Подробный мануал по изготовлению экструдера прутка. Автор ianmcmill. Часть 2
Добавлено в закладки: 3
Фабрика прутка для 3D принтера. Часть 2
Автор ianmcmill
Оригинал мануала можно изучить по этой ссылке.
Это продолжение. Первую часть читайте по этой ссылке.
Шаг 8. Сопло
Нужно заранее запастись заглушками для трубы, потому что подбор отверстия сопла дело долгое и кропотливое. Автор предлагает начать с отверстия диаметром 1,5 мм для изготовления 1,75 мм прутка.
Так как автор кидает в экструдер пластик различного происхождения, он предлагает сразу поставить фильтр от камней, волос и пузырьков, взятый из смесителя (на кухне или в ванной) и обрезанного по размеру.
Шаг 9. Нагреватель и термопара
Сверлим отверстие 2 мм в крайней части удлинителя водопроводной трубы для помещения туда термопары. Только не насквозь!
С термопары снимаем корпус и немного оплётки.
Помещаем её в подготовленное отверстие и закрепляем каптоновым скотчем.
Наматываем на резьбу фум ленту и накручиваем заглушку-сопло.
Впереди крепим на жёсткой проволоке обрезок 10 см алюминиевой трубки диаметром 10 мм. Она даёт дополнительное охлаждение прутку на выходе из сопла.
Обматываем нагреватель и сопло утеплителем.
Шаг 10. Охлаждение
В передней части сопла и на моторе нужно охлаждение.
Пруток очень горячий и мягкий на входе из сопла и чтобы он неконтролируемо не растягивался при падении вниз его нужно охлаждать. Чем лучше вы охладите пруток в начале, тем проще будет контролировать диаметр потом.
Мотор нужно обязательно охлаждать
Шаг 11. Электроника
Теперь, когда большинство механических частей установлено, пришло время для электроники. Но прежде возьмём кусок фанеры и установим туда три выключателя, PID контроллер температуры и регулятор оборотов мотора.
Схема подключения электроники
Схема PID контроллера температуры (у вас может быть другая)
Подключите шнур питания через выключатель к блоку питания.
Подключите PID контроллер температуры через выключатель к источнику питания.
Подключите сигнальные порты (3 и 4) твердотельного реле к PID контроллеру (порт 6 и 8). Подключите порт 1 реле к 200В в порт L блока питания. Порт 2 реле подключите к нагревателю, свободный порт нагревателя подключите к блоку питания в порт N.
Для чего нужно реле? PID контроллер коммутирует только 12В, а нагревателю нужно 220В. Поэтому реле соединяет 12В PID с 220В нагревателя. А PID через реле включает или отключает нагрев. Идея состоит в том, чтобы контролировать устройство большой мощности с помощью устройства малой мощности.
Подключите контроллер оборотов мотора через выключатель к источнику питания. Затем подключите мотор к контроллеру оборотов.
Два вентилятора подключите в те же порты, что и контроллер оборотов.
Различные схемы подключения:
- Схема Filastruder
- Схема Filabot Wee
- Схема Sestos PID контроллера (использованный автором)
- Инструкция на PID REX C-100
Схема на PID REX-C100 (из комментариев)
Шаг 11. Настройка экструзии и PID
Различным материалам нужны разные настройки экструзии. Для чистого ABS достаточно температуры 190 градусов Цельсия. PLA нуждается в меньшей температуре, а смесь ABS/PC требует 260- 270 градусов.
PID контроллер используется для автоматической поддержки заданной температуры.
Для установки параметров автонастройки держите SET в течении 3 секунд. Вы увидите надпись HIAL на дисплее. Теперь жмите кнопку Down, пока не увидите Ctrl и настройте его на “2“. Это число для функции автонастройки. Теперь нажмите SET снова пока не увидите температуру. Установите желаемую температуру используя кнопки Up/Down и ждите пока дисплей не перестанет мигать. Подожите 10-15 минут пока не поднимется температура.
Включите мотор и ждите первой экструзии. Теперь нужно настраивать скорость двигателя. По опыту автора, на половине скорости по потенциометру и температуре 270 градусов ABS/PC давится очень хорошо.
Обсудим мой перевод и конструкцию этого экструдера на форуме?
  
2015-11-15  
  
Раздел: Обзор, Своими руками, Экструдер прутка  
нити по чертежам своими руками
Появление первых 3D принтеров поспособствовало ускоренному развитию сегмента IT. Уникальность оборудования, способного воспроизводить конструкции в трехмерном формате, стала причиной его высокой стоимости.
Экструдер
Поэтому появление самодельных устройств, обладающих подобными функциями, не стало неожиданностью. Их используют в бытовых условиях, а при работе с ними требуется расходный материал. Чаще к нему относят нитевидный пластик, к примеру, ABS или PLA. Человек, который хочет своими руками собрать 3D принтер или его отдельную часть (экструдер), должен обладать необходимыми знаниями и опытом. Он обязан знать о калибровке экструдера, охлаждении Cool-end и Hot-end.
О чём пойдет речь:
Механические компоненты
Детали для сборки реально приобрести в комплекте, но те, кто не ищут легких путей, часто решаются на самостоятельное изготовление. Им понадобятся:
- крепежные детали для формирования каркаса;
- рабочая площадка;
- устройство для нагрева и регулировки температурного режима;
- направляющие из металла;
- шестерни для электроприводов;
- экструдер.
Главной трудностью при изготовлении 3D принтера считается правильная конфигурация последних трех элементов. Большое значение имеет привод, который устанавливают для передвижения платформы на одной оси. Вторая становится залогом перемещения печатающей головки.
Детали для сборки 3d-экструдера
Самостоятельная сборка механической части осуществляется благодаря использованию листов из фанеры, шурупов подходящего размера и зажимов, обеспечивающих фиксацию. На фото стандартный набор для изготовления 3D принтера с двумя печатающими головками.
Электротехнические составляющие
Особенностью конструкции является экструдер нити для 3d принтера. Благодаря ему происходит выход расходного материала и непосредственно создание рисунка. Чаще его не рискуют делать самостоятельно, а приобретают в специализированных магазинах. Сборку начинают с подготовки необходимых деталей.
Блок Cool-end
К его функциям относится подача филамента (нити из пластика). Он состоит из электрического мотора, прутка и шестерней. Нити намотаны на предусмотренную для этого катушку.
Блок Cool-end
Hot-end
Он представляет собой дуэт сопла и элемента для нагрева. Филамент проходит через последний и изменяет агрегатное состояние, превращаясь в вязкую массу, которая после выдавливается с помощью сопла. Завершающим этапом становится послойное нанесение данного состава.
hotend насадка
Детали этой части 3d принтера с двумя экструдерами производятся из сплавов латуни или алюминия. Благодаря этому тепло проводится достаточно быстро. Блок состоит из проволочной спирали, термопара (он регулирует температуру) и двух резисторов. Охлаждение элеватора осуществляется из-за термоизолирующей вставки. Она располагается между Cool-end и Hot-end. Данная деталь изображена на фото.
Сборка экструдера
Производство экструдера для 3D принтера своими руками происходит следующим образом.
Подбирается двигатель
Чаще данную деталь заменяют рабочим мотором от принтера или сканера, приобрести его можно на радиорынке.
17 Шаговый Двигатель 1.75 мм 1.7
Если двигатель для экструдера оказался слишком слабым, дополнительно потребуется редуктор. Подходящей заменой покупной детали станет та, что ранее была частью шуруповерта. Также редуктор понадобиться экструдеру прутка для 3d принтера. Присоединение двигателя происходит за счет корпуса, прижимного ролика и хот-энда, располагать их нужно как на фото.
Регулировка прижимного ролика
Обязательным условием является продуманное взаимодействие этого элемента и пружины. Последняя устанавливается из-за возможных недочетов в расчете параметров прутка 3D принтера.
Слишком сильное сцепление нитей с механизмом подачи провоцирует отделение частиц расходного материала.
Создание хот-энда
Его гораздо проще приобрести, большинство мастеров так и поступают. Для самостоятельного изготовления потребуется чертежи, которые можно скачать из интернета. Для радиатора понадобиться алюминиевый сплав.
Радиатор экструдера (хотэнда) 3D принтера
Этот элемент отводит теплый воздух от ствола прибора, который представляет собой полую трубку. В ее функциях соединение элемента нагрева и радиатора. Это предупреждает перегрев принтера.
Удачным вариантом считается светодиодный радиатор, при этом охлаждение прибора будет происходить с помощью вентилятора. Ствол хот-энда 3D принтера представляет собой металлическую полую трубку. При создании экструдера необходимо учитывать время плавления нитей. Если они плавятся раньше, чем положено, то произойдет засорение сопла.
Сборка элемента нагрева
В первую очередь понадобиться алюминиевая пластина. В ней делают ходы для крепления терморезистора, хот-энда и резистора.
Алюминиевая пластина
В принтере, работающем в формате 3D, может быть больше одного экструдера, например, как на фото. Данный факт следует учитывать при создании чертежа устройства. Функциональность такого оборудования на порядок выше, чем у стандартного, например, печать в двух цветах и изготовление конструкций из растворимых полимерных материалов.
К завершающему этапу создания 3D принтера своими руками относят калибровку экструдера, подключение электроники, регулировку процесса печати, внедрение подходящего ПО.
Обзор принтера Bigrep One
Данная модель характеризуется наличием двух экструдеров, наличием подогрева рабочей платформы и внушительными габаритами. Bigrep One (изображен на фото) предназначен для профессионалов, специализирующихся на производстве качественных изделий в 3D формате.
Еще одним плюсом 3d принтера Bigrep One 2 с двумя экструдерами считается его стоимость. На фоне цен на аналогичные устройства она более приемлема, поэтому пользуется большим спросом.
Принтер Bigrep One
Отмечают следующие преимущества принтера Bigrep One:
- Рабочий объем 1,3 м3.
- Низкая себестоимость 3D моделей.
- Отсутствие необходимости в оснастке готовых изделий.
- Повсеместность применения.
- Экономичность и производительность.
- Наличие камеры 3D печати.
- Обширный ряд возможных филаментов (нити ABS и PLA, нейлон, гибкие эластомеры).
Bigrep One представляет собой новое поколение принтеров, употребление которых расширяет сферу использования 3D технологий.
Вывод
Экструдер – это значимый узел 3D принтера. Он влияет на качество готовых предметов, саму процедуру печати. Неполадки в нем влекут за собой потерю дорогостоящих нитей из пластика. Недочеты в расчете диаметра прутков, отсутствие калибровки, неправильное расположение осей корпуса приводят к отрицательным результатам производства. Пример на фото.
Поэтому, перед тем как начинать сборку принтера, проведите обзор возможных конструкций этого устройства, определите точные параметры прутка и количество экструдеров (один, два или более).
Делаем сами пластик для 3d принтера. Экструдер для самостоятельного изготовления филамента. Точность на экструдере достаточно высокая
Небольшой отчет о покупке и установке комплекта экструдера для 3D принтера. Для тех, кто хочет добавить цветную печать в свой принтер.
Давно назрел апгрейд 3D принтер, особенно хотелось попробовать цветную печать — обзавестись двойным экструдером на принтере Tevo Tarantula. В свое время не было в наличии версии Large и Dual, взял просто Large, но с прицелом, что когда нибудь…
Но это когда-нибудь настало. Заранее были приобретены комплекты для апгрейда: (extruder coolend) с высокомоментным двигателем, а также «горячая» часть — с двумя каналами для двух цветов пластика. В комплекте были нужные провода, нагреватели, термодатчики.
Для доработки потребуется:
— высокомоментный двигатель. То есть шаговик, который будет крутиться не быстро, но точно. А момент нужен, чтобы «продавливать» пластик через сопло. И если сопло стоит 0,8 мм, то высокий момент не нужен, то для маленьких сопел с отверстием 0,3…0,2 мм нужен обязательно, момент возрастает в несколько раз. Как вариант — использование двигателя с редуктором.
— скоба крепления двигателя.
— провод подключения двигателя. Обычно правда сразу идет в комплекте с двигателем.
— если на плате отсутствует выход под второй (третий) двигатель экструдера, то необходимо будет купить разветвитель-адаптер 2-in-1 для установки драйвера нового двигателя.
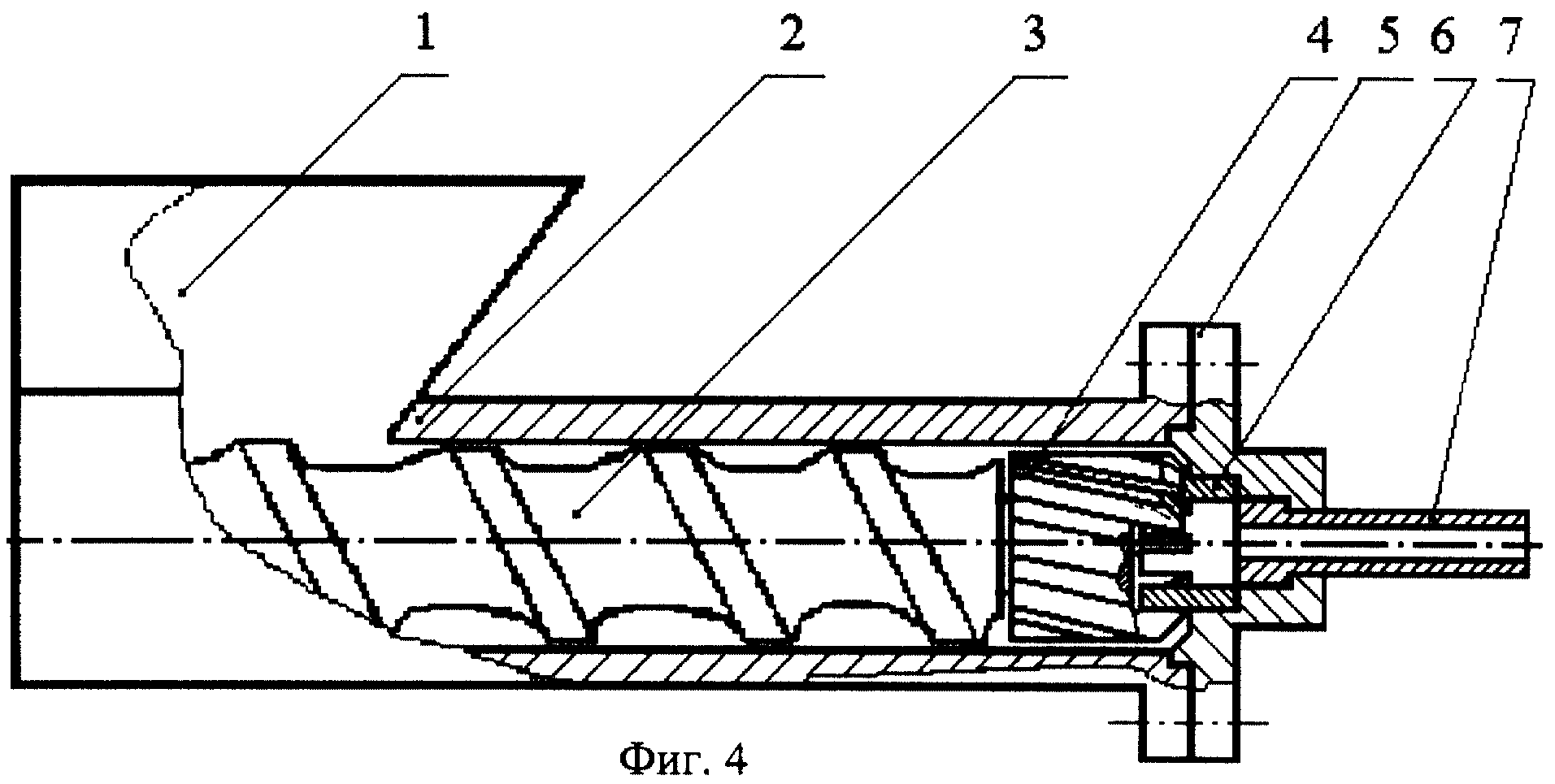
— трубка подачи пластика (тефлоновая трубка OD=4/ID=2, то есть внешний диаметр 4 мм, внутренний 2 мм. трубки с внутренним диаметром 4 мм обычно идут не для 1,75 прутка, а для 3мм прутка) — трубка «боудена».
для «горячей части»:
— два радиатора Е3D или один двойной.
— два нагревательных блока
— нагревательные картриджи и термисторы.
— вентилятор обдува термобарьера.
Для сборки и настройки:
— прямые руки
— модифицированная прошивка
Несколько слов про популярные микширующие/двойные Хотэнды.
Это так называемые Химера и Циклоп.
— это глубокая модификация E3D хотэнда с плоским радиатором, двумя входами (фланцы) и двумя нагревательными блоками.
Циклоп (Ciclop) — аналог Химеры, тот же радиатор и два канала, но общий нагревательный блок и одно сопло.
Внутри блока два канала сводятся в один
Смена пластика происходит ретрактом одного прутка и подачей другого. Минус — пластики должны иметь близкую температуру плавления, так как нагреватель один, общий и общий термодатчик. То есть «подружить» PLA и, например, ABS не получится. А вот ABS и HIPS — вполне. Соответственно не подходит для печати поддержек PVA пластиком, так как PVA имеет низкую температуру плавления и при 200-210° С уже перегревается и получается пробка в канале.
Есть еще Diamond hotend, заострять внимание на нем не буду, так как кроме нестандартного сопла на 0,4мм за бешеные деньги они не могут ничего предложить.
Итак, решено было взять комплектом все, перестраховываясь от различных несовместимостей и дополнительного ожидания. Был заказан комплект механизм подачи+двигатель и отдельно комплект двойного экструдера.
Характеристики комплекта MK7/MK8 All Metal Remote Extruder Kit
Диаметр прутка — 1,75 мм
Материал механизма — анодированный алюминий («7075 авиационный» сплав)
Размещение: Слева, справа, по центру.
— 2 фитинга для PTFE трубки с диаметром 4 мм
— кабель подключения двигателя
— двигатель 17hd40005-22b
— скоба крепления
— MK7 зубчатое колесо с проточкой
— шестигранник
— пружина
— комплект винтов.
Теперь чуть более подробно про купленный комплект. Пришло все в простом пакете и в пупырке. Посылка достаточно тяжелая.
Огромный плюс — фуллметалл, то есть отсутствие пластиковых деталей в механизме экструдера. Почему плюс — потому что в моей уже люфты (выработка), плюс повреждено пластиковое крепление. Перепечатывал, но не торт. Лучше пусть все будет металлическое.
Так что при доставке ничего не пострадало. Распаковываем смело!
Маркировка высокомоментного шагового двигателя.
Зубчатая шестеренка с проточкой.
Дополнительная информация для тех, кто хочет купить по отдельности комплект
Характеристики
Сравните с характеристиками «обычного»
Далее . Бывает трех видов: для установки слева, справа, по центру. Отличаются фрезеровкой на «ручке» — рычаге, на который нажимают при заправке пластика. Можно оценить, если знаете уже место расположения экструдера.
В этом комплекте идет прямая зубчатая шестерня, если брать , то это еще плюсом.
Можно взять вот
Хотэнд
И к нему
Плюс термистор, нагревательный картридж, фланцы для пластика, трубка.
Можно на радиатор установить не блок-циклоп, а обычные блоки типа volcano, две штуки. Только трубки-горловины нужны без резьбы.
Основное все. ИМХО, дешевле купить все в наборе, с нагревателями, термисторами и вентилятором.
Начинаем собирать комплект. Тут дело не хитрое.
Устанавливаем шестерню. Потребуется с шестигранник на 1,5.
Далее в таком порядке: скоба-основание-рычаг-пружина.
Естественно скоба сначала крепится на нужное место принтера, иначе у вас не будет возможности закрепить, так как пазы окажутся под корпусом двигателя. Для наглядности я соберу сначала без установки на принтер.
Обратите внимание на разную длину и диаметр винтов. Каждый предназначен для своего отверстия.
Далее устанавливаем рычаг и пружины
Получилось как то вот так.
Затем прикручиваем фланцы для прутка
Вот фотография комплекта до «примерки»
Примеряем к принтеру. На принтере сейчас штатно установлен простой экструдер с модифицированный E3D (который имеет трубку до самого сопла). Для установки хотэнда Циклоп потребуется заменить каретку оси Х.
Для окончательной установки мне еще предстоит напечатать крепление для экструдера, либо найти удобное положение скобы для крепления на профиль 2020.
Итак, несколько слов о модификации прошивки Tevo Tarantula.
Заходим в онлайн конструктор прошивки
И сразу же загружаем свой Configuration.h. Мы получаем возможность модифицировать заведомо рабочую прошивку своего принтера.
На четвертой вкладке «Tools» нажимаем «добавить экструдер». По умолчанию у нас только один, Extruder0.
Добавляем Extruder1.
И конфигурируем его. Указываем pin по необходимости.
Обратите внимание, что если у вас микширующий хотэнд с одним нагревателем и одним термистором, это тоже необходимо указать в прошивке.
Нагреватель0 и Темп0 для основного экструдера. Если отдельный блок нагревателя у второго — то указываем Нагреватель2 и Темп2 для второго экструдера. Далее сохраняем, заливаем в принтер и пробуем.
В управляющей программе либо с дисплея даем задание на подачу N мм прутка. Например, 100 мм. И затем измеряем результат: могло вылезти больше или меньше. Учитываем разницу, вводим поправочный коэффициент в прошивку и перепроверяем еще раз. Операцию лучше всего проводить со снятой трубкой боудена.
Вот сюда в файле Configuration.h в разделе «default settings» прописываем количество шагов DEFAULT_AXIS_STEPS_PER_UNIT для экструдера (четвертое значение, первые три — оси Х, У, Z).
#define DEFAULT_AXIS_STEPS_PER_UNIT {80,80,1600,100} // custom steps per unit for TEVO Tarantula
Высчитываем поправочный коэффициент и заносим. Например, выдавило больше чем надо, не 100, а 103 мм. Делим 100/103, полученный результат заносим в прошивку.
#define DEFAULT_AXIS_STEPS_PER_UNIT {80,80,1600,97.0874} // custom steps per unit for TEVO Tarantula
Сохраняем, компилируем, заливаем, проверяем.
Дополнительная информация — расчет количества шагов экструдера
Если что — расчет количества шагов экструдера DEFAULT_AXIS_STEPS_PER_UNIT считается по формуле:
steps per mm=micro steps per rev * gear ratio / (pinch wheel diameter * pi)
где micro steps per rev — количество микрошагов двигателя для 1 оборота = 3200, то есть 16 микрошагов на шаг, 200 шагов за оборот
— количество микрошагов двигателя для 1 оборота
gear ratio — соотношение количества зубьев в редукторе экструдера. В моем Тево редуктора нет, поэтому =1
pinch wheel diameter — диаметр впадины толкающего винта
После расчета всеравно проверять по указанной выше методике.
В группе FB есть некоторые публикации на
Любой из принтеров 3D обладает своими особенностями конструкции. Основным в таких устройствах является , его еще называют печатающей головкой. Роль головки в работе принтера предельно проста. Ее роль в выдавливании пластика через сопло, в следствии чего, складывается рисунок в трехмерном формате. Возникает закономерный вопрос: возможно ли сделать своими руками?
Какие особенности в этих устройствах
Во время работы принтера с использованием 3D технологий, как правило, используется нитевидный . Он есть разных видов, но для таких принтеров в основном берут PLA или ABS. Но, большой выбор исходного материала мало влияет на конструкцию печатающей головки, как правило, разными производителями они изготовляются по схожему типу. Вот какая конструкция экструдера у современного 3d принтера поступает в продажу:
- Cool-end это блок подающий филамент. В его конструкции обязательно присутствуют несколько шестерней и электрический мотор. Пластиковую нить из соответственной катушки извлекают от процесса вращения шестерней, далее она проходит через нагревательный элемент, где на пластик воздействует высокая температура и он становится мягким.
Это позволяет далее это вязкий пластик выдавливать посредством использования сопла и придавать ему необходимые очертания.
- Другой hot-end блок это сопло со своим нагревательным элементом. При его изготовлении используют алюминиевые или латунные сплавы. Этому блоку присуща очень высокая тепло проводимость. В составе компонента нагревания встроена проволочная спираль, два резистора, и термопара для регулировки температуры нагревания прибора. При работе hot-end нагревается и тем самым, проходит процесс плавления пластика. Очень важным моментом в работе обеох блоков является охлаждение рабочих платформ. Это обеспечивает специальная термоизолирующая вставка между блоками.
Возможно ли сделать самодельный экструдер для 3d принтера
Если вы все-таки решились самостоятельно смастерить экструдер к 3d принтеру, необходимо выбрать двигатель. Но, здесь возможно применение и старых моторов от принтера или сканера (рабочий, естественно). Если вы не уверены, с каким именно мотором лучше всего будет работать самодельный экструдер для 3d принтера форум со специалистами, в этой области, поможет вам во всем разобраться. Чтобы закрепить двигатель, необходим корпус из подходящего материала, хот-энд, а так же ролик – его функция прижимание. Чтобы сделать сам корпус, могут быть использованы разные материалы, как и его форму, вы можете сделать по своему усмотрению. Для регулирования прижимного ролика обязательно использовать пружину, так как по толщине прутик не обязательно идеально соответствует требованиям. Материал обязательно сцепляется с подающим компонентом. Но оно так же нельзя делать тесным, так как в этом случае частички пластика могут отколоться в процессе печати.
Хот-энд вы можете приобрести, хотя это и не самое дешевое приобретение, в таком случае самодельный экструдер для 3д принтера станет неплохим вложением денег. Хотя вы можете найти и изучить его чертежи и сделать самому. Итак, из алюминиевого сплава создают радиаторы, он необходим для отведения теплого воздуха от ствола прибора. Тогда можно будет легко избежать чрезмерного перегрева устройства во время печати. Очень практично использование светодиодного радиатора, а охлаждение производить вентилятором. Для создания ствола хот-энда используется полая трубка из металла. Она соединяет радиатор с нагревательным элементом.
Для самостоятельного конструирования элемента нагревания в 3d-экструдере выбирается пластина из алюминиевых сплавов. В этой пластине сверлите дырку для того, чтобы закрепить хот-энд. После чего просверливаются отверстия для болтов крепления, резистора и терморезистора. Резистор нагревает пластину, а терморезистор, как раз эту температуру нагревания регулирует. Для создания сопла, как правило, используется гайка с закруглённым концом. Проще всего поддается обработке гайка из латунного или медного сплава. Болт закрепляется тисками, после чего накручиваете на него гайку и сверлите в центре отверстие. Это и есть способ не слишком хлопотного создания экструдера в домашних или полевых условиях.
Для некоторых моделей таких принтеров в оснащение входят два экструдера, это дает возможность печати изображения в двух цветах или создавать структуры из растворимого полимера. Но, если у вас получилось сделать один экструдер для 3d принтера своими руками то и двойной смастерить так же станет возможным.
Достаточно высокая стоимость расходных материалов для 3d принтеров все еще остается серьезной проблемой, как для производителей, так и для потребителей.
Принтеры, способные превращать трехмерные чертежи в физические предметы из или ряда других материалов становятся все доступнее. Готовых 3d-моделей, становиться все больше, но без доступа к действительно дешевым расходным материалам, бурного развития рынка 3d-печати, по мнению специалистов, ожидать не стоит.
Шаг на пути снижения стоимости расходных материалов сделала британская компания Noztek, представив свою последнюю разработку: экструдер для ABS / PLA нити Noztek Pro.
Как отмечают в компании, большинство выпускаемых сегодня экструдеров существую лишь в виде комплектов для сборки, и доступны только энтузиастам. В отличии от них, Noztek Pro это экструдер, готовый к работе через 15 минут после распаковки. Все, что необходимо, это засыпать специальные гранулы и выставить на панели управления необходимые параметры экструзии.
Аппарат позволяет производить 1кг пластиковой нити за 45 минут используя гранулы для производства ABS и PLA пластмасс. В зависимости от температуры экструзии и типа используемого пластика аппарат производит до 1 м метра нити диаметром 1,75 мм с допустимым отклонением не более 0,04 мм.
В Noztek считают, что экономия для конечного потребителя составит около 70%.
Тестирование прибора проводилось именно на ABS и PLA гранулах, но это не значит, что его возможности на этом ограничиваются. По заявлениям компании некоторые клиенты с успехом используют HDPE, HIPS, UPV материалы. Кроме того экструдер способен перерабатывать другие виды пластмасс и даже сами 3d-модели.
Еще одним плюсом использования экструдера является более свободный выбор цветов нитей, экспериментируя и смешивая гранулы различных цветов можно добиться интересных цветовых решений, недоступных в продаже.
Команда инженеров Noztek непрерывно работают над улучшением скорости экструзии и повышением уровней допуска. Аппарат оснащен модернизированным мотор-редуктором и возможностью изменять скорость экструзии, именно это позволяет настраивать его для экструзии различных видов пластика. Экструдер разработан с учетом возможности дальнейшей модернизации, это означает, что пользователи в скором времени смогут приобрести обновление для контроля всего процесса с помощью USB интерфейса. Кроме того, компания планирует оснастить следующее поколение Noztek Pro механизмом для автоматической намотки нити на бухту.
Мы надеемся, что люди будут иметь возможность печатать столько моделей, одежды, инструментов, игр и так далее, сколько захотят, не беспокоясь о стоимости материалов.
Стивен Форстер
Технические характеристики
- Преобразует разнообразные пластиковые гранулы: (протестирован только на ABS и PLA) в нить толщиной 1.
75mm или 3мм (Обе головки в комплекте)
- Температура экструзии: 180-220 Цельсия
- Допуски для нити: 1.75mm (+ 0,04 / — 0,04)
- Полностью собран и готов к работе прямо из коробки (не сборочный комплект)
- Производит до 1 метра нити в минуту (в зависимости от температуры экструзии и типа пластика)
- Производительность: 1 кг за 45 мин
Цена на экструдер Noztek Pro составляет: £595 ($992, €723)
Мнение редакции:
Сегодня на рынке стоимость 1 кг ABS нити для 3d-принтеров составляет 30-60 долларов (производство КНР, Россия), цена на нить производства США может составлять более 100 долларов. Стоимость цветных гранул для производства ABS пластика варьируется в пределах 3-4 долларов. При использовании вторичное сырья цена может быть еще ниже. Поэтому экономия от применения экструдеров налицо, остается только вопрос с качеством производимой нити.
сайт
Видео рабочего процесса Noztek Pro
В настоящее время самая доступная цена на пластиковую нить для 3D принтеров составляет более 20$ за 1 кг, стоимость филамента от надежных производителей или с какими-либо особенными характеристиками (цвет, добавки) достигает 50$.
Таким образом, при печати 3D моделей, снижение расхода материала и его стоимости становятся ключевыми факторами повышения экономичности и, соответственно, доходности 3D печати.
Экструдер Лимана
Первым публичным шагом к этому стало объявленное в марте 2013 года изобретение с открытым источником – экструдер для самостоятельного создания пластиковой нити для 3D принтеров. Изобретатель Хью Лиман представил свою машину на конкурс и выиграл главный приз от фонда Кауфмана и Maker Faire. Одним из главных условий конкурса была цена устройства – не более 250$. Победивший экструдер позволяет выдавливать нить диаметром 1,75 или 3 мм с погрешностью в 0,01мм, причем это был уже второй вариант представленного устройства, первый не прошел по цене. Изобретение Лимана с открытым исходным кодом, что позволяет любому использовать и строить его.
С помощью самодельного экструдера, вы сможете экономить до 80%. Качественный филамент стоит около 50$ за 1 кг, тогда как покупка килограмма гранул обойдется только в 10$.
А если вы покупаете упаковку гранул в 25 кг, то каждый килограмм обойдется всего в 5$.
Экструдер Фишера
Вдохновленный экструдером Лимана, Бен Фишлер из Сан-Диего (Калифорния) решил попробовать создать простую в использовании версию для пользователей. STRUdittle является ультра-компактным устройством и может делать нити из ABS пластика со скоростью экструзии 30-60 см в мин.
Точность на экструдере достаточно высокая:
- Погрешность 0,05 мм при свободном выводе филамента;
- Погрешность 0,03 мм при использовании автоматически сматывающей готовую нить катушки.
Проект Фишлера запущен на Kickstarter для того, чтобы сделать этот продукт доступным для масс. Необходимые средства уже собраны, и комплектное устройство предлагается участникам со финансирования по 385$. Причем, кроме полного комплекта, уже имеющим подобный экструдер также предлагается отдельно только механизм для автоматического сматывания филамента за 100$. А само устройство поставляется с размерами сопла по выбору заказчика, в том числе вообще без него – для изготовления материалов нестандартных размеров.
Всем добра. Так случилось что у меня появился 3д принтер. Побаловавшись им я понял что АБС нити для него в наших краях найти трудно или очень дорого. Кое где есть 1.75мм по заоблачной цене, 3мм нигде не нашел. Посмотрев статью, Лимана про его экструдер, решил сделать что то подобное. Заказал с мешок гранул. Пока он шел, из остатков пластика, который был в комплекте с принтером соорудил аппарат)))) благо Китай рядом. Термопара, нагреватель, драйвера мотора привезли за неделю примерно. Шнековую пару сделал из 2х частей. Горячая часть была заказана у местных токарей, которые за пару часов из цельного куска железа выточили мне ее. Термовставка из стеклотекстолита. Так называема часть была напечатана из остатков былой роскоши. Обычное сверло по дереву, пара подшипников простых, один упорный. Несколько дней пыхтел. В итоге вот что получилось. Килограмм гранул перерабатывается в нить 1.70-1.77мм за 3.5 часа.
Если есть вопросы или предложения, обращайтесь.
Аппарат находиться еще в стадии доводки до идеала.
В планах сделать охлаждение мотора, т.к. при длительной работе он разогревается до 100-120 градусов. Шестерни в редукторе пластиковые, боюсь что долго при такой температуру они не проживут.
автоматическую намотку, т.к. вручную намотать около 500 метров прутка на катушку очень трудно.
Да и хотелось бы чутка переделать «холодную» часть шнековой пары, получилась она немного неудачная.
PS: писать много текста не люблю и не умею, так что сильно не пинайте.
блок так сказать управления. кнопка включения термопары, кнопка включения мотора шнека, и регулятор вращения шнека или регулятор толщины нити.
Система автоматической подачи гранул… LoL вмещает в себя ровно 1 кг пластика
Собственно сам аппарат….
Сборка домашнего 3D-принтера своими руками: рекомендации из личного опыта
3D-печать и сборка 3D-принтеров — мое хобби и увлечение. Здесь я не буду делиться детальными схемами и чертежами, их более чем достаточно на профильных ресурсах. Главная цель этого материала — рассказать, с чего начать, куда копать и как избежать ошибок в процессе сборки домашнего 3D-принтера. Возможно, кто-нибудь из читателей вдохновится на прикладные инженерные свершения.
Зачем нужен 3D-принтер? Сценарии использования
Впервые с идеей 3D-печати я столкнулся в далеких 90-х, когда смотрел сериал Star Trek. Помню, как меня впечатлил момент, когда герои культового сериала печатали необходимые им во время путешествия вещи прямо на борту своего звездолета. Печатали они все что угодно: от обуви до инструментов. Я думал, что было бы здорово когда-нибудь тоже иметь такую штуку. Тогда это все казалось чем-то невероятным. За окном — хмурые 90-е, а «нокиа» с монохромным экраном была вершиной прогресса, доступной лишь избранным.
Годы шли, все менялось. Примерно с 2010 в продаже начали появляться первые рабочие модели 3D-принтеров. Вчерашняя фантастика стала реальностью. Однако стоимость таких решений, мягко говоря, обескураживала. Но IT-индустрия не была бы собой без любознательного комьюнити, где происходит активный обмен знаниями и опытом и которому только дай покопаться в мозгах и потрохах новых железок и ПО. Так, чертежи и схемы принтеров стали все чаще всплывать в Сети. Сегодня самым содержательным и объемным ресурсом по теме сборки 3D-принтеров является RepRap — это огромная база знаний, которая содержит детальные гайды по созданию самых разных моделей этих машин.
Первый принтер я собрал около пяти лет назад. Моя личная мотивация собрать собственное устройство довольно прозаична и основана на нескольких факторах. Во-первых, появилась возможность попробовать реализовать старую мечту иметь собственное устройство, навеянную фантастическим сериалом. Второй фактор — иногда нужно было отремонтировать какие-то домашние вещи (например, детскую коляску, элементы автомобиля, бытовую технику и другие мелочи), а нужных деталей найти не удавалось. Ну и третий аспект применения — «околорабочий». На принтере я изготавливаю корпусы для различных IoT-устройств, которые собираю дома.
Согласитесь, лучше разместить свое устройство на основе Raspberry Pi или Arduino в эстетически приятном «кузове», который не стыдно поставить в квартире или взять в офис, чем организовывать компоненты, например, в пластиковом судочке для еды. И да, можно печатать детали для сборки других принтеров 🙂
Сценариев применения 3D-принтеров огромное множество. Думаю, каждый сможет найти что-то свое.
Сложная деталь с точки зрения чертежа, которую я печатал на своем принтере. Да, это просто фигурка, но она имеет множество мелких элементов
Готовое решение vs своя сборка
Когда технология обкатана, ее стоимость на рынке заметно снижается. То же произошло и в мире 3D-принтеров. Если раньше готовое решение стоило просто заоблачных денег, то сегодня обзавестись такой машиной — дело более гуманное для кошелька, но тем не менее не самое доступное для энтузиаста. На рынке присутствует ряд уже собранных и готовых к домашнему использованию решений, их ценовой диапазон колеблется от $500-700 (не самые лучшие варианты) и до бесконечности (адекватные решения стартуют с ценника около $1000). Да, есть варианты и за $150, но на них мы, по понятным, надеюсь, причинам, останавливаться не будем.
Если коротко, рассматривать готовую сборку стоит в трех случаях:
- когда печатать вы планируете совсем не много и редко;
- когда точность печати играет критическую роль;
- вам нужно печатать формы для серийного изготовления деталей.
Очевидных плюсов у собственноручной сборки несколько. Первый и самый главный — стоимость. Покупка всех необходимых компонентов обойдется вам максимум в пару сотен долларов. Взамен вы получите полноценное решение для 3D-печати с приемлемым для бытовых нужд качеством производимых продуктов. Второе преимущество заключается в том, что, собирая принтер собственноручно, вы разберетесь с принципами его устройства и работы. Поверьте, эти знания пригодятся вам в процессе эксплуатации даже дорогого готового решения — любой 3D-принтер необходимо регулярно обслуживать, и делать это без понимания основ может оказаться затруднительным.
Основной минус сборки — необходимость большого количества времени. На свою первую сборку я потратил около 150 часов.
Что нужно, чтобы собрать принтер самому
Самое главное здесь — наличие желания. Что касается каких-то особых навыков, то, по большому счету, чтобы собрать свой первый принтер, умение паять или писать код не критично. Конечно, понимание основ радиоэлектроники и базовые умения в области механики (то есть «прямые руки») существенно упростят задачу и сократят количество времени, которое нужно уделить сборке.
Также для старта нам понадобится обязательный набор деталей:
- Экструдер — элемент, который непосредственно отвечает за печать, печатная головка.
На рынке есть множество вариантов, но для бюджетной сборки я рекомендую модель MK8. Из минусов: не получится печатать пластиками, которые требуют высокой температуры, есть заметный перегрев во время интенсивной работы, который может вывести элемент из строя. Если бюджет позволяет, то можно посмотреть на MK10 — там все минусы учтены.
- Процессорная плата. Хорошо подойдет знакомая многим Arduino Mega. Я не заметил минусов у этого решения, но можно потратить на пару долларов больше и приобрести что-то более мощное, с заделом на будущее.
- Плата управления. Я использую RAMPS 1.4, которая прекрасно работает в связке с Arduino Mega. Более дорогая, но более надежная плата — Shield, которая уже совмещает в себе процессорную плату и плату управления. В современных реалиях рекомендую обратить внимание именно на нее. В довесок к ней нужно приобрести минимум 5 микрошаговых контроллеров шаговых двигателей, например — А4988. И лучше иметь пару таких в запасе для замены.
- Стол с подогревом. Это часть, на которой будет находиться печатаемый элемент. Подогрев необходим из-за того, что большинство пластиков не будут держаться на холодной поверхности. Например, для печати PLA пластиком необходимая температура поверхности стола составляет 60-80°C, для ABS — 110-130°C, а для поликарбоната она будет еще выше
В выборе стола тоже есть два варианта — подешевле и подороже. Дешевые варианты, по сути, представляют собой печатные платы с проложенной разогреваемой проводкой. Для эксплуатации на стол такого типа потребуется класть боросиликатное стекло, которое будет царапаться и трескаться в процессе эксплуатации. Поэтому лучшее решение — стол из алюминия. - Шаговые двигатели. Для большинства моделей, включая i2 и i3, используются двигатели типового размера NEMA 17: два для оси Z и по одному для осей X и Y. Готовые экструдеры обычно идут со своим шаговым двигателем в комплекте. Двигатели лучше брать мощные с током в обмотке двигателя от 1А и более, чтобы мощности хватило для подъема экструдера и печати без пропуска шагов на высокой скорости.
- Базовый комплект пластиковых креплений.
- Ремень и шестеренки для его привода.
Примеры внешнего вида элементов: 1) экструдер MK8; 2) процессорная плата Arduino; 3) плата управления RAMPS; 4) контроллеры двигателей; 5) алюминиевый стол с подогревом; 6) шаговый двигатель NEMA 17; 7) набор пластиковых креплений; 8) шестерни привода; 9) ремень привода
Это перечень необходимых к покупке элементов. Хардкорные пользователи могут собирать некоторые из них собственноручно, но новичкам я настоятельно рекомендую приобрести уже готовые решения.
Да, еще будет нужна различная мелочевка (шпильки, подшипники, гайки, болты, шайбы…) для сборки корпуса. На практике оказалось, что использование стандартной шпильки м8 приводит к низкой точности печати на оси Z. Я бы порекомендовал сразу заменить ее на трапециевидную того же размера.
Трапециевидная шпилька м8 для оси Z, использование которой сэкономит вам кучу времени и нервов. Доступна для заказа на всех крупных онлайн-площадках
Также необходимо приобрести адаптированные пластиковые детали для оси X, например, эти из комплекта модификации MendelMax.
Большинство деталей доступно в ближайшем строительном магазине. На RepRap можно найти полный список нужных мелочей со всеми размерами и схемами. Нужный вам комплект будет зависеть от выбора платформы (о платформах поговорим дальше).
Что сколько стоит
Прежде чем углубиться в некоторые аспекты сборки, давайте разберемся, во сколько же обойдется такое развлечение для вашего кошелька. Ниже — перечень необходимых к покупке деталей с усредненной ценой.
Деталь | Количество, ед. | Средяя стоимость, USD |
Экструдер МК8 | 1 | 17 |
Экструдер МК10 | 1 | 45 |
Стол с подогревом | 1 | 11 |
Плата Arduino | 1 | 10 |
Плата RAMPS 1.![]() | 1 | 10 |
Двигатель NEMA 17 | 4 | 7 |
END-стопы (концевики) | 3 | 1 |
Набор пластиковых креплений | 1 | 30 |
Приводной ремень G2 | 2 | 1 |
Шестеренки для валов двигателей | 2 | 1 |
Шпильки м8 | 2 | 10 |
Шестеренки для валов двигателей | 2 | 1 |
Катушка пластика для печати | 1 | 12 |
Итого с МК8 | 135 | |
Итого с МК10 | 163 |
В таблице представлены примерные цены основных компонентов. Также не забудьте о гайках, шайбах, подшипниках. Эти мелочи могут потянуть еще на $20-30.
Выбор платформы
Для сборки принтеров сообщество уже разработало ряд различных платформ — наиболее оптимальных конструкций корпуса и расположения основных элементов, поэтому изобретать велосипед вам не придется.
Ключевыми платформами для корпусов самосборных принтеров являются i2 и i3. Также существует множество их модификаций с различными улучшениями, но начинающим рассматривать следует именно эти две классические платформы, так как они не требуют особых навыков и тонкой настройки.
Собственно, иллюстрация платформ: 1) платформа i2; 2) платформа i3
Из плюсов i2: она обладает более надежной и устойчивой конструкцией, хотя немного сложнее в сборке; шире возможности для дальнейшей кастомизации.
Вариант i3 требует больше специальных пластиковых деталей, которые нужно докупать отдельно, и имеет низкую скорость печати. Однако более прост в сборке и обслуживании, имеет более эстетически приятный внешний вид. За простоту придется платить качеством печатаемых деталей — корпус имеет меньшую, чем i2, устойчивость, что может влиять на точность печати.
Лично я начинал свои опыты в сборке принтеров с платформы i2. О ней и пойдет речь дальше.
Этапы сборки, сложности и улучшения
В данном блоке я затрону только ключевые этапы сборки на примере платформы i2. Полные пошаговые инструкции можно найти здесь.
Общая схема всех основных компонентов выглядит примерно так. Чего-то особо сложного здесь нет:
Также я рекомендую добавить в вашу конструкцию дисплей. Да, без этого элемента можно легко обойтись, выполняя операции на ПК, но так работать с принтером будет гораздо удобнее.
Понимая, как будут связаны все компоненты, переходим к механической части, где у нас есть два основных элемента — рама и координатный станок.
Собираем раму
Детальная инструкция по сборке рамы доступна на RepRap. Из важных нюансов — вам потребуется набор пластиковых деталей (об этом я уже говорил выше, но лучше повторюсь), который вы можете либо приобрести отдельно, либо попросить напечатать товарищей, у которых уже есть 3D-принтер.
Каркас i2 является довольно устойчивым благодаря форме трапеции.
Вот так выглядит каркас с уже частично установленными деталями. Для большей жесткости я укрепил конструкцию листами фанеры
Координатный станок
На эту деталь крепится экструдер. За ее движение отвечают шаговые двигатели, отображенные на схеме выше. После установки необходима калибровка по всем основным осям.
Из важного — вам потребуется приобрести (или же самостоятельно изготовить) каретку для передвижения экструдера и крепление для приводного ремня. Приводной ремень я рекомендую GT2.
Каретка, напечатанная принтером с предыдущей картинки, после завершения его сборки. На деталь уже установлены подшипники LM8UU под направляющие и крепление для ремня (сверху)
Калибровка и настройка
Итак, мы произвели процесс сборки (как и говорил, у меня он занял 150 часов) — каркас собран, станок установлен. Теперь еще один важный шаг — калибровка этого самого станка и экструдера. Здесь тоже есть маленькие тонкости.
Настраиваем станок
Я рекомендую проводить калибровку станка при помощи электронного штангенциркуля. Не поскупитесь на его приобретение — вы сэкономите много времени и нервов в процессе.
На скрине ниже отображены правильные константы для прошивки Marlin, которые нужно подобрать, чтобы установить корректное количество шагов на единицу измерения. Считаем коэффициент, перемножаем, подставляем в прошивку, после чего заливаем ее на плату.
Константы для прошивки Marlin
Для качественной калибровки я рекомендую в замерах опираться на цифры побольше — брать не 1-1,5 см, а около 10. Так погрешность будет более заметной, и исправить ее станет проще.
Калибруем экструдер
Когда собран каркас, станок откалиброван, мы приступаем к настройке экструдера. Здесь тоже не все так просто. Основная задача данной операции — правильно отрегулировать подачу пластика.
Если подача недостаточная, то напечатанный тестовый предмет будет с заметными пробелами, как тестовый кубик 1. И наоборот, результат будет выглядеть раздутым при чрезмерной подаче пластика (кубик 2)
Приступаем к печати
Нам остается запустить какой-нибудь CAD или загрузить уже готовые .stl, которые описывают структуру печатаемого материала. Далее эту структуру необходимо преобразовать в набор команд, понятных нашему принтеру. Для этого я использую программу Slicer. Ее тоже нужно корректно настроить — указать температуру, размер сопла экструдера. После этого данные можно отправлять на принтер.
Интерфейс Slicer
В качестве сырья для печати я рекомендую начать с обычного ABS-пластика — он довольно крепкий, изделия из него долговечны, а для работы с ним не требуется высоких температур. Для комфортной печати ABS-пластиком стол нужно разогреть до температуры 110-130 °С, а сопло экструдера — в пределах 230-260 °С.
Немного важных мелочей. Перед печатью откалибруйте станок по оси Z. Сопло экструдера должно находиться примерно в половине миллиметра от стола и ездить вдоль него без перекосов. Для такой калибровки лучше всего подойдет обычный лист бумаги формата А4, вставленный между соплом и поверхностью стола с подогревом. Если лист можно двигать с незначительным усилием, калибровка выполнена правильно.
Еще один момент, о котором не стоит забывать — обработка поверхности стола с подогревом. Обычно перед печатью поверхность стола покрывают чем-то, к чему хорошо пристает разогретый пластик. Для ABS-пластика это может быть, например, каптоновый скотч. Минусом скотча является необходимость его переклеивать через несколько циклов печати. Кроме этого, придется буквально отдирать от него приставшую деталь. Все это, поверьте, отнимает много времени. Поэтому, если есть возможность избежать этой возни, лучше ее избежать.
Альтернативный вариант, который я использую вместо скотча — нанесение нескольких слоев обычного светлого пива с последующим нагревом стола до 80-100 °С до полного высыхания поверхности и повторного нанесения 7-12 слоев. Наносить жидкость необходимо при помощи тряпочки, смоченной напитком. Из преимуществ такого решения: ABS-пластик самостоятельно отделяется от стола при остывании примерно до 50 °С и снимается без усилий, стол не придется отдраивать, а одной бутылки пива вам хватит на несколько месяцев (если использовать напиток только в технических целях :)).
После того как мы все собрали и настроили, можно приступать к печати. Если у вас есть ЖК-экран, то файл можно передать на печать при помощи обычной SD-карты.
Первые результаты могут иметь неровности и другие артефакты — не расстраивайтесь, это нормальный процесс «притирки» элементов принтера, который закончится спустя несколько циклов печати.
Рекомендации, которые смогут упростить жизнь (а иногда — сэкономить деньги)
Кроме небольших рекомендаций, приведенных в тексте выше, в этом разделе я дам еще краткий перечень советов, которые значительно упростят эксплуатацию 3D-принтера и жизнь его владельца.
- Не экспериментируйте с форсунками. Если вы планируете сразу печатать из материалов, которые требуют высоких температур, то лучше сразу возьмите экструдер МК10.
На МК8 можно «навесить» специальные форсунки, поддерживающие высокотемпературные режимы. Но такие модификации часто вызывают сложности и требуют особого опыта. Лучше избежать этой возни еще «на берегу», просто поставив подходящий для вас экструдер.
- Добавьте реле стартера для стола с подогревом. Усовершенствование системы питания этой важной для печати детали при помощи реле стартера поможет решить известную проблему RAMP 1.4 — перегрев транзисторов, управляющих питанием стола, который может привести к выходу платы из строя. Я сделал такой апгрейд после того, как пришлось выбросить несколько RAMPS 1.4.
- Выберите правильный диаметр пластика для печати. Рекомендую брать пластик диаметром 1,75 мм для MK8 и MK10. Если взять пластик, например, в 3 мм, то экструдеру просто не хватит сил, чтобы проталкивать его с приемлемой скоростью — печататься все будет значительно дольше, а качество упадет. Для MK8 идеально подходит ABS-пластик, MK10 сможет производить изделия из поликарбоната.
- Используйте только новые и точные направляющие по осям X и Y. Это влияет на качество печати. Сложно рассчитывать на хорошее качество при гнутых или деформированных направляющих по осям.
- Позаботьтесь об охлаждении. В ходе моих экспериментов с различными экструдерами лучшие результаты показал МК10 — он печатает довольно точно и быстро. Также МК10 может печатать пластики, требующие более высокой температуры печати, чем ABS, например поликарбонат. Хоть он и не так сильно подвержен перегреву, как его младший брат МК8, все же я рекомендую позаботиться о его охлаждении, добавив в вашу конструкцию кулер. Он должен быть постоянно включен, эту опцию можно настроить в Slicer. Также можно добавить кулеры для поддержания приемлемой температуры шаговых моторов, однако следите, чтобы их потоки воздуха не попадали на печатаемую деталь, так как это может привести к ее деформации из-за слишком быстрого охлаждения.
- Предусмотрите сохранение тепла.
Да, с одной стороны, мы боремся с перегревом элементов. С другой — равномерная температура вокруг принтера будет способствовать качественной печати (пластик будет более податливым). Для достижения равномерной температуры можно поставить наш принтер, например, в картонную коробку. Главное — перед этим подключить и настроить кулеры, о чем написано выше.
- Подумайте о термоизоляции стола. Стол с подогревом нагревается до больших температур. И если часть этого тепла уходит с толком, подогревая печатаемую деталь, то вторая часть (снизу) — просто уходит вниз. Чтобы сконцентрировать тепло от стола на детали, можно провести операцию по его термоизоляции. Для этого я просто креплю к его нижней части пробковый коврик для мыши при помощи канцелярских зажимов.
Выводы
Уверен, в процессе сборки вы столкнетесь с рядом трудностей, присущих именно вашему проекту. От этого не застрахуют ни этот текст, ни даже самые подробные гайды.
Как я и написал во вступительной части, изложенное не претендует на статус детального мануала по сборке. Описать все-все этапы и их тонкости практически невозможно в рамках одного такого текста. Прежде всего, это обзорный материал, который поможет вам подготовиться к процессу сборки (как мысленно, так и материально), понять, нужно ли лично вам заморачиваться самосбором — или же махнуть на все рукой и купить готовое решение.
Для меня сборка принтеров стала увлекательным хобби, которое помогает закрывать некоторые вопросы в домашних и рабочих делах, отвлечься от программирования и сделать что-то интересное своими руками. Для моих детей — развлечением и возможностью получить необычные и уникальные игрушки. Кстати, если у вас есть дети, которым возраст позволяет возиться с подобными штуками, такое занятие может стать хорошим подспорьем для входа в мир механики и технологий.
Для каждого векторы использования 3D-принтеров будут самыми разными и весьма индивидуальными. Но, если уж вы решитесь посвятить личное время такому увлечению, поверьте, обязательно найдете, что печатать 🙂
Буду рад ответить на комментарии, замечания и вопросы.
Что почитать/посмотреть
Підписуйтеся на Telegram-канал «DOU #tech», щоб не пропустити нові технічні статті.
Про взаємоповагу між розробниками та рекрутерами. Подкаст DOU #24
Грануляторы полимеров
Гранулятор для пластика: виды и функционал
По видам перерабатываемого материала грануляторы бывают:
- Универсальные грануляторы – предназначены для переработки таких полимеров, как полипропилен (ПП), полиэтилен (высокого и низкого давления – ПВД и ПНД), стрейч (линейный полиэтилен высокого давления), полистиролы (ПСС, УПС, АБС) – чаще всего грануляторы полимеров приобретаются именно для этих видов сырья.
Грануляторы пленки тоже относятся к категории универсальных. ГК «Апрель» поставляет высокопроизводительные грануляторы для пленки.
- Специализированные грануляторы – предназначены для переработки более сложных материалов:
- Грануляторы для ПЭТ (дробленные пластиковые бутылки)
- Грануляторы для ПВХ
- Грануляторы твердых полимеров, таких как полиамид (ПА), поликарбонат (ПК)
- Грануляторы-компаундеры – предназначены для производства композитных материалов, в том числе наполнения полимеров стеклом, мелом, красителями и другими добавками.
По количеству шнеков грануляторы делятся на одношнековые (стандартные) и двухшнековые, применяющиеся для смешивания различных типов сырья. Двухшнековые грануляторы часто используются для получения композитов (грануляторы-компаундеры).
По количеству каскадов (по числу установленных экструдеров) грануляторы можно разделить на однокаскадные и двухкаскадные. Однокаскадные грануляторы подходят для переработки чистых пластиковых отходов. Сырье с загрязнениями рекомендуется перерабатывать на двухкаскадных грануляторах, так как основная часть загрязнений остается на сетке фильтра первого каскада, а во второй каскад поступает уже чистый расплав.
На шнековых грануляторах полимеров предусмотрены зоны дегазации: через специальные отверстия в материальном цилиндре экструдера выделяется пар от влажного сырья, а также продукты горения грязи и краски.
Какой гранулятор выбрать
Как подобрать гранулятор полимеров для Вашего типа сырья? В идеале, каждый вид пластика лучше перерабатывать на отдельном грануляторе, параметры которого специально подобраны под грануляцию пленки, дробленки или агломерата. Однако в этом случае проекты по переработке были бы весьма дорогостоящими. Экономические реалии заставляют переработчиков искать универсальные варианты.
ГК «Апрель» предлагает универсальные грануляторы, на которых можно перерабатывать как дробленку, агломерат, так и дробленую пленку (пушонку) или пленку целиком, подавая ее напрямую в экструдер. На наших грануляторах влажного сырья можно перерабатывать и материалы с большим содержанием влаги, так как в их конструкции предусмотрен отвод воды.
Устройство типового гранулятора:
- Станина с закрепленным на ней экструдером (шнек в гильзе)
- Двигатель, вращающий шнек
- Шкаф управления
- Фильера (голова)
- Ванна охлаждения
- Стренгорезка
Гранулятор можно комплектовать горячей резкой (воздушная – производительность до 100кг/ч, водяная – производительность свыше 100кг/ч), когда полимер нарезается в гранулу сразу при выходе из фильеры.
Вы всегда можете посмотреть грануляторы в работе у нас или у наших клиентов в Вашем регионе. Звоните, наши специалисты с удовольствием проконсультируют Вас и помогут с оптимальным выбором гранулятора!
▶▷▶▷ как сделать экструдер для корма своими руками
▶▷▶▷ как сделать экструдер для корма своими рукамиИнтерфейс | Русский/Английский |
Тип лицензия | Free |
Кол-во просмотров | 257 |
Кол-во загрузок | 132 раз |
Обновление: | 10-08-2019 |
как сделать экструдер для корма своими руками — Как сделать экструдер для кормов своими руками nalugahruinventarkak-sdelat-ehkstruder-dlya-kormov Cached Как сделать экструдер своими руками из старого пылесоса, из запчастей для сельхозмашин и для больших объемов комбикорма Экструдер своими руками, экструдер для кормов — YouTube wwwyoutubecom watch?vJ8n22Lk0MNg Cached Экструдер своими руками , экструдер для кормов Экструдер для биотопливных брикетов Как сделать КРУТУЮ Как Сделать Экструдер Для Корма Своими Руками — Image Results More Как Сделать Экструдер Для Корма Своими Руками images Экструдер для кормов своими руками: как и из чего fermerznaetcomselhoztehnikaobrabotka-kormovsamodelny Cached Экструдер своими руками , сделать довольно сложно, но при определённых навыках проблем это не составит Как сделать зерновой экструдер своими руками? moezernorutexnikakak-sdelat-zernovoj-ekstruder-svoimi Cached 2 Как сделать экструдер своими руками Изготовление экструдера зернового своими руками задача не из простых Но сложно не значит нереально Как сделать экструдер для кормов своими руками agrolainrugrain-equipmentekstruder-dlya-kormov-svoimi Cached Экструдер для кормов своими руками — полезные советы и чертежи Сравнительный анализ заводского и самодельного экструдера Самодельный экструдер кормов — YouTube wwwyoutubecom watch?v5yPsjaChFSs Cached Изготовление шнекового гранулятора своими руками !!! Часть 1Шнек Screw granulator Гранулятор Как сделать экструдер для кормов своими руками fermagururazvedenie-zhivotnyhkak-sdelat-ekst Cached Как сделать экструдер для кормов своими руками Жизнь фермера полна забот, об этом многим известно Облегчить тяжелый труд можно с помощью современной техники либо станков Как сделать самодельный экструдер своими руками agronomwikirukak-sdelat-samodelnyj-ekstruder Cached Есть несколько способов, как сделать экструдер своими руками : Для больших объемов сырья, Из запчастей для сельхозтехники, Из пылесоса Экструдер своими руками для кормов (кормовой) — как сделать? moezernorutexnikacrusherkak-sdelat-ekstruder-svoimi Cached В качестве решения можно сделать экструдер для кормов своими руками 1 Как работает кормовой экструдер ? Прежде чем сделать экструдер своими руками , нужно разобраться с принципом его работы Как сделать экструдер для кормов своими руками agrojofome738678html Cached Не все спешат приобретать его в хозяйство свое из-за непосильной цены Экструдер для своими кормов руками позволит снизить затраты, хорошего получить помощника в хозяйстве Promotional Results For You Free Download Mozilla Firefox Web Browser wwwmozillaorg Download Firefox — the faster, smarter, easier way to browse the web and all of 1 2 3 4 5 Next 2,150
- Самодельный экструдер может переработать до 40 кгч.
Производительность зависит от мощности двигателя
- , установленного на агрегате. Качество корма будет иное, животному придется отдать больше сил на его переработку. Производить полезные комбикорма на экструдере достаточно просто. Кстати в бизнесе по
- переработку.
Производить полезные комбикорма на экструдере достаточно просто. Кстати в бизнесе по приготовлению экструдированных кормов можно одновременно снизить себестоимость продукции и повысить качество корма.
Экструдер позволяет получать уникальные корма нового поколения — Экструдированные корма — это экологиче ( меньше ) Сигнализатор своими руками. как сделать сигнализатор поклевки своими руками видео. схема,и принцип… Экструдер своими руками чертежи. Экструдер…
Кроме того, в сети можно без особого труда найти довольно большое количество чертежей и схем сборки экструдера. …ту или иную сторону и помимо прочего, необходимо следить за правильной подачей корма…
В наше время для облегчения обработки зерна используют специализированные приборы, которые помогают ускорить работу и увеличить производительность труда, а еще улучшить качество корма.
Экстр. Как устроен экструдер? Экструдер это общее название нескольких видов машин, где применяется данный механизм. … Экструдер состоит из шнекового пресса, бункера с дозатором и электропривода. (Большой эн цикло педи чес кий поли техни ческий словарь. Если вы задаетесь вопросом: окупится ли экструдер, то ответ однозначный да. 1 В чем плюсы корма в гранулах. Экструдер для домашнего использования. Прокрутив через экструдер, получаем достаточно калорийный гранулированный корм, который кроликам очень нравится, не пропадает ни одного грамма. Хотя большей частью с таким условием, что эти корма придется изготавливать самостоятельно.. Процесс переработки сырья в экструдере происходит за счет термической обработки при высоком давлении. В процессе экструдирования корма меняются его строение и свойства, а поэтому и энергетическая эффективность.
получаем достаточно калорийный гранулированный корм
не пропадает ни одного грамма. Хотя большей частью с таким условием
- как сделать экструдер своими руками : Для больших объемов сырья
- из запчастей для сельхозмашин и для больших объемов комбикорма Экструдер своими руками
- easier way to browse the web and all of 1 2 3 4 5 Next 2
Нажмите здесь , если переадресация не будет выполнена в течение нескольких секунд как сделать экструдер для корма своими руками Поиск в Все Картинки Ещё Видео Новости Покупки Карты Книги Все продукты Экструдер для кормов своими руками как и из чего Фермер fermerznaetcomsamodelnyjekstruder Экструдер своими руками , сделать довольно сложно, но при определённых навыках проблем это не составит Экструдер своими руками , экструдер для кормов YouTube янв Самодельный экструдер кормов Двигатель , кВт, обмин сеть В, диаметр шнека myoutubecom Зерновой экструдер как сделать своими руками в moezernorukaksdelatzernovoj Как сделать зерновой экструдер своими руками ? Экструдированные корма для откорма домашних животных Что такое экструдер? Как сделать экструдер Как сделать экструдер для кормов своими руками agrolainruekstruderdlyakormov Экструдер для кормов своими руками полезные советы и чертежи Сравнительный анализ заводского и Принцип работы Можно ли сделать своими Экструдер для кормов своими руками описание Agronomu Мы привели пример того, как можно собрать экструдер Описание и назначение Как сделать своими руками Картинки по запросу как сделать экструдер для корма своими руками Как сделать экструдер для кормов своими руками На лугах nalugahrukaksdelatehkstruderdlya Как сделать экструдер своими руками из старого пылесоса, из запчастей для сельхозмашин и для больших Как сделать экструдер для кормов своими руками Fermaguru Кормовой экструдер для чего он нужен, устройство агрегата, как его сделать собственными руками , несколько Зерновой экструдер для кормов своими руками чертежи wwwportalteplicruekstruderdlja Но если сделать экструдер для кормов своими руками , то можно хорошо сэкономить Только в данном случае Как сделать экструдер для кормов своими руками Tomo wwwcntomocomkaksdelat июн О высокой эффективности дробилки для злаков знают многие собственники животноводческих Как сделать самодельный экструдер своими руками spasagrorukaksdelat кормов домашним своими руками , Самодельный экструдер кормов FermerRu ФермерРу Главный сен Ктонибудь пробовал делать экструдер ? Есть пока такая схема и некоторое техническое Экструдер для кормов своими руками GuruAnimalru Экструдер своими руками предпочитают делать большинство фермеров Дело в том, что стоимость заводских Самодельный экструдер кормов своими руками Экструдер своими руками Экструдер Зерновой Своими Руками Чертежи Видео авг Экструдированные корма для появились на рынке Как сделать экструдер своими руками Кормовой экструдер своими руками в Украине Сравнить Кормовой экструдер своими руками Экструдер кормов ЭГК В, кВт, кгчас с бункером дозатором Экструдер что это такое, для чего он предназначен окт Экструдер для кормов своими руками , почему он должен быть в каждом хозяйстве Жизнь фермера полна Можно ли самостоятельно сделать экструдер ? Своими руками Экструдер для кормов что это такое Экструдированные Производство экструдированных кормов своими руками Чтобы приготовить комбинированный состав для Экструдер для кормов Самое разное Форум птицеводов forumpticevodcomekstruderdlya фев экструдер для кормов своими руками можно взять и попробовать сделать , вот только вещь и как сделать экструдер для кормов своими руками Econcifras econcifrascomkaksdelatekstruderdl май как сделать экструдер для кормов своими руками tm sasXML mln answers found found thsd Как самостоятельно сделать измельчитель кормов ? mastertraktorruizmelchitelikormov В результате, вы получаете довольно производительный измельчитель, сделанный своими руками Отметим экструдер своими руками часть экструдер своими мар по шаговые видео фрагменты делания экструдера Экструдер для кормов своими руками РосЭкструдер рос экструдер рфekstruderdlyakormov Экструдер для кормов своими руками обеспечит снижение затрат и получение более высокой прибыли, а также Самодельный Экструдер Очумелые ручки Конференция wwwgazruсамодельный дек Самодельный Экструдер Экструдирует любое зерно,на корм для скотины ,говорят Мне этот эр обошолся в грн,где можно купить за такую цену, подскажи? Like Экструдер гранулятор для кормов ЯФЕРМЕРRU yafermerruekstruder авг Экструдер гранулятор для кормов Вы можете сделать чертежи экструдера на кгчас? Сколько это Здравствуйте! Хочу купить у Вас экструдер гранулятор кгчас Гранулятор своими руками Самодельный гранулятор akomrublogitem Гранулятор это крайне полезная и нужная вещь для производства экструдированного корма или комбикорма с Готовим гранулированный корм для кроликов Hrunyaru Мы опишем, как приготовить гранулы своими руками и что для этого нужно В экструдер засыпают уже измельченные зерна, траву и тп Молоть Гранулированный корм своими руками Грануляторы кормов своими руками в России Сравнить Грануляторы кормов своими руками Продажа Экструдер металлический для моделирования Makins, дисков Сварочный экструдер своими руками ccmmskcom Экструдер своими руками для кормов кормовой как сделать ? Как работает кормовой экструдер ? Из Экструдер своими руками Все о сварке expertsvarkiru переработка кормов ;; производство пластика и полиэтилена;; изготовление труб;; пищевое производство Но есть экструдеры , которые можно сделать своими руками Наиболее простыми Экструдер гранулятор для кормов своими руками чертеж docplayerruEkstruder Экструдер гранулятор для кормов своими руками чертеж СкачатьЭкструдер Как сделать арбалет чертеж Экструдированный корм КОРМ UA Многие фермеры уже успели приобрести, или сделать своими руками экструдер для кормов При помощи Как сделать гранулы в домашних условиях Как сделать апр В принципе, сделать пеллеты своими руками реально, Самый простой по строению шнековый экструдер Бизнес по производству гранулированного корма для животных Как улучшить кормоэкструдер модернизация своими руками kaksvoimirukamicomkakuluchshit янв Модернизация кормоэкструдера своими руками Мы хотели делать собственные корма пределы корпуса экструдера в специально приспособленный пластиковый ящик Процесс пошел дешевый экструдер для изготовления июл Процесс пошел дешевый экструдер для изготовления прутка , Экструдер своими руками его конусовать нет необходимости, только отверстие сделать правильным Горизонтальный гранулятор Изготовление гранулятора апр Низкое качество покупных кормов , стремление Как сделать гранулятор для комбикорма своими руками из мясорубки Даже самое Рекомендовано приобрести экструдер При помощи экструдера можно делать отличный недорогой апр друзья всем добрый день сегодня мы делаем очередную партию корма для своих рыб подробное описание чертежи и размеры зернового мини экструдер зерновой своими руками чертежи Экструдер для кормов , чертежи экструдера , экструдер продам, пресс экструдеры Как сделать самодельный экструдер своими Комбикорм для кур несушек своими руками рецепты фев Чтобы создать корм для птиц своими руками , существуют Чтобы приготовить такой комбикорм по госту, необходимо В бункер экструдера засыпается зерносмесь Экструдер корма шнековый для зерна В купить в Мир mirpticruekstruder korma , Экструдер корма шнековый для зерна В КЭШ Цена, отзывы покупателей, фото , характеристики, описание Пресс экструдеры производство пресс экструдеров favorerucatalogpressekstrudery Купить оборудование для сельхозпереработки в компании Фавор, Оборудование для высококачественных кормов для домашнего скота и других животных Что делать с падежом скота и с отходами животноводства? оборудование для производства корма для животных kootopequipment_for Компоненты корма поочередно подаются в бункер экструдера с пре кондиционером, из которого с помошью как сделать экструдер для ремонта шаровых своими руками remstroymontrukaksdelatekstruder мар как сделать экструдер для ремонта шаровых своими руками видео ШАРОВОЙ опоры ремонт своими руками Самодельный экструдер кормов Станок для восстановления Оборудование для производства комбикорма Как выбрать июл экструдеры для производства комбикормов Он способен подготавливать корм как для крупного Еще приготовление комбикорма своими руками это залог Предлагаемый продукт можно приготовить дома, Свой бизнес по производству кормов для домашних животных openbusinessru Согласно расчету окупаемости производства кормов для домашних животных, К примеру, экструдер при изготовлении влажных кормов работает при более идей способов отстроиться от конкурентов и сделать Пресс гранулятор для комбикорма Kormocehru kormocehrupressgranulyatordlya Рекомендуется экструдер для кормов купить компаниям, стремящимся к повышению качества своей продукции Линия свой бизнес, сделать его более прибыльным и конкурентоспособным Производство экструдированных кормов своими руками Производство экструдированных кормов своими руками Процесс Работать с экструдером достаточно легко Корм для кроликов своими руками в домашних условиях Корм для кроликов своими руками в домашних условиях Технология Экструдер Фермер всегда может приготовить новую порцию из свежих ингредиентов, а значит его подопечные будут Состав комбикорма для кроликов, приготовление своими это можно сделать и на Рекомендации по эффективности использования фев Схема последовательности выполнения процессов производства экструдированного зерна Запросы, похожие на как сделать экструдер для корма своими руками экструдер для сена своими руками экструдер из мясорубки шнек для экструдера своими руками экструдер своими руками для полипропилена экструдер для кукурузных палочек своими руками экструдер своими руками чертежи экструдер для пластики своими руками экструдер для кормов След Войти Версия Поиска Мобильная Полная Конфиденциальность Условия Настройки Отзыв Справка
Самодельный экструдер может переработать до 40 кгч. Производительность зависит от мощности двигателя, установленного на агрегате. Качество корма будет иное, животному придется отдать больше сил на его переработку.
Производить полезные комбикорма на экструдере достаточно просто. Кстати в бизнесе по приготовлению экструдированных кормов можно одновременно снизить себестоимость продукции и повысить качество корма.
Экструдер позволяет получать уникальные корма нового поколения — Экструдированные корма — это экологиче ( меньше ) Сигнализатор своими руками. как сделать сигнализатор поклевки своими руками видео. схема,и принцип… Экструдер своими руками чертежи. Экструдер…
Кроме того, в сети можно без особого труда найти довольно большое количество чертежей и схем сборки экструдера. …ту или иную сторону и помимо прочего, необходимо следить за правильной подачей корма…
В наше время для облегчения обработки зерна используют специализированные приборы, которые помогают ускорить работу и увеличить производительность труда, а еще улучшить качество корма.
Экстр. Как устроен экструдер? Экструдер это общее название нескольких видов машин, где применяется данный механизм. …
Экструдер состоит из шнекового пресса, бункера с дозатором и электропривода. (Большой эн цикло педи чес кий поли техни ческий словарь.
Если вы задаетесь вопросом: окупится ли экструдер, то ответ однозначный да. 1 В чем плюсы корма в гранулах. Экструдер для домашнего использования.
Прокрутив через экструдер, получаем достаточно калорийный гранулированный корм, который кроликам очень нравится, не пропадает ни одного грамма. Хотя большей частью с таким условием, что эти корма придется изготавливать самостоятельно..
Процесс переработки сырья в экструдере происходит за счет термической обработки при высоком давлении. В процессе экструдирования корма меняются его строение и свойства, а поэтому и энергетическая эффективность.
RepRapable Recyclebot: Экструдер для трехмерной печати с открытым исходным кодом для преобразования пластика в волокно для трехмерной печати
https://doi.
Аннотация
Для помощи исследователям Чтобы изучить весь потенциал распределенной переработки бытовых полимерных отходов, в этой статье описывается робот-рециклинг, который представляет собой экструдер для пластиковых отходов, способный производить нить для трехмерной печати коммерческого качества. В конструкции устройства используются преимущества как аппаратной методологии с открытым исходным кодом, так и парадигмы, разработанной сообществом самовоспроизводящихся быстрых прототипов (RepRap) 3-D принтеров с открытым исходным кодом.В частности, в этой статье описывается конструкция, изготовление и работа RepRapable Recyclebot, что относится к способности Recyclebot предоставить нить, необходимую для большей репликации деталей Recyclebot на любом типе RepRap 3-D принтера. Устройство стоит менее 700 долларов в материалах и может быть изготовлено примерно за 24 часа. Нить производится со скоростью 0,4 кг / ч при использовании 0,24 кВт-ч / кг при диаметре ± 4,6%. Таким образом, филамент может быть изготовлен из коммерческих гранул по цене <22% от стоимости коммерческих филаментов.Кроме того, он может производить из переработанных пластиковых отходов нити за 2,5 ц / кг, что в 1000 раз меньше коммерческих затрат на нити. Система может изготавливать нить из полимеров с температурами экструзии <250 ° C и, таким образом, способна изготавливать нестандартные нити из широкого диапазона термополимеров и композитов для материаловедческих исследований новых материалов и исследований возможности вторичной переработки, а также исследований новых применений сплавленных материалов. 3-D печать на филаментной основе.
Ключевые слова
Аппаратные средства с открытым исходным кодом
Открытые аппаратные средства
3-D печать
Изготовление плавленых волокон
RepRap
Вторичная переработка
Полимеры
Пластик
Recyclebot
пластикЭкструдер
Upcycle
Циркулярная экономика
Материаловедение
Рекомендуемые статьиЦитирующие статьи (0)
© 2018 Авторы. Опубликовано Elsevier Ltd.
Рекомендуемые статьи
Цитирующие статьи
Экструзия пластмасс — 3D-модели CAD и 2D-чертежи
Экструзия пластмасс — это крупносерийный производственный процесс, в котором необработанный пластик плавится и формируется в непрерывный профиль. Экструзия производит такие изделия, как трубы / трубки, уплотнители, ограждения, перила палубы, оконные рамы, пластиковые пленки и защитное покрытие, термопластические покрытия и изоляцию проводов.
Этот процесс начинается с подачи пластикового материала (гранул, гранул, хлопьев или порошков) из бункера в цилиндр экструдера.Материал постепенно плавится за счет механической энергии, генерируемой вращением винтов и нагревателей, расположенных вдоль ствола. Затем расплавленный полимер нагнетают в фильеру, которая придает полимеру форму, которая затвердевает во время охлаждения. [1]
История
Первые предшественники современного экструдера были разработаны в начале 19 века. В 1820 году Томас Хэнкок изобрел резиновый «мастикатор», предназначенный для регенерации переработанных обрезков резины, а в 1836 году Эдвин Чаффи разработал двухвалковую машину для смешивания добавок в резину. [2] Первая экструзия термопласта была произведена в 1935 году Полем Тростером и его женой Эшли Гершофф в Гамбурге, Германия. Вскоре после этого Роберто Коломбо из LMP разработал первые двухшнековые экструдеры в Италии. [3]
Процесс
При экструзии пластмасс сырьевая смесь обычно имеет форму гранул (маленьких шариков, часто называемых смолой), которые под действием силы тяжести загружаются из установленного сверху бункера в цилиндр экструдера. Часто используются такие добавки, как красители и ингибиторы УФ-излучения (в жидкой или гранулированной форме), и их можно смешивать со смолой до поступления в бункер.Этот процесс имеет много общего с литьем пластмасс под давлением с точки зрения технологии экструдера, хотя отличается тем, что обычно является непрерывным процессом. Хотя при пултрузии можно получить множество аналогичных профилей непрерывной длины, обычно с добавлением армирования, это достигается вытягиванием готового продукта из фильеры вместо экструзии расплава полимера через фильеру.
Материал входит через горловину подачи (отверстие рядом с задней частью цилиндра) и входит в контакт с шнеком.Вращающийся винт (обычно вращающийся, например, со скоростью 120 об / мин) толкает пластиковые шарики вперед в нагретый цилиндр. Желаемая температура экструзии редко бывает равна заданной температуре цилиндра из-за вязкого нагрева и других эффектов. В большинстве процессов для ствола устанавливается профиль нагрева, в котором три или более независимых зоны нагрева с ПИД-регулированием постепенно повышают температуру ствола от задней части (куда входит пластик) к передней части. Это позволяет пластиковым шарикам постепенно плавиться по мере их проталкивания через цилиндр и снижает риск перегрева, который может вызвать деградацию полимера.
Дополнительное тепло создается за счет сильного давления и трения внутри ствола. Фактически, если экструзионная линия работает с некоторыми материалами достаточно быстро, нагреватели могут быть отключены, а температура расплава поддерживается только за счет давления и трения внутри цилиндра. В большинстве экструдеров присутствуют охлаждающие вентиляторы, чтобы поддерживать температуру ниже установленного значения, если выделяется слишком много тепла. Если принудительного воздушного охлаждения оказывается недостаточно, используются залитые рубашки охлаждения.
В передней части ствола расплавленный пластик покидает винт и проходит через сетчатый фильтр для удаления любых загрязнений из расплава.Экраны усилены отбойной пластиной (толстая металлическая шайба с множеством просверленных отверстий), поскольку давление в этой точке может превышать 5000 фунтов на квадратный дюйм (34 МПа). Узел грохота / отбойной пластины также служит для создания противодавления в стволе. Противодавление требуется для равномерного плавления и надлежащего перемешивания полимера, а то, какое давление создается, можно «настроить», варьируя состав пакета сит (количество сит, размер их переплетения проволоки и другие параметры). Эта комбинация пластины прерывателя и пакета экрана также устраняет «память вращения» расплавленного пластика и вместо этого создает «продольную память».
После прохождения через пластину прерывателя расплавленная пластмасса попадает в матрицу. Штамп — это то, что придает конечному продукту его профиль, и он должен быть спроектирован таким образом, чтобы расплавленный пластик равномерно стекал от цилиндрического профиля к форме профиля продукта. Неравномерный поток на этой стадии может привести к образованию продукта с нежелательными остаточными напряжениями в определенных точках профиля, которые могут вызвать коробление при охлаждении. Можно создавать самые разные формы, ограничиваясь непрерывными профилями.
Теперь продукт необходимо охладить, что обычно достигается путем протягивания экструдата через водяную баню.Пластмассы — очень хорошие теплоизоляторы, поэтому их трудно быстро охладить. По сравнению со сталью пластик отводит тепло в 2000 раз медленнее. В экструзионной линии для труб или труб на герметичную водяную баню воздействует тщательно контролируемый вакуум, чтобы не допустить разрушения вновь образованной и все еще расплавленной трубы или трубы. Для таких продуктов, как пластиковая пленка, охлаждение достигается за счет протягивания через набор охлаждающих валков. Для пленок и очень тонких листов воздушное охлаждение может быть эффективным в качестве начальной стадии охлаждения, как при экструзии пленки с раздувом.
Экструдеры для пластмасс также широко используются для переработки переработанных пластиковых отходов или другого сырья после очистки, сортировки и / или смешивания. Этот материал обычно экструдируют в нити, подходящие для измельчения в шарики или гранулы для использования в качестве прекурсора для дальнейшей обработки.
Винтовая конструкция
В винте из термопласта есть пять возможных зон. Поскольку терминология не стандартизирована в отрасли, эти зоны могут относиться к другим названиям.Различные типы полимеров имеют разную конструкцию шнеков, некоторые из которых не включают все возможные зоны.
Простой пластиковый экструзионный шнекУ большинства винтов есть три зоны:
- Зона подачи (также называемая зоной транспортировки твердых частиц): эта зона подает смолу в экструдер, и глубина канала обычно одинакова по всей зоне.
- Зона плавления (также называемая переходной зоной или зоной сжатия): большая часть полимера плавится в этой части, и глубина канала становится все меньше.
- Зона дозирования (также называемая зоной транспортировки расплава): в этой зоне плавятся последние частицы и смешиваются до однородной температуры и состава. Как и в зоне подачи, глубина канала постоянна по всей этой зоне.
Дополнительно вентилируемый (двухступенчатый) шнек будет иметь:
- Зона декомпрессии. В этой зоне, примерно на две трети ниже шнека, канал внезапно становится глубже, что снижает давление и позволяет отводить любые захваченные газы (влага, воздух, растворители или реагенты) с помощью вакуума.
- Вторая зона замера. Эта зона аналогична первой зоне измерения, но с большей глубиной канала. Он служит для повышения давления в расплаве, чтобы он выдержал сопротивление экранов и матрицы.
Часто длина винта зависит от его диаметра как отношения L: D. Например, винт диаметром 6 дюймов (150 мм) при 24: 1 будет иметь длину 144 дюйма (12 футов), а при 32: 1 — 192 дюйма (16 футов) в длину. Отношение L: D 25: 1 является обычным явлением, но некоторые машины повышают его до 32: 1 для большего перемешивания и большей производительности при том же диаметре шнека.Двухступенчатые (вентилируемые) винты обычно имеют соотношение 36: 1 с учетом двух дополнительных зон.
Каждая зона оборудована одной или несколькими термопарами или RTD в стенке цилиндра для контроля температуры. «Температурный профиль», то есть температура каждой зоны, очень важен для качества и характеристик конечного экструдата.
Типовые экструзионные материалы
Типичные пластмассовые материалы, которые используются при экструзии, включают, помимо прочего: полиэтилен (PE), полипропилен, ацеталь, акрил, нейлон (полиамиды), полистирол, поливинилхлорид (PVC), акрилонитрилбутадиенстирол (ABS) и поликарбонат. [4]
Типы штампов
Для экструзии пластмасс используются различные фильеры. Несмотря на то, что между типами фильер и их сложностью могут быть значительные различия, все фильеры позволяют осуществлять непрерывную экструзию расплава полимера, в отличие от прерывистой обработки, такой как литье под давлением.
Экструзия пленки с раздувом
Производство пластиковой пленки для таких продуктов, как пакеты для покупок и непрерывная пленка, осуществляется с использованием линии для производства пленки с раздувом. [5]
Этот процесс аналогичен обычному процессу экструзии до штампа.В этом процессе используются три основных типа матриц: кольцевые (или крейцкопфные), крестовины и спиральные. Кольцевые фильеры являются самыми простыми и полагаются на то, что расплав полимера проходит по всему поперечному сечению фильеры перед выходом из фильеры; это может привести к неравномерному потоку. Матрицы Spider состоят из центральной оправки, прикрепленной к внешнему кольцу матрицы через ряд «ножек»; хотя поток более симметричен, чем в кольцевых фильерах, образуется ряд сварных линий, ослабляющих пленку. Спиральные матрицы устраняют проблему линий шва и асимметричного потока, но на сегодняшний день являются наиболее сложными. [6]
Расплав немного охлаждают перед выходом из фильеры, чтобы получить слабую полутвердую трубу. Диаметр этой трубки быстро увеличивается за счет давления воздуха, и трубка тянется вверх роликами, растягивая пластик как в поперечном направлении, так и в направлении вытяжки. Вытягивание и выдувание делают пленку тоньше, чем экструдированная трубка, а также предпочтительно выравнивают молекулярные цепи полимера в направлении, в котором наблюдается наибольшая пластическая деформация. Если пленку вытягивают больше, чем выдувают (конечный диаметр трубы близок к диаметру экструдированной), молекулы полимера будут сильно выровнены по направлению вытяжки, создавая пленку, которая будет прочной в этом направлении, но слабой в поперечном направлении. .Пленка, диаметр которой значительно превышает диаметр экструдированного материала, будет иметь большую прочность в поперечном направлении, но меньшую в направлении вытяжки.
В случае полиэтилена и других полукристаллических полимеров, когда пленка охлаждается, она кристаллизуется на так называемой линии замерзания. По мере того, как пленка продолжает охлаждаться, ее протягивают через несколько наборов прижимных роликов, чтобы сплющить ее в плоскую трубку, которую затем можно намотать или разрезать.
Экструзия листа / пленки
Экструзия листа / пленки используется для экструзии пластиковых листов или пленок, слишком толстых для выдувания.Используются два типа плашек: Т-образные и плечики. Назначение этих матриц — переориентировать и направить поток полимерного расплава от единственного круглого выхода из экструдера к тонкому плоскому плоскому потоку. Оба типа фильер обеспечивают постоянный равномерный поток по всей площади поперечного сечения фильеры. Охлаждение обычно осуществляется путем протягивания через набор охлаждающих валков (каландровые или охлаждающие валки). При экструзии листов эти валки не только обеспечивают необходимое охлаждение, но также определяют толщину листа и текстуру поверхности. [7] Часто коэкструзия используется для нанесения одного или нескольких слоев поверх основного материала для получения определенных свойств, таких как поглощение УФ-излучения, текстура, сопротивление проникновению кислорода или отражение энергии.
Обычным процессом постэкструзии пластиковых листов является термоформование, при котором лист нагревают до мягкости (пластика) и формуют с помощью пресс-формы в новую форму. Когда используется вакуум, это часто называют вакуумным формованием. Ориентация (т.е. способность / доступная плотность листа, который может быть вытянут в форму, глубина которого обычно может варьироваться от 1 до 36 дюймов) очень важна и сильно влияет на время цикла формования для большинства пластиков.
Экструзия труб
Экструдированные трубы, такие как трубы из ПВХ, производятся с использованием штампов, очень похожих на те, что используются при экструзии пленки с раздувом. Положительное давление может быть приложено к внутренним полостям через штифт, или отрицательное давление может быть приложено к внешнему диаметру с помощью вакуумного калибратора, чтобы гарантировать правильные окончательные размеры. Дополнительные просветы или отверстия могут быть введены путем добавления соответствующих внутренних оправок в матрицу.
Многослойные трубки также широко используются в автомобильной, водопроводной и отопительной промышленности, а также в упаковочной промышленности.
Экструзия поверх оболочки
Экструзия поверх оболочки позволяет наносить внешний слой пластмассы на существующий провод или кабель. Это типичный процесс изоляции проводов.
Существует два различных типа штампа, используемого для нанесения покрытия на проволоку, трубку (или оболочку) и давление. В оснастке для создания оболочки расплав полимера не касается внутренней проволоки до момента, когда он находится непосредственно перед кромкой штампа. В инструментах, работающих под давлением, расплав контактирует с внутренней проволокой задолго до того, как достигнет кромки штампа; это делается под высоким давлением, чтобы обеспечить хорошее сцепление расплава.Если требуется плотный контакт или адгезия между новым слоем и существующей проволокой, используется инструмент для давления. Если адгезия нежелательна / необходима, вместо нее используется инструмент для изготовления кожухов.
Коэкструзия
Коэкструзия — это одновременная экструзия нескольких слоев материала. В этом типе экструзии используются два или более экструдера для плавления и доставки стабильного объемного расхода различных вязких пластмасс к одной экструзионной головке (фильере), которая будет экструдировать материалы в желаемой форме.Эта технология используется в любом из описанных выше процессов (экструзионная формовка пленки, нанесение внешней оболочки, трубка, лист). Толщина слоя регулируется относительными скоростями и размерами отдельных экструдеров, доставляющих материалы.
Во многих реальных сценариях один полимер не может удовлетворить все требования приложения. Экструзия компаундов позволяет экструдировать смешанный материал, но при совместной экструзии отдельные материалы сохраняются в виде разных слоев в экструдированном продукте, что позволяет надлежащим образом размещать материалы с различными свойствами, такими как проницаемость для кислорода, прочность, жесткость и износостойкость.
Экструзионное покрытие
Экструзионное покрытие — это процесс экструзии с раздувом или литьем пленки для нанесения дополнительного слоя на существующий рулон бумаги, фольги или пленки. Например, этот процесс можно использовать для улучшения характеристик бумаги, покрывая ее полиэтиленом, чтобы сделать ее более водостойкой. Экструдированный слой также можно использовать в качестве клея для соединения двух других материалов. Тетрапак — коммерческий пример этого процесса.
Составные экструзии
Экструзия компаундов — это процесс смешивания одного или нескольких полимеров с добавками для получения пластиковых компаундов.Сырьем могут быть гранулы, порошок и / или жидкости, но продукт обычно находится в форме гранул для использования в других процессах формования пластмасс, таких как экструзия и литье под давлением. Как и в случае с традиционной экструзией, существует широкий диапазон размеров машин в зависимости от области применения и желаемой производительности. Хотя в традиционной экструзии можно использовать одно- или двухшнековые экструдеры, необходимость адекватного перемешивания при экструзии с компаундированием делает двухшнековые экструдеры практически обязательными. [8] [9]
Существует два подтипа двухшнековых экструдеров: вращающиеся в одном направлении и в противоположном направлении.Эта номенклатура относится к относительному направлению вращения каждого винта по сравнению с другим. В режиме совместного вращения оба винта вращаются либо по часовой стрелке, либо против часовой стрелки; при вращении против часовой стрелки один винт вращается по часовой стрелке, а другой — против часовой стрелки. Было показано, что для данной площади поперечного сечения и степени перекрытия (зацепления) осевая скорость и степень перемешивания выше в двойных экструдерах, вращающихся в одном направлении. Однако в экструдерах с противовращением давление выше. [10]
Преимущества
Большим преимуществом экструзии является то, что профили, такие как трубы, можно изготавливать любой длины. Если материал достаточно гибкий, можно изготавливать трубы большой длины, даже наматывая их на катушку. Еще одно преимущество — экструзия труб со встроенной муфтой, включающей резиновое уплотнение. [11]
См. Также
DIY Экструдер Dies
Не ограничивайтесь тем, что экструдер может добавить в вашу студию. Изготовленные на заказ матрицы могут иметь большое значение, и их легко сделать. Для тех из вас, у кого нет экструдера, приготовьтесь изучить совершенно новый способ работы со своими горшками! В большинстве общественных студий экструдер стоит где-нибудь в углу.Я хотел бы поделиться некоторыми идеями о том, как использовать этот иногда забытый инструмент.
Использование экструдера
Основная идея заключается в том, что глина загружается в трубку, на одном конце которой есть фитинг, который удерживает диск с заданным отверстием или отверстием (см. 2), определяющим форму экструдированной глины. Это называется кубиком. На другом конце имеется толкатель или толкатель, который со значительной силой проталкивает глину через матрицу. Существует два основных типа штампа: цельный (для ручки или катушки) и полый (для трубки).На рынке представлено множество типов коммерческих экструдеров, для многих из которых вы можете изготовить матрицы. Если вы подумываете о покупке экструдера (1), имейте в виду, что если вы хотите создавать твердые формы, вам понадобится экструдер меньшего размера. Экструдеры большего размера (используемые для полых форм) могут изготавливать трубы от 4 дюймов шириной / в диаметре до очень большой ширины (большие размеры облегчаются за счет расширительной камеры, прикрепленной к концу экструдера (см. 1, справа)) .
Изготовление нестандартных штампов
У меня есть довольно большая коллекция нестандартных штампов (2).За эти годы я сделал сотни штампов (показаны не все), на изготовление каждой из которых уходит всего 10 минут с помощью пилы для свитков. Я беру лом полиэтилена сверхвысокой молекулярной массы (СВМП) у местного производителя пластика. Это чрезвычайно прочный, устойчивый к истиранию недорогой пластик, который используется в широком диапазоне износа. Он идеально подходит для изготовления штампов, поскольку режет гладко и может гнуться, не ломаясь.
Чтобы сделать высокую вазу, мне нужна нестандартная полая матрица с закругленными углами и нестандартная сплошная матрица, чтобы сделать окантовку крышки на вазе.Начнем с рисунка шапки (3). Добавьте пунктирные линии, чтобы обозначить, как изделие будет опираться на глиняную трубку. С помощью резинового клея приклейте рисунок к заготовке из пластика. Просверлите две круглые области, отмеченные точкой — этот тип пластика очень легко режется или просверливается. Затем используйте спиральную пилу (4) или зажмите пластик в тисках и используйте копировальную пилу с острым мелкозубчатым лезвием, чтобы вырезать остальную часть формы. Для начала вставьте лезвие в одно из двух просверленных отверстий.Обрежьте заусенцы универсальным ножом.
Из-за нагрузки на матрицу с полой трубкой я увеличил толщину пластика до дюйма. Полые матрицы имеют внешнюю и внутреннюю части, а простые U-образные болты используются для удержания частей на месте (5). При затяжке болтов полезно использовать прокладки, чтобы обеспечить равномерную толщину стенки (расстояние между пластиковыми секциями). При использовании глина проталкивается через трубку экструдера, сначала она отделяется, когда проходит через изгиб U-образного болта, а затем превращается в твердую массу к тому времени, когда она проходит через головку. Совет: Более мягкую глину намного легче выдавливать. Жесткая глина будет тянуться к штампу, часто имеет изъяны и вдвое труднее нажимать. При этом со слишком мягкой глиной будет труднее обращаться с формами, выходящими из экструдера.
Экструзия деталей вазы
Сначала закрепите полую головку в нижней части экструдера и загрузите цилиндр мягкой глиной. Присоедините рукоятку гидроцилиндра и выдавите воздух из экструдера. Когда глина начнет выступать, отрегулируйте упорную платформу на желаемую длину выдавливания.Обрежьте основание экструдера и слегка расширьте его, чтобы он стал шире и придал вазе большую устойчивость. Совет: Приготовьте несколько маленьких бит с отверстиями в центре. Отверстие в бите позволяет воздуху заполнять внутреннюю часть экструзии, поэтому она не разрушается во время экструзии. Дальше самое интересное! Одной рукой сильно надавите битой на нижнюю часть экструзии, а другой рукой потяните за шток. Это действие заставляет глину круто раскрываться. Когда форма будет удовлетворена, продолжайте нажимать на плунжер и выдавливать, пока деталь не коснется упорной платформы (6).Верх аккуратно отрезать проволокой и отложить в сторону.
Далее прикрепляем дно к вазе. Очень тщательно надрежьте нижнюю часть трубы и проверьте, нет ли выбоин (дыр или слабых мест в стенках). Подготовьте большую плиту, положите ее на газету, затем забейте и сдвиньте (7). Осторожно переверните трубку на плиту и слегка покачивайте, чтобы трубка приклеилась к дну. Обрежьте лишнюю глину у основания. Чтобы обеспечить хорошее соединение, либо сожмите детали вместе, либо воспользуйтесь небольшим деревянным инструментом, чтобы приподнять глину снизу над швом. Это соединение стало проще, потому что обе секции на этом этапе еще влажные.
Чтобы выдавить накладку крышки на вазе, замените полую головку цельной головкой, изготовленной ранее в этом процессе. Я использую для этого 2-дюймовый экструдер. Выдавите несколько отрезков из матрицы (8). Отложите их, пока вы переходите к штамповке.
Украшение вазы
Мой любимый материал для штампов — дерево; однако глина, обожженная бисквитом, работает очень хорошо. Я модифицировал простые деревянные блоки с помощью горелки для дерева, чтобы создать символы для семян, корней, стволов деревьев, ветвей и верхушек деревьев (9).
Поскольку на этом этапе ваза должна оставаться мягкой, я вставляю квадратный деревянный брусок в трубку, чтобы он поддерживал штамповку. Я покрываю деревянную подставку кулинарным спреем, чтобы она легко скользила внутри глиняной трубки. Теперь вы можете поднимать, поворачивать и штамповать мягкую трубку без повреждений (10). Когда штамповка будет завершена, обрежьте верхнюю часть уровня вазы (см. Боковую панель выше) и оберните верхний край пластиком, чтобы он не высох, пока вы будете делать верхнюю крышку.
Создание верхних крышек
Измерьте и отрежьте углы 45 ° на выступах верхней крышки.Соберите эти части, как мини-рамки для картин, наденьте, наденьте и прижмите их вместе (11). Очистите щеткой и отложите их в сторону. Переверните рамки для картин вверх ногами, наденьте и сдвиньте обе части, затем осторожно прижмите их и пошевелите, чтобы соединиться (12). Очистите влажной кистью и воспользуйтесь деревянным инструментом, чтобы разгладить внутреннее соединение. Вы хотите, чтобы все детали оставались достаточно влажными, поэтому двигайтесь быстрее или продолжайте обматывать их полиэтиленом.
Я не считаю, что верх должен быть идеальным и прямым, когда нижняя часть сделана немного шаткой, поэтому надавите на верх (13).Это также весело и дает мне чувство художественного самовыражения (14).
Глазирование и обжиг
Полностью просушите форму и затем обожгите до бисквитного обжига. После бисквитного обжига я использую комбинацию двух глазурей. Один из них — надежная глазурь с темным лайнером; другой — прозрачная глазурь, которая хорошо сочетается с глазурью для лайнера. За прошедшие годы я испытал множество комбинаций глазури и ищу определенные характеристики для типа работы, глины, температуры и атмосферы. Например, моя темно-коричневая глазурь для лайнера сохраняет свой цвет независимо от того, насколько толстая или тонкая она нанесена.Для второй глазури я модифицировал прозрачную базовую глазурь небольшим количеством карбоната меди, чтобы придать ей зеленый оттенок. Затем я добавил дополнительную фритту, чтобы она стекала по кастрюле. По мере того, как он течет, он захватывает часть темно-коричневой глазури и создает интересное движение.
Первый слой необходимо разбавить, чтобы он вошел во все крошечные щели. Затем я протираю основную поверхность губкой, чтобы выделить текстуру (15). Я использую эту же глазурь для внутренней части вазы, затем окунаю край в ведро для глазури. Второй слой наносится толстой кистью массирующими движениями, так я могу контролировать толщину глазури на дне горшка. Я всегда использую толстую вату, когда стреляю, потому что ты просто не можешь все контролировать.
Более 20 лет назад, когда я впервые начал работать с глиной, я был очарован инструментом в углу классной комнаты. Попробуйте, у него большой потенциал!
Том Квест — гончар, живущий в Омахе, штат Небраска. Чтобы узнать больше, посетите www.Кириллович .
Recyclebot — RepRap
Для получения инструкций по последней версии recyclebot см .: RepRapable Recyclebot: экструдер с открытым исходным кодом для трехмерной печати для преобразования пластика в нить для трехмерной печати.
Источник: Обри Л. Верн, Джозеф Р. МакКаслин, Адам М. Прингл и Джошуа М. Пирс. RepRapable Recyclebot: экструдер для трехмерной печати с открытым исходным кодом для преобразования пластика в нить для трехмерной печати. HardwareX 4C (2018) e00026 doi: https: // doi.org / 10.1016 / j.ohx.2018.e00026 открытый доступ
Для того, чтобы помочь исследователям изучить весь потенциал распределенной рециркуляции бытовых полимерных отходов, в этой статье описывается recyclebot, который представляет собой экструдер для пластиковых отходов, способный производить нить для трехмерной печати коммерческого качества. В конструкции устройства используются преимущества как аппаратной методологии с открытым исходным кодом, так и парадигмы, разработанной сообществом самовоспроизводящихся быстрых прототипов (RepRap) 3-D принтеров с открытым исходным кодом. В частности, в этой статье описывается конструкция, изготовление и работа RepRapable Recyclebot, что относится к способности Recyclebot предоставить нить, необходимую для большей репликации деталей Recyclebot на любом типе RepRap 3-D принтера.Устройство стоит менее 700 долларов в материалах и может быть изготовлено примерно за 24 часа. Нить производится со скоростью 0,4 кг / ч при использовании 0,24 кВт-ч / кг при диаметре ± 4,6%. Таким образом, филамент может быть изготовлен из коммерческих гранул по цене <22% от стоимости коммерческих филаментов. Кроме того, он может производить из переработанных пластиковых отходов нити за 2,5 ц / кг, что в 1000 раз меньше коммерческих затрат на нити. Система может изготавливать нить из полимеров с температурами экструзии <250 ° C и, таким образом, способна изготавливать нестандартные нити из широкого диапазона термополимеров и композитов для материаловедческих исследований новых материалов и исследований возможности вторичной переработки, а также исследований новых применений сплавленных материалов. 3-D печать на филаментной основе.
Фон
Это порт в стадии строительства из Аппропедии [1] и [2], где находится проект и все еще продолжается. Полный список металлических компонентов v2.2 доступен на Thingiverse. Полностью автоматизированный RecycleBot подробно описан здесь для версии 2.3, а весь код Arduino размещен на Thingiverse.
Дополнительная информация: Кристиан Бэклер, Мэтью ДеВуоно и Джошуа М. Пирс, «Распределенная переработка отработанного полимера в сырье RepRap» Rapid Prototyping Journal, 19 (2), стр.118-125 (2013). бесплатная копия в открытом доступе
Следуя модели с открытым исходным кодом, RepRap сделал возможным использование 3D-печати в мелкомасштабном производстве для содействия устойчивому развитию, как описано в разделе «Трехмерная печать соответствующих технологий с открытым исходным кодом для самостоятельного устойчивого развития». Пластмассовое сырье для RepRap — это одна из областей, где можно снизить стоимость. Здесь представлены описание и анализ конструкции для производства нити для RepRap из пластиковых отходов, включая свойства компонентов, процедуры испытаний и результаты экструзии.Успех этого устройства еще больше повысит доступность RepRap за счет снижения эксплуатационных расходов. Альтернативным источником дохода могло бы стать производство филаментов. Кроме того, он позволяет переработать пластик в домашних условиях с использованием побочных продуктов. Это имеет значение в области управления отходами, поскольку переработка в домашних условиях может избежать выбросов парниковых газов и экономических затрат, связанных с муниципальными программами переработки, за счет обхода сбора и транспортировки отходов.
История
Информацию о первом recyclebot можно найти здесь: Recyclebot v1.0. Это было отличным подтверждением концепции и основывалось на конструкции с ручным приводом, хотя с экологической точки зрения она не позволяла создать нить достаточно высокого качества, чтобы быть особенно полезной для 3D-принтеров.
На конструкцию экструдера для отходов пластика (Recyclebot v2.0 и v2.1), показанного ниже, сильно повлиял экструдер Web4Deb, который экструдирует HDPE для использования в качестве среды для роста в аквапонике.Подробности дизайна Web4Deb можно найти в блоге Web4Deb. В рамках курса машиностроения Королевского университета, Mech 461 под руководством Дж. М. Пирса [3], Кристиан Бэклер разработал Recyclebot v2.0 — устройство для автоматического преобразования бытовых пластиковых отходов в пригодный для использования материал, который затем будет загружен в небольшие машины для быстрого прототипирования, такие как RepRap. Этот дизайн был улучшен внутри группы — особенно с помощью Мэтью ДеВуоно.
Recyclebot v2.2 в настоящее время выполняется Michigan Tech in Open Sustainability Technology Research Group.
Recyclebot v2.0 / v2.1
Инженерное дело
Недавно было предложено использовать 3D-принтеры с открытым исходным кодом для обеспечения устойчивого развития [4]. Для того, чтобы это стало реальностью, критически важно разрабатывать сырье из материалов, доступных на местном уровне, с тем чтобы не допустить эрозии экономических преимуществ для местного производства. Использование доступных на местном уровне материалов для изготовления соответствующей технологии с открытым исходным кодом (OSAT) не только гарантирует, что данное сообщество будет меньше зависеть от иностранной помощи в случае возникновения проблем с технологией, но также создает ощущение расширения возможностей, поскольку технология не распространяется. как форма благотворительности, способствующая зависимости от иностранной помощи.Это может быть достигнуто за счет использования сырья, созданного из отходов (например, пластиковых пакетов или бутылок), или за счет использования доступных местных материалов, таких как биополимеры. Огромное количество пластика в бытовых отходах (включая пакеты, бутылки, упаковку для продуктов питания и развлечений) является реальностью в большинстве несельских общин, но эти отходы можно использовать повторно. Можно использовать процесс для создания нити из отходов пластика для использования в RepRap. Таким образом, необходим экструдер для пластика, который мог бы нагревать пластик и выдавливать его как нить, которую можно использовать в трехмерном принтере.Следует отметить, что производство исходного материала для филамента является сложной задачей, поскольку диаметр должен быть точным, а нить должна быть очень круглой (не овальной), иначе экструдер будет производить детали низкого качества или замятие, что часто случается, когда владельцы RapMan покупают замену филамента.
локально. Экструдер с бункером может не так сильно зависеть от размерных свойств материала, а также надежные достижения в использовании гранулированного исходного материала в сочетании с гранулятором — еще один вариант, который можно изучить.
Цель исследования
Цель этого исследовательского проекта — разработать, построить и испытать экструдер для RepRap, который может принимать полимерные отходы в качестве сырья.
Обзор литературы
Перейдите по этой ссылке, чтобы получить доступ к полной версии «Экструдер для пластика: обзор литературы». В обзоре исследуется ряд литературы по вопросам технологии быстрого прототипирования с открытым исходным кодом, обращения с пластиковыми отходами и их вторичной переработки, свойств материалов и технологии экструзии, среди прочего.
Общественная осведомленность и поддержка
Устойчивое развитие и трехмерная печать сегодня привлекают значительное внимание общественности, и организации, которые могли бы помочь с поддержкой и сотрудничеством, уже существуют. Проект Perpetual Plastic [5], запущенный дизайнерским агентством Better Future Factory [6], в настоящее время работает над продвижением очень похожей концепции. Похоже, их цель — выявить потерянные пластиковые отходы, превратив их в ресурс, который можно использовать для создания нити накала и печати новых продуктов в одном месте. Это может быть возможностью для участников RepRap сотрудничать с Perpetual Plastic Project, который, похоже, хочет распространять свою технологию.
Проект
Описание конструкции, включая подробные инструкции по сборке, можно найти ниже.
Экструдер
На конструкцию экструдера для пластиковых отходов сильно повлиял экструдер, разработанный «Web4Deb» (имя пользователя в сети), который экструдирует HDPE для использования в качестве среды для роста в аквапонике. Подробности этого дизайна можно найти в блоге Web4Deb и на вики-странице устройства RepRap. Было решено, что эта конструкция будет использована в качестве основы и модифицирована для производства 3-миллиметровой нити для использования с 3D-принтером RepRap.
Конструкция имеет следующие особенности. Дополнительные сведения см. В разделе «Инструкции по сборке».
- Труба 3/4 «(внутренний диаметр) для цилиндра экструдера.
- разделен на 3 отдельные секции, которые собираются вместе (зубчатая передача, бункер и нагреватель).
- 3/4 «-17» Судовой шнек — вставлен в ствол. Бункер
- приварен к секции бункера. Сюда вставлен измельченный пластик. Шнек
- повернут с помощью электродвигателя стеклоочистителя (бывшая в употреблении модель Dodge Neon 1994 года выпуска) Цепно-звездочный привод
- , передаточное число 2: 1 (снижает скорость, увеличивает крутящий момент).
- упорный подшипник / шайба в сборе для ограничения движения в осевом направлении и противодействия силе, прилагаемой к шнеку при транспортировке пластмассы.
- нагревательная секция (описана ниже) и матрица с отверстием 3 мм.
Нагревательная секция
- Нихромовая проволока 14 калибра, намотанная на ствол.
Закреплен термостойкой каптоновой лентой.
Для предотвращения короткого замыкания на цилиндр нагревательной секции нанесен печной цемент - . (можно избежать за счет использования изолированного нихрома).
- достиг температуры 225 o C при использовании блока питания ноутбука 15 В, 5 А.
- Каптонная лента может предотвратить короткое замыкание через цилиндр, но ограничена областями ниже 250 o C. Эта высокая температура необходима, если экструдируется ABS или PET.
- Температура внутри нагревательного цилиндра имела тенденцию отставать примерно на 30 o C.
Проволока четырнадцатого калибра была выбрана для того, чтобы создать зону нагрева с минимальными требованиями к мощности.В настоящее время температура нихромовой проволоки составляет 225 o C, что достигается при мощности 75 Вт (15 В, 5 А). Температуру можно регулировать, изменяя ток, проходящий через нихромовую проволоку. Увеличение тока увеличивает температуру проволоки. В настоящее время в секции имеется только одна зона равномерного нагрева, однако были предусмотрены две зоны нагрева, если более постепенный нагрев пластика окажется полезным. Во многих коммерческих процессах используется постепенный нагрев для обеспечения равномерного нагрева материала (Rosato, 1997).На этом веб-сайте есть спецификации по сопротивлению каждого калибра провода и току, необходимому для нагрева каждого калибра до различных температурных порогов. Данные с этого сайта были использованы для первоначальных расчетов проекта.
В настоящее время нагревательная секция неизолирована, однако добавление изоляции, вероятно, улучшит характеристики. Время нагрева при первом запуске машины может быть сокращено, а в цилиндре экструдера могут быть достигнуты более высокие температуры. В качестве изоляции можно использовать обертки из стекловолокна / кевлара, а также домашний ватин из стекловолокна.
Списки запчастей
В конструкцию включены несколько дополнительных модификаций и нестандартных деталей. К двигателю стеклоочистителя ветрового стекла был добавлен удлинитель вала, чтобы увеличить диаметр вала и обеспечить достаточно места для установки звездочки. Втулка была создана между валом и зубчатой передачей, которая удерживает шнек на месте и позволяет установить упорный подшипник. Каждая из этих нестандартных деталей представлена на рисунках ниже.
Экструдер был сконструирован из комбинации специально разработанных и стандартных материалов.В приведенном ниже списке представлены материалы на складе вместе со ссылками на их поставщиков.
Складские материалы:
Все перечисленные номера деталей относятся к деталям, использованным в прототипах экструдеров. Могут быть заменены другие марки и детали. Многие из этих деталей могут быть доступны в использованном или утильском виде. Я нашел много деталей бесплатно, таких как фанера и деревянные доски, застежки и зажимы из крокодиловой кожи. Детали, выделенные курсивом, представляют собой материалы, которые потребуются для корпуса экструдера. В моем случае эти материалы были включены в стоимость механической обработки в механическом цехе машиностроения и материаловедения Королевского университета. Для подготовки деталей к сборке в экструдере требуется дополнительное производство. Необходимые инструменты должны быть в состоянии резать металл (например, шлифовальный станок, универсальные пилы, кислородно-ацетиленовая горелка и т. Д.) И выполнять простую сварку. В моем случае эти детали были изготовлены на заказ, как описано ниже.
Пользовательские детали
Детали по индивидуальному заказу изготавливались в Королевском университете, на факультете механического оборудования и обработки материалов.Особая благодарность мистеру Энди Брайсону и его команде за их помощь в изготовлении. Большинство деталей изготовлено с использованием сварочного, режущего и сверлильного оборудования. В некоторых случаях для изготовления требовался токарный станок. Файлы STL для каждой из пользовательских деталей можно найти ниже, а также производственные чертежи отдельных компонентов. Файлы показывают размеры, используемые для этого конкретного экструдера, и были выбраны на основе предыдущего экструдера Web4Deb и подходят для других компонентов (например, шнека).Оптимизация размеров экструдера не исследовалась.
Файлы изображений деталей
Экструдер для пластиковых отходов: напильники
Инструкции по сборке
Ниже приведены инструкции по полной сборке конструкции экструдера, прототип которой был разработан для курса Mech 461:
Основной корпус в сборе
Основной корпус состоит из:
- Нагреватель, бункер и редуктор
- 6 фланцев
- матрица
- опорная плита подшипника
- хомут
- Подшипник упорный и шайбы
- шнек
- большая звездочка
Детали, выделенные курсивом, являются нестандартными деталями.Строительные чертежи можно найти в разделе файлов деталей. Большинство этих деталей должны быть изготовлены с помощью инструментов для резки и сверления металла. Их размеры такие же, как у прототипа экструдера Mech 461, но могут быть изменены в соответствии с индивидуальным дизайном.
После того, как каждая часть построена. Была соблюдена следующая процедура:
- Фланец был приварен к каждому концу секции нагрева, бункера и шестерни. Это позволяет соединять отдельные секции вместе.Наличие их в отдельных секциях позволяет работать над каждой секцией отдельно от остальной части тела. В частности, полезно иметь отдельную зону нагрева, с которой можно работать отдельно и изолировать от остальной части экструдера. Примечание. Возможно изготовление экструдера с однокорпусной конструкцией.
- Из части 1: У вас должен быть узел редуктора, бункера и нагревательной секции, состоящий из соответствующих трубопроводов и 2 фланцев каждый.
- Бункер приварен к открытому участку трубы в зоне бункера.
- Вырезан квадрат из фанеры размером примерно с полку. Его помещали между бункером и секциями нагрева, чтобы уменьшить теплопередачу между зоной нагрева и зоной бункера.
Секция бункера, секция нагрева и фанера соединялись крепежом через отверстия фланца.
- Матрица может быть прикреплена к другому концу нагревательной секции тем же способом.
- Шнек вставлен в цилиндр экструдера.
- На хвостовик шнека насажено нестандартное кольцо сверху.Хомут ограничен увеличением диаметра шнека от хвостовика до лопасти. Манжета с меньшим внешним диаметром расположена ближе всего к лопасти шнека. Он помещается внутри цилиндра экструдера. Больший внешний диаметр ограничивает движение шнека в осевом направлении по направлению к зоне нагрева, поскольку он слишком велик, чтобы поместиться в цилиндре экструдера.
- Далее на шнек были наложены игольчатый упорный подшипник и шайбы (шайба, шайба подшипника).
- Подшипниковый узел закреплен опорной пластиной подшипника.«Это было связано с крепежом к фланцу на секции зубчатой передачи. Упорный подшипник компенсирует осевое усилие, действующее на шнек, когда он толкает пластик.
- На шнеке была обработана плоскость, чтобы обеспечить лучший контакт с установочным винтом звездочки.
Это было признано необходимым во время испытаний, так как звездочка проскальзывает по хвостовику до того, как будет создана плоскость.
- Большая звездочка была насажена на хвостовик, и установочный винт затянут на секции с плоскостью.
На этом сборка основного корпуса экструдера завершена.
Отопительная секция
Зона нагрева — показана нихромовая проволока, закрепленная каптоновой лентой.Нагревательная секция состоит из следующих компонентов:
- узел нагревательной секции (см. Узел основного корпуса)
- Проволока нихромовая (изолированная или неизолированная)
- Каптонная лента
- медный провод
- Адаптеры зажимов типа «крокодил»
При использовании неизолированного нихрома :
Конструкция зоны нагрева представляет собой довольно простой, но важный узел экструдера для пластиковых отходов.Процедура немного отличается при использовании изолированной или неизолированной нихромовой проволоки. Если вы используете изолированный провод , пропустите шаг 1 ниже.
- Покройте корпус нагревательной секции (трубопровод) тонким слоем термостойкого цемента. Я использовал Bomix Pyromix. Проверьте список компонентов, чтобы найти ссылку на продукт. Сделайте слой как можно тоньше, но убедитесь, что на нем нет оголенного металла.
- оберните нихромовую проволоку вокруг ствола от одного конца до другого. Одной секции, покрывающей весь ствол, должно быть достаточно, но две отдельные зоны нагрева могут иметь преимущества (более постепенный, равномерный нагрев; меньшее напряжение через любой провод).Я эффективно использовал одну зону. Если вы используете неизолированный провод , убедитесь, что катушки не соприкасаются, иначе произойдет короткое замыкание.
- Закрепите провод каптоновой лентой. Каптоновая лента рассчитана на 250 o C. Если вы будете достигать более высоких температур (требуемых для экструзии АБС и ПЭТ), вы можете закрыть устройство другим слоем печного цемента.
- Присоедините медный провод к зажимам типа «крокодил» и используйте их в качестве проводов для подключения к источнику питания.
- Протестируйте и при необходимости измените.
Я использовал старый адаптер питания ноутбука (15 В, 5 А) и получил 225 o C. Максимальную температуру можно регулировать, изменяя ток через провод. Это можно сделать, добавив сопротивление или заменив источники питания. В будущем ведется работа по разработке системы микроконтроллера для мониторинга и контроля температуры. Это было сделано в прошлом на экструдере Web4Deb и для экструзионных сопел в 3D-принтере RepRap.
Опорная конструкция
Опорная конструкция состоит из деревянной основы с 8 опорами, которые удерживают корпус экструдера от осевых, вертикальных и крутильных движений.Приведенные ниже инструкции описывают процесс создания экструдера Mech 461. Большая часть этого дизайна может быть изменена для удовлетворения различных потребностей. Этот дизайн претерпел несколько изменений. Увеличенная опора была добавлена после того, как одна из деревянных опор сломалась во время использования. Изменились также тип и расположение опор. Строительная документация для различных опор будет добавлена в ближайшее время.
в процессе
Привод
Электродвигатель стеклоочистителя, используемый для привода шнека экструдера.Крепится к подвижной платформе, что позволяет легко натянуть цепь.Система трансмиссии состоит из следующих компонентов:
- большая и малая звездочка
- Мотор стеклоочистителя
- Удлинитель вала (файл детали доступен здесь)
- цепь
- устройство натяжения
- Резьбовые стержни 2 x 1/4 «-16»
- Гайки 8 1/4 «
- деревянная опора
- металлическая обвязка
Каждый из этих компонентов является стандартным, за исключением удлинителя вала, который был изготовлен на заказ. Большая звездочка также была модифицирована для уменьшения внутреннего и внешнего диаметров отверстия.
Сборка системы трансмиссии выполнялась в соответствии со следующей процедурой. Строительные схемы будут добавлены в ближайшее время.
в процессе
Шлифовальный пластик
Чтобы превратить пластиковые бутылки в жизнеспособное сырье с помощью этого метода, их сначала нужно было измельчить на мелкие кусочки.Для этого был исследован ряд методов.
Следуя работе студентов Делфтского университета, ряд обычных кухонных приборов был протестирован на их шлифовальную способность [7]. Были протестированы кухонный комбайн, кофемолка и блендер, причем блендер оказался наиболее эффективным. В соответствии с результатами работы группы U из Делфта было обнаружено, что блендер работал лучше всего, когда добавлялась вода для охлаждения машины и сдерживания размалываемого пластика.
Однако это решение было недостаточно эффективным для измельчения в больших количествах, так как требовало слишком много времени.Кроме того, измельченный пластик нужно было высушить, прежде чем его можно будет использовать в экструдере. Более эффективный метод был найден с использованием офисного шредера Staples®, который был разработан для измельчения кредитных карт и компакт-дисков. Это оказалось гораздо более экономичным по времени и энергии и позволило избежать использования воды. Использованный измельчитель был найден в местной деревне Value Village за 24,99 доллара.
Тестирование показало, что этого метода достаточно. Некоторые проблемы возникли с более толстыми пластиковыми бутылками, поскольку измельчитель не мог полностью разрезать их на мелкие кусочки.Режущая кромка шнека все еще могла обрабатывать большинство этих образцов после того, как они прошли через измельчитель. Чтобы обеспечить бесперебойную работу машины и постоянную скорость экструзии, использовались ножницы, чтобы разрезать самые большие куски на более мелкие, прежде чем они были помещены в бункер.
Полный метод подготовки пластика был следующим:
- мойка пластиковых бутылок
- снятие наклеек и крышек
- нарезка на управляемые части для измельчителя
- измельчение
Ручка и крышки не использовались, так как они не могли проходить через измельчитель. Этапы резки и измельчения чередовались, чтобы гарантировать, что измельчитель не перегреется, как это происходит при непрерывном измельчении в течение 15-минутного периода. Прерывистое измельчение в течение часа не вызвало никаких проблем с измельчителем.
Дальнейшая работа должна быть сосредоточена на устройстве для измельчения, которое не требует резки бутылок и которое может производить более мелкую пластиковую стружку, подаваемую в бункер.
Тестирование
Испытания экструзии и разработка исходного сырья для 3-миллиметровой нити продолжаются.Будущие обновления.
Работа в будущем
Шлифовальное устройство
- создание недорогого устройства для измельчения домашних весов.
- следует измельчать бутылки на мелкие кусочки (площадь <1 см 2 )
- предварительная нарезка не требуется
- может принимать ручки, крышки и т. Д.
См. Также Информация о Recyclebot
Внешние ссылки
От искусства к науке: меняющееся лицо экструзии
Экструзия является одной из самых инновационных и быстро развивающихся областей производства медицинских устройств.
Продолжается выпуск нового оборудования, которое позволяет производить более мелкие детали с очень жесткими допусками, обеспечивая уровни контроля и возможностей, намного превосходящие то, что было возможно всего несколько лет назад.Стандартные инструменты доступны в меньших и меньших размерах. Даже при повсеместном стремлении к использованию труб меньшего размера, все большее число производителей оригинального оборудования (OEM) также хотят иметь толстостенные трубки большего размера, что может затруднить поиск экструзионного оборудования, отвечающего такому широкому диапазону технических характеристик трубок.
Кроме того, технологии онлайн-измерений теперь очень надежны и способны измерять меньшие размеры и с большей точностью по сравнению с оборудованием предыдущих поколений.На рынке продолжают появляться улучшенные материалы, часто с новыми пластификаторами поливинилхлорида (ПВХ) или альтернативными материалами для применения в ПВХ. Многие производители оригинального оборудования стараются изготавливать собственные трубки для экономии денег и времени. Это работает для основных нужд трубок; однако для более сложных проектов OEM-производители, как правило, обращаются за решениями к своим партнерам по экструзии, ожидая, что у них будет оборудование, ноу-хау и терпение, чтобы воплотить эти более сложные конструкции в реальность с очень жесткими допусками.
«С приобретением многих экструзионных производств в более крупные корпорации, кажется, многие компании пытаются изготавливать все свои собственные трубки», — сказал Тайлер Уэр, владелец и президент GenX Medical, поставщика медицинских изделий на заказ. трубка. «Когда они передают работу на аутсорсинг, это обычно означает, что они не могут выполнить ее самостоятельно из-за трудностей, будь то материал, процесс или и то, и другое».
По мере того, как занятые OEM-производители производят более мелкие и сложные продукты, часто из современных или чувствительных материалов, они начинают понимать, что у них нет внутренних ресурсов, чтобы оставаться в курсе быстрых изменений, происходящих в экструзионной науке; Затем они решают, что совместная разработка и параллельный инжиниринг с проверенными экструдерами является наиболее эффективным подходом к рационализации разработки продукта и более быстрому выводу на рынок передовых продуктов.
Производители медицинских устройств (MDM) сталкиваются со все более сложными требованиями к экструзии, которые требуют очень точных спецификаций размеров, материалов и конструкции. Они часто работают в тесном сотрудничестве с партнерами по экструзии, чтобы полностью понять технологичность продукции и разработать инновационные и / или нестандартные решения для экструзии. Иногда для этого требуется подход, даже совершенно новый для отрасли. Производители оригинального оборудования также хотят сократить сроки разработки, даже если их продукты более сложные и требуют больше времени на производство.Например, устройства меньшего размера для менее инвазивных хирургических процедур (таких как нейроваскулярные) бросают вызов традиционным технологиям экструзии и требуют очень жестких допусков. «Это особенно влияет на технологию экструзионного плетения и оплавления для труб с микроканальным армированием», — сказал Адам Надо, менеджер по исследованиям и разработкам подразделения медицины, фильтрации и электроники Saint-Gobain Performance Plastics, производителя высокопрочных материалов в Нортборо, штат Массачусетс. высокопроизводительные трубки для медицинской промышленности.«Примерами являются экструзия пасты ультратонкой оболочки из политетрафторэтилена [ПТФЭ] [0,0005 дюйма и тоньше], плетение очень тонкой проволокой для уменьшения общей толщины стенок и экструзия слоев тонкостенной оболочки, которые являются ключевыми компонентами сосудисто-нервных катетеров.
”
Экструзионное оборудование продолжает совершенствоваться, чтобы соответствовать этим сложным проектным требованиям. Шестерни и двигатели становятся более точными, а «конструкция шнеков и металлургия цилиндров значительно улучшились», — сказала Шаран Тэтхенд, технический менеджер компании Fluortek, Истон, Пенсильвания.-поставщик медицинских трубок, медицинских термоусадочных трубок, а также медицинских фторполимеров и термопластов. «Органы управления также претерпели значительные улучшения. Например, задняя панель экструдера становится все более сложной, в то время как интерфейс человек-машина стал еще удобнее, чем когда-либо ».
Несмотря на то, что новости о медицинских устройствах, кажется, сосредоточены на трубках меньшего диаметра и более жестких допусках, существует также тенденция, движущаяся в противоположном направлении. «Многим нашим клиентам требуется внешний диаметр до 0.5 дюймов или более, при этом желая сохранить относительно тонкие стены », — сказал Уэр. Более широкие трубки часто используются для улучшения функциональности устройства за счет увеличения пропускной способности для большего количества люменов, проводки и других компонентов.
В отрасли наблюдается повышенный интерес к консолидации поставщиков, поскольку решение «производить вместо покупки» «побуждает все больше OEM-производителей оценивать свои цепочки поставок», — сказал Кристиан Херрилд, директор по стратегиям роста Teel Plastics, Барабу, Висконсин. -производитель медицинских трубок и поставщик услуг по сборке и разработке.«Это привело к некоторому возобновлению интереса к тому, чтобы просить такие компании, как Teel, которые сосредоточены на узкоспециализированных приложениях, рассмотреть продукты, которые больше относятся к категории товаров массового потребления. Тенденция OEM, похоже, уходит от наличия большого количества нишевых поставщиков ».
Качество, скорость и стоимость возглавляют список OEM. Поддержание системы менеджмента качества, соответствующей международным стандартам, таким как ISO 13485: 2016, является обязательным условием для MDM и их контрактных производителей. Они хотят, чтобы их экструдеры постоянно соответствовали жестким габаритным характеристикам, таким как внешний диаметр (OD) трубы, внутренний диаметр (ID), стенка, концентричность и овальность. Им также нужны данные об оборудовании и проверках, которые используются для сертификации их продукции. «Производители оригинального оборудования хотят знать, что у вас есть конкретные данные, подтверждающие качество каждой детали или каждой катушки, а не просто план статистической выборки», — сказал Херрилд. «Мы удовлетворяем эти запросы, расширяя нашу онлайн-систему измерения и обновляя наше программное обеспечение.
«Производители оригинального оборудования хотят, чтобы их продукция была произведена вовремя, в соответствии с их спецификациями и доставлена с исключительным качеством», — добавил Мэтт Карчиди, вице-президент по операциям GenX Medical. «Экструзии и сопроводительная документация должны быть правильными и точными при поступлении на предприятие».
Производители оригинального оборудования стремятся к равномерной экструзии, что становится все более сложной задачей по мере того, как трубки становятся все меньше и тоньше, с более жесткими допусками. «Большинство наших клиентов перерабатывают наши трубы вторично, поэтому однородные трубы означают минимальную регулировку процесса на их конце», — сказал Тэтхенд.«Спецификации с каждым днем становятся все уже, что ставит перед экструдерами новые задачи. В компании Fluortek мы успешно достигли размеров экструдера с допуском менее ± 0,0005 дюйма ».
OEM-производители больше полагаются на отдельных поставщиков для экструзии различных полимерных материалов — не только из-за их опыта, такого как руководство по выбору материалов, но и для сокращения своих цепочек поставок и ускорения вывода на рынок. «Производители комплектного оборудования все чаще ищут поставщика, способного предоставить не только трубы, но и дополнительные технологические процессы с добавленной стоимостью», — сказал Надо.«Это включает в себя такие процессы, как опрокидывание, формование, склеивание, сверление / зуботочение, печать, нанесение покрытия, плетение и оплавление».
Тенденции в новых технологиях
Технологии экструзии продолжают развиваться. Трубки могут быть изготовлены с термопластичными оболочками из различных материалов, включая пебаксы, нейлон и уретаны. Армирующая оплетка и / или катушка может быть встроена в стенки трубок для увеличения прочности и соответствия определенным требованиям к давлению разрыва. Решения для трубок все чаще настраиваются с очень жесткими допусками — например, некоторые производственные технологии могут достигать ± 0.00025 дюймов допуски на внешний диаметр.
Когда дело доходит до экструзии с несколькими просветами для целей НИОКР, производители оригинального оборудования ищут сочетание цены, скорости и функциональности. Многопросветная экструзия — это смесь искусства и науки, особенно с учетом того, что изготовление устройств становится все сложнее. «На проектирование и производство инструментов требуется не только время, но и несколько различных итераций наборов инструментов для изготовления трубок в точном соответствии со спецификациями заказчика», — сказал Уэр. «Когда наши OEM-производители связываются с нами для быстрой доставки многолучевых конструкций, мы можем предоставить исследования и разработки, необходимые для сокращения затрат и времени выполнения заказа, при этом обеспечивая функциональность продукта для тестирования, даже если он может быть не совсем подходящим. указанные размеры.”
MicroLumen, компания-производитель высококачественных медицинских трубок из Олдсмара, штат Флорида, изготавливает трубки без экструзии. Технология заключается в нанесении очень тонких слоев жидкого полимера на проволоку в непрерывном процессе; затем проволоку удаляют, чтобы получить трубку. Этот метод позволяет выдерживать очень жесткие допуски по внутреннему диаметру и толщине стенки. Его также можно использовать для создания трубок с несколькими слоями материала, включая оплетку и арматуру спиралей.
«Большая часть того, что мы производим, имеет толщину стенок менее 0.005 дюймов », — сказала Кэролайн Либерти, инженер по применению MicroLumen. «Мы производим трубы с четырьмя слоями материала на стенке толщиной до 0,0025 дюйма. В целом, мы можем выдерживать допуски ± 0,00025 дюймов по толщине стенки или ± 0,0005 дюймов по наружному диаметру ».
Самая маленькая коммерческая деталь Teel Plastics имеет наружный диаметр 0,027 дюйма со стенками 0,002 дюйма с допусками 0,0004 дюйма. «Заказчику этого продукта требуется максимальная согласованность, поэтому мы проводим непрерывный контроль наружного диаметра и стенок в режиме онлайн», — сказал Херрилд.Затем данные передаются в электронном виде во внутреннюю систему качества, которая сопоставляет точные кадры детали с результатами онлайн-измерения на момент производства детали. «Мы работаем с 1,33 + Cpk и прекращаем экономить, когда детали выходят за рамки спецификации, что бывает редко, поскольку мы можем видеть это и вносить коррективы», — добавил он.
OEM-производители также требуют более точной длины. Тил недавно приобрел резак, изготовленный по индивидуальному заказу, который может выдерживать допуски до ± 0,002 по длине на линии для деталей от 3.Общая длина от 0 до 6,5 дюймов. «Разработка оборудования — это итеративный процесс, в котором участвовали наш поставщик оборудования и наша команда инженеров», — сказал Херрилд. «Ключевым моментом было использование независимых сервоприводов для всего, что могло бы общаться друг с другом для синхронизации. Мы заказали больше и планируем сделать это оборудование стандартом для всей нашей медицинской продукции ».
Поддержание качества и соответствия труб с такими жесткими требованиями к допускам требует наличия передовых систем контроля. «Контроль качества перешел на новый уровень», — сказал Тэтхенд.«Лазерные измерительные системы, которые интегрируются с последующими процессами, исключают сбор деталей, не указанных в спецификации. Кроме того, в линию используются системы видеонаблюдения с расширенными возможностями обнаружения поверхностных дефектов на 360 градусов, которые также интегрируются с последующим оборудованием для отделения неисправных деталей. Индустрия продолжает двигаться к надежной системе с минимальным возможным человеческим взаимодействием ».
Экструдеры привыкают к постоянному спросу на более высокую производительность, меньшие размеры, более быстрое выполнение работ, более длительный жизненный цикл, снижение затрат, отслеживаемость и проверку / валидацию. МДМ рассчитывают на то, что они превратят все свои проекты в коммерческий успех, раздвинув границы технологии трубок — и все это при сохранении низких затрат.
Однако есть предел тому, что поставщики трубок могут предоставить с использованием современных материалов и технологий. Лучший способ оставаться на переднем крае технологий, материаловедения и передового опыта — и снижать расходы — это принять Индустрию 4.0. Индустрия 4.0 — это цифровизация производства. Сотни датчиков, встроенных в производственное оборудование, измеряют, хранят и передают данные, которые можно использовать для оптимизации операций.
«Внедрение датчиков на экструзионной линии и подключение датчиков и оборудования через систему диспетчерского управления и сбора данных (SCADA) позволяет ускорить разработку процесса, более быстрый запуск и повысить точность / качество», — сказал Надо.
Teel Plastics имеет штатного программиста в штате, который работает с внутренними командами, чтобы сделать Индустрию 4. 0 и Интернет вещей (IoT) реальностью на производстве. «Теперь у нас есть системы, которые будут взаимодействовать примерно с 70% оборудования на полу», — сказал Херрилд.«Мы можем отправлять инструкции и собирать данные практически обо всем на объекте с помощью программируемого логического контроллера. Это позволяет нам передавать параметры настройки на линию удаленно, собирать данные о том, что делает каждая единица оборудования на линии, прогнозировать время работы и использование материалов, а также позволяет инженерам проверять, как выполняется задание, со своих рабочих мест. . »
Автоматизация — ключевая часть Индустрии 4.0 и важная часть сегодняшней экструзионной технологии, особенно с учетом того, что производители оригинального оборудования уделяют особое внимание жестким допускам.Даже малейшие колебания в работе машины могут вывести трубы из допустимого диапазона — риск, который сводится к минимуму или даже устраняется с помощью автоматизации.
«Последние экструдеры оснащены программами с обратной связью, которые интегрируются с последующим оборудованием, таким как съемник / резак и лазерная измерительная система», — сказал Тэтхенд. «Эта интеграция делает экструдер достаточно интеллектуальным, чтобы изменять скорость для сохранения размеров продукта. Это также помогает отделить плохие части от хороших. С развитием средств контроля сбор данных стал ключевым аспектом.Сбор данных не только полезен для изучения процесса, но и помогает устранять неполадки. В связи с растущими нормативными требованиями валидация процессов становится обязательной. Благодаря возможностям сбора данных проверки становятся более точными и беспроблемными ».
Teel Plastics продолжает автоматизировать как можно больше процессов. Херрилд отмечает, что поначалу окупаемость была незаметной, но теперь она «меняет правила игры» на их процессы экструзии. «Теперь мы можем легко увидеть проблемы на рабочих местах до закрытия рабочего задания», — сказал он.«Мы можем точно отслеживать, как была создана линия, кем и кто ее подтвердил. У нас меньше проблем с вещами, не оптимизированными для заданных значений. Это вызывает коррекцию, а не реакцию, и мы видим, что объем брака по всему предприятию падает. Фактически, мы обнаружили проблемы, о которых даже не подозревали, потому что они были невидимы, когда данные не поступали в режиме реального времени. Как только вы начнете путь в Промышленность. 4.0, преимущества настолько очевидны, что пути назад нет ».
Аддитивное производство (AM), еще одна ключевая отрасль 4.0, еще не оказала существенного влияния на производство самих НКТ. Однако некоторые экструдеры используют AM для создания прототипов и ускорения процесса проектирования. Например, AM может быть полезен при создании макетов фитингов, инструментов, приспособлений, форм и сопрягаемых деталей, которые помогают максимизировать процесс экструзии.
«Мы также использовали 3D-печать для разработки некоторых приборов для более разумных и удобных методов контроля качества», — сказал Тэтхенд. «Инструменты для экструзии никогда не были такими точными, и я еще не видел 3D-принтер — металлический или пластиковый — который мог бы выдерживать допуск ± 0.0005 дюймов ».
Технология экструзии продолжает быстро развиваться, чтобы соответствовать спросу на меньшие и более тонкие трубки, которые могут вмещать больше люменов для выполнения множества функций. Достижение сверхтонких стенок раздвигает границы технологии труб и воспроизводимости — например, футеровка внутренних стенок может иметь толщину в несколько тысячных дюйма. Стены также должны быть достаточно прочными, чтобы соответствовать требованиям к испытаниям под давлением и воспроизводимости производства, что часто требует индивидуального армирования.Переходные трубки материалов, в которых один материал переходит в другой по длине трубки, тщательно спроектированы так, чтобы иметь разные механические свойства в определенных точках вдоль трубки. Высокотехнологичные материалы имеют очень специфические физические параметры; трубки также могут быть разработаны для защиты светочувствительных растворов и чувствительных фармацевтических ингредиентов.
Хотя многие производители оригинального оборудования имеют свои собственные экструзионные производства, они также осознают свои знания и технологические ограничения для сложных продуктов; поэтому они передают их доверенным вертикально интегрированным экструдерам в своих цепочках поставок, которые могут выполнять другие обязанности, связанные с трубами, включая выбор материалов. «Некоторые производители оригинального оборудования могут не совсем понимать, что существует множество различных типов и сортов полимерных материалов, доступных для их продукции, особенно для некоторых новых продуктов, находящихся на стадии разработки», — сказал Надо. «Следовательно, некоторые альтернативные полимеры могут удовлетворить требования к их продукту, обладая такими преимуществами, как простота обработки и цена».
Поскольку требования к трубкам и толщине стенок продолжают уменьшаться, системы качества и технологии измерения также должны не отставать, например, системы измерения наружного диаметра рентгеновских лучей / стенок / контроля для медицинских трубок меньшего размера.Хотя современные рентгеновские технологии проще использовать для измерений, чем ультразвуковые системы, они недостаточно точны, чтобы надежно измерять трубки меньшего размера. Другой проблемой является измерение внутреннего наружного диаметра и толщины стенок многопросветных трубок.
Несмотря на сложность, экструдеры уверены, что обладают технологиями и ноу-хау для создания инновационных, даже уникальных решений.
«Никогда не бойтесь проектировать», — сказал Либерти. «Наша работа — находить решения для проблем проектирования.Мы всегда готовы пробовать новое и применять свои знания и опыт для новых подходов. Мы не боимся проявлять творческий подход при решении дизайнерских задач и не хотим, чтобы наши клиенты боялись спрашивать. Мы с энтузиазмом работаем в тесном сотрудничестве с нашими клиентами и рассматриваем наши отношения как партнерские ».
По мере того, как OEM-производители продолжают выпускать продукты, которые выходят за рамки экструзионных технологий и выходят за рамки их собственных внутренних знаний, они с большей готовностью формируют коллективные команды с инженерами по экструзии и принимают их советы относительно технологичности.
Херрилд считает это хорошим знаком, потому что OEM-производители отказываются от устаревших представлений о прошлом.
«Клиенты думают, что с помощью экструзии что-то невозможно сделать, потому что это было невозможно 10 лет назад», — сказал он. «Все изменилось за этот период. Детали точнее. Оборудование лучше. Элементы управления более сложные. Датчики более эффективны. Сейчас существуют материалы, которых не было в прошлом году, не говоря уже о 10 лет назад. Если вы в последнее время не пробовали что-то делать с экструзией, поговорите со своей базой снабжения — вы будете поражены тем, что они могут предложить.
Лучший (и самый простой) способ сделать процесс экструзии максимально рентабельным и успешным, подчеркнул Уэр, — это поддерживать открытый обмен информацией между OEM-дизайнером и экструзионным заводом, особенно в отношении конечного использования трубы и того, как ожидается выполнение. «Часто мы просто делаем то, о чем просят, не зная о конечном использовании», — сказал Уэр. «Когда мы можем обсудить с проектировщиком перед тем, как изготовить трубку, есть шанс улучшить процесс экструзии, а также производительность трубки в ее конечном применении.”
Марк Кроуфорд — штатный внештатный писатель по бизнесу и маркетингу / коммуникациям из Мэдисона, штат Висконсин.

«Драгоценный пластик» стремится сделать 3D-печать экологически чистой и пригодной для вторичной переработки
Возможно, самая большая жалоба на зарождающуюся отрасль 3D-печати заключается в том, что, если говорить о ней, если у вас нет особого робота , скорее всего, ваши проекты печати предметов своими руками будут выполнены из пластика.По-прежнему, будущее, мой мальчик, , с использованием столь оклеветанного синтетического твердого вещества практически неизбежно, когда дело доходит до большей части аддитивного производства. Это не значит, что все пластики плохие — PLA, один из двух пластиков, в основном используемых в 3D-печати на основе экструзии, получают из возобновляемых источников, включая кукурузный крахмал и тапиоку, — но их все еще трудно продать, учитывая, что только 23% 50 миллиардов пластиковых бутылок с водой, которые американцы используют каждый год, перерабатываются.
Precious Plastic , набор «пластиковых машин», созданный для мелкомасштабной переработки пластика своими руками, призван изменить все это: созданный дизайнером Дэйвом Хаккенсом из известности Phonebloks, инъекция , ротация , экструзия , и шредер — четыре жизнеспособных механических ответа на постоянно актуальный вопрос: «Что мне делать со всем этим пластиком?»
Вот объяснение Хаккенса:
Важно отметить, что такого рода машины не «новые», а, скорее, являются адаптацией стандартов пластмассовой промышленности для условий домашней мастерской.По словам Хаккенса: «Литье под давлением — наиболее часто используемая технология в пластмассовой промышленности. Обычно эти машины очень быстрые — [ инжекция ] намного медленнее и более ручная, но все же может производить продукт каждые пару минут. Вставленный пластик нагревается, а затем прессуется в форму ».
Проще говоря, эти машины могут произвести революцию в переработке вторичного сырья, сделав его домашним решением для постфордианского скопления контейнеров на вынос.
Экструзия , еще одна машина Хаккенса, в конечном итоге может быть использована для производства нитей для 3D-печати.«Пластмассовый измельчитель помещается в ведро, — объясняет Хаккенс, — винт внутри трубки прижимает хлопья вперед, и нагревательные элементы плавят пластик по пути. Результатом этого процесса является линия формованного пластика — форма зависит от форма сопла «.
Теоретически можно было бы даже перепечатать с неисправными, поврежденными или опечатанными формовками — запретами индустрии аддитивного производства, в надежде сделать 3D-печать поистине безотходным процессом.
Хаккенс объясняет: «Пока весь этот проект все еще находится в разработке, машины находятся в открытом доступе онлайн и улучшаются сообществом.[…] Наша цель — вместе разработать совершенное оборудование для производства пластмасс и поделиться этим открытым исходным кодом в Интернете. Мы хотим, чтобы люди во всем мире могли загружать проекты, создавать эти машины и открывать местный центр по переработке пластика. В этих центрах местные пластиковые отходы собираются, превращаются в новые продукты, что позволяет превращать пластиковые отходы в новые продукты ».
По сути, будущее переработки и 3D-печати стало еще ярче. Ниже, Дэйва Хаккенса. Precious Plastic , машины, их чертежи и продукция, на которую они способны:
Посетите PreciousPlastic.com, чтобы узнать больше о революционных машинах для вторичной переработки Дэйва Хаккенса. h / t designboom
Связано:
Autodesk 3D-печатает будущий горизонт Сан-Франциско
[видео] Crystal Nano Flowers и будущее архитектурной химии
Великие планы Фредини по сохранению острова Кони Forever By 3D Printing It
Что такое 3D-печать? Как работает 3D-принтер? Изучите 3D-печать
3D-печать или аддитивное производство — это процесс создания трехмерных твердых объектов из цифрового файла.
Создание объекта 3D-печати осуществляется с помощью аддитивных процессов. В аддитивном процессе объект создается путем наложения последовательных слоев материала до тех пор, пока объект не будет создан. Каждый из этих слоев можно рассматривать как тонко срезанное поперечное сечение объекта.
3D-печать — это противоположность субтрактивного производства, при котором вырезают / выдалбливают кусок металла или пластика, например, на фрезерном станке.
3D-печать позволяет изготавливать сложные формы с использованием меньшего количества материала, чем традиционные методы производства.
Присоединяйтесь к нашему списку рассылкиНаша информационная рассылка бесплатна, и вы можете отказаться от подписки в любое время.
Как работает 3D-печать?
Все начинается с 3D-модели. Вы можете создать его с нуля или загрузить из 3D-библиотеки.
Программное обеспечение 3D
Доступно множество различных программных инструментов. От промышленного уровня до открытого исходного кода. Мы создали обзор на нашей странице программного обеспечения для 3D.
Мы часто рекомендуем новичкам начать с Tinkercad.Tinkercad бесплатен и работает в вашем браузере, вам не нужно устанавливать его на свой компьютер. Tinkercad предлагает уроки для начинающих и имеет встроенную функцию для экспорта вашей модели в виде файла для печати, например .STL или .OBJ.
Теперь, когда у вас есть файл для печати, следующий шаг — подготовить его для вашего 3D-принтера. Это называется нарезкой.
Нарезка: от файла для печати к 3D-принтеру
Нарезка в основном означает разбиение 3D-модели на сотни или тысячи слоев и выполняется с помощью программного обеспечения для нарезки.
Когда ваш файл нарезан, он готов для вашего 3D-принтера. Загрузку файла на принтер можно выполнить через USB, SD или Wi-Fi. Теперь ваш нарезанный файл готов к 3D-печати слой за слоем .
Промышленность 3D-печати
Внедрение 3D-печати достигло критической массы, поскольку те, кому еще предстоит интегрировать аддитивное производство в свою цепочку поставок, теперь являются частью постоянно сокращающегося меньшинства. Если на ранних этапах 3D-печать подходила только для создания прототипов и разового производства, то сейчас она быстро превращается в производственную технологию.
Большая часть текущего спроса на 3D-печать носит промышленный характер. Acumen Research and Consulting прогнозирует, что к 2026 году мировой рынок 3D-печати достигнет 41 миллиарда долларов.
По мере своего развития технология 3D-печати призвана преобразовать практически все основные отрасли и изменить наш образ жизни, работы и развлечений в будущем.
Примеры 3D-печати
3D-печать включает в себя множество форм технологий и материалов, поскольку 3D-печать используется практически во всех отраслях, о которых вы можете подумать.Важно рассматривать его как кластер различных отраслей с множеством различных приложений.
Несколько примеров:
- — товары народного потребления (очки, обувь, дизайн, мебель)
- — продукция промышленного назначения (инструменты для изготовления, прототипы, функциональные части конечного использования)
- — Стоматологические изделия
- — протезирование
- — архитектурные макеты и макеты
- — реконструкция окаменелостей
- — копирование древних артефактов
- — реконструкция улик в судебной патологии
- — реквизит для фильмов
Быстрое прототипирование и быстрое производство
Компании использовали 3D-принтеры в процессе проектирования для создания прототипов с конца семидесятых. Использование 3D-принтеров для этих целей называется быстрое прототипирование .
Зачем использовать 3D-принтеры для быстрого прототипирования?
Вкратце: это быстро и относительно дешево. От идеи до 3D-модели и до прототипа в руках — вопрос дней, а не недель. Итерации проще и дешевле производить, и вам не нужны дорогие формы или инструменты.
Помимо быстрого прототипирования, 3D-печать также используется для быстрого производства . Быстрое производство — это новый метод производства, при котором предприятия используют 3D-принтеры для мелкосерийного / мелкосерийного производства по индивидуальному заказу.
История по теме
3D-печать как производственная технология
Автомобильная промышленность
Производители автомобилей уже давно используют 3D-печать. Автомобильные компании печатают запасные части, инструменты, приспособления и приспособления, а также детали конечного использования. 3D-печать позволила производить продукцию по запросу, что привело к снижению уровня запасов и сокращению циклов проектирования и производства.
Автомобильные энтузиасты по всему миру используют детали, напечатанные на 3D-принтере, для восстановления старых автомобилей.Один из таких примеров — когда австралийские инженеры напечатали детали, чтобы вернуть к жизни Delage Type-C. При этом им приходилось печатать детали, которые не выпускались десятилетиями.
История по теме
Как 3D-печать меняет автомобилестроение
Авиация
Авиационная промышленность использует 3D-печать по-разному. Следующий пример знаменует собой важную веху в производстве 3D-печати: GE Aviation напечатала на 3D-принтере 30 000 кобальто-хромовых топливных форсунок для своих авиационных двигателей LEAP.Они достигли этого рубежа в октябре 2018 года, и, учитывая, что они производят 600 принтеров в неделю на сорока 3D-принтерах, это, вероятно, намного выше, чем сейчас.
Около двадцати отдельных деталей, которые ранее приходилось сваривать, были объединены в один компонент, напечатанный на 3D-принтере, который весит на 25% меньше и в пять раз прочнее. Двигатель LEAP является самым продаваемым двигателем в аэрокосмической отрасли из-за его высокого уровня эффективности, и GE экономит 3 миллиона долларов на самолет за счет 3D-печати топливных форсунок, поэтому эта единственная 3D-печатная деталь приносит сотни миллионов долларов финансовой выгоды.
Топливные форсунки GE также попали в Boeing 787 Dreamliner, но это не единственная деталь, напечатанная на 3D-принтере в 787. Конструктивные элементы длиной 33 сантиметра, которые крепят кормовой кухонный гарнитур к планеру, напечатаны на 3D-принтере компанией под названием Norsk Titanium. Компания Norsk решила специализироваться на титане, поскольку он имеет очень высокое соотношение прочности и веса и является довольно дорогостоящим, а это означает, что сокращение отходов за счет 3D-печати оказывает более значительное финансовое воздействие, чем по сравнению с более дешевыми металлами, где затраты на отходы материалов равны легче впитывается.Вместо того, чтобы спекать металлический порошок с помощью лазера, как в большинстве металлических 3D-принтеров, Norsk Merke 4 использует плазменную дугу для плавления металлической проволоки в процессе, называемом Rapid Plasma Deposition (форма направленного энергетического осаждения), который может наносить до 10 кг титана. в час. Для изготовления 2-килограммовой титановой детали обычно требуется 30-килограммовый блок титана, что дает 28 кг отходов, но для 3D-печати той же детали требуется всего 6 кг титановой проволоки.
История по теме
GE получает сертификат летной годности USAF для Metal AM Critical Part
Строительство
Можно ли распечатать здание? — Да, это. 3D-печатные дома уже доступны в продаже. Некоторые компании печатают сборные детали, а другие делают это на месте.
История по теме
Здание для получения композитного фасада произвольной формы на 3D-принтере
Большинство статей о печати на бетоне, которые мы рассматриваем на этом веб-сайте, сосредоточены на крупномасштабных системах печати на бетоне с довольно большими соплами для большой скорости потока. Он отлично подходит для быстрой и повторяемой укладки бетонных слоев. Но для действительно сложной бетонной работы, в которой в полной мере используются возможности 3D-печати, требуется что-то более проворное и более тонкое.
История по теме
Производство добавок к бетону усложняется
Потребительские товары
Когда мы впервые начали вести блог о 3D-печати в 2011 году, 3D-печать не была готова к использованию в качестве метода производства для больших объемов. В настоящее время существует множество примеров потребительских товаров, предназначенных для конечного использования на 3D-принтере.
Обувь
Линия 4D Adidas имеет полностью напечатанную на 3D-принтере межподошву и печатается в больших объемах.Тогда мы написали статью, в которой объясняли, как Adidas изначально выпускал для широкой публики всего 5000 пар обуви и намеревался продать к 2018 году 100000 пар обуви, наполненной AM.
С их последними версиями обуви кажется, что они превзошли эту цель или находятся на пути к ее достижению. Обувь доступна по всему миру в местных магазинах Adidas, а также в различных сторонних онлайн-магазинах.
История по теме
Кроссовки с 3D-принтом в 2021 году
Очки
Прогнозируется, что рынок очков, напечатанных на 3D-принтере, достигнет 3 долларов.4 миллиарда к 2028 году. Быстро увеличивающийся раздел — это рамы для конечного использования. 3D-печать является особенно подходящим методом производства оправ для очков, потому что измерения человека легко обрабатываются в конечном продукте.
История по теме
Fitz Frames 3D-печать детских очков с помощью приложения
Но знаете ли вы, что линзы можно также печатать на 3D-принтере? Традиционные стеклянные линзы не кажутся тонкими и легкими; они вырезаны из гораздо более крупного куска материала, называемого заготовкой, около 80% которого уходит в отходы.Если учесть, сколько людей носит очки и как часто им нужно приобретать новую пару, 80% этих цифр — пустая трата времени. Вдобавок к этому лаборатории должны хранить огромные запасы заготовок для удовлетворения индивидуальных потребностей своих клиентов. Наконец, однако, технология 3D-печати достаточно продвинулась, чтобы предоставлять высококачественные офтальмологические линзы по индивидуальному заказу, избавляясь от прошлых затрат на отходы и складские запасы. В 3D-принтере Luxexcel VisionEngine используется акрилатный мономер, отверждаемый ультрафиолетом, для печати двух пар линз в час, которые не требуют какой-либо полировки или постобработки. Фокусные области также могут быть полностью настроены, так что определенная область линзы может обеспечивать лучшую четкость на расстоянии, в то время как другая область линзы обеспечивает лучшее видение вблизи.
История по теме
Линзы для 3D-печати для умных очков
Ювелирные изделия
Есть два способа изготовления украшений на 3D-принтере. Вы можете использовать прямой или косвенный производственный процесс. Прямое относится к созданию объекта прямо из 3D-дизайна, в то время как непрямое производство означает, что объект (шаблон), который напечатан на 3D-принтере, в конечном итоге используется для создания формы для литья по выплавляемым моделям.
Здравоохранение
В наши дни нередко можно увидеть заголовки об имплантатах, напечатанных на 3D-принтере. Часто эти случаи носят экспериментальный характер, и может показаться, что 3D-печать по-прежнему является второстепенной технологией в медицине и здравоохранении, но это уже не так. За последнее десятилетие GE Additive напечатала на 3D-принтере более 100000 замен тазобедренного сустава.
Чашка Delta-TT, разработанная доктором Гвидо Граппиоло и LimaCorporate, изготовлена из трабекулярного титана, который характеризуется регулярной трехмерной гексагональной структурой ячеек, имитирующей морфологию губчатой кости.Трабекулярная структура увеличивает биосовместимость титана, стимулируя рост кости в имплант. Некоторые из первых имплантатов Delta-TT все еще работают более десяти лет спустя.
Еще один компонент здравоохранения, напечатанный на 3D-принтере, который делает все возможное, чтобы быть необнаружимым, — это слуховой аппарат. Почти каждый слуховой аппарат за последние 17 лет был напечатан на 3D-принтере благодаря сотрудничеству между Materialise и Phonak. Компания Phonak разработала Rapid Shell Modeling (RSM) в 2001 году. До RSM для создания одного слухового аппарата требовалось девять трудоемких шагов, включая лепку вручную и изготовление форм, и результаты часто не подходили. В RSM технический специалист использует силикон для снятия слепка слухового прохода, этот слепок сканируется в 3D, и после некоторых незначительных корректировок модель печатается в 3D на полимерном 3D-принтере. Электроника добавляется и отправляется пользователю. С помощью этого процесса каждый год печатаются на 3D-принтере сотни тысяч слуховых аппаратов.
Стоматологическая
В стоматологической индустрии мы видим, что формы для прозрачных элайнеров, возможно, являются самыми трехмерными печатными объектами в мире. В настоящее время пресс-формы печатаются на 3D-принтере с использованием процессов 3D-печати на основе смолы и порошка, а также методом струйной печати.Коронки и зубные протезы уже напрямую напечатаны на 3D-принтере вместе с хирургическими шаблонами.
История по теме
3 способа 3D-печати революционизируют цифровую стоматологию
Биопечать
В начале двухтысячного периода технология 3D-печати изучалась биотехнологическими фирмами и академическими кругами для возможного использования в тканевой инженерии, где органы и части тела строятся с использованием струйных технологий. Слои живых клеток наносятся на гелевую среду и медленно наращиваются, образуя трехмерные структуры.Мы называем эту область исследований термином: биопечать.
История по теме
Сотрудничество в отрасли открывает путь к созданию легких, напечатанных на 3D-принтере
Продукты питания
Аддитивное производство давно вторглось в пищевую промышленность. Такие рестораны, как Food Ink и Melisse, используют это как уникальный торговый аргумент для привлечения клиентов со всего мира.
Образование
Педагоги и студенты уже давно используют 3D-принтеры в классе.3D-печать позволяет студентам быстро и доступно воплощать свои идеи в жизнь.
В то время как дипломы, связанные с аддитивным производством, довольно новы, университеты уже давно используют 3D-принтеры в других дисциплинах. Есть много образовательных курсов, которые можно пройти, чтобы заняться 3D-печатью. Университеты предлагают курсы по смежным с 3D-печатью предметам, таким как САПР и 3D-дизайн, которые на определенном этапе можно применить к 3D-печати.
Что касается прототипов, многие университетские программы обращаются к принтерам.Есть специализации в аддитивном производстве, которые можно получить, получив степень в области архитектуры или промышленного дизайна. Печатные прототипы также очень распространены в искусстве, анимации и моде.
История по теме
3D-печать в образовании
Типы технологий и процессов 3D-печати
Американское общество испытаний и материалов (ASTM) разработало набор стандартов, которые классифицируют процессы аддитивного производства по 7 категориям.Это:
- НДС Фотополимеризация
- Стереолитография (SLA)
- Цифровая обработка света (DLP)
- Непрерывное производство раздела жидкостей (CLIP)
- Струйная обработка материалов
- Распыление связующего
- Экструзия материалов
- Моделирование наплавленного осаждения (FDM)
- Производство плавленых волокон (FFF)
- Порошковая кровать Fusion
- Многоструйная сварка (MJF)
- Селективное лазерное спекание (SLS)
- Прямое лазерное спекание металла (DMLS)
- Ламинирование листа
- Направленное распределение энергии
НДС Фотополимеризация
3D-принтер, основанный на методе фотополимеризации в чане, имеет контейнер, заполненный фотополимерной смолой.Смола затвердевает под воздействием УФ-излучения.
Схема фотополимеризации чана. Источник изображения: lboro.ac.ukСтереолитография (SLA)
SLAбыл изобретен в 1986 году Чарльзом Халлом, который в то же время основал компанию 3D Systems. В стереолитографии используется емкость с жидкой отверждаемой фотополимерной смолой и ультрафиолетовый лазер для создания слоев объекта по одному. Для каждого слоя лазерный луч отслеживает поперечное сечение узора детали на поверхности жидкой смолы.Воздействие ультрафиолетового лазерного излучения отверждает и укрепляет рисунок, нанесенный на смолу, и сплавляет его с нижележащим слоем.
После того, как рисунок был нанесен, платформа подъемника SLA спускается на расстояние, равное толщине одного слоя, обычно от 0,05 до 0,15 мм (от 0,002 до 0,006 дюйма). Затем лезвие, заполненное смолой, проходит по поперечному сечению детали, повторно покрывая его свежим материалом. На этой новой поверхности жидкости прослеживается рисунок последующего слоя, соединяющий предыдущий слой.В зависимости от ориентации объекта и печати SLA часто требует использования вспомогательных структур.
Цифровая обработка света (DLP)
DLP или цифровая обработка света относится к методу печати, в котором используются свет и светочувствительные полимеры. Хотя он очень похож на SLA, ключевым отличием является источник света. DLP использует другие источники света, например дуговые лампы. DLP относительно быстр по сравнению с другими технологиями 3D-печати.
Непрерывное производство раздела жидкостей (CLIP)
Один из самых быстрых процессов с использованием фотополимеризации в ванне называется CLIP, сокращение от Continuous Liquid Interface Production , разработанный Carbon.
Цифровой синтез света
В основе процесса CLIP лежит технология Digital Light Synthesis . В этой технологии свет от настраиваемого высокопроизводительного светодиодного источника света проецирует последовательность УФ-изображений, обнажающих поперечное сечение 3D-печатной детали, что приводит к частичному отверждению УФ-отверждаемой смолы точно контролируемым образом. Кислород проходит через проницаемое для кислорода окно, создавая тонкую жидкую поверхность раздела неотвержденной смолы между окном и печатной частью, известную как мертвая зона.Мертвая зона составляет всего десять микрон. Внутри мертвой зоны кислород не позволяет свету отверждать смолу, расположенную ближе всего к окну, тем самым обеспечивая непрерывный поток жидкости под печатной частью. Прямо над мертвой зоной направленный вверх ультрафиолетовый свет вызывает каскадное отверждение детали.
Простая печать с использованием одного только оборудования Carbon не позволяет реализовать свойства конечного использования в реальных приложениях. После того, как свет сформировал деталь, второй программируемый процесс отверждения позволяет достичь желаемых механических свойств путем запекания детали, напечатанной на 3D-принтере, в термальной ванне или духовке.Программируемое термическое отверждение задает механические свойства, вызывая вторичную химическую реакцию, заставляющую материал укрепляться, достигая желаемых конечных свойств.
Компоненты, напечатанные с использованием технологии Carbon, соответствуют деталям, изготовленным методом литья под давлением. Цифровой синтез света обеспечивает стабильные и предсказуемые механические свойства, создавая действительно изотропные детали.
Струйная очистка материала
В этом процессе материал наносится каплями через сопло малого диаметра, аналогично тому, как работает обычный струйный бумажный принтер, но он наносится слой за слоем на платформу для сборки, а затем затвердевает под воздействием ультрафиолетового излучения.
Схема струйной печати материалов. Источник изображения: custompartnet.comBinder Jetting
При нанесении связующего используются два материала: порошковый основной материал и жидкое связующее. В камере формирования порошок распределяется равными слоями, а связующее наносится через форсунки, которые «склеивают» частицы порошка в требуемой форме. После завершения печати оставшийся порошок счищается, и его можно повторно использовать для печати следующего объекта. Эта технология была впервые разработана в Массачусетском технологическом институте в 1993 году.
Схема Binder JettingЭкструзия материала
Моделирование наплавления (FDM)
Схема FDM (Изображение предоставлено Википедией, сделанное пользователем Zureks)FDM работает с использованием пластиковой нити, которая разматывается с катушки и подается на экструзионное сопло, которое может включать и выключать поток. Сопло нагревается для плавления материала и может перемещаться как в горизонтальном, так и в вертикальном направлении с помощью механизма с числовым программным управлением. Изделие изготавливается путем экструзии расплавленного материала с образованием слоев, поскольку материал затвердевает сразу после экструзии из сопла.
FDM был изобретен Скоттом Крампом в конце 80-х. После патентования этой технологии он основал компанию Stratasys в 1988 году. Термин Fused Deposition Modeling и его аббревиатура FDM являются товарными знаками Stratasys Inc.
.Производство плавленых волокон (FFF)
Точно эквивалентный термин, Fused Filament Fabrication (FFF), был придуман участниками проекта RepRap, чтобы дать фразу, использование которой не ограничивалось бы законом.
Порошковая кровать Fusion
Селективное лазерное спекание (SLS)
SLS использует лазер высокой мощности для сплавления мелких частиц порошка в массу, которая имеет желаемую трехмерную форму.Лазер избирательно плавит порошок, сначала сканируя поперечные сечения (или слои) на поверхности порошкового слоя. После сканирования каждого поперечного сечения слой порошка опускается на один слой. Затем поверх наносится новый слой материала и процесс повторяется до тех пор, пока объект не будет готов.
Схема SLS (Изображение предоставлено Википедией от пользователя Materialgeeza)Multi Jet Fusion (MJF)
ТехнологияMulti Jet Fusion была разработана Hewlett Packard и работает с подметающим рычагом, который наносит слой порошка, а затем с другим рычагом, оснащенным струйными форсунками, который выборочно наносит связующее на материал.Кроме того, струйные принтеры наносят детализирующий агент вокруг связующего для обеспечения точных размеров и гладкости поверхностей. Наконец, слой подвергается выбросу тепловой энергии, которая вызывает реакцию агентов.
Прямое лазерное спекание металла (DMLS)
DMLS в основном такой же, как SLS, но вместо него используется металлический порошок. Весь неиспользованный порошок остается как есть и становится опорной структурой для объекта. Неиспользованный порошок можно повторно использовать для следующего отпечатка.
Из-за повышенной мощности лазера DMLS превратился в процесс лазерного плавления.Подробнее об этой и других технологиях обработки металлов читайте на нашей странице с обзором технологий обработки металлов.
История по теме
3D-печать на металле: обзор наиболее распространенных типов
Лист для ламинирования
При ламинировании листов используется материал в листах, который скрепляется внешней силой. Листы могут быть металлическими, бумажными или полимерными. Металлические листы свариваются между собой послойно ультразвуковой сваркой, а затем фрезерованием на станке с ЧПУ придают нужную форму. Также можно использовать листы бумаги, но они склеиваются клеевым клеем и вырезаются по форме точными лезвиями.
Упрощенная схема ультразвуковой обработки листового металла (Изображение предоставлено Википедией от пользователя Mmrjf3)Направленное нанесение энергии
Этот процесс в основном используется в металлургической промышленности и в системах быстрого производства. Устройство для 3D-печати обычно прикрепляется к многоосной роботизированной руке и состоит из сопла, которое наносит металлический порошок или проволоку на поверхность, и источника энергии (лазер, электронный луч или плазменная дуга), который плавит его, образуя твердый объект.
Направленное осаждение энергии с помощью металлического порошка и лазерного плавления (Изображение предоставлено: проект Merlin)Материалы
В аддитивном производстве можно использовать несколько материалов: пластмассы, металлы, бетон, керамику, бумагу и некоторые продукты питания (например,г.