Свариваемость сталей | Мир сварки
Содержание
- Свариваемость сталей
- Литература
Свариваемость сталей
Основными характеристиками свариваемости сталей является их склонность к образованию трещин и механические свойства сварного шва.
По свариваемости стали подразделяют на четыре группы:
1 | — | хорошая свариваемость; |
2 | — | удовлетворительная свариваемость; |
3 | — | ограниченная свариваемость; |
4 | — | плохая свариваемость. |
К группе 1 относят стали, сварка которых может быть выполнена без подогрева до сварки и в процессе сварки и без последующей термообработки. Но применение термообработки не исключается для снятия внутренних напряжений.
К группе 2 относят преимущественно стали, при сварке которых в нормальных производственных условиях трещины не образуются, а также стали, которые для предотвращения трещин нуждаются в предварительном нагреве, стали, которые необходимо подвергать предварительной и последующей термообработке.
К группе 3 относят стали, склонные к образованию трещин в обычных условиях сварки. Их предварительно подвергают термообработке и подогревают. Большинство сталей этой группы термически обрабатывают и после сварки.
К группе 4 относят стали, наиболее трудно сваривающиеся и склонные к образованию трещин. Сваривают обязательно с предварительной термообработкой, подогревом в процессе сварки и последующей термообработкой.
Низкоуглеродистые стали отличаются хорошей свариваемостью. Снижать свариваемость могут вредные примеси, если содержание их превышает норму. Вредные примеси могут ухудшать свариваемость даже и при среднем содержании, не выходящем за норму, если они образуют местные скопления, например вследствие ликвации. Вредными для сварки элементами в низкоуглеродистой стали могут являться углерод, фосфор и сера, причем последняя, особенно склонна к ликвации с образованием местных скоплений.
Отрицательное влияние на свариваемость может оказывать также засоренность металла газами и неметаллическими включениями. Засоренность металла вредными примесями зависит от способа его производства, и о ней частично можно судить по маркировке металла: сталь повышенного качества сваривается лучше, чем сталь обычного качества соответствующей марки; сталь мартеновская лучше, чем сталь бессемеровская, а сталь мартеновская спокойная – лучше, чем кипящая. При изготовлении ответственных сварных изделий указанные отличия в свариваемости низкоуглеродистых сталей должны обязательно приниматься во внимание и учитываться при выборе марки основного металла.
Углеродистые стали, содержащие более 0,25% углерода, обладают пониженной свариваемостью по сравнению с низкоуглеродистыми, причем свариваемость постепенно снижается по мере повышения содержания углерода. Стали с повышенным содержанием углерода легко закаливаются, что ведет к получению твердых хрупких закалочных структур в зоне сварки и может сопровождаться образованием трещин. С повышением содержания углерода растет склонность металла к перегреву в зоне сварки.
При содержании свыше 0,4-0,5% углерода сварка стали становится одной из сложных задач сварочной техники. Углеродистые стали вообще обладают пониженной свариваемостью и, если это возможно, рекомендуется заменять их низколегированными конструкционными сталями, которые дают ту же прочность при значительно меньшем содержании углерода за счет других легирующих элементов. При сварке углеродистых сталей плавлением обычно не придерживаются соответствия химического состава присадочного и основного металлов, стремясь получить наплавленный металл равнопрочным с основным за счет легирования марганцем, кремнием и др. при пониженном содержании углерода.
Сварка углеродистых сталей часто выполняется с предварительным подогревом и последующей термообработкой, причем, если возможно, во многих случаях стремятся совместить термообработку с процессом сварки, например, с газовой сваркой мелких деталей, с газопрессовой, точечной, со стыковой контактной сваркой и т. д.
Большинство низколегированных конструкционных сталей обладает удовлетворительной свариваемостью. Ввиду возросшего значения сварки конструкционная низколегированная сталь новых марок, как правило, отличается удовлетворительной свариваемостью. Если же испытания пробных партий стали показывают недостаточно удовлетворительную свариваемость, то обычно для улучшения свариваемости изготовители корректируют состав стали. В некоторых случаях требуется небольшой предварительный подогрев стали до 100-200 °С, реже приходится прибегать к последующей термообработке. Для предварительной грубой качественной оценки свариваемости низколегированных сталей иногда прибегают к подсчету эквивалента углерода по химическому составу стали по следующей эмпирической формуле:
где символы элементов означают процентное содержание их в стали. При эквиваленте углерода меньше 0,45 свариваемость стали может считаться удовлетворительной, если же эквивалент углерода больше 0,45, то необходимо принимать специальные меры, например, проводить предварительный подогрев и последующую термообработку. Метод оценки свариваемости по эквиваленту углерода является ориентировочным и далеко не всегда дает верные результаты.
По структуре низколегированные стали относятся обычно к перлитному классу, большое разнообразие химического состава низколегированных сталей весьма затрудняет получение одинакового состава наплавленного и основного металлов при сварке плавлением, что требует большого разнообразия присадочных материалов. Поэтому, за исключением некоторых особых случаев, когда требуется соответствие химического состава основного и наплавленного металлов (например, получение устойчивости против коррозии, крипоустойчивости и т. п.), обычно ограничиваются получением необходимых механических свойств наплавленного металла, не принимая во внимание его химический состав. Это позволяет при сварке многих сортов сталей пользоваться немногими видами присадочных материалов, что является существенным практическим преимуществом. Например, электродами УОНИ-13 успешно свариваются десятки марок углеродистых и низколегированных сталей.
Из высоколегированных сталей обладают хорошей свариваемостью и находят широкое применение в сварных конструкциях стали аустенитного класса. Наиболее широко применяются хромоникелевые аустенитные стали, например общеизвестная нержавеющая сталь 18-8 (18% Сr и 8% Ni). Хромоникелевые аустенитные стали применяются как нержавеющие, а при более высоком легировании, например при содержании 25% Сr и 20% Ni, они являются и жароупорными сталями. Содержание углерода в хромоникелевых аустенитных сталях должно быть минимальным, не превышающим 0,10-0,15%, иначе возможно выпадение карбидов хрома, резко снижающее ценные свойства аустенитной стали.
Для частей машин, работающих на истирание, например для щек камнедробилок, а также для рельсовых крестовин, применяется обычно в форме отливок сравнительно дешевая марганцовистая аустенитная сталь, содержащая 13-14% Мn и 1-1,3% С.
Сварка аустенитных сталей должна, как правило, сохранить структуру аустенита в сварном соединении и связанные с аустенитом ценные свойства: высокое сопротивление коррозии, высокую пластичность и т. д. Распад аустенита сопровождается выпадением карбидов, образуемых освобождающимся из раствора избыточным углеродом. Распаду аустенита способствуют нагрев металла до температур ниже точки аустенитного превращения, уменьшение содержания аустенитообразующих элементов, повышение содержания углерода в низкоуглсродистых аустенитных сталях, загрязнение металла примесями и т. д. Поэтому при сварке аустенитных сталей следует сокращать до минимума продолжительность нагрева и количество вводимого тепла и применять возможно более интенсивный отвод тепла от места сварки – посредством медных подкладок, водяного охлаждения и т.
Аустенитная сталь, предназначенная для изготовления сварных изделий, должна быть высшего качества, с минимальным количеством загрязнений. Поскольку распад хромоникелевого аустенита вызывается образованием и выпадением карбидов хрома, стойкость аустенита может быть повышена введением в металл карбидообразователей более сильных, чем хром. Для этой цели оказались пригодными титан и ниобий, в особенности первый элемент, к тому же не являющийся дефицитным. Титан весьма прочно связывает освобождающийся углерод, не позволяя образовываться карбидам хрома, и тем самым предотвращает распад аустенита. Для сварки рекомендуется применять аустенитную сталь с небольшим содержанием титана. Хорошей свариваемостью отличается, например, нержавеющая аустенитная хромоникелевая сталь X18Н9T типа 18-8 с небольшим количеством титана (не свыше 0,8%).
Более строгие требования, естественно, предъявляются к присадочному металлу, который должен быть аустенитным, желательно с некоторым избытком легирующих элементов, с учетом возможного их выгорания при сварке и со стабилизирующими добавками – титаном или ниобием. ГОСТ 2240-60 предусматривает аустенитную присадочную проволоку для сварки нержавеющих и жароупорных сталей. Аустенитная присадочная проволока иногда применяется и для сварки сталей мартенситного класса. Дефицитность и высокая стоимость аустенитной хромоникелевой проволоки заставляют разрабатывать более дешевые заменители.
Стали мартенситного класса, отличающиеся высокой прочностью и твердостью, находят применение как инструментальные стали, как броневые и т. д. Сварка их связана с известными трудностями. Стали легко и глубоко закаливаются, поэтому после сварки обычно необходима последующая термообработка, заключающаяся в низком или высоком отпуске. Часто необходим также предварительный подогрев изделия. Существенное значение может иметь предшествующая термообработка изделия перед сваркой; желательно по возможности равномерное мелкодисперсное распределение структурных составляющих. При сварке плавлением часто отказываются от сходства наплавленного и основного металла не только по химическому составу, но и по механическим свойствам, стремясь в первую очередь обеспечить повышенную пластичность наплавленного металла и устранить образование в нем трещин. Для этой цели при дуговой сварке довольно часто применяют, например, электроды из аустенитной стали.
Стали карбидного класса применяют главным образом как инструментальные, и на практике чаще приходится иметь дело не со сваркой, а с наплавкой этих сталей при изготовлении и восстановлении металлорежущего инструмента, штампов и т. п. Предварительный подогрев и последующая термообработка для этих сталей по большей части обязательны. Для дуговой сварки и наплавки применяются электродные стержни легированных сталей, близких по свойствам к основному металлу, а также стержни низкоуглеродистой стали с легирующими покрытиями, содержащими соответствующие ферросплавы. По окончании сварки или наплавки обычно производится термообработка, состоящая из закалки и отжига.
Стали ферритного класса отличаются тем, что в них совершенно подавлено или ослаблено образование аустенита при высоких температурах за счет введения больших количеств стабилизаторов феррита. Существенное практическое значение имеют хромистые ферритные стали с содержанием 16-30% Сr и не свыше 0,1-0,2% С, отличающиеся кислотоупорностью и исключительной жаростойкостью. Стали могут быть сварены с присадочным металлом того же состава или аустенитным. Обязателен предварительный подогрев; по окончании сварки производится продолжительный отжиг в течение нескольких часов, за которым следует быстрое охлаждение.
Литература
- Сварка, резка и пайка металлов / К.К. Хренов. М., Машиностроение, 1970, 408 с.
- Справочник конструктора–машиностроителя. Т.3 / В.И. Анурьев. М.: Машиностроение. 2000. 859 с.
- Марочник сталей и сплавов / В.Г. Сорокин, А.В. Волосникова. – М.: Машиностроение, 1989. – 640 с.
- Инструментальные стали. Справочник / Л.А. Позняк. М., Металлургия, 1977, 168 с.
Свариваемость сталей
Содержание страницы
- Понятие о свариваемости
- Свариваемость сталей
- Влияние элементов, содержащихся в сталях, на их свариваемость
- Классификация сталей по свариваемости
Понятие о свариваемости
Свариваемостью называется свойство металла (или другого материала) образовывать при установленной технологии сварки соединение, отвечающее требованиям, обусловленным конструкцией и эксплуатацией изделия (ГОСТ 2601).
Свариваемость различных металлов и их сплавов существенно отличается.
Степень свариваемости оценивают изменением свойств сварного соединения по отношению к основному металлу. Степень свариваемости сплава тем выше, чем больше способов сварки и режимов при каждом способе можно применить. Примером хорошей свариваемости является малоуглеродистая сталь.
Под технологической свариваемостью понимают отношение металла к конкретному способу сварки и режиму.
Физическая свариваемость определяется процессами, протекающими в зоне сплавления свариваемых металлов, по завершении которых образуется неразъемное сварное соединение. Все однородные металлы обладают физической свариваемостью. Свойства разнородных металлов зачастую препятствуют протеканию необходимых физико-механических процессов в зоне сплавления. В этом случае металлы не обладают физической свариваемостью.
Свариваемость сталей
Влияние элементов, содержащихся в сталях, на их свариваемостьУглерод. Малоуглеродистые стали хорошо свариваются всеми видами сварки. С увеличением содержания углерода в стали повышается твердость и снижается пластичность. Металл в сварном соединении закаливается, и образуются трещины. В результате интенсивного окисления углерода при сварке образуется значительное количество газовых пор.
Марганец. В количестве 0,3…0,8 % марганец не ухудшает свариваемость стали. Является хорошим раскислителем и способствует уменьшению содержания кислорода в стали. При содержании марганца 1,5…2,5 % свариваемость ухудшается и возможно появление трещин из-за увеличения твердости стали и образования закалочных структур.
Кремний. Содержание кремния в углеродистых сталях незначительно (0,03…0,35 %). Кремний вводят как раскислитель, и при содержании до 1 % он не влияет на свариваемость. С увеличением содержания кремния более 1 % свариваемость ухудшается, так как образуются тугоплавкие окислы, которые приводят к появлению шлаковых включений. Металл сварного шва имеет повышенные прочность, твердость и хрупкость.
Хром. В углеродистых сталях содержание хрома не превышает 0,25 % и в таком количестве его влияние на свариваемость не значительно. Конструкционные стали типа 15Х, 20Х, 30Х, 40Х содержат от 0,7 до 1,1 % хрома. При таком содержании хрома твердость увеличивается, а свариваемость ухудшается, особенно с увеличением содержания углерода. Стали, содержащие значительное количество хрома (Х5, 1X13, Х17) имеют самую плохую свариваемость. При сварке образуются тугоплавкие окислы, снижается химическая стойкость стали и образуются закалочные структуры.
Никель. Никель повышает прочность и пластичность металла сварного соединения и не ухудшает свариваемость.
Молибден. В теплоустойчивых сталях содержание молибдена составляет 0,2…0,8 %, а в специальных сталях, предназначенных для работы при высоких температурах, увеличивается до 2…3 %. Молибден значительно повышает прочность и ударную вязкость стали, но вызывает склонность к образованию трещин, как в самом шве, так и в переходной зоне.
Ванадий. Ванадий повышает прочность сталей. Содержание его в инструментальных и штамповых сталях достигает 1,5 %. Ванадий ухудшает свариваемость, так как способен сильно окисляться и при сварке необходимо вводить в зону плавления активные раскислители.
Вольфрам. Содержание вольфрама в специальных (инструментальных и штамповых) сталях составляет до 2 %. Стали с содержанием вольфрама имеют значительную твердость и прочность при высоких температурах. Вольфрам ухудшает свариваемость, сильно окисляется и поэтому сварка требует особых приемов.
Титан и ниобий. Титан и ниобий улучшают свариваемость стали. При сварке высоколегированных хромистых и хромоникелевых сталей углерод взаимодействует с хромом и образуются карбиды хрома. Это приводит к уменьшению содержания хрома по границам зерен, образованию межкристаллитной коррозии и разрушению сварных швов. При введении в стали титана или ниобия в количестве 0,5…1 % происходит их взаимодействие с углеродом, что препятствует образованию карбидов хрома.
Медь. В сталях, используемых для ответственных конструкций, содержание меди составляет 0,3…0,8 %. Медь улучшает свариваемость, повышает прочность, пластические свойства, ударную вязкость и коррозионную стойкость сталей.
Сера. Повышенное содержание серы приводит при сварке к образованию горячих трещин. Наибольшее допускаемое содержание серы до 0,06 %.
Фосфор. Повышенное содержание фосфора ухудшает свариваемость, так как вызывает при сварке появление холодных трещин. Допускается содержание фосфора в углеродистых сталях не более 0,08 %.
Кислород. Кислород ухудшает свариваемость стали, снижая ее механические свойства – прочность, пластичность, ударную вязкость.
Азот. Азот из окружающего воздуха при охлаждении сварочной ванны образует нитриды железа, которые повышают прочность и твердость стали и значительно снижают пластичность.
Водород. Водород попадает в сварочную ванну из влаги и коррозии на поверхности металла, скапливается в отдельных местах сварного шва, образует газовые пузырьки, вызывает появление пористости и мелких трещин.
Свариваемость сталей оценивается такими признаками как склонность к образованию трещин и механические свойства сварного соединения.
Количественной характеристикой свариваемости стали является эквивалентное содержание углерода Сэк, которое определяют по формуле
Сэк = С + (Мn/6) + [(Cr + Mo +V)/5 + (Ni + Cu)/15] ,
где С – содержание углерода, %;
Мn, Cr, Mo, V, Ni, Cu – содержание легирующих элементов (марганец, хром, молибден, ванадий, никель, медь), %.
Наибольшее влияние на свариваемость стали оказывает количество содержащегося в ней углерода и легирующих компонентов.
Стали по свариваемости делят на четыре группы: хорошо сваривающиеся стали, удовлетворительно сваривающиеся, ограниченно сваривающиеся и плохо сваривающиеся стали.
К первой группе относятся стали, сварку которых выполняют по обычной технологии без подогрева. Возможно применение термообработки для снятия внутренних напряжений.
Ко второй группе относятся стали, у которых при сварке в нормальных условиях, как правило, трещин не образуется. Для сварки сталей этой группы имеются ограничения по толщине свариваемого изделия и температуре окружающей среды.
К третьей группе относятся стали, склонные в обычных условиях сварки к образованию трещин. При сварке их предварительно подвергают термообработке и подогревают. Кроме того, большинство сталей, входящих в эту группу, подвергают термообработке после сварки.
К четвертой группе относятся стали, наиболее трудно поддающиеся сварке и склонные к образованию трещин. Эти стали свариваются ограниченно, поэтому сварку их выполняют с обязательной предварительной термообработкой, с подогревом в процессе сварки и последующей термообработкой.
В табл. 1 приведена свариваемость и условия сварки сталей различных видов и марок.
Таблица 1. Свариваемость сталей и условия сварки
Группа свариваемости | Эквивалентное содержание углерода, Сэк | Углеродистые стали | Легированные стали | Высоколегированные стали | Условия сварки |
I Хорошая | До 0,25 | ВСт1, ВСт2, ВСт3, ВСт4, Стали 08, 10, 15, 20, 25 | 15Г, 20Г, 15Х, 20Х, 15ХМ, 20ХГСА, 10ХСНД, 10ХГСНД, 15ХСНД | 08Х20Н14С2, 20Х23Н18, 08Х18Н10, 12Х18Н9Т, 15Х5 | Без ограничений, в широком диапазоне режимов сварки независимо от толщины металла, жесткости конструкции, температуры окружающей среды |
II Удовлетворительная | Свыше 0,25 и до 0,35 | ВСт5, Стали 30, 35 | 12ХН2, 12ХН3А, 20ХН, 20ХН3А, 30Х, 30ХМ, 25ХГСА | 30Х13, 25Х13Н2, 9Х14А, 12Х14А | Сварка при температуре окружающей среды не ниже + 5 оС и толщине металла до 20 мм при отсутствии ветра |
III Ограниченная | Свыше 0,35 и до 0,45 | ВСт6 Стали 40, 45 | 35Г, 40Г, 45Г, 40Г2, 35Х, 40Х, 45Х, 40ХМФА, 40ХН, 30ХГС, 30ХГСА, 35ХМ, 20Х2Н4МА | 17Х18Н9Т, 12Х18Н9, 36Х18Н25С2, 40Х9С2 | Сварка с предварительным или сопутствующим подогревом до 250 оС в жестком диапазоне режимов сварки |
IV Плохая | Свыше 0,45 | Стали 50, 55, 60, 65, 70, 75, 80, 85 | 50Г, 50Г2, 50Х, 50ХН, 45ХН3МФА, 6ХС, 7Х3 | 40Х10С2М, 40Х13, 95Х18, 40Х14Н14В2М, 40Х10С2М, Р18, Р9 | Сварка с предварительным и сопутствующим подогревом, термообработкой после сварки |
Просмотров: 3 337
Свариваемость сталей и сплавов — презентация онлайн
Похожие презентации:
Технология перевозочного процесса
Влияния состава и размера зерна аустенита на температуру фазового превращения и физико-механические свойства сплавов
Организация работы и расчет техникоэкономических показателей участка механической обработки детали
Газовая хроматография
Грузоподъемные машины. (Лекция 4.1.2)
Безопасное проведение работ на высоте
Геофизические исследования скважин
Искусственные алмазы
Трансформаторы тока и напряжения
Транзисторы
1. Свариваемость сталей и сплавов
1Свариваемость – способность стали
(металла) или сочетания металлов
образовывать при установленной
технологии сварки соединение,
отвечающее эксплуатационным
требованиям.
2
3. В сварочной практике различают свариваемость физическую и технологическую
Физическая свариваемость — свойствоматериалов давать монолитное соединение с
химической связью. Такой свариваемостью
обладают практически все технические сплавы и
чистые металлы, а также ряд сочетаний металлов
с неметаллами
Технологическая свариваемость отражает реакцию
материала на тепловое, силовое и
металлургическое воздействие сварки.
Эта реакция
оценивается при сравнении механических свойств
металла сварных соединений и одноименных
свойств основного металла (например, прочности,
пластичности, ударной вязкости и др.

3
При сварке плавлением свариваются
металлы, имеющие хорошую
взаимную растворимость. Хорошую
свариваемость имеют все однородные
металлы, например сталь со сталью,
чугун с чугуном, медь с медью и т. п.
Любые металлы при сварке
плавлением могут образовывать
сварные соединения
удовлетворительного качества.
4
5. Физическая свариваемость
56. Технологическая свариваемость
Стойкость к образованию горячихи холодных трещин
6
7. Технологическая свариваемость
Отсутствие пор и шлаковых включений7
8. Технологическая свариваемость
Отсутствие оксидных пленок наповерхности металла
8
При сварке плавлением свариваются
только те металлы, которые имеют
хорошую взаимную растворимость.
Хорошо свариваются все однородные
металлы
Для обеспечения свариваемости
разнородных металлов применяют
третий металл, обладающий взаимной
растворимостью со свариваемыми
металлами
9
Разница между металлами,
обладающими хорошей и плохой
свариваемостью, заключается в том,
что при сварке последних необходима
более сложная технология (строгое
соблюдение параметров режима,
предварительный подогрев,
термическая обработка, облицовка
кромок, последующая термообработка
и т.
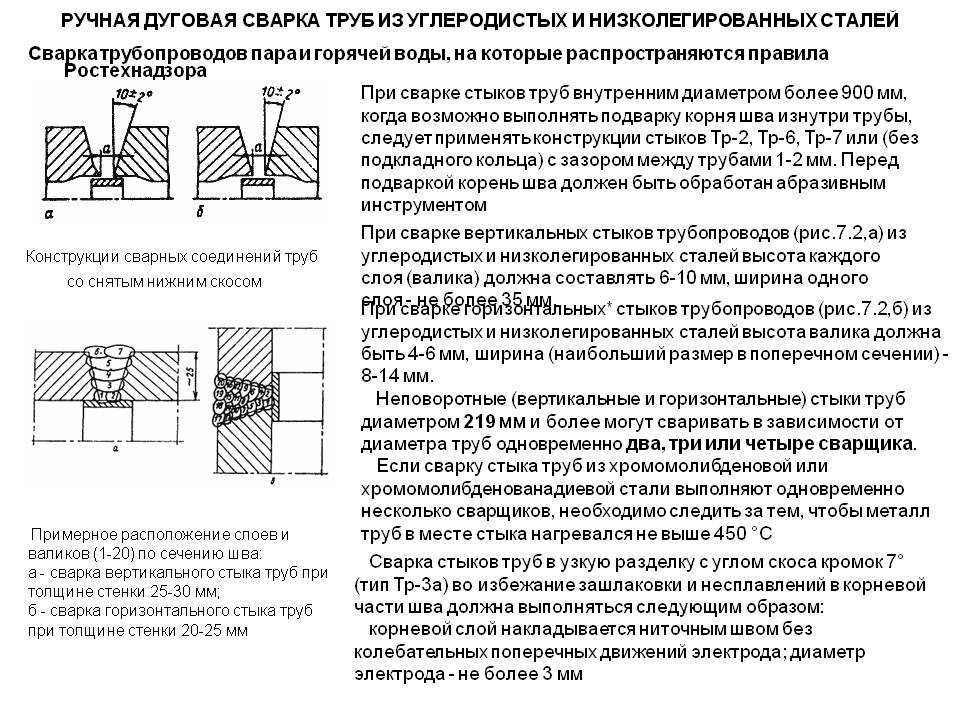
10
11. Признаки плохой свариваемости
Склонность металла кперегреву
образованию закалочных структур
охрупчиванию в зоне сварки
образованию трещин в металле шва и
переходной зоне
Образованию других дефектов при сварке
(пор, раковин, несплавлений и т.д.)
11
Существует примерно
150 способов
определения свариваемости
металлов и их сплавов
12
13. Оценка стойкости материалов против образования горячих (кристаллизационных) трещин
а) составная листовая проба МГТУ;в) проба Ходдкрофта – «рыбья кость»;
и Mg сплавы)
б) проба ИМЕТ;
в) крестовидная проба
(Al
13
14. Оценка стойкости материалов против образования горячих (кристаллизационных) трещин
а) проба Пеллини;б) кольцевая сегментная
проба;
в) проба с кольцевым
многослойным швом;
г) образец с канавками
14
15. Оценка стойкости материалов против образования холодных трещин
Метод МГТУПроба «Тэккен»
Крестовая проба (Канада)
15
16.

стали оказывает количество содержащегося
в ней
углерода
легирующих компонентов
С увеличением содержания углерода
и ряда легирующих элементов
свариваемость сталей ухудшается.
16
17. Количественная характеристика свариваемости: Эквивалентное содержание углерода
где С – содержание углерода, %;Mn, Cr… — содержание легирующих элементов, %
17
18. Количественная характеристика свариваемости
1819. Особенности сварки сталей разных групп свариваемости
1920
21. Оценка склонности сталей к образованию трещин
Наиболее простым способом оценки свариваемостисталей является оценка их склонности к образованию
горячих трещин по расчету показателя UCS
(по ЕN 1011—2) на основе содержания (%) легирующих
элементов. Метод оценки разработан в России.
UCS— единицы склонности к горячим трещинам.
Для углеродистых и низколегированных сталей расчет ведут
по выражению:
UCS = 230С + 190S + 75Р + 45Nb — 12,3Si — 5,4Мп – 1
При UCS < 10 сталь имеет высокую сопротивляемость
образованию трещин, а при UCS > 30 низкую.

21
22. Оценка склонности сталей к образованию трещин
Склонность низколегированных сталейк образованию холодных трещин можно
использовать расчет по эквиваленту углерода Сэкв (%)
по соотношению:
Сэкв = С + Мn/6 + Si/24 + Сг/5 +
Ni/40 + Мо/4 + V/14 + Сu/13 + Р/2
Медь и фосфор учитывают, если их содержание:
Сu >0,5
%, Р >0,05 %.
Стали, у которых Сэкв > 0,35%, считают склонными к
образованию холодных трещин.
Увеличение толщины свариваемого материала ухудшает его
свариваемость и в ряде случаев это надо учитывать.
22
23. Оценка склонности сталей к образованию трещин
Для низкоуглеродистых сталей:Сэкв = С + Мn/6 + 0,0025S ≤ 0,5 %
Для легированных сталей:
Сэкв = С + Мn/20 + Ni/15 + (Сг + Мо +
V)/10 + 0,0025S ≤ 0,45 %
Если полученная величина Сэкв. выше указанных
значений, то при сварке стали следует
производить ее предварительный подогрев,
температуру которого определяют по
соотношению
Тпод = 350√Сэкв – 0,25
23
24.

English Русский Правила
Свариваемость конструкционных сталей
Сопутствующая информация
1. ВВЕДЕНИЕ
1.1 Краткое описание процесса сварки
Сварка – это процесс соединения, в котором совместное производство может быть достигнуто с использованием высоких температур, высокого давления или того и другого одновременно. . В этой лекции обсуждается только использование высоких температур для изготовления соединения, поскольку это, безусловно, самый распространенный метод сварки конструкционных сталей. По сути, это процесс, при котором интенсивный источник тепла воздействует на соединяемые поверхности для достижения локального плавления. Обычно в расплавленную сварочную ванну добавляют дополнительный «присадочный металл», чтобы перекрыть зазор между поверхностями и получить требуемую форму и размеры сварного шва при охлаждении. В наиболее распространенных процессах сварки стальных конструкций используется электрическая дуга, поддерживаемая между стержнем присадочного металла и заготовкой, чтобы обеспечить интенсивный источник тепла.
Расплавленный металл в сварочной ванне без защиты может легко поглощать кислород и азот из атмосферы. Это поглощение может привести к пористости и хрупкости затвердевшего металла сварного шва. Методы, используемые для предотвращения поглощения газа в сварочной ванне, различаются в зависимости от процесса сварки. Ниже более подробно рассмотрены основные процессы сварки, применяемые для соединения конструкционных сталей.
1.2 Основные сварочные процессы
а. Ручная дуговая сварка металлическим электродом (MMA)
В этом процессе сварщик использует металлический стержневой электрод с плавким минеральным покрытием в держателе, подключенном к источнику электропитания. Между электродом и зоной сварки зажигается дуга, которая замыкает цепь возврата к источнику электроэнергии. Дуга плавит как электрод, так и область поверхности заготовки. Электромагнитные силы, создаваемые в дуге, помогают выбрасывать капли расплавленного электрода на расплавленную область заготовки, где два металла сплавляются, образуя сварочную ванну.
Покрытие электрода из флюса вносит свой вклад в содержание сварочной ванны за счет прямого добавления металла и металлургических реакций, которые очищают расплавленный металл. Флюс также создает локальную газообразную атмосферу, которая предотвращает поглощение атмосферных газов металлом сварного шва.
Существует множество типов электродов. Основные отличия между ними заключаются во флюсовом покрытии. Три основных класса электродов показаны ниже:
1. Рутил: электроды общего назначения для применений, не требующих строгого контроля механических свойств. Эти электроды содержат большое количество оксида титана в флюсовом покрытии.
2. Основной: Эти электроды обеспечивают сварку с большей прочностью и ударной вязкостью, чем рутиловые. Электроды имеют покрытие, содержащее карбонат кальция и другие карбонаты и плавиковый шпат.
3. Целлюлозный: Дуга, создаваемая этим типом электрода, имеет очень проникающую способность. Эти электроды имеют высокую долю горючих органических материалов в своем покрытии.
б. Дуговая сварка под флюсом (SAW)
В этом процессе используется электрод из неизолированной проволоки и флюс, добавляемый отдельно в виде гранул или порошка поверх дуги и сварочной ванны. Флюс защищает расплавленный металл, образуя слой шлака, а также стабилизирует дугу.
Этот процесс используется главным образом в механической системе подачи непрерывного отрезка проволоки из катушки, в то время как сварочный провод перемещается вдоль соединения. Машина SAW может подавать несколько проволок, одну за другой, так что может быть выполнен многопроходный сварной шов. Дуговая сварка под флюсом обеспечивает более прочные соединения, чем ручная сварка, но она не подходит для труднодоступных мест.
в. Сварка в среде защитного газа
В этом процессе используется электрод из неизолированной проволоки, а вокруг дуги и сварочной ванны подается защитный газ. Этот газ предотвращает загрязнение электрода и сварочной ванны воздухом. Существует три основных варианта этого процесса, как показано ниже:
1. Сварка MIG (металл в инертном газе) – для защиты используется аргон или гелий. Этот процесс обычно используется для цветных металлов.
2. Сварка MAG (металл-активный газ) – двуокись углерода (обычно смешанная с аргоном) используется для защиты. Этот процесс обычно используется для углеродистых и углеродисто-марганцевых сталей.
3. TIG (вольфрамовый инертный газ) – аргон или гелий используется для защиты и зажигания дуги между заготовкой и неплавящимся вольфрамовым электродом. Этот процесс обычно используется для тонколистовой обработки и точной сварки.
1.3 Проектирование и подготовка сварного соединения
Существует два основных типа сварных соединений, известных как стыковые и угловые швы [1]. Схематические изображения этих двух типов сварных швов показаны на рис. 1. Фактическая форма сварного шва определяется подготовкой соединяемой области. Тип подготовки под сварку зависит от процесса сварки и технологии изготовления. Примеры различных видов подготовки под сварку показаны на рис. 2. Сварной шов должен быть расположен и сформирован таким образом, чтобы он был легко доступен с точки зрения как процесса сварки, так и положения сварки. Детализированная форма сварного шва спроектирована таким образом, чтобы адекватно распределять имеющееся тепло и помогать контролировать проникновение металла сварного шва и, таким образом, создавать прочное соединение. Трудно избежать дефектов, вызванных оператором, таких как непровар и непровар, если подготовка и конструкция шва препятствуют хорошему доступу для сварки.
1.4 Влияние термического цикла сварки на микроструктуру
Интенсивное выделение тепла в процессе сварки влияет на микроструктуру как металла шва, так и основного металла вблизи границы плавления (граница между твердым и жидким металлом). Таким образом, цикл сварки влияет на механические свойства соединения.
Расплавленная сварочная ванна быстро охлаждается, так как соединяемые металлы действуют как эффективный теплоотвод. Это охлаждение приводит к тому, что металл шва имеет микроструктуру кокильного литья. При сварке конструкционных сталей присадочный металл обычно не имеет того же состава, что и основной металл. Если бы составы были одинаковыми, быстрое охлаждение могло бы привести к образованию твердых и хрупких фаз, т.е. мартенсита, в микроструктуре металла шва. Этой проблемы можно избежать, используя присадочные металлы с более низким содержанием углерода, чем основная сталь.
Основной металл вблизи расплавленной сварочной ванны быстро нагревается до температуры, которая зависит от расстояния до границы сплавления. Вблизи границы плавления достигаются пиковые температуры, близкие к точке плавления, в то время как материал, находящийся всего в нескольких миллиметрах от него, может достигать лишь нескольких сотен градусов по Цельсию. Исходный материал вблизи границы плавления нагревается в поле аустенитной фазы. При охлаждении эта область трансформируется в микроструктуру, отличную от остального исходного материала. В этой области скорость охлаждения обычно высока и, следовательно, существует тенденция к образованию структур низкотемпературного превращения, таких как бейнит и мартенсит, которые более твердые и более хрупкие, чем основная масса основного металла. Эта область известна как зона термического влияния (ЗТВ).
На микроструктуру ЗТВ влияют три фактора:
- Химический состав основного металла
- Скорость подведения тепла при сварке
- Скорость охлаждения в ЗТВ после сварки
Химический состав основного металла важен, поскольку он определяет прокаливаемость ЗТВ. Скорость подвода тепла имеет большое значение, поскольку она напрямую влияет на размер зерна в ЗТВ. Чем дольше время нахождения выше температуры укрупнения зерна основного металла при сварке, тем грубее структура в ЗТВ. Как правило, высокая скорость подвода тепла приводит к более длительному термическому циклу и, следовательно, к более грубой микроструктуре ЗТВ. Следует отметить, что скорость тепловложения также влияет на скорость охлаждения в ЗТВ. Как правило, чем выше скорость подвода тепла, тем ниже скорость охлаждения. Величина подводимого тепла зависит от параметров процесса сварки: напряжения дуги, тока дуги и скорости сварки. Помимо скорости подводимого тепла, на скорость охлаждения в ЗТВ влияют еще два фактора. Во-первых, важны конструкция и толщина шва, поскольку они определяют скорость отвода тепла от сварного шва во время охлаждения. Во-вторых, температура соединяемых деталей, т. е. любой предварительный нагрев, имеет большое значение, поскольку определяет температурный градиент, существующий между сварным швом и основным металлом.
1.5 Остаточные сварочные напряжения и деформация
Интенсивное тепло, связанное со сваркой, вызывает расширение зоны сварки. При охлаждении происходит сокращение. Окружающий холодный материал сопротивляется этому расширению и последующему сжатию, что приводит к возникновению поля остаточных напряжений вблизи сварного шва. В металле сварного шва остаточное напряжение носит преимущественно растягивающий характер. Это остаточное растягивающее напряжение уравновешивается сжимающим напряжением, возникающим в основном металле [2]. Схематическое изображение поля остаточных напряжений, полученное для продольной усадки сварного шва, показано на рис. 3. Растягивающие остаточные напряжения по величине достигают предела текучести в металле шва и ЗТВ. Важно отметить, что остаточные напряжения возникают из-за локальных пластических деформаций материала. Эта деформация может привести к растрескиванию металла шва и ЗТВ во время сварки, деформации соединяемых деталей или способствовать хрупкому разрушению в процессе эксплуатации.
Поперечные и продольные сжатия в результате сварки могут привести к деформации, если горячий металл шва несимметричен относительно нейтральной оси изготовления [2]. Типичный угловой поворот в одинарном V-образном стыковом шве показан на рис. 4а. Вращение происходит из-за того, что большая часть сварного шва находится на одной стороне нейтральной оси пластины, что вызывает большее сжимающее напряжение на этой стороне. Это приводит к искажению, известному как перекос при изготовлении пластины, как показано на рисунке 4b. Деформацию сварного шва можно контролировать путем предварительной настройки или предварительного изгиба узла соединения, чтобы компенсировать деформацию, или путем сдерживания сварного шва, чтобы противостоять деформации. Примеры обоих этих методов показаны на рис. 5. Проблем с деформацией легче всего избежать, используя правильную подготовку сварного шва. Использование несимметричных двусторонних сварных швов, таких как показанные на рис. 2e и 2i, компенсирует деформации. Деформация с меньшей стороны сварного шва (созданная первой) устраняется, когда больший шов накладывается на другую сторону. Этот метод известен как сбалансированная сварка.
Невозможно точно предсказать искажение геометрически сложной конструкции, но следует придерживаться одного основного правила. Это правило заключается в том, что сварку желательно начинать в центре изделия, а все последующие сварные швы выполнять от центра к краям, что способствует возникновению усадок в свободном состоянии.
Если искажение не контролируется, есть два метода его исправления: силовое и тепловое. Искажение световых сечений можно устранить простым применением силы, т.е. применение гидравлических домкратов и прессов. В случае более тяжелых секций требуется локальный нагрев и охлаждение, чтобы вызвать термические напряжения, противодействующие уже существующим.
1.6 Снятие остаточного напряжения
Наиболее распространенным и эффективным способом снятия остаточного напряжения является нагрев. Повышение температуры приводит к снижению предела текучести и способствует ползучести. Ползучесть снимает остаточные напряжения за счет пластической деформации. Стальные сварные детали обычно нагревают до слабого красного каления (600°C) во время обработки для снятия напряжений. Скорости нагрева и охлаждения во время этого снятия теплового напряжения должны тщательно контролироваться; в противном случае в сварном компоненте могут образоваться дополнительные образцы остаточных напряжений. Существует ограничение по размеру конструкций, с которых может быть снято термическое напряжение, как из-за размера необходимых печей, так и из-за возможности деформации конструкции под собственным весом. Однако возможна термическая обработка отдельных стыков в большой конструкции путем размещения вокруг стыков небольших печей или использования электрических нагревательных элементов.
Другие методы снятия напряжения основаны на тепловом расширении, создающем механические силы, способные противодействовать первоначальным остаточным напряжениям. Этот метод можно применять на месте, но очень важно точно знать расположение остаточных сжимающих напряжений; в противном случае уровень остаточного напряжения может увеличиться, а не уменьшиться. Чисто механическое снятие напряжения также может быть применено при условии, что оно достаточно для компенсации необходимой пластической деформации.
Читать Подробнее
Сварка металлургии и свариваемость нержавеющих сталей
ПРЕДИСЛОВИЕ XV
1 ВВЕДЕНИЕ 1
1.1 Определение из нержавеющей стали 2
1.2 4
1.4 Коррозионная стойкость 5
1.5 Производство нержавеющей стали 6
Ссылки 7
2 ФАЗОВЫЕ ДИАГРАММЫ 8
2.1 Система железо-хром 9
2,2 Система железа — хромий -углерод 10
2,3 Система железа -хромий -никель 12
2,4 фазовые диаграммы для конкретных систем сплава 15
Список литературы 18
,11 3 Элементы и диаграммы конституции 19994,1,111.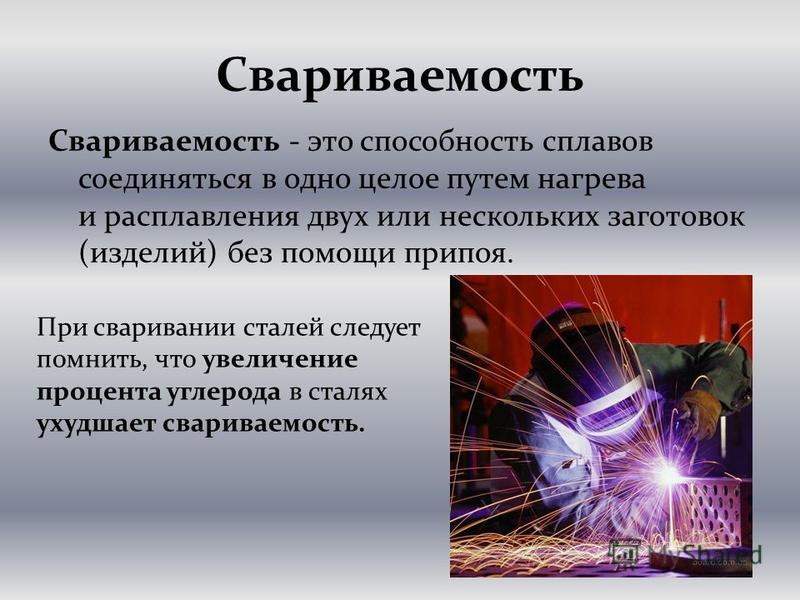
3,1,1 Хром 20
3,1,2 Никель 20
3,1,3 Марганец 21
3,1,4 Кремний 21
3,1,5 Молибден 22
3,1,6 Элементы корневистового формы 22 9.5 22
3,1,6.0009
3,1,7 Элементы с осадками 23
3,1,8 Интерстициальные элементы: углерод и азот 23
3,1,9 Другие элементы 24
3,2 Ферритные профроты по сравнению с Austenite-Promoting Elements 24
3,3 Конституционные диаграммы 25
8 3.3.1 Системы аустенитно-ферритных сплавов: первые диаграммы и отношения эквивалентности 25
3.3.2 Диаграмма Шеффлера 29
3.3.3 Диаграмма Делонга 33
88 и WRC-1992 Диаграммы 40
3,4 Austenitic-Martensitic Systems 43
3,5 Ферритные-мартенситные сплавные системы 46
3,6 Прогнозирование фермерского феррита. Сплавы и расходные материалы 57
4.2 Физико-механическая металлургия 59
4.3 Сварочная металлургия 63
4.3.1 Зона плавления 63
4. 3.2 Зона термического влияния 67
4.3.3 Фазовые преобразования 70
4.3.4 Посточевая тепловая обработка 71
4.3.5 Предварительное разогрев, интернет и руководящие принципы термообработки по постолдке 74
4.4 Механические свойства сварных плат 77
4.5. 77
4.5.11. Затвердевание и ликвационное растрескивание 78
4.5.2 Растрескивание при повторном нагреве 78
4.5.3 Растрескивание, индуцированное водородом 79
4.6 Супермартенситные нержавеющие стали 80
4.7 Практический пример: расчет температуры МС мартенситных сталей
Список литературы 86
5 Ферритные нержавеющие стали 87
5.1 Стандартные сплавы и расходные материалы 88
5,2 Физическая и механическая металлургия 92
5.2.1. Эффект добавления сплаты на микроструктуру 95 9000
5.2.2.
5.2.3 Явление охрупчивания 96
5.2.3.1 Охрупчивание при 475°C 97
5.2.3.2 Сигма- и Хи-фазное охрупчивание 97
5. 2.3.3 Высокотемпературное охрупчивание 98
5.2.3.4 Чувствительность Notch 103
5.2.4 Механические свойства 104
5.3 Сварная металлургия 104
5.3.1 Зона слияния 104
5.3.1
5.3.1.3 Прогнозирование микроструктуры 111
5.3.2 Зона термического влияния 112
5.3.3 Сварные швы в твердом состоянии 113
5.4 Механические свойства сварных соединений 1140009
5.4.2 Средние сплавы среднего хромиума 116
5.4.3 Сплавы с высоким хромием 119
5.5 Сварная сварная установка 123
5.5.1 Перевертка сварки. -Индуцированное растрескивание 126
5.6 Коррозионная стойкость 126
5.7 Тепловая обработка после Вудда 130
5.8 Выбор металла наполнителя 132
5.9 ТЕЗИЧЕСКИ ЗТВ Тип 430 135
Список литературы 137
6 Аустенитные нержавеющие стали 141
6.1 Стандартные сплавы и расходные материалы 143
6.2 Физическая и механическая металлургия 147
6.2.1. Эволюция микроструктуры 153
6.3.1.1 Тип A: Полностью аустенитный затвердевающий 154
6.3.1.2 Тип AF Затвердевший 155
6.3.1.3 Тип FA Затвердевший 155
6.3.1.4 Тип F Затвердевание 158
6.3.2 Интерфейсы в однофазной Austenitic Weld Metal 162
6.3.2.1 Границы затвердевания. 162
6.3.2
6.3.3 Зона, затронутая тепло, 164
6.3.3.1 Рост зерна 165
6.3.3.2.
6.3.4 Предварительная и межпроходная температура и термообработка после Келд 166
6.3.4.1. Промежуточная температурная охррение 167
6.4 Механические свойства сварных сварных средств 168
6.5 Сварка 173
6.5.1 Разрешивание сварки. Положительные эффекты первичного затвердевания феррита 175
6.5.1.2 Использование прогнозных диаграмм 177
6.5.1.3 Влияние примесных элементов 179
6.5.1.4 Измерение феррита 181
6.5.1.5 Влияние быстрого затвердевания 182
6.5.1.6 Морфология перелома затвердевания.
6.5.4 Растрескивание погружением в пластичность 194
6.5.5 Растрескивание при повторном нагреве 196
6.5.6 Растрескивание при загрязнении медью 199
6.5.7 Растрескивание при загрязнении цинком 200
80009
6.6 Коррозионная стойкость 200
6.6.1 Межгранулярная коррозия 201
6.6.1.1 Предотвращение сенсибилизации 204
6.6.1.2 Атака ножниц 205
6.6.1.3.
6.6.3 Точечная и щелевая коррозия 208
6.6.4 Микробиологическая коррозия 208
6.6.5 Селективная атака феррита 209
6.7 Специальные сплавы 211
Все термостойкие0009
6.7.2 Сплавы с высоким содержанием азота 214
6.8 Практический пример: выбор подходящего присадочного металла 220
6.9 Практический пример: что не так с моим плавательным бассейном? 223
6.10 ТЕХКОЕ ИССЛЕДОВАНИЕ: Требование в зоне затронутой тепла 224
Ссылки 225
7 Дуплексные нержавеющие стали 230
7.1 Стандартные сплавы и расходные материалы 231
7. 2 Физическая металлургия 234
7. Баланс фаз 234
7.2.2 Реакции осаждения 237
7.3 Механические свойства 237
7.4 Сварная металлургия 238
7.4.1 Поведение затвердевания 238
7.4.2 Роль азота 240
7.4.3 Вторичный Austenite 244
7.4.4 Контроль баланса феррита -аустенита 250
7.5.1. Вход тепла 251
7.5.2 Эффекты скорости охлаждения 251
7.5.3 Прогнозирование и измерение ферритов 253
7.6.0009
7.6.2, вызванное водородом растрескивание 254
7.6.3. Промежуточная температурная обтекания 255
7.6.3.1 Альфа-острая охлаждения 256
7,6.3.2 Фаза SIGMA. Стойкость 261
7.8.1 Коррозионное растрескивание под напряжением 261
7.8.2 Точечная коррозия 261
Каталожные номера 262
0008 8.1 Стандартные сплавы и расходные материалы 265
8.2 Физическая и механическая металлургия 267
8.2.1. Нержавеющая сталь 276
8.3 Металлургия сварки 277
8. 3.1 Эволюция микроструктуры 278
8.3.2 Термическая обработка после сварки 278
8.4 Механические свойства сварных изделий 279
8.5 Свартоваемость 280
8.6 Коррозионная стойкость 285
Список литературы 285
9 Дизное сварка из нержавеющих сталей 287
9,1 Применение сварки диссимиляра 287
9.2. 9.2.1 Определение состава металла шва 288
9.2.2 Область перехода границы плавления 291
9.2.3 Характер границ типа II 294
9.3 Свариваемость 296
9.3.1 Затвердевание трещины 296
9.3.2 Осну «Отсутствие 298
9.3.3 РАСПОЛОЖДЕНИЕ КРУГКА В ЗАКАХ Углеродной или низкопластной стали 299
9.4 Другие комбинации диссимила 301
9.4 Ожидается, что расплавленная зона будет содержать некоторое количество феррита или затвердеет в виде первичного феррита
301
9.4.2 Номинально аустенитные сплавы, расплавленная зона которых, как ожидается, будет содержать некоторое количество феррита, полностью сваренные с аустенитной нержавеющей сталью
301
9. 4.3 Аустенитная нержавеющая сталь, соединенная с дуплексной нержавеющей сталью 302
9.4.4 Аустенитная нержавеющая сталь, соединенная с ферритной нержавеющей сталью 302
9.4.5 Аустенитная нержавеющая сталь, соединенная с мартенситной нержавеющей сталью 302
9.4.6 Мартенситная нержавеющая сталь Соединение с ферритной нержавеющей сталью 302
9.4.7 Присадочный металл из нержавеющей стали для трудносвариваемых сталей 303
9.4.8 Сплавы на основе меди, соединенные с нержавеющими сталями 305
9.4.9 сплавов с никелевой базой соединены со нержавеющими сталями 306
Список литературы 307
10 Тестирование свартоваемости 309
10.1 ВВЕДЕНИЕ 309
10.1.1. Испытание 311
10.2.1 Методика количественной оценки растрескивания при затвердевании сварного шва 312
10.2.2 Методика количественной оценки ликвационного растрескивания ЗТВ 316
10.3 Испытание на горячую пластичность 319
10.4 Тест изгиба Fissure Bend 323
10. 5 Тест на деформацию в обработке 328
10.6 Другие тесты сварки 329
Список литературы 329
Appendix 1 Номинальные композиции из Stainless Steels 331
Appendix 2 Etching Techniques For Stainless Welds 3433 349
Приложение 2.
АВТОРСКИЙ УКАЗАТЕЛЬ 347
ТЕМАТИЧЕСКИЙ УКАЗАТЕЛЬ 353