★ Зона термического влияния — Вики .. | Информация
★ Зона термического влияния
Зона термического влияния — объем основного материала, металла или термопластичного материала, который при сварке не довели до точки плавления, но его микроструктура и свойства меняются под воздействием тепла.
Скорость изменения свойств материала в зоне зависит от основного материала, присадочного металла шва, объема и концентрации тепла в процессе сварки. в результате микроструктура, в свою очередь, влияет как на прочность сварного шва и прочность конструкции.
Зона термического влияния при сварке стальных полос из низкоуглеродистой мартенситной, его ширина составляет около 50 мкм, это полоса с переходом структуры из низкоуглеродистый мартенсит и бейнит с использованием тонкого слоя феррита-перлита в ферритно-перлитной структуры основного металла.
Распределение температуры нагрева зона термического влияния состоит из следующих разделов:
- Зона сварки, температуры от 1250 С до температуры плавления.
- Сюжет старение температура 200 (Plot an aging temperature of 200) — 300 с.
- Фазы освобождения, температура 250 (The phase of release, temperature 250) — 650 с.
- Температура нормализации сюжет 840 (Temperature normalization of the plot is 840) — 1000 с.
- Сюжет температуру перегрева 1000 (Plot the temperature of the overheating 1000) — 1250 С.
- Площадь неполное температуры рекристаллизации 700 (The area of incomplete recrystallization temperature of 700) — 870 с.
Коэффициент температуропроводности свариваемого материала играет важную роль для ХАЗ — если коэффициент диффузии материала является высокой, скорости охлаждения сварного шва и зоны термического влияния относительно небольшой. количество тепла, образующегося в процессе сварки в ЗТВ также играет важную роль, так что в процессе сварки используется кислород с высокой погонной энергией, увеличивая размер зоны термического влияния. процессы, такие как лазерная и электронно-лучевой сварки высокой концентрацией энергии в ограниченном количестве выделяется тепло, результат — ХАЗ имеет небольшие размеры.
где Q = кДж тепла / мм V = напряжение в Вольтах I = и тока S = скорость сварки мм / мин. Коэффициент Efficiency (Эффективность) зависит от процесса сварки, ручная дуговая сварка металла это значение 0.75 для газовой дуговой сварки металла электродом и дуговой сварки — 0.9, для дуговой сварки вольфрамовым 0.8.
ⓘ Энциклопедия — Зона термического влияния
ⓘ Зона термического влияния
Зона термического влияния — объём основного материала, металла или термопластика, который при сварке не доводится до плавления, однако его микроструктура и свойства меняются под воздействием выделяемого тепла.
Степень изменения свойств материала в зоне зависит от основного материала, присадочного металла шва, объёма и концентрации теплоты в процессе сварки. Полученная микроструктура, в свою очередь, влияет как на прочность сварного соединения, так и на прочность конструкции.
Зона термического влияния при сварке стали имеет полосу из низкоуглеродистого мартенсита, её ширина — около 50 мкм, за ней расположена полоса с переходной структурой — от низкоуглеродистого мартенсита через бейнит и тонкий слой феррит-перлита в феррит-перлитную структуру основного металла.
По распределению температур нагрева зона термического влияния разделяется на следующие участки:
- Участок околошовный, температура от 1250 С до температуры плавления.
- Участок нормализации, температура 840 — 1000 С;
- Участок старения, температура 200 — 300 С;
- Участок неполной перекристаллизации, температура 700 — 870 С;
- Участок отпуска, температура 250 — 650 С;
- Участок перегрева, температура 1000 — 1250 С
Температуропроводность свариваемого материала играет большую роль для зоны термического влияния — если коэффициент диффузии материала является высоким, скорость охлаждения шва и ЗТВ относительно невелика. Количество теплоты, выделяемое в процессе сварки также играет для ЗТВ важную роль, так в процессе кислородной сварки используется высокая погонная энергия, при этом увеличивается размер зоны термического влияния. Такие процессы, как лазерная и электронно-лучевая сварка проходят при высокой концентрации энергии при ограниченном количестве выделяемой теплоты, в результате — ЗТВ мала по размерам. Дуговая сварка занимает промежуточное положение между этими двумя крайними для ЗТВ процессами. Для расчета выделяемой теплоты при дуговой сварке используется следующая формула:
где Q = теплота кДж/мм, V = напряжение Вольт, I = сила тока А, S = скорость сварки мм/мин. Коэффициент Efficiency зависит от процесса сварки, для ручной дуговой сварки металла он имеет значение 0.75, для газовой дуговая сварка металлическим электродом и дуговой сварки — 0.
Зона термического влияния алюминия
При сварке чистого алюминия и сплавов, не упрочняемых термообработкой, в зоне теплового воздействия наблюдается лишь рост зерна и некоторое их разупрочнение, вызванное снятием нагартовки (если сплав сваривался в нагартированном состоянии). Интенсивность роста зерна и разупрочнения нагартованного сплава при сварке может изменяться в зависимости от метода сварки, режимов и величины предшествовавшей нагартовки. Практика показывает, что даже в условиях газовой сварки, отличающейся наиболее длительным нагревом металла, сварные соединения, выполненные из этих сплавов, по прочности не уступают прочности основного металла в отожженном состоянии.
Тепловая свариваемость алюминиево-магниевых сплавов с большим содержанием
магния (АМг5В и АМг6), относящихся также к группе сплавов, не упрочняемых
термически, осложняется повышенной чувствительностью их к нагреву и склонностью
к вспучиванию в участках основного металла, непосредственно примыкающих к шву.
Большинство авторов работ, посвященных исследованию этого явления, приходит к выводу, что основной причиной вспучивания и образования несплошностей могут быть реакция магния с парами воды, накопление водорода в несплошностях и увеличение в них давления.
В настоящее время установлено, что вспучивание в околошовных зонах
наблюдается лишь при сварке металла определенных полуфабрикатов и плавок.
Вспучивание металла при нагреве вызывает молекулярный водород, заполняющий
микронесплошности, образовавшиеся в процессе деформации и обжатия мелких газовых
пузырьков, которые возникают при кристаллизации слитка на базе дисперсных
оксидных включений, имеющихся в недостаточно тщательно рафинированном металле.
Концентрация растворенного водорода в металле промышленных слитков, отлитых непрерывным литьем, не превышает 0,15— 0,3 см3/100 г, что совпадает с расчетными данными растворимости водорода в сплаве при температурах нижней границы эффективного интервала кристаллизации. В связи с этим для контроля качества свариваемого металла необходимо в первую очередь определять в нем содержание молекулярного водорода.
Для этих целей предназначена тепловая проба МАТИ. Цилиндрический образец
диаметром 15 мм, длиной 25 мм, изготовленный из контролируемого металла,
нагревают в печи при температуре 580 + 5°С в течение 15 мин. После остывания из
образца изготовляют шлиф. Наличие в металле образца макронесплошностей и
расслоений свидетельствует о недостаточно высоком качестве металла и повышенном
содержании молекулярного водорода.
При сварке сплавов, упрочняемых термообработкой, в зонах около шва происходят изменения, существенно снижающие свойства свариваемого металла. Замеры твердости и изучение структуры металла в зоне термического влияния сварных соединений из сплавов, упрочняемых термообработкой, позволяют обнаружить в ней участки металла с различной степенью распада твердого раствора и коагуляции упрочнителя.
Самое опасное изменение, вызывающее в большинстве случаев резкое снижение
свойств металла и образование трещин, — оплавление границ зерен. Появление
жидких прослоек между зернами приводит к снижению механических свойств металла в
нагретом состоянии и нередко к образованию трещин. После сварки в участках
оплавления металл хрупко разрушается и прочность его снижается.
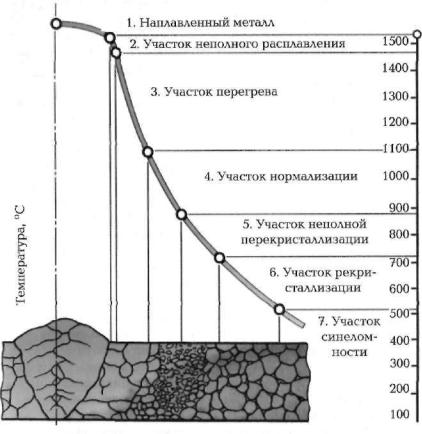
Наиболее простой моделью для изучения процессов, протекающих в околошовных зонах при сварке, может быть двойной алюминиево-медный сплав, содержащий 4 % Сu.
При медленном охлаждении сплава, содержащего 4 % Сu, от температуры выше
эвтектической концентрация меди уменьшается в соответствии с кривой
растворимости (
Рис. 9.5. Алюминиевый угол
диаграммы состояния системы Al-Сu
При быстром охлаждении этого же сплава из области α-твердого раствора до
нормальной температуры выделение фазы СuА12 можно задержать и зафиксировать медь
в растворе. Если не учитывать, что в сплаве присутствуют нерастворимые фазы,
образованные примесями, то после быстрого охлаждения сплав должен представлять
собой однородный раствор меди в алюминии с содержанием 4 % Сu.
Пересыщенный раствор меди в алюминии неустойчив. Даже при нормальной температуре в нем протекают процессы, приводящие к повышению его прочности и снижению пластичности,— происходит старение сплава.
При естественном старении выделение второй фазы отсутствует, и пересыщенный раствор меди в алюминии сохраняется. Повышение прочности металла объясняется перемещением атомов меди на небольшие расстояния, сопровождающиеся собиранием ее на плоскостях куба (100) решетки в двумерные пластинчатые образования, названные зонами Гинье—Престона. Эта неравномерность п распределении атомов меди приводит к искажениям решетки, увеличению прочности и твердости сплава.
Нагрев сплава выше температуры 150 °С вызывает дальнейшее развитие возникших
образований. Плоскости, обогащенные медью, занимают определенный порядок между
соседними плоскостями алюминиевых атомов. Появление сверхструктуры
рассматривается как переходная стадия к выделению из раствора упрочнителя. При
нагреве до температуры выше 200 °С на базе сверхструктуры образуется
промежуточная фаза θ’; ее состав соответствует фазе θ (СuАl2), а кристаллическая
решетка отличается от решетки алюминия и фазы 6.
При температуре выше 300 °С образуется стабильная фаза θ. Появление метастабильной фазы θ’ приводит к значительному упрочнению сплава и снижению его пластичности.
В соответствии со сказанным различают естественное старение, протекающее при нормальных температурах, и искусственное при температуре выше 150— 200 °С. Первый вид старения назван И. Н. Фрлдляндером зонным старением, а второй — фазовым.
Для понимания процессов, протекающих в околошовных зонах при сварке сплавов, упрочняемых термообработкой, важное значение имеют некоторые особенности распада пересыщенных твердых растворов. Появление частицы новой фазы другого объема сопровождается упругими искажениями решетки матрицы.
Если упругая энергия, концентрирующаяся вокруг частицы новой фазы, велика, то
появление ее становится более вероятным в первую очередь на границе зерен, где
имеются дефекты решетки. Этому же способствует повышенная концентрация на
границах зерен растворенных атомов, имеющих атомный радиус, отличающийся от
атомного радиуса растворителя.
В связи с этим при быстром нагреве пересыщенного раствора до высоких температур, характерном для условий сварки, можно ожидать появления второй фазы, в первую очередь по границе зерен.
При сварке отожженного сплава в зоне термического влияния но мере повышения максимальной температуры нагрева металла в соответствии с диаграммой состояния происходят процессы растворения выпавшего упрочнителя. Особенно заметны процессы растворения дисперсных выделений второй фазы в объеме зерна в участке металла, нагревавшемся выше температуры 350 °С. На границе этого участка наблюдается как бы просветление фона за счет исчезновения более мелких частиц упрочнителя, выделившегося по объему зерна, и повышение твердости раствора.
По мере повышения температуры нагрева более четко начинают просматриваться
границы зерен в связи с укрупнением выделений упрочнителя на их границах. Этот
процесс продолжается в участке металла, нагревавшемся от 500 °С до температуры
плавления эвтектики (548 °С). В этом участке по мере повышения температуры
нагрева наряду с утолщением границ зерен становится
более
заметной белая полоска обедненной медью периферийной части зерна,
примыкающей к выделениям второй фазы на границе раздела зерен (рис.
9.6).
Рис. 9.6. Оплавление границ
зерен в участке околошовной зоны сварного соединения сплава алюминия с 4 %
Сu:
1 — оплавленная граница зерна; 2 — светлая оторочка периферии зерна; 3 —
участок зерна с нормальной травимостью
На участке металла, нагревавшемся в интервале температуры между солидусом и
температурой плавления эвтектики (548 °С), по границам зерен появляются жидкие
прослойки, что, по-видимому, можно объяснить развитием контактного плавления
между частицами упрочнителя — фазы СuАl2 — и твердым раствором. Процесс
контактного плавления, сопровождающийся появлением на границе зерна жидких
прослоек, приводит к обеднению медью периферийных участков зерна, примыкающих к
оплавленной границе.
При сварке закаленного и искусственно состаренного сплава заметное изменение травимости зерен и более четкое выявление их границ наблюдается в участках металла, нагревавшихся в процессе сварки до температуры выше 500 °С. По-видимому, это связано с частичной коагуляцией упрочнителя, выделившегося в объеме зерна и по границам зерен. Однако согласно равновесной диаграмме состояния системы Аl—Сu (см. рис. 9.5) при температуре 500 °С вместо коагуляции выделившегося упрочнителя должно было бы произойти его дополнительное растворение.
Причина кажущегося несоответствия обнаруженных структурных изменений с равновесной диаграммой состояния состоит в следующем. Распад раствора при высоких температурах начинается с появления устойчивых зародышей второй фазы на границах зерна, их развития за счет притока атомов меди из пограничных участков зерна и затем выделения упрочнителя в объеме зерна.
Для теплового воздействия при сварке характерны быстрый нагрев металла до
максимальных температур и более медленное последующее его охлаждение.
При сварке искусственно состаренного сплава в период быстрого нагрева до температуры 500 °С коагуляция упрочнителя происходить не успевает. Наоборот, начиная с температуры 500 °С и выше возможно даже частичное растворение дисперсных выделений второй фазы в объеме зерна. В процессе последующего охлаждения, начиная с температуры 500 °С и ниже, продолжается высокотемпературный распад твердого раствора, сопровождающийся образованием зародышей упрочнителя, в первую очередь по границам зерна, и их развитием за счет притока атомов меди из прилежащих периферийных участков зерен, что приводит к появлению светлых оторочек по их границам и усилению травимости основной части зерна за счет коагуляции дисперсных выделений второй фазы в объеме зерна.
По мере повышения температуры максимального нагрева увеличивается время
существования металла в интервале температур 500—300 °С и создаются условия для
более полного распада раствора и коагуляции выпавшего упрочнителя. Поэтому по
мере приближения к шву постепенно снижается твердость металла, утолщаются
границы зёрен и резче выявляются светлые оторочки на границах зерен,
представляющие собой обедненный медью раствор алюминия.
В интервале температур между солидусом и температурой плавления эвтектики наблюдается оплавление границ зерен. Оплавление границ и в этом случае вызывает контактное плавление, развивающееся между частицами фазы СuАl2, выделявшимися по границам зерен, и твердым раствором меди и алюминия.
Рассмотренный выше механизм оплавления границ зерна характерен для большинства термообрабатываемых сплавов, способных подвергаться старению. В отличие от бинарного алюминиево-медного сплава, рассмотренного в качестве модели при сварке сплавов сложного легирования, меняется состав упрочняющих фаз и образующихся в результате контактного плавления эвтектик.
Приведенная выше точка зрения на причины и механизм оплавления границ зерен
при сварке сплавов, упрочняемых термообработкой, не является единственной и
общепринятой. Существует также мнение, что основная причина оплавления границ
зерен связана с наличием в сплаве равновесной эвтектики при высокой степени
легирования сплавов или неравновесной эвтектики, образующейся при кристаллизации
слитка в условиях, далеких от равновесных.
Некоторые исследователи склоняются также к мысли о том, что оплавление границ зерен происходит в участке металла зоны термического влияния, нагревающегося в процессе сварки выше температуры солидуса — высокотемпературной области. Зона, обедненная упрочнителем, и оплавленная эвтектика появляются в процессе последующей неравновесной кристаллизации оплавленной границы зерна.
Опыт сварки сплавов типа дуралюминов (Д1 и Д16) показывает, что независимо от метода сварки и исходного состояния металла во всех случаях в непосредственной близости от шва наблюдается зона оплавления границ зерна. Ширина этой зоны меняется в зависимости от метода и режимов сварки. Наиболее широкая зона появляется при газовой сварке и более узкая — при автоматической дуговой.
Характер распределения эвтектики в этой зоне изменяется в зависимости от
исходного состояния сплава. В сварных соединениях, полученных при дуговой сварке
закаленного сплава, эвтектика располагается в виде сплошной прослойки вокруг
зерен твердого раствора, в то время как в соединениях из отожженного металла в
залегании эвтектики появляются несплошности.
При газовой сварке дуралюмина Д16 в закаленном состоянии трудно получить соединение без трещин. При дуговой сварке в аргоне и по флюсу прочность соединений из закаленного сплава колеблется в пределах 290-320 МПа, а при сварке в отожженном состоянии около 220 МПа.
В связи с наличием сплошной сетки оплавленной эвтектики сварные соединения из закаленного металла имеют низкую пластичность и легко разрушаются при небольшой деформации и вибрационных или динамических нагрузках. При сварке жестких узлов из закаленного металла по границе сплавления часто возникают трещины. Последующей термообработкой не удается восстановить свойства металла в этой зоне. При сварке образцов из алюминиевых сплавов типа дуралюминов с применением очень резкого охлаждения удалось значительно сократить ширину зоны с оплавленными границами зерен и повысить свойства сварных соединений. Однако применение таких скоростей охлаждения в производственных условиях трудноосуществимо.
Проблема сварки высокопрочных алюминиевых сплавов, упрочняемых
термообработкой, может быть решена при условии создания специальных свариваемых
сплавов этой группы. Вопросам создания свариваемых высокопрочных сплавов,
упрочняемых термообработкой, уделяется много внимания. В нашей стране разработан
ряд сплавов этой группы, имеющих лучшую тепловую свариваемость: ВАД1, М40 и др.
Перспективны самозакаливающиеся сплавы, построенные на основе тройной системы
Аl-Zn-Mg (В92Ц, АЦМ, 1915 и др.), а также сплавы на основе системы А1-Сu-Мn
(типа 1201) и сплавы на основе системы Аl-Mg-Li (типа 1420).
Закономерности структурообразования зоны термического влияния при термической резке металлов Текст научной статьи по специальности «Технологии материалов»
УДК621.791
ЗАКОНОМЕРНОСТИ СТРУКТУРООБРАЗОВАННЯ ЗОНЫ ТЕРМИЧЕСКОГО ВЛИЯНИЯ ПРИ ТЕРМИЧЕСКОЙ РЕЗКЕ МЕТАЛЛОВ
А.В. Сумец, асп., В.Д. Кассов, проф., д.т.н., Донбасская государственная машиностроительная академия, г. Краматорск
Аннотация. Исследованы особенности фазных и структурных превращений при термической резке сталей. Приведено влияние способа резки на глубину оплавленного и переходного участков. Описаны явления, связанные с процессом затвердевания после резки. Детально рассмотрено влияние скорости охлаждения на структуру металлов в зоне резки.
Ключевые слова: термическая резка, зона термического влияния, скорость резки, структура.
3AKOHOMIPHOCTI СТРУКТУРОУТВОРЕННЯ ЗОНИ ТЕРМ1ЧНОГО ВПЛИВУ П1Д ЧАС ТЕРМ1ЧНОГО Р13АННЯ МЕТАЛ1В
А.В. Сумец, асп., В.Д. Кассов, проф., д.т.н., Донбаська державна машинобуд1вна академ1я, м. Краматорськ
Анотац1я. Досл1джено особливост1 фазних i структурних перетворенъ у процеа терм1чного р1зання сталей. Наведено вплив способу р1зання на глибину оплавлено! та nepexidno! дтянок. Описано явища, що пов’язат з процесом затвердтня теля р1зання. Детально розглянуто вплив швидкост1 охолодження на структуру метал1в у зот р1зання.
Ключов1 слова: терм1чне р1зання, зона терм1чного впливу, швидюстъ р1зання, структура.
REGULARITIES OF THE STRUCTURE FORMATION OF THE THERMAL ZONE DURING THERMAL CUTTING OF METAL
A. Sumets, P. G., V. Kassov, Prof., D. Sc. (Eng.), Donbass State Engineering Academy, Kramatorsk
Abstract. The features ofphase and structural transformations during thermal cutting of steel are investigated. The influence of the cutting method on the depth of the melted and transition sections is given. The phenomena connected with the process of solidification after cutting are described. The influence of the cooling rate on the structure of metal in the cutting zone is considered.
Key words: thermal cutting, thermal zone, cutting velocity, structure.
Введение
Структурные превращения в условиях термической резки металла (аргоно-плазменной, воздушно-плазменной и кислородно-флюсовой) значительно отличаются от превращений при обычной термической обработке [1, 2]. Данные отличия объясняются, прежде всего, спецификой термодеформационного цикла резки [3]. В условиях термической резки распад твёрдых растворов в зоне резки протекает
в более сложной и непрерывно изменяющейся обстановке, а наличие химической неоднородности в зоне термического нагрева во многих случаях коренным образом изменяет кинетику распада твёрдых растворов [4, 5]. Поэтому процессы кристаллизации металла и структурные превращения в зоне резки в большинстве случаев предопределяют дальнейшие технологические и эксплуатационные свойства металла.
Анализ публикаций
Материал и методика исследований
С процессом затвердевания металла после резки связаны многие нежелательные явления, в том числе и формирование химической неоднородности [1, 6-9]. Микроскопическая химическая неоднородность, имеющая место в зоне термической резки, в первую очередь определяется характером первичной кристаллизации стали и зависит от количества и природы легирующих элементов, примесей и условий охлаждения [7-12].
Цель и постановка задачи
Целью работы является исследование особенностей фазовых и структурных превращений в металле при термической резке.
При неравновесной кристаллизации диффузия не будет успевать выравнивать состав внутренних и наружных слоев твердого раствора. Таким образом, после охлаждения подвергнутая резке сталь, скорее всего, будет иметь неоднородный или слоистый состав. В таких условиях кристаллизации, если легирующий элемент или примесь имеет в жидкой фазе большую растворимость, чем в твёрдой, будет иметь место обогащение междуосного и меж-дендридного пространства. Дендритная неоднородность хорошо выявляется на микроструктуре металла после термической резки в виде поверхностного рельефа. При очень большом обогащении в междуосных и междендритных пространствах на последних стадиях кристаллизации наблюдаются неравновесные структуры (рис. 1).
Рис. 1. Микроструктура оплавленного участка стали У10 (*250) после аргоно-плазменной (а), воздушно-плазменной (б) и кислородно-флюсовой резки (в)
Способность элемента обогащать междуос-ные и междендритные промежутки характеризуется коэффициентом распределения К, представляющим собой отношение раство-римостей элемента в твёрдой и жидкой фазах: Ств/Сж.
В нашем случае исследований особый интерес представляют процессы, протекающие в зоне резки (термического нагрева/плавления), от структуры и химического состава которой зависят свойства зоны термической резки. Аналитическое выражение процесса диффузии на границе сплавления для оценки распределения в ней легирующих элементов и примесей в зависимости от коэффициента диффузии в твёрдой Бт и жидкой Бж фазах, продолжительности процесса X и коэффициента распределения К в нашем случае имеют следующий вид:
Ст СТо
Ст — К ■
10 ж0
К ■ +1
+1 +
у/ж
■е у Ну,
(1)
С = С
Ст — К • с.
Жо
К • От
+1—
%/л
Вт
2Ну ,(2)
где СТ0 и Сж0 — начальные концентрации элементов в твёрдой и жидкой фазах; у -расстояние от межфазной границы раздела вглубь жидкого металла в процессе резки.
Неравновесная концентрация атомов примесей и легирующих элементов, являющаяся следствием повышенных скоростей охлаждения в результате резки, способствует значительному упрочнению металла (табл. 1, 2).
X
2
О
1
0
2
у
■е
0
Таблица 1 Влияния способа резки на глубину термически обработанных слоев
Марки стали
Глубина термически © <с © Н 0 ел ^
обработанных слоев, мм Ы о СП о о £ 09Г2( 40Х 0 СП <м X 0 СП § <м К 00 X 00 0 к 1> х СП 0
Аргоно-плазменная ОУ 0,08 0,45 0,10 0,08 0,04 0,15 0,40 0,20 0,13 0,35 0,90
ПУ 2,00 3,00 2,50 1,70 2,30 1,05 0,40 0,70 1,10 2,10 1,60
Е 2,08 3,45 2,60 1,78 2,034 1,20 0,80 0,90 1,23 2,45 2,50
Воздушно-плазменная ОУ 0,18 0,80 0,10 0,15 0,15 0,08 0,35 0,15 0,13 0,14 0,40
ПУ 1,50 0,60 1,80 0,60 1,50 0,13 0,15 0,10 1,60 1,03 1,04
Е 1,68 1,40 1,90 0,75 1,65 0,21 0,50 0,25 1,73 1,17 1,44
Кислородно-флюсовая ОУ 0,10 0,25 0,05 0,50 0,40 0,13 0,58 0,15 0,18 0,43 2,72
ПУ 1,50 7,00 1,40 2,00 1,70 2,15 1,70 3,20 1,70 4,30 3,30
Е 1,60 7,025 1,45 2,50 2,10 2,28 2,28 3,35 1,88 4,73 6,02
Примечание: ОУ — глубина оплавленного участка, мм; ПУ — глубина переходного участка, мм; Е — сумма ОУ и ПУ.
Таблица 2 Влияние способа резки на микротвердость
Марки стали
Микротвердость, кг/мм2 ы о СП о 0 £ 09Г2С 40Х 30X13 Х12МФ 30ХМА 25Х1МФ 08Х18Н10Т 03Х17Н14М3
Аргоно-плазменная ОУ 420 572 900 383 514 724 724 385 350 383 380
ПУ 290 350 510 270 260 640 642 350 240 236 297
ом 180 263 330 210 226 270 350 227 232 220 254
Воздушно-плазменная ОУ 170 572 420 193 420 824 950 383 350 272 254
ПУ 220 322 380 200 380 640 642 383 237 274 254
ом 180 263 330 210 226 270 350 227 232 220 254
Кислородно-флюсовая ОУ 193 322 824 181 464 642 724 383 420 383 274
ПУ 210 275 500 160 350 724 946 350 382 279 274
ом 180 263 330 210 226 270 350 227 232 220 254
Примечание: ОУ — глубина оплавленного участка, мм; ПУ — глубина переходного участка, мм; ОМ — основной металл.
Увеличение скорости охлаждения в интервале кристаллизации способствует измельчению первичной структуры металла в зоне резки, особенно для легированных сталей. Металл, образовавшийся в результате термической резки на среднелегированных сталях, охлаждённых с повышенными скоростями, по механическим свойствам значительно превосходит основной металл. По-видимому, изменение механических свойств происходит не только в результате измельчения первичной структуры, но также ослабления степени химической неоднородности, определяемой соотношением концентраций элементов в ликвационной межкристаллитной прослойке и в теле столбчатого кристаллита. Таким образом, скорее всего, зависимость изменения
свойств металла в зоне термической резки от скорости охлаждения определяется изменениями не степени ликвации, а главным образом, размеров столбчатых кристаллитов и ширины обогащённых межкристаллитных границ. -у-превращенне. По мере перегрева выше температуры Ас3 аустенитное зерно растёт и даже при незначительной продолжительности пребывания в условиях высоких температур успевает вырасти до значительных размеров. Тип структуры, образующейся в участке перегрева, зависит от характера термического процесса резки и состава металла. Так, в некоторых случаях в этом участке формируется видманштеттова структура. В легированных сталях участки металла, нагревающиеся при резке выше температуры Ас3, в результате быстрого охлаждения приобретают структуры закалки. Однако структура зоны по ширине от участка сплавления до участка, имевшего при резке максимальную температуру только несколько выше Ас3, будет одинаковой. В результате распада крупных аустенитных зёрен в участках, прилегающих к границе сплавления и нагревающихся при резке выше 1200 °С, образуется более крупнопластинчатый мартенсит, чем в участках металла, нагревающихся при резке выше Ас3. Структура зоны сплавления является почти такой же, как и структура участка перегрева.
-у-превращення, до 1100-1150 °С. Ширина данного участка 0,7-1,0 мм. В низкоуглеродистых и низколегированных сталях в участке перекристаллизации обычно образуется мелкодисперсная (зернистая) структура, характеризующаяся в целом достаточно высоким комплексом механических свойств. В средне- и высоколегированных сталях в металле данного участка часто образуется мелкопластинчатый мартенсит или смесь мартенсита и продуктов промежуточного превращения, т.е. те же структуры, что и в участке перегрева, но более дисперсные. Следующий, четвёртый, участок включает в себя металл, нагретый от температур Ас1 до тем-
пературы Ас3. Металл участка подвергается только частичной перекристаллизации, и поэтому его можно назвать участком неполной перекристаллизации. Металл этого участка в низкоуглеродистых и низколегированных сталях характеризуется почти неизменяющимся ферритным зерном, и некоторым дроблением и сфероидизацией перлитных участков. В средне- и высоколегированных сталях после охлаждения формируется структура частичной закалки.
Следующий участок — пятый — можно назвать участком рекристаллизации. Он включает металл, который нагревался от 500 °С до температур несколько ниже Ась Отдельные участки данной зоны, нагревавшиеся ниже Ась по своей структуре и свойствам могут быть различными в зависимости от исходного состояния металла перед термической резкой. Если металл перед резкой подвергался холодной пластической деформации, то при нагреве до температур ниже Ас1 происходит рекристаллизация, приводящая к значительному росту зерна.
Шестой участок включает металл, который нагревался в интервале температур 100500 °С. Этот участок в процессе резки не претерпевает видимых структурных изменений.
Высоколегированные аустенитные стали не претерпевают видимых фазовых превращений в условиях термического воздействия на них при резке. Вследствие этого зона термического нагрева этих сталей имеет менее сложное строение, чем зона при резке обычных конструкционных сталей. Размер зоны сплавления высоколегированных сталей сравнительно невелик и определяется температурным градиентом и интервалом кристаллизации. Если температурный градиент мал, а интервал кристаллизации сравнительно велик, то ширина зоны сплавления возрастает. Свойства зоны термического воздействия при резке неразрывно связаны с состоянием границ зёрен в ней. В зоне термического воздействия под влиянием термического цикла резки происходит энергичный рост зёрен, а также подплавление границ в зоне сплавления и последующее развитие в ней химической микронеоднородности. В связи с этим по границам зёрен локализуются различного рода разрушения, что обусловливает существенное влияние их на механические свойства. В зоне сплавления образуются границы
двух типов — первичные и вторичные. Первичные границы формируют более мелкие зёрна, вторичные (тонкие) крупные зёрна. Первичные и вторичные границы, как правило, расположены по отношению друг к другу произвольно. Первичные границы содержат повышенное количество легирующих элементов [13-16], причём уровень химической неоднородности сопоставим с дендритной неоднородностью, развивающейся при кристаллизации зоны сплавления. Это даёт основание полагать, что первичные границы возникают вследствие образования и последующего затвердевания жидкой фазы.
Выводы
Проведенные исследования особенностей структурообразования зоны термического влияния, образующейся при аргоно-плаз-менной, воздушно-плазменной и кислородно-флюсовой резки металлов 11 марок стали, показали, что наиболее эффективным и целесообразным является воздушно-плазменная резка.
Литература
1. Эсибян Э. М. Воздушно-плазменная рез-
ка: состояние и перспективы / Э.М. Эсибян // Автоматическая сварка. — 2000. -№. 12. — С. 6-20.
2. Голобородько Ж.Г. Влияние плазмооб-разующей среды при резке на образование пор при сварке судокорпусных сталей / Ж.Г. Голобородько, В.В Квас-ницкий// 36. наук. праць УДМТУ. -2002. — № 5 (383). — С. 25-31.
3. Пащенко В.М. Плазмове р1зання з вико-ристанням складних газових сумшей / В.М. Пащенко, В.Д. Кузнецов // Зб1рник наукових праць НУК. — 2005. — № 1 (400). — С. 40-49.
4. Голобородько Ж.Г. Опыт Херсонского судостроительного завода по применению плазменной резки / Ж.Г. Голобородько // Автоматическая сварка. — 2013. — С. 43-48.
5. Лященко Г.И. Качество реза при плаз-менно-дуговой резке / Г.И. Лященко // Сварщик. — 2012. — №4. — С. 34-39.
6. Васильев А.Н. Сравнительные исследования воздушно-плазменной и кисло-
родно-плазменной резки / А. Н. Васильев, ВВ. Внук, В.И. Зиновьев, ТВ. Коть-кина // Известия МГТУ. — 2014. -№2 (20). — С. 13-18.
7. Орлов A.C. Термодеформационные процессы при термической резке тонкостенных цилиндрических изделий: монография / A.C. Орлов. — Ростов-на-Дону: ДГТУ, 2004. — 170 с.
8. Григорьянц А.Г. Лазерная резка металлов / А.Г. Григорьянц, A.A. Соколов. -М: Высшая школа, 1988. — 128 с.
9. Носуленко В.И. Размерная обработка металлов электрической дугой / В.И. Носуленко // Электронная обработка материалов. — 2005. — №1. — С. 8-17.
10. Базров Б.М. Основы технологии машиностроения / Б.М. Базров. — М.: Машиностроение, 2005. — 763 с.
11. Пат. 92865 UA, МПК F23C 7/00. Cnoci6 кисневого р1зання метал1в великих тов-щин / В. М. Литвинов, O.I. Волошин, К.П. Шаповалов, В.А. Белшський, С.Л. Василенко, O.I. Коровченко; заяв-ник та патентовласник ДДМА. -№ и2014 02889; заявл. 21.03.14; опубл. 10.09.14, Бюл. №17. — 3 с.
12. Банов М.Д Сварка и резка / М.Д. Банов, Ю.В. Казаков. — М.: Академия, 2001. -313 с.
13. Литвинов М.В. Кислородная резка металлов больших толщин на заводе ЗАО «НКМЗ» / В.М. Литвинов, ЮН. Лысенко, С. А. Чумак и др. // Вестник Донбасской машиностроительной академии. -2010. — №2. — С. 64-167.
14. Литвинов В.М. Газопламенная обработка метал лов. Новые тенденции в создании горелочных устройств / В.М. Литвинов, Ю.Н. Лысенко, С.А. Чумак // Штрипс. — 2008. — №4. — С. 30-32.
15. Казаков С.И. Сварка плавлением и термическая резка металлов: учебное пособие / С.И. Казаков. — Курган: Издательство КГУ, 20014. — 365 с.
16. Сварка. Резка. Контроль: справочник: в 2 т./ под общ. ред. Н.П. Алешина, Г.Г. Чернышова. — М.: Машиностроение, 2004. — Т. 1. — 624 с.
Рецензент: Д.Б. Глушкова, профессор, д.т.н., ХНАДУ.
Тепловое действие сварочного пламени на наплавленный и основной металл
увеличении содержания серы могут образоваться горячие трещины.. Поэтому при сварке металлов, чувствительных к таким примесям (например, никеля), необходимо применять только хорошо очищенный ацетилен.
24. Тепловое действие сварочного пламени на наплавленный
и основной металл
При нагреве изделия пламенем газовой горелки, помимо расплавления металла, происходит изменение структуры металла в зоне теплового воздействия, изменяется форма изделия, возникают так называемые внутренние напряжения.
Если сварный шов разрезать поперек, отшлифовать и обработать специальным реактивом, то на таком образце, называемом макрошлифом, можно заметить невооруженным глазом, что наплавленный металл шва отличается от основного металла. Это отличие объясняется тем, что металл в сварном шве является литым, а свариваемые Детали большей частью изготовляются из прокатного, металла.» При прокатке металла в горячем состоянии его механические свойства улучшаются. Литой металл шва, не подвергающийся подобной обработке, имеет крупнозернистую структуру и худшие по сравнению с прокатным механические свойства.
Основной металл, расположенный рядом с наплавленным металлом, нагревается в процессе сварки до различных температур (но-ниже температуры плавления), а затем вновь охлаждается до температуры окружающей среды. Часть основного металла, подвергнутая такому нагреву при сварке, называется зоной термического (теплового) влияния, или околошовной зоной (фиг. 43). Зона термического влияния состоит из нескольких участков, имеющих неоднородную структуру металла. Размер этих участков и сруктуру можно увидеть,, рассматривая микрошлиф под микроскопом (микрошлиф — образец,, отполированный, а затем протравленный раствором азотной кислоты в спирте). Размер зоны термического влияния зависит от степени нагрева металла в процессе сварки и скорости охлаждения. Скорость охлаждения зависит от толщины свариваемого металла,, а степень нагрева — от способа и режима газовой сварки. Так, например, при сварке стали правым способом ширина зоны термического влияния меньше, чем при сварке левым способом. Режим сварки в основном определяется мощностью применяемой горелки и скоростью перемещения пламени. При нормально установленных мощности пламени и скорости сварки зона термического влияния имеет меньшую ширину, чем при чрезмерно большой мощности и малой, скорости сварки.
ОБРАЗОВАНИЕ ШВА И ОКОЛОШОВНОЙ ЗОНЫ
В сварочной ванне расплавленные основной и, если используют, дополнительный металлы перемешиваются. По мере перемещения источника теплоты вслед за ним перемещается и сварочная ванна. В результате потерь теплоты на излучение, теплоотвод в изделие, а при электрошлаковой сварке — и в формирующие ползуны в хвостовой части ванны происходит понижение температуры расплавленного металла, который, затвердевая, образует сварной шов. Форма и объем сварочной ванны зависят от способа сварки и основных параметров режима. Ее объем может составлять от миллиметров до сотен кубических сантиметров.
1 результате этого изменяются и усло — iiHii затвердевания (кристаллизации) металла сварочной ванны, которые также зависят от условий теплоотвода, т. е. от толщины свариваемого металла, типа сварного соединения, способа сварки, наличия шлака па поверхности сварочной ванны и т. д. Таким образом, названные выше условия определяют и неодинаковое время существования в расплавленном состоянии металла в различных участках сварочной ванны.
Кристаллизация металла сварочной ванны у границы с нерасплавившимся основным металлом (границы сплавления) протекает очень быстро. Но мере удаления от нее к центру ванны длительность пребывания металла в расплавленном состоянии увеличивается. Переход металла из жидкого в твердое состояние — первичная кристаллизация на границе сплавления начинается от частично оплавленных зерен основного или ранее наплавленного металла (рис. 108) в виде дендрптов, растущих в направлении, обратном теплоотводу, т. с. в глубь сварочной ванны. Таким образом, возникают общие зерна. При многослойной сварке, когда кристаллизация начинается от частично оплавленных зерен предыдущего шва, возможно прорастание кристаллов из слоя в слой — образуется транскржсталличная структура.
Б различные этапы кристаллизации металла сварочной ванны и роста дендрптов состав кристаллизующего жидкого металла не одинаков. Первые порции металла менее загрязнены примесями, чем последние. Б результате образуется зональная и впут- ридендритная химическая неоднородность металла. Неоднородность химического состава в различных участках одного дендрита, когда его поверхностные слон более загрязнены примесями — внутридендритная ликвация, имеет преимущественное развитие в сварном шве. Ликвация в сварном шве зависит от его химического состава, формы сварочной ванны и скорости кристаллизации. Способ сварки оказывает существенное влияние на развитие ликвации.
Первичная кристаллизация металла сварочной ванны имеет прерывистый характер, вызванный выделением перед фронтом кристаллизации скрытой теплоты кристаллизации. Это приводит к характерному слоистому строению шва и появлению ликвации н виде слоистой неоднородности, которая в наибольшей степени проявляется вблизи границы сплавления. Слоистая ликвация также зависит от характеру и скорости кристаллизации металла сварочной ванны. Слоистая и дендритная ликвации уменьшаются при улучшении условий диффузии ликвирутощих элементов в твердом металле.
Образовавшиеся в затвердевшем металле шва в результате первичной кристаллизации столбчатые кристаллиты имеют аустенитную микроструктуру (диаграмма состояния системы Fe—С сплавов на рис. 109, справа). При дальнейшем охлаждении металла, при температуре аллотропического превращения Ас3 начинается процесс перестройки атомов пространственной решетки — перекристаллизация. В результате перекристаллизации происходит распад части аустенита и превращение его в феррит. Так как растворимость углерода в феррите меньше, чем в аустените, выделяющийся углерод вступает в химическое соединение с железом, образуя цементит.
Дальнейшее охлаждение стали ниже температуры превращения Лсг приводит к образованию эвтсктоидной смеси феррита и цементита — перлита. Вторичная кристаллизация сопровождается значительным увеличением числа зерен, так как в пределах первичного зерна аустенита образуется несколько зерен перлита и феррита. Это благоприятно влияет на механические свойства стали. С увеличением в стали содержания углерода количество перлита возрастает. Одновременно может наблюдаться и рост величины зерен. Количество и строение перлитной фазы зависит также от скорости охлаждения металла шва.
При некоторых условиях может образоваться видманштеттова структура, характеризующаяся выделением феррита из аустенита не только но границам зерен, но и по кристаллографическим пдоско — сгям отдельных кристаллитов. Видманштеттова структура в сварных соединениях не желательна, так как снижает их механические свойства. Металл шва при комнатной температуре и обычных для сварки скоростях охлаждения в области температур перекристаллизации имеет ферритно-перлитную или сорбитообразную структуру.
Теплота, выделяемая при сварке, распространяется вследствие теплопроводности в основной металл. Этот процесс характеризуется термическим циклом. В каждой точке околошовной зоны температура вначале нарастает, достигая максимума, а затем снижается. Чем ближе точка расположения к границе сплавления, тем быстрее происходит нагрев металла в данном участке и тем выше максимальная температура, достигаемая в нем. При значительном удалении от шва нагрев основного металла практически не происходит.
Таким образом, различные участки основного металла характеризуются различными максимальными температурами и различными скоростями нагрева и охлаждения, т. е. подвергаются своеобразной термообработке. Поэтому структура и свойства основного металла в различных участках сварного соединения различны. Зону основного металла, в которой под воздействием термического цикла при сварке произошли фазовые и структурные изменения, называют зоной термического влияния. Характер этих превращений и протяженность зоны термического влияния зависят от состава и теплофизических свойств свариваемого металла, способа и режима сварки, типа сварного соединения и т. п.
На рис. 109 слева показаны поперечное сечение стыкового сварного соединения при однослойной сварке низкоуглеродистой стали, кривая распределения температур по поверхности сварного соединения в момент, когда металл шва находится в расплавленном состоянии, и структуры различных участков зоны термического влияния шва после сварки, образованные в результате действия термического цикла сварки. Эта схема — условная, так как кривая распределения температур по поверхности сварного соединения во время охлаждения меняет свой характер.
На участке неполного расплавления объемы металла нагре
вались в интервале температур между солидусом и ликвидусом, что приводило к частичному расплавлению (оплавлению) зерен металла. Пространство между нерасплавившимися зернами заполнено жидкими прослойками, связанными с металлом сварочной ванны. Поэтому в него могли проникать и элементы, вводимые в металл сварочной ванны. В результате состав металла на этом участке может отличаться от состава основного металла, а за счет нерасплавившихся зерен основного металла — и от состава металла шва.
Слоистая ликвация способствует увеличению химической неоднородности металла на этом участке по сравнению с металлом шва. Состав и структура металла в этой зоне зависят также от диффузии элементов, которая может проходить как из основного нерасплавившегося металла в жидкий металл, так и наоборот. Этот участок по существу и является местом сварки. Его протяженность зависит от состава и свойств металла, способа сварки и обычно не превышает 0,5 мм, но свойства металла в нем могут оказывать решающее влияние на свойства всего сварного соединения.
На участке перегрева металл нагревался в интервале температур от 1100—1150°С до линии солидуса. Металл, нагревавшийся выше температуры Ас3, полностью переходит в состояние аустенита, при этом происходит рост зерна, размеры которого увеличиваются тем больше, чем выше температура металла. Даже непродолжительное пребывание металла при температурах свыше 1100° С приводит к значительному увеличению размера зерен. Крупнозернистая структура металла на этом участке перегрева после охлаждения может привести к образованию неблагоприятной видманштеттовой структуры. Металл, нагретый незначительно выше температур Лс3, имеет мелкозернистую структуру с высокими механическими свойствами. Этот участок называется участком нормализации (перекристаллизации). На участке неполной перекристаллизации металл нагревался до температуры между Л, и Ас3. Поэтому он характеризуется почти неизменным ферритным зерном и некоторым измельчением и сфероидизацией перлитных участков.
Металл, нагревавшийся в интервале температур 500—550° С до Асг (участотї рекристаллизации), по структуре незначительно отличается от основного. Если до сварки металл подвергался пластической деформации, то при нагреве в нем происходит сращивание раздробленных зерен основного металла — рекристаллизация. При значительной выдержке при этих температурах может произойти значительный рост зерен. Механические свойства металла этого участка могут несколько снизиться вследствие разупрочнения ввиду снятия наклепа.
При нагреве металла в интервале температур 100—500° € (участок старения) его структура в процессе сварки нс претерпевает видимых изменений. Однако в некоторых сталях, содержащих повышенное количество кислорода и азота (обычно кипящих), их нагрев при температурах 150—350° С сопровождается резким снижением ударной вязкости и сопротивляемости разрушению.
Многослойная сварка ввиду многократного воздействия термического цикла сварки на основной металл в околошовной зоне изменяет строение и структуру зоны термического влияния. При сварке длинными участками после каждого последующего прохода предыдущий шов подвергается своеобразному отпуску.
При сварко короткими участками шов и околошовная зона длительное время находятся в нагретом состоянии. Помимо изменения структур, это увеличивает и протяженность зоны термического влияния. Последующие слои термически воздействуют на ранее наплавленные швы, имеющие структуру литого металла, и создают в них зону термического влияния, строение и структура которой значительно отличаются от зоны термического влияния в основном металле, подвергавшемся прокатке. Эта зона на участке перегрева обычно не имеет крупного зерна и характеризуется мелкозернистыми структурами с повышенными пластическими свойствами.
Структура металла тпвов при электрошлаковой сварке может характеризоваться наличием трех зон (рис. 110, а): зона 1 крупных столбчатых кристаллов, которые растут в направлении, обратном отводу теплоты; зона 2 тонких столбчатых кристаллов с меньшей величиной зерна и несколько большим их отклонением в сторону теплового центра; зона 3 равноосных кристаллов, располагающаяся посередине шва. В зависимости от способа электрошлаковой сварки, химического состава металла шва и режима сварки может быть получено различное строение швов. Повышение содержания в шве углерода и марганца увеличивает, а уменьшение интенсивности теплоотвода уменьшает ширину зоны 1.
Направленность кристаллизации зависит от коэффициента формы шва. При его увеличении за счет уменьшения скорости подачи электродной проволоки (рис. 110, б) происходит отклонение роста кристаллов в сторону теплового центра сварочной ванны. Подобные швы имеют повышенную стойкость против кристаллизационных трещин. Медленное охлаждение швов при электрошлаковой сварке в интервале температур фазовых превращений способствует тому, что их структура характеризуется грубым ферритно-перлитным строением с утолщенной оторочкой феррита по границам кристаллов.
Термический цикл околошовпой зоны при электрошлаковой сварке характеризуется длительным ее нагревом и выдержкой при температурах перегрева и медленным охлаждением. Поэтому
в ней могут образовываться грубые видманштеттовы структуры, которые по мере удаления от линии сплавления сменяются нормализованной мелкозернистой структурой. Б зоне перегрева может наблюдаться падение ударной вязкости, что устраняется последующей термообработкой (нормализация с отпуском). Термический цикл электрошлаковой сварки, способствуя распаду аустенита в области перлитного и промежуточного превращений, благоприятен при сварке низколегированных сталей, так как способствует подавлению образования закалочных структур.
Основным фактором, определяющим после окончания сварки конечную структуру металла в отдельных участках зоны термического влияния, является термический цикл, которому подвергался металл этого участка при сварке. Решающими факторами термического цикла сварки являются максимальная температура, достигаемая металлом в рассматриваемом объеме, и скорость его охлаждения. Ширина и конечная структура различных участков зоны термического влияния определяются способом и режимом сварки, составом и толщиной основного металла. Общая протяженность зоны термического влияния может достигать 30 мм. При более концентрированных источниках теплоты протяженность зоны меньше.
Рассмотренное разделение зоны термического влияния — приближенно. При переходе от одного структурного участка к другому имеются промежуточные структуры. Кроме того, диаграмму железо — углерод мы рассматривали статично, в какой-то момент существования сварочной ванны. В действительности температура в точках зоны термического влияния изменяется во времени в соответствии с термическим циклом сварки.
Повышение прочности низколегированных сталей достигается легированием их элементами, которые растворяются в феррите и измельчают перлитную составляющую. Наличие этих элементов при охлаждении тормозит процесс распада аустенита и действует равносильно некоторому увеличению скорости охлаждения. Поэтому при сварке в зоне термического влияния на участке, где металл нагревался выше температур Aclt при повышенных скоростях охлаждения могут образовываться закалочные структуры. Металл, нагревавшийся до температур значительно выше Ас3, будет иметь более грубозернистую структуру.
При сварке термически упрочненных сталей на участках рекристаллизации и старения может произойти отпуск металла с образованием структуры сорбита отпуска и понижением прочностных свойств металла. Технология изготовления сварных конструкций из низколегированных сталей должна предусматривать минимальную возможность появления в зоне термического влияния закалочных структур, способных привести к холодным трещинам, особенно при сварке металла больших трещин. При сварке термически упрочненных сталей следует принимать меры, предупреждающие разупрочнение стали на участке отпуска.
Рассматриваемые стали обладают хорошей свариваемостью. Технология их сварки должна обеспечивать определенный комплекс требований, основные из которых — обеспечение надежности и долговечности конструкций (особенно из термически упрочняемых сталей, обычно используемых при изготовлении ответственных конструкций). Важное требование при сварке рассматриваемых сталей — обеспечение равнопрочное™ сварного соединения с основным металлом и отсутствие дефектов в сварном шве. Для этого механические свойства металла шва и околошовной зоны должны быть не ниже нижнего предела соответствующих свойств основного металла.
В некоторых случаях конкретные условия работы конструкций допускают снижение отдельных показателей механических свойств сварного соединения. Однако во всех случаях, особенно при сварке ответственных конструкций, швы не должны иметь трещин, непроваров, пор, подрезов. Геометрические размеры и форма швов должны соответствовать требуемым. Сварное соединение должно быть стойким против перехода в хрупкое состояние. Иногда к сварному соединению предъявляют дополнительные требования (работоспособность при вибрационных и ударных нагрузках, пониженных температурах и т. д.). Технология должна обеспечивать максимальную производительность и экономичность процесса сварки при требуемой надежности конструкции.
Таблица 47. Средний химический состав металла шва, %
|
Механические свойства металла шва и сварного соединения зависят от его структуры, которая определяется химическим составом, режимом сварки, предыдущей и последующей термообработкой. Химический состав металла шва при сварке рассматриваемых сталей незначительно отличается от состава основного металла (табл. 47). Это различие сводится к снижению содержа
ния в металле шва углерода для предупреждения образования структур закалочного характера при повышенных скоростях охлаждения. Возможное снижение прочности металла шва, вызванное уменьшением содержания в пом углерода, компенсируется легированием металла через проволоку, покрытие или флюс марганцем, кремнием, а при сварке низколегированных сталей — также и за счет перехода этих элементов из основного металла.
Таким образом, химический состав металла шва зависит от доли участия основного и дополнительного металлов в образовании металла шва и взаимодействий между металлом, шлаком и газовой фазой. Повышенные скорости охлаждения металла шва также способствуют йовышению его прочности (рис. 111), однако при этом снижаются его пластические свойства и ударная вязкость. Это объясняется изменением количества и строения перлитной фазы. Критическая температура перехода металла однослойного шва в хрупкое состояние практически не зависит от скорости охлаждепия. Скорость охлаждения металла шва определяется толщиной свариваемого металла, конструкцией сварного соединения, режимом сварки и начальной температурой изделия.
Влияние скорости охлаждения в наибольшей степени проявляется при дуговой сварке однослойных угловых швов и последнего слоя многослойных угловых и стыковых швов при наложении их на холодные, предварительно сваренные швы. Металл многослойных швов, кроме последних слоев, подвергающийся действию повторного термического цикла сварки, имеет более благоприятную мелкозернистую структуру. Поэтому он обладает более низкой критической температурой перехода в хрупкое состояние.
Марка | Вид термообработки | кгс/мм2 | V кгс/мм2 | % | ’1, % |
ВСтЗки | Отжиг…………………………… | 10.4 | 39,3 | 35.9 | 61,0 |
Нормализация………………. | 25.5 | 41.8 | 32,8 | 64.1 | |
Закалка в масле…………… | 3J.8 | 50.6 | 29.4 | 68,5 | |
Закалка в водо……………… | 42,1 | 58,8 | 18,2 | 67,9 | |
19Г | Отжиг.. | 26.7 | 48 | 34.9 | 62,9 |
Нормализации………………. | 31,9 | 53,3 | 29.8 | — | |
Закалка в масло…………… | 43.7 | 62,2 | 28,1 | 73.2 | |
Закалка в воде……………… | 47,4 | 67,6 | 10,0 | 53,1 | |
14Г2 | Отжиг…………………………… | 20.4 | 50.3 | 34,9 | 67.2 |
Нормализация………………. | 33,8 | 53,2 | 30,1 | 65.5 | |
Закалка в масло….. | 52.8 | 73,9 | 23.4 | 61,6 | |
Закалка в водо…………….. | 88 | 101.4 | 13.6 | 50,4 |
Пластическая деформация, возникающая в металле шва под воздействием сварочных напряжений, также повышает предел текучести металла шва.
Обеспечение равнопрочности металла шва при дуговых способах сварки низкоуглеродистых и низколегированных нетермо — упрочпепных сталей обычно не вызывает затруднений. Механические свойства металла околошовной зоны зависят от конкретных условий сварки и от вида термообработки стали перед сваркой.
При сварке низкоуглеродистых горячекатаных (в состоянии поставки) сталей при толщине металла до 15 мм на обычных режимах, обеспечивающих небольшие скорости охлаждения, структуры металла шва и околошовной зоны примерно такие, как было рассмотрено выше (рис. 109). Повышение скоростей охлаждения при сварке на форсированных режимах металла повышенной толщины, однопроходных угловых швов, при отрицательных температурах и т. д. может привести к появлению в металле шва и околошовной зоны закалочных структур на участках перегрева и полной и неполной рекристаллизации.
Как видно из данных табл. 48 и рис. 112, скорость охлаждения для низкоуглеродистых сталей оказывает большое влияние на их механические свойства. При повышении содержания марганца это влияние усиливается. Поэтому даже при сварке горячекатаной низкоуглеродистой стали марки ВСтЗ при указанных выше условиях не исключена возможность получения в сварном соединении закалочных структур. Если сталь перед сваркой прошла термическое упрочнение — закалку, то в зоне термического влияния шва на участках рекристаллизаций и старения будет наблюдаться отпуск металла, т. е. снижение его прочностных свойств. Уровень
изменения этих свойств зависит от погонной энергии, типа сварного соединения и условий сварки.
При сварке низколегированных сталей изменение свойств металла шва и околошовной зоны проявляется более значительно. Сварка горячекатаной стали способствует появлению (см. рис. 109) закалочных структур на участках перегрева и нормализации. Уровень изменения механических свойств металла больше, чем при сварке низкоуглеродистых сталей. Термообработка низколегированных сталей, наиболее часто — закалка (термоупроч — пение) с целью повышения их прочностных показателей при сохранении высокой пластичности (табл. 48) усложняет технологию сварки.
На участках рекристаллизации и старения происходит разупрочнение стали иод действием высокого отпуска с образованием
структур преимущественно троостита или сорбита отпуска. Это разупрочнение телі больше, чем выше была прочность основного металла, полученная после тормообработки. При температурах выше Ас3 разупрочнение обусловлено совместно протекающими процессами высокого отпуска и фазовой перекристаллизации. В этих процессах решающее значение имеют скорость охлаждения металла шва (рис. 112) и в первую очередь погонная энергия при сварке (табл. 49).
Таким образом, при сварке низколегированных сталей (особенно термоупрочненных) получение равнопрочного сварного соединения вызывает некоторые трудности и поэтому требует применения определенных технических приемов (сварка короткими участками нетермоупрочненных сталей и длинными термоупрочненных и др.). Протяженность участков зоны термического влияния, где произошло заметное изменение свойств основного металла под действием термического цикла сварки (разупрочнение или закалка), зависит от способа и режима сварки, состава и толщины металла, конструкции сварного соединения др.
Повышение погонной энергии сварки (рис. ИЗ) сопровождается расширением разупрочненной зоны и снижением твердости металла в ней. Это вызвано увеличением объема металла, подвергавшегося высокому сварочному нагреву, и замедлением темпа охлаждения. Кроме того, повышение погонной энергии уменьшает скорость охлаждения в субкритическом интервале температур, что уменьшает количество неравновесных структур (снижает твердость) в прилегающих к шву участках перегрева и полной нерекристад-
а)
Рис. 113. Влияние погонной энергии на турной области, возникает распределение твердости металла по похолодней пластическая де — перечному сечению шва на стали 14ХГС:
формация. Попадая при п) g/v = 2Ю0 кал/см; б) g/v = 11 800 кал/см;
__ * I — шов; II — зона перекристаллизации; III —
наложении ПОСЛедуЮЩИХ основной металл
швов под сварочный нагрев до температур около 300° С, эти зоны становятся участками деформационного старения, приводящего к снижению пластических и повышению прочностных свойств металла и возможному возникновению трещин, особенно при низких температурах или в копцентраторах напряжений.
Высокий отпуск при температурах G00—650° С в этих случаях служит эффективным средством восстановления свойств металла (рис. 114). Высокий отпуск применяют и для снятия сварочных напряжений. Нормализации подвергают сварные конструкции для улучшения структуры отдельных участков сварного соединения и выравнивания их свойств. Термообработка, кроме закалки сварных соединений, в которых шов и околошовная зона охлаждались с повышенными скоростями, приведшими к образованию на некоторых участках неравновесных структур закалочного характера (угловые однослойные швы, последние проходы, выполненные на полностью остывших предыдущих), приводит к снижению прочностных и повышению пластических свойств металла в этих участках (табл. 48 и 50).
При сварке короткими участками по горячим предварительно наложенным швам
замедленная скорость охлаждения металла шва и околошовттой зоны способствует получению равновесных структур. Влияние термообработки в этом случае сказывается незначительно. При электрошлаковой сварке, когда скорость остывания металла шва околошовной зоны сопоставима со скоростями охлаждения при термообработке, последующая термообработка мало изменяет механические свойства металла рассматриваемых зон. Однако нормализация приводит к резкому возрастанию ударной вязкости.
Таблица 50. Влияние термообработки на механические свойства металла шва про сварке низкоуглеродистой стали
Примечание. Состав металла шва: при сварке под флюсом 0,12% С; 0,75% Мп; 0,22% Si; ври электрошлаковой сварке 0,14% С; 0,80% Мп; 0,07% Si. |
Швы, сваренные на низкоуглеродистых сталях всеми способами сварки, обладают удовлетворительной стойкостью против образования кристаллизационные трещин. Это обусловлено низким содержанием в них углерода. Однако для низкоуглеродистых сталей, содержащих углерод по верхнему пределу (свыше 0,20%), при сварке угловых швов и первого корневого шва в многослойных швах, особенно с повышенным зазором, возможно образование кристаллизационных трещин, что связано в основном с неблагоприятной формой провара (узкая глубокая форма провара с коэффициентом формы 0,8—1,2). Легирующие добавки в низколегированных сталях могут повышать вероятность образования кристаллизационных трещин.
Низкоуглеродистые и низколегированные стали хорошо свариваются практически всеми способами сварки плавлением.
(парные соединения для фиксации входящих в них деталей шпосительно друг друга и выдерживания необходимых зазоров перед сваркой собирают в сборочных приспособлениях или при помощи прихваток. Длина прихваток зависит от толщины и изменяете)! в пределах 20—120 мм при расстоянии между ними 500— 800 мм. Сечение прихваток равно примерно 1/3 сечения шва, но по более 25—30 мм2. Прихватки выполняют обычно покрытыми нлоктродами или полуавтоматами в углекислом газе. Их рекомендуется накладывать со сторопы, обратной наложению основного однопроходного шва или первого слоя в многопроходных швах. При сварке прихватки следует переплавлять полностью, так как м них могут образовываться трещины ввиду высокой скорости теплоотвода. Поэтому перед сваркой прихватки тщательно зачищают и осматривают. При наличии в прихватке трещины ее вырубают или удаляют другим способом.
При электрошлаковой сварке детали, как правило, устанавливают с зазором, расширяющимся к концу шва. Взаимное положение деталей фиксируют скобами, установленными на расстоянии 500—1000 мм друг от друга и удаляемыми по мере наложения шва. При автоматических способах дуговой сварки и электрошлаковой сварке в начале и конце шва устанавливают входные и выходные планки для обеспечения сварки начала шва с установившимся термическим циклом (требуемыми размерами шва) и вывода кратера с основного шва.
Сварку стыковых швов вручную или полуавтоматами в защитных газах и порошковыми проволоками обычно выполняют па весу. При автоматической сварке предусматривают применение приемов, обеспечивающих предупреждение прожогов и качественный провар корпя шва. Для предупреждения образования в швах пор, трещин, непроваров и других дефектов свариваемые кромки перед сваркой тщательно зачищают от шлака, оставшегося после термической резки, ржавчины, масла и других загрязнений.
Дуговую сварку ответственных конструкций лучше проводить г двух сторон. Более благоприятные результаты получаются при многослойной сварке. В этом случае, особенно на толстом металле, достигаются более благоприятные структуры в металле шва и околошовной зоне. Однако выбор способа заполнения разделки при многослойной сварке зависит от толщины металла и термообработки стали перед сваркой. При появлении в швах дефектов (нор, трещин, непроваров, подрезов и т. д.) металл в месте дефекта удаляется механическим путем, газопламенной, воздушно-ду — I оной или плазменной строжкой и после зачистки подваривается.
Гледует помнить, что при сварке низколегированных сталей выбор техники и режима сварки влияет на форму провара, долю участия основного металла в формировании шва, а также на его состав и свойства.
Ручная дуговая сварка покрытыми электродами
В зависимости от назначения конструкций и типа стали электроды можно выбирать согласно табл. 51. Режим сварки выбирают в зависимости от толщины металла, типа сварного соединения и пространственного положения сварки.
Таблица 51. Марки электродов, применяемых при сварке
иизкоуглеродистых п низколегированных сталей
При сварке корневых швов в разделке на металле толщиной 10 мм и более используют электроды диаметром 3—4 мм. Рекомендуемые для данной марки электрода значения сварочного тока, его род и полярность выбирают согласно паспорту электрода, в котором обычно приведены и его сварочно-технологические свойства, типичный химический состан шва и механические свойства. Рядовые и ответственные конструкции из низкоуглеродистых сталей сваривают электродами типа Э42 и Э46 (табл. 51 и 52).
При сварке этих сталей обычно обеспечиваются достаточно высокие механические свойства сварного соединения и поэтому в большинстве случаев не требуются специальные меры, направленные на предотвращение образования в нем закалочных структур. Однако при сварке угловых вівов на толстом металле и первого слоя многослойного шва для повышения стойкости металла против кристаллизационных трещин может потребоваться предварительный подогрев до температуры 120—150° С.
Тип электрида но ГОСТ 9467-75 | Марки электродов | |
342 | ОММ-5, СМ-5, ЦМ-7, КПЗ-32Г, АНО-1, АНО-6, ОМА-2, ВСІМ, ВСЦ-2 | АНО-5, |
Э42А | УОНИ-13/45, СМ-11, УП-1/45, УП-2/45, ОЗС-2 | |
Э46 | АНО-3, АНО-4, МР-1, МР-3, ОЗС-З, ОЗС-4, ЭРС-1; ЭРС-2, РБУ-4, РВУ-5 | 03C-G, |
040А | Э-138/45Н | |
Э50 | ВСН-3 | |
Э50А | УОНИ-13/55, УП-1/55, УП-2/55, ДСК-50, Э-138/50Н | К-5А, |
Для сварки рядовых конструкций из пи з к о л о ги р о в а н н ы х сталей обычно применяют электроды типа Э42А, а ответственных — типа Э51)А. Это обеспечивает получение металла швов с достаточной стойкостью против кристаллизационных трещин и требуемыми прочностными и пластическими свойствами. Легирование металла шва за счет провара основного металла легирующими элементами, входящими в основной металл, и повышенные скорости охлаждения позполяют получить металл шва с более высокими, чем при сварке иизкоуглеродистых сталей, прочностными показателями.
Техника заполнения швов и определяемый ею термический цикл сварки зависят от предварительной термообработки стали. Сварка толстого металла каскадом и горкой, замедляя скорость охлаждения металла шва и околошовной зоны, предупреждает образование в них закалочных структур. Это же достигается при предварительном подогрене до температуры 150—200 ЭС. Поэтому эти способы дают благоприятные результаты на нетормоупрочпел — ных сталях. При сварке термоупрочнеппых сталей для уменьшения разупрочнения стали в околошовной зоне рекомендуется сварка длинными швами по охлажденным предыдущим швам.
Следует выбирать режимы сварки с малой погонной энергией. При этом достигается и уменьшение протяженности зоны разу- прочненного металла в околошовной зоне. При исправлении дефектов в сварных швах низколегированных п иизкоуглеродистых сталей повышенной толщины швами малого сечения вследствие значительной скорости охлаждения металл подварочного шва и его околошовной зоны обладает пониженными пластическими свойствами. Поэтому дефектные участки следует подваривать швами нормального сечения длиной не менее 100 мм или предварительно подогревать до температуры 150—200 °С.
Сварка под флюсом
Автоматическую сварку обычно выполняют электродной проволокой диаметром 3—5 мм, полуавтоматическую проволокой диаметром 1,2—2 мм. Равноирочность соединения достигается за
счет подбора соответствующих составов флюсов и электродных проволок и выбора режимов и техники сварки. При сварке пин коуглеродистых сталей в большинстве случаев применяют флюсы марок АН-348-А и ОСЦ-45 и низкоуглеродистые электродные проволоки марок Св-08 и Си 08А. При сварке ответственных кон струкдий, а также ржавого металла рекомендуется использовать электродную проволоку марки Св-08ГА.
Использование указанных материалов позволяет получи*, металл шва с механическими свойствами, равными или превышающими свойства основного металла. При сварке низколегированных сталей используют те же флюсы и электродные проволоки марок Св-08ГА, Си-ЮГА и Св-10Г2. Легирование металла шва марганцем за счет проволок и кремнием за счет провара основного металла при подборе соответствующего термического цикла (погонной энергии) позволяет получить металл шва с требуемыми механическими свойствами. Использованием указанных материалов достигается высокая стойкость металла швов против образования пор и кристаллизационных трещин.
В конструкциях из низкоуглеродистых и низколегированных сталей наряду со сваркой с разделкой кромок широко применяется сварка стыковых швов и швов без разделки кромок. Увеличение доли основного металла в металле шва, характерное для этого случая, и некоторое увеличение содержания в нем углерода могут повысить прочностные свойства и понизить пластические свойства металла шва.
Таблица 53. Режимы сварки под флюсом
|
Е.
Примечание. Ток постоянной обратной полярности. |
Технология сварки низкоуглеродистых и низколегированных сталей отличается незначительно. Режимы сварки зависят от конструкции соединения, типа шва и техники сварки (табл. 53). Свойства металла околошовной зоны зависят от термического цикла сварки. При сварке угловых однослойных швов и стыковых н угловых швов на толстолистовой стали типа ВСтЗ па режимах с малой погонной энергией в околошовной зоне возможно образование закалочных структур с пониженной пластичностью. Предупредить это можно увеличением сечения швов или применением двухдуговой сварки.
Для низколегированных термоупрочпепных сталей с целью предупреждения разупрочнения шва в зоне термического влияния следует использовать режимы с малой погонной анергией, а для нетермоупрочненных — наоборот, с повышенной. Для обеспечения пластических свойств металла шва и околошовной зоны на уровне свойств основного металла, во втором случае следует выбирать режимы, обеспечивающие получение швов повышенного сечения, применять двухдуговую сварку или проводить предварительный подогрев металла до температуры 150—200 °С.
В зависимости от условий сварки и охлаждения свойства сварных соединений на низкоуглеродистых и низколегированных сталях изменяются в широких пределах.
Кинетика размягчения в докритической зоне термического влияния двухфазных стальных швов
org/ScholarlyArticle»> 1.Федеральный регистр , 2009, т. 74. С. 49454–789.
W. Gan, S.S. Babu, N. Kapustaka, R.H. Wagoner: Metall. Mater. Транс А , 2006, т. 37А, стр. 3221–31.
Артикул CAS ОБЪЯВЛЕНИЯ Google ученый
С. Хашимото, С. Канбе и М. Судо: Пер. ISIJ , 1981, т.21. С. B-497.
Google ученый
Н. Ямаути, Т. Така, К. Кунисигэ и Н. Нагао: Пер. ISIJ , 1982, т. 22, стр. B-107.
Google ученый
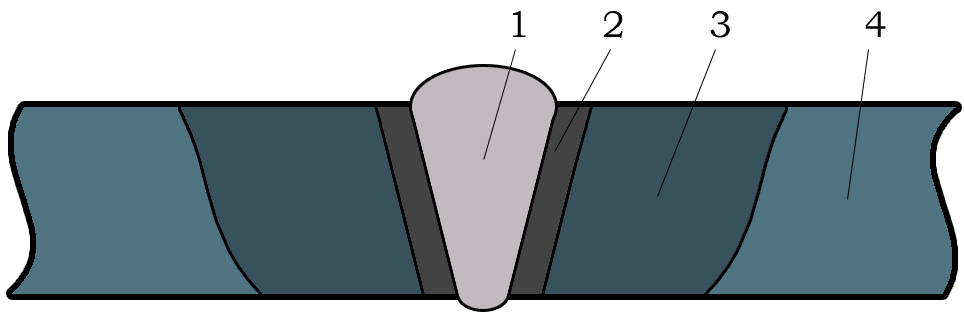
Т. Така, К. Кунисигэ, Н. Ямаути и Н. Нагао: ISIJ Int. , 1989, т. 29. С. 503–10.
Артикул CAS Google ученый
Э. Биро и А. Ли: Конференция по сварке листового металла XII , AWS, Ливония, Мичиган, 2006.
Google ученый
P.K. Гош, П.С. Гупта, Рамавтар и Б.К. Jha: Weld. J. , 1991, т. 70, с. 7с – 14с.
М. Ся, Э. Биро, З. Тиан, Ю.Н. Чжоу: ISIJ Int. , 2008, т. 48. С. 809–14.
Артикул CAS Google ученый
Э. Биро и А. Ли: Конференция по сварке листового металла XI , AWS, Sterling Heights, MI, 2006.
Google ученый
P.K. Гош, П.С. Гупта, О. Пал, Р. Автар, Б.К. Джа, В. Двиведи: ISIJ Int. , 1993, т. 33. С. 807–15.
Артикул CAS Google ученый
Н. Юриока, Х. Судзуки, С. Охшита и С. Сайто: Weld.J. , 1983, т. 62, стр. 147с-53с.
Google ученый
J.C. Ion, K.E. Истерлинг, М.Ф. Эшби: Acta Metall. , 1984, т. 32, стр. 1949–62.
Артикул CAS Google ученый
K.W. Эндрюс, Д.Дж. Дайсон и С. Keown: Interpretation of Electron Diffraction Patterns , 2 nd ed., Plenum Press, New York, NY, 1971, стр.181–91.
Google ученый
М. Юнг, С. Дж. Ли и Й. К. Ли: Металл. Mater. Пер. А. , 2009, т. 40А, стр. 551–59.
Артикул CAS ОБЪЯВЛЕНИЯ Google ученый
Y. Wang, S. Denis, B. Appolaire, P. Archambault: J. Phys. IV Франция , 2004, т. 120. С. 103–10.
CAS Google ученый
J.W. Кристиан: Теория превращений в металлах и сплавах, часть I, Равновесие и общая кинетическая теория , 2 nd изд. , Pergamon Press, Oxford, UK, 1975, стр. 19–20.
Google ученый
E.J. Mittemeijer, A. Van Gent и P.J. Van der Schaaf: Metall. Пер. А , 1986, т. 17A, стр. 1441–45.
CAS ОБЪЯВЛЕНИЯ Google ученый
М.И. Луппо и Х. Оверхеро-Гарсия: Mater. Charact. , 1998, т. 40. С. 189–96.
Артикул CAS Google ученый
C.S. Roberts, B.L. Авербах и М. Коэн: Trans. AIME , 1953, т. 45. С. 576–603.
Google ученый
E.C. Bain: Легирующие элементы в стали , 1 st изд., ASM, Кливленд, Огайо, 1939, стр.146–260.
Google ученый
Сварка
Определение сварки
Сварка — это производственный процесс, в ходе которого материалы, обычно металлы или термопласты, соединяются путем коалесценции. Часто это делается путем плавления заготовок и добавления присадочного материала для образования ванны расплавленного материала (сварочной ванны), которая остывает, чтобы стать прочным соединением, но иногда давление используется в сочетании с теплом или само по себе, чтобы произвести сварка.Это контрастирует с пайкой и пайкой, которые включают плавление материала с более низкой температурой плавления между деталями для образования связи между ними без плавления деталей.
Рисунок 1 Дуговая сварка
Для сварки можно использовать множество различных источников энергии, включая газовое пламя, электрическую дугу (рис. 1), лазер, электронный луч, трение и ультразвук. Хотя сварка часто является промышленным процессом, ее можно выполнять в самых разных средах, в том числе на открытом воздухе, под водой и в космосе.Однако независимо от местоположения сварка остается опасной, и необходимо соблюдать меры предосторожности, чтобы избежать ожогов, поражения электрическим током, ядовитых паров и чрезмерного воздействия ультрафиолетового света.
До конца XIX века единственным процессом сварки была кузнечная сварка, которую кузнецы веками использовали для соединения металлов путем нагрева и измельчения. Дуговая сварка и кислородная сварка были одними из первых процессов, разработанных в конце века, и вскоре последовала контактная сварка.Технологии сварки быстро развивались в начале 20-го века, поскольку Первая и Вторая мировые войны вызвали спрос на надежные и недорогие методы соединения. После войн было разработано несколько современных методов сварки, в том числе ручные методы, такие как дуговая сварка защищенным металлом; В настоящее время это один из самых популярных методов сварки, а также полуавтоматические и автоматические процессы, такие как газовая дуговая сварка, дуговая сварка под флюсом и дуговая сварка порошковой проволокой. Развитие продолжилось с изобретением лазерно-лучевой сварки и электронно-лучевой сварки во второй половине века.Сегодня наука продолжает развиваться. Роботизированная сварка становится все более обычным явлением в промышленных условиях, и исследователи продолжают разрабатывать новые методы сварки и лучше понимать качество и свойства сварных швов.
1.2 Газокислородная сварка и резка
Газокислородная сварка (обычно называемая кислородно-ацетиленовой сваркой) и газокислородная резка — это процессы, в которых для сварки и резки металлов используются топливные газы и кислород соответственно. Кислородно-топливная смесь — один из старейших сварочных процессов, хотя в последние годы он стал менее популярным в промышленности.Французские инженеры Эдмон Фуш и Шарль Пикар первыми разработали кислородно-ацетиленовый сварочный аппарат в 1903 году. Он до сих пор широко используется для сварки труб и труб, а также при ремонтных работах. Кислородно-топливное оборудование универсально, оно подходит не только для сварки некоторых видов чугуна или стали, но также для пайки, пайки-сварки, нагрева металла (для гибки и формовки) и для использования на объектах, где нет источника питания.
При кислородно-топливной сварке для сварки металлов используется сварочная горелка.Сварка металла происходит, когда две детали нагреваются до температуры, при которой образуется общая ванна расплавленного металла. В ванну расплава обычно добавляют дополнительный металл, называемый наполнителем. Присадочный материал зависит от свариваемых металлов.
При газокислородной резке для нагрева металла до температуры воспламенения используется резак. Затем поток кислорода, направленный на металл, соединяется с металлом, который затем вытекает из пропила (пропила) в виде оксидного шлака.
1.3 Ручная дуговая сварка металла (MMA)
Процесс сварки металлической дугой вручную (также известный как сварка стержнем) происходит, когда две проволоки, составляющие часть электрической цепи, соединяются, а затем медленно разводятся, на их концах образуется электрическая искра.Эта искра, или дуга, как ее еще называют, имеет температуру до 3600 ° C. Поскольку дуга ограничена очень небольшой площадью, она может почти мгновенно расплавить металл. Если один из этих проводов подсоединен к заданию, а другой — к катанке или электроду, как его обычно называют, тепло дуги расплавляет как металл работы, так и острие электрода. Расплавленный металл из электрода смешивается с расплавленным металлом и образует сварной шов.
1.4 Сварка в металлической среде с активным газом (MAGS)
Сварка в среде активного газа в среде защитного газа (MAGS), которую иногда называют подтипами Дуговая сварка в газовой среде (GMAW) или сварка в среде инертного газа (MIG), представляет собой полуавтоматический или автоматический процесс дуговой сварки, в котором непрерывный и плавящийся проволочный электрод и через сварочный пистолет подается защитный газ.Источник постоянного напряжения постоянного тока чаще всего используется с MAGS, но могут использоваться системы постоянного тока, а также переменного тока.
Сварка MAGS, первоначально разработанная для сварки алюминия и других цветных металлов в 1940-х годах, вскоре стала применяться для обработки черных сталей, поскольку она позволяла сократить время сварки по сравнению с другими сварочными процессами. Стоимость инертного газа ограничивала его использование в сталях до тех пор, пока несколько лет спустя не стали широко использоваться полуинертные газы, такие как диоксид углерода.Дальнейшие разработки в 1950-х и 1960-х годах придали этому процессу большую гибкость, и в результате он стал широко используемым промышленным процессом. Сегодня сварка MAGS является наиболее распространенным процессом промышленной сварки, предпочтительным из-за ее универсальности, скорости и относительной простоты адаптации процесса к роботизированной автоматизации.
1.5 Сварка металла в активной газовой среде (MAGS)
Дуговая сварка вольфрамовым электродом в среде защитных газов (TAGS), также известная как сварка вольфрамовым электродом в среде инертного газа (TIG), представляет собой процесс дуговой сварки, в котором для получения сварного шва используется неплавящийся вольфрамовый электрод.Зона сварки защищена от атмосферного загрязнения защитным газом (обычно, но не всегда инертным газом, например, аргоном), и обычно используется присадочный металл, хотя для некоторых сварных швов, известных как автогенные сварные швы, он не требуется. Сварочный источник постоянного тока вырабатывает энергию, которая проходит через дугу через столб высокоионизированного газа и паров металлов, известный как плазма.
Сварка TAGS чаще всего используется для сварки тонких секций нержавеющей стали и цветных металлов, таких как алюминий, магний и медные сплавы.Этот процесс предоставляет оператору больший контроль над сваркой по сравнению с конкурирующими процедурами, такими как дуговая сварка металлическим электродом в защитных оболочках и дуговая сварка металлическим электродом в среде газа, что позволяет получать более прочные и качественные сварные швы. Однако сварка TAGS сравнительно более сложна и трудна для освоения, и, кроме того, она значительно медленнее, чем большинство других методов сварки.
1.6 Плазменная резка
Плазменная резка — это процесс, который используется для резки стали и других металлов разной толщины (или иногда других материалов) с помощью плазменной горелки.В этом процессе инертный газ (в некоторых установках — сжатый воздух) с большой скоростью выдувается из сопла; в то же время электрическая дуга образуется через этот газ от сопла к разрезаемой поверхности, превращая часть этого газа в плазму. Плазма достаточно горячая, чтобы расплавить разрезаемый металл, и движется достаточно быстро, чтобы сдуть расплавленный металл от разреза.
Ключевые моменты обучения
- Определить зону термического влияния при сварке
- Определите, почему разные методы резки и сварки имеют разные зоны термического влияния
2.1 зона теплового воздействия (HAZ)
Зона термического влияния (HAZ) на рис. 2 — это область основного материала, будь то металл или термопласт, микроструктура и свойства которого были изменены в результате сварки или операций термической резки. Тепло от процесса сварки и последующего повторного охлаждения вызывает это изменение в области, окружающей сварной шов. Степень и величина изменения свойств зависит в первую очередь от основного материала, присадочного металла сварного шва, а также количества и концентрации тепла, подводимого в процессе сварки.
Температуропроводность основного материала играет большую роль — если коэффициент диффузии высокий, скорость охлаждения материала высока, а ЗТВ относительно мала. В качестве альтернативы, низкий коэффициент диффузии приводит к более медленному охлаждению и большей ЗТВ. Количество тепла, поступающего в процессе сварки, также играет важную роль, поскольку в таких процессах, как кислородная сварка, используется большое количество тепла и увеличивается размер ЗТВ. Такие процессы, как сварка TAGS, где гораздо больше контроля над параметрами сварки, дают высококонцентрированное ограниченное количество тепла, что приводит к небольшой ЗТВ.Дуговая сварка находится между этими двумя крайностями, при этом отдельные процессы несколько различаются по тепловложению.
Рис.2 Поперечный разрез зоны термического влияния стыкового шва
Поперечное сечение сварного стыкового соединения, показанное выше, где самый темный серый цвет представляет зону сварного шва или плавления, средний серый цвет — зону термического влияния, а самый светлый серый цвет — основной материал.
2.2 Изменения в зоне термического влияния (HAZ)
Процессы резки и сварки с использованием сильного нагрева, такие как газокислородная резка или сварка, вызывают тепловые эффекты вблизи края реза или сварного шва, которые приводят к микроструктурным и металлургическим изменениям в металле. Все процессы термической резки и сварки создают в металле ЗТВ.
Изменения, вызванные теплом, могут включать:
- Изменение микроструктуры определенных сталей, приводящее к увеличению твердости ЗТВ по сравнению с основным металлом.
- Изменение микроструктуры определенных сталей, приводящее к снижению прочности ЗТВ.
- Образование нитридов или нитридов на кромке среза, которые могут повлиять на свариваемость кромки среза.
- Потемнение или изменение цвета поверхности металла рядом с ЗТВ («тепловой оттенок»).
Некоторые изменения, например тепловой оттенок, носят косметический характер и не имеют значения для некоторых приложений. Для других применений, таких как нержавеющая сталь, изменение цвета может иметь большое значение. На ширину теплового оттенка влияет состояние поверхности металла. Любые поверхностные загрязнения или покрытия, такие как краска, окисление, масло и даже отпечатки пальцев, будут влиять на формирование теплового оттенка. На ширину ЗТВ влияет только термическая история металла. Важно помнить, что ЗТВ находится не только на поверхности, но и в глубине металла.
2.3 Зона теплового воздействия (HAZ) от термической резки
Другие изменения в металле после термической резки, такие как деформация или закалка, влияют на свариваемость и пригодность металла после термической резки. Перед использованием металлической детали может потребоваться частичное или полное удаление HAZ (шлифованием или каким-либо другим способом).
На ширину ЗТВ от термической резки влияют:
- Скорость резания — как правило, более высокие скорости приводят к меньшей ЗТВ.
- Ампер (при использовании плазмы) — для данной толщины металла более высокая сила тока (и, следовательно, более высокая скорость резки) приводит к меньшей ЗТВ.
- Тип разрезаемого металла. Разные металлы передают тепло с разной скоростью и по-разному реагируют на повышенные температуры. Повышенные температуры и более длительное время резки приведут к более широкой ЗТВ.
Например, плазменный резак можно использовать для резки любого электропроводящего материала, но при прочих равных условиях он будет создавать ЗТВ различной ширины на алюминии, чем на низкоуглеродистой стали такой же толщины.
- Еще одна вещь, которую следует отметить в отношении HAZ, заключается в том, что при резке более толстых металлов ширина зоны может быть меньше в верхней части обрезной кромки и шире в нижней части.
Ключевые моменты обучения
- Определите, какие единицы СИ
- Определите единицу СИ для температуры
- Продемонстрируйте связь между Кельвином и градусом Цельсия
3.1 Международная система единиц (СИ)
Международная система единиц (СИ) определяет семь единиц измерения как базовый набор, из которого происходят все остальные единицы СИ. Эти основные единицы СИ и их физические величины: метр для длины, килограмм для массы, второй для времени, ампер для электрического тока, кельвин для температуры, кандела для силы света и моль для количества вещества.
3.2 Единица СИ для измерения температуры
«Кельвин, единица термодинамической температуры, представляет собой долю 1/273.16 термодинамической температуры тройной точки воды ». 13-й CGPM (1967/68, Резолюция 4; CR, 104). Шкала Кельвина начинается с абсолютного нуля, который составляет -273,16 ºC, и увеличивается в единицах, называемых Кельвинами, которые равны Чтобы получить значение в градусах Цельсия, необходимо вычесть 273 из градуса Цельсия, чтобы получить значение в градусах Цельсия, или прибавить 273 к температуре в градусах Кельвина, чтобы получить значение в градусах Цельсия.
Ключевые моменты обучения
- Определите опасности, связанные с тепловыми процессами
- Укажите меры безопасности, которые необходимо соблюдать, чтобы свести к минимуму эти опасности
- Укажите меры предосторожности, которые следует принимать для защиты других
- Определите важность соблюдения разрешений на работу систем, а также поддержания и соблюдения требований разрешений на проведение огневых работ.
4.1 Опасности, связанные с тепловыми процессами
Опасности для здоровья и безопасности, связанные с термическими процессами, такими как газокислородная резка, сварка и электросварка, включают многие из следующих:
- Опасности от баллонов со сжатым газом
- Поражение электрическим током
- Лучевые ожоги,
- Тепловые ожоги
- Пожары и взрывы,
- шум,
- Пары и газы от сварочного процесса.
- Дым и газы от покрытий на основном металле.
Воздействие любого из них или всех из них можно минимизировать, используя эффективную комбинацию мер контроля.
4.2 Меры безопасности, которые необходимо соблюдать при тепловых процессах
При сварке или резке с использованием кислородно-топливного оборудования сварочной установки оператор должен быть надлежащим образом обучен и находиться под наблюдением, а также соблюдать все общие безопасные рабочие процедуры, необходимые для тепловых процессов. Несмотря на то, что это не исчерпывающий список, некоторые конкретные моменты, которые следует отметить для кислородно-топливных процессов, следующие:
Кислородно-топливные процессы
- Всегда носите защитную одежду, например, огнестойкий комбинезон.
- Всегда надевайте подходящие очки.
- Всегда держите ключ шпинделя в клапане баллона с ацетиленом.
- Всегда держите цилиндры закрепленными в вертикальном положении.
- Всегда проверяйте герметичность с помощью мыльного раствора, НИКОГДА не открывайте огонь.
- Никогда не выполняйте временный ремонт сварочного оборудования.
- Никогда не допускайте контакта масла или смазки с кислородным оборудованием.
- Никогда не сваривайте закрытую емкость, например бочки с бензином / маслом, пока они не будут тщательно очищены.
- Никогда не работайте в закрытом сосуде самостоятельно и всегда оставляйте баллоны снаружи. При работе в закрытом резервуаре необходимо обеспечить соответствующую вентиляцию и оборудование для пожаротушения.
- В случае серьезного воспоминания или возгорания погрузите нагнетательную трубку в ведро с холодной водой, оставив поток кислорода, чтобы вода не попала в нагнетательную трубку.
- В случае повреждения шлангов отключите подачу газа в баллон и сообщите об этом своему инструктору.
- Не забывайте, что это оборудование при неправильном использовании или повреждении может быть опасным. В случае сомнений обратитесь за помощью и разъяснениями к своему инструктору.
Процессы электросварки
- Убедитесь, что нет открытых участков кожи, поскольку ультрафиолетовые лучи от сварочной дуги могут обжечь кожу.
- Носите только негорючий комбинезон, так как при дуговой сварке образуется большое количество горячих искр, которые воспламеняют легковоспламеняющуюся одежду. Для защиты от искр при сварке над головой следует надевать соответствующий кожух.
- При дуговой сварке образуются тепло, блики, искры, ультрафиолетовые и инфракрасные лучи и вредные пары.
Сварочные рукавицы необходимо носить постоянно.
- Маски для лица предназначены для отвода паров, поэтому их следует держать близко к лицу.
- Убедитесь, что на лицевой маске установлены сварочные фильтры правильного оттенка, соответствующие типу выполняемой сварки.
- Очки для газовой сварки не обеспечивают защиту лица от сильного света или излучения при электродуговой сварке, и их нельзя использовать.
- Всегда надевайте защитные очки при измельчении шлака.
- Обеспечьте соответствующую вентиляцию источника при сварке внутри зданий. Это требование закона, предназначенное для защиты оператора и других лиц.При сварке некоторых материалов (например, оцинкованной стали) выделяются высокотоксичные пары
- Проверьте свое окружение: когда вы работаете за темной маской, вы не замечаете, что происходит вокруг вас. Очистите окружающую среду от легковоспламеняющихся материалов и убедитесь в наличии огнетушителя.
- Проверьте все сварочные кабели на предмет неплотных соединений, которые могут вызвать искривление и создать опасность.
Убедитесь, что ваше окружение сухое и по возможности стоит на деревянной «утиной доске».
- При сварке в ограниченном пространстве, пожалуйста, обратитесь к отдельному обучению, необходимому для входа и работы в ограниченном пространстве, поскольку для этого требуются специальные знания, подготовка и оборудование.
- Не покрывать краской / маслами / консистентными смазками / растворителями, так как зажигание дуги будет затруднено и будут образовываться токсичные пары
4.3 Защита других
- Перед сваркой убедитесь, что окружающие защищены от лучей дуги, установив экраны.Ультрафиолетовые лучи вызывают состояние, известное как «дугообразный глаз», которое на самом деле является конъюнктивитом. При поражении глаза следует тщательно промыть глазной ванночкой. Если состояние не исчезнет, следует обратиться за медицинской помощью.
- Человек, получивший удар электрическим током, все еще может находиться в контакте с источником энергии, поэтому его следует удалить с использованием непроводящего материала для защиты спасателя.
- Наблюдатели за процессом сварки должны быть проинформированы о необходимости носить защитную одежду и СИЗ.
- Предупредите посторонних о зажигании дуги.
4.4 Общие меры безопасности
- Перед началом любых сварочных или горячих работ всегда проверяйте, что у вас есть соответствующие разрешения на проведение огневых работ и подписан соответствующий персонал, а также соблюдены все требования разрешения на проведение огневых работ.
- Убедитесь, что подходящий огнетушитель и противопожарное одеяло легко доступны и легко доступны в случае небольшого пожара.Противопожарные покрытия могут использоваться для защиты небольших окружающих участков от искр при выполнении врезных или локальных сварных швов.
- Убедитесь, что рабочая зона чистая, и все горючие / легковоспламеняющиеся материалы удалены из рабочей зоны, чтобы гарантировать, что они не воспламеняются от чрезмерного тепла или случайных искр.
- Обеспечьте свободный доступ к рабочей зоне в случае аварии или травмы.
На выходах не должно быть препятствий.
- Убедитесь, что соблюдаются надлежащие меры предосторожности при обращении с горячими материалами и что они не остаются без присмотра, чтобы ничего не подозревающие прохожие могли прикоснуться к ним.
- Выполните процедуру закрытия в конце рабочего периода или в случае длительного перерыва.
Перед выполнением любых сварочных работ проконсультируйтесь с вашим инструктором по поводу требований безопасности на рабочем месте.
Рис. 3 Защитная одежда / оборудование для термических процессов
Ключевые моменты обучения
- Определите ключевые слова, используемые в терминологии сварки
- Укажите различные типы соединений, используемых при сварке
5.1 Терминология сварки
Корень
Позиция в подготовленном стыковом соединении, где соединяемые детали находятся ближе всего друг к другу,
или
В квадратном стыковом соединении кромки сварных поверхностей, наиболее удаленные от граней предполагаемого сварного шва,
или
В угловом сварном шве — вершина угла, образованного двумя сварными поверхностями.
Корневая поверхность
Поверхность, образованная «скруглением» корневого края сплавленной поверхности, чтобы избежать острого края у основания препарирования.
Корневой прогон
Первый прогон размещается в корне стыка, если предполагается более одного прогона.
Бег
Металл плавился или осаждался за один проход электрода или выдувной трубы.
Уплотнение
Небольшой сварной шов, нанесенный на корневую сторону стыкового или углового соединения после завершения основного сварного шва.
Уплотнительный шов
Сварной шов — это не прочный сварной шов, используемый для создания герметичного соединения.
Брызги
При сварке шарики металла выбрасываются наружу.
Толщина горловины
Кратчайшее расстояние от корня сварного шва до поверхности углового шва,
или
Толщина сварочного металла в стыковом шве, измеренная по его средней линии.
Носок сварного шва
Линия соединения поверхности сварного шва с основным металлом,
или
Линия, где поверхность сварного шва соединяется с лицевой стороной ранее нанесенного прогона.
Weld Face
Поверхность сварного шва, видимая со стороны, с которой был выполнен сварной шов.
Сварной шов
Граница между зоной плавления и зоной термического влияния.
Сварной металл
При сварке весь металл расплавился и остался в шве.
Сварочная ванна
Ванна из жидкого металла, образовавшаяся при сварке плавлением.
Зона сварки
Зона, включающая металл шва, зону плавления и зону термического влияния.
Последовательность сварки
Порядок и направление, в котором должны выполняться соединения, сварные швы или участки.
5.2 Выполнение стыковых, нахлесточных и угловых сварных швов в плоском положении
Цифры, указанные в этом разделе для снятия фаски и расстояния, являются рекомендациями для средней работы. Точность подготовки, размер электродов и их тип, а также навыки сварщика будут влиять на все указанные размеры. В большинстве производственных цехов такая информация будет предоставлена в отношении процедуры сварки и чертежей.
Два основных типа сварного шва
Стыковые швы толщиной более 6 мм обычно требуют подготовки путем снятия фаски.На рис. 3 приведен пример сварочной пластины толщиной 10 мм.
Различные типы стыковых или угловых сварных швов
- Подготовьте пластины со скосом 60 ° или 70 ° и с требуемой поверхностью основания и настройкой зазора.
- Скрепите пластины вместе.
- Отложение пробега 1, буртик.
- После очистки отбойным молотком и металлической щеткой, пробег 2.
- Наконец, снова после очистки нанесите укупорочный слой с легким «переплетением».Дайте готовому сварному шву медленно остыть.
Угловой шов — это соединение двух поверхностей, пересекающихся под прямым углом. Порядок выполнения угловых и нахлесточных швов показан на рисунках ниже.
Пример процедуры сварки листа толщиной 10 мм
Угловые и нахлесточные швы
На рисунках ниже показаны примеры процедур испытаний для стыковых и угловых швов соответственно.
Пример процедуры испытания стыковых швов
Пример процедуры испытаний Т-образных угловых швов
Заголовок | Автор | Арт.Код |
Вводная книга, «Кодекс поведения и рекомендации по охране здоровья и безопасности» | СОЛАС | |
Базовая сварка и изготовление | Вт Кеньон | ISBN 0-582-00536-L |
Основы производства и сварочного производства | FJM Smith | ISBN 0-582-09799-1 |
Процессы, практики и материалы семинаров, 3-е издание, Elsevier Science & Technology | Черный, Брюс Дж. | ISBN-13: 9780750660730 |
Новые инженерные технологии | Лоуренс Смит и Лиам Хеннесси | ISBN 086 1674480 |
Источник: http: // local.ecollege.ie/Content/APPRENTICE/liu/pipefitting/word/M2_U1_Introduction%20to%20thermal%20Process%20and%20Safety.doc
Если вы являетесь автором приведенного выше текста и не соглашаетесь поделиться своими знаниями для преподавания, исследования, стипендии (для добросовестного использования, как указано в авторском праве США), отправьте нам электронное письмо, и мы быстро удалим ваш текст.
Добросовестное использование — это ограничение и исключение из исключительного права, предоставленного законом об авторском праве автору творческой работы.В законах США об авторском праве добросовестное использование — это доктрина, разрешающая ограниченное использование материалов, защищенных авторским правом, без получения разрешения от правообладателей. Примеры добросовестного использования включают комментарии, поисковые системы, критику, репортажи, исследования, обучение, архивирование библиотек и стипендии. Он предусматривает легальное, нелицензионное цитирование или включение материалов, защищенных авторским правом, в работы другого автора в соответствии с четырехфакторным балансирующим тестом. (источник: http://en.wikipedia.org/wiki/Fair_use)
Информация о медицине и здоровье, содержащаяся на сайте, носит общий характер и цель , которая является чисто информативной и по этой причине не может в любом случае заменить совет врача или квалифицированного лица, имеющего законную профессию.
Тексты являются собственностью соответствующих авторов, и мы благодарим их за предоставленную нам возможность бесплатно делиться своими текстами с учащимися, преподавателями и пользователями Интернета, которые будут использоваться только в иллюстративных образовательных и научных целях.
ScienceCentral
Аннотация
Флюсы играют важную роль в определении свойств металла шва. Сильно ухудшаются свойства сварных швов в зоне HAZ. В этом исследовании была сделана попытка оценить влияние состава флюса на ширину ЗТВ.Исследование показывает, что и FeMn, и NiO оказывают значительное влияние на ширину ЗТВ. Комбинированный эффект CaF 2 , FeMn и CaF 2 , NiO также является значительным. Это исследование может помочь в выборе флюса для минимальной ширины ЗТВ в сварных деталях.
Ключевые слова: SAW, BI, HAZ, Flux
1. Введение
При сварке под флюсом дуга возникает между электродом и заготовкой. Поскольку дуга покрыта толстым слоем гранулированного флюса, это называется дуговой сваркой под флюсом.Процесс сварки может быть ручным или автоматическим. Этот процесс сварки обеспечивает высокое качество соединения, поскольку достигается двойная защита от атмосферных газов. 1) . Пила — это автоматический процесс.

2. Зона теплового воздействия
Зона термического влияния может быть определена как область основного металла, который не расплавляется, но на его свойства влияет высокая температура сварки. Свойства ЗТВ изменяются из-за изменения микроструктуры. Изменение микроструктуры происходит в результате нагрева и последующего охлаждения. Степень и величина изменения свойств зависят от основного металла, процесса сварки, состава флюса и подводимого тепла в процессе сварки. 4) . Изменение ЗТВ происходит в два этапа.На первом этапе происходят микроструктурные изменения, такие как рост зерен, а на втором этапе происходит дисперсионное твердение и охрупчивание металла 5) .

Зона термического влияния влияет на механические свойства сварочного материала, так как микроструктура ЗТВ оказывает сильное влияние на свойства сварного соединения.Предел прочности на разрыв, ударная вязкость и водородное растрескивание являются основными проблемами, связанными с ЗТВ. Состав флюса также оказывает определенное влияние на ширину, глубину, площадь проплавления, площадь усиления и разбавление сварного шва в мягких сталях, поэтому изучение и контроль HAZ очень важны. HAZ также увеличивает вероятность усталостного разрушения в наиболее слабой зоне, вызванного нагревом и охлаждением зоны сварного шва.
3. Методика эксперимента
Флюсы были приготовлены методом агломерации.Основные компоненты CaO, SiO 2 и Al 2 O 3 были смешаны в соотношении 7: 10: 2 на основании тройных и бинарных фазовых диаграмм.
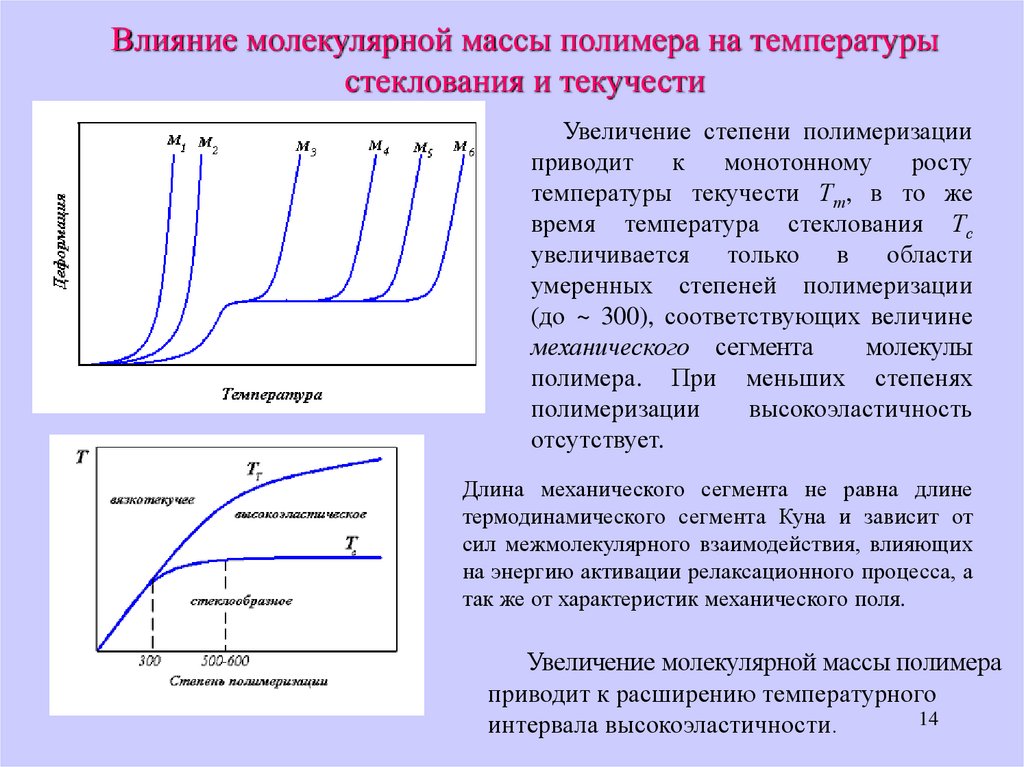
Таблица 1
Матрица проектирования в кодированной форме
№ эксперимента | CaF 2 мас.% | FeMn мас.% | NiO мас.% |
---|---|---|---|
1 | +1 | -1 | -1 |
2 | 0 | +1 | 0 |
3 | +1 | -1 | +1 |
4 | -1 | -1 | -1 |
5 | 0 | 0 | 0 |
6 | 0 | 0 | 0 |
7 | +1 | +1 | +1 |
8 | 0 | 0 | 0 |
9 | 0 | -1 | 0 |
10 | +1 | 0 | 0 |
11 | 0 | 0 | +1 |
12 | -1 | -1 | +1 |
13 | 0 | 0 | 0 |
14 | 0 | 0 | 0 |
15 | +1 | +1 | -1 |
16 | -1 | 0 | 0 |
17 | 0 | 0 | 0 |
18 | 0 | 0 | -1 |
19 | -1 | +1 | +1 |
20 | -1 | +1 | -1 |
Таблица 2
Отображение трех факторов и их уровней
Факторы | Добавки% | Нижний уровень (-1) | Средний уровень (0) | Высокий 1 уровень (+1) |
---|---|---|---|---|
A | CaF 2 | 2 | 5 | 8 |
B | FeMn | 2 | 5 | 8 |
C | NiO | 2 | 5 | 8 |
Таблица 3
Отображение состава проводов и пластин
Композиция | Углерод% | Кремний% | Марганец% | Сера% | Фосфор% | Никель% |
---|---|---|---|---|---|---|
Опорная плита | 0.![]() | 0,07 | 0,34 | 0,017 | 0,022 | — |
Провод | 0,11 | 0,09 | 0,45 | 0,021 | 0,021 | — |
Таблица 4
S.No. | Напряжение | Текущий | Скорость передвижения |
---|---|---|---|
1 | 30 вольт | 475 ампер | 20 см / мин. |
Таблица 5
Флюс NO | CAF 2 (%) | FeMn (%) | НИО (%) | Ширина ЗТВ (мм) | Mn | ∆Mn | Ni |
---|---|---|---|---|---|---|---|
1 | 8 | 2 | 2 | 3,45 | 0,17 | -0,267 | 0,177 |
2 | 5 | 8 | 5 | 3.![]() | 0,37 | -0,069 | 0,702 |
3 | 8 | 2 | 8 | 4,38 | 0,23 | -0,209 | 0,544 |
4 | 2 | 2 | 2 | 2,63 | 0,17 | -0,269 | 0,374 |
5 | 5 | 5 | 5 | 2,19 | 0.35 | -0,089 | 0,388 |
6 | 5 | 5 | 5 | 1,91 | 0,31 | -0,129 | 0,25 |
7 | 8 | 8 | 8 | 2,35 | 0,38 | -0,059 | 0,477 |
8 | 5 | 5 | 5 | 1,77 | 0,34 | -0.![]() | 0,27 |
9 | 5 | 2 | 5 | 2,17 | 0,34 | -0,099 | 0,474 |
10 | 8 | 5 | 5 | 3,56 | 0,42 | -0,019 | 0,744 |
11 | 5 | 5 | 8 | 1,28 | 0,15 | -0,289 | 1.33 |
12 | 2 | 2 | 8 | 3,80 | 0,57 | 0,131 | 0,44 |
13 | 5 | 5 | 5 | 1,75 | 0,38 | -0,059 | 0,32 |
14 | 5 | 5 | 5 | 2,23 | 0,39 | -0,049 | 0,32 |
15 | 8 | 8 | 2 | 5.![]() | 0,24 | -0,199 | 0,054 |
16 | 2 | 5 | 5 | 3,68 | 0,25 | -0,189 | 0,344 |
17 | 5 | 5 | 5 | 2,25 | 0,50 | 0,061 | 0,452 |
18 | 5 | 5 | 2 | 2,02 | 0.29 | -0,149 | 0,366 |
19 | 2 | 8 | 8 | 2,64 | 0,33 | -0,109 | 0,502 |
20 | 2 | 8 | 2 | 6.![]() | 0,33 | -0,109 | 0,288 |
(1)
Ожидаемый состав = разбавление * состав базовой пластины 100 + (100 — разбавление) * состав проволоки 100 Наплавные швы на пластину с помощью дуговой сварки под флюсом выполнялись на пластинах толщиной 18 мм.Состав базовой пластины и проволоки приведены в таблице 3. Сварочные параметры, такие как напряжение, ток и скорость хода были сделаны постоянной таблице 4. Четыре гранулы наложены друг на друга, с тем чтобы свести к минимуму эффект разбавления. В этом исследовании рассматривалось 10% разбавление базовой пластины. После изготовления шариков порошок был извлечен из верхнего шарика с помощью дрели для химического анализа. Результаты измерений приведены в Таблице 5, а полированные образцы валика и ширины ЗТВ показаны на Рис.1 (а) и (б).Рис.1
(а) Фотографии валика на сварных швах пластин, (б) Показанная ширина ЗТВ
4.

Таблица 6
ANOVA Таблица ширины зоны термического влияния
ANOVA для приведенной квадратичной модели | поверхности отклика|||||||
---|---|---|---|---|---|---|---|
Таблица дисперсионного анализа [Неполная сумма квадратов — Тип III] | |||||||
Сумма | Среднее | F | p-значение | ||||
Источник | Квадраты | df | Квадрат | Значение | Вероятность.![]() | ||
Модель | 27,88987 | 8 | 3,486 | 70,05 | <0,0001 | значительный | |
A-CaF 2 | 0,00025 | 1 | 0,000 | 0,01 | 0,9448 | ||
B-FeMn | 0,81796 | 1 | 0,818 | 16,44 | 0,0019 | значительный | |
C-NiO | 2.2 | 0,449046 | 1 | 0,449 | 9,02 | 0,0120 | значительный |
Остаток | 0,547448 | 11 | 0,050 | ||||
Отсутствие соответствия | 0,274114 | 6 | 0,046 | 0,84 | 0,5899 | незначительно | |
Чистая ошибка | 0.![]() | 5 | 0,055 | ||||
Кор Итого | 28,43732 | 19 |
Стд. Dev. | 0,224 | R-квадрат | 0,98107 |
Среднее | 2,92 | Adj R-Squared | 0,9667 |
С.V.% | 7,65 | Пред R-квадрат | 0,9203 |
ПРЕССА | 2,19 | Adeq Precision | 31,91 |
5.

Квадратичная модель второго порядка, разработанная для ширины ЗТВ с использованием методологии поверхности на основе экспериментальных результатов, представлена в уравнении. Прогнозируемое уравнение дано с точки зрения фактических факторов, приведенных в уравнении 2.
(2)
Ширина ЗТВ = 3,491−1,530 * CaF2 + 0,172 * FeMn + 0,862 * NiO-0,0360 * CaF2 * FeMn − 0,145 * FeMn * NiO + 0,1739CaF22 + 0,0678 * FeMn2−0,0448 * NiO26. Результаты ANOVA для ширины HAZ
Результаты дисперсионного анализа для ширины ЗТВ приведены в Таблице 6. Значение F модели, равное 70,05, означает, что модель значима. Вероятность того, что такое большое «модельное F-значение» может возникнуть из-за шума, составляет всего 0,01%. Из таблицы 6 видно, что факторы B и C, взаимодействия BC и AC и квадратичные члены A 2 , B 2 и C 2 — все они оказывают значительное влияние на ширину HAZ.Коэффициент множественной регрессии модели равен 0,9812.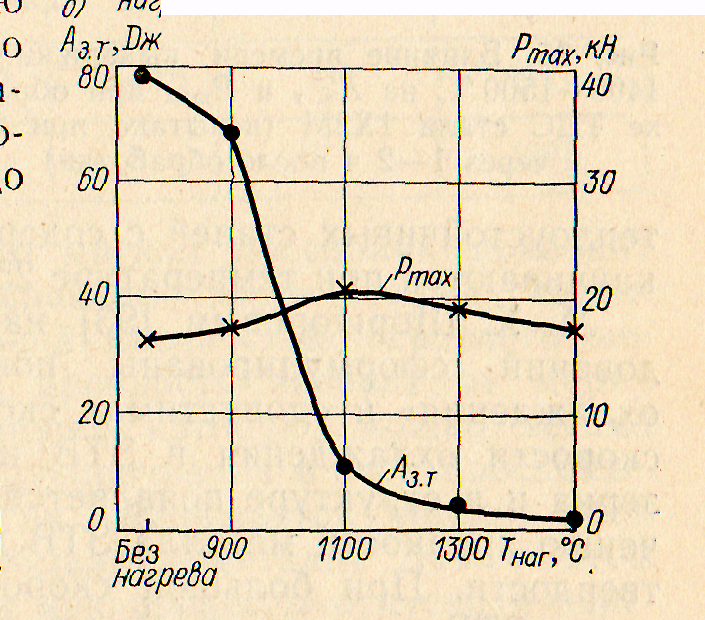
Рис.2
Нормальный график остатков для ширины ЗТВ
Рис.3
Прогнозируемые и фактические значения для ширины ЗТВ
7. Влияние добавки FeMn на ширину ЗТВ
Влияние содержания FeMn на ширину ЗТВ показано на рис.4. Это показывает, что после начального уменьшения ширина ЗТВ увеличивается. Это можно объяснить изменением содержания кислорода в сварном шве, которое, как следствие, влияет на поверхностное натяжение жидкого флюса и геометрию валика.
Рис.4
Влияние FeMn на ширину ЗТВ
Рис.5
Изменение ширины ЗТВ при сварке Mn
Фиг.6
Вариация HAZ с кислородом сварного шва
8.
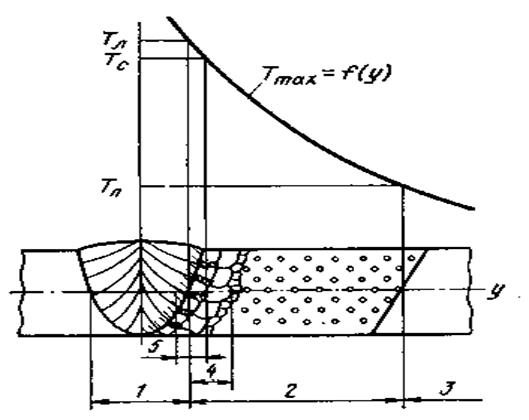
Рис.

Влияние NiO на ширину ЗТВ
Рис.8
Корреляция Ni с шириной ЗТВ
9. Валидация модели
Проверка модели проводилась путем выбора двух потоков в заданном диапазоне. Результаты приведены в таблице 7, приведенной ниже, и ошибка находится в пределах допустимого предела. Это показывает, что модель может быть использована для прогнозирования значений ширины ЗТВ для данного состава потока.Таблица 7
Прогнозируемые и экспериментальные значения
С.№ | CaF 2 % | FeMn% | NiO% | Расчетная ширина ЗТВ сварного шва | Экспериментальное значение ширины ЗТВ | Ошибка% |
---|---|---|---|---|---|---|
1 | 2 | 2 | 5 | 3,34 | 3,50 | 4,7 |
2 | 5 | 2 | 8 | 6,74 | 6,3 | 6,5 |
10.
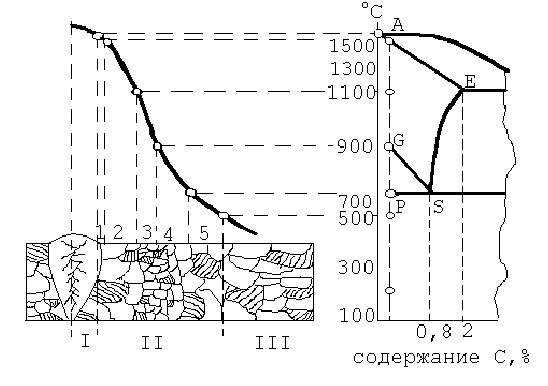
1) Добавки FeMn и NiO по отдельности оказывают синергетический эффект на ширину ЗТВ, но в смеси они оказывают антисинергетический эффект на ширину ЗТВ.
2) После уменьшения до минимума ширина ЗТВ увеличивается с увеличением добавки FeMn.
3) Ширина ЗТВ уменьшается с увеличением содержания NiO во флюсе, но содержание Mn в сварном шве не влияет на ширину ЗТВ. Однако он уменьшается с увеличением добавки Ni.
4) Ширина ЗТВ имеет тенденцию к уменьшению с увеличением содержания Ni.
5) Квадратичное моделирование можно использовать для прогнозирования влияния магнитного потока на ширину ЗТВ.
Что такое зона теплового воздействия?
Преимущественная коррозия зоны термического влияния — широко известное явление. Высокотемпературное воздействие и сварка могут значительно повлиять на микроструктуру и свойства зоны термического влияния, что делает их более подверженными коррозии. Изменения микроструктуры, которые происходят в зонах термического влияния, включают выделение карбида и образование интерметаллической фазы.
Зоны термического влияния могут быть разного размера и прочности. Протяженность и величина ЗТВ обратно пропорциональны коэффициенту температуропроводности и скорости охлаждения материала:
- Если коэффициент температуропроводности высокий, скорость охлаждения материала высока, а ЗТВ мала.
- Там, где коэффициент температуропроводности низкий, скорость охлаждения ниже и ЗТВ больше.
Степень и величина изменения свойств зависит в первую очередь от:
- Основного материала
- Сварочного присадочного металла
- Количество и концентрация подводимого тепла в процессе сварки
На ширину ЗТВ влияют:
- Скорость резания — Как правило, более высокие скорости приводят к меньшей ЗТВ.
- Сила тока (при использовании плазмы) — Для данной толщины металла более высокая сила тока (и, следовательно, более высокая скорость резки) приводит к меньшей ЗТВ.
- Тип разрезаемого металла — Повышенная температура и увеличенное время резки приводят к более широкой ЗТВ.
Все процессы термической резки создают в разрезанном металле зону термического влияния. Количество тепла, выделяемого в процессе сварки, играет важную роль:
- При кислородно-топливной сварке используется большое количество подводимого тепла и увеличивается размер ЗТВ.
- Лазерная и электронно-лучевая сварка дает высококонцентрированное ограниченное количество тепла, что приводит к небольшой ЗТВ.
- Дуговая сварка находится между этими двумя крайностями.
Тепло от процесса сварки и последующего повторного охлаждения вызывает изменение границы раздела сварного шва до прекращения чувствительной температуры в основном металле. Эти изменения можно минимизировать, соблюдая надлежащие процедуры сварки и используя низкоуглеродистые сплавы нержавеющей стали.
% PDF-1.OO \ /? [? _ U ~ ۿ_ ‘_ 1: nu [L>, & zw ޗ Da1qYLxFyv [`puZ`OBya1cZLl = D:` b -, & ڦ Di1D 㰘 hDvheŨb (, (Fe #, & ZŨbtVfA1 * bYP, 0Ff # 3cdf1DYXecXLTPf1b ,, 2Ufa1Y`27YZ, (FeCPfA1 * a1, (Fe [L2Q̂bTf12YXe # 31, & b (b ,, 2Ufa1Y`2cDY: ,, 2 QPfc, 2 QPfaQ1 , & b (a1Qeodf9t, 2b (a1QeCUfa1Y`n1QeCx2d # 3dcXL43cdf1bY`, 4FXL43ff2Kx \ 2b (YXhe2- & ZŨbtVfA1 * Y«` & b (a1Qeodfy] ob (Y« 2Ufa1Y`n1QeCUfa1Yh’Of12Of1D3Yha1,0Ff #, & BcD3Yhhfo (te1 * ,, 2QVfA1 * bYP« Fhe2b (Y`a1QeCUfa1Y`2cDYXe
е [YXeCŨbD + YXn1, (Fe [L2Qcdfa1Y`, 0ư2c *, 0FXLTPf1b ,, 2UfaƓYy9. x2d # 3cdf1D3Yhn1,0FfYpOf1̂c | 21, & d, 8ưYh’a1’Of1bOf1̂cDB
e0FeCPfA1 * a1, (Fe [L2Q̂bTf12YXe # 31, & b (b ,, 2Ufa1Y`2cDY ؾ r8.QPfa1YP ,, FXL2Q̂bTfa1D + Y`, 0FfCc *, 0ư2cDYXe #, & b (a1QeodfocY *, `, 4ưhf # 3cdf1bY`, 4FXL437Y [YXeCŨbD + YXn1, (Fe [L2Qcdfa1Y`, 0ư2c *, 0FXLTPf1b« 2Ufa2a, FeCPfA1 * a1, (Fe [L2QY1BTf12YXe` 2 & b (b« 2- & b (Of1cdf1Bcff12bY`, 4FXL43ff12a1, pPf e1 *« 2QVfA1 * bYP« Fhe2b (Y`a1QeCUfa1Y`2cDYXe #, &
e-pY ,, 2̂bTfa1bYP ,, Fhe2- & ZŨcdf12,0FfcXLTPf1DYXe #, & b (a1QeC *} # 3˸-Pf12YXe #, & b (b ,, 2- & b (Of1cdf1Bcff12bY`, 4FXL43ff12a1 *, pPQL43ff12a1 *, , Fhe2b (Y`a1QeCUfa1Y`2cDYXe #, &
e-pY ,, 2̂bTfa1bYP ,, Fhe2- & ZŨcdf12,0FfcXLTPf1DYXe #, & b (a1QeC *} # 3KLe1Y`, 0FfC *, 0F2ct *, 4ƓYh’Yh’bY`, 4ưhf # 3cdf1XLYC`, 4ưhf # 3cdf1XLYC`, 4ưhf # 3cdf1XLYC [L2Qcdfa1Y`, 0ư2c *, 0FXLTPf1b ,, 2Ufa2i, FeCPfA1 * a1, (Fe [L2Q̂bTf12YXe # 31, & b (b ,, 2Ufa1Y`2cDY ؾ Oe1Y`, 0FfC *, 0F2ct` *, 4ưbYh’c, 4ưbYh ‘ , 4FXL437Y [YXeCŨbD + YXn1, (Fe [L2Qcdfa1Y`, 0ư2c *, 0FXLTPf1b ,, 2Ufa2Kx \ 2b (YXhe2- & ZŨbtVfA1 * Y` ,, 2Ufa1Y`a1QeC *, 0FXLTPf\ @ q9 ~ 9 # f [x1c) RP
KbRa3b8SbRHXpXNJ! 1c):% f (Č 딘 3; SbRHXb6) f0 # f0 # f0tXgL1 ֙ bR3 «u) f0EwXgKbStu) f0EwXgKb [f, EJ! 1c) RX3b: SbRu
K 딘 3 «) 1C) $ f, EwXa3BbRtuJP
# o1;) f (Čh2c) RXNK1) 1C) $ f, E8SbRHXpXa3BbRtuJP
K) 1C) $ fl1? `GX333b: 3L1c) R`pXgKbS: SX3; 3Ōh2): SX3; 3Ōh2} -f0EJ! 1c) RX3b: SbRuJP
K 딘 3 «) 1C) $ f, EwXa3BbRtuJP
# o1; h2C) $ f, EKbRLuJXNJ! 1c) a3BbR:% f (Č 딘 3; SbRHXNJ! 1c} 47) 1c) R`G`G`3b83Ōh2) a) f, ELL1c) R`3 «L1c) R `3» Û) f (Čh2c) RXNK1) 1C) $ f, E8SbRHXpXa3BbRtuJP
K) 1C) $ ftx «) f, EK1) 1c):% f (ČuJP
K 딘 3; SbRHXNJ! 1c):% f (Č-fm: LKbS
S
SLua) f, ELL1c) R`pXgKbStu) f0EwXgKbStu) fl8LbRHX3 «Ō PB K) 1C) $ f, EwXa3Bb [N7) RP KbRa3b8SbRHXpXNJ! 1c):% f (Č 딘 3; SbRHXbvN7) 1c) R`G`G`3b83Ōh2) a) f, ELL1c) R`3 «L1c) R`3» 7) RP KbRa3b8SbRHXpXNJ! 1c):% f (Č 딘 3; SbRHXyYsx «) f, EK1) 1c):% f (ČuJP K 딘 3; SbRHXNJ! 1c):% f (Čh2C) $ f, EKbRLuJXNJ! 1c) a3BbR:% f (Č 딘 3; SbRHXNJ! 1c} d1xČh2) 1) 1): S`3 «u) f0E83Ōh2): SX3; 3Ōh2): SX3Gbh2C) $ f, EKbRLuJXNJ! 1c) a3BbR:% f (Č 딘 3; SbRHXNJ! 1c} -f / 7) RP KbRa3b8SbRHXpXNJ! 1c):% f (Č 딘 3; SbRHXbxČh2) 1) 1): S`3 «u) f0E83Ōh2): SX3; 3Ōh2): SX3Gbh2C) $ f, EKbRLuJXNJ (ČBR: a) ; SbRHXNJ! 1c} -f / 7) RP KbRa3b8SbRHXpXNJ! 1c):% f (Č 딘 3; SbRHXYb = LM3 # f4tX # f4pX # f0 # f4E833 «LMLMLML # o1oAS3» Ōh2c):% f, pXNJ! 1c) a3BbRtuJP K) 1C) $ f, EwX>? H4BbR) f, tXČ 딘 3 «) 1C) $ f, E8SbRHXNJ! 1c):% f (Č 딘 3G ݷ) f0 # f0 # f0tXgL1 ֙ bR3» u) f0EwXgKbXgKb [Ew ) f (Čh2c) RXNK1) 1C) $ f, E8SbRHXpXa3BbRtuJP K) 1C) $ fpx «) f, EK1) 1c):% f (ČuJP K 딘 3; SbRHXNJ! 1c):% f (Č-f0 # f, ELLL1 ֙ bSu) f0E83Ōh2) a) f, EL ֙ bRa) f, EL ֙ bR> px «) f, EK1) 1c):% f (ČuJP K 딘 3; SbRHXNJ! 1c):% f (ČoS3 «Ōh2c):% f, pXNJ! 1c) a3BbRtuJP K) 1C) $ f, EwX> loS
a) f0pXgKbS: SX3 «֙ bRa) f, EL ֙ bRa) f, Ehuhguy {? ؗ ǵ} uc] u ^ _} # XGW] n ~ _5? T7] _4} ܗ z uWK_ ط_ ~ mVeb ¼} XzerC: ﳯ y) _9 {} ߪ A ܯ uOm | -u} ֭ ڵ u 鵿 ~? 4j ~ N {: cuo? s. b װ5- & zDi1yZLtD0u: LtDG: LtDYLХ% = — tt6] q
Аналитическое моделирование зоны термического влияния при лазерном фрезеровании стали AerMet100, Международный журнал передовых производственных технологий
По сравнению с обычным фрезерованием, лазерное фрезерование (LAM) повышает производительность обработки труднообрабатываемых материалов и является экологически чистым процессом из-за отсутствия охлаждающей жидкости.Однако этот процесс с нагревом может вызвать образование зоны вредного термического влияния (HAZ, обычно называемой зоной фазового превращения) в заготовке. В данной статье представлена аналитическая модель для прогнозирования ЗТВ, образованной лазерным нагревом в LAM стали AerMet100, в которой размер ЗТВ определяется путем сравнения устойчивого температурного поля с температурой фазового превращения материала заготовки. Для проверки модели HAZ проводится серия экспериментов по лазерному нагреву и LAM.Метод XRD используется для анализа микроструктуры в нагретых и обработанных поверхностных слоях. Фазовый состав и содержание остаточного аустенита каждого образца сравнивают с таковым в основном материале. Результаты показывают, что предложенная модель осуществима. Кроме того, обсуждается влияние различных параметров лазера на ЗТВ. Размер ЗТВ значительно увеличивается с увеличением мощности лазера и значительно уменьшается с увеличением скорости подачи. Ширина ЗТВ увеличивается с увеличением размера лазерного пятна, а для глубины ЗТВ наблюдается противоположное изменение.Эту работу можно применить для определения параметров процесса в LAM, которые не дадут остаточной HAZ в заготовке после обработки.
中文 翻译 :
AerMet100 激光 辅助 铣削 中 热 影响 区 的 分析 模型
与 传统 铣削 相比 , 激光 辅助 铣削 (LAM) 可以 提高 难 切削 材料 的 生产率 , 消除 了 冷却 剂 , 因此 是 绿色 但是 , 这种 热 在 中 产生(HAZ , 通常 称为 相 变 区)。 本文 提出 了 一种 分析 模型 AerMet100 钢 的 LAM 中 激光 加热 的 热 影响 , 其中 通过 将确定 热 影响 区 的 大小。 进行 了 的 激光 加热 LAM 实验 以 验证 HAZ 。XRD 技术 用于 分析 加热 和.