технология, стыки и особенности работ
Сварка рельс может быть осуществлена различными способами. Наиболее популярной и эффективной считается алюминотермитная сварка. Этот метод обеспечивает надежность и прочность соединения рельсов, которые относятся к объектам повышенного значения. Алюминотермитная сварка рельсов может использоваться, как при их прокладке, так и при ремонте.
Способы сварки рельсов
Рельсы изготавливаются из высокоуглеродистых сталей, особенностью которых является плохая свариваемость. При выборе способа соединения рельсов необходимо учитывать химический состав сплавов, из которых изготовлены рельсы, их текучесть и пластичность. Выбирать надо из следующих имеющихся технологий:
- электродуговая;
- электроконтактная;
- алюмотермитная;
- газопрессовая.
Каждая технология имеет свои преимущества.
Наиболее привычным является электродуговой способ. Сварка рельсовых стыков электродами применяется следующим образом:
- Подлежащие соединению концы рельс укладывают с небольшим зазором между ними величиной в несколько миллиметров.
- Их концы проваривают электродами, расплавляемыми посредством температуры сварочной электрической дуги.
- Расплав постепенно начнет заполнять весь стык.
- После того, как окончательно закончится охлаждение сварной ванны, полученный стык подвергают зачистке, убирают окалину, поверхность рельса в месте стыка выравнивают.
Для получения тока, переменного или постоянного, используется передвижная сварочная станция. В качестве оборудования применяются трансформаторы, выпрямители и инверторы.
Предварительно необходимо решить вопрос, какими электродами варить рельсы. Диаметр у них должен быть размером приблизительно 5-6 миллиметров. Применяются электроды, имеющие основной вид покрытия. Среди электродов, выпускаемыми в нашей стране, можно порекомендовать УОНИ 13/45 и УОНИ 13/55, а среди импортных — LB 52U. Перед тем, как сваривать рельсу встык электродами, необходимо подвергнуть их прокаливанию.
Разновидностью дугового способа, которую можно назвать удачной, является сварка рельс ванным способом. Он состоит в том, что у рельсов заранее обрезаются торцы. Затем их укладывают с небольшим зазором четко вдоль протяженности путей, но при небольшом поднятии. Между уложенными таким образом кусками рельс вводят электрод и пропускают ток величиной приблизительно 300-350 Ампер.
Образовавшаяся раскаленная масса начинает растекаться вдоль зазора, пока не заполнит его полностью. Это происходит постепенно и равномерно. Чтобы стекание не начинало происходить наружу, зазор ограждают блокираторами. Качественное соединение рельсов получается также при контактной сварке.
Сварка осуществляется в автоматическом режиме. Рельсы размещают поблизости с их постоянным местонахождением. Микроструктура стыкового контактного сварного шва рельсов должна по возможности соответствовать основному составу. К недостаткам контактной сварки можно отнести необходимость участия в этом процессе нескольких сварщиков, трудность доставки оборудования, длительность процесса, высокая стоимость оборудования.
Газопрессовой способ основан на соединении стыков рельс при более низких температурах, но при высоком давлении. Необходимо производить подготовительные операции, заключающиеся в тщательной обработке свариваемых концов рельс, чтобы обеспечить необходимую плотность прилегания.
Рельсы в ходе процесса сдавливают гидравлическим прессом со значительным усилием и разогревают горелкой до температуры 1200 градусов. К преимуществам этого метода относится однородность получаемого шва и его прочность, а к недостаткам не слишком высокую производительность. Газопрессовую сварку имеет смысл применять для ремонта железнодорожных путей, где нагрузка на рельсы имеет большое значение.
Суть алюминотермитного метода
Термитная сварка рельс относится к наиболее сбалансированным методам соединения стыков. Она отвечает современным требованиям к качеству швов на этом важном участке. Технология соединения рельсов таким способом предполагает использование особой смеси. Термитная смесь содержит 77% оксида железа, а остальные 23% приходятся на крошку из алюминия. Возможны небольшие отклонения в процентном составе.
Наличие слова «термитный» в названии метода свидетельствует о том, что при сваривании необходимо нагревание. Сильный разогрев будет способствовать образованию прочного надежного шва. Для того, чтобы приблизить состав смеси к параметрам свариваемого материала, в нее добавляют частички стали и легирующие элементы.
Сущность этой технологии заключается в том, что под воздействием окислов алюминия из оксидов происходит восстановление железа. Такая реакция сопровождается значительным выделением тепла, количество которого будет достаточным для того, чтобы металлические рельсы начали плавиться.
После разогрева металла до температуры 2000 градусов его заливают в особую форму, которую перед этим устанавливают на место стыка.
Существуют следующие варианты термитной сварки:
- Соединение встык.
- Промежуточное литье.
- Комбинированный вид.
- Дуплекс.
К наиболее простому и доступному способу относится метод с промежуточным литьем:
- над стыком устанавливают особую металлическую конструкцию, имеющую форму емкости;
- внутри емкости размещают смесь крошек алюминия и оксида железа;
- на стыке рельс, подлежащему соединению, производят установку заливочной формы, конфигурация которой должна совпадать с формой профиля рельс;
- при помощи воздействия воспламенителя емкость подвергается разогреву до температуры 1000 градусов;
- возникает алюмотермитная реакция, проходящая с выделением тепла, в результате чего смесь разогревается до температуры 2000 градусов;
- получившийся расплав переливается в заливочную форму;
- торцы рельс сильно разогреваются и оплавляются;
- при постепенном охлаждении происходит еще большее уплотнение, при котором шлак выдавливается наружу.
На финишной стадии необходимо произвести отбивание шлака молотком и отделку шва с помощью угловой шлифовальной машины или болгарки.
Алюмотермитная сварка обладает неоспоримыми преимуществами:
- Высокая скорость процесса. Продолжительность сваривания одного стыка рельсов составляет не более получаса. В течение часа одной бригадой может быть выполнено более десятка соединений.
- Не существует привязки к стационарным источникам тока. Мобильные установки имеют небольшие размеры с весом менее килограмма. Они осуществляют работу автономно.
- Отсутствие повышенных требований к опыту и квалификации исполнителей. Достаточным является следование указаниям технологического процесса.
- При использовании оборудования, находящегося в исправном состоянии, и соблюдением правил проведения сварочных работ степень безопасности можно назвать высокой.
- Эффективность метода, как при прокладывании новых путей различного назначения, так и при ремонте уже имеющихся.
- Отличные характеристики шва в области дальнейшей эксплуатации.
- Высокая производительность.
- Невысокая стоимость.
Необходимо следить за тем, чтобы в емкости не происходило попадание воды. Сварка рельсовых стыков алюминотермитным методом является гарантией безопасного движения транспортных средств.
Интересное видео
Алюминотермитная сварка | Главный механик
Для сварки рельсов используется такой способ сварочных работ, как алюминотермитный. Он подразумевает использование порошка, в состав которого входит алюминий, железная окалина и магний. Эта смесь называется термитом.
Особенности алюминотермитной сварки
Алюминотермитная сварка не столь распространена, как контактная. Однако, этот способ сварочных работ имеет ряд существенных преимуществ. К ним можно отнести следующие.
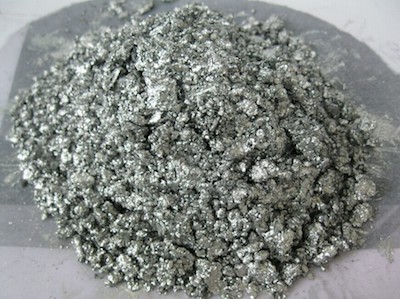
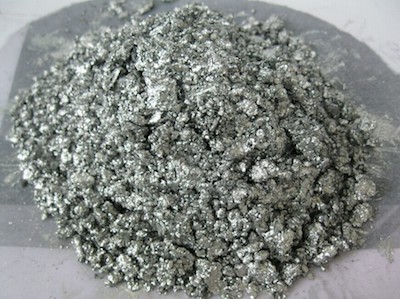
- Требует минимальных трудозатрат. Для выполнения сварочных работ алюминотермитным способом требуется минимальное количество рабочих рук. Справится с данной работой способна бригада, состоящая из 3 человек.
- Для выполнения алюминотермитной сварки не требуется сложного оборудования. А вес используемого составляет до 400 кг.
- Данный способ осуществления сварочных работ значительно быстрее по сравнению с контактным методом сварки. Продолжительность сварки для одного стыка рельс занимает меньше часа.
- Для осуществления алюминитермитной сварки применяется порошкообразное сочетание алюминия, железной окалины и магния, которое расфасовано определенным образом. Элементы, которые требуют нагревания, заформовывают материалом, устойчивым к воздействию высоких температур. Затем осуществляется нагрев этих деталей. При помощи электродуги или запала зажигают термит и разогревают до жидкого состояния. Расплавленный металл заливают на место, требующее сварки.
- Сварочные работы с использованием термита осуществляются с использованием автономных источников электропитания.
В результате правильно осуществленной алюминотермитной сварки получается довольно надежное соединение. Применяется этот вид сварочных работ для соединения стальных и чугунных изделий.
Алюминитермитная сварка для стыковки рельсов
Наиболее часто сварочные работы с помощью термита на основе алюминия используют при проведении железнодорожных работ. Обусловлено это преимуществами данного способа сварки.
Алюминотремитная сварка рельсов помогает оперативно изготовить стыки без продолжительного перерыва в движении поездов. Так, например, бригада из 3 человек за два часа способна сварить 3 рельсовых соединения. Оперативность проведения ремонтных и сварочных работ крайне важна при организации движения на железных дорог.
Но более важным фактором является надежность соединений. Алюминотермитная сварка рельсов наилучшим образом обеспечивает прочность стыков.
Таким образом, сочетая в себе наиболее важные факторы, надежность и оперативность, сварка при помощи термита на основе алюминия является наиболее подходящим способом для изготовления стыков рельс. Потому данный способ проведения сварочных работ широко применятся именно на железных дорогах России. Важно, что такая сварка может применятся даже при ремонте и стыковки стрелочных переводов. Ну и, конечно же, на перегонах основной части пути.
Преимущества использования алюминотермитной сварки рельсов
По мимо описанных выше особенностей и преимуществ, сварочные работы алюминиевым термитом имеют ряд существенных преимуществ относительно применения именно для обслуживания железных дорог. Таковыми являются следующие:
- Значительное сокращение расходов на содержание и обслуживание железнодорожного пути.
- Сокращение интенсивности износа. Это касается колес поездов и другого подвижного состава. А также самих стыков рельс.
- Предотвращает появление дефектов на окончаниях рельс.
- Обеспечивает плавность и скорость хода подвижного состава.
- Гарантия устанавливается по количеству пропущенного по рельсам груза. Она предусматривает пропуск общей массой до 120 милионнов тонн брутто для рельсов Р65. Гарантия имеет ограничения по времени – не более 5 лет использования.
Технология сварки рельс алюминотермитным способом и осуществление контроля качества
Сварка на основе алюминотермитного способа является бесшовной. Происходит этот процесс при помощи перетекания молекул одного вещества в другое.
Для осуществления алюминтермитных сварочных работ имспользуется специальное оборудование – воспламинитель. При помощи однопорционного заряда происходит повышение температуры до 1 тыс. градусов. Такая температура является подходящей для того, чтобы расплавить большинство видов рельс. Эта процедура занимает менее полминуты, около 20 секунд. При этом образуется металл в жидком виде и шлаки, которые поднимаются к верху.
Далее расплавленная металлическая масса перетекает в форму. При достижении пределов сердечника металл растекается равномерным слоем. При этом нагревательный элемент разогревает окончания рельс. Жидкий металл растекаясь, заполняет люфт разогретых рельс.
Алюминотермитные сварочные работы подходят даже для рельс из закаленного металла, упроченных и неупроченных видов.
Для качественного выполнения работ потребуется операционный аудит, т.е. за правильностью проведения сварки необходимо следить на всех без исключения этапах. Производить операцию по свариванию рельс должен профессиональный сварщик-термист при наличии защитной и сигнальной экипировки.
Алюминотермитный способ сварки включает в себя следующие этапы
- Проведение подготовительных работ. Рельсы на месте сварки должны быть полностью зачищены от грязи и ржавчины, а соединительные элементы должны быть удалены. Крепления, которые расположены рядом со свариваемым элементом ослабляются, поверхность рельсов должна быть гладкой. Затем элементы требуют выпрямления до горизонтального или вертикального положения. Сами рельсы ставятся с соблюдением зазора в 2,5 см. При помощи резака рельсы режут с последующим очищением от шлака.
- Выравнивание рельсов. В целях обеспечения безопасности и прочности сварки рельсы требуется выпрямить. Для этого вначале устанавливаются клинья с обеих сторон рельс взамен удаленным прокладкам креплений. При помощи металлической линейки длиной в 1 метр осуществляется контроль точности положения рельсы. С целью компенсации шовной усадки допускается люфт, который не превышает 1 мм.
- Проведение установки форм и их герметизации. На должном расстоянии устанавливается зажимающее устройство. Определяет его позицию измеритель. Поверх оси рельс, в центре предполагаемого шва, устанавливается горелка. Шпателем проводится герметизация, который плотно прижимают, тем самым обеспечивая тонкую грань между песком и металлом. Головка рельсов запирается крышками.
- Нагревание, металл и сварка. Сердечник сварочного оборудования требует дополнительного прогрева и просушки. Осуществляется это при помощи газа-пропана с давлением равным 1,5 бара и кислорода с уровнем давления равным 5 Барам. Затем начинается подача пламени на металл рельс, которая происходит не дольше 120 секунд. Осуществляется это при помощи горелки. После прогрева рельс, она снимается. На ее место должен быть установлен сердечник. После этого осуществляется поворот тигеля. Необходимо зажечь однопорционный заряд с целью осуществления сварочных работ. Для этого используют запал с высоким уровнем температуры. Пока металл плавится, необходимо чтобы тигель достиг стабильного положения. После чего расплавленный металл заливают в форму. После того, как он полностью перетечет в зазор, удаляют тигель с поддонами для шлака и крышками. Далее начинается процесс отвердения металла, длительностью около четырех минут.
- Финальные операции и процесс шлифовки. Для безопасности передвигающихся по рельсам составов и долговечности стыка, он должен быть гладким. Требуется его шлифовка по бокам и поверхности катания. Для этого наплывы в течение 10 минут разогревают при помощи горелки до горячего состояния. Затем механическим путем происходит срез излишков металла. По завершению данной процедуры при помощи инструментов абразивного типа выполняют шлифовку металла до прямолинейного состояния. Правильность шлифовки определяется при помощи металлической линейки и щупа. Допустимо отклонение от требуемого размера в пределах до 1 мм.
- Проверка качественности сварки. Для этого требуется провести испытание статичного изгиба. Здесь допустимо применение растяжения по головке изделия или его подошве. Также опытные образцы могут доводится до излома.
При правильно выполненной алюминетермитной сварки, качественный стык будет обеспечивать долговечность рельс и колес подвижных составов при минимальных временных и финансовых затратах на проведение ремонта и обслуживания железнодорожного пути.
Внимание покупателей подшипников Уважаемые покупатели, отправляйте ваши вопросы и заявки по приобретению подшипников и комплектующих на почту или звоните сейчас: +7(499)403 39 91
Доставка подшипников по РФ и зарубежью. Каталог подшипников на сайте themechanic.ru
|
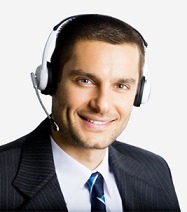
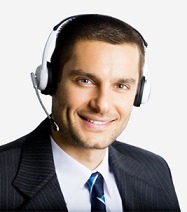
Внимание покупателей подшипников
Уважаемые покупатели, отправляйте ваши вопросы и заявки по приобретению подшипников и комплектующих на почту или звоните сейчас:
tel:+7 (495) 646 00 12
[email protected]
Доставка подшипников по РФ и зарубежью.
Каталог подшипников на сайте
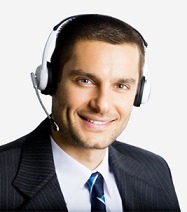
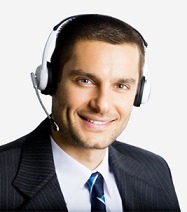
Внимание покупателей подшипников
Уважаемые покупатели, отправляйте ваши вопросы и заявки по приобретению подшипников и комплектующих на почту или звоните сейчас:
tel:+7 (495) 646 00 12
[email protected]
Доставка подшипников по РФ и зарубежью.
Каталог подшипников на сайте
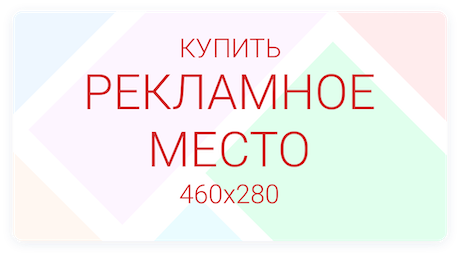
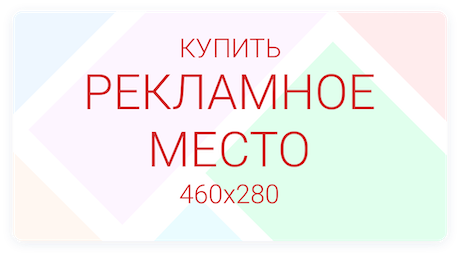
Изготовление термита. Применение алюминотермитной технологии для сварки рельс на железной дороге. Соединение рельс с помощью алюминотермитной сварки
ТЕРМИТ
(от греч. therme-тепло, жар), порошкообразная смесь стехиометрич. кол-в металлов или сплавов (т. наз. горючее) с оксидами менее активных металлов (окислитель), сгорающая при воспламенении с выделением большого кол-ва теплоты. Осн. горючее-Аl, Mg, Ca-Si, Сu-Аl, Fe-Mn, окислители- Fe 2 O 3 , Fe 3 O 4 , CuO, NiO, Pb 3 O 4 , MnO 2 . При экзотермич. окислит.-восстановит. р-ции идет металла оксида; продукты р-ции (преим. жидкие шлаки) нагреваются до т-ры ~ 2000 °С. Т-ра горения Т. 2000-2800 °С, т. воспл. > 800 °С (для наиб.
распространенного Т.-смеси А1 с Fe 3 O 4 -1300°C). Кол-во теплоты, выделяющееся при горении, зависит от состава Т., напр, в случае железоалюминиевого Т.: 8Аl + 3Fe 3 O 4: : 4А1 2 О 3 +9 Fe + 3478 кДж.
Производят Т. в виде порошка или шашек. Для поджигания используют смесь ВаО 2 и Mg или особые термитные спички.
Применяют Т. в качестве зажигательных составов, для термитной сварки, в металлотермии для произ-ва Мn, Сr, V, W, ферросплавов и разл. лигатур цветных и редких металлов, для дробления руды. Для сварочных работ (термитно-муфельная проводов, сварка и стыковка рельсов, приварка заземляющих проводников к металлич. конструкциям, сварка труб и др.) широко используют след. термитные составы-CuO, ферромарганец, сплав Cu-Al; Fe 3 О 4 , Аl, Mg, ферромарганец; Fe 3 O 4 , Mg, Al и др. Для получения феррованадия, феррохрома и др. применяют Т., содержащие Fe 3 O 4 и оксиды этих металлов.
Лит.: Шевченко Г. Д., Сварка, пайка и термическая резка металлов, М., 1966; Боровинская И. П., Мержанов А. Г., в сб.: Металлотермические процессы в химии и металлургии, Новосиб., 1971; Шидловский А. А., Основы пиротехники, 4 изд., М., 1973; Brauer К. О., Handbook of pyrotechnics, N. Y., 1974; Barbour R.T., Pyrotechnics in industry, N.Y., 1981. H. А. Силин.
Химическая энциклопедия. — М.: Советская энциклопедия . Под ред. И. Л. Кнунянца . 1988 .
Синонимы :Смотреть что такое «ТЕРМИТ» в других словарях:
1. ТЕРМИТ см. Термиты. 2. ТЕРМИТ, а; м. [от греч. thermē жар, тепло] Порошкообразная смесь алюминия (реже магния) с окислами некоторых металлов, при воспламенении которой образуется очень высокая температура (используется в технике при сварке,… … Энциклопедический словарь
Термит: Термиты отряд насекомых. Термитная смесь горючая смесь алюминия или магния с оксидами различных металлов. П 15 «Термит» противокорабельная ракета … Википедия
— (термитная смесь) (от греч. therme жар тепло), порошкообразная смесь алюминия (реже магния) с оксидами различных металлов (обычно железа), интенсивно сгорающая при воспламенении с выделением большого количества теплоты. Применяется в производстве … Большой Энциклопедический словарь
Толковый словарь Ушакова
1. ТЕРМИТ1, термита, муж. (от лат. termes) (зоол.). Насекомое жарких стран, живущее сообществами в разнообразных по форме и часто очень больших гнездах и приносящее громадный вред человеку. Укусы термитов чрезвычайно болезненны. 2. ТЕРМИТ2,… … Толковый словарь Ушакова
ТЕРМИТ 1, а, м. (спец.). Порошкообразная смесь, дающая при горении очень высокую температуру. Толковый словарь Ожегова. С.И. Ожегов, Н.Ю. Шведова. 1949 1992 … Толковый словарь Ожегова
ТЕРМИТ 2, а, м. Общественное насекомое жарких стран, живущее большими колониями, вредитель древесины, кожи, бумаги, сельскохозяйственных продуктов. Толковый словарь Ожегова. С.И. Ожегов, Н.Ю. Шведова. 1949 1992 … Толковый словарь Ожегова
Занятие №1 «Классификация зажигательных веществ и их свойства».
Понятия о зажигательном оружие. Классификация зажигательных средств (напалм, пирогели, электрон, термит, белый фосфор) и их свойства
2. Средства применения зажигательных веществ
Введение.
Огонь является одним из наиболее древних видов оружия. Более семи столетий вплоть до 15 века на полях сражений использовался «Греческий огонь», представляющий собой смесь горючих масел, смол, серы, селитры и других веществ, которыми снаряжались сосуды и перебрасывались в расположение противника метательными машинами. А с появлением огнестрельного оружия зажигательные вещества не утратили своего значения. В период первой мировой войны были разработаны конструкции термитносегментного снаряда и фугасного огнемета с пороховым генератором давления, которые и в настоящее время являются основой конструкции современных зажигательных боеприпасов и средств их применения. Перед второй мировой войной и в период ее ведения были созданы танковые, фугасные и ранцевые минометы. Известный скачок в развитии зажигательного оружия был сделан в 1942 году, когда была разработана предложена для военного использования горючая смесь на основе бензинов с загустителем, состоящим из алюминиевых солей нафтеновой и пальмитовой кислот. С тех пор зажигательные смеси на основе углеводородного горючего, содержащие загустители, принято называть НАПАЛМАМИ. Американская авиация широко применяла напалм в боевых действиях против Японии на острове в Тихом океане, а после второй мировой войны – в войне в Корее, южном Вьетнаме. В 1980 году в Женеве состоялась конференция Организации Объединенных Наций по ограничению применения зажигательного оружия по мирному гражданскому населению. Протоколом конференции запрещено применение зажигательного оружия по гражданскому населению и гражданским объектам. В настоящее время в капиталистических странах п
Использование алюмотермитного способа сварки на железных дорогах Текст научной статьи по специальности «Химические технологии»
УДК 625.143.48
ЩЕРБИНИНА Ю.В., старший преподаватель (Донецкий институт железнодорожного
транспорта)
Использование алюмотермитного способа сварки на железных дорогах
SCHERBININA Y.V., Senior Lecturer (DRTI)
The use of aluminum-thermite method of welding on Railways
Введение
На железных дорогах бесстыковый путь является основной конструкцией пути.
В ряде случаев при выборе того или иного способа сварки руководствуются только его
продуктивностью и стоимостью выполняемых работ, что приводит к появлению в соответствующих конструкциях сварных соединений низкого качества. На получение качественного сварного соединения большое влияние оказывает
свариваемость материала, из которого изготовлены детали, которые соединяются. Свариваемость -комплексная характеристика металла, которая характеризует его реакцию на физико-химическое действие процесса сварки и способность образовывать сварное соединение, которое соответствует заданным
эксплуатационным требованиям [1].
Рельсовая сталь содержит большое количество углерода и относится к группе материалов, которые плохо свариваются, которые при сварке склонны к образованию трещин.
Трещины в таких конструктивных элементах, как рельсы, недопустимы, поскольку, будучи концентраторами напряжения, могут в любой момент привести к разрушению стыка. В данное время стыковая сварка рельсов
осуществляется двумя видами: стыковая контактная сварка и сварка алюминотермитным способом.
Стыковая контактная сварка достаточно хорошо зарекомендовала себя при получении длинных рельсовых плетей в стационарных условиях и на перегонах. Следует отметить, что при проведении ремонтных работ рельсового пути данным способом необходимы дорогие путевые рельсосварочные машины, продолжительные «окна» для их доставки на место сварки и дальнейшей эвакуации, кроме того, необходима достаточно большая бригада рабочих. Дефицит рабочего времени в ряде случаев заставляет нарушать технологический процесс, что приводит к получению сварного стыка невысокого качества [2].
Одним из существенных недостатков стыковой контактной сварки является невозможность сварки стыков в стрелочных переводах. В настоящее время для сварки таких стыков безальтернативной и
обеспечивающей хорошее качество сварного шва, является
алюминотермитная сварка [4].
Следует отметить, что в странах западной Европы и Америки этот способ завоевал очень большую популярность — им сваривают стыки не только в районе стрелочных переводов, но и на перегонах основного пути.
Анализ последних исследований и публикаций
Вопросы исследования свойств алюминотермитной сварки достаточно активно поднимаются в научных публикациях. В научных статьях авторов Тихомировой Л.Б.,
Ильиных А.С., Галай М.С.,
Сидорова Э.С, «Исследование
структуры и механических свойств алюминотермитных сварных
соединений» и автора Игнатовой Е.Л. «Вопросы алюминотермитной сварки в развитии высокоскоростного движения» рассмотрены достоинства
алюминотермитной сварки рельсов перед стыковой контактной сваркой и сделаны выводы о том, что повышение механических и эксплуатационных характеристик алюминотермитных сварных соединений может быть достигнуто за счет применения термической обработки (нормализации) и модифицированием литейного компонента.
Цель работы
Рассмотреть технологический процесс производства алюмотермитной сварки (АТС) и осуществление контроля за его выполнением специалистами, которые знают процессы, происходящие при сварке и в период эксплуатации сварных конструкций.
Основная часть
Технологический процесс АТС.
Операция № 1. Подготовка к АТС на месте проведения работ.
С персоналом бригады и дефектоскопистом проводится
инструктаж по технике безопасности,
пожарной безопасности и охране труда на рабочем месте.
Технологическое оборудование, оснащение и материалы, после их перевозки непосредственно к месту проведения АТС, располагается в удобном для работы положении с обязательным соблюдением требований безопасности.
Контролируется закрытие
движения поездов на участке пути, где запланировано проведение сварочных работ по АТС рельсов.
Выполняется ограждение места производства работ.
Операция № 2. Подготовка тигля к работе и демонтаж стыка.
Выполняется осмотр тигля для плавильного процесса, проверяется отсутствие трещин, сколов и других дефектов. Исправный тигель
вставляется в обечайку, уплотняется место контакта с обечайкой формировочной смесью и
просушивается при температуре не менее 25-30°С в течение 24 часов, устанавливается тигель на
вспомогательной стойке [3].
Выполняется демонтаж стыка:
— демонтировать скрепление: на трёх шпалах в каждую сторону от стыка для прямых участков пути или на шести шпалах в каждую сторону — для кривых;
— демонтировать стыковые накладки, подрельсовые подкладки и прокладки;
— вырезка балласта из шпального ящика в подрельсовой зоне стыка;
— удалить мазут и грязь с поверхностей, которые сваривают на расстоянии 100-120 мм от торца рельса, который сваривается.
Операция № 3 Подготовка к сварке.
Формирование зазора.
Выполняется формирование
стыкового зазора между торцами
рельсов 25±1 мм.
Измеряется существующий зазор.
Выполняется, при необходимости, обрезка рельсов механическим способом.
Выполняется очистка торцов рельсов и приторцевой поверхности от ржавчины металлической щёткой.
Установка рельсов в рабочее положение. Выправить рельсы в рабочее положение для выполнения АТС — с целью компенсации оседания сварного шва выполнить повышение концов рельсов с помощью клиньев по вертикальной оси стыка на высоту 2,0+0,5 мм. Контроль установки концов рельсов перед сваркой выполняется с помощью линейки длиной 1 м и штангенциркуля или щупа.
Подготовка тигля к сварке.
Тигель перед началом сварки дополнительно просушить кислородо-пропановым пламенем с излишком кислорода.
Подготовка литейного
комплекта.
Приготовить литейный
компонент — одну порцию. Установить литейный зазор в тигле. Для этого в реакционном тигле, расположенном на вспомогательной стойке, с помощью фрезы очистить отверстие для установки литника.
Литейный зазор установить в нижнем отверстии тигля таким образом, чтобы верхние его кромки находились на 8-10 мм выше днища тигля.
Установить оправку на литейный зазор.
Место контакта литейного зазора с тиглем уплотнить магнезитовым порошком. Засыпать в тигель приготовленную порцию литейного компонента, который соответствует типу рельсов, которые сваривают. Удалить оправку из тигля.
Операция № 4. Процесс сварки методом промежуточного литья.
Установка технологического оборудования в зоне стыка. Установить комбинированную стойку на головку рельса таким образом, чтобы держатели частей литейной формы находились сбоку по оси зазора, который сваривается.
Установить механизм настройки горелки вместе с горелкой на комбинированную стойку и
отрегулировать положение сопла относительно зазора, который сваривается.
Установить на свариваемом стыке литейную форму, которая состоит из двух полуформ. На одной полуформе удалить ослабленную стенку литейного жёлоба для отвода шлака.
Зафиксировать полуформы
относительно стыкового зазора так, чтобы центр зазора совпал с вертикальной осью литейной формы, а сами полуформы прилегали друг к другу без уступов по всему периметру стыковки.
На литейную форму со стороны жёлоба для отвода шлаков установить ковш, внутреннюю поверхность которого обмазать формировочной смесью толщиной 5 мм. При сварке на пути ковш установить во внутренней стороне пути.
Сделать вручную обмазку с целью уплотнения места контакта ковша с литейной формой.
Установить подготовленный
тигель с литейным компонентом, перенеся его со вспомогательной на комбинированную стойку, и проверить центрирование литника относительно вертикальной оси зазора, который сваривается. При необходимости сделать регулирование для совмещения осей литника и зазора. Контроль
осуществить визуально. После этого повернуть тигель на 90 градусов в сторону от зазора.
Подготовить две лопатки с формировочной смесью для устранения свища в случае его образования в процессе литья в литейной форме.
Подогрев концов рельсов.
Установить на газовых редукторах давление пропана 1,0-1,2 атм. и давление кислорода 4,5-5,0 атм. Зажечь газовую горелку, отрегулировать пламя до нормального горения и установить газовую горелку на вспомогательную стойку.
Переместить газовую горелку с нормально отрегулированным пламенем на комбинированную стойку в зону сварки для нагрева концов рельсов. Длительность прогрева для рельса Р65 составляет 7-9 минут.
Температуру нагрева металла рельсов до 800-900°С контролировать визуально по цветам нагретого металла до светло-красных цветов или пирометром.
За одну минуту до окончания подогрева концов рельсов нагреть литейный мостик формы, удерживая его специальными щипцами.
Плавильный процесс.
Снять газовую горелку с комбинированной стойки. Установить нагретый литейный мостик в литейную форму.
Повернуть тигель с литейным компонентом и установить его таким образом, чтобы ось литника совпадала с осью зазора.
Зажечь от пламени горелки термитную спичку, вставить её в литейный компонент, который находится в тигле, и накрыть тигель конической крышкой с отверстием для выпуска газов.
Установить горелку на
вспомогательную стойку.
Контролировать визуально и по времени процесс плавления литейного компонента и заливку расплавленного металла в литейную форму, которая состоится через 20-28 с автоматически.
Контролировать время
кристаллизации металла литейного шва, которое в зависимости от массы порции литейного компонента для рельсов Р65 длится 3,0-3,5 минуты. После чего демонтировать литейное оборудование.
Демонтаж литейного
оборудования после затвердения металла.
Снять ковш со шлаком. Запустить двигатель гидроагрегата обрезного станка и подключить обрезное приспособление.
Снять тигель и перенести его на вспомогательную стойку. Снять комбинированную стойку и держатели литейных полуформ. Снять
металлические рамки, которые удерживают литейные полуформы.
Демонтаж верхней части литейной формы.
Очистить зубилом боковые и верхние контуры головки рельсов от формовочной смеси и шлаков.
Выполнить отделение, с помощью кузнечных клещей, верхней части литейной формы. Очистить головку рельса от песка металлической щёткой.
Формирование головки рельса в зоне литейного шва
Установить гидравлическое
обрезное приспособление для исключения дополнительной части литейного шва.
В течение 10-15 секунд сделать обрезку дополнительной части литейного шва по головке и снять обрезное приспособление.
Удалить излишки шлака, обрезки металла и срубить при помощи молотка и зубила или гидравлических ножниц остатки литейной системы, подрубив
литники в горячем состоянии.
Установить на поверхности головки рельса гидравлический шлифовальный станок и выполнить предварительную шлифовку
дополнительной части литейного шва до высоты приблизительно 1 мм над верхом головки рельса.
Операция № 5 Выдержка стыка до полного охлаждения.
Выдержать литейный шов до его полного охлаждения, когда температура металла шва и рельса на расстоянии 2 м от шва будут одинаковыми.
Ориентировочное время
охлаждения 90-120 минут, в зависимости от температуры
окружающего воздуха.
Операция № 6. Окончательная шлифовка стыка и контроль качества.
Окончательная шлифовка.
Отбить литники.
Окончательно очистить литейный шов от остатков литейной формы и песка металлической щёткой.
Выполнить окончательную
шлифовку головки рельса в зоне стыка шлифовальным станком. Выполнить крепление рельса к шпалам в зоне литейного шва. Засыпать балласт в шпальный ящик в подрельсовой зоне стыка.
Контроль качества АТС на месте выполнения работ.
В процессе подготовки и проведения АТС рельсов руководитель бригады сварщиков должен выполнять пооперационный контроль за качеством всех операций. По окончанию технологического процесса АТС должен быть проведён визуальный контроль литейного шва в стыке. Наличие на поверхностях шва трещин, а также пор и шлаковых включений не допускается.
Операция № 7. Приведение сварного шва и участка рельса в рабочее
состояние.
Установить инвентарные
стыковые накладки (при
необходимости) на рельс в зоне литейного стыка.
Демонтировать приспособление, собрать инструмент, включая клины, для выправки рельсов.
Собрать остатки литейных материалов.
Вывод
Свое развитие алюминотермитная сварка получила благодаря следующим позитивным факторам: полная независимость от электроэнергии и газа; простота и доступность технологии; отсутствие сложного технологического оборудования; возможность
выполнения работ в линейных или полевых условиях [5].
Алюминотермитная сварка стыков позволяет:
— значительно сократить расходы на текущее содержание пути;
— предотвратить образование дефектов на концах рельсов, тем самым избежать преждевременной замены рельсов;
— уменьшить интенсивность износа колес подвижного состава;
— увеличить скорость хода подвижного состава;
— увеличить плавность хода подвижного состава [6].
Список литературы:
1. Коненков В.И. Алюмотермитная сварка // Евразия. Вести. — 2003. — № 9. — 22 с.
2. Малкин Б.В., Воробьев А.А. Термитная сварка. М. : Минкоммхоз, 1963. — 104 с.
3. ТУ-0921-127-011243 23 -2005.
Сварка рельсов алюминотермитная методом промежуточного литья.
4. https://helpiks.org/1-136097.html.
5.http://www.zaosnk.ru/services/alyu minotermitnaya_svarka_relsov.
Аннотации:
В статье детально рассмотрены технологический процесс производства алюминотермитной сварки (АТС) и осуществление контроля за его выполнением.
Приведены выводы о состоятельности использования этого способа сварки на стыках
стрелочных переводов отечественных железных дорог.
Ключевые слова: алюминотермитная сварка, стык, руководитель, бригада, контроль, стрелочный перевод.
In the article details considered the technological process of production of aluminum-thermal welding (PBX) and monitoring its implementation.
The above conclusions about the viability of using this welding method at the junction turnouts for local Railways.
Key words, aluminothermic welding, joint, leader, team, control, switches transfer.
Параметры твёрдости стыков рельсов, сваренных алюминотермитным способом Текст научной статьи по специальности «Технологии материалов»
Общетехнические и социальные проблемы
Современные технологии — транспорту
УДК 625.143.48 А. Л. Алехин
ПАРАМЕТРЫ ТВЁРДОСТИ СТЫКОВ РЕЛЬСОВ, СВАРЕННЫХ АЛЮМИНОТЕРМИТНЫМ СПОСОБОМ
Увеличение сроков службы рельсов в пути — одно из направлений ресурсосбережения. Важным фактором, влияющим на этот показатель, является твердость металла поверхности катания. Приведены результаты экспериментов по определению твердости металла на поверхности катания головки рельса в зоне стыков, сваренных алюминотермитной сваркой. Приведена формула определения нарастания твердости металла стыка в зоне рекристаллизации. Выдвинуты предложения по организации контроля, а также текущего содержания пути в зоне стыков, сваренных алюминотермитным способом.
алюминотермитная сварка, стык, твердость.
Введение
В последнее время много внимания уделяется ресурсосберегающим технологиям. Одним из направлений ресурсосбережения является увеличение сроков службы рельсов в пути. Одной из причин их «выхода» являются дефекты в зоне стыка, а также усиленный износ рельсов в зоне стыка за счет повышенных динамических нагрузок.
Устранение подобных проблем возможно путем сварки рельсов. На данный момент на сети железных дорог России применяются два вида сварки рельсов: электроконтактная и алюминотермитная. Каждый из этих видов имеет свои сферы применения. Электроконтактная сварка обеспечивает высокие физико-механические свойства сварного стыка и применяется практически повсеместно на железных дорогах России, за исключением тех мест, где применение данной сварки невозможно (в пределах стрелочных переводов) или экономически нецелесообразно. Алюминотермитная сварка при более низких физико-механических показателях сварного стыка позволяет выполнять сварку стыков на стрелочных переводах, а также является экономически более выгодной при выполнении небольших объемов сварочных работ, например при восстановлении целостности рельсовых плетей.
ISSN 1815-588 Х. Известия ПГУПС
2010/2
Общетехнические и социальные проблемы
61
1 Сущность алюминотермитной сварки
Алюмотермитная сварка осуществляется с использованием термитной смеси, которая является источником тепла и соединительного материала. Термит представляет собой механическую смесь мелкоизмельченных окислов и восстановителей. Алюмотермитный порошок состоит из окислов железа и алюминия с размером частиц 0,1-2,5 мм. Первичный алюминий содержит 98-99% чистого алюминия. В качестве окислов железа используют перемолотую железную окалину, которая должна быть хорошо обожжена с целью удаления влаги и масла. Содержание кислорода в окалине не должно быть ниже 25%. Химическая реакция смеси происходит, если смесь нагреть до температуры 1200-1300°С. Эта реакция идет с большим выделением тепла. Данная реакция выражается следующим уравнением:
3Fe3O4 + 8Al = 9Fe + 4AI2O3.
Подставив в формулу молекулярный вес входящих элементов, получим:
696 + 216 = 504 + 408.
Таким образом, 696 г железной окалины и 216 г алюминия дают после реакции 504 г железа и 408 г окиси алюминия. Термитная смесь содержит по весу 23,7% алюминия и 76,3% окалины. При сгорании 1 кг термитной смеси выделяется 762 ккал тепла, что позволяет получить температуру около 3000 °C.
Для лучшего использования тепла, выделяемого при реакции, в смесь добавляется измельченная сталь, а для получения определенного химического состава сплава — легирующие элементы в виде ферросплавов [1].
В технологии выполнения работ по алюминотермитной сварке рельсов необходимо обратить особое внимание на следующие операции, влияющие на качество сварного шва: очистка свариваемой поверхности, установка стыкового зазора и стыка по геометрии, предварительный прогрев стыка.
2 Исследование твёрдости стыков, сваренных алюминотермитной сваркой
Процесс эксплуатации стыков, сваренных аллюминотермитным способом, является недостаточно изученным в условиях эксплуатации на российских железных дорогах. Одним из направлений изучения стыков сваренных алюминотермитной сваркой служит исследование твердости поверхности катания в зоне стыка и влияние ее на прямолинейность поверхности катания рельса.
ISSN 1815-588 Х. Известия ПГУПС
2010/2
Общетехнические и социальные проблемы
Для исследования этих процессов были выполнены замеры твердости на станциях направления Санкт-Петербург — Москва Октябрьской железной дороги. Замеры проводились согласно схеме контроля твердости сварных стыков (рис. 1) согласно ТУ 0921-127-01124323-2005, а также замеры по оси рельса на расстоянии 250, 500 и 750 мм в обе стороны от оси сварного стыка. Измерения проводились с учетом направления движения поездов. Испытанию подвергались стыки, сваренные по технологии фирмы «СНАГА».
Рис. 1. Схема контроля твердости металла литейного шва
На основании полученных данных была составлена характерная картина изменения твердости по оси рельса и оси сварного шва (рис. 2).
Рис. 2. Характеристики твердости металла сварного шва в зависимости
от наработки тоннажа
На графике видно, что с увеличением пропущенного тоннажа твердость на всем протяжении поверхности катания рельсов в том числе в зоне сварного стыка, повышается. Однако процесс изменения твердости
ISSN 1815-588 Х. Известия ПГУПС
2010/2
Общетехнические и социальные проблемы
63
является неоднородным. Скорости нарастания твердости в зоне влияния сварного стыка и остального рельса различны. Также различными являются скорости нарастания твердости в различных точках зоны влияния сварки. Наиболее интенсивно идет нарастание твердости в точках удаленных на расстояние 25 и 75 мм от оси сварного стыка, что соответствует зонам нормализации и отпуска металла.
При этом, если твердость металла в зоне нормализации одинакова независимо от направления движения, то для зоны отпуска металла характерным является то, что твердость на отдающем конце рельса ниже твердости на принимающем на 3%, что может являться следствием повышенных динамических нагрузок на принимающий конец рельса из-за недостаточной частоты шлифовки сварного стыка после сварки. По оси сварного стыка, а также в зонах рекристаллизации, расположенных на расстоянии 50 мм от нее, нарастание твердости идет менее интенсивно. И если по оси шва и на принимающем конце в зоне рекристализации скорости нарастания сопоставимы, то на отдающем конце в данной зоне она ниже (рис. 3), что может быть следствием резкого изменения твердости поверхности катания с более твердого непосредственно на самом рельсе к менее твердому в зоне влияния сварного стыка.
=Г 2
Рис. 3. График нарастания твердости металла по оси стыка и в зонах рекристаллизации
в зависимости от пропущенного тоннажа
ISSN 1815-588 Х. Известия ПГУПС
2010/2
Общетехнические и социальные проблемы
Скорость нарастания твердости на отдающем конце в зоне рекристаллизации можно выразить формулой:
ДНВ = 2 0,4 М| — 4,44М| + 113,16МТ,
где АНВ — нарастание твердости по стыку в единицах по Бринеллю;
Мт — пропущенный тоннаж по стыку, сваренному алюминотермитной сваркой, млн т брутто.
Как видно из графика (см. рис. 2), перепады твердости довольно значительны при наработке соответствующего тоннажа, что может являться причиной возникновения коротких изолированных неровностей в зоне сварного стыка.
Для дальнейшего подтверждения данного факта были проведены измерения прямолинейности поверхности катания в зоне сварного стыка с помощью траекториографа. В зоне стыков, сваренных алюминотермитной сваркой, были обнаружены при наработке 78,78 млн т брутто пропущенного тоннажа короткие изолированные неровности трех видов: горбы, впадины, синусоидальные неровности. Максимальные величины данных неровностей составляли: горбов — до 2,0 мм; впадин — до 1,0 мм; синусоидальных неровностей — до 1 мм.
Заключение
На основании приведенных данных предлагается ввести контроль прямолинейности стыков в ходе их эксплуатации с назначением работ по шлифовке рельсов в случае необходимости. Учитывая тезисы, изложенные в статье «Волнообразный износ рельсов и скорость движения» [2], предлагается назначить шлифовку рельсов в зоне стыков, сваренных алюминотермитной сваркой, в зависимости от скоростей движения: 140 км/ч — после пропуска 40 млн т брутто, при скорости 100 км/ч — после 70 млн т брутто, при скорости движения 60 км/ч — 160 млн т брутто.
Важным является контроль за состоянием пути в зоне стыков, сваренных алюминотермитной сваркой. Предполагается осуществлять контроль геометрии поверхности катания головки рельса в зоне стыков с помощью профилографа и траекториографа при плановых проверках пути вагоном-путеизмерителем.
Библиографический список
1. Технология алюминотермитной сварки : учебное пособие / ред. Н. Н. Воронин. -М. : МИИТ, 2008. — С. 72-73.
2. Волнообразный износ рельсов и скорость движения / В. И. Абросимов,
А. Н. Трофимов, Л. Н. Фролов // Путь и путевое хозяйство. — 2001. — № 8. — С. 5-7.
Статья поступила в редакцию 16.04.2010;
ISSN 1815-588 Х. Известия ПГУПС
2010/2
Обучение сварщиков железнодорожных путей алюмотермической сварке
EUROJOIN 6, Сантьяго-де-Компостела, Испания, 28-30 июня 2006 г.
Сводка
1 октября 2004 г. стартовал европейский проект RAILSAFE. Целью проекта является гармонизация обучения, подготовки, квалификации и сертификации сварщиков железнодорожных путей в области алюмотермической сварки в Европе.
В 5 странах были проведены семинары по формулированию требований к алюмотермическим сварщикам и по согласованному обучению и обучению.
В этом документе рассказывается, как можно решить существующие национальные и международные различия.
Введение
Что такое алюмотермическая сварка?
В процессе алюмотермической сварки расплавленная сталь заливается в форму, окружающую зазор между соединяемыми концами рельсов. Концы рельсов соединены жидким металлом. Принцип алюминотермической сварки основан на экзотермической химической реакции порошка алюминия и оксида железа с выделением тепла, достаточного для плавления.
Перед тем, как начать плавление, концы рельсов обрезаются, чтобы создать определенный зазор, и рельсы выравниваются. Затем огнеупорную форму крепят вокруг зазора с помощью стальных башмаков. Утечки в формах предотвращаются специальным фиксирующим материалом. После предварительного нагрева обоих рельсов начинается экзотермическая реакция порошка алюминия и оксида железа в повторно используемом или «одноразовом» тигле, и жидкий металл течет в форму. Металл заполняет изложницу, и шлак выгружается в шлаковые чаши.После периода охлаждения излишки металла в головке рельса удаляются, и можно начинать шлифование рельса.
Поскольку сварка довольно часто происходит на действующих путях, скорость сварки и безопасность сварщиков являются важными аспектами сварки на железнодорожных путях.
Почему RAILSAFE?
Безопасность железнодорожного движения во многом зависит от качества путей, сварных швов на путях и, следовательно, от навыков сварщика. Во всей Европе наблюдается отсутствие единообразия в обучении и тестировании алюмотермических сварщиков, отсутствие общих учебных программ и отсутствие мобильности квалифицированных сварщиков.Это верно не только между странами, но и внутри некоторых стран. Направление сварщиков для работы в других компаниях или в других странах часто затрудняется из-за различных процедур и разной квалификации сварщиков.
Политика Европейской комиссии состоит в том, чтобы способствовать взаимодействию между отдельными национальными железнодорожными системами и повышать безопасность. (См. Белая книга ЕС: Европейская транспортная политика на 2010 год: время решать, 2001 год)
Другая политика Европейской комиссии состоит в том, чтобы стимулировать через «Программу действий Сообщества Леонардо да Винчи по профессиональному обучению» образование и обучение в рамках процесса обучения на протяжении всей жизни, чтобы улучшить возможности трудоустройства и сделать работу вне национальных границ возможной: свободное перемещение людей в Европейском Союзе.
Европейская организация по стандартизации, CEN, и, в частности, TC256 / SC1 / WG4, разрабатывает стандарты по процедурам сварки железнодорожных путей и по обучению сварщиков алюмотермической сварке, prEN 14730. Эти стандарты предназначены для комментариев и еще не вступили в силу.
1 октября 2004 г. стартовал трехлетний европейский проект: «Разработка гармонизированной системы обучения, квалификации и сертификации сварщиков железнодорожных путей», RAILSAFE. Проект частично финансируется программой ЕС «Программа профессионального обучения Сообщества Леонардоды Винчи».
Целью проекта RAILSAFE является разработка гармонизированной системы обучения, квалификации и сертификации сварщиков железнодорожных путей.
Гармонизированное образование, обучение и квалификация делают возможным обмен сварщиками на национальном и европейском уровнях. Сертификация гарантирует непрерывное профессиональное образование для получения компетенций на протяжении всей жизни. Квалификация и сертификация также обеспечивают видимую проверку компетентности сварщика в соответствии с согласованными европейскими директивами, которые признаются и принимаются соответствующими работодателями и властями по всей Европе.Таким образом можно избежать многократных или повторных испытаний сварщиков.
Результаты проекта также способствуют улучшению «интероперабельности» между национальными железнодорожными системами, более эффективному обслуживанию, сокращению времени владения путями и повышению безопасности персонала, а также свободному перемещению сварщиков в ЕС.
Новые стандарты prEN 14730 служат основой для деятельности RAILSAFE, особенно стандарта по процедурам. Однако в проекте стандартов не указывается подробно уровень подготовки или компетентности сварщиков.Результаты RAILSAFE будут включать эти детали.
Ожидаемые результаты проекта:
- Отраслевые требования в отношении рабочих характеристик для алюмотермических сварщиков, а также согласованного обучения и подготовки.
- Руководство по обучению, обучению, квалификации и сертификации сварщиков железнодорожных путей
- База данных квалифицированных и сертифицированных сварщиков
- Пилотные курсы с экзаменом и квалификацией
- План организации эксплуатации системы
- Распространение результатов проекта в Европе
Проект выполняется 9 партнерами из 7 разных стран: подрядчиком по строительству железных дорог, консультантом по качеству и гармонизации сварки, европейской организацией, представляющей институты сварки и сами институты сварки, обладающие опытом в области образования, обучения, квалификации и сертификации сварщики.
Во время семинаров в 5 европейских странах специалисты по железнодорожным путям определили отраслевые требования в отношении образования и обучения сварщиков.
Требования к образованию и обучению
Мастерские
Около 50 специалистов по сварке рельсов приняли участие в семинарах в Копенгагене, Кембридже, Генуе, Ганновере и Братиславе. В нем приняли участие представители железнодорожных властей, подрядчиков, поставщиков технологических процессов, исследовательских и консультационных организаций, учебных заведений и институтов сварки.
Эксперты обсудили проекты предложений по рабочим характеристикам, процедурам технических требований к сварке, базе данных для сертифицированных сварщиков и структуре для работы гармонизированной системы.
Из — иногда противоречивых — комментариев были получены следующие результаты, которые снова являются предметом обсуждения среди участников семинара.
Структура образования, обучения, квалификации и сертификации
Гармонизированная система предусматривает теоретическое обучение и практическую подготовку алюминотермических сварщиков, их экзамен, выдачу диплома, действительного в течение всего срока действия владельца, и сертификатов с ограниченным сроком действия.
Квалификация, в результате которой выдается диплом, требует теоретического образования, практической подготовки, а также теоретических и практических экзаменов.
Для сертификациитребуется квалификация, указанная выше, плюс удовлетворительный опыт сварки гусениц.
Теоретическое образование и экзамен на получение диплома являются общими, а практическая подготовка и экзамен на получение диплома зависят от конкретного процесса. После сдачи экзаменов сварщик получит общий диплом, действующий на протяжении всей жизни.
Обладатели диплома должны продемонстрировать годичный контролируемый, документально подтвержденный и удовлетворительный опыт, чтобы получить сертификат, который зависит от процесса. Это относится к Сертификату процесса, в котором сварщик был обучен для получения Диплома, а также к дополнительным Сертификатам в других процессах. Чтобы получить сертификат в других процессах, сварщик также должен пройти практическое обучение в этом процессе.
Сертификаты действительны в течение двух лет.Чтобы продлить Сертификат еще на двухлетний период, держатели должны продемонстрировать подтвержденный документально подтвержденный и удовлетворительный опыт в процессе, за который был выдан сертификат, в течение периода действия сертификата.
Общая структура
Европейская организация по сварке рельсов (будет назначена или создана Европейским сообществом по сварке рельсов) разрабатывает специальные правила для уполномоченных национальных органов (ANB) в каждой стране, которая желает внедрить схему обучения, квалификации и сертификации сварщиков рельсов.Эти правила потребуют от ANB создать Национальный комитет специалистов по сварке рельсов для этой деятельности с представителями национального сектора железнодорожной промышленности. Презентация этого комитета будет включать:
- Управление железных дорог
- подрядчиков по сварке рельсов
- поставщики сварочного оборудования для рельсов, действующие в соответствующей стране
- организаций по обучению сварщиков рельсов.
Этот национальный комитет специалистов по сварке рельсов будет отвечать за реализацию схемы на национальном уровне от имени руководящего совета ANB.
ANB оценивают и утверждают утвержденные учебные органы (ATB) и уполномоченных экзаменаторов (AE) ANB.
Группа специалистов по сварке рельсов создана на европейском уровне для соблюдения согласованных руководящих принципов и правил. В эту группу будут входить железнодорожные власти, подрядчики, поставщики процессов, обучающие организации и ANB.
Цели деятельности
Участники семинара определили рабочие характеристики алюминотермического сварочного аппарата.Цели деятельности — это утверждения, которые определяют конкретные знания и навыки, которые человек должен получить и продемонстрировать в результате своего образования и обучения. Они описаны в терминах «ожидаемых результатов». Рабочие характеристики лягут в основу Руководства «Минимальные требования к образованию, обучению, квалификации и сертификации» европейского алюмотермического сварщика.
В следующей таблице представлена структура, в которой определены целевые показатели эффективности.
Также включено указание количества учебных часов.
Модуль | Подмодуль | Рекомендуемые часы обучения |
---|---|---|
I. Теоретическое образование |
| 8 24 8 |
Общий модуль I | 40 | |
II.Практические занятия |
| 64 16 |
Общий модуль II | 80 | |
Общий курс | 120 |
В следующих таблицах приведены два примера целевых показателей эффективности с точки зрения ожидаемых результатов: один в модуле «Теоретическое образование», подмодуле «Материалы и их поведение во время сварки» и один в модуле «Практическое обучение». подмодуль «Алюминотермическая сварка».
Модуль I — Теоретическое образование | 40 |
I.1 Материалы и их поведение при сварке | |
I.1.1 Основы металлургии | 4 |
Ожидаемые результаты | |
|
Модуль II — Практическое обучение | 80 |
II.1.1 Алюминотермическая сварка | 64 |
Ожидаемые результаты | |
|
Методики сварки
В связи с появлением стандарта prEN 14730-1 CEN многие участники семинара подумали, что документ о процедуре сварки не потребуется.
Введена форма «Спецификация практического теста» для определения обучения и проверки практической части квалификации (диплома).
База данных
База данных по-прежнему вызывает споры. Большинство подрядных компаний и железнодорожных властей имеют базы данных для квалифицированных и сертифицированных сварщиков. Международная база данных рассматривается многими участниками семинара как столь необходимая мгновенная общеевропейская проверка квалификации / сертификации сварщика.Однако другие считают, что такая база данных не нужна.
Поскольку база данных является продуктом проекта, RAILSAFE разработает базу данных, которая будет основана на Интернете. Данные будут предоставлены ATB и вставлены ANB.
Данные основаны на одном пожизненном дипломе и одном или нескольких сертификатах с ограниченным сроком действия, выданных сварщику, и сварщик / работодатель должен согласиться (или не согласиться) с данными, хранящимися в базе данных.
Продолжение
Принимая во внимание все отраслевые требования, в рамках проекта будет продолжена разработка Руководства по обучению, квалификации и сертификации сварщиков, Спецификации практических испытаний, базы данных квалифицированных и сертифицированных сварщиков, пилотных курсов с квалификацией и сертификацией, а также дальнейшего распространения система в Европе.
Партнеры по проекту организуют в конце 2006 г. общеевропейский семинар для обсуждения результатов проекта со специалистами по сварке железных дорог из всех европейских стран.
Наблюдения
Из обсуждений на семинаре можно сделать вывод, что RAILSAFE принесет пользу в плане мобильности и признания, и принесет национальную и европейскую гармонизацию существующей компетенции сварщиков.
RAILSAFE добавит детали к стандартам CEN: единые цели производительности для сварщиков и руководство по образованию, обучению, квалификации и сертификации, чтобы подкрепить стандарты, и обеспечит надежную мгновенную общеевропейскую проверку квалификации / сертификации сварщика по базе данных.
.алюминиотермический набор для заварки рельса 400в 1500уф для распределительной станции
Комплект для алюминотермической сварки рельсов 400 В 1500 мкФ для распределительной станции
Характеристики:
1. long life : до 5000 ч
2. Высокая удельная мощность : до 3000 Вт / кг
3. Low ESR : может использоваться в качестве перезаряжаемой батареи и идеально подходит для целей резервного копирования.
4. Быстрая зарядка : зарядка от 10 секунд до 10 минут для достижения номинальной емкости более 95%
5. Стандарт качества : ISO 9001: 2000; ISO 9001: 2008; ISO 14001: 2004
6. Превосходный сервис : обеспечение качества продукции, обещание одного года послепродажного обслуживания, не беспокойтесь f2
алюминотермический Комплект для сварки рельсов 400 В 1500 мкФ для распределительной станции
Применения: широко используется в беспроводных телефонах, сотовых телефонах, цифровых камерах, интеллектуальных электрических приборах, электронных игрушках, интеллектуальных дверных замках, интеллектуальных счетчиках, MP3, КПК, DVD, видеомагнитофонах, GPS , PLC, факс, аудиооборудование, электрическая плита, электрический водонагреватель, супер-фонарик с автономным питанием, принтер, задний фонарь, электронные игрушки, кассовый аппарат, ИБП, солнечная энергия, энергия ветра, система утилизации энергии, партнер по батареям и т. Д. .
почему выбрали нас?
1. Ведущие производители алюминиевых электролитических конденсаторов.
2.Суперконденсаторы и ведущие производители модулей.
3. Ведущий разработчик высококачественных электронных материалов.
4. Ведущие мировые электронные компоненты лучшие дистрибьюторы
.
Сварка термитом |
Применительно к восстановлению оксидов железа экзотермическая реакция генерирует достаточно энергии, чтобы поднять температуру продукта реакции до уровня, превышающего 3000 ° C, при котором и металл, и оксид алюминия являются жидкими:
Оксид железа | + | Алюминий | > | Оксид алюминия | + | Утюг | + | Тепло |
3FeO | + | 2Al | > | Al2O3 | + | 3Fe | + | 880 кДж |
Fe2O3 | + | 2Al | > | Al2O3 | + | 2Fe | + | 850 кДж |
Этот процесс был впервые использован для обеспечения тепловой энергией для метода ковочной сварки рельсов в 1899 году, когда на трамвае Эссена было установлено несколько сварных соединений.Впервые этот процесс был использован в Великобритании для сварки трамвайных рельсов, установленных в Лидсе в 1904 году.
Дальнейшая разработка, ведущая к добавлению легирующих элементов в основную алюминотермическую реакцию, позволила получить сталь с совместимой металлургией основных рельсов, что позволило разработать процесс сварки плавлением. В то время как первые сварные швы производились путем заливки стали Thermit в формы, изготовленные вручную, включающие два рельса, которые необходимо было соединить вместе, последующее развитие привело к внедрению предварительно сформированных огнеупорных форм, предназначенных для соответствия конкретным профилям рельсов.
Хотя основной процесс алюминотермической сварки по-прежнему составляет основу сварочных процессов Thermit, постоянное развитие в сочетании с современными производственными технологиями, статистическим контролем процесса и контролем качества привело к созданию процессов, которые более чем соответствуют требованиям обслуживания современных высоких скоростей и высоких нагрузок на ось. железнодорожные системы.
- Обычные рельсы «с плоским дном» или «виньоль»
- Рельсы специальные секции
- Рельсы трамвайные рифленые
- Рельсы для тяжелых секционных кранов
- Рельсы для электрических проводов
Кроме того, доступны изделия для специальных типов опор направляющих, ограниченного пространства, ограничений окружающей среды, а также для соединения рельсов разных типов или с различной степенью износа.
Процесс термитной сварки
Сварка термитом — это эффективный, высокомобильный метод соединения стальных конструкций большого диаметра, таких как рельсы. По сути, процесс литья, высокая погонная энергия и металлургические свойства стали Thermit делают этот процесс идеальным для сварки высокопрочных сталей с высокой твердостью, таких как те, которые используются для современных рельсов.
Thermit Welding — это квалифицированный сварочный процесс, который не должен выполняться лицами, не прошедшими обучение и сертификацию для его использования.
Подробные инструкции по эксплуатации предоставляются для каждого из наших процессов, но все методы сварки состоят из 6 основных элементов:
1- Между двумя рельсами должен быть сделан тщательно подготовленный зазор, который затем должен быть точно выровнен с помощью линейки, чтобы конечный стык был идеально прямым и плоским.
2- Предварительно отформованные огнеупорные формы, которые изготавливаются таким образом, чтобы точно соответствовать определенному профилю рельса, зажимаются вокруг зазора рельса, а затем герметизируются на месте.Затем собирается оборудование для размещения горелки предварительного нагрева и контейнера Thermit.
3- Сварочная полость, образованная внутри формы, предварительно нагревается с помощью кислородно-газовой горелки с точно установленным давлением газа в течение заданного времени. Качество готового сварного шва будет зависеть от точности этого процесса предварительного нагрева.
4- По завершении предварительного нагрева контейнер устанавливают на верхнюю часть форм, часть зажигается, и последующая экзотермическая реакция дает расплавленную термитную сталь.Контейнер включает в себя автоматическую систему выпуска, позволяющую жидкой стали, имеющей температуру выше 2500 ° C, выходить непосредственно в сварочную полость.
5- Сварному стыку дают остыть в течение заданного времени, прежде чем излишки стали и пресс-формы будут удалены с верхней части рельса с помощью гидравлического устройства обрезки.
6- В холодном состоянии стык очищается от мусора, а рабочие поверхности рельсов прецизионно шлифуют профиль.Готовый сварной шов необходимо затем проверить, прежде чем он будет признан готовым к эксплуатации.
Видео:
См. Также: http://www.asa.transport.nsw.gov.au/sites/default/files/asa/railcorp-legacy/disciplines/civil/tmc-222.pdf
Источник: thermit-welding.com
.Порошок для алюминотермической сварки— Купить порошок для алюминотермической сварки на Alibaba.com
2 доллара США.98–44,98 долларов США / Кусок | 20 шт. / Шт. (Минимальный заказ)
- Перевозка:
- Поддержка Экспресс · Морские перевозки · Наземный фрахт · Авиаперевозка
- Время выполнения заказа:
Кол-во (шт.) 1–1000 1001–5000 5001–10000 > 10000 Приблиз.Срок (дни) 10 15 20 Торг
- Настройка:
Индивидуальная упаковка (Мин.Заказ: 10 шт.)