Сталь цвета нагрева — Энциклопедия по машиностроению XXL
При термической обработке необходимо соблюдать температурный режим, так как нарушение его может привести к браку. Для точного определения температурного режима используют различные приборы. Без приборов температуры устанавливают приблизительно. Обычно это делает опытный термист. Температуру определяют по цвету побежалости и излучению (цвету каления). Цвета побежалости — радужные цвета, возникающие в результате появления тонкого слоя окислов на чистой поверхности углеродистой стали при нагреве от 220 до 330 °С (табл. 9.1). Ими можно пользоваться при низком отпуске и закалке с самоотпуском. [c.175]Отпуск стали по цветам побежалости. Температуру отпуска часто определяют по цветам побежалости. Этот метод основан на наблюдении, показывающем, что светлая, зачищенная поверхность стали при нагреве окисляется, покрываясь тончайшей окисной пленкой. С повышением температуры отпуска толщина окисной пленки увеличивается и цвет поверхности изменяется. Каждому цвету побежалости свойственна определенная температура (табл. 6). Цвета побежалости зависят не только от температуры нагрева, но и от продолжительности нагрева, т. е. времени выдержки.
Цвета побежалости. Это радужные цвета, возникающие в результате появления тонкого слоя окислов на чистой поверхности углеродистой стали при нагреве ее в интервале температур 150—350°С и на легированной стали при более высоких температурах. [c.90]
Посредством отпуска можно сообщить стали строго определенные механические свойства, уменьшить хрупкость и увеличить вязкость, что особенно необходимо для деталей, работающих при толчках и ударах. Чем выше температура отпуска, тем более вязкой становится сталь. Температуру отпуска контролируют по цветам побежалости, появляющимся на поверхности стали при нагреве. [c.532]
Если очищенный напильником или наждачной шкуркой кусок стали начать нагревать, то на его поверхности появляются различной толщины пленки окислов железа.
Марка стали Режим нагрева Цвет полированной поверхности шлифа, видимой невооруженным глазом Цвет составляющих под микроскопом при увеличении 315-4Ю раз [c.54]
При нагревании стали до температуры выше указанной цвет металла также изменяется в зависимости от температуры. Цвет стали при нагреве выше 330° С называется цветом каления. [c.84]
Температуру самоотпуска нередко определяют по цветам побежалости, т. е. по цветам, появляющимся па шлифованной поверхности стали при нагреве до температуры 200—300° С и зависящим от толщины возникающей окисной пленки.
Таблица 3 Цвета нагрева стали при различных температурах |
Цвета нагрева стали 307 [c.781]
При нагреве стали выше 530° сталь начинает светиться. С повышением температуры свечение стали меняется. Цвета, принимаемые сталью при нагреве выше 530°, называются цветами каления. [c.70]
Температура и цвет нагрева при отжиге, закалке и отпуске резцов из быстрорежущей стали [c.114]
Температуру нагретой стали приближенно можно определить на глаз по цветам нагрева, приведенным в табл. 45. [c.112]
Определяют температуру нагрева по цветам побежалости или цветам нагрева стали непосредственно под ядром пламени (табл. 38). [c.238]
Цвет побежалости Температура в град. 1 Цвет нагрева стали Температура в град. [c.238]
При температурах от 330—350 до 530° С цвета побежалости не наблюдаются. При 530° С сталь начинает светиться. С повышением температуры свечение стали меняется и зависит от продолжительности нагрева. Цвета, принимаемые сталью при нагреве выше 530° С, называются цветами каления. Определить температуру по цветам побежалости и каления можно только при наличии соответствующего опыта работы.
[c.75]
Из имеющейся в продаже окиси хрома, предназначенной, по-видимому, для применения в качестве пигмента, а не абразивного материала, получается довольно тупая паста. Значительно легче и быстрее достигается яркий блеск при пользовании окисью хрома приготовленной сжиганием хромпика (двухромовокислого натрия или двухромовокислого калия) с серой. Измельченный хромпик смешивают с измельченной серой (удобнее пользоваться мелким порошком серы, поступающим в продажу под названием серного цвета ) в соотношении 10 массовых долей натриевого хромпика на 1,4 части серы для получения примерно 6 частей окиси хрома или на 10 массовых долей калиевого хромпика 1,2 частей серы для получения примерно 5 долей окиси хрома (сера везде берется в небольшом избытке, а выход готовой окиси указан приблизительно, ибо он зависит от аккуратности работы при сжигании). Тщательно перемешанную смесь помещают на противень (предпочтительно из хромистой жароупорной стали) и нагревают до полного сгорания, остужают, размельчают, отмывают горячей водой от легкорастворимого сернокислого натрия (или, соответственно, —
Таблица 2. Цвета нагрева стали |
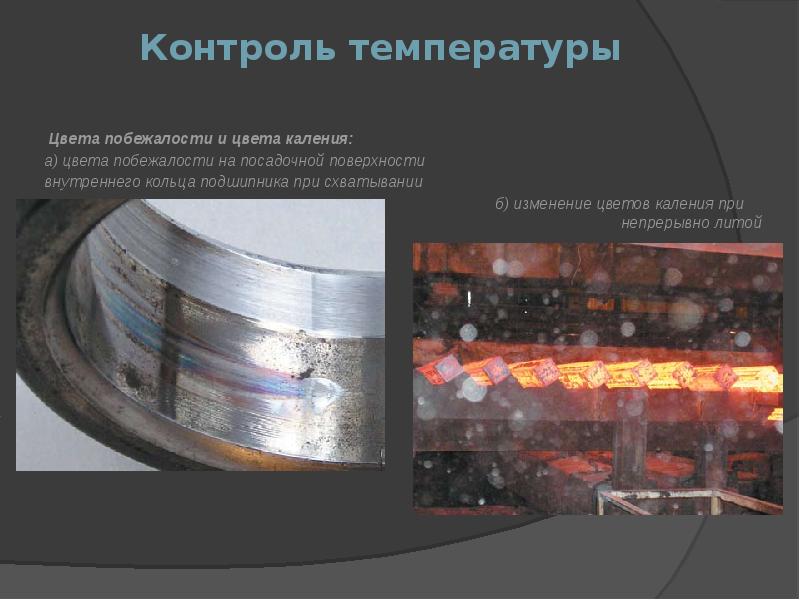
Сталь принимает закалку, начиная с марки Ст. 5 и. выше. Температуру нагрева при закалке обычно определяют по цвету раскаленного изделия (цвета накала). [c.19]
Примечание. Приведенное в таблице соответствие между температурой нагрева и цветом поверхности металла относится к углеродистым сталям. У легированных сталей такое соотношение не имеет места, так как они обладают большей стойкостью против окисления. [c.218]
Проведение травления довольно просто. Шлиф после полирования слегка подтравливают. Благодаря этому проявляются границы зерен и одновременно удаляется оказывающий вредное влияние на окончательные результаты деформированный слой. Некоторые авторы, например Скортези и Дюранд [56], рекомендовали неоднократное травление и полирование. Хорошо обезжиренный образец помещают полированной стороной вверх на медную плиту или песчаную баню и нагревают. За поверхностью образца следует непрерывно наблюдать. По достижении желаемой окраски шлифа образец охлаждают в ртутной ванне или, если не стремятся избежать слабого дополнительного развития цветов побежалости, на холодной металлической плите. Горячее травление на воздухе можно применять в первую очередь для незакаленных сталей при нагреве практически неизбежны изменения мартенсита. Несмотря на это, Ханке и Хенкель [57] травили этим методом мартенситные и аустенитные образцы при этом они смогли очень хорошо выявить обе фазы.
Светлая закалка. При этом способе закалки детали нагревают в нейтральной безокислительной атмосфере или в расплавленных нейтральных солях. При светлой закалке нагрев деталей или инструмента осуществляют в жидких солях, не вызывающих окисления металла, с последующим охлаждением их в расплавленных едких-щелочах в нагревательных печах с применением контролируемой защитной газовой амтосферы, позволяющей регулировать взаимодействие печных газов со сталью при нагреве в вакуумных (10 —мм рт.
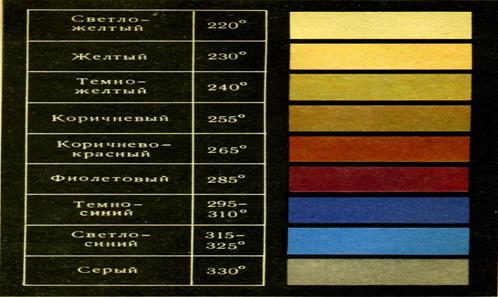
И. В. Гутман [68] изучал влияние нагрева (60, 100, 200, 300, 400 и 500 °С) на защитные свойства фосфатной пленки, полученной из раствора железомарганцового фосфата (препарат ВИМ), на образцах из углеродистой, никелевой и кремнистой сталей. Образцы нагревали в муфельной печи в течение 1 ч при температуре опыта. Наблюдения показали, что при нагревании до 150 °С видимых изменений фосфатной пленки не наступало. В интервале температур 150—200 °С на отдельных образцах наблюдалось легкое пожелтение пленки, которое стало особенно заметным при нагревании выше 350 °С. При 500 °С фосфатная пленка приобрела бурый цвет. Изменение цвета пленки связано с образованием окисных соединений вследствие термического разложения вторичных и третичных фосфатов железа и марганца. Защитные свойства фосфатных пленок, подвергавшихся нагреву, определялись погружением в 3% раствор ]ЧаС1 и оценивались по продолжительности испытаний в нем до появления первых признаков коррозии (табл. 19).
Отпуск обязательно производят после закалки в целях уменьшения хрупкости и внутренних напряжений, полученных при резком охлаждении стали. Температура нагрева при отпуске для инструментов — 200—320°, для деталей машин — 500—600°. Охлаждение производят в воде или на воздухе. Чем выше нагрев стали при отпуске, тем ббльшую вязкость она приобретает, но тем больше и падение твердости. Температура нагрева инструментов при отпуске может быть приближенно определена по цветам побежалости, т, е. цветам пленок окиси, образующихся на поверхности нагретого куска стали светло-желтый цвет соответствует 220—240° оранжевый — 240—260°, красно-фиолетовый— 260—280°, синий — 280—300°. [c.275]
Все конструкции до подачи их со склада на монтажную площадку рассортировывают по назначению, маркам и очередности монтажа и тщательно осматривают для выявления повреждений. Местные искривления, перегибы и вмятины выправляют обычно с подогревом дефектных мест ацетилено-кислородными резаками. Сталь следует нагревать до светло-красного цвета на участке, превышающем дефектный в 1,5—2 раза. Выпуклости и другие аналогичные дефекты выправляют кувалдой через гладилку. Удары наносят, начиная с краев и приближаясь к середине. В результате выпуклость растягивгется по всей площади. При нескольких выпуклостях, расположенных рядом, удары наносят по перешейкам, сводя все выпуклости к одной. Затем действуют, как описано выше. Профильные элементы выправляют переносными скобами или ручными домкратами. .
При нагревании сталь окисляется, и на ее поверхности появляются пленки окислов, которые приобретают различную окраску, зависящую от толщины пленки и температуры нагрева. Такая окраска металла -называется цветом побежалости. При температурах свыше 330° С цвета побежалости исчезают. При нагревании стали свыше 330° С цвет ее также изменяется в зависимости от температуры. Цвет стали при нагреве выше 330° С называется цветом каления. В табл. 1 и 2 приведены цвета побежалости и каления стали, соответствующие определенным темпеоатурам нагрева. [c.28]
Термическое травление. Тщательно отполированный образец, который можно предварительно протравить в растворе 1.1 или 2.1, постепенно нагревают до красноватого цвета. Для этого образец помещают на нагретую до 300° С песчаную баню. Поверхность следует защитить от песка. Затем образец быстро охлаждают сжатым воздухом Ферритные зерна сильно окращиваются. Цементит также окрашивается, а большинство сложных карбидов не приобретают окраски и поэтому хорошо заметны. Для низкоуглеродистых сталей достаточно непродолжительного нагрева, чтобы выявить различие между фер-ритными зернами. Нержавеющие стали требуют нагрева до более высоких температур, так как аустенит окрашивается медленнее, чем феррит [1. 3, 40 421 [c.40]
Резкое падение прочности при высоких температурах (рис. 158, а) может привести к разрушению (проваливанию) твердого металла нерасплавившейся части кромок под действием веса сварочной ванны. В связи с высокой жидкотекучестью алюминий моягет вытекать через корень шва. Размеры сварочной ванны трудно контролировать, так как алюминий при нагреве практически не меняет своего цвета. Для предотвращения провалов или прожогов при однослойной сварке или сварке первых слоев многопроходных швов на большой погонной энергии необходимо применять формирующие подкладки из графита пли стали.
[c.354]
На рис. 4-6 показана зависимость степени черноты от температуры для покрытия черный хром , полученного электроосаждением из. хромового ангидрида, растворенного в кремнефтористо-водородпой кислоте [53]. Степень черноты при температурах 815— 1100 К равнялась 0,89. После испытаний цвет покрытий из.менился с черного на зеленый. В течение первого определения излучательной способности (покрытие наносилось на подложку из нержавеющей стали) степень черноты в интервале указанных температур оставалась в пределах 0,88. Во время повторного нагрева степень черноты увеличилась с 0,89 при 815 до 0,92 яри 1100 К цвет образца также изменился с черного на зеленый. При увеличении темпе- [c.100]
На поверхности стальных шлифов при нагреве на воздухе образуются тонкие окисные слои, которые растут в зависимости от температуры и продолжительности травления. Наблюдаемые при этом цвета побежалости являются результатом интерференции. При микроскопическом наблюдении обнаруживают, что поверхность шлифа окрашивается на отдельных зернах одной и той же фазы в зависимости от ориентировки зерен относительно поверхности шлифа образуются слои разной толш,ины. Толщина окисных слоев также неодинакова на разных фазах в стали цементите и феррите. Это явление используют для получения цветных изображений структуры. [c.96]
Травитель 62 [термическое травление].
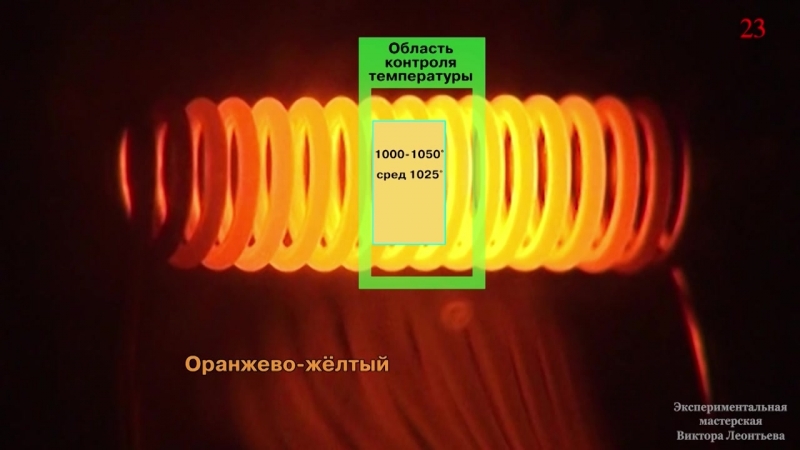
При нагреве до синего цвета, что соответствует температуре 250 — 300° С, обработку стали производить нельзя, так как при этой температуре она становится очень хрупкой — синеломкой (фиг. 48). [c.497]
Д. К. Чернов ещё в 1868 г. установил наличие в стали критических точек (точки Чернова), в которых при нагреве и охлаждении происходят фазовые превращения. Первая точка, соответствующая тёмновишнёвому цвету каления стали, названа Черновым точкой а, вторая, соответствующая красному цвету каления,— точкой б. [c.476]
При температурах 200—300° С наблюдается снижение пластичности стали ( > и При этом уменьшение пластичности и вязкости стали в области тегчператур 200— 300° С носит название синеломкости, которое происходит от синего цвета побежалости при нагреве стали до 300° С. [c.41]
Отжиг концов труб из стали марок 15ХМ или 12МХ производится так же, как и углеродистых труб, но с нагревом до температуры 680—700° С (темнокрасный цвет металла) и выдержкой при этой температуре из расчета 3 мин. на каждый миллиметр толщины стенки. Затем трубы снимаются с горна и производится медленное охлаждение каждого конца, для чего он тщательно обертывается асбестовым матрацем или погружается в сухой, слегка подогретый песок.
[c.198]
Гибка труб из углеродистых сталей может производиться с подогревом ТВЧ или газопламенной горелкой. Температура нагрева трубы — от 700 до 1000° С, при этом труба раскаляется до вишнево-красного цвета. Подогрев воздушноацетиленовым пламенем допускается также для гибки труб из алюминиевого сплава типа АМгМ при наружном диаметре трубы > 18 мм. [c.100]
изменение цвета при нагреве, интерфенции цвета
Визуальное определение температуры нагретого металла
Термическую обработку стальных деталей проводят в тех случаях, когда необходимо либо повысить прочность, твердость, износоустойчивость или упругость детали или инструмента, либо наоборот, сделать металл более мягким, легче поддающимся механической обработке.
В зависимости от температуры нагрева и способа последующего охлаждения различают следующие виды термической обработки: закалка, отпуск и отжиг.
В любительской практике для определения температуры раскаленной детали по цвету можно использовать приведенную таблицу.
Цвет каления стали | Температура нагрева, °С |
Темно-коричневый (заметен в темноте) Коричнево-красный Темно-красный Темно-вишнево-красный Вишнево-красный Светло-вишнево-красный Светло-красный Оранжевый Темно-желтый Светло-желтый Ярко-желтый | 530-580 580-650 650-730 730-770 770-800 800-830 830-900 900-1050 1050-1150 1150-1250 1250-1350 |
Шкала цветов побежалости
Толщина окисных пленок определяется температурой и временем нагрева, а существующие шкалы цветов побежалости носят довольно условный характер.
- Во-первых, визуальная оценка — очень субъективный процесс, результаты которого определяются освещенностью и практическим опытом.
- Во-вторых, плотность окисной пленки определяется и химсоставом сплава.
Поэтому таблицы соответствия разнятся (шкалы для углеродистых, жаростойких, нержавеющих сталей), и можно говорить только об ориентировочном соответствии. Но усредненная таблица цветов побежалости выглядит следующим образом
Цвета | Температура нагрева, °С |
бледно-желтый | 220 |
бледно-соломенно-желтый | 230 |
золотисто -желтый | 246 |
коричнево-желтый до бурого | 256 |
пурпурно-красный | 265 |
пурпурный | 275 |
лиловый | 280 |
голубой | 290 |
васильковый | 295 |
индиго | 300 |
светло-синий | 310 |
цвет морской воды | 320 |
Например, при продолжительном нагреве при 220 °С можно вызвать посинение стали. Или желаемый цвет получается при кратковременном нагреве до температуры, более высокой, чем указанная в таблице. Но для каждого цвета побежалости существует температурный минимум, ниже которого нужный цвет не получится.
Закалка стальных деталей
Закалка придаёт стальной детали большую твердость и износоустойчивость.
Для этого деталь нагревают до определенной температуры, выдерживают некоторое время, чтобы весь объём материала прогрелся, а затем быстро охлаждают в масле (конструкционные и инструментальные стали) или в воде (углеродистые стали).
Обычно детали из конструкционных сталей нагревают до 880–900°C (цвет каления светло-красный), из инструментальных – до 750–760°С (цвет темно-вишнево-красный), а из нержавеющей стали – до 1050–1100°С (цвет темно-желтый).
Нагревают детали вначале медленно (примерно до 500°С), а затем быстро. Это необходимо для того, чтобы в детали не возникли внутренние напряжения, что может привести к появлению трещин и деформации материала.
В ремонтной практике применяют в основном охлаждение в одной среде (масле или воде), оставляя в ней деталь до полного остывания. Однако этот способ охлаждения непригоден для деталей сложной формы, в которых при таком охлаждении возникают большие внутренние напряжения.
Детали сложной формы сначала охлаждают в воде до 300–400°С, а затем быстро переносят в масло, где и оставляют до полного охлаждения. Время пребывания детали в воде определяют из расчета: 1с на каждые 5–6 мм сечения детали. В каждом отдельном случае это время подбирают опытным путём в зависимости от формы и массы детали.
Качество закалки в значительной степени зависит от количества охлаждающей жидкости. Важно, чтобы в процессе охлаждения детали температура охлаждающей жидкости оставалась почти неизменной, а для этого масса ее должна быть в 30–50 раз больше массы закаливаемой детали. Кроме того, перед погружением раскаленной детали жидкость необходимо тщательно перемешать, чтобы выровнять ее температуру по всему объему.
В процессе охлаждения вокруг детали образуется слой газов, который затрудняет теплообмен между деталью и охлаждающей жидкостью. Для более интенсивного охлаждения деталь необходимо постоянно перемещать в жидкости во всех направления.
Можно ли повысить твердость металлов и их сплавов?
Технологии придания большей твердости металлам и сплавам совершенствовались в течение долгих веков. Современное оборудование позволяет проводить термическую обработку таким образом, чтобы значительно улучшать свойства изделий даже из недорогих материалов.
Закалка стали и сплавов
Закалка (мартенситное превращение) — основной способ придания большей твердости сталям. В этом процессе изделие нагревают до такой температуры, что железо меняет кристаллическую решетку и может дополнительно насытиться углеродом. После выдержки в течение определенного времени, сталь охлаждают.
Это нужно сделать с большой скоростью, чтобы не допустить образования промежуточных форм железа.В результате быстрого превращения получается перенасыщенный углеродом твердый раствор с искаженной кристаллической структурой. Оба эти фактора отвечают за его высокую твердость (до HRC 65) и хрупкость.
Большинство углеродистых и инструментальных сталей при закаливании нагревают до температуры от 800 до 900С, а вот быстрорежущие стали Р9 и Р18 калятся при 1200-1300С.
Микроструктура быстрорежущей стали Р6М5: а) литое состояние; б) после ковки и отжига; в) после закалки; г) после отпуска. ×500.
Режимы закалки
Нагретое изделие опускают в охлаждающую среду, где оно остается до полного остывания Это самый простой по исполнению метод закалки, но его можно применять только для сталей с небольшим (до 0,8%) содержанием углерода либо для деталей простой формы. Эти ограничения связаны с термическими напряжениями, которые возникают при быстром охлаждении — детали сложной формы могут покоробиться или даже получить трещины.
При таком способе закалки изделие охлаждают до 250-300С в соляном растворе с выдержкой 2-3 минуты для снятия термических напряжений, а затем завершают охлаждение на воздухе. Это позволяет не допускать появления трещин или коробления деталей. Минус этого метода в сравнительно небольшой скорости охлаждения, поэтому его применяют для мелких (до 10 мм в поперечнике) деталей из углеродистых или более крупных — из легированных сталей, для которых скорость закалки не столь критична.
Начинается быстрым охлаждением в воде и завершается медленным — в масле. Обычно такую закалку используют для изделий из инструментальных сталей. Основная сложность заключается в расчете времени охлаждения в первой среде.
- Поверхностная закалка (лазерная, токами высокой частоты)
Применяется для деталей, которые должны быть твердыми на поверхности, но иметь при этом вязкую сердцевину, например, зубья шестеренок. При поверхностной закалке внешний слой металла разогревается до закритических значений, а затем охлаждается либо в процессе теплоотвода (при лазерной закалке), либо жидкостью, циркулирующей в специальном контуре индуктора (при закалке током высокой частоты)
Таблица температур закалки и отпуска сталей
№ п/п | Марка стали | Твёрдость (HRCэ) | Температ. закалки, град.С | Температ. отпуска, град.С | Температ. зак. ТВЧ, град.С | Температ. цемент., град.С | Температ. отжига, град.С | Закал. среда | Прим. |
1 | 2 | 3 | 4 | 5 | 6 | 7 | 8 | 9 | 10 |
1 | Сталь 20 | 57…63 | 790…820 | 160…200 | 920…950 | Вода | |||
2 | Сталь 35 | 30…34 | 830…840 | 490…510 | Вода | ||||
33…35 | 450…500 | ||||||||
42…48 | 180…200 | 860…880 | |||||||
3 | Сталь 45 | 20…25 | 820…840 | 550…600 | Вода | ||||
20…28 | 550…580 | ||||||||
24…28 | 500…550 | ||||||||
30…34 | 490…520 | ||||||||
42…51 | 180…220 | Сеч. до 40 мм | |||||||
49…57 | 200…220 | 840…880 |
Источник: https://www.m-deer.ru/tehnologiya/zakalka_still.html
Отпуск закаленных деталей
Отпуск закаленных деталей уменьшает их хрупкость, повышает вязкость и снимает внутренние напряжения. В зависимости от температуры нагрева различают низкий, средний и высокий отпуск.
Низкий отпуск применяют главным образом при обработке измерительного и режущего инструмента. Закаленную деталь нагревают до температуры 150–250°С (цвет побежалости – светло-желтый), выдерживают при этой температуре, а затем охлаждают на воздухе. В результате такой обработки материал, теряя хрупкость, сохраняет высокую твердость и, кроме того, в нем значительно снижаются внутренние напряжения, возникшие при закалке.
Средний отпуск применяют в тех случаях, когда хотят придать детали пружинящие свойства и достаточно высокую прочность при средней твердости. Для этого деталь нагревают до 300–500°С и затем медленно охлаждают.
И, наконец, высокому отпуску подвергают детали, у которых необходимо полностью снять все внутренне напряжение. В этом случае температура нагрева еще выше – 500–600°С.
Термообработку (закалку и отпуск) деталей постой формы (валики, оси, зубила, кернера) часто делают за один раз. Нагретую до высокой температуры деталь опускают на некоторое время в охлаждающую жидкость, затем вынимают. Отпуск происходит за счет тепла, сохранившегося внутри детали.
Небольшой участок детали быстро зачищают абразивным брусочком и следят за сменой цветов побежалости на нем. Когда появится цвет, соответствующий необходимой температуре отпуска (220°С – светло-желтый, 240°С – темно-желтый, 314°C – светло-синий, 330°С – серый), деталь вновь погружают в жидкость, теперь уже до полного охлаждения.
Происхождение
В природе цвета побежалости образуются на поверхности многих минералов, включая пирит и халькопирит. Из-за окисления они покрываются тонкой оксидной пленкой, преломляющий солнечный свет. В результате интерференции поверхности металла окрашивается в разные цвета. Яркость побежалости зависит от толщины оксидной пленки и длины волны. Наиболее яркие цвета побежалости образуются на медных минералах. Также цвет зависит от качественного состава металла. Если в элементе присутствует большое количество ионов металлов, то он окрашивается в синие цвета. При наличии хромофоров минералы становятся красными.
Также цвета побежалости могут образовывать в естественных условиях на поверхностях старых стекол или монет. Изменение окраса может быть обусловлено длительным контактом этих материалов с землей. Если на них присутствует жировая пленка, то они окрашиваются в радужный цвет. Побежалость скрывает настоящий цвет металла. Поэтому нельзя определять его истинный окрас на свежем изломе. Рекомендуется определять цвет при рассмотрении оксидной пленки.
Искусственно цвета побежалости образуются на поверхности металлических заготовок при сварке или закалке. Они появляются при нагревании металлов до критических температур без участия молекул воды или иных жидкостей. Во время нагревания происходит процесс образования оксидной пленки. Ее толщина составляет несколько молекул и уменьшается по мере нагрева. Это обусловлено явлением диффузии – процессом проникновения мельчайших частиц одного химического элемента в другой. В данном случае происходит взаимодействие атомов металла и кислорода. На углеродистых сталях пленки из оксидов возникают быстрее, чем на легированных.
Процедура покрытия стали и железа слоем оксидной пленки называется воронением. После проведения этой процедуры повышается коррозийная стойкость изделия. Обработанные детали не покрываются ржавчиной. Процедура воронения позволяет придать изделию окрас, даже если металлическая поверхность по условиям эксплуатации не подлежит покраске. Во время воронения заготовку протирают минеральным маслом и нагревают на железном листе. После выгорания масляной жидкости на заготовке появляются цвета побежалости. Для нужного окраса необходимо нагреть деталь до соответствующей температуры. Получившийся слой окисла является влагоустойчивым и не подвергается воздействию воздуха.
На скорость образования окисных пленок влияют следующие факторы:
- Структура поверхности: закаленные детали окисляются с большей скоростью.
- Загрязненность изделия: поверхности, покрытые маслом, при длительном нагреве обугливаются, что приводит к возникновению сажи. По этой причине образуется неровная и тонкая оксидная пленка.
- Наличие шероховатостей: если нагревается заготовка с шершавой поверхностью, то оксидная пленка получается плотной. Если перед процедурой термообработки отполировать деталь, то образуется тонкая пленка из оксидов.
- Оборудование для нагрева: если при термообработке применяются специальные нагревательные печи, способные поддерживать устойчивую температуру, то окисная пленка будет плотной. В бытовых условиях можно также использовать духовые шкафы, газовые горелки или металлургические печи (горны).
Тонкие оксидные пленки поглощают световые волны с меньшей длиной волны, но отражают – с большей. Цвет металлических деталей меняется в зависимости от температуры и плотности оксидной пленки. Чем толще оксидная пленка, тем светлее окраска. Синий или фиолетовый цвет получается, когда из спектра отражаются наиболее длинные волны. Если пленка из оксидов отражает волны с малой длиной волны, то металлическая поверхность становится желтой. Светлые цвета соответствуют высокой температуре нагрева, светлые – более низкой. По этой причине многие мастер часто определяют при помощи цветов побежалости степень закалки изделий, стальной стружки и режущих инструментов, применяемых во время проведения токарных работ.
Несмотря на эти факторы, при помощи цветов побежалости нельзя точно определить температуру металла, потому что на величину этого показателя оказывают влияние следующие факторы:
- время нагрева: промежуток времени, в течение которого металлическая деталь нагревается до температуры окружающей среды при отсутствии теплоотдачи.
- наличие различных примесей в составе металла;
- особенности освещения в помещении, где проводилась сварка или закалка заготовок;
- скорость разогревания: изменение температуры изделия в единицу времени при его нагревании.
В современной промышленности контроль температуры производится при помощи специальных приборов – пирометров. Они оснащены специальными датчиками, определяются степень нагрева заготовки при помощи лазера.
Цвета побежалости используются при изготовлении рабочих инструментов, лазерной маркировке и внешней обработке изделий из железа, меди, алюминия и латуни. Если требуется изготовить инструментарии с высокой плотностью (бритвенные лезвия, предметы для проведения хирургических операций, режущие кромки резцов и грабштихели), то побежалость должна быть яркого цвета: красного, оранжевого или желтого. До пурпурных и зеленых тонов нагревают инструменты, применяющихся в деревообрабатывающем секторе. Для достижения упругости при изготовлении пил, ножей, вил и пружин необходимо нагреть заготовки до появления синих или черных цветов.
В процессе нагревания металлическая заготовка становится гибкой, что позволяет мастеру придать ей необходимую форму. После данного процесса изделие закаляется при определенных температурах. Согласно рекомендациям специалистов, оптимальной температурой для закалки металлов является 700–800 °C. В этом случае изделие окрашивается в разные оттенки красного или розового цветов. При превышении этих значений на 300 °C заготовка становится оранжевой или желтой. При больших температурах происходит перекал, что негативно сказывается на прочности изделия.
Закалка улучшает следующие параметры металлической поверхности:
- Твердость: этот показатель является номинальным. Он прописан в шкале Роквелла и измеряется в HRC. Твердость определяет степень сопротивляемости металла к механическим повреждениям. На мягких изделиях при длительном соприкосновении с иными поверхностями остаются следы, что ухудшает их режущие свойства. Твердость ножей европейского образца составляет 60 HRC, азиатских – 70 HRC.
- Упругость: данный параметр определяет степень деформации металла при изгибах и ударах. Если сталь закалена, при изгибе на 10–30° она вернется в исходное положение.
При перегреве снижается упругость поверхности, что приводит к поломке инструментов.
- Износостойкость: данный критерий показывает общую стойкость металла (сопротивление абразивному износу, стойкость к большим нагрузкам). При правильной закалке изделие сможет стабильно функционировать в течение более длительного срока.
После закалки заготовка приобретает высокую твердость. Для восстановления ее прочности необходимо провести процедуру отпуска, представляющую собой повторную термообработку детали. Металлическое изделие нагревается до более низких температур и охлаждается. Между закалкой и охлаждением также осуществляется полное остывание металлической поверхности при помощи его погружения в раствор соли или в масло. При выборе отпуска необходимо учитывать следующие особенности:
- Для изделий, подвергающимся деформациям или ударным нагрузкам, нужно использовать высокотемпературный отпуск: до 700 °C.
- Для легких клинков используется среднетемпературный отпуск: до 500 °C.
- Для обеспечения оптимальной твердости применяется низкотемпературный отпуск: до 250 °C. Но в этом случае изделие не сможет выдерживать высокие ударные нагрузки и будет легко деформироваться.
Температура цветов побежалости и каления
Во время отпуска возникают цвета каления. По ним можно определить, до какой температуры нагрелась заготовка. В отличие от побежалости, цвета каления меняются в процессе охлаждения металлической поверхности. Переход между цветами осуществляется в строгой последовательности, но с быстрой скоростью, поэтому мастер должен тщательно контролировать процесс термообработки.
Отжиг стальных деталей
Чтобы облегчить механическую или пластическую обработку стальной детали, уменьшают ее твердость путем отжига.
Так называемый полный отжиг заключается в том, что деталь или заготовку нагревают до температуры 900°С, выдерживают при этой температуре некоторое время, необходимое для прогрева ее по всему объему, а затем медленно (обычно вместе с печью) охлаждают до комнатной температуры.
Внутренние напряжения, возникшие в детали при механической обработке, снимают низкотемпературным отжигом, при котором деталь нагревают до температуры 500–600°С, а затем охлаждают вместе с печью. Для снятия внутренних напряжений и некоторого уменьшения твердости стали применяют неполный отжиг – нагрев до 750–760°С и последующее медленное (также весте с печью) охлаждение.
Отжиг используется также при неудачной закалке или при необходимости перекаливания инструмента для обработки другого металла (например, если сверло для меди нужно перекалить для сверления чугуна). При отжиге деталь нагревают до температуры несколько ниже температуры, необходимой для закалки, и затем постепенно охлаждают на воздухе. В результате закаленная деталь вновь становится мягкой, поддающейся механической обработке.
Отжиг и закаливание дюралюминия
Отжиг
дюралюминия производят для снижения его твердости. Деталь или заготовку нагревают примерно до 360°С, как и при закалке, выдерживают некоторое время, после чего охлаждают на воздухе. Твердость отожженного дюралюминия вдвое ниже, чем закаленного.
Приближенно температуру нагрева дюралюминия детали можно определить так. При температуре 350–360°С деревянная лучина, которой проводят по раскаленной поверхности детали, обугливается и оставляет темный след. Достаточно точную температуру детали можно определить с помощью небольшого (со спичную головку) кусочка медной фольги, который кладут на ее поверхность. При температуре 400°С над фольгой появляется небольшое зеленоватое пламя.
Отожженный дюралюминий обладает небольшой твердостью, его можно штамповать и изгибать вдвое, не опасаясь появления трещин.
Закаливание
. Дюралюминий можно повергать закаливанию. При закаливании детали из этого металла нагревают до 360–400°С, выдерживают некоторое время, затем погружают в воду комнатной температуры и оставляют там до полного охлаждения. Сразу после этого дюралюминий становится мягким и пластичным, легко гнется и куется. Повышенную твердость он приобретает спустя три-четыре дня. Его твердость (и одновременно хрупкость) увеличивается настолько, что он не выдерживает изгиб на небольшой угол.
Наивысшую прочность дюралюминий приобретает после старения. Старение при комнатной температуре называют естественным, а при повышенных температурах – искусственным. Прочность и твердость свежезакаленного дюралюминия, оставленного при комнатной температуре, с течением времени повышается, достигая наивысшего уровня через пять–семь суток. Этот процесс называется старением дюралюминия.
Отжиг меди и латуни
Отжиг меди
. Термической обработке подвергают и медь. При этом медь можно сделать либо более мягкой, либо более твердой. Однако в отличии от стали закалка меди происходит при медленном остывании на воздухе, а мягкость медь приобретает при быстром охлаждении в воде.
Если медную проволоку или трубку нагреть докрасна (600°С) на огне и затем быстро погрузить в воду, то медь станет мягкой. После придания нужной формы изделие вновь можно нагреть на огне до 400°С и дать ему остыть на воздухе. Проволока или трубка после этого станет твердой.
Если необходимо выгнуть трубку, ее плотно заполняют песком, чтобы избежать сплющивания и образования трещин.
Отжиг латуни
позволяет повысить ее пластичность. После отжига латунь становится мягкой, легко гнется, выколачивается и хорошо вытягивается. Для отжига ее нагревают до 500°С и дают остыть на воздухе при комнатной температуре.
Цвета каления
При продолжении нагревания на смену цветам побежалости приходят цвета каления.
Поскольку каление представляет из себя свечение материала, объективная оценка самых темных его цветов, возможна только в темноте. А более светлых, как минимум, при затемнении. Первый, различимый глазом цвет каления красновато-коричневый, означающий, что температура каления в области его проявления находится в диапазоне 530 – 580 градусов по Цельсию. В отличие от цветов побежалости, цвета каления при охлаждении не сохраняются, а изменяются в обратном порядке.
Если на поверхности образовалась окалина, ее цвет возвращается к светло серому оттенку. При нагревании магнитных, железоуглеродистых сплавов выше 768 С их магнитные свойства исчезают. И появляются вновь, после охлаждения ниже этой температуры.
Это явление можно использовать как дополнительное средство контроля температур. Цвета каления отражают температуру нагрева не только металлических тел, но и не металлических тоже. Например, изделий из керамики, графита и других.
Железо цвета побежалости — Справочник химика 21
Отполированную сталь и железо можно подвергнуть воронению, благодаря чему их поверхность покрывается красивым слоем окисла, стойким по отношению к влаге из воздуха. Для воронения поверхность протирают маслом (минеральным) и, положив на железный лист, нагревают на листе в пламени примуса до выгорания масла и почернения поверхности. Стальную деталь, не прибегая к смазыванию маслом, можно нагреть до появления того или иного цвета побежалости и затем для закрепления его опустить в расплавленный парафин или льняное масло (гл. 2, 2). Нагревая стальную пластинку с одной из ее сторон, можно получить и закрепить целую гамму цветов побежалости. [c.155]Этому опыту было дано такое объяснение. В местах, подвергнутых слабому нагреву, где нет видимых изменений, образовалась тонкая и сплошная пленка окисла. Она защищала металл от соприкосновения с ионами Си , и реакция (У1,6) была невозможна. В зоне цветов побежалости образовавшаяся пленка окисла настолько толста, что не может остаться сплошной, растрескивается и обнажает железо. В местах дефектов пленки происходит реакция ( 1,6). На поверхности, оставшейся холодной, пленки либо нет вообще, либо она настолько пориста, что реакция (VI,6) протекает беспрепятственно, [c.209]
Термический способ (воронение и синение) применяют для обработки мелких проволочных, а также полированных изделий (часовых стрелок и волосков, винтов, лент, пружин и т. п.). Прр воронении изделия смазывают тонким слоем асфальтового или масляного лака, растворимого в бензине, подсушивают на воздухе и загружают (на железных сетках) на 12— 20 мин. в печь при температуре 350—450° С после того как изделия приобрели черную окраску, их выгружают из печи и охлаждают в минеральном масле. В результате такой обработки на металле образуется защитная пленка из окислов железа, на которой имеется тонкий слой сплавленного асфальта или осмоленного масла. Для синения изделия помещают в печь при температуре 310—350° С и выгружают из нее в момент появления на поверхности металла цветов побежалости. Печи снабжены слюдяным или кварцевым стеклом для наблюден ия за ходом процесса. [c.211]
Удельный вес никеля, наносимого гальваническим пз тем, равен 8,9 точка плавления 1455° С. Электрическая проводимость никеля составляет лишь 15% электрической проводимости меди. При высокой температуре на никеле появляются цвета побежалости, однако в окисляющей атмосфере при температуре до 800° С никель не изменяет своих свойств. Обычные загрязнения-железо, марганец, кобальт, кислород (в виде окиси) и сера (в виде сульфида). В щелочах и органических кислотах никель не растворяется, в серной и со- тяной кислотах он растворяется медленно, в азотной кислоте хорошо. [c.149]
Особенности хромового покрытия. Хромовое покрытие стойко против действия большинства газов, щелочей, растворов кислот и солей хром растворяется в горячей серной и азотной кислотах. Блеск и цвет хромового покрытия не изменяются от воздействия атмосферы. При нагревании твердость хро.мового покрытия уменьшается. При температуре нагрева от 200 до 600° С уменьшение твердости происходит медленно, а при температуре свыше 600° С — очень быстро. Для появления цветов побежалости критической температурой является 450° С. При нагреве до температуры, близкой к 450° С, хромовое покрытие начинает менять цвет. С точки зрения противокоррозийной защиты хром как электроотрицательный металл в принципе защищает железо от ржавления. Но поскольку на воздухе хром пассивируется (на покрытии образуется тонкая пленка окиси хрома), то его электроотрицательные и защитные свойства снижаются. Это относится только к тонким пористым хромовым покрытиям. [c.164]
Физические свойства. Уран — блестящий металл, напоминающий по виду в свежем срезе или окисленном состоянии железо. Поверхность свежеполированного металла имеет сильный блеск, но после нескольких часов пребывания на воздухе покрывается цветами побежалости. Уран имеет плотность 19,07 г/сж . Он на 80% тяжелее свинца, пластичен и ковок. [c.9]
Непосредственно вслед за шлифовкой поверхности железа производилось ее окисление. Для получения клиновидных пленок один конец железной полоски нагревался до появления окалины, в то время как другой находился в хорошем контакте с медным зажимом, иногда охлаждаемым проточной водой. Благодаря этому холодный конец образца сохранял свой металлический блеск. Между холодным и горячим концами всегда можно было наблюдать цвета побежалости различных оттенков. [c.25]
Относительно толстые окисные пленки, снятые с железа, имеющего последние цвета побежалости, в проходящем свете дают коричневатую окраску, а в отраженном имеют блестящий, почти металлический вид На более тонких пленках коричневый цвет и металлический блеск становятся менее четкими. [c.80]
Следует заметить, что легкость отделения пленок, возникших при обычных температурах, сильно меняется в зависимости от физического и химического характера железа. Снятие таких пленок со стали обычно невозможно, хотя пленки со стали, нагретой до цветов побежалости, снимаются легко. Применение йодного метода для отделения пленок от железа, обработанного в растворе хромовокислого калия, упомянуто на стр. 379 эти пленки снимаются более легко, чем пленки, возникшие на воздухе. [c.81]
Несколько опытов, произведенных в Кембридже с желе-. 50М, покрытым видимой пленкой, иллюстрируют этот факт. Железо было очищено абразивом, нагрето до полу Гения цвета побежалости первого порядка и испытано в 0,1 Л серной кислоте. Цвета быстро изменились и скоро исчезли. Даже 0,002 М кислота вызывает утонение пленки в течение минуты. Из этого можно было бы сделать тот вывод, что кислота разрушает пленки окиси железа. Тогда опыт был повторен с железом, нагретым до появления более толстых пленок (цвета [c.89]
Если это объяснение правильно, то становится возможным воспрепятствовать. восстановлению пленки (замедляя таким образом ее разрушение) при помощи окислительных агентов. Опыты подтвердили это предположение. Было установлено, что 0,01 М серная кислота, содержащая хромовую кисло Уу (0,1 /П), ие изменяет железо с цветами побежалости, хотя 0,01 М серная кислота (без хромовой кислоты) дает заметное изменение в 5 сек. и полное разрушение более ранних окрасок в 1 йин. [c.90]
Описанные опыты делают очевидным то, что видимые окисные пленки на железной поверхности совершенно у с т о й ч и в ы в кислоте в анодных условиях. Были затем проведены опыты с анодом из железа без цветов побежалости, пассивированного в разбавленной серной кислоте применением тока высокой плотности. В этом случае также было обнаружено, что некоторые короткие перерывы тока могут быть допущены без потери пассивности однако более долгие перерывы возвращают металлу его способность растворяться при низких плотностях тока. Трудно не притти к заключению, что оба случая анодного иммунитета являются следствием наличия окисных пленок, хотя на ненагретом железе пленка еще слишком тонка, чтобы дать интерференционные цвета. [c.91]
Опыты, проведенные в лаборатории в Кембридже также показали, что существуют окислы железа, стойкие к азотной кислоте. Полоски электролитического железа нагревались с одного конца, так же как и при получении обычных интерференционных цветов, обязанных возникновению окисным пленкам другой конец полоски при этом остается без изменения. Когда эти полосы были помешены в азотную кислоту уд, веса 1,4, никаких изменений цветов не было замечено даже спустя ЗУа часа при 23° если бы кислота была способна быстро растворять окислы, дающие цвета побежалости, то последние быстро исчезли бы. При повторении этого опыта с более разбавленной кислотой (уд. вес 1,2), железо подверглось сильной коррозии у конца, свободного от цветов побежалости у противоположного конца железо около пленок было подъедено, а сами пленки отстали в виде шероховатых микроскопической величины чешуек, похожих на чешуйки. [c.394]
Видимые пленки, образующиеся иа металлах при действии азотной кислоты. Имеется много указаний, что при действии азотной кислоты на металле может образоваться пленка. Во многих произведенных в Кембриджской лаборатории опытах по исследованию действия разбавленной азотной кислоты на железо было замечено, что в тех случаях, когда красные пары, получающиеся в ходе реакции, проходят над поверхностью железа, поднимаясь к уровню кислоты, получается последовательный ряд интерференционных цветов (желтоватый, красновато-лиловый, синий и т. д.), указывающих на наличие пленки. Достижение видимой толщины доказывало, что вещество пленки не имело здесь защитного характера и, во всяком случае, было установлено, что площадь, покрытая цветами побежалости, в этом случае является активной по отношению к пробе с азотнокислой медью. Однако возможно, что некоторое изменение условий может дать пленки гораздо более ровные и менее пористые и такие пленки, не достигая толщины, необходимой для появления цветов побежалости, могут вместе с тем сделать металл пассивным. Очевидно такие условия осуществляются в концентрированной азотной кислоте. [c.395]
Одно время высказывались сомнения в том, что цвет побежалости на железе действительно зависит от толщины пленки. Указывали, что если это так, то должно быть возможным изменение цветов в обратном порядке при уменьшении толщины пленки ранние опыты сошлифовывания пленки на железе, окрашенном в голубой цвет первого порядка, не дали пурпурного и желтого цветов, характерных для более тонких пленок, хотя последующие опыты были более успешны Но сошлифовывание не подходящий метод для получения столь тонких пленок. Катодная обработка железа с цветами побежалости в разбавленной соляной кислоте дает более однородное уменьшение толщины и ожидаемое изменение цветов было в действительности получено в данном случае уменьшение толщины зависит от катодного восстановления окиси железа до закиси, которая очень быстро растворяется в кислоте скорость реакции зависит только от силы тока и таким образом легко получить необходимую однородность уменьшения толщины пленки. Следовательно, указанное выше возражение по отношению к интерференционному объяснению цветов тонких пленок устранено. [c.841]
В чистом воздухе пассивирующая пленка и лежащий под ней металл будут химически устойчивы. В загрязненном промышленном воздухе агрессивные газы химически разрушают пассивирующую окисную пленку. При этом изменяется цвет поверхности деталей, на ней появляются цвета побежалости, темные и цветные пятна и т. д. Повышение температуры увеличивает скорость разрушения пассивирующей окисной пленки, а солнечный свет, наоборот, препятствует ее разрушению. Доказано, например, что детали из железа и цинка на солнечном свету химически более устойчивы, чем в темноте. Скорость коррозии резко возрастает также при наличии на поверхностях деталей пыли. В пыльном воздухе коррозия идет значительно интенсивнее. [c.94]
Подобный процесс называется диффузией, причём, благодаря диффузии атомов А, исчезает разность концентраций и устанавливается стехиометриЧеское равновесие. Примером может служить известное явление цветов побежалости, наблюдаемое, например, при образовании тонких слоёв окислов на железе. При этом атом А на рис. 134 соответствует железу, а атом В—кислороду, т. е. слева мы имеем чистое железо, а справа — окислительную атмосферу кислорода. [c.298]
На более сильно нагретом конце полосы цвета побежалости, обусловленные интерференцией, исчезают, и внешний вид определяется специфическим цветом окисла. Обычно пленка имеет синевато-серый или черный цвет но на медной полосе, когда резким изгибом удается отделить пленку в виде тонких чешуек, видно, что, хотя наружный ее слой почти черный и состоит обычно из окиси меди (СиО), внутренний слой — красный и состоит из закиси меди (СигО). Никель образует только один слой (N 0), а железо иногда образует три слоя (см. ниже). [c.30]
Наблюдение за цветами побежалости само собой не позволяет измерить количество окисла на или непосредственно под поверхностью металла. Вернон и его сотрудники нашли, что выше 200° (когда шлифованное железо окисляется однородно по параболическому закону) количество окисла, находящегося в пленке, эквивалентно всему поглощенному кислороду. При нагревании ниже 200° С, когда окислы проникают в металл и окисление подчиняется логарифмическому закону, этого явления не наблюдается. В области более низких температур в снятой пленке кислорода было значительно меньше, чем общее количество поглощенного кислорода. Цвета побежалости отсутствовали (или ограничивались слабым соломенным цветом), даже тогда, когда общее количество поглощенного кислорода, как можно судить по увеличению веса, было достаточно, чтобы образовалась окраска (если допустить, что пленка однородная) [c.58]
Потемнение, замеченное на кухонной посуде, объясняется различным образом. Одни авторы рассматривают его как начало образования пленок, дающих благодаря явлениям интерференции цвета побежалости, другие же связывают этот эффект с действием железа. Третьи снова постулируют образование мелких частичек металлического алюминия, вкрапленных в окись или гидроокись. Если, например, коррозия происходит по границам зерен, которые превращаются в окись, а внутренние участки зерна сохраняют металлическое состояние, то любой световой луч, падающий на поверхность, теряется в результате многократного отражения от металлических частиц. Это обусловливает потемнение поверхности по тем же оптическим эффектам, которые объясняют темный цвет мелкодисперсной платины. Возможно, что все эти факторы играют роль при различных обстоятельствах. [c.101]
На одинаково нагретых полосках меди или железа цвета побежалости ПОЯВЛЯЮТСЯ практически в той же последовательности, но на железе окраска в толстых пленках может быть слабее или вовсе отсутствовать. Окисел железа менее прозрачен, чем окисел меди, поэтому отражение от внутренней поверхности при толстой пленке становится слабее. Тот факт, что последовательность цветов для всех металлов приблизительно одинакова, показывает, что окраска зависит от толщины пленки и не является специфическим свойством окисла. Повторение одного и того же цвета последовательно несколько раз легко объясняется. Если толщина пленки такова, что пути лучей света, отраженных от внутренней и наружной поверхностей пленки, соответственно отличаются на величину, равную половине длины волны зеленого цвета, то произойдет частичное затухание зеленых лучей и образец, рассматриваемый при дневном свете, будет казаться красно-фиолетовым, так как этот цвет является дополнительным к зеленому. Однако до некоторой степени такой же цвет получится, когда пленка утолщилась настолько, что разница в пути лучей стала Р/а, 2V2 или З /а длины зеленой волны. Таким образом, красноватое окрашивание последовательно повторяется несколько раз, хотя его оттенки при повторных появлениях различны. Не только оттенки окраски, но и последовательность цветов второго порядка немного отличается от таковых первого порядка по причинам, которые объяснены на стр. 719. Таблицы толщин пленок различных цветов приведены на стр. 55, 56. [c.30]
Полученные этим автором результаты по сухому сероводороду приведены на рис. 128. По данным привеса видно, что коррозия исключительно слаба. Все металлы делятся автором на три группы. К первой группе относятся металлы, не изменяющие даже внешнего вида (магний, алюминий и сплав авиаль), а также те, которые сохраняют естественный вид, но покрываются либо цветами побежалости (цинк), либо мелкими черными пятнышками (сталь 18-8). Ко второй группе относятся металлы, меняющие лишь свой цвет,— никель, железо и свинец. К третьей — металлы, изменяющие свой внешний вид,— серебро, латунь и медь. [c.193]
ЦВЕТА ПОБЕЖАЛОСТИ — радужные цвета поверхности материала. Появляются при образовании тонких пленок в результате изменения (напр., окисления) поверхностного слоя. Так, при низком или среднем отпуске стали в окислительной среде (напр., на воздухе) на поверхности образуются п.ченки окислов, толщина к-рых увеличивается с повышением т-ры нагрева и продолжительности выдержки. Появление Д. п. связано с интерференцией белого цвета в этих пленках, вследствие чего погашаются лучи той или иной длины волны. По Ц. п. можно судить о т-ре нагрева и продолжительности выдержки изделия нри этой т-ре, поскольку длина волны погашенного луча зависит от толщины пленки. При нагреве в те-.чение нескольких минут на поверхности железа и нелегированной углеродистой стали появляется Д. п. слабо-желтый — при т-ре 215 С, светло-соломенный — 220° С, светло-желтый — 230 С, тускло-желто-соломенный — 235 С, соломенный — 240 С, густо-соломенный — 250° С, желтовато-коричневый — 255° С, коричневый — 265 С, коричневопурпурный — 270° С, пурпурный — [c.712]
Приведем некоторые данные, полученные методом эллиптической поляризации отраженного света. На мягкой стали (0,04% С) в азотной кислоте образуется пленка толщиной б = 25-г 30 А [26]. На нержавеющей стали (—0,1% С, —18% Сг, 8% N1) в этих же условиях б я 10 А. Такую же толщину имеет пленка, образованная на железе в сухом воздухе. Железо и никель испытывались соответственно в 0,5 н. NaOH 1 н. N82804 и в 0,1 н. КаОН 0,3 н. На2304. Образцы подвергались анодной поляризации, благоприятствующей образованию окисла, и катодной, восстанавливающей его. После первой анодной поляризации б = 20 40 А. При повторных анодных и катодных поляризациях, приводящих к разрыхлению поверхности, на электродах наблюдались цвета побежалости, т. е. б сильно увеличивалась. [c.89]
У. Р. Эванс [17] нагревал железную пластинку на воздухе так, чтобы на одном ее конце стали видны цвета побежалости, а другой конец оставался бы холодным и без видимых изменений. После охлаждения в разных местах поверхнйсти пластинки наносились капли раствора нитрата меди. На конце пластинки, остававшемся холодным, немедленно происходило окисление железа ионом Си [c.209]
ВОН кислоты в слое улучшает его стойкость. На рис. 1.93 показано влияние содержания кремния в сплаве на состав слоя и на коррозионные потери сплава в 10% растворе хлорного железа. На сплавах, содержащих молибден, последний выделяется в форме окисла. Повышенная стойкость этих сплавов основана на совместном действии кремневой кислоты и молибдена [281, 282]. В толстых слоях (300—500 А), которые образуются под действием воЗ духа при нагревании, хром содержится в повышенном, а никель — в уменьшенном количествах. Эти слои являются кристалличс скими, показывают цвета побежалости и построены по типу шпинели [283]. Скорость их роста лимитируется скоростью движения ионов металла и кислорода в слое. [c.103]
Опыт V.10. Стальную пластину бОх 10×2 мм зачистить наждачной бумагой, протереть органическим растворителем (ацетоном) для обезжиривания и нагреть с одного конца в пламени газовой горелки в течение 2—3 мин до появления цветов побежалости. Дать пластинке остыть и затем пипеткой нанести на пластинку по ее длине равномерно на некотором расстоянии друг от друга 3—4 капли 2%-ного раствора нитрата меди. Заметить время появления пятен меди в зависимости от того, в какой степени была нагрета пластинка. На том конце пластинки, который совсем не нагревался, медь не выделяется, потому что тонкая окисная пленка на железе защищает металл и не пропускает раствора Си(МОз)а. На противоположном конце пластинки почти мгновенно появляется большое желтое пятно меди. Этот конец нагревался больше всего и здесь образовалась наиболее толстая, но и менее эластичная пленка оксида она растрескивается при высоких температурах и потому не обладает защитными свойствами и пропускает к железу раствор Си(МОз)2- [c.322]
Практически толщина оксидного слоя может колебаться от сотых долей микрона до 10 л и более. Защитные свойства оксидной тленки, а также механическая прочность ее в значительной степени зависят от применяемого способа оксидирования. Так, тонкие слои, дающие цвета побежалости, получаемые на железе термическим способом, обладают малой механической прочностью вследствие их крайне незначительной толщины, но более высокими защитными свойствами, чем пленки, получаемые химическим способом. В последнем случае защитные окисные пленки отличаются большей пористостью. На скорость образования оксидной пленки влияет состав и структура металла изделия. Малоуглеродистая легированная сталь труднее оксидируется. Для нее требуется повышенная температура оксидирования и большая продолжительность процесса. Как правило, оксидированию подвергаются изделия, предназначенные для использования в закрытых помещениях, а также для временной защиты готовых обработанных изделий. В сухом воздухе окисные пленки достаточно стойки. Во влажной атмосфере и осо- [c.334]
Углерод. Влияние углерода на реакции взаимодействия железа с кислородсодержащими газами определяется в большой мере обезуглероживанием при температурах выше приблизительно 700° С. Как известно и как это неоднократно подтверждалось (см., например, работу Остина [745]), обезуглероживание стали водородом сильно ускоряется в присутствии водяного пара или при использовании листовой стали с цветами побежалости. Если углеродсодержащее железо соприкасается с газом, содержащим кислород даже в малой примеси, то образующаяся окись углерода создает значительное давление. зависяп1ее от температуры, концентрации углерода в стали и концентрации кислорода с. газовой среде. Ясно, что выделение окиси углерода (наряду с углекислым газом) должно отразиться на окислении сталей. Этот выделяющийся газ препятствует н какой-то мере созданию [c.320]
Ванадий. В сплавах железа с ванадием последним обогащены внутренние слои, прилегающие к металлу, тогда, как в наружных слоях его обнаруживается мало [116, 446, 729] вследствие сравнительно больщой свободной энергии образования окислов ванадия и малой скорости диффузии его ионов. Ванадий не способен улучшать сопротивление сталей окислению [446, 773]. Наоборот, как наблюдал Бандель [747], добавка ванадия в количестве 4,4% вызывала при 1100° С образование на поверхности сталей цветов побежалости. Фактически легкоплавкая пятиокись ванадия, как это показано несколько дальше, принадлежит к числу самых худших соединений, вызывающих катастрофическое окисление. [c.332]
Другим рациональным методом задержки катодного восстановления пленок является анодная обработка образца с цветами побежалости. Для этого нужно соединить образец с электрической батареей до введения его в кислоту в противном случае пленки будут разрушены до того, как начнется анодная обработка. Когда железо, имеющее цвет первого порядка, становится с момента его погружения в кислоту анодом, не наблюдается никакой коррозии и никаких изменений цвета образец ведет себя как пассивный анод и выделяется кислород. Оказалось возможным также прервать ток на доли секунды (иногда даже на несколько секунд) без на-пу1 1ения пассивности или исчезновения цвета. В таких случаях [c.90]
Толщина пленок, образовавшихся при взаимодействии металла с сухим воздухом или окислителями, различна и зависит от рода металла, характера среды, температуры и других факторов. Толщина пленок на меди и железе в обычных aт ю фepныx условиях составляет 10—30 А (А= ЫО мм). Такие пленки невидимы и настолько тонки, что метал.л сохраняет свой блеск. Наличие пленки можно установить по изменению отражательной способности поверхности металла. Так. называемые цвета побежалости на металлах обусловлены образованием пленок толщиной 400—5000 А. [c.128]
Закись железа, магнетит, а также Y-oк i6ь железа имеют кубическую кристаллическую структуру можно считать, что Рвз04 образуется из РеО удалением четверти железа (некоторые двухвалентные ионы должны стать трехвалентными, чтобы сохранить электронейтральность). Возможно дальнейшее удаление железа и получение серии твердых растворов с кубической структурой, в которых последним является -Ре Оз. Обычно полагают, что «у-окисел не стоек при высоких температурах устойчивая форма а-РеаОз, которая является главной составляющей пленки и обусловливает цвета побежалости. Эта форма окисла имеет ромбоэдрическую структуру. В результате новых электронно-дифракционных исследований, проведенных в лаборатории Коэна в Оттаве на железе, нагретом при 320° С в течение 1740 мин. в кислороде при давлении 20 мм, найдено присутствие малых количеств у-РеаОз между слоями магнетита и а-РеаОз, что позволяет пред- [c.32]
Магнетит —фаза устойчивая даже при низких температурах и можно предполагать, что в области цветов побежалости пленки окиси железа (которые способствуют окраске, будучи совершенно прозрачными) отделяются от металла относительно непрозрачным магнетитом. Для пленок с цветами второго и более высокого порядка это имеет место, но, по-видимому, также верно и для пленок первого порядка в течение некоторого времени. Определенная окраска может быть получена длительной выдержкой при низкой температуре или меньшей выдержкой при более высокой температуре. При втором способе окрашенная пленка окиси железа обыч1 о находится непосредственно на поверхности металла [c.34]
Сцепление окисла и металла на шлифованной поверхности. Ранее проведенная работа по снятию пленки в Кембридже и более подробное исследование в Теддингтоне показали, что через тонкие пленки на железе и меди (включая те, которые дают цвета побежалости первого порядка) происходит значительное окисление металла. Под гомогенной окисной пленкой появляется смешанная зона металла и окисла. Современная работа по изучению электронной эмиссии, проведенная в Глазго, подтверждает это и указывает на удивительно глубокое проникновение смешанной зоны. Нестойкий деформированный окисел, образовавшийся под поверхностью шлифованного металла, может испускать электроны при освещении определенными длинами волн в условиях, когда относительно устойчивая пленка окисла на поверхности не способна к этому. Алюминий, шлифованный на воздухе карборундовой бумагой средней зернистости, после выдержки на воздухе в течение [c.55]
В 0,001 н. растворе, проводимость которого низка, защитное действие краев может распространяться лишь на ограниченное расстояние от них (фиг. 29, б). В 0,0001 н. растворе защищенная область становится очень узкой основная часть центральной области претерпевает изменения, но на ранней стадии коррозия, начавшись в различных точках поверхности, защищает от поражения область, непосредственно к ней примыкающую, так что каждая темная точка коррозии окружена светлым не изменившимся участком. Внеэтих участков основная часть поверхности покрыта пленками цветов побежалости, что указывает на то, что в этих местах защита недостаточна для того, чтобы помешать движению катионов железа наружу через пленку. Однако катионы движутся наружу медленно и осаждаются щелочью и кислородом, как только они выходят из поверхности металла таким образом, на поверхности металла образуется пленка, толщина которой достаточна для того, чтобы давать интерференционные окраски и защищать металл от коррозии в течение некоторого времени. [c.109]
Для того чтобы удостовериться в том, действительно ли жидкость, образующаяся на начальных точках коррозии, может разрушать окисную пленку, были проведены специальные опыты с образцами железа, нагретого до появления окрашивания, на котором была нанесена царапина, до частичного погружения его (царапина вертикальна) в раствор хлористого натрия. Вскоре около царапины начинался процесс коррозии и коррозионные продукты, опускаясь вниз, разрушали окисные плецки на дугообразной области. Для того чтобы это не вызывало сомнений, опыт был поставлен так, что коррозионные продукты из царапины на полупогруженном образце попадали на второй образец, помещенный под первым без электрического контакта с ним (так что сложность, обусловленная дифференциальной аэрацией, была устранена) в этом случае пленки с цветами побежалости опять исчезали в области, на которую попадали продукты коррозии, но не везде. Если продукты коррозии могут разрушить относительно толстые пленки, образующиеся при нагревании, то они определенно разрушат невидимые пленки, имеющиеся на не подвергнутых нагреву образцах. [c.112]
Постоянное залечивание слабых мест в пленке происходит на железе и стали в областях, где образующаяся на катоде щелочь является доминирующей одним из примеров может служить область ватерлинии частично погруженного образца, на котором возникают пленки с характерными окрасками типа цветов побежалости, но нет активной коррозии (стр. 87). Эти положения, однако, лучше показать на примере поведения капель раствора хлористого натрия или калия, помещенных на горизонтальную стальную поверхность. Распределение анодных и катодных участков удобно демонстрировать с помощью добавок к электролиту так называемого ферроксил — [c.112]
Изменения начинаются, как и на других металлах, в изолированных точках, которые более многочисленны около краев однако вместо образования свободных, плохо сцепленных с поверхностью продуктов, как это наблюдается на железе и цинке, на меди появляются овальные области ярких цветов побежалости на хорошо отшлифованных образцах и грязнокоричневые пятна на грубо отшлифованных образцах. Твердая хлористая медь, образующаяся при анодной реакции, будучи трудно растворимой, превращается тут же на месте в окись меди благодаря взаимодействию со щелочью, возникающей за счет катодной реакции и растекающейся по поверхности. Таким образом, образующаяся пленка дает характерное окрашивание. Тем временем на остальной поверхности возникают более слабые цвета, которые вызваны пленками, образованными при взаимодействии ионов одновалентной меди, двигающихся через начальную пленку в жидкость со щелочью, образующейся на катоде если это так, то это окрашивание можно рассматривать аналогично тому, которое наблюдается в районе ватерлинии на цинке или железе. [c.118]
Коррозия имеет место, если максимальная скорость доставки ингибитора меньше, чем скорость образования ионов металла в результате анодной реакции в отсутствие ингибитора. Сокращение фронта диффузии к чувствительному участку у конца менисковой щели будет, несомненно, снижать скорость доставки ингибитора, однако в такой же степени будет уменьшаться скорость миграции ионов, так как любое сокращение сечения, независимо от его геометрической формы, будет увеличивать сопротивление диффузии и электрическое сопротивление по той же причине. Таким образом, вероятность разрушений в точке, расположенной в мениске, будет точно такой, как в любой другой. Пиирс, однако, обнаружил, что особая чувствительность точек в менисковой области имеет место только в том случае, если на металле есть пленка (например, железо, нагретое до температуры, вызывающей цвета побежалости) или если электролит содержит соединения, образующие пленку (например, ингибитор). Если [c.143]
Для чего проводят термическую обработку
Термическая обработка стали
Классификация видов термообработки стали. Виды термической обработки стали (отжиг, отпуск, закалка).
Термическая обработка (термообработка) стали— процесс изменения структуры стали, цветных металлов, сплавов при нагревании и последующем охлаждении с определенной скоростью. Термическая обработка (термообработка) приводит к существенным изменениям свойств стали, цветных металлов, сплавов. Химический состав металла не изменяется.
Виды термической обработки стали
Отжиг
Отжиг — термическая обработка (термообработка) металла, при которой производится нагревание металла, а затем медленное охлаждение. Эта термообработка (т. е. отжиг) бывает разных видов (вид отжига зависит от температуры нагрева, скорости охлаждения металла).
Закалка
Закалка — термическая обработка (термообработка) стали, сплавов, основанная на перекристаллизации стали (сплавов) при нагреве до температуры выше критической; после достаточной выдержки при критической температуре для завершения термической обработки следует быстрое охлаждение. Закаленная сталь (сплав) имеет неравновесную структуру, поэтому применим другой вид термообработки — отпуск.
Отпуск
Отпуск — термическая обработка (термообработка) стали, сплавов, проводимая после закалки для уменьшения или снятия остаточных напряжений в стали и сплавах, повышающая вязкость, уменьшающая твердость и хрупкость металла.
Нормализация
Нормализация — термическая обработка (термообработка), схожая с отжигом. Различия этих термообработок (нормализации и отжига) состоит в том, что при нормализации сталь охлаждается на воздухе (при отжиге — в печи).
Среди основных видов термической обработки следует отметить:
Отжиг (гомогенизация и нормализация). Целью является получение однородной зёренной микроструктуры и растворение включений. Последующее охлаждение является медленным, препятствующим образованию неравновесных структур типа мартенсита.
Закалку проводят с повышенной скоростью охлаждения с целью получения неравновесных структур типа мартенсита. Критическая скорость охлаждения, необходимая для закалки зависит от материала.
Отпуск необходим для снятия внутренних напряжений, внесённых при закалке. Материал становится более пластичным при некотором уменьшении прочности.
Дисперсионное твердение (старение). После проведения отжига проводится нагрев на более низкую температуру с целью выделения частиц упрочняющей фазы. Иногда проводится ступенчатое старение при нескольких температурах с целью выделения нескольких видов упрочняющих частиц.
Термическая обработка металлов разделяется на обработку черных металлов и цветных. Ниже пойдет речь конкретно об видах термической обработке стали. Также можете ознакомится с термической обработкой цветных металлов.
Обжигание — нагревание стального изделия до температуры 840—900 °С, выдержка при этой температуре не меньше 2 ч и охлаждение вместе с печью. Этот метод применяют при изготовлении из закаленного изделия другого или же когда предыдущий закал был неудачный и инструмент нужно снова закалить. Если закаливать необожженные детали, то в них могут возникнуть трещины, структура металла станет неоднородной, что резко ухудшает качество изделия. Мелкие детали отжигают, нагревая на массивных накаленных стальных штабах, с которыми их охлаждают. Иногда изделие нагревают ацетиленовой горелкой, которую постепенно отдаляют от изделия, чтобы изделие постепенно остыло.
Нормализация – это нагревание стальных изделий к соответствующей температуре и охлаждению на воздухе.
Закаливание – нагревание углеродных или некоторых легированных сталей к определенной температуре и быстрое ее охлаждение. В результате этого изменяется кристаллическая структура металла – он становится твердее и более антикоррозийным. Мало-углеродные стали с содержимым углерода до 0,3 % не закаливаются. В зависимости от марки сталь нагревают до определенной температуре. Так, стали У7, У7А нагревают до 770—790 °С; У8-У13А — до 760—780; Р9-Р18 К5-Ф2 – до 1235—1280 °С. При нагревании выше этой температуры сталь теряет свои свойства «Пережиг» — непоправимый брак. Это также касается отжига и отпускания. В небольших мастерских или в домашних условиях температуру определяют за цветом разжаривания (в затененном месте), которое приобретает изделие во время нагревания:
Цвет. Температура, °С Темно-коричневый………. 530-580 Коричнево-красный ……..580-650 Темно-красный ……………650-730 Темно-вишневый …………730-770 Вишнево-красный ………..770-800 Светло-вишневый………. 800-830 Светло-красный …………830-900 Оранжевый ………………..900-1050 Темно-желтый …………..1050-1150 Светло-желтый ………….1150-1250 Светло-белый …………….1250-1350
Мелкие изделия, для того чтоб не пережечь, лучше нагревать на предварительно нагретой металлической подставке (например, штабе). Температура нагревания равно температуре нагревания изделия. Быстрое охлаждение приводит к твердому закалу, вследствие чего могут возникнуть большие внутренние напряжения и даже трещины. Медленное охлаждение может не дать нужного по твердости закала Охлаждающими средами могут быть вода (обычной температуры или нагретая до температуре 50-50 °С), водные растворы, масло и воздух. Кухонная соль, едкий натр или селитра, которые добавляют к охладителям, ускоряют охлаждение. Для уменьшения скорости охлаждения к воде добавляют раствор мыла, масляную эмульсию, жидкое стекло, известковое молоко и т.п.. Чрезмерно быстрое охлаждение водой часто приводит к дефектам изделия (внутренние напряжения, трещины, деформация), а повышение температуры воды уменьшает ее закальные свойства. Поэтому при последовательном закале нескольких деталей, чтобы они имели одинаковую закалку, воду часто заменяют или используют большой сосуд. Равномерно и довольно быстро сталь охлаждается в 8-12 %-ном водном растворе кухонной соли или едкого натра при температуре 20 °С. Некоторые стали для лучшего закала охлаждают в 30 %-ном растворе едкого натра. Как охлаждающую среду можно применять расплавленные соли калиевой или натриевой селитры. Нагревание масла к 60-90 °С не уменьшает скорости охлаждения, т.е. не влияет на его закаливальные свойства. Охлаждающей средой для сталей может быть воздух (для тонких деталей) или воздух под давлением (от вентилятора, компрессора). Некоторые плоские детали (ножи) из нержавеющий стали охлаждают между двумя металлическими штабами.
Отпускание — нагревание деталей к определенной температуре, выдерживанию при этой температуре и быстрое охлаждение. Его применяют после охлаждения детали в процессе закаливания, чтобы уменьшить хрупкость и частично твердость. Есть три вида отпускания: низкое, среднее и высокое соответственно в интервале температур до 350 °С, 350—500 и 500—680 °С. Наиболее распространенное низкое отпускание. Нагревание до 170 °С только снимает внутренние напряжения, но не изменяет твердости стали. Температуру нагревания при отпускании определяют специальным термометром, а если его нет, то за цветами побежалости, т.е. цветами окислительной пленки, которая возникает на зачищенной поверхности изделия во время нагревания:
Цвет. Температура, °С Светло-соломенный ……..200 Светло-желтый ……………225 Соломенно-желтый ……..240 Коричнево-желтый ………255 Красно-коричневый ……..265 Пурпурно-красный ………275 Фиолетовый ………………..285 Синий …………………………295 Светло-синий ……………..315 Серый (морская вода) ….330
После появления желательного цвета в процессе нагревания, деталь охлаждают. У легированных сталей цвета побежалости появляются при температурах на 12-17 °С ниже от приведенных. Не имея достаточного опыта, нагревать закаленные изделия для отпускания лучше всего на расплавленном свинце, олове, цинка (для пружин) или в расплавленной смеси (поровну) калиевой и натриевой селитры. Это гарантирует быстрое и равномерное нагревания и его постоянную температуру. Можно отпускание соединить с охлаждением. Для этого нагретый рабочий конец инструмента погружают во время закаливания на 20-25 мм в воду и держат, пока металл не потемнеет. Потом инструмент вынимают из воды, быстро очищают от охлажденной части окалину напильником или куском шлифовального круга. Как только появится, нужен цвет побежалости, инструмент погружают в воду сначала наполовину, а потом полностью и держат до охлаждения.
Термообработка сплавов является неотъемлемой частью производственного процесса чёрной и цветной металлургии. В результате такой процедуры металлы способны изменить свои характеристики до необходимых значений. В данной статье мы рассмотрим основные виды термообработки, применяемые в современной промышленности.
Сущность термической обработки
В процессе производства полуфабрикаты, металлические детали подвергаются термической обработке для придания им нужных свойств (прочности, устойчивость к коррозии и износу и т. д.). Термическая обработка сплавов – это совокупность искусственно созданных процессов, в ходе которых в сплавах под действием высоких температур происходят структурные и физико-механические изменения, но сохраняется химический состав вещества.
Назначение термообработки
Металлические изделия, которые используются ежедневно в любых отраслях народного хозяйства, должны отвечать высоким требованиям устойчивости к износу. Металл, как сырьё, нуждается в усилении нужных эксплуатационных свойств, которых можно добиться воздействием на него высокими температурами. Термическая обработка сплавов высокими температурами изменяет изначальную структуру вещества, перераспределяет составляющие его компоненты, преобразует размер и форму кристаллов. Всё это приводит к минимизации внутреннего напряжения металла и таким образом повышает его физико-механические свойства.
Виды термической обработки
Термообработка металлических сплавов сводится к трём незатейливым процессам: нагреву сырья (полуфабриката) до нужной температуры, выдерживанию его в заданных условиях необходимое время и быстрому охлаждению. В современном производстве используется несколько видов термообработки, отличающихся между собой некоторыми технологическими особенностями, но алгоритм процесса в общем везде остаётся одинаковым.
По способу совершения термическая обработка бывает следующих видов:
- Термическая (закалка, отпуск, отжиг, старение, криогенная обработка).
- Термо-механическая включает обработку высокими температурами в сочетании с механическим воздействием на сплав.
- Химико-термическая подразумевает термическую обработку металла с последующим обогащением поверхности изделия химическими элементами (углеродом, азотом, хромом и др.).
Отжиг
Отжиг – производственный процесс, при котором металлы и сплавы подвергаются нагреванию до заданного значения температуры, а затем вместе с печью, в которой происходила процедура, очень медленно естественным путём остывают. В результате отжига удаётся устранить неоднородности химического состава вещества, снять внутренне напряжение, добиться зернистой структуры и улучшить её как таковую, а также снизить твёрдость сплава для облегчения его дальнейшей переработки. Различают два вида отжига: отжиг первого и второго рода.
Отжиг первого рода подразумевает термическую обработку, в результате которой изменения фазового состояния сплава незначительны или отсутствуют вовсе. У него также есть свои разновидности: гомогенизированный – температура отжига составляет 1100-1200 , в таких условиях сплавы выдерживают в течение 8-15 часов, рекристаллизационный (при t 100-200 ) отжиг применяется для клёпаной стали, то есть деформированной уже будучи холодной.
Отжиг второго рода приводит к значимым фазовым изменениям сплава. Он также имеет несколько разновидностей:
- Полный отжиг – нагрев сплава на 30-50 выше критической температурной отметки, характерной для данного вещества и охлаждения с указанной скоростью (200 /час – углеродистые стали, 100 /час и 50 /час – низколегированные и высоколегированные стали соответственно).
- Неполный – нагрев до критической точки и медленное охлаждение.
- Диффузионный – температура отжига 1100-1200.
- Изотермический – нагрев происходит так же, как при полном отжиге, однако после этого проводят быстрое охлаждение до температуры несколько ниже критической и оставляют остывать на воздухе.
- Нормализованный – полный отжиг с последующим остыванием металла на воздухе, а не в печи.
Закалка
Закалка – это манипуляция со сплавом, целью которой является достижение мартенситного превращения металл, обеспечивающее понижение пластичности изделия и повышение его прочности. Закалка, равно как и отжиг, предполагает нагрев металла в печи выше критической температуры до температуры закалки, отличие состоит в большей скорости охлаждения, которое происходит в ванне с жидкостью. В зависимости от металла и даже его формы применяют разные виды закалки:
- Закалка в одной среде, то есть в одной ванне с жидкостью (вода – для крупных деталей, масло – для мелких деталей).
- Прерывистая закалка – охлаждение проходит два последовательных этапа: сперва в жидкости (более резком охладителе) до температуры приблизительно 300 , затем на воздухе либо в другой ванне с маслом.
- Ступенчатая – по достижению изделием температуры закалки, его охлаждают какое-то время в расплавленных солях с последующим охлаждением на воздухе.
- Изотермическая – по технологии очень похожа на ступенчатую закалку, отличается только временем выдержки изделия при температуре мартенситного превращения.
- Закалка с самоотпуском отличается от других видов тем, что нагретый метал охлаждают не полностью, оставив в середине детали тёплый участок. В результате такой манипуляции изделие приобретает свойства повышенной прочности на поверхности и высокой вязкости в середине. Такое сочетание крайне необходимо для ударных инструментов (молотки, зубила и др.)
Отпуск
Отпуск – это завершающий этап термической обработки сплавов, определяющий конечную структуру металла. Основная цель отпуска является снижение хрупкости металлического изделия. Принцип заключается в нагреве детали до температуры ниже критической и охлаждении. Поскольку режимы термической обработки и скорость охлаждения металлических изделий различного назначения могут отличаться, то выделяют три вида отпуска:
- Высокий – температура нагрева от 350-600 до значения ниже критической. Данная процедура чаще всего используется для металлических конструкций.
- Средний – термообработка при t 350-500, распространена для пружинных изделий и рессор.
- Низкий – температура нагрева изделия не выше 250 позволяет достичь высокой прочности и износостойкости деталей.
Старение
Старение – это термическая обработка сплавов, обуславливающая процессы распада пересыщенного металла после закалки. Результатом старения является увеличение пределов твёрдости, текучести и прочности готового изделия. Старению подвергаются не только чугун, но и цветные металлы, в том числе и легко деформируемые алюминиевые сплавы. Если металлическое изделие, подвергнутое закалке выдержать при нормальной температуре, в нём происходят процессы, приводящие к самопроизвольному увеличению прочности и уменьшению пластичности. Это называется естественное старение металла. Если эту же манипуляцию проделать в условиях повышенной температуры, она будет называться искусственным старением.
Криогенная обработка
Изменения структуры сплавов, а значит, и их свойств можно добиться не только высокими, но и крайне низкими температурами. Термическая обработка сплавов при t ниже нуля получила название криогенной. Данная технология широко используется в самых разных отраслях народного хозяйства в качестве дополнения к термообработкам с высокими температурами, поскольку позволяет существенно снизить расходы на процессы термического упрочнение изделий.
Криогенная обработка сплавов проводится при t -196 в специальном криогенном процессоре. Данная технология позволяет существенно увеличить срок службы обработанной детали и антикоррозионные свойства, а также исключить необходимость повторных обработок.
Термомеханическая обработка
Новый метод обработки сплавов сочетает в себе обработку металлов при высоких температурах с механической деформацией изделий, находящихся в пластичном состоянии. Термомеханическая обработка (ТМО) по способу совершения может быть трёх видов:
- Низкотемпературная ТМО состоит из двух этапов: пластической деформации с последующим закалкой и отпуском детали. Главное отличие от других видов ТМО – температура нагрева до аустенитного состояния сплава.
- Высокотемпературная ТМО подразумевает нагрев сплава до мартенситного состояния в сочетании с пластической деформацией.
- Предварительная – деформация производится при t 20 с последующей закалкой и отпуском металла.
Химико-термическая обработка
Изменить структуру и свойства сплавов возможно и с помощью химико-термической обработки, которая сочетает в себе термическое и химическое воздействие на металлы. Конечной целью данной процедуры помимо придания повышенной прочности, твёрдости, износостойкости изделия является и придание детали кислотоустойчивости и огнестойкости. К данной группе относятся следующие виды термообработки:
- Цементация проводится для придания поверхности изделия дополнительной прочности. Суть процедуры заключается в насыщении металла углеродом. Цементация может быть выполнена двумя способами: твёрдая и газовая цементация. В первом случае обрабатываемый материал вместе с углём и его активатором помещают в печь и нагревают до определённой температуры с последующей выдержкой его в данной среде и охлаждением. В случае с газовой цементацией изделие нагревается в печи до 900 под непрерывной струёй углеродосодержащего газа.
- Азотирование – это химико-термическая обработка металлических изделий путём насыщения их поверхности в азотных средах. Результатом данной процедуры становится повышение предела прочности детали и увеличение его коррозионной устойчивости.
- Цианирование – насыщение металла одновременно и азотом и углеродом. Среда может быть жидкой (расплавленные углерод- и азотсодержащие соли) и газообразной.
- Диффузионная металлизация представляет собой современный метод придания металлическим изделиям жаростойкости, кислотоустойчивости и износостойкости. Поверхность таких сплавов насыщают различными металлами (алюминий, хром) и металлоидами (кремний, бор).
Особенности термической обработки чугуна
Литейные сплавы чугуна повергаются термической обработке по несколько иной технологии, чем сплавы цветных металлов. Чугун (серый, высокопрочный, легированный) проходит следующие виды термообработки: отжиг (при t 500-650 ), нормализация, закалка (непрерывная, изотермическая, поверхностная), отпуск, азотирование (серые чугуны), алитирование (перлитные чугуны), хромирование. Все эти процедуры в результате значительно улучшают свойства конечных изделий чугуна: увеличивают эксплуатационный срок, исключают вероятность возникновения трещин при использовании изделия, повышают прочность и жаростойкость чугуна.
Термообработка цветных сплавов
Цветные металлы и сплавы обладают отличными друг от друга свойствами, поэтому обрабатываются разными методами. Так, медные сплавы для выравнивания химического состава подвергаются рекристаллизационному отжигу. Для латуни предусмотрена технология низкотемпературного отжига (200-300 ), поскольку этот сплав склонен при влажной среде к самопроизвольному растрескиванию. Бронза подвергается гомогенизации и отжигу при t до 550 . Магний отжигают, закаляют и подвергают искусственному старению (естественное старение для закалённого магния не происходит). Алюминий, равно как и магний, подвергается трём методам термообработки: отжигу, закалке и старению, после которых деформируемые алюминиевые сплавы значительно повышают свою прочность. Обработка титановых сплавов включает: рекристаллизационный отжиг, закалку, старение, азотирование и цементацию.
Резюме
Термическая обработка металлов и сплавов является основным технологическим процессом, как в чёрной, так и в цветной металлургии. Современные технологии располагают множеством методов термообработки, позволяющих добиться нужных свойств каждого вида обрабатываемых сплавов. Для каждого металла свойственна своя критическая температура, а это значит, что термообработка должна производиться с учётом структурных и физико-химических особенностей вещества. В конечном итоге это позволит не только достичь нужных результатов, но и в значительной степени рационализировать производственные процессы.
Термообработка — основополагающий химический процесс, проводимый при работе со сплавами. В черной и цветной металлургии методика берется за основу и имеет огромное количество различных вариаций. От правильного проведения операции зависят химические, технические и механические свойства металла. Все виды термообработки стали подразделяются на определённые группы, что позволяет подбирать рациональные вариации.
Основные виды термической обработки
На промышленных предприятиях все процессы автоматизированы и человек принимает в них лишь косвенное участие. Все технологии практически идентичные, но имеют отличия по условиям температуры и другим факторам. В первую очередь сплав нагревается до определённой температуры, далее его выдерживают в этих температурных режимах. На последнем этапе происходит моментальное охлаждение. Таким образом, термообработанная сталь будет иметь уникальные технические характеристики. Основные типы технологий:
- Термическое воздействие включает в себя закалку, старение, отпуск, криогенный нагрев.
- Термомеханические методики. Сопровождаются не только нагревом, но и механическими воздействиями.
- Термохимические технологии. После воздействия температурой происходит обработка различными типами жидкостей или газов, что может упрочнять сплав.
Любой способ подразумевает под собой получение требуемых условий, поэтому в случае возникновения сложностей вторичная обработка будет неприемлемой. Каждая технология по-своему уникальна, но при этом основывается на нагревании металлов.
Поэтому требуется более основательно разобраться с различиями и другими факторами. Это позволит получить более конкретную информацию обо всех интересующих аспектах.
Отжиг металлов в печи
Стандартная методика, при которой заготовки отправляют в печь и нагревают. В дальнейшем остывание происходит не в отдельных камерах, а в той же печи. Таким образом, начинается естественный процесс остывания за счет температуры окружающей среды. Если рассматривать виды термообработки металлов, то представленная технология — одна из самых простых. Технология позволяет получить следующие свойства:
- Уменьшается твердость, в дальнейшем легко перерабатывать сплавы.
- Повышается зернистость структуры.
- Исчезают неоднородные сегменты.
- Исчезает внутреннее напряжение.
В настоящее время представленная технология реализуется в нескольких разнообразных вариациях. Как указывает технологический справочник, для различных нужд создаются оптимальные условия. На промышленных предприятиях данные работы должны проводиться в специальных печах. Сегодня отжиг стальных заготовок применяется для получения высококачественной стали. Такие методики очень важны для промышленности и развития индустрии в этом сегменте.
Технология закалки
Один из самых распространённых методов термической обработки — это закалка. Технология представляет собой термические манипуляции с металлами и нагрев их до критических температур. Результатом технологии становится повышение пластичности и прочности сплавов. Отличием закалки от отжига является довольно быстрое охлаждение. Для этих целей применяются ванны с водой, что в значительной степени ускоряет процессы. С технической точки зрения это уникальная методика. Существует несколько основных разновидностей закалки:
- Технология, где используют только один тип жидкости для охлаждения.
- Прерывистая методика. Сначала металл нагревают до критического показателя и опускают в воду. После остывания до температуры 300 градусов оставляют на воздухе или в масле.
- Ступенчатая. В этом случае применяется методика охлаждения в воде, потом в специальных солях и на последнем этапе оставляют остывать на воздухе. Таким образом, на каждом этапе металл приобретает более уникальные технические характеристики.
- Изотермическая — практически идентична ступенчатой закалке.
- Частичная закалка. Охлаждение происходит только по краям металла, в середине он остается горячим. Такая методика применяется при изготовлении отбойных инструментов, так как сплав получается вязким в середине и прочным по краям.
Технология закалки очень часто используется в кузницах как основной метод термообработки. Его эффективность подтверждается многими годами использования и указывает на невероятные преимущества. В настоящее время на каждом этапе технологического процесса нужно контролировать показатели. Это позволит получить металл с требуемыми характеристиками.
Отпуск и старение сплавов
Если нет информации о том, какая обработка стальных изделий характеризуется улучшением технических показателей, то можно выбрать любую методику. Все связано с тем, что каждая технология имеет определённые преимущества и достоинства. Отпуск — это методика, используемая на последнем этапе обработки металлов, таким образом, за счет нее придаются различные физические свойства конечного формата. Для этого металлическую деталь нагревают до температуры, которая должна быть ниже критической, и проводят охлаждения. В настоящее время известно несколько основных типов отпуска:
Процесс старения применяется для обработки чугуна и различных типов цветных металлов. Технология очень распространена, так как позволяет увеличивать пределы текучести и прочности металлов. Проводят старение после отжига при нормальной температуре, это позволяет добиться требуемого эффекта без каких-либо сторонних технологий.
Особенность любого типа термической обработки заключается в профессионализме исполнителей. У каждого специалиста, работающего с металлом, есть свои секреты, которые он применяет на практике. Удается получать металл с уникальными техническими характеристиками. В заводских условиях нужно придерживаться технического регламента, поэтому металл всегда одинакового формата, это иногда является большой проблемой. Технические стандарты остаются постоянными.
Криогенное воздействие
В настоящее время техника и технология постоянно развиваются, появляются новые варианты воздействий на сплавы. Сегодня можно использовать не только высокие температуры, но и низкие. То есть холод также улучшает качество материалов. Существуют специальные криогенные камеры, в которых и проводятся технологические процедуры. Температура, при которой находятся детали и заготовки, равна -196 градусов Цельсия. Преимущество технологии заключается в том, что не требуется повторная обработка.
Конечно же, технология не всегда бывает подходящей и имеет множество различных нюансов. Рекомендуется пользоваться технологическими регламентами, что позволит в значительной степени повысить качество продукта. Также при такой обработке в значительной степени снижаются затраты. Достаточно использовать холодильник, при высоких температурах нужны сторонние ресурсы на разогрев печи и так далее.
Термомеханическое воздействие
Из всех перечисленных технологий представленная методика в промышленных масштабах используется уже давно. Суть заключается в предварительном нагревании металла до пластичного состояния и в дальнейшем механическом воздействии. Термомеханическая обработка может быть нескольких видов:
- Низкотемпературная обработка. Ее отличие заключается в том, что металл нагревается до аустенитного состояния. Технология включает в себя пластическую деформацию, закалку и отпуск. Все делается в соответствии с техническим регламентом.
- Высокотемпературная обработка. Металл нагревается до мартенситного состояния, проводится пластическая деформация.
- Предварительная обработка.
Выбрать нужный метод позволяют практика и те цели, которые вы преследуете. С технологической точки зрения каждый метод любого типа термической обработки подходит только для определённых металлов и сплавов. Именно этим фактором обусловлено разнообразие. То есть ни в коем случае нельзя подвергать сталь воздействию определенного типа, если оно не подходит. Это приведет к ухудшению качества материалов.
Химическая обработка
Химические реакции с металлами в совокупности с термическими воздействием приводят к повышению износостойкости, устойчивости к воздействию кислот и щелочей. В настоящее время существуют специализированные промышленные условия для проведения большого количества процессов. Важно различать методики и использовать их в нужный момент. Типы термохимических реакций:
- Цианирование — металл подвергают одновременному воздействию углерода и азота. Основа методики заключается в насыщении сплава данными элементами.
- Азотирование — технология, позволяющая повысить коррозионную устойчивость металлов до максимальных показателей, также повышается прочность. Для этого сплавы погружают в азотную среду.
- Диффузионная металлизация — очень сложная технология, но схожая с предыдущими. Благодаря ее проведению металл становится более прочным, износостойким и не подвергается воздействию агрессивных средств. Для этого поверхность сплавов обрабатывают бромом, хромом, алюминием.
- Цементация — методика, повышающая прочность металла. Для этого используют углерод, который в газовом состоянии непрерывно подается на металл в печи.
В каждом отдельном случае важно соблюдать все правила технологического сопровождения. Сплав при неправильном воздействии может потерять свои технические характеристики и будет отправлен на дополнительную переплавку. В таких ситуациях используются контрольно-измерительные приборы, исключающие нарушение технологии.
Цветные сплавы
Каждый отдельный цветной металл или сплав отличается от других физическими и химическими свойствами, что не скажешь о черных металлах. Поэтому рекомендуется для каждого отдельного случая подбирать свои методики, чтобы не потерять качество. Рекристализационный отжиг проводится для меди, что в значительной степени повышает качество, и происходит термоупрочнение. Различают такие особенности:
- Латунь ни в коем случае нельзя сильно нагревать, предел — 250−300 градусов Цельсия. При неправильной обработке либо высоких температурах происходит растрескивание структуры.
- Бронзу нужно гомогенизировать и в последующем нагревать до 600 градусов Цельсия.
- Магний можно обрабатывать различными методами: старение, отжиг и так далее.
- Титановые сплавы можно закаливать, отжигать, подвергать старению, цементации.
В настоящее время существуют специальные справочники и технические пособия, позволяющие подбирать соответствующие методики для повышения технических свойств металлов. Специалисты, работающие на промышленных предприятиях, действуют по заранее заложенным планам и техническим документам. Таким образом, каждая методика по-своему уникальна и делает металлы и сплавы более качественными и подходящими для технических и промышленных нужд.
Промышленные компании применяют практически все существующие методы, что дает возможность получить сплавы различного формата. Очень важно придерживаться регламентов и стандартов ГОСТ. Каждая рассмотренная термическая обработка имеет свои стандарты и технические нормативы. Любое отклонение приведет к получению некачественного материала, и, следовательно, будет брак.
Измерение температур металла
Для измерения температур при термической обработке используют специальные приборы — пирометры.
Наибольшее распространение получили термоэлектрические и оптические пирометры.
Схема термоэлектрического пирометра приведена на рисунке:
Он представляет собой термопару с гальванометром. Термопара — это две проволочки из разнородных металлов или сплавов, сваренные между собой.
Если место спая проволочек поместить в расплавленный металл, температуру которого мы хотим определить, то на свободных концах проволочек КК возникнет термоэлектродвижущая сила, тем большая, чем больше разность температур «горячего спая» — спая, погруженного в металл, и свободных концов — «холодного спая».
Отклонение стрелки гальванометра, подключенного к свободным концам термопары, при постоянной температуре окружающей среды будет пропорционально температуре исследуемого металла.
Для удобства пользования гальванометром на нем имеется температурная шкала.
Для термопар используют различные
металлы и сплавы.Так, например, для измерения температур 1000–1300° термопару изготовляют из платины и сплава платины с родием.
Для температур 700–950° применяют термопару — хромель (хромоникелевый сплав) и алюмель (алюминеникелевый сплав), еще при более низких температурах используют железо-константановую (медно-никелевый сплав) и медно-константановую термопары.
Температуру раскаленного металла можно определять оптическим пирометром — путем сравнения яркости его свечения с накалом нити электрической лампочки.
На рис. 63, а показан оптический пирометр. Объектив пирометра направляют на раскаленный предмет. Внутри пирометра светится электрическая лампочка. В поле зрения окуляра видны одновременно нить накала и раскаленный металл.
Изменяя с помощью реостата силу электрического постоянного тока, питающего электрическую лампу, подбирают такой ток, чтобы яркость нити накала электрической лампы и раскаленного металла совпала (рис. 63, б).
В зависимости от величины тока стрелка прибора отклонится по шкале на различный угол. Для удобства шкала отградуирована на градусы Цельсия.
Приближенные методы определения значения температуры металла
Помимо перечисленных методов, в практике термической обработки используют приближенные методы, дающие только, ориентировочные значения температуры металла. К таким методам следует отнести определение температуры металла по цветам каления при нагреве под закалку или отжиг и определение температуры металла при отпуске по цветам побежалости, появляющимся на светлой поверхности деталей (рис. 64).
§
Статья о термообработке ножевых сталей
Термообработка металла
Журнал «Моделист-конструктор«, №5 за 1994 г., с.24
А. Виноградов
ТЕРМООБРАБОТКА МЕТАЛЛА
Моделистам постоянно приходится сталкиваться с необходимостью повысить прочность и твёрдость металла или инструмента, а иногда, наоборот, сделать металл более мягким, легче поддающимся обработке. Этого можно достичь термическим воздействием, заключающимся в нагреве материала до определённой температуры с последующим быстрым или медленным охлаждением.
Нагревание деталей, конечно, удобнее всего производить в электрических муфельных печах; но можно использовать и паяльные лампы, бензиновые и газовые горелки и даже конфорки домашних газовых плит — для нагрева мелких деталей.
Важнейшим условием правильной термообработки сталей является подбор необходимого температурного режима в зависимости от марки стали. Но ввиду того, что в свободной продаже имеется ограниченное число марок стали, приходится в основном использовать либо вторичное сырьё, либо изготавливать одни инструменты из других.
Маркировки углеродистой стали обыкновенного качества обозначаются двумя буквами и цифрой (Ст.1 — Ст.7). Цифра в данном случае показывает примерное содержание углерода в сотых долях процента.
В марках углеродистых качественных сталей — конструкционных (сталь 30; сталь 45) и автоматных сталях (А12; А30) цифры также показывают примерное содержание углерода в сотых долях процента. Наиболее широкоприменяемые стали — инструментальные (У7; У8; У8А; У10А…) — цифра в их маркировке означает содержание углерода в десятых долях процента; буква А в конце марки показывает, что в этих сталях пониженное содержание вредных примесей.
Легированные стали маркируются буквами и цифрами. Буквы обозначают наличие в стали одного или целой группы легирующих компонентов: В — вольфрам; Г — марганец; К — кобальт; М — молибден; Н — никель; С — кремний; Ф — ванадий; Х — хром; Ю — алюминий. Например, сталь марки 65Х13 имеет в своём составе 0,065% углерода и 0,013% хрома.
Наиболее ходовые марки сталей для изготовления инструмента приведены в таблице 1.
Таблица 1.
Инструмент | Марка стали |
Зубила, отвёртки, топоры, клейма для стали Пуансоны, матрицы, пробойники, стамески Керны, деревообрабатывающий инструмент Молотки, кувалды, гладилки, плотницкий инструмент Метчики Надфили Напильники Ножовочные полотна станочные Ножовочные полотна ручные Ножовки по дереву Ножи фуговальных станков Пилы циркулярные Пилы лесопильных рам Плашки Полотна лучковых пил Пилы поперечные Пилы продольные Резцы для твёрдых металлов Резцы токарные и строгальные Свёрла спиральные по дереву Свёрла по металлу Фрезы |
У7А У8; У8А У10; У10А У7 У11; Р9; 9ХС У10 — У12 У10 — У13; ШХ6 Р9; Р18; ШХ15 У8 — У12 У8ГА 9Х5ВФ 85ХФ 85ХВ 9ХС У8ГА; 85ХФ У8ГА; У10 85Х У13; У13А У10; У10А 9ХС; 9Х5ВФ Р9; Р18 Р9; Р18 |
Термическая обработка стали разделяется на закаливание, отпуск и отжиг.
Закаливание стали применяется для повышения её твёрдости. Мягкие малоуглеродистые стали (Ст.25) и «железо» (Ст.10; Ст.20) не калятся; углеродистые (сталь 45; сталь 50) и инструментальные (У8; У9; У10; У10А и другие) увеличивают свою твёрдость при закалке в три-четыре раза.
Процесс закаливания состоит в нагревании стали до температуры калки (для каждой марки своя) и в быстром охлаждении в масле или воде. Температурные режимы закалки приведены в таблице 2.
Таблица 2.
Марка |
Закалка C° |
Отпуск C° |
Отжиг C° |
Охлаждающая среда для закалки |
Охлаждающая среда для отпуска |
У7; У7А У8; У8А У10; У10А У11; У11А У12; У12А У13; У13А У8ГА Р9 Р18 ШХ6 ШХ9 ШХ15 9ХС 9Х5ВФ 50ХГА 60С2 60С2ХА 65С2ВА 85ХВ |
800 800 790 780 780 780 800 1250 1300 810 830 845 860 950 840 870 870 850 830 |
170 170 180 180 180 180 180 580 580 200 280 400 170 270 315 325 315 330 250 |
780 770 770 750 750 750 770 860 860 780 780 780 730 800 810 840 840 820 790 |
вода вода вода вода вода вода вода масло масло масло масло масло масло масло вода вода вода вода вода |
вода, масло вода, масло вода, масло вода, масло вода, масло вода, масло вода, масло воздух в печи воздух в печи воздух воздух воздух воздух воздух воздух воздух воздух воздух воздух |
В домашних условиях, при отсутствии приборов температуру нагрева приближённо можно определить по цвету. Для ориентации цвета каления стальных изделий в неосвещённой солнцем комнате приведены по порядку их появления в зависимости от температуры (в °С):
тёмно-коричневый (заметен в темноте) 530-580
коричнево-красный 580-650
тёмно-красный (вишнёвый) 650-730
вишнёво-красный (багровый) 730-770
вишнёво-алый 770-800
светло-вишнёво-алый 800-830
ярко-красный 830-870
красный 870-900
оранжевый 900-1050
тёмно-жёлтый 1050-1150
светло-жёлтый 1150-1250
жёлто-белый 1250-1300
ослепительно белый св. 1300.
В закалённом состоянии сталь обладает большой твёрдостью, но вместе с тем и хрупкостью. Чтобы придать ей вязкость, производится отпуск стали после закалки. Для этого её нагревают до температуры 220-300°С и медленно охлаждают в воздухе. Твёрдость стали при этом несколько уменьшается, структура её изменяется, и она становится более вязкой. Меняя температуру отпуска, можно получить разные механические свойства. При нагреве стали на воздухе её поверхность окрашивается в различные цвета, называемые цветами побежалости. Каждый цвет побежалости соответствует вполне определённой температуре и может служить указателем для определения степени нагрева при отпуске стали. Термические режимы и соответствующие им цвета побежалости приведены в таблице 3.
Таблица 3.
Инструмент |
Температура отпуска, C° |
Цвет побежалости |
Свёрла перовые, плашки, матрицы и пуансоны, фрезы Резцы, метчики, полотна ножовок, лобзики, центры Кусачки, стамески, ножницы по металлу, зубила Молотки слесарные и медницкие Матрицы и пуансоны вытяжные Ролики для накаток Перки столярные, железки рубаночные, отвёртки, обжимки Долота столярные, ножи, призмы разметочные, державки резцов Ключи гаечные, пассатижи, круглогубцы, плоскогубцы Полотна пил по дереву |
200 225 240 255 265 275 285 295 310 325 |
светло-соломенный светло-жёлтый соломенно-жёлтый коричнево-жёлтый красно-коричневый пурпурно-красный фиолетовый ярко-синий светло-синий серый |
Отпуск выполняется следующим образом: стальную деталь зачищают в каком-нибудь месте до блеска, помещают в огонь и следят за появлением цветов побежалости. Отпуск закалённой детали должен быть проведён в течение 24 часов после её закалки.
Отжиг стали служит для выполнения задачи обратной закалки в случаях, когда закалённую деталь требуется обработать режущим инструментом, согнуть или разрезать. Отжиг стали заключается в нагревании её до температуры 800-900°С с последующим медленным охлаждением. После отжига сталь легко поддаётся обработке.
* * *
Подписная научно-популярная серия «Сделай сам» (издательство «Знание»), №1 за 1990 г., с. 88, 89.
Отжиг цветных металлов. При обработке цветных металлов (чеканка, выколотка и др.) иногда приходится снимать напряжения, возникшие при обработке. Для этого необходимо отжечь заготовку. Отжиг цветных металлов проводят при следующих температурах:
Металл |
Температура отжига, C° |
Охлаждающая среда |
Медь Латунь Л96 Латунь Л90-Л62 Мельхиор Нейзильбер Серебро Алюминий Дюралюминий |
500 — 600 540 — 600 600 — 700 650 — 700 700 — 750 650 — 700 300 — 350 360 — 380 |
Вода На открытом воздухе На открытом воздухе Вода Вода Вода На открытом воздухе Охлаждение в печи |
Дополнительные услуги: | Термическая обработка изделийТермическая обработка (термообработка) стали, цветных металлов — процесс изменения структуры стали, цветных металлов, сплавов при нагревании и последующем охлаждении с определенной скоростью. Термическая обработка (термообработка) приводит к существенным изменениям свойств стали, цветных металлов, сплавов. Химический состав металла не изменяется. Виды термической обработки сталиОтжигОтжиг — термическая обработка (термообработка) металла, при которой производится нагревание металла, а затем медленное охлаждение. Эта термообработка (т. е. отжиг) бывает разных видов (вид отжига зависит от температуры нагрева, скорости охлаждения металла). ЗакалкаЗакалка — термическая обработка (термообработка) стали, сплавов, основанная на перекристаллизации стали (сплавов) при нагреве до температуры выше критической; после достаточной выдержки при критической температуре для завершения термической обработки следует быстрое охлаждение. Закаленная сталь (сплав) имеет неравновесную структуру, поэтому применим другой вид термообработки — отпуск. ОтпускОтпуск — термическая обработка (термообработка) стали, сплавов, проводимая после закалки для уменьшения или снятия остаточных напряжений в стали и сплавах, повышающая вязкость, уменьшающая твердость и хрупкость металла. НормализацияНормализация — термическая обработка (термообработка), схожая с отжигом. Различия этих термообработок (нормализации и отжига) состоит в том, что при нормализации сталь охлаждается на воздухе (при отжиге — в печи). Нагрев заготовкиНагрев заготовки — ответственная операция. От правильности ее проведения зависят качество изделия, производительность труда. Необходимо знать, что в процессе нагрева металл меняет свою структуру, свойства и характеристику поверхностного слоя и в результате от взаимодействия металла с воздухом атмосферы, и на поверхности образуется окалина, толщина слоя окалины зависит от температуры и продолжительности нагрева, химического состава металла. Стали окисляются наиболее интенсивно при нагреве больше 900°С, при нагреве в 1000°С окисляемость увеличивается в 2 раза, а при 1200°С — в 5 раз. Хромоникелевые стали называют жаростойкими потому, что они практически не окисляются. Легированные стали образуют плотный, но не толстый слой окалины, который защищает металл от дальнейшего окисления и не растрескивается при ковке. Углеродистые стали при нагреве теряют углерод с поверхностного слоя в 2-4 мм. Это грозит металлу уменьшением прочности, твердости стали и ухудшается закаливание. Особенно пагубно обезуглероживание для поковок небольших размеров с последующей закалкой. Заготовки из углеродистой стали с сечением до 100 мм можно быстро нагревать и потому их кладут холодными, без предварительного прогрева, в печь, где температура 1300°С. Во избежание появлений трещин высоколегированные и высокоуглеродистые стали необходимо нагревать медленно. При перегреве металл приобретает крупнозернистую структуру и его пластичность снижается. Поэтому необходимо обращаться к диаграмме «железо-углерод», где определены температуры для начала и конца ковки. Однако перегрев заготовки можно при необходимости исправить методом термической обработки, но на это требуется дополнительное время и энергия. Нагрев металла до еще большей температуры приводит к пережогу, от чего происходит нарушение связей между зернами и такой металл полностью разрушается при ковке. ПережогПережог — неисправимый брак. При ковке изделий из низкоуглеродистых сталей требуется меньше число нагревов, чем при ковке подобного изделия из высокоуглеродистой или легированной стали. При нагреве металла требуется следить за температурой нагрева, временем нагрева и температурой конца нагрева. При увеличении времени нагрева — слой окалины растет, а при интенсивном, быстром нагреве могут появиться трещины. Известно из опыта, что на древесном угле заготовка 10-20 мм в диаметре нагревается до ковочной температуры за 3-4 минуты, а заготовки диаметром 40-50 мм прогревают 15-25 минут, отслеживая цвет каления. Химико-термическая обработкаХимико-термическая обработка (ХТО) стали — совокупность операций термической обработки с насыщением поверхности изделия различными элементами (углерод, азот, алюминий, кремний, хром и др.) при высоких температурах. Поверхностное насыщение стали металлами (хром, алюминий, кремний и др.), образующими с железом твердые растворы замещения, более энергоемко и длительнее, чем насыщение азотом и углеродом, образующими с железом твердые растворы внедрения. При этом диффузия элементов легче протекает в решетке альфа-железо, чем в более плотноупакованной решетке гамма-железо. Химико-термическая обработка повышает твердость, износостойкость, кавитационную, коррозионную стойкость. Химико-термическая обработка, создавая на поверхности изделий благоприятные остаточные напряжения сжатия, увеличивает надежность, долговечность. Цементация сталиЦементация стали — химико-термическая обработка поверхностным насыщением малоуглеродистой (С<0,2%) или легированных сталей при температурах 900…950°С — твердым (цементация твердым карбюризатором), а при 850…900°С — газообразным (газовая цементация) углеродом с последующей закалкой и отпуском. Цель цементации и последующей термической обработки — повышение твердости, износостойкости, также повышением пределов контактной выносливости поверхности изделия при вязкой сердцевине, что обеспечивает выносливость изделия в целом при изгибе и кручении. Детали, предназначенные для цементации, сначала очищают. Поверхности не подлежащие науглероживанию, покрывают специальными предохранительными противоцементными обмазками. 1-ый состав простейшей обмазки: огнеупорная глина с добавлением 10% асбестового порошка, вода. Смесь разводят до консистенции густой сметаны и наносят на нужные участки поверхности изделия. После высыхания обмазки можно производить дальнейшую цементацию изделия. 2-ой состав применяемой обмазки: каолин — 25%, тальк — 50%: вода — 25%. Разводят эту смесь жидким стеклом или силикатным клеем. Цементацию делают после полного высыхания обмазки. Вещества, которые входят в состав обмазки, называют карбюризаторами. Они бывают твердые, жидкие и газообразные. В условиях домашней небольшой мастерской удобнее осуществлять цементацию с помощью пасты. Это цементация в твердом карбюризаторе. В состав пасты входят: сажа — 55%, кальцинированная сода — 30%, щавелевокислый натрий — 15%, вода для образования сметанообразной массы. Пасту наносят на нужные участки изделия, дают высохнуть. Затем изделие помещают в печь, выдерживая при температуре 900-920°С в течение 2-2,5 часов. При использовании такой пасты цементация обеспечивает толщину науглероженного слоя 0,7-0,8 мм. Жидкостная цементация также возможна в небольшой мастерской при наличии печи-ванной, в которой и происходит науглероживание инструментов и других изделий. В состав жидкости входят: сода — 75-85%, 10-15% хлористого натрия, 6-10% карбида кремния. Печь-ванну наполняют этим составом и погружают изделие или инструмент. Процесс протекает при температуре 850-860°С в течение 1,5-2 часов; толщина науглероженного слоя достигает при этом 0,3-0,4 мм. Газовую цементацию производят в смеси раскаленных газов, содержащих метан, окись углерода в специальных камерах при температуре 900-950°С и только в производственных условиях. После цементации детали охлаждают вместе с печью, затем закаляют при 760-780°С е окончательным охлаждением в масле. Азотирование сталиАзотирование стали — химико-термическая обработка поверхностным насыщением стали азотом путем длительной выдержки ее при нагреве до б00…650°С в атмосфере аммиака NН3. Азотированные стали обладают очень высокой твердостью (азот образует различные соединения с железом, алюминием, хромом и другими элементами, обладающие большей твердостью, чем карбиды). Азотированные стали обладают повышенной сопротивляемостью коррозии в таких средах, как атмосфера, вода, пар. Азотированные стали сохраняют высокую твердость, в отличие от цементованных, до сравнительно высоких температур (500…520°С). Азотированные изделия не коробятся при охлаждении, так как температура азотирования ниже, чем цементации. Азотирование сталей широко применяют в машиностроении для повышения твердости, износостойкости, предела выносливости и коррозионной стойкости ответственных деталей, например, зубчатых колес, валов, гильз цилиндров. Нитроцементация (цианирование) сталиНитроцементация (цианирование) стали — химико-термическая обработка с одновременным поверхностным насыщением изделий азотом и углеродом при повышенных температурах с последующими закалкой и отпуском для повышения износо- и коррозионной устойчивости, а также усталостной прочности. Нитроцементация может проводиться в газовой среде при температуре 840..860°С — нитроцианирование, в жидкой среде — при температуре 820…950°С — жидкостное цианирование в расплавленных солях, содержащих группу NaCN. Нитроцементация эффективна для инструментальных (в частности, быстрорежущих) сталей; она используется для деталей сложной конфигурации, склонных к короблению. Однако, поскольку этот процесс связан с использованием токсичных цианистых солей, он не нашел широкого распространения. Борирование сталиБорирование стали — химико-термическая обработка насыщением поверхностных слоев стальных изделий бором при температурах 900…950°С. Цель борирования — повышение твердости, износостойкости и некоторых других свойств стальных изделий. Диффузионный слой толщиной 0,05…0,15 мм, состоящий из боридов FeB и Fе2В, обладает весьма высокой твердостью, стойкостью к абразивному изнашиванию и коррозионной стойкостью. Борирование особенно эффективно для повышения стойкости (в 2…10 раз) бурового и штампового инструментов. Цинкование (Zn), алюминирование (Аl), хромирование (Сr), силицирование (Si) сталейЦинкование (Zn), алюминирование (Аl), хромирование (Сr), силицирование (Si) сталей выполняются аналогично цементации с целью придания изделиям из стали некоторых ценных свойств: жаростойкости, износостойкости, коррозионной устойчивости. В настоящее время все большее распространение получают процессы многокомпонентного диффузионного насыщения Термомеханическая обработка (ТМО) сталиТермомеханическая обработка (ТМО) стали — совокупность операций термической обработки с пластической деформацией, которая проводится либо выше критических точек (ВТМО), либо при температуре переохлажденного (500… 700°С) аустенита (НТМО). Термомеханическая обработка позволяет получить сталь высокой прочности (до 270 МПа). Формирование структуры стали при ТМО происходит в условиях повышенной плотности и оптимального распределения дислокаций. Окончательными операциями ТМО являются немедленная закалка во избежании развития рекристаллизации и низкотемпературный (Т=100…300 °С) отпуск. Термомеханическая обработка с последующими закалкой и отпуском позволяют получить очень высокую прочность ( s= 2200…3000 МПа) при хорошей пластичности (d = 6…8%, y= 50…60%) и вязкости. В практических целях большее распространение получила ВТМО, обеспечивающая наряду с высокой прочностью хорошее сопротивление усталости, высокую работу распространения трещин, а также сниженные критическую температуру хрупкости, чувствительность к концентраторам напряжений и необратимую отпускную хрупкость. ВТМО осуществляется в цехах прокатного производства на металлургических заводах, например, при упрочнении прутков для штанг, рессорных полос, труб и пружин. Отпуск сталиОтпуск стали смягчает действие закалки, уменьшает или снимает остаточные напряжения, повышает вязкость, уменьшает твердость и хрупкость стали. Отпуск производится путем нагрева деталей, закаленных на мартенсит до температуры ниже критической. При этом в зависимости от температуры нагрева могут быть получены состояния мартенсита, тростита или сорбита отпуска. Эти состояния несколько отличаются от соответственных состояний закалки по структуре и свойствам: при закалке цементит (в троостите и сорбите) получается в форме удлиненных пластинок, как в пластинчатом перлите. А при отпуске он получается зернистым, или точечным, как в зернистом перлите. Преимуществом точечной структуры является более благоприятное сочетание прочности и пластичности. При одинаковом химическом составе и одинаковой твердости сталь с точечной структурой имеет значительно более высокое относительное сужение, ударную вязкость, повышенное удлинение и предел текучести по сравнению со сталью с пластинчатой структурой. Отпуск разделяют на низкий, средний и высокий в зависимости от температуры нагрева. Для определения температуры при отпуске изделия пользуются таблицей цветов побежалости.
Тонкая пленка окислов железа, придающая металлу различные быстро меняющиеся цвета — от светло-желтого до серого. Такая пленка появляется, если очищенное от окалины стальное изделие нагреть до 220°С; при увеличении времени нагрева или повышении температуры окисная пленка утолщается и цвет ее изменяется. Цвета побежалости одинаково проявляются как на сырой, так и на закаленной стали. При низком отпуске (нагрев до температуры 200-300° ) в структуре стали в основном остается мартенсит, который, однако, изменяется решетку. Кроме того, начинается выделение карбидов железа из твердого раствора углерода в альфа-железе и начальное скопление их небольшими группами. Это влечет за собой некоторое уменьшение твердости и увеличение пластических и вязких свойств стали, а также уменьшение внутренних напряжений в деталях. Для низкого отпуска детали выдерживают в течение определенного времени обычно в масляных или соляных ваннах. Если для низкого отпуска детали нагревают на воздухе, то для контроля температуры часто пользуются цветами побежалости, появляющимися на поверхности детали.
Появление этих цветов связано с интерференцией белого света в пленках окисла железа, возникающих на поверхности детали при ее нагреве. В интервале температур от 220 до 330 ° в зависимости от толщины пленки цвет изменяется от светло-желтого до серого. Низкий отпуск применяется для режущего, измерительного инструмента и зубчатых колес. При среднем (нагрев в пределах 300-500°) и высоком (500-700°) отпуске сталь из состояния мартенсита переходит соответственно в состояние тростита или сорбита. Чем выше отпуск, тем меньше твердость отпущенной стали и тем больше ее пластичность и вязкость. При высоком отпуске сталь получает наилучшее сочетание механических свойств, повышение прочности, пластичности и вязкости, поэтому высокий отпуск стали после закалки ее на мартенсит назначают для кузнечных штампов, пружин, рессор, а высокий — для многих деталей, подверженных действию высоких напряжений (например, осей автомобилей, шатунов двигателей). Для некоторых марок стали отпуск производят после нормализации. Этот относится к мелкозернистой легированной доэвтектоидной стали (особенно никелевой), имеющий высокую вязкость и поэтому плохую обрабатываемость режущим инструментом. Для улучшения обрабатываемости производят нормализацию стали при повышенной температуре (до 950-970°), в результате чего она приобретает крупную структуру (определяющую лучшую обрабатываемость) и одновременно повышенную твердость (ввиду малой критической скорости закалки никелевой стали). С целью уменьшения твердости производят высокий отпуск этой стали. Дефекты закалкиК дефектам закалки относятся:
Главная причина трещин и поводки — неравномерное изменение объема детали при нагреве и, особенно, при резком охлаждении. Другая причина — увеличение объема при закалке на мартенсит. Трещины возникают потому, что напряжения при неравномерном изменении объема в отдельных местах детали превышают прочность металла в этих местах. Лучшим способом уменьшения напряжений является медленное охлаждение около температуры мартенситного превращения. При конструировании деталей необходимо учитывать, что наличие острых углов и резких изменений сечения увеличивает внутреннее напряжение при закалке. Коробление (или поводка)возникает также от напряжений в результате неравномерного охлаждения и проявляется в искривлениях деталей. Если эти искривления невелики, они могут быть исправлены, например, шлифованием. Трещины и коробление могут быть предотвращены предварительным отжигом деталей, равномерным и постепенным нагревом их, а также применением ступенчатой и изотермической закалки. Обезуглероживание стали с поверхности — результат выгорания углерода при высоком и продолжительном нагреве детали в окислительной среде. Для предотвращения обезуглероживания детали нагревают в восстановительной или нейтральной среде (восстановительное пламя, муфельные печи, нагрев в жидких средах). Образование окалины на поверхности изделия приводит к угару металла, деформации. Это уменьшает теплопроводность и, стало быть, понижает скорость нагрева изделия в печи, затрудняет механическую обработку. Удаляют окалину либо механическим способом, либо химическим (травлением). Выгоревший с поверхности металла углерод делает изделия обезуглероженным с пониженными прочностными характеристиками, с затрудненной механической обработкой. Интенсивность, с которой происходит окисление и обезуглерожевание, зависит от температуры нагрева, т. е. чем больше нагрев, тем быстрее идут процессы. Образование окалины при нагреве можно избежать, если под закалку применить пасту, состоящую из жидкого стекла — 100 г, огнеупорной глины — 75 г, графита — 25 г, буры — 14 г, карборунда — 30 г, воды — 100 г. Пасту наносят на изделие и дают ей высохнуть, затем нагревают изделие обычным способом. После закалки его промывают в горячем содовом растворе. Для предупреждения образования окалины на инструментах быстрорежущей стали применяют покрытие бурой. Для этого нагретый до 850°С инструмент погружают в насыщенный водный раствор или порошок буры Антикоррозионная обработка изделий после термической обработкиПосле термической обработки, связанной с применением солей, щелочей, воды и прочих веществ, могущих вызывать при длительном хранении изделий коррозию, следует провести антикоррозионную обработку стальных изделий, заключающуюся в том, что очищенные, промытые и высушенные изделия погружают на 5 минут в 20 – 30% водный раствор нитрита натрия, после чего заворачивают в пропитанную этим же раствором бумагу. или отправьте онлайн заявку |
Тинт (закалка) цветов на поверхности из нержавеющей стали, нагреваемой на воздухе — Британская ассоциация нержавеющей стали
Введение
Цвет, образующийся при нагревании нержавеющей стали в печи или в зоне термического влияния сварных швов, зависит от нескольких факторов, связанных со стойкостью стали к окислению. Образующийся тепловой оттенок или умеренный цвет вызывается постепенным утолщением поверхностного оксидного слоя, и поэтому при повышении температуры цвета меняются.Стойкость к окислению нержавеющих сталей
Однако существует несколько факторов, влияющих на степень изменения цвета, поэтому не существует единой таблицы цвета и температуры, которая представляла бы все случаи. Сформированные цвета могут использоваться только как указатель температуры, до которой была нагрета сталь.
Факторы, влияющие на формирование цветов теплового оттенкаСостав стали
Содержание хрома является наиболее важным фактором, влияющим на стойкость к окислению.Чем выше содержание хрома, тем более жаропрочная сталь и, таким образом, замедляется проявление оттенков тепла.
Атмосфера
Уровень кислорода, доступного для процесса окисления, также влияет на образующиеся цвета. Обычно предполагается нагрев на воздухе (т.е. около 20% кислорода). При сварке эффективность защитного газа или покрытия электрода и другие параметры сварки, такие как скорость сварки, могут влиять на степень теплового оттенка цвета, образующегося вокруг сварного шва.
Время
Лабораторные испытания, проведенные для установления опубликованных цветовых диаграмм теплового оттенка, обычно основывались на нагревании в течение одного часа. По мере увеличения времени выдержки можно ожидать, что цвета заката станут более насыщенными, то есть создадут впечатление, что могла быть использована более высокая температура выдержки.
Обработка поверхности
Исходная обработка поверхности стали может повлиять на скорость окисления и внешний вид образовавшегося цвета. Более грубые поверхности могут окисляться с большей скоростью и поэтому могут иметь более глубокий цвет при любом заданном наборе условий.Поскольку цвета формируются за счет световых помех, гладкость поверхности также может влиять на внешний вид сформированных цветов. Нет опубликованных конкретных данных, которые сравнивали бы эффект отделки поверхности, но стоит отметить, что качество поверхности может повлиять на вывод о температуре нагрева, исходя из видимых цветов.
Таблица цветов теплового оттенкаВ таблице ниже представлены цвета закалки, которые могут образоваться на нержавеющей стали типа 1.4301 (AISI 304) при нагревании на воздухе.
ДАННУЮ ИНФОРМАЦИЮ ДОЛЖНО ИСПОЛЬЗОВАТЬСЯ С ОСТОРОЖНОСТЬЮ ПРИ ИССЛЕДОВАНИИ ЦВЕТОВ ОТТЕНОК НАБЛЮДЕНИЯ НА ПОВЕРХНОСТИ ИЗ НЕРЖАВЕЮЩЕЙ СТАЛИ, поскольку УСЛОВИЯ НАГРЕВА НЕ УКАЗАНЫ.
Цветная форма | Приблизительная температура o C |
бледно-желтый | 290 |
соломенно-желтый | 340 |
темно-желтый | 370 |
коричневый | 390 |
пурпурно-коричневый | 420 |
темно-фиолетовый | 450 |
синий | 540 |
темно-синий | 600 |
← Вернуться к предыдущей
↑ Начало
Почему сталь синеет при нагревании? — Сделать из металла
Если вы такой же машинист, как я, вы, вероятно, всегда пытаетесь сделать эти красивые синие шестерки и девятки для стружки, когда режете сталь.Если вы сварщик, то цветовая гамма, следующая за вашим валиком, — обычное дело. Если вы случайно уронили нож в костер, вы, вероятно, задаетесь вопросом, означает ли синий цвет, что вы только что сломали нож.
Почему сталь синеет при нагревании? Сталь становится синей из-за тонкого оксидного слоя, образующегося на поверхности металла. Тонкая пленка мешает световым волнам, которые усиливают одни длины волн, уменьшая другие. Толщина пленки изменит некоторые длины волн света, отражающегося от поверхности металла, тем самым изменив цвет стали.
На самом деле сталь может окрашиваться в несколько разных цветов в зависимости от толщины оксидного слоя. Цвет стали — отличный способ определить, насколько горячим был металл. В этом посте я немного поясню, как работает этот эффект тонкой пленки, как он формируется и почему он так полезен со сталью для натренированного глаза.
Как работают свет и цвет
На самом деле, свет — довольно сложная вещь, и он реагирует с разными объектами, создавая цвет по-разному.Вот почему в этом посте я упрощу его до того, как это работает в отношении цвета металла.
Каждый цвет — это просто свет с разной длиной волны. Например, то, что мы видим как красный, — это просто световая волна с длиной волны 700 нанометров, фиолетовый — 400 нанометров и т. Д.
Обычный свет, подобный тому, который мы получаем от солнца или «белой» лампочки, известен просто как «белый свет». Белый свет содержит каждый цвет (и, следовательно, каждую длину световой волны), но поскольку все они включены равномерно, один из них не более различим, чем другой.Вот почему он нам кажется белым.
Итак, белый — это все цвета, упакованные в один. Это не коричневый цвет, как когда вы растапливаете все свои мелки вместе. Крайола просто теребит вашу голову.
Чтобы воспринимать цвет, нам нужно либо уменьшить, либо увеличить некоторые из этих длин волн.
Интерференция тонкой пленки
Это явление, при котором металл меняет цвет. Когда у вас есть тонкая пленка чего-либо, свет, отражающийся от верхней и нижней границы этой пленки, будет вести себя по-разному.
Часть света будет отражаться от верхнего слоя пленки, часть света будет отражаться от нижнего слоя. Это немного смещает длины волн света, в зависимости от того, откуда этот свет исходит.
Если длина волны пленки кратна одной четверти длины волны определенного цвета, свет, отраженный от верхней части пленки, будет мешать свету, отраженному от нижней части пленки. В результате он будет уменьшен.
Если длина волны пленки кратна половине длины волны определенного цвета, результатом является усиление.
Вот пример того, как это работает:
Допустим, мы хотим, чтобы что-то стало синим. Длина волны синего цвета составляет около 470 нанометров. Это означает, что если пленка имеет толщину 235 нанометров, она усилит эту длину волны и сделает поверхность более синей.
Если пленка имеет 3/4 длины волны синего цвета или около 350 нанометров толщиной, она будет мешать длине волны и удалять синий цвет с поверхности.
Хорошо, на самом деле это немного сложнее, и эти цифры не на 100% верны, но они достаточно близки, чтобы донести до сути суть.Физика света никогда не бывает такой простой.
Как свет работает на металле
Если сталь имеет «нормальную» неокисленную поверхность и не имеет тонкой пленки, она отражает весь свет в спектре. Он не выглядит белым просто потому, что не отражает достаточно света. Чем меньше света вы отражаете, тем ближе к черному цвету вы. Полный черный цвет — это полное отсутствие света.
Так что же заставляет его менять цвет?
Толщина этого слоя определяет, какие световые волны блокируются.Толщина оксидного слоя зависит от температуры, которой подвергается сталь при контакте с кислородом. Также немного зависит от количества углерода в стали.
Другими словами, тепло инициирует химическую реакцию между железом в стали и кислородом воздуха. Это образует оксидный слой, который представляет собой тонкую пленку, которая будет фильтровать одни длины волн, усиливая другие, в зависимости от своей толщины. Так меняется цвет.
На самом деле, сталь — не единственный металл, который становится синим, и не только оксид железа может совершить этот интересный подвиг.Другой пример металла, который при нагревании становится синим (и другим цветом), — это титан. Оксид титана может дать такой же результат, хотя для его достижения потребуются разные температуры.
Почему краска для стали так полезна
По мнению некоторых, окраска стали была первым полезным применением эффекта тонкой пленки. Причина этого в том, что он позволяет нам узнать, насколько нагрелся кусок стали при воздействии кислорода, который обычно находится в воздухе.
Чем горячее становится сталь, тем толще становится этот оксидный слой.Это означает, что световые волны различной длины либо приглушаются, либо усиливаются, тем самым изменяя цвет стали.
На самом деле, это один из наиболее распространенных способов управления отпуском при термообработке стали. Когда кусок средне- или высокоуглеродистой стали нагревается до ярко-красного / оранжевого цвета, а затем быстро закаливается в масле или воде, он становится чрезвычайно твердым, но также и очень хрупким.
Если позволить металлу «пропитаться» при более низкой температуре после охлаждения, сталь станет более жесткой и менее хрупкой.Он также станет немного менее твердым. Мы можем использовать цвет стали, чтобы определить, когда она достигла желаемой температуры для этого процесса отпуска.
Машинисты также будут использовать эту цветовую индикацию нагрева, чтобы определить, когда условия резания идеальны для обработки стали. Голубые фишки означают, что тепло поглощается и отводится стружкой, а не заготовкой или режущим инструментом.
Вот загружаемый список различных цветов, в которые сталь меняет цвет в зависимости от температуры:
Теперь разные марки стали будут иметь разную толщину оксидного слоя при разных температурах.Этот список основан на инструментальных сталях со средним содержанием углерода.
Нержавеющая стальособенно требует более высоких температур, поскольку они более устойчивы к коррозии и, следовательно, требуют больше тепла для создания этого слоя оксида железа.
В конечном счете, эффект тонкой пленки чрезвычайно полезен для всех, кто работает со сталью. Это позволяет нам определять температуру металла на глаз и тем самым контролировать свойства металла или давать представление о процессе, который мы выполняем.
Цветовая температура (Кельвин)
Что такое цветовая температура?
- Цветовая температура — это способ описания внешнего вида света лампочки. Он измеряется в градусах Кельвина (K) по шкале от 1000 до 10000.
- Обычно температура Кельвина для коммерческого и жилого освещения падает где-то в диапазоне от 2000K до 6500K.
- Цветовая температура лампочки позволяет нам узнать, как будет выглядеть излучаемый свет.
- Цветовая температура лампочки назначается на основе коррелированной цветовой температуры (CCT).
- Например, если вы нагреете металлический предмет, он будет светиться. В зависимости от температуры Кельвина, при которой нагревается металлический объект, свечение будет разных цветов, например, оранжевого, желтого или синего. Цветовая температура лампочек должна повторять температуру Кельвина металлического объекта.
Какая цветовая температура мне подходит?
Понимание температуры Кельвина (K) упрощает выбор освещения, которое дает вам желаемый внешний вид.
- В нижней части шкалы, от 2000K до 3000K, излучаемый свет называется «теплым белым» и имеет цвет от оранжевого до желто-белого цвета.
- Цветовая температура от 3100K до 4500K называется «холодный белый» или «ярко-белый». Лампочки в этом диапазоне излучают более нейтральный белый свет и даже могут иметь слегка голубой оттенок.
- Выше 4500K вводит нас в «дневную» цветовую температуру света.Лампочки с цветовой температурой 4500K и выше излучают бело-голубой свет, имитирующий дневной свет.
Знаете ли вы, что титан изменит цвет? — Металлический титан
В последние годы титановые горшки, изготовленные из чистого титана, стали популярными на всех кухнях благодаря своей коррозионной стойкости, легкому весу, устойчивости к высоким температурам и отсутствию осаждения тяжелых металлов. После того, как титановый горшок использовался долгое время, многие люди обнаружили, что он меняет цвет.Например, при варке он был желтым; когда горшок остыл, он снова стал серебристо-белым. Почему титановый горшок меняет цвет? Это во многом связано с используемым титановым материалом.
Титан очень стабилен на воздухе при комнатной температуре, и изменение цвета происходит только при нагревании в течение определенного периода времени. Это происходит главным образом потому, что при нагревании титана на воздухе он окисляется кислородом с образованием плотной оксидной пленки. Эта оксидная пленка не только защищает поверхность титана, но и является основным источником изменения цвета титана.
Уравнение реакции окисления титана: Ti + O2 == TiO2, а условия реакции — высокотемпературный нагрев. Когда температура нагрева низкая, оксидная пленка на поверхности титана почти прозрачна, что трудно обнаружить невооруженным глазом, но при повышении температуры оксидная пленка в горшке будет постепенно утолщаться и мешать свету. . В глазах людей они также будут показывать разные цвета. Следовательно, толщина оксидной пленки определяет цвет поверхности титана.
Согласно соответствующим исследованиям, после нагревания на воздухе в течение получаса поверхность титана, нагретого до 200 ° C, становится серебристо-белой, 300 ° C — светло-желтой, 400 ° C — золотисто-желтой, 500 ° C — голубой, 600 ° C. C — фиолетовый, 700 ° C (до) — 800 ° C для серо-красного, 900 ° C для серого, все изменение цвета можно охарактеризовать как красочное. Температура воспламенения природного газа составляет 270-540 ° C, температура воспламенения сжиженного нефтяного газа составляет 365-460 ° C, а температура воспламенения городского газа составляет 270-605 ° C, что может достигать температуры окислительного обесцвечивания. титан.Если ваш титановый горшок может менять цвет, это означает, что вы купили чистый титановый горшок.
Оксидная пленка титана не только меняет цвет титана, но и значительно улучшает коррозионную стойкость титана. Однако чем толще оксидная пленка титана, тем лучше коррозионная стойкость. Когда температура нагрева ниже 500 ° C, кислород и титан образуют плотную оксидную пленку TiO2, которая оказывает определенное защитное действие на поверхность титана; Когда температура нагрева достигает 600-700 ° C, оксидная пленка на поверхности титана становится толще; После того, как температура превышает 700 ° C, оксидная пленка, хотя толщина пленки увеличивается, она становится рыхлой, легко разрушаемой и теряет свой защитный эффект.Следовательно, титан обычно имеет хорошую коррозионную стойкость при нормальной температуре.
Для получения дополнительной информации посетите https://www.samaterials.com/.
ВСЕ О БАЛАНСЕ БЕЛОГО, ЦВЕТОВОЙ ТЕМПЕРАТУРЕ И ОТТЕНОК В ФОТОГРАФИИ — Фотоучитель
Вы когда-нибудь задумывались, почему ваши объекты становятся желтыми при съемке в помещении? Или почему вспышка вашей камеры может сделать их синими? Тщательное понимание концепции баланса белого и того, как он работает, очень важно в цифровой фотографии, потому что его неправильная установка может испортить изображение, добавить всевозможные нежелательные цветовые оттенки и сделать оттенки кожи очень неестественными.В этой статье я объясню, как вы можете настроить это на своей камере или на пост-обработке, чтобы получить точные цвета.
Определение баланса белого
Проще говоря, баланс белого в цифровой фотографии означает настройку цветов так, чтобы изображение выглядело более естественным. Мы настраиваем цвета, чтобы в первую очередь избавиться от цветовых оттенков, чтобы изображение соответствовало тому, что мы видели при съемке. Почему мы должны это делать? Потому что большинство источников света (солнце, лампочки, фонарики и т. Д.) Не излучают чисто белый цвет и имеют определенную «цветовую температуру».Человеческий мозг обрабатывает информацию, поступающую от наших глаз, и автоматически регулирует цветовую температуру, поэтому мы обычно правильно видим цвета. Если вы возьмете белый лист бумаги и посмотрите на него снаружи, он, скорее всего, будет выглядеть таким же белым, как если бы вы смотрели на него в помещении. Однако большинство людей не осознают, что существует огромная разница в цветовой температуре между ярким солнечным светом и вольфрамовым светом в помещении.
Если вы лыжник или сноубордист, попробуйте этот быстрый эксперимент: наденьте лыжные очки и посмотрите на снег — он должен измениться по цвету.Если у вас есть лыжные очки с желтым оттенком, снег будет желтоватым. Однако после того, как вы немного покатаетесь на лыжах, ваши глаза и мозг приспособятся к цвету, и снег снова станет белым. Когда вы снимаете лыжные очки после катания на лыжах, снег какое-то время будет казаться голубоватым, а не чисто белым, пока ваш мозг снова не вернет цвета к норме. Этот пример доказывает тот факт, что мы оснащены очень сложной цветовой системой, которая автоматически регулирует цвета в различных ситуациях освещения.
В то время как наш мозг автоматически обрабатывает цвета таким умным способом, цифровые камеры могут только угадывать цветовую температуру, наблюдая за окружающим светом. В большинстве случаев современные цифровые фотоаппараты могут довольно хорошо угадывать, однако в некоторых ситуациях допускают ошибки. Из-за этих ошибок некоторые изображения могут казаться голубоватыми или желтоватыми, а телесные тона могут выглядеть неестественными.
Вот пример правильного и неправильного баланса белого:
более естественный, и оттенки кожи выглядят правильно
изображение явно требует настройки баланса белого для устранения желтых оттенков
ЦВЕТОВАЯ ТЕМПЕРАТУРА
Цветовая температура описывает спектр света, который излучается «черным телом» с такой температурой поверхности.Черное тело — это объект, который поглощает весь падающий свет, но не отражает его и не позволяет ему проходить. Грубый аналог излучения черного тела в нашей повседневной жизни может быть при нагревании металла или камня: говорят, что они становятся «раскаленными», когда достигают одной температуры, а затем «раскалены добела» при еще более высоких температурах. Точно так же черные тела при разных температурах также имеют разные цветовые температуры «белого света». Несмотря на свое название, свет, который может казаться белым, не обязательно содержит равномерное распределение цветов в видимом спектре:
Относительная интенсивность нормализована для каждой температуры (в Кельвинах).
Обратите внимание, что 5000 K дают примерно нейтральный свет, тогда как 3000 K и 9000 K дают световой спектр, который смещается, чтобы содержать больше оранжевых и синих длин волн соответственно. По мере повышения цветовой температуры распределение цветов становится холоднее. Это может показаться не интуитивным, но связано с тем, что более короткие волны содержат свет более высокой энергии.
Почему цветовая температура является полезным описанием света для фотографов, если они никогда не имеют дела с истинными черными телами? К счастью, такие источники света, как дневной свет и вольфрамовые лампы, точно имитируют распределение света, создаваемое черными телами, хотя другие источники света, такие как флуоресцентное и большинство коммерческого освещения, значительно отличаются от черных тел.Поскольку фотографы никогда не используют термин «цветовая температура» для обозначения истинного источника света черного тела, термин подразумевается как «коррелированная цветовая температура» с таким же окрашенным черным телом. Следующая таблица представляет собой практическое руководство по коррелированной цветовой температуре некоторых распространенных источников света:
Цветовая температура | Источник света |
1000-2000 К | Свечи |
2500-3500 К | Лампа накаливания (бытовая) |
3000-4000 К | Восход / закат (чистое небо) |
4000-5000 К | Люминесцентные лампы |
5000-5500 К | Электронная вспышка |
5000-6500 К | Дневной свет с ясным небом (солнце над головой) |
6500-8000 К | Небо умеренно пасмурно |
9000-10000 К | Тень или сильно пасмурное небо |
Баланс белого в камере
Большинство камер имеют возможность вручную устанавливать или настраивать баланс белого.Типичные настройки включают «солнце», «тень», «вольфрам» и «флуоресцентный». Некоторые камеры имеют возможность вручную установить цветовую температуру, выбрав определенное значение в градусах Кельвина.
Давайте посмотрим на несколько примеров:
На изображении слева вы можете увидеть, как оранжевые лампочки выглядят, когда в камере установлен нейтральный баланс белого, но когда он изменен на цветовую температуру ламп (вручную или с предустановленным балансом белого) , они выглядят нормально. Это почему? Камера «охлаждает» цветовую температуру ламп, добавляя синий цвет к фотографии, создавая впечатление белого света.Обратите внимание, что в то время как лампочки теперь выглядят белыми, боке на заднем плане теперь выглядит синим.
Возьмем еще один пример. Взгляните на эти изображения той же сцены, сделанные при дневном свете:
Теперь, когда наступил дневной свет, вы можете видеть, что 5500 K — это правильный баланс белого для цветовой температуры. Что произойдет, если при дневном свете установить баланс белого на 3050 К? Изображение станет синим! Вот сколько синего было добавлено к фотографии оранжевых ламп накаливания, чтобы сбалансировать оранжевый цвет и сделать цветовую температуру лампы накаливания нормальной.
Постобработка баланса белого
Если вы не хотите беспокоиться об изменении баланса белого в вашей камере для различных ситуаций, пока вы снимаете в формате RAW, вы всегда можете настроить баланс белого ваших изображений с помощью программного обеспечения для постобработки, такого как Adobe Photoshop или Lightroom. Иногда это называют «цветокоррекцией». В вашем программном обеспечении вы, вероятно, увидите панель, которая выглядит примерно так:
Так же, как и при установке баланса белого в вашей камере, вы можете вручную установить баланс белого либо путем регулировки значения температуры, либо с помощью пипетки слева и щелкнув нейтральную или белую часть изображения.Как и в вашей камере, вы также можете выбрать предустановленный баланс белого:
Вот то же изображение сверху, прямо из камеры и с балансом белого, настроенным в Lightroom. Сравните это с изображением, на котором настройка баланса белого была произведена в камере:
Помните, это возможно только при съемке изображений RAW. Если вы снимаете в формате JPEG, вы сможете внести небольшие корректировки баланса белого в свои изображения, но не сможете вносить кардинальные исправления.
Вот еще один пример настройки баланса белого при постобработке. Эта фотография была сделана во время сеанса помолвки, который начался при дневном свете, поэтому для камеры установлен баланс белого 5500 K. Когда солнце начало садиться, свет становился все теплее и теплее, придавая этому изображению очень оранжевый оттенок.
Закат — Баланс белого камеры: 5500 K
Закат — Баланс белого камеры: 5500 KНекоторые люди могут захотеть, чтобы изображение заката было таким теплым, но ему нужно было немного остыть, чтобы действительно выделить розовые и голубые цвета в небе, не говоря уже о том, чтобы их кожа выглядела немного более нормально.В Lightroom баланс белого был отрегулирован таким образом, чтобы температура была на уровне 4500 K, что придает изображению более естественный вид:
Связь между цветовой температурой и балансом белого
Теперь, когда вы знаете разницу между цветовой температурой и балансом белого, вы должны увидеть взаимосвязь между ними. Они противоположности! К сожалению, поскольку фотографы в основном работают с балансом белого, мы иногда путаемся, когда говорим о значениях цветовой температуры.
Практически всегда рекомендуется снимать при фиксированном значении Кельвина около 5500 K. При съемке интерьеров, освещенных лампами накаливания, все изображения выглядят оранжевыми. Если вы снимаете в формате RAW, это не проблема! В Lightroom вы можете просто «охладить их», изменив баланс белого примерно на 3000 К. Что касается тени, вы «разогреете» тени, изменив баланс белого примерно на 6500 К. Более высокие значения Кельвина начинают приравниваться к теплому свету. и более низкие значения Кельвина начинают приравниваться к холодному свету.
Но помните, что баланс цветовой температуры! На самом деле вы добавляете к изображению противоположную цветовую температуру, чтобы оно выглядело естественно.
Итак, теперь главный вывод, который вы можете сделать из всего этого. Если вы установите баланс белого на цветовую температуру снимаемой сцены, все должно выглядеть великолепно! Если вы фотографируете лампочки с цветовой температурой 3000 К и устанавливаете баланс белого камеры на 3000 К, свет должен выглядеть белым! А теперь самое плохое.На самом деле нет способа измерить цветовую температуру, поэтому вам остается приближение или корректировка при постобработке.
Предустановленные настройки баланса белого
Авто — Параметр «Авто» помогает автоматически регулировать баланс белого в соответствии с различными условиями освещения, но вы можете попробовать другие режимы для получения лучших результатов.
Tungsten — Этот режим используется для освещения под маленькой лампочкой, например, вольфрамовой, и часто используется при съемке в помещении.Вольфрамовая настройка цифровой камеры снижает цветовую температуру на фотографиях.
Флуоресцентный — этот режим используется для получения более ярких и теплых снимков с компенсацией холодного оттенка флуоресцентного света.
Дневной свет — Этот режим предназначен для нормального дневного света при съемке на открытом воздухе. Многие камеры не имеют режима дневного света.
Облачно — этот режим идеально подходит для съемки в пасмурный день. Это потому, что он нагревает объект и окружающую среду и позволяет делать более качественные снимки.
Вспышка — Режим вспышки требуется при недостаточном освещении. Этот режим помогает выбрать правильный баланс белого в условиях низкой освещенности.
Оттенок — в затененном месте обычно получаются более холодные или голубые изображения, поэтому при съемке затененных объектов необходимо согреть окружающую обстановку.
Использование автоматического баланса белого
Если вы предпочитаете снимать в формате JPEG или просто не хотите беспокоиться о цветокоррекции после того, как изображение было снято, большинство (если не все) камеры и программное обеспечение для постобработки имеют возможность использовать автоматический баланс белого или AWB.Благодаря AWB ваша камера оценивает сцену, которую вы фотографируете, и выбирает лучший баланс белого для использования. Обычно он ссылается на нейтральный цвет в вашей сцене, такой как белый или серый, чтобы определить правильный баланс белого. В зависимости от вашей камеры и сцены, которую вы снимаете, ваши результаты будут варьироваться от идеальных до совсем не очень.
Использование автоматического баланса белого в камере
При использовании автоматического баланса белого в камере ваши результаты будут зависеть от условий освещения, в которых вы снимаете.Например, если вы снимаете при дневном свете, баланс белого на ваших фотографиях обычно будет правильным. К сожалению, смешанное освещение действительно может создавать проблемы с AWB, поэтому вам все равно может потребоваться регулировка баланса белого при постобработке.
Даже дневной свет может нарушить автоматический баланс белого. Вот набор изображений оранжевой лисы на коричневом столе, которые действительно демонстрируют, насколько непоследовательным может быть автоматический баланс белого без нейтрального цвета на изображении для справки вашей камерой:
Автоматический баланс белого — Как снято 3600 KAuto Баланс белого — Как снято 2850 KAuto Баланс белого — Как снимок 5600 KAuto Баланс белого — Скорректировано 5600KВсе эти изображения были сфотографированы при одинаковом освещении.Вы можете увидеть, насколько сильно изменится фон при использовании автоматического баланса белого. На третьем изображении простое добавление белого фона помогло камере получить правильный баланс белого. Вы можете видеть, что последнее изображение такое же, как и второе, только с правильным балансом белого (настроенным в Lightroom).
Различные камеры имеют разные возможности автоматического баланса белого. Как и в случае с любой другой технологией, более современные камеры кажутся более точными, чем старые. У вас также обычно есть более продвинутые возможности в более дорогих камерах.Нельзя сказать, что системы AWB в камерах начального уровня не очень хороши. Например, iPhone 6 хорошо справляется с AWB, но есть вероятность, что Nikon D810 лучше справляется с этой задачей более последовательно.
Использование автоматического баланса белого при постобработке
Большинство, если не все программное обеспечение для постобработки, такое как Adobe Photoshop или Lightroom, поставляется с опцией автоматического баланса белого. Это никогда не бывает так точно, как съемка с AWB в камере, но может служить хорошей отправной точкой, если вы пытаетесь настроить баланс белого на своем изображении и просто не можете сделать это правильно.
Вот пример использования автоматического баланса белого в Lightroom на простой солнечной фотографии:
Баланс белого, установленный в камере: 5400 K Автоматический баланс белого в Lightroom: 4050 KПОЛЬЗОВАТЕЛЬСКИЙ БАЛАНС БЕЛОГО: ВЫБОР НЕЙТРАЛЬНОЙ ССЫЛКИ
Нейтральный эталон часто используется для проектов, критичных к цвету, или в ситуациях, когда ожидается, что автоматический баланс белого столкнется с проблемами. Нейтральные отсылки могут быть либо частью вашей сцены (если вам повезет), либо переносным предметом, который вы носите с собой.Ниже приведен пример удачной ссылки в синеватой сумеречной сцене.
С другой стороны, готовые переносимые ссылки почти всегда более точны, так как можно легко обмануть, думая, что объект нейтрален, когда это не так. Портативные справочные материалы могут быть дорогими и специально разработаны для фотографии или могут включать менее дорогие предметы домашнего обихода. Идеальный серый эталон — это тот, который одинаково отражает все цвета в спектре и может стабильно делать это в широком диапазоне цветовых температур.Пример готовой серой ссылки показан ниже:
Обычные домашние нейтральные ссылки — это нижняя сторона крышки контейнера для кофе или принглов. Они недорогие и достаточно точные, хотя лучше всего подходят сделанные на заказ фотографии (например, карты, показанные выше). Изготовленные на заказ устройства можно использовать для измерения цветовой температуры падающего или отраженного источника света. Большинство нейтральных эталонов измеряют отраженный свет, тогда как такие устройства, как измеритель баланса белого или «ExpoDisc», могут измерять падающий свет (и теоретически могут быть более точными).
Следует проявлять осторожность при использовании нейтрального эталона с высоким уровнем шума изображения, поскольку щелчок по кажущейся серой области может фактически выбрать цветной пиксель, вызванный цветовым шумом:
Низкий уровень шума (гладкий бесцветный серый)
Высокий уровень шума (цветные участки)
Оттенок
Помимо цветовой температуры, свет может иметь оттенок. В то время как цветовая температура находится в пределах оранжевого / синего спектра, оттенок находится в пределах зеленого / пурпурного спектра.При цветокоррекции изображений, сделанных при дневном свете, обычно не требуется значительная регулировка оттенков. Если вы склонны фотографировать объекты, освещенные искусственными источниками света, такими как вольфрамовые, флуоресцентные, светодиодные или ртутные лампы, вы обнаружите, что настраиваете оттенок гораздо больше, чем при естественном свете.
Вот пример сцены, освещенной флуоресцентными лампами:
Флуоресцентный свет — температура: 4450 K, оттенок: -5 Флуоресцентный свет — температура: 4450 K, оттенок: +50Вы можете видеть, что первое изображение имеет очень сильный зеленый оттенок.Баланс белого был скорректирован путем изменения оттенка (добавления пурпурного), но без изменения цветовой температуры.
Оттенок не предназначен для компенсации цвета, который отражается на вашем объекте от близлежащих объектов, например, на этом изображении:
Мелисса стояла перед зеленой дверью специально, чтобы продемонстрировать этот сценарий. Хотя баланс белого на изображении правильный, на теневой стороне ее лица есть зеленый оттенок, который не имеет ничего общего с цветовой температурой.Это отражение света от зеленой двери, и его нельзя исправить, изменив оттенок изображения.
Так же, как отраженный свет, который приобрел цветовой оттенок, цветные или гелеобразные огни на вашем объекте также нелегко исправить путем настройки оттенка вашего изображения. Например, на этом изображении со свадьбы в канун Нового года есть все, что вы хотели бы от изображения, сделанного ровно в полночь: растяжки, празднование, счастливые зеленые лица на женихе и невесте… подождите, что?
NIKON D810 + 35 мм f / 1.4 @ 35 мм, ISO 1600, 1/160, f / 1.4К сожалению, это нельзя исправить, регулируя баланс белого. К счастью, он по-прежнему неплохо смотрится в черно-белом цвете.
NIKON D810 + 35 мм f / 1,4 @ 35 мм, ISO 1600, 1/160, f / 1,4В СМЕШАННОМ ОСВЕЩЕНИИ
Использование нескольких источников света с разной цветовой температурой может еще больше усложнить выполнение баланса белого. В некоторых ситуациях освещения может даже не быть действительно «правильного» баланса белого, и это будет зависеть от того, где точность цветопередачи наиболее важна.
При смешанном освещении автоматический баланс белого обычно вычисляет среднюю цветовую температуру для всей сцены, а затем использует ее в качестве баланса белого. Этот подход обычно приемлем, однако автоматический баланс белого имеет тенденцию преувеличивать разницу в цветовой температуре для каждого источника света по сравнению с тем, что мы воспринимаем нашими глазами.
Чрезмерная разница в цветовой температуре часто наиболее заметна при смешанном внутреннем и естественном освещении. Для критических изображений может даже потребоваться другой баланс белого для каждой области освещения.С другой стороны, некоторые могут предпочесть оставить цветовую температуру как есть.
Обратите внимание, что в здании слева довольно тепло, а небо несколько прохладное. Это связано с тем, что баланс белого был установлен на основе лунного света, что подчеркивает теплую цветовую температуру искусственного освещения внизу. Баланс белого на основе естественного света часто дает более реалистичную фотографию. Выберите «камень» в качестве эталона баланса белого и посмотрите, как небо становится нереально синим.
Заключение
Пока вы снимаете в формате RAW, знание цветовой температуры различных источников света не так важно.Большинству фотографов достаточно простого понимания базовой концепции цветовой температуры. Важно знать, как и когда настраивать баланс белого: в камере перед созданием изображения или в программе пост-обработки после создания изображения.
Как только вы освоитесь с настройкой баланса белого ваших изображений, вы можете начать творчески использовать баланс белого в своих изображениях, либо нагревая их, либо охлаждая, чтобы изменить ощущение всей сцены. Хотя мы не собираемся сейчас вдаваться в подробности, следите за будущей статьей о творческом использовании баланса белого.
Как это:
Нравится Загрузка …
Light Guide: Color Metrics
Light, как и все формы лучистая энергия, представлена на электромагнитном спектр. Путешествуя волнами, свет отличается от другие формы лучистой энергии, такие как тепло и рентгеновские лучи частота и длина его формы волны. Узкая полоса на спектр — видимый свет, состоящий из разных цвета / длины волн, от фиолетового при 380 нм до красного при 620-760 нм.Равномерный баланс этих световых волн составляет белый видимый свет. Чтобы увидеть этот принцип воочию посмотрите на радугу, которая возникает от солнечного света преломляться каплями влаги в воздухе, или просто направьте луч белого света через стеклянную призму, чтобы Сделайте так, чтобы радуга цветов появлялась на другом сторона.
Видимый свет не может быть видно, однако. Если включить фонарик в темной комнате, луч света, который мы видим, на самом деле свет отражается от множества частиц пыли в воздухе.Следовательно, мы видим объекты только тогда, когда свет отражается или испускается из них. Вот как мы видим цвет.
Все объекты химически ориентированы на поглощение определенных длин волн света и отражение другие. Те, что отражены, воспринимаются человеческий глаз должен быть цветом объекта. Красный объект пораженный видимым белым светом поглощает все длины волн кроме красного, который отражается, и поэтому мы видим объект как красный.Чистый белый объект отражает все длины волн и не поглощает. Чистый черный объект поглощает все длины волн и ничего не отражает.
Вот где большое количество искусства приходит в освещение, потому что немногие типы ламп производят чистый белый свет. Некоторые лампы излучают насыщенный свет. синим и зеленым, другие — красным и желтым. Красный объект пораженный светом, который содержит только синий и зеленый длины волн не будут красными, как если бы они находились ниже Солнечный свет.Натриевая лампа низкого давления излучает свет насыщенного желтого цвета, что означает, что все объекты, пораженные он будет желтым, черным или с оттенком серого. Главная у всех производителей ламп есть литература и экспонаты, продемонстрировать влияние света на цвет. Слоган одного: «Цвет — это то, как вы его зажигаете».
Метрики
Чтобы понять, как лампа свет повлияет на цвет предметов в пространстве, три метрики, в том числе спектральная мощность распределение , цветовая температура и цвет рендеринг .
Спектральная мощность распределение показывает спектр видимого света и состав длины волны для света от лампы (см. иллюстрацию). Шипы указывают на то, что свет горит. сильнее проявляет определенные цвета.
А спектральное распределение мощности кривая для лампы 4000К с трифосфором (красный, синий, зеленый) покрытие для улучшения цветопередачи.Предоставлено Osram Sylvania |
Цветовая температура , выражается по шкале Кельвина (K), это внешний вид цвета самой лампы и излучаемого ею света.
Согласно Общество инженеров освещения Северной Америки (IESNA), цветовая температура — это «абсолютная температура излучатель черного тела, имеющий цветность, равную цветности источник света.«
Представьте себе стальной блок который постоянно нагревается, пока он не загорится сначала оранжевым, затем желтый и так далее, пока он не станет синим или голубовато-белым. В в любое время во время нагрева мы могли измерить температура металла Кельвина (Цельсия + 273) и присвоить это значение производимому цвету, в результате в «цветовой температуре». Компьютерное программное обеспечение выполняет это функция для современных ламп, придавая им цветовую температуру Рейтинг найден в литературе производителей.
Для ламп накаливания цветовая температура — это «истинное» значение; для люминесцентных и разрядные лампы высокой интенсивности (HID), значение приблизительный и поэтому называется коррелированным цветом температура . В промышленности оба термина — — цвет температура и соответствующая цветовая температура — — часто используются взаимозаменяемо. Цветовая температура ламп составляет их визуально «теплый», «нейтральный» или «холодный» свет источники.
Светильники с нижним цветом температура (3500К или меньше) иметь теплый или красно-желтый / оранжево-белый внешний вид. Свет насыщен в красном и оранжевом диапазоне длин волн, выделяя более теплый объект более насыщенные цвета, такие как красный и оранжевый.
Лампы среднего цвета температура (от 3500K до 4000K) имеет нейтральный или белый цвет. внешний вид. Свет более сбалансирован по цвету длины волн.
Светильники с высшим цветом температура (4000К и выше) имеет холодный или голубовато-белый цвет. внешний вид. Летний солнечный свет выглядит очень прохладно в около 5500К. Свет насыщен зеленым и синим длины волн, выделяя более холодные цвета объекта, такие как зеленый и синий более насыщенный.
Эти три фотографии имитируют влияние цветовых температур на объекты.(Слева) а используется теплый источник света, усиливающий красные и апельсины, приглушенные синим и зеленым; (В центре) а используется нейтральный источник; (Справа) крутой источник используется усиление синего и зеленого цветов при приглушении красных и апельсины. Предоставлено Osram Sylvania |
Как только цветовая температура указанному, используйте данные о спектральном распределении мощности, чтобы помочь в выборе конкретной лампы.
Цветопередача , выражается как рейтинг по индексу цветопередачи (CRI) , от 0 до 100, описывает, как источник света делает цвет объекта кажется человеческому глазу и насколько хорошо выявляются тонкие вариации цветовых оттенков. Выше рейтинг CRI, тем лучше его цветопередача способность.
Согласно IESNA, цветопередача — это «мера степени изменения цвета. объекты претерпевают при освещении источником света как по сравнению с цветом тех же предметов при освещении эталонным источником сопоставимого цвета температура.«
Представьте себе два объекта, один красный, один синий, которые освещены холодным источником света с низкий индекс цветопередачи. Красный объект выглядит приглушенным, в то время как синий объект приобретает насыщенный синий цвет. Теперь выньте лампу и вставьте крутой источник света с высоким индексом цветопередачи. Синий объект все еще кажется насыщенно-синим, но красный объект больше похож на его истинный цвет.
Лампы накаливания стандартные иметь рейтинг CRI 100.Люминесцентные лампы находятся в Диапазон 52-95, в зависимости от лампы. Достижения в люминофоре технологии позволили люминесцентным и HID лампам продвинуться вперед сильно в цветопередаче.
Как указано в IESNA определение, чтобы сравнить любые две данные лампы, они должны иметь одинаковая цветовая температура для сравнения, чтобы иметь любую смысл.
Указание Цвет
При указании цвета характеристики лампы, многочисленные психологические факторы необходимо учитывать в зависимости от целей освещения для Космос.Вот несколько общих советов.
Источники теплого света обычно предпочтительнее для дома, ресторанов и розничной торговли приложения, чтобы создать ощущение тепла и комфорта, а нейтральные и прохладные источники обычно предпочтительны для офисов и аналогичные приложения, чтобы создать ощущение настороженность.
Дополнительно в рознице приложений, цвет является критическим дизайнерским решением, потому что покупатели должны иметь возможность выбирать товары правильного цвет, как для увеличения шансов его продажи, так и для уменьшения шанс его возврата, как только покупатель выйдет на улицу и видит это под солнечным светом.В этом или любом другом приложении где обитатель должен видеть правильный цвет, хороший цвет качество важно.
В других приложениях, например как и на стоянках, цвет не имеет значения, поэтому могут быть указаны лампы с низкой цветопередачей.
Подробнее Световоды
Световоды © 2012 inter.Light, Inc. Все права защищены.Заявление об отказе от ответственности
Электрополировка удаляет тепловую окраску нержавеющей стали
Предотвращение теплового обесцвечивания с помощью электрополировкиКогда нержавеющая сталь нагревается в печи или в зоне термического влияния (например, при сварке), иногда возникающая окраска известна как тепловой оттенок. Часто при наличии теплового оттенка образуется внешний слой, богатый хромом. Это, скорее всего, со временем повлияет на коррозионную стойкость детали.
Факторы исследования, связанные с тепловым оттенком
Существует большое количество факторов, влияющих на степень изменения цвета.Не существует единой таблицы цветов, которая могла бы точно представить температуру во всех случаях. Появляющиеся цвета могут использоваться только как предположение о температуре, до которой была нагрета сталь. Факторы, влияющие на цвета теплового оттенка, могут включать:
Состав металла
Наиболее важным фактором, связанным с стойкостью стали к окислению, является хром. Чем выше содержание хрома, тем выше будет жаропрочность металла. И, как следствие, откладывается проявление теплых оттенков цветов.
атмосфера
Уровень кислорода, доступного для процесса окисления, также влияет на цветовой оттенок. Обычно предполагается нагревание на воздухе (примерно 20 процентов кислорода). При сварке эффективность защитного газа или покрытия электрода и другие сварочные факторы, такие как скорость, могут влиять на цвет теплового оттенка, образующийся вокруг сварного шва.
Сроки
Лабораторные испытания, проводимые для создания цветовых диаграмм теплового оттенка металла, обычно основывались на нагревании в течение примерно одного часа.При дополнительном времени экспонирования можно ожидать, что цвета теплового оттенка станут более глубокими, создавая впечатление, будто использовалась более высокая температура воздействия.
Поверхность
Цвета, появляющиеся на металле из-за теплового оттенка, могут точно указывать на текстуру поверхности. Окисление и внешний вид образовавшегося цвета (а также скорость его образования) во многом зависят от исходной отделки поверхности стали. Шероховатые или неровные поверхности имеют тенденцию к более высокому окислению.Из-за этого цвета могут казаться темнее в самых разных условиях.