Основные направления механизации сварочного производства — Студопедия
Вообще, когда речь идет о механизации сварочных работ, различают два основных типа механизации:
· механизация отдельных технологических процессов
· механизация всего производства в целом.
Первое направление включает в себя установку механизмов, которые сокращают ручной труд при подаче деталей к месту сварки и перемещению сварочного оборудования. Сюда же включается и создание совершенно уникальных сварочных установок, позволяющих ускорить работу сварщика. Применение такого пути механизации приводит к объединению высокотехнологичных механизированных операций с ручным трудом профессионала. Но стоит отметить, что на общей трудоемкости процесса такой путь сказывается не очень сильно. Расчеты показывают, что даже замена половины ручных операций механическими может снизить трудоемкость сварочного процесса лишь на 10%. Также не слишком сильно сокращается и общее время выполнения сварочных работ.
Второе направление считается наиболее эффективным способом повысить качество всего сварочного процесса и ускорить производство сварных конструкций. Для внедрения такого пути механизации требуется комплексный подход ко всему процессу, замена практически всего ручного оборудования на механическое. Но результатом таких действий становится соблюдение всех требований к качеству любой сварной конструкции и общее повышение производительности труда в разы.
Общие сведения одной из главных технических и социальных задач в сварочном производстве является замена ручного труда сварщиков механизированной и автоматизированной сваркой. Эта задача решается заменой ручной сварки механизированной для конструкций, где сложно использовать автоматическую сварку (короткие швы, сложное пространственное положение), широкого использования робототехники, применения механизированных и автоматизированных сварочных установок с использованием усовершенствованных и новых сварочных процессов.
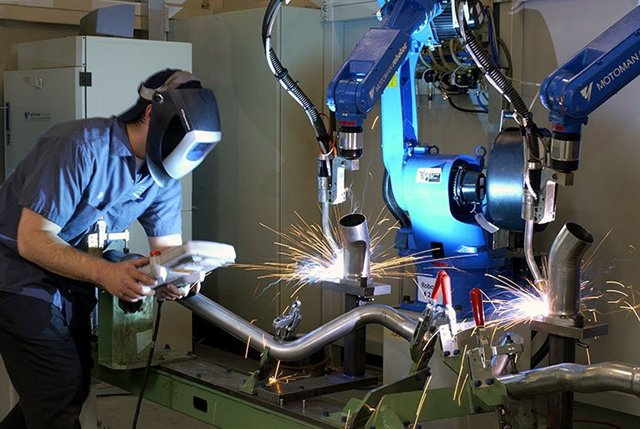
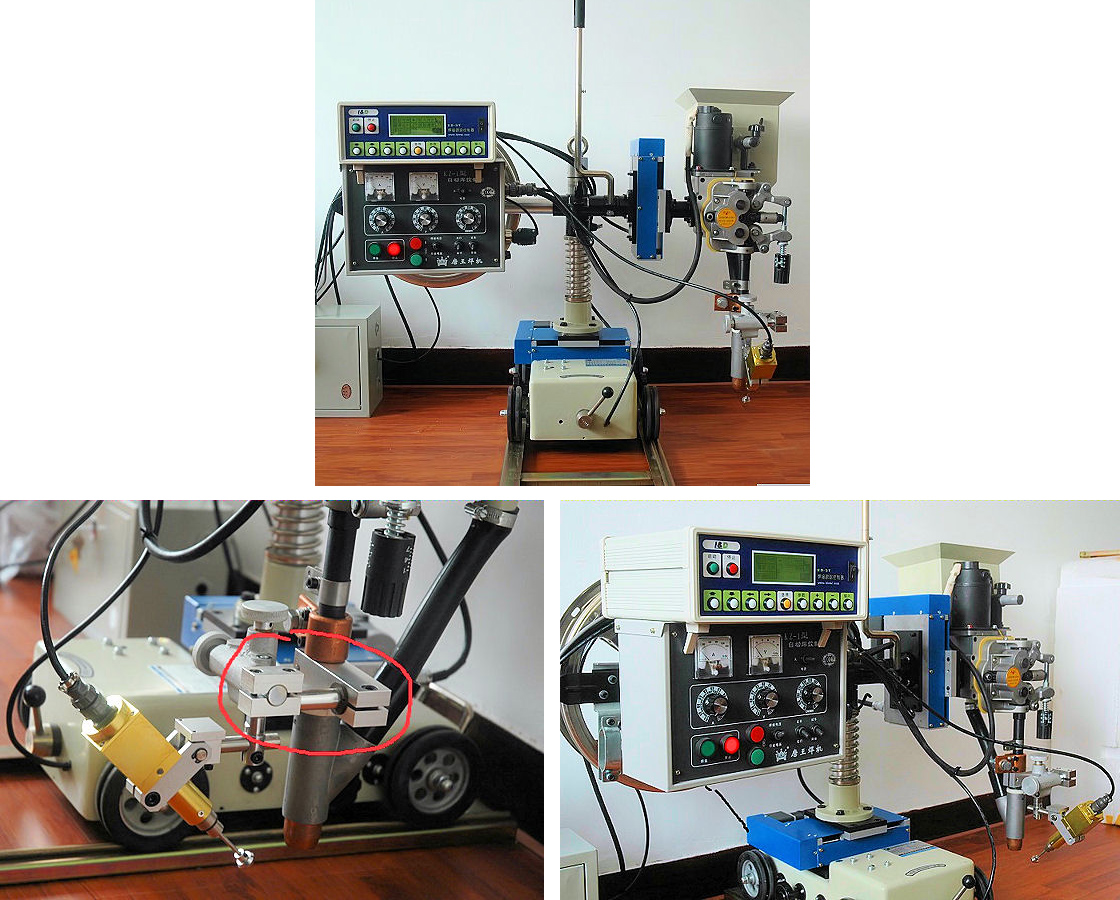
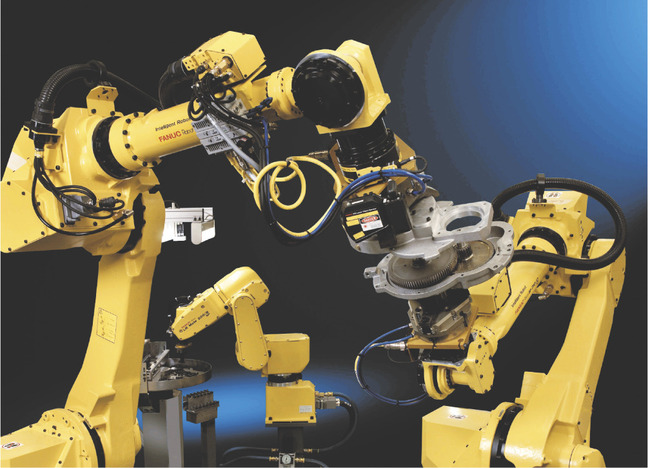
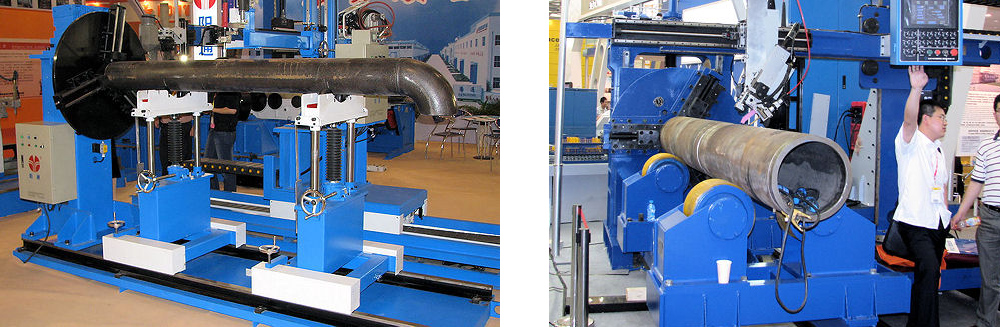
Универсальные приспособления общего назначения (сборочные плиты, стеллажи, манипуляторы, кантователи, роликовые стенды) используют для сборки и сварки изделий широкой номенклатуры и различных размеров. Для изделий определенного типа, но разных размеров используют универсальные приспособления специального назначения, которые конструируют в индивидуальном порядке. Универсальные приспособления применяют в единичном и мелкосерийном производстве. Помимо универсальных и специальных приспособлений в мелкосерийном и единичном производстве применяют универсально-сборочные приспособления, представляющие собой набор различных конструктивных элементов — универсальные плиты с продольными и поперечными пазами, типовые сменные упоры, фиксаторы, штыри, прихваты, планки, крепежные детали и т.

Поточные механизированные и автоматизированные линии Поточная линия — комплекс оборудования, взаимно связанного и работающего согласованно с определенным заданным ритмом по единому технологическому процессу. В сборочно-сварочные механизированные поточные линии входит оборудование для выполнения сборки, сварки, а иногда и операций подготовки металла, его раскроя, контроля готовой продукции и т. д. Первая поточная линия с применением автоматической сварки под флюсом была создана в годы Великой Отечественной войны для производства корпусов танков Т-34. По признаку механизации и автоматизации различают несколько типов поточных линий: с частичной механизаций, при которой используется ручная и полуавтоматическая сварка, а остальные процессы производственного цикла — раскрой металла, резка, сборка, окраска и др.

Вопросы для самопроверки:
1. Какие процессы в сварочном производстве могут быть механизированы?
2.
Литература:
Базовая:
6. А.Д. Гитлевич, Механизация и автоматизация сварочного производства, М., Машиностроение, 1979г. – стр.290.
Вспомогательная:
1. С.А. Куркин, Сварные конструкции, М., Высшая школа, 1991г. – стр.398;
7. М.С. Львов, Автоматика и автоматизация сварочных процессов, М. , Машиностроение, 1982г. – стр.302;
8. В.А. Тимченко, А.А. Сухомлин, Роботизация сварочного производства, К., Техника, 1989г. – стр.175;
9. Г. Герден, Сварочные работы, М., Машиностроение, 1988г. – стр.288;
10. Методические указания к выполнению практических работ по дисциплине «Технологическое оборудование».
Вебинар «Автоматизация сварочных процессов»
Компания «Вебер Комеханикс» приглашает Вас на семинар в формате онлайн «АВТОМАТИЗАЦИЯ СВАРОЧНЫХ ПРОЦЕССОВ».
Мероприятие пройдёт 21 мая 2020 года в 14-00 по московскому времени и будет состоять из 2-х секций каждая длительностью 30 минут.
Ключевые темы семинара:
- Варианты автоматизации сварки и их преимущества для современного сварочного производства.
- Обзор решений, предлагаемых «Вебер Комеханикс», для повышения эффективности сварочного производства. Реализованные проекты.
- Основные узлы и компоненты роботизированных сварочных комплексов (РСК).
- Обзор типовых сварочных ячеек и планировочных решений на базе промышленных роботов.
Механизация и автоматизация сварочных процессов открывают большие перспективы в развитии производства и ориентированы на снижение трудоемкости технологических процессов, увеличение выпуска и совершенствование качества конечного продукта, сокращение трудозатрат. Комплексы автоматической сварки позволяют выполнять типовые и сверхсложные задачи наиболее эффективным способом.
«Вебер Комеханикс» более 20 лет является поставщиком сварочного оборудования на предприятия автомобилестроения, крупного машиностроения, производителей мебели, радиаторов, дверей, оконных конструкций, котельного и трубопроводного оборудования и др. За это время мы накопили большой опыт, стали экспертами в сварке и готовы предложить технологии и оборудование для автоматизации Вашего производства: сварочные колонны, вращатели, установки для автоматической сварки кольцевых и продольных швов, роботизированные сварочные комплексы.
Чтобы принять участие в онлайн-семинаре, необходимо отправить письмо на электронный адрес [email protected] с указанием Ваших контактных данных и названия предприятия. В ответ Вы получите ссылку для входа на мероприятие.
Также вы можете зарегистрироваться на мероприятие на нашем сайте.
Основные направления механизации сборочно-сварочного производства в судостроении Вьетнама Текст научной статьи по специальности «Механика и машиностроение»
УДК 629.5.024.002
Фам Куанг Тиен
Астраханский государственный технический университет (Социалистическая Республика Вьетнам)
ОСНОВНЫЕ НАПРАВЛЕНИЯ МЕХАНИЗАЦИИ СБОРОЧНО-СВАРОЧНОГО ПРОИЗВОДСТВА В СУДОСТРОЕНИИ ВЬЕТНАМА
Судостроение Социалистической Республики Вьетнам находится на начальной стадии своего развития. В последние 5 лет наблюдается скачок в развитии судостроительного производства. Однако на первом этапе развития перед судостроительным производством стоит ряд проблем, в том числе преодоление низкого технологического уровня сборочносварочного производства — одного из основных видов судостроительных производств. Для повышения технологического уровня сборочносварочного производства необходимо осуществлять механизацию производственных процессов. Ниже рассматриваются некоторые положения механизации сборочно-сварочного производства для судостроения Вьетнама.
Сборочно-сварочное производство включает в себя работы по изготовлению узлов, секций, блоков и модулей металлического корпуса судна. На ее долю приходится 15-18 % общей трудоемкости постройки судна. Сборочно-сварочное производство объединяет следующие виды работ: разметочно-проверочные (7-10 %), пригоночные (12-17 %), сборочные (24-41 %), сварочные (25-46 %), правочные работы (7-8 %) [1].
Одним из путей повышения производительности труда в сборочносварочном производстве является механизация производственного процесса, под которой понимают полную или частичную замену ручного труда машинами, механизмами, аппаратами. Механизация начинается с момента разработки технологического процесса сборки и сварки конструкций и заканчивается внедрением его в производство. Эффективность механизации во многом зависит от уровня намеченной технологии и организации производства. Высшая ступень механизации — это комплексная механизация, когда ручной труд на основных и вспомогательных операциях заменяется работой машин, механизмов, установок. Комплексная механизация позволяет интенсифицировать технологические процессы. Она тесно связана с осуществлением массового производства и является основой его автоматизации, при которой весь производственный процесс осуществляется машинами, механизмами, специальными устройствами и приборами. Роль человека сводится только к контролю и отладке автоматизированного производства [2].
Современное развитие сборочно-сварочного производства характеризуется высоким уровнем механизации и автоматизации сварочных работ, составляющих 75-78 % от общего их объема. В то же время механизация сборочных, разметочных и проверочно-пригоночных работ состав-
ляет всего 28-48 %. Это связано с тем, что процесс сварки конструкций легче поддается механизации и автоматизации путем разработки и применения сравнительно малогабаритного сварочного оборудования стационарного и переносного типов, а уровень развития сварочной науки и техники обеспечивает создание и широкое применение его в производстве. Остальные операции изготовления сварных конструкций (разметка, сборка, проверка, прихватка, пригонка) для механизированного выполнения требуют создания и применения довольно сложного и крупногабаритного оборудования и металлоемкой технологической оснастки. Конструкции этих механизмов и оснастки находятся в прямой зависимости от конструктивного оформления изготовляемого изделия. При индивидуальной и мелкосерийной постройке судов они нерентабельны. От этого отчасти зависит низкий уровень механизации сборочных работ. Другой причиной низкого уровня механизации сборочных операций является отсутствие апробированных в производстве рациональных конструкций сборочно-сварочной оснастки и средств механизации этих процессов, а также недостаточность научных разработок, освещающих пути создания и внедрения эффективных конструкций механизмов и оснастки, удовлетворяющих механизированному, комплексномеханизированному и автоматизированному производствам [3].
В основу механизации сборочно-сварочного производства положены следующие основные принципы:
— технологичность корпусных конструкций в условиях комплексной механизации производства, т. е. пригодность конструкций к изготовлению на механизированных линиях или участках;
— конструктивно-технологическое сходство узлов и секций корпуса;
— организация поточного производства с принудительным ритмом, специализацией рабочих мест и синхронизацией их работы;
— типизация технологических процессов и оборудования для механизации изготовления типовых конструкций [3].
Можно сформулировать ряд общих требований к технологичности конструкций, выполнение которых обусловливает возможности механизации и автоматизации процессов. Во всех случаях необходимо стремиться к упрощению формы как всего корпуса судна, так и отдельных его конструкций. Упрощение формы обводов корпуса позволяет увеличить количество унифицированных деталей, узлов и секций корпуса, расширить область применения средств механизации и автоматизации и повысить их эффективность, сократить номенклатуру оснастки и уменьшить производственные площади для изготовления корпусных конструкций.
В составе корпуса современного крупнотоннажного судна может насчитываться несколько сот секций, несколько десятков тысяч узлов. В связи с этим весьма эффективной является организация изготовления узлов и секций на основе групповой технологии. Групповая технология заключается в том, что все изделия распределяют по технологическим группам и изготовляют по типовому технологическому процессу, характеризующемуся общностью технологического оборудования и оснастки. Основой групповой технологии является применение прогрессивных технологиче-
ских процессов и высокопроизводительного механизированного оборудования и оснастки [4].
Исходя из принципов групповой технологии, всю продукцию, выпускаемую сборочно-сварочным цехом, можно разделить на группы, положив в основу тип конструкций, ее форму, массу, а также соотношение основных размеров. Классификация объектов сборки по конструктивнотехнологическим признакам показана на рисунке [5]. Характерным признаком групп узлов является соотношение размеров в трех измерениях, поскольку оно непосредственно влияет на выбор технологического процесса изготовления. Главным конструктивно-технологическим признаком секций являются: форма ограничивающих поверхностей (плоская или криволинейная), соотношение высот набора и число балок разного направления, отношение высоты секции к ее размерам в плане.
Конструктивно-технологическая классификация сборочных единиц корпуса судна
К основным положениям организации производства при механизированном изготовлении узлов и секций корпуса относится предметная специализация линий и участков для изготовления определенных типов узлов и секций. Внедрение этого организационного принципа обеспечива-
ет повышение производительности труда примерно на 20-25 % путем более эффективного освоения приемов работ, характерных для каждой группы узлов и секций, а также путем использования специализированного оборудования, инструмента, приспособлений и оснастки; применением поточных форм организации производства на специализированных линиях и участках, где основной формой организации является поточнопозиционная с принудительным ритмом; применением системы автоматизированного запуска-выпуска узлов и секций на линиях и участках с определением рациональной последовательности их изготовления.
Важной задачей является обеспечение ритмичной работы механизированных поточных линий. Основной причиной нарушения ритмичности являются пригоночные работы, которые связаны с устранением погрешностей изготовления деталей и узлов, подаваемых на сборку. Для ликвидации пригоночных работ необходимо повысить точность изготовления корпусных деталей путем их типизации и унификации, широкого внедрения процессов плазменной и лазерной резки, совершенствования системы контроля.
Унификация типов и размеров создаваемого оборудования, включая отдельные агрегаты и узлы, является важным условием успешного решения задач комплексной механизации сборочно-сварочного производства. В данном случае унификация — это рациональное сокращение конструкции машин, их элементов и процессов изготовления до экономически и технически обоснованного минимума. Трудность создания унифицированного оборудования в судостроении объясняют рядом конструктивнотехнологических и организационных факторов: различием конструктивного оформления корпусов судов в зависимости от их типов, назначения и марок применяемого материала, многономенклатурностью программы судостроительных предприятий, выполняющих, как правило, одновременную постройку нескольких типов судов, характеристиками действующих сборочно-сварочных цехов, имеющих конкретные производственные площади, размерами пролетов и высот до подкрановых путей и грузоподъемным оборудованием. Отмеченные факторы показывают, что создание унифицированного оборудования является сложной задачей, которая должна решаться комплексно. Одним из путей решения следует считать создание типовых рядов оборудования на базе габаритов заказных листов.
Расчеты показывают, что внедрение механизированных производств в цехах верфей Социалистической Республики Вьетнам с использованием типовых решений может обеспечить повышение производительности труда в 2-2,2 раза. Срок окупаемости затрат на средства механизации составит 4-6 лет в зависимости от объема производства [6].
СПИСОК ЛИТЕРА ТУРЫ
1. Механизация и автоматизация судостроительного производства: Справ. / Л. Ц. Адлерштейн, Л. А. Клестов, Е. С. Нахамкин и др. — Л.: Судостроение, 1988.
2. Галкин В. А. Справочник технолога-судосборщика. Судокорпусное производство. — Л.: Судостроение, 1985.
3. Соколов В. Ф. Технологическое оборудование и автоматизация корпусосборочного производства: Учеб. пособие. — Л.: Судостроение, 1985.
4. Галкин В. А. Сборочно-сварочная оснастка цехов, верфи. — Л.: Судостроение, 1974.
5. Технология судостроения / Под общ. ред. А. Д. Гармашева. — СПб.: Профессия, 2003.
6. Website: www.vinashin.com
Получено 17.02.05
MAIN TRENDS
IN MECHANIZATION OF ASSEMBLY-WELDING MANUFACTURE IN SHIP-BUILDING INDUSTRY OF VIETNAM
Fam Kuang Tien
Adaptability to manufacturing of hull construction in the conditions of complex mechanization of manufacture i. e. fitness of constructions for manufacturing in mechanized lines or sections; structurally technological resemblance of units and hull of sections; creation of line production with forced rithm, specialization of jobs and timing their work, standardization of technological processes and equipment for mechanization of manufacturing standard structuresare put into the basis of this research. Mechanization promotes to increase labour productivity in assembly-welding manufacturing by 2-2,2 times.
Преимущества и применение робототехники для автоматической сварки
Сварочные аппараты получат широкое распространение в сварочной промышленности. В процессе сварочного производства степень механизации и автоматизации будет увеличена примерно на 15%, а степень автоматизации сварки достигнет 40-50%. Давайте посмотрим на преимущества и возможности применения роботизированной технологии автоматической сварки. 1. Повышение эффективности производства
Время отклика сварочного робота короткое, а действие быстрое.Скорость сварки составляет 60-3000 пикселей / мин, что намного выше, чем при ручной сварке. Робот может работать непрерывно, без пауз и отдыха в процессе работы. При условии обеспечения внешних условий воды и электричества, эффективность производства может быть незаметно улучшена.
2. Повышение качества продукции
В процессе сварки, если заданы параметры сварки и движущаяся дорожка, робот будет точно повторять это действие.Параметры сварки, такие как сварочный ток, напряжение, скорость сварки и длина сварочной проволоки, играют решающую роль в результатах сварки. Когда применяется роботизированная сварка, параметры сварки каждого сварного шва постоянны, и на качество сварки меньше влияет человеческий фактор, что снижает требования к технологии работы рабочих. Таким образом, качество сварки остается стабильным, что гарантирует качество нашей продукции.
3. Снижение затрат предприятия
Снижение стоимости сварочного робота в основном отражается в крупносерийном производстве.Один робот может заменить от 2 до 4 промышленных рабочих, что зависит от конкретной ситуации на предприятии. Кроме того, благодаря применению высокоскоростной и эффективной технологии сварки с использованием роботизированной сварки снижение затрат становится более очевидным.
4. Простота составления производственного плана
Поскольку у робота высокая воспроизводимость, пока указаны параметры, он всегда будет действовать в соответствии с инструкциями, поэтому цикл роботизированной сварки продукта ясен и легко контролируется выходом продукта.Производственный ритм робота фиксирован, поэтому график производства очень четкий. Точный производственный план может максимизировать эффективность производства и всестороннее использование ресурсов.
5. Сократить период преобразования продукта
Роботавтоматическая сварка может сократить период преобразования продукта и снизить затраты на соответствующее оборудование. Он может реализовать автоматизацию сварки мелкосерийных изделий. Самая большая разница между роботом и специальной машиной заключается в том, что он может изменять программу для адаптации к производству различных деталей.
Поскольку роботизированная дуговая сварка может в любой момент изменить сварочный путь и последовательность сварки с помощью программы, она лучше всего подходит для изделий с большим разнообразием деталей с короткими сварными швами и сложными формами. И этот вид продукции чаще всего появляется на кузове автомобиля, что как раз соответствует характеристикам автомобильной промышленности. Кроме того, становится все больше и больше автомобильных стилей, и скорость обновления теперь выше. Внедрение автомобильной производственной линии с роботизированным оборудованием может соответствовать быстрому развитию автомобильной промышленности в современном обществе.Робот-автомат для сварки широко используется в автомобильной промышленности, в частности в производстве автомобильных шасси, каркаса сиденья, направляющей, глушителя и гидравлического преобразователя крутящего момента, особенно при сварке автомобильных шасси.
Архивы автоматизированной сварки Dyna-Torque Technologies
Сварка стала основой различных отраслей промышленности по всему миру благодаря бесшовному соединению различных материалов, просто подвергая их воздействию тепла. Однако для получения точной и безупречной сварки необходимо наличие подходящих параметров и правильного инструмента. Поэтому пользователям необходимо с умом выбирать оборудование, чтобы реализовывать безупречные проекты в срок. Примечательно, что автоматизированное сварочное оборудование оказывается огромным подспорьем в этом отношении из-за его удобных функций. Различные отрасли, включая производство, производство клапанов, производство электроэнергии, переработку металлов, нефть и газ и т. Д., Дружно приняли этот особый метод сварки.
Помощь промышленным предприятиям
Для правильного изготовления в цехе необходимо различное оборудование, чтобы сделать процедуру простой, эффективной и менее трудоемкой.Обладая адекватными знаниями о параметрах и точным обучением, каждый становится опытным экспертом и может увеличить отдачу с помощью автоматизированных инструментов.
Широкий выбор автоматических сварочных аппаратов может удовлетворить основные потребности в производстве труб в цехе как для морских, так и для наземных трубопроводных предприятий. Целью разработки и проектирования этой автоматизированной системы было повышение долговечности и производительности в обрабатывающей промышленности. Кроме того, использование этой машины сокращает как рабочее время, так и затраты, что является огромной экономией для любой отрасли.
Лучшие преимущества
Из всех методов сварки, таких как защитная головка, механический и другие, автоматизированное сварочное оборудование приобрело популярность благодаря своему превосходному опыту и безопасному обращению. Сама машина регулирует параметры соответствующим образом, чтобы получать прекрасные результаты с помощью ручной помощи пользователя. Его простая процедура и точное использование металлов и наполнителей делают его предпочтительным выбором компаний.
В заключение отметим, что важность правильного сварочного аппарата неоспорима для своевременного выполнения и выполнения точных проектов.Таким образом, будет разумной игрушкой выбрать и использовать автоматическое сварочное оборудование для фантастического создания всех ваших производственных предприятий!
Гибкая автоматизация сварки в действии
Ранее этим летом базирующаяся в Ванкувере компания Novarc Technologies провела свой первый день открытых дверей в своей штаб-квартире в дополнение к дням открытых дверей, которые она недавно организовала на объектах дистрибьюторов в США. Восторженный отклик участников свидетельствует о том, что преимущества приложений для совместных роботов (коботов) будут стимулировать дальнейший рынок проникновение этих систем в самые разные конфигурации.
Комфортная сварка труб
Компания Novarc впервые появилась на рынке со своим совместным роботом для сварки катушек (SWR) два года назад. Полуавтоматическая роботизированная установка предназначена для сварки труб, изготовления сосудов под давлением и других сварочных работ.
В устройстве используется 3-осевая роботизированная рука на конце манипулятора с большим радиусом действия, который разработан для повышения ловкости и гибкости человека-оператора. Это позволяет им выполнить сварной шов от корня до верха трубы с полным проплавлением.
В действии он явно облегчает жизнь сварщику труб, который привык выполнять сварку вручную. Оператор перемещает робота к стыку и после ввода параметров на сенсорном экране может быстро начать сварку; навыки программирования не требуются.
Камера настроена для наблюдения за процессом наплавки, поэтому оператор может реагировать на это в режиме реального времени, изменяя параметры сварки по ходу дела. Это означает, что оператор подвергается меньшему воздействию сварочного дыма и не испытывает усталости от того, что сгорбился над сварным швом.Сварные швы также легко повторить, потому что система сохраняет ранее использованные сварочные процедуры.
SWR позволяет операторам выбирать между однопроходными или предварительно запрограммированными многопроходными сварными швами. Горелка с водяным охлаждением работает от источника питания на 500 А.
Способ установки системы на подвесной стреле позволяет сварщику перемещаться от стыка к стыку в радиусе 15 футов от основания, работая с несколькими позиционерами; не требуется никакого ограждения, что позволяет поднимать систему, чтобы она не мешала движению других магазинов, когда она не используется.
SWR может сохранять и пересчитывать данные сварных швов для цехового анализа и статистической отчетности.
Сварочное ноу-хау, поддержка автоматизации
Посетители дня открытых дверей Novarc в ее штаб-квартире в Северном Ванкувере наблюдают за работой технологии с использованием нового продукта компании ArcHood.
Крис Туроу, менеджер по качеству и сварочным технологиям, Samuel Pressure Vessel Group, посетил один из недавних дней открытых дверей компании и увидел, насколько автоматизация имеет смысл для работы, которую выполняет его компания.
«Мы всегда ищем способы, которыми мы можем больше использовать автоматизацию в нашем бизнесе», — сказал он. «Во всех трех наших офисах проблема заключается в укомплектовании персоналом; если бы у нас было больше квалифицированных сварщиков, мы бы это сделали. Даже когда мы находим квалифицированных сварщиков, им может потребоваться время, чтобы научиться выполнять конкретную работу, которую мы выполняем ».
Туроу сказал, что ценит эту технологию за то, что она устраняет повторяющиеся детали из работы.
«Оператору не нужно беспокоиться о действии переплетения, так как сварной шов остается на одном уровне со швом.Вместо этого он может сосредоточиться на нестандартных проблемах, связанных с этим типом работы, например, когда корневой разрыв становится больше », — пояснил он. «Вам по-прежнему нужен квалифицированный сварщик, но им немного легче управлять, потому что камера получает лучший угол сварного шва, чем ручной сварщик, и вы можете настраивать подгонку по ходу дела.
«Это открывает возможности для тех, кто действительно разбирается в процессе, но не всегда может собрать все воедино при ручной сварке, потому что есть на что реагировать.На самом деле, во время этого типа сварки происходит так много всего, что ваши реакции должны быть почти инстинктивными. Наблюдение за тем, что делает дуга, на эффект изменения переплетения, регулировки ампер и вольт — это нечто среднее между искусством и научным процессом — отслеживать все это одновременно ».
Туроу в восторге от того, как коботы в целом меняют наш взгляд на автоматизацию.
«Если у вас есть процесс, который предусматривает последовательную настройку и размещение деталей, полная автоматизация — отличный подход к работе», — сказал он.«В подобном процессе нет настоящего интеллекта; вы просто устанавливаете свои настройки и отслеживаете их по мере продвижения, но он разработан для того, чтобы каждый раз все шло по плану. Но в нашем магазине мы почти никогда не берем два металлических квадрата и не свариваем их. Скатанные скорлупы или формованные головы — это большая часть того, с чем мы работаем. При жесткой автоматизации обычно требуется что-то для поддержки сварного шва, а не открытый корень или швы с полным проплавлением. Используя такие коботы, как эта система, вы получаете преимущества как автоматизации, так и ноу-хау опытного сварщика.Технология делает то, что технология делает лучше всего, а сварщик делает все остальное. Коботу просто нужно знать конфигурацию фаски, толщину материала и корневые зазоры ».
Работа без шлема
На днях открытых дверей в Ванкувере Novarc также продемонстрировала свой новый продукт ArcHood ™, который прикрепляется к вытяжному рукаву, а затем перемещается на место вокруг сварочной горелки. Это устраняет необходимость в сварочных масках при работе с механизированным сварочным оборудованием.Дугу по-прежнему можно увидеть через окно автозатемнения на передней панели ArcHood, но его размещение сводит к минимуму воздействие сварочных искр, дыма, чрезмерного тепла и ультрафиолетового излучения. На картинке изображен гость, наблюдающий за демонстрацией сварного шва, используя вытяжку.
Дополнительные преимущества такого инструмента также очевидны. Использование такого кожуха устраняет необходимость в сварочных экранах, освобождая производственное пространство вокруг сварочной установки.
Участник дня открытых дверей смотрит на готовый сварной шов.
С редактором Робертом Колманом можно связаться по адресу [email protected].
Novarc Technologies Inc., novarctech.com
Автоматизация сварки трубопроводов и сосудов высокого давления с помощью адаптивного планирования и управления
org/ScholarlyArticle»> 1.А. Залкинд, Информационный бюллетень по сварке . Отчет Американского общества сварщиков (2007).
Дж. Уилки, Блог [Интернет] (2015). https://awo.aws.org/2015/11/the-future-remains-bright-for-skilled-welders/.По состоянию на 11 ноября 2019 г.
С. Бабу, Введение в интегрированное моделирование сварных швов , том 22 (Справочник ASM, Огайо, 2010 г.).
С. Мишра и Т. Деброй, Настройка геометрии газо-вольфрамовой дуговой сварки с использованием генетического алгоритма и нейронной сети, обученной расчетам конвективного теплового потока. Mater. Sci. Англ. А 454455, 477 (2007).
Артикул Google ученый
N.Львов, Дж. Чжун, Х. Чен, Т. Лин и С. Чен, Управление проваром в реальном времени во время динамического процесса GTAW с помощью звукового определения длины дуги. Внутр. J. Adv. Manuf. Technol. 74 (1–4), 235 (2014).
Артикул Google ученый
S.B. Чен и Н. Львов, Развитие исследований интеллектуальных технологий для процесса дуговой сварки. J. Manuf. Процесс. 16 (1), 109 (2014).
Артикул Google ученый
Дж. П. Стил, К. Мних, К. Дебруннер, Т. Винсент и С. Лю, Разработка управления процессами роботизированной сварки с обратной связью. Ind. Robot Int. J. 32 (4), 350 (2005).
Артикул Google ученый
Код ASME, ASME для котлов и сосудов под давлением, Стандарт (2017)
Р.Д. Конрой, Орбитальный процесс GTAW с узкой зазором становится все более заметным. Weld. J. 72 (12), 15 (1993).
Google ученый
B.K. Henon, Orbital GTAW увеличивает производство герметичных труб. Weld. J. 85 (6), 56 (2006).
MathSciNet Google ученый
D. Baek, H.S. Мун и С. Park, Разработка автоматической системы орбитальной сварки с надежным контролем ширины переплетения и функцией отслеживания шва для узких канавок. Внутр. J. Adv. Manuf. Technol. 93 (1–4), 767 (2017).
Артикул Google ученый
J.K. Татман, Л. Маккракен, Т. Hicks, Разработка новых уравнений тепловложения и разбавления сварного шва для дуговой сварки газом вольфрамовым электродом — Часть 1, Документ конференции (2013).
Дж. К. Татман, Разработка улучшенных уравнений для управления тепловложением и разбавлением сварного шва — часть 2, доклад конференции (2018).
М. Стадлер, П. Фретон и Ж.-Ж. Гонсалес, Влияние параметров сварки на размеры и форму сварочной ванны в конфигурации TIG. Заявл. Sci. 7 (4), 373 (2017).
Артикул Google ученый
Командури Р., Хоу З. Термический анализ процесса дуговой сварки: общие решения части I, Metall. Матер. Пер. В 31 (6), 1353–1370 (2000).
Артикул Google ученый
Ю. Ли, Ю.Ф. Ли, К.Л. Ван, Д. Сюй и М. Тан, Измерение и обнаружение дефектов сварного шва на основе онлайн-визуального контроля. IEEE Trans. Instrum. Измер. 59 (7), 1841–1849 (2010)
Статья Google ученый
RobotWorx — Эволюция роботизированной сварки —
С тех пор, как первобытный человек начал изготавливать инструменты, производство было неотъемлемой частью жизни каждого человека. Смотреть по сторонам. Все, что вы видите, чего не существует в природе, было произведено где-то в мире. От машин, в которых мы едем, до кресел, в которых мы сидим, многие из этих вещей были затронуты роботизированной сваркой. Но как мы перешли от первобытного человека к сварочной робототехнике?
Первоначально изделия изготавливались самими людьми, а затем, в более поздние века, мастерами в небольших мастерских. Когда в 18 веке началась промышленная революция, товары перемещались из магазинов на крупные фабрики. После того, как Эли Уитни изобрел механизированную сборочную линию в 1797 году, зародилось современное производство.
Одним из ключевых процессов производства металлических изделий является сварка.Сварка, процесс соединения двух металлических частей с помощью тепла и давления, в той или иной форме применялась с первых дней существования человека. Египтяне использовали сварку давлением еще в 3000 году до нашей эры.
Только в 1860-х годах Генри Уайльд использовал доступные электрические источники и запатентовал первую форму электросварки. Отсюда с начала до середины двадцатого века были разработаны различные типы сварочных процессов — дуговая сварка, сварка порошковой проволокой, электронно-лучевая сварка и т. Д.В то время как процесс сварки помещал людей в опасную среду с экстремальной жарой и токсичными парами, применение было необходимо для производства.
Затем, в 1962 году, все изменилось.
В том же году началась роботизированная сварка, когда General Motors начала использовать на своем автомобильном заводе первого промышленного робота — UNIMATE, разработанного Джорджем Деволом и Джозефом Энгельбергером. UNIMATE выполнил точечную сварку автомобилей, проходящих с конвейера.
В то время как Unimation была первой робототехнической компанией, основанной Деволом и Энгельбергером, в 1960-х и 1970-х годах на сцену вышли многие другие производители роботов, такие как KUKA, FANUC и Motoman.
Сварочные роботы начали развиваться только в 1980-х годах, когда другие автомобильные компании последовали примеру GM и начали использовать роботов для точечной сварки. Именно тогда отрасли начали расти и понимать преимущества сварочных роботов.
К 2005 году в Северной Америке работало более 60 000 роботизированных сварочных ячеек. В то время как компании, возможно, раньше задушили свои цели автоматизации из-за высокой цены, теперь затраты начали снижаться, поскольку все больше и больше компаний переходят на автоматизацию сварочной робототехники.
В последние годы популярность процесса дуговой сварки возросла, и по мере того, как промышленные сварочные аппараты-роботы становятся все более сложными с большим количеством осей (для лучшего движения) и трехмерным зрением (для повышения точности сварки), многие предприятия используют только роботизированные сварочные ячейки для их сварочные процессы.
Учитывая внутреннее увлечение человека металлами и производством, легко понять, почему роботизированная сварка — это путь будущего.
Роботы-сварщики создают высококачественные и точные сварные швы и повышают производительность сборочной линии.Эти роботы экономят производственные деньги производителей на трудозатратах из-за их скорости, способности работать без перерывов и их способности уменьшать количество ошибок.
Они также повышают уровень безопасности в цехах, убирая рабочих из опасной сварочной среды, от дыма и сильной жары. В то время как люди выводятся из опасной зоны, роботам по-прежнему нужны люди для программирования и функционирования, что показывает, что, хотя ручная сварка может стать устаревшей, люди всегда будут важной частью процесса сварки и производства.
RobotWorx, сертифицированный интегратор для KUKA, Universal Robots, Motoman, ABB и FANUC robotics, работает с производителями, чтобы найти правильное решение для роботизированной сварки для своего предприятия. Если вы производитель, стремящийся автоматизировать процесс сварки, свяжитесь с RobotWorx сегодня по телефону 740-251-4312 и узнайте больше о вариантах роботизированной сварки.
IRJET-Запрошенная вами страница не была найдена на нашем сайте
IRJET приглашает статьи из различных инженерных и технологических дисциплин, научных дисциплин для Тома 8, выпуск 3 (март-2021)
Отправить сейчас
IRJET Vol-8, выпуск 3, Март 2021 г. Публикация продолжается…
Обзор статей
IRJET получил «Импакт-фактор научного журнала: 7,529» за 2020 год.
Проверить здесь
IRJET получил сертификат регистрации ISO 9001: 2008 для своей системы управления качеством.
IRJET приглашает специалистов по различным инженерным и технологическим дисциплинам, научным дисциплинам для Тома 8, выпуск 3 (март-2021 г.)
Отправить сейчас
IRJET Vol-8, выпуск 3, март 2021 г. Публикация продолжается…
Обзор статей
IRJET получил «Импакт-фактор научного журнала: 7,529» за 2020 год.
Проверить здесь
IRJET получил сертификат регистрации ISO 9001: 2008 для своей системы управления качеством.
IRJET приглашает специалистов по различным инженерным и технологическим дисциплинам, научным дисциплинам для Тома 8, выпуск 3 (март-2021 г.)
Отправить сейчас
IRJET Vol-8, выпуск 3, март 2021 г. Публикация продолжается…
Обзор статей
IRJET получил «Импакт-фактор научного журнала: 7,529» за 2020 год.
Проверить здесь
IRJET получил сертификат регистрации ISO 9001: 2008 для своей системы управления качеством.
IRJET приглашает специалистов по различным инженерным и технологическим дисциплинам, научным дисциплинам для Тома 8, выпуск 3 (март-2021 г.)
Отправить сейчас
IRJET Vol-8, выпуск 3, март 2021 г. Публикация продолжается…
Обзор статей
IRJET получил «Импакт-фактор научного журнала: 7,529» за 2020 год.
Проверить здесь
IRJET получил сертификат регистрации ISO 9001: 2008 для своей системы управления качеством.
IRJET приглашает специалистов по различным инженерным и технологическим дисциплинам, научным дисциплинам для Тома 8, выпуск 3 (март-2021 г.)
Отправить сейчас
IRJET Vol-8, выпуск 3, март 2021 г. Публикация продолжается…
Обзор статей
IRJET получил «Импакт-фактор научного журнала: 7,529» за 2020 год.
Проверить здесь
IRJET получил сертификат регистрации ISO 9001: 2008 для своей системы управления качеством.
IRJET приглашает специалистов по различным инженерным и технологическим дисциплинам, научным дисциплинам для Тома 8, выпуск 3 (март-2021 г.)
Отправить сейчас
IRJET Vol-8, выпуск 3, март 2021 г. Публикация продолжается…
Обзор статей
IRJET получил «Импакт-фактор научного журнала: 7,529» за 2020 год.
Проверить здесь
IRJET получил сертификат регистрации ISO 9001: 2008 для своей системы управления качеством.
IRJET приглашает специалистов по различным инженерным и технологическим дисциплинам, научным дисциплинам для Тома 8, выпуск 3 (март-2021 г.)
Отправить сейчас
IRJET Vol-8, выпуск 3, март 2021 г. Публикация продолжается…
Обзор статей
IRJET получил «Импакт-фактор научного журнала: 7,529» за 2020 год.
Проверить здесь
IRJET получил сертификат регистрации ISO 9001: 2008 для своей системы управления качеством.
IRJET приглашает специалистов по различным инженерным и технологическим дисциплинам, научным дисциплинам для Тома 8, выпуск 3 (март-2021 г.)
Отправить сейчас
IRJET Vol-8, выпуск 3, март 2021 г. Публикация продолжается…
Обзор статей
IRJET получил «Импакт-фактор научного журнала: 7,529» за 2020 год.
Проверить здесь
IRJET получил сертификат регистрации ISO 9001: 2008 для своей системы управления качеством.
Датчики для роботизированной дуговой сварки и программирование в промышленных приложениях | Международный журнал машиностроения и материаловедения
Введение
Промышленные роботы и механизированное оборудование стали незаменимыми для промышленной сварки при высокой производительности, поскольку ручная сварка дает низкие производственные показатели из-за суровых условий труда и экстремальных физических требований (Laiping et al. 2005). Динамичное поведение рынка и жесткая конкуренция вынуждают компании-производители искать оптимальные производственные процедуры. Как показано на рис. 1 (Pires et al. 2003), для малых / средних объемов производства роботизированное производство дает лучшие затраты на единицу производительности по сравнению с ручной и жесткой автоматизацией. Помимо конкурентоспособных удельных затрат, роботизированные сварочные системы обладают и другими преимуществами, такими как повышенная производительность, безопасность, качество сварки, гибкость и использование рабочего пространства, а также снижение затрат на рабочую силу (Robot et al.2013a; Роберт и др. 2013). Расширение диапазона применений технологии роботизированной сварки привело к необходимости уменьшить вмешательство оператора и улучшить автоматизированный контроль над параметрами сварки, траекторией движения робота, обнаружением неисправностей и исправлением неисправностей (Schwab et al. 2008). Несмотря на то, что уровень сложности и сложности этих роботизированных систем высок, их способность адаптироваться к изменениям в условиях окружающей среды в реальном времени не может сравниться со способностью человеческих органов чувств адаптироваться к среде сварного шва (Hohn and Holmes 1982).
Зона промышленной робототехники (Pires et al. 2003; Myhr 1999)
Согласно данным Института робототехники Америки, робот — это «перепрограммируемый многофункциональный манипулятор, предназначенный для перемещения материалов, деталей, инструментов или специализированных устройств с изменяемыми запрограммированными движениями для выполнения различных задач». Хотя первый промышленный робот был разработан Джозефом Энгельбургером еще в середине 1950-х годов, только в середине 1970-х годов роботизированная дуговая сварка была впервые использована в производстве.Впоследствии робототехника была использована во многих сварочных процессах. Преимущества роботизированной сварки варьируются от процесса к процессу, но общие преимущества обычно включают улучшенное качество сварки, повышенную производительность, снижение затрат на сварку и повышенную стабильность повторяемости сварки (Lane, 1987).
Роботы для дуговой сварки
Сварка является неотъемлемой частью передового промышленного производства, а роботизированная сварка считается основным символом современной сварочной технологии (Cui et al. 2013). В самых ранних применениях роботизированной сварки, так называемых роботизированных сварочных системах первого поколения, сварка выполнялась как двухпроходная сварочная система, в которой первый проход был посвящен изучению геометрии шва, а затем следовало фактическое отслеживание и сварка шва за второй проход. С развитием технологий появилось второе поколение роботизированных сварочных систем, которые отслеживали шов в реальном времени, одновременно выполняя этапы обучения и отслеживания шва.Новейшая технология роботизированной сварки — это системы третьего поколения, в которых система не только работает в режиме реального времени, но и изучает быстро меняющуюся геометрию шва, работая в неструктурированной среде (Pires et al. 2006). На рисунке 2 показаны основные компоненты роботизированной системы дуговой сварки (Cary and Helzer 2005).
Роботизированная система дуговой сварки (Cary and Helzer 2005)
В следующих разделах кратко обсуждаются некоторые ключевые аспекты робототехники в сварочной технике.
Конфигурации роботов
Роботов можно разделить на категории на основе таких критериев, как степени свободы, кинематическая структура, технология привода, геометрия рабочего пространства и характеристики движения (Tsai 2000). При выборе роботов для конкретного применения необходимо учитывать все эти факторы. В зависимости от геометрии рабочего места роботы с поворотной (или шарнирной) конфигурацией являются наиболее часто используемым типом в промышленной роботизированной дуговой сварке (Росс и др., 2010). На рисунке 3 показан пример робота с вращающейся конфигурацией.
Рис. 3Вертикально шарнирный (поворотная конфигурация) робот с пятью поворотными шарнирами (Росс и др. 2010)
Этапы сварочных операций
Операция сварки состоит из трех различных фаз, которые требуют критического рассмотрения при проектировании полностью автоматизированной роботизированной сварочной системы для достижения хороших рабочих характеристик и качества сварки (Pires et al. 2006):
Подготовительный этап
На этом этапе сварщик настраивает свариваемые детали, оборудование (источник питания, робот, программу робота и т. Д.).) и параметров сварки, а также типа газовой и электродной проволоки. Когда используется CAD / CAM или другое автономное программирование, предварительная программа роботизированной сварки доступна и размещается в режиме онлайн. Следовательно, роботизированной программе может потребоваться лишь небольшая настройка для калибровки, которую может легко выполнить оператор сварки, выполняющий выбранное онлайн-моделирование процесса.
Фаза сварки
Автоматическое оборудование требует тех же возможностей, что и ручная сварка, т.е.е. система должна быть способна поддерживать ориентацию горелки, которая следует желаемой траектории (которая может отличаться от запланированной), выполнять отслеживание шва и изменять параметры сварки в реальном времени, таким образом имитируя адаптивное поведение ручных сварщиков.
Этап анализа
Этап анализа, как правило, является этапом после сварки, когда оператор сварки исследует полученный сварной шов, чтобы убедиться, что он приемлем или требуются ли изменения на предыдущих двух этапах.Использование современных датчиков, таких как 3D-лазерные камеры, позволяет выполнять этот этап в режиме онлайн на этапе сварки.
Режимы программирования роботов
Существуют различные методы обучения или программирования контроллера робота; а именно ручные методы, онлайн-программирование (сквозное, сквозное) и автономное программирование. Ручные методы в основном используются для роботов-захватчиков и не используются для роботов для дуговой сварки (Cary and Helzer 2005).
Онлайн-программирование
Эта категория программирования роботов включает сквозное и пошаговое программирование.Использование ручного метода онлайн-программирования не требует специального оборудования или программного обеспечения на месте, кроме того, которое используется в производственном процессе. Основным недостатком онлайн-программирования является то, что оно довольно негибкое и может управлять только простыми путями робота (Pan et al. 2012a). При пошаговом методе оператор вручную перемещает горелку через желаемую последовательность движений, которые записываются в память для воспроизведения во время сварки. Метод прохода был принят в нескольких первых сварочных роботах (Cary and Helzer 2005), но не получил широкого распространения.Традиционный метод программирования сварочных роботов — это онлайн-программирование с помощью обучающего пульта, т. Е. Сквозное программирование. В этом подходе программист толкает робота в желаемое положение с помощью клавиш управления на обучающем пульте, и желаемое положение и последовательность движений записываются. Основным недостатком метода онлайн-обучения является то, что программирование робота вызывает перебои в производстве на этапе программирования (McWhirter 2012).
Режим обучения и воспроизведения имеет ограниченную гибкость, поскольку он не может адаптироваться ко многим проблемам, которые могут возникнуть при сварке, например, ошибкам при предварительной обработке и подгонке заготовки, а также тепловым искажениям в процессе что приводит к изменению размера зазора. Таким образом, передовые приложения роботизированной сварки требуют автоматической системы управления, которая может адаптировать и регулировать параметры сварки и движения сварочных роботов (Hongyuan et al. 2009). Hongyuan et al. (2009) разработали замкнутую систему управления для роботов, которая использовала обучение и воспроизведение на основе визуального контроля в реальном времени для определения ширины верхней части сварочной ванны и зазора шва для управления образованием сварного шва при газовой вольфрамовой дуговой сварке с изменением зазора в многопроходном режиме. сварка. Несмотря на все вышеупомянутые недостатки, онлайн-программирование по-прежнему является единственным выбором программирования для большинства малых и средних предприятий (МСП).Методы онлайн-программирования с использованием более интуитивно понятных человеко-машинных интерфейсов (HMI) и сенсорной информации были предложены несколькими учреждениями (Zhang et al. 2006; Sugita et al. 2003). Вспомогательное онлайн-программирование можно разделить на вспомогательное онлайн-программирование и онлайн-программирование с сенсорным управлением.
Несмотря на значительный прогресс, достигнутый в том, чтобы сделать онлайн-программирование более интуитивным, менее зависимым от навыков оператора и более автоматическим, большинство результатов исследований коммерчески недоступны, за исключением Sugita et al.2003.
Автономное программирование
Автономное программирование (OLP) с помощью программного обеспечения для моделирования позволяет программировать путь сварки и последовательность операций с компьютера, а не с самого робота. Для OLP требуются 3D-модели CAD деталей, роботов и приспособлений, используемых в ячейке. Программное обеспечение для моделирования соответствует этим 3D-моделям САПР, позволяя программировать траекторию сварки робота с компьютера вместо обучающего пульта в сварочной камере, как при онлайн-программировании.После моделирования и тестирования программы инструкции можно экспортировать с компьютера в контроллер робота через сеть связи Ethernet. Однако текущие исследования показывают, что использование сенсорных технологий позволит полностью запрограммировать конечную траекторию только с помощью OLP (Miller Electric Mfg Co., 2013). Pan et al. (2012a) разработал автоматизированный метод автономного программирования с программным обеспечением, которое позволяет автоматическое планирование и программирование (с использованием моделей САПР в качестве входных данных) для роботизированной сварочной системы с высокой степенью свободы без каких-либо усилий по программированию.Основными преимуществами OLP являются его многократно используемый код, гибкость для модификации, возможность генерировать сложные траектории и сокращение времени простоя производства на этапе программирования для настройки новой детали. Тем не менее, OLP в основном используется для создания сложных путей роботов для больших объемов производства, потому что время и затраты, необходимые для создания кода для сложных роботизированных систем, аналогичны, если не больше, чем при онлайн-программировании (Pan et al.
2012a). В настоящее время для сложного производственного процесса с небольшим или средним объемом производства используется очень мало роботизированных решений для автоматизации, чтобы заменить ручное производство из-за этих дорогостоящих и трудоемких накладных расходов на программирование.Хотя OLP имеет вышеупомянутые преимущества, он не пользуется популярностью среди пользователей малого и среднего бизнеса (SME) из-за своих очевидных недостатков. Трудно экономически оправдать OLP для продуктов с меньшей стоимостью из-за высокой стоимости пакета OLP и накладных расходов на программирование, необходимых для настройки программного обеспечения для конкретного приложения. Разработка индивидуального программного обеспечения для автономного программирования занимает много времени и требует навыков программирования высокого уровня. Как правило, эти навыки недоступны инженерам-технологам и операторам, которые сегодня часто выполняют программирование роботов в процессе.Поскольку методы OLP основаны на точном моделировании робота и рабочей ячейки, дополнительные процедуры калибровки с использованием дополнительных датчиков во многих случаях неизбежны для удовлетворения требований (Pan et al.
2012b).
Интеллектуальный робот
Очень сложно и даже невозможно предвидеть и идентифицировать все ситуации, которые робот мог бы сделать во время выполнения своей задачи. Поэтому разработчик программного обеспечения должен указать категории ситуаций и предоставить роботу достаточный интеллект и способность решать задачи любого класса своей программы.Иногда, когда ситуации неоднозначны и неопределенны, робот должен уметь оценивать различные возможные действия. Если среда робота не меняется, роботу дается модель окружающей среды, чтобы он мог предсказать результат своих действий. Но если окружающая среда изменится, робот должен научиться. Это среди других предпосылок, требующих разработки и внедрения в роботов системы искусственного интеллекта (ИИ), способной учиться, рассуждать и решать проблемы (Tzafestas and Verbruggen 1995).
Большинство сварочных роботов, используемых в практическом производстве, по-прежнему являются обучающими и воспроизводящими, и они не могут полностью соответствовать требованиям качества и диверсификации сварочного производства, потому что эти типы роботов не имеют автоматических функций для адаптации к изменениям обстоятельств и неопределенным возмущениям (ошибки предварительного механическая обработка и подгонка заготовки, теплопроводность, рассеивание во время процесса сварки) во время процесса сварки (Tarn et al. 2004; Tarn et al. 2007). Чтобы преодолеть или ограничить различную неопределенность, которая влияет на качество сварного шва, было бы эффективным подходом к разработке и совершенствованию интеллектуальной технологии сварочных роботов, такой как визуальное зондирование, мульти-зондирование для сварочных роботов, распознавание сварочной среды, самовыражение. -управление и отслеживание швов, а также интеллектуальные процедуры управления сварочными роботами в режиме реального времени.С этой целью разработка интеллектуальной технологии для улучшения текущего метода обучения и использования для воспроизведения программирования для сварочных роботов имеет важное значение для достижения высокого качества и гибкости, ожидаемых от сварных изделий (Chen and Wu 2008; Chen 2007).
Ожидается, что интеллектуальные роботы будут играть активную роль в работе по соединению, которая составляет такую же значительную часть в машиностроении, как и работа по механической обработке. Интеллектуальный робот может выполнять высокоточные сборочные работы, собирая заготовку из беспорядочно уложенных друг на друга заготовок на лотке, собирая ее с точностью установки зазора 10 мкм или меньше с помощью датчиков силы, а также обеспечивая высокоскоростную стойкую точечную дуговую сварку при автомобильной сварке и сварке. картина.Тем не менее, у промышленных интеллектуальных роботов все еще есть задачи, в которых они не могут конкурировать с квалифицированными рабочими, хотя у них высокий уровень навыков, как было объяснено до сих пор. Например, сборка гибких объектов, таких как жгут проводов, в мире ведется ряд исследований и разработок, направленных на решение этих проблем (Nof 2009).
Проблемы роботизированной сварки
Несмотря на преимущества использования роботизированных систем, связанные с ними проблемы требуют должного внимания.Проблемы включают следующее:
Консистенция, необходимая для изготовления детали за деталью, которая при отсутствии надлежащего контроля может колебаться из-за плохой фиксации или отклонений в процессе обработки металла.
В случае малых и средних объемов производства или ремонтных работ время и усилия, затрачиваемые на программирование робота для сварки новой детали, могут быть довольно высокими (Dinham and Fang 2013).
Роботизированная сварка требует правильной конструкции соединения, постоянных условий зазора и допуска зазора не более 0,5–1 мм. Изменение состояния зазора требует использования сенсорных технологий для заполнения зазора (Robot et al. 2013b).
Автоматизация сварки с помощью роботизированных систем имеет высокую начальную стоимость, поэтому точный расчет окупаемости инвестиций (ROI) очень важен (Rochelle 2010).
Возможная нехватка квалифицированных сварщиков с необходимыми знаниями и подготовкой создает ограничения.
В отличие от адаптивного человеческого поведения, роботы не могут самостоятельно принимать автономные корректирующие решения и должны дополняться использованием датчиков и надежной системы управления для принятия решений.
Роботизированная сварка не может быть легко выполнена в некоторых областях, таких как сосуды высокого давления, внутренние резервуары и корпуса судов из-за ограничений рабочего пространства (Robotics Bible 2011).
Большинство доступных на рынке интеллектуальных систем на основе датчиков не интегрированы плотно с контроллером робота, что ограничивает производительность робототехнической системы, поскольку большинство промышленных роботов предлагают только около 20 Гц петли обратной связи через интерфейс программирования.
Следовательно, робот не может быстро реагировать на информацию датчика, что приводит к вялой, а иногда и нестабильной работе.
Датчики в роботизированной сварке
Потребность в датчиках в роботизированной сварке
В настоящее время сварочные роботы используются преимущественно в автоматических производственных процессах, в большинстве из которых используются обучающие и воспроизводящие роботы, которые требуют много времени для обучения и планирования пути, Кроме того, обучение и программирование необходимо повторить, если размеры сварных деталей изменяются, поскольку они не могут самостоятельно исправляться в процессе сварки.В частности, на практике положение шва часто нарушается из-за различных проблем. Использование датчиков — это способ решения этих проблем в автоматизированных процессах роботизированной сварки (Xu et al. 2012). Основное применение датчиков в роботизированной сварке — это обнаружение и измерение характеристик и параметров процесса, таких как геометрия стыка, геометрия и расположение сварочной ванны, а также оперативное управление процессом сварки. Датчики дополнительно используются для проверки сварных швов на дефекты и оценки качества (Pires et al. 2006).Идеальный датчик для применения робота должен измерять точку сварки (предотвращение несоосности отслеживания), должен обнаруживать заранее (определение начальной точки шва, распознавание углов, предотвращение столкновений) и должен быть как можно меньше (без ограничений в доступности). ). Идеальных датчиков, сочетающих все три требования, не существует; поэтому необходимо выбрать датчик, который подходит для каждой отдельной сварочной работы (Bolmsjö and Olsson 2005). Датчики, измеряющие геометрические параметры, в основном используются для обеспечения робота возможности отслеживания шва и / или поиска, что позволяет адаптировать траекторию робота в соответствии с геометрическими отклонениями от номинального пути.Технологические датчики измеряют параметры сварочного процесса на предмет его стабильности и в основном используются для мониторинга и / или контроля (Pires et al. 2006).
В таблице 1 представлены различные применения датчиков, а также краткие сведения о преимуществах и недостатках для определенного времени во время операции сварки.
Датчики контактного типа, такие как сопла или пальчиковые, дешевле и проще в использовании, чем бесконтактные.Однако этот тип датчиков нельзя использовать для стыковых соединений и тонких соединений внахлестку. Бесконтактные датчики, называемые датчиками сквозной дуги, могут использоваться для тройников, U- и V-образных канавок или соединений внахлест определенной толщины. Эти типы датчиков подходят для сварки больших деталей с плетением, когда нет необходимости в контроле проплавления. Однако это не применимо к материалам с высокой отражательной способностью, таким как алюминий. Сварщики уделяют большое внимание обнаружению соединений с 1980-х годов.Основными типами датчиков для промышленной дуговой сварки являются оптические датчики и датчики дуги (Nomura et al. 1986). Некоторые из наиболее важных применений датчиков в роботизированной сварке обсуждаются ниже:
Поиск швов
Обнаружение шва (или поиск стыка) — это процесс, в котором стык определяется с помощью одного или нескольких поисков, чтобы убедиться, что сварной шов точно укладывается в стык. Поиск шва осуществляется путем установки роботизированного манипулятора и сварочной горелки в правильное положение и ориентацию по отношению к сварочной канавке или путем настройки программы машины перед сваркой (Servo Robot Inc 2013a).Многие роботизированные приложения, особенно в автомобильной промышленности, включают производство серии коротких и повторяющихся сварных швов, для которых не требуется отслеживание в реальном времени; однако необходимо начинать каждый сварной шов в правильном месте, что требует использования датчиков шва (Meta Vision Systems Ltd 2006).
Отслеживание шва
Отслеживание шва позволяет сварочной горелке автоматически следовать за канавкой сварного шва и соответствующим образом регулировать робот-манипулятор; чтобы противостоять эффектам изменения шва, вызванного деформацией, неравномерной теплопередачей, изменчивостью размера зазора, смещением краев и т. д.(Сюй и др., 2012).
Надежные датчики отслеживания шва имеют следующие преимущества (Björkelund 1987):
Автоматическая вертикальная и горизонтальная коррекция траектории (даже изменения траектории, вызванные тепловыми искажениями)
Менее строгие требования к точности для объектов и приспособлений
Адаптация параметров сварки
Сокращенное время программирования
Более низкий уровень брака
Повышенное качество сварки
Жизнеспособность коротких серий
Адаптивное управление
При сварке с адаптивным управлением, т. е.е., замкнутая система, использующая устройства с обратной связью и адаптивное управление, есть система управления процессом, которая автоматически обнаруживает изменения в условиях сварки с помощью датчиков и направляет оборудование для принятия соответствующих мер. При сварке с адаптивным управлением необходимы датчики для обнаружения стыка, оценки проникновения корня, проведения укладки валика и отслеживания шва, а также для обеспечения надлежащего заполнения стыка (Cary and Helzer 2005). Использование датчиков обеспечивает адаптивное управление для контроля в реальном времени и регулировки параметров процесса, таких как сварочный ток и напряжение.Например, возможности датчиков по обнаружению швов, идентификации проплавления и заполнения стыка, а также обеспечения проплавления корня и приемлемой формы сварного шва означают, что корректирующее изменение соответствующих параметров сварки выполняется таким образом, чтобы поддерживать постоянное качество сварки (Cary and Helzer 2005 ; Дрюс и Старк 1986).
Адаптивный сварочный робот должен иметь возможность решать два основных аспекта. Первый аспект — это управление траекторией и ориентацией концевого эффектора, чтобы робот мог отслеживать свариваемое соединение с высокой точностью.Второй — это управление параметрами процесса сварки в режиме реального времени, например, контроль количества осаждения металла в стыке в соответствии с размерами зазора, разделяющего свариваемые детали.
Chen et al. (2007) изучали использование лазерного зондирования для адаптивной сварки алюминиевого сплава, в котором скорость подачи проволоки и сварочный ток регулируются автоматически в соответствии с условиями канавки. Датчик использовался для точного измерения сварной канавки и для автоматического отслеживания шва, включая автоматическое выравнивание положения горелки и регулировку высоты горелки во время сварки.Применялось адаптивное программное обеспечение, которое рассчитывало скорость подачи проволоки в зависимости от изменения зазора и площади сварного шва. Программное обеспечение включало извлечение геометрии канавки, расчет и фильтрацию, запрос адаптивной таблицы (таблица ADAP, как показано в таблице 2) и генерацию управляющего выходного сигнала.
На рис. 4 показан модуль управления потоком для адаптивного управления параметрами сварки для системы.
Рис. 4Схема адаптивного управления параметрами сварки (Chen et al. 2007)
Процесс адаптивного управления состоял из вычисления площади канавки по геометрическим данным, передаваемым из модуля обработки изображения, с последующей фильтрацией данных вычисленной площади для удаления недопустимых данных и шума. Затем модуль запросил таблицу ADAP, чтобы получить правильные параметры сварки, то есть сварочный ток и скорость подачи проволоки. Затем соответствующие значения аналоговых сигналов передавались для управления источником питания и механизмом подачи проволоки (Chen et al. 2007).
Контроль качества
Использование автоматических систем контроля качества сварки приводит к сокращению производственных затрат за счет сокращения рабочей силы, необходимой для контроля. Автоматическая система обнаружения сварки должна уметь классифицировать дефекты сварного шва, такие как пористость, разбрызгивание металла, неправильная форма валика, чрезмерное укрепление корня, неполные проплавления и прожоги.Большинство коммерческих систем мониторинга работают аналогичным образом: напряжение, ток и другие технологические сигналы измеряются и сравниваются с заданными номинальными значениями. Тревога срабатывает, когда любое отклонение от предустановленных значений превышает заданный порог. Пороговые значения срабатывания сигнализации соотносятся с реальными дефектами сварного шва или со спецификациями, определенными в спецификации процедуры сварки (WPS) (Pires et al. 2006). В настоящее время общие методы неразрушающего контроля сварного шва включают рентгенографию, ультразвуковое исследование, визуальное обнаружение, магнитное обнаружение, а также измерения вихревых токов и акустических измерений (Abdullah et al.2013).
Quinn et al. (1999) разработали метод обнаружения дефектов при автоматической газовой сварке металлическим электродом при постоянном напряжении (GMAW) с использованием сигналов технологического тока и напряжения. Они использовали семь алгоритмов обнаружения дефектов для обработки сигналов тока и напряжения, чтобы получить параметры качества и отметки сварных швов, которые отличались от базовых данных ранее сделанных бездефектных сварных швов. Система может эффективно определять плавление, потерю защитного газа и маслянистые части, которые вызывают поверхностную и подповерхностную пористость.
На рисунке 5 показан пример системы визуального контроля сварных швов (VIRO wsi от Vitronic GmbH), состоящей из датчика на основе камеры, вычислительного блока и программного обеспечения, имеющего возможность полностью автоматизированного трехмерного контроля шва с комбинированием 2D и 3D. машинное зрение. Он может обнаруживать все соответствующие дефекты и их положение в режиме реального времени. Эту информацию можно сохранить для последующего наблюдения, документирования и статистической оценки (VITRONIC 2010).
Трехмерный контроль сварного шва с помощью VIRO WSI (VITRONIC 2010)
На рис. 6 показан пример датчика контроля сварного шва, основанного на сканирующем термическом профиле под названием ThermoProfilScanner (TPS) от HKS Prozesstechnik GmbH, для оценки качества сварного шва и перекоса сварных швов во время охлаждения. В качестве характеристик теплового профиля (симметрия, ширина тепловой зоны, максимальная температура и т. Д.)) и качество шва напрямую связаны, аномалии шва, такие как недостаточный провар, смещение сварного шва, отверстия, отсутствие плавления и т. д., могут быть обнаружены с помощью TPS. Корреляции между термическим профилем и качеством сварного шва из предыдущего опыта можно использовать для сравнения желаемых значений и допусков. При превышении пределов допуска выдаются предупреждающие сигналы, обозначающие дефектные точки, и процесс сварки может быть остановлен (HKS Prozesstechnik 2013).
Измерение теплового поля шва во время охлаждения сварочной установки TPS ( a ), дефектного шва ( b ) и аномального термического профиля ( c ) дефектного шва (HKS Prozesstechnik 2013)
Датчики отслеживания и обнаружения шва
В продаже имеется несколько датчиков для роботизированной сварки, в основном для отслеживания шва и контроля качества.Некоторые из наиболее известных сенсорных продуктов в области роботизированной сварки описаны ниже:
Robo-Find (Servo Robot Inc)
Датчик в системе Robo-Find для поиска швов при роботизированной сварке основан на системе лазерного зрения. . Robo-Find предоставляет решение для автономных приложений поиска швов, в которых детали и / или элементы должны быть сначала обнаружены при изменении траектории инструмента. Он определяет местонахождение, обнаруживает и измеряет сварные швы без какого-либо контакта с деталью, а затем сигнализирует роботу о необходимости корректировать траекторию резака менее чем за 1 с.Некоторые функции и преимущества Robo-Find (Servo Robot Inc) перечислены ниже (Servo Robot Inc 2013a):
Он невосприимчив к дуговым процессам, таким как брызги, и выдерживает тепловое излучение.
Он может найти швы для всех свариваемых материалов.
Он имеет встроенную цветную видеокамеру для удаленного мониторинга и программирования.
Имеет возможность автоматически распознавать тип соединения.
Сокращает ремонт и переделку.
Может быть дооснащен существующим оборудованием.
В нем используется технология интеллектуальной камеры со встроенным блоком управления (нет отдельного контроллера со всем, что находится внутри самой камеры), поэтому настройку можно выполнить с помощью простого интерфейса ноутбука.
Robo-Find доступен с одним из двух типов лазерных камер, основанных либо на точечном лазерном датчике, либо на системе линейных лазерных датчиков. На рисунке 7 показана система Robo-Find SF / D-HE, основанная на системе линейного лазера, и система SENSE-I / D-V, основанная на точечном лазере. Примерное сравнение времени, необходимого для работы лазерного датчика зрения и механического тактильного датчика для поиска швов и сварки, показано на рис.8.
Рис.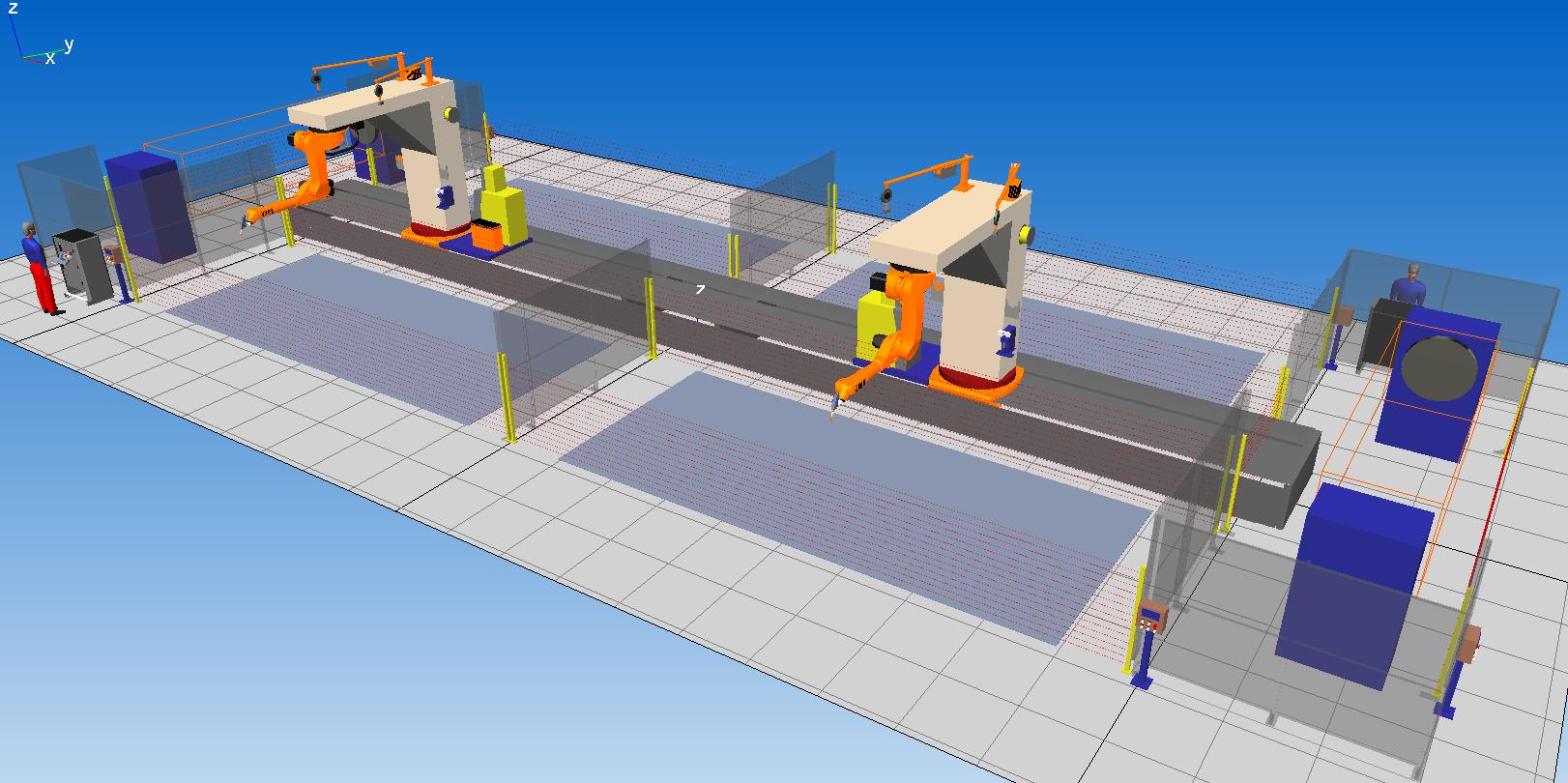
a Линейный лазерный датчик Robo-Find SF / D-HE и b Точечный лазерный датчик Robo-Find SENSE-I / D-V (Servo Robot Inc 2013a)
Рис. 8Сравнение лазерного зрения и тактильной сенсорной системы для поиска швов и сварки (Servo Robot Inc 2013a)
Power-Trac (Servo Robot Inc)
Этот датчик имеет возможность отслеживания швов в реальном времени и автономного поиска швов на основе системы лазерного зрения.Траектория резака постоянно изменяется, чтобы компенсировать изменения в реальном времени, такие как деформация, вызванная подводом тепла во время процесса сварки. Некоторые из функций и преимуществ, упомянутых производителем, следующие (Pires et al. 2006):
- 1.
Это полностью интегрированная система с лазерной камерой, блоком управления и программным обеспечением.
- 2.
Он предлагает автоматическое отслеживание стыков и управление траекторией сварочной горелки в реальном времени.
- 3.
Имеется опция модуля контроля для контроля качества сварных швов.
- 4.
Он невосприимчив к дуге, например брызгам, и выдерживает тепловое излучение.
- 5.
На систему не влияет окружающее освещение, и она может отслеживать все свариваемые материалы.
- 6.
Система предлагает точные трехмерные лазерные измерения геометрических размеров суставов.
- 7.
Высокоскоростной цифровой лазерный датчик делает возможным быстрое и надежное распознавание суставов.
- 8.
Система подходит для высокоскоростных сварочных процессов, таких как тандемная газовая дуговая сварка металлическим электродом и гибридная лазерная сварка.
- 9.
Система имеет прямой интерфейс с роботами большинства производителей с помощью усовершенствованного протокола связи по последовательному каналу или Ethernet.
- 10.
Включена большая библиотека соединений, которая позволяет отслеживать и геометрически измерять практически любой сварной шов на любом свариваемом материале.
- 11.
Адаптивный сварочный модуль может регулировать изменчивость геометрии стыка для оптимизации размера сварного шва и, таким образом, устранения дефектов и уменьшения переварки.
На рис. 9 показана роботизированная дуговая сварка в сочетании с системой Power-Trac для поиска и отслеживания швов (Servo Robot Inc 2013b).
Рис.9Роботизированная дуговая сварка с помощью Power-Trac (Servo Robot Inc 2013b)
Laser Pilot (Meta Vision Systems Ltd.)
Этот датчик с лазерным зрением позволяет определять фактические свариваемые детали для обнаружения швов и отслеживания швов.Он исправляет ошибки позиционирования деталей, а также ошибки, вызванные термической деформацией во время процесса сварки. Некоторые варианты системы Laser Pilot описаны ниже:
Лазерный пилот MTF
Laser Pilot MTF — это искатель шва, который может использоваться в роботизированной сварке, которая включает серию коротких сварных швов, как это обычно бывает в автомобильной промышленности, которые не требуют отслеживания в реальном времени, хотя правильное размещение сварочной горелки в необходимо начало сварного шва.MTF использует стандартный интерфейс для связи с контроллером робота.
Лазерный пилот MTR
Laser Pilot MTR — это устройство для отслеживания швов, доступное с возможностью взаимодействия с продуктами различных ведущих производителей роботов. Помимо функции поиска швов, он может отслеживать швы в режиме реального времени во время сварки (Meta Vision Systems Ltd 2006).
Датчик сварки системы кругового сканирования
Система кругового сканирования (CSS) Weld-Sensor (Oxford Sensor Technology Ltd.) состоит из маломощного лазерного диода, который проецирует лазерный луч через внеосевую линзу на анализируемую поверхность, как показано на рис. 10. Линейный ПЗС-детектор просматривает пятно через ту же внеосевую линзу. Расстояние между датчиком сварки CSS и измеряемой поверхностью рассчитывается на основе метода триангуляции. Встроенный двигатель вращает внеосевую линзу, заставляя лазерное пятно вращаться и формируя коническое сканирование (Mortimer 2006). Технология кругового сканирования позволяет измерять углы трехмерной формы за одно измерение и имеет преимущество в увеличенной степени обнаружения по сравнению с другими датчиками (Bergkvist 2004).Датчик сварки CSS также может использоваться с материалами с высокой отражающей способностью, такими как алюминий (Mortimer 2006).
Рис.10Расположение деталей со смещенной линзой в CSS (Braggins 1998)
Производственная система, разработанная Thyssen-Krupp-Drauz-Nothelfer (TKDN) со встроенным датчиком сварки CSS в сочетании со сварочной горелкой MIG и роботом ABB 2400–16, использовалась при приварке алюминиевой стойки C к алюминиевой крыше. часть спортивного автомобиля Jaguar XK, как показано на рис.11. Эта сварка имеет важное значение как с эстетической точки зрения, так и с точки зрения прочности, поскольку разрез находится на уровне глаз и не должно быть видимых внешних стыков и дефектов. Датчик считывает положение, ширину, глубину и ориентацию шва. Процесс сварки включает шесть или восемь измерений, каждое из которых занимает менее 400 мс. В системе использовался один датчик сварки CSS для измерения истинного положения шва перед сваркой, что позволяло оптимизировать запрограммированную траекторию сварки путем автоматической корректировки допусков компонентов и вариаций подгонки (Nomura et al.1986).
Рис. 11Робот ABB 2400–16 со сварочной горелкой MIG и датчиком сварки OST CSS, установленным на конце руки (HKS Prozesstechnik 2013)
ABB Weldguide III
Weldguide III — это датчик слежения за швом по дуге, разработанный ABB, который использует два внешних датчика сварочного тока и напряжения дуги. Он имеет измерительную способность при 25000 Гц для быстрой и точной корректировки траектории и может быть интегрирован с различными режимами переноса, такими как струйная дуга, короткая дуга и импульсная дуга GMAW.
Weldguide III имеет базовый, расширенный и многопроходный режимы слежения. Основные режимы слежения состоят из режима «резак-рабочий» или режима осевой линии. В режиме от резака к работе измеряется высота, а в фиксированном режиме от резака к работе расстояние поддерживается путем измерения заданного тока и регулировки высоты для сохранения настройки, как показано на рис. 12a. Режим средней линии используется с плетением, где импеданс измеряется при перемещении резака из стороны в сторону с использованием параметра смещения, как показано на рис.12b (ABB Group 2010).
Фиг.12a Резак в рабочий режим и b режим средней линии (ABB Group 2010)
В режиме адаптивного заполнения, разновидности расширенного режима отслеживания, робот может определять и корректировать отклонения в допусках соединений. Если ширина сустава изменится, переплетение робота будет увеличиваться или уменьшаться, и скорость движения регулируется соответствующим образом, как показано на рис.13.
Рис. 13Режим адаптивного заполнения (ABB Group 2010)
Для многопроходной сварки Weldguide III отслеживает первый проход и сохраняет фактический отслеживаемый путь, чтобы он мог смещаться для последующих проходов, как показано на рис. 14.
Рис. 14Многопроходная сварка с помощью Weldguide III ( ABB Group 2010)
Практический пример: MARWIN
Целевая проблема
Доступные в настоящее время сварочные технологии, такие как ручная сварка и сварочные роботы, имеют несколько недостатков.Ручная сварка отнимает много времени, а существующие роботы недостаточно эффективны для производства небольших партий продукции, но они также часто сталкиваются с несоответствиями при необходимости перепрограммирования. Это перепрограммирование также занимает очень много времени.
В ноябре 2011 года был начат проект MARWIN, являющийся частью рамок проекта FP7 Европейского исследовательского агентства (CORDIS 2015). Его цель заключалась в разработке сварочного робота на основе технического зрения, подходящего для малых и средних предприятий (МСП) с автоматическим расчетом колеи, выбором параметров сварки и встроенной системой контроля качества (Chen et al.2007). MARWIN может извлекать параметры сварки и рассчитывать траекторию рабочего органа непосредственно из моделей САПР, которые затем проверяются с помощью 3D-сканирования и регистрации в реальном времени (Родригес и др. 2013a). Основная проблема для малых и средних предприятий, пытающихся использовать роботизированную сварку, заключается в том, что продукты меняются после небольших партий, а необходимость обширного перепрограммирования является дорогостоящей и требует много времени. Ограничения текущего OLP включают производственные допуски между САПР и заготовками, а также неточности в размещении заготовок и смоделированной рабочей ячейке (TWI Ltd 2012).На рисунке 15 показана общая схема процесса для системы MARWIN.
Рис.15Схема процесса системы MARWIN (TWI Ltd. 2012)
Программирование
Система MARWIN состоит из управляющего компьютера с пользовательским интерфейсом и органов управления для системы технического зрения и сварочного робота. Новая методология автономного программирования роботов (OLP) решает проблему автоматического создания программ непосредственно из 3D-моделей САПР и проверки посредством онлайн-3D-реконструкции.Система технического зрения способна реконструировать трехмерное изображение деталей с использованием структурированного света и распознавания образов, которое затем сравнивается с чертежом реальной сборки в САПР. Он извлекает параметры сварки и рассчитывает траектории робота непосредственно из моделей САПР, которые затем проверяются с помощью 3D-сканирования и регистрации в реальном времени. Компьютер определяет оптимальную траекторию движения робота на основе ввода данных пользователем. Автоматическая корректировка траектории выполняется по восстановленному изображению. Параметры сварки автоматически выбираются из встроенной базы данных процедур сварки (TWI Ltd 2012).Роль пользователя ограничивается подробным описанием сварочного задания и подтверждением и / или изменением параметров и последовательностей сварки, как это предлагает MARWIN (Rodrigues et al. 2013a). Концепция MARWIN проиллюстрирована на рис. 16.
Рис. 16Концепция MARWIN (TWI Ltd. 2012)
Обнаружение
Система технического зрения MARWIN основана на методе сканирования структурированного света. Как показано на рис. 17, на целевую поверхность проецируется множество световых плоскостей известного рисунка, который фиксируется камерой.Затем пространственное соотношение между источником света и камерой комбинируется с формой захваченного рисунка, чтобы получить трехмерное положение поверхности вдоль рисунка. Преимущества такой системы заключаются в том, что и камеру, и проектор можно разместить как можно ближе друг к другу, что может дать преимущества для миниатюризации дизайна. Более того, математическая формулировка такой компоновки проще, чем у стандартных сканеров, что приводит к меньшему количеству вычислительных циклов, что делает параллельную конструкцию более подходящей для обработки 3D в реальном времени (Rodrigues et al.