Капиллярная дефектоскопия
Капиллярная дефектоскопияРостБизнесКонсалт
Профессиональная переподготовка
Повышение квалификации
Рабочие специальности
Специальная оценка условий труда
Повышение квалификацииБолее 2000 программ
Короткие сроки
Дистанционно
Выгодные цены
Профессиональная переподготовкаБолее 1000 программ
Короткие сроки
Дистанционно
Выгодные цены
Обучение по рабочим специальностямБолее 2000 программ
Короткие сроки
Дистанционно
Выгодные цены
Задать вопрос
Я принимаю условия пользовательского соглашения и даю согласие на обработку персональных данных.
Капиллярная дефектоскопия – это комплекс операций по выявлению скрытых и мелких изъянов на основе действия индикаторных жидкостей. Капиллярный контроль, или контроль проникающими веществами признается одним из самых чувствительных и информативных методик неразрушающего контроля.
Он может применяться для проверки объектов практически любых размеров, форм и материалов почти во всех областях промышленности от энергетики до строительства ядерных реакторов. Неразрушающий контроль проникающими веществами также используется при установлении нарушений герметичности. Для некоторых материалов такой способ неразрушающего контроля является единственным средством диагностики соответствия качества.
Преимущества капиллярного метода дефектоскопии:
- высокая чувствительность и достоверность;
- широкая применимость;
- возможность получения не только информации о наличии дефектов, но и сведений об их природе и возможных факторах появления;
- легкость операций;
-
несложное оборудование.
Основные виды капиллярного контроля по способу проявления индикатора делятся на:
- люминесцентный, в основе которого использование люминесцирующего вещества, различимого в уф-свете на исследуемом участке;
- контрастный
- люминесцентно-цветной, являющийся комбинацией первых двух и применяющий пенетранты, видимые как при уф-излучении, так и дневном свете;
- яркостный, где контрастным выступает ахроматический узор индикатора.
В зависимости от используемого вида набор для капиллярной дефектоскопии может меняться, однако в целом для проведения такого исследования необходимы:
- индикаторы для цветной дефектоскопии;
- флуоресцентные индикаторы;
- наборы очистителей, проявителей, пенетрантов;
- распылитель;
- пневмогидропистолет;
- УФ-лампы;
-
тест-панели.
Материалы в специализированных наборах должны быть совместимыми между собой и применимыми к конкретному объекту по условиям его эксплуатации и техническим характеристикам.
Общая технология капиллярного контроля заключается в последовательном выполнении следующих этапов:
- Очистка проверяемой области водой или специальным раствором для равномерного проникновения индикатора.
- Нанесение пенетранта, на срок от 5 минут до получаса.
- Снятие излишков вещества с поверхности и последующее просушивание.
- Нанесение проявителя на область обследования.
- Проверка и фиксация следов индикатора.
В силу использования специфических материалов и оборудования проведение капиллярного контроля регламентируется ГОСТом 18442-80 «Контроль неразрушающий. Капиллярные методы. Общие требования».
Помимо знания методики обследования и следования ГОСТу каждый специалист должен пройти обязательную аттестацию по правилам ПБ 03-440-02, утвержденным постановлением Госгортехнадзора РФ от 23.
Компания «РостБизнесКонсалт» предлагает записаться на дистанционный курс подготовки к аттестации по неразрушающему контролю. Программа предполагает дистанционное обучение в соответствии с нормами сдачи всех квалификационных экзаменов. Наши преподаватели подготовили полную информационную научно-методическую базу, проводят вебинары и консультации в режиме реального времени. По итогам финального тестирования мы отдаем документы в аттестующий орган для завершения процедуры.
Качество нашего обучения гарантирует всем слушателям подготовительного курса получение удостоверения установленного образца по неразрушающему контролю капиллярным методом.
Чтобы уточнить детали и задать интересующие вопросы. Оставьте заявку на сайте или позвоните по телефону 8 800 333-96-76.
Источник: https://rostbk.com/o-kompanii/stati/kapillyarn-defektoskop/
Оформите заявку сейчас
Мы ответим на все вопросы и предложим выгодную цену!
Я принимаю условия пользовательского соглашения и даю согласие на обработку персональных данных.
Нам доверяют
Все компании
Отзывы и благодарности
Все отзывы
Поиск по сайту:
О компании- Наши клиенты
- Способы оплаты
- Доставка документов
- Гарантии
- Часто задаваемые вопросы
- Новости
- Статьи
- СМИ о нас
- Отзывы
- Видеоотзывы
- Карьера в РБК
- Контакты
Вся Россия
8 800 333-96-76Звонок по России бесплатно
Телефон
Ваше имя
Время В любое время08:00 — 09:0009:00 — 10:0010:00 — 11:0011:00 — 12:0012:00 — 13:0013:00 — 14:0014:00 — 15:0015:00 — 16:0016:00 — 17:0017:00 — 18:00
Я принимаю условия пользовательского соглашения и даю согласие на обработку персональных данных.
- А
- Абакан
- Анадырь
- Ангарск
- Архангельск
- Астрахань
- Б
- Барнаул
- Белгород
- Бийск
- Брянск
- В
- Владивосток
- Владимир
- Волгоград
- Воронеж
- Е
- Екатеринбург
- И
- Иваново
- Ижевск
- Иркутск
- К
- Казань
- Калининград
- Калуга
- Кемерово
- Киров
- Краснодар
- Красноярск
- Курск
- Л
- Липецк
- М
- Магадан
- Махачкала
- Москва
- Мурманск
- Н
- Набережные Челны
- Нижний Новгород
- Нижний Тагил
- Новокузнецк
- Новороссийск
- Новосибирск
- Новый Уренгой
- Ноябрьск
- О
- Омск
- Орел
- Оренбург
- П
- Пенза
- Пермь
- Петропавловск-Камчатский
- Р
- Ростов-на-Дону
- Рязань
- С
- Самара
- Санкт-Петербург
- Саратов
- Севастополь
- Симферополь
- Смоленск
- Сочи
- Ставрополь
- Сургут
- Т
- Тверь
- Тольятти
- Томск
- Тула
- Тюмень
- У
- Улан-Удэ
- Ульяновск
- Уфа
- Х
- Хабаровск
- Ханты-Мансийск
- Ч
- Чебоксары
- Челябинск
- Чита
- Ю
- Южно-Сахалинск
- Я
- Якутск
- Ярославль
Нет моего региона (Будут отображаться контакты головного офиса)
× Мы используем файлы cookie, чтобы улучшить работу и повысить эффективность сайта.
Продолжая пользование данным сайтом, вы соглашаетесь с использованием файлов cookie.
Капиллярный метод неразрушающего контроля (кнк) (капиллярная дефектоскопия) armtorg.ru
Капиллярный метод неразрушающего контроля (кнк) (капиллярная дефектоскопия) Капиллярный метод неразрушающего контроля (кнк) (капиллярная дефектоскопия)
Этот метод пригоден только для выявления дефектов, проявляющихся на поверхности контролируемого объекта. Он основан на проникновении специальной жидкости — пенетранта — в полости поверхностных и сквозных несплошностей объекта контроля, в извлечении пенетранта из дефектов с помощью проявляющего покрытия и фиксировании пенетранта. Глубина дефектов, обнаруживаемых КНК должна значительно превышать их ширину. Если ширина поверхностного повреждения больше его глубины (риска, царапина), то оно легко заполняется пенетрантом и так же легко удаляется из повреждений. Такие дефекты, как правило, КНК не выявляются.
КНК обычно используют для обнаружения дефектов, не видимых невооруженным глазом. Его абсолютную чувствительность определяют средним раскрытием дефекта типа трещин длиной 3-5 мм. выявляемого с заданной вероятностью.
Индикаторные рисунки, образующиеся при контроле, либо обладают способностью люминесцировать в ультрафиолетовых лучах, либо имеют окраску, вызываемую избирательным поглощением (отражением) части падающих на них световых лучей. Линии индикаторного рисунка имеют ширину от 0.05 до 0.3 мм (на расстоянии наилучшего зрения это соответствует угловой ширине от 15″ до Г30″). яркостный контраст 30-60% и более, а также высокий цветовой контраст. Это значительно выше соответствующих параметров поверхностных дефектов, обнаруживаемых визуально (угловой размер от Г до 10″. яркостный контраст 0-5%. цветовой контраст отсутствует).
При КНК ставятся следующие задачи: обнаружение дефекта, определение направления дефекта относительно конфигурации детали, определение размеров и формы дефекта.
В процессе КНК осуществляется следующая маркировка дефектов;
а — по количеству дефектов: А — одиночные дефекты. Б — множественные дефекты. В — сплошные дефекты:
б — по направлению дефектов:
|| -дефекты, параллельные направлению изделия:
_|_ — дефекты, перпендикулярные направлению изделия;
Z -дефекты, расположенные под углом к направлению изделия.
Основными объектами КНК являются неферромагнитные материалы: лопатки турбин из никелевых сплавов, в том числе авиационных турбин: титановый крепеж для летательных и космических аппаратов: литые детали из цветных металлов для электроники и систем автоматического управления: детали приборов и аппаратов нефтяной и химической промышленности.
КНК позволяет диагностировать объекты контроля любых размеров и форм, изготовленных из чёрных и цветных металлов и сплавов, пластмасс, стекла, керамики, а также других твёрдых неферромагнитных материалов. При этом выявляются такие дефекты, как трещины, пористость, рыхлоты.
При КНК применяют следующие материалы:
1. В качестве пенетранта — различные жидкие растворы, чаше всего на основе керосина, в который добавляются красители или люминофоры, светящиеся под действием ультрафиолетового излучения. Например, пенетрант «А» состоит из 700 мл керосина, 300 мл бензина Б-70. 30 г тёмно-красного красителя. Пенетрант «Е» состоит из керосина (800 мл), бензола (200 мл) и тёмно- красного красителя. Существуют пенетранты. у которых в керосин добавлены ацетон, бензин и краситель, или трансформаторное масло, скипидар и краситель, и ряд других.
Люменисцирующие пенетранты представляют собой смеси органических растворителей, масел, керосина с добавками поверхностно-активных веществ (ПАВ) и люминесцирующих веществ: масел, нефти, норнола, эмульсола и др.
2. Очищающую жидкость, которая предназначена для удаления пенетранта с поверхности контролируемого объекта. В качестве очищающих жидкостей используются вода, вода с добавлением ПАВ. органические растворители, смесь масла с керосином и другие жидкости. Например, масло МК-8-65% объема, толуол — 30%. эмульгатор ОП-7
3. Гаситель, который представляет собой состав для устранения окраски или люминесцентных остатков пенетранта без удаления его с контролируемой поверхности. В качестве гасителей используется, например, вода с кальцинированной содой (гаситель О201). спирт с поверхностно активным веществом ОП-7 (гаситель О300) и другие вещества.
4. В качестве проявляющих веществ — агар-агар, крахмал, порошок окиси магния, суспензия каолина в ацетоне и многие другие материалы, которые адсорбируют пенетрант. проникший в дефекты, и тем самым позволяют фиксировать их на поверхности контролируемого объекта.
Для выполнения КНК применяется следующая аппаратура:
1 — ванны для мойки и насыщения изделия пенетрантом:
2 — шкафы для сушки изделий:
3 — устройства для нанесения пенетранта:
4 — оптические устройства для фиксации дефектов визуально, с помощью фотосъёмок и для облучения пенетранта ультрафиолетовыми лучами в случае применения люминесцирующих веществ.
Проникающую жидкость наносят на предварительно очищенную поверхность деталей, чтобы заполнить полости возможных поверхностных дефектов. Продолжительность контакта жидкости с поверхностью детали зависит от физических свойств жидкости, характера обнаруживаемых дефектов и способа заполнения жидкостью полостей дефектов.
В табл. 4.1 приведены способы заполнения полостей дефектов пенетрантом. Наиболее простым и распространенным в производственных условиях является капиллярный способ. При этом для улучшения проникновения жидкости в полости может подогреваться проникающая жидкость или проверяемая деталь.
При вакуумном способе деталь помешают в герметичную камеру, из которой откачивают воздух. После подачи проникающей жидкости камеру разгерметизируют. Жидкость заполняет полости дефектов под действием капиллярного и атмосферного давлений. При разрежении около 1 Па выявляются трещины шириной на порядок меньше, чем при капиллярной пропитке.
При компрессионном способе жидкость быстро заполняет полости дефектов под действием капиллярного и внешнего избыточного давлений. При этом достигается более полное заполнение полостей дефектов, однако многие пенетранты изменяют свои свойства при увеличении давления — увеличивается вязкость, ухудшается смачиваемость твердых тел. в результате эффективность способа невелика.
При ультразвуковом способе ускоряется процесс заполнения полостей дефектов, особенно загрязненных. Высокой эффективности способ достигает при использовании пенетрантов средней и высокой вязкости (нориола, шубнкола. смесей масла с керосином), когда направление колебаний совпадает с плоскостью полости дефекта.
Под воздействием статических сил увеличивается ширина раскрытия полости дефектов, улучшаются условия заполнения этих полостей н выявления дефектов ннзковязкимн жидкостями.
При обычных условиях, например, заполнение поверхностных трещин раскрытием 0. 002 мм и глубиной происходит за 20 с: такая же трещина глубиной 3 мм полностью заполняется примерно за 40 с.
Скорость заполнения сквозных дефектов зависит от их размеров и конфигурации, время заполнения измеряется секундами.
Индикаторные пенетранты для красок и люминофоров, приготовленные на основе растворителей (керосин, бензин и т.п.). достаточно быстро испаряются. Длительная выдержка пенетранта на контролируемой поверхности может привести к его высыханию и выпадению в виде осадка из частиц красителя или люминофора. Эти частицы, являясь сорбентом, могут привести к извлечению пенетранта из устья дефекта: в результате выявление дефектов при контроле ухудшается. Для предотвращения высыхания можно периодически наносить дополнительно пенетрант. однако это процесс трудоемкий, особенно при контроле больших площадей, поэтому время нахождения пенетранта на контролируемой поверхности обычно ограничено 3-5 мин. После этого индикаторный пенетрант необходимо удалить с поверхности КО.
Способы удаления проникающей жидкости с поверхности выбирают с учетом необходимости сохранения ее в полостях дефектов, а также типа пенетранта. шероховатости поверхности, условий контроля, объема работ и требуемой производительности труда. При локальном контроле условиях в случае использования невысыхающих жидкостей детали протирают ветошью или бумагой. При большом объеме работ или при контроле шероховатых деталей (с чистотой обработки поверхности ниже пятого класса) этот способ непригоден. В этих случаях применяют промывку органическими растворителей!, водой и пр. Для удаления невысыхающих жидкостей применяют обдувку струей песка, дроби, косточковой крошки, опилок и т.п. Гашением устраняется люминесценция или окраска при использовании специальных проникающих жидкостей. При контроле массовых деталей в цеховых условиях применяют комбинированный способ удаления проникающей жидкости с поверхности деталей.
Полноту удаления пенетранта определяют визуально или (при люминисцентном методе) в ультрафиолетовом свете. Оценку считают удовлетворительной, если отсутствует светящийся или окрашенный фон.
Если фон обнаружен, для повторной очистки используют очиститель типа O-l или 0-2. При температуре окружающего воздуха ниже 8°С индикаторный пенетрант с поверхности КО снимают бязью, смоченной в спирте. Влагу с поверхности изделия удаляют влажной бязью до полного исчезновения с нее капель воды, после чего поверхность считается подготовленной к следующей операции. Проявитель чаще всего наносят кистью. При этом расход проявителя значительно меньше, чем при нанесении его краскораспылителем, окружающий воздух меньше насыщается вредными для человека парами растворителей и аэрозолей.
В цеховых условиях применяют также способ посыпания и способ наложения липких пленок. Затем происходит медленное перемещение мениска в глубь трещины (рис. 4.2) и незначительное увеличение индикаторного следа. Размер индикаторного следа определяется объемом пенетранта. извлеченного из устья трещины, после образования мениска по всей ее протяженности.
Средняя ширина индикаторного следа определяется в основном раскрытием поверхностной единичной трещины. Следовательно, для надежного выявления поверхностных дефектов при проведении технологических операций контроля необходимо обеспечить сохранение пенетранта в устье дефекта от момента нанесения до момента его извлечения из дефекта, поэтому операции по нанесению и удалению проникающей жидкости и нанесению проявителя должны проводиться непосредственно одна за другой с минимальным интервалом времени, не следует допускать длительной сушки поверхности после удаления пенетранта. длительной промывки КО и т.п.
Освещенность исследуемой поверхности должна быть не ниже 50 лк. Контроль проводят в затененном помещении, а в полевых условиях — при местном затемнении. При цветном контроле естественное или искусственное освещение на контролируемом участке должно быть не менее 3000 лк. С поверхностей деталей, прошедших контроль и признанных годными, удаляют проявитель и следы других дефектоскопических материалов одним из перечисленных способов: протиркой, промывкой, анодной обработкой, выжиганием, органическими растворителями.
В некоторых случаях в условиях производства возникает необходимость многократного контроля. Перед повторным контролем проводят полный цикл подготовки изделий, тщательно промывая КО ацетоном, бензином или другими растворителями для удаления остатков дефектоскопических материалов из поверхностных дефектов. Небольшие изделия перед повторным контролем рекомендуется помещать на несколько часов в растворители индикаторного красителя. В качестве иллюстрации влияния первичного контроля на последующие проверки на рис. 4.3 приведены результаты двух серий (каждая по пять раз) контроля образцов из стали, на которых при первичном осмотре было обнаружено 11 единичных трещин.
Осмотр контролируемой поверхности, как правило, проводят дважды: через 5-6 мин для обнаружения крупных дефектов и через 25-60 мин для обнаружения мелких. При люминесцентном методе контроля используют ультрафиолетовое излучение с длиной волны Сумма площадей индикаторных следов, обнаруженных на образцах, изменяется в зависимости от числа проведенных ранее испытаний.
Между сериями испытаний образцы помешали на 8-10 ч в растворители индикаторного красителя. Из рис. 4.3 видно, что такая обработка образцов почти полностью исключает влияние загрязнений дефектов остатками дефектоскопических материалов, используемых на предыдущих стадиях контроля.
КНК подразделяется на четыре уровня, как указано в табл. 4.2.
У КНК есть верхний и нижний пределы чувствительности. Верхний предел определяется наибольшей шириной дефекта, при которой пенетрант полностью вытекает из него, образуя размытое облако. Нижний предел определяется настолько малым дефектом, что проникшего в него пенетранта недостаточно для обнаружения.
Чувствительность КНК определяется геометрическим к. и оптическим ко факторами: KKHK=f(kr. ko). где f- знак функции.
Геометрический фактор определяется как k=l-y/b, где у— ширина устья дефекта, a b — ширина выделившегося пенетранта. как показано на рис. 4.4.
Здесь 1 — контролируемое изделие. 2 — проявитель. 3 — дефект. В6 и Ва — интенсивности света, отражённого от проявителя (фон) и от выделившегося из дефекта пенетранта. Оптический фактор определяется отношением интенсивностей света: ко= В./ Вп .
Приборы для КНК выпускаются серийно. В качестве примеров приведём отечественный прибор ЛДА-3 н прибор США «Тнн-Kq) АФБ». Последний позволяет контролировать в течение часа до 500 лопаток турбин.
Основные положения, которые необходимо знать при КНК. следующие.
1. Подготовку изделий к контролю (удаление жидкостей из поверхностных дефектов) можно проводить путем их нагрева или нанося на их поверхность проявитель. При нагреве изделий выше температуры кипения жидкостей происходит удаление жидкости из дефектов за счет образования пузырьков пара. Температура, при которой происходит выброс жидкости из дефекта, зависит от величины раскрытия дефекта. При широких является практически мгновенно. При нагреве изделий ниже температуры кипения жидкости очистка дефектов происходит за счет испарения жидкостей и пленочного массопереноса ее по стенкам дефекта. Нанесение проявителя на контролируемую поверхность обеспечивает удаление жидкости из устья дефектов приблизительно за 20 мин.
2. Размер индикаторного следа от поверхности единичной трещины определяется в основном объемом индикаторного пенетранта. находящегося в устье трещины, поэтому надежное выявление поверхностных дефектов обеспечивается при условии сохранения пенетранта в устье дефекта от момента его нанесения до момента извлечения его из дефекта.
3. Осмотру с целью обнаружения дефекта не подвергаются детали, состояние проявителя в зонах контроля которых затрудняет видимость индикаторных рисунков. Например, при цветовом варианте КНК осмотру не подвергаются детали, если в слое проявителя имеются пятна не удаленной красной проникающей жидкости, пятна и потеки масляно-керосиновой смеси, непокрытые проявляющей краской участки зоны контроля, частицы пыли, ветоши, следы каких-либо посторонних материалов (из-за применения загрязненных инструментов, приспособлений — краскораспылителей, кистей, захватов и др. ).
Общий осмотр проводят невооруженным глазом или с применением луп малого увеличения с большим полем зрения 2.
Размер индикаторного следа от поверхности единичной трещины определяется в основном объемом индикаторного пенетранта. находящегося в устье трещины, поэтому надежное выявление поверхностных дефектов обеспечивается при условии сохранения пенетранта в устье дефекта от момента его нанесения до момента извлечения его из дефекта.
3. Осмотру с целью обнаружения дефекта не подвергаются детали, состояние проявителя в зонах контроля которых затрудняет видимость индикаторных рисунков. Например, при цветовом варианте КНК осмотру не подвергаются детали, если в слое проявителя имеются пятна не удаленной красной проникающей жидкости, пятна и потеки масляно-керосиновой смеси, непокрытые проявляющей краской участки зоны контроля, частицы пыли, ветоши, следы каких-либо посторонних материалов (из-за применения загрязненных инструментов, приспособлений — краскораспылителей, кистей, захватов и др. ).
Общий осмотр проводят невооруженным глазом или с применением луп малого увеличения с большим полем зрения. При осмотре отыскивают окрашенный или люминесцирующнй индикаторный рисунок, обращая внимание на основные признаки:
— Трещины любого происхождения, волосовины, закаты, неслитнны. непровары. неспаи, плены выявляются в виде четких, иногда прерывистых окрашенных линий различной конфигурации (рис.4.5. 4.6)
— Растрескивание материала, межкристаллнтная коррозия участков поверхности крупнозернистых сплавов проявляются в виде группы отдельных коротких линий или сетки (рис.4.7. б)
— Межкристалльная коррозия участков поверхности мелкозернистых сплавов выявляется в виде пятен, размытых полос:
— Поры, язвенная коррозия, выкрашивание материала, эрозионные повреждения поверхности выявляются отдельными точками, звездочками (рис.4.7, а).
Обнаружение рисунка, соответствующего указанным выше основным признакам, служит основанием для анализа допустимости дефекта по его размеру, положению, характеру.
К недостаткам КНК следует отнести высокую трудоемкость контроля при отсутствии механизации; сложность механизации и автоматизации процесса контроля: большую длительность процесса (от 0.5 до 1.5 ч): снижение достоверности результатов при отрицательных температурах, необходимость удаления лакокрасочных покрытий и тщательной предварительной очистки контролируемых деталей: низкую вероятность обнаружения дефектов, перекрытых окисными пленками или сжатых значительными остаточными или рабочими напряжениями в детали: громоздкость стационарного оборудования: вредность некоторых дефектоскопических материалов для персонала и необходимость использования защитных приспособлений и вентиляции: субъективность контроля, зависимость достоверности результатов от умения и состояния контролера: ограниченный срок хранения дефектоскопических материалов, зависимость их свойств от продолжительности хранения и температуры среды.
Поделиться
Капиллярный контроль.
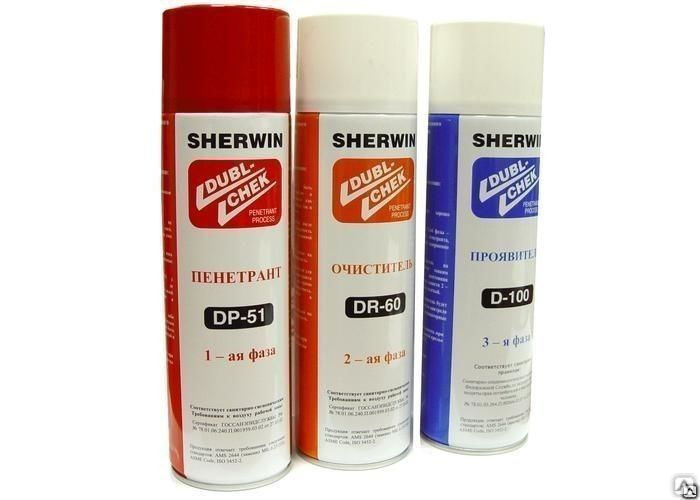
Капиллярный метод исследования дефектов представляет собой понятие, которое основано на проникновении определенных жидких составов в поверхностные слои необходимых изделий, осуществляемое при помощи капиллярного давления. Используя данный процесс, можно значительно повысить световые эффекты, которые способны определять более досконально все дефектные участки.
Виды методов капиллярного исследования
Довольно частым явлением, которое может встречаться в неразрушающем методе дефектоскопии, это не достаточно полное выявление необходимых дефектов. Такие результаты очень часто являются настолько маленькими, что общий визуальный контроль не способен воссоздавать все дефектные участки различных изделий. Например, при помощи такого измерительного оборудования, как микроскоп или простая лупа, невозможно определить поверхностные дефекты. Это происходит в результате недостаточной контрастности имеющегося изображения. Поэтому в большинстве случаев, наиболее качественным методом контроля является капиллярная дефектоскопия. Такой способ использует индикаторные жидкости, которые полностью проникают в поверхностные слои исследуемого материала и образуют индикаторные отпечатки, при помощи которых происходит дальнейшая регистрация визуальным способом. Ознакомиться с материалами для каппилярной дефектоскопии вы можете на нашем сайте.
Требования для капиллярного метода
Самым главным условием качественного метода обнаружения различных дефектных нарушений в готовых изделиях по типу капиллярного метода является приобретение специальных полостей, которые полностью свободны от возможности загрязнения, и имеют дополнительный выход на поверхностные области объектов, а также укомплектованы параметрами глубин, которые намного превышают ширину их раскрытия. Значения капиллярного метода исследования разделяются на несколько категорий: основные, которые поддерживают только капиллярные явления, комбинированные и совмещенные, использующие соединение нескольких методов контроля.
Основные действия капиллярного контроля
Дефектоскопия, которая использует капиллярный метод контроля, предназначена для исследования самых скрытных и недоступных дефектных мест. Таких как трещины, разнообразные виды коррозии, поры, свищи и другие. Данная система применяется для правильного определения расположения, протяжности и ориентации дефектов. Ее работа основана на тщательном проникновении индикаторных жидкостей в поверхностные и неоднородные полости материалов контролируемого объекта. Образцы для капиллярного контроля.
Использование капиллярного метода
Капиллярный контроль в основном применяется для любых видов и форм изделий, которые имеют черные, цветные, легированные, чугунные, металлические, стеклянные, керамические и многие другие сплавы. Такое обнаружение дефектов используется в авиации, судостроении, металлургии, строительстве, машиностроении и во многом различном производстве. В большинстве случаев данный метод является единственным допустимым условием для понятия пригодности необходимых изделий. Также капиллярная дефектоскопия может использоваться в материалах, которые имеют ферромагнитные составы. Но единственным исключающим звеном в этой системе может являться наличие необходимой чувствительности магнитопорошкового действия и определенные условия эксплуатации используемого объекта. Также не нужно забывать, что важным условием капиллярного метода является наличие полостей, которые должны быть полностью свободны от посторонних веществ и загрязнений, довольно часто располагающихся на поверхностях исследуемых объектов. Еще одной областью обнаружения дефектов может быть течеискание, которое применяется вместе с другими методами, в совокупности с мониторингом основных объектов, а также в процессе эксплуатации.
Преимущества капиллярной дефектоскопии
Основным достоинством данного метода является простота системы контролирования, большой обхват материалов и применение несложной конструкции оборудования. Также система неразрушающего контроля обнаружения дефектов при помощи капиллярного метода, помогает исследовать не только поверхностные слои изделий, но и располагает дополнительной информацией, способной определить расположение, протяженность, форму и ориентацию дефекта. И даже может легко найти причины их возникновения.
Для создания индикаторных жидкостей применяют органические соединения люминофоров, которые создают достаточно яркое свечение, при помощи ультрафиолетовых лучей и дополнительных красителей. Обнаружение дефектных мест, которые располагаются на поверхности, можно воссоздать, используя специальные индикаторные вещества, исходящие из середины полости самих дефектов. Тем самым можно получить полную картину результатов проведенных исследований.
Что такое капилляр?
Понятие значения слова капилляр можно объяснить , как трещина, которая выходит на поверхность только с одной стороны контролируемого объекта. Такое действие называется поверхностной несплошностью. А противоположные стенки, которые помогают соединять используемый объект, называют сквозными. Затем нужно определить не являются- ли такие значения дефектами. Если подозрения подтверждаются, тогда данную систему называют поверхностный или сквозной дефект. А изображение, которое получается в местах нахождения разрыва сплошного соединения, называется индикаторным рисунком. Также существуют такие понятия, как глубина и ширина несплошности. Глубина подразумевает наличие размеров разрыва изделий внутри исследуемого объекта. А ширина – это понятие продольного размера несплошностей контролируемого изделия. Еще имеется значение раскрытия, которое подразумевает поперечные результаты размеров, располагаемые на поверхности материалов. Самым важным условием капиллярного контроля является наличие действия выхода на поверхность контролируемого объекта. Также обязательно необходимо полностью контролировать загрязненность, глубину и ширину их раскрытия. Для более качественного выполнения контролируемой работы необходимо наносить такое вещество, как пенетрант, которое используется для очищения поверхностей.
Приборы для капиллярного метода контроля
Изделия, которые необходимы для цветной дефектоскопии Spotcheck от фирмы Magnaflux. Материалы люминесцентного направления Ziglo той же фирмы. Наборы, необходимые для капиллярного контроля Sherwin, Magnaflux, Helling. Также используются пульверизаторы, пневмогидропистолеты, приборы ультрафиолетового освещения, панели для проведения тестов и контрольные материалы, применяемые в цветной дефектоскопии.
Чувствительные значения капиллярного контроля
Наиболее чувствительные данные – это проявление размеров несплошностей, имеющие заданную вероятность и применяемую определенно направленный способ. Также такое понятие может носить характер контролируемой и пенетрантной системы. Учитывая все стандарты, необходимые для определения чувствительности, классификация контроля определяется с учетом минимального размера отображения дефектов. Также дефектные значения имеют свою ширину раскрытия, которая составляет около ноля целых пяти десятых миллиметра.
При помощи чувствительности первого класса контролируются лопатки турбореактивных двигателей, разнообразные клапаны и гнезда, расположенные на поверхности объекта, уплотнительные прокладки и другие. Применяя второй класс чувствительности, можно определять разнообразные коррозии редакторов, сварочные соединения, детали подшипников, а также трещины и поры, которые могут иметь разные величины.
Система чувствительности капиллярного контроля, а также явления промежуточной очистки, располагаются на специальных дисплеях цветного контроля, то есть на определенной металлической шероховатости, которая дополняется отдельными искусственно выведенными трещинами. Классификация контролируемой чувствительности может колебаться в зависимости от размеров имеющихся дефектов. Такое понятие зачастую определяют либо в натуральных изделиях, либо в искусственных объектах. Используя разнообразные размеры дефектов, можно получить класс контролируемой чувствительности. Также для выявления параметров размера необходимо использовать поперечные значения дефектов. Данный способ может существенно повлиять на быстроту нахождения дефектных мест. Не нужно забывать, что минимальный размер раскрытия может ограничиваться из –за небольшого наличия пенетранта, которое содержится в середине дефекта. А максимальное значение порога, которое получается путем выявления из широких дефектных мест, имеет пенетрант, создающийся в случае появления лишнего количества на поверхности.
Классификация чувствительности
К первому относится менее одного мкм дефекта. Ко второму – от одного до десяти. К третьему – от десяти до ста, и к четвертому – от ста до пятисот мкм.
Установлено 5 классов чувствительности (по нижнему порогу) в зависимости от размеров дефектов:
Класс чувствительности |
Ширина раскрытия дефекта, мкм |
I |
Менее 1 |
II |
От 1 до 10 |
III |
От 10 до 100 |
IV |
От 100 до 500 |
технологический |
Не нормируется |
Физические понятия капиллярного метода
Исследование при помощи капиллярного метода представляет собой целостное проникновение в дефектную зону специальной индикаторной жидкости, которая направлена на выявление поверхностных дефектов. Такой способ исследования помогает воссоздать достаточно четкую картинку различных несплошностей, которые имеют поперечные размеры от ноля целых одной сотой до пятисот мкм. Также различаются неоднородности в цветных, черных, керамических, стеклянных и многих других сплавах.
На поверхность контролируемого изделия наноситься цветной пенетрант, который способствует подбору необходимых физических параметров вещества. К таковым относятся: вязкость, плотность, натяжение на поверхности, которое происходит при наличии капиллярных сил и полное проникновение в самые мелкие участки дефектов. Далее возникает необходимость нанесения проявителя, который располагается на поверхности контролируемого объекта. После чего, нужно аккуратно удалить вещество пенетрант, и в результате происходит полное растворение красителя, который находится внутри дефектного участка. Затем моментально проявляется достаточная контрастность , которая помогает увидеть все образовавшиеся дефекты.
Стадии процесса нахождения дефектов
1)необходимое очищение поверхности. 2) использование пенетранта. 3)удаление лишнего образование вещества. 4)добавление проявителя. 5)проведение контроля.
Метод очищения поверхности
Для того чтобы произошло правильное распределение красителя в дефектные участки, необходимо провести тщательное очищение при помощи воды или специального органического очистителя. Наличие таких веществ, как ржавчина, металлизация или другие покрытия, обязательно должны удаляться с контролируемого места расположения. Затем нужно хорошо высушить верхнюю часть объекта, до полного отсутствия воды или используемого очистителя. После этого необходимо нанести пенетрант красноватого цвета при помощи кисти. Он обязательно должен полностью пропитать все труднодоступные уголки изделия. Далее важно удалить лишнее количество вещества, используя при этом специальную салфетку или же просто воду. Не забывайте, что пенетрант удаляется только с поверхности объекта, но не с полости. Следующим процессом является нанесение проявителя, который чаще всего имеет белый цвет.
Система контроля
Контрольный процесс начинается после завершения работы проявителя, и длиться приблизительно около тридцати минут. Наличие насыщенности цветности говорит о размере дефекта. Чем меньшая концентрация цвета, тем меньше размер дефектного участка. Более насыщенная цветовая гамма проявляется в основном в глубоких трещинах. После завершения контроля, обязательно нужно удалить проявитель водой или специальным очистителем. Именно благодаря эффекту пенетранта, происходит полное проникновение в самые труднодоступные места дефектов. А проявитель, который наносится на поверхность изделия, дает тщательное растворение красителя, который находится во внутренней полости дефекта. Данный процесс дает полностью понять, где располагаются дефектные участки, и при этом появляются цветовые следы, которые имеют линейный вид, и целенаправленно указывают на все трещины, царапины и поры.
Самым практичным распылителем являются аэрозольные баллоны. Но также можно производить нанесение проявителя и простым погружением. Обязательно знать, что сухие составы наносятся только в вихревой камере или электростатическим способом. В завершении процесса, необходимо немного подождать, в зависимости от размеров дефектов. Время ожидания может меняться от пяти минут до одного часа. Проявление выглядит, как простые следы красного цвета на белом основании. А объекты, которые будут иметь сквозные трещины, можно увидеть при помощи нанесения проявителя и пенетранта с нескольких сторон. Проявляющий краситель, который попадает сквозь контролируемый участок, будет хорошо просматриваться на фоне проявителя.
Вещество пенетрант
Пенетрант – это материал, который имеет значение капиллярного дефектоскопического эффекта, обладающего специальными проникновениями в прерывистые участки изделия, а также имеющий способности нахождения необходимых дефектов. Пенетрант имеет в своем составе вещества, которые обладают красящими препаратами, или дополнительными люминесцентными добавками. Такие вещества являются отличным вспомогательным звеном при обнаружении разнообразных трещин и дефектных мест.
Действия проявителя
Такое вещество, как проявитель является целенаправленным дефектоскопическим препаратом, которые отвечает за правильность извлечения пенетранта из участка капиллярной несплошности. Тем самым проявитель преследует основную цель для образования яркого индикаторного изображения, а также для проявления основного контрастирующего фона. Полное понятие предназначения проявителя заключается в процессе извлечения пенетранта, которое происходит за счет капиллярных сил. А также существует и другая сторона данного вещества, которая помогает осуществлять создание контрастного фона, расположенного на контролируемой поверхности. Вся технология данной системы проявления имеет ширину, которая может превышать размеры дефекта в двадцать раз, а цветность возрастает до пятидесяти процентов. Такой процесс обнаружения дефектов, который происходит при помощи вспомогательных препаратов, является наиболее эффективным методом выявления всевозможных дефектных участков.
Что касается порядка операций капиллярного метода контроля описано в этой статье Порядок операций капиллярного контроля
Основные данные физического капиллярного контроля
Процесс изменения насыщенности рисунка и отображения дефекта можно изменять двумя способами. Один из них подразумевает полировку верхних слоев контролируемого объекта, который в последствие выполняет травление при помощи кислот. Такая обработка результатов контролируемого объекта создает заполнение веществами коррозии, что дает потемнение и затем проявление на светлом материале. Данный процесс имеет несколько определенных запретов. К таковым относятся: нерентабельные поверхности, которые могут быть плохо отпалированны. Также нельзя использовать такой способ выявления дефектов, если применяются неметаллические изделия.
Вторым процессом изменения является светоотдача дефектов, которые подразумевает их полное заполнение специальными цветовыми или индикаторными веществами, так называемыми пенетрантами. Обязательно нужно знать, что если в пенетранте находится люминесцентные составы, тогда данная жидкость будет носить название – люминесцентная. А если главное вещество относится к красителям, тогда вся дефектоскопия будет называться цветной. Такой метод контроля содержит красители только насыщенных красных оттенков.
Последовательность операций при капиллярном контроле:
Предварительная очистка |
Механически, щеткой |
Струйным методом |
Обезжиривание горячим паром |
Очистка растворителем |
Предварительная просушка |
||||
Нанесение пенетранта |
Погружение в ванну |
Нанесение кистью |
Нанесение из аэрозоли / распылителя |
Нанесение электростатическим способом |
Промежуточная очистка |
Пропитанной водой не ворсистой тканью или губкой |
Пропитанной водой кистью |
Сполоснуть водой |
Пропитанной специальным растворителем не ворсистой тканью или губкой |
Сушка |
Высушить на воздухе |
Протереть не ворсистой тканью |
Обдуть чистым, сухим воздухом |
Высушить теплым воздухом |
Нанесение проявителя |
Погружением (проявитель на водной основе) |
Нанесение из аэрозоли / распылителя (проявитель на спиртовой основе) |
Электростатическое нанесение (проявитель на спиртовой основе) |
Нанесение сухого проявителя (при сильной пористости поверхности) |
Проверка поверхности и документирование |
Контроль при дневном или искусственном освещении мин. При использовании флуоресцентного пенетранта: Освещение: < 20 Lux Интенсивность УФ: 1000μW/cm2 |
Документация на прозрачной пленке |
Фотооптическое документирование |
Документирование с помощью фото- или видеосъемки |
Основные капиллярные методы неразрушающего контроля подразделяют в зависимости от типа проникающего вещества на следующие:
· Метод проникающих растворов — жидкостный метод капиллярного неразрушающего контроля, основанный на использовании в качестве проникающего вещества жидкого индикаторного раствора.
· Метод фильтрующихся суспензий — жидкостный метод капиллярного неразрушающего контроля, основанный на использовании в качестве жидкого проникающего вещества индикаторной суспензии, которая образует индикаторный рисунок из отфильтрованных частиц дисперсной фазы.
Капиллярные методы в зависимости от способа выявления индикаторного рисунка подразделяют на:
· Люминесцентный метод, основанный на регистрации контраста люминесцирующего в длинноволновом ультрафиолетовом излучении видимого индикаторного рисунка на фоне поверхности объекта контроля;
· контрастный (цветной) метод, основанный на регистрации контраста цветного в видимом излучении индикаторного рисунка на фоне поверхности объекта контроля.
Контрастный (красно-белый) метод: |
· люминесцентно-цветной метод, основанный на регистрации контраста цветного или люминесцирующего индикаторного рисунка на фоне поверхности объекта контроля в видимом или длинноволновом ультрафиолетовом излучении;
· яркостный метод, основанный на регистрации контраста в видимом излучении ахроматического рисунка на фоне поверхности объекта контроля.
Всегда в наличии! У нас Вы можете купить материалы для капиллярного контроля (цветной дефектоскопии) по низкой цене со склада в Москве: пенетрант, проявитель, очиститель Sherwin, капиллярные системы Helling, Magnaflux, ультрафиолетовые фонари, ультрафиолетовые лампы, ультрафиолетовые осветители, ультрафиолетовые светилники и контрольные образцы (эталоны) для цветной дефектоскопии ЦД.
Доставляем расходные материалы для цветной дефектоскопии по России и СНГ транспортными компаниями и курьерскими службами.
Капиллярная дефектоскопия | Независимая Экспертиза Волгоград
Капиллярная дефектоскопия
Капиллярный контроль
Капиллярный метод неразрушающего контроля
Капиллярная дефектоскопия — метод дефектоскопии, основанный на проникновении определенных жидких веществ в поверхностные дефекты изделия под действием капиллярного давления, в результате чего повышается свето- и цветоконтрастность дефектного участка относительно неповрежденного.
Различают люминесцентный и цветной методы капиллярной дефектоскопии.
В большинстве случаев по техническим требованиям необходимо выявлять настолько малые дефекты, что заметить их при визуальном контроле невооруженным глазом практически невозможно. Применение же оптических измерительных приборов, например лупы или микроскопа, не позволяет выявить поверхностные дефекты из-за недостаточной контрастности изображения дефекта на фоне металла и малого поля зрения при больших увеличениях. В таких случаях применяют капиллярный метод контроля.
При капиллярном контроле индикаторные жидкости проникают в полости поверхностных и сквозных несплошностей материала объектов контроля, и образующиеся индикаторные следы регистрируются визуальным способом или с помощью преобразователя.
Контроль капиллярным методом осуществляется в соответствии с ГОСТ 18442-80 “Контроль неразрушающий. Капиллярные методы. Общие требования. ”
Необходимым условием выявления дефектов типа нарушения сплошности материала капиллярными методами является наличие полостей, свободных от загрязнений и других веществ, имеющих выход на поверхность объектов и глубину распространения, значительно превышающую ширину их раскрытия.
Капиллярные методы подразделяют на основные, использующие капиллярные явления, и комбинированные, основанные на сочетании двух или более различных по физической сущности методов неразрушающего контроля, одним из которых является капиллярный контроль (капиллярная дефектоскопия).
Назначение капиллярного контроля (капиллярной дефектоскопии)
Капиллярная дефектоскопия (капиллярный контроль) предназначен для выявления невидимых или слабо видимых невооруженным глазом поверхностных и сквозных дефектов (трещины, поры, раковины, непровары, межкристаллическая коррозия, свищи и т.д.) в объектах контроля, определения их расположения, протяженности и ориентации по поверхности.
Капиллярные методы неразрушающего контроля основаны на капиллярном проникновении индикаторных жидкостей (пенетрантов) в полости поверхностных и сквозных несплошностей материала объекта контроля и регистрации образующихся индикаторных следов визуальным способом или с помощью преобразователя.
Применение капиллярного метода неразрушающего контроля
Капиллярный метод контроля применяется при контроле объектов любых размеров и форм, изготовленных из черных и цветных металлов, легированных сталей, чугуна, металлических покрытий, пластмасс, стекла и керамики в энергетике, авиации, ракетной технике, судостроении, химической промышленности, металлургии, при строительстве ядерных реакторов, в автомобилестроении, электротехники, машиностроении, литейном производстве, штамповке, приборостроении, медицине и других отраслях. Для некоторых материалов и изделий этот метод является единственным для определения пригодности деталей или установок к работе.
Капиллярная дефектоскопию применяют также и для неразрушающего контроля объектов, изготовленных из ферромагнитных материалов, если их магнитные свойства, форма, вид и месторасположение дефектов не позволяют достигать требуемой по ГОСТ 21105-87 чувствительности магнитопорошковым методом и магнитопорошковый метод контроля не допускается применять по условиям эксплуатации объекта.
Необходимым условием выявления дефектов типа нарушения сплошности материала капиллярными методами является наличие полостей, свободных от загрязнений и других веществ, имеющих выход на поверхность объектов и глубину распространения, значительно превышающую ширину их раскрытия.
Капиллярный контроль используется также при течеискании и, в совокупности с другими методами, при мониторинге ответственных объектов и объектов в процессе эксплуатации.
Достоинствами капиллярных методов дефектоскопии являются: простота операций контроля, несложность оборудования, применимость к широкому спектру материалов, в том числе к немагнитным металлам.
Преимуществом капиллярной дефектоскопии является то, что с его помощью можно не только обнаружить поверхностные и сквозные дефекты, но и получить по их расположению, протяженности, форме и ориентации по поверхности ценную информацию о характере дефекта и даже некоторых причинах его возникновения (концентрация напряжений, несоблюдение технологии и пр. ).
В качестве индикаторных жидкостей применяют органические люминофоры — вещества, дающие яркое собственное свечение под действием ультрафиолетовых лучей, а также различные красители. Поверхностные дефекты выявляют с помощью средств, позволяющих извлекать индикаторные вещества из полости дефектов и обнаруживать их присутствие на поверхности контролируемого изделия.
Капилляр (трещина), выходящий на поверхность объекта контроля только с одной стороны, называют поверхностной несплошностью, а соединяющий противоположные стенки объекта контроля, — сквозной. Если поверхностная и сквозная несплошности являются дефектами, то допускается применять вместо них термины «поверхностный дефект» и «сквозной дефект». Изображение, образованное пенетрантом в месте расположения несплошности и подобное форме сечения у выхода на поверхность объекта контроля, называют индикаторным рисунком, или индикакацией.
Применительно к несплошности типа единичной трещины вместо термина «индикация» допускается применение термина «индикаторный след». Глубина несплошности — размер несплошности в направлении внутрь объекта контроля от его поверхности. Длина несплошности — продольный размер несплошности на поверхности объекта. Раскрытие несплошности — поперечный размер несплошности у ее выхода на поверхность объекта контроля.
Необходимым условием надежного выявления капиллярным методом дефектов, имеющих выход на поверхность объекта, является относительная их незагрязнённость посторонними веществами, а также глубина распространения, значительно превышающая ширину их раскрытия (минимум 10/1). Для очистки поверхности перед нанесением пенетранта используют очиститель.
Капиллярные методы дефектоскопии подразделяют на основные, использующие капиллярные явления, и комбинированные, основанные на сочетании двух или более различных по физической сущности методов неразрушающего контроля, одним из которых является капиллярный.
Приборы и оборудования для капиллярного контроля:
- Наборы для капиллярной дефектоскопии (очистители, проявители, пенетранты)
- Пульверизаторы
- Пневмогидропистолеты
- Источники ультрафиолетового освещения (ультрафиолетовые фонари, осветители)
- Испытательные панели (тест-панель)
Контрольные образцы для цветной дефектоскопии
Чувствительность капиллярной метода дефектоскопии
Чувствительность капиллярного контроля – способность выявления несплошностей данного размера с заданной вероятностью при использовании конкретного способа, технологии контроля и пенетрантной системы. Согласно ГОСТ 18442-80 класс чувствительности контроля определяют в зависимости от минимального размера выявленных дефектов с поперечными размером 0,1 — 500 мкм.
Выявление дефектов, имеющих ширину раскрытия более 0,5 мм, капиллярными методами контроля не гарантируется.
С чувствительностью по 1 классу с помощью капиллярной дефектоскопии контролируют лопатки турбореактивных двигателей, уплотнительные поверхности клапанов и их гнезд, металлические уплотнительные прокладки фланцев и др. (выявляемые трещины и поры величиной до десятых долей мкм). По 2 классу проверяют корпуса и антикоррозийные наплавки реакторов, основной металл и сварные соединения трубопроводов, детали подшипников (выявляемые трещины и поры величиной до нескольких мкм).
Чувствительность дефектоскопических материалов, качество промежуточной очистки и контроль всего капиллярного процесса определяются на контрольных образцах (эталонах для цветной дефектоскопии ЦД), т.е. на металлических определенной шероховатости с нанесенными на них нормированными искусственными трещинами (дефектами).
Класс чувствительности контроля определяют в зависимости от минимального размера выявляемых дефектов. Постигаемую чувствительность в необходимых случаях определяют на натурных объектах или искусственных образцах с естественными или имитируемыми дефектами, размеры которых уточняют металлографическими или другими методами анализа.
Согласно ГОСТ 18442-80 класс чувствительности контроля определяется в зависимости от размера выявляемых дефектов. В качестве параметра размера дефекта принимается поперечный размер дефекта на поверхности объекта контроля – так называемая ширина раскрытия дефекта. Поскольку глубина и длина дефекта также оказывают существенное влияние на возможность его обнаружения (в частности, глубина должна существенно больше раскрытия), эти параметры считаются стабильными. Нижний порог чувствительности, т.е. минимальная величина раскрытия выявленных дефектов ограничивается тем, что весьма малое количество пенетранта; задержавшееся в полости небольшого дефекта, оказывается недостаточным, чтобы получить контрастную индикацию при данной толщине слоя проявляющего вещества. Существует также верхний порог чувствительности, который определяется тем, что из широких, но неглубоких дефектов пенетрант вымывается при устранении излишков пенетранта на поверхности.
Установлено 5 классов чувствительности (по нижнему порогу) в зависимости от размеров дефектов:
Класс чувствительности |
Ширина раскрытия дефекта, мкм |
I |
Менее 1 |
II |
От 1 до 10 |
III |
От 10 до 100 |
IV |
От 100 до 500 |
технологический |
Не нормируется |
Физические основы и методика капиллярного метода контроля
Капиллярный метод неразрушающего контроля (ГОСТ 18442-80) основан на капиллярном проникновении внутрь дефекта индикаторной жидкости и предназначен для выявления дефектов, имеющих выход на поверхность объекта контроля. Данный метод пригоден для выявления несплошностей с поперечными размером 0,1 — 500 мкм, в том числе сквозных, на поверхности черных и цветных металлов, сплавов, керамики, стекла и т.п. Широко применяется для контроля целостности сварного шва.
Цветной или красящий пенетрант наносится на поверхность объекта контроля. Благодаря особым качествам, которые обеспечиваются подбором определенных физических свойств пенетранта: поверхностного натяжения, вязкости, плотности, он, под действием капиллярных сил, проникает в мельчайшие дефекты, имеющие выход на поверхность объекта контроля
Проявитель, наносимый на поверхность объекта контроля через некоторое время после осторожного удаления с поверхности пенетранта, растворяет находящийся внутри дефекта краситель и за счет диффузии “вытягивает” оставшийся в дефекте пенетрант на поверхность объекта контроля.
Имеющиеся дефекты видны достаточно контрастно. Индикаторные следы в виде линий указывают на трещины или царапины, отдельные точки — на поры.
Процесс обнаружения дефектов капиллярным методом разделяется на 5 стадий (проведение капиллярного контроля):
1. Предварительная очистка поверхности (используют очиститель)
2. Нанесение пенетранта
3. Удаление излишков пенетранта
4. Нанесение проявителя
5. Контроль
Предварительная очистка поверхности. Чтобы краситель мог проникнуть в дефекты на поверхности, ее предварительно следует очистить водой или органическим очистителем. Все загрязняющие вещества (масла, ржавчина, и т.п.) любые покрытия (ЛКП, металлизация) должны быть удалены с контролируемого участка. После этого поверхность высушивается, чтобы внутри дефекта не оставалось воды или очистителя.
Нанесение пенетранта. Пенетрант, обычно красного цвета, наносится на поверхность путем распыления, кистью или погружением ОК в ванну, для хорошей пропитки и полного покрытия пенетрантом. Как правило, при температуре 5-50 0С, на время 5-30 мин.
Удаление излишков пенетранта.
Нанесение проявителя. После просушки сразу же на ОК наносится проявитель, обычно белого цвета, тонким ровным слоем.
Контроль. Инспектирование ОК начинается непосредственно после окончания процесса проявки и заканчивается согласно разным стандартам не более чем через 30 мин. Интенсивность окраски говорит о глубине дефекта, чем бледнее окраска, тем дефект мельче. Интенсивную окраску имеют глубокие трещины. После проведения контроля проявитель удаляется водой или очистителем.
Красящий пенетрант наносится на поверхность объекта контроля (ОК). Благодаря особым качествам, которые обеспечиваются подбором определенных физических свойств пенетранта: поверхностного натяжения, вязкости, плотности, он, под действием капиллярных сил, проникает в мельчайшие дефекты, имеющие выход на поверхность объекта контроля. Проявитель, наносимый на поверхность объекта контроля через некоторое время после осторожного удаления с поверхности пенетранта, растворяет находящийся внутри дефекта краситель и за счет диффузии “вытягивает” оставшийся в дефекте пенетрант на поверхность объекта контроля. Имеющиеся дефекты видны достаточно контрастно. Индикаторные следы в виде линий указывают на трещины или царапины, отдельные точки — на поры.
Наиболее удобны распылители, например аэрозольные баллоны. Можно наносить проявитель и окунанием. Сухие проявители наносятся в вихревой камере, либо электростатически. После нанесения проявителя следует выждать время от 5 мин для крупных дефектов, до 1 часа для мелких дефектов. Дефекты будут проявляться, как красные следы на белом фоне.
Сквозные трещины на тонкостенных изделиях можно обнаруживать, нанося проявитель и пенетрант с разных сторон изделия. Прошедший насквозь краситель будет хорошо виден в слое проявителя.
Пенетрантом (пенетрант от английского penetrate — проникать) называют капиллярный дефектоскопический материал, обладающий способностью проникать в несплошности объекта контроля и индицировать эти несплошности. Пенетранты содержат красящие вещества (цветной метод) или люминесцирующие добавки (люминесцентный метод), или их комбинацию. Добавки позволяют отличать пропитанную этими веществами область слоя проявителя над трещиной от основного (чаще всего белого) сплошного без дефектов материала объекта (фон).
Проявителем (проявитель) называют дефектоскопический материал, предназначенный для извлечения пенетранта из капиллярной несплошности с целью образования четкого индикаторного рисунка и создания контрастирующего с ним фона. Таким образом, роль проявителя в капиллярном контроле заключается, с одной стороны, в том, чтобы он извлекал пенетрант из дефектов за счет капиллярных сил, с другой стороны, — проявитель должен создать контрастный фон на поверхности контролируемого объекта, чтобы уверенно выявлять окрашенные или люминесцирующие индикаторные следы дефектов. При правильной технологии проявления ширина следа в 10 … 20 и более раз может превосходить ширину дефекта, а яркостный контраст возрастает на 30 … 50 %. Этот эффект увеличения позволяет опытным специалистам даже невооруженным глазом выявлять очень маленькие трещины.
Последовательность операций при капиллярном контроле:
Предварительная очистка |
Механически, щеткой |
Струйным методом |
Обезжиривание горячим паром |
Очистка растворителем |
Предварительная просушка |
||||
Нанесение пенетранта |
Погружение в ванну |
Нанесение кистью |
Нанесение из аэрозоли / распылителя |
Нанесение электростатическим способом |
Промежуточная очистка |
Пропитанной водой не ворсистой тканью или губкой |
Пропитанной водой кистью |
Сполоснуть водой |
Пропитанной специальным растворителем не ворсистой тканью или губкой |
Сушка |
Высушить на воздухе |
Протереть не ворсистой тканью |
Обдуть чистым, сухим воздухом |
Высушить теплым воздухом |
Нанесение проявителя |
Погружением (проявитель на водной основе) |
Нанесение из аэрозоли / распылителя (проявитель на спиртовой основе) |
Электростатическое нанесение (проявитель на спиртовой основе) |
Нанесение сухого проявителя (при сильной пористости поверхности) |
Проверка поверхности и документирование |
Контроль при дневном или искусственном освещении мин. При использовании флуоресцентного пенетранта: Освещение: < 20 Lux Интенсивность УФ: 1000μW/cm2 |
Документация на прозрачной пленке |
Фотооптическое документирование |
Документирование с помощью фото- или видеосъемки |
Основные капиллярные методы неразрушающего контроля подразделяют в зависимости от типа проникающего вещества на следующие:
· Метод проникающих растворов — жидкостный метод капиллярного неразрушающего контроля, основанный на использовании в качестве проникающего вещества жидкого индикаторного раствора.
· Метод фильтрующихся суспензий — жидкостный метод капиллярного неразрушающего контроля, основанный на использовании в качестве жидкого проникающего вещества индикаторной суспензии, которая образует индикаторный рисунок из отфильтрованных частиц дисперсной фазы.
Капиллярные методы в зависимости от способа выявления индикаторного рисунка подразделяют на:
· Люминесцентный метод, основанный на регистрации контраста люминесцирующего в длинноволновом ультрафиолетовом излучении видимого индикаторного рисунка на фоне поверхности объекта контроля;
· контрастный (цветной) метод, основанный на регистрации контраста цветного в видимом излучении индикаторного рисунка на фоне поверхности объекта контроля.
Контрастный (красно-белый) метод: |
· люминесцентно-цветной метод, основанный на регистрации контраста цветного или люминесцирующего индикаторного рисунка на фоне поверхности объекта контроля в видимом или длинноволновом ультрафиолетовом излучении;
· яркостный метод, основанный на регистрации контраста в видимом излучении ахроматического рисунка на фоне поверхности объекта контроля.
Физические основы капиллярной дефектоскопии. Люминесцентная дефектоскопия (ЛД). Цветная дефектоскопия (ЦД).
Изменить соотношение контрастностей изображения дефекта и фона можно двумя способами. Первый способ заключается в полировке поверхности контролируемого изделия с последующим травлением ее кислотами. При такой обработке дефект забивается продуктами коррозии, чернеет и становится заметным на светлом фоне полированного материала. Этот способ имеет целый ряд ограничений. В частности, в производственных условиях совершенно нерентабельно полировать поверхность изделия, особенно сварных швов. К тому же способ неприменим при контроле прецизионных полированных деталей или неметаллических материалов. Способ травления чаще применяют для контроля каких-то локальных подозрительных участков металлических изделий.
Второй способ состоит в изменении светоотдачи дефектов заполнением их с поверхности специальными свето- и цветоконтрастными индикаторными жидкостями — пенетрантами. Если в состав пенетранта входят люминесцирующие вещества, т. е. вещества, дающие яркое свечение при облучении их ультрафиолетовым светом, то такие жидкости называют люминесцентными, а метод контроля соответственно — люминесцентным (люминесцентная дефектоскопия — ЛД). Если же основой пенетранта являются красители, видимые при дневном свете, то метод контроля называют цветным (цветная дефектоскопия — ЦД). В цветной дефектоскопии используют красители ярко-красного цвета.
Сущность капиллярной дефектоскопии заключается в следующем. Поверхность изделия очищают от грязи, пыли, жировых загрязнений, остатков флюса, лакокрасочных покрытий и т. п. После очистки на поверхность подготовленного изделия наносят слой пенетранта и некоторое время выдерживают, чтобы жидкость смогла проникнуть в открытые полости дефектов. Затем поверхность очищают от жидкости, часть которой остается в полостях дефектов.
В случае люминесцентной дефектоскопии изделие освещают ультрафиолетовым светом (ультрафиолетовый осветитель) в затемненном помещении и подвергают осмотру. Дефекты хорошо заметны в виде ярко светящихся полосок, точек и т. п.
При цветной дефектоскопии выявить дефекты на этой стадии не удается, так как разрешающая способность глаза слишком мала. Чтобы повысить выявляемость дефектов, на поверхность изделия после удаления с нее пенетранта наносят специальный проявляющий материал в виде быстро сохнущей суспензии (например, каолина, коллодия) или лаковые покрытия. Проявляющий материал (обычно белого цвета) вытягивает пенетрант из полости дефектов, что приводит к образованию на проявителе индикаторных следов. Индикаторные следы полностью повторяют конфигурацию дефектов в плане, но больше их по размерам. Такие индикаторные следы легко различимы глазом даже без использования оптических средств. Увеличение размеров индикаторного следа тем больше, чем глубже дефекты, т.е. чем больше объем пенетранта, заполнившего дефект, и чем больше времени прошло с момента нанесения проявляющего слоя.
Физической основой капиллярных методов дефектоскопии является явление капиллярной активности, т. е. способность жидкости втягиваться в мельчайшие сквозные отверстия и открытые с одного конца каналы.
Капиллярная активность зависит от смачивающей способности твердого тела жидкостью. В любом теле на каждую молекулу со стороны других молекул действуют молекулярные силы сцепления. В твердом теле они больше, чем в жидком. Поэтому жидкости в отличие от твердых тел не обладают упругостью формы, но обладают большой объемной упругостью. Молекулы, находящиеся на поверхности тела, взаимодействуют как с одноименными молекулами тела, стремящимися втянуть их внутрь объема, так и с молекулами окружающей тело среды и обладают наибольшей потенциальной энергией. По этой причине перпендикулярно к границе в направлении внутрь тела возникает нескомпенсированная сила, называемая силой поверхностного натяжения. Силы поверхностного натяжения пропорциональны длине контура смачивания и, естественно, стремятся его уменьшить. Жидкость на металле в зависимости от соотношения межмолекулярных сил будет растекаться по металлу или соберется в каплю. Жидкость смачивает твердое тело, если силы взаимодействия (притяжения) жидкости с молекулами твердого тела больше, чем силы поверхностного натяжения. В этом случае жидкость будет растекаться по твердому телу. Если же силы поверхностного натяжения больше, чем силы взаимодействия с молекулами твердого тела, то жидкость соберется в каплю.
При попадании жидкости в капиллярный канал ее поверхность искривляется, образуя так называемый мениск. Силы поверхностного натяжения стремятся уменьшить величину свободной границы мениска, и в капилляре начинает действовать дополнительная сила, приводящая к всасыванию смачивающей жидкости. Глубина, на которую жидкость проникает в капилляр, прямо пропорциональна коэффициенту поверхностного натяжения жидкости и обратно пропорциональна радиусу капилляра. Иными словами, чем меньше радиус капилляра (дефекта) и лучше смачиваемость материала, тем жидкость быстрее и на большую глубину проникает в капилляр.
У нас Вы можете купить материалы для капиллярного контроля (цветной дефектоскопии) по низкой цене со склада в Москве: пенетрант, проявитель, очиститель Sherwin, капиллярные системы Helling, Magnaflux, ультрафиолетовые фонари, ультрафиолетовые лампы, ультрафиолетовые осветители, ультрафиолетовые светилники и контрольные образцы (эталоны) для цветной дефектоскопии ЦД.
Доставляем расходные материалы для цветной дефектоскопии по России и СНГ транспортными компаниями и курьерскими службами.
Капиллярный контроль. Капиллярный метод. Неразрушающий контроль. Капиллярная дефектоскопия.
Наша приборная база
Специалисты организации Независимая Экспертиза готовы помочь как физическим, так и юридическим лицам в проведении строительно-технической экспертизы,техническое обследование зданий и сооружений, капиллярная дефектоскопия.
У Вас нерешенные вопросы или же Вы захотите лично пообщаться с нашими специалистами или заказать независимую строительную экспертизу, всю необходимую для этого информацию можно получить в разделе «Контакты».
С нетерпением ждем Вашего звонка и заранее благодарим за оказанное доверие
Вернуться: экспертиза
Капиллярная дефектоскопия проводится
400074, г. Волгоград, ул. Иркутская, 7 (остановка ТЮЗ, отдельный вход с торца здания).
Заключение независимой экспертной организации имеет статус официального документа доказательного значения и может быть использовано в суде.
Капиллярный контроль
Капиллярный контроль.
ООО «Диаформ» имеет все необходимое для качественного проведения капиллярного контроля.
Капиллярная дефектоскопия — метод дефектоскопии, основанный на проникновении определенных жидких веществ в поверхностные дефекты изделия под действием капиллярного давления, в результате чего повышается свето- и цветоконтрастность дефектного участка относительно неповрежденного.
Различают люминесцентный и цветной методы капиллярной дефектоскопии.
В большинстве случаев по техническим требованиям необходимо выявлять настолько малые дефекты, что заметить их при визуальном контроле невооруженным глазом практически невозможно. Применение же оптических измерительных приборов, например лупы или микроскопа, не позволяет выявить поверхностные дефекты из-за недостаточной контрастности изображения дефекта на фоне металла и малого поля зрения при больших увеличениях. В таких случаях применяют капиллярный метод контроля.
Получить консультацию
При капиллярном контроле индикаторные жидкости проникают в полости поверхностных и сквозных несплошностей материала объектов контроля, и образующиеся индикаторные следы регистрируются визуальным способом или с помощью преобразователя.
Контроль капиллярным методом осуществляется в соответствии с ГОСТ 18442-80 “Контроль неразрушающий. Капиллярные методы. Общие требования.”
Необходимым условием выявления дефектов типа нарушения сплошности материала капиллярными методами является наличие полостей, свободных от загрязнений и других веществ, имеющих выход на поверхность объектов и глубину распространения, значительно превышающую ширину их раскрытия.
Капиллярные методы подразделяют на основные, использующие капиллярные явления, и комбинированные, основанные на сочетании двух или более различных по физической сущности методов неразрушающего контроля, одним из которых является капиллярный контроль (капиллярная дефектоскопия).
Назначение капиллярного контроля (капиллярной дефектоскопии)
Капиллярная дефектоскопия (капиллярный контроль)предназначен для выявления невидимых или слабо видимых невооруженным глазом поверхностных и сквозных дефектов (трещины, поры, раковины, непровары, межкристаллическая коррозия, свищи и т.д.) в объектах контроля, определения их расположения, протяженности и ориентации по поверхности.
Капиллярные методы неразрушающего контроля основаны на капиллярном проникновении индикаторных жидкостей (пенетрантов) в полости поверхностных и сквозных несплошностей материала объекта контроля и регистрации образующихся индикаторных следов визуальным способом или с помощью преобразователя.
Применение капиллярного метода неразрушающего контроля
Капиллярный метод контроля применяется при контроле объектов любых размеров и форм, изготовленных из черных и цветных металлов, легированных сталей, чугуна, металлических покрытий, пластмасс, стекла и керамики в энергетике, авиации, ракетной технике, судостроении, химической промышленности, металлургии, при строительстве ядерных реакторов, в автомобилестроении, электротехники, машиностроении, литейном производстве, штамповке, приборостроении, медицине и других отраслях. Для некоторых материалов и изделий этот метод является единственным для определения пригодности деталей или установок к работе.
Капиллярная дефектоскопию применяют также и для неразрушающего контроля объектов, изготовленных из ферромагнитных материалов, если их магнитные свойства, форма, вид и месторасположение дефектов не позволяют достигать требуемой по ГОСТ 21105-87 чувствительности магнитопорошковым методом и магнитопорошковый метод контроля не допускается применять по условиям эксплуатации объекта.
Необходимым условием выявления дефектов типа нарушения сплошности материала капиллярными методами является наличие полостей, свободных от загрязнений и других веществ, имеющих выход на поверхность объектов и глубину распространения, значительно превышающую ширину их раскрытия.
Капиллярный контроль используется также при течеискании и, в совокупности с другими методами, при мониторинге ответственных объектов и объектов в процессе эксплуатации.
Достоинствами капиллярных методов дефектоскопии являются: простота операций контроля, несложность оборудования, применимость к широкому спектру материалов, в том числе к немагнитным металлам.
Преимуществом капиллярной дефектоскопии является то, что с его помощью можно не только обнаружить поверхностные и сквозные дефекты, но и получить по их расположению, протяженности, форме и ориентации по поверхности ценную информацию о характере дефекта и даже некоторых причинах его возникновения (концентрация напряжений, несоблюдение технологии и пр.).
В качестве индикаторных жидкостей применяют органические люминофоры — вещества, дающие яркое собственное свечение под действием ультрафиолетовых лучей, а также различные красители. Поверхностные дефекты выявляют с помощью средств, позволяющих извлекать индикаторные вещества из полости дефектов и обнаруживать их присутствие на поверхности контролируемого изделия.
Лекция 5. Капиллярная дефектоскопия — Студопедия
Поделись
План лекции Классификация капиллярных методов НК, цветная дефектоскопия (ЦД). Физическая сущность ЦД — контроля: пенетрация, краевой угол смачивания, капиллярные явления и уравнение Лапласа. Технологическая схема ЦД — контроля, чувствительность метода. Дефектоскопические материалы для ЦД — контроля
Метод контроля основан на капиллярном проникновении индикаторных жидкостей (пенетрантов) в полости поверхностных и сквозных несплошностей материала объектов контроля и регистрации образующихся индикаторных следов визуальным способом или с помощью преобразователя.
Капиллярный НК предназначен для обнаружения невидимых или слабовидимых невооруженным глазом поверхностных и сквозных дефектов в объектах контроля, определения их расположения, протяженности (для дефектов типа трещин) и ориентации по поверхности. Этот вид контроля позволяет диагностировать объекты любых размеров и форм, изготовленные из черных и цветных металлов и сплавов, пластмасс, стекла, керамики, а также других твердых неферромагнитных материалов.
Капиллярный контроль применяют также для объектов, изготовленных из ферромагнитных материалов, если их магнитные свойства, форма, вид и месторасположение дефектов не позволяют достичь требуемой по ГОСТ 21105—75 чувствительности магнитопорошковым методом или магнитопорошковый метод контроля не допускается применять по условиям эксплуатации объекта.
Капилляр, выходящий на поверхность объекта контроля только с одной стороны, называют поверхностной несплошностью, а соединяющий противоположные стенки объекта контроля, — сквозной.
Изображение, образованное пенетрантом, в месте расположения несплошности и подобное форме ее сечения у выхода на поверхность объекта контроля называют индикаторным рисунком (след).
Капиллярные методы подразделяют на основные, использующие капиллярные явления, и комбинированные.
Основные капиллярные методы контроля подразделяют в зависимости от типа проникающего вещества:
1. Метод проникающих растворов — жидкостный метод — основанный на использовании в качестве проникающего вещества жидкого индикаторного раствора.
2. Метод фильтрующихся суспензий — жидкостный метод, основанный на использовании в качестве жидкого проникающего вещества индикаторной суспензии, которая образует индикаторный рисунок из отфильтрованных частиц дисперсной фазы.
В зависимости от способа выявления индикаторного рисунка подразделяют на люминисцентные, основанный на регистрации контраста люминесцирующсго в длинноволновом ультрафиолетовом излучении видимого индикаторного рисунка на фоне поверхности объекта контроля,
— цветной, основанный на регистрации контраста цветного в видимом излучении индикаторного рисунка па фоне поверхности объекта контроля;
— люминесцентно – цветной, Рис. 5.1, основанный на регистрации контраста цветного или люминесцирующего индикаторного рисунка на фоне поверхности объекта контроля ввидимом или длинноволновом ультрафиолетовом излучении;
Рисунок 5.1 Люминесцентно- цветная дефектоскопия 1 — деталь, 2 – дефект заполненный пенетрантом, 3. – слой проявителя, 4. – индикаторный след, 5. – источник ультрофиолетового излучения, Вн — свечение индекаторного следа, Вф – свечение фона, Xи – размер индикаторного следа, Xд – размер дефекта на поверхности
— яркостный, основанный на регистрации контраста в видимом излучении ахроматического рисунка на фоне поверхности объекта контроля.
Комбинированные методы капиллярного неразрушающего контроля сочетают два или более различных по физической сущности методов неразрушающего контроля, один из которых обязательно жидкостный.
Капиллярно-электростатический метод основан на обнаружении индикаторного рисунка, образованного скоплением электрически заряженных частиц у поверхностной или сквозной несплошности неэлектропроводящего объекта, заполненного ионогенным пенетрантом.
Капиллярно-электроиндуктивный метод основан на электроиндуктивном обнаружении электропроводящего индикаторного пенетранта в поверхностных и сквозных несплошностях неэлектропроводящего объекта.
Капиллярно-магнитопорошковый метод основан на обнаружении комплексного индикаторного рисунка, образованного пенетрантом и ферромагнитным порошком, при контроле намагниченного объекта.
Жидкостный капиллярно-радиационный метод излучения основан на регистрации ионизирующего излучения соответствующего пенетранта в поверхностных и сквозных несплошностях, а капиллярно-радиационный метод поглощения — на регистрации поглощения ионизирующего излучения соответствующим пенетрантом в поверхностных и сквозных несплошностях объекта контроля.
6 наиболее важных методов испытаний на трещины при неразрушающем контроле материалов
6 наиболее важных методов испытаний на трещины при неразрушающих испытаниях материалов
В последние годы неразрушающие испытания материалов прочно вошли в процесс контроля. Благодаря своей эффективной работе эта процедура проверки стала решающей для всестороннего контроля процесса. В то же время во многих отраслях уже недостаточно проверять только геометрические размеры компонента. Это связано с тем, что все чаще предъявляются повышенные требования к тестированию компонентов параллельно с непрерывной работой. Поэтому необходимы гораздо более обширные испытания, чтобы подтвердить соответствующие свойства в течение всего срока службы.
Зачем нужны неразрушающие испытания материалов?
Во многих критически важных с точки зрения безопасности приложениях или с крупным экономическим косвенным ущербом компоненты выходят из строя или не соответствуют требованиям. Если, например, американские горки разваливаются во время работы, человеческая жизнь подвергается немедленной опасности. Если трубопроводы здания выходят из строя, может последовать значительный ущерб от воды с последующими высокими затратами на ремонт.
В соответствии с этим определяются стандарты в автомобильной и многих других отраслях. Они обеспечивают непрерывный и тщательный контроль важных для безопасности компонентов в процессе производства и перед установкой.
Какие дефекты могут быть обнаружены в компонентах?
Каталог дефектов от клиентов разнообразен. Например, решающими факторами влияния являются область применения компонента, материал, из которого он изготовлен, и его размеры. Наиболее распространенными типами дефектов, обнаруживаемых при осмотре поверхности, являются:
- Трещины
- Полости
- Вмятины
- Шлифовальный ожог
- Твердые участки
- Мягкие места
- Магнитные включения (остатки)
Классические дефекты компонентов представляют собой трещины, обнаруженные на поверхности материала. Здесь обычно используется вихретоковый контроль. Это связано с тем, что даже самые маленькие трещины, которые изначально не представляют проблемы, могут увеличиваться и расширяться под постоянной нагрузкой. В худшем случае это может привести к выходу из строя компонента. Вспомните трещину в тормозном диске: есть вероятность, что после определенного периода эксплуатации тормозной диск сильно порвется при торможении. В дорожном движении такой неисправный компонент может быстро привести к опасным для жизни ситуациям.
По этой причине клиенты ожидают, что даже самые мелкие дефекты глубиной всего в несколько микрометров будут обнаружены и надежно отображены в процессе контроля. Например, для проверки этого обычно используется контрольно-измерительный прибор STATOGRAPH от FOERSTER. Размер дефекта, который еще можно устранить с помощью STATOGRAPH, зависит от компонента и его материала, а также от частоты тестирования и используемого датчика. Благодаря оптимальной конструкции можно обнаружить даже трещины глубиной всего 30 мкм.
Какие существуют методы обнаружения трещин в литых компонентах?
Существует несколько методов тестирования компонентов. Различают два классических подхода:
- Разрушающий контроль
- Неразрушающий контроль
Компоненты из партий, которые впоследствии перепродаются и устанавливаются, могут быть проверены только случайным и разрушающим образом. По мере увеличения потребности в тестировании стоимость брака, вызванного тестом, возрастает. В результате полная проверка методологически невозможна.
На этой ноте была развита область неразрушающего контроля. Исходя из этого, в зависимости от задачи тестирования доступны различные методы:
- Визуальный осмотр (VT)
- Испытания на проникающие красители (PT)
- Вихретоковый контроль (ET)
- Термографические испытания (ТТ)
- Магнитопорошковый контроль (МТ)
- Ультразвуковой контроль (УЗК)
В зависимости от применения используются разные методы испытаний. Существенными влияющими факторами являются тестовый материал, размер, структура дефектов и тестовое задание, а также необходимое время цикла и доступный бюджет.
1. Испытание на трещины с визуальным контролем (VT)
невооруженным глазом или с помощью оптических устройств (например, увеличительных стекол, микроскопов или эндоскопов). Перед всеми другими методами разрушающего и неразрушающего контроля визуальный контроль первоначально проводится в комплексном тесте и используется для различных форм продукта в соответствии с указанными инструкциями по тестированию.
Процедура испытаний реализуется в виде прямого и косвенного визуального осмотра в рамках производственного контроля, осмотра и исследования повреждений компонентов, систем или других объектов испытаний. Результаты тестирования сильно зависят от опыта и субъективной оценки тестировщика. Поэтому трудно добиться сопоставимости.
2. Испытание на растрескивание методом капиллярного контроля (PT)
Испытание на проникновение красителя является еще одним методом неразрушающего контроля поверхностей материалов. В основе этого процесса лежит капиллярное действие. Процесс проникновения используется как визуальное свидетельство поверхностных дефектов, таких как трещины или поры.
Процесс в основном используется для металлов. При необходимости испытание на проникновение красителя также может выявить дефекты пластика и керамики. Как и в случае визуального контроля, контроль проникновения цвета является субъективным методом, который зависит от опыта инспектора.
3. Контроль трещин с помощью вихретоковых приборов (ET)
Для контроля поверхности токопроводящих деталей вихретоковый метод (англ. «eddy current testing», сокращенно ECT) зарекомендовал себя как доминирующая технология. . Системы вихретокового контроля состоят из испытательного прибора с соответствующим щупом и, при необходимости, дополнительных программных модулей. Испытательный щуп содержит катушку возбуждения (первичную катушку) и дифференциальную катушку (вторичную катушку). Испытательный щуп подключается к испытательному прибору, например, STATOGRAPH CM для испытаний на трещины.
Катушка возбуждения работает с переменным полем и индуцирует вторичное поле в дифференциальной катушке, которое изменяет амплитуду и фазу сигнала при изменении поверхности. Это изменение сигнала регистрируется тестовым прибором с очень высокой скоростью передачи данных. Позже эта информация передается на завод-изготовитель. В результате неисправная часть может быть распознана и отсортирована.
В зависимости от характера неисправности и материала объекта испытаний необходимо выбрать правильную конфигурацию испытательного прибора и испытательного щупа. Существуют различные способы настройки параметров теста, чтобы они максимально оптимально реагировали на определенные шаблоны ошибок. В то же время это способствует тому, что нерелевантные ошибки могут быть найдены хуже. Последующие программы также могут помочь в оценке тестовых данных. Одни и те же данные оцениваются с помощью разных методов фильтрации и, таким образом, оптимизируются для множественных шаблонов ошибок.
STATOVISION является примером такого нижестоящего программного обеспечения, способного улучшить качество сигнала. После сбора необработанных данных программное обеспечение использует методы цифровой фильтрации. Это особенно необходимо, если требования к размеру обнаруживаемой ошибки очень высоки. Типичные глубины ошибок, которые, как ожидается, будут обнаружены с помощью вихретокового метода, находятся в диапазоне от 30 мкм до 1 мм.
Предпосылками для вихретокового контроля поверхностных дефектов являются, с одной стороны, общепроводящие компоненты, с другой — вращательная симметрия объектов контроля. Вращательная симметрия необходима для максимально эффективного выполнения теста. Компонент поворачивается для тестирования, и датчик параллельно сканирует его поверхность. Если нет симметрии, возможно, придется использовать другой метод испытаний.
4. Испытание на трещины с помощью термографического оборудования (ТТ)
Вихретоковый контроль всегда является предпочтительным методом, когда речь идет о проводящих и осесимметричных материалах. Кроме того, эти компоненты должны иметь как можно более гладкие поверхности, чтобы их можно было сканировать датчиком. Если эти условия не выполняются, используются дополнительные методы испытаний. Обнаружение трещин с помощью термографии неуклонно растет в промышленности. Термографические испытания на трещины обычно проводят импульсным термографическим методом или термографическим методом Lock-In. Здесь компонент локально нагревается короткими импульсами с источником энергии (например, индукцией, оптическим путем с помощью ламп или лазера). Поверхность фиксируется термографической камерой. Трещины и другие локальные различия на поверхности по-разному реагируют на прикладываемое тепло. Трещина аккумулирует меньше тепла и четко выделяется на термографическом изображении из своего окружения.
Различные источники тепла также оказывают разное воздействие. Если, например, проводящий компонент возбуждается индуктором, на концах трещины выделяется больше тепла, чем в других точках испытуемой детали. Вихревые токи здесь сконденсировались и погонная энергия выше. Изображения, записанные с помощью термографической камеры, поступают в качестве входных данных в программное обеспечение для обработки данных. Для оценки изображения используются специальные алгоритмы обработки. Несколько последовательных снимков показывают, помимо прочего, изменение теплового потока во времени и предоставляют дополнительную информацию. Основное преимущество термографического метода обнаружения трещин заключается в том, что компоненты могут иметь высокую степень свободы в отношении их размеров и геометрии. Кроме того, метод может быть применен к непроводящим компонентам. В этих случаях для ввода энергии обычно необходим оптический метод.
Кроме того, метод относительно устойчив к воздействиям окружающей среды. Однако испытуемая поверхность по возможности должна быть свободна от загрязнений. Измененные свойства поверхности могут привести к различным тепловым потокам, которые могут проявляться как псевдоошибки при оценке. Автоматизированные процессы с обработкой компонентов сегодня могут быть достигнуты относительно легко. Сейчас также доступны хорошие термографические камеры, поэтому этот процесс постепенно внедряется в производственные линии. Эта технология может заменить магнитопорошковую дефектоскопию, которая до сих пор широко распространена.
5. Испытание на трещины с помощью магнитопорошковой дефектоскопии (MT)
Вероятно, самым старым методом обнаружения трещин в материалах является магнитопорошковая дефектоскопия. Согласно этому методу ферромагнитные компоненты намагничиваются и напыляются магнитным порошком. Дефекты в контрольной детали по-разному реагируют на намагничивание. В этот момент магнитное поле проявляется сильнее на поверхности. Соответственно, магнитный порошок может лучше прилипать. При добавлении в магнитный порошок флуоресцентного материала дефекты «светятся» по-разному при определенных условиях освещения. Основным недостатком этой процедуры является то, что сортировка испытуемой части на хорошие или плохие результаты осуществляется на основе субъективной оценки инженера-испытателя. Только опыт инспектора определяет, будет ли трещина оценена как большая или маленькая, или степень ошибки будет такой величины, которая может быть оценена как серьезная. Кроме того, очистка компонентов после теста требует больших усилий, так как магнитный порошок прилипает к тестируемым деталям. Автоматизация систем магнитопорошкового тестирования может быть довольно сложной. Таким образом, процедура тестирования полезна только в том случае, если количество тестовых заданий не слишком велико.
6. Испытание на трещины с помощью ультразвуковых приборов (UT)
Вихретоковый контроль является предпочтительным методом обнаружения открытых трещин в проводящих компонентах. Однако этот метод достигает своих пределов в случае трещин или аномалий материала, расположенных внутри испытуемого образца. Это связано с тем, что глубина проникновения этого метода зависит от используемой частоты. Если это в диапазоне кГц, глубина проникновения уменьшается относительно быстро до нескольких миллиметров. Поэтому еще одним общепринятым методом испытаний является испытание на трещины с помощью ультразвуковых устройств. Ультразвуковой метод подходит для проверки компонентов на глубину. С помощью этого метода любой материал может быть полностью «просвечен». Для этого на исследуемую деталь помещают измерительную головку с ультразвуковым излучателем и приемником. Ультразвук, генерируемый в измерительной головке, передается в испытуемую деталь через связующую среду, обычно типа воды. Хорошая связь важна для эффективного тестирования.
Ультразвук проникает в испытательный образец, и эхо ультразвуковых волн создается отражениями от задней стенки. Дефекты, такие как трещины или включения, приводят к дополнительному отражению ультразвука. Они записываются в поисковый блок. Тип и размер рефлексов позволяют сделать выводы о том, где в образце расположена обнаруженная аномалия. Производство ультразвуковых поисковых установок очень сложное. Кроме того, из-за связующей среды требуются закрытые системы. Кроме того, связующая среда должна быть как можно более свободной от примесей и образования пузырьков, поскольку они мешают ультразвуковому пути и действуют как дефект материала.
Какой кряк — какой процесс?
Подписи
A = Лучший подходящий
B = вид OK для использования
C = не так хороша
D = во всех подходящих
Заключение
Все неразрушающие методы показанные здесь испытания на трещины оправданы. Подходящий метод испытаний определяется на основе типа ошибки и используемого материала. Также возможно использовать комбинацию различных методов испытаний, которые могут быть объединены в одну испытательную линию.
Неразрушающий контроль – контроль проникающей жидкости
Контроль проникающей жидкости (DPI), также называемый контролем проникающей жидкости (LPI) или контролем проникающей жидкости (PT), является одним из старейших и упрощенных методов неразрушающего контроля, в то время как его самые ранние версии (с использованием смесь керосина и масла) восходит к 19 веку.
Капиллярная дефектоскопия используется для обнаружения любых неоднородностей, связанных с поверхностью, таких как трещины от усталости, закалки и шлифовки, а также изломов, пористости, неполного сплавления и дефектов в соединениях.
Принципы
DPI основан на капиллярном действии, при котором жидкость с низким поверхностным натяжением проникает в чистые и сухие разрывы поверхности. Пенетрант можно наносить на испытуемый компонент погружением, распылением или кистью. По истечении достаточного времени проникновения излишки пенетранта удаляются и наносится проявитель. Проявитель помогает вывести пенетрант из дефекта, где невидимый признак становится видимым для инспектора. Проверка проводится в ультрафиолетовом или белом свете, в зависимости от типа используемого красителя — флуоресцентного или нефлуоресцентного (видимого).
Материалы
Пенетранты классифицируются по уровням чувствительности. Видимые пенетранты обычно красного цвета и обладают самой низкой чувствительностью. Флуоресцентные пенетранты содержат два или более красителей, которые флуоресцируют при возбуждении ультрафиолетовым (УФ-А) излучением (также известным как черный свет). Поскольку флуоресцентная пенетрантная дефектоскопия проводится в затемненной среде, а возбужденные красители излучают яркий желто-зеленый свет, сильно контрастирующий с темным фоном, этот материал более чувствителен к дефектам.
При выборе уровня чувствительности необходимо учитывать множество факторов, включая окружающую среду, в которой будет проводиться испытание, качество поверхности образца и размер искомых дефектов. Необходимо также убедиться, что тестовые химикаты совместимы с образцом, чтобы исследование не вызывало стойкого окрашивания или деградации. Этот метод может быть довольно портативным, поскольку в его простейшей форме для осмотра требуется всего 3 аэрозольных баллончика, несколько безворсовых салфеток и достаточное видимое освещение. Стационарные системы со специальными станциями нанесения, промывки и проявки более дороги и сложны, но обеспечивают лучшую чувствительность и более высокую производительность по образцам.
Наносится красный пенетрант
Удаление излишков пенетранта
Нанесен белый проявитель
Этапы проверки
- Предварительная очистка.
несоответствующие или ложные показания. Методы очистки могут включать растворители, щелочную очистку, обработку паром или струйную очистку. Конечная цель этого шага — чистая поверхность, на которой любые присутствующие дефекты открыты, сухая и свободная от загрязнений. Обратите внимание, что если используется пескоструйная обработка, она может «обработать» небольшие дефекты в детали, и в качестве постструйной обработки рекомендуется травильная ванна.
- Нанесение пенетранта..
Затем пенетрант наносится на поверхность испытуемого объекта. Пенетранту дается «время выдержки», чтобы впитаться в любые дефекты (обычно от 5 до 30 минут). Время выдержки в основном зависит от используемого пенетранта, тестируемого материала и размера искомых дефектов. Как и ожидалось, небольшие дефекты требуют более длительного времени проникновения. Из-за их несовместимости необходимо соблюдать осторожность и не наносить пенетрант на основе растворителя на поверхность, которая должна быть проверена водосмываемым пенетрантом. - Удаление избытка пенетранта..
Излишки пенетранта удаляются с поверхности. Метод удаления определяется типом используемого пенетранта. Обычно выбирают смываемые водой, удаляемые растворителем, липофильные постэмульгируемые или гидрофильные постэмульгируемые. Эмульгаторы представляют собой самый высокий уровень чувствительности и химически взаимодействуют с маслянистым пенетрантом, делая его удаляемым с помощью распыления воды. При использовании средства для удаления растворителя и безворсовой ткани важно не распылять растворитель непосредственно на тестируемую поверхность, так как это может удалить пенетрант с дефектов. Если избыток пенетранта не удален должным образом, после нанесения проявителя он может оставить фон в проявленной области, который может маскировать признаки или дефекты. Кроме того, это также может привести к ложным показаниям, которые серьезно помешают вам провести надлежащую проверку. - Нанесение проявителя..
После удаления излишков пенетранта на образец наносится белый проявитель.Доступны несколько типов проявителей, в том числе неводный влажный проявитель, сухой порошковый проявитель, суспендируемый в воде и водорастворимый. Выбор проявителя определяется совместимостью пенетранта (нельзя использовать водорастворимый или суспендирующий проявитель с водосмываемым пенетрантом) и условиями контроля. При использовании неводного влажного проявителя (NAWD) или сухого порошка образец должен быть высушен перед нанесением, в то время как растворимые и суспендируемые проявители наносятся на деталь, еще влажную после предыдущего шага. NAWD коммерчески доступен в аэрозольных баллончиках и может использовать ацетон, изопропиловый спирт или пропеллент, представляющий собой комбинацию этих двух веществ. Проявитель должен образовывать полупрозрачное ровное покрытие на поверхности.
Проявитель выводит пенетрант из дефектов на поверхность, чтобы сформировать видимый признак, известный как вытекание. Любые вытекающие области могут указывать на расположение, ориентацию и возможные типы дефектов на поверхности.Интерпретация результатов и характеристика дефектов по обнаруженным показаниям может потребовать некоторой подготовки и/или опыта.
- Инспекция..
Инспектор будет использовать видимый свет с достаточной интенсивностью (обычно 100 фут-кандел или 1100 люкс) для видимого проникающего красителя. Ультрафиолетовое (УФ-А) излучение достаточной интенсивности (обычно 1000 микроватт на квадратный сантиметр) наряду с низким уровнем окружающего освещения (менее 2 фут-кандел) для флуоресцентных пенетрантных исследований. Осмотр тестируемой поверхности следует проводить через 10–30 минут времени проявления, в зависимости от типа продукта. Эта временная задержка позволяет осуществить действие блоттинга. Инспектор может наблюдать за образцом для формирования индикации при использовании видимого красителя. Также хорошей практикой является наблюдение за признаками по мере их формирования, потому что характеристики вытекания являются важной частью интерпретации характеристик дефектов. - Последующая очистка..
Тестовая поверхность часто очищается после проверки и регистрации дефектов, особенно если запланированы процессы нанесения покрытия после проверки.
Преимущества и недостатки
Основные преимущества и недостатки по сравнению с другими методами НК:
Преимущества
- Высокая чувствительность (можно обнаружить небольшие разрывы).
- Несколько ограничений по материалам (могут проверяться металлические и неметаллические, магнитные и немагнитные, проводящие и непроводящие материалы).
- Быстрый осмотр больших площадей и объемов.
- Подходит для деталей сложной формы.
- Индикация производится непосредственно на поверхности детали и представляет собой визуальное представление дефекта.
- Портативный (материалы доступны в аэрозольных баллончиках)
- Низкая стоимость (материалы и сопутствующее оборудование относительно недороги)
Недостатки
- Могут быть обнаружены только дефекты разрушения поверхности.
- Можно проверять только материалы с относительно непористой поверхностью.
- Предварительная очистка имеет решающее значение, поскольку загрязнения могут маскировать дефекты.
- Металлические пятна от механической обработки, шлифовки, пескоструйной или пароструйной обработки должны быть удалены.
- Инспектор должен иметь прямой доступ к проверяемой поверхности.
- Чистота и шероховатость поверхности могут повлиять на чувствительность проверки.
- Необходимо выполнять и контролировать несколько технологических операций.
- Требуется последующая очистка приемлемых деталей или материалов.
- Требуется химическая обработка и надлежащая утилизация.
Стандарты
Международная организация по стандартизации (ISO)
- ISO 3452-1, Неразрушающий контроль. Капиллярный контроль. Часть 1. Общие принципы
- ISO 3452-2, Неразрушающий контроль. Капиллярный контроль. Часть 2.
Испытание пенетрантных материалов
- ISO 3452-3, Неразрушающий контроль. Капиллярный контроль. Часть 3. Контрольные образцы
- ISO 3452-4, Неразрушающий контроль. Капиллярный контроль. Часть 4. Оборудование
- ISO 3452-5, Неразрушающий контроль. Капиллярный контроль. Часть 5. Капиллярный контроль при температуре выше 50°C
- ISO 3452-6, Неразрушающий контроль. Капиллярный контроль. Часть 6. Капиллярный контроль при температуре ниже 10°C
- ISO 3059, Неразрушающий контроль. Капиллярный контроль и магнитопорошковый контроль. Условия просмотра
- ISO 12706, Неразрушающий контроль. Капиллярный контроль. Словарь
- ISO 23277, Неразрушающий контроль сварных швов. Капиллярный контроль сварных швов. Уровни приемлемости
Европейский комитет по стандартизации (CEN)
- EN 1371-1, Литье. Контроль проникающей жидкости. Часть 1. Литье под давлением в песчаные формы, под давлением и под низким давлением
- EN 1371-2, Литье.
Контроль проникающей жидкости. Часть 2. Литье по выплавляемым моделям
- EN 10228-2, Неразрушающий контроль стальных поковок. Часть 2. Капиллярный контроль
- EN 10246-11, Неразрушающий контроль стальных труб. Часть 11. Контроль проникающей жидкости бесшовных и сварных стальных труб для обнаружения дефектов поверхности
Американское общество по испытаниям и материалам (ASTM)
- ASTM E 165, Стандартная практика для исследования проникающей жидкости в промышленности общего назначения
- ASTM E 1417, Стандартная практика для капиллярных испытаний
Американское общество инженеров-механиков (ASME)
- Кодекс ASME по котлам и сосудам под давлением, раздел V, ст. 6, Капиллярная экспертиза
- Кодекс ASME по котлам и сосудам под давлением, раздел V, ст. 24 Стандартный метод испытания пенетранта SE-165 (идентичен ASTM E-165)
Испытание на проникновение красителя (DPT, LPI, PT) – неразрушающий контроль – сварка и неразрушающий контроль
Испытание на проникновение красителя (DPT) является одним из самых недорогих методов неразрушающего контроля (NDT), используется для проверки неровностей поверхности любого компонента. Этот метод тестирования популярен под многими названиями, а именно:
- Контроль проникающей жидкости (LPI)
- Испытание на проникновение жидкости или испытание на проникновение жидкости (LPT)
- Пенетрантное испытание или пенетрантное испытание (PT)
Испытание проникающей жидкостью является одним из наиболее широко используемых методов неразрушающего контроля (НК). Его можно использовать для проверки практически всех непористых материалов, таких как металлы, пластмассы, керамика и т. д. С помощью этого метода испытаний мы можем обнаружить любые неровности поверхности (или неровности), такие как поверхностные трещины, пористость, точечные отверстия и т. д.
Принцип: DPT основан на принципах КАПИЛЛЯРНОЕ ДЕЙСТВИЕ . В силу этого жидкость имеет тенденцию течь или просачиваться в любое узкое отверстие, даже несмотря на внешние силы, такие как гравитация. Это явление происходит из-за молекулярного притяжения.
Процедура проверки методом проникающей жидкости может варьироваться в зависимости от таких факторов, как используемая пенетрантная система, а также условия и среда, в которых проводится проверка. Однако общие шаги, которые необходимо выполнить, приведены ниже;
Подготовка поверхности: Поверхность должна быть тщательно очищена от грязи, масла, краски, жира, воды или других загрязнений. Для очистки можно использовать сухую ткань, растворители, очиститель, средство для удаления ржавчины и т. д. в зависимости от состояния проверяемой поверхности.
Нанесение пенетранта: После тщательной очистки наносится пенетрант. Пенетрант представляет собой жидкость красного цвета. Его можно наносить на поверхность распылением (чаще всего) или кистью или путем погружения всей поверхности в пенетрантную ванну.
Температура поверхности должна быть в пределах от 5 O C до 52 O C.
Период выдержки: Оставьте пенетрант в том виде, в котором он есть, на поверхности на минимальный период времени (известный как Время выдержки или Период выдержки). За время выдержки пенетрант просачивается в дефекты (при их наличии на контролируемой поверхности), из-за капиллярного действия. Период выдержки варьируется от 5 минут до 60 минут или даже больше в зависимости от материала и условий его эксплуатации. Производитель пенетранта также указывает период выдержки на самом продукте. Тем не менее, нет ничего плохого в том, чтобы превысить минимальный период выдержки, при условии, что температура должна быть окружающей, потому что при повышенной температуре всегда будет возможность испарения пенетранта. Следовательно, при повышенной температуре следует строго ограничивать рекомендуемое время выдержки.
Удаление избытка пенетранта: После ухода с поверхности в течение рекомендуемого периода выдержки пенетрант необходимо очистить, для очистки излишков пенетранта использовать ткань и удалить пенетрант.
При очистке излишков пенетранта необходимо позаботиться о двух вещах;
- Очистка должна быть однонаправленной, т.е. очистка должна производиться только в одном направлении. Следует избегать круговой чистки.
- Средство для удаления/очистки пенетранта не следует наносить непосредственно на поверхность. Нанесите средство для удаления/очистителя пенетранта на ткань, и эту ткань следует использовать для очистки.
(метод очистки может различаться в зависимости от типа используемого пенетранта)
Применение проявителя: После тщательной очистки наносится тонкий слой проявителя. При распылении проявителя необходимо учитывать две вещи;
- Тщательно встряхнуть флакон
- Сохраняйте расстояние от 10 до 12 дюймов от поверхности при распылении проявителя
- После распыления проявителя подождите от 10 до 60 минут (время проявления)
Проявитель всасывает пенетрант, захваченный на поверхности, из дефектов (если они есть). То есть пенетрант вытекает на поверхность и приобретает ярко-красный цвет. Проявитель представляет собой жидкость белого цвета, и, следовательно, пенетрант имеет ярко-красный цвет, поэтому мы можем легко определить дефекты.
Осмотр: После подачи заявки разработчика подождите от 10 до 60 минут и затем проведите осмотр. Соответствующее освещение необходимо для обнаружения признаков любых дефектов, которые могут присутствовать. Минимальный требуемый свет составляет 1000 люкс или 100 фут-кандел.
- Одним из основных преимуществ цветного пенетрантного теста (DPT) является его портативность. Набор для тестирования пенетранта (пенетрант/очиститель/проявитель) очень легкий и небольшой по размеру, поэтому его можно легко транспортировать в любом месте. Испытание на проникновение красителя
- довольно недорого по сравнению с другими неразрушающими методами, а именно.
MT, UT, RT, ET и т. д.
- DPT очень чувствителен, и небольшие неоднородности также могут быть легко обнаружены.
- Почти все непористые материалы, такие как металлы, пластмассы, керамика и т. д., могут быть проверены с помощью DPT.
- Этот тест занимает очень мало времени; следовательно, материал можно было быстро проверить.
- Также можно легко контролировать сложные геометрические формы.
- Одним из основных недостатков капиллярной дефектоскопии (DPT) является то, что можно проверить только поверхностные дефекты или несплошности.
- Требуется предварительная очистка проверяемой поверхности.
- Можно проверять только непористые материалы.
- Требуется последующая очистка
- Требуется надлежащее обращение и утилизация химикатов.
Также ознакомьтесь с основами ультразвукового контроля (УЗК)
См. также: Радиографические испытания (RT)
См. также: Расчет углового датчика для ультразвукового контроля (UT)
. См. также: Диапазон толщины для квалификационного теста сварщика /Urdu ), чтобы понять этапы проведения теста на проникающую краску.
Посмотрите это демонстрационное видео ( на английском языке ), чтобы понять шаги, связанные с выполнением капиллярного теста. Следующие фотографии предназначены для вашего лучшего понимания;
Метод вихретоковой дефектоскопии бесшовных стальных труб
Неразрушающий контроль стальных труб — это технология обнаружения, которая выявляет внутренние или внешние дефекты при условии, что стальные трубы не повреждаются. В последние годы он широко используется крупными производителями стальных труб. Методы неразрушающего контроля, используемые при производстве 9Бесшовные стальные трубы 0005 в основном включают ультразвуковые испытания, магнитные испытания, вихретоковые испытания и испытания на проникновение. Различные методы дефектоскопии имеют свою область применения.
1. Преимущества и недостатки различных видов дефектоскопии
Преимущества вихретоковой дефектоскопии Результат дефектоскопии может быть напрямую выведен электрическим сигналом, что удобно для автоматического обнаружения; за счет бесконтактного метода скорость дефектоскопии очень высокая; подходит для дефектоскопии поверхностных дефектов. Недостатки: невозможность обнаружения дефектов в более глубоких частях под поверхностью; легко генерировать загроможденные сигналы; трудно напрямую судить о типе дефектов по сигналам отображения, полученным при обнаружении.
Испытание на проникновение — это метод дефектоскопии, основанный на смачивании жидкостей твердыми телами и капиллярных явлениях (включая явления пенетрации и подъема). По сравнению с другими методами дефектоскопии преимущества дефектоскопии проникающими веществами заключаются в том, что оборудование и дефектоскопические материалы просты, дефекты могут отображаться интуитивно, и одновременно могут отображаться различные дефекты во всех направлениях. Недостатком является то, что он может осматривать только те дефекты, которые открываются на поверхность, а процесс эксплуатации усложняется.
2. Метод вихретокового контроля бесшовных стальных труб
В соответствии с характеристиками промышленного неразрушающего контроля, чтобы реализовать автоматическое управление системой контроля, большинство вихретоковых испытаний бесшовных стальных труб ниже 180 мм на предприятиях по производству стальных труб применяют традиционный метод испытаний змеевиков. Для бесшовных стальных труб диаметром более 180 мм, если для испытаний используется традиционный сквозной вихретоковый метод, возникнет множество проблем, которые не разрешены национальными стандартами. Проникающая катушка обнаруживает окружную поверхность поверхности стальной трубы. При вихретоковой дефектоскопии с использованием проникающей катушки чем больше диаметр обнаруживаемой стальной трубы, тем больше площадь окружности, обнаруживаемая катушкой, и тем ниже отношение сигнал/шум. Именно по этой причине стандарт вихретокового контроля для стальных труб предусматривает, что внешний диаметр вихретокового контроля с использованием катушки сквозного типа не должен превышать 180 мм. Кроме того, существуют определенные трудности намагничивания и размагничивания стальной трубы при сквозной дефектоскопии стальных труб большого диаметра. Поэтому, будь то отечественное или зарубежное, для дефектоскопии стальных труб большого диаметра обычно используется точечное вихретоковое дефектоскопное оборудование.
3. Вихретоковый метод дефектоскопии бесшовных стальных труб разного калибра
Чувствительность точечного вихретокового контроля очень высока, и он имеет высокую скорость обнаружения трещин и складчатых дефектов, распределенных вдоль оси трубы. стальная труба; кроме того, точечный вихретоковый контроль также подавляет температуру окружающей среды и трансмиссионную вибрацию заготовки. эффект влияния. Что еще более важно, форма точечного вихретокового преобразователя может быть адаптирована к требованиям дефектоскопии стальных труб различного диаметра.
(1) Во-первых, в соответствии с реальной ситуацией на производственной линии определяется метод дефектоскопии стальной трубы, вращающейся по спирали вдоль производственной линии, и фиксируемого зонда. Заставляя стальную трубу вращаться вперед, дайте точечному зонду приблизиться к поверхности стальной трубы, чтобы завершить сканирование всей внешней поверхности.
(2) Определить структуру системы дефектоскопии. Сначала поместите шестиканальный вихретоковый датчик в тележку для датчиков, отрегулируйте тележку для датчиков в соответствии с требованиями диаметра стальной трубы, подлежащей испытанию, путем регулировки винта, а затем используйте метод толкания и точной настройки цилиндра, чтобы сделать Датчик обнаружения всегда плотно прижимается к заготовке. Осматривается поверхность заготовки, и на обоих концах тележки зонда устанавливается пара универсальных колес, чтобы сохранять определенное расстояние между ней и контролируемой заготовкой.
(3) Определите количество зондов. В методе дефектоскопии с точечным щупом необходимо использовать несколько щупов для увеличения шага сканирования и повышения скорости обнаружения. Вихретоковые точечные преобразователи обычно имеют небольшие размеры и высокую чувствительность обнаружения, но за счет скорости обнаружения. Увеличение охвата области обнаружения зонда может улучшить скорость обнаружения, но чувствительность обнаружения снизится.
Идите сюда, если вы ищете « 3 Обычно используемые методы неразрушающего контроля бесшовных стальных труб »
NDT Уровень 3 Услуги – Ресурсы
NDT – это неразрушающий контроль, также известный как NDE (неразрушающий контроль). Существует множество методов и приемов неразрушающего контроля, и вот краткое описание наиболее часто используемых из них. Цель неразрушающего контроля состоит в том, чтобы найти дефекты в тестируемом материале, и успешное применение теста во многом зависит от навыков оператора и используемого оборудования.
Магнитные испытания (МТ)
Также известен как MPI (контроль магнитных частиц). Это метод, который можно использовать для обнаружения поверхностных и приповерхностных дефектов в ферромагнитных материалах, таких как сталь и железо.
В этом методе используется принцип, заключающийся в том, что магнитные силовые линии (поток) искажаются из-за наличия дефекта таким образом, что его присутствие становится очевидным. Дефект (например, трещина) располагается от «натекания флюса», следующего за нанесением на исследуемый участок мелких железных частиц. Существуют различные способы применения магнитного поля, но все они зависят от вышеуказанного принципа.
Частицы железа можно наносить сухим или влажным способом; взвешенные в жидкости, окрашенные или флуоресцентные. Хотя магнитопорошковая дефектоскопия в основном используется для обнаружения поверхностных дефектов, ее также можно использовать для обнаружения подповерхностных дефектов. Но его эффективность быстро снижается в зависимости от глубины и типа дефекта.
Неровности поверхности и царапины могут дать ложные показания. Поэтому необходимо обеспечить тщательную подготовку поверхности перед проведением магнитопорошкового контроля.
Капиллярные испытания (PT)
Также известен как контроль проникающих жидкостей (DPI), контроль проникающих жидкостей (LPI) или контроль флуоресцентных пенетрантов (FPI). Это метод, который используется для выявления дефектов разрушения поверхности путем вытекания цветного или флуоресцентного красителя из дефекта.
Методика основана на способности жидкости втягиваться в «чистую» поверхность, разрушая дефект за счет капиллярного действия. По истечении времени проникновения излишки поверхностного пенетранта удаляются и наносится проявитель. Это «вытягивает» пенетрант из дефекта, чтобы выявить его присутствие. Цветовые контрастные (или «видимые») пенетранты требуют хорошего белого света, в то время как флуоресцентные пенетранты необходимо использовать в затемненных условиях с ультрафиолетовым светом (также известный как черный свет).
Капиллярный контроль можно использовать практически для любого непористого материала. Важно предварительно тщательно очистить материал, иначе пенетрант не сможет проникнуть в дефект. Если поверхностный пенетрант не будет удален полностью, это приведет к вводящим в заблуждение показаниям.
Ультразвуковой контроль (UT)
Ультразвуковой контроль использует звуковые волны короткой длины и высокой частоты для обнаружения дефектов или измерения толщины материала. Он используется для проверки сварных швов, отливок и кованых изделий, например. листовой прокат или поковки. Применяются ручной и иммерсионный методы.
Ручное испытание включает звуковые волны (импульсные лучи высокочастотного ультразвука), передаваемые через переносной преобразователь, который помещается на образец. «Связующая жидкость» используется для того, чтобы звук проходил от преобразователя к тестируемому компоненту. Любой звук от импульса, который возвращается к преобразователю (эхо), отображается на экране, который показывает амплитуду импульса и время, необходимое для возврата к преобразователю. Дефекты в любом месте толщины образца отражают звук обратно к преобразователю. Размер дефекта, расстояние и отражательная способность могут быть интерпретированы.
Метод погружения заключается в помещении компонента в резервуар с водой и пропускании звуковых волн через воду в компонент.
В последнее время разработаны такие методы ультразвукового контроля, как ультразвуковой контроль с фазированной решеткой (PAUT) и времяпролетная дифракция (TOFD). PAUT использует многоэлементные зонды, которые возбуждаются индивидуально под управлением компьютера. Возбуждая каждый элемент контролируемым образом, можно генерировать сфокусированный пучок ультразвука. Программное обеспечение позволяет управлять лучом. Можно создавать двух- и трехмерные изображения, показывающие размеры и расположение любых обнаруженных дефектов. TOFD также управляется компьютером и основан на дифракции ультразвуковых волн на вершинах несплошностей, в отличие от отражения звука обратно от несплошностей. Когда ультразвук падает на линейный разрыв, такой как трещина, на его концах происходит дифракция в дополнение к нормальной отраженной волне.
Из-за его сложности требуется значительная подготовка и навыки технического персонала.
Радиографический контроль (RT)
Также известен как рентгенография и гамма-радиография. Рентгеновские лучи производятся высоковольтными рентгеновскими аппаратами, тогда как гамма-лучи производятся радиоактивными изотопами, такими как иридий-192 и кобальт-60. Рентгеновские или гамма-лучи помещаются близко к проверяемому материалу и проходят через материала, а затем записываются на пленку. Затем эта пленка обрабатывается, и изображение получается в виде серии оттенков серого между черным и белым. Преимущество гамма-источников заключается в их портативности, что делает их идеальными для использования в полевых условиях.
Рентгеновские и гамма-лучи очень опасны. При проведении рентгенографии необходимо соблюдать особые меры предосторожности. Поэтому оператор будет использовать их внутри защитного кожуха или с соответствующими барьерами и предупредительными сигналами, чтобы гарантировать отсутствие опасности для персонала.
Цифровая рентгенография — новейшая форма рентгенографической визуализации. Поскольку пленка не требуется, цифровые рентгенографические изображения захватываются либо с помощью специальных люминесцентных экранов, либо с помощью плоских панелей, содержащих микроэлектронные датчики. Изображения могут быть улучшены в цифровом виде для большей детализации и могут быть легко заархивированы.
Существует ряд форм цифровой рентгенографии, в том числе:
- Компьютерная рентгенография (CR): процесс цифровой визуализации, в котором используется специальная пластина для визуализации, в которой используются запоминающие люминофоры.
- Рентгенография в реальном времени (RTR): форма рентгенографии, позволяющая получать и просматривать электронные изображения в режиме реального времени.
- Прямая рентгенография (DR): форма рентгенографии в реальном времени, в которой используется специальный плоскопанельный детектор.
- Компьютерная томография (КТ): использует систему проверки в режиме реального времени, использующую систему позиционирования образца и специальное программное обеспечение.
Вихретоковый контроль (ET)
ET — это электромагнитный метод, который можно использовать только на проводящих материалах. Его области применения варьируются от обнаружения трещин до быстрой сортировки мелких компонентов на наличие дефектов, различий в размерах или материалах. Обычно он используется в аэрокосмической, автомобильной, морской и обрабатывающей промышленности.
Когда катушку под напряжением приближают к поверхности металлического компонента, в образце индуцируются вихревые токи. Эти токи создают магнитное поле, которое имеет тенденцию противодействовать исходному магнитному полю. Импеданс катушки, находящейся в непосредственной близости от образца, определяется наличием наведенных вихревых токов в образце.
Когда вихревые токи в образце искажаются из-за наличия дефектов или изменений материала, импеданс катушки изменяется. Это изменение измеряется и отображается таким образом, который указывает тип дефекта или состояние материала.
Визуальное тестирование (VT)
Также известный как визуальный контроль, VT является одним из методов неразрушающего контроля, который широко используется для оценки состояния или качества сварного шва или компонента. Он легко проводится, недорог и обычно не требует специального оборудования.
Он используется для контроля сварных швов и других компонентов, где быстрое обнаружение и исправление дефектов или проблем, связанных с технологическим процессом, может привести к значительной экономии средств. Это основной метод оценки многих программ контроля качества.
VT требует хорошего зрения, хорошего освещения и знания того, что искать. Визуальный осмотр можно улучшить с помощью различных методов, начиная от маломощных увеличительных стекол и заканчивая бороскопами. Эти устройства также могут использоваться с системами телевизионных камер. Подготовка поверхности может варьироваться от протирания тканью до пескоструйной очистки и обработки химическими веществами, чтобы показать детали поверхности.
Он может определить, где наиболее вероятно возникновение сбоя, и определить, когда сбой начался. VT часто усиливается другими методами контроля, которые могут выявить дефекты, которые трудно увидеть невооруженным глазом.
Чтобы связаться с NDT Level 3 Services, перейдите на страницу контактов.
Традиционный неразрушающий контроль – контроль неразрушающего контроля
Являясь лидером отрасли в области неразрушающего контроля ( NDT ), MISTRAS предлагает обширный набор традиционных решений NDT в качестве основы для многих наших программ защиты активов. .
Неразрушающий контроль ( NDT ) – также известный как неразрушающий контроль ( NDE ) и неразрушающий контроль (NDI), в зависимости от отрасли, — это эффективный способ проверки оборудования, поскольку нет необходимости останавливать или вводить актив, что увеличивает время безотказной работы и производительность. В отличие от своего аналога, разрушающего контроля ( DT ), неинтрузивное применение неразрушающего контроля существенно не влияет на целостность проверяемого актива.
Каждый метод NDT предназначен для обнаружения и/или количественной оценки конкретных повреждений. Например, ультразвуковой контроль ( UT ) эффективны для обнаружения и отслеживания активных дефектов, коррозии и эрозии, а акустическая эмиссия ( AE ) является эффективным выбором для усталости, утечек и трещин.
Поскольку многие клиенты нуждаются в инспекции на высоте, в замкнутом пространстве и под водой, инспекционные услуги MISTRAS NDT включают в себя группы канатного доступа, сертифицированных пилотов беспилотных систем и обученных дайверов для проверки активов в труднодоступных местах. места проверяются так регулярно, как это необходимо.
MISTRAS предлагает широкий спектр методов неразрушающего контроля , а также экспертов в данной области для помощи в выборе подходящего метода. В дополнение к решениям, упомянутым ниже, ознакомьтесь со списком OneSource, чтобы узнать больше о широком спектре доступных традиционных решений MISTRAS NDT , включая:
- Акустическая эмиссия ( AE )
- Вихревой поток ( ET )
- Магнитная частица ( MT )
- Капиллярные испытания ( PT )
- Положительная идентификация материала ( PMI )
- Радиографический контроль ( RT )
- Ультразвуковой контроль ( UT )
- Визуальное тестирование ( VT )
Акустическая эмиссия (АЭ) — это мощный метод исследования поведения материалов, деформирующихся под нагрузкой. Аппаратура АЭ «слушает» звуки роста трещин, обрыва волокон и многих других режимов активного разрушения нагруженного материала. Небольшие повреждения обнаруживаются задолго до отказа, поэтому АЭ можно использовать в качестве метода неразрушающего контроля (НК) для обнаружения дефектов во время контроля качества (КК), структурных контрольных испытаний и эксплуатации предприятия. AE также предлагает уникальные возможности для исследования и разработки материалов в лаборатории.
Мелкие повреждения обнаруживаются задолго до выхода из строя, поэтому AE можно использовать в качестве неразрушающего метода для обнаружения дефектов во время структурных контрольных испытаний и эксплуатации установки. AE также предлагает уникальные возможности для исследования и разработки материалов в лаборатории. Наконец, оборудование AE можно адаптировать ко многим формам контроля качества продукции ( QC ), включая контроль сварных швов и обнаружение утечек.
Узнайте больше об инспекции AE.
Вихретоковые испытания (ET)Вихретоковые испытания (EC) индуцируют электрический ток в проводящем материале. Любые изменения тока из-за геометрии, изменений материала или дефектов, таких как питтинг, эрозия, коррозия, истирание перегородки, растрескивание или другие аномалии, нарушают поток вихревого тока, потенциально указывая на наличие повреждений. Он чувствителен к небольшим и подповерхностным трещинам и дефектам.
Вихретоковый контроль обычно используется для проверки немагнитных (цветных) и слабомагнитных сплавов, обладающих электропроводностью. Вихретоковый контроль очень чувствителен к небольшим дефектам, таким как коррозионное растрескивание под напряжением. Интерпретация данных вихревых течений очень сложна, поэтому MISTRAS предоставляет сертифицированных инспекторов с многолетним опытом для правильной характеристики сигнальных образований.
Узнайте больше об инспекции ET.
MT — это быстрый и экономичный метод неразрушающего контроля для обнаружения поверхностных и приповерхностных несплошностей, доступный в полевых условиях или в лаборатории. В МТ специалисты MISTRAS намагничивают ферромагнитный материал и наносят на него мелкоизмельченные частицы железа, покрытые красящим пигментом. Частицы указывают на неоднородность материала, группируясь непосредственно над ним, что можно визуально обнаружить при надлежащем освещении.
MISTRAS использует методы сухого порошкового и влажного флуоресцентного магнитопорошкового контроля ( MT ) для обнаружения поверхностных/приповерхностных дефектов в ферромагнитных материалах. MT требует, чтобы квалифицированный техник различал релевантные и нерелевантные показания. Он часто используется для обнаружения растрескивания металла, проверки сварных швов и обнаружения коррозионного растрескивания под напряжением.
Узнайте больше о проверке МТ.
Капиллярные испытания (PT)Традиционный, относительно простой метод неразрушающего контроля в полевых или лабораторных условиях, пенетрантный контроль (ПТ) используется для обнаружения разрывов поверхности на относительно гладких непористых поверхностях. Он основан на свойствах капиллярного действия или феномене подъема или подъема жидкости, когда она ограничена небольшим отверстием. После удаления избытка пенетранта и нанесения проявителя обученный инспектор может определить любой оставшийся пенетрант, который может указывать на дефект.
Также называется инспекцией проникающей жидкостью ( LPT ). Испытание пенетрантной жидкостью ( PT ) используется на цветных материалах, таких как металлы, композиты и керамика, для выявления поверхностных аномалий, таких как трещины, швы, расслоения, газовые пробоины. , нахлесты, внешние разрывы и дефекты сварки.
Узнайте больше о проверке PT.
Радиографический контроль (РТ)Радиографический контроль (РТ) При контроле используются источники рентгеновского или гамма-излучения для просмотра и оценки внутренней структуры актива. RT чувствителен к коррозии, изменениям толщины, пустотам, трещинам и изменениям плотности материала и способен обнаруживать как поверхностные, так и подповерхностные дефекты с минимальной необходимой подготовкой поверхности. RT используется как в полевых условиях, так и в лаборатории, и особенно полезен, поскольку он обеспечивает постоянную запись инспекции, что делает его полезным для оценки активов до и после обработки и на различных этапах их эксплуатации.
Радиографический контроль ( RT ) позволяет техническим специалистам точно определить местонахождение, размер и идентификацию внутренних и внешних дефектов. RT — распространенное и эффективное решение для инспекции ( NDT ) широкого спектра активов, включая трубопроводы, трубопроводы, сосуды под давлением, резервуары для хранения и многое другое. Наш штат квалифицированных, сертифицированных профессиональных рентгенологов работает в соответствии со строгими параметрами безопасности и использует наш значительный отраслевой опыт для производства высококачественных рентгенограмм.
Узнайте больше о проверке RT.
Ультразвуковой контроль (УЗК)Обычный ультразвуковой контроль (УЗК) — широко используемый метод неразрушающего контроля (НК), который измеряет распространение механических колебаний (ультразвуковых волн) через материал для изучения свойств, измеряйте толщину, определяйте эластичность и обнаруживайте ряд неоднородностей, включая коррозию/эрозию, дефекты, трещины и т. д.
Ан НК ), технические специалисты MISTRAS используют обычный ультразвуковой контроль ( UT ) для обнаружения поверхностных и подповерхностных дефектов и предоставления точных показаний относительно размера и формы несплошностей. Ультразвуковые исследования используются в качестве основного метода контроля для программ эрозии/коррозии на заводе и широко используются на наших многочисленных вечнозеленых объектах по всему миру.
Узнайте больше об УЗ-контроле.
Визуальное тестирование (VT)Самая старая и самая основная форма неразрушающего контроля, традиционная визуальная проверка включает в себя техников MISTRAS, которые осматривают оборудование своими глазами, чтобы определить любые визуальные дефекты. MISTRAS предлагает визуальных инспекторов, сертифицированных в соответствии с различными отраслевыми нормами и правилами.
Часто это первый метод, который MISTRAS использует в начале проекта. MISTRAS предоставляет различные услуги визуального контроля ( VT ) для различных отраслей промышленности. Этот метод полезен для определения масштаба проекта, установления степени существующего ущерба и информирования технического специалиста о том, где необходимы более сложные и углубленные проверки.