Дефектоскоп импульсный ультразвуковой — Энциклопедия по машиностроению XXL
Для ультразвуковой дефектоскопии применяют метод звуковой тени (теневая дефектоскопия), импульсный и резонансный методы. [c.244]В СССР четкая классификация импульсных ультразвуковых дефектоскопов определена ГОСТ 23049—84. В зависимости от области применения ультразвуковые дефектоскопы (УД) подразделяют на две группы общего назначения — УД и специализированные — уде, а в зависимости от функционального назначения— на четыре группы (табл. 4.1), Условное обозначение дефектоскопа состоит из букв УД (или УДС), номера группы и порядкового номера модели, а также буквы М с номером модернизации и номера исполнения по устойчивости к воздействию внешней среды. [c.179]
В практике неразрушающего контроля наиболее широко используют ручные импульсные ультразвуковые дефектоскопы 2-й и 3-й групп общего или специального назначения.
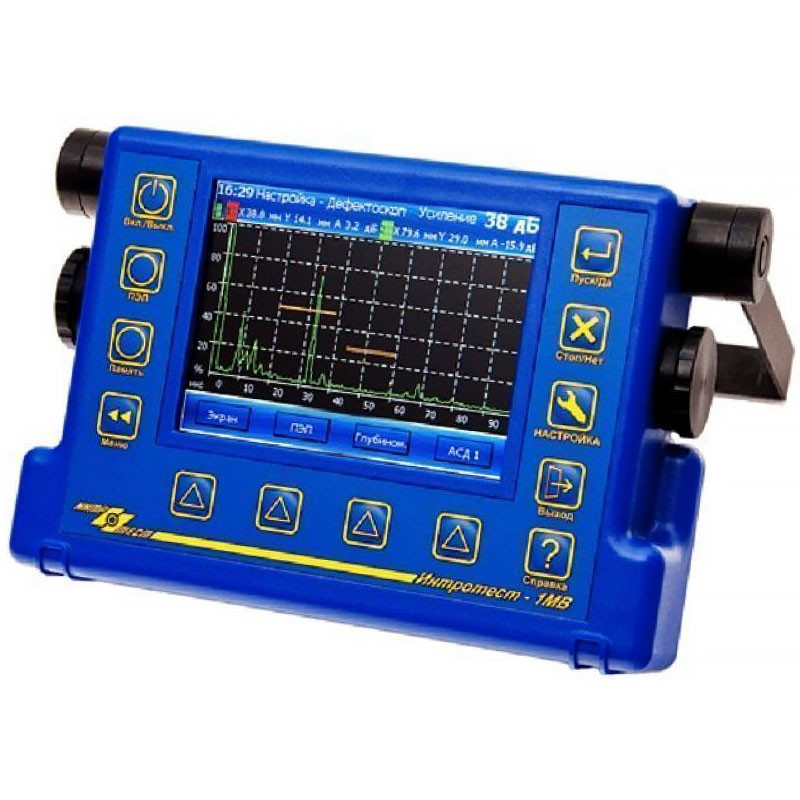
Первые импульсные ультразвуковые дефектоскопы с электронным глубиномером и звуковым индикатором разработаны НИИ мостов ЛИИЖТа в 1955 г. [c.180]
Импульсные ультразвуковые дефектоскопы. Основными параметрами сигнала в методе отражений, подлежащими измерению, являются амплитуда U (дБ) и временной сдвиг Т (мкс) принятого сигнала (импульса) относительно излученного, называемого зондирующим сигналом (импульсом). [c.180]
Качественным скачком в развитии импульсной ультразвуковой дефектоскопии рельсов является создание в СССР портативных приборов для обнаружения дефектов на расстоянии до 10. .. 20 м от преобразователя (рис. 4.5). Это позволяет перейти от сплошного к пошаговому сканированию, что повышает производительность контроля рельсов.
Современные импульсные ультразвуковые дефектоскопы применяются главным образом для проверки качества изделий машиностроения. Исключение составляют массивные отливки, имеющие крупнозернистую структуру. Эта структура сильно поглощает и рассеивает ультразвуковые колебания, поэтому приходится уменьшать их частоту (так как при малых частотах поглощение и рассеяние звуковой энергии уменьшается), но при этом сильно падает чувствительность дефектоскопа. В то же время сильное поглощение и рассеяние ультразвуковых колебаний крупными зернами чугуна позволяют применять ультразвуковые дефектоскопы для определения зерен графита в чугуне и судить о структуре. Для определения структуры некоторых металлов в настоящее время изготовляются ультразвуковые дефектоскопы с частотой звуковых колебаний более 15 МГц.
Установлено, что качество электрошлаковой сварки можно проверять при помощи импульсных ультразвуковых дефектоскопов, так как микроструктура наплавленного металла таких швов в большинстве случаев получается однородной, мелкозернистой, в особенности после термической обработки. Для контроля качества толстостенных швов в ЦНИИТМАШе разработан специальный импульсный ультразвуковой дефектоскоп. Дефектоскоп имеет электронный глубиномер для точного определения глубины залегания дефектов и ряд других усовершенствований.
[c.265]
Наиболее совершенным и широко распространенным в дефектоскопии является эхо-метод, который поясняется блок-схемой импульсного ультразвукового дефектоскопа, [c.505]
Импульсный ультразвуковой эхо-дефектоскоп типа УДМ-1М предназначен для обнаружения и определения координат дефектов, являющихся нарушениями сплошности (раковины, расслоения, пористость, треш,ины и т. д.), которые расположены на глубине от 1 до 2500 мм под поверхностью в крупных металлических заготовках, полуфабрикатах и изделиях для обнаружения различных дефектов в сварных соединениях для контроля макроструктуры стали, а также для измерения толщины изделия при одностороннем доступе к нему.

На рис. 31 приведена принципиальная схема импульсного ультразвукового дефектоскопа. Высокочастотный генератор, образуя кратковременные импульсы переменного напряжения высокой частоты, передает их на пьезоэлектрический вибратор, который преобразует эти колебания в упругие колебания той же частоты. При соприкосновении вибратора (щупа) с деталью импульсы упругих колебаний поступают в металл и распространяются в нем в виде слегка расходящегося пучка. Если на пути распространения импульсов упругих колебаний встречается дефект, то часть
Рнс. 31. Принципиальная схема импульсного ультразвукового дефектоскопа [c.58]
В турбостроении широко применяют дефектоскопы УДМ-1М и УЗД-7Н, работающие на принципе импульсных ультразвуковых колебаний. Дефектоскопы предназначены для выявления в деталях таких дефектов, как трещины, пустоты, рыхлости, шлаковые включения, зоны ликвации, флокены и т. д. Этими дефектоскопами можно обнаруживать внутренние дефекты в поковках, прокате и сварных швах. Глубина залегания дефекта и толщина изделия определяются глубиномером. Максимальная глубина прозвучивания для стали при пользовании прямым искателем доходит до 2,5 м, призматическим искателем — до 1,2 м, а минимальная глубина прозвучивания при применении специальных призматических искателей равна 1—2 мм. При замере толщины металла свыше 100 мм погрешность составляет не более 2,5%. Дефектоскоп очень чувствителен. На глубине 1 м дефектоскоп обнаруживает дефект площадью 3—4 мм , а на глубине 300 мм — до 1—2 мм.
[c.447]
Импульсный ультразвуковой дефектоскоп (рис. 4.12) состоит из задающего генератора 3, генератора импульсов 2, генератора 4, усилителя импульсов 1, электронно-лучевой трубки (ЭЛТ) 5, источника питания (ГОСТ 23667—79). Задающий генератор вырабатывает колебания, запускающие генератор импульсов и генератор развертки. Генератор импульсов формирует высокочастотные электрические импульсы, которые подаются на пьезоэлемент преобразователя 6 и возбуждают его. Пьезоэлемент, колеблясь с частотой генератора, передает эти колебания изделию 7, в котором колеба-
В современных импульсных ультразвуковых дефектоскопах (табл. 4.16) применяют преобразователи «(искательные головки), рассчитанные на работу в контактном и иммерсионном вариантах с возбуждением в контролируемом изделии ультразвуковых волн. В соответствии с ГОСТ 14782—76 по конструктивному выполнению они могут быть раздельными, совмещенными и раздельно-совмещенными, прямыми, угловыми (призматическими), с плоской или фигурной контактной поверхностью. [c.123]
Ультразвуковой контроль. Широкое распространение в промышленности и строительстве получили импульсные ультразвуковые дефектоскопы (УЗД), предназначенные для обнаружения внутренних дефектов в материалах и сварных соединениях, работающие в диапазоне частот 0,02.
Рис. 3.2. Импульсный ультразвуковой дефектоскоп |
Рис. 116. Импульсный ультразвуковой дефектоскоп |
На рис. 11.4.17 приведена схема импульсного ультразвукового дефектоскопа. При контроле детали к ее поверхности подводят излучатель ультразвуковых колебаний, который питается от генератора. Если дефекта в детали нет, то ультразвуковые колебания, отразившись от противоположной стороны детали, возвратятся обратно и возбудят электрический сигнал в приемнике. При этом на экране электронно-лучевой трубки будут видны два всплеска слева — излученный импульс и справа — отраженный от противоположной стенки детали (донный).
[c.79]
В импульсных ультразвуковых дефектоскопах (типа УЗД-7Н) ультразвуковая волна, распространяющаяся в исследуемом материале, при встрече с препятствием в виде дефекта отражается от него. Отраженные волны принимаются, усиливаются и передаются на показывающий индикатор. Импульсные дефектоскопы могут работать с одним или с двумя щупами, прикладываемыми к изделию только с одной стороны. Это является одним из важных преимуществ импульсных дефектоскопов, позволяющих производить контроль изделия при доступе к нему только с одной стороны в отличие от теневых дефектоскопов.
Переносные импульсные ультразвуковые рельсовые дефектоскопы ДУК-13, УЗД-56, УЗД-63 (рис. 55) и другие также находят применение в зависимости от конкретных условий. [c.260]
ШВОВ применяются импульсные ультразвуковые дефектоскопы, принципиальная скелетная схема которых изображена на фиг. 22. [c.689]
В импульсных дефектоскопах используются ультразвуковые волны, посылаемые через короткие интервалы такой интервал, называемый паузой, необходим для того, чтобы сигнал мог распространяться до задней стенки образца через материал и возвратиться обратно (рис. 11-10). Регистрация отраженных от задней стенки и от имеющихся дефектов или включений сигналов лежит в основе эхо-метода, который используется в большинстве импульсных дефектоскопов. Для передачи ультразвуковых колебаний от генератора и для приема отраженных волн используются пьезоэлектрические преобразователи — искатели. Иногда излучающий и приемный искатели объединяют в одной искательной головке.
Рис. 57. Схема импульсного ультразвукового дефектоскопа |
Импульсный ультразвуковой дефектоскоп УДМ-1М предназначен для обнаружения и определения координат дефектов, расположенных на глубине от 1 до 2500 мм. Кроме того, он позволяет [c.346]
Так, на заводе Электроточприбор Молдавского СНХ /спешно освоен серийный выпуск дефектоскопов различных битов электромагнитных индуктивных, магнитных передвижных и переносных импульсных ультразвуковых и др. [c.6]
Для лучшего совпадения результатов измерения размеров и конфигурации дефекта, величины а и к, характеризующие гео—метрию и работу искателя импульсного ультразвукового дефектоскопа, следует подбирать на опыте, так как обычно свойства пьезопреобразователей, применяемых в ультразвуковой дефектоскопии, весьма далеки от идеальных характеристик, на которых основывался расчет формулы (23). В формулах (7), (23) и (24) отсутствуют члены, зависящие от коэффициента затухания ультразвука и изменяющиеся с увеличением расстояния между искателем и дефектом. Это объясняется следующим если глубина залегания дефекта значительно превышает его размеры, смещение по поверхности изделия от точки ( =0, х=1) можно рассматривать как смещение по окружности, центром которой является дефект. Вследствие этого расстояние между дефекто.м и искателем остается неизменным, а значит, и отношение к не зависит от коэффициента затухания. Уменьшение сигнала при смещении искателя происходит только из-за отклонения прямой, соединяющей искатель и дефект от направления их акустических осей.
[c.138]
В последние годы интенсивно проводятся исследования по разработке теории импульсного ультразвукового метода дефектоскопии. В частности, выведены уравнения, определяющие зависи.мость амплитуды ультразвукового сигнала от размеров и глубины залегания торцового дефекта. Благодаря этому удалось решить ряд практически важных задач, например, определить эквивалентную площадь обнаруженных дефектов и настройку чувствительности дефектоскопа. В этом случае измерялась лишь а.мплитуда отраженных сигналов.
[c.141]
Для указанных целей разработан прибор Акон-4 , имеющий абсолютную погрешность измерения времени распространения УЗК 0,01—0,03 мкс, габаритные размеры 170Х 280Х 350 мм, массу 7 кг. Прибор разработан на основе унифицированного импульсного ультразвукового дефектоскопа типа УД-ППУ. Параметры контролируемых шпилек (болтов) следующие М18…М140 при отношении длины к диаметру до семи максимальная длина в направлении прозвучивания — до 800 мм, минимальная — 30 мм. Возможная абсолютная погрешность определения напряжений (10- 50) МПа. Прибор позволяет осуще [c.285]
На практике большее распространение получили ультразвуковые дефектоскопы, работающие на принципе использования импульсных ультразвуковых колебаний. В указанных приборах пьезоэлектрическим излучателем, возбуждаемым радиоимпульсами специального генератора, посылаются в исследуемый металл не непрерывные (незатухающие) упругие колебания, а чрезвычайно короткие импульсы =0,5-5- Юмкс) с относительно продолжительными промежутками между ними ( = 1 -5- 5 мс), распространяющиеся узким пучком.
[c.41]
Чувствительность (разрешающая способность) импульсных ультразвуковых дефектоскопов с приемом отраженных сигналов значительно выше, чем теневых дефектоскопов. При помощи импульсных дефектоскопов можно прозвучивать более толстые слои материалов и при этом выявлять мельчайшие дефекты. [c.264]
На рис. 2 показана схема установки, моделирующей узел трения при распространении в ней импульсных ультразвуковых колебаний. Процесс прохождения импульса через зазор, заполненный смазкой, может наблюдаться на экране прибора с помощью ос-циллоскопической трубки. В работе использовался дефектоскоп типа УДМ-1М, снабженный устройством электронная лупа , позволяющим выделить на экране интересующий нас участок. На рис. 3 показаны два случая прохождения импульса высокочастотных колебаний через зазор б, заполненный смазкой. В случае а на экране прибора отчетливо виден отраженный импульс ОИ. В случае
[c.296]
Несомненно, что надежность и долговечность каждой детали во многом зависят от ее качества, наличия трещин, пустот, рыхлостей и других аналогичных дефектов в детали, от свойств металла, качества термообработки, толщины покрытий, неоднородности металла по сечению, наклепа и внутренних напряжений. Для ознакомления с методами неразрушающего контроля материала, выявления перечисленных дефектов и оценки свойств деталей студентам предлагается выполнить лабораторную работу Изучение конструкций и областей применения дефектоскопов в целях повышения надежности изделий . При выполнении данной работы студенты изучают конструкции и принципы действия электро-индуктивного дефектоскопа ЭМИД-4М, люминесцентного дефектоскопа типа ЛД-4, импульсного ультразвукового эходефектоскопа типа УДМ-1М и магнитного дефектоскопа типа ДМП-2, а также с помощью указанных приборов производят ряд экспериментальных исследований. [c.306]
Фиг.![]() |
Структурная схема импульсного ультразвукового эходефектоскопа приведена на рис. 8.8. Электроакустический преобразователь ЭАП (пьезоэлектрический искатель) служит для преобразования электромагнитных колебаний в ультразвуковые, излучения их в изделие и приема колебаний, отраженных от дефектов. Усилитель сигналов УС состоит из усилителя высокой частоты с коэффициентом усиления 10 —10 и детектора. Генератор зондирующих импульсов ГИ вырабатывает высокочастотные импульсы напряжения, возбуждающие ультразвуковые колебания ЭАП. Синхронизатор С предназначен для обеспечения синхронной работы узлов дефектоскопа. Он обеспечивает одновременный запуск генератора ГИ и генератора линейно изменяющегося напряжения ГЛИН, который служит для формирования напряжения развертки электронно-лучевой трубки ЭЛТ. Измеритель времени ИВ предназначен для измерения времени прохождения импульса до дефекта и обратно. Регистрирующее устройство РУ селектирует эхосигнал от дефекта по времени и по амплитуде и фиксирует его на самописце. Блок регулировки чувствительности РЧ служит для выравнивания амплитуд сигналов от дефектов, залегающих на разной глубине.
[c.376]
Основные характеристики отечественных дефектоскопов общего назначения приведены в табл. 3.7. С их помощью осуществляется ручной контроль сварных соединений эхо-ме-тодом, теневым и зеркально-теневым методами. Наиболее распространенный импульсный ультразвуковой дефектоскоп УД2-12 показан на рис. 3.2. Эти дефектоскопы позволяют определять глубину залегания дефектов по цифровому индикатору и оценивать условные размеры дефектов путем измерения отношений амплитуд сигналов, отраженных от дефектов.
[c.469]
В про1иышленности широко применяются неразрушающие физические методы обнаружения пороков в изделиях. Импульсные ультразвуковые эхо-дефектоскопы успешно обнаруживают скрытые в материале изделия дефекты, а в некоторых случаях позволяют определить их размеры. Методика определения размеров дефектов состоит в сравнении сигнала от дефекта, обнаруженного в изделии, с сигналом от некоторого стандартного дефекта, расположенного на такой же глубине в эталонном образце [1. При этом требуется найти эталонный образец с искусственным дефекто.м, сигнал от которого равен сигналу от естественного дефекта в изделии. Но этот метод практически неприменим при контроле крупных деталей, так как набор эталонных образцов с искусственными дефектами в этом случае и.меет большие габариты, а образцы должны выполняться из того же материала, что и контролируе. мое изделие.
[c.128]
Рассмотрим акустический тракт импульсного ультразвукового эхо-дефектоскопа при однощуповом варианте контроля изделий (рис. 1). Буквами Л и 5 помечены соответственно искатель дефектоскопа и дефект изделия. При расположении искателя в точке О, принадлежащей поверхности изделия, сигнал от дефекта достигает максимальной величины = р (О, г), а при смещении искателя от точки О на вектор Ь сигнал уменьшается до [c.130]
Импульсный метод ультразвуковой дефектоскопии — Справочник химика 21
ИМПУЛЬСНЫЙ МЕТОД УЛЬТРАЗВУКОВОЙ ДЕФЕКТОСКОПИИ [c.83] ТЕНЕВОЙ МЕТОД ДЕФЕКТОСКОПИИ — метод дефектоскопии, основанный на ослаблении дефектами интенсивности упругих колебаний ультразвуковой частоты один из методов ультразвуковой дефектоскопии. Впервые применен (1928) сов. исследователем С. Я. Соколовым. Для осуществления контроля в исследуемое изделие с одной стороны вводят ультразвуковые колебания (импульсные, непрерывные с частотной модуляцией или без нее), используя различные излучатели (напр. , облучающую головку). С другой стороны изделия с помощью датчика, установленного напротив излучателя, регистрируют интенсивность этих колебаний, прошедших через толщу материала. Если на пути колебаний окажется дефект, то часть их отразится, и интенсивность колебаний, поступающих на датчик, уменьшится. Для Т. м. д. используют дефектоскопы типа УЗД, ДУК и др. Т. м, д. применяют для обнаружения расслоений, инородных включений, раковин и др. дефектов в металлах, бетоне и т. д. [c.516]
Ультразвуковой метод обнаружения скрытых дефектов основан на свойстве ультразвука проходить через металлические изделия и отражаться от границы раздела двух сред, в том числе и от дефекта. В зависимости от способа приема сигнала от дефекта различают два метода ультразвуковой дефектоскопии — метод просвечивания и импульсный метод. [c.97]
Ультразвуковой импульсный метод контроля не дает возможности с полным основанием судить о характере дефекта. С помощью серийных ультразвуковых дефектоскопов можно лишь с достаточной для практики точностью определить координаты и условную площадь дефекта чтобы судить о характере дефекта, необходимо провести дополнительные исследования. [c.481]
Как отмечалось во введении, эхометод— основной метод АК, поэтому он здесь рассмотрен наиболее полно. Контроль этим методом выполняют с помощью импульсного ультразвукового дефектоскопа. [c.92]
Эхо-импульсный метод измерения толщины основан на регистрации времени прохождения ультразвукового импульса через изделие. Эхо-импульсный толщиномер работает так же, как и ультразвуковой дефектоскоп. Пьезоэлектрический преобразователь при воздействии электрического сигнала от импульсного генератора посылает в изделие импульс упругих колебаний, который распространяется со скоростью, зависящей от химического [c.50]
Эхо-импульсный метод дефектоскопии заключается в посылке в изделие искателем ультразвуковых импульсов и приеме тем же или другим искателем сигналов, отраженных от дефектов и от противоположной поверхности изделия. Различают два способа контроля основной и реверберационный. [c.85]
Наиболее совершенным и широко распространенным в дефектоскопии является эхо-метод, который поясняется блок-схемой импульсного ультразвукового дефектоскопа, работающего по принципу отражения ультразвуковых импульсов от дефектов в изделии (рис. 4.25). [c.282]
Книга посвящена методам ультразвукового контроля, применяемым в промышленности, а также воздействию мощных ультразвуковых колебаний на различные технологические процессы. Большое внимание уделено импульсным ультразвуковым методам дефектоскопии и физико-химических исследований. [c.2]
Измерение скоростей распространения продольных и поперечных ультразвуковых волн, а также поглощения ультразвука в твердых телах позволяет исследовать ряд вопросов, относящихся к физике твердого тепа. Из них наиболее ванметод определения упругих постоянных и метод измерения величины зерна в металлах. Хотя подобные методы исследования применимы, кроме металлов, и к ряду других материалов, однако большинство экспериментальных данных на сегодняшний день относится к исследованию металлов. Это в некоторой стенени объясняется тем, что аппаратура, предназначенная для измерения скорости и поглощения ультразвука, во многом аналогична импульсным ультразвуковым дефектоскопам, применяемым для исследования металлов. Поэтому первые опыты в этом направлении проводились с помощью упомянутых выше дефектоскопов. И лишь в дальнейшем, в связи с необходимостью повышения точности измерений и расширения диапазона частот, для этих целей были изготовлены специальные установки, позволившие существенно расширить круг вопросов, решаемых данным методом. [c.146]
Ультразвуковой метод дефектоскопии использует ЗВ высокой частоты (20 кгц — 25 Мгц). Известны два основных метода ультразвукового контроля — теневой (метод сквозного прозвучивания) п эхо-метод (метод отражения) имеются варианты иммерсионного и контактного ультразвукового методов, отличающиеся способом ввода ЗВ в исследуемый материал. При этом методе используется аппаратура, блок-схема к-рой аналогична схеме импульсного прибора для ультразвуковых испытаний полимерных материалов (см.
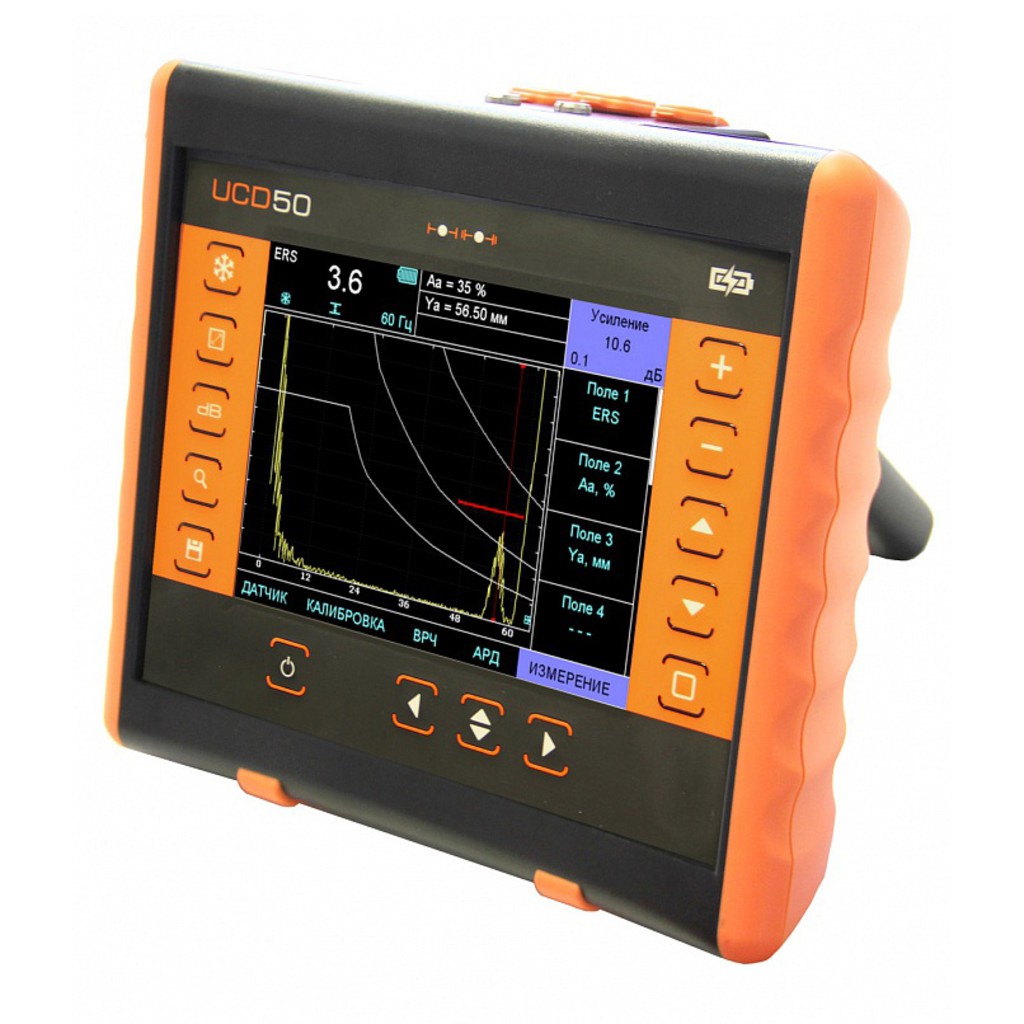
При контроле детали ультразвуковым дефектоскопом, основанном на импульсном методе, к ее поверхности подводят излучатель ультразвуковых колебаний, который одновременно может быть приемником. Если дефекта в детали нет, то ультразвуковые колебания, возбуждаемые генератором, отразившись от противоположной стороны детали, возвращаются обратно и возбуждают электрический сигнал в приемнике. После усиления и развертки сигнала на экране электрон-но-лучевой трубки будут видны два всплеска от излученного и отраженного от противоположной стенки импульсов. Если в детали имеется дефект, то ультразвуковые колебания отражаются от дефекта и на экране появляется промежуточный всплеск. Этот метод обладает высокой чувствительностью и применяется при обнаружении внутренних дефектов в деталях большой толщины, а также в труднодоступных местах. [c.98]
Ультразвуковой метод является основным для выявления внутренних пороков крупногабаритных изделий, отливок и дефектов в. прокате большого сечения. Широкое применение он находит при контроле сварных швов и в первую очередь швов больших толщин. Принцип действия этого метода основан на свойстве ультразвуковых волн малой длины распространяться в виде направленного луча, отражаться и преломляться на границе раздела двух сред. Ультразвуковые дефектоскопы подразделяются на импульсные с приемом отраженного сигнала и теневые с непрерывным излучением. [c.155]
Импульсный ультразвуковой дефектоскоп типа ДУК-8 предназначен для обнаружения дефектов контактным и иммерсионным методами контроля в материалах с большим коэффициентом затухания. [c.206]
На фиг. 4 приведена схема прозвучивания изделий импульсным методом, получившим наибольшее применение в ультразвуковой дефектоскопии металлов. [c.35]
Повышение чувствительности ультразвуковой когерентно-импульсной фурье-ин-троскопии на основе метода нуль-вре-менного анализа комплексных огибающих синтезированных импульсных характеристик // Дефектоскопия. 1997. № 6. С. 3-9. [c.840]
Физические методы контроля применяют с целью выявления в сварных соединениях возможных внутренних дефектов (трещин, непроваров, пор, шлаковых включений и др.). Ультразвуковой контроль осуществляют с помощью импульсных дефектоскопов УДМ-З, ДУК-66П и др. [c.148]
Импульсный дефектоскоп благодаря наличию пауз свободен от большинства помех дефектоскопа с непрерывным излучением. Может быть задана большая мощность импульса без перегрузки кварца, интерференция практически отсутствует, дифракция и многократное отражение не сказываются на выявлении дефекта. Большим преимуществом метода являются значительная глубина проникновения (до 3,5 м), исследование с одной стороны детали и отсутствие погружения детали в жидкость. К недостаткам ультразвукового метода относятся необходимость чисто обработанной поверхности размерами не менее 30 X 60 мм, неудобство контроля деталей сложной формы и наличие неконтролируемых ( мертвых ) зон, простирающихся на глубину 10 мм от передней грани детали и на 5 % [c. 378]
Общеизвестно применение ультразвуковой дефектоскопии для контроля внутренних пороков, дефектов в металлоизделиях. Большая проникающая способность ультразвуковых колебаний ставит ее на одно из первых мест среди прочих разнообразных физических методов дефектоскопии без разрушения испытуемых изделий. Область применения импульсной ультразвуковой дефектоскопии металлов весьма многообразна детали турбин и двигателей внутреннего сгорания, детали автомобилей, паровозов и самолетов, рельсы, поковки, листовые материалы, трубопроводы, крепежные шпильки, закленочныо соединения котлов и самая разнообразная продукция прокатных, кузнечных и прессовых цехов. Кроме импульсных методов ультразвуковой дефектоскопии, существует несколько различных по своей физической природе методов дефектоскопии с помощью незатухающих колебаний. К ним следует отнести проверку резонансным методом толщин изделий, доступ к которым возможен с одной стороны. С подобного вида измерениями мы встречаемся при проверке зон коррозионного разъедания стенок котлов, трубопроводов и общивки судов. Незатз хающие [c.7]
Использование незатухающих (непрерывных) колебаний в ультразвуковой дефектосконии известно с 1928 г. [56]. Существует несколько различных по своей физической природе методов ультразвуковой дефектоскопии с помощью незатухающих колебаний. Эти методы до сих пор используются для целей обнаружения внутренних дефектов в различных материалах наряду с рассмотренными выше импульсными методами, так как в ряде случаев они имеют некоторые преимущества перед ними и позволяют, тем самым, расширить возможности ультразвуковой дефектоскопии. [c.125]
При контроле крз пногабаритиых прессованных и катаных полуфабрикатов (профилей, плит и других деталей) рядом ценных преимуществ по сравнению с обычным методом импульсной ультразвуковой дефектоскопии обладает так называемый иммерсиопньпг метод [94, 95, 96]. В этом случае контролируемое изделие полностью погружается в воду, что значительно улучшает акустический контакт пьезопреобразователей (щ шов) с поверхностью изделия.
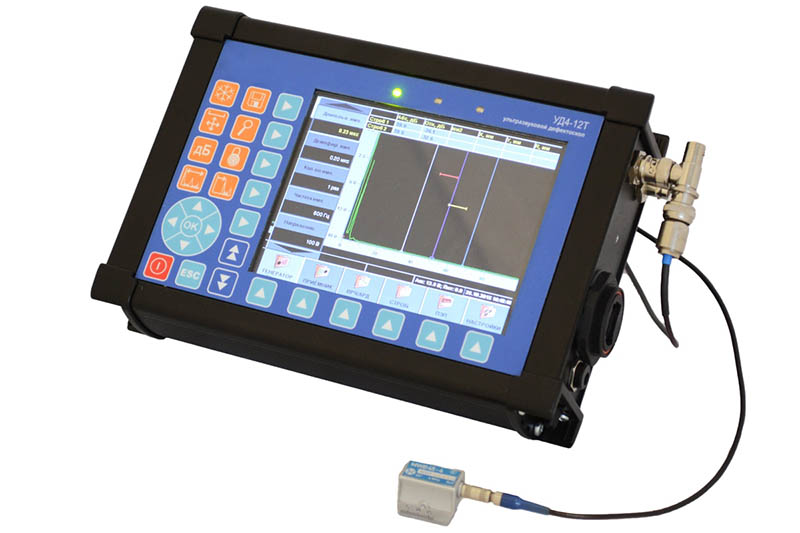
В настоящее время существует несколько типов приборов, позволяющих производить испытания качества бетона в толще до 20-> 30 м. Испытания обычно производятся импульсным методом. В качестве пьезопреобразователей используются щуиы с пакетами пз сегнетовой соли, имеющие значительно большую чувствительность, чем обычно применяемые в ультразвуковой дефектоскопии металлов щупы с пластинками кварца или титаната бария. Кроме того, ввиду неровной поверхности изделий из бетона, применяют специальные нхуиы с топким резиновым донышком (см. рис. 65). [c.134]
Метод неразрушающей дефектоскопии сварных соединений выбирают исходя из возможности обеспечения наиболее полного и точного выявления дефектов. При этом применяют следующие основные методы ультразвуковой контроль с помощью импульсных дефектоскопов УДМ-3, ДУК-66П и др. рентгенонросвечивание с помощью аппаратов РУ-12-5-1, РИПА-1Д, РИНА-2Д, РАП-160-ЮН и др., гаммагрифирование с помощью дефектоскопов Гаммарид-13, Гаммарид-15, Гаммарид-2, Гамма-рид-23, РИД-21М и др. цветную дефектоскопию. [c.128]
Ультразвуковыми волнами называют упругие механические колебания (звуки), имеющие частоту более 20 кГц. Этот вид дефектоскопии применяют для обнаружения подповерхностных и глубоко залегающих пороков деталей независимо от материала, из которого они изготовлены. Ультразвуковая дефектоскопия используется как для контроля отдельных деталей, так и деталей, находящихся в сборке например, можно выявить дефекты подступичной части оси колесной пары, шеек коленчатого вала, не снятого с дизеля, в болтах крепления полюсов электрических машин, в зубьях шестерен тяговых редукторов, находящихся под тепловозом, и т. д. В локомотивных депо и на ремонтных заводах распространен дефектоскоп УЗД-64, работающий по эхо-импульсному методу (рис. 9). Генератор импуль- [c.32]
К физическим методам контроля, выявляющим внутренние дефекты сварных соединений (трещины, непровары, поры, шлаковые включения и др.), относятся ультразвуковая дефектоскопия, радиографическая дефектоскопия (рентгено- и гаммаграфирование). Ультразвуковую дефектоскопию вьшолняют с помощью импульсных дефектоскопов УДМ-3, ДУК-66П и др. Для рентгенографиро- [c.123]
Следует отметить, что ультразвуковой метод импульсной дефектоскопии применяется не только для исследования металлов, но и таких материалов, как фарфор, стекло, пластмассы и др. Нан1)имер, в фарфоровых изоляторах с помощью ультразвука определяются внутренние дефекты [971, качество склейки и пористость [98]. [c.124]
Измерения поглощения в большинстве металлов и сплавов проводятся импульсным ультразвуковым методом. При этом наблюдается затухание импульсов, многократно отраженных от граней испытуемого образца. Сопоставление данных ультразвукового метода с металлографическими данными о размерах зерен металла позволяет уточнить характер зависимости поглощения звука от структуры металла. Блок-схема ультразвуковой установки для контроля структуры металлов аналогична схемам импл льсных дефектоскопов, т. е. состоит из синхронизирующего генератора, генератора высокой частоты, усилителя [c.148]
При использовании ультразвукового метода для возбуждения продольных и поперечных колебаний в испытуемых образцах применяются соответственно кристаллы X- и Г-срезов. Продольные волны вводятся в образцы через промежуточный слой смазки, например слой трансформаторного масла. Для ввода поперечных волн необходим слой смазки, обладающий упругостью сдвига. В этом случае применяется минеральный воск, полиизобутилен и др. Ультразвуковые волны, прошедшие через испытуемый образец, принимаются приемным кристаллом и через усилитель подаются на экран электронно-лучевой трубки. Интервалы времени между двумя последовательно отраженными импульсами и будут характеризовать величину скорости распространения звука. При использовании для этих целей ультразвукового импульсного дефектоскопа точность измерений величины скорости распространения звука составляет1 — 3%. Следовательно, с такой же (или несколько меньшей) точностью могут быть измерены и упругие постоянные материалов. Однако следует отметить, что это относится к материалам с малой величиной рассеяния звука при постоянной температуре во всей толще испытуемого изделия. В противном случае скорость распространения звука будет различной для разных участков испытуемого образца и интерпретация результатов измерений будет затруднительной. Это, естественно, скажется на точности данного метода. Несмотря на это, ультразвуковой метод измерения упругих постоянных твердых тел является вполне надежным, и с помощью его уже получено много полезных результатов. Так, он с успехом нашел применение для измерения модулей упругости высоковольтных изоляторов, для которых требуется повышенная механическая прочность [97]. Простота и высокая точность измерений, характеризующие импульсный ультразвуковой метод, обусловливают широкое применение этого метода для измерения упругих постоянных каучуков [20], пластмасс, стекла [130], фарфора [131], бетона [109], льда [132] и металлов.
[c.155]
Сплошность сцепления. На заводах-изготовителях для контроля качества гомогенной освинцовки используют переносные и стационарные рентгеновские установки. Контроль осуществляют как на стадии нанесения гомогенной освинцовки на поверхность стального листа, так и покрытия аппарата. Контроль проводят выборочно (отдельных участков) или всей поверхности. В условиях монтажной площадки для контроля сплощности сцепления щироко используют ультразвуковой метод. Его часто применяют также для определения толщины покрытия. Испытания проводят как импульсными, так и резонансными дефектоскопами. Сигналы фиксируются ло шкале прибора или на слух с использованием наушников. При хорошем сцеплении не происходит отражения сигналов от поверхности раздела сталь — свинец. Наличие сильных сигналов показывает на полное отсутствие связи обычно это имеет место, если площадь отслоения превышает размер головки прибора. При меньших размерах дефектов поступают слабые сигналы. Контур отслоения покрытия легко выявляется с помощью прибора. Испытания проводят с наружной стороны корпуса. Поверхность должна быть чистой от сварочных брызг, окалины, глубоких пор, трещин и других дефектов. Для обеспечения акустического контакта между искательной головкой и металлом его поверхность тщательно протирают ветошью и на нее наносят слой масла или вазелина. [c.279]
В центральной лаборатории треста Южгазстрой объединения Росгазспецстрой были проведены экспериментальные работы по применению ультразвукового метода контроля сварных швов при строительстве газопроводов различных диаметров и толщины стенки. Результаты контроля были сопоставлены с данными магнитографического, рентгенографического, гамма-графического контроля и механических испытаний. При проведении экспериментальных работ использовались импульсный дефектоскоп УДМ-1М, магнитографический дефектоскоп МГК-1, рентгеновский аппарат ИРА-1Д, гамма-графический аппарат ГУП-Цезий. [c.128]
Физические методы контроля (рентгено- и гаммаграфирование) производят, чтобы выявить в сварных соединениях возможные внутренние дефекты (трещины, непровары, поры, шлаковые включения и др. ). Ультразвуковой контроль вьшолняют с помощью импульсных дефектоскопов УДМ-1М, УЗД-7Н, УЗД-НИИМ-5, УЗД-НИИМ-3 и др. [c.137]
Ультразвуковой дефектоскоп сварных швов для контроля сварных соединений
Ультразвуковой дефектоскоп – сканер, предназначенный для выявления подповерхностных дефектов в толще изделий из металлов, бетона, камня, полимеров, других материалов без нарушения целостности исследуемого объекта, его поверхности. Для получения данных о скрытых инородных вкраплениях, пустотах, трещинах, несплошностях, порах и других дефектах используется метод генерации ультразвуковых волн, которые, неравномерно отражаясь от материалов различной плотности, возвращаются к датчику прибора в искаженном виде. Прибор фиксирует сигнал, дешифрует его и отображает на экране в виде графика, числовых значений, общих снимков, что позволяет специалисту определять не только наличие, но и точные координаты дефектов.
Сферы применения
Наиболее распространенной является ультразвуковая дефектоскопия сварных швов, металлических изделий, ответственных конструкций. Метод позволяет осуществлять контроль качества на этапе приемки металлических изделий/конструкций, проводить плановые проверки в процессе эксплуатации, что позволяет своевременно выявлять возникающие проблемы, предупреждать аварийные ситуации. Эти свойства определяют области применения приборов:
- Металлургическая промышленность
- Инженерия – строительство мостов, опор, несущих конструкций, энергетических коммуникаций – нефте-газопроводов, водоснабжения
- Авиакосмическая отрасль
- Машиностроение, железнодорожное (ультразвуковая дефектоскопия рельсов) и общее строительство
Наиболее распространенным является метод эхо-импульсного исследования. Импульсный ультразвуковой дефектоскоп генерирует импульс, сам же его принимает и дешифрует. То есть, используется только один преобразователь, что упрощает задачу для специалиста.
Технические особенности представленных в компании «ПОВЕРКОН» ультразвуковых дефектоскопов
В компании «ПОВЕРКОН» вы можете купить ультразвуковой дефектоскоп, цена которого зависит от его функциональных особенностей, технических возможностей. Среди важных характеристик отдельных моделей:
- Использование фазированных решеток (до 32 параллельных каналов) – ультразвуковой дефектоскоп на фазированных решетках позволяет получать результаты контроля в виде сканированных изображений на дисплее без использования дополнительных модулей (функция визуализации)
- Универсальность – возможность проведения исследований различными методами (Эхо-импульсного, зеркального, зеркально-теневого, электромагнитно-акустического) с применением одного прибора
- Настройка скорости ультразвука в широком диапазоне – до 15000 м/с
- Возможность обнаружения дефектов на глубине свыше 2000 мм при максимальной длине образца до 6000 мм
- Оснащение морозостойкими TFT дисплеями – диапазон эксплуатационных температур от -20 до +50 градусов Цельсия
- Сохранение результатов во внутренней памяти, передача на внешние носители, подключение к ПК
- Автономная работа от перезаряжаемых батарей – в среднем до 8-12 часов в непрерывном режиме
- Встроенные в интерфейс подсказки
- Дополнительные аксессуары в комплектации – защитные чехлы, пеналы, сумки, сменные аккумуляторные батареи
Каждый ультразвуковой дефектоскоп для контроля сварных соединений, купить который в компании «ПОВЕРКОН» можно прямо со страниц каталога, поставляется с гарантией в готовом к использованию виде. За помощью в выборе и любой дополнительной информацией обращайтесь напрямую к нашим техническим специалистам одним из предложенных в разделе «Контакты» способов.
Ультразвуковые дефектоскопы Sonatest
КОМПЛЕКСНЫЙ ПОДХОД К ВЫЯВЛЕНИЮ ДЕФЕКТОВ МНОГОСЛОЙНЫХ КОНСТРУКЦИЙ ИЗ КОМПОЗИТНЫХ МАТЕРИАЛОВ
Представлены экспериментальные результаты применения современных тепловизионных систем серии ТН-9100 и ультразвуковых импульсных дефектоскопов серии SONATEST 700 для выявления дефектов в конструкциях из композиционных материалов, используемых в авиационной промышленности и технике.
В процессе отработки технологии и изготовления крупногабаритных изделий из композиционных материалов возникает необходимость проведения оперативного контроля значительных площадей конструкций, с последующим уточнением параметров выявленных дефектов (размера, глубины залегания и формы).
В данной работе
рассмотрены возможности применения методов ИК-термографии и
ультразвукового метода контроля для решения
рассматриваемой проблемы.
В последние годы методы ИК-термографии рассматриваются как одно из перспективных направлений в технике неразрушающих испытаний изделий, в том числе и конструкций из композиционных материалов [1]. Практическое применение методов ИК-термографии в ряде случае затруднено и связано с необходимостью использования опытных специалистов для интерпретации результатов контроля и их анализа. В ряде работ рассмотрена возможность передачи функций анализа температурной информации и автоматизированного обнаружения дефектов, используя достаточно сложные алгоритмы теории распознавания образов [2]. Данные направления работ представляют значительный интерес, однако в настоящее время не вышли за рамки лабораторных исследований.
Для выявления
признаков наличия дефекта методом ИК-термографии необходимо выяснить может ли
временное изменение температуры быть описано одномерным приближением для
однородной среды или нет. Это позволяет провести упрощенный анализ и
выявить признаки наличия дефектов по кривой изменения температур.
Кривая временного изменения температуры при наличии дефектов типа включений или расслоений с воздушными промежутками располагается выше кривой охлаждения изделия без дефектов [3]. Для включений с повышенной теплоемкостью, например, при увлажнении полостей расслоений, кривая временной зависимости охлаждения образца будет располагаться ниже кривой охлаждения образца в бездефектной зоне (рис 1).
Рис.1.
Кривые охлаждения в зонах бездефектного (2) и дефектных (1,3)
участков.
Как видно из
графиков, разность температур поверхности над дефектом, по сравнению с
бездефектным участком, на начальном временном периоде увеличивается, а затем
уменьшается. Как правило, превышение температуры для определенной глубины
залегания дефекта имеет максимум или минимум для включений с отличными от
основного материала теплофизическими свойствами.
В области регулярного (установившегося) теплообмена, изменение температуры в двойных логарифмических координатах описывается линейной функцией. Для бездефектной области функция временного изменения температуры описывается линейной функцией с фиксированным отрицательным углом наклона, что следует из решения нестационарного уравнения теплопроводности для однородного полупространства. Наличие дефекта изменяет скорость распространения тепловой волны так, что при наблюдении за температурой на поверхности изделия, дефекты обнаруживаются в виде зон с отличающейся (относительно бездефектных областей) температурой. Глубоко расположенные дефекты наблюдаются с большей задержкой по времени и уменьшенным температурным контрастом.
Время от начала
импульсного воздействия до обнаружения температурной аномалии пропорционально
квадрату глубины залегания дефекта. Абсолютная величина температурного контраста
изменяется во времени ипримерно обратно
пропорциональна кубу глубины расположения дефекта от поверхности
облучения и контроля. Длительность наблюдения проявления дефекта от начала
температурного переходного процесса пропорциональна квадрату
глубины залегания дефекта и обратно пропорциональна коэффициенту α
температуропрводности материала [4].
Для типичных композитных пластиковых материалов значение α ≈1·10-7м2/с (органопластики) и α ≈5·10-7м2/с (углепластики). Признаки расслоений с характерным размером, сопоставимым с глубиной залегания, обнаруживаются сравнительно легко при обеспечении необходимого импульсного энергетического воздействия на поверхность объекта контроля, или при остывании предварительно нагретого объекта в атмосфере.
В данной работе
исследования проводились на стеклопластиковых и углестеклопластиковых
многослойных образцах толщиной 5…10мм, в которых были выполнены искусственные
дефекты, ориентированные параллельно поверхности, так и фрагментов натурных
конструкций с естественными технологическими дефектами типа расслоений. Диаметр искусственных дефектов в указанных образцах составлял от 3 до 20
мм. Глубина залегания дефектов составляла от 1 до 5 мм.
В опытах использован тепловизор серии ТН-9100 фирмы NEC (Япония), с температурным разрешением ~0,05К. и ультразвуковой импульсный дефектоскоп типа SONATEST 700 фирмы Sonatest (Великобритания).
Термограммы процесса остывания объекта получены в режиме отрицательного теплового воздействия (остывания предварительно равномерно нагретого фрагмента объекта в свободной атмосфере). Подобное тепловое воздействие наиболее близко моделирует тепловой переходный процесс в технологическом процессе изготовления изделий. Характерные термограммы процесса свободного остывания фрагмента изделия из углестеклопластика приведены на рис.2, а из стеклопластика — на рис. 3.
Рис.2. Термограммы фрагмента конструкции из
углестеклопластика. Область выявленного расслоения показана стрелкой.
Рис. 3. Термограммы процесса остывания изделия из стеклопластика. Области выявленных расслоений показаны стрелками.
Как видно из приведенных термограмм, дефекты надежно обнаруживаются без привлечения сложных методов обработки тепловых изображений. Из термограмм следует, что превышение температуры поверхности (в области максимального контраста) достигает ΔТ= 4°С, что более чем на порядок превышает предел температурного разрешения используемой тепловизионной системы.
К достоинствам описанного подхода следует отнести возможность осуществления оперативного контроля состояния протяженных поверхностей в ходе технологического процесса в тех случаях, когда имеют место переходные тепловые режимы.
Наряду с
описанными преимуществами термографический метод контроля не свободен от
недостатков, главным из которых является требование обеспечения оптического
доступа к поверхности объекта, а также обеспечение однородности излучательных
свойств и начальной температуры контролируемой поверхности. В ряде случаев
отмеченные особенности можно преодолеть путем применения дифференциального
анализа термограмм, а также применения дублирующих методов контроля, например,
ультразвукового метода.
Ультразвуковой
контроль локализованных термографическим методом зон выполнялся ультразвуковым дефектоскопом
SONATEST 700, работающим в эхо-импульсном режиме на частоте 1 МГц, с
применением прямого преобразователя раздельно-совмещенного типа. Для
одновременного наблюдения дефектов (расслоений) по толщине контролируемого
изделия, а также за качеством акустического контакта преобразователя,
в ультразвуковом дефектоскопе SONATEST 700 предусмотрено выделение временных строб-импульсов. Это
обеспечивает выдачу сигнализации при появлении эхо-сигналов от дефектов в
области первого строба, так и нарушение акустического контакта при пропадании
донного импульса в область второго строба.
Основной задачей ультразвукового контроля являлось подтверждение результатов обнаружения дефектов термографическим методом, а также точное определение глубины залегания расслоений. Данный вид контроля предполагается использовать при осуществлении технологического процесса изготовления конструкций из многослойных композитных материалов.
Типичные изображения на экране дефектоскопа, полученные в бездефектной и дефектной зонах конструкции, приведены на рис. 4. Горизонтальные стробирующие сигналы 1 и 2, изображенные на экране ультразвукового дефектоскопа SONATEST 700 (рис 4 и рис.5), показывают области потенциального расположения дефекта (зона контроля) и донного эхо-сигнала для контроля качества акустического контакта.
Рис. 4.
Изображение на экране дефектоскопа SONATEST 700:
а)- бездефектная
зона изделия из композиционного углестеклопластикового
материала; б)-дефектная зона изделия.
При наличии в дефектной зоне небольших по площади дефектов (непроклеев), расположенных на разной глубине (рис. 5,а), наряду с эхо-сигналами от дефектов отображается также донный эхо-сигнал.
Рис. 5. а) —
отображение двух небольших по площади расслоений материала;
б)- дефекты
увеличенной площади: 1, 2 – строб-импульсы; 3- донный сигнал; 4-эхо- сигналы от
дефектов.
С увеличением площади непроклея пропадает донный сигнал и наблюдаются только эхо-сигналы от непроклеев (рис. 5 б). Следует отметить, что при отсутствии акустического контакта ультразвукового преобразователя с контролируемым изделием, все эхо-сигналы отсутствуют.
Макрошлиф
дефектного участка, выявленного термографическим и подтвержденного
ультразвуковым эхо-импульсным методами в конструкции из композиционного
стеклопластикового материала, приведен на рис. 6.
Рис. 6. Макрошлиф дефектного участка конструкции из стеклопластика, выявленного термографическим и ультразвуковым методами контроля.
В результате исследований установлено, что эхо-импульсный ультразвуковой метод контроля ультразвуковым дефектоскопом SONATEST 700 многослойных конструкций на основе стекло- и угле-пластиковых композитных материалов обеспечивает обнаружение более меньших по площади дефектов (расслоений, непроклеев), в сравнению с тепловым и теневым ультразвуковым методами контроля. Как и тепловой метод, ультразвуковой эхо- метод не требует двустороннего доступа к контролируемому объекту, что часто реализуется на практике.
Таким образом,
полученные результаты показывают на перспективность применения комбинированного
подхода к контролю, сочетающего возможности оперативного контроля
значительных площадей объекта термографическим методом, с последующим уточнением
параметров выявленных дефектов (размера, глубины залегания и формы)
ультразвуковым эхо-импульсным методом.
Тепловизоры
серии ТН-9100 и ультразуковые импульсные дефектоскопы типа SONATEST 700
по своим техническим характеристикам позволяют обеспечить возможность
достоверного обнаружение непроклеев и расслоений, при относительно низкой
трудоемкости контроля крупногабаритных композиционных изделий, подобных лопастям
вертолетных винтов и др.
ВЫВОДЫ
Предложенный в
работе подход, основанный на использовании нескольких методов диагностики,
эффективен для дефектоскопии изделий непосредственно в ходе технологической цепи
их производства, где требуется оперативная локализация наличия дефектных
участков (непроклеев, расслоений). Определение основных характеристик
дефектов (размера и глубины залегания) может быть произведено
ультразвуковым методом локации. Необходимость решения указанных задач подобной
постановки возникает как на этапе отработки технологии изготовления
изделий, так и проведении стендовых испытаний конструкций. Близкие по
характеру задачи связаны с обнаружением образовавшихся дефектов и
увлажнений композиционных и сотовых конструкций в процессе эксплуатации
авиационной техники.
Предварительная проработка методических аспектов контроля, с учетом технологических особенностей изготовления изделий, является необходимым атрибутом успешного использования применяемых средств дефектоскопии.
ЛИТЕРАТУРА:
1. Вавилов В.П. Тепловые методы неразрушающего контроля. М.:, «Машиностроение» 1991, 240 с.
2. N P Avdelidis, A Moropoulou, Z P Marioli-Riga, “Invited Paper: The technology of composite patches and their structural reliability inspection using infrared imaging”, Journal of Progress in Aerospace Sciences, Vol. 39, No 4, pp 317-328, 2003.
3. D Bates, G Smith, D Lu, J Hewitt, “Rapid thermal non-destructive
testing of aircraft components”, Journal of Composites Part B: Engineering, Vol. 31, No 3, pp 175-185, 2000.
4. D.A. González, C. Ibarra-Castanedo, M. Pilla, M. Klein, J.M. López-Higuera, X. Maldague, Automatic Interpolated Differentiated Absolute Contrast Algorithm for the Analysis of Pulsed Thermographic Sequences, Proceedings of 7th International Conference on Quantitative Infrared Thermography (QIRT’04), 2004
Купить ультразвуковые дефектоскопы и толщиномеры, предварительно ознакомившись с их работой, Вы можете в ООО «ПАНАТЕСТ». Наши квалифицированные специалисты обеспечивают качественное гарантийное и постгарантийное обслуживание приборов.
Обращайтесь по телефонам: +7 (495) 918-09-30, 362-78-73, 673-02-23. Менеджеры компании оперативно ответят на любой Ваш вопрос. г. Москва, ул. Авиамоторная 12, офис 405; Тел./факс: +7 (495) 789-37-48, +7 (495) 587-82-98.
Дефектоскопы ультразвуковые портативные Интротест-1М, Интротест-1МВ, Интротест-1МН
ОПИСАНИЕ ТИПА СРЕДСТВА ИЗМЕРЕНИЙ Дефектоскопы ультразвуковые портативные «Интротест-1МВ», «Интротест-1МН» Назначение средства измерений
Дефектоскопы ультразвуковые портативные «Интротест-1МВ», «Интротест-1МН» (далее — дефектоскопы) предназначены для обнаружения дефектов, измерения глубин (координат) их залегания, измерения отношения амплитуд сигналов от дефектов и для ультразвуковой толщинометрии.
Подробное описание
Принцип действия дефектоскопа заключается в измерении амплитудных и временных параметров электрических импульсов ультразвукового пьезоэлектрического преобразователя и основан на излучении в направлении объекта контроля импульсных ультразвуковых колебаний, вводимых в объект контроля от ультразвуковых пьезоэлектрических преобразователей через промежуточные контактные звукопроводящие среды, с последующей регистрацией ультразвуковым пьезоэлектрическим преобразователем (далее — ПЭП) импульсных ультразвуковых колебаний, прошедших или отраженных от дефекта или раздела двух сред, в результате взаимодействия с объектом контроля. Глубины (координаты) залегания дефектов и толщины объектов контроля рассчитываются дефектоскопом на основании измеренных временных параметров электрических импульсов ПЭП и вводимой с клавиатуры информации о параметрах ПЭП и объекте контроля.
Дефектоскоп является: по области применения — дефектоскопом общего назначения, по конструктивному исполнению — портативным, по устойчивости к механическим воздействиям -обыкновенным, по степени участия оператора в процессе ультразвукового неразрушающего контроля — ручным.
Электронный блок дефектоскопа оборудован устройством генерации импульсов возбуждения ПЭП, устройством усиления электрических импульсов ПЭП, устройством обработки информации на базе микропроцессора, дисплеем и клавиатурой. Для излучения и приема импульсных ультразвуковых колебаний к электронному блоку дефектоскопа подключается ПЭП из комплекта ультразвуковых преобразователей дефектоскопа.
Ультразвуковые преобразователи из комплекта дефектоскопа являются контактными ПЭП общего назначения, в комплект входят прямые совмещенные и раздельно-совмещенные ПЭП, наклонные совмещенные ПЭП. Условное обозначение ПЭП из комплекта дефектоскопа соответствует требованиям Приложения 2 ГОСТ 26266-90, основные показатели соответствуют требованиям таблицы 1 ГОСТ 26266-90.
Дефектоскоп реализует эхо-импульсный, зеркально-теневой и теневой методы ультразвукового неразрушающего контроля. Дефектоскоп позволяет измерять толщину объекта контроля, а также регистрировать в памяти прибора параметры настройки и информацию о дефектах.
Дефектоскоп имеет модификации:
— »Интротест-1МВ», применяется для контроля материалов с малым затуханием ультразвуковых колебаний;
— »Интротест-1МН», применяется для контроля материалов с высоким затуханием ультразвуковых колебаний.
Общий вид дефектоскопа приведен на рисунке 1, общий вид ПЭП приведен на рисунке 2, схема пломбировки корпуса дефектоскопа приведена на рисунке 3.
Работа дефектоскопов осуществляется под управлением встроенного программного обеспечения (далее — ПО), которое отдельно от дефектоскопов не функционирует. Встроенное ПО вычисляет непосредственный результат измерения. При этом аппаратная и программная части дефектоскопов, работая совместно, обеспечивают заявленные точности результатов измерений.
После изготовления дефектоскопа доступ к встроенному ПО со стороны пользователя и (или) других технических (программных) средств полностью исключён. Защита программного обеспечения от непреднамеренных и преднамеренных изменений — уровень А по МИ 3286-2010.
Идентификацию встроенного ПО проводят считыванием идентификационного наименования программного обеспечения и номера версии ПО с дисплея дефектоскопа. Идентификационное наименование программного обеспечения считывают при включении дефектоскопа, а номер версии программного обеспечения — при подключении к дефектоскопу блока питания 220/20 В или в момент выключения дефектоскопа согласно таблице.
Идентификационное наименование программного обеспечения |
Номер версии (идентификационный номер) программного обеспечения |
Цифровой идентификатор программного обеспечения (контрольная сумма исполняемого кода) |
Алгоритм вычисления цифрового идентификатора программного обеспечения |
Ультразвуковой дефектоскоп Интротест-1МВ, -1МН |
2.1.5 |
нет доступа к исполняемому файлу |
нет доступа к исполняемому файлу |
Технические данные
Наименование характеристики |
Значение характеристики |
Диапазон измерения глубин залегания дефектов (для скорости распространения ультразвуковых колебаний 6000 м/с), мм |
от 0,5 до 6399,0 |
Диапазон измерения координат залегания дефектов (для скорости распространения ультразвуковых колебаний 3000 м/с), мм |
от 0,5 до 3199,0 |
Пределы допускаемого значения абсолютной погрешности измерения глубин (координат) дефекта, мм |
±(0,5 + 0,01-И), где И — измеряемая глубина (координата), мм |
Диапазон измерения толщины для модификации «Интротест-1МВ», мм |
от 0,5 до 100,0 |
Диапазон измерения толщины для модификации «Интротест-1МН», мм |
от 5 до 100 |
Пределы допускаемого значения погрешности измерения толщины, мм |
±(0,05 + 0,01-И), И — измеряемая толщина, мм |
Диапазон измерения времени задержки сигналов, мкс |
от 0,2 до 2133,0 |
Пределы допускаемого значения абсолютной погрешности измерения времени задержки сигналов, мкс |
±(0,01 + 0,005-T), T — измеряемое время задержки, мкс |
Диапазон установки скоростей распространения ультразвуковых колебаний, м/с |
от 2000 до 10000 |
Шаг установки скорости распространения ультразвуковых колебаний, м/с |
5 |
Наименование характеристики |
Значение характеристики | |
Пределы допускаемого значения абсолютной погрешности измерения отношения амплитуд сигналов на входе приемника в диапазоне усиления от 0 до 70 дБ, дБ |
±1,0 | |
Границы амплитудной характеристики приемного тракта при нелинейности ±2 % высоты экрана дефектоскопа, % высоты экрана дефектоскопа |
от 5 до 90 | |
Погрешность настройки (зона нечувствительности) порогового индикатора на уровне 55 % высоты экрана дефектоскопа, дБ |
±0,5 | |
Динамический диапазон временной регулировки чувствительности (ВРЧ), дБ |
60±1 | |
Амплитуда зондирующего импульса, В, не менее |
300 | |
Диапазон регулировки длительности зондирующего импульса, нс |
от 75 до 325 | |
Полосы пропускания фильтров приемника по уровню минус 3 дБ, МГц | ||
модификация «Интротест-1МВ» |
фильтр 1,25 МГц |
от 0,6 до 2 |
фильтр 2,50 МГц |
от 1,3 до 3,8 | |
фильтр 5,00 МГц |
от 2,5 до 7,5 | |
фильтр 15,00 МГц |
от 7 до 20 | |
модификация «Интротест-1МН» |
фильтр 0,07 МГц |
от 0,04 до 0,1 |
фильтр 0,40 МГц |
от 0,1 до 0,7 | |
фильтр 1,25 МГц |
от 0,6 до 2 | |
фильтр 2,50 МГц |
от 1,3 до 3,8 | |
Максимальная чувствительность приемника на частоте максимальной амплитуды для соответствующих фильтров, мкВ, не более | ||
модификация «Интротест-1МВ» |
фильтр 1,25 МГц |
60 |
фильтр 2,50 МГц |
80 | |
фильтр 5,00 МГц |
100 | |
фильтр 15,00 МГц |
150 | |
модификация «Ин1ротесг-1МН» |
фильтр 0,07 МГц |
60 |
фильтр 0,40 МГц |
60 | |
фильтр 1,25 МГц |
60 | |
фильтр 2,50 МГц |
80 | |
Отклонение эффективной частоты эхо-импульса ультразвуковых преобразователей из комплекта дефектоскопа от номинального значения, % |
±10 % | |
Отклонение угла ввода наклонных ультразвуковых преобразователей из комплекта дефектоскопа от номинального значения |
±2 | |
Запас чувствительности для ультразвуковых преобразователей из комплекта дефектоскопа, дБ, не менее | ||
П111-1,8-К20, П111-2,5-К12 |
60 | |
П111-5-К6, П121-1,8-40 |
55 | |
П121-1,8-50, П112-2,5-12/2, П121-2,5-40, П121-2,5-50 |
50 | |
П112-5-12/2, П112-5-6/2, П121-2,5-65, П121-2,5-70, П121-5-40, П121-5-65 |
45 | |
П121-1,8-65 П121-2,5-75 П121-5-50 |
40 | |
П112-10-6/2 П121-5-70 |
35 | |
П121-5-75 |
30 |
Наименование характеристики |
Значение характеристики |
Рабочие условия эксплуатации: — температура окружающего воздуха, °С — относительная влажность воздуха (без конденсации влаги), % — атмосферное давление, кПа |
от минус 10 до 40 от 30 до 80 (при 35 °С) от 84,0 до 106,7 |
Электропитание от сети переменного тока: — напряжение, В — частота, Гц Электропитание от блока аккумуляторов: — напряжение, В |
от 176 до 253 от 49 до 51 от 10,8 до 12,0 |
Потребляемая мощность, Вт, не более |
10 |
Габаритные размеры (ширинахвысотахглубина), мм, не более |
250х170х60 |
Масса, кг, не более |
1,5 |
Средний срок службы, лет, не менее |
10 |
Средняя наработка на отказ, ч, не менее |
12 000 |
Утвержденный тип
Знак утверждения типа наносят на корпус дефектоскопа путем наклейки полимерной пленки с нанесенным типографским способом текстом и на титульный лист руководства по эксплуатации типографским способом.
Комплект
Наименование изделия |
Обозначение изделия |
Кол-во |
Дефектоскоп ультразвуковой портативный «Интротест-1МВ» («Интротест-1МН») с аккумуляторным блоком |
ТУ 4276-004-20872624-2013 |
1 |
Кабель для подключения ПЭП |
2 | |
Блок питания 220/20 В |
1 | |
Ультразвуковые преобразователи |
ТУ 4276-004-20872624-2013 |
* |
Методика поверки |
МП 04-011-2013 |
1 |
Руководство по эксплуатации |
42 7610.003.00.000 РЭ |
1 |
Свидетельство об упаковывании |
1 | |
* — по заявке заказчика |
Информация о поверке
осуществляется по документу МП 04-011-2013 «Дефектоскопы ультразвуковые портативные «Интротест-1МВ», «Интротест-1МН». Методика поверки», утвержденному ФБУ «УРАЛТЕСТ» 28 октября 2013 г.
Перечень эталонов, применяемых для поверки:
— осциллограф цифровой TDS2012B, полоса пропускания от 0 до 100 МГц, диапазон коэффициента отклонения Ко от 10 мВ/дел до 5 В/дел, пределы допускаемой относительной погрешности коэффициента отклонения ±3 %;
— генератор сигналов произвольной формы 33250A, диапазон частот выходного синусоидального сигнала от 1-10-6 Гц до 80 МГц, пределы допускаемой относительной погрешности установки частоты выходного сигнала ±2-10-6;
— магазин затуханий МЗ-50-3, диапазон частот от 0 до 50 МГц; диапазон установки затуханий от 0,0 до 82,1 дБ, пределы допускаемой абсолютной погрешности по разностному затуханию от ±0,1 до ±0,2 дБ;
Лист № 6 Всего листов 6
— комплекс программно-аппаратный USStudio-2, номер по Госреестру 45385-10;
— образцы контрольные №2 и №3 из комплекта контрольных образцов и вспомогательных устройств КОУ-2, номер по Госреестру 6612-99;
— комплект образцовых ультразвуковых мер толщины КМТ176М-1, диапазон воспроизведения эквивалентной ультразвуковой толщины от 0,2 до 100,0 мм, третий разряд по ГОСТ Р 8. 756-2011.
Методы измерений
42 7610.003.00.000 РЭ «Дефектоскопы ультразвуковые портативные «Интротест-1МВ», «Интротест-1МН. Руководство по эксплуатации»
Нормативные и технические документы, устанавливающие требования к дефектоскопам ультразвуковым портативным «Интротест-1МВ», «Интротест-1МН»
ТУ 4276-004-20872624-2013 «Дефектоскопы ультразвуковые портативные «Интротест-1МВ», «Интротест-1МН». Технические условия»;
ГОСТ Р 8.756-2011 «ГСИ. Государственная поверочная схема для средств измерений скорости распространения продольных ультразвуковых волн в твердых средах»;
ГОСТ 26266-90 «Контроль неразрушающий. Преобразователи ультразвуковые. Общие технические требования».
Рекомендации
Дефектоскопы могут применяться при выполнении работ по оценке соответствия промышленной продукции и продукции других видов, а также иных объектов установленным законодательством Российской Федерации обязательным требованиям.
Ультразвуковой дефектоскоп для контроля сварных соединений
Неразрушающий контроль соединений – современный метод диагностики наличия и глубины дефектов в узлах и деталях. В отношении оценки последующей работоспособности сварных соединений особенно эффективной признана ультразвуковая дефектоскопия. Дело в том, что в подавляющем большинстве производственных ситуаций имеющиеся неоднородности сварного шва располагаются так, что хорошо отражают именно акустические волны сверхвысокой частоты. Этот метод проверки и заключает в себе ультразвуковой дефектоскоп.
В чём заключается эффективность неразрушающего контроля сварных соединений?
Идеально однородные среды в процессе взаимодействии с источником ультразвуковых колебаний не ослабляют амплитуду звуковых волн. Совсем иное происходит, если сканируются реальные объекты. При наличии в них участка с искажениями первоначальной структуры всегда наблюдается существенное искажение и уменьшение амплитуды звукового давления, которое количественно проявляется в виде ослабления или даже полного поглощения ультразвуковых волн.
Интенсивность таких искажений устанавливается законом ослабления
P=Р0 exp(-αd),
где: Р0 – исходное значение амплитуды звукового давления; Р – значение на выходе из диагностируемого сварного шва; d – толщина шва; α – коэффициент ослабления.
Поскольку параметр d чаще представляют как расстояние до источника ультразвукового излучения, то считается, что звуковая волна имеет вид полусферы, а потому ослабление будет равномерным по всем направлениям. В практике измерений оно обычно устанавливается в децибелах (дБ), поэтому может быть вычислено по формуле
α = 20/d∙lg(P0/Р)
Промышленный ультразвуковой дефектоскоп, применяемый для определения сплошности и качества сварных швов, оценивает интенсивность эхо-сигнала, которая пропорциональна амплитуде звукового давления:
p0/P = H0/H
где: Н0 и Н соответственно — амплитуды звукового сигнала на входе и выходе из прибора.
Для практически применяемого диапазона частот 1…15 МГц (что и случается для подавляющего большинства металлических изделий) интенсивность эхо-сигналов соотносится с относительным ослаблением ультразвукового сигнала следующими соотношениями:
Н/Н0 | 1,26 | 1,78 | 2,82 | 5,01 | 10,0 | 21,62 |
Мощность сигнала, дБ | 2 | 5 | 9 | 14 | 20 | 30 |
Из представленной таблицы следует, что применение оценочного критерия логарифмической интенсивности ультразвукового сигнала может эффективно фиксировать изменения в его амплитуде.
Причинами ослабления ультразвуковых волн происходит вследствие поглощения и рассеивания сигналов. Энергия поглощения превращает колебательную энергию в тепловую. Она пропорциональна частоте ультразвуковых колебаний, поэтому ультразвуковые дефектоскопы для контроля сварных соединений изготавливаются с максимально возможными генерируемыми частотами.
С повышением частоты облегчается фокусировка прибора, благодаря чему распознавание неоднородностей или дефектов улучшается. При этом должны соблюдаться следующие условия:
- Размер оцениваемой неоднородности должен быть больше половины длины волны.
- Направление сканирования должно быть перпендикулярным направлению хода звукового луча.
- Прибор не должен использовать так называемые критические частоты (для металлических конструкций это, например, частоты близкие к 6 МГц), при которых из-за явления дифракции ультразвуковых волн чувствительность метода резко снижается.
Энергия рассеивания более существенна для поликристаллических тел. Поэтому для крупнозернистых структур (например, чугуна) ультразвуковая дефектоскопия малочувствительна. Также неэффективно ультразвуковое сканирование при пониженных температурах окружающей среды.
Для получения ультразвуковых колебаний применяются два вида источников: магнитострикционные генераторы и пьезоэлектрические преобразователи. Каждое из устройств имеет свои рациональные области применения.
Конструкции ультразвуковых пьезоэлектрических дефектоскопов
Пьезоэффект заключается в том, что при силовом воздействии на определённые кристаллические вещества (изоляторы с полярно расположенными осями) в них возникают напряжения определённого знака, которые, в свою очередь, инициируют электрические поверхностные заряды. При этом величина напряжений прямо пропорциональна механической нагрузке, что очень важно именно в конструктивном смысле, поскольку упрощает конструкцию прибора. Таким образом цена ультразвукового дефектоскопа для контроля сварных соединений будет невысокой.
Пьезоэлектрический эффект обратим, а потому использующие его ультразвуковые дефектоскопы быстро переналаживаются, и не нуждаются в сложной регулировке. При этом при помощи прямого пьезоэффекта ультразвуковые волны обнаруживаются, а при помощи обратного – генерируются.
Принцип работы пьезогенератора дефектоскопа следующий. На конденсаторные пластины, которые наложены на кристалл, подаётся переменное электрическое напряжение. Это вызывает колебание кристалла с той же частотой. В качестве преобразователей используют такие материалы, как кварц, титанат бария, сульфат лития и др. При наличии внешнего давления атомы в структурной ячейке пьезоэлемента сдвигаются, что и является моментом начала разряда конденсаторных пластин. При изготовлении ультразвукового дефектоскопа для контроля сварных соединений, использующего подобный принцип, излучатель вырезается таким образом, чтобы плоскость колебания по отношению к толщине рассматриваемого сварного шва излучала продольные волны. Если требуется оценить неравномерность структуры соединения на значительной площади, то используют пластину, вырезанную в перпендикулярном направлении. Тогда с приложением напряжения она будет излучать поперечные волны, которые будут равномерно распространяться в толще исследуемого соединения.
Корпуса пьезоизлучателей изготавливают из керамики, что повышает уровень требований к условиям работы ультразвуковых дефектоскопов для контроля сварных соединений. В частности, им противопоказаны удары и сотрясения корпуса.
Магнитострикционные преобразователи ультразвуковых дефектоскопов
Магнитоскрикция заключается в деформации ферромагнитной детали, которая размещена в силовом магнитном поле. Длина этой детали изменяется в зависимости от вида силовых линий магнитного поля, её материала, температуры и степени намагниченности. В ультразвуковых дефектоскопах используются ферромагнетики, относительное изменение длины которых – не менее 10-5.
Работают такие преобразователи следующим образом. В приборе создаётся переменное электромагнитное поле, при этом ферромагнитный стержень начинает совершать колебания удвоенной амплитуды. Поскольку линейная деформация магнитостриктора не зависит от направления силовых линий магнитного поля, то подмагничивания такого элемента не требуется.
Как и пьезоэффект, магнитострикция обратима. В качестве излучателей применяются химически чистый никель, а также его сплавы с медью или железом. Минимальная частота, при которой обнаружение дефектов сварных конструкций окажется эффективным, составляет 60 Гц, хотя в приборах обычно реализуются частоты от 300 Гц.
Магнитострикционные преобразователи конструктивно проще, однако уступают пьезогенераторам по параметрам минимальной площади диагностируемой зоны: она должна быть достаточно большой. Кроме того, такие ультразвуковые дефектоскопы теряют свою чувствительность при обследовании только что полученных сварных швов. Ещё одним ограничением магнитострикционных источников получения ультразвуковых волн считается их повышенная энергоёмкость. Зато они более компактны, а потому применимы в стеснённых для диагностики условиях.
Промышленные конструкции ультразвуковых дефектоскопов для контроля сварных соединений
Для измерения необходимы:
- Сам регистрирующий прибор.
- Искательная головка (передатчик).
- Контрольная головка (приёмник).
- Устройство отображения (монитор или цифровой дисплей).
Напряжение от источника переменного тока (аккумулятор или генератор — для стационарных дефектоскопов) подаётся на излучатель, а от него ультразвуковые волны передаются в исследуемый сварной шов. Интенсивность ослабления исходного сигнала определяет степень неоднородности шва. Возникающая амплитуда сигнала далее усиливается и регистрируется, при этом возможна как визуальная оценка качества, так и запись результатов на цифровой носитель информации.
Перед использованием ультразвуковой дефектоскоп для контроля сварных соединений подлежит юстировке. Как образец, используется сварной стык с идеальными параметрами качества, при этом отклонение шкалы/стрелки должно быть максимально возможным.
В качестве приёмника дефектоскопы некоторых фирм используют преобразователь изображения. При этом фиксируется фактическое значение плотности энергии звукового поля за швом. Этот способ получения конечной информации более нагляден, но требует определённого пространства за исследуемым соединением.
Излучение звуковой энергии в ультразвуковых дефектоскопах может быть выполнено двумя способами – резонансным или импульсным. В первом случае излучение ультразвука происходит непрерывно, а применяемые частоты находятся в диапазоне 1…12,5 кГц. При импульсном методе используется сигнал (эхо) звуковой волны, который отражается от дефектной зоны или задней поверхности сварного стыка. Подача звукового импульса происходит через 1…2 мкс, чем обеспечивается высокая точность сканирования объекта. Конечный импульс отражается на мониторе, и может регистрироваться цифровым устройством записи. Энергопотребление дефектоскопов такого типа значительно меньше.
Признанным мировым лидером в производстве переносных дефектоскопов для контроля сварных соединений, цена которых вполне соответствует их качеству, считаются аппараты от компании SONATEST (Франция). Данные приборы отличаются компактностью и точностью получаемых данных. Например, применяемые для тестирования качества сварки труб, листовых материалов и т.п. ультразвуковые дефектоскопы линейки Harfang Veo характеризуются следующими эксплуатационными достоинствами:
- большим диапазоном регулировки направления и силы излучения, а также скорости диагностики;
- точностью измерения;
- воспроизводимостью результатов, включая и 3D-моделирование структуры сварного шва;
- удобствами настройки;
- возможностью подключения для целей сканирования нескольких источников;
- ёмкими батареями, допускающими замену непосредственно в ходе измерений.
Лазерно-ультразвуковой дефектоскоп
Предлагаемое изобретение относится к неразрушающим методам исследования и может быть использовано для контроля внутренних структур объектов их геометрических параметров и определения их физических характеристик.
Известен ультразвуковой дефектоскоп, содержащий импульсный лазер, оптически прозрачную пластину, пластину из поглощающего оптическое излучение материала и приемник ультразвука, при этом оптически поглощающая пластина выполнена в виде плоско-вогнутой линзы, а поглощающая пластина — в виде плоско-выпуклой линзы, которые сопряжены между собой сферическими поверхностями (1).
Недостатком данного устройства является невозможность его использования при одностороннем доступе к объекту контроля.
Наиболее близким к предлагаемому лазерно-ультразвуковому дефектоскопу является устройство, описанное в (2). Оно содержит импульсный лазер, соединенный через оптическое волокно с оптико-акустическим преобразователем, а также пьезоприемник, соединенный через усилитель с аналого-цифровым преобразователем, подключенным к компьютеру. К недостаткам известного устройства следует отнести необходимость пропускания излучения лазера сквозь приемник ультразвука, что создает значительные трудности при практической реализации.
Предлагаемое устройство отличается от известного тем, что оптико-акустический преобразователь в нем выполнен в виде единого блока и содержит пластину оптико-акустического генератора, помещенную между исследуемым объектом и прозрачным цилиндром, на торце которого расположен пьезопреобразователь, а фаска цилиндра сопряжена через оптическую систему с оптоволокном. При этом акустические импедансы пластины и цилиндра равны.
Возможность реализации.
На Фиг.1 приведена схема лазерно-ультразвукового дефектоскопа. Он содержит:
1 — лазер с модуляцией добротности и высокой частотой повторения импульсов, содержащий на выходе адаптер для ввода излучения в оптическое волокно;
2 — силовое оптическое волокно для передачи лазерного излучения в оптико-акустический преобразователь;
3 — оптико-акустический преобразователь для преобразования лазерных импульсов в акустические, передачи их в исследуемую среду и регистрации отраженных и рассеянных назад акустических сигналов, содержащий оптико-акустический генератор, оптико-акустическую призму, широкополосный пьезопреобразователь и зарядовый предусилитель;
4 — скоростной прецизионный аналого-цифровой преобразователь, обеспечивающий перевод электрического сигнала оптико-акустического преобразователя в цифровую форму, временное запоминание его и передачу по скоростной линии в компьютер;
5 — комбинированный многофункциональный блок питания, обеспечивающий электропитание лазера, оптико-акустического преобразователя и аналого-цифрового преобразователя;
6 — систему обработки данных, включающую компьютер, связанный скоростной линией передачи данных с аналого-цифровым преобразователем и программным обеспечением, обеспечивающим прием цифровых данных, их спектральную обработку и отображение результатов на экране монитора, а также интерактивное управление процессом передачи и обработки данных;
7 — специализированный изолированный корпус, в котором помещаются лазер, аналого-цифровой преобразователь и блок питания.
Управление и работа системы осуществляются от компьютера, а синхронизация работы лазера производится специальными сигналами, вырабатываемыми в блоке аналого-цифрового преобразователя. Старт-считывание сигнала осуществляется по импульсу фотодиода, согласованному с лазерным импульсом.
Схема оптико-акустического преобразователя 3 приведена на Фиг.2. Оптико-акустический преобразователь 3 содержит прозрачный для лазерного излучения цилиндр 8 с плоскопараллельными основаниями, на которых размещены оптико-акустический генератор 9 и широкополосный пьезоприемник 10. Оптико-акустический генератор 9 представляет собой плоскопараллельную пластину, выполненную из материала, поглощающего лазерное излучение, имеющего высокое значение коэффициента теплового расширения и согласованного по акустическому импедансу с материалом цилиндра 8 (например, из полимера). Облучение оптико-акустического генератора производится коротким лазерным импульсом с помощью формирующей лазерный пучок оптической системы 11, сопрягаемой с волокном 2, через фаску 12 на поверхности цилиндра 8, образованной на его торце с закрепленным пьезоприемником 10.
Дефектоскоп работает следующим образом. Оптико-акустический генератор 9 приводится в акустический контакт с исследуемым объектом 13. Лазерный импульс поступает с лазера 1 через оптоволокно 2, оптическую систему 11, фаску 12 и прозрачное тело цилиндра 8 на пластину оптико-акустического генератора 9. Последний излучает акустический импульс в прозрачный цилиндр 9 и исследуемый объект 13. Рассеянные в объекте акустические импульсы через оптико-акустический генератор 10 и прозрачный цилиндр 9 попадают на пьезоприемник 11, и его электрический сигнал, усиленный усилителем 14, поступает в аналого-цифровой преобразователь 4.
На Фиг.3 показан пример сигнала оптико-акустического преобразователя. По времени прихода рассеянных импульсов определяют глубину нахождения дефекта, а по измеренной толщине объекта и времени прихода сигнала, отраженного от его тыльной поверхности, — скорость ультразвука в объекте контроля.
Источники информации
1. Авторское свидетельство СССР №849072, кл. G01N 29/04.
2. Патент России №2232983, кл. G01N 29/04.
Ультразвуковой эхо-импульсный метод — ZfP
Лаура-Кристин Шольц, январь 2016 г.
Ультразвуковой эхо-импульсный метод или эхо-импульсный метод — это метод неразрушающего контроля с использованием ультразвуковых волн для обнаружения дефектов в материалах.
Принцип эхо-импульсного метода показан на рисунке 1. Излучатель (Т) генерирует ультразвуковую импульсную волну, которая отражается неоднородностью, такой как дефект или задняя стенка образца, и принимается приемником (Р).Полученный сигнал отображается на экране, см. Рисунок 2. [1]