Как отливают чугунные отливки методом литья в землю? Основные этапы.
Литьё чугуна в землю является экономически недорогим и простым процессом, который используют на протяжении более 500 лет. Таким образом отливаются формы массой до 200 тонн, один из прекрасных примеров литья чугуна в землю – это отлитая в 1586 году «Царь пушка». На данный момент литьё в землю используется в машиностроении, станкостроении, автомобилестроении. Многие памятники так же были изготовлены этим способом. У литья в землю есть свои преимущества и недостатки, которые будут рассмотрены ниже.
Модели для литья в землю
Чтобы получить готовое изделие, предварительно изготавливается модель, которая в точности повторяет будущее изделие. Обязательное условие при литье чугуна в землю – это превышение размера модели на процент усадки чугуна. Дело в том что расплавленные металлы имеют свойство расширятся, а при охлаждении масса металла уменьшается в объёме, то есть, говоря по-другому – металл имеет усадку. Чтобы готовое изделие имело точный размер, модель делают большего размера с учётом будущей усадки.
Модели для литья могут быть разборные, полнотелые, пустотелые, с разными дополнительными съёмными частями. Для художественного литья используют выплавляемые модели, либо выжигаемые (из пенонаполненного пластика). Несложные художественные формы изготавливают по неразборным моделям ( часто односторонним, плоским).
Пустотелые отливки изготавливают с применением стержней, которые устанавливают в формы. Стержни формируют в будущей отливке полости и глубокие выемки. Таким образом изготавливали крупные памятники, полости внутри позволяют экономить металл и получить более качественную отливку. Дело в том что меньший слой металла имеет меньшую усадку, что положительно сказывается на качество получаемой поверхности, уменьшает количество раковин и других браков отливки.
Модели для литья чугуна в землю изготавливают из различных материалов, для этого используют дерево, пластик, различные легкоплавкие материалы, пенопласт. Так же модели изготавливают из металлов – чугуна, бронзы, латуни, алюминия. В качестве материалов для моделей используют глину или гипс, эти материалы не такие прочные, но позволяют делать модели для малосерийных отливок. На продвинутых производствах для изготовления форм для будущих отливок используют станки с ЧПУ, управляемые специальным программным обеспечением. В этом случае модели получаются наиболее качественные, выполненные с высокой точностью.
Обработку моделей производят любым подходящим инструментом, то есть, используются фрезеровочные, токарные, точильные станки, а так же, как было упомянуто выше, многофункциональные роботизированные станки с ЧПУ. В последнее время для изготовления особо сложных моделей, применяются 3D принтеры. Они с максимальной точностью позволяют реализовать реальную модель, спроектированную в программе моделирования.
Опоки для отливки
Опока для отливки – это ёмкость (ящик, коробка), которая предназначена для изготовления самой литейной формы из модели. Форма в опоке формируется из нескольких полуформ. Выплавляемые модели позволяют изготавливать неразборные формы, которые после заливки и остывания металла просто разбиваются. Формы в опоке могут быть многоразовые или одноразовые. Как правило, формы для литья изготавливают одноразовые. Раньше отливки особо крупных размеров использовали в качестве опоки саму землю. То есть, форма для литья формировалась непосредственно в слое земли. Сейчас в качестве опоки используются ящики из металла и немного реже из дерева.
Стержни для литья
Стержни в форме для литья необходимы, чтобы формировать в отливках полости разного объёма, размера и длины. Стержни подвергаются воздействию расплавленного металла, поэтому они должны выполняться из газопроницаемых, прочных, термостойких материалов. В зависимости от размеров отливки, заливаемого металла, свойств сплава, для стержней используют специально подобранные смеси. В основном стержни делают из смесей кремнезёмистых элементов, песка, графита, каолина, шамота. Стержни могут быть изготовлены с внутренними полостями, таким образом, в эти полости будут удаляться образующиеся при литье чугуна газы. Так же наличие полостей в стержнях позволяет легче их удалить из уже готового изделия. Для примера можно привести литьё чугунных батарей. В этом изделии внутренняя полость, образуемая с помощью стержней определённой формы, имеет внутренние пустые пространства. Без наличия полостей в стержнях, удалить их будет проблематично.
Формовка для заливки
Формовка формы (тут немного технической тавтологии) производится разными способами. Если изделие несложной формы, то формовку выполняют заливкой (либо заполнением) формовочной смесью. В основном используют кремнезёмистые составы, основной состав которых это смесь глины и песка, с дополнительными компонентами. Так в основном производится изготовления форм для заливки чугуна в землю. При формовке производится трамбовка формообразующего состава, последующая сушка и дополнительный прогрев.
Заливка чугуна в готовые формы
Заливку чугуна производят в подготовленную, собранную форму. Предварительно форма высушивается и дополнительно прогревается. В зависимости от тиража форма на модели, как правило, разъёмная, предварительно собирается и готовится для заливки металла. В подготовленную высушенную и прогретую форму уже можно производить заливку расплавленного чугуна. Залитая металлом форма остывает, затем изделие освобождают от внешней формовочной смеси, а также удаляют внутренние стержни. Затем готовое изделие проходит тщательную очистку и механическую обработку. Дальше изделие может подвергаться дополнительной химической пассивации, окраске и упаковывается.
Данная технология литья чугуна в землю в техническом плане практически не перенесла изменений в течении последних 50-ти лет. Хотя технологическая сторона стала более эффективна и имеет поточное производство. Сотни тысяч современных изделий льются из чугуна именно в песчано-земляные формы. Из положительных сторон данной технологии можно отметить её невысокую стоимость и простоту. Отрицательным моментом можно считать невысокое качество поверхности, а также брак некоторых изделий. Но всё же технология продолжает работать и будет востребована ещё продолжительное время.
КАК СДЕЛАТЬ ЗАКАЗ?Если у вас возникли вопросы или вы хотите узнать цены, обращайтесь в отдел сбыта по телефону:
+7 (4842) 75-10-21 (многоканальный)
или на e-mail:
Профессиональные сотрудники предоставят Вам дополнительную информацию и помогут оформить заявку.
Отправляя заявку я даю свое согласие на обработку моих персональных данных
подать заявку на заказ
Подать заявку на заказ продукции
Возникли вопросы?
Свяжитесь с нами по телефону +7 (4842) 75-10-21
Удобнее связаться по электронной почте?
Напишите нам на [email protected]
ОПОКА (в литейном производстве) — это… Что такое ОПОКА (в литейном производстве)?
- ОПОКА (в литейном производстве)
- ОПОКА (в литейном производстве)
ОПО́КА в литейном производстве, приспособление (в виде жесткой рамы или открытого ящика) для удержания формовочной смеси при изготовлении форм, транспортировании их и заливке металлом. Изготовляют литьем, сваркой, штамповкой и другими методами из стали, чугуна, алюминиевых сплавов.
Энциклопедический словарь. 2009.
- ОПОКА (в геологии)
- ОППМАН Евгений Максимилианович
Смотреть что такое «ОПОКА (в литейном производстве)» в других словарях:
Опока (в литейном пр-ве) — Опока в литейном производстве, приспособление, служащее для удержания формовочной смеси при её уплотнении, т. е. для получения литейной формы и при заливке формы расплавленным металлом. Простейшая О. для разовой литейной формы представляет собой… … Большая советская энциклопедия
Опока — Опока меловой известняк; известковатый суглинок; белая сероватая глина, для обмазки щелей в избе, особ. мергель, глина для отливки чугуна, меди. Опока в литейном производстве, приспособление, служащее для удержания формовочной смеси… … Википедия
ОПОКА — в литейном производстве приспособление (в виде жесткой рамы или открытого ящика) для удержания формовочной смеси при изготовлении форм, транспортировании их и заливке металлом. Изготовляют литьем, сваркой, штамповкой и другими методами из стали,… … Большой Энциклопедический словарь
опока — 1. ОПОКА, и; ж. Спец. Ящик или рама без дна и верха для изготовления литейной формы. ◁ Опоковый, ая, ое. 2. ОПОКА, и; ж. Геол. Твёрдая, лёгкая горная порода, богатая кремнезёмом. ◁ Опоковый, ая, ое. * * * опока I (геол.), лёгкая, твёрдая,… … Энциклопедический словарь
ОПОКА — ОПОКА, опоки, жен. 1. В литейном производстве ящик, рама, в которой заключена земляная форма для литья (тех.). 2. Плотная глина, содержащая в себе кремнезем (геол.). Толковый словарь Ушакова. Д.Н. Ушаков. 1935 1940 … Толковый словарь Ушакова
ОПОКА — 1) О. вгеологии твёрдая микро пористая лёгкая порода серой или чёрной окраски; состоит гл. обр. из опала (до 90% ) с примесью зёрен кварца, полевых шпатов и др. минералов, глинистых частиц, скелетных остатков кремневых микроорганизмов. Содержание … Большой энциклопедический политехнический словарь
Опока — [molding box (flask)] в литейном производстве приспособление для удержания формовочной смеси при изготовлении литейной формы, транспортировке и заливке жидким металлом. По конструкции опоки подразделяются на прямоугольные, квадратные, круглые и… … Энциклопедический словарь по металлургии
Опока — I Опока (геол.) прочная пористая кремнистая осадочная горная порода. О. состоит в основном из микрозернистого водного аморфного кремнезёма (до 97%) обычно с примесью глины, песка, глауконита и др.; присутствуют плохо сохранившиеся остатки … Большая советская энциклопедия
Формовка — в литейном производстве, процесс изготовления литейной формы (См. Литейная форма), предназначенной для получения фасонной отливки (См. Фасонная отливка). Различают Ф. ручную и машинную. Первая применяется главным образом в единичном и… … Большая советская энциклопедия
Литьё — Литьё технологический процесс изготовления заготовок (реже готовых деталей), заключающийся в заполнении предварительно изготовленной литейной формы жидким материалом (металлом, сплавом, пластм … Википедия
Литье из гипса: технология, силиконовые формы изготовление
Гипс — доступный и легкий в обработке материал. С доисторических времен литье из гипса наравне с лепкой из глины использовалось для изготовления различных поделок, игрушек и ритуальных фигурок.


И в наши дни гипс сохраняет свою популярность как поделочный материал. Из него делают также украшения и детали масштабных моделей техники.
Процесс литья из гипса
Процесс литья из гипса состоит из нескольких этапов. Само литье в гипсовые формы занимает минуты, гораздо больше времени уходит на подготовительные и завершающие операции. К подготовительным относятся:
- Изготовление модели изделия.
- Проектирование и изготовление формы, или опоки.
- Подготовка материалов для литья смазывания формы.


Процесс литья из гипса
Проверьте, чтобы все необходимые материалы, оборудование и инструменты были под рукой, отмыты и очищены после прошлого раза. Счет при отливке идет на минуты.
Непосредственно перед литьем в гипс следует произвести смазывание опоки и смешивание раствора для литья. Заливать растров в отверстие следует тонкой струйкой, обязательно давая воздуху возможность выйти. После заливки форму надо повращать и слегка потрясти, чтобы добиться максимального прилегания раствора к мелким деталям рельефа.
Завершающие операции не менее важны. Они так же определяют качество изделия. К ним относятся
- Сушка (при естественной температуре или на радиаторе). Слишком быстрая сушка может привести к растрескиванию отливки.
- Разборка формы. Если она плохо отходит от изделия, можно легонько обстучать ее деревянным или резиновым молоточком.
- Удаление литников и доработка деталей готового изделия.
- Очистка опоки (если планируется еще одна или несколько отливок).
Литье в гипсовые формы немного отличается от литья в формы из силикона. Силикон не нуждается в смазке, он упруг и из него легче извлекать отливку, к тому же он дает больше возможностей для проработки деталей.
Необходимое оборудование и материалы
Для отливки изделий из гипса не требуется высокопрофессиональное оборудование. Процесс вполне доступен в любительской домашней мастерской.
Важно: подготовка, сам процесс литья и завершающие операции связаны с появлением большого количества пыли. Обязательно должна быть обеспечена качественная вентиляция и уборка помещения. Не стоит заниматься этим в жилых помещениях и в домах, где живут аллергики. Кроме того, смесь воздуха и пыли в определенной концентрации взрывоопасна. Избегайте использования открытого огня в мастерской.


Формы для отливки из гипса
Основным оборудование является форма для отливки. Для ее изготовления сначала следует подготовить модель изделия. Для этого подходит пластилин, полимерная глина, любой пластичный материал. Если делают копию, то моделью является сам оригинал. Обязательно нужно наметить на модели линию стыка половинок будущей формы.
Важно правильно подобрать материал для опоки. Если готовится маленькая формочка для литья кулона или деталей масштабной модели техники — подойдет жесткий картон. Для литья крупных отливок лучше взять многослойную фанеру — ее не разопрет большой массой гипса.


Опока из жесткого картона для литья из гипса
Понадобятся также:
- Емкость для смешивания гипса с водой.
- Стакан с носиком для заливки гипса.
- Резинки для стягивания частей формы.
- Кисточки для смазки.
- Дрель для сверления отверстий.
- Шпатели и ножи.
- Картон и скотч.
Гипс для литья следует выбирать самый лучший. Строительный алебастр можно применять, в крайнем случае, его лучше просеять через сито 0.2 мм, убедиться в том, что он достиг «пуховой» консистенции, не содержит комочков и посторонних включений.


Смазка формы для литья из гипса
Смазку для формы можно приобрести готовую, а можно изготовить самостоятельно из натертого на терке детского мыла, воды и подсолнечного масла.
Изготовление форм для литья из гипса
Наиболее используемыми материалами являются сам гипс и силикон.
Формы из гипса являются традиционными и привычными для многих поколений мастеров. Они более требовательны к уровню мастерства при изготовлении. В последние десятилетия их все больше теснят формы из силикона.
Формы, которые сделаны из силикона, отличаются высокой точностью, возможностью проработки мелких деталей, легкостью изготовления и снятия ее с отливки. Несколько дороже обходится исходный состав, но это компенсируется повышенной технологичностью и долговечностью.
При проектировании и изготовлении формы важно обращать внимание на:
- Тщательность проработки деталей.
- Способ соединения половинок формы и их последующей разборки
- Способ фиксации половинок друг относительно друга
- Расположение отверстий для литья. Оно должно позволить жидкому гипсу проникать во все уголки формы и полностью заполнять ее.
- Конфигурация опоки должна давать пузырькам воздуха свободный выход.
Для фиксации частей опоки друг относительно друга обычно используют резиновые ленты. Для маленьких изделий подходят резинки для денег, для более крупных их вырезают из велосипедных или автомобильных камер.
Изготовление гипсовых форм для литья
Литье в гипсовые формы требует определенного навыка, хорошего планирования и точной координации действий мастера. Как сделать форму для литья из гипса?
Сначала вокруг модели будущего изделия строится опока — ящичек из картона, обклеенного скотчем, или жесткого пластика. Щели между основанием и стенками помазываются пластилином. Модель покрывается смазкой и размещается внутри опоки на равных расстояниях от дна и стенок. В качестве подпорки используют кусочки пластика, картона. Иногда просто подвешивают модель на нитках.


Гипс разводят до консистенции сметаны
Гипс разводят до консистенции сметаны, кисточкой наносят на сложные элементы рельефа модели — углы, впадины и т.п. Все готово к литью. Потом заливают модель до линии стыка половинок опоки и оставляют гипс загустевать.


Гипсовая форма для литья
После загустевания проверяют, насколько хорошо модель отделяется от нижней половинки, смазывают ее и модель и заливают верхнюю половину формы. После загустевания верхней половинки по углам сверлят отверстия для штифтов, которые будут фиксировать половинки при отливке. После этого верхнюю половинку снимают, модель удаляют. Опока готова к отливке. Если вы начинающий мастер, запланируйте достаточно времени на приобретение опыта и наработку навыков. Литье в гипс может получиться не с первого раза.
Область применения литья из гипса
Литье из гипса применяется как на промышленных предприятиях для изготовления деталей отделки помещений, так и в авторских мастерских. Мастера льют из гипса весьма широкий ассортимент
- Авторские элементы декора помещений
- Статуэтки и даже большие статуи, вплоть до моделей для последующего литья из металлов
- Небольшие украшения
- Игрушки
- Детали для масштабных моделей техники
Этим перечнем область применения не ограничивается. Мастера придумывают все новые и новые области применения литья из гипса — везде, где нужно создать детали со сложными поверхностями и рельефом, а требования к прочности и износостойкости не являются критически важными.
Вакуумное литьё по выплавляемым восковым моделям.
ВАКУУМНОЕ ЛИТЬЁ ПО ВЫПЛАВЛЯЕМЫМ ВОСКОВЫМ МОДЕЛЯМ.
Существует большое количество способов литья, применяемых в современной ювелирной промышленности:
— литьё в землю (в т.ч. при помощи различной оснастки)
— этилсиликатное литьё
— литьё в одноразовые опоки
— центробежные виды литья
— и, наконец, вакуумные виды литья.
Именно его мы и будем рассматривать подробно, так как на сегодняшний день, как мы уже выяснили, это и есть самый широко применяемый способ литья для изготовления ювелирной и сувенирной продукции.
Итак, вакуумное литьё по выплавляемым восковым моделям.
И начинается в нём всё с качественной восковой модели или, как принято её называть среди ювелиров, — восковки. Конечно, качественную восковку невозможно получить без качественно изготовленной пресс-формы, которая, в свою очередь, должна быть снята с качественно разработанной и обработанной мастер-модели. Однако, мастер-модели и пресс-формы – это тема отдельная, которая в рамках этой статьи рассматриваться не будет, в силу того, что тема литья и так очень обширная и мы, не перегружая эту статью, прибережём её для отдельной публикации.
Как же изготавливаются «восковки»?
— при помощи пресс-формы и инжекторного бачка
— вырезаются вручную или на фрезерных ЧПУ-станках из скульптурного воска
— при помощи иных способов (обливные, инжектированные в металлические формы, изготовленные вручную нестандартными технологиями)
— печатаются из выжигаемых полимеров на 3D-принтерах
При первом способе (а это основной способ для серийного производства), воск в пресс-форму попадает при помощи инжекции (впрыска, подачи под давлением) из заливного клапана инжекторного бачка. Эти бачки, в свою очередь, возможно разделить на несколько типов:
— с ручным насосом
— с подключением к компрессору
— вакуумные (с подключением к воздушному и вакуумному компрессорам)
— полуавтоматические
— автоматические
Принципиальная разница существует между вакуумными и не вакуумными бачками, так как первые, непосредственно перед инжекцией воска в пресс-форму, откачивают из неё воздух. В то время, как из вторых воздух выдавливается как раз в процессе впрыска воска через специальные технологические резы – выпоры. Отсюда же вытекает и разница в употреблении различным образом изготовленных пресс-форм – для вакуумного бачка пресс-форма изготавливается отличным образом от пресс-форм, предназначенных для работы с обычными, не вакуумными инжекторными бачками.
Как бы то ни было, любая пресс-форма делается разъёмной, чтобы после того, как инжектированный в неё воск застыл, была возможность извлечь его для последующего использования, а саму пресс-форму приготовить к дальнейшим повторяющимся операциям.
Какие требования предъявляют к изготавливаемым при помощи пресс-форм восковкам?
1. Не должно присутствовать непоправимых деформаций
2. Не допускается наличия заметных швов и смещений
3. Не допускается наличие пузырьков воздуха или любых других включений, в том числе внутри восковой модели(контроль на просвет)
4. Вся геометрия очертаний восковой модели должна полностью повторять мастер-модель, с которой снята пресс-форма
5. Качество поверхностей восковки должно в разумной степени повторять качество поверхностей мастер-модели, с которой снята пресс-форма
После того, как восковая модель готова и её качество проверено, она размещается (путём припаивания) в специальном восковом блоке, часто называемом, в силу внешней похожести, «восковым деревом» или «ёлкой». Существует несколько техник сборки ёлок, однако имеются несколько основных принципов, применяемых в этом процессе:
— сверху ёлки припаиваются более мелкие и лёгкие детали, а внизу – более крупные
— детали на ёлке помещаются под углом менее 90 градусов по отношению к основному литнику(называется иногда стояком)
— восковки, размещаемые на ёлке не должны касаться друг друга и основного литника
— восковки припаиваются на ёлку таким образом, чтобы места их присоединения к литнику были максимально гладкими и не имели непропаев или любых зазоров.
После сборки ёлки попадают на участок формовки, где их размещают на специальных резиновых подставках – «башмаках» или «подошвах» и помещают в опоки – специальные металлические цилиндры, что позволяет в дальнейшем залить их формовочной массой.
Устройства, при помощи которых происходит процесс смешивания формовочной смеси и розлив её в подготовленные опоки, называют вакуумными миксерами, так как в современных условиях весь этот процесс происходит полностью в вакууме. После заливки формовочной массой, опоки с ёлками внутри оставляют в покое на несколько часов для качественного застывания гипса и предварительного высыхания.
Если на производстве применяется паровая вытопка воска, то после формовки и отстаивания, опоки помещают в неё. В ней из опок выплавляется большая часть содержащегося воска. После прохождения этой обработки опокам снова необходимо отстояться. И , после всех описанных процедур, опоки могут наконец оказаться в муфельной печи.
Для ювелирного и сувенирного производства используется довольно большая номенклатура формовочных смесей, основой которых в любом случае является кристобалит – довольно редко встречающийся в природе минерал, высокотемпературная полиморфная модификация кварца, при нагреве меняющий свою структуру. Кроме него в формовочных смесях присутствует гипс, а также большое количество различных присадок выполняющих адаптивные функции. Выбор подходящей формомассы для литья – один из важнейших элементов процесса получения качественных отливок.
Ювелирные муфельные печи устроены таким образом, чтобы обеспечить совокупность осуществления необходимых процессов при прохождении прокалочного цикла опок. Нагревательные элементы(обыкновенно спирального типа) в них расположены как в стенках, так и в дверце (существуют редкие конструкции с нагревателями в полу или потолке печи), обязательно наличие программатора, в паре с термопарой, позволяющего управлять нагревом, а также шиберного отверстия, необходимого для отвода образующихся при выжиге воска испарений. Существуют очень разные конструкции печей, например, позволяющие штатно размещать внутри себя опоки в несколько этажей, цилиндрической формы и оборудованные ротационным механизмом, с различными системами слива воска или принудительного оттока воздуха и т.д. Все эти усовершенствования позволяют, как правило, положительно повлиять на результат прокалки, однако в минимальной комплектации, наличие многостороннего нагрева, термопары с контроллером и шиберного отверстия является нормой, а остальное относится к разряду желаемого.
Прокалочный цикл в печах программируется таким образом, чтобы добиться наилучшим образом сочетания двух факторов – удаления из опоки всех остатков воска и хорошей полимеризации формовочной смеси. График прокалки опок в печи напоминает по виду лестницу: набор температуры, выдержка на заданной «полке», снова набор, снова выдержка формовочной смеси, то есть удаления из неё излишков влаги. Дальнейшие «полки» ступенчатым образом выводят печь на максимальную температуру программы – чаще всего 740 градусов Цельсия, в процессе чего формомасса полимеризуется и приобретает необходимые для заливки в неё в вакууме металла свойства.. Затем, после прохождения всего прокалочного цикла, температура опускается до заданной для заливки металла. Весь стандартный прокалочный цикл продолжается обычно не менее 12 часов, с момента постановки опок в печь, а часто значительно дольше.
После прохождения прокалочного цикла, опоки готовы к розливу в них металла. В современных литьевых цехах и мастерских этот процесс, как правило, происходит при помощи литьевых машин. Конструкции этих машин весьма разнообразны, условно могут быть разделены по способу плавки металла и по способу залива, по наличию/отсутствию и составу инертной среды, степени автоматизации процесса.
По способу плавки различают машины со спиральными нагревателями и индукционным нагревательным элементом; по способу розлива: донный розлив, «перевёртыши», розлив через край; по инертной среде — одно и двухгазовые машины и машины без инертной среды; по автоматизации процесса — ручного розлива, полуавтоматические и автоматические.
Розлив металла производится под воздействием глубокого вакуума на опоку, при температуре немного превышающей его температуру плавления, по возможности, или в вакууме, или в инертной среде, для предотвращения контакта расплава с кислородом воздуха.
После розлива металла в опоки, они охлаждаются в естественных условиях, затем помещаются в размывочные ванны, после чего, извлечённые описанным образом из опок литьевые полуфабрикаты в виде «ёлок», обрабатываются в водоструйной кабине с целью удаления с них остатков формовочной массы. При необходимости отбеливаются в водных растворах кислот. Очищенные отлитые ёлки могут быть подвергнуты, кроме того, очистке в УЗВ, обработке паром при помощи парогенератора и, иногда, галтованию в магнитной галтовочной машине. После очистки «ёлки» сушат (чаще всего или в специальной камере, или при помощи промышленного фена). Затем производят процесс «раскусывания», т.е. срезают отлитые детали с «ёлки», состригают с деталей избыточной длины литники и получившуюся продукцию сдают на склад, где она сортируется, приходуется и производится отбраковка деталей, не прошедших ОТК. Полученные таким образом литьевые полуфабрикаты могут быть переданы в ювелирный цех для дальнейшей обработки.
Автор статьи: Иван Геннадьевич Скворцов.
Основатель и генеральный директор производственной компании 3D Avtozavod.
Что такое опока в ювелирном деле? Процесс литья ювелирного украшения
Разглядывая витрины дорогих ювелирных магазинов, мы приходим в восторг от красоты изделий и мастерства ювелиров. Искусство превращать драгоценный металл в предмет роскоши в воображении многих людей является неким таинством, особым умением, которым может овладеть далеко не каждый. Как же рождаются на свет манящие своей красотой кольца? Какой путь проходит драгоценный металл от эскиза до воплощения в дорогое украшение? Что такое опока в ювелирном деле и для чего она используется?
Особенности профессии ювелира
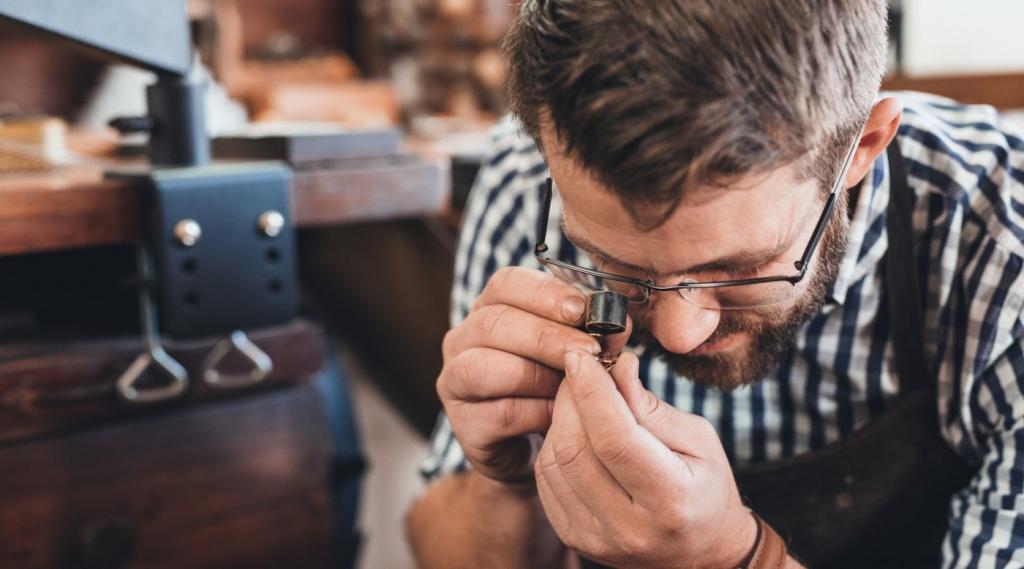
Профессия ювелира требует не только творческого подхода. Ювелир должен быть аккуратен и терпелив. В этом деле множество нюансов, соблюдение которых требует предельной точности. Ювелир работает с высокими температурами и раскаленным металлом, опасность этой профессии требует выдержки и физической силы. Мастер ювелирного дела — это не только дизайнер, придумывающий эскизы и работающий напильником под ярким светом лампы. Это еще и работник литейного цеха, управляющийся с раскаленными печами и расплавленным металлом, поднимающий тяжелые гипсовые формы и следящий за соблюдением технологии. В арсенале мастера ювелирного дела полно необычных приспособлений, о которых простой обыватель даже не слышал. Например, опока. Что такое опока и для чего используется это приспособление? Об этом расскажет наша статья.
Опока в ювелирном деле
Несмотря на все новшества и высокий уровень технологии изготовления украшений, многие методы работы ювелира остаются неизменными с древних времен. Процесс литья колец, например, мало чем изменился. Чтобы ответить на вопрос о том, что такое опока, следует узнать, как происходит процесс литья ювелирных изделий.
Чтобы сделать кольцо из драгоценного металла, ювелир использует специальный огнеупорный цилиндр, в который заливается раскаленный металл, формовочная масса и помещаются восковые заготовки. Это и есть опока.
Это приспособление служит для того, чтобы удерживать формовочную смесь при ее уплотнении в процессе получения литейной формы, в которую заливается драгоценный металл. Изготовить опоку можно самостоятельно, главное — чтобы она была из огнеупорного материала. Некоторые умельцы делают опоку из обрезка трубы или сворачивают ее из листа железа. На фото представлена современная опока из металла.
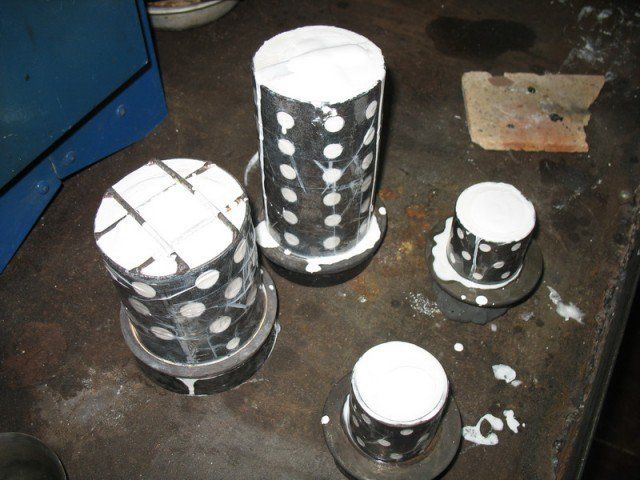
В эту опоку уже залита формовочная масса, внутри которой находятся восковые заготовки. Следующий шаг — прокалка опоки в раскаленной печи, эта процедура происходит в литейном цехе.
Применение опоки в литейном цехе
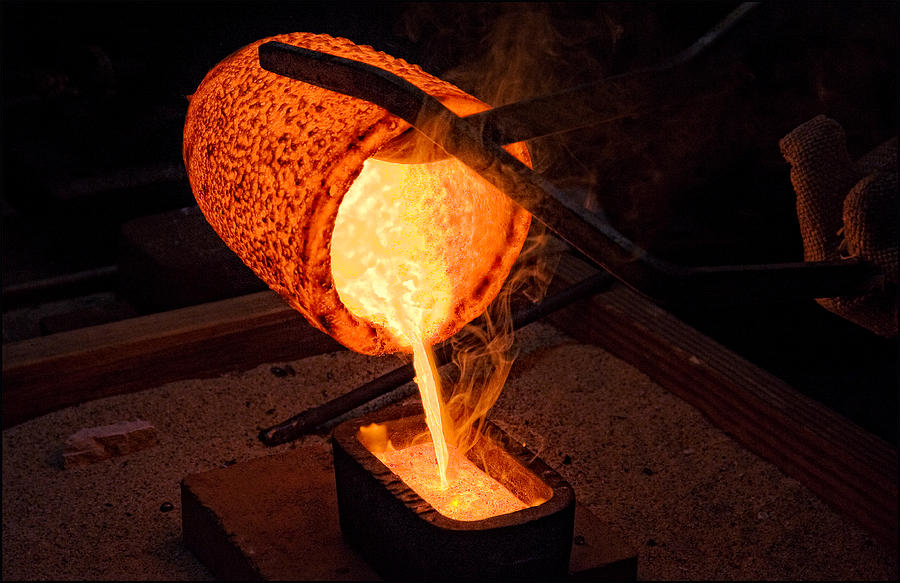
Какими бы утонченными ни были в итоге украшения, они проходят весьма суровый путь через раскаленные печи литейного цеха. Вот как выглядит процесс литья:
- Изделия поступают в литейный цех в виде восковых заготовок, которые проходят процесс формовки.
- Восковая заготовка помещается в специальный огнеупорный металлический цилиндр — опоку для литья.
- Затем опока ставится в раскаленную печь для прокалки. Температура в такой печи может достигать 1000 градусов. Воск из опоки выплавляется, и в этой форме появляется место для драгоценного металла.
- После прокалки опоки и образования формы в нее заливается металл. Процесс отливки украшений происходит в вакууме, предотвращается образование пустот и попадание инородного мусора в форму.
- На финальном этапе из опоки для литья ювелирных изделий литейщик достает украшение и приступает к его финальной обработке и шлифовке.
Гипсовые опоки для изготовления украшений
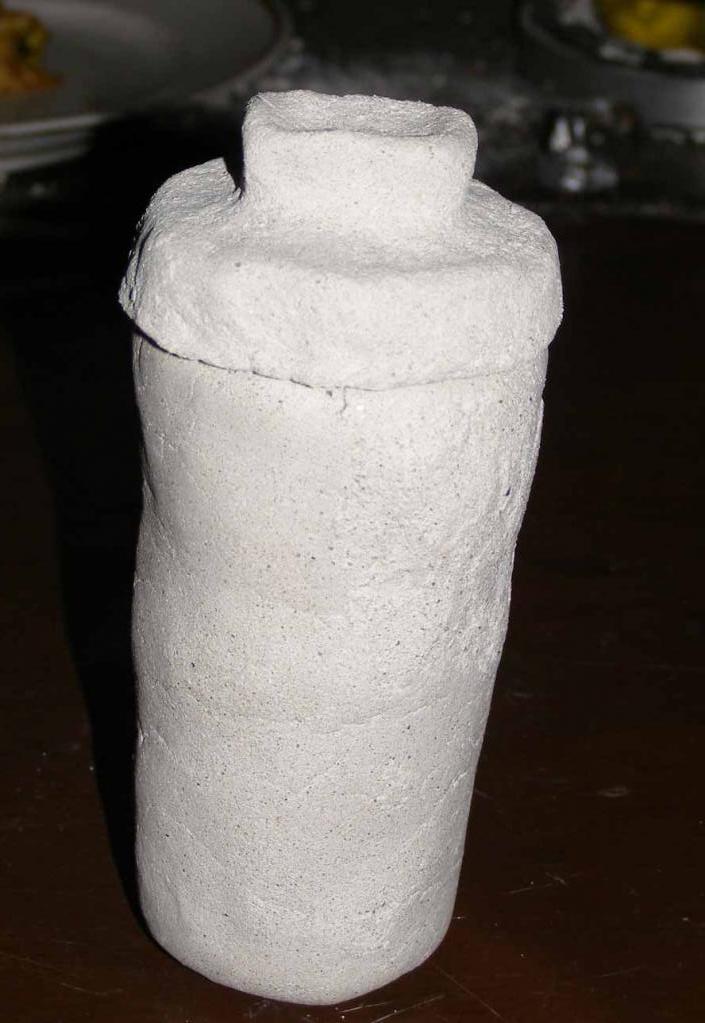
Что такое опока из гипса? По форме она не отличается от более распространенной металлической. Единственное ее отличие — это материал и необходимость ступенчатого нагрева. Гипсовые опоки чаще всего используются для мелкого ювелирного литья, а не для промышленного. Для того чтобы процесс литья с использованием гипсовой опоки был успешным, следует соблюдать температурный режим, иначе форма треснет и станет непригодной для работы. Удобнее всего это делать в специальной электрической печи для отжига, так как там можно регулировать температуру. Отжиг гипсовой опоки производится в несколько этапов:
- Нагрев при температуре менее 100 °С. Выдерживать опоку в такой температуре нужно не менее часа.
- Затем форма должна находиться в печи при температуре 250 °С от двух до двух с половиной часов.
- По истечении этого времени, температуру следует поднять до 450 °С и отжигать опоку еще полтора часа.
- Только после этого можно поднимать температуру до максимальных 750 °С и отжигать форму еще около трех часов.
Время отжига зависит от размеров опокич: чем она больше, тем дольше нужно ее отжигать.
Одноразовые опоки
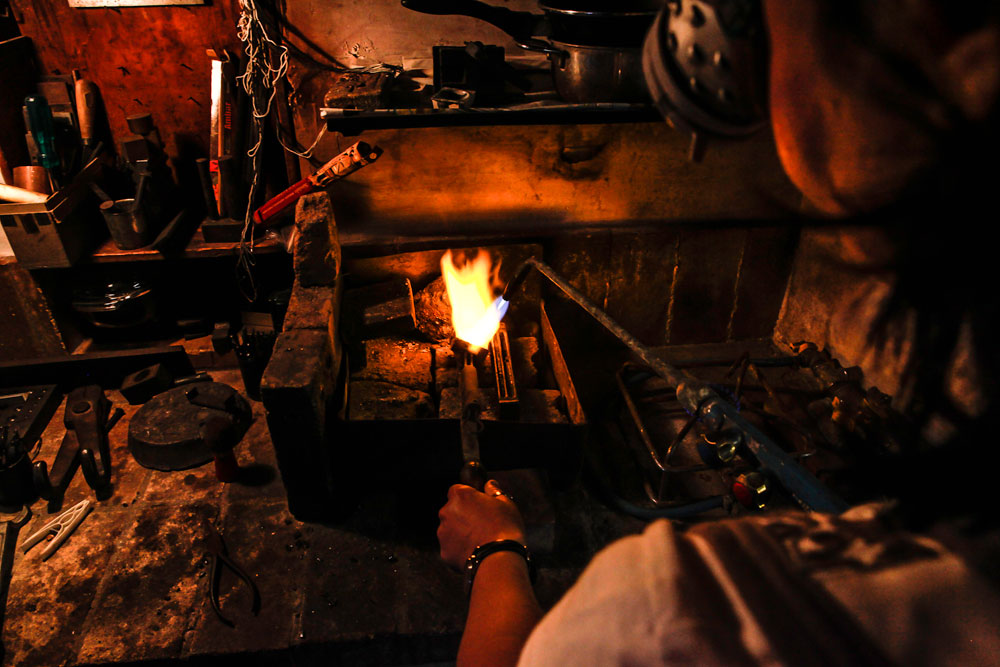
Узнав, что такое опока и как она используется, проще вникнуть в тонкости процесса. Он уже не кажется таким уж сложным, скорее, интересным и простым. Современные технологии позволяют попробовать самостоятельно изготовить ювелирное украшение практически в домашних условиях. Китайский рынок предлагает широкий ассортимент одноразовых опок с уже готовыми формами. Все что нужно для работы с такой формой, — это необходимое количество драгоценного металла и возможность его расплавить. Ими пользуются как ювелиры, не имеющие собственного литейного цеха, так и свободные мастера, изготавливающие украшения на заказ.
сущность литья, технология, изготовление песчаных форм
Литье в песок (литье в песчано-глинистые формы) — один из самых распространенных методов получения литых заготовок во многих отраслях промышленности – станкостроение, автомобильная отрасль и многое другое. Этот способ широко применяют при единичном, серийном и массовом производстве.


Технология литья в песчаные формы
Технология литья в формы из песка не отличается сложностью. Такой метод литья применяют для изготовления отливок и деталей из серого чугуна, низкоуглеродистые стальные сплавы. Иногда, литье в песчаные формы используют для обработки цветных металлов – алюминия, меди и пр.
Выбирая такое литье в песок технолог, должен понимать, что качество готовых деталей будет довольно низким. Это связано в первую очередь с тем, использование такой технологии не может гарантировать того, что в жидкий сплав не попадут посторонние включения. При литье в песчаные формы весьма бурно происходить газообразование, особенно этот процесс, проявляет себя при литье во влажные формы. Допустимо использовать такую форму литья для получения деталей со сложной геометрией. Но ряд ограничений на получение таких заготовок накладывает то, что изъятие готовой отливки сопряжено с определенными сложностями.
Литье в песок позволяет получать заготовки до сотен тонн весом. Таким образом, производят станины для металлорежущего оборудования, корпусные детали и пр.
Между тем точность получаемых заготовок ниже 14 квалитета, кроме того, на поверхности отлитых деталей можно встретить раковины, посторонние включения. Именно поэтому те поверхности, которые будут контактировать с другими деталями, всегда подвергают механической обработке.
Литейная продукция
Литье в песок или землю применяют для производства множества деталей. Для удобства потребителей их можно систематизировать в несколько групп.
Группа А – к этой группе относят отливки простой формы – кольца, колеса, маховики и пр.
Группа Б – к этой группе относят элементы арматуры, подшипниковые корпуса, сложные поверхности с тупым или острым углом.
Группа В – она включает в себя заготовки для зубчатых колес, станины, кожуха и пр.
Группа Г – это отливки для производства станочных станин, сложные корпусные детали.
Группа Д – это отливки, которые получают методом формования по модели.
Таким образом, можно сделать вывод, что в формы из песка можно выполнять отливку и канализационных люков, и детали со сложной геометрической формы, например, кожуха ступеней компрессоров и пр.
При проектировании формы из песка, конструктор должен учитывать то, что в том направлении куда будет извлекаться готовая отливка не должна иметь никаких препятствий в виде выступающих стержней и пр.
Литейные модели
Модели для такой формы литья в песок должны выдерживать довольно большое давление, которое возникает при набивке опоки литейной землей. Именно поэтому для изготовления литьевых форм применяют металл, твердую древесину. Все материалы, которые допустимо использовать для изготовления литьевых форм допускается комбинировать. То есть их можно собирать на резьбовых соединениях, склеивать и пр. Для устранения пор на деревянных частях моделей из тщательно обрабатывают абразивной шкуркой. Затем, ее покрывают лаком. При изготовлении литейных форм необходимо учитывать то, что необходимо выдерживать углы наклона вертикальных плоскостей. Наличие этих углов впоследствии облегчит изъятие готовой отливки из формы.


Основные элементы литья в песчано-глиняные формы
Одним из ключевых факторов, определяющих качество выполнения литья – это свойства песка (земли), применяемого для получения литьевой оснастки. Практика показывает то, что чем мельче и чище песок, тем качество получаемой отливки будет выше.
Нельзя забывать и о стержнях, которые могут быть много- или одноразовые.
Общая классификация песчаных формовочных смесей
В зависимости от применения смеси можно разделить на следующие подвиды:
- облицовочные их применяют при создании рабочей поверхности формы;
- диные (наполнительные), их применяют непосредственно для создания формы.


Общая классификация песчаных формовочных смесей
Облицовочные материалы обладают толщиной, которая определяется толщиной будущей отливки, она может составлять 20 – 100 мм. Сверху смеси, применяемой для облицовки, может быть засыпана наполнительная смесь.
Наполнительную или единую смесь применяют для набивки всей формы и применяют для производства оснастки при всех видах производства, начиная от единичных изделий и заканчивая массовым.
Изготовление литейной песчаной формы
Литье в песчаные формы начинается с ее создания. Отличительной чертой песчаной оснастки является то, что их можно использовать только один раз и для получения новой детали необходимо изготавливать новую.
Оснастку производят, имея на руках модель будущей детали. Ее устанавливают в опоку (деревянная или металлическая коробка для формовочной смеси), засыпают землю. Затем необходимо уплотнить засыпанную песчаную смесь. Для этого используют ручной или механизированный инструмент ударного действия и приспособления. По достижении смесью необходимой кондиции, то есть необходимой плотности, модель извлекают и в распоряжении литейщиков останется готовая технологическая оснастка.
Для получения полостей расположенных внутри будущей отливки применяют стержни. Их как правило, изготавливают из того же материала, что и саму оснастку.
В процесс производства литейной формы из песка входят следующие основные этапы.
- установка модели в опоку;
- уплотнение песчаной смеси;
- изъятие модели из опоки.
Трудоемкость и технология производства литейной оснастки во многом зависит от следующих параметров:
- размера будущей отливки;
- количества полостей;
- типа оснастки.
Если изготавливаемая форма требует дополнительного нагрева или запекания, то затраты времени на ее производство резко вырастут. Для облегчения изъятия готовой отливки на рабочие поверхности наносят различные смазки, например, солидол.
Сборка песчаной литейной формы
После того как оснастка для литья произведена, ее готовят для заливания расплава. Рабочие поверхности необходимо смазать специальным составом, который способствует свободному извлечению готовой отливки. После подготовки рабочих поверхностей выполняют установку литьевых стержней.


Процесс изготовления формы
На завершающем этапе, полуформы соединяют между собой и надежно скрепляют. Надежность сборки не позволит расплаву вытечь за пределы формы.
Типы песчаных форм
Многообразие песчаных форм для литья позволило их разделить на несколько групп, предназначенных для получения отливок с разными характеристиками.


Песчаные литейные формы
Всего можно назвать 7 групп литейной технологической оснастки или модельных комплектов.
- Модельный набор, произведенный из металла, в состав, которого входят дополнительные приспособления для выполнения машинной формовки.
- Набор, выполненный из металла, в его состав включены дополнительные приспособления, которые предназначены для выполнения машинной и ручной формовки.
- Модельный набор, используемый для выполнения машинной и ручной формовки. Сами модели произведены из металла, а некоторые части, например, стержни для формирования полостей выполнены их древесины разных пород.
- Набор для производства ручной и машинной формовки. Модели и стержни, подвергаемые сильному износу, выполняют из металла.
- Набор для формовки отливок из твердых пород древесины.
- Набор для формирования отливок, выполненный из мягких пород древесины.
- Наборы для выполнения ручной формовки отливок.
Сырая песчаная форма
Для производства литьевой оснастки используют смеси, состоящие из песка, воды, глины и какого-либо связующего материала. Типовой рецепт выглядит примерно так:
- 90% песка;
- 3% воды;
- 7% глины.


Сырая песчаная форма
Оснастку такого типа относят к весьма экономичным и широко используемым.
Подсушенная песчаная форма
Производство такой оснастки похоже на производство сырой формы, но в рецептуру вводят дополнительные материалы, предназначенные для связывания компонентов смеси.


Подсушенная песчаная форма
Рабочие поверхности оснастки просушивают прогреванием. Такой подход к изготовлению форм приводит к росту точности размеров заготовок и их качества. Производство таких форм требует больших затрат времени и в результате их стоимость растет, а выпуск деталей нижается.
Сухая песчаная форма
В оснастке такого типа используют добавки органического типа. Их задача связывание компонентов смеси в единое целое. Окончательную обработку производят в печи. К явным достоинствам этих изделий можно отнести точность выполненной отливки. Но надо понимать, что эти формы обладают высокой стоимостью изготовления и низкой производительностью выполнения отливок.
Химически твердеющая песчаная форма
В формовочный состав химически твердеющей оснастки вводят смолы. Они обеспечивают формирование модели на открытом воздухе без использования термической обработки.


Химически твердеющая песчаная форма
В основе смеси лежит кварцевый песок. Кроме, песка в состав смеси входит жидкое стекло и едкий натр. Добавление этого химиката оказывает влияние на технологические свойства литейной формы. В частности, будет продлен срок ее эксплуатации. После затвердевания, ее прочность будет выше, чем у смесей другого типа.
Характеристики литейного песка
Выполняя литье в песчаную оснастку надо понимать, что качество отливки напрямую зависит от состава и свойств литейного песка. Практикой литейного дела определены пять ключевых параметров, которые определяют качество литейного песка.


Физические характеристики песка
- прочность;
- газопроницаемость;
- стабильность при воздействии температуры;
- способность к просадке;
- возможность многократного использования.
Прочность
Прочностью называют способность смеси сохранять заданные параметры во время выполнения литейной операции и транспортировки опоки внутри производственного помещения.
Газопроницаемость
Газопроницаемость – это способность песка пропускать через себя газы, образовывающиеся при затвердевании расплава. Если смесь обладает высокой проницаемостью, будет снижена пористость отливки. Если проницаемость низкая, то качество поверхности будет значительно лучше. Газопроницаемость напрямую зависит состава и фракции песчаной смеси.
Термическая стабильность
Возможность оснастки при воздействии температуры сохранять заданную форму, оказывать сопротивление растрескиванию и появлению иных дефектов, проявляющихся при действии большой температуры расплавленного металла, называют термической стабильностью.
Способность к просадке
Способность формовочной смеси плотно сжиматься в процессе затвердевания отлитой детали. Если бы песок не обладал таким свойством, то отлитая заготовка не имела бы возможности изменять размеры внутри формы. А это в результате привело бы к растрескиванию заготовки и проявлению других дефектов, возникающих при разливе расплавленного металла.
Повторное применение
Это обозначает возможность использования формовочной смеси для производства оснастки, предназначенных для формирований новой партии отливок.
как создать форму для отливки за неделю / Блог компании iQB Technologies / Хабр
3D-технологии, интегрированные в технологическую цепочку литейного производства, обеспечивают предприятию реальную выгоду. Как показать все преимущества 3D-сканирования и 3D-печати? Нагляднее всего – продемонстрировать процесс создания детали с нуля аддитивными методами и провести сравнение с традиционными технологиями. С этой целью мы обратились к Павлу Чадушкину, ведущему специалисту производственного направления RP-центра компании iQB Technologies.
– Итак, наша задача – создать эталонную деталь на основе цифровой модели для последующей отливки реального изделия. С чего начинается этот процесс, если мы применяем 3D-технологии?
– Прежде всего, нам необходимо исходное изделие, которое нужно отсканировать, а затем выполнить обратное проектирование (реверс-инжиниринг). Конечно, оно должно быть новое, не бывшее в употреблении, чтобы не было износа детали. Мы оцениваем, насколько сложна ее геометрия и после этого задаем только один вопрос: какой должен быть допуск по точности? Уже по внешнему виду можно понять, каким образом эта деталь производится. Чаще всего это литье (высокоточное или в землю), фрезерование или изготовление на токарном станке. У каждой из этих методик производства есть свои допуски.
После того, как мы имеем представление о технологии производства и допуске, мы выбираем оборудование, а именно – 3D-сканер с нужными нам параметрами точности, и производим оцифровку изделия. Например, ручной сканер Creafrom HandyScan 700 или стационарный Solutionix C500. Такие устройства метрологического класса уже хорошо зарекомендовали себя на производственных предприятиях. Получив 3D-модель, мы переносим ее в программное обеспечение Geomagic Design X, позволяющее быстро и легко обработать данные 3D-сканирования с целью выполнения контроля геометрии и реверс-инжиниринга. Затем к работе подключается инженер, который по результатам сканирования обрисовывает эту деталь и создает твердотельную модель.
В процессе обрисовки инженер исключает из твердотельной модели различные недостатки изделия. Здесь нужно подчеркнуть, что абсолютно любое изделие имеет производственные деформации. Они могут быть обусловлены разными факторами – например, неверно подобранным материалом, сложной формой, деформацией во время транспортировки, изношенным инструментом, с помощью которого производилось изделие.
В любом случае, какой бы объект мы ни взяли для 3D-сканирования, он будет содержать дефекты и отклонения от эталона, а наша задача – создать этот самый эталон. Если деталь круглая, то совершенно точно можно сказать, что отверстие в ней будет не круглым, а эллипсовидным. Соответственно, инженер с помощью ПО этот эллипс исключает и создает окружность правильной формы. Таким путем, обрисовывая каждый элемент геометрии, мы исправляем все недостатки. Когда деталь полностью обрисована, у нас получается твердое тело, которое можно запускать в производство.
Отливка перепускного клапана стравливания избыточного давления газа (в разрезе)
– Мы получили CAD-модель. Теперь нужно определить, каким способом производить изделие.
– Традиционный способ – подготовка оснастки для литья восковых моделей на станке с ЧПУ. В этом случае модель должна адаптироваться под станок, со своими допусками, уклонами, скруглениями – все зависит от оборудования и инструментов, с помощью которых деталь будет производиться.
Но теперь есть и второй путь – 3D-печать, которая является идеальным решением для прототипирования и изготовления малых серий.
Ключевое преимущество аддитивных технологий – возможность создавать изделия максимально сложной формы (в том числе с мельчайшими деталями), которые нельзя произвести традиционными методами. Кроме того, при запуске печати необязательно учитывать сложность геометрии. Это особенно актуально для производства изделий путем металлического и пластикового литья.
Если изделие имеет простую форму, то зачастую целесообразнее его производить на станке с ЧПУ. Если же геометрия сложная, то 3D-печать – оптимальный вариант.
Когда нам нужен не один рабочий прототип, а малая серия – от 10 до 1000 изделий, используется литье в силикон, или двухкомпонентное литье. Для этого нужно получить мастер-модель – эталон, по которому будет создаваться силиконовая форма, в которую затем заливается пластик или воск.
– Мы выяснили, что 3D-печать – незаменимое решение при производстве продукции с использованием металлического и пластикового литья. Можете привести пример создания конкретной детали?
– Возьмем корпус обыкновенного телефона из пластика. Во-первых, он делится на две половины, нижнюю и верхнюю. Чтобы произвести одну из половин, надо сделать матрицу и пуансон – это оснастка для литья пластика под давлением. Металлическая форма, состоящая из двух половин, смыкается, затем в нее под давлением подается пластик, который принимает форму внутренней геометрии изделия.
При традиционном производстве на станке с ЧПУ вытачивают внешнюю и внутреннюю форму каждой половины. Но если у нас есть 3D-принтер, мы печатаем сразу готовое изделие целиком, металлическую оснастку делать не нужно. Мало того что ее долго изготавливать, она будет баснословно дорогая для тиража в десять штук. Таким образом, выгода 3D-печати очевидна – отпадает необходимость фрезерования для получения оснастки.
Телефон – продукт массового производства, и речь идет не о десяти, а о тысячах изделий. Как раз в этом случае нужны матрица и пуансон, и постоянная штамповка большого тиража. Кроме того, если понадобится внести какое-то небольшое изменение в конструкцию, мы можем оперативно исправить CAD-модель, сразу напечатать прототип и проверить его на собираемость, посмотреть, правильно ли мы разработали геометрию.
– При создании выплавляемых и выжигаемых мастер-моделей для литья с помощью 3D-принтера используется, соответственно, воск и фотополимер (технология печати MJP, технология литья QuickCast). Как выглядит производственная цепочка с использованием этих материалов и в чем их различия?
– Использование напечатанных на 3D-принтере выплавляемых восковых и выжигаемых фотополимерных моделей имеет одну и ту же механику, немного различаются алгоритмы действия.
У нас есть напечатанная восковая модель. Мы создаем для нее корку (то есть форму, в которую заливается металл), обмазывая мелкодисперсным порошком толщиной не менее 6-8 мм. Вид материала и толщина корки зависит не только от сложности геометрии и габаритов изделия, но и от металла, который будет литься в будущую форму. Затем деталь помещается в печь. В печи воск выплавляется, а сама корка отвердевает, и у нас получается твердая форма для литья металла.
Восковая и фотополимерная модели перепускного клапана, напечатанные на 3D-принтерах
Что касается выжигаемого фотополимера, то мы так же кладем изделие в печь, но если воск вытапливается при температуре +200⁰С градусов, то фотополимер – при +950⁰С. Корка так же затвердевает, а материал, из которого была создана модель, выгорает.
Далее в получившуюся форму заливается раскаленный металл – это может быть и алюминий, и титан, и даже магний. Форма остывает, после чего корка разбивается молотком или вибромашиной, и мы получаем отливку.
Следующий этап – мехобработка. Она заключается в том, чтобы сделать поверхность детали более гладкой – обрезать литники, по которым заливался металл, зашлифовать их, снять излишнюю шероховатость изделия. На этой стадии нам также может потребоваться сверление отверстия или подгонка крепежных элементов – для этого применяются станки с ЧПУ для финальной обработки изделия до его конечного варианта (шлифовальные, пескоструйные, сверлильные и т.д.).
– От чего зависит выбор воска или фотополимера?
– Восковые машины относительно дешевы, при этом расходный материал – дорогой. С фотополимерными 3D-принтерами ситуация обратная. В сравнении с фотополимером воск достаточно хрупкий материал, это его недостаток. Но на сегодня восковая 3D-печать обеспечивает самую точную и самую гладкую поверхность. К тому же, восковое литье является традиционным для всех литейных производств в России. Соответственно, фотополимер подойдет там, где нужны модели большего размера, а прочность и детализация менее критичны. Пользователь должен сделать выбор, исходя из того, какие объемы он будет печатать, насколько часто он будет обращаться к прототипированию.
Так, на литейных предприятиях по всему миру, в России в том числе, активно используются профессиональные 3D-принтеры от 3D Systems, ведущего мирового производителя аддитивных установок. При этом ряд компаний имеют свой парк 3D-оборудования, другие заказывают услуги 3D-печати у подрядчиков.
– Мы подробно рассмотрели, как и в каких случаях выгодно использовать 3D-принтеры и 3D-сканеры. Если резюмировать: почему литейному предприятию необходимо внедрять аддитивные технологии?
– Для сокращения сроков производства при изготовлении опытных образцов и деталей малого тиража. Мы экономим и время, и деньги.
Вернемся к сравнению традиционного процесса с аддитивным. В первом случае это выглядит следующим образом:
1. Конструктор разрабатывает деталь, затем передает свою разработку инженеру.
2. Инженер адаптирует ее под методику производства вместе с технологом.
3. Дальнейшая адаптация заключается в том, что создается чертеж будущей формы матрицы и пуансона или чертеж, по которому деталь будет вытачиваться на фрезеровочном станке.
4. Затем на станке изготавливают матрицу и пуансон и отдают их на производство.
Так вот, с момента выдачи конструктором готового проекта инженеру и до получения формы, по которой будет отливаться изделие, проходит от полугода до года. И прошло, допустим, полгода, сделали десять опытных образцов, отдали их конструктору, он примерил эти металлические болванки, а они не совпадают с посадочными местами. Он понимает, почему они не совпадают, дорабатывает эту модель, и дальше цикл повторяется. Проходит еще минимум полгода до следующей примерки.
С помощью 3D-принтера конструктор фактически нажатием одной кнопки отправляет на печать свое изделие и отдает его сразу на производство в отливку. Срок сокращается с года или полугода до недели максимум. Это самое главное преимущество. Плюс, мы экономим значительные средства на изготовление формы. И, наконец, мы имеем возможность создавать изделия с геометрией любой сложности и, при необходимости, быстро оптимизировать конструкцию в программном обеспечении.