Плазменная резка для начинающих.
Плазменная резка металлов для начинающих.
Уважаемые покупатели, в этой статье мы хотим вам рассказать что такое плазменная резка металлов, показать ее основные преимущества, рассказать об устройстве плазменных аппаратов и как их использовать, а теперь обо всем этом по порядку.
Иногда наши покупатели приобретая аппарат плазменной резки с удивлением узнают, что для его работы необходим компрессор. Компрессор необходим для того, чтобы выдувать металл который вы режете. Без компрессора резать плазмой невозможно. Компрессор подключается к аппарату, а к аппарату подключается плазматрон (плазменная горелка), так вот, когда возникает дежурная дуга между катодом и соплом, воздух эту дугу выдувает наружу, где дуга переходит в основную дугу при соприкосновении с металлом; далее происходит процесс плавления металла и выдувания его жидкой части из зоны расплава. При выборе компрессора стоит обратить особое внимание на его качество и на его параметры. Корректная работа аппарата плазменной резки возможно только в сочетании с хорошим компрессором. Мы рекомендуем использовать компрессоры способные выдавать 5-6 атмосфер.
Еще одна немаловажная деталь, на которую мы хотим обратить ваше внимание. В компрессоре должен стоять фильтр воздуха, он может быть встроен в компрессор изначально, а может подключаться отдельно. Воздух, который будет проходить через аппарат плазменной резки и выходить из плазматрона, должен быть чистым, в него не должны попадать никакие посторонние предметы и вещества. Недопустимо попадание паров и частиц масла, мельчайшей частицы металлической стружки, пыль и грязь. Особенно это важно, если вы планируете использовать плазму на пыльных производствах, в гаражах, цехах с бетонными полами и т.д. Чем чище воздух – тем лучше рез!
Если вы будете соблюдать эти условия, аппарат будет работать корректно и без сбоев.
Плазма или газорезка?
Мы не будем говорить о том, что газорезка хуже чем плазменная резка. У газорезки есть ряд преимуществ перед плазмой, например при резе металлолома в больших количествах вам не справиться с этой задачей если использовать плазменную резку. Плазменная резка экономически целесообразна при толщине металла до 50 мм, при большей толщине преимущество переходит к кислородной резке. Но качество и скорость раскроя всегда на стороне плазменной резки.
Для газорезки нужен газ, для плазмы нужно электричество. Выделим два основных преимущества плазмы: первое – вам не нужен газ (ацетилен) вы не связываетесь с взрывоопасными газами, второе — вы можете резать различные типы металлов (сталь, нержавейка, медь, алюминий и пр.)
Таким образом кому-то необходима газорезка, кому-то подойдет плазма, выбор за вами.
Как правильно выбрать аппарат плазменной резки?
Здесь все очень просто. Чем мощнее плазменный аппарат, тем толще металл он может резать. Если вы планируете резать разные толщины, вам лучше выбрать мощные аппарат, если вы будете резать тонкие металлы, вам нет необходимости покупать мощные аппарат, достаточно приобрести сорока амперный аппарат. Обратите внимание на такое понятие, как качество реза. Рез может быть «грязный» и «чистый». Грязный рез – это когда вам нужно просто отрезать кусок металла и для вас не имеет значение какой срез будет, аккуратный или нет. Чистый рез — это максимально ровно отрезанный металл. Как правило, производители указывают в параметрах грязный рез. Чтобы понять чистый рез, вам нужно отнять порядка 25% от указанной толщины. Так например если производитель указал 12 мм – значит чистый рез составит 8-9 мм. Не думайте, что производители вас обманывают, это всемирная практика указать в параметрах грязный рез, а не чистый. Этот параметр показывает максимальную возможность аппарата, а вы уже сами выбираете как вам резать металл, по “грязному” или по “чистому”.
Кроме того, перед покупкой желательно понять как часто вы будете включать аппарат плазменной резки. Обратите внимание на ПВ приобретаемого аппарата. Если ПВ аппарата 60% — значит в 10 минутном цикле вы можете резать 6 минут, а 4 минуты аппарат будет отдыхать, если ПВ 100% — значит можно не отрываться от работы, аппарат будет работать постоянно.
Расходные части.
Покупая аппарат плазменной резки, мы рекомендуем вам узнать у поставщика как обстоят дела с расходкой для плазменной горелки. Практически все производители вместе с аппаратом кладут расходные части, вы можете приступать к резке незамедлительно, но расходка горит, независимо от производителя. И когда встает вопрос о замене, выясняется, что там где аппарат покупался – “расходки” нет. Мы часто сталкиваемся с такими случаями, когда помогаем людям подобрать расходку, и стоит признать, что не всегда это получается. Расходка не всегда стыкуется. Так, например, расходка для аппаратов китайского происхождения не подходит к европейским товарам или американским. Кроме того, нет возможности поменять плазматрон (плазменную горелку) – разные разъемы. В нашем интернет-магазине продаются аппараты плазменной резки произведенные в Китае, все расходные части для горелок CUT всегда в наличии и как показывает практика, китайская расходка подходит практически на все аппараты сделанные в Китае.
Скорость с которой резать металл.
Этот вопрос нам часто задают покупатели. Определенного ответа на него нет, вы поймете, как быстро вам надо будет вести плазматрон по металлу только в процессе обучения, приноровиться очень просто. Все зависит от толщины металла и амперажности, которую вы выставите. Когда вы приступите к резу, вы сразу увидите — если вы ведете плазматрон очень быстро (в таком случае металл не будет прорезаться полностью) если очень медленно (в этом случае вы просто будете расходовать воздух и электроэнергию). Перед тем как резать нужные вам заготовки или отрезки, мы рекомендуем потренироваться на ненужных обрезках, чтобы выбрать оптимальный режим и скорость реза.
Еще один совет, когда вы включите аппарат – поставьте ток на максимум, а во время реза уменьшайте его, пока не поймете, что этого тока достаточно для реза вашей толщины металла. Начинайте с больших токов, затем идите на понижение.
И ещё, не старайтесь ставить максимальный ток, чтобы отрезать побыстрее, так как чем больше ток, тем быстрее выходит из строя расходка; не делайте слишком частые поджиги, поскольку именно в момент поджига происходит интенсивное «выветривание» тугоплавкой вставки на катоде и преждевременный выход его из строя, т.е. нажали на кнопку и режьте непрерывно. Если по условиям работы вам необходимо делать короткие резы, например резать сетку – приготовьтесь к частой замене расходки.
Как все работает.
Установки плазменной резки имеют напряжение холостого хода 250-300 В.
При нажатии на кнопку подаётся сжатый воздух и одновременно между катодом и соплом во внутренней камере плазмотрона прикладывается это напряжение холостого хода, но чтобы пробить этот промежуток и зажечь плазму, необходима поджигающая искра – эту функцию поджига выполняет осциллятор (напряжение поджига порядка 5-10 кВ). Как только дуга зажглась (и дуга в этот момент называется дежурной) воздух выдувает плазму наружу. Ток дежурной дуги как правило в мощных аппаратах ограничен внутри мощным сопротивлением для экономии расходки, для реза не предназначен; дежурная дуга горит 2-3 сек. Если в течение этого времени дуга не коснулась металла или металл по каким-то причинам не соединён с «+» установки (например, обрыв обратного кабеля), то дуга гаснет. Если же всё прошло нормально, то дежурная дуга переходит в основную дугу, блок осциллятора отключается. Далее происходит плавление металла дугой и одновременное выдувание расплавленного материала из расплава. Горение основной дуги происходит между тугоплавкой вставкой из гафния, впрессованной в торец катода и материалом изделия. Наибольшее разрушение этой вставки происходит именно в момент поджига, поэтому лучше стараться избегать слишком частых включений в целях экономии расходки.
Выбрать аппарат плазменной резки можно здесь.
Для наглядности, мы провели несколько тестов. Аппарат Сварог CUT 100 разрезал металл толщиной 10 мм. с увеличением до 35 мм. Ток резки был выставлен 90 Ампер.
Аппарат Сварог CUT 40 разрезал пластину толщиной 4 мм. Ток резки 20 Ампер.
Технические характеристики аппаратов AuroraPro →← Про расходные части для горелок CUT доступным языком.
Как резать металл при помощи плазмореза?
Плазменная резка получила широкое распространение в самых разнообразных отраслях производства, ведь с ее помощью становится возможным — разрезать фактически любые токопроводящие металлы: от алюминия и нержавейки до углеродистой стали и титана. Данный способ применяют как на больших предприятиях, так и в маленьких частных мастерских. Овладев основными приемами плазменной резки, Вы сумеете легко исполнять прямые и фигурные резы, делать проемы и отверстия в металлических заготовках, выравнивать кромки листов, а так же исполнять более трудные работы.
Впервые работая с плазморезом, хочется, чтобы результат оправдал ожидания. Однако, к сожалению, не у всех начинающих резчиков это получается. Для примера приведем особенно распространенный случай из практики. Пользователь работает с купленным недавно плазморезом. Однако отчего-то появляются проблемы: то дуга нестабильная, то пламя гаснет, то агрегат совсем отключается. Возникает сомнение — недоброкачественный ток в центральной электросети. Пока время уходит на поиск и устранение неполадок, работа стоит. А на самом деле причина может быть в другом. Сколько раз случалось, когда пользователи во всем винили центральную проводку, а на деле оказывалось, что было неправильно выставлено давление воздуха либо сила тока. Для того чтобы подобного не случилось, при работе с плазморезом необходимо учесть множество нюансов.
Освоить азы спецтехнологии плазменной резки не так трудно, главное — подробно во всем разобраться. Мы расскажем обо всем по порядку. А начать необходимо с вопроса безопасности проведения работ. Ведь от соблюдения правил зависит Ваше здоровье.
Что необходимо знать о технике безопасности?
Вначале перечислим факторы, которые представляют опасность при работе с агрегатом плазменной резки: электрический ток, высокая температура, ультрафиолетовое излучение, раскаленный металл. Для того чтобы защитить себя, необходимо выполнять работу в специальной экипировке. Глаза должны быть защищены очками либо щитком сварщика (стекла 4 или 5 класса затемнения), руки — перчатками, ноги — штанами из плотной ткани, а так же закрытой обувью. Следует отметить, что при работе с резаком образуется газ с примесями озона, водорода и частиц металла. Особенно опасными являются окислы марганца, соединения кремния и хрома, окись титана, которые представляют угрозу не только для легких, но и для других внутренних органов. Для того чтобы не вдыхать эти пагубные пары, необходимо обеспечить в помещении отличную вентиляцию, а на лицо надевать защитную маску.
Что касается электробезопасности, то необходимо соблюдать несколько обязательных требований:
— Плазменная резка должна подключаться в сеть с предохранителем либо автоматическим выключателем.
— Параметры тока в электросети должны полностью соответствовать характеристикам устройства.
— Непременно убедитесь в том, что обеспечено отличное заземление розеток, а также рабочей подставки агрегата и находящихся неподалеку металлических предметов.
— Проверьте электрические и силовые кабели на предмет повреждений. Не используйте их, в том случае, если изоляция повреждена.
Ответственный подход и соблюдение мер безопасности помогут Вам избежать травм, а также снизить риск получения профессиональных заболеваний.
Как подготовить агрегат к работе?
Подробнейший алгоритм подключения плазмореза к электросети и источнику сжатого воздуха Вы найдете в инструкции, именно поэтому, мы не будем заострять внимание на этом этапе. Лучше обозначим особенно важные аспекты, которые оказывают существенное влияние на качество выполнения работ.
— Установите агрегат таким образом, чтобы к его корпусу был обеспечен доступ воздуха для охлаждения. Это позволит работать продолжительное время, а так же избежать отключений оборудования в связи с перегревом. При этом на него не должны попадать капли расплавленного металла и какие-нибудь жидкости.
— Позаботьтесь о подаче высококачественного воздуха от пневмосети либо компрессора. Установите влагомаслоотделитель, для того чтобы частицы масла и воды не попали в резак. В противном случае увеличится износ расходных материалов, а также может прийти в негодность сам плазмотрон. Убедитесь, что давление подаваемого воздуха полностью соответствует параметрам агрегата плазменной резки. При неудовлетворительном давлении дуга будет нестабильна (появятся наплывы и шлак в месте реза), а при избыточном могут прийти в негодность значимые рабочие элементы.
— Тщательно подготовьте заготовку перед тем, как ее резать. В том случае, если на поверхности есть краска либо ржавчина, необходимо ее счистить, для того чтобы при нагреве металла не выделялись ядовитые пары. Помимо этого, не рекомендуется резать без предварительной чистки резервуара и емкости, в которых были горючие вещества.
Помните, что грамотно проведенные подготовительные работы являются гарантией производительности применения плазменной резки. Теперь перейдем к рассмотрению самого процесса резки металла.
Как грамотно подобрать силу тока?
Для того чтобы получить ровный и опрятный рез, без окалины, наплывов и шлака, необходимо грамотно выставить на агрегате силу тока, нужную для разрезания строго определенной заготовки. Для этого необходимо знать, какая сила тока приходится на расплавление 1 мм материала. Для самых различных видов металла будет свое значение:
— При работе с чугуном и сталью — 4 А.
— При работе с цветными металлами, а так же их сплавами — 6 А.
Например, для обработки стального листа толщиной 20 мм на агрегате необходимо выставить силу тока не менее 80 А, а для работы с алюминиевым листом такой же толщины — 120 А. Однако это еще не все, что необходимо учесть при работе. Для того чтобы металл успел расплавиться в месте реза, но при этом не деформировался при тепловом воздействии плазмы, важно подобрать оптимальную скорость ведения резака. Она может быть от 0,2 до 2 м/мин., в зависимости от выставленной силы тока, толщины заготовки и вида металла. Естественно, первое время новичку будет трудно измерить скорость и подобрать наиболее подходящую, это придет с опытом. А на первое время запомните примитивное правило: ведите горелку так, чтобы искры были видны с обратной стороны разрезаемой заготовки. В том случае, если их не видно — металл разрезан не насквозь, скорость большая. Однако слишком неторопливое ведение резака, особенно при высокой силе тока, может стать причиной образования окалины, угасания дуги и ухудшению качества реза.
Как разжигать плазменную дугу?
Прежде чем приступать к резке, необходимо сделать продувку резака газом. Для этого нажмите и отпустите кнопку поджига на резаке, плазмотрон перейдет в режим продувки. Выждите не менее 30 секунд, прежде чем зажигать дугу, за это время из резака должен удалиться конденсат и инородные частицы. Сразу же после этого можно нажимать на кнопку розжига — возникнет дежурная либо, как ее называют, пилотная дуга. Как правило, пилотная дуга горит не больше 2 секунд. Именно поэтому, за это время должна зажечься рабочая дуга. У самых различных моделей плазморезов это происходит по-различному, в зависимости от типа поджига. Различают:
— Контактный — для получения рабочей дуги нужно короткое замыкание, которое возникает следующим образом: сразу же после того, как зажглась дежурная дуга, при нажатии на кнопку блокируется подача воздуха — контакт замыкается. После автоматического открытия воздушного клапана контакт размыкается, а поток воздуха выводит искру из сопла. Между электродом с отрицательной полярностью, а так же металлом с положительной полярностью появляется плазменная дуга. Помните, что контактный поджиг не значит, что необходимо прислонять сопло к металлу.
— Бесконтактный — такой тип розжига применяется в агрегатах, сила тока которых превышает 50 А (его еще называют осциллятором либо высокочастотным зажиганием). Дежурная дуга имеет высокую частоту тока и высокое напряжение, она появляется между электродом и соплом. При приближении сопла к поверхности разрезаемой заготовки образуется рабочая дуга.
Сразу же после зажигания рабочей дуги, пилотная гаснет. В том случае, если Вам не удалось с первого раза получить рабочую дугу, то необходимо отпустить кнопку на резаке и опять нажать ее — это будет новый цикл. Дуга может не разжигаться из-за неудовлетворительного давления воздуха в пневмосистеме, неправильной сборки плазмотрона либо неполадок в работе электроэлементов. Отключите агрегат, проверьте правильность подключения и давление на входе. Еще раз попробуйте осуществить розжиг.
Также стоит помнить, что в процессе резки рабочая дуга может гаснуть. Это может случиться по причине износа электрода, однако чаще всего проблемы появляются при несоблюдении расстояния между резаком и деталью. Безусловно, это сказывается на скорости выполнения работ и на качестве реза.
Как поддерживать расстояние между горелкой и металлом?
Бывают аппараты плазменной резки, которые рассчитаны на разрезание металла с упором на сопло, т.е., вплотную к заготовке — соблюдать расстояние не нужно. Однако множество моделей оборудования для этого не предназначено — сопло будет стремительно изнашиваться, резак будет отключаться. Для них оптимальным расстоянием между заготовкой и соплом будет 1,6-3 мм. В том случае, если превысить его, то дуга будет затухать, придется поджигать ее вновь — опрятного реза не получится. Особенно значимо поддерживать идентичное расстояние при выполнении кропотливых работ, к примеру, фигурной резки. Для того чтобы удерживать зазор, многие пользователи устанавливают на резак особую дистанционную направляющую, и опираются ею на заготовку, а не соплом.
Не забывайте, что держать резак необходимо таким образом, чтобы сопло было перпендикулярно заготовке. Угол отклонения не должен превышать 10-50 градусов, иначе рез будет неаккуратным. В том случае, если Вы режете металлическую заготовку, толщина которой не превышает 25% от максимально допустимой изготовителем, держите горелку не перпендикулярно поверхности, а под небольшим углом. Так Вы сумеете избежать сильной деформации тонкого металла. При этом следите, чтобы расплавленный металл не попадал на сопло резака.
Помните, что сопло и электрод являются оснасткой, которая подвержена наибольшему износу при выполнении работ. Своевременно заменяйте эти элементы, согласно требованиям инструкции. Тогда в процессе плазменной резки будет обеспечена стабильная дуга, не будет наплывов и шлака на обрабатываемой поверхности — рез будет опрятным и ровным.
Верим, что наша статья была Вам полезна, и эту информацию Вы будете удачно использовать на практике. Подробнее о том, как применять плазменную резку, Вы узнаете из инструкции конкретной модели агрегата. Соблюдая все правила, Вы быстро «набьете руку» и будете справляться как с примитивными работами, к примеру, нарезкой профиля либо металлических листов, так и с более трудными — вырезанием отверстий и самых разнообразных фигур.
Типичные ошибки оператора при плазменной резке и способы их избежания
Все знают что простои в работе из-за выхода оборудования из строя несут большие убытки для производства, тогда как их можно было бы избежать при правильном использовании оборудования.
Обращая внимание на вещи описанные ниже в статье и проводя своевременные процедуры можно избежать простоев и крупных поломок, сэкономив деньги на ремонте, не потерять оборудование на время его ремонта (или же не потерять вовсе из-за неремонтопригодности) и в целом увеличить ресурс его работы.
Особое внимание, естественно, стоит уделить износу расходных материалов поскольку они со временем изнашиваются, а качество и точность реза уменьшается. Увеличенный краевой скос и деформация края являются важными признаками для оператора, что требуется замена непригодной детали.
Чтобы устранить эти проблемы, оператор нередко заменяет весь набор расходных материалов сразу — электрод, сопло и защитную крышку, вместо того, чтобы оценивать каждый компонент по отдельности. Это приводит к чрезмерному использованию расходных материалов, что отрицательно сказывается на общей стоимости эксплуатации и увеличивает стоимость производства.
Эта статья поможет вам избежать лишних трат и своевременно реагировать на проблемы, а также заблаговременно предупредить их.
Итак, вот список ошибок, которые стоит избегать.
Использование расходных материалов до тех пор, пока они не выйдут из строя
Если посмотреть на ряд деталей одного типа, которые были вырезаны при таком подходе, можно безошибочно определить те детали, на которых сопло или электрод были уже «на подходе». Использование сильно изношенных сопел и электродов может не только привести к браку при вырезке детали, но и стать причиной дорогостоящего ремонта пламенного резака и даже аппарата плазменной резки, во время которого машина плазменной резки будет простаивать. Выход из строя сопел и электродов можно легко предупредить по нескольким признакам, которые выдают изношенные расходники. Опытный оператор по звуку резки и цвету пламени дуги (при выгорании циркониевой вставки оно приобретает зеленоватый оттенок), а также по необходимости уменьшать высоту плазмотрона при пробивке, всегда скажет Вам, когда пора менять электрод. Также, одним из лучших способов оценки состояния деталей резака является качество реза. Если качество реза внезапно начинает ухудшаться, то это повод проверить состояние сопла и электрода. Разумным подходом является ведение журнала со средним временем работы электрода или сопла от замены до замены. Сопло и электрод могут выдерживать разное количество пробивок в зависимости от тока резки, типа и толщины материала. Например, при резке нержавеющей стали требуется более частая замена расходников.
Однажды определив по такому журналу среднее время жизни электрода для каждого конкретного вида вырезаемых деталей, можно выполнять плановую замену сопел и электродов, не доводя до появления брака в вырезаемых деталях или до поломки пламенного резака.
Новая деталь | Изношенная деталь | |
Защитная насадка Её следует заменять только при наличии видимых повреждений, таких как образование шлака, вмятины или ожоги, или если его трудно надеть на горелку или защитная крышка не может быть ровно установлена из-за повреждений. |
|
![]() |
Защитная крышка
Как следует из его названия, защитный колпачок заглушает защитный газ с целью дополнительного охлаждения сопел и улучшения края режущей кромки. Отверстие в защитной крышке имеет решающее значение для качества реза, поэтому его следует заменить, когда оно становится сожженным, согнутым, когда на него попадает шлак и оно становится не круглым. Для удаления брызг (шлака), который застрял на защитной крышке, можно использовать абразивную щётку. Всегда проверяйте уплотнительные кольца на предмет возможных повреждений, таких как трещины и разрывы. Убедитесь, что уплотнительные кольца правильно смазаны с использованием рекомендованной производителем смазки. Инструкции по смазке см. в руководстве изготовителя. |
![]() |
![]() |
Внутреннее защитное кольцо Эта деталь имеет медный корпус с нажимным изоляционным кольцом для размещения в защитной крышке. Цель внутреннего удерживающего колпачка состоит в том, чтобы циркулировать охлаждающую жидкость вокруг внешней части сопла и распределять газ на защитный колпачок через крошечные отверстия в изоляторном кольце. Эта деталь не изнашивается плазменной дугой и может легко выдерживать до 30 или более замен электродов. Заменяйте только в том случае, если отверстие сожжено, согнуто или повреждено и не является круглым, или если повреждено изоляционное кольцо или отверстия по периметру. |
![]() |
![]() |
Сопло Сопло – один из важнейших элементов плазмотрона. Сопло формирует струю плазмы, которая, проходя через отверстие, осуществляет рез. Когда оно новое, это отверстие будет идеально круглым с четко определенным острым краем. Сопло должно быть заменено, когда отверстие начинает изнашиваться во внешнем или внутреннем отверстии, делая края менее острыми и ухудшая качество реза. На внутренней стороне сопла могут возникать более светлые участки, вызванные пуском дуги, но это не является причиной замены. Для наивысшего качества резки следует заменять сопло в два раза чаще, чем электрод. |
![]() |
![]() |
Завихрительное кольцо (шазовый диффузор) Вихревое кольцо изготовливается из высокотемпературного материала, такого как Vespel или керамики, и поэтому не изнашивается плазменной дугой. Оно служит для завихрения плазмообразующего газа вокруг электрода и направления его в сопло. Вихревое кольцо также изолирует отрицательно заряженный электрод от положительно заряженного сопла. Диффузор влияет на множество факторов, и без него вы получите гораздо более короткий срок службы всех остальных расходных частей и плохое качество реза. Необходимо следить за тем, чтобы маленькие отверстия не содержали грязи и мусора, и их следует заменять, если обнаружены трещины или сколы, так как даже микроскопическая трещина может нарушить газовый поток. Всегда проверяйте уплотнительные кольца на предмет возможных повреждений, таких как трещины и разрывы. Убедитесь, что уплотнительные кольца правильно смазаны с использованием рекомендованной производителем смазки. Инструкции по смазке см. в руководстве изготовителя. В среднем 1 диффузор способен пережить более 50 замен электрода. |
![]() |
![]() |
Электрод Электрод является основным и расходным материаом в плазменной резке и требует наиболее частой замены. Электрод может быть изготовлен из меди или серебра или их комбинации и содержит отдельную вставку из эмиттерного стержня, изготовленную из гафния или вольфрама. Эмиттерный стержень обладает меньшим сопротивлением току, чем медь, что предотвращает сжигание электрода при генерировании большого тока дуги. Медь обладает низким электрическим сопротивлением, из-за чего электрическая дуга может пройти на корпус, что повлечёт повреждение других элементов — сопла, защитной крышки, а также самого плазмотрона. Чтобы этого не допустить, электрод следует менять в тот момент, когда на вставке появится ямка по размерам равная диаметру самой вставки. |
![]() |
![]() |
Безопасное значение глубины износа эмиттера составляет примерно 0,040 дюйма (1,02 мм) для медных электродов и 0,1 дюйма (2,54 мм) для серебряных электродов. |
![]() |
Слишком частая замена сопел и электродов
Среди использованных сопел и электродов достаточно часто можно встретить такие, которые еще можно использовать при резке. Излишне частая замена расходников также очень распространена среди операторов металлорежущих станков с ЧПУ, и в особенности, машин плазменной резки. При замене сопла или электрода оператор должен четко знать, на что обращать внимание. Сопло требует замены в следующих ситуациях:
1. Если сопло имеет деформации снаружи или изнутри. Это часто бывает при слишком маленькой высоте пробивки и при непрорезе металла. Расплавленный металл попадает на внешнюю поверхность сопла или защитного колпака и деформирует ее.
2. Если выходное отверстие сопла по форме отличается от окружности. При большой высоте пробивки, если движение начинается до прореза металла, то дуга отклоняется от перпендикуляра к листу и проходит через край отверстия сопла. Чтобы определить, изношен ли электрод, нужно посмотреть на вставку из металла серебристого цвета на торце медного электрода (как правило, используется сплав циркония, гафния или вольфрама). В общем случае, электрод считается работоспособным, если этот металл вообще есть и глубина лунки на его месте не превышает 2 мм для воздушно-плазменной или кислородно-плазменной резки. Для резки плазмой в среде защитного газа (азота или аргона) глубина лунки может достигать 2,2 мм. Завихритель нуждается в замене лишь в том случае, если при тщательном осмотре можно выявить забитые отверстия, трещины, следы вызванные попаданием дуги, или сильный износ. Завихрители особенно часто заменяются преждевременно. То же самое касается и защитных колпаков которые нуждаются в замене только в случае физического повреждения. Очень часто защитные колпачки могут быть очищены наждачной бумагой и использованы вновь.
Использование неправильных настроек параметров плазменной резки и расходных материалов
Выбор расходников при плазменной резке зависит от вида разрезаемого металла (сталь, медь, латунь, нержавейка и т.д.), от его толщины, выставленного тока дуги на аппарате плазменной резки, плазмообразующего и защитного газов и т.д. Справочное руководство оператора машины плазменной резки описывает, какие расходные материалы использовать в случае разных режимов процесса резки. Указанные в инструкции оператора режимы, рекомендации относительно настроек плазменной резки следует соблюдать. Использование расходных материалов (сопел, электродов) несоответствующих текущему режиму плазменной
резки обычно приводит к ускоренному выходу расходников из строя и к значительному ухудшению качества пламенного реза. Очень важно выполнять плазменную резку металла именно с тем током дуги, на который рассчитаны используемые расходные материалы. Например, не стоит резать металл плазмой на 100 амперах, если в плазменном резаке стоит сопло на 40 ампер, и т.д. Самое высокое качество реза достигается, когда ток на аппарате плазменной резки выставлен на 95% от номинального тока резки, на который рассчитано сопло. Если установлен режим плазменной резки с заниженным током дуги, то рез будет зашлакованный, и на обратной стороне вырезаемых деталей будет значительное количество грата, пламенный рез будет неудовлетворительного качества. Если установленный на установке плазменной резки ток слишком высок, то срок службы сопла значительно сокращается.
Неправильная сборка плазменного резака
Пламенный резак должен быть собран таким образом, чтобы все его детали плотно прилегали друг к другу, и не было бы впечатления «разболтанности». Плотность прилегания деталей плазмотрона обеспечивает хороший электрический контакт и нормальную циркуляцию воздуха и охлаждающей жидкости через плазменный резак. Во время замены расходных материалов нужно стараться разбирать плазменный резак на чистой поверхности, чтобы грязь и металлическая пыль, образующиеся при плазменной резке, не загрязнили плазмотрон. Чистота при сборке/разборке плазменного резака очень важна и, тем не менее, это требование часто не соблюдается.
Невыполнение регулярного планового обслуживания плазмотрона
Плазменный резак может работать в течение многих месяцев, и даже лет без должного обслуживания. И, тем не менее, газовые каналы и каналы охлаждающей жидкости внутри плазменного резака должны содержаться в чистоте, посадочные места сопел и электродов должны проверяться на предмет загрязнения или повреждений. Грязь, металлическая пыль должны удаляться из плазменного резака. Для чистки плазмотрона следует использовать чистую хлопчатобумажную тряпочку и жидкость для чистки электрических контактов либо перекись водорода.
Резка металла без проверки давления плазмообразующего газа или подачи охлаждающей жидкости в плазморез
Расход и давление плазмообразующего газа и охлаждающей жидкости нужно проверять ежедневно. Если расход недостаточный, детали резака не будут в должной степени охлаждаться и их срок службы будет снижен. Недостаточный проток охлаждающей жидкости из-за изношенного насоса, забитых фильтров, недостаточного количества охлаждающей жидкости, является распространенной причиной поломок плазменных резаков. Постоянное давление плазмообразующего газа очень важно для поддержания режущей дуги и для качественного реза. Избыточное давление плазмообразующего газа является распространенной причиной затрудненного поджига плазменной дуги, притом, что все остальные требования к настройкам, параметрам и процессу плазменной резки полностью удовлетворены. Слишком высокое давление плазмообразующего газа является причиной быстрого выхода из строя электродов. Плазмообразующий газ обязательно должен быть очищен от примесей, т.к. его чистота оказывает сильное влияние на срок службы расходных материалов и плазмотрона в целом. Компрессоры, подающие воздух в аппараты плазменной резки имеют тенденцию к загрязнению воздуха маслами, влагой и мелкими частицами пыли.
Пробивка при малой высоте плазмотрона над металлом
Расстояние между заготовкой и срезом сопла плазмотрона оказывает огромное влияние, как на качество реза, так и на срок службы расходных материалов. Даже небольшие изменения в высоте плазменного резака над металлом могут значительно повлиять на скосы на кромках вырезаемых деталей. Высота плазменного резака над металлом во время пробивки особенно важна. Распространенной ошибкой является пробивка при недостаточной высоте плазмотрона над металлом. Это приводит к тому, что расплавленный металл выплескивается из лунки, образованной при пробивке и попадает на сопла и защитные колпачки, разрушая эти детали. Тем самым существенно ухудшается качество реза. Если пробивка происходит, когда плазменный
резак касается металла, то может произойти «втягивание» дуги. Если дуга «втягивается» в плазмотрон, то электрод, сопло, завихритель, а иногда, и резак целиком — разрушаются. Рекомендуемая высота пробивки равна 1.5-2 величины толщины разрезаемого плазмой металла. Следует отметить, что при пробивке достаточно толстого металла рекомендуемая высота получается слишком большой, дежурная дуга не достает до поверхности листа металла, следовательно, процесс резки на рекомендуемой высоте начать невозможно. Однако если пробивка будет производиться на высоте, на которой плазморез может зажечь дугу, то брызги расплавленного металла могут попасть на плазмотрон. Решением этой проблемы может быть применение технологического приема под названием «подпрыжка». При отработке команды на включение резки, плазменная резка включается на небольшой высоте, затем резак поднимается вверх на заданную высоту подпрыжки, на которой брызги металла не достают до резака. После отработки пробивки резак опускается на высоту врезки и начинается движение по контуру.
Плазменная резка металла на слишком большой, либо слишком малой скорости
Несоответствие скорости плазменной резки выбранному режиму существенно сказывается на качестве реза. Если установленная скорость резки слишком низкая, на вырезаемых деталях будет большое количество облоя и разнообразных наплывов металла по всей длине реза на нижней части кромки деталей. Низкие скорости резки могут стать причиной увеличения ширины реза и большого количества брызг металла на верхней поверхности деталей. Если установлена слишком высокая скорость резки, дуга будет загибаться назад, вызывая деформацию кромок вырезаемой детали, будет узкий рез, и небольшие бусинки грата и облоя в нижней части кромки реза. Грат образованный при высокой скорости резки тяжело удаляется. При правильно выбранной скорости резки количество грата, облоя и наплывов металла будет минимальным. Поверхность кромки пламенного реза при правильно выбранной скорости должна быть чистой и механическая обработка должна быть минимальной. В начале и конце реза может произойти «отклонение» дуги от перпендикуляра. Это происходит из-за того, что дуга не успевает за резаком. Отклонение дуги приводит к тому, что она врезается в боковую поверхность сопла, нарушая тем самым его геометрию. Если выполняется врезка с кромки, центр отверстия сопла должен находиться точно на линии кромки детали. Это особенно важно в комбинированных станках, в которых применяется и дыропробивная головка и плазморез. Отклонение дуги может произойти и когда плазмотрон при включенной резке проходит через край листа, или если линия выхода из контура с резкой (lead out) пересекает старый рез. Необходима точная настройка параметров времени, чтобы уменьшить проявления этого эффекта.
Механическое повреждение или поломка плазменного резака
Столкновения резака с листом, вырезанными деталями или ребрами раскроечного стола могут полностью вывести резак из строя. Столкновений резака с вырезаемыми деталями можно избежать, если в управляющей программе задавать холостые проходы вокруг, а не над вырезанными деталями. Например, в программе оптимального раскроя ProNest производства MTC-Software присутствует такая возможность, что позволяет свести риск поломки плазмотрона к минимуму и сэкономить значительные средства. Стабилизаторы высоты резака также обеспечивают некоторую защиту от столкновений с металлом. Однако, если используется только лишь датчик высоты резака по напряжению дуги, то в конце реза могут происходить «клевки», т.к. напряжение дуги меняется в результате ее «отклонения» и резак опускается вниз чтобы его компенсировать. В системах ЧПУ применяется многоуровневая система защиты от столкновения с металлом. Используется как датчик касания, измеряющий сопротивление между антенной вокруг резака и листом, емкостной датчик и датчик
напряжения дуги. Это позволяет в полной мере использовать преимущества каждого из типов датчиков. Также, для защиты резака можно применять «ломкие» кронштейны, которые при столкновении сломаются быстрее, чем плазменный резак. Таким образом, грамотный оператор машины плазменной резки может сэкономить своему предприятию огромные деньги, время и накладные расходы на плазменную резку. Результатом работы хорошего оператора МТР будет возросшая рентабельность плазменной резки и увеличение прибыли предприятия в целом. Надеемся, что изложенные в этой статье рекомендации по плазменной резке металла позволят выполнить настройку плазменной резки и подобрать режимы реза для каждого конкретного случая.
Аппарат для плазменной резки металла, все о ручных плазморезах
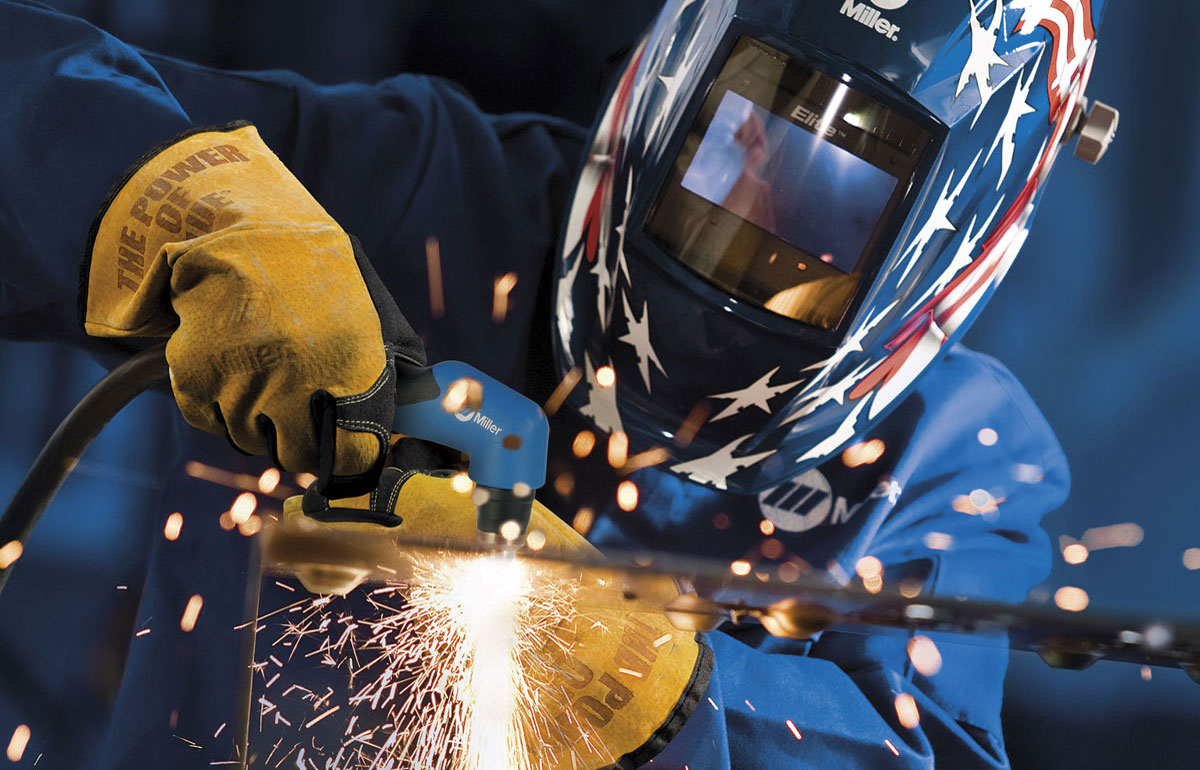
- Содержимое:
- Что такое плазморез, что им можно делать
- Принцип работы плазмореза, как устроен плазморез
- Какой и как выбрать плазморез для дома
- Как правильно резать плазморезом
- Ручная газовая и плазменная резка металла, что лучше
Обычные сварочные аппараты не удобны при резке металлов и требуют особых навыков и практики у человека, использующего их для проведения работ по раскрою. Плазменные устройства более удобны и просты в эксплуатации.
Первые модели плазменных резаков использовались исключительно в промышленных целях: машино- и судостроении, изготовлении металлоконструкций и т. д., то современный плазморез можно встретить и в обычном гараже используемую для личных нужд. Аппарат для плазменной резки металла позволяет точнее управлять технологическим процессом, а также значительно облегчает проведение работ.
Что такое плазморез, что им можно делать
Переносная ручная плазменная резка металла в бытовых целях используется в основном во время капитального строительства. Плазморез позволяет заменить малоэффективную и опасную болгарку. С помощью плазмореза можно раскраивать необходимый листовой металлопрокат и трубы.
Еще одна сфера, где пригодится ручной аппарат плазменной резки металла — это художественная обработка материала. Точность, простота в эксплуатации и доступность использования плазменной установки практически в любых условиях, позволяет использовать оборудование в следующих целях:
- Промышленность — аппарат воздушно-плазменной резки металла в основном применяется в случаях, где существует необходимость в быстром разрезании любого токопроводящего материала. В промышленных целях используют не только аппарат для ручной плазменной резки металла, но и специальные плазменные станки позволяющие автоматизировать и сократить время выполнения работ.
Бытовые цели — в этой сфере оборудование для ручной плазменной резки металла пока не получило широкого распространения. В основном это связано с тем, что ручные плазморезы сравнительно недавно поступили в свободную продажу. В основном применение плазмореза в бытовых целях связано с фигурной резкой металла. Некоторые строительные бригады используют оборудование во время кровельных, сантехнических и других работ.
В зависимости от основного назначения, аппарат для резки металла плазмой может отличаться техническими характеристиками и возможностями. Перед выбором плазменного оборудования следует определиться, как именно будет использоваться резак.
Принцип работы плазмореза, как устроен плазморез
Воздушно-плазменная резка основана на принципе подачи разогретого воздуха под давлением на обрабатываемую поверхность. Что такое плазма — это воздух, который разогревается до температуры 25 – 30 тыс. градусов с помощью электрической дуги.
Что происходит при этом? Принцип действия плазмореза основан на изменении свойств воздуха при его моментальном разогревании до максимально высоких температур. В этот момент воздух ионизируется и благодаря этому начинает пропускать электрический ток.
Двойное воздействие плазмы и электричества позволяет ускорить процесс резки металла. Чтобы это стало возможным в конструкцию резака входят следующие узлы:
Плазмотрон — это резак, с помощью которого и выполняются все основные задачи. Устройство горелки плазмореза может быть прямого и косвенного воздействия:- Плазморез прямого воздействия используется для обработки токопроводящих материалов, в таких случаях заготовка включается в электрическую цепь и отвечает за возникновение искры.
- Плазморез косвенного воздействия применяется в более дорогих и сложных устройствах и используется для обработки материалов, не проводящих электричество. Электрод в таких устройствах находится непосредственно в резаке.
- Плазморез прямого воздействия используется для обработки токопроводящих материалов, в таких случаях заготовка включается в электрическую цепь и отвечает за возникновение искры.
Сопло — одна из самых функциональных деталей плазматрона. В зависимости от диаметра сопла, плазморезом можно делать либо простые операции, либо сложную фигурную резку. Скорость разрезания материала в основном зависит от длины сопла. Максимальным считается соотношение 1,5; 1,8 к диаметру сопла.- Электрод — используется в дорогих моделях плазморезов косвенного воздействия. Преимущественно электроды изготавливаются из гафния.
- Компрессор — чтобы трансформировать воздух в плазму необходимо не только довести его до определенной температуры, но и создать поток определенной скорости. Именно по этой причине для плазмореза нужен компрессор. К качеству компрессора предъявляются высокие требования. Так, чтобы была возможность производства плазмы, воздух в горелку должен подаваться сухой и без примесей машинного масла. Важным является обеспечение равномерного потока воздушных масс без пульсации. Ручные плазменные резаки по металлу со встроенным компрессором являются оптимальным вариантом, так как в них производитель установил оборудование полностью соответствующее требованиям для проведения работ. В плазморезах со встроенным компрессором по умолчанию установлен влагоочиститель или осушитель. Плазморез с компрессором обеспечивает максимальную производительность и увеличивает срок эксплуатации резака.
Для мощных промышленных устройств понадобится отдельно приобрести не только компрессор, но и осушитель воздуха. При выборе плазмореза необходимо проследить, чтобы параметры каждого из этих узлов подходили остальным устройствам.
Какой и как выбрать плазморез для дома
При выборе плазмореза для дома необходимо учитывать не только технические параметры и производительность самой установки, но и комплектующие устройства. Обратить внимание необходимо на следующее:
- Тип питания — оборудование может подключаться как к обычной сети в 220В, так и трехфазной в 380В. От этой особенности во многом зависит производительность плазмореза и скорость резки. Для бытовых нужд лучше выбрать ручной плазморез с тем типом подключения, который есть в наличии. Производительности бытовой модели работающей от розетки будет достаточно для проведения всех необходимых работ по дому.
Параметры мощности — наиболее популярными для бытового применения являются модели с производительностью 60-90 ампер. Бытовые плазморезы легко справляются с толстым металлом толщиной до 3 см. Если планируется ручная резка металла до 100 мм плазмой, тогда лучше выбрать модели, выдающие на выходе 90-170 ампер.- Продолжительность работы — этот коэффициент можно посмотреть в технической документации установки. Обычно он обозначается сокращением ПВ. Если указано соотношение 80%, тогда плазморезом надо пользоваться в течение 8 минут, не больше. Для бытовых нужд будет достаточно оборудования с индексом ПВ 50-60%.
- Сопло для плазмореза — скорость резки напрямую связано с соплом. На скорость раскроя влияет соотношение диаметра к длине сопла. Скорость резки также указывается в технической документации. Выбор комплектующих зависит от используемой силы тока. Чем больше диаметр сопла, тем больше может быть напряжение на выходе.
- Дополнительные расходники к плазморезу. Стол-копир для ручной плазменной резки позволяет выполнять самые сложные детали, если процесс поставлен на конвейер. Часто даже в домашних условиях требуется воссоздать точную копию сделанной заготовки, для этого и проведения остальных работ, и предназначен стол-копир. Помимо стола понадобится определиться с другими комплектующими и приспособлениями, предназначенными для проведения работ с помощью плазмореза.
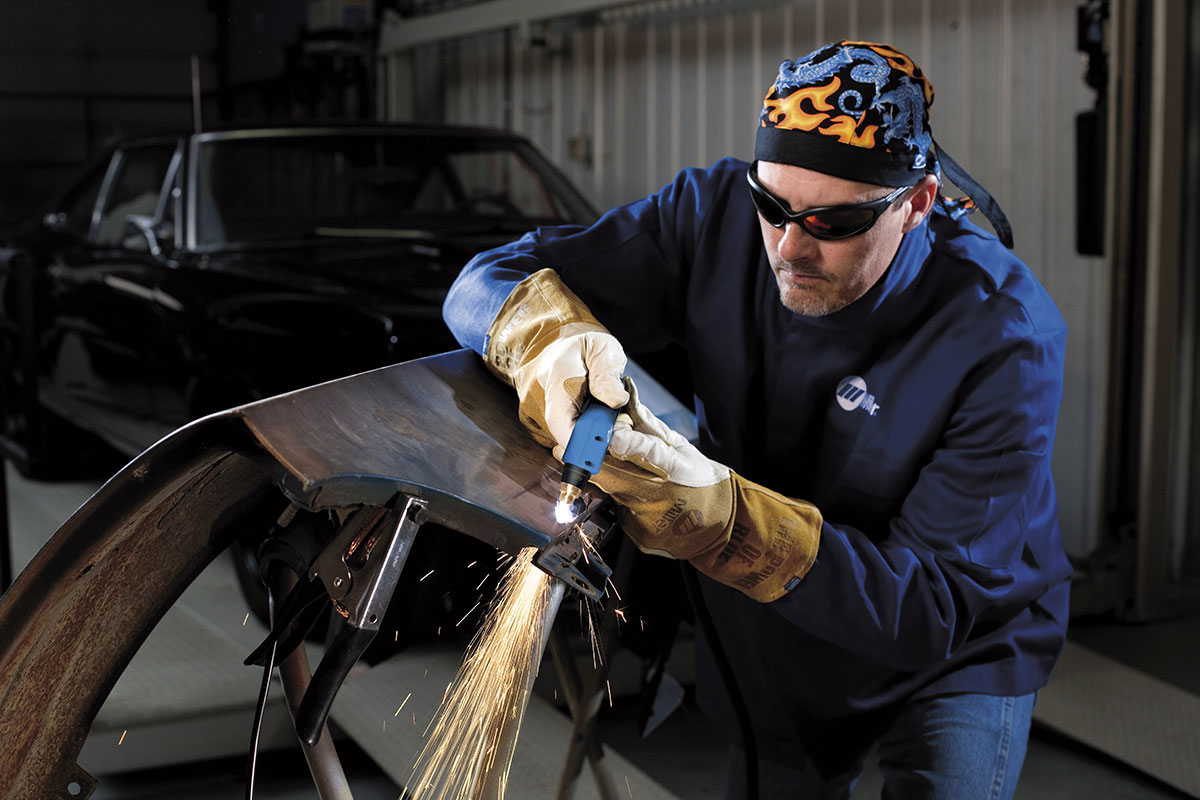
Многие критерии критичные для промышленного оборудования практически не влияют на производительность бытовой модели. Продолжительности работы плазмореза с индексом ПВ 50% будет достаточно для проведения работ в доме. Промышленное оборудование обычно имеет коэффициент равный 100%.
Как правильно резать плазморезом
Правильно работать плазморезом можно научиться практически с первого раза. Качественный рез достигается благодаря практике. Основные принципы работы с плазменным оборудованием следующие:
На начальной стадии работ в аппарат подается сжатый воздух под давлением.- Выполняется несколько надрезов при более высоком токе, после чего его силу уменьшают до необходимых параметров.
- Разрез делают в соответствии с выбранными параметрами. Неправильно подобранная сила тока или скорость резки свидетельствует окалинами, которые появляются в процессе резки.
- Держак для плазмореза располагают под углом около 40 градусов.
- После окончания резки, на горелку будет еще какое-то время подаваться воздух для охлаждения нагретого элемента.
При работе с плазматроном необходимо соблюдать требования относительно использования средств индивидуальной защиты. Потребуется одевать очки для плазменной резки и перчатки, даже если планируется использовать аппарат относительно короткое время.
Ручная газовая и плазменная резка металла, что лучше
Выбирая, что именно лучше следует учитывать цели, которые планируется достичь с использованием данной установки, желаемое качество выполнения работ и другие факторы.
Минусами газовой резки является зависимость от баллонов, что не всегда удобно, а для бытовых условий заправить их часто проблематично.
Плазменная резка имеет свои минусы, связанные в основном с тем, что качество реза напрямую зависит от профессионализма мастера. Также подаваемый воздух должен соответствовать определенным критериям, что требует использования дополнительного оборудования.
При плазменной резке может понадобиться использовать не только очки для работы, но и респираторную маску, и другие средства защиты. Проводить работы в помещении без хорошей вентиляции запрещается.