ПЛАЗМЕННАЯ СВАРКА [видео, состав оборудования, технология]
Сегодня все большую актуальность приобретает [плазменная сварка], которая позволяет производить работу со многими современными сплавами, в том числе и с цветными металлами, а также с нержавейкой.
Сварка плазмой обеспечивает максимально прочное сцепление обрабатываемых поверхностей, притом, что качество и плотность шва получаются на высоком уровне.
Сварка плазменной дугой и резка выполняются на специальном оборудовании, эксплуатация которого возможна и в домашних условиях, правда его цена достаточно высокая.
За счет прямого действия на обрабатываемые сварочные поверхности воздушно-газовой смесью, которая используется при плазменной сварке, удается избежать разбрызгивания расплавленного металла.
В настоящее время плазменная сварка и резка используются на многих промышленных объектах и позволяет выполнять качественное соединение металлических поверхностей практически любой сложности.
Сварочные аппараты для данного вида сварки представляют собой достаточно компактные устройства, которые дополнительно оснащаются системой для подачи воздушно-газовой смеси.
Плазменная сварка и резка имеет достаточно простой принцип работы, который заключается в том, что расплавление металла в заданном месте происходит от прямого действия потока плазмы в воздушно-газовой защитной смеси.
Принцип работы, который производит аппарат сварки плазмой можно увидеть на видео, которое размещено ниже в статье.
Особенности работы
Плазменная сварка и резка в чем-то схожа с аргоновой, при этом при помощи нее посредством прямого действия осуществляется расплавление металлических поверхностей в заданном месте.
В процессе работы используется воздушно-газовая смесь, которая исполняет роль своеобразной защиты сварочной ванны от агрессивного атмосферного действия.
Вообще, непосредственно под плазмой принято понимать ионизированный газ, структуру которого составляют сильно заряженные ионы и электроны, кроме этого, в процессе участвуют и нейтральные молекулы атомов.
В некотором смысле к плазме можно отнести и стандартную дугу, однако она не может сравниться с тем потенциалом, которым обладает сама плазма.
Для того чтобы увеличить, как мощность, так и температуру обыкновенной дуги, необходимо произвести в принудительном порядке вдувание в нее специального плазмообразующего газа, либо выполнить ее сжатие, что сделать не так просто.
Все эти процессы происходят в плазмотроне, который исполняет роль резака.
Главной отличительной особенностью плазменной сварки является достаточно высокая температура плазменной дуги, которая может достигать показателей в тридцать тысяч градусов по Цельсию.
В момент прямого действия плазменной дуги особым образом осуществляется подача воздушно-газовой смеси, что дает оптимальную возможность добиться высокоскоростного течения дуги непосредственно из самого плазмотрона.
Здесь следует отметить, что при выполнении данной сварки происходит соединение тепловой и кинетической энергии, вследствие чего образуется дуга с более мощным потоком.
Плазменная дуга, в отличие от обычной, имеет и значительно более высокое давление на обрабатываемые поверхности, а ее рабочий диаметр получается, наоборот, значительно меньшим.
Кроме этого, форма плазменной дуги является полностью цилиндрической. Следует отметить и то, что данный вид сварки является более универсальным, что позволяет производить работу на более сложных поверхностях.
За счет прямого действия плазменной сварки удается добиться более глубокого проплавления металла. При соблюдении определенных условий может выполняться плазменная сварка своими руками.
В этом случае необходимо отметить то, что цена на такой аппарат достаточно высокая, а для многих домашних мастеров именно цена является определяющим фактором при выборе оборудования.
На видео ниже можно увидеть, как выполняется сварка и резка плазмой в домашних условиях.
Видео:
Основные разновидности
Условно данную сварку прямого действия можно поделить на различные типы в зависимости от силы тока и способа подачи воздушно-газовой смеси.
Так, сегодня доступны аппараты с большими и средними токами, а также микроплазменные аппараты. Сварка и резка, выполняемые на средних токах, по некоторым своим характеристикам схожи с аргоновой, однако более безопасная и мощная.
По своим возможностям такое сваривание плазмой может только превзойти лазерная или сварка электронным лучом.
В момент выполнения работы плазменная дуга оказывает более высокое давление на сварочную ванну, чем обыкновенная.
Это дает возможность в несколько раз увеличить передачу тепла непосредственно в самую глубь обрабатываемой металлической поверхности.
Следует отметить, что при работе на средних токах нет необходимости дополнительно использовать присадочную проволоку, что несколько снижает затраты на выполнение соответствующих работ.
При выполнении работ на больших токах, металлические поверхности подвергаются еще более мощному воздействию плазмы. В этом случае для начала происходит своеобразная разрезка металла, после чего она заваривается с еще большей прочностью.
Данный тип сварки особенно актуален для изделий из меди, титана, либо легированных сталей.
При выполнении данного типа сварки микротоками, используются токи с относительно малой величиной, при этом обязательно наличие воздушно-газовой смеси с достаточным уровнем ионизации.
Данный тип сварки используется преимущественно тогда, когда необходимо произвести соединение тонких металлов, а также при необходимости закрепить на металлической поверхности некоторых элементов.
Суть данного процесса заключается в том, что для начала образуется дежурная дуга, которая зажигает основную в тот момент, когда к рабочей поверхности подводится непосредственно сам плазмотрон.
Плазмотрон имеет два независимых сопла. Одно из них предназначено для подачи газа, образующего само пламя, а другое подает воздушно-газовую защитную смесь.
При этом в процессе работы происходит непрерывное охлаждение горелки за счет подачи воды.
Состав используемых газовых смесей при данном типе сварке зависит, главным образом, от типа металла, который нужно соединить между собой.
Оборудование, предназначенное для сварки плазмой, может функционировать по своему прямому назначению в нескольких различных режимах.
Сварка алюминия сопряжена с некоторыми трудностями. Сплавы алюминия обладают неудовлетворительной свариваемостью.
Решить многие проблемы свариваемости сплавов из алюминия поможет сварка и резка плазмой. Действие плазмы постоянного тока обратной полярности повышает качество сварных швов сплавов из алюминия.
Выбор технологии плазменной сварки и резки алюминия и режима определяется составом сплава из алюминия.
Наиболее часто применяется автоматическая сварка алюминия плазмой с подачей присадочной проволоки.
На видео, которое размещено ниже, показано, как выполняется сварка алюминия плазмой.
Видео:
Состав оборудования
Любое современное оборудование данного типа можно отнести к двум различным типам. Основное различие здесь заключается в характеристиках вырабатываемой дуги.
В любом случае, дуга должна обязательно обеспечивать не только высокий КПД самого процесса, но и относительно малый участок температурного действия на рабочие поверхности обрабатываемых материалов.
Используемое оборудование должно полностью соответствовать нормам безопасности и обеспечивать сравнительно небольшой расход используемых в процессе работы защитных газов.
Также сварка данного типа должна иметь возможность осуществлять соединение тонколистовых стальных поверхностей с различными неметаллами.
Кроме этого, на обрабатываемых поверхностях могут оставаться только несущественные деформации.
Во многом характеристики таких установок определяет цена, и чем она выше, тем больше функциональных возможностей имеет такой аппарат.
На видео, которое размещено ниже, подробно показан процесс выполнения плазменной сварки.
Когда вы выбираете аппарат данного типа, в первую очередь необходимо руководствоваться тем, какие именно поверхности планируется обрабатывать с его помощью.
Следует отметить и то, что данное оборудование выпускается как в ручном варианте, так и в автоматическом.
В устройствах данного типа основным питающим элементом является специальный инвертор, который обеспечивает подачу тока с определенными параметрами.
При использовании устройств данного типа, можно не только повысить общую скорость выполнения соответствующей работы, но и значительно снизить количество отходов.
Видео:
Для работы самого обыкновенного плазменного аппарата необходимо только лишь электричество, а также струя воздуха определенного давления.
Также, качество шва во многом зависит и от используемого в процессе работы плазмотрона, который является, по сути, основным рабочим инструментом.
Более подробно о том, как работает плазменный аппарат, рассказано на видео в нашей статье.
Плазменная сварка
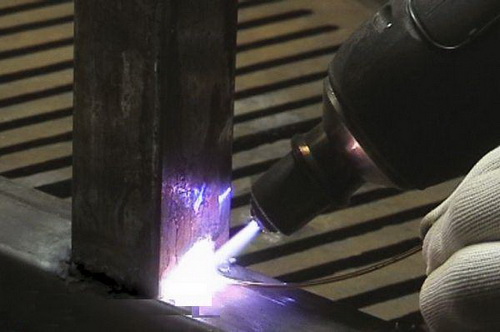
Современные производственные технологии не стоят на месте, поэтому теперь появилось огромное количество методов сваривания металлов. Плазменная сварка входит в это число, ведь она является самой продвинутой и современной из всех возможных.
Сварка плазмой позволяет облегчить процесс сваривания металлов быстрым и удобным, металлические детали при необходимости хорошо разрезаются при помощи специализированного аппарата, ну а монтажные работы становятся более легкими при применении плазмы. Также такое сваривание является довольно безопасным, вот только не стоит забывать об осторожности сварщика, ведь нужно обязательно соблюдать все нормы безопасности при сваривании специальными аппаратами.
Плазменное сваривание и для чего оно нужно
Сплавы и металлы, к примеру, нержавеющая сталь, металлы цветные или разнообразные соединения, тяжело поддаются свариванию, они тяжело обрабатываются и соединения в большинстве случаев получаются не особенно качественными и крепкими. Поэтому теперь появился новый метод сваривания при помощи сварки плазмой, которая позволяет сделать этот процесс надежным.
Данный тип сваривания основан на специальных характеристиках плазмы, поэтому ее в основном применяют при строительных работах.
Плазменная дуговая сварка сильно напоминает сварку аргоном, вот только в этом случае не используется обыкновенная дуга, ведь температуры могут достигнуть 30 000 градусов по Цельсию.
Поэтому при сваривании плазмой при помощи специализированных приспособлений можно соединять различные конструкции, которые вообще невозможно соединить обычным способом, в котором самая высокая температура плавления достигает лишь 5000 градусов.
Данный процесс основан на расплавлении металлических сегментов на поверхности при большой скорости ионизированных газов, который состоит из частей, проводящих ток.
В процессе потоки ионизируются при нагревании быстро движущейся дуги, которая выходит из плазмотрона. Ионизация становится выше во время роста температур и газов.
Плазменная дуга, имеющая высокие мощности и температуры, получается из обыкновенной дуги при сжигании и выдувании в дугу, ну а плазмообразующий газ сформировывает ее до необходимого состояния. Обычно данным газом является аргон или смесь его гелия и водорода.
При ионизации кинетические частицы, содержащиеся в газах начинают увеличивать тепло дуги и энергии. При этом дуга из плазмы начинает сильно давить на металлы, ведь ее диаметр существенно уменьшаться.
Положительные стороны сваривания плазмой
Если сравнивать сваривание плазмой с обычной сваркой, то стоит отдельно отметить некоторые положительные стороны плазменно-дугового сваривания:
- аппарат можно использовать при сваривании металлических конструкций;
- металлы большой толщины 50 — 200 мм легко разрезаются при плазменной сварке;
- значительно экономятся затраты на газы, ведь здесь вполне можно обойтись без бутана, пропана и ацетилена;
- швы при сварке плазмой точные, ровные и аккуратные;
- металлы при сварке не деформируются;
- сварка плазмой безопасна при соблюдении всех норм и технологий, ведь не требуется применение газовых баллонов.
Микроплазменная сварка и ее особенности
Сварку плазмой можно подразделить на три разновидности, которые напрямую зависят от того, какая сила тока применяется во время процесса:
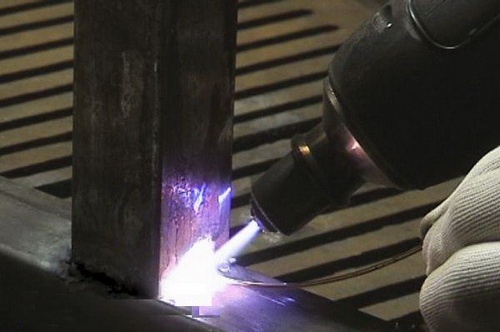
сваривание при использовании большого тока более 150 А;
сваривание на среднем режиме тока от 50 до 150 А;

сваривание микроплазменное при силе тока от 0,1 до 25 А.
Микроплазменное сваривание является довольно распространенным способом из всех разновидностей сваривания плазмой. Данный вариант подразумевает под собой воздействие тока всего в нескольких Амперах, это приводит к образованию дежурной дуги, которая постоянно горит между медным водоохлаждающим соплом и вольфрамовыми электродами, имеющими диаметр от 1 до 2 мм.
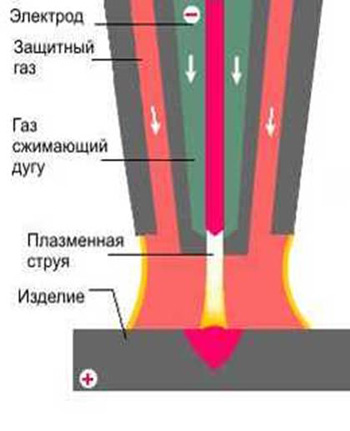
Основная дуга приходит в действие тогда, когда плазма подводится к металлическому изделию для последующей обработки. Плазмотронное сопло диаметром 0,5 — 1,5 мм подает газы, которые и начинают образовывать плазму.
Плазменная сварка и резка металла
Плазменная дуга имеет диаметр максимум 2 мм, именно поэтому значительные тепловые энергии сосредотачиваются на небольшом сегменте металлических заготовок. Данная разновидность сваривания имеет довольно качественный эффект для изделий, в которых толщина не превышает 1,5 мм.
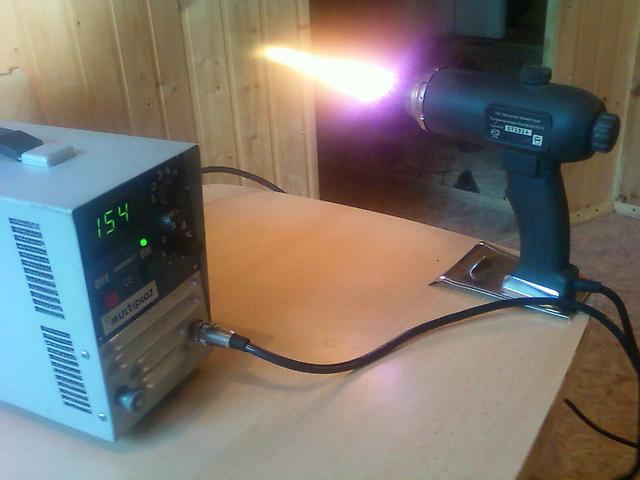
Важно! Чтобы образовался защитный газ и плазма рекомендуется пользоваться аргоном при сваривании такого типа. Иногда можно применять разнообразные добавки для сваривания, это напрямую зависит от обрабатываемых материалов.
Аппарат для плазменной сварки данной разновидности способен сваривать металлические детали и конструкции в разных режимах. С его помощью можно изготавливать тонкостенные трубы и емкости, производить ювелирную продукцию и украшения, сваривание фольги и разнообразных креплений, а также многие остальные операции.
Сварка при средней силе тока и ее особенности
Сваривание на среднем режиме тока применяется при помощи раскаленных газов, сила тока здесь должна быть 50 — 150 Ампер. Она должна находиться между сварочной дугой и лучом электронного типа (лазерным).
Использование данного способа сильно напоминает аргоновую сварку при применении вольфрамовых электродов. Однако сваривание на средней силе тока плазменного типа имеет более мощную дугу, поэтому и оказывает сильное действие на определенные участки свариваемых металлов, что обеспечивает высокую эффективность и качество соединения.
Плазморез и работа с ним
Аппарат плазменной сварки действует на среднем режиме тока, поэтому металлические изделия расплавляются качественно и глубоко. Шов при этом становится довольно узким, чем когда обыкновенная дуга оказывает действие на заготовки.
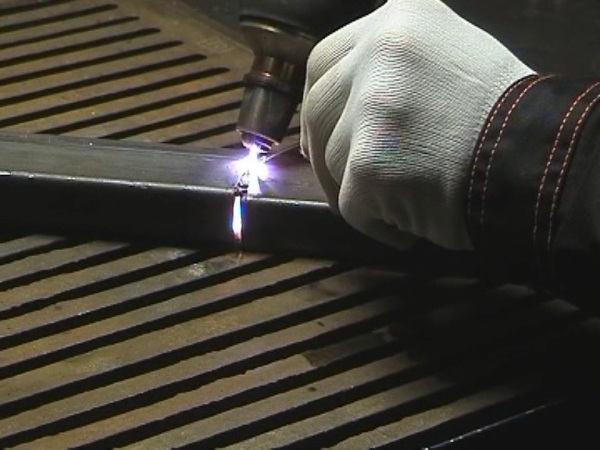
Получается прекрасный результат из-за высокой энергии и большого воздействия плазменной дуги на ванну сваривания.
В результате под дугой начинает образовываться жидкий металл небольшой толщины.
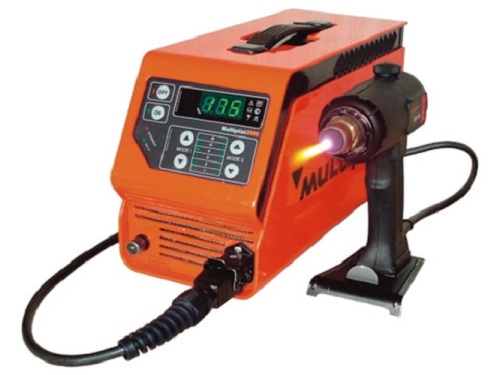
Также металлические заготовки прекрасно прогреваются на необходимой глубине, поэтому и получается сваривание металлов самого высокого качества.
Плазменная сварка при большом токовом режиме
Применение плазменной сварки на токах большого размера больше 150 Ампер дает еще более высокую мощность на металлические заготовки. Дуга оказывает самое мощное воздействие на металлы при использовании не плавящихся электродов.
Заготовка при этом способе проплавляется полностью. Сварочная ванная начинает образовывать сквозное отверстие. Весь процесс сваривания металлов сначала разрезает заготовки, а затем заваривает их с высокой прочностью. Расплавленные металлы, которые выступают из сквозного отверстия, удерживаются в необходимом месте при силе поверхностного натяжения.
Сущность плазменной сварки при высокой силе тока необходима при обрабатывании титановых заготовок и сплавов, медных и алюминиевых деталей, легированных сталей и с низким содержанием углерода, а также многих других изделий.
При использовании данного метода сваривания можно значительно сократить расходы, связанные с качественной сваркой металлических конструкций и сооружений, работа будет происходить с большей быстротой и качеством.
Аппарат для плазменной сварки
Самыми распространенными аппаратами для плазменной сварки являются аппараты для газовой, электрической, инверторной и плазменной сварки. Плазменный аппарат является самым высокотехнологичным и современным.
По большей части все мастера и специалисты в своем деле стараются приобретать и пользоваться именно плазменными сварочными аппаратами. Вед данные приспособления помогают значительно сократить время процесса сваривания, причем получить самое высокое качество и прочность соединения необходимых металлов и конструкций.
Чтобы сварочный аппарат такого типа прекрасно функционировал, необходима только подача электрического тока и использование сжатого воздуха. Такое оборудование также радует профессионалов тем, что при ремонте требует замены лишь сопла и электрода, ну а газовое оборудование постоянно необходимо заправлять и заменять присадки.
Сварочное оборудование для плазменной сварки подразделяется на два вида, это напрямую зависит от того, какого типа будет плазменная струя, прямая или косвенная.
Сварочная дуга прямого типа бывает цилиндрической формы, главным ее отличием является высокая температура. В данных устройствах для сваривания более хорошо проработана система охлаждения.
Аппараты с прямой дугой имеют более большой КПД, в сравнении с косвенной дугой. Именно поэтому ими пользуются в большинстве случаев при разрезании, наплавлении и сваривании металлических изделий, а косвенные аппараты чаще предназначены для нагревания и напыления.
Технология плазменной сварки
Плазменная сварка имеет отличия от остальных способов сваривания материалов. Именно поэтому следует учитывать некоторые особенности данного процесса. Необходимо заблаговременно подготовить необходимое оборудование и материалы, а затем придерживаться точной технологии во время всего процесса.
Необходимо для нормального сваривания заточить электрод под наклоном около 30 градусов. Образовавшийся конус должен быть равен 5 — 6 диаметрам электрода. Конец не должен быть слишком острым.
Для сваривания листов из металла следует тщательно следить за образованиями зазоров, которые будут больше 1,5 мм. Сварные стыки должны совпадать с остальными, чтобы соединение получилось надежным и качественным.
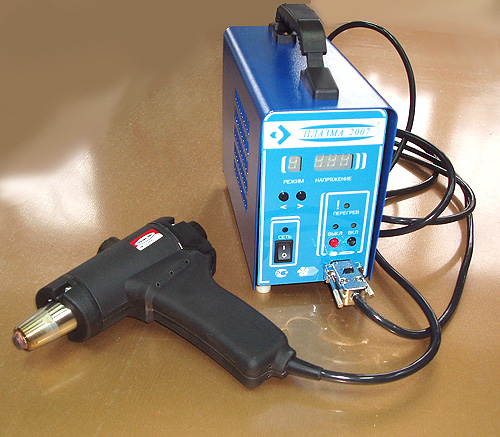
Процесс сваривания следует проводить при применении постоянного тока. Газ необходимо подавать к необходимому месту за 15 секунд до того момента, как возбудится плазменная дуга.
Оборудование для плазменной сварки нужно держать на расстоянии меньше 1 см от поверхности.
Во время процесса сваривания нужно смотреть, чтобы дуга не оборвалась. Если это случилось, то необходимо тщательно зачистить данное место. Сварка возобновляется немного раньше того места, где произошел обрыв.
При соблюдении правил эксплуатации данного прибора процесс станет качественным, быстрым, а главное безопасным.
Плазменные сварочные аппараты: видео, фото, своими руками
Аппараты плазменного вида в огромном количестве современных сварочных устройств, заняли важное место. Это многофункциональное устройство. Его используют:
- выполняя сварочный процесс;
- резку;
- термическую обработку;
- спаивание;
- воронение.


Работа данного аппарата основана на плазменном потоке, подаваемом под влиянием высокого давления. Это дает возможность производить не только сварку, но и резку. Многие считают данный факт нереальным, но высокотемпературный поток получается из самой обычной воды. Под действием испарителя она переходит в парообразное состояние. Выход через сопло становиться только одним вариантом для передвижения пара. Но, на этом выходе пар обрабатывают анодно-катодным действием, и таким путем он становится разогретой плазмой с очень высокой температурой (от 6 до 7 тыс. градусов).
Главная особенность такого аппарата состоит в его возможности быстро достигать показателей очень высоких температур. Буквально за несколько секунд создают поток плазмы с температурным показателем в 30 тыс. градусов.
Все современные устройства этого типа оснащают системой, которая регулирует температуру. Это превращает сварочный процесс в комфортную работу.
Объем факела легко контролируется специальной гайкой. Она помогает выставить не только размер, но и форму факела.
Функционирует сварочный аппарат от сетевого обеспечения, равного 220 В. А небольшая масса и компактность агрегата позволяют применить его и в гараже, и в доме. Это оборудование превосходно справляется с такими задачами:
- нарезка металла толщиною в 5 мм;
- соединение и резка керамики, стеклянных изделий и натурального камня.
В основу плазменного аппарата для сварки положили устройство — плазмотрон. Многие отмечают, что в этом названии есть что-то фантастическое. Он бывает двух типов:
- Прямого действия. Их подключают, когда нужна генерация дуги.
- Косвенного действия. Их подключают, когда необходима генерация струи плазмы.
Сварочный аппарат прямого действия использую немного чаще, зато устройства косвенного типа оснастили лучшей системой охлаждения. В процессе работы агрегатов прямого действия, дуга образуется в части между стержнем из вольфрама (он и является электродом) и изделиями, на которых проводят сварочные мероприятия. Данный сварочный аппарат на выходе образует дугу, которая имеет четкую форму цилиндра. Она немного расширена возле поверхности для работы. Эта дуга имеет очень высокую температуру, из-за чего данный вид агрегатов применяют для наплавок, резки и сварки изделий.


Типы дуг плазмотронов
Аппарат косвенного вида образует совсем другую форму дуги. Она конусовидная. И температура в данном случае немного ниже. Естественно, что и КПД такого устройства немного меньше. По вышеуказанным причинам, плазменные аппараты с косвенным действием используют только для напылений и для прогрева.
Кроме больших температурных показателей, плазменный аппарат имеет еще одну особенность. Он соединяет не только металлы, но и стекло, пластик, и даже разные по химическому составу материалы (например, заготовка из пластика и заготовка из металла). Для применения в быту эти устройства называют наиболее подходящим вариантом.
- Схема работы плазменного сварочного аппарата
- Принцип работы плазменного сварочного аппарата
Изготовление плазменного сварочного аппарата своими руками
Данный сварочный аппарат для полноценного функционирования потребует сжатого воздуха и электричества. Если для работы используется компрессорное оборудование, то аппарату будет нужно только электричество. Исходя из этого факта, при сварочных работах придется менять электроды и сопло.
- Сборочный чертеж плазмотрона
- Детали для самодельного плазмотрона
Самостоятельная сборка устройства – это очень кропотливая работа. В первую очередь разрабатывают схему блока питания. От него зависит то, насколько полноценно будет работать сварочный аппарат.
Для работы необходимо:
- Дроссель, который используют для обычных сварочных аппаратов. Он стабилизирует напряжение. Без этого плазма будет гаситься постоянными скачками напряжения. А для сварочных мероприятий это недопустимо.
- Трехфазный тиристорный выпрямитель. Его включают в схему для выполнения ограничений подачи тока (в пределах 50 А).
- Машинный стартер. Он выполняет поджег в автоматическом режиме. Также для этой цели можно использовать трамблер.
- Создание корпуса требует особого внимания. Если запастись нужными материалами и хорошими станками для обработки металла, то самостоятельное изготовление завершиться качественным результатом.
Для того, чтобы получить полное представление о том, как должен выглядеть сварочный аппарат, советуют выучить его схему. В сети есть огромное количество вариантов.
Горелка. Ей в устройстве принадлежит одна из главных ролей. Это простая рукоятка, где располагается анод и катод. Анод также является соплом, его изготавливают из меди. Во время работы он охлаждается водой. В роли катода используют вольфрам. Оба элемента между собою не контактируют, потому, что изолируют спецматериалами (чаще всего, для этого применяется асбест).
Для образования дуги плазмы между анодом и катодом используют постоянное напряжение (в 100 В). Эта дуга нагревает газ до нужных температурных показателей. Сварка начинает действовать, при этом появляется плазменный поток, в который помешают заготовки для сварки или производят резку.
Подводя итог, можно заключить, что плазменная сварка своими руками — это реальная вещь. В результате можно рассчитывать на качественное соединение деталей из металла. Такой аппарат придет на помощь во многих ситуациях, особенно актуальным он будет при ремонтных работах автомобиля.
Плазменная сварка принцип работы
пер.Каштановый 8/14 51100 пгт.Магдалиновка

Nikolaenko Dmitrij
Плазменная сварка принцип работы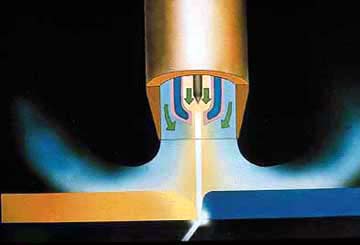
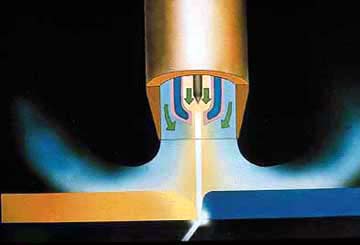
- 5
- 4
- 3
- 2
- 1
Плазменная сварка, принцип работы которой описан ниже, применяется для сваривания металлов любой температуры плавления, хотя рекомендовано использовать технологию для работы с тугоплавкими сплавами. Один и тот же аппарат успешно справляется как со свариванием, так и с резкой, поэтому это достаточно универсальный инструмент и технология, благодаря чему она и получила широкое распространения в промышленности и бытовых условиях.
Принцип работы плазменной сварки основан на локальном разогреве металла потоком плазмы, которая генерируется в плазмотроне. Плазма представляет собой ионизированный газ, который под давлением выбрасывается через сопло плазмотрона. В этом газе содержаться заряженные частицы, которые отличаются способностью проводить электрический ток. Процесс ионизации газа производится непосредственно в плазмотроне под воздействием сжатой электрической дуги высокой мощности.
Температура генерируемой плазмы находится в пределах от 5 000 — 30 000 градусов по шкале Цельсия, чего достаточно, чтобы расплавить любой тугоплавкий металл. Важно отметить, что на «выходе», обычный, бытовой плазменный аппарат способен выдать до 7 000 градусов Цельсия. При соблюдении ряда технологических требований и создании должных условий, с помощью плазмы возможно сваривание металлических и не металлических деталей.
На чем работает сварка этого типа?
Не смотря на внушительные характеристики, приведенные выше, плазменная сварка, принцип работы которой не сложен, достаточно проста в устройстве и обслуживании. Как упоминалось выше, в этой технологии применяется направленная плазменная дуга, генерируемая подаваемым электрическим током требуемой сил (А). В свою очередь плазменная дуга образуется из так называемой «дежурной» (обычной). Основными характеристиками установки является следующие три качества:
- Минимальный диаметр плазменной струи;
- Высокая мощность;
- Высокие рабочие температуры.
Перечисленные характеристики вносят свои корректировки и в саму конструкцию, что вполне логично (можно читать и наоборот). Для достижения описанных выше характеристик, обязательным образом выполняются следующие условия:
- Интенсивное охлаждение стенок плазмотрона производится непрерывно;
- Используется не плавящийся вольфрамовый электрод, производимый с присадками тория;
- Обязательно организуется защита электрода путем подачи инертного газа (аргона).
Плазменная сварка принцип работы или как с ней работать?
Плазменная сварка принцип работы которой заключается в следующих действиях, имеет высокую производительность и качество сварных соединений. Итак, вот основополагающие принципы сваривания металлов плазменной сваркой:
- сварочный аппарат передает ток в плазмотрон, где возбуждается дуга. Затем подводится газ, образующий плазму. Газ нагревается дугой и ионизируется. Этот газ состоит из заряженных ионов и электронов, а также нейтральных молекул и атомов;
- получается плазма, которая вырывается из горелки со скоростью более 2000 км/ч. Она имеет температуру 100000 С;
- сжатие плазменной дуги происходит устройством плазмотрона, которое охлаждается водой;
- после этого необходимо взять присадочную проволоку, одеть средства защиты и подвести сопло горелки к стыку детали на расстоянии 5 мм. Горелку держать под углом 70<sup>0</sup>;
- поверхность нагревать до расплавления на стыке и образования сварной ванны. Для качественной сварки необходимо поддерживать одно расстояние между соплом и стыком детали. Выбрать скорость перемещения горелки такой, при которой не будет происходить выдувания металла. При необходимости используется присадочная проволока.
Такая технология плазменной сварки металла позволяет качественно производить соединение деталей с наименьшими затратами времени, энергии и ресурсов. Процесс практически аналогичен и для использования этой технологии как на производстве, так и в бытовых условиях.
Плазменная резка, сварка, наплавка и обработка материалов.
Содержание страницы
1. Физическая сущность генерирования плазмы
Плазма – это частично или полностью ионизированный газ. Источником ионизации являются электрические разряды (дуговой, искровой, тлеющий и пр.). Степенью ионизации называют отношение числа ионизованных атомов к полному их числу в единице объёма плазмы. В зависимости от степени ионизации различают слабо, сильно и полностью ионизированную плазму. Степень ионизации плазмы зависит от многих факторов и прежде всего от температуры. Различают низкотемпературную плазму T ≤ 105 K и высокотемпературную T > 106…108 K
Существование плазмы поддерживается непрерывно протекающим процессом ионизации. Интенсифицировать процесс плазмообразования можно путём обдува соосным потоком газа. Если часть столба электрической дуги поместить в узкий канал с охлаждаемыми стенками, то будет достигнута дальнейшая интенсификация плазмообразования. Это связано с тем, что в узком канале столб дуги сжимается, особенно при обдуве её соосным потоком газа. С увеличением электрического тока столб дуги из-за ограничивающего действия стенок канала расширяться не может, температура газа и степень ионизации резко повышаются. Практически весь газ, проходящий сквозь столб сжатой дуги ионизируется и превращается в плазму.
Различают плазменные дуги прямого и косвенного действия.
В дуге прямого действия (рисунок 1.11) в качестве анода используется обрабатываемый материал. В этом случае плазменная струя совмещена со столбом дуги по всей длине, начиная от входного среза канала сопла и кончая анодным пятном на фронтальной поверхности полосы реза. Тепловая энергия вводится в разрезаемый металл струей плазмы и столбом дуги. При этом коэффициент полезного действия (КПД) прямой плазменной дуги составляет 60–70%. Недостатком дуги прямого действия является невозможность обработки диэлектрических материалов.
Дуга косвенного действия возбуждается и горит между электродами, которые не связаны с обрабатываемым материалом. Катодом служит электрод плазмотрона, а в качестве анода используется его формирующее сопло. Объект обработки не включен в электрическую цепь. Столб дуги расположен внутри плазмотрона. Плазмообразующий газ контактирует со столбом дуги на коротком участке, протяженностью от торца электрода до выходного среза канала сопла. Далее плазма существует независимо от столба дуги. Вследствие этого температура и скорость истечения струи плазмы по мере удаления от выходного среза сопла резко уменьшается, а КПД при использовании дуги косвенного действия не превышает 30–40 %.
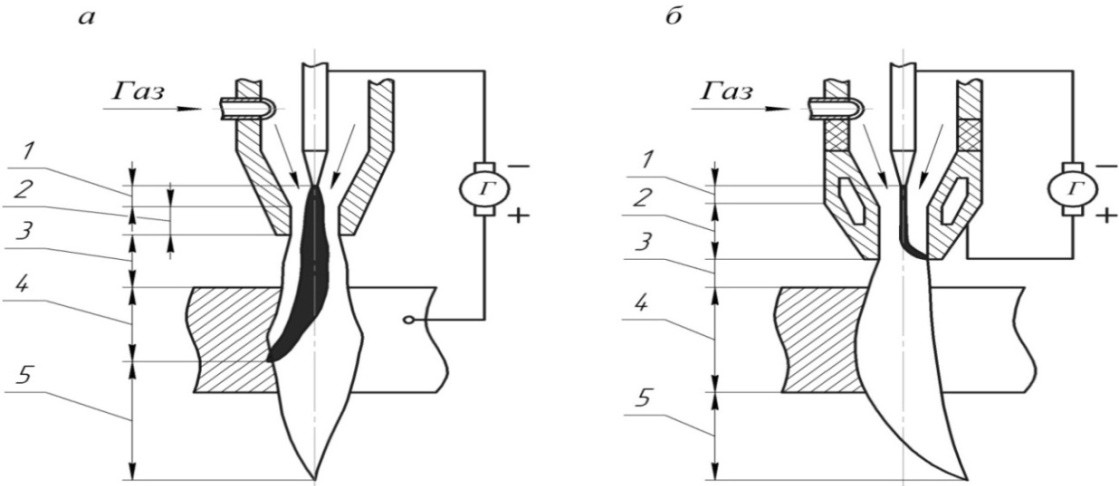
Рисунок 1.11 – Элементы схем плазменных дуг прямого (а) и косвенного (б) действия и их участки: 1 – закрытый; 2 – сжатый; 3 – открытый; 4 – рабочий; 5 – факел; Г – генератор тока
2. Плазмообразующие среды
В качестве плазмообразующих сред применяют аргон, гелий, азот, воздух, водород, воду.
Аргон – химически инертный газ с низкой теплопроводностью, поэтому он хорошо защищает от перегрева и разрушения электрод и сопло. Однако, аргон малоэффективен для преобразования электрической энергии дуги в тепловую. Он обладает самой низкой напряженностью поля столба дуги, т. е. аргоновая плазма вызывает значительное падение напряжения на дуге. Это означает, что при одинаковом токе в аргоновой плазме выделяется минимальное количество энергии по сравнению с другими плазмообразующими газами.
Гелий – в отличие от аргона обладает большей теплопроводностью. В случае его применения для плазменной резки происходит быстрый нагрев и разрушение сопла. Гелий обеспечивает высокую напряженность дугового столба примерно в четыре раза более высокую, чем у аргоновой плазмы. Гелий, в отличие от аргона, является более эффективным преобразователем энергии дуги в тепло и применяется в смеси с аргоном.
Азот является наиболее приемлемым газом для стабилизации плазменной дуги. Теплоёмкость азотной плазмы в пять раз выше аргоновой. Напряженность поля столба дуги в азоте более высокая, чем в аргоне. Поэтому использование азота в качестве плазмообразующего газа эффективно для преобразования электрической энергии в тепловую.
Воздух является сильным окислителем металлов. При использовании воздуха по сравнению с азотом скорость резки углеродистых и низколегированных сталей при тех же параметрах дуги возрастает более, чем в 1,5 раза.
Водород обеспечивает высокую напряженность поля дугового столба. Диссоциация и ионизация водорода происходит при более низких температурах, чем аргона и гелия. Теплоёмкость водородной плазмы несколько ниже азотной, но в четыре раза выше аргоновой. Водород обладает высокой теплопроводностью и является эффективным преобразователем энергии дуги в тепло. Использование водорода в качестве плазмообразующего газа приводит к быстрому разрушению сопла в результате интенсивного нагрева. Поэтому водород применяют как добавку к аргону или азоту.
Вода может использоваться в качестве плазмообразующей среды самостоятельно, в виде пара или как добавка к рабочему газу. Применение воды обеспечивает интенсивное охлаждение периферийных участков столба дуги и концентрирует его. В результате температура в ядре дуги возрастает, увеличивается его проплавляющая способность.
Анализ рассмотренных плазмообразующих сред показывает, что ни один из газов не может обеспечить самостоятельно весь комплекс положительных свойств идеальной плазмообразующей среды. Поэтому используют смеси из различных газов. Хорошо зарекомендовали себя смеси аргона и азота в сочетании с водородом. В сочетании с азотом и воздухом применяется вода. Плазмообразующая среда оказывает существенное влияние на изменение фазового состава металла прилегающего к поверхности реза, на его химический состав и механические свойства.
3. Ввод компонентов плазмообразующей среды в электрическую дугу
Способы ввода плазмообразующей среды в электрическую дугу можно разделить на четыре группы: аксиальный (осевой), тангенциальный (вихревой), распределённый, транспирационный (рис. 1.12).
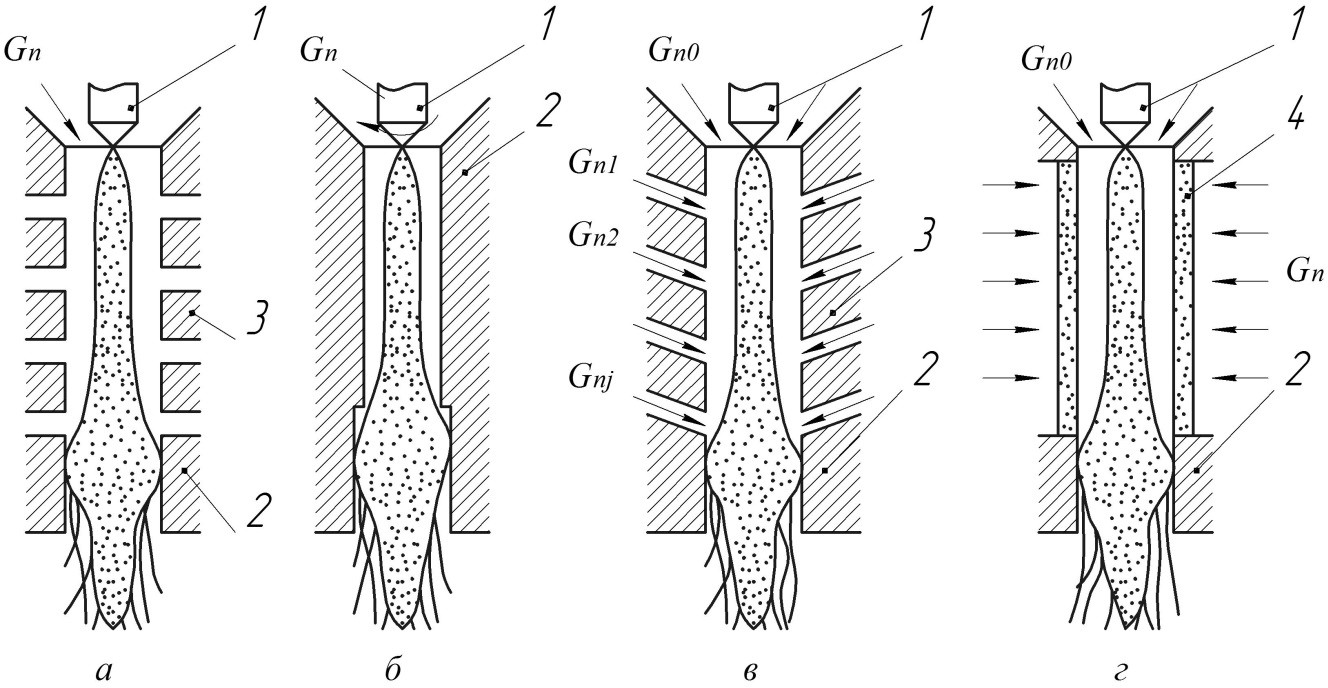
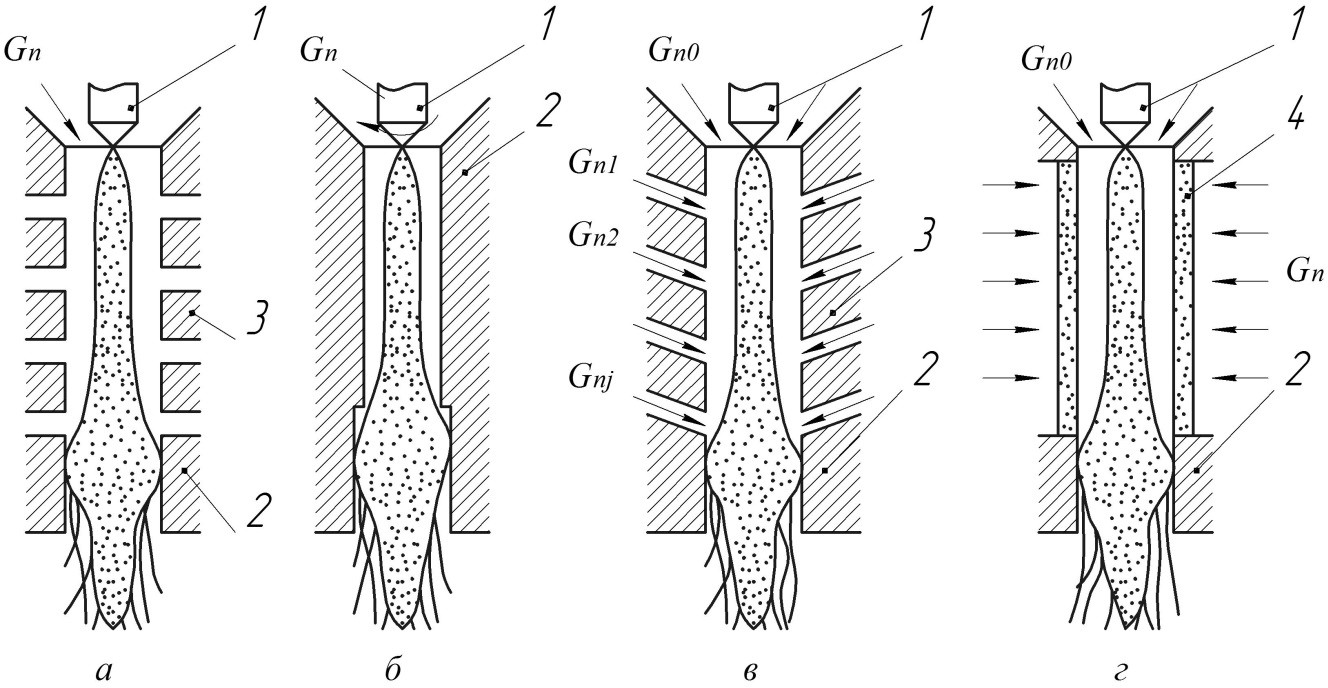
Рисунок 1.12 – Схемы ввода плазмообразующей среды в дуговой разряд: а – аксиальный; б – тангенциальный; в – распределённый; г – транспирационный; 1, 2 – электроды; 3 – межэлектродные вставки; 4 – пористая стенка; Gno– стабилизирующий газ; Gn, Gn1…Gnj – плазмообразующие газы
Аксиальный ввод используется в различных плазменных устройствах, применяемых в основном для обработки дисперсных материалов, для сварки, плавки, рафинирования металлов, требующих аксиального потока плазмы. Он позволяет обеспечить хорошую стабилизацию разряда, снижения турбулентных пульсаций в плазме, возможность получения ламинарных потоков, повышение однородности прогрева газа в разряде, равномерность его распределения по сечению канала.
Тангенциальный ввод используется для повышения термоизоляции плазмы. Газ подается в разрядную камеру по специальным каналам, в результате чего образуется газовый вихрь, обдувающий столб дуги и генерируемую плазменную струю. Слой холодного газа под действием центробежных сил располагается у стенки, предохраняя её от контакта с дугой.
Плазмотроны с тангенциальным вводом газа, в отличие от аксиального, имеют больший термический КПД; более высокую эффективность преобразования электрической энергии в тепловую; хорошую пространственную стабилизацию разряда.
К недостаткам данного способа относятся: образование вихревой плазменной струи с повышенным рассеиванием мощности; сложности ввода исходного материала в плазменный поток; невозможность получения ламинарных потоков; высокий уровень шума.
Распределённый ввод во многом аналогичен аксиальному вводу газа. В этом случае повышается термоизоляция плазмы от стенок канала и возможно создание плазмотронов с высоким термическим КПД (более 80 %). Длина дуги может быть значительно увеличена, и в связи с этим достигнута необходимая мощность плазмотронов при высоких напряжениях и низких токах дуги.
Недостатками данного способа являются: усложнение конструкции плазмотрона; трудность равномерного распределения газа по сечению разрядного канала; низкое теплосодержание потока плазмы в связи с большим расходом газа.
Транспирационный ввод – это способ ввода газа через пористую стенку. При этом имеет место интенсивное взаимодействие газа со стенкой. Поэтому разрядные каналы с пористыми стенками обеспечивают высокий термический КПД более 90 %. Кроме того обеспечивается равномерность ввода газа в дугу и улучшается её стабилизация.
4. Устройство плазмотронов
Плазмотрон – это устройство, предназначенное для генерации плазмы. Применяется множество конструкций плазмотронов, схема одного из них представлена на рисунок 1.13.
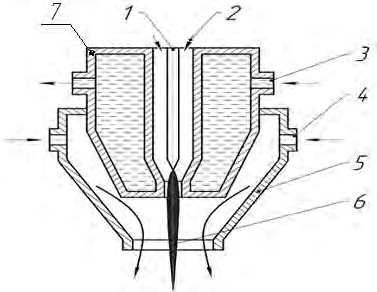
Рисунок 1.13 – Схема конструкции плазмотрона: 1 – электрод; 2 – вход плазмообразующего газа; 3 – водяное охлаждение; 4 – вход защитного газа; 5 – сопло; 6 – факел плазмы; 7 – корпус
Для каждой конструкции плазматрона существует вполне определённая конструкция дуговой камеры. Различают конструктивные и технологические параметры плазмотронов.
К конструктивным параметрам относятся: диаметр канала плазмотрона; длина канала плазмотрона; форма разрядной области; угол оформляющей части входного электрода; диаметр, длина, угол раскрытия выходного электрода; расстояние между рабочей поверхностью входного электрода и входной частью канала.
К технологическим параметрам относятся: ток дуги; расход плазмообразующей среды; способ ввода плазмообразующей среды в плазмотрон; КПД плазмотрона.
Электроды плазмотрона по типу и конструкции зависят от состава плазмообразующей среды. В качестве материала для электродов, работающих в окислительных средах, используют гафний, так как его соединения обладают высокими эмиссионными свойствами, устойчивы к термическим колебаниям токового и газового режимов, а так же условиям охлаждения.
Теплофизические константы гафния и его соединений существенно ниже соответствующих теплофизических констант вольфрама – теплопроводность в три – четыре раза, а температура плавления – в два раза.
Электроды, работающие с нейтральными газами, чаще всего изготавливают из вольфрама. Преимущественно используется вольфрам, легированный окислами лантана и иттрия. Эти добавки существенно улучшают эмиссионные свойства вольфрама, повышая ресурс работы катода и надёжность плазмотрона.
Сопло является основным элементом плазмотрона, определяющим его технические характеристики и ресурс работы.
Назначение сопла – формирование геометрических и энергетических параметров дуги.
Сопло выполняет так же роль электрода, обеспечивающего зажигание вспомогательной дуги. С её помощью осуществляется переход к возбуждению основной дуги, горящей между электродом плазмотрона и обрабатываемым изделием. К основным параметрам сопла относятся диаметр и высота канала, геометрия дуговой камеры плазмотрона. Диаметр и высота канала сопла устанавливаются в зависимости от величины рабочего тока, состава и расхода плазмообразующего газа. При этом находят наиболее благоприятные сочетания таких показателей, как технологические возможности и надежность работы плазмотрона, т. е. стойкость сопла и электрода.
5. Плазменная резка
Плазменная резка широко применяется для обработки конструкционных сталей всех марок толщиной 1-40 мм; коррозионностойких высоколегированных сталей толщиной 3-70 мм; алюминия и его сплавов толщиной 3-80 мм; меди и её сплавов толщиной 2-70 мм.
Процесс резки состоит в проплавлении мощным дуговым разрядом, локализованном на малом участке поверхности разрезаемого металла, с последующим удалением расплавленного металла из зоны реза высокоскоростным газовым потоком.
Струя плазмы формируется путём обжатия столба дуги в канале сопла. Под воздействием стенок канала сопла и струи плазмообразующего газа столб дуги сжимается, его поперечное сечение уменьшается, а температура в центральной части столба повышается до 10000-50000 ºС. В результате внутренний слой газа, соприкасающийся со столбом дуги, превращается в плазму, а наружный слой, обтекающий стенки канала сопла, остается сравнительно холодным, образуя электрическую и тепловую изоляцию между потоком плазмы и поверхностью сопла. Этот охлаждённый слой газа препятствует отклонению столба дуги от заданного направления и замыкания его на стенку канала сопла.
Напряжение сжатой дуги соответствует 60-200 В, что в 3-10 раз больше, чем в свободной дуге. Плотность тока сжатой дуги достигает 100 A/мм2 , т. е. на порядок больше, чем у свободной, а удельная мощность достигает 2·106 Вт/см2.
Процесс плазменной резки, как правило, сопровождается водяной защитой (рис. 1.14). При этом используют резку листов, уложенных над поверхностью или на поверхности воды (а, б), погруженных в воду (в). Возможны сочетания одной из схем (а–г) с
круговой водяной защитой. В этих условиях вода улучшает санитарно- гигиенические условия процесса; обеспечивает повышение качества кромок вырезаемых изделий; способствует снижению тепловых деформаций материала; поглощаются водой вредные выделения.
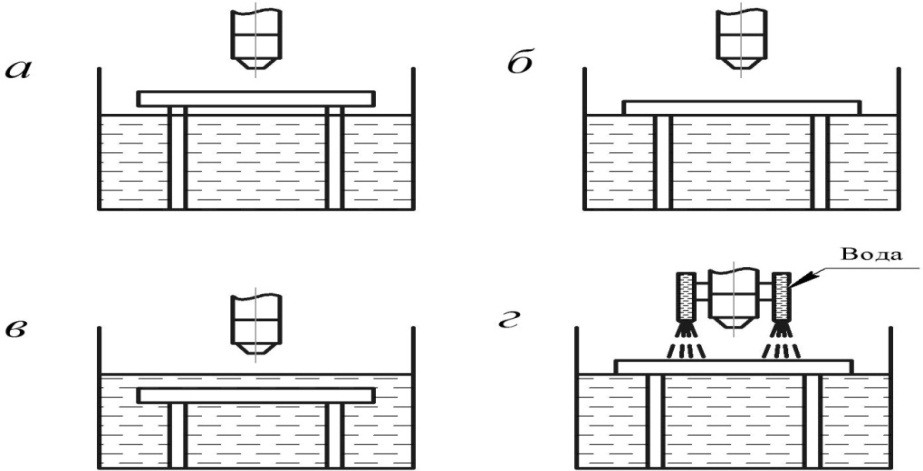
Рисунок 1.14 – Схемы плазменной резки с водяной защитой
На процесс плазменной резки оказывает влияние множество технологических факторов: сила тока, напряжение дуги, скорость резки, расход плазмообразующего газа, скорость его истечения из сопла, диаметр и длина канала сопла, плотность разрезаемого металла и др.
При резке углеродистых и низколегированных сталей толщиной 6-30 мм, исходя из нормальной стойкости электродов (около 2 ч горения дуги), силу тока дуги обычно выбирают в пределах 270±30 А. Уменьшение силы тока снижает скорость резки, увеличение – заметно ускоряет износ электродов.
Сила тока и напряжение режущей дуги не равноценны по интенсивности влияния на скорость резки. Экспериментально установлено, что повышение напряжения более эффективно влияет на скорость резки, чем увеличение силы тока.
Возбуждение дуги происходит при слабом потоке плазмообразующего газа при его расходе 3-5 л/мин. Повышение расхода сверх рекомендуемого приводит к обрыву дуги. Если расход слишком мал, плазменную дугу, горящую внутри резака, не удается выдуть наружу из сопла, или она столь коротка, что её длины не хватает для создания токопроводящего мостика между электродом и металлом. В этом случае режущая дуга не возникает.
После возбуждения дуги увеличение расхода плазмообразующего газа (60-90 л/мин) приводит к обжатию плазменного столба дуги, ширина реза уменьшается, скорость реза увеличивается, напряжение дуги повышается.
Ширину реза устанавливают с учетом суммарного воздействия ряда факторов: диаметра сопла, силы тока, скорости резки, состава и расхода плазмообразующего газа, расстояния от нижнего среза сопла до поверхности разрезаемого металла. В первом приближении ширину реза на верхней кромке можно принимать равной двум диаметрам сопла. Для обеспечения надежной работы при силе тока примерно 300 А и разрезаемой толщине 3-10 мм целесообразно использовать сопла диаметром 1-2 мм. Для стали толщиной 10-30 мм целесообразно использовать сопла диаметром 3 мм, для стали толщиной 31-50 мм применяют сопла с большим диаметром.
В таблице 1.6 приведены рекомендуемые режимы резки углеродистых и низколегированных сталей толщиной 6-30 мм. При этом сила тока составляет 270±30 А, расход газа 80-90 л/мин, расстояние от резака до поверхности металла 10-12 мм, ширина реза по нижней кромке 3-3,5 мм.
Таблица 1.6 – Параметры режимов плазменной резки углеродистых и низколегированных сталей
Параметр | Толщина разрезаемой стали, мм | |||||||
6 | 8 | 10 | 12 | 14 | 16 | 20 | 30 | |
Скорость | 5- | 4-4,1 | 3,15- | 2,8- | 2,5- | 2,16- | 1,66- | 1,0- |
резки, см/с | 5,1 | 3,3 | 3,0 | 2,65 | 2,33 | 1,83 | 1,1 | |
Напряжен | 140 | 145- | 150- | 155- | 160- | 160- | 165- | 170- |
ие дуги, В | – | 150 | 155 | 160 | 165 | 165 | 170 | 175 |
145 |
Алюминий и его сплавы относятся к материалам, для которых применение плазменной резки наиболее эффективно, так как высокая скорость резки сочетается с хорошим качеством реза.
Наиболее полную защиту расплавленного алюминия от окисления и насыщения водородом достигают при использовании аргона в качестве плазмообразующего газа. Преимуществом аргона является так же способность поддерживать плазменную дугу при небольших напряжениях и малой силе тока. Аргоновую плазму обычно применяют при ручной резке листов из алюминиевых сплавов сравнительно небольшой толщины (до 12-20 мм). Недостаток аргоновой плазмы – относительно малая проплавляющая способность дуги и, как следствие скорость резки меньше, чем при использовании других плазмообразующих газов.
Скорость резки можно существенно повысить за счет добавки к аргону водорода. Аргона-водородные смеси, содержащие 35-50 % водорода, обеспечивают минимальную шероховатость реза. По мере увеличения толщины разрезаемого металла рекомендуют увеличивать содержание водорода в смеси, доводя его до 60-80% при толщине 80- 100 мм. Для резки алюминиево-марганцевых сплавов и сплавов типа дуралюмина используют смеси с меньшим содержанием водорода, а так же азотно-водородные смеси.
Ориентировочные параметры режимов плазменной резки алюминиевых сплавов с применением аргона, азота, водорода приведены в таблице 1.7.
Таблица 1.7 – Ориентировочные параметры режимов плазменной резки алюминиевых сплавов
Толщина металла, мм | Диаметр сопла, мм | Сила тока, А | Напряжение на дуге, В | Мощность, кВт | Расход газа, л/мин | Скорость резки мм/с | |
аргона/ азота | водорода | ||||||
15 | 35 | 250 | 140-160 | 40 | 12/24 | 8,5 | 17 |
30 | 180-200 | 18 | 10 | ||||
50 | 5 | 450 | 160-180 | 50 | 24 | 18 | 7,5 |
80 | 30 | 24 | 7,0 |
Медь и медные сплавы характеризуются высокой теплоемкостью и теплопроводностью. Поэтому при их резке используют более мощные дуги, чем при резке стали. В качестве плазмообразующего газа применяют воздух и азотно-водородные смеси с высоким содержанием водорода.
Титан и его сплавы хорошо подвергаются резанию плазменной дугой. Наибольшая производительность достигается при использовании воздуха и кислорода в качестве плазмообразующего газа. При резке воздушной плазмой кромки реза на глубине 0,1–0,2 мм содержат в 1,5 раза больше кислорода, чем основной металл, в 7–10 раз больше азота, в 4-8 раз больше водорода. Поэтому кромки титановых заготовок после плазменной резки подлежат механической обработке.
6. Плазменная сварка
Свойство плазменной дуги глубоко проникать в металл используется для сварки достаточно толстых (10-15 мм) металлов без предварительной разделки кромок и присадочного материала.
В качестве плазмообразующего газа обычно применяют аргон или его смеси с водородом или гелием, а для защиты металла сварочной ванны от окисления при сварке легированной стали, меди, никеля и сплавов на его основе – смесь аргона с 5-8 % водорода. При сварке низкоуглеродистой и низколегированной стали в качестве защитного газа можно применять углекислый газ.
Расход плазмообразующего газа устанавливают таким образом, чтобы истечение плазмы из сопла не было турбулентным, а силовое воздействие плазменной струи на поверхность сварочной ванны не приводило к разбрызгиванию расплавленного металла.
Плазменной дугой сваривают листы толщиной до 9,5 мм встык без разделки кромок и присадочного металла. В ряде случаев успешно
сваривают за один проход листы толщиной до 13 мм. При сварке листов толщиной до 25 мм требуется V- или U-образная подготовка кромок. При плазменно-дуговой сварке количество присадочного металла снижается примерно в 3 раза. Наибольшее преимущество сварки плазменной дугой проявляется при соединении толстых листов без разделки кромок и использования присадочного металла.
Плазменно-дуговая сварка может быть выполнена практически в любом пространственном положении. Режимы сварки плазменной дугой некоторых металлов и сплавов приведены в таблице 1.8.
Таблица 1.8 – Режимы сварки плазменной дугой стыковых соединений без присадочного металла
Металл | Толщина листов, мм | Скорость сварки, м/мин | Диаметр сопла, мм | Параметры дуги | Плазмообразующий газ | Фокусирующий и защитный газ | |||
Сила тока, А | Напряжение, В | Состав | Расход м3/ч, | Состав | Расход м3/ч, | ||||
Коррозионностойкая сталь | 2,4 | 0,97 | – | 160 | 31 | Ar+7,5 % H2 | 0,14 | Ar+ 7,5 % H2 | 0,99 |
3,2 | 0,61 | 145 | 32 | 0,28 | |||||
4,8 | 0,41 | 240 | 38 | 0,34 | 1,27 | ||||
6,4 | 0,36 | 0,5 | 1,41 | ||||||
12,7 | 0,19 | 2, 4 | 305 | 35 | Ar | 0,14 | 1,4 | ||
Титан | 3,2 | 0,51 | – | 185 | 21 | 0,23 | Ar | 0,85 | |
4,8 | 0,38 | 190 | 26 | 0,34 | 1,27 | ||||
12,7 | 0,25 4 | 2, 4 | 285 | 38 | 0,113 | 0,85 | |||
Инконель 600 | 3,5 | 0,4 | 180 | 27 | 0,34 | 1,13 | |||
Низкоуглеродистая сталь | 6,4 | 0,25 4 | 305 | 35 | 0,057 | 1,4 | |||
Алюминий | 85 | 27 | He+Ar | 0,085 +0,02 8 | 0,85 |
Комбинированный процесс точечной плазменно-дуговой сварки. Дуговую точечную сварку нахлесточных соединений различных металлов и сплавов выполняют обычно плавящимся электродом с предварительным сверлением и зенковкой отверстий в верхнем листе. Диаметр отверстий превышает диаметр электрода не менее чем на 3-8 мм. Такая технология обеспечивает проплавление верхнего листа и уменьшение выпуклости электрозаклепочного шва. Однако сверление отверстий увеличивает трудоемкость работ, производимых перед общей сборкой и сваркой металлоконструкций. Более технологичным представляется комбинированный процесс
точечной сварки (рис. 1.15), предусматривающий свободное проплавление листов с использованием плазменной горелки 1 и последующую заварку полученных отверстий дугой с плавящимся электродом 2.
Расстояние от оси горелки мундштука с плавящимся электродом регулируют в диапазоне 30-100 мм. Питание плазменного и дугового разрядов осуществляют от раздельных источников 3 и 5, управляемых программируемым устройством 4.
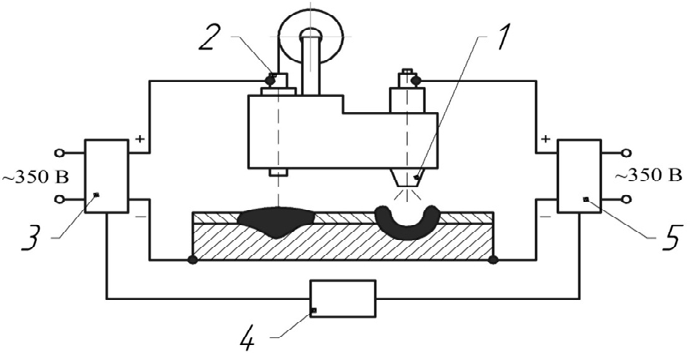
Рисунок 1.15 – Схема комбинированного процесса точечной плазменно- дуговой сварки
Внешний вид точечных соединений, полученных комбинированным способом плазменно-дуговой сварки, характеризуется равномерным формированием швов, стабильной глубиной проплавления.
7. Плазменная наплавка
Наплавка относится к наиболее эффективным методам нанесения защитных и упрочняющих покрытий. Наплавку используют преимущественно для восстановления изношенных или повреждённых деталей машин. На многих производствах наплавка является обязательным технологическим процессом, который применяют при изготовлении новых изделий. Корпуса атомных реакторов и химических установок, трубопроводная арматура, засыпные устройства доменных печей, буровой инструмент, клапаны двигателей внутреннего сгорания, шнеки экструдеров и другие изделия современного машиностроения не могут быть изготовлены без наплавки нержавеющими, износостойкими, жаропрочными или другими материалами с особыми эксплуатационными свойствами.
Изготовительная наплавка быстроизнашивающихся или наиболее тяжело нагруженных деталей позволяет увеличить срок их
службы, избавить промышленность от необходимости производить большое количество запасных частей, повысить работоспособность и надежность машин, сократить расходы на их эксплуатацию. По этой причине применение изготовительной наплавки обеспечивает прогресс в различных отраслях машиностроения.
7.1 Плазменная наплавка проволокой
Плазменная наплавка осуществляется двумя способами: с боковой или осевой подачей присадочной проволоки. Присадочная проволока может быть токоведущей или нейтральной.
Принципиальная схема наплавки с боковой подачей токоведущей проволоки представлена на рисунке 1.16 а.
Дуга горит между вольфрамовым электродом и присадочной проволокой, подаваемой сбоку. Дуга между неплавящимся электродом и присадочной проволокой представляет собой независимый от изделия источник нагрева, что позволяет раздельно регулировать нагрев и плавление основного и присадочного металла.
Основной металл нагревается за счёт теплового воздействия струи плазмы и теплоты, переносимой каплями присадочного металла. Эффективная тепловая мощность такого источника нагрева зависит не только от силы тока электрической дуги, но и от расстояния между проволокой и поверхностью основного металла.
Так как энергия плазменной струи передается основному металлу через слой жидкого присадочного металла, то наплавку плазменной струей с токоведущей проволокой можно рассматривать как своеобразную заливку поверхности изделия перегретым присадочным металлом.
Этот способ наплавки обеспечивает высокую прочность соединения наплавленного и основного металлов.
Схема наплавки с боковой подачей нейтральной проволоки представлена на рисунке 1.16 б. С точки зрения нагрева основного металла плазменная дуга является более эффективным и более локальным тепловым источником, чем плазменная струя. Эффективный КПД нагрева основного металла плазменной дугой 50-75 %, а плазменной струёй 20-45 %.
При использовании этого способа плавления присадочного материала происходит за счёт теплоты, получаемой от столба дуги путем конвективного и лучистого теплообмена. Массовую скорость плавления определяют теплофизические и газодинамические параметры плазмы, их распределение по радиусу столба дуги и площади теплообмена. В зависимости от этих факторов присадочная проволока может плавиться на различном расстоянии от оси дуги, начиная от
точки ввода проволоки в столб дуги и кончая точкой выхода из него. В первом случае скорость плавления проволоки минимальна, во втором – максимальна для данного режима горения дуги. Массовая скорость плавления возрастает не только с увеличением длины нагреваемого участка проволоки, но и при увеличении её диаметра или замены проволоки лентой, что увеличивает поверхность теплообмена.
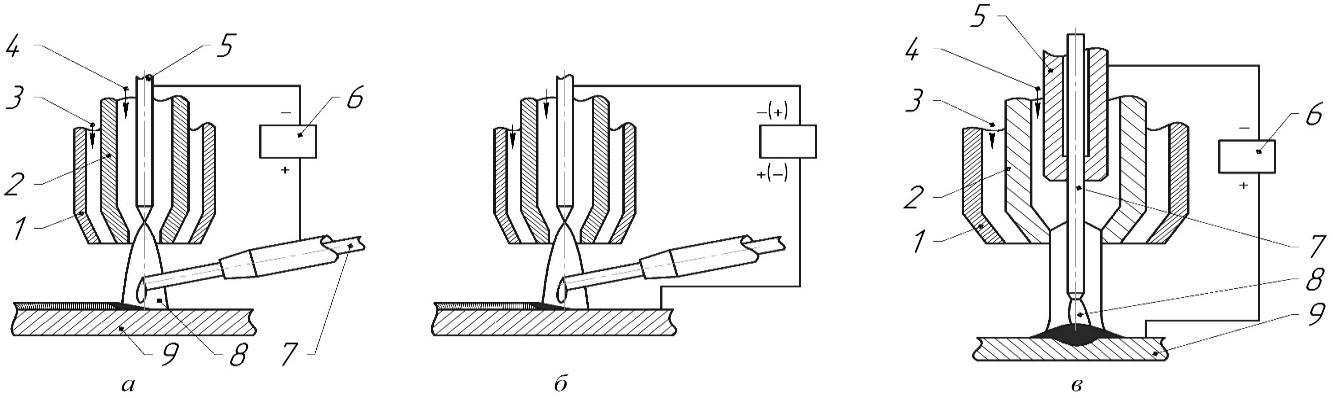
Рисунок 1.16 – Схемы плазменной наплавки с боковой присадочной проволокой (а, б) и осевой (в): 1 – защитное сопло; 2 – плазмообразующее сопло; 3 – защитный газ; 4 – плазмообразующий газ; 5 – электрод; 6 – источник питания дуги; 7 – проволока; 8 – плазменная дуга; 9 – изделие
Схема плазменной наплавки с осевой подачей токоведущей проволоки представлена на рисунке 1.16 в.
Процесс плазменной наплавки начинается с возбуждения электрической дуги, после чего в течение 0,1 с самопроизвольно возникает стабильная плазменная дуга между соплом и изделием.
В зависимости от силы тока дуги плавящейся проволоки возможны два вида переноса металла. При силе тока меньше некоторого критического значения столб дуги плавящегося электрода имеет цилиндрическую или слегка коническую форму, а перенос металла происходит каплями, движущимися вдоль оси дуги. Разбрызгивание отсутствует, однако глубина проплавленного основного металла значительна, так как тепловой поток дуги и капель сосредоточен на небольшой площади.
При больших тепловых потоках капельный перенос переходит во вращательно-струйный. Для него характерны большая длина расплавленной части электрода, изгиб её по спирали и вращение вокруг оси горелки. Например, конец стальной электродной проволоки диаметром 1,2 мм при силе тока 300 А описывает окружность диаметром около 8 мм.
Скорость вращения расплавленного конца электродной проволоки и дуги зависит от многих параметров режима (вылета электрода, силы тока и др.). Режимы наплавки с вращением дуги отличаются повышенной производительностью.
Достоинствами плазменной наплавки проволокой, определяющими возможные области её применения, являются: малая глубина проплавленного слоя основного металла, что важно в тех случаях, когда разбавление основного металла в наплавленном приводит к ухудшению свойств наплавленного металла; отсутствие при наплавке технических проблем, связанных с плохой отделяемостью шлаковой корки; этот способ находит широкое практическое применение при наплавке сплавов на основе цветных металлов.
7.2 Плазменно-порошковая наплавка
Плазменная наплавка с присадкой порошка в наибольшей степени отличается от других способов наплавки применяемыми материалами. Порошки могут быть получены практически из любого пригодного для наплавки материала, независимо от твердости, пластичности, степени легирования и других свойств. Применяют в качестве присадки порошки (гранулы) размером от 2,5–3,0 мм до тонко измельченных частиц размером до 0,1 мм.
Порошковый присадочный материал могут распределять на поверхность изделия непосредственно перед наплавкой или вводить в дугу в процессе наплавки. Ввод порошка в дугу может осуществляться внутри плазмотрона или вне его.
На рисунке 1.17 представлена схема наплавки по слою гранулированной присадки. Присадочный материал в гранулах размером 0,5-3,0 мм заранее насыпают равномерным слоем по наплавляемой поверхности с помощью специального устройства. Расплавляют присадочный материал плазмотроном, который совершает поперечные движения, в соответствии с шириной насыпанного слоя. Тяжёлые крупные гранулы не раздуваются дугой и защитным газом. Поэтому нет необходимости закреплять их на поверхности каким-либо связующим веществом.
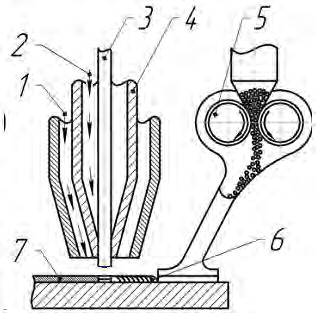
Рисунок 1.17 – Схема наплавки по слою гранулированной присадки: 1 – ввод защитного газа; 2 – ввод плазмообразующего газа; 3 – электрод; 4 – сопло; 5 – питатель подачи крупки; 6 – слой крупки; 7 – наплавленный металл
Недостатки процесса – сложность наплавки криволинейных или цилиндрических поверхностей; необходимость применения формирующих приспособлений при наплавке кромок; невозможность наплавки тонких слоёв.
Схема наплавки порошком с внутренним вводом представлена на рисунке 1.18 а. Порошок вводится в дугу под углом 25-80º через воронкообразную щель между коническими поверхностями внутреннего и наружного сопел. В этом случае двухфазный поток транспортирующего газа и порошка концентричен дуге. Поэтому он не только смешивается, но и повышается его стабильность. Дуга косвенного действия горит между электродом и внутренним соплом и служит, в основном, для обеспечения устойчивой работы плазмотрона. Роль её в нагреве порошка незначительна. Более мощная дуга прямого действия обеспечивает необходимый нагрев поверхности изделия, плавление присадочного металла и образование сварочной ванны.
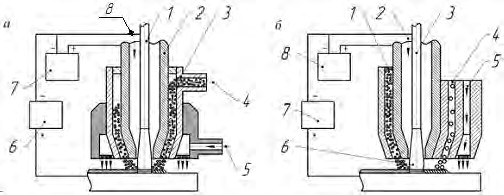
Рисунок 1.18 – Схемы плазменной наплавки с вводом присадочного порошка в дугу внутри плазмотрона (а) и снаружи (б): а) 1 – электрод; 2, 3 – соответственно внутреннее и наружное сопла; 4 – ввод присадочного порошка транспортирующим газом; 5 – ввод защитного газа; 6, 7 – соответственно источники питания дуг прямого и косвенного действия; 8 – ввод плазмообразующего газа; б) 1 – ввод присадочного порошка транспортирующим газом; 2 – ввод плазмообразующего газа; 3 – электрод; 4 – ввод дополнительного присадочного порошка; 5 – ввод защитного газа; 6 – плазменная дуга; 7, 8 – источники питания соответственно дуг прямого и косвенного действия
При плазменной наплавке с внешней подачей присадочного порошка (рис. 1.18 б), последний подают в зону наплавки через отверстие в торцах плазмотрона. При наплавке композиционных сплавов дополнительный канал служит для подачи упрочняющих частиц карбида вольфрама. Канал расположен сзади дуги и имеет угол, обеспечивающий попадание зерен карбида в сварочную ванну, минуя
дугу. Это позволяет устранить или уменьшить их растворение в расплаве. Сварочная ванна образуется за счёт расплавления основного металла; защитного покрытия, нанесенного на зёрна карбида вольфрама; порошка сплава-связки, который подают вместе с карбидом либо отдельно от него по боковым каналам. В любом случае, наплавленный металл имеет гетерогенную структуру, состоящую из относительно легкоплавкой матрицы и нерасплавившихся зерен карбида.
Плазменно-порошковая наплавка обладает всеми достоинствами плазменной наплавки проволокой. Кроме того, применение в качестве присадочного материала порошка, который может быть получен практически из любого сплава, значительно расширяет круг сплавов, наплавляемых механизированными способами. Стоимость порошков на 10-30% ниже стоимости прутков и проволоки аналогичного состава. Качество порошков, в частности, их химический состав, контролировать легче, чем качество порошковой проволоки. Порошки можно смешивать для получения требуемого состава.
Важными достоинствами плазменной наплавки порошком является небольшая толщина слоя (при необходимости) и хорошее его формирование, благодаря чему снижаются расход наплавочных материалов и трудоёмкость механической обработки наплавленных изделий.
Просмотров: 317
Плазменная сварка — Плазма и газ-резка, сварка, напыление
Требования предъявляемые к плазматронамПри конструировании плазмотронов, предназначенных для различных видов обработки материалов следует учитывать ряд общих требований, предъявляемых к ним:
- Плазмотрон должен обеспечивать многократное надежное зажигание и стабильное горение плазменной дуги в заданном диапазоне рабочих токов и напряжений. Это требование удовлетворяется при определенных соотношениях между диаметром электрода, сопла, длиной последнего, и зазором между ними, а также при правильном конструктивном решении узла формирования и стабилизации дуги.
- Элементы, наиболее подверженные действию тепла (электрод, сопло), должны выдерживать длительную тепловую нагрузку при максимальной мощности плазмотрона. Это требование выполняется при правильном выборе материала теплонапряженных элементов и си-стемы их охлаждения.
- Электрическая изоляция между электродами и соплом должна быть рассчитана на максимальное напряжение, возникающее на дуговом промежутке при возбуждении дуги и ее обрыве. При возбуждении дуги с помощью осциллятора это напряжение составляет 2-5 кв в диапазоне частот 0,3-1 Мгц.
- Элементы водяных и газовых коммуникаций плазмотрона (шланги, уплотнения, прокладки и пр.) должны выдерживать давление не ниже 10 атм.
- Для обеспечения маневренности плазмотрона подсоединяемые к нему шланги и электрические провода должны быть гибкими и прочными.
- Плазмотрон должен быть технологичным в изготовлении, в ремонте и удобным в эксплуатации. Особо важно обеспечить легкость его разборки и сборки и возможность быстрой замены наиболее часто изнашиваемых деталей (катода и сопла).
- Конструкция плазмотрона должна быть экономичной, т. е. должна предусматривать возможность применения недифицитных материалов для его изготовления и обеспечивать минимальное потребление охлаждающей воды, рабочего газа и минимальные потери тепла.
- К плазмотронам предъявляется и ряд специальных требований, обусловленных особенностями технологического процесса.
- Плазмотроны для сварки и наплавки должны обеспечивать надежную защиту шва от вредного воздействия окружающей среды, плазмотроны для напыления — высокие скорость течения и теплосодержание плазменной струи при минимальной ее загрязненности продуктами эрозии электродов, плазмотроны для резки — высокую концентрацию теплового потока плазменной струи. Ручной плазменный резак должен быть легким и удобным в обращении.
- отсутствие любых водо-, электро- или газоподводящих шлангов в рабочем пространстве печи;
- водоохлаждение всех металлических частей;
- защита от излучения всех уплотнений и неметаллических деталей водоохлаждаемыми или термоизоляционными экранами;
- возможность ввода плазмотрона в печную камеру через уплотнение.
В ряде случаев выдвигаются особые требования к системе управления плазмотроном, к способу его охлаждения, к защите от воздействия окружающей среды, к повышенной надежности его в условиях работы на поточной линии и др.
Плазматроны: схемы, классификация
При создании плазмотрона первым шагом является составление схемы его устройства. Исходя из особенностей технологического процесса и условий работы плазмотрона выбираем систему его охлаждения, род тока, плазмообразующую среду, вид и материал электрода, способ стабилизации дуги, перемещения ее электродных пятен и т. д. Различные варианты схем плазмотронов удобнее всего представить в виде классификации (рис.). Данная классификация составлена таким образом, что один из вариантов каждого подраздела является необходимым составным элементом общей схемы плазмотрона любого типа.
В первую очередь все плазмотроны разделяются на две группы по виду дуги (см. рис.): плазмотроны с дугой прямого и косвенного действия (схемы 1 и 2). Различие тепловых свойств обоих типов плазмотронов и области их применения уже рассматривались выше.
рис. 1 Классификация плазмотронов по критериям
По системе охлаждения электрода и сопла плазмотроны также делятся на два основных типа: с воздушным и с водяным охлаждением (схемы 3, 4). Теплоемкость воды намного выше теплоемкости воздуха и других газов. Поэтому наиболее эффективной и распространенной является водяная система охлаждения, при которой допускаются высокие тепловые нагрузки на электрод и сопло, т. е. обеспечивается нормальная работа плазмотрона при больших токах и высокой степени обжатия плазменной дуги. Однако водяное охлаждение несколько усложняет конструкцию плазмотрона, утяжеляет его из-за наличия водоподводящих шлангов и удорожает эксплуатацию плазменной установки. Чистота воды существенно влияет на эффективность теплоотвода. При больших расходах воды плазменную установку целесообразно оснащать циркуляционной системой охлаждения с использованием дистиллированной воды во избежание образования накипи. Система воздушного охлаждения ввиду низкой эффективности применяется реже, главным образом для охлаждения малоамперных плазменных горелок и ручных плазменных резаков, предназначенных для монтажных работ в зимних условиях. В таких резаках рабочий ток обычно не превышает 300-400 а. В обеих системах охлаждающая среда чаще всего проходит последовательно электродный и сопловой узел через изолирующий корпус плазмотрона. При этом существенную роль с точки зрения эффективности охлаждения играет профиль полостей охлаждения, температура и давление поступающей в плазмотрон охлаждающей среды. Основная задача при выборе системы охлаждения состоит в том, чтобы обеспечить максимальную интенсивность отвода тепла стенками сопла, так как чем выше величина теплового потока, отводимого соплом, тем круче температурный градиент газовой прослойки между столбом дуги и стенками канала сопла и, следовательно, тем выше плотность тока и мощность столба дуги.
рис. 2 Классификация плазмотронов по методам стабилизации дуги
Плазмотроны можно классифицировать и по способу стабилизации дуги. Система стабилизации дуги, обеспечивающая сжатие столба и строгую фиксацию его по оси электрода и сопла плазмотрона, является наиболее важным элементом плазмотрона. Существуют три вида стабилизации дуги: газовая, водяная и магнитная. Наиболее простой и распространенной является газовая стабилизация, при которой наружный холодный слой рабочего плазмообразующего газа, омывая стенки столба дуги, охлаждает и сжимает его. При этом в зависимости от способа подачи газа (вдоль или перпендикулярно оси столба) газовая стабилизация может быть аксиальной или вихревой (схемы 5, 6). Наибольшее обжатие дуги достигается при вихревой ее стабилизации, поэтому этот способ используется главным образом в плазмотронах для резки и напыления. При аксиальной стабилизации поток газа, обдувающего столб дуги, имеет более спокойный, ламинарный характер, что обеспечивает лучшие условия защиты нагреваемого изделия от воздействия окружающей среды. Поэтому аксиальная стабилизация применяется в плазмотронах для сварки и наплавки. Иногда применяют двойную стабилизацию дуги (схема 7), при которой сочетается аксиальная подача газа через первичное и вихревая подача через вторичное сопло или наоборот. Столб дуги можно стабилизировать, омывая его водяной струей (схема 8). Образуемый из струи водяной пар служит плазмообразующей средой. При водяной стабилизации можно достигнуть наиболее высокой степени сжатия и температуры столба дуги до 50 000 °К. Однако присутствие паров воды вблизи катодной области приводит к интенсивному сгоранию электродов из любых материалов. В плазмотронах с водяной стабилизацией, предназначенных для резки, используется графитовый электрод, автоматически перемещаемый по мере его сгорания. Плазмотроны с водяной стабилизацией отличаются сложностью конструкции, малой надежностью системы автоматического регулирования подачи электрода и сложностью способов возбуждения дуги. Магнитная стабилизация (схема 9), при которой создается продольное магнитное поле, сжимающее столб дуги, менее эффективно, чем газовая и водяная. Кроме того, надетый на сопло соленоид усложняет конструкцию плазмотрона. Преимущество способа магнитной стабилизации состоит в возможности регулирования степени сжатия столба дуги независимо от расхода рабочего газа, в то время как при газовой и водяной стабилизации рабочий газ является одновременно плазмообразующим и стабилизирующим. На практике наложение продольного магнитного поля применяется не столько для стабилизации дуги, сколько для вращения ее анодного пятна по внутренним стенкам сопла с целью повышения стойкости последнего. Например, в плазмотронах, применяемых для напыления, магнитное вращение анодного пятна газовихревым способом позволяет значительно снизить эрозию сопла и, следовательно, загрязненность плазменной струи.
Классификация плазмотронов по виду электрода
По виду электрода-катода плазмотроны постоянного тока можно разделить на две группы: плазмотроны со стержневым и плазмотроны с распределенным катодом.В плазмотронах со стержневым катодом, катодное пятно фиксируется на торце электрода, а в плазмотронах с распределенным катодом — интенсивно перемещается с помощью газовихревого или магнитного вращения по развитой поверхности электрода.
В плазмотронах для обработки металлов применяются в основном стержневые катоды, подразделяемые на три основных вида: расходуемый, газозащищенный и пленкозащитный (схемы 1, 2, 3).
Расходуемый, чаще всего графитовый, электрод был показан в схеме плазмотрона с водяной стабилизацией. Несмотря на то, что графит обладает высокой температурой плавления, при нагревании до этой температуры он не плавится, а возгоняется, чем и обусловлен его повышенный расход.
Газозащищенный вольфрамовый электрод — самый распространенный из всех видов электродов. При работе в инертной (аргон, гелий) и восстановительной (азот, водород) средах катод из тугоплавкого вольфрамового стержня при нагрузке 15-20 а/мм2 практически не расходуется. Вольфрамовый катод по сравнению с графитовым значительно прочнее и обладает во много раз большей электропроводностью.
Для улучшения условий работы катоды дуговых плазмотронов изготовляют из вольфрама с небольшой добавкой окиси тория или лантана (1,5-2%). Существует мнение, что торированные вольфрамовые электроды обладают некоторой радиационной способностью, поэтому в последнее время чаще используются лантанированные вольфрамовые электроды. Примеси окиси тория или лантана повышают эмиссионные свойства вольфрамового катода (работа выхода электронов понижается с 4,5 до 2,63 эв), что обеспечивает лучшие условия зажигания, более высокую допустимую плотность тока и устойчивость горения дуги. Кроме того, вольфрам с указанными добавками имеет температуру рекристаллизации на 600° К выше, чем чистый вольфрам и, следовательно, сохраняет волокнистое строение и пластичность до более высокой температуры. Однако стойкость вольфрамового электрода при добавлении кислорода к газовой среде в связи с образованием летучих соединений резко снижается. Например, в плазмотронах, применяемых для резки, при использовании технического азота, содержащего 3-5% О2, на вольфрамовом катоде через 2-3 ч работы при токе 300-400 а образуется кратер, смещение центра которого относительно оси сопла вызывает соответствующее смещение столба дуги и приводит к явлению двойного дугообразования. Поэтому при работе с кислородосодержащей плазмообразующей средой в первичное сопло подается аргон, защищающий вольфрамовый электрод от воздействия рабочего кислородосодержащего газа, подаваемого во вторичное сопло. Система с двойным газовым потоком имеет существенные недостатки. При использовании дешевого рабочего газа, например воздуха, все же остается необходимость в использовании дефицитного аргона. При этом усложняется конструкция плазмотрона и ухудшается нагрев рабочего газа, так как наиболее эффективно газ нагревается вблизи катодной области. Сравнительно недавно появился новый вид катода — пленкозащитный стержневой катод, обладающий высокой стойкостью в газах, содержащих кислород (в воздухе, углекислом газе, техническом азоте). Он представляет собой стержень из циркония или его сплавов, запрессованный в медной обойме. Механизм работы такого электрода должен быть еще детально изучен, но можно уже считать установленным, что достаточно высокая термостойкость циркония, имеющего относительно низкую температуру плавления (2125° К), в значительной мере обусловлена образованием стойкой тугоплавкой пленки из его окислов и нитридов, защищающей чистый цирконий от испарения. Тугоплавкие соединения, образующие пленку, при обычных температурах являются диэлектриками, а при температурах, близких к температуре плавления (3200° К), теряют свои диэлектрические свойства и становятся проводниками с ионной проводимостью (σ >= 1 ом-1*см-1). Таким образом, стойкость циркониевого катода определяется его термохимическим взаимодействием с плазмообразующей средой. Не-обходимыми условиями, обеспечивающими высокую стойкость катода, является наличие в составе газовой среды кислорода и азота, а также такая интенсивность его охлаждения, при которой температура катодного пятна не превышала бы температуру разложения туго-плавких соединений. Эрозия циркониевого катода резко повышается при большем процентном содержании кислорода, чем в воздухе (более 20%) и особенно при наличии в газовой среде водорода. Особо важное значение с точки зрения повышения стойкости циркониевого катода имеет его конструкция и система охлаждения. В настоящее время в плазмотронах для воздушно-плазменной резки достигнута вполне удовлетворительная стойкость циркониевого катода при работе на токах до 400 а. Применение пленкозащитного электрода в плазмотронах переменного тока исключается ввиду его активного разрушения в полупериоды обратной полярности. Особенностью работы циркониевой вставки является постепенное углубление ее нижнего основания в медную обойму по мере эрозии. Циркониевая вставка расходуется главным образом при включении дуги, очевидно, вследствие разрушения пленки от термоудара. При определенном углублении нижней поверхности вставки последующее зажигание дуги осуществляется с медной обоймы, поэтому для перемещения катодного пятна на циркониевую вставку и для жесткой фиксации его необходимо применять газовихревую или магнитную стабилизацию дуги, обеспечивающую строгую соосность столба дуги с электродом и соплом плазмотрона. При использовании циркониевого электрода допускается большая плотность тока, достигающая 80-100 а/мм2, чем при использовании вольфрамового электрода. При работе плазмотрона с окислительной плазмообразующей средой на больших токах (1000 а и выше) используются разнообразные виды распределенных катодов, наиболее распространенными из которых являются полый, дисковый и кольцевой (схемы 4, 5 и 6). Недостатками распределенных катодов являются сложность их конструкции, трудность равномерного перемещения катодного пятна по всей поверхности электрода, низкая стабильность горения дуги, возрастание напряжения прикатодной области дуги и связанное с этим увеличение потерь мощности в электроде. Поэтому в плазмотронах для обработки металлов распределенные катоды не нашли практического применения. Существует классификация плазмотронов и по плазмообразующей среде. Состав плазмообразующей среды диктуется технологическим процессом и в свою очередь является определяющим фактором при выборе схемы плазмотрона.
По химическому воздействию на обрабатываемое изделие и электроды плазмотрона все плазмообразующие среды можно разделить на три большие группы: инертная, восстановительная и окислительная. Физические свойства и оценка роли каждого из плазмообразующих газов уже рассматривались выше.
Классификация плазмотронов по роду тока
По роду тока плазмотроны отличаются наибольшим разнообразием вариантов. Поэтому рассмотрим лишь основные из них. Подавляющее большинство плазмотронов для обработки металлов выполняется на постоянном токе прямой полярности (схема 1). Это объясняется, прежде всего, физической особенностью дуги, заключающейся в том, что на аноде дуги выделяется большее количество тепла, чем на катоде. Тепловая мощность, выделяемая в электроде плазмотрона, в отличие от плавящегося электрода сварочной дуги является не только бесполезной, но и вредной. Наименьшую тепловую нагрузку несет электрод, являющийся катодом. Достаточно отметить, что предельно допустимая токовая нагрузка на лантанированный вольфрамовый электрод на переменном токе примерно в два раза, а на обратной полярности при использовании постоянного тока в десять раз ниже, чем на прямой полярности. Поэтому плазмотроны постоянного тока имеют наиболее высокий коэффициент полезного использования мощности. Столб интенсивно сжатой дуги должен быть жестко стабилизирован по оси электрода и сопла плазмотрона. При смене полярности электрода эта стабилизация нарушается, поэтому дугу переменного тока сжать труднее, чем дугу постоянного тока.
Важным преимуществом плазмотронов постоянного тока по сравнению с плазмотронами переменного тока является большая стабильность горения дуги. Прохождение тока через нуль может вызвать погасание дуги, поэтому обычно напряжение холостого хода источника питания переменным током не менее чем вдвое превышает рабочее напряжение дуги. При питании плазмотронов постоянным током можно достичь отношения uд/uxx равного 0,8-0,9. Следовательно, при одинаковой мощности дуги установленная мощность и габариты источника постоянного тока меньше, чем мощность и габариты источника переменного тока. Кроме того, источник постоянного тока обеспечивает равномерную загрузку трехфазной сети. Существовавшая раньше проблема выпрямления постоянного тока в настоящее время практически решена благодаря созданию и широкому выпуску электропромышленностью мощных малогабаритных полупроводниковых вентилей. Первоначальные затраты и расходы на эксплуатацию плазменных установок переменного и постоянного тока приблизительно равны. Поэтому с учетом перечисленных выше преимуществ для большинства процессов обработки материалов целесообразно применять плазмотроны постоянного тока. Плазмотроны переменного тока применяются в ряде случаев в силу технологических требований процесса. Например, плазменную сварку алюминиевых сплавов необходимо вести на переменном токе, так как в периоды обратной полярности за счет действия эффекта катодного распыления разрушается тугоплавкая пленка окиси алюминия, препятствующая нормальному процессу сплавления металла.
При плазменной плавке в случае параллельной работы нескольких мощных плазмотронов постоянного тока на общую ванну-анод возникает трудноустранимое магнитное взаимодействие между дугами. Поэтому в этих условиях могут быть использованы плазмотроны переменного тока. В этом случае целесообразно использовать плазмотроны в количестве, кратном трем, что обеспечивает равномерную загрузку трехфазной сети. Рассмотрим три основные схемы плазмотронов переменного тока. На схемах 2 и 3 плазмотроны питаются от однофазного трансформатора. В схеме 3 осуществлена вентильная коммутация тока таким образом, что электрод функционирует только как катод (в полупериод прямой полярности), а сопло — как анод (в полупериод обратной полярности). При такой схеме обеспечивается большая стойкость вольфрамового электрода. Однако с увеличением тока ухудшаются условия работы сопла, а при работе на токах ниже определенного предела (~150 а) нарушается стабильность горения дуги. На схеме 4 плазмотрон питается от трехфазного трансформатора. В этом случае обеспечивается высокая стабильность горения дуги, однако электроды и сопло находятся в сравнительно тяжелых условиях работы. Кроме того, значительно усложняется конструкция плазмотрона. В целях повышения стабильности горения дуги переменного тока некоторые плазмотроны выполняют комбинированными. В этом случае основную дугу переменного тока прямого действия стабилизируют вспомогательной маломощной дугой постоянного тока, горящей либо между электродом и соплом (схема 5), либо между двумя соплами (схема 6), одно из которых (катод) является формирующим. Второе сопло (анод) выполняется с большим внутренним диаметром. Благодаря этому оно подвержено меньшему тепловому воздействию столба основной дуги.
Наряду с дуговыми плазмотронами, работающими на переменном токе промышленной частоты, за последнее время были разработаны высокочастотные (ВЧ) и сверхвысокочастотные (СВЧ) плазмотроны [7, 8]. Принцип работы высокочастотного индуктивного или безэлектродного плазмотрона (схема 7) заключается в нагреве газа до состояния плазмы в электромагнитном поле индуктора. Для этого в полость индуктора, питаемого от высокочастотного генератора (частотой 1-40 Мгц, напряжением до 10 кв и мощностью до 50 кВт), помещается трубка из термостойкого изолирующего материала, например, кварца. В трубку подается плазмообразующий газ и кратковременно вводится металлический или графитовый пруток. Последний раскаляется под действием поля индуктора и вызывает нагрев и первоначальную ио-низацию окружающего газа. Когда электропроводность газа возрастает до определенной величины, начинается интенсивный его нагрев и ионизация вихревыми токами, создаваемыми полем индуктора. После развития самостоятельного кольцевого разряда пруток удаляется из полости трубки. Продуваемый через трубку газ, проходя через кольцевой разряд, нагревается и истекает в виде плазменной струи, температура которой достигает 15 000-20 000° К, а скорость истечения в десятки раз меньше, чем скорость истечения плазменной струи дуговых плазмотронов. Высокочастотная энергия сравнительно дорога, высокочастотные генераторы сложны и имеют ограниченную мощность. Поэтому очень чистый (ввиду отсутствия электродов) и мягкий факел индукционного плазмотрона нашел применение для обработки особо чистых тугоплавких порошковых материалов, выращивания монокристаллов и других специальных процессов, не требующих высокой производительности.
В сверхвысокочастотных (СВЧ), или электронных плазмотронах, газ также нагревается электромагнитным полем, создаваемым электродом-излучателем (схема 8). Плазменный высокочастотный факел возникает у электрода при остроконечной форме электрода и высокой напряженности поля вблизи него. В высоковольтном и сверхвысокочастотном электрическом поле свободные электроны ускоряются и приобретают такую кинетическую энергию, что при столкновении с частицами газа вызывают их диссоциацию и ионизацию. Электрод плазмотрона подключен к магнетронному генератору частотой 2000-3000 Мгц и мощностью 2-5 кет. Плазменный факел электронного плазмотрона интересен тем, что в нем нет термического равновесия: температура электронов на порядок выше температуры ионов и свободных атомов. Например, при температуре факела 3500° К электронная температура достигает 35 000° К. Такая высокая температура электронов позволяет проводить в плазменной струе химические реакции синтеза некоторых специальных материалов.