Дефектоскопист по ультразвуковому контролю
Выучиться на дефектоскописта
Конечно же труд дефектоскописта должен быть основан на обширных знаниях, которые можно получить, пройдя курсы дефектоскопистов. Обучение по профессии дефектоскопист в Москве проводят специальные независимые органы по аттестации персонала системы неразрушающего контроля. Получив образование, проводится аттестация дефектоскописта, по результатам которой выдается удостоверение инженера дефектоскописта. Наша компания поможет Вам и Вашим сотрудникам выучиться на дефектоскописта различных видов, в данном случае, дефектоскопист по ультразвуковому методу НК, без отрыва от производства.
Зачем нужна аттестация дефектоскописта?
Согласно ПБ 03-440-02, все специалисты неразрушающего контроля (дефектоскописты) должны проходить аттестацию, при проведении контроля методами установленными п.17 ПБ 03-440-02 методами на объектах, установленных Приложением 1.
Аттестацией своих специалистов должны заниматься предприятия и организации, осуществляющие деятельность по неразрушающему ультразвуковому контролю при технической диагностике, ремонте, реконструкции зданий и сооружений, а также их частей и технических устройств на производственных объектах связанных с повышенной опасностью. Также организации, занимающиеся аттестацией, повышением квалификации персонала должны пройти аттестацию в специальных независимых органах по аттестации персонала системы неразрушающего контроля.
3 уровня квалификации дефектоскописта:
I уровень квалификации — специалист НК, обладающий умениями, знаниями и навыками согласно п. 1.2 Приложения 4.
Специалист НК I уровня квалификации может выполнять работы по незразрущающему контролю определенным методом НК, определенных объектов, согласно инструкции, строго соблюдая технологию и методику НК и под контролем персонала уровня квалификации выше, чем у него.
В обязанности дефектоскописта по ультразвуковому контролю I уровня входит:
- настройка оборудования, которое используется для осуществления НК соответствующим методом;
- выполнение НК методом, на который аттестован;
- описание результатов наблюдения и контроля.
Специалист I уровня квалификации не может осуществлять самостоятельный выбор метода НК, оборудования, технологии и режима контроля, проводить оценку результатов контроля.
II уровень квалификации — специалист НК, обладающий знаниями, умениями и навыками согласно пп 2.2 и 2.3 Приложения 4.
Специалист НК II уровня квалификации может выполнять работы по незразрушающему контролю, обладает достаточной квалификацией для руководства НК в соответствии с нормативно-технической документацией, для выбора способа контроля, ограничения области применения метода. Производит настройку оборудования, проводит оценку качества объекта или элемента в соответствии с документами, документирует полученные результаты, разрабатывает инструкции и различные документы по конкретной продукции в области своей аттестации, подготавливает и руководит специалистами I уровня. Специалист II уровня квалификации НК производит выбор технологии и средств контроля, делает заключение по результатам контроля, который осуществляет он сам или специалист НК I уровня.
III уровень квалификации — специалист НК, обладающий знаниями, умениями и навыками согласно п.3 Приложения 4.
Специалист НК III уровня квалификации обладает квалификацией, необходимой для руководства любыми операциями по методу НК, по которому он аттестован, осуществляет самостоятельный выбор методов и способов НК, персонала и оборудования. Руководит работой персонала I и II уровней, и выполняет работы, которые входят в обязанности этих уровней. Контролирует и согласовывает технологическую документацию, которая разработана специалистами II уровня. Занимается разработкой методических документов и технических регламентов по НК, а также оценкой и интерпретацией результатов контроля. Участвует в подготовке, аттестации персонала на I, II, III уровни, если уполномочен Независимым органом. Инспектирует работы, которые выполнены персоналом I и уровней, занимается выбором технологии и средств контроля, делает заключение по его результатам, которое он выполнил сам, или же специалист I уровня под его наблюдением.
Существуют также различные разряды дефектоскопистов, которые они получают непосредственно на предприятиях, где они работают.
Вы можете пройти обучение независимо от того, какую квалификацию уже имеете на данный момент. Если у вас уже есть стаж работы по профессии, и вы хотите повысить свой статус до дефектоскописта 6 разряда, вам необходимо пройти повышение квалификации дефектоскопистов. Для специалистов с недостаточным стажем и знаниями существуют курсы, где проходит профессиональная подготовка дефектоскопистов, где вы сможете учиться на дефектоскописта «с нуля».
ВАЖНО
Для того, чтобы заниматься деятельностью по неразрушающему контролю работнику необходимо получить заключение врача
Список документов для аттестации персонала в области неразрушающего контроля (дефектоскопист по ультразвуковому методу НК):
- Регистрационная карта с подписью кандидата(об-но указать опыт работы)
- Заявление о согласии на обработку персональных данных
- Заявка
- Копия документа об образовании заверенная
- Документ, подтверждающий практический стаж работы по заявленному методу НК
- Справка о состоянии здоровья(заключение терапевта и окулиста)
- Сведения о работах,проведенных кандидатом за последний год (кроме кандидатов, претендующих на I уровень)
- Оригиналы ранее выданных уд-ий , для переоформления(квалификационное+ПБ)
- Фото 4 шт
- Соглашение о сотрудничестве
Срок действия аттестации дефектоскописта по ультразвуковому методу НК I, II уровней — 3 года, III уровня — 5 лет с момента аттестации.
Стоимость удостоверения дефектоскописта рассчитывается только по заявке, исходя из того, по каким работам и видам деятельности будет производится аттестация!
ГОСТ УЗК, проверка соединений трубопроводов – Сертификация и обучение на Svarka.guru
Для проверки металлических деталей и конструкций на предмет целостности и однородности в промышленности применяется ультразвуковая дефектоскопия, благодаря такой методике обнаруживаются мельчайшие дефекты. Например, для толстого металла используются волны с частотой до 20 МГц, а для тонких изделий достаточно ультразвука с частотой в пределах 0,5—10,0 МГц.
Краткое объяснение методики

Ультразвуковая дефектоскопия – это метод контроля без разрушения изделия, в основу которого входят исследования распространения звука внутри различных материалов с частотой волн до 25 МГц, а также проведение анализа величины амплитуд, времени прохождения и особенностей формы, при этом используются специальные мобильные устройства, называемые дефектоскопами.
Проверки проводятся на основании документов, прописанных в ГОСТ ультразвуковой контроль, подробное описание легко найти в интернете или справочной литературе. Эта методика занимает 32% от всего объёма аналогичных проверок на производстве, но, несмотря на высокую автоматизацию производственных процессов, такие проверки производятся только вручную.
Неразрушающий ультразвуковой контроль основывается на введении в проверяемую конструкцию высокочастотных волн, которые полностью отражают картину внутренней целостности объекта и выводят данные на экран. Используют два принципа: время прохождения ультразвуковой волны внутри изделия и измерение полученной амплитуды отражённого сигнала.
Методы проверки
Повсеместно применяются такие методы неразрушающего ультразвукового контроля:
- Эхо-импульсный вариант — волны пропускаются сквозь изделие, а затем происходит регистрация их отражения от обнаруженного внутри изъяна.
- Теневая методика подразумевает использование минимум двух излучателей, устанавливаемых с противоположных сторон проверяемого объекта. Одно из устройств излучает акустические волны, а другой преобразователь, расположенный строго по направлению движений волн, исполняет роль приёмника. Пропадание колебаний показывает, что внутри изделия обнаружен скрытый дефект.
- При эхо-зеркальном варианте используются также два преобразователя, но установка осуществляется на одной стороне проверяемого изделия. Генерируемые волны отражаются от, например, обнаруженной трещины и происходит регистрация на приёмнике. На практике такая методика получила широкое применение при поиске микротрещин в сварочных швах.
- Зеркально-теневая методика — это теневой вариант, но два преобразователя располагаются на одной стороне проверяемого изделия, а регистрация происходит отражённых от обнаруженной полости волн. Если отражённые ультразвуковые колебания пропадают, т. к. полость или трещина создаёт тень, то техника фиксирует обнаружение дефекта.
Сегодня на практике в основном применяется первый вариант ультразвукового контроля (УЗК), очень редко второй, не говоря уже о последующих методиках.

Принцип УЗК
Проверка сварных швов ультразвуком относится, как уже упоминалось ранее, к неразрушающей методике контроля целостности аналогичных соединений и чаще всего применяется на практике. Звуковые волны быстро распространяются внутри твёрдых тел, проникая на всю глубину, отражение затеняется границами трещин или пустот, т. к. эти образования обладают другими свойствами, нежели материал проверяемого изделия.
Во время проверки сварных швов ультразвуковые дефектоскопы направляют волны сквозь проверяемый объект и улавливают отражение, а на экране появляются импульсы, интенсивность и расположение которых позволяет оператору определить точное расположение, а также основные параметры обнаруженного изъяна. При такой проверке производится тщательная диагностика всего шовного соединения, чтобы с точностью определить его внутреннее состояние.
Схема дефектоскопа, области применения
Основа схематического изображения ультразвукового дефектоскопа — это генератор электрических импульсов, который возбуждает ультразвуковые волны и направляет их движение. Волны пронизывают всё изделие и отражаются от противоположной стенки объекта, если дефектов не выявлено, или происходит их отражение от границ изъяна.
Отражённые импульсы улавливаются преобразователем и направляются на усилитель, затем в электронно-лучевую трубку и далее на генератор развёртки. На экране отображается плотность внутренней части изделия в виде графика, по которому анализируются два основных параметра: пики амплитуды и время возвращения сигнала.
Область применения аналогичных устройств довольна обширна, укажем только основные из них: нефтяная и химическая промышленность, машиностроение, строительство, приборостроительное и механическое производство, исследовательские лаборатории, проверка соединений трубопроводов. Аппаратура способна обнаружить и замерить пустоты в изделиях, определить плотность сварочных швов, клеевого соединения, имеется возможность проверять качество деталей прямо на конвейере.


И. П. Никодимов, образование: МГСУ, специальность: дефектоскопист по визуальному и измерительному контролю, опыт работы: с 1998 года: «Ультразвуковой контроль сварных соединений имеет ограничения — если дефекты менее четверти длины применяемой волны, то на мониторе такие нарушения не отражаются».

Особенности настройки
Перед началом проверки оборудование УЗК настраивается следующим образом:
- вначале производят регулировку пьезоэлектрического преобразователя;
- по эталонам параметров контроля осуществляется настройка дефектоскопа.
ПЭП настраивается на стандартных образцах, которые используют на предприятии, типа СО-1,2 или 3. При втором варианте настройка производится таким методом:
- вначале осуществляется настрой скорости прохождения ультразвуковых волн сквозь контролируемый объект;
- затем регулируется чувствительность по эталонам или стандартными образцами предприятия.
СОП изготавливаются из такого же материала, что и объект для проверки, а искусственный изъян внутри имеет минимальные размеры, которые допустимы для аналога изделия. Методика контроля осуществляется с требованиями ГОСТ УЗК, при этом учитываются действующие стандарты в отрасли на аналогичный вид контроля.
Осуществление контроля

- Удаление краски и следов коррозии со шва, а также на расстоянии не менее 50 мм с обеих сторон.
- Для улучшения прохождения ультразвуковых волн и удаления воздуха между корпусом излучателя, поверхность обработать машинным маслом, возможна замена техническим вазелином или солидолом.
- Осуществляется предварительный настрой аппаратуры, что напрямую зависит от решения поставленной задачи по проведению диагностики.
- Корпус искателя перемещается вдоль шва зигзагообразно, при этом исполнитель плавно проворачивает его вокруг оси на несколько градусов.
- Искатель максимально разворачивается во время первого появления сигнала на экране прибора, чтобы провести расширенный поиск с появлением максимальной амплитуды ультразвуковой волны.
- Уточняется — не вызвано ли появление колебания из-за отражения волны от рядом расположенных швов, если всё в норме, то оператор фиксирует изъян с записью координат расположения.
- Аналогичный контроль проводится не менее, как за два прохода.
- Тавровые швы с прямым углом проверяются эхо-методикой.
- Результат проверки оператор записывает в таблицу, чтобы было легко осуществить повторное обнаружение выявленных дефектов и последующее устранение.
В исключительных случаях для определения точного характера обнаруженных дефектов применяют такие исследования, как гамма-дефектоскопия или рентгенодефектоскопия.
Достоинства и недостатки
Положительные качества методики:
- при проверке детали остаются в целости и сохранности;
- низкая себестоимость проверки и быстрота работы исполнителя;
- не представляет опасности для работающего персонала;
- проверка осуществляется для изделий из любого материала;
- высокая мобильность ультразвукового оборудования.
Благодаря малым габаритам, проверка ультразвуковым способом проводится в любом месте.
Без негативных свойств никогда не обходится:
- нужна довольно тщательная предварительная подготовка, чтобы между искателем дефектоскопа и изделием не было воздушной прослойки;
- трудности с проверкой изделий и конструкций сложной формы ил малых размеров.
Иногда аналогичная методика не позволяет получение реальных размеров обнаруженного дефекта.
Как определяют параметры изъянов?
Чувствительность ультразвуковых дефектоскопов для внутреннего контроля изделий напрямую зависит от минимального размера эталонного образца, поэтому мельчайшие изъяны внутри изделия могут не определиться на дисплее прибора. Роль эталона часто выполняют прямые или боковые отверстия с плоским дном, иногда это специальные зарубки, расположение которых строго перпендикулярно направлению распространения звуковых волн.
При проверке ультразвуком сварочных швов выявленные изъяны оцениваются исходя из следующих параметров:
- амплитуда ультразвука;
- условная протяжённость, пространственные габариты дефекта;
- форма обнаруженного объекта.
Условная длина изъяна сварочного соединения определяется величиной расстояния перемещения излучателя вдоль изделия, когда сигнал, исходящий от дефекта, поступает непрерывно. Перемещая излучатель перпендикулярно оси шва, определяется условная ширина, аналогичная высота оценивается разницей между интервалом времени, когда был получен сигнал от излучённой и отражённой от дефекта волны, при этом излучатель находится в крайнем положении.
Точность получаемых данных зависит от следующих основных факторов:
- Уровня подготовки исполнителя (оператора).
- Тщательности проводимого обследования и внимательности оператора.
- Соответствия измеренных параметров с теми, которые были предусмотрены соответствующей инструкцией.
Довольно затруднительно точно установить истинную величину обнаруженного изъяна в сварном шве во время проведения ультразвуковой диагностики, поэтому на практике достаточно вычислить его площадь или диаметр, т. к. это эквивалентные показатели.

Выводы
Ультразвуковая дефектоскопия относится к сложному оборудованию, хотя габариты прибора довольно небольшие, что позволяет увеличить мобильность и использовать приборы внутри помещения и снаружи, даже в труднодоступных местах. Операторами работают специально обученные люди, которые по графику изменения частот определяют месторасположение изъяна, например, Московский строительный университет готовит инженеров для работы с ультразвуковыми дефектоскопами на производстве.
Дефектоскопия трубопроводов – ультразвуковой способ контроля труб, сварных швов и соединений
В течение длительного периода использования, трубопроводы попадают под негативное внешнее и внутреннее воздействие окружающей среды. В итоге – металл деградирует, на нем образуются коррозийные образования, появляются трещины и сколы, и другие типы дефектов. Казалось бы, при создании проекта трубопровода используя современные технологии, должна быть обеспеченна полная защита магистральных коммуникаций.
Но, к сожалению, исключить в полной мере возникновение повреждений невозможно. Чтобы небольшие дефекты не превратились в серьезную проблему, используют различные виды контроля.
Одним из них, который не предусматривает вывода в ремонт магистральной системы – является дефектоскопия трубопроводов.
Этот метод диагностики получил широкое распространение. Его применение позволяет выявить следующие виды дефектов:
- потеря уровня герметичности;
- потеря контроля состояния напряженности;
- нарушение сварных стыков;
- разгерметизация сварных швов другие параметры, которые ответственны за надежное функционирование магистралей.
Проверять таким образом можно:
- теплосеть;
- газоподающую сеть;
- нефтепроводы;
- водоподающие трубопроводы и др.
Дефектоскопия на 100% способна выявить недостатки и предупредить серьезные аварии. Методы поиска дефектов постоянно усовершенствуются, обновляется оборудование, и испытываются новые модели дефектоскопов. Плюс ко всему этому проводятся различные анализы для того, что бы в последствие улучшить работу средств.
Ультразвуковая дефектоскопия
Ультразвуковая дефектоскопия трубопровода впервые была предоставлена Соколовым С.Я. в 1928 году. Она создана на основе изучения передвижения ультразвуковых колебаний, которые находились под контролем дефектоскопа.
Описывая принцип работы этих устройств, необходимо отметить, что волна звука не меняет направление своего передвижения в среде, имеющем одинаковую структуру. Когда среда разделяется удельным акустическим препятствием, то получается отражение волны.
Видео: Магнитопорошковая дефектоскопия сварных швов
Чем выше количество таких препятствий, тем больше волн будет отражена от границы, которая разделяет среду. Возможность обнаружить небольшие дефекты отдельно один от другого определяет длина звуковой волны. А она при этом зависима от того, насколько часты звуковые колебания.
Многообразные задачи, стоящие при проведении ультразвуковой дефектоскопии, привели к тому, что появились большие возможности этого способа поиска неисправностей. Из них выделяют пять основных вариантов:
- Эхо – локация.
- Теневой метод.
- Зеркально-теневой.
- Зеркальный.
- Дельта – способ.
Приборы современного производства для ультразвуковой проверки оснащают несколькими возможностями измерения одновременно. И делают это в разных сочетаниях.
Эти механизмы отличаются очень высокой точностью, в результате остаточное пространственное разрешение и достоверность итогового вывода о дефективности трубопровода или его деталей получается максимально правдивым.
Ультразвуковой анализ не приносит повреждений исследуемой конструкции, и дает возможность провести все работы с максимально быстро и без вреда человеческому здоровью.
Ультразвуковая дефектоскопия – это доступная во всех отношениях система контроля мест соединения и швов. То, что в основе этого метода положена высокая возможность проникновения ультразвуковых волн сквозь металл.
Анализ сварных швов
Дефектоскопия сварных швов трубопроводов является обязательной процедурой перед запуском в эксплуатацию магистральных коммуникаций, особенно проходящих под землей.
В любой конструкции сварной шов являлся слабым местом, по этим причинам их качество всегда должно быть под контролем. На сварных швах лежит важная ответственность – они определяют герметичность и качество готового сооружения в целом.
Суть различных подходов для анализа таких стыков состоит в оценке тех или других физических свойств, характеризующих надежность и прочность трубопровода. Дефектоскопия определяет не только размер дефектов, но и оценивает качественное состояние швов. В эту оценку входит:
- показатель прочности;
- возможность противостоять коррозийным образованиям;
- степень пластичности;
- структура металла шовного соединения и области возле него;
- количество о габариты дефекта.
Способ ультразвукового исследования – это один из основных методов выявления дефектов на сварных швах.
Видео: Обзор дефектоскопа магнитопорошкового
Дефектоскопия сварных соединений трубопроводов имеет следующие преимущества.
- Быстрое проведение ревизии.
- Высокая точность исследования.
- Небольшая стоимость.
- Абсолютная безвредность для человека.
- Мобильность используемых для проверки устройств.
- Возможность выполнять проверку качества функционирующего трубопровода.
Самая простая процедура дефектоскопии – это визуальный осмотр. Визуально – измерительный способ позволяет на основе первых полученных результатов при внешнем осмотре определить наличие многих дефектов.
С помощью данного осмотра проверяют уровень качества готовых сварных стыков. Этот вид исследования применяют независимо от других типов контроля. Чаще всего он является очень информативным, и кроме этого, он самый дешевый.
Этим методом выявляют отклонения от номинальных размеров. При этом поверхность трубопровода тщательно очищают от грязи, металлических брызг, ржавых образований, окалины, масла и прочих загрязнений.
В зону внимания попадают сварные швы и прилегающая к ним зона. Все найденные на этом этапе недостатки устраняют до выполнения иных способов дефектоскопии.
Например, заметно выраженные различия в высоте сварного шва свидетельствуют о том, что дуга во время сварочных работ прерывалась.
На период проверочных мероприятий такие стыки рекомендуют обработать 10% раствором азотной кислоты. Если будут заметны грубые геометрические нарушения, то это свидетельствует о нарушении качества сварного шва.
Видео: В видео представлен краткий обзор ультразвуковых приборовTG 110-DL, Avenger EZ
Преимущества данного метода исследования следующие:
- Чаще всего на такую операцию нужно немного времени.
- Небольшая стоимость проверки.
- Безопасность данной процедуры для человеческого здоровья.
- Можно проверить действующий трубопровод.
Ну и куда же без недостатков:
- Возможность разрушающего действия.
- Потребность в спецреактивах и иных расходных материалах.
- Опытные образцы после этого процесса не всегда подлежали восстановлению.
Дефектоскопия стыков трубопроводов
Дефектоскопия соединений трубопроводов – это довольно ответственный процесс, который начинают только после того, как сварной шов готовый. Место состыковки должно остыть и его необходимо очистить от загрязнений.
Еще одним методом проверки является цветная дефектоскопия трубопроводов, ее по-другому называют капиллярный контроль. В основе данной проверке лежит капиллярная активность жидкости. Поры и потрескавшиеся образования создают сетку в стыке.
Когда они контактируют с жидкостью, то они просто пропускают ее сквозь себя. Такой способ дает возможность обнаружить скрытие проблемные образования. Проводят такую процедуру в соответствии к ГОСТу 1844-80.
Часто для этого вида поверки применяют магнитную дефектоскопию. В ее основу положили такое явление, как электромагнетизм. Возле проверяемой зоны механизм создает магнитное поле. Его линии свободно проходят сквозь металл, но когда присутствует повреждение, то линии теряют ровность.
Видео: Проведение внутритрубной диагностики магистральных трубопроводов
Чтобы зафиксировать полученное изображение, используют магнитографическую или магнитопорошковую дефектоскопию. Если применяют порошок, то его накладывают сухим или в виде влажной массы (в нее добавляют масло). Порошок станет скапливаться только в проблемных местах.
Внутритрубная проверка
Внутритрубная дефектоскопия магистральных трубопроводов – это самый эффективный вариант обнаружения проблем, основанный на прогоне по системе труб спецустройств.
Ими стали внутритрубные дефектоскопы, с установленными специальными приборами. Эти механизмы определяют конфигурационные особенности поперечного сечения, выявляют вмятины, утончения и коррозийные образования.
Также есть внутритрубные механизмы, которые созданы для решения конкретных заданий. Например, оборудование, имеющее видео и фотокамеры, инспектирует внутреннюю часть магистрали и определяет степень кривизны и профиль конструкции. Также оно обнаруживает трещины.
Эти агрегаты передвигаются по системе потоком и оснащаются разнообразными датчиками, они накапливают и хранят информацию.
Внутритрубная дефектоскопия магистральных трубопроводов имеет весомые преимущества. Она не выставляет требований ставить устройства, которые ведут систематический контроль.
К сказанному необходимо добавить, что, используя это вид диагностики, можно производить регулярный контроль деформационных изменений по всему участку действующей конструкции с высоким уровнем производительности.
Таким путем можно вовремя установить участок, который несет аварийную угрозу всей системе, и своевременно провести ремонтные работы по устранению неполадок.
Говоря об этом методе, важно заметить, что есть ряд технических трудностей по его внедрению. Основное – он является дорогим. А второй фактор – это наличие устройств только для магистральных трубопроводов с большими объемами.
Видео
По этим причинам этот метод чаще всего применяют для относительно новых газопроводных систем. Внедрить этот способ для других магистралей можно посредством выполнения реконструкции.
Помимо оговоренных технических трудностей, этот метод отличается максимально точными показателями с обработкой проверочных данных.
Для исследования магистральных трубопроводов не обязательно выполнять все процедуры, чтобы убедиться в отсутствии проблем. Каждый участок магистрали можно проверить тем или другим наиболее подходящим способом.
Чтобы выбрать оптимальный вариант проверки нужно оценить, насколько важна ответственность стыка. И уже, исходя из этого, подбирать метод исследования. Например, для домашнего производства часто хватает визуального осмотра или других бюджетных видах проверок.
Ультразвуковая дефектоскопия — Википедия. Что такое Ультразвуковая дефектоскопия
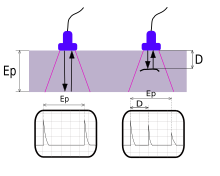
Ультразвукова́я дефектоскопи́я — метод, предложенный С. Я. Соколовым в 1928 году и основанный на исследовании процесса распространения ультразвуковых колебаний с частотой 0,5 — 25 МГц в контролируемых изделиях с помощью специального оборудования — ультразвукового преобразователя и дефектоскопа[1]:125. Является одним из самых распространенных методов неразрушающего контроля.
Принцип работы
Звуковые волны не изменяют траектории движения в однородном материале. Отражение акустических волн происходит от границы раздела сред с различными удельными акустическими сопротивлениями. Чем больше различаются акустические сопротивления, тем большая часть звуковых волн отражается от границы раздела сред. Так как включения в металле обычно содержат газ (смесь газов) возникающих вследствие процесса сварки, литья и т. п. И не успевают выйти наружу при затвердевании металла, смесь газов имеет на пять порядков меньшее удельное акустическое сопротивление, чем сам металл, то отражение будет практически полное.
Разрешающая способность акустического исследования, то есть способность выявлять мелкие дефекты раздельно друг от друга, определяется длиной звуковой волны, которая в свою очередь зависит от частоты ввода акустических колебаний. Чем больше частота, тем меньше длина волны. Эффект возникает из-за того, что при размере препятствия меньше четверти длины волны, отражение колебаний практически не происходит, а доминирует их дифракция. Поэтому, как правило, частоту ультразвука стремятся повышать. С другой стороны, при повышении частоты колебаний быстро растёт их затухание, что сокращает возможную область контроля. Практическим компромиссом стали частоты в диапазоне от 0,5 до 10 МГц.
Возбуждение и приём ультразвука
Существует несколько методов возбуждения ультразвуковых волн в исследуемом объекте. Наиболее распространенным является использование пьезоэлектрического эффекта. В этом случае излучение ультразвука производится с помощью преобразователя, который преобразует электрические колебания в акустические путём обратного пьезоэлектрического эффекта. Пройдя через контролируемую среду, ультразвуковые колебания попадают на приёмную пьезопластину преобразователя и, вследствие прямого пьезоэлектрического эффекта вновь становятся электрическими, которые и регистрируются измерительными цепями. В зависимости от конструкции и подключения, пьезопластины преобразователя могут выполнять роль только излучателя ультразвуковых колебаний или только приёмника, либо совмещать в себе обе функции.
Ультразвуковые пьезоэлектрические преобразователи, использующиеся при ручном контроле: прямой B1S-O, миниатюрный наклонный MWB 70-4, наклонный WK45-2Также используются электромагнитно-акустический (ЭМА) метод, основанный на приложении сильных переменных магнитных полей к металлу. КПД этого метода гораздо ниже, чем у пьезоэлектрического, но зато может работать через воздушный зазор и не предъявляет особых требований к качеству поверхности.
Классификация методов исследования
Существующие акустические методы неразрушающего контроля подразделяют на две большие группы — активные и пассивные.
Активные
Активные методы контроля подразумевают под собой излучение и приём акустических волн.
Отражения
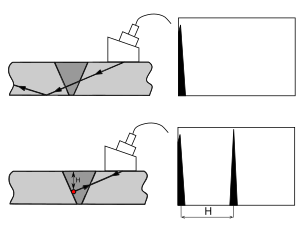
- Эхо-метод или эхо-импульсный метод — наиболее распространённый: преобразователь генерирует колебания (то есть выступает в роли генератора) и он же принимает отражённые от дефектов эхо-сигналы (приёмник). Данный способ получил широкое распространение за счёт своей простоты, так как для проведения контроля требуется только один преобразователь, следовательно при ручном контроле отсутствует необходимость в специальных приспособлениях для его фиксации (как, например, в дифракционно-временном методе) и совмещении акустических осей при использовании двух преобразователей. Кроме того, это один из немногих методов ультразвуковой дефектоскопии, позволяющий достаточно точно определить координаты дефекта, такие как глубину залегания и положение в исследуемом объекте (относительно преобразователя).
- Зеркальный или Эхо-зеркальный метод — используются два преобразователя с одной стороны детали: сгенерированные колебания отражаются от дефекта в сторону приёмника. На практике используется для поиска дефектов расположенных перпендикулярно поверхности контроля, например трещин.

- Дифракционно-временной метод — используется два преобразователя с одной стороны детали, расположенные друг напротив друга. Если дефект имеет острые кромки (как, например, трещины) то колебания дифрагируют на концах дефекта и отражаются во все стороны, в том числе и в сторону приёмника. Дефектоскоп регистрирует время прихода обоих импульсов при их достаточной амплитуде. На экране дефектоскопа одновременно отображаются оба сигнала от верхней и от нижней границ дефекта, тем самым можно достаточно точно определить условную высоту дефекта. Способ достаточно универсален, позволяет производить ультразвуковой контроль на швах любой сложности, но требует специального оборудования для фиксации преобразователей, а также дефектоскоп, способный работать в таком режиме. Кроме того, дифрагированные сигналы достаточно слабые.
- Дельта-метод — разновидность зеркального метода — отличается механизмом отражения волны от дефекта и способом принятия сигнала. В диагностике используется для поиска специфично расположенных дефектов. Данный метод очень чувствителен к вертикально-ориентированным трещинам, которые не всегда удаётся выявить обычным эхо-методом.
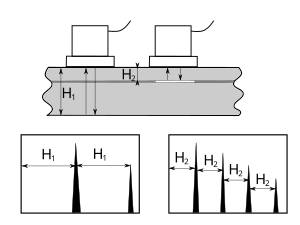
- Ревербационный метод — основан на постепенном затухании сигнала в объекте контроля. При контроле двухслойной конструкции, в случае качественного соединения слоёв, часть энергии из первого слоя будет уходить во второй, поэтому ревербация будет меньше. В обратном случае будут наблюдаться многократные отражения от первого слоя, так называемый лес. Метод используется для контроля сцепления различных видов наплавок, например баббитовой наплавки с чугунным основанием. Основным недостатком данного метода является регистрация дефектоскопом эхо-сигналов от границы соединения двух слоёв. Причиной этих эхо-сигналов является разница скоростей упругих колебаний в материалах соединения и их различное удельное акустическое сопротивление. Например на границе баббит-сталь возникает постоянный эхо-сигнал даже в местах качественного сцепления. В силу конструкционных особенностей некоторых изделий, контроль качества соединения материалов ревербационным методом может быть невозможен именно из-за наличия на экране дефектоскопа эхо-сигналов от границы соединения.
- Акустическая микроскопия благодаря повышенной частоте ввода ультразвукового пучка и применению его фокусировки, позволяет обнаруживать дефекты, размеры которых не превышают десятых долей миллиметра. Широкое применение в промышленности затруднено в связи с крайне низкой производительностью метода. Данный метод подходит для исследовательских целей, диагностике, а также радиоэлектронной промышленности.
- Когерентный метод — по сути является разновидностью Эхо-импульсного метода. Помимо двух основных параметров эхо-сигнала, таких как амплитуда и время прихода, используется дополнительно фаза эхо-сигнала. Использование когерентного метода, а точнее нескольких идентичных преобразователей, работающих синфазно. При использовании специальных преобразователей, таких как преобразователь бегущей волны или его современный аналог — преобразователь с фазированной решёткой. Исследования применимости данного метода к реальным объектам контроля ещё не завершены. Метод находится на стадии научно-исследовательских изысканий.
Прохождения
Методы прохождения подразумевают под собой наблюдение за изменением параметров ультразвуковых колебаний, прошедших через объект контроля, так называемых сквозных колебаний. Изначально для контроля применялось непрерывное излучение, а изменение его амплитуды сквозных колебаний расценивалось как наличие дефекта в контролируемом объекте, так называемой звуковой тени. Отсюда появилось название теневой метод. Со временем непрерывное излучение сменилось импульсным, а к фиксируемым параметрам помимо амплитуды добавились также фаза, спектр и время прихода импульса и появились другие методы прохождения. Термин теневой потерял свой первоначальный смысл и стал означать один из методов прохождения. В англоязычной литературе метод прохождения называется through transmission technique или through transmission method, что полностью соответствует его российскому названию. Термин теневой в англоязычной литературе не применяется.
- Теневой — используются два преобразователя, которые находятся по две стороны от исследуемой детали на одной акустической оси. В данном случае один из преобразователей генерирует колебания (генератор), а второй принимает их (приёмник). Признаком наличия дефекта будет являться значительное уменьшение амплитуды принятого сигнала, или его пропадание (дефект создаёт акустическую тень).
- Зеркально-теневой — используется для контроля деталей с двумя параллельными сторонами, развитие теневого метода: анализируются отражения от противоположной грани детали. Признаком дефекта, как и при теневом методе, будет считаться пропадание отраженных колебаний. Основное достоинство этого метода в отличие от теневого заключается в доступе к детали с одной стороны.

- Временной теневой основан на запаздывании импульса во времени, затраченного на огибание дефекта. Используется для контроля бетона или огнеупорного кирпича.
- Метод многократной тени аналогичен теневому, с тем исключением, что ультразвуковая волна несколько раз проходит через параллельные поверхности изделия.
- При эхо-сквозном методе используют два преобразователя, расположенные по разные стороны объекта контроля друг напротив друга. В случае отсутствия дефекта, на экране дефектоскопа наблюдают сквозной сигнал и сигнал, двукратно отражённый от стенок объекта контроля. При наличии полупрозрачного дефекта, также наблюдают отражённые сквозные сигналы от дефекта.
- Ревербационно-сквозной метод включает в себя элементы ревербационного метода и метода многократной тени. На небольшом расстоянии друг от друга, как правило, с одной стороны изделия, устанавливают два преобразователя — передатчик и приёмник. Ультразвуковые волны, посылаемые в объект контроля после многократных отражений, в конечном счете попадают на приёмник. Отсутствие дефекта позволяет наблюдать стабильные отраженные сигналы. При наличии дефекта изменяется распространение ультразвуковых волн — изменяется амплитуда и спектр принятых импульсов. Метод применяется для контроля многослойных конструкций и полимерных композитных материалов.
- Велосиметрический метод основан на регистрации изменения скорости упругих волн в зоне дефекта. Применяется для контроля многослойных конструкций и для изделий из полимерных композиционных материалов.
Собственных колебаний
Основаны на возбуждении в объекте контроля свободных или вынужденных колебаний и измерению их параметров: собственных частот и величины потерь.
Вынужденных колебаний
- Интегральный
- Локальный
- Акустико-топографический
Свободных колебаний
Свободные колебания возбуждают путём кратковременного воздействия на объект контроля, после чего объект колеблется в отсутствии внешних воздействий. Источником кратковременного воздействия может быть любой механический удар, например молотком.
- Интегральный
- Локальный
Импедансные
- Изгибных волн
- Продольных волн
- Контактного импеданса
Пассивные
Пассивные методы контроля заключаются в приёме волн, источником которых является сам объект контроля.
Современные дефектоскопы точно замеряют время, прошедшее от момента излучения до приёма эхо-сигнала, тем самым измеряя расстояние до отражателя. Это позволяет добиться высокого лучевого разрешения исследования. Компьютеризированные системы позволяют провести анализ большого числа импульсов и получить трёхмерную визуализацию отражателей в металле.
Преимущества
Ультразвуковой контроль изделий в ГДР, 1977 годУльтразвуковой контроль не разрушает и не повреждает исследуемый образец, что является его главным преимуществом. Возможно проводить контроль изделий из разнообразных материалов, как металлов, так и неметаллов. Кроме того можно выделить высокую скорость исследования при низкой стоимости и опасности для человека (по сравнению с рентгеновской дефектоскопией) и высокую мобильность ультразвукового дефектоскопа.
Недостатки
Использование пьезоэлектрических преобразователей требует подготовки поверхности для ввода ультразвука в металл, в частности создания шероховатости поверхности не ниже класса 5, в случае со сварными соединениям ещё и направления шероховатости (перпендикулярно шву). Ввиду большого акустического сопротивления воздуха, малейший воздушный зазор может стать непреодолимой преградой для ультразвуковых колебаний. Для устранения воздушного зазора, на контролируемый участок изделия предварительно наносят контактные жидкости, такие как вода, масло, глицерин. При контроле вертикальных или сильно наклоненных поверхностей необходимо применять густые контактные жидкости с целью предотвращения их быстрого стекания.
Для контроля изделий с внешним диаметром менее 200 мм, необходимо использовать преобразователи, с радиусом кривизны подошвы R, равным 0,9-1,1R радиуса контролируемого объекта, так называемые притертые преобразователи, которые в таком виде непригодны для контроля изделий с плоскими поверхностями. Например для контроля цилиндрической поковки, необходимо производить перемещение преобразователя в двух взаимно перпендикулярных направлениях, что подразумевает под собой использование двух притёртых преобразователей — по одному для каждого из направлений.
Как правило ультразвуковая дефектоскопия не может дать ответ на вопрос о реальных размерах дефекта, лишь о его отражательной способности в направлении приемника. Эти величины коррелируют, но не для всех типов дефектов. Кроме того, некоторые дефекты практически невозможно выявить ультразвуковым методом в силу их характера, формы или расположения в объекте контроля.
Практически невозможно производить достоверный ультразвуковой контроль металлов с крупнозернистой структурой, таких как чугун или аустенитный сварной шов (толщиной свыше 60 мм)[2][3] из-за большого рассеяния и сильного затухания ультразвука. Кроме того, затруднителен контроль малых деталей или деталей со сложной формой. Также затруднен ультразвуковой контроль сварных соединений из разнородных сталей (например аустенитных сталей с перлитными сталями) ввиду крайней неоднородности металла сварного шва и основного металла.
Применение
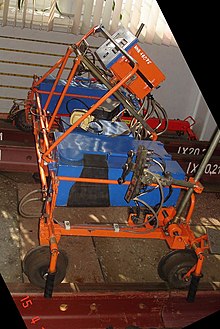
Применяется для поиска дефектов материала (поры, волосовины, различные включения, неоднородная структура и пр.) и контроля качества проведения работ — сварка, пайка, склейка и пр. Ультразвуковой контроль является обязательной процедурой при изготовлении и эксплуатации многих ответственных изделий, таких как части авиационных двигателей, трубопроводы атомных реакторов или железнодорожные рельсы.
Ультразвуковой контроль сварных швов
Сварные швы являются самой массовой областью применения ультразвуковой дефектоскопии. Это достигается за счёт мобильности ультразвуковой установки, высокой производительности контроля, точности, чувствительности к внутренним (объёмным — поры, металлические и неметаллические включения; плоскостным — непровары, трещины), а также внешним, то есть поверхностным дефектам сварных швов.
Многие ведомственные документы подразумевают обязательный ультразвуковой контроль сварных швов, либо альтернативный выбор ультразвукового или радиационного контроля, либо контроль обоими методами.
Основным документом в России по ультразвуковому контролю сварных швов является ГОСТ Р 55724-2013, в котором рассмотрены в полном объёме методы контроля стыковых, тавровых, нахлесточных и угловых сварных швов, выполненных различными способами сварки. Также в нём подробно описаны стандартные образцы (эталоны) СО-1, СО-2 (СО-2А), СО-3 и СО-4 и стандартные образцы предприятия, необходимые для настройки дефектоскопа, а также их параметры для их изготовления.
Объёмы контроля и нормы оценки качества сварного соединения устанавливаются различными нормативными документами в соответствии с требованиями прочности к конкретной сварной конструкции. На предприятиях, изготавливающих особо ответственные изделия, а также различными надзорными органами могут выпускаться собственные методические материалы для оценки качества сварных швов[4]. Примером может служить РД РОСЭК-001-96, разработанный Российской экспертной компанией по объектам повышенной опасности «РосЭК», и утвержденный Ростехнадзором для оценки качества сварных соединений для грузоподъёмных машин.
Нормативно-техническая документация
- ГОСТ Р 55724-2013 Контроль неразрушающий. Соединения сварные. Методы ультразвуковые.
- ГОСТ 24507-80 Контроль неразрушающий. Поковки из черных и цветных металлов. Методы ультразвуковой дефектоскопии.
- ГОСТ 22727-88 Прокат листовой. Методы ультразвукового контроля.
- ГОСТ 21120-75 Прутки и заготовки круглого и прямоугольного сечения. Методы ультразвуковой дефектоскопии.
- РД РОСЭК-001-96 Машины грузоподъемные. Конструкции металлические. Контроль ультразвуковой. Основные положения.
- ОП 501 ЦД-97 Энергетическое оборудование. Сосуды давления. Трубопроводы пара, воды.
- ПНАЭ Г-7-010-89 Оборудование и трубопроводы атомных энергетических установок. Сварные соединения и наплавки. Правила контроля.
- ПНАЭ Г-10-032-92 Правила контроля сварных соединений элементов локализующих систем безопасности атомных станций.
- ПНАЭ Г-7-032-91 Унифицированные методики контроля основных материалов полуфабрикатов), сварных соединений и наплавки оборудования и трубопроводов атомных энергетических установок. Ультразвуковой контроль. Часть IV. Контроль сварных соединений из сталей аустенитного класса.
См. также
Примечания
- ↑ В. Н. Волченко, А. К. Гурвич, А. Н. Майоров, Л. А. Кашуба, Э. Л. Макаров, М. Х. Хусанов. Контроль качества сварки / Под ред. В. Н. Волченко. — Учебное пособие для машиностроительных вузов. — М.: Машиностроение, 1975. — 328 с. — 40 000 экз.
- ↑ ПНАЭ Г-7-032-91 Ультразвуковой контроль. Часть IV. Контроль сварных соединений из сталей аустенитного класса. П.1.4.
- ↑ Клюев В. В. Неразрушающий контроль. Том 3.: Справочник. В 7-и книгах / Под ред. Клюева В. В. — М.: Машиностроение, 2004.
- ↑ Некоторые «болезненные» вопросы УЗК традиционными методами, журнал «В мире неразрушающего контроля», № 2(60) — июнь 2013.
Литература
- Шрайбер Д. С. Ультразвуковая дефектоскопия //М.: Металлургия. — 1965. — Т. 392. — С. 29.
- Гурвич А. К., Ермолов И. Н. Ультразвуковая дефектоскопия сварных швов — Киев: Техника, 1972, 460 с.
- Выборнов Б. И. Ультразвуковая дефектоскопия — М.: Металлургия, 1985.
- Щербинский В. Г., Пафос С. К., Гурвич А. К. Ультразвуковая дефектоскопия: вчера, сегодня, завтра //В мире неразрушающего контроля. — 2002. — №. 4. — С. 18.
- Ермолов И. Н. Достижения в теоретических вопросах ультразвуковой дефектоскопии, задачи и перспективы //Дефектоскопия. — 2004. — №. 10. — С. 13-48.
- Кретов Е. Ф. Ультразвуковая дефектоскопия в энергомашиностроении. — Изд.3-е, перераб.и доп. -Санкт-Петербург: СВЕН, 2011, 312с., ISBN 978-5-91161-014-2
- Марков А. А., Шпагин Д. А. Ультразвуковая дефектоскопия рельсов, — Изд. 2-е, исправл. и доп. — СПб.: Образование — Культура, 2013, 283с., ISBN 5-88857-104-0