Подводная резка металлов — презентация онлайн
1. Подводная резка
ПОДВОДНАЯ РЕЗКАВыполнил:Маркевич Николай 41 гр.
Подводная резка металлов необходима при
ремонте судов, подводной части металлических
конструкций портовых гидротехнических и
других сооружений. Находясь под водой,
рабочий-резчик стеснен в своих движениях, так
как кроме сопротивления воды и состояния
невесомости он одет в специальное водолазное
снаряжение. Видимость ограничена, особенно во
время резки, когда выделяется значительное
количество оксидов железа, образующих бурый
раствор в воде, мешающий ориентированию
резчика и обзору разрезаемой конструкции.
3. В подводных условиях применяют различные способы резки:
1) механические;2) термические;
3) кумулятивные (взрывом).
Наибольшее распространение получили способы
термической резки:
1) электродуговая;
2) электрокислородная;
3) газокислородная;
4) плазменная.
При подводной резке используется тепло концентрированных
источников дуги или плазмы и тепло, выделяющееся в
металлом. Поскольку разрезаемый металл находится в воде и
интенсивно охлаждается, то источник тепла должен иметь
высокую концентрацию его в месте реза.
4. ЭЛЕКТРОДУГОВАЯ РЕЗКА
Подводная электродуговая резка отличается от дуговойподводной сварки повышенными значениями сварочного тока и
приемами выполнения работ. Поэтому дуговую резку под водой
можно выполнять на том же оборудовании, что и подводную
сварку. Целесообразно использование постоянного тока прямой
полярности, так как это приводит к выделению большого
количества тепла в полости реза.
Электроды для резки отличаются от электродов для сварки
размерами, толщиной и составом обмазки. Электроды
изготовляются из проволоки диаметром 5 – 7 мм, длинной 500 –
700 мм.
При выборе режимов тока для резки следует применять
коэффициент K равным 60 –80 А/мм.

электродами диаметром 5 мм можно успешно резать металл
толщиной больше 50 мм при силе тока 350 – 500А.
Режимы резки, обеспечивающие максимальную
производительность процесса, находят опытным путем.
Резка осуществляется непрерывным перемещением
электрода. Она начинается с кромки или отверстия и
производится пилообразными движениями конца
электрода. Металл не большой толщины (до 10 –15 мм)
разрезается непрерывным перемещением конца
электрода вдоль линии реза (рис. 5.1.1). При резке
металла большой толщины (рис.5.1.1) движение
электрода от верхней поверхности к нижней
осуществляется медленно, подъем его к верху – быстро.
ПРОИЗВОДИТЕЛЬНОСТЬ И РАСХОД
ЭЛЕКТРОДОВ ПРИ РЕЗКЕ
Таблица 5.1.
Из табл.5.1. видно, что с увеличением толщины металла
производительность дуговой резко падает, а расход электродов на один
погонный метр реза растет.
7. электрокислородная резка
ЭЛЕКТРОКИСЛОРОДНАЯ РЕЗКАЭлектрокислородная резка впервые
применена в 1915г и в настоящее время
является самой распространенной. Способ
электрокислородной резки удачно объединил
преимущество дугового разряда и струи
режущего кислорода. За счет тепла дуги
происходит нагрев и плавление металла, а за
счет струи кислорода – сгорание и выдувание
металла из полости реза. В основном
применяют трубчатые электроды с осевым
каналом для режущего кислорода и
специальные электроды из карборунда.
Стержни электродов изготовляют из
толстостенной цельнотянутой трубки из
малоуглеродистой стали наружным диаметром 5 –
7 мм и внутренним 1,5 – 2 мм (см. рис. 5.2.1). Длина
электродов 350 – 400 мм. Трубчатый электрод
покрывают обмазкой толщиной 1 – 1,2 мм. Время
сгорания такого электрода 1 мин. Электроды из
карборунда получили название керамических (рис.
5.2.1). Керамический электрод из карборунда
длиной 250 мм сгорает через 15 мин.
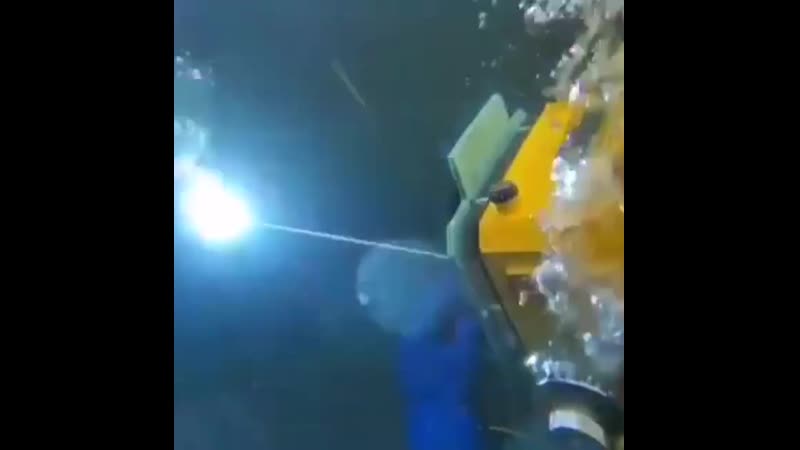
больших размеров (диаметр 15 – 20 мм)
керамические электроды могут быть
рекомендованы для резки сплошного металла
толщиной до 30 мм.
9. Для электрокислородной резки применяют электродержатели специальной конструкции типа ЭКД4 и ЭКД4 – 60 (рис. 5.2.2).
Электрокислородную резку применяют длярезки черных и цветных металлов толщиной
до 100 – 120 мм на глубинах до100 м. По
производительности электрокислородная
резка электродуговой и газокислородной
резки (табл. 5.2).
10. ПОКАЗАТЕЛИ ЭЛЕКТРОКИСЛОРОДНОЙ РЕЗКИ
11. ГАЗОКИСЛОРОДНАЯ РЕЗКА
Газокислородная резка основана на сгоранииметалла в струе кислорода и выдувании окислов и
металла из полости реза. Она возможна только при
постоянном существовании газового пузыря вокруг
подогревающего пламени (рис. 3.3). Создание
газового пузыря возможно за счет продуктов
сгорания подогревающего пламени, для которого
используют ацетилен, водород, другие углеводороды
специальной конструкцией наконечника подводного
резака и подачей защитного газа – воздуха или
кислорода. В воде металл интенсивно охлаждается и
поэтому для его подогрева требуется пламя в 10-15
раз больше, чем для аналогичных работ на воздухе.
Газокислородная резка основана на сгорании
металла в струе кислорода и выдувании окислов и
металла из полости реза. Она возможна только при
постоянном существовании газового пузыря вокруг
подогревающего пламени (рис. 3.3). Создание
газового пузыря возможно за счет продуктов
сгорания подогревающего пламени, для которого
используют ацетилен, водород, другие углеводороды
и бензин. Устойчивость пузыря обеспечивается
специальной конструкцией наконечника подводного
резака и подачей защитного газа – воздуха или
кислорода. В воде металл интенсивно охлаждается и
поэтому для его подогрева требуется пламя в 10-15
раз больше, чем для аналогичных работ на воздухе.
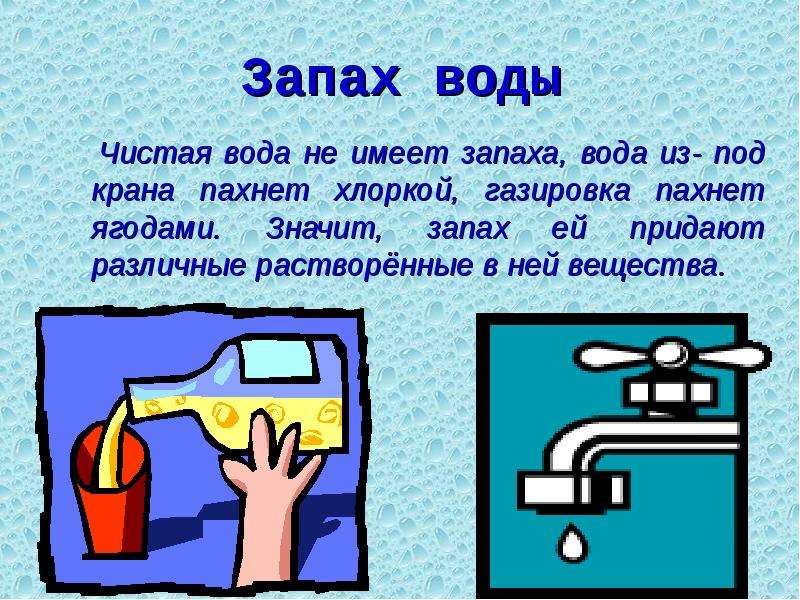
Рис.5.3.1. Схема водороднокислородной резки: 1, 2 –
мундштуки; 3 — колпачок; 4 –
режущий кислород; 5 – горючая
смесь; 6 – воздух; 7 –
подогревающее пламя; 8 – струя
режущего кислорода; 9 –
воздушный пузырь; вода.
Водород и кислород поступают по шлангам из баллонов, а
воздух по отдельному шлангу от компрессора или баллона. На
глубине 30-40 м водородно-кислородным резаком можно резать
сталь толщиной до 70 мм; рабочее давление газов составляет,
кгс/см2: 6,6 – кислород, 5,5 – водород, 5 – воздух. Средний
часовой расход водорода и кислорода 4-10 м3, воздуха 20 м3.
Использование бензина для подводных работ стало
возможным благодаря разработке новых конструктивных
принципов построения бензорезов, сущность которых состоит в
том, что бензин предварительно не испаряется, а распыляется
виде тончайшей бензиновой пыли. Продукты сгорания пламени
содержат много неконденсирующихся газов, образующих
устойчивый газовый пузырь, что исключает подведения
дополнительного воздуха или кислорода, упрощает и
удешевляет установку и ее эксплуатацию
16. 5.4. ПЛАЗМЕННАЯ РЕЗКА
Для плазменно-дуговой резки разработанаспециализированная установка типа ОППР-1,
обеспечивающая резку в пресной и морской воде.
Плазменную резку металла толщиной 8-40 мм на
глубинах до 10 м производят при силе тока 200-600
А и напряжении дуги 120-140 В со скоростью 5-24
м/ч.
Применение плазмотронов с циркониевым
катодом позволяет использовать сжатый воздух,
который повышает тепловую мощность плазменной
дуги и улучшает ее режущие способности.
Присутствие кислорода в воздухе повышает
эффективность резки стали Ст3С (табл. 5.4)
17. Эффективность воздушно-плазменной резки
Обеспечение безопасности. Сдерживающим фактором внедренияплазменной резки является обеспечение безопасной
эксплуатацией электрооборудования.

в соленной воде измерялось напряжение между различными
частями макета водолазного снаряжения и оборудования, когда
напряжение разомкнутой цепи составляло 180 В и токи утечки
70 А. Максимальная разница потенциала (14 В) наблюдалась
между правой рукой и правой галошей макета водолаза.
Следовательно, процесс плазменной резки может быть
безопасным, если резак достаточно изолирован.
18. Основные методы резки под водой
19. . Организация работ при подводной сварке и резке
. ОРГАНИЗАЦИЯ РАБОТ ПРИПОДВОДНОЙ СВАРКЕ И РЕЗКЕ
Успех сварки под водой в значительной степени зависит
от четкой и правильной организации работ.
Кадры подводных сварщиков и резчиков готовятся из
опытных водолазов достаточно высокой квалификации.
Работы производятся в тяжелом мягком водолазном
снаряжении, в зимних рубахах с закрытыми кистями рук.
Вся аппаратура должна быть высокого качества в полной
исправности, и, безусловно, проверена.
Подводная сварка, дуговая и электрокислородная резка
производятся, как правило, на постоянном токе прямой
полярности. Переменный ток не рекомендуется из-за
меньшей устойчивости дуги и повышенной опасности
для работающих.
Газовая сварка различных металлов | Презентация урока для интерактивной доски на тему:
Газовая сварка металловСлайд 2
02.05.17 Газовая сварка сталей Низкоуглеродистые стали с содержанием углерода до 0, 25% свариваются без ограничений. Для сварки применяют нормальное пламя с расходом ацетилена – 100-300 л/ч на 1 мм толщины металла при правом способе и 120-150 л/ч – при левом. В качестве присадочного материала используют сварочную проволоку марок: Св.- 08, Св.- 08А, Св.- 08ГА, Св. – 10ГА, Св. – 10Г2. Применение флюса не требуется. Иногда применяют последующую термообработку.
Слайд 3
02.05.17 Газовая сварка сталей В среднеуглеродистых сталях с содержанием уг-лерода свыше 0,3% возможно образование тре-щин при температурах, близких к температуре кристаллизации металла (горячие трещины), и при охлаждении после сварки (холодные трещи-ны). Повышение содержания углерода способ-ствует образованию хрупких прослоек по грани-цам зёрен металла. Трещины в таких сталях могут образовываться как в околошовной зоне, так и в металле шва. Для сварки таких сталей (с содержанием углерода 0,3 – 0,6%) применяют пламя с меньшим расходом ацетилена – 75 – 100 л/ч на 1 мм толщины металла. Используют только нормальное пламя. При толщине метал-ла более 3 мм рекомендуется применять общий
Слайд 4
02.05.17 Газовая сварка сталей предварительный подогрев изделия до 250 – 350 0 С. Применяют также местный подогрев горелками околошовной зоны до температуры 650 – 700 0 С. Структуру металла шва и околошовной зоны пос-ле сварки можно улучшить отпуском при 600 – 650 0 С. Повышение механических свойств нап-лавленного металла при сварке среднеуглеро-дистых сталей может быть достигнуто использо-ванием присадочной проволоки, легированной хромом (0,5 – 1,0%) и никелем (2 – 4%), например Св. – 06Н3, Св. – 18ХГС.
Слайд 5
02.05.17 Газовая сварка сталей Высокоуглеродистые стали содержат 0,6 – 2,0% углерода. Эти стали свариваются хуже, чем среднеуглеродистые. Приёмы сварки применяют те же, что и при сварке среднеуглеродистых сталей. Расход ацетилена составляет 75 л/ч на 1 мм толщины металла. Рекомендуется левый способ сварки. Применяют нормальное или слегка науглероживающее пламя и присадочную проволоку с низким содержанием углерода. При сварке сталей, содержащих более 0,7% углерода, рекомендуется применять флюс (буру). Удовлетворительное сварное соединение высокоуглеродистых сталей можно получить при толщине металла не более 3 мм.
Слайд 6
02.05.17 Газовая сварка сталей Обычно сварку ведут с предварительным подогревом до 250 – 350 0 С в сочетании с местным подогревом до 650 -700 0 С. После сварки применяют термообработку по режиму, установленному для данной марки стали.
Слайд 7
02.05.17 Газовая сварка сталей Низколегированные стали перлитного класса (10ХСНД, 15ХСНД) характеризуются повышенной прочностью, хорошей свариваемостью и высокой стойкость к коррозии в атмосферных условиях. При газовой сварке указанных сталей применяют нормальное пламя с расходом ацетилена 75 – 100 л/ч (при левой сварке) и 100м – 130 л/ч (при правой сварке) на 1 мм толщины металла. Используют присадочную проволоку Св. – 08А и Св. – 08Г2С. Флюс не применяют.
Слайд 8
02.05.17 Газовая сварка сталей Молибденовые и низколегированные стали марок 15М, 25МЛ содержат 0,4 – 0,6% молиб-дена и предназначены для работы при темпе-ратурах 500 – 550 0 С. При сварке этих сталей применяют только нормальное пламя с рас-ходом ацетилена 100 л/ч на 1 мм толщины металла. Применяются сварочные проволоки марок Св. – 08ХМ, Св. – 10НМ, Св. – 18ХМА, Св. — 10ХМ. Сварку ведут небольшими участками 15 – 25 мм, поддерживая весь свариваемый учас-ток при температуре светло-красного каления. При сварке кромки должны быть зачищены до металлического блеска. При толщине металла до 5 мм сварку ведут в один слой, при большей толщине применяют многослойную сварку.
Слайд 9
02.05.17 Газовая сварка сталей Сварку следует вести с минимальным коли-чеством перерывов. При возобновлении сварки после перерыва необходимо рав-номерно подогреть шов в данном месте (при сварке труб – весь стык!) до 250 – 300 0 С для предупреждения появления трещин.
Слайд 10
02.05.17 Газовая сварка сталей Хромомарганцевые стали (типа 30ХГСА) обладают большой прочностью, упругостью и хорошо выдерживают вибрационные и ударные нагрузки. В термически обработанном состоянии они имеют прочность 800 МПа и относительное удлинение 10%. Для предупреждения выгорания хрома и кремния сварку ведут наконечником с расходом ацетилена 75 – 100 л/ч на 1 мм толщины металла. В качестве присадочного металла используют низкоуглеродистую проволоку Св. – 08 и Св. – 08А или легированную проволоку Св. – 18ХМА. Перед сваркой листы прихватывают через 20 – 30 мм при толщине металла 0,5 – 1,5 мм и через 40 -60 мм при толщине металла более 2 мм. Прихватки следует располагать на расстоянии 10 – 15 мм от края листа или угла сварного соединения.
Слайд 11
02.05.17 Газовая сварка сталей Необходима тщательная зачистка и подгонка кромок, а также точное соблюдение зазора между ними, который должен быть одинаковым по всей длине шва, что проверяется шаблоном. Сварку ведут в один слой. При резком охлаждении возможно образование трещин в шве и околошовной зоне, поэтому при окончании сварки пламя следует отводить от шва медленно, подогревая факелом конечный участок на площади радиусом 20 – 40 мм. Сварку необходимо вести как можно быстрее, без перерывов, не задерживая пламя горелки на одном месте и не перегревая металла сварочной ванны.
Слайд 12
02.05.17 Сварка легированных сталей К среднелегированным сталям относятся стали, содержащие 2,5 – 10% легирующих элементов. Высоколегированными считаются стали с содержанием легирующих элементов более 10% (кроме углерода). По своей структуре эти стали могут быть мартенситного, мартенситно-ферритного, ферритного и аустенитного классов. При их сварке необходимо стремиться сохранить первоначальный состав и структуру стали в сварном соединении для того, чтобы свойства его не отличались в значительной степени от специфических свойств основного металла (коррозионная стойкость, жаростойкость, износостойкость и др.). Свариваемость этих сталей определяется их химическим составом
Слайд 13
02.05.17 Сварка легированных сталей и особенно содержанием в них углерода. В сварных соединениях наиболее широко используют хромистые и хромоникелевые коррозионно-стойкие, жаростойкие и жаропрочные стали. Они находят применение при изготовлении химической аппаратуры. Хромистые стали могут содержать 4 – 30% хрома. Стали с содержанием хрома в пределах 4 – 14% относятся к мартенситному классу, 13 – 18% — к мартенситно-ферритному, 23 – 30% — к ферритному. Структура стали зависит также от содержания в ней углерода. Повышение содержания углерода способствует образованию мартенситной структуры.
Слайд 14
02.05.17 Сварка легированных сталей Среднелегированные хромистые стали, содержащие до 0,15% углерода, применяют в конструкциях, где необходима коррозионная стойкость. Высоколегированные хромистые стали могут содержать до 0,35% углерода. При длительном нагреве высокохромистые стали склонны к росту зерна, что снижает их прочность, поэтому газовой сваркой эти стали сваривать не рекомендуется. Сварку хромистых сталей для предупреждения излишнего перегрева и уменьшения коробления выполняют нормальным пламенем с пониженным расходом ацетилена (70 л/ч на 1 мм толщины металла). При сварке применяют присадочную проволоку марок СВ. – 04Х19Н9 и Св. – 06Х19Н9Т.
Слайд 15
02.05.17 Сварка легированных сталей Сварку необходимо вести как можно быстрее, без перерывов и повторного нагрева одного и того же места шва пламенем горелки. Тонкие листы сваривают левым способом, металл большой толщины – только правым. Рекомендуется ис-пользовать флюс следующего состава: 55% борной кислоты, 10% оксида кремния, 10% фер-ромарганца, 10% феррохрома, 5% ферротитана, 5% титановой руды, 5% плавикового шпата. Пос-ле сварки рекомендуется подвергать изделие термообработке, предусмотренной, для данной марки стали
Слайд 16
02.05.17 Сварка легированных сталей Хромоникелевые аустенитные стали содержат до 0,12% углерода и 17 – 19% хрома. Эти стали обладают высокой коррозионной стойкостью, жаростойкостью и жаропрочностью. Газовую сварку хромоникелевых сталей выполняют нормальным пламенем с расходом ацетилена 70 — 75 л/ч на 1 мм толщины металла. Окислительное пламя применять нельзя ввиду сильно выгорания хрома с образованием тугоплавких оксидов. Присадочную проволоку применяют с малым содержанием углерода (Св. – 01Х19Н9, Св. – 06Х19Н9 или Св. – 07Х19Н10Б). Сварку ведут с возможно максимальной скоростью, держа конец присадочной проволоки погруженным в сварочную ванну. Можно применять правый и левый способы сварки. Для защиты сварочной ванны используют флюс на основе буры .
Слайд 17
02.05.17 Сварка легированных сталей Флюсы необходимо тщательно удалять после сварки , так как они образуют на шве агрессив-ную плёнку, которая может способствовать воз-никновению межкристаллитной коррозии. Флюс разводят в воде и в виде пасты наносят на кром-ки за 15 – 20 минут до сварки. Флюс наносят так-же с обратной стороны шва для предупрежде-ния образования оксидов хрома в корне шва. Остатки флюса после сварки удаляют тщатель-ной промывкой швов после сварки в горячей воде.
Слайд 18
02.05.17 Сварка легированных сталей Газовую сварку целесообразно применять для хромоникелевых сталей толщиной не более 1,5 – 2,0 мм, при этом достигаются удовлет-ворительное качество соединения и доста-точная производительность процесса. После сварки, если позволяет конструкция, реко-мендуется термообработка – нагрев до 1050 – 1100 0 С с последующим охлаждением в воде.
Слайд 19
02.05.17 Рассмотрим особенности газовой сварки чугуна
Слайд 20
02.05.17 Чугун является трудносвариваемым сплавом. При сварке в металле шва и околошовной зоне наблю-даются большие скорости охлаждения. В результате этого образуются хрупкие структуры отбела и закал-ки, которые не поддаются механической обработке. Повышенная склонность чугуна к образованию хруп-ких структур связана с высоким содержанием в нем углерода. При газовой сварке, обеспечивающей большую зону нагрева и меньшие скорости охлаж-дения, образование структур закалки и отбела менее вероятно по сравнению с дуговыми способами свар-ки.
Слайд 21
02.05.17 Трещины в сварном соединении чугуна могут возникать из-за неравномерного нагрева и ох-лаждения изделий, литейной усадки металла шва, жесткости свариваемого изделия. Холодные трещины развиваются мгновенно со значительным механическим и звуковым эф-фектом. Наиболее благоприятные условия для трещинообразования создаются в околошовной зоне. Менее склонны к трещинообразованию мелкозернистые чугуны с перлитной структурой и мелкими графитовыми выделениями. Лучше свариваются чугуны, имеющие мелкозернистую структуру и излом
Слайд 22
02.05.17 светло-серого цвета, хуже – чугуны с крупнокристал-лическим изломом, имеющие крупные включения графита. Плохо свариваются чугуны с изломом чер-ного цвета. При сварке чугуна происходит интенсив-ное газовыделение из сварочной ванны, которое мо-жет привести к образованию пор в наплавленном ме-талле. Образование пор, вызванное присутствием водорода и азота, связано с изменением их раство-римости в металле при изменении его температуры. В расплавленном состоянии металл сварочной ван-ны может растворить значительное количество водо-рода и азота. По мере остывания металла раствори-мость газов снижается.
Слайд 23
02.05.17 Резкое скачкообразное снижение растворимости отмечается в момент кристаллизации металла. Образующиеся при этом газовые пузырьки могут полностью выйти на поверхность сварочной ванны или запутаться между кристаллитами и вызвать по-ристость в металле шва. Образование пор, вызван-ное нерастворимыми в чугуне водяными парами и оксидом углерода, имеет другую природу. Если эти газы образуются в жидкой сварочной ванне, то они могут интенсивно выделяться из нее (кипение ван-ны). При удалении они увлекают из ванны другие газы и неметаллические включения. В этом случае обеспечивается получение плотного металла шва.
Слайд 24
02.05.17 При газовой сварке чугуна основной способ устра-нения пористости – уменьшение скорости кристал-лизации сварочной ванны. Это достигается тем, что по окончании заполнения разделки дефекта сварщик прогревает жидкую ванну пламенем горелки, созда-вая этим условия для удаления газов. В некоторых случаях, обнаружив в ванне газовые пузырьки, целе-сообразно временно прекратить расплавление при-садочного материала и дополнительно прогреть ванну до видимого удаления газовых пузырьков.
Слайд 25
02.05.17 Способы сварки чугуна С общим нагревом С местным нагревом Без подогрева («холодная сварка») Температура подогрева составляет 300 – 400 0 С. После сварки деталь должна медленно остывать для получения однородной равномерной структуры серого чугуна и предупреждения возникновения трещин.
Слайд 26
02.05.17 Материалы для горячей сварки чугуна Пруток А (С = 3,0-3,5%, Si = 3 ,0-3,4%, S ≤ 0,08%, P ≤ 0 ,4%, Mn = 0,5 – 0,8%, Cr ≤ 0 ,05%, Ni ≤ 0,3% ) Пруток Б (С = 3,0-3,5%, Si = 3 ,5-4,0%, S ≤ 0,08%, P ≤ 0 ,5%, Mn = 0,5 – 0,8%, Cr ≤ 0 ,05%, Ni ≤ 0,3% )
Слайд 27
02. 05.17 Материалы для горячей сварки чугуна Флюс № 1 – бура прокаленная 100% Флюс № 2 — бура прокаленная – 56%, углекислый натрий – 22%, углекислый калий – 22% Флюс № 3 — бура прокаленная – 50%, сода двууглекислая – 47%, кремнезем – 3% Флюс № 4 — углекислый натрий – 50%, сода двууглекислая – 50% Флюс № 5 — бура прокаленная – 23%, углекислый натрий – 27%, Азотнокислый натрий – 50%
Слайд 28
02.05.17 Технология газовой сварки чугуна с нагревом Предварительный нагрев до 500 — 600 0 С Прогрев основного металла вокруг сварки до 850 0 С (до светло – красного цвета) Нанести флюс на поверхность свариваемого металла при-садочным прутком Расплавить присадочный пруток и заполнить разделку шва, периодически добавляя флюс на кончике присадочного прутка Держать сварочную ванну в жидком состоянии до полного заполнения разделки (для полного удаления газов и неме-таллических включений из сварочной ванны В конце сварки уменьшить скорость охлаждения сварочной ванны (плавно отводить горелку на расстояние 50 – 60 мм от сварочной ванны)
Слайд 29
02.05.17 Процесс замедленного охлаждения контролировать визуально с помощью защитных очков: по перифе-рии шва должно образоваться темное кольцо охлаж-дающегося металла. После распространения этого кольца на центр наплавленного металла пламя го-релки выключают. Для замедленного охлаждения деталь засыпают сухой землей или накрывают лис-товым асбестом. Для уменьшения внутренних напря-жений и предупреждения образования трещин дета-ли большой толщины и сложной конфигурации реко-мендуется подвергать вторичному нагреву (отжигу) в горне или печи при температуре 650 – 750 0 С и ох-лаждать вместе с печью.
Слайд 30
02.05.17 Технология газовой сварки чугуна без подогрева Установить максимально возможную мощность пламени горелки Перед заполнением сварочной ванны необходимо подогреть участки прилегающие к месту сварки Нанести флюс Расплавить присадочный пруток и заполнить сварочную ванну Вновь подогреть прилегающие участки в течении 2 – 3 мин. , постепенно удаляя сварочную горелку. Засыпать заваренный участок сухим песком или накрыть листовым асбестом для замедленного остывания.
Слайд 31
02.05.17 Технология холодной газовой сварки чугуна (пайкосварка) Такая технология применяется тогда, когда после из-готовления чугунной детали остаются малые при-пуски на механическую обработку и нельзя устра-нять дефекты после литья сваркой с подогревом, так как это приведет к возникновению внутренних термических напряжений и деформаций, которые уже нельзя исправить и компенсировать последу-ющей механической обработкой. В этом случае применяется пайкосварка, при которой сварное со-единение образуется так же как и при пайке, без расплавления основного металла.
Слайд 32
02.05.17 Технология холодной газовой сварки чугуна (пайкосварка) В начале низкотемпературной пайкосварки жидкая ванна не образуется, и наплавку производят отдельными каплями. Капли жидкого присадочного металла, попадая не основной металл, разогретой ниже температуры кристаллизации при-поя, и соприкасаясь с ним, отдают ему часть своей тепло-ты, вследствие чего повышается температура поверхност-ного слоя основного металла. Капля жидкого припоя под действием флюса и давлении пламени легко растекается тонким слоем по основному металлу. Часть жидкого метал-ла под действием капиллярных сил заполняет пустоты, об-разующиеся в чугуне в результате поверхностного выкра-шивания или окисления графита.
Слайд 33
02.05.17 Технология холодной газовой сварки чугуна (пайкосварка) Подготовку к сварке осуществляют механическим путём (сверление и вырубка) с плавными радиусными перехода-ми для того, чтобы обеспечить равномерный прогрев и сво-бодный выход газов в сторону от наконечника газовой го-релки. В качестве присадочного материала могут приме-няться чугунные прутки марок НЧ-2 (углерод-3,0…3,5%, кремний-3,5…4,0%, марганец-0,6…0,7%, фосфор-0,2…0,4%, никель-0,4…0,6%, титан-0,15…0,2%, медь-не бо-лее 0,1%, сера — не более-0,05%) и УНЧ-2 (углерод-3,4…3,7%, кремний-3,5…3,8%, марганец-0,6…0,7%, фосфор-0,2…0,4%, никель-0,4…0,6%, титан-0,15…0,2%, медь-не более 0,1%, сера — не более-0,03%)
Слайд 34
02. 05.17 Технология холодной газовой сварки чугуна (пайкосварка) Угол наклона горелки – 20…30 0 Присадочный пруток расположен от ядра пламени на расстоянии до 23 мм Флюс МАФ-1 Процесс протекает при температуре 750-800 0 С Допускается предварительный нагрев до температуры 300-400 0 С
Слайд 35
02.05.17 Технология холодной газовой сварки чугуна (пайкосварка) Чаще пайкосварку чугуна осуществляют латунными припоями марок ЛО 59-1-03, ЛОМНА 49-05-10-4-04 с использованием флюсов ФПСН -1 или ФПСН — 2 Пламя горелки устанавливают слегка окислительное. Режимы прогрева такие же как и при пайкосварке чугунными присадочными прутками
Слайд 36
02.05.17 Сварка меди Для обеспечения высококачественной сварки меди необходи-мо раскислять сварочную ванну. При этом оксиды из сва-рочной ванны удаляют путем связывания их флюсами или восстановления оксидов меди активными элементами, ок-сиды которых всплывают на поверхность этой ванны. Активные элементы могут быть введены в состав приса-дочного металла. Применение в качестве присадочного ме-талла меди, не содержащей раскислителей, можно реко-мендовать для сварки неответственных, малонагруженных конструкций. Эффективно применение присадочного ме-талла, содержащего в качестве раскислителей кремний, марганец и др. Хорошие результаты даёт легирование присадки серебром, оловом, магнием, которые понижают температуру плавления меди.
Слайд 37
02.05.17 Сварочные материалы для газовой сварки меди Присадочный пруток – МСр1 (магния — 0,8…1,2%) по ГОСТ 16130-72 Флюсы (пасты и порошки): № 1 (прокаленная бура – 100%) № 2 (борная кислота – 100%) № 3 (прокаленная бура – 50%, борная кислота – 50%) № 4 (прокаленная бура – 75%, борная кислота – 25%) № 5 (прокаленная бура – 50%, борная кислота – 35%, гидрофосфат натрия – 15%) № 6 (прокаленная бура – 50%, гидрофосфат натрия – 15%, кварцевый песок – 15%, древесный уголь – 20%) № 7 (поваренная соль – 20%,рокаленная бура – 80%) № 8 (поваренная соль – 22%, карбонат калия – 22%, прокаленная бура – 56%)
Слайд 38
02. 05.17 Технология сварки меди Применяются в основном стыковые и угловые соединения, реже – нахлёсточные и тавровые. Стыковые соединения толщиной до 1,5…2,0 мм сваривают без присадочного металла (в зазор подкладывают асбест или графит) Угол разделки не менее 90 0 Стыковое соединение толщиной более 10 мм сваривают вертикально снизу вверх одновременно 2 газосварщика. При сварке следует избегать резких переходов Пламя горелки строго нормальное, мягкое Присадочный пруток надо держать как можно ближе к поверхности сварочной ванны (это уменьшит его окисление) Сварку надо выполнять в один слой! Для повышения пластичности шов надо проковать сразу после сварки.
Слайд 39
02.05.17 Технология сварки латуни Латунь – это сплав меди с цинком (иногда латунь легируют алюминием, никелем, железом, оловом, свинцом, крем-нием, марганцем). При сварке латуней применение флюсов обязательно (иск-лючение для самофлюсующегося присадочного прутка марки ЛКБ 62 -0,2-0,04-0,5) При сварке латуни образуются основные оксиды, поэтому на-до применять кислые флюсы ( например, борный ангидрид В 2 О 3 ), можно применять флюс БМ-1 Применяется преимущественно левый способ. Нельзя касаться ядром пламени горелки поверхности свароч-ной ванны и присадочного прутка – это вызывает перегрев и насыщение ванны водородом. Хорошие результаты получаются с применением присадочного прутка марки ЛК62-0,5 с флюсом: бура
Слайд 40
02.05.17 Технология сварки латуни Флюс № 1 (бура – 100%) Флюс № 2 (бура – 50%, борная кислота – 35%, ортофосфат натрия – 15%) Флюс № 3 (бура – 20%, борная кислота – 80%) ВМ – 1 (метиловый спирт – 25%, метилборат – 75%)
Слайд 41
02.05.17 Технология сварки латуни Пламя горелки окислительное (защита от выгорания цинка) Присадочная проволока должна быть всё время погружена в сварочную ванну Кромки свариваемого металла должны быть тщательно зачищены напильником, щетками и протравлены 10% раствором азотной кис-лоты с последующей промывкой в горячей воде. Расход ацетилена не более 35-40 л/ч на 1 мм толщины металла
Слайд 42
02. 05.17 Технология сварки бронзы Бронза – это сплав меди с оловом, а также с алюминием, марганцем, кремнием, бериллием, железом и др. Оловянные бронзы сваривают только нормальным пламенем, так как окислительное пламя приводит к выгоранию олова, о науглероживающее пламя увеличивает пористость из-за растворения в металле водорода. Расход ацетилена – 70-120 л/ч на 1 мм толщины металла Предварительный подогрев до 500-600 0 С Пламя должно быть мягким (давление кислорода надо снижать) чтобы не раздувать сварочную ванну После сварки – отжиг при температуре 750 0 С и закалка при температуре 600-650 0 С (в воде)
Слайд 43
02.05.17 Технология сварки бронзы Сварка безоловянных бронз проводится нормаль-ным пламенем с расходом ацетилена 100 – 150 л/ч на 1 мм толщины металла. Предварительный подогрев до температуры 300 – 350 0 С После сварки – отжиг и закалка Сварка алюминиевых бронз затруднена образова-нием тугоплавкого оксида алюминия Al 2 O 3 , поэто-му надо использовать флюсы для сварки алюми-ния (АФ-4А) Скорость сварки должна быть максимальной Сварку выполняют без подогрева, но лучше варить такую бронзу аргонодуговой сваркой!
Слайд 44
02.05.17 Сварка алюминия и его сплавов Алюминиевые сплавы обладают высокими механическими свойствами при малой плотности, большой удельной проч-ностью, высокими тепло — и электропроводностью, стойкос-тью против коррозии и хорошими технологическими свойст-вами. Высоких механических свойств достигают введением в алюминиевые сплавы легирующих элементов, например марганца, меди, магния, кремния, цинка, хрома, никеля и др. Алюминиевые сплавы подразделяют на две основные группы: деформируемые и литейные. Деформируемые: АМц, АМг2, АМг3, АМг5 . Большинство этих сплавов отличается высокими пластичностью и сопротив-лением к коррозии и хорошей свариваемостью. Однако прочность их сравнительно невелика. К ним также относят-ся дюралюминиевые сплавы: Д1,Д16, АВ, АК, В95. Литейные сплавы используют для изготовления фасонных де-талей, имеющих сложную конфигурацию и они должны об-ладать высокими литейными свойствами (силумины).
Слайд 45
02.05.17 Сварка алюминия и его сплавов При сварке алюминиевых сплавов возможно образо-вание пористости в металле шва. Это обусловлено тем, что при взаимодействии расплавленного алю-миния с парами воды происходит образование атомарного водорода, который хорошо растворя-ется в металле сварочной ванны. Высокая ско-рость кристаллизации препятствует выходу газа в атмосферу и создает благоприятные условия для образования пор. Предварительный подогрев и уменьшение скорости сварки, способствующие за-медлению процесса кристаллизации, позволяют уменьшить вероятность образования пористости. При газовой сварке алюминиевых сплавов допусти-мо применение в качестве горючего газа ацетиле-на и водорода, а также пропан-бутановой смеси .
Слайд 46
02.05.17 Сварочные материалы для газовой сварки алюминиевых сплавов Пруток АК5 Пруток АМц Пруток СвАК5 Пруток СвАК10 Пруток СвАМг3 Пруток СвАК12 Присадочные прутки перед сваркой должны быть очищены и обезжирены!
Слайд 47
02.05.17 Сварочные материалы для газовой сварки алюминиевых сплавов Сварочные флюсы: № 1 – хлористый калий – 45%, хлористый натрий – 30%, хлористый литий – 15%, сернокислый натрий – 7%, фтористый калий – 3% № 2 — хлористый калий – 45%, хлористый натрий – 30%, хлористый литий – 15%, фтористый калий – 10% № 3 — хлористый калий – 50%, хлористый натрий – 15%, криолит – 35% № 4 — хлористый калий – 50%, хлористый натрий – 30%, криолит – 20% № 5 — хлористый калий – 45%, хлористый натрий – 20%, фтористый калий – 35% № 6 — хлористый калий – 50%, хлористый натрий – 28%, хлористый литий – 22%
Слайд 48
02.05.17 Технология сварки алюминиевых сплавов Подготовка кромок — на станках – заусенцы и шероховатости не допускаются Необходим подварочный шов с обратной стороны Кромки должны быть очищены от грязи, краски, жиров и масел металлическими щетками и напильниками. Применение шкурок не допускается! Обязательна очистка и околошовной зоны на ширину 25-30 мм по обе стороны будущего шва Перед сваркой детали протравливают в азотной кислоте при температуре 65 0 С в течение 2…5 мин. Потом промывка в теплой воде и сушка. Сварка выполняется не позднее чем через 8 часов после такой обработки
Слайд 49
02.05.17 Технология сварки алюминиевых сплавов Пламя горелки должно быть нормальным, допускается небольшой избыток ацетилена, особенно не допускается избыток кислорода, так как это приводит к образованию тугоплавких оксидов алюминия. Сварка ядром пламени не допускается Угол наклона горелки почти 90 0 Применяется левый способ сварки Сварка должна выполняться с большой скоростью, чтобы нет перегреть металл Нельзя начинать сварку с самого края, так как могут образоваться трещины в самом начале шва Подварка по готовому шву не допускается! После сварки желательно провести термообработку Допускается проковка шва для повышения его пластичности. Остатки флюса надо обязательно удалять!!!
Слайд 50
02.05.17 Задание на дом Повторить технологию газовой сварки различных металлов Повторить устройство и назначение газовой аппаратуры Подготовиться к тестовым контрольным по газовой сварке
Слайд 51
02.05.17 Благодарю за внимание!!!
XI Промышленный конгресс юга России
Научно-практическая конференция «Инновационные технологии в машиностроении и металлургии».
Программа конференции:
Регистрация посетителей.
Доклады по секциям:
— Секции «Машиностроение» и «Станкоинструмент».
Место проведения: конференц-зал Бета, 2-й этаж.
Вопросы для рассмотрения:
— Приспособление контроля несоосности элементов передач.
— Демпфирующие свойства гофрированного картона сотовой структуры.
-Исследование рационального спектрального состава колебаний ходовой системы зерноуборочного комбайна.
— Экспресс-оценка ресурса при разработке конструктивных вариантов деталей.
— Оптимальная траектория укладки детонирующей ленты, обеспечивающая максимальное воздействие на заглубленный объект.
— Определение распределений интенсивности оптических полей при измерении перемещений поверхностей объектов контроля лазерным интерферометром.
— Основные направления совершенствования оптических интерференционных средств измерения малых перемещений.
— О моделировании волновых процессов при диагностике состояния слоистых анизотропных материалов.
— Алюминирование поверхности деталей нагревательных приборов из стали в процессе вибрационной механико-термической обработки.
— Распространение ударных волн при виброволновой упрочняющей обработке деталей.
— Нанесение твердосмазочного покрытия на поверхность деталей из алюминиевых сплавов в процессе вибрационной механохимической обработке.
— Виброволновая стабилизирующая обработка деталей из алюминиевых и титановых сплавов.
— Виброволновая обработка в процессе изготовления пьезокерамических элементов.
— Виброволновая обработка трубчатых деталей водонагревательных устройств на операции подготовки поверхности под покрытие.
— Энергетическая модель формирования вибрационных механохимических покрытий.
— Секция «Инновационные технологии сварочного производства».
Место проведения: конференц-зал Вега, 3-й этаж.
— Тенденции развития сварочных технологий в России и за рубежом.
— Особенности сварки под водой металлических конструкций.
— Современные тенденции развития сварочного производства при изготовлении котельного оборудования.
— Организация аттестации специалистов сварочного производства на ОАО ТКЗ «Красный Котельщик»
— Состояние сварочного производства и тенденции его развития на НЭВЗе.
— Оборудование и инструмент для сварки трением с перемешиванием.
— Сварка трением с перемешиванием разнородных соединений.
— Разработка компетенции свариваемости разнородных материалов способами сварки: плавлением, давлением, наплавки, пайки и напыления.
— Секция «Промышленная безопасность».
Место проведения: конференц-зал Дельта, 2-й этаж.
— Мобильные вентиляционные комплексы для улучшения условий труда сварщиков при работах в стеснённых условиях и ограниченных пространствах.
— Проектирование центробежных пылеуловителей на основе параллельных сравнительных испытаний с применением компьютерного моделирования.
— Использование метода математического моделирования для прогнозирования уровня производственного травматизма в ООО «ПК «НЭВЗ».
— Применение группового метода для анализа и оценки состояния производственного травматизма в ООО «Ростовский Прессово-Раскройной завод».
— Определение уровней звуковой мощности редукторов при их эксплуатации.
— Виброакустические характеристики станка ТВМ-12 с базовой и экспериментальной шпиндельной бабкой.
— Акустические характеристики скрипных гидравлических ножниц.
— Шумовые характеристики в рабочей зоне многодисковых ножниц.
— Анализ условий труда при зачистке сварных швов кузовов электровозов.
Организатор: Федеральное государственное бюджетное образовательное учреждение высшего профессионального образования «Донской государственный технический университет» (ДГТУ), ВЦ «ВертолЭкспо».
В Росатоме создали инновационный комплекс для подводной сварки
Группа ученых Государственного научного центра АО «НПО «ЦНИИТМАШ» (входит в машиностроительный дивизион «Росатома» – АО «Атомэнергомаш») представила испытательный стенд для отработки технологии подводной сварки и рассказала о ходе научно-исследовательской работы в этом направлении. Презентация прошла в рамках Международной научной конференции «Сварка и родственные технологии для изготовления оборудования специального и ответственного назначения». Работа ведется по заказу Ленинградской АЭС для новых блоков ВВЭР-1200, генеральный подрядчик работ – ООО «Специальное конструкторско-технологическое бюро прикладной робототехники», в проекте также заняты специалисты ЦНИИТМАШ и ООО «АПС РАДИС».
В ходе научно-исследовательской работы на тему «Разработка и согласование технологии для ремонта облицовки бассейна выдержки методом автоматической роботизированной подводной сварки» ЦНИИТМАШ разрабатывает уникальную технологию подводной сварки, а также сварочные материалы, обладающие особыми сварочно-технологическими характеристиками: порошковую проволоку, подходящую для работ под водой. Для разработки состава проволоки и отработки технологии подводной сварки в Сварочно-технологическом центре ЦНИИТМАШ был смонтирован тренировочный стенд. Первые этапы отработки технологии проводились в контейнере с водой с применением самозащитных порошковых проволок различных производителей, а также проволок сплошного сечения с применением защитного газа и без.
Более того, при участии специалистов ЦНИИТМАШ разрабатывается технологическое оборудование, способное выдерживать радиацию и активную среду бассейна выдержки АЭС. Специалисты ООО «АПС РАДИС» разработали подводную сварочную систему, полностью обеспечивающую выполнение разрабатываемой технологии, что позволит ликвидировать потенциальный дефект. Это лишь один из рабочих органов пятикоординатного робота, на схвате которого смогут находиться также система зачистки и ультразвуковая система поиска трещин (созданием систем занимается генеральный подрядчик работ – ООО «СКТБ ПР»). На аналогичном стенде пройдут обучение сотрудники новых блоков ВВЭР-1200 ЛАЭС, которые впоследствии будут инспектировать состояние бассейна выдержки в реальных условиях.
Для тестирования сварочной системы группой ученых был разработан испытательный стенд: он состоит из транспортной системы, перемещающей в различных направлениях сварочный аппарат, и бассейна с водой. Стенд позволяется имитировать давление воды на разной глубине. Именно здесь будут отработаны синергетические режимы сварки путем моделирования всех возможных сценариев развития дефекта в бассейне.
«Работы в рамках этой НИР подразумевают много сложностей. Одна из них состоит в разработке сварочных материалов – специальных порошковых проволок, аналогов которым в России пока не существует. Проведенные патентные исследования показали, что не только материалы, но и все технические решения, которые будут использованы при ремонте бассейнов выдержки АЭС посредством подводной сварки, имеют патентную чистоту на территории РФ. В частности, в данный момент мы решаем проблему подбора материалов и химических элементов, способствующих образованию устойчивого защитного газового пузыря, необходимого для качественной сварки, – рассказывает координатор проекта, старший научный сотрудник института сварки ЦНИИТМАШ Сергей Волобуев. – Ранее ремонтные работы под слоем воды выполнялись либо в специальных камерах сухим методом, либо с помощью водолазных работ штучными электродами. Оба способа не подходят для агрессивной среды и ограниченности пространства бассейна выдержки, поэтому мы и решили исследовать другие возможности».
Технология и комплекс для подводной сварки в перспективе имеют широкую область применения. В частности, они могут быть использованы в судостроении, при проведении сварочных работ на глубине, при прокладке подводных трубопроводов, выполнении различных ремонтных работ на объектах портовой инфраструктуры и в других сферах.
1 Технология ручной дуговой сварки презентация, доклад, проект
Текст слайда:Траектория движения электрода
Правильное поддержание дуги и ее перемещение является залогом качественной сварки. Слишком длинная дуга способствует окислению и азотированию расплавленного металла, разбрызгивает его капли и создает пористую структуру шва. Красивый, ровный и качественный шов получается при правильном выборе дуги и равномерном ее перемещении, которое может происходить в трех основных направлениях.
Поступательное движение сварочной дуги происходит по оси электрода. При помощи этого движения поддерживается необходимая длина дуги, которая зависит от скорости плавления электрода. По мере плавления электрода, его длина уменьшается, а расстояние между электродом и сварочной ванной — увеличивается. Для того чтобы это не происходило, электрод следует продвинуть вдоль оси, поддерживая постоянную дугу. Очень важно при этом поддерживать синхронность. То есть, электрод продвигается в сторону сварочной ванны синхронно с его укорочением. Продольное перемещение электрода вдоль оси свариваемого шва формирует так называемый ниточный сварочный валик, толщина которого зависит от толщины электрода и скорости его перемещения. Обычно ширина ниточного сварочного валика бывает на 2 — 3 мм больше диаметра электрода. Собственно говоря, это уже есть сварочный шов, только узкий. Для прочного сварочного соединения этого шва бывает недостаточно. И поэтому по мере перемещения электрода вдоль оси сварочного шва выполняют третье движение, направленное поперек сварочного шва.
Поперечное движение электрода позволяет получить необходимую ширину шва. Его совершают колебательными движениями возвратно-поступательного характера. Ширина поперечных колебаний электрода определяется в каждом случае индивидуально и во многом зависит от свойств свариваемых материалов, размера и положения шва, формы разделки и требований, предъявляемых к сварному соединению. Обычно ширина шва лежит в пределах 1,5 — 5,0 диаметров электрода.
Таким образом все три движения накладываются друг на друга, создавая сложную траекторию перемещения электрода.
Презентация на тему: Газовая сварка
Недостатком газовой сварки является меньшая по сравнению с дуговой скорость нагрева металла и большая зона теплового воздействия (зона термического влияния) на металл. При газовой сварке концентрация тепла меньше, а коробление свариваемых деталей больше.
Ацетилен наиболее широко применяется для газовой сварки и резки, так как дает высокую температуру пламени при сгорании в смеси с кислородом (около 3150оС).
Технический ацетилен получают из карбида кальция путем разложения последнего водой:
1. Получение карбида кальция (СаС2) – сплавление известняка и кокса в дуговых электропечах.
2.Получение ацетилена:
СаС2 + 2Н2О = С2Н2 + Са(ОН)2 + Q
Ацетиленовый генератор – аппарат, служащий для получения газообразного ацетилена из карбида кальция при воздействии на него водой.
Схема инжекторной ацетиленовой горелки:
Основные способы газовой сварки: а – левый — горелку перемещают справа налево, а присадочную проволоку передвигают впереди пламени;
б – правый — горелку ведут слева направо, присадочную проволоку перемещают вслед за горелкой.
СВАРКА ДАВЛЕНИЕМ
При сварке давлением, сближение атомов и молекул и активация поверхности соединяемых материалов достигаются в результате совместной упруго-пластической деформации. Сварку давлением проводят либо без нагрева, либо нагревом до температуры текучести, либо взрывом, ультразвуком, трением и пр.
Контактная сварка
Контактная сварка объединяет большую группу способов сварки, наиболее распространёнными из которых являются точечная, шовная и стыковая.
Сущность точечной сварки заключается в следующем. Если через два листа стали (рис. 1, а), уложенные внахлестку, и через сжимающие их два конусообразных медных электрода пропустить электрический ток большой силы, то стальные листы в точке прохождения электрического тока разогреются.
Рис. 1. Схема контактной сварки: а — точечной, б — роликовой; 1 — электроды, 2 — свариваемый материал
Роликовая сварка.
Для получения сплошного сварного шва применяют роликовую сварку, которая является разновидностью точечной. Листы стали зажимают между электродами (рис. 1, б), которые имеют вид дисков. Верхнему диску сообщается прерывистое движение, нижний поворачивается свободно. Сварка происходит с небольшими интервалами, так как ток пропускается только в момент движения электродов. Под действием электрического тока стальные листы между электродами нагреваются, размягчаются и свариваются. В следующий момент ток автоматически выключается для охлаждения шва и одновременно останавливается электрод. Затем цикл повторяется и таким образом получается непрерывный сварной шов.
Стыковая сварка — способ, при котором детали соединяются (свариваются) по всей плоскости их касания под воздействием нагрева и сжимающего усилия. Детали одинакового или близкого по размерам сечения закрепляют в электродах-губках машины, к которым подводят ток. При нагреве и пластической деформации металла в зоне стыка часть элементарных частиц — зерен металла разрушается с одновременным образованием новых (общих для обеих деталей) зерен. Кроме того, обязательным условием получения надежного соединения является удаление пленки окислов на торцах деталей или ее разрушение.
В Росатоме создали инновационный комплекс для подводной сварки
Группа ученых Государственного научного центра АО «НПО «ЦНИИТМАШ» (входит в машиностроительный дивизион «Росатома» – АО «Атомэнергомаш») представила испытательный стенд для отработки технологии подводной сварки и рассказала о ходе научно-исследовательской работы в этом направлении. Презентация прошла в рамках Международной научной конференции «Сварка и родственные технологии для изготовления оборудования специального и ответственного назначения». Работа ведется по заказу Ленинградской АЭС для новых блоков ВВЭР-1200, генеральный подрядчик работ – ООО «Специальное конструкторско-технологическое бюро прикладной робототехники», в проекте также заняты специалисты ЦНИИТМАШ и ООО «АПС РАДИС».
В ходе научно-исследовательской работы на тему «Разработка и согласование технологии для ремонта облицовки бассейна выдержки методом автоматической роботизированной подводной сварки» ЦНИИТМАШ разрабатывает уникальную технологию подводной сварки, а также сварочные материалы, обладающие особыми сварочно-технологическими характеристиками: порошковую проволоку, подходящую для работ под водой. Для разработки состава проволоки и отработки технологии подводной сварки в Сварочно-технологическом центре ЦНИИТМАШ был смонтирован тренировочный стенд. Первые этапы отработки технологии проводились в контейнере с водой с применением самозащитных порошковых проволок различных производителей, а также проволок сплошного сечения с применением защитного газа и без.
Более того, при участии специалистов ЦНИИТМАШ разрабатывается технологическое оборудование, способное выдерживать радиацию и активную среду бассейна выдержки АЭС. Специалисты ООО «АПС РАДИС» разработали подводную сварочную систему, полностью обеспечивающую выполнение разрабатываемой технологии, что позволит ликвидировать потенциальный дефект. Это лишь один из рабочих органов пятикоординатного робота, на схвате которого смогут находиться также система зачистки и ультразвуковая система поиска трещин (созданием систем занимается генеральный подрядчик работ – ООО «СКТБ ПР»). На аналогичном стенде пройдут обучение сотрудники новых блоков ВВЭР-1200 ЛАЭС, которые впоследствии будут инспектировать состояние бассейна выдержки в реальных условиях.
Для тестирования этой системы группой ученых был разработан испытательный стенд: он состоит из транспортной системы, перемещающей в различных направлениях сварочный аппарат, и бассейна с водой. Стенд позволяется имитировать давление воды на разной глубине. Именно здесь будут отработаны синергетические режимы сварки путем моделирования всех возможных сценариев развития дефекта в бассейне.
«Работы в рамках этой НИР подразумевают много сложностей. Одна из них состоит в разработке сварочных материалов – специальных порошковых проволок, аналогов которым в России пока не существует. Проведенные патентные исследования показали, что не только материалы, но и все технические решения, которые будут использованы при ремонте бассейнов выдержки АЭС посредством подводной сварки, имеют патентную чистоту на территории РФ. В частности, в данный момент мы решаем проблему подбора материалов и химических элементов, способствующих образованию устойчивого защитного газового пузыря, необходимого для качественной сварки, – рассказывает координатор проекта, старший научный сотрудник института сварки ЦНИИТМАШ Сергей Волобуев. – Ранее ремонтные работы под слоем воды выполнялись либо в специальных камерах сухим методом, либо с помощью водолазных работ штучными электродами. Оба способа не подходят для агрессивной среды и ограниченности пространства бассейна выдержки, поэтому мы и решили исследовать другие возможности».
Технология и комплекс для подводной сварки в перспективе имеют широкую область применения. В частности, они могут быть использованы в судостроении, при проведении сварочных работ на глубине, при прокладке подводных трубопроводов, выполнении различных ремонтных работ на объектах портовой инфраструктуры и в других сферах.
Семинар по подводной сварке и контролю
Презентация на тему: «Семинар по подводной сварке и контролю» — стенограмма презентации:
1 Семинар по подводной сварке и осмотру
4/12/2018 Семинар по подводной сварке и осмотру Саламу алейкум и доброе утро, цель моей сегодняшней презентации — познакомить вас с подводным миром.Но здесь вы увидите не рыб, кораллов или других подводных существ. Здесь вы узнаете о другой стороне атмосферной сварки — подводной сварке. . Я представляю это от имени команды, которая работала над элементом «Признание» после совещания по процессу согласования команд (TAP). НАЖМИТЕ Али Малик Саадун Отдел инженерных дел Багдадского университета
2
Цель: Целью этого семинара является ознакомление только с тем, как выполняется «подводная сварка».Здесь также делается упор на безопасность, поскольку мы имеем дело с двумя видами деятельности: дайвингом и сваркой. Следует помнить, что подводная сварка — это другой мир, поэтому для максимальной безопасности сварщика / дайвера соблюдаются особые меры предосторожности.
3 Список содержания: 1- Введение 2- Использование 3- Сварщик / дайвер
4- Классификация 5- Принцип работы 6- Коды, стандарты и спецификации 7- Характеристики хорошей подводной сварки 8- Применение подводной сварки 9- Некоторые характеристики подводной сварки 10- Подводный осмотр 11- Вовлеченный риск 12- Безопасность 13- Разработки 14- Ссылки: 15-Приложение
4 4/12/2018 1- Введение. Подводная сварка началась во время Первой мировой войны, когда британский флот использовал ее для временного ремонта кораблей.Этот ремонт заключался в приварке негерметичных заклепок корпусов судов. Подводная сварка также была ограничена только аварийно-спасательными работами и аварийным ремонтом. Кроме того, он был ограничен глубиной ниже поверхности не более 30 футов (10 метров). Сначала подводная сварка применялась только для приваривания заплатки, пока не удалось провести более тщательный ремонт. Но как только был накоплен больший опыт, амбициозные люди и компании объединили свои усилия, чтобы улучшить результаты и установить достижимые спецификации.В настоящее время подводная сварка становится все более сложной и может выполняться на большей глубине. GTAW использовалась для сварки труб на глубине 200 футов (61 м) и позволила получить сварные швы рентгеновского качества, соответствующие требованиям стандарта API 1104. Морские разведки нефти повысили интерес к подводной сварке.
5
2-Использование: Хотя подводная сварка использовалась для нового строительства и монтажа морских сооружений, подводных трубопроводов и портовых сооружений, она чаще всего используется для технического обслуживания и ремонта.Сюда входит ремонт повреждений, вызванных коррозией, усталостью и авариями морских сооружений, таких как нефтяные платформы, ремонт и замена поврежденных участков подводных трубопроводов, ремонт отверстий в корпусах судов или повреждения портовых сооружений в результате столкновения.
6 Использование (продолжение) Фотографии, представленные ниже, очевидно, что эти конструкции необходимо отремонтировать. И один из инструментов ремонта — подводная сварка.Поврежденная морская конструкция, опускающаяся на морскую конструкцию
7 3- Сварщик / дайвер: сварщик / дайвер — сертифицированный сварщик, который также является профессиональным водолазом, способным выполнять задачи, связанные с коммерческими подводными работами, настройкой и подготовкой сварных швов, и который имеет способность выполнять сварку в соответствии с AWS D3. .6, Технические условия на подводную сварку (влажную или сухую) и другие связанные с этим виды деятельности. Квалификация сварщика / водолаза, необходимая для выполнения определенного задания, варьируется от проекта к проекту.Большинство подрядчиков по подводному плаванию хотели бы, чтобы их сварщик / дайвер был «мастером на все руки». Это означает, что сварщик / дайвер должен знать, как выполнять подводную резку, установку и оснастку, инспекцию и неразрушающий контроль, а также подводную фотографию. Сварка Резка
8 4- Классификация в соответствии с AWS D3.6M: 2010:
В настоящее время используются пять основных методов подводной сварки: (1) Сварка в сосуде высокого давления, в котором давление снижается примерно до одной атмосферы, независимо от глубины (сухая сварка при одной атмосфере).(2) Сварка при атмосферном давлении в большой камере, из которой вода была вытеснена в атмосферу, при которой сварщик / дайвер не работает в водолазном снаряжении (сухая сварка в помещении). (3) Сварка при атмосферном давлении в простой сухой камере с открытым дном, которая вмещает, как минимум, голову и плечи сварщика / дайвера в полном снаряжении для дайвинга (сварка в сухой камере). (4) Сварка при атмосферном давлении в небольшом, прозрачном, заполненном газом корпусе со сварщиком / водолазом снаружи в воде (сухая точечная сварка). (5) Сварка при атмосферном давлении, когда сварщик / дайвер находится в воде без каких-либо механических барьеров между водой и сварочной дугой (мокрая сварка).
9 Итак, подводная сварка подразделяется на две категории.
Сварка во влажной среде = в основном использовалась для аварийного ремонта и аварийно-спасательных работ на мелководье из-за низкого качества сварных швов. Сварка в сухой среде = этот метод позволяет получать высококачественные сварные швы, соответствующие требованиям к рентгеновским лучам и нормам.
10 Сварка во влажной среде
4/12/2018 Сварка во влажной среде Подводная мокрая сварка выполняется в среде, где основной металл и дуга полностью окружены водой. Используемые типы электродов соответствуют классификации AWS E6013. Для гидроизоляции электродов их оборачивают водонепроницаемой лентой или погружают в специальные смеси силиката натрия и дают им высохнуть.Источником питания является машина постоянного тока номиналом 300 или 400 ампер. Сила дуги создает пузырь из смеси газов, который позволяет плавлению и соединению металла более или менее нормально. Сила дуги создает пузырь из смеси газов, который позволяет плавлению и соединению металла происходить более или менее нормально, как показано на фотографии выше.
11 Сварка во влажном состоянии (продолжение):
4/12/2018 Сварка во влажном состоянии (продолжение): Ниже представлена типичная установка оборудования для подводной сварки.Водонепроницаемый электрододержатель Источник питания _ + электрод В методе мокрой подводной сварки используются водонепроницаемые сварочные электроды. Сила дуги создает пузырь из смеси газов, который позволяет плавлению и соединению металла более или менее нормально. рабочий ножевой переключатель
12 Преимущества мокрой сварки
Мокрая подводная сварка MMA (ручная металлическая дуга) уже много лет широко используется при ремонте морских платформ.Преимущества мокрой сварки: — 1) Универсальность и низкая стоимость мокрой сварки делают этот метод очень востребованным. 2) Другие преимущества включают скорость. С которой проводится операция. 3) Это менее затратно по сравнению с сухой сваркой. 4) Сварщик может дотянуться до частей морских конструкций, которые нельзя сварить другими методами. 5) Никаких ограждений не требуется, и время на строительство не теряется. Используются доступные стандартные сварочные аппараты и оборудование. Оборудование, необходимое для выполнения работ по мокрой сварке, минимально.
13 Недостатки мокрой сварки
Хотя мокрая сварка широко используется для подводных производственных работ, она страдает следующими недостатками: — 1) Быстрая закалка металла шва окружающей водой. Хотя закалка увеличивает прочность сварного шва на растяжение, она снижает пластичность и ударную вязкость сварного изделия, а также увеличивает пористость и твердость.2) Водородное охрупчивание — в области сварного шва присутствует большое количество водорода в результате диссоциации водяного пара в области дуги. H3 растворяется в зоне термического влияния (HAZ) и в металле сварного шва, что вызывает охрупчивание, трещины и микроскопические трещины. Трещины могут разрастаться и привести к катастрофическому разрушению конструкции. 3) Еще один недостаток — плохая видимость. Сварщик иногда не умеет правильно сваривать.
14 Сварка в сухой среде
Сварку в сухой среде можно разделить на две основные категории: Гипербарическая сварка, при которой камера герметизируется вокруг свариваемой конструкции и заполняется пригодным для дыхания газом при преобладающем давлении. .Сварка коффердама, которая выполняется в сухом помещении, на воздухе, когда жесткая стальная конструкция для размещения сварщиков герметично прилегает к стороне свариваемой конструкции и открыта для атмосферы.
15 Сварка в сухой среде:
4/12/2018 Сварка в сухой среде: Гипербарическая сварка выполняется с использованием сварочной камеры или помещения. Этот метод обеспечивает высокое качество сварных соединений, отвечающих требованиям рентгенографии и норм.Камера герметична в конструкции или трубопроводе и заполнена пригодной для дыхания смесью гелия и кислорода (90-95% гелия и 5-10% кислорода). Сварочная камера Нижняя часть камеры находится под открытым небом и закрыта решеткой. Это делается для выравнивания давления в камере с давлением воды снаружи на определенной глубине. Камера предоставляет сварщику / водолазу все необходимое сварочное оборудование для сварки в сухой среде. Сварочная камера Внутренняя
16 Сварка в сухом состоянии (продолжение)
Сварка коффердамом также представляет собой тип сухой сварки, при котором жесткая стальная конструкция, в которой размещаются сварщики, прилегает к стороне свариваемой конструкции и открыта для атмосферы.Обычно он используется для портовых работ или ремонта судов.
17 Сварка в сухом состоянии (продолжение)
На фотографиях ниже приведены примеры коффердамской сварки. Фиктивная структура Фактическая структура
18
19 Преимущества сухой сварки
1) Безопасность сварщика / дайвера — Сварка выполняется в камере, защищенной от океанских течений и морских животных. Теплая и сухая среда обитания хорошо освещена и имеет собственную систему экологического контроля (ECS). 2) Сварные швы хорошего качества — этот метод позволяет получать сварные швы с качеством, сравнимым со сварными швами на открытом воздухе, поскольку вода больше не присутствует для закалки сварного шва, а уровень h3 намного ниже, чем у влажных сварных швов. 3) Контроль поверхности — подготовка стыков, выравнивание труб, контроль неразрушающего контроля и т. Д. Контролируются визуально. 4) Неразрушающий контроль (NDT) — неразрушающему контролю также способствует сухая среда обитания.
20 Недостатки сухой сварки
1) Сварка в среде обитания требует большого количества сложного оборудования и большого количества вспомогательного оборудования на поверхности.Камера очень сложная. 2) Стоимость сварки среды обитания чрезвычайно высока и увеличивается с увеличением глубины. Глубина обработки влияет на сварку рабочей зоны. На большей глубине дуга сужается и требуются соответствующие более высокие напряжения. Этот процесс дорогостоящий — за одну сварку взимается плата в долларах. Нельзя использовать одну и ту же камеру для другой работы, если она другая.
21 год 5- Принцип работы:
4/12/2018 На рисунке справа показано общее устройство для подводной сварки.Подводная сварка всегда должна осуществляться аппаратом постоянного тока, заземленным на судно. Схема сварки включает рубильник, который по сигналу сварщика / водолаза приводится в действие помощником на поверхности. Рубильный выключатель отключает сварочный ток и сконструирован таким образом из соображений безопасности. В держателе электрода используется поворотная головка для захвата электрода. Рабочий кабель прикрепляется на расстоянии не более 3 футов от места сварки и отлично изолирован, чтобы избежать утечек. Сварочная цепь должна иметь отрицательный электрод постоянного тока.
22 6- Коды, стандарты и спецификации:
4/12/2018 6- Коды, стандарты и спецификации: Подводная сварка рассматривается в: Спецификации AWS D3.6 для подводной сварки. ASME N-516 Подводная сварка Раздел XI Div. 1 BS EN ISO: 2002 Квалификационные испытания сварщиков для подводной сварки. ASTM ANSI / AWS D3.6 предоставляет важную информацию: Инженеру по сварке — для выбора рекомендуемого процесса сварки под водой (мокрый или сухой) Инженеру по стрессу — для проверки соответствия требованиям.Инженер-проектировщик — для уточнения деталей при изготовлении конструкций. Покупатель — для установления приемочных требований. Подрядчик — для оценки средств и стоимости проекта.
23 7-Характеристики хорошей подводной сварки
Характеристики хорошего процесса подводной сварки следующие: (a) Требуется недорогое сварочное оборудование, низкая стоимость сварки, простота в эксплуатации и гибкость во всех положениях.(b) Минимальная опасность поражения электрическим током, минимальная скорость сварки 20 см / мин. (d) Обеспечьте хорошую видимость. (e) Выполнять сварные швы хорошего качества и надежно. (v) Оператор должен уметь обеспечивать себя. (vi) Легко автоматизировать.
24 8- Применение подводной сварки
Важными областями применения подводной сварки являются: (а) морское строительство для добычи морских ресурсов, (б) временные ремонтные работы, вызванные столкновениями судов или неожиданными авариями.(c) Спасение затонувших в море судов. (d) Ремонт и техническое обслуживание судов. (e) Строительство больших судов, превышающих вместимость существующих доков.
25 9- Некоторые характеристики подводной сварки
1. Быстрое охлаждение На микроструктуру сварного шва влияет высокая скорость охлаждения при подводной сварке. Использование диаграммы непрерывного охлаждения (CCT) может объяснить эту микроструктуру.Рисунок (1) представляет собой CCT смоделированных однопроходных сварных швов на стали A516 Gr 70, которые были созданы с использованием машины Gleeble. Микроструктуры и соответствующие температуры, при которых каждая из них начинается и заканчивается, могут быть идентифицированы на диаграмме. Поскольку представляющие интерес образцы сварных швов были многопроходными сварными швами, вводится важная переменная, известная как отпуск валика. Последующие проходы сварки и их влияние на микроструктуру предыдущего прохода. На рисунке (2) показано, как несколько сварочных проходов могут повлиять на ЗТВ предшествующего ему сварного прохода.Многократные сварочные проходы обеспечивают отпуск валика по сравнению с предыдущим сварочным проходом, который измельчает крупные зерна в ЗТВ, где обычно присутствует водород при растрескивании валика.
26 Рис. (1) Диаграмма трансформации при непрерывном охлаждении для однопроходного сварного шва на стали A516 Grade 70
Рис. (2) Схематическая диаграмма микроструктуры HAZ многопроходного сварного шва
27 9- Некоторые характеристики подводной сварки (продолжение)
2.Водородное растрескивание. Склонность к водородному растрескиванию подводных сварных деталей, сделанных на высокопрочных сталях, является серьезной проблемой. Четыре условия, которые должны присутствовать для возникновения водородного растрескивания: 1) Чувствительная микроструктура 2) Критическая концентрация диффундирующего водорода 3) Интенсивность напряжения 4) Относительно низкая температура менее 200 ° C. Как и следовало ожидать, все четыре условия существуют в подводной экранированной среде. Дуговая сварка металла SMAW. Очевидно, что мартенситная микроструктура ЗТВ вблизи линии плавления является чувствительной, поскольку она твердая и хрупкая.При диссоциации водорода вблизи сварочной дуги водород неизбежно попадает в металл шва. Из-за высоких ограничений, накладываемых на сварную деталь, и наложения больших температурных градиентов в сварном шве могут возникать высокие напряжения. Наконец, температура любого подводного объекта, в котором можно проводить работы, определенно ниже 200 ° C. Комментарии, сделанные во всех подразделах раздела C, ясно показывают, что водородное растрескивание под бортом подводных мокрых сварных швов на ферритной стали весьма вероятно, если углеродный эквивалент стали и содержание углерода не поддерживаются на достаточно низком уровне.
28 год 10- Подводный осмотр:
Подводный осмотр также включает визуальный и фотографический осмотр подводных конструкций и ремонт, а также неразрушающий контроль, такой как MT, UT и RT. Типичный подводный инспектор, оснащенный фонарями и камерой. Подводная конструкция со следами коррозии.
29 Подводный контроль (продолжение)
Неразрушающий контроль, такой как UT, RT и MT, также можно проводить под водой.Техник по подводному неразрушающему контролю, использующий испытание магнитными частицами на подводных опорах конструкций. Примечание: существует неразрушающий контроль подводных сварных стальных конструкций.
30 Подводный осмотр (продолжение)
Визуальный, видео- и фотографический осмотр также может проводиться во время технического осмотра любых подводных конструкций, как показано ниже. Для проведения надлежащей визуальной проверки и неразрушающего контроля необходимо провести абразивоструйную очистку, чтобы удалить все организмы морской воды, которые растут на подводной конструкции, как показано на этой фотографии.
31 год Подводная инспекция (продолжение)
Последней разработкой в области подводной инспекции является использование ROV. Это машины, которыми управляет пилот ROV. ROV Pilot Submarine Rescue Machine ROV машина
32 Подводная инспекция (продолжение)
Всемирный центр TWI по технологии соединения материалов Предлагаемые курсы: подводная инспекция — подводное обучение и экзамены CSWIP 3.1U — NDT Inspection Diver CSWIP 3.2U — NDT Inspection Diver CSWIP 3.3U — ROV Inspector CSWIP 3.4U — Контроллер подводного осмотра CSWIP Общие визуальные инспекторы для морских сооружений и сооружений
33 11- Вовлеченный риск: Ниже приведены некоторые риски, связанные с подводной сваркой:
Поражение электрическим током — существует вероятность поражения электрическим током, если оборудование не изолировано должным образом, или когда источник питания не отключается сразу после того, как сварщик выключает сварку. дуга во время сварки.Взрыв-дуговая сварка производит водород и кислород. Могут накапливаться газовые карманы, и они потенциально взрывоопасны. Азотный наркоз — опасность для здоровья, с которой обычно сталкиваются дайверы во время занятий дайвингом, когда не соблюдаются меры безопасности на определенном уровне. Любопытно, что риск утопления не входит в список опасностей, связанных с подводной сваркой. Для сварных конструкций проверка сварных швов после сварки может быть сложнее, чем сварных швов, выполненных над водой. Существует риск дефектов, которые могут остаться незамеченными и в конечном итоге привести к отказу.
34 12- Безопасность: Стандарт OSHA 1915.6 — Коммерческое дайвинг
Стандарт OSHA — Подводное плавание с аквалангом, том IV, выпуск 3, 3 квартал 2002 г. Информационный бюллетень по охране труда — Коммерческое дайвинг Неотложная медицинская помощь в Саудовской Аравии
35 год Безопасность: (продолжение) Приложение D к AWS D3.6 — Рекомендуемое руководство по безопасности при подводной сварке Область применения ограничивается рекомендованными безопасными методами, конкретно относящимися к подводной сварке и связанным с ней работам, выполняемым в сухой (гипербарической) или влажной среде. .Приложение D включает меры безопасности, подводную связь, электрооборудование, ручные электроинструменты, подготовку к работе, выполнение работ, а также проверки и проверки.
36 Безопасность (продолжение) Сварка:
Необходимо соблюдать необходимые меры предосторожности, такие как: Соблюдайте правила техники безопасности работодателя. Пары и газы могут быть опасны для вашего здоровья. Лучи дуги могут повредить глаза и кожу.Во время сварки используйте соответствующую вентиляцию. Носите подходящие средства защиты глаз и защитную одежду. Не прикасайтесь к токоведущим электрическим частям. Надевайте резиновые перчатки. Заменяйте электрод только в холодном состоянии.
37
13- События. Последние разработки в области строительства морских нефтяных платформ увеличили спрос на подводную сварку. Использование барокамер для получения сварного шва нормального качества очень дорого в эксплуатации.Исследователь Sea Grant доктор Чон Цай разработал новый сварочный электрод для влажной сварки, получивший прозвище «Черная красавица» из-за черного внешнего вида его водонепроницаемого покрытия. Электрод демонстрирует превосходный внешний вид и профиль, микротрещины сварного шва устранены, рабочие характеристики превосходят другие имеющиеся в продаже электроды, и электрод дает подходящие результаты при использовании в любом положении.
38 Разработки (продолжение)
Влажная и сухая сварка — Сухие гипербарические камеры или среды обитания чрезвычайно дороги.Это потому, что он должен быть построен для специальных применений, таких как ремонт или врезка горизонтально проложенных труб. Последние усовершенствования позволили использовать процесс GMAW (газовая дуговая сварка) при подводной сварке с использованием специальных сопел, куполов или миниатюрных камер. При использовании этого типа аппарата сварщик / водолаз находится в воде, но сопло сварочного пистолета и свариваемый материал находятся в сухой атмосфере. Эти локализованные камеры с сухой газовой средой недороги, малы и легки.Он изготовлен из прозрачного материала или имеет достаточное количество окон, чтобы сварщик мог видеть изнутри, чтобы правильно управлять сварочным пистолетом и направлять его. Этот процесс можно использовать для сварки на глубине до 125 футов (35 м) от поверхности воды.
39 14- Ссылки: TWI Knowledge Summary — Underwater Welding
Underwater Magazine — Commercial Diving Divers Academy International Atlantic Welding & Fabrication Center Special Applications of Welding — Underwater Welding Blakemore, G.Р. (2000): Подводное вмешательство 2000 — Хьюстон, Ян Чен В., Чжан Х и др. (1998): Proc SPIE, Vol. 3550. С. 287–297. Чен Х. Б., Ли Л., Брукфилд Д. Д. и др. (1993): Многочастотные оптоволоконные датчики для контроля качества лазерной сварки в процессе. Proc NDT E Int., Vol. 26, № 2, с. 268–274. Давас К. (ред.) (1992): Laser Welding, Mc. Graw-Hill, N. York. Duley W. W. (редактор) (1999): Laser Welding, John Wiley & Sons, Inc., N. York, стр. 1 Датта Маджумдар, Дж. И Манна, I. (2003): Sadhana, Vol.28, стр. 495. Фарсон Д., Али А., Санг Ю. (1998): Weld Res Suppl., Vol. 77, №: 4, с. 142–148. Хаддад, Г. Н., Фармер, А. Дж. (1985): Weld. J., Vol. 64, No. 12, p Hugel H, Matthias G, Muller G, et al. (1999): Proc SPIE, Vol. 3571. С. 52–60. Ирие Т., Оно Й., Мацусита Х. и др. (1997): Труды 16-го ОМАЭ, стр. 43–50. Керн, М., Бергер, П., Угель, Х. Х. (2000), Weld. J., Vol. 3, стр. 72. Кханна, О. П. (2004): Учебник технологии сварки, Dhanpat Rai Publications (P) Ltd., Н. Дели, Индия. Круузинг, А.(2004): Оптика и лазеры в технике, Vol. 41. С. 329–352. Ланчестер, Дж. Ф. (1987): Физика сварки плавлением — Часть I: Электрическая дуга в сварке, IEE Proc., Vol. 134, стр. Oates W. A. (ed.) (1996): Welding Handbook, Vol. 3, Американское общество сварки, Майами, США. Огава Ю., Ирие Т., Оно Ю. и др. (1998): Материалы 17-го ОМАЭ. Огава Ю. (1998): Материалы восьмой Международной конференции по морской и полярной инженерии, т. 4.
40 15- Приложение: Сухая подводная сварка
41 год Мокрая подводная сварка
42 Вопросов
43 год «Спасибо»
44 год Список условных обозначений: MMA: Ручная дуговая сварка металлом (впервые изобретена в России в 1888 году.В нем использовался стержень из чистого металла без покрытия из флюса для защиты от газа) NDT: неразрушающий контроль ECS: Система экологического контроля CCT: Непрерывное охлаждение HAZ: Зона теплового воздействия. MT: Испытание магнитными частицами UT: Ультразвуковое испытание RT: Радиографическое испытание ROV: Дистанционно управляемый подводный аппарат
Подводная сварка — [PPTX Powerpoint]
- 1. ПОДВОДНАЯ СВАРКА Мухаммед Лабееб
2. СОДЕРЖАНИЕ Важность подводной сварки Принцип классификации операций Подводная сварка в мокрой / сухой среде Преимущества и недостатки Связанные с риском и применения для обеспечения безопасности Ссылки на будущее 3. Четверг, 8 мая 2014 г. 3 4. ПОДВОДНАЯ СВАРКА Подводная сварка — это процесс сварки при повышенных давлениях, обычно под водой. Подводная сварка может происходить как в воде, так и в сухом состоянии внутри специально сконструированного корпуса с избыточным давлением и, следовательно, в сухой среде. Обычно ее называют «гипербарической сваркой» в сухой среде и «подводной сваркой» во влажной среде. Применения подводной сварки разнообразны: она часто используется для ремонта судов, морских нефтяных платформ и трубопроводов.Сталь является наиболее распространенным свариваемым материалом. 5. ПРИНЦИП РАБОТЫ Сварочная цепь обычно должна включать рубильник, который приводится в действие на поверхности и управляется сварщиком и используется в целях безопасности. При использовании постоянного тока с положительной полярностью будет иметь место электролиз, который приведет к быстрому разрушению любых металлических компонентов в держателе электрода. Для влажной сварки переменный ток не используется из-за электробезопасности и сложности поддержания дуги под водой _ Электропитание — + работа Электрод с ножевым выключателем Водонепроницаемый держатель электрода 6.КЛАССИФИКАЦИЯ Подводная сварка может быть классифицирована как 1) Мокрая сварка 2) Сухая сварка При мокрой сварке сварка выполняется под водой, непосредственно во влажной среде. При сухой сварке рядом с зоной сварки создается сухая камера, и сварщик выполняет свою работу, оставаясь внутри камеры. 7. ВЛАЖНАЯ СВАРКА Как следует из названия, влажная подводная сварка выполняется в среде, где основной металл и дуга полностью окружены водой. При мокрой сварке используется MMA (ручная дуговая сварка металлом).Используется специальный электрод, и сварка выполняется вручную, как и при сварке на открытом воздухе. Повышенная свобода движений делает мокрую сварку наиболее эффективным, действенным и экономичным методом. Источник сварочного тока расположен на поверхности с подключением к водолазу / сварщику с помощью кабелей 8. ВЛАЖНАЯ СВАРКА При мокрой сварке используется MMA (ручная дуговая сварка металлическим электродом).
Используемый источник питания: Полярность постоянного тока: -ve полярность (прямая полярность). При использовании постоянного тока с положительной полярностью произойдет электролиз, который приведет к быстрому разрушению любых металлических компонентов в держателе электрода.Для мокрой сварки переменный ток не используется из-за электробезопасности и трудности поддержания дуги под водой. 9. ВЛАЖНАЯ СВАРКА Источником питания должен быть аппарат постоянного тока с номиналом 300 или 400 ампер. Сварочные аппараты с электродвигателем-генератором чаще всего используются для подводной сварки во влажной среде. Применяется постоянный ток с отрицательным электродом (прямая полярность). Используются специальные держатели сварочных электродов с дополнительной изоляцией от воды. Используемые типы электродов соответствуют классификации AWS E6013 (высокое содержание диоксида титана, калия, DC +).Электроды должны быть гидроизолированы. Все соединения должны быть тщательно изолированы, чтобы вода не могла контактировать с металлическими частями. 10. ПРЕИМУЩЕСТВА ВЛАЖНОЙ СВАРКИ. Самый дешевый и быстрый метод. Высокая прочность на растяжение. Легкий доступ к месту сварки. времени НЕДОСТАТКИ Быстрая закалка снижает ударную вязкость и пластичность Водородное охрупчивание, трещины Плохая видимость в воде 11. СУХАЯ СВАРКА ИЛИ ГИПЕРБАРИЧЕСКАЯ СВАРКА Гипербарическая сварка — это сварка, при которой камера герметизируется вокруг свариваемой конструкции и заполняется пригодным для дыхания газом (обычно гелий, содержащий 0.5 бар кислорода) при преобладающем давлении. на котором должна производиться сварка. Этот метод обеспечивает получение высококачественных сварных соединений. Для этого процесса используется процесс газовой вольфрамовой дуговой сварки. Область под полом Хабитата открыта для воды. Таким образом, сварка выполняется в сухой, но при гидростатическом давлении морской воды, окружающей среду обитания 12. Сухая сварка 12 13. ПРЕИМУЩЕСТВА СУХОЙ СВАРКИ Безопасность сварщика / водолаза Хорошее качество сварных швов Контроль поверхности Неразрушающий контроль НЕДОСТАТКИ Более высокая стоимость процесса, обучения и т.
… Большое количество дорогостоящего и сложного оборудования. Для большей глубины требуется больше энергии Невозможно сваривать, если место сварки находится в недоступных местах 14. РИСК И МЕРЫ БЕЗОПАСНОСТИ Сварщик / дайвер может получить удар электрическим током. Меры предосторожности включают обеспечение надлежащей электроизоляции сварочного оборудования. риск взрыва для сварщика / дайвера Необходимо принять меры предосторожности, чтобы избежать скопления газовых карманов, которые потенциально являются взрывоопасными. Другой основной областью риска является для жизни или здоровья сварщика / дайвера азот, попавший в кровь. пар во время контакта с воздухом при повышенном давлении. Меры предосторожности включают обеспечение аварийной подачи воздуха или газа, резервных водолазов и декомпрессионных камер, чтобы избежать азотного наркоза после быстрого всплытия после погружения с насыщением 15.СПИСОК ЛИТЕРАТУРЫ Справочник по металлам ASM, 9-е изд., Том 9, Сварка, пайка и пайка, ASM, Metals Park, (1983) Степат М. Д., Подводная сварка и резка медленно поддаются исследованию, Инженер по сварке, апрель 1973 г.
Под водой Сварочный семинар ppt
Подводная сварка — установка больших участков, а также установка подходящих проушин представляет для дайвера более сложную проблему, чем подводная резка.Необходима значительная практика для достижения неизменно высоких стандартов подводной сварки при аварийно-спасательных работах. В результате методы подводной сварки дайвером должны соответствовать приемлемым стандартам. Кроме того, океан действует как большой радиатор и отводит тепло от электрода. Это может вызвать образование дыр и возможную потерю прочности между заплатой и корпусом. Это верно, потому что газ не может выйти из расплавленной металлической ванны из-за внезапного охлаждения окружающей водой. Несмотря на вышеупомянутые недостатки, возможны подводные сварные швы хорошей прочности, приемлемые для аварийно-восстановительных работ. Если не указано иное, термин «подводная сварка», используемый в данном руководстве, относится к технике влажной сварки, при которой сварочная дуга не отделяется от окружающей воды механическим барьером.
В данном руководстве рассматриваются два типа сварки:
- Мокрая сварка и
- Сухая сварка в процессе сварки в зоне разбрызгивания, которая выполняется под водой. Используется в нефтяной компании, судовой компании.
Мокрая сварка означает, что сварка выполняется под водой, в непосредственном контакте с влажной средой.Используется специальный электрод, и сварка выполняется вручную, как и при сварке на открытом воздухе. Увеличенная свобода движений делает мокрую сварку наиболее эффективным, действенным и экономичным методом. Источник питания для сварки расположен на поверхности с подключением к водолазу / сварщику с помощью кабелей и шлангов.
Сухая сварка:Гипербарическая сварка выполняется в камере, герметичной вокруг свариваемой конструкции. Камера заполнена газом (обычно гелий, содержащий 0.5 бар кислорода) при преобладающем давлении. Помещение герметично закрывается на трубопроводе и заполняется пригодной для дыхания смесью гелия и кислорода при давлении окружающей среды, при котором должна проводиться сварка, или немного выше него. Этот метод обеспечивает получение высококачественных сварных соединений, соответствующих требованиям к рентгеновскому излучению и нормам. Для этого процесса используется процесс газовой дуговой сварки вольфрамом. Область под полом Хабитата открыта для воды. Таким образом, сварка выполняется в сухой среде, но при гидростатическом давлении морской воды, окружающей среду обитания.
Полный отчет семинара по подводной сварке, тезисы и презентация скачать
Загрузите отчеты по подводной сваркеПодводная сварка
Сварка — неизбежный процесс современного машиностроения? гражданские, электрические, механические, автомобильные, морские авиационные? во всех отраслях. Он используется при изготовлении и возведении инфраструктур и установок. Соединяет металлы или термопласты. Образуется лужа расплавленной массы? сварочная лужа? и дать ему остыть, чтобы он стал прочным, является основой процесса сварки. Для ремонта под водой существует отдельный процесс. Это называется подводной сваркой. Если поврежденные корабли подлежат ремонту, в качестве базовой технологии следует использовать подводную сварку. Это узкоспециализированная профессия? больше занятых в нефтяной или судоходной промышленности, а также в оборонных операциях.
Процесс подводной сварки подразделяется на две категории.
? Мокрая сварка
? Сухая сварка
Мокрая сварка:
В случае мокрой сварки операция завершается под водой, в непосредственном контакте с влажной средой. Для этого используется электрод другого типа. Функция выполняется вручную. Сварщику разрешается свобода передвижения. Следовательно, мокрая сварка — наиболее эффективный, действенный и экономичный процесс.
Сварочный блок питания и питания размещается на поверхности и подключается к сварочному аппарату с помощью кабелей и шлангов.
Преимущества:
* Расход очень минимальный. В отличие от сухой сварки.
* Скорость операции чрезвычайно высока.
* Поскольку оборудования очень мало, сварку можно выполнить в более короткие сроки с минимальным планированием.
Недостатки:
* Сварной шов очень быстро закаливается под водой.Это снижает пластичность и ударную вязкость, а также делает сварной шов очень пористым.
* Видимость сварщика недостаточна.
* Количество используемого напряжения очень ограничено. Необходимо соблюдать осторожность, чтобы сварщик не пострадал от возможного поражения электрическим током.
Сухая сварка:
В случае сухой сварки, иначе известной как гипербарическая сварка, вся операция завершается в камере, герметизированной вокруг свариваемой конструкции.Камера заполнена газом? обычно гелий? содержащий 0,5 бар кислорода. Камера устанавливается на трубопровод и заполняется пригодной для дыхания смесью воздуха. Операция проводится при более высоком давлении. Используется процесс газовой дуговой сварки вольфрамом.
Преимущества:
* Сварка может выполняться без воздействия океанских течений и морских животных.
* Можно использовать сварные швы более высокого качества.
* С самой поверхности есть возможность визуально контролировать подготовку стыка и выравнивание труб.
Недостатки:
* Камера очень сложная. На поверхности необходимо большое вспомогательное оборудование для поддержки камеры.
* Расход будет очень высоким. Стоимость увеличивается пропорционально глубине под водой.
* Возможность повторного использования камеры ограничена.
Риски и меры предосторожности:
В опасности и сварщик, и конструкция. Сварщик должен защищаться от поражения электрическим током.Сварщик должен быть изолирован. Напряжение сварочных аппаратов необходимо контролировать. Карманы кислорода и водорода, образованные дугой, могут быть потенциально взрывоопасными. Сварщик должен принимать меры предосторожности, потому что азот будет накапливаться в кровотоке сварщика при контакте с воздухом под высоким давлением под поверхностью воды. Осмотр хоть и очень сложен, но является обязательным требованием. Никаких дефектов остаться не должно. В дополнение ко всем этим мерам предосторожности необходимо соблюдать меры предосторожности при дуговой сварке.
Подводная сварка чаще всего применяется в морской технике? в установках нефтегазовых вышек. Подводную сварку можно классифицировать в зависимости от типов оборудования и применяемых процедур. Самый распространенный процесс подводной сварки, известный как ручное дуговое строительство (MMA), используется для глубоководного ремонта. Процесс сварки коффердамом и процесс гипербарической сварки обычно выполняются для подводных сварочных работ.Они используются для сварки стальных трубопроводов, других морских конструкций, подводных частей больших судов и подводных конструкций, поддерживающих гавань. Меры безопасности включают аварийную подачу воздуха или газа, дежурных водолазов и декомпрессионные камеры.
Источник:
Загрузите отчеты по подводной сварке
Объявления
Рекламные ссылки: —
Краткое изложение 26 вакансий для подводной сварки в среде обитания | OTC Offshore Technology Conference
РЕФЕРАТ
Сварка под водой, в сухих условиях и в среде обитания стала эффективным инструментом, когда было непрактично поднимать трубы на поверхность для крепления фланцев или ремонта.Обобщено 26 работ, при которых сварные швы плавлением были выполнены в среде для подводной сварки. Не являясь механическими соединениями, исключается возможность утечки и проблем с окружающей средой. Техника использовалась для соединения новых трубопроводов, стояков, ремонта и модификации существующих трубопроводов, конструкций и применима к линиям сброса канализации, кабелям связи и т.д. Патент Осборна 1954 года, в котором описывалось подводное ограждение, которое должно было стать предшественником сварочных помещений, используемых сегодня.Патент опередил свое время и не получил особого внимания до истечения срока его действия. За прошедшие семнадцать лет морские трубопроводы продвигались из болот в открытое море во все возрастающем количестве после первой морской скважины в 1947 году в 42 милях к югу от Морган-Сити, штат Луизиана.
Технология прокладки морских трубопроводов шла в ногу с увеличением глубины воды, даже несмотря на то, что диаметры труб значительно увеличились. Однако технология стыковки фланцевых труб большого диаметра на морском дне и постановка длинных стояков на глубоководье не дала результатов.Это оставалось очень трудоемкими и трудными задачами. Сварка в среде обитания стала эффективным инструментом, когда было непрактично поднимать трубы на поверхность для крепления фланцев или ремонта.
Примерно в 1966 году компании, которые занимались дайвингом и другими подобными видами деятельности, построили различные типы подводных сварочных комплексов, провели несколько ремонтов морских платформ и трубопроводов, а также выполнили несколько горячих врезок. Поскольку крупнейшим заказчиком Тейлора было и остается подразделение морских трубопроводов Brown & Root, и поскольку дайвинг также был нашим бизнесом, мы тоже начали рассматривать сварку среды обитания.
Как следует из названия, в этой статье рассматривается 26 работ по сварке в условиях сухого подводного грунта, выполняемых в основном в Мексиканском заливе. Размеры включали номинальный диаметр от 6 дюймов до внешнего диаметра 48 дюймов, соединенные на глубине от 8 футов до 540 футов морской воды. Двадцать три работы были сварными швами кольцевыми стыковыми соединениями горизонтальных труб; 3 были сварными швами углового типа, связанными с ремонтом труб. Из общего числа 12 работ были выполнены только с использованием оборудования для подводной сварки (UWH), а 14 включали использование UWH в сочетании с подводной установкой для выравнивания труб (SPAR).
ОБОРУДОВАНИЕ
Первое место для подводной сварки Тейлора (UWH-1) было 8 на 8 на 9 футов в высоту и по форме напоминало хижину Quonset (рис. 1). Он нес 9 тонн балласта, имел дверные уплотнения с гидравлическим приводом и ствол-туннель для обеспечения беспрепятственного входа и выхода водолазов-сварщиков при любых обстоятельствах. Он был спроектирован для труб диаметром не более 24 дюймов и имел прокладки из катаных пластин для работы с трубами диаметром до 6 дюймов. Шланг подсоединялся к крыше жилого помещения с помощью фланца.
Во время строительства UWH-1 сварщики, которые с тех пор стали водолазами, практиковали сварку с использованием процесса газо-вольфрамовой дуговой сварки (GTAW) с упором на получение внутреннего валика во время корневого прохода.
Презентация по подводной сварке
Подводная сварка и осмотрПрезентация
Представлено: Сайфул Ризал Уаян VID / QCU 19 декабря 2004 г.
Цель: Цель данной презентации — дать общие знания о том, как выполняется подводная сварка.Здесь также делается упор на безопасность, поскольку мы имеем дело с двумя видами деятельности: дайвингом и сваркой. Следует помнить, что подводная сварка — это другой мир, поэтому для максимальной безопасности сварщика / дайвера соблюдаются особые меры предосторожности.
Краткое содержание: Введение Использует принцип классификации сварщиков / водолазов, коды, стандарты и спецификации
Подводный осмотр Риск, связанный с разработками в области безопасности
Введение: подводная сварка началась во время Первой мировой войны, когда британский флот использовал ее для временного ремонта кораблей.Этот ремонт заключался в приварке негерметичных заклепок корпусов судов. Подводная сварка также была ограничена только аварийно-спасательными работами и аварийным ремонтом. Кроме того, он был ограничен глубиной ниже поверхности не более 30 футов (10 метров). Сначала подводная сварка применялась только для сваривания заплатки, пока не удалось выполнить более тщательный ремонт. Но как только был накоплен больший опыт, амбициозные люди и компании объединили свои усилия, чтобы улучшить результаты и установить достижимые спецификации.
Использование: Хотя подводная сварка использовалась при строительстве и установке новых морских сооружений, подводных трубопроводов и портовых сооружений, она чаще всего используется для технического обслуживания и ремонта. Сюда входит ремонт повреждений, вызванных коррозией, усталостью и авариями морских сооружений, таких как нефтяные платформы, ремонт и замена поврежденных участков подводных трубопроводов, ремонт отверстий в корпусах судов или повреждения портовых сооружений в результате столкновения.
Использование (продолжение) Судя по фотографиям, приведенным ниже, очевидно, что эти конструкции требуют ремонта.И один из инструментов ремонта — подводная сварка.
Поврежденная морская конструкция
Морская подводная конструкция
Сварщик / водолаз: Сварщик / водолаз — сертифицированный сварщик, который также является профессиональным водолазом, способным выполнять задачи, связанные с коммерческими подводными работами, настройкой и подготовкой сварных швов, и у которого есть способность выполнять сварку в соответствии с AWS D3.6, Технические условия для подводной сварки (мокрой или сухой) и другие связанные с этим виды деятельности. Квалификация сварщика / водолаза, необходимая для выполнения определенного задания, варьируется от проекта к проекту.Большинство подрядчиков по подводному плаванию хотели бы, чтобы их сварщик / дайвер был мастером на все руки. Это означает, что сварщик / дайвер должен знать, как выполнять подводную резку, установку и оснастку, инспекцию и неразрушающий контроль, а также подводную фотографию.
Сварка
Резка
Классификация: Подводная сварка подразделяется на две категории.
1. Сварка во влажной среде = в основном использовалась для аварийного ремонта и аварийно-спасательных работ на мелководье из-за низкого качества сварных швов.
2. Сварка в сухой среде = с помощью этого метода получаются высококачественные сварные швы, соответствующие требованиям к рентгеновским лучам и нормам.
Сварка во влажной среде Как следует из названия, влажная сварка под водой выполняется в среде, где основной металл и дуга полностью окружены водой. Используемые типы электродов соответствуют классификации AWS E6013. Для гидроизоляции электродов их оборачивают водонепроницаемой лентой или погружают в специальные смеси силиката натрия и дают им высохнуть.Источником питания является машина постоянного тока номиналом 300 или 400 ампер.
Мощность дуги создает пузырь из смеси газов, который позволяет плавлению и соединению металла происходить более или менее нормально, как показано на фотографии выше.
Сварка в мокрой среде (продолжение): Ниже представлена типичная установка подводного сварочного оборудования. Водонепроницаемый источник питания держателя электродов
_
+
Работа электродов
Ножевой выключатель
Сварка в сухой среде Сварка Сухая среда снова делится на две части:
Гипербарическая сварка, при которой камера герметизируется вокруг свариваемой конструкции и заполняется пригодным для дыхания газом при преобладающем давлении.
Сварка коффердама, которая выполняется в сухом помещении на воздухе, когда жесткая стальная конструкция для размещения сварщиков герметично прилегает к свариваемой стороне конструкции и является открытой для атмосферы.
Сварка в сухой среде: Гипербарическая сварка выполняется с использованием сварочной камеры или помещения. Этот метод обеспечивает высокое качество сварных соединений, отвечающих требованиям рентгенографии и норм. Камера герметична в конструкции или трубопроводе и заполнена пригодной для дыхания смесью гелия и кислорода (90-95% гелия и 5-10% кислорода).
Сварочная камера
Сварочная камера Внутренняя
Сварка в сухом состоянии (продолжение) Сварка коффердамом также является типом сухой сварки, при которой жесткая стальная конструкция, в которой размещаются сварщики, прилегает к стороне свариваемой конструкции и открыт для атмосферы. Обычно он используется для портовых работ или ремонта судов.
Сварка на суше (продолжение) На фотографиях ниже приведены примеры коффердамской сварки.
Макет конструкции
Фактическая конструкция
Принцип действия: На рисунке справа показано общее устройство для подводной сварки.Подводная сварка всегда должна осуществляться аппаратом постоянного тока, заземленным на судно. Схема сварки включает рубильник, который по сигналу сварщика / водолаза приводится в действие помощником на поверхности. Рубильный выключатель отключает сварочный ток и сконструирован таким образом из соображений безопасности. В держателе электрода используется поворотная головка для захвата электрода. Рабочий кабель прикрепляется на расстоянии не более 3 футов от места сварки и отлично изолирован, чтобы избежать утечек. Сварочная цепь должна иметь отрицательный электрод постоянного тока.
Коды, стандарты и спецификации: Подводная сварка подпадает под:
AWS D3.6 Specification for Underwater Welding.
ASME N-516 Секция подводной сварки XIDiv. 1
BS EN ISO 15618-1: 2002 Квалификационные испытания сварщиков для подводной сварки.
Saudi Aramco SAEP-1117 Welding TestSupplement S17 для SMAW, Wet Welding
AWS D3.6M 1999 Краткое описание технических условий для подводной сварки Эта спецификация охватывает требования к сварке конструкций или компонентов под водой.Он включает сварку как в сухой, так и во влажной среде. Разделы с 1 по 6 представляют собой общие требования к подводной сварке, а разделы с 7 по 10 содержат специальные требования, применимые к четырем отдельным классам сварных швов: Класс A Сравним со сваркой над водой. Класс B Для менее ответственных приложений. Класс C, где несущая способность не является приоритетным.
Класс O Для соответствия требованиям другого установленного кода или спецификации.
Корпус N-516-3 Подводная сварка ASME Раздел XI Объем и общие требования Требования к подводной сварке в мокром и сухом состоянии.
Дополнительные переменные для сухой подводной сварки Процедура и квалификация производительности.
Дополнительные переменные для сварки под водой «мокрым способом». Процедура и аттестация характеристик.
Аттестация присадочного металла Каждый присадочный металл испытывается в соответствии с применимыми спецификациями ОТВС.
Альтернативные квалификационные требования процедуры ByCharpy V-notch.
Осмотр NDE.
Saudi Aramco Инженерная процедура: SAEP 1117 Приложение к испытаниям сварки S17 для SMAW, Мокрая сварка Объем: Это приложение к испытаниям регулирует испытания сварщиков с процессом дуговой сварки защищенным металлом (SMAW), последовательность сварки вертикально вниз, для мокрой сварки основы из углеродистой стали металлы.Это дополнение должно использоваться для проверки способности сертифицированных сварщиков, нанятых Saudi Aramco, выполнять подводную (мокрую) сварку на морских объектах Saudi Aramco.
Подводный осмотр: Подводный осмотр также включает визуальное и фотографическое обследование подводных конструкций и ремонт, а также неразрушающий контроль, такой как MT, UT и RT.
На фотографии слева показан типичный подводный инспектор, оснащенный фонарями и камерой.
На фотографии справа показана подводная конструкция со следами коррозии.
Подводный осмотр (продолжение) Неразрушающий контроль, такой как UT, RT и MT, также можно проводить под водой. На фотографии справа показан специалист по подводному неразрушающему контролю, использующий испытание магнитными частицами на опорах подводных конструкций.
Книги также доступны на рынке для справки, например;
Неразрушающий контроль подводных сварных стальных конструкций.
Подводная влажная сварка и резка. Технология подводного ремонта. Руководство профессионального дайвера по мокрой сварке.
Подводный осмотр (продолжение) Визуальный, видео- и фотографический осмотр также может проводиться во время технического осмотра любых подводных конструкций, как показано ниже. удалите все морские организмы, которые растут на подводной конструкции, как показано на этой фотографии.
Подводная инспекция (продолжение) Последней разработкой в области подводной инспекции является использование ROV. Это машины, которыми управляет пилот ROV.
ROV Pilot
ROV machine
Подводная спасательная машина
Подводная инспекция (продолжение) Всемирный центр технологии соединения материалов TWI Предлагаемые курсы:
Подводная инспекция Подводная подготовка и экзамены
CSWIP 3.1U NDTW Inspection CSWIP 3.3U ROV Inspector CSWIP 3.4U Контроллер подводного осмотра CSWIP Общие визуальные инспекторы для морских сооружений и сооружений
Риски, связанные с подводной сваркой: Ниже приведены некоторые риски, связанные с подводной сваркой: Поражение электрическим током. , или когда источник питания не отключается сразу, когда сварщик прекращает дугу во время сварки
Подводная сварка и осмотр: краткая презентация, часть 2 из 2
Коды, стандарты и спецификации:
Подводная сварка распространяется под:
- AWS D3.6 Спецификация подводной сварки.
- ASME N-516 Подводная сварка, раздел XI Div. 1
- BS EN ISO 15618-1: 2002 Квалификационные испытания сварщиков для подводной сварки.
AWS D3.6M 1999 Спецификации для подводной сварки:
- Класс C — где нагрузка не является приоритетным.
- Класс O — для соответствия требованиям другого обозначенного кода или
Корпус N-516-3 Подводная сварка ASME Раздел XI:
Объем и общие требования —
- Требования к подводной сварке «мокрым» и «сухим» способом.
- Дополнительные переменные для сухой подводной сварки — процедура и квалификация выполнения.
- Дополнительные переменные для подводной мокрой сварки — процедура и аттестация.
- Аттестация присадочного металла — каждый присадочный металл испытывается в соответствии с применимыми спецификациями SFA.
- Альтернативные квалификационные требования процедуры — по Шарпи с V-образным надрезом.
- Экспертиза — NDE.
Подводная инспекция:
Подводный осмотр также включает визуальный и фотографический осмотр подводных конструкций и ремонт, а также неразрушающий контроль, такой как MT, UT и RT.
Рис. 5: Различные методики проверки и испытаний
Неразрушающий контроль, такой как UT, RT и MT, также можно проводить под водой.
На фотографии на рис. 5 (рис. 5) изображен специалист по подводному неразрушающему контролю, использующий испытание магнитными частицами на подводных конструкционных опорах.
Книги также доступны на рынке для справки, например;
- Неразрушающий контроль подводных сварных стальных конструкций.
- Подводная влажная сварка и резка.
- Технология подводного ремонта.
- Пособие профессионального дайвера по мокрой сварке.
Визуальный, видео- и фотографический осмотр также может проводиться во время технического осмотра любых подводных конструкций, как показано ниже
Для проведения надлежащей визуальной проверки и неразрушающего контроля необходимо провести абразивоструйную очистку, чтобы удалить все организмы морской воды, которые растут на подводной конструкции, как показано на фотографии на рис. 5.
Последней разработкой в области подводного контроля является использование ROV.Это (рис. 6) машины, которыми управляет пилот ТПА.
Рис. 6: Последние достижения в области подводного контроля.
Вовлеченный риск:
Ниже приведены некоторые риски, связанные с подводной сваркой:
- Поражение электрическим током — существует вероятность поражения электрическим током, если оборудование не изолировано должным образом или если источник питания не отключается сразу после прекращения дуги сварщиком во время сварки.
- Взрыв — дуговая сварка производит водород и кислород.Могут накапливаться газовые карманы, и они потенциально взрывоопасны.
- Азотный наркоз — опасность для здоровья, с которой обычно сталкиваются дайверы во время занятий дайвингом, когда не соблюдаются меры безопасности на определенном уровне. Любопытно, что риск утопления не входит в список опасностей, связанных с подводной сваркой.
- Для сварных конструкций проверка сварных швов после сварки может быть сложнее, чем сварных швов, выполненных над водой. Существует риск дефектов, которые могут остаться незамеченными и в конечном итоге привести к отказу.
Безопасность:
- Стандарт OSHA 1915.6 — Коммерческое дайвинг
- Стандарт OSHA 1910.424 — Подводное плавание с аквалангом
- Том IV, выпуск 3, 3 квартал 2002 г.
- Информационный бюллетень по гигиене труда — коммерческий
Безопасность при сварке:
- Необходимо принять необходимые меры предосторожности, например:
- Соблюдайте правила техники безопасности работодателя.
- Пары и газы могут быть опасными для вашего здоровья.
- Дуговые лучи могут повредить глаза и кожу.
- Во время сварки используйте соответствующую вентиляцию.
- Носите подходящие средства защиты глаз и защитную одежду.
- Не прикасайтесь к токоведущим частям.
- Наденьте резиновые перчатки.
- Заменяйте электрод только в холодном состоянии.
Разработки:
- Последние разработки в области строительства морских нефтяных платформ увеличили спрос на подводную сварку.Использование барокамер для получения сварного шва нормального качества очень дорого в эксплуатации.
- Исследователь Sea Grant доктор Чон Цай разработал новый сварочный электрод для влажной сварки, получивший название «Черная красавица» за черный внешний вид его водонепроницаемого покрытия. Электрод демонстрирует превосходный внешний вид и профиль, микротрещины сварного шва устранены, рабочие характеристики превосходят другие имеющиеся в продаже электроды, и электрод дает подходящие результаты при использовании в любом положении.