , краткое.
2
Напомним, что согласно закону Джоуля (W = 0,24 RI t) потребляемая энергия W является функцией тока I тока и времени сварки t при равном сопротивлении R. Таким образом, такое же значение W может быть достигнуто с помощью:
— Я слабый x длинный
— I сильная x короткая т
Если выбрать слабый вариант I, то получится:
— Температура металлической сборки повышается, но не достигает плавления.
— Убытки увеличиваются
— Износ электродов
Во всех случаях тепловой баланс будет намного выше, как:
— Я был, на подъеме
— T слабое, убывающее
Допускается, что время сварки обратно пропорционально квадрату силы тока.
График зависимости энергии сварки ( Вт, ) от интенсивности ( I ) и времени ( t ) отражен на следующем графике No.8:
Anuncios
Рисунок № 8: Энергетическая диаграмма сварки
, в котором мы можем определить различные зоны как:
— Зона A = Зона склейки металла
— Зона B = Зона сварки металла
— Зона C = Зона внешних выступов на острие металла
Практический способ настройки сварочного аппарата для данного металла и давления сварки:
— Схема сварки должна быть построена, ищу:
o Предел сцепления
o Предел проекции
Все это под конкретный отвод трансформатора.Затем такая же операция выполняется для следующего большего и меньшего дубля.
Получаются три зоны сварки, из которых выберем самую большую, регулируя машину на 50%.
C.- Влияние размеров точки сварки
Факторы, влияющие на размеры точки сварки:
— Толщина металла
— Величина перекрытия кромок, которую мы обозначили C
— Длина точки сварки L, которая является функцией скорости сварки vs.
Наиболее благоприятные условия даются при аккредитива = 1 . В такой точке тепло сварного шва распределяется правильно и получается равномерно цепочка горячих точек.
Если L / C = 2 , условия не столь благоприятны, потому что в этой точке тепло сварного шва распределяется плохо, и может быть получена альтернативная последовательность горячих точек и прилипших (холодных) точек. См. Рисунок № 9
Рисунок № 9: Схема точек сварки
МЕТАЛЛУРГИЯ УКАЗАТЕЛЬНОЙ СВАРКИ
1º.- Период отопления:
— Прохождение тока вызывает локальный нагрев, который достигает плавления материала, соответствующего двум частям
— При нагревании чечевица материала расширяется, понимая под чечевицей зону расплавленного материала, имеющую эту форму.
— Для нейтрализации толкающей силы расплавленного металла требуется большая сила сжатия.
— Если сила сжатия слишком мала, металл вырывается в виде выступов.
— При сварке возникают серьезные внутренние дефекты (полости, поры…).
2º.- Тепловое состояние острия при отключении сварочного тока:
— Зона A = плавленый металл
— Зона B = пастообразный металл
— Зона C = критическая температура
— Зона D = температура ниже критической
— Зона E = Температура окружающей среды
См. Рисунок № 10:
Рисунок № 10: Тепловое состояние точки сварки
— Температурный градиент составляет несколько миллиметров от 1500 ° C до температуры окружающей среды.
— Прекращение сварочного тока знаменует начало охлаждения.
3º.- Фаза охлаждения:
— Ядро расплавленного металла находится в большой охлаждающей массе, состоящей из:
o Сварные детали
o Электроды охлаждаемые
— Теплообменники быстрые
— Кристаллизация осуществляется по направлению к центру точки:
Anuncios
o Зона D = Без изменения структуры
o Зона C = Зерно очищено
o Зона B = тонкая структура
o Зона A = тонкая структура
В случае неправильного охлаждения под давлением сварки может произойти образование пузырей.Тепловое сжатие также может вызвать внутреннее напряжение в определенных точках.
ИССЛЕДОВАНИЕ СВАРОЧНОЙ ЦЕПИ
1º.- Проблемы, возникающие при сварке
— Геометрия внутренней сварки.
Внутренняя сварка всегда бывает неравномерной, с волнами, расплавленным металлом, острыми краями — все это отрицательно сказывается на хорошей защите с помощью покрывающего лака.
— Однородность наплавленного металла
o Повышение скорости сварки или
o Уменьшение значения нахлеста шва при одинаковой скорости
вызывает слабые места в сварке, которые проявляются разрывами во внутренней сварке
2º.- Описание сварочной схемы
Рассмотрим стандартную сварочную схему, которая в основном включает:
— Шкив верхний (большой диаметр)
— Шкив нижний (малый диаметр)
— Трансформатор сварочный
Эта схема отличается тем, что два шкива имеют разный диаметр, поэтому контактные поверхности разные, что подразумевает:
1º.- R2
Это означает, что сварной шов внутри более горячий, чем снаружи.
2º.- Кроме того, уже сформированные точки поддерживают определенную более высокую температуру в части, уже сделанной из соединения внахлест, которая в задней части еще не осознает, что будет холоднее.
3º.- Поскольку проволока дольше остается в контакте с внешним электродом, внешняя сварка охлаждается быстрее.
Следовательно, можно сказать, что распределение температуры асимметрично, уменьшаясь от:
— Изнутри наружу
— спереди назад
Исследование показывает, что точка на внутренней стороне сварного шва характеризуется следующими тремя элементами:
— а) След точки
— б) Край кромки листа
— в) Гирлянда из расплавленного металла, выдавленная из сварного шва.
Вертикальный рисунок № 11.
Рисунок № 11: Элементы внутренней поверхности сварного шва
3º.- Последствия:
Поперечное сечение сварного шва показывает, что точка сварного шва образует выступ вперед (самая горячая часть), поскольку:
1º.-Неудовлетворительное распределение температуры приводит к тому, что металл остается в пастообразном состоянии между двумя последовательными точками сварного шва, этот металл подвергается нагрузке со стороны шкива в момент, когда следующий импульс наносится на сварной шов.
2 .- Этот металл, который толкается, не подвергается давлению ковки и не охлаждается шкивом, поэтому существует риск неоднородности сварного шва.
3º.- Если условия сварки таковы, что соотношение L / C неблагоприятное:
— Липкие точки создаются между самыми горячими точками.
— Увеличить дефицитное распределение энергии.
Следовательно, металл в пастообразном состоянии подвергается нагрузке со стороны шкива, образуя прилипшую, но не сваренную точку.
Anuncios
4º.- Расширение металла, вызванное нагревом, не может происходить по вертикали, а должно происходить горизонтально в области образования гребня. Следовательно, после охлаждения в области сварного шва создается сжатие и зона растяжения, что представляет опасность хрупкости.
См. Рисунок № 12:
Рисунок № 12: Напряжения при сварке после охлаждения
Процесс роликовой шовной сварки резервуаров и установка для контактной сварки роликовых швов для проведения процесса
УРОВЕНЬ ТЕХНИКИ
Изобретение относится к процессу роликовой шовной сварки и к машине для контактной сварки роликовым швом, предназначенной для осуществления этого процесса.
Известно использование машин для сварки роликовых швов, в частности, для сварки топливных баков автомобилей. Два сварочных ролика, верхний и нижний, каждый из которых питается проволочным электродом, повторяют контур наложенных друг на друга сварных фланцев половин резервуара, причем эти фланцы были соединены прихватками перед сваркой. В частности, для сварки резервуаров, приварные фланцы которых лежат в одной плоскости, на практике обычно предусматривают стол для заготовок, чтобы удерживать прикрепленный контейнер, причем этот стол имеет контур, т.е.грамм. внешний контур, соответствующий контуру свариваемого резервуара. Затем стол для заготовок перемещается по его контуру, в результате чего сварочный фланец бака, прикрепленный к столу, перемещается между сварочными роликами, которые установлены в фиксированном положении на машине. Этот способ перемещения резервуара с приводом стола известным способом с помощью зубьев шестерни на внешнем контуре стола, с которыми зацепляется ведущая шестерня, и с помощью ведомого рычага (называемого пантографом), зацепляющегося со столом для сохранения касательности. контура к направлению сварки, обеспечил эффективную технику сварки резервуаров с ровным приварным фланцем.
Производители транспортных средств требуют все более сложных форм резервуаров, при изготовлении которых используются неровные соединительные поверхности резервуаров, то есть неровные приварные фланцы. Для сварки резервуаров такой формы технические разработки до сих пор были сосредоточены на соответствующем манипулировании резервуаром, при этом сварочный фланец по-прежнему проходит мимо сварочных роликов, установленных в фиксированном положении. В частности, для управления резервуаром был предложен стол для заготовок, который позволяет наклонять резервуар вокруг оси наклона (японская полезная модель 4-470).Кроме того, предлагалось управлять танком с помощью промышленного робота (DE-A 3603919). Было обнаружено, что при таком способе сварки точное следование пути сварки, заданное с очень жесткими допусками, часто невозможно. Трехмерным движением танка сложно управлять, особенно в случае больших и тяжелых танков. Скорость сварки, которая для эффективного производства резервуаров должна быть как можно более высокой, может быть снижена.
Таким образом, задачей изобретения является создание способа для роликовой шовной сварки резервуаров сложной формы, в которых приварной фланец не лежит в одной плоскости.Это должно позволить максимально простым способом достичь точно выровненного сварочного пути и высокой скорости сварки.
Целью изобретения также является создание машины для контактной сварки роликовым швом, с помощью которой может осуществляться процесс. Эта машина должна позволять отслеживать путь сварки максимально простым и в то же время чрезвычайно точным способом, обеспечивать высокую скорость сварки и позволять сваривать фланцы, которые повторяют трехмерный профиль, при сварке высокая скорость сварки даже на больших и тяжелых резервуарах.
СУЩНОСТЬ ИЗОБРЕТЕНИЯ
Настоящее изобретение относится к способу и устройству для сварки роликовым швом контейнера, в частности топливного бака транспортного средства, в котором приварной фланец не лежит в одной плоскости, а движения, выполняемые посредством резервуар во время сварки целиком находится в одной плоскости движения. Предусмотрен стол с управляемыми контурами для удержания резервуара, а рычаг, приводимый как минимум в двух осях, перемещает стол. При сварке неровных или неплоскостных участков приварного фланца оси сварочных роликов смещаются как единое целое по отношению к плоскости движения резервуара, так что сварочные ролики следуют профилю приварного фланца. .
Было обнаружено, что путем разделения манипуляций с резервуаром в соответствии с изобретением, назначения движения в плоскости держателю резервуара и назначения третьего измерения движению сварочных роликов можно добиться совмещения сварного шва и сварного шва превосходного качества. получается даже в приварном фланце со сложным трехмерным профилем. Более того, манипулирование резервуаром несложно, так как оно происходит полностью внутри самолета; и это верно даже для больших и тяжелых танков.Однако движением сварочных роликов можно точно управлять, поскольку все параметры известны и не зависят от размера или веса резервуара.
КРАТКОЕ ОПИСАНИЕ ЧЕРТЕЖЕЙ
Варианты осуществления изобретения теперь будут объяснены в качестве примеров со ссылкой на единственный чертеж, показывающий схематический вид в перспективе машины согласно изобретению.
ОПИСАНИЕ ПРЕДПОЧТИТЕЛЬНЫХ ВАРИАНТОВ ОСУЩЕСТВЛЕНИЯ
Аппарат 1 для контактной сварки сопротивлением роликовых швов, показанный на чертеже, имеет стол 2 для заготовок.Стол заготовки 2 снабжен зубьями 7 шестерни по внешнему контуру. Внешний контур стола заготовки соответствует проекции необходимого пути сварки на приварной фланец 6 свариваемого бака 3 транспортного средства, который установлен на столе заготовки. Стол 2 перемещается ведущей шестерней 4, которая входит в зацепление с зубьями шестерни 7. Контр-ролик 5 удерживает шестерню в надежном зацеплении, когда стол 2 для заготовок находится в движении. Ось шестерни 4 определяет первую ось U движения резервуара.
Стол для заготовок также соединен с рычагом 16, который будет называться пантографом. Пантограф снабжен первым приводом 20, например. винтовой шпиндельный привод. С помощью этого привода 20 пантограф вместе со столом 2 для заготовок перемещается таким образом, что сохраняется касательность контура к направлению сварки. Пантограф с приводом устанавливает вторую ось V. Возможные движения стола для заготовок, которые были описаны до сих пор, с осями U и V, придают резервуару возможность перемещения в плоскости.Фланец 6 резервуара 3 расположен для сварки между сварочными роликами 10 и 11, на каждый из которых подается проволочный электрод 12. Каждый из сварочных роликов вращается вокруг своей центральной оси, и резервуар 3 приводится в движение в описанным выше способом, так что сварочные ролики 10 и 11 движутся по заданной траектории сварки на приварном фланце 6.
На машине 1, показанной на чертеже, сварочные ролики установлены на головке 14, которая может быть расположена вертикально. пройдено вверх или вниз.Это позволяет паре сварочных роликов следовать неровному профилю фланца, то есть поднимающемуся или опускающемуся. Для этого головка 14 может перемещаться вертикально вдоль оси Z с помощью приводного механизма. Как будет объяснено ниже, привод по оси Z управляется числовым программным управлением.
В примере, показанном на чертеже, станок снабжен дополнительной осью B, вокруг которой можно наклонять головку 14. Это наклонное действие позволяет удерживать точку сварки на сварочных роликах в том же месте, когда головка 14 перемещается в направлении Z, как и при сварке ровной части приварного фланца 6.Указанное движение резервуара 3 в плоскости в сочетании с устройством вертикального перемещения и, предпочтительно, устройством наклона B головки позволяет без проблем сваривать трехмерные профили фланцев. Маневренность головки 14 со сварочными роликами позволяет точно следовать контуру сварочного фланца, когда он поднимается или опускается. Это дает уже описанные преимущества.
Пантограф 16 разделен на две части 17 и 18.Секция 18 шарнирно прикреплена к секции 17 посредством шарнира 19 и снабжена независимым приводом 21. Эта секция пантографа с приводом устанавливает дополнительную ось, ось W, машины. Этот дополнительный привод обеспечивает сохранение касательной в тех ситуациях, когда возникает неопределенность. Это тот случай, когда пантограф находится в выдвинутом положении. Привод 21 может также иметь форму привода винтового шпинделя. До настоящего времени не было известной практики приводить в движение ось W пантографа, когда стол 2 уже перемещается управляемым образом с помощью оси U.Однако такой комбинированный привод оказался очень выгодным для реализации оптимальной точности слежения за сваркой. Для сварки резервуаров очень важна точность слежения (а также точность скорости), поскольку возрастает потребность в сварке резервуаров очень сложной формы, а также из-за того, что сварочный фланец относительно узкий. Поскольку во время сварки возникают поперечные силы, поддерживать точность отслеживания непросто, но это достигается с помощью приводов U, V, W, которые были проиллюстрированы.В результате получается замкнутая кинематическая цепочка. Предпочтительно, как показано на чертеже, привод оси W также расположен сзади пантографа и прикреплен к машине и действует на переднюю часть 18 пантографа через параллелограммную связь. Это обеспечивает точный привод с низкой инерцией.
Управление машиной осуществляется с помощью числового программного управления. Управление движением стола 2 известно из существующих машин, работающих только в плоскости. Кроме того, теперь блок управления должен взять на себя управление головкой 14.Головку 14 необходимо перемещать и, при необходимости, наклонять, чтобы приваренные ролики смещались в соответствии с требуемым подъемом или опусканием приварного фланца 6. Наклон головки 14 происходит в зависимости от требуемого градиента подъема. или падение фланца 6 так, чтобы зона сварки между роликами оставалась в одной и той же точке, независимо от вертикального движения головки 14. Эти дополнительные функции управления могут обычно выполняться с помощью обычного числового управления того типа, который уже используется использовать на аналогичных сварочных аппаратах.
Патенты и заявки на патенты на роликовые электроды (класс 219/81)
Номер патента: 5676862
Реферат: Сварщик сопротивлением сваривает, горячее обжатие, закаливание и шлифовку металлических заготовок внахлест. Сварщик включает в себя два трансформатора (50, 60), которые подключены к двум комплектам колесных электродов (26, 28 и 36, 38).Электрический ток от первого трансформатора (50) проходит через детали (16) и возвращается через второй трансформатор (60). Первый набор колесных электродов (26, 28) создает сварное соединение, а второй набор (36, 38), в зависимости от формы, площади и давления колес, либо уменьшает толщину сварного шва, смягчает сварное соединение, либо оба. Схема управления (72) включает датчик тока (70) и регулятор коэффициента мощности (80). Датчик тока определяет ток, протекающий через первый трансформатор во время процесса сварки.При изменении тока, особенно когда наборы колесных электродов входят в зацепление и расцепление деталей, регулятор коэффициента мощности (72) регулирует коэффициент мощности, чтобы поддерживать постоянный нагрев деталей.
Тип: Грант
Подано: 27 сентября 1996 г.
Дата патента: 14 октября 1997 г.
Цессионарий: Корпорация Тейлор Уинфилд
Изобретатель: Роберт П.Matteson
Преимущества роликов для сварки и формовки нитрида кремния
Шовная сварка — один из наиболее распространенных способов соединения стыковых поверхностей незавершенных цилиндрических профилей (труб, трубок и т. Д.). В нем используется принцип, аналогичный стандартной точечной сварке, для получения прочного продольного шва по всей длине трубчатой заготовки. Процесс обычно автоматизирован, чтобы обеспечить однородное твердотельное соединение, а точность гарантируется благодаря использованию сварочных и формовочных роликов.
Сварочные ролики или прижимные ролики являются неотъемлемыми компонентами типичных систем высокочастотной контактной сварки сопротивлением (HF-ERW). Они выполняют двойную функцию: прикладывают давление и перемещают заготовку через сварочный аппарат. Ролики из кованой стали широко используются при сварке продольным швом, несмотря на их сравнительно низкие характеристики и срок службы по сравнению с технической керамикой, такой как нитрид кремния (Si 3 N 4 ).
В этом сообщении в блоге International Syalons более подробно исследует принципы работы и преимущества сварочных роликов из нитрида кремния.
Описание сварочных роликов
Электрическая контактная сварка (ERW) включает в себя ряд методов соединения, при которых стыковые поверхности нагреваются до точки плавления за счет электрического сопротивления. Это выполняется с помощью сварочной головки, которая прикладывает как постоянное давление, так и постоянный электрический ток, создавая трение и используя температурный коэффициент материала. При продольной сварке электрический ток обычно подается с помощью набора медных электродов, в то время как давление прикладывается рядом сварочных роликов.
Трубы из алюминия, латуни и нержавеющей стали обычно изготавливаются из горячекатаного листа, который обрезан и сформирован в отдельные цилиндрические профили с прилегающими поверхностями в одной плоскости. Этот профиль подается на конвейер сварочного аппарата HF-ERW, где он сжимается сварочными роликами и транспортируется с хирургической точностью через рабочую катушку или под контактные электроды сварочного аппарата. Это обеспечивает сверхточную точку сварки по всей длине профиля.
Сварные ролики Syalon 101
Проблемы, стоящие перед сварочными роликами
Этот высокотемпературный процесс является механически интенсивным, для него требуются чрезвычайно прочные и износостойкие материалы, которые могут выдерживать сильный термический удар.Хотя сварочные ролики из нержавеющей стали обеспечат значительное повышение точности, они выйдут из строя из-за термического и механического разрушения намного быстрее, чем нитрид кремния. Электропроводность сварочных роликов из нержавеющей стали также может быть проблематичной, вызывая проблемы захвата материала, которые являются обычным явлением при соединении цветных металлов.
Сварочные ролики из нитрида кремния значительно превосходят по характеристикам стальные альтернативы, обладая значительно улучшенной стойкостью к термическому удару и прочностью, несмотря на непроводимость материала.Syalon 101 — это запатентованный нитрид кремния от International Syalons, обладающий прочностью на сжатие до 3500 МПа и термостойкостью Δ900 ° C. Это превышает требования к шовной сварке, обеспечивая ряд преимуществ по сравнению с обычными сварочными роликами, включая лучшее качество продукции, меньшее количество отказов сварных швов, меньшие требования к техническому обслуживанию роликов и меньшее время охлаждения. Впоследствии сварочные ролики из нитрида кремния могут снизить мощность HF-ERW до 30% и могут превзойти стальные компоненты в 12 раз.
Процесс формирования трубы — Изображение предоставлено: Shutterstock
Сварочные ролики из нитрида кремния от International Syalons
International Syalons специализируется на производстве продуктов из нитрида кремния для тяжелых промышленных применений, предлагая решения с добавленной стоимостью для сложных и непрерывных процессов. Если вам нужна дополнительная информация о свойствах Syalon 101 или общие вопросы о нитриде кремния в промышленных помещениях, просто свяжитесь с одним из членов команды International Syalons сегодня.
СвязанныеСварка сопротивлением — обзор
10.5.3 Термокомпрессионное соединение (TCB)
Сварка сопротивлением — это метод, используемый для соединения двух плоских металлических заготовок друг с другом путем пропускания через них электрического тока. Необходимое сварочное тепло создается за счет электрического сопротивления металлов, контактного сопротивления между ними и электрического тока. Никакого присадочного металла и флюса не требуется. TCB — это особый вид контактной сварки, который можно использовать для соединения изолированных металлических поверхностей.Электрод TCB состоит из двух ножек, соединенных между собой кончиком. Таким образом, электрический ток проходит только через электрод и выделяет сварочное тепло непосредственно на наконечнике. Вырабатываемое тепло мгновенно разрушает любые изоляционные слои металлов.
В отличие от контактной сварки, когда электрический ток выделяет тепло точно в месте сварки, тепло, генерируемое TCB, должно течь от кончика электрода к месту сварки на границе раздела двух металлов.В результате к верху двух металлов передается больше тепла, чем к низу. Это, наряду с необходимой температурой плавления, ограничивает выбор соединяемых металлов. Поэтому технологический интервал для TCB меньше, чем для контактной сварки. Обзор некоторых комбинаций металлов дан в AVIO (2011).
TCB имеет три основных параметра процесса: мощность сварки (P), время сварки (T) и давление наконечника (P). Эти параметры обычно сохраняются в пределах заданного окна для обеспечения качества.Стандартное сварочное оборудование управляет процессом с помощью регулируемого импульса тока (I), напряжения (V) или мощности (P). Режим управления зависит от конфигурации материала, и важно различать диффузионную сварку и сварку плавлением. Диффузионное связывание (твердотельное соединение) происходит при температурах плавления от 70 до 80% металлов обрабатываемой детали. Такие связки обладают очень хорошей прочностью на сдвиг и разрывом, но менее желательной прочностью на отслаивание. Сварка плавлением происходит выше точек плавления деталей.Эти связки обладают очень хорошей прочностью на сдвиг, разрывной вязкостью и прочностью на отслаивание (Zhou, 2008).
На рисунке 10.5 схематично показан процесс TCB. Электрод помещают с определенным давлением на заготовки; в этом примере на медную площадку прижимается проволока. Затем сварной шов отпускается с тщательно контролируемой формой импульса, определенной энергией и временем. Твердая рабочая поверхность имеет решающее значение для качественной сварки. Прочность сварного шва можно достоверно проверить только путем разрушения сварного шва, например, с помощью испытания на отслаивание.Сварочный шов создается в течение от нескольких миллисекунд до нескольких секунд, в зависимости от размеров и материалов двух заготовок. Сварка сопротивлением и термокомпрессионная сварка обычно используются для электрических катушек, электродвигателей и лампочек. Полный цикл сварки занимает от 3 до 10 секунд при автоматической настройке процесса. Крупные компании, которые в настоящее время производят блоки управления сваркой, сварочные головки и электроды, включают Miyachi, Avio, Kombitec, Lingl и Resistronic. На рисунке 10.6 показано место сварки проволоки на поверхности печатной платы.Форму сварочного электрода можно четко определить. Сама проволока непосредственно вплетается в ткань ПЭТ, а ткань ПЭТ и изоляция провода вокруг нее плавятся и испаряются во время процесса сварки, тем самым приваривая провод к печатной плате.
10.5. (а, б) Процесс сварки УТС.
10.6. Приварите тканую проволоку к печатной плате (Sefar AG).
Приводы ServoWeld от Tolomatic для автомобильной точечной сварки сопротивлением
Новые приводы ServoWeld от Tolomatic модернизированы для повышения производительности и имеют меньший вес по сравнению с другими винтовыми технологиями.Приводы ServoWeld с роликовыми винтами, разработанными и изготовленными Tolomatic, созданы специально для контактной точечной сварки (RSW) в автомобильной промышленности. По словам Tolomatic, приводы ServoWeld обеспечивают 20 миллионов сварных швов или больше, что намного дольше, чем у конкурирующих технологий, таких как шарико-винтовые передачи и приводы с перевернутым роликом.
Привод ServoWeld Advanced (SWA) основан на самой современной технологии роликового винта, которая обеспечивает максимальное количество сварных швов.Привод ServoWeld Base (SWB) построен на альтернативной конструкции роликового винта, чтобы обеспечить более длительный срок службы, чем у обычных шарико-винтовых и перевернутых роликовинтовых передач, но по более экономичной цене, чем привод SWA.
Модели SWA и SWB ServoWeld доступны в двух размерах: меньший размер 3 для облегченных графиков сварки и размер 4 для тяжелых условий эксплуатации. Оба размера доступны с различными шагами резьбы винтовых роликов (5 мм и 10 мм), напряжениями двигателя (230 В переменного тока и 460 В переменного тока) и множеством вариантов для концов стержней, обратной связи и разъемов, а также водяного охлаждения.Эти модели могут создавать силы привода на штоке до 4000 фунтов силы / 17,8 кН, выдерживая более 20 миллионов сварных швов и сохраняя повторяемость усилия +/- 3% в течение всего срока службы привода. Каждая модель в стандартной комплектации оснащена отверстием для повторной смазки, что позволяет легко обслуживать привод без демонтажа из сварочного пистолета, что продлевает срок его службы.
Компания Tolomatic имеет большой опыт работы в автомобильной промышленности точечной сварки сопротивлением и ее предшественник — привод GSWA ServoWeld. Благодаря этому опыту приводы ServoWeld SWA и SWB имеют файлы двигателей для бесшовной интеграции роботов со всеми основными поставщиками, включая ABB, Comau, Fanuc, Kawasaki, Kuka, Motoman, Nachi и многими другими.
Для получения дополнительной информации посетите www.tolomatic.com.
Инновационная машина для роликовой точечной сварки For Welding Efficacy
Повысьте производительность ваших сварочных процессов, используя безупречность. Аппарат для роликовой точечной сварки доступен на сайте Alibaba.com. Эти. Аппараты для роликовой точечной сварки представлены в широком ассортименте, включающем множество моделей, форм и размеров. Соответственно, покупатели из разных слоев общества всегда найдут для себя наиболее подходящий. роликовый точечный сварочный аппарат применим к своим ситуациям на объекте.
Изучая сайт Alibaba.com, вы наверняка столкнетесь с ним. Роликовый точечный сварочный аппарат , изготовленный из прочных и инновационных материалов. Это делает их очень надежными и способными служить пользователям в течение долгого срока службы. Файл. Роликовый точечный сварочный аппарат основан на передовых технологиях, которые делают его чрезвычайно энергоэффективным. Они потребляют незначительное количество электроэнергии, что гарантирует, что вы меньше тратите на свои счета за электроэнергию.Простота установки и использования. Аппарат для роликовой точечной сварки делает их идеальным выбором для всех.
The. Аппарат для роликовой точечной сварки Производители внедрили удивительные средства безопасности, чтобы защитить операторов от сильной жары и света.