Ультразвуковой контроль сварных соединений (швов)
Сварные швы независимо от времени их создания и особенностей конструкций должны систематически подлежать контролю, который должен осуществлять специалист. Для ревизии разработаны разные методы, но самый прогрессивный и популярный из них – ультразвуковой контроль сварных соединений. По результативности он лучше, чем, например, рентгеноскопия или магнитная дефектоскопия.
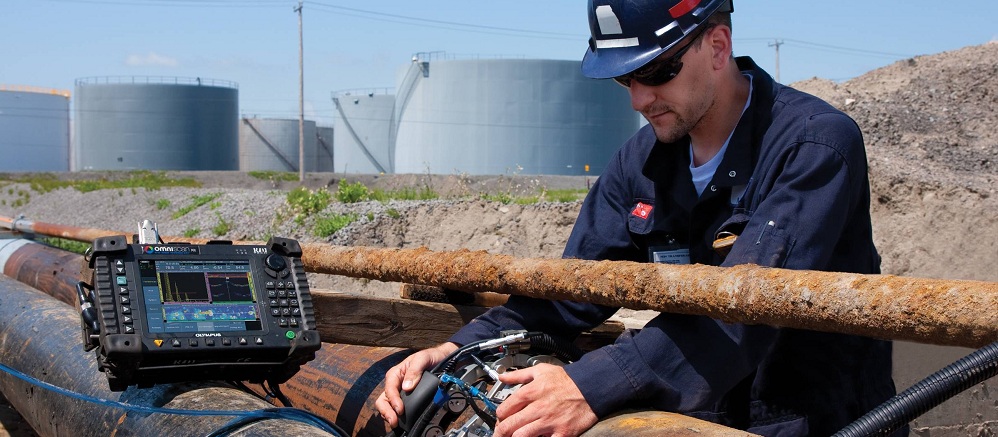
Стоит заметить, что такой способ контроля сварных соединений не новинка. Его впервые начали использовать эксперты в 30-х годах прошлого века. С помощью излучаемого аппаратурой ультразвука можно выявить практически любые отклонения от нормы и дефекты внутри швов. Как показывает практика, особенно важно выявлять дефекты внутри различных сварных соединений изделий. Чаще всего именно они становятся причиной деструктивных процессов в конструкции.
Выгодная услуга от группы компаний «МЦК»
Если вам необходимо провести контроль качества сварных швов, группа компаний «МЦК» готова предложить свои услуги по доступной стоимости. Мы начали свою деятельность в 1997 году, и за весь период работы заслужили безупречную репутацию и положительные отзывы довольных клиентов. Наш штат состоит из опытных специалистов своей сфере.
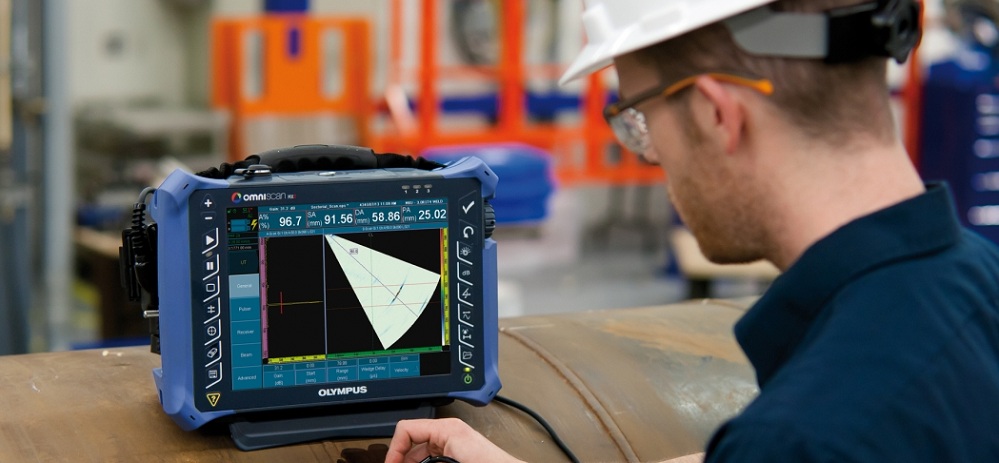
Для проведения манипуляций мы используем действенные технологии и оборудование. В завершение нашей работы каждый заказчик получает отчет или же протокол с объективной и детальной информацией о проделанных манипуляциях. Такие документы являются официальными. Они имеют силу в суде, например, для решения спорных ситуаций между заказчиком и исполнителем (изготовителем конструкции со сварными швами).
Особенности технологии
Ультразвуковые волны практически не воспринимают человеческие уши. Тем не менее, исследования с помощью таких волн являются эффективными. Поэтому их используют для разных видов диагностики. Метод относится к неразрушающим способам контроля для выявления отклонений от установленных норм.
Заказать ультразвуковой контроль сварных соединений
Стоит заметить, такой способ ревизии хоть и эффективный, но он во многом зависит от некоторых факторов: калибровка оборудования, чувствительность приборов, опыт человека, который ими орудует.
Что представляет собой процедура?
Ультразвуковой контроль сварных соединений представляет собой ревизию швов разных типов конструкций с помощью специального ультразвукового оборудования. Таким способом можно выявить даже мельчайшие дефекты как механического, так и химического характера. УЗК даст возможность найти пустоты с воздухом, шлаковые вкрапления и неоднородности в материале (металле). Также с помощью исследования можно определить наличие неметаллических элементов.
Важно!
Ревизия швов (ГОСТ 14782-86) уполномоченной организацией важна для получения разрешительной документации для введения конструкции в эксплуатацию.
Принцип процедуры
Манипуляция заключается в проникновении ультразвуковых излучений в металл и отражении их от пустот, неровностей и других дефектов.
Прибор излучает высокочастотную волну на исследуемую зону. Излучение проникает внутрь материала, и если под поверхностью находится скрытый дефект, то направление дальнейшего распространения волны изменяется. Датчик прибора фиксирует это и сообщает о возникшей проблеме специалисту.
Специалист, проводящий ультразвуковой контроль сварных соединений, видит изменения распространения волн и может дать отклонениям от нормы характеристики:
- параметры дефекта;
- технические особенности;
- расстояние до найденной проблемной зоны.
Методы ультразвукового исследования
Теневой
Такой способ базируется на определении уменьшения амплитуды колебаний отраженного и внедренного импульсов. Теневая диагностика считается эффективной и популярной. В ней задействуется сразу несколько преобразователей – излучатель и, соответственно, приемник. Их нужно устанавливать по разные стороны объекта и только перпендикулярно по отношению к исследуемой области.
Если в идущем потоке ультразвуковых волн появляется глухая точка, это свидетельствует о том, что на пути излучателя есть дефекты.
Эхо-импульсный
Согласно стандартам, для проведения исследования используется один ультразвуковой дефектоскоп. Он издает высокочастотные волны, и он же их принимает. Технология подразумевает отражение волн от зон с наличием дефектов. Если ультразвук прошел и не отразился на оборудовании, значит, в исследуемом предмете дефектов нет. Отражение свидетельствует о наличии проблем в швах.
Эхо-зеркальный
Такой способ ревизии считается разновидностью вышеуказанной процедуры. Основное отличие в том, что для эхо-зеркального исследования эксперты задействуют два аппарата, один из них приемник, а другой – излучатель. Оборудование устанавливается по одну сторону предмета со швами. Излучатель выделяет волны под углом, при попадании на зоны с дефектами они отражаются, далее информация поступает на приемник. Это наиболее эффективный метод ультразвукового контроля сварных швов для выявления трещин.
Зеркально-теневой
Исследование сочетает в себе особенности зеркального и теневого изучения материалов. Приборы располагаются по одной стороне объекта исследования. Излучатель издает волны косого типа, которые отражаются от стенок конструкции и принимаются прибором для приема ультразвука. Если изъянов нет, волны проходят без каких-либо изменений. Появление глухой зоны говори о наличии проблем.
Дельта
Метод контроля заключается в переизлучении изъяном волн вглубь шва. Ультразвуковые колебания разделяются переизлучаемые и зеркальные. Прибор для приема может ловить не все колебания. Как правило, он хорошо улавливает излучение, которое движется прямо на него.
Дельта-контроль не считается самым эффективным. Многое зависит от настроек прибора, к тому же в показаниях могут быть незначительные погрешности. Тем не менее, эксперты его практикуют, так как отклонения в большинстве случаев допустимые.
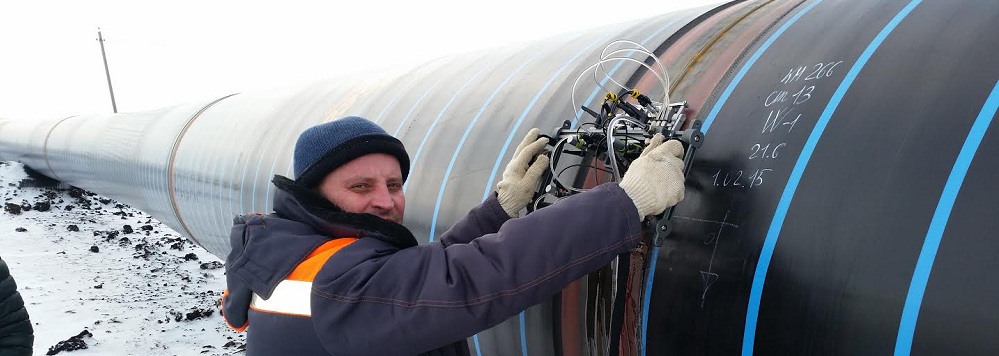
Для проверки на качество таким способом должны быть соблюдены строгие правила в плане чистоты швов.
Оптимальный вариант неразрушающей ревизии определит специалист после ознакомления с перечнем задач. Контроль в нашей компании осуществляется разными способами, но независимо от выбранного варианта специалисты используют корректно настроенное оборудование, которое позволяет получить достоверные результаты.
Пример реализации теневого метода на практике согласно установленным стандартам (ГОСТ)
Прежде всего, сварные швы зачищаются от пыли и загрязнений. Также очищаются места возле них. Следует очистить не менее 50 сантиметров рабочей поверхности с каждой стороны.
Для оптимизации процесса специалисты нередко наносят на рабочую зону специальную смазку. Для примера, в медицине во время УЗИ врачи также используют гель. Для работы с металлами в качестве смазки можно использовать техническое масло, глицерин или же обычный солидол.
Заказать ультразвуковой контроль сварных соединений
Включаются приборы и проводятся подготовительные настройки. Устанавливается излучатель и приемник перпендикулярно изделию. Приборы базируются с разных сторон конструкции.
Приемником совершаются зигзагообразные передвижения вдоль шва. Допустимо и даже желательно его немного поворачивать туда и обратно (примерно на 13⁰). Глухая точка является признаком дефекта. На приборе о его наличии говорит максимальная амплитуда. Как правило, исследование осуществляется за несколько проходов.
Полученная в ходе ультразвукового контроля информация записывается сперва в журнал, а после этого она фигурирует в отчете, который получает заказчик услуги.
Важный нюанс:
Как правило, приборы рассчитаны на диагностику гладких поверхностей. Есть случаи, когда снаружи шов неровный, но внутри изъянов нет. Однако прибор сигнализирует о проблеме. Поэтому важно убедиться, что в появлении негативного показателя не сыграло роль именно наружное состояние шва.
Особенности оценивания полученных данных
Во многом провести объективную оценку позволяет уровень чувствительности оборудования. Если аппарат корректно настроен, можно выявить все важные параметры найденной проблемы.
Профессионально проведенный ультразвуковой контроль сварного соединения позволяет узнать численность дефектов, даже если они расположены совсем близко один к другому.
В определении количества изъянов и их оценке помогают такие факторы:
- протяжность сигнала;
- амплитуда ультразвуковой волны.
Протяжность выявляется с помощью передвижения излучателя по направлению вдоль сварного стыка. Геометрическая форма изъянов определяется с помощью формы сигнала, который был показан на экране узкоспециализированного оборудования.
Несмотря на прогрессивность и точность приборов, важно, чтобы их показания правильно интерпретировал оператор, который заносит показания в технический журнал.
Ключевые преимущества контроля швов с помощью ультразвука
Исследование обладает такими преимуществами:
- Процесс протекает довольно быстро.
- Возможность выбрать оптимально подходящий способ.
- Высокие показатели точности диагностики.
- Доступная цена по сравнению с другими исследованиями.
- Безопасность для здоровья людей, так как нет вредных излучений.
- Оборудование переносное, поэтому проводить диагностику удобно как с выездом оператора, так и в офисе компании.
- Деталь, подлежащая контролю, не портится. Все ее свойства сохраняются.
- Можно без остановки прибора обследовать разные части деталей.
- Оборудование работает с разными типами металлов.
Недостатки процедуры
Наряду с многочисленными достоинствами недостатки у описываемого метода тоже имеются. Расскажем о них подробней.
Заказать ультразвуковой контроль сварных соединений
Не во всех случаях можно выявить формы изъянов, даже при корректно настроенных приборах. Так может быть из-за разной плотности материалов, например металла и шлака. Поэтому отражение будет также разное.
Не всегда можно узнать особенности дефектов в сложных конструкциях из-за того, что ультразвук может отразиться на другой зоне детали. Исследование может усложниться, если у детали зернистая фактура, так как потолки лучей будут рассеиваться.
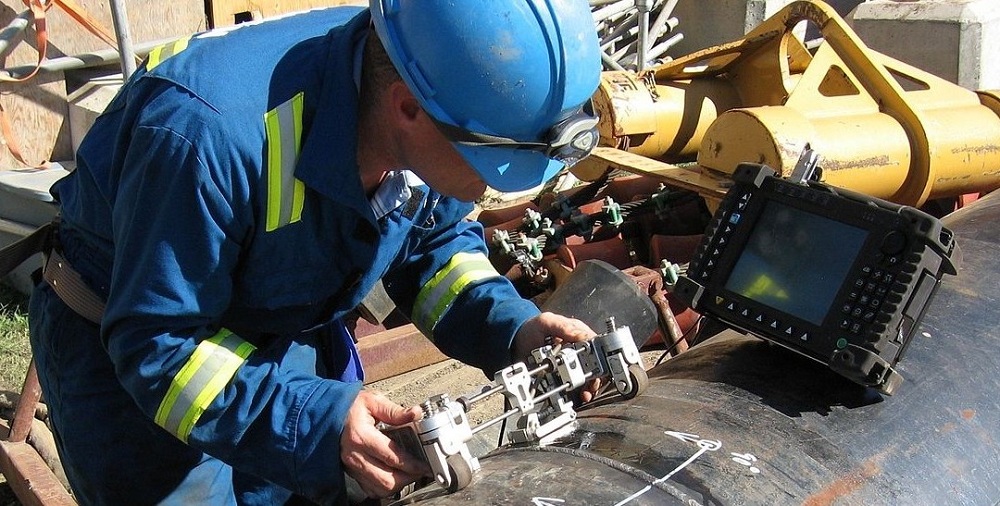
Загрязнения поверхности могут негативно отразиться на корректности получаемых сведений. Поэтому важно делать тщательную зачистку рабочей зоны.
Ультразвуковой контроль сварных соединений – гарантия того, что изделие сделано качественно и может исправно функционировать. Также это один из важных шагов к разрешению введения изделия в эксплуатацию.
Чтобы процедура была сделана качественно, доверяйте ее проведение опытным специалистам. Группа компаний «МЦК» предлагает свою услугу по доступной цене. Мы гарантируем профессиональный подход, своевременное выполнение задач и достоверную информацию. Также мы всегда готовы вас проконсультировать по всем техническим вопросам.
Обращайтесь к нам, и мы вас не подведем!
!Подробная информация, уточнение цен и приём заказов по телефону:
Контроль сварных швов | ||||
1 | Ультразвуковой контроль сварных соединений толщиной 0 — 10 мм (1 п.м.) | — Подготовка и настройка оборудования — Проведение контроля — Обработка результатов — Ведение журналов — Оформление протоколов |
ГОСТ Р 55724-2013 СП 70.13330.2012 |
1 000 |
2 | Ультразвуковой контроль сварных соединений толщиной 10 — 20 мм (1 п.м.) | — Подготовка и настройка оборудования — Проведение контроля — Обработка результатов — Ведение журналов — Оформление протоколов |
ГОСТ Р 55724-2013 СП 70.13330.2012 |
1 200 |
3 | Ультразвуковой контроль сварных соединений толщиной 20 — 30 мм (1 п.м.) | — Подготовка и настройка оборудования — Проведение контроля — Обработка результатов — Ведение журналов — Оформление протоколов |
ГОСТ Р 55724-2013 СП 70.13330.2012 |
1 500 |
4 | Ультразвуковой контроль сварных соединений толщиной 30 — 40 мм (1 п.м.) | — Подготовка и настройка оборудования — Проведение контроля — Обработка результатов — Ведение журналов — Оформление протоколов |
ГОСТ Р 55724-2013 СП 70.13330.2012 |
2 000 |
5 | Ультразвуковой и визуальный контроль качества (дефектоскопия) сварных соединений арматуры (1 стык) | — Подготовка и настройка оборудования — Проведение контроля — Обработка результатов — Оформление протоколов |
РД 03-606-03 ГОСТ 23858-79 ГОСТ Р 55724-2013 |
700 |
6 | Ультразвуковая дефектоскопия одним преобразователем сварных соединений перлитного класса с двух сторон, прозвучивание поперечное. Трубопроводов диаметром до 36 мм, толщина стенки до 6 мм. (1 стык) | — Подготовка и настройка оборудования — Проведение контроля — Обработка результатов — Ведение журналов — Оформление протоколов |
ГОСТ Р 55724-2013 РД 153-34.1-003-01 |
590 |
7 | Ультразвуковая дефектоскопия одним преобразователем сварных соединений перлитного класса с двух сторон, прозвучивание поперечное. Трубопроводов диаметром до 57 мм, толщина стенки до 6 мм. (1 стык) | — Подготовка и настройка оборудования — Проведение контроля — Обработка результатов — Ведение журналов — Оформление протоколов |
ГОСТ Р 55724-2013 РД 153-34.1-003-01 |
630 |
8 | Ультразвуковая дефектоскопия одним преобразователем сварных соединений перлитного класса с двух сторон, прозвучивание поперечное. Трубопроводов диаметром до 76 мм, толщина стенки до 6 мм. (1 стык) | — Подготовка и настройка оборудования — Проведение контроля — Обработка результатов — Ведение журналов — Оформление протоколов |
ГОСТ Р 55724-2013 РД 153-34.1-003-01 |
680 |
9 | Ультразвуковая дефектоскопия одним преобразователем сварных соединений перлитного класса с двух сторон, прозвучивание поперечное. Трубопроводов диаметром до 89 мм, толщина стенки до 6 мм. (1 стык) | — Подготовка и настройка оборудования — Проведение контроля — Обработка результатов — Ведение журналов — Оформление протоколов |
ГОСТ Р 55724-2013 РД 153-34.1-003-01 |
720 |
10 | Ультразвуковая дефектоскопия одним преобразователем сварных соединений перлитного класса с двух сторон, прозвучивание поперечное. Трубопроводов диаметром до 108 мм, толщина стенки до 8 мм. (1 стык) | — Подготовка и настройка оборудования — Проведение контроля — Обработка результатов — Ведение журналов — Оформление протоколов |
ГОСТ Р 55724-2013 РД 153-34.1-003-01 |
690 |
11 | Ультразвуковая дефектоскопия одним преобразователем сварных соединений перлитного класса с двух сторон, прозвучивание поперечное. Трубопроводов диаметром до 114 мм, толщина стенки до 8 мм. (1 стык) | — Подготовка и настройка оборудования — Проведение контроля — Обработка результатов — Ведение журналов — Оформление протоколов |
ГОСТ Р 55724-2013 РД 153-34.1-003-01 |
790 |
12 | Ультразвуковая дефектоскопия одним преобразователем сварных соединений перлитного класса с двух сторон, прозвучивание поперечное. Трубопроводов диаметром до 159 мм, толщина стенки до 8 мм. (1 стык) | — Подготовка и настройка оборудования — Проведение контроля — Обработка результатов — Ведение журналов — Оформление протоколов |
ГОСТ Р 55724-2013 РД 153-34.1-003-01 |
960 |
13 | Ультразвуковая дефектоскопия одним преобразователем сварных соединений перлитного класса с двух сторон, прозвучивание поперечное. Трубопроводов диаметром до 219 мм, толщина стенки до 8 мм. (1 стык) | — Подготовка и настройка оборудования — Проведение контроля — Обработка результатов — Ведение журналов — Оформление протоколов |
ГОСТ Р 55724-2013 РД 153-34.1-003-01 |
1 160 |
14 | Ультразвуковая дефектоскопия одним преобразователем сварных соединений перлитного класса с двух сторон, прозвучивание поперечное. Трубопроводов диаметром до 273 мм, толщина стенки до 8 мм. (1 стык) | — Подготовка и настройка оборудования — Проведение контроля — Обработка результатов — Ведение журналов — Оформление протоколов |
ГОСТ Р 55724-2013 РД 153-34.1-003-01 |
1 280 |
15 | Ультразвуковая дефектоскопия одним преобразователем сварных соединений перлитного класса с двух сторон, прозвучивание поперечное. Трубопроводов диаметром до 325 мм, толщина стенки до 8 мм. (1 стык) | — Подготовка и настройка оборудования — Проведение контроля — Обработка результатов — Ведение журналов — Оформление протоколов |
ГОСТ Р 55724-2013 РД 153-34.1-003-01 |
1 480 |
16 | Ультразвуковая дефектоскопия одним преобразователем сварных соединений перлитного класса с двух сторон, прозвучивание поперечное. Трубопроводов диаметром до 377 мм, толщина стенки до 8 мм. (1 стык) | — Подготовка и настройка оборудования — Проведение контроля — Обработка результатов — Ведение журналов — Оформление протоколов |
ГОСТ Р 55724-2013 РД 153-34.1-003-01 |
1 920 |
17 | Ультразвуковая дефектоскопия одним преобразователем сварных соединений перлитного класса с двух сторон, прозвучивание поперечное. Трубопроводов диаметром до 426 мм, толщина стенки до 10 мм. (1 стык) | — Подготовка и настройка оборудования — Проведение контроля — Обработка результатов — Ведение журналов — Оформление протоколов |
ГОСТ Р 55724-2013 РД 153-34.1-003-01 |
2 240 |
18 | Ультразвуковая дефектоскопия одним преобразователем сварных соединений перлитного класса с двух сторон, прозвучивание поперечное. Трубопроводов диаметром до 530 мм, толщина стенки до 10 мм. (1 стык) | — Подготовка и настройка оборудования — Проведение контроля — Обработка результатов — Ведение журналов — Оформление протоколов |
ГОСТ Р 55724-2013 РД 153-34.1-003-01 |
2 560 |
19 | Ультразвуковая дефектоскопия одним преобразователем сварных соединений перлитного класса с двух сторон, прозвучивание поперечное. Трубопроводов диаметром до 720 мм, толщина стенки до 8 мм. (1 стык) | — Подготовка и настройка оборудования — Проведение контроля — Обработка результатов — Ведение журналов — Оформление протоколов |
ГОСТ Р 55724-2013 РД 153-34.1-003-01 |
2 760 |
20 | Ультразвуковая дефектоскопия одним преобразователем сварных соединений перлитного класса с двух сторон, прозвучивание поперечное. Трубопроводов диаметром до 820 мм, толщина стенки до 14 мм. (1 стык) | — Подготовка и настройка оборудования — Проведение контроля — Обработка результатов — Ведение журналов — Оформление протоколов |
ГОСТ Р 55724-2013 РД 153-34.1-003-01 |
2 920 |
21 | Ультразвуковая дефектоскопия одним преобразователем сварных соединений перлитного класса с двух сторон, прозвучивание поперечное. Трубопроводов диаметром до 1020 мм, толщина стенки до 14 мм. (1 стык) | — Подготовка и настройка оборудования — Проведение контроля — Обработка результатов — Ведение журналов — Оформление протоколов |
ГОСТ Р 55724-2013 РД 153-34.1-003-01 |
3 200 |
22 | Ультразвуковая дефектоскопия одним преобразователем сварных соединений перлитного класса с двух сторон, прозвучивание поперечное. Трубопроводов диаметром до 1220 мм, толщина стенки до 14 мм. (1 стык) | — Подготовка и настройка оборудования — Проведение контроля — Обработка результатов — Ведение журналов — Оформление протоколов |
ГОСТ Р 55724-2013 РД 153-34.1-003-01 |
3 760 |
Ультразвуковая дефектоскопия УЗК сварных швов и соединений
Во время сваривания металлических деталей подбирается правильный режим, специальные расходные материалы, добавочные предметы, улучшающие свойства сваривания, а также сама технология. Но это все равно полностью не защищает от возможного появления брака. Если появился заметный дефект, то это еще не так страшно, потому как часто встречаются скрытые поры, трещины, раковины и прочее. Чтобы их обнаружить, требуются особые методы, одним из которых является ультразвуковая дефектоскопия сварных швов. Как понятно из названия, здесь используются ультразвуковые волны, а точнее, их принцип отражения от границ поверхностей с различным уровнем плотности.

Ультразвуковая дефектоскопия сварных швов
Такой метод является очень распространенным и набрал большие обороты популярности. Сейчас встречаются такие приборы, которые могут проводить анализ не только в качестве стационарной установки, но и как мобильные устройства. Это позволяет проводить контроль практически в любом удобном месте. Но для проведения анализа необходимо иметь определенные знания, так далеко не каждый человек сможет правильно расшифровать полученные сигналы. Ультразвуковой контроль сварных швов проходит по ГОСТ 14782-86.

Контроль сварных швов
Преимущества 
- Это очень распространенный и недорогой способ неразрушающего контроля сварных швов;
- Скорость проведения является достаточно высокой и результатов не придется долго ждать;
- Безопасность для здоровья человека;
- Исследуемую деталь не нужно отделять от всей конструкции;
- Есть много вариантов приборов для проведения процедуры;
- Можно подвергать анализу достаточно широкие области изделия;
- Помогает точно определить место, где находится тот или иной дефект, а также его характер.
Недостатки 
- Для использования прибора необходим специалист, который сможет правильно расшифровать полученные данные;
- Затруднительно проводить анализ при большой толщине детали;
- Нет высокого уровня точности, которые дают некоторые другие разновидности контроля.
Теория акустической технологии 
Проверка сварных швов ультразвуком основана на свойствах ультразвука. Стоит сразу отметить, что человеческое ухо не ловит такие волны. Для его распространения, а также последующего считывания требуется специальный ультразвуковой дефектоскоп для контроля сварных соединений. Благодаря тому, что звук не слышно, он стал использоваться в самых различных методах, а не только в сфере сварки. Практически ни в какой из областей ультразвуковые волны не наносят вреда исследуемому объекту во время контроля. Он помогает локализовать дефекты, даже если речь идет об относительно небольших участках, но все это зависит от размеров и особенностей самого прибора.

Ультразвуковой дефектоскоп
Чтобы определить, насколько качественно пройдет УЗК сварных швов, требуется учитывать такие факторы как чувствительность приборов, калибровка и правильность настройки, опыта оператора и прочего. В данной области УЗК помогает определиться, подходит ли то или иное изделие по допускам, которые выдвигаются к швам в конкретном случае, так как иногда небольшие дефекты все же допускаются.
Особенности проведения данной процедуры 
Проверка сварных швов ультразвуком хоть и обладает универсальностью применения, в ней все же есть определенные ограничения. При правильном применении и качественной настройке техника даст полное представление об имеющемся дефекте. Но здесь встречаются следующие рамки:
Выявляемые дефекты:
- Поры;
- Области, где имеется искаженный геометрический размер;
- Непроваренные участки шва;
- Участки с инородным химическим составом;
- Трещины в зоне около шва;
- Расслоение наплавленного металла;
- Зоны, в которых имеется ржавчина;
- Наслоение шва и несплошности;
- Провисание частей металла снизу шва;
- Свищи.
Подробные данные ультразвуковое исследование сварных швов может обеспечить в следующих разновидностях металлов:
- Медь и ее сплавы;
- Легированная сталь;
- Чугун;
- Аустенитная сталь;
- Металл с плохими свойствами проведения ультразвука.
Геометрические рамки проведения процесса:
- Максимальная толщина металла, с которой ведется работа – 500-800 мм;
- Минимальная толщина металла, с которой ведется работа 8-10мм;
- Максимальная глубина, на которой может находиться шов для распознания его нюансов – 10 метров;
- Минимальная глубина, на которой может находиться шов для распознания его нюансов – 3 мм.
Стоит отметить, что все данные зависят от марки прибора и могут иметь некоторые отличия.
К проверке пригодны следующие виды сварных соединений и швов:
- Сваренные трубы;
- Тавровые соединения;
- Стыковые соединения;
- Кольцевые швы;
- Продольные;
- Плоские швы.
Устройство дефектоскопа 
В качестве одного из компонентов здесь имеется генератор электроимпульсов. Он создает сигналы, которые потом подаются на преобразователь. Во время анализ обращен к образцу, чтобы звуковой испульс попал именно на него. Когда волна будет возвращаться от столкновения с поверхностью, то она попадает на преобразователь, который передает сигнал на усилитель. Затем его принимает электронно-лучевая трубка, соединенная с генератором развертки.

Дефектоскоп для ультразвуковой проверки сварных швов
Принцип работы 
Проверка сварочных швов ультразвуком основана на том, что звуковые волны отражаются от плотных поверхностей при столкновении с ними. Когда волна проходит сквозь шов в котором есть трещины, то на переходе между границей металла и воздуха будет еще одно отражение волны звука. Оно придет раньше, чем отражение от перехода на нижней грани. Преобразователь сможет уловить не только разницу во времени, но и локализовать место нахождения дефекта. Усилитель, который передает сигнал на трубку, помогает построить график, по которому специалист сможет определить все особенности проверяемого шва.
Методика
УЗК контроль сварных соединений проводится по следующему методу:
- Сначала подготавливается металл, с которого убирается шлак, ржавчина и краска в области около 10 см диаметром;
- Чистая поверхность металла обрабатывается машинным или трансформаторным малом, чтобы улучшить прохождение сигнала;
- Устройство настраивают согласно заданному стандарту, относительно параметров металла и способа обнаружения (при толщине до 2 см используются стандартные настройки, а если выше, то нудна настройка АРД-диаграмм).;
- Искатель перемещается зигзагообразно вдоль исследуемой поверхности шва, с поворотом около 15 градусов;
- Если проявляется устойчивый сигнал на экране устройства, то искатель нужно максимально развернуть;
- Поиск проводится до тех пор, пока на дисплее не появится сигнал, у которого имеется максимальная амплитуда
- По ГОСТ ультразвуковой контроль сварных швов проводится два раза;
- Если работа ведется с тавровыми швами, то они проверяются эхо-методом;
- После результатов проверки создается таблица данных, по которой можно будет легко найти обнаруженные дефекты.
«Важно!
При выявлении колебаний дефекта нужно проверить все несколько раз, чтобы убедиться в точности предположения, после чего можно фиксировать дефект.»
Меры по технике безопасности
Дефектоскопия сварных швов ультразвуком является достаточно безопасной процедурой, при которой нужно соблюдать правила электробезопасности и инструкции того места, где проводится сам процесс.
Ультразвуковой контроль сварных соединений
Темы: Контроль качества сварки, Сварные соединения .
Метод ультразвуковой дефектоскопии металлов и других материалов впервые был разработан и практически осуществлен в Советском Союзе в 1928—1930 гг. проф. С. Я. Соколовым.
Еще страницы, относящиеся к теме
Ультразвуковой контроль сварных соединений
:
Свойства ультразвуковых волн.
Ультразвуковые волны представляют собой упругие колебания материальной среды, частота которых лежит за пределами слышимости в диапазоне от 20 кгц (волны низкой частоты) до 500 Мгц (волны высокой частоты).
Ультразвуковые колебания бывают продольные и поперечные. Если частицы среды перемещаются параллельно направлению распространения волны, то такая волна является продольной, если перпендикулярно-поперечной. Для отыскания дефектов в сварных швах используют в основном поперечные волны, направленные под углом к поверхности свариваемых деталей.
Ультразвуковые волны способны проникать в материальные среды на большую глубину, преломляясь и отражаясь при попадании на границу двух материалов с различной звуковой проницаемостью. Именно эта способность ультразвуковых волн используется в ультразвуковой дефектоскопии сварных соединений.
Ультразвуковые колебания могут распространяться в самых различных средах — воздухе, газах, дереве, металле, жидкостях.
Скорость распространения ультразвуковых волн C определяют по формуле:
C = fλ
где f — частота колебаний, гц;
λ — длина волны, см.
Для выявления мелких дефектов в сварных швах следует пользоваться коротковолновыми ультразвуковыми колебаниями, так как волна, длина которой больше размера дефекта, может не выявить его.
Получение ультразвуковых волн.
Ультразвуковые волны получают механическим, термическим, магнитострикционным (Магнитострикция — изменение размеров тела при намагничивании) и пьезоэлектрическим (Приставка «пьезо» означает «давить») способами.
Наиболее распространенным является последний способ, основанный на пьезоэлектрическом эффекте некоторых кристаллов (кварца, сегнетовой соли, титаната бария): если противоположные грани пластинки, вырезанной из кристалла, заряжать разноименным электричеством с частотой выше 20 000 гц, то в такт изменениям знаков зарядов пластинка будет вибрировать, передавая механические колебания в окружающую среду в виде ультразвуковой волны. Таким образом электрические колебания преобразовываются в механические.
В различных системах ультразвуковых дефектоскопов применяют генераторы высокой частоты, задающие на пьезоэлектрические пластинки электрические колебания от сотен тысяч до нескольких миллионов герц.
Пьезоэлектрические пластинки могут служить не только излучателями, но и приемниками ультразвука. В этом случае под действием ультразвуковых волн на гранях кристаллов-приемников возникают электрические заряды малой величины, которые регистрируются специальными усилительными устройствами.
Методы выявления дефектов ультразвуком.
Существуют в основном два метода ультразвуковой дефектоскопии: теневой и эхо-импульсный (метод отраженных колебаний.)
Рис. 1. Схемы проведения ультразвуковой дефектоскопии : а — теневым; б — эхо импульсным методом; 1 — щуп-излучатель; 2 — исследуемая деталь; 3 — щуп приемник; 4 — дефект.
При теневом методе (рис. 1, а) ультразвуковые волны, идущие через сварной шов от источника ультразвуковых колебаний (щупа-излучателя), при встрече с дефектом не проникают через него, так как граница дефекта является границей двух разнородных сред (металл — шлак или металл — газ). За дефектом образуется область так называемой «звуковой тени». Интенсивность ультразвуковых колебаний, принятых щупом-приемником, резко падает, а изменение величины импульсов на экране электронно-лучевой трубки дефектоскопа указывает на наличие дефектов. Этот метод имеет ограниченное применение, так как необходим двусторонний доступ к шву, а в ряде случаев требуется снимать усиление шва.
При эхо-импульсном методе щуп-излучатель посылает через сварной шов импульсы ультразвуковых волн, которые при встрече с дефектом отражаются от него и улавливаются щупом-приемником. Эти импульсы фиксируются на экране электроннолучевой трубки дефектоскопа в виде пиков, свидетельствующих о наличии дефекта. Измеряя время от момента посылки импульса до приема обратного сигнала, можно определить и глубину залегания дефектов. Основное достоинство этого метода состоит в том, что ультразвуковой контроль сварных соединений можно проводить при одностороннем доступе к сварному шву без снятия усиления или предварительной обработки шва. Этот метод получил наибольшее применение при ультразвуковой дефектоскопии сварных швов.
Импульсные ультразвуковые дефектоскопы.
Ультразвуковой контроль сварных соединений осуществляется при помощи ультразвуковых дефектоскопов, которыми можно выявлять трещины» непровары, газовые и шлаковые включения в стыковых, угловых, тавровых и нахлесточных соединениях, выполненных дуговой, электрошлаковой сваркой, газовой и контактной сваркой. Контролировать можно как сварку сталей, так и сварку цветных металлов и их сплавов.
Рис. 2. Конструктивная схема призматического щупа : 1 — кольцо изоляционное; 2 — асбестовая прокладка; 3 — накладка контактная; 4 — втулка изоляционная; 5 — втулка; 6 — пластинка из титаната бария; 7 — корпус;8 — призма из плексигласа.
Электрическая схема дефектоскопов, состоящая из отдельных электронных блоков, смонтирована в металлическом кожухе, на передней панели которого находится экран электроннолучевой трубки и расположены рукоятки управления. Дефектоскопы укомплектованы призматическими щупами-искателями (рис. 2) с углами ввода ультразвукового луча 30, 40 и 50° (0,53; 0,7 и 0,88 рад). Придаются также и прямые щупы, при помощи которых ультразвуковые колебания вводятся перпендикулярно поверхности контролируемого изделия. Комплект щупов позволяет выбирать для каждого конкретного случая необходимую схему прозвучивания. Во всех щупах в качестве пьезоэлектрического преобразователя используются пластинки титаната бария.
В зависимости от количества щупов и схемы их включения ультразвуковые дефектоскопы могут быть двухщуповыми, в которых один щуп является излучателем, а другой приемником, или однощуповыми, где функция ввода и приема ультразвуковых колебаний выполняются одним щупом. Это возможно потому, что прием отраженного сигнала происходит во время пауз между импульсами, когда никаких других сигналов, кроме отраженных, на пьезоэлектрическую пластинку не поступает.
Рис. 3. Блок-схема импульсного ультразвукового дефектоскопа УЗД-7Н : 1 — задающий генератор; 2 — генератор импульсов; 3 — пьезоэлектрический щуп; 4 — генератор развертки; 5 — приемный усилитель; 6 — электроннолучевая трубка; 7 — контролируемое изделие.
В качестве индикаторов дефектов применяются электроннолучевые трубки. Ряд дефектоскопов оснащен также световым (электрической лампочкой на искательной головке щупа) и звуковым (динамиком и телефонными наушниками) индикаторами.
Типовая блок-схема импульсного ультразвукового дефектоскопа, работающего по однощуповой схеме, приведена на рис. 3.
Задающий генератор, питаемый переменным током, вырабатывает электрические колебания, передаваемые на генератор импульсов и пьезоэлектрический щуп. В последнем высокочастотные электрические колебания преобразуются в механические колебания ультразвуковой частоты и посылаются в контролируемое изделие. В интервалах между отдельными посылами высокочастотных импульсов пьезоэлектрический щуп при помощи электронного коммутатора подключается к приемному усилителю, который усиливает полученные от щупа отраженные колебания и направляет их на экран электроннолучевой трубки. Таким образом, пьезоэлектрический щуп попеременно работает как излучатель и приемник ультразвуковых волн.
Генератор развертки обеспечивает развертку электронного луча трубки, который прочерчивает на экране электроннолучевой трубки светящуюся линию с пиком начального импульса.
При отсутствии дефекта в контролируемом изделии импульс дойдет до нижней поверхности изделия, отразится от нее и возвратится в пьезоэлектрический щуп. В нем механические колебания ультразвуковой частоты снова преобразуются в высокочастотные электрические колебания, усиливаются в приемном усилителе и подаются на отклоняющие пластины электроннолучевой трубки. При этом на экране возникает второй пик донного импульса (как бы отраженного от дна изделия).
Если на пути прохождения ультразвука встретится дефект, то часть волн отразится от него раньше, чем донный сигнал достигнет пьезоэлектрического щупа. Эта часть волн усиливается приемным усилителем, подается на электроннолучевую трубку и на ее экране между начальным и донным импульсами возникнет пик импульса от дефекта.
Благодаря синхронной работе генератора развертки луча, генератора импульсов и других устройств дефектоскопа взаимное расположение импульсов на экране электроннолучевой трубки характеризует глубину расположения дефекта. Расположив на экране трубки масштабные метки времени, можно сравнительно точно определить глубину залегания дефекта.
Методика ультразвукового контроля.
Перед началом ультразвукового контроля зачищают поверхность сварного соединения на расстоянии 50—80 мм с каждой стороны шва, удаляя брызги металла, остатки шлака и окалину. Зачистку выполняют ручной шлифовальной машинкой, а при необходимости еще и напильником или наждачной шкуркой.
Рис. 4. Схема проведения ультразвукового контроля : а — перемещение призматического щупа по поверхности изделия; б — контроль прямым лучом; в — контроль отраженным лучом.
Чтобы обеспечить акустический контакт между щупом-искателем и изделием, зачищенную поверхность металла непосредственно перед контролем тщательно протирают и наносят на нее слой контактной смазки. В качестве смазки применяют автол марок 6, 10, 18, компрессорное, трансформаторное или машинное масло.
Рис. 5. Держатели призматических щупов : а — для контроля стыковых швов отраженным лучом; б — для контроля стыковых швов прямым лучом; в — для контроля угловых швов.
Затем проверяют правильность показаний дефектоскопа на эталонах сварных швов с заранее определенными дефектами.
Ультразвуковой контроль стыковых соединений проводят путем поочередной установки щупа по обеим сторонам проверяемого шва.
В процессе контроля щуп-искатель плавно перемещают вдоль обеих сторон шва по зигзагообразной линии (рис. 4, а), систематически поворачивая его на 5—10° в обе стороны для выявления различно расположенных дефектов.
Прозвучивание производят как прямым (рис. 4, б), так и отраженным (рис. 4, в) лучом. Стыковые соединения при толщине металла более 20 мм обычно проверяют прямым лучом. При толщине металла менее 20 мм усиление шва не дает возможности установить щуп так, чтобы ультразвуковой луч проходил через корень шва. В этих случаях ультразвуковой контроль сварных соединений осуществляют однократно или двукратно отраженными лучами. При толщине металла менее 8 мм его прозвучивают многократно отраженным лучом.
Рис. 6. Схема определения размеров дефекта в стыковом шве: а — протяженности l; б — высоты h.
Пределы перемещения щупа поперек шва зависят от угла ввода луча и способа прозвучивания и определяются по номограммам, прилагаемым к инструкции на эксплуатацию дефектоскопа. Чтобы обеспечить перемещение щупов в заданных пределах, их устанавливают в специальный держатель (рис. 5).
При обнаружении дефекта в сварном шве на экране дефектоскопа появляется импульс. Условную протяженность его измеряют длиной зоны перемещения щупаискателя вдоль шва, в пределах которой наблюдается появление и исчезнование импульса (рис. 6, а). Условную высоту дефекта определяют как разность глубин, измеренных в крайних положениях щупаискателя, в которых появляется и исчезает импульс при перемещении щупа перпендикулярно оси шва (рис. 6, б). Условную высоту дефектов, имеющих большую протяженность, измеряют в месте, где импульс от дефекта имеет наибольшую амплитуду.
Рис. 7. Конструктивная схема жидкостного глубиномера : 1 — генератор дефектоскопа; 2 — цилиндр; 3 — компенсирующий объем; 4 — глубиномер; 5 — механизм перемещения поршня; 6 — жидкость; 7 — поршень; 8 — пьезоэлектрическая пластинка.
Глубину залегания дефекта определяют при помощи глубиномеров. Жидкостной глубиномер (рис. 7) состоит из пьезоэлектрической пластинки, которая возбуждается от генератора дефектоскопа одновременно с основной излучающей пьезоэлектрической пластинкой щупаискателя. Эта пластинка помещена в цилиндр с компенсирующим объемом. Цилиндр наполнен жидкостью и имеет поршень, связанный со шкалой глубиномера. При прозвучивании сварного шва на экране электроннолучевой трубки вместе с начальным и донным сигналом появляется так называемый служебный импульс, отраженный от поршня цилиндра глубиномера. Положение его на экране трубки дефектоскопа определяется положением поршня в цилиндре. Передвигая поршень, совмещают служебный импульс с импульсом, отраженным от дефекта, и по шкале глубиномера определяют глубину залегания дефекта. При совмещении поршня с донным импульсом можно определить толщину металла. Подобные глубиномеры могут быть присоединены к любому ультразвуковому импульсному дефектоскопу.
Повышения скорости контроля можно достичь применением несложных устройств (рис. 8), позволяющих осуществлять перемещение дефектоскопа вдоль шва и возвратно-поступательное движение щупа. Щуп-искатель устанавливается на тележке устройства и соединяется с ультразвуковым дефектоскопом. На этой же тележке находится механизм передвижения, состоящий из электродвигателя мощностью 12 вт, червячных пар и кривошипного механизма.
Рис. 8. Схема автоматизированного контроля стыков трубопроводов с помощью специального приспособления: 1 — контрольный механизм; 2 — труба; 3 — роликовая цепь; 4 — коробка со щупом; 5 — ультразвуковой дефектоскоп.
Значительно увеличивается надежность и скорость контроля при использовании автоматического ультразвукового дефектоскопа ДАУЗ-169, позволяющего контролировать сварные соединения при толщине листов от 6 до 16 мм. Он представляет собой датчик, установленный на автоматически передвигающейся каретке, соединенной гибким кабелем со шкафом с электронными блоками.
Дефекты регистрируются записью на диаграммной ленте и краскоотметчиком на контролируемом шве, работа которого дублируется световой сигнализацией. Скорость контроля составляет 1 м/мин. Применение его значительно увеличивает надежность и производительность процесса контроля сварных швов.
Оформление результатов контроля.
Результаты ультразвуковой дефектоскопии согласно ГОСТ 14782—69 фиксируют в журнале или в заключении, обязательно указывая:
а) тип сварного соединения; индексы, присвоенные данному изделию и сварному соединению; длину проконтролированного участка шва;
б) технические условия, по которым выполнялась дефектоскопия;
в) тип дефектоскопа;
г) частоту ультразвуковых колебаний;
д) угол ввода луча в контролируемый металл или тип искателя, условную или предельную чувствительность;
е) участки шва, которые не подвергались дефектоскопии;
ж) результаты дефектоскопии;
з) дату дефектоскопии;
и) фамилию оператора.
При сокращенном описании результатов дефектоскопии каждую группу дефектов указывают отдельно.
Характеристика протяженности дефекта обозначается одной из букв А, Б, В. Цифрами обозначают: количество дефектов в шт.; условную протяженность дефекта в мм; наибольшую глубину залегания дефекта в мм; наибольшую условную высоту дефекта в мм.
Буква А указывает, что протяженность дефекта не превышает допускаемую техническими условиями. Буква Б используется для характеристики дефекта большей протяженности, чем типа А. Буквой В обозначают группу дефектов, отстоящих друг от друга на расстоянии не более величины условной протяженности для дефектов типа А.
Ниже приводится пример сокращенной записи результатов дефектоскопии в журнале или в заключении.
На участке шва сварного соединения С15 (ГОСТ 5264—69), обозначенном индексом МН-2, длиной 800 мм обнаружены: два дефекта типа А на глубине 12 мм, один дефект типа Б условной протяженностью 16 мм на глубине 14—22 мм, условной высотой 6 мм и один дефект типа В условной протяженностью 25 мм на глубине 5—8 мм.
Сокращенная запись результатов испытания выглядит так:
С15, МН-2, 800; А-2-12; Б-1-16-22-6; В-1-25-8.
Техника безопасности при ультразвуковом контроле.
К работе с ультразвуковыми дефектоскопами допускают лиц, прошедших инструктаж по правилам техники безопасности и имеющих соответствующее удостоверение. Перед проведением контроля на большой высоте, в труднодоступных местах или внутри металлоконструкций оператор проходит дополнительный инструктаж, а его работу контролирует служба техники безопасности.
Ультразвуковой дефектоскоп при работе заземляют медным проводом сечением не менее 2,5 мм2. Работать с незаземленным дефектоскопом категорически запрещается. При отсутствии на рабочем месте розетки подключать и отключать дефектоскоп может только дежурный электрик.
Запрещается проводить ультразвуковой контроль сварных соединений вблизи сварочных работ при отсутствии защиты от лучей электрической дуги.
- < Сопротивление образованию горячих трещин
- Дефекты сварных соединений >
Ультразвуковой метод контроля сварных соединений
Ультразвуковой метод контроля основан на применении ультразвуковых упругих колебаний материальной среды, частота которых лежит выше предела слышимых звуков, т. е. более 20 тысяч колебаний в секунду.
При ультразвуковой дефектоскопии сварных соединений обычно применяются частоты, достигающие миллионов колебаний в секунду (1,2÷5,0МГц).
Физические свойства ультразвуковых волн высокой частоты близки физическим свойствам электромагнитных световых волн. Проходя через толщу металла, волны вызывают колебания его частиц и отражаются при встрече с несплошностью.
В том случае, когда направление распространения ультразвуковой волны совпадает с направлением колебания частиц, волна называется продольной, или волной сжатия. Если колебания частиц перпендикулярны направлению распространения ультразвуковой волны, она называется поперечной.
Скорость распространения продольных волн больше, чем поперечных, в два раза. При движении ультразвука в стали скорость распространения его продольной волны равна 5860 м/с, а длина волны при частоте ультразвуковых колебаний 2,5 МГц составляет 2,34 мм. Для Обнаружения дефектов в контролируемом материале длина ультразвуковой волны должна быть меньше размера дефекта, который необходимо обнаружить.
Ультразвуковые колебания получают чаще всего магнитострикционным и пьезоэлектрическим способами. Для ультразвуковой дефектоскопии применяется в основном пьезоэлектрический способ, заключающийся в следующем.
Если, например, к пластинке кварца, вырезанной так, что две ее грани перпендикулярны электрической оси кристалла, подвести переменное напряжение высокой частоты, то пластинка будет колебаться с той же частотой. При сжатии или растяжении пластинки на ее гранях образуются электрические заряды. Кроме кварца такими свойствами обладают, например, титанат бария и сегнетовая соль.
Для ввода ультразвука в исследуемый металл поверхность его предварительно покрывают тонким слоем трансформаторного, машинного или турбинного масла. Затем на эту поверхность ставят пьезоэлектрический щуп ультразвукового дефектоскопа, который посылает в металл ультразвуковые колебания.
Распространяющиеся в металле упругие колебания его частиц при встрече с дефектами частично отражаются и, возвращаясь обратно к пьезоэлектрическому щупу, давят на него. Образовавшиеся электрические заряды пьезоэлемента усиливаются и подаются в электронно-лучевую трубку, на экране которой возникает всплеск (отклонение от горизонтали) электронного луча.
Чтобы ультразвуковые колебания не накладывались на отраженные, их посылают с паузами. Продолжительность пауз превышает время посылки колебаний в материал.
С помощью ультразвука проверяют качество основного металла и сварных соединений толщиной от миллиметров до нескольких метров.
В контролируемый шов ультразвук вводится под углом к поверхности, через основной металл с помощью призматических щупов.
Изготавливаются и применяются разнообразные ультразвуковые дефектоскопы, например дефектоскоп УДМ-1М (рис. 190) и специализированные установки для контроля ультразвуком.
Рис. 190. Ультразвуковой дефектоскоп УДМ-1М.
Контроль сварных соединений ультразвуком регламентирован ГОСТ 14782 «Швы сварных соединений. Методы ультразвуковой дефектоскопии».