Ультразвуковые дефектоскопы Sonatest
Программное обеспечение УЗКарта
Для эффективной подготовки средств ультразвукового контроля (ультразвуковых дефектоскопов) к проведению дефектоскопии сварных швов, компанией «Панатест» было разработано программное обеспечение, получившее название УЗКарта.
С помощью созданного ПО стало возможным моделирование процесса ультразвукового контроля всех типов сварных швов с различной разделкой кромок.
ПО отображает ход ультразвукового луча в ОК в зависимости от выбранного ПЭП, типа шва, а также характера разделки кромок шва и предназначено для определения параметров зоны ультразвукового контроля (зоны подготовки для сканирования), выбора оптимального режима контроля и ПЭП из библиотеки данных.
Программа применяется для ультразвуковой дефектоскопии стыковых (в т.ч. разнотолщинных), угловых, тавровых и нахлесточных сварных соединений и предназначено для работы с ультразвуковыми дефектоскопами SiteScan, MasterScan, Harfang Prisma UT производства Sonatest, Великобритания.
ПО предназначено для ускорения процесса обучения ультразвуковой диагностике сварных соединений, в первую очередь, начинающих пользователей ультразвуковых дефектоскопов.
В процессе подготовки к проведению ультрафиолетовой дефектоскопии оператор создает Библиотеку ПЭП. Для этого вводятся параметры преобразователей, с которыми предполагается проведение контроля: маркировка ПЭП, габаритные размеры, угол ввода, значение стрелы и т.д.
Далее в программу вводится тип контролируемого сварного шва и его геометрические характеристики: толщины свариваемых материалов, катеты шва и т.д.
В результате ПО строит ход ультразвукового луча в объекте контроля с учетом введенных параметров.
С помощью созданной программы пользователь ультразвукового дефектоскопа может наблюдать за ходом луча по сечению сварного шва, виртуально перемещая ПЭП поперек соединения.
UTility Lite / UTility Pro (программа управления данными)
Программа Utility Lite имеет все необходимое для обработки контрольных данных. Стандартная версия (Lite) является БЕСПЛАТНОЙ и позволяет просматривать, перемещать и управлять калибровками, данными А-скана, В-скана и записями толщины как на экране дефектоскопа, так и на мониторе ПК. С помощью Utility Lite можно создавать образцы отчетов проверки, удалять и вставлять данные в другие приложения, создавать документы в формате pdf для печати.
Она позволяет
- Загружать, сохранять данные, управлять файлами на ПК и дефектоскопе
- Сохранять, анализировать, выполнять цветовую кодировку и экспортировать данные регистрации толщины в программу для обработки электронных таблиц.
- Обновлять программное и аппаратное обеспечение дефектоскопа по мере появления обновлений на нашем сайте.
Программа Utility Pro представляет собой профессиональную версию и работает совместно с режимом обнаружения коррозии, предлагает пользователю создавать и управлять планами инспекционных проверок, заметками, архивными данными измерения толщины и другой информацией оценочного характера. Программа позволяет
- Подготовить шаблоны для выполнения проверок (сетки), заметки и примечания
- Импортировать ранее полученные показания в план проверки
- Экспортировать данные плана проверки в базы данных для обслуживания установки и табличные программы.
DAC
До 20 справочных точек можно задействовать для построения цифровой кривой DAC, выбрав вариант JIS/ASME или EN1714. Пользователь может выбрать кривую DAC или Gate 1 (канал 1) в качестве контрольного уровня. Амплитуда эхосигнала отображается в дБ DAC, % DAC или % полноэкранной высоты.
Библиотека кривых DAC
Пользователь располагает предварительно запрограммированными уровнями дБ, соответствующие стандартам
- EN1714 (-6дБ, -14дБ)
- ASME (-2дБ, -6дБ, -10дБ)
- JIS DAC (+6дБ, -6дБ, -12дБ)
Любой из существующих уровней можно использовать в качестве контрольной схемы. Выбранный для мониторинга уровень подсвечен другим цветом для выделения на экране.
Пользовательская кривая DAC
До 3 пользовательских кривых можно добавить в библиотеку кривых DAC. Пользователь может выбрать уровень в пределах +/- 20дБ для каждой из 3 кривых. Таким образом, обеспечивается соответствие всем международным стандартам.
Динамическая кривая DAC
Широкий динамический ряд DAC можно использовать для повышения точности измерения слабых эхосигналов. Высоту кривых DAC можно отрегулировать с помощью уставочного усиления. Соотношение между кривой DAC и справочными точками предварительно записывается и контрольный режим «T-loss» передает затухание от тестового блока на образец.
Преобразование кривой DAC в TCG
Кривую DAC можно преобразовать в кривую TCG и наоборот. При конверсии используются справочные точки, затем сохраняется уставочное (справочное) усиление для самой левой справочной точки, все справочные эхосигналы заданы на уровне 80% FSH.
ПЛЮС! Если Ваш дефектоскоп Sonatest требует обновления программного обеспечения, опция «Utility» позволяет получить последнюю версию обновления по сети интернет и обновить программу дефектоскопа без обращения в сервис-центр.
ПРОТОКОЛ производственных испытаний ультразвукового дефектоскопа c фазированными антенными решетками OmniScan SX
Во исполнение решений VII-го отраслевого совещания «Состояние и основные направления развития неразрушающего контроля качества сварных соединений объектов ПАО «Газпром» (сентябрь 2017 г., г. Н. Новгород) по дальнейшему внедрению технологий ультразвукового контроля (УЗК) фазированными антенными решетками (ФАР), а также достигнутых взаимных договоренностей АО «Газстройдеталь» и ООО «ТЕХКОН» провели 17.01.18 г. совместные производственные испытания ультразвукового дефектоскопа с ФАР, модель OmniScan SX производства компании «Olympus».
64-канальный автоматизированный дефектоскоп OmniScan SX является прибором нового поколения, который реализует такие передовые технологии УЗК, как применение многоэлементных преобразователей (до 64 элементов для данной модели), электронное сканирование с программно управляемым полем излучения-приема ультразвука, полное документирование и томографическую визуализацию результатов контроля. В настоящее время дефектоскоп OmniScan c ФАР широко применяется при УЗК объектов ПАО «Газпром», ПАО «Транснефть», ГК «Росатом» и других ответственных объектов.
Испытания проведены с целью проверки технических возможностей и целесообразности применения дефектоскопа OmniScan SX с ФАР при УЗК деталей и изделий, производимых АО «Газстройдеталь».
В ходе испытаний в цехе АО «Газстройдеталь» дефектоскопом OmniScan SX с ФАР выполнен демонстрационный УЗК сварного шва №1 тройника ТР II 1420 (75) × 1020 (45) №168, (продольный стыковой сварной шов с толщиной стенки 75×75 мм, V-образной разделкой кромок, материал – сталь 09Г2С). При этом были показаны с необходимыми пояснениями основные этапы работы с дефектоскопом – настройка для контроля сварного шва, сканирование сварного шва, анализ полученных данных, создание отчета по результатам контроля. Специалисты АО «Газстройдеталь» были ознакомлены с основными функциональными возможностями и техническими характеристиками дефектоскопа.
Результаты испытаний дефектоскопа OmniScan SX с ФАР.
Для многоканального автоматизированного дефектоскопа OmniScan SX является достаточно легким и компактным (вес – 3,4 кг, габаритные размеры 267×208×94 мм). Дефектоскоп имеет ударопрочный обрезиненный и герметичный корпус (без отверстий для охлаждения, степень защиты IP66), сменный аккумулятор обеспечивает работу прибора не менее 6 часов. Такая конструкция обеспечивает достаточно удобное и безопасное применение дефектоскопа при УЗК в цеховых условиях.
Дефектоскоп может комплектоваться большим количеством ФАР с различными характеристиками, сменными призмами к ним, а также датчиками пути и сканерами различных моделей для решения разнообразных задач по УЗК. Сменные призмы (наклонные и прямые) позволяют применять одну и ту же ФАР как для контроля сварных швов, так и для контроля основного металла. На сменные призмы могут быть установлены специальные насадки, которые предохраняют призмы и ФАР от механического износа и повреждений, что значительно увеличивает срок их эксплуатации.
Программный интерфейс дефектоскопа является русскоязычным, достаточно простым и понятным. Многие операции автоматизированы и сопровождаются наглядным отображением на дисплее дефектоскопа, напр., трассировка хода ультразвуковых лучей ФАР в сварном шве. Все это позволяет оперативно производить настройку, контроль объекта, анализ результатов и другие операции с дефектоскопом.
Настройка и проверка параметров контроля дефектоскопа может быть выполнена с применением калибровочных и настроечных образцов (СО и СОП), изготовленных согласно действующей документации по УЗК, в т. ч. с применением образцов, которыми оснащена лаборатория УЗК АО «Газстройдеталь». Кроме того, дефектоскоп может использоваться с любыми типами контактной жидкости, применяемыми при УЗК.
ФАР за счет электронного сканирования с переменным углом ввода ультразвука заменяет несколько одноэлементных преобразователей с фиксированным углом ввода, а также позволяет проводить УЗК сварного шва без поперечных перемещений преобразователя, что существенно сокращает время контроля. Кроме того, это позволяет уменьшить ширину зоны зачистки и сократить время подготовки сварного шва для УЗК. В ходе испытаний контроль стыкового сварного шва толщиной 75 мм проводился ФАР без поперечных перемещений, при этом скорость сканирования вдоль продольной оси сварного шва составляла до 3 м/мин, ширина зоны перемещения ФАР не превышала 30 мм от края валика усиления сварного шва.
При контроле дефектоскоп выполнял автоматический сбор исходных данных – массива А-сканов по всем точкам электронно-механического сканирования в количестве 31000 А-сканов на 1 п. м. шва (при контроле с одной стороны шва). При этом расстояние между контрольными поперечными сечениями сварного шва, в которых проводился сбор данных, составляло 1 мм.
При сканировании дефектоскоп в режиме реального времени выполнял томографическую обработку данных и отображал результаты контроля как пространственные виды и сечения объекта контроля. Применялась типовая комбинация А‑, В‑ (S-) и С-сканов, которая в сумме позволяет получить объемное 3D-представление результатов контроля. На S‑сканах отображались результаты контроля в поперечных сечениях шва, в т. ч. положение дефектов по ширине и глубине шва с привязкой к границам шва. На С-скане отображались результаты контроля как на проекционном «виде сверху» (аналог радиографического снимка), в т. ч. положение дефектов по длине шва. При необходимости дефектоскоп позволяет применять и другие типы сканов.
Наглядное представление данных по трем пространственным координатам с привязкой к границам сварного шва делает анализ результатов контроля, полученных дефектоскопом OmniScan с ФАР, более быстрым и достоверным по сравнению с обычным 1-канальным дефектоскопом, который отображает только одиночный А-скан. Например, можно быстрее и точнее оценить тип и форму дефекта, определить его характеристики (максимальную амплитуду эхо-сигнала, координаты, условные размеры), а также выделить индикации от дефектов-несплошностей и ложные индикации (от «обратного валика» сварного шва и т. п.), что и было показано в ходе испытаний.
При контроле сварного шва был выявлен дефект типа несплавления по кромке в корне шва и определены его характеристики – максимальная амплитуда эхо‑сигнала, координаты и условные размеры (условная высота и условная протяженность).
После сканирования сварного шва результаты контроля, включая исходный массив А‑сканов, были сохранены в сменной карте памяти дефектоскопа (тип SDHC, емкость до 64 Гб), откуда они могут быть скопированы стандартными средствами (USB‑порты в дефектоскопе или картридер для карты памяти) на другие носители информации. Полное сохранение данных позволяет, при необходимости, проводить анализ результатов контроля в режиме постобработки. Анализ результатов может быть проведен как на дефектоскопе, так и на внешнем компьютере, что позволяет при больших объемах контроля использовать дефектоскоп только для сбора данных.
Дефектоскоп имеет удобные программные функции для анализа результатов контроля, такие как маркеры по всем координатным осям, которые позволяют определять размеры дефектов, автоматически формируемая таблица дефектов с указанием их характеристик, автоматическая генерация отчета по результатам контроля. В отчет входят данные по дефектоскопу, ФАР и объекту контроля, параметры контроля, заданные при настройке, таблица дефектов, включающая их характеристики и сканы, которые отображают расположение дефектов в сварном шве, а также другая информация по усмотрению дефектоскописта. Указанный отчет имеет формат HTML, может быть просмотрен как на дефектоскопе, так и скопирован стандартными средствами и просмотрен на внешнем компьютере. Пример отчета по проконтролированному в ходе испытаний сварному шву с выявленным дефектом приведен в Приложении к настоящему Протоколу.
Выводы по результатам испытаний дефектоскопа OmniScan SX c ФАР.
Применение 64-канального дефектоскопа OmniScan SX с ФАР вместо простых 1‑канальных дефектоскопов может быть перспективным по следующим причинам.
Дефектоскоп OmniScan c ФАР способен обеспечить более надежное выявление дефектов — за счет гарантированной высокой плотности электронно-механического сканирования, в т. ч. с переменным углом ввода, наглядного томографического отображения результатов контроля (по различным сечениям в трех координатах), полного документирования результатов контроля с возможностью их последующего анализа;
Дефектоскоп OmniScan SX с ФАР позволяет сократить время контроля за счет замены некоторых видов механического сканирования (многократных поперечных перемещений преобразователя при контроле сварных швов) более быстрым электронным сканированием, что особенно актуально при контроле сварных швов больших толщин.
Отчёт OmniScan
Дата отчёта | Версия отчёта | Имя файла | Дата контроля | Версия контроля | Реж. сохр. |
17.![]() |
MXU — 4.4R3 | File0014.opd | 17.01.2018 | MXU — 4.4R3 | Данные контроля |
Тип OmniScan | Серийн.№ OmniScan | Тип модуля | Серийн.№ модуля | Имя файла | |
OmniScan SX | QC-010253 | OMNISX-PA1664PR | QC-010253 | File#### |
PA 1
Хар-ка ПЭП
Модель ПЭП | Серийн. № ПЭП | ||||
2.![]() |
S1975 | ||||
Частота ПЭП | Макс. частота | Модель призмы | Угол призмы | Апертура ПЭП | |
2.25 MHz | N/A | SA10-N55S 2.25L16 | 36.10º | N/A | |
Низкая частота | Высок. частота | Центр. частота | Полоса проп.(МГц) |
Полоса проп.![]() |
|
–6 дБ | N/A | N/A | N/A | N/A | N/A |
–20 дБ | N/A | N/A | N/A | N/A | N/A |
Дата | Время | Процедура | Калибров.образец | Характер. усил. | A% |
N/A | N/A | N/A | N/A | N/A | N/A |
Настройка
A:40.![]() |
|||||
Задерж. луча | Начало (полупуть) | Диапазон (полупуть) | Макс.скор.сбора | Тип | Фактор усред. |
9.9 µs | 0.00 mm | 130.56 mm | 60 | PA | 1 |
Тип шкалы | Коэф. масшт. | Видео фильтр | Предв. запуск | Детектирование | Фильтр |
Сжатие | 26 | Вкл. | 0.00 µs | FW |
Нет (1.![]() |
Напряжение | Усил. | Режим | Тип волны | Скорость звука | Длит.импульса |
40 (Низк.) | 39.96 dB | И-Э (имп.-эхо) | Попереч. | 3240.0 m/s | 220.00 ns |
Смещ.скан. | Смещ.индекс. | Наклон ПЭП | Врем. разреш. С-скана | Частота оцифровки | Врем.разреш. А-скан |
70.00 mm | -60.00 mm | 90.0º | 10.0 ns | 100 MHz |
260.![]() |
Строб |
Начало | Ширина | Порог | Синхр. | Выбор макс. |
I | Off | Off | Off | Off | Off |
A | 14.42 mm | 61.90 mm | 40.00 % | Импульс | Максимум |
B | Off | Off | Off | Off | Off |
Номер точки ВРЧ |
Полож.![]() |
Усил. |
1 | 15.92 mm | 0.0 dB |
2 | 68.97 mm | 14.0 dB |
3 | 79.57 mm | 16.0 dB |
Калькулятор
Кол-во использ. эл-тов | Перв. элемент | Послед. элемент | Разреш. | Тип волны | Скорость в мат-ле |
16 | 1 | 16 |
1.![]() |
Попереч. | 3240.0 m/s |
Начал. угол | Конеч. угол | Разреш. угла | Глубина фокуса | Конфиг.закон | Наклон луча |
40.00º | 70.00º | 1.00º | 50.00 mm | Секторн. | 0.00º |
Объект
Материал | Геометрия | Толщина |
СТАЛЬ, МАЛОУГ. | Пластина |
75.![]() |
Зона скан.
Начало скан. | Длина скан. | Разреш. скан. |
0.00 mm | 3000.00 mm | 1.00 mm |
Синхр. | Макс.скор.сканир. | |
Кодировщик | 60.00 mm/s |
Ось |
Кодировщик | Тип кодировщика | Разреш. кодировщика | Полярность | ||||||||
Скан | 1 | Квадратура |
12.![]() |
S(m-r) (mm) | S(r) (mm) | S(m) (mm) | U(m-r) (mm) | AdBA (dB) | ||||
- | 1 | 1905.00 | -60.00 | PA 1 | 47.00º | 72.68 | июл.15 | 44.79 | 1898.61 | 1943.40 | 13.14 | 12.апр |
Опор.![]() |
S(m-r) | S(r) | S(m) | U(m-r) | AdBA | |||||||
- | 1 | 1905.00 mm | -60.00 mm | PA 1 | 47.00º | 72.68 mm | 7.15 mm | 44.79 mm | 1898.61 mm | 1943.40 mm | 13.14 mm | 12.4 dB |
Коммент.
-Дефект типа несплавления по кромке в корне шва
Дефектоскоп для ручного контроля сварных швов Olympus NDT EPOCH 1000i
Olympus NDT EPOCH 1000i — дефектоскоп на фазированных решетках
Переносной дефектоскоп EPOCH 1000i позволяет проводить неразрушающий контроль в соответствии со всеми стандартами и нормами ультразвуковых исследований, при этом применяя расширенные возможности фазированных решеток. Основное предназначение дефектоскопа— контроль сварных швов (вт.ч. по AWS D1.1/D1.5), литых и кованых изделий, а также поиск дефектов и отслоений в композитных материалах.
Дефектоскопы EPOCH 1000 сочетают в себе традиционный ультразвук нового поколения и возможности визуализации фазированных решёток. Модели EPOCH 1000, 1000iR и 1000i оснащены экраном VGA с высоким качеством изображения при ярком солнечном свете. Ручка прокрутки и курсорные кнопки по обеим сторонам экрана дают больше возможностей для настройки параметров и навигации в интерфейсе прибора. Кроме того, приборы соответствуют требованиям стандарта EN12668-1. В дополнение к традиционному ультразвуку нового поколения в модели EPOCH 1000i присутствуют полнофункциональные возможности визуализации фазированных решёток.
EPOCH 1000 — УЗК НОВОГО ПОКОЛЕНИЯ
EPOCH 1000 — это ультразвуковой дефектоскоп в расширенным набором функций УЗК и возможностью активации фазированных решёток в специализированном центре обслуживания Olympus.
EPOCH 1000iR — УЗК НОВОГО ПОКОЛЕНИЯ + ПОДДЕРЖКА ФР
EPOCH 1000iR обладает всеми функциями EPOCH 1000, а также позволяет удалённо активировать функцию фазированных решёток.
EPOCH 1000i — УЗК НОВОГО ПОКОЛЕНИЯ + ФАЗИРОВАННЫЕ РЕШЕТКИ
В EPOCH 1000i, в дополнение ко всем основным функциям EPOCH 1000, также встроена и активизирована функция фазированных решёток.
Применение дефектоскопа
- контроль сварных швов
- контроль и определение размеров трещин
- Энергетическая промышленность
- контроль сварных швов AWS D1.1/D1.5
- контроль литых и кованых изделий
- определение размеров дефектов по АРД-диаграммам
- Использование с промышленными системами контроля и сканерами
- обнаружение дефектов и отслоений в композитах
- аэрокосмическая промышленность и техническое обслуживание
- автомобильная и транспортная промышленность
Переносной дефектоскоп для ручного контроля
Ультразвуковые дефектоскопы на фазированных решетках EPOCH 1000i соответствует евростандарту IP66. Измерительные приборы успешно прошли испытания на устойчивость к вибрациям и ударам, на безопасную эксплуатацию во взрывоопасной атмосфере и стабильно работали при самых разных температурах. Можно сполной уверенностью сказать, что новые дефектоскопы EPOCH 1000i созданы для работы вне благоприятных условиях.
Оцените преимущество фазированных решеток
Благодаря фазированным решеткам повышается вероятность обнаружения дефектов. Одновременное сканирование множественными законами фокусировки под разными углами позволяет повысить КПД инспекции. Отпадает необходимость использования нескольких датчиков и призм. С помощью EPOCH 1000i можно проводить контроль в соответствии со стандартами ультразвуковых исследований, но с использованием возможностей визуализации фазированных решёток. EPOCH 1000i поддерживает конфигурацию ФР 16:16, функции А-скана и S-скана (секторное сканирование), а также опорные и измерительные курсоры для измерения размеров дефекта. Среди стандартных функций EPOCH 1000i особо можно выделить DAC/ВРврЧ для каждого закона фокусировки. На основе кривой DAC и А-скана определяются параметры дефекта.
Модели EPOCH 1000, EPOCH 1000iR и EPOCH 1000i поддерживают широкий спектр функций традиционного ультразвука как для стандартных задач, так и для сложных случаев контроля. Эти портативные приборы могут интегрироваться в небольшие системы высокоскоростного сканирования с традиционным ультразвуком. Во всех стандартных комплектациях присутствуют такие функции, как: частота повторения зондирующего импульса (ЧЗИ) до 6 кГц для точного высокоскоростного сканирования со сбором информации «за один приём»; настраиваемый генератор прямоугольных импульсов с технологией Perfect Square; цифровой приёмник с большим динамическим диапазоном, а также полный набор цифровых фильтров для обеспечения оптимального соотношения сигнал-шум.
Ультразвуковой метод контроля качества сварных соединений
Рекомендуем приобрести:
Установки для автоматической сварки продольных швов обечаек — в наличии на складе!
Высокая производительность, удобство, простота в управлении и надежность в эксплуатации.
Сварочные экраны и защитные шторки — в наличии на складе!
Защита от излучения при сварке и резке. Большой выбор.
Доставка по всей России!
Свойства ультразвуковых волн
Метод ультразвуковой дефектоскопии металлов и других материалов впервые был разработан и практически осуществлен в Советском Союзе в 1928—1930 гг. проф. С. Я. Соколовым.
Ультразвуковые волны представляют собой упругие колебания материальной среды, частота которых лежит за пределами слышимости в диапазоне от 20 кгц (волны низкой частоты) до 500 Мгц (волны высокой частоты).
Ультразвуковые колебания бывают продольные и поперечные. Если частицы среды перемещаются параллельно направлению распространения волны, то такая волна является продольной, если перпендикулярно-поперечной. Для отыскания дефектов в сварных швах используют в основном поперечные волны, направленные под углом к поверхности свариваемых деталей.
Ультразвуковые волны способны проникать в материальные среды на большую глубину, преломляясь и отражаясь при попадании на границу двух материалов с различной звуковой проницаемостью. Именно эта способность ультразвуковых волн используется в ультразвуковой дефектоскопии сварных соединений.
Ультразвуковые колебания могут распространяться в самых различных средах — воздухе, газах, дереве, металле, жидкостях.
Скорость распространения ультразвуковых волн C определяют по формуле:
C = fλ
где f — частота колебаний, гц;
λ — длина волны, см.
Для выявления мелких дефектов в сварных швах следует пользоваться коротковолновыми ультразвуковыми колебаниями, так как волна, длина которой больше размера дефекта, может не выявить его.
Получение ультразвуковых волн
Ультразвуковые волны получают механическим, термическим, магнитострикционным (Магнитострикция — изменение размеров тела при намагничивании) и пьезоэлектрическим (Приставка «пьезо» означает «давить») способами.
Наиболее распространенным является последний способ, основанный на пьезоэлектрическом эффекте некоторых кристаллов (кварца, сегнетовой соли, титаната бария): если противоположные грани пластинки, вырезанной из кристалла, заряжать разноименным электричеством с частотой выше 20 000 гц, то в такт изменениям знаков зарядов пластинка будет вибрировать, передавая механические колебания в окружающую среду в виде ультразвуковой волны. Таким образом электрические колебания преобразовываются в механические.
В различных системах ультразвуковых дефектоскопов применяют генераторы высокой частоты, задающие на пьезоэлектрические пластинки электрические колебания от сотен тысяч до нескольких миллионов герц.
Пьезоэлектрические пластинки могут служить не только излучателями, но и приемниками ультразвука. В этом случае под действием ультразвуковых волн на гранях кристаллов-приемников возникают электрические заряды малой величины, которые регистрируются специальными усилительными устройствами.
Методы выявления дефектов ультразвуком
Существуют в основном два метода ультразвуковой дефектоскопии: теневой и эхо-импульсный (метод отраженных колебаний.)
Рис. 41. Схемы проведения ультразвуковой дефектоскопии
а — теневым; б — эхо импульсным методом; 1 — щуп-излучатель; 2 — исследуемая деталь; 3 — щуп приемник; 4 — дефект
При теневом методе (рис. 41, а) ультразвуковые волны, идущие через сварной шов от источника ультразвуковых колебаний (щупа-излучателя), при встрече с дефектом не проникают через него, так как граница дефекта является границей двух разнородных сред (металл — шлак или металл — газ). За дефектом образуется область так называемой «звуковой тени». Интенсивность ультразвуковых колебаний, принятых щупом-приемником, резко падает, а изменение величины импульсов на экране электронно-лучевой трубки дефектоскопа указывает на наличие дефектов. Этот метод имеет ограниченное применение, так как необходим двусторонний доступ к шву, а в ряде случаев требуется снимать усиление шва.
При эхо-импульсном методе (рис. 41,6) щуп-излучатель посылает через сварной шов импульсы ультразвуковых волн, которые при встрече с дефектом отражаются от него и улавливаются щупом-приемником. Эти импульсы фиксируются на экране электроннолучевой трубки дефектоскопа в виде пиков, свидетельствующих о наличии дефекта. Измеряя время от момента посылки импульса до приема обратного сигнала, можно определить и глубину залегания дефектов. Основное достоинство этого метода состоит в том, что контроль можно проводить при одностороннем доступе к сварному шву без снятия усиления или предварительной обработки шва. Этот метод получил наибольшее применение при ультразвуковой дефектоскопии сварных швов.
Импульсные ультразвуковые дефектоскопы
Контроль сварных соединений осуществляется при помощи ультразвуковых дефектоскопов, которыми можно выявлять трещины» непровары, газовые и шлаковые включения в стыковых, угловых, тавровых и нахлесточных соединениях, выполненных дуговой, электрошлаковой, газовой и контактной сваркой. Контролировать можно как сварку сталей, так и сварку цветных металлов и их сплавов.
Электрическая схема дефектоскопов, состоящая из отдельных электронных блоков, смонтирована в металлическом кожухе, на передней панели которого находится экран электроннолучевой трубки и расположены рукоятки управления. Дефектоскопы укомплектованы призматическими щупами-искателями (рис. 42) с углами ввода ультразвукового луча 30, 40 и 50° (0,53; 0,7 и 0,88 рад). Придаются также и прямые щупы, при помощи которых ультразвуковые колебания вводятся перпендикулярно поверхности контролируемого изделия. Комплект щупов позволяет выбирать для каждого конкретного случая необходимую схему прозвучивания. Во всех щупах в качестве пьезоэлектрического преобразователя используются пластинки титаната бария.
Рис. 42. Конструктивная схема призматического щупа
1 — кольцо изоляционное; 2 — асбестовая прокладка; 3 — накладка контактная; 4 — втулка изоляционная; 5 — втулка; 6 — пластинка из титаната бария; 7 — корпус;8 — призма из плексигласа
В зависимости от количества щупов и схемы их включения ультразвуковые дефектоскопы могут быть двухщуповыми, в которых один щуп является излучателем, а другой приемником, или однощуповыми, где функция ввода и приема ультразвуковых колебаний выполняются одним щупом. Это возможно потому, что прием отраженного сигнала происходит во время пауз между импульсами, когда никаких других сигналов, кроме отраженных, на пьезоэлектрическую пластинку не поступает.
В качестве индикаторов дефектов применяются электроннолучевые трубки. Ряд дефектоскопов оснащен также световым (электрической лампочкой на искательной головке щупа) и звуковым (динамиком и телефонными наушниками) индикаторами.
Типовая блок-схема импульсного ультразвукового дефектоскопа, работающего по однощуповой схеме, приведена на рис. 43.
Рис. 43. Блок-схема импульсного ультразвукового дефектоскопа УЗД-7Н
1 — задающий генератор; 2 — генератор импульсов; 3 — пьезоэлектрический щуп; 4 — генератор развертки; 5 — приемный усилитель; 6 — электроннолучевая трубка; 7 — контролируемое изделие
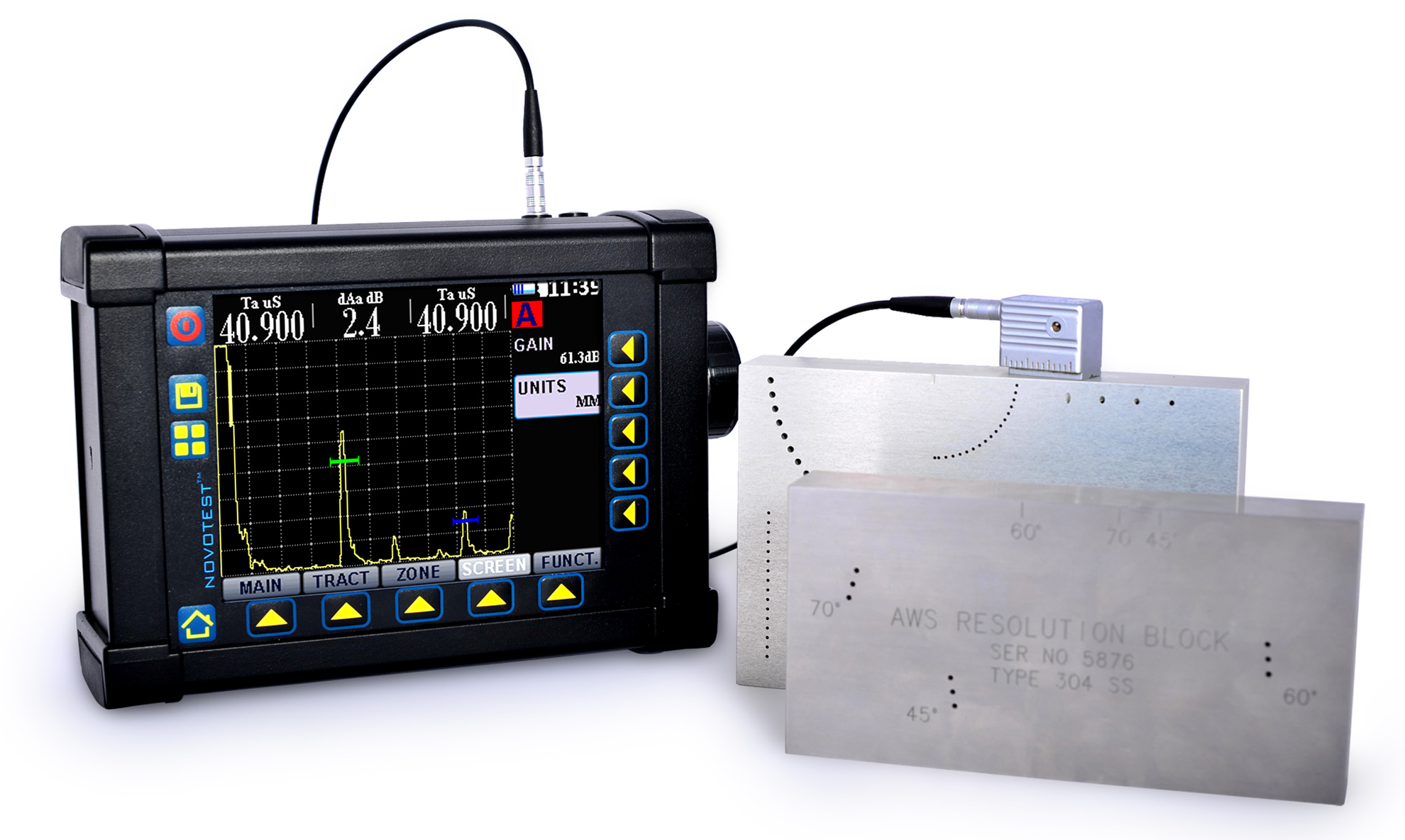
Генератор развертки обеспечивает развертку электронного луча трубки, который прочерчивает на экране электроннолучевой трубки светящуюся линию с пиком начального импульса.
При отсутствии дефекта в контролируемом изделии импульс дойдет до нижней поверхности изделия, отразится от нее и возвратится в пьезоэлектрический щуп. В нем механические колебания ультразвуковой частоты снова преобразуются в высокочастотные электрические колебания, усиливаются в приемном усилителе и подаются на отклоняющие пластины электроннолучевой трубки. При этом на экране возникает второй пик донного импульса (как бы отраженного от дна изделия).
Если на пути прохождения ультразвука встретится дефект, то часть волн отразится от него раньше, чем донный сигнал достигнет пьезоэлектрического щупа. Эта часть волн усиливается приемным усилителем, подается на электроннолучевую трубку и на ее экране между начальным и донным импульсами возникнет пик импульса от дефекта.
Благодаря синхронной работе генератора развертки луча, генератора импульсов и других устройств дефектоскопа взаимное расположение импульсов на экране электроннолучевой трубки характеризует глубину расположения дефекта. Расположив на экране трубки масштабные метки времени, можно сравнительно точно определить глубину залегания дефекта.
Методика ультразвукового контроля
Перед началом ультразвукового контроля зачищают поверхность сварного соединения на расстоянии 50—80 мм с каждой стороны шва, удаляя брызги металла, остатки шлака и окалину. Зачистку выполняют ручной шлифовальной машинкой, а при необходимости еще и напильником или наждачной шкуркой.
Чтобы обеспечить акустический контакт между щупом-искателем и изделием, зачищенную поверхность металла непосредственно перед контролем тщательно протирают и наносят на нее слой контактной смазки. В качестве смазки применяют автол марок 6, 10, 18, компрессорное, трансформаторное или машинное масло.
Затем проверяют правильность показаний дефектоскопа на эталонах сварных швов с заранее определенными дефектами.
Контроль стыковых соединений проводят путем поочередной установки щупа по обеим сторонам проверяемого шва.
Рис. 44. Схема проведения ультразвукового контроля
а — перемещение призматического щупа по поверхности изделия; б — контроль прямым лучом; в — контроль отраженным лучом
В процессе контроля щуп-искатель плавно перемещают вдоль обеих сторон шва по зигзагообразной линии (рис. 44, а), систематически поворачивая его на 5—10° в обе стороны для выявления различно расположенных дефектов.
Прозвучивание производят как прямым (рис. 44, б), так и отраженным (рис. 44, в) лучом. Стыковые соединения при толщине металла более 20 мм обычно проверяют прямым лучом. При толщине металла менее 20 мм усиление шва не дает возможности установить щуп так, чтобы ультразвуковой луч проходил через корень шва. В этих случаях контроль осуществляют однократно или двукратно отраженными лучами. При толщине металла менее 8 мм его прозвучивают многократно отраженным лучом.
Пределы перемещения щупа поперек шва зависят от угла ввода луча и способа прозвучивания и определяются по номограммам, прилагаемым к инструкции на эксплуатацию дефектоскопа. Чтобы обеспечить перемещение щупов в заданных пределах, их устанавливают в специальный держатель (рис. 45).
Рис. 45. Держатели призматических щупов
а — для контроля стыковых швов отраженным лучом; б — для контроля стыковых швов прямым лучом; в — для контроля угловых швов
Рис. 46. Схема определения размеров дефекта в стыковом шве
а — протяженности l; б — высоты h
Рис. 47. Конструктивная схема жидкостного глубиномера
1 — генератор дефектоскопа; 2 — цилиндр; 3 — компенсирующий объем; 4 — глубиномер; 5 — механизм перемещения поршня; 6 — жидкость; 7 — поршень; 8 — пьезоэлектрическая пластинка
При обнаружении дефекта в сварном шве на экране дефектоскопа появляется импульс. Условную протяженность его измеряют длиной зоны перемещения щупаискателя вдоль шва, в пределах которой наблюдается появление и исчезнование импульса (рис. 46, а). Условную высоту дефекта определяют как разность глубин, измеренных в крайних положениях щупаискателя, в которых появляется и исчезает импульс при перемещении щупа перпендикулярно оси шва (рис. 46, б). Условную высоту дефектов, имеющих большую протяженность, измеряют в месте, где импульс от дефекта имеет наибольшую амплитуду.
Глубину залегания дефекта определяют при помощи глубиномеров. Жидкостной глубиномер (рис. 47) состоит из пьезоэлектрической пластинки, которая возбуждается от генератора дефектоскопа одновременно с основной излучающей пьезоэлектрической пластинкой щупаискателя. Эта пластинка помещена в цилиндр с компенсирующим объемом. Цилиндр наполнен жидкостью и имеет поршень, связанный со шкалой глубиномера. При прозвучивании сварного шва на экране электроннолучевой трубки вместе с начальным и донным сигналом появляется так называемый служебный импульс, отраженный от поршня цилиндра глубиномера. Положение его на экране трубки дефектоскопа определяется положением поршня в цилиндре. Передвигая поршень, совмещают служебный импульс с импульсом, отраженным от дефекта, и по шкале глубиномера определяют глубину залегания дефекта. При совмещении поршня с донным импульсом можно определить толщину металла. Подобные глубиномеры могут быть присоединены к любому ультразвуковому импульсному дефектоскопу.
Повышения скорости контроля можно достичь применением несложных устройств (рис. 48), позволяющих осуществлять перемещение дефектоскопа вдоль шва и возвратно-поступательное движение щупа. Щуп-искатель устанавливается на тележке устройства и соединяется с ультразвуковым дефектоскопом. На этой же тележке находится механизм передвижения, состоящий из электродвигателя мощностью 12 вт, червячных пар и кривошипного механизма.
Рис. 48. Схема автоматизированного контроля стыков трубопроводов с помощью специального приспособления
1 — контрольный механизм; 2 — труба; 3 — роликовая цепь; 4 — коробка со щупом; 5 — ультразвуковой дефектоскоп
Значительно увеличивается надежность и скорость контроля при использовании автоматического ультразвукового дефектоскопа ДАУЗ-169, позволяющего контролировать сварные соединения при толщине листов от 6 до 16 мм. Он представляет собой датчик, установленный на автоматически передвигающейся каретке, соединенной гибким кабелем со шкафом с электронными блоками.
Дефекты регистрируются записью на диаграммной ленте и краскоотметчиком на контролируемом шве, работа которого дублируется световой сигнализацией. Скорость контроля составляет 1 м/мин. Применение его значительно увеличивает надежность и производительность процесса контроля сварных швов.
Оформление результатов контроля
Результаты ультразвуковой дефектоскопии согласно ГОСТ 14782—69 фиксируют в журнале или в заключении, обязательно указывая:
а) тип сварного соединения; индексы, присвоенные данному изделию и сварному соединению; длину проконтролированного участка шва;
б) технические условия, по которым выполнялась дефектоскопия;
в) тип дефектоскопа;
г) частоту ультразвуковых колебаний;
д) угол ввода луча в контролируемый металл или тип искателя, условную или предельную чувствительность;
е) участки шва, которые не подвергались дефектоскопии;
ж) результаты дефектоскопии;
з) дату дефектоскопии;
и) фамилию оператора.
При сокращенном описании результатов дефектоскопии каждую группу дефектов указывают отдельно.
Характеристика протяженности дефекта обозначается одной из букв А, Б, В. Цифрами обозначают: количество дефектов в шт.; условную протяженность дефекта в мм; наибольшую глубину залегания дефекта в мм; наибольшую условную высоту дефекта в мм.
Буква А указывает, что протяженность дефекта не превышает допускаемую техническими условиями. Буква Б используется для характеристики дефекта большей протяженности, чем типа А. Буквой В обозначают группу дефектов, отстоящих друг от друга на расстоянии не более величины условной протяженности для дефектов типа А.
Ниже приводится пример сокращенной записи результатов дефектоскопии в журнале или в заключении.
На участке шва сварного соединения С15 (ГОСТ 5264—69), обозначенном индексом МН-2, длиной 800 мм обнаружены: два дефекта типа А на глубине 12 мм, один дефект типа Б условной протяженностью 16 мм на глубине 14—22 мм, условной высотой 6 мм и один дефект типа В условной протяженностью 25 мм на глубине 5—8 мм.
Сокращенная запись результатов испытания выглядит так:
С15, МН-2, 800; А-2-12; Б-1-16-22-6; В-1-25-8.
Техника безопасности при ультразвуковом контроле
К работе с ультразвуковыми дефектоскопами допускают лиц, прошедших инструктаж по правилам техники безопасности и имеющих соответствующее удостоверение. Перед проведением контроля на большой высоте, в труднодоступных местах или внутри металлоконструкций оператор проходит дополнительный инструктаж, а его работу контролирует служба техники безопасности.
Ультразвуковой дефектоскоп при работе заземляют медным проводом сечением не менее 2,5 мм2. Работать с незаземленным дефектоскопом категорически запрещается. При отсутствии на рабочем месте розетки подключать и отключать дефектоскоп может только дежурный электрик.
Запрещается проводить контроль вблизи сварочных работ при отсутствии защиты от лучей электрической дуги.
Л.П. Шебеко, А.П. Яковлев. «Контроль качества сварных соединений»
Сварные дефектоскопия — Энциклопедия по машиностроению XXL
Ультразвуковой контроль основан на способности ультразвуковых волн отражаться от поверхности раздела двух сред.
Объем дефектоскопии при изготовлении резервуара включал контроль качества в объеме 100% длины сварных швов оболочки резервуара методом ультразвуковой дефектоскопии и 15% длины сварных швов в местах пересечении меридиональных и горизонтальных (поясных) швов радиографическим методом. Механические испытания и металлографические исследования сварных соединений выполнялись а объеме требований ОСТ 26-291.

Объем контроля ультразвуковой дефектоскопией или радиографическим методов стыковых, угловых, тавровых и других сварных соединений сосудов и их элементов (днищ, [c.49]
Указанный объем контроля относится к каждому сварному соединению. Места сопряжений (пересечений) сварных соединений подлежат обязательному контролю ультразвуковой дефектоскопией или радиографическим методом. [c.50]
При невозможности осуществления ультразвуковой дефектоскопии или радиографического контроля из-за недоступности отдельных сварных соединений или при неэффективности этих методов контроля (в частности, швов приварки штуцеров и труб внутренним диаметром менее 100 мм) контроль качества этих сварных соединений должен производиться другими методами в соответствии с инструкцией, согласованной с Госгортехнадзором России. Указания об использованном методе контроля заносятся в паспорт сосуда. [c.50]
При диагностировании технического состояния сварных сосудов и аппаратов ультразвуковой метод применяется при толщинометрии и дефектоскопии. Применяются приборы трех типов
[c.197]
Ультразвуковая дефектоскопия (УЗД) наряду с радиографической является регламентируемым методом контроля качества сварных сосудов и аппаратов в соответствии с требованиями действующих НТД. [c.203]
Ультразвуковая дефектоскопия аппаратов должна проводиться в соответствии с требованиями ГОСТ 14782 и ОСТ 26-2044. УЗД предназначена для контроля продукции на наличие дефектов (обнаружение дефектов) типа нарушений сплошности и однородности материалов и их сварных соединений для измерения глубины и координат их залегания. [c.203]
Правильность показаний дефектоскопа проверяют на эталонах сварных швов с заранее определенными дефектами. [c.205]
Очевидно, трудно ожидать других результатов, когда вся методология диагностирования почти полностью нацелена на поиск дефектов. Не отрицая важности результатов дефектоскопии, следует все же признать, что такой подход явно недостаточен для таких крупногабаритных конструкций, каковыми являются сварные сосуды и особенно колонные аппараты, реакторы и т. п.
[c.209]
При изготовлении сварных сосудов и аппаратов в соответствии с требованиями ОСТ 26-291 цветная дефектоскопия является регламентируемым методом контроля качества сварных соединений. Цветной или магнитопорошковой дефектоскопии следует подвергать сварные швы, не доступные для осуществления контроля радиографическим или ультразвуковым методом (в частности, швов приварки штуцеров и труб внутренним диаметром менее 100 мм), а также сварные швы сталей, склонных к образованию трещин при сварке. [c.219]
Цветная дефектоскопия сварных соединений должна проводиться в соответствии с ГОСТ 18422 и ОСТ 26-5. [c.219]
Ультразвуковой дефектоскопии (УЗД) или просвечиванию необходимо подвергать до 100% от общей длины сварных швов обследуемого сосуда, причем обязательному контролю следует подвергать все продольные швы обечаек корпуса, места пересечения продольных и кольцевых швов, стыки днищ с обечайкой корпуса, а также сварные швы приварки штуцеров диаметром > 100 мм. Зачистка мест контроля под УЗД от окалины ржавчины до металлического блеска производится вдоль стыков шириной по 140-150 мм по обе стороны шва.
[c.249]
Цветной дефектоскопии (ЦЦ) следует подвергать те участки сварных соединений, где имеется вероятность образования поверхностных трещин при изготовлении и эксплуатации. К таким местам относятся узлы вварки наиболее нагруженных при эксплуатации штуцеров диаметром > 100 мм, перекрещивающиеся швы, места исправления швов. Контролю Ц Д подлежат ремонтные сварные швы и зона вокруг них шириной не менее 30 мм. [c.249]
Пневматические испытания проводятся с соблюдением особых мер предосторожности только при положительных результатах тщательного внешнего и внутреннего осмотров, диагностики технического состояния аппарата неразрушающими методами контроля (ультразвуковой и цветной дефектоскопии сварных соединений, толщинометрии и замеров твердости), а также прочностных расчетов основных несущих элементов с учетом их фактических толщин.
[c.250]
НВ трещина длиной 300 мм, а методами ультразвуковой дефектоскопии зафиксировано ее развитие в металле шва на расстояние 1200 мм. Характер разрушения хрупкий, поверхность излома покрыта продуктами коррозии, растрескивание начинается от непровара (рис. 13). В зоне термического влияния под корневым слоем в области очага разрушения обнаружен участок укрупненного бейнитного зерна с твердостью 266-285 НУ. В следующих далее слоях сварного соединения в зоне термического влияния наблюдается мелкозернистая нормализованная структура с твердостью 210-221 НУ. Сероводородное растрескивание сварного соединения инициировал концентратор напряжений — непровар в сочетании с бейнитной структурой металла, обладающей высокой твердостью. [c.42]
Такие дефекты, как изменение толщины стенки трубы, потеря металла, отложение, вмятина, вздутие, закат, включение, расслоение, выявленные внутритрубной дефектоскопией, одно-.значно идентифицируются в том случае, когда каждый из них имеет явно выраженные признаки своего типа, и отсутствует наложение посторонних сигналов. На практике дефекты, как правило, имеют сложную форму. Часто наблюдаются схожие признаки (включение или расслоение, водородное расслоение или вмятина, вздутие или отложение и другие). В области сварных швов происходят потери сигнала, которые значительно снижают информативность измерений.
[c.98]
Цветная, магнитопорошковая или вихретоковая дефектоскопия сварных швов и основного металла мест вварки штуцеров и патрубков, приварки горловин люков, зон сопряжений обечайки с днишами, мест приварки опорных узлов, зон проведенного ранее ремонта (внутри и снаружи сосуда или трубопровода) производится в соответствии с [98-101, ПО]. [c.162]
Неразрушающий контроль сварных соединений и ПОУ методами ультразвуковой дефектоскопии осуществляют в соответствии с [102, 103, 113-115]. [c.162]
Гамма-дефектоскоп Газпром (см, табл. 10) предназначен для просвечивания сварных стыков трубопровода через две стенки. [c.297]
Гамма-дефектоскопы ДАР-2 и ДАР-3 предназначены для радиографического контроля качества сварных соединений труб с трубными досками теплообменных агрегатов, используемых на тепловых и атомных электростанциях. Аппараты обеспечивают просвечивание сварного соединения панорамным пучком излучения за одну экспозицию. Чувствительность контроля стальных и титановых сварных соединений составляет 0,15—0,2 мм в диапазоне толщин труб и их диаметров, приведенных в табл. 13.
[c.297]
Сталь. Методы ультразвукового контроля. Общие требования Контроль неразрушающий. Швы сварные. Методы ультразвуковые Аппараты рентгеновские аналитические. Общие технические условия Источники излучения с изотопом цезий-137 для гамма-дефектоскопов. Типы, основные параметры и размеры [c.473]
С помощью пьезометрического щупа ультразвукового дефектоскопа, помещаемого на поверхность сварного соединения, в металл посылают направленные ультразвуковые колебания (рис. 80). Ультразвук вводят в изделие отдельными импульсами под углом к поверхности металла. При встрече с дефектом возникает отраженная ультразвуковая волна, которая воспринимается либо другим щупом (приемным в случае двухщуповой схемы), либо тем же (подающим при однощуповой схеме) во время паузы между импульсами. Отраженный ультразвуковой сигнал преобразуется в электрический, усиливается и подается на трубку осциллографа, где фиксируется наличие дефекта в соединении в виде пика на экране осциллографа.
[c.151]
В горизонтальных сосудах допускается местное перекрытие седловыми опорами кольцевых (поперечных) сварных швов на общей длине не более 0,35 t D, а при наличии гилд-кладного листа — не более 0,5 яО, где D — наружный диаметр сосуда. При этом перекрываемые участки сварных швов ни всей длине должны быть проверены методом радиографии или ультразвуковой дефектоскопии. [c.44]
Ультразвуковая дефектоскопия и радиографический кон-i роль производятся с целью выявления в сварных соединениях вну фенних дефектов (трещин, непроваров, пор, шлаковых включений и др.). [c.49]
В настоящее время для обнаружения и идентификации дефектов используется широкий спектр методов неразрушающего контроля (НК). Современная классификация методов НК включает девять видов контроля электрический, магнитный, вихретоковый, радиоволновой, тепловой, визу-ально-измерительный, радиационный, акустический и проникающими веществами. По причинам конструктивного и эксплуатационного характера при диагностировании сварных аппаратов используются, в основном, следующие методы НК магнитный контроль (ГОСТ 24450), капиллярный контроль (ГОСТ 24522), акустический контроль (ультразвуковая дефектоскопия ГОСТ 14782 и толщинометрия, метод акустической эмиссии), радиационные методы (ГОСТ 7512 рентгеновский, гамма- и бета-излучением). При этом следует отметить, что радиационные методы применяются преимущественно на стадии изготовления аппаратов, а использование магнитного метода носит эпизодический харак гер. Руководящие документы по оценке 1екущего состояния
[c.175]
Вначале рассмотрим нормирование дефектов в сварных соединениях, не склонных к квазихрупким (хрупким) разрушениям. При разработке данной методики норми1ювания необходимо учитывать влияние местоположения дефектов на прочность сварных соединений, а также реальные возможности производства и уровень развития дефектоскопии. Удобным является так называемое жесткое нормиро-
[c. 108]
Визуальный контроль основных материалов, сварных соединений и изделий проводится невооруженным глазом и с применением оптических приборов (луп, микроскопов, визуально-оптических приборов — цистоскопов, эндоскопов, бароскопов, флексоскопов, биноклей, перископических дефектоскопов, зеркал, зрительных труб и др.). [c.140]
В настоящее время наиболее распространенным из отечественных УЗ-дефектоскопов является дефектоскоп марки УД2-12, а толщиномеров — УТ-93П. В ЦНИИТМАШе разработан УЗ-дефектоскоп УДЦ -105 М, который обеспечивает автоматизированное измерение эхо-сигнала и его отображение на цифровом табло. В дефектоскопе марки УДЦ-100 также имеются 1налогичные возможноеги, а на цифровом табло отображаются координаты залегания дефектов. Высокой степенью автоматизации обладает дефектоскоп УЗД-18, предназначенный для контроля сварных соединений с толщиной до 60 мм. Дефектоскоп УЗД-22М (МГТУ им. Баумана) обладает гювышенной чувствительностью и имеет возмож-тюсть выдавать распечатку координат и формы дефектов.
[c.179]
В отличие от методов просвечивания, ультразв>тсовые методы позволяют успешно выявлять именно трещиноподобные дефекты. Спецификой ультразвукового метода контроля является то, что он не дает конкретной информации о характере дефекта, так как на экране дефектоскопа появляется импульс, величина которого пропорциональна отражающей способности обнаруженного дефекта. Последняя зависит от многих факторов размеров дефекта, его геометрии и ориентации по отношению к направлению распространения ультразвуковых колебаний. В связи с тем, что эти параметры при контроле остаются неизвестными, обнар> -женные дефекты обычно характеризуются эквивалентной площадью, которая устанавливается в зависимости от интенсивности полученного сигнала Достоинствами л льтразвукового метода являются его меньшая по сравнению с методами просвечивания трудоемкость, а также возможность достаточно точного определения координат обнаруженного дефекта. Как показала практика применения ультразвукового метода, он не позволяет достаточно надежно обнаружить дефекты, лежащие вблизи поверхности изделия в связи с экранированием сигнала от дефекта сигналом ог поверхности. Это обстоятельство также необходимо ч читы-вать при практическом использовании данного метода контроля. Ультразвуковые методы используют как для контроля дефектов металла листов и поковок на стадии их изготовления, так и для контроля сварных соединений, для диагностики трубопроводного транспорта. На данном принципе созданы внутритрубные инспекционные снаряды (ВИС) — Ультраскан-СД, которые, двигаясь внутри трубы, считывают информацию о техническом состоянии трубопроводов. При этом фиксируется толщина стенки, коррозионные каверны, расслоения мета.лла, дефекты стресс-коррозионного происхождения.
[c.61]
Метод цветной дефектоскопии применяют для обнаружения трещин, невидимых невооруженным глазом. Трещины выявляются после нанесения на предварительно зачищенную поверхность проникающего, смывающего и проявляющего растворов в соответствии с Методическими указаниями по цветнс й дефектоскопии деталей и сварных швов . [c.99]
Гамма-дефектоскопы Магистраль и Магистраль 1 (см.
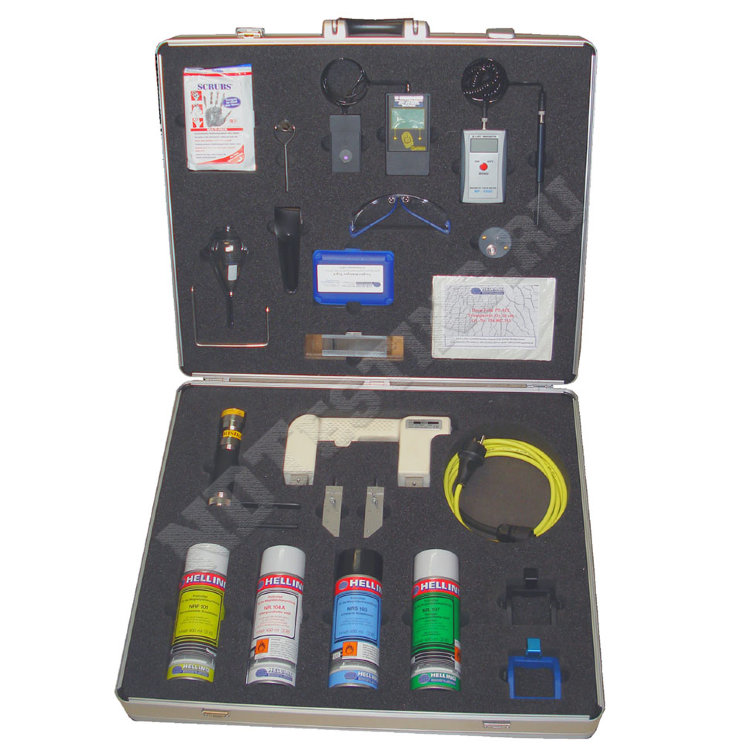
Контроль неразрушающйй. Дефектоскопы ультразвуковые. Методы измерения основных параметров 23694—79 Контроль неразрушающий. Паста магнитная для магнитно-порошковой дефектоскопии КМ-К. Технические условия 23702—79 Контроль неразрушающий. Преобразователи ультразвуковые. Основные параметры и методы их измерений 23764—79 Гамма-дефектоскопы. Общие технические условия 23829—79 Контроль неразрушающйй акустический. Термины и определения 23858—79 Соединения сварные стыковые и тавровые арматуры железобетонных конструкций. Ультразвуковые методы контроля качества. Правила приемки
[c.474]
Клюев В. В., Малкес Л. Я. и др. Материалы для капиллярной и магиитио-люминесцентной дефектоскопии. — Сб. Передовой опыт неразрушающего контроля качества сварных соединений. Киев Изд. ИЭС им. Патона АН УССР, 1979, с. 113-126. [c.477]
Воспроизводящее устройство УВ-ЗОГ (более совершенное по сравнению с дефектоскопом МДУ-2У) предназначено для считывания и воспроизведсния на экране электронно-лучевой трубки полей рассеяния от дефектов, зафиксированных на магнитной ленте в процессе магнитографического контроля стыковых сварных соединений трубопроводов, резервуаров и других конструкций. Оно используется также в полевых испытательных лабораториях, передвижных автолабораториях в условиях строительства магистральных трубопроводов и в заводских лабораториях.
[c.44]
Принцип действия дефектоскопа основан на построчном считывании с магнитной ленты полей, зафиксированных в процессе контроля сварных соединений и преобразований информации в электрические сигналы многоэлементным микроферрозондо-вым преобразователем, с последующей обработкой и частотной селекцией сигналов и регистрацией результатов на электрохимической бумаге. Запись сигналов ведется по четырем каналам — по одному каналу записывается плоскостное полутоновое изображение рельефа магнитного поля, записи по остальным каналам дают возможность судить по амплитуде сигнала от дефектов и их местоположении по толщине изделия. Получение в дефектоскопе двухмерного плоскостного изображения достигается за счет возвратно-поступательного движения по электрохимической бумаге подвижного электрода и пропускания через пишущие электроды (подвижный и неподвижный) электрического тока, пропорционального величине сигнала, поступающего с феррозондов. Подвижный электрод движется синхронно с движением феррозондов над магнитной лентой. Степень потемнения бумаги оказывается тем большей, чем больший по амплитуде сигнал снимается с феррозондов.
[c.46]
Автоматизированные феррозондовые дефектоскопы для контроля труб выпускает ин-т д-ра Ферстера в ФРГ. Дефектоскоп типа Дискомат-6251 предназначен для комбинированного контроля (методом вихревых токов и методом считывания полей дефектов) качества продольного сварного шва ферромагнитных труб с помощью вращающегося измерительного преобразователя в форме диска. Диаметр контролируемых изделий 57—600 мм, скорость контроля при сплошном сканировании— до 1,0 м/с. В дефектоскопе предусмотрены раздельная индикация внешних и внутренних дефектов, а также регулирование границ сортировки. К дефектоскопу можно подключать устройства для маркировки дефектных труб и оценки размеров дефектов, а также блок управления сортирующим устройством, производящим автоматическую разбраковку труб на две или три группы, [c.57]
Ферромагнитные сварные трубы диаметром до 60 мм контролируют дефектоскопом ЭЗТМ. Проходной трансформаторный ВТП, выполненный в виде трех одновитковых катушек из полых проводников, внутри которых циркули-
[c.140]
При контроле сварных швов толщиной 200 мм и более чувствительность дефектоскопа иногда оказывается не достаточной. Применяют преобразо ватели с малыми углами наклона пониженными частотами, пьезопла СТИНЫ большого размера (см. табл. 19) контроль только прямым лучом. [c.260]
Стол дефектоскопии представляет собой сварную раму, на верхней плоскости которой смонтированы поворотные плиты с преобразователями дефектоскопов. Поворотные плиты используют при настройке дефектоскопов, для чего преобразователи поворачивают на такой угол, при котором пруток можно перемен1,ать вручную. На раме стола дефектоскопа смонтирован пульт управления линии. Все пять ведущих роликов приводятся в движение от общего привода, установленного на подающем роликовом конвейере. [c.327]
Ультразвуковой контроль сварных швов · SONOTEC
Контрольное оборудование
Требуется цифровой ультразвуковой дефектоскоп (например, SONOSCREEN ST10 или SONOWALL 70 с обновлением дефектоскопа). Прибор должен быть способен передавать и принимать ультразвуковые импульсы и отображать их в полностью выпрямленном виде (А-скан). Наклонные преобразователи, поддерживающие автоматические тригонометрические расчеты и программное обеспечение DAC, DGS или AWS, являются абсолютным минимумом для контроля сварных швов. Крайне важно, чтобы устройство было откалибровано и изготовлено в соответствии со стандартом EN-12668-1.В большинстве отраслей оборудование, используемое для официального контроля сварных швов, должно калиброваться по этому стандарту не реже одного раза в год.
Ультразвуковые датчики: двухэлементные датчики с прямым лучом (например, серии TS и TL), датчики с наклонным лучом (например, серии WS, WM и WL) — выбор датчика сильно зависит от контролируемого материала; необходимо учитывать его геометрию, тип сварного шва, толщину, минимальный размер обнаруживаемого дефекта и многие другие факторы. Чтобы упростить процесс выбора датчика, общее эмпирическое правило состоит в том, чтобы использовать датчики с частотой 4 МГц для диапазона толщины от 8 до 50 мм и датчики с частотой 2 МГц для толщины 50 мм и выше. Для правильной проверки необходимо использовать два угла. Для более тонких сварных швов до 20 мм рекомендуются углы 70° и 60°. Для более толстых объектов предпочтительны 45° и 60°.
Экзаменационный эскиз
Следующим шагом является рисование экзаменационного эскиза. На нем должны четко отображаться зона движения преобразователя, часть сварного шва, охваченная контролем, и точка, в которой ультразвуковой луч попадает на деталь. На испытуемом объекте должна быть постоянно установлена и отмечена на эскизе нулевая точка измерения.Должна быть обеспечена возможность точного воспроизведения процедуры испытаний на основе отчета, сделанного после завершения испытаний.
Контактное вещество
Обычно это гель на водной основе, масло, жир или клей для обоев. Очень важно, чтобы одна и та же контактная жидкость использовалась на протяжении всей процедуры тестирования (т. е. калибровки, оценки потерь при переносе, настройки чувствительности и тестирования).
Портативный ультразвуковой дефектоскоп, Мастер обнаружения дефектов leeb530 Детектор сварных швов, Измерение пузырьков трещин: Amazon.

В настоящее время недоступен.
Мы не знаем, будет ли этот товар снова в наличии. ]]>
Технические характеристики для данного элемента
Фирменное наименование | YARUIFANSEN |
---|---|
Ean | 0723093734330 |
Part Number | leeb530 |
UNSPSC Код | 41110000 |
СКП | 723093734330 |
Амазон.
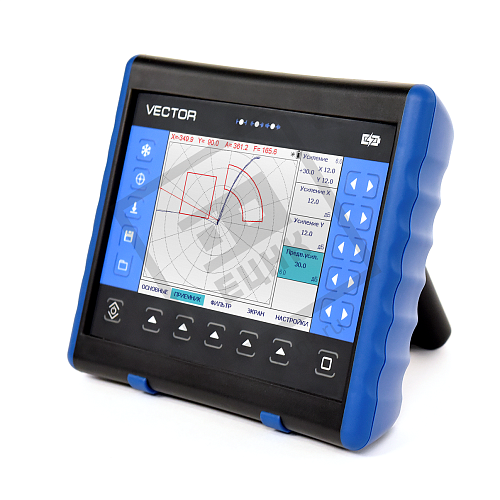
В настоящее время недоступен.
Мы не знаем, будет ли этот товар снова в наличии.
- Убедитесь, что это подходит, введя номер модели.
- Цифровой ультразвуковой дефектоскоп Производитель MFD550B, основанный на ультразвуковом принципе, цифровой ультразвуковой дефектоскоп, вы можете быстро и точно тестировать, направлять, оценивать и диагностировать различные дефекты, такие как трещины, укорачивание, воздушные отверстия внутри заготовки без разрушения.
- С диапазоном 0-9999 мм он может соответствовать требованиям общего контроля дефектов в обрабатывающей промышленности, металлургической промышленности, металлообрабатывающей промышленности, химической промышленности и т. д.
Примечание. Изделия с электрическими вилками предназначены для использования в США.Розетки и напряжение различаются в зависимости от страны, и для этого продукта может потребоваться адаптер или преобразователь для использования в вашем регионе. Пожалуйста, проверьте совместимость перед покупкой.
Спецификации ETher NDE WeldCheck | ||
Зонд | Проверка сварки 2 | WeldCheck+ |
Соединители | 12-ходовой Lemo 2b (абсолютный, мостовой и отраженный) и соединение Lemo 00 (для одноэлементных абсолютных датчиков). | Возможна одновременная работа зонда с использованием 12-ходового Lemo и Lemo 00 |
Поворотный | 600–3000 об/мин — ETher Mercury Drive (ADR002), Hocking 33A100, Rohmann MR3, SR1 и SR2 Drive (требуется специальный адаптер) | |
Частота | Одиночная частота.![]() | Двойная частота. = 10 Гц — 12,8 МГц |
Усиление | ||
Комбинезон | от -18 до +100 дБ, 0.Шаги 1, 1 и 6 дБ (максимум 100 дБ) | |
Вход | 0 дБ или 12 дБ | |
Привод | 0 дБ, 6 дБ и 10 дБ (эталонное значение 0 дБ 1 мВт на 50 Ом) | |
Макс. отношение X/Y | +/-100,0 дБ | |
Фаза | ||
Диапазон | 0,0–359,9°, шаг 0,1° | |
Автофаза | Позволяет автоматически устанавливать фазовый угол на заранее установленный угол | |
Фильтры | ||
Нормальный фильтр верхних частот | от постоянного тока до 2 кГц или фильтр нижних частот, в зависимости от того, что ниже с шагом 1 Гц.![]() | |
Нормальный фильтр нижних частот | от 1 Гц до 2 кГц или четверть самой низкой испытательной частоты, в зависимости от того, что ниже, с шагом в 1 Гц | |
Баланс | ||
Руководство | 14 внутренних балансировочных грузов; 2,2 мкГн, 5,0 мкГн, 6,0 мкГн, 6,5 мкГн, 7,0 мкГн, 7,5 мкГн, 8,2 мкГн, 12 мкГн, 15 мкГн, 18 мкГн, 22 мкГн, 30 мкГн, 47 мкГн, 82 мкГн | |
Автоматический | Выбор оптимальной сбалансированной нагрузки | |
Тревоги | ||
Коробка | Полностью настраиваемый, стоп-кадр, тональный или визуальный | |
Сектор | Полностью настраиваемый, стоп-кадр, тональный или визуальный | |
Выход | Трансформатор с открытым коллектором (50 В пост.![]() | |
Дисплей | ||
Тип | 5.7 дюймов (145 мм), 18-битный цвет, читаемость при дневном свете | |
Видимая область | 115,2 мм (по горизонтали) x 86,4 мм (по вертикали) | |
Разрешение | 640 x 480 пикселей | |
Флип | Ручное или автоматическое изменение ориентации экрана для использования левой или правой рукой | |
Цветовые схемы | Настраиваемый пользователем темный, яркий и черно-белый | |
Конфигурируемый экран | Полноэкранный, одиночный, двухточечный или двухпанельный с переменным размером, расположением и функциями e.г. XY, временная база, водопад и счетчик | |
Режимы отображения | Spot, Time base (0,1–20 секунд x 1–200 разверток и до 55 секунд), Waterfall и Meter с удержанием пика и % считывания | |
Гратикулы | Нет, сетка (4 размера 5, 10, 15 и 20 % FSH), полярная (4 размера 5, 10, 15 и 20 % FSH) | |
Смещение | Точечное положение: Y = от -50 до +50, X = от -65 до +65 % | |
Цифровой спот | Отображение по осям X,Y или R,θ | |
Сводка показаний позиции | Отображение всех настроек в устаревшем формате | |
Съемный накопитель данных | ||
Хранилище настроек | Micro SD до 32 ГБ, вмещает более 10 000 настроек | |
Сохраненный экран | Micro SD до 32 ГБ, вмещает более 10 000 снимков экрана | |
Выстрелы | Комплексное воспроизведение и хранение записей | |
Повтор записи | Запись данных трассировки в режиме реального времени и воспроизведение на приборах и настольных ПК до 164 секунд | |
Выходы | ||
Подключение к ПК | USB (полное дистанционное управление ПК плюс данные в реальном времени) | |
Цифровая беспотенциальная сигнализация | On Lemo 12-ходовой транзистор с открытым коллектором (36 В постоянного тока при макс.![]() | |
VGA | Полный 15-канальный выход VGA | |
Общий | ||
Языки | английский, французский, испанский, русский, японский, китайский, турецкий | |
Уровень проверки | При поставке система включает детальную функциональную проверку и калибровку 2-го уровня верификации сроком действия 2 года в соответствии со стандартом ISO 15548-1:2013 | .|
Самотестирование при включении | Система выполняет самотестирование при запуске внешней оперативной памяти, оперативной памяти SD, акселерометра, карты Micro SD, буфера ЖК-экрана | |
Мощность | ||
Внешний | 100–240 В, 50–60 Гц, 30 Вт | |
Аккумулятор | Внутренний 7.![]() | |
Время работы | До 8 часов с щупом-карандашом 2 МГц, фоновой подсветкой 30 % и до 6 часов с вращающимся приводом при 3000 об/мин, рабочий цикл 50 % | |
Время зарядки | 2,5 часа. время зарядки, одновременная зарядка и работа | |
Физический | ||
Вес | 1,2 кг, 2,7 фунта | |
Размер (ШхВхГ) | 237.5 мм x 144 мм x 52 мм / 9,4 дюйма x 5,7 дюйма x 2,1 дюйма | |
Материал | Алюминиевый сплав Mg Si 0,5 с порошковым покрытием | |
Рабочая температура | от -20 до +60 °С | |
Температура хранения | Хранение до 12 месяцев от -20 до +35 °C Номинальная +20 °C | |
Степень защиты IP | 54 |
Все о дефектоскопах, включая ультразвуковое и вихретоковое обнаружение
Изображение предоставлено: rumruay/Shutterstock. ком
— это электронные устройства, используемые в различных производственных процессах для выявления несоответствий на поверхностях или в нижележащих материалах, таких как сварные швы. Дефектоскопы используют ультразвуковые или вихретоковые средства для выявления дефектов материалов и могут быть переносными или стационарными установками. Ключевые характеристики включают тип датчика, диапазон обнаруживаемых дефектов или толщин, а также предполагаемое применение. Информацию о других датчиках см. в нашей статье «Типы датчиков».
Ультразвуковой
Звуковые волны обеспечивают глубоко проникающий неразрушающий метод проверки металлов и композитов на наличие таких дефектов, как пористость, неправильная зернистая структура, расслоение и т. д. Контроль сварных швов является самым большим применением технологии, где она используется для обнаружения включений, пористости. , отсутствие проникновения и отсутствие сплавления. Другое использование — обнаружение усталостных трещин в машинах. При этом высокочастотные (0,1-15 МГц) звуковые волны передаются в материал через преобразователь и пленку контактной смазки, а результирующее эхо записывается и отображается для анализа.Анализ данных остается чем-то вроде искусства и обычно проводится сертифицированными ультразвуковыми инспекторами — по крайней мере, для оценки сварных швов. Стандарты доступны в таких организациях, как Американское общество сварщиков (AWS), которые предоставляют эталоны для испытательных образцов с известными геометрическими характеристиками или дефектами.
При типичном испытании сварного шва датчик перемещается по обеим сторонам сварного шва. Поверхностные несоответствия, такие как сварочные брызги или вершина самого сварного шва, могут препятствовать передаче ультразвуковых волн в материал и должны быть устранены (в случае брызг) или измерения должны выполняться под углом (в случае сварки). Корона).В специальных преобразователях используются пластиковые клинья, вставленные между зондом и деталью, для преобразования продольных волн в сдвиговые, поперечные, поверхностные или лэмбовские колебательные моды путем дифракции.
Импульсно-эхо-системы являются наиболее распространенными системами, в которых используется один преобразователь, но иногда используются системы сквозной передачи, в которых используются отдельные передающие и приемные преобразователи.
Доступны как ручные, так и автоматические ультразвуковые дефектоскопы. Автоматические системы иногда погружают деталь и датчик в водяную баню, чтобы исключить необходимость непосредственного контакта датчика с деталью и, следовательно, износ поверхности датчика.
Ограничения ультразвуковой дефектоскопии включают форму объекта, шероховатость поверхности, размер зерна, структуру материала, ориентацию любых дефектов, избирательность несплошностей и навыки оператора. ЭМАП, или электромагнитно-акустические передатчики, полагаются на магнитострикционный эффект для передачи и приема сигналов. Они могут работать на небольшом расстоянии от детали, что исключает необходимость использования контактных жидкостей или удаления накипи. Специальные датчики предназначены для других сложных задач контроля, таких как проверка точечных сварных швов. Также доступны датчики для использования с композитными конструкциями.
Вихревой поток
Вихретоковый контроль с неглубоким проникновением используется для измерения толщины термической обработки, глубины корпуса, покрытия и т. д. в металлических деталях, а также для обнаружения несплошностей или изменений материала. Вихревые токи индуцируются в металлах всякий раз, когда они попадают в магнитное поле переменного тока. Эти вихревые токи создают вторичное магнитное поле, которое противодействует индуцирующему полю, изменяя кажущееся сопротивление индуцирующей катушки.Вихревые токи высокой частоты чувствительны к поверхностным дефектам, в то время как вихревые токи низкой частоты могут проникать глубже в материал.
Вихретоковое сканирование широко используется в авиационной промышленности в качестве как стационарных, так и переносных систем для проверки колес, тормозов и шасси, крепежных деталей и крепежных отверстий, поверхностей крыльев и шарниров, опор двигателя и т. д. Мобильность систем делает их эффективными в электроэнергетике и нефтегазовой промышленности, где они достаточно компактны, чтобы их можно было использовать в местах с доступом по канату.Автопроизводители, переработчики металлов и операторы железных дорог также используют вихретоковый контроль для обнаружения поверхностных трещин и подповерхностных дефектов и коррозии, для контроля сварных швов, для сортировки черных и цветных металлов и т. д.
Вихретоковая дефектоскопия предлагает альтернативу магнитопорошковой дефектоскопии для обнаружения поверхностных трещин. Обычно используются зонды типа «карандаш» или «блин», некоторые из которых способны обнаруживать трещины размером до 0,1 мм. Экранированные датчики можно использовать для обнаружения несплошностей вблизи краев или между разнородными материалами, такими как крепежные детали из железа в алюминиевых конструкциях.Специальные вращающиеся щупы облегчают осмотр отверстий в планерах и т. д.
Осмотр планера использует энергию низкой частоты (110 Гц-10 кГц) для обнаружения подповерхностных трещин глубиной до 10 мм в алюминии и подобных материалах, которые были бы невидимы под поверхностью или покрыты покрытиями. Обычно рекомендуется, чтобы диаметр зонда был в два раза больше глубины предполагаемого дефекта, но не больше. Частоты испытаний определяют глубину проникновения из-за явления переменного тока, называемого «скин-эффектом».Глубина проникновения тока – это глубина, на которой вихревые токи равны 37% их поверхностного значения.
Различают абсолютные и дифференциальные испытательные катушки. Абсолютный тест катушек без использования эталонного объекта в другой катушке. Вместо этого в дифференциальных катушках используются две катушки, соединенные последовательно друг с другом. Катушки могут иметь круглую форму, катушку или зонд для окружающих объектов, вставки в отверстия или перемещения по поверхностям.
Как и для большинства методов неразрушающего контроля, для вихретоковой дефектоскопии требуется должным образом обученный оценщик.Одним из главных преимуществ этого метода является то, что он подходит для автоматизированных процессов, когда приборы могут быть настроены на игнорирование всех, кроме неожиданных аномалий в проверяемых материалах.
Вихретоковая дефектоскопия применяется в некоторых неожиданных местах, включая аттракционы, светофоры, решетки тюремных камер и т. д., а также в некоторых более распространенных местах, таких как стальные здания и мосты.
Радиографические и визуальные системы
Гамма- и рентгеновский контроль являются давними методами оценки качества сварных швов.Эти методы упоминаются здесь лишь вскользь, поскольку они не относятся к категории датчиков/детекторов. То же самое можно сказать и о системах технического зрения, способных обнаруживать дефекты поверхности, такие как отслаивание краски и т. д.
Резюме
В данной статье представлено краткое обсуждение дефектоскопов с акцентом на ультразвуковой и вихретоковый методы дефектоскопии. Для получения дополнительной информации о других продуктах обратитесь к другим нашим руководствам или посетите платформу поиска поставщиков Thomas, чтобы найти потенциальные источники поставок или просмотреть подробную информацию о конкретных продуктах. Конкретную информацию о контроле сварных швов можно найти на сайте Американского общества сварщиков.
Другие датчики Артикул
Еще из раздела Инструменты и элементы управления
Автоматическое обнаружение дефектов на изображениях TOFD для неразрушающего контроля во время сварки
Шон В. Лоусон, Исследовательская группа по мехатронным системам и робототехнике, Университет Суррея. Эта статья появляется в ноябрьском/декабрьском выпуске журнала Inspectioneering Journal за 1996 год. Основной подход к процедуре осмотра и ремонта при сварке почти не изменился за три десятилетия. Обычной практикой по-прежнему является проверка сварного шва только после завершения программы сварки. Таким образом, к моменту обнаружения дефекта значительное время и деньги тратятся на завершение сварки бракуемого компонента. Кроме того, обычно на дефект наносится большое количество дополнительных сварных швов, что увеличивает стоимость ремонта и снижает качество компонента.
Если бы неразрушающий контроль (НК) выполнялся во время сварки в режиме реального времени, это дало бы значительные преимущества в плане затрат и программ для широкого круга отраслей промышленности. Бракованные сварные швы могут быть идентифицированы как таковые, прежде чем тратить время и деньги на завершение сварки. Кроме того, ремонт можно было бы выполнить быстрее и экономичнее, если бы он выполнялся до дальнейшего наплавления, а обнаружение большого количества дефектов во время сварки позволило бы соответствующим образом отрегулировать параметры процесса до завершения производственного цикла.Таким образом, если контроль неразрушающего контроля может проводиться между проходами сварки без задержки в процедуре сварки, то некоторый уровень улучшенного контроля и отсутствие простоев практически гарантированы. Более того, если бы результат проверки также можно было интерпретировать автоматически, то можно было бы предвидеть комплексный онлайн-контроль процесса сварки.
Этот контент доступен зарегистрированным пользователям и подписчикам
Зарегистрируйтесь сегодня, чтобы разблокировать эту статью бесплатно.
Создайте бесплатную учетную запись и получите доступ к:
|
Текущие подписчики и зарегистрированные пользователи могут войти в систему сейчас.
ВИХРЕТОКОВЫЙ ДЕФЕКТОСКОР WELDCHECK
Products
Двойной CP ROV Bottleпродукты — Подводная система UT
Подводная система UT Products — Система насоса AUT System Autshan Aut Pump Products — CP ROV BLASH Oceanshan CP ROV Botton С ROVEДвойной CP ROV Bottle
AncaScan EFG ROV CP Bottle
Rental
LinkQuest UWM2000H Подводный модем
RDT Videovave System
Satel 3ASD Radio Modem
Rental Sastlyne Dunker 6
5 — подводные и оффшор — геофизический — Поддонный профилограф
KLEIN K-CHIRP 3310 ПОДДОННЫЙ ПРОФИЛЕРАренда — Подводный и морской — Геофизический — Гидролокатор бокового обзора
KLEIN 3000 ЦИФРОВАЯ СИСТЕМА БОКОВОГО СКАНИРОВАНИЯГЕОАКУСТИЧЕСКАЯ СИСТЕМА KLEIN03 БУКСИРУЕМАЯ DSCAN TOWFISH DEPRESSOR
Edgetech 4200 300/600 кГц
Edgetech 4200 300/900 кГц
Аренда — подводная ND Offshore — Геофизические магнитометры
Геометрические моменты G880 Marine Cesesium MagnetometerGeometrics G882 Marine Cesesium Pavor MagnetoMer
Marine Magnetics Explorer Mini Magnetometer 300M
Marine Magnetics Sea Spy Magnetometer 1000 METER
Аренда — Подводная и оффшор — Гидрография и обследование — Multibeam / Батимиметрический
Valeport Midas SVPValeport MIDAS SVP
Renishaw Mern SVS
Renishaw Merlin Laser Scanner
TreiTech Seanet Seabat
Teledyne Reson Seabat 7125 8125 Multibeam Echosounders
Tritech Seeking 704
Nexus MKV Мультиплексор
Nexus MKIV MKIV Multixer
Macartne Nexus MK I оптоволоконный мультиплексор
HYPACK / HYSWEEP MBES COMPITION и POST Обработка
R2sonic I2NS SIM-ящик и IP68 IMU (Appleanix Waveticaster)
Valeport Swift SVP
R2sonic 2024 широкополосный Multibeam Echo Sounder 170 KHZ 450 KHZ
R2sonic 2024 широкополосный Multibeam Echo Sounder UHR 700 кГц
R2sonic 2022 Multibeam Echo Sounder
R2sonic 2022 широкополосный Multibeam Echo Sounder 3000m
— подводные и оффшорные — Гидрография и опрос — Echo Sounders
Knudsen двойной частоты ECHO ECHOODOM ECHOTRAC MKIII DF3200 C / W 24/200 кГц преобразователей
Оффшор — Гидрография и обследование — Глубинные датчики
TRITech Seaking 704Паритуационный 8CDP 700-I Digiquartz Интеллектуальные Глубинные Датчики
Valeport Mini IPS Интеллектуальная Датчик Датчик Давления
— Подводные и оффшорные и оффшорные — Гидрография и обследование — Winch и Cable Catchers
Klein PUrfish Аренда Depressor— Подводные и оффшорные — Гидрография и обследование — Пакеты сбора данных / обработки данных
Coda DA2000 Система сбораSoda F180 Прецизионные системы и позиционирования
Аренда — Подводные и оффшорные — Гидрография и обследование — Термальные принтеры
EPC 1086NT СЕРИЯ 2000 ТЕПЛОВАЯ СЕТЕВАЯ ПЕЧАТЬ RGeoprinter 93315CTP Dual Interface Thermal Recorder
Ultra 3710 Thermal Recorder
Аренда
— Подводные и оффшорные — Гидрография и опрос — Altimeters
Multi-Repeat Alteimeters3 DataSonics PSA900 Программируемый сонар AltimeterАренда — Подводные и оффшорные — ROV Датчики — Камеры
Macartney Luxus Compact Low Light CameraImenco Reef Arch Camera
Imenco Bull Arcuk HD Camera
Nexus MKV Multilexer
Macartney Luxus Low Light Camera
IMENCO Hammerhead Color / Zoom Camera
Imenco Basking Shark Camera
Imenco Silvertip широкоугольная камера
Imenco Tiger Shark Camera
Tritech Seaspy Mini Camera C / W Light Ring
Treitech Oceanspy Mini Camera C / W Light Congspy
Kongsberg Asprey 1366 MKII Zoom Coongsberg
Kongsberg osprey 1386 P & T Camera
Kongsberg osprey 14-102 Rotate и Tilt
Kongsberg OE14-208 ЦИФРОВАЯ ФОТОКАМЕРА СО ВСПЫШКОЙ И НОУТБУКОМ
KONGSBERG OE 14-308 Diver Digital Starts Camera
Kongsberg OE 14-376 Камера для инструментов
Oceanscan VS3003 Цифровые фотоаппараты C / W VS3003 PC
CONALSCAN VS3870 Цветовая камера
Oceanscan DTR100Z ADF взрывозащищенная камера
Nexus MKIV мультиплексор
Macartney Nexus MK I оптоволоконный мультиплексор
Konsberg Аренда OE14-366
— Подводные и оффшорные — ROV Датчики — Труба и кабельное Отслеживание6
Оптимальная система отслеживания ОрионTSS 440 Система отслеживания труб
TSS 350 Система отслеживания кабеля
ELSEC 5000 Diver Удерживаемый магнитометр
Innovalatum Tone Generator
Tinsley 5915 Tone Generator
Tinsley 5910 Тестовый набор
Nexus MKV Мультиплексор
Nexus MKV Мультиплексор
Macartne Nexus Mk I Оптоволоконный мультиплексор
Аренда — Подводные и оффшорные — ROV Датчики — Допплерские Logs
0 KHZ Workhorse
CDL MINIPOS NAV DOPPLER
NEXUS MKV MULTIPLEXER
NEXUS MKIV MULTIPLEXER
Аренда Macartney Nexus Mk I Волоконно-оптический мультиплексор
— Подводные и оффшорные — ROV Датчики — Sonars / Profillers 92016
Tritech Gemini 720IS Multibeam Imaging Sonar 4000M VDSLBlueView M900 2D Визуализация SONAR
TRITECH Seant Control Unite
TRITECH MULTICOMM UNDICATE BOX
BlueView P900E Multi-Beam Imaging Sonar
Kongsberg Mesotech 1071 серии Sonar
Kongsberg Mesotech 1000 SONAR
TRITECH Super MeaPrine DST
Tritech Super Seaking Dual Profific Profific Conar
Nexus MKV Мультиплексор
Nexus MKIV Мультиплексор
Macartney Nexus MK I Pibele Optix Multibexer
Gemini 720IM Multibeam SONAR
BLUEVIEW M2250-900 Двойная частота
ARIS Explorer 3000
ARIS Rotator AR2
Tritech Gemini 720is Multibeam Imaging Sonar 1000M VDSL
Rental — Подводные и оффшорные — ROV-датчики — Gyros
IXSEA Octans NanoTeledyne TSS Meridian Surveyer Gyrocompass
IXSEA OCTANS MKIV 3000 метров 9002 3 IXSEA OCTANS MKIII 3000 метров F.

Nexus MKV Мультиплексор
Nexus MKIV мультиплексор
Macartney Nexus Mk I Волоконно-оптический мультиплексор
IXSEA IXSEA Инерциальная навигационная система
IXSEA Rovins Gyro Inits Enabled
Rovins Nano 2020
Nortek DVL1000 — 4000 м
Аренда — Подводные и оффшорные — ROV Датчики — Датчики движения
TSS DMS-05 Датчик движенияCDL Mini Tilt
Nexus MKV Мультиплексор
Nexus MKIV мультиплексор
Macartney Nexus Mk I Волоконно-оптический мультиплексор
Аренда — Подводные и оффшорные — ROV Датчики — Инерционные системы
IXSEA Rovins Gyro ins ФИН-Инерционная навигационная системаNexus MKIV Мультиплексор
RDI 300/600/1200 KHZ Workhorse Navigator
Nexus MKV Мультиплексор
Macartney Nexus Mk I Волоконно-оптический мультиплексор
— Подводные и оффшорные — ROV Датчики — Лампы и лазеры
океан ГЕНЕРАТОРMACARTNEY LUXUS POWER LED
OSPREY 1130 U/W ПРОЖЕКТОР ДЛЯ КАМЕРЫ 90 023 OSPREY 1132 U/W SPOT LAMP
OSPREY 1135 U/W SPOT LAMP
ROS WDL-75 WET & DRY LAMP
IMENCO ANGEL SHARK LASER
NEXUS MKV MULTIPLEXER
NEXUS MKIV MULTIPLEXER
4 — Rambe Multiplexer и Offshore датчики
4 — Аренда 906s
Valeport SVX2Аренда — Подводные и оффшорные — CTD / SVP
Valeport Monitor CTDValeport CTD606 Самостоятельная запись
Valeport CTD604 MK3
Valeport CTD606 MK3
Valeport Midas SVP
Valeport Mini SVS
Valeport CTD600
Valeport SVX2
Аренда — подводные и оффшорные — экологические — экологические — барометры
Air DB2 Digital Barometerаренду — подводные и оффшорные экологические — текущие метры
RDI 300/600/1200 KHZ Workhorse NavigatorValeport 308 текущий счетчик
Valeport 803 ROV (ЭЛЕКТРОМАГНИТНЫЙ)
VALEPORT BFM 106 ИЗМЕРИТЕЛЬ ТОКА
Аренда — подводные и морские — экологические — уровнемеры 906 16
Valeport Midas TMS TIDE & ECHOURY MONITORING SYSTELValeport 740 Tide Maene
Aanderaa WLR7 & WLR8
Valeport Aanderaa WLR7 & WLR8
Valeport Midas WLR
— подводные и оффшорные — ROVS
Seabotix LBV300-5
Seabotix LBV200-4
Buddy Rov TMS
Outland 1000
Outland 2000
VideOray ROV Pro 4 Rugged Base
VideOray ROV Pro 4 Стандартная база
Прокат Seabotix LBV300-5
Seabotix LBV300-5
— подводное обеспечение и оффшорное оборудование для дайвера.
Баня Бандли
RSL FMD System
Teledyne CDL Diverlevel
UFM7 / UPRS6 Комбинированное магнитное поле, УФ и окружающий световой счетчик
ASAMS 3 Подводная магнитная система инспекции частиц
ASAMS 12 Подводная магнитная система инспекции частиц
прокат — подводное и оффшорное средство — акустическое положение — USBL
SONARDYNE 8271SONARDYNE 8190
EASYTRAK АЛЬФ Портативный
Kongsberg Cnode Maxi Transponders
HPR 410P — система SSBL
Ranger 2 Simrad Rep
Kongsberg Simrad RPT 319
Kongsberg Simrad RPT 324
Kongsberg Simrad MPT 319
Kongsberg Simrad SPT 314 319
SIMRAD SIMRAD SPT 314 319
SONARDYNE SIMRAD SUB-MINI TRANSPONDER RESPONDER WSM
Прикладная акустика 219 Micro Beacon / Transponders
Применяемая акустика 945 MIDI Beacon / Transponders
962/965 и 972 Fat Boy BeaCon / Transponders
PAM 2520
Применяемая акустика 982 Универсальное зарядное устройство
Прикладная акустика 935H MIDI Beacon / Transponders
Sonardyne Ant Transponder Тестовый набор
Sonardyne Compatt 6 Transponder
Sonardyne Iwand 6G
Sonardyne Rovnav 6
Active Acoustics 1019 Mini BeaCon
Прикладная акустика 1082 Smart Switch
Применяемая акустика 3510 PAM Портативный
IXBLUE GAPS USBL
Sonardyne Mini-Ranger 2 USBL
WSM 6+ AUV / ROV позиционирование маяка (USBL)
KONGSBERG CNODE MINI S
Аренда — подводная И оффшор — акустическое позиционирование — LBL
Sonardyne Compatt 5Sonardyne Ant Transponder Test
Sonardyne Mini Rovnav
Sonardyne Data Fusion Engine
Sonardyne Rovnav EHF / MF
Sonardyne Compatt 6 Transponder
Sonardyne Dunker 6
Sonardyne Iwand 6G
Sonardyne Rovnav 6 Прокат
— подводные и оффшорные — мультиплексоры
MATRIX MK II +Macartne Nexus Mk II +
Macartney Nexus Mk I Nexus MKV мультиплексор
Nexus MKIV мультиплексор
5 — подводные и оффшорные — ROV Tooling — Zip Jeam
Macartney Nexus MK I Fiber Оптический мультиплексорTritech Ultra Zipjet Насосная система
Nexus MKV Мультиплексор
Nexus MKV Мультиплексор
— подводные и оффшорные — ROV Tooling — резания, очистки и крутящий момент
WebTool Rutter RCV75HDTorque Tool Class 1-4 (API 17D)
Аренда — Подводные и морские установки — ROV Tooling — Caviblasters
CAVIBL ASTER 1222 E50/60Аренда — Подводная инспекция — Подводная толщинометрия — Подводный толщиномер в руках водолаза
CYGNUS DIVE MK2CYGNUS DIVE
CYGNUS THICKNESS GAUGE DIVER HELD
Прокатный толщиномер — Подводный толщиномер Inspected — Subsea Gauge Inspection
CYGNUS MK5 ROV ROV — подводная проверка — обнаружение недостатки. Подводная инспекция — обнаружение подводных недостатков — подводные MPI
UFM7 / UPRS6 Комбинированное магнитное поле, УФ и окружающий световой счетчик
Bowtech ROV Подводный черный свет
ASAMS 3 Подводная магнитная система инспекции частиц
ASAMS подводная ультрафиолетовая лампа
Аренда — Подводная инспекция — Подводная дефектоскопия Tion — ACFM
U31D ACFM подводный дайверный дайверACFM Crack Microgauge Amigo
Amigo
— подводная инспекция — Подводная проверка — Подводная проверка. Системы подводной камеры
Imenco Bull Arcark HD CameraImenco Hammerhead Color / Zoom Camera
Imenco Basking Shark Camera
Imenco Silvertip Широкоугольная камера
Imenco Tiger Shark Camera
TRITECH Seaspy Mini Camera C / W Light Ring
Tritech Oceanspy Mini Camera C / W Light Ring
Kongsberg Osprey 1366 MKII Zoom Camera
Kongsberg Asprie 1386 P & T Camera
Kongsberg osprey 14-102 вращается и Tilt
Kongsberg OE14-208 Цифровая фотокамера с Flash и ноутбуком
Kongsberg OE 14-308 Diver Digital Starts Camera
Kongsberg OE 14-376 Камера для инструментов
Oceanscan VS3003 Digital Sharts C / W Flash & ноутбук PC
Oceanshan VS3870 Цветная камера
Oceanshan ВЗРЫВОЗАЩИЩЕННАЯ КАМЕРА DTR100Z ADF
КАМЕРА ДЛЯ СЛАБОГО ОСВЕЩЕНИЯ MACARTNEY LUXUS
KONSBERG OE14-366
Аренда — Подводная инспекция — мониторинг коррозии
БатакоррометрОкеанский CP ROV бутылки и на заказ программное обеспечение с зондом
CP контактный зонд
CP Beoxity Shate
Buckley Marine Survey Kit
DUAL CP ROV бутылка
Oceanscan EFG ROV CP бутылка
— подводная инспекция — Определение затопленного члена
RESL FMD System Rental — Topside NDT & Inspection — обнаружение дефектов — Вихреемое текущее дефектное обнаружение Eddyfi Sharck Rested Atdy Actore Artray (ECA)Nortec 600
PHASEC3 Addy нынешние дефекты Deletors
WeeldCheck
PEC-GS Lyft Probe
Eddyfi Lyft Импульсный вихревой ток (PEC)
EDDYFI EECTANE 2 Addy нынешний Atte Artray (ECA)
Eddyfi PECA Probe
EDDYFI Reddy
Rental — Topside NDT & Ispection — обнаружение дефектов — Ультразвуковое обнаружение дефектов
Olympus EPOCH XTOLYMPUS EPOCH LTC
OLYMPUS EPOCH IV
SONATEST SITESCAN СЕРИЯ D+
G E’s USM GO
OLYMPUS EPOCH 600
ZONOTIP
SITESCAN D-50
MASTERSCAN D-70
MICAGE III серии
RAILSCAN 125+
CTS-30C
Siui Smartor
Аренда Olympus Epoch 650
— Topside NDT & Inscection — обнаружение дефектов — Обнаружение дефектов поэтапных массивов / TOFD / сопоставление коррозии6
Olympus TOFD Scanner
Olympus Omniscan SX PA
Olympus Omniscan MX2 16: 128 Олимпус
Olympus Omniscan MX2 32: 128PR
Olympus Hydroform Rest
Scanner Cobra
Scanner Cobra
Scanner
Olympus HSMT Flex Scanner
Seanscan Aut Насосная система
Phoenix Wren ToFD Kit
Phoenix Remen ToFD AWP & CWP
Gekko
Rental — Topside NDT & Ispection — обнаружение дефектов — вычисленная рентгенография
DURR CR35 NDTRental — Topside NDT & Инспекция – обнаружение дефектов – цифровая рентгенография
СИСТЕМА GE’S INSPECTION DXR250U-W Аренда – неразрушающий контроль и проверка верхнего строения Comption — Обнаружение дефектов — Tube Iris Probe
Eddyfi Iris Probe
Eddyfi MagniSi Software
Olympus MultiScan M MS 5800 Tube Accessection System
Eddyfi Electane 2 Addy Tooth Array (ECA)
Аренда — Topside NDT & Inspection — Обнаружение дефектов — Магнитная частица Осмотр
oeanscan My2 yoke с портативным пакетом аккумулятораJohnson & Allen Polymag постоянный магнит
BAUA и WEEDON LUMACHECK двойной УФ и белый свет, проверка
Lumazon двойной ультрафиолетовый и белый свет светодиодный инспектор лампы
Levyhill двойной светодиодный счетчик
Spectroline Bib-150p UV лампа
Magnaflux 10-ДЮЙМОВАЯ МАГНИТНАЯ КАТУШКА
ПОСТОЯННЫЙ МАГНИТ KEIYU
ELY TOPSIDE UV LIGHT
LABINO BIGBEAM HELIOS UV LED DUO MID-LIGHT
S-LED
Аренда — неразрушающий контроль и проверка верхней части — дефектоскопия — дефектоскопия — магнитопорошковая дефектоскопия — MY2 YOCE
Аренда — Неразрушающий контроль и проверка верхнего строения — Дефектоскопия — ACFM
ACFM Krack Microgauge AmigoPace
Amigo
Pace
Amigo 2
AmiGo 2
Floormap3dim-R
— Topside NDT & Inspection — обнаружение дефектов — Addy end Array
Аренда — Topside NDT & Ispection — Толщина Толщина — Ультразвуковая толщина 4
Cygnus 4 Многократный эхо Ультразвуковой цифровая толщина 20023 Olympus 38DL Plus SystemOlympus Panametrics 37DL Plus System
Olympus Panametrics 36DL PLUS System
Sonatest T-Gage V серия
Cygnus 6+ Pro
Zonotip
CTS-30C
Danatronics Echo DLW9
Rental — Topside Неразрушающий контроль и контроль – Толщиномер – Ультразвуковой прецизионный толщиномер
DANATRONICS UPG-07DLCW ПРЕЦИЗИОННЫЙ ТОЛЩИНОМЕРMICROGAGE III SERIES
Аренда – Верхний НК и контроль – Толщинометрия – Ультразвуковая искробезопасная толщиномер 0EECS5
CY — Неразрушающий контроль и инспекция верхнего строения — Измерение толщины — Карьерный отдел H IMUGING ELCOMETER 119 PIT-CAMENT прокат — Topside NDT & Inspection — визуальный осмотр — дистанционная визуальная проверка (RVI) OLYMPUS IPLEX ULTRALITEOLYMPUS MXR VIDOCOPOPE (3 метра)
WOHLER VIS220 20 MTR.

Pearpoint P332 FlexiProbe 120 M
INUKTUN SPECTRUM 45 P & T CAMERA
FORTE Visio Prime Inspector (6 м)
WOHLER VIS 250
WOHLER VIS 350 Rental Arrand Camera
— Topside NDT & Inspection — визуальный осмотр — искробезопасные видеооскоты
PEARPOINT P374 ZONE 0 34-ММ КАМЕРА И КАМЕРА 61MTSАренда — Неразрушающий контроль и осмотр верхних строений — Визуальный осмотр — Тепловое изображение
ТЕПЛОВАЯ КАМЕРА FLIR Аренда — Неразрушающий контроль и осмотр верхнего строения — Визуальный осмотр — Лазерное сканирование SCANNER
FARO LASER SCANNER FOCUS 3D
Аренда — Неразрушающий контроль и проверка верхней части — Твердость T ESTING
EQUOTIP 3 Портативный твердотельный тестерEquostat 3 портативный твердотельный тестер
PROCEQ EQUOTIP 550
PROCEQ EQUOTIP LIVE UCI
PROCEQ EQUOTIP Live Leeb-D
PROCEQ EQUOTIP 550 — UCI
PROCEQ EQUOTIP 550 — Rockwell
ProCeq Equotip 550 — Leeb-D
Аренда — Topside NDT & Inspection — Газ и радиация — RAD Мониторы
NDS 1000S Radiation MonitorTracerco T404 PED Radiation Monitor
Valeport SVX2
Rental — Topside NDT & Inspection — PCD 1-20 кВ
Pipple / Holiday DelectorELCOMETER 319 DEWPOINT METER
ELCOMETER 456 Толщина покрытия Метры
Пряжки Детектор Праздник PD130
Аренда PD130
— Topside NDT & Inspection — Ferits Content Meter
Fischer Feritscope FMP30— Topside NDT & Invection — PMI Guns / Gas Анализаторы
THERMO SCIENTIFIC NITON XL2 GOLDD XRF ANALYSER/PMI GUNTHERMO SCIENTIFI C NITON XL2 Analyzer
Аренда Olympus XRF Vanta
— Topside NDT & Inspection — Тестирование бетона6
PROCEQ GPR Live
Расходные материалы — Зонды — Phoenix
Расходные материалы — Кабели и потенциальные материалы6
Ультразвуковые приводыТекущие потенциальные потенциалы
Расходные материалы — Couplatt
Сонагель W Соединительные материалыРасходные материалы — MPI / DPI Чернила и краска — Aerosol Paint
Fluxo 3Fluco 5
Fluco R175
Fluco P1215
Fluco S190
Fluxo 6
Fluxo 4
Fluxo Pht
Fluxo Rht
Fluxo NHT
Расходные материалы NHT
— MPI / DPI чернила и краска — порошок
Расходные материалы — MPI / DPI чернила и краска — подводные МПИ чернила и аксессуары6
Neoaastra DGCUWSaterland Flask
Burmah Castrol полосы
ARDOX 8544
Расходные материалы — испытательные блоки
ИСПЫТАТЕЛЬНЫЙ БЛОК ФАЗИРОВАННОЙ РЕШЕТКИИСПЫТАТЕЛЬНЫЙ БЛОК DAC
ИСПЫТАТЕЛЬНЫЙ БЛОК A5
4 Step Block
A6 Test Block
A6 Тестовый блок
Эдди Тестовый блок
5 Step Block
A7 Тестовый блок
V2 Тестовый блок
V1 Тестовый блок
Расходные материалы — CR Визуализация Пластины
5 Расходные материалы — Фильм
AGFA Обычная рентгенография ФильмРасходные материалы — Разное
Магнитный правительАналоговый магнитометр / гаус-метр
Цифровые магнитометры / гаусс, метры
A8L Светодиодный рентгеновский просмотр фильма
A2 Светодиодный рентгеновский режим просмотра фильма
CR PHANTOM
Magnetive Materage Meter / Ferromaster
TAM Parel
ГАЗОВЫЙ ДЕТЕКТОР
Обслуживание и калибровка – Разное
S-LEDS-LED
.
