Бронза Термообработка — Энциклопедия по машиностроению XXL
В некоторых медных сплавах, обрабатываемых давлением (бериллиевая, алюминиевая и хромистая бронза), термообработка — закалка и старение — чрезвычайно эффективно повышает механические свойства сплава. [c.711]Двухфазные бронзы (а + у ) имеют повышенную прочность до 600 МПа, но пластичность заметно ниже 5 =(35.. 45)%. Эти сплавы упрочняются термообработкой и дополнительно легируются Ре, N1, Мп. [c.116]
Красноломкость может наблюдаться у пересыщенных твердых растворов при испытании в зоне температур облагораживания. Так, по нашим данным хромистая бронза при 400—500°С хрупка (ф = 4 %, 6=1 %) Если понизить способность хромистой бронзы к облагораживанию, то зона хрупкости сужается, а пластичность увеличивается. Испытания облагороженной (закалка с 980 °С и отпуск при 450 Х) и отожженной при 700 °С хромистой бронзы показали, что режим термообработки существенно влияет на красноломкость отожженный сплав значительно пластичнее.
ТАБЛИЦА 80. ВЛИЯНИЕ ТЕРМООБРАБОТКИ, ХИМИЧЕСКОГО СОСТАВА И ТЕМПЕРАТУРЫ НА ОТНОСИТЕЛЬНОЕ СУЖЕНИЕ ХРОМИСТОЙ БРОНЗЫ [c.183]
По табл. 8.4 для червяка принимаем сталь 40Х с термообработкой улучшение заготовки до твердости 269…302 НВ и закалка т.в.ч. до твердости поверхности витков 45…50 ННСэ. Витки шлифуют и полируют, так как выбранная бронза имеет пониженные противозадирные свойства. [c.227]
Скорость коррозии бронзы с 7—9% А1 при об. т. и доступе воздуха в зависимости от способа термообработки [c.387]
Для закалки трубок перед формовкой в сильфоны трубки нагревают в атмосфере диссоциированного аммиака. Отформованные из трубок бериллиевые сильфоны и сильфоны из бронз Бр.БНТ для придания им высоких упругих свойств, прочности и твердости подвергаются особому виду термообработки — облагораживанию.
Термическая обработка трубок из фосфористой бронзы состоит из отжига перед вытяжкой и отжига перед формованием трубок в сильфоны. Целью термообработки является снятие наклепа после глубокой вытяжки и обеспечение достаточных пластических свойств перед формованием. [c.95]
Термообработка трубок аналогична термообработке трубок из фосфористой бронзы. Промежуточная термообработка ведется при нагреве до 600—650° С, выдержка в печи 30—40 мин. Охлаждение на воздухе. [c.96]
К четвертой группе относят металлы, рекомендуемые для использования при температурах ниже —196°С. Для работы при таких температурах пригодны лишь высоколегированные стали, содержащие обычно 18—20 % хрома и 9—14 % никеля. Перспективными в этой области являются также алюминиевые сплавы. Улучшаемые термообработкой алюминиевые сплавы, содержащие до 14 % меди, используют при температурах до —253 °С. Применяют сплавы, содержащие 6 % меди и 0,15 % циркония, титановые сплавы на основе а-фазы, бериллиевую бронзу.
Материалы для шарикоподшипников. Кольца подшипников изготавливают из сталей ШХ, реже из сталей У10, У12, ЭИ 347 Ш, из бериллиевой бронзы, которая после термической обработки приобретает твердость, близкую к твердости закаленной стали, так, например, твердость стали после термообработки HR 55—60, а бериллиевой бронзы HR 43—45. [c.48]
НИКОВ С ТОЛСТЫМИ стенками и крупногабаритных с пористым слоем, расположенным на внутренней поверхности подшипника. В последнем случае пористый слой спекается под действием центробежных сил. Напеченный слой бронзы затем подвергается четырехкратной вакуумной пропитке водной суспензией фторопласта, что обеспечивает удовлетворительное заполнение пор. Термообработка фторопласта состоит из промежуточной сушки при 90 °С в течение 2 ч и спекания при 370 С в течение 1 ч. [c.45]
Бронза Бр.АЖ9-4 имеет температуру заливки 1120—1140° С при литье в кокиль и 1060—1100″ С при литье в землю.

Бериллиевая бронза поддается электросварке при использовании металлических и угольных электродов, дуговой сварке в атмосфере инертного газа и шовной сварке методом сопротивления, а также пайке серебром и мягкими припоями. Однако газовая сварка и пайка твердыми припоями (бронзой) не дают удовлетворительных результатов. Поскольку температуры, при которых производят все виды сращивания бериллиевой бронзы, за исключением пайки мягкими припоями, превышают температуры термообработки, после термообработки сварку производить нельзя. [c.71]
К сожалению, из-за недостатка экспериментальных данных учесть перечисленные факторы при расчете передач винт-гайка в настоящее время не представляется возможным. Допускаемое давление [р] условно определяют только в зависимости от термообработки винта, выполняемого обычно стальным, и материала гайки. В частности для пар закаленная сталь-бронза, 10… 15 МПа, незакаленная сталь — бронза 7… 8 МПа, незакаленная сталь — чугун
[c.396]
Оловянные бронзы имеют высокие антифрикционные свойства и коррозионную стойкость. Бронзы алюминиевые и кремнистые обладают высокими механическими свойствами и коррозионными свойствами, дешевле оловянных. Марганцовистые бронзы имеют хорошую коррозионную стойкость и повышенную жаропрочность. Бериллиевые бронзы после термообработки приобретают прочность, сопоставимую с прочностью стали. Химический состав типовых марок меди и ее сплавов приведены в табл. 12.8. [c.454]
Никель резко смещает однофазную область а при понижении температуры в сторону медного угля и придает возможность облагораживания алюминиевых бронз термообработкой. Никель повышает механические, физические и эк плyaтaциon Iыe свойства.
Для червячных колес из безоловяни тых бронз и латуней (II группа) н чугуна (III группа) допуск емые контактные напряжения, при которых обеспечивается сопр тпвление заеданию, выбирают в зависимости от скорости сколь) гния, материала червяка и его термообработки по табл. 1.11. [c.19]
Произвести проверочный прочностный расчет червячной передачи редуктора строительного полноповоротного крана Пионер грузоподъемностью 5000 И (500 кгс). Усилие в канате, наматываемом на барабан диаметром 160 мм, составляет 2500 Н (при двухкратном полиспасте). Червячное колесо, закрепленное на одном валу с барабаном, изготовлено из бронзы АЖ 9-4, имеет гг = 27, т = 8 мм, ширину венца ba=60 мм. Червяк архимедов одиозаходный из стали Ст 5 ГОСТ 380—71, термообработка — нормализация, шлифованный, частота вращения п,= = 1460 об/мин.
Материалы. Тела качения и кольца изготовляют из высокоуглеродистых хромистых подшипниковых сталей ШХ15, ШХ15СГ и других с термообработкой до твердости ННСбО.. . 65 и последующими шлифованием и полированием. Сепараторы чаще всего штампуют из низкоуглеродистой листовой стали. Для быстроходных подшипников изготовляют массивные сепараторы из бронзы, латуни, текстолита, капрона и т. п. [c.418]
Широко применяют среднеуглеродистую качественную сталь 45 и 50, легированную сталь 12ХНЗА, 40Х, 40ХН и др. Посредством термообработки обеспечивают высокую твердость червяка HR 45, при венце червячного колеса из безоловянной бронзы такая твердость необходима в случае оловянных бронз допустима и меньшая твердость, но целесообразнее применять червяки высокой твердости, так как при этом нагрузочная способность передачи повышается.
В качестве материала червяка принимаем сталь 45, термообработка-закалка материал колеса — бронза БрОФ10-1, отливка заготовки в кокиль. Допускаемое контактное напряжение [о, ] = = 190 МПа. [c.384]
Решение. 1. Материалы винта и гайки. Для винта принимаем сталь 45, термообработка — улучшение (по табл. 8.4 От = 540 Н/мм ), для гайки— бронзу БрО10Ф1. [c.204]
Антифрикционные свойства. Зависимость коэффициентов трения от величины нагрузки при трении стали по бронзе никель фосфорному н хромовому покрытиям приведена на рис 6 Как видно из приведенных кривых, возрастание коэффициента трения для никель фосфорных покрытий наблюдается при повышении нагрузки свыше 6 О, а для хромовых покрытий после 6.5 МПа Довольно низкие коэффициенты трения ннкель-фосфорных покрытий объясняются, в частности, их хорошей прирабатываемостью Приме нение смазочного материала существенно снижает силу трения Важное значение имеет определение максимальных нагрузок до заедания, выдерживаемых никель фосфорными покрытиями Эти характеристики получены при использовании машины трения 77МТ 1 в условиях возвратно-поступательного движения при смазке маслом АМГ 10 и комнатной температуре Величина предельных нагрузок до заедания выдерживаемых никель фосфорными покрытиями существенно возрастает после часовой термообработки в интервале температур 300— 750 °С и доходит до 42 МПа
15]
Один из таких элементов — контактная пружина из фосфорной бронзы. Она изготовляется из листового материала, прокатанного с целью получения определенной толщины и твердости материала. Для установки пружины на посадочное место термокомпрессионным методом ее конец должен быть термически обработан для снижения твердости. Обычно это делается с помощью специальных приспособлений (масок) в печах, однако в этом случае на небольших деталях очень трудно локализовать процесс термообработки. Импульсное лазерное технологическое оборудование позволяет подводить строго дозированное количество тепловой энергии к тому участку детали, который нуждается в отпуске [82]. Участок обрабатываемой пружины, подлежащий отпуску, имеет следующие размеры толщина 0,2 мм, ширина 0,7 мм и длина 2,54 мм. Обработка концов пружины проводилась импульсами на алюмоиттриевом гранате с энергией до 16 Дж при длительности импульсов 10 мс и 20 мс. Диаметр пятна фокусирования излучения составлял 0,7 мм. Энергия импульса 16 Дж являлась пороговым значением, выше которого начинался процесс нежелательного плавления материала. Испытания пружины, обработанной лазерным излучением, дали положительные результаты, что свидетельствует о перспективности использования импульсных ОКГ для выполнения операций разупрочнения материала.
[c.112]
Алюминиевая бронза, содержащая > 8 % А1, имеет очень хорошие прочностные характеристики и хорошую коррозионную стойкость при условии, что сплав не содержит богатой алюминием «у-фазы, которая очень чувствительна к селективному коррозионному деалюминирова-нию. Чтобы понизить опасность возникновения 1)-фазы, следует обеспечивать подходящие условия термообработки и сварки материала. Опасность можно понизить также, вводя в сплав добавки никеля, железа и марганца. Никельалюминиевая бронза является прочным и коррозионностойким материалом, который хорошо зарекомендовал себя для морских применений, например судовых винтов, кранов и трубных досок в теплообменниках. [c.137]
В до X — от об. до 90°С в растворах с концентрацией до 80%. Алюминиевые бронзы устойчивее меди и большинства ее сплавов. Например, в 5—6%-ной аэрированной h3SO4 при 20°С для меди У м = 16 г/м -24 ч, для красной латуни с 9% Sn, 3,6% РЬ и 2,3% Zn Уп = 14 г/м2-24 ч, для фосфористой бронзы с 11,3% Sn VoM = 9,8 г/м -24 ч, для алюминиевой бронзы с 10,6% А1 Упм = 3,5 г/м -24 ч. Большое значение для устойчивости алюминиевых бронз имеет термообработка.
[c.386]
Долговечность аксиально-поршневых гидромашин в основном зависит от работы деталей распределительных и поршневых устройств. Эти пары, как правило, изготовляют из высококачественных материалов с соответствующей термообработкой. Так, например, в гидромашине бескарданного типа 210.25 блок цилиндров изготовлен из высокооловянистой бронзы БрО—12 или БрОЦСб—б—3, а распределитель и поршни — из азотированной стали 38Х2МЮА. Несмотря на качественное изготовление указанных деталей, составляющих пары трения скольжения, они все же имеют ограниченную износостойкость. К тому же применение дефицитной бронзы значительно удорожает производство, так как масса деталей из нее в разных моделях гидромашин колеблется от 2 до 8 кг. Поэтому возникла актуальная задача, связанная не только с повышением износостойкости ответственных пар трения гидромашин, но и с подбором более дешевых материалов [27].
[c.193]
Удельный вес наполненных фторопластов зависит от удельного веса применяемого наполнителя и его количества с увеличением количества наполнителя удельный вес композиции возрастает. Однако избыток наполнителя может вызвать увеличение пористости и, как следствие, уменьшение удельного веса материала. Наибольшим удельным весом обладают фторопласты, наполненные бронзой, дисульфидом молибдена, медью (при содержании меди 50% удельный вес композиции — 4,84 Г1см ). Зная удельный вес фторопласта и наполнителя, можно рассчитать теоретический удельный вес композиции и, замерив истинный удельный вес, определить пористость материала. Удельный вес наполненных фторопластов зависит также от режима прессования и термообработки. [c.190]
Рабочая поверхность шеек подлежит термообработке, если подшипники имеют заливку из свинцовистой бронзы (см. гл. VIII). Требуемая твёрдость поверхности около 300 Нв или 30 R -
[c.502]
Коренные и кривошипные шейки нала цементуются и закаливаются, если подшипники имеют.заливку из свинцовистой бронзы. При подшипниках с баббитовой заливкой шейки оставляют без термообработки. [c.502]
Пружины из бериллиевой бронзы (табл. 7 и 9) обязательно подвергаются термообработке, состоящей из а) длительного постепен-ногб нагрева до температуры 800° под закалку, [c.662]
Для термически необработанных винтов применяют сталь марок 45 50 Ст5. Если материал подвергается термообработке (закалка и высокотемпературный отпуск), применяют сталь 45, 50, 40Х и 65Г. Гайки изготовляют из бронзы БрОФ 6,5-0,15 БрОФ 10—1 БрОЦС 6—6—3 БрАЖЭ—4 из чугуна антифрикционного АСЧ—I, АВЧ—1, АКЧ—2. [c.238]
Хорошие антифрикционные свойства перлито-ферритных ковких чугунов не зависят от способа изготовления последних повышенного содержания марганца в металле перед заливкой его в формы ускоренного охлаждения при 2-й стадии графитизации (700—760°) применения последующей термообработки—нормализации уже готовых отливок из ковкого чугуна после отжига получения ковкого чугуна из вагранки или дуплекс-процессом. Поэтому наш вывод распространяется на все перлито-ферритные ковкие чугуны, независимо от способа их изготовления. Это обстоятельство имеет весьма большое практическое значение, позволяя заводу применительно к его производственным возможностям изготовлять для своих нужд тем или другим способом антифрикционный ковкий чугун как заменитель бронзы. Исключение составляет сферои-дизованный ковкий чугун, который нельзя рекомендовать в качестве антифрикционного материала, так как в ряде случаев износ стального кольца (вала) превышает износ образца (втулки).
[c.348]
Кольца изготовляют из материала, обладающего достаточной упругостью и антифрикционными свойствами. Распространены кольца из серого чугуна твердость колец после термообработки 98—106 НВ. Модуль упругости материала колец должен находиться в пределах (9—10) X X 10 кПсм . Применяются также кольца из бронзы, текстолита, графита и металлографитовой массы. [c.503]
Свойства бериллиевон бронзы зависят от условий холодной обработки давлением и термообработки, как это показывают приведенные в табл. 15 данные, характеризующие высокопрочный материал 130]. Закалку высокопрочных бериллиевых бронз на твердый раствор проводят при 788° с последующим состариванием в интервале температур 316—343° бронзы с высокой электропроводностью закаливают при 927°, а состаривают в интервале температур 454—482°.
[c.71]
бронзы, баббиты. Влияние термообработки на степень упрочнения сплавов
Использование операций термической обработки сталей и сплавов существенно повышает степень фрикционного упрочнения и долговечность работы в условиях трения и износа. В таблице 2 приведены составы литейных бронз, применяемые для антифрикционных деталей. ( одержание фосфора в бронзе Бр08Ф — 0,25…0,35 %, а в бронзе БрОбФ — 0.1…0,15%.
Влияние термообработки на степень упрочнения сплавов
Сплав | Вид термической обработки | Степень фрикционного упрочнения |
Алюминиевый сплав АК7 | Т5 — закалка и старение | 1,2…1,3 |
Цинковый сплав ЦАМ 10-5 | Состояние поставки | 1,3…1,6 |
Сталь 30ХГСА | Изотермическая закалка | 2,9…3,6 |
Бронза БрОЮФ1 | Литое состояние | 2,1…2,6 |
Серый чугун СЧ 20 (0,1 % Р) | Без термообработки | 3,1…3,6 |
Сталь 45Л, 40JI | После закалки и отпуска | 4,0…4,6 |
Сталь 40ХФЛ | После закалки и отпуска | 4,8…5,3 |
Медь Ml | После отжига | 2,6…2,9 |
Ковкие чугуны КЧ 60-5, | Нормализация | 3,9…4,1 |
КЧ 45-7 | ||
Высокопрочные чугуны | После отжига | 2,4…3,5 |
АЧВ-1, АЧВ-3 | Литое состояние | 3,4…4,4 |
АЧВ-2, АЧВ-4 | Нормализация | 4,5…5,2 |
Свинец | Состояние поставки | 1,0…1,1 |
Графитизированная сталь | После отжига и нормализации | 4,9…5,7 |
Чугун ВЧ 100 | Изотермическая закалка и отпуск | 5,1…5,8 |
Чугун ВЧ 70 | Нормализация | 4,2…4,8 |
Составы и свойства бронз для антифрикционных деталей
Марка | Состав, % (Си — остальное) | Предел прочности, МПа | Относи- | Твердость | ||||||
Sn | Zn | Pb | А1 | Fe | Mn | Ni | удлинение, % | НВ | ||
Бр08Ф | 7…8 | — | — | — | — | — | — | — | — | — |
БрОбФ | 6…7 | — | — | — | — | — | — | 250…350 | 2 | о оо о |
Бр04Ц4С2 | 3…5 | 3…5 | 1,5…3,5 | — | — | — | — | 350 | 15…20 | 60 |
Бр04Ц4С 17 | 3…5 | 2…5 | 14…20 | — | — | — | — | — | — | — |
БрА10М2Ц | — | — | — | 9… 11 | — | 1,5…2,5 | — | 500 | 12 | 120 |
БрА9Ж4 | — | — | — | 8…10 | 3,5…5,5 | — | — | 500 | 10 | 100 |
БрА10Ж4Н4 | — | — | — | 9…11 | 3,5…5,5 | — | 3,5…5,5 | 600 | 5 | 170 |
Применение смазочного материала в узле трения может повлечь за собой необходимость замены материала по крайней мере одной из трущихся деталей, что связано с изменением вида изнашивания и, как следствие, с иным расположением пар трения по износостойкости. В амортизационных устройствах шасси самолетов в качестве рабочей жидкости применяли спиртоглицериновую смесь, при использовании которой в качестве смазочного материала буксы из бронзы БрАЖМц в паре со стальной поверхностью быстро изнашивались. Бронза интенсивно обогащалась медью, налипала на стальную поверхность, наращивалась на ней толстым слоем и отлушивалась, частично при этом налипая на поверхность буксы.
Бронзы других марок вследствие избирательного переноса при трении во много раз более износостойки. Переход на бронзу типа БрОФ является целесообразным, однако существенной разницы в износостойкости безоловянной бронзы БрАЖМц и бронзы БрОФ при трении по стали и смазывании АМГ-10 не установлено. Для букс амортизаторов, работающих на этой жидкости, рентабельнее использовать бронзу БрАЖМц.
Бронзы и латуни применяют для сложных нажимных винтов, венцов червячных колес, сепараторов подшипников и деталей судо- и авиастроения при литье в кокиль, под давлением, в песчано-глинистые формы, жидкой штамповкой и др. Значительное развитие получили методы точного литья, применение которых позволяет получать детали по безотходной технологии, не требующие дальнейшей механической обработки.
Бронзы и латуни выплавляют, как правило, в индукционных тигельных (при производстве оловянных бронз) и индукционных канальных (при производстве безоловянных бронз и латуней) печах. Для снижения содержания примесей в медных сплавах используются методы обработки флюсами, фильтрации и раскисления, обеспечивающих снижение газов и неметаллических включений в литых изделиях.
Для улучшения прирабатываемости в бронзу вводят свинец, который снижает ее твердость и увеличивает пластичность. Оловянно-цинково-свинцовую бронзу Бр04Ц4С17 применяют в виде холоднокатаных лент для изготовления тонкостенных втулок. Бронзы типа БрАЖН имеют повышенную твердость и применяются для деталей, работающих при высоких температурах (например, из них изготовляют направляющие выпускных клапанов двигателей внутреннего сгорания). Направляющие впускных клапанов изготовляют из бронзы типа БрАЖ твердостью 70… 100 НВ.
Свинец в свинцовых бронзах находится в виде отдельных включений равномерно распределенных в матрице. Эти бронзы имеют хорошие антифрикционные свойства и применяются в подшипниках с высокими нагрузками и скоростями скольжения. Для лучшей прирабатываемости такие подшипники электролитически покрывают тонким слоем свинца; для устранения возможной коррозии подшипников из свинцовой бронзы в смазочное масло вводят противоокислительные присадки. Толщина заливки вкладышей подшипников бронзой 0,5…0,8 мм. Рабочую поверхность подшипников растачивают алмазным или твердосплавным резцом.
Подшипниковые материалы из мягких металлов Sn, Pb, Cd, Sb, Zn, характеризующиеся наличием твердых структурных составляющих в пластичной матрице, называют баббитами. Их заливают на подогретые вкладыши (250 °С) при температуре сплава 450…480 °С. Чаще применяют центробежную заливку. Заливают в кокиль и под давлением; толщина отливки в подшипниках 1…3 мм. Баббиты имеют высокие антифрикционные свойства, хорошо прирабатываются, имеют низкий коэффициент трения при граничной смазке, способны работать при попадании небольшого количества абразивных частиц в зазор подшипника. Твердость вала при работе с баббитовыми подшипниками должна быть 25…35 HRC. Для по- лучения долговечности подшипников твердость валов увеличивают до М)…55 HRC.
Из подшипниковых сплавов хорошо изучены и широко применяют ся высокооловянистые баббиты, структура которых подчиняется принципу Шарпи: в мягкой матрице (в-Sn) распространены твердые частицы (Pb, Sn, CuSn). Такая структура способствует повышению антифрикционных свойств сплава. Однако классические подшипниковые сплавы,
структура которых удовлетворяют принципу Шарпи, оказались непригодными для биметаллических подшипников с тонким слоем заливки баббита. В то же время отметим, что принцип Шарпи, сформулированный применительно к цветным сплавам, в дальнейшем был распространен на износостойкие чугуны и стали.
Недостатком баббитов является их малое сопротивление усталости, особенно при повышении температуры более 100 °С. С уменьшением толщины заливки подшипника и повышением жесткости системы вкла- дыш постель вкладыша сопротивление усталости увеличивается. Минимальная толщина заливки баббита допускается 0,25…0,4 мм.
Для экономии олова разработаны низкооловянные баббиты, которые имеют несколько худшие антифрикционные свойства по сравнению с высокооловянными. В таблице 3 приведены составы и свойства оловянных и свииицовых баббитов.
Составы и свойства баббитов
Марка баббита | Состав, % | Твер- | Плот- | Предел прочности, МПа | Относительное удлинение, % | |||||||||
Sn | Sb | Си | РЬ | Са | As | Cd | Na | А1 | дость НВ | ность, г/см3 | при растяже нии | при сжа тии | ||
Б83 | 82… 84 | 10… 12 | 5,5… 6,5 | 0,3 | — | — | — | — | — | 30 | 7,3 | 90 | 115 | 60 |
Б16 | 15… 17 | 15… 17 | 1,5… 2,0 | 64… 68 | — | — | — | — | — | 30 | 9,5 | 80 | 120 | 2 |
БС6 | 5…6 | 5…6 | 0,1… 0,3 | 88…90 88…90 | — | — | — | — | — | 16 | — | 68 | 100 | 12 |
БН | 9…11 | 13… 15 | 1,5… 2,0 | 70… 75 | 1,2… 1,7 | 0,5… 0,9 | 0,1… 0,7 | — | — | 30 | 9,5 | 70 | 130 | 17 |
БКА | — | — | — | 98… 99 | 0,9… 1,2 | — | — | 0,6… 0,9 | 0,1… 0,2 | 30 | 105 | 80…100 | 120… 150 | 25…30 |
Высокие антифрикционные свойства позволяют получить технологические процессы облучения цветных сплавов и литья биметаллических и многослойных изделий.
Применение биметаллических и многослойных изделий, в которых достигается сочетание требуемых свойств, дифференцированных по объему и поверхности — одно из перспективных направлений рационального использования материалов в различных отраслях промышленности. Основной причиной, сдерживающей более широкое применение биметаллов, является получение качественного соединения компонентов по всей поверхности.
Авторами предложен принципиально новый способ получения биметаллических заготовок, в котором соединение компонентов в заготовках происходит в жидкофазном состоянии без перемешивания. Получены образцы биметаллов Al-Sn, Al-Pb, Pb-Sn, Sn-Zn, Al-Pb. Металло- графические исследования показали наличие четкой волнообразной границы раздела в биметаллических образцах Al-Sn, Al-Zn, Al-Pb, Pb-Sn и размытой в образце Sn-Zn. В обоих случаях достигнуты высокая плотность и сплошность соединения компонентов. Методом дюрометриче- ского анализа биметаллических образцов обнаружено наличие диффузионной зоны в Al-Sn шириной 0,2…0,3 мм; в Al-Zn — 0,5…0,6 мм. В образцах Аl-Рb и Pb-Zn диффузионная зона не выявлена. В образцах Zn-Sn ярко выраженной поверхности раздела нет. Результаты рентгеноструктурного анализа и ультразвукового зондирования подтвердили наличие диффузионной зоны в образцах Аl—Sn, Al-Zn и ее отсутстние у Рb-Аl. Полученные результаты позволяют перейти к теоретическим и экспериментальным исследованиям по литью биметаллических заготовок цилиндрического профиля для деталей типа втулок, валов и т.п.
Для исследования свойств композитов предложен новый метод ультразвукового зондирования, позволяющий возбуждать в исследуемом звукопроводе как объемную, так и приповерхностную акустические волны.
Разработанное устройство является преобразователем торцового типа. Пьезоэлектрическая пластина с напаянным на нее электродом крепилась на торце прямоугольной призмы исследуемого образца биметалла, параллельно поверхности контакта металлов. Как показали исследования, для нормальной работы преобразователя необходимо, чтобы электрод пьезопластины располагался напротив одного из ребер образца, а его ширина стремилась к нулю.
В описанном устройстве использовался преобразователь из калийнатриевого ниобата, связанный при помощи эпоксидного компаунда. Этот пьезоэлектрический материал интересен тем, что обладает высокой.
диэлектрической проницаемостью. Длина электрода выбиралась порядка 20Х, где X — длина волны; устройство работало на центральной частоте 60 МГц; акустический импульс имел ширину 0,1 мм.
Режимы эксплуатации литых композитов и многослойных изделий, работающих в условиях трения и изнашивания, чрезмерно многообразны, а прогнозирование их износостойкости представляется весьма сложной задачей в связи с многочисленностью определяющих ее факторов. Важнейшими из них являются: удельные нагрузки, условия смазки, условия теплоотвода, скорость и характер взаимодействия материалов пары между собой, со средой и продуктами износа; структура и свойства изнашиваемого материала.
Широкое применение серого износостойкого чугуна в машиностроении обусловлено его многими ценными качествами: высокими литейными, антифрикционными и прочностными свойствами, хорошей обрабатываемостью, высокой стойкостью, способностью поглощать вибрации благодаря высокой циклической вязкости и усталостной прочностью. При этом требования к качеству серого чугуна, его прочностным, технологическим и служебным свойствам с каждым годом ужесточаются. Постоянно повышаются требования к структуре металлической матрицы и учитывается температура эвтектического превращения чугуна при его микролегировании. На рисунке показаны изменения температуры эвтектических превращений чугуна в зависимости от его микролегирования РЗМ.
Влияние микролегирования РЗМ на температуру эвтектического превращения (проба 0 20 мм) в фосфористых чугунах:
1 — 0,08 % Р, без РЗМ; 2 — 0,08 % Р и 0,03 % РЗМ; 3 — 0,08 % Р и 0,07 % РЗМ; 4 — 0,07 % Р и 0,16 % РЗМ; 5 — 0,16 % Р, без РЗМ; б — 0,16 % Р и 0,03 % РЗМ; 7 — 0,16 % Р и 0,08 % РЗМ; 5-0,16 % Р и 0,16 % РЗМ
В качестве комплексной характеристики многокомпонентного химического состава чугуна наибольшее распространение получила степень эвтектичности (Sc), которой многие исследователи придают определяющую роль при установлении зависимости состав-свойства. Однако объективное представление о структуре чугуна может быть получено только при совместном рассмотрении всех процессов ее формирования, прежде всего кристаллизации и перекристаллизации. Поэтому для производства высококачественных чугунов важен контроль не только химического состава, но и количественного соотношения первичного аустенита, графита, эвтектики, неметаллических включений и примесей, так как именно эти параметры позволяют установить пока еще неизвестные соотношения между составом, структурой и свойствами. При этом необходимо отметить, что фазовый состав и их структурные составляющие опреде- ляют физико-механические свойства серого износостойкого чугуна в значительно большей степени, чем, например, химический состав. Значительное распространение износостойких чугунов объясняется тем, что особенности их структуры позволяют в широких пределах регулировать надежность, долговечность и эксплуатационные свойства в литых изделиях. В таблице приведен средний износ образцов из различных литейных сплавов, используемых в промышленности, в зависимости от характера трения и структуры.
Средний износ образцов из литейных сплавов
Материал | Твер дость НВ | Структура | Средний износ образцов, г | |
Трение без смазки | Трение со смазкой | |||
Чугун с шаровидным графитом, нормализованный | 236 | Сорбитизирован- ный перлит, феррит (20 %) | 0,053… 0,067 | 0,0015… 0,0345 |
Чугун с шаровидным графитом, после закалки | 257 | Троостит, феррит (30 %), аустенит (15 %) | 0,02 | 0,0011 |
Чугун с шаровидным графитом, после закалки с отпуском | 263 | Троостит, сорбит, феррит (20%) | 0,0329 | 0,00205 |
Твер | Средний износ образцов, г | |||
Материал | дость НВ | Структура | Трение без смазки | Трение со смазкой |
Чугун с шаровидным графитом, после изотермической закалки | 241 | Троостит, феррит (30 %), аустенит (30 %) | 0,012 | 0,0006 |
Латунь ЛЦ40С Бронза БрОЮФ1 | 75 90 | а+в а+в | 2,975 2,86 | 0,00114 0,00105 |
Ковкий чугун с зернистым перлитом | 163… 187 | Зернистый перлит и углерод отжига | 0,04… 0,2 | 0,002… 0,029 |
Термоулучшенный высокопрочный ковкий чугун | 285 | Бейнит, зернистый перлит (20 %) | 0,03 | 0,007 |
Литейные сплавы, приведенные в таблице при испытании в условиях интенсивного абразивного изнашивания в соответствии с методом по ГОСТ 17367-88 и в условиях гидроабразивного изнашивания показали низкую износостойкость. Высокую износостойкость в таких условиях имели легированные белые чугуны.
Контроль твёрдости изделий из бериллиевой бронзы
Автор статьи: Кадышкин Б.А.
октябрь 2013 г.Санкт-Петербург
Бериллиевая бронза БрБ2 дисперсионно-твердеющий сплав, в закаленном состоянии мягкий и высокопластичный.
После искусственного старения бронза приобретает высокую твердость, высокий предел упругости, усталостной прочности и высокой износостойкости.
Химический состав бронзы БрБ2 (ГОСТ 493-54):
Be | Ni | Al | Cu | Примеси, не более | |||
Si | Pb | Fe | |||||
% | 1,9-2,2 | 0,2-0,5 | 0,15 | ост. | 0,15 | 0,005 | 0,15 |
Твердость бронзы, поставляемой в виде полосы различной толщины, в различном состоянии имеет следующие значения (ГОСТ 1189-70):
- после закалки – HV ≤ 130
- после закалки и наклепа – HV ≥ 170
- после закалки и старения — HV ≥ 320
- после закалки, наклепа и старения — HV ≥ 360
Закалка изделий из БрБ2 производится с температуры 110-190 °С в воду.
Нагрев под закалку тонкостенных изделий толщиной ≤ 0,5 проводится в заневоленном состоянии (специальная технологическая оснастка).
Перегрев при закалке изделий из бронзы БрБ2 приводит к снижению их упругости и прочностных свойств, повышению хрупкости материала из-за увеличения размера зерна, и оплавление границ зерен. Недогрев при закалки изделий из бронзы приводит к недостаточной концентрации бериллия в α-растворе, что после старения снижает предел упругости и твердости.
Упрочнение бронзы при старении происходит за счет выделения в ее структуре мелкодисперсионной фазы (Cu, Be) из неравновесного твердого раствора α-фазы.
Старение изделий из бронзы БрБ2 при температуре более высокой (˃ 340-360 °С) приводит к коагуляции частиц -фазы, что приводит к снижению механических свойств материалов.
Контроль качества т/обр (старение) изделий из бериллиевой бронзы БрБ2 производится измерением твердости (HV) этих изделий.
Контроль твердости изделий толщиной ≥ 2 мм производится либо на стационарных твердомерах измерения HV при нагрузке 5 кг, либо на портативных ультразвуковых твердомерах. Следует отметить, что этот контроль можно производить по измерению электропроводности изделий.
При контроле твердости изделий толщиной ≤ 0,2 мм необходимо исключить затраты энергии вдавливаемого индентора на линейную деформацию контролируемого участка, которая функционально не связана с твердостью контролируемого материала и определяется только его размерами (толщиной, профилем, массой) и величиной прилагаемой нагрузки.
Для исключения дополнительных потерь механической энергии индентора на линейную деформацию контролируемого участка (стационарным твердомером, ультразвуковым твердомером) необходимо использовать под контролируемым участком изделия подложку с высокой твердостью (HRC ≥ 55 или HV ≥ 750).
При измерении электропроводности контролируемого изделия необходимо выполнить следующие требования: температура контролируемого изделия должна соответствовать температуре контролируемых образцов по электропроводности (прилагаются к прибору), тонкостенные изделия (контрольные образцы) при измерении их электропроводности укладываются на изоляционную подложку, для контролируемого участка малых размеров для исключения краевого эффекта необходимо обеспечить строгое позиционирование датчика прибора относительно контролируемого участка (разработка и изготовление технологических насадок на датчик прибора, изготавливается из непроводящего материала – текстолит, эбонит и т. п.)
Для примера на рис.1 приведены зависимости электропроводности и сигнала датчика УЗ твердомера образцов бериллиевой бронзы (∅ 25, h = 3 мм) от времени их старения при оптимальной температуре.
Видно, что изменение электропроводности бронзы БрБ2 более надежно и объективно отслеживает время старения образцов БрБ2.
На рис.2 приведена зависимость сигнала датчика ультразвукового твердомера ТКМ-459 от твердости образцов из бронзы БрБ2 толщиной 0,15-0,2 мм. Наблюдается высокозначимая зависимость (R2 …), при этом для толщин 0,15-0,2 мм можно практически пренебречь разницей в толщине этих образцов.
На рис.3 приведены зависимости электропроводности МСим∙м (в отн. ед.) от твердости образцов бронзы толщиной 0,15-0,2 мм.
Наблюдается существенная разница этих зависимостей от толщин контролируемого образца, что связано с большой глубиной проникновения вихревых токов датчика прибора ВЭ27НЦ (δ ≈ 1,2-1,5 мм).
Однако, даже в этом случае четко различаются образцы с твердостью (HV) HV ≤ 250 от образцов с твердостью HB ≥ 200.
Выводы:
- Отработана методика контроля твердости (HV) изделий из БрБ2 толщиной 0,15-0,2 мм с помощью ультразвуковых портативных твердомеров.
- Установлена принципиальная возможность использования вихретокового метода измерения электропроводности для контроля качества т/об (старения) с оценкой твердости (HV) изделий из бериллиевой бронзы БрБ2.
По вопросам и предложениям обращайтесь по телефону +7 (812) 640-40-13
СВОЙСТВА БРОНЗ
БРОНЗЫ и БРОНЗОВЫЙ ПРОКАТ
Классификация бронзовых сплавов
Бронзами называются сплавы на основе меди, в которых основными легирующими элемен-тами являются олово, алюминий, железо и другие элементы (кроме цинка, сплавы с которым относятся к латуням). Маркировка бронз состоит из сочетания «Бр», букв, обозначающих основ-ные легирующие элементы и цифр, указывающих на их содержание.
По химическому составу бронзы классифицируются по названию основного легирующего элемента. При этом бронзы условно делят на два класса: оловянные (с обязательным присут-ствием олова) и безоловянные.
По применению бронзы делят на деформируемые, технологические свойства которых допускают производство проката и поковок, и литейные, используемые для литья. В то же время многие бронзы, из которых производится прокат, используются и для литья.
Химический состав и марки бронзовых сплавов определены в следующих ГОСТах:
Литейные: оловянные в ГОСТ 613-79, безоловянные в ГОСТ 493-79.
Деформируемые: оловянные в ГОСТ 5017-2006, безоловянные в ГОСТ 18175-78
Многообразие бронз отражает приведенная ниже таблица. В ней представлены практически все деформируемые и часть литейных бронз. Бронзы, используемые исключительно как литейные, помечены «звездочкой». В дальнейшем будут рассматриваться преимущественно деформируемые бронзы. Структура бронзовых сплавов кратко рассмотрена в — Структура и свойства сплавов.
ОЛОВЯННЫЕ БРОНЗЫ | ||||
БрО5* | БрОФ4-0.25 | БрОЦ4-3 | БрОС8-12* | БрОЦС4-4-2.5 |
БрО10* | БрОФ6.5-0.15 | БрОЦ8-4* | БрОС5-25* | БрОЦС4-4-17* |
БрО19* | БрОФ7-0.2 | БрОЦ10-2* | БрОС10-10* | БрОЦС5-5-5* |
БрОФ10-1* | БрОС6-15* | БрОЦС6-6-3* | ||
АЛЮМИНИЕВЫЕ БРОНЗЫ | ||||
БрА5 | БрАМц9-2 | БрАЖ9-4 | БрАЖМц10-3-1.![]() | БрАЖН10-4-4 |
БрА7 | БрАМц10-2* | БрАЖНМц10-4-4-1 | БрАЖН11-6-6* | |
КРЕМНИСТЫЕ | БЕРИЛЛИЕВЫЕ | КАДМИЕВЫЕ | МАГНИЕВЫЕ | ХРОМОВЫЕ |
БрКМц3-1 | БрБ2 | БрКд1 | БрМг0.3 (0.5 и 0.8) | БрХ0.8 |
БрКН1-3 | БрБ2.5 | БрКдХ0.5-0.15 | БрХ1 | |
БрКН0.5-2 | БрБНТ-1.9 | БрХ1Цр | ||
СЕРЕБРЯНЫЕ | ЦИРКОНИЕВЫЕ | СВИНЦОВЫЕ | МАРГАНЦЕВЫЕ | |
БрСр0.1 | БрЦр0.2 | БрС30* | БрМц5 |
Физические свойства бронзовых сплавов
Модуль упругости Е разных марок меняется в широких пределах: от 10000 (БрОФ, БрОЦ) до 14000 (БрКН1-3, БрЦр). Модуль сдвига G меняется в пределах 3900-4500. Эти величины сильно зависят от состояния бронзы (литье, прокат, до и после облагораживания). Для нагартованных лент наблюдается анизотропия по отношению к направлению прокатки.
Обрабатываемость резанием практически всех бронз составляет 20% (по отношению к ЛС63-3). Исключение составляют оловянно-свинцовые бронзы БрОЦС с очень хорошей обраба-тываемостью ( 90% для БрОЦС5-5-5).
Ударная вязкость меняется в широких пределах, в основном она меньше, чем для меди (для сопоставимости результатов все значения приведены для литья в кокиль):
БрОФ 10-1 | БрОФ 6.5-0.4 | БрАЖ 9-4 | БрА5 | Медь | БрМц5 |
БрОЦС 6-6-3 | БрОЦС 4-4-2.![]() | БрАЖМц | БрА7 | ||
БрОС 5-25 | БрОЦ4-3 | БрАМц 9-2 | БрКМц3-1 | ||
Значение ударной вязкости >> увеличение >> | |||||
1 – 3 | 4 – 6 | 6 – 8 | 15 – 16 | 16 – 18 | 20 |
Электропроводность большинства бронзовых сплавов существенно ниже, чем у чистой меди и многих латуней (значения удельного сопротивления приведены в мкОм*м):
БрКд | ||||||
Медь | БрМг | Л63 | БрОЦ4-3 | БрАМц | БрКМц | БрОФ7-0.![]() |
БрСр | БрЦр | ЛС59-1 | БрОЦС5-5-5 | БрА7 | БрАЖМц | |
БрХ | БрАЖ9-4 | БрАЖН | ||||
Значения удельного электросопротивления >> ухудшение электропроводности>> | ||||||
0.02 | 0.02 — 0.04 | 0.065 | 0.![]() | 0.1-0.13 | 0.15 | 0.19 |
Сопротивление серебряной бронзы (медь легированная серебром до 0.25%) такое же как у чистой меди, но такой сплав имеет большую температуру рекристаллизации и малую ползучесть при высоких температурах.
Низкое удельное сопротивление имеют низколегированные бронзовые сплавы БрКд, БрМг, БрЦр, БрХ.. Величина электропроводности имеет существенное значение для бронз, используемых для изготовления коллекторных полос, электродов сварочных машин, для пружинящих электрических контактов. Приведенные значения являются ориентировочными, т.к. на величину сопротивления оказывает влияние состояние материала. Особенно сильно оно может измениться под влиянием облагораживания (в сторону уменьшения, это касается БрХ, БрЦр, БрКН, БрБ2 и др.). Например электросопротивление БрБ2 до и после облагораживания составляют 0. 1 и 0.07 мкОм*м.
Теплопроводность большинства бронз существенно ниже теплопроводности меди и ниже теплопроводности латуней (значения приведены в кал/cм*с*С):
Медь | БрКд | БрКН1-3 | Л63 | БрАЖН | БрАМц | БрОФ10-1 | БрКМц |
БрСр | БрМг | БрА5 | ЛС59-1 | БрБ2 | БрАЖ | БрМц5 | |
БрХ | БрОЦ4-3 | БрАЖМц | |||||
Значения теплопроводности >> ухудшение >> | |||||||
0.![]() | 0.8-0.6 | 0.25 | 0.25 | 0.25-0.18 | 0.17-0.14 | 0.13-0.12 | 0.1-0.09 |
Высокую теплопроводность имеют низколегированные бронзы. Облагораживание улучшает теплопроводность. Высокая теплопроводность особенно важна для обеспечения отвода тепла в узлах трения и в электродах сварочных машин. Низкая теплопроводность облегчает процесс сварки бронзовых деталей.
Механические свойства бронзового проката
Если из всего разнообразия латуней массово производится прокат только двух марок (ЛС59-1 и Л63), то для массового производства полуфабрикатов из бронзы используется значительно большее количество марок. Бронзовый прокат включает в себя круги, трубы, проволоку, ленты, полосы и плиты.
Бронзовые круги
Бронзовые круги выпускаются прессованными, холоднодноформированными и методом непрерывного литья. Способ производства и диапазон производимых диаметров определяется технологическими свойствами конкретной бронзы. В таблице указано соответствие между марками бронз, диаметром прутка и способом производства.
Общее представление об основных механических свойствах бронзовых кругов дает следующая гистограмма.
Непрерывнолитые круги.
Методом непрерывного литья массово производятся БрОЦС5-5-5, БрАЖ9-4, реже БрОФ10-1 и БрАЖМц10-3-1.5. В изделиях, полученных этим способом, отсутствуют дефекты, характерные для литья в кокиль или песчаную форму. Поэтому по своим свойствам непрерывнолитые полуфабрикаты существенно превосходят отливки в кокиль и близки к прессованным полуфабрикатам.
Круги из БрОЦС5-5-5 и БрОФ10-1 имеют относительно гладкую поверхность, нарушаемую неглубокими вмятинами от тянущего устройства. Круги этих марок производятся только непрерывнолитым способом.
Круги из БрАЖ и БрАЖМц, полученные методом непрерывного литья, могут иметь на поверхности опоясывающие трещины глубиной до 1 мм. По твердости, прочности и пластичности непрерывнолитые круги незначительно уступают прессованным, антифрикционные свойства у них практически одинаковы, а стоимость их существенно ниже. При необходимости качественные круги больших диаметров (свыше 100 мм) и короткой длины можно отливать методом центробежного литья.
Прессованные и холоднодеформированные круги.
Они производятся по ГОСТ 1628-78, а также ГОСТ 6511-60 (БрОЦ4-3), ГОСТ10025-78 (БрОФ6.5-0.15 и БрОФ7-0.2) и ГОСТ 15835-70 (БрБ2) и многочисленным ТУ.
Массово производятся и имеются в свободной продаже прессованные круги из БрАЖ9-4 диаметром 16-160 мм.
Доступны также круги из БрАЖМц10-3-1.5, БрАЖН10-4-4 и БрАЖНМц9-4-4-1, но они значительно дороже. Прессованные круги других марок выпускаются под заказ.
Холоднодеформированные (тянутые) круги выпускаются в разном состоянии поставки диаметром до 40 мм. На гистограмме представлены данные для прутков из БрОЦ4-3. БрКМц3-1, БрОФ7-0.2 (твердое состояние), БрАМц9-2 (полутвердое состояние) и прутков БрБ2 в состояниях «М» и «Т» Следует отметить, что холоднодеформированные круги производятся под заказ и являются большим дефицитом.
Бронзовые трубы и заготовки для втулок
Прессованные трубы общего назначения производятся из БрАЖМц10-3-1.5, БрАЖН10-4-4 (ГОСТ 1208-90). Трубы специального назначения выпускаются из других марок по различным ТУ. Методом непрерывного литья выпускаются трубные заготовки из БрОЦС5-5-5, БрАЖ9-4, БрАЖМц10-3-1.5. Механические свойства труб практически совпадают с таковыми для соответствующих кругов.
Заготовки для втулок отливаются в кокиль или методом центробежного литья. При этом чаще используются марки БрАЖ9-4, БрОЦС5-5-5, БрОФ10-1, БрОЦ10-2.
Особенности свойств различных бронзовых сплавов
Выбор бронзы для использования в конкретных целях не определяется только величинами ?в и НВ, которые отражают лишь часть механических свойств. Выбор той или иной марки производится с учетом всего комплекса физических, механических, технологических и антифрикционных свойств, коррозионной стойкости, поведения при высоких или низких температурах и т.д. Ниже в таблице сопоставлены свойства и марки бронзовых сплавов.
Свойства | Марка бронзы |
Наибольшая электро- и теплопроводность | БрСр, БрКд, БрМг, БрЦр, БрХЦр, БрХ |
Жаропрочность | БрМц, БрАЖ, БрАЖМц, БрАЖН, БрАЖНМц |
Жаропрочность в сочетании с высокой электропроводностью | БрХЦр, БрХ, БрКН |
Износостойкость | БрОФ6. |
Износостойкость в сочетании с высокой электропроводностью | БрКд, БрМг |
Хорошая свариваемость | БрКМц3-1, оловянные бронзы |
Эрозионная и кавитационная устойчивость | БрАЖМц, БрАЖН, БрАЖНМц |
Высокий предел ползучести | БрА7, БрАЖН |
Сопротивление коррозионной усталости | БрБ2 |
ПРИМЕНЕНИЕ БРОНЗОВЫХ СПЛАВОВ В УЗЛАХ ТРЕНИЯ
(Антифрикционные бронзы)
Бронзы очень широко используются в качестве антифрикционных материалов. К числу бронз, которые импользуются в качестве антифрикционных материалов относится большинство оловянных (кроме БрОЦ4-3) бронз, а из безоловянных — БрАМц, БрАЖ, БрАЖМц, БрАЖН. Эти бронзы применяются главным образом для изготовления 1) опор подшипников скольжения, 2) колес (венцов) червячных передач и 3) гаек в передачах «винт-гайка».
Анти-фрикционные свойства составляют отдельную группу свойств и не связаны напрямую с их механическими свойствами. Антифрикционные свойства определяются свойствами поверхностного слоя, тогда как механические свойства определяются объемными свойствами материала.
Это неочевидное утверждение можно проиллюстрировать на примере двух бронз — БрС30 и БрАЖ9-4 при их использовании в подшипниках скольжения. БрС30 существенно уступает бронзе БрАЖ9-4 по всем механическим показателям (прочность, твердость, относительное удлиение). Однако, именно она применяется в особо ответственных подшипниках, допускающих высокие скорости и высокие нагрузки ( в т.ч. ударные).
Поэтому при выборе бронзы для использования в узлах трения учитывают прежде всего антифрикционные, а затем — механические свойства. Для этих целей массово используются круги и полые заготовки БрАЖ9-4 и БрАЖМц10-3-1.5 БрОЦС5-5-5, БрОФ10-1. Для направляющих используются катаные полосы из БрАМц9-2 и плиты (литые и отфрезерованные) из БрАЖ9-4 и БрОЦС5-5-5.
Критерии выбора той или иной марки бронзы зависят от вида узла трения и условий его работы. Для наиболее распространенных случаев общие рекомендации могут быть следующими.
Подшипники скольжения.
При скоростях скольжения > 5-6 м/с предпочтительно применять БрОФ10-1. При скоростях < 5-6 м/с можно применять БрАЖ9-4 или БрОЦС5-5-5. Если опорная поверхность вала закалена, то можно применять любую из этих бронз, но БрАЖ допускает вдвое большие радиальные нагрузки. Если опорная поверхность вала незакалена, можно применять только БрОЦС.
Колеса (венцы) червячных передач.
При скоростях скольжения > 8-12 м/с применяется БрОФ10-1. При скоростях 4-10 м/с применяется БрОЦС5-5-5. При скоростях <4-6 м/с применяется БрАЖ9-4.
Более подробно вопросы применения бронз в узлах трения рассматривается на странице Антифрикционные материалы. Соответствующие рекомендации могут быть полезны при проведении ремонтных работ в отсутствии технической документации на изделие.
Круги и заготовки из основных марок бронз имеются на складе — см. стр. сайта «БРОНЗОВЫЕ КРУГИ и ТРУБЫ»
В некоторых бронзах при понижении температуры растворимость легирующей компоненты резко падает и её выделение из твердого раствора приводит к эффекту дисперсионного твердения. Этот процесс сопровождается резким изменением физических и механических свойств.
Бронзы, способные к дисперсионному твердению, позволяют осуществлять упрочнение изделий из них за счет специальной термообработки (старение, облагораживание). В результате возрастают твердость, пределы текучести и прочности, улучшается коррозионная стойкость, повышается тепло- и электропроводность.
К бронзам с эффектом дисперсионного твердения относятся бериллиевые, хромистые, циркониевые, кремнисто-никелевые и некоторые сложные сплавы (см. таблицу марок бронз). Полуфабрикаты из таких бронз (прутки, ленты, плиты, проволока) имеют следующие состояния поставки:
— Без термообработки.
Это горячекатаные плиты или прессованные прутки, остывшие со скоростью естественного охлаждения.
— С термообработкой (закалка).
В этом случае полуфабрикат нагревается до некоторой «высокой» температуры после чего производится его закалка в воду для получения пересыщенного твердого раствора. Это закаленные полуфабрикаты, состояние которых обычно маркируется буквой «М». Такая термообработка повышает пластичность и позволяет в дальнейшем производить операции гибки, вытяжку, прокатку и другие виды холодной деформации. Твердость, пределы текучести и прочности, пластичность закаленных бронз несколько выше, чем у прессованных.
— С термообработкой (закалка) и последующей холодной деформацией.
Холодная деформация повышает пределы текучести и прочности и увеличивает твердость закаленных полуфабрикатов. Холоднодеформированный полуфабрикат после закалки обычно маркируется буквой «Т».
Второй этап термообработки – отпуск, обычно производится уже над изделием. Отпуск производится при «низкой температуре» в течение определенного времени. В процессе отпуска происходит выделение избыточной фазы с упорядоченным распределением легирующего элемента. Эти выделения связаны со значительными напряжениями кристаллической решетки, которые вызывают повышение прочности и твердости.
Таким образом, облагораживание такого класса бронз состоит из двух операций. Вначале производится быстрая закалка, затем длительный отпуск. Между закалкой и отпуском может производиться упрочнение холодной деформацией или изготовление детали. Режимы облагораживания сильно зависят от химического состава бронзы. Для БрБ2 температура закалки 750-790 С, температура отпуска 300 – 350 С в течение 2 – 4 часов. Для БрХ0.5 температура закалки 950 С, температура отпуска 400 С в течение 4 часов.
Эффект термообработки для прутка из БрБ2 показан на гистограмме, а для лент — в таблице. Там же, в таблице, приведен эффект облагораживания для хромистой бронзы БрХ0.5.
БрБ2 | БрХ0.5 | |||
После закалки (М) | После закалки и отпуска | После закалки (М) | После закалки и отпуска | |
Модуль упругости Е, МПа | 9500 | 10500 | 11200 |
|
Предел текучести, МПа | 200 — 350 | 950 — 1350 | 500 | 270 |
Предел прочности, МПа | 400 — 600 | 1100-1500 | 240 | 410 |
Относительное удлинение | 20 | 2 | 50 | 22 |
Твердость HV | <130 | 330 | 65 | 130 |
Электрическое сопротивление | 0. | 0.04 — 0.07 | 0.04 | 0.02 |
Дисперсионное твердение изделий, изготовленных из термоупрочняемых бронз (БрБ2, БрХ, БрХЦр, БрКН) и сплавов (МНМц20-30) существенно повышают показатели прочности и твердости в сравнении с исходным материалом поставки. Наибольший эффект от облагораживания имеют изделия из бериллиевых бронз.
ПРИМЕНЕНИЕ БРОНЗОВЫХ СПЛАВОВ ДЛЯ ИЗГОТОВЛЕНИЯ ПРУЖИН
(Упругие свойства бронзовых сплавов)
Для изготовления пружин используются материалы с высоким пределом упругости и минимальным уровнем неупругих явлений (упругий гистерезис, низкий уровень релаксации и др.).
Для изготовления пружин и пружинящих деталей используются ленты, прутки и проволока из БрКМц3-1, БрОФ6. 5-0.15, БрОФ7-0.2, БрОЦ4-3, бериллиевых бронз. Высокая пластичность этих бронз даже в твердом состоянии позволяет использовать для навивки пружин не только проволоку, но и прутки диаметром до 10-15 мм.
В зависимости от вида пружины на её материал действуют нормальные (сжатие-растяжение) или касательные напряжения. Жесткость пружины определяется модулем упругости E или модулем сдвига G соответственно. Область допустимых нагрузок тем больше, чем больше соответствующий предел упругости (текучести), но при расчетах допустимые нагрузки и деформации рассчитывают по пределу прочности при растяжении с учетом расчетных коэффициентов.
В таблице представлены свойства лент из БрОФ, БрОЦ, БрКМц (в твердом состоянии) и БрБ2 (после дисперсионного твердения из состояния «Т»).
ГОСТ | 4748-92 | 1761-79 | 1789-70 | |
Марка бронзы | БрКМц3-1 | БрОФ6,5-0,15 | БрОЦ4-3 | БрБ2 |
Модуль упругости Е, МПа | 12000 | 9500 | 9500 | 12000 |
Предел упругости ?0.![]() | 260 — 530 | 320- 480 | 300-450 | |
Предел текучести ?0.2 , МПа | 510 — 750 | 550 — 720 | 520-680 | 1150-1600 |
Предел прочности ?В , МПа | 600 — 770 | 580 — 760 | 550-700 | 1150-1600 |
Относ. удлинение ? | 2 | 3 | 2 | — |
Твердость HV | 180 — 250 | 170 -220 | 170-210 | 360 |
Для изготовления плоских пружин используется также лента из БрА7.

После изготовления пружин из облагораживаемых материалов (бериллиевые бронзы и сплав МНМц20—20) производится их дисперсионное твердение.
Технологический процесс изготовления винтовых цилиндрических пружин из материалов этой группы включает следующие основные операции: закалка, навивка заготовок, разрезка длинных заготовок на отдельные пружины, обработка торцов пружин, дисперсионное твердение. Процесс изготовления плоских пружин включает: резку материала на ленты требуемой ширины, закалку, штамповку пружин, дисперсионное твердение.
В результате такой термообработки повышается твердость, упругость, износостойкость и значительно повышается усталостная прочность материала пружин.
ПРИМЕНЕНИЕ БРОНЗОВЫХ СПЛАВОВ ДЛЯ ЭЛЕКТРОДОВ И ПРОВОДНИКОВ ТОКА
(Электродные и проводящие сплавы)
Среди многочисленных марок бронз выделяется группа сплавов с малым (0. 3 – 1%) содержанием легирующих элементов. Они отличаются тем, что обладают практически такой же электро- и теплопроводностью, как и чистая медь, но при этом они имеют большую твердость, предел текучести, износостойкость, предел усталости, и сохраняют работоспособность до более высоких температур за счет повышенной (по сравнению с чистой медью) температуры начала рекристаллизации.
К таким сплавам относятся:
Кадмиевые бронзы (Cd: 0.9-1.2%) — прутки, ленты и коллекторные полосы.
Хромокадмиевые бронзы (Cd: 0.2-0.5%, Cr: 0.35-0.65%) — прутки
Магниевые бронзы (Мg: 0.3-0.8%) — коллекторные полосы и проволока.
Серебряные бронзы (Ag до 0.25%) – прутки, проволока, полосы.
Хромистые бронзы (Cr: 0.5 – 1.0) – прутки, плиты, полосы для коллекторных пластин, проволока.
Циркониевые (Zr: 0.2 – 0.7%) – коллекторные полосы, трубы, полосы
Хромисто-циркониевые бронзы – прутки, плиты
Эти бронзы имеют два основных применения.
1. Использование в производстве силовых подвижных контактов (контактные кольца, коллекторные пластины). Здесь в первую очередь важна высокая износостойкость, а также работоспособность при повышенных температурах.
2. Для изготовления электродов сварочных машин. Электродные сплавы должны иметь высокую температуру размягчения, высокую твердость и предел текучести в области рабочих температур (500 — 700 С).
На рисунке (Б) показано изменение твердости меди, кадмиевой и хромистой бронз с повышением температуры. Видно несомненное преимущество БрХ при высоких температурах. Ещё лучшие результаты имеют БрХЦр, БрБНТ и другие сплавы, но их применение ограничивается высокой ценой и доступностью.
На соседнем рисунке (А) видна принципиальная разница между облагораживаемой хромистой бронзой с одной стороны и обычной бронзой (БрКд) или медью с другой.
Отжиг холоднодеформированных прутков из меди или БрКд уменьшает твердость. При температурах выше температуры рекристаллизации разрушается текстура и металл разупрочняется. В то же время в БрХ при 400оС происходит дисперсионное твердение и его твердость после отжига, наоборот, возрастает. Если бы дисперсионное твердение не происходило, то твердость уменьшалась бы по пунктирной кривой (происходило бы разупрочнение). Это означает, что после изготовления электродов из сплавов типа БрХ, БрХЦр, они должны быть соответствующим образом термообработаны для улучшения их физико-механических свойств.
НАЗАД на ГЛАВНУЮ
Бериллиевая бронза БрБ2
БрБ2 — это безоловянная бериллиевая бронза, обрабатываемая давлением. Химический состав сплава БрБ2 описан в ГОСТ 18175-78 и включает в себя следующие компоненты: медь 96,9-98,0 %, бериллий 1,8-2,1 %, никель 0,2-0,5 % и до 0,5 % примесей.
Сплав выделяется среди прочих бронз высокой износостойкостью и стойкостью к коррозионной усталости. Наряду с другими бронзами БрБ2 обладает хорошими антифрикционными и пружинящими свойствами, а также средними тепло и электропроводностью, что обуславливает применение ленты и проволоки БрБ2. Кроме того можно улучшить механические качества этого сплава, если подвергнуть его процедурам закалки и старения. Так, например, широко используют пруток БрБ2Т.
Свойства БрБ2
Рассмотрим свойства бериллиевой бронзы марки БрБ2 — химические, технологические, механические, физические.
Химический состав БрБ2
Fe | Si | Ni | Al | Cu | Pb | Be | Примесей |
до 0.15 | до 0.15 | 0.2 — 0.5 | до 0.15 | 96.9 — 98 | до 0.005 | 1.8 — 2.1 | всего 0.5 |
Примечание: Cu — основа; процентное содержание Cu дано приблизительно
Температура плавления БрБ2 | 955 °C |
Температура горячей обработки БрБ2: | 750 — 800 °C |
Температура отжига БрБ2: | 530 — 650 °C |
Сортамент | Предел кратковременной прочности sв | Предел пропорциональности (предел текучести дляостаточной деформации) sT | Относительное удлинение при разрыве d5 |
— | МПа | МПа | % |
Проволока мягк.![]() |
343-686 | 15-60 | |
Проволока тверд.,ГОСТ 15834 — 77 | 735-1372 | ||
Полоса мягк., ГОСТ1789-70 | 390-590 | 20-30 | |
Полоса твердая, ГОСТ1789-70 | 590-930 | 2.5 | |
Сплав мягкий , ГОСТ1789-70 | 400-600 | 196-344 | 40-50 |
Сплав твердый, ГОСТ1789-70 | 600-950 | 588-930 | 2-4 |
Твердость прутков из БрБ2 прописана в ГОСТ 15835-2013 (взамен ГОСТ 15835-70)
Твердость БрБ2, Пруток мягкий ГОСТ 15835-2013 | HB 10 -1= 100 — 150 МПа |
Твердость БрБ2, Пруток твердый ГОСТ 15835-2013 | HB 10 -1= 150 МПа |
HB — Твердость по Бринеллю бериллиевой бронзы
Температура T | Модуль упругости первого рода E 10-5 | Коэффициент температурного (линейного) расширения a10 6 | Теплоемкость l | Плотность | Удельная теплоемкость C | Удельное электросопротивление R 109 |
Град | МПа | 1/Град | Вт/(м·град) | кг/м3 | Дж/(кг·град) | Ом·м |
20 | 1.![]() |
84 | 8200 | 70 | ||
100 | 16.6 | 419 |
США | Германия | Япония |
DIN,WNr | JIS | |
Применение бериллиевой бронзы БрБ2
Прутки из бронзы БрБ2 применяются в приборостроении и автомобилестроении. Ленты БрБ2 также применяются в приборостроении и производстве упругих и пружинящих деталей. Аналогичное применение нашла проволока в машиностроении и приборостроении. Бронза БрБ2 используется в различных областях производства. Из неё изготавливают антифрикционные детали и пружинящие детали: пружинящие детали и пружины. Из неё изготавливают детали ответственного назначения. Также из неё изготавливают неискрящие инструменты.
Технологические характеристики позволяют изготавливать из бериллиевых бронз сложные отливки высокого качества, но обычно детали из них производят из заготовок, подвергнутых предварительной пластической деформации (листы и полосы, проволока, ленты и др). Широкое применение сплавов бериллиевой группы обусловлено еще и тем, что они хорошо поддаются различным видам обработки, а для соединения деталей из них можно использовать все известные способы (сварка и пайка).
Пайка и сварка БрБ2
Пайку бериллиевых бронз следует выполнять сразу же, как была выполнена тщательная механическая зачистка соединяемых элементов. В качестве припоя при выполнении такой технологической операции используются сплавы на основе серебра, а в защитном флюсе, использование которого необходимо, должны в обязательном порядке содержаться фтористые соли. Высокое качество пайки деталей из данных сплавов обеспечивает технология, предполагающая выполнение соединения в вакууме и использование слоя защитного флюса.
Детали из бериллиевых бронз не соединяют при помощи электродуговой сварки, для этого успешно используют другие технологии: точечную, шовную, роликовую и сварку в среде инертных газов. Такое ограничение в применении электродуговой сварки обусловлено тем, что сплавы данной группы обладают большим температурным интервалом кристаллизации. Кроме этого, сварку бронз бериллиевой группы нельзя выполнять после термической обработки, что обусловлено их особыми механическими свойствами.
Износостойкость и коррозионной устойчивость бронзы БрБ2
Детали из бериллиевой бронзы не истираются и в то же время бережно воздействуют на сопрягаемые механизмы, хорошо сопрягаются с друг другом, полируются и идеальным образом взаимодействуют в механизмах при заданных параметрах. Но даже если условия эксплуатации нарушены, детали из БрБ2 способны выдерживать большие нагрузки трения и других механических воздействий. При работе механизмов в ходе изнашивания БрБ2 не откалывается большими кусками, а истирается постепенно, давая очень мелкую стружку.
Коррозионная усталость – это один из показателей коррозионной стойкости металлов. Когда детали работают под воздействием большой массы, циклических динамических нагрузок в коррозионной среде, велика вероятность выхода из строя конструкций, в которых они используются. Сплав БрБ2 хорошо проявляет себя в различных коррозионных средах и может быть использован для изготовления ответственных деталей, так как коррозия проявляется достаточно медленно и не оказывает значительного воздействия на механические и физические свойства деталей из этого материала долгое время. Однако, под действием влажных паров аммиака и воздуха бериллиевые бронзы склонны к межкристаллизационной коррозии и растрескиванию. В газовой среде, насыщенной галогенами (фтором, бромом, хлором и йодом), на их поверхности образуются галогениды бериллия, из-за чего происходят уменьшение его концентрации в сплаве. Особенно активно процесс взаимодействия с галогенами происходит при повышенных температурах. В связи с этим, бериллиевую бронзу БрБ2 не рекомендуют использовать для изготовления деталей, эксплуатируемых в указанных газах.
Облагораживание и закалка БрБ2
Путём облагораживания изделия из БрБ2 получаются более твёрдыми и более пластичными. Соответственно выпускаются полуфабрикаты в мягком (М) и твёрдом (Т) состоянии. В ходе процедуры закалки металл нагревают до некоторой температуры, после чего остужают в воде. В результате пластичные свойства металла повышаются и его применяют для изготовления деталей путём прокатки, ковки, вытяжки и гибки в холодном состоянии. Также выпускаются полуфабрикаты из БрБ2 с закалкой и холодной деформацией. БрБ2 закаливают при температуре 750-790 °C, после чего сплав отпускают при температуре в пределах 300-350 °C. После холодной деформации механические качества твёрдости, прочности и текучести улучшаются. БрБ2 Т выделяется среди прочих бронз самым высоким показателем прочности на растяжение. Медно-бериллиевый сплав БрБ2, подвергаемый термическому закаливанию, становится более прочным, упругим и пластичным. Первоначально его приводят в мягкое состояние, нагревая до 760-780°С, а затем подвергают старению в воде при температуре 310-330°С в течение 3 часов. При нагревании и последующем охлаждении сплава до комнатной температуры бериллий растворяется в меди с образованием насыщенного твердого раствора. Последующая закалка приводит к его осаждению, в результате чего бронза БрБ2 приобретает высокую твердость до 350 — 400 НВ.
Перспективы закалки сталей и сплавов в газовой среде высокого давления | Шевченко
Открытый доступ Доступ для подписчиковПерспективы закалки сталей и сплавов в газовой среде высокого давления
С. Ю. Шевченко, А. Е. Смирнов, Мин Хтет Вай Ян, Ю. Н. Рожкова, Д. П. Слепцова
Аннотация
Рассмотрены перспективы применения закалки в азоте высокого давления для средне- и высоколегированных сталей, а также дисперсионно-твердеющих сплавов. Представлена методика прогнозирования структуры и свойств сталей и сплавов после закалки. Показано, что закалка в газе обеспечивает высокий уровень механических свойств при сохранении геометрии прецизионных изделий из-за отсутствия окисления поверхности.
Ключевые слова
закалка; закалка в газе; охлаждающая способность; легированные стали; бериллиевая бронза; прецизионный пружинный сплав; hardening; hardening in gas; cooling capacity; alloy steels; beryllium bronze; precision spring alloy
Полный текст:
PDFЛитература
Lior N. The cooling process in gas quenching // Journal of materials processing technology. 2004. № 2. P. 1881 — 1888.
Pritchard J., Rush S. Vacuum hardening high strength steels: oil versus gas quenching // Heat treating progress. 2007. May/June. P. 19 — 23.
Shevchenko S. Y., Melnik Y. A., Smirnov A. E., Wai Yan Min Htet. Comparative evaluation of methods for the determination of heat transfer coefficients of liquid and gaseous quenching media // Mechanics & Industry. 2017. V. 18. Р. 703 — 708.
Шевченко С. Ю., Смирнов А. Е., Кириллов И. В., Курпякова Н. А. Исследование закалочного охлаждения в газовых средах // МиТОМ. 2016. № 8. С. 15 — 19.
Попова Л. Е., Попов А. А. Диаграммы превращения аустенита в сталях и бета-раствора в сплавах титана. М.: Металлургия, 1991. 503 с.
Пастухова Ж. П., Рахштадт А. Г. Пружинные сплавы цветных металлов. 2-е изд. М.: Металлургия, 1983. 364 с.
Смирнов А. Е., Шевченко С. Ю., Шевчуков А. П. и др. Исследование структуры и свойств бериллиевой бронзы после закалки в азоте высокого давления // Технология металлов. 2018. № 4. С. 25 — 30.
DOI: https://doi.org/10.30906/mitom.2020.2.37-42
© Издательский дом «Фолиум», 1993–2021
Внимание! эта страница распознана автоматически, поэтому мы не гарантируем, что она не содержит ошибок. Для того, чтобы увидеть оригинал, Вам необходимо Если Вы являетесь автором данной книги и её распространение ущемляет Ваши авторские права или если Вы хотите внести изменения в данный документ или опубликовать новую книгу свяжитесь с нами по по . Страницы: 1 2 3… 181 182 183 184 185 186 187… 382 383 384
Страницы: 1 2 3… 181 182 183 184 185 186 187. Внимание! эта страница распознана автоматически, поэтому мы не гарантируем, что она не содержит ошибок. Для того, чтобы увидеть оригинал, Вам необходимо скачать книгу |
Ковка из бронзы — Ковка в Куин-Сити
Применение в ковке из бронзыБронза — один из нескольких сплавов для ковки меди. Он состоит в основном из меди, а также из добавок, включая олово, алюминий, фосфор, цинк, кремний и иногда мышьяк.
Добавки придают бронзовым поковкам различные характеристики. Безграничное разнообразие делает бронзу одним из самых универсальных сплавов. Вот некоторые из типичных приложений:
- Гидравлические системы
- Корпуса насосов
- Музыкальные инструменты
- Клапаны
- Спринклеры
- Фитинги
- Трубопровод
- Монеты
- Втулки
- Подшипники
Есть много дополнительных применений для бронзы.Важнейшая часть любого проекта — выбор правильной подготовки. Ковка — основное средство придания бронзе полезных форм.
Оптимальная обработка зависит от конструктивного решения бронзовой детали. Например, отжиг, форма термической обработки, изменяет микроструктуру бронзовой поковки в механических или электрических целях. Более высокая концентрация меди в бронзовых сплавах улучшает электропроводность.
Добавки от 0,5% до 1% олова повышают ударную вязкость и прочность.Олово также снижает коэффициент трения (CoE), сохраняя при этом высокое сопротивление усталости за счет измельчения зерна. Эти характеристики делают оловянную бронзу превосходно подходящей для электротехнических изделий, шайб и пружин. Фосфор дает многие из тех же преимуществ, хотя добавляется всего лишь от 0,01% до 0,35%.
Никель — еще одна распространенная добавка благодаря своей средней прочности и относительно высокой коррозионной стойкости. Никелевая бронза находит множество применений на море, поскольку она защищает детали от соленой морской воды и морских биологических повреждений. Некоторые из других применений никелевой бронзы включают оборудование для производства продуктов питания и напитков, оптическое оборудование и музыкальные инструменты.
Есть несколько причин инвестировать в ковку из бронзы. Например, кованый материал имеет высокую точность размеров, высокую плотность и блестящую поверхность. Некоторые из других преимуществ ковки бронзы включают следующие предметы.
Предел прочностиПрочность на растяжение измеряет максимальное напряжение, которое материалы могут выдержать при растяжении или растяжении.Хрупкие материалы, такие как чистый цинк, алюминий или чугун, имеют низкую прочность на разрыв и относительно легко растрескиваются. Бронза, наряду с медью, латунью и другими коваными сплавами, обладает более высокой пластичностью и прочностью на разрыв.
Конструирование из кованой бронзы — это один из способов гарантировать более высокую прочность на разрыв по сравнению с другими материалами. Процесс ковки обеспечивает правильный поток зерна, что увеличивает сопротивление усталости. Тот же подход применяется к ковке меди и ковке латуни для улучшения механических свойств.
Bronze идеально подходит для промышленных предприятий, особенно с агрессивными химическими веществами. Производители оригинального оборудования рекомендуют поковки из бронзового сплава для защиты от этих агрессивных сред. Дополнительные преимущества — самосмазывание, низкий коэффициент теплопроводности и электрическая проводимость.
Латунь, бронза и медные сплавы без содержания железа не подвержены коррозии. Со временем появляется зеленый налет из оксида меди, который защищает структуру от дальнейшего повреждения.
Формуемость Подобно другим медным сплавам, бронза может быть выкована для получения мелких деталей и согласованности с допусками на размеры, превосходящими другие сплавы, такие как сталь. Детали в оснастке более плотно захватываются при ковке бронзы и других медных сплавов.
Бронзовые сплавы с высоким содержанием меди сохраняют повышенную и надежную проводимость. Такие материалы, как бронза, остаются весьма желательными для удовлетворения этих требований по сравнению с более дорогими материалами, такими как серебро или алюминий, склонный к диэлектрической коррозии.
Ковка бронзы в кузнечной компании Куин-СитиQueen City Forging является лидером в области ковки мирового класса с 1881 года. Наш многолетний опыт очевиден в отмеченных наградами процессах ковки, передовых исследованиях и квалифицированном персонале. Инженеры-конструкторы OEM, металлурги-конструкторы OEM и агенты по закупкам доверяют нам, когда им нужны доступные и высококачественные бронзовые детали.
Queen City Forging гордится своей непревзойденной приверженностью качеству и удовлетворенности клиентов. Мы подбираем подходящее оборудование и ковочные изделия для металлургии, чтобы вы всегда получали наилучшие производственные результаты. Если вам нужна кованая бронза, медь, латунь или кремниевые сплавы, у нас есть все, что вам нужно.
Если вам нужна бронзовая ковка, кузница Королевского города поможет вам. Свяжитесь с нами сегодня для всех ваших потребностей в бронзе.
Часто задаваемые вопросы Можно ли ковать латунь?Да, латунь можно ковать. То же относится и к поковкам из меди. Производители используют горячую, холодную и горячую ковку для приготовления сплавов в зависимости от их окончательной формы.
Горячая ковка идеально подходит для придания латуни или меди определенной конфигурации. Эти материалы обладают высокой ковкостью; позволяя обрабатывать сложные геометрические формы. Готовые поковки часто не требуют дополнительной обработки.
Ограниченное количество латуни и меди позволяет использовать холодную штамповку для специальных применений. Холодная штамповка может улучшить твердость в соответствии с проектными требованиями. Холодная штамповка может обеспечить экономию средств, повышение точности размеров и превосходную чистоту поверхности.
Независимо от того, какой метод выбирают производители, ковка латуни идеально подходит для обработки и долговечности. Полированная латунь может создать очень привлекательную эстетическую поверхность, когда требуется косметический вид.
Можно ли ковать алюминиевую бронзу?Да, ковка бронзы с алюминием возможна. Готовые детали обычно содержат от 90% до 95% меди в расчете на общую массу. Добавление алюминия обеспечивает дополнительные и альтернативные свойства, что делает сплав желательным для конкретных применений.
Можно ли закалить бронзу? Да и нет. Некоторые бронзовые сплавы успешно закаливаются, в то время как другие могут быть ослаблены этим процессом. Как правило, сплавы, содержащие цинк, чаще подходят для процесса отпуска.
В некоторые сплавы добавляют небольшое количество кремния для улучшения отделки поверхности и повышения коррозионной стойкости. Добавление кремния улучшает твердость поверхности, что делает ее пригодной для несущих и нагрузочных свойств.Он особенно полезен для проставок, дорожек качения и сепараторов подшипников, используемых в аэрокосмической промышленности.
Закалка и отпуск Алюминиевая бронза? : Metallurgy
Никель-алюминиевая бронза — один из немногих медных сплавов, которые можно подвергнуть закалке и отпуску для повышения прочности, хотя механизм упрочнения отличается от закаленной и отпущенной стали. С достаточно высоким содержанием Al бинарные сплавы Cu-Al образуют твердый раствор с ОЦК (β-фаза) при высоких температурах. Медленное охлаждение из этой области до комнатной температуры позволяет ему разложиться на обогащенный медью твердый раствор α и интерметаллическую γ2 фазу с эвтектоидной микроструктурой, которая ухудшает коррозионную стойкость и механические свойства. Если вместо этого его закалить до комнатной температуры, произойдет мартенситное превращение, в результате чего получится относительно твердый, но хрупкий материал, который можно подвергнуть отпуску для улучшения пластичности. Отвечая на ваш вопрос, да, для упрочнения бинарной Cu-Al бронзы можно использовать закалку и отпуск.
Большинство коммерческих алюминиевых бронз содержат железо и, как правило, никель. Комбинированный эффект этих добавок вызывает образование преципитатов (известных под общим названием κ-фазы) при охлаждении, а не γ2-фазы.Эти осадки упрочняют материал, не оказывая такого сильного воздействия на пластичность, хотя некоторые фазы все же могут отрицательно сказаться на стойкости к коррозии. Если коррозионная стойкость не является для вас серьезной проблемой, я думаю, что добавление 5% Fe и предпочтительно 5% Ni может улучшить механические свойства. Я считаю, что марганец можно использовать для замены обоих компонентов в некоторой степени, и он имеет дополнительное преимущество, заключающееся в улучшении текучести и литейных свойств. Я далек от эксперта в этой области, поэтому, если вы хотите узнать больше, я рекомендую прочитать следующие документы:
Термическая обработка сложных алюминиевых бронз
Морфология, кристаллография и химия фаз в никеле в литом состоянии. Алюминиевая бронза
Обзор литературы, связанной с разработкой микроструктуры во время лазерной обработки поверхности никель-алюминиевой бронзы
Руководство по никель-алюминиевой бронзе для инженеров
Избранные диаграммы медных сплавов, иллюстрирующие основные типы фазового превращения
В чем разница: отпуск против .Отжиг?
Закалка и отжиг — это оба метода термической обработки металла. Целью термической обработки является намеренное изменение физических (и химических) свойств металла, чтобы подготовить его к производству. Термическая обработка может повлиять на многие свойства металлического изделия, включая прочность, твердость, формуемость, пластичность, пластичность и обрабатываемость.
Закалка и сталь после отжига: термическая обработка металлических изделий
Как правило, на термическую обработку металла влияют три переменных:
- Температура, до которой его нагревают производители
- Как долго он остается при этой температуре
- Способ или скорость охлаждения
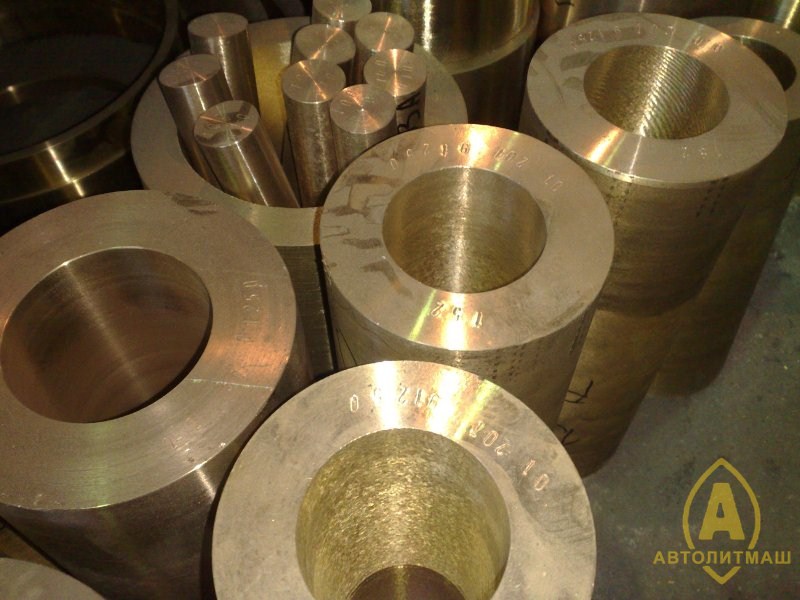
Несмотря на то, что существует множество методов термической обработки металла, сегодня мы рассмотрим только два из них: отжиг и отпуск.
Процесс отжига
Как работает отжиг?
В процессе отжига производители нагревают материал до идеальной температуры, а затем выдерживают его при этой температуре в течение определенного времени. Скорость охлаждения при отжиге также очень низкая.Допустим, вы что-то готовили в духовке, и время пошло. Если вместо того, чтобы удалить его, вы позволите ему остыть в духовке, это будет похоже на предпосылку отжига.
Основная причина, по которой производители отжигают материал, состоит в том, чтобы снизить его твердость для более плавного процесса обработки. Кроме того, производители могут потребовать, чтобы металл имел более высокую удельную электропроводность, которая также может быть повышена за счет отжига.
Три этапа отжига
Процесс отжига включает три отдельных этапа:
- Восстановление
- Рекристаллизация
- Рост зерна
Давайте подробнее рассмотрим, что происходит на каждом этапе.
Этап отжига 1: восстановление
Первым этапом процесса отжига является восстановление. Во время восстановления производители полностью нагревают металл. Чаще всего для этого вида обработки металла используют печь. Это может быть газовая, электрическая или индукционная печь, но цель стадии восстановления — нагреть металл до температуры, при которой металл может расслабиться и стать пластичным.
Этап отжига 2: рекристаллизация
Различия между темперированием и отпуском.Отжиг стали начинается на этом этапе процесса. Во время перекристаллизации производители снова нагревают до критической температуры. Целью является температура, которая выше температуры рекристаллизации металла, но не выше температуры его плавления.
Когда материал удерживается в этой зоне наилучшего восприятия, во внутренней структуре металла начинают развиваться новые зерна без образования ранее существовавших напряжений.
Этап отжига 3: рост зерен
Третья стадия процесса отжига — рост зерна. На этой заключительной стадии зерна из второй стадии могут полностью развиться. Контролируя процесс охлаждения и поддерживая определенную скорость, рост зерен дает более пластичный и менее твердый материал.
Процесс закалки
Как работает закалка?
Закалка — это термообработка, которая улучшает вязкость твердых, хрупких сталей, чтобы они могли удерживаться во время обработки. Для отпуска требуется, чтобы металл достиг температуры ниже так называемой нижней критической температуры — в зависимости от сплава эта температура может находиться в диапазоне 400–1300 ° F.
Когда сталь достигает своей нижней критической температуры, производитель поддерживает ее на этом уровне в течение заранее определенного периода времени. Тип стали определяет критическую температуру и время выдержки материала при этой температуре.
Другие переменные, влияющие на отпуск, включают продолжительность пребывания металла при критической температуре, а также скорость охлаждения. Оба эти фактора влияют на механические свойства материала.
Визуальное влияние отпуска и стали после отжига
Также известно, что отпуск влияет на цвета, которые появляются на поверхности стали, в отличие от процесса отжига, который имеет небольшой визуальный эффект. Эти цвета, которые могут варьироваться от светло-желтого до оттенков синего, указывают на окончательные свойства стали. Например, наши улучшенные пружинные стали — 1075 и 1095 — имеют синий цвет, но из-за явных различий в контакте с углеродом их оттенок синего и другие физические свойства различаются.Вы можете просмотреть подробное сравнение здесь.
Медь, бронза и латунь. Как их лечить. — Металлообработка, пайка и металлическая арматура
Ссылка в первом посте голая основная. Существует буквально много тысяч медных сплавов, каждый из которых предназначен для определенных целей.
Латунь, продаваемая для хобби, представляет собой сплав меди с цинком 75/25 и находится в полутвердом состоянии. Латунь в гильзах огнестрельного оружия — 70/30. Большинство медных сплавов деформируются, что значительно увеличивает прочность, но также делает их более хрупкими.Например, если вы протягиваете отожженную (также называемую «мягкой» или «мертвенно-мягкой») латунную проволоку через волочильную пластину, вам придется отжечь ее после двух протяжек. Один розыгрыш сделает его полутвердым. В третий раз он не потянется, обычно он просто ломается, а в противном случае он будет настолько хрупким, что сломается при сгибании.
Отжиг большинства медных сплавов проводится, как описано в Wefalk: нагрейте их до тех пор, пока они не загорятся, а затем немедленно закалите в воде. Результат нагрева до тех пор, пока он не начнет светиться, и дать ему остыть, очень непредсказуем.Если латунь нагреть примерно до 800 F и закалить, она частично отожжется до примерно полутвердости.
Темно-синяя латунь представляет собой сплав меди, цинка и олова, который сохраняет цвет латуни, а также имеет более высокую коррозионную стойкость, чем бронза. Это латунный сплав, который использовался на кораблях. Металл Muntz — это сплав меди / цинка 60/40 со следами железа, который после изобретения в 1832 году часто использовался для обшивки корпуса по гораздо более низкой цене, чем медь. См. Пример его использования на веб-сайте Cutty Sark .Он очень похож на латунь, но немного белее.
Настоящая бронза содержит от 8% до 12% олова. Архитектурная и коммерческая бронза на самом деле изготавливается из латуни с цинком вместо олова, а иногда также содержит свинец. Вот почему современные «бронзовые» статуи становятся зелеными, в то время как некоторые из более старых статуй, отлитых из настоящей бронзы, остаются такими же темно-красновато-коричневыми, какими были при отливке 200 лет назад.
Медь также легирована никелем для обеспечения высокой коррозионной стойкости, особенно в морской воде; наиболее широко используемый для этой цели — монель — содержит 45% меди, 55% никеля.Другой медно-никелевый сплав (обычно с некоторым количеством цинка), известный как немецкое серебро, не содержит серебра, но очень похож на него. Если у вас когда-либо было «серебряное» кольцо, делавшее ваш палец зеленым, то оно было сделано из немецкого серебра. Нейзильбер — это стандартизированный сплав меди / никеля / цинка (60/20/20, опять же без серебра), используемый (среди прочего) для рельсов в модельных железных дорогах, потому что оксид, который он образует, также белый, защищает металл от дальнейшее окисление и проводит электричество. Он также используется для изготовления большинства музыкальных инструментов из белого металла профессорского уровня, в отличие от инструментов из желтой латуни более низкого качества.
Извините, если я представил больше информации, чем вы хотите или вам нужно знать, но я провел всю свою сознательную жизнь, работая с металлом, и до сих пор очарован и поражен тем, что с ним можно сделать.
Коды отпуска ASTM B601 для термообработки медных сплавов
ASTM B601 Коды отпуска при термообработке для металлической меди и медных сплавов
Из-за большого разброса важных физических свойств в зависимости от истории обработки сплава, это непреодолимо.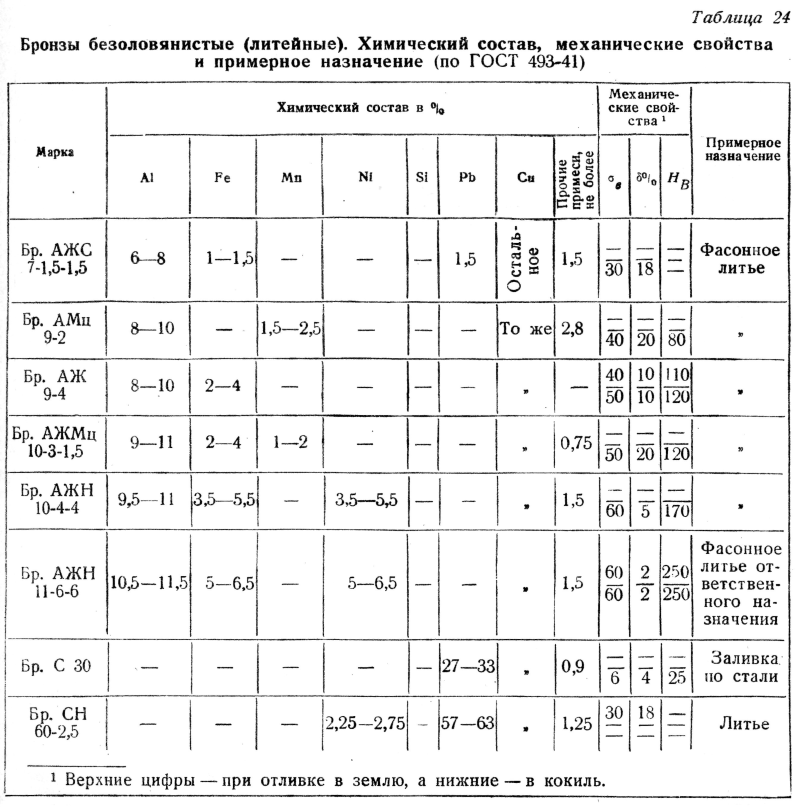
|
|
Ссылки
Чтобы получить более общую информацию о более чем 2500 конкретных технических паспортах меди, латуни и бронзовых сплавов, выберите одну из следующих ссылок или воспользуйтесь одним из наших методов поиска для поиска конкретных продуктов. В дополнение к атрибутам, связанным с термообработкой, таким как температура старения, температура отжига и температура горячей обработки, MatWeb имеет полный список механических и термических свойств и спецификаций состава для сплавов на основе меди.
Разница между отжигом и отпуском
В чем разница между отжигом и отпуском?
Разница между отжигом и отпуском заключается в том, как они обрабатываются. Отжиг включает нагрев стали до заданной температуры, а затем охлаждение с очень медленной и контролируемой скоростью, тогда как отпуск включает нагрев металла до точной температуры ниже критической точки и часто проводится в воздухе, вакууме или инертной атмосфере.
Термическая обработка
Термическая обработка используется для изменения физических и механических свойств металла без изменения его формы. Это важные процессы в производстве металла, которые улучшают желаемые характеристики металла, позволяя при этом производить дальнейшую обработку.
Различные процессы термообработки включают тщательно контролируемый нагрев и охлаждение металла. Сталь, например, обычно подвергается термической обработке для использования во множестве коммерческих применений.
Общие цели термической обработки:
- Увеличить силу
- Повышение твердости
- Повысить ударную вязкость
- Улучшить обработку
- Улучшить формуемость
- Увеличить пластичность
- Повысить эластичность
Этап охлаждения оказывает различное воздействие в зависимости от металла и процесса. Когда сталь охлаждается быстро, она затвердевает, тогда как стадия быстрого охлаждения при отжиге в растворе приводит к размягчению алюминия.
Существует много видов термообработки, но двумя важными из них являются отжиг и отпуск.
Отжиг
Отжиг включает нагрев стали до заданной температуры и затем очень медленное и контролируемое охлаждение.
Отжиг обычно используется для:
- Размягчение металла для холодной обработки
- Повышение обрабатываемости
- Повышение электропроводности
Отжиг также восстанавливает пластичность. Во время холодной обработки металл может затвердеть до такой степени, что дальнейшая работа приведет к растрескиванию.За счет предварительного отжига металла холодная обработка может происходить без риска образования трещин, поскольку отжиг снимает механические напряжения, возникающие во время обработки или шлифования.
Отжиг используется для стали, однако другие металлы, включая медь, алюминий и латунь, могут подвергаться процессу, называемому отжигом в растворе.
Большие печи используются для отжига стали. Внутренняя часть духовки должна быть достаточно большой, чтобы воздух мог циркулировать вокруг металла. Для больших кусков используются газовые конвейерные печи, в то время как печи с вагонным подом более практичны для небольших кусков металла.
В процессе отжига металл нагревается до определенной температуры, при которой может происходить рекристаллизация. На этом этапе устраняются дефекты, вызванные деформацией металла. Металл выдерживают при этой температуре в течение фиксированного периода времени, а затем охлаждают до комнатной температуры.
Процесс охлаждения должен выполняться очень медленно, чтобы получить улучшенную микроструктуру и, таким образом, добиться максимальной мягкости. Часто это делается путем погружения горячей стали в песок, золу или другие вещества с низкой теплопроводностью или путем выключения печи и предоставления стали остыть вместе с печью.
Закалка
Закалка используется для повышения ударной вязкости сплавов железа, особенно стали. Незакаленная сталь очень твердая, но слишком хрупкая для большинства применений. Закалка обычно проводится после закалки, чтобы уменьшить излишнюю твердость.
Закалка используется для изменения:
- Твердость
- Пластичность
- Прочность
- Прочность
- Структурная устойчивость
Закалка включает нагрев металла до точной температуры ниже критической точки и часто проводится на воздухе, в вакууме или в инертной атмосфере.
Температура регулируется в зависимости от степени жесткости, которую необходимо уменьшить. Хотя он варьируется в зависимости от типа металла, обычно низкие температуры уменьшают хрупкость при сохранении большей части твердости, в то время как более высокие температуры снижают твердость, что увеличивает эластичность и пластичность, но приводит к потере некоторой текучести и прочности на разрыв.
Важно нагревать металл постепенно, чтобы не допустить растрескивания стали. Затем металл выдерживают при этой температуре в течение фиксированного периода времени.Приблизительная норма — один час на дюйм толщины. За это время в металле снимаются внутренние напряжения. Затем металл охлаждают на неподвижном воздухе.
Обновление видео
Нет времени читать блог? Вы можете посмотреть наше видео о термообработке ниже, в котором более подробно рассматривается разница между отжигом и отпуском.
Металлические Супермаркеты
Metal Supermarkets — крупнейший в мире поставщик металла небольшими партиями, имеющий более 100 обычных магазинов в США, Канаде и Великобритании. Мы эксперты по металлу и обеспечиваем качественное обслуживание клиентов и продукцию с 1985 года.
В Metal Supermarkets мы поставляем широкий ассортимент металлов для различных областей применения. В нашем ассортименте: низкоуглеродистая сталь, нержавеющая сталь, алюминий, инструментальная сталь, легированная сталь, латунь, бронза и медь.
У нас в наличии широкий ассортимент форм, включая стержни, трубы, листы, пластины и многое другое. И мы можем разрезать металл в точном соответствии с вашими требованиями.
Посетите одно из более чем 100 наших офисов по всей Северной Америке сегодня.
Кремниевая бронза 651 — Vegas Fastener Manufacturing
Вам нужны индивидуальные крепежи, изготовленные из Silicon Bronze 651? С момента основания Vegas Fastener Group решила все задачи по предоставлению качественных, своевременных и экономичных решений для специальных крепежных изделий. Каждый продукт создается в соответствии с вашими спецификациями, при необходимости с использованием ваших отпечатков.
Ниже приведены технические характеристики прутковой ложи 651 из кремниевой бронзы, которая может удовлетворить ваши потребности.
Бронза с низким содержанием кремния B, UNS C65100, OSO35 Закалочный стержень
Подкатегория: Бронза; Медный сплав; Металл; Цветной металл Ключевые слова: CDA 651, ISO CuSi1, CEN C115C
Компонент | Вт. % |
Cu | 98,5 |
Fe | Макс 0,8 |
Mn | Макс 0,7 |
Пб | Макс 0.05 |
Si | 0,8 — 2 |
Zn | Макс 1,5 |
Примечания по материалам: Устойчивость к коррозии от хорошей до отличной. Отличная обрабатываемость в горячем и холодном состоянии. Производится путем формовки и гибки, высадки и высадки, горячей штамповки и прессования, нарезания резьбы и накатки валков, выжимания и обжимки. Области применения: трубопроводы гидравлического давления , анкерные винты, болты, кабельные зажимы, винты с головкой под ключ, крепежные винты, морское оборудование, гайки, оборудование для полюсов, заклепки, U-образные болты, электрические трубопроводы, трубки теплообменника, сварочный стержень.
Образец для испытаний: стержень диаметром 25 мм.
Физические свойства | Метрическая система | Английский | Комментарии |
Плотность | 8,75 г / куб. См | 0,316 фунт / дюйм³ | при 20 ° C (68 ° F) |
Механические свойства | |||
Твердость по Роквеллу F | 55 | 55 | |
Предел прочности на разрыв | 275 МПа | 39900 фунтов на кв.![]() | |
Предел прочности при растяжении | 105 МПа | 15200 фунтов на кв. Дюйм | 0.Расширение на 5% под нагрузкой |
Удлинение при разрыве | 50% | 50% | дюйм 50 мм |
Модуль упругости | 115 ГПа | 16700 тысяч фунтов / кв. Дюйм | |
Обрабатываемость | 30% | 30% | UNS C36000 (автоматная латунь) = 100% |
Модуль сдвига | 44 ГПа | 6380 тысяч фунтов / кв. Дюйм | |
Электрические свойства | |||
Удельное электрическое сопротивление | 1.44e-005 Ом-см | 1.![]() | |
Тепловые свойства | |||
КТР, линейный 250 ° C | 18 мкм / м- ° C | 10 мкдюймов / дюйм-° F | от 20 до 300 ° C (68-570 ° F) |
Теплоемкость | 0,38 Дж / г- ° C | 0,0908 БТЕ / фунт- ° F | |
Теплопроводность | 57 Вт / м-К | 396 БТЕ-дюйм / час-фут²- ° F | при 20 ° C (68 ° F) |
Точка плавления | 1030-1060 ° С | 1890 — 1940 ° F | |
Солидус | 1030 ° С | 1890 ° F | |
Ликвидус | 1060 ° С | 1940 ° F | |
Свойства обработки | |||
Температура отжига | 475 — 675 ° С | 887 — 1250 ° F | |
Температура горячей обработки | 700-875 ° С | 1290–1610 ° F |
Ссылки доступны для этого материала.