с древних времен и до современности
Можно с уверенностью сказать, что сварка на сегодняшний день — это одна из основ развития человечества. И это не голословное утверждение. Именно благодаря этому процессу люди имеют возможность возводить небоскребы, прокладывать инженерные коммуникации, развивать промышленность и науку. И конечно же возникает закономерный вопрос: а когда появилась сварка? Когда люди научились соединять между собой тугоплавкие материалы? Может, 50-100 лет назад? Или это одно из новейших открытий человечества? Постараемся разобраться в этом вопросе и рассмотреть, какая история развития сварки.
Древние времена и Средневековье
Способ получения цельных металлических конструкций путем сварки и пайки пришел к нам с глубокой древности. Доказательством этому служат золотые украшения с оловянной пайкой, которые были найдены во время раскопок в египетских пирамидах и свинцовые водопроводные трубы с поперечным паянным швом, которые были найдены во время раскопок в итальянском городе Помпеи.
Технологический процесс сварки развивался и в Средние века. Примером этому служит огромная пушка Дол Грайет, созданная в 1382 году. Пушка представляла собой кованную трубу, которая была усилена наружными металлическими обручами, присоединенными к ней с помощью кузнечной сварки. Такой способ изготовления артиллерийских орудий применялся во всем мире. Самые большие экземпляры таких пушек были изготовлены в XVI веке в Индии. Вес орудий был более 50 тонн, а общая длина — более 9 метров.
Большинство древних строений предусматривали наличие мощной несущей конструкции из камня, а в качестве балок и перекладин использовались деревянные брусья. Однако в некоторых случаях при создании особо крупных конструкций были необходимы узлы, которые работали на растяжение. Для их создания использовались металлические анкера, изготовленные путем кузнечной сварки или ковки.
Индустриализация и появление сварочных электродов
Благодаря быстрым темпам развития научного и технического прогресса, многие элементы сооружений, которые ранее изготавливались из камня и дерева, были заменены металлом. Преобладающим материалом все так же являлось железо или более крепкие сплавы на его основе — стали.
Большинство сварочных процессов и технологий были разработаны в начале ХХ века, хотя уже в XIX веке они использовались в единичных случаях. Например, в 1802 году профессор медико-хирургической академии в Санкт-Петербурге Василий Владимирович Петров открыл явление дугового разряда. В ходе дальнейших исследований профессором была доказана возможность использования дугового разряда для плавления и освещения металлов.
Изначально при применении электрической дуговой сварки не использовались расходные сварочные материалы, а применялся неплавящийся угольный электрод. Впервые сварка с использованием такого электрода была применена в 1881 году, а уже в 1888 году российский ученый Н. Г. Славянов заменил его металлическим электродом. Однако постоянную температуру горения дуги было очень сложно поддерживать, к тому же процесс сварки сопровождался образованием пористых поверхностей и неровностей на металлических конструкциях.
Первые флюсы были изготовлены в 1902 году. Металлические стержни электродов опускались в пасту, которая состояла из окисей металлов и карбонатов, смешанных с водой. Такое покрытие высыхало при обычной температуре (20-40 градусов), после чего электрод был готов к использованию. Несмотря на то, что по современным стандартам применение такого флюса считается достаточно примитивным, такое покрытие электродов обеспечивало стабилизацию электрической дуги и обеспечивало газовую защиту.
Новое время и развитие современных видов сварки
Развитие истории сварки особо активно продолжалось в ХХ столетии. Большинство изобретений в данной сфере, которые были придуманы и разработаны ещё в начале века, используются и по сей день. Единственная разница «наших» сварочных аппаратов от аппаратов прошлого столетия — это технологический уровень. Принцип работы остался точно таким же.
В 1903 году французскими учеными Эдмоном Фуше и Шарлем Пикаром была сконструирована первая ацетиленокислородная сварочная горелка. Конструкция, которая была предложена ими, принципиально не изменилась до наших дней. В 1906 году появились первые надежные ацетиленовые генераторы, после чего началось промышленное использование данного вида сварки для создания газопроводов, технологического оборудования и других конструкций.
В 1912 году было создано толстое электродное покрытие, которое представляло собой обертку из синего асбеста. Электроды с толстым покрытием, которые были пропитаны жидким стеклом, нашли свое применение в военной промышленности и кораблестроении. Толстое флюсовое покрытие использовалось благодаря тому, что оно не только обеспечивало защиту от загрязнения, но и стабилизировало горение электрической дуги благодаря ионизируемым компонентам. Благодаря этому стало возможно создавать сварочные швы без дефектов, а плотность шва впервые стала такой же, как и плотность самого металла.
В 1940 году был впервые применен вольфрамовый электрод, электрическая дуга которого поддерживалась в гелии. Инертный газ обеспечивал самый высокий уровень стабилизации дуги и защиты от загрязнения. В связи с потребностью более чистых инертных газов для сварки реактивных металлов и алюминиевых конструкций в 1946 году стал использоваться аргон, который зарекомендовал себя как наиболее чистый и безопасный для работы инертный газ.
В 1960 году была разработана новая технология сварки, которая предусматривала использование нескольких электродов. Технология заключалась в следующем: две или более сварочные проволоки под флюсом подаются в одну сварочную ванну, причем они могут использоваться как в качестве присадки, так и находится под напряжением. Данный технологический процесс позволяет существенно увеличить скорость плавления металла и улучшить эксплуатационную гибкость.
60-е годы ХХ столетия отметились наибольшим количеством новейших разработок в области процесса сварки. Именно тогда впервые были изобретены, а впоследствии распространились по всему миру процесс сварки металлов с помощью порошкового электрода в инертном газе и без него, электрогазосварка и так далее.
В конце 70-х и начале 80-х годов началась разработка газолазерной резки. На тот момент она считалась наиболее перспективной среди всех существующих способов резки металла.
История сварки по нашему мнению будет писаться ещё очень долго.
Как и когда появилась сварка, и как она развивалась
Некоторые открытия человечества были настолько полезными, что используются до сих пор.
Познавательная информация
В Ирландии сегодня хранятся маленькие короба из золота, созданные сваркой давлением. Она не предполагала нагрева материала, и изделия изготавливались путем пластичной деформации при обычной температуре. Они созданы около двух тысяч лет назад. В железном веке научились сваривать металлические куски. Изготовленные таким способом приспособления датированы примерно 1000 годом до нашей эры.
В Средние века появилось кузнечное искусство. В эту пору некоторые детали стали свариваться ковкой.
Ацетилен открыл Эдмунд Дэвисон, а первым дуговой разряд между угольными стержнями описал химик Гемфри Дэви в начале XIX века. Для этого он использовал изделия, подключенные к полюсам электробатареи, сложенной из двух тысяч гальванических деталей. Середина XIX века — эпоха появления электрогенератора.
В 1881 году во Франции тепло электродуги было впервые применено для сплава свинцовых пластин аккумуляторов. Открытие принадлежит российскому инженеру Николаю Бернадосу, который также разработал первый электродержатель.
Сварка посредством графитового стержня по сути была примитивной, однако тогда ее использовали для соединения свинцовых и железных изделий. В конце XIX века этот способ был востребованным. В 1890 году представлен металлоперенос (расплавление стального стержня под действием тока с последующей кристаллизацией) через дугу.
В 1900 году в Великобритании был создан первый электрод из стали, который тонко покрывали известь и глина, способствующие стабилизации дуги. В это же время была изобретена контактная сварка. Сегодня же вы можете легко приобрести у нас сварочный инвертор по выгодной цене.
Сварка, к которой мы так привыкли, имеет длинную историю. Конечно, сейчас, в пик развития технологий, мы получаем удобные и миниатюрный аппарат. А вот история еще помнит, громоздкие самодельные сварочные аппараты. Самая первая электрическая дуга, которая в дальнейшем использовалась в сварочных работах, была открыта более чем 200 лет назад, но еще 80 лет после открытия она не применялась. А вот с 1881 года начали очень активно проводить опыты со сваркой с использованием электрической дуги. Что забавно, опыты проводили двое незнакомых людей и делали это одновременно, как говорится: «Мысли гениев сходятся». Бернандос и Славянский — стали основоположниками современной сварки. Не смотря на то, что дуга появилась в 18 веке, сварочный аппарат, который напоминает привычный для нас, появился через 100 лет. В 1905 году. Русский ученый – электротехник В. Миткевич путем опытов пришел к тому, что электрическая дуга возбуждается от трехфазного тока. Но прийти к той сварке, которая для нас стала родной, как не странно, помогла война. В годы холодной войны США и СССР соревновались не только в транспорте и оружие, но и в сварочных аппаратах. На первый взгляд, это кажется глупостью, какая сварка, когда самолеты строят, но все же. Если задуматься для строительства любой, даже самой простой военной техники нужны сваривальные работы. Благодаря этому соревнование мы в результате имеем Вращатель сварочный М31050А и плазменную сварку. Развитие сварочных аппаратов и всех аксессуаров для этого процессов, сейчас находится на небывалой высоте, но идеалу нет предела. До сих пор сварка постоянно развивается и улучшает свои характеристики. Ведь нужды людей растут неимоверно. Еще вчера, было достаточно приварить два куска металла, а уже сегодня душа зовет покорять космические пространства. Для звездолетов обычные сварочные аппараты не подходят. Пока что мы даже представить не можем, каким станет сварочный аппарат через 50 лет, но известно, что будет развиваться он всегда, ведь человеческие желания безграничны. |
Контроль и регулировка импульсной сварочной дуги с LORCH ХТ: самый высокий уровень сварки
Контроль и регулировка импульсной сварочной дуги с LORCH ХТ: самый высокий уровень сварки
02 мая 2016 г.
В 2016 году LORCH обрадовал разработкой и внедрением новых возможностей в регулировке сварочной дуги, а именно ее длины и динамики в импульсных сварочных полуавтоматах Lorch S и Lorch S SpeedPulse — функция ХТ. Данный процесс был создан и запатентован исключительно LORCH, что ставит данного производителя на ступень выше среди конкурентов и аналогов. Благодаря внедрению новой технологии ХТ, сварочный процесс становится еще более стабильным, а сварка совершеннее.
ХТ — это EXTRA надежность EXTRA вариативность EXTRA малое образование брызг!
Как сварщик регулирует процесс сварки? Ранее вся регулировка сварочного процесса сводилась к изменению напряжения и скорости подачи проволоки. Регулировкой напряжения мы увеличиваем или уменьшаем длину сварочной дуги, что в конечном итоге сказывается на сварочной ванне: либо она широкая, либо более узкая. Размер ванны влияет также на провар изделия. Если ванна узкая, то сварочная дуга более сконцентрированная и провар получается более глубоким. Если сварочная ванна шире, то необходимо затратить больше энергии на то, чтобы расплавить как основной, так и присадочный металл. Ведь если ванна широкая нам нужно больше проволоки для того, чтобы заполнить ее металлом. Сам сварочный шов при этом выглядит более широким. Если сварщику, например, нужно больше наплавить металла, получить определенный катет, то он увеличивает скорость подачи проволоки. Регулируя подачу проволоки сварщик меняет количество подаваемого присадочного металла и сварочный шов получается в итоге более бугристым, либо напротив более вогнутым.
В основном сварщики любят варить на короткой дуге, поскольку сварка на длинной очень нестабильна, кроме того она ведет к большому каплеобразованию. А это затраты денег и времени на дальнейшую доработку сварочного шва.
С приходом синергетического управления, процесс сварки стал проще. Например, в сварочных полуавтоматах LORCH для настройки сварщику необходимо только выбрать металл, диаметр проволоки и используемый защитный газ. Далее выбирается толщина свариваемого металла, а все остальные параметры, в том числе напряжение и скорость подачи проволоки, выставляется аппаратом самостоятельно. В процессе сварки вручную сварщик лишь корректирует скорость подачи проволоки. Однако для идеальной сварки этого оказалось недостаточно…
Как получить идеальную импульсную дугу?
Как показала практика, для формирования качественной импульсной дуги необходимы 3 составляющих:
- Регулировка длины сварочной дуги
- Регулировка динамики сварочной дуги
- Компенсация внешних воздействий
Причем компенсация внешнего влияния должна происходить в автоматическом режиме, т. к. ручная регулировка сильно тормозит процесс сварки. Раньше сварщики, увеличивая/уменьшая длину сварочной дуги косвенно влияли на размер сварочной ванны, делая ее шире или уже. С 2016 года, в линейке импульсных сварочных полуавтоматов LORCH S SpeedPulse появилась возможность корректировки не только длины, но и динамики сварочной дуги. Динамика позволяет делать ванну шире/уже независимо от длины дуги. Длина дуги остается неизменной. Т.е. теперь, можно варить на короткой дуге и при этом делать ванну того размера, который нужен сварщику для комфортной работы. Однако LORCH на этом не остановился, ведь мало дать сварщику возможность регулировать сварочные параметры. Необходимо сделать их независимыми от сварщика, выставляемыми автоматически и при этом, независимо от внешних условий.
Как известно, на процесс сварки большое влияние оказывает воздействие внешних факторов (падение напряжение в сети, качество газа, включения в металле, наличие прихваток и т.п.). Самый распространенный пример: сварка по прихваткам. В месте прихватки, как правило, сварка становится крайне не стабильной и данное место становится изъяном сварочного шва — при проходе прихваток образуется много капель. Что сделал LORCH? Немецкий производитель профессионального сварочного оборудования LORCH внес принципиальное изменение в природу самого сварочного импульса.
Новый импульс вместе с ХТ
Стандартный импульс представляет собой чередование «пауза/импульс/пауза/импульс» (так называемая I-I регулировка). Это делает перенос металла контролируемым, но более медленным в сравнении со стандартной сваркой. LORCH внедрил специальны сварочный процесс SpeedPuls, который позволил увеличить скорость стандартной импульсной сварки практически вдвое.
Основной специфической характеристикой, отличающей SpeedPuls от традиционных импульсных процессов – за направляющей каплей следует вторичный переход металла — результатом является более быстрый перенос металла. В процессе данной сварки импульс стал выглядеть иначе: «пауза/импульс с резким изменением тока/пауза/импульс с резким изменением тока» (I-I-I регулировка). Благодаря контролю 3-й фазы регулировки сварочного тока LORCH усовершенствовал импульсную сварку и сделал ее быстрее стандартной сварки на 48%.
Следующим шагом, реализованным в 2016 году стало новое измемение импульса: регулировка стала правной, что позволило сделать сварку еще более стабильной и избавиться от влияния внешних факторов. Новый вид импульсной сварки получил название ХТ. Благодаря изменению самого импульса, внешне процесс сварки выглядит практически таким же, как SpeedPuls, однако он имеет ряд преимуществ:
- Более высокий уровень наплавка
- Высококонцентрированная дуга (глубокое проплавление, хорошее формирование корня шва, глубокая дуга, без подрезов)
- В результате более высокая скорость сварки как результат нескольких факторов влияния на дугу.
Что дает специальный процесс сварки ХТ?
Для импульсной сварки одним важным факторам воздействия на вводимую энергию является частота импульсов и различные точки регулировки. SpeedPulse XT объединяет все лучшие характеристики, что создает более простую, комфортную, лучшую в управлении“ импульсную сварку с регулировкой напряжения.
Если в SpeedPuls частота импульсов переменная, то в SpeedPuls XT частота импульсов постоянна. Это позволяет получить мгновенную но более мягкую регулировку (реакция происходит в одной и той же фазе импульса). Так LORCH получает собственное пропорциональное регулирование и компенсацию внешних воздействий в автоматическом режиме. Так, XT объединяет в себе лучшее от 2-х типов регулировки. В результате мы получаем:
- Вариативность регулировки – без немедленного вмешательства
- Более интуитивный контроль за дугой
- Хорошая реакция на изменения при сварке в ограниченном пространстве
- Улучшенная сварка зазоров путем изменения вылета электрода
- Активное противодействие отклонениям дуги путем уменьшение длины дуги (уменьшая расстояние горелка — деталь)
- Лучший контроль при сварке в ограниченном пространстве: угловые соединения и тд
Результат
Нагляднее всего новый тип сварки можно увидеть в процессе сварки поверх прихваток. Если раньше проходя прихватку процесс сварки становился в месте прихватки крайне нестабильным, то с ХТ все иначе.
LORCH сделал сварку по прихваткам обсолютно стабильной. Шов не меняет своей равномерности независимо от наличия прихваток на сварочном изделии.С импульсными сварочными полуатвоматами нового поколения LORCH S-SpeedPulse XT вы получаете:
- Стабильность без скачков напряжения/тока
- Малое образование брызг
- Без слышимых изменений частоты
- При SpeedPulse XT – умеренная регулировка длины дуги
- Простой и удобный процесс сварки
- Уменьшение затрат на обработку детали после сварки
Кроме того, возможность регулировки динамики сварочной дуги оказывает влияние на формирование сварочного шва. Например, при сварке нержавеющей стали динамика дуги влияет на профиль проплавления, при более высокой динамике профиль шва более вогнутый, повышая надежность образования хорошего корня шва и сторон шва, даже при неидеальном положении горелки.
Если у вас появились вопросы, будем рады ответить на них по тел.: +7 (3952) 745-542
история появления, эволюция и след Украины
Сегодня в Киеве есть 5 действующих автомобильных мостов, перекинутых через крупнейшую реку страны – Днепр. Строительство одного из них началось в 1940 году и длилось до 1953 года.
На момент возведения это был самый большой в Европе цельносварной мост. Впервые в истории инженерного строительства все его швы были выполнены с помощью автоматической сварки. В проектировании этого чуда инженерии непосредственное участие принимал выдающийся ученый Евгений Патон, именем которого и назвали мост, которым пользуются жители столицы Украины.
Какова роль Патона в мировой эволюции электросварки и что собой представляет сварка металлов?
С незапамятных времен человечество пыталось соединять фрагменты металлических изделий и слитки металлов природного происхождения. Это позволяло увеличить их размеры, создавать предметы сложной формы, а также исправлять дефекты, полученные в процессе литья. Но из-за многих технологических ограничений процесс был несовершенным. На помощь приходила физическая сила и один из немногих известных на тот момент процессов обработки металлов давлением – ковка (холодная и высокотемпературная). Также производилась литейная сварка: погружение деталей, которые нужно соединить, в расплавленный металл. После этого мастера ждали, пока конструкция затвердеет. Такие соединения нельзя было назвать прочными и надежными.
Но сталь все сильнее проникала в разные сферы жизни и экономики, поэтому перед учеными и технологами все чаще возникали теоретические и практические вопросы обработки и соединения металлов.
И в итоге появился новый способ соединения металлических изделий! Что такое сварка металла? В этом процессе детали соединяются между собой посредством межатомных связей в результате нагрева и пластического деформирования.
Когда появилась электросварка металла?
На рубеже XVIII-XIX веков была открыта электрическая дуга, стартовало исследование возможностей ее практического применения. В 1802 году русский физик и электротехник Василий Петров первым выдвинул идею, что высокая температура, которую дает электрическая дуга, может быть использована для расплавления металлов. После этого ученые всего мира, в том числе и такие известные, как британец Майкл Фарадей, проводили различные эксперименты с электрической дугой, которые десятилетиями ограничивались теоретическими изысканиями.
Переход на практический уровень произошел в конце XIX века. В этот же период истории на промышленные рельсы вышло производство стали и чугуна. Все чаще требовалось соединение металлических деталей простым и надежным способом.
В 1881 году в Париже ученый Николай Бернардос продемонстрировал способ сварки с применением угольного электрода. Это был аппарат «ЭлектроГефестЪ», который завоевал золотую медаль на Парижской международной выставке. Примечательно, что Бернардос хоть и имел греческие корни, но родился в селе на территории современной Николаевской области Украины, а учился в Киевском университете.
В 1888 году русский ученый Николай Славянов создал и запатентовал сварочное оборудование, в котором использовались плавящиеся металлические электроды, которые были схожи по характеристикам со свариваемыми металлами. Именно эта технология стала основой для распространения дуговой электросварки по всему миру.
С помощью первого сварочного оборудования удавалось устранять брак, возникавший при литье деталей, восстанавливать изношенные части оборудования. На рубеже веков электросварка становилась все более совершенной. Например, были предложены способы использования электрической дуги, возбуждаемой трехфазным и переменным током. И на этом процесс не останавливался.
В 1906 году швед Оскар Чельберг усовершенствовал изобретение Славянова. Он запатентовал сварочный электрод, который был покрыт флюсом. Это специальный материал, защищающий место сварки от окисления и накопления вредных примесей. Его изобретение дошло до наших дней практически без изменений.
Киев как центр мировой сварки
В 1904 году молодой ученый Евгений Патон, который родился во Франции и закончил Дрезденский технологический университет, получил предложение создать кафедру строительства мостов на базе Киевского политехнического института. В те годы мостостроение было неразрывно связано с металлургией и другими смежными процессами. Поэтому в 1930-х Патон увлекся электросваркой. Со временем кафедра, которую он возглавлял, эволюционировала в Институт электросварки при Академии Наук. Евгений Патон был его руководителем с момента основания в 1934 году и до своей смерти в 1953 г.
Именно киевский институт электросварки стал одним из мировых центров изучения сварки. Сделанные здесь открытия и изобретения нашли практическое применение во многих сферах промышленности и экономики.
Например, во время Второй мировой войны институт внес значительный вклад в обороноспособность СССР, предложив технологию сварки специальных сталей для танковых башен, которые до того были клепаными или цельнолитыми.
Но главным изобретением Евгения Патона стало развитие идей Бенардоса и Чельберга – скоростная автоматическая сварка под флюсом, которая была названа «методом Патона». Для этого были созданы механизированные самоходные аппараты – сварочные тракторы. Они движутся непосредственно по поверхности свариваемых изделий и перемещают электрическую дугу вдоль сварного шва, подают флюс и обеспечивают другие вспомогательные процессы без участия человека. Наиболее активный период развития автоматической сварки пришелся на 1959-1965 гг. Сегодня она используется во многих отраслях промышленности: для сварки листового металла, труб, корпусов техники, бытовых изделий и многого другого.
Сила тока
Важнейшей составляющей электросварки является источник тока. Сначала это были очень громоздкие сварочные генераторы, но по мере распространения процесса возникала потребность в более компактном оборудовании. Заметное уменьшение его габаритов произошло в начале 1940-х годов, когда на верфях и танковых заводах все чаще использовалась сварка, а не клепка деталей.
Это были трансформаторные аппараты или трансформаторы, подключаемые к электросети. После Второй мировой войны они стали доступны в мирных секторах экономики и даже для использования в быту.
Сейчас наиболее популярны инверторные сварочные аппараты. В их основе лежит сложная система преобразования сварочного тока с помощью микросхем и транзисторов. Это прибор скорее похож на компьютер. Он позволяет в одном компактном устройстве совместить несколько видов сварки: от ручной дуговой и до плазменной резки.
Соответственно, современный сварщик – это высококвалифицированный специалист, который должен пройти сложное обучение. По его окончанию можно получить не только диплом, но и сертификат соответствующего образца. Прохождение аттестации дает допуск к таким сложным работам как судоремонт и судостроение, производство котельного и нефтехимического оборудования, тяжелое станкостроение, автомобильная и аэрокосмическая отрасль.
Современность и будущее сварки
Сегодня насчитывается более 150 различных способов сварки. Одна из основных классификаций этого процесса соединения металлов – по форме используемой тепловой энергии, так называемый, «термический класс». Она определяет виды сварки в зависимости от используемой тепловой энергии. Ключевыми разновидностями сварки по данному критерию являются:
- дуговая;
- газовая;
- электронно-лучевая;
- плазменная;
- электрошлаковая;
- лазерная и др.
В электрической дуговой сварке источником дуги является переменный, постоянный или пульсирующий ток, который пропускается между двумя электродами (один из них – это свариваемое изделие). От вида тока зависят сферы применения электросварки и металлы, которые свариваются.
Тепло, которое выделяется из дуги, оплавляет края свариваемого изделия и электрод, что приводит к появлению сварочной ванны. Это небольшой объем жидкого металла, который после затвердевания образует сварное соединение.
Наиболее популярные виды электродуговой сварки:
- ручная дуговая сварка;
- автоматическая сварка под флюсом;
- полуавтоматическая сварка в среде защитных газов.
Сварка плавящимся электродом хорошо автоматизируется и обеспечивает высокую производительность.
Во второй половине ХХ века автоматизация процесса электросварки вышла на очень высокий уровень. Были разработаны специальные роботы, работающие без вмешательства человека. Сегодня без них невозможно представить практически ни один сегмент машиностроения.
В 1969 году электросварка пришла в космонавтику. Это были эксперименты на космическом корабле «Союз-6». Сварочные работы проводились электронным лучом со сжатой дугой низкого давления и плавящимся электродом. В 1984 году при помощи сварочного аппарата «УРИ», созданного в Институте электросварки им. Е.О. Патона, была проведена электронно-лучевая сварка за пределами космического корабля, то есть в открытом космосе.
Эти эксперименты подтвердили эффективность электросварки в условиях вакуума и невесомости. Возможно, именно их результаты станут одним из необходимых условий для колонизации других планет. И американец Илон Маск, который уже планирует экспедиции на Марс, будет восхищаться не только Сергеем Королевым и ракетами «Южмаша», но и сварочными аппаратами, созданными в Киеве последователями династии Патонов.
Дуговая сварка в защитном газе: описание технологии, режимы, способы
Дуговая сварка в защитном газе представляет собой метод, который значительно повышает качество результата работы. Эта технология имеет ряд особенностей. Прежде чем применять ее, мастер должен ознакомиться с основами дуговой сварки, которая проводится в среде защитных газов. Об особенностях этой технологии будет рассказано далее.
Особенности методики
Одним из подвидов дугового соединения металлических изделий, заготовок является дуговая сварка в защитных газах. ГОСТом регламентирован процесс, во время которого в точку плавления подается газ. Это может быт аргон, кислород, азот или прочие разновидности. Существуют определенные особенности подобного процесса.
Каждый сварщик знает, что качество сварного шва зависит не только от умений мастера, а еще и от условий в точке плавления. В идеальном случае здесь должны присутствовать только электрод и присадочные материалы. Если сюда попадают иные элементы, они способны оказать негативное воздействие на сварку. Место спайки будет из-за этого недостаточно прочным.
Технология ручной дуговой сварки в защитном газе появилась еще в 1920 году. Применение подобных субстанций позволяет сделать швы без шлака. Они характеризуются высокой чистотой, не покрываются микротрещинами. Этот метод активно применяется в промышленности при создании разных элементов из металла.
Особые пропорции защитных газов позволяют снять напряжение в зоне расплава. Здесь не возникают поры, что заметно повышает качество спайки. Шов становится прочнее.
В промышленных условиях в ходе сварочных работ применяют стержни, смешанные с аргоном и диоксидом углерода. Благодаря такой комбинации дуга становится постоянной, оберегая зону расплава от сквозняков. Это позволяет соединить тонкие листы металла.
Если же требуется выполнить глубокую проплавку, смешивают углекислый газ и кислород. Этот состав обладает окислительными свойствами, защищает шов от пористости. Существует множество методик, которые предполагают применять разные газы в ходе сварочных работ. Выбор зависит от особенностей проведения этого процесса.
Техника сварки
Существуют разные режимы дуговой сварки в среде защитного газа. Применяется две основные методики. Первая из них предполагает применение плавящихся шпилей. По ним проходит ток, а стержень из-за этого расплавляется, образуя прочный шов. Этот материал обеспечивает прочное соединение.
Вторая методика предполагает проведение дуговой сварки в защитном газе неплавящимся электродом. В этом случае ток также проходит по стержню, но материал соединяется благодаря расплавлению краев металлических деталей, заготовок. Материал электрода не становится частью шва.
В ходе проведения подобных манипуляций применяются разные газы:
- Инертные.
Такие субстанции не имеют запаха и цвета. У атомов присутствует плотная оболочка из электродов. Это обуславливает их инертность. К инертным газам относятся аргон, гелий и т. д.
- Активные. Растворяются в металлической заготовке, вступая с ней в реакцию. К таким средам относятся диоксид углерода, водород, азот и т. д.
- Комбинированные. В ходе определенных процессов нужно применять обе разновидности газов. Поэтому сварка проходит в среде как активных, так и инертных газов.
Чтобы выбрать газовую среду, учитывают состав металла, экономичность самой процедуры, а также свойства спайки. Могут учитываться и прочие нюансы.
В ходе применения инертных газов устойчивость дуги повышается, что позволяет выполнить глубокую расплавку. Подобные вещества подаются в зону расплава несколькими потоками. Если он идет параллельно стержню, это центральный поток. Также есть боковые и концентрические струи. Также газ может подаваться в подвижную насадку, установленную над рабочей средой.
Стоит отметить, что при дуговой сварке, которая происходит в газовой ванне, тепловые параметры приемлемые для производства шва требуемой модели, качества и размера. Выбор режима Чтобы соответствовать требованиям ГОСТ, дуговая сварка в защитных газах может проводиться в разных режимах. Для этого в большинстве случаев требуется применение инверторов полуавтоматического типа. При помощи такой аппаратуры становится возможным регулировать поток электричества, его напряжения.
Инверторные полуавтоматы служат источником питания. Они могут отличаться мощностью, а также опциями. Эксплуатационные качества зависят от модели. Для большинства стандартных операций, в ходе которых не требуется проведение сварки толстых или нечасто используемых сплавов, применяются простые аппараты.
Автоматическая дуговая сварка в среде защитных газов различается массой параметров:
- Радиус проволоки.
- Диаметр проволоки.
- Сила электричества.
- Напряжение.
- Скорость подачи контакта.
- Расход газа.
Существующие полуавтоматические режимы дуговой сварки в защитных газах также разделяют на локальные и общие. В первом случае защитный газ поступает из сопла в зону сварки. Этот вариант применяется чаще. При помощи локальной сварки можно соединить разные материалы, но результат не всегда может быть удовлетворительным.
При использовании локальной подачи газа в зону расплава может попадать воздух. Это снижает качество шва. Чем больше заготовка, которую нужно сварить, тем хуже будет результат при использовании такой методики.
Если нужно сварить крупногабаритные детали, применяются камеры, в которых регулируется атмосфера. Из них откачивается воздух, создается вакуум. Дальше в камеру закачивают нужный по технологии газ. При помощи дистанционного управления производится сварка.
Подготовка к сварке
Чтобы правильно выполнить процедуру соединения металлических заготовок, нужно понимать сущность дуговой сварки в защитном газе. Сварка требует правильной подготовки. Эта процедура всегда одинаковая, независимо от технологии сварки. Сначала кромкам придают правильную геометрию. Это определяется ГОСТом 14771-76.
Механизированная дуговая сварка в защитном газе применяется для полной проварки сплава, что позволяет полностью соединить края заготовки. Зазора между ними не остается. Если же присутствует определенный отступ, разделка краев, проварку можно провести для заготовки, толщина которой не превышает 11 мм.
Для увеличения производительности в процессе автоматической сварки проводится разделка краев заготовок без откосов.
После проведения сварки в углекислом газе потребуется очищать всю плоскость шва от грязи и шлака. Чтобы загрязнение было менее значительным, поверхности обрабатывают особыми составами. Чаще всего это аэрозоли, которые распыляют на металл. Ждать его высыхания не нужно.
В ходе последующей сборки применяются стандартные запчасти, например, клинья, прихватки, скобы и т. д. Конструкция перед началом работы требует тщательного осмотра.
Преимущества и недостатки
Ручная и автоматическая дуговая сварка в защитных газах имеет как преимущества, так и недостатки.
К положительным качествам этого метода относятся:
- Качество шва получается очень высокое. Этого не могут обеспечить иные методики сварки.
- Большинство защитных газов стоит относительно недорого, поэтому процесс сварки не удорожается сильно. Даже дешевые газы обеспечивают качественную защиту.
- Опытный сварщик, который ранее применял иные методики, легко освоит и эту технологию, поэтому поменять специфику маневров сможет даже крупное предприятие с большим количеством сотрудников в штате.
- Процесс универсальный, позволяет сварить как тонкие, так и толстые листы металла.
- Производительность высокая, что положительно сказывается на результатах работы производства.
- Методика применяется не только для сварки черных, но и цветных металлов и сплавов.
- Процесс сварки при использовании газовой защитной ванны легко поддается модернизации. Его можно переделать из ручного в автоматический.
- Процесс сварки можно приспособить ко всем тонкостям производства.
Автоматическая и ручная дуговая сварка в среде защитных газов имеет и определенные недостатки:
- Если сварка производится на открытом участке, нужно обеспечить хорошую герметичность камеры. В противном случае защитные газы могут выветриваться.
- Если же сварка проводится в помещении, здесь обязательно должна быть обустроена качественная система вентиляции.
- Некоторые разновидности газов стоят дорого (например, аргон). Это повышает себестоимость продукции, удорожает весь процесс производства.
Разновидности газов
Дуговая сварка в среде защитных газов производится в разных средах. Они могут быть активными или инертными. К последним относятся такие вещества как Ar, He и прочее. Они не растворяются в железе, не вступают с ним в реакцию.
Инертные газы применяют для сварки алюминия, титана и прочих популярных материалов. Дуговая сварка в защитном газе неплавящимся электродом применяется для стали, которая плохо поддается плавлению.
Активные газы также применяются в ходе проведения подобных работ. Но в этом случае чаще используют дешевые разновидности, например, азот, водород, кислород. Одним из самых популярных веществ, которые применяются в ходе сварки, является двуокись углерода. По цене это самый выгодный вариант.
Особенности газов, чаще всего применяемых в ходе процесса сварки, следующие:
- Аргон не воспламеняется, а также не взрывоопасен. Он обеспечивает качественную защиту сварного шва от неблагоприятных внешних воздействий.
- Гелий поставляется в баллонах с повышенной устойчивостью к давлению, которое здесь достигает 150 атм. Сжижается газ при очень низкой температуре, достигающей -269ºС.
- Двуокись углерода является неядовитым газом, который не имеет запаха и цвета.
Это вещество добывают из дымовых газов. Для этого применяется специальное оборудование.
- Кислород является веществом, которое способствует горению. Его получают при помощи охлаждения из атмосферы.
- Водород при контакте с воздухом становится взрывоопасным. При обращении с таким веществом важно соблюдать все требования безопасности. Газ не обладает цветом и запахом, помогает процессам воспламенения.
Особенности сварки в углекислоте, азоте
Дуговая сварка в защитном газе плавящимся электродом проводится при использовании углекислоты. Это самая дешевая методика, которая сегодня пользуется большим спросом. Под воздействием сильного нагрева в зоне плавления СО₂ превращается в СО и О. Чтобы уберечь поверхность от окислительной реакции, в проволоке присутствуют кремний и марганец.
Это также приводит к некоторым неудобствам. Кремний и марганец вступают между собой в реакцию, образуя шлак. Он проступает на поверхности шва, требуя устранения. Это выполнить несложно. На качество сварного шва это обстоятельство никакого воздействия не имеет.
Перед началом работы из баллона удаляют воду, для чего его переворачивают. Это нужно делать с определенной периодичностью. Если не выполнить такую манипуляцию, шов станет пористым. Его прочностные качества будут невысокими.
Дуговая сварка в защитном газе может выполняться при помощи азота. Эта технология применяется для спайки медных заготовок или деталей из нержавейки. С этими сплавами азот не вступает в химическую реакцию. В ходе проведения сварки применяются графитовые или угольные электроды. Если применять для этих целей вольфрамовые контакты, это вызывает их перерасход.
Важно правильно настраивать оборудование. Это зависит от сложности сварки, типа материала и прочих условий. Чаще всего применяется оборудование с напряжением 150-500 А. Оно создает дугу 22-30 В, а расход газа при этом составляет 10 л/мин.
Процесс сварки
Дуговая сварка в защитном газе является эффективной методикой. Но чтобы этого добиться, мастер должен выполнять все требования, выдвигаемые стандартами к этому процессу. Эта методика несколько отличается от иных техник, что мастер должен обязательно учитывать.
Сначала металл готовят для проведения процесса сварки. При использовании такой технологии эта процедура оказывает меньшее воздействие на результат, но проводить ее нужно. Далее проводится настройка оборудования в соответствии с параметрами сварки. Учитывается толщина и тип материала.
Когда оборудование будет готово, производится розжиг дуги. При этом подпаливают пламя горелки. Некоторые разновидности сварки предполагают проведение предварительного прогрева заготовки. Для этого сначала включают горелку, при помощи которой производится предварительная обработка металла.
Когда вокруг дуги начнет образовываться сварочная ванна, начинают подавать проволоку. Для этого оборудование оснащают специальным подающим устройством. Оно поставляет проволоку в зону расплава с определенной скоростью. Если нужно сделать длинный шов, это удобно, так как дугу не придется разрывать. Для этого применяется неплавкий электрод, который поддерживает дугу длительное время.
Если сварка происходит при использовании постоянного тока, его полярность должна быть обратной. Это сокращает вероятность разбрызгивания, но повышается расход металла. Коэффициент наплавления при использовании подобной методики заметно снижается. При прямой полярности он возрастает в 1,5 раз.
Ванну желательно вести слева направо (если мастер правша). Так будет видно процесс формирования шва. Также все действия нужно выполнять по направлению к себе. Шов создается просто, от мастера требуется только ровно вести аппарат на перманентной скорости.
Дуга отрывается от заготовки в обратном направлении относительно движения сварки. В некоторых случаях после такой манипуляции может потребоваться дополнительный прогрев.
Оборудование
Дуговая сварка в защитном газе производится при помощи специального оборудования. Оно применяет стандартные источники электропитания, а также обладает функцией регулировки напряжения.
Агрегаты для сварки оснащаются устройством, передающим проволоку. Также здесь предусмотрены узлы для подачи газов в зону плавления при помощи шлангов из баллонов. Процедура сварки производится при постоянной высокой частотности тока. От правильности регулировки зависит стабильность дуги. Также настраивается скорость подачи проволоки. Наиболее популярными агрегатами для проведения подобной сварки являются:
- «Импульс 3А». Применяется для сварки алюминия, но недостатком является малая функциональность прибора. Его также можно применять для сварки черных металлов, а также создания потолочных швов.
- «ПДГ-502». Применяется для проведения спайки в углекислом газе. Аппарат надежный и производительный. Работает от сети как 220 В, так и 380 В. Электричество может регулироваться от 100 А до 500 А.
- «УРС 62А». Применяется при сварке в полевых условиях.
Преимущественно используется для сварки алюминия, но может и обработать титан.
Средства защиты
Сварочные работы при использовании газа отличаются высокой степенью опасности, особенно при использовании взрывоопасных веществ. Поэтому сварщик должен применять в работе индивидуальные средства защиты. Они должны закрывать кожу, глаза, не позволять мастеру вдыхать вредные пары.
Даже если проводится кратковременная сварка в собственном гараже, мастер должен применять специальную маску, респиратор и термоустойчивые краги. В этом случае работа будет выполняться в безопасном режиме, что также сильно отражается на качестве результата.
что это такое? В чем заключается сущность процесса, ГОСТ, область применения
Электрошлаковая сварка появилась не так давно – несмотря на это, она уже успела завоевать популярность среди специалистов в своей области. Этот вариант сваривания деталей относится к перспективным технологическим процессам, так как позволяет соединять металлические изделия с различной толщиной.
Что это такое?
Электрошлаковую сварку относят к термическим видам плавки металла. Источником нагрева в данном случае выступает тепло, которое выделяется энергетическим носителем в процессе прохождении ванны из шлака. Обычно такая сварка используется при необходимости вертикально соединить всевозможные элементы конструкций и заготовок.
Характеристика процесса подразумевает нагрев рабочей области теплом из ванны со шлаком, что присутствует в составе. Процедура нагревания масс шлака возможна благодаря наличию электротока. Суть проведения данной процедуры заключается в плавке и быстром последующем охлаждении заготовки. Чтобы электрошлаковая сварка прошла успешно, мастерам необходимо воспользоваться специальным оборудованием.
Классификация электросварки происходит с учетом количества электродов и возможностей его колебаний. В ГОСТах присутствует вся информация, которая касается требований, условий, иных моментов, что обязательно должны учитываться во время сварки. В ГОСТ 30482-97 описаны правила сварочных процедур, в ГОСТ 9087-81 имеется информация о сварочных материалах, а в ГОСТ 15164-78 указаны виды, габариты и элементы процесса.
Плюсы и минусы
Главной положительной характеристикой ЭШС считается возможность сваривать крупногабаритные предметы. Благодаря этому у людей появилась возможность возводить массивные конструкции и делать их ремонт. Иными преимуществами процесса можно считать:
- высокую производительность при работе с пластинками большого размера;
- экономию использования электрической энергии и других вспомогательных веществ;
- высокое качество скрепления, у которого имеется непосредственная схожесть с основой материала;
- невозможность деформирования материалов после процедуры сваривания;
- отсутствие надобности разделывать кромки, благодаря чему облегчается подготовительный процесс.
Помимо всего вышесказанного, специалисты отмечают экономность сварки, так как в ходе процедуры получается сделать шов с любой толщиной в один проход.
Недостатками электрошлаковой сварки считаются такие моменты:
- исключительно вертикальная ориентация сварочного шва;
- невозможность делать перерывы при сварке, так как это может повлечь за собой появление дефектов;
- необходимость устанавливать дополнительное оборудование;
- крупнозернистость сварочных швов;
- для увеличения показателя прочности требуется проводить термообработку сваренных деталей.
Описание процесса
Сущность ЭШС зависит от варианта используемого электрода.
- Электродная проволока. Процедура основана на использовании проволочных электродов, диаметр которых составляет около 3-х мм. При этом стоит учитывать, что скорость передачи их в ванну должна характеризоваться постоянством. Этот метод обычно используют во время сваривания металла толщиной менее 50 мм. Чтобы сварить детали с большой толщиной, стоит воспользоваться парой электродных проволок. Перемещение электродов происходит возвратными и поступательными движениями.
- Электроды с большим сечением.
В этом случае используются пластинки и стержни с квадратными и круглыми типами сечений. На размеры и число электродов оказывает влияние габариты обрабатываемых поверхностей, а также форма и габариты отверстий в них. Данный способ сваривания при помощи ЭШС считается актуальным для работы с толстыми металлическими элементами, высота которых менее 100 см.
- Плавящийся мундштук. Данный вид электрошлаковой сварки включает в себя особенности двух предыдущих вариантов. При этом в зазор на границе деталей устанавливают стальную пластину, чтобы в процессе сварки он оставался недвижимым.
Во время ЭШС детали стоит фиксировать вертикально, оставив зазор на границе кромок. Шов на поверхности в этом случае осуществляет принудительное формирование. В зону сваривания происходит подача электродов, флюсовых стержней, которые вызывают первоначальное возгорание дуги. После того как образуется достаточный объем шлаковой ванны, дуга погасает, а электричество передается исключительно через флюс.
Тепло, образующееся при сварке, плавит флюс, электроды и окраины материалов, что подвергаются свариванию. Расплавленный металл приводит к формированию сварочной ванны, что стекает ко дну ванны из шлака. Ползуны из меди в совокупности со сварочной головкой перемещаются по обрабатываемым изделиям с нижней части к верхней, при этом удерживая их.
Охлаждение ползунов, которые формируют металлический шов, осуществляется водой, циркулирующей в каналах.
При вертикальном передвижении ползуна пластинчатый зазор постепенно заполняется. После этого происходит охлаждение металла, его кристаллизация и образования сварочного шва вдоль всей кромки изделия, что подвергается сварке.
Оборудование и материалы
С учетом элементов конструкции и источника тока выделяют несколько видов оборудования для ЭШС. Благодаря наличию специальных устройств осуществляется передвижение электрода вдоль по ванне. Данная особенность обеспечивает равномерность прогрева элементов. Наличие боковых ограничивающих узлов и мундштука с проволокой обеспечивают поднятие соединений вверх.
Еще в СССР разработали аппараты для ЭШС следующих видов:
- рельсовый агрегат передвигается вдоль по вертикальным направляющим сварного шва;
- безрельсовый аппарат крепят к материалу, который обрабатывается путем механической фиксации, после чего перемещают по нему;
- шагающий механизм перемещается по конструкции с помощью магнитов.
Агрегаты и установки для электрошлакового процесса сваривания бывают полуавтоматическими и автоматическими. В конструкцию каждого из вышеперечисленных приспособлений входят следующие составные элементы:
- источники питания;
- головки сварки;
- ползуны с принудительным удержанием сварочных ванн;
- механизмы передвижения агрегата сварки и электродов;
- катушки с проволокой;
- инструменты контроля;
- флюсовые бункера;
- приборы контроля за местонахождением сварочных ванн.
Большой популярностью у мастеров ЭШС пользуется станок А535. Он считается оптимальным вариантом для однопроходного процесса с переменным напряжением. Однако этот вид установки подходит для ограниченных сварочных процедур. Приспособление способно справиться со спайкой кольцевого и продольного шва, диаметр которых не превышает 30 см.
А также потребители отдают предпочтение агрегату А550, который сваривает элементы аналогично с предыдущим приспособлением. Отличием аппарата являются некоторые конструкционные моменты и функциональные возможности. Чтобы сделать качество изделия лучше, можно добавлять разные виды присадок. Их подача осуществляется непосредственно в резервуар, где происходит перемешивание с основным веществом.
Область применения
Главной областью использования электрошлаковой сварки является тяжелое машиностроение. Здесь ее применяют для следующих целей:
- для соединения пластин и изделий с толстыми стенками, к примеру, в бронированных корпусах корабля, гидравлических турбинах, станинах мощного пресса, станках прокатного типа, танковой брони, котельных барабанах с высоким давлением;
- для сварки металла с разным химическим составом;
- при сооружении доменных кожухов;
- при изготовлении конструкций сварно-кованого и сварно-литого типа;
- в производстве оборудования для тяжелой промышленности.
Электрошлаковая сварка считается довольно эффективной при сваривании металла с небольшой толщиной, например, от 14 до 30 мм. К таким элементам относят монтажные стыки корпусов судов на стапеле.
Часто ЭШС используют при строительстве крупногабаритного транспорта, к примеру, торгового судна. Не обойтись без нее во время возведения мостов, в которых важное место отводится качеству и прочности соединения, так как от них зависят человеческие жизни.
Все об электрошлаковой сварке смотрете в видео ниже.
История сварки | Fairlawn Tool Inc.
Современное производство металлов было бы невозможно без сварки, но откуда взялась эта технология? Кто его открыл и что мы можем наблюдать о том, как он изменился за эти годы? Вот ответы на некоторые из ваших самых насущных вопросов об одном из самых значительных достижений в области производства металлов.
Когда возникла сварка?
Как вы понимаете, сварка существует уже довольно давно.Мы можем предположить, что он существовал в той или иной форме еще в железном и бронзовом веках. Есть свидетельства того, что египтяне научились сваривать железо, и мы нашли небольшие золотые ящики со сварными соединениями внахлестку более 2000 лет назад.
Тем не менее, тип сварки, распространенный тогда и в средние века, был очень рудиментарным типом сварки, который обычно заключался в соединении двух кусков металла под действием тепла до тех пор, пока они не соединились. Обычная сварка в том виде, в каком мы ее знаем, появилась только в 19 веке.
Кто изобрел сварку?
Ни один человек не претендует на изобретение сварки. Некоторые из первых прорывов в сторону традиционной сварки произошли еще в 1800 году. В том же году сэр Хамфри Дэви произвел первую электрическую дугу между двумя угольными электродами с помощью батареи. В 1836 году Эдмунд Дэви открыл ацетилен. Но процесс, который мы сегодня называем сваркой, появился только в 1881 году.
Все началось с Огюста де Меритенса, который использовал тепло дуги для соединения свинцовых пластин.Его русский ученик Николай Бенардос затем запатентовал метод электродуговой сварки угольными стержнями. После этого сварочные процессы быстро развивались. Николай Славынов придумал, как использовать металлические электроды для сварки. После этого К.Л. Коффин, американский инженер, открыл процесс дуговой сварки с использованием металлического электрода с покрытием, который стал предшественником дуговой сварки защищенным металлом.
История сварки Хронология
История сварки — это богатое исследование человеческой изобретательности и духа.После своего изобретения сварка продолжала развиваться, приведя ее к современному виду. Древняя сварка выглядит совсем иначе, чем сейчас. Но каждый шаг на временной шкале сварки — это впечатляющий скачок в машиностроении. Вот некоторые из ключевых моментов в истории сварки.
- 4000 г. до н.э.: Историки считают, что древние египтяне разработали самые ранние формы сварки примерно в это время. Цивилизации начали сваривать медь и со временем перешли на другие металлы, такие как железо, бронза, золото и серебро.
- 3000 г. до н.э.: Египтяне использовали древесный уголь для выработки тепла, чтобы превратить железную руду в рыхлое вещество, называемое «губчатое железо». Затем они соединили разрозненные частицы вместе, чтобы соединить детали в первом случае сварки давлением.
- 1330 г. до н.э.: Египтяне начали паять и выдувать трубы, соединяя куски металла вместе.
- 60 Н.э.: Историк Плиний записал информацию о процессе пайки золотом. Он включил информацию об использовании соли в качестве флюса и даже упомянул, как цвет металла указывает на сложность его пайки.
- 310 г. н.э.: Индийские сварщики создали Железный столб Дели, который стоит до сих пор, используя железо из метеоритов.
Столб остается впечатляющим примером раннего мастерства, его высота составляет 25 футов, а вес — шесть тонн.
- 1375 CE: Кузнечная сварка была на переднем крае в этот период. Кузнецы нагревали металлические детали и сбивали их вместе, пока они не соединялись.
- XVI век: В этот период сварщики продвинулись в своем ремесле.Рукописи этого века содержат первые упоминания слова «сварка». Итальянский ювелир Бенвенуто Челлини писал о процессе пайки, используемом для пайки серебра и меди.
- 18 век: Технологии сварки резко возросли в 18 веке благодаря промышленной революции, которая проложила путь обществу, которое мы знаем сегодня. Для достижения своих целей отраслям промышленности требовались более передовые методы сварки. Сварщики разработали инновационные технологии сварки, чтобы удовлетворить этот спрос.Пара новых достижений включала разработку доменных печей и открытие кислорода.
- XIX век: В этом веке сэр Хамфри Дэви открыл электрическую дугу.
Другие изобретатели также внедрили и запатентовали сварку плавлением, сварку электродом без покрытия и дуговую сварку угольным электродом. Грабители использовали факел, чтобы ворваться в банковское хранилище, дав первое представление о преднамеренном использовании факелов для плавления металла.
- ХХ век: Термитная сварка впервые появилась в 1903 году.В 1919 году CJ Holslag изобрел сварку переменным током, заменив электродуговую сварку как наиболее распространенную форму сварки в Соединенных Штатах. Сварка продолжала расти и пользовалась большим спросом из-за Первой и Второй мировых войн. Президент Вудро Вильсон учредил Комитет США по сварке военного времени, чтобы увеличить производство сварного оборудования.
Как изменилась современная сварка?
С 19 века люди разрабатывают все более эффективные методы точной, быстрой и эффективной сварки.Сегодня у нас даже есть роботизированная сварка, метод, который становится все более популярным и использует компьютерное управление для сварки металла гораздо быстрее и точнее, чем это возможно при ручной сварке. Это также значительно снижает или устраняет любые риски для работающих людей. Мы можем только представить, какие невероятные новые процессы сварки принесет 21 век.
Выберите инструмент Fairlawn для ваших современных потребностей в сварке
С каждым веком сварка становится все более упорядоченным процессом. Сварщики прошлого могли только мечтать о наших современных достижениях.Если вашему бизнесу требуются услуги сварки среднего или крупного масштаба, Fairlawn Tool — это компания, в которую можно обратиться.
Мы предоставляем высококачественную автоматизированную сварку и резку, а также гибку труб, револьверную штамповку с ЧПУ и широкий спектр других современных услуг по изготовлению металла для удовлетворения ваших потребностей в металлообработке. Чтобы узнать больше о сварке и других процессах изготовления металлов или узнать, как Fairlawn Tool может помочь вашему бизнесу, свяжитесь с нами сегодня.
Последнее обновление: 4 июня 2021 г.
История сварки
На протяжении тысячелетий металлы использовались в соответствии с желаниями и потребностями человека. Но от примитивных молотков и наковален до высокотехнологичных роботизированных лазеров, человеческие методы манипулирования со временем сильно изменились и эволюционировали. Благодаря достижениям в области сварки были построены небоскребы, автомобили и даже ядерные реакторы, но зарождение сварки не имело ничего общего с передовыми технологиями, которыми мы располагаем сегодня. Прокладывая путь к современным конструкциям и более безопасным машинам, сварка играет решающую роль в нашей повседневной жизни.
Истоки современной сварки восходят к бронзовому веку. Древние жители Месопотамии использовали пайку для изготовления золотых шкатулок. Пайка работает при гораздо более низкой температуре, чем сварка, и поэтому не вызывает плавления, но принципы металлообработки были заложены, и вскоре после этого на передний план вышла кузнечная сварка. Кузнецы сталкивали нагретые металлы вместе, пока не произошло соединение. Этого метода хватило на долгие годы, и с помощью кузнечной сварки были созданы впечатляющие сооружения, такие как Железный столб Дели.Процесс сварки не претерпевал никаких изменений в течение многих лет, пока не была изобретена электрическая дуга.
В 1800 году сэр Хамфри Дэви, британский химик, изобрел электрическую дугу, используя угольный электрод, прикрепленный к батарее. Развитие этого изобретения увеличило время, в течение которого могла поддерживаться дуга. Углеродная дуговая сварка, разработанная в 1885 году, была первой разработкой, использованной для сварки. Этот метод сварки создает дугу между угольным электродом и заготовкой, создавая температуру до 5000 ° F.Угольный электрод был неплавящимся и создавал дугу только для плавления заготовок, но это изобретение проложило путь к новым инновациям в области дуговой сварки в будущем.
Спустя сто лет после изобретения электрической дуги А. П. Строменгер представил в 1900 году металлический электрод с покрытием. Это покрытие из извести стабилизировало дугу и предотвратило неплотность сварных швов. В 1907 году процесс дуговой сварки металлическим электродом был завершен. Для этого метода электрод с покрытием является расходным материалом и предназначен для затекания в заготовки.Смесь между заготовками и присадочным металлом создает связь, которая часто сильнее, чем первоначальная прочность заготовок. Появление покрытых и расходуемых электродов определило современную сварку с новыми и технологически продвинутыми методами, восходящими к основным принципам электрической дуги, защитного агента и расходуемого присадочного металла.
С появлением расходуемого металлического наполнителя появилась автоматизация подачи. Эта автоматика легла в основу сварки МИГ, разработанной в 1948 году.По мере того, как расходуемый металл втекает в заготовку, через горелку автоматически подается дополнительная расходуемая проволока вместе с защитным газом для защиты сварного шва от загрязнения. Сварка MIG быстро стала одной из самых популярных форм сварки из-за простоты использования для сварки листового металла. Это хорошо отразилось на автомобильной промышленности и резко увеличило популярность метода.
Поскольку автоматизация и робототехника заняли центральное место в производственном процессе, роботизированная сварка перешла из научной фантастики в реальность.Многие считают сварку искусством, в котором используются разные методы от сварщика к сварщику. Появление робототехники перевернуло это представление с ног на голову в 1980-х годах, когда роботы смогли стабильно производить сварные швы высокого качества. Это устранило проблему человеческого фактора, значительно снизив количество дефектов сварки. Роботизированная сварка является одним из многих технологических достижений, от которых сварка выиграла за последние 30 лет. Гибридная лазерная дуговая сварка также зарекомендовала себя как ценный метод сварки. Использование лазера в сочетании с электрической дугой для создания сварного шва дает преимущество в меньшей зоне термического влияния и более глубоком проплавлении.
Металлообработка далеко ушла от своих примитивных кузнечных корней. Изобретение электродуговой сварки перенесло нас в современную эпоху и заложило основу для будущих разработок в области технологий. Сварка подняла стандарт, по которому оценивают металлические изделия. Благодаря возможности большей структурной целостности, чем ковка, металл стал более популярным в качестве ресурса и раскрыл потенциал металлических конструкций.
Характеристика режимов отказа для различных процессов сварки нержавеющих сталей AISI/SAE 304
https://doi.org/10.1016/j.engfailanal.2011.04.008Получить права и содержаниеAbstract
Сварные соединения, изготовленные с использованием сварочного электрода типа 308L и тремя различными способами дуговой сварки: дуговая сварка металлическим электродом в среде защитного газа (SMAW), дуговая сварка металлическим электродом в среде защитного газа (GMAW) и Дуговая сварка с флюсовой проволокой (FCAW) в стали AISI/SAE 304 изучалась с целью сравнения механизмов отказа, связанных с их механическими и микроструктурными свойствами. Химический состав был проанализирован с помощью оптической эмиссионной спектроскопии, а также были определены ферритные числа (FN) сварных швов.Соответствующие микроструктурные характеристики различных процессов были проанализированы методами микроскопии. Наконец, были проведены испытания на усталость для изучения изменений механических свойств каждого процесса и анализа их наиболее вероятных режимов отказа с помощью фрактографического исследования, в ходе которого были определены характерные морфологии каждого из них (зарождение, распространение, окончательный разрыв). с помощью оптической стереоскопии и сканирующей электронной микроскопии (СЭМ). В сварных соединениях были обнаружены три различных режима разрушения, которые показали корреляцию с микроструктурными изменениями, происходящими в процессе сварки.Первый вид разрушения показал, что зарождение трещины произошло в корне шва. Второй вид разрушения возник в зоне термического влияния (ЗТВ), где трещина зародилась из-за изменения размера зерна, вызванного процессом, а затем распространилась дальше по кромке сварного шва.
Третий вид разрушения возник из-за наличия экзогенных включений, образованных в процессе сварки, которые выступали в качестве концентраторов напряжений в сварном шве и приводили к зарождению и дальнейшему распространению трещины.Наконец, некоторые сварочные процессы представляли собой комбинацию предыдущих режимов разрушения и, следовательно, множественных мест зарождения трещин.
Особенности
► В сварных швах были обнаружены три различных режима разрушения, коррелирующих с микроструктурными изменениями. ► Первый вид разрушения показал, что зарождение трещины произошло в корне шва. ► Второй вид разрушения сформировался в зоне термического влияния (ЗТВ). ► Третий вид разрушения возник из-за наличия экзогенных включений, образовавшихся в процессе сварки.► Наконец, некоторые сварочные процессы представляли собой комбинацию предыдущих режимов разрушения и, следовательно, множественных мест зарождения трещин.
ключевые слова нержавеющая сталь
AISI / SAE 304
AISI / SAE 304.
Рекомендуемые статьи
Ссылки на статьи
Связана ли электродуговая сварка с марганцем или болезнью Паркинсона?
Марганец и его неорганические соединения широко используются во многих отраслях промышленности и считаются профессиональными нейротоксинами, которые вызывают отчетливую и приводящую к инвалидности клиническую картину, манганизм, на нескольких видах работ, особенно при контакте с пылью.Имеются неубедительные и непоследовательные данные о том, что у представителей этих профессий субклинические неврологические эффекты, обнаруживаемые только нейроповеденческими исследованиями, могут быть вызваны низкими дозами. Это вызвало переоценку пределов профессионального облучения. Некоторые страны, в том числе Великобритания, уже требуют гораздо более высокого уровня защиты от облучения, чем 5 лет назад. Сварка является наиболее распространенным источником профессионального облучения, поскольку марганец является важным компонентом стали и, следовательно, его соединения являются неизбежными компонентами дыма, выделяемого при сварке стали. Там он находится во вдыхаемых частицах, часто в виде сложных оксидов (шпинелей), иногда внутри ядра, защищенного оболочкой из оксида кремния, в отличие от гораздо более простой формы частиц, образующихся в результате распада в таких процессах, как добыча полезных ископаемых и измельчение руды, где присутствует марганец. был поставлен убедительный диагноз. Миллионы рабочих подвергаются риску воздействия марганецсодержащих соединений в дымах при электродуговой сварке стали. В последние годы утверждалось, что неврологические и нейроповеденческие расстройства могут развиваться в результате воздействия дыма при сварке стали и что работа сварщиком связана с необычно ранним началом болезни Паркинсона.Установлены причинно-следственные связи. Было зарегистрировано, что сварщики подвергались воздействию высоких концентраций марганецсодержащих паров, особенно когда они работали в закрытых невентилируемых помещениях, хотя, судя по ограниченным данным, это скорее исключение, чем правило. Даже в этом случае получаемая доза обычно меньше, чем при добыче полезных ископаемых или дроблении руды.
Если принять меры для исключения воздействия в процессе наплавки, горения и дуговой резки, где марганец может составлять высокий процент дыма, соединения марганца обычно составляют относительно небольшой процент состава частиц сварочного дыма, <2.0%, сильно перевешивает железо. Хотя эти частицы сварочного дыма, содержащие соединения марганца, нерастворимы в воде, соединения марганца в частицах, которые задерживаются в альвеолах, могут абсорбироваться, по крайней мере, частично. Концентрации марганца в образцах биологических материалов в некоторых группах, подвергшихся воздействию, отражают это по сравнению с не подвергавшимися воздействию рабочих. Некоторые из систем переноса для абсорбции и транспорта, в том числе через гематоэнцефалический барьер, используются в качестве конкуренции с железом, которое в изобилии присутствует в сварочном дыму.Это может снизить абсорбцию марганца сварщиками и, таким образом, уменьшить вероятность того, что достаточные дозы вызовут нейротоксикологические последствия.
Изучение литературы, охватывающей последние 40 лет, выявило только пять случаев, которые соответствуют достаточным критериям для манганизма, чтобы просто пересечь диагностический порог, и даже тогда они несут в себе определенную степень сомнения. Одна только эта низкая заболеваемость свидетельствует о том, что сварщики не подвергались и не подвергаются высокому риску клинически очевидных повреждений от воздействия марганца.Если это необходимо еще раз подчеркнуть, то в литературе нет подтвержденных случаев манганизма у сварщиков. Утверждения об аномальных результатах нейроповеденческих исследований сварщиков повысили вероятность существования субклинической формы манганизма с потерей контроля над мелкой моторикой в качестве одной из ее особенностей. Хотя наблюдения за такими изменениями у рабочих в других отраслях промышленности заставили регулирующие органы в некоторых странах применять более строгие меры контроля воздействия, пока результаты не обладают убедительной последовательностью, и нет никаких указаний на какую-либо взаимосвязь между дозой и эффектом.
Если сварочный дым может иметь эти двигательные эффекты, это будет тяжелым ударом и, возможно, концом карьеры для тех, кто пострадал. Было бы неблагоразумно отмахиваться от предостережений, прозвучавших по результатам исследований сварщиков, какими бы несовершенными ни были эти исследования, но разумнее и лучше действовать энергичнее, чтобы уменьшить облучение и контролировать эффективность этой дополнительной защиты, проводя при этом качественные исследования. чтобы сделать обоснованные выводы о том, действительно ли существует субклиническое расстройство.Идиопатическая болезнь Паркинсона является распространенным заболеванием, поражающим 1-2% населения в возрасте старше 65 лет. На основе ошибочных и оспариваемых доказательств было высказано предположение, что заболевание вызывает не сварка, а скорее то, что работа сварщиком сопряжена с риском развития этого заболевания в более молодом возрасте, чем если бы эта профессия не использовалась. Марганец в сварочном дыму был назван нейротоксином.
Это может быть биологически осуществимо, если марганец разрушает недостаточное количество рецепторных клеток, чтобы вызвать клинический манганизм, но достаточное, чтобы усилить эффекты сниженного поступления дофамина, чтобы дать проявления уже развивающейся идиопатической болезни Паркинсона раньше в ходе разрушения черной субстанции, чем если бы все рецепторы были целы.
Опасность синего света при дуговой сварке малоуглеродистой стали в CO2 | Анналы рабочих воздействий и здоровья
Аннотация
Цели: Цель состояла в том, чтобы количественно определить опасность синего света от CO 2 дуговой сварки мягкой стали. Методы: Спектральная яркость дуги при дуговой сварке низкоуглеродистой стали СО 2 измерялась для сплошных и порошковых проволок при сварочных токах 120–480 А. Эффективная яркость синего света и максимально допустимая продолжительность воздействия рассчитывались из спектральное излучение, используя их определения в рекомендациях Американской конференции государственных промышленных гигиенистов. Результаты. Эффективная яркость синего света колебалась от 22,9 до 213,1 Вт/см -2 ср -1 . Соответствующая максимально допустимая продолжительность воздействия составляла всего 0,47–4,36 с, что означает, что суммарное суточное воздействие сварочной дуги без защиты глаз не должно превышать эту продолжительность. Выводы: Очень опасно наблюдать за дугой при дуговой сварке низкоуглеродистой стали CO 2 . Сварщики и их помощники должны использовать соответствующие защитные очки во время этих операций дуговой сварки. Кроме того, им следует избегать прямого воздействия света при начале дуговой сварки.
ВВЕДЕНИЕ
Ультрафиолетовое излучение, создаваемое дуговой сваркой, часто вызывает у рабочих эритему и кератоконъюнктивит, как хорошо известно, но производимый свет (видимый свет) также опасен. Сообщалось о световом повреждении сетчатки у людей, которые смотрели на сварочную дугу без надлежащей защиты (Würdemann, 1936; Minton, 1949; Naidoff and Sliney, 1974; Romanchuk et al. , 1978; Uniat et al. ). , 1986; Cellini et al., 1987; Британия, 1988 год; Мощность и др. , 1991; Fich и др. , 1993; Аренд и др. , 1996). Это повреждение проявляется изменениями сетчатки, такими как отек или отверстие, и сопровождается такими симптомами, как снижение остроты зрения, нечеткость зрения или скотома. Эти симптомы появляются сразу или в течение нескольких часов после воздействия, а затем постепенно улучшаются в течение нескольких недель. В некоторых случаях пациенты полностью выздоравливают в течение нескольких недель или месяцев, тогда как в других случаях симптомы сохраняются через несколько месяцев.
Механизм светоиндуцированного повреждения сетчатки, связанного с дуговой сваркой, не является термическим, поскольку повышение температуры сетчатки оценивается как недостаточное, чтобы вызвать ожог; поэтому механизм повреждения считается фотохимическим (Naidoff, Sliney, 1974).
Фотохимическое повреждение сетчатки, известное как фоторетинопатия, вызывается светом преимущественно в диапазоне длин волн 400–500 нм. Поскольку свет в этой области кажется глазу голубым, его называют голубым светом.Опасность синего света обычно измеряется эффективной яркостью синего света, которая получается путем взвешивания спектральной яркости источника света по сравнению с функцией опасности синего света (рис. 1) и интегрирования ее в диапазоне длин волн 305–700. нм (ICNIRP, 1997; ACGIH, 2009). Максимально допустимая продолжительность облучения рассчитывается путем деления 100 Дж/см -2 ср -1 на эффективную яркость синего света. Таким образом, измерение эффективного синего излучения сварочной дуги является первым шагом к предотвращению фоторетинопатии, вызванной дуговой сваркой.
Рис. 1.
Функция опасности синего света (ICNIRP, 1997; ACGIH, 2009). Функция опасности синего света показывает способность света вызывать фотохимическое повреждение сетчатки в зависимости от длины волны.
Рис. 1.
Функция опасности синего света (ICNIRP, 1997; ACGIH, 2009). Функция опасности синего света показывает способность света вызывать фотохимическое повреждение сетчатки в зависимости от длины волны.
В нескольких исследованиях измерялся синий свет сварочной дуги (Marshall et al., 1977; Окуно, 1986; Хиетанен, 1998 г.; Пэн и др. , 2007), и только два из них определили эффективное излучение синего света, отчасти из-за технических трудностей. Маршалл и др. (1977) экспериментально определили эффективное излучение дуги в синем свете для различных процессов дуговой сварки в общей сложности в 20 условиях. Они показали, что эффективное излучение дуги в синем свете находится на потенциально опасном уровне для всех оцениваемых процессов, хотя опасность сильно варьируется в зависимости от процесса и условий.Окуно (1986) также определил эффективное излучение синего света сварочной дуги при 14 условиях, но в целом обнаружил гораздо более низкие уровни эффективного излучения синего света. В этих двух исследованиях эффективная освещенность синего света (спектральная освещенность, взвешенная по отношению к функции опасности синего света) была измерена на расстоянии от сварочной дуги, а затем эффективная освещенность синего света была рассчитана путем деления эффективной освещенности синего света на расчетный размер (площадь) дуги и умножение на квадрат расстояния измерения. Однако, поскольку сварочная дуга не имеет определенных границ и, следовательно, определенного размера, этот метод является приблизительным и может не давать точных результатов.
В предыдущем всестороннем обзоре опасностей синего света мы рассмотрели дуговую сварку СО 2 (разновидность дуговой сварки металлическим газом, при которой используется газ СО 2 для защиты сварного шва) мягкой стали и дуговую сварку защитным металлом из мягкая сталь, а также многие другие источники света (Okuno et al. , 2002). Мы экспериментально измерили спектральную яркость сварочной дуги и рассчитали эффективную яркость синего света на основе спектральной яркости.Было показано, что эти сварочные процессы излучают опасные уровни синего света в используемых условиях, что указывает на необходимость дальнейшего изучения сварочных процессов. В частности, имеет практическое значение более подробное изучение дуговой сварки CO 2 , поскольку в настоящее время это наиболее широко используемый процесс сварки в Японии, и поэтому многие рабочие потенциально подвергаются воздействию его синего света. В настоящей работе экспериментально определена эффективная мощность синего света дуг при дуговой сварке низкоуглеродистой стали СО 2 сплошной и порошковой проволокой при сварочных токах 120–480 А.
МЕТОДЫ
Мы использовали сварочного робота (Arcman-Ron, Kobe Steel, Ltd., Кобе, Япония) для создания дуги CO 2 дуговой сварки на плоской пластине из мягкой стали толщиной 12 мм, помещенной на приводной электродвигатель. подвижная ступень (рис. 2). Запрограммированный заранее робот автоматически зажигает и гасит дугу, перемещает горелку (дугу), подает проволоку и подает защитный газ. Металлические поверхности не соединялись. Дуга перемещалась с минимальной устанавливаемой скоростью 12 см/мин -1 для облегчения измерения света.Для достижения достаточной относительной скорости для сварки пластину из мягкой стали перемещали на 60 см мин -1 в противоположном направлении. Синий свет оценивали для сплошной проволоки (MG-50T, Kobe Steel, Ltd. ) и порошковой проволоки (DW-Z100, Kobe Steel Ltd.) при сварочных токах 120–480 А и интервалах 40 А. Таблица 1 суммированы условия сварки.
Опорная плита | Мягкая сталь, 100 мм × 75 мм × 12 мм | |
Проволока | Сплошная проволока (Kobe Steel Ltd.MG-50T), провод с флюсом (kobe Steel Ltd. dw-z100), 1,2 мм в диаметре | |
проволочной кормления | Undukna | |
проводной проводной длиной | 15 мм | |
Shield Gas | CO 2 GAS, 20 л Мин -1 -1 | |
Скорость сварки | 72 см | 72 см MIN -1 |
Ткан сварки | 120 A до 480 a с интервалом в 40 а | |
Дуга напряжение | Unduke |
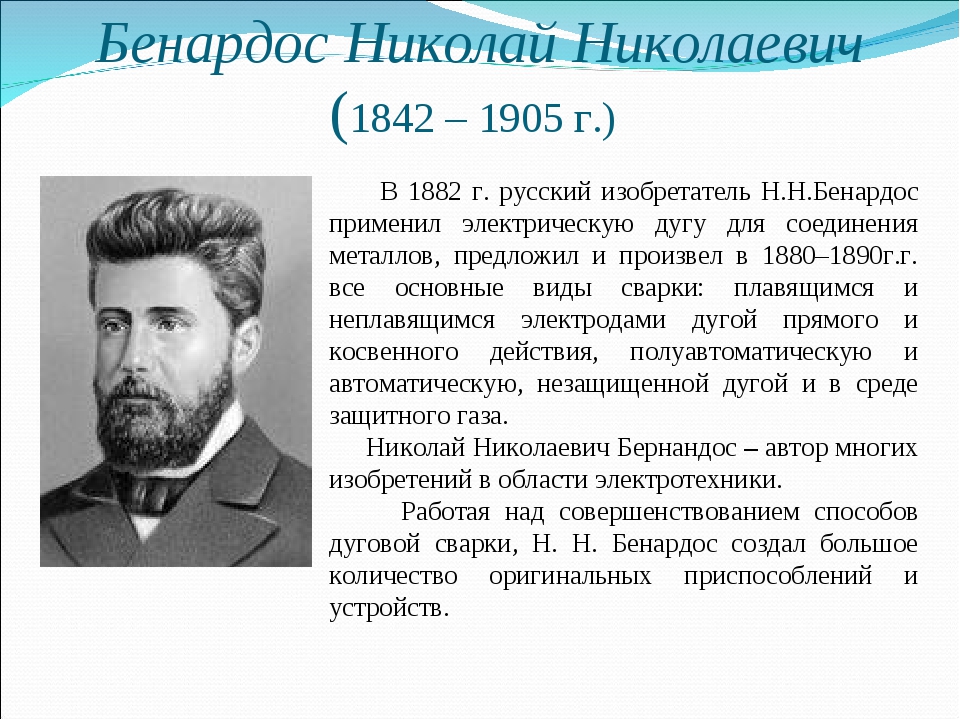

Рис.2.
Схема экспериментальной установки.
Рис. 2.
Схема экспериментальной установки.
Спектрорадиометр (PR-705, Photo Research Inc., Chatsworth, CA, USA) использовали для измерения спектральной яркости сварочных дуг в диапазоне длин волн 380–780 нм с интервалом 2 нм. Измерительное поле спектрорадиометра было установлено на диаметр 1/8°, а к апертуре спектрорадиометра была прикреплена конверсионная линза (KR2005, Kenko Co. , Ltd., Токио, Япония), чтобы уменьшить поле измерения до диаметр 1/16°.Два дополнительных фильтра нейтральной плотности (ND) с пропусканием ~1% (ND-100) и пропусканием ~10% (ND-10) и фильтр нейтральной плотности для использования в камере с пропусканием ~12,5% (PRO ND8, Kenko Co., Ltd. ) были прикреплены к апертуре, потому что свет от сварочной дуги слишком интенсивен для прямого измерения. Также был прикреплен прозрачный защитный фильтр для камеры (MC Protector, Kenko Co., Ltd.) для защиты апертуры от сварочной пыли и брызг. Спектрорадиометр внутренне вносит поправки на спектральный коэффициент пропускания двух дополнительных фильтров нейтральной плотности.Поправки на спектральный коэффициент пропускания преобразующего объектива, нейтрального фильтра камеры и прозрачного защитного фильтра были сделаны путем деления измеренного спектрального излучения на их спектральный коэффициент пропускания после измерения. Время экспозиции было установлено на 40 мс. Перед проведением измерений спектрорадиометр был откалиброван производителем.
Спектральное излучение было измерено, когда сварочная дуга удерживалась на пластине из мягкой стали в течение 10 с, перемещаясь на 2 см по горизонтали. Спектрорадиометр располагали под углом 15° и на расстоянии ∼0.8 м от центра траектории дуги и был направлен в центр (рис. 2). В этой установке измерительное поле в положении дуги представляло собой круг диаметром 0,8 мм, и измерялась средняя спектральная яркость по этому полю.
Эксперимент проводился в большом проветриваемом помещении, но вокруг сварочной дуги и спектрорадиометра вентиляционного обдува практически не было.
Эффективное излучение сварочной дуги в синем свете было получено путем взвешивания измеренного спектрального излучения по функции опасности синего света (рис.1) и интегрирование его по длине волны. Однако интегрирование было начато при 380 нм вместо 305 нм. Эта модификация приемлема, поскольку функция опасности синего света очень мала в диапазоне длин волн 305–380 нм, и поэтому ожидается, что энергия излучения в этом диапазоне будет вносить небольшой вклад в эффективное излучение синего света для источников белого света, таких как как сварочные дуги. Например, простой расчет показывает, что вклад этого диапазона длин волн составляет всего 1% для источников света с плоским спектральным распределением.
Эффективная яркость синего света измерялась 18 раз для каждого условия, после чего рассчитывались среднее значение (M) и стандартное отклонение (SD). Некоторые измерения показали чрезвычайно низкие значения, очевидно, из-за того, что измерительное поле не попало точно в дугу. Эти аномальные измерения были исключены путем исключения значений меньше (M — SD), а среднее значение и стандартное отклонение были пересчитаны. Максимально приемлемая продолжительность воздействия рассчитывалась исходя из эффективного излучения синего света для каждого условия.
РЕЗУЛЬТАТЫ
Для каждого условия можно было провести не менее 13 достоверных измерений, которые использовались для расчета средней спектральной яркости и средней эффективной яркости синего света. От одного до пяти из 18 измерений были исключены как аномальные измерения для каждого условия, что привело к увеличению средней эффективной яркости синего света на 3–20% и снижению стандартного отклонения на 5–33%.
Спектральная яркость сварочной дуги имела характерную форму с множеством эмиссионных линий (рис. 3 и 4).Общая интенсивность свечения дуги в целом увеличивалась с увеличением сварочного тока для каждой сварочной проволоки, но спектральные характеристики оставались неизменными.
Рис. 3.
Спектральное излучение дуги в CO 2 Дуговая сварка малоуглеродистой стали сплошной проволокой.
Рис. 3.
Спектральное излучение дуги в CO 2 Дуговая сварка малоуглеродистой стали сплошной проволокой.
Рис. 4.
Спектральное излучение дуги в CO 2 Дуговая сварка малоуглеродистой стали порошковой проволокой.
Рис. 4.
Спектральное излучение дуги в CO 2 Дуговая сварка низкоуглеродистой стали порошковой проволокой.
Точно так же эффективная яркость синего света, рассчитанная по спектральной яркости сварочной дуги, обычно увеличивается с увеличением сварочного тока; при больших сварочных токах эффективная яркость синего света была выше для сплошной проволоки, чем для порошковой. Эффективная яркость синего света варьировалась от 33,7 до 213,1 Вт·см -2 ср -1 для сплошной проволоки и от 22.9 до 162,9 Вт·см −2 ср −1 для порошковой проволоки (рис. 5). Соответствующая максимально допустимая продолжительность воздействия составила 0,47–2,97 с для сплошной проволоки и 0,61–4,36 с для порошковой проволоки, что означает, что суммарное суточное воздействие сварочной дуги без средств защиты глаз не должно превышать эту продолжительность.
Рис. 5.
Эффективное излучение дуги в синем свете в CO 2 Дуговая сварка мягкой стали. Максимально допустимая продолжительность воздействия указана на правой шкале.
Рис. 5.
Эффективное излучение дуги синего света в CO 2 Дуговая сварка мягкой стали. Максимально допустимая продолжительность воздействия указана на правой шкале.
ОБСУЖДЕНИЕ
Это исследование показывает, что дуги при дуговой сварке низкоуглеродистой стали CO 2 не должны наблюдаться в течение >0,47–4,36 с всего в день. Таким образом, при дуговой сварке CO 2 каждый сварщик и помощники, наблюдающие за дугой и объектами вблизи дуги, должны носить защитные очки с фильтром соответствующего номера затемнения и смотреть через фильтр, чтобы защитить себя от синий свет.Кроме того, поскольку они надевают защитные очки (фильтр), им следует избегать прямого воздействия света при зажигании дуги. Хотя воздействие при поджигании дуги длится всего доли секунды, сварщики обычно выполняют эту задачу много раз в день и, следовательно, общая продолжительность воздействия может превысить лимит. Таким образом, сварщики и их помощники должны убедиться, что они надели защитные очки перед зажиганием дуги, когда они начинают операцию дуговой сварки.
Наши данные (рис. 5) согласуются с эффективной яркостью синего света, которую Marshall et al. (1977) определили для СО 2 дуговой сварки малоуглеродистой стали, хотя использовали другой метод измерения (17,5 и 53,7 Вт·см -2 ср -1 при сварочных токах 90 и 150 А соответственно). Это поддерживает надежность наших методов и результатов, несмотря на технические трудности определения эффективного излучения синего света сварочных дуг.
Когда сварочная дуга рассматривается как небольшой источник света, стягивающий угол <0,011 рад, можно использовать критерии для малых источников света, чтобы обеспечить более длительное воздействие (ICNIRP, 1997; ACGIH, 2009).Например, Marshall и др. (1977) сделал фотографии дуг для различных процессов дуговой сварки и измерил площадь внутри контура, соответствующую уровню излучения 1/e (~37%), умноженному на пиковое излучение на фотографии. Они установили, что размер дуги при дуговой сварке низкоуглеродистой стали СО 2 составляет 1,2–9,2 мм 2 , что соответствует диаметру 1,2–3,4 мм, если дуга предполагается круговой. Когда сварщик смотрит на эту дугу с расстояния 50 см, дуга образует угол 0.0024–0,0068 рад, что составляет <0,011 рад, и можно использовать критерии малого источника света. Однако сварочная дуга не имеет определенных границ и, следовательно, определенного размера, поэтому к сварочным дугам обычно трудно применить критерий малого источника света.
Критерии (ICNIRP, 1997; ACGIH, 2009) прямо не указывают, но подразумевают, что эффективное излучение синего света должно быть усреднено по кругу с угловым диаметром 0,011 рад. Таким образом, опасность синего света, определенная в этом исследовании, считается для расстояния просмотра 7.3 см, так как эффективная яркость синего света определялась при усредняющем поле зрения диаметром 0,8 мм, что соответствует угловому диаметру 0,011 рад на этом расстоянии наблюдения. Однако сварочная дуга обычно видна на большем расстоянии. В этом случае эффективное излучение синего света может быть ниже в зависимости от размера дуги, поскольку оно усредняется по большей площади, и, следовательно, опасность синего света может быть ниже.
Поскольку эффективное излучение дуги в синем свете может сильно различаться в зависимости от процесса и условий сварки, необходимо провести дополнительные исследования для других процессов и условий сварки.Например, дуговая сварка алюминиевых сплавов должна оцениваться, потому что ее дуги кажутся более белыми, чем дуги при дуговой сварке стали, что указывает на то, что они излучают большое количество синего света.
ВЫВОДЫ
Это исследование показывает, что очень опасно наблюдать за дугой при дуговой сварке низкоуглеродистой стали CO 2 . Сварщики и их помощники должны использовать соответствующие защитные очки во время этих операций дуговой сварки. Кроме того, им следует избегать прямого воздействия света при начале дуговой сварки.
ФИНАНСИРОВАНИЕ
Исследовательский проект «Вредные агенты, связанные с процессами дуговой сварки» (P20-02).
Каталожные номера
ACGIH
,TLV и BEI
,2009
Цинциннати, Огайо
ACGIH
, , , et al.Макулопатия сварщиков, несмотря на использование защитных линз
,Сетчатка
,1996
, том.16
(стр.257
—9
).Ожоги сетчатки, вызванные воздействием сварочных дуг MIG: отчет о двух случаях
,Br J Ophthalmol
,1988
, том72
(стр.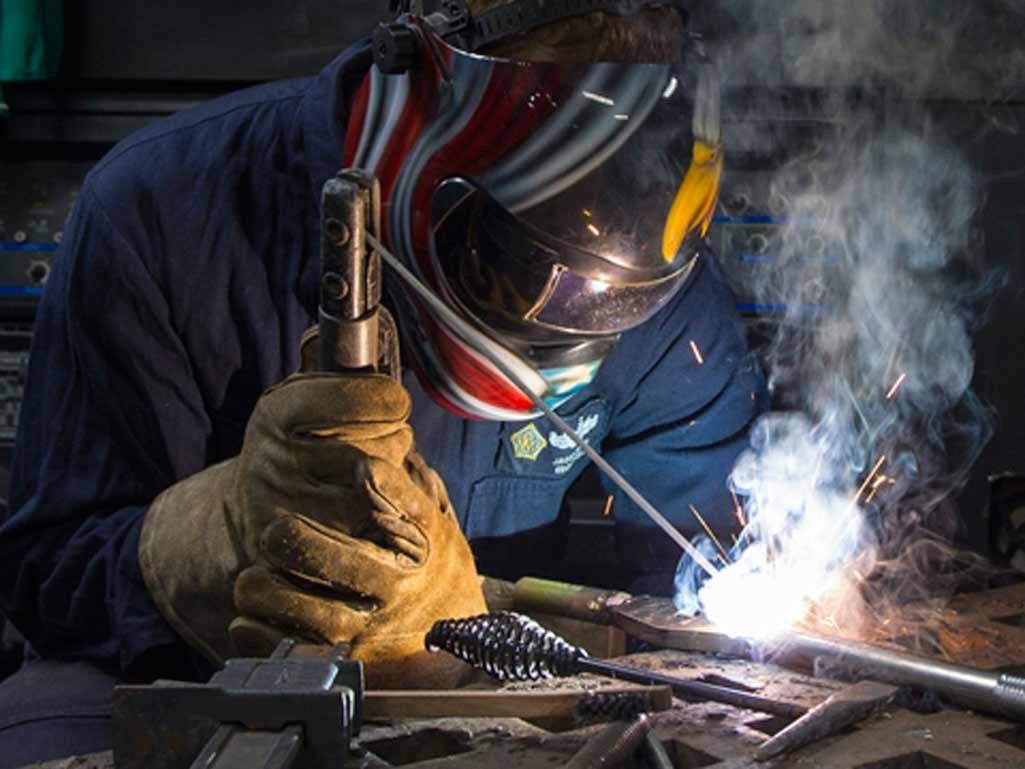
570
—5
), , , и др.Световая макулопатия при дуговой сварке. История болезни
,Int Ophthalmol
,1987
, vol.10
(стр.157
—9
), , , и др.Макулопатия, вызванная сварочной дугой. Отчет о 3 случаях
,Acta Ophthalmologica
,1993
, vol.71
(стр.402
—4
). , .Измерения оптического излучения, испускаемого сварочными дугами
,Измерения опасностей оптического излучения
,1998
Мюнхен, Германия
Märkl-Druck
(стр.553
—7
)ICNIRP
Рекомендации по пределам воздействия широкополосного некогерентного оптического излучения (от 0,38 до 3 мкм)
,Health Phys
,1997
73
(стр.539
—54
), , , и др. ,Оценка потенциальной опасности для сетчатки глаза от оптического излучения, генерируемого электрической сваркой и режущей дугой
,1977
Абердинский испытательный полигон, Мэриленд
Агентство гигиены окружающей среды армии США
.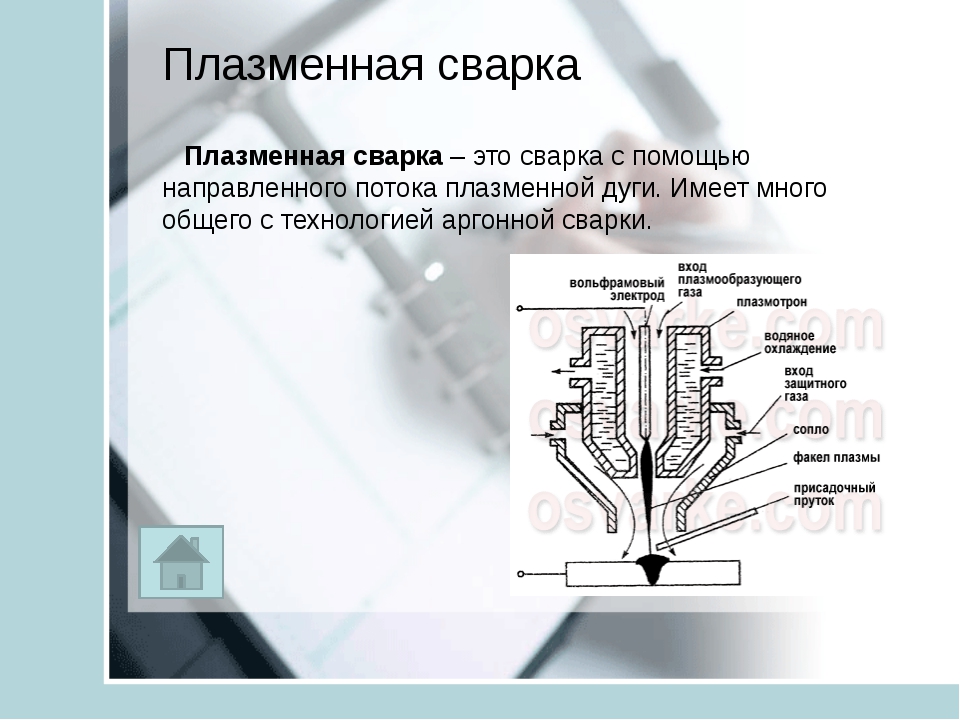
Профессиональные заболевания хрусталика и сетчатки
,Br Med J
,1949
, vol.41
(стр.392
—4
), .Повреждение сетчатки сварочной дугой
,Am J Офтальмол
,1974
, том.77
(стр.663
—8
).Измерение эффективного излучения сварочной дуги в синем свете
24
(стр.213
—26
), , .Оценка опасности синего света от различных источников света
,Dev Ophthalmol
,2002
, том35
(стр.104
—12
), , , и др.Оценка воздействия излучения при дуговой сварке алюминия
93
(стр.298
—306
), , .Макулопатия сварочной дуги и флуфеназин
,Br J Ophthalmol
,1991
, том.75
(стр.433
—5
), , .Ожог сетчатки глаза сварочной дугой
,Can J Ophthalmol
,1978
, том.13
(стр.120
—2
), , .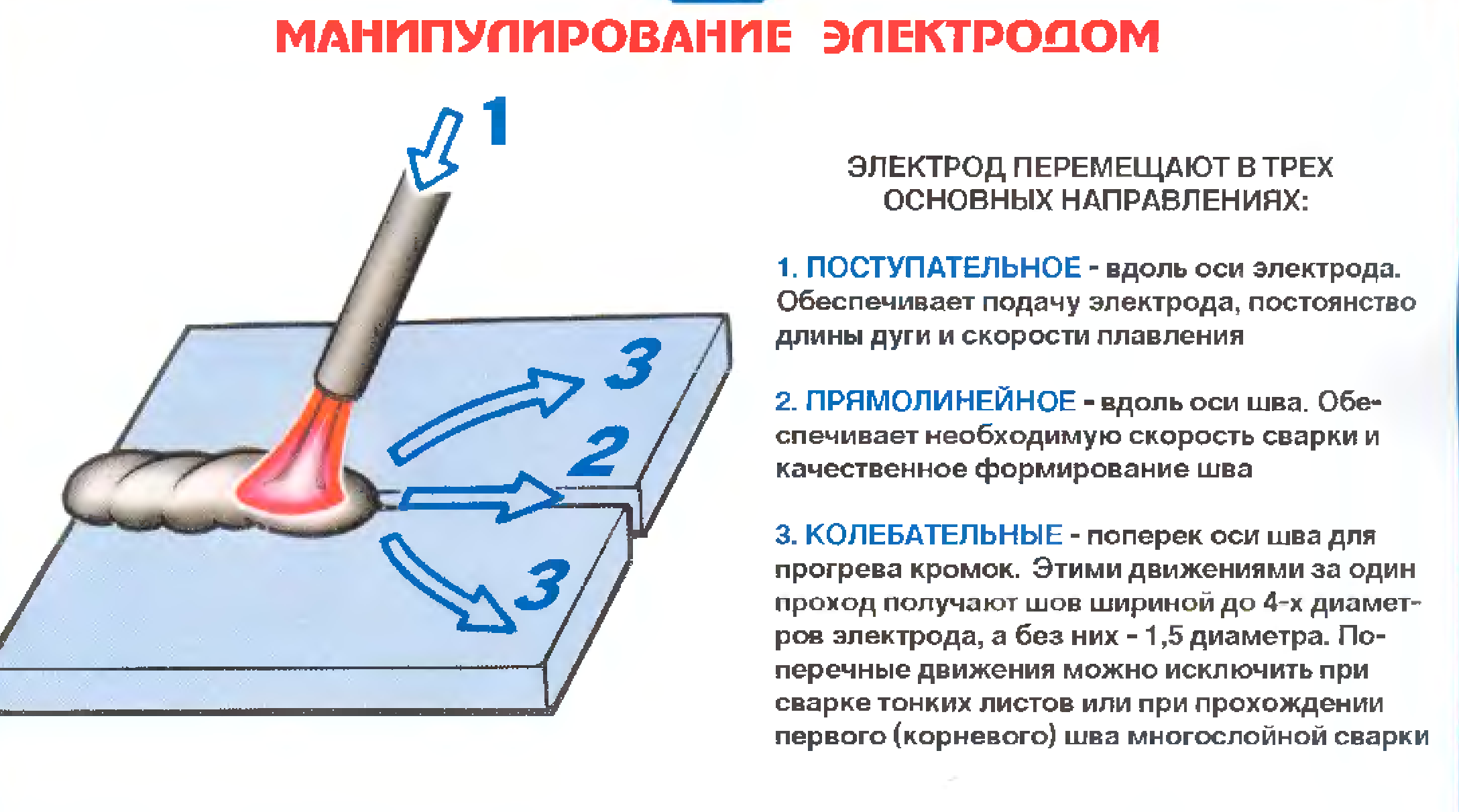
Макулопатия сварочной дуги
,Am J Офтальмол
,1986
, том.102
(стр.394
—5
).Образование отверстия в макуле. Легкий ожог от воздействия электросварки
,Am J Офтальмол
,1936
, том.19
(стр.457
—60
)© Автор, 2009 г. Опубликовано Oxford University Press от имени Британского общества гигиены труда
.Воздействие сварочного дыма и газов. Охрана труда и техника безопасности
Воздействие сварочного дыма и газов
Воздействие сварочного дыма сильно варьируется из-за нескольких факторов воздействия.
- Джером Э.Копье
- 01 июня 2011 г.
Сварочный дым представляет собой очень мелкие частицы, образующиеся при быстрой конденсации испаряющегося металла на воздухе. Обычно они слишком малы, чтобы их можно было увидеть невооруженным глазом, но все вместе образуют видимый шлейф. Воздействие на здоровье паров металлов зависит от конкретных металлов, присутствующих в дымах; они могут варьироваться от кратковременных заболеваний, таких как лихорадка металлического дыма (т. е. гриппоподобные симптомы), до долговременных повреждений легких и/или неврологических расстройств.
При сварке также образуются газы, которые могут включать окись углерода (CO), озон и оксиды азота. CO представляет собой бесцветный газ без запаха, который может образовываться при неполном сгорании покрытия электрода или флюса и при использовании двуокиси углерода (CO 2 ) в качестве защитного газа. Чрезмерное воздействие угарного газа ингибирует эритроциты в организме, чтобы в достаточной степени переносить кислород к другим тканям тела, что впоследствии приводит к удушью. Также существует вероятность образования атмосферы с недостатком кислорода при сварке в ограниченном или замкнутом пространстве, если в качестве защитного газа используется инертный газ (например, аргон).
Озон, двуокись азота и окись азота образуются при взаимодействии ультрафиолетового света (от сварочной дуги) с окружающим воздухом. Эти соединения раздражают глаза, нос и горло. Высокое воздействие также может вызвать жидкость в легких и другие долговременные легочные заболевания.
Если металл был обезжирен хлорированным растворителем, другие содержащиеся в воздухе газы (такие как фосген, хлористый водород, газообразный хлор и т.) может быть произведено. Эти газы обычно вызывают раздражение глаз, носа и дыхательной системы, и симптомы могут проявляться с задержкой.
Первым шагом в оценке потенциального воздействия сварочного дыма и газов является понимание общих процессов сварки, их относительной скорости образования дыма (FGR) и других факторов потенциального воздействия.
Общие сварочные процессы
Различные сварочные процессы имеют разные FGR. Обзор распространенных сварочных процессов и их FGR представлен ниже:
- Дуговая сварка защитным металлом (SMAW, «сварка стержнем») обычно используется для сварки низкоуглеродистой стали, низколегированной стали и нержавеющей стали.В SMAW электрод удерживается вручную, и электрическая дуга течет между электродом и основным металлом. Электрод покрыт флюсом, который обеспечивает защитный газ для сварки, помогая свести к минимуму загрязнения. Электрод расходуется в процессе, а присадочный металл способствует сварке. SMAW может производить высокие уровни металлического дыма и воздействия фтора; однако считается, что SMAW имеет небольшой потенциал для образования озона, оксида азота и газообразного диоксида азота.
- Дуговая сварка металлическим газом (GMAW) также известна как сварка металлов в среде инертного газа (MIG). GMAW обычно используется для большинства типов металлов и работает быстрее, чем SMAW. Этот процесс включает в себя протекание электрической дуги между основным металлом и расходуемым электродом со сплошным сердечником, непрерывно питаемым с катушки.
Защитный газ подается извне, электрод не имеет флюсового покрытия или сердцевины. Хотя GMAW требует более высокого электрического тока, чем SMAW, GMAW производит меньше дыма, поскольку в электроде нет флюса.
- Дуговая сварка с флюсовым сердечником (FCAW) обычно используется для сварки низкоуглеродистой стали, низколегированной стали и нержавеющей стали. Этот процесс сварки имеет сходство как с SMAW, так и с GMAW. Расходуемый электрод непрерывно подается с катушки, и между электродом и основным металлом протекает электрическая дуга. Электродная проволока имеет центральную жилу, содержащую флюс, а дополнительный защитный газ может подаваться извне. Этот процесс сварки приводит к образованию значительного количества дыма из-за высоких электрических токов и использования электрода с флюсовой сердцевиной.FCAW производит мало озона, оксида азота и газообразного диоксида азота.
- Дуговая сварка вольфрамовым электродом в среде защитного газа (GTAW) также известна как сварка вольфрамовым электродом в среде инертного газа (TIG).
GTAW используется на таких металлах, как алюминий, магний, низкоуглеродистая сталь, нержавеющая сталь, латунь, серебро и медно-никелевые сплавы. В этом методе используется неплавящийся вольфрамовый электрод. Присадочный металл подается вручную, а защитный газ подается извне. Используются высокие электрические токи, что приводит к тому, что в этом процессе образуются значительные количества озона, оксида азота и газообразного диоксида азота.Однако GTAW производит очень мало дыма.
- Дуговая сварка под флюсом (SAW) — еще один распространенный процесс сварки, используемый для сварки толстых листов из низкоуглеродистой и низколегированной стали. В этом процессе сварки электрическая дуга течет между основным металлом и плавящимся проволочным электродом; однако дуга не видна, потому что она погружена под флюсовый материал. Этот флюсовый материал удерживает пары на низком уровне. Также мало генерируются газы озона, оксида азота и диоксида азота. Главной потенциальной опасностью, переносимой по воздуху с ПАВ, являются соединения фтора, образующиеся из флюсового материала.
Скорость образования дыма
Основными источниками информации при определении компонентов, которые могут находиться в дыме, являются паспорт безопасности материала и/или паспорт технических данных производителя расходуемого электрода/провода. От 90 до 95 процентов дыма образуется из присадочного металла и флюсового покрытия/сердцевины расходуемых электродов (Lyttle, 2004). Поскольку сварочная ванна из основного металла намного холоднее, чем кончик электрода, основной металл дает лишь незначительную долю общего количества дыма.Однако основной металл может быть существенным фактором воздействия дыма, если металл или остатки на поверхности содержат высокотоксичное вещество (например, хроматсодержащие покрытия, краски на основе свинца и т. д.).
Помимо процесса сварки, на FGR также влияют следующие факторы (Spear, 2010):
- Электрический ток: В общем, FGR экспоненциально пропорционален току.
- Напряжение дуги: FGR обычно увеличивается при увеличении напряжения дуги.
- Диаметр электрода: Диаметр электрода оказывает незначительное влияние на скорость образования дыма из-за различий в напряжении и силе тока. Как правило, электрод малого диаметра имеет более высокую FGR, чем электрод большого диаметра, при прочих равных условиях. Однако при использовании электродов большего диаметра обычно происходит увеличение электрического тока.
- Угол электрода: Угол электрода к заготовке оказывает незначительное (но непредсказуемое) влияние на FGR.
- Защитный газ: при дуговой сварке в защитных газах FGR имеет тенденцию быть выше, когда в качестве защитного газа используется 100-процентный диоксид углерода (CO 2 ), по сравнению с аргоном.
- Скорость сварки: по мере увеличения скорости сварки скорость образования дыма, очевидно, увеличивается.
- Сварка постоянным/импульсным током: Технология продвинулась до источников питания, которые могут работать в импульсном режиме. Исследования (Wallace et al., 2001) показали, что при использовании импульсного тока во время сварки образуется меньше дыма, чем при сварке постоянным током.
В целом, FCAW производит наибольшую скорость образования дыма (для низколегированной сварки), за ней следует SMAW.Однако при сварке хромсодержащей стали содержание Cr(VI) в дымовых газах, образующихся при SMAW, обычно больше, чем Cr(VI), образующегося при FCAW. Щелочные металлы, такие как натрий и калий, стабилизируют Cr(VI) и часто являются покрытиями электродов SMAW, а также могут присутствовать во флюсе FCAW (Fiore, 2006), что может объяснить, почему концентрации Cr(VI) в операциях SMAW часто выше, чем Концентрации Cr(VI) из FCAW. GMAW обычно имеет умеренный относительный FGR. GTAW и SAW по своей природе являются процессами с низким уровнем образования дыма.
Другие вспомогательные процессы (такие как строжка воздушной дугой и резка плазменной дугой) также могут генерировать значительное количество дыма из-за высокого электрического тока и напряжения дуги, связанных с этими процессами. Потенциальное облучение не только оператора, но и другого персонала в рабочей зоне может быть значительным в результате таких процессов, особенно в закрытых и замкнутых пространствах.
Факторы воздействия шестивалентного хрома28, 2006 г., в котором рассматривается воздействие Cr(VI) на рабочем месте (OSHA, 2006 г.). OSHA определило, что правило Cr(VI) необходимо для снижения значительного риска для здоровья из-за воздействия Cr(VI).
Металлический хром содержится в нержавеющей стали и многих низколегированных материалах, электродах и присадочных материалах. Хром, присутствующий в электродах, сварочной проволоке и основных материалах, находится в форме Cr(0), поэтому сварщики обычно не работают с материалами, содержащими Cr(VI). Именно высокие температуры, создаваемые при сварке, окисляют хром в стали до шестивалентного состояния.
Воздействие сварочного дыма сильно варьируется из-за нескольких факторов воздействия. Эти факторы следует учитывать при оценке потенциального воздействия Cr(VI). Первичные факторы воздействия Cr(VI) следующие:
1. Процесс сварки (как описано выше)
2. Содержание хрома и флюсы в расходных материалах
3. Хромовые покрытия на основном материале
4. Скорость сварки
5. Относительное положение при сварке (например, горизонтальное, горизонтальное, вертикальное и/или потолочное положение при сварке)
6.Местная вытяжная вентиляция (ЛВВ)
7. Сварочная среда (внутри или в замкнутом пространстве)
8. Общая/приточно-вытяжная вентиляция и естественные притоки воздуха
9. Прочая сварка (или вспомогательные/сопутствующие процессы), выполняемая в зоне
Оценка воздействия сварочного дыма и газов
Приведенную выше информацию следует учитывать при проведении мониторинга воздействия во время сварочных работ. Процесс сварки и состав материала (в первую очередь ингредиенты электрода, если только сталь не имеет покрытия) должны быть основой для классификации групп аналогичного воздействия (SEG).
SEG могут дополнительно определяться конкретной задачей, положением заготовки (относительно зоны дыхания сварщика), наличием или отсутствием LEV и/или другими факторами, связанными с работой.
Эта статья впервые появилась в июньском выпуске журнала Occupational Health & Safety за 2011 год.
Об авторе
Джером Э.Спир, CSP, CIH, является директором J.E. Spear Consulting, LP в Магнолии, штат Техас. Чтобы связаться с ним, позвоните по телефону 281-252-0005 или посетите сайт www.jespear.com.
Технология; Проверка качества сварки
В некоторых конфигурациях информация дополняется оптическими датчиками. Наблюдая за световыми волнами, испускаемыми электрической дугой, выходящей из сварочной горелки, и, в некоторых случаях, за расплавленным сварочным материалом, можно проверить информацию о подводе тепла и многое узнать о присутствующих материалах.Если к сварному шву примешивается пыль или какой-либо нежелательный газ, световые волны, излучаемые во время сварки, будут изменены. Что еще более важно, когда поверхность сварки защищена аргоном, чтобы предотвратить реакцию нагретого металла с кислородом в воздухе, системы оптического контроля показывают, когда экран сломался.
Фрэнк Кирни, инженер, возглавлявший группу разработчиков устройства реального времени, говорит, что на сегодняшний день разработано около 10 различных конфигураций стоимостью от 1000 до 20 000 долларов.Сварщику кажется, что это всего лишь пара проводов, прикрепленных к пистолету. Микропроцессор находится далеко от рабочей станции. Систему можно подключить к динамикам, которые сообщают сварщику, когда нужно внести коррективы.
Первые полевые испытания системы реального времени были проведены на гидроэлектростанции на реке Арканзас в 1977 году. Сейчас ее тестирует Allis-Chalmers, подрядчик, выбранный для ремонта семи больших гидроэлектростанций, построенных на плотинах на этой реке. Г-н Кирни сказал, что компания ожидает, что система наполовину сократит количество сварных швов, требующих ремонта, что сэкономит 600 000 долларов.