Ультразвуковой дефектоскоп для контроля сварных соединений

Неразрушающий контроль соединений – современный метод диагностики наличия и глубины дефектов в узлах и деталях. В отношении оценки последующей работоспособности сварных соединений особенно эффективной признана ультразвуковая дефектоскопия. Дело в том, что в подавляющем большинстве производственных ситуаций имеющиеся неоднородности сварного шва располагаются так, что хорошо отражают именно акустические волны сверхвысокой частоты. Этот метод проверки и заключает в себе ультразвуковой дефектоскоп.
В чём заключается эффективность неразрушающего контроля сварных соединений?
Идеально однородные среды в процессе взаимодействии с источником ультразвуковых колебаний не ослабляют амплитуду звуковых волн. Совсем иное происходит, если сканируются реальные объекты. При наличии в них участка с искажениями первоначальной структуры всегда наблюдается существенное искажение и уменьшение амплитуды звукового давления, которое количественно проявляется в виде ослабления или даже полного поглощения ультразвуковых волн.
Интенсивность таких искажений устанавливается законом ослабления
P=Р0 exp(-αd),
где: Р0 – исходное значение амплитуды звукового давления; Р – значение на выходе из диагностируемого сварного шва; d – толщина шва; α – коэффициент ослабления.
Поскольку параметр d чаще представляют как расстояние до источника ультразвукового излучения, то считается, что звуковая волна имеет вид полусферы, а потому ослабление будет равномерным по всем направлениям. В практике измерений оно обычно устанавливается в децибелах (дБ), поэтому может быть вычислено по формуле
α = 20/d∙lg(P0/Р)
Промышленный ультразвуковой дефектоскоп, применяемый для определения сплошности и качества сварных швов, оценивает интенсивность эхо-сигнала, которая пропорциональна амплитуде звукового давления:
p0/P = H0/H
где: Н0 и Н соответственно — амплитуды звукового сигнала на входе и выходе из прибора.
Для практически применяемого диапазона частот 1…15 МГц (что и случается для подавляющего большинства металлических изделий) интенсивность эхо-сигналов соотносится с относительным ослаблением ультразвукового сигнала следующими соотношениями:
Н/Н0 | 1,26 | 1,78 | 2,82 | 5,01 | 10,0 | 21,62 |
Мощность сигнала, дБ | 2 | 5 | 9 | 14 | 20 | 30 |
Из представленной таблицы следует, что применение оценочного критерия логарифмической интенсивности ультразвукового сигнала может эффективно фиксировать изменения в его амплитуде.
Причинами ослабления ультразвуковых волн происходит вследствие поглощения и рассеивания сигналов. Энергия поглощения превращает колебательную энергию в тепловую. Она пропорциональна частоте ультразвуковых колебаний, поэтому ультразвуковые дефектоскопы для контроля сварных соединений изготавливаются с максимально возможными генерируемыми частотами.
С повышением частоты облегчается фокусировка прибора, благодаря чему распознавание неоднородностей или дефектов улучшается. При этом должны соблюдаться следующие условия:
- Размер оцениваемой неоднородности должен быть больше половины длины волны.
- Направление сканирования должно быть перпендикулярным направлению хода звукового луча.
- Прибор не должен использовать так называемые критические частоты (для металлических конструкций это, например, частоты близкие к 6 МГц), при которых из-за явления дифракции ультразвуковых волн чувствительность метода резко снижается.
Энергия рассеивания более существенна для поликристаллических тел. Поэтому для крупнозернистых структур (например, чугуна) ультразвуковая дефектоскопия малочувствительна. Также неэффективно ультразвуковое сканирование при пониженных температурах окружающей среды.
Для получения ультразвуковых колебаний применяются два вида источников: магнитострикционные генераторы и пьезоэлектрические преобразователи. Каждое из устройств имеет свои рациональные области применения.
Конструкции ультразвуковых пьезоэлектрических дефектоскопов
Пьезоэффект заключается в том, что при силовом воздействии на определённые кристаллические вещества (изоляторы с полярно расположенными осями) в них возникают напряжения определённого знака, которые, в свою очередь, инициируют электрические поверхностные заряды. При этом величина напряжений прямо пропорциональна механической нагрузке, что очень важно именно в конструктивном смысле, поскольку упрощает конструкцию прибора. Таким образом цена ультразвукового дефектоскопа для контроля сварных соединений будет невысокой.
Пьезоэлектрический эффект обратим, а потому использующие его ультразвуковые дефектоскопы быстро переналаживаются, и не нуждаются в сложной регулировке. При этом при помощи прямого пьезоэффекта ультразвуковые волны обнаруживаются, а при помощи обратного – генерируются.
Принцип работы пьезогенератора дефектоскопа следующий. На конденсаторные пластины, которые наложены на кристалл, подаётся переменное электрическое напряжение. Это вызывает колебание кристалла с той же частотой. В качестве преобразователей используют такие материалы, как кварц, титанат бария, сульфат лития и др. При наличии внешнего давления атомы в структурной ячейке пьезоэлемента сдвигаются, что и является моментом начала разряда конденсаторных пластин. При изготовлении ультразвукового дефектоскопа для контроля сварных соединений, использующего подобный принцип, излучатель вырезается таким образом, чтобы плоскость колебания по отношению к толщине рассматриваемого сварного шва излучала продольные волны. Если требуется оценить неравномерность структуры соединения на значительной площади, то используют пластину, вырезанную в перпендикулярном направлении. Тогда с приложением напряжения она будет излучать поперечные волны, которые будут равномерно распространяться в толще исследуемого соединения.
Корпуса пьезоизлучателей изготавливают из керамики, что повышает уровень требований к условиям работы ультразвуковых дефектоскопов для контроля сварных соединений. В частности, им противопоказаны удары и сотрясения корпуса.
Магнитострикционные преобразователи ультразвуковых дефектоскопов
Магнитоскрикция заключается в деформации ферромагнитной детали, которая размещена в силовом магнитном поле. Длина этой детали изменяется в зависимости от вида силовых линий магнитного поля, её материала, температуры и степени намагниченности. В ультразвуковых дефектоскопах используются ферромагнетики, относительное изменение длины которых – не менее 10-5.
Работают такие преобразователи следующим образом. В приборе создаётся переменное электромагнитное поле, при этом ферромагнитный стержень начинает совершать колебания удвоенной амплитуды. Поскольку линейная деформация магнитостриктора не зависит от направления силовых линий магнитного поля, то подмагничивания такого элемента не требуется.
Как и пьезоэффект, магнитострикция обратима. В качестве излучателей применяются химически чистый никель, а также его сплавы с медью или железом. Минимальная частота, при которой обнаружение дефектов сварных конструкций окажется эффективным, составляет 60 Гц, хотя в приборах обычно реализуются частоты от 300 Гц.
Магнитострикционные преобразователи конструктивно проще, однако уступают пьезогенераторам по параметрам минимальной площади диагностируемой зоны: она должна быть достаточно большой. Кроме того, такие ультразвуковые дефектоскопы теряют свою чувствительность при обследовании только что полученных сварных швов. Ещё одним ограничением магнитострикционных источников получения ультразвуковых волн считается их повышенная энергоёмкость. Зато они более компактны, а потому применимы в стеснённых для диагностики условиях.
Промышленные конструкции ультразвуковых дефектоскопов для контроля сварных соединений
Для измерения необходимы:
- Сам регистрирующий прибор.
- Искательная головка (передатчик).
- Контрольная головка (приёмник).
- Устройство отображения (монитор или цифровой дисплей).
Напряжение от источника переменного тока (аккумулятор или генератор — для стационарных дефектоскопов) подаётся на излучатель, а от него ультразвуковые волны передаются в исследуемый сварной шов. Интенсивность ослабления исходного сигнала определяет степень неоднородности шва. Возникающая амплитуда сигнала далее усиливается и регистрируется, при этом возможна как визуальная оценка качества, так и запись результатов на цифровой носитель информации.
Перед использованием ультразвуковой дефектоскоп для контроля сварных соединений подлежит юстировке. Как образец, используется сварной стык с идеальными параметрами качества, при этом отклонение шкалы/стрелки должно быть максимально возможным.
В качестве приёмника дефектоскопы некоторых фирм используют преобразователь изображения. При этом фиксируется фактическое значение плотности энергии звукового поля за швом. Этот способ получения конечной информации более нагляден, но требует определённого пространства за исследуемым соединением.
Излучение звуковой энергии в ультразвуковых дефектоскопах может быть выполнено двумя способами – резонансным или импульсным. В первом случае излучение ультразвука происходит непрерывно, а применяемые частоты находятся в диапазоне 1…12,5 кГц. При импульсном методе используется сигнал (эхо) звуковой волны, который отражается от дефектной зоны или задней поверхности сварного стыка. Подача звукового импульса происходит через 1…2 мкс, чем обеспечивается высокая точность сканирования объекта. Конечный импульс отражается на мониторе, и может регистрироваться цифровым устройством записи. Энергопотребление дефектоскопов такого типа значительно меньше.
Признанным мировым лидером в производстве переносных дефектоскопов для контроля сварных соединений, цена которых вполне соответствует их качеству, считаются аппараты от компании SONATEST (Франция). Данные приборы отличаются компактностью и точностью получаемых данных. Например, применяемые для тестирования качества сварки труб, листовых материалов и т.п. ультразвуковые дефектоскопы линейки Harfang Veo характеризуются следующими эксплуатационными достоинствами:
- большим диапазоном регулировки направления и силы излучения, а также скорости диагностики;
- точностью измерения;
- воспроизводимостью результатов, включая и 3D-моделирование структуры сварного шва;
- удобствами настройки;
- возможностью подключения для целей сканирования нескольких источников;
- ёмкими батареями, допускающими замену непосредственно в ходе измерений.
Дефектоскопия сварных швов, соединений: капиллярная, магнитная
Контроль качества полученных соединений обязательно должен проходить перед вводом в эксплуатацию каких-либо изделий. В особенности это касается теплотрасс, трубопроводов и прочих вещей, где требуется создание герметичных соединений. Дефектоскопия сварных швов помогает определиться с тем, какие отклонения от нормы присутствуют в полученном соединении. Каждый дефект уменьшает прочность соединения, поэтому, изделие может оказаться непригодным для использования, так как не выдержит возлагаемые на него нагрузки. В швах могут образовываться раковины и поры, встречаться непроваренные места, также могут случаться посторонние вкрапления, что также уменьшает прочность изделия.

Дефектоскопия сварных швов
Дефектоскопия сварных швов может проводиться по ГОСТ 18442-42. Не обязательно подвергать анализам все предметы из выпускаемой серии. Для этого берется несколько образцов, над которыми и ставят опыты, чтобы проверить всю технологию соединения. Проверяются те или иные физические свойства изделий. Проверке подвергается стойкость к коррозии, прочность, пластичность, структура металла после температурной обработки. Также учитывается форма и размер имеющихся дефектов. Все это в совокупности определяет насколько пригоден объект для использования.
Различные методы дефектоскопии сварных швов применяются в производстве. Чем больше ответственность требуемых соединений, тем больше необходимо использовать методов проверки. При частных соединениях такой жесткий контроль не требуется.
Преимущества дефектоскопии сварных швов 
- Зачастую на операцию требуется относительно немного времени;
- Стоимость проверки является невысокой;
- Большинство методов безопасны для здоровья человека;
- Существуют мобильные ультразвуковые дефектоскопы, которые могут применяться нестационарно;
- Есть возможность делать проверку действующих труб и прочих изделий.
Недостатки дефектоскопии 
- Присутствуют разрушающие способы;
- Для некоторых разновидностей необходимо использовать специальные реактивы и прочие расходные материалы;
- Опытные образцы порой не восстанавливаются после проведения данного процесса.
Общий принцип работы 
Дефектоскопия это очень ответственный процесс, так как благодаря ему можно проверить работоспособность целой партии изделий. Ее проводят только после того, когда шов полностью завершен. Месту соединения дают остыть, а затем происходит обработка. С него оббивается шлак, зачищается поверхность, чтобы можно было сделать визуальный осмотр. На самом деле, если шлак не оббивать, то соединение будет более надежным, так как покрытая поверхность лучше защищена от коррозии, но в таком случае невозможно сделать визуальный осмотр.
Затем происходит дефектоскопия сварных швов трубопроводов и прочих изделий.

Процесс дефектоскопии сварных соединений
Для каждого вида отбираются несколько экземпляров. Далеко не всегда одна деталь проходит через все виды испытаний. Это обосновано как скоростью проведения испытательных работ, так и чистотой эксперимента, чтобы изделие подвергалось только одному виду воздействия. Это помогает определить максимальные пределы его стойкости.
Методы дефектоскопии 
Визуальный осмотр является первоочередной и самой простой процедурой. С его помощью можно определить наличие как наружных, так и внутренних дефектов. Если высота шва постоянно разная, то значит, что дуга во время сваривания часто обрывалась. Во время осмотра можно обработать соединения 10% раствором азотной кислоты. При наличии грубых геометрических отклонений все будет сразу видно и без последующих анализов. Это метод не разрушаемого контроля сварных швов и соединений, не требующий финансовых затрат.
Цветная дефектоскопия сварных швов, которая еще носит название капиллярного контроля, основана на капиллярной активности жидкостей благодаря чему и получила свое название.

Набор для капиллярной дефектоскопии
Трещины и поры образуют сеть в соединении. При контакте с жидкостью они могут попросту пропускать ее через себя. Чем выше смачиваемость в выбранной жидкости, тем выше скорость ее прохождения. Данный метод подходит для любых форм и марок металла. Капиллярная дефектоскопия сварных швов позволяет выявить скрытые дефекты поверхности. Зачастую здесь применяется керосин. Сама процедура проводится по ГОСТ 18442-80.
Магнитная дефектоскопия 
Во время контроля таким способом используется явление электромагнетизма. Устройство образует магнитное поле возле исследуемой области. Линии поля проходят через металл, но если в изделии есть дефекты, то линии искривляются. Для фиксации данного искажения применяется два основных метода. Одним из них является магнитографическая, а также магнитопорошковая дефектоскопия. При использовании порошка, его наносят в сухом виде или во влажной смеси, где дополнительно используется масло. Порошок скапливается в тех местах, где имеются дефекты.

Процесс магнитной дефектоскопии
Ультразвуковая дефектоскопия сварных соединений основана на принципе отражения звуковых волн от границ, которые разделяют различные среды. Волна посылается прибором на участок металла. Когда она достигает границы, то звуковые волны разделяются от акустических свойств каждой поверхности. Дойдя до нижнего предела заготовки, часть волны снова возвращается и фиксируется датчиками. Если внутри шва имеются дефекты, то волна искажается и датчик фиксирует это. Данный способ очень удобен в применении, поэтому стал очень широко распространенным. Недостатком способа является сложность расшифровки получаемых сигналов. Для крупнозерновых металлов такой способ также не подходит.
Дефектоскопия сварных швов радиационным методом основывается на свойствах проникновения гамма излучения и рентгеновских лучей сквозь металлическую поверхность. Дефекты фиксируются на фотопленке. Но это достаточно дорогостоящий способ. Также это самый вредный для здоровья человека способ.
Выбор метода
Далеко не всегда требуется проводить все процедуры, чтобы сказать с уверенностью, что в изделии нет дефектов. Для каждого случая будет уместен тот или иной способ. Чтобы подобрать какой именно будет наиболее подходящим, стоит определиться с тем, где именно будет использоваться заготовка и насколько высока ответственность шва. Для самых сложных случаев целесообразно использовать радиационный способ, несмотря на его сложность и опасность, так как он дает подробные данные о состоянии шва.
Если необходимо просто проверить, есть ли дефекты в соединении и насколько они сильные, то здесь подойдет магнитный или ультразвуковой. Второй способ более простой и универсальный. Он предпочтительнее благодаря наличию компактных устройств для проведения дефектоскопии.
«Важно!
Ультразвуковые волны нужно уметь правильно расшифровывать, так что неспециалистам данный метод не подойдет.»
При домашнем производстве будет достаточно визуального осмотра. Дефектоскопия сварных соединений с низким уровнем ответственности производится бюджетными способами.
Меры по технике безопасности
Инструкция охраны труда предполагает ношение свинцовой защиты при использовании радиационного метода. Помещение для проведения процедуры должно быть обустроено металлическими пластинами из свинца. В остальном же следует дождаться полного остывания материала, прежде чем приступать к анализу.
Ультразвуковой дефектоскоп для контроля сварных соединений
Необходимость в контроле сварных соединений перед их вводом в эксплуатацию является очень важным этапом во многих сферах. Сварка является часто используемым методом соединения металлических изделий, поэтому. Она используется как для ответственных металлоконструкций, так и для частной сферы. Отсутствие дефектов в соединении позволяет использовать их по прямому назначению. При наличии какого-либо брака, применять такие изделия запрещено, так как это может привести к непредсказуемым последствиям. Для анализа внутреннего состояния шва используют специальные устройства, одним из которых является ультразвуковой дефектоскоп для контроля сварных соединений.

Ультразвуковой дефектоскоп для контроля сварных соединений
Благодаря данному устройству можно проводить ультразвуковой анализ, который на данный момент является одним из самых популярных. За все время существования появилось большое разнообразие моделей такого устройства, позволяющие проводить анализ не только в условиях стационарных помещений, но и с возможностью переноски. Принцип действия практически у всех одинаковый, но встречаются отличия в параметрах. Также имеется несколько особенностей использования, которые нужно знать специалисту, так как для обыкновенного человека трудно будет справиться с проведением анализа и расшифровкой полученных данных. Дефектоскоп сварных швов доложен соответствовать ГОСТ 23667-85.

Дефектоскоп для сварных швов согласно ГОСТ 23667-85
Виды методов 
Дефектоскоп для проверки сварных швов может иметь несколько видов методов проверки. Среди них выделяют:
- Эхо-метод, который основывается на испускании коротких ультразвуковых импульсов. Прибор регистрирует их время прихода и активность звуковой волны. При встрече с несплошностью, который зачастую выступает тот или иной дефект, волна в этом месте возвращается раньше, чем в остальных. Пр. Благодаря эхо-дефектоскопу можно обнаружить дефекты, как на поверхности, так и внутри шва, расположенные в различных пространственных положениях.
- Теневой метод ультразвуковой дефектоскопии сварных соединений работает на принципе отражения звукового колебания, который встречается с дефектом на своем пути. Отражение происходит в обратном направлении. О том, что дефект действительно присутствует, можно понять по тому, как изменяется фаза принимаемого сигнала звука, так как звук огибает дефект. Применяется как метод неразрушающего контроля сварных соединений рельсов и прочих крупных металлических изделий.
- Зеркально-теневой применяется как дополнение или замена эхо-дефектоскопам. Он хорошо подходит для определения относительно небольших дефектов, дающих слабый уровень отражения. Направление распределения волн здесь раздельно-совмещенное с преобразователем. Разнообразные дефекты, такие как вертикальные трещины и прочие, зачастую ориентируются перпендикулярно основной поверхности, где проходит преобразователь. Все это дает рассеянный слабый донный сигнал, так как на поверхности продольная волна приобретает вид головной. Она же в свою очередь излучает боковые волны, которые уносят энергию. Зеркально-теневой метод используется для выявления вертикальных трещин.
Устройство 
Основным элементом устройства, который испускает звуковые волны, является генератор импульсов. Образуемые им сигналы передаются на следующий элемент, которым выступает преобразователь. Он повернут непосредственно к образцу исследуемого металла, чтобы отраженный сигнал мог попасть точно на его поверхность. После возвращения волны она попадает на поверхность преобразователя, который отправляет сигнал на следующий компонент – усилитель. Он необходим для того, чтобы получаемый относительно слабый импульс был усилен для нормального восприятия электронно-лучевой трубкой. При помощи генератора развертки электронно-лучевая трубка выводит изображение полученного анализа.
Принцип работы 
Ультразвуковой дефектоскоп сварных швов имеет следующий принцип работы. Когда волна генерируется при помощи соответствующего элемента устройства, она моментально начинает распространяться в воздушном пространстве. Но в то время, когда она сталкивается со средой, плотность которой отличается от той, в которой она проходила до этого, то часть волн возвращается. При одной плотности шва это должно происходить на момент вхождения ее в шов и на момент выхода, то есть график должен быть ровным. Но если внутри есть неровности и воздушные прослойки, что говорит о наличии дефекта, то волна будет приходить назад неравномерно. Преобразователь помогает определить данную особенность, а усилитель обеспечивает показания сигнала так, чтобы человек смог локализовать найденный дефект.
Технические характеристики 
На примере такой модели как дефектоскоп контроля сварных швов УД1 можно рассмотреть основные технические характеристики данных устройств:
Параметр | Значение |
Диапазон возможных размеров глубины стали, мм | 6000 |
Регулируемый диапазон усиления | 115 дБ |
Регулировка чувствительности | до 70 дБ, кривая строится по 16 основным точкам, которые вводятся вручную или по специальным контрольным отражателям |
Контролируемая зона | Ширина и начало измерений в используемой развертке |
Импульс зондирования | Переменный с возможностью настройки, амплитуда импульса достигает до 350 В, максимальная измеряемая длительность составляет от 12,5 до 500 нс, |
Память | Запоминание настроек с А-сканом (Б-сканом, С-сканом), ее размер ограничен только вместительностью SD-карты. |
Интерфейс | Блютуз, SD-card |
Диапазон рабочих температур | От -20 да +50 градусов Цельсия |
Модели и отличительные особенности 
Каждый ультразвуковой дефектоскоп для контроля сварных швов обладает собственными параметрами, которые обеспечивают ему свою сферу применения. Среди основных распространенных моделей можно выделить:
- УД4 12Т используется для анализа однородности металла, пластика и прочих твердых материалов. Применяется в машиностроении, в строительстве, металлургической промышленности, а также при ремонте транспортных средств.

Ультразвуковой дефектоскоп УД4 12Т
- УСД 50 – универсальная модель, которая обладает цветным дисплеем, что построен по технологии TFT. Экран большого размера, поддерживающий разрешение 640х480 точек. Вес устройства около 2 кг, работа прибора идет от аккумуляторов. Это отличный выбор для профессионалов.

Ультразвуковой дефектоскоп УСД 50
- УСД 60 – универсальная модель, которая обладает TFT дисплеем, размером 135х100 мм. Сигналы выводятся в виде каналов А, В и С. Может записывать большие объемы данных. Есть функция автоматического формирования отчетов с последующим выводом на печать. Устройство отличается высокой точностью и тонкой коррекцией. Есть поддержка подключения многоканальных систем сканирования.

Ультразвуковой дефектоскоп УСД 60
- УД 25 П45 – не имеет функции сохранения данных, а также не подключается к ПК. Используется для поиска дефектов и измерения толщины деталей.
- ФОКУС РХ – применяется как один из компонентов автоматических систем контроля. Работает на собственном программном обеспечении ФОКУС ПК. Обладает хорошими характеристиками в параметрах сигнал-шум и скорости контроля.
Производители
Среди производителей на современном рынке выделяются такие компании как:
- Novotest;
- АКС;
- Helling;
- Orient;
- Пульсар.
что это такое, гост, методика проведения
Первичный контроль качества сварных соединений выполняется методом визуального осмотра. На ответственных конструкциях для выявления изъянов невидимых невооруженным глазом дополнительно проводится цветная дефектоскопия. Этим способом выявляют местоположение и размеры трещин, пор, непроваров, раковин на поверхности сварного шва. Метод универсален, проводится без применения сложной аппаратуры работниками с низкой квалификацией.
Суть метода цветной дефектоскопии
Способ основан на капиллярном проникновении, сорбции, диффузии жидкостей. В сущности, цветная дефектоскопия ― это усовершенствованный визуальный контроль. Для обнаружения изъянов размером от 1 микрона применяют индикаторные жидкости и растворы с большой текучестью. При нанесении на поверхность они заполняют мельчайшие капилляры. После обработки проявителем дефекты становятся контрастными, что облегчает визуальное выявление. Методом цветной дефектоскопии проверяют качество и герметичность сварных швов на конструкциях любой сложности.
Необходимые материалы
Основной материал ― это индикаторная жидкость с добавкой красителя, которая называется пенетрант (от английского слова проникать). Для приготовления простого состава смешивают керосин, трансформаторное масло, скипидар, анилиновый краситель. Пропорции нормируются ГОСТом. Цвет раствора должен быть хорошо виден при нормальном освещении. Обычно его делают темно-красного оттенка. Порошкообразные индикаторы широкого распространения не получили, так как для проведения проверки требуется нагрев или смешивание со специальными жидкостями.
В полном объеме цветная дефектоскопия проводится с применением дополнительных материалов:
- Проявители необходимы для создания фона, на котором образуется индикаторный рисунок. Их делают из водных растворов мела или каолина, водорастворимой краски белого цвета.
- Очистителями удаляют пенетрант после проведения контроля. Для очистки возможно применение моющих средств, ПВА (поверхностно-активных веществ), этилового спирта, 50% раствора кальцинированной соды.
- Гасителем пенетранта смывают проявитель с проверяемой поверхности.
Технология проведения
При проведении цветной дефектоскопии сварных швов руководствуются требованиями ГОСТ 18442-80. Проверку выполняют при температуре 5 — 50°C в следующем порядке:
- С поверхности сварных соединений и зоны возле шва металлической щеткой удаляют грязь и шлак. Мелкие шероховатости обрабатывают мелкозернистым абразивом. Очищенную поверхность обезжиривают бензином или ацетоном. Их наносят тряпкой или распыляют. Детали небольшого размера целиком опускают в сосуд с обезжиривающим средством. Если помещение не оборудовано вытяжной вентиляцией процедуру выполняют водным раствором порошковых синтетических составов.
- После просушки кистью или распылителем наносят 3 — 5 слоев пенетранта и оставляют на 5 — 30 минут. Длительность ожидания зависит от конфигурации соединения и материала заготовок (чугун, нержавеющая или углеродистая сталь, алюминий, пластик). Слои наносят так, чтобы нижние не успевали засохнуть. Каждый новый слой должен быть по площади больше предыдущего. Это позволит избежать ошибок, так как резкий переход или наплыв может быть принят за трещину.
- Лишний пенетрант удаляют мягкой тряпочкой смоченной очистителем. Поверхность протирают до тех пор, пока на ней не будет следов индикатора.
- Проявитель равномерным слоем наносят на шов и поверхность рядом с ним. Ждут высыхания или просушивают феном.
- Для обнаружения изъянов соединение осматривают через лупу с увеличением не меньше 5-кратного. Сначала через 3 — 5 минут и повторно спустя полчаса.
Проверку швов емкостей и трубопроводов цветной дефектоскопией на герметичность проводят по упрощенной методике. На наружную сторону наносят водный раствор мела, после просушки внутреннюю часть соединения обрабатывают керосином. Появление темных пятен на лицевой поверхности означает, что на шве есть сквозные дефекты.
Важно!
Проверку выполняют при температуре 5 — 50°C.
Меры безопасности
Поскольку контроль качества сварных соединений методом цветной дефектоскопии проводится легковоспламеняющимися материалами, персонал обеспечивают спецодеждой из негорючей ткани. Вблизи от места проведения проверки не должно быть источника открытого огня или искр. В помещении для постоянной работы устанавливают таблички с запретом курения и правилами пожарной безопасности. Отработанный обтирочный материал должен складываться в емкость из негорючего материала.
Цветной дефектоскопией невозможно выявить внутренние дефекты. Поэтому при проверке конструкций с высокими требованиями по прочности ее дополняют магнитным, радиационным или ультразвуковым контролем. После получения полной картины о состоянии соединения выбирают способ устранения обнаруженных изъянов.
применяемые материалы и порядок проведения
Цветная дефектоскопия сварных швов относится к методу капиллярной дефектоскопии неразрушающего контроля. В ее основе лежит явление проникания смачивающей жидкости в поверхностные дефекты сварных соединений.
Цель – обнаружение поверхностных дефектов под воздействием средств, изменяющих светоотдачу дефектных зон, что приводит к изменению контрастности неповрежденных и поврежденных участков.
Цветной способ, который еще называют методом красок, применяется для обнаружения невидимых и слабо видимых невооруженным взглядом поверхностных изъянов в сварных швах:
Цветная дефектоскопия дополняет рентгеновский и ультразвуковой методы контроля по выявлению поверхностных мелких дефектов, размеры которых находятся за пределами чувствительности данных способов дефектоскопии.
Принцип действия
В основе цветной дефектоскопии лежат физические явления:
- капиллярное проникновение, сорбция, диффузия;
- световой и цветовой контрасты.
Индикаторные жидкости просачиваются в полости поверхностных и сквозных дефектов, что приводит к образованию цветного индикаторного рисунка (следа дефекта). Индикаторная жидкость имеет яркую окраску. След дефекта чаще всего ярко-красный на белом фоне проявителя. Индикаторный след регистрируется.
Метод красок проводится при естественном, с применением ламп накаливания или комбинированном освещении.
ГОСТы
Способ цветной дефектоскопии сварных швов регламентирован ГОСТами.
- 24522-80 «Контроль неразрушающий капиллярный. Термины и определения».
Разделы документа:
- общие понятия;
- методы капиллярного неразрушающего контроля;
- средства капиллярного неразрушающего контроля;
- аппаратура капиллярного неразрушающего контроля;
- алфавитный указатель терминов.
ГОСТ содержит 2 справочных приложения.
- 18422.80 «Контроль неразрушающий. Капиллярные методы. Общие требования».
Содержание межгосударственного стандарта:
- основные положения и область применения;
- дефектоскопические материалы;
- аппаратура;
- проведение исследования;
- оформление результатов;
- требования безопасности.
ГОСТ имеет 6 справочных приложений.
Другие нормативные документы
Исследование сварных соединений способом красок также регулируется отраслевыми стандартами:
- ОСТ 26-5-99 «Контроль неразрушающий. Цветной метод контроля сварных соединений, наплавленного и основного металла».
- ОСТ 36-76-83 «Контроль неразрушающий. Сварные соединения трубопроводов и конструкций. Цветной метод».
Применяемые материалы
Основным капиллярным дефектоскопическим материалом метода красок является индикаторный пенетрант (в переводе с английского – проникать). Пенетранты содержат красящие вещества определенного цветового тона, наблюдаемого в видимом свете. Это раствор или суспензия жирорастворимого темно-красного красителя.
Вспомогательные материалы:
- Проявитель – служит для извлечения пенетранта из несплошности с целью образования индикаторного рисунка и формирования контрастирующего фона. В качестве проявителей используют суспензии порошкообразных сорбентов и белые проявляющие лаки.
- Очиститель – состав для удаления индикаторного пенетранта с поверхности исследуемого образца. Используют моющие порошки, ПАВ (поверхностно-активные вещества), этиловый спирт.
- Гаситель пенетранта – состав, служащий для устранения фоновой окраски.
Порядок проведения
С помощью способа красок производится выявление трещин и иных изъянов, выходящих на поверхность сварочного шва. Этот метод исследования не требует применения аппаратуры.
Технологическая последовательность цветной дефектоскопии сварного шва включает этапы:
- Очищение поверхности образца от загрязнений.
- Нанесение в 3-4 приема слоя подкрашенного индикаторного пенетранта. Время выдержки проникновения красящего вещества в дефекты составляет 15-20 минут.
- Удаление избытка пенетранта способом промывки поверхности сварного шва 50% водным раствором кальцинированной соды. Просушивание или вытирание поверхности светлой салфеткой. При наличии на салфетке следов обработка повторяется.
- Нанесение проявителя – водного раствора каолина. Просушивание поверхности подогретым воздухом до появления красного индикаторного рисунка на белом фоне каолина.
- Осмотр поверхности шва на предмет выявления дефектов. Рекомендуется проводить дважды: с интервалом 3-5 минут и 20-30 минут.
- Обработка и оформление результатов исследования.
преимущества процедуры и особенности ее проведения
Вне зависимости от видов сварные соединения являются наиболее уязвимым местом любой конструкции. Поэтому завершающим этапом сварки должна быть дефектоскопия сварных швов. Ее проведение позволяет оценить физико-химические свойства деталей, изменить параметры и выявить проблемы. Дефектоскопия сварных соединений используется для выявления проницаемости швов, которая становится причиной нарушения герметичности. Проведение дефектоскопии особенно важно для элементов, которые будут работать под высоким давлением.
Преимущества и недостатки
Применение дефектоскопии для проверки качества и надежности сварных швов обладает рядом преимуществ:
- используемые методы безопасны для человека, поэтому зачастую не требуют использования даже средств индивидуальной защиты;
- проведение проверки занимает немного времени;
- стоимость проверки находится на доступном уровне;
- для выполнения проверки вне лаборатории или мастерской может использоваться мобильный ультразвуковой дефектоскоп для проверки сварных швов;
- возможность использовать для проверки свежих швов и уже действующих соединений.
Несмотря на явные преимущества дефектоскопии, существуют и некоторые недостатки данной процедуры. К ним относится:
- некоторые методы дефектоскопии обладают разрушительным действием;
- для определенных способов требуется использовать узкоспециализированные реактивы и расходные материалы;
- вероятность повреждения опытного образца.
Однако в большинстве случае проведение дефектоскопии опытными мастерами гарантирует минимальный риск повреждения детали и обеспечения гарантии надежности сварного соединения.
Виды дефектоскопии
Существуют видимые и невидимые дефекты сварочных швов, поэтому для их выявления рекомендуется применять различные методы. Наиболее простым и доступным способом обнаружить дефекты внутри сварочного шва является визуальный осмотр. Способы контроля сварных швов разделяются на разрушающие и неразрушающие. Первый вариант используется в том случае, если требует провести проверку значительного объема, используя при этом небольшой контрольный образец.
К неразрушающим видам дефектоскопии относится:
- Магнитопорошковая дефектоскопия сварных швов. Заключается в создании магнитного поля, пронизывающего тело шва. Чаще всего данный метод включает в себя использования ферромагнитного порошка, который собирается в месте дефекта. Магнитопорошковый контроль сварных соединений может выполняться и с помощью ферромагнитной ленты.
- Визуальный осмотр. Позволяет выявить не только видимые дефекты, но и наличие непроваров. Для начала шов очищается, обрабатывается спиртом и азотной кислотой, после чего на поверхности видны любые трещинки и поры.
- Цветная дефектоскопия сварных швов. Заключается в нанесение на поверхность шва одного из растворов на основе воды, керосина или масла. Данные растворы обладают сильной цветовой концентрацией, что дает возможность окрасить дефект. Жидкости имеют цветной и люминесцентный эффект.
- Радиационный контроль. Один из самых надежных способов обнаружить дефекты шва, но для его проведения требуется использование дорогого оборудования.
- Ультразвуковая дефектоскопия. Для использования этого метода требуется знания и опыт расшифровке полученных результатов.
Выбор оптимального способа дефектоскопии учитывается особенности сварных швов, наличие опыта пользования методиками, определенных реактивов и оборудования.
Интересное видео
Вихретоковая дефектоскопия сварных соединений
Физические основы метода вихретоковой дефектоскопии можно пояснить следующим образом. Если установить рядом две катушки индуктивности L1 и L2 (например, трансформаторы без сердечников) и по катушке L1 (рис. 36) пропустить ток, то при изменении силы тока в ней или взаимного расположения катушек в катушке L2 будет наводиться электродвижущая сила.
При вихретоковой дефектоскопии функцию одной из катушек индуктивности выполняет металлическая пластина 1, в которой наводятся вихревые токи 2 (рис. 37), текущие в поверхностном слое металла со стороны катушки. Плотность и распределение вихревых токов в металле зависят от его геометрических и электрофизических параметров.
Если в схеме, изображенной на рис. 37, металлическую пластину заменить сварным соединением, содержащим дефекты, то увеличится сопротивление поверхностного слоя, что приведет к ослаблению вихревых токов, которое регистрируется катушкойдатчиком.
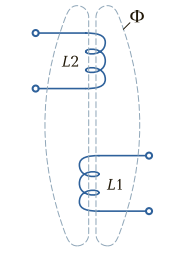
Рис. 36. Схема из двух взаимосвязанных катушек индуктивности L1 и L2: Ф — магнитный поток
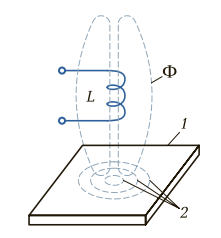
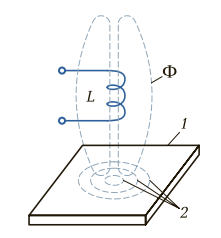
Рис. 37. Схема образования вихревых токов в металлической пластине: 1 — металлическая пластина; 2 — вихревые токи; L — катушка индуктивности; Ф — магнитный поток
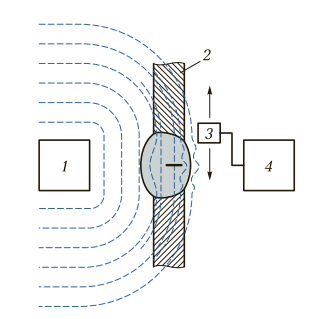
Рис. 38. Схема контроля сварного соединения методом вихретоковой дефектоскопии (стрелками показаны направления перемещения датчика): 1 — полезадающая система; 2 — сварное соединение; 3 — датчик; 4 — регистрирующий прибор
Методика контроля. Процесс контроля методом вихретоковой дефектоскопии (рис. 38) включает в себя выполнение следующих основных операций:
- внешний осмотр сварного соединения и устранение наружных дефектов, препятствующих проведению контроля;
- установка полезадающей системы 1 на контролируемое сварное соединение 2 и пропускание тока через катушку возбуждения;
- сканирование поверхности сварного соединения датчиком 3 и регистрация сигнала прибором 4;
- расшифровка результатов контроля и оценка качества соединения.
Вихретоковая дефектоскопия используется для контроля точечной сварки алюминиевых сплавов. При наличии литого ядра электропроводность сплавов марок Д16 и АМг в его зоне уменьшается на 10 … 15 % по сравнению с электропроводностью основного металла. Электропроводность сплавов В95, АМг6 и других может уменьшаться на 15 … 30 %. При наличии дефектов типа слипания или непровара электропроводности литого ядра и основного металла примерно одинаковые.
Метод вихревой дефектоскопии пока не нашел широкого применения при контроле сварных швов, так как электропроводность отдельных зон шва и околошовной зоны значительно изменяется, что создает сильные помехи при выявлении дефектов сварки.
Чувствительность метода. На чувствительность метода вихретоковой дефектоскопии значительное влияние оказывает зазор между датчиком и поверхностью контролируемого объекта, а также их взаимное расположение, форма и размеры. С увеличением зазора чувствительность метода резко снижается. Допустимый максимальный зазор составляет 2 мм. Структурная неоднородность сварного соединения также существенно снижает чувствительность данного метода.
Этот метод позволяет обнаруживать поверхностные и подповерхностные трещины высотой 0,1 … 0,2 мм и протяженностью более 1 мм, расположенные на глубине до 1 мм.
Вихретоковая дефектоскопия может использоваться для измерения толщины гальванических, лакокрасочных и теплоизоляционных покрытий, стенок труб, пустотелых деталей и тонколистовых конструкций при одностороннем доступе к ним, а также диаметров прутков и проволоки. Однако в ряде случаев практическое применение этого метода затрудняется неоднородностью свойств материалов соединения и отклонением размеров деталей от заданных даже в пределах допусков.
Классификация полезадающих систем. Полезадающие системы, или вихретоковые преобразователи (ВТП), подразделяются на наружные проходные — в которых катушка с током охватывает контролируемое сварное соединение (рис. 39, а), внутренние проходные — в которых катушку вводят в соединение (рис. 39, б), и накладные — в которых катушку устанавливают на соединение торцом (рис. 39, в). В ВТП первых двух типов электромагнитная волна от полезадающей системы распространяется в направлении контролируемого соединения, а в ВТП третьего типа — вдоль его поверхности.

Рис. 39. Схемы наружной проходной (а), внутренней проходной (б) и накладной (в) полезадающих систем электромагнитного контроля (стрелками показаны направления распространения электромагнитных волн): 1 — сварное соединение; L — катушка индуктивности; Н — вектор напряженности магнитного поля
Измерительные катушки (датчики) выполняются отдельно от полезадающих (генераторных) и размещаются вблизи от поверхности сварного соединения.
Наружные проходные ВТП используют для контроля линейнопротяженных объектов и мелких деталей.
С помощью внутренних проходных ВТП контролируют внутреннюю поверхность труб и отверстий в различных деталях.
Накладные ВТП применяют в основном для контроля качества объектов с плоскими поверхностями и объектов сложной формы, а также в тех случаях, когда требуется уменьшить зону контроля и обеспечить высокую чувствительность. Накладные преобразователи выполняются с ферромагнитным сердечником или без него. Такой сердечник (обычно ферритовый) повышает абсолютную чувствительность преобразователя и уменьшает зону контроля за счет локализации магнитного потока.
Дефектоскопы с проходными преобразователями. Для автоматизированного высокоскоростного бесконтактного контроля качества эффективно использование дефектоскопов с проходными преобразователями, позволяющими проверять в широком диапазоне типоразмеров протяженные объекты (трубы, прутки, проволоку с поперечными размерами 0,15 … 135 мм) и мелкие детали (шарики и ролики подшипников, метизы и т. д.). При этом производительность контроля может достигать 50 м/с (для проволоки) или нескольких тысяч мелких деталей в час. Производительность контроля труб и прутков ограничивается инерционностью устройств транспортирования и разбраковки и редко превышает 3 м/с.
Основной параметр дефектоскопа — порог чувствительности — определяется минимальными размерами дефекта заданной формы, при которых отношение сигнал/помеха равно двум. Порог чувствительности обычно устанавливается с помощью калиброванного образца с искусственными дефектами различной формы, например в виде отверстий разных диаметров и глубин в трубах и прутках, продольных рисок на проволоке и т. д. Реальный порог чувствительности дефектоскопа зависит от уровня помех, связанных с вариацией параметров объекта (например, от шероховатости поверхности). Порог чувствительности дефектоскопа с проходным преобразователем обычно определяется глубиной узкого длинного продольного дефекта, выраженной в процентах от поперечного размера (диаметра) объекта.
Дефектоскопы отличаются друг от друга главным образом конструкцией: наличием или отсутствием блоков сортировки, представления и регистрации информации, маркировки дефектных участков, подмагничивания и т. д. В настоящее время широко применяются отечественные дефектоскопы моделей ИПП-1М, ТНМ1М, ИДП-1, АСК-12, ЭЗТМ, ДКВ-2, ВД-20П и -30П.
Дефектоскоп ИПП-1М предназначен для выявления в условиях поточного производства поверхностных дефектов в прутках с круглым и шестигранным профилями диаметром 4 … 47 мм, выполненных из ферромагнитных и неферромагнитных металлов и сплавов. Глубина залегания порогового дефекта для него составляет 1 … 2 % от диаметра, но не менее 0,1 мм, а длина — 2 мм.
Дефектоскоп ИДП-1 используется для обнаружения в прутках диаметром 1 … 5 мм из неферромагнитных и ферромагнитных металлов и сплавов поверхностных дефектов: трещин, волосовин, раковин и т. п. Глубина залегания порогового дефекта для него составляет 0,05 мм.
Качество ферромагнитных сварных труб диаметром до 60 мм контролируют с помощью дефектоскопа ЭЗТМ. Проходной преобразователь, выполненный в виде трехвитковой трансформаторной системы, обеспечивает надежную работу такого дефектоскопа в условиях высоких температур даже при наличии окалины и масел. С его помощью выявляют непровары в сварном шве, и его применение позволяет исключить гидроиспытания.
Для контроля качества протяженных сварных конструкций с широким диапазоном типоразмеров и видов материалов разработан универсальный дефектоскоп ВД-30П.
Из зарубежных моделей данного типа наиболее эффективны дефектоскопы, разработанные в Институте Ферстера (Германия). В нашей стране их используют для контроля труб, прутков и проволоки преимущественно из ферромагнитных, а также из неферромагнитных материалов.
Дефектоскопы с накладными преобразователями. Для контроля линейно-протяженных объектов с круглым сечением (прутков, труб) применяют сканирующие дефектоскопы с вращающимися вокруг объекта накладными преобразователями: ВД-40Н, -41Н и -43Н. Эти дефектоскопы предназначены для обнаружения поверхностных дефектов в сварных соединениях из ферромагнитных и слабомагнитных сталей, а также из цветных металлов и сплавов.
Для контроля плоских сварных соединений и соединений, имеющих малую кривизну поверхности, разработан ряд переносных малогабаритных дефектоскопов с преобразователями, вращающимися в плоскости, параллельной поверхности объекта. Дефектоскоп ЭДМ-65 используется для выявления поверхностных дефектов в зачищенных сварных швах из алюминиевых сплавов.
Сканирующие дефектоскопы, имеющие головку сравнительно большого диаметра, трудно применять для контроля сварных соединений сложной конфигурации. В этих случаях обычно используются переносные и малогабаритные дефектоскопы с преобразователями малого диаметра, работающими в статическом режиме.
Наиболее распространены дефектоскопы серии ДНМ и ВД20НСТ. Дефектоскопы серии ДНМ (ДНМ-15, -500, -2000) предназначены для контроля качества поверхности сварных соединений из алюминиевых и жаропрочных сплавов, а ВД-20НСТ позволяет обнаруживать поверхностные дефекты в ферромагнитных и неферромагнитных материалах. Для контроля мелких деталей (в основном деталей подшипников) разработаны дефектоскопы СК-27-МДШ5, -31, -39, МДР-1, -2 и -3 отраслевого назначения.
Из зарубежных дефектоскопов данного типа распространены различные модификации серий «Циркограф» и «Дефектометр», разработанные в Институте Ферстера. Дефектоскопы серии «Циркограф» с вращающимися накладными преобразователями снабжены сменными сканирующими головками, позволяющими контролировать качество объектов диаметром 2 … 120 мм. Для контроля коротких деталей и узлов, имеющих поверхность вращения сложной формы, к ним подключается гребенка с плавающими преобразователями, закрепленная в специальных державках. Дефектоскопы серии «Циркограф», предназначенные для контроля внутренней поверхности труб, имеют внутренние вращающиеся преобразователи, которые можно устанавливать в стационарном или переносном (в виде ручной дрели) устройстве.
Просмотров: 517