Выплавка стали: история и современность
Что необходимо, чтобы приготовить какое-либо блюдо? Температура! Если пару веков назад ее давал открытый огонь костра из дров или угля, то сегодня на кухнях используют газовые или электрические плиты.
На металлургической кухне выплавка стали происходит по похожему сценарию: в огромную «кастрюлю» засыпают сырье (шихту) и «варят» в условиях высокой температуры по определенной технологии (рецепту). А нужная температура также достигается либо с помощью газа, либо электроэнергии.
Сейчас есть три основных промышленных способа выплавки стали в мире:
- мартеновский;
- кислородно-конвертерный;
- электрометаллургический.
История выплавки стали
Человечество научилось получать железо еще в средние века. Но вплоть до середины XIX века это были небольшие объемы низкокачественного материала. Его производили, как правило, в сыродутных печах и дорабатывали в кузнях, где мастера получали штучный товар. Интересно, что остатки средневековых сыродутных печей (также известных как гамарни) найдены на территории современной Украины. Что наиболее примечательно, они находились в западной части страны, которая сегодня не является центром металлургии.
Но в существовавших до XIX века технологиях производства железных изделий был один существенный недостаток. Фактически это было либо очень мягкое железо, либо хрупкая сталь, которую получали из железа доработкой в кузнях. И такие материалы нельзя было в чистом виде использовать — предметы быстро тупились или легко ломались.
Сейчас известно, что железный сплав обладает таким свойством как упругость. Оно появляется лишь при формировании четкой кристаллической структуры из расплава. А средневековые технологии не позволяли расплавить металл с нужной пропорцией железа и углерода. Для этого требовалась недостижимая в те времена температура 1450 С°.
Промышленная революция привела к резкому росту спроса на новый конструкционный и оружейный материал: прочный, долговечный и поддающийся механической обработке.
Как результат, в XIX веке появились истоки всех трех современных способов выплавки стали.
Мартеновское производство: преимущества и модернизация
Вплоть до середины XX века мартеновские печи были основной технологией, которая позволяла плавить сталь. Впервые ее построил француз Эмиль Мартен в 1864 году. Среди ее преимуществ были: возможность использования стального лома в шихте (его было много благодаря активному развитию железных дорог) и большой сортамент качественных марок стали, которые можно было производить благодаря длительной плавке (до 13 часов).
Первые мартены на территории современной Украины построил валлиец Джон Юз в 1879 году. В середине XX века с использованием этой технологии, по разным оценкам, выплавлялось от 50% до 80% всей мировой стали.
Однако из-за длительного времени плавки, необходимости постоянного внешнего подогрева печи, удорожания природного газа, неэкологичности процесса и других сложностей мартены уступили свои позиции новым технологиям.
В большинстве действующих мартеновских цехов используются не классические мартены, а, так называемые двухванные сталеплавильные агрегаты. В них объединены элементы конвертерной и мартеновской технологий. Грубо говоря, это две мартеновских печи, которые объединены между собой, что позволяет подогревать железный расплав изнутри кислородом, а не только внешнюю часть печи природным газом. Это дает существенную экономию ресурсов и возможность сократить длительность одной плавки до 3-4 часов.
Конвертерное производство: в поисках кислорода
Предтеча конвертерного способа выплавки стали – бессемеровский процесс – появился раньше мартенов. Англичанин Генри Бессемер получил патент на свое изобретение в 1856 году.
В 1878 году еще один англичанин Сидни Гилкрист Томас усовершенствовал изобретение своего земляка. Томасовские печи позволили выводить из расплава часть вредных примесей, таких как фосфор. Благодаря этому технология получила распространение в Бельгии и Люксембурге, где добывались высокофосфористые железные руды.
Однако, в обеих технологиях качество стали оставалось низким по сравнению с мартенами вплоть до начала 1930 годов. Именно тогда начались попытки внедрения кислородного дутья. В бессемеровских конвертерах жидкую сталь продували не воздухом, а чистым кислородом, получаемым в криогенных установках. Считается, что одни из первых опытов по использованию такой технологии проводились Николаем Мозговым в Киеве на заводе Большевик. Параллельно велись пробные плавки в Германии и Австрии. Но Вторая мировая война затормозила технологический прогресс в металлургии.
Лишь после окончания войны с развитием криогенных технологий кислородные конвертеры начали вытеснять мартеновское производство. Первые промышленные цеха заработали в 1952 году. Производство конвертерной стали оказалось более производительным и экономным. Некоторое время на эту технологию переводили устаревшие бессемеровские цеха, но все чаще строили новые более совершенные производственные линии.
Современные кислородные конвертеры представляют собой сосуды грушевидной формы, изготовленные из стали. Внутри они обложены специальным огнеупорным материалом. Сверху в них погружаются фурмы, через которые под высоким давлением подается чистый кислород. С помощью этого газа дожигается углерод до требуемого в стали уровня.
Дуговые электросталеплавильные печи: сила тока
Еще в 19 веке стало известно, что не только газы, но и постоянный электрический ток может восстанавливать металлы из окислов, а также расплавлять их с помощью электрической дуги. Однако отсутствие мощных источников электроэнергии сдерживало развитие технологии выплавки стали в электрических печах.
Лишь в 30-х годах 20 века начали появляться мощные электростанции, которые позволили задуматься о промышленном внедрении электрометаллургии. Сначала это был цветмет. Впоследствии технология пришла и в черную металлургию. Одним из наиболее наглядных примеров внедрения электрометаллургии является Запорожье. В этом городе в 1932 году запустили первые турбины ДнепроГЭС. После этого здесь один за другим появились предприятия электрометаллургии, которые производили алюминий, титан, ферросплавы и специальные стали.
Сегодня дуговые сталеплавильные печи (ДСП) используют не только для выплавки специальных, но и рядовых марок стали. Из них, как правило, производят квадратную заготовку и длинномерный стальной прокат. В печи, заполненные шихтой, погружают три огромных графитовых электрода, на которые подается переменный или постоянный ток. Возникает электрическая дуга, которая создает высокую температуру внутри печи и плавит лом. На базе ДСП обычно строят так называемые мини-заводы (mini-mills) – небольшие металлургические предприятия годовой мощностью 0.5-2 млн. тонн стали. Распространены они в странах с доступной электроэнергией и большими источниками ломообразования.
Как и в кислородных конвертерах, в электрометаллургии достаточно короткий период плавки – 40-60 минут. На первых этапах развития этих технологий скорость была и основным недостатком – возникали сложности с освоением большого количества марок стали. Ведь за несколько часов плавки в мартенах, в шихту постепенно вводили флюсы, раскислители, легирующие элементы, которые влияли на характеристики материала. А заводские лаборатории успевали за это время провести анализ полученного продукта и дать рекомендации сталеварам. Однако сейчас это преимущество мартенов практически нивелировано внедрением внепечной обработки. Сталь из конвертеров и ДСП дорабатывается в вакууматорах и установках печь-ковш до необходимого состояния и химсостава и уже после этого подается на машины непрерывной разливки.
Сырье: как найти нужную пропорцию шихты
Все три основных способа выплавки на выходе дают один продукт – жидкую сталь. При ее производстве используются разные сырьевые компоненты и их пропорции.
В мартенах при классической плавке около 33% шихты составляет лом черных металлов. Остальное – жидкий чугун из доменных печей. В отдельных случаях доля лома доходила до 66%. Это, так называемый, скрап-процесс, который активно использовался в мартенах при машиностроительных или трубных предприятиях. Ведь там во время обработки металлопродукции образовывалось огромное количество стальных отходов. Но чем больше лома, тем более высокая температура требуется для его расплавления. И мартены благодаря внешнему обогреву природным газом обеспечивали нужный уровень тепла.
А вот в кислородных конвертерах возможности внешнего обогрева нет. Поэтому доля лома в шихте здесь существенно ниже – около 15-25%. Иначе расплав получится слишком холодным. Кроме того, этот способ выплавки стали начал активно распространяться параллельно с непрерывной разливкой, которая привела к сокращению оборотного лома на металлургических предприятиях. Чтобы его не закупать на стороне, приходилось увеличивать долю горячего чугуна.
В электрометаллургических печах нет сложностей с достижением нужной температуры. Поэтому здесь до 100% шихты может быть сформировано из лома черных металлов. Однако, некоторые современные ДСП были построены вместо мартенов в составе интегрированных металлургических комбинатов с действующим доменным производством. Поэтому их конструкцией предусмотрено использование до 40% жидкого чугуна в составе шихты. Но страны, в которых распространены ДСП, имеют свои особенности. Например, в США около 70% стали выплавляется таким способом. Это объясняется высоким уровнем ломообразования: американцы часто меняют автомобили и бытовую технику, в этой стране развито машиностроение. В Турции около 68% электростали, но гораздо меньше источников ломообразования. Поэтому эта ближневосточная страна является крупнейшим в мире импортером лома.
Выплавка стали в Украине производится всеми тремя рассмотренными способами. По итогам 2019 года согласно данным www.worldsteel.org в мире было произведено 1,87 млрд. тонн стали. Из них – почти 72% в конвертерах, чуть менее 28% в ДЭСП, и лишь 0,3% в мартенах. Полный список стран по выплавке стали можно посмотреть на сайте ассоциации Worldsteel.
В любом случае можно уверенно говорить, что на современной металлургической кухне при соблюдении технологии (рецепта) и хорошей подготовке компонентов (сырья) получится качественное блюдо… то есть сталь. И при этом не важно, в какой печи его готовишь – электрической или газовой.
А то, что это хорошо получается у металлургов Украины, подтверждено географией экспорта их металлопродукции – от ближайших соседей до самых отдаленных уголков земли.
Археологи выявили, что плавить железо на Алтае начали на 3 века раньше
Археологи ТГУ получили данные радиоуглеродного датирования железоплавильных печей кош-агачского типа, обнаруженных в Горном Алтае. Раньше считалось, что эти печи появились в древнетюркскую эпоху в VI–X вв. нашей эры, однако радиоуглеродный анализ показал, что они возникли на 300–400 лет раньше – в III–IV вв. нашей эры, то есть еще до того, как сложился Тюркский каганат. Результаты исследований были представлены на международной конференции Archaeometallurgy in Europe в Мишкольце (Венгрия).
Археологи ТГУ при поддержке гранта РНФ «Генезис черной металлургии в Южной Сибири» изучают, кто, когда и каким именно способом стал добывать железо на Алтае и в Шории. Первая часть проекта – исследование древних железоплавильных печей Горного Алтая (Россия).
Всего там было открыто 15 печей кош-агачского типа – это крупнейшие для того времени печи во всей Центральной Азии. Исследования велись в 1970–1980-х годах, и тогда их появление связали с первым Тюркским каганатом. После этого больше 40 лет на территории Горного Алтая исследования по археометаллургии железа не велись.
В 2018 году археологи ТГУ провели раскопки древних мастерских по выплавке железа на берегу реки Куяхтанар. Для обнаружения печей и рудных выработок ученые использовали аэрофотосъемку и магнитную разведку. Именно с помощью магнитной разведки была обнаружена печь прекрасной сохранности, что впервые позволило полностью восстановить конструкцию и понять древнюю технологию выплавки железа.
– Проведенная работа позволила провести переоценку дат возникновения печей данного типа на Алтае. Радиоуглеродные даты показали, что печи кош-агачского типа появились уже в III-IV вв. нашей эры. Очень похожие печи встречаются позднее в Юго-Восточной Азии, – рассказал руководитель проекта, сотрудник лаборатории социально-антропологических исследований ФИПН ТГУ Евгений Водясов. – Это переворот представлений о развитии металлургии. Раз такие сложные и производительные печи появились на Алтае раньше, чем в Юго-Восточной Азии, то теперь нужно переосмысливать существующие представления о распространении технологий. В этом нам могут очень помочь исследования на пограничных российскому Алтаю территориях Монголии, Казахстана и Китая.
В печах кош-агачского типа можно было получить за одну плавку железную крицу весом около одной тонны. Для сооружения печи использовалось 1500 кг глины и каменные плиты весом 1200 кг.
– Мы изучили подземную камеру и наземную часть печи, где происходил процесс восстановления железа из руды. В этом году будем искать место, где обрабатывали полученную крицу, и надеемся найти кузницу, – пояснил Евгений Водясов.
Результаты своей работы томские ученые представили на международной конференции Archaeometallurgy in Europe в Мишкольце (Венгрия). Это единственная специализированная европейская конференция по археометаллургии, которая проходит раз в три года. В этом году в ней приняли участие ученые из Италии, Греции, Болгарии, Австрии, Франции и других стран. Археологи ТГУ стали одними из немногих представителей России и единственными представителями данного научного направления из Сибири. Помимо исследования железоплавильных печей в Горном Алтае, они рассказали об особенностях металлургии кузнецких татар и предварительных итогах исследований железоплавильных и кузнечных горнов в Горной Шории.
Доклады томских ученых получили высокую оценку и вызвали оживленную дискуссию. Несколько зарубежных лабораторий предложили им рассмотреть возможность совместных проектов.
Переработка черных металлов | Полезная информация от компании «Втортехмикс»
Добыча металлов из рудных материалов – это сложный и дорогостоящий процесс. Он повышает себестоимость изделий и требует от предприятий специального оснащения, квалифицированных рабочих. Поэтому практически все металлургические заводы принимают лом черных металлов для вторичной переработки. После переплавки сталь, чугун, железо приобретают такие же характеристики, что и первичное сырье. Можно перерабатывать черные металлы множество раз без потери свойств. В то же время, технология вторичной переработки значительно сокращает энергетические затраты предприятия, снижает негативное воздействие производства на окружающую среду, сохраняет природные запасы руды.
Вторсырье наиболее востребовано для изготовления проволоки и стальной тары. Переработанные черные металлы также применяют для производства металлоконструкций в некоторых отраслях строительства и машиностроения. Рассмотрим технологию переплавки лома подробнее.
Оборудование для переработки черных металлов
1. Плавильные печи.
2. Пакетировочные прессы для подготовки проволоки и листов.
3. Пресс-ножницы с острыми ножевыми балками для быстрого реза металлических отходов.
4. Аллигаторные ножницы рычажного типа для резки труб, стального проката, армированного кабеля.
5. Аппараты плазменной резки металлов.
6. Дозаторы для введения легирующих компонентов.
7. Дробилки и сортирующее оборудование.
8. Перегружатели.
9. Шредеры.
10. Грузоподъемное оборудование.
Относительно недавно на рынке появились мини-заводы по переработке металлолома. Их часто устанавливают в пунктах приема. С помощью мини-завода можно перерабатывать вторсырье и сразу выпускать из него готовую продукцию: катанку, строительную арматуру, швеллеры, балки, мелющие шары и т. д.
Прием и сортировка
Черные металлы отделяют от цветных еще в приемном пункте, но на заводе лом сортируют дополнительно по габаритам и химическому составу. Одновременно металл очищают от мусора и примесей. В современных промышленных комплексах процесс сортировки лома автоматизирован. Для пуска в линию предварительно отделяют тяжелые элементы от легких.
Сортировка по химическому составу производится на основании лабораторных анализов. Черные металлы разделяют по количеству углерода и еще по нескольким качественным показателям.
Раскрой лома
Перерабатывающие заводы предъявляют свои требования к параметрам металлолома для вторичной переработки. Большие куски конструкций режут с использованием газоплазменного оборудования или гидравлических ножниц. Мелкие элементы прессуют в брикеты под высоким давлением. Крупные металлические листы нарезают на фрагменты для удобной транспортировки.
На некоторых современных пунктах приема лома установлено специальное оборудование для прессования металла в бруски. Это значительно упрощает последующие процессы погрузки/выгрузки и транспортировки вторсырья на завод.
Очистка металлов
Черный лом в виде брикетов, брусков, элементов конструкций направляют в специальную дробилку. Аппарат разделяет металл на мелкие куски для определения вида загрязнителя. После этого лом очищают от пыли, следов ГСМ и неметаллических включений методом сепарации.
1. Механические твердые примеси выдувают из массы металла с помощью пневматической установки.
2. Неметаллические примеси отсеивают с помощью магнитов. Для этого лом помещают на конвейер. Металлические части удерживаются магнитами, а неметаллические по ленте ссыпаются в бункер. По типу конструкции сепараторы бывают не только конвейерными, но и барабанными. Мощность магнитов регулируется в соответствии с весом и размером кусков металла.
Переплавка лома
Нарезанный и очищенный черный металл направляют в плавильные плазменные или электрические печи. Плазменные установки дешевле, но и КПД у них ниже, поэтому они постепенно выводятся из эксплуатации.
Электрические печи бывают:
- дуговые (постоянного и переменного тока). По сравнению с плазменным оборудованием, такие установки имеют высокую производительность при меньшем расходе на энергоносители и капитальное строительство. В рабочей камере дуговой печи можно плавить металл массой от 50 тонн с одновременной продувкой;
- индукционные тигельные средней частоты. Плавление происходит за счет непосредственного нагрева металла без сопутствующих теплопотерь, поэтому печи имеют высокий КПД. Индукционные установки экономичны в эксплуатации, обеспечивают садочный режим плавки. В них можно получать сталь и чугун с высоким содержанием стальной стружки и скрапа. Индукционные тигельные печи средней частоты используют для скоростной плавки небольшими партиями;
- индукционные канальные промышленной частоты.
Крупные установки для выплавки и накопления цветных металлов. Такие печи обычно работают ночью, когда стоимость электроэнергии ниже, а днем выполняют непрерывную разливку в крупные формы.
Процесс переплавки включает следующие этапы.
1. Металлолом засыпают в ковш с тугоплавким покрытием.
2. Сверху на вторсырье заливают чугун и продувают массу кислородом. Окисление металла позволяет избавиться от примесей серы, фосфора и кремния, которые часто бывают в сталях. Эти элементы снижают прочность сплавов, делают их хрупкими. Для эффективного выжигания примесей дополнительно используют специальные присадки.
3. В расплав добавляют легирующие компоненты согласно технологической карте. Это может быть никель, хром, кобальт, ванадий. Легированные стали износостойкие, поэтому более востребованные на рынке.
Процессы плавления автоматизированы. Рабочие параметры контролирует компьютер и оператор, который имеет возможность выполнять ручную регулировку при необходимости. На металлургических комбинатах черные металлы после плавки могут подвергать прокатке для изготовления слитков. В таком виде перевозить материалы дешевле и удобнее. Предприятия с прокатными станами имеют большую доходность.
В США и в странах Европы ежегодно выделяют большие средства из частных фондов и государственного бюджета на совершенствование технологий вторичной переработки черных металлов. Расходы на исследования окупаются экономией на процессах переработки среды и снижением налогов на предприятии за счет улучшения экологических показателей. Можно сказать, что вопрос переработки чермета – один из главных в металлургической отрасли. В ближайшие годы технологии будут совершенствоваться, а качество переплавленного металла – повышаться.
Обработка металла в древности. Как человечество вошло в железный век
Как известно, основным материалом, из которого первобытные люди изготавливали орудия труда, был камень. Не зря сотни тысяч лет, прошедшие между появлением человека на земле и возникновением первых цивилизаций называют каменным веком.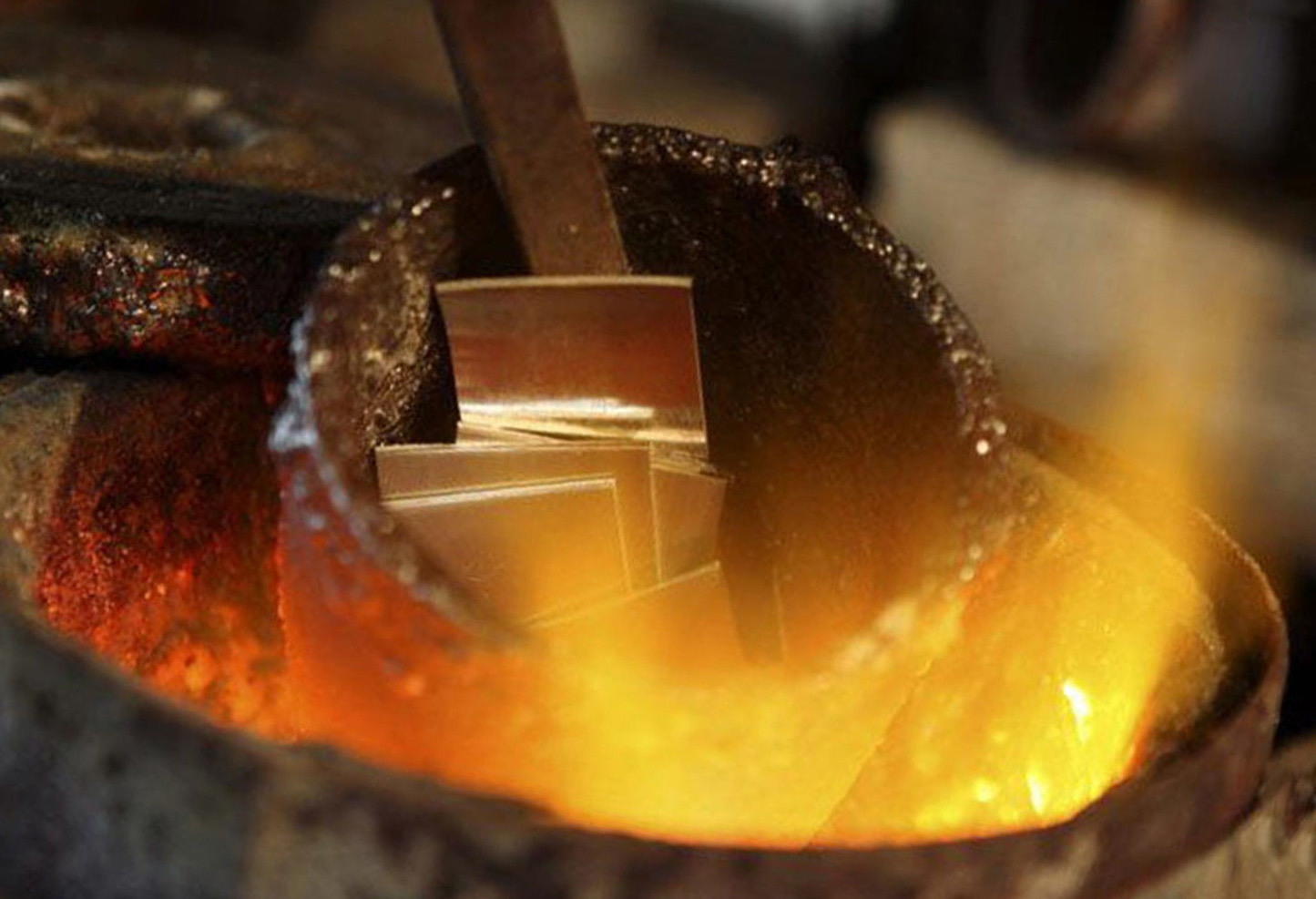
Скорее всего, первое время человек относился к металлу точно так же, как к камню. Он находил, например, медные самородки и пытался обрабатывать их точно так же, как камень, т. е. с помощью обивки, шлифования, отжатия отщепов и т. д. Но очень быстро стала ясна разница между камнем и медью. Может быть, даже, первоначально люди решили, что от металлических самородков толку не будет, тем более что медь была достаточно мягкой, и орудия, которые из нее изготавливались, быстро выходили из строя. Кто придумал плавить медь? Теперь мы никогда не узнаем ответа на этот вопрос. Скорее всего, все получилось случайно. Раздосадованный человек бросил камешек, который показался ему неподходящим для изготовления топора или наконечника стрелы, в костер, а затем с удивлением заметил, что камешек растекся блестящей лужицей, а после прогорания огня – застыл. Потом понадобилось только немного поразмыслить – и идея плавки была открыта. На территории современной Сербии был найден медный топор, созданный за 5 500 лет до Рождества Христова.
Правда, медь, конечно, уступала по многим характеристикам даже камню. Как уже говорилось выше, медь – слишком мягкий металл. Его основным преимуществом являлась плавкость, позволявшая изготавливать из меди самые различные предметы, но по прочности и остроте она оставляла желать лучшего. Конечно, до открытия, например, златоустовской стали (Статья «Русский булат из Златоуста»), должно было пройти еще несколько тысячелетий. Ведь технологии создавались постепенно, сначала – неуверенными, робкими шажками, методом проб и бесчисленных ошибок. Вскоре медь была вытеснена бронзой, сплавом меди и олова. Правда, олово, в отличие от меди, встречается далеко не везде. Не зря в древности Британия носила название «Оловянные острова» – многие народы снаряжали туда торговые экспедиции за оловом.
Медь и бронза стали основой древнегреческой цивилизации. В «Илиаде» и «Одиссее» мы постоянно читаем о том, что греки и троянцы были одеты в медные и бронзовые доспехи, использовали бронзовое оружие. Да, в древности металлургия во многом обслуживала именно военных. Пахали землю нередко по старинке, деревянным плугом, да и, например, водостоки можно было сделать из дерева или глины, но на поле битвы бойцы выходили в прочных металлических доспехах. Однако бронза как материал для оружия имела один серьезный недостаток: она была слишком тяжелой. Поэтому со временем человек научился выплавлять и обрабатывать сталь.
Железо было известно еще в те времена, когда на Земле шел бронзовый век. Однако сыродутное железо, получавшееся в результате обработки при небольшой температуре, было чересчур мягким. Большей популярностью пользовалось метеоритное железо, но оно было очень редким, найти его можно было лишь по случайности. Однако оружие из метеоритного железа было дорогим, иметь его было очень престижно. Египтяне называли кинжалы, выкованные из упавших с неба метеоритов, Небесными.
Принято считать, что широкое распространение обработка железа получила у живших на Ближнем Востоке хеттов. Именно они около 1200 г до н. э. научились выплавлять настоящую сталь. На некоторое время ближневосточные державы стали невероятно могущественными, хетты бросали вызов самому Риму, а филистимляне, о которых упоминается в Библии, владели огромными территориями на современном Аравийском полуострове. Но вскоре их технологическое преимущество сошло на нет, ведь технологии выплавки стали, как оказалось, было не так уж сложно позаимствовать. Главной проблемой было создание горнов, в которых можно было достичь той температуры, при которой железо превращалось в сталь. Когда окрестные народы научились строить такие плавильные печи, производство стали началось буквально во всей Европе. Конечно, многое зависело от сырья. Ведь люди лишь относительно недавно научились обогащать исходное сырье дополнительными веществами, придающими стали новые свойства. Например, римляне насмехались над кельтами, ведь у многих кельтских племен сталь была настолько плохой, что их мечи гнулись в сражении, и воины должны были отбежать в задний ряд, чтобы выпрямить клинок. Зато римляне преклонялись перед изделиями мастеров-оружейников из Индии. Да и у некоторых кельтских племен сталь не уступала знаменитой дамасской. (Статья «Дамасская сталь: мифы и реальность»)
Но, в любом случае, человечество вступило в железный век, и его уже нельзя было остановить. Даже широчайшее распространение пластмасс, произошедшее в ХХ веке, не смогло вытеснить металл из большинства сфер человеческой деятельности.
Возврат к списку
Зеркала способны испарять металл! 4000 градусов? Да пожалуйста! | Огниво
Описывая возможность плавления металлов зеркалами и линзами, не мог пройти мимо относительно современных установок использующих потрясающую своей силой и бесконечностью — энергию солнца. Ну неужели, если даже я понимаю огромную выгоду от использования бесплатной энергии, никто не попытался в современном мире её применить с целью генерации электроэнергии, плавки металлов, парогенерации? И всё это помощью простых зеркал!
Простота установки поражает! Достаточно оклеить «спутниковую тарелку» зеркалами, добавить установку, которая будет следить за солнцем, не давая ему уползать из фокуса и пожалуйста — плавьте, режьте, грейте. Стоимость такой установки — гроши! Я даже думал сделать, благо зеркала достаточно часто выкидывают, как и «ледянку» после зимних покатушек, найти не проблема, а стеклорез есть!
Пора заводить тетрадку проектов. 🙂 Благодаря этому каналу, я уже должен поехать в раскопанное поселение, где жили люди с собачьими головами, найти болотную руду, выплавить из неё железо…Вот теперь ещё солнечный концентратор…
Оказывается пытались, да ещё как.
В 1986 году на территории полуострова Крым, была построена первая в СССР опытная солнечная электростанция.
Крымская СЭС-5 Конструкция СЭС-5 базировалась на концентраторе ( это поле солнечных гелиостатов) и солнечном парогенераторе с турбинами и системой автоматического слежения за Солнцем плюс система теплового аккумулирования. Ели солнца не было, работал накопительный аккумулятор и полноценно обеспечивал работу станции в течение 3-4 часов плюс еще около 10 часов в режиме пониженной мощности. Проектная мощность станции составляла 5 МВт, это мощность первой советской атомной электростанции. После распада СССР Крымская СЭС -5 проработала еще пару лет, и была закрыта за недостатком финансирования. Зеркала гелиостатов и парогенератор очутились в металлоломе.
Сейчас, судя по яндекс картам, там пара ветряков стоит — восстанавливают небось.. Простите, не удержался.. 🙂
Ешё один очень интересный проект и тоже в Крыму, до сих пор, несмотря на разруху, вызывает интерес иностранных специалистов..
Здесь проводились исследования и разработка покрытия для космических кораблей, спутников. Очевидцы говорят, что устройства достаточно простые, однако позволяли наловить солнечных зайчиков аж на 4000 градусов цельсия.. А от комментаторов моих статей, я узнал, что на солнышке всего-то 6000. Установка была способна буквально испарять металлы.
Вот ещё выдержки из статьи «Солнечная металлургия»(https://helpiks.org/6-72117.html»
Еще в начале 60‑х годов в Ташкенте была создана солнечная печь. Около нее слева находился оптический прибор – гелиостат, который отраженные от зеркал солнечные лучи собирал в пучок. Справа находилось параболическое зеркало диаметром 2 метра. Ориентируясь по Солнцу, гелиостат направляет пучок параллельных лучей на зеркало, которое концентрирует их в кружок диаметром 14–16 миллиметров. Здесь создается температура 3000°С и выше. На этой гелиоустановке проводились опыты по резке и сварке металлов.
Ученые Ереванских отделений ВНИИ ПКТИ источников тока и ВНИИ кабельной промышленности за создание импульсной гелиоустановки старения материалов получили золотую медаль на международной Лейпцигской ярмарке.
В ходе теоретических и экспериментальных разработок, проведенных в СССР, Японии, США и других странах, получены данные, достаточные для того, чтобы внедрить высокотемпературные установки в исследовательскую и полупромышленную практику.![]()
Мы рассмотрели некоторые возможные пути развития металлургии будущего. Приведенные факты свидетельствуют о том, что ученые и инженеры уже сейчас работают над созданием новых способов добычи железа. Мы можем быть спокойны за судьбу металла‑труженика. Он еще долго будет служить человечеству.
И я полностью согласен с авторами статьи, Более того, мои предположения, о похожих установках в глубокой древности, позволяющие плавить металлы там, где не было лесов, кстати, знаете какой аргумент есть у историков, на вопрос откуда в таком количестве металлы, в местах, где нет растительного топлива? Их два. Первый — плавили в печах на сушёных какахах скота и второй- вот потому и нет леса, что весь вырубили для угля, чтоб тот металл выплавить. 🙂
И, в заключении, порадую моего критика. 🙂 Как же сделать параболическое зеркало в древности? Я тут прикинул.. Ну найти округлый валун в реке, обмазать его глиной с соломой, получится «спутниковая тарелка» и обклеить кусочками полированной меди, (были же медные зеркала) или, возможно, есть какие-то минералы в виде пластинок… 🙂
Благо дарю Вам. С Уважением к Вашему мнению — Крес
Несмотря на рекомендации ДЗЕНа, мой канал так и не получил определённый вектор. Здесь я не зарабатываю, а делюсь с Вами своим мнением, выслушиваю Ваше мнение, учусь у Вас. Поэтому, на канале многие смогут найти для себя что-то интересное. Ну, я надеюсь, 🙂
Отдельная благодарность за отметку «Нравится»
КАНАЛ ОГНИВО
Наиболее обсуждаемые статьи — Маленькая шпилька историкам, Нашёл древний артефакт(шуточная с подтекстом), Готовитесь встречать весну-масленицу в феврале?? Когда на самом деле приходит весна, Что кроется за словом «ТАРТАРИЯ» страна или территория?, Даю совет- что почитать, Загадка бронзового века, Кирпичная цивилизация.
Может ли свеча теоретически расплавить железо?
Тепло накапливается?
Это немного двусмысленный вопрос, но да, это «накопительный». Если вы положите немного тепла во что-то, оно останется горячим, если это тепло не будет снято. Установка 10 единиц тепла за раз — это то же самое, что установка 1 единицы за 10 раз, опять же при условии, что вы можете сохранить тепло в объекте.
Аналогия здесь ведро с отверстиями. Тепло, как вода, которую вы кладете, температура — это уровень воды. Неважно, если вы положите воду сразу или мелкими кусочками, но как только вы добавите немного воды, она начнет вытекать. Так что, если вы не торопитесь, вы, возможно, никогда не получите достаточно воды, и чем больше воды в ведре, тем быстрее оно вытекает.
Можно ли расплавить железо свечой?
Возможно нет. Я думаю, что самая большая проблема заключается в том, что тепло течет от горячих вещей к холодным вещам. Если утюг достигнет той же температуры, что и газ, поступающий из пламени, он не получит дальнейшего нагрева. Если ваша целевая температура (точка плавления) на самом деле ниже этого, вы застрянете.
Как это бывает, температура плавления железа составляет около 1600 ° С. Пламя восковой свечи достигает максимума при 1500С, но это крошечная область в центре — средняя температура составляет 1000С.
Вы можете решить эту проблему, используя экзотическую свечу из необычных материалов. Например, термит горит достаточно горячо, чтобы расплавить сталь, ацетиленовые горелки могут довести вас до 3500C. Но когда вы говорите «свеча», я предполагаю, что вы имели в виду восковую свечу, а не термитную «свечу».
Даже с горящей свечой у вас все еще есть проблема небольшого теплового потока. Ты говоришь:
скорость потери тепла ниже скорости получения тепла
Конечно, но это легче сказать, чем сделать. Если у вас есть волшебное железо, которое никогда не теряет тепло, хорошо, но в реальной жизни горячий утюг будет нагревать воздух в комнате (свеча не будет гореть в вакууме), горячий воздух уплывает, и в результате вы будете в конечном итоге нагревать всю комнату, потому что все это в тепловом контакте. Это требует много от свечи, но если у вас была свеча с бесконечным количеством топлива и она горела бесконечно, то в конечном итоге вы могли бы обогреть всю комнату выше температуры плавления железа (она должна быть выше, потому что само плавление требует некоторого подвод тепла) и да, он растает — но мы сейчас говорим об очень необычной свече. Не говоря уже о том, что масса такой свечи может действовать как теплоотвод, или она может воспламениться в вашей огненной буре в комнате, поэтому существует целый ряд практических проблем.
Итак, в заключение, какую свечу потребуется, чтобы расплавить железо? Тебе нужно:
- Огонь горячее, чем 1500С.
- Изолированная среда, которая может достичь этой температуры и остаться там.
- Достаточно большая свеча, чтобы гарантировать, что скорость потери тепла всегда меньше усиления (помните, что потеря тепла быстрее, когда разница температур больше).
Такое устройство называется кузницей.
Что, если бы можно было плавить металл руками?
Представьте, что вы настолько сильны и мощны, что можете плавить металл руками! Золото, железо и даже титан.
Что бы вы растопили? Есть ли способы сделать это сегодня? И какой температуры должны быть ваши руки?
Технически да, вы можете плавить металл руками, но не со всеми типами металлов. Есть металл, который настолько мягкий, что может плавиться при температуре чуть ниже 30 ° C (85,6 ° F).
Это известно как галлий, и после пары секунд поигрывания с ним он быстро превращается в жидкость.Есть и другие металлы, которые имеют такую же температуру плавления, например, франций и цезий. Но вам стоит держаться от них подальше, поскольку они радиоактивны и могут загореться, если с ними не обращаться должным образом.
Самое замечательное в галлии — это то, что он абсолютно безопасен для вас. По сути, это просто чрезвычайно дорогой пластилин Play-Doh.
Но мы уже можем плавить эти материалы. Но как бы это было, если бы вы могли плавить любой металл?
Плавить металл довольно сложно. Обычное пламя костра не поможет.
Для плавления металла требуется невероятно высокая температура. И для этого люди используют литейные производства. Литейные производства используются для достижения чрезвычайно высоких температур и поддержания их.
В зависимости от того, что вы хотите расплавить, например, золото, температура должна быть около 1000 ° C (1832 ° F). Это означает, что для того, чтобы расплавить металл, ваши руки должны быть как минимум такими горячими.
И поскольку максимальная температура, которую может достичь ваше тело перед смертью, составляет жалкие 44 ° C (115.7 ° F), вы бы растаяли, если бы ваше тело нагрелось до этой температуры. Но допустим, вы выжили.
Если вы хотите плавить металл, вам понадобится шагающая печь. Вы сможете плавить не только алюминий, железо и сталь, но и все остальное, к чему вы прикасаетесь. Это потому, что ты был бы горячим, как расплавленная лава.
Вы были бы гигантским огненным шаром разрушения. Но как только вы уничтожите все вокруг себя, вас так же легко уничтожить.Но как?
Предположим, вы занимаетесь своим делом и сжигаете металл. Внезапно начинается дождь — или из-за того, что вы горите, кто-то проливает на вас немного воды. Внезапно произойдет мощный взрыв.
Это происходит из-за реакции воды с горячим расплавленным металлом. Если вода или какая-либо влага коснется плавящегося металла, он расширится в 1600 раз больше своего первоначального объема. Это создает мощный паровой взрыв, который разносит горячий жидкий металл.
Если вы не будете предельно осторожны, вы непременно нанесете серьезный ущерб вещам и людям, которым не хотите причинять вред. Плавление металла голыми руками может показаться забавным, но нет причин, по которым вы когда-либо хотели бы это делать.
Помимо красивого вида, металл используется во всех видах электроники, автомобилях и даже в некоторых лекарствах, отпускаемых по рецепту. Металлы — неотъемлемая часть мира, в котором мы живем, и мы определенно не хотели бы разрушать и плавить их все. Но что, если бы металла никогда не существовало?
Подпишитесь на What-If на Youtube или следите за шоу на Facebook Watch.
Источники
Какие металлы можно плавить дома?
Это, наверное, очень похоже на свинец.
Алюминий плавится выше цинка, олова и свинца, но не так высоко, как медь.
Подойдет электрическая печь или пропановая горелка.
Какой металл плавить легче всего? — Quora. Галлий — это металл, который плавится при взятии в руки и имеет температуру плавления около 29 градусов Цельсия.
Обычные металлы для литья включают цинк, медь, олово, алюминий и серебро. Конструирование и создание ваших собственных металлических предметов поддается множеству различных видов ремесел.
Литейный завод — это завод по производству металлических отливок. Металлам придают формы путем плавления их в жидкости, заливки металла в форму и удаления материала формы после того, как металл затвердеет по мере его охлаждения.
Как плавить алюминий в домашних условиях?
Плавление алюминия
- Первый шаг, который вам нужно сделать, это раздавить банки, чтобы вы могли загрузить как можно больше в тигель.
- Разожгите печь или печь до 1220 ° F.
- Наденьте защитные очки и термостойкие перчатки.
- Открыть печь.
- Залейте жидкий алюминий в форму.
Если вы хотите расплавить металл, вам нужно найти способ нагреть его. Это можно сделать с помощью литейного цеха или горелки. В литейном производстве металл можно превратить в жидкость, из которой затем придать любую форму. С помощью горелки вы можете расплавить металл и разрезать его на самые разные формы.
Металлы в жидкой форме называются расплавленными. Когда металл нагревается, его температура повышается. Это называется нагревом. Состояние ликвидуса металла называется его расплавленным состоянием.
Можно ли плавить сталь в домашних условиях?
Чтобы создать нестандартные изделия, вам нужно либо расплавить металл и отлить его в форму, либо нагреть, пока он не станет достаточно мягким, чтобы придать ему форму молотком. Правильное плавление металлов может быть немного опасным в нашем домашнем магазине, но мы можем приготовить кузницу для кофе для всех наших домашних кузнечных нужд.
Другими действительно хорошими металлами для литья являются олово и алюминий. У меня никогда не было достаточно дешевого олова, чтобы с ним справиться, поэтому я не могу сказать вам никаких подробностей. Наверное, это очень похоже на свинец. Алюминий плавится выше цинка, олова и свинца, но не так высоко, как медь.
Можно ли отливать низкоуглеродистую сталь?
Из-за того, что в чугуне присутствует дополнительный углерод, его расплавленная форма более текучая, что облегчает отливку материала сложной формы.Это очень удобно для литья больших и тяжелых предметов. С мягкой сталью также легко работать, но чугун обладает более высокой литейной способностью.
Как расплавить металл в литейном цехе
Плавка металла — это процесс, при котором металл превращается из твердого в жидкий. Процесс плавления варьируется в зависимости от технологии. Здесь мы даем объяснение того, как плавить металл в литейном цехе, а также общие точки плавления металлов и протокол защиты.
Литейный цех в основном занимается обработкой расплавленного металла для придания формы различным литейным изделиям . Не будет преувеличением признать, что плавление металла — это сердце литейного производства.
Плавка металла — это незаменимый процесс литья, при котором твердый металл разжижается для заливки в форму и формирования отливки любой формы. Вкратце, во время рабочего процесса металл помещается в плавильное устройство, называемое печью, и перегревается до определенной точки плавления, чтобы преобразовать твердый металлический материал в жидкий.
При плавке металла используются разные технологии, в основном в зависимости от типа используемой плавильной печи.В этом посте мы поможем вам ответить на вопрос «Как плавить металл» , указав основные технологии плавильных печей на литейных заводах сегодня, а также температуру плавления обычных металлов, а также рекомендации по обеспечению безопасности в процессе плавки.
Оставайтесь с нами и копайте знания!
Что такое плавящийся металл?
Плавление, также называемое плавлением, представляет собой переходный процесс, который изменяет состояние металлического материала от твердого до жидкого за счет выделения достаточного количества тепла.
Процесс плавления металла ослабляет плотную упаковку молекул металла. В результате плавление дает металлическую жидкость из твердого материала.
Плавление чистого и твердого металла происходит при определенной фиксированной температуре, называемой точкой плавления, в то время как нечистые металлические материалы плавятся при другой температуре, которая варьируется в зависимости от типа и процентного содержания примесей.
Являясь сердцем литейного производства, процесс плавления металла обеспечивает жидкую текучую среду, которую можно использовать для заливки в форму, и она затвердевает в различные формы по мере необходимости.Плавка металлов — это энергоемкая работа, на которую приходится 55% энергозатрат в металлообрабатывающей промышленности.
Это очень важный этап, потому что расплав металла не только является материалом для процесса литья, но также сильно влияет на физические и химические свойства конечных продуктов литья.
Процесс плавки металла
Те, кто задается вопросом, как плавить металл в литейном производстве, могут обнаружить, что процесс плавления металла обычно включает следующие краткие этапы:
- Определение соотношения смешанных металлов
- Подготовка и загрузка металла
- Плавление металла
- Рафинирование и обработка расплавленного металла
- Транспортировка расплавленного металла
Выбор смешанного металла соотношение
Для каждого вида литья требуются разные механические свойства металла, которые можно изменить, регулируя соотношение смеси металлов.Производитель литейного производства имеет формулу смешивания металлов в соответствии с конкретным классом материала и требованиями.
Например, соотношение компонентов смеси для литья алюминиевых деталей на нашем металлургическом заводе часто составляет 40% алюминиевых слитков + 50% алюминиевого лома + 10% других. В котором 10% других составляют некоторые добавки, такие как сплавы Zn, Mn, Cu, Si и т. Д.
Подготовка металла
Слитки и металлолом — основной состав материала, используемый в процессе плавки, составляющий до 80% от соотношения компонентов смеси.
Перед загрузкой в печь слитки и металлолом (банки, лом деталей машин, контейнеры или подъездные пути) необходимо удалить грязь, а также предварительно нагреть и высушить. Этот шаг предназначен для удаления влаги, предотвращения возможности исследования в печи, ограничения образования шлака и повышения плавильной способности.
В частности, для металлолома требуется удаление краски, машинного масла и других загрязнений, обычно термическим способом.
Погрузка и плавка металла
Печь загружается путем добавления источника топлива (древесный уголь, природный газ, электричество).В процессе нагрева металл непрерывно загружается в печь вместо партии для экономии энергии и эффективности работы.
Расплавленный металл в литьеПечь работает в чрезвычайно жестких условиях, где расплавленный металл, футеровка печи, атмосферные газы и продукты сгорания топлива имеют очень высокую температуру, что требует строгих средств защиты рабочего. Печь бывает разного размера, формы, принципа работы и энергии, поэтому плавильная мощность каждой печи отличается от других.
При фиксированной температуре плавления металл переходит из твердого состояния в жидкое. Температура плавления варьируется от металла к металлу и составляет от 350 до 2000 ° C.
Рафинирование и обработка жидкого металла
Этот процесс предназначен для дегазации расплава, удаления нежелательных твердых частиц и корректировки состава сплава, как ожидалось. Добавочные материалы, особенно некоторые из черных металлов, для повышения механических свойств жидкого металла (прочность, пластичность, жесткость, эластичность).
Этот шаг очень важен, потому что он может повлиять на качество окончательного литья.
Транспортировка расплавленного металла
После плавления жидкий расплав перекачивается из печи в формовочную линию по системе разливки.
Технологии плавки металлов
В основе процесса плавки металла лежит плавильная печь, которая напрямую влияет на эффективность процесса плавки. Существуют различные технологии плавки, которые влияют на способ плавления металла и решают, какая печь используется.
Как выбрать плавильную печь
Плавильная печь сильно влияет не только на эффективность работы литейного цеха, но и на конечные результаты литья, поэтому очень важно принять во внимание, какие технологии печи следует применять.
Как вы знаете, печи для плавки металлов различаются по форме, геометрии, топливу и мощности.
Эти нижеприведенные факторы строго определяют, какая плавильная печь подходит для вашего литейного производства.
- Наличие места: проверьте свою производственную площадь. Куда будешь печь ставить?
- Тип плавкого сплава и его температура плавления
- Производительность плавки и количество металла
- Энергоэффективность
- Капитальные вложения
- Эксплуатационные расходы
- Требования к техническому обслуживанию
- Эмиссия и проблема окружающей среды
Конечно, не существует универсального варианта, но производители литейного производства должны учитывать, какие критерии важнее других.У каждого литейного завода будут свои собственные критерии приоритета при выборе плавильной печи, которая соответствует их потребностям и масштабу производства.
После разъяснения этих соображений, второй шаг — выбрать тот, который работает на вашем литейном цехе. Здесь мы рассмотрим самые популярные на сегодняшний день плавильные печи в литейном производстве. Давай проверим.
Текущие и новые технологии плавильных печей в литейном производстве
Для плавки металла в металлообработке используются печи разных типов.Их классифицируют по источнику тепла, эксплуатационным характеристикам и конструкции печи.
Тигельные и ваграночные печи представляют собой традиционные методы плавки, в то время как индукционные и электродуговые печи представляют собой современные передовые технологии плавления.
Тигельная печь
Электрическая тигельная печьТигельная печь — старейшая, простейшая и оригинальная плавильная печь, применяемая в литейных цехах. Это основное плавильное устройство изготовлено из жаропрочных материалов, которые часто представляют собой керамические или тугоплавкие материалы.
Тигельная печь может поставляться в очень маленькой чаше, которая обычно используется для плавления ювелирных изделий (золота, серебра), в большую емкость, которая применяется для небольших партий.
Топливом для тигля обычно является кокс, газ, нефть или электричество. В то время как электрический тигель имеет максимальную производительность 2,5 т / ч, тигель для газа или жидкого топлива может плавиться до 4 т / ч.
Тигельная печь не является энергоэффективным устройством с потерей более 60% тепла на излучение.
Эта печь подходит для цветных металлов, которые особенно применяются для плавки алюминия. Хорошо работают с любыми алюминиевыми сплавами. Одним из преимуществ является то, что тигель очень прост в эксплуатации и обслуживании, что снижает затраты. Кроме того, его низкая капитальная стоимость привлекает небольшие литейные предприятия вкладывать свои деньги.
Однако эта печь подходит только для небольших объемов производства и использования металла с низкой температурой плавления из-за ее низкой энергоэффективности.
Купольные печи
Купольная печь считается одной из самых экономичных технологий плавки. В этой печи в настоящее время выплавляется почти серый чугун.
По конструкции, купол может быть любой формы и размера, но его диаметр может составлять от 0,5 до 4 м, а высота — около 6-11 м. Купол выполнен в виде вертикально-цилиндрического сосуда, вероятно, в виде большой трубы.
Конструкция купольной печиВагранки стена, как правило, изготовлена из стали и выровнена с огнеупорной кирпичной стеной. Дно печи облицовано аналогичным образом, но часто используется смесь глины и песка, поскольку эта футеровка носит временный характер.Некоторые вагранки снабжены охлаждающими слоями кожуха для охлаждения и добавлением кислорода для более интенсивного горения кокса.
Топливом для обогрева вагранки является кокс с некоторыми присадками. Для запуска производственной партии в печь добавляют слои кокса и зажигают горелкой. Когда кокс загорается, воздух попадает в слои кокса через вентиляционные отверстия. В качестве топочного топлива также можно использовать древесину, уголь или горючие газы.
Когда кокс достаточно горячий, твердые металлы подают в печь через отверстие в верхней части.В процессе плавления между топливом и входящим воздухом происходит термодинамическая реакция.
Углерод в коксе соединяется с кислородом воздуха с образованием монооксида углерода, который продолжает гореть до диоксида углерода. Определенное количество углерода растворяется в падающих каплях жидкого металла и, следовательно, увеличивает содержание углерода в металле. В процессе плавки производятся разные марки чугуна и стали.
Купольная печь может применяться для плавки любых черных металлов, в основном применяемых для плавки чугуна в больших объемах.По статистике 60% чугунного литья выплавляется с помощью вагранки. Его энергоэффективность также высока, считая порядка 40-70%.
Электродуговые печи
Электродуговая печь (ДСП) — это печь, в которой энергия электрической дуги используется для нагрева и плавления материала.
Он колеблется от 1 тонны (обычно для производства чугуна) до 400 тонн (для вторичной стали). Промышленные электродуговые печи могут достигать температуры 1800 ° C (3272 ° F), в то время как лабораторные сосуды могут достигать температуры более 3000 ° C (5432 ° F).
Конструкция электродуговой печиКак расплавить металл в электродуговой печи?
В электродуговой печи материал находится в прямом контакте с электричеством дуги, и электрический ток проходит через материал. Следовательно, плавление более эффективно, чем другие технологии, использующие внешнее тепло.
Электродуговая печь часто используется для плавки стали (учтите 87%), а 13% — для плавки железа. Они могут хорошо перерабатывать стальной автомобильный измельченный лом с высоким содержанием остаточных элементов, что неэффективно при вагранке.
Индукционная печь
Индукционная печь — это электрическая печь, использующая принцип электромагнитной индукции. Итак, как расплавить металл с помощью этой технологии плавки?
Металл загружается в тигель, окруженный медной катушкой из проволоки, по которой проходит переменный электрический ток. После включения индукционной печи катушка быстро создает обратное магнитное поле, которое проникает через металл. Магнитное поле создает вихревые токи — круговой электрический ток, протекающий внутри металла.В результате циркуляция этих токов создает очень высокие температуры, плавящие металлы.
Конструкция индукционной печиПлавильная мощность индукционных печей составляет от менее 1 кг до 100 тонн, обычно используемых для плавки чугуна, стали, меди, алюминия и драгоценных металлов.
По сравнению с другими технологиями плавки металлов преимущество индукционных печей состоит в том, что они являются экологически чистыми, энергоэффективными и простыми в управлении процессом плавки.
Однако ограничения индукционной печи на металлолом и некоторые легирующие элементы могут привести к потере из-за окисления.
Температура плавления металла
Большинство металлов, существующих на Земле, в нормальном состоянии находятся в твердом состоянии. Однако в металлообрабатывающей промышленности, особенно в литье и металлургии, металл необходимо сжижать, чтобы получить новый продукт. Чтобы металл стал жидким, его необходимо нагреть до точки плавления.
Следовательно, знать температуру плавления веществ так же важно, как и при плавлении металла. Это упрощает обработку металлического литья.Специалисты могут точно рассчитать время формования, плавления и застывания отливок. Это помогает неэффективному производству и в то же время предоставляет необходимые решения для резервного копирования на случай возникновения чрезвычайных ситуаций.
Что такое точка плавления?
Точка плавления, также известная как температура разжижения, — это температура, при которой происходит процесс плавления твердого металла. Это точка, в которой металл переходит из твердой фазы в жидкую.Температура плавления варьируется от металла к металлу.
На практике температуру плавления считают относительной. Нечувствителен к давлению. Некоторые аморфные вещества, такие как стекло, не имеют фиксированной температуры плавления.
Температура плавления варьируется от металла к металлу.Какой металл имеет самую высокую температуру плавления?
Вольфрам (W), также известный как вольфрам, — это металл с самой высокой температурой плавления (3422 ° C; 6192 ° F) , самым низким давлением пара (при температурах выше 1650 ° C, 3000 ° F) и самым высоким предел прочности.
Самый простой для плавления металл
До этого момента металл с самой низкой температурой плавления составляет ртутного столба с температурой плавления -38,830 ° C. Это единственный металл на Земле в жидком состоянии при нормальной, стандартной химической температуре и давлении.
В настоящее время ртуть в основном используется в качестве термометра, манометра, поплавкового клапана, ртутного переключателя и т. Д.
Температура плавления чугуна и стали
Сегодня железо является наиболее используемым металлом в мире, на него приходится 95% от общего годового производства металла.
Чистое железо мягкое и гибкое. Но при добавлении углеродного компонента в количестве 0,002% — 2,1% получается стальной сплав с выдающейся твердостью, пластичностью и несущей способностью.
Железо имеет температуру плавления 1538 ° C, а сталь 1370 ° C . В настоящее время железо и сталь — это два металла, которые широко используются в области машиностроения, автомобилестроения, судостроения, строительства и т. Д.
Температура плавления алюминия
Алюминий имеет температуру плавления 933.47 К (660,32 ° C, 1220,58 ° F) . Температура плавления алюминия невысока по сравнению с другими металлами.
В периодической таблице алюминий обозначается как Al; Атомный номер 13, плотность 2,9 г / см3. Алюминий легкий, мягкий, с отличной коррозионной стойкостью и хорошей литейной способностью. Это самый распространенный металл в земной коре. Алюминиевое литье широко используется в деталях машин, двигателях и внешней отделке городов.
Металл | точка плавления (° C) | точка плавления (° F) | ||
Алюминий | 660.32 | 1220,58 | ||
Алюминиевый сплав | 463-671 | 865-1240 | ||
Кованое железо | 1482-1593 | 2700-2900 | ||
2060 — 2200 | ||||
Чугун, ковкий | 1149 | 2100 | ||
Свинец | 327,5 | 621 | ||
Углеродистая сталь | ||||
1540 | 2600 — 2800 | |||
Нержавеющая сталь | 1510 | 2750 |
Руководство по технике безопасности при плавке металла
При плавке металла ежедневно приходится иметь дело с экстремальным нагревом (до 2000 ° C), что является очень опасной рабочей средой.
Можно сказать, что плавка — одно из самых опасных работ, вызывающих неожиданные аварии на литейном производстве. Подробнее о том, как работает литейное производство.
Следовательно, для защиты здоровья и жизни рабочего и предотвращения потери и повреждения свойств литейного цеха, существуют строгие правила, которые производители литейных цехов должны учитывать.
Обеспечение инфраструктуры литейного производства
- Зона плавления должна быть устроена отдельно, чтобы избежать опасности для неуполномоченных рабочих
- Должна быть вентиляция, а конструкция крыши литейного цеха должна быть высокой для циркуляции воздуха
- Печь должна обеспечивать качество и безопасность при использовании
- Должна быть оборудована с автоматической или полуавтоматической системой заливки и дозаправки для ограничения воздействия на человека и несчастных случаев.
- Взрывобезопасное и противопожарное оборудование должно быть всегда наготове
Обеспечить рабочему защитную защитную одежду
Плавильщик во время смены должен быть одет в полную защитную одежду. Шапка, очки, перчатка, маска, плотная одежда и обувь являются обязательными аксессуарами.
Работа на плавильной печиЧто можно и нельзя
- Разместите предупреждающий знак для зоны плавления
- Ограничьте доступ неуполномоченных рабочих в зону плавления
- Регулярно проверяйте печь и вентиляционную систему и убедитесь, что неэффективная одна из них отремонтирована немедленно
- Очистите и высушите металлический материал перед плавлением
- Сделайте предварительный нагрев печи и огнеупоры перед использованием
- Подготовьте план действий в чрезвычайных ситуациях
- Не разрешайте курить, есть, пить в зоне плавления
Резюме
В приведенном выше содержании мы предоставили подробное объяснение Как плавить металл в литейном цехе .Надеюсь, он расскажет вам о некоторых интересных идеях о процессе плавки металла.
Подробнее о нашем блоге, посвященном процессу литья в металлообрабатывающих цехах, читайте здесь.
Кратко представленная компания VIC — производитель литейных изделий для литья металлов, специализирующийся на производстве и поставке деталей для литья металлов на мировой рынок. Если вам это нужно, свяжитесь с нами, чтобы оформить заказ и получить консультацию по лечению гипсом.
Номер ссылки
Министерство энергетики США (2005 г.). Передовые технологии плавления: концепции и возможности энергосбережения для индустрии литья металлов . Https://www.energy.gov/sites/prod/files/2013/11/f4/advancedmeltingtechnologies.pdf.
Безопасная работа, Австралия (2013 г.). Руководство по управлению рисками, связанными с литейными работами. https://www.safeworkaustralia.gov.au/system/files/documents/1702/guide-managing-risks-associated-foundry-workl.pdf
Плавление чугуна по методу Ваупака
Плавление чугуна в литейном цехе Ваупака
Процесс плавления чугуна начинается в Литейном цехе Ваупака с выбора из множества материалов, соответствующих уникальным спецификациям отливок из серого чугуна и высокопрочного чугуна.
В больших печах железо расплавляется при температуре от 2600 до 2800 градусов по Фаренгейту. Компьютеризированные системы постоянно контролируют температуру.
По мере того, как утюг перемещается по линии формования, температура постепенно снижается примерно с 2600 до 1200 градусов. Когда чугунные отливки охлаждаются, они вступают в процесс вытряхивания, при котором формы стряхиваются, а песок перерабатывается для повторного использования. Когда наши отливки из серого чугуна и высокопрочного чугуна опускаются ниже 140 градусов, они очищаются и обрабатываются.
Плавление железа в стиле Ваупака
Все начинается с включения тепла. Плавление чугуна осуществляется одним из двух способов: вагранкой, представляющей собой цилиндрическую шахтную печь; или электрическая плавильная печь.
Во всех наших литейных цехах, кроме двух, используется вагранка для плавления чугуна, которая нагнетает воздух со сверхзвуковой скоростью в базовое топливо — кокс, чтобы поднять температуру до 2800 градусов по Фаренгейту. Специальная смесь материалов в вагранке включает чушковый чугун, переработанное железо из нашего производственного процесса, чугунный лом и новые металлы, как указано.Изменяя процентное содержание и состав этих материалов, мы меняем химический состав готового железа. Когда чугун плавится, он просачивается сквозь кокс и попадает в наши печи для выдержки.
Наши литейные производства в
Маринетт, Висконсин и Лоуренсвилль, Пенсильвания, имеют электроплавильные печи, в которых магнитные свойства железа используются для создания трения и нагрева. В этих печах также хранится жидкое железо.
Почему не тает внутренняя часть купола?
Кожухи наших вагранок охлаждаются снаружи водой и футерованы в зоне плавления огнеупорными материалами.В вагранке железо будет плавиться до 12 дней, затем мы открываем дверцы створки и выкидываем золу и неиспользованный кокс, обнажаем внутреннюю часть, затем осматриваем и ремонтируем участки, если это необходимо.
Новая теория объясняет, как металлы плавятся и замерзают
Физики обнаружили, как процесс плавления работает при экстремальных давлениях, таких как те, которые обнаруживаются внутри ядра Земли.
Ученые разработали новую теорию замерзания и плавления металлов, таких как железо или медь.
Новые результаты опубликованы в Интернете в научном журнале Nature Communications.
Ученые, стоящие за новым исследованием, надеются, что теория приблизит их к пониманию того, как металлы развиваются под экстремальным давлением внутри Земли и как жидкие металлы затвердевают, когда они теряют тепло в окружающую среду и остывают.
Температура плавления повышается с увеличением давления
Новые результаты показывают, как температура плавления вещества — точка плавления — изменяется при более высоком давлении.
Новая модель описывает, как кристалл переходит в жидкость при разных давлениях. Прогнозы модели соответствуют фактическим наблюдениям. (Иллюстрация: Ульф Педерсен)
«Температура плавления обычно повышается, когда мы увеличиваем давление. Например, железо плавится при температуре 1538 градусов по Цельсию при давлении в одну атмосферу. Но при высоком давлении ядра Земли железо сначала плавится при температуре более 5000 градусов », — говорит ведущий автор исследования Ульф Рёрбек Педерсен из Университета Роскилле в Дании.
«Вопрос в том, как изменяются явления плавления и замерзания при увеличении давления. Интересным предположением является теория Линдеманна 1910 года, — говорит Педерсен.
Когда вы нагреваете кристалл, молекулы начинают двигаться, колеблясь вокруг своих позиций внутри кристалла. Линдеманн предполагает, что в какой-то момент вибрации становятся настолько сильными, что кристалл просто разрушается и плавится.
«Теперь мы впервые можем понять, насколько сильными должны быть колебания, прежде чем кристалл расплавится, и это зависит от давления, что противоречит тому, что думал Линдеманн», — говорит Педерсен.
Теперь физики могут предсказать, как быстро жидкость плавится при достижении точки плавления и, наоборот, как быстро атомы организуются, когда вещество начинает кристаллизоваться.
Подробнее: прорыв в физике может привести к новому взгляду на магнетизм
Как долго экзопланеты сохраняют тепло
Теперь физики могут начать отвечать на такие ключевые вопросы, как: Почему металл плавится и замерзает при определенном давлении? Затем они могут рассчитать, как этот процесс изменяется в различных условиях, например, при экстремальных давлениях.
«Я надеюсь, что наша теория может быть использована для моделирования экстремальных условий, которые встречаются в центре Земли и других планет, включая экзопланеты», — говорит Педерсен.
«Теория может сказать нам, как быстро растут внутренние кристаллы, что упрощает подсчет времени, необходимого для остывания планеты», — говорит он.
Новые результаты могут показать, как долго экзопланеты — планеты, вращающиеся вокруг звезд, помимо Солнца — могут оставаться теплыми достаточно долго, чтобы поддерживать жидкую воду на своей поверхности и, следовательно, жизнь.
Подробнее: Новое открытие: маленькие планеты имеют круговые орбиты
————-
Прочтите датскую версию этой статьи на Videnskab.dk
Переведено: Catherine Jex
Научные ссылки
Внешние ссылки
Сопутствующее содержание
3 основных типа плавильных печей, используемых при литье металлов
Типы плавильных печей
При литье металла необходимо воздействуют на металл, чтобы достичь его точки плавления, наносят через печи.Печь используется для плавления металлов на начальных этапах металлургического процесса. При литье используются разные типы плавильных печей, и в каждой печи используется разная технология. Литейные производства проектируют плавильную печь таким образом, чтобы она потребляла как можно меньше тепла и топлива для плавления металла.
Купольная печьЭтот тип высокой цилиндрической печи является одной из старейших плавильных печей, используемых для литья. Внутренняя часть купола выложена глиной, кирпичами или блоками, которые защищают внутреннюю часть печи от высоких уровней тепла, истирания и даже окисления.Для плавки металла литейщики закладывают в печь несколько слоев ферросплавов, кокса и известняка. Осадочная порода, используемая в качестве строительного материала, вступит в реакцию с металлом, в результате чего примеси в печи всплывут на поверхность плавящегося металла.
Индукционная печьКак следует из названия, в этих плавильных печах используется индукционная технология с переменным электрическим током для подачи необходимого тепла для плавления металла. Электрическая печь, используемая для плавки металлов, делает процесс более энергоэффективным по сравнению с другими типами плавильных печей.Большинство литейных заводов по всему миру используют индукционные печи вместо вагранки для плавки латуни или чугуна.
Кроме того, индукционные печи предпочтительны для плавки множества металлов, включая сталь, железо, алюминий и медь. Поскольку он использует индукцию вместо горения, тепловой энергии, необходимой для плавления металла, будет достаточно; таким образом, это приведет к экономии средств для литья под давлением. Печь может плавить от менее 1 кг до 100 тонн.
Печь с открытым подомЛитейные заводы используют подовую печь для плавки цветных металлов в меньших количествах.Он использует распыленную тяжелую нефть или природный газ для создания тепла, с помощью которого материал расплавляется. Мартеновский процесс также используется как средство для повышения температуры внутри металлургической печи, которая использует отходы или неиспользованное тепло, вытесняемое из печи. Затем отработанное тепло перенаправляет дымовые газы через кирпичную кладку, которая образует насадку. Подовая печь используется в основном в промышленности в качестве кислородной печи или электродуговой печи.
Металлическая вставка в дереве | Бернзоматик
Мне всегда нравилось ощущение контрастности материалов, особенно металла и дерева.Металл — это инь по сравнению с янь дерева: холодный, четкий и неумолимый, в то время как дерево предлагает гладкие, гибкие и органичные узоры. Когда я действительно хочу выделить какую-то фигуру, я приложу немного усилий, чтобы найти этих маловероятных партнеров, чтобы они играли друг с другом ради визуального интереса, и немного поинтересовался, «как они это сделали?». Моей младшей из них исполняется 5 лет в этом месяце, и я конструирую шкатулку для подарков, которая, я надеюсь, будет у нее до конца жизни — реликвия, которую я хочу выделить как вневременную, личную и знакомую.Я решил, что металлическая инкрустация ее инициала будет отличным способом сделать его своим. Добавить металлическую вставку в проект проще, чем вы думаете, с помощью всего нескольких простых инструментов, я использовал роторный инструмент, паяльную лампу Bernzomatic TS8000 и чугунный ковш. Металлические слитки можно было купить в Интернете по цене около 30 долларов за штуку, что более чем достаточно для нескольких проектов инкрустации.
Направления
Шаг 1. Создайте свой проект
Я делаю подарочную коробку размером 8 x 12 дюймов с загнутыми краями вишневыми краями и твердой крышкой из орехового дерева.Серебристый металл действительно выделяется на вершине из темного ореха. Я собрал все вместе и срезал верхнюю часть, затем отшлифовал квадрат, ровно и разгладил до зернистости 800. На этом этапе верхней части коробки уделяется немного меньше внимания, так как мы будем снимать слой, чтобы металл был на одном уровне. Коробка была практически готова на этом этапе, за исключением верхней части и хорошего слоя отделки. Я отложил все остальное, кроме верха, и принялся за подготовку.
Шаг 2. Создайте дизайн
После того, как коробка была построена, я измерил размер и расположение инкрустации, а затем распечатал ее на бумаге.При использовании вставок из расплавленного металла избегайте слишком большого количества деталей или тонких участков, которые могут выгореть при нагревании. Кроме того, просто — это классно, не так ли? Я распылил клей на бумагу и аккуратно приклеил туда, где хотел. Как только он хорошо приклеился, я осторожно разгладил его пластиковой картой, чтобы удалить воздух и складки. На этом этапе действительно дважды проверьте свою работу. Это момент невозврата, поэтому несколько вдохов перед погружением того стоят.
Шаг 3: Трассировка и оценка
Я использую острый бритвенный нож, чтобы аккуратно надрезать дерево по контуру рисунка.Обязательно получите каждый ракурс. Как только он будет полностью набран, разорвите рисунок и обведите контур перманентным маркером, чтобы получить темный силуэт, с которым можно работать. Будьте очень уверены в линиях, так как теперь легче вносить коррективы, чем когда вы начинаете резать.
Шаг 4: Удалите древесину
Я использовал фрезу с треугольным острием на фрезере для ладони, чтобы удалить большую часть дерева из конструкции. Не беспокойтесь о том, чтобы получить все, вы можете очистить это позже с помощью меньшего, более управляемого вращающегося инструмента.Следите за своей глубиной, цель состоит в том, чтобы пройти через кусок дерева только наполовину, но не менее 1/8 — 1/4 дюйма для хорошей удерживающей способности. Как только центр выйдет наружу, у вас должно получиться хорошее углубление, которое можно подрезать небольшой шпоночной коронкой на вращающемся инструменте. Это необходимо для того, чтобы металл держался за древесину под поверхностью и не выскакивал при движении или использовании древесины. Я осторожно просверливаю отверстие, затем делаю углубление под небольшим углом и удаляю древесину. Делайте это медленно и, если он дымится, немного отпустите и дайте дереву немного остыть.
Шаг 5: Точная настройка
На этом этапе внимательно посмотрите на верхний край контура и удалите неровности или неровности. Обратите внимание на области поднутрения: они достаточно глубокие и широкие, чтобы обеспечить достаточную удерживающую способность. Я также удалил клей и всю оставшуюся бумагу с выкройки.
Шаг 6: Подготовка области
Когда мы будем готовы к заливке, уделите минуту, чтобы как следует подготовить область. Расплавленный металл принадлежит вашей заготовке, а не ноге.Я удалил все легковоспламеняющиеся материалы и убедился, что заготовка стабильно стоит на столе. Я открываю дверцы и убеждаюсь, что вентиляция будет очищать воздух, но не дует прямо на заготовку. Я также составил план, где установить горячую горелку и нагретый ковш, когда закончу с ним. Я также спланировал, где начать заливку, чтобы ускорить течение расплавленного металла.
Я отрезал хороший кусок слитка, который поместился в чашу ковша. Я использовал ленточную пилу, но вы можете использовать ножовку или просто оплавить конец в чашку ковша.
Шаг 7: Залейте металл
Я медленно плавил металл, прикладывая пламя непосредственно к слитку. Температура плавления составляет около 460 градусов по Фаренгейту, поэтому он растает всего за несколько секунд.
Перед заливкой убедитесь, что он хорошо нагрет, чтобы избежать преждевременного затвердевания заготовки. Я начал заливку на несколько дюймов выше начала канала и позволил ей течь до конца.
Важно нанести достаточное количество материала в каждую область вкладки, прежде чем она начнет охлаждаться и застывать.Древесина сразу задымится, но не беспокойтесь, она выветрится.
Я использовал металлический зонд, чтобы убедиться, что он вошел во все маленькие края. Материал немного выходит за пределы контура, но его можно отшлифовать, поэтому дайте ему остыть и не пытайтесь сильно двигаться, пока он остывает или могут возникнуть трещины.
Шаг 8: Завершение проекта металлической инкрустации
Металл можно отшлифовать, как только он остынет на ощупь. Я использовал ленточную шлифовальную машину для большей части материала и орбитальную шлифовальную машину с зернистостью до 800, чтобы по-настоящему отполировать ее.Я протер слой полиуретана, чтобы запечатать и защитить его. Теперь он готов к передаче следующему поколению для хранения коллекции особых воспоминаний по мере того, как он превращается в собственное сокровище.
Советы
Что следует учитывать при работе с расплавленным металлом и деревом
— Оставайтесь в безопасности. Это расплавленный металл, и он обязательно обожжет все, к чему прикасается. Держите руки и другую кожу покрытыми огнестойким материалом, например, кожаными перчатками и фартуком.Также убедитесь, что все детали устойчивы и не опрокинутся при нагревании или перемещении металла.