Методы контроля качества сварных соединений
Среди обязательных этапов любых сварочных работ находится проверка качества швов. Благодаря такому подходу, специалист может выявить недоработки, которые негативно сказываются на прочности соединения. Своевременное устранение производственных дефектов позволяет продлить срок службы металлоконструкции. Как проверить качество сварного шва? Конечно, это можно оценить визуально. Но это далеко не точный и не единственно доступный метод контроля.
Ни один специалист, даже самый опытный, визуально не сможет определить наличие пустот и трещин внутреннего характера. Здесь необходим совершенно иной подход. На больших предприятиях качество мониторится контроллером сварочных работ. А во всех остальных случаях ответственность ложится на плечи самого исполнителя. Далее мы рассмотрим разные существующие варианты проверки швов, помимо визуального контроля.
СОДЕРЖАНИЕ
- Методы контроля качества сварных швов
- Визуальный контроль
- Капиллярный контроль
- Проверка сварных швов на герметичность
- Магнитное поле
- Ультразвук
- Радиография
- Заключение
Методы контроля качества сварных швов
На практике применяются разные средства технического контроля, которые отличаются нюансами в работе; обладают разными достоинствами и недостатками. Тем не менее, весь их функционал ориентирован на то, чтобы определить прочность и долговечность сварочного шва. Качество соединения двух металлических заготовок можно предсказать. Ведь в большей части оно зависит от мастерства исполнителя и качества используемых расходников. Обладая этими данными, несложно предусмотреть итог контроля. Однако, лучше выполнить несложные процедуры контроля, чтобы объективно убедиться в надежности соединения.
Самым распространенным способом определения качества сварного шва остается визуальный. Наряду с ним используются магнитный, капиллярный и радиационный виды контроля. Конечно, существуют и другие варианты, но перечисленный выше являются максимально простыми и наиболее часто востребованными. Желательно практиковать пооперационный контроль качества. Сначала сварочный шов осматривается, после этого выполняется капиллярное исследование образца и т.д.
Читайте также: Дефекты и способы испытания сварных швов
Визуальный контроль
Наиболее доступный способ определить качество сварных соединений. Для внешнего осмотра не нужны никакие дополнительные приборы или материалы. Достаточно иметь хорошее зрение и обладать внимательностью к деталям. Сварное соединение необходимо рассматривать как можно тщательнее. Говорить о хорошем качестве можно только тогда, если нет видимых дефектов, сколов, трещин; а шов характеризуется одинаковой шириной (высотой) по всей длине. Очень важно, чтобы не было грубых дефектов сварки: складок, наплывов, непроваренных участков.
Чтобы максимально эффективно контролировать качество сварного шва, стоит в перечень используемых инструментов включить хорошую лампу, лупу, штангенциркуль и рулетку. Эти инструменты понадобятся, чтобы найти дефект, определить его размеры и наметить пути устранения проблемы. Простейшие приспособления, конечно, не позволяют полноценно контролировать качество сварки, но станут первым шагом на пути к этому.
Читайте также: Визуальный контроль качества сварных соединений
Капиллярный контроль
Проверенный временем способ дает возможность проверить сварной шов на прочность. Суть его сводится к тому, что для проверки применяются специальные жидкости с высокой текучестью. Они проникают в самые тонкие пустоты, которые принято называть капиллярами.
Данный метод дает возможность проверить качество сварного соединения с любого состава. Он отлично подходит в ситуациях, когда есть потребность в проверке скрытых дефектов сварного соединения при ограниченном бюджете на проверку. Здесь нет потребности в дорогостоящем оборудовании, а исполнить манипуляции сможет даже новичок.
Жидкости, которые применяются в капиллярной методе оценки, называются пенетрантами. Это походное слово от английского «penetrant», что переводится как «проникающая жидкость». Для них характерно малое поверхностное натяжение. Благодаря такому свойству, субстанция легко проникает в капилляры, которые могут образоваться во время сварки. Говоря проще, пенетранты проникают в пустоты, окрашивают их, делая видимыми для человеческого глаза.
На практике используются разные растворы, каждый из которых можно приготовить самостоятельно. Они отличаются не только химическим составом, но и свойствами. На практике чаще всего применяются пенетранты, изготовленные на основе воды либо другой органической жидкости – бензола, скипидара и т.д. Именно они наиболее чувствительны к самым незначительным дефектам.
Для улучшения качества и увеличения скорости работ, вы всегда можете воcпользоваться нашими верстаками собственного производства от компании VTM.
Проверка сварных швов на герметичность
На капиллярно методе испытания сварочного шва не заканчиваются. Важно определить степень герметичности стыка. Метод, который применяется в данных целях, называется по-разному: пузырьковый, гидроиспытание, течеискание и много иных вариаций. Их объединяет общая суть – обнаружение дефектов герметичности.
Герметичность стыка проверяется при помощи газа или жидкости. Суть метода идентична капиллярному. Разница заключается только в том, что кислород, азот или вода подаются под высоким давлением.
Пневматический метод контроля базируется на использовании воздуха или газовоздушной смеси, которые подаются к тестируемой области под давлением. Предварительно место стыка обильно смазывается раствором из воды и мыла. Подвидом пневматического метода является контроль с использованием вакуума. Сварочный шов промазывается мыльным раствором. После этого конструкция или деталь помещается в безвоздушную среду, созданную специальным оборудованием. Если существуют сквозные дефекты, то будут образовываться мыльные пузыри.
Для приготовления мыльного раствора необходимо использовать один кусок мыла на литр воды. В случаях, когда предполагается использовать раствор при отрицательной температуре, необходимо половину воды заменить техническим спиртом. Не лишним будет подключение манометра к емкости, где создается вакуум или нагнетается давление. Изменения в показаниях прибора будут свидетельствовать о наличии дефектов сварочного шва.
Есть очень простой и надежный способ контроля качества шва, который заключается в погружении испытуемой детали в воду. Не требуется ни мыльный раствор, ни герметичные резервуары или нагнетательное оборудование. В случаях, когда присутствуют дефекты, то из детали, погруженной в воду, будут подыматься мелкие пузырьки воздуха. Данный метод называют полевом. Несмотря на свою простоту, он достаточно эффективный.
Еще одна разновидность пневматического контроля основывается на проверке соединений при помощи аммиака. Он подается на соединение вместо воды или газа. Предварительно стыки покрываются бумажной лентой. Аммиак проникает во все доступные полости и, если шов имеет пустоты, то на поверхности бумажной ленты образуются красные пятна.
При гидравлическом методе контроля давление создается при помощи масла или воды. В зависимости от вида металла деталь выдерживается в жидкости от 5 до 15 минут. В это время зона по периметру сварочного шва обстукивается молоточком. Даже при слабых ударах жидкость станет вытекать в случаях, когда шов имеет сквозные дефекты.
Читайте также: Виды сварных соединений и швов
Магнитное поле
В основу метода легла технология использования электромагнетизма в промышленности. С помощью специального приспособления вокруг сварочного шва создается магнитное поле, имеющее свой рисунок электромагнитных линий. Если они ровные, то можно смело сказать, что работа выполнена качественно. В случаях наличия дефектов, линия будут иметь явное искажение.
Для визуализации магнитных линий достаточно на поверхность проверяемых деталей насыпать ферримагнитный порошок. В случае искажения магнитного поля он скапливается в том месте, где присутствует дефект. В силу объективных обстоятельств данный метод приемлем только при работе с ферримагнитными металлами. Качество сварки меди, алюминия, стали с большой долей никеля или хрома проверить не получится. Помимо этого, технология является достаточно затратной. Они востребована только в случаях, когда есть необходимость точной проверки соединения особо важных узлов.
Ультразвук
Для контроля над качеством сварного шва используются также уникальные свойства ультразвука. Звуковые волны по-разному отражаются от монолитной и деформированной поверхности. Сколы и трещины имеют свои акустические особенности, которые фиксируются специальной аппаратурой. Проще говоря, на сварочный шов подается ультразвук. Если он сталкивается с пустотой, сколом или иным дефектом, то отображается от металла под другим углом. Более того, разные виды дефектов отражают ультразвук неодинаково, что позволяет диагностировать их.
Благодаря тому, что ультразвуковой метод диагностики является сравнительно недорогим и стабильно эффективным, он используется повсеместно. Распространению способствует и простота использования. К примеру, не нужно учитывать физико-химические особенности металлических сплавов, как в случаях с магнитным или радиационным контролем. Да и приобретение дорогостоящей оснастки тоже не требуется. Недостатком является необходимость наличия специальных знаний и навыков. То есть для контроля привлекается специалист со стороны. Сварщик выполнить процедуру самостоятельно не сможет.
Радиография
Радиационный контроль сварных швов является миниатюрной версией всем знакомого медицинского рентгена. Гамма-лучи прошивают металл и оставляют свой след на специальной пленке. Соответственно, отображаются и скрытые от глаз внутренние дефекты сварочного стыка. Данный метод является самым передовым и позволяет точно обрисовать картину внутреннего состояния соединения.
Наряду с этим, метод имеет и недостатки. Прежде всего, это необходимость приобретения дорогостоящего оборудования. Другой нюанс – требуется предварительная подготовка специалиста. Плюс ко всему, нельзя работать с оборудованием длительной время, поскольку это негативно сказывается на состоянии здоровья.
С недавних пор есть возможность приобрести цифровой радиограф, работающий с компьютерной программой. Вместо пленки в этом случае применяются многоразовые пластины, которые реагируют с любыми лучами. Ключевое отличие от классического рентген-аппарата заключается в том, что изображение сразу отображается на мониторе компьютера. Его можно масштабировать и редактировать. Перспективой технологии является полная автоматизация процесса.
Заключение
Специалист, выполняющий контроль качества сварных соединений металлоконструкций, должен максимально ответственно относиться к своим обязанностям. От его внимательности зависит функциональность и срок службы конструкции. Нужно фиксировать все отклонения от нормы, которые поддаются диагностированию. Чтобы получить максимально детальную картинку, желательно комбинировать несколько методов контроля. Строго воспрещается прибегать к методам, которые могут нанести вред сварному соединению.
Методы контроля качества сварных соединений
Среди обязательных этапов любых сварочных работ находится проверка качества швов. Благодаря такому подходу, специалист может выявить недоработки, которые негативно сказываются на прочности соединения. Своевременное устранение производственных дефектов позволяет продлить срок службы металлоконструкции. Как проверить качество сварного шва? Конечно, это можно оценить визуально. Но это далеко не точный и не единственно доступный метод контроля.
Ни один специалист, даже самый опытный, визуально не сможет определить наличие пустот и трещин внутреннего характера. Здесь необходим совершенно иной подход. На больших предприятиях качество мониторится контроллером сварочных работ. А во всех остальных случаях ответственность ложится на плечи самого исполнителя. Далее мы рассмотрим разные существующие варианты проверки швов, помимо визуального контроля.
СОДЕРЖАНИЕ
- Методы контроля качества сварных швов
- Визуальный контроль
- Капиллярный контроль
- Проверка сварных швов на герметичность
- Магнитное поле
- Ультразвук
- Радиография
- Заключение
Методы контроля качества сварных швов
На практике применяются разные средства технического контроля, которые отличаются нюансами в работе; обладают разными достоинствами и недостатками. Тем не менее, весь их функционал ориентирован на то, чтобы определить прочность и долговечность сварочного шва. Качество соединения двух металлических заготовок можно предсказать. Ведь в большей части оно зависит от мастерства исполнителя и качества используемых расходников. Обладая этими данными, несложно предусмотреть итог контроля. Однако, лучше выполнить несложные процедуры контроля, чтобы объективно убедиться в надежности соединения.
Самым распространенным способом определения качества сварного шва остается визуальный. Наряду с ним используются магнитный, капиллярный и радиационный виды контроля. Конечно, существуют и другие варианты, но перечисленный выше являются максимально простыми и наиболее часто востребованными. Желательно практиковать пооперационный контроль качества. Сначала сварочный шов осматривается, после этого выполняется капиллярное исследование образца и т.д.
Читайте также: Дефекты и способы испытания сварных швов
Визуальный контроль
Наиболее доступный способ определить качество сварных соединений. Для внешнего осмотра не нужны никакие дополнительные приборы или материалы. Достаточно иметь хорошее зрение и обладать внимательностью к деталям. Сварное соединение необходимо рассматривать как можно тщательнее. Говорить о хорошем качестве можно только тогда, если нет видимых дефектов, сколов, трещин; а шов характеризуется одинаковой шириной (высотой) по всей длине. Очень важно, чтобы не было грубых дефектов сварки: складок, наплывов, непроваренных участков.
Чтобы максимально эффективно контролировать качество сварного шва, стоит в перечень используемых инструментов включить хорошую лампу, лупу, штангенциркуль и рулетку. Эти инструменты понадобятся, чтобы найти дефект, определить его размеры и наметить пути устранения проблемы. Простейшие приспособления, конечно, не позволяют полноценно контролировать качество сварки, но станут первым шагом на пути к этому.
Читайте также: Визуальный контроль качества сварных соединений
Капиллярный контроль
Проверенный временем способ дает возможность проверить сварной шов на прочность. Суть его сводится к тому, что для проверки применяются специальные жидкости с высокой текучестью. Они проникают в самые тонкие пустоты, которые принято называть капиллярами.
Данный метод дает возможность проверить качество сварного соединения с любого состава. Он отлично подходит в ситуациях, когда есть потребность в проверке скрытых дефектов сварного соединения при ограниченном бюджете на проверку. Здесь нет потребности в дорогостоящем оборудовании, а исполнить манипуляции сможет даже новичок.
Жидкости, которые применяются в капиллярной методе оценки, называются пенетрантами. Это походное слово от английского «penetrant», что переводится как «проникающая жидкость». Для них характерно малое поверхностное натяжение. Благодаря такому свойству, субстанция легко проникает в капилляры, которые могут образоваться во время сварки. Говоря проще, пенетранты проникают в пустоты, окрашивают их, делая видимыми для человеческого глаза.
На практике используются разные растворы, каждый из которых можно приготовить самостоятельно. Они отличаются не только химическим составом, но и свойствами. На практике чаще всего применяются пенетранты, изготовленные на основе воды либо другой органической жидкости – бензола, скипидара и т.д. Именно они наиболее чувствительны к самым незначительным дефектам.
Для улучшения качества и увеличения скорости работ, вы всегда можете воcпользоваться нашими верстаками собственного производства от компании VTM.
Проверка сварных швов на герметичность
На капиллярно методе испытания сварочного шва не заканчиваются. Важно определить степень герметичности стыка. Метод, который применяется в данных целях, называется по-разному: пузырьковый, гидроиспытание, течеискание и много иных вариаций. Их объединяет общая суть – обнаружение дефектов герметичности.
Герметичность стыка проверяется при помощи газа или жидкости. Суть метода идентична капиллярному. Разница заключается только в том, что кислород, азот или вода подаются под высоким давлением. Субстанции распределяются по пустотам и в случае негерметичности стыка, выходят наружу. Классификация методологий зависит от вида применяемого материала. Он бывает гидравлическим или пневматическим. Последний делится на подвиды: вакуумный или нагнетательный.
Пневматический метод контроля базируется на использовании воздуха или газовоздушной смеси, которые подаются к тестируемой области под давлением. Предварительно место стыка обильно смазывается раствором из воды и мыла. Подвидом пневматического метода является контроль с использованием вакуума. Сварочный шов промазывается мыльным раствором. После этого конструкция или деталь помещается в безвоздушную среду, созданную специальным оборудованием. Если существуют сквозные дефекты, то будут образовываться мыльные пузыри.
Для приготовления мыльного раствора необходимо использовать один кусок мыла на литр воды. В случаях, когда предполагается использовать раствор при отрицательной температуре, необходимо половину воды заменить техническим спиртом. Не лишним будет подключение манометра к емкости, где создается вакуум или нагнетается давление. Изменения в показаниях прибора будут свидетельствовать о наличии дефектов сварочного шва.
Есть очень простой и надежный способ контроля качества шва, который заключается в погружении испытуемой детали в воду. Не требуется ни мыльный раствор, ни герметичные резервуары или нагнетательное оборудование. В случаях, когда присутствуют дефекты, то из детали, погруженной в воду, будут подыматься мелкие пузырьки воздуха. Данный метод называют полевом. Несмотря на свою простоту, он достаточно эффективный.
Еще одна разновидность пневматического контроля основывается на проверке соединений при помощи аммиака. Он подается на соединение вместо воды или газа. Предварительно стыки покрываются бумажной лентой. Аммиак проникает во все доступные полости и, если шов имеет пустоты, то на поверхности бумажной ленты образуются красные пятна.
При гидравлическом методе контроля давление создается при помощи масла или воды. В зависимости от вида металла деталь выдерживается в жидкости от 5 до 15 минут. В это время зона по периметру сварочного шва обстукивается молоточком. Даже при слабых ударах жидкость станет вытекать в случаях, когда шов имеет сквозные дефекты.
Читайте также: Виды сварных соединений и швов
Магнитное поле
В основу метода легла технология использования электромагнетизма в промышленности. С помощью специального приспособления вокруг сварочного шва создается магнитное поле, имеющее свой рисунок электромагнитных линий. Если они ровные, то можно смело сказать, что работа выполнена качественно. В случаях наличия дефектов, линия будут иметь явное искажение.
Для визуализации магнитных линий достаточно на поверхность проверяемых деталей насыпать ферримагнитный порошок. В случае искажения магнитного поля он скапливается в том месте, где присутствует дефект. В силу объективных обстоятельств данный метод приемлем только при работе с ферримагнитными металлами. Качество сварки меди, алюминия, стали с большой долей никеля или хрома проверить не получится. Помимо этого, технология является достаточно затратной. Они востребована только в случаях, когда есть необходимость точной проверки соединения особо важных узлов.
Ультразвук
Для контроля над качеством сварного шва используются также уникальные свойства ультразвука. Звуковые волны по-разному отражаются от монолитной и деформированной поверхности. Сколы и трещины имеют свои акустические особенности, которые фиксируются специальной аппаратурой. Проще говоря, на сварочный шов подается ультразвук. Если он сталкивается с пустотой, сколом или иным дефектом, то отображается от металла под другим углом. Более того, разные виды дефектов отражают ультразвук неодинаково, что позволяет диагностировать их.
Благодаря тому, что ультразвуковой метод диагностики является сравнительно недорогим и стабильно эффективным, он используется повсеместно. Распространению способствует и простота использования. К примеру, не нужно учитывать физико-химические особенности металлических сплавов, как в случаях с магнитным или радиационным контролем. Да и приобретение дорогостоящей оснастки тоже не требуется. Недостатком является необходимость наличия специальных знаний и навыков. То есть для контроля привлекается специалист со стороны. Сварщик выполнить процедуру самостоятельно не сможет.
Радиография
Радиационный контроль сварных швов является миниатюрной версией всем знакомого медицинского рентгена. Гамма-лучи прошивают металл и оставляют свой след на специальной пленке. Соответственно, отображаются и скрытые от глаз внутренние дефекты сварочного стыка. Данный метод является самым передовым и позволяет точно обрисовать картину внутреннего состояния соединения.
Наряду с этим, метод имеет и недостатки. Прежде всего, это необходимость приобретения дорогостоящего оборудования. Другой нюанс – требуется предварительная подготовка специалиста. Плюс ко всему, нельзя работать с оборудованием длительной время, поскольку это негативно сказывается на состоянии здоровья.
С недавних пор есть возможность приобрести цифровой радиограф, работающий с компьютерной программой. Вместо пленки в этом случае применяются многоразовые пластины, которые реагируют с любыми лучами. Ключевое отличие от классического рентген-аппарата заключается в том, что изображение сразу отображается на мониторе компьютера. Его можно масштабировать и редактировать. Перспективой технологии является полная автоматизация процесса.
Заключение
Специалист, выполняющий контроль качества сварных соединений металлоконструкций, должен максимально ответственно относиться к своим обязанностям. От его внимательности зависит функциональность и срок службы конструкции. Нужно фиксировать все отклонения от нормы, которые поддаются диагностированию. Чтобы получить максимально детальную картинку, желательно комбинировать несколько методов контроля. Строго воспрещается прибегать к методам, которые могут нанести вред сварному соединению.
Ультразвуковой контроль качества сварных швов и соединений трубопроводов и металлоконструкций
Контроль сварного шва средствами дефектоскопии позволяет выявить трещины, шлаки, непровар и поры, обычно скрытые в толще металла. Внутренние дефекты ослабляют прочность и нарушают герметичность конструкции. Поэтому после окончания сварочных работ выполняется тщательный контроль качества сварного шва.
Разнообразные способы обследования неразъемных соединений разделяют на неразрушающие, например ультразвуковой контроль, и разрушающие, требующие вскрытия шва. Современные методы отличаются степенью эффективности, принципом действия и сложностью оснащения. Наиболее востребован контроль качества сварных швов, не влияющий на целостность зон стыковки элементов.
Безопасные и производительные методы контроля сварных швов, не разрушающие соединенные участки, подразделяются на виды:
• визуальный осмотр, позволяющий выявить внешние повреждения;
• ультразвуковой контроль, базирующийся на сканировании объектов высокочастотными волнами;
• магнитный способ, включающий магнитопорошковую, индукционную и магнитографическую разновидности;
• контроль сварных швов для выявления негерметичности металлических соединений жидкими проникающими веществами;
• акустическая эмиссия, радиационный, вихретоковой, тепловой, электрический и виброакустический методы, построенные на анализе реакции объекта на различные воздействия.
Выбор методики проверки зависит от сложности и ответственности деталей конструкции. Самым простым считается внешний осмотр, требующий предварительной очистки проверяемых участков. Ультразвуковой контроль сварных швов, намагничивание и прочие виды физического воздействия используются для точной оценки прочности и однородности шва.
Для выявления масштабов разрушения структуры и определения толщины материала без прямого контакта с ним обычно применяют функциональный вихретоковый способ. Универсальный ультразвуковой контроль швов помогает оценить качество всех видов сварки не только металлических, но и пластмассовых, композитных и керамических объектов. Для решения конкретной задачи целесообразно выбирать дефектоскоп, принцип действия которого позволит выявить все изъяны околошовных зон.
Согласно ГОСТ 15467-79, сварные изделия, в частности, трубопроводы, должны отвечать своему прямому назначению, иметь высокие технические и эксплуатационные свойства, а главное, быть безопасными в использовании. Поэтому контроль качества сварных швов и соединений играет особую роль в цепочке технологического процесса. Дефекты, обнаруженные в термической зоне шва, приводят к снижению прочности сварки, а, следовательно – надежности изделия в целом. Вовремя обнаруженный брак позволяет принять верные технологические решения еще на этапе его производства.
Существует несколько методов контроля качества сварных швов. Самый простой – это визуальный осмотр сварных швов и соединений, который помогает обнаружить явные изъяны сварки. Также их можно проверить на изъяны с помощью гамма-лучей, магнитной томографии, химическим и т. д.
ООО «Измерение» проводит все виды контроля качества сварки и сварных соединений трубопроводов в Екатеринбурге по оптимальной цене:
- Визуальный осмотр на наличие явных дефектов. Это самый простой контроль качества сварных соединений;
- Просвечивание трубопроводов гамма-лучами;
- Метод обнаружения поля рассеяния, при намагничивании металлоконструкции;
- Ультразвуковой контроль с замером частоты звуковых волн и преобразующихся от них электрическим импульсом;
- Метод вскрытия шва путем вскрытия подозрительного участка;
- Нанесение на место сварки химических реагентов;
- Цветная дефектоскопия: на место предполагаемого дефекта наносится флуоресцентный раствор и проявляющая белая краска;
- Проба керосином;
- Испытание повышенным атмосферным давлением;
- Вакуумный метод;
- Проверка на склонность к коррозии;
- Проверка на твердость по окружности сварки.
Вовремя сделанный контроль качества сварных швов трубопроводов позволит оперативно устранить такие распространенные дефекты как: наплывы, прожоги, подрезы, непровар, трещины, посторонние шлаковые включения, газовые поры и т. д. Каждый вид контроля качества сварки лучше всего выделяет определенные типы брака. Каждый из них имеет свои плюсы и минусы.
Так, например, ультразвуковой контроль качества сварных соединений хорошо выявляет плоскостные изъяны сварки трубопроводов, но при этом «не замечает» дефектные поры на соединениях металлоконструкций до 1 мм. А радиационный контроль качества сварки наоборот, хорошо выявляет мельчайшие поры размером от 0.1 мм., но не эффективен при обнаружении непроваров, трещин и т. д.
ООО «Измерение» проведет контроль качества сварки металлоконструкций и их соединений в зависимости от особенностей трубопроводов. Наши клиенты – это известные строительные и промышленные предприятия Екатеринбурга. Обратившись к нам, вы узнаете настоящее качество сварки и вовремя сможете принять необходимые меры.
Контроль сварного шва – оперативно, качественно и результативно
Гарантировать надежность сварного шва, выполненного даже специалистом самого высокого разряда, достаточно проблематично. Ведь на качество работ влияет не только человеческий фактор, но и много других составляющий, в том числе оборудование и характеристики материала. Поставить окончательную точку в этом вопросе, позволит профессиональный контроль качества шва посредством специализированного оборудования. Заказать такую услугу в Екатеринбурге, вы можете в нашей современной лаборатории.
Исследование сварочных швов: от визуального осмотра до химических испытаний
В зависимости от исследуемого объекта и его технических особенностей, команда наших профессионалов подберет наиболее эффективные варианты контроля сварных швов:
- Визуальный;
- Магнитный;
- Проникающими веществами;
- Радиационный и т.д.
Результатом проведенных испытаний станут многопараметрические экспертные заключения, соответствующие требованиям законодательства. При выявлении дефектов, мы не оставляем клиента с его проблемой. Наши специалисты окажут профессиональную консультацию по подбору решений устранения недостатков объекта, а после их реализации, проведем повторный неразрушающий контроль качества стыковых швов. Стоимость наших услуг доступна и демократична, поэтому совместное сотрудничество будет не только результативным, но и выгодным как для крупного производственного предприятия, так и среднего бизнеса.
Как автоматизированный контроль качества сварки повышает производительность
По мере развития технологий материалов и производства производители расширяют возможности конструкций, используемых в автомобильной, строительной, морской, энергетической и многих других отраслях. Все эти отрасли используют сварку в своих повседневных производственных задачах, и, поскольку сварные швы используются для соединения двух или более металлических поверхностей, эти соединения могут подвергаться нагрузкам и усталости в течение срока службы продукта. Всегда есть шанс, что эти продукты могут потерпеть неудачу, если они не будут созданы в соответствии с надлежащей спецификацией.
Если возможен сбой продукта, не следует ли нам подумать, как уменьшить или даже полностью исключить вероятность ошибок в процессе?
Сегодня автоматический контроль качества сварки обычно представляет собой компактный 3D-датчик, используемый для повышения качества, управления автоматизацией и снижения производственных затрат для автоматизированных сварочных роботов. Это система, ориентированная на процесс, которая больше фокусируется на предотвращении проблем с качеством, чем на общих проблемах процесса. Все дело в оптимизации процессов, использовании данных в упреждающем, а не реактивном режиме, чтобы снизить процент отказов.
Этот производственный процесс в режиме реального времени позволяет нам получать информацию все быстрее и быстрее, без необходимости ждать. Датчики, программное обеспечение и компьютеры эволюционировали, чтобы иметь возможность обрабатывать карты/файлы поверхности сварных швов с высоким разрешением, отсканированные лазером, и инструменты измерения размеров для проверки размеров сварных швов, когда они происходят. Вопрос в том, соответствуем ли мы спецификациям и стандартам ваших клиентов? Да или нет, и каков количественный результат?
Информация о качестве, подобная этой, сегодня является фундаментальной для передовых производственных компаний. Большая часть программного обеспечения, используемого сегодня, более удобна для пользователя, чем в прошлом, и проста в использовании; что делает анализ, внесение корректировок в процесс до того, как будут изготовлены дефектные детали, и выявление потенциальных проблем для снижения процента брака — все это часть процесса улучшения.
Для ABICOR BINZEL нашей системой обеспечения качества является система контроля сварных швов SmartRay 3D. Эта технология использует лазер для освещения сварной детали, а затем захватывает весь этот шов для измерения размеров. Информация, предоставляемая датчиками, включает в себя надежные контрольные размеры сварных швов и дефекты сварных швов для доработки. Автоматизация процесса контроля сварных швов увеличивает скорость производства и обеспечивает надежность за счет последовательного использования датчика. В конечном счете, информация, собранная с помощью системы SmartRay, будет использоваться для установления базовых показателей того, соответствуете ли вы жестким требованиям обеспечения качества сварки. Как только вы ознакомитесь с системой и лучше поймете, как она может вам помочь, разрыв между выполненным и не выполненным заданием начнет уменьшаться.
Одним из важнейших аспектов этой технологии, который следует учитывать, является идея прослеживаемости — это основа всего, что мы делаем в этой отрасли. Отслеживаемость может означать несколько вещей, но в основном речь идет о том, чтобы отслеживать все данные сварки. Открывая ящик для каждой детали на протяжении всего срока ее службы, они могут идентифицировать, учитывать и находить все производственные данные для этой детали. Большинство систем обеспечения качества сварки оснащены программным обеспечением для сбора базы данных для всех данных сварки и деталей. Ответственность, которую это влечет за собой, имеет важное значение. Наличие базы данных с возможностью поиска защитит не только клиента от любых непредвиденных проблем, но и вашу ответственность.
Еще одним преимуществом использования этой системной технологии является будущая выгода от наличия передовых технологий в вашем учреждении. Внедрение этого раньше, чем позже, даст вашему учреждению время изучить и понять не только то, как работают подобные системы, но и то, как они разработаны, чтобы приносить вам пользу. Сварочные системы продолжают становиться умнее, как и оборудование, используемое в этих системах. По мере того, как этот снежный ком продолжает расти, наш доступ к большему количеству данных будет только увеличиваться, что приведет к тому, что фабрики станут все более и более эффективными.
Каждый раз, когда есть технология, которую можно использовать автоматически, бесконтактно, это впечатляет. Что делает автоматические системы обеспечения качества сварки еще более впечатляющими, так это то, как быстро они могут предоставлять данные реальным рабочим, окружающим свариваемую деталь. Нам нравится ссылаться на технологию интеллектуальной автоматизации такого калибра. 3D-сканер, работа которого состоит в том, чтобы сканировать только что сваренные детали, чтобы определить, соответствуют ли они стандартам, и одновременно создавать документацию в виде данных в режиме реального времени, просто невероятен. Именно такие вещи меняют производственный мир в целом. Чем более интеллектуальные технологии развиваются и понимаются сегодня экспертами в этой области, тем лучше будут развиваться сварочные цеха с точки зрения более высокой производительности и эффективности.
Поскольку передовое производство в значительной степени зависит от анализа данных, автоматизированное обеспечение качества сварки всегда будет опираться на немедленную обратную связь. В основном с использованием датчиков, программных алгоритмов, гибкого потока деталей и подключенных линий. В конце концов, именно связь между этими сварочными инструментами, связанными друг с другом в цифровом виде, создает и обменивается информацией, что приводит к полезной информации, которая позволяет устранять неполадки, устанавливать первопричину, предпринимать корректирующие действия и абсолютно необходима для производительности.
Ориентированная на надежность оптимизация обеспечения качества сварки
И. Э. Экенгву , О. К. Окафор , Х. К. Олисакве , У. Д. Огбонна
Факультет машиностроения, Университет Ннамди Азикиве, Авка, штат Анамбра, Нигерия
Адрес для переписки: О. К. Окафор, факультет машиностроения, Университет Ннамди Азикиве, Авка, штат Анамбра, Нигерия.
Электронная почта: |
Copyright © 2021 Автор(ы). Опубликовано Scientific & Academic Publishing.
Эта работа находится под лицензией Creative Commons Attribution International License (CC BY).
http://creativecommons.org/licenses/by/4.0/
Аннотация
Качество и надежность сварных конструкций в основном зависят от таких факторов, как: сварочный ток и напряжение, скорость прохода шва, угол разделки, тип присадочного материала, характеристики основного металла и способ охлаждения/закалки сварного шва. Исследовательские усилия были больше сосредоточены на влиянии этих факторов, исключая угол разделки и закалочное вещество, на качество и надежность сварного соединения. Это исследование было основано на измерении надежности сварных конструкций с использованием метода оптимизации с учетом двух факторов, определяющих качество сварки, — угла разделки разделки и типа охлаждающего/закалочного вещества. В разработанном эксперименте, использованном в процессе оптимизации, использовались входные переменные угла канавки (55°-60°) и типа закалочного вещества. В качестве измеренных характеристик использовались механические свойства сварного соединения. Результаты показали, что сварной шов с воздушной закалкой для угла разделки кромок 60° имел самый высокий предел текучести, пластичность и желаемое минимальное процентное уменьшение площади. Закаленный в воде сварной шов с углом разделки кромок 60° обеспечивает высокую предельную прочность на растяжение и твердость. При закалке сварного шва пальмовым маслом с углом разделки кромок 59° имел самую высокую инженерную прочность на излом.
Угол канавки 60° и воздух в качестве охлаждающего вещества считались лучшей комбинацией факторов для достижения хороших характеристик сварки с точки зрения прочности, пластичности и процентного уменьшения (площади) по результатам оптимизации.
Ключевые слова: Сварка, оптимизация, сталь, угол разделки, охлаждение, механические свойства
Процитируйте эту статью: И. Э. Экенгву, О. К. Окафор, Х. К. Олисакве, У. Д. Огбонна, Оптимизация обеспечения качества сварных изделий, ориентированная на надежность, Журнал машиностроения и автоматизации , Vol. 10 № 1, 2021, стр. 1-11. doi: 10.5923/j.jmea.20211001.01.
Описание статьи
- 1. Введение
- 2. Материалы и метод
- 2.1. Материалы
- 2.2. Метод
- 2.2.1. План эксперимента
- 2.
2.2. Подготовка образцов и сварка
- 2.2.3. Закалка образцов
- 2.2.4. Лабораторные испытания образцов
- 2.2.5. Статистический анализ
- 2.2.6. Техника оптимизации
- 3. Результаты и обсуждение
- 3.1. Статистические тесты – ANOVA
- 3.2. Методология поверхности отклика – оптимизация переменных
- 3.3. Оптимальное сочетание факторов
- 3.4. Графики напряжения-деформации сварного изделия из мягкой стали
- 4. Выводы
1. Введение
- Сварка – это операция, которая включает соединение (сварку) двух одинаковых или разнородных материалов посредством тепла и/или давления с использованием или без использования наполнителей. Во время сварочных работ для облегчения процесса могут использоваться другие вспомогательные материалы, такие как: защитные газы, флюсы или пасты.
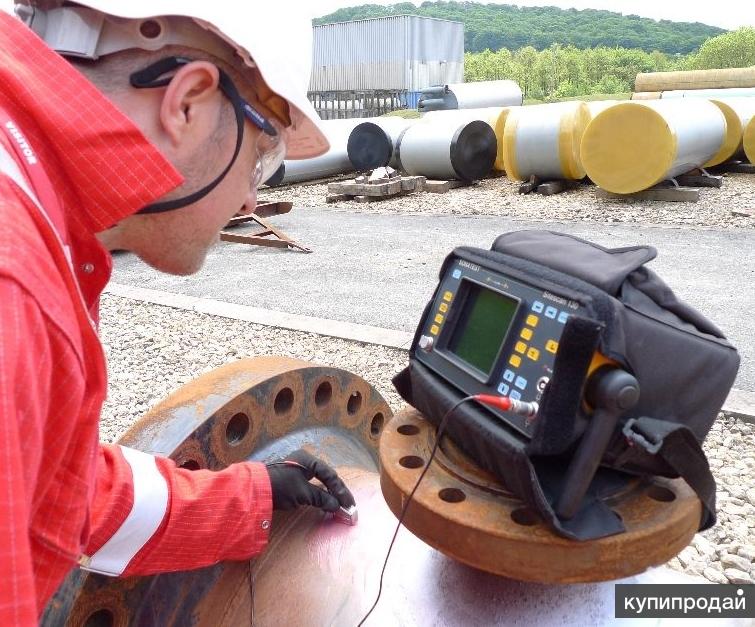


Рисунок 1 . Взаимосвязь входных и ответных переменных для процесса сварки SMAW |
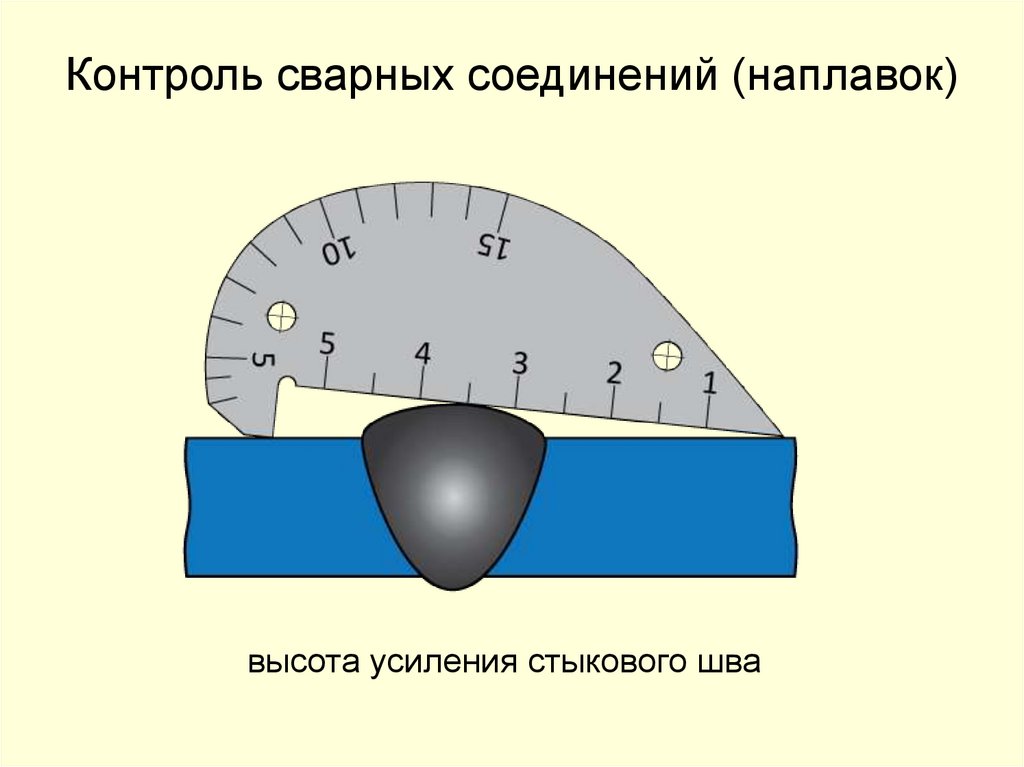
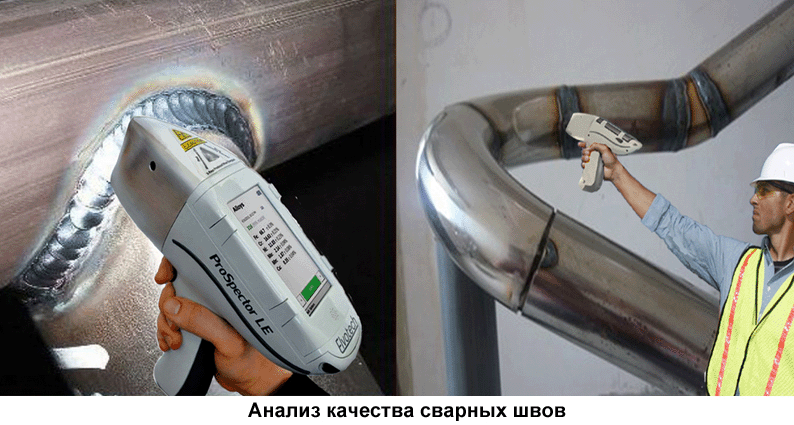

2. Материалы и методы
2.1. Материалы
- В этом исследовании использовались следующие материалы: мягкая сталь AISI/SAE 1020 (размеры: 100 мм × 46 мм × 1 мм), полировальный реагент (алмазный порошок и порошок оксида алюминия), вода, реагенты для травления (азотная кислота и этанол), гасящие вещества (пальмовое масло, вода и воздух), наждачная бумага, электроды (основного типа, поскольку они обеспечивают хорошее проплавление дуги и отличные механические свойства). Химический состав образца мягкой стали, использованного в этом исследовании, показан в таблице 1.
|
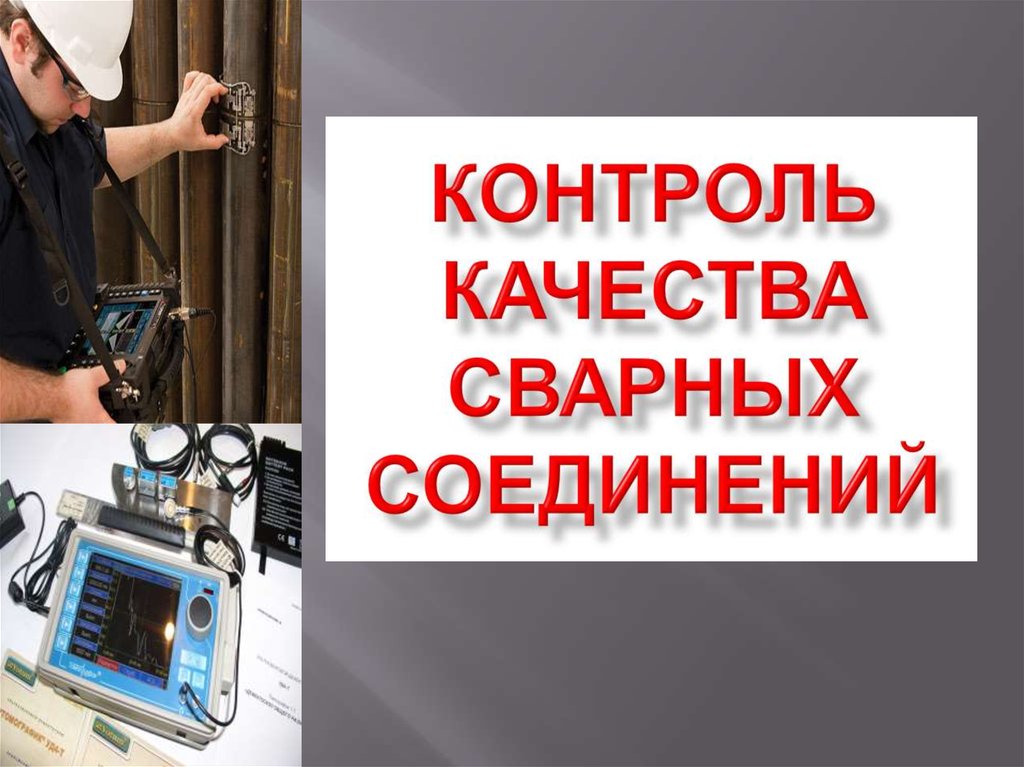
- Метод исследования, использованный в этом исследовании, основан на планировании экспериментов посредством подготовки образцов и сварки, закалки образцов, механических испытаний и оптимизации реакции в поисках оптимальных факторных характеристик для хорошей целостности сварного шва или рабочих характеристик. В следующих разделах представлено подробное описание методов исследования.
2.2.1. Дизайн эксперимента
- Программное обеспечение Design Expert 11.0 использовалось при разработке эксперимента с использованием инструмента методологии поверхности отклика для проведения механического анализа сварного соединения. Эксперимент был спланирован с использованием входных факторов: типа закалочных веществ (вода, воздух и пальмовое масло) и различных углов одиночных V-образных канавок (А). Используемые переменные отклика: предел текучести, предельное растягивающее напряжение, инженерное напряжение разрушения, пластичность в процентах и обжатие.

2.2.2. Подготовка образцов и сварка
- Одиннадцать (11) образцов были приготовлены путем вырезания двух пластин из мягкой стали, которые должны были получить размеры 100 мм × 46 мм × 1 мм при сборке вместе, тщательно следуя запланированному эксперименту. Затем две металлические детали были соединены вместе с помощью дуговой сварки в защитном металле (SMAW). Используемые параметры сварки: сварочный ток 180А, сварочное напряжение 220В переменного тока.
2.2.3. Закалка образцов
- Сразу после сварки образцы каждый из них опускали в соответствующие охлаждающие вещества — воду, пальмовое масло и воздух с помощью ручного щипца.

Рисунок 2 . (a) Образец, закаленный водой (b) Образец, закаленный маслом (c) Образец с воздушным охлаждением |
2.2.4. Лабораторные испытания образцов
- а. Испытание на растяжение Прочность образцов на растяжение была испытана при растяжении до разрушения путем установки каждого образца на зажимы тензиометра, к которому прикладывалась постепенно возрастающая нагрузка, а начальная площадь и ширина образцов были отмечены как 140 мм.
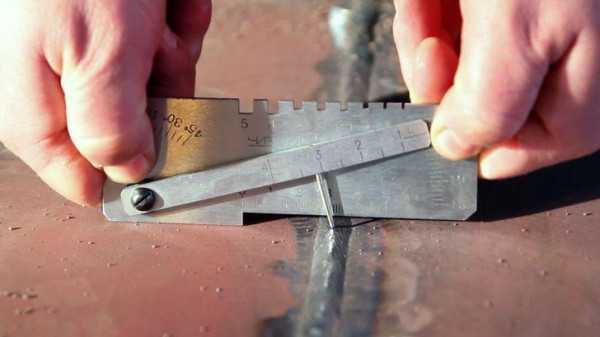
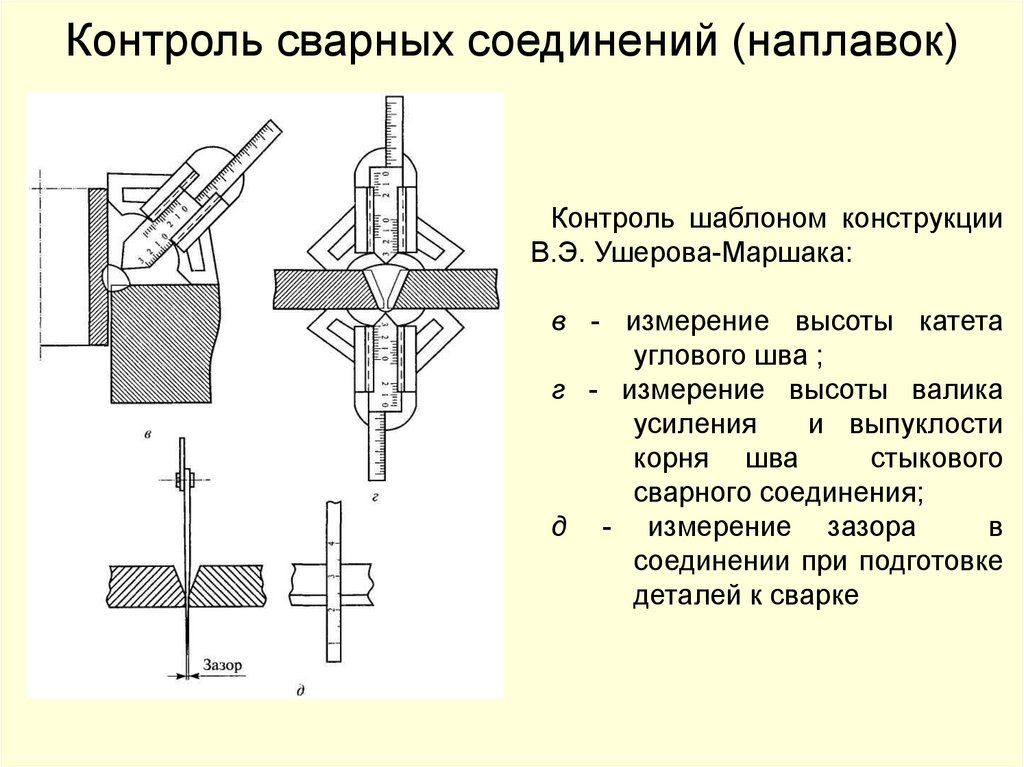
2.2.5. Статистический анализ
- Статистический тест (дисперсионный анализ-ANOVA) был проведен для каждой из рассматриваемых переменных, чтобы установить их существенное влияние на характеристики сварки металла из мягкой стали. Определяли реакцию, имеющую как индивидуальное, так и комбинированное/интерактивное двухфакторное воздействие. Дисперсионный анализ (ANOVA) представляет собой набор статистических моделей и связанных с ними процедур оценки (таких как вариации между группами и между группами), используемых для анализа различий между средними значениями в выборке. Он обеспечивает статистическую проверку того, равны ли два или более средних значений генеральной совокупности.
2.2.6. Техника оптимизации
- Значения всех рассмотренных откликов, использованных в плане эксперимента, были определены и соответствующим образом зарегистрированы. Затем инструмент методологии поверхности отклика был использован для оптимизации откликов, чтобы получить наилучшую комбинацию факторов, которая обеспечила бы хорошие характеристики сварного шва с точки зрения его механических свойств — предела текучести, предельного напряжения растяжения, инженерного напряжения разрушения, процентной пластичности и обжатия.

3. Результаты и обсуждение
3.1. Статистические тесты – ANOVA
- а. Предел текучести Результат анализа дисперсионного анализа, выполненного для переменной отклика – предела текучести материала из мягкой стали, показан в таблице 2. ANOVA Анализ реакции 1- Предел текучести

|
|
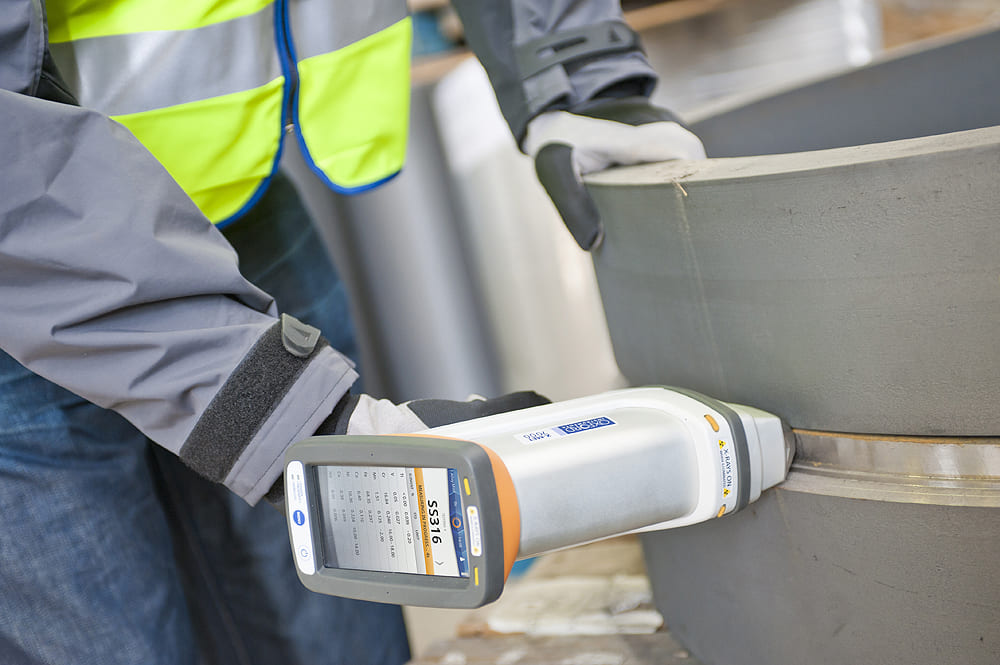
|
|
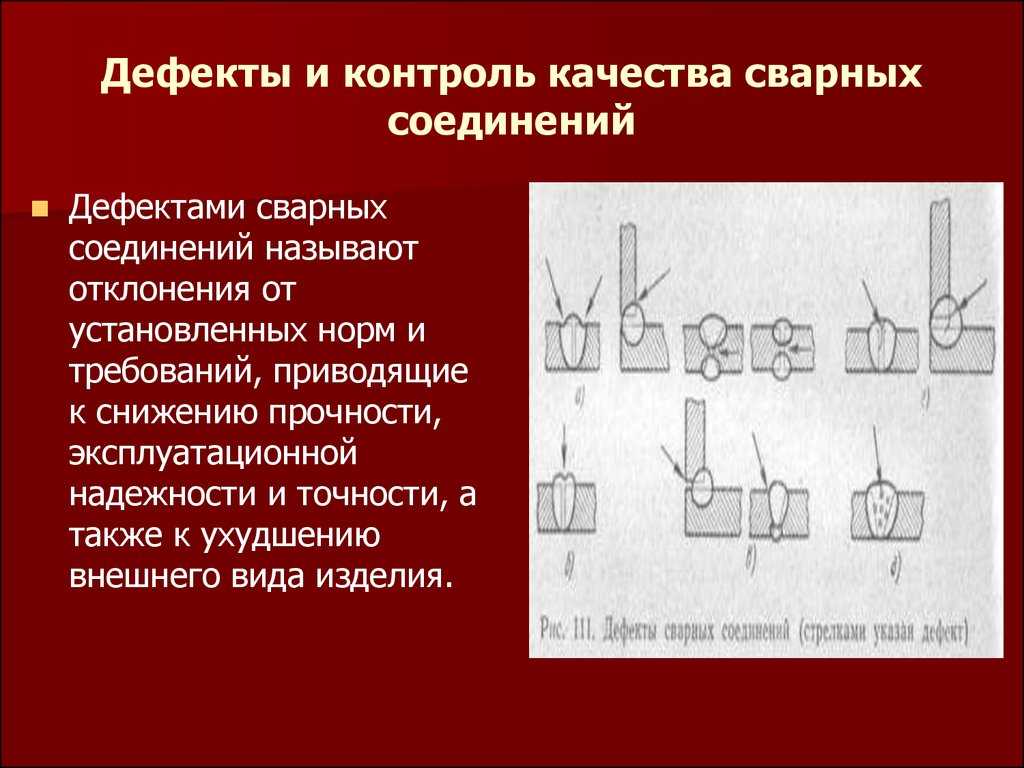
|
3.2. Методология поверхности отклика – оптимизация переменных
- Операция оптимизации направлена на максимизацию предела текучести, предела прочности при растяжении, инженерной прочности на излом, пластичности в процентах и твердости по Роквеллу сварного шва из мягкой стали.

Рисунок 3 . (a) График желательности в зависимости от угла разделки (b) График желательности в зависимости от закалочной среды |

Рисунок 4 . (a) График зависимости предела текучести от угла разделки (b) График зависимости предела текучести от закалочного вещества |

Рисунок 5 . (a) График предельного растягивающего напряжения в зависимости от угла канавки (b) График предельного растягивающего напряжения в зависимости от закалочной среды |
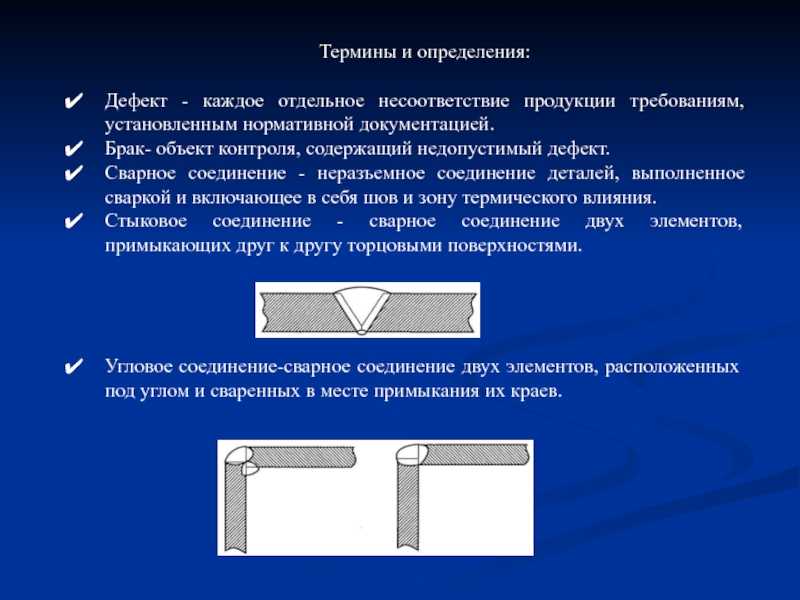
Рисунок 6 . (a) График инженерного напряжения разрушения в зависимости от угла канавки (b) График инженерного напряжения разрушения в зависимости от гасящего вещества |

Рисунок 7 . (a) График пластичности в зависимости от угла разделки (b) График пластичности в зависимости от закалочной среды |
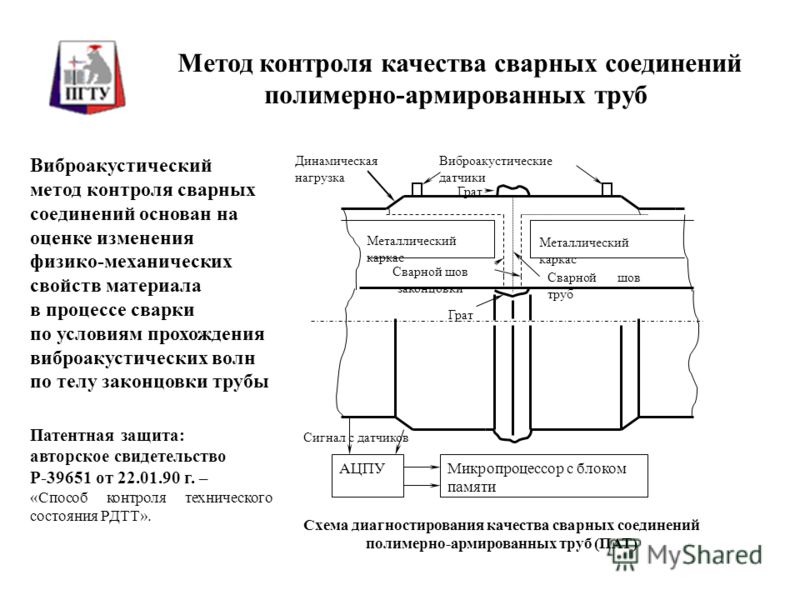