Π‘ΡΠ΅Π΄ΡΡΠ²Π° ΠΌΠ΅Ρ Π°Π½ΠΈΠ·Π°ΡΠΈΠΈ ΠΈ Π°Π²ΡΠΎΠΌΠ°ΡΠΈΠ·Π°ΡΠΈΠΈ
ΠΡΠΎΡΠ΅ΡΡ ΠΏΡΠΎΠ²Π΅Π΄Π΅Π½ΠΈΡ ΡΠ²Π°ΡΠΎΡΠ½ΡΡ ΡΠ°Π±ΠΎΡ Π΄Π΅Π»ΠΈΡΡΡ Π½Π° Π²ΡΠ΅ΠΌΡ ΠΏΡΠΎΠ²Π΅Π΄Π΅Π½ΠΈΠ΅ ΠΎΡΠ½ΠΎΠ²Π½ΡΡ ΠΈ Π²ΡΠΏΠΎΠΌΠΎΠ³Π°ΡΠ΅Π»ΡΠ½ΡΡ ΡΠ°Π±ΠΎΡ. ΠΠ° Π±ΠΎΠ»ΡΡΠΈΠ½ΡΡΠ²Π΅ ΠΌΠ°ΡΡΠΎΠ²ΡΡ ΠΈ ΠΏΠΎΡΠΎΡΠ½ΡΡ ΠΏΡΠΎΠΈΠ·Π²ΠΎΠ΄ΡΡΠ²Π°Ρ , Π²ΡΠΏΠΎΠ»Π½Π΅Π½ΠΈΠ΅ ΠΎΡΠ½ΠΎΠ²Π½ΡΡ ΡΠ²Π°ΡΠΎΡΠ½ΡΡ ΡΠ°Π±ΠΎΡ ΠΏΠΎΠ»Π½ΠΎΡΡΡΡ ΠΌΠ΅Ρ Π°Π½ΠΈΠ·ΠΈΡΠΎΠ²Π°Π½ΠΎ. ΠΠ»Ρ ΠΏΠΎΠ²ΡΡΠ΅Π½ΠΈΡ ΠΏΡΠΎΠΈΠ·Π²ΠΎΠ΄ΠΈΡΠ΅Π»ΡΠ½ΠΎΡΡΠΈ Π½ΡΠΆΠ½ΠΎ ΡΠ°ΡΡΠΌΠ°ΡΡΠΈΠ²Π°ΡΡ ΡΠΏΠΎΡΠΎΠ±Ρ ΠΎΠΏΡΠΈΠΌΠΈΠ·Π°ΡΠΈΠΈ Π²ΡΠ΅ΠΌΠ΅Π½ΠΈ, ΡΡ ΠΎΠ΄ΡΡΠ΅Π³ΠΎ Π½Π° ΠΏΡΠΎΠ²Π΅Π΄Π΅Π½ΠΈΡ Π²ΡΠΏΠΎΠΌΠΎΠ³Π°ΡΠ΅Π»ΡΠ½ΡΡ ΡΠ°Π±ΠΎΡ. ΠΠ²ΡΠΎΠΌΠ°ΡΠΈΡΠ΅ΡΠΊΠ°Ρ ΠΏΠΎΠ΄Π°ΡΠ° Π΄Π΅ΡΠ°Π»Π΅ΠΉ Π½Π°Β Π°ΠΏΠΏΠ°ΡΠ°Ρ ΠΊΠΎΠ½ΡΠ°ΠΊΡΠ½ΠΎΠΉ ΡΠ²Π°ΡΠΊΠΈΒ ΠΈ ΡΡΡΠ°Π½ΠΎΠ²ΠΊΠ° ΠΈΡ ΠΏΠΎΠ΄ ΡΠ»Π΅ΠΊΡΡΠΎΠ΄Ρ, ΡΠ΅Π°Π»ΠΈΠ·ΠΎΠ²Π°Π½Π° Π½Π΅ Π±ΠΎΠ»Π΅Π΅ ΡΠ΅ΠΌ Π½Π° 10%.
ΠΠΎΠ²ΡΡΠ΅Π½ΠΈΠ΅ ΠΏΡΠΎΠΈΠ·Π²ΠΎΠ΄ΠΈΡΠ΅Π»ΡΠ½ΠΎΡΡΠΈ ΡΡΡΠ΄Π° Π½Π° ΡΠ²Π°ΡΠΎΡΠ½ΠΎΠΌ ΠΏΡΠΎΠΈΠ·Π²ΠΎΠ΄ΡΡΠ²Π΅ Π·Π°Π²ΠΈΡΠΈΡ Π½Π΅ ΠΎ ΠΌΠΎΡΠ½ΠΎΡΡΠΈ ΠΈΡΠΏΠΎΠ»ΡΠ·ΡΠ΅ΠΌΠΎΠ³ΠΎ ΠΎΠ±ΠΎΡΡΠ΄ΠΎΠ²Π°Π½ΠΈΡ, Π° Π² Π±ΠΎΠ»ΡΡΠ΅ΠΉ ΡΡΠ΅ΠΏΠ΅Π½ΠΈ ΠΎΡ Π°Π²ΡΠΎΠΌΠ°ΡΠΈΠ·Π°ΡΠΈΠΈ ΠΏΠΎΠ΄Π°ΡΠΈ Π΄Π΅ΡΠ°Π»Π΅ΠΉ ΠΈ ΠΈΡ ΠΏΠΎΡΠ»Π΅Π΄ΡΡΡΠ΅ΠΉ ΡΠ²Π°ΡΠΊΠΈ. ΠΠ²Π΅Π΄Π΅Π½ΠΈΠ΅ Π² ΠΏΡΠΎΠΈΠ·Π²ΠΎΠ΄ΡΡΠ²ΠΎ Π°Π²ΡΠΎΠΌΠ°ΡΠΈΡΠ΅ΡΠΊΠΈΡ Π»ΠΈΠ½ΠΈΠΉ, Π³Π΄Π΅ Π²Π΅ΡΠΎΠΌΠ°Ρ Π΄ΠΎΠ»Ρ ΡΠ΅Ρ Π½ΠΎΠ»ΠΎΠ³ΠΈΡΠ΅ΡΠΊΠΈΡ ΠΎΠΏΠ΅ΡΠ°ΡΠΈΠΉ Π²ΡΠΏΠΎΠ»Π½ΡΠ΅ΡΡΡ Π°ΠΏΠΏΠ°ΡΠ°ΡΠ½ΠΎ, Π±Π΅Π· ΠΏΡΠΈΠΌΠ΅Π½Π΅Π½ΠΈΡ ΡΠΈΠ·ΠΈΡΠ΅ΡΠΊΠΎΠ³ΠΎ ΡΡΡΠ΄Π° ΡΠ΅Π»ΠΎΠ²Π΅ΠΊΠ°, Π΄Π°Π΅Ρ ΡΠ²Π΅Π»ΠΈΡΠ΅Π½ΠΈΠ΅ ΡΡΡΠ΅ΠΊΡΠΈΠ²Π½ΠΎΡΡΠΈ ΡΠ°Π±ΠΎΡΠ΅Π³ΠΎ ΠΏΡΠΎΡΠ΅ΡΡΠ° Π² Π½Π΅ΡΠΊΠΎΠ»ΡΠΊΠΎ ΡΠ°Π·.Β
Π‘ΠΏΠ΅ΡΠΈΡΠΈΠΊΠ° ΡΠ°Π±ΠΎΡΡ Π½Π° Π»ΠΈΠ½ΠΈΠΈ, Π² ΠΊΠΎΡΠΎΡΠΎΠΉ ΠΎΡΠ½ΠΎΠ²Π½ΡΠΌ ΡΠ΅Ρ
Π½ΠΎΠ»ΠΎΠ³ΠΈΡΠ΅ΡΠΊΠΈΠΌ ΡΠ·Π»ΠΎΠΌ ΡΠ²Π»ΡΠ΅ΡΡΡ Π°ΠΏΠΏΠ°ΡΠ°Ρ ΠΊΠΎΠ½ΡΠ°ΠΊΡΠ½ΠΎΠΉ ΡΠ²Π°ΡΠΊΠΈ, Π½Π°ΠΊΠ»Π°Π΄ΡΠ²Π°Π΅Ρ ΠΎΠΏΡΠ΅Π΄Π΅Π»Π΅Π½Π½ΡΠ΅ ΡΡΠ΅Π±ΠΎΠ²Π°Π½ΠΈΡ ΠΈ Π½Π° ΠΌΠ΅Ρ
Π°Π½ΠΈΠ·Π°ΡΠΈΡ ΠΏΡΠΎΡΠ΅ΡΡΠ°:
-ΡΠΎΠΊΠΎΠ²ΡΠ΅ ΡΠ»Π΅ΠΌΠ΅Π½ΡΡ ΠΎΠ±ΠΎΡΡΠ΄ΠΎΠ²Π°Π½ΠΈΡ Π΄ΠΎΠ»ΠΆΠ½Ρ Π±ΡΡΡ ΠΏΠΎΠ»Π½ΠΎΡΡΡΡ ΠΈΠ·ΠΎΠ»ΠΈΡΠΎΠ²Π°Π½Ρ,
-ΡΠ΅Ρ Π½ΠΎΠ»ΠΎΠ³ΠΈΡΠ΅ΡΠΊΠΈΠ΅ ΡΠ·Π»Ρ, ΠΏΡΠΈΠ½ΠΈΠΌΠ°ΡΡΠΈΠ΅ ΡΡΠ°ΡΡΠΈΠ΅ Π² ΡΠΎΡΠ΅ΡΠ½ΠΎΠΉ ΠΈΠ»ΠΈ ΡΠΎΠ²Π½ΠΎΠΉ ΡΠ²Π°ΡΠΊΠ΅, ΡΠ΅ΠΊΠΎΠΌΠ΅Π½Π΄ΡΠ΅ΡΡΡ ΡΡΡΠ°Π½Π°Π²Π»ΠΈΠ²Π°ΡΡ Π½Π° Π½ΠΈΠΆΠ½Π΅ΠΌ ΡΠ»Π΅ΠΊΡΡΠΎΠ΄Π΅, Ρ.ΠΊ. ΡΡΡΠ°Π½ΠΎΠ²ΠΊΠ° Π½Π° ΠΏΠ»Π°Π²Π°ΡΡΠ΅ΠΉ ΠΎΠΏΠΎΡΠ΅ Π΄Π°Π΅Ρ ΠΌΠ΅Π½ΡΡΠΈΠΉ ΠΈΠ·Π½ΠΎΡ ΡΠ°Π±ΠΎΡΠ΅ΠΉ ΠΏΠΎΠ²Π΅ΡΡ Π½ΠΎΡΡΠΈ ΡΠ»Π΅ΠΊΡΡΠΎΠ΄Π°,
-Π²ΠΈΠ΄ Π²ΡΠΏΠΎΠΌΠΎΠ³Π°ΡΠ΅Π»ΡΠ½ΡΡ ΠΏΠ΅ΡΠ΅Π½ΠΎΡΠ½ΡΡ ΡΡΡΡΠΎΠΉΡΡΠ² Π΄ΠΎΠ»ΠΆΠ΅Π½ ΡΠΎΠΎΡΠ²Π΅ΡΡΡΠ²ΠΎΠ²Π°ΡΡ ΡΠ°Π·ΠΌΠ΅ΡΠ°ΠΌ ΠΏΠ΅ΡΠ΅Π½ΠΎΡΠΈΠΌΠΎΠ³ΠΎ ΠΈΠ·Π΄Π΅Π»ΠΈΡ,
-Π²ΡΠΏΠΎΠΌΠΎΠ³Π°ΡΠ΅Π»ΡΠ½ΡΠ΅ ΡΡΡΡΠΎΠΉΡΡΠ²Π° Π½Π΅ Π΄ΠΎΠ»ΠΆΠ½Ρ Π·Π°Π³ΡΠΎΠΌΠΎΠΆΠ΄Π°ΡΡ ΠΏΡΠΎΡ ΠΎΠ΄ ΠΊ ΠΌΠ΅ΡΡΡ ΠΏΡΠΎΠ²Π΅Π΄Π΅Π½ΠΈΡ ΡΠ²Π°ΡΠ½ΡΡ ΡΠ°Π±ΠΎΡ,
-ΠΌΠ°ΠΊΡΠΈΠΌΠ°Π»ΡΠ½Π°Ρ ΡΠΎΠΎΡΠ½ΠΎΡΡΡ Π΄Π΅ΡΠ°Π»Π΅ΠΉ ΠΏΡΠΈ ΡΡΡΠΊΠΎΠ²ΠΎΠΉ ΠΈΠ»ΠΈ ΡΠΎΡΡΠ΅Π²ΠΎΠΌ ΡΠΏΠΎΡΠΎΠ±Π΅ ΡΠ²Π°ΡΠΊΠΈ Π΄ΠΎΡΡΠΈΠ³Π°Π΅ΡΡΡ ΠΏΡΠΈ ΠΎΠ±Π΅ΡΠΏΠ΅ΡΠ΅Π½ΠΈΠΈ Ρ ΠΎΡΠΎΡΠ΅ΠΉ ΠΆΠ΅ΡΡΠΊΠΎΡΡΠΈ ΠΏΡΠΈΡΠΏΠΎΡΠΎΠ±Π»Π΅Π½ΠΈΠΉ.
ΠΠ° ΠΌΠ°ΡΡΠΎΠ²ΡΡ ΠΏΡΠΎΠΈΠ·Π²ΠΎΠ΄ΡΡΠ²Π°Ρ ΡΠ²Π΅Π»ΠΈΡΠΈΠ²Π°ΡΡ Π°Π²ΡΠΎΠΌΠ°ΡΠΈΠ·Π°ΡΠΈΡ Π½ΡΠΆΠ½ΠΎ ΠΏΡΡΠ΅ΠΌ Π²Π²Π΅Π΄Π΅Π½ΠΈΡ Π² ΠΏΡΠΎΠΈΠ·Π²ΠΎΠ΄ΡΡΠ²ΠΎ ΠΏΠΎΡΠΎΡΠ½ΡΡ Π»ΠΈΠ½ΠΈΠΉ, ΠΎΠ±ΠΎΡΡΠ΄ΠΎΠ²Π°Π½ΠΈΠ΅ ΠΊΠΎΡΠΎΡΡΡ ΠΌΠΎΠΆΠ½ΠΎ Π±ΡΡΡΡΠΎ ΠΏΠ΅ΡΠ΅Π½Π°ΡΡΡΠΎΠΈΡΡ Π½Π° Π²ΡΠΏΡΡΠΊ Π΄ΡΡΠ³ΠΎΠ³ΠΎ ΡΠΈΠΏΠ° Π΄Π΅ΡΠ°Π»Π΅ΠΉ. ΠΠ° Π½Π΅Π±ΠΎΠ»ΡΡΠΎΠΌ ΠΏΡΠΎΠΈΠ·Π²ΠΎΠ΄ΡΡΠ²Π΅ Π½Π° Π»ΠΈΠ½ΠΈΡ Π²Π½Π΅Π΄ΡΡΡΡ Π±ΡΡΡΡΠΎΠ΄Π΅ΠΉΡΡΠ²ΡΡΡΠ΅Π΅ ΠΎΠ±ΠΎΡΡΠ΄ΠΎΠ²Π°Π½ΠΈΠ΅ Ρ Π°Π²ΡΠΎΠΌΠ°ΡΠΈΠ·ΠΈΡΠΎΠ²Π°Π½Π½ΡΠΌ ΠΏΡΠΎΡΠ΅ΡΡΠΎΠΌ ΡΠ²Π°ΡΠΊΠΈ. ΠΠ»Ρ Π°Π²ΡΠΎΠΌΠ°ΡΠΈΠ·Π°ΡΠΈΠΈ Π²ΡΠΏΠΎΠΌΠΎΠ³Π°ΡΠ΅Π»ΡΠ½ΡΡ ΡΠ°Π±ΠΎΡ Π²Π²ΠΎΠ΄ΡΡ Π² ΡΠΊΡΠΏΠ»ΡΠ°ΡΠ°ΡΠΈΡ ΡΠ½ΠΈΠ²Π΅ΡΡΠ°Π»ΡΠ½ΡΠ΅ ΠΏΡΠΈΡΠΏΠΎΡΠΎΠ±Π»Π΅Π½ΠΈΡ Π΄Π»Ρ ΡΠ±ΠΎΡΠΊΠΈ, ΡΠ΅Π΄ΡΠΊΡΠΎΡΡ, ΠΏΠΎΠ²ΠΎΡΠΎΡΠ½ΡΠ΅ ΠΊΡΠ°Π½Ρ ΠΈ Π΄ΡΡΠ³ΠΎΠ΅ ΠΎΠ±ΠΎΡΡΠ΄ΠΎΠ²Π°Π½ΠΈΠ΅, ΠΏΠΎΠ²ΡΡΠ°ΡΡΠ΅Π΅ ΡΡΡΠ΅ΠΊΡΠΈΠ²Π½ΠΎΡΡΡ ΠΈ ΡΠΌΠ΅Π½ΡΡΠ°ΡΡΠ΅Π΅ Π²ΡΠ΅ΠΌΡ Π½Π° Π²ΡΠΏΠΎΠ»Π½Π΅Π½ΠΈΠ΅ ΡΠ°Π±ΠΎΡ.
ΠΡΡΠ°Π»ΠΈΡΡ Π²ΠΎΠΏΡΠΎΡΡ?
ΠΠ΅Ρ Π°Π½ΠΈΠ·Π°ΡΠΈΡ ΠΈ Π°Π²ΡΠΎΠΌΠ°ΡΠΈΠ·Π°ΡΠΈΡ ΡΠ²Π°ΡΠΎΡΠ½ΠΎΠ³ΠΎ ΠΏΡΠΎΠΈΠ·Π²ΠΎΠ΄ΡΡΠ²Π°
ΠΠ΅Ρ Π°Π½ΠΈΠ·Π°ΡΠΈΡ ΠΈ Π°Π²ΡΠΎΠΌΠ°ΡΠΈΠ·Π°ΡΠΈΡ ΡΠ²Π°ΡΠΊΠΈ ΠΎΡΠΊΡΡΠ²Π°ΡΡ Π±ΠΎΠ»ΡΡΠΈΠ΅ ΠΏΠ΅ΡΡΠΏΠ΅ΠΊΡΠΈΠ²Ρ Π² ΡΠ°Π·Π²ΠΈΡΠΈΠΈ ΡΠ²Π°ΡΠΎΡΠ½ΠΎΠ³ΠΎ ΠΏΡΠΎΠΈΠ·Π²ΠΎΠ΄ΡΡΠ²Π°: ΠΏΠΎΠ²ΡΡΠ΅Π½ΠΈΠ΅ ΠΏΡΠΎΠΈΠ·Π²ΠΎΠ΄ΠΈΡΠ΅Π»ΡΠ½ΠΎΡΡΠΈ ΡΡΡΠ΄Π°, ΡΠΎΠ²Π΅ΡΡΠ΅Π½ΡΡΠ²ΠΎΠ²Π°Π½ΠΈΠ΅ ΠΊΠ°ΡΠ΅ΡΡΠ²Π° ΠΏΡΠΎΠ΄ΡΠΊΡΠΈΠΈ, ΡΠΎΠΊΡΠ°ΡΠ΅Π½ΠΈΠ΅ ΡΠΈΡΠ»Π΅Π½Π½ΠΎΡΡΠΈ ΠΏΠ΅ΡΡΠΎΠ½Π°Π»Π° ΠΈ ΡΠ½ΠΈΠΆΠ΅Π½ΠΈΠ΅ ΡΡΠ΅Π±ΠΎΠ²Π°Π½ΠΈΠΉ ΠΊ ΠΌΠ°ΡΡΠ΅ΡΡΡΠ²Ρ ΡΠ²Π°ΡΡΠΈΠΊΠ°, Ρ.ΠΊ. ΠΎΠ½ ΡΡΠ°Π½ΠΎΠ²ΠΈΡΡΡ ΠΎΠΏΠ΅ΡΠ°ΡΠΎΡΠΎΠΌ, ΠΊΠΎΠ½ΡΡΠΎΠ»ΠΈΡΡΡΡΠΈΠΌ ΠΈ ΡΠΏΡΠ°Π²Π»ΡΡΡΠΈΠΌ ΠΏΡΠΎΡΠ΅ΡΡΠΎΠΌ.
ΠΠ΅Ρ Π°Π½ΠΈΠ·Π°ΡΠΈΡ ΠΈ Π°Π²ΡΠΎΠΌΠ°ΡΠΈΠ·Π°ΡΠΈΡ ΠΌΠΎΠ³ΡΡ Π±ΡΡΡ ΡΠ°ΡΡΠΈΡΠ½ΡΠΌΠΈ ΠΈ ΠΊΠΎΠΌΠΏΠ»Π΅ΠΊΡΠ½ΡΠΌΠΈ. Π§Π°ΡΡΠΈΡΠ½Π°Ρ ΠΌΠ΅Ρ Π°Π½ΠΈΠ·Π°ΡΠΈΡ ΠΈ Π°Π²ΡΠΎΠΌΠ°ΡΠΈΠ·Π°ΡΠΈΡ ΠΎΡ Π²Π°ΡΡΠ²Π°ΡΡ ΠΎΡΠ΄Π΅Π»ΡΠ½ΡΠ΅ ΠΎΠΏΠ΅ΡΠ°ΡΠΈΠΈ ΠΏΡΠΎΠΈΠ·Π²ΠΎΠ΄ΡΡΠ²Π΅Π½Π½ΠΎΠ³ΠΎ ΠΏΡΠΎΡΠ΅ΡΡΠ°. ΠΡΠΈ ΠΊΠΎΠΌΠΏΠ»Π΅ΠΊΡΠ½ΠΎΠΌ ΡΠ΅ΡΠ΅Π½ΠΈΠΈ Π²Π΅ΡΡ ΠΏΡΠΎΠΈΠ·Π²ΠΎΠ΄ΡΡΠ²Π΅Π½Π½ΡΠΉ ΡΠΈΠΊΠ» Π²ΡΠΏΠΎΠ»Π½ΡΠ΅ΡΡΡ Ρ ΠΏΠΎΠΌΠΎΡΡΡ ΠΌΠ°ΡΠΈΠ½ ΠΈ ΠΌΠ΅Ρ Π°Π½ΠΈΠ·ΠΌΠΎΠ², ΡΡΡΠ°Π½ΠΎΠ²Π»Π΅Π½Π½ΡΡ Π² ΠΏΠΎΡΡΠ΄ΠΊΠ΅, ΡΠΎΠΎΡΠ²Π΅ΡΡΡΠ²ΡΡΡΠ΅ΠΌ ΡΠ΅Ρ Π½ΠΎΠ»ΠΎΠ³ΠΈΡΠ΅ΡΠΊΠΎΠΌΡ ΠΌΠ°ΡΡΡΡΡΡ. Π ΡΠ²Π°ΡΠΎΡΠ½ΠΎΠΌ ΠΏΡΠΎΠΈΠ·Π²ΠΎΠ΄ΡΡΠ²Π΅ ΠΌΠ΅Ρ Π°Π½ΠΈΠ·Π°ΡΠΈΡ ΠΈ Π°Π²ΡΠΎΠΌΠ°ΡΠΈΠ·Π°ΡΠΈΡ Π΄ΠΎΡΡΠΈΠ³Π°ΡΡΡΡ Π·Π° ΡΡΠ΅Ρ ΠΏΡΠΈΠΌΠ΅Π½Π΅Π½ΠΈΡ ΡΠ°Π·Π»ΠΈΡΠ½ΡΡ ΠΏΡΠΈΡΠΏΠΎΡΠΎΠ±Π»Π΅Π½ΠΈΠΉ, ΡΠΏΠ΅ΡΠΈΠ°Π»ΡΠ½ΡΡ ΡΠ²Π°ΡΠΎΡΠ½ΡΡ ΡΡΡΠ°Π½ΠΎΠ²ΠΎΠΊ, ΠΈΡΠΏΠΎΠ»ΡΠ·ΠΎΠ²Π°Π½ΠΈΡ ΡΠΎΠ±ΠΎΡΠΎΡΠ΅Ρ Π½ΠΈΠΊΠΈ, ΡΠΎΠ·Π΄Π°Π½ΠΈΡ ΠΏΠΎΡΠΎΡΠ½ΡΡ ΠΌΠ΅Ρ Π°Π½ΠΈΠ·ΠΈΡΠΎΠ²Π°Π½Π½ΡΡ ΠΈ Π°Π²ΡΠΎΠΌΠ°ΡΠΈΠ·ΠΈΡΠΎΠ²Π°Π½Π½ΡΡ Π»ΠΈΠ½ΠΈΠΉ, Π½Π° ΠΊΠΎΡΠΎΡΡΡ ΠΌΠ΅Ρ Π°Π½ΠΈΠ·ΠΈΡΠΎΠ²Π°Π½Π½ΡΠΌΠΈ ΡΠΏΠΎΡΠΎΠ±Π°ΠΌΠΈ ΠΎΡΡΡΠ΅ΡΡΠ²Π»ΡΡΡΡΡ ΡΠ°Π±ΠΎΡΡ ΠΏΠΎ Π·Π°Π³ΠΎΡΠΎΠ²ΠΊΠ΅, ΡΠ±ΠΎΡΠΊΠ΅, ΡΠ²Π°ΡΠΊΠ΅ ΠΈ ΡΡΠ°Π½ΡΠΏΠΎΡΡΠΈΡΠΎΠ²ΠΊΠ΅ ΡΠ²Π°ΡΠ½ΡΡ ΠΈΠ·Π΄Π΅Π»ΠΈΠΉ, Π° Π² ΡΡΠ΄Π΅ ΡΠ»ΡΡΠ°Π΅Π² — ΠΈΡ ΠΏΠΎΡΠ»Π΅ΡΠ²Π°ΡΠΎΡΠ½ΠΎΠΉ ΠΎΠ±ΡΠ°Π±ΠΎΡΠΊΠΈ.
ΠΠ΅Ρ Π°Π½ΠΈΠ·Π°ΡΠΈΡ ΠΈ Π°Π²ΡΠΎΠΌΠ°ΡΠΈΠ·Π°ΡΠΈΡ ΠΎΡΡΡΠ΅ΡΡΠ²Π»ΡΠ΅ΡΡΡ Π² Π·Π°Π²ΠΈΡΠΈΠΌΠΎΡΡΠΈ ΠΎΡ Π·Π°Π΄Π°ΡΠΈ Π·Π° ΡΡΠ΅Ρ ΡΡΡΠ°Π½ΠΎΠ²ΠΊΠΈ ΡΡΠ°Π½Π΄Π°ΡΡΠ½ΠΎΠ³ΠΎ ΠΎΠ±ΠΎΡΡΠ΄ΠΎΠ²Π°Π½ΠΈΡ ΠΈΠ»ΠΈ ΡΠΏΠ΅ΡΠΈΠ°Π»ΡΠ½ΠΎΠ³ΠΎ, ΠΈΠ·Π³ΠΎΡΠΎΠ²Π»Π΅Π½Π½ΠΎΠ³ΠΎ ΡΠΎΠ³Π»Π°ΡΠ½ΠΎ ΡΡΠ΅Π±ΠΎΠ²Π°Π½ΠΈΡΠΌ ΠΠ°ΠΊΠ°Π·ΡΠΈΠΊΠ°.
Π‘Π²Π°ΡΠΎΡΠ½ΡΠ΅ Π²ΡΠ°ΡΠ°ΡΠ΅Π»ΠΈ
Π‘Π²Π°ΡΠΎΡΠ½ΡΠ΅ Π²ΡΠ°ΡΠ°ΡΠ΅Π»ΠΈ ΡΠ»ΡΠΆΠ°Ρ Π΄Π»Ρ ΡΡΡΠ°Π½ΠΎΠ²ΠΊΠΈ ΠΈΠ·Π΄Π΅Π»ΠΈΠΉ Π² ΡΠ΄ΠΎΠ±Π½ΠΎΠ΅ Π΄Π»Ρ ΡΠ²Π°ΡΠΊΠΈ ΠΏΠΎΠ»ΠΎΠΆΠ΅Π½ΠΈΠ΅ ΠΏΡΡΠ΅ΠΌ ΠΏΠΎΠ²ΠΎΡΠΎΡΠ° ΠΈΡ Π²ΠΎΠΊΡΡΠ³ ΠΎΡΠ΅ΠΉ ΠΈ Π²ΡΠ°ΡΠ΅Π½ΠΈΡ ΠΈΡ ΡΠΎ ΡΠΊΠΎΡΠΎΡΡΡΡ ΡΠ²Π°ΡΠΊΠΈ. Π‘ΡΡΠ΅ΡΡΠ²ΡΠ΅Ρ Π±ΠΎΠ»ΡΡΠΎΠ΅ ΠΊΠΎΠ»ΠΈΡΠ΅ΡΡΠ²ΠΎ Π²ΡΠ°ΡΠ°ΡΠ΅Π»Π΅ΠΉ ΡΠ°Π·Π»ΠΈΡΠ½ΡΡ ΠΊΠΎΠ½ΡΠΈΠ³ΡΡΠ°ΡΠΈΠΉ, ΠΎΡΠ»ΠΈΡΠ°ΡΡΠΈΡ ΡΡ ΠΊΠΎΠ»ΠΈΡΠ΅ΡΡΠ²ΠΎΠΌ ΠΎΡΠ΅ΠΉ, Π³ΡΡΠ·ΠΎΠΏΠΎΠ΄ΡΠ΅ΠΌΠ½ΠΎΡΡΡΡ, ΡΠΊΠΎΡΠΎΡΡΡΡ Π²ΡΠ°ΡΠ΅Π½ΠΈΡ ΠΏΠ»Π°Π½ΡΠ°ΠΉΠ±Ρ ΠΈ Ρ.Π΄. Π Π½Π°ΡΠ΅ΠΌ ΠΊΠ°ΡΠ°Π»ΠΎΠ³Π΅ ΠΏΡΠ΅Π΄ΡΡΠ°Π²Π»Π΅Π½Ρ Π½Π°ΠΈΠ±ΠΎΠ»Π΅Π΅ ΡΠ°ΡΠΏΡΠΎΡΡΡΠ°Π½Π΅Π½Π½ΡΠ΅ ΡΠΈΠΏΡ ΡΠ²Π°ΡΠΎΡΠ½ΡΡ Π²ΡΠ°ΡΠ°ΡΠ΅Π»Π΅ΠΉ.
Π£Π½ΠΈΠ²Π΅ΡΡΠ°Π»ΡΠ½ΡΠΉ (Π΄Π²ΡΡ ΠΎΡΠ΅Π²ΠΎΠΉ) ΡΠ²Π°ΡΠΎΡΠ½ΡΠΉ Π²ΡΠ°ΡΠ°ΡΠ΅Π»Ρ.
Π£Π½ΠΈΠ²Π΅ΡΡΠ°Π»ΡΠ½ΡΠΉ ΡΠ²Π°ΡΠΎΡΠ½ΡΠΉ Π²ΡΠ°ΡΠ°ΡΠ΅Π»Ρ ΠΈΠΌΠ΅Π΅Ρ Π΄Π²Π΅ ΠΎΡΠΈ: ΠΎΡΡ Π½Π°ΠΊΠ»ΠΎΠ½Π° ΠΈ ΠΎΡΡ Π²ΡΠ°ΡΠ΅Π½ΠΈΡ ΠΏΠ»Π°Π½ΡΠ°ΠΉΠ±Ρ. ΠΠ°ΠΊ ΠΏΡΠ°Π²ΠΈΠ»ΠΎ ΠΎΡΡ Π²ΡΠ°ΡΠ΅Π½ΠΈΡ ΠΏΠ»Π°Π½ΡΠ°ΠΉΠ±Ρ ΠΌΠΎΠΆΠ΅Ρ Π½Π°ΠΊΠ»ΠΎΠ½ΡΡΡΡΡ Π² Π΄ΠΈΠ°ΠΏΠ°Π·ΠΎΠ½Π΅ ΠΎΡ 0ΠΎ Π΄ΠΎ 90ΠΎ. ΠΠΎΠ΄ΠΎΠ±Π½ΡΠΉ ΡΠΈΠΏ Π²ΡΠ°ΡΠ°ΡΠ΅Π»Ρ ΠΏΠΎΠ·Π²ΠΎΠ»ΡΠ΅Ρ ΠΏΠΎΠ·ΠΈΡΠΈΠΎΠ½ΠΈΡΠΎΠ²Π°ΡΡ ΠΈ Π²ΡΠ°ΡΠ°ΡΡ ΠΈΠ·Π΄Π΅Π»ΠΈΡ ΠΏΠΎΠ΄ ΡΠ°Π·Π»ΠΈΡΠ½ΡΠΌΠΈ ΡΠ³Π»Π°ΠΌΠΈ, ΡΡΠΎ ΡΠ°ΡΡΠΈΡΡΠ΅Ρ ΠΎΠ±Π»Π°ΡΡΡ Π΅Π³ΠΎ ΠΏΡΠΈΠΌΠ΅Π½Π΅Π½ΠΈΡ Π² ΡΠ²Π°ΡΠΎΡΠ½ΠΎΠΌ ΠΏΡΠΎΠΈΠ·Π²ΠΎΠ΄ΡΡΠ²Π΅. ΠΠ΅Π΄ΠΎΡΡΠ°ΡΠΊΠΎΠΌ Π΄Π°Π½Π½ΠΎΠ³ΠΎ Π²ΡΠ°ΡΠ°ΡΠ΅Π»Ρ ΡΠ²Π»ΡΠ΅ΡΡΡ Π½Π°Π»ΠΈΡΠΈΠ΅ Π±ΠΎΠ»ΡΡΠΎΠ³ΠΎ ΠΈΠ·Π³ΠΈΠ±Π°ΡΡΠ΅Π³ΠΎ ΠΌΠΎΠΌΠ΅Π½ΡΠ° ΠΏΡΠΈ Π½Π°ΠΊΠ»ΠΎΠ½Π΅ ΠΏΠ»Π°Π½ΡΠ°ΠΉΠ±Ρ Ρ ΠΎΡΠ½ΠΎΡΠΈΡΠ΅Π»ΡΠ½ΠΎ Π΄Π»ΠΈΠ½Π½ΡΠΌ ΠΈ ΠΌΠ°ΡΡΠΈΠ²Π½ΡΠΌ ΠΈΠ·Π΄Π΅Π»ΠΈΠ΅ΠΌ Π½Π° Π½Π΅ΠΉ. Π’Π°ΠΊΠΈΠΌ ΠΎΠ±ΡΠ°Π·ΠΎΠΌ, ΠΏΡΠΈ Π½Π°ΠΊΠ»ΠΎΠ½Π΅ ΠΏΠ»Π°Π½ΡΠ°ΠΉΠ±Ρ Π³ΡΡΠ·ΠΎΠΏΠΎΠ΄ΡΠ΅ΠΌΠ½ΠΎΡΡΡ Π²ΡΠ°ΡΠ°ΡΠ΅Π»Ρ ΠΎΡΠ½ΠΎΡΠΈΡΠ΅Π»ΡΠ½ΠΎ Π½ΠΎΠΌΠΈΠ½Π°Π»ΡΠ½ΡΡ Π·Π½Π°ΡΠ΅Π½ΠΈΠΉ Π·Π½Π°ΡΠΈΡΠ΅Π»ΡΠ½ΠΎ ΡΠ½ΠΈΠΆΠ°Π΅ΡΡΡ. ΠΡΠ° ΠΎΡΠΎΠ±Π΅Π½Π½ΠΎΡΡΡ Π΄ΠΎΠ»ΠΆΠ½Π° ΡΡΠΈΡΡΠ²Π°ΡΡΡΡ ΠΏΠΎ
ΠΠ²ΡΠΎΠΌΠ°ΡΠΈΠ·Π°ΡΠΈΡ ΡΠ²Π°ΡΠΎΡΠ½ΡΡ ΠΏΡΠΎΡΠ΅ΡΡΠΎΠ²
Π Π΅ΠΊΠΎΠΌΠ΅Π½Π΄ΡΠ΅ΠΌ ΠΏΡΠΈΠΎΠ±ΡΠ΅ΡΡΠΈ:
Π£ΡΡΠ°Π½ΠΎΠ²ΠΊΠΈ Π΄Π»Ρ Π°Π²ΡΠΎΠΌΠ°ΡΠΈΡΠ΅ΡΠΊΠΎΠΉ ΡΠ²Π°ΡΠΊΠΈ ΠΏΡΠΎΠ΄ΠΎΠ»ΡΠ½ΡΡ
ΡΠ²ΠΎΠ² ΠΎΠ±Π΅ΡΠ°Π΅ΠΊ — Π² Π½Π°Π»ΠΈΡΠΈΠΈ Π½Π° ΡΠΊΠ»Π°Π΄Π΅!
Π‘Π²Π°ΡΠΎΡΠ½ΡΠ΅ ΡΠΊΡΠ°Π½Ρ ΠΈ Π·Π°ΡΠΈΡΠ½ΡΠ΅ ΡΡΠΎΡΠΊΠΈ — Π² Π½Π°Π»ΠΈΡΠΈΠΈ Π½Π° ΡΠΊΠ»Π°Π΄Π΅!
ΠΠ°ΡΠΈΡΠ° ΠΎΡ ΠΈΠ·Π»ΡΡΠ΅Π½ΠΈΡ ΠΏΡΠΈ ΡΠ²Π°ΡΠΊΠ΅ ΠΈ ΡΠ΅Π·ΠΊΠ΅. ΠΠΎΠ»ΡΡΠΎΠΉ Π²ΡΠ±ΠΎΡ.
ΠΠΎΡΡΠ°Π²ΠΊΠ° ΠΏΠΎ Π²ΡΠ΅ΠΉ Π ΠΎΡΡΠΈΠΈ!
ΠΠ΅Ρ
Π°Π½ΠΈΠ·Π°ΡΠΈΡ ΡΠ»Π΅ΠΊΡΡΠΎΠ΄ΡΠ³ΠΎΠ²ΠΎΠΉ ΡΠ²Π°ΡΠΊΠΈ Π½Π° Π±Π°Π·Π΅ Π°Π²ΡΠΎΠΌΠ°ΡΠΈΡΠ΅ΡΠΊΠΈΡ
ΡΠ²Π°ΡΠΎΡΠ½ΡΡ
ΠΊΠ°ΡΠ΅ΡΠΎΠΊ ΠΎΡ ΠΊΠΎΠΌΠΏΠ°Π½ΠΈΠΈ Β«ΠΠ΅Π»ΡΡΠ°Π‘Π²Π°ΡΒ»
ΠΠ΅ΠΎΠ±Ρ ΠΎΠ΄ΠΈΠΌΠΎΡΡΡ Π°Π²ΡΠΎΠΌΠ°ΡΠΈΠ·Π°ΡΠΈΠΈ ΡΠ²Π°ΡΠΎΡΠ½ΡΡ ΠΏΡΠΎΡΠ΅ΡΡΠΎΠ² ΠΎΠΏΡΠ΅Π΄Π΅Π»ΡΠ΅ΡΡΡ, ΠΏΡΠ΅ΠΆΠ΄Π΅ Π²ΡΠ΅Π³ΠΎ, ΡΠ°ΠΊΠΈΠΌΠΈ ΠΈΡ Ρ Π°ΡΠ°ΠΊΡΠ΅ΡΠ½ΡΠΌΠΈ ΠΎΡΠΎΠ±Π΅Π½Π½ΠΎΡΡΡΠΌΠΈ, ΠΊΠ°ΠΊ Π²ΡΡΠΎΠΊΠΈΠ΅ ΡΠ½Π΅ΡΠ³Π΅ΡΠΈΡΠ΅ΡΠΊΠΈΠ΅ ΠΏΠ°ΡΠ°ΠΌΠ΅ΡΡΡ, ΡΠΊΠΎΡΠΎΡΠ΅ΡΠ½ΠΎΡΡΡ ΠΎΡΠ΄Π΅Π»ΡΠ½ΡΡ ΡΡΠ°ΠΏΠΎΠ² ΡΠ½Π΅ΡΠ³Π΅ΡΠΈΡΠ΅ΡΠΊΠΈΡ ΠΏΡΠ΅ΠΎΠ±ΡΠ°Π·ΠΎΠ²Π°Π½ΠΈΠΉ ΠΈ ΠΏΡΠΎΡΠ΅ΡΡΠ° ΡΠΎΡΠΌΠΈΡΠΎΠ²Π°Π½ΠΈΡ ΡΠ²Π°ΡΠ½ΠΎΠ³ΠΎ ΡΠΎΠ΅Π΄ΠΈΠ½Π΅Π½ΠΈΡ, ΡΡΡΠ΄Π½ΠΎΠ΄ΠΎΡΡΡΠΏΠ½ΠΎΡΡΡ Π·ΠΎΠ½Ρ ΡΠ²Π°ΡΠΊΠΈ Π΄Π»Ρ Π½Π΅ΠΏΠΎΡΡΠ΅Π΄ΡΡΠ²Π΅Π½Π½ΠΎΠ³ΠΎ ΠΈΠ·ΠΌΠ΅ΡΠ΅Π½ΠΈΡ ΠΈ ΠΊΠΎΠ½ΡΡΠΎΠ»Ρ, ΠΏΠΎΠ²ΡΡΠ΅Π½Π½ΡΠΉ ΡΡΠΎΠ²Π΅Π½Ρ Π²ΡΠ΅Π΄Π½ΡΡ Π²ΠΎΠ·Π΄Π΅ΠΉΡΡΠ²ΠΈΠΉ Π½Π° Π·Π΄ΠΎΡΠΎΠ²ΡΠ΅ ΡΠ΅Π»ΠΎΠ²Π΅ΠΊΠ° ΠΈ Π½Π΅ΠΎΠ±Ρ ΠΎΠ΄ΠΈΠΌΠΎΡΡΡ ΠΎΠΏΠ΅ΡΠ°ΡΠΈΠ²Π½ΠΎΠΉ ΠΎΠΏΡΠΈΠΌΠΈΠ·Π°ΡΠΈΠΈ ΡΠ²Π°ΡΠΎΡΠ½ΡΡ ΠΏΡΠΎΡΠ΅ΡΡΠΎΠ² Π² ΡΠΎΠΎΡΠ²Π΅ΡΡΡΠ²ΠΈΠΈ Ρ Π²ΡΠ±ΡΠ°Π½Π½ΡΠΌ ΠΊΡΠΈΡΠ΅ΡΠΈΠ΅ΠΌ.
Π ΠΎΠ±ΡΠ΅ΠΌ ΠΎΠ±ΡΠ΅ΠΌΠ΅ ΠΎΠΏΠ΅ΡΠ°ΡΠΈΠΉ ΠΏΠΎ ΠΏΡΠΎΠΈΠ·Π²ΠΎΠ΄ΡΡΠ²Ρ ΡΠ²Π°ΡΠ½ΡΡ ΠΊΠΎΠ½ΡΡΡΡΠΊΡΠΈΠΉ Π½Π° ΠΏΡΠΎΡΠ΅ΡΡ ΡΠ²Π°ΡΠΊΠΈ ΠΎΠ±ΡΡΠ½ΠΎ ΠΏΡΠΈΡ ΠΎΠ΄ΠΈΡΡΡ 15…20%, ΠΎΠ΄Π½Π°ΠΊΠΎ ΠΎΠ½ ΠΎΠΏΡΠ΅Π΄Π΅Π»ΡΠ΅Ρ ΡΠ²ΠΎΠΉΡΡΠ²Π° ΠΈ ΡΠΊΡΠΏΠ»ΡΠ°ΡΠ°ΡΠΈΠΎΠ½Π½ΡΡ Π½Π°Π΄Π΅ΠΆΠ½ΠΎΡΡΡ ΠΊΠΎΠ½ΡΡΡΡΠΊΡΠΈΠΉ. ΠΠΎΠ»ΡΡΠΎΠ΅ ΠΊΠΎΠ»ΠΈΡΠ΅ΡΡΠ²ΠΎ ΠΏΠ°ΡΠ°ΠΌΠ΅ΡΡΠΎΠ², Π²Π»ΠΈΡΡΡΠΈΡ Π½Π° Ρ ΠΎΠ΄ ΡΠ²Π°ΡΠΎΡΠ½ΡΡ ΠΏΡΠΎΡΠ΅ΡΡΠΎΠ², ΠΈ Π²ΡΡΠΎΠΊΠΈΠ΅ ΡΠΊΠΎΡΠΎΡΡΠΈ ΠΈΡ ΠΈΠ·ΠΌΠ΅Π½Π΅Π½ΠΈΡ ΡΡΠ΅Π±ΡΡΡ Π΄Π»Ρ ΡΠΏΡΠ°Π²Π»Π΅Π½ΠΈΡ ΠΈΠΌΠΈ ΠΎΠ±ΡΠ°Π±ΠΎΡΠΊΠΈ Π·Π½Π°ΡΠΈΡΠ΅Π»ΡΠ½ΠΎΠ³ΠΎ ΠΎΠ±ΡΠ΅ΠΌΠ° ΠΈΠ½ΡΠΎΡΠΌΠ°ΡΠΈΠΈ Π² Π΅Π΄ΠΈΠ½ΠΈΡΡ Π²ΡΠ΅ΠΌΠ΅Π½ΠΈ, ΠΏΠΎΡΡΠΎΠΌΡ Π°Π²ΡΠΎΠΌΠ°ΡΠΈΠ·Π°ΡΠΈΡ ΠΎΠΊΠ°Π·ΡΠ²Π°Π΅ΡΡΡ ΠΎΠ±ΡΠ·Π°ΡΠ΅Π»ΡΠ½ΡΠΌ ΡΡΠ»ΠΎΠ²ΠΈΠ΅ΠΌ ΡΡΠΏΠ΅ΡΠ½ΠΎΠ³ΠΎ ΠΈ ΠΊΠ°ΡΠ΅ΡΡΠ²Π΅Π½Π½ΠΎΠ³ΠΎ Π²ΡΠΏΠΎΠ»Π½Π΅Π½ΠΈΡ ΡΠ²Π°ΡΠΎΡΠ½ΡΡ ΠΏΡΠΎΡΠ΅ΡΡΠΎΠ². ΠΠ΅Π²ΠΎΠ·ΠΌΠΎΠΆΠ½ΠΎΡΡΡ ΠΏΠΎΠ΄Π΄Π΅ΡΠΆΠ°Π½ΠΈΡ Π½Π΅ΠΏΡΠ΅ΡΡΠ²Π½ΠΎΠΉ Π²ΠΎΠ»ΡΡΠΎΠ²ΠΎΠΉ Π΄ΡΠ³ΠΈ ΠΏΡΠΈ ΡΠ²Π°ΡΠΊΠ΅ ΠΏΠ»Π°Π²ΡΡΠΈΠΌΡΡ ΡΠ»Π΅ΠΊΡΡΠΎΠ΄ΠΎΠΌ ΠΎΠ±ΡΡΠ»ΠΎΠ²ΠΈΠ»Π° ΡΠΎΠ·Π΄Π°Π½ΠΈΠ΅ Π°Π²ΡΠΎΠΌΠ°ΡΠΈΡΠ΅ΡΠΊΠΎΠ³ΠΎ ΡΠ΅Π³ΡΠ»ΡΡΠΎΡΠ° Π. Π. Π‘Π»Π°Π²ΡΠ½ΠΎΠ²ΡΠΌ, ΡΡΠΎ ΠΈ ΠΎΠ±Π΅ΡΠΏΠ΅ΡΠΈΠ»ΠΎ ΡΠ΅Π°Π»ΡΠ½ΡΡ Π²ΠΎΠ·ΠΌΠΎΠΆΠ½ΠΎΡΡΡ ΠΏΡΠΎΠΌΡΡΠ»Π΅Π½Π½ΠΎΠ³ΠΎ ΠΏΡΠΈΠΌΠ΅Π½Π΅Π½ΠΈΡ Π΄ΡΠ³ΠΎΠ²ΠΎΠΉ ΡΠ²Π°ΡΠΊΠΈ ΠΏΠ»Π°Π²ΡΡΠΈΠΌΡΡ ΡΠ»Π΅ΠΊΡΡΠΎΠ΄ΠΎΠΌ.
Π¦Π΅Π»Ρ Π°Π²ΡΠΎΠΌΠ°ΡΠΈΠ·Π°ΡΠΈΠΈ ΡΠ²Π°ΡΠΎΡΠ½ΡΡ ΠΏΡΠΎΡΠ΅ΡΡΠΎΠ² — ΠΏΠΎΠ»ΡΡΠ΅Π½ΠΈΠ΅ ΡΠ²Π°ΡΠ½ΡΡ ΡΠΎΠ΅Π΄ΠΈΠ½Π΅Π½ΠΈΠΉ Ρ ΡΡΠ΅Π±ΡΠ΅ΠΌΡΠΌΠΈ ΡΠ²ΠΎΠΉΡΡΠ²Π°ΠΌΠΈ ΠΏΡΠΈ Π½Π°ΠΈΠ»ΡΡΡΠΈΡ ΡΠ΅Ρ Π½ΠΈΠΊΠΎ-ΡΠΊΠΎΠ½ΠΎΠΌΠΈΡΠ΅ΡΠΊΠΈΡ ΠΏΠΎΠΊΠ°Π·Π°ΡΠ΅Π»ΡΡ Π±Π΅Π· Π½Π΅ΠΏΠΎΡΡΠ΅Π΄ΡΡΠ²Π΅Π½Π½ΠΎΠ³ΠΎ ΡΡΠ°ΡΡΠΈΡ ΡΠ΅Π»ΠΎΠ²Π΅ΠΊΠ°. ΠΠ²ΡΠΎΠΌΠ°ΡΠΈΠ·Π°ΡΠΈΡ ΡΠ²Π°ΡΠΎΡΠ½ΡΡ ΠΏΡΠΎΡΠ΅ΡΡΠΎΠ², ΠΏΡΠΈ ΠΊΠΎΡΠΎΡΠΎΠΉ ΠΏΠΎΠ²ΡΡΠ°Π΅ΡΡΡ ΡΠΎΡΠ½ΠΎΡΡΡ ΡΠΏΡΠ°Π²Π»Π΅Π½ΠΈΡ ΠΈ ΠΊΠΎΠ½ΡΡΠΎΠ»Ρ, Π° ΡΠ°ΠΊΠΆΠ΅ ΠΈΡΠΊΠ»ΡΡΠ°Π΅ΡΡΡ Π²Π»ΠΈΡΠ½ΠΈΠ΅ Π½Π° ΡΠ΅Ρ Π½ΠΎΠ»ΠΎΠ³ΠΈΡΠ΅ΡΠΊΠΈΠΉ ΠΏΡΠΎΡΠ΅ΡΡ ΡΡΠ±ΡΠ΅ΠΊΡΠΈΠ²Π½ΡΡ ΡΠ°ΠΊΡΠΎΡΠΎΠ² (ΠΌΠ°ΡΡΠ΅ΡΡΡΠ²ΠΎ ΡΠ°Π±ΠΎΡΠ΅Π³ΠΎ, Π΅Π³ΠΎ ΡΡΠΎΠΌΠ»ΡΠ΅ΠΌΠΎΡΡΡ ΠΈ Ρ. ΠΏ.), Π½Π°ΠΏΡΠ°Π²Π»Π΅Π½Π° ΠΏΡΠ΅ΠΆΠ΄Π΅ Π²ΡΠ΅Π³ΠΎ Π½Π° ΠΏΠΎΠ²ΡΡΠ΅Π½ΠΈΠ΅ ΠΊΠ°ΡΠ΅ΡΡΠ²Π° ΡΠ²Π°ΡΠ½ΡΡ ΡΠΎΠ΅Π΄ΠΈΠ½Π΅Π½ΠΈΠΉ ΠΈ Π΅Π³ΠΎ ΡΡΠ°Π±ΠΈΠ»ΠΈΠ·Π°ΡΠΈΡ Π² ΠΏΡΠ΅Π΄Π΅Π»Π°Ρ ΠΏΠ°ΡΡΠΈΠΈ ΠΎΠ΄Π½ΠΎΡΠΈΠΏΠ½ΡΡ ΠΈΠ·Π΄Π΅Π»ΠΈΠΉ. ΠΡΠΊΠ»ΡΡΠ΅Π½ΠΈΠ΅ ΠΈΠ»ΠΈ ΡΠ²Π΅Π΄Π΅Π½ΠΈΠ΅ ΠΊ ΠΌΠΈΠ½ΠΈΠΌΡΠΌΡ ΠΊΠΎΠ»ΠΈΡΠ΅ΡΡΠ²Π° Π½Π΅Π΄ΠΎΠΏΡΡΡΠΈΠΌΡΡ Π΄Π΅ΡΠ΅ΠΊΡΠΎΠ² ΡΠ²Π°ΡΠ½ΡΡ ΡΠ²ΠΎΠ² ΡΠ½ΠΈΠΆΠ°Π΅Ρ ΠΏΠΎΡΠ΅ΡΠΈ ΡΠ°Π±ΠΎΡΠ΅Π³ΠΎ Π²ΡΠ΅ΠΌΠ΅Π½ΠΈ, ΡΠ½Π΅ΡΠ³Π΅ΡΠΈΡΠ΅ΡΠΊΠΈΡ ΠΈ ΠΌΠ°ΡΠ΅ΡΠΈΠ°Π»ΡΠ½ΡΡ ΡΠ΅ΡΡΡΡΠΎΠ², ΡΠ²ΡΠ·Π°Π½Π½ΡΠ΅ Ρ ΠΈΡΠΏΡΠ°Π²Π»Π΅Π½ΠΈΠ΅ΠΌ Π±ΡΠ°ΠΊΠ°.
ΠΠ²ΡΠΎΠΌΠ°ΡΠΈΠ·Π°ΡΠΈΡ ΡΠ²Π°ΡΠΎΡΠ½ΡΡ ΠΏΡΠΎΡΠ΅ΡΡΠΎΠ² ΡΠΎΠΏΡΠΎΠ²ΠΎΠΆΠ΄Π°Π΅ΡΡΡ ΡΠ΅Π°Π»ΡΠ½ΡΠΌ ΠΏΠΎΠ²ΡΡΠ΅Π½ΠΈΠ΅ΠΌ ΠΏΡΠΎΠΈΠ·Π²ΠΎΠ΄ΠΈΡΠ΅Π»ΡΠ½ΠΎΡΡΠΈ ΡΡΡΠ΄Π° ΠΈ ΡΠΊΠΎΠ½ΠΎΠΌΠΈΠ΅ΠΉ ΡΡΡΠ΄ΠΎΠ²ΡΡ ΡΠ΅ΡΡΡΡΠΎΠ².
Π‘ΠΎΡΠΈΠ°Π»ΡΠ½ΡΠΉ Π°ΡΠΏΠ΅ΠΊΡ Π°Π²ΡΠΎΠΌΠ°ΡΠΈΠ·Π°ΡΠΈΠΈ ΠΏΡΠ΅Π΄ΠΏΠΎΠ»Π°Π³Π°Π΅Ρ ΠΎΡΠ²ΠΎΠ±ΠΎΠΆΠ΄Π΅Π½ΠΈΠ΅ ΡΠ΅Π»ΠΎΠ²Π΅ΠΊΠ° ΠΎΡ Π½Π΅ΠΏΠΎΡΡΠ΅Π΄ΡΡΠ²Π΅Π½Π½ΠΎΠ³ΠΎ Π²ΡΠΏΠΎΠ»Π½Π΅Π½ΠΈΡ ΡΠ²Π°ΡΠΎΡΠ½ΡΡ ΠΎΠΏΠ΅ΡΠ°ΡΠΈΠΉ ΠΈ ΡΠΏΡΠ°Π²Π»Π΅Π½ΠΈΡ ΡΠ²Π°ΡΠΎΡΠ½ΡΠΌ ΠΎΠ±ΠΎΡΡΠ΄ΠΎΠ²Π°Π½ΠΈΠ΅ΠΌ ΠΏΡΠ΅ΠΆΠ΄Π΅ Π²ΡΠ΅Π³ΠΎ Π² ΡΡΠ»ΠΎΠ²ΠΈΡΡ Π²ΡΠ΅Π΄Π½ΡΡ , Π»ΠΈΠ±ΠΎ ΠΎΠΏΠ°ΡΠ½ΡΡ Π΄Π»Ρ Π·Π΄ΠΎΡΠΎΠ²ΡΡ, Π° ΡΠ°ΠΊΠΆΠ΅ ΠΏΡΠΈ Π²ΡΠΏΠΎΠ»Π½Π΅Π½ΠΈΠΈ ΡΡΡΠΈΠ½Π½ΡΡ ΠΎΠΏΠ΅ΡΠ°ΡΠΈΠΉ Π½Π΅ΡΠ²ΠΎΡΡΠ΅ΡΠΊΠΎΠ³ΠΎ Ρ Π°ΡΠ°ΠΊΡΠ΅ΡΠ°. ΠΠ²ΡΠΎΠΌΠ°ΡΠΈΠ·Π°ΡΠΈΡ ΡΠΎΠΏΡΠΎΠ²ΠΎΠΆΠ΄Π°Π΅ΡΡΡ ΡΠΎΠ·Π΄Π°Π½ΠΈΠ΅ΠΌ Π½ΠΎΠ²ΡΡ ΡΡΠ΅Π΄ΡΡΠ² ΠΏΡΠΎΠΈΠ·Π²ΠΎΠ΄ΡΡΠ²Π°, ΠΊΠΎΡΠΎΡΡΠ΅ Π² ΡΠ²ΠΎΡ ΠΎΡΠ΅ΡΠ΅Π΄Ρ ΡΠ»ΡΠΆΠ°Ρ ΠΎΡΠ½ΠΎΠ²ΠΎΠΉ ΡΠ°Π·ΡΠ°Π±ΠΎΡΠΊΠΈ ΠΈ ΠΏΡΠΈΠΌΠ΅Π½Π΅Π½ΠΈΡ ΠΏΡΠΎΠ³ΡΠ΅ΡΡΠΈΠ²Π½ΡΡ ΡΠ΅Ρ Π½ΠΎΠ»ΠΎΠ³ΠΈΠΉ ΡΠ²Π°ΡΠΊΠΈ.
ΠΠ΅ΠΏΠΎΡΡΠ΅Π΄ΡΡΠ²Π΅Π½Π½ΠΎΠ΅ ΡΠ΅ΡΠ΅Π½ΠΈΠ΅ ΠΎΠ±ΡΠ΅ΠΉ Π·Π°Π΄Π°ΡΠΈ Π°Π²ΡΠΎΠΌΠ°ΡΠΈΠ·Π°ΡΠΈΠΈ ΡΠ²Π°ΡΠΎΡΠ½ΠΎΠ³ΠΎ ΠΏΡΠΎΠΈΠ·Π²ΠΎΠ΄ΡΡΠ²Π° Π·Π°ΡΡΡΠ΄Π½Π΅Π½ΠΎ ΠΌΠ½ΠΎΠ³ΠΎΠΌΠ΅ΡΠ½ΠΎΡΡΡΡ ΠΎΠ±ΡΠ΅ΠΊΡΠΎΠ². ΠΡΠ±ΠΎΡ ΠΎΠΏΡΠΈΠΌΠ°Π»ΡΠ½ΠΎΠ³ΠΎ Π²Π°ΡΠΈΠ°Π½ΡΠ° ΡΡΡΠ°ΡΠ΅Π³ΠΈΠΈ ΡΠΏΡΠ°Π²Π»Π΅Π½ΠΈΡ ΡΠ²Π°ΡΠΎΡΠ½ΡΠΌΠΈ ΠΏΡΠΎΡΠ΅ΡΡΠ°ΠΌΠΈ ΠΎΠΏΡΠ΅Π΄Π΅Π»ΡΠ΅ΡΡΡ ΡΠΈΠΏΠΎΠΌ ΡΠ΅Ρ Π½ΠΎΠ»ΠΎΠ³ΠΈΡΠ΅ΡΠΊΠΎΠ³ΠΎ ΠΏΡΠΎΡΠ΅ΡΡΠ° ΠΈ ΠΎΡΠ½ΠΎΠ²Π½ΡΠΌΠΈ ΡΠ΅Π»ΡΠΌΠΈ. ΠΠΏΠΏΠ°ΡΠ°ΡΡΡΠ° ΠΈ ΡΠΈΡΡΠ΅ΠΌΡ ΡΠΏΡΠ°Π²Π»Π΅Π½ΠΈΡ ΠΊΠ»Π°ΡΡΠΈΡΠΈΡΠΈΡΡΡΡΡΡ ΠΏΠΎ Π°Π»Π³ΠΎΡΠΈΡΠΌΡ ΡΠΏΡΠ°Π²Π»Π΅Π½ΠΈΡ, ΠΊΠΎΡΠΎΡΡΠΉ ΠΎΠΏΡΠ΅Π΄Π΅Π»ΡΠ΅Ρ Π²ΡΠ±ΠΎΡ Π°Π»ΡΡΠ΅ΡΠ½Π°ΡΠΈΠ²Π½ΠΎΠΉ ΡΠ΅Π»ΠΈ ΡΠΏΡΠ°Π²Π»Π΅Π½ΠΈΡ. ΠΡΠΈ ΡΡΠΎΠΌ ΠΌΠΎΠΆΠ½ΠΎ Π²ΡΠ΄Π΅Π»ΠΈΡΡ ΡΠ»Π΅Π΄ΡΡΡΠΈΠ΅ Π³ΡΡΠΏΠΏΡ ΡΠΈΡΡΠ΅ΠΌ ΡΠΏΡΠ°Π²Π»Π΅Π½ΠΈΡ.
ΠΠ»Ρ ΡΠ΅ΡΠ΅Π½ΠΈΡ ΠΏΡΠΎΡΡΠ΅ΠΉΡΠΈΡ
Π·Π°Π΄Π°Ρ Π°Π²ΡΠΎΠΌΠ°ΡΠΈΠ·Π°ΡΠΈΠΈ ΡΠ²Π°ΡΠΎΡΠ½ΡΡ
ΠΏΡΠΎΡΠ΅ΡΡΠΎΠ² ΡΠ°ΠΊΠΈΡ
, ΠΊΠ°ΠΊ ΠΏΠ΅ΡΠ΅ΠΌΠ΅ΡΠ΅Π½ΠΈΠ΅ ΠΈΡΡΠΎΡΠ½ΠΈΠΊΠ° Π½Π°Π³ΡΠ΅Π²Π°, ΠΏΠΎΠ΄Π°ΡΠ° ΠΏΡΠΈΡΠ°Π΄ΠΎΡΠ½ΠΎΠ³ΠΎ ΠΌΠ°ΡΠ΅ΡΠΈΠ°Π»Π° ΠΏΡΠΈ ΡΠ²Π°ΡΠΊΠ΅ ΠΏΠ»Π°Π²Π»Π΅Π½ΠΈΠ΅ΠΌ, ΠΈΠ·ΠΌΠ΅Π½Π΅Π½ΠΈΠ΅ ΡΠΈΠ»Ρ ΡΠ²Π°ΡΠΎΡΠ½ΠΎΠ³ΠΎ ΡΠΎΠΊΠ° ΠΏΡΠΈ ΠΊΠΎΠ½ΡΠ°ΠΊΡΠ½ΠΎΠΉ ΡΠ²Π°ΡΠΊΠ΅, ΠΏΡΠΈΠΌΠ΅Π½ΡΡΡ ΠΏΡΠΎΠ³ΡΠ°ΠΌΠΌΠ½ΠΎΠ΅ ΡΠΏΡΠ°Π²Π»Π΅Π½ΠΈΠ΅ Ρ ΡΠ°Π·ΠΎΠΌΠΊΠ½ΡΡΡΠΌ ΡΠΈΠΊΠ»ΠΎΠΌ (ΡΠΈΡ. 1.5, Π°). ΠΡΠΎΠ³ΡΠ°ΠΌΠΌΠΈΡΡΡΡΠ΅Π΅Β Β ΡΡΡΡΠΎΠΉΡΡΠ²ΠΎΒ Β (ΠΠ£)Β Β ΠΈΠ·ΠΌΠ΅Π½ΡΠ΅ΡΒ Β ΡΠΏΡΠ°Π²Π»ΡΡΡΠ΅Π΅ Π²ΠΎΠ·Π΄Π΅ΠΉΡΡΠ²ΠΈΠ΅ Π₯y ΠΏΠΎ Π·Π°ΠΊΠΎΠ½Ρ, Π·Π°Π΄Π°ΡΡΠ΅ΠΌΡ ΡΡΠ΅Π±ΡΠ΅ΠΌΡΠ΅ ΠΈΠ·ΠΌΠ΅Π½Π΅Π½ΠΈΡ ΡΠΏΡΠ°Π²Π»ΡΠ΅ΠΌΠΎΠΉ Π²Π΅Π»ΠΈΡΠΈΠ½Ρ Π² ΡΠ²Π°ΡΠΎΡΠ½ΠΎΠΌ ΠΏΡΠΎΡΠ΅ΡΡΠ΅ ΠΊΠ°ΠΊ ΠΎΠ±ΡΠ΅ΠΊΡΠ΅ ΡΠΏΡΠ°Π²Π»Π΅Π½ΠΈΡ (ΠΠ£). ΠΠ»Ρ ΠΏΡΠ΅Π΄ΡΠΏΡΠ΅ΠΆΠ΄Π΅Π½ΠΈΡ Π²ΡΠ΅Π΄Π½ΠΎΠ³ΠΎ Π²Π»ΠΈΡΠ½ΠΈΡ Π½Π° ΡΠ²Π°ΡΠΎΡΠ½ΡΠΉ ΠΏΡΠΎΡΠ΅ΡΡ ΠΎΡΠ΄Π΅Π»ΡΠ½ΡΡ
ΠΎΠΆΠΈΠ΄Π°Π΅ΠΌΡΡ
Π²ΠΎΠ·ΠΌΡΡΠ΅Π½ΠΈΠΉ, Π½Π°ΠΏΡΠΈΠΌΠ΅Ρ, ΠΈΠ·ΠΌΠ΅Π½Π΅Π½ΠΈΡ Π½Π°ΠΏΡΡΠΆΠ΅Π½ΠΈΡ ΡΠ΅ΡΠΈ, ΠΈΡΠΏΠΎΠ»ΡΠ·ΡΡΡ ΡΠ°Π·ΠΎΠΌΠΊΠ½ΡΡΡΠ΅ ΡΠΈΡΡΠ΅ΠΌΡ ΠΊΠΎΠΌΠΏΠ΅Π½ΡΠ°ΡΠΈΠΈ, ΠΎΠ±Π»Π°Π΄Π°ΡΡΠΈΠ΅ ΠΏΠΎΠ²ΡΡΠ΅Π½Π½ΡΠΌ Π±ΡΡΡΡΠΎΠ΄Π΅ΠΉΡΡΠ²ΠΈΠ΅ΠΌ (ΡΠΈΡ. 1.5, Π±). ΠΡΠΈ Π²ΠΎΠ·Π½ΠΈΠΊΠ½ΠΎΠ²Π΅Π½ΠΈΠΈ Π²ΠΎΠ·ΠΌΡΡΠ΅Π½ΠΈΡ Π ΠΎΠ½ΠΎ ΠΏΡΠ΅ΠΎΠ±ΡΠ°Π·ΡΠ΅ΡΡΡ ΠΈΠ·ΠΌΠ΅ΡΠΈΡΠ΅Π»Π΅ΠΌ Π²ΠΎΠ·ΠΌΡΡΠ΅Π½ΠΈΠΉ ΠΠ Π² ΠΊΠΎΠΌΠΏΠ΅Π½ΡΠΈΡΡΡΡΠΈΠΉ ΡΠΈΠ³Π½Π°Π», ΡΡΡΡΠ°Π½ΡΡΡΠΈΠΉ Π²Π»ΠΈΡΠ½ΠΈΠ΅ Π²ΠΎΠ·ΠΌΡΡΠ΅Π½ΠΈΡ Π Π½Π° Π²ΡΡ
ΠΎΠ΄Π½ΠΎΠΉ ΠΏΠ°ΡΠ°ΠΌΠ΅ΡΡ Π₯
Π Π·Π°ΠΌΠΊΠ½ΡΡΡΡ ΡΠΈΡΡΠ΅ΠΌΠ°Ρ Π°Π²ΡΠΎΠΌΠ°ΡΠΈΡΠ΅ΡΠΊΠΎΠ³ΠΎ ΡΠ΅Π³ΡΠ»ΠΈΡΠΎΠ²Π°Π½ΠΈΡ (Π‘ΠΠ ) ΠΈΠ·ΠΌΠ΅Π½Π΅Π½ΠΈΠ΅ ΡΠ΅Π³ΡΠ»ΠΈΡΡΡΡΠ΅Π³ΠΎ Π²ΠΎΠ·Π΄Π΅ΠΉΡΡΠ²ΠΈΡ Π₯Ρ (ΡΠΈΡ. 1.6), ΠΎΠΏΡΠ΅Π΄Π΅Π»ΡΡΡΠ΅Π³ΠΎ ΠΈΠ·ΠΌΠ΅Π½Π΅Π½ΠΈΠ΅ ΡΠ΅Π³ΡΠ»ΠΈΡΡΠ΅ΠΌΠΎΠΉ Π²Π΅Π»ΠΈΡΠΈΠ½Ρ Π₯Π²ΡΡ , ΠΏΡΠΎΠΈΡΡ ΠΎΠ΄ΠΈΡ Π΄ΠΎ ΡΠ΅Ρ ΠΏΠΎΡ, ΠΏΠΎΠΊΠ° Π₯Π²ΡΡ Π½Π΅ Π΄ΠΎΡΡΠΈΠ³Π½Π΅Ρ ΡΡΠ΅Π±ΡΠ΅ΠΌΠΎΠ³ΠΎ Π·Π½Π°ΡΠ΅Π½ΠΈΡ ΠΈ Π½Π΅ Π²ΠΎΡΡΡΠ°Π½ΠΎΠ²ΠΈΡΡΡ ΡΠ°Π²Π½ΠΎΠ²Π΅ΡΠΈΠ΅ ΡΠΈΡΡΠ΅ΠΌΡ ΡΠ΅Π³ΡΠ»ΠΈΡΠΎΠ²Π°Π½ΠΈΡ, ΠΎΠΏΡΠ΅Π΄Π΅Π»ΡΠ΅ΠΌΠΎΠ΅ ΡΡΠ»ΠΎΠ²ΠΈΡΠΌΠΈ:
ΠΡΡΠΎΡΠ½ΠΈΠΊΠΎΠΌ ΠΊΠΎΡΡΠ΅ΠΊΡΠΈΡΡΡΡΠ΅Π³ΠΎ Π²ΠΎΠ·Π΄Π΅ΠΉΡΡΠ²ΠΈΡ Π½Π° ΡΠΈΡΡΠ΅ΠΌΡ ΡΠ»ΡΠΆΠΈΡ Π³Π»Π°Π²Π½Π°Ρ (ΠΎΡΡΠΈΡΠ°ΡΠ΅Π»ΡΠ½Π°Ρ) ΠΎΠ±ΡΠ°ΡΠ½Π°Ρ ΡΠ²ΡΠ·Ρ, ΡΠΈΠ³Π½Π°Π» Π₯ΠΎ.Ρ ΠΊΠΎΡΠΎΡΠΎΠΉ ΠΎΠΏΡΠ΅Π΄Π΅Π»ΡΠ΅ΡΡΡ ΡΠΎΠ»ΡΠΊΠΎ ΠΎΡΠ»ΠΈΡΠΈΠ΅ΠΌ ΠΈΠ·ΠΌΠ΅ΡΠ΅Π½Π½ΠΎΠ³ΠΎ Π·Π½Π°ΡΠ΅Π½ΠΈΡ Π₯Π²ΡΡ ΠΎΡ Π·Π°Π΄Π°Π²Π°Π΅ΠΌΠΎΠ³ΠΎ Π₯Π²Ρ , ΠΈ Π½Π΅ Π·Π°Π²ΠΈΡΠΈΡ ΠΎΡ ΠΏΠ°ΡΠ°ΠΌΠ΅ΡΡΠΎΠ² ΠΈ ΠΌΠ΅ΡΡΠ° ΠΏΡΠΈΠ»ΠΎΠΆΠ΅Π½ΠΈΡ Π²ΠΎΠ·ΠΌΡΡΠ΅Π½ΠΈΠΉ Π. ΠΠ±ΡΠ°ΡΠ½ΡΠ΅ ΡΠ²ΡΠ·ΠΈ Π²ΡΠΏΠΎΠ»Π½ΡΡΡ Π½Π° ΠΎΡΠ½ΠΎΠ²Π΅ ΠΈΠ·ΠΌΠ΅ΡΠΈΡΠ΅Π»Π΅ΠΉ ΡΠΈΠ»Ρ ΡΠ²Π°ΡΠΎΡΠ½ΠΎΠ³ΠΎ ΡΠΎΠΊΠ°,Β Π½Π°ΠΏΡΡΠΆΠ΅Π½ΠΈΡ,ΡΠ°Π·Π»ΠΈΡΠ½ΡΡ Π²ΠΈΠ΄ΠΎΠ² ΠΈΠ·Π»ΡΡΠ΅Π½ΠΈΠΉ ΠΈΠ· Π·ΠΎΠ½Ρ ΡΠ²Π°ΡΠΊΠΈ, ΠΏΠΎΠ»ΠΎΠΆΠ΅Π½ΠΈΡ Π³ΡΠ°Π½ΠΈΡΡ ΡΠ»Π°ΠΊ-ΠΌΠ΅ΡΠ°Π»Π» ΠΏΡΠΈ ΡΠ»Π΅ΠΊΡΡΠΎΡΠ»Π°ΠΊΠΎΠ²ΠΎΠΉ ΡΠ²Π°ΡΠΊΠ΅, ΠΏΠ΅ΡΠ΅ΠΌΠ΅ΡΠ΅Π½ΠΈΠΉ ΡΠ»Π΅ΠΊΡΡΠΎΠ΄ΠΎΠ² ΠΈΠ»ΠΈ Π·Π°Π³ΠΎΡΠΎΠ²ΠΎΠΊ ΠΏΡΠΈ ΠΊΠΎΠ½ΡΠ°ΠΊΡΠ½ΠΎΠΉ ΡΠ²Π°ΡΠΊΠ΅ ΠΈ Π΄ΡΡΠ³ΠΈΡ ΠΏΠ°ΡΠ°ΠΌΠ΅ΡΡΠΎΠ² ΡΠ²Π°ΡΠΎΡΠ½ΠΎΠ³ΠΎ ΠΏΡΠΎΡΠ΅ΡΡΠ°. ΠΠ°ΠΌΠΊΠ½ΡΡΡΠ΅ Π‘ΠΠ ΠΏΡΠΈΠΌΠ΅Π½ΡΡΡ ΠΏΡΠ΅ΠΆΠ΄Π΅ Π²ΡΠ΅Π³ΠΎ Π΄Π»Ρ ΡΡΠ°Π±ΠΈΠ»ΠΈΠ·Π°ΡΠΈΠΈ ΡΠ½Π΅ΡΠ³Π΅ΡΠΈΡΠ΅ΡΠΊΠΈΡ ΠΏΠ°ΡΠ°ΠΌΠ΅ΡΡΠΎΠ² ΡΠ²Π°ΡΠΎΡΠ½ΡΡ ΠΏΡΠΎΡΠ΅ΡΡΠΎΠ².
ΠΡΡΠ΅ΠΊΡΠΈΠ²Π½ΠΎΡΡΡ Π°Π²ΡΠΎΠΌΠ°ΡΠΈΠ·Π°ΡΠΈΠΈ ΡΠ²Π°ΡΠΎΡΠ½ΡΡ ΠΏΡΠΎΡΠ΅ΡΡΠΎΠ² Π²ΠΎ ΠΌΠ½ΠΎΠ³ΠΎΠΌ ΠΎΠΏΡΠ΅Π΄Π΅Π»ΡΠ΅ΡΡΡ ΡΠΎΡΠ½ΠΎΡΡΡΡ ΠΏΠΎΠ΄Π³ΠΎΡΠΎΠ²ΠΊΠΈ Π·Π°Π³ΠΎΡΠΎΠ²ΠΎΠΊ ΠΈ ΠΈΡ ΡΠ±ΠΎΡΠΊΠΎΠΉ.
Π Π°Π·ΠΌΠ΅ΡΡ Π·Π°Π³ΠΎΡΠΎΠ²ΠΎΠΊ ΠΏΠΎΠ»ΡΡΠ°ΡΡΡΡ ΠΈΠ· ΠΏΡΠ΅Π΄ΡΠ΅ΡΡΠ²ΡΡΡΠΈΡ ΡΠ²Π°ΡΠΊΠ΅ ΡΠ΅Ρ Π½ΠΎΠ»ΠΎΠ³ΠΈΡΠ΅ΡΠΊΠΈΡ (Π·Π°Π³ΠΎΡΠΎΠ²ΠΈΡΠ΅Π»ΡΠ½ΡΡ ) ΠΎΠΏΠ΅ΡΠ°ΡΠΈΠΉ ΠΈ, ΡΠ»Π΅Π΄ΠΎΠ²Π°ΡΠ΅Π»ΡΠ½ΠΎ, ΠΏΡΠ΅Π΄ΠΎΠΏΡΠ΅Π΄Π΅Π»ΡΡΡ Π»ΠΈΠ½ΠΈΠΈ ΡΡΡΠΊΠΎΠ² Ρ ΠΈΡ Π½Π΅ΡΠΎΡΠ½ΠΎΡΡΡΠΌΠΈ ΠΏΠΎ Π½Π°ΠΏΡΠ°Π²Π»Π΅Π½ΠΈΡ, Π·Π°Π·ΠΎΡΡ, ΠΏΡΠ΅Π²ΡΡΠ΅Π½ΠΈΡ ΠΊΡΠΎΠΌΠΎΠΊ ΠΈ Π΄Ρ. ΠΠΎΡΡΠΎΠΌΡ Π°Π²ΡΠΎΠΌΠ°ΡΠΈΠ·Π°ΡΠΈΡ ΡΠ²Π°ΡΠΎΡΠ½ΡΡ ΠΏΡΠΎΡΠ΅ΡΡΠΎΠ² ΡΠ΅Π»Π΅ΡΠΎΠΎΠ±ΡΠ°Π·Π½Π° ΠΈ ΡΡΡΠ΅ΠΊΡΠΈΠ²Π½Π° ΡΠΎΠ»ΡΠΊΠΎ ΠΏΡΠΈ Π½Π°Π»ΠΈΡΠΈΠΈ ΠΌΠ΅Ρ Π°Π½ΠΈΠ·Π°ΡΠΈΠΈ ΠΈ Π°Π²ΡΠΎΠΌΠ°ΡΠΈΠ·Π°ΡΠΈΠΈ Π·Π°Π³ΠΎΡΠΎΠ²ΠΈΡΠ΅Π»ΡΠ½ΡΡ ΠΈ ΡΠ±ΠΎΡΠΎΡΠ½ΡΡ ΠΎΠΏΠ΅ΡΠ°ΡΠΈΠΉ. ΠΠ°ΠΆΠ΅ ΠΏΡΠΈ Π²ΡΠΏΠΎΠ»Π½Π΅Π½ΠΈΠΈ ΡΡΠΈΡ ΡΡΠ»ΠΎΠ²ΠΈΠΉ Π½Π΅ΠΈΠ·Π±Π΅ΠΆΠ½Ρ ΠΎΡΠΊΠ»ΠΎΠ½Π΅Π½ΠΈΡ ΠΏΠΎΠ»ΠΎΠΆΠ΅Π½ΠΈΡ ΠΈ ΡΠΎΡΠΌΡ ΡΠΎΠ΅Π΄ΠΈΠ½Π΅Π½ΠΈΠΉ Π² ΡΠ΅Π·ΡΠ»ΡΡΠ°ΡΠ΅ Π·Π½Π°ΡΠΈΡΠ΅Π»ΡΠ½ΡΡ ΡΠ΅ΠΌΠΏΠ΅ΡΠ°ΡΡΡΠ½ΡΡ Π΄Π΅ΡΠΎΡΠΌΠ°ΡΠΈΠΉ ΠΈ ΠΏΠ΅ΡΠ΅ΠΌΠ΅ΡΠ΅Π½ΠΈΠΉ ΡΠ²Π°ΡΠΈΠ²Π°Π΅ΠΌΡΡ Π΄Π΅ΡΠ°Π»Π΅ΠΉ Π²ΡΠ»Π΅Π΄ΡΡΠ²ΠΈΠ΅ Π½Π΅ΡΠ°Π²Π½ΠΎΠΌΠ΅ΡΠ½ΠΎΡΡΠΈ Π½Π°Π³ΡΠ΅Π²Π° ΠΈΠ·Π΄Π΅Π»ΠΈΡ ΠΏΡΠΈ ΡΠ²Π°ΡΠΊΠ΅.
ΠΠ»Ρ Π°Π²ΡΠΎΠΌΠ°ΡΠΈΡΠ΅ΡΠΊΠΎΠ³ΠΎ Π²Π΅Π΄Π΅Π½ΠΈΡ ΡΠ»Π΅ΠΊΡΡΠΎΠ΄Π° ΠΏΠΎ ΠΎΡΠΈ ΡΡΡΠΊΠ° ΠΏΡΠΈ Π΄ΡΠ³ΠΎΠ²ΠΎΠΉ ΡΠ²Π°ΡΠΊΠ΅ ΠΏΡΠΈ Π½Π°ΡΡΡΠ΅Π½ΠΈΠΈ ΠΏΡΡΠΌΠΎΠ»ΠΈΠ½Π΅ΠΉΠ½ΠΎΡΡΠΈ ΡΡΡΠΊΠ° Π²ΡΠ»Π΅Π΄ΡΡΠ²ΠΈΠ΅ ΠΏΠΎΠ³ΡΠ΅ΡΠ½ΠΎΡΡΠ΅ΠΉ ΠΈΡ ΠΏΠΎΠ΄Π³ΠΎΡΠΎΠ²ΠΊΠΈ ΠΏΠΎΠ΄ ΡΠ²Π°ΡΠΊΡ, ΡΠ΅ΠΏΠ»ΠΎΠ²ΡΡ Π΄Π΅ΡΠΎΡΠΌΠ°ΡΠΈΠΉ, Π° ΡΠ°ΠΊΠΆΠ΅ ΠΏΡΠΈ ΡΠ²Π°ΡΠΊΠ΅ ΠΊΡΠΈΠ²ΠΎΠ»ΠΈΠ½Π΅ΠΉΠ½ΡΡ ΡΠ²ΠΎΠ² ΠΏΡΠΈΠΌΠ΅Π½ΡΡΡ ΡΠ»Π΅Π΄ΡΡΠΈΠ΅ ΡΠΈΡΡΠ΅ΠΌΡ. Π ΡΠ°ΠΊΠΈΡ ΡΠΈΡΡΠ΅ΠΌΠ°Ρ Π·Π°ΠΊΠΎΠ½ ΠΈΠ·ΠΌΠ΅Π½Π΅Π½ΠΈΡ Π·Π°Π΄Π°ΡΡΠ΅Π³ΠΎ Π²ΠΎΠ·Π΄Π΅ΠΉΡΡΠ²ΠΈΡ y(t) β Π·Π°ΡΠ°Π½Π΅Π΅ Π½Π΅ΠΈΠ·Π²Π΅ΡΡΠ½Π°Ρ ΡΡΠ½ΠΊΡΠΈΡ Π²ΡΠ΅ΠΌΠ΅Π½ΠΈ, ΠΎΠΏΡΠ΅Π΄Π΅Π»ΡΠ΅ΠΌΠ°Ρ ΡΠ΅ΠΊΡΡΠΈΠΌΠΈ ΠΎΡΠΊΠ»ΠΎΠ½Π΅Π½ΠΈΡΠΌΠΈ Π»ΠΈΠ½ΠΈΠΈ ΡΠΎΠΏΡΡΠΆΠ΅Π½ΠΈΡ ΡΠ²Π°ΡΠΈΠ²Π°Π΅ΠΌΡΡ Π΄Π΅ΡΠ°Π»Π΅ΠΉ ΠΈΠ»ΠΈ ΠΏΠ°ΡΠ°ΠΌΠ΅ΡΡΠΎΠ² ΡΡΡΠΊΠ° (Π·Π°Π·ΠΎΡΠ°, ΡΠ΅ΡΠ΅Π½ΠΈΡ ΡΠ°Π·Π΄Π΅Π»ΠΊΠΈ) ΠΎΡ ΡΠ°ΡΡΠ΅ΡΠ½ΡΡ Π·Π½Π°ΡΠ΅Π½ΠΈΠΉ. Π ΠΊΠ°ΡΠ΅ΡΡΠ²Π΅ ΡΡΠ΅Π΄ΡΡΠ² ΠΈΠ·ΠΌΠ΅ΡΠ΅Π½ΠΈΡ ΡΠ°ΠΊΠΈΡ ΠΎΡΠΊΠ»ΠΎΠ½Π΅Π½ΠΈΠΉ ΠΈΡΠΏΠΎΠ»ΡΠ·ΡΡΡ ΠΊΠ°ΠΊ ΡΡΡΡΠΎΠΉΡΡΠ²ΠΎ ΠΏΡΡΠΌΠΎΠ³ΠΎ ΠΊΠΎΠΏΠΈΡΠΎΠ²Π°Π½ΠΈΡ, ΡΠ°ΠΊ ΠΈ ΡΠ°Π·Π»ΠΈΡΠ½ΡΠ΅ ΡΠ»Π΅ΠΊΡΡΠΎΠΌΠ΅Ρ Π°Π½ΠΈΡΠ΅ΡΠΊΠΈΠ΅, Π±Π΅ΡΠΊΠΎΠ½ΡΠ°ΠΊΡΠ½ΡΠ΅ (ΠΌΠ°Π³Π½ΠΈΡΠ½ΡΠ΅, ΡΠΎΡΠΎΡΠ»Π΅ΠΊΡΡΠΈΡΠ΅ΡΠΊΠΈΠ΅) Π΄Π°ΡΡΠΈΠΊΠΈ, Π²ΠΈΠ΄Π΅ΠΎΡΠ΅Π½ΡΠΎΡΠ½ΡΠ΅ ΠΈ Π΄ΡΡΠ³ΠΈΠ΅ ΠΏΠΎΠ΄ΠΎΠ±Π½ΡΠ΅ ΡΡΡΡΠΎΠΉΡΡΠ²Π°.
Π ΠΎΠ±ΡΠ΅ΠΌ ΡΠ»ΡΡΠ°Π΅ Π°Π²ΡΠΎΠΌΠ°ΡΠΈΠ·Π°ΡΠΈΡ ΡΠ²Π°ΡΠΎΡΠ½ΡΡ ΠΏΡΠΎΡΠ΅ΡΡΠΎΠ² ΠΎΡΡΡΠ΅ΡΡΠ²Π»ΡΠ΅ΡΡΡ Π½Π° ΠΎΡΠ½ΠΎΠ²Π΅ ΡΠΎΠ²ΠΌΠ΅ΡΡΠ½ΠΎΠ³ΠΎ ΠΈΡΠΏΠΎΠ»ΡΠ·ΠΎΠ²Π°Π½ΠΈΡ ΡΠΊΠ°Π·Π°Π½Π½ΡΡ ΡΠΈΡΡΠ΅ΠΌ. Π’Π°ΠΊ, ΠΏΡΠΎΠ³ΡΠ°ΠΌΠΌΠ½ΠΎΠ΅ ΡΠΏΡΠ°Π²Π»Π΅Π½ΠΈΠ΅ ΠΏΠΎΡΠ»Π΅Π΄ΠΎΠ²Π°ΡΠ΅Π»ΡΠ½ΠΎΡΡΡΡ ΠΎΠΏΠ΅ΡΠ°ΡΠΈΠΉ ΡΠ²Π°ΡΠΎΡΠ½ΠΎΠ³ΠΎ ΡΠΈΠΊΠ»Π° ΠΈ ΠΏΠ΅ΡΠ΅ΠΌΠ΅ΡΠ΅Π½ΠΈΡ ΡΠ²Π°ΡΠΎΡΠ½ΠΎΠ³ΠΎ ΠΈΠ½ΡΡΡΡΠΌΠ΅Π½ΡΠ°, ΠΈΠ·ΠΌΠ΅Π½Π΅Π½ΠΈΡΠΌΠΈ ΠΏΠ°ΡΠ°ΠΌΠ΅ΡΡΠΎΠ² ΡΠ΅ΠΆΠΈΠΌΠ°, Π² ΡΠ°ΡΡΠ½ΠΎΡΡΠΈ ΠΏΡΠΈ Π·Π°ΠΆΠΈΠ³Π°Π½ΠΈΠΈ Π΄ΡΠ³ΠΈ, Π·Π°Π²Π°ΡΠΊΠ΅ ΠΊΡΠ°ΡΠ΅ΡΠ° ΠΈ Ρ. ΠΏ. ΠΎΠ±ΡΡΠ½ΠΎ Π΄ΠΎΠΏΠΎΠ»Π½ΡΠ΅ΡΡΡ Π»ΠΎΠΊΠ°Π»ΡΠ½ΡΠΌΠΈ Π‘ΠΠ (ΡΠ΅Π³ΡΠ»ΡΡΠΎΡΠ°ΠΌΠΈ) Π²Π°ΠΆΠ½Π΅ΠΉΡΠΈΡ ΠΏΠ°ΡΠ°ΠΌΠ΅ΡΡΠΎΠ² ΡΠ΅ΠΆΠΈΠΌΠ° ΡΠ²Π°ΡΠΊΠΈ. ΠΠΎ ΡΡΡΠ΅ΡΡΠ²Ρ Π»ΠΎΠΊΠ°Π»ΡΠ½ΡΠ΅ ΡΠ΅Π³ΡΠ»ΡΡΠΎΡΡ ΠΏΡΠ΅Π΄ΡΡΠ°Π²Π»ΡΡΡ ΡΠΎΠ±ΠΎΠΉ ΠΌΠ°Π»ΡΠ΅ Π²ΡΡΠΈΡΠ»ΠΈΡΠ΅Π»ΠΈ, ΠΊΠΎΡΠΎΡΡΠ΅ Π² ΠΎΠ±ΡΠ΅ΠΌ ΡΠ»ΡΡΠ°Π΅ ΡΠ΅ΡΠ°ΡΡ ΡΡΠ°Π²Π½Π΅Π½ΠΈΡ ΡΠΈΠΏΠ°
Π³Π΄Π΅ Π0, Π1, Π2 —Β ΠΊΠΎΡΡΡΠΈΡΠΈΠ΅Π½ΡΡ, ΠΎΠΏΡΠ΅Π΄Π΅Π»ΡΠ΅ΠΌΡΠ΅ ΠΏΠ°ΡΠ°ΠΌΠ΅ΡΡΠ°ΠΌΠΈ Π½Π°ΡΡΡΠΎΠΉΠΊΠΈ ΡΡΡΡΠΎΠΉΡΡΠ² 3 ΠΈ 4 ΡΠ΅Π³ΡΠ»ΡΡΠΎΡΠ° (ΡΠΌ. ΡΠΈΡ. 1.6). ΠΡΠ±ΡΡ Π·Π°Π΄Π°ΡΡ Π°Π²ΡΠΎΠΌΠ°ΡΠΈΠ·Π°ΡΠΈΠΈ ΡΠ²Π°ΡΠΎΡΠ½ΡΡ ΠΏΡΠΎΡΠ΅ΡΡΠΎΠ² ΠΊΠ°ΠΊ ΡΠ°ΡΡΠ½ΡΠΉ ΡΠ»ΡΡΠ°ΠΉ ΠΎΠ±ΡΠ΅ΠΉ ΠΏΡΠΎΠ±Π»Π΅ΠΌΡ ΠΎΠ±ΡΠ°Π±ΠΎΡΠΊΠΈ ΠΈΠ½ΡΠΎΡΠΌΠ°ΡΠΈΠΈ ΠΌΠΎΠΆΠ½ΠΎ ΠΏΡΠ΅Π΄ΡΡΠ°Π²ΠΈΡΡ ΡΠΎΠ²ΠΎΠΊΡΠΏΠ½ΠΎΡΡΡΡ ΠΎΡΠ΄Π΅Π»ΡΠ½ΡΡ ΠΎΠΏΠ΅ΡΠ°ΡΠΈΠΉ, Π²ΡΠΏΠΎΠ»Π½ΡΠ΅ΠΌΡΡ Π² ΠΎΠΏΡΠ΅Π΄Π΅Π»Π΅Π½Π½ΠΎΠΉ ΠΏΠΎΡΠ»Π΅Π΄ΠΎΠ²Π°ΡΠ΅Π»ΡΠ½ΠΎΡΡΠΈ. Π£Π½ΠΈΠ²Π΅ΡΡΠ°Π»ΡΠ½ΡΠΌ ΡΡΡΡΠΎΠΉΡΡΠ²ΠΎΠΌ ΡΠΎΠ²ΡΠ΅ΠΌΠ΅Π½Π½ΡΡ Π²ΡΡΠΈΡΠ»ΠΈΡΠ΅Π»ΡΠ½ΡΡ ΡΠΈΡΡΠ΅ΠΌ, ΡΠ΅Π°Π»ΠΈΠ·ΡΡΡΠΈΡ Π·Π°Π΄Π°Π½Π½ΡΠΉ ΠΏΡΠΎΠ³ΡΠ°ΠΌΠΌΠΎΠΉ ΠΏΡΠΎΡΠ΅ΡΡ ΡΠ΅ΡΠ΅Π½ΠΈΡ Π·Π°Π΄Π°ΡΠΈ, ΡΠ²Π»ΡΠ΅ΡΡΡ ΠΌΠΈΠΊΡΠΎΠΏΡΠΎΡΠ΅ΡΡΠΎΡ. Π‘ΠΎΠ·Π΄Π°Π½Π½ΡΠ΅ Π½Π° ΠΎΡΠ½ΠΎΠ²Π΅ ΠΌΠΈΠΊΡΠΎΠΏΡΠΎΡΠ΅ΡΡΠΎΡΠΎΠ², Π΄ΠΎΠΏΠΎΠ»Π½Π΅Π½Π½ΡΡ ΠΏΠ°ΠΌΡΡΡΡ, Π²Π½Π΅ΡΠ½ΠΈΠΌΠΈ ΡΡΡΡΠΎΠΉΡΡΠ²Π°ΠΌΠΈ ΠΈ ΡΡΠ΅Π΄ΡΡΠ²Π°ΠΌΠΈ ΡΠ²ΡΠ·ΠΈ, ΠΌΠΈΠΊΡΠΎΠΠΠ Ρ Π°ΡΠ°ΠΊΡΠ΅ΡΠΈΠ·ΡΡΡΡΡ ΠΌΠ°Π»ΡΠΌΠΈ ΡΠ°Π·ΠΌΠ΅ΡΠ°ΠΌΠΈ, Π½ΠΈΠ·ΠΊΠΎΠΉ ΡΡΠΎΠΈΠΌΠΎΡΡΡΡ, Π²ΡΡΠΎΠΊΠΎΠΉ Π½Π°Π΄Π΅ΠΆΠ½ΠΎΡΡΡΡ ΠΈ ΡΠΊΠΎΠ½ΠΎΠΌΠΈΡΠ΅ΡΠΊΠΈ ΠΎΠΏΡΠ°Π²Π΄Π°Π½Ρ Π½Π΅ ΡΠΎΠ»ΡΠΊΠΎ Π΄Π»Ρ Π³ΡΡΠΏΠΏΠΎΠ²ΠΎΠ³ΠΎ, Π½ΠΎ ΠΈ Π΄Π»Ρ ΠΈΠ½Π΄ΠΈΠ²ΠΈΠ΄ΡΠ°Π»ΡΠ½ΠΎΠ³ΠΎ ΡΠΏΡΠ°Π²Π»Π΅Π½ΠΈΡ ΡΠ±ΠΎΡΠΎΡΠ½ΠΎ-ΡΠ²Π°ΡΠΎΡΠ½ΡΠΌΠΈ ΡΡΡΠ°Π½ΠΎΠ²ΠΊΠ°ΠΌΠΈ ΠΈ Π΄Π°ΠΆΠ΅ ΠΎΡΠ΄Π΅Π»ΡΠ½ΡΠΌΠΈ ΡΡΡΡΠΎΠΉΡΡΠ²Π°ΠΌΠΈ ΡΡΡΠ°Π½ΠΎΠ²ΠΊΠΈ. ΠΡΠΈΠΌΠ΅Ρ ΠΌΠΈΠΊΡΠΎΠΏΡΠΎΡΠ΅ΡΡΠΎΡΠ½ΠΎΠΉ ΡΠΈΡΡΠ΅ΠΌΡ ΡΠΏΡΠ°Π²Π»Π΅Π½ΠΈΡ Π΄ΡΠ³ΠΎΠ²ΠΎΠΉ ΡΠ²Π°ΡΠΊΠΎΠΉ ΠΏΡΠΈΠ²Π΅Π΄Π΅Π½ Π½Π° ΡΠΈΡ. 1.7.
ΠΡΠΈΠΌΠ΅Π½Π΅Π½ΠΈΠ΅ ΠΠΠ Π² ΡΠΈΡΡΠ΅ΠΌΠ°Ρ Π°Π²ΡΠΎΠΌΠ°ΡΠΈΠ·Π°ΡΠΈΠΈ ΠΏΠΎΠ·Π²ΠΎΠ»ΡΠ΅Ρ ΡΠ΅Π°Π»ΠΈΠ·ΠΎΠ²ΡΠ²Π°ΡΡ Π°Π΄Π°ΠΏΡΠΈΠ²Π½ΠΎΠ΅ ΡΠΏΡΠ°Π²Π»Π΅Π½ΠΈΠ΅ ΡΠ²Π°ΡΠΎΡΠ½ΡΠΌΠΈ ΠΏΡΠΎΡΠ΅ΡΡΠ°ΠΌΠΈ, ΠΊΠΎΡΠΎΡΠΎΠ΅ ΠΏΡΠ΅Π΄ΠΏΠΎΠ»Π°Π³Π°Π΅Ρ ΡΠ°ΠΌΠΎΠ½Π°ΡΡΡΠΎΠΉΠΊΡ ΡΠΈΡΡΠ΅ΠΌΡ ΠΏΡΠΈ ΠΈΠ·ΠΌΠ΅Π½Π΅Π½ΠΈΠΈ Π²Π½Π΅ΡΠ½ΠΈΡ ΡΡΠ»ΠΎΠ²ΠΈΠΉ ΠΈ Π½Π° ΠΎΡΠ½ΠΎΠ²Π΅ ΠΈΠ½ΡΠΎΡΠΌΠ°ΡΠΈΠΈ ΠΎΠ± ΡΡΠ»ΠΎΠ²ΠΈΡΡ ΠΈ ΠΊΠ°ΡΠ΅ΡΡΠ²Π΅ ΡΠΎΡΠΌΠΈΡΠΎΠ²Π°Π½ΠΈΡ ΡΠ²Π°ΡΠ½ΠΎΠ³ΠΎ ΡΠΎΠ΅Π΄ΠΈΠ½Π΅Π½ΠΈΡ. ΠΠ»Ρ ΡΡΠΎΠ³ΠΎ Π² ΡΠΈΡΡΠ΅ΠΌΠ΅ Π΄ΠΎΠ»ΠΆΠ½ΠΎ Π±ΡΡΡ ΡΠ΅Π°Π»ΠΈΠ·ΠΎΠ²Π°Π½ΠΎ Π²ΡΠΏΠΎΠ»Π½Π΅Π½ΠΈΠ΅ ΡΡΠ΅Ρ ΡΡΠ½ΠΊΡΠΈΠΉΒ Β Β Β Β Β Β Β Β Β ΠΈΠ΄Π΅Π½ΡΠΈΡΠΈΠΊΠ°ΡΠΈΠΈΒ Β Β (ΠΎΠΏΡΠ΅Π΄Π΅Π»Π΅Π½ΠΈΠ΅ΠΌΠ³Π½ΠΎΠ²Π΅Π½Π½ΠΎΠ³ΠΎ ΡΠΎΡΡΠΎΡΠ½ΠΈΡ ΠΏΡΠΎΡΠ΅ΡΡΠ° ΠΈΠ»ΠΈ ΡΠΈΡΡΠ΅ΠΌΡ), ΠΏΡΠΈΠ½ΡΡΠΈΡ ΡΠ΅ΡΠ΅Π½ΠΈΠΉ (ΠΏΡΠΎΠ³ΡΠ°ΠΌΠΌΠ° Π½Π°ΡΡΡΠΎΠΉΠΊΠΈ), Π½Π°ΡΡΡΠΎΠΉΠΊΠΈ (ΡΠΈΠ·ΠΈΡΠ΅ΡΠΊΠ°Ρ ΡΠ΅Π°Π»ΠΈΠ·Π°ΡΠΈΡ ΠΏΡΠΈΠ½ΡΡΠΎΠ³ΠΎ ΡΠ΅ΡΠ΅Π½ΠΈΡ), ΠΊΠΎΡΠΎΡΡΠ΅ ΠΏΠΎΠ·Π²ΠΎΠ»ΡΡΡ Π³ΠΈΠ±ΠΊΠΎ ΡΠ΅Π°Π³ΠΈΡΠΎΠ²Π°ΡΡ Π½Π° ΠΏΠΎΡΠ²Π»Π΅Π½ΠΈΠ΅ ΡΠ°Π·Π»ΠΈΡΠ½ΡΡ Π²ΠΎΠ·ΠΌΡΡΠ΅Π½ΠΈΠΉ.
ΠΡΠΈΠΌΠ΅ΡΠΎΠΌ ΠΌΠΎΠΆΠ΅Ρ ΡΠ»ΡΠΆΠΈΡΡ Π΄Π΅ΠΉΡΡΠ²ΡΡΡΠ°Ρ Π°Π΄Π°ΠΏΡΠΈΠ²Π½Π°Ρ ΡΠΈΡΡΠ΅ΠΌΠ° ΡΠΏΡΠ°Π²Π»Π΅Π½ΠΈΡ ΡΠ²Π°ΡΠΊΠΎΠΉ Π½Π΅ΠΏΠΎΠ²ΠΎΡΠΎΡΠ½ΡΡ ΡΡΡΠΊΠΎΠ² ΡΡΡΠ± ΠΌΠ°Π»ΠΎΠ³ΠΎ Π΄ΠΈΠ°ΠΌΠ΅ΡΡΠ° Ρ Π°Π²ΡΠΎΠΌΠ°ΡΠΈΡΠ΅ΡΠΊΠΎΠΉ ΡΡΠ°Π±ΠΈΠ»ΠΈΠ·Π°ΡΠΈΠ΅ΠΉ Π²ΡΠΏΡΠΊΠ»ΠΎΡΡΠΈ Π² ΠΊΠΎΡΠ½Π΅ ΡΠ²Π°. Π‘ΠΈΡΡΠ΅ΠΌΠ° ΠΎΠ±Π΅ΡΠΏΠ΅ΡΠΈΠ²Π°Π΅Ρ ΠΎΡΠ΅Π½ΠΊΡ ΠΈΠ½ΡΠ΅Π³ΡΠ°Π»ΡΠ½ΠΎΠ³ΠΎ ΡΡΡΠ΅ΠΊΡΠ° ΡΠΎΠ²ΠΌΠ΅ΡΡΠ½ΠΎΠ³ΠΎ Π²Π»ΠΈΡΠ½ΠΈΡ ΡΠ΅Ρ Π½ΠΎΠ»ΠΎΠ³ΠΈΡΠ΅ΡΠΊΠΈΡ Π²ΠΎΠ·ΠΌΡΡΠ΅Π½ΠΈΠΉ, Ρ Π°ΡΠ°ΠΊΡΠ΅ΡΠ½ΡΡ Π΄Π»Ρ ΠΊΠ°ΠΆΠ΄ΠΎΠ³ΠΎ ΡΡΡΠΊΠ°, ΠΏΠΎ ΡΠ½Π΅ΡΠ³ΠΎΠ²Π»ΠΎΠΆΠ΅Π½ΠΈΡ, Π½Π΅ΠΎΠ±Ρ ΠΎΠ΄ΠΈΠΌΠΎΠΌΡ Π΄Π»Ρ Π΄ΠΎΡΡΠΈΠΆΠ΅Π½ΠΈΡ ΡΠΊΠ²ΠΎΠ·Π½ΠΎΠ³ΠΎ ΠΏΡΠΎΠ²Π°ΡΠ° Π½Π° Π½Π°ΡΠ°Π»ΡΠ½ΠΎΠΌ ΡΡΠ°ΡΡΠΊΠ΅ ΡΠ²Π°ΡΠΊΠΈ — ΡΡΠ°ΡΡΠΊΠ΅ ΠΈΠ΄Π΅Π½ΡΠΈΡΠΈΠΊΠ°ΡΠΈΠΈ. ΠΠ° ΠΎΡΠ½ΠΎΠ²Π°Π½ΠΈΠΈ ΡΡΠΎΠΉ ΠΈΠ½ΡΠΎΡΠΌΠ°ΡΠΈΠΈ ΡΠΏΡΠ°Π²Π»ΡΡΡΠ°Ρ ΠΌΠΈΠΊΡΠΎΠΠΠ Π²ΡΡΠΈΡΠ»ΡΠ΅Ρ ΠΈΠ·ΠΌΠ΅Π½Π΅Π½ΠΈΠ΅ ΠΏΠ°ΡΠ°ΠΌΠ΅ΡΡΠΎΠ² ΡΠ²Π°ΡΠΎΡΠ½ΠΎΠ³ΠΎ ΡΠ΅ΠΆΠΈΠΌΠ° Π΄Π»Ρ ΠΎΡΠ½ΠΎΠ²Π½ΠΎΠΉ ΡΠ°ΡΡΠΈ ΡΡΡΠΊΠ° ΠΈ ΠΎΠ±Π΅ΡΠΏΠ΅ΡΠΈΠ²Π°Π΅Ρ Π²Π²ΠΎΠ΄ ΡΡΡΠ°Π²ΠΎΠΊ Π² Π·Π°Π΄Π°ΡΡΠΈΠ΅ ΡΡΡΡΠΎΠΉΡΡΠ²Π° ΡΠ΅Π³ΡΠ»ΡΡΠΎΡΠΎΠ² ΠΏΠ°ΡΠ°ΠΌΠ΅ΡΡΠΎΠ² ΡΠ²Π°ΡΠΎΡΠ½ΠΎΠ³ΠΎ ΡΠ΅ΠΆΠΈΠΌΠ°.
Π‘ ΡΠΎΡΠΊΠΈ Π·ΡΠ΅Π½ΠΈΡ Π°ΠΏΠΏΠ°ΡΠ°ΡΡΡΡ ΠΈ ΡΠΈΡΡΠ΅ΠΌ ΡΠΏΡΠ°Π²Π»Π΅Π½ΠΈΡ ΡΠ»Π΅ΠΊΡΡΠΎΡΠ²Π°ΡΠΎΡΠ½ΠΎΠ΅ ΠΎΠ±ΠΎΡΡΠ΄ΠΎΠ²Π°Π½ΠΈΠ΅ ΡΠ»Π΅Π΄ΡΠ΅Ρ ΡΠ°Π·Π΄Π΅Π»ΠΈΡΡ Π½Π° ΡΠ»Π΅Π΄ΡΡΡΠΈΠ΅ Π²ΠΈΠ΄Ρ; ΠΎΠ±ΠΎΡΡΠ΄ΠΎΠ²Π°Π½ΠΈΠ΅ ΠΎΠ±ΡΠ΅Π³ΠΎ ΠΏΡΠΈΠΌΠ΅Π½Π΅Π½ΠΈΡ, ΡΠΏΠ΅ΡΠΈΠ°Π»ΡΠ½ΡΠ΅ ΠΌΠ°ΡΠΈΠ½Ρ ΠΈ ΡΡΡΠ°Π½ΠΎΠ²ΠΊΠΈ, ΡΠ±ΠΎΡΠΎΡΠ½ΠΎ-ΡΠ²Π°ΡΠΎΡΠ½ΡΠ΅ Π»ΠΈΠ½ΠΈΠΈ, ΡΠ²Π°ΡΠΎΡΠ½ΡΠ΅ ΡΠ°Π±ΠΎΡΡ. Π‘ΡΡΠ΅ΡΡΠ²ΡΠ΅Ρ ΠΌΠ½ΠΎΠΆΠ΅ΡΡΠ²ΠΎ ΡΠΈΠΏΠΎΠ² Π°ΡΡ ΠΈΡΠ΅ΠΊΡΡΡΡ Π°ΠΏΠΏΠ°ΡΠ°ΡΠ½ΡΡ ΡΡΠ΅Π΄ΡΡΠ², Π½Π° ΠΎΡΠ½ΠΎΠ²Π΅ ΠΊΠΎΡΠΎΡΡΡ ΠΌΠΎΠΆΠ½ΠΎ ΡΠ΅Π°Π»ΠΈΠ·ΠΎΠ²Π°ΡΡ ΡΠ°Π·Π»ΠΈΡΠ½ΡΠ΅ Π²Π°ΡΠΈΠ°Π½ΡΡ ΡΡΡΠ°ΡΠ΅Π³ΠΈΠΈ ΡΠΏΡΠ°Π²Π»Π΅Π½ΠΈΡ ΡΠ²Π°ΡΠΎΡΠ½ΡΠΌΠΈ ΠΏΡΠΎΡΠ΅ΡΡΠ°ΠΌΠΈ ΠΈ ΠΎΠ±ΠΎΡΡΠ΄ΠΎΠ²Π°Π½ΠΈΠ΅ΠΌ β ΠΊΠΎΠ½ΡΡΠΎΠ»Π»Π΅ΡΡ Π°Π²ΡΠΎΠ½ΠΎΠΌΠ½ΡΠ΅ (ΠΎΠ±ΠΎΡΡΠ΄ΠΎΠ²Π°Π½ΠΈΠ΅ ΠΎΠ±ΡΠ΅Π³ΠΎ ΠΏΡΠΈΠΌΠ΅Π½Π΅Π½ΠΈΡ β Π°Π²ΡΠΎΠΌΠ°ΡΡ ΠΈ ΠΏΠΎΠ»ΡΠ°Π²ΡΠΎΠΌΠ°ΡΡ Π΄Π»Ρ Π΄ΡΠ³ΠΎΠ²ΠΎΠΉ ΡΠ²Π°ΡΠΊΠΈ, ΠΌΠ°ΡΠΈΠ½Ρ ΠΊΠΎΠ½ΡΠ°ΠΊΡΠ½ΠΎΠΉ ΡΠ²Π°ΡΠΊΠΈ ΠΈ Π΄Ρ.), Π»ΠΈΠ½Π΅ΠΉΠ½ΡΠ΅ ΠΈ ΡΠΈΡΡΠ΅ΠΌΠ½ΡΠ΅ (ΡΠΈΡΡΠ΅ΠΌΡ ΡΠΏΡΠ°Π²Π»Π΅Π½ΠΈΡ Ρ ΡΠ°ΡΠΏΡΠ΅Π΄Π΅Π»Π΅Π½Π½ΠΎΠΉ Π²ΡΡΠΈΡΠ»ΠΈΡΠ΅Π»ΡΠ½ΠΎΠΉ ΠΌΠΎΡΠ½ΠΎΡΡΡΡ ΠΈ ΡΠ°ΡΠΏΡΠ΅Π΄Π΅Π»Π΅Π½Π½ΠΎΠΉ ΠΊΠΎΠ½ΡΡΡΡΠΊΡΠΈΠ΅ΠΉ Π² ΠΊΠ°ΡΠ΅ΡΡΠ²Π΅ Π»ΠΎΠΊΠ°Π»ΡΠ½ΠΎΠ³ΠΎ ΡΠ΅Π³ΡΠ»ΡΡΠΎΡΠ°; ΡΠΈΡΡΠ΅ΠΌΡ ΡΠΏΡΠ°Π²Π»Π΅Π½ΠΈΡ ΡΡΡΠ°Π½ΠΎΠ²ΠΊΠ°ΠΌΠΈ, Π»ΠΈΠ½ΠΈΡΠΌΠΈ, ΡΠΎΠ±ΠΎΡΠ°ΠΌΠΈ).
ΠΠ°ΡΠΎΠ½ Π.Π. «ΠΠ°ΡΠΈΠ½ΠΎΡΡΡΠΎΠ΅Π½ΠΈΠ΅ ΠΠ½ΡΠΈΠΊΠ»ΠΎΠΏΠ΅Π΄ΠΈΡ Ρ.IV-6. ΠΠ±ΠΎΡΡΠ΄ΠΎΠ²Π°Π½ΠΈΠ΅ Π΄Π»Ρ ΡΠ²Π°ΡΠΊΠΈ»
ΠΠ²ΡΠΎΠΌΠ°ΡΠΈΠ·Π°ΡΠΈΡ
Π£Π»ΡΡΡΠΈΡΡ ΠΊΠ°ΡΠ΅ΡΡΠ²ΠΎ ΡΠ²Π°ΡΠ½ΡΡ ΡΠΎΠ΅Π΄ΠΈΠ½Π΅Π½ΠΈΠΉ ΠΈ ΡΠ΅Ρ Π½ΠΈΠΊΠΎ-ΡΠΊΠΎΠ½ΠΎΠΌΠΈΡΠ΅ΡΠΊΠΈΠ΅ ΠΏΠΎΠΊΠ°Π·Π°ΡΠ΅Π»ΠΈ ΡΠ°ΠΌΠΎΠ³ΠΎ ΠΏΡΠΎΠΈΠ·Π²ΠΎΠ΄ΡΡΠ²Π°, ΠΏΠΎΠ²ΡΡΠΈΡΡ ΠΏΡΠΎΠΈΠ·Π²ΠΎΠ΄ΠΈΡΠ΅Π»ΡΠ½ΠΎΡΡΡ ΠΈ ΡΠΌΠ΅Π½ΡΡΠΈΡΡ ΡΡΠΎΠΈΠΌΠΎΡΡΡ ΠΏΡΠΎΠΈΠ·Π²ΠΎΠ΄ΡΡΠ²Π° ΠΏΠΎΠ·Π²ΠΎΠ»ΡΠ΅Ρ Π°Π²ΡΠΎΠΌΠ°ΡΠΈΠ·Π°ΡΠΈΡ ΡΠ²Π°ΡΠΎΡΠ½ΠΎΠ³ΠΎ ΠΏΡΠΎΡΠ΅ΡΡΠ°.
Π ΡΠ΅Π·ΡΠ»ΡΡΠ°ΡΠ΅ Π°Π²ΡΠΎΠΌΠ°ΡΠΈΠ·Π°ΡΠΈΠΈ ΠΌΠΈΠ½ΠΈΠΌΠΈΠ·ΠΈΡΡΠ΅ΡΡΡ ΡΠ΅Π»ΠΎΠ²Π΅ΡΠ΅ΡΠΊΠΈΠΉ ΡΠ°ΠΊΡΠΎΡ, ΡΠΎΠΊΡΠ°ΡΠ°Π΅ΡΡΡ ΠΊΠΎΠ»ΠΈΡΠ΅ΡΡΠ²ΠΎ Π±ΡΠ°ΠΊΠΎΠ²Π°Π½Π½ΡΡ ΠΈΠ·Π΄Π΅Π»ΠΈΠΉ, Π·Π½Π°ΡΠΈΡΠ΅Π»ΡΠ½ΠΎ ΡΠ²Π΅Π»ΠΈΡΠΈΠ²Π°Π΅ΡΡΡ ΡΠΊΠΎΡΠΎΡΡΡ ΠΈΠ·Π³ΠΎΡΠΎΠ²Π»Π΅Π½ΠΈΡ ΠΏΡΠΎΠ΄ΡΠΊΡΠΈΠΈ. Π‘ΠΎΠΊΡΠ°ΡΠ°ΡΡΡΡ ΡΡΡΠ΄ΠΎΠ·Π°ΡΡΠ°ΡΡ ΠΊΠ²Π°Π»ΠΈΡΠΈΡΠΈΡΠΎΠ²Π°Π½Π½ΡΡ ΡΠΎΡΡΡΠ΄Π½ΠΈΠΊΠΎΠ², Ρ.ΠΊ. Π±ΠΎΠ»ΡΡΡΡ ΡΠ°ΡΡΡ ΡΠ°Π±ΠΎΡΡ Π²ΡΠΏΠΎΠ»Π½ΡΡΡ ΡΡΡΡΠΎΠΉΡΡΠ²Π°, ΡΠ΅ΡΠΊΠΎΡΡΡ ΡΠ°Π±ΠΎΡΡ ΠΊΠΎΡΠΎΡΡΡ Π·Π°Π²ΠΈΡΠΈΡ ΠΎΡ ΠΏΡΠ°Π²ΠΈΠ»ΡΠ½ΠΎΡΡΠΈ ΠΈΡ Π½Π°Π»Π°Π΄ΠΊΠΈ. Π‘ ΡΡΠΎΠΉ ΡΠΎΡΠΊΠΈ Π·ΡΠ΅Π½ΠΈΡ ΡΡΠ΅Π±ΡΠ΅ΡΡΡ Π²ΡΡΠΎΠΊΠ°Ρ ΠΊΠ²Π°Π»ΠΈΡΠΈΠΊΠ°ΡΠΈΡ ΠΎΠΏΠ΅ΡΠ°ΡΠΎΡΠ°, ΠΊΠΎΡΠΎΡΡΠΉ Π½Π°ΡΡΡΠ°ΠΈΠ²Π°Π΅Ρ ΠΎΡΠ½ΠΎΠ²Π½ΡΠ΅ ΠΏΠ°ΡΠ°ΠΌΠ΅ΡΡΡ ΡΠ²Π°ΡΠΊΠΈ ΠΈ ΠΊΠΎΠ½ΡΡΠΎΠ»ΠΈΡΡΠ΅Ρ ΡΠ°ΠΌ ΠΏΡΠΎΡΠ΅ΡΡ.
Π‘ ΠΏΠΎΠΌΠΎΡΡΡ Π°Π²ΡΠΎΠΌΠ°ΡΠΈΠΊΠΈ ΠΌΠΎΠΆΠ½ΠΎ ΠΎΠ±Π΅ΡΠΏΠ΅ΡΠΈΠ²Π°ΡΡ ΠΏΠΎΠ΄Π°ΡΡ ΡΠ»Π΅ΠΊΡΡΠΎΠ΄Π° ΠΏΠΎ ΠΌΠ΅ΡΠ΅ Π΅Π³ΠΎ ΠΏΠ»Π°Π²Π»Π΅Π½ΠΈΡ Π² Π΄ΡΠ³Ρ, ΠΏΠ΅ΡΠ΅ΠΌΠ΅ΡΠ΅Π½ΠΈΠ΅ Π΄ΡΠ³ΠΈ Π²Π΄ΠΎΠ»Ρ ΡΠ²Π°, ΠΊΠΎΠ½ΡΡΠΎΠ»Ρ ΠΎΠΏΡΠΈΠΌΠ°Π»ΡΠ½ΡΡ ΠΏΠ°ΡΠ°ΠΌΠ΅ΡΡΠΎΠ² ΡΠ°Π±ΠΎΡΡ ΠΈ ΠΏΡ.
ΠΡΠ½ΠΎΠ²Π½ΡΠΌΠΈ ΠΌΠ΅Ρ Π°Π½ΠΈΠ·ΠΌΠ°ΠΌΠΈ, ΠΊΠΎΡΠΎΡΡΠ΅ Π²Ρ ΠΎΠ΄ΡΡ Π² ΡΠΎΡΡΠ°Π² ΡΡΡΠ°Π½ΠΎΠ²ΠΊΠΈ Π΄Π»Ρ Π²ΡΠΏΠΎΠ»Π½Π΅Π½ΠΈΡ Π°Π²ΡΠΎΠΌΠ°ΡΠΈΠ·ΠΈΡΠΎΠ²Π°Π½Π½ΠΎΠΉ ΡΠ²Π°ΡΠΊΠΈ, ΡΠ²Π»ΡΡΡΡΡ:
- Π‘Π²Π°ΡΠΎΡΠ½ΡΠ΅ Π³ΠΎΠ»ΠΎΠ²ΠΊΠΈ β ΡΡΡΡΠΎΠΉΡΡΠ²Π°, ΠΏΠΎΠ΄Π΄Π΅ΡΠΆΠΈΠ²Π°ΡΡΠΈΠ΅ ΠΎΠΏΡΠΈΠΌΠ°Π»ΡΠ½ΡΡ ΡΠ°Π±ΠΎΡΡ Π΄ΡΠ³ΠΈ ΠΈ Π²ΡΠΏΠΎΠ»Π½ΡΡΡΠΈΠ΅ ΠΏΠΎΠ΄Π°ΡΡ ΠΏΡΠΎΠ²ΠΎΠ»ΠΎΠΊΠΈ Π² ΠΏΡΠΎΡΠ΅ΡΡΠ΅ ΡΠ°Π±ΠΎΡΡ.
- Π‘Π²Π°ΡΠΎΡΠ½ΡΠ΅ ΡΡΠ°ΠΊΡΠΎΡΡ ΠΈ ΠΊΠ°ΡΠ΅ΡΠΊΠΈ — ΡΠ°ΠΌΠΎΡ ΠΎΠ΄Π½ΡΠ΅ Π°Π²ΡΠΎΠΌΠ°ΡΡ Π΄Π»Ρ ΡΠ²Π°ΡΠΊΠΈ, ΠΊΠΎΡΠΎΡΡΠ΅ Π΄Π²ΠΈΠ³Π°ΡΡΡΡ ΠΏΠΎ Π²Π΅ΠΊΡΠΎΡΡ ΡΠ²Π°ΡΠΈΠ²Π°Π΅ΠΌΡΡ ΠΊΡΠΎΠΌΠΎΠΊ ΠΏΠΎ ΠΏΠΎΠ²Π΅ΡΡ Π½ΠΎΡΡΠΈ ΠΈΠ·Π΄Π΅Π»ΠΈΡ Π»ΠΈΠ±ΠΎ ΡΠ΅Π»ΡΡΠΎΠ²ΠΎΠΌΡ ΠΏΡΡΠΈ.
- Π‘Π²Π°ΡΠΎΡΠ½ΡΠ΅ ΠΏΠΎΠ·ΠΈΡΠΈΠΎΠ½Π΅ΡΡ ΠΈ ΡΠΎΠ»ΠΈΠΊΠΎΠ²ΡΠ΅ Π²ΡΠ°ΡΠ°ΡΠ΅Π»ΠΈ β ΡΡΡΡΠΎΠΉΡΡΠ²Π°, ΠΏΠΎΠ·Π²ΠΎΠ»ΡΡΡΠΈΠ΅ ΡΠ²Π°ΡΡΠΈΠΊΡ Π·Π°ΡΠΈΠΊΡΠΈΡΠΎΠ²Π°ΡΡ Π΄Π΅ΡΠ°Π»ΠΈ Π² Π½ΡΠΆΠ½ΠΎΠΌ Π΅ΠΌΡ ΠΏΠΎΠ»ΠΎΠΆΠ΅Π½ΠΈΠΈ.
- Π‘Π²Π°ΡΠΎΡΠ½ΡΠ΅ ΠΊΠΎΠ»ΠΎΠ½Π½Ρ β ΡΡΡΡΠΎΠΉΡΡΠ²Π°, ΠΏΡΠΈΠΌΠ΅Π½ΡΠ΅ΠΌΡΠ΅ Π΄Π»Ρ ΡΠ²Π°ΡΠΊΠΈ ΠΏΡΠΎΠ΄ΠΎΠ»ΡΠ½ΠΎΠ³ΠΎ, ΠΊΠΎΠ»ΡΡΠ΅Π²ΠΎΠ³ΠΎ ΡΠ²ΠΎΠ², ΠΊΠ°ΠΊ Π²Π½ΡΡΡΠΈ, ΡΠ°ΠΊ ΠΈ ΡΠ½Π°ΡΡΠΆΠΈ ΠΈΠ·Π΄Π΅Π»ΠΈΠΉ.
- ΠΠ±ΠΎΡΡΠ΄ΠΎΠ²Π°Π½ΠΈΠ΅ Π΄Π»Ρ ΠΎΡΠ±ΠΈΡΠ°Π»ΡΠ½ΠΎΠΉ ΡΠ²Π°ΡΠΊΠΈ, ΠΏΡΠΈ ΠΊΠΎΡΠΎΡΠΎΠΉ Π΄ΡΠ³Π° ΠΏΠΎΠ²ΠΎΡΠ°ΡΠΈΠ²Π°Π΅ΡΡΡ Π²ΠΎΠΊΡΡΠ³ ΡΡΠ°ΡΠΈΡΠ΅ΡΠΊΠΎΠΉ Π·Π°Π³ΠΎΡΠΎΠ²ΠΊΠΈ.
ΠΠΎΠΌΠΏΠΎΠ½Π΅Π½ΡΡ Π°Π²ΡΠΎΠΌΠ°ΡΠΈΠ·Π°ΡΠΈΠΈ ΡΠ²Π°ΡΠΎΡΠ½ΠΎΠ³ΠΎ ΠΏΡΠΎΡΠ΅ΡΡΠ° Π»Π΅Π³ΠΊΠΎ Π²ΠΆΠΈΠ²Π»ΡΡΡΡΡ Π² ΡΠΆΠ΅ ΡΡΡΠ΅ΡΡΠ²ΡΡΡΠΈΠ΅ Π½Π° ΠΏΡΠΎΠΈΠ·Π²ΠΎΠ΄ΡΡΠ²Π΅ ΡΠ΅Ρ Π½ΠΎΠ»ΠΎΠ³ΠΈΡΠ΅ΡΠΊΠΈΠ΅ ΡΠ΅ΠΏΠΎΡΠΊΠΈ ΠΈ ΠΏΠΎΠ·Π²ΠΎΠ»ΡΡΡ Π·Π½Π°ΡΠΈΡΠ΅Π»ΡΠ½ΠΎ ΡΠ°ΡΡΠΈΡΠΈΡΡ ΡΠΏΠ΅ΠΊΡΡ Π²ΡΠΏΠΎΠ»Π½ΡΠ΅ΠΌΡΡ ΡΠ°Π±ΠΎΡ. ΠΠ½Π΅Π΄ΡΠ΅Π½ΠΈΠ΅ ΡΠ°ΠΊΠΈΡ ΡΠ»Π΅ΠΌΠ΅Π½ΡΠΎΠ² Π² ΠΌΠ°ΡΡΠΎΠ²ΠΎΠ΅ ΠΈ ΠΊΡΡΠΏΠ½ΠΎΡΠ΅ΡΠΈΠΉΠ½ΠΎΠ΅ ΠΏΡΠΎΠΈΠ·Π²ΠΎΠ΄ΡΡΠ²ΠΎ Π·Π½Π°ΡΠΈΡΠ΅Π»ΡΠ½ΠΎ ΠΏΠΎΠ²ΡΡΠ°Π΅Ρ ΡΡΡΠ΅ΠΊΡΠΈΠ²Π½ΠΎΡΡΡ ΡΠ°Π±ΠΎΡΡ ΠΏΡΠ΅Π΄ΠΏΡΠΈΡΡΠΈΡ ΠΏΡΠΈ ΠΎΡΠ½ΠΎΡΠΈΡΠ΅Π»ΡΠ½ΠΎ Π½Π΅Π±ΠΎΠ»ΡΡΠΈΡ Π²Π»ΠΎΠΆΠ΅Π½ΠΈΡΡ .
ΠΠ²ΡΠΎΠΌΠ°ΡΠΈΠ·Π°ΡΠΈΡ ΡΠ²Π°ΡΠΎΡΠ½ΡΡ ΠΏΡΠΎΡΠ΅ΡΡΠΎΠ² Π² Π³. ΠΠΊΠ°ΡΠ΅ΡΠΈΠ½Π±ΡΡΠ³
ΠΠΠ «ΠΠ΅Π»Π΄ΠΏΡΠΎΠΌ» ΡΠ°ΡΠΏΠΎΠ»Π°Π³Π°Π΅Ρ ΡΠΈΡΠΎΠΊΠΈΠΌ Π°ΡΡΠΎΡΡΠΈΠΌΠ΅Π½ΡΠΎΠΌ ΠΎΠ±ΠΎΡΡΠ΄ΠΎΠ²Π°Π½ΠΈΡ Π΄Π»Ρ Π°Π²ΡΠΎΠΌΠ°ΡΠΈΠ·Π°ΡΠΈΠΈ ΠΏΡΠΎΡΠ΅ΡΡΠ° ΡΠ²Π°ΡΠΊΠΈ. ΠΡ Π½Π΅ ΡΠΎΠ»ΡΠΊΠΎ ΡΠ΅Π°Π»ΠΈΠ·ΡΠ΅ΠΌ Π²ΡΡΠΎΠΊΠΎΠΊΠ°ΡΠ΅ΡΡΠ²Π΅Π½Π½ΡΡ ΡΠ΅Ρ Π½ΠΈΠΊΡ ΠΎΡΠ΅ΡΠ΅ΡΡΠ²Π΅Π½Π½ΠΎΠ³ΠΎ ΠΈ ΠΈΠΌΠΏΠΎΡΡΠ½ΠΎΠ³ΠΎ ΠΏΡΠΎΠΈΠ·Π²ΠΎΠ΄ΡΡΠ²Π°, Π½ΠΎ ΠΈ ΠΎΡΡΡΠ΅ΡΡΠ²Π»ΡΠ΅ΠΌ ΠΏΡΡΠΊΠΎ-Π½Π°Π»Π°Π΄ΠΊΡ ΠΈ ΠΎΠ±ΡΠ»ΡΠΆΠΈΠ²Π°Π½ΠΈΠ΅ ΠΎΠ±ΠΎΡΡΠ΄ΠΎΠ²Π°Π½ΠΈΡ. ΠΠ° ΠΏΠΎΠ΄ΡΠΎΠ±Π½ΠΎΠΉ ΠΈΠ½ΡΠΎΡΠΌΠ°ΡΠΈΠ΅ΠΉ ΠΏΠΎ ΠΏΡΠ΅Π΄ΡΡΠ°Π²Π»Π΅Π½Π½ΠΎΠΌΡ Π² ΠΊΠ°ΡΠ°Π»ΠΎΠ³Π΅ ΠΎΠ±ΠΎΡΡΠ΄ΠΎΠ²Π°Π½ΠΈΡ ΠΈ ΡΡΠ»ΠΎΠ²ΠΈΡΠΌ ΡΠΎΡΡΡΠ΄Π½ΠΈΡΠ΅ΡΡΠ²Π° ΠΎΠ±ΡΠ°ΡΠ°ΠΉΡΠ΅ΡΡ ΠΏΠΎ ΡΠ΅Π»Π΅ΡΠΎΠ½Ρ, ΡΠΊΠ°Π·Π°Π½Π½ΠΎΠΌΡ Π² ΡΠ°ΠΏΠΊΠ΅ ΡΠ°ΠΉΡΠ°.
ΠΠ΅Ρ Π°Π½ΠΈΠ·Π°ΡΠΈΡ ΠΈ Π°Π²ΡΠΎΠΌΠ°ΡΠΈΠ·Π°ΡΠΈΡ ΡΠΎΡΠ΅ΡΠ½ΠΎΠΉ ΠΈ ΡΠΎΠ²Π½ΠΎΠΉ ΡΠ²Π°ΡΠΊΠΈ
Π Π΅ΠΊΠΎΠΌΠ΅Π½Π΄ΡΠ΅ΠΌ ΠΏΡΠΈΠΎΠ±ΡΠ΅ΡΡΠΈ:
Π£ΡΡΠ°Π½ΠΎΠ²ΠΊΠΈ Π΄Π»Ρ Π°Π²ΡΠΎΠΌΠ°ΡΠΈΡΠ΅ΡΠΊΠΎΠΉ ΡΠ²Π°ΡΠΊΠΈ ΠΏΡΠΎΠ΄ΠΎΠ»ΡΠ½ΡΡ
ΡΠ²ΠΎΠ² ΠΎΠ±Π΅ΡΠ°Π΅ΠΊ — Π² Π½Π°Π»ΠΈΡΠΈΠΈ Π½Π° ΡΠΊΠ»Π°Π΄Π΅!
ΠΡΡΠΎΠΊΠ°Ρ ΠΏΡΠΎΠΈΠ·Π²ΠΎΠ΄ΠΈΡΠ΅Π»ΡΠ½ΠΎΡΡΡ, ΡΠ΄ΠΎΠ±ΡΡΠ²ΠΎ, ΠΏΡΠΎΡΡΠΎΡΠ° Π² ΡΠΏΡΠ°Π²Π»Π΅Π½ΠΈΠΈ ΠΈ Π½Π°Π΄Π΅ΠΆΠ½ΠΎΡΡΡ Π² ΡΠΊΡΠΏΠ»ΡΠ°ΡΠ°ΡΠΈΠΈ.
Π‘Π²Π°ΡΠΎΡΠ½ΡΠ΅ ΡΠΊΡΠ°Π½Ρ ΠΈ Π·Π°ΡΠΈΡΠ½ΡΠ΅ ΡΡΠΎΡΠΊΠΈ — Π² Π½Π°Π»ΠΈΡΠΈΠΈ Π½Π° ΡΠΊΠ»Π°Π΄Π΅!
ΠΠ°ΡΠΈΡΠ° ΠΎΡ ΠΈΠ·Π»ΡΡΠ΅Π½ΠΈΡ ΠΏΡΠΈ ΡΠ²Π°ΡΠΊΠ΅ ΠΈ ΡΠ΅Π·ΠΊΠ΅. ΠΠΎΠ»ΡΡΠΎΠΉ Π²ΡΠ±ΠΎΡ.
ΠΠΎΡΡΠ°Π²ΠΊΠ° ΠΏΠΎ Π²ΡΠ΅ΠΉ Π ΠΎΡΡΠΈΠΈ!
Π‘Π²Π°ΡΠΎΡΠ½ΡΠ΅ ΠΌΠ°ΡΠΈΠ½Ρ Π΄Π»Ρ ΡΠΎΡΠ΅ΡΠ½ΠΎΠΉ ΠΈ ΡΠΎΠ²Π½ΠΎΠΉ ΡΠ²Π°ΡΠΊΠΈ ΠΎΠ±Π΅ΡΠΏΠ΅ΡΠΈΠ²Π°ΡΡ ΠΏΠΎΡΡΠΈ ΠΏΠΎΠ»Π½ΡΡ Π°Π²ΡΠΎΠΌΠ°ΡΠΈΠ·Π°ΡΠΈΡ ΠΏΡΠΎΡΠ΅ΡΡΠ°. ΠΠ»Ρ ΡΠΎΠΊΡΠ°ΡΠ΅Π½ΠΈΡ ΠΆΠ΅ Π΄Π»ΠΈΡΠ΅Π»ΡΠ½ΠΎΡΡΠΈ Π²ΡΠΏΠΎΠΌΠΎΠ³Π°ΡΠ΅Π»ΡΠ½ΡΡ ΠΎΠΏΠ΅ΡΠ°ΡΠΈΠΉ ΠΈ ΠΏΠΎΠ²ΡΡΠ΅Π½ΠΈΡ ΠΏΡΠΎΠΈΠ·Π²ΠΎΠ΄ΠΈΡΠ΅Π»ΡΠ½ΠΎΡΡΠΈ Π²ΡΠ΅Π³ΠΎ ΡΠ΅Ρ Π½ΠΎΠ»ΠΎΠ³ΠΈΡΠ΅ΡΠΊΠΎΠ³ΠΎ ΠΏΡΠΎΡΠ΅ΡΡΠ° ΡΠΈΡΠΎΠΊΠΎ ΠΏΡΠΈΠΌΠ΅Π½ΡΡΡ ΡΠ°Π·Π½ΡΠ΅ ΠΌΠ΅Ρ Π°Π½ΠΈΠ·ΠΈΡΠΎΠ²Π°Π½Π½ΡΠ΅ ΠΏΡΠΈΡΠΏΠΎΡΠΎΠ±Π»Π΅Π½ΠΈΡ, ΠΌΠ°ΡΠΈΠ½Ρ-Π°Π²ΡΠΎΠΌΠ°ΡΡ, Π°Π²ΡΠΎΠΌΠ°ΡΠΈΡΠ΅ΡΠΊΠΈΠ΅ Π»ΠΈΠ½ΠΈΠΈ ΠΈ ΠΏΡΠΎΠΌΡΡΠ»Π΅Π½Π½ΡΠ΅ ΡΠΎΠ±ΠΎΡΡ.
Π‘Π±ΠΎΡΠΎΡΠ½ΠΎ-ΡΠ²Π°ΡΠΎΡΠ½ΡΠ΅ ΠΏΡΠΈΡΠΏΠΎΡΠΎΠ±Π»Π΅Π½ΠΈΡ β ΡΡΠΎ ΡΠ°Π±Π»ΠΎΠ½Ρ, ΠΊΠΎΠ½Π΄ΡΠΊΡΠΎΡΡ, ΡΡΠ°ΠΏΠ΅Π»ΠΈ, ΡΠ±ΠΎΡΠΎΡΠ½ΡΠ΅ ΡΡΠ΅Π½Π΄Ρ, Π½Π° ΠΊΠΎΡΠΎΡΡΡ ΠΎΡΡΡΠ΅ΡΡΠ²Π»ΡΡΡ ΡΠ±ΠΎΡΠΊΡ, ΠΏΡΠΈΡ Π²Π°ΡΠΊΡ ΠΈ ΡΠ²Π°ΡΠΊΡ ΡΠ·Π»ΠΎΠ². Π¨ΠΈΡΠΎΠΊΠΎ ΠΈΡΠΏΠΎΠ»ΡΠ·ΡΡΡΡΡ ΡΠ°ΠΊΠΆΠ΅ ΠΏΠΎΠ΄Π΄Π΅ΡΠΆΠΈΠ²Π°ΡΡΠΈΠ΅ (Π²ΡΡΠ°Π²Π½ΠΈΠ²Π°ΡΡΠΈΠ΅) ΠΏΡΠΈΡΠΏΠΎΡΠΎΠ±Π»Π΅Π½ΠΈΡ, ΠΏΠΎΠ·Π²ΠΎΠ»ΡΡΡΠΈΠ΅ ΠΎΡΠΈΠ΅Π½ΡΠΈΡΠΎΠ²Π°ΡΡ ΡΠ·Π΅Π» ΠΎΡΠ½ΠΎΡΠΈΡΠ΅Π»ΡΠ½ΠΎ ΡΠ»Π΅ΠΊΡΡΠΎΠ΄ΠΎΠ² ΠΈΠ»ΠΈ ΡΠΎΠ»ΠΈΠΊΠΎΠ² ΡΠ²Π°ΡΠΎΡΠ½ΠΎΠΉ ΠΌΠ°ΡΠΈΠ½Ρ (ΡΠΈΡ. 20.20). ΠΠ΅ΡΠ΅ΠΌΠ΅ΡΠ°ΡΡΡΡ ΡΠ·Π»Ρ Π»ΠΈΠ±ΠΎ Π²ΡΡΡΠ½ΡΡ β ΡΠΎΠ»ΠΈΠΊΠ°ΠΌΠΈ ΠΌΠ°ΡΠΈΠ½Ρ, Π»ΠΈΠ±ΠΎ ΡΠΏΠ΅ΡΠΈΠ°Π»ΡΠ½ΡΠΌΠΈ ΠΌΠ΅Ρ Π°Π½ΠΈΠ·ΠΌΠ°ΠΌΠΈ, Π½Π°ΠΏΡΠΈΠΌΠ΅Ρ ΡΠ°Π³ΠΎΠ²ΡΠΌΠΈ Π΄Π²ΠΈΠ³Π°ΡΠ΅Π»ΡΠΌΠΈ (ΡΠ»Π΅ΠΊΡΡΠΎΠΌΠ°Π³Π½ΠΈΡΠ½ΡΠΌΠΈ ΠΌΡΡΡΠ°ΠΌΠΈ), ΠΏΠΎ Π·Π°Π΄Π°Π½Π½ΡΠΌ ΡΠΈΡΡΠ΅ΠΌΠΎΠΉ ΡΠΏΡΠ°Π²Π»Π΅Π½ΠΈΡ ΠΊΠΎΠΌΠ°Π½Π΄Π°ΠΌ.
ΠΠ°ΡΠΈΠ½Ρ-Π°Π²ΡΠΎΠΌΠ°ΡΡ Π΄ΠΎΠ²ΠΎΠ»ΡΠ½ΠΎ ΡΠΈΡΠΎΠΊΠΎ ΠΏΡΠΈΠΌΠ΅Π½ΡΡΡΡΡ ΠΏΡΠΈ ΠΈΠ·Π³ΠΎΡΠΎΠ²Π»Π΅Π½ΠΈΠΈ Π°ΡΠΌΠ°ΡΡΡΠ½ΡΡ ΡΠ΅ΡΠΎΠΊ, ΡΠΎΠΏΠ»ΠΈΠ²Π½ΡΡ Π±Π°ΠΊΠΎΠ² Π°Π²ΡΠΎΠΌΠΎΠ±ΠΈΠ»Π΅ΠΉ, ΠΊΠΎΡΠΏΡΡΠΎΠ² Ρ ΠΎΠ»ΠΎΠ΄ΠΈΠ»ΡΠ½ΠΈΠΊΠΎΠ², ΡΠ°Π΄ΠΈΠΎΡΠ»Π΅ΠΊΡΡΠΎΠ½Π½ΠΎΠΉ Π°ΠΏΠΏΠ°ΡΠ°ΡΡΡΡ ΠΈ Ρ.Π΄. ΠΡΠΈ ΡΡΠΎΠΌ ΠΈΡΠΏΠΎΠ»ΡΠ·ΡΡΡΡΡ ΠΏΠΈΡΠ°ΡΠ΅Π»ΠΈ, Π²ΡΠ°ΡΠ°ΡΡΠΈΠ΅ΡΡ ΡΡΠΎΠ»Ρ, ΠΊΠΎΠ½Π²Π΅ΠΉΠ΅ΡΡ Π΄Π»Ρ ΠΏΠΎΠ΄Π°ΡΠΈ Π΄Π΅ΡΠ°Π»Π΅ΠΉ Π² Π·ΠΎΠ½Ρ ΡΠ²Π°ΡΠΊΠΈ, ΠΎΠ±Π΅ΡΠΏΠ΅ΡΠΈΠ²Π°ΡΡΠΈΠ΅ ΠΏΡΠΎΠΈΠ·Π²ΠΎΠ΄ΠΈΡΠ΅Π»ΡΠ½ΠΎΡΡΡ Π΄ΠΎ 200β300 ΡΠΎΠ΅Π΄ΠΈΠ½Π΅Π½ΠΈΠΉ Π² ΠΌΠΈΠ½ΡΡΡ.
ΠΠ²ΡΠΎΠΌΠ°ΡΠΈΡΠ΅ΡΠΊΠΈΠ΅ Π»ΠΈΠ½ΠΈΠΈ Π·Π°Π΄Π΅ΠΉΡΡΠ²ΡΡΡΡΡ ΠΏΡΠΈ ΠΌΠ°ΡΡΠΎΠ²ΠΎΠΌ ΠΏΡΠΎΠΈΠ·Π²ΠΎΠ΄ΡΡΠ²Π΅ Π°Π²ΡΠΎΠΌΠΎΠ±ΠΈΠ»Π΅ΠΉ, ΡΠ΅Π»ΡΡΠΊΠΎΡ ΠΎΠ·ΡΠΉΡΡΠ²Π΅Π½Π½ΠΎΠΉ ΡΠ΅Ρ Π½ΠΈΠΊΠΈ Π² Π²Π°Π³ΠΎΠ½ΠΎΡΡΡΠΎΠ΅Π½ΠΈΠΈ, ΡΠ°Π΄ΠΈΠΎΡΠ»Π΅ΠΊΡΡΠΎΠ½ΠΈΠΊΠ΅, ΠΏΡΠΈ ΠΏΡΠΎΠΈΠ·Π²ΠΎΠ΄ΡΡΠ²Π΅ ΡΡΡΠ±Π½ΡΡ Π·Π°Π³ΠΎΡΠΎΠ²ΠΎΠΊ ΠΈ Ρ. Π΄.
ΠΠ°ΠΏΡΠΈΠΌΠ΅Ρ, ΡΠ²Π°ΡΠΊΠ° ΡΠ»ΠΎΠΆΠ½ΠΎΠ³ΠΎ ΠΈ ΠΊΡΡΠΏΠ½ΠΎΠ³ΠΎ ΡΠ·Π»Π°-ΠΎΡΠ½ΠΎΠ²Π°Π½ΠΈΡ ΠΊΡΠ·ΠΎΠ²Π° Π°Π²ΡΠΎΠΌΠΎΠ±ΠΈΠ»Ρ Β«ΠΠΎΠ»Π³Π°Β» (ΠΌΠ°ΡΡΠΎΠΉ ~ 150 ΠΊΠ³) ΠΈΠ· 200 Π΄Π΅ΡΠ°Π»Π΅ΠΉ ΠΏΡΠΎΠΈΠ·Π²ΠΎΠ΄ΠΈΡΡΡ Π² 870 ΡΠΎΡΠΊΠ°Ρ . ΠΠ° Π»ΠΈΠ½ΠΈΠΈ ΡΡΡΠ°Π½ΠΎΠ²Π»Π΅Π½ΠΎ ΡΠ΅ΠΌΡ ΠΌΠ½ΠΎΠ³ΠΎΡΠ»Π΅ΠΊΡΡΠΎΠ΄Π½ΡΡ ΠΌΠ°ΡΠΈΠ½, Π·Π°Π³ΡΡΠ·ΠΎΡΠ½ΡΡ ΠΈ ΠΏΠΎΠ²ΠΎΡΠΎΡΠ½ΡΡ ΠΏΡΠΈΡΠΏΠΎΡΠΎΠ±Π»Π΅Π½ΠΈΠΉ, ΡΠΎΠ΅Π΄ΠΈΠ½Π΅Π½Π½ΡΡ ΠΊΠΎΠ½Π²Π΅ΠΉΠ΅ΡΠΎΠΌ, Π΄Π²ΠΈΠΆΡΡΠΈΠΌΡΡ ΡΠΎ ΡΠΊΠΎΡΠΎΡΡΡΡ 1,5 ΠΌ/Ρ; ΡΠ°ΡΠΎΠ²Π°Ρ ΠΏΡΠΎΠΈΠ·Π²ΠΎΠ΄ΠΈΡΠ΅Π»ΡΠ½ΠΎΡΡΡ Π»ΠΈΠ½ΠΈΠΈ β Π΄ΠΎ 40 ΠΈΠ·Π΄Π΅Π»ΠΈΠΉ. ΠΡΠΈ ΠΈΠ·Π³ΠΎΡΠΎΠ²Π»Π΅Π½ΠΈΠΈ ΠΎΡΠΎΠΏΠΈΡΠ΅Π»ΡΠ½ΡΡ ΡΠ°Π΄ΠΈΠ°ΡΠΎΡΠΎΠ² (ΡΠΈΡ. 20.21) ΡΡΠ°Π»ΡΠ½Π°Ρ Π»Π΅Π½ΡΠ° ΠΈΠ· ΡΡΠ»ΠΎΠ½Π° ΠΏΠΎΠ΄Π°Π΅ΡΡΡ ΡΠΎ ΡΠΊΠΎΡΠΎΡΡΡΡ Π΄ΠΎ 20 ΠΌ/ΠΌΠΈΠ½ Π² ΡΠΎΡΠΌΠΎΠ²ΠΎΡΠ½ΡΡ ΠΊΠ»Π΅ΡΡ, Π³Π΄Π΅ ΡΡΠ°ΠΌΠΏΡΡΡΡΡ ΠΏΠΎΠ»ΠΎΠ²ΠΈΠ½Ρ ΡΠ°Π΄ΠΈΠ°ΡΠΎΡΠ°. Π Π²Π΅ΡΡ Π½Π΅ΠΉ Π·Π°Π³ΠΎΡΠΎΠ²ΠΊΠ΅ Π½Π° ΠΌΠ°ΡΠΈΠ½Π΅ ΠΏΡΠΈΠ²Π°ΡΠΈΠ²Π°Π΅ΡΡΡ ΡΡΡΡΠ΅Ρ Π·Π°Π³ΠΎΡΠΎΠ²ΠΊΠΈ Π΄Π°Π»Π΅Π΅ ΠΏΡΠΈΡ Π²Π°ΡΡΠ²Π°ΡΡΡΡ ΡΠΎΡΠΊΠ°ΠΌΠΈ ΠΈ ΡΠ²Π°ΡΠΈΠ²Π°ΡΡΡΡ Π³Π΅ΡΠΌΠ΅ΡΠΈΡΠ½ΡΠΌ ΡΠ²ΠΎΠΌ. ΠΠ° Π²ΡΡ ΠΎΠ΄Π΅ Π»ΠΈΠ½ΠΈΠΈ ΡΠ°Π΄ΠΈΠ°ΡΠΎΡΡ ΠΎΡΡΠ΅Π·Π°ΡΡΡΡ Π½ΠΎΠΆΠ½ΠΈΡΠ°ΠΌΠΈ.
ΠΡΠΎΠΌΡΡΠ»Π΅Π½Π½ΡΠ΅ ΡΠΎΠ±ΠΎΡΡ ΡΠΈΡΠΌΡ Β«UnimaiionΒ» (Π‘Π¨Π) ΠΏΡΠΈΠΌΠ΅Π½ΡΡΡΡΡ Π΄Π»Ρ ΡΠΎΡΠ΅ΡΠ½ΠΎΠΉ ΡΠ²Π°ΡΠΊΠΈ Ρ ΡΠ΅ΡΠ΅Π΄ΠΈΠ½Ρ 1960 Π³ΠΎΠ΄ΠΎΠ². Π ΠΊΠ°ΠΏΠΈΡΠ°Π»ΠΈΡΡΠΈΡΠ΅ΡΠΊΠΈΡ ΡΡΡΠ°Π½Π°Ρ Π±ΠΎΠ»ΡΡΠ°Ρ ΡΠ°ΡΡΡ ΡΠ²Π°ΡΠΎΡΠ½ΡΡ ΡΠΎΠ±ΠΎΡΠΎΠ² (Π΄ΠΎ 60 β 70%, ΠΈΠ»ΠΈ 30β40 ΡΡΡ.) ΠΏΡΠ΅Π΄Π½Π°Π·Π½Π°ΡΠ΅Π½Π° Π΄Π»Ρ ΡΠΎΡΠ΅ΡΠ½ΠΎΠΉ ΡΠ²Π°ΡΠΊΠΈ. Π Π½Π°ΡΠ΅ΠΉ ΡΡΡΠ°Π½Π΅ ΡΠΎΠ±ΠΎΡΡ ΠΈΡΠΏΠΎΠ»ΡΠ·ΡΡΡΡΡ ΠΈΠ»ΠΈ ΠΊΠ°ΠΊ Π°Π²ΡΠΎΠΌΠ°ΡΠΈΡΠ΅ΡΠΊΠΈ ΠΏΠ΅ΡΠ΅ΠΌΠ΅ΡΠ°ΡΡΠΈΠ΅ΡΡ ΡΠ²Π°ΡΠΎΡΠ½ΡΠ΅ ΠΌΠ°ΡΠΈΠ½Ρ, Π½Π°ΠΏΡΠΈΠΌΠ΅Ρ, Ρ ΠΊΠ»Π΅ΡΠ°ΠΌΠΈ, ΠΈΠ»ΠΈ ΠΊΠ°ΠΊ ΡΡΠ°Π½ΡΠΏΠΎΡΡΠ½ΡΠ΅ ΡΡΡΡΠΎΠΉΡΡΠ²Π°, ΠΏΠ΅ΡΠ΅Π΄Π²ΠΈΠ³Π°ΡΡΠΈΠ΅ ΡΠ·Π΅Π» ΠΎΡΠ½ΠΎΡΠΈΡΠ΅Π»ΡΠ½ΠΎ ΠΎΠ±ΡΡΠ½ΠΎΠΉ ΡΡΠ°ΡΠΈΠΎΠ½Π°ΡΠ½ΠΎΠΉ ΠΌΠ°ΡΠΈΠ½Ρ (ΠΠΠ‘Π’ 26054β85). Π¨ΠΈΡΠΎΠΊΠΎ ΠΈΠ·Π²Π΅ΡΡΠ½Ρ ΡΠΎΠ±ΠΎΡΡ ΡΠΈΡΠΌ Β«Kawasaki UnimateΒ» (Π―ΠΏΠΎΠ½ΠΈΡ), Β«ASEAΒ» (Π¨Π²Π΅ΡΠΈΡ), Β«UnimationΒ» (Π‘Π¨Π) ΠΈ Ρ. Π΄. Π Π°Π±ΠΎΡΠΈΠΉ ΠΎΡΠ³Π°Π½ ΡΠΎΠ±ΠΎΡΠ° β ΡΡΠΊΠ° β ΠΈΠΌΠ΅Π΅Ρ Π΄ΠΎ ΡΠ΅ΡΡΠΈ ΡΡΠ΅ΠΏΠ΅Π½Π΅ΠΉ ΡΠ²ΠΎΠ±ΠΎΠ΄Ρ ΠΈ ΠΏΠ΅ΡΠ΅ΠΌΠ΅ΡΠ°Π΅ΡΡΡ Π² ΠΏΡΡΠΌΠΎΡΠ³ΠΎΠ»ΡΠ½ΠΎΠΉ ΡΠΈΠ»ΠΈΠ½Π΄ΡΠΈΡΠ΅ΡΠΊΠΎΠΉ ΠΈΠ»ΠΈ ΡΡΠ΅ΡΠΈΡΠ΅ΡΠΊΠΎΠΉ ΡΠΈΡΡΠ΅ΠΌΠ΅ ΠΊΠΎΠΎΡΠ΄ΠΈΠ½Π°Ρ Ρ ΡΠΎΡΠ½ΠΎΡΡΡΡ ΠΏΠΎΠ·ΠΈΡΠΈΠΎΠ½ΠΈΡΠΎΠ²Π°Π½ΠΈΡ Π΄ΠΎ 0,1β0,2 ΠΌΠΌ. ΠΡΡΠ·ΠΎΠΏΠΎΠ΄ΡΠ΅ΠΌΠ½ΠΎΡΡΡ ΡΠΎΠ±ΠΎΡΠ° Π΄ΠΎΡΡΠΈΠ³Π°Π΅Ρ 200 ΠΊΠ³, ΠΌΠ°ΠΊΡΠΈΠΌΠ°Π»ΡΠ½ΠΎΠ΅ ΡΠ²Π°ΡΠΎΡΠ½ΠΎΠ΅ ΡΡΠΈΠ»ΠΈΠ΅ β 5 ΠΊΠ, ΠΏΡΠΎΠΈΠ·Π²ΠΎΠ΄ΠΈΡΠ΅Π»ΡΠ½ΠΎΡΡΡ 100 ΡΠΎΡΠ΅ΠΊ/ΠΌΠΈΠ½. Π§Π°ΡΡΠΎ ΡΠ²Π°ΡΠΎΡΠ½ΡΠ΅ ΡΡΠ°Π½ΡΡΠΎΡΠΌΠ°ΡΠΎΡΡ Π²ΡΡΡΠ°ΠΈΠ²Π°ΡΡΡΡ Π² ΡΡΠΊΡ ΡΠΎΠ±ΠΎΡΠ°, ΡΠΏΡΠ°Π²Π»Π΅Π½ΠΈΠ΅ β ΠΌΠΈΠΊΡΠΎΠΏΡΠΎΡΠ΅ΡΡΠΎΡΠ½ΠΎΠ΅. ΠΠ΅ΡΡΠΌΠ° ΠΏΠ΅ΡΡΠΏΠ΅ΠΊΡΠΈΠ²Π½Ρ ΠΌΠΎΠ΄ΡΠ»ΡΠ½ΡΠ΅ ΡΠΎΠ±ΠΎΡΡ, Π½Π°ΠΏΡΠΈΠΌΠ΅Ρ ΡΠΈΡΠΌΡ Β«Sciaky Electric Welding MashineΒ» (Π€ΡΠ°Π½ΡΠΈΡ), ΠΎΡΠΎΠ±Π΅Π½Π½ΠΎΡΡΡ ΠΊΠΎΡΠΎΡΡΡ β ΡΠ½ΠΈΠ²Π΅ΡΡΠ°Π»ΡΠ½ΡΠ΅ ΡΠΌΠ΅Π½Π½ΡΠ΅ Π±Π»ΠΎΠΊΠΈ (ΠΌΠΎΠ΄ΡΠ»ΠΈ), ΠΎΡΡΡΠ΅ΡΡΠ²Π»ΡΡΡΠΈΠ΅ Π»ΠΈΠ½Π΅ΠΉΠ½ΠΎΠ΅ ΠΈΠ»ΠΈ Π²ΡΠ°ΡΠ°ΡΠ΅Π»ΡΠ½ΠΎΠ΅ Π΄Π²ΠΈΠΆΠ΅Π½ΠΈΠ΅. ΠΠ· Π½ΠΈΡ ΠΌΠΎΠΆΠ½ΠΎ ΡΠΎΠ±ΠΈΡΠ°ΡΡ ΡΠΎΠ±ΠΎΡΡ Ρ ΠΌΠΈΠ½ΠΈΠΌΠ°Π»ΡΠ½ΡΠΌ ΡΠΈΡΠ»ΠΎΠΌ ΡΡΠ΅ΠΏΠ΅Π½Π΅ΠΉ ΡΠ²ΠΎΠ±ΠΎΠ΄Ρ ΠΏΡΠΈΠΌΠ΅Π½ΠΈΡΠ΅Π»ΡΠ½ΠΎ ΠΊ ΡΡΠ΅Π±ΠΎΠ²Π°Π½ΠΈΡΠΌ ΠΏΡΠΎΠΈΠ·Π²ΠΎΠ΄ΡΡΠ²Π°, Π½Π°ΠΏΡΠΈΠΌΠ΅Ρ, ΠΏΡΠΈ ΠΈΠ·Π³ΠΎΡΠΎΠ²Π»Π΅Π½ΠΈΠΈ ΠΊΡΠ·ΠΎΠ²Π° Π°Π²ΡΠΎΠΌΠΎΠ±ΠΈΠ»Ρ. Π Π°Π·ΡΠ°Π±Π°ΡΡΠ²Π°ΡΡΡΡ ΡΠΎΠ±ΠΎΡΡ Ρ Π°Π΄Π°ΠΏΡΠΈΠ²Π½ΡΠΌ ΡΠΏΡΠ°Π²Π»Π΅Π½ΠΈΠ΅ΠΌ, ΠΊΠΎΡΠΎΡΡΠ΅ ΠΌΠΎΠ³ΡΡ ΠΈΠ·ΠΌΠ΅Π½ΡΡΡ ΡΠ΅ΠΆΠΈΠΌ ΡΠ°Π±ΠΎΡΡ Π² ΡΠΎΠΎΡΠ²Π΅ΡΡΡΠ²ΠΈΠΈ Ρ ΠΊΠΎΠ½ΠΊΡΠ΅ΡΠ½ΡΠΌΠΈ ΡΡΠ»ΠΎΠ²ΠΈΡΠΌΠΈ ΡΠ²Π°ΡΠΊΠΈ.
Π ΠΎΠ±ΠΎΡΡ ΡΠ°ΠΌΠΈ ΠΏΠΎ ΡΠ΅Π±Π΅ ΠΈΠ»ΠΈ Π² ΡΠΎΡΠ΅ΡΠ°Π½ΠΈΠΈ Ρ ΠΎΠ±ΡΡΠ½ΡΠΌΠΈ (ΠΌΠ½ΠΎΠ³ΠΎΡΠ»Π΅ΠΊΡΡΠΎΠ΄Π½ΡΠΌΠΈ) ΠΌΠ°ΡΠΈΠ½Π°ΠΌΠΈ ΠΎΠ±ΡΠ΅Π΄ΠΈΠ½ΡΡΡΡΡ Π² ΡΠΎΠ±ΠΎΡΠΎΡΠ΅Ρ Π½ΠΈΡΠ΅ΡΠΊΠΈΠΉ ΠΊΠΎΠΌΠΏΠ»Π΅ΠΊΡ (ΡΠΈΡ. 20.22). ΠΠ·Π΄Π΅Π»ΠΈΠ΅ 8 ΠΊΠΎΠ½Π²Π΅ΠΉΠ΅ΡΠΎΠΌ 1 Ρ ΠΏΠΎΠΌΠΎΡΡΡ ΠΎΠΏΡΡΠΊΠ½ΠΎΠΉ ΡΠ΅ΠΊΡΠΈΠΈ 2 ΠΏΠΎΠ΄Π°Π΅ΡΡΡ Π½Π° ΠΏΡΠ»ΡΡΠΈΡΡΡΡΠΈΠΉ Π½Π°ΠΏΠΎΠ»ΡΠ½ΡΠΉ ΠΊΠΎΠ½Π²Π΅ΠΉΠ΅Ρ 7, Π²Π΄ΠΎΠ»Ρ ΠΊΠΎΡΠΎΡΠΎΠ³ΠΎ ΡΡΡΠ°Π½ΠΎΠ²Π»Π΅Π½Ρ ΡΠΎΠ±ΠΎΡΡ 9 Π² Π²ΡΠ΅ΠΌΠΊΠ°Ρ 11 ΠΈΠ»ΠΈ Π½Π° ΡΡΡΠ°ΠΊΠ°Π΄Π°Ρ 10. Π‘Π²Π°ΡΠΎΡΠ½ΡΠ΅ ΡΡΠ°Π½ΡΡΠΎΡΠΌΠ°ΡΠΎΡΡ 5 ΡΡΡΠ°Π½ΠΎΠ²Π»Π΅Π½Ρ Π½Π° Π΄Π²ΡΡ ΠΌΠΎΠ½ΠΎΡΠ΅Π»ΡΡΠ°Ρ 4 Π²Π΄ΠΎΠ»Ρ ΠΊΠΎΠ½Π²Π΅ΠΉΠ΅ΡΠ° ΠΈ ΡΠ²ΡΠ·Π°Π½Ρ Ρ ΠΊΠ»Π΅ΡΠ°ΠΌΠΈ Π³ΠΈΠ±ΠΊΠΈΠΌΠΈ ΠΊΠ°Π±Π΅Π»ΡΠΌΠΈ. ΠΠΈΠ½ΠΈΡ ΡΠΏΡΠ°Π²Π»ΡΠ΅ΡΡΡ Ρ ΠΏΡΠ»ΡΡΠ° 3. ΠΠΎΡΠ»Π΅ ΡΠ²Π°ΡΠΊΠΈ ΠΎΠΏΡΡΠΊΠ½Π°Ρ ΡΠ΅ΠΊΡΠΈΡ 6 ΡΠ½ΠΈΠΌΠ°Π΅Ρ ΠΊΡΠ·ΠΎΠ² Ρ ΠΊΠΎΠ½Π²Π΅ΠΉΠ΅ΡΠ° ΠΈ ΠΏΠ΅ΡΠ΅Π΄Π°Π΅Ρ Π΅Π³ΠΎ Π½Π° ΠΎΡΠ΄Π΅Π»ΠΎΡΠ½ΡΠΉ ΡΡΠ°ΡΡΠΎΠΊ.
Π ΡΡΠ΄Π΅ ΡΡΡΠ°Π½ ΠΎΠ±ΡΠ΅ΠΌ ΠΏΡΠΈΠΌΠ΅Π½Π΅Π½ΠΈΡ ΡΠΎΠ±ΠΎΡΠΎΠ² Π² Π°Π²ΡΠΎΠΌΠΎΠ±ΠΈΠ»Π΅ΡΡΡΠΎΠ΅Π½ΠΈΠΈ Π΄ΠΎΡΡΠΈΠ³Π°Π΅Ρ 25 % ΠΎΡ ΠΎΠ±ΡΠ΅Π³ΠΎ ΠΎΠ±ΡΠ΅ΠΌΠ° ΠΎΠ±ΠΎΡΡΠ΄ΠΎΠ²Π°Π½ΠΈΡ. ΠΡΠΈ ΡΡΠΎΠΌ ΡΡΠΎΠΈΠΌΠΎΡΡΡ Π·Π°ΡΡΠ°Ρ ΡΠ½ΠΈΠΆΠ°Π΅ΡΡΡ Π½Π° 50β60%, ΠΏΡΠΎΠΈΠ·Π²ΠΎΠ΄ΠΈΡΠ΅Π»ΡΠ½ΠΎΡΡΡ Π²ΠΎΠ·ΡΠ°ΡΡΠ°Π΅Ρ Π² 1,5β2 ΡΠ°Π·Π°. ΠΠ°ΠΏΡΠΈΠΌΠ΅Ρ, ΠΏΠ΅ΡΠ΅ΡΡΡΠΎΠΉΠΊΠ° ΡΠΎΠ±ΠΎΡΠ° Π½Π° Π½ΠΎΠ²ΡΡ ΠΌΠΎΠ΄Π΅Π»Ρ ΠΊΡΠ·ΠΎΠ²Π° Π·Π°Π½ΠΈΠΌΠ°Π΅Ρ 0,5 Ρ Π²ΠΌΠ΅ΡΡΠΎ 24β200 Ρ ΠΏΡΠΈ ΠΎΠ±ΡΡΠ½ΡΡ ΡΡΠ΅Π΄ΡΡΠ²Π°Ρ Π°Π²ΡΠΎΠΌΠ°ΡΠΈΠ·Π°ΡΠΈΠΈ. ΠΠ΅ΡΠΌΠΎΡΡΡ Π½Π° Π²ΡΡΠΎΠΊΡΡ ΡΡΠΎΠΈΠΌΠΎΡΡΡ ΡΠΎΠ±ΠΎΡΠΎΠ² (700β100 ΡΡΡ. Π΄ΠΎΠ»Π».), ΠΎΠ½ΠΈ ΠΎΠΊΡΠΏΠ°ΡΡΡΡ Π·Π° Π΄Π²Π°βΡΡΠΈ Π³ΠΎΠ΄Π°.
ΠΠΎΠ»ΡΠ΅Π½ΠΊΠΎ Π.Π. Π‘Π²Π°ΡΠΊΠ° ΠΈ ΡΠ²Π°ΡΠΈΠ²Π°Π΅ΠΌΡΠ΅ ΠΌΠ°ΡΠ΅ΡΠΈΠ°Π»Ρ Ρ.2. -M. 1996
Π‘ΠΌ. ΡΠ°ΠΊΠΆΠ΅: ΠΠΎΠ½ΡΠ°ΠΊΡΠ½Π°Ρ ΡΠ²Π°ΡΠΊΠ°, Π’ΡΠ΅Π±ΠΎΠ²Π°Π½ΠΈΡ ΠΊ ΡΠ²Π°ΡΠ½ΡΠΌ ΠΊΠΎΠ½ΡΡΡΡΠΊΡΠΈΡΠΌ ΠΏΡΠΈ ΡΠΎΡΠ΅ΡΠ½ΠΎΠΉ ΠΈ ΡΠΎΠ²Π½ΠΎΠΉ ΡΠ²Π°ΡΠΊΠ΅, ΠΠΎΠ½ΡΡΠΎΠ»Ρ ΠΊΠ°ΡΠ΅ΡΡΠ²Π° ΡΠΎΠ΅Π΄ΠΈΠ½Π΅Π½ΠΈΠΉ ΡΠΎΡΠ΅ΡΠ½ΠΎΠΉ ΠΈ ΡΠΎΠ²Π½ΠΎΠΉ ΡΠ²Π°ΡΠΊΠΈ, ΠΡΠΎΠΌΡΡΠ»Π΅Π½Π½ΠΎΠ΅ ΠΏΡΠΈΠΌΠ΅Π½Π΅Π½ΠΈΠ΅ ΡΠΎΡΠ΅ΡΠ½ΠΎΠΉ ΠΈ ΡΠΎΠ²Π½ΠΎΠΉ ΡΠ²Π°ΡΠΊΠΈ
ΠΠ²ΡΠΎΠΌΠ°ΡΠΈΠ·Π°ΡΠΈΡ ΠΏΡΠΎΠΈΠ·Π²ΠΎΠ΄ΡΡΠ²Π° — Svarcom
ΠΠ²ΡΠΎΠΌΠ°ΡΠΈΠ·Π°ΡΠΈΡ ΠΏΡΠΎΠΈΠ·Π²ΠΎΠ΄ΡΡΠ²Π° ΡΠ»Π΅ΠΊΡΡΠΎΠ΄ΡΠ³ΠΎΠ²ΠΎΠΉ ΡΠ²Π°ΡΠΊΠΈ ΠΌΠΎΠΆΠ΅Ρ Π±ΡΡΡ ΠΏΡΠΈΠΌΠ΅Π½Π΅Π½Π° Π½Π° Π²ΡΠ΅Ρ ΡΡΠΎΠ²Π½ΡΡ ΡΠ»ΠΎΠΆΠ½ΠΎΡΡΠΈ Π²ΡΠΏΠΎΠ»Π½Π΅Π½ΠΈΡ ΡΠ²Π°ΡΠ½ΡΡ ΡΠΎΠ΅Π΄ΠΈΠ½Π΅Π½ΠΈΠΉ, Ρ ΡΠ°ΠΌΠΎΠ³ΠΎ ΠΏΡΠΎΡΡΠ΅ΠΉΡΠ΅Π³ΠΎ Π΄ΠΎ ΡΠ²Π΅ΡΡ ΡΠ»ΠΎΠΆΠ½ΠΎΠ³ΠΎ. Β Π‘Π²Π°ΡΠΎΡΠ½ΠΎΠ΅ ΠΎΠ±ΠΎΡΡΠ΄ΠΎΠ²Π°Π½ΠΈΠ΅ Π±ΡΠ»ΠΎ ΠΏΠ΅ΡΠ²ΠΎΠ½Π°ΡΠ°Π»ΡΠ½ΠΎ ΡΠ°Π·Π΄Π΅Π»Π΅Π½ΠΎ Π½Π° ΡΡΡΠ½ΡΡ (Π½Π°ΠΏΡΠΈΠΌΠ΅Ρ, ΠΏΡΠΈ ΠΈΡΠΏΠΎΠ»ΡΠ·ΠΎΠ²Π°Π½ΠΈΠΈ ΡΠ»Π΅ΠΊΡΡΠΎΠ΄ΠΎΠ² Ρ ΠΏΠΎΠΊΡΡΡΠΈΠ΅ΠΌ), ΠΏΠΎΠ»ΡΠ°Π²ΡΠΎΠΌΠ°ΡΠΈΡΠ΅ΡΠΊΠΎΠ΅ (Π΄Π»Ρ ΡΠ²Π°ΡΠΊΠΈ MIG / MAG, Ρ ΠΌΠ΅Ρ Π°Π½ΠΈΠ·ΠΈΡΡΠ΅ΠΌΠΎΠΉ ΠΏΠΎΠ΄Π°ΡΠ΅ΠΉ ΡΠ²Π°ΡΠΎΡΠ½ΠΎΠΉ ΠΏΡΠΎΠ²ΠΎΠ»ΠΎΠΊΠΈ) ΠΈ Π°Π²ΡΠΎΠΌΠ°ΡΠΈΡΠ΅ΡΠΊΠΎΠ΅ (Π½Π°ΠΏΡΠΈΠΌΠ΅Ρ Π΄Π»Ρ Π΄ΡΠ³ΠΎΠ²ΠΎΠΉ ΡΠ²Π°ΡΠΊΠΈ, Ρ ΠΌΠ΅Ρ Π°Π½ΠΈΠ·ΠΈΡΠΎΠ²Π°Π½Π½ΠΎΠΉ ΠΏΠΎΠ΄Π°ΡΠ΅ΠΉ ΠΏΡΠΈΡΠ°Π΄ΠΎΡΠ½ΠΎΠΉ ΠΏΡΠΎΠ²ΠΎΠ»ΠΎΠΊΠΈ ΠΈ ΠΌΠ΅Ρ Π°Π½ΠΈΡΠ΅ΡΠΊΠΎΠ³ΠΎ ΠΏΠ΅ΡΠ΅ΠΌΠ΅ΡΠ΅Π½ΠΈΡ ΡΠ²Π°ΡΠΎΡΠ½ΠΎΠΉ Π³ΠΎΠ»ΠΎΠ²ΠΊΠΈ).
ΠΡΠΈΠΌΠ΅Π½Π΅Π½ΠΈΠ΅ ΡΠ²Π°ΡΠΎΡΠ½ΠΎΠ³ΠΎ ΡΠΎΠ±ΠΎΡΠ° ΠΎΠ±ΡΡΠ»Π°Π²Π»ΠΈΠ²Π°Π΅Ρ Π½Π΅ ΡΠΎΠ»ΡΠΊΠΎ Π½Π°ΡΠ°Π»ΠΎ ΠΈ ΠΊΠΎΠ½Π΅Ρ ΡΠ²Π°ΡΠΊΠΈ, Π½ΠΎ ΠΈ ΠΏΡΠΎΠ³ΡΠ°ΠΌΠΌΠ½ΠΎ-ΡΠΏΡΠ°Π²Π»ΡΠ΅ΠΌΡΠ΅ Π΄Π²ΠΈΠΆΠ΅Π½ΠΈΠ΅ ΠΌΠ΅ΠΆΠ΄Ρ ΡΠ°Π·Π½ΡΠΌΠΈ ΠΏΠΎΠ»ΠΎΠΆΠ΅Π½ΠΈΡΠΌΠΈ ΡΠ²Π°ΡΠΊΠΈ. ΠΠΎΠ»Π½ΠΎΡΡΡΡ Π°Π²ΡΠΎΠΌΠ°ΡΠΈΡΠ΅ΡΠΊΠ°Ρ ΡΠ²Π°ΡΠΊΠ°, Π²ΠΊΠ»ΡΡΠ°Ρ ΡΡΡΠ°Π½ΠΎΠ²ΠΊΡ Π΄Π΅ΡΠ°Π»Π΅ΠΉ ΠΈ Π²ΡΠ³ΡΡΠ·ΠΊΠΈ Π³ΠΎΡΠΎΠ²ΠΎΠ³ΠΎ ΠΈΠ·Π΄Π΅Π»ΠΈΡ, ΠΊΠΎΠ½ΡΡΠΎΠ»ΠΈΡΡΠ΅ΡΡΡ ΠΠΈΠ±ΠΊΠΈΠΌΠΈ ΠΡΠΎΠΈΠ·Π²ΠΎΠ΄ΡΡΠ²Π΅Π½Π½ΡΠΌΠΈ Π‘ΠΈΡΡΠ΅ΠΌΠ°ΠΌΠΈ (ΠΠΠ‘). ΠΡΠΈ ΡΠΈΡΡΠ΅ΠΌΡ ΠΎΠ±ΡΡΠ½ΠΎ ΠΈΡΠΏΠΎΠ»ΡΠ·ΡΡΡΡΡ Π΄Π»Ρ ΡΠ²Π°ΡΠΊΠΈ Π² ΡΡΠ΅Π΄Π΅ Π·Π°ΡΠΈΡΠ½ΡΡ Π³Π°Π·ΠΎΠ² ΠΌΠ°Π»ΡΡ ΠΈ ΡΡΠ΅Π΄Π½ΠΈΡ Π΄Π΅ΡΠ°Π»Π΅ΠΉ.
ΠΠ΅Ρ Π°Π½ΠΈΠ·ΠΈΡΠΎΠ²Π°Π½Π½Π°Ρ ΡΠ²Π°ΡΠΊΠ° ΠΏΠΎΠ²ΡΡΠ°Π΅Ρ ΠΏΡΠΎΠΈΠ·Π²ΠΎΠ΄ΠΈΡΠ΅Π»ΡΠ½ΠΎΡΡΡ, ΠΊΠ°ΡΠ΅ΡΡΠ²ΠΎ ΡΠ²Π°ΡΠ½ΡΡ ΡΠ²ΠΎΠ² ΠΈ ΡΡΠ»ΠΎΠ²ΠΈΡ ΡΠ°Π±ΠΎΡΡ. ΠΠ΅Ρ Π°Π½ΠΈΠ·Π°ΡΠΈΡ ΡΠ²Π°ΡΠΎΡΠ½ΡΡ ΠΏΡΠΎΡΠ΅ΡΡΠΎΠ² ΠΏΡΠΈΠΌΠ΅Π½ΡΠ΅ΡΡΡ Π΄Π»Ρ Π²ΡΠΏΠΎΠ»Π½Π΅Π½ΠΈΡ ΡΠΎΠ΅Π΄ΠΈΠ½Π΅Π½ΠΈΠΉ, ΠΊΠΎΡΠΎΡΡΠ΅ Π½Π΅Π²ΠΎΠ·ΠΌΠΎΠΆΠ½ΠΎ Π²ΡΠΏΠΎΠ»Π½ΠΈΡΡ ΠΏΡΠΈ ΠΏΠΎΠΌΠΎΡΠΈ ΡΡΡΠ½ΡΡ ΠΏΡΠΎΡΠ΅ΡΡΠΎΠ². ΠΡΠΈΠΌΠ΅ΡΠΎΠΌ ΡΠ²Π»ΡΠ΅ΡΡΡ ΡΠ²Π°ΡΠΊΠ° Π² ΡΠ·ΠΊΡΡ ΡΠ°Π·Π΄Π΅Π»ΠΊΡ.
Β
1. Π‘Π²Π°ΡΠΊΠ° Π² ΡΠ·ΠΊΡΡ ΡΠ°Π·Π΄Π΅Π»ΠΊΡ
Π‘Π²Π°ΡΠΊΠ° Π² ΡΠ·ΠΊΡΡ ΡΠ°Π·Π΄Π΅Π»ΠΊΡ ΠΈΠΌΠ΅Π΅Ρ ΡΠ»Π΅Π΄ΡΡΡΠΈΠ΅ ΠΏΡΠ΅ΠΈΠΌΡΡΠ΅ΡΡΠ²Π°:
β ΡΠ½ΠΈΠΆΠ΅Π½ΠΈΠ΅ ΡΠ½Π΅ΡΠ³ΠΎΠ·Π°ΡΡΠ°Ρ;
-ΡΠΌΠ΅Π½ΡΡΠ΅Π½ΠΈΠ΅ ΠΊΠΎΠ»ΠΈΡΠ΅ΡΡΠ²Π° ΠΏΠ΅ΡΠ΅ΠΏΠ»Π°Π²Π»Π΅Π½Π½ΠΎΠ³ΠΎ ΠΌΠ°ΡΠ΅ΡΠΈΠ°Π»Π°;
-ΡΠΊΠΎΠ½ΠΎΠΌΠΈΡ Π²ΡΠ΅ΠΌΠ΅Π½ΠΈ;
-ΡΠΌΠ΅Π½ΡΡΠ΅Π½ΠΈΠ΅ ΡΠ²Π°ΡΠΎΡΠ½ΡΡ Π΄Π΅ΡΠΎΡΠΌΠ°ΡΠΈΠΉ.
Π‘Π²Π°ΡΠΊΠ° Π² ΡΠ·ΠΊΡΡ ΡΠ°Π·Π΄Π΅Π»ΠΊΡ ΠΏΡΠΈΠΌΠ΅Π½ΠΈΠΌΠ° Π΄Π»Ρ ΡΠΎΠ΅Π΄ΠΈΠ½Π΅Π½ΠΈΡ Π»ΠΈΡΡΠΎΠ² ΠΈ ΠΏΠ»Π°ΡΡΠΈΠ½ Π² Π΄ΠΈΠ°ΠΏΠ°Π·ΠΎΠ½Π΅ ΡΠΎΠ»ΡΠΈΠ½ 25-300 ΠΌΠΌ. ΠΡΠΎΠΌΠΊΠΈ ΠΏΠΎΠ΄Π³ΠΎΡΠ°Π²Π»ΠΈΠ²Π°ΡΡΡΡ Ρ ΠΏΠ°ΡΠ°Π»Π»Π΅Π»ΡΠ½ΡΠΌΠΈ ΡΡΠΎΡΠΎΠ½Π°ΠΌΠΈ ΠΈΠ»ΠΈ ΡΠ»Π΅Π³ΠΊΠ° UβΠΎΠ±ΡΠ°Π·Π½ΠΎΠΉ Β ΡΠΎΡΠΌΠΎΠΉ, ΠΊΠ°ΠΊ ΠΏΠΎΠΊΠ°Π·Π°Π½ΠΎ Π½Π° Π ΠΈΡ.1. ΠΡΠΎΠΌΠΊΠΈ Ρ ΠΏΠ°ΡΠ°Π»Π»Π΅Π»ΡΠ½ΡΠΌΠΈ ΡΡΠΎΡΠΎΠ½Π°ΠΌΠΈ Π΄Π΅ΡΠ΅Π²Π»Π΅ Π² ΠΈΠ·Π³ΠΎΡΠΎΠ²Π»Π΅Π½ΠΈΠΈ, Π½ΠΎ Ρ Π΄ΡΡΠ³ΠΎΠΉ ΡΡΠΎΡΠΎΠ½Ρ Π²ΠΎΠ·Π½ΠΈΠΊΠ°Π΅Ρ Π²Π΅ΡΠΎΡΡΠ½ΠΎΡΡΡ Π½Π΅ ΠΏΠΎΠ»Π½ΠΎΠ³ΠΎ ΠΏΡΠΎΠ²Π°ΡΠ° ΠΊΠΎΡΠ½Ρ ΡΠ²Π°.
Π ΠΈΡΡΠ½ΠΎΠΊ 1. Π‘Π²Π°ΡΠΊΠ° Π² ΡΠ·ΠΊΡΡ ΡΠ°Π·Π΄Π΅Π»ΠΊΡ
Β Β Β Β Β Β Β Β Β Β Β Π Π΅ΠΊΠΎΠΌΠ΅Π½Π΄ΡΠ΅ΡΡΡ ΠΈΡΠΏΠΎΠ»ΡΠ·ΠΎΠ²Π°ΡΡ U-ΠΎΠ±ΡΠ°Π·Π½ΡΡ ΡΠ°Π·Π΄Π΅Π»ΠΊΡ ΠΊΡΠΎΠΌΠΎΠΊ, ΡΠ°ΠΊ ΠΊΠ°ΠΊ ΡΡΠΎ ΡΠΌΠ΅Π½ΡΡΠ°Π΅Ρ Π²ΠΎΠ·ΠΌΠΎΠΆΠ½ΡΠ΅ ΡΠ»ΠΎΠΆΠ½ΠΎΡΡΠΈ Β ΠΈ ΡΠ½ΠΈΠΆΠ°Π΅Ρ Π²Π΅ΡΠΎΡΡΠ½ΠΎΡΡΡ Π±ΡΠ°ΠΊΠ°, ΠΏΠΎΡΠΊΠΎΠ»ΡΠΊΡ, ΠΏΡΠΎΡΠ΅ ΡΠ°ΡΠΏΠ»Π°Π²ΠΈΡΡ ΡΡΠ΅Π½ΠΊΠΈ ΡΠ²Π° Ρ Π½ΠΈΠΆΠ½Π΅Π³ΠΎ ΠΊΡΠ°Ρ, ΡΠ°Π²Π½ΠΎΠΌΠ΅ΡΠ½ΠΎΠ΅ ΠΎΡΡΡΠ²Π°Π½ΠΈΠ΅ ΡΠ²Π°ΡΠ΅Π½Π½ΡΡ
Π΄Π΅ΡΠ°Π»Π΅ΠΉ.
ΠΠΊΠΎΠ½ΠΎΠΌΠΈΡΠ΅ΡΠΊΠΈΠ΅ ΠΏΡΠ΅ΠΈΠΌΡΡΠ΅ΡΡΠ²Π° ΡΠ²Π°ΡΠΊΠΈ Π² ΡΠ·ΠΊΡΡ ΡΠ°Π·Π΄Π΅Π»ΠΊΡ Π²ΠΎΠ·ΠΌΠΎΠΆΠ½ΠΎ ΠΏΠΎΠ»ΡΡΠΈΡΡ Π±Π»Π°Π³ΠΎΠ΄Π°ΡΡ Π½ΠΈΠ·ΠΊΠΎΠΌΡ ΡΠ½Π΅ΡΠ³ΠΎΠΏΠΎΡΡΠ΅Π±Π»Π΅Π½ΠΈΡ, Π·Π°ΡΡΠ°ΡΡ ΠΌΠ΅Π½ΡΡΠ΅Π³ΠΎ ΠΊΠΎΠ»ΠΈΡΠ΅ΡΡΠ²Π° ΠΏΡΠΈΡΠ°Π΄ΠΎΡΠ½ΠΎΠ³ΠΎ ΠΌΠ°ΡΠ΅ΡΠΈΠ°Π»Π°, Π²ΠΌΠ΅ΡΡΠ΅ Ρ Π±ΠΎΠ»Π΅Π΅ ΠΊΠΎΡΠΎΡΠΊΠΈΠΌ Π²ΡΠ΅ΠΌΠ΅Π½Π΅ΠΌ, Π½Π΅ΠΎΠ±Ρ
ΠΎΠ΄ΠΈΠΌΡΠΌ Π΄Π»Ρ Π²ΡΠΏΠΎΠ»Π½Π΅Π½ΠΈΡ ΡΠ²Π°.
ΠΡΡΠ³ΠΈΠ΅ ΡΠ°ΠΊΡΠΎΡΡ Π²ΠΊΠ»ΡΡΠ°ΡΡ Π² ΡΠ΅Π±Ρ ΠΌΠ΅Π½Π΅Π΅ ΡΠ»ΠΎΠΆΠ½ΡΡ ΡΠΎΠ²ΠΌΠ΅ΡΡΠ½ΡΡ ΠΏΠΎΠ΄Π³ΠΎΡΠΎΠ²ΠΊΡ ΠΊΡΠΎΠΌΠΎΠΊ, ΡΠΎΠΊΡΠ°ΡΠ΅Π½ΠΈΠ΅ Π²ΡΠ΅ΠΌΠ΅Π½ΠΈ Π½Π° ΠΏΠΎΠ²ΡΡΠ΅Π½ΠΈΠ΅ ΡΠ°Π±ΠΎΡΠ΅ΠΉ ΡΠ΅ΠΌΠΏΠ΅ΡΠ°ΡΡΡΡ ΠΈ ΠΌΠ΅Π½ΡΡΠ΅ Π΄Π΅ΡΠΎΡΠΌΠ°ΡΠΈΠΉ Β ΠΈΠ·-Π·Π° ΠΌΠ΅Π½ΡΡΠ΅Π³ΠΎ ΠΎΠ±ΡΠ΅ΠΌΠ° ΡΠ²Π°. ΠΠ΅ΠΎΠ±Ρ ΠΎΠ΄ΠΈΠΌΡΠΌ ΡΡΠ»ΠΎΠ²ΠΈΠ΅ΠΌ Π΄Π»Ρ ΡΡΠΏΠ΅ΡΠ½ΠΎΠ³ΠΎ ΡΠ΅Π·ΡΠ»ΡΡΠ°ΡΠ° Π΅ΡΡΡ ΠΏΡΠ°Π²ΠΈΠ»ΡΠ½ΠΎΠ΅ ΡΠΏΡΠ°Π²Π»Π΅Π½ΠΈΠ΅ ΠΏΡΠΎΡΠ΅ΡΡΠΎΠΌ, ΡΠ²Π°ΡΠΎΡΠ½ΡΠ΅ Π³ΠΎΠ»ΠΎΠ²ΠΊΠΈ ΡΠΏΠ΅ΡΠΈΠ°Π»ΡΠ½ΠΎΠΉ ΠΊΠΎΠ½ΡΡΡΡΠΊΡΠΈΠΈ Ρ ΡΠΎΡΠ½ΡΠΌ ΠΌΠ΅Ρ Π°Π½ΠΈΡΠ΅ΡΠΊΠΈΠΌ ΡΠΏΡΠ°Π²Π»Π΅Π½ΠΈΠ΅ΠΌ. Π‘Π²Π°ΡΠΊΠ° Π² ΡΠ·ΠΊΡΡ ΡΠ°Π·Π΄Π΅Π»ΠΊΡ Π²ΡΠΏΠΎΠ»Π½ΡΠ΅ΡΡΡ ΡΠΏΠΎΡΠΎΠ±Π°ΠΌΠΈ MIG/MAG, TIG ΠΈ ΡΠ»Π΅ΠΊΡΡΠΎΠ΄ΡΠ³ΠΎΠ²ΠΎΠΉ ΡΠ²Π°ΡΠΊΠΎΠΉ ΠΏΠΎΠ΄ ΡΠ»ΡΡΠΎΠΌ.
Π‘Π²Π°ΡΠΊΠ° Π² ΡΠ·ΠΊΡΡ ΡΠ°Π·Π΄Π΅Π»ΠΊΡ ΠΏΡΠΈ ΠΏΠΎΠΌΠΎΡΠΈ MIG.
ΠΠ»Ρ ΠΎΠ±Π΅ΡΠΏΠ΅ΡΠ΅Π½ΠΈΡ Π½Π°Π΄Π»Π΅ΠΆΠ°ΡΠ΅Π³ΠΎ ΠΏΡΠΎΠΏΠ»Π°Π²Π»Π΅Π½ΠΈΠ΅ ΡΡΠΎΡΠΎΠ½ ΡΠ²Π° Π΄ΡΠ³Π° Π΄ΠΎΠ»ΠΆΠ½Π° ΠΏΠΎΠΏΠ΅ΡΠ΅ΠΌΠ΅Π½Π½ΠΎ Π³ΠΎΡΠ΅ΡΡ Π½Π° Π»Π΅Π²ΡΡ ΠΈ ΠΏΡΠ°Π²ΡΡ ΡΡΠΎΡΠΎΠ½Ρ ΡΠΎΠ΅Π΄ΠΈΠ½Π΅Π½ΠΈΡ. ΠΡΠ³Ρ ΡΠ°ΠΊΠΆΠ΅ ΠΌΠΎΠΆΠ½ΠΎ ΠΊΠΎΠ½ΡΡΠΎΠ»ΠΈΡΠΎΠ²Π°ΡΡ ΠΏΡΡΠ΅ΠΌ ΠΏΠΎΠ΄Π°ΡΠΈ Π΄Π²ΡΡ ΠΏΡΠΈΡΠ°Π΄ΠΎΡΠ½ΡΡ ΠΏΡΠΎΠ²ΠΎΠ»ΠΎΠΊ ΡΡΠ΄ΠΎΠΌ Π΄ΡΡΠ³ Ρ Π΄ΡΡΠ³ΠΎΠΌ, ΡΡΠΎ Π·Π°ΡΡΠ°Π²Π»ΡΠ΅Ρ Π΄ΡΠ³Ρ ΠΏΠΎΡΡΠΎΡΠ½Π½ΠΎ ΠΎΡΠ΄Π²ΠΈΠ³Π°ΡΡΡΡ ΠΎΡ ΠΎΡΠΈ ΠΌΠ΅ΠΆΠ΄Ρ Π½ΠΈΠΌΠΈ.
Π ΠΈΡΡΠ½ΠΎΠΊ 2. MIG ΡΠ²Π°ΡΠΊΠ° Π΄Π²ΡΡ ΡΠ°ΡΠΈΠΊΠΎΠ² ΡΡΠ΄ΠΎΠΌ Π΄ΡΡΠ³ Ρ Π΄ΡΡΠ³ΠΎΠΌ ΠΏΠΎ ΠΎΠ΄Π½ΠΎΠΌΡ Ρ Π²ΠΎΠ·ΠΌΠΎΠΆΠ½ΠΎΡΡΡΡ Π²ΡΠ°ΡΠ΅Π½ΠΈΡ ΡΠ²Π°ΡΠΎΡΠ½ΠΎΠΉ Π³ΠΎΠ»ΠΎΠ²ΠΊΠΈ.
Π‘Π²Π°ΡΠΊΠ° Π² ΡΠ·ΠΊΡΡ ΡΠ°Π·Π΄Π΅Π»ΠΊΡ ΠΏΡΠΈ ΠΏΠΎΠΌΠΎΡΠΈ TIG.
TIG ΠΏΠΎΠ·Π²ΠΎΠ»ΡΠ΅Ρ ΠΏΠΎΠ»ΡΡΠΈΡΡ Π²ΡΡΠΎΠΊΠΎΠΊΠ°ΡΠ΅ΡΡΠ²Π΅Π½Π½ΡΠΉ ΠΌΠ΅ΡΠ°Π»Π» ΡΠ²Π° Π²ΠΎ Π²ΡΠ΅Ρ ΠΏΠΎΠ»ΠΎΠΆΠ΅Π½ΠΈΡΡ ΡΠ²Π°ΡΠΊΠΈ. ΠΡΠΎ ΠΎΡΠΎΠ±Π΅Π½Π½ΠΎ ΠΏΠΎΠ»Π΅Π·Π½ΠΎ ΠΏΡΠΈ ΡΠ²Π°ΡΠΊΠ΅ Π² ΡΡΡΠ΄Π½ΠΎΠ΄ΠΎΡΡΡΠΏΠ½ΡΡ ΠΌΠ΅ΡΡΠ°Ρ ΠΈ Π½Π΅ ΠΏΠΎΠ²ΠΎΡΠΎΡΠ½ΡΡ ΡΠ²ΠΎΠ², Ρ ΠΎΡΡ Ρ Π΄ΡΡΠ³ΠΎΠΉ ΡΡΠΎΡΠΎΠ½Ρ ΠΈΠΌΠ΅Π΅Ρ Π½ΠΈΠ·ΠΊΡΡ ΠΏΡΠΎΠΈΠ·Π²ΠΎΠ΄ΠΈΡΠ΅Π»ΡΠ½ΠΎΡΡΡ. ΠΠ°ΠΈΠ±ΠΎΠ»Π΅Π΅ Π²Π°ΠΆΠ½ΡΠΌ ΡΠ°ΠΊΡΠΎΡΠΎΠΌ ΠΏΠΎΠ»ΡΡΠ΅Π½ΠΈΠ΅ ΠΊΠ°ΡΠ΅ΡΡΠ²Π΅Π½Π½ΠΎΠ³ΠΎ ΡΠΎΠ΅Π΄ΠΈΠ½Π΅Π½ΠΈΠ΅ Π΅ΡΡΡ ΠΊΠ°ΡΠ΅ΡΡΠ²ΠΎ Π³Π°Π·ΠΎΠ²ΠΎΠΉ Π·Π°ΡΠΈΡΡ, ΡΠ°ΠΊΠΆΠ΅ Π½Π΅ΠΎΠ±Ρ ΠΎΠ΄ΠΈΠΌΠΎ ΠΎΠ±Π΅ΡΠΏΠ΅ΡΠΈΡΡ Π΄ΠΎΡΡΠΈΠΆΠ΅Π½ΠΈΠ΅ Π΄ΡΠ³ΠΈ ΠΊΠΎΡΠ½Ρ ΡΠ²Π°. ΠΡΠΎΡ ΠΌΠ΅ΡΠΎΠ΄ ΠΈΡΠΏΠΎΠ»ΡΠ·ΡΠ΅ΡΡΡ Π² ΠΎΡΠ½ΠΎΠ²Π½ΠΎΠΌ Π΄Π»Ρ Π½Π΅ΡΠΆΠ°Π²Π΅ΡΡΠ΅ΠΉ ΠΈ Π½ΠΈΠ·ΠΊΠΎΠ»Π΅Π³ΠΈΡΠΎΠ²Π°Π½Π½ΠΎΠΉ ΡΡΠ°Π»Π΅ΠΉ.
Π ΠΈΡΡΠ½ΠΎΠΊ 3. Π‘Π²Π°ΡΠΊΠ° ΠΏΠΎΠ΄ ΡΠ»ΡΡΠΎΠΌ Π² ΡΠ·ΠΊΡΡ ΡΠ°Π·Π΄Π΅Π»ΠΊΡ
Π‘Π²Π°ΡΠΊΠ° Π² ΡΠ·ΠΊΡΡ ΡΠ°Π·Π΄Π΅Π»ΠΊΡ ΠΏΡΠΈ ΠΏΠΎΠΌΠΎΡΠΈ ΡΠ²Π°ΡΠΊΠΈ ΠΏΠΎΠ΄ ΡΠ»ΡΡΠΎΠΌ.
ΠΠΎΠ»ΠΎΠ²ΠΊΠ° Π΄Π»Ρ ΡΠ²Π°ΡΠΊΠΈ ΠΏΠΎΠ΄ ΡΠ»ΡΡΠΎΠΌ Π΄Π»Ρ Π²ΡΠΏΠΎΠ»Π½Π΅Π½ΠΈΡ ΡΠ²Π°ΡΠΊΠΈ Π² ΡΠ·ΠΊΡΡ ΡΠ°Π·Π΄Π΅Π»ΠΊΡ Π΄ΠΎΠ»ΠΆΠ½Π° Π±ΡΡΡ ΡΠ°ΠΌΠ° ΠΏΠΎ ΡΠ΅Π±Π΅ ΡΠ·ΠΊΠΎΠΉ. ΠΡΡΡΠΈΠΌ ΡΠΏΠΎΡΠΎΠ±ΠΎΠΌ ΡΠ²Π»ΡΠ΅ΡΡΡ Π½Π°ΠΏΠ»Π°Π²Π»ΡΡΡ ΡΠ»ΠΎΠΉ Π·Π° ΡΠ»ΠΎΠ΅ΠΌ ΠΏΠΎΠΎΡΠ΅ΡΠ΅Π΄Π½ΠΎ ΡΠ»Π΅Π²Π° ΠΈ ΡΠΏΡΠ°Π²Π°.
ΠΠ»Π΅ΠΊΡΡΠΎΠ΄ Π΄ΠΎΠ»ΠΆΠ΅Π½ Π±ΡΡΡ ΡΠ°ΡΠΏΠΎΠ»ΠΎΠΆΠ΅Π½ ΠΏΠΎΠ΄ ΡΠ³Π»ΠΎΠΌ ΠΊ ΡΡΠ΅Π½ΠΊΠ΅ ΡΠ°Π·Π΄Π΅Π»ΠΊΠΈ ΠΈ Π±ΡΡΡ ΡΠΎΡΠ½ΠΎ ΡΡΡΠ°Π½ΠΎΠ²Π»Π΅Π½. ΠΡΠΈ ΠΏΡΠ°Π²ΠΈΠ»ΡΠ½ΠΎΠΌ Π²ΡΠΏΠΎΠ»Π½Π΅Π½ΠΈΠΈ ΡΠ²Π° ΡΠ»Π°ΠΊ ΠΎΡΠΏΠ°Π΄ΡΡ ΡΠ°ΠΌ ΠΏΠΎ ΡΠ΅Π±Π΅, ΡΠ°ΠΊ Π½Π°ΠΏΡΠΈΠΌΠ΅Ρ, ΠΏΡΠΈ ΡΠ²Π°ΡΠΊΠ΅ ΡΠΈΠ»ΠΈΠ½Π΄ΡΠΈΡΠ΅ΡΠΊΠΈΡ ΠΈΠ·Π΄Π΅Π»ΠΈΠΉ Ρ ΠΈΡ Π²ΡΠ°ΡΠ΅Π½ΠΈΠ΅ΠΌ β ΡΠ»Π°ΠΊ Π²ΡΠΏΠ°Π΄Π΅Ρ ΡΠ°ΠΌ ΠΏΠΎ ΡΠ΅Π±Π΅.
2. ΠΠ»Π΅ΠΊΡΡΠΎΠ΄ΡΠ³ΠΎΠ²Π°Ρ ΡΠ²Π°ΡΠΊΠ° ΠΏΡΠΈ ΠΏΠΎΠΌΠΎΡΠΈ ΡΠΎΠ±ΠΎΡΠ°.
Π ΠΎΠ±ΠΎΡΠΈΠ·ΠΈΡΠΎΠ²Π°Π½Π½Π°Ρ ΡΠ²Π°ΡΠΎΡΠ½Π°Ρ ΠΏΠΎΠ·ΠΈΡΠΈΡ.
Π ΠΎΠ±ΠΎΡΠΈΠ·ΠΈΡΠΎΠ²Π°Π½Π½Π°Ρ ΡΠ²Π°ΡΠΎΡΠ½Π°Ρ ΠΏΠΎΠ·ΠΈΡΠΈΡ ΠΎΠ±ΡΡΠ½ΠΎ ΡΠΎΡΡΠΎΠΈΡ ΠΈΠ· ΡΠΎΠ±ΠΎΡΠ° Ρ Π΅Π³ΠΎ ΡΠΏΡΠ°Π²Π»ΡΡΡΠΈΠΌ ΠΎΠ±ΠΎΡΡΠ΄ΠΎΠ²Π°Π½ΠΈΠ΅ΠΌ, ΠΌΠ°Π½ΠΈΠΏΡΠ»ΡΡΠΎΡΠ° Π·Π°Π³ΠΎΡΠΎΠ²ΠΊΠΈ, ΠΈΡΡΠΎΡΠ½ΠΈΠΊΠ° ΡΠ²Π°ΡΠΎΡΠ½ΠΎΠ³ΠΎ ΡΠΎΠΊΠ° ΠΈ Π΄ΡΡΠ³ΠΎΠ³ΠΎ ΡΠ²Π°ΡΠΎΡΠ½ΠΎΠ³ΠΎ ΠΎΠ±ΠΎΡΡΠ΄ΠΎΠ²Π°Π½ΠΈΡ. Π ΠΎΠ±ΠΎΡ Π² ΠΎΡΠ½ΠΎΠ²Π½ΠΎΠΌ ΠΈΠΌΠ΅Π΅Ρ ΡΠ΅ΡΡΡ ΠΎΡΠ΅ΠΉ Π΄Π²ΠΈΠΆΠ΅Π½ΠΈΡ, Π½ΠΎ ΡΠ°ΠΊΠΆΠ΅ ΠΌΠΎΠΆΠ΅Ρ Π΄ΠΎΠ±Π°Π²Π»ΡΡΡΡΡ ΠΎΠ΄Π½Π° ΠΈΠ»ΠΈ Π±ΠΎΠ»ΡΡΠ΅ ΠΎΡΠ΅ΠΉ Π½Π° ΠΌΠ°Π½ΠΈΠΏΡΠ»ΡΡΠΎΡΠ΅ Π·Π°Π³ΠΎΡΠΎΠ²ΠΎΠΊ. ΠΠ°Π½ΠΈΠΏΡΠ»ΡΡΠΎΡ ΠΌΠΎΠΆΠ΅Ρ ΠΏΡΠ΅Π΄ΡΡΠ°Π²Π»ΡΡΡ Π΄Π²ΡΡ ΡΡΠΎΡΠΎΠ½Π½ΡΡ ΠΊΠΎΠ½ΡΡΡΡΠΊΡΠΈΡ, ΠΏΠΎΠΊΠ° ΠΎΠΏΠ΅ΡΠ°ΡΠΎΡ ΠΌΠΎΠ½ΡΠΈΡΡΠ΅Ρ Π·Π°Π³ΠΎΡΠΎΠ²ΠΊΠΈ Π½Π° ΠΎΠ΄Π½ΠΎΠΉ ΡΡΠΎΡΠΎΠ½Π΅, ΡΠΎΠ±ΠΎΡ Π²ΡΠΏΠΎΠ»Π½ΡΠ΅Ρ ΡΠ²Π°ΡΠΊΡ Π½Π° Π΄ΡΡΠ³ΠΎΠΉ ΡΡΠΎΡΠΎΠ½Π΅, ΠΏΠΎΡΠΎΠΌ ΡΡΠΎΡΠΎΠ½Ρ ΠΌΠ΅Π½ΡΡΡΡΡ, ΠΊΠ°ΠΊ ΠΏΠΎΠΊΠ°Π·Π°Π½ΠΎ Π½Π° Π ΠΈΡ. 4.
Π ΠΈΡΡΠ½ΠΎΠΊ 4. Π ΠΎΠ±ΠΎΡΠΈΠ·ΠΈΡΠΎΠ²Π°Π½Π½ΡΠΉ ΠΊΠΎΠΌΠΏΠ»Π΅ΠΊΡ
ΠΡΠΎΠ³ΡΠ°ΠΌΠΌΠΈΡΠΎΠ²Π°Π½ΠΈΠ΅ ΡΠΎΠ±ΠΎΡΠ°.
Π ΠΎΠ±ΠΎΡ ΠΏΡΠΎΠ³ΡΠ°ΠΌΠΌΠΈΡΡΠ΅ΡΡΡ Π΄Π»Ρ ΡΠ²Π°ΡΠΊΠΈ Ρ ΠΎΠ΄Π½ΠΎΠΉ ΡΠΎΡΠΊΠΈ Π² Π΄ΡΡΠ³ΡΡ ΠΏΡΡΠΌΠΎ Π½Π° Π·Π°Π³ΠΎΡΠΎΠ²ΠΊΠ΅. ΠΠΏΠ΅ΡΠ°ΡΠΎΡ ΡΠΏΡΠ°Π²Π»ΡΠ΅Ρ ΡΠΎΠ±ΠΎΡΠΎΠΌ ΠΏΡΠΈ ΠΏΠΎΠΌΠΎΡΠΈ Π΄ΠΆΠΎΠΉΡΡΠΈΠΊΠ° ΠΈ ΠΎΠΏΡΠ΅Π΄Π΅Π»ΡΠ΅Ρ ΡΠ°Π·Π½ΡΠ΅ ΠΏΠΎΠ·ΠΈΡΠΈΠΈ ΠΈΠ½ΡΡΡΡΠΌΠ΅Π½ΡΠ°, Π½Π°ΠΏΡΠ°Π²Π»Π΅Π½ΠΈΡ, ΡΠ°ΠΌ, Π³Π΄Π΅ ΡΠΎΠ±ΠΎΡ ΠΈΠ·ΠΌΠ΅Π½ΡΠ΅Ρ Π½Π°ΠΏΡΠ°Π²Π»Π΅Π½ΠΈΠ΅, ΠΈΠ·ΠΌΠ΅Π½ΡΠ΅Ρ ΡΠ²Π°ΡΠΎΡΠ½ΡΠ΅ ΠΏΠ°ΡΠ°ΠΌΠ΅ΡΡΡ ΠΈΠ»ΠΈ ΠΎΠΏΡΠ΅Π΄Π΅Π»ΡΠ΅Ρ Π½Π°ΡΠ°Π»ΠΎ ΠΈΠ»ΠΈ ΠΊΠΎΠ½Π΅Ρ ΡΠ²Π°ΡΠΊΠΈ. ΠΠΎΠΎΡΠ΄ΠΈΠ½Π°ΡΡ ΠΏΠΎΠ·ΠΈΡΠΈΠΉ Π²ΠΌΠ΅ΡΡΠ΅ Ρ Π΄ΠΎΠΏΠΎΠ»Π½ΠΈΡΠ΅Π»ΡΠ½ΡΠΌΠΈ ΠΈΠ½ΡΡΡΡΠΊΡΠΈΡΠΌΠΈ ΡΠΎΡ ΡΠ°Π½ΡΠ΅ΡΡΡ Π² ΠΏΠ°ΠΌΡΡΠΈ ΡΠΎΠ±ΠΎΡΠ°. ΠΠ»Ρ Π΄ΡΠ³ΠΎΠ²ΠΎΠΉ ΡΠ²Π°ΡΠΊΠΈ Π²Π°ΠΆΠ½ΠΎ Π½Π΅ ΡΠΎΠ»ΡΠΊΠΎ ΠΏΠΎΠ·ΠΈΡΠΈΠΈ ΡΠ»Π΅ΠΊΡΡΠΎΠ΄Π°, Π½ΠΎ ΡΠ°ΠΊΠΆΠ΅ Π²Π°ΠΆΠ΅Π½ ΡΠ³ΠΎΠ» Π½Π°ΠΊΠ»ΠΎΠ½Π° ΠΈ Π²ΡΠ»Π΅Ρ ΡΠ»Π΅ΠΊΡΡΠΎΠ΄Π°. ΠΡΡΠ³ΠΈΠ΅ Π΄Π°Π½Π½ΡΠ΅ ΡΠ²Π°ΡΠΊΠΈ, ΡΠ°ΠΊΠΈΠ΅ ΠΊΠ°ΠΊ: ΡΠΊΠΎΡΠΎΡΡΡ ΠΏΠΎΠ΄Π°ΡΠΈ ΠΏΡΠΎΠ²ΠΎΠ»ΠΎΠΊΠΈ, Π½Π°ΠΏΡΡΠΆΠ΅Π½ΠΈΠ΅ ΠΈ ΡΠΊΠΎΡΠΎΡΡΡ ΡΠ²Π°ΡΠΊΠΈ ΡΠ°ΠΊΠΆΠ΅ ΠΏΡΠΎΠ³ΡΠ°ΠΌΠΌΠΈΡΡΡΡΡΡ Π² ΠΏΠ°ΠΌΡΡΡ ΡΠΎΠ±ΠΎΡΠ°. ΠΡΠ»ΠΈ Π½Π΅ΠΎΠ±Ρ ΠΎΠ΄ΠΈΠΌΠΎ ΠΊΠΎΠ»Π΅Π±Π°Π½ΠΈΠ΅, ΡΠΎ ΠΎΠ½ΠΎ ΠΌΠΎΠΆΠ΅Ρ Π±ΡΡΡ ΡΠ΅Π°Π»ΠΈΠ·ΠΎΠ²Π°Π½ΠΎ Π³ΠΎΠ»ΠΎΠ²Π½ΡΠΌ Π΄Π²ΠΈΠΆΠ΅Π½ΠΈΠ΅ΠΌ ΡΠΎΠ±ΠΎΡΠ°.
Π ΡΠΎΠ±ΠΎΡΠΈΠ·ΠΈΡΠΎΠ²Π°Π½Π½ΡΠΉ ΠΊΠΎΠΌΠΏΠ»Π΅ΠΊΡ ΠΎΠ±ΡΡΠ½ΠΎ Π²ΠΊΠ»ΡΡΠ°ΡΡ ΠΌΠ°Π½ΠΈΠΏΡΠ»ΡΡΠΎΡ Π΄Π»Ρ ΠΏΠΎΠ·ΠΈΡΠΈΠΎΠ½ΠΈΡΠΎΠ²Π°Π½ΠΈΡ Π·Π°Π³ΠΎΡΠΎΠ²ΠΊΠΈ Π½Π΅ ΡΠΎΠ»ΡΠΊΠΎ Π΄Π»Ρ ΠΎΠ±Π΅ΡΠΏΠ΅ΡΠ΅Π½ΠΈΡ Π΄ΠΎΡΡΠΈΠΆΠ΅Π½ΠΈΡ ΡΠΎΠ±ΠΎΡΠΎΠΌ Π²ΡΠ΅Ρ Π½Π΅ΠΎΠ±Ρ ΠΎΠ΄ΠΈΠΌΡΡ ΠΌΠ΅ΡΡ, Π½ΠΎ ΠΈ Π²ΡΠΏΠΎΠ»Π½ΡΡΡ ΡΠ²Π°ΡΠΎΡΠ½ΡΠ΅ ΡΠ²Ρ Π² ΠΎΠΏΡΠΈΠΌΠ°Π»ΡΠ½ΠΎΠΌ ΠΏΠΎΠ»ΠΎΠΆΠ΅Π½ΠΈΠΈ. Π‘Π²Π°ΡΠΈΠ²Π°Π΅ΠΌΠ°Ρ Π΄Π΅ΡΠ°Π»Ρ ΠΌΠΎΠΆΠ΅Ρ ΡΠ°ΠΌΠ° Π²ΡΠΏΠΎΠ»Π½ΠΈΡΡ Π½Π΅ΠΎΠ±Ρ ΠΎΠ΄ΠΈΠΌΡΠ΅ Π΄Π²ΠΈΠΆΠ΅Π½ΠΈΡ.
ΠΡΠΎΠ³ΡΠ°ΠΌΠΌΠΈΡΠΎΠ²Π°Π½ΠΈΠ΅ ΠΎΠ±ΡΡΠ½ΠΎ ΠΏΡΠΎΡ ΠΎΠ΄ΠΈΠΌ ΠΏΡΡΠΌΠΎ ΠΏΠΎ ΡΠ²Π°ΡΠΈΠ²Π°Π΅ΠΌΠΎΠΉ Π΄Π΅ΡΠ°Π»ΠΈ (ΠΎn-line), Π½ΠΎ ΡΠ°ΠΊΠΆΠ΅ ΠΌΠΎΠΆΠ΅Ρ Π±ΡΡΡ Π²ΡΠΏΠΎΠ»Π½Π΅Π½Π° ΡΠ°ΡΡΡ ΠΏΡΠΎΠ³ΡΠ°ΠΌΠΌΡ ΠΏΡΠΈ ΠΏΠΎΠΌΠΎΡΠΈ ΡΠΏΠ΅ΡΠΈΠ°Π»ΡΠ½ΠΎΠ³ΠΎ ΠΏΡΠΎΠ³ΡΠ°ΠΌΠΌΠ½ΠΎΠ³ΠΎ ΠΎΠ±Π΅ΡΠΏΠ΅ΡΠ΅Π½ΠΈΡ ΠΈ ΠΎΡΠ΄Π΅Π»ΡΠ½ΠΎΠ³ΠΎ ΠΊΠΎΠΌΠΏΡΡΡΠ΅ΡΠ° (ΠΎff-line). Off-line ΠΏΡΠΎΠ³ΡΠ°ΠΌΠΌΠΈΡΠΎΠ²Π°Π½ΠΈΠ΅ ΠΏΡΠΈΠΌΠ΅Π½ΡΡΡΡ Π² ΡΠΎΠΌ ΡΠ»ΡΡΠ°Π΅, Π΅ΡΠ»ΠΈ Π½Π΅Ρ Π²ΠΎΠ·ΠΌΠΎΠΆΠ½ΠΎΡΡΠΈ ΠΎΡΡΠ°Π½ΠΎΠ²ΠΊΠΈ ΡΠΎΠ±ΠΎΡΠΈΠ·ΠΈΡΠΎΠ²Π°Π½Π½ΠΎΠ³ΠΎ ΠΊΠΎΠΌΠΏΠ»Π΅ΠΊΡΠ° ΠΈΠ»ΠΈ Π΄Π»Ρ ΠΈΠ·Π±Π΅Π³Π°Π½ΠΈΡ Π΄ΠΎΡΠΎΠ³ΠΎΡΡΠΎΡΡΠ΅Π³ΠΎ ΠΏΡΠΎΡΡΠΎΡ. ΠΡΠΈ ΡΠ²Π°ΡΠΊΠ΅ Π±ΠΎΠ»ΡΡΠΈΡ Π΄Π΅ΡΠ°Π»Π΅ΠΉ ΡΠ²Π°ΡΠΊΠ° ΠΌΠΎΠΆΠ΅Ρ Π·Π°Π½ΠΈΠΌΠ°ΡΡ ΡΠ°ΡΡ, Π½ΠΎ ΠΏΡΠΎΠ³ΡΠ°ΠΌΠΌΠΈΡΠΎΠ²Π°Π½ΠΈΠ΅ ΠΌΠΈΠ½ΡΡΡ ΡΠ²Π°ΡΠΊΠΈ, ΡΠ°ΠΊΠΆΠ΅ Π·Π°Π½ΠΈΠΌΠ°Π΅Ρ ΡΠ°ΡΡ.
Π‘Π°ΠΌΡΠΌ ΠΏΡΠΎΠ΄Π²ΠΈΠ½ΡΡΡΠΌ ΡΠΏΠΎΡΠΎΠ±ΠΎΠΌ ΠΎff-line ΠΏΡΠΎΠ³ΡΠ°ΠΌΠΌΠΈΡΠΎΠ²Π°Π½ΠΈΡ ΡΠ²Π»ΡΠ΅ΡΡΡ ΠΈΡΠΏΠΎΠ»ΡΠ·ΠΎΠ²Π°Π½ΠΈΠ΅ 3Π Π³ΡΠ°ΡΠΈΠΊΠΈ. Π‘ ΠΏΠΎΠΌΠΎΡΡΡ ΡΠΏΠ΅ΡΠΈΠ°Π»ΡΠ½ΠΎΠ³ΠΎ ΠΏΡΠΎΠ³ΡΠ°ΠΌΠΌΠ½ΠΎΠ³ΠΎ ΠΎΠ±Π΅ΡΠΏΠ΅ΡΠ΅Π½ΠΈΡ, ΠΊΠΎΡΠΎΡΠΎΠ΅ ΡΠΎΠ΄Π΅ΡΠΆΠΈΡ Π² ΡΠ΅Π±Π΅ Π²ΡΡ ΠΈΠ½ΡΠΎΡΠΌΠ°ΡΠΈΡ ΠΎ ΡΠΎΠ±ΠΎΡΠ΅ ΠΈ ΠΎ Π·Π°Π³ΠΎΡΠΎΠ²ΠΊΠ΅, Π²ΡΠ΅ Π½Π΅ΠΎΠ±Ρ ΠΎΠ΄ΠΈΠΌΡΠ΅ ΠΏΠ΅ΡΠ΅Π΄Π²ΠΈΠΆΠ΅Π½ΠΈΠ΅ ΠΌΠΎΠ΄Π΅Π»ΠΈΡΡΡΡΡΡ ΠΏΡΡΠΌΠΎ Π½Π° ΡΠΊΡΠ°Π½Π΅. ΠΠΎΠ½Π΅ΡΠ½ΠΎ, ΡΠ»Π΅Π΄ΡΠ΅Ρ ΠΈΡΠΏΠΎΠ»ΡΠ·ΠΎΠ²Π°ΡΡ Π‘ΠΠΠ ΡΠΈΡΡΠ΅ΠΌΡ Π΄Π»Ρ ΠΌΠΎΠ΄Π΅Π»ΠΈΡΠΎΠ²Π°Π½ΠΈΡ Π·Π°Π³ΠΎΡΠΎΠ²ΠΎΠΊ, Π° ΠΏΠΎΡΠΎΠΌ ΠΈΡ ΠΊΠΎΠ½Π²Π΅ΡΡΠΈΡΠΎΠ²Π°ΡΡ Π΄Π»Ρ ΡΡΠ΅Π½ΠΈΡ ΠΏΡΠΎΠ³ΡΠ°ΠΌΠΌΠ½ΡΠΌ ΠΎΠ±Π΅ΡΠΏΠ΅ΡΠ΅Π½ΠΈΠ΅ΠΌ ΠΏΡΠΈΠ²Π΅Π΄Π΅Π½Π½ΡΠΌ Π²ΡΡΠ΅. Β ΠΡΠΎ ΡΠΈΠ»ΡΠ½ΠΎ ΡΠΎΠΊΡΠ°ΡΠ°Π΅Ρ Π²ΡΠ΅ΠΌΡ ΠΏΡΠΎΡΡΠΎΡ ΡΠΎΠ±ΠΎΡΠ°.
ΠΡΡ ΠΎΠ΄Π½ΠΈΠΌ Π²ΠΈΠ΄ΠΎΠΌ ΠΎff-line ΠΏΡΠΎΠ³ΡΠ°ΠΌΠΌΠΈΡΠΎΠ²Π°Π½ΠΈΡ ΡΠ²Π»ΡΠ΅ΡΡΡ ΠΊΠΎΡΡΠ΅ΠΊΡΠΈΡΠΎΠ²Π°Π½ΠΈΠ΅ ΠΊΠΎΠΎΡΠ΄ΠΈΠ½Π°Ρ ΡΠΎΡΠ΅ΠΊ Π² ΡΠΎΠΎΡΠ²Π΅ΡΡΡΠ²ΠΈΠΈ Ρ Π΄ΡΡΠ³ΠΈΠΌ ΠΈΠ·Π΄Π΅Π»ΠΈΠ΅ΠΌ, Π½ΠΎ ΡΡΠΎΡ Β ΡΠΏΠΎΡΠΎΠ± ΡΡΠ΅Π±ΡΠ΅Ρ Π²ΡΡΠΎΠΊΠΎΠΉ ΡΡΠ΅ΠΏΠ΅Π½ΠΈ ΠΏΠΎΠ΄ΠΎΠ±Π½ΠΎΡΡΠΈ ΠΈΠ·Π΄Π΅Π»ΠΈΠΉ.
Π‘Π²Π°ΡΠΊΠ° Π² Π³ΠΈΠ±ΠΊΠΈΡ ΠΏΡΠΎΠΈΠ·Π²ΠΎΠ΄ΡΡΠ²Π΅Π½Π½ΡΡ ΡΠΈΡΡΠ΅ΠΌΠ°Ρ .
Π‘Π²Π°ΡΠΊΠ° Π² Π³ΠΈΠ±ΠΊΠΈΡ ΠΏΡΠΎΠΈΠ·Π²ΠΎΠ΄ΡΡΠ²Π΅Π½Π½ΡΡ ΡΠΈΡΡΠ΅ΠΌΠ°Ρ Π²ΠΊΠ»ΡΡΠ°Π΅Ρ ΡΠΈΡΡΠ΅ΠΌΡ ΡΠΈΠΊΡΠ°ΡΠΈΠΈ Π·Π°Π³ΠΎΡΠΎΠ²ΠΎΠΊ, Π½Π΅ΡΠΊΠΎΠ»ΡΠΊΠΎ ΠΏΡΡΠ΅ΠΉ ΡΡΡΠ°Π½ΠΎΠ²ΠΊΠΈ Π·Π°Π³ΠΎΡΠΎΠ²ΠΎΠΊ ΠΈ Π½Π΅ΡΠΊΠΎΠ»ΡΠΊΠΎ ΠΏΡΡΠ΅ΠΉ ΡΠ½ΡΡΠΈΡ ΠΈΠ·Π΄Π΅Π»ΠΈΠΉ. Π‘ΠΈΡΡΠ΅ΠΌΡ ΠΌΠΎΠ³ΡΡ ΠΈΡΠΏΠΎΠ»ΡΠ·ΠΎΠ²Π°ΡΡ ΠΎΠ΄ΠΈΠ½ ΠΈΠ»ΠΈ Π±ΠΎΠ»ΡΡΠ΅ ΡΠΎΠ±ΠΎΡΠΎΠ² ΠΈ Π½Π΅ΡΠΊΠΎΠ»ΡΠΊΠΎ ΡΠ°Π·Π½ΡΡ Π²ΠΈΠ΄ΠΎΠ² ΠΈΠ·Π΄Π΅Π»ΠΈΠΉ ΠΊΠΎΡΠΎΡΡΠ΅ ΠΌΠΎΠ³ΡΡ Π±ΡΡΡ ΡΠ²Π°ΡΠ΅Π½Ρ ΠΎΠ΄Π½ΠΎ Π· Π΄ΡΡΠ³ΠΈΠΌ Ρ ΠΎΡΠ΅Π½Ρ ΠΊΠΎΡΠΎΡΠΊΠΈΠΌ Π²ΡΠ΅ΠΌΠ΅Π½Π΅ΠΌ ΠΏΠ΅ΡΠ΅Π½Π°Π»Π°Π΄ΠΊΠΈ. ΠΡΠΈ ΠΈΡΠΏΠΎΠ»ΡΠ·ΠΎΠ²Π°Π½ΠΈΠΈ ΠΏΡΠΎΠΌΠ΅ΠΆΡΡΠΎΡΠ½ΠΎΠ³ΠΎ Π½Π°ΠΊΠΎΠΏΠ»Π΅Π½ΠΈΡ ΠΏΡΠΎΠΈΠ·Π²ΠΎΠ΄ΡΡΠ²ΠΎ ΠΌΠΎΠΆΠ΅Ρ ΠΏΡΠΎΡ ΠΎΠ΄ΠΈΡΡ Π±Π΅Π· ΠΎΡΡΠ°Π½ΠΎΠ²ΠΎΠΊ. ΠΡΡ ΡΠΈΡΡΠ΅ΠΌΠ° ΠΏΠΎΠ΄ΡΠΈΠ½ΡΠ΅ΡΡΡ Π³ΠΎΠ»ΠΎΠ²Π½ΠΎΠΉ ΠΊΠΎΠΌΠΏΡΡΡΠ΅ΡΡ.
Π ΠΈΡΡΠ½ΠΎΠΊ 5. ΠΠΈΠ±ΠΊΠΈΠ΅ ΠΏΡΠΎΠΈΠ·Π²ΠΎΠ΄ΡΡΠ²Π΅Π½Π½ΡΠ΅ ΡΠΈΡΡΠ΅ΠΌΡ
Π£Π²Π΅Π»ΠΈΡΠ΅Π½ΠΈΠ΅ Π·ΠΎΠ½Ρ ΡΠ°Π±ΠΎΡΡ ΡΠΎΠ±ΠΎΡΠ°.
ΠΡΡΡ Π½Π΅ΡΠΊΠΎΠ»ΡΠΊΠΎ ΡΠΏΠΎΡΠΎΠ±ΠΎΠ² Π΄Π»Ρ ΡΠ²Π΅Π»ΠΈΡΠ΅Π½ΠΈΡ Π·ΠΎΠ½Ρ ΡΠ°Π±ΠΎΡΡ ΡΠΎΠ±ΠΎΡΠ°, ΡΡΠΎ ΠΌΠΎΠΆΠ΅Ρ ΠΏΡΠΈΠ³ΠΎΠ΄ΠΈΡΡΡ ΠΏΡΠΈ ΡΠ²Π°ΡΠΊΠ΅ Π±ΠΎΠ»ΡΡΠΈΡ ΠΈΠ·Π΄Π΅Π»ΠΈΠΉ, ΡΡΡΠ°Π½ΠΎΠ²ΠΈΡΡ ΡΠΎΠ±ΠΎΡ Π½Π° ΡΠ΅Π»ΡΡΠΎΠ²ΡΠ΅ Π½Π°ΠΏΡΠ°Π²Π»ΡΡΡΠΈΠ΅ ΠΈΠ»ΠΈ ΠΏΠΎΠ΄Π²Π΅ΡΠΈΡΡ Π΅Π³ΠΎ Π½Π° ΠΏΠ΅ΡΠ΅Π΄Π²ΠΈΠΆΠ½ΠΎΠΉ ΠΏΠΎΡΡΠ°Π». ΠΡΠΎ ΠΎΠ·Π½Π°ΡΠ°Π΅Ρ, ΡΡΠΎ ΠΊ ΡΠ΅ΡΡΠΈ ΠΎΡΡΠΌ ΡΠΎΠ±ΠΎΡΠ° ΠΈ Π΄Π²ΡΠΌ ΠΎΡΡΠΌ ΠΌΠ°Π½ΠΈΠΏΡΠ»ΡΡΠΎΡΠ° Π΄ΠΎΠ±Π°Π²ΠΈΡΡΡ Π΅ΡΠ΅ ΠΎΠ΄Π½Π° ΠΎΡΡ ΠΏΠ΅ΡΠ΅ΠΌΠ΅ΡΠ΅Π½ΠΈΡ ΡΠΎΠ±ΠΎΡΠ°, ΠΌΡ ΡΠΆΠ΅ ΠΏΠΎΠ»ΡΡΠΈΠ»ΠΈ Π΄ΠΎΠΏΠΎΠ»Π½ΠΈΡΠ΅Π»ΡΠ½ΠΎ ΡΡΠΈ ΠΎΡΠΈ Π΄Π²ΠΈΠΆΠ΅Π½ΠΈΡ. Π‘ΠΎΠ²ΡΠ΅ΠΌΠ΅Π½Π½ΡΠ΅ ΡΠΈΡΡΠ΅ΠΌΡ ΡΠΏΡΠ°Π²Π»Π΅Π½ΠΈΡ ΡΠΎΠ±ΠΎΡΠ° ΠΌΠΎΠΆΠ΅Ρ ΠΎΠ±Π΅ΡΠΏΠ΅ΡΠΈΡΡ ΠΏΠΎΠ»Π½ΡΡ ΠΊΠΎΠΎΡΠ΄ΠΈΠ½Π°ΡΠΈΡ Π΄Π²ΠΈΠΆΠ΅Π½ΠΈΠ΅ Π½Π° Π²ΡΠ΅Ρ ΠΎΡΡΡ , ΡΠΎ Π΅ΡΡΡ ΡΠΎΠ±ΡΡΠ²Π΅Π½Π½ΡΡ ΠΎΡΠ΅ΠΉ ΡΠΎΠ±ΠΎΡΠ° ΠΈ Π²Π½Π΅ΡΠ½ΠΈΡ ΠΎΡΠ΅ΠΉ.
Π Π°ΡΡΠΈΡΠ΅Π½Π½ΡΠΉ ΡΠ°Π±ΠΎΡΠΈΠΉ Π΄ΠΈΠ°ΠΏΠ°Π·ΠΎΠ½ ΡΠ°ΠΊΠΆΠ΅ ΠΌΠΎΠΆΠ΅Ρ Π±ΡΡΡ ΠΈΡΠΏΠΎΠ»ΡΠ·ΠΎΠ²Π°Π½ Π΄Π»Ρ ΠΏΠ΅ΡΠ΅Π΄Π²ΠΈΠΆΠ΅Π½ΠΈΡ ΡΠΎΠ±ΠΎΡΠ° ΠΌΠ΅ΠΆΠ΄Ρ ΠΌΠ΅ΡΡΠ°ΠΌΠΈ ΡΠ²Π°ΡΠΊΠΈ, ΡΠ°ΠΊ ΡΡΠΎ ΠΎΠ½ ΠΌΠΎΠΆΠ΅Ρ Π±ΡΡΡ ΠΈΡΠΏΠΎΠ»ΡΠ·ΠΎΠ²Π°Π½ Ρ Π½Π΅ΡΠΊΠΎΠ»ΡΠΊΠΈΠΌΠΈ ΠΈΠ·Π΄Π΅Π»ΠΈΡΠΌΠΈ.
ΠΠ΅Π·ΠΎΠΏΠ°ΡΠ½ΠΎΡΡΡ.
Π ΠΎΠ±ΠΎΡΠΈΠ·ΠΈΡΠΎΠ²Π°Π½Π½ΡΠ΅ ΠΊΠΎΠΌΠΏΠ»Π΅ΠΊΡΡ ΠΎΠ³ΠΎΡΠΎΠΆΠ΅Π½Ρ Π΄Π»Ρ ΠΏΡΠ΅Π΄ΡΠΏΡΠ΅ΠΆΠ΄Π΅Π½ΠΈΡ Π²ΠΎΠ·ΠΌΠΎΠΆΠ½ΠΎΡΡΠΈ ΡΡΠ°Π²ΠΌΠΈΡΠΎΠ²Π°Π½ΠΈΡ Π»ΡΠ΄Π΅ΠΉ. ΠΠ΅ΡΠ°Π½ΠΊΡΠΈΠΎΠ½ΠΈΡΠΎΠ²Π°Π½Π½ΡΠΉ ΠΏΠ΅ΡΡΠΎΠ½Π°Π» Π½Π΅ ΠΌΠΎΠΆΠ΅Ρ Π½Π°Ρ ΠΎΠ΄ΠΈΡΡΡΡ Π² ΠΏΡΠ΅Π΄Π΅Π»Π°Ρ ΡΠ°Π±ΠΎΡΠ΅ΠΉ Π·ΠΎΠ½Ρ ΡΠΎΠ±ΠΎΡΠ°, ΠΏΠΎΠΊΠ° ΠΎΠ½ Π½Π°Ρ ΠΎΠ΄ΠΈΡΡΡ Π² ΡΠΊΡΠΏΠ»ΡΠ°ΡΠ°ΡΠΈΠΈ. ΠΠ±ΡΡΠ½ΠΎΠΉ ΡΠΎΡΠΌΠΎΠΉ Π·Π°ΡΠΈΡΡ ΡΠ²Π»ΡΠ΅ΡΡΡ Π²ΡΡΠΎΠΊΠΈΠΉ Π·Π°Π±ΠΎΡ, Π²Ρ ΠΎΠ΄Ρ Π·Π°ΡΠΈΡΠ΅Π½Ρ ΡΠ²Π΅ΡΠΎΠ²ΡΠΌΠΈ Π»ΡΡΠ°ΠΌΠΈ. ΠΠ΅ΡΠ΅ΡΠ΅ΡΠ΅Π½ΠΈΠ΅ Π»ΡΡΠ° Ρ ΡΠ΅ΠΌ-Π»ΠΈΠ±ΠΎ Π°Π²ΡΠΎΠΌΠ°ΡΠΈΡΠ΅ΡΠΊΠΈ ΠΎΡΡΠ°Π½ΠΎΠ²ΠΈΡ ΠΌΠ°Π½ΠΈΠΏΡΠ»ΡΡΠΎΡ ΠΈ ΡΠΎΠ±ΠΎΡ. Π’ΠΎΠ»ΡΠΊΠΎ ΡΠΏΠ΅ΡΠΈΠ°Π»ΡΠ½ΠΎ ΠΎΠ±ΡΡΠ΅Π½Π½ΡΠ΅ ΠΏΡΠΎΠ³ΡΠ°ΠΌΠΌΠΈΡΡΡ ΠΈΠ»ΠΈ ΡΠ°Π±ΠΎΡΠ½ΠΈΠΊΠΈ ΡΠ΅ΡΠ²ΠΈΡΠ½ΠΎΠΉ ΡΠ»ΡΠΆΠ±Ρ ΠΌΠΎΠ³ΡΡ ΡΠ°Π±ΠΎΡΠ°ΡΡ Π² ΡΠ°Π±ΠΎΡΠ΅ΠΉ Π·ΠΎΠ½Π΅ ΡΠΎΠ±ΠΎΡΠ°, Π΄Π° ΠΈ ΡΠΎ Ρ ΠΎΡΠΎΠ±ΠΎΠΉ Π·Π°ΡΠΈΡΠ½ΠΎΠΉ ΠΏΡΠΎΡΠ΅Π΄ΡΡΠΎΠΉ. ΠΡΠΎΠΌΠ΅ ΡΠΎΠ³ΠΎ, ΠΈΠΌΠ΅ΡΡΡΡ ΠΊΠ½ΠΎΠΏΠΊΠΈ Π°Π²Π°ΡΠΈΠΉΠ½ΠΎΠΉ ΠΎΡΡΠ°Π½ΠΎΠ²ΠΊΠΈ, ΠΊΠΎΡΠΎΡΡΠ΅ Π΄ΠΎΠ»ΠΆΠ½Ρ Π±ΡΡΡ ΠΏΡΠΎΡΡΠΎ ΡΠ±ΡΠΎΡΠ΅Π½Ρ ΠΏΠΎΡΠ»Π΅ Π½Π°ΠΆΠ°ΡΠΈΡ.
ΠΠ½ΡΡΡΡΠΌΠ΅Π½ΡΡ ΠΈ ΡΠ΅Ρ Π½ΠΈΡΠ΅ΡΠΊΠΎΠ΅ ΠΎΠ±ΡΠ»ΡΠΆΠΈΠ²Π°Π½ΠΈΠ΅.
Π‘Π²Π°ΡΠΎΡΠ½ΡΠ΅ Π³ΠΎΡΠ΅Π»ΠΊΠΈ ΠΌΠΎΠ³ΡΡ Π±ΡΡΡ ΠΎΡΠΈΡΠ΅Π½Ρ ΠΎΡ Π±ΡΡΠ·Π³ ΡΠ΅ΡΠ΅Π· ΠΎΠΏΡΠ΅Π΄Π΅Π»Π΅Π½Π½ΡΠ΅ ΠΏΡΠΎΠΌΠ΅ΠΆΡΡΠΊΠΈ Π²ΡΠ΅ΠΌΠ΅Π½ΠΈ. Π ΠΎΠ±ΠΎΡ ΠΏΠ΅ΡΠ΅ΠΌΠ΅ΡΠ°Π΅ΡΡΡ Π² ΡΠΏΠ΅ΡΠΈΠ°Π»ΡΠ½ΠΎΠ΅ ΠΏΠΎΠ»ΠΎΠΆΠ΅Π½ΠΈΠ΅, Π² ΠΊΠΎΡΠΎΡΠΎΠΌ ΡΠ²Π°ΡΠΎΡΠ½ΠΎΠ΅ ΡΠΎΠΏΠ»ΠΎ ΠΌΠ΅Ρ Π°Π½ΠΈΡΠ΅ΡΠΊΠΈ ΠΈΠ»ΠΈ ΠΏΠ½Π΅Π²ΠΌΠ°ΡΠΈΡΠ΅ΡΠΊΠΈ ΠΎΡΠΈΡΠ°Π΅ΡΡΡ. Π‘ΡΡΠ΅ΡΡΠ²ΡΡΡ ΡΠ°ΠΊΠΆΠ΅ ΡΠΈΡΡΠ΅ΠΌΡ ΡΠΌΠ΅Π½Ρ ΠΈΠ½ΡΡΡΡΠΌΠ΅Π½ΡΠ°, Π½Π°ΠΏΡΠΈΠΌΠ΅Ρ: Π·Π°ΠΌΠ΅Π½Ρ ΡΠ²Π°ΡΠΎΡΠ½ΠΎΠΉ Π³ΠΎΡΠ΅Π»ΠΊΠΈ Π½Π° Π΄ΡΡΠ³ΡΡ Π³ΠΎΡΠ΅Π»ΠΊΡ, Π΄Π»Ρ ΠΈΠ·ΠΌΠ΅Π½Π΅Π½ΠΈΡ ΠΏΡΠΎΡΠ΅ΡΡΠ° ΡΠ²Π°ΡΠΊΠΈ ΠΈΠ»ΠΈ Π΄Π°ΠΆΠ΅ Π΄Π»Ρ ΠΏΠ΅ΡΠ΅Ρ ΠΎΠ΄Π° ΠΊ ΡΠΎΠ²Π΅ΡΡΠ΅Π½Π½ΠΎ Π΄ΡΡΠ³ΠΎΠΉ Π·Π°Π΄Π°ΡΠ΅, Π½Π°ΠΏΡΠΈΠΌΠ΅Ρ, ΡΠ»ΠΈΡΠΎΠ²Π°Π½ΠΈΠ΅.
Π’ΠΎΡΠ½ΠΎΡΡΡ.
Π’ΠΎΡΠ΅ΡΠ½Π°Ρ ΡΠ²Π°ΡΠΊΠ° ΡΠΎΠ±ΠΎΡΠ°ΠΌΠΈ ΡΠ²Π»ΡΠ΅ΡΡΡ ΠΏΡΠΈΠ·Π½Π°Π½Π½ΡΠΌ ΠΌΠ΅ΡΠΎΠ΄ΠΎΠΌ, ΠΊΠΎΡΠΎΡΡΠΉ ΡΡΠΏΠ΅ΡΠ½ΠΎ ΠΈΡΠΏΠΎΠ»ΡΠ·ΡΠ΅ΡΡΡ Ρ Π½Π°ΡΠ°Π»Π° 1970-Ρ . ΠΡΠΎ ΠΏΠΎΡΠΎΠΌΡ, ΡΡΠΎ ΡΡΠ΅Π±ΡΠ΅ΠΌΠ°Ρ ΡΠΎΡΠ½ΠΎΡΡΡ ΠΏΠΎΠ·ΠΈΡΠΈΠΎΠ½ΠΈΡΠΎΠ²Π°Π½ΠΈΡ ΡΠΎΡΠ΅ΡΠ½ΡΡ ΡΠ²Π°ΡΠ½ΡΡ ΡΠ²ΠΎΠ² Π²ΡΠ΅Π³ΠΎ +/- 1 ΠΌΠΌ, ΠΊΠΎΡΠΎΡΡΠΉ ΡΠΎΠΎΡΠ²Π΅ΡΡΡΠ²ΠΎΠ²Π°Π» Ρ ΡΠΎΡΠ½ΠΎΡΡΡΡ ΠΏΠΎΠ²ΡΠΎΡΡΠ΅ΠΌΠΎΡΡΠΈ ΠΏΠ΅ΡΠ²ΠΎΠ³ΠΎ ΠΏΠΎΠΊΠΎΠ»Π΅Π½ΠΈΡ ΡΠΎΠ±ΠΎΡΠΎΠ². Π‘Π²Π°ΡΠΎΡΠ½ΡΠ΅ ΠΊΠ»Π΅ΡΠΈ ΡΡΡΠ°Π½Π°Π²Π»ΠΈΠ²Π°ΡΡΡΡ, Π° Π·Π°ΡΠ΅ΠΌ Π·Π°ΠΊΡΡΠ²Π°ΡΡΡΡ, ΡΡΠΎΠ±Ρ ΡΠΆΠ°ΡΡ Π΄Π²Π΅ ΡΠ°ΡΡΠΈ ΠΌΠ΅ΡΠ°Π»Π»Π° β ΠΏΡΠΎΠΈΡΡ ΠΎΠ΄ΠΈΡ ΡΠ²Π°ΡΠΊΠ°.
ΠΡΠΈ Π΄ΡΠ³ΠΎΠ²ΠΎΠΉ ΡΠ²Π°ΡΠΊΠ΅, Π² ΠΎΡΠ»ΠΈΡΠΈΠ΅ ΠΎΡ ΠΊΠΎΠ½ΡΠ°ΠΊΡΠ½ΠΎΠΉ, ΡΡΠ΅Π±ΡΠ΅Ρ Π·Π½Π°ΡΠΈΡΠ΅Π»ΡΠ½ΠΎ Π±ΠΎΠ»Π΅Π΅ ΠΆΠ΅ΡΡΠΊΠΈΠ΅ Π΄ΠΎΠΏΡΡΠΊΠΈ, Π² ΠΎΡΠ½ΠΎΠ²Π½ΠΎΠΌ, ΠΌΠΎΠΆΠ½ΠΎ ΡΠ²Π°ΡΠΈΡΡ Π½Π΅Π±ΠΎΠ»ΡΡΠΈΠ΅ ΠΈ ΡΡΠ΅Π΄Π½ΠΈΠ΅ Π΄Π΅ΡΠ°Π»ΠΈ Π±Π΅Π· ΠΈΡΠΏΠΎΠ»ΡΠ·ΠΎΠ²Π°Π½ΠΈΡ ΡΠΈΡΡΠ΅ΠΌ ΡΠ»Π΅ΠΆΠ΅Π½ΠΈΡ Π·Π° ΡΡΡΠΊΠΎΠΌ. ΠΠ·ΠΌΠ΅Π½Π΅Π½ΠΈΠ΅ Π² ΠΏΠΎΠ»ΠΎΠΆΠ΅Π½ΠΈΠΈ Π΄ΡΠ³ΠΈ ΠΌΠ΅ΠΆΠ΄Ρ ΠΏΠΎΠ·ΠΈΡΠΈΡΠΌΠΈ Π·Π°Π³ΠΎΡΠΎΠ²ΠΊΠΈ Π½Π΅ Π΄ΠΎΠ»ΠΆΠ½ΠΎ ΠΏΡΠ΅Π²ΡΡΠ°ΡΡ, ΠΊΠ°ΠΊ ΠΏΡΠ°Π²ΠΈΠ»ΠΎ +/- 0,5 ΠΌΠΌ, ΠΈ Π΄Π»Ρ Π΄ΠΎΡΡΠΈΠΆΠ΅Π½ΠΈΡ ΡΡΠΎΠΉ ΡΠ΅Π»ΠΈ Π½Π΅ΠΎΠ±Ρ ΠΎΠ΄ΠΈΠΌΡ Π²ΡΡΠΎΠΊΠΎΠ΅ ΠΊΠ°ΡΠ΅ΡΡΠ²ΠΎ Π²ΡΠΏΠΎΠ»Π½Π΅Π½ΠΈΡ Π·Π°Π³ΠΎΡΠΎΠ²ΠΎΠΊ ΠΈ Π²ΡΡΠΎΠΊΠ°Ρ ΡΠΎΡΠ½ΠΎΡΡΡ ΡΠ±ΠΎΡΠΊΠΈ.
Π‘Π²Π°ΡΠΎΡΠ½Π°Ρ ΠΏΡΠΎΠ²ΠΎΠ»ΠΎΠΊΠ° ΡΠ²Π»ΡΠ΅ΡΡΡ ΠΏΠΎΡΠ»Π΅Π΄Π½ΠΈΠΌ Π·Π²Π΅Π½ΠΎΠΌ Π² ΡΠ΅ΠΏΠΈ. ΠΠ»Π΅ΠΊΡΡΠΎΠ΄ ΡΠ΅Π΄ΠΊΠΎ ΡΠ°Π·ΠΌΠ΅ΡΠ°Π΅ΡΡΡ ΠΏΡΡΠΌΠΎ ΠΏΠΎ ΡΠ΅Π½ΡΡΡ, ΠΊΠΎΠ³Π΄Π° ΠΎΠ½ Π²ΡΡ ΠΎΠ΄ΠΈΡ ΠΈΠ· ΠΊΠΎΠ½ΡΠ°ΠΊΡΠ½ΠΎΠ³ΠΎ Π½Π°ΠΊΠΎΠ½Π΅ΡΠ½ΠΈΠΊΠ°. ΠΠΌΠ΅ΡΡΠΎ ΡΡΠΎΠ³ΠΎ, ΡΠ°ΡΡΠΎ ΡΠ»Π΅Π³ΠΊΠ° ΡΠΎΠ³Π½ΡΡ ΠΈ Π΅ΡΠ»ΠΈ ΠΊΠΎΠ½ΡΠ°ΠΊΡΠ½ΡΠΉ Π½Π°ΠΊΠΎΠ½Π΅ΡΠ½ΠΈΠΊ ΠΈΠ·Π½ΠΎΡΠ΅Π½, ΡΡΡΠ΅ΡΡΠ²ΡΠ΅Ρ ΡΠΈΡΠΊ Π²ΡΡ ΠΎΠ΄Π° ΠΈΠ· Π½Π΅ΠΎΠ±Ρ ΠΎΠ΄ΠΈΠΌΡΡ ΡΡΠ΅Π±ΠΎΠ²Π°Π½ΠΈΠΉ Π΄ΠΎΠΏΡΡΠΊΠ°. ΠΠ΅Π·Π½Π°ΡΠΈΡΠ΅Π»ΡΠ½ΡΠΉ ΠΏΡΠ΅Π΄Π²Π°ΡΠΈΡΠ΅Π»ΡΠ½ΡΠΉ ΠΈΠ·Π³ΠΈΠ± ΡΠ²Π°ΡΠΎΡΠ½ΠΎΠΉ ΠΏΡΠΎΠ²ΠΎΠ»ΠΎΠΊΠΈ ΠΏΡΠ΅Π΄Π½Π°Π·Π½Π°ΡΠ΅Π½ Π΄Π»Ρ ΠΎΠ±Π΅ΡΠΏΠ΅ΡΠ΅Π½ΠΈΡ ΡΠΎΠΊΠΎΡΡΠ΅ΠΌΠ° Ρ ΠΊΠΎΠ½ΡΠ°ΠΊΡΠ½ΠΎΠ³ΠΎ Π½Π°ΠΊΠΎΠ½Π΅ΡΠ½ΠΈΠΊΠ°. ΠΠ΄Π½Π°ΠΊΠΎ, ΠΏΡΠΈ ΠΏΡΠΈΠΌΠ΅Π½Π΅Π½ΠΈΠΈ ΡΠ²Π°ΡΠΎΡΠ½ΡΡ ΡΠΎΠ±ΠΎΡΠΎΠ², Π²Π°ΠΆΠ½ΠΎ, ΡΡΠΎΠ±Ρ ΡΡΠΎΡ ΠΏΡΠ΅Π΄Π²Π°ΡΠΈΡΠ΅Π»ΡΠ½ΡΠΉ ΠΈΠ·Π³ΠΈΠ± Π½Π΅ ΡΠ²Π»ΡΠ»ΡΡ ΡΡΠ΅Π·ΠΌΠ΅ΡΠ½ΡΠΌ ΠΈ ΠΊΠΎΠ½ΡΠ°ΠΊΡΠ½ΡΠ΅ Π½Π°ΠΊΠΎΠ½Π΅ΡΠ½ΠΈΠΊΠΈ Π·Π°ΠΌΠ΅Π½ΡΡΡΡΡ Π΄ΠΎΡΡΠ°ΡΠΎΡΠ½ΠΎ ΡΠ°ΡΡΠΎ.
ΠΠ°Ρ ΠΎΠΆΠ΄Π΅Π½ΠΈΠ΅ ΡΠ²Π° ΠΈ ΡΠ»Π΅ΠΆΠ΅Π½ΠΈΠ΅ Π·Π° ΡΠ²ΠΎΠΌ.
Π Π±ΠΎΠ»ΡΡΠΈΠ½ΡΡΠ²Π΅ ΡΠ»ΡΡΠ°Π΅Π² ΠΌΠΎΠΆΠ½ΠΎ ΠΎΠ±Π΅ΡΠΏΠ΅ΡΠΈΡΡ ΡΠΎΡΠ½ΠΎΡΡΡ ΡΠ°Π·ΠΌΠ΅ΡΠ΅Π½ΠΈΠ΅ ΡΠ²Π°ΡΠΎΡΠ½ΡΡ ΡΠ²ΠΎΠ² ΠΈ Π½Π΅ ΠΈΡΠΏΠΎΠ»ΡΠ·ΠΎΠ²Π°ΡΡ ΠΎΠ±ΠΎΡΡΠ΄ΠΎΠ²Π°Π½ΠΈΠ΅ Π΄Π»Ρ ΡΠ»Π΅ΠΆΠ΅Π½ΠΈΡ Π·Π° ΡΠ²ΠΎΠΌ. ΠΠ΄Π½Π°ΠΊΠΎ ΠΏΡΠΈ ΡΠ²Π°ΡΠΊΠ΅ Π±ΠΎΠ»ΡΡΠΈΡ Π΄Π΅ΡΠ°Π»Π΅ΠΉ ΠΎΠ±Π΅ΡΠΏΠ΅ΡΠΈΡΡ Π΄ΠΎΡΡΠ°ΡΠΎΡΠ½ΡΡ ΠΏΠΎΠ²ΡΠΎΡΡΠ΅ΠΌΠΎΡΡΡ ΡΠ°Π·ΠΌΠ΅ΡΠ΅Π½ΠΈΠ΅ ΡΠ²Π°ΡΠΎΡΠ½ΡΡ ΡΠ²ΠΎΠ² Π½Π΅Π²ΠΎΠ·ΠΌΠΎΠΆΠ½ΠΎ ΠΈ, ΠΊΠ°ΠΊ ΡΠ»Π΅Π΄ΡΡΠ²ΠΈΠ΅, Π½Π΅Π²ΠΎΠ·ΠΌΠΎΠΆΠ½ΠΎ Π²ΡΠΏΠΎΠ»Π½ΠΈΡΡ ΡΠ²Π°ΡΠΊΡ.
ΠΠ°Ρ ΠΎΠΆΠ΄Π΅Π½ΠΈΠ΅ ΡΠ²Π°.
Π ΠΏΡΠΎΡΡΠ΅ΠΉΡΠ΅ΠΌ ΡΠ»ΡΡΠ°Π΅ ΡΡΡ ΠΎΠΏΠ΅ΡΠ°ΡΠΈΡ Π½ΡΠΆΠ½ΠΎ ΠΏΡΠΎΠ²ΠΎΠ΄ΠΈΡΡ ΡΠΎΠ»ΡΠΊΠΎ Ρ ΠΎΠ΄Π½ΠΈΠΌ ΡΠ²ΠΎΠΌ Π΄Π»Ρ ΠΎΠΏΡΠ΅Π΄Π΅Π»Π΅Π½ΠΈΡ ΠΌΠ΅ΡΡΠΎ ΡΠ°ΡΠΏΠΎΠ»ΠΎΠΆΠ΅Π½ΠΈΡ. ΠΡΠΎ Π²ΡΠΏΠΎΠ»Π½ΡΠ΅ΡΡΡ ΠΏΠ΅ΡΠ΅Π΄ Π½Π°ΡΠ°Π»ΠΎΠΌ ΡΠ²Π°ΡΠΊΠΈ. Π ΠΎΠ±ΠΎΡ ΠΎΠΏΡΠ΅Π΄Π΅Π»ΡΠ΅Ρ ΠΏΠΎΠ·ΠΈΡΠΈΡ Π² ΠΏΡΠΎΡΡΡΠ°Π½ΡΡΠ²Π΅ ΠΏΡΡΠ΅ΠΌ ΠΊΠ°ΡΠ°Π½ΠΈΡ Π³ΠΎΡΠ΅Π»ΠΊΠΈ (ΡΠ»Π΅ΠΊΡΡΠΈΡΠ΅ΡΠΊΠΎΠ³ΠΎ ΠΊΠΎΠ½ΡΠ°ΠΊΡΠ°) Β Π² ΡΡΠ΅Ρ ΡΠ°Π·Π½ΡΡ ΡΠΎΡΠΊΠ°Ρ , ΡΠ°ΠΊ ΡΠΎΠ±ΠΎΡ ΠΎΠΏΡΠ΅Π΄Π΅Π»ΡΠ΅Ρ ΡΠ°ΠΊΡΠΈΡΠ΅ΡΠΊΠΎΠ΅ ΡΠ°ΡΠΏΠΎΠ»ΠΎΠΆΠ΅Π½ΠΈΠ΅ ΠΏΠ»ΠΎΡΠΊΠΎΡΡΠΈ ΠΈΠ·Π΄Π΅Π»ΠΈΡ ΠΈ ΠΊΠ°ΠΊ ΠΈΡΠΎΠ³ ΡΠ΅Π°Π»ΡΠ½ΠΎΠ΅ ΡΠ°ΡΠΏΠΎΠ»ΠΎΠΆΠ΅Π½ΠΈΠ΅ ΡΠ²Π°ΡΠ½ΠΎΠ³ΠΎ ΡΠ²Π°.
ΠΠΎΠΈΡΠΊ ΠΌΠΎΠΆΠ΅Ρ Π±ΡΡΡ Π²ΡΠΏΠΎΠ»Π½Π΅Π½ ΠΏΡΡΠ΅ΠΌ ΠΎΠΏΡΠ΅Π΄Π΅Π»Π΅Π½ΠΈΡ ΡΡΠ΅Ρ ΠΏΠ»ΠΎΡΠΊΠΎΡΡΠ΅ΠΉ Π½Π° Π΄Π΅ΡΠ°Π»ΠΈ Π² ΠΏΠ΅ΡΠΏΠ΅Π½Π΄ΠΈΠΊΡΠ»ΡΡΠ½ΠΎΠΌ Π½Π°ΠΏΡΠ°Π²Π»Π΅Π½ΠΈΠΈ. Π’Π°ΠΊΠΈΠΌ ΠΎΠ±ΡΠ°Π·ΠΎΠΌ, ΡΠΎΠ±ΠΎΡ ΠΏΠΎΠ²Π΅ΡΠ½ΡΡ Π·Π°ΠΏΡΠΎΠ³ΡΠ°ΠΌΠΌΠΈΡΠΎΠ²Π°Π½Π½ΡΠ΅ ΡΠΎΡΠΊΠΈ ΠΊ ΡΠ΅Π°Π»ΡΠ½ΠΎΠΌΡ ΡΠ°ΡΠΏΠΎΠ»ΠΎΠΆΠ΅Π½ΠΈΡ Π΄Π΅ΡΠ°Π»ΠΈ ΠΈ ΡΠΌΠΎΠΆΠ΅Ρ Π²ΡΡΠΈΡΠ»ΠΈΡΡ ΡΠΎΡΠΊΡ Π½Π°ΡΠ°Π»Π° ΡΠ²Π°ΡΠΊΠΈ.
Β
Π ΠΈΡΡΠ½ΠΎΠΊ 6. ΠΠ°Ρ ΠΎΠΆΠ΄Π΅Π½ΠΈΠ΅ Π·Π°Π³ΠΎΡΠΎΠ²ΠΊΠΈ ΡΠΎΠ±ΠΎΡΠΎΠΌ
Π‘Π»Π΅ΠΆΠ΅Π½ΠΈΠ΅ Π·Π° ΡΡΡΠΊΠΎΠΌ.
Π‘Π»Π΅ΠΆΠ΅Π½ΠΈΠ΅ Π·Π° ΡΡΡΠΊΠΎΠΌ ΠΏΡΠΈΠΌΠ΅Π½ΡΠ΅ΡΡΡ ΠΏΡΠΈ ΡΠ²Π°ΡΠΊΠ΅ ΠΏΡΠΎΡΡΠΆΡΠ½Π½ΡΡ ΡΠ²ΠΎΠ² Π΄Π»Ρ ΠΎΠΏΡΠ΅Π΄Π΅Π»Π΅Π½ΠΈΡ ΡΡΠ΅ΠΏΠ΅Π½ΠΈ ΠΊΠΎΡΡΠ΅ΠΊΡΠΈΠΈ ΠΌΠ΅ΠΆΠ΄Ρ Π·Π°ΠΏΡΠΎΠ³ΡΠ°ΠΌΠΌΠΈΡΠΎΠ²Π°Π½Π½ΡΠΌ ΠΈ ΡΠ΅Π°Π»ΡΠ½ΡΠΌ ΡΠ°ΡΠΏΠΎΠ»ΠΎΠΆΠ΅Π½ΠΈΠ΅ΠΌ ΡΠ²Π°. Π§Π°ΡΠ΅ Π²ΡΠ΅Π³ΠΎ ΡΠ°ΠΌΡ Π΄ΡΠ³Ρ ΠΈΡΠΏΠΎΠ»ΡΠ·ΡΡΡ ΠΊΠ°ΠΊ ΡΠ΅Π½ΡΠΎΡ. ΠΡΠΏΠΎΠ»ΡΠ·ΡΠ΅ΡΡΡ ΠΊΠΎΠ»Π΅Π±Π°Π½ΠΈΠ΅ Π΄ΡΠ³ΠΈ ΠΏΠΎΠΏΠ΅ΡΠ΅ΠΊ ΡΠ²Π° ΠΈ Π² ΡΡΠΎΡ ΠΌΠΎΠΌΠ΅Π½Ρ ΠΈΠ·ΠΌΠ΅ΡΡΠ΅ΡΡΡ Π½Π°ΠΏΡΡΠΆΠ΅Π½ΠΈΠ΅ ΠΈ ΡΠΎΠΊ Π½Π° Π΄ΡΠ³Π΅. Π’Π°ΠΊΠΈΠΌ ΠΎΠ±ΡΠ°Π·ΠΎΠΌ, ΠΌΠΎΠΆΠ½ΠΎ ΠΎΠΏΡΠ΅Π΄Π΅Π»ΠΈΡΡ ΡΠ΅Π°Π»ΡΠ½ΠΎΠ΅ ΠΏΠΎΠ»ΠΎΠΆΠ΅Π½ΠΈΠ΅ ΡΡΡΠΊΠ° ΠΎΡΠ½ΠΎΡΠΈΡΠ΅Π»ΡΠ½ΠΎ ΠΊΡΠ°ΠΉΠ½ΠΈΡ ΡΠΎΡΠ΅ΠΊ ΠΊΠΎΠ»Π΅Π±Π°Π½ΠΈΡ. ΠΡΠΎΡ ΡΠΏΠΎΡΠΎΠ± ΡΠ²Π»ΡΠ΅ΡΡΡ ΡΠ°ΠΌΡΠΌ ΠΏΠΎΠΏΡΠ»ΡΡΠ½ΡΠΌ, ΠΏΠΎΡΠΊΠΎΠ»ΡΠΊΡ Π½Π΅ ΡΡΠ΅Π±ΡΠ΅ΡΡΡ ΡΡΡΠ°Π½ΠΎΠ²ΠΊΠΈ Π΄ΠΎΠΏΠΎΠ»Π½ΠΈΡΠ΅Π»ΡΠ½ΠΎΠ³ΠΎ ΠΎΠ±ΠΎΡΡΠ΄ΠΎΠ²Π°Π½ΠΈΡ, ΠΊΠΎΡΠΎΡΠΎΠ΅, Π² ΡΠ²ΠΎΡ ΠΎΡΠ΅ΡΠ΅Π΄Ρ, ΠΏΠΎΠ²ΡΡΠ°Π΅Ρ Π³Π°Π±Π°ΡΠΈΡ (Π ΠΈΡ.7)
Π ΠΈΡΡΠ½ΠΎΠΊ 7. ΠΠ·ΠΌΠ΅Π½Π΅Π½ΠΈΠ΅ Π΄Π»ΠΈΠ½Ρ Π΄ΡΠ³ΠΈ Π² Π·Π°Π²ΠΈΡΠΈΠΌΠΎΡΡΠΈ ΠΎΡ ΠΏΠΎΠ»ΠΎΠΆΠ΅Π½ΠΈΡ ΡΠ²Π°ΡΠΎΡΠ½ΠΎΠΉ Π³ΠΎΡΠ΅Π»ΠΊΠΈ ΠΏΠΎΠΏΠ΅ΡΠ΅ΠΊ ΡΠ²Π°.
Β Β Β Β Β Β Β Β Β Β Β Π’Π°ΠΊΠΆΠ΅ ΠΈΡΠΏΠΎΠ»ΡΠ·ΡΡΡΡΡ ΠΎΠΏΡΠΈΡΠ΅ΡΠΊΠΈΠ΅ ΡΡΠ΅Π΄ΡΡΠ²Π° ΡΠ»Π΅ΠΆΠ΅Π½ΠΈΡ Π·Π° ΡΡΡΠΊΠΎΠΌ, ΡΠ°ΠΊΠΈΠ΅ ΠΊΠ°ΠΊ, Π»Π°Π·Π΅ΡΠ½ΡΠΉ ΡΠΊΠ°Π½Π΅Ρ Π΄Π»Ρ ΠΎΠ±Π½Π°ΡΡΠΆΠ΅Π½ΠΈΡ ΡΠ²Π° Π½Π° ΠΏΠΎΠ²Π΅ΡΡ Π½ΠΎΡΡΠΈ ΠΏΠ΅ΡΠ΅Π΄ Π΄ΡΠ³ΠΎΠΉ.
ΠΡΠ΅ΠΈΠΌΡΡΠ΅ΡΡΠ²Π° ΠΈ Π½Π΅Π΄ΠΎΡΡΠ°ΡΠΊΠΈ.
Π ΡΡΠΎΠΈΠΌΠΎΡΡΠ½ΠΎΠΌ Π²ΡΡΠ°ΠΆΠ΅Π½ΠΈΠΈ, ΡΠ²Π°ΡΠΎΡΠ½ΡΠΉ ΡΠΎΠ±ΠΎΡ Π΄Π»Ρ MIG/MAG ΡΠ²Π°ΡΠΊΠΈ ΡΠ²Π»ΡΠ΅ΡΡΡ ΡΠΊΠΎΠ½ΠΎΠΌΠΈΡΠ΅ΡΠΊΠΈ ΠΎΠ±ΠΎΡΠ½ΠΎΠ²Π°Π½Π½ΡΠΌ ΠΏΡΠΈ ΠΏΡΠΎΠ΄ΡΠΊΡΠΈΠ²Π½ΠΎΡΡΠΈ 1000 ΠΈ 60 000 Π΅Π΄ΠΈΠ½ΠΈΡ Π² Π³ΠΎΠ΄. ΠΠ»Ρ ΡΠΈΡΠ΅Π», ΠΌΠ΅Π½ΡΡΠΈΡ , ΡΡΠΎΠΈΠΌΠΎΡΡΡ ΠΏΡΠΎΠ³ΡΠ°ΠΌΠΌΠΈΡΠΎΠ²Π°Π½ΠΈΡ ΡΠΎΠ±ΠΎΡΠ° ΠΈ ΠΏΡΠΎΠΈΠ·Π²ΠΎΠ΄ΡΡΠ²Π΅Π½Π½ΡΡ ΠΏΡΠΈΡΠΏΠΎΡΠΎΠ±Π»Π΅Π½ΠΈΠΉ Π²ΡΡΠ΄ Π»ΠΈ Π±ΡΠ΄Π΅Ρ ΠΏΡΠΈΠ½ΠΎΡΠΈΡΡ Π΄ΠΎΡ ΠΎΠ΄, Π² ΡΠΎ Π²ΡΠ΅ΠΌΡ ΠΊΠ°ΠΊ ΠΏΡΠΈ Π±ΠΎΠ»ΡΡΠΈΡ ΠΊΠΎΠ»ΠΈΡΠ΅ΡΡΠ²Π°Ρ , Π±ΡΠ»ΠΎ Π±Ρ Π»ΡΡΡΠ΅ ΠΈΠ½Π²Π΅ΡΡΠΈΡΠΎΠ²Π°ΡΡ Π² Π±ΠΎΠ»ΡΡΠΈΠ΅ ΠΈΠ»ΠΈ Π±ΠΎΠ»Π΅Π΅ ΡΠ»ΠΎΠΆΠ½ΡΠ΅ ΡΡΡΠ°Π½ΠΎΠ²ΠΊΠΈ. Π’Π΅ΠΌ Π½Π΅ ΠΌΠ΅Π½Π΅Π΅, Π² Π½Π΅ΠΊΠΎΡΠΎΡΡΡ ΡΠ»ΡΡΠ°ΡΡ , Π΄Π°ΠΆΠ΅ Π½Π΅Π±ΠΎΠ»ΡΡΠΎΠ΅ ΠΏΡΠΎΠΈΠ·Π²ΠΎΠ΄ΡΡΠ²ΠΎ ΠΌΠΎΠΆΠ΅Ρ Π±ΡΡΡ ΡΠ΅Π»Π΅ΡΠΎΠΎΠ±ΡΠ°Π·Π½ΠΎ, Π΅ΡΠ»ΠΈ ΠΌΠΎΠΆΠ½ΠΎ ΠΈΡΠΏΠΎΠ»ΡΠ·ΠΎΠ²Π°ΡΡ Π³ΠΈΠ±ΠΊΠΈΠ΅ ΠΏΡΠΎΠΈΠ·Π²ΠΎΠ΄ΡΡΠ²Π΅Π½Π½ΡΠ΅ ΡΠΈΡΡΠ΅ΠΌΡ ΠΈ ΠΏΡΠΎΠ³ΡΠ°ΠΌΠΌΠΈΡΠΎΠ²Π°Π½ΠΈΡ off-line. ΠΡΠ΅ΠΈΠΌΡΡΠ΅ΡΡΠ²Π°ΠΌΠΈ ΡΠΎΠ±ΠΎΡΠΈΠ·ΠΈΡΠΎΠ²Π°Π½Π½ΠΎΠ³ΠΎ ΠΊΠΎΠΌΠΏΠ»Π΅ΠΊΡΠ° Β Π΄Π»Ρ Π΄ΡΠ³ΠΎΠ²ΠΎΠΉ ΡΠ²Π°ΡΠΊΠΈ ΡΠ²Π»ΡΡΡΡΡ:
β Π±ΠΎΠ»Π΅Π΅ Π²ΡΡΠΎΠΊΠ°Ρ ΠΏΡΠΎΠΈΠ·Π²ΠΎΠ΄ΠΈΡΠ΅Π»ΡΠ½ΠΎΡΡΡ β ΡΠ°ΠΊΡΠΎΡ Π²ΡΠ΅ΠΌΠ΅Π½ΠΈ Π΄ΡΠ³ΠΈ ΠΏΠΎΠ΄Π½ΠΈΠΌΠ°Π΅ΡΡΡ Ρ 30-40 % Π΄ΠΎ 60-80%, ΡΠΊΠΎΡΠΎΡΡΡ ΡΠ²Π°ΡΠΊΠΈ ΡΠ²Π΅Π»ΠΈΡΠΈΠ²Π°Π΅ΡΡΡ;
β ΠΎΠ΄ΠΈΠ½ ΠΎΠΏΠ΅ΡΠ°ΡΠΎΡ ΡΠΎΠ±ΠΎΡΠ° Π·Π°ΠΌΠ΅Π½ΡΠ΅Ρ 2-4 ΡΡΡΠ½ΡΡ ΡΠ²Π°ΡΡΠΈΠΊΠ°;
-ΠΊΠ°ΡΠ΅ΡΡΠ²ΠΎ ΡΠ²Π°ΡΠΊΠΈ ΡΡΠ°Π½ΠΎΠ²ΠΈΡΡΡ Π±ΠΎΠ»Π΅Π΅ ΠΏΡΠ΅Π΄ΡΠΊΠ°Π·ΡΠ΅ΠΌΠΎ ΠΈ, ΠΊΠ°ΠΊ ΠΏΡΠ°Π²ΠΈΠ»ΠΎ, Π²ΡΡΠ΅;
-ΡΡΠ»ΠΎΠ²ΠΈΡ ΡΡΡΠ΄Π° ΡΠ»ΡΡΡΠ°ΡΡΡΡ, ΡΠ°ΠΊ ΠΊΠ°ΠΊ ΠΎΠΏΠ΅ΡΠ°ΡΠΎΡΡ Π½Π΅ Π½ΡΠΆΠ½ΠΎ ΡΡΠΎΡΡΡ Π² Π±Π»ΠΈΠ·ΠΎΡΡΠΈ ΠΎΡ Π΄ΡΠ³ΠΈ;Β Β Β Β Β Β Β Β -Π½Π΅ΠΎΠ±Ρ ΠΎΠ΄ΠΈΠΌΠ°Ρ ΠΎΡΠ³Π°Π½ΠΈΠ·Π°ΡΠΈΡ ΠΈ ΡΠ»ΡΡΡΠ΅Π½ΠΈΠ΅ ΠΊΠΎΠ½ΡΡΠΎΠ»Ρ ΠΏΠ΅ΡΠΈΡΠ΅ΡΠΈΠΉΠ½ΠΎΠΉ Π΄Π΅ΡΡΠ΅Π»ΡΠ½ΠΎΡΡΠΈ, ΡΠ²ΡΠ·Π°Π½Π½ΠΎΠΉ Ρ Π²Π²Π΅Π΄Π΅Π½ΠΈΠ΅ΠΌ ΡΠΎΠ±ΠΎΡΠ°, ΠΎΠΊΠ°Π·ΡΠ²Π°ΡΡ Π±Π»Π°Π³ΠΎΡΠ²ΠΎΡΠ½ΠΎΠ΅ Π²Π»ΠΈΡΠ½ΠΈΠ΅ Π½Π° ΠΎΠ±ΡΡΡ ΡΡΡΠ΅ΠΊΡΠΈΠ²Π½ΠΎΡΡΡ.
ΠΠ΅Π΄ΠΎΡΡΠ°ΡΠΊΠΈ :
-Π·Π½Π°ΡΠΈΡΠ΅Π»ΡΠ½Π°Ρ ΠΏΠΎΡΡΠ΅Π±Π½ΠΎΡΡΡ Π² ΠΎΠ±ΡΡΠ΅Π½ΠΈΠΈ, ΠΊΠ°ΠΊ Π΄Π»Ρ ΠΏΡΠΎΠ³ΡΠ°ΠΌΠΌΠΈΡΠΎΠ²Π°Π½ΠΈΡ ΡΠ°ΠΊ ΠΈ Π΄Π»Ρ ΠΎΠ±ΡΠ»ΡΠΆΠΈΠ²Π°Π½ΠΈΡ;
-ΠΆΠ΅ΡΡΡΠ΅ Π΄ΠΎΠΏΡΡΠΊΠΈ Π½Π° Π·Π°Π³ΠΎΡΠΎΠ²ΠΊΡ, ΡΠ±ΠΎΡΠΊΡ ΠΈ Π½Π° ΠΏΠΎΠ·ΠΈΡΠΈΠΎΠ½ΠΈΡΠΎΠ²Π°Π½ΠΈΠ΅;
β Π²ΡΡΠΎΠΊΠ°Ρ Π²Π΅ΡΠΎΡΡΠ½ΠΎΡΡΡ ΡΠ΅ΠΊΠΎΠ½ΡΡΡΡΠΊΡΠΈΠΈ Π·Π°Π³ΠΎΡΠΎΠ²ΠΈΡΠ΅Π»ΡΠ½ΠΎΠΉ ΡΠ°ΡΡΠΈ, ΡΡΠΎΠ±Ρ ΡΠ΄Π΅Π»Π°ΡΡ Π·Π°Π³ΠΎΡΠΎΠ²ΠΊΠΈ ΠΏΡΠΈΠ³ΠΎΠ΄Π½ΡΠΌΠΈ Π΄Π»Ρ ΡΠΎΠ±ΠΎΡΠΈΠ·ΠΈΡΠΎΠ²Π°Π½Π½ΠΎΠΉ ΡΠ²Π°ΡΠΊΠΈ.
3. ΠΠ΅Ρ Π°Π½ΠΈΠ·ΠΈΡΠΎΠ²Π°Π½Π½Π°Ρ TIG ΡΠ²Π°ΡΠΊΠ°
ΠΠ΅Ρ Π°Π½ΠΈΠ·ΠΈΡΠΎΠ²Π°Π½Π½Π°Ρ TIG ΡΠ²Π°ΡΠΊΠ° Π΄Π°Π΅Ρ Π²ΠΎΠ·ΠΌΠΎΠΆΠ½ΠΎΡΡΡ ΠΏΠΎΠ»ΡΡΠΈΡΡ Π²ΡΡΠΎΠΊΠΎΠΊΠ°ΡΠ΅ΡΡΠ²Π΅Π½Π½ΡΠΉ ΠΈ ΡΡΡΠ΅ΡΠΈΡΠ΅ΡΠΊΠΈΠΉ ΡΠΎΠ². ΠΡΠΎΡ ΡΠΈΠΏ ΡΠ²Π°ΡΠΊΠΈ ΠΏΡΠΈΠΌΠ΅Π½ΡΠ΅ΡΡΡ Π΄Π»Ρ ΡΠ²Π°ΡΠΊΠΈ Π½Π΅ΡΠΆΠ°Π²Π΅ΡΡΠΈΡ ΡΡΠ°Π»Π΅ΠΉ, Π½ΠΈΠΊΠ΅Π»Π΅Π²ΡΡ ΡΠΏΠ»Π°Π²ΠΎΠ² ΠΈ Π°Π»ΡΠΌΠΈΠ½ΠΈΡ. Π‘ΠΏΠ΅ΡΠΈΠ°Π»ΡΠ½ΡΠ΅ Π°ΠΏΠΏΠ°ΡΠ°ΡΡ ΡΠ°ΡΠΏΡΠΎΡΡΡΠ°Π½Π΅Π½Ρ Π΄Π»Ρ ΡΠ²Π°ΡΠΊΠΈ ΡΡΡΠ± ΠΈΠ· Π½Π΅ΡΠΆΠ°Π²Π΅ΡΡΠΈΡ ΡΡΠ°Π»Π΅ΠΉ ΠΈ ΡΠ²Π°ΡΠΊΠΈ ΡΡΡΠ±Π½ΡΡ Π΄ΠΎΡΠΎΠΊ.
ΠΡΠΈΡΠ°Π΄ΠΎΡΠ½Π°Ρ ΠΏΡΠΎΠ²ΠΎΠ»ΠΎΠΊΠ°
ΠΡΠΈΡΠ°Π΄ΠΎΡΠ½Π°Ρ ΠΏΡΠΎΠ²ΠΎΠ»ΠΎΠΊΠ° Π½Π΅ΠΎΠ±Ρ ΠΎΠ΄ΠΈΠΌΠ° Π΄Π»Ρ Π·Π°ΠΏΠΎΠ»Π½Π΅Π½ΠΈΡ ΡΠ°Π·Π΄Π΅Π»ΠΊΠΈ ΡΠ²Π°, ΠΈ ΠΎΠ½Π° ΠΏΠΎΡΡΡΠΏΠ°Π΅Ρ Ρ ΠΌΠ΅Ρ Π°Π½ΠΈΠ·ΠΌΠ° ΠΏΠΎΠ΄Π°ΡΠΈ ΠΏΡΠΈΡΠ°Π΄ΠΎΡΠ½ΠΎΠΉ ΠΏΡΠΎΠ²ΠΎΠ»ΠΎΠΊΠΈ. ΠΡΠΎΠ²ΠΎΠ»ΠΎΠΊΠ° ΠΏΠΎΠ΄Π°ΡΡΡΡ ΠΏΡΡΠΌΠΎ Π² ΡΠ²Π°ΡΠΎΡΠ½ΡΡ Π²Π°Π½Π½Ρ, ΡΠ°ΡΠ΅ ΠΏΠ΅ΡΠ΅Π΄ Π΄ΡΠ³ΠΎΠΉ Π±Π΅Π· ΠΏΡΠ΅Π΄Π²Π°ΡΠΈΡΠ΅Π»ΡΠ½ΠΎΠ³ΠΎ ΡΠ°ΡΠΏΠ»Π°Π²Π»Π΅Π½ΠΈΡ ΡΠ΅ΠΏΠ»ΠΎ ΡΠ²Π°ΡΠΎΡΠ½ΠΎΠΉ Π΄ΡΠ³ΠΈ.
ΠΠ°ΠΊ Π²Π°ΡΠΈΠ°Π½Ρ: ΠΏΠΎΠ΄Π°ΡΠ° ΠΏΡΠΈΡΠ°Π΄ΠΎΡΠ½ΠΎΠΉ ΠΏΡΠΎΠ²ΠΎΠ»ΠΎΠΊΠΈ, ΠΊΠΎΡΠΎΡΠ°Ρ ΠΏΠΎΠ΄ΠΎΠ³ΡΠ΅ΡΠ° ΠΎΡΠ΄Π΅Π»ΡΠ½ΡΠΌ ΠΈΡΡΠΎΡΠ½ΠΈΠΊΠΎΠΌ ΡΠ½Π΅ΡΠ³ΠΈΠΈ. Π’ΠΎΠΊ Π½Π°Π³ΡΠ΅Π²Π° Π΄ΠΎΠ»ΠΆΠ΅Π½ ΡΠΎΠΎΡΠ²Π΅ΡΡΡΠ²ΠΎΠ²Π°ΡΡ ΡΠΊΠΎΡΠΎΡΡΠΈ ΠΏΠΎΠ΄Π°ΡΠΈ ΠΏΡΠΈΡΠ°Π΄ΠΎΡΠ½ΠΎΠΉ ΠΏΡΠΎΠ²ΠΎΠ»ΠΎΠΊΠΈ. Π‘ΠΊΠΎΡΠΎΡΡΡ ΡΠ²Π°ΡΠΊΠΈ ΠΌΠΎΠΆΠ΅Ρ Π±ΡΡΡ ΡΠ²Π΅Π»ΠΈΡΠ΅Π½Π°, ΡΠ°ΠΊ ΠΊΠ°ΠΊ ΠΌΠ΅Π½ΡΡΠ΅ ΡΠ½Π΅ΡΠ³ΠΈΠΈ ΠΎΡ Π΄ΡΠ³ΠΈ ΠΎΡΠ±ΠΈΡΠ°Π΅ΡΡΡ Π½Π° ΠΏΠΎΠ΄ΠΎΠ³ΡΠ΅Π² ΠΏΡΠΈΡΠ°Π΄ΠΎΡΠ½ΠΎΠΉ ΠΏΡΠΎΠ²ΠΎΠ»ΠΎΠΊΠΈ. ΠΡΠ΅ΠΈΠΌΡΡΠ΅ΡΡΠ²ΠΎ:
β ΠΌΠ΅Π½ΡΡΠ΅ ΡΠΈΡΠΊ ΡΠΎΡΠΌΠΈΡΠΎΠ²Π°Π½ΠΈΠ΅ ΠΏΠΎΡ, ΠΏΠΎΠ΄ΠΎΠ³ΡΠ΅ΡΠ°Ρ ΠΏΡΠΎΠ²ΠΎΠ»ΠΎΠΊΠ° ΠΏΠΎΠΌΠΎΠ³Π°Π΅Ρ Π³Π°Π·Π°ΠΌ ΠΏΠΎΠΊΠΈΠ΄Π°ΡΡ ΡΠ²Π°ΡΠΎΡΠ½ΡΡ Π²Π°Π½Π½Ρ;
β Π²ΡΡΠΎΠΊΠ°Ρ ΡΠΊΠΎΡΠΎΡΡΡ ΠΏΠ΅ΡΠ΅ΠΏΠ»Π°Π²Π°, Π΄ΠΎ 8 ΠΊΠ³/Ρ;
β ΠΌΠ΅Π½ΡΡΠ΅ ΡΠ΅ΠΏΠ»ΠΎΠ²Π»ΠΎΠΆΠ΅Π½ΠΈΠ΅ ΠΈ ΠΌΠ΅Π½ΡΡΠΈΠΉ ΡΠΈΡΠΊ ΡΡΠ΅ΡΠΈΠ½.
Π‘Π²Π°ΡΠΎΡΠ½ΠΎΠ΅ ΠΎΠ±ΠΎΡΡΠ΄ΠΎΠ²Π°Π½ΠΈΠ΅ Π΄ΠΎΠ»ΠΆΠ½ΠΎ Π±ΡΡΡ Π΄ΠΎΠΏΠΎΠ»Π½Π΅Π½ΠΎ Π΄ΠΎΠΏΠΎΠ»Π½ΠΈΡΠ΅Π»ΡΠ½ΡΠΌ ΡΡΡΡΠΎΠΉΡΡΠ²ΠΎΠΌ ΠΏΠΎΠ΄Π°ΡΠΈ ΠΏΡΠΎΠ²ΠΎΠ»ΠΎΠΊΠΈ, Π²ΠΌΠ΅ΡΡΠ΅ ΡΠΎ ΡΠΏΠ΅ΡΠΈΠ°Π»ΡΠ½ΠΎΠΉ ΡΠ²Π°ΡΠΎΡΠ½ΠΎΠΉ Π³ΠΎΡΠ΅Π»ΠΊΠΎΠΉ Π΄Π»Ρ ΠΏΠΎΠ΄Π°ΡΠΈ ΠΏΡΠΈΡΠ°Π΄ΠΎΡΠ½ΠΎΠΉ ΠΏΡΠΎΠ²ΠΎΠ»ΠΎΠΊΠΈ. ΠΡΠΎΠ²ΠΎΠ»ΠΎΠΊΠ° ΠΏΠΎΠ΄Π°Π΅ΡΡΡ Π² ΡΠ²Π°ΡΠΎΡΠ½ΡΡ Π²Π°Π½Π½Ρ ΠΏΠΎΠ΄ ΡΠ³Π»ΠΎΠΌ ΠΎΠΊΠΎΠ»ΠΎ 40Β°, ΠΈ Π½Π°Π³ΡΠ΅Π²Π°Π΅ΡΡΡ ΠΎΡ ΡΠ΅ΡΠΈ ΠΏΠ΅ΡΠ΅ΠΌΠ΅Π½Π½ΠΎΠ³ΠΎ ΡΠΎΠΊΠ°, ΡΡΠΎΠ±Ρ ΡΠΌΠ΅Π½ΡΡΠΈΡΡ ΠΌΠ°Π³Π½ΠΈΡΠ½ΠΎΠ΅ Π΄ΡΡΡΡ Π½Π° Π΄ΡΠ³Π΅.
ΠΠΎΠ½ΡΡΠΎΠ»Ρ Π²ΡΠ»Π΅ΡΠ° ΡΠ»Π΅ΠΊΡΡΠΎΠ΄Π°.
ΠΠ»Ρ ΠΎΠ±Π΅ΡΠΏΠ΅ΡΠ΅Π½ΠΈΡ ΠΏΠΎΡΡΠΎΡΠ½Π½ΠΎΠ³ΠΎ Π²ΡΠ»Π΅ΡΠ° ΡΠ»Π΅ΠΊΡΡΠΎΠ΄Π° ΠΎΡΠ½ΠΎΡΠΈΡΠ΅Π»ΡΠ½ΠΎ ΡΠ²Π°ΡΠΈΠ²Π°Π΅ΠΌΡΡ Π΄Π΅ΡΠ°Π»Π΅ΠΉ Π² ΠΎΠ±ΠΎΡΡΠ΄ΠΎΠ²Π°Π½ΠΈΠ΅ Π²ΠΊΠ»ΡΡΠ°Π΅ΡΡΡ ΠΌΠΎΠ΄ΡΠ»Ρ ΠΊΠΎΠ½ΡΡΠΎΠ»Ρ Π½Π°ΠΏΡΡΠΆΠ΅Π½ΠΈΡ Π½Π° Π΄ΡΠ³Π΅, ΠΊΠΎΡΠΎΡΠΎΠ΅ Π΄Π°Π΅Ρ ΡΠΈΠ³Π½Π°Π» Π½Π° ΡΠΌΠ΅Π½ΡΡΠ΅Π½ΠΈΠ΅ ΠΈΠ»ΠΈ ΡΠ²Π΅Π»ΠΈΡΠ΅Π½ΠΈΠ΅ Π²ΡΠ»Π΅ΡΠ° ΡΠ»Π΅ΠΊΡΡΠΎΠ΄Π°, Π² ΡΠ΅Π»ΠΎΠΌ ΠΏΠΎΠ·Π²ΠΎΠ»ΡΠ΅Ρ ΡΠΎΡ ΡΠ°Π½ΠΈΡΡ Π²ΡΠ»Π΅Ρ ΠΏΠΎΡΡΠΎΡΠ½Π½ΡΠΌ.
Β ΠΡΠΎΡΠΈΠ΅ ΠΊΠΎΡΡΠ΅ΠΊΡΠΈΡΠΎΠ²ΠΊΠΈ
ΠΠ±ΠΎΡΡΠ΄ΠΎΠ²Π°Π½ΠΈΠ΅ Π΄Π»Ρ ΠΌΠ΅Ρ Π°Π½ΠΈΠ·ΠΈΡΠΎΠ²Π°Π½Π½ΠΎΠΉ ΡΠ²Π°ΡΠΊΠΈ ΡΠΏΠΎΡΠΎΠ±ΠΎΠΌ TIG ΡΠ°ΡΡΠΎ Π²ΠΊΠ»ΡΡΠ°Π΅Ρ Π² ΡΠ΅Π±Ρ ΠΏΠ΅ΡΠ΅Π΄ΠΎΠ²ΡΠ΅ ΡΡΠ΅Π΄ΡΡΠ²Π° ΡΠΏΡΠ°Π²Π»Π΅Π½ΠΈΡ, ΡΠ°ΠΊΠΈΠ΅ ΠΊΠ°ΠΊ Β«ΠΊΠΎΠΌΠΏΠ»Π΅ΠΊΡΠ½ΠΎΒ» ΠΏΡΠΎΠ³ΡΠ°ΠΌΠΌΠΈΡΡΠ΅ΠΌΡΠ΅ ΠΏΠ°ΡΠ°ΠΌΠ΅ΡΡΡ ΡΠ²Π°ΡΠΊΠΈ, ΡΡΠΎΠ±Ρ ΡΠ΄ΠΎΠ²Π»Π΅ΡΠ²ΠΎΡΠΈΡΡ ΠΎΠΏΡΠ΅Π΄Π΅Π»Π΅Π½Π½ΡΠ΅ ΡΠΈΠΏΡ ΡΠ²ΠΎΠ² ΠΈΠ»ΠΈ ΠΌΠ°ΡΠ΅ΡΠΈΠ°Π»ΠΎΠ². ΠΠ°ΡΠ°ΠΌΠ΅ΡΡΡ, ΠΊΠΎΡΠΎΡΡΠ΅ ΠΎΠ±ΡΡΠ½ΠΎ ΠΊΠΎΠ½ΡΡΠΎΠ»ΠΈΡΡΡΡΡΡ ΡΠ°ΠΊΠΈΠΌ ΠΎΠ±ΡΠ°Π·ΠΎΠΌ, ΠΌΠΎΠ³ΡΡ Π²ΠΊΠ»ΡΡΠ°ΡΡ Π² ΡΠ΅Π±Ρ ΡΠ²Π°ΡΠΎΡΠ½ΡΠΉ ΡΠΎΠΊ, ΠΏΡΠ»ΡΡΠ°ΡΠΈΠΈ, ΡΠΊΠΎΡΠΎΡΡΡ ΠΏΠΎΠ΄Π°ΡΠΈ ΠΏΡΠΎΠ²ΠΎΠ»ΠΎΠΊΠΈ ΠΈ Ρ.Π΄.
ΠΠ»Ρ ΡΠ²Π°ΡΠΊΠΈ ΡΡΡΠ± ΡΠ²Π°ΡΠΎΡΠ½ΠΎΠ΅ ΠΎΠ±ΠΎΡΡΠ΄ΠΎΠ²Π°Π½ΠΈΠ΅ ΠΈΡΠΏΠΎΠ»ΡΠ·ΡΡΡ ΡΠΏΠ΅ΡΠΈΠ°Π»ΡΠ½ΡΠ΅ ΠΈΠ½ΡΡΡΡΠΌΠ΅Π½ΡΡ, ΠΊΠ°ΠΊ ΠΏΠΎΠΊΠ°Π·Π°Π½ΠΎ Π½Π° ΡΠΈΡΡΠ½ΠΊΠ΅ 9. ΠΡΠΈ ΡΠ²Π°ΡΠΊΠ΅ Π³ΠΎΡΠΈΠ·ΠΎΠ½ΡΠ°Π»ΡΠ½ΡΡ ΡΡΡΠ±, ΡΠ²Π°ΡΠΎΡΠ½Π°Ρ Π³ΠΎΠ»ΠΎΠ²ΠΊΠ° Π΄ΠΎΠ»ΠΆΠ½Π° Π΄Π²ΠΈΠ³Π°ΡΡΡΡ ΠΏΠΎ ΠΊΡΡΠ³Ρ, ΡΡΠΎ ΠΎΠ·Π½Π°ΡΠ°Π΅Ρ, ΡΡΠΎ Π΅Π΅ ΡΠ³ΠΎΠ» Π΄ΠΎΠ»ΠΆΠ΅Π½ ΠΏΠΎΡΡΠΎΡΠ½Π½ΠΎ ΠΌΠ΅Π½ΡΡΡΡΡ. Π§ΡΠΎΠ±Ρ ΡΠ΅ΠΆΠΈΠΌ ΡΠΎΠΎΡΠ²Π΅ΡΡΡΠ²ΠΎΠ²Π°Π» ΠΏΠΎΠ»ΠΎΠΆΠ΅Π½ΠΈΡ, ΠΌΠΎΠΆΠ½ΠΎ Π·Π°ΠΏΡΠΎΠ³ΡΠ°ΠΌΠΌΠΈΡΠΎΠ²Π°ΡΡ ΡΠ°Π·Π»ΠΈΡΠ½ΡΠ΅ ΠΏΠ°ΡΠ°ΠΌΠ΅ΡΡΡ ΡΠ²Π°ΡΠΊΠΈ Π΄Π»Ρ ΡΠ°Π·Π½ΡΡ ΡΡΠ°ΡΡΠΊΠΎΠ² ΡΠ²Π°ΡΠ½ΠΎΠ³ΠΎ ΡΠ²Π°.
Π ΠΈΡΡΠ½ΠΎΠΊ 9. Π‘Π²Π°ΡΠΎΡΠ½ΠΎΠ΅ ΠΎΠ±ΠΎΡΡΠ΄ΠΎΠ²Π°Π½ΠΈΠ΅ Π΄Π»Ρ ΠΌΠ΅Ρ Π°Π½ΠΈΠ·ΠΈΡΠΎΠ²Π°Π½Π½ΠΎΠΉ TIG ΡΠ²Π°ΡΠΊΠΈ ΠΈ ΡΠ°Π·Π½ΡΠΌΠΈ ΡΠΏΠ΅ΡΠΈΠ°Π»ΡΠ½ΡΠΌΠΈ Π²ΠΈΠ΄Π°ΠΌΠΈ ΠΎΠ±ΠΎΡΡΠ΄ΠΎΠ²Π°Π½ΠΈΡ Π΄Π»Ρ ΡΠ²Π°ΡΠΊΠΈ ΡΡΡΠ±
4. Π’ΡΠ΅Π±ΠΎΠ²Π°Π½ΠΈΡ ΠΊ ΠΊΠ°ΡΠ΅ΡΡΠ²Ρ ΠΌΠ΅Ρ Π°Π½ΠΈΠ·ΠΈΡΠΎΠ²Π°Π½Π½ΠΎΠΉ ΡΠ²Π°ΡΠΊΠΈ
ΠΠ±ΡΠΈΠ΅ ΠΈΠ·ΠΌΠ΅ΡΠ΅Π½ΠΈΡ.
ΠΠΎΠ³Π΄Π° ΠΎΠΏΡΡΠ½ΡΠΉ ΡΠ²Π°ΡΡΠΈΠΊ Π²ΡΠΏΠΎΠ»Π½ΡΠ΅Ρ ΡΠ²Π°ΡΠ½ΠΎΠ΅ ΡΠΎΠ΅Π΄ΠΈΠ½Π΅Π½ΠΈΠ΅ Π²ΡΡΡΠ½ΡΡ, ΠΎΠ½ ΡΡΠ°Π·Ρ Π·Π°ΠΌΠ΅ΡΠΈΡ, Π΅ΡΠ»ΠΈ ΡΡΠΎ-ΡΠΎ ΠΏΠΎΡΠ»ΠΎ Π½Π΅ ΡΠ°ΠΊ. ΠΠ½ Π±ΡΠ΄Π΅Ρ ΡΠ»Π΅Π΄ΠΈΡΡ Π·Π° ΠΏΡΠΎΡΠ΅ΡΡΠΎΠΌ, Π·Π° ΡΠ°Π±ΠΎΡΠΎΠΉ ΠΎΠ±ΠΎΡΡΠ΄ΠΎΠ²Π°Π½ΠΈΡ ΠΈ ΡΡΠ°Π·Ρ Π²Π½Π΅ΡΠ΅Ρ ΠΈΡΠΏΡΠ°Π²Π»Π΅Π½ΠΈΠ΅ ΡΠ°ΠΊ, ΡΡΠΎΠ±Ρ ΡΠ²Π°ΡΠΎΡΠ½ΡΠΉ ΡΠΎΠ² ΠΏΠΎΠ»ΡΡΠΈΠ»ΡΡ ΠΏΡΠΈΠ΅ΠΌΠ»Π΅ΠΌΠΎΠ³ΠΎ ΠΊΠ°ΡΠ΅ΡΡΠ²Π°. ΠΠ΅Ρ Π°Π½ΠΈΠ·ΠΈΡΠΎΠ²Π°Π½Π½Π°Ρ ΡΠ²Π°ΡΠΊΠ° Π²Π΅ΡΠ½ΠΎ ΠΈ ΡΠΎΡΠ½ΠΎ ΠΏΠΎΠ²ΡΠΎΡΡΠ΅Ρ Π·Π°ΠΏΡΠΎΠ³ΡΠ°ΠΌΠΌΠΈΡΠΎΠ²Π°Π½Π½ΡΠ΅ Π΄Π²ΠΈΠΆΠ΅Π½ΠΈΡ. ΠΠΎΡΡΠΎΠΌΡ Π²Π°ΠΆΠ½ΠΎ, ΡΡΠΎΠ±Ρ Π²ΡΠ΅ ΡΠ°ΠΊΡΠΎΡΡ Π½Π°Ρ ΠΎΠ΄ΠΈΠ»ΠΈΡΡ Π΄ΠΎΡΡΠ°ΡΠΎΡΠ½ΠΎ ΠΏΠΎΡΡΠΎΡΠ½Π½ΡΠΌ, ΡΡΠΎΠ±Ρ ΠΎΠ±Π΅ΡΠΏΠ΅ΡΠΈΡΡ ΡΡΠΏΠ΅ΡΠ½ΡΠΉ ΡΠ΅Π·ΡΠ»ΡΡΠ°Ρ. ΠΡΠ½ΠΎΠ²Π½ΠΎΠΉ ΠΏΡΠΈΠ½ΡΠΈΠΏ Π·Π°ΠΊΠ»ΡΡΠ°Π΅ΡΡΡ Π² ΡΠΎΠΌ, ΡΡΠΎ Π΄ΠΎΠΏΡΡΠΊ ΡΠΎΡΠ½ΠΎΡΡΠΈ ΡΠ²Π°ΡΠΎΡΠ½ΠΎΠ³ΠΎ ΠΏΡΠΎΡΠ΅ΡΡΠ° ΠΌΠΎΠΆΠ΅Ρ Π±ΡΡΡ Π±ΠΎΠ»ΡΡΠ΅, ΡΠ΅ΠΌ Π»ΡΠ±ΡΠ΅ ΠΎΡΠΊΠ»ΠΎΠ½Π΅Π½ΠΈΡ. Π ΡΠΎΠΆΠ°Π»Π΅Π½ΠΈΡ, ΠΏΡΠΈΠ΅ΠΌΠ»Π΅ΠΌΡΠ΅ Π΄ΠΎΠΏΡΡΠΊΠΈ ΠΈΠΌΠ΅ΡΡ ΡΠ΅Π½Π΄Π΅Π½ΡΠΈΡ ΠΊ ΡΠ½ΠΈΠΆΠ΅Π½ΠΈΡ, Π² ΡΠΎΠΆΠ΅ Π²ΡΠ΅ΠΌΡ ΡΡΠ΅Π±ΠΎΠ²Π°Π½ΠΈΠ΅ ΠΏΠΎΠ΄Π½ΡΡΠΈΡ ΠΏΡΠΎΠΈΠ·Π²ΠΎΠ΄ΠΈΡΠ΅Π»ΡΠ½ΠΎΡΡΠΈ β ΡΠ²Π΅Π»ΠΈΡΠΈΠ²Π°Π΅ΡΡΡ. Π’Π°ΠΊΠΈΠΌ ΠΎΠ±ΡΠ°Π·ΠΎΠΌ, Π½Π°ΠΌ ΠΏΡΠΈΠ΄Π΅ΡΡΡ ΠΈΡΠΏΠΎΠ»ΡΠ·ΠΎΠ²Π°ΡΡ Π΄ΠΎΠΏΠΎΠ»Π½ΠΈΡΠ΅Π»ΡΠ½ΠΎΠ΅ ΠΎΠ±ΠΎΡΡΠ΄ΠΎΠ²Π°Π½ΠΈΠ΅ Π΄Π»Ρ ΠΊΠΎΠ½ΡΡΠΎΠ»Ρ ΠΊΠ°ΡΠ΅ΡΡΠ²Π°.
Π’ΠΈΠΏΠΈΡΠ½ΡΠΌΠΈ ΠΏΡΠΈΠΌΠ΅ΡΠ°ΠΌΠΈ ΡΠ°ΠΊΡΠΎΡΠΎΠ², ΠΊΠΎΡΠΎΡΡΠ΅ ΠΌΠΎΠ³ΡΡ Π½Π΅Π³Π°ΡΠΈΠ²Π½ΠΎ ΠΏΠΎΠ²Π»ΠΈΡΡΡ Π½Π° ΠΏΡΠΎΡΠ΅ΡΡ, ΡΠ²Π»ΡΡΡΡΡ:
-ΡΠΈΡΠΈΠ½Π° Π·Π°Π·ΠΎΡΠ° Π² ΡΠ²Π°ΡΠ½ΠΎΠΌ ΡΠΎΠ΅Π΄ΠΈΠ½Π΅Π½ΠΈΠΈ;
-ΠΏΠΎΠ»ΠΎΠΆΠ΅Π½ΠΈΠ΅ Π½Π°ΠΊΠΎΠ½Π΅ΡΠ½ΠΈΠΊΠ° ΡΠ»Π΅ΠΊΡΡΠΎΠ΄Π° ΠΎΡΠ½ΠΎΡΠΈΡΠ΅Π»ΡΠ½ΠΎ ΡΡΡΠΊΠ°;
-ΠΏΡΠΎΠ±Π»Π΅ΠΌΡ Ρ ΠΏΠΎΠ΄Π°ΡΠ΅ΠΉ ΠΏΡΠΎΠ²ΠΎΠ»ΠΎΠΊΠΈ.
Π‘Π»Π΅Π΄ΡΡΡΠΈΠ΅ ΡΠ°ΠΊΡΠΎΡΡ Π²Π°ΠΆΠ½Ρ Π΄Π»Ρ ΠΏΠΎΠ΄Π΄Π΅ΡΠΆΠΊΠΈ ΠΊΠ°ΡΠ΅ΡΡΠ²Π°:
-ΡΠΎΠΎΡΠ²Π΅ΡΡΡΠ²ΠΈΠ΅ ΠΊΠΎΠ½ΡΡΡΡΠΊΡΠΈΠΈ Ρ ΡΠΈΠΏΠΎΠΌ ΡΠ²Π°ΡΠΎΡΠ½ΠΎΠ³ΠΎ ΡΠΎΠ΅Π΄ΠΈΠ½Π΅Π½ΠΈΡ;
-ΠΈΡΠΏΠΎΠ»ΡΠ·ΡΠΉΡΠ΅, ΠΏΠΎ Π²ΠΎΠ·ΠΌΠΎΠΆΠ½ΠΎΡΡΠΈ, Π½Π°ΠΈΠ±ΠΎΠ»Π΅Π΅ Π±Π»Π°Π³ΠΎΠΏΡΠΈΡΡΠ½ΡΠ΅ Π΄Π»Ρ ΡΠ²Π°ΡΠΊΠΈ ΠΏΠΎΠ»ΠΎΠΆΠ΅Π½ΠΈΠ΅;
-ΠΏΡΠΎΡΠΈΠ»Π°ΠΊΡΠΈΡΠ΅ΡΠΊΠΎΠ΅ ΠΎΠ±ΡΠ»ΡΠΆΠΈΠ²Π°Π½ΠΈΠ΅ ΠΎΠ±ΠΎΡΡΠ΄ΠΎΠ²Π°Π½ΠΈΡ;
-ΠΈΡΠΏΠΎΠ»ΡΠ·ΠΎΠ²Π°Π½ΠΈΠ΅ ΡΠ²Π°ΡΠΎΡΠ½ΠΎΠ³ΠΎ ΠΎΠ±ΠΎΡΡΠ΄ΠΎΠ²Π°Π½ΠΈΡ, ΠΊΠΎΡΠΎΡΠΎΠ΅ ΠΌΠΎΠΆΠ΅Ρ ΠΊΠΎΠ½ΡΡΠΎΠ»ΠΈΡΠΎΠ²Π°ΡΡ ΠΈ ΠΏΠΎΠ΄Π΄Π΅ΡΠΆΠΈΠ²Π°ΡΡ Π·Π°Π΄Π°Π½Π½ΡΠ΅ ΠΏΠ°ΡΠ°ΠΌΠ΅ΡΡΡ ΡΠ²Π°ΡΠΊΠΈ;
-ΠΈΡΠΏΠΎΠ»ΡΠ·ΠΎΠ²Π°Π½ΠΈΠ΅ ΠΎΠ±ΠΎΡΡΠ΄ΠΎΠ²Π°Π½ΠΈΡ Π΄Π»Ρ ΠΌΠΎΠ½ΠΈΡΠΎΡΠΈΠ½Π³Π°;
Π‘ΠΏΠ΅ΡΠΈΠ°Π»ΡΠ½ΡΠ΅ ΠΌΠ΅ΡΠΎΠ΄Ρ ΠΌΠΎΠ³ΡΡ Π±ΡΡΡ ΠΈΡΠΏΠΎΠ»ΡΠ·ΠΎΠ²Π°Π½Ρ Π΄Π»Ρ ΡΠ΅ΡΠ΅Π½ΠΈΡ ΡΠ»ΠΎΠΆΠ½ΡΡ ΡΠΈΡΡΠ°ΡΠΈΠΉ:
-ΠΊΠΎΠ»Π΅Π±Π°Π½ΠΈΠ΅ ΠΈΠ»ΠΈ ΠΏΠ΅ΡΠ΅ΠΌΠ΅Π½Π½ΠΎΠ΅ ΡΠ΅ΠΏΠ»ΠΎΠ²ΠΎΠ΅ Π²Π»ΠΎΠΆΠ΅Π½ΠΈΠ΅ ΠΌΠΎΠΆΠ΅Ρ ΡΠ΄Π΅Π»Π°ΡΡ ΠΏΡΠΎΡΠ΅ΡΡ ΠΌΠ΅Π½Π΅Π΅ ΡΡΠ·Π²ΠΈΠΌΡΠΌ ΠΊ ΠΈΠ·ΠΌΠ΅Π½Π΅Π½ΠΈΡΠΌ, Π½Π°ΠΏΡΠΈΠΌΠ΅Ρ, Π·Π°Π·ΠΎΡΠ° Π·Π°Π³ΠΎΡΠΎΠ²ΠΎΠΊ;
-ΡΠ»Π΅ΠΆΠ΅Π½ΠΈΡ Π·Π° ΡΡΡΠΊΠΎΠΌ.
ΠΠΎΠ½ΠΈΡΠΎΡΠΈΠ½Π³.
Π‘ΡΠ°Π½Π΄Π°ΡΡΡ ΠΊΠ°ΡΠ΅ΡΡΠ²Π° ΡΡΠ΅Π±ΡΡΡ ΠΌΠΎΠ½ΠΈΡΠΎΡΠΈΠ½Π³Π° Π·Π° ΠΏΠ°ΡΠ°ΠΌΠ΅ΡΡΠ°ΠΌΠΈ ΡΠ²Π°ΡΠΊΠΈ, ΠΊΠΎΡΠΎΡΡΠ΅ Π±ΡΠ΄ΡΡ ΠΎΠΏΠΈΡΠ°Π½Ρ Π² ΡΠ΅Ρ Π½ΠΎΠ»ΠΎΠ³ΠΈΠΈ ΡΠ²Π°ΡΠΊΠΈ Π‘ΠΏΠ΅ΡΠΈΡΠΈΠΊΠ°ΡΠΈΡ(WPS). ΠΠΏΡΠ΅Π΄Π΅Π»Π΅Π½Π½Π°Ρ ΡΠΎΡΠΌΠ° ΠΌΠΎΠ½ΠΈΡΠΎΡΠΈΠ½Π³Π° Π΄ΠΎΠ»ΠΆΠ½Π° Π±ΡΡΡ ΠΈΡΠΏΠΎΠ»ΡΠ·ΠΎΠ²Π°Π½Π° Π΄Π»Ρ ΡΠΎΠ³ΠΎ, ΡΡΠΎΠ±Ρ ΠΏΠΎΠ΄Π΄Π΅ΡΠΆΠΈΠ²Π°Π»ΠΈΡΡ ΡΠΊΠ°Π·Π°Π½Π½ΡΠ΅ ΠΏΠ°ΡΠ°ΠΌΠ΅ΡΡΡ ΡΠ²Π°ΡΠΊΠΈ.
ΠΠ°ΠΏΠΈΡΡ.
ΠΡΠΎΡΡΠ΅ΠΉΡΠ°Ρ ΡΠΎΡΠΌΠ° ΠΌΠΎΠ½ΠΈΡΠΎΡΠΈΠ½Π³Π° Π·Π°ΠΏΠΈΡΠΈ ΡΠΎΠΎΡΠ²Π΅ΡΡΡΠ²ΡΡΡΠΈΡ ΠΏΠ°ΡΠ°ΠΌΠ΅ΡΡΠΎΠ², Π²ΠΎΠ·ΠΌΠΎΠΆΠ½ΠΎ, ΡΠΎΠΏΡΠΎΠ²ΠΎΠΆΠ΄Π°Π΅ΡΡΡ Π²ΠΈΠ·ΡΠ°Π»ΡΠ½ΡΠΌ ΠΎΡΠΎΠ±ΡΠ°ΠΆΠ΅Π½ΠΈΠ΅ΠΌ. Π’ΠΈΠΏΠΈΡΠ½ΡΠ΅ ΠΏΠ°ΡΠ°ΠΌΠ΅ΡΡΡ Π΄Π»Ρ ΡΠ°ΠΊΠΎΠ³ΠΎ ΠΌΠΎΠ½ΠΈΡΠΎΡΠΈΠ½Π³Π° Π²ΠΊΠ»ΡΡΠ°ΡΡ ΡΠΎΠΊ, Π½Π°ΠΏΡΡΠΆΠ΅Π½ΠΈΠ΅, ΡΠΊΠΎΡΠΎΡΡΡ ΠΏΠΎΠ΄Π°ΡΠΈ ΠΏΡΠΎΠ²ΠΎΠ»ΠΎΠΊΠΈ, ΡΠ°ΡΡ ΠΎΠ΄ Π³Π°Π·Π° ΠΈΠ»ΠΈ Π»ΠΈΠ½Π΅ΠΉΠ½Π°Ρ ΡΠΊΠΎΡΠΎΡΡΡ ΡΠ²Π°ΡΠΊΠΈ. ΠΠ±ΠΎΡΡΠ΄ΠΎΠ²Π°Π½ΠΈΠ΅ Π΄ΠΎΠ»ΠΆΠ½ΠΎ Π±ΡΡΡ ΡΠΎΠ²ΠΌΠ΅ΡΡΠΈΠΌΠΎ Π΄Π»Ρ ΠΏΠΎΠ΄ΠΊΠ»ΡΡΠ΅Π½ΠΈΡ ΠΊ ΠΠ Π΄Π»Ρ ΠΏΡΠ΅Π΄ΡΡΠ°Π²Π»Π΅Π½ΠΈΡ ΠΈ Π΄ΠΎΠΊΡΠΌΠ΅Π½ΡΠ°ΡΠΈΠΈ ΠΈ ΠΈΠ½ΡΠΎΡΠΌΠ°ΡΠΈΠΈ Π² ΡΠ»Π΅ΠΊΡΡΠΎΠ½Π½ΠΎΠΌ Π²ΠΈΠ΄Π΅.
ΠΠ°Π΄Π·ΠΎΡ Ρ Π³ΡΠ°Π½ΠΈΡ ΡΡΠ΅Π²ΠΎΠ³ΠΈ.
Π£ΡΡΠ°Π½ΠΎΠ²ΠΈΠ² ΡΠΎΠΎΡΠ²Π΅ΡΡΡΠ²ΡΡΡΠΈΠ΅ Π΄ΠΎΠΏΡΡΡΠΈΠΌΡΠ΅ ΠΏΡΠ΅Π΄Π΅Π»Ρ, ΠΎΠ±ΠΎΡΡΠ΄ΠΎΠ²Π°Π½ΠΈΠ΅ ΠΌΠΎΠΆΠ΅Ρ Π³Π΅Π½Π΅ΡΠΈΡΠΎΠ²Π°ΡΡ Π°Π²Π°ΡΠΈΠΉΠ½ΡΠ΅ ΡΠΈΠ³Π½Π°Π»Ρ, Π΅ΡΠ»ΠΈ Π»ΡΠ±ΠΎΠΉ ΠΈΠ· ΠΊΠΎΠ½ΡΡΠΎΠ»ΠΈΡΡΠ΅ΠΌΡΡ ΠΏΠ°ΡΠ°ΠΌΠ΅ΡΡΠΎΠ² Π²ΡΡ ΠΎΠ΄ΠΈΡ Π·Π° ΠΏΡΠ΅Π΄Π΅Π»Ρ Π΄ΠΎΠΏΡΡΡΠΈΠΌΠΎΠ³ΠΎ Π΄ΠΈΠ°ΠΏΠ°Π·ΠΎΠ½Π°. Π‘ΠΈΠ³Π½Π°Π»Ρ ΡΡΠ΅Π²ΠΎΠ³ΠΈ ΠΌΠΎΠ³ΡΡ Π±ΡΡΡ ΡΠ³Π΅Π½Π΅ΡΠΈΡΠΎΠ²Π°Π½Ρ ΡΠ°Π·Π½ΡΠΌΠΈ ΠΏΡΠΈΠ½ΡΠΈΠΏΠ°ΠΌΠΈ. ΠΡΠ°ΡΠΊΠΎΠ²ΡΠ΅ΠΌΠ΅Π½Π½ΡΠΉ Π²ΡΡ ΠΎΠ΄ Π·Π° ΠΏΡΠ΅Π΄Π΅Π»Ρ ΠΌΠΎΠΆΠ΅Ρ Π±ΡΡΡ ΠΏΡΠΎΠΈΠ³Π½ΠΎΡΠΈΡΠΎΠ²Π°Π½ ΠΈ ΠΏΡΠΎΡΡΠΎ Π±ΡΡΡ Π·Π°ΠΏΠΈΡΠ°Π½, ΡΠΎΡΠΌΠΈΡΡΠ΅ΡΡΡ ΡΠ°ΠΊΠΆΠ΅ Π²ΡΠΎΡΠΎΠΉ ΡΡΠΎΠ²Π΅Π½Ρ Π³ΡΠ°Π½ΠΈΡ β ΠΏΡΠ΅Π΄Π΅Π»ΡΠ½ΡΠΉ β Π²ΡΡ ΠΎΠ΄ Π·Π° ΠΊΠΎΡΠΎΡΡΠΉ ΠΎΡΡΠ°Π½Π°Π²Π»ΠΈΠ²Π°Π΅Ρ ΡΠ°Π±ΠΎΡΡ ΠΎΠ±ΠΎΡΡΠ΄ΠΎΠ²Π°Π½ΠΈΡ.
ΡΠΎΠ±ΠΎΡΠΎΡΠ΅Ρ Π½ΠΈΠΊΠ°, ΡΠ²Π°ΡΠΎΡΠ½ΡΠ΅ ΠΏΡΠ΅ΡΡΡ, ΠΊΠΎΠ½ΡΡΠΎΠ»Ρ ΡΡΡΡΠΎΠΉΡΡΠ²Π°
ΠΠ΅Π· ΡΠ²Π°ΡΠΊΠΈ ΠΌΠ΅ΡΠ°Π»Π»ΠΎΠ² Π½Π΅ ΠΎΠ±Ρ ΠΎΠ΄ΠΈΡΡΡ Π½ΠΈ ΠΎΠ΄ΠΈΠ½ ΠΏΡΠΎΠΈΠ·Π²ΠΎΠ΄ΡΡΠ²Π΅Π½Π½ΡΠΉ ΠΏΡΠΎΡΠ΅ΡΡ. ΠΠΎΠ±ΠΈΡΡΡΡ ΠΎΡΠ»ΠΈΡΠ½ΠΎΠ³ΠΎ ΠΊΠ°ΡΠ΅ΡΡΠ²Π° ΡΠΎΠ΅Π΄ΠΈΠ½Π΅Π½ΠΈΡ Π΄Π΅ΡΠ°Π»Π΅ΠΉ ΠΌΠΎΠΆΠ½ΠΎ ΠΏΡΡΠ΅ΠΌ ΡΠΎΠ²Π΅ΡΡΠ΅Π½ΡΡΠ²ΠΎΠ²Π°Π½ΠΈΡ Π°Π²ΡΠΎΠΌΠ°ΡΠΈΠ·Π°ΡΠΈΠΈ ΡΠ²Π°ΡΠΊΠΈ. ΠΠ΅ΠΎΠ±Ρ ΠΎΠ΄ΠΈΠΌΡΠ΅ ΡΠ²ΠΎΠΉΡΡΠ²Π° ΡΠ²Π° Π²ΡΠΏΠΎΠ»Π½ΡΡΡΡΡ Π·Π° ΡΡΠ΅Ρ ΠΌΠ½ΠΎΠΆΠ΅ΡΡΠ²Π° ΠΏΡΠΎΠ³ΡΠ°ΠΌΠΌ, Π° ΠΎΡΡΡΡΡΡΠ²ΠΈΠ΅ Π²ΠΈΠ΄ΠΈΠΌΡΡ Π΄Π΅ΡΠ΅ΠΊΡΠΎΠ² ΠΎΠ±ΡΠ°Π·ΡΠ΅ΡΡΡ Π±Π»Π°Π³ΠΎΠ΄Π°ΡΡ ΠΏΠΎΠ»Π½ΠΎΠΉ ΠΌΠ΅Ρ Π°Π½ΠΈΠ·Π°ΡΠΈΠΈ ΡΠ²Π°ΡΠΊΠΈ. ΠΠ½Π° Π·Π°Π²ΠΈΡΠΈΡ ΠΎΡ ΡΡΠ°ΡΠ΅Π»ΡΠ½ΠΎΠΉ ΠΏΠΎΠ΄Π³ΠΎΡΠΎΠ²ΠΊΠΈ ΠΈΠ·Π΄Π΅Π»ΠΈΠΉ Π΄Π»Ρ ΡΠ°Π±ΠΎΡΡ, ΠΈΡΠΏΡΠ°Π²Π½ΠΎΡΡΠΈ Π²ΡΠ΅Π³ΠΎ ΠΎΠ±ΠΎΡΡΠ΄ΠΎΠ²Π°Π½ΠΈΡ, ΠΎΠΏΡΡΠ° ΡΠ°Π±ΠΎΡΡ ΡΠ²Π°ΡΡΠΈΠΊΠ°. ΠΠ²ΡΠΎΠΌΠ°ΡΠΈΠ·Π°ΡΠΈΡ ΡΠ²Π°ΡΠΊΠΈ ΠΎΡΠ½ΠΎΠ²Π°Π½Π° Π½Π° ΠΏΠΎΠ»Π½ΠΎΠΌ ΠΏΠ΅ΡΠ΅Ρ ΠΎΠ΄Π΅ Π²ΡΠ΅Π³ΠΎ ΡΠΏΡΠ°Π²Π»Π΅Π½ΠΈΡ ΠΊ ΠΌΠ°ΡΠΈΠ½Π°ΠΌ, Π° ΡΠ²Π°ΡΡΠΈΠΊ Π»ΠΈΡΡ ΠΎΡΡΡΠ΅ΡΡΠ²Π»ΡΠ΅Ρ ΠΊΠΎΠ½ΡΡΠΎΠ»Ρ Π½Π°Π΄ ΡΡΠ½ΠΊΡΠΈΠΎΠ½ΠΈΡΠΎΠ²Π°Π½ΠΈΠ΅ΠΌ Π²ΡΠ΅Π³ΠΎ ΠΎΠ±ΠΎΡΡΠ΄ΠΎΠ²Π°Π½ΠΈΡ.
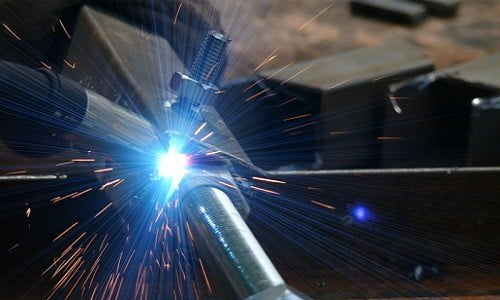
ΠΡΠΎΡΠ΅ΡΡ ΡΠ²Π°ΡΠΊΠΈ ΠΏΡΠΎΠΈΡΡ ΠΎΠ΄ΠΈΡ ΠΏΡΡΠ΅ΠΌ Π½Π°Π³ΡΠ΅Π²Π° ΠΌΠ΅ΡΠ°Π»Π»Π° ΠΏΡΠΈ ΠΏΠΎΠΌΠΎΡΠΈ ΡΠΎΠΊΠ°.
ΠΡΠ΅ΠΈΠΌΡΡΠ΅ΡΡΠ²Π° ΡΡΠΎΠ²Π΅ΡΡΠ΅Π½ΡΡΠ²ΠΎΠ²Π°Π½ΠΈΡ ΠΏΡΠΎΡΠ΅ΡΡΠ° ΡΠ²Π°ΡΠΎΡΠ½ΡΡ ΡΠ°Π±ΠΎΡ
ΠΡΠΏΠΎΠ»ΡΠ·ΠΎΠ²Π°Π½ΠΈΠ΅ ΠΌΠ°ΡΠΈΠ½ ΠΏΠΎΠ·Π²ΠΎΠ»ΡΠ΅Ρ ΠΎΡΡΡΠ΅ΡΡΠ²ΠΈΡΡ ΠΌΠ΅Ρ Π°Π½ΠΈΠ·Π°ΡΠΈΡ ΡΠ²Π°ΡΠΊΠΈ, Π° ΡΠ°Π±ΠΎΡΠΈΠΉ Π±Π΅ΡΠ΅Ρ Π½Π° ΡΠ΅Π±Ρ ΡΠΏΡΠ°Π²Π»Π΅Π½ΠΈΠ΅ ΠΏΡΠΎΠΈΠ·Π²ΠΎΠ΄ΡΡΠ²ΠΎΠΌ. ΠΡΠΎΡΠ΅ΡΡ Π²ΡΠΏΠΎΠ»Π½Π΅Π½ΠΈΡ ΡΠ°Π±ΠΎΡΡ ΠΏΠΎΠ΄ΡΠ°Π·Π΄Π΅Π»ΡΠ΅ΡΡΡ Π½Π° ΡΠ°ΡΡΠΈΡΠ½ΠΎΠ΅ ΠΈ ΠΊΠΎΠΌΠΏΠ»Π΅ΠΊΡΠ½ΠΎΠ΅ ΠΈΡΠΏΠΎΠ»Π½Π΅Π½ΠΈΠ΅. ΠΠ²ΡΠΎΠΌΠ°ΡΠΈΠ·Π°ΡΠΈΡ ΡΠΎΡΡΠΎΠΈΡ ΠΈΠ· ΠΎΡΠ΄Π΅Π»ΡΠ½ΡΡ ΠΎΠΏΠ΅ΡΠ°ΡΠΈΠΉ ΠΈΠ»ΠΈ ΠΎΡ Π²Π°ΡΡΠ²Π°Π΅Ρ Π²Π΅ΡΡ ΡΠ°Π±ΠΎΡΠΈΠΉ ΠΏΡΠΎΡΠ΅ΡΡ. ΠΡΠ½ΠΎΠ²Π½ΡΠΌΠΈ ΡΠΎΡΡΠ°Π²Π»ΡΡΡΠΈΠΌΠΈ ΠΏΡΠΎΡΠ΅ΡΡΠ° ΠΌΠ΅Ρ Π°Π½ΠΈΠ·Π°ΡΠΈΠΈ ΡΠ²Π»ΡΡΡΡΡ:
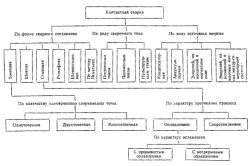
Π’Π°Π±Π»ΠΈΡΠ° ΠΊΠ»Π°ΡΡΠΈΡΠΈΠΊΠ°ΡΠΈΠΉ ΠΊΠΎΠ½ΡΠ°ΠΊΡΠ½ΠΎΠΉ ΡΠ²Π°ΡΠΊΠΈ.
- ΠΏΡΠΈΡΠΏΠΎΡΠΎΠ±Π»Π΅Π½ΠΈΡ Π΄Π»Ρ ΡΠ°Π±ΠΎΡΡ;
- ΡΠ²Π°ΡΠΎΡΠ½ΡΠ΅ ΠΈΠ½ΡΡΡΡΠΌΠ΅Π½ΡΡ;
- ΡΠ»Π΅ΠΌΠ΅Π½ΡΡ ΡΠΎΠ±ΠΎΡΠΎΡΠ΅Ρ Π½ΠΈΠΊΠΈ;
- Π»ΠΈΠ½ΠΈΠΈ Π°Π²ΡΠΎΠΌΠ°ΡΠΈΠ·Π°ΡΠΈΠΈ.
ΠΡΠΈΠΌΠ΅Π½ΡΡ Π°Π²ΡΠΎΠΌΠ°ΡΠΈΠ·Π°ΡΠΈΡ ΡΠ²Π°ΡΠΊΠΈ, ΠΌΠΎΠΆΠ½ΠΎ Π΄ΠΎΠ±ΠΈΡΡΡΡ ΠΎΡΡΡΠ΅ΡΡΠ²Π»Π΅Π½ΠΈΡ ΡΠ°ΠΊΠΈΡ Π·Π°Π΄Π°Ρ, ΠΊΠ°ΠΊ:
- ΡΠΎΠ·Π΄Π°Π½ΠΈΠ΅ Π±Π°Π·Ρ ΠΌΠ°ΡΠ΅ΡΠΈΠ°Π»ΠΎΠ² Π΄Π»Ρ ΡΠ°Π±ΠΎΡΡ;
- ΡΡΡΠ°Π½ΠΎΠ²Π»Π΅Π½ΠΈΠ΅ ΡΠ΅ΠΆΠΈΠΌΠΎΠ² ΡΠΎΠ΅Π΄ΠΈΠ½Π΅Π½ΠΈΡ ΠΌΠ°ΡΠ΅ΡΠΈΠ°Π»ΠΎΠ²;
- ΠΏΡΠΈΠΎΠ±ΡΠ΅ΡΠ΅Π½ΠΈΠ΅ Π½Π΅ΠΎΠ±Ρ ΠΎΠ΄ΠΈΠΌΠΎΠ³ΠΎ ΠΊΠΎΠ»ΠΈΡΠ΅ΡΡΠ²Π° Π΄Π΅ΡΠ°Π»Π΅ΠΉ Π΄Π»Ρ ΡΠ²Π°ΡΠΊΠΈ;
- ΡΡΡΠ°Π½ΠΎΠ²ΠΊΠ° ΡΠ΅Ρ Π½ΠΎΠ»ΠΎΠ³ΠΈΡΠ΅ΡΠΊΠΈΡ Π·Π°Π΄Π°Π½ΠΈΠΉ Π΄Π»Ρ ΠΊΠ°ΠΆΠ΄ΠΎΠ³ΠΎ ΡΡΠ°ΠΏΠ° ΡΠ°Π±ΠΎΡΡ.
ΠΠ½ΠΎΠ³ΠΈΠ΅ ΠΏΡΠ΅Π΄ΠΏΡΠΈΡΡΠΈΡ ΠΎΡΠ½Π°ΡΠ΅Π½Ρ ΡΠ²Π°ΡΠΎΡΠ½ΡΠΌΠΈ ΡΠΈΡΡΠ΅ΠΌΠ°ΠΌΠΈ Π² Π²ΠΈΠ΄Π΅ ΡΠΎΠ±ΠΎΡΠ°. ΠΠ³ΠΎ ΠΏΡΠΈΠΎΠ±ΡΠ΅ΡΠ΅Π½ΠΈΠ΅ ΠΈ ΡΡΡΠ°Π½ΠΎΠ²ΠΊΠ° ΡΠΊΠΎΠ½ΠΎΠΌΠΈΡΠ΅ΡΠΊΠΈ Π²ΡΠ³ΠΎΠ΄Π½Ρ, Ρ. ΠΊ. Π² Ρ ΠΎΠ΄Π΅ ΡΠ°Π±ΠΎΡΡ ΠΏΠΎΠ»ΡΠ·ΠΎΠ²Π°ΡΠ΅Π»Ρ ΠΏΠΎΠ»ΡΡΠ°Π΅Ρ:
- ΡΠΈΡΡΠ΅ΠΌΡ, ΠΎΡΡΡΠ΅ΡΡΠ²Π»ΡΡΡΡΡ ΠΌΠ΅Ρ Π°Π½ΠΈΠ·Π°ΡΠΈΡ ΡΠ²Π°ΡΠΊΠΈ;
- ΡΠΊΠΎΠ½ΠΎΠΌΠΈΡ Π΄Π΅Π½Π΅Π³ Π½Π° ΠΏΠΎΠ²ΡΡΠ΅Π½ΠΈΠΈ ΠΊΠ²Π°Π»ΠΈΡΠΈΠΊΠ°ΡΠΈΠΈ ΡΠ°Π±ΠΎΡΠΈΡ .
Π‘Π²Π°ΡΡΠΈΠΊ Π²ΡΠΏΠΎΠ»Π½ΡΠ΅Ρ ΡΠ²ΠΎΡ ΡΠ°Π±ΠΎΡΡ, ΠΈΡΠΏΠΎΠ»ΡΠ·ΡΡ Π΄ΠΎΠΏΠΎΠ»Π½ΠΈΡΠ΅Π»ΡΠ½ΡΠ΅ ΠΏΠ΅ΡΠ΅ΡΡΠ²Ρ, Π° ΡΠΎΠ±ΠΎΡ ΡΡΡΠ΄ΠΈΡΡΡ Π±Π΅ΡΠΏΡΠ΅ΡΡΠ²Π½ΠΎ, Π° ΠΊΠΎΡΡΡΠΈΡΠΈΠ΅Π½Ρ Π΅Π³ΠΎ Π΄Π΅ΡΡΠ΅Π»ΡΠ½ΠΎΡΡΠΈ ΡΠΎΡΡΠ°Π²Π»ΡΠ΅Ρ 70-75%. Π‘Π²Π°ΡΠΊΠ° ΠΏΡΡΠ΅ΠΌ ΠΌΠ΅Ρ Π°Π½ΠΈΠ·Π°ΡΠΈΠΈ ΠΏΡΠΎΠΈΠ·Π²ΠΎΠ΄ΡΡΠ²Π° Π²ΡΠΏΠΎΠ»Π½ΡΠ΅ΡΡΡ Π³ΠΎΡΠ°Π·Π΄ΠΎ Π±ΡΡΡΡΠ΅Π΅, ΡΠ΅ΠΌ Π²ΡΡΡΠ½ΡΡ. ΠΠ΅Ρ Π°Π½ΠΈΠ·Π°ΡΠΈΡ ΡΠ²Π°ΡΠΊΠΈ ΠΎΠ±Π΅ΡΠΏΠ΅ΡΠΈΠ²Π°Π΅ΡΡΡ ΡΠ°ΠΊΠΈΠΌ Π΄ΠΎΡΡΠΈΠΆΠ΅Π½ΠΈΠ΅ΠΌ ΠΏΡΠΎΠ³ΡΠ΅ΡΡΠ°, ΠΊΠ°ΠΊ ΡΠΎΠ±ΠΎΡΠΎΡΠ΅Ρ Π½ΠΈΠΊΠ°:
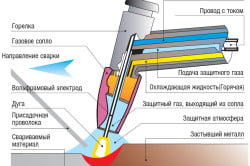
Π‘Ρ Π΅ΠΌΠ° Π΄ΡΠ³ΠΎΠ²ΠΎΠΉ ΡΠ²Π°ΡΠΊΠΈ.
- ΠΏΠΎΡΡΠ°Π»ΡΠ½ΡΠΌ ΡΠ²Π°ΡΠΎΡΠ½ΡΠΌ ΠΎΠ±ΠΎΡΡΠ΄ΠΎΠ²Π°Π½ΠΈΠ΅ΠΌ;
- ΠΎΠΏΡΠΎΠ²ΠΎΠ»ΠΎΠΊΠΎΠ½Π½ΠΎΠΉ Π»Π°Π·Π΅ΡΠ½ΠΎΠΉ ΡΡΡΠ°Π½ΠΎΠ²ΠΊΠΎΠΉ;
- ΠΊΠ°ΠΌΠ΅ΡΠΎΠΉ Π΄Π»Ρ ΡΠΎΠ΅Π΄ΠΈΠ½Π΅Π½ΠΈΡ ΡΠ»Π΅ΠΌΠ΅Π½ΡΠΎΠ² ΡΠ°ΠΌΠΎΠ»Π΅ΡΠΎΠ².
ΠΠ»Ρ Π°Π²ΡΠΎΠΌΠ°ΡΠΈΠ·Π°ΡΠΈΠΈ Π²ΡΠ΅Π³ΠΎ ΠΏΡΠΎΡΠ΅ΡΡΠ° ΠΈΡΠΏΠΎΠ»ΡΠ·ΡΡΡ ΡΡΠ°Π»ΡΠ½ΡΠ΅ ΡΠ²Π°ΡΠ½ΡΠ΅ ΠΊΠΎΠ»ΠΎΠ½Π½Ρ: ΡΡΡΠΏΠ΅Π½ΡΠ°ΡΡΠ΅, ΡΠ°Π·Π΄Π΅Π»ΡΠ½ΡΠ΅, Ρ ΠΏΠΎΡΡΠΎΡΠ½Π½ΡΠΌ ΡΠ΅ΡΠ΅Π½ΠΈΠ΅ΠΌ. ΠΠ½ΠΈ ΠΎΡΡΡΠ΅ΡΡΠ²Π»ΡΡΡ ΠΊΠΎΠ½ΡΡΠΎΠ»Ρ Π½Π°Π΄ ΡΠ²Π°ΡΠΎΡΠ½ΠΎΠΉ Π³ΠΎΡΠ΅Π»ΠΊΠΎΠΉ ΠΈ ΠΏΠ΅ΡΠ΅ΠΌΠ΅ΡΠ°ΡΡ Π΅Π΅ Ρ ΡΠΎΡΠ½ΠΎ ΡΡΡΠ°Π½ΠΎΠ²Π»Π΅Π½Π½ΠΎΠΉ ΡΠΊΠΎΡΠΎΡΡΡΡ. ΠΡΠΏΠΎΠ»ΡΠ·ΡΡΡ ΠΊΠΎΠ»ΠΎΠ½Π½Ρ ΠΏΡΠΈ Π°ΡΠ³ΠΎΠ½ΠΎΠ΄ΡΠ³ΠΎΠ²ΠΎΠΉ, ΠΏΠ»Π°Π·ΠΌΠ΅Π½Π½ΠΎΠΉ ΡΠ²Π°ΡΠΊΠ΅. ΠΠ½ΠΈ ΠΏΡΠΈΠ³ΠΎΠ΄Π½Ρ Π΄Π»Ρ ΠΏΠ΅ΡΠ΅ΠΌΠ΅ΡΠ΅Π½ΠΈΡ Π°ΠΏΠΏΠ°ΡΠ°ΡΠΎΠ² Π΄Π»Ρ ΡΠ²Π°ΡΠΊΠΈ Ρ ΠΏΠΎΡΠ»Π΅Π΄ΡΡΡΠ΅ΠΉ ΠΈΡ ΡΡΡΠ°Π½ΠΎΠ²ΠΊΠΎΠΉ. ΠΠΎΠ»ΠΎΠ½Π½Π° ΡΠ½Π°Π±ΠΆΠ°Π΅ΡΡΡ Π²ΡΠ΄Π²ΠΈΠΆΠ½ΠΎΠΉ ΠΈΠ»ΠΈ Π½Π΅ΠΏΠΎΠ΄Π²ΠΈΠΆΠ½ΠΎΠΉ ΠΊΠΎΠ½ΡΠΎΠ»ΡΡ. Π‘Π²Π°ΡΠΎΡΠ½ΡΠ΅ Π°Π²ΡΠΎΠΌΠ°ΡΡ ΠΎΡΠ½Π°ΡΠ°ΡΡΡΡ ΠΊΠΎΠ»ΠΎΠ½Π½Π°ΠΌΠΈ, ΠΈΠΌΠ΅ΡΡΠΈΠΌΠΈ ΠΎΡΠ½ΠΎΠ²Π½ΡΠ΅ ΠΏΠ°ΡΠ°ΠΌΠ΅ΡΡΡ. ΠΠ°ΠΈΠ±ΠΎΠ»ΡΡΠ°Ρ Π²ΡΡΠΎΡΠ° ΠΊΠΎΠ»ΠΎΠ½Π½Ρ β ΠΎΡ 1600 Π΄ΠΎ 6300 ΠΌΠΌ, Π²ΡΠ»Π΅Ρ ΠΊΠΎΠ½ΡΠΎΠ»ΠΈ ΡΠΎΡΡΠ°Π²Π»ΡΠ΅Ρ ΠΎΡ 1120 Π΄ΠΎ 4500 ΠΌΠΌ. Π‘ΠΊΠΎΡΠΎΡΡΡ ΠΏΠ΅ΡΠ΅ΠΌΠ΅ΡΠ΅Π½ΠΈΡ ΡΡΠ°Π½Π³ΠΈ ΡΠΎΡΡΠ°Π²Π»ΡΠ΅Ρ 2,0 ΠΌ/ΠΌΠΈΠ½.
ΠΡΡΡΠ΅ΡΡΠ²Π»Π΅Π½ΠΈΠ΅ ΠΌΠ΅Ρ Π°Π½ΠΈΠ·Π°ΡΠΈΠΈ ΡΠ²Π°ΡΠΊΠΈ ΠΊΠΎΠ½ΡΠ°ΠΊΡΠ½ΡΠΌ ΡΠΏΠΎΡΠΎΠ±ΠΎΠΌ
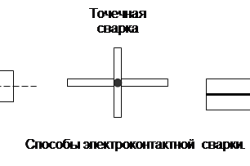
Π‘ΠΏΠΎΡΠΎΠ±Ρ ΠΊΠΎΠ½ΡΠ°ΠΊΡΠ½ΠΎΠΉ ΡΠ²Π°ΡΠΊΠΈ.
ΠΠ°ΡΠΈΠ½Ρ, Π²ΡΠΏΠΎΠ»Π½ΡΡΡΠΈΠ΅ ΠΎΠ±ΡΠ΅ΠΌ ΡΠ°Π±ΠΎΡΡ, ΠΏΠΎΠ΄ΡΠ°Π·Π΄Π΅Π»ΡΡΡ Π½Π° ΡΠΏΠ΅ΡΠΈΠ°Π»ΡΠ½ΡΠ΅ ΠΈ ΡΠ½ΠΈΠ²Π΅ΡΡΠ°Π»ΡΠ½ΡΠ΅. ΠΠ½ΠΈ Π±ΡΠ²Π°ΡΡ Π°Π²ΡΠΎΠΌΠ°ΡΠΈΡΠ΅ΡΠΊΠΈΠ΅ ΠΈ ΠΏΠΎΠ»ΡΠ°Π²ΡΠΎΠΌΠ°ΡΠΈΡΠ΅ΡΠΊΠΈΠ΅, ΠΈΡΠΏΠΎΠ»ΡΠ·ΡΠ΅ΠΌΡΠ΅ ΠΏΡΠΈ Π±ΠΎΠ»ΡΡΠΎΠΉ ΠΌΠΎΡΠ½ΠΎΡΡΠΈ ΠΈ Π² ΠΏΠΎΡΠΎΡΠ½ΡΡ Π»ΠΈΠ½ΠΈΡΡ . ΠΠ°ΡΠΈΠ½Ρ-Π°Π²ΡΠΎΠΌΠ°ΡΡ ΠΎΡΠ½Π°ΡΠ΅Π½Ρ Π±ΠΎΠ»ΡΡΠΈΠΌ ΠΊΠΎΠ»ΠΈΡΠ΅ΡΡΠ²ΠΎΠΌ ΠΏΡΠΎΠ³ΡΠ°ΠΌΠΌ, ΠΈΠΌΠ΅ΡΡ Π² ΡΠ²ΠΎΠ΅ΠΌ ΡΠΎΡΡΠ°Π²Π΅ Π½Π΅ΡΠΊΠΎΠ»ΡΠΊΠΎ ΠΎΡΠ½ΠΎΠ²Π½ΡΡ ΡΠ·Π»ΠΎΠ²:
- ΡΠ²Π°ΡΠΎΡΠ½ΡΠΉ ΡΡΠ°Π½ΡΡΠΎΡΠΌΠ°ΡΠΎΡ;
- ΡΠ΅Π³ΡΠ»ΡΡΠΎΡΡ ΠΌΠΎΡΠ½ΠΎΡΡΠΈ;
- ΠΌΠ΅Ρ Π°Π½ΠΈΠ·ΠΌ ΠΎΡ Π»Π°ΠΆΠ΄Π΅Π½ΠΈΡ;
- ΠΏΡΠΈΠ²ΠΎΠ΄Ρ Π³ΠΈΠ΄ΡΠ°Π²Π»ΠΈΡΠ΅ΡΠΊΠΈΠ΅.
Π Π°Π²ΡΠΎΠΌΠΎΠ±ΠΈΠ»Π΅ΡΡΡΠΎΠ΅Π½ΠΈΠΈ Π΄Π»Ρ ΡΡΡΠ°Π½ΠΎΠ²Π»Π΅Π½ΠΈΡ Π°Π²ΡΠΎΠΌΠ°ΡΠΈΠ·Π°ΡΠΈΠΈ ΡΠ²Π°ΡΠΊΠΈ Π΅ΡΡΡ Π½Π΅ΡΠΊΠΎΠ»ΡΠΊΠΎ ΠΏΡΠΈΡΠΈΠ½:
- ΠΈΡΠΏΠΎΠ»ΡΠ·ΠΎΠ²Π°Π½ΠΈΠ΅ Π»ΠΈΡΡΠΎΠ²ΠΎΠ³ΠΎ ΠΌΠ΅ΡΠ°Π»Π»Π°;
- Π½Π°Π»Π°ΠΆΠΈΠ²Π°Π½ΠΈΠ΅ ΠΊΠΎΠ½ΡΡΠΎΠ»Ρ Π½Π°Π΄ ΠΎΡΠΈΡΡΠΊΠΎΠΉ ΡΠ»Π΅ΠΊΡΡΠΎΠ΄ΠΎΠ²;
- Π·Π°ΠΌΠ΅Π½Π° ΡΡΡΠ½ΠΎΠ³ΠΎ Π½Π΅ΠΊΠ²Π°Π»ΠΈΡΠΈΡΠΈΡΠΎΠ²Π°Π½Π½ΠΎΠ³ΠΎ ΡΡΡΠ΄Π°.
ΠΡΠΏΠΎΠ»ΡΠ·ΡΡΡΡΡ Π΄Π»Ρ ΡΠ²Π°ΡΠΊΠΈ ΡΠΎΠ±ΠΎΡΠΎΡΠ΅Ρ Π½ΠΈΡΠ΅ΡΠΊΠΈΠ΅ Π»ΠΈΠ½ΠΈΠΈ, ΠΎΠ±Π΅ΡΠΏΠ΅ΡΠΈΠ²Π°ΡΡΠΈΠ΅ ΡΠ±ΠΎΡΠΊΡ, ΡΡΠ°Π½ΡΠΏΠΎΡΡΠΈΡΠΎΠ²ΠΊΡ, Π°Π²ΡΠΎΠΌΠ°ΡΠΈΠ·Π°ΡΠΈΡ ΠΏΡΠΎΡΠ΅ΡΡΠ°. Π ΠΎΠ±ΠΎΡ Π΄Π»Ρ ΠΊΠΎΠ½ΡΠ°ΠΊΡΠ½ΠΎΠΉ ΡΠ²Π°ΡΠΊΠΈ ΡΠΎΡΡΠΎΠΈΡ ΠΈΠ· ΡΡΠ΅Ρ ΡΠ·Π»ΠΎΠ²:
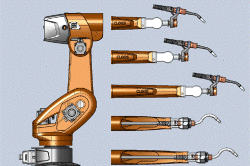
Π ΠΎΠ±ΠΎΡ Π΄Π»Ρ ΡΠ²Π°ΡΠΊΠΈ Ρ Π½Π°ΡΠ°Π΄ΠΊΠ°ΠΌΠΈ Π΄Π»Ρ ΡΠ°Π·Π½ΡΡ Π²ΠΈΠ΄ΠΎΠ² ΡΠ²Π°ΡΠΊΠΈ.
- Π Π°Π±ΠΎΡΠ΅Π³ΠΎ.
- ΠΠ»Π΅ΠΊΡΡΠΎΠ½Π½ΠΎ-Π²ΡΡΠΈΡΠ»ΠΈΡΠ΅Π»ΡΠ½ΠΎΠ³ΠΎ ΠΎΡΠ³Π°Π½Π°.
- ΠΠ°ΠΏΠΎΠΌΠΈΠ½Π°ΡΡΠ΅Π³ΠΎ ΡΡΡΡΠΎΠΉΡΡΠ²Π°.
ΠΠ½ ΡΠ°Π±ΠΎΡΠ°Π΅Ρ, ΠΈΡΠΏΠΎΠ»ΡΠ·ΡΡ Π±ΠΎΠ»ΡΡΠΎΠ΅ ΠΊΠΎΠ»ΠΈΡΠ΅ΡΡΠ²ΠΎ ΠΏΡΠΎΠ³ΡΠ°ΠΌΠΌ, Π² Π·Π°Π²ΠΈΡΠΈΠΌΠΎΡΡΠΈ ΠΎΡ Π½Π°Π»ΠΈΡΠΈΡ ΡΠ·Π»ΠΎΠ², ΠΏΠΎΠ΄Π»Π΅ΠΆΠ°ΡΠΈΡ ΡΠ²Π°ΡΠΈΠ²Π°Π½ΠΈΡ. Π ΠΎΠ±ΠΎΡ ΠΈΠΌΠ΅Π΅Ρ 6 ΡΡΠ΅ΠΏΠ΅Π½Π΅ΠΉ ΡΠ²ΠΎΠ±ΠΎΠ΄Ρ. Π Π°Π±ΠΎΡΠ°Ρ ΡΠ°ΡΡΡ Π²Π΅ΡΠΈΡ ΠΎΡ 100 ΠΊΠ³, ΡΠ³ΠΎΠ» ΠΏΠΎΠ²ΠΎΡΠΎΡΠ° ΡΠΎΡΡΠ°Π²Π»ΡΠ΅Ρ 200Β°. Π‘ΠΎΠ²ΡΠ΅ΠΌΠ΅Π½Π½ΡΠ΅ ΡΠΎΠ±ΠΎΡΠΈΠ·ΠΈΡΠΎΠ²Π°Π½Π½ΡΠ΅ ΠΊΠΎΠΌΠΏΠ»Π΅ΠΊΡΡ ΡΠΎΠ·Π΄Π°Π½Ρ Π½Π° ΠΎΡΠ½ΠΎΠ²Π΅ ΠΌΠΎΠ΄ΡΠ»Π΅ΠΉ. ΠΠ°Π½ΠΈΠΏΡΠ»ΡΡΠΎΡ ΠΎΠ±ΡΠ°Π·ΡΠ΅Ρ ΡΠ°Π±ΠΎΡΡΡ Π·ΠΎΠ½Ρ, Π° ΠΊΠΎΠ½ΡΡΡΡΠΊΡΠΈΡ ΠΌΠΎΠ½ΡΠΈΡΡΠ΅ΡΡΡ Π½Π° ΠΆΠ΅ΡΡΠΊΡΡ ΠΏΠΎΠ΄ΡΡΠ°Π²ΠΊΡ, ΠΎΠ±Π΅ΡΠΏΠ΅ΡΠΈΠ²Π°ΡΡΡΡ ΡΠ΄ΠΎΠ±Π½ΠΎΠ΅ ΠΏΠ΅ΡΠ΅ΠΌΠ΅ΡΠ΅Π½ΠΈΠ΅ Π²ΡΠ΅Π³ΠΎ ΠΊΠΎΠΌΠΏΠ»Π΅ΠΊΡΠ°. Π‘Π²Π°ΡΠΎΡΠ½Π°Ρ ΡΡΡΠ°Π½ΠΎΠ²ΠΊΠ° ΡΠΎΡΡΠΎΠΈΡ ΠΈΠ· ΠΎΡΠ½ΠΎΠ²Π½ΡΡ ΠΌΠ΅Ρ Π°Π½ΠΈΠ·ΠΌΠΎΠ²:
- ΠΌΠ°Π½ΠΈΠΏΡΠ»ΡΡΠΎΡΠ°;
- Π±Π»ΠΎΠΊΠ° ΠΠΠ£;
- ΠΏΠΎΠ²ΠΎΡΠΎΡΠ½ΠΎΠ³ΠΎ ΡΡΠΎΠ»Π°;
- ΠΈΡΡΠΎΡΠ½ΠΈΠΊΠ° ΡΠΎΠΊΠ°.
Π‘Π²Π°ΡΠΊΠ° Ρ ΠΏΡΠΈΠΌΠ΅Π½Π΅Π½ΠΈΠ΅ΠΌ ΠΌΠ΅Ρ Π°Π½ΠΈΠ·ΠΌΠΎΠ², ΠΎΡΡΡΠ΅ΡΡΠ²Π»ΡΡΡΠΈΡ ΡΠΎΡΠ΅ΡΠ½ΠΎΠ΅ ΠΈ ΡΠ΅Π»ΡΠ΅ΡΠ½ΠΎΠ΅ ΡΠΎΠ΅Π΄ΠΈΠ½Π΅Π½ΠΈΠ΅
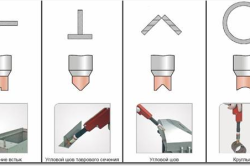
Π’ΠΎΡΠ΅ΡΠ½ΠΎΠ΅ ΡΠΎΠ΅Π΄ΠΈΠ½Π΅Π½ΠΈΠ΅ ΡΠ²Π°ΡΠΊΠΈ.
ΠΠ΅ΡΡ ΠΏΡΠΎΡΠ΅ΡΡ ΡΠ²Π°ΡΠΊΠΈ ΠΎΡΡΡΠ΅ΡΡΠ²Π»ΡΠ΅ΡΡΡ Ρ ΠΏΡΠΈΠΌΠ΅Π½Π΅Π½ΠΈΠ΅ΠΌ ΠΌΠ°ΡΠΈΠ½-Π°Π²ΡΠΎΠΌΠ°ΡΠΎΠ², ΡΠΎΠ±ΠΎΡΠΎΠ², ΠΏΡΠΎΠΌΡΡΠ»Π΅Π½Π½ΡΡ Π»ΠΈΠ½ΠΈΠΉ. ΠΠ½ΠΈ ΡΠ°Π·Π»ΠΈΡΠ°ΡΡΡΡ ΠΌΠ΅ΠΆΠ΄Ρ ΡΠΎΠ±ΠΎΠΉ ΠΏΠΎ ΠΌΠ½ΠΎΠ³ΠΈΠΌ ΠΏΠ°ΡΠ°ΠΌΠ΅ΡΡΠ°ΠΌ: ΠΊΠΎΠ½ΡΡΡΡΠΊΡΠΈΠΈ ΠΌΠ΅Ρ Π°Π½ΠΈΠ·ΠΌΠΎΠ², ΡΠΏΠΎΡΠΎΠ±Π°ΠΌ ΠΏΡΠ΅ΠΎΠ±ΡΠ°Π·ΠΎΠ²Π°Π½ΠΈΡ ΡΠ½Π΅ΡΠ³ΠΈΠΈ. Π‘Π²Π°ΡΠΎΡΠ½ΡΠ΅ ΠΏΡΠ΅ΡΡΡ ΠΎΠ±Π»Π°Π΄Π°ΡΡ ΠΌΠΎΡΠ½ΠΎΡΡΡΡ 150-660 ΠΊΠΠ. ΠΠ΅Ρ Π°Π½ΠΈΠ·ΠΌΡ Π΄Π»Ρ Π°Π²ΡΠΎΠΌΠ°ΡΠΈΠ·Π°ΡΠΈΠΈ ΡΠ²Π°ΡΠΊΠΈ ΠΎΡΠ½Π°ΡΠ΅Π½Ρ ΡΡΠ°Π½ΠΈΠ½ΠΎΠΉ, ΡΡΠ°Π½ΡΡΠΎΡΠΌΠ°ΡΠΎΡΠΎΠΌ, ΡΠΎΠΊΠΎΠΏΠΎΠ΄Π²ΠΎΠ΄ΡΡΠΈΠΌ ΡΡΡΡΠΎΠΉΡΡΠ²ΠΎΠΌ. Π£ΠΏΡΠ°Π²Π»Π΅Π½ΠΈΠ΅ ΠΎΡΡΡΠ΅ΡΡΠ²Π»ΡΠ΅ΡΡΡ Π·Π° ΡΡΠ΅Ρ ΡΠ»Π΅ΠΊΡΡΠΈΡΠ΅ΡΠΊΠΎΠΉ ΠΈ Π³ΠΈΠ΄ΡΠ°Π²Π»ΠΈΡΠ΅ΡΠΊΠΎΠΉ Π°ΠΏΠΏΠ°ΡΠ°ΡΡΡΡ. ΠΠΎΠ½ΡΠ°ΠΊΡΠΎΡ ΡΡΡΠ°Π½Π°Π²Π»ΠΈΠ²Π°ΡΡ Π² ΠΌΠ΅Ρ Π°Π½ΠΈΠ·ΠΌΠ°Ρ Π±ΠΎΠ»ΡΡΠΎΠΉ ΠΌΠΎΡΠ½ΠΎΡΡΠΈ. ΠΠ³Π½ΠΈΡΡΠΎΠ½Π½ΡΠΉ ΠΊΠΎΠ½ΡΠ°ΠΊΡΠΎΡ ΡΠ°Π±ΠΎΡΠ°Π΅Ρ ΠΎΡ Π½ΠΎΠΌΠΈΠ½Π°Π»ΡΠ½ΠΎΠ³ΠΎ ΡΠΎΠΊΠ° Π² 500 Π, 1000 Π, 2000 Π. Π’ΠΈΡΠΈΡΡΠΎΡΠ½ΡΠ΅ ΠΊΠΎΠ½ΡΠ°ΠΊΡΠΎΡΡ ΡΡΠ½ΠΊΡΠΈΠΎΠ½ΠΈΡΡΡΡ ΠΎΡ ΡΠΎΠΊΠ° 230-1600 Π (Π²Π΅Π»ΠΈΡΠΈΠ½Π° Π·Π°Π²ΠΈΡΠΈΡ ΠΎΡ ΠΏΡΠΎΠ΄ΠΎΠ»ΠΆΠΈΡΠ΅Π»ΡΠ½ΠΎΡΡΠΈ ΠΈΠΌΠΏΡΠ»ΡΡΠ° ΡΠΎΠΊΠ°). ΠΠ²ΡΠΎΠΌΠ°ΡΠΈΡΠ΅ΡΠΊΠΈΠ΅ ΠΌΠ΅Ρ Π°Π½ΠΈΠ·ΠΌΡ Π΄Π»Ρ ΡΠΎΡΠ΅ΡΠ½ΠΎΠΉ ΡΠ²Π°ΡΠΊΠΈ ΠΏΠΎΠ΄ΡΠ°Π·Π΄Π΅Π»ΡΡΡ ΠΏΠΎ ΠΊΠΎΠ»ΠΈΡΠ΅ΡΡΠ²Ρ ΡΠ²Π°ΡΠΈΠ²Π°Π΅ΠΌΡΡ ΡΠ»Π΅ΠΌΠ΅Π½ΡΠΎΠ² (ΡΠΎΡΠ΅ΠΊ) Π½Π° ΡΡΡΡΠΎΠΉΡΡΠ²Π°:
- ΠΎΠ΄Π½ΠΎΡΠΎΡΠ΅ΡΠ½ΡΠ΅;
- ΠΌΠ½ΠΎΠ³ΠΎΡΠΎΡΠ΅ΡΠ½ΡΠ΅.
ΠΠ½ΠΈ ΠΏΠΎΠ΄ΡΠ°Π·Π΄Π΅Π»ΡΡΡΡΡ Π½Π° ΡΠ»Π΅Π΄ΡΡΡΠΈΠ΅ Π²ΠΈΠ΄Ρ, Π² Π·Π°Π²ΠΈΡΠΈΠΌΠΎΡΡΠΈ ΠΎΡ ΠΊΠΎΠ½ΡΡΡΡΠΊΡΠΈΠΈ ΠΏΡΠΈΠ²ΠΎΠ΄Π° Π΄Π»Ρ ΡΠ»Π΅ΠΊΡΡΠΎΠ΄ΠΎΠ²:
- ΡΠ»Π΅ΠΊΡΡΠΎΠΌΠ΅Ρ Π°Π½ΠΈΡΠ΅ΡΠΊΠΈΠ΅;
- ΠΏΠ΅Π΄Π°Π»ΡΠ½ΡΠ΅;
- Π³ΠΈΠ΄ΡΠ°Π²Π»ΠΈΡΠ΅ΡΠΊΠΈΠ΅;
- ΠΏΠ½Π΅Π²ΠΌΠ°ΡΠΈΡΠ΅ΡΠΊΠΈΠ΅.
ΠΠΎΠ΄Π²Π΅ΡΠ½ΡΠ΅ ΠΌΠ΅Ρ Π°Π½ΠΈΠ·ΠΌΡ Π΄Π»Ρ ΡΠ²Π°ΡΠΊΠΈ ΡΠ°Π±ΠΎΡΠ°ΡΡ ΠΎΡ Π½ΠΎΠΌΠΈΠ½Π°Π»ΡΠ½ΠΎΠ³ΠΎ ΡΠΎΠΊΠ° 6,3-8 ΠΊΠ. ΠΠΎΡΠ½ΠΎΡΡΡ ΡΠΎΡΡΠ°Π²Π»ΡΠ΅Ρ 75,156,170, 80,25 ΠΊΠ.Π. ΠΠ½ΠΈ ΡΠ²Π°ΡΠΈΠ²Π°ΡΡ Π΄Π΅ΡΠ°Π»ΠΈ ΠΈΠ· Π½ΠΈΠ·ΠΊΠΎΡΠ³Π»Π΅ΡΠΎΠ΄ΠΈΡΡΠΎΠΉ ΡΡΠ°Π»ΠΈ ΡΠΎΠ»ΡΠΈΠ½ΠΎΠΉ Π»ΠΈΡΡΠ° 1,2-1,2 ΠΌΠΌ; 0,5+0,5+4,4 ΠΌΠΌ. ΠΠ°ΠΊΡΠΈΠΌΠ°Π»ΡΠ½Π°Ρ ΠΏΡΠΎΠΈΠ·Π²ΠΎΠ΄ΠΈΡΠ΅Π»ΡΠ½ΠΎΡΡΡ ΡΠΎΡΡΠ°Π²Π»ΡΠ΅Ρ: Π΄Π»Ρ ΠΏΠΎΠ΄Π²Π΅ΡΠ½ΡΡ ΡΡΠ°Π½ΡΡΠΎΡΠΌΠ°ΡΠΎΡΠΎΠ² β 80-120 ΡΠΌ/ΠΌΠΈΠ½, Π° Π΄Π»Ρ Π²ΡΡΡΠΎΠ΅Π½Π½ΡΡ ΠΌΠ΅Ρ Π°Π½ΠΈΠ·ΠΌΠΎΠ² β ΠΎΡ 40 Π΄ΠΎ 120 ΡΠΌ/ΠΌΠΈΠ½. ΠΡΠΏΠΎΠ»ΡΠ·ΡΡΡ ΠΊΠΎΠ½Π΄Π΅Π½ΡΠ°ΡΠΎΡΠ½ΡΠ΅ ΠΈ ΡΠΏΠ΅ΡΠΈΠ°Π»ΡΠ½ΡΠ΅ ΡΡΡΡΠΎΠΉΡΡΠ²Π° Π΄Π»Ρ ΡΠΎΡΠ΅ΡΠ½ΠΎΠΉ ΡΠ²Π°ΡΠΊΠΈ.
ΠΠ²ΡΠΎΠΌΠ°ΡΠΈΠ·Π°ΡΠΈΡ ΡΠΎΠ²Π½ΠΎΠΉ ΡΠ²Π°ΡΠΊΠΈ
Π¨ΠΈΡΠΎΠΊΠΎ ΠΏΡΠΈΠΌΠ΅Π½ΡΡΡΡΡ Π΄Π»Ρ ΡΠ°Π±ΠΎΡΡ ΡΠΏΠ΅ΡΠΈΠ°Π»ΡΠ½ΡΠ΅ ΠΈ Π½Π°ΠΈΠ±ΠΎΠ»Π΅Π΅ ΡΡΡΠ΅ΠΊΡΠΈΠ²Π½ΡΠ΅ ΡΠ½ΠΈΠ²Π΅ΡΡΠ°Π»ΡΠ½ΡΠ΅ ΠΌΠ΅Ρ Π°Π½ΠΈΠ·ΠΌΡ. ΠΠ½ΠΈ ΡΠ²Π°ΡΠΈΠ²Π°ΡΡ ΠΌΠ΅ΡΠ°Π»Π»Ρ ΠΈΠ΄Π΅Π½ΡΠΈΡΠ½ΡΡ ΠΌΠ°ΡΠΎΠΊ ΠΈΠ»ΠΈ ΠΎΠ΄Π½ΠΎΡΠΈΠΏΠ½ΡΠ΅ Π΄Π΅ΡΠ°Π»ΠΈ.
ΠΠ°ΡΠΈΠ½Ρ ΡΠ°Π·Π»ΠΈΡΠ°ΡΡΡΡ ΠΌΠ΅ΠΆΠ΄Ρ ΡΠΎΠ±ΠΎΠΉ ΠΏΠΎ ΡΠ°ΠΊΠΈΠΌ ΠΏΠ°ΡΠ°ΠΌΠ΅ΡΡΠ°ΠΌ, ΠΊΠ°ΠΊ ΠΊΠΎΠ½ΡΡΡΡΠΊΡΠΈΠ²Π½ΡΠ΅ ΠΏΡΠΈΠ·Π½Π°ΠΊΠΈ, Ρ Π°ΡΠ°ΠΊΡΠ΅Ρ Π²ΡΠ°ΡΠ΅Π½ΠΈΡ ΡΠΎΠ»ΠΈΠΊΠΎΠ², ΠΏΠΈΡΠ°Π½ΠΈΠ΅ ΠΎΡ ΡΠ»Π΅ΠΊΡΡΠΎΡΠΎΠΊΠ°.
ΠΠ»Ρ ΡΠ²Π°ΡΠΊΠΈ ΠΎΠ½ΠΈ ΠΈΠΌΠ΅ΡΡ ΡΠ°Π·Π½ΡΡ ΠΌΠ°ΡΡΡ ΠΈ Π΄ΠΎΡΡΠ°ΡΠΎΡΠ½ΠΎ ΠΌΠΎΡΠ½ΡΠΉ ΡΡΠ°Π½ΡΡΠΎΡΠΌΠ°ΡΠΎΡ. ΠΠΎΡΡΠ΅Π±Π»ΡΠ΅ΠΌΠ°Ρ ΠΌΠΎΡΠ½ΠΎΡΡΡ ΠΎΡ 30 ΠΊΠβ’Π Π΄ΠΎ 100 ΠΊΠΠ. Π‘ΠΈΠ»Π° ΡΠΎΠΊΠ° Π² ΠΏΡΠ΅Π΄Π΅Π»Π°Ρ ΠΎΡ 16 ΠΊΠ Π΄ΠΎ 308 ΠΊΠ. ΠΠ°ΡΠΈΠ½Ρ Π΄Π»Ρ ΡΠ²Π°ΡΠΎΡΠ½ΡΡ ΡΠ°Π±ΠΎΡ Π²ΡΠΏΡΡΠΌΠ»ΡΡΡ ΡΠΎΠΊ Π²ΡΠΎΡΠΈΡΠ½ΠΎΠ³ΠΎ ΠΊΠΎΠ½ΡΡΡΠ°. ΠΠ½ΠΈ ΡΠΎΠ΅Π΄ΠΈΠ½ΡΡΡ ΠΌΠ΅ΠΌΠ±ΡΠ°Π½Π½ΡΠ΅ ΠΈ ΡΠΈΠ»ΡΡΠΎΠ½Π½ΡΠ΅ ΡΠ·Π»Ρ, Π½ΠΈΠ·ΠΊΠΎΡΠ³Π»Π΅ΡΠΎΠ΄ΠΈΡΡΡΠ΅ ΡΡΠ°Π»ΠΈ ΠΈ ΡΠΈΡΠ°Π½ΠΎΠ²ΡΠ΅ ΡΠΏΠ»Π°Π²Ρ. Π‘Π²Π°ΡΠΎΡΠ½ΡΠΉ ΡΠΎΠΊ ΠΈΡΠΏΠΎΠ»ΡΠ·ΡΡΡ ΠΎΡ 12 Π΄ΠΎ 80 ΠΊΠ. Π‘ΠΊΠΎΡΠΎΡΡΡ ΡΠ²Π°ΡΠΊΠΈ ΠΊΠΎΠ»Π΅Π±Π»Π΅ΡΡΡ ΠΎΡ 0,1-1,5 Π΄ΠΎ 0,2-8 ΠΌ/ΠΌΠΈΠ½.
ΠΠΎΠ½ΡΡΡ ΠΌΠ°ΡΠΈΠ½Ρ ΠΏΠΎΠ΄ΠΊΠ»ΡΡΠ΅Π½ ΠΊ Π²ΡΠΏΡΡΠΌΠ»Π΅Π½Π½ΠΎΠΌΡ ΡΠΎΠΊΡ, ΠΊΠΎΡΠΎΡΡΠΉ ΠΏΡΠΎΡ ΠΎΠ΄ΠΈΡ ΠΈΠΌΠΏΡΠ»ΡΡΠ°ΠΌΠΈ ΠΈΠ»ΠΈ ΡΠ΅ΡΠ΅Ρ Π½Π΅ΠΏΡΠ΅ΡΡΠ²Π½ΠΎ. Π£Π½ΠΈΠ²Π΅ΡΡΠ°Π»ΡΠ½ΡΠ΅ ΠΌΠ΅Ρ Π°Π½ΠΈΠ·ΠΌΡ Π΄Π»Ρ ΡΠΎΠ²Π½ΠΎΠΉ ΡΠ²Π°ΡΠΊΠΈ ΡΠ°Π±ΠΎΡΠ°ΡΡ ΠΎΡ ΡΠΎΠΊΠ° 10-32 ΠΊΠ. Π‘Π²Π°ΡΠΈΠ²Π°Π΅ΠΌΡΠ΅ Π΄Π΅ΡΠ°Π»ΠΈ ΠΈΠΌΠ΅ΡΡ ΡΠΎΠ»ΡΠΈΠ½Ρ 1,2-1,2 ΠΌΠΌ Π΄ΠΎ 3+3 ΠΌΠΌ. Π‘ΠΊΠΎΡΠΎΡΡΡ ΡΠ²Π°ΡΠΊΠΈ ΡΠΎΡΡΠ°Π²Π»ΡΠ΅Ρ 0,5-4,5 Π΄ΠΎ 1-5 ΠΌ/ΠΌΠΈΠ½. ΠΠΎΡΠ½ΠΎΡΡΡ ΠΈΡΠΏΠΎΠ»ΡΠ·ΡΠ΅ΠΌΠΎΠ³ΠΎ ΡΠ»Π΅ΠΊΡΡΠΎΠ΄Π²ΠΈΠ³Π°ΡΠ΅Π»Ρ Ρ ΠΏΡΠΈΠ²ΠΎΠ΄ΠΎΠΌ β 0,27-1,1 ΠΊΠΡ. ΠΠ΅Ρ ΠΌΠ΅Ρ Π°Π½ΠΈΠ·ΠΌΠΎΠ² ΠΊΠΎΠ»Π΅Π±Π»Π΅ΡΡΡ ΠΎΡ 500 Π΄ΠΎ 1550 ΠΊΠ³.
ΠΡΠΈΠ²ΠΎΠ΄ Π²ΡΠ°ΡΠ΅Π½ΠΈΡ ΡΠΎΡΡΠΎΠΈΡ ΠΈΠ· ΠΌΡΡΡΡ, ΡΠ½Π°Π±ΠΆΠ΅Π½Π½ΠΎΠΉ ΡΠ»Π΅ΠΊΡΡΠΎΠΌΠ°Π³Π½ΠΈΡΠΎΠΌ. ΠΠΎΡΡΠΎΡΠ½Π½ΠΎ ΠΈΡΠΏΠΎΠ»ΡΠ·ΡΠ΅ΡΡΡ ΡΠ΅ΠΆΠΈΠΌ ΡΠ°Π±ΠΎΡΡ, ΠΏΠΎΠ·Π²ΠΎΠ»ΡΡΡΠΈΠΉ Π½Π°Π»Π°Π΄ΠΈΡΡ ΠΏΡΠ΅ΡΡΠ²ΠΈΡΡΠΎΠ΅ Π²ΡΠ°ΡΠ΅Π½ΠΈΠ΅ ΡΠΎΠ»ΠΈΠΊΠΎΠ². ΠΠ°ΡΠΈΠ½Π° ΡΠ½Π°Π±ΠΆΠ΅Π½Π° ΠΏΠ½Π΅Π²ΠΌΠ°ΡΠΈΡΠ΅ΡΠΊΠΈΠΌ ΠΈ ΡΠ»Π΅ΠΊΡΡΠΈΡΠ΅ΡΠΊΠΈΠΌ ΠΏΡΠΈΠ²ΠΎΠ΄ΠΎΠΌ Π΄Π»Ρ ΡΠΆΠ°ΡΠΈΡ ΡΡΡΡΠΎΠΉΡΡΠ²Π° Π΄Π»Ρ ΡΠ»Π΅ΠΊΡΡΠΎΠ΄ΠΎΠ².
ΠΠ²ΡΠΎΠΌΠ°ΡΠΈΠ·Π°ΡΠΈΡ ΠΈ ΠΌΠ΅Ρ Π°Π½ΠΈΠ·Π°ΡΠΈΡ ΡΠ²Π°ΡΠΎΡΠ½ΡΡ ΡΠ°Π±ΠΎΡ Π² ΡΠΎΠ²ΡΠ΅ΠΌΠ΅Π½Π½ΠΎΠΉ ΠΏΡΠΎΠΌΡΡΠ»Π΅Π½Π½ΠΎΡΡΠΈ ΠΏΠΎΠ·Π²ΠΎΠ»ΡΡΡ ΡΠ½ΠΈΠ·ΠΈΡΡ ΡΡΡΠ΄ΠΎΠ΅ΠΌΠΊΠΎΡΡΡ ΠΏΡΠΎΡΠ΅ΡΡΠ°, ΠΏΠΎΠ²ΡΡΠΈΡΡ ΠΊΡΠ»ΡΡΡΡΡ ΡΡΡΠ΄Π°, Π΄ΠΎΡΡΠΈΡΡ Π±ΠΎΠ»ΡΡΠΈΡ ΡΠ΅Ρ Π½ΠΈΡΠ΅ΡΠΊΠΈΡ ΠΈ ΡΠΊΠΎΠ½ΠΎΠΌΠΈΡΠ΅ΡΠΊΠΈΡ ΡΡΡΠ΅ΠΊΡΠΎΠ².