Технология ультразвуковой сварки: особенности, принцип действия, аппараты и оборудование
В данной статье мы разберем суть сварки ультразвуком (будем говорить преимущественно об ультразвуковой сварки металлов), рассмотрим особенности УЗ-микросварки, опишем принцип действия установок и аппаратов ультразвуковой сварки.
Ультразвуковая сварка металлов
Технология ультразвуковой сварки представляет собой соединение деталей под воздействием ультразвуковых волн, которые преобразуются в механические колебания и вызывают пластическую деформацию плоскостей в месте их соприкосновения, одновременно разрушая оксидные пленки. Свойства металлов почти не изменяются. Установка ультразвуковой сварки состоит из следующих компонентов:
- источник питания;
- преобразователь;
- сварочная головка;
- волноводы.
Электричество преобразуется в звук высокой частоты, необходимый для сварки, головка обеспечивает сжатие рабочих деталей, волноводы передают энергию в ту точку, где сваривают поверхности.
Сфера промышленного применения данного вида сварки достаточно широка. Ее используют для соединения проволоки, фольги, термочувствительных материалов. Также используется при изготовлении мобильных телефонов, микросхем, оптических и других приборов. Современное автомобилестроение и производство звуковой техники также не обходится без сварки ультразвуковым способом. Данный метод ценят за высокую производительность, точность и прочность, а также за возможность сваривать различные сплавы, для которых обычная сварка недоступна.
Преимущества ультразвуковой сварки
Данный вид сварки широко используется и успел доказать многочисленные преимущества:
- Отсутствие сильного нагревания позволяет сваривать даже те металлы, которые характеризуются химической активностью.
- Сварка осуществляется с высокой скоростью.
- Повышается прочность соединения разнородных материалов, которое при высокой температуре, сопровождающей обычную сварку, оказалось бы хрупким.
- Устраняются технологические ограничения, касающиеся сварки алюминия или меди.
- Толщина свариваемых ультразвуковым способом деталей не ограничена, они могут быть тонкими или даже сверхтонкими (например, фольга), причем толщина соединяемых сваркой элементов может различаться.
- Требования к чистоте поверхностей при использовании ультразвука менее строги, чем при обычном способе сварки, допускается наличие оксидной или изоляционной пленки.
- Сварочное усилие невелико, что позволяет избежать сильной деформации в зоне стыка.
- Конструкция установки для УЗ сварки не отличается сложностью.
Экологическая безопасность и гигиеничность также относится к числу достоинств ультразвуковой технологии. Такая сварка требует меньших трудозатрат, ведь она может быть автоматизирована. Сварка ультразвуком не предполагает расходных материалов, что делает ее чрезвычайно экономичной.
Ультразвуковая микросварка
Одной из разновидностей ультразвуковой сварки является УЗ микросварка. Основная сфера ее применения – это микроэлектроника. Когда монтируются полупроводниковые кристаллы, между контактными площадками и выводами создаются проволочные или ленточные перемычки, которые обеспечивают электрическое соединение. Сваривать сверхтонкие детали можно только с помощью ультразвука, контролируя с помощью специальной установки его параметры:
- мощность;
- давление;
- время воздействия.
Процесс сварки основан на взаимодействии электронов со смежными молекулами, соединение тончайшей проволоки происходит на уровне атомов методом диффузии. Современные аппараты для ультразвуковой микросварки позволяют максимально снизить трудоемкость процесса и расширить круг материалов, которые можно сваривать таким методом. Сварка с применением ультразвука используется не только для металлических деталей, но и для изделий из пластика при наложении точечных швов.
Установки ультразвуковой микросварки
Ультразвуковая сварка в микроэлектронике нашла широчайшее применение.
Разберем основные аппараты ультразвуковой микросварки.
- Установка УМС-1АК предназначена для автоматической и полуавтоматической ультразвуковой и термозвуковой сварки золотой проволоки методом «шарик-клин» и алюминиевой, золотой проволоки методом «клин-клин». Управление автоматической установкой производится с помощью специализированной системы управления на базе персонального компьютера, позволяющая производить программирование до 100 технологических параметров: высота, длина, угол наклона перемычки и т. д.
Установка оснащена системой машинного зрения для распознавания образов контактных площадок полупроводниковых приборов. Установка комплектуется ультразвуковым генератором с возможностью автоматической подстройки резонансной частоты в процессе сварочного импульса, при этом используются ультразвуковые пьезокерамические преобразователи с резонансной частотой 62 кГц; 108 кГц. - Аппарат ультразвуковой микросварки УМС-1УТ используется для ультразвуковой сварки внахлест алюминиевой и золотой проволоки «клин-клин». Установка комплектуется дополнительным ручным механическим приводом для опускания сварочной головки по оси Z с помощью – «ручки» с целью точного позиционирования сварочного электрода относительно контактной площадки и для оперативной коррекции уровня сварки с разновысотностью до 6 мм и глубиной «колодца» до 18 мм (при длине электрода 21мм, 3 мм остаются на закрепления электрода в ультразвуковом преобразователе).
- Установка УМС-2ШК предназначена для автоматизированной термозвуковой сварки золотых проволочных выводов методом «шарик-клин», с дополнительным закреплением «клина» «шариком», с возможностью присоединения золотых шариков на контактные площадки (бампирование) и «внахлест» методом «клин-клин» Кроме того установка предназначена для автоматизированной ультразвуковой сварки алюминиевой проволоки и сварки ленты.
- Установка УЗ сварки УМС-21У используется для ультразвуковой сварки алюминиевой проволоки диаметром от 100 мкм до 500 мкм внахлест методом «клин-клин».
Установка изготавливается в двух вариантах: при сборке приборов проволокой диаметром от 100 до 350 мкм, отделение проволоки от второго сварного соединения происходит с помощью зажимных губок; при монтаже проволокой диаметром 400-500 мкм с обрезкой сварочной проволоки после второй сварки с помощью «ножа».
- Установка сварки ультразвуком УМС-2ТКУ, предназначенная для точечного присоединения золотых проволочных выводов диаметром от 15 до 50 мкм к контактным площадкам без корпусных диодов методом термокомпрессионной и термозвуковой микросварки (для проволочного монтажа гибридных интегральных микросхем).
Что такое ультразвуковая сварка металлов?
Екатерина
На данный момент существует около сотни самых разнообразных способов сварки металлов. У каждого из них есть свои достоинства и недостатки, особенности и сферы применения. Какие-то методы незаменимы на опасных объектах, а какие-то становятся основополагающими в практике домашних мастеров. Но существуют и такие способы сварки, о которых мы мало что слышим в силу узкого применения.
Один из таких способов — сварка ультразвуком. Ультразвуковая сварка нечасто на слуху, но она все же широко применяется при сварке микроэлектроники, проволоки, листового металла и прочих тонких или просто маленьких изделий. В этой статье мы подробно объясним, что такое ультразвуковая сварка и как работает данный метод соединения металлов.
Содержание статьи
- Общая информация
- Технология
- Достоинства и недостатки
- Оборудование
- Вместо заключения
Общая информация
Ультразвуковая сварка металлов — метод сварки, в основе которого лежит применение ультразвуковых колебательных волн. Широко применяется не только для сварки металлов, но и для соединения деталей из пластмассы, ткани, натуральной кожи. Также с помощью ультразвука вы сможете сварить стекло с металлом. Вы можете комбинировать ультразвуковую сварку с точечной, контурной или шовной сваркой.
Интересный факт: в конце 60-х годов прошлого века с помощью ультразвуковой сварки был собран автомобиль, изготовленный из пластмассы. Именно благодаря ультразвуковому оборудованию этот проект удалось успешно завершить.
Читайте также: Ультразвуковая сварка пластмасс
Существуют даже специализированные приборы для ультразвуковой сварки. Например, большой популярностью пользуется ультразвуковая швейная машина для сварки полимеров (брезента или подобных изделий). Но про оборудование мы подробнее поговорим позже.
Технология
Ультразвуковая сварка металлов может выполняться с использованием самых разнообразных типов сварных соединений. Вы можете сварить две детали внахлест, раздавить кромки и сварить их, можете встык сварить круглую деталь с плоской, и так далее. Словом, возможности практически безграничны.
Достоинства и недостатки
У ультразвуковой сварки (как и у любого другого метода) есть достоинства и недостатки. Давайте рассмотрим их подробнее, чтобы вы могли понять, в каких целях стоит применять ультразвук, а в каких от этой идеи лучше отказаться.
Первое достоинство — отсутствие необходимости в тщательной подготовке металла под сварку. Единственное, что необходимо сделать — обезжирить поверхность. Все. Можно даже не удалять грязь или ржавчину. При других методах сварки подготовительный процесс отнимает много времени и сил, а вот с применением ультразвука эта проблема легко решается.
Второй плюс — местный нагрев. Металл нагревается только в том месте, где планируется сварное соединение. По этой причине исключены какие-либо деформации металла из-за избыточного нагрева. Это достоинство особенно заметно при сварке пластмассовых деталей.
Третий плюс — возможность варить даже в труднодоступных местах, при этом вся сварка производится очень быстро, ведь металл успевает нагреться менее чем за секунду. К тому же, вы без труда сварите очень тонкий металл. И говоря «тонкий» мы подразумеваем даже металлические листы толщиной не более 0,001 миллиметра. Впечатляет!
Но, поскольку наш материал объективен, мы расскажем и о недостатках. Учтите, что все они не так существенны.
Во-первых, в некоторых ситуациях все же приходится приобретать дорогие генераторы ультразвуковых волн, если бюджетные модели не справляются. Но, справедливости ради, случается это крайне редко. В нашей практике еще не было ни одного случая, когда бы недорогой ультразвуковой генератор не справился со своей работой.
Также иногда бывают ситуации, когда ультразвук не может сварить толстый металл. Эту проблему можно решить, если подбирать вогнутые детали. Они будут фокусировать ультразвук в зоне сварки и тем самым даже толстый металл быстро расплавится.
Оборудование
Раз уж мы дважды упомянули оборудование, остановимся подробнее на этой теме. Существует три типа аппаратов для ультразвуковой сварки:
- Аппараты, выполняющие точечно-контурную сварку
- Сварочники, выполняющие шовную или шовно-шаговую сварку
- Мобильные (переносные) аппараты малой мощности, например, сварочные пистолеты.
При этом мощность аппарата может быть от 100 до 1500Вт, в зависимости от его цены, назначения и размеров.
На сварочных аппаратах, произведенных до конца 70-х, использовался магнитострикционный принцип генерации ультразвука. Но на данный момент такие аппараты не выпускаются, им на смену пришли установки, в которых ультразвук генерируется с помощью встроенного пьезоэлектрического преобразователя.
На данный момент такое оборудование производят многие страны Европы и мира, в том числе Россия. Качество отечественной продукции вполне приемлемо, особенно учитывая невысокую стоимость по сравнению с зарубежными конкурентами. Вообще производство ультразвуковых сварочных аппаратов началось еще в Советском союзе. Тогда такие аппараты в основном использовались для сварки микросхем. Сейчас же сфера применения стала куда шире.
Вместо заключения
Сварка ультразвуком незаменима при работе с маленькими и тонкими деталями, которые просто невозможно сварить вручную или с применением других технологий. Благодаря ультразвуку металл не деформируется и не растекается, а образует прочное соединение. Также сварка ультразвуком позволяет беспроблемно варить металлы, покрытые окисной пленкой. Например, алюминий, с которым у сварщиков обычно много проблем.
К тому же, оборудование для ультразвуковой сварки стоит не так уж дорого. Поэтому рекомендуем испробовать в своей практике этот метод соединения металлов. Если вы когда-либо выполняли ультразвуковую сварку своими руками, то расскажите об этом. Ваш опыт будет полезен для многих новичков. Желаем удачи в работе!
Похожие публикации
Ультразвуковая сварка металлов | Публикации Виндэк
Тарас Никифоров
Технический центр «Виндэк» (Россия, г. Подольск)
Владимир Гуреев
TELSONIC AG (Швейцария)
На мировом рынке только за последнее десятилетие объем продаж оборудования для ультразвуковой сварки увеличился в несколько раз, и эксперты пророчат ему дальнейший рост. Благодаря новым достижениям в разработке технологии данные сварочные системы позволяют решать уникальные задачи в электронной, электротехнической, автомобильной промышленности, а также при производстве аккумуляторов, конденсаторов, солнечных батарей и систем нагрева воды.
В наши дни ультразвуковая сварка металлов находит все более широкое применение и позиционируется чуть ли ни как инновационный продукт. Вместе с тем, мало кто знает, что данный метод был открыт еще в 30-40 годы прошлого столетия, причем, совершенно случайно. При подготовке поверхности алюминия к контактной сварке экспериментаторы, применившие для этой вспомогательной цели ультразвуковые колебания, неожиданно для себя отметили, что соединение металлических пластин происходит еще до пропускания через них сварочного тока. Вот так и было положено начало совершенно новому виду сварки.
Как работает?
Область применения такого метода соединения простирается в диапазоне от пластмасс до цветных металлов. Однако, независимо от свариваемых материалов, оборудование для ультразвуковой сварки традиционно состоит из высокочастотного генератора, блока управления, механической колебательной системы и привода давления.
Ультразвуковой генератор преобразует ток электрической сети в ток высокой частоты, который по получении сигнала с блока управления подается на пьезоэлементы колебательной системы. Преобразование колебаний электрического тока высокой частоты в механические и введение их в зону сварки обеспечивается механической колебательной системой. Последняя, в свою очередь, состоит из конвертера (преобразователь), бустера (усилитель) и волновода (сонотрод) и является главным узлом технологии ультразвуковой сварки.
Для доступности понимания сравним колебательную систему, обеспечивающую практическую реализацию метода, например, с автомобилем (Рис.2). Конвертер выступает в роли мотора, преобразовывая ток высокой частоты в механические колебания с соответствующей частотой. Далее бустер, действуя как коробка передач, изменяет амплитуду колебаний в зависимости от передаточного числа и переадресует их на волновод. Волновод, увеличивая при необходимости амплитуду механических колебаний высокой частоты, передает их непосредственно в зону сварки, приводя в движение верхнюю свариваемую деталь.
В основу работы пьезокерамического конвертера положен хорошо известный многим еще со школьной скамьи пьезоэлектрический эффект. При воздействии на пьезоэлемент переменного давления возникает переменное электрическое напряжение, а под воздействием переменного электрического поля возникают механические напряжения, которые вызывают упругие деформации материала в следствии чего пьезоэлемент начинает сжиматься и увеличиваться на определенную величину с частотой равной частоте тока.
Величина изменения размера пьезоэлемента соответствует амплитуде механических колебаний (Рис.3), которая зависит от мощности и конфигурации конвертера. Так, при частоте 20кГц амплитуда колебаний пьезокерамического конвектора, как правило, не превышает 10мкм. Однако, за счет увеличения амплитуды бустером и волноводом можно получить максимальную амплитуду в зоне сварки — до 70мкм. Для ультразвуковой сварки обычно используется частота от 20кГц и выше. Применение той или иной частоты зависит от материала и габаритов свариваемого изделия.
Применительно к реальным технологиям это явление может иметь очень положительный эффект. Вот и в процессе ультразвуковой сварки металлов колебательные движения волновода совместно с усилием прижатия передаются на верхнюю свариваемую деталь. Она по определению должна быть подвижной относительно нижней детали, прочно закрепленной на наковальне. В результате между деталями возникает трение с определенной частотой и амплитудой, способствующее их сращиванию между собой (Рис.4). Именно поэтому ультразвуковую сварку можно еще классифицировать, как механическую сварку трением с высокой частотой без ввода сварочного тока в зону сварки.
В процессе сварки микроскопические смещения деталей относительно друг друга вызывают стирание шероховатостей, разрушение оксидных пленок и возникновение узлов схватывания. При повышение температуры в зоне сварки, за счет трения и дальнейшей деформации свариваемых деталей, наблюдается повышение пластичности поверхностных слоев металла, вытеснение оксидных пленок и загрязнений из зоны сварки. Все это приводит к интенсивному разрастанию зон схватывания, диффузии одного материала в другой, локальному плавлению верхних атомарных слоев, появлению новых и стойких межатомных связей. Данные структурные изменения можно воочию наблюдать на фотографии микрошлифа покрытых серебром медных проводов, которые были сварены между собой при помощи ультразвука.
Плюсы применения
Ультразвуковая сварка металлов обладает уникальными технологическими свойствами, которые в практическом применении дают ей сто очков вперед на многих направлениях. Перечислим только главные из них.
Прежде всего, это возможность производить сварку без предварительной подготовки поверхности соединяемых деталей и при весьма незначительном температурном воздействии, оказываемом непосредственно на них. Отсюда вытекает такое существенное преимущество ультразвуковой сварки, как умение накрепко и без печальных последствий соединять между собой термочувствительные элементы.
Более того, допустима сварка деталей разной толщины, а также разнородных металлов (медь-алюминий, алюминий-никель и др. ). При ультразвуковой сварке достигаются отличные электрические свойства и незначительное переходное сопротивление.
Что очень даже существенно, прочность обеспечиваемых ультразвуком соединений приближается к 70% от прочности основного материала. Дополнительно следует отметить высокую скорость, экологическую чистоту и экономичность процесса.
Проверено практикой
Как уже было сказано, инновационная технология ультразвуковой сварки металлов благодаря своим особым свойствам находит все более широкое применение в самых различных отраслях промышленности. Например, в автомобилестроении метод активно используется при соединении медных многожильных проводов жгутов электропроводки (Рис.6). В России данную технологию весьма успешно применяют, в частности, такие производители автокомпонентов, как Leoni Group, Prettl, ИВК, Завод радиоаппаратуры, ПТОО ОАО «АВТОВАЗ» и другие. Конкурентными преимуществами собственной продукции они во многом обязаны внедрению у себя ультразвуковой технологии. Так ультразвуковые системы TelsoSplice, выпускаемые швейцарской фирмой Telsonic AG, способны сваривать многожильные медные провода суммарным сечением от 0,5 до 45мм2. Также ультразвуковая сварка используется при производстве электромоторов и патронов для подушек безопасности.
Масштабное применение ультразвуковая сварка обрела в электронной и электротехнической промышленности. И ничего удивительного здесь нет. Ведь ультразвук умеет соединять как миниатюрные изделия, так и проводку большого суммарного сечения до 200мм2 . Впрочем, в последнем случае описываемые нами системы оснащаются генераторами мощностью в 10кВт и наделяются способностью оказывать усилие в 8000Н.
С помощью ультразвуковой технологии, например, на «Свердловском заводе трансформаторов тока» к медному контакту присоединяют многожильные провода. Тем же способом специалисты ОАО «Протвинский опытный завод «ПРОГРЕСС» приваривают многожильные медные провода к шинам электрических шкафов. Наглядной демонстрацией преимуществ ультразвуковой сварки можно назвать и ее применение в компании Bosch. В частности, там при изготовлении электродвигателей соединяют провода с контактами без снятия с них защитной эмали, что позволило полностью автоматизировать процесс сборки автомобильных электромоторчиков.Или еще примеры. Растущая потребность в солнечных батареях и системах нагрева воды повлекла за собой использование ультразвуковой шовной сварки металлов в процессе создания и такого рода устройств. Компания «Элеконд» применяет ультразвук в соединении алюминиевой фольги и контактов. Кстати будет сказать, что технология применима также и в изготовлении самой алюминиевой фольги. Но продолжим о применениях, так сказать, по прямому назначению.
При производстве литий-ионных аккумуляторов компания VARTA при помощи ультразвука сваривает между собой алюминиевую, медную и никелевую фольгу. На заводе им. Фрунзе при изготовлении предохранителей тем же способом сваривают медные и биметаллические пластины. ФГУП ВНИИА им. Н.Л. Духова, используя технологию ультразвуковой сварки, соединяет алюминиевую фольгу толщиной всего от 5мкм.
Примером уникальности метода и его нацеленности на решение сложных задач, недоступных другим технологиям, может служить и соединение медных проводников с контактами в керамической подложке (Рис. 8). Впрочем, как в оценке всего нового, не будем спешить с конечным выводом. В самом ближайшем будущем нам еще предстоит узнать, на что еще способна ультразвуковая сварка.
А о том, что это обозримая перспектива свидетельствует опыт уже упомянутой компании TELSONIC AG. Она выпускает прецизионные сварочные системы, способные работать как автономно, так и в составе автоматизированных линий. Причем, неустанно продолжает поиск новых применений. Официальным дилером этой компании в России является ООО «Технический центр «Виндэк» из подмосковного Подольска.
Подводя итог, следует сказать, что использование ультразвуковых технологий существенно облегчает получение требуемых характеристик сварного соединения и повышает эффективность производства.
Ультразвуковая сварка – возможности применения в жгутовом производстве и не только
Еще в 40-е годы прошлого века появились разработки в области промышленного применения ультразвукового излучения. Одним из направлений разработок была предварительная очистка поверхностей свариваемых деталей ультразвуком. Параллельно получило развитие использование ультразвука для сварки металлов и других материалов. Во время проведения испытаний и лабораторных исследований разработчики отметили, что металлические образцы сваривались под воздействием ультразвука еще до воздействия электрическим током. Можно сказать, что этот процесс был открыт в какой-то степени случайно.
Сегодня трудно найти отрасли производства, где бы не применялась ультразвуковая сварка. Наиболее активно она используется в автомобильной, электротехнической промышленности, в производстве бытовой электроники, холодильных установок, аккумуляторных батарей, в солнечной энергетике, все чаще ее применяют в специальных отраслях, в том числе авиационно-космической.
Рассмотрим подробнее эту технологию и области ее применения.
В системах ультразвуковой сварки высокочастотная электрическая энергия преобразуется в механические колебания в преобразователе (рис 1). Частота генерируемого ультразвука составляет от 20 кГц. Ультразвуковая металлическая сварка — это диффузионный процесс в твердом состоянии при одновременном воздействии на свариваемые поверхности высокочастотных колебаний, прижимного давления и теплового воздействия. Высокочастотные колебания, приложенные под нагрузкой, разрушают поверхностные пленки и оксиды, образуя чистое, контролируемое, диффузионное сварное соединение (рис 2). Происходит сухое и чистое трение, в результате которого образуются узлы схватывания. Атомы свариваемых деталей образуют между собой связи, что и создает такое соединение.
Для качественного процесса ультразвуковой сварки важно обеспечить оптимальное соотношение трех ключевых параметров:
- времени — продолжительность воздействия ультразвуковыми колебаниями;
- амплитуды колебаний — величина смещения в процессе колебаний;
- величины прижимного усилия.
У процесса есть ряд существенных преимуществ:
- возможность сваривать поверхности без предварительной очистки.
Окислы и другие поверхностные загрязнения очищаются в процессе сварки под воздействием ультразвука;
- возможность сварки тонких материалов и приварки тонких материалов к материалам большой толщины;
- относительно низкие температуры процесса. Нагрев не более чем до 1/3 температуры плавления материалов, не вносящий существенных изменений в физические свойства металлов;
- отсутствие вредных выделений и безопасность процесса для рабочего персонала;
- высокая прочность сварного соединения;
- высокие токопроводящие свойства соединения и низкое переходное сопротивление;
- возможность соединения однородных и разнородных материалов;
- низкая стоимость сварных соединений.
Российские производители жгутовой и другой электротехнической продукции уже оценили все преимущества использования ультразвуковых соединений. Пока эта технология больше применяется в гражданском сегменте, но производители специальной техники также проявляют к ней интерес.
Решения, которые предлагает ГК Остек для ультразвуковой сварки от наших партнеров, компании Branson (Emerson), позволяют технологам в минимальное время подобрать необходимые режимы и параметры (рис 3). Высокие прочностные характеристики, достигающие 70 % от базового материала, позволяют обеспечить высокое качество и надежность жгутового соединения.
О компании Branson-Emerson
В 1942 году Норман Брэнсон (Norman Branson) разработал ультразвуковые решения для использования в промышленности. В 1984 компания Branson стала частью корпорации Emerson. По версии Fortune в 2010 году Emerson заняла 3-е место из компаний электронной индустрии в категории «World’s Most Admired Companies» — «Наиболее авторитетные компании». Направлением ультразвуковой сварки в компании занимаются более 1800 человек.
Помимо производственных мощностей в США и Европейском Союзе есть собственные лаборатории и технические центры. Среди клиентов Branson-Emerson такие компании как LEAR, Nissan, Tesla, Sony, Panasonic, Hitachi, Samsung, LG
Одна из запатентованных разработок компании в области ультразвуковой сварки
Приведем примеры использования ультразвуковой сварки для различных решений.
Первый — ультразвуковая сварка ленточного провода с контактными выводами (рис 4).
В журнале «Вектор высоких технологий» № 4 (33)1 мы рассказывали о том, что ленточные провода активно используются в приборостроении. Машина ультразвуковой сварки логично дополняет автоматизированный комплекс лазерной обработки ленточных проводов БАУМ-ЛЗ-50. Заказчик может получить решение не только для обработки ленточных проводов (лазерной зачистки и мерной резки), но и для сварки жил шлейфа с контактами соединителя.
Другой пример использования ультразвуковой сварки — это сварка разнородных материалов. Благодаря этому возможно комбинировать в изделии различные проводные материалы и соединители (рис 5). В T1 представлена совместимость различных материалов. Помимо использования этой информации мы рекомендуем при подборе оборудования проводить тестирование материалов. Это можно сделать в демонстрационном зале Остека или получить тестовое заключение от производителя оборудования вместе с результатами pull-test и peel-test.
Еще один пример: в жгутовом и приборном производстве представлены контакты, соединители и разъемы из различных материалов, поэтому в ряде случаев ультразвуковая сварка может стать хорошей альтернативой традиционной опрессовке и пайке. Возрастающая интеграция жгутов с электронными компонентами, модулями и устройствами также расширяет возможности ее применения.
С помощью ультразвуковой сварки можно делать сращивание проводных заготовок с высокими прочностными характеристиками (рис 6).
Такой способ дает широкие возможности разработчикам и конструкторам при проектировании геометрии жгутовых изделий и комбинировании проводных материалов в жгутовом изделии, становится меньше ограничений в технологической реализации конструкторских решений.
Еще одна возможность повышения технологичности и одновременно снижения массогабаритных характеристик жгутовых изделий — сварка наконечников обработанных проводов, когда жилы провода спрессовываются и свариваются в единое целое (рис 7). Такая сварка позволяет отказаться от контактов и наконечников.
Ультразвуковая сварка жилы провода позволила одному из наших заказчиков обеспечить существенную экономию на контактах для клеммных разъемов без потери в качестве проводного соединения как с точки зрения механической прочности, так и токопроводящих свойств.
Еще одно применение ультразвуковой сварки — производство солнечных элементов, литий-ионных и аккумуляторных батарей, используемых в электромобилях. Для таких изделий важно обеспечить соединение элементов с минимальными значениями переходного сопротивления, поэтому производители по достоинству оценили возможности ультразвука.
Ультразвуковая сварка — это возможность создать прочные соединения с высокими токопроводящими свойствами.
Опыт применения технологии в различных отраслях позволяет в короткие сроки обосновать применение ультразвуковой сварки в отраслях специального применения. В ряде зарубежных стандартов, в частности IPC/WHMA-A-620, прописаны критерии контроля качества ультразвуковых сварных соединений. Остек, совместно со своим партнером, компанией Branson, предлагает следующие технологические решения: адаптацию оснастки машин ультразвуковой сварки под конкретные задачи заказчика, экспертное заключение о возможности сварки тех или иных материалов, предоставление результатов тестирования сварных соединений.
Наименования металлов | Медь | Алюминий | Железо | Никель | Серебро | Другие | |||||||||||||||||||||||||||||||||||||
99.![]() |
Фосфорная медь | Теллуровая медь | Бериллиевая медь | Хромированная медь | Красная латунь | Латунь с низким содержанием цинка | Латунь 70% медь и 30% цинк | Желтая латунь | Освинцованная латунь | Морская латунь | Фосфорная бронза | Алюминиевая бронза | Кремниевая бронза | Чистый 99 % | 0.4% содержание свинца | 0.55% содержание свинца | Железо (мягкое) | Сталь | Чугун | Нержавеющая сталь | Чистый Никель | Сплав Никель-Медь (NiCu) | Сплав Никель-Железо (NiFe) | Сплав Никель-Хром-Железо | Чистое серебро | Серебро 925 пробы | Сплав серебро кадмий | Тантал | Литий | Свинец | Золото | Магниевые сплавы | Титан | Кобальтовые сплавы | Цинковые сплавы | Вольфрамовые сплавы | Платиновые сплавы | Магнитные сплавы | |||||
Медь |
99.![]() |
X | X | X | X | X | X | X | X | X | X | X | |||||||||||||||||||||||||||||||
Фосфорная медь | X | X | X | X | X | X | X | X | X | X | X | ||||||||||||||||||||||||||||||||
Теллуровая медь | |||||||||||||||||||||||||||||||||||||||||||
Бериллиевая медь | X | X | X | X | X | X | X | X | X | X | X | ||||||||||||||||||||||||||||||||
Хромированная медь | X | X | X | X | X | X | X | X | X | X | X | ||||||||||||||||||||||||||||||||
Красная латунь | X | X | X | X | X | X | X | X | |||||||||||||||||||||||||||||||||||
Латунь с низким содержанием цинка | X | X | X | X | X | X | X | X | |||||||||||||||||||||||||||||||||||
Латунь 70% медь и 30% цинк | X | X | X | X | X | X | X | X | |||||||||||||||||||||||||||||||||||
Желтая латунь | X | X | X | X | X | X | X | X | |||||||||||||||||||||||||||||||||||
Освинцованная латунь | |||||||||||||||||||||||||||||||||||||||||||
Морская латунь | X | X | X | X | X | X | X | X | |||||||||||||||||||||||||||||||||||
Фосфорная бронза | X | X | X | X | |||||||||||||||||||||||||||||||||||||||
Алюминиевая бронза | X | X | X | X | |||||||||||||||||||||||||||||||||||||||
Кремниевая бронза | X | X | X | X | |||||||||||||||||||||||||||||||||||||||
Алюминий | Чистый 99 % | X | X | X | X | X | X | X | X | ||||||||||||||||||||||||||||||||||
0.![]() |
|||||||||||||||||||||||||||||||||||||||||||
0.55% содержание свинца | |||||||||||||||||||||||||||||||||||||||||||
Железо | Железо (мягкое) | X | X | X | X | X | X | X | X | X | X | X | X | X | X | X | X | X | |||||||||||||||||||||||||
Сталь | X | X | X | X | X | X | X | X | X | X | X | X | X | X | X | X | |||||||||||||||||||||||||||
Чугун | X | X | X | X | X | X | X | X | X | X | X | X | X | X | X | X | |||||||||||||||||||||||||||
Нержавеющая сталь | X | X | X | X | X | X | X | X | X | X | X | X | X | X | X | ||||||||||||||||||||||||||||
Никель | Чистый Никель | X | X | X | X | ||||||||||||||||||||||||||||||||||||||
Сплав Никель-Медь (NiCu) | X | X | X | X | |||||||||||||||||||||||||||||||||||||||
Сплав Никель-Железо (NiFe) | X | X | X | X | |||||||||||||||||||||||||||||||||||||||
Сплав Никель-Хром-Железо | X | X | X | X | |||||||||||||||||||||||||||||||||||||||
Условные обозначения | Серебро | Чистое серебро | X | X | X | X | |||||||||||||||||||||||||||||||||||||
Серебро 925 пробы | X | X | X | X | |||||||||||||||||||||||||||||||||||||||
Отлично | Сплав серебро кадмий | X | X | X | X | ||||||||||||||||||||||||||||||||||||||
Другие | Тантал | X | X | X | X | X | X | X | |||||||||||||||||||||||||||||||||||
Хорошо | Литий | X | X | X | X | X | X | ||||||||||||||||||||||||||||||||||||
Свинец | |||||||||||||||||||||||||||||||||||||||||||
X | Возможно | Золото | X | X | |||||||||||||||||||||||||||||||||||||||
Магниевые сплавы | X | X | |||||||||||||||||||||||||||||||||||||||||
Плохая или неизвестно | Титан | X | X | X | |||||||||||||||||||||||||||||||||||||||
Кобальтовые сплавы | |||||||||||||||||||||||||||||||||||||||||||
Цинковые сплавы | X | ||||||||||||||||||||||||||||||||||||||||||
Вольфрамовые сплавы | |||||||||||||||||||||||||||||||||||||||||||
Платиновые сплавы | X | ||||||||||||||||||||||||||||||||||||||||||
Магнитные сплавы |
Ультразвуковая сварка нетканых материалов — УЛЬТРАЗВУКОВАЯ ТЕХНИКА — ИНЛАБ
С. С. ВОЛКОВ, канд. техн. наук
МГТУ им. Н.Э. Баумана
Изготовление нетканых материалов посредством скрепления волокнистых холстов ультразвуковой сваркой
В
последние годы большое значение приобрели изделия их химических волокон, в
частности нетканые материалы. Эти материалы обладают хорошими фильтрационными
свойствами и высокой прочностью. Сущность технологии изготовления нетканых
полотен заключается в получении волокнистых холстов и образовании между
волокнами прочных связей [1]. Холст – это определенным образом сформировавшийся
слой, состоящий из равномерно распределенных в нем нескрепленных волокон. К
преимуществам способов изготовления нетканых материалов можно отнести:
производительность, значительно превышающую производительность ткацких станков;
возможность автоматизации процессов и объединения в поточную линию агрегатов
для изготовления или подготовки волокон, формирования волокнистых холстов,
скрепление волокон в холсте и отделки материала; низкую стоимость получаемых
материалов; возможность использования в ряде материалов в качестве сырья
непрядевых отходов текстильного и других производств; широкий диапазон
пористости и плотности материалов.
Широко распространен клеевой способ изготовления нетканых материалов, при котором связь между волокнами определяется адгезией связующего к волокнам. Помимо этого способа, применяют различные механические технологии, когда скрепление волокон в холстах осуществляется вязально-прошивным, иглопробивным и валяльно-войлочным способами. Применяют также способы горячего прессования, бумагоделательный, получение нетканых материалов из расплава полимера и др.[1,2].
Наряду с несомненными достоинствами указанным способам присущи и недостатки, обусловливающие хаотическую ориентацию волокон, ограниченную толщину получаемого материала и его низкую прочность. В большинстве случаев прочность волокон не превосходит 20% прочности материала.
На
кафедре «Технологии сварки и диагностики» МГТУ им. Н. Э. Баумана ведутся
исследования в области создания нетканых материалов посредством ультразвуковой
сварки холстов, сформированных из термопластичных волокон либо из их смеси с
натуральными или химическими волокнами, а также разработки технологии и
оборудования для изготовления материалов с помощью ультразвука. Сущность
способа заключается в том, что волокна холста, которые могут быть ориентированы
или распределены случайно, скрепляются посредством ультразвуковой сварки. При
этом холст может состоять из термопластичных волокон (полипропилена, капрона,
лавсана, сарана, хлорина и др.) либо из их смеси с хлопком, вискозой, шерстью и
другими нетермопластичными волокнами. В последнем случае размягченная
термопластичная составляющая обволакивает нетермопластичные волокна, образуя
прочные соединения. С увеличением содержания нетермопластичных волокон прочность
нетканых материалов падает практически линейно. Причем предельно допустимым
содержанием нетермопластичных волокон считать 65%.
Из
всего разнообразия карбо – и гетероцепных волокон исследовали по одному типу
волокон каждого класса: полипропиленовые и полиэтилентерефталатные
(лавсановые). Такой выбор обусловлен исключительными свойствами этих волокон, в
частности, гидрофобностью, делающей их незаменимыми для изготовления
волокнистых фильтров, работающих во влажной среде [3]. Поскольку волокнистые холсты
характеризуются большим коэффициентом затухания, то их скрепление можно
выполнять по схеме контактной ультразвуковой сварки [4].
Для непрерывного осуществления процесса наиболее приемлем способ шовно-шаговой сварки, являющейся разновидностью прессовой сварки, с шаговым перемещением материала. При такой схеме сварки предотвращаются деформации и разрывы нескрепленного холста при сварке и транспортировке готового материала на заданный шаг. При этом сварные швы располагают как в направлении, перпендикулярном продольной оси холста, так и под углом к оси (рис.1,а,б). Протяженные швы можно получить при использовании нескольких сварочных головок, установленных таким образом, чтобы обеспечивалось перекрытие сварных швов (рис.1,в).
Первые
эксперименты по ультразвуковой сварке волокнистых холстов различного развеса
только из термопластичных волокон, проведенные на режимах для сварки сплошных
полимерных материалов, не дали положительных результатов. Возникла
необходимость исследования особенностей процесса теплообразования в волокнистых
термопластичных материалах под действием ультразвуковых колебаний, так как
режим сварки определяет количество энергии, вводимой в свариваемый материал и,
следовательно, возможность разогрева зоны сварки до температуры вязкотекучего состояния.
Процесс образования сварного соединения в этом случае можно условно разбить на
три стадии.
На
первой – происходит частичное размягчение поверхности волокон, расположенных в
слоях, прилегающих к волноводу. Шов имеет спрессованную волокнистую структуру и
незначительное усилие разрыва. На второй стадии волокна, расположенные в слоях,
прилегающих к волноводу, полностью переходят в вязкотекучее состояние и
размягченный термопластичный полимерный материал вдавливается сварочным
давлением во внутренние слои холста, скрепляя их. Шов имеет при этом
характерный матовый оттенок и значительную прочность. Третья стадия
характеризуется полным переходом термопластичного материала между волноводом и
опорой в вязкотекучее состояние. Шов приобретает вид прозрачной пленки толщиной
15-20 мкм, прочность его незначительна.
Все эксперименты проводили на лабораторной установке с использованием магнитострикционного преобразователя мощностью 1,6 кВт и резонансной частотой 22 кГц, с ножевым экспотенциальным волноводом из титанового сплава ВТ5. В качестве опоры использовали стальную плиту толщиной 20 мм.
Сварку
выполняли по циклу сварочное давление – ультразвук – сварочное давление. Такой
цикл позволяет охлаждать сварной шов под сварочным давлением после отключения
ультразвуковых колебаний, что существенно влияет на повышение прочности сварных
соединений холста и, кроме того, предотвращает расползание волокон в
расплавленном состоянии [4]. Сварку проводили на отработанных оптимальных
режимах: для холстов, сформированных их полипропиленовых волокон, амплитуда
смещений А=30 мкм, сварочное давление рст= 3,5 МПа, время сварки tсв=0,25 с; для
холстов, сформированных из полиэтилентерефталатных волокон, А=35 мкм, рст=2,7
МПа, tсв=0,3
с.
Можно предположить, что основным источником теплоты при ультразвуковой сварке волокнистых термопластичных материалов, являются гистерезисные потери от циклического деформирования. Явление разогрева полимерных материалов при циклическом деформировании изучалось до сих пор в связи с усталостной прочностью этих материалов [5]. Установлено, что интенсивное теплообразование в испытуемом образце происходит после достижения определенной критической температуры, что обусловлено резким изменением релаксационных характеристик волокнистого полимерного материала – динамического модуля и механических потерь [5,6]. Критическая температура не зависит от амплитуды нагрузки, круговой частоты, условий теплоотвода в волновод и опору и определяется только физико-механическими свойствами волокнистого полимерного материала, режимом нагружения и температурой окружающей среды [7].
Для
сравнения кинетики разогрева волокнистых полимерных материалов и сплошных
полимерных материалов при циклическом деформировании проводили
термографирование процесса ультразвуковой сварки волокнистых полимерных
материалов с помощью электронно-лучевого осциллографа [7]. К преимуществам
этого способа относится его практически полная безынерционность в отличие от
светолучевых способов осциллографирования. Длительное послесвечение
электронно-лучевой трубки позволяет наблюдать визуально и производить
фотографирование термограммы с экрана осциллографа.
В экспериментах использовали хромель-копелевые термопары, имеющие высокую термоэдс. Для одновременного наблюдения двух и более кривых термического цикла, помимо многолучевых осциллографов, можно использовать различные типы коммутаторов. В данном случае использовали коммутатор на шаговом искателе, что позволило получить четкие осциллограммы с двух или трех термопар при исследовании распределения температур по толщине свариваемого термопластичного волокнистого материала.
Из
сравнения кривых термических циклов
различных точек объема волокнистого материала, находящегося под волноводом, со
схематическими кривыми, приведенными в работах [3,7], следует, что режим разогрева
во всех точках волокнистого материала высокотемпературный. В слоях, прилегающих
к волноводу, к концу сварки наступает тепловое равновесие, во внутренних слоях
это не наблюдается.
Характер
термических циклов при сварке волокнистых холстов (рис.2) сходен с характером
термических циклов при сварке сплошных термопластичных мягких материалов,
например, полиэтилена толщиной до 5 мм (рис.3). Критическая температура Ткр перехода к интенсивному
разогреву составляет 100ОС при сварке материалов из полипропиленовых
волокон и 130ОС – материалов из полиэтилентерефталатных волокон при
температуре окружающей среды 23ОС. Время достижения Ткр в различных точках
неодинаково. Это связано с неравномерностью распределения амплитуд напряжений и
деформаций и температурными условиями на границах волновод — материал и
материал – опора. Интенсивность тепловыделения в некоторой степени зависит от
механических потерь ? в термопластичном материале, которые больше у волокнистых
полимерных материалов, чем сплошных. Следовательно, время разогрева до
температур вязкотекучего состояния (сварки) волокнистых материалов будет
гораздо меньше, чем сплошных. Кроме того, по сравнению со сплошными
теплопроводность волокнистых материалов ниже из-за наличия воздушных прослоек.
Можно предположить, что разогрев волокнистых материалов при ультразвуковой сварке будет приближаться к адиабатическому, т. е. протекать без теплообмена с окружающей средой. Зону, выделенную сварочным давлением в волокнистом материале, можно представить как эквивалентный ему сплошной вязкоупругий стержень, по которому распространяются продольные колебания (рис.4).
Примем,
что стержень закреплен на конце х=0,
так как податливость материала опоры много ниже податливости полимерного
материала, боковая поверхность стержня теплоизолирована, теплофизические и
релаксационные характеристики материала не зависят от температуры, вся
механическая энергия, затрачиваемая на циклическое деформирование стержня,
переходит в тепловую. При этих допущениях задача о разогреве волокнистого
материала под действием ультразвуковых колебаний сводится к решению
дифференциального уравнения
dT/d?=d2T/d?2 + q(ch?1? + cos?2?),
где Т, ?, ?, q – безразмерные параметры; ?1,?2 – факторы механических потерь.
Предположим,
что в сечении х=0 температура
практически равна начальной температуре стержня, а в сечении х=l происходит
теплообмен между поверхностью нагретого полимерного волокнистого материала и
холодным волноводом. Для волокнистых полимерных материалов, толщина которых
превышает 5 мм, ?1 > 1,35,
поэтому наибольшая температура разогрева будет непосредственно под волноводом.
Исходя из этого, представим кинетику образования сварного соединения при ультразвуковой сварке волокнистых полимерных материалов следующим образом. В начальный момент сварки непосредственно под волноводом образуется вязкотекучая прослойка, поскольку здесь развиваются наибольшие температуры. Под действие м статического сварочного давления расплавленный полимерный материал вдавливается во внутренние слои волокнистого холста. При малой поверхностной плотности полимерного материала вязкая масса проникает на противоположную сторону, подогревая его по всей толщине, что значительно сокращает время сварки. Когда толщина волокнистого материала сравнима с расстоянием, на которое перемещается вязкая масса под действием заданного сварочного давления, время сварки должно изменяться незначительно. Дальнейшее увеличение поверхностной плотности волокнистого материала приведет к резкому возрастанию времени сварки.
При
проведении экспериментов волокнистые полимерные материалы с различной
поверхностной плотностью сваривали до полного проплавления, которое фиксировали
по образования сварного шва в виде характерной прозрачной пленки (рис. 5). При
этом амплитуду смещения рабочего торца волновода поддерживали на минимальном
уровне – 20 мкм, а давление, близкое к максимальному, составляло 4 МПа.
Поверхностную плотность образцов определяли на аналитических весах второго
класса. Наличие на кривых участков, соответствующих тем значениям поверхностей
плотности, при которых время проплавления изменяется незначительно, и точек
перегиба, после которых наблюдается резкое увеличение времени проплавления,
подтверждает правильность выдвинутого предположения о кинетике образования
сварного шва при ультразвуковой сварке волокнистых полимерных материалов.
Для
исследования структуры с помощью рентгенографического метода выполняли сварку
волокнистых полимерных холстов, из которых затем вырезали сварные швы. При этом
амплитуду смещения рабочего торца волновода и сварочное давление поддерживали
на оптимальном уровне (отмеченном выше), а время пропускания ультразвукового
импульса изменялось от 0,2 до 1 с.
Структуру сварных швов исследовали на приборах УРС-70 и ДРОМ-1 на медном излучении с никелевым фильтром. Степень ориентации кристаллов определяли по кривой азимутального распределения интенсивности рефлекса 110.
Для определения степени упорядоченности кристаллитов образцы быстро вращали вокруг первичного рентгеновского луча при медленном вращении счетчика.
Рентгенограмма
исходного волокна полипропилена свидетельствует о высокой степени ориентации
кристаллов в волокне. При воздействии
ультразвуком в зоне шва происходит локальный перегрев, температура при этом
достигает температуры плавления, что при времени воздействия 0,2 и 0,3 с
приводит к образованию пленки, в которой просматриваются отдельные волокна, а
при 0,4с – полной прозрачной пленки. При воздействии ультразвуком в течение 0,2
и 0,3с происходит значительная разориентация кристаллов, а дальнейшая выдержка
— приводит к их полной переориентации.
На
рис. 6 приведены дифрактограммы исходного волокна, подвергавшегося воздействию
ультразвука в течение 0,3 и 0,4с. Если при времени воздействия tи=0,3с
значительные изменения в дифрактограмме на наблюдаются, то при tи=0,4с
происходит резкое расширение рефлексов вплоть до их слияния. Полуширина
рефлекса возрастает в 2 раза, что свидетельствует об увеличении дефектности
кристаллитов. Степень кристалличности образцов практически не изменяется.
Поскольку сварные швы, полученные при времени протекания ультразвукового
импульса 0,3с и выше, имеют значительное разрывное усилие, можно предположить,
что это обусловлено отжигом и появлением ?-текстуры. Для проверки этого
предположения из полипропиленовой пленки толщиной 30 мкм, ориентированной в
двух направлениях, вырезали образцы размером 50х50 мм для проведения отжига. В
исходном состоянии в пленке выявили две кристаллические текстуры с осью С и осью ?. Вероятно ?-текстура
появилась при термофиксации пленки в процессе ее изготовления. Отжиг проводили
в термошкафу при температуре около 170ОС, близкой к температуре
плавления полипропилена, с выдержкой от 1 до 5 мин. Для предотвращения
коробления образцы закладывали между двумя фторопластовыми прокладками и
зажимали в специальном приспособлении.
Установили, что при выдержке в течение 2 мин текстура практически не изменяется. Увеличение выдержки сопровождается переориентацией кристаллов уже в течение 15 мин происходит полная разориентация кристаллитов.
Результаты
испытания образцов, вырезанные из исходной и отожженной пленок, на разрыв
показали, что прочность при этом изменяется незначительно. Следовательно, само
наличие ?-текстуры не должно проводить к резкому уменьшению разрывного усилия
сварного шва. Однако известно, что переориентация кристаллов и образование
?-текстуры сопровождается релаксацией полимерных цепей и возникновением
внутренних напряжений. Это приводит к росту дефектности кристаллитов, о чем
свидетельствует расширение рефлексов на дифрактограммах (см. рис. 6) и, по-видимому, к образованию
микротрещин, что обуславливает снижение разрывного усилия сварных швов.
Необходимо отметить, что с увеличение значений параметров режимов сварки
разрывное усилие швов не падает до нуля. Поскольку изменение разрывного усилия
в большей мере обусловлено уточнением полимерного материала в процессе сварки,
то и остаточная толщина шва остается неизменной при сварке на этих режимах. Это
явление, названное автостабилизацией толщины шва, впервые обнаружено при сварке
полимерных пленок [4]. Стабильность толщины шва в этом случае можно объяснить
тем, что в процессе утонения зоны сварки происходит постоянное
перераспределение теплоты, выделяющейся в полимере вследствие гистерезисных
потерь в материале, и теплоты, отводимой в холодные волновод и опору. Очевидно,
что при определенной минимальной толщине шва наступает тепловое равновесие или
количество отводимой теплоты даже превалирует над количеством теплоты,
выделяющейся в полимере, вследствие чего температура в зоне сварки начинает
падать.
Увеличение времени пропускания ультразвукового импульса при сварке волокнистых холстов из полиэтилентерефталатных волокон свыше 0,3 с практически не влияют на разрывное усилие и толщину шва. При воздействии ультразвуком от 0,2 до 0,5с значительные изменения в структуре зоны шва на рентгенограммах не зафиксированы.
Чтобы
уменьшить теплоотвод в волновод и опору проводили сварку лавсановых и
полипропиленовых волокон через целлофановые и бумажные прокладки. В результате
разрывное усилие сварного шва понизилось с 110 до 40 Н. При этом в структуре
материала шва наблюдали некоторую амортизацию и полную разориентацию
кристаллитов. Для выявления микротрещин и других дефектов проводили
электронно-микроскопическое исследование сварных швов. Предварительные
эксперименты по отработке методики испытаний показали, что для получения
качественных срезов необходима фиксация волокон. В качестве химического
фиксатора поверхности волокон использовали 2%-ный раствор четырехоксида осмия.
Фиксацию проводили при Т=4ОС
в течение 24 ч, а также 7, 21 и 30 суток. Затем волокна промывали дистиллированной водой,
обрабатывали 96О-ным спиртом и заливали смесью эпоксидных смол
ЭПОН-812. Полимеризацию проводили в термостате при 60ОС в течение 24
ч. Полученные блоки разрезали на ультрамикротоме фирмы «Рейхерт», а срезы
просматривали на световом и электронном микроскопах.
Установили, что только при фиксации в течение 30 суток в срезах довольно прочно удерживается более 90% волокон.
В электронном микроскопе срезы волокон полипропилена имели вид овалов или кругов с неправильным по толщине темным кругом. При очень больших увеличениях (50 000 – 80 000) на поверхности волокон четко видны частицы металла, располагающиеся неравномерным по толщине слоем.
Для
исследования сварных швов проводили предварительную фиксацию волокон указанным
выше способом. После фиксации, сварки на различных режимах и заливки смесью
эпоксидных смол сварные блоки резали на микротоме.
После просвечивания на электронном микроскопе получили типичную картину взаимодействия двух соседних волокон. В отдельных участках происходило полное слияние волокон до исчезновения границы раздела. Однако на некоторых участках такое слияние не происходило, и между волокнами сохранились пустоты, которые, по-видимому, снижали прочность сварного шва нетканых материалов.
Необходимо отметить, что нетканые фильтровальные материалы из ультратонких волокон, разработанные и изготовленные в соответствии с предложенным способом, отвечают всем требованиям, предъявляемым к материалам фильтров предварительной очистки и, следовательно, могут быть рекомендованы для использования в качестве предфильтров, в частности для фильтрации газовых сред от аэрозолей.
ВЫВОДЫ
Контактная
прессовая шовно-шаговая сварка наиболее приемлема для изготовления нетканых
материалов с помощью ультразвука и позволяет избежать деформаций и разрывов
волокнистых холстов при сварке и транспортировке. Такая схема позволяет также
создать универсальное сварочное оборудование.
При ультразвуковом воздействии наиболее интенсивно разогреваются слои волокнистого холста, прилегающие к волноводу, поэтому оптимальной является толщина волокнистого холста, соответствующая поверхностной плотности, равной 0,4 кг/м2.
Для образования прочного сварного соединения наибольшее количество нетермопластичных добавок не должно превышать 65% общего количества волокон в холсте.
Список литературы
- Назаров Ю. П., Афанасьев В. М. Нетканые
текстильные материалы. М.: Легкая индустрия, 1974. 200 с.
- Тихомиров В. Б. Физико-химические
основы получения нетканых материалов. М.: Легкая индустрия, 1971. 328 с.
- Справочник по сварке и склеиванию
пластмасс/А. Н. Шестопалов, Ю. С. Васильев, Э. А. Минеев и др./ Под. общ. ред.
А. Н. Шестопалова. Киев.: Технiка,
1986. 192 с.
- Волков С.
С., Черняк Б. Я. Сварка пластмасс ультразвуком. 2-е изд., перераб. и доп. М.: Химия, 1986. 256 с.
- Урожумцев Ю. С., Скалозуб С. Л.
Акустическая усталость полимеров//Механика полимеров. 1969. № 1. С. 108-111.
- Ратнер С. Б., Бугло С. Т. Влияние
режима нагружения на разогрев пластмасс при циклическом
деформировании//пластические массы. 1969. № 3. С. 465-469.
- Черняк Б. Я., Волков С. С., Орлов Ю. Н. Процесс теплообразования при ультразвуковой сварке пластмасс//Сварочное производство. 193. № 8. С. 53-55.
Версия для печати
Ультразвуковая сварка | Сварка и сварщик
При сварке ультразвуком неразъемное соединение образуется при совместном воздействии на детали механических сдвигающих колебаний с ультразвуковой частоты (f = 20…230 Кгц), относительно небольшом сдавливающем усилии, приложенном перпендикулярно к свариваемым поверхностям и тепловом эффекте вследствие трения при их возвратно-поступательных перемещениях. В результате в зоне сварки наблюдается небольшая пластическая деформация.
В начальный момент действия с ультразвуковых колебаний на свариваемых поверхностях возникает сухое трение, приводящее к разрушению окисных и адсорбированных пленок. После появления ювенильных поверхностей процесс сухого трения переходит в чистое трение, сопровождающееся образованием узлов схватывания. Схватыванию способствует малая амплитуда колебаний трущихся поверхностей и возвратно-поступательный характер этих колебаний.
Для получения механических колебаний ультразвуковой частоты используется открытый Р. Джулен в 1847 г. магнитострикционный эффект. Этот эффект заключается в том, что под действием переменного магнитного поля, направленного вдоль магнитопровода, происходит его укорочение или удлинение.
Основной узел машины для ультразвуковой сварки — магнитострикционный преобразователь (рис. 1), обмотка которого питается током ультразвуковой частоты 20…180 Кгц от генератора. Охлаждаемый водой магнитострикционный преобразователь 1 служит для превращения энергии тока высокой частоты в механические колебания. Высокочастотные упругие колебания передаются через волновод в виде продольных механических перемещений на верхний наконечник
При сварке изделие 4 зажимают между наконечниками, к которым прикладывают усилие, необходимое для создания давления в процессе сварки.
Наиболее распространенными схемами ультразвуковой сварки являются точечная, шовная и по контуру. При точечной сварке наконечниками служат круглые или другой формы стальные пуансоны, при шовной стальные ролики.
Рис. 1. Схема установки для сварки ультразвуком:
1 — магнитострикционный преобразователь; 2 — волновод; 3 — наконечники; 4 — свариваемые детали.
Основные параметры режимов ультразвуковой сварки: мощность преобразователя, частота и амплитуда колебаний инструмента, усилие сжатия, время сварки.
Мощность ультразвукового преобразователя выбирается в зависимости от толщины и свойств металла свариваемых деталей. Обычно она равна 4…6 кВт. Амплитуда колебаний инструмента (Обычно в пределах 10…20 мкм) является одной из важнейших характеристик сварочного процесса, влияющей на свойства сварного соединения и на его прочность.
Усилие сжатия необходимо для обеспечения требуемого физического контакта между деталями. Он составляет 100…2000 кН. Сила трения при смещении детали друг относительно друга под воздействием ультразвуковых колебаний также зависит от усилия сжатия.
Время сварки тоже оказывает существенное влияние на прочность сварного соединения. При малом времени сварки соединение получается непрочным, так как углы схватывания занимают небольшую часть поверхности контакта. Если же время сварки слишком большое, то на деталях образуются глубокие вмятины от электродов, наблюдается усталостное разрушение сварного соединения и схватывание электродов с деталями. Время сварки при точечном соединении 0.5…3 с.
Процесс ультразвуковой сварки сопровождается выделением тепла в месте образования соединения в результате трения в контакте между деталями. Максимальная температура в зоне сварки не превышает 0.5…0.7 температуры плавления. В некоторых случаях детали перед сваркой подогревают.
Предварительный подогрев приводит к уменьшению времени сварки и способствует повышению прочности соединения. Однако слишком высокая температура нагрева не позволяет повысить прочность вследствие увеличения текучести металла и обусловленного этим ухудшения передачи ультразвуковых волн в зону сварки.
Имеющийся опыт применения сварки ультразвуком выявил следующие преимущества этого способа:
1. Сварка ультразвуком позволяет соединить разные металлы, хорошо свариваются алюминий, медь, никель, удовлетворительно — высоколегированные стали. Получены соединения на ряде тугоплавких металлов — ниобии, тантале, молибдена и вольфраме. Существенные успехи получены при сварке металлов с неметаллами (полупроводниками, стеклом и некоторыми другими материалами). С помощью ультразвука сваривают детали из пластмасс, получают соединения биологических тканей, что является одним из уникальных примеров использования сварки ультразвуком и одновременно характеризует ее широкие возможности.
2. Возможны соединения тонких и ультратонких деталей, сварка пакетов из фольги, можно приваривать тонкие обшивки и фольгу к элементам несущей конструкции, толщина которых практически не ограничена.
3. Сварка ультразвуком происходит в твердом состоянии без существенного нагрева места сварки, что позволяет соединять химически активные металлы или пары металлов.
4. Не требуется предварительная зачистка поверхности детали, в связи с чем возможна сварка плакированных и оксидированных деталей.
5. Небольшие сдавливающие усилия вызывают незначительную деформацию поверхности деталей в месте их соединения.
6. Сварка ультразвуком более экономична, так как применяется сварочное оборудование малой мощности. Например, для контактной точечной сварки алюминия толщиной 1 мм необходима машина мощностью 100…150 кВт, при ультразвуковой сварке того же соединения — 2.5…5 кВт.
Недостатки ультразвуковой сварки заключаются в следующем. Прежде всего толщина свариваемых деталей ограничена 2,0 мм. Для больших толщин необходимо увеличить частоту колебаний, что приводит к разрушению волновода. Неустойчивость параметров сварки вследствие нестабильности количества энергии, поступающей в зону сварки из-за отклонений в размерах деталей, различного состояния их поверхностей, нестабильности в работе ультразвукового генератора, механизма сжатия и т. п. вызывает значительные колебания прочности сварных соединений.
Ультразвуковая сварка нашла широкое применение для соединения тонких деталей в приборостроении, радиоэлектронной промышленности и особенно в микроэлектронике, а также для полимерных пленок, полимеров.
Что такое ультразвуковая сварка? Соединение/преобразование термопластов
Ультразвуковая сварка пластмасс (USW) — это соединение или преобразование термопластов с использованием тепла, выделяемого высокочастотным механическим движением. Это достигается путем преобразования высокочастотной электрической энергии в высокочастотное механическое движение. Это механическое движение, наряду с приложенной силой, создает тепло трения на сопрягаемых поверхностях пластиковых компонентов (в области соединения), поэтому пластик плавится и образует молекулярную связь между деталями.
Основной принцип ультразвуковой сварки
1- Детали в приспособлении 2- Спуски и контакты рупора 3- Приложенное усилие 4- Время сварки 5- Время удержания 6- Втягивание рупора размещаются вместе, один поверх другого, в поддерживающем гнезде, называемом приспособлением.
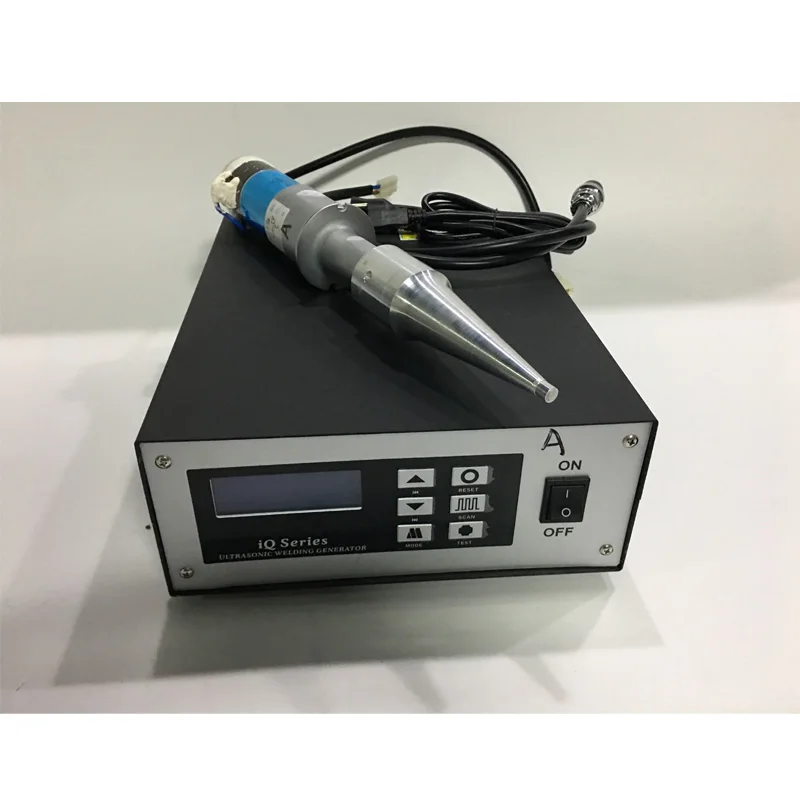
Преимущества ультразвуковой сварки
Быстрое время цикла
Очень точный
Высокая воспроизводимость, отлично подходит для больших объемов и автоматизации
Экологически безопасный
Универсальный, хорошо подходит для различных применений
Без расходных материалов
Материальное вознаграждение
- Для склеивания двух термопластичных деталей необходимо, чтобы материалы были химически совместимы. В противном случае, даже если оба материала могут расплавиться вместе, молекулярной связи не будет.
- Хорошим примером может быть попытка сварки полиэтилена с полипропиленом. Оба этих полукристаллических материала имеют схожий внешний вид и многие общие физические свойства. Однако они химически несовместимы и поэтому не могут быть сварены друг с другом.
- Подобные термопласты (т. е. материалы с одинаковыми химическими свойствами) будут сваривать друг с другом. Например, одна деталь из АБС-пластика будет привариваться к другой детали из АБС-пластика.
- Разнородные термопласты могут быть совместимы, только если их температура плавления находится в пределах 40ºF (6ºC) и они имеют одинаковую молекулярную структуру. Например, вполне вероятно, что деталь из АБС-пластика можно приварить к детали из акрила, поскольку их химические свойства совместимы.
- Вообще говоря, только подобные аморфные полимеры имеют высокую вероятность сваривания друг с другом. Химические свойства любого полукристаллического материала делают его совместимым только с самим собой. Когда свариваемые материалы совместимы, на адгезионное соединение деталей могут влиять несколько других факторов.
Эти факторы включают гигроскопичность, смазки для форм, смазки, пластификаторы, наполнители, антипирены, измельчение, пигменты и сорта смолы.
Особенности конструкции соединения
Конструкция соединения сопрягаемых деталей имеет решающее значение для достижения оптимальных результатов сборки. Конструкция зависит от таких факторов, как тип пластика, форма детали и требования к сварке.
Существует множество различных конструкций соединений, каждая из которых имеет свои преимущества. Некоторые из этих конструкций обсуждаются далее в этом разделе. К конструкции соединения предъявляются три основных требования:
- Однородная площадь контакта
- Небольшая начальная контактная площадка
- Средство выравнивания
Другие сварочные процессы
УЛЬТРАЗВУКОВАЯ СВАРКА ПЛАСТИКА
ВИБРАЦИОННАЯ СВАРКА
ВРАЧ
СВАРКА
ИНФРАКРАСНЫЙ
СВАРОЧНЫЙ
ГОРЯЧАЯ СВАРКА
УЛЬТРАЗВУКОВАЯ ОБРАБОТКА ПЛЕНКИ И ТКАНЕЙ
Как работает ультразвуковая сварка? Полное руководство (с фотографиями)
Последнее обновление
Ультразвуковая сварка, или УЗС, — это метод сварки, в котором используются механические вибрации выше слышимого диапазона. Процесс осуществляется путем преобразования высокочастотной электрической энергии в высокочастотное механическое движение. Механические движения, прилагаемые вместе с силой, генерируют фрикционную теплоту в области пластического соединения. Это приводит к плавлению пластика, образуя молекулярную связь между деталями. Этот метод является быстрым, экономичным, легко автоматизируемым и хорошо подходит для массовой сварки термопластичных материалов.
Основы ультразвуковой сварки
В процессе используется высокая частота ультразвуковых колебаний, обычно от 20 до 40 кГц, для соединения двух пластиковых деталей. Свариваемые пластмассовые детали обычно помещают между наковальней и сонотродом. Эти детали обычно изготавливаются из алюминия или титана. При сварке сонотрод подключается к преобразователю, что приводит к излучению акустических колебаний. Затем эти вибрации передаются от преобразователя на свариваемые детали через сонотрод с высокочастотными скоростями в диапазоне от 16 кГц до 75 кГц.
Основные части ультразвуковой сварки
1. Пресс-машинаПресс-машина используется для удержания сварочной системы и приложения силы к заготовкам. Он состоит из опорной плиты, используемой для удержания охлаждающего приспособления, и пневматического цилиндра для регулирования давления. Пресс-машина также имеет манометр и регулятор для регулировки силы сварки. Функциональность манометров зависит от сварочного усилия аппарата. Чтобы точно сравнить сварочное усилие машины, вам необходимо откалибровать его сварочное усилие, используя локальную ячейку.
2. Генератор Генератор ультразвуковой машины преобразует электроэнергию от однофазного основного источника в необходимое напряжение и частоту. Затем преобразователь преобразует электрическую энергию в механические колебания, используемые для сварки. Микропроцессорный блок генератора управляет сварочным циклом и обеспечивает сварщика важными сварочными данными через пользовательский интерфейс. Пользовательский интерфейс также позволяет оператору вводить необходимые параметры сварки.
3. Сварочный блокПосмотреть этот пост в Instagram
Пост, опубликованный Rim Rock Wire & Assembly (MC) (@rimrockwire)
Это основная часть сварочного аппарата, отвечающая за создание ультразвуковых колебаний аппарата. Сварочный комплект состоит из трех частей: преобразователя, усилителя и сварочного рожка. Все эти три детали смонтированы на прессе сварочного аппарата в центральной точке усилителя. Сварочный блок обычно представляет собой настроенный резонатор для оптимального функционирования. Для получения качественных результатов частота сварочного блока должна близко совпадать с частотой электрического сигнала генератора.
Преобразователь, также известный как преобразователь, используется для преобразования электрической энергии генератора в механические колебания, используемые при сварке. Преобразователь состоит из нескольких пьезоэлектрических керамических дисков, зажатых между двумя металлическими титановыми блоками. Между дисками находится тонкая металлическая пластина, выполняющая роль электрода.
5. УсилительЭта секция служит двум основным целям: усиление механических вибраций, создаваемых на конце преобразователя, и передача их на сварочный рожок. Другая функция заключается в том, что он выступает в качестве основания для установки штабеля на сварочном прессе. Всякий раз, когда энергия преобразователя достигает усилителя, он заставляет его расширяться и сжиматься, усиливая вибрации.
6. Сварочный рожок Сварочный рожок служит для передачи энергии свариваемым деталям. Сварочный рожок также является настроенным устройством, обеспечивающим механическое усиление ультразвуковой машины. Эти компоненты изготовлены из алюминия или титана. Однако алюминий применим только в небольших объемах, поскольку он быстро изнашивается, что приводит к деформации сварных швов. Чтобы контролировать ношение рогов, большинство из них имеют закаленные кончики.
Основание пресса используется для поддержки инструмента, поддерживающего заготовки при сварке. Опорный инструмент был разработан, чтобы прочно удерживать нижние компоненты во время применения ультразвука. Вспомогательный инструмент также спроектирован так, чтобы соответствовать контурам заготовок.
Посмотреть этот пост в Instagram
Сообщение, опубликованное VIAL Automation d.o.o. (@viaautomation)
Применение ультразвуковой сварки
Ультразвуковая сварка широко используется во многих отраслях промышленности благодаря ее способности создавать качественные сварные швы без непосредственного нагрева. Вот обзор применения ультразвуковой сварки.
В автомобильной промышленности ультразвуковая сварка используется для сборки крупных пластмасс и электрических компонентов. Эти компоненты включают дверные панели, приборные панели, рулевые колеса, воздуховоды, обивку и компоненты двигателя. В этой отрасли сварщики предпочитают ультразвуковую сварку из-за низких капитальных затрат, гибкости, короткого времени цикла и автоматизации. Метод также не повреждает отделку поверхности. Это связано с высокочастотными вибрациями, препятствующими образованию следов на изготовленных деталях.
В аэрокосмической промышленности ультразвуковая сварка используется для соединения калибровочных металлов и других легких деталей самолетов, таких как фонари. Ультразвуковая сварка также полезна при сварке алюминия, широко используемого при изготовлении различных деталей самолетов.
2. Компьютерная и электротехническая промышленность Ультразвуковая сварка используется в компьютерной промышленности для соединения проводных соединений для создания небольших и чувствительных цепей. Этот метод также используется для предохранения соединений жгутов проводов, используемых для распределения электроэнергии и сигналов. Ультразвуковая сварка также используется при сборке трансформаторов, электродвигателей, конденсаторов и катушек возбуждения.
Ультразвуковая сварка используется при сборке носителей информации, таких как флэш-накопители и компьютерные диски, из-за необходимости больших объемов. По оценкам, время цикла компьютерного диска, сваренного ультразвуком, составляет менее 300 миллисекунд.
Метод применяется при проведении исследований и экспериментов с микросхемами. Связи, созданные в этом процессе, надежны и предотвращают загрязнение или термическую деформацию компонентов. Метод применим также для соединения проводов, лент и микросхем при изготовлении микросхем.
3. Медицинская промышленность Ультразвуковая сварка используется в медицинской промышленности, поскольку она предотвращает разрушение сварных швов. По этой причине метод используется при производстве специализированных машин для уборки помещений. Автоматизация ультразвуковой сварки обеспечивает строгий контроль допусков на размеры, предотвращая биосовместимость свариваемых деталей. Это снижает производственные затраты без ущерба для качества функций.
Посмотреть этот пост в Instagram
Сообщение, опубликованное VIAL Automation d.o.o. (@viaautomation)
Ультразвуковая сварка используется для изготовления медицинских изделий, таких как иглы для внутривенных инъекций или фильтры, лицевые маски, фильтры для крови и газов, диализные трубки, резервуары для кардиометрии, артериальные и анестезиологические фильтры. Этот метод также используется в производстве медицинских тканей, таких как трансдермальные пластыри, ткани для уборки, стерильная одежда и больничные халаты. Ультразвуковая сварка эффективна при пошиве медицинских тканей благодаря ее способности предотвращать загрязнение и снижать риск инфекций.
В упаковочной промышленности ультразвуковая сварка часто используется для изготовления, упаковки и запечатывания блистерных упаковок, тюбиков и контейнеров. Этот метод также имеет решающее значение при упаковке опасных материалов, которые требуют герметичности и не могут подвергаться воздействию высоких температур. К таким предметам относятся фейерверки, взрывчатые вещества и реактивные химические вещества, такие как калий. Ультразвуковая сварка также используется при упаковке боеприпасов и пороха. Известно, что эти упаковки выдерживают давление и напряжение, защищая потребителя от ненужных несчастных случаев во время применения.
Пищевая промышленность также использует ультразвуковую сварку для упаковки, поскольку она выполняется быстро и может использоваться для изготовления герметичных швов. Бумажные уплотнения, используемые для упаковки, обычно покрываются пластиковыми материалами, такими как полипропилен, перед сплавлением с помощью ультразвуковой сварки для создания воздухонепроницаемого уплотнения. Ультразвуковая сварка также используется для герметизации пищевых продуктов, таких как упаковки для замороженных продуктов, контейнеры для напитков и обертки для шоколадных батончиков.
Преимущества ультразвуковой сварки
Ультразвуковая сварка нашла свое применение в большинстве отраслей и областей применения благодаря своей способности смешиваться с термопластами и другими сварочными материалами, такими как полипропилен. Вот некоторые преимущества ультразвуковой сварки:
1. СкоростьУльтразвуковая сварка использует передачу высокочастотных ультразвуковых акустических колебаний для нагрева, сварки и охлаждения. Все эти процессы происходят очень быстро и позволяют сварить больше изделий за считанные минуты. При использовании ультразвуковой сварки вы получите высокую производительность и короткое время выполнения работ.
2. Непревзойденная безопасность Ультразвуковая сварка очень безопасна. В процедуре используется целенаправленная энергия, что снижает травматизм сварщиков. Тепло, выделяемое во время сварки, локализовано, минимально и быстро рассеивается на требуемых сварных соединениях и материалах. Этот процесс не наносит никакого ущерба сварным швам и окружающей среде.
3. НадежностьПосмотреть этот пост в Instagram
Пост, которым поделилась Грейс Ся (@dizo_ultrasonic)
Известно, что ультразвуковые машины и оборудование долговечны. После того, как они будут собраны и испытаны, вы сможете выполнять массовую сварку с минимальными поломками и неисправностями. В зависимости от вашего проекта сварки вы можете автоматизировать процесс, чтобы уменьшить вмешательство человека. Это уменьшит эксплуатационные расходы и повысит качество сварных швов.
4.
Вы можете использовать методы ультразвуковой сварки для сварки различных материалов. Собираетесь ли вы сваривать термопласты или металлы, вы можете использовать этот метод, не опасаясь неровных швов. Этот метод широко используется для сварки разнородных материалов.
5. Минимальные затраты на материалыПоскольку процесс выполняется быстро, выполнение сварочного проекта требует меньше времени, денег и ресурсов. Процесс сварки не требует соединительных болтов, припоев и клеевых материалов. Таким образом, вы значительно сэкономите на материальных затратах. Благодаря высокой точности ультразвуковая сварка обеспечивает гладкую поверхность с минимальными отходами.
6. Качество соединения Точность ультразвуковой сварки гарантирует высокое качество соединения. В этих соединениях не будет пластических заусенцев, деформаций или дефектов. В результате получается чистый и почти невидимый шов, который не нуждается в ретуши.
Недостатки ультразвуковой сварки
Хотя ультразвуковая сварка имеет свои преимущества, она также имеет недостатки, которые могут снизить эффективность сварочного проекта. Ниже приведены некоторые недостатки метода:
1. Ограничения МатериалХотя ультразвуковая сварка гибка и эффективна для большинства материалов, она плохо работает с некоторыми термопластами. Если вы собираетесь использовать термопласты с высоким содержанием влаги, ультразвуковая сварка становится неэффективной. Этот метод также неприменим при сварке твердых и прочных термопластов, таких как полипропилен.
2. Ограничения по размерамПосмотреть этот пост в Instagram
Пост, которым поделился сварочный аппарат для пластика (@ultrasonic_welding_machine)
Хотя этот метод применим для широкого спектра металлов, он не может работать с изделиями со швами более 150 мм, поскольку выходной сигнал преобразователя находится в диапазоне 100-150 мм. Сварка более толстых материалов, таких как полипропилен, также представляет собой проблему, поскольку для разрыва молекулярных связей требуется много энергии.
Основное оборудование и инструменты для ультразвуковой сварки являются дорогостоящими. Дальнейшее повышение цен на автоматические ультразвуковые сварочные аппараты.
4. Ограничения по типам соединенийУльтразвуковая сварка может использоваться только для соединений внахлестку. Эти соединения перекрывают друг друга, используя плоскую поверхность. Техника непригодна для сварки таких соединений, как угловые, стыковые, тавровые и кромочные.
5. Время выполнения заказа Для ультразвуковой сварки требуется ряд оборудования, инструментов и процессов. Добавление еще одной детали или оборудования в процесс приведет к общему увеличению времени выполнения заказа. Дополнительные инструменты или оборудование требуют индивидуальной настройки инструментов.
Часто задаваемые вопросы
1. Какова минимальная частота, которую можно использовать при ультразвуковой сварке?Минимальная частота, необходимая для ультразвуковой сварки, составляет 20 000 Гц.
2. Как разорвать ультразвуковой сварной шов?Вы можете сломать, сжав сварной шов с противоположных углов, чтобы треснуть и открыть его по линиям сварки. Этот процесс обычно сложен из-за молекулярных связей, образующихся в результате сварки. Вы также можете расколоть сварной шов, ударив по нему молотком.
3. Какие электронные компоненты наиболее подвержены повреждению при ультразвуковой сварке и почему?Посмотреть этот пост в Instagram
Пост, которым поделилась Селена (@se_lena6415)
При сварке ультразвуковым методом обычно вибрируют верхние секции, соединенные сонотродом. Любые другие электронные компоненты, механически прикрепленные к вибрирующим частям, изменят характер вибрации, повреждая сварные швы. Повреждение, вероятно, произойдет в зонах концентрации высоких напряжений, таких как небольшие площади поперечного сечения или участки с острыми углами. Чтобы легко решить эту проблему, изолируйте электрические компоненты от верхней части вибрирующих частей сборки.
Под сварочным зазором понимается разница в высоте между сварочными материалами и конечными сварными швами. Сварщики обычно обеспечивают предполагаемый сварочный зазор около 0,025 мм для размещения слоя расплава. Однако вы можете проверить этот зазор, разработав направляющую энергии на деталях, подлежащих ультразвуковой сварке. Функция директора по энергетике заключается в контроле мощности, необходимой для производства и формирования сварных швов.
Всякий раз, когда вы настраиваете процесс сварки с использованием направляющих энергии, следите за тем, чтобы они не расплавлялись полностью во время сварки. Полное расплавление этих направляющих энергии приведет к вытеканию расплава из соединения, что приведет к вспышке, ослабляющей связи сварного шва.
Для достижения идеальной точности вам следует выбрать ультразвуковой аппарат, который может выполнять сварку на точном расстоянии, автоматически определяя длину конечного шва. Использование небольшого регулятора энергии также является отличной альтернативой, так как его можно увеличить, когда возникнет необходимость.
Заключение
Ультразвуковая сварка требует точности и аккуратности. По этой причине персонал, обслуживающий машины и процессы, должен быть хорошо обучен и иметь высокую квалификацию. Безопасность также имеет первостепенное значение в этом процессе. Таким образом, ультразвуковые сварщики должны быть соответствующим образом подготовлены для уменьшения телесных повреждений и воздействия вредных паров и газов, выделяемых при сварке. Чтобы увеличить срок службы ультразвуковых сварочных аппаратов, убедитесь, что вы регулярно проводите техническое обслуживание и ремонт. При покупке ультразвукового аппарата убедитесь, что вы пользуетесь аутсорсингом у лицензированного поставщика, и проверьте наличие знака качества оборудования.
Изображение.
- 1. Аэрокосмическая и автомобильная промышленность
- 2. Компьютерная и электрическая промышленность
- 3. Медицинская индустрия
- 4. Упаковочная индустрия
- 1. Скорость
- 2. Неуказанная безопасность
- 3. Reliation
- 4.
- 5. Минимальные материальные затраты
- 6. Качество соединения
- 1. Ограничения по материалу
- 2. Ограничения по размерам инвестиций A Высокий начальный
- 3.0014
- 4. Ограничения по типам соединений
- 5. Время выполнения заказа
- 1.
Какова минимальная частота, которую можно использовать при ультразвуковой сварке?
- 2. Как разорвать ультразвуковой сварной шов?
- 3. Какие электронные компоненты наиболее подвержены повреждению при ультразвуковой сварке и почему?
- 4. Каков правильный зазор для ультразвуковой сварки поликарбоната?
Ультразвуковая сварка – процесс и оборудование
Профессиональные знания 61
Обзор процесса
Ультразвуковая сварка компонентов, отлитых под давлением из термопластов, представляет собой процесс, в котором используются механические вибрации выше слышимого диапазона. Вибрации, создаваемые сварочным сонотродом или, как известно, рупором, используются для размягчения или плавления термопластичного материала на линии стыка. Соединяемые компоненты удерживаются вместе под давлением и подвергаются вибрации, обычно с частотой 20 или 40 кГц.
Нажмите здесь, чтобы посмотреть наши последние технические подкасты на YouTube .
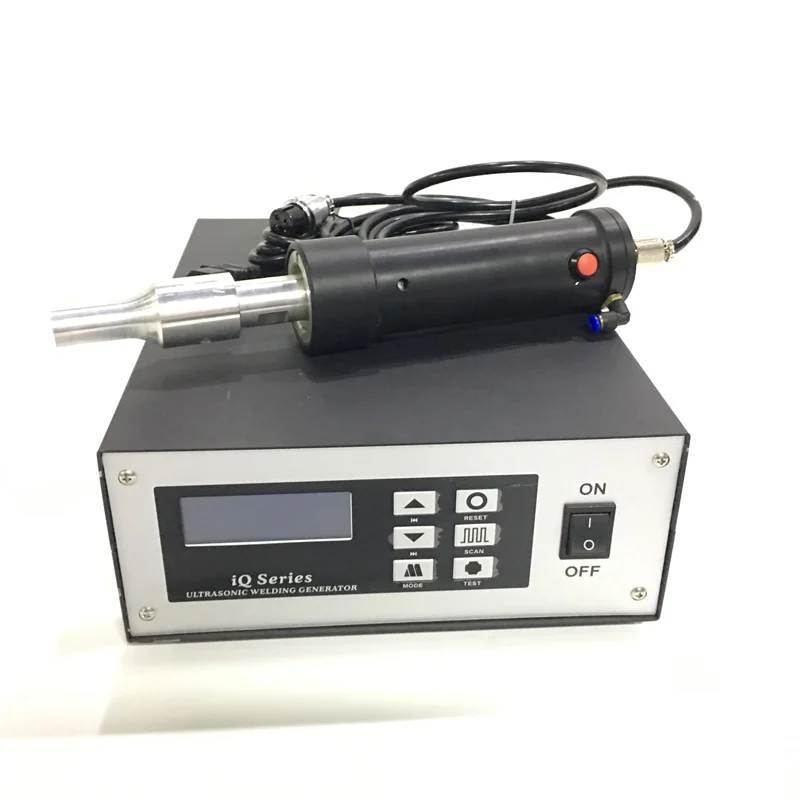
Возможность успешной сварки компонента определяется конструкцией оборудования, механическими свойствами свариваемого материала, а также конструкцией компонентов и соединения. Время ультразвуковой сварки короткое (обычно менее одной секунды), что делает этот процесс идеальным для массового производства. Этот процесс широко применяется во многих приложениях, начиная от автомобильных осветительных приборов и заканчивая продуктами бытовой электроники, такими как корпуса мобильных телефонов.
Рис.1. Ультразвуковой сварочный аппарат
Оборудование
Ультразвуковое сварочное оборудование состоит из пресса, генератора, преобразователя или преобразователя, усилителя, сонотрода или звукового сигнала и инструментов для поддержки компонентов.
Рис.2. Схема аппарата ультразвуковой сварки
Генератор
Генератор преобразует электроэнергию из однофазной сети в нужную частоту и напряжение, чтобы преобразователь преобразовал их в механические вибрации. Микропроцессорный блок управляет циклом сварки и передает ключевую информацию о сварке пользователю через пользовательский интерфейс. Пользовательский интерфейс также позволяет оператору вводить необходимые параметры сварки.
Машинный пресс
Стойка станка предназначена для удержания сварочной системы или штабеля и приложения усилия, необходимого для сварки. Он состоит из опорной плиты, удерживающей инструментальное приспособление, и пневматического цилиндра для приложения усилия.
Аппарат оснащен манометром и регулятором для регулировки силы сварки. Следует отметить, что определенное манометрическое давление, установленное на одной части оборудования для ультразвуковой сварки, не обязательно будет обеспечивать такое же сварочное усилие, как другое устройство, настроенное на то же манометрическое давление.
Сварочное усилие следует откалибровать с помощью тензодатчика, чтобы можно было провести прямое сравнение сварочных усилий от машины к машине.
Также имеется клапан управления потоком, позволяющий регулировать скорость, с которой сварочная головка приближается к свариваемому компоненту. Некоторые производители оборудования внедрили систему приложения электромагнитной силы вместо традиционного пневматического цилиндра. Это дает лучший контроль скорости подхода и может быть полезным при сварке небольших или хрупких компонентов.
Сварочный блок
Это часть машины, обеспечивающая ультразвуковые механические колебания. Как правило, это блок из трех частей, состоящий из преобразователя, усилителя и сварочного рожка, установленный на сварочном прессе в центральной точке секции усилителя. Стек представляет собой настроенный резонатор, скорее похожий на камертон музыкального инструмента. Для работы резонансная частота настроенного сварочного блока должна близко совпадать с частотой электрического сигнала от генератора (с точностью до 30 Гц).
Преобразователь
Преобразователь, также известный как преобразователь, преобразует электрическую энергию генератора в механические колебания, используемые в процессе сварки. Он состоит из нескольких пьезоэлектрических керамических дисков, зажатых между двумя металлическими блоками, обычно титановыми.
Между каждым из дисков находится тонкая металлическая пластина, образующая электрод. По мере того как синусоидальный электрический сигнал подается на преобразователь через электроды, диски расширяются и сжимаются, производя осевое движение от пика к пику от 15 до 20 мкм.
Датчики — хрупкие устройства, с которыми следует обращаться осторожно. Как только элементы сломаны, преобразователь не будет работать.
Усилитель
Секция усилителя сварочной колонны служит двум целям, в первую очередь для усиления механических вибраций, создаваемых на конце преобразователя, и передачи их на сварочный рожок. Его вторичное назначение — предоставить место для установки пакета на сварочном прессе.
Усилитель расширяется и сжимается по мере того, как преобразователь подает ультразвуковую энергию.
Рис.3. Ультразвуковые сварочные усилители
Усилитель, как и другие элементы сварочного комплекта, представляет собой настраиваемое устройство, поэтому он должен резонировать на определенной частоте, чтобы передавать ультразвуковую энергию от преобразователя к сварочному рупору. Для успешного функционирования бустер должен быть либо половиной длины волны ультразвука в материале, из которого он изготовлен, либо кратным этой длине. Обычно это половина длины волны.
Сварочный рожок
Сварочный рожок — это элемент сварочного комплекта, который подает энергию на свариваемый компонент. Типовой сварочный рожок показан на рис. 4 . Конструкция сварочного рожка имеет решающее значение для успешной сварки. Настоятельно рекомендуется, чтобы изготовление сварочного рожка осуществлялось только компаниями, специализирующимися на ультразвуковой сварке.
Рис.4 Ультразвуковой сварочный рожок
Сварочный рожок, как и усилительный элемент, представляет собой настраиваемое устройство, которое в большинстве случаев также обеспечивает механическое усиление. Обычно он изготавливается из алюминия или титана. Алюминиевые сварочные рожки, как правило, используются для небольших объемов работ, поскольку износ может быть особой проблемой для этого материала. Некоторые сварочные рожки имеют специально закаленные наконечники для уменьшения износа во время сварки.
Как и в случае усилителя, длина сварочного рупора должна быть равна половине длины волны ультразвука в материале, из которого он изготовлен, или кратна этой длине. Это обеспечивает достаточную амплитуду на конце сварочного рожка для осуществления сварки.
Амплитуда обычно составляет от 30 до 120 мкм. Форма сварочного рупора важна, так как напряжение, вызванное осевым расширением и сжатием рупора, может привести к растрескиванию в приложениях с большой амплитудой. В некоторых случаях сварочный рожок изготавливается с прорезями в осевом направлении. Это необходимо для обеспечения максимальной амплитуды вибрации в продольном направлении.
Наконечник сварочного рожка подает ультразвуковую энергию на свариваемый компонент. Наконечник должен быть специально разработан, чтобы соответствовать компоненту. Это обеспечит максимальную передачу энергии между рупором и компонентом. Обычно кончик рупора профилирован, чтобы соответствовать контурам компонента.
Опорный инструмент
Наконец, основание машинного пресса поддерживает инструменты, поддерживающие компоненты во время операции сварки. Опорный инструмент предназначен для предотвращения перемещения нижнего компонента во время применения ультразвука. Его часто обрабатывают, чтобы точно соответствовать контурам поверхности компонента.
Следующая статья будет посвящена конструкции компонентов и параметрам сварки.
Часть 2: Конструкция компонентов
См. дополнительную информацию о сварке полимеров или свяжитесь с нами.
Процесс ультразвуковой сварки. Принцип работы, составные части, преимущества и недостатки при применении
Что такое ультразвуковая сварка
Ультразвуковая сварка (USW) — это метод сварки, в котором для сварки двух деталей используется ультразвуковая вибрация высокой частоты. Он чаще всего используется для сварки термопластичных материалов и разнородных материалов. Металл с тонким сечением также можно сваривать УЗВ.
Принцип работы
Ультразвуковая вибрация высокой частоты (от 20 до 40 кГц) используется для соединения двух пластмассовых деталей. Высокочастотная вибрация генерирует тепловую энергию на границе раздела двух частей и расплавляет материал. Расплавленный материал сплавлялся друг с другом, образуя прочный сварной шов при охлаждении и затвердевании.
Обычно используется частота 15, 20, 30, 35 или 40 кГц.
Основные части
Различные основные части или компоненты ультразвуковой сварки
- A Пресс: Используется для приложения давления к двум соединяемым пластиковым деталям. Он может быть с пневматическим или электрическим приводом.
- Гнездо или наковальня или приспособление: Это зажимное устройство, которое используется для удерживания и зажима двух пластиковых деталей вместе. Он допускает высокочастотную вибрацию, направленную на поверхность раздела двух частей.
- Ультразвуковой стек : Он состоит из трех компонентов: преобразователя или пьезоэлектрического преобразователя, усилителя и рупора или сонотрода. Эти три элемента настроены на работу на резонансной частоте 15 кГц, 20 кГц, 30 кГц, 35 кГц или 40 кГц.
- Преобразователь: Преобразует электрические сигналы в высокочастотные механические вибрации. И делает это благодаря пьезоэлектрическому эффекту.
- Усилитель: Механически изменяет амплитуду вибрации. В некоторых стандартных системах используется для зажима стопки в прессе.
- Горн или сонотрод: Он вибрирует с высокой частотой и передает механическую вибрацию на две свариваемые детали. Он также механически изменяет амплитуду. Он принимает форму детали. Рог изготовлен из титана или алюминия.
- Ультразвуковой генератор: Генерирует и подает высокочастотные электрические сигналы, соответствующие резонансной частоте стека.
- Контроллер: Используется для управления движением пресса и подачей ультразвуковой энергии.
Читайте также:
- Лазерная сварка – оборудование, принцип работы, преимущества и недостатки
- Что такое подводная сварка и как она работает?
- Сварка сопротивлением – принцип, работа и применение
Рабочий процесс ультразвуковой сварки
- Две соединяемые пластмассовые детали собираются в гнезде (наковальня или приспособление)
- в верхней части изделия.
- К двум деталям прикладывается давление на приспособление. Давление подается с помощью пресса с пневматическим или электрическим приводом.
- Рупор вибрирует вертикально на очень высокой частоте (от 20 кГц до 40 кГц), передавая механическую вибрацию двум пластмассовым частям. Это генерирует тепловую энергию на контактном наконечнике двух поверхностей и расплавляет их.
- К двум частям прикладывается зажимное усилие в течение заданного периода времени, чтобы сплавить их вместе, образуя прочный сварной шов при охлаждении и затвердевании.
- После затвердевания зажимное усилие снимается и рог втягивается. Сварная пластиковая деталь вынимается из приспособления как единое целое.
Для лучшего понимания посмотрите видео ниже:
Применение
В основном используется в компьютерной и электротехнической, аэрокосмической и автомобильной, медицинской и упаковочной промышленности.
- Компьютерная и электротехническая промышленность: Здесь он используется для соединения проводных соединений и создания соединений в небольших чувствительных цепях.
- Аэрокосмическая и автомобильная промышленность
В автомобильной промышленности он используется для сборки крупных пластиковых и электрических компонентов, таких как дверные панели, приборные панели, воздуховоды, лампы, рулевые колеса, обивка и компоненты двигателя.
В аэрокосмической отрасли используется для соединения тонких листов и легких материалов, таких как алюминий.
- Медицинская промышленность
Не загрязняет сварной шов и не разрушает его. Именно поэтому его используют в медицинской промышленности.
Такие изделия, как фильтры для анестезии, артериальные фильтры, фильтры для крови, диализные трубки, пипетки, фильтры для крови/газа, резервуары для кардиометрии и т. д., могут быть изготовлены методом ультразвуковой сварки.
4 . Упаковочная промышленность
Используется для упаковки различных материалов в пищевой промышленности.
Используется для упаковки опасных материалов, таких как взрывчатые вещества, фейерверки и химикаты.
Читайте также:
- Процесс электронно-лучевой сварки – оборудование, принцип работы со схемой
- Основные 8 преимуществ дуговой сварки
- Процесс плазменно-дуговой сварки – принцип, основные части, работа, преимущества и недостатки с применением4
Преимущества
- Это быстрый процесс сварки.
- Имеет быстрое время высыхания, т.е. изделия не остаются долго сохнуть в приспособлениях
- Его можно легко автоматизировать.
- Обеспечивает чистое и точное соединение.
- Имеет чистые места сварки и не требует подкраски.
- Оказывает низкое термическое воздействие на материалы.
Недостатки
- Нельзя использовать для изготовления больших швов (более 250 х 300 мм).
- Для этого требуются специально разработанные соединения, чтобы он мог соприкасаться наконечниками в процессе сварки.
- Высокая стоимость оснастки для приспособлений.
- Процесс ультразвуковой сварки ограничен соединениями внахлестку.
Многообещающая технология для сварки пластмасс и металлов
Крепление, сшивание и склеивание — некоторые из популярных методов, которые мы используем для соединения двух материалов. Однако нельзя отрицать тот факт, что сварка дает наилучшие результаты.
Сварные швы обеспечивают прочное соединение, которое длится значительно дольше, чем большинство других форм соединений.
В настоящее время используется множество способов сварки. Каждый тип отличается по-своему и используется в зависимости от требований и типа используемого материала.
Одним из самых современных методов сварки является ультразвуковая сварка.
СВЯЗАННЫЕ С: ПОДВОДНАЯ СВАРКА: ОДНА ИЗ САМЫХ ОПАСНЫХ ПРОФЕССИЙ В МИРЕ
Ультразвуковая сварка использует ультразвуковую вибрацию для соединения различных материалов. Одним из самых больших преимуществ ультразвуковой сварки является то, что ее можно использовать не только с металлами, но и с термопластами.
При воздействии ультразвуковой вибрации на точки контакта высокая вибрация вызывает плавление материала. Типичный диапазон частот, используемый при ультразвуковой сварке, находится между от 15 до 40 кГц .
Поскольку ультразвуковое сварочное оборудование может концентрировать вибрацию в очень ограниченном месте, сварка получается очень точной.
Детали ультразвуковой сварки
Ультразвуковые сварочные аппараты созданы для эффективного преобразования электроэнергии в механические колебания.
Машины оснащены микропроцессором, который считывает температуру и соответствующим образом регулирует нагрев.
Некоторые другие компоненты, составляющие стек машины:
Источник питания: Аппарат для высокочастотной ультразвуковой сварки требует источника питания высокого напряжения.
Преобразователь: Преобразователь принимает ток высокого напряжения и преобразует его в высокочастотные колебания.
Усилитель: Работает как усилитель, улавливая высокие частоты и делая их еще более мощными.
Сонотрод или рупор: Сонотрод или рупор, как его обычно называют, является посредником между свариваемыми материалами и машиной. Он фокусирует ультразвуковые колебания в определенной точке.
Свариваемые материалы обычно закрепляют на наковальне или приспособлениях, удерживающих их вместе. К машине часто прикрепляют пневматический пресс, чтобы можно было передать давление на материалы с помощью рога.
Как ультразвуковая сварка расплавляет материалы?
Ультразвук используется при сварке для создания небольших, но быстрых вибраций. Когда рупор или сонотрод прикреплены к материалам, ультразвуковые колебания заставят материалы колебаться примерно на полмиллиметра или около того при движении вперед и назад.
Такого минутного движения достаточно, чтобы расплавить материал, потому что скорость вибрации довольно высока. Эти вибрации заставляют материалы тереться друг о друга, и в результате трения между ними выделяется тепло.
Вы можете воспроизвести подобное окружение, быстро потирая руки. Вы почувствуете тепло, выделяющееся между ладонями.
Самый популярный
И если вы продолжите быстро тереть, становится довольно неудобно. Представьте себе тепло, выделяющееся внутри материалов, когда они трутся друг о друга со скоростью, которую трудно уловить человеческому глазу!
Трение повышает температуру до такой степени, что точки контакта между материалами плавятся, прокладывая путь для молекулярной связи.
Вот как ультразвуковая сварка сваривает пластмассы.
Однако при сварке металлов есть небольшая разница. Ультразвуковая сварка используется для нагрева металла до одной трети его температуры плавления.
В этот момент молекулы двух металлов будут пересекать друг друга, создавая прочную молекулярную связь. В металлах нет плавления.
Преимущества ультразвуковой сварки
Ультразвуковая сварка имеет много преимуществ по сравнению с традиционными технологиями сварки. Многие отрасли промышленности используют ультразвуковую сварку из-за этих специфических комбинаций достоинств.
Не требует внешнего источника тепла: Основным преимуществом ультразвуковой сварки является отсутствие необходимости во внешнем источнике тепла. Тепло самогенерируется между материалами.
Быстро: Поскольку частота вибрации очень высока, ультразвуковая сварка является одним из самых быстрых методов сварки, доступных в отрасли.
Возможность автоматизации: Ультразвуковая сварка несложна во многих отношениях, поэтому ее легко автоматизировать. Ультразвуковая машина оснащена датчиками, которые постоянно контролируют температуру.
Чистое и прочное соединение: Контактные поверхности плавятся/плавятся при сварке, в результате получается очень чистое и прочное соединение.
О чем следует помнить при использовании ультразвукового сварочного аппарата
Ультразвуковая сварка очень эффективна при герметизации или сварке пластмасс. Однако, вы не можете сваривать все виды пластика.
Как и металлы, пластмассы также бывают разных типов. И очень важно следить за тем, чтобы свариваемые пластмассы были химически совместимы.
Если попробовать сварить полиэтилен и полипропилен, они могут расплавиться, но химической связи не будет. Химическая связь важна для создания прочных сварных соединений.
Еще один фактор, о котором следует помнить при сварке любого материала с помощью ультразвуковой сварки, — поддержание однородной площади контакта.
При сварке металлов ультразвуковые колебания распространяются параллельно плоскости.
Недостатки ультразвуковой сварки
Как и все процессы соединения, ультразвуковая сварка также имеет некоторые недостатки, которые могут повлиять или не повлиять на вас в зависимости от вашего варианта использования. Однако вы должны понимать их.
Только для соединения внахлестку: Ультразвуковая сварка может использоваться только для сварки соединений внахлестку. Ее нельзя использовать для других типов соединений, так как для этого потребуются специально разработанный рожок и приспособления, и опять же, успех не гарантируется.
Ограниченная область сварки: Мы обсудили, как ультразвуковая сварка создает высоко локализованные сварные швы. Следовательно, вы не можете ожидать, что сварка обеспечит более крупные швы, чем площадь 250×250 мм 2 .
Нельзя сваривать толстые и твердые металлы: Толстые и твердые металлы вибрируют не так сильно, как тонкие и мягкие.
Это предохраняет их от механических колебаний.
Ультразвуковая сварка используется в различных областях. Один из лучших примеров его использования — спортивная обувь. Соединения, которые вы видите в верхних частях, выполнены не сшиванием, а ультразвуковой сваркой.
Ультразвуковая сварка обеспечивает гораздо лучшую отделку, чем сшивание или склеивание.
СВЯЗАННЫЕ: МОЩНЫЙ АЛЮМИНИЕВЫЙ СПЛАВ ТЕПЕРЬ ПОДХОДИТ ДЛЯ СВАРКИ БЛАГОДАРЯ НАНОТЕХНОЛОГИЯМ
Ультразвуковая сварка термопластов широко используется в медицинской промышленности, автомобилестроении и производстве бытовой техники. Поскольку для надежного соединения не требуются дополнительные материалы, ультразвуковая сварка не увеличивает общий вес готового изделия.
Ультразвуковая сварка — это технология, появившаяся в 1940-х годах, но она по-прежнему используется для создания чистых и прочных соединений между различными материалами.
Разработки в области ультразвуковой сварки все еще ведутся, чтобы увеличить масштабы ее использования.
More Stories
инновации Безвоздушные шины, использующие технологии НАСА, могут положить конец проколам, сократить количество отходов и революционизировать отрасль
Крис Янг| 15.09.2022
культураУмнее Эйнштейна? У этих людей самый высокий IQ в мире
Майя Мулко| 15.09.2022
транспортШкольные электробусы чище и дешевле в обслуживании — но у них есть 2 проблемы
Разговор| 10.09.2022
Что такое ультразвуковая сварка и подходит ли она мне? — Часть
Что такое ультразвуковая сварка и подходит ли она мне?
Изучая способы соединения пластиковых деталей, вы почти наверняка остановитесь на процессе, подпадающем под одну из следующих категорий: механическое соединение, склеивание или сварка.
Механические процессы, такие как защелкивание, винты или заклепки, отлично подходят, если продукт необходимо разобрать в течение срока его службы или если продукт будет работать в небольшом объеме. Клеи, такие как клей, образуют более прочную связь и превосходно склеивают два разнородных материала. Процессы сварки пластмасс носят непрерывный характер, не требуют расходных материалов и используют комбинацию тепла и давления для сплавления деталей. При оценке методов производства нельзя упускать из виду один конкретный метод сварки: ультразвуковую сварку.
Что такое ультразвуковая сварка?
Проще говоря, ультразвуковая сварка использует высокочастотные вибрации для нагрева и соединения двух частей, соприкасающихся под давлением. Эти высокочастотные вибрации в большинстве случаев превышают предел человеческого слуха. Диапазон человеческого слуха составляет от 20 Гц до 20 кГц, в то время как ультразвуковые частоты, используемые в этих сварочных аппаратах, обычно находятся в диапазоне от 15 кГц до 75 кГц.
Техника была запатентована в 60-х годах и впервые использовалась в индустрии игрушек. С тех пор технология продолжает развиваться и используется в таких отраслях, как медицина, электроника, упаковка и автомобилестроение. Ультразвуковая сварка может использоваться как для пластмасс, так и для металлов, но в этой статье основное внимание будет уделено сварке пластмасс. Чтобы лучше понять ультразвуковую сварку, давайте рассмотрим компоненты сварочного аппарата.
Блок питания . Каждый ультразвуковой сварочный аппарат начинается с источника питания. Источник питания иногда называют генератором частоты, потому что он потребляет стандартную электрическую мощность (обычно 115 В) с частотой 60 Гц и преобразует ее в рабочую частоту примерно 20 кГц или 20 000 циклов в секунду. Другие широко доступные выходные частоты находятся в диапазоне от 15 до 70 кГц. Затем этот высокочастотный ток направляется по специальному кабелю в ультразвуковой блок.
Ультразвуковой стек.
Стек — это не одно целое, а скорее комбинация трех основных компонентов: преобразователь, усилитель и сварочный рупор. В сварочном аппарате для пластика ультразвуковой блок выровнен вертикально и расположен над свариваемыми деталями в опорной колонне.
Преобразователь. Преобразователь представляет собой пьезоэлектрический преобразователь, на который подается ток высокой частоты от источника питания и который выдает механические колебания той же частоты. Преобразователь работает за счет пьезоэлектрического эффекта — вспомните кварцевые часы. Таким образом, пьезоэлектрический эффект возникает, когда механическая деформация (изменение формы из-за давления) возникает в материале-кандидате, который, в свою очередь, генерирует электрический заряд. Пьезоэлектрический эффект работает и в обратную сторону. Если к материалу приложить электрическое поле, он изменит форму. Пьезоэлектрические преобразователи, используемые в ультразвуковых преобразователях, состоят из множества пьезоэлектрических керамических дисков, покрытых с обеих сторон металлическими пластинами.
Все они хранятся под давлением в титановом цилиндре. Источник питания посылает на это устройство высокочастотный ток, генерирующий быстро меняющиеся электрические поля. Эти быстро меняющиеся электрические поля вызывают быстрое изменение формы пьезоэлектрического материала, что приводит к высокочастотным вибрациям. Титановый цилиндр помогает передавать эту вибрацию усилителю.
Бустер. Усилитель является реактивным компонентом преобразователя и помогает усилить или ослабить вибрацию. Колебания, исходящие от преобразователя, имеют приблизительную амплитуду (от нуля до пика) 8 микрометров (диаметр эритроцита). Эта амплитуда должна часто изменяться, чтобы успешно передать требуемую энергию сварному соединению. Усилитель увеличивает или уменьшает
амплитуду вибрации в определенном соотношении. Это соотношение определяется геометрией и распределением массы ракеты-носителя, каждая из которых точно спроектирована для достижения этого соотношения. Например, бустеры с большей массой возле рупора уменьшают выходную амплитуду.Типичные передаточные числа бустера составляют 1: 0,6 (амплитуда уменьшения) и 1: 2,0 (двойная амплитуда), и обычно они изготавливаются из титана или алюминия. Отношение также может быть выражено как «усиление», где усиление равно выходной амплитуде, деленной на входную амплитуду. Бустер — не единственный компонент стека, который может изменять амплитуду акустических волн.
Горн или сонотрод. За пределами США рупор иногда чаще называют сонотродом. Рупор принимает вибрации от усилителя и дополнительно усиливает или ослабляет амплитуду акустических волн. Рог также отвечает за передачу этих вибраций на свариваемые детали путем прямого контакта. В пластиковом сварочном аппарате рупор и усилитель вибрируют в осевом направлении с рабочей частотой, установленной источником питания. Рупор контактирует с верхней пластиковой деталью и применяет эти вибрации перпендикулярно поверхности детали. Напротив, металлические рога сварщика лежат горизонтально, а вибрации прикладываются параллельно поверхности деталей.
Рупор уникально спроектирован так, чтобы его концы постоянно двигались в противоположных направлениях, в то время как центр рупора оставался на месте. Умножая выходную амплитуду преобразователя на усиление усилителя и усиление рупора, вы можете найти эффективную выходную амплитуду стека, применяемую к части. Титан является предпочтительным материалом для изготовления рупора из-за его механических свойств, таких как высокая усталостная прочность и твердость, но также существуют экономичные алюминиевые и стальные рупоры для правильного применения. Существует множество форм рупора, каждая из которых имеет свое уникальное применение, и для особых случаев могут быть изготовлены специальные рупоры. Круглый рожок, например, полезен, когда детали должны быть сварены по окружности. Прежде чем рог сможет воздействовать на заготовку вибрацией, ее необходимо сначала опустить на место.
Привод. Привод отвечает за опускание пакета на свариваемые детали. Он также должен прикладывать усилие, соответствующее желаемому приложению.
Ультразвуковые сварочные приводы обычно имеют пневматический или электрический привод и обеспечивают усилие сварки в диапазоне 50-750 фунтов. Приводы, используемые в аппарате для ультразвуковой сварки металла, могут приводиться в действие гидравликой и воспринимать большее усилие. Точное усилие будет определяться исходя из конструкции свариваемых деталей.
Гнездо или наковальня. Обычно свариваются две детали — верхняя половина и нижняя половина. Нижняя половина находится в приспособлении, называемом гнездом. Гнездо будет направлять вибрации на поверхность раздела между двумя частями. Когда приспособление, удерживающее нижнюю часть, более плоское, его можно назвать наковальней. При сварке длинных швов некоторые машины имеют подвижную наковальню, которая перемещает деталь, удерживая сварщика на месте.
Процесс ультразвуковой сварки. Теперь, когда вы знаете основные компоненты ультразвукового сварочного аппарата, пришло время понять, как работает типичный цикл сварки:
Первым шагом является загрузка деталей в гнездо вручную или с помощью автоматизации — автоматизация используется при выполнении больших объемов работ.Далее органы управления сварочным аппаратом будут работать в одном из четырех режимов:
Сварка по времени. Сварка по времени запускает последовательность сварки в течение заданного времени. В течение многих лет это был стандартный способ сварки. Недостатком этого процесса является то, что это система без обратной связи (без обратной связи). С появлением строгих требований к качеству в таких отраслях, как медицина, метод сварки по времени не всегда может обеспечить требуемый уровень стабильности. Если одна часть отличается от другой очень незначительно, обратной связи, объясняющей различия, не существует. Это приводит к изменению качества сварки и общих характеристик детали. Благодаря тому, что новые датчики и усовершенствованные элементы управления становятся более доступными, были разработаны более совершенные режимы сварки.
Общая энергия. Одна из теорий успешной сварки заключается в том, что для данной детали необходимо приложить определенное количество энергии к границе раздела деталей для получения удовлетворительного сварного шва.
Режим полной энергии работает путем измерения мощности, потребляемой сварщиком, и регулировки продолжительности процесса сварки для достижения желаемого энергопотребления (мощность x время = энергия). Этот метод, хотя и хорош в теории, трудно предсказать фактическую энергию, приложенную к сварному шву, из-за потерь в машине (например, потери энергии в приспособлении).
Свернуть (относительное) расстояние. С помощью линейного энкодера система управления может измерять расстояние, на которое рупор погружает верхнюю часть в нижнюю во время сварки. Измерение начинается, когда рупор впервые соприкасается с верхней частью (когда привод опускается), и заканчивается после достижения заданного расстояния. Это предустановленное расстояние представляет собой расстояние разрушения — величину, на которую плавится поверхность раздела между двумя частями. Этот метод является предпочтительным во многих ситуациях, поскольку позволяет точно контролировать глубину сварки.
Абсолютное расстояние.
Когда габаритные размеры свариваемой детали являются критическими, предпочтительным методом является «абсолютное расстояние». Используя линейный энкодер, сварщик будет продолжать цикл сварки до тех пор, пока не будет достигнут определенный общий размер детали (обычно общая высота). Методы полной энергии, расстояния коллапса и абсолютного расстояния включают в себя петли обратной связи, что делает их системами с обратной связью.
После того, как выбран режим управления, привод опускает стек. В конце концов рупор соприкасается с верхней частью, и прикладывается нагрузка. Между тем, источник питания подает ток на преобразователь, который выдает высокочастотную вибрацию через усилитель и звуковой сигнал. Рог подает эту ультразвуковую волну на свариваемые детали. Одна из частей обычно имеет направляющую энергии на границе раздела. Директор энергии представляет собой небольшой формованный гребень высотой чуть менее 1 миллиметра и сторонами под углом 60-9°.0 градусов. Из-за вибраций и трения направляющая энергии расплавится и создаст молекулярную связь с поверхностью другой детали.
Время сварки обычно занимает менее секунды, после чего сварной шов быстро охлаждается из-за того, что температура плавления остается локализованной на границе раздела деталей. Времени на лечение тоже нет. После этого привод полностью убирается, и детали можно снять вручную или с помощью автоматики.
Лучшие практики проектирования.
При оценке ультразвуковой сварки как метода изготовления важно иметь в виду, что некоторые пластики свариваются лучше, чем другие.
• Благодаря своему химическому составу и тонкой структуре термопластичные пленки и ткани легко свариваются ультразвуковыми методами.
• Аморфные термопласты (например, ABS) также являются идеальными кандидатами.
• Полукристаллические термопласты (такие как нейлон) сложнее, но можно.
• С другой стороны, термопластичные эластомеры очень плохо подходят для ультразвуковой сварки и, как правило, не рекомендуются.
Различные материалы имеют разные диапазоны амплитуд, необходимые для эффективной сварки.Большинство поставщиков ультразвуковых сварочных аппаратов могут предоставить эталонные настройки для различных материалов. Сварка двух разных пластиков может быть достигнута, если их настройки не слишком отличаются.
Размер деталей также является важным фактором. Ультразвуковая сварка отлично подходит для мелких деталей. Насколько велик слишком большой? Вот несколько практических правил:• Чем сложнее материал, тем меньше может быть его максимальный размер. Нейлон (сложный) может быть только около 3,5 дюймов, а АБС (легкий) может быть около 10 дюймов.
• Для более низких частот (15 кГц) требуются более крупные инструменты (10 дюймов). Для более высоких частот (40 кГц) требуются инструменты меньшего размера (2,5 дюйма)
Геометрия детали влияет на возможность получения чистых сварных швов. Ультразвуковая сварка хорошо работает с тонкостенными деталями, длинными неподдерживаемыми стенками и внутренними сварными швами. Сложная геометрия и глубокие контуры плохо подходят для ультразвуковой сварки.
При проектировании интерфейса между деталями важно добавить направляющую энергии. Энергетический директор работает, чтобы сконцентрировать энергию от рога, чтобы инициировать быстрое плавление. Обычно это треугольный профиль, расположенный в центре стены по всей длине стены. Рекомендуется размещать регулятор энергии на части, касающейся рупора. Хорошей отправной точкой является угол 60-9.0 градусов при высоте, равной 1/8 толщины стенки. Эмпирическое правило для требуемой силы привода составляет 1 фунт-сила на каждый погонный миллиметр направляющей энергии. Дизайн деталей должен включать элементы, которые помогают их выравнивать. Эти предложения являются лишь отправной точкой и должны быть оценены инженером по применению. Проверенный набор эмпирических данных вместе с установленными процедурами сварки являются ключом к успешному проекту.Преимущества
Ультразвуковая сварка имеет много преимуществ по сравнению с альтернативными методами:
• Высокопрочные сварные швы
• Без расходных материалов — без крепежа или клея
• Быстро — без отверждения или времени высыхания.
- Это быстрый процесс сварки.