Сварочные электроды
Электроды изготавливаются из электропроводного материала и предназначены для подвода электрического тока к месту сварки. Виды электродов:
- металлические – стальные, чугунные, медные, латунные, вольфрамовые, бронзовые и др.;
- неметаллические (неплавящиеся) – угольные и графитовые электроды.
- плавящиеся металлические электроды – покрытые и комбинированные электроды, сварочные пластины и ленты сплошного сечения;
- неплавящиеся металлические электроды – электродные стержни из вольфрама, электроды для контактной сварки;
Покрытые электроды для ручной дуговой сварки
Покрытые электроды для ручной сварки представляют собой стержни длиной, как правило, от 250 до 700 мм, изготовленные из сварочной проволоки с нанесенным на нее слоем покрытия. Один из концов электрода длиной 20–30 мм не имеет покрытия для его крепления в электрододержателе.
Длина электрода зависит от его диаметра и химического состава стержня. Например, стержни малого диаметра, состоящие из высоколегированных сталей, делаются более короткими, чтобы уменьшить электрическое сопротивление (и нагрев) при сварке, а стержни малого диаметра из низкоуглеродистых сталей обладают высокой электропроводностью и, следовательно, могут быть длинными.
Сварочные электроды должны обеспечивать:
- устойчивое горение дуги, равномерное плавление металла и стабильный перенос его в сварочную ванну;
- достаточную защиту расплавленного электродного металла и металла сварочной ванны от воздуха;
- получение металла шва требуемого химического состава и механических свойств;
- хорошее формирование шва, минимальные потери на угар и разбрызгивание;
- возможно высокую производительность процесса сварки;
- хорошую отделимость и легкую удаляемость шлака с поверхности шва;
- достаточную стойкость покрытий против механических повреждений (осыпание, откалывание при относительно легких ударах, в процессе нагрева электрода при сварке и др.
) и недопустимость резкого ухудшения свойств в процессе хранения;
- минимальную токсичность газов, выделяющихся при сварке, соблюдение санитарно-гигиенических норм.
Данные требования обеспечиваются благодаря подбору компонентов покрытия электрода. Вещества, из которых состоит покрытие, можно разделить на следующие группы.
Газообразующие компоненты
Шлакообразующие компоненты обеспечивают шлаковую защиту расплавленного и кристаллизующегося металла от воздуха. При расплавлении они образуют шлак, который всплывает на поверхность сварочной ванны. Шлаком также покрыты капли электродного металла. Шлакообразующие компоненты (кислые окислы SiO2, TiO2, Al2O3; основные окислы CaO, MnO, MgO; галогены CaF2) содержатся в мраморе, граните, гематите, кварцевом песке, рудах, ильменитовом и рутиловом концентрате.
Раскисляющие компоненты позволяют восстановить часть металла, находящегося в сварочной ванне в виде оксидов. К ним относятся железосодержащие соединения – ферромарганец, ферротитан и ферросилиций.
Стабилизирующие компоненты обеспечивают стабильное горение дуги за счет присутствия в них элементов с низким потенциалом ионизации – натрия, калия, кальция и др. Последние содержатся в мраморе, меле, полевом шпате, кальцинированной соде, поташе и других веществах.
Легирующие компоненты придают металлу шва дополнительные свойства, например, повышенную прочность, коррозионную стойкость и др. Добавляются в покрытие в виде железосодержащих сплавов – феррохрома, ферротитана, феррованадия. Основным способом легирования металла шва является легирование через стержень электрода, дополнительным – через покрытие.
Связующие компоненты связывают порошковые материалы покрытия в однородную массу.
Добавление в покрытие железного порошка (до 60% от массы покрытия) позволяет повысить производительность сварки.
Некоторые материалы покрытия выполняют несколько функций. Например, мрамор является газообразующим, шлакообразующим и стабилизирующим минералом.
Покрытия сварочных электродов
Электродные покрытия могут создаваться по-разному. В одних возможно преобладание газообразующих компонентов, в других – шлакообразующих. В качестве газообразующих компонентов могут применяться минералы или органические соединения. Выведение из металла шва водорода может осуществляться с помощью фтора или кислорода. В различной степени может выполняться очистка металла шва от нежелательных включений, в том числе от фосфора и серы.
В зависимости от используемого подхода выделяют четыре базовых типа покрытия.
Кислое покрытие (обозначается по ГОСТ 9466-75 буквой «А») создается на основе материалов рудного происхождения. В качестве шлакообразующих компонентов используются оксиды, газообразующих – органические составляющие. При плавлении покрытия в расплавленном металле и в зоне горения дуги выделяется большое количество кислорода. Поэтому в покрытие добавляют много раскислителей – марганца и кремния.
Преимущества кислого покрытия электродов:
- низкая склонность к образованию пор при удлинении дуги и при сварке металла с окалиной и ржавыми кромками;
- высокая производительность сварки за счет выделения теплоты при окислительных реакциях;
- стабильное горение дуги при сварке на постоянном и переменном токе.
К недостаткам этого покрытия относятся пониженные пластичность и ударная вязкость металла шва, что связано с невозможностью легирования шва из-за окисления легирующих добавок. Ввиду отсутствия в покрытии кальция в металле шва присутствуют сера и фосфор, повышающие вероятность образования кристаллизационных трещин. Одним из главных недостатков данного покрытия является выделение большого количества вредных примесей вследствие повышенного содержания в аэрозолях соединений марганца и кремния. Поэтому сварочные электроды с кислым покрытием используются в последнее время редко.
Область применения электродов с кислым покрытием – сварка неответственных конструкций из низкоуглеродистых сталей.
Основное покрытие (обозначается по ГОСТ 9466-75 буквой «Б») создается на основе фтористых соединений (плавиковый шпат CaF2), а также карбонатов кальция и магния (мрамор CaCO3, магнезит MgCO3 и доломит CaMg(CO3)2). Газовая защита осуществляется за счет углекислого газа, который выделяется при разложении карбонатов:
CaCO3 → CaO + CO2
С помощью кальция металл шва хорошо очищается от серы и фосфора. Фтор вводится в ограниченных количествах (чтобы сохранить стабильность горения дуги) и связывает водород и пары воды в термические стойкие соединения:
CaF2 + H2O → CaO + 2HF
2CaF2 + 3SiO2 → 2CaSiO3 + SiF4
SiF4 + 3H → SiF + 3HF
Из-за низкого содержания водорода в металле шва сварочные электроды с основным покрытием также называют «низководородными».
Преимущества основного покрытия электродов:
- низкая вероятность образования кристаллизационных трещин, высокая пластичность и ударная вязкость металла шва, обусловленные малым содержанием в наплавленном металле кислорода и водорода, а также его хорошим рафинированием;
- высокая стойкость против хладноломкости – появлению или возрастанию хрупкости с понижением температуры;
- широкие возможности легирования ввиду низкой окислительной способности покрытий;
- меньшая токсичность по сравнению с кислыми покрытиями;
- повышенный коэффициент наплавки при введении железного порошка.
Недостатки основного покрытия:
- склонность к образованию пор при увеличении длины дуги, повышении влажности покрытия, наличии ржавчины и окалины на свариваемых кромках, что требует более высокой квалификации сварщика, а также необходимости в предварительной очистке кромок и прокалке электродов перед сваркой;
- более низкая устойчивость горения дуги из-за фтора, имеющего высокий потенциал ионизации, в связи с чем сварку электродами с основным покрытием обычно выполняют короткой дугой на постоянном токе обратной полярности.
Область применения электродов с основным покрытием:
- сварка ответственных конструкций из углеродистых сталей, работающих при знакопеременных нагрузках или отрицательных температурах до -70°C;
- сварка конструкционных, жаропрочных, коррозионно-стойких, окалиностойких, а также других специальных сталей и сплавов;
- сварка легированных сталей.
В связи с присутствием в аэрозолях фтористых соединений при сварке в закрытом помещении необходимо обеспечение качественной вентиляции воздуха, а сварщикам рекомендуется работать со средствами индивидуальной защиты дыхательных органов или с подачей чистого воздуха в зону дыхания.
Рутиловое покрытие (обозначается по ГОСТ 9466-75 буквой «Р») создается на базе рутилового концентрата TiO2, обеспечивающего шлаковую защиту, а также алюмосиликатов (полевой шпат, слюда, каолин) и карбонатов (мрамор, магнезит). Газовую защиту обеспечивают карбонаты и органические соединения (целлюлоза). В качестве легирующего компонента и раскислителя используется ферромарганец, в некоторые покрытия вводится железный порошок (обозначаются по ГОСТ 9466-75 буквами«РЖ»). С помощью кальция, присутствующего в карбонате CaCO3, из металла шва удаляются сера и фосфор.
Преимущества сварочных электродов с рутиловым покрытием:
- более высокий коэффициент наплавки при введении железного порошка;
- низкая токсичность;
- по сравнению с электродами с основным покрытием – стабильность горения дуги при сварке на постоянном и переменном токе, более высокая стойкость против образования пор, лучшее формирование шва с плавным переходом к основному металлу, меньшая чувствительность к увеличению длины дуги, меньше коэффициент разбрызгивания металла, более удобная сварка в вертикальном и потолочном положениях (при отсутствии в них железного порошка или его содержании менее 20%).
Недостатки электродов с рутиловым покрытием:
- пониженные пластичноcть и ударная вязкость металла шва из-за включений SiO2;
- не используются для сварки конструкций, работающих при высоких температурах;
- по сравнению с электродами с основным покрытием – меньшее сопротивление наплавленного металла сероводородному растрескиванию, приводящего к разрушению сварных трубопроводов в месторождениях с сероводородными соединениями; ниже стойкость против кристаллизационных трещин; сильнее окисляют легирующие элементы и железо и поэтому не используются для сварки средне- и высоколегированных сталей; повышенное содержание фосфора в наплавленном металле и склонность к хладноломкости.
Область применения сварочных электродов с рутиловым покрытием:
- сварка и наплавка ответственных конструкций из низкоуглеродистых и некоторых типов низколегированных сталей, за исключением конструкций, работающих при высоких температурах;
- в ряде случаев для сварки среднеуглеродистых сталей, если в покрытии содержится большое количество железного порошка.
Целлюлозное покрытие (обозначается по ГОСТ 9466-75 буквой «Ц») создается на основе органических соединений (до 50%) – целлюлозы, муки, крахмала, обеспечивающих газовую защиту. Для шлаковой защиты в небольшом количестве применяются рутиловый концентрат, мрамор, карбонаты, алюмосиликаты и другие вещества. На сварном шве образуется тонкий слой шлака. Легирование наплавленного металла выполняется легирующими добавками стержня, а также за счет добавления в покрытие ферросплавов и металлических порошков. В качестве раскислителей используют ферросплавы марганца. Металл шва по химическому составу соответствует полуспокойной или спокойной стали.
Преимущества сварочных электродов с целлюлозным покрытием:
- качественный провар корня шва;
- возможность сварки в труднодоступных местах в связи с малой толщиной покрытия;
- сварка во всех пространственных положениях.
Недостатки целлюлозного покрытия:
- повышенное разбрызгивание (до 15%) из-за небольшого количества шлакообразующих компонентов и высокого поверхностного натяжения расплавленного металла;
- повышенное количество водорода в металле шва.
Область применения электродов с целлюлозным покрытием – сварка первого (труднодоступного) слоя неповоротных стыков трубопроводов.
Также используются и смешанные покрытия: кислорутиловое (обозначается по ГОСТ 9466-75 буквами «АР»), рутилово-основное (обозначается по ГОСТ 9466-75 буквами«РБ»), рутилово-целлюлозное (обозначается по ГОСТ 9466-75 буквами «РЦ»), а также прочие (обозначаются по ГОСТ 9466-75 буквой «П»).
Таблица. Обозначение покрытий сварочных электродов
Тип покрытия | Обозначение по ГОСТ 9466-75 | Международное обозначение ISO | Старое обозначение по ГОСТ 9467-60 |
кислое | А | A | Р – руднокислое |
основное | Б | B | Ф – фтористокальциевое |
рутиловое | Р | R | Т – рутиловое (титановое) |
целлюлозное | Ц | C | О – органическое |
смешанные покрытия | |||
кислорутиловое | АР | AR | |
рутилово-основное | РБ | RB | |
рутилово-целлюлозное | РЦ | RC | |
прочие (смешанные) | П | S | |
рутиловые с железным порошком | РЖ | RR |
Тип сварочного электрода характеризует свойства металла шва. Для конструкционных сталей – это механические свойства (временное сопротивление разрыву, ударная вязкость, относительное удлинение, угол загиба), для легированных сталей со специальными свойствами (теплоустойчивые, жаропрочные, коррозионно-стойкие и др.) – химический состав (содержание углерода, кремния, хрома, марганца, никеля и других элементов). Обозначение типа электрода (регламентируется ГОСТ 9467-75 и ГОСТ 10052-75) содержит букву «Э», после которой ставится временное сопротивление на разрыв δВ(кг/мм2). Например, «Э46А» означает, что металл, наплавленный этими электродами, имеет прочность 46 кг/мм2 (460 МПа) и улучшенные пластические свойства. Для сварки легированных конструкционных сталей повышенной и высокой прочности тип электрода может быть Э70, Э85, Э100, Э125, Э150.
Примеры обозначений типа электрода для сварки сталей со специальными свойствами:
- «Э09Х2М» – в металле шва содержится примерно 0,09% углерода, 2% хрома, 1% молибдена;
- «Э10Х25Н13Г2Б» – в металле шва содержится примерно 0,1% углерода, 25% хрома, 13% никеля, 2% марганца, 1% ниобия.
Электроды покрытые
Электроды рекомендуют использовать при сварке, ремонте стальных конструкций из металла толщиной до 20 мм. Они позволяют выполнять сварку стыковых соединений с повышением зазором, а также при наличии на свариваемых кромках ржавчины, окалины и других поверхностных загрязнений.
Электроды АНО-36 отличаются легким начальным и повторным зажиганием, мягким и стабильныма горением дуги, обеспечивают малые потери металла от разбрызгивания, равномерное плавление покрытия, отличное формирование металла шва, легкую отделимость шлаковой корки. Электроды малочувствительны к качеству подготовки кромок, наличию ржавчины и других поверхностных т тзагрязнений. Электроды имеют герметическую трехслойную (полиэтилен-картон-полтэтилен) упаковку.
Транспортная тара – деревянные поддоны, обернутые стрейч-пленкой и затянутые полипроопиленовой лентой.
Электродное производство специализируется на изготовлении электродов для ручной дуговой сварки, используемых при сварке конструкций из углеродистых, низколегированных и высоколегированных сталей, а также для сварки чугуна и наплавки поверхностей с особыми свойствами.
Для изготовления электродов применяется проволока сварочная по ГОСТ 2246-70 следующих марок: Св-08, Св-08А, Св-08АА, Св-ЗОХ25Н16Г7, Св-01Х19Н9, Св-04Х19Н9 Св-07Х19Н10Б, Св-04х19Н11МЗ, Св-07Х25Н13, Св-06Х19Н10МЗТ. Технические требования к электродам приведены в таблице 1,2.
Упаковка электродов
Электроды упаковываются в коробки из картона для потребительской тары или равноценного ему по характеристикам и по согласованию с потребителем с последующей упаковкой каждой коробки в термоусадочную полиэтиленовую пленку.
Коробки с электродами укладываются или в ящики из гофрированого картона или в крупногабаритные деревянные ящики массой не более 1 100 кг.
Ящики из гофрированного картона пакетируются па деревянных поддонах размером 800×1200 мм с помощью металлической ленты.
Качество электродов
Качество электродов марок УОНИ-13/45, УОНИИ-13/45А, УОНИ-13/45СМ УОНИ-13/55, АНО-ТМ, УОНИ- 13/55М,УОНИ-13/55СМ подтверждено сертификате ом Морского Регистра Судоходства России, а марок УОНИ-13/55, УОНИИ- 13/45А и АНО-ТМ сертификатом Морского Регистра Ллойда (Англия).
Покрытые электроды для дуговой сварки и наплавки
S 3. СВАРОЧНЫЕ ПОКРЫТЫЕ ЭЛЕКТРОДЫ ДЛЯ ДУГОВОЙ СВАРКИ и НАПЛАВКИ [c.92]ПОКРЫТЫЕ ЭЛЕКТРОДЫ ДЛЯ ДУГОВОЙ СВАРКИ И НАПЛАВКИ [c.24]
Стальной электрод для дуговой сварки и наплавки состоит из проволочного стержня, покрытого специальной обмазкой. Различают тонкие или стабилизирующие покрытия (обмазки) и толстые или качественные. [c.190]
Электроды с толстым покрытием для дуговой сварки и наплавки конструкционной и легированной стали [c.182]
Стальные электроды применяются при дуговой электрической сварке конструкционных, легированных сталей, сталей с особыми свойствами, при сварке чугунов и при наплавке.
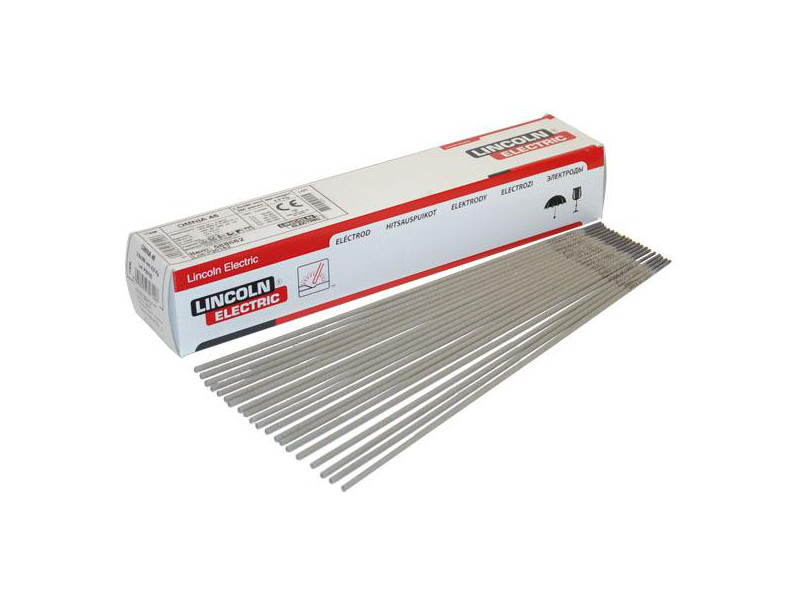
Электроды покрытые металлические для ручной дуговой сварки и наплавки. В соответствии с ГОСТ 9466—75 электроды подразделяют по назначению (буквами дано условное обозначение) [c.330]
Электроды для ручной дуговой сварки и наплавки представляют собой металлические стержни из сварочной проволоки по ГОСТ 2246—70, покрытые обмазками различного назначения. При восстановлении деталей автомобилей чаще всего используют проволоку из малоуглеродистой стали марок Св-08 и Св-08А. [c.93]
Наиболее распространенные компоненты покрытий электродов для ручной дуговой сварки и наплавки
[c. 93]
Ручную дуговую сварку и наплавку применяют для устранения небольших повреждений и восстановления деталей сложной формы. Электродом при ручной сварке и наплавке служит стальной стержень с покрытием (обмазкой). [c.119]
Покрытые электроды для ручной дуговой сварки и наплавки [c.66]
Электроды для дуговой сварки. Электроды должны иметь паспорт, в котором указываются его марка, тип и назначение, марки свариваемой стали и электродной проволоки, состав или группа покрытия, род тока, рекомендуемые режимы сварки, механические свойства металла шва, коэффициент наплавки, режимы сушки и Термообработки. [c.346]
Металлические электроды для дуговой сварки изготовляют Б соответствии с ГОСТ 9466—75 Электроды покрытые металлические для ручной дуговой сварки сталей и наплавки. Классификация, размеры и общие технические требования . Установленные этим ГОСТом размеры электродов следующие [c.141]
Покрытые металлические электроды для сварки и наплавки являются важнейшим и наиболее используемым видом сварочных материалов. Несмотря на интенсивное развитие механизированных и автоматических видов сварки, преобладающим способом изготовления сварных конструкций, как в нашей стране, так и за рубежом является дуговая сварка покрытыми металлическими электродами. В общем объеме производства сварных конструкций около 60 % изготовляется с применением ручной дуговой сварки.
[c.98]
ГОСТ на электроды. Общие требования ко всем металлическим плавящимся электродам для сварки стали и наплавки определяются ГОСТ 9466—60 Электроды металлические плавящиеся для дуговой сварки конструкционных и теплоустойчивых сталей . Длина электродов устанавливается в зависимости от диаметра металлического стержня и состава проволоки. Установлены следующие длины электродов (в мм) 225—250 350 400—450, Предусмотрены два типа электродов закрепляемые в электрододержателе, имеющие конец длиной 30 мм, очищенный от покрытия привариваемые к электроде-держателю, имеющие покрытие по всей длине стержня.
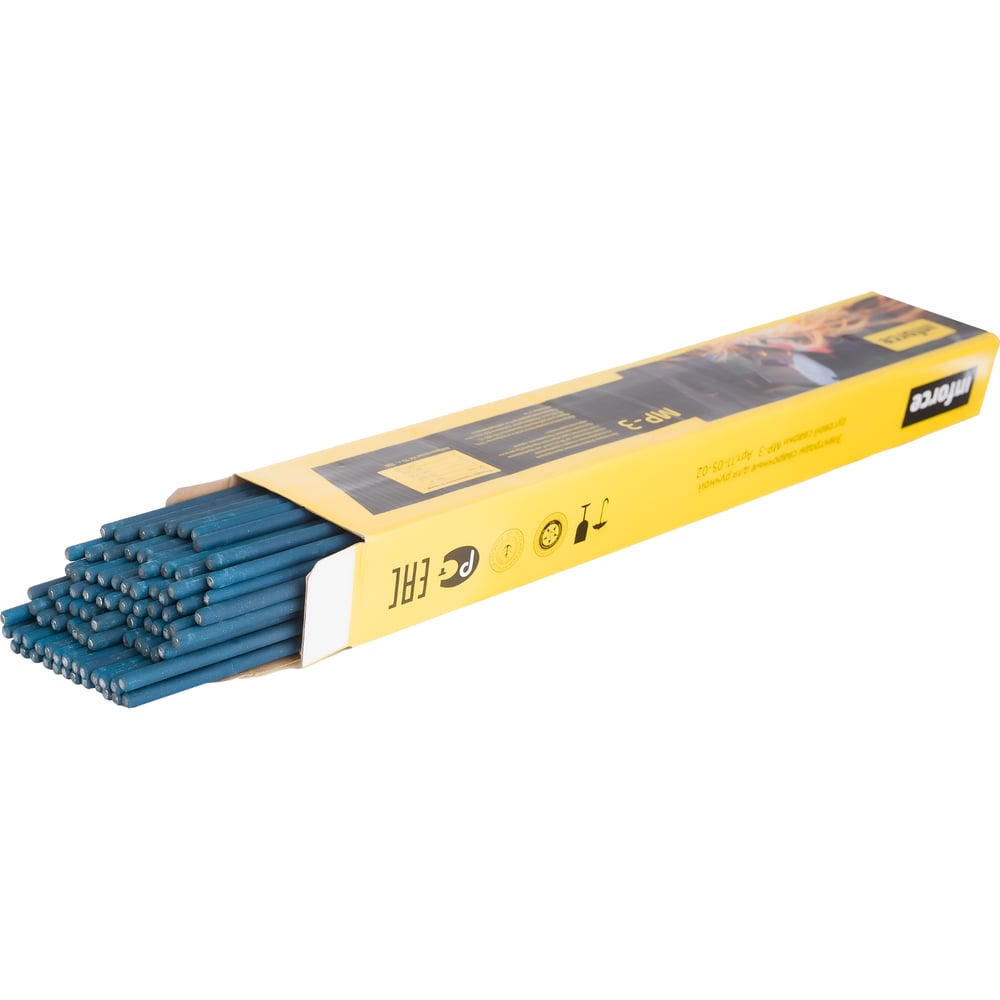
Металлические электроды, предназначенные для дуговой сварки, наплавки и резки металлов, как правило, имеют специальные покрытия (обмазки). Назначение покрытий—повышение устойчивости или стабилизации сварочной дуги п улучшение качества наплавленного металла. [c.127]
В соответствии с действующими стандартами покрытые электроды для ручной дуговой сварки сталей и наплавки классифицируются по различных признакам. [c.44]
Размеры и общие технические требования на покрытые металлические электроды для ручной дуговой сварки сталей и наплавки поверхностных слоев из сталей и сплавов приведены в ГОСТ 9466-75. [c.24]
Ручная дуговая сварка покрытыми электродами. Учитывая требования к свойствам сварного соединения, выбирается тип электрода, затем (см. гл. 2) по справочным данным или паспорту на электроды, где приводятся их технологические и другие показатели, с учетом условий выполнения сварки и имеющихся источников сварочного тока выбирается марка электрода. Часто выбор марки электродов производится сразу по их паспортным данным. В паспорте на электроды приводятся сведения о их назначении, типичные химический состав и механические свойства металла шва, технологические особенности сварки, рекомендуемые род и сила сварочного тока, производительность наплавки, расход электродов и др. Следует помнить, что химический состав металла шва по его длине изменяется. Это связано с нагревом электрода по мере его расплавления, а значит с изменением скорости его расплавления, т.е. изменяется уо. Геометрические размеры швов задаются по соответствующим ГОСТ или ТУ. Точность их исполнения зависит от квалификации сварщика и проверяется специальным шаблоном. При сварке многопроходных швов стыковых соединений первые проход (корневой) должен выполняться электродами диаметром 3.
.. 4 мм для удобства провара корня шва. Следует иметь ввиду, что максимальная площадь поперечного сечения металла шва, наплавленного за один проход 30. .. 40 мм . При сварке угловых швов, за один проход, рекомендуется выполнять швы с катетом 8. .. 9 мм. При необходимости выполнения швов с большим катетом применяется сварка за два прохода и более.
[c.242]
Структура условного обозначения покрытых металлических электродов для ручной дуговой наплавки поверхностных слоев с особыми свойствами установлена ГОСТ 9466-75 такой же, как и электродов для сварки сталей (рис. 4.5). [c.174]
Стандарт DIN 8555 регламентирует обозначение электродов для наплавки одновременно для щести основных видов сварки плавлением, а не только покрытых металлических электродов для ручной дуговой наплавки, как по ГОСТ 10051-75, поэтому в обозначении не указывают вид покрытия, род и полярность тока. Для каждого вида сварки устанавливают свой буквенный индекс (табл. 4. 47).
[c.175]
Размеры и общие технические требования на покрытые металлические электроды для ручной дуговой сварки сталей и наплавки приведены в ГОСТ 9466—75. [c.23]
Электроды покрытые металлические для ручной дуговой наплавки поверхностных слоев с особыми свойствами 24 —для ручной дуговой сварки конструкционных и теплоустойчивых сталей —= Назначение 25, 26 — Типы 23, 24 [c.557]
Эти металлы и сплавы приобретают все большее значение как конструкционные материалы. Вольфрам и молибден применяют для производства электро- и радиоламп, высоковольтных выпрямителей, рентгеновской, радио- и сварочной аппаратуры, электровакуумных приборов и пр. Из проволоки и прутков вольфрама изготовляют электроды горелок для аргоно-дуговой сварки, а из молибдена — электроды для плавки стекла, так как последний наиболее устойчив против жидкого стекла. Из лент и проволоки вольфрама и молибдена изготовляют нагревательные элементы для электропечей, способные работать при 1800—3000° С.

Сварочная проволока и электроды. Качество наплавленного материала и производительность процесса сварки или наплавки во многом определяются материалом электродов и их покрытий. В зависимости от способа сварки применяют сварочную проволоку, плавящиеся и неплавящиеся электродные стержни, пластины и ленты. Наибольшее применение в качестве электродного материала находит выпускаемая промышленностью электродная сварочная проволока. При механизированных способах сварки ее используют без покрытия, а для ручной дуговой сварки проволоку рубят на стержни длиной 350…400 мм и на их поверхность наносят покрытие. Плавящийся стержень с нанесенным на его поверхность покрытием называют сварочным электродом.
[c.71]
ГОСТ 9466—75 на электроды покрытые металлические для ручной дуговой сварки сталей и наплавки устанавливает некоторые характеристики электродных покрытий. По толщине нанесенного покрытия электроды подразделяются с тонким покрытием М при отношении 0/(1) ],2 (Д —диаметр электрода с покрытием, ё — диаметр стержня) со средним покрытием С при (Д/с ) 1,45 с толстым покрытием Д при (/)/й()> (1,45—1,8) с особо толстым покрытием Г при ОМ) >1,8. [c.134]
Наплавку меди или бронзы на стальные, медные и бронзовые детали осуществляют ручной дуговой сваркой покрытыми электродами, дуговой сваркой в инертных газах неплавящимися вольфрамовыми электродами и угольными электродами с применением защитного флюса, нанесенного на присадочный пруток. Для наплавки используют электроды со стержнем из меди или бронзы. Применяют электроды марки К-100 ( Комсомолец-100 ) со стержнем из меди М1 и покрытием, замешанным на жидком стекле и состоящим из ферромарганца (47,5%), полевого шпата (12,5 %), плавикового шпата (15 %) и кремнистой меди (20%). Этими электродами сваривают медные детали между собой или выполняют наплавку меди на сталь.
[c.262]
Классификация электродов. Классификацию и размеры электродов, технические требования к ним, правила приемки, методы испытаний, упаковку, транспортирование и хранение электродов для ручной дуговой сварки сталей и наплавки устанавливает ГОСТ 9466—75 ( Электроды покрытые металлические для ручной дуговой сварки сталей и наплавки ). [c.104]
Голландская фирма Филипс в 1946—1947 гг. начала изготовлять электроды с железным порошком в покрытии для сварки методом опирания. Такие же электроды, с содержанием 30—бО /о железного порошка, выпускаются в США, Англии, Франции, Бельгии и других странах. Они пользуются большим спросом, так как обладают повышенным коэффициентом наплавки и, следовательно, позволяют значительно повысить производительность ручной дуговой сварки (в некоторых случаях на 150— 180 /о) по сравнению со сваркой обычными электродами.
[c.90]
Электроды покрытые металлические для ручной дуговой сварки сталей и наплавки. [c.35]
ГОСТ 9466-75 в ред. 1997 г. распространяется на изготовленные способом опрессовки покрытые металлические электроды для ручной дуговой сварки сталей и наплавки поверхностных слоев из сталей и сплавов. Стандарт не распространяется на электроды для наплавки поверхностных слоев из цветных металлов и их сплавов. [c.35]
Электроды покрытые металлические для ручной дуговой сварки сталей и наплавки. Классификация, размеры и общие технические требования [c.458]
Классификация стальн.ых покрытых элек-т р о д о в. Металлические электроды для дуговой сварки сталей и наплавки изготовляют в соответствии с ГОСТ 9466-75 Электроды покрытые металлические для ручной дуговой сварки сталей и наплавки. Классификация, размеры и общие технические требования . Стальные покрытые электроды для ручной дуговой сварки и наплавки подразделяются по назначению (ГОСТ 9467-75)
[c. 50]
При сварке чугунных деталей применяют как газовую (для сложных деталей горячую с температурой нагрева 600—650° С), так и электродуговую (обычно холодную) сварку. Для растворения тугоплавких окислов при газовой сварке применяют флюсы. При холодной дуговой сварке используют специальные электроды и обмазки. С целью уменьшения отбела металла при сварке деталей из серого и ковкого чугуна применяют также газовую пайку присадочными прутками из цветных сплавов, имеющих температуру плавления ниже, чем у чугуна. Типы и марки электродов, сварочной проволоки и присадочных прутков, гзриме-няемых для сварки, наплавки и пайки автомобильных деталей из серого и ковкого чугуна, приведены в табл. 85. В табл. 86 дз1.ы составы покрытий специальных электродов для сварки чугуна, в табл. 87 указан химический состав чугунных присадочных прутков, а в табл. 88 — компоненты наиболее распространенных флюсов, применяемых для газовой сварки и наплавки чугунных деталей. [c.107]
На металлические электроды для ручной дуговой сварки и наплавки в стране действует четыре стандарта.


Условное обозначение электродов для дуговой сварки сталей и наплавки состоит из обозначения марки и типа электрода, диаметра стержня и номера стандарта. В условном обозначении электродов для сварки конструкционных и теплоустойчивых сталей указан также вид покрытия. Например, условное обозначение электрода АНО-7 Э50А-5,0-Ф ГОСТ 9467—60 расшифровывается следующим образом АНО-7 — марка электрода Э50А — тип электрода (Э — электрод для дуговой сварки, 50 — минимальное гарантируемое временное сопротивление металла шва в кгс/мм А — гарантирование получения повышенных пластических свойств металла шва) 5,0 — диаметр электродного стержня в мм Ф — фтористо-кальциевое покрытие ГОСТ 9467—60— номер стандарта на данный электрод. [c.308]
Покрытые электроды. Для наплавки различных деталей применяют электроды, предназначенные для сварки различных сталей и сплавов, и специальные электроды. Общие технические требования к металлическим электродам для дуговой сварки сталей и наплавки регламентированы ГОСТ 9466—60. ГОСТ 10051—62 предусматривает 25 типов электродов, например ЭН-14Г2Х, ЭН-У30Х28С4Н4 и др. В основу деления электродов на типы положен конкретный химический состав наплавленного металла. Каждому типу может соответствовать несколько марок электродов, отличающихся составом стержня, покрытия и сварочно-технологическими свойствами.
[c.711]
Стальные покрытые электроды для ручной дуговой сварки также подразделяются по назначению. Для сварки низколегированных и конструкционных сталей с временным сопротивлением разрыву до 60 кгс/мм , имеют обозначение У. Для сварки легированных конструкционных сталей с временным сопротивлением разрыву свыше 60 кгс/мм , обозначаются — Л. Для сварки легированных теплоустойчивых сталей — Т. Сварка высоколегированных сталей с особыми сво 1ствами — В. Для наплавки поверхностных слоев с особыми свойствами — Н. [c.152]
Для различных пар металлов применяют сварку плавлением и наплавку дуговую в среде заищгных газов неплавящимся и плавящимся электродом, плазменной струей, электродами с толстым покрытием (типа Д), под слоем флюса, электронно-лучевую, лазерную.
[c.485]
Электроды для сварки алюминий и его сплавов. Ручную дуговую сварку чистого алюминия выполняют электродами марки ОЗА-1. Стержень изготавливается из алюминиевой проволоки марки АД-1 или АВ-2Т. Покрытие тгроскопично, поэтому перед сваркой электроды следует просушить при 160— 200°С в течение 2 ч. Коэффициент наплавки равен 6,25—6,5 т/А-ч. Для сварки литейных алюминиево-кремнистых сплавов АЛ- [c.97]
Подготовка к дуговой С. Дуговая. С., как и С. газовым пламенем, применяется для соединений стыковыми и галтельными швами и для наплавочных работ. Подготовка к сварке производится таким же путем, как и при газовой сварке, но для образования сварочнога угла достаточен скос каждой кромки в 30°. Только в случае применения покрытых электродов при С. более толстых листов делают скосы под ббльшими углами в целях более легкого удаления шлаков при С. потолочной с применением таких электродов доходят даже до общего угла в 120°. Для предупреждения перекоса листов при дуговой С. их предварительно сваривают по длине через определенные промежутки. Сначала сваривают листы в обоих концах шва, затем в середине, после чего С. производится каждый раз посредине между каждыми двумя последними сваренными точками так поступают до тех пор, пока расстояние между каждыми двумя соседними сваренными пунктами не составит всего 15 см. Если в целях прихватки листов производят С. точками подряд, начиная с одного конца шва, то-вследствие неравномерного нагрева листов может произойти разрыв шва. При С. галтель-ным швом и при наплавке (где дуговая С. является особенно пригодной) других каких-либо подготовительных мероприятий, кроме очистки сварочных поверхностей, не требуется.
[c.114]
Аппараты для ручной сварки покрытыми электродами, инверторные, | 8515391800 |
Машины и аппараты для дуговой сварки металлов, полуавтоматические; для ручной сварки покрытыми электродами, укомплектованные приспособлениями для сварки, | 8515399000 |
Установка для автоматической наплавки твердосплавного покрытия при помощи газовой дуговой сварки металлическим электродом для промышленности, серийный номер E0429210.![]() | 8515310000 |
СВАРОЧНЫЙ АППАРАТ ДЛЯ ДУГОВОЙ РУЧНОЙ СВАРКИ ПОКРЫТЫМИ ЭЛЕКТРОДАМИ | 8515391300 |
Трансформатор для питания одного поста переменным током 50 Гц при ручной дуговой сварке (резке и наплавке) на переменном токе малоуглеродистых и низколегированных сталей покрытыми электродами типа АНО-4, АНО-6,АНО-24,МР-3 | 8504320002 |
Оборудование электросварочное: аппараты для ручной сварки покрытыми электродами, аппараты для аргонодуговой сварки, аппараты для полуавтоматической сварки, | 8515391800 |
Оборудование для ручной сварки покрытым электродом: выпрямители инверторные, напряжение 230В «MOST», | 8515391800 |
Оборудование для сварки: аппарат для ручной дуговой сварки штучными электродами с покрытием | 8515399000 |
Установка дозировки порошкообразных материалов покрытия электродов для дуговой сварки и наплавки | 8423829000 |
Оборудование электросварочное промышленное: Аппарат для ручной электросварки металлов покрытыми электродами | 8515391300 |
СВАРОЧНЫЙ АППАРАТ ДЛЯ ДУГОВОЙ РУЧНОЙ СВАРКИ ПОКРЫТЫМИ ЭЛЕКТРОДАМИ, ПОСТАВЛЯЕМЫЕ С ТРАНСФОРМАТОРАМИ, В МЕТАЛЛИЧЕСКОМ КОРПУСЕ | 8515391300 |
Аппаратура для нанесения гальванических покрытий: электрод-карандаш | 8543300000 |
МАШИНА СВАРОЧНАЯ-ИНВЕРТОР РУЧНОЙ ДУГОВОЙ СВАРКИ ПЛАВЯЩИМСЯ ПОКРЫТЫМ ЭЛЕКТРОДОМ | 8515391800 |
Оборудование электросварочное промышленное: сварочные установки для ручной сварки покрытыми электродами, | 8515391300 |
Оборудование для физико-механической обработки материалов: комплексы для опрессовки покрытых металлических электродов, | 8479899708 |
Оборудование сварочное: аппарат плазменно-дуговой сварки покрытыми электродами, сварочный комплекс (трактор) для автоматической дуговой сварки, | 8515391800 |
Оборудование сварочное: аппарат сварочный для ручной дуговой сварки металлов покрытыми плавящимися электродами, со встроенным трансформатором, | 8515391300 |
машины и аппараты для дуговой сварки: АППАРАТЫ ДЛЯ РУЧНОЙ ИНВЕРТОРНОЙ АРГОННО-ДУГОВОЙ СВАРКИ НЕПЛАВЯЩИМСЯ(ВОЛЬФРАМОВЫМ) ПОКРЫТЫМ ЭЛЕКТРОДОМ, | 8515391800 |
Наименование | Кол-во | Цена за ед.![]() |
Стоимость, ₽ |
---|---|---|---|
Электроды ОЗЛ-6-4,0 ОКПД2 25.93.15.120 Электроды с покрытием |
20 кг |
563,33 |
11 266,60 |
Электроды ОЗЛ-6-3,0 ОКПД2
25. |
40 кг |
570,00 |
22 800,00 |
Электроды АНО-21-2,0 ОКПД2 25.93.15.120 Электроды с покрытием |
12 кг |
183,33 |
2 199,96 |
Электроды УОНИ 13/55-3,0 ОКПД2
25. |
100 кг |
118,67 |
11 867,00 |
Электроды ЦЛ-11-4,0 ОКПД2 25.93.15.120 Электроды с покрытием |
15 кг |
500,00 |
7 500,00 |
Электроды АНО-21-3,0 ОКПД2
25. |
200 кг |
120,67 |
24 134,00 |
Электроды ЦНИИН-4-4,0 ОКПД2 25.93.15.120 Электроды с покрытием |
300 кг |
550,00 |
165 000,00 |
Электроды Т-590-5,0 ОКПД2
25. |
20 кг |
183,33 |
3 666,60 |
Электроды ОЗЛ-25-4,0 ОКПД2 25.93.15.120 Электроды с покрытием |
40 кг |
3 250,00 |
130 000,00 |
Электроды АНО-4-3,0 ОКПД2
25. |
200 кг |
118,00 |
23 600,00 |
Электроды ОЗЛ-25Б-4,0 ОКПД2 25.93.15.120 Электроды с покрытием |
40 кг |
3 166,67 |
126 666,80 |
Электроды ОЗАНА-2-5,0 ОКПД2
25. |
4 кг |
1 386,67 |
5 546,68 |
Электроды ЦЛ-11-3,0 ОКПД2 25.93.15.120 Электроды с покрытием |
30 кг |
510,00 |
15 300,00 |
Электроды ОЗЛ-25Б-3,0 ОКПД2
25. |
50 кг |
3 166,67 |
158 333,50 |
Электроды УОНИ 13/45-4,0 ОКПД2 25.93.15.120 Электроды с покрытием |
70 кг |
118,00 |
8 260,00 |
Электроды ОЗЛ-25-3,0 ОКПД2
25. |
10 кг |
3 250,00 |
32 500,00 |
Электроды АНО-4-5,0 ОКПД2 25.93.15.120 Электроды с покрытием |
100 кг |
116,67 |
11 667,00 |
Электроды АНО-21-4,0 ОКПД2
25. |
250 кг |
119,33 |
29 832,50 |
Электроды АНО-4-4,0 ОКПД2 25.93.15.120 Электроды с покрытием |
500 кг |
116,67 |
58 335,00 |
Электроды УОНИ 13/55-4,0 ОКПД2
25. |
150 кг |
117,33 |
17 599,50 |
Электроды с покрытием — типы, назначение, сферы применения
Дуговая сварка с покрытыми металлическими электродами уже больше ста лет является самым эффективным и удобным способом получения соединений металлических деталей путем их сваривания. Роль электродов – в сварочной цепи выступать передатчиком электрического тока от аппарата к свариваемому изделию. Производятся электроды и- проволоки специального состава, которую маркируют СВ08Г2С или СВ08А.
Немного истории
Патент на первые покрытые электроды был получен шведским инженером Оскаром Кельбергом, который впервые стал покрывать электроды из металла не проводящим электрический ток материалом, к тому стойким к высоким температурам. Тем не менее, первые покрытые электроды в промышленности стали применяться только в 1928 году. Они были покрыты порошкообразным веществом на клеящем растворе. В нашей стране электроды с покрытием внедрял Ленинградский институт металлов и его руководитель А.Горячевым. Поэтому первые советские электроды выпускались под маркировкой ЛИМ.
Сегодня на рынке электродуговой сварки представлено более 500 марок электродов с самыми разными покрытиями, каждое из которых имеет свое назначение. Самые востребованные покрытия таких типов:
• кислые;
• основные;
• ильментиновые;
• рутиловые;
• целлюлозные;
• смешанные.
Кислые электроды (с кислым покрытием)
В покрытии присутствуют оксиды кремния или алюминия и ферромарганец, а для газовой защиты в состав включены декстрин и крахмал. Преимущество этого типа электродов в том, что ими можно варить заржавленный и корродированный металл. Благодаря эффективной дегазации в ванне расплава в сварных швах отсутствует пористость и они получаются достаточно прочными. Недостаток электродов с кислым покрытием в том, что сварной шов насыщается кислородом и в него попадают неметаллические включения. Это приводит к снижению ударной вязкости и возможности появления «горячих» и кристаллизационных трещин, поэтому их не применяют на ответственных конструкциях. Еще один минус кислых электродов – высокая токсичность газов по причине высокого содержания соединений марганца.
Электроды с основным покрытием
Такое покрытие еще называется низководородным. В состав покрытия входят такие компоненты: карбонаты (мел, мрамор), фтористые соединения (плавиковый шпат), ферросплавы. Такие электроды применяют для сварки постоянным током с обратной полярностью. Чтобы применять их для сварки переменным током, то надо выбирать модели, в покрытии которых есть жидкое стекло или поташ. Для сварки применяется короткая дуга. Свариваемые поверхности надо тщательно подготовить – очистить от загрязнений, ржавчины и высушить. Шов отличается высокой устойчивостью нагрузкам, полным отсутствием кристаллизационных и «горячих» трещин. А еще эти швы не подвержены старению. Сами электроды очень чувствительны к влаге и перед применением их обязательно надо высушить. Применяют основные электроды для сваривания ответственных швов, в том числе на металлоконструкциях с толстым сечением, а также, сталей, содержащих повышенную концентрацию фосфора и серы.
Рутиловое покрытие электродов
Основа его – рутиловый концентрат (природный диоксид титана), а также, небольшие включения мрамора, магнезита, шпата, каолина и некоторых органических соединений. Сварка такими электродами дает самые стойкие к образованию трещин швы. Кроме того, такое покрытие обеспечивает очень стабильную сварку переменным током короткой и длинной дугой, низкое разбрызгивание металла, красивую форму шва. Рутиловые электродами можно сваривать окисленные, корродированные и неочищенные поверхности. Применение – сложные сварки, в том числе, угловые, пространственные, в конструкциях, подвергаемых большим нагрузкам.
Ильментиновые электроды
Это промежуточный вариант между кислыми и рутиловыми электродами. Основа – ильменитовый концентрат (природное соединение диоксидов титана и железа). При сварке выделяется мало газов, а качество шва достаточно высокое. Используются такие электроды для сварки низкоуглеродистых сталей во всех пространственных положениях.
Электроды с целлюлозным покрытием
В состав обмазки включают органические компоненты – почти 50%. Чаще всего – это целлюлоза. Из неорганических элементов применяют рутил, марганец, некоторые другие. Шлака образуется мало, так как концентрация защитного газа достаточно высокая. Сфера применения достаточно широкая: сварка переменным током конструкций без предварительной подготовки. Этими электродами можно проваривать вертикальные швы сверху вниз и наоборот. Минус – из-за высокой концентрации кислорода в сварной ванне качество шва снижено в сравнении с рутиловыми электродами.
Электроды со смешанным покрытием
Покрытия смешанного типа – это сочетание основного рутилового компонента с различными добавками. Это позволяет улучшить характеристики рутиловых электродов в зависимости от сферы применения и повысить качество шва.
Поделитесь информацией
Покрытие электродов— обзор
2.5 Ограничения на создание газовой защиты в самозащитных проводах
Ингредиенты минерального флюса, используемые для создания газовой защиты (например, CaCO 3 ), находятся на внешней стороне сердечника проволоки флюса. покрытый электрод, но они находятся внутри оболочки трубчатого электрода. Как показано в Таблице 2.4, карбонаты, обычно используемые в покрытиях электродов (CaCO 3 и MgCO 3 ), разлагаются и выделяют CO2 при относительно низких температурах (в среднем около 600 ° C), и давление газа, создаваемое внутри трубки, имеет тенденцию к раздувать плавящуюся оболочку, вызывая разбрызгивание. Сообщалось (10, 17, 18, 21), что разбрызгивание увеличивается с увеличением зависимости от создания газовой защиты с помощью самозащитных проводов. Это накладывает серьезные ограничения на количество карбонатов, используемых в самозащитной проволоке (см. Приложение A), по сравнению с примерно 30% CaCO 3 в покрытии электрода E7018 и до 50% CaCO 3 в покрытии E7016. электрод.
Таблица 2.4. Температуры разложения, плавления и кипения / испарения некоторых ингредиентов флюсов, используемых в самозащитной порошковой проволоке, и некоторых продуктов реакции.