Дефекты сварки и способы их устранения
Дефекты сварки и способы их устранения
Дефекты сварных швов появляются в результате либо неправильного выбора, либо нарушения технологии изготовления сварной конструкции, а также в результате использования некачественных сварочных материалов и невысокой квалификации сварщика.
Дефекты подразделяются на внешние и внутренние. Причем внешние дефекты можно выявить путем осмотра невооруженным глазом или с помощью лупы с десятикратным увеличением, в то время как для установления внутренних дефекте требуется использование специальных методов: металлографии ческие исследования, химический анализ, механические испытания, просвечивание рентгеновскими или гамма-лучами, магнитные и ультразвуковые методы контроля. Для выявления:! дефектов сварное соединение нужно предварительно очистить: от шлака, окалины и металлических брызг.
К внешним дефектам относятся: нарушение размеров формы шва, подрез зоны сплавления, прожог, наплыв, непровар, поверхностное окисление, незаваренные кратеры, поверх^ ностные поры, продольные и поперечные трещины.
К внутренним дефектам относятся следующие: внутренние поры, непровар, неметаллические включения и микре трещины.
Нарушение размеров и форм шва проявляется в чрезмерном усилении и резких переходах от основного металла к наплавленному, а также в неполномерности высоты и ширины шва. При ручной сварке данные дефекты возникают в результате неаккуратной подготовки свариваемых кромок, неправильного выбора сварочного тока, невысокого качества сборки под сварку и низкой квалификации сварщика. Дефекты формы шва могут возникнуть и в результате колебания напряжения в сети при выполнении работы. При автоматизированной сварке нарушения размеров и формы швов могут быть из-за несоблюдения режима сварочного процесса (скорости сварки, скорости подачи электродов, сварочного тока) и неправильной разделки шва.
Подрез зоны сплавления выглядит в виде узкого углубления в основном металле вдоль края сварного шва. Этот дефект возникает при усиленной мощности горелки, при сварке удлиненной дугой, неправильном положении электрода или горелки и присадочного прутка, а также при сварке большим током.
Прожог представляет собой сквозное отверстие в сварном шве. Основные причины его возникновения следующие: малая толщина свариваемого металла, завышенная мощность пламени горелки, большой сварочный ток, незначительное притупление свариваемых кромок и неравномерный зазор между ними по расстоянию.
Наплыв — натекание металла шва на непрогретую поверхность свариваемого металла или прежде выполненного валика без сплавления с ним. Дефект возникает при некачественных электродах и несоответствии скорости сварки и сварочного тока разделке шва, а также при низкой квалификации сварщика.
Непровар проявляется в виде местного несплавления свариваемых кромок основного и наплавленного металлов и может быть результатом плохой подготовки свариваемых кромок (отсутствие зазора, большое притупление, незначительный угол скоса), смещения электрода к одной из кромок, быстрого перемещения электрода по шву.
Поверхностное окисление — окисление металла шва и примыкающего к нему основного металла главным образом из-за сильно окисляющей среды, очень высокой мощности пламени сварочной горелки, большой длины дуги, слишком сильного сварочного тока, медленного перемещения электрода или горелки вдоль шва.
Поверхностные и внутренние поры являются результатом попадания в металлический шов различных газов, образующихся при сварке (азот, водород, углекислый газ и др.). АзоТ попадает в шов из атмосферного воздуха при недостаточно тщательной защите расплавленного металла в зоне сварки. Из компонентов покрытия электродов, воды и масла образуется водород. Оксид углерода возникает в процессе сварки стали при сгорании содержащегося в ней углерода. Дело в том, что при повышенном содержании углерода в электродах и свариваемой стали, а также при дефиците в сварочной ванне рас-кислителей и высокой скорости сварки оксид углерода не успевает улетучиться и остается в металле. Итак, пористость — итог неаккуратной подготовки свариваемых кромок (ржавчина, замасленность, загрязненность), недостатка раскислителей, использования влажного флюса, электродов с сырым покрытием и больших скоростей сварки.
Наружные и внутренние трещины (микротрещины) возникают главным образом в результате появляющихся в металле напряжений из-за его неравномерного нагревания, охлаждения и усадки. Легированные и высокоуглеродистые стали при охлаждении после сварки закаливаются; в результате этого могут появиться трещины. Высокое содержание в стали вредных примесей (серы и фосфора) также может вызвать образование трещин. Следует заметить, что наружные и внутренние трещины являются наиболее опасными и недопустимыми дефектами швов.
Чердак — это помещение, которое находится между крышей и верхним (чердачным) перекрытием здания. Как правило, в нем устанавливают водяные баки, прокладки разводных труб отопления и размещают сборные каналы и камеры вентиляции.
В индивидуальном доме проветривание чердака осуществляется через слуховые окна, а также через приточные отверстия под карнизом и вытяжные в коньке крыши. Данные приспособления призваны бороться с конденсатом, который образуется в результате проникновения влажного воздуха из кухни, санузлов и лестничных клеток.
Слуховые окна изобрел русский мастер Слухов, который, возглавляя артель, осуществлял строительство московского Манежа в 1824 г.
Чердачное пространство можно использовать для хозяйственных целей, например разместить в нем мастерскую. Для этого необходимо укрепить чердачное перекрытие, чтобы избежать его провисания. Кроме этого, надо позаботиться об освещении, которое может быть естественным и искусственным. Для обеспечения первого требуется устройство чердачных окон, для второго — электрическая проводка.
Чердак можно также оборудовать под помещение для сушки белья. Для этого следует предусмотреть наличие дополнительных вентиляционных устройств.
Чердачное помещение может служить в качестве кладовки для хранения различных материалов и инструментов.
Однако в последнее время развитие строительства, разработка рациональных планировочных решений, появление новых высококачественных материалов сделало возможным использование чердака в качестве жилого помещения.
Читать далее:
Сварочные флюсы
Сварочные электроды
Общие сведения о сварке арматуры
Противопожарные мероприятия при сварке
Безопасность труда при сварке технологических трубопроводов
Безопасность труда при сварке строительных металлических и железобетонных конструкций
Защита от поражения электрическим током при сварке
Техника безопасности и производственная санитария при сварке
Управление качеством сварки
Статистический метод контроля
Дефекты металла при сварке.
Дефекты сварных соединений металла
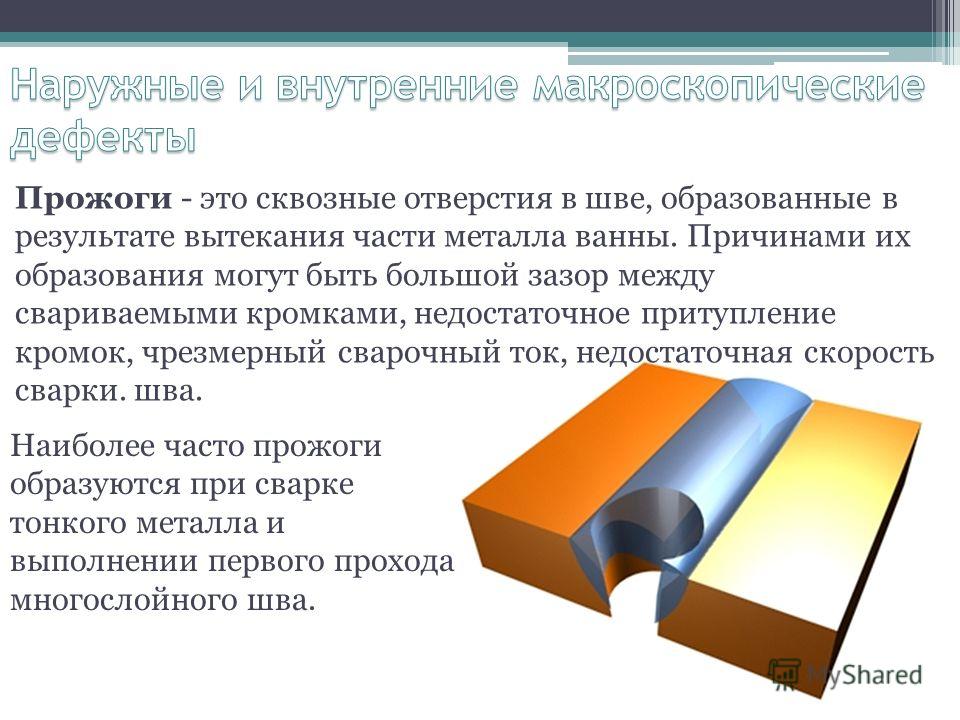
Не менее распространенными являются и дефекты металла, возникающие в результате его сваривания.
Вообще, стоит сказать, что дефектами сварных соединений считаются все возможные отклонения от установленных требований и норм, снижающие прочностные и эксплуатационные характеристики сварных швов, соединений, а соответственно и конструкции в целом.
То-есть дефекты- отклонения по геометрии сварных швов и соединений, подрезы, канавки, рябь, несплавления, пустоты, излишек металла, угловые или линейные смещения, образующиеся при использовании неподходящей техники сварки и не правильной технике узлов конструкции.
Виды сварных дефектов
Различают такие группы дефектов:
- изменения форм или размера шва, соединений,
- изменения микро- и макроструктуры,
- деформация сварных соединений.
Итак, рассмотрим эти самые дефекты подробнее.
Трещины, пузыри, подрезы и не только
Достаточно часто при сварке в наплавке металла образуются трещины темного цвета в разломах, они могут быть очень окисленными или светлыми. Трещины бывают продольными или поперечными.
Основной причиной появления таких трещин является:
- плохо подобранный присадочный материал или некачественные присадочная проволока, обмазка, флюс;
- не подходящий режим или техника сварки;
- высокое внутришовное напряжение или наличие пористостей и включений шлака.
В сварных швах и зонах перехода могут располагаться холодные трещины, которые образуются в момент снижения температуры материала, в процессе сваривания стали высокой толщины, с низким содержанием легирующих элементов.
Обычно они образуются в переходных зонах из-за использования неподходящей техники сваривания или не того присадочного материала.
Помимо холодных трещин в зонах перехода могут располагаться извилистые горячие трещины-темного цвета, и значительно окисленные в разломе. Маленькие трещинки шва и надрыва-образующиеся по тем же причинам, что и другие.
При термической обработке могут возникать трещины различных направлений. Причина их образования- применение неподходящих режимов термообработки свариваемых соединений, а так же из-за нетехнологичности узлов самой конструкции.
При неправильной технологии изменения изделия возникают рихтовочные трещины, которые располагаются в любых направлениях по отношению ко шву.
Такой дефект, как несплавление основного металла с наплавленным, образуется в самом шве, в его кромке, и между различными слоями — проходами при многопроходной сварке.
Наличие углублений в зонах соединения основного и наплавленного металла по всему сварному шву может свидетельствовать о наличии подрезов; а сквозных отверстий в нем о прожогах.
Наличие пузырей разного размера, заполненных газом, возникает в следствии наличия этих газов поглощаемых жидким металлом при сваривании, говорит о наличии в металле пор и раковин.
Наличие в шве шлаковых включений и окислов — является дефектом. Их размеры и формы может быть совершенно различными.
Опубликовано: 18.11.2016
Дефекты точечной и шовной сварки
Контактная сварка может производиться двумя способами – точечным и шовным. В первом случае элементы соединяются с помощью расплавления посредством электрического тока отдельных участков поверхностей, во втором образуется непрерывное сварное соединение. Точечная сварка применяется, например, тогда, когда нужно наварить металлический лист или ленту на каркас или крестообразно скрепить арматуру, а шовная – в основном для получения герметичных соединений при производстве каких-либо емкостей.
Однако при отсутствии должного навыка или невнимательности мастера результат сварки может оказаться далеким от идеала. Проще говоря, работа окажется выполненной с браком. Погрешности делятся на две разновидности – внешние и внутренние.
Внешние дефекты точечной и шовной сварки
- Трещины
Образуются при слишком жестких режимах сварки (в частности, при большом значении сварочного тока) или из-за чрезмерно сильного сжатия свариваемых деталей. В результате уменьшения прочности металла эксплуатация такого соединения может завершиться отрывом основной массы металла от сварной точки.
- Пережог и прожог
Причиной их становится слишком большая величина тока в сочетании с недостаточным сжатием деталей и чересчур длительным временем сварки. Внешними признаками являются: очень глубокая вмятина, губчатая поверхность шва или точки, а также, как правило, большой участок цветов побежалости (пленки окислов, образующейся на поверхности нагретого металла и имеющей радужную окраску) на детали. При прожоге слоев металла образуется сквозной свищ, в поперечнике равный диаметру рабочей поверхности электрода.
Так выглядят цвета побежалости на перегретом металле
- Выплеск металла
Выбрасывание из свариваемого места части расплава с повышенным образованием искр. Причины появления этого дефекта – те же, что и в случае пережога, плюс наличие загрязнений. В результате выплеска вмятина на поверхности детали получается слишком большой, электрод приваривается к изделию и в дальнейшем требует зачистки или замены.
Внешние дефекты ухудшают не только вид изделия, но и прочность сварки
- Вырыв точек и разрыв металла у кромки соединения
Причина появления данных дефектов – стремление сэкономить там, где не следует, за счет уменьшения нахлестки металла, из-за чего сварка выполняется слишком близко к краю.
- Темная поверхность сварного шва или точек
Потемнение сварной точки – признак того, что металл окислился. Спровоцировать появление этого дефекта могут те же самые факторы, которые вызывают пережог и выплеск металла.
- Чрезмерно глубокие либо неправильной формы вмятины от электродов
Глубина вмятины считается приемлемой, если она не превышает 10 % толщины одной детали. Если же на свариваемых поверхностях остались слишком глубокие следы от электродов, это показатель того, что соединение окажется непрочным, а «добиться» столь нежелательного эффекта можно, если слишком сильно сдавить детали, включить слишком большой ток или пользоваться при сварке изношенными электродами.
- Выдавливание металла на поверхность точки или шва
Причина данного дефекта – форсированный режим сварки и неправильное закрепление электродов, возможно, с перекосом.
Правильная установка электродов – важное условие получения качественного сварного соединения
- Гофрирование поверхности свариваемых металлических листов
Возникает при неправильном порядке сваривания деталей из-за их деформации при нагревании (при хорошем качестве отдельных точек или шва). Однако не стоит предпринимать попытку устранить коробление фрагмента изделия путем сваривания в местах выпячивания металла, так как подобное «лечение» может оказаться хуже «болезни» и привести к прожогу деталей. Для устранения этого дефекта существует только один способ – профилактический: правильно продуманный порядок сварки изделия.
Внутренние дефекты точечной и шовной сварки
- Непровар
В этом случае в сварной точке литое ядро или не сформировалось вовсе, или оказалось слишком малым, то есть детали в данном месте не скреплены либо соединены непрочно. Итогом может оказаться разрушение изделия в ходе использования (точечное соединение) или утечка жидкости или газа (шовное соединение). Причины непровара:
- Малое значение сварного тока или недостаточное время его протекания.
- Слишком сильное сдавливание деталей между электродами.
- Увеличенная рабочая поверхность электродов.
- Нарушение технологии при сложном режиме сварки.
- Случайное касание электродом изделия.
- Малый шаг точек (в этом случае ток ответвляется через ранее проваренную точку, т.к. она обладает хорошей проводимостью по сравнению с не успевшим прогреться и расплавиться местом текущего наложения электродов).
- Грязные поверхности сварки.
- Внутренние выплески, раковины и поры
Еще один набор погрешностей сварки, также снижающих прочность соединения.
Внутренние дефекты оказываются куда более коварными, чем те, что поддаются выявлению при внешнем осмотре, потому что они могут серьезно повлиять на безопасность людей (например, как вам понравится брак в сварном шве котла высокого давления?). Поэтому очень важно не только выбрать качественный сварочный аппарат, но и задать правильный режим его работы, поскольку обнаружить внутренние дефекты можно только при использовании неразрушающих методов контроля (проверки ультразвуком или рентгеновской дефектоскопии).
Основные дефекты сварки
Сварка при производстве электромонтажных работ
Наиболее часто встречаются следующие дефекты сварных швов (рис. 2-2): отклонения от заданных размеров, подрезы, непровары, наплывы, трещины, шлаковые и газовые включения (раковины), незаделанные кратеры, пережог металла.
Отклонения от заданных размеров сечения шва могут повлиять на его прочность (сечение меньше нормального) или вызвать перерасход металла (слишком большое усиление).
Подрезы — это подплавления основного металла у кромки шва, расположенные вдоль шва участками большей или меньшей длины. Причинами подрезов являются: слишком большая сила сварочного тока, неправильное формирование шва, неправильное плавление присадочного прутка.
Непровары — это отсутствие сплавления между основным и наплавленным в шов металлом. Причинами непроваров являются: малая сила тока, малый зазор между свариваемыми кромками, неправильная разделка кромок, неправильная форма подкладки под швом, слишком большая скорость сварки. Непровары в корне шва иногда можно исправить подваркой с обратной стороны.
Наплывы — это натеки расплавленного металла на неуспевшие расплавиться кромки основного металла. Причинами наплывов являются: неправильное ведение процесса сварки, когда Одна из свариваемых кромок нагревается больше, чем другая; слишком быстрое сплавление в шов присадочного материала при чрезмерном его сечении и др.
Наиболее серьезным дефектом сварных швов являются трещины, снижающие механическую прочность соединений. Трещины появляются в результате внутренних напряжений в металле, например при изменении объема во время застывания металла (литейная усадка), вследствие неравномерного распределения температур при нагревании и охлаждении, а также вследствие различных структурных превращений, сопровождающихся изменением объема (например, закалка). Причинами трещин являются также неправильная последовательность сварки при выполнении шва и жесткое закрепление деталей при сварке.
Пустоты (раковины) и включения в швах, могут возникать при слишком быстром нагревании и охлаждении металла, когда растворенные газы не успевают выделиться, а шлаки — подняться на поверхность ванны. Разбрызгивание металла при сварке может
вызвать пористость, так как окисленные с поверхности брызги, попадая в шов, не сплавляются с основным металлом, а образуют своеобразные металлические включения.
Рис. 2-2. Дефекты сварных соединений: а — отклонения от заданных размеров швов; 6 — подрезы; в — непровары; г — наплывы
1 »— шов с нормальным усилением; 2 — ослабленный шов; 3 шов с чрезмерным
усилением
S
В месте действия электрической дуги поверхность металла имеет вогнутую форму, что приводит к образованию углубления кратера — при обрыве дуги или в конце шва. Углубления в конце шва могут возникать также в результате усадки при сварке некоторых металлов (например, алюминия). Незаделанные кратеры и усадочные раковины, уменьшая сечение шва, ослабляют? его.
Пережог металла — это окисление, связанное с длительным нагреванием металла до высокой температуры; пережог алюминия и меди возможен при электросварке токами, меньшими нормаль-/ ных.
Обеспечение безопасности при выполнении сварочных работ, а также выполнение необходимых требований промышленной санитарии являются важнейшей частью комплекса мероприятий по организации электромонтажного производства. При сварочных работах следует учитывать возможные несчастные случаи, …
В электромонтажной практике сварка пластмасс находит применение при монтаже соединительных муфт на кабелях с поливинилхлоридными оболочками. При этом корпус с муфты, также изготовленный. из поливинилхлорида, приваривают внахлестку к оболочке. Наиболее …
15-1. Сварка свинца Сварка свинца в электромонтажной практике применяется только при монтаже свинцово-кислотных аккумуляторных батарей. При этом производится приварка ушек аккумуляторных пластин к соединительным полосам. До недавнего времени сварку свинца …
Распространенных дефектов сварки — Welders Universe
Хотя сварка — несложный процесс, металл — это динамичный материал, поэтому вы можете ожидать много поворотов на этом пути.
Ваши заготовки могут расширяться при нагревании. Структура зерен может ослабнуть и стать причиной ломкости. Кроме того, форма металла может деформироваться, вызывая трещины, которые со временем могут распространяться и потенциально разрушать сварной шов.
Излишне говорить, что такие ужасные возможности заставляют инспекторов быть в напряжении, а инженеров лежать без сна в ночи, гадая, правильно ли их проекты предвидели все, что может пойти не так.
Конструкции, подобные мосту Золотые Ворота (который был склепанным, а не сварным), демонстрируют, что сталь является основным строительным материалом, когда речь идет о прочности.
Хорошее, плохое и уродливое — Сварка валиков вдоль тренировочной пластины показывает, что может пойти не так, когда сварщик использует неправильную технику или неправильные настройки машины.
Низкоуглеродистая сталь (также известная как мягкая) широко используется для строительных работ, поскольку она с большей вероятностью сохранит свою пластичность, чем другие металлы при перегреве.Даже если вы слишком быстро погасите его в воде, ему удастся (в большинстве случаев) пережить шок испытания. Но жизнь не так проста для алюминия, чугуна, титана, нержавеющей или высокоуглеродистой стали.
Помимо хрупкости, другие распространенные дефекты сварных швов, такие как деформация, растрескивание и сквозное плавление, могут снизить долговечность металлов (включая низкоуглеродистую сталь).
Следовательно, нормы и стандарты, разработанные Американским сварочным обществом, точно определяют, как должно выглядеть соединение после завершения работы.В зависимости от приложения, другие группы также могут иметь право голоса в проекте, например, Американское общество инженеров-механиков (ASME), Американский институт нефти (API) и Американское общество неразрушающего контроля (ASNT). Проще говоря, при соблюдении кодов такие события, как отказ косынок на мосту I-35 в Миннеаполисе, могли не произойти в августе 2007 года, что привело к обрушению конструкции. Еще более смертоносным было обрушение двух эстакад в отеле Hyatt Regency в Канзас-Сити в 1981 году.(См. Фото ниже.)
Технические требования для сварки касаются окончательной формы, размеров и степени любых аномалий в готовом сварном шве. Одиночная трещина считается дефектом сварного шва и автоматически не проверяется. Однако другие проблемы, известные как разрывы, могут быть достаточно мелкими, чтобы избежать тяжелой руки правосудия. Что приемлемо для инспектора, прописано в коде.
Обрушение эстакады в Канзас-Сити было связано с ошибками инженерного проектирования, устраненными дальнейшими изменениями, внесенными на строительной площадке во время строительства.Сварные швы и другие крепежные детали не выдержали веса людей, толпившихся на дорожке во время чаепития.
Технические требованиядля сварки касаются окончательной формы, размеров и степени любых аномалий в готовом сварном шве. Одиночная трещина считается дефектом сварного шва и автоматически не проверяется. Однако другие проблемы, известные как разрывы, могут быть достаточно мелкими, чтобы избежать тяжелой руки правосудия. Что приемлемо для инспектора, прописано в коде.
Взгляните на фото ниже.Он показывает относительно однородный сварной шов с хорошей врезкой, слегка выпуклую поверхность и отсутствие брызг, кратеров или других видимых неоднородностей. Создание подобных сварных швов требует как практики, так и понимания того, как металлы реагируют на нагрев и окисление.
Чтобы освоить сварку по кодам, вы также должны получить информацию о дефектах, которые приводят к отклонению сварных швов.Помните, что у большинства проблем, с которыми вы столкнетесь, есть единственная причина и решение, которые можно установить. Более того, эта причина может не иметь ничего общего с вашей способностью уложить сварочный валик. Вместо этого виновником окажется один из следующих:
- Плохая конструкция и подгонка стыков
- Неправильные настройки машины
- Неправильный защитный газ или расход • несоответствующая предварительная или последующая термообработка
- Использование неправильного (или неисправного) стержня / проволоки
- Высокая или низкая температура окружающей среды, высокая влажность или другие атмосферные условия
По мере того, как вы приобретете навыки работы с различными сварочными процессами и рабочими материалами, вы научитесь устранять любые проблемы и быстро вносить изменения. А до тех пор обязательно прекращайте сварку, как только заметите, что что-то не так. Прежде чем продолжить, посоветуйтесь с коллегой, руководителем или инструктором. Помните, что чем больше тепла вы применяете к металлу, тем больше нарушается его молекулярная или химическая структура. Поэтому по возможности следует избегать повторных переделок.
По мере того, как вы приобретете навыки работы с различными сварочными процессами и рабочими материалами, вы научитесь устранять любые проблемы и быстро вносить изменения. А до тех пор обязательно прекращайте сварку, как только заметите, что что-то не так.Прежде чем продолжить, посоветуйтесь с коллегой, руководителем или инструктором. Помните, что чем больше тепла вы применяете к металлу, тем больше нарушается его молекулярная или химическая структура. Поэтому по возможности следует избегать повторных переделок.
Трещины Независимо от того, насколько мала, каждая трещина считается дефектом, и требуется всего одна, чтобы не пройти проверку сварного шва. Это потому, что трещина со временем распространяется. В отличие от столярных работ, вы не можете просто заполнить отверстие небольшим количеством клея и опилок.Трещины необходимо отшлифовать напильником или болгаркой, затем выполнить новую сварку. Вот четыре распространенных типа, на которые следует обратить внимание:
Горячее растрескивание — Эта трещина появляется вскоре после сварки, обычно внутри сварного шва, в результате чего-то, что называется горячей короткостью. Причиной может быть плохая подгонка или конструкция, но присутствие серы в основе или металле сварного шва также может вызывать проблемы, как и разные скорости охлаждения внутри сварного шва. Часто трещина образуется вдоль оси (центра) соединения, когда две стороны расходятся.
Холодная трещина — Это не появляется сначала, но в течение дня или около того после сварки. Это вызвано водородом, поглощенным сварным швом через сварочную ванну. Водород может присутствовать из-за просачивания влаги в электрод перед сваркой, поэтому так важно хранить стержни с низким содержанием водорода в печи до тех пор, пока они не понадобятся. Другой причиной холодных трещин является загрязнение основного металла, поэтому обязательно очистите любой старый, загрязненный или обесцвеченный металл перед началом сварки.
Микротрещина — это скорее будущая трещина, которая развивается в течение срока службы сварного шва.Он возникает в результате сейсмического возмущения, усталости металла или напряжений в зоне термического влияния или ЗТВ.
Кратерная трещина — Эта трещина появляется на конце стыка, когда сварщик не засыпает зазор. Стандартная практика — приваривать немного дальше конца стыка или идти назад и поверх металла шва, чтобы убедиться, что не осталось кратера.
Чтобы избежать трещин в сварных швах, подгонка всегда должна быть максимально точной, как если бы вы были мастером-краснодеревщиком.Не думайте, что любой зазор можно легко устранить, добавив дополнительный металл сварного шва. Опять же, металл — совсем другое животное, чем дерево. Он расширяется при нагревании, из-за чего трудно компенсировать то здесь, то там стороны, которые не подходят друг к другу. Даже если соединение может выглядеть нормально сразу после того, как вы его сварили, чаще всего ваши рабочие пластины возвращаются в исходную ориентацию после остывания сварного шва. Вот рецепт, как это обойти:
- Потратьте необходимое время на шлифовку, очистку, опиливание и / или удаление заусенцев с краев пластин, чтобы они легко стыковались друг с другом.
- Предварительно нагрейте обе стороны стыка (при необходимости).
- Зажмите и / или скрепите пластины вместе.
- Перед сваркой проверьте настройки вашего аппарата, чтобы убедиться, что вы набрали нужное количество тепла.
Пористость — это технический термин для обозначения пузырьков газа. Они образуются внутри или на поверхности сварных швов, поскольку металл в расплавленном состоянии очень уязвим для загрязнений. По этой причине в большинстве сварочных процессов используется защитный газ (или газовые компоненты в стержнях). Пористость может быть вызвана одной из следующих причин:
- Установлено слишком большое значение расходомера на баллоне защитного газа.
- Вы используете неправильную газовую смесь или стержень / проволоку.
- Сварочная ванна загрязнена из-за нечистого металла, поверхностной влаги или контакта между разнородными металлами.
- Ваша скорость сварочного хода слишком велика, что не позволяет защитному газу или ингредиентам стержневого флюса выполнить свою работу.
- Сквозняк или свежий ветер на открытом воздухе выдувают газ из сварочной ванны.
Кислород и водород — два главных врага сварщиков. Окисленные поверхности, которые проявляются как ржавчина, коррозия или прокатная окалина в черных металлах, должны быть удалены со всех свариваемых участков непосредственно перед сваркой (а не накануне). Помните, вода состоит из двух частей водорода и кислорода. Как только водород попадает внутрь металла, он создает состояние, известное как водородное охрупчивание.
Засорение газового сопла сварочного пистолета MIG также может препятствовать попаданию защитного газа в сварочную ванну, поэтому не забывайте регулярно чистить отверстие.При сварке штангой электроды следует хранить вдали от источников влаги. В частности, стержни с низким содержанием водорода, такие как E7018, должны быть помещены в печь для стержней, установленную на 250 градусов по Фаренгейту, после открытия коробки. (Однако не нагревайте стержни других типов, так как это приведет к разрушению их целлюлозного покрытия.)
При сварке MIG всегда проверяйте настройку расходомера перед началом первой сварки и убедитесь, что газовая смесь (аргон, CO2 и т. Д.) Является подходящей для вашего применения.
Отсутствие проникновения и слияния GoWelding.com Этот сварной шов не проникает в основной металл и не имеет сплавления с обеих сторон. Таким образом, он не будет служить своей цели — обеспечить прочное, длительное соединение между двумя пластинами.
В зависимости от стыка вам, возможно, придется сваривать до дна или пластин, чтобы достичь так называемого полного проникновения в стык (CJP). С другой стороны, для большинства угловых сварных швов требуется только частичное проплавление стыка (PJP). В любом случае вам необходимо настроить сварочный аппарат так, чтобы у вас было достаточное напряжение и ток для выполнения работы.
Сварной валик, который просто скользит по поверхности основного металла, легко обнаружить, потому что валик выглядит как поезд с пулями. Достаточное проникновение достигается путем установки правильной силы тока или напряжения на сварочном аппарате. Слишком высокая скорость движения или слишком высокое расположение резака над суставом обычно ограничивают проникновение. (Для некоторых металлов, таких как алюминий и нержавеющая сталь, вам придется двигаться быстрее, потому что они оба чувствительны к нагреванию.)
Fusion означает привязку сторон сварного шва к основному металлу так, чтобы не было разделительной линии. Это требует немного больше времени и внимания для швов с разделкой кромок с открытым корнем, так как там остается много места для заполнения. Любой зазор приведет к появлению трещин. Трещины в конечном итоге будут расширяться и привести к утечкам (в случае трубы) или отслоению и неспособности выдержать нагрузку (в конструкционной стали).
Здесь нет проникновения или сплавления с нижней пластиной. На стоящей пластине вы видите неравномерное проникновение и зазор внизу.
Чтобы соединить стороны стыка, сварщик должен ненадолго остановиться с каждой стороны при нанесении сварочного металла.Как правило, вы быстро перемещаетесь по центру сварного шва, чтобы не допустить налипания нового металла в этой области. Но стороны стыков склонны к подрезанию, поэтому необходима пауза, чтобы эти зазоры не образовывались. Таким образом, получается плоский или слегка выпуклый валик с хорошей закрепкой на носках сварного шва.
В этом сварном шве гораздо лучше выполняется проплавление и сплавление сторон основного металла. Поверхность сварного шва слегка выпуклая, что обычно предпочтительнее плоской или вогнутой формы.
При контактной сварке мягкой стали электроды E6010 или 6011 являются стандартными стержнями, поскольку они предназначены для глубокого проплавления. Затем сварщик переключается на другой тип стержня, часто с низким содержанием водорода E7018 для наполнителя и проходов крышки.
ПодрезкаКак отмечалось ранее, отсутствие хорошей стыковки обоих пальцев сварного шва может привести к подрезу. Это потому, что металл по краям плавится быстрее, чем по центру. На Т-образном соединении, подобном показанному выше, опорная плита чаще всего приваривается к краю, где она более подвержена плавлению.Поскольку нижняя пластина приварена посередине, имеет смысл направлять на нее больше тепла, когда вы перемещаетесь по стыку. Многие сварщики начального уровня забывают это основное практическое правило о том, как металл реагирует на тепло.
WeldReality.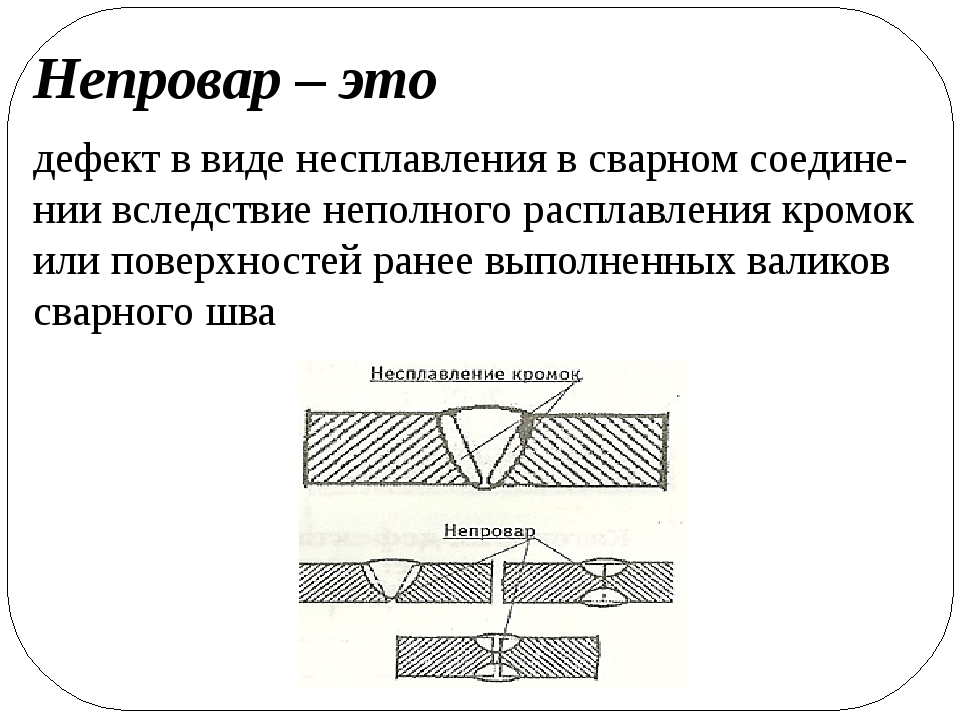
Пальцы этого сварного шва сильно подрезаны. Это происходит из-за того, что сварщик не останавливается достаточно долго на каждой стороне сварного шва, когда он делает зигзагообразные движения (или катит фигурную букву Q) вдоль стыка. Кроме того, сварной шов прошел сквозь стоящую пластину, что свидетельствует о приложении большого количества тепла (или тока).
Вы также можете подрезать мысок на нижней пластине, если не потратите достаточно времени на сварку этой стороны соединения. Таким образом, в дополнение к сосредоточению на нем большего количества тепла, не забудьте манипулировать электродом в боковом направлении, задерживаясь на каждом пальце ноги, чтобы сварочная лужа покрывала оба этих края соединения. Это важный навык, который нужно освоить, так как он будет неоднократно повторяться практически в каждом типе сварочного задания, которое вы выполняете.
Правильное движение из стороны в сторону обеспечивает сплавление с основным металлом на каждом сварочном проходе. Когда вы дойдете до последнего прохода (заглушки), убедитесь, что сварочная лужа достигает и закрывает любой палец.
По мере того, как вы практикуете движения из стороны в сторону, вы научитесь выполнять эту манипуляцию с достаточной скоростью, чтобы избежать перегрева, и в то же время не откладывать слишком много материала через горловину сустава.
ПерекрытиеВ то время как слишком большое количество тепла вызывает поднутрение, слишком маленькое создает перекрытие, когда два отдельных слоя металла остаются вдоль носка.Сварка по нормам требует тщательного сплавления основного металла.
Это крайний край, противоположный поднутрению. Здесь металл сварного шва течет по основному металлу у носка, не производя плавления между ними. Это может быть вызвано недостаточным количеством тепла для плавления основного металла и / или неправильным обращением с электродом. Убедитесь, что ваш стержень или рабочий угол пистолета правильный; иначе тепло не будет направлено на палец ноги.
Поскольку металл расширяется при нагревании, а затем сжимается после охлаждения, две стороны соединения могут смещаться в процессе сварки.Вот почему прихватывание и / или использование зажимов является неотъемлемой частью многих сварочных операций. Нержавеющая сталь особенно подвижна.
TWIОсновной металл будет загибаться внутрь по направлению к поверхности сварного шва, если он не зафиксирован на месте. Иногда вы можете предварительно расположить пластины с небольшим наклоном в противоположном направлении, чтобы компенсировать неизбежное искажение.
При сварке с разделкой кромок или других многопроходных сварных швах две опорные пластины также могут начать сжиматься и сгибаться в направлении соединения, независимо от прихваток или зажимов.Контроль нагрева (т.е. правильные настройки машины, высокая скорость движения и т. Д.) Поможет предотвратить деформацию. Изменение последовательности сварных швов или расположения стыка или выполнение меньшего количества проходов также может помочь снизить риск. Иногда вы можете начать первый сварной шов с пластинами, слегка наклоненными в сторону от направления, в котором они должны сгибаться. Это компенсирует неизбежное загибание внутрь. Как правило, чем крупнее сварной шов и чем меньше размер пластин, тем больше вероятность усадки, скручивания или коробления.
Когда профилактика не помогает, попробуйте пост-термическую обработку, чтобы ослабить любые термически индуцированные искажения. Иногда можно заставить пластины согнуться в прежнее состояние. А иногда и не получается.
Брызги, дуговые разряды и другие повреждения поверхностиПри сварке в соответствии с требованиями норм поддержание безупречной поверхности рабочих плит или секций труб — это большое дело. Даже один заусенец, оставшийся после шлифовки, может помешать механической сборке или зацепиться за одежду или кожу другого рабочего и вызвать травму.(Заусенцы также могут блокировать течение сварочного металла во время сварочной операции.)
Вмятина в металле, оставленная случайным попаданием дуги, может быть началом поперечной трещины. Поэтому всегда бейте дуги внутри стыка перед сварным швом, или по краю рабочих пластин, или по другой области, которая будет отшлифована или удалена позже.
Spatter описывает частицы расплавленного металла, которые вылетают из сварного шва при использовании процесса дуговой сварки. Этот материал затвердевает в маленькие шарики, которые прикрепляются к поверхности сварных пластин.При сварке штангой разбрызгивание возникает из-за чрезмерного напряжения или слишком длинной дуги. При сварке MIG слишком большое значение подачи проволоки приведет к тому же результату. В некоторых случаях вы можете отшлифовать или отшлифовать любые пятна на металлических поверхностях перед вызовом инспектора. Для других работ вы можете использовать только ручные файлы для обработки металла после сварки.
Изменение цвета вокруг сварных швов — обычное явление, которое обычно не считается дефектом. Однако в случае более термочувствительных металлов, таких как алюминий и нержавеющая сталь, чрезмерное изменение цвета в ЗТВ может указывать на перегрев металла, что изменило его механические свойства или химический состав.В этом случае шлифовка цвета не устранит проблемы. Проконсультируйтесь с руководителем или инструктором, как действовать дальше.
Ресурсы / документы Фотографии дефектов сварных швов
Sumit Waghmare
Разрывы сварных швов
WeldingEngineer.com
Дефекты сварных швов — их причины и способы их устранения ESAB
Проверка дефектов труб
Tafaseel Engineering
Дефекты сварных швов и контроль качества (PDF)
Как управлять искажениями
Lincoln Electric
Консультанты по сварке водородной хрупкости.com
Дефект сварного шва — обзор
17.6.2 Радиографический контроль
Рентгенография, рентгенография, считается высшей степенью внутреннего контроля и наиболее затратной. Рентгенография хороша тем, что постоянная запись обследования доступна для просмотра в любое время. Он используется в основном для сварных швов, а также для критических участков отливок. Компоненты можно отнести к стационарному рентгеновскому оборудованию. Большие компоненты или сборки подвергаются рентгенографии с использованием радиоактивных изотопов. Необходимо соблюдать строгие меры безопасности.Ввиду его важности для целостности высокопроизводительных вентиляторов этот метод описан очень подробно.
Наиболее технически продвинутые компании в индустрии вентиляторов имеют оборудование, которое за счет использования методов реального времени сокращает временные дефекты примерно на две трети, что позволяет улучшить производство и доставку. Система (рис. 17.1) более чувствительна, она также обеспечивает гораздо более комплексные и легкодоступные системы: предыдущие рентгеновские аппараты. На каждую движущуюся часть наносится штамп, все рентгеновские снимки автоматически архивируются на 50-миллиметровом лазере.30 лет, обеспечивая полную отслеживаемость компонентов.
Рисунок 17.1. Рентгенографическая система в реальном времени в помещении
Осмотр с помощью рентгеновских лучей выполняется путем облучения одной поверхности образца рентгеновскими лучами, в то время как чувствительный к излучению электронный датчик изображения прижимается к противоположной поверхности. Излучение, проходя через образец, по-разному поглощается неоднородностями, вызванными дефектами, пустотами, изменениями толщины или плотности материала, и изображение изменений, интегрированное по толщине образца, создается на поверхности электронного чувствительного экрана.
После уменьшения шума в электронном изображении оно отображается на экране, где вариации внутри образца проявляются в виде теневых объектов с разными полутонами, из которых можно получить информацию о наличии дефектов. Запись, полученная таким образом, называется рентгенограммой в реальном времени. В реальном времени, потому что изображение отображается в реальном времени, и если образец перемещается, рентгеновская рентгенограмма изменяется, чтобы показать соответствующую падающую тень на дисплее изображения. Использование рентгеновских лучей для получения рентгенограммы называется рентгенографией.На рисунках 17.2 и 17.3 показаны два примера рентгенограмм лопастей рабочего колеса.
Рисунок 17.2. Пример приемлемой рентгенографии лезвия
Рисунок 17.3. Пример неприемлемой рентгенографии с лезвием
Рентгеновские лучи представляют собой форму электромагнитного излучения, которое может генерироваться, заставляя поток быстро движущихся электронов высокой энергии поражать металлическую цель. Внезапное замедление электронов вызывает излучение фотонов (рентгеновское излучение) с непрерывным энергетическим спектром.
Рентгеновские лучи обладают большой проникающей способностью, которая увеличивается с увеличением энергии волн (увеличением частоты или уменьшением длины волны).Рентгеновское оборудование определяется напряжением питания, которое обычно может находиться в диапазоне от 25 кВ до 15 м В. Рентгеновские лучи могут использоваться для исследования предметов, от слоев бумаги до стали толщиной до 0,5 метра. Рентгеновские лучи проникают во все материалы, но чем больше плотность, тем меньше проницаемость.
Коротковолновое излучение, создаваемое мишенью с высоким потенциалом, считается высокоэнергетическим и описывается как жесткий рентгеновский луч с большей проникающей способностью. Более длинноволновое излучение, создаваемое более низким потенциалом цели, называется низкоэнергетическим и описывается как мягкое рентгеновское излучение с более низкой проникающей способностью.
Проникающая способность рентгеновского излучения может быть выражена в терминах заданной толщины материала (например, стали или алюминия), который может быть надлежащим образом исследован.
Для низкоэнергетических генераторов рентгеновского излучения с постоянным потенциалом интенсивность пучка, создаваемого рентгеновской трубкой, в основном определяется величиной тока нити накала и, в меньшей степени, потенциалом мишени. Между током накала и током пучка существует почти линейная зависимость, поэтому выходную способность такой лампы принято выражать через ток накала.
Качество рентгеновского снимка в реальном времени почти всегда определяется количеством деталей, различимых на изображении индикатора качества изображения (IQI) того же материала, что и образец, помещенный на поверхность образца. Эта чувствительность IQI зависит от используемой рентгенографической техники, типа IQI и толщины образца. При рентгенографии других материалов, кроме стали, обычно используют таблицы преобразования, относящиеся к материалу и энергии излучения, чтобы получить приблизительные эквивалентные коэффициенты толщины.
В Великобритании рекомендуются два разных образца IQI, известные как тип «проволока» и тип «ступенчатое отверстие», и один или другой обычно используется в большинстве европейских стран. В США обычно используется табличка ASTM.
Чувствительность IQI выражается в процентах, то есть размер минимально различимых деталей IQI выражается в процентах от толщины образца, таким образом, меньшее числовое значение означает лучшую чувствительность. Типичная радиографическая чувствительность находится в диапазоне от 0.5 и 2,5 процента в зависимости от контрольных переменных.
Рекомендуемая процедура для сообщения о дефектах сварных швов и отливок на рентгенограмме заключается в использовании трехкомпонентного кода:
- (1)
Число, обозначающее горизонтальное или вертикальное расстояние в дюймах между «контрольной меткой или точкой отсчета». наименьшее число на рентгенограмме и начало дефекта.
- (2)
Кодовая буква или буквы для обозначения типа дефекта (см. Сокращения в Таблице 17.1).
Таблица 17.1. Тип сокращенного обозначения дефекта
Неровности поверхности Код Описание SXP Избыточное проникновение 9064 SR902 902 9064 SRI заполненная канавка SGS Усадочная канавка SUC Поднутрение SSP Сварочные брызги SED 902 902 902 Подфальцовка 902 SMC Отколы SMH Отбойники STS Рваная поверхность SPT Выкрашивание поверхности 9025 9025 9025 9025 9025 9025 e Описание K Трещина KL Продольная трещина 902 902 902 902 902 902 902 902KT Поперечная трещина - 4
902 902 902 902 L Отсутствие сварки LS Отсутствие боковой сварки LR Отсутствие корневого слияния LI LI Lack Lack LI Неполное корневое проникновение I Включение IL Линейное включение IT Вольфрамовое включение PG МедьIC МедьIC Включение ICP Пористость PU Равномерная пористость PL Локализованная пористость PP Линейная пористость EC Удлиненные полости CP64 902 902 902 902 902 902 902 902 902 902 902 902 902 902 902 902 902 902 902 902 902 902 902 902 Кратерная труба BT Прогорание DM Дифракционные крапинки - 4
- (3)
Число, обозначающее длину дефекта, которая составляет приблизительную длину в дюймах .
Например, изображение рентгеновского снимка, показывающее отсутствие плавления, начинающееся в 50 мм (2 дюйма) от референтной отметки на длине 25 мм (1 дюйм), и повторение дефекта на 150 мм (6 дюймов) от) референтной метки на длине 25 мм (1 дюйм), а также локализованной пористости на 19 мм (0,75 дюйма) на расстоянии 150 мм (6 дюймов) от референтной метки, код будет 2-L- 1: 6-PL-0,75: 8,5-L-0,5.
Радиографические устройства в реальном времени используются в любом из следующих режимов:
- a)
Промежуточный контроль продукта или промежуточная радиография.Как правило, когда изделия отливаются, проверка на этом этапе выделяет хорошие отливки и отбраковывает их до того, как литье будет добавлена какая-либо ценность. Это сводит к минимуму потерю времени перед обработкой отливки и ее очисткой от заусенцев и чрезмерных материалов.
Радиографический метод обычно определяется для разных продуктов. Этот этап проверки может проводиться любое количество раз до этапа готовой продукции. В этом режиме отчеты о проверке продукта обычно не требуются.Хорошие отливки передаются на следующий этап производства, и браки обрабатываются соответствующим образом.
- б)
Промежуточная рентгенография с сохранением изображений. Требования к качеству продукции могут предусматривать минимальное приемочное качество для размеров и типа дефекта. Подтверждение приемки на основе записей может потребоваться независимыми инспекторами. После того, как продукты будут приняты на следующий этап, могут потребоваться рентгенографические записи для кратковременного хранения, возможно, от 6 до 24 месяцев.
- c)
Рентгенография в реальном времени с регистрацией и долгосрочным хранением цифровых или аналоговых изображений. Для продуктов, критически важных для безопасности и чувствительных к применению, обычно требуется, чтобы протоколы проверок хранились в архивах на протяжении всего срока службы продукта. Необходимо вести полную историю продукта. Предусмотрены строгие требования к контролю качества, соблюдение которых является обязательным.
Рекомендуемые процедуры требуют:
- 1.
Каждый предмет, подлежащий проверке, идентифицируется с помощью уникальной системы нумерации.
- 2.
Каждый тип продукта соответствует методам радиографического контроля. Такая установка обеспечит повторяемый и надежный контроль отливок.
- 3.
Каждое рентгенографическое изображение будет идентифицировано уникальным ссылочным номером продукта, который проштампован на отливках.
- 4.
Для нескольких изображений продукта могут потребоваться разные настройки и они будут последовательно записаны на видео.
- 5.
Оператор вручную регистрирует результаты осмотра, записывая вердикт изображения и общую приемлемость предметов.
Следует отметить, что внутренние дефекты могут быть определены только такими методами, как рентгенография и ультразвуковое исследование. Было много случаев, когда явно хорошее литье не удавалось, только чтобы выявить довольно серьезные внутренние дефекты.
Подповерхностные дефекты включают усадку, горячие разрывы и включения, а именно:
- a)
Усадка — под поверхностью: это часто называют усадкой по средней линии, поскольку она возникает около средней точки стенки отливки, которая является последний, чтобы затвердеть.Поскольку усадка — это подповерхностное состояние, ее следует оценивать с помощью рентгенографии.
- b)
Горячие разрывы: Разрывы отливки обычно появляются в точках перехода толщины и связаны с напряжениями сжатия во время охлаждения и низкой кольцевой прочностью отливки.
- c)
Включения: Подповерхностные неметаллические включения, такие как песок, шлак и газовые карманы или пористость, легко идентифицируются во время радиографического контроля.
17.6.2.1 Критерии приемки для рентгеновского исследования
Очевидно, что прочность и целостность тесно связаны с качеством литого компонента. Критерии приемлемости, как правило, описаны в стандарте ASTM E155 вместе с его эталонными рентгенограммами. Следует принять процедуру, определяющую процесс проверки. Перед проведением рентгеновских или рентгеноскопических исследований необходимо выполнить следующие проверки:
- •
В отливках из алюминия не должно быть видимых признаков пористости или трещин на поверхности.
- •
В отливках из алюминия в песчаные формы не должно быть видимых следов раковин или перекоса формы.
- •
Термообработанные алюминиевые отливки следует проверять на твердость.
- •
Держатели лезвий из ковкого чугуна не должны иметь раковин или царапин на поверхности.
Для лопаток и ступиц даны дополнительные критерии в соответствии с нагрузками, прилагаемыми к ним во время работы.
Лезвия можно разделить на 3 основные категории, как показано на рисунке 17.4, где области, требующие высокой целостности, показаны заштрихованными, а области, требующие более низкого уровня целостности, показаны простыми.
Рисунок 17.4. Критерии приемки для лезвий (области с высокой или низкой степенью целостности)
Области с высокой степенью целостности должны быть практически без каких-либо дефектов, максимально допустимые значения:
- •
Площадь пористости не более 5 мм в диаметре на микрофотографии образца Нет.1, как определено в ASTM E155.
- •
Одиночный изолированный дефект диаметром не более 2 мм.
В областях с низкой целостностью максимально допустимый дефект должен быть:
- •
Площадь пористости не более 10 мм в диаметре.
- •
Одиночный изолированный дефект диаметром не более 5 мм.
Дефекты не должны находиться в пределах 5 мм от границы отливки, и в каждом компоненте должен быть допустим только один дефект.
Ступицы для осевых рабочих колес показаны на рисунке 17.5.
Рисунок 17.5. Критерии приемки для ступиц
Критерии приемки для литых алюминиевых ступиц и зажимных пластин должны быть:
- 1.
На отливке не должно быть видимой пористости поверхности.
- 2.
Не должно быть пористости, прорывающейся в отверстия с сердцевиной.
- 3.
Не должно быть пористости в пределах 10 мм от любой граничной поверхности, смотрящей в осевом направлении.
- 4.
Не должно быть включений диаметром более 1 мм.
- 5.
Не должно быть группы включений (каждое диаметром менее 1 мм) диаметром более 10 мм в сумме и должно соответствовать требованиям 3. выше.
- 6.
В примечании 5 должно быть не более двух таких групп, и они не должны соседствовать друг с другом.
- 7.
Газовые отверстия или пористость допустимы, если они соответствуют 1.до 6. выше. Не допускаются усадочные полости и пористость, посторонние предметы, микроусадка и т. Д.
- 8.
Уровень пористости не должен превышать пористость пластины 4 алюминий — газ (круглая) согласно ASTM E155.
- 9.
Между вставкой и алюминиевой отливкой во время рентгеновского излучения не должно быть сплошной линии дефектов. Длина дефектов не должна превышать 3 мм. Суммарные дефекты не должны превышать 6 мм и не должны прилегать друг к другу.
- 10.
При механической обработке отливки допускается наличие тонкой линии «Свидетель» до тех пор, пока тонкий указатель не проникает глубже, чем на 0,5 мм.
- 11.
Отслаивание или точечная коррозия на участке между вставкой и алюминием недопустимы.
Описанные методы будут действовать как мощный инструмент для определения областей, требующих улучшения, или для изменения переменных процесса для улучшения общего качества продукта.Важно, чтобы была принята процедура проектирования и испытаний, в которой признается, что основная причина отказа, особенно в рабочих колесах с осевым потоком, связана с недостаточным знанием критериев усталости и того, как на них влияет качество литья.
Тесное сотрудничество между конструкторским и производственным отделами необходимо для обеспечения заявленного срока службы. Тем не менее, постоянная бдительность проявляется в постоянных исследованиях, направленных на улучшение знаний. Благодаря такой бдительности можно гарантировать целостность продукта.
Дефекты сварки и способы их устранения / Блог RodOvens.com
Эта запись была опубликована 28 марта 2015 г. автором admin.
Это статья будет охватывать некоторые сварочных дефектов, которые иногда игнорируются или не учитываются. считается. Каждый сварочный проект требует тщательного рассмотрения. Они включают:
- Процесс, вид сварки т.е. палка, MIG, TIG.
- Состав и толщина основного металла.
- Положение при сварке, т.е.е. плоские, вертикальные, горизонтальные, накладные.
- Сварное соединение и тип.
- Электроснабжение и оборудование.
- И, наконец, используемые методы сварки.
Дефект сварки устраняет
Кому свести к минимуму вероятность дефектов сварки обязательно учитывать 1) скорость движения перевала; 2) размер и тип электрода; 3) настройки машины; 4) убедитесь, что Сварка производится в соответствии с планом и текущими условиями.
Мост некоторые или многие дефекты сварки можно определить невооруженным глазом. Зная, что может вызвать дефекты сварки, вы узнаете, как избежать их. Производство без дефектов экономит время, материалы, затраты на ремонт и снижает в производительности.
Две следующие причины брака сварного шва не должны быть, но часто игнорируются 1) владеет ли сварщик применяемым процессом? 2) сварочный стержень поставка в соответствии со стандартами? Одним из способов устранения дефектов сварки является использование только правильно хранящихся, высушенных и обслуживаемых сварочных швов. стержни.(Ознакомьтесь со всем нашим ассортиментом печей для сварки прутков.)
Сварка дефекты включают плохое проникновение. Это выход из строя сварочного стержня и основания металл, чтобы сплавиться вместе. Это вызвано слишком большой поверхностью корня; корневое отверстие это слишком мало; электрод слишком большого размера; низкая скорость движения или машина настройка слишком низкая.
Плохо сплавление — это неспособность соединить слои металла шва с основанием. металл. Отсутствие слияния вызвано «.. . отказ поднять до плавления острие основного металла или наплавленного металла шва »(Miller Electric Mfg. Co.) Это вызвано неправильным флюсованием; грязные поверхности плит; неподходящий электрод размер или тип; неверные текущие настройки. Электроды, не соответствующие требованиям хранения, Это также может быть вызвано требованиями к сушке и техническому обслуживанию.
Подрезка это еще одна проблема, которая вызывает дефекты сварки. Выгорает основной металл на носке сварного шва. Это вызвано слишком высокой настройкой тока; слишком длинный дуговой промежуток или невозможность полного заполнения кратера сварным швом металл.
Пористость выглядит «как губка» или как крошечные «пузырьки» в сварном шве. Это вызванный газами, выделяемыми остывающим сварным швом, потому что текущая настройка слишком высокая или дуга слишком длинная.
Шлак включение происходит, когда шлак не отколот и не очищен должным образом, а затем еще один пропуск делается сверху. Во избежание: 1) подготовьте канавку и сварите как следует перед каждый проход; 2) тщательно очищать между проходами; сверьте настройки машины с предложенные производителем; 3) возьмите сварочную ванну меньшего размера.
Узнать подробнее о правильной технике сварки.
Equinor исследует дефекты сварки на корпусе Castberg FPSO
Собственная следственная группа норвежской компании Equinor изучила отклонения в качестве сварки и осмотр производственного судна Johan Castberg, которое в настоящее время строится на верфи Sembcorp Marine в Сингапуре.
Во время строительства корпуса производственного судна Johan Castberg на предприятии Sembcorp Marine в Сингапуре Equinor выявила отклонения качества в отношении сварки и контроля сварки.
В сентябре 2020 года норвежское агентство по надзору за безопасностью морских операций, Управление по безопасности нефти Норвегии (PSA), начало расследование проблем, связанных с завершением строительства корпуса и оборудования для FPSO Йохана Кастберга Equinor.
В октябре 2020 года Equinor сообщила, что реализация проекта Йохана Кастберга будет отложена на один год с запланированным запуском производства в четвертом квартале 2023 года.
Основной причиной задержки является пандемия Covid-19 и связанные с ней меры инфекционного контроля, введенные на верфях в Сингапуре, Сторде, Вердале и Санднесшёне.
Другие проблемы включают прогресс в Сингапуре и отклонения в качестве сварки.
Equinor сообщил в понедельник, что проводятся обширные работы по обеспечению качества и перекрестной проверке сварных швов и устранению сварочных дефектов, чтобы убедиться, что судно соответствует применимым требованиям безопасности и целостности, прежде чем покинуть верфь.
«Безопасность — главный приоритет Equinor. В настоящее время мы проводим обширную перекрестную проверку и ремонт сварных швов, чтобы убедиться, что производственное судно Johan Castberg соответствует требованиям безопасности и целостности.Когда Йохан Кастберг войдет в строй, не должно быть никаких сомнений в том, что судно безопасно », — сказал Гейр Тунгесвик , старший вице-президент Equinor по разработке проектов.
Equinor отметил, что верфь несет ответственность за исправление всех отклонений в качестве, а затраты, связанные с ремонтом сварочных дефектов, покрываются Sembcorp Marine в соответствии с контрактом. Перекрестные проверки и улучшения почти завершены, и Equinor внимательно следит за ними.
«Чтобы обеспечить обучение и избежать подобных ситуаций в других проектах или на других верфях, мы провели тщательное расследование», — сказал Тунгесвик.
Согласно Equinor, группа расследования не обнаружила ни одного события, которое могло бы быть прямой причиной проблем с качеством сварки, но указала на причинные факторы, которые, как считается, оказали влияние.
Сюда входит тот факт, что подрядчик (SCM) не смог предоставить достаточно компетентных сварщиков и инспекторов по сварке для выполнения объема работ и не соблюдал в достаточной степени процессы и рабочие процедуры для выполнения и контроля сварочных и инспекционных работ.
Кроме того, Equinor недостаточно соблюдает собственные рабочие процессы и процедуры для управления рисками, управления строительством и контроля на строительной площадке.
Даже если группа наблюдения Equinor обнаружила признаки низкого качества на ранней стадии, степень и степень серьезности не были поняты. Поэтому достаточные меры не были реализованы.
Наконец, у команды Equinor не было достаточного количества персонала с опытом и знаниями в области сварки и контроля сварки, и она не использовала технический опыт компании в этих областях достаточно рано, заявила норвежская компания.
«Мы готовим план с конкретными действиями по отслеживанию результатов, и мы поделимся своим опытом», — сказал Тунгесвик.
Следственной группой изучены причины отклонений качества сварки в период с января 2017 года по октябрь 2019 года.
На основании этой работы команда рекомендует Equinor улучшить процесс предварительной квалификации для новых поставщиков, практику последующих действий на строительных площадках, включая управление рисками, а также процесс найма для последующих групп и состав команд.
Иллюстрация производственного судна Johan Castberg. (Иллюстрация: Equinor)Когда Equinor летом 2019 года проверила ультразвуковую проверку сварных швов корпуса Sembcorp в районе лунного бассейна с помощью собственного персонала, она обнаружила более высокий процент отказов, чем сообщалось. Тогда было решено перепроверить все монтажные швы. Позднее были выявлены необычно высокие показатели отказов производственных сварных швов.
«Поэтому мы повторно оценили все структурные сварные швы на корпусе.Это очень ответственная работа, поскольку корпус уже построен, однако безопасность превыше всего. Судно должно соответствовать требованиям, включенным в план развития и эксплуатации (PDO), и получить сертификат класса DNV перед выходом на месторождение », — сказал Тунгесвик.
Была проведена переоценка всех сварных швов и обширная перекрестная проверка с использованием неразрушающего контроля (NDT), включая ультразвук.
«Equinor должна была обнаружить степень сварочных дефектов раньше, однако корпус все еще находится в доке, что позволяет нам отремонтировать дефекты до его спуска на воду», — сказал Тунгесвик.
Корпус производственного судна Johan Castberg планируется доставить в Сторд на борту тяжеловесного судна Boka Vanguard в конце 2021 года, однако пандемия Covid-19 по-прежнему добавляет неопределенности ко всем графикам, заключил Equinor.
Прогресс в устранении дефектов сварных швов на новом FPSO
Equinor Изображение предоставлено Equinor. От Морской исполнительный 19.04.2021 09:09:27
Проблемы с качеством сварки, о которых сообщалось ранее, на борту недавно построенного FPSO на месторождении Йохан Кастберг тщательно ремонтируются, и, по словам оператора Equinor, работа близится к завершению.
Equinor сообщил в понедельник, что проблемы с дефектом сварного шва Johan Castberg возникают по нескольким причинам. Сложное судно строится в Sembcorp Marine в Сингапуре, и хотя отклонения начались еще в январе 2017 года, проблемы были впервые обнаружены, когда собственный персонал Equinor проверил районы в прошлом году.
«Безопасность — главный приоритет Equinor. В настоящее время мы проводим обширную перекрестную проверку и ремонт сварных швов, чтобы убедиться, что производственное судно Johan Castberg соответствует требованиям безопасности и целостности.Когда Johan Castberg войдет в строй, не должно быть никаких сомнений в том, что судно безопасно », — говорит Гейр Тунгесвик, старший вице-президент Equinor по разработке проектов. «Чтобы обеспечить обучение и избежать подобных ситуаций в других проектах или на других верфях, мы провели тщательное расследование».
КомандаТунгесвик определила четыре точки общей ответственности за результат и не возложила вину исключительно на верфь. Он пришел к выводу, что:
— Sembcorp якобы «не смогла предоставить достаточно компетентных сварщиков и инспекторов по сварке для выполнения объема работ и не соблюдала в достаточной степени процессы и рабочие процедуры для выполнения и последующих действий.«
— Персонал Equinor не полностью следовал собственным рабочим процессам и процедурам фирмы в отношении управления рисками, управления строительством и последующих действий.
— Даже если группа наблюдения Equinor обнаружила признаки низкого качества на ранней стадии, степень и степень серьезности не были поняты.
— В команде Equinor не хватает персонала с опытом и знаниями в области сварки и контроля сварки.
В ответ, обзор рекомендует Equinor улучшить процесс предварительного отбора новых поставщиков; усиление контроля на месте и управления рисками; и улучшить состав последующих групп, чтобы охватить все области требуемых знаний.
Согласно Equinor, Sembcorp несет ответственность за исправление всех отклонений в качестве и затрат, связанных с ремонтом сваркой, в соответствии с контрактом. Перекрестные проверки и улучшения почти завершены, и Equinor заявляет, что внимательно следит за ними.
сварочных дефектов | Part2b
Поскольку сварные соединения находят применение в критически важных элементах, где отказ приводит к катастрофе, процедуры проверки и стандарты утверждения имеют гораздо большее значение, чем в прошлом.Критерии приемки представляют собой минимальное качество сварного шва и зависят от испытания сварных образцов, содержащих несколько несплошностей. Обычно для получения последнего стандарта приемки добавляется коэффициент запаса прочности.
Теперь мы рассмотрим нарушения сплошности сварных швов, обычно наблюдаемые в сварных швах, их причины, способы устранения и их важность. Небольшие дефекты, которые вызывают некоторое отклонение от типичных средних свойств металла шва, называются несплошностями. Когда разрыв достаточно велик, чтобы повлиять на назначение соединения, это называется серьезным дефектом.
Стандартные нормы допускают ограниченную степень дефектов на основе основ механики разрушения, принимая во внимание их эксплуатационные состояния при изготовлении. Независимо от этого, изготовитель должен попытаться предотвратить появление дефектов сварного шва в первом случае, а также исправить их, когда они действительно возникнут.
ОБЩАЯ ТАБЛИЦА ДЕФЕКТОВ СВАРКИ
Следующая таблица сгенерирована в соответствии с набором услуг, которые Part2b.com предоставляет
X указывает на то, что в сварных швах, полученных в результате процесса, может возникать несплошность.Номер
R указывает на то, что дефект этого типа в этих сварных швах встречается очень редко.
A.UNDERCUT
Выражение используется для обозначения канавки, вплавленной в основной металл, рядом с носком сварного шва и оставленной незаполненной от металла сварного шва. Кроме того, в нем описывается плавление боковой стенки сварочной канавки на краю покрытия или валика. Это плавление канавки образует острую выемку в боковой стенке в области, в которой должен сплавиться другой слой или валик.Таким образом, поднутрение — это канавка, которая может различаться по глубине, а также по резкости в ее основании.
Видимые поднутрения обычно связаны с неправильными методами сварки или избыточным сварочным током, или даже с тем и другим вместе. Обычно это параллель к месту пересечения металла сварного шва и основного металла в корне или подошве сварного шва. Дефекты поднутрения создают на поверхности механические надрезы. Когда поднутрение находится в пределах этих спецификаций и не дает резких или глубоких надрезов, это обычно приемлемо.
Термин поднутрение может использоваться в мастерской для объяснения плавления поверхности канавки стыка на краю слоя или валика сварочного металла. Это поднутрение образует выемку на комбинированной поверхности, где следующий слой или валик металла сварного шва должен сплавиться с основным сплавом. Если толщина плавления в этом месте слишком мала при нанесении следующего слоя сварочного металла, в зоне плавления могут остаться пустоты. Эти пустоты можно было бы правильно распознать как неполное слияние. Этот подрез обычно связан с ошибочными манипуляциями со сварочным электродом при нанесении сварного шва или покрытия помимо поверхности соединения.В результате происходит ослабление сварного шва и заготовки.
ПРИЧИНЫ ПОДКРЕПЛЕННЫХ ДЕФЕКТОВ И СПОСОБ УСТРАНЕНИЯ ПРИ СВАРОЧНЫХ ОПЕРАЦИЯХ
B. ЗАПОЛНЕНИЕ
Недостаточное заполнение — это термин, используемый для соединения, которое не было полностью заполнено до поверхности основного металла, но края соединения были сплавлены. Этот дефект сварки возникает просто из-за неспособности сварщика или оператора сварки выполнить соединение с металлом шва, как указано в спецификации процедуры сварки или на чертеже конструкции.Обычно условие исправляется добавлением пары дополнительных слоев сварочного металла на стыке перед последующей обработкой.
Возможные корни этих дефектов:
- с помощью небольших электродов;
- сварного шва недостаточно;
- отсутствие способности сварщика
В. ТРЕЩИНЫ
Трещины можно классифицировать по форме (продольные, поперечные или разветвленные) и месту (ЗТВ, основной сплав, осевая линия, кратер).Сварочный подрядчик редко классифицирует перелом как тип до тех пор, пока не будет проведена оценка; в большинстве случаев невозможно установить причину перелома. Положение и форма — правда, все — предположение. Металлы склонны к линейным разрывам, которые называются трещинами. Хотя иногда они широкие, они часто находятся на довольно узком расстоянии от сварного шва или основного металла. Обычно заметна небольшая деформация. Обычно выделяют три основных класса трещин: горячие трещины, холодные трещины и макротрещины.Все виды могут встречаться в сварном шве или основном металле.
Существует множество различных трещин, в том числе трещины под бортом, трещины на пальцах ног, трещины кратера, продольные трещины и поперечные трещины. Даже трещина под полом, ограниченная в основном сталью, является трещиной основного металла, обычно связанной с водородом. Трещины на носке в стали могут иметь аналогичное происхождение. В других металлах (включая высоколегированные и нержавеющую сталь) трещины на носке часто называют границей трещин сварного шва, что связано с горячим растрескиванием вблизи линии плавления.Кратерные трещины — это трещины из-за усадки, возникающие в результате внезапного прекращения дуги.
ПРИЧИНЫ ДЕФЕКТОВ ТРЕЩИНЫ И СПОСОБ УСТРАНЕНИЯ ПРИ СВАРКЕ
D. ПОРИСТОСТЬ
Пористость — это наличие группы газовых пор в сварном шве, вызванное захватом газа во время затвердевания (если затвердевание происходит слишком быстро). Это небольшие сферические полости, разбросанные или сгруппированные локально. Время от времени захваченный газ может образовывать одну большую полость, которая называется дыхалкой.Растворенные газы обычно находятся в расплавленном металле сварного шва. Пористость образуется по мере затвердевания сварочного сплава, если растворенные газы обнаруживаются в количествах, превышающих их пределы растворимости в твердом состоянии. Причины пористости металла шва связаны с технологией сварки и, в некоторых случаях, с типом и химическим составом основного металла. Процесс сварки, процедура сварки и тип основного металла напрямую влияют на количество и виды газов, присутствующих в расплавленной сварочной ванне. Процесс сварки и процесс сварки контролируют скорость затвердевания, которая, в свою очередь, влияет на величину пористости металла шва.Соответствующие процедуры сварки для любой конкретной комбинации процедуры сварки и основного металла должны создавать сварные швы, которые в основном не имеют пористости.
ПОВЕРХНОСТНЫЕ ПОРЫ:
Иногда поры образуются на поверхности сварного шва. Рисунок может отличаться от одной поры каждые несколько миллиметров до нескольких пор на миллиметр. Поры образовались из-за неправильных условий сварки, таких как более высокий ток, недостаточное экранирование или неправильная полярность. Недостаточная газовая защита также может отрицательно сказаться на сварном шве.Защита от газа обычно лучше в основании сварной канавки, чем вблизи ее поверхности. Улучшение внешнего вида сварного шва может быть достигнуто путем изменения таких условий сварки, как полярность или длина дуги. Крайне важно удалить поверхностные поры, поскольку они могут привести к улавливанию шлака при других сварочных проходах.
ПОРИСТИЧЕСКИЕ ДЕФЕКТЫ В ПРОЦЕССЕ СВАРКИ
E. ВКЛЮЧЕНИЕ ШЛАКА
Этот термин используется для описания оксидов и других неметаллических твердых материалов, которые удерживаются в металле сварного шва или между металлом сварного шва и основным металлом.Включение шлака может быть вызвано загрязнением металла шва атмосферой, но они обычно происходят из материалов покрытия электродов или флюсов, используемых в операциях дуговой сварки; или при многослойных сварочных операциях, если не удается удалить шлак между проходами. Этого можно избежать путем соответствующей подготовки канавки перед нанесением каждого валика и корректировки контуров, через которые будет трудно полностью проникнуть при последовательных перемещениях. Уловленный шлак — это продукт реакции флюса и расплавленного металла шва.Оксиды, нитриды и другие примеси могут растворяться из шлака и очищать металл шва. Плотность шлака значительно меньше плотности металла шва, поэтому шлаки обычно всплывают на поверхность. Во время сварки шлак формируется и вытесняется под поверхность расплавленного металла шва под действием перемешивающей дуги. Шлак также может течь впереди дуги, а поверх него может осаждаться металл. Последнее особенно верно, когда многопроходные сварные швы выполняются без надлежащей очистки. В любом случае шлак имеет тенденцию подниматься на поверхность из-за меньшей плотности.
ДЕФЕКТЫ И ПРИЧИНЫ ВКЛЮЧЕНИЯ ШЛАКА ПРИ СВАРОКЕ
Возможные формы шлака
F. НЕПОЛНОЕ ПРЕОБРАЗОВАНИЕ
Это происходит из-за того, что соседний валик не сваривается и не сваривается сплавлением металла и основного металла. Это может произойти из-за того, что не удалось повысить температуру основного металла или не очистить или обезжирить поверхности перед сваркой.
НЕПОЛАДКА ПОВРЕЖДЕНИЯ ПРИЧИНЫ И СПОСОБ УСТРАНЕНИЯ ПРИ СВАРОЧНЫХ ОПЕРАЦИЯХ
Неполное слияние
г.ОТСУТСТВИЕ ПРОНИКАНИЯ
Этот дефект возникает, когда сварочный сплав не достигает начала соединения, а затем полностью сплавляет корневые поверхности. Это вызвано неправильным размером электрода, соответствующим форме стыка, низким сварочным током, недостаточной конструкцией стыка и сборкой. Чаще всего это происходит при сварке в вертикальном и потолочном положениях.
ОТСУТСТВИЕ ПРОНИКНОВЕНИЯ ДЕФЕКТЫ ПРИЧИНЫ И МЕРЫ
Непробиваемость
H.БРЫЗГИ
Брызги возникают, когда мелкие частицы от сварного шва зацепляются за окружающую поверхность. Особенно часто это происходит при дуговой сварке металлическим электродом в газе. Как бы вы ни старались, полностью устранить это не удастся. Однако есть несколько способов свести его к минимуму.
ПРИЧИНЫ БЫТОВЫХ ДЕФЕКТОВ И СПОСОБЫ УСТРАНЕНИЯ
Дефекты разбрызгивания при сварке
I. КОРРОЗИЯ ШВОВ
I.1. ГАЛЬВАНИЧЕСКАЯ КОРРОЗИЯ
Эта коррозия возникает, когда два соприкасающихся металла подвергаются воздействию проводящей среды.Разность электрических потенциалов действует как движущая сила, вызывающая коррозию одного из металлов в паре при протекании электрического тока. Активные металлы вызывают коррозию больше, чем благородные металлы.
Гальваническая коррозия может возникать в сварных швах, если присадочный металл имеет другой состав, чем основной металл. Иногда это может происходить из-за литого сварочного металла и деформируемого основного металла. Сравнительно большая площадь благородного по сравнению с активным металлом ускоряет атаку.
I.2. КОРРОЗИЯ РЕЗКИ
В расщелине условия окружающей среды со временем могут стать более агрессивными по сравнению с близлежащей открытой поверхностью.Трещины в сварных соединениях могут возникать по-разному: пористость поверхности, трещины, подрезы, недостаточный провар и дефекты конструкции. Некоторые материалы более восприимчивы к нему, чем другие. Такими примерами являются материалы, которые образуют оксидную пленку для защиты, например алюминий и нержавеющая сталь. Этим материалам может быть разрешено изменить свое поведение, вместе с разработкой минимизации щелей и технического обслуживания для поддержания чистоты поверхностей — некоторые из способов предотвратить проблему.
I.3. МЕЖГРАНУЛЯРНАЯ КОРРОЗИЯ
Атомное несоответствие на границах зерен делает его более популярным местом для сегрегации и осаждения.Коррозия обычно возникает из-за того, что коррозионный агент предпочитает воздействовать на участки, потерявшие атом или элемент, необходимый для адекватной коррозионной стойкости. Подверженность межкристаллитному разрушению обычно является побочным продуктом термической обработки, например, карбиды хрома выделяются на границах зерен, когда сталь нагревается до 650 ° C. Это вызывает межкристаллитную коррозию в массиве лент от сварного шва, температура которого достигла 650 ° C. Эту проблему можно предотвратить с помощью отжига после сварки.
I.4. КОРРОЗИЯ НАПРЯЖЕНИЯ
Смесь растягивающего напряжения и агрессивной среды вызывает растрескивание металла. Многие сплавы уязвимы для этой атаки, но, к счастью, количество вызывающих ее комбинаций сплава и коррозии относительно невелико. Напряжения, которые вызывают это, возникают из-за остаточного давления из-за холодной сварки, работы, термообработки и могут быть отнесены на счет приложенных извне сил во время изготовления и технического обслуживания. Трещины могут иметь межкристаллитный или трансгранулярный характер.Есть тенденция к разветвлению трещин. В следующем списке приведены некоторые характеристики коррозионного растрескивания под напряжением:
- Коррозия под напряжением требует растягивающего напряжения. Ниже порогового значения трещин не возникает.
- Растрескивание кажется макроскопически хрупким, хотя материал может быть пластичным из-за отсутствия коррозии.
- Коррозия под напряжением зависит от металлургического состояния металла.
- В конкретном металле растрескивание вызывают несколько определенных коррозионных веществ.
- Коррозия под напряжением может происходить в средах, которые в остальном являются умеренными для коррозии. Могут пройти длительные периоды времени (часто годы), пока не станут видимыми трещины. Затем трещины быстро распространяются и могут вызвать неожиданный отказ.
- Коррозия под напряжением в большинстве случаев еще не известна, хотя в настоящее время имеется много данных, помогающих избежать этой проблемы.
Как снизить затраты на сварные детали
Сварочные подрядчики начали осознавать, что самые большие затраты, связанные со сваркой в этой области, — это оплата труда.Были разработаны новые инновационные сварочные решения для повышения производительности и снижения затрат на рабочую силу в этой области. Пора спросить себя, получаю ли я лучший сервис для моих проектов. Пришло время обновить мою сварочную службу или поставщика. Примерно 80% стоимости сварного шва в полевых условиях составляет оплата труда. Сварщики — высококвалифицированные мастера, но окружающая среда и другие виды деятельности на рабочем месте часто ограничивают продуктивность вашей рабочей силы. Другой фактор, влияющий на производительность и качество на рабочем месте, — это развивающаяся рабочая сила.Многие опытные сварщики уходят на пенсию, и трудно заменить 30-40-летний опыт работы в связи с изменениями в отрасли. Новые технологии могут повысить безопасность и качество продукции в этой области. Подумайте о сотовых телефонах и телевизорах, которые сейчас выглядят совершенно иначе, чем 10 лет назад. Эти достижения и технологии актуальны и для сварочной отрасли. Подумайте, какой уровень технологий используют ваши поставщики в ваших сварочных проектах. Простые технологии, такие как дистанционное управление, могут улучшить безопасность и производительность на рабочих местах.
Влияние конструкции и других цен на сварочные процессыВероятно, наиболее важной причиной для расчета стоимости является определение способов снижения производственных затрат. На затраты влияет стадия проектирования, а также дополнительные факторы ввода до производства. Ниже приведены некоторые примеры. Самая большая стоимость ручной сварки — это трудозатраты. Один из способов уменьшить это — ввести автоматизацию или приспособление, описанный ниже. Это может повлиять на различные части общего времени работы: метод сварки с более высокой скоростью наплавки сокращает время дуги, в то время как полное изменение метода может также сделать возможным сокращение времени, необходимого для замены электродов, удаления шлаковой стружки и удаления брызг, тем самым сокращение общего времени.
Оборудование для удержания заготовки или манипулирования ею, чтобы обеспечить хорошее положение при сварке, помогает при сварке. Планирование работы тоже очень важно, так как, возможно, только 30% общего времени составляет продуктивное время дуги. Иногда можно избежать бессмысленных сварных швов или использовать другие производственные процессы, такие как гибка. Часть рабочего времени — это время дуги. Даже при использовании данного метода сварки его все еще можно улучшить за счет правильного выбора параметров процесса сварки и электродов и / или за счет предотвращения наплавки большего количества металла шва, чем необходимо.Например, на этапе проектирования определяется конструкция стыка и толщина сварного шва углового шва. Конструкция соединения может сводить к минимуму количество необходимого сварочного металла, естественно, с учетом необходимых требований к характеристикам. Слишком большая толщина шва всегда приводит к большему количеству сварочного металла: при толщине шва 5 мм используется на 60% больше металла сварного шва, чем при толщине шва 4 мм. также важно спланировать подготовку стыков, собрать вместе и удерживать детали и сварку, чтобы не было наплавлено больше металла шва, чем необходимо: это также будет иметь дополнительное преимущество в виде уменьшения сварочной деформации. Если дополнительно можно использовать проплавление углового сварного шва для уменьшения номинальной толщины сварного шва, произойдет дальнейшее уменьшение количества металла сварного шва. Использование присадочных материалов также может быть затронуто, хотя эти затраты должны быть связаны с затратами на рабочую силу. Если затраты на рабочую силу могут быть уменьшены за счет гораздо более эффективной сварки, сокращения подготовки и отделки, например, удаления брызг, предотвращения двусторонней сварки, повышения качества и т. Д., Дополнительные затраты на присадочные материалы могут быть оправданы.Не забывайте также об общем производственном процессе. Правильное качество материалов, наполнителей, тщательная подготовка стыков и сборка деталей — все это способствует сварке, сокращая общее время и минимально влияя на другие процессы. Правильно сделанный сварной шов вызывает меньше проблем, связанных с проверкой и исправлением.
сварочных дефектов | SpringerLink
- Nisith R. Mandal
First Online:
Часть Серия Springer по военно-морской архитектуре, морской инженерии, судостроению и судоходству серия книг (НАМЕСС, том 2)Реферат
В процессе сварки в сварном шве могут быть дефекты.Дефекты в зависимости от их размера, расположения и типа могут рассматриваться как дефекты. Как только эти дефекты обнаружены, необходимо принять меры по их устранению, поскольку конструкция не может быть введена в эксплуатацию с дефектами. Дефекты — это не что иное, как дефекты сварного соединения. Процедура сварки, особенности соединения, доступ и техника сварки будут иметь прямое влияние на дефекты изготовления. Неправильная процедура или плохая техника могут привести к дефектам, ведущим к преждевременному отказу в обслуживании.Большинство дефектов сварных конструкций связано, прежде всего, с неправильной сваркой. Как только причины установлены, оператор может легко устранить проблему. Наиболее часто встречающиеся дефекты / дефекты сварки — это непровар (отсутствие проплавления корня), отсутствие плавления, включения шлака, подрезы, пористость и трещины сварного шва.
Ключевые слова
Сварка металла Сварочная ванна Скорость сварки сварным швомЭти ключевые слова были добавлены машиной, а не авторами.Это экспериментальный процесс, и ключевые слова могут обновляться по мере улучшения алгоритма обучения.
Это предварительный просмотр содержимого подписки,
войдите в, чтобы проверить доступ.
Ссылки
1.
Сварочные дефекты. (2005).
Классификация трещин по DIN 8524 часть 3. ISF: Аахен.
Google Scholar2.
Лукас Б., Мазерс Г. и Эйлинз К.
Дефекты / дефекты сварных швов — включения шлака, Рабочие знания 43, Институт сварки.
Google Scholar
Информация об авторских правах
© Springer Nature Singapore Pte Ltd.