Как правильно сваривать полипропиленовые трубы?
Для создания комфортных условий жизни постоянно разрабатываются новые технологии, изобретаются новые материалы, воплощаются новые идеи. На протяжении последних нескольких десятилетий для монтажа водопроводной системы, канализации, а в последнее время – системы отопления, используют пластиковые трубы, в частности полипропиленовые. Они имеют массу преимуществ по сравнению с чугунными или металлическими и кардинально отличаются методом монтажа — сварка при помощи специального аппарата паяльника. К тому же сварку полипропиленовых труб может произвести самостоятельно, не прибегая к помощи наемных работников. Немного потренировавшись, можно с легкостью установить трубопровод в новом доме или заменить старую водопроводную систему.
На чем основан принцип монтажа полипропиленовых труб
Для установки полипропиленовых труб применяются физические свойства материала. При нагревании полипропилен плавится, после чего переходит в жидкое состояние.
Безусловно, для качественного монтажа необходим навык и опыт работы. Но для того, чтоб технология сварки полипропиленовых труб была соблюдена в полном объеме, необходимо иметь сварочный аппарат, который обеспечит необходимый температурный режим.
Технология сварки полипропиленовых труб
Какое сварочное оборудование необходимо иметь и как сварить полипропиленовые трубы поговорим далее.
Разновидности аппаратов для монтажа полипропиленовых труб
Аппарат для сварки представляет собой корпус, на котором расположен нагревательный элемент, насадки разных диаметров.
- Аппарат для муфтового соединения. Это наиболее распространенный вид для сварки полипропилена. Его конструкция очень проста, а работа с ним происходит в ручном режиме. Сварка полипропиленовых труб своими руками ручным прибором может пройти качественно и быстро.
- Прибор для стыкового соединения. В быту применяется редко из-за высокой стоимости и сложности управления, но при его помощи можно легко сварить две трубы диаметром более 40 мм. Аппарат полностью механизирован. Он оборудован ножом для резки, нагревательного диска, устанавливаемого между двумя деталями, и после окончания времени нагрева убирается. Сжатие также происходит автоматически.
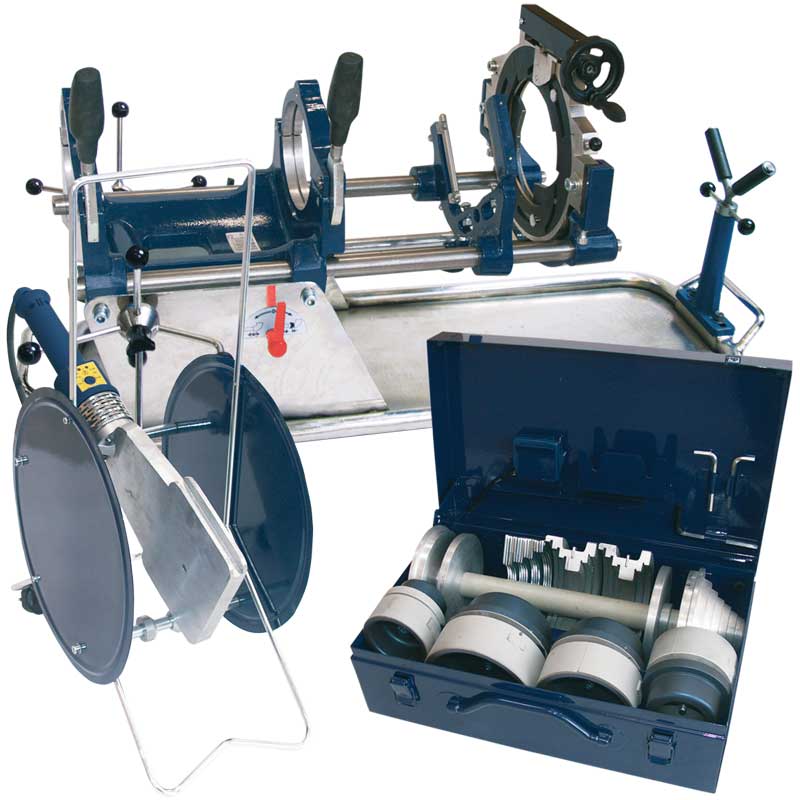
Профессиональные мастера советуют обращать на страну изготовителя комплектов сварочного оборудования для полипропилена. Лучшим оборудованием признано европейское. Уступает по качеству, срокам эксплуатации, цене турецкое и китайское оборудование (он может сразу выйти из строя или использовать для набора опыта, таким образом, новичкам можно остановить свой выбор на этих производителях).
Температурный режим пайки
Необходимо, чтоб температура сварки полипропиленовых труб была около 260о
С. Как правило, любой паяльник (с регулировкой температуры или без) может обеспечить такое значение.На качество швов сварки полипропиленовых труб отражается выбор оптимального температурного режима и время выдержки материала под нагревом. Если эти параметры ниже необходимого значения, то стык получается недостаточно крепким, с течением времени может дать течь. Когда время нагрева и температура завышены – материал сильно расплавляется, шов получается слишком большим и некрасивым. Кроме того, попав внутрь может значительно уменьшить диаметр.
Стоит учитывать и температуру вокруг аппарата для сварки, если она низкая необходимо увеличивать время выдержки на 2 секунды, если высокая, наоборот, уменьшать. Придерживаясь этих простых правил, сварка полипропиленовых труб своими руками пройдет легко.
Диаметр трубы тоже имеет большое значение. В таблице описаны необходимые параметры при + 20оС как правильно сваривать полипропиленовые трубы.
Наружный диаметр труб, мм | Время нагрева, с |
---|---|
16 | 5 |
20 | 5 |
25 | 7 |
32 | 8 |
40 | 12 |
50 | 18 |
63 | 20 |
75 | 30 |
90 | 40 |
110 | 50 |
Аппарат для стыковой сварки полипропиленовых труб большого диаметра
Процесс соединение труб при помощи паяльника
Технология сварки полипропиленовых труб довольно проста, но не стоит забывать о некоторых моментах.
- Перед началом работы необходимо разогреть сварочный аппарат. Но перед тем как включить его в электрическую сеть, нужно установить, подходящую по размеру диаметра, насадку. Температуру нужно выставить на 260оС, только после этого включить в розетку. После того как температура будет набрана, сработает сигнализация или погаснет индикаторная лампочка (смотря какая используется модель аппарата для сварки). Это будет означать, что паяльник для сварки полипропиленовых труб готов и можно приступать к работе.
- Подготовка комплектующих. Неправильные, кривые с заусенцами, задирами срезы могут свести на нет все усилия по установке системы. Резку производят специальными ножницами. Их применяют следующим образом. На держатель, который надежно фиксирует материал в неподвижном состоянии, укладывается деталь, а режущая часть находится сверху и легко делается срез. Единственный недостаток при этом процессе устают руки. Можно воспользоваться для порезки болгаркой, но в этом случае много времени уйдет на обработку среза и его зачистку.
Перед тем как сваривать, необходимо обезжирить, высушить все детали. - Проведение сваривания полипропиленовых труб и инструкция по нагреву была описана выше, поэтому повторяться не будем. Обратите внимание, для хорошего, а также качественного шва все комплектующие для водопровода, канализации или отопления необходимо покупать от одного производителя. Это обеспечит подходящие по диаметру фитинги к диаметру труб (в холодном состоянии они должны с усилием соединяться). После нагрева соединительных частей снять с нагревательного элемента и соединить между собой, сразу устанавливая горизонтальное положение. После остывания исправить положение деталей между собой будет невозможно без деформации стыка. Процесс сваривания требует затраты физических усилий на несколько секунд. Соединение необходимо оставить на 2-3 минуты для остывания и после этого можно продолжать монтировать цепь далее.
Это и вся технология. Теперь Вы знаете, как варить полипропиленовые трубы самостоятельно.
Закончив работу с паяльником, обязательно требуется очищение его от материала, что остался при помощи любого мягкого куска ткани.
Оборудование для сваривания полипропиленовых труб работает от электричества и с высокими температурами, поэтому при проведении работ на нем необходимо соблюдать правила безопасности:
- следить за тем, чтоб была надежная изоляция электрических составляющих;
- не прикасаться к нагревающим элементам.
110 фото предварительной подготовки и сварки
В современном производстве при изготовлении водопроводных труб чаще всего используется пластик. На замену металлу пришел практичный полипропилен.
Такие конструкции имеют ряд преимуществ:
- Длительное использование. Некоторые поставщики гарантируют эксплуатацию сроком до 50 лет.
- Устойчивость к коррозии.
- Небольшой вес.
- Легкость монтажа.
Каждый может справиться со сваркой полипропиленовых труб своими руками. Для этого необходимо приобрести соответствующее оборудование и ознакомиться с технологией установки.
Краткое содержимое статьи:
Виды труб из полипропилена
На рынке строительных материалов встречаются пластиковые трубы 4 цветов. Белые, зеленые и серые не отличаются по своим свойствам. Их обычно используют в помещениях.
Изделия черного цвета обладают особой устойчивостью к солнечным лучам, что позволяет использовать их для организации системы полива.
Специалисты выделяют несколько типов труб:
- Используемые в холодной воде. Такое оборудование выдерживает температуру до +45°С. Для маркировки применяется полоса, имеющая голубой цвет.
- Устойчивые к высоким температурам. Трубы, по которым течет горячая вода, должны выдерживать до +85°С.
При покупке на изделии стоит искать красную полоску.
- Универсальные. Такой товар помечен сразу двумя полосками – голубого и красного цветов.
Полипропиленовые трубы имеют свою маркировку:
PN10. Данная отметка говорит о том, что водопровод предназначен только для холодной воды. При этом толщина изделия является небольшой.
PN16. Такие трубы выдерживают более высокую температуру, но также не предназначены для горячего водоснабжения.
PN20. Эта маркировка ставится на конструкции с толстыми стенками. Данный тип используется как для холодной, так и очень горячей воды.
PN25 имеют самую большую толщину стенок и дополнительную защиту в виде фольги или стекловаты. Такие трубы предназначены для отопительной системы.
Способы монтажа
Современные технологии позволяют прокладывать водопровод как открытого типа, когда конструкции прилегают к стене, так и закрытого, при этом изделия прячутся в специальных углублениях.
В любом случае понадобятся держатели, которые по форме напоминают клипсы. Они могут быть одинарными или двойными и устанавливаются на расстоянии в среднем по полметра друг от друга.
Предварительная подготовка
Нужно уделить особое внимание подготовке аппарата, чтобы в ходе работы верно выполнить все пункты инструкции сварки полипропиленовых труб:
Перед началом сварки на рабочую платформу устанавливаются необходимые насадки. Обычно это гильза и дорн. Далее следует выставить нужную температуру на регуляторе.
Опытные рабочие рекомендуют +260°.
Следующим этапом является подключение к сети и ожидание нагрева.
Особое внимание нужно уделить правильному срезу трубы. Качество сварки зависит от отсутствия недостатков разреза. Этого можно добиться с помощью специальных ножниц.
После проведения разреза поверхности следует тщательно обезжирить и высушить.
Технология сварки полипропиленовых труб
Полипропилен, в качестве материала для производства водопроводных труб, является достаточно жестким по своим характеристикам. При монтаже понадобятся тройники, переходники, уголки и прочие фитинги. Данные детали припаиваются к основной конструкции путем нагревания до очень высокой температуры.
Существуют специальные фитинги, состоящие из двух частей. Одна соединяется с металлическими конструкциями, а вторая часть сделана из полипропилена.
Аппарат для сварки полипропиленовых труб часто называют паяльником. По своей форме он является небольшой платформой с электрической спиралью внутри и насадками снаружи. Спираль нагревает рабочую поверхность.
Сварка пластиковых конструкций состоит их нескольких этапов:
Нагрев поверхностей до +260°. При такой высокой температуре происходит расплавление металла. Сварочная платформа при этом соединена с двумя металлическими насадками, которые имеют покрытие из тефлона.
Первая насадка называется дорн. Он имеет небольшой диаметр и служит для расплавления внутренней части детали. Вторая носит название гильза. Ее предназначение – нагревать наружную часть.
Через несколько секунд, когда соединяемые детали дойдут до нужного состояния, их следует плотно прижать друг к другу. При этом произойдет сварка конструкции.
Полезные замечания
Установка полипропиленовых водопроводных конструкций не требует особо сложных навыков и осуществляется в короткие сроки. При использовании качественного аппарата для сварки полипропиленовых труб можно быть уверенным, что процесс монтажа пройдет без неприятностей.
Однако, стоит обратить внимание на некоторые моменты:
Нужно внимательно измерять участки трубы перед резкой, так как при неправильной длине детали могут не сойтись друг с другом.
Сварка в труднодоступных местах, таких как углы, может привлечь дополнительные трудности. С ними можно справиться при использовании сразу двух комплектов насадок.
При выборе сварочного аппарата не стоит экономить денежные средства, так как использование дешевых насадок может привести к некачественной сварке конструкций. Лучше приобрести небольшой агрегат, который поможет существенно сэкономить силы и время при ремонте.
Фото сварки полипропиленовых труб
Также рекомендуем посетить:
Сварка полипропиленовых листов с применением термического оборудования
Сварка листового полипропилена строительным феном и экструдером
Одним из самых распространенных методов соединения полипропилена является его сварка. Такая технология является самой востребованной и эффективной, это объясняется термопластичностью и прочностью материалов. Сварка листового полипропилена происходит вследствие их соединения встык или под прямым углом. Для соединения также можно использовать экструдер, фен или стыковой сварочный станок.
Лист полипропилена: природа материала для заготовки
Данный материал производится путем выдавливания гранул вещества полимера из специальных отверстий. Такая технология позволяет получить в итоге лист любой длины и ширины. Сам лист полностью состоит из гранул. Покрытие такого материала может быть или глянцевым или матовым, если лист покрыт глянцем, то сверху накрывается пленкой.
Основными преимуществами полипропилена является:
- диэлектричность;
- достаточная гидрофобность;
- стойкость к стиранию;
- химическая прочность.
Благодаря особым характеристикам сварка листов полипропилена не представляет самой объемный процесс и отличается доступностью. Весь процесс сварки заключается в доведении краев материала до вязкого состояния и сильно прижатия друг к другу. Такой механизм поможет получить в последующем цельную деталь.
Диффузионная сварка
Перед началом работы, необходимо подготовить рабочее место и весь материал.
Чтобы швы склейки были как можно ровными и незаметными, следует с полной серьезностью подойти к процессу и выбрать такой способ сварки, который будет для вас наиболее доступным и удобным.
Одним из наиболее эффективных способов соединения листового полипропилена является диффузная сварка. Такой механизм соединяется на специально оборудованном сварочном станке.
Сварка полипропиленовых листов происходит с помощью укладки двух частей на станок и их фиксации. Концы листов будут прижиматься к нагревательному элементу.
Для получения наилучшего эффекта листы следует нагревать продолжительное время. После достижения необходимой температуры, листы прижимаются с помощью фиксирующего механизма.
Шов, который получается с помощью оборудования для сварки, будет являться самым прочным и надежным.
Рекомендуем! Прямая и обратная полярность при сварке инверторным аппаратом
Очень важным при такой сварке является чистота и пониженная влажность воздуха в помещении, температура воздуха должна быть теплой.
Одним из главных преимуществ шва будет не только его прочность, но и скорость получения качественного материала. Такой метод подходит для листов любой ширины, и дает возможность сваривать полипропиленовые листы в рулоны.
При большом количестве работы, сварочный станок станет незаменимой вещью.
Сварка с помощью экструдера
Такой метод предполагает наличие особого инструмента – экструдера. Такой аппарат оснащен различными насадками, которые позволяют сваривать самые сложные и громоздкие конструкции. Огромным преимуществом есть и небольшой размер оборудования.
Экструдер оснащен автоматической подачей теплого воздуха, что позволяет размягчать листы и избегать каких-либо повреждений при сварке.
Работа таким методом предполагает оперативность в действиях, так как из-за высокой температуры (около 270С) возможна деформация около внутренних слоев полипропилена.
Такой процесс не требует выделения отдельного помещения и соединения возможно прямо на рабочем месте, благодаря компактности устройства.
Шов, полученный с помощью экструдера, является вторым по прочности, после сварочного станка.
Недостатком такого метода является необходимость соединять полипропилен одинакового состава, класса, в противном случае швы будут получаться непрочными и неравномерными.
Сварка листового полипропилена строительным феном
Для сварки листового полиэтилена феном, вам понадобится строительный фен большой мощности и тонкие
полимерные листы, а также полипропиленовая проволока (подобранная под размер и толщину листов, которые необходимо соединить).
Важным является фактор подбора материала, листы и проволока должны состоять из одинакового класса материалов.
Пренебрежение данного момента существенно повлияет на качество полученного шва и его прочность, так как фен не сможет одновременно довести до одинаковой нужной температуры разные виды материалов.
Для нормальной стыковки листов, их необходимо разместить на ровной поверхности и края обработать наждачной бумагой. Важным моментом подготовки является разделка кромок под углом 45.
Подготовленные листы полипропилена для сварки встык
Процесс нагревания феном и расплавки прута занимает примерно от 5 до 10 минут. Далее идет сам процесс сварки. Пластиковый пруток вставляется в насадку сварочного фена и в процессе заполнения шва непрерывно подается в зону сварного шва.
Рекомендуем! Сварка полуавтоматом нержавеющей стали
После соблюдения всех процедур, соединенный материал можно использовать. Полученный шов, при сварке ПНД с помощью строительного фена, является менее прочным, чем при сварке станком или экструдером, однако такой метод будет идеальным для соединения материала с небольшой толщиной.
Склеивание листового полипропилена
Склеивание полипропилена – очень трудоемкий процесс, требующий специальной подготовки. Это обуславливается тем, что такой вид пластмассы является особенно трудносклеиваемым.
На современном рынке существует большое множество клеев, которые без каких-либо проблем способны склеить пластмассу, основным вопросом будет выбор специального раствора.
Особая подготовка к склеиванию материала будет заключаться в предварительной сборке всех деталей, чтобы поставить необходимые метки, ведь неправильное соединение полипропиленовых листов или банальная ошибка в процессе может стоить вам испорченного материала.
Главными рекомендациями при склеивании и сварке полипропилена своими руками будут:
- необходимо приобретать клей, обращая внимание, прежде всего на его марку, но никак не на цену. Свой опыт в таком вопросе будет для вас дополнительным бонусом. Иногда клей из высокой ценовой категории по качеству может уступать более дешевым аналогам;
- очень важным будет уделить внимание заточке и обработке краев полипропиленовых листов, при правильном выполнении этого требования, шов получится очень аккуратным;
- выбирайте способ сваривания в зависимости от ширины листа, а также его размера.
Чем правильней будет выбрана техника соединения, тем прочнее шов получится на выходе.
Источник: https://svarkagid.ru/tehnologii/svarka-listov-polipropilena.html
Полипропиленовый лист: методы сварки и обработки
Работы, связанные с механической обработкой и сваркой листов из полипропилена достаточно сложные, и требуют детального ознакомления со свойствами и особенностями такого материала, которых на самом деле не мало.
В первую очередь, полипропилен плавится при невысоких температурных показателях, поэтому, при работе с этим материалом необходимо аккуратно работать со сверлами, пилами, и другими фрезами, которые могут нагреть пластик.
Механическая обработка такого материала как полипропилен и полиэтилен требует соблюдения следующих условий:
- Режущий инструмент должен быть заточен
- При резке кромка инструмента должна едва касаться материала
- Стружка, которая образуется в процессе резки должна вовремя устраняться
- В случае, когда материал сильно разогреется необходимо прервать работу, либо провести охлаждение материала.
Основой полипропиленовых резервуаров, таких как гальванические ванны или бассейны является полипропиленовый лист.
Для его соединения можно применять заклепки, болты, но лучшим способом соединения материала является полифузионная сварка, или ручная сварка экструдером.
Обязательно стоит отметить, что худший способ соединения полипропиленовых листов, это склеивание, так как это совершенно не надежно.
Сварка полипропиленовых листовобычно проводится тремя способами:
- Методом полифузионной сварки;
- Методом экструзивной сварки;
- При помощи пистолета с горячим воздухом.
Стыковая полифузионная сварка – это самый качественный метод, так как процесс направлен на разогрев краев материала и их скрепление под давлением. Так делают даже тогда, когда листы имеют очень большую толщину, и результат качества шва всегда превышает 90% от прочности самого материала.
При помощи экструдера шов формируется за счет нанесения специального сварочного прутка, которая перед нанесением проходит процесс плавления в винтовом роторе устройства.
Так как такой агрегат как экструдер, в первую очередь ручного управления, то выполнять сварку равномерно используя равноценное количество материала достаточно трудно.
Тем не менее, используя этот метод можно добиться склеивания пропиленовых листов очень большой толщины.
Что касается сварки пистолетом с горячим воздухом, то это не очень эффективно и качественно, так как разогрев будет проводиться не равномерно. А в случае если детали изделия будут иметь разные показатели нагрева, то при склеивании это вызовет очень серьезные проблемы: пока один полимер будет разогреваться, второй уже начнет плавиться.
Полифузионная сварка не требует дополнительного материала для склеивания, а вот в случае с экструдером и пистолетом наличие полипропиленового или полиэтиленового сварочного прутка обязательно.
Цена на полипропиленовый лист низкая, поэтому из него очень выгодно производить как промышленные технические резервуары, так и емкости для дома, такие как купели, бассейны, резервуары для воды и многое другое.
Купить полипропиленовый лист различных размеров и цверов и в любом необходимом для вас количестве, вы сможете без труда, всего лишь обратившись в нашу компанию.
Источник: http://pplist.ru/infopolimer/sposobyi-obrabotki-listov/polipropilenovyij-list-metodyi-svarki-i-obrabotki.html
Сварка полипропилена
Для сварки листового полипропилена в промышленных условиях в основном используются следующие технологии:
- Сварка горячим воздухом (или сварка феном)
- Сварка ручным экструдером
- Сварка при помощи нагревательного элемента встык
Для сварки полипропиленовых труб могут использоваться также электромуфтовая сварка, раструбная сварка и т.д. В данном разделе описываются основные виды сварки листового полипропилена.
Сварка полипропилена горячим газом (сварка феном)
Наиболее простой и бюджетный, с точки зрения оборудования, способ сварки, широко распространенный при сварке листов малой толщины и/или линейных размеров.
При этой технологии основные материалы и присадочный материал (сварочный пруток) свариваются подогретым газом (чаще всего воздухом) с использованием прижимного давления на соединяемых поверхностях которое создается вручную оператором. Проводка (подача прутка) также осуществляются вручную.
Воздух подогревается электрическими нагревательными элементами (феном) до температуры необходимой для сварки. Нагрев места сварки и сварочного прутка происходит одновременно с помощью специальной сварочной насадки на фен.
Форма и размеры насадки, в основном, определяются формой и сечением сварочного прутка.
Основные параметры процесса:
60-7060-7060-70 | 280-320280-320280-320 | ок.![]() |
Сварка полипропилена ручным экструдером
Данный способ применяется, в частности, при сварке толстостенных деталей, также требующий использования присадочного материала (сварочного прутка, реже – гранулята.) Экструдер при сварке не должен останавливаться (из-за опасности разложения).
В принципе, экструзионная сварка двух деталей заключается во впрыскивании расплавленного присадочного материала в зону сварки. Например, при взаимно перпендикулярном расположении двух листов присадочный материал впрыскивается в угол между ними, образуя т.н. шов K-типа.
Основные параметры процесса сварки полипропилена ручным экструдером:
210-240 | 210-300 | 300 |
ВНИМАНИЕ!
Ряд производителей полуфабрикатов инженерных пластиков рекомендуют применять для сварки листов из полипропилена-гомополимера (PP-H) пруток из полипропилена-блок-сополимера (PP-B).
Основаниями для данных рекомендаций являются следующие соображения:
Ударная прочность полипропилена-блок-сополимера (PP-B), согласно ISO 179
в 5-8 раз выше чем у полипропилена-гомополимера (PP-H).
В отличие от материала листа сварные швы часто имеют небольшие риски или зарубки и применение сварного прутка из полипропилена-блок-сополимера (PP-B) значительно уменьшает риск образования трещин.
Кроме того, другая величина фактора пластичности A4 полипропилена-блок-сополимера (PP-B) согласно DVS 2205 при 20º С по сравнению с PP-H придает месту шва дополнительную надежность
С учетом того, что швы преимущественно выполняются в местах соединения горизонтальных и вертикальных поверхностей, и напряжения, испытываемые материалом, в основном носят изгибающий характер, дополнительная пластичность полипропилена-блок-сополимера (PP-B) является дополнительным преимуществом.
Сварка прутком из полипропилена-блок-сополимера (PP-B) несколько проще, что уменьшает риск ошибок.
Большая стойкость к образованию трещин и разломов полипропилена-блок-сополимера (PP-B) является дополнительным преимуществом при образовании микроотверстий, как результата усадки материала в процессе сварки
Индекс текучести расплава листов полипропилена-гомополимера (PP-H) и прутка из полипропилена-блок-сополимера (PP-B) находится в пределах одной группы, согласно DIN EN ISO 1873-1, а именно группы 003” (230ºС/2.16 кг 0.2 – 0.4 г/10 мин.) В связи с этим данные материалы являются полностью совместимыми с точки зрения сварки.
Тем не менее, следует крайне осторожно подходить к возможности сварки листов из полипропилен-гомополимера (PP-H) прутком из полипропилена-блок-сополимера (PP-B) в случаях, когда режим эксплуатации изделия (например верхняя граница диапазона рабочих температур) является критическим для последнего материала.
Сварка полипропилена с помощью нагревательного элемента (Butt Welding)
Сварка полипропилена с помощью нагревательного элемента (называемая также сваркой встык) применяется для сварки плит, блоков и других профилей полуфабрикатов. Чрезвычайно широко данный вид сварки применятся для сварки трубопроводов из термопластов. В отличие от предыдущих двух способов сварки данный метод не требует использования присадочного материала.
Для сварки с помощью нагревательного элемента применяются т.н.
машины для сварки встык, принцип действия которых (разогрев с помощью нагревательного элемента различной формы) одинаков, и отличающиеся между собой лишь типом привода (ручной, механический, пневматический и т.д.
), передающего сдвижное усилие на свариваемые элементы. Кроме того, машины для сварки встык могут отличаться комплектацией специальным оборудованием и всевозможными опциями- например для сварки листов под углом, для сворачивания свариваемых листов.
При сварке полипропилена встык необходимое тепло подводится непосредственно от подогревающего элемента в зону сварки соединяемых поверхностей.
При этом достигается более благоприятное распределение тепла, так что ни одна из зон материала не нагружена теплом больше, чем другая.
Кроме этого стыкующиеся поверхности подогревающего элемента должны быть чистыми и полностью прилегать.
Такой вид сварного шва показывает небольшое внутреннее напряжение и его можно нагружать практически также, как и исходный материал.
Источник: http://www.engplast.ru/content.php?1046-%D0%A1%D0%B2%D0%B0%D1%80%D0%BA%D0%B0-%D0%BF%D0%BE%D0%BB%D0%B8%D0%BF%D1%80%D0%BE%D0%BF%D0%B8%D0%BB%D0%B5%D0%BD%D0%B0
Сварочный экструдер для листов полипропилена
За последние десятилетия полипропилен занял значительную нишу в строительной сфере, вытеснив многие другие материалы. Данный материал имеет ряд весомых преимуществ, одно из которых заключается в довольно простом монтаже.
Одним из способов создания полипропиленовых конструкций является сваривание, позволяющая получить аккуратные и полностью герметичные швы.
Рассмотрим один из вариантов сварки полипропилена при помощи экструдера, который применяется при создании разного рода емкостей.
Листовой полипропилен
Полипропилен в виде листов получается путем пропускания расплавленного материала под специальными валиками. Он находит широкое применение при создании емкостей, изготовлении труб больших диаметров, в качестве изоляционного материала. Этому способствуют следующие характеристики:
- Устойчивость к влаге;
- Высокая механическая прочность;
- Устойчивость к химическим веществам;
- Инертность к ультрафиолетовым лучам.
Кроме того, материал универсален с точки зрения обработки и монтажа. Его можно фрезеровать, резать и соединять различными способами. На данный момент наибольшей популярностью пользуются 3 способа соединения:
- Механический. Требует использование крепежа и не дает высоких изоляционных характеристик конструкции;
- Склеивание. Устойчивость к химическим воздействиям позволяет склеивать материал без ущерба для него;
- Сварка листов полипропилена. Позволяет получить прочное и надежное соединение благодаря использованию специальных инструментов для сварки полипропилена.
Технология сварки
Главная особенность сводится к тому, что при сваривании не происходит изменений в химическом составе листов. Для этого применяется стыковочный материал, а также пруток для сварки, хотя процесс может обходиться и без него.
Основные процессы сводятся к трем пунктам:
- Нагрев соединяемых элементов до образования вязкой поверхности;
- Стыковка расплавленных частей механическим способом;
- Остывание деталей в фиксированном состоянии.
Для получения швов высокого качества необходимо соблюдение ряда условий:
- Температура внешней среды не менее 15°С;
- Соответствие присадок свариваемому полипропилену;
- Высокое качество свариваемых поверхностей;
- Правильный выбор инструмента и насадок для него.
Сварка полипропиленовых листов
Сварка для полипропилена выпускается в виде устройств ручного и автоматического использования в зависимости от применяемых инструментов для сварки. В рамках данной статьи рассмотрим ручные способы.
Методы ручной сварки
Различаются несколько способов:
- Экструзионный. Монтирование деталей производится экструдером для сварки. Это ручной аппарат достаточно небольших размеров, но при этом он позволяет создавать достаточно надежное соединение полипропиленовых листов. Показатели прочности сварных конструкций дают результат в 0,8 по сравнению с 1 исходного материала. Использование экструдера позволяет осуществлять сварку листового полипропилена толщиной от 16 мм. Принцип данного метода заключается в подаче горячего воздуха, который расплавляет материал в зоне проведения сварочных работ. Экструдер подает размягченный состав и перемешивает его до однородности, что позволяет получить шов высокой прочности.
- Строительный фен. Фен для сварки подает разогретый до 180° воздух на края поверхностей, которые оплавляются. Их соединяют и ждут остывания. Полученный результат не может похвастаться высокой прочностью, но такой способ имеет право на существование для соединения полипропилена своими руками.
Метод можно применять для малых элементов, которые не будут испытывать больших нагрузок. Рекомендован для материала толщиной 20 мм.
- Полифазный способ. Данный метод применим для листов самой различной толщины. Его осуществление производится на специальных подвижных столах. Шов, полученный таким способом, имеет высокие показатели прочности и герметичности.
Ручные способы имеют важные преимущества благодаря своей мобильности, что позволяет создавать различные конструкции.
Подведем итоги
Сварка полипропиленовых листов в последнее время находит все больше сфер применения, так как позволяет получить изделия с высокими эксплуатационными характеристиками. Качество производимых работ в большой мере связаны с выбором инструмента и его правильного применения.
Большое распространение при сварочных работах с полипропиленом имеет ручной инструмент, применение которого возможно как в быту, так и в промышленности. Ручной инструмент типа экструдера позволяет получать надежные соединения без потери мобильности монтажа.
Сергей Одинцов
Источник: http://electrod.biz/varim/ekstruder-dlya-listov-polipropilena.html
Сварка листового полипропилена
На смену традиционным материалам прошлого века со всеми их преимуществами и недостатками пришел новый, недорогой, эффективный, незаменимый в отдельных сферах, материал будущего. Полипропилен обладает рядом очевидных преимуществ.
Несложные способы монтажа позволяют его использовать в качестве конструктивного строительного материала.
Сварка листового полипропилена включает в себя термомеханические и термические технологии, которые обеспечивают высокопрочные, абсолютно герметичные соединения.
Свойства материала
Получаемый методом каландрирования расплавленной массы через валки заданных размеров, материал производится в листах. Широко используется в строительстве, изготовлении бытовых предметов, производстве труб, как гидроизоляционный материал. Его важные свойства, такие как:
- гидрофобность;
- стойкость к механическим воздействиям, истиранию;
- химическая стойкость,
- инертность к воздействию ультрафиолета,
объясняют широкую популярность полипропилена, который является к тому же отличным диэлектриком.
Листовой полипропилен высокого качества используется для гальванопластики, изготовления ванн, бассейнов, вентиляционных конструкций, производства ёмкостей, очистных сооружений, профильных труб, бытовых изделий, пантонов. Материал используют в строительстве, горном деле, нефтехимии.
Виды полипропилена
Уникальные свойства материала способствуют его широкому применению. Полипропилен бывает:
- экструдированным;
- кашированным;
- прессованным,
каждый вид имеет собственное назначение, виды монтажа, сварки, склейки.
Маркировка листового полипропилена РР зависит от дополнительных технических характеристик. Маркировка и свойства:
- H – химическая стойкость;
- R – химостойкость дополненная повышенной прочностью, устойчивостью к высоким температурам;
- S – химическая устойчивость, не горючий материал;
- S-el – инертность к химическим реагентам, не горючесть, электропроводность.
Такая маркировка используется на территории страны и за рубежом.
Листовой полипропилен делится на типы по способу производства:
- плотный;
- ячеистый;
- вспененный,
каждый, из них имеет свои технические и технологические особенности. Плотный имеет жесткость, ячеистый имеет структуру упаковочного материала, вспененный ценится как материал для эффективной изоляции.
Особенности сварки листового полипропилена
Все виды и типы листового полипропилена являются универсальным материалом с точки зрения обработки. Фрезеровка, резка, машинная обработка механическое соединение и сварка – применяются к любому из типов, видов этого материала. Как можно соединять листы полипропилена:
- механическим способом, с использованием крепёжного материала, метод не предполагает сохранение герметичности, водонепроницаемости конструкции;
- методом склеивания, химическая инертность материала позволяет создавать достаточно прочные герметичные конструкции без его повреждения;
- сварка, метод с использованием экструдера, фена прочего сварочного оборудования обеспечивает прочные надёжные, абсолютно герметичные соединения.
Метод соединения выбирается в зависимости от производственных целей, технических характеристик материала, наличия технических возможностей.
Методы ручной сварки листового полипропилена
Сварочное оборудование производится как для ручного использования, так и для автоматического применения. Ручная сварка осуществляется следующими методами:
- Экструзионный метод. Соединение осуществляют небольшим по размерам аппаратом, который называется ручной экструдер. Применение ручного экструдера позволяет формировать достаточно надёжные соединения с коэффициентом прочности по отношению к исходному материалу – 0,8, позволяет производить стыковку листов толщиной не менее 16мм. Данным методов производят сварку крупных изделий сложной конфигурации.
Принцип состоит в подаче воздуха, размягчающего и нагревающего пластмассу в зоне сварки, куда встраивается полипропиленовая проволока. Размягчённый состав с помощью присадки подающейся экструдером соединяется с составом разогретого листа, перемешиваясь до однородной массы. Соединения получаются сверхпрочными, с высокого качества швом.
- Стыковка строительным феном. Под воздействием струи горячего воздуха (180°) расплавляются края листов полипропилена, соединяются и остывают. Метод действенен только при соединениях листов в 20мм толщиной. Шов не отличается высокой механической прочностью. Применение метода рекомендовано для сварки мелких элементов, не предназначенных для серьёзных нагрузок.
- Стыковой или полифузный метод. Применяется для стыковки элементов разной толщины, в том числе и самой большой. Производится с помощью подвижных специальных столов. Шов при стыковой сварке обладает высокой прочностью, надёжностью.
Стыковочные работы проводятся с определённой последовательностью мероприятий. Подготовка рабочего места, очищение от грязи и пыли. Обработка материала абразивными материалами, для придания лучших адгезионных характеристик.
Важнейшее преимущество ручного сварочного оборудования состоит в том, что оно позволяет производить соединительные работы непосредственно на месте, это широкие возможности для создания самых разных конструкций.
Аппараты ручной сварки предполагают использование присадочных материалов. Часто используется полипропиленовая проволока круглого или треугольного сечения разного диаметра (1- 6мм).
Автоматическая сварка
Принцип полифузного сваривания, автоматической сварки состоит в нагреве деталей в месте соединения и стыковки под высоким давлением.
- Края свариваемых деталей фиксируются специальным устройством,
- нагреваются до требуемой температуры,
- прижимаются друг к другу с помощью давления.
Качество получаемого соединения оценивается как очень высокое, надёжность подобных соединений подтверждена практикой.
Преимущества автоматической сварки:
- стыковка листов между собой без швов;
- сварка листов в рулоны;
- соединение под прямым углом;
- торцевое, угловое соединение гарантировано высокой прочности;
- не требуется регулировки давления, оно поддерживается на заданном уровне;
- не происходит перегрева и деформации шовного соединения благодаря автоматическому поддерживанию заданной температуры.
- Автоматика обеспечивает монолитность соединений.
Осуществляются операции на специальном оборудовании. Используются швейцарские станки Leister, немецкие Rothenberger, российские Ingenia, это машины с автоматическим циклом, числовым программным управлением, в арсенале имеющие три цикла сварки.
Сварка отдельных видов полипропилена
Сварка применима для прессованного, экструдированного полипропилена всех марок и типов. Автоматическая или ручная, полифузная, с помощью фена или экструдера сварка применяется для решения различных производственных задач.
Среди всех видов полипропилена выделяется кашированный. Это полипропилен, склеенный с тканевым материалом. Одну сторону листа, с повышенной адгезией соединяют с тканевым материалом из полиэфирных волокон или стеклоткани.
Соединяют путём каландрирования, то есть, в процессе экструзии пластмассу механически прижимают к тканевому полотну, ткань внедряется в слой полимера.
Так получается уникальный по своим физико-техническим свойствам полипропилен, сочетающтй в себе все самые превосходные качества стеклопластика и полимера:
- прочность;
- повышенная несущая способность;
- улучшенные возможности для пищевых ёмкостей;
- химическая стойкость самой высокой степени.
Максимально прочное соединение ткани и полимера происходит за счёт клеящих составов изготовленных на основе полиэфирной, эпоксидной смолы, других клеев промышленных составов.
Основы технологии сварки листового полипропилена
Основа технологии состоит в том, что соединение элементов термическим способом не влечёт за собой изменения их химического состава.
Сварка происходит с использованием стыковочного материала, используется пруток, но сварку осуществляют и без него.
Доведение соединяемых поверхностей до вязкого состояния путём нагрева, принудительная стыковка механическим образом, рождает цельную деталь определённой прочности после остывания.
Для обеспечения нормального технологического процесса сварки требуются некоторые обязательные условия:
- Чистое светлое помещение с минимальной температурой воздуха 15°;
- Соответствие присадочных материалов основному;
- Правильный выбор сварочного инструмента и насадок к нему;
- Допустимое качество используемых материалов, лист должен иметь правильную геометрию, ровную поверхность, однородность цвета, пруток ровное сечение, структуру без пузырьков или иных вкраплений;
- Наличие дополнительного инструмента, ножей, наждачных шкурок, растворителей для снятия жира, прочего
- Края свариваемых листов перед сваркой обработать фрезером, для предания угла наклона края 45° к плоскости листа. Соединить листы обработанными краями, так, чтобы образовался паз, в который затем нужно подавать расплавленный полипропилен через экструдер.
- При соединении листов методом спайки феном и склейки, края листов обрабатываются под 90° к плоскости листа.
Соблюдение условий гарантирует надёжное качество стыковочных сварных работ любым известным способом.
Источник: http://www.m-deer.ru/tehnologiya/svarka-listovogo-polipropilena.html
Сварка листового полипропилена — выбираем сварочный аппарат для сварки полимера
Полипропиленовые листы в настоящее время широко используются в производстве ёмкостей для предприятий электронной, химической, нефтехимической, радиотехнической, пищевой, металлургической и других промышленностей. Данный материал также используется при изготовлении бассейнов.
Нередко полипропилен сравнивают с «королём» пластмасс. Он не является наиболее популярным и востребованным полимером в данное время, однако по темпам роста производства он является бесспорным лидером.
Основные технические показатели полипропилена
Полипропилен, как синтетически неполярный термопластичный материал, получают в промышленности из макромолекул изотактического строения. При комнатной температуре материал не растворяется в органических жидкостях, однако он может растворяться в некоторых видах растворителей при нагревании до высоких температур.
Полипропилен устойчив к щелочам, кислотам, растворам солей и иным неорганическим агрессивным средам, имеет низкий уровень влагопоглощения, высокие показатели электроизоляционных свойств, хорошие механический свойства, повышенную жёсткость и высокий уровень ударопрочности.
Технология и общие принципы сварки полипропилена
Сварка листового полипропилена заключается в соединении деталей посредством нагрева материала без изменения его химического состава. Полимер соединяется между собой при создании вязко-текучего состояния при нагревании.
Сварка полипропилена своими руками может осуществляться при помощи специального пистолета с подачей горячего воздуха (фена). В конструкции такого устройства воздух нагревается равномерно, что образует хорошую среду для сварки полимерных деталей.
Экструдер, как аппарат для сварки полипропилена, также нередко используется в производстве. Данный процесс осуществляется в сухом тёплом помещении. Стыковые поверхности (края) свариваемых деталей обязательно должны быть зачищены мелкой шкуркой.
В экструдер поступает специальный присадочный пруток, который при разогревании сваривает нужные элементы. Время остывания такой сварки – ориентировочно 5-7 минут.
Механический сварочный аппарат для полипропилена применяется в основном в тех случаях, когда нужно приложить максимум усилий, чтобы края деталей соприкасались друг с другом. Не всегда с помощью подручных средств можно достичь этого.
Сварка полипропилена (видео находится на сайте) механическим путём подразумевает использование специальной опорной рамы с приборным блоком и гидроагрегатом. На данной раме с обеих сторон имеются специальные захваты, между которыми устанавливаются вкладыши для поддержания оптимального распределения давления на соединяемые элементы.
Сварочный аппарат для полипропилена имеет нагревательный элемент, который представляет собой диск со специальным покрытием. Внутри данного диска имеются нагревательные компоненты (ТЭНы), а снаружи – датчики контроля температуры и терморегуляторы.
Чем точнее показания термодатчика, который встроен в аппарат для сварки полипропилена, тем качественней сам аппарат. Наиболее качественными считаются агрегаты с электронными терморегуляторами (терморезисторами, которые способны измерять температуру близко около муфт и дорнов).
Сварка листового полипропилена в некоторых случаях подразумевает также использование разных вспомогательных материалов (калиброватель, фаскосниматель, ножницы, торцеватель, очищающая жидкость и др.).
Требования по технике безопасности для сварки полипропилена
Во время процесса сварки полимерных изделий должно соблюдаться несколько правил:
- рабочая температура – не ниже 5оС;
- сварка листового полипропилена может осуществлять не только в закрытом помещении, но и на открытом воздухе;
- при низких температурах (ниже 5оС) технологическая пауза может быть слишком приближена к нулю;
- перед выполнением сварочных работ обязательным условием является очистка сварочных насадок во избежание возгорания остатков пластмассы и выделения углекислого газа;
- если помещение, где осуществляется сварка, плохо вентилируется, возможно выделение и скопление вредных газов;
- для проведения сварочных работ с полипропиленом рекомендуется иметь специальные защитные рукавицы и очки (защитную маску для лица).
Для более подробного ознакомления с процессом соединения двух полимерных листовых изделий рекомендуется посмотреть сварка полипропилена видео.
Источник: http://swarka-rezka.ru/svarka-listovogo-polipropilena-vybi/
Сварка листов из полипропилена и ПНД
Их можно резать, фрезеровать, строгать или подвергать обработке на машинах таких же или подобных тем, которые используются для обработки дерева.
Соединять листы из полипропилена и листы ПНД можно механически при помощи заклепок или болтов. При этом необходимо помнить о склонности материала к линейному расширению.
Хотя такое соединение и является разъемным, оно не обладает водонепронецаемыми качествами, в некоторых случаях оно даже недостаточно прочно, поэтому считается не очень подходящим для соединения полипропиленовых деталей.
Данный материал обладает высокой химической стойкостью, поэтому может контактировать со многими растворимыми клеями. Однако применять клей при работе с ним можно, только проконсультировавшись со специалистами.
Поверхность полипропилена и полиэтилена обладает «жирными» свойствами, что делает невозможным адгезию к нему многих материалов.
Наиболее выгодным и надежным, а, следовательно, и наиболее часто используемым способом соединения деталей из полипропилена и полиэтилена является сваривание. В настоящее время известно три способа сварки.
- Самый качественный — полифузионная сварка. Концы соединяемых деталей при помощи специального прибора нагреваются в течение определенного периода времени до достижения нужной температуры, затем они с необходимым усилием прижимаются друг к другу. Возникший таким образом шов наиболее прочный из всех применяемых способов сварки (достигает примерно 80-90% прочности материала). Таким способом можно сваривать листы любой толщины.
- Шов, сделанный при помощи ручного экструдера, не настолько прочный. Сваривание термопластов экструдером осуществляется нанесением добавочного материала (присадочная полипропиленовая проволока ), предварительно расплавленного в винтовом роторе экструдера. Экструдер – ручной аппарат, поэтому невозможно обеспечить всегда одинаковое давление и скорость сварки, что в свою очередь сказывается на качестве шва. Таким способом можно сваривать листы большой толщины.
- Немного ниже прочностью обладает шов, полученный в результате сварки пистолетом с горячим воздухом ( феном ). В данном случае локально нагревается деталь, предназначенная для соединения, и добавочный материал. Конструкция такого прибора, дает возможность поддерживать одинаковую температуру нагреваемого воздуха, но температура свариваемых деталей зависит от скорости сварки. Применяя ручные аппараты для сварки, необходимо помнить, что при очень медленном сваривании деталей материал вокруг шва может перегреться, что приведет в дальнейшем к деградации материала, а следовательно и к снижению качества шва. То же произойдет, если материал будет недостаточно нагрет.Шов, полученный в процессе ручной сварки пистолетом с горячим воздухом, достаточно надежен. Таким способом рекомендуется соединять листы и детали, толщина которых не превышает 25мм.
При сваривании отдельных деталей необходимо следить за тем, чтобы соединяемые материалы принадлежали к одному классу. Добавляемый материал тоже должен совпадать по классу свариваемости с основными.
На нашем производстве мы выпускаем специальный полипропиленовый сварочный пруток (проволоку).
Сварочный пруток ООО “Русполимер” изготавливается из блок-сополимера полипропилена марки PPH 2464 (Германия) и идеально подходит для сваривания полипропиленовой продукции нашего производства.
Пруток различного сечения: круглый 4мм, треугольный 5мм и 7мм, овальный. Цвета: натуральный (белый), голубой, синий, серый, зеленый. Цены на сварочный пруток.
Полипропиленовые листы и листы ПНД используются для производства емкостей для предприятий нефтехимической, химической, электронной, радиотехнической, металлургической, пищевой промышленности. Мы также применяем листы из полипропилена при изготовлении бассейнов.
Коэффициент прочности полученного шва
Стыковая сварка. Листы из полипропилена.Полифузионная (стыковая) сварка
0,9
Сварка ручным экструдером. Листы из полипропиленаЭкструзионная сварка
0,8
Стыковая сварка. Листы из полипропилена.Пистолет с горячим воздухом
0,7
Источник: http://www.rospolymerplast.ru/polypropylene-scope/9-%D0%BB%D0%B8%D1%81%D1%82%D0%BE%D0%B2%D0%BE%D0%B9-%D0%BF%D0%BE%D0%BB%D0%B8%D0%BF%D1%80%D0%BE%D0%BF%D0%B8%D0%BB%D0%B5%D0%BD
Обработка и сварка листов из полипропилена и полиэтилена
При проведении работ по механической обработки и сварки полиэтиленовых и полипропиленовых листов следует учитывать их особые свойства.
Одной из основных особенностей листов из полипропилена (PP) и полиэтилена (PE) – относительно низкая температура плавления материала, в связи с чем при использовании инструмента необходимо избегать повышенного трения сверла, фрезы или пилы с обрабатываемой поверхностью полимерного материала.
Высокая теплота трения может вызвать оплавление обрабатываемой поверхности полипропиленового или полиэтиленового листа. Чтобы этого избежать, при механической обработке полимерных листов необходимо обеспечить максимальный отвод тепла, т.е. уменьшить тепловую нагрузку на материал.
При механической обработке листов из полипропилена и полиэтилена необходимо соблюдать следующие правила:
- кромки режущего инструмента должны быть хорошо заточены
- режущий инструмент должен быть установлен так, чтобы режущая кромка только касалась полимера
- следует обеспечить хорошее удаление стружки с режущего инструмента
- в случае большого тепловыделения должно быть обеспечено охлаждение
Соединять полимерные листы можно как механически (при помощи заклепок, болтов и т.п.), так и методом сварки.
Неподходящим методом соединения считается при помощи клея – склеивание.Данный материал обладает высокой химической стойкостью, поэтому может контактировать со многими растворимыми клеями. Однако применять клей при работе с ним можно, только проконсультировавшись со специалистами.
Наиболее выгодным и надежным способом соединения листов из полипропилена и полиэтилена является сваривание.
Сварка листового полипропилена и полиэтилена осуществляется тремя способами: полифузионная сварка, сваривание экструдером и пистолетом с горячим воздухом.
Первый способ является самым качественным. Соединяемые концы нагреваются специальным прибором до достижения нужной температуры и с усилием прижимаются друг к другу. Такой шов достигает 80-90% прочности материала. Таким способом соединяют листы любой толщины.
Шов термопластов при помощи экструдера осуществляется нанесением вспомогательного материала (сварочной проволки), расплавленного предварительно в винтовом роторе экструдера.
Так как экструдер – ручной аппарат, одинаковую скорость варки и одинаковое давление обеспечить тяжело, что сказывается на качестве шва.
Сварка листовых полимерных материалов экструдером применяется в случае большой толщины листов
Сварка пистолетом с горячим воздухом дает шов самого плохого качества. Конструкция прибора не дает одинаковой температуры нагреваемого воздуха.
Важный момент: необходимо следить за тем, чтобы свариваемые детали были изготовлены из материала одного класса. Добавляемый материал тоже должен совпадать по классу свариваемости с основными.
При сварки вторым и третьим способом применяется специальный полипропиленовый или полиэтиленовый сварочный пруток (проволка).
Коэффициент прочности полученного шва
Полифузионная (стыковая) сварка (сварка на стыковой машине) | Экструзионная сварка (сварка ручным экструдером) | Пистолет с горячим воздухом (сварка ручным феном) |
0,9 | 0,8 | 0,7 |
Источник: http://smp-agru.ru/o-materialah/obrabotka-svarka-pp-pe
Проектирование и выбор трубопроводов. Оптимальный диаметр трубопровода
Трубопроводы для транспортировки различных жидкостей являются неотъемлемой частью агрегатов и установок, реализующих рабочие процессы, относящиеся к различным областям применения. При выборе труб и конфигураций трубопроводов большое значение имеет стоимость самих труб и стоимость арматуры. Окончательная стоимость передачи среды по трубопроводу во многом определяется размером труб (диаметром и длиной).Для расчета этих значений используются специально разработанные формулы, специфичные для определенных типов операций.
Труба — это полый цилиндр из металла, дерева или другого материала, используемый для транспортировки жидких, газообразных и гранулированных сред. Переносимая среда может включать воду, природный газ, пар, нефтепродукты и т. Д. Трубы используются повсеместно, начиная с различных отраслей промышленности и заканчивая домашним хозяйством.
Различные материалы, такие как сталь, чугун, медь, цемент, пластик, например АБС-пластик, поливинилхлорид, хлорированный поливинилхлорид, полибутилен, полиэтилен и т. Д., можно использовать при производстве труб.
Диаметр трубы (внешний, внутренний и т. Д.) И толщина стенки, измеряемая в миллиметрах или дюймах, являются основными размерами трубы. Также используется такое значение, как номинальный диаметр или условное отверстие — номинальное значение внутреннего диаметра трубы, также измеряемое в миллиметрах (обозначается Ду ) или дюймах (обозначается DN). Значения номинального диаметра стандартизованы, что является основным критерием при выборе трубы и соединительной арматуры.
Соответствие номинального диаметра в [мм] и [дюймах] указано ниже.
По ряду причин, указанных ниже, трубы с круглым (круглым) поперечным сечением являются предпочтительным вариантом по сравнению с другими геометрическими сечениями:
- Circle имеет минимальное отношение периметра к площади; применительно к трубам это означает, что при одинаковой пропускной способности расход материала для труб круглой формы будет минимальным по сравнению с трубами другой формы. Это также подразумевает минимально возможные затраты на изоляционные и защитные покрытия;
- Круглое поперечное сечение — наиболее выгодный вариант для перемещения жидких или газообразных сред с гидродинамической точки зрения.Кроме того, благодаря минимально возможной внутренней площади трубы на единицу ее длины трение между перекачиваемой жидкостью и трубой сводится к минимуму.
- Круглая форма наиболее устойчива к внутреннему и внешнему давлению;
- Процесс производства круглых труб достаточно прост и удобен в реализации.
Трубы могут сильно различаться по диаметру и конфигурации в зависимости от назначения и области применения. Поскольку магистральные трубопроводы для перекачки воды или нефтепродуктов могут достигать почти полуметра в диаметре при довольно простой конфигурации, а змеевики, также выполненные в виде трубы малого диаметра, имеют сложную форму с большим количеством витков.
Невозможно представить любой сектор промышленности без трубопроводной сети. Расчет любой трубопроводной сети включает в себя выбор материалов труб, разработку ведомости материалов, которая включает данные о толщине, размере, маршруте и т.д. трубы. Сырье, промежуточный продукт и / или готовый продукт проходят различные стадии производства, перемещаясь между различными аппаратами и агрегатами. , которые соединяются трубопроводами и арматурой. Правильный расчет, выбор и установка системы трубопроводов необходимы для надежного выполнения всего технологического процесса и обеспечения безопасной передачи рабочих сред, а также для герметизации системы и предотвращения утечки переносимых веществ в атмосферу.
Не существует универсальной формулы или правила для выбора трубопровода для любого возможного применения и рабочей среды. Каждая область применения трубопровода включает ряд факторов, которые следует принимать во внимание и которые могут оказать значительное влияние на требования к трубопроводу. Например, при работе с жидким навозом крупногабаритный трубопровод не только увеличит стоимость установки, но и создаст трудности в эксплуатации.
Обычно трубы выбираются после оптимизации материальных затрат и эксплуатационных затрат.Чем больше диаметр трубопровода, т.е. чем больше первоначальные вложения, тем меньше перепад давления и, соответственно, меньше эксплуатационные расходы. И наоборот, небольшой размер трубопроводов позволит снизить начальную стоимость труб и арматуры; однако повышенная скорость повлечет за собой повышенные потери и приведет к затратам дополнительной энергии на прокачку среды. Значения скорости, фиксированные для различных приложений, основаны на оптимальных расчетных условиях. Эти ставки с учетом области применения используются при расчетах размеров трубопроводов.
Трубопроводы — PetroWiki
Трубопроводная система, которая передает добычу отдельной скважины или группу скважин от центрального объекта к центральной системе или местоположению терминала, представляет собой сборный трубопровод. Как правило, система сборных трубопроводов представляет собой серию трубопроводов, которые текут от скважинных производственных мощностей на добывающем месторождении к сборному «магистральному» трубопроводу.
Системы сбора
Системы сбораобычно делятся на одну из четырех категорий:
- Одноствольные системы с «боковыми» линиями от каждой скважины производственного объекта.
- Петельные системы, в которых основная леска имеет форму петли вокруг поля.
- Многоствольная система, в которой несколько основных линий отходят от центральной точки.
- Комбинации категорий с 1 по 3.
Для выбора наиболее желательной компоновки требуется экономическое исследование, которое учитывает множество переменных, таких как:
- Тип резервуара
- Форма резервуара
- Способ использования земли над водохранилищем
- Имеющийся и допустимый расход
- Давление и температура подачи и закрытия
- Климат и рельеф местности
- Основной пункт назначения нефти или газа
Системы сбора обычно требуют труб малого диаметра, которые проходят на относительно короткие расстояния.Отводные боковые линии обычно имеют длину от 2 до 8 дюймов. Системы сбора должны быть спроектированы таким образом, чтобы минимизировать падение давления без использования труб большого диаметра или без использования механического оборудования для повышения давления (насосы для жидкости и компрессоры для газа) для перемещения объема жидкости. Для линий сбора природного газа можно использовать уравнение Веймута для определения размера трубы.
Магистральные трубопроводы
Магистральные трубопроводы «по пересеченной местности» будут собирать продукт из многих источников «поставки» и «доставлять» его одному или нескольким конечным потребителям.Есть три основные категории магистральных трубопроводов:
- Природный газ — только природный газ
- Товар
- Относить ряд переработанных или очищенных нефтепродуктов, таких как:
- Переработанный сжиженный природный газ — бутан и пропан
- Бензин
- Дизель
- Топливные нефтепродукты
Транспортировать нерафинированную сырую нефть с участков добычи на большие складские площади или непосредственно на нефтеперерабатывающие заводы
Для магистральных трубопроводов обычно требуются трубы гораздо большего размера, чем для систем сбора.Системы передачи обычно рассчитаны на большие расстояния и потребуют оборудования для повышения давления на маршруте.
Наземные трубопроводы
При проектировании, строительстве и эксплуатации трубопроводной системы необходимо учитывать множество факторов. После определения основного внутреннего диаметра трубы с использованием соответствующей формулы расхода необходимо рассмотреть другие важные проектные параметры.
Для приложений в США трубопроводы сбора, передачи и распределения регулируются постановлениями и законами, которые на национальном уровне находятся в ведении США.S. Департамент транспорта (DOT). Правила содержатся в Сводах федеральных правил (CFR), раздел 49:
- Часть 190 [1] Правоприменительные процедуры
- Части 191 [2] и 192 [3] Трубопроводы природного газа
- Часть 193 [4] Трубопроводы для сжиженного природного газа
- Часть 194 [5] Планы реагирования на нефтепровод
- Part 195 [6] Трубопроводы для опасных жидкостей (например, сырой нефти и нефтепродуктов)
- Часть 198 [7] Государственные гранты
- Part 199 [8] Тестирование на наркотики
Правила включают отраслевые кодексы, руководства и стандарты, включая ANSI / ASME B31.4, B31.8 и другие.
На международном уровне многие страны приняли правила США, а также отраслевые кодексы, руководства и стандарты. В некоторых странах действуют разные требования, законы и постановления, и с каждой из них следует проконсультироваться перед проектированием и строительством трубопровода. По большей части эти правила аналогичны правилам в США, и, следовательно, следующие ниже комментарии, основанные на стандартах США, в целом справедливы и для других стран. Даже трубопроводы, на которые не распространяются специальные правила, следует проектировать, строить и эксплуатировать в соответствии с отраслевыми нормами, правилами и стандартами, поскольку они основаны на надежной инженерии и опыте эксплуатации.
Выбор трубы и толщина стенки
Тип трубы и толщина стенки должны определяться для каждого случая применения. Следуя проектным требованиям Части 192 для природного газа, Части 193 для сжиженного природного газа (СПГ) и Части 195 для трубопроводов сырой нефти и нефтепродуктов, материалы труб и толщину стенок могут быть определены с использованием соответствующей формулы. Как описано на странице, посвященной расчетам падения давления в трубопроводах и трубопроводных системах, толщина стенки будет определяться:
- Давление рабочее (максимальное и нормальное)
- Рабочая температура
- Прочие расчетные факторы (в зависимости от типа трубопровода и применимых нормативов)
- Материал трубы
ПВХ, стекловолокно, полипропилен и другие материалы могут использоваться в системах низкого давления и коммунальных услугах.Нормы ANSI / ASME B31.4, B31.8 и DOT допускают использование альтернативных материалов в очень ограниченных областях применения. Тем не менее, стальные трубы потребуются в большинстве случаев добычи нефти и газа и трубопроводов. ANSE / ASME A53 [9] и A106 [10] и API 5L [11] бесшовные стальные трубы, сваренные под флюсом и сваренные под флюсом стальные трубы (SAW) коммерчески доступны и чаще всего используются в трубопроводных системах. Бесшовные трубы редко используются в трубопроводах из-за более высокой стоимости единицы и ограниченной доступности.С точки зрения конструкции и нормативных требований, трубы, изготовленные с использованием швов ВПВ и ПАВ, эквивалентны бесшовным трубам и являются менее дорогостоящими. Примечание: это неверно для трубопроводных систем, разработанных в соответствии со стандартом ANSI / ASME B31.3. [12]
Обычно для трубопроводов высокого давления выбираются трубы более высокого качества (например, API 5L, классы X42, X52, X60 и X65), поскольку можно использовать трубы с гораздо более тонкими стенками, что значительно снижает затраты на трубы. Также достигается экономия затрат на строительство, поскольку сокращается время сварки и снижаются затраты на транспортировку / погрузочно-разгрузочные работы.
Выбор материала
Трубные фитинги, фланцы и клапаны должны соответствовать спецификации и классу давления трубы, выбранной для трубопроводов. Материалы для трубопроводов обычно соответствуют отраслевым нормам и стандартам, включая:
- Стандарт ANSI / ASME B16.5 [13]
- Стандарт ANSI / ASME B16.9 [14]
- Стандарт ANSI / ASME B31.4 [15]
- Стандарт ANSI / ASME A105 [16]
- Стандарт ANSI / ASME A106 [10]
- Стандарт ANSI / ASTM A234 [17]
- Стандарт ANSI / ASTM A420 [18]
- Стандарт ANSI / ASTM A694 [19]
- Стандарт API 6D [20]
- Стандарт API 6H [21]
- MSS Spec.44 [22]
- MSS Spec. 75 [23]
Фитинги могут быть адаптированы к трубам более высокого класса API 5L, класса X. Подробная информация о материалах обсуждается на странице по номинальным значениям для клапанов, фитингов и фланцевых давлений.
Выбор маршрута и обследование
Выбор маршрута очень важен для успешного проектирования трубопровода. Это требует внимательного изучения:
- Местность
- Естественные препятствия, такие как
- Искусственные препятствия, такие как
- Шоссе
- Дороги
- Железные дороги
- Здания
- Плотность населения
Некоторые полезные средства в процессе маршрутизации включают:
- Топографические карты
- Аэрофотосъемка
- Спутниковый снимок
- Карты собственности
- Физический осмотр
Конструктивность является важным фактором при выборе маршрута.Как правило, минимальная рабочая полоса отвода трубопровода (ROW) для 2-дюймовой. Ширина трубопровода составляет от 35 до 40 футов, а рабочая зона должна быть достаточно ровной. Для трубы большего диаметра требуется более широкая полоса отвода, потому что для большей трубы требуется более крупное оборудование для обработки труб (боковые стрелы), более широкие канавы и более широкие отвалы. Строительные рабочие полосы шириной от 80 до 100 футов являются типичными для ширины полосы от 4 до 12 дюймов. Ширина полосы отвода трубопровода и конструкции более 200 футов является обычной для труб диаметром от 30 до 36 дюймов. Предлагаемый маршрут должен быть исследован для:
- Определить точную длину предполагаемого трубопровода
- Определить физический рельеф
- Обнаружение естественных и искусственных препятствий
- Проверка границ собственности
После подтверждения работоспособного маршрута начинается получение разрешений на полосу отвода земли и регулирующих органов.
Полоса отвода (ROW)
Приобретение частных и государственных полос землеотвода и соответствующих государственных разрешений является основным компонентом процесса строительства трубопровода. В аренде нефти и газа часто есть положения, позволяющие добытчику устанавливать скважины, выкидные трубопроводы, производственные мощности, а также перерабатывающие и складские помещения без необходимости приобретения дополнительных участков землеотвода или объектов собственности. Однако производители не имеют права скрещивать:
- Дороги общего пользования
- Автомагистрали, железные дороги
- Реки
- Ручьи / ручьи юрисдикции
- Болота
- Существующие ранее сервитуты или полосы отвода
Для трубопроводов сбора и передачи необходимо приобрести полосу отвода или сервитут, который требуется для системы трубопроводов.Как правило, приобретаются сервитуты, которые предоставляют владельцу трубопровода право эксплуатировать и обслуживать трубопровод и сопутствующие объекты. В некоторых случаях земля отвода может быть приобретена «за плату», если сервитут приобретается в собственность.
Разрешения и особые условия
Разрешения необходимы для прокладки трубопроводов через дороги общего пользования, дороги, улицы и любые другие виды общественного транспорта. Разрешения должны быть получены от федерального, государственного или местного органа власти, обладающего юрисдикционными полномочиями.Специальные сервитуты или разрешения также должны быть получены от железных дорог и других трубопроводов.
Существуют специальные требования к конструкции труб, проложенных через шоссе, дороги, улицы и железные дороги, которые предусмотрены в ANSI B31.4, B31.8 и правилах DOT. Трубы с более толстыми стенками (требуются из-за более низких расчетных факторов снижения номинальных характеристик), обсадные трубы, гидростатические и неразрушающие испытания и другие особые требования оговариваются в действующих нормах, правилах и отраслевых стандартах.
Особые требования к установке являются обычными, так как небольшое количество автомагистралей, дорог общего пользования или улиц, если таковые имеются, можно вырубить открытым способом и окопать. Железные дороги не допускают установку традиционных траншей в карьерах. Трубопровод должен устанавливаться методами мокрого или сухого бурения, туннелирования или горизонтально-направленного бурения (ГНБ). Эти методы описаны позже.
Экологические требования имеют большое влияние на трубопроводную промышленность. Трубопроводы не могут быть построены на определенных заболоченных территориях, болотах, болотах, реках, ручьях или ручьях, где установка и эксплуатация трубопровода может повлиять на чувствительную экологию и окружающую среду.В США Инженерный корпус армии США (COE) имеет основную юрисдикцию над этими территориями, а другие федеральные агентства, такие как Служба охраны рыбных ресурсов и дикой природы США, имеют вторичную юрисдикцию. Во всех штатах теперь есть природоохранные или аналогичные агентства, которые также обладают юрисдикцией во многих из этих областей. На международном уровне во многих странах действуют законы и постановления, защищающие природные ресурсы. Перед окончательным выбором маршрута необходимо изучить несколько вопросов, включая, помимо прочего:
- Исторически значимые памятники
- Археологические памятники
- Вымирающие виды
Для работы на чувствительных территориях и вокруг них необходимо получать специальные разрешения.В США разрешения от COE требуются для пересечения рек, судоходных ручьев / ручьев, водно-болотных угодий и других регулируемых вод.
Нормативы и требования по охране окружающей среды и природных ресурсов применяются не только к регулируемым трубопроводам сбора, передачи и распределения, но также применяются к выкидным трубопроводам и производственным объектам, построенным в рамках договоров аренды нефти и газа. Потенциальное влияние этих проблем на стоимость должно быть серьезно рассмотрено в процессе проектирования трубопровода.
Защита от коррозии
Стальные трубы и трубопроводы должны быть защищены от воздействия внешней и внутренней коррозии.Материалы трубопроводов из цветных металлов, такие как стекловолокно, ПВХ и полипропилен, не подвергаются таким же коррозионным воздействиям и требуют небольшого внимания. Промышленные нормы и стандарты, а также правила DOT требуют, чтобы трубопроводы, вспомогательное оборудование и оборудование были защищены от воздействия коррозии. NACE имеет стандарты, предписывающие защиту от коррозии, необходимую для трубопроводов — стандарт NACE MR01-76, [24], RP200, [25] и RP572. [26]
Внутренняя коррозия
Внутренняя коррозия может быть вызвана присутствием CO 2 , воды, H 2 S, хлоридов (соленая вода), бактерий, жидкостей заканчивания заканчивания или других веществ в добываемых углеводородах.Когда CO 2 или H 2 S смешивается с кислородом и / или водой, образуются кислоты, которые разрушают сталь. Когда CO 2 или H 2 S смешивается с кислородом и / или соленой водой, возникает сильная коррозия. Определенные типы бактерий, часто встречающиеся в продуктивных пластах, также могут атаковать и разрушить сталь. Любой из внутренних коррозионных агентов по отдельности или в комбинации может вызвать утечки и серьезные выбросы.
Потенциальные коррозионные вещества обычно можно определить по химическому анализу добытых углеводородов.В случаях, когда присутствуют высокие концентрации CO 2 , H 2 S или других высококоррозионных химикатов, в конструкцию трубы может быть добавлена дополнительная толщина стенки трубы, чтобы учесть потенциальные коррозионные эффекты. Обычно это не рекомендуется, поскольку коррозия может быть локализована, а ее скорость трудно предсказать. В большинстве случаев удаления кислорода и воды из жидкости достаточно для борьбы с возможной коррозией. Если это нецелесообразно, используются химические вещества, ингибирующие коррозию, внутренние покрытия и коррозионно-стойкие материалы.
Внутренняя коррозия также может быть вызвана эрозией или износом. Чрезмерно высокие скорости в жидкостных и многофазных жидкостных системах могут вызвать эрозию или износ внутренней стенки трубы, а также фитингов и клапанов. Условия, вызывающие механическую эрозию, можно смягчить за счет правильного выбора размера и конструкции трубы.
Коррозионное воздействие углеводородного флюида может со временем измениться по мере изменения химического состава добываемого флюида или развития бактерий, которых раньше не было. Если после начала эксплуатации образуются неизвестные коррозионные вещества, лучшим решением может быть химическая обработка.
Внешняя коррозия — подземные трубопроводы
Внешняя коррозия поражает подземные и наземные трубы. Закопанная труба подвергается катодным и гальваническим воздействиям. Надземная труба подвержена атмосферной коррозии и гальваническому воздействию.
Катодное воздействие происходит, когда стальная труба проложена под землей. Железо и другие материалы, например, почвы, обладают небольшими электрическими потенциалами. В естественном процессе преобразования металлов обратно в их элементарное или естественное состояние имеет место электролитическая проводимость.Незащищенная стальная труба становится анодом (положительно заряженным) и переносит материал посредством электронов на катодный (отрицательно заряженный) материал, которым является почва или окружающая среда. Металл трубы буквально уносится за счет электрического тока между анодом и катодом. Вода, содержащаяся в почве и других средах, служит электролитом, способствующим переносу электронов.
Для противодействия катодному воздействию труба покрывается антикоррозийными материалами, а на трубопровод устанавливаются системы катодной защиты.Покрытие должно обеспечивать эффективную «изоляцию» от окружающей среды, но должно быть достаточно прочным, чтобы выдерживать рабочие температуры, быть устойчивым к почве и выдерживать физические нагрузки.
Существует ряд экономичных и коммерчески доступных систем покрытия, в том числе:
- Экструдированные системы (полиэтилен или полипропилен поверх асфальтовой мастики или бутилового клея)
- Ленточные покрытия (полиэтилен, поливинил или каменноугольная смола поверх бутилмастичного клея)
- Эпоксидная смола Fusion Bonded (тонкая пленка)
- Каменноугольное эпоксидное покрытие
Эпоксидное покрытие, связанное плавлением (FBE), является наиболее популярными системами покрытий, поскольку они:
- Отличные изоляторы
- Устойчивы к углеводородам, кислотам и щелочам
- Не подвержены влиянию температуры
- Не требует грунтовки
- Может наноситься на готовые сварные швы (монтажные стыки).
Системы ленточных покрытий и системы каменноугольной эмали становятся все менее популярными.Ленточное покрытие сложно наносить, и особенно трудно его использовать на трубах большого диаметра. Ряд систем с ленточным покрытием испытали отказы в течение относительно коротких промежутков времени из-за неправильного применения. Каменноугольная эпоксидная смола становится все менее востребованной из-за некоторых проблем со здоровьем и окружающей средой, возникающих во время ее нанесения.
В дополнение к антикоррозийным системам покрытия труб, к трубопроводу добавляются системы катодной защиты для защиты трубы в местах разрыва системы покрытия.В системе катодной защиты используется либо подаваемый ток, либо расходуемый анод для защиты подземной трубы. Система катодной защиты изменяет процесс электролитической проводимости и использует приложенный электрический ток или другой металлический предмет (расходуемый анод), чтобы сделать трубу катодом. Проще говоря, приложенный ток меняет естественный поток электронов из трубы в окружающую среду, чтобы предотвратить потерю ионов металлов. Жертвенный анод, сделанный из металла с более высоким потенциалом, такого как магний, находится в контакте с трубой и окружающей средой.Анод отдает свои электроны (металл) вместо стальной трубы.
Системы с протекторным анодом проще и дешевле, чем системы с подаваемым током. В наземных трубопроводах обычно используется магний, а в морских — цинковые или алюминиевые аноды. Системы с наложенным током намного сложнее и требуют внешних источников питания и инверторов переменного / постоянного тока или выпрямителей для подачи тока в трубу.
Проектирование систем катодной защиты требует специальной подготовки и может быть очень сложным.Необходимо провести подробные исследования почвы для определения электрического потенциала и удельного сопротивления почвы или окружающей среды, потенциалов между трубами и почвой и ряда других критериев. Дизайн системы должен выполняться специалистом по катодной защите.
Гальваническая коррозия
Еще одним важным аспектом антикоррозионной системы является предотвращение гальванической коррозии. Гальваническая коррозия вызывается границей раздела разнородных металлов с разными электролитическими потенциалами. Разные металлы будут приобретать или терять электроны друг от друга или друг от друга, в результате один из металлов эффективно утекает и теряет материал.Стальная труба, которая претерпевает резкие изменения в среде, будет вести себя как разнородные металлы и вызывать гальваническое воздействие. Труба, переходящая из-под земли в надземную, может испытывать гальваническую коррозию. Соединение материалов, таких как углеродистая сталь с нержавеющей сталью, вызовет коррозию углеродистой стали.
Изоляционные фланцы или соединения могут использоваться для противодействия гальваническим воздействиям. Следует приложить усилия, чтобы избежать взаимодействия разнородных материалов в конструкции системы.
Атмосферная коррозия
Эффекты атмосферной коррозии очевидны. Голая сталь быстро подвергается коррозии при воздействии:
- Влажность
- Соль
- Химические вещества (загрязнение)
- Тепло
- Холодный
- Воздух (кислород)
Трубопроводы и оборудование, ежедневно подвергаемые атмосферным воздействиям, должны быть защищены антикоррозийными покрытиями. Хорошие системы лакокрасочного покрытия, такие как эпоксидные смолы, и регулярное техническое обслуживание обычно обеспечивают надлежащую защиту надземных сооружений.
Объектам, подвергающимся тяжелой эксплуатации, например, на море, могут потребоваться более обширные системы защиты. Существует ряд альтернативных систем покрытия, которые обсуждаются в разделе о морских трубопроводах.
Сварка и соединение труб
Способы, используемые для соединения стыков или сегментов труб, очень важны и имеют решающее значение для конструкции трубопровода. Стандарты ANSI / ASME B31.3, [12] B31.4, [14] и B31.8, [27] , а также правила DOT определяют методы сварки и соединения труб.Для каждого типа материала трубы используются методы соединения или соединения, предназначенные для обеспечения того, чтобы соединение было таким же прочным, как соединение трубы, или прочнее. Стекловолоконные, ПВХ и другие типы пластиковых труб могут иметь раструбные и гладкие соединения, которые являются механическими, резьбовыми или клееными. Полипропиленовые и полиэтиленовые трубы, которые часто используются в системах с углеводородами очень низкого давления, используют сварное соединение плавлением. Однако для большинства трубопроводов углеводородов требуются стальные трубы.
Для большинства стальных трубопроводов сварка является предпочтительным методом соединения труб.Стандарт API 1104 [28] и ASME Sec. IX норм по котлам и сосудам высокого давления определяют требования к сварке стальных труб. Ручные и автоматические сварочные процессы используются на трубопроводах как на суше, так и на море. Экранированная дуговая сварка металлом (SMAW), или сварка «палкой», является наиболее распространенным ручным процессом, применяемым на трубопроводах из углеродистой стали, но разработка и использование труб из углеродистой стали более высокого качества (например, API 5L X65 и X70) потребовали разработки процессов сварки и металлургии, совместимых с высокоуглеродистыми сплавами.Для нержавеющих сталей и других сплавов могут потребоваться специальные сварочные процессы.
Разработка надежных и экономичных автоматических сварочных аппаратов также оказала значительное влияние на трубопроводную промышленность. Автоматические сварочные аппараты могут быть внешними или внутренними для труб большого диаметра.
Необходимо спроектировать каждое сварное соединение и разработать спецификацию процедуры сварки (WPS) для трубы. Каждый WPS определяет:
- Тип свариваемой трубы (спецификация, марка и т. Д.)
- Тип и спецификация трубного соединения [например, указать фаску (и), угол, уступ и расстояние / выравнивание]
- Толщина материала или диапазон применимых толщин
- Тип и размер сварочных стержней
- Положение и направление сварного шва
- Напряжение / сила тока
- Предварительный / последующий нагрев
- Снятие напряжения
WPS должно быть физически подтверждено путем фактической сварки испытательного «ниппеля» и проведения разрушающих испытаний в соответствии с требованиями API и / или ASME.Как только спецификация подтверждена, записывается квалификационная запись процедуры (PQR), подтверждающая WPS. Сварщики должны иметь квалификацию для выполнения сварных швов в соответствии со стандартом API 1104 [28] или ASME Sec. IX. [29] Каждый сварщик выполнит пробную сварку трубы с помощью WPS и будет квалифицирован в соответствии с процедурой. Стандарт API 1104, [28] ASME Sec. IX, [29] и DOT определяют и определяют квалификацию сварщика.
Существуют и другие приемлемые методы соединения труб.Стальная труба может иметь резьбу и соединение или иметь различные механические соединения. Применение стальных труб с резьбой обычно ограничивается небольшими диаметрами, 4 дюйма и меньше. Трубы большего диаметра сложно правильно соединить, а трубопроводы с резьбой большого диаметра не всегда доступны. Стеклопластиковые трубы, используемые в промышленности, могут иметь резьбу или соединения, сваренные растворителем. ПВХ может иметь соединения, выполненные сваркой растворителем, или могут иметь раструбные механические соединения. Отраслевые нормы и стандарты, а также правила DOT признают другие методы соединения, но ограничивают использование труб, кроме стальных.
Процесс строительства трубопровода
Далее описывается традиционный процесс строительства наземного трубопровода.
Очистка / подготовка полосы отвода
Перед началом строительных работ должны быть завершены любые отложения, контроль эрозии, строительные ограждения и другие подготовительные работы. Вся растительность очищена и выкорчевана, верхний слой почвы удален (при необходимости), а рабочая полоса отвода профилирована.
Трубопровод
После подготовки полосы отвода труба загружается на грузовики-платформы.Перед разгрузкой салазки трубопровода (обычно бревна лиственных пород размером 4 дюйма × 6 дюймов × 4 фута) сбрасываются вдоль полосы отвода и размещаются под трубой. Грузовики едут по полосе землеотвода, а труба разгружается, стык за стыком / конец в конец, с помощью боковых стрел или кранов.
Углубление
Канава выкапывается вдоль осевой линии трубопровода с использованием землеройных машин, экскаваторов, экскаваторов-погрузчиков и другого землеройного оборудования. Трубопроводы обычно заглубляются с минимальным покрытием 36 дюймов (нормативные требования DOT).В уплотненных породах минимальное покрытие колеблется от 18 до 24 дюймов. Покрытие для участков класса 1 составляет 18 дюймов; покрытие для классов 2–4 (железные дороги, автомагистрали и дороги общего пользования) составляет 24 дюйма.
Сварка
Труба, натянутая вдоль полосы отвода, сваривается прогрессивным способом. Боковые балки будут работать вдоль полосы отвода, поднимая трубу, в то время как бригада выравнивает трубу для подготовки к сварному шву «стрингера». Как правило, сварщик или сварщики (в зависимости от размера трубы) будут работать с бригадой по выравниванию, выравнивать трубу и наносить первоначальный сварной валик.Группа сварщиков будет следовать сразу за сварщиком (-ами) стрингера и наложить «горячий проход» валик или герметичный шов. Следующие сварщики будут выполнять последние проходы сварочного материала.
Монтажные стыки и антикоррозийное покрытие и контроль
Когда сварка завершена, бригады монтажных соединений очищают области сварных швов и короткие прилегающие стальные поверхности с обеих сторон сварного шва и наносят покрытие монтажных швов. Любой неразрушающий контроль сварных швов, такой как рентгеновский контроль, будет завершен до нанесения покрытия на стыки.После завершения нанесения покрытия на полевые стыки труба проверяется с помощью оборудования для обнаружения «выходных дней» (низковольтное оборудование постоянного тока, которое показывает, где покрытие трубы и полевые стыки имеют отказы или разрывы), и устраняются аномалии и нарушения в покрытии.
Трубка опускная
По завершении нанесения полевого стыка и проверки покрытия трубу опускают и укладывают в канаву с помощью боковых стрел или другого спускового оборудования.
Засыпка, очистка и восстановление
После завершения спуска трубы траншея засыпается, а полоса отвода очищается и протравливается.Полоса отвода тщательно заделана, трава и растительность заново засажены, и все специальные меры по восстановлению или очистке выполнены.
Переходы автомобильные, автомобильные, железнодорожные и речные
Автомагистраль, дорожные переходы редко устанавливаются традиционными методами открытой траншеи. Как правило, эти переходы устанавливаются методом мокрого или сухого прохода. Бурение выполняется с помощью буровых установок, которые похожи на очень маленькие буровые установки, которые уложены горизонтально и помещены в предварительно выкопанные ямы уровня бурения.”Буровая установка сверлит под зоной пересечения, и труба или обсадная труба устанавливаются. Мокрый метод использует буровую установку и обеспечивает циркуляцию воды или бурового раствора через буровую штангу, чтобы открыть небольшое пилотное отверстие, затем протягивает режущую головку размером с трубу или обсадную колонну обратно к буровой установке, вырезает отверстие, достаточно большое для размещения трубы или обсадной колонны. . Метод «сухого» ствола аналогичен, но обсадная труба или несущая труба оснащена режущей головкой и используется для просверливания отверстия и остается на месте после завершения бурения.Отверстие просверливается всухую и не использует воду или жидкость для облегчения операции бурения. Железнодорожные переезды никогда не бывают открытыми и всегда надоедают. Как правило, железные дороги требуют, чтобы отверстия выполнялись методом сухого сверления. И мокрый, и сухой методы ствола ограничены расстоянием, на котором они эффективны и практичны.
Переходы через реки в настоящее время обычно устанавливаются методом ГНБ. Инженерный корпус США может разрешить рытье рек открытым способом, но установка ГНБ стала более экономичной.В методе ГНБ используется буровая установка с компьютерным управлением, которая управляет направленным пилотным буровым станком с мокрым стволом, которым можно точно управлять с буровой установки. Наклонно-направленное бурение может пробурить пилотную скважину на расстояние до мили или более и пробить отверстие до буровой установки, достаточно большое для установки несущей трубы. «Бурильная» колонна или тяговая секция трубы свариваются вместе со стороны выхода бурового снаряда, проходят предварительные испытания, а затем отводятся обратно на сторону буровой установки вслед за расширителем.
Метод HDD может использоваться для устройства длинных автомагистралей и автомобильных переходов, таких как межгосударственные автомагистрали и автострады.Методы мокрого и сухого ствола ограничены длиной в несколько сотен футов, что требует многократного просверливания, чтобы пересечь расстояния, обычно требуемые для пересечения межгосударственных автомагистралей и автострад.
Галстуки
Бригада, или бригады, как правило, выполняет все врезки трубопроводов вдоль строительного коридора. Бригада по монтажу выполняет окончательную сварку в местах соединения, где прогрессивная сварка не может выполнить окончательные швы. Врезки производятся в таких местах, как шоссе, дороги, железные дороги, пересечения рек и ручьев, а также на участках сопротивления и т. Д.Бригада по монтажу обычно имеет оборудование для земляных работ и обработки труб, а также специальных сварщиков.
Конструктивные особенности
Рис. 1 от до Рис. 11 иллюстрируют типичные детали конструкции. Администратор по охране труда. (OSHA) является агентством DOT и предоставляет дополнительные федеральные правила и нормы, касающиеся проектирования, строительства и испытаний трубопроводов. [30] , [31]
Фиг.1 — Типичная полоса отвода через обсаженный железнодорожный переезд (любезно предоставлено AMEC Paragon).
Рис. 2 — Типичная полоса отвода с обсаженной магистралью / пересечением дорог (любезно предоставлено AMEC Paragon).
Рис. 3 — Типовые детали уплотнения корпуса, изолятора и вентиляционного трубопровода для Рис. 1 и Рис. 2 (любезно предоставлено AMEC Paragon).
Рис. 4 — Типичные детали закладки трубопровода (любезно предоставлено AMEC Paragon).
Рис. 5 — Типичные детали минимального зазора между несколькими пересечениями трубопровода (любезно предоставлено AMEC Paragon).
Рис. 6 — Типичные детали покрытия трубопровода в переходной зоне, чуть ниже и чуть выше отметок (любезно предоставлено AMEC Paragon).
Рис. 7 — Типичная полоса отвода дороги / пересечения дороги без покрытия (любезно предоставлено AMEC Paragon).
Рис. 8 — Типичная полоса отвода, пересекающая небольшой ручей, канал или канаву без обсаженного грунта (предоставлено AMEC Paragon).
Рис. 9 — Различные типы анкеров плотности и обычные механические анкеры (любезно предоставлено AMEC Paragon).
Рис. 10 — Типичные насадочные массы железобетонного трубопровода (любезно предоставлены AMEC Paragon).
Фиг.11 — Типовой предупреждающий знак на трубопроводе природного газа для установки на железной дороге, шоссе / дороге, пересечениях канав, границ собственности и т. Д. (Любезно предоставлено AMEC Paragon).
Морские трубопроводы
Конструкция морского трубопровода отличается в первую очередь требованиями окружающей среды и процессом установки. Трубы, используемые в морских условиях, подвергаются высоким изгибающим напряжениям — потенциальным силам сжатия на трубу, установленную на большой глубине и в среде с низкой плотностью.До недавнего времени размер трубопровода был сильно ограничен, но технологические разработки и усовершенствованные методы строительства позволили морским трубопроводам продолжать увеличиваться в размерах и пропускной способности. Трубопроводы строятся все глубже и глубже. Трубопроводы до 28 дюймов. диаметром теперь устанавливаются в глубоководных приложениях до 7000 футов воды.
Дизайн
Материалы трубопроводов, используемых в морских трубопроводах, по существу те же, что и материалы, используемые в береговых трубопроводах.Когда трубопровод спроектирован в соответствии со стандартом ANSI / ASME B31.8, расчетный коэффициент 0,72 используется для большей части расчета толщины стенки трубопровода, а расчетный коэффициент 0,50 используется в стояке и часто на первых 300 футах трубы. примыкает к стояку. Труба больше 10 дюймов. номинальный размер, установленный в соленой воде с низкой плотностью, обычно имеет тенденцию плавать. Иногда это можно преодолеть, используя большую толщину стенки, чем это необходимо для утяжеления трубы. Обычно более экономично использовать утяжеляющее бетонное покрытие или прокладывать линию во влажном состоянии для получения необходимой устойчивости на дне.Как правило, трубы рассчитаны на удельный вес 1,35.
Труба должна иметь достаточную толщину стенки, чтобы выдерживать внутреннее рабочее давление, напряжения изгиба и внешние силы сжатия. Высокопрочные высококачественные трубы, такие как API 5L Grade X65 и выше, часто используются для строительных, конструктивных, эксплуатационных и экономических соображений.
Расчет минимального радиуса изгиба для трубы с бетонным покрытием выражается в Ур. 9,36 .
где
R | = | радиус изгиба, дюйм, |
E | = | Модуль упругостидля бетона = 3 000 000 фунтов на квадратный дюйм, |
C | = | радиус трубы + толщина эмали + толщина бетона, дюймы, |
и | ||
S B | = | 2500 фунтов на квадратный дюйм. |
Минимальный радиус изгиба стали выражается как
где
S Y | = | Минимальный предел текучести, указанный для трубы, фунт / кв. Дюйм |
P | = | расчетное давление, фунт / кв. Дюйм |
D | = | Наружный диаметр трубы, дюйм. |
т | = | Толщина стенки трубы, дюйм. |
R | = | радиус изгиба, дюйм. |
E | = | Модуль упругостидля стали = 30 000 000 фунтов на квадратный дюйм. |
C | = | радиус трубы, дюйм. |
и | ||
f | = | Коэффициент напряжения: используйте от 75 до 85% для морского проектирования. |
На большой глубине доступны компьютерные программы для расчета напряжения, которое должно выдерживаться на трубе для поддержания приемлемого радиуса изгиба.Это сложный расчет, который должен учитывать конкретные возможности укладочной баржи. На большой глубине толщину стенки могут определять напряжения укладки и напряжения обрушения. Кроме того, могут потребоваться ограничители пряжки для ограничения длины пряжки, если она вызвана проблемой установки (например, потерей достаточного натяжения).
Строительство
Морские трубопроводы сооружаются с использованием барж-укладчиков или специальных судов. Каждая операция в процессе строительства трубопровода, за исключением закладки труб, происходит на барже-укладчике.Трубу хранят, подготавливают, сваривают, покрывают, проверяют и спускают с укладочного судна. Труба опускается с задней части баржи с помощью сложной системы динамических позиционеров, роликов, натяжителей тросов, поплавков и длинной регулируемой стрелы или стингера. Труба протягивается позади и ниже укладочной баржи и принимает S-образную или J-образную форму. При S-образной прокладке труба укладывается горизонтально на барже, что позволяет использовать несколько сварочных станций. Труба покидает баржу через жало, контролирующее кривизну «перегиба».«Натяжение якорей баржи контролирует радиус кривизны« прогиба », который возвращает трубу в горизонтальное положение на морском дне. На очень большой глубине невозможно контролировать перегиб с помощью стингера, и поэтому используется J-образная укладка, когда труба выходит из баржи вертикально. J-образная укладка требует, чтобы на барже была мачта, чтобы удерживать длину трубы, в то время как все сварочные работы выполняются в одном месте.
Независимо от того, какая система используется, труба испытывает огромные изгибающие силы, вызванные весом трубы, движением судна и радиусом изгиба.Радиус регулируется системами натяжителей. Труба должна быть спроектирована так, чтобы напряжение, вызванное осевым растяжением и изгибающим моментом, находилось в допустимых пределах.
Скорость укладки, волнение моря и другие факторы могут вызвать коробление трубы. Чем глубже прокладка, тем больше вероятность изгиба трубы. Трубу можно прокладывать на мелководье, не более 50 футов, с помощью буровой баржи или самоподъемной баржи. Буровые и самоподъемные баржи работают так же, как и укладочные баржи.
Закапывание труб производится плугом или водометом. Плуги используются на глубоководных и более плотных глинах и могут использоваться одновременно с укладочной баржей. Струйные системы могут использоваться в воде на глубине примерно до 300 футов. Дайверы могут вручную спустить трубу на мелководье, но чаще струйная установка используется для закапывания трубы после ее укладки. На мелководье (50 футов или меньше) для рытья траншеи для труб можно использовать земснаряд.
В США минимальное покрытие трубопровода на глубине до 200 футов составляет 36 дюймов.Нет требований к заглублению трубы в воду на глубине более 200 футов. Обычно труба заглубляется с 5-футовым покрытием на протяжении первых 300 футов от стояка платформы, 16 1/2 футов в зонах якорной стоянки и 10 футов на фарватерах. Посторонние трубопроводы обычно пересекаются, и может возникнуть необходимость опустить заграничный трубопровод. Минимум 18 дюймов Должно сохраняться разделение, и часто между линиями укладываются сочлененные бетонные маты с резиновым покрытием.
Контроль коррозии
Те же принципы защиты от коррозии и катодной защиты, которые применяются к наземным трубопроводам, также применимы к морским трубопроводам.Линия трубы обычно покрывается FBE или подобной системой, и, если требуется дополнительный вес, на нее будет нанесено покрытие из бетона.
Надводные трубопроводы обычно покрываются многослойной эпоксидной краской. Специальный участок трубы с вулканизированным резиновым покрытием, прикрепленный к трубе, «Splashtron», часто используется в зоне сильнокоррозионных брызг на границе раздела вода / воздух.
Жертвенные цинковые или алюминиевые аноды крепятся к трубе в виде браслета.Аноды обычно рассчитаны на минимальный срок службы 20 лет. Очень сложно спроектировать и поддерживать систему подаваемого тока на длинном морском трубопроводе.
Гидростатические и неразрушающие испытания и контроль
Каждая трубопроводная система должна быть проверена и проверена, чтобы гарантировать, что система может работать безопасно. Правила DOT определяют требования к испытаниям и проверкам, а также стандарты ANSI / ASME B31.3, B31.4 и B31.8 и стандарты API 1104, [28] 571, [32] и 574. [33]
Гидростатические испытания
Правила DOT, часть 192, подраздел J, параграфы 192.501–192.517; Часть 193, подраздел D, пункты 193.2319 и 193.2323; и часть 195, подраздел E, предписывают требования к испытаниям под давлением и прочности трубопроводов для природного газа, СПГ и опасных жидкостей, соответственно. Стандарты ANSI / ASME и API также предписывают требования к испытаниям. Пневматические испытания разрешены для некоторых трубопроводных систем низкого давления, но большинство трубопроводов испытывается водой.
Перед проведением гидростатическое испытание, профиль испытательной секции должны быть разработаны с указанием максимальных и минимальных отметок, максимальное допустимое рабочее давление (МДРД) определяется в самой нижней точке подъема, расположение заполнения и давления насоса, минимальное давление требуется в насосе давления, определяемый:
- Максимальное давление на самой низкой отметке
- Качество источника воды
- Точка выпуска / утилизации
Профиль тестового сегмента обеспечивает графическое представление тестового сегмента, который помогает инженеру по тестированию определить расположение вентиляционных отверстий, а также скорость заполнения и скорость скребка, необходимые для предотвращения захвата воздуха, и проверить что испытание не вызовет чрезмерного или пониженного давления в трубе в сегменте.Перепад высот может стать важным фактором. Когда радикальные изменения высоты происходят на коротких расстояниях, может возникнуть необходимость разделить исходный сегмент на более короткие тестовые сегменты. Каждые 100 футов перепада высоты представляют собой приблизительно 43,3 фунта на квадратный дюйм перепада давления, что может привести к понижению давления в высоких точках и избыточному давлению в нижних точках во время испытания. Профиль испытаний также используется для документирования расположения наполняющего насоса, испытательного насоса, манометра и оборудования для регистрации давления / температуры. На рис. 12 показан типичный сегмент испытательного профиля.
Рис. 12 — Высота испытания целостности трубопровода в зависимости от номера станции (любезно предоставлено AMEC Paragon).
Типичное испытательное оборудование, необходимое для проведения гидростатических испытаний:
- Временный заправочный коллектор с клапанами (номинальное давление, как минимум, в 1,5 раза превышающее максимальное испытательное давление)
- Коллектор для обезвоживания в комплекте с клапанами (также номинальное давление не ниже 1.5-кратное максимальное испытательное давление)
- Чуши для пенопласта или уретана
- Насос наполнения низкого / большого объема с фильтрующим оборудованием, поршневой насос высокого давления
- Манометр (и) сертифицированный
- Регистратор давления диаграммный
- Регистратор температуры воды карточный
- Регистратор температуры окружающего воздуха диаграммный
- Манометры, рассчитанные на 50-75% максимального испытательного давления
- Источник сжатого воздуха или азота для обезвоживания
- Оборудование для фильтрации выпускаемой воды
Кроме того, могут потребоваться временные резервуары для хранения воды или резервуары для хранения воды для подачи резервной воды для испытаний или для использования в качестве устройств для удержания или отстаивания для обезвоживания.
Неразрушающий контроль
Неразрушающий контроль и контроль сварных швов требуется в соответствии с правилами Министерства транспорта США, часть 192, подраздел E, параграф 192.243 [3] для трубопроводов природного газа; Часть 193, подраздел D, пункт 193.2321 [4] для линий СПГ; и часть 195, подраздел D, параграф 195.234 [6] для трубопроводов для опасных жидкостей. Стандарты ANSI / ASME B31.3, [12] B31.4, [15] и B31.8 [27] также предписывают требования неразрушающего контроля.
Инспекция
Каждый из правил и отраслевых кодексов требует визуального контроля сварных швов и процесса строительства.
Контрольно-измерительные приборы
Системы управления трубопроводом могут состоять из простых устройств, таких как автоматические клапаны регулирования давления, до сложной системы полного диспетчерского управления и сбора данных (SCADA). Система SCADA может отслеживать и контролировать в реальном времени всю систему трубопроводов. Система SCADA может открывать и закрывать клапаны, запускать и останавливать насосы / компрессоры, отслеживать и регулировать поток, отбирать образцы продукта, контролировать и регулировать давление и температуру, а также выполнять многие другие функции.Системы SCADA обычно не нужны и не практичны для небольших сборных трубопроводных систем.
Компрессорным станциям, насосным станциям и связанным с ними объектам может потребоваться оборудование аварийной изоляции для защиты трубопровода. Системы аварийного отключения (ESD) состоят из автоматических запорных запорных клапанов, расположенных на главном входе и выходе на станции / сооружения, и скоординированных систем сброса давления между запорными клапанами. Система ESD защищает как трубопровод, так и объект, останавливая поток внутрь и из объекта и ограничивая источник питания в случае пожара, взрыва или другой аварийной ситуации.
Базовая контрольно-измерительная аппаратура трубопровода включает в себя стратегически расположенные манометры и приборы для контроля давления, датчики температуры и приборы контроля, а также оборудование для контроля / ограничения и сброса давления.
Ссылки
- ↑ Заголовок 49 CFR США, Часть 190, Программы безопасности трубопроводов и процедуры разработки правил. 1998. Вашингтон, округ Колумбия: Министерство транспорта США, Правительство США. Типография.
- ↑ US DOT Title 49 CFR Part 191, Транспортировка природного и другого газа по трубопроводам: годовые отчеты, отчеты об инцидентах и отчеты о состоянии безопасности.1998. Вашингтон, округ Колумбия: Министерство транспорта США, Правительство США. Типография.
- ↑ 3,0 3,1 US DOT Title 49 CFR Part 192, Транспортировка природного и другого газа по трубопроводам. 1998. Вашингтон, округ Колумбия: Министерство транспорта США, Правительство США. Типография.
- ↑ 4,0 4,1 US DOT Title 49 CFR Part 193, Оборудование для сжиженного природного газа. 1998. Вашингтон, округ Колумбия: Министерство транспорта США, Правительство США. Типография.
- ↑ US DOT Title 49 CFR Part 194, Планы реагирования для береговых нефтепроводов.1998. Вашингтон, округ Колумбия: Министерство транспорта США, Правительство США. Типография.
- ↑ 6.0 6.1 US DOT Title 49 CFR Part 195, Транспортировка опасных жидкостей по трубопроводам. 1998. Вашингтон, округ Колумбия: Министерство транспорта США, Правительство США. Типография.
- ↑ US DOT Title 49 CFR Part 198, Положения о грантах в помощь государственным программам безопасности трубопроводов. 1998. Вашингтон, округ Колумбия: Министерство транспорта США, Правительство США. Типография.
- ↑ US DOT Title 49 CFR Part 199, Тестирование на наркотики и алкоголь.1998. Вашингтон, округ Колумбия: Министерство транспорта США, Правительство США. Типография.
- ↑ Стандарт ANSI / ASME A53, Стандарт на бесшовные трубы из углеродистой стали для работы при высоких температурах. 2002. Нью-Йорк: ANSI / ASME.
- ↑ 10,0 10,1 Стандарт ANSI / ASME A106, Стандарт на бесшовные трубы из углеродистой стали для работы при высоких температурах. 2002. Нью-Йорк: Ошибка ссылки ANSI / ASME: недопустимый тег
- ↑ Стандарт API 5L, Спецификации для трубопроводов, девятнадцатое издание.2004. Вашингтон, округ Колумбия: API.
- ↑ 12,0 12,1 12,2 Стандарт ANSI / ASME B31.3, Стандарт для трубопроводов химических заводов и нефтеперерабатывающих заводов. 2002. Нью-Йорк: ANSI / ASME.
- ↑ Стандарт ANSI / ASME B16.5, Стандарт для стальных трубных фланцев и фланцевых фитингов от NPS 1/2 до NPS 24 Метрические / дюймовые. 2003. Нью-Йорк: ANSI / ASME.
- ↑ 14.0 14.1 Стандарт ANSI / ASME B16.9, Стандарт на заводские фитинги из кованой стали для стыковой сварки.2003. Нью-Йорк: ANSI / ASME.
- ↑ 15,0 15,1 Стандарт ANSI / ASME B31.4, Стандарт для систем транспортировки жидких углеводородов, сжиженного нефтяного газа, безводного аммиака и спиртов. 2002. Нью-Йорк: ANSI / ASME.
- ↑ Стандарт ANSI / ASME A105, Стандарт на поковки из углеродистой стали для трубопроводов. 2002. Нью-Йорк: ANSI / ASME.
- ↑ Стандарт ANSI / ASME A234, Стандартные спецификации для трубных фитингов из кованой углеродистой стали и легированной стали для умеренных и повышенных температур.2002. Нью-Йорк: ANSI / ASME.
- ↑ Стандарт ANSI / ASME A420, Стандартные спецификации для трубных фитингов из кованой углеродистой и легированной стали для работы при низких температурах. 2002. Нью-Йорк: ANSI / ASME.
- ↑ Стандарт ANSI / ASME A694, Углеродистая и легированная сталь для трубных фланцев, фитингов, клапанов и деталей для систем передачи высокого давления. 2000 г. Нью-Йорк: ANSI / ASME.
- ↑ Стандарт API 6D, Стандартные спецификации для стальных затворов, пробок и обратных клапанов для трубопроводов, двадцать первое издание.1998. Вашингтон, округ Колумбия: API.
- ↑ Стандарт API 6H, Стандартные спецификации для торцевых затворов, соединений и вертлюгов. 1998. Вашингтон, округ Колумбия: API.
- ↑ Спецификация 44, Спецификация на фланцы стальных трубопроводов. 1998. Вена, штат Вирджиния: Manufacturer’s Standardization Soc. компании Valves and Fittings Industry Inc.
- ↑ Спецификация 75, Спецификация на арматуру для стыковой сварки, прошедшую высокие испытания. 1998. Вена, штат Вирджиния: Manufacturer’s Standardization Soc. компании Valves and Fittings Industry Inc.
- ↑ Стандарт NACE MR01-76, Стандартные технические условия на металлические материалы для штанговых насосов для агрессивных сред на нефтяных месторождениях. 2000. Хьюстон, Техас: NACE.
- ↑ NACE RP200, Рекомендуемая практика для стальных трубопроводов, разд. 3 и 5. 2003. Хьюстон, Техас: NACE.
- ↑ NACE RP572, Рекомендуемая практика по проектированию, установке, эксплуатации и техническому обслуживанию глубинных грунтовых пластов с наложенным током, разд. 3 и 5. 2003. Хьюстон, Техас: NACE.
- ↑ 27.0 27,1 ANSI / ASME: Стандарт B31.8, Стандарт для систем трубопроводов передачи и распределения газа. 1999 г. Нью-Йорк: ANSI / ASME.
- ↑ 28,0 28,1 28,2 28,3 Стандарт API 1104, Стандартные технические условия на сварку трубопроводов и связанных с ними объектов, девятнадцатое издание. 1999. Вашингтон, округ Колумбия: API.
- ↑ 29,0 29,1 Нормативы ASME по котлам и сосудам высокого давления 2004 г., Раздел IX: Квалификация по сварке и пайке.2004 г. Фэрфилд, Нью-Джерси: ASME.
- ↑ OSHA, раздел 29, часть 1910 CFR, Стандарты безопасности и гигиены труда для общей промышленности. 1981. Вашингтон, округ Колумбия: Министерство транспорта США, Правительство США. Типография.
- ↑ OSHA 2207, часть 1926 CFR, приложения A-F, Строительные стандарты, касающиеся земляных работ, части 1926.650, 1926.651 и 1926.652. 1981. Вашингтон, округ Колумбия: Министерство транспорта США, Правительство США. Типография.
- ↑ Стандарт API 571, Стандартные спецификации для кодов трубопроводов — проверка, ремонт, изменение и переоценка действующих трубопроводных систем, второе издание.1999. Вашингтон, округ Колумбия: API.
- ↑ Стандарт API 574, Стандартные требования к методам контроля компонентов трубопроводной системы, второе издание. 1999. Вашингтон, округ Колумбия: API.
Интересные статьи в OnePetro
Используйте этот раздел, чтобы перечислить статьи в OnePetro, которые читатель, желающий узнать больше, обязательно должен прочитать
Внешние ссылки
Используйте этот раздел для предоставления ссылок на соответствующие материалы на других веб-сайтах, кроме PetroWiki и OnePetro.
См. Также
Газопроводы
Трубопроводы и трубопроводные системы
Очистка трубопровода
Соображения и стандарты проектирования трубопроводов
Оценка падения давления на трубопроводе
PEH: Трубопроводы и трубопроводы
Метод установки трубы большого диаметра: горизонтально-направленное бурение
/>
Как установить трубу большого диаметра, не нанося ущерба чувствительной экологической среде и не разрушая высоко урбанизированные сообщества? За последние два десятилетия подрядчики все чаще обращаются к методу, называемому горизонтально-направленным бурением (ГНБ).ГНБ — это управляемый бестраншейный метод установки всего, от трубы до кабеля, с минимальным размером конструкции и незначительным воздействием на окружающие территории.
При рассмотрении вопроса об установке труб большого диаметра, который может превышать метр (39 дюймов) в диаметре, метод бестраншейной прокладки потенциально может решить множество проблем. Здесь мы обсудим преимущества и варианты использования установки ГНБ для труб большого диаметра и рассмотрим недавнее тематическое исследование, демонстрирующее этот метод в действии.
Каковы преимущества использования ГНБ при прокладке труб большого диаметра?
Хотя методы рытья траншей и земляных работ более просты, они могут быть непрактичными в современных случаях использования из-за окружающей среды (например, переход через реку), ландшафта (например, экологических соображений) или социально-экономического воздействия (например, дороги и дома).
Enter HDD, который обеспечивает очень точное бурение с неглубокими дугами и позволяет обходить подземные препятствия, такие как другие трубы или русла рек.Этот метод управляемого бурения начинается с создания пилотного отверстия, которое просверливается и направляется по заданной траектории. Когда буровая головка достигает конца траектории и вырезает поверхность, последняя траектория сверления завершается. Теперь к буровым штангам прикрепляют заднюю развертку, а затем втягивают заднюю развертку по траектории ствола. По мере того, как задний расширитель продвигается вперед, он одновременно увеличивает диаметр траектории сверления и одновременно протягивает трубу на место ( 1 ).
Выбор материала трубы и стандартного соотношения размеров (SDR) будет зависеть от трех требований: давления, рабочих нагрузок и обратного усилия.
Выбор материала трубы большого диаметра для метода ГНБ
Труба может быть изготовлена из таких материалов, как полиэтилен, полипропилен, высокопрочный чугун, сталь и ПВХ — практически из любых материалов, которые можно протянуть по траектории сверления. Однако сама природа HDD поощряет использование материалов, которые могут выдерживать различные нагрузки и другие переменные, присутствующие во время цикла обратного хода.
Трубы из полиэтилена (PE) очень хорошо дополняют метод ГНБ благодаря своей высокой прочности, гибкости, превосходной целостности соединений, малому весу и долгому сроку службы, что обеспечивает более высокую рентабельность по сравнению со многими конкурирующими материалами.Кроме того, полиэтиленовые трубы обладают высокой коррозионной стойкостью и химически устойчивы — они способны переносить множество соединений без разложения ( 2 ). Полиэтиленовые трубы также могут быть изготовлены в соответствии с потребностями вашего проекта, включая очень толстые трубы из полиэтилена высокой плотности с массивными стенками.
ГНБ установила трубу большого диаметра под рекой Шпрее, Германия
Хотя трубы большого диаметра на самых высоких концах шкалы никогда не устанавливались с использованием ГНБ, такие трубы, как AGRULINE PE 100-RC, соответствуют всем техническим требованиям к нагрузкам и испытаны и одобрены PAS 1075 для методов бестраншейной прокладки.
В 2016 году сочетание наводнений, деликатных экологических соображений и высокой стоимости ремонта традиционными методами вынудило использовать ГНБ для обхода многотрубного разрыва водопровода Нохтен возле реки Шпрее, Германия. Эти трубы подземных вод и шахтных вод необходимы для близлежащих горнодобывающих предприятий, поставляющих бурый уголь, необходимый для питания электростанции Schwarze Pumpe.
Новая установка методом ГНБ с трубами из PE 100-RC была самым экономичным и простым в реализации решением ( 3 ).Эти трубы постоянно устойчивы к коррозии, вызванной переносимой шахтной водой. Кроме того, учитывая их высокую гибкость, также возможны промывочные отверстия с небольшими установочными радиусами. Наконец, трубы допускают значительную деформацию, которая может возникнуть в результате проседания грунта без опасности появления трещин или разрывов.
Для окончательной установки потребовались две трубы длиной примерно 220 м (721,8 фута), которые должны были быть предварительно изготовлены с НД 1200 мм (47,2 дюйма) и НД 1400 мм (55,1 дюйма) с толщиной стенки SDR 17.Сегменты длиной 13 м (42,7 фута) будут сварены вместе на месте. При общей массе 76 тонн каждый был использован специальный роликовый блок для уменьшения усилия, необходимого для их втягивания.
Хотя технология строительства ГНБ широко использовалась в различных отраслях промышленности в течение многих лет, этот инженерный проект был первым в мире, представляя реальный случай установки полиэтиленовой трубы большого диаметра методом ГНБ. Йорн Стулинга, консультант по горизонтально-направленному бурению в Visser & Smit, сказал: «Мы гордимся тем, что первыми успешно уложили трубы из полиэтилена 100 такого большого диаметра с использованием процесса промывочного бурения.Их легко было сваривать, и их очень легко втягивать благодаря их гибкости ».
Труба высокопрочная большого диаметра для магистральных газопроводов высокого давления
1 Труба большого диаметра высокопрочная для магистральных газопроводов высокого давления М.K. Gräf Europipe GmbH H.-G. Hillenbrand Europipe GmbH C. J. Heckmann Mannesmann Forschungsinstitut GmbH K. A. Niederhoff Mannesmann Forschungsinstitut GmbH ISOPE 2003 26-30 мая 2003 г., Гонолулу, Гавайи, США TP53
2 Высокопрочные трубы большого диаметра для протяженных газопроводов высокого давления M. K. Gräf 1, H.-G. Hillenbrand 2, CJ Heckmann 3, KA Niederhoff 3 1 Europipe GmbH 2 Europipe GmbH 3 Mannesmann Forschungsinstitut Mülheim, Германия Ратинген, Германия Дуйсбург, Германия РЕЗЮМЕ Постоянно растущий спрос на природный газ будет и дальше влиять на тип его транспортировки в будущем, как со стратегической и экономической точки зрения.Трубопроводы большой протяженности являются безопасным и экономичным средством транспортировки газа от мест добычи до конечных потребителей. Энергетический сценарий в последние годы быстро меняется. Международные исследования прогнозируют, что спрос на природный газ вырастет почти вдвое. Расстояние между объектами добычи газа и конечными потребителями увеличивается, что подразумевает необходимость строительства сложных газотранспортных трубопроводных сетей, когда использование танкеров для СПГ невозможно или неэкономично. Это сделает транспортировку природного газа под высоким давлением по трубопроводам все более интересным.Уже было показано, что использование линейных труб класса X 80 приводит к значительной экономии затрат. В данной статье представлены результаты испытаний эксплуатационных труб марки Х 80, поставляемых для наземных и морских проектов. Но экономичная транспортировка газа на очень большие расстояния требует дополнительного сокращения затрат. Решением может стать использование класса X100 и / или X120. Таким образом, рассматриваются преимущества использования высокопрочных линейных труб и современные технические ограничения на их производство. Представлены лабораторные и производственные результаты высокопрочных труб большого диаметра для описания свойств материалов, а также поведения при эксплуатации.Уже разработаны процедуры кольцевой сварки, охватывающие механизированные и ручные методы. ВВЕДЕНИЕ В данной статье дается обзор развития высокопрочных низколегированных марок линейных труб. Представлены некоторые из текущих проектов для трубопроводов класса X 80 и преимущества использования трубы X 80. Также обсуждаются важные аспекты свойств основного материала и сварных швов. Разработка марок материалов до X 100 или X 120 представляет собой одну из больших проблем и возможностей в будущем.Особое внимание уделяется влиянию бора на механические свойства материалов марок от> X 80 до X 120. Кроме того, рассматриваются различные аспекты производственных сварных швов и свариваемости в полевых условиях. СНИЖЕНИЕ СТОИМОСТИ ПРОЕКТА Снижение затрат на проект может быть результатом совокупности различных выгод, которые могут быть получены при использовании высокопрочных сталей / 1 /, даже если цена за тонну трубы увеличивается с увеличением сорта материала. К преимуществам относятся: меньшее количество стали; меньшие затраты на транспортировку труб; меньшие затраты на укладку труб.Использование линейных труб класса X 80 при строительстве первого трубопровода Ruhrgas X80 привело к экономии материала около тонны по сравнению с трубами класса X 70 (Рисунок 1) за счет уменьшения толщины стенки с 20,8 мм для труб X 70 до 18,3 мм для X 80. Это привело также к сокращению затрат на укладку труб из-за снижения затрат на транспортировку труб и значительного снижения затрат на сварку за счет сокращения времени сварки, необходимого для более тонких стенок. Использование материалов с еще более высокой прочностью, таких как марка X 100 или марка X 120, может привести к дополнительной экономии материала, как это дополнительно показано на Рисунке 1.Вес трубопровода [т] X70 X80 X100 X120 Марка стали по API Рис. 1: Возможная экономия материала за счет использования высокопрочного материала. Бумага № SYMP-03 Gräf 1
3 Предварительная экономическая оценка / 2 / подчеркнула, что трубопроводы высокого давления X 100 могут дать экономию инвестиционных затрат примерно на 7% по сравнению с трубопроводом класса X 80. В этом исследовании утверждается, что при сравнении X 70 и X 100 экономия затрат достигает 30%.Учитывая, что в сложной трубопроводной сети, работающей при высоком давлении, капитальные затраты очень высоки, становится понятно, насколько более привлекательным может быть вариант из высокопрочной стали. С другой стороны, из рисунка 2 становится ясно, что снижение стоимости производства на тонну трубы при данной транспортной пропускной способности трубопровода увеличивается не только за счет повышения качества стали, но и за счет уменьшения по толщине стенки трубы. С точки зрения производителей труб уменьшение толщины стенки трубы не является предпочтительным вариантом.Уменьшение диаметра трубы при постоянной толщине трубы и одновременное увеличение рабочего давления в трубопроводе, по нашему мнению, представляет собой более благоприятное решение проблемы. Производственные затраты на метрическую тонну X60 X80 X100 X120 Марка стали по API Рисунок 2: Стоимость производства на тонну труб для различных марок стали и толщины стенки, которые будут использоваться при постоянной транспортной способности 12,7 мм 15,9 мм 19,1 мм 25,4 мм РАЗРАБОТКА ВЫСОКОПРОЧНЫХ МАРК СТАЛИ Усовершенствованный метод обработки используемых в настоящее время высокопрочных сталей, таких как X 80 и выше, состоит термомеханической прокатки (возникла в 80-е годы) с последующим ускоренным охлаждением.С помощью этого метода стало возможным производить высокопрочный микролегированный материал NbTi, имеющий пониженное содержание углерода и, следовательно, превосходную свариваемость в полевых условиях. Добавки молибдена, меди и никеля позволяют повысить уровень прочности до уровня X 100, когда сталь перерабатывается в лист термомеханической прокаткой с модифицированным ускоренным охлаждением. Разработка высокопрочной стали для труб марки X 120 заключается в дальнейшей оптимизации термомеханической обработки и использовании ниобия, титана и бора в качестве элементов микролегирования.Первые результаты этой разработки в отношении механических свойств нового материала очень обнадеживают. СОРТА X 80 X 80 Проекты и соответствующие свойства труб За последние два десятилетия компания EUROPIPE провела обширную работу по разработке высокопрочных сталей марок X 80 и X 100, чтобы помочь клиентам в их стремлении снизить вес труб и затраты на укладку труб. С 1984 года прямошовная сварная под флюсом труба марки Х 80 использовалась при реализации нескольких трубопроводных проектов в Европе и Северной Америке (рис. 3).В 1984 году компания EUROPIPE произвела линейную трубу класса X 80, впервые в истории установленную на трубопроводе Megal II. Марганец-ниобий-титановая сталь, дополнительно легированная медью и никелем, была использована для производства трубы с наружным диаметром 44 x 13,6 мм WT. Последующая оптимизация производственных параметров позволила выполнить заказ ЧССР с использованием марганцево-ниобий-титановой стали без добавок меди и никеля. ГОД ЗАКАЗА ГЕОМЕТРИЯ ТРУБЫ ДЛИНА ТРУБОПРОВОДА 1984 Megal II 44 «x 13.6 мм 3,2 км 1985 CSSR 56 дюймов x 15,5 мм 1,5 км 1991/92 Ruhrgas 48 дюймов x 18,3 мм 250 км CNRL 24 дюйма x 25,4 мм 12,7 км Transco 48 дюймов x 14,3 / 15,1 мм 158 км + Рисунок 3: Проекты Europipe, выполненные с трубопроводы из марки X80 Первым трубопроводом с использованием GRS 550 (X 80) на всей его длине 250 км был проект трубопровода Ruhrgas Werne-to-Schlüchtern, реализованный в Германии в EUROPIPE, который поставил все трубы диаметром 48 с толщиной стенки до 19,3 мм и необходимые индукционные изгибы. Поскольку прочность уменьшается с увеличением толщины стенки, в то время было необходимо незначительно повысить уровни углерода и марганца.Концентрации всех остальных элементов не изменились. Измеренные значения прочности на растяжение и энергии удара во всех случаях полностью соответствовали требованиям спецификации. Стандартное отклонение значений текучести и прочности на разрыв было очень низким. Значения энергии удара, измеренные на образцах с V-образным надрезом по Шарпи при 0 ° C, были очень высокими, в среднем около 180 Дж. Температуры перехода 85% площади сдвига, определенные в испытаниях на разрыв падающим грузом (DWT), были намного ниже 0 C. В 2002 и 2003 годах трубы X 80 (L555MB) были снова произведены для проектов Transco в Великобритании.Изготовлен трубопровод для нескольких участков газопроводных сетей протяженностью около 158 км. EUROPIPE поставила трубы диаметром 48 и толщиной 14,3 мм и 15,1 мм. Заказано еще 52 км. На рис. 4 показан вид на строительную площадку трубопровода Транско. После завершения сварки, неразрушающего контроля и покрытия стыков на стыках участки трубопровода с кольцевым сварным швом опускались на подготовленное дно траншеи. Результаты испытаний, проведенных EUROPIPE на производственных трубах в контексте сертификации труб, показаны на рисунках 5 и 6.Все результаты проведенных испытаний на растяжение и удар были в пределах спецификации для класса X 80. Стандартное отклонение составляло 15 МПа для значений предела текучести и 13 МПа для значений предела прочности. Среднее значение энергии удара составило 227 Дж для основного металла и 134 Дж для металла шва. Документ № SYMP-03 Gräf 2
4 цистерны, материал трубопровода X 80 с толщиной стенки 33 мм.Рисунки 7 и 8 дают представление об установке такого танкера PNG. На одно судно можно отгрузить около тонны газа, и нет необходимости обрабатывать или охлаждать газ. Одобрение этой концепции было дано DNV. Рис. 4: Вид на операцию по укладке труб (проект Транско) Расчетное давление, 250 бар Случайное давление, бар Высота: прибл. 36 метров I.D .: 1000 мм Объемы: Вес каждого цилиндра: прибл. 31 Mt Кол-во цилиндров: 3600 Общий вес цилиндров: Mt Расчетные условия: Материал трубопровода X80 WT 33 мм.Рисунок 7: Конструкция защитных цилиндров для танкеров PNG Рисунок 5: Прочность на растяжение трубы Transco класса X 80 (48 OD x 15,1 мм WT) Рисунок 8: Конструкция танкера PNG Механические свойства труб X 80, используемых для цилиндров, являются Обобщено на Рисунке 9. Все значения испытаний на растяжение и удар соответствовали требованиям. Энергия удара по Шарпи с V-образным надрезом, измеренная при -10 ° C, превысила 200 Дж. Поскольку это не применяется в арктических условиях, ни высокая ударная вязкость при низких температурах, ни испытания BDWT не требуются.Операции по формовке и сварке труб не доставили никаких проблем. Сварка в полевых условиях трубы марки X 80 Рис. 6. Прочностные характеристики трубы марки Transco марки X 80 (48 OD x 15,1 мм WT) Одним из самых сложных проектов, с которыми столкнулись в 2001 году, была установка горячего пара для CNRL в Канаде / 3 /. Линейная труба с продольным сварным швом была аттестована для использования при температурах до 354 ° C. Высокотемпературные свойства были определены и признаны удовлетворительными. Для нового участка трубопровода горячего пара недавно было заказано еще 7,7 км труб.Чтобы продемонстрировать технологичность толстостенных труб класса X 80, компания EUROPIPE разработала конструкцию защитных цилиндров для строительства трубопровода ПНГ, требующих сварочных работ с использованием ручного SMAW и автоматического GMAW. Эти методы сварки хорошо зарекомендовали себя в настоящее время и считаются достаточно проверенными для широкомасштабного использования / 4-6 /. Помимо ручного SMAW, автоматический GMAW становится все более важным экономичным процессом из-за сокращения времени сварки, необходимого для узких зазоров. Узкие зазоры требуют меньшего количества отдельных проходов.Один из очень эффективных используемых процессов автоматической сварки GMA — это процесс CRC, который также частично использовался при строительстве трубопровода Верне-Шлюхтерн и недавних проектах Transco. На рисунке 10 показана процедура сварки, применяемая к трубам X 80. На рисунке 11 показаны механические свойства и вязкость кольцевых сварных швов, которые комфортно соответствуют стандартным требованиям спецификации. Документ № SYMP-03 Gräf 3
5 РАЗРАБОТКА МАРКИ X100 / X120 Чтобы соответствовать требованиям рынка, предъявляемым к трубам повышенной прочности, EUROPIPE приложила все усилия для разработки марки X 100.Никаких технологических прорывов в прокатке ТМ и ускоренном охлаждении не потребовалось. Для производства листа марки Х 100 потребовалась только оптимизация существующей технологии. В результате производственное окно стало уже. очевидно, что в обработке пластины или трубы не было необходимости. С 1995 года компания EUROPIPE разработала различные подходы к производству высокопрочных материалов / 1 /. Как видно на фиг. 12, обычно возможны три различных подхода к выбору химического состава и условий прокатки листа.Рис. 9: Механические свойства толстостенной трубы класса X 80 для защитных цилиндров PNG Проход Корневой проход Горячий проход Заполнитель Заглушка Проход Расходные материалы Торговое наименование dia. [мм] Защитный газ Thyssen K Nova Thyssen NiMo 80 Thyssen NiMo 80 Thyssen NiMo Ar / CO 2 75/25 CO 2 CO2 Ar / CO 2 75/25 Ток [A] 190 / / / Напряжение [В] 19/21 24 / 26 22/25 20/22 Скорость сварки [см / мин] Рис. 10: Типичные параметры сварки для GMAW класса X 80 с использованием процесса CRC / 45 26/41 Осцилляция nnyy Рис. 12: Различные подходы для достижения уровня прочности сорт X 100 путем изменения химического состава стали, а также параметров охлаждения во время производства листа / 7 / Подход A (Таблица 1), в котором используется относительно высокий углеродный эквивалент при 0.49, имеет недостаток, заключающийся в том, что характеристики ударной вязкости при остановке трещин невысоки, и поэтому требования по предотвращению продолжительных трещин могут быть не выполнены. Более того, этот подход также вреден, например свариваемости в полевых условиях. Типичный результат этого подхода был следующим: Прочность [МПа] Прочностные характеристики (поперечная сварка плоского образца) 550 YS 690 TS Вязкость CVN Вязкость разрушения WM -30 C WM 0 C HAZ 0 C Рис. 11: Результаты испытаний кольцевых швов X 80 (CRC технологический процесс) размер трубы OD X WT C Mn Si Mo Ni Cu Nb Ti N CEIIW PCM I 30 дюймов x 19.1 мм I Предел текучести R t0,5 * предел текучести R m * Подход A Отношение текучести к растяжению R t0,5 / R m * CVN (20 C) DWTT Температура перехода 739 МПа 792 МПа% C * Испытания на поперечное растяжение на образцах круглого прутка Относительное удлинение A 5 * Таблица 1: Подход A для производства листа класса API X100 Подход B (Таблица 2), в котором используется углеродный эквивалент всего 0,43 и который используется в сочетании с высокой скоростью охлаждения на толстолистовом стане до очень низкая температура остановки охлаждения, приводит к образованию больших фракций мартенсита в микроструктуре, что Документ № SYMP-03 Gräf 4
6 отрицательно влияет на ударную вязкость основного металла.Этот эффект нельзя адекватно компенсировать за счет использования чрезвычайно низкого содержания углерода. Кроме того, наблюдалось размягчение зоны термического влияния. Подход B превышает 200 Дж во всех случаях. Гарантировать значения, превышающие 300 Дж при низких температурах на производственной основе, кажется невозможным. На рисунке 14 показаны результаты испытания DWT при 20 ° C для различной толщины стенок. Как правило, значения площади сдвига выше для тонкостенного материала X 100. Из-за относительно высокого углеродного эквивалента и высокого уровня прочности ударная вязкость металла продольного шва и ЗТВ ограничена.Изготовленный материал X 100 благоприятно реагирует на ручную и механизированную сварку в полевых условиях, что можно объяснить пониженным содержанием углерода / 8, 9 /. Размер трубы II OD X WT C Mn Si Mo Ni Cu Nb Ti N CEIIW PCM 30 дюймов x 15,9 мм Предел текучести II R t0,5 * предел текучести R m * отношение текучести к растяжению R t0,5 / R m * удлинение A 5 * CVN (20 C) DWTT Температура перехода 755 МПа 820 МПа% C Таблица 2: Подход B для производства листа из класса API X100 Накопленный опыт показывает, что подход C (Таблица 3) является лучшим выбором.Такой подход позволяет достичь желаемого профиля свойств за счет оптимизированного двухступенчатого процесса прокатки в сочетании со средним содержанием углерода, средним эквивалентом углерода и оптимизированным процессом охлаждения. Особый потенциал существующего прокатного и охлаждающего оборудования в значительной степени способствует успеху этого подхода. Рисунок 13: Прочность на растяжение труб X 100 с различной толщиной стенки Среднее содержание углерода, используемое в подходе C, обеспечивает превосходную ударную вязкость, а также полностью удовлетворительную свариваемость в полевых условиях, несмотря на относительно высокий эквивалент углерода, примерно при примерно. цель текущей стандартизации.EUROPIPE уже произвела сотни тонн труб класса X 100, применяя подход C. Недавние испытания охватили диапазон толщины стенки от 12,7 до 25,4 мм. Было продемонстрировано, что можно использовать тот же состав стали, и потребуется лишь незначительное изменение условий прокатки. III размер трубы OD X WT Подход CC Mn Si Mo Ni Cu Nb Ti N CEIIW PCM 56 дюймов x 19,1 мм Рис. 14: Влияние толщины стенки на результаты испытаний DWT при 20 C (трубы X 100) IV 36 дюймов x 16,0 мм III выход прочность R t0.5 * предел прочности при растяжении R m * отношение текучести к растяжению R t0,5 / R m * удлинение A 5 * CVN (20 C) DWTT температура перехода 737 МПа 800 МПа% 200 Дж — 20 ° C IV 752 МПа 816 МПа% 270 Дж ~ — 50 CJ * Испытания на поперечное растяжение на образцах круглого прутка ** -60 C для WT 12,7 мм -10 C для WT 25 мм Таблица 3: Подход C для производства листа из класса API X100 Как видно на Рисунке 13, результаты на производственные трубы демонстрируют однородные прочностные характеристики при любой испытанной толщине стенки. Испытания на растяжение проводились на образцах круглого прутка.Отношение текучести к растяжению все еще было относительно высоким. Значения удлинения ниже, чем известные для класса X 70. Измеренная энергия удара (CVN) представлена на Рисунке 15: Результаты испытаний по Шарпи на трубе 36 OD x 16 мм WT класса X 100 в состоянии поставки и старении. Бумага № SYMP- 03 Gräf 5
7 По причинам технической осуществимости и рентабельности производства, в контексте сорта X 100 необходимо переоценить и пересмотреть некоторые требования к механическим свойствам с учетом ожидаемых условий эксплуатации.Произведенные трубы были подвергнуты различным испытаниям для оценки эксплуатационных характеристик. На рисунке 15 показано влияние обработки старением на кривую перехода Шарпи. Наблюдалось лишь небольшое снижение характеристик ударной вязкости после термообработки в течение 30 минут при 250 C. Полевые испытания на холодный изгиб также были завершены с удовлетворительными результатами. На рисунке 16 показаны фотографии полномасштабных серийных испытаний, которые были проведены CSM в рамках исследовательского проекта, финансируемого ECSC / 10 /. На сегодняшний день наш опыт показывает, что без использования трещинопоглотителей невозможно установить трубопровод марки Х100 в арктических регионах.EUROPIPE предлагает промышленности различные типы гасителей трещин. Рисунок 16: Полномасштабные испытания на разрыв, проведенные на трубах 56 x 19,1 мм и 36 x 16,0 мм класса X 100 Рисунок 17: Влияние бора на предел текучести высокопрочного материала трубопроводов (толщина стенки 15-18 мм) Микролегирование с бор также позволил производить материал марки Х 120. Конструкция из сплава, которая позволяет производить этот сверхвысокопрочный материал, также отличается пониженным содержанием углерода. Помимо Cu, Ni, Cr, Nb и Ti, он содержит добавки V и B.Углеродный эквивалент CE IIW химического состава, использованного в первоначальных исследованиях, составлял 0,55%. Используя узкие диапазоны температур для отдельных стадий прокатки, которые основывались на точно измеренных температурах A r3, можно было достичь очень высокого уровня прочности. Кроме того, значения энергии удара 215 Дж были измерены при 30 ° C. Механические свойства перечислены на рисунке 18. Влияние бора на высокопрочные стали для трубопроводов марок от X 80 до X 120 Это имеет первостепенное значение для производителя труб и, в конечном итоге, заказчику, чтобы обеспечить достижение требуемых свойств с минимумом легирующих добавок, чтобы контролировать затраты на производство труб и сделать более привлекательным использование трубопроводов из высокопрочной стали для транспортировки газа под высоким давлением на большие расстояния.Было необходимо подходящее сочетание химического состава труб и параметров термомеханической обработки, обеспечивающее правильный баланс между прочностью, ударной вязкостью и свариваемостью. Помимо ниобия, титана и ванадия, эффективным считался микролегирующий элемент бор. Поэтому была проведена серия лабораторных испытаний листовой прокатки с хорошо известным химическим составом материала марки X 80, начиная с чрезвычайно низкого CE IIW, всего лишь 0,38%. Помимо скорости охлаждения (ок.15 и 25 ° C / с), все условия прокатки и охлаждения поддерживались постоянными. На рисунке 17 показано влияние бора на предел текучести листа по сравнению с плавками без бора. Как видно из рисунка, свойства листа класса X 100 для толщины стенки 20 мм были достигнуты с CE IIW около 0,41%, что очень мало. Увеличение предела текучести, достигаемое за счет добавления бора, составляет примерно от 70 до 100 МПа по сравнению с материалом, не содержащим бор. Во всех случаях основной материал характеризовался преимущественно бейнитной микроструктурой.Энергия Шарпи с V-образным надрезом, измеренная при 40 ° C, превышала 200 Дж. Только сплавы на основе микролегированных бором сплавов, содержащие 0,06% C, показали более низкие значения Шарпи, от 100 до 170 Дж при 40 ° C. Рис. X 120 Аспекты, которые необходимо решить при сварке продольного шва Многопроволочный процесс дуговой сварки под флюсом, широко используемый для наплавки двухпроходного продольного шва на трубе, связан с большим тепловложением и приводит к проблемам, которые невозможно решить. занижена в случае марок X 100 и X 120, нацеленных на.Первая проблема — разупрочнение основного материала, прилегающего к продольному шву сварного шва. Эта проблема в некоторой степени существует также в случае материалов марок X 80 и X 100. Но степень проблемы здесь такова, что с ней можно легко справиться. Документ № SYMP-03 Gräf 6
8 Вторая проблема связана с продолжением использования проверенной дуговой сварки под флюсом и достижением адекватной прочности и ударной вязкости металла шва двухпроходного продольного шва из материала X 120 с наивысшей прочностью.Эту проблему нельзя решить путем выбора подходящего химического состава только для металла шва. Было бы скорее необходимо уменьшить подвод тепла за проход. Среднее тепловложение за проход, которое составляет 2 кДж на сантиметр сварного шва и на миллиметр толщины стенки трубы, необходимо значительно снизить (например, до 1,5 кДж на сантиметр сварного шва и на миллиметр толщины стенки трубы). . Имеющийся на сегодняшний день производственный опыт в этой связи недостаточен для оценки разупрочнения основного материала, прилегающего к сварному шву.Это зависит также от толщины стенки трубы. Наконец, такой подход ограничен необходимостью сварки с достаточным перекрытием и, следовательно, достаточной производственной безопасностью. Если невозможно снизить тепловложение при двухпроходной сварке под флюсом до необходимой степени без ущерба для безопасности производства, следует искать альтернативные методы сварки, включающие многослойную сварку. Эти методы, в свою очередь, неизменно приводят к высокой стоимости инвестиций в трубные заводы. Кроме того, будет нелегко быстро переключиться с существующих методов сварки на требуемые новые методы.Поэтому необходимые решения в этом контексте чреваты неопределенностью для производителя труб. Производство листов и сварка в полевых условиях (разработка сварочных материалов) уже хорошо развиты. Кольцевая сварка в полевых условиях X 100 / X 120 Ручная сварка SMA и механизированная сварка GMA в полевых условиях высокопрочных трубопроводов марок X 100 и X 120 не представляет серьезных проблем. Химический состав марки X100 будет практически таким же, как у толстостенной трубы марки X 80 (дополнительно легированной молибденом).С классом X 120 можно использовать такое же низкое содержание C, но с несколько более высоким эквивалентом C (от 0,50 до 0,55% согласно IIW). Рисунок 19: Факторы, влияющие на склонность к образованию холодных трещин во время строительства трубопровода (сварка в полевых условиях) Углеродный эквивалент высокопрочных марок стали для трубопроводов сам по себе не оказывает существенного влияния на пиковую твердость при типичных условиях полевой сварки (сокращенно t 8/5 охлаждение раз, рисунки 20 и 21). В кольцевых сварных швах, которые всегда характеризуются временем охлаждения t 8/5 = от 2 до 6 с, максимальная твердость ЗТВ корневого шва изначально определяется 100% мартенситной структурой и, следовательно, зависит только от содержания углерода.Этот аспект следует принимать во внимание при включении ограниченных углеродных эквивалентов в стандарты и спецификации для обсуждаемых высокопрочных сталей. То же самое и с классом X 120, представляющим наивысший целевой уровень прочности. Следовательно, нет никакой разницы в поведении основного материала при холодном растрескивании между классами X 100 и X 120. Пиковая твердость в ЗТВ кольцевых швов играет важную роль в предрасположенности к холодному растрескиванию (Рисунок 19). Значительное влияние также оказывают высокие остаточные напряжения, возникающие в зоне сварного шва в критический период между сваркой корневого шва и сваркой горячего шва.По мере нанесения горячего шва твердость ЗТВ корневого шва снижается в результате повторного нагрева (эффекты нормализации и отпуска), так что риск холодного растрескивания, которое предпочтительно может возникать на зазубринах корневого шва, значительно увеличивается. уменьшено. Теоретически остаточные напряжения увеличиваются с увеличением прочности материалов. С этой проблемой можно справиться, используя мягкие целлюлозные электроды для нанесения корневого прохода. Однако этот аспект и повышенная твердость ЗТВ не будут иметь никакого значения при условии, что температура сварного шва поддерживается при температуре 50 ° C во время критической начальной стадии и любых незапланированных перерывов во время последующей сварки.Хорошо известно, что холодное растрескивание кольцевых сварных швов может возникать только тогда, когда температура между проходами падает значительно ниже плюс 50 ° C. Рисунок 20: Сравнение способности к упрочнению более старого материала трубопровода X 70 с современным материалом трубопровода X 100 в отношении типичного диаметра кольца. условия сварки (расчет по формулам Маннесмана) Таким образом, необходимо подчеркнуть, что это не основной материал, а металл сварочного шва, наплавленный сверхпрочными основными вертикальными вниз электродами, который более чувствителен и, следовательно, играет главную роль в предотвращении образования холодных трещин при сварке материалов класса X 100 и особенно X 120.Выбираемая температура предварительного нагрева должна соответствовать химическому составу металла шва и документу № SYMP-03 Gräf 7
.9 Ввод водорода при сварке. Это означает, что температура предварительного нагрева должна быть такой, чтобы водород мог адекватно истекать из сверхвысокопрочного основного металла шва в заполнении и прохождении крышки до того, как сварной шов остынет до комнатной температуры.Все эти меры сегодня являются обычным явлением и не предполагают очень больших дополнительных затрат. Производство сварочных материалов, соответствующих классам X 100 и X 120, должно быть в принципе возможным как для SMA, так и для GMAW. Огромное давление на цены на природный газ вынуждает операторов трубопроводов изучать все возможности для снижения стоимости трубопроводных проектов в будущем. Производитель трубок может помочь ему в его начинаниях, поставив высококачественные трубы. Влияние качества труб на снижение проектных затрат будет более значительным, когда трубопровод будет построен до проектного состояния.Наконец, производители труб вносят свой вклад в снижение эксплуатационных расходов на трубопровод в течение его срока службы, определяя путем исследований усталостные, коррозионные и старение свойств труб и материалов труб. Эти свойства в значительной степени влияют на целостность трубопровода и, следовательно, на эксплуатационные расходы. Эти свойства в настоящее время активно изучаются. Знания, полученные в результате этих исследований, могут быть доступны операторам трубопроводов при планировании нового проекта трубопровода или при оценке остаточного срока службы стареющих трубопроводов.СПИСОК ЛИТЕРАТУРЫ / 1 / М. К. Граф, Х.-Г. Хилленбранд: Высококачественная труба — необходимое условие для снижения стоимости проекта, 11-е совместное техническое совещание PRCI-EPRG, Арлингтон, Вирджиния, апрель 1997 г. / 2 / Л. Барсанти, Х.-Г. Хилленбранд, Дж. Маннуччи, Дж. Демофонти и Д. Харрис: Возможное использование новых материалов для строительства трубопроводов высокого давления: отверстие в стали класса X100, Международная конференция по трубопроводам, Калгари, Альберта, сентябрь 2002 г. Рис. 21: Прокаливаемость стали для трубопроводов марки X 100 и X 120 (расчет согласнопо формулам Маннесманна) ВЫВОДЫ Прогнозируемый рост энергопотребления в ближайшие десятилетия требует серьезных усилий для экономичной транспортировки больших объемов природного газа к конечным потребителям. Трубопроводы большого диаметра — лучшее и самое безопасное средство передвижения. В этой статье представлен обзор текущих требований к высокопрочным сталям и связанных с ними разработок. Описаны технические возможности. Также в будущем могут быть реализованы дополнительные существенные улучшения.Несколько трубопроводов, установленных в Европе и Северной Америке за последние два десятилетия, показывают, что использование трубопровода X 80 не вызывает проблем с точки зрения механических свойств и сварки. В результате опытно-конструкторских работ был сделан вывод о возможности достижения механических свойств класса X 100. Свойства защиты от трещин для труб определенных размеров были проверены в натурных испытаниях на разрыв. Первые результаты работы по разработке марки X 120 обнадеживают с точки зрения свойств основного материала.Не только марка стали, но также коэффициент использования и рабочее давление постоянно растут. С точки зрения производителей, необходимо соблюдать определенные моменты при использовании материалов повышенной прочности. Минимальная толщина должна составлять 12 мм для трубы класса X 80 и 16 мм для трубы класса X 100. Увеличение рабочего давления в сочетании с меньшим диаметром и постоянной толщиной стенки должно быть предпочтительным по сравнению с уменьшением толщины стенки. В любом случае отношение толщины к диаметру высокопрочной трубы большого диаметра должно быть более 1% или лучше 1.5%. / 3 / М. Д. Бишоп, О. Рипмайер, Х.-Г. Хилленбранд, Дж. Шредер и А. Лиссем: Прямошовные сварные трубы X80 для высокотемпературного паропровода высокого давления, 3 R international 41 (2002) No. 2/4 / H. Engelmann, A. Engel, PA Peters, C. Дюрен и Х. Мюш: Первое использование труб большого диаметра из стали GRS 550 TM (X80); 3R International 25 (1986), No. 4, / 5 / V. Chaudhari, H.P. Ritzmann, G. Wellnitz, H.-G. Хилленбранд и В. Виллингс: в газопроводе Германии впервые используются трубопроводы нового поколения; Oil & Gas Journal, январь 1995 г. / 6 / H.-Г. Хилленбранд, К. А. Нидерхофф, Г. Хаук, Э. Пертенедер и Г. Веллнитц: Установлены методика и рекомендации по сварке трубопровода X80; Oil & Gas Journal, 15 сентября 1997 г. / 7 / В. Швинн, П. Флесс и Дж. Бауэр: «Производство и работа над пластинами для труб с уровнем прочности X80 и выше», Международная конференция по применению и оценке высококачественные трубопроводы в неблагоприятных условиях окружающей среды, Иокогама, Япония, ноябрь 2002 г. / 8 / Л. Барсанти, Г. Поццоли и Х.-Г. Хилленбранд: Производство и оценка свариваемости трубопровода X100 в полевых условиях, 13-е совместное совещание PRCI-EPRG, Новый Орлеан, США 2001/9 / H.-Г. Hillenbrand, A. Liessem, G. Knauf, KA Niederhoff и J. Bauer: Разработка трубы большого диаметра из класса X100 Отчет о современном состоянии с точки зрения производителя, Международная конференция по трубопроводным технологиям, Брюгге, Бельгия, май 2000 г. / 10 / Дж. Демофонти, Дж. Маннуччи, Д. Харрис, Х.-Г. Хилленбранд и Л. Барсанти: Поведение при разрыве газопровода X100 при полномасштабных испытаниях, Международная конференция по применению и оценке высокопроизводительных трубопроводов в агрессивных средах, Иокогама, Япония, ноябрь 2002 г. Документ № SYMP-03 Gräf 8
10 Документ № SYMP-03 Gräf 9
Посмотреть наш каталог универсальных гофрированных дренажных труб
Применение дренажных труб
Наша одностенная труба используется во многих условиях, в том числе в сельском хозяйстве, жилом секторе, при строительстве водопропускных труб и в рекреационных целях.В 1987 году ADS представила гладкую внутреннюю двустенную трубу N-12®, которая сегодня по всей стране используется в диаметрах от 4 до 60 дюймов для муниципальных ливневых стоков и канализации шоссе, обеспечивая исключительную гидравлику и прочность. В 2008 году ADS представила гладкие двустенные и трехстенные трубы N-12 HP и SaniTite HP диаметром 12–60 дюймов, изготовленные исключительно из полипропиленовой смолы. Санитарная труба SaniTite® HP была добавлена к уже зарекомендовавшей себя линейке продуктов N-12 и была специально разработана для рынка самотечной канализации.
Преимущества использования гофрированной трубы ADS
Наши продукты работают лучше, их легче устанавливать и они более экономичны, чем традиционные материалы. Инертные материалы PP и HDPE устойчивы к воздействию химикатов, истиранию, горячим почвам и сточным водам. Отличительная зеленая полоса ADS на наших трубах гарантирует, что вы получите высококачественные дренажные изделия для труб из HDPE, которые соответствуют строгим стандартам качества.
Гофрированная гладкая внутренняя труба из полиэтилена высокой плотности (HDPE)
Гладкая внутренняя стена, гофрированный внешний вид, превосходная устойчивость к коррозии и истиранию.Труба N-12 доступна с герметичным (ST), водонепроницаемым (WT) концом и гладким концом, каждая из которых предлагает варианты соединения в виде раструба и втулки, прокладки, раструба или пары с номинальным давлением 10,8 фунтов на квадратный дюйм.
Труба для самотечной канализации
Благодаря передовой технологии производства полипропиленовых смол и эксклюзивной конструкции с тройными стенками, SaniTite HP является логичным выбором для самотечных канализационных труб. SaniTite HP предлагает превосходные характеристики соединений, химическое истирание, ударопрочность, а также дополнительные резервы и факторы безопасности, которых нет у сопоставимых продуктов.Он также изготавливается с повышенной жесткостью трубы, прочностью балки и целостностью соединений для длительного срока службы.
Гофрированная гладкая внутренняя труба из полипропилена (ПП)
HP Storm — это высококачественная полипропиленовая (ПП) труба для самотечного ливневого дренажа и идеальный выбор, когда требуются превосходные характеристики соединения и / или большая жесткость трубы.
Гофрированная труба из полиэтилена высокого давления с гладкой внутренней поверхностью
ADS MEGA GREEN HDPE труба — идеальный выбор для экологически безопасных инфраструктурных проектов.Эта двустенная гофрированная труба из полиэтилена высокой плотности, обеспечивающая водонепроницаемость и долгий расчетный срок службы, соответствует стандарту ASTM F2648 и обеспечивает гладкую внутреннюю часть (для гидравлической эффективности) и кольцевую внешнюю гофру.
Гофрированные трубы Двустенные трубы и фасонные части Системы гофрированных труб из ПНД
Гофрированные трубы уже много лет используются в ведущих странах Европы, США и Японии; имеют высокую прочность на сжатие и имеют зубчатую наружную трубку, имеющую округлый вид.EN 13476-1 и DIN 16961-16566 производятся в соответствии со стандартом hdp, производство гофрированных труб наряду с развивающимися технологиями во всех новых проектах, которые сейчас интенсивно используются. Гофрированные трубы с двойными стенками обычно используются для транспортировки сточных вод и сточных вод, что является одной из главных причин, по которой предпочитают высокую прочность и экономичность. Ребристая система на внешней поверхности гофрированной трубы используется для повышения устойчивости трубы к внешнему давлению. Что касается других пластиковых труб, химическая стойкость является одной из наиболее важных характеристик гофрированных труб, наши трубы устойчивы к истиранию и обладают высокой химической стойкостью.
Инфраструктура
— В оросительной системе
— Канализационные и жилые соединения
— Дождевая вода
— Промышленное применение
— Дренажные системы
— Очистные сооружения
— В системе водного транспорта используется сила тяжести.
Характеристики гофрированных труб
Гофрированные трубы; высокая прочность за счет высокой прочности ребер, коррозионная стойкость за счет полиэтилена, полная герметичность, 50-летний срок службы, износостойкий органический состав, гладкая внутренняя поверхность, легко транспортируется и укладываются в короткие сроки.
Если мы исследуем вещества;
— Гофрированная труба Обеспечивает отличную стойкость к истиранию и воздействию химикатов.
— Благодаря внешнему виду и ребрам, стойким к большим нагрузкам. Ударная гофрированная труба — это труба с максимальной прочностью против нагрузки и движения грунта.
— Разжижение почвы под подземными водопроводными трубами, известное в истории против возникающих деформаций и напряжений, является прочностью трубы.
— Гофрированные трубы легкие, легко транспортируемые, благодаря такой конструкции нет необходимости в специальном оборудовании и рабочей силе, до определенного диаметра.
— Гофрированная труба HDPE имеет метод легкого склеивания, они соединяются с ветеринаром, чтобы заглушить уплотнительную втулку прокладки.
— Гофрированная труба HDPE имеет уплотнение до давления 0,5 бар.
— Гофрированная труба Hdpe обеспечивает ремонт и обслуживание.
— Внутренние поверхности могут быть выполнены в любом цвете.
— Гофрированные трубы из полиэтилена должны выполнять свою функцию в течение многих лет, не подвергаясь влиянию условий окружающей среды. Полиэтилен — одна из самых важных характеристик; Земля из гофрированных труб может перемещаться даже при землетрясениях.Они остаются износостойкими по сравнению с химическим сырьем. Потери на трение сведены к минимуму и не подвержены коррозии. Гофрированная пластиковая труба экономична; Экономия времени на транспортировку, рабочую силу и время за счет многолетнего срока службы может продолжаться без проблем. Двустенная гофрированная труба была экономичным и незаменимым вариантом.
Технические характеристики | единиц | Значение | Метод испытаний | г / см3 | 0,950 — 0,960 | ISO 1183 | |||||
Расход расплава (MFR) при 190 ° C — 5,0 кг | г / 10 дак. | 0,4 — 0,7 | ISO1183 | ||||||||
Удлинение при разрыве | % | > 600 | 1 / 2-27, TS1398 | ||||||||
Напряжение при пределе текучести | МПа | 22-27 | ISO 527-2 / 1B / 50, модуль TS1398 | ||||||||
МПа | ≥900 | ISO 527-2 / 1B / 50, TS1398 | |||||||||
Количество черного углерода | 28 28% 9 5 | ISO 6964 | |||||||||
Твердость | Shore D | 59-60 | ISO 868 | ||||||||
Термическая стабильность | Dak | ≥20 | EN 728 | ||||||||
Vicat C Температура размягчения 9113 0002 0002 Vicat 0002 ISO 306 (МЕТОД A) | |||||||||||
Температурная хрупкость | ° C | ASTM D-746 | |||||||||
911 2063 911 2063 911 2063 9112 911 911 9102 9102 911 2063 Теплопроводность Вт / мк | 0,4 | DIN 52612 | |||||||||
Теплопроводность (150 ° C) | Вт / мк | 03||||||||||
ESRC (50 ° C’de), F50 | Часы | > 1000 | ASTM D-1693 |
Гофрированная труба со спирально-навитой структурой, поскольку гофрированная труба обеспечивает более прочную и высококачественную продукцию.Благодаря плавному потоку для высоких гофрированных труб пропускает трансмиссионную жидкость в трубы меньшего диаметра.
— Также из-за гофрированных труб большого диаметра с низким коэффициентом трения не создает отложений и мусора в гофрированных трубах.
— Отличная стойкость к трещинам и ударам.
— Имеет форму множественной муфты, облегчает проект.
— На месте из-за наличия технического углерода не подвержены воздействию УФ-лучей.
— Реализация проекта консолидации будет осуществляться на месте.
— Внутренняя часть изготовлена из полиэтилена и обладает высокой устойчивостью к истиранию.
— Поскольку высокопрочные гофрированные трубы Hdpe из гофрированной трубы легко переносить, быстро укладывать, техническое обслуживание, транспортировка, труд и установка являются экономичными. Операционные расходы низкие. Другая прокладка гофрированная труба пэ в стоимости самая низкая.
Гофрированные трубы HDPE работают двумя способами, которые мы объясним ниже.
Это: Заглушить процесс связывания с помощью сварных швов или прокладок.Системная конструкция стыков не должна протекать.
Проблема уплотнения на самом деле очень важная проблема, которую необходимо вычесть и которая должна быть для нас главным приоритетом.
-Потому что утечка имеет место, будет мешать в нашем месте под протекающими канализационными трубами и начнет исчезать из нашего подземного богатства.
БЕТОННАЯ ТРУБА | Гофрированная труба | ||||||||||||
Внутренний диаметр Выходной сигнал 4 | % Выход 4 | % | Внутренний диаметр | Выход при 100% полном расходе | Полный поток при 60% | ||||||||
с | Mm л / с | мм | л / с | л / с | |||||||||
1000 | 2.309 | 1.524 | 900 | 2.492 | 1.644 | ||||||||
800 | 800 | 933 | |||||||||||
400 | 225 | 148 | 350 | 237 350 | 237 | 237 | 237 0003 | 104 | 69 | 250 | 97 | 64 |
Гладкая внутренняя поверхность обеспечивает высокую скорость текучести.Осадки в гофрированной трубе не возникает. Обеспечивается полная герметизация.
Рассчитан по нормам ATV-110.
DN 200 — DN 1200 График уклона, потока, диаметра, скорости
Канализационные трубы — это продукт, производимый из полипропилена и полиэтилена в группе полиолефинов. Выпускается гофрированная труба диаметром до Ø450 мм; полиэтилен и полипропилен производятся из сырья, гофрированные трубы производятся из полиэтилена.Больше предпочтительнее, потому что значение прочности полипропиленового кольца такой же толщины стенки выше. Методом прокатки изготавливаются трубы диаметром 500 мм и диаметром. Разделены на три основные группы в зависимости от процентного содержания полиэтилена, плотности и кристаллической структуры;
• Сырье полиэтилена низкой плотности (LDPE)
• Сырье полиэтилена средней плотности (MDPE)
• Сырье полиэтилена высокой плотности (HDPE)
Полиэтилен высокой плотности является наиболее химически чистым полиэтиленом.HDPE имеет очень хорошую химическую стойкость ко многим химическим веществам и растворителям.
Наиболее предпочтительно, чтобы продукты, связанные с подробной информацией о полиэтиленовых трубах и фитингах из полиэтилена высокой плотности, СЫРЬЕ ИЗ ПОЛИЭТИЛЕНА находили все подробности о полиэтилене под названием ТРУБА и формировании высокой производительности по сравнению с другими видами сырья в своей области и экономия, как из-за длительной силы, пока вы не сможете найти подробную информацию о продолжительности.
1-й тип: Гомополимер полипропилена: молекулы, полученные из пропилена и этилена, не учитываются.Поэтому из-за мягкого мешка с мягким полипропиленом гомополимер используется при производстве таких материалов, как полиэтиленовые пакеты.
2-й тип: Сополимер полипропилена Bloco: Вклад этилена (3%) в сырье. Мукаввемет температура сырья, используемого при производстве пластиковых труб для использования только в линиях холодной воды, ниже.
3-й тип: Статистический сополимер полипропилена: Опять же, это вклад этилена в сырье. Количество этилена составляет 3-7%.4 Области применения — это места с высокими значениями давления и температуры. Все подробности, касающиеся полипропиленового сырья, молекулы пропилена, полученного из веществ, нафтовых концах получают молекулы большего размера путем добавления конца, полученного таким образом путем полимеризации белого материала, формирование информации касается времени до использования PPRC Pipe и страницы фитингов «полипропиленовое сырье и СВОЙСТВА »вы найдете в разделе.