Ковка ножа из советского вторичного сырья
Вторичное сырье не позволит сделать клинок высочайшего качества. Но многим нравится ощущение перерождения других материалов в режущие и колющие предметы. Например, ковка ножа из напильника или цепи, рессоры, клапана, подшипника, троса, сверла.
Нож из подшипника
Для ножей используются подшипники от автомобилей, обычно диаметром сантиметров 10-15.
Ножи из троса
Из троса получаются хорошие клинки, но дамасские свойства не высокие из-за крупных рисунков. Ножи из троса содержат небольшое количество углерода, поэтому к их телам нужно приваривать режущую кромку из дамаска.
Ножи из рессоры
Многие предпочитают делать ножи своими руками из рессоры, которая была изготовлена еще в советский период. Тогда использовалась для рессоры высококачественная сталь 65Г. Свойства металла рессоры повышаются за счет правильного соотношения составных частей и технологичной термообработки. Если ножи из рессоры перекалить, то они станут хрупкими.
Ножи из цепи
Широко применяется для ковки такой вторичный материал, как цепи. Чаще это цепи от бензопилы, но бывают и моторные цепи от бензинового двигателя.
Ножи из клапана
Для изготовления ножей своими руками из клапана берутся пустотелые выпускные клапаны. Не каждый умелец знает, как грамотно оттянуть нож из клапана. Поэтому это не лучший вариант.
Ножи из сверла
Хорошие ножи получаются из сверла. Инструментальная сталь, из которой изготовлены сверла, говорит сама за себя. Если правильно закалить клинок, сделанный своими руками из сверла, то он не будет ломаться при ударных нагрузках и сможет противостоять высокой нагрузке на изгиб.
Ножи из напильников
Чтобы изготовить нож из напильника своими руками нужно сначала нарисовать эскиз – форму лезвия и ручки, выбрать способ крепления, как на видео.
Ножи из пилы
Альтернативой может быть использование механической пилы для железнодорожного рельса. Их прочность даже выше, чем у напильников. Оба эти изделия как нельзя лучше подходят для ковки ножей в домашних условиях. Так как старый напильник более доступен, то технологию ручной ковки из него и рассмотрим более подробно. Также процесс можно посмотреть на видео.
Этапы переделки напильника в нож
Ковка в домашних условиях должна происходить при строгом соблюдении всех мер предосторожности.
Будем пользоваться:
- Напильником (желательно советским).
- Материалом для изготовления рукоятки (пластик, кость, дерево и др).
- Обувным кремом и воском.
- Газовой плитой или другим нагревательным устройством.
- Станком, тисками и болгаркой.
- Магнитом.
- Наждачной бумагой.
- Материалом для заклепок (желательно латунь).
- Клеем для кожи и металла.
Шаг 1
Сначала производим обжиг напильника в печи, как на видео. Накаливаем его на протяжении 6 часов и оставляем там до полного остывания. Это делаем для того, чтобы сталь стала такой, как перед заводской обработкой. Вместо печи можно использовать раскаленные угли костра. В домашних условиях для этого можно использовать газовую конфорку. На нее кладут будущий нож тем местом, где предполагается режущая часть. Сверху ставят металлический тепловой экран так, чтобы он не касался напильника. Заготовку посыпают солью, которая при нагревании должна расплавиться. Время процесса – 6 часов.
Шаг 2
Затем отрезают от заготовки все лишнее, чтобы она соответствовала нарисованному эскизу. Теперь нужно просверлить отверстия для клепок и закалить будущий нож. Заготовку равномерно прогревают до накаливания одного цвета. Рукоятку можно не закаливать. Если сталь закалилась, то она не будет магнититься. Это сигнал к дальнейшим действиям. На этой стадии заготовка должна царапать стекло, если все сделано правильно.
Шаг 3
Самая ответственная часть дела закончена, можно приступать к отпуску – процессу изменения свойств стали, с целью снижения хрупкости. Для этого нужно прогреть нож в духовке два часа. Затем нож шлифуется, доводится до гладкого состояния поверхности, как на видео.
Шаг 4
Следующим этапом будет травление стали хлорным железом. Результатом станет образование оксидной пленки, она защитит металл от коррозии. Если хлорного железа нет, то можно воспользоваться уксусом или лимонным соком.
Шаг 5
Завершающий шаг – рукоятка. Она садится на клей и приклепывается. Заточка предполагается ручная, как на видео, так как царапин нож не боится. Во всяком случае, лучше ручная заточка, чем неумелая на станке. Теперь лезвие нужно натереть воском. Затачивать ножи целесообразно до окончательной закалки металла.
Вместо накладной рукоятки можно использовать кожу, которую надо равномерно намотать и с помощью крема для обуви довести до состояния однородности.
Надо заметить, что ножи, сделанные в домашних условиях, очень устойчивы к механическим обработкам и после закалки, править их можно будет только на алмазной заточной машинке. На обычном точиле получиться поправить только ручную заточку.
Похожие статьиКак сделать нож из рессоры. Изготовление ножа из автомобильной рессоры
Как сделать нож из рессоры своими руками
У хорошего ножа лезвие долго не тупится, а клинок возвращается в исходное состояние после изгибания. Этим требованиям в полной мере соответствует нож из рессоры. Этот материал используется для промышленного и самостоятельного изготовления. В зависимости от назначения ножи из рессоры своими руками делают из амортизаторов легковых или грузовых автомобилей.
Особенности ножа из рессоры
Популярность ножей из рессорной стали объясняется доступностью и дешевизной. Материал обладает характеристиками необходимыми для качественных клинков:
- пластичностью;
- вязкостью;
- стойкостью к ударным нагрузкам;
- твердостью;
- износостойкостью.
Чаще всего делают нож из рессорной стали марки 65Г, из 50ХГСА и 50ХГА реже. Незначительные различия характеристик металлов не влияют на качество клинка. Независимо от марки рессорная сталь хорошо поддается термообработке. К недостаткам относится подверженность коррозии.
Применение рессорной стали
Универсальность характеристик стали 65Г позволяет делать из рессор ножи различного назначения. С ежедневной работой на кухне дешевые самоделки справляются не хуже чем дорогие фирменные модели. По этой же причине туристы, охотники и рыболовы предпочитают рессорную сталь для ножей, сделанных самостоятельно или мастерами. Они также популярны у военных. Солдаты во время прохождения службы нередко занимаются изготовлением армейских ножей для своих нужд, потому что их можно сделать из рессоры доступными инструментами.
Из длинных полос от большегрузных автомобилей куют мечи для ролевых игр. Для обрубки веток и борьбы с разросшимся кустарником делают мачете. Из толстых рессор получаются удобные топорики для разрубания тушек птицы и крупных кусков мяса.
Делаем нож из рессоры своими руками
Отслужившие свой срок рессоры обычно выкидывают на улицу. Поэтому найденный материал перед началом работы очищают от грязи и ржавчины. Выгнутые листы выправляют нагреванием до красного каления с медленным остыванием до температуры окружающего воздуха. Чтобы первый блин не получился комом, нужно знать последовательность как из рессоры делают нож.
Заготовка клинка
За счет того, что ковка повышает прочность металла, ножи, сделанные этим способом, будут надежней и долговечней. Сначала из рессоры вырезают заготовку по размерам близкую к профилю будущего клинка. Этот способ выбирают, когда из рессоры делают кованые топоры, мечи, длинные мачете. После нагрева до красного каления ковкой придают металлу нужную форму и ширину, заостряют конец, делают скосы для лезвия. После окончания работы заготовку оставляют медленно остывать.
Прежде, чем начать делать нож из рессоры без ковки, предварительно снимают внутреннее напряжение металла путем нагрева до температуры 420 — 460⁰C. После медленного остывания сталь становится более пластичной и легче обрабатывается. Затем делают картонный шаблон формы клинка и, приложив к рессоре, переносят его контуры на металл с помощью карандаша, фломастера, чертилки.
В зависимости от имеющегося инструмента заготовку вырезают:
- ленточной пилой;
- болгаркой, не допуская перегрева металла;
- просверливают ряд отверстий рядом с контуром сверлильным станком или дрелью с последующим спиливанием перегородок;
- ножовкой по металлу.
После подгонки заготовки по профилю размечают скосы. Их выпиливают шлифовальной машинкой, болгаркой или напильником. На этом этапе нельзя оставлять недоделки, так как после термической обработки исправить их будет трудно.
Закалка лезвия
Закалка необходима для восстановления характеристик металла, которые он утратил после предварительного снятия напряжения в начале работы. Иначе самодельный нож придется точить после открывания каждой консервной банки. При отсутствии кузнечного горна закалку выполняют на костре, в котором горит каменный уголь. Заготовку нагревают до 840 — 880⁰C. Если нет термометра с нужным диапазоном измерения, температуру определяют магнитом. Он перестает притягиваться к металлу после нагрева до нужного значения.
При изготовлении ножа из рессоры закаливают только режущую кромку или весь клинок. В первом варианте греют только край лезвия и погружают в машинное или растительное масло. Вынимают после прекращения образования пузырьков. Закаливать всю заготовку нецелесообразно, так как у рессорной стали достаточно упругости и прочности для сохранения формы даже при значительных нагрузках. Тем более что при неправильной полной закалке лезвие может повести, а при исправлении треснуть.
Закалку завершают низким отпуском металла, нагревая до 180 -200⁰C. Для создания такой температуры достаточно простого костра, печи, духового шкафа. После разогрева металл оставляют медленно остывать.
Изготовление рукоятки
У ножей мастеров не только качественные лезвия, но и красивые рукояти. Их делают из дерева, кожи, пластика, кости, отливают из эпоксидной смолы. Импозантно смотрятся рукоятки, набранные из чередующихся слоев кожи и бересты или разноцветного пластика. Уникальные ручки делают из кости украшенной резьбой.
Новички обычно изготавливают рукоятки из деревянных или пластиковых накладок закрепленных на хвостовике заклепками. Если нужно скрыть крепеж в плашках сверлят глухие отверстия и устанавливают на штифты, предварительно смазав клеем внутреннюю сторону. Для лучшего сцепления деталей между собой ручку зажимают в тисах. Если внешний вид не важен накладки закрепляют болтиками с гайками.
При подгонке формы черновую обработку выполняют напильником, чистовую ― наждачной бумагой. Для защиты от гниения деревянные рукоятки пропитывают маслом. После такой обработки улучшится внешний вид ручки, так как проявится структура древесины.
Заточка ножа
Чтобы хорошо вручную наточить кухонный нож потребуется не менее получаса, а с длинным кованым клинком придется поработать не один день. Поэтому для экономии времени желательно обзавестись электрической или механической точилкой. Если ее нет, заточку выполняют бруском (точильным камнем), соблюдая следующие правила:
- клинок ведут от одного конца бруска к другому так, чтобы режущая кромка была впереди;
- движения вдоль и поперек точильного камня (от рукоятки к острию) должны быть синхронными;
- между бруском и лезвием необходимо выдерживать угол 20 — 25⁰.
Первичную заточку выполняют на крупнозернистом бруске до появления заусенца. Затем переходят на камень с мелким зерном. Завершают заточку шлифовкой режущей кромки на самом мелкозернистом бруске, осторожно удаляя заусенцы. После полировки клинка нож готов к применению.
Эффектно выглядят ножи с вороненым лезвием черного цвета. Для этого клинок нагревают в масле, после чего у металла также повышается стойкость к коррозии. На лезвии можно сделать желобки или украсить гравировкой.
Видео изготовления ножа из рессоры своими руками
youtube.com/embed/HJMvCjMAxj8?feature=oembed»/>Феномен ножа из рессоры
В истории российского холодного оружия не так уж много примеров того, когда модель ножа или кинжала получила широкое признание не только на родине, но и во всем мире. Но ножи тульского мастера Егора Петровича Самсонова исключение.
Знаменитые «медвежьи» кинжалы Самсонова были широко известны в России и за рубежом, причем еще при жизни автора и тем более после его смерти цены на его ножи увеличивались многократно.
Сегодня трудно понять, почему в конце XIX века такое внимание уделяли так называемым «медвежьим» кинжалам и ножам.
Но объясняется это просто.
Хороший кинжал считался оружием последнего шанса, а с учетом того, что многие охотники еще пользовались дульнозарядным оружием, быстро перезарядить которое не представлялось возможным, важно было иметь хороший и крепкий нож, способный дать охотнику пусть небольшой, но шанс при нападении на него крупного и опасного зверя (в принципе в России все так и осталось, кроме дульнозарядного оружия).
За границей же оружием последнего шанса стал крупнокалиберный револьвер или пистолет, и большой охотничий нож стал чисто декоративным или статусным предметом.
Но вернемся в девятнадцатый век. Охотникам нужен был хороший, крепкий и, что немаловажно, красивый нож.
Абсолютное лидерство в этом сегменте принадлежало американским ножам компании «Роджерс» (Joseph Rodgers & Sons Ltd), крупнейшего производителя ножей в городе Шеффилде. Это были огромные, традиционные для Америки ножи по типу Боуи, с неповторимым дизайном.
Судя по всему, именно они, широко представленные в российских каталогах, стали прототипом или, по крайней мере, идеей создания ножа Самсонова.
В каталоге торгового дома Фальковского подобный нож можно найти под № 358, он описывается как «охотничий нож-кинжал Роджерса, небольшого размера, но с более широким клинком длиной около 5 1/8 дюйма, работа высокого качества.
Самсонов был мастером-кустарем, великолепно умевшим работать со сталью, но не обладавшим достаточным опытом в проектировании самих клинков, а точнее, их форм.
Ничем другим нельзя объяснить тот факт, что форму ножа предложил не Самсонов, а егермейстер великого князя Николая Николаевича младшего Михаил Владимирович Андриевский.
В 1894 году в журнале «Природа и охота» он опубликовал статью «По поводу вновь изобретенной механической рогатины», в которой подробно описал историю создания «медвежьего» ножа: «Самым удобным я считаю нож американской системы с небольшими, сделанными лично мною изменениями в форме.
Фото Андрея Чугина.
Этот нож имеет обоюдоострый клинок, который заострен к концу. С выемками по бокам, шесть вершков длины (26,7 см), один вершок ширины (4,45 см) и восемь миллиметров толщины. Лезвие ножа отделяется от рукояти стальной перекладиной; рукоятка, изготовленная из крепкопородного дерева, держится на клинке широким винтом.
Носится этот нож на черном поясном ремне в деревянных, обтянутых черной кожей ножнах, концы которых отделаны вороненой сталью.
Размеры ножа и его баланс рассчитаны так, что он удобно держится в руке и им отлично можно рубить, резать, колоть и вспарывать брюхо натиском кверху или книзу. Первый такой нож отлично изготовил мне тульский мастер Егор Самсонов, а затем такие ножи стали делать на Златоустовском казенном заводе».
В дневнике за апрель 1887 года имеется запись о ноже, послужившем Андриевскому образцом: «Всегда ношу с собой охотничий американский нож, которым можно и рубить, и колоть; им соорудили плот».
При этом егермейстер прямо сказал, что за основу им был взят нож Боуи фабрики «Роджерс», в которые он внес ряд удачных изменений.
Новый нож Самсонова, как и его американский прототип, был достаточно большим — 25–26 см длиной, до 1 см толщиной и до 5 см шириной. Сегодня такие размеры, особенно толщина клинка, кажутся чудовищными, но тогда это было нормой.
Фото Андрея Чугина.
С появлением ножа связана интересная история. У Михаила Владимировича был постоянный оппонент — князь Ширинский-Шихматов, известный охотник-медвежатник, написавший множество статей и книг об охоте на медведя.
Даже он признал (впрочем, не назвав автора дизайна), что нож Самсонова и его форма очень удачны. «Из охотничьих ножей, — писал он в своей книге, — пригодных для охоты на медведей, по моему личному мнению, лучший — это нож, изготовленный Самсоновым в Туле».
Одним из секретов ножей Самсонова является высокое качество применяемых сталей. Для изготовления клинков американских ножей использовали широко распространенную тогда сталь Cast Steel, что в переводе означает «литая, или тигельная сталь» (ее часто применяли для производства пружин и рессор).
Сегодня этот сорт стали известен в Великобритании как EN8 или 080М40, в Европе она именуется С40, С45, у немцев это 1.0511, 1.1 186, у американцев — 1039, 1040, 1042, 1043, 1045.
Это сталь с высоким содержанием углерода (0,36–0,44 %), кремния (0,1–0,4 %), марганца (0,6–1,0 %). При цементации (поверхностной закалке) твердость изделия из нее можно довести до показателя 50–55 HRC.
В то время получить такую твердость и далеко не хрупкий клинок было нелегко, поэтому основной секрет заключался в обработке стали.
В литературе встречается мнение, что ножи Самсонова делались из каретной рессорной стали. Что ж, вполне возможно, но мне наиболее вероятным кажется, что клинки перековывались из рессор железнодорожных вагонов, возможно сломанных.
Есть версия, что рессорная сталь, долгое время находящаяся под нагрузкой и даже ржавеющая, приобретает особые свойства. В пользу этого мнения говорит то, что в 1869 году в Туле были созданы паровозные мастерские, которые занимались не чем иным, как ремонтом подвижного состава — паровозов и вагонов всех систем, поэтому проблем с рессорами у Самсонова не было.
Повторить качество стали мастера попытались в советское время на заводе «Серп и Молот», и результаты получились хорошие: клинки выдерживали давление пресса от 10 до 12 тонн. Однако достичь показателей клинков Самсонова 14 тонн так и не удалось.
Реплики ножа Самсонова могут быть очень высокого качества. Фото Андрея Чугина.
До нас дошло описание процесса изготовления клинка: «Рессорная сталь отжигалась в кузнечном горне, куда загружался березовый или дубовый уголь. Воздух подавался с помощью ручных мехов.
Затем раскаленные листы правились на наковальне. Из них ручным слесарным способом заготавливались клинки.
После этого все детали подвергались цементации, регенерации, закалке, отпуску и старению. В продолговатую канавку, сделанную в горящем угле горна, закладывались заготовки клинков. Сверху и снизу они засыпались карбюризатором и древесным углем.
Все это нагревалось до 900–925° и выдерживалось в течение 4–5 часов из расчета, что в один час проникновение углерода в деталь происходит на глубину 0,1 мм. После охлаждения заготовки нагревались вновь до 900°, но уже без карбюризатора.
В течение трех часов происходила регенерация цементируемого зерна, то есть равномерное распределение углерода по всей поверхности детали. Затем каждая из них погружалась в ванну с маслом.
Наполовину остывшие заготовки выдерживались на воздухе до появления синего цвета, то есть до температуры отпуска в 300–325°.
После этого их опять погружали в ванну с маслом, где они окончательно охлаждались, и сразу же их вновь разогревали до температуры 150–175°, выдерживая в таком режиме в течение двенадцати часов.
После охлаждения все детали вытирались ветошью и подвергались окончательной механической обработке. Режущие грани охотничьего ножа доводились оселком».
До революции ножи Самсонова были широко представлены в каталогах оружейных дворов. Фото Андрея Чугина.
Но надо учитывать, что Самсонов был кустарем, у него не было инструментов и оборудования, которые позволили бы точно выдерживать температуру; он все делал исключительно по интуиции. В этом было что-то магическое: мастер-индивидуалист создавал клики, которые невозможно повторить в заводских условиях.
Возможно, именно поэтому ножи Самсонова высоко ценились при жизни мастера и еще больше после его смерти.
Надо отметить, что ножи были высоко оценены и официальными представителями «от охоты». Так, Самсонов получил право называться поставщиком Императорского охотничьего общества и право наносить на клинки шестиконечную звезду, подтверждающую признание высокого качества.
Кроме того, на клинках мастера ставилось его личное клеймо:
«ВЪ ТУЛЪ ЕГОРЪ САМСОНОВЪ» или «ЕГОРЪ САМСОНОВЪ ВЪ ТУЛЪ».
Фото Андрея Чугина.
Отделка ножа проста и даже аскетична; как сказали бы сегодня, нож обладает функциональным и лаконичным дизайном. На заказ выпускались украшенные образцы, но все украшения находились на ножнах, что подчеркивало высокую функциональность оружия.
Форма клинка была очень удачной и не принадлежала эксклюзивно Самсонову, поэтому параллельно выпускались ножи такой же формы, но сделанные «Златоустом» или «ШАФом» как более доступные, нежели ножи от Самсонова.
Сегодня можно встретить реплики «медвежьих» ножей в большом разнообразии, причем от вполне доступных по цене до дорогих, претендующих на то, что современным мастерам удалось раскрыть секрет Самсонова и повторить характеристики его клинков
Нож из рессоры своими руками
Фотоотчёт о том, как я изготовил нож своими руками из автомобильной рессоры. Было это уже давно, я только сейчас откопал эти фото. Я в тот момент работал электриком в больнице, и у меня было много свободного времени. Вот я и тратил его на изготовление различных предметов. Точнее, я учился этому, поскольку я совсем не профессионал, а лишь любитель. Очень люблю ножи, и всегда хотел сделать нож себе сам. Думаю, многие из вас разделяют мои мысли, что, каким бы ни был ваш нож – главное, что вы его сделали сами, своими руками!
На вид мой нож из рессоры от грузового автомобиля получился не очень подходящим под различные шаблоны и критерии, но зато он имеет весьма оригинальную форму. Думаю, многим из вас приходили в голову мысли, как изготовить нож своими руками. Так что, возможно, этот отчёт будет полезен для вас, а если не полезен – так, во всяком случае, интересен!
Материал для клинка я тупо нашёл на улице. Это автомобильная рессора, предположительно от КамАЗа, которая, видимо, отлетела у него на кочке. Я взял и притащил её к себе на работу. Взял болгарку и распилил её на 3 части. Рессора имеет закруглённую форму и неравную толщину. Поэтому я выбрал подходящий кусок и отпилил его. Получились две равные заготовки для двух моих будущих клинков.
Заготовка для одного из клинков. Сталь 65г.
После работы с болгаркой идёт муторная и весьма кропотливая работа с наждаком. Нужно вывести форму клинка, снять ненужное. А ненужного оказалось довольно много. Толщина рессоры была около 8 мм. Ну где вы видели нож с такой толщиной в обухе? Так что я снял около 2-3 мм, потом плюнул – и решил оставить такую толщину. Пускай мой нож и будет слегка толстоватым.
Затем пошла работа с мелкими брусками. Так как у меня не было возможности поставить на наждак другие бруски (их просто не было), то пришлось работать вручную и скоблить клинок камнем. На фото видна разница после работы с крупнозернистым бруском и более мелким.
Затем снял немного лишнего с хвостовика.
Получилась вот такая форма. Причём полировать весь клинок я не стал и оставил на спусках следы от крупного бруска. На электрическом наждаке можно было бы, но руками – это очень муторно. Кто когда-нибудь делал это, тот поймёт! Скажете, а почему ты просто не купил мелкозернистый камень и не поставил на наждак? Просто как-то не доходили руки до этого. Сидел на работе и неспеша скоблил его бруском. Другие в карты играют, а я сижу и наяриваю! Кому что)) Размеры: длина клинка без хвостовика 13.5 см ширина 3.5 см, толщина в обухе 6 мм.
Затем я взял кусок войлока, пасту ГОИ и начал полировать клинок, приблизительно до зеркального блеска. На фото клинок до обработки ГОИ.
Затем я в одном из своих походов заготовил бересту для рукояти. Но, правда, слегка разошёлся и заготовил чуть больше, чем требовалось.
Добрые люди подогнали мне своих обрезков кожи толщиной 3 мм. Кожа пошла на рукоять и на ножны. Вырезал из кожи вот такие квадратики, проделывал отверстия для хвостовика. Кожа толстая – режется очень трудно. Использовал только шило и нож.
Сообщества › Сделай Сам › Блог › Нож из рессоры.Якут?
Попробовал себя в ножетворении. Из-за недостаточности материалов огрехов достаточно… Бумагу режет, в лес в роли тесака пойдет. Материал рессора от моей первой машины Москвич 2140 SL, закален в масле. Рукоять береза (долго не протянет) вымоченная в льняном масле.
Сам собой доволен! По крайней мере еще попробую, но поменьше для кухни, уж очень острый получился и заточку держит хорошо! Спасибо что прочли! Небольшое видео
Смотрите также
Комментарии 53
Нормальный нож. И за правильно приложенные руки однозначно лайк. Но…
Это не якут…
Для якутов характерна прямая рукоять без изысков, обычно и без больстера. Всадной монтаж лезвия. Деревянные ножны… И самое главное это спуски.
Спуск со стороны выямки прямой, а с другой стороны выпуклая линза. Прообраз ножа это часть кости.
Якут это как бы нож сделанный в очень полевых условиях и для простых полевых задач. Постругать деревяшку, просверлить-проковырять дырочку. Разделать тушку… эти ножи делаются чуть ли не на коленке во время стоянки.
Не плох. Но похоже весьма и весьма тяжёл
А средину на ноже сваркой прожигают так ?
Ковал. Подшипник к арматуре приварил и пробивал.
классика.Рессора и Якут, начало всех ножеманов. О форме клинка якута везде спорят. В принципе, прообраз клина была кость, расщепленная вдоль. Не самый удобный клин для повседневного пользования, но как первый витринник пойдет. Вообщем друг сердешный, путь тебе на ганзу. Хобби замечательное!
классика.Рессора и Якут, начало всех ножеманов. О форме клинка якута везде спорят. В принципе, прообраз клина была кость, расщепленная вдоль. Не самый удобный клин для повседневного пользования, но как первый витринник пойдет. Вообщем друг сердешный, путь тебе на ганзу. Хобби замечательное!
Я с мехпилы начинал. Ты прав это не якут.
Попытка попробывать себя в ножеделании конечно же хорошая, но это как бы не много не совсем Якут. Если лезвие еще можно назвать похожим, то рукоять и наличее такого больстера ни как подходит к определению якутского ножа. Хотя художника может обидеть каждый ;).
Спасибо за отзыв. В заголовке Якут написал со знаком ?
Да, да конечно же вопросительный знак я видел, поэтому и написал
Спасибо за отзыв. В заголовке Якут написал со знаком ?
зря молотил углубления имитацию под кость. нож итак получилс нормальный без додумок))
Поддержу. Мне то же понравился. Просто работяга для хоз.нужд. И сломать не жалко с точки зрения себестоимости его. Но к вам есть вопрос.
Ответьте, если вы правша, то резать линзой к себе, во внутрь так сказать своего тела — удобно? Нет ощущения, что клин при резке шмота сала гуляет?
Есть, гуляет. Рубит шикарно…
Я не просто так спросил об этом. Вам нужен клин с линзой от себя! Что бы линза работала в отвал. Это разрыв шаблона… Просто устоявшиеся многими мнени — что это есть настоящий якут — ошибка (ИМХО), что вот ваш образ под правшу. В идеале он под левшу. Попробуйте собрать нож по моему совету — он вас приятно удивит. К себе нужно работать плоскостью, а линзу пускать в отвал. По сути якут это тоже самое — танто, только с выраженным долом. У танто одна сторона ножа (танто — не нож, а небольшой меч) плоская, вторая линзовидная (выпуклая). Если танто не для реза а махового движения — обе стороны в линзу. Вот он рубит зачетнее якута. Удачи.
заполируй его и будет хорошо!
Отличный нож я считаю, тем более для первого опыта, думаю если бы я взялся за изготовление подобного, то мой и до половины вашего не дотянул.) Если продолжите заниматься этим, уверен что дальше будет только лучше.
Отлично! Полицаи не доколебаются?))
Я оч хочу сделать по подобию Фербейн-Сикса, да пока не из чего и нечем(
Вбил в яндекс Фербейн-Сикс очень интересный результат)))
Х) со словом секс в дефисе могут результаты и похлеще быть)))
Вбил в яндекс Фербейн-Сикс очень интересный результат)))
Fairbairn-Sykes, так лучше)))) культовый кинжал, коллекционная вещица. Хотя бы копию сделать
Отлично! Полицаи не доколебаются?))
Я оч хочу сделать по подобию Фербейн-Сикса, да пока не из чего и нечем(
Наверное доколебаются))) Хотя у нас в деревне в каждом дворе холодное оружие, или чуть теплое.
))) ахха, не, ну если участковый нормальный, то все ОК. С собой не таскайте, а то могут быть вариации на тему, бывали прецеденты. Теперь в машине только киянка резиновая лежит)))
Чуть тёплое — это вилы?;)
я тоже влезу… без обид… мне понравилось…молодец!
А одежу для ножика? У якутов ручка прямая делается, но тут под себя делали и полного ” аутентика” не требовалось?
Скоро рессоры от уаза высвобожу и как заделаю ножей))))
Из низ мечи с шашками ковать можно…
Для кухни не пойдет, ржаветь будет
Серьезный!Ковал или просто вырезал?
Отлично.только держи всегда в смазке.Как в старину очень любят уход.Ржой покрываются бысттро.Свой заворонил.
Чем и как воронил?
Углеродка хорошо в ортофосфорной кислоте оксидируется — спрайт, кола хорошо покрывают, единственное надо дождаться выхода газов а то пятнами покроет
Это недолговечное и непрочноное покрытие. Я думал народ ржавым лаком балуется )))
Любое воронение не долговечно, я делаю в основнос бысрорезов, там хлорное железо или купорос рулят
Ржавый лак рулит. Но изготовление этого так называемого ржавого лака ядовито и занимает много времени. Да и сам процесс воронения длительный. Но покрытие очень надежное и прочное.
Любое воронение не долговечно, я делаю в основнос бысрорезов, там хлорное железо или купорос рулят
если по этому способу заворонить глюкофон (если не знаете — херовина из небольшого газового баллона — ru.wikipedia.org/wiki/%D0…A%D0%BE%D1%84%D0%BE%D0%BD) то нормально будет?
предмет то округлый во первых, во вторых кроме голых рук к нему ничего прикасаться не будет.
На быстрорезах и углеродках не облазит, даже на кухонниках, шх15 практически не покрывается, хотя травится хорошо, лучше попробовать на обрезках, не могу ссылку вставить, в моем блоге есть запись о травлении якута, принцип тот же только по времени меньше держать
блог обязательно гляну.
скажите пожалуйста, а пятилитровый газовый баллон из какого металла делают?
Честно не знаю, но явно не ст, скорее углеродки с добавлением марганца или других легирующих добавок, там прочность на разрыв нужна. Если не найдете данных по составу, попробуйте на точиле или болгарке на средних оборотах ” на искру”. Простая ст даст жиденькую едва желтенькую искру, углеродка ярко желтые пышные искры, лигатуры типа быстрорезов красные пышные. В гугле можно забить определение металла по искре, там наглядные таблицы есть, но все это приблизительно
ну да, явно не простая сталь, я скорее сужу по тому что, как Вы сказали, прочность на разрыв, ну и по звуку тоже, металл как раз для муз интструмента — очень звонкий.
но ржавеет, даже на атмосферном воздухе. к тому же с рук будет попадать человеческий пот и жир. так что металл надо защищать. а покраска плохо влияет на звук — изначальная настройка сразу херится. поэтому надо что найти помимо краски.
я вот думаю насчет воронения другу посоветовать. мне кажется это единственное что не будет оказывать влияния (большого) на звук.
спасибо за информацию.
Сильно ржавучий — однозначно углеродка, купорос покроет. Про инструмент напишете потом, заинтерисовали?
да ничего особенного, пилят баллон, делают ударный лепестковый муз. инструмент:
но вот в первом видео человек настроил, а потом красил. но после покраски (как утверждает мой друг) настройка меняется. и это моему другу не нравится (он в этом разбирается (в отличии от меня) — закончил муз.школу, много лет играл (на гитаре) с друзьями в рок группе), он категорически против грунтовок и красок.
мы пришли к выводу что надо воронИть. но в инете пишут всякую дичь — греть, потом в отработку, или еще какая фигня. можно ж как то и перегреть, например. в общем, мы искали способ попроще.
Чем и как воронил?
Классика.маслом.лусше касторку или льняное.и прогрев равномерный.нагрев на 10-20 град больше температуры кипения масла.но и в инете много инфы.
Отлично.только держи всегда в смазке.Как в старину очень любят уход.Ржой покрываются бысттро.Свой заворонил.
Да, совет верный!
Хороший нож, рабочий!
Хороший ломик, функциональный и вполне гармоничный.
Как сделать нож из рессоры
Умельцы ножевого ремесла, ухитряются выполнять клинки из чего угодно. Завалялась железяка в сарае – пара дней работы, клинок готов. Не удивляться таким людям просто нонсенс. Неизменно отдельные изделия получаются произведением искусства. А нож из рессоры – выглядит уникально по-своему. Освятим тему кропотливого труда мастера.
Особенности ножа из рессоры
Характерной чертой рессорных марок стали, является свойство изделия принимать первоначальную форму после деформирования – скручивания или изгиба. Детали, принимающие участие в механизмах со специфическими нагрузками, обязаны иметь непростые свойства.
Сплав активно использующийся профессиональными ножеделами, позволяет получить клинок с уникальными свойствами. Высочайшая прочность плюс пластичность и износостойкость материала, позволяет мастерам изготавливать достойные внимания клинки.
Рессорно-пружинная сталь – недорогой вариант углеродистой стали. Химсостав придаёт ей упругость и ударную вязкость. Закалка сплава придаёт твёрдость 60-62 единицы по Роквеллу. Современные мастера берутся изготавливать изделия из стали 65Г, считая её самой подходящей.
Свойства рессорной стали
Существует множество мнений о рессорах автомобилей родом из СССР. Якобы они являются реально хорошим материалом для клинка. Спорить бесполезно, проще узнать из какой марки стали состоит изделие. Бывалые металлурги утверждают, что рессорно-пружинная сталь включает в себя немало марок:
- пружины для железнодорожных вагонов и рессоры для автомобилей производят из: 50ХГ и 50ХГА, 50ХГФА;
- машиностроение, тракторостроение использует 55С2;
- сверхпрочные пружинные механизмы и рессоры изготавливают из55С2ГФ;
- детали наименее подверженные ударным нагрузкам используют 65Г.
Список довольно продолжительный и освящать весь нет смысла. Но отметить приблизительную сходность данных марок стали и по химсоставу, и по физическим свойствам, стоит.
Главным ориентиром создания таких изделий, является способность восстановления первоначальной формы, после различных нагрузок, т.е. – пружинить. Недопустима малейшая деструкция во время работы изделия. В соответствии с ГОСТом к подобным сплавам предъявляются завышенные требования.
Применение рессорной стали для изготовления ножа
Пружинный материал 65Г применяют для изготовления ножей ножеделы любители. Благодаря уникальным характеристикам металл находит своё применение в различных сферах.
Клинки для кухни, охоты, туризма – все показывают отличные режущие качества. При особой надобности, реально выковать меч либо топор. После закалки сталь приобретает хорошую жёсткость, что позволяет изделием рубить. Примеры использования рессорной стали:
- Кухонный нож. В не лучшие времена для страны, после распада СССР, не все люди могли позволить себе хороший кухонный набор ножей. Приходилось выкручиваться. Рессоры и пластины из стали 65Г были легкодоступны. На кухнях постсоветского пространства часто встречались самодельные изделия. Рукоять изготавливали из подручного материала: дерево, простая эпоксидка, и изолента – не мешали ножам оставаться на высоте.
- Туристический нож. Минус пружинного металла – он подвержен коррозии, требует постоянного ухода после использования. Нож подойдёт для применения в походных условиях. Важным моментом является закалка. При слабой – лезвие быстро затупится о консервную банку. Следует знать твёрдость ножа.
- Армейский. Тактические или в нынешнее время – армейские ножи, отлично справляются со своими обязанностями. Серрейторная заточка увеличит сферы применения клинка. Колющие удары выдерживает без проблем. В бытовых условиях бойцу или «выживальщику» станет ценным помощником.
- Топор, мачете или меч. Сплав 65Г и аналоги, позволяет изготовить действительно грозное оружие. Непременно толщина изделия играет немалую роль. Производя такой шедевр, необходимо запастись рессорой от грузовика, или раздобыть длинную пластину.
При правильной обработке металла мы гарантировано получим отличный клинок. Мало опыта с изготовлением изделий из стали, ерунда. Далее, в статье предоставим подробное описание изготовления ножей из рессоры, различными способами.
Как сделать нож из рессоры с помощью ковки
Работа с металлом – дело тонкое. Ковка изделия требует определённых навыков. Нет ничего зазорного, испортить одну заготовку. Полученный опыт пригодится при очередной попытке. Работать будем с рессорой, ориентировочно марки стали 65Г, выяснить точно сплав поможет цвет заготовки при накаливании.
Профессионалы считают ковочный метод более практичным. При многократном нагревании и охлаждении металла происходят процессы на молекулярном уровне. Уплотнение металла и изменение структуры, скажутся на качестве изделия.
Инструменты и материалы
Работы следует проводить на свежем воздухе или в просторном гараже с вытяжкой. Стоит позаботиться о своём здоровье, найти маску и жаропрочные перчатки. Набор для ковки выглядит так:
- стальная заготовка из рессоры;
- горн или печь;
- молот большой 4-5 кг, молот маленький 1-1,5 кг;
- наковальня, щипцы;
- шлифовальный станок;
- сварочный аппарат, УШМ.
В качестве нагревательного элемента вполне подойдёт простой костёр с подачей воздуха. Закинуть каменного угля и трудностей с нагревом не возникнет.
Ковка клинка
Все пружинные изделия проходят закалку на предприятии. Сталь необходимо отжечь. Процесс производят постепенным нагреванием заготовки до температуры до 800-900 °С и оставляют остывать на воздухе. Деталь готова к работе:
- После отжига металл становится более податливым к любым манипуляциям. Проще приварить пруток, для удобства в дальнейшей работе, щипцы не понадобятся.
- Если заготовка имеет изогнутую форму, стоит её нагреть докрасна и малым молотом выпрямить. Следить за температурой обязательно. Не работать с остывшим металлом.
- Ковочная температура 1000-1100 °С, не имея термометра, определять её стоит на глаз (темно-жёлтый), либо магнитом – заготовка перестанет прилипать к нему. Цвет и термометр подсказывают, что сталь реально марки 65Г.
- Крупным молотом проковываем изделие и вытягиваем в длину. Рессоры в основном имею толщину в 5-6 мм, вытягивание следует продолжать до толщины в 3-4 мм.
- Лучше выковать спуски и носик к острию клинка сразу, в будущем меньше мороки на шлифовальном станке.
Приобретя вид клинка, изделие следует остудить на воздухе, срезать болгаркой пруток. Разметив конкретнее спуски и хвостовик, продолжить обработку на шлифовальном станке. Процессы изготовления рукояти и закалки клинка, обязательно опишем ниже.
Как выточить нож из рессоры своими руками
Резать или ковать – персональный выбор ножедела. Чтобы выгнуть заготовку нужна печь. Рессору лучше взять потоньше, иначе будет много возни с толщиной заготовки: устанешь её убирать и сотрёшь несколько кругов. Требуемый инструмент немного отличается от ковочного варианта
- УШМ, шлифовальный станок, круги к ним с разным зерном;
- печь и заготовка рессоры;
- напильники, молоток, наковальня;
- маркер, бумага;
- наждачка с разным зерном.
Молотом работать не придётся, больше мороки с болгаркой и шлифстанком. Приступая к работе, защитите глаза и руки.
Процесс изготовления ножа из рессоры
Следуя инструкции, клинок выйдет не хуже кованного. Важно, не перегреть заготовку и точно провести закалку:
- Произведя процесс отжига, и выпрямив заготовку, необходимо изготовить шаблон будущего клинка. Фантазия ножедела и интернет позволят создать уникальный шаблон клинка.
- Эскиз выполнить необходимо с запасом в пару миллиметров, на случай перегрева металла. Обвести его маркером на заготовке и приступить к трудоёмкому процессу – вырезанию.
- Толстую рессору придётся снять до 3-4 мм, сделать это поможет УШМ или шлифстанок. Снарядив болгарку отрезным кругом, и закрепив заготовку в тиски, вырезаем по контуру будущий клинок. Следите за цветом металла, не допускайте его изменения. Меняет цвет – перегрев. Поливайте больше водой.
- По заключению процесса вырезания снять заусенцы помогут напильники. Разметьте симметрично спуски и на шлифмашине снимите их.
Получив изделие близкое к клинку, затачивать сразу не следует. Не забывайте обработать хвостовик. Нож почти готов, осталось несколько нюансов.
Закалка лезвия
Вариантов закалки достаточно. Работая со сталью 65Г и аналогами, профессионалы рекомендуют, производить её в масле. Но присутствует мнение, что предпочтительнее процесс провести на воздухе. Остановимся на масляном методе.
Разогрев печь до 900 °С, ниже отметки ковки, аккуратно помещаем клинок и следим за нагревом. Достигнув оранжевого цвета детали, вынимаем клещами и на 3-и сек опускаем в масло. Вытаскиваем, ждём полного остывания. Опять помещаем в печь, нагреваем и в масло. Время выдержки увеличиваем на 1-у сек.
Сделать процедуру необходимо 3-и раза с постепенным увеличением времени окунания на 1-у сек. Клинок приобретёт высокую твёрдость и не потеряет пластичных качеств. Наш ресурс содержит более подробную процедуру закалки ножей в домашних условиях.
Важный момент – отпуск клинка. Производят отпуск при температуре от 200 до 300 °С. Процесс произвести реально в духовом шкафу газовой плиты. Нагрев заготовку до необходимой отметки, следует оставить её на 2-3 часа, не уменьшая показатели термометра.
Изготовление рукоятки
Существует 2-а типа рукояти: накладная и всадная. Для клинков с высокой твёрдостью применяют 1-ый вариант.
Способ несложный, потребуется:
- брусок древесины;
- дрель, свёрла;
- эпоксидный клей, штифты;
- наждачку;
- шлифовальный станок.
Древесину дозволительно заменить на: пластик, оргстекло и т.д. Материал подойдёт для применения различный. Вырезав подходящие по размеру накладки, насверливаем отверстия в хвостовике. В заготовках рукояти аналогично.
Доведя накладки наждачной бумагой до идеальной плоскости, приклеиваем их к хвостовику и вставляем штифты – их можно заклепать. Струбцинами закрепляем конструкцию, оставляем на 24 часа высыхать. На шлифовальном станке доводим рукоять до необходимых размеров.
Дерево обязательно требуется пропитать маслами или средствами против старения древесины. На нашем ресурсе имеется подробная статья о монтаже рукояти.
Заточка ножа
Твёрдость получившегося ножа составит 60-62 единицы по шкале Роквелла. Убедившись в симметричности спусков, можно приниматься за заточку. Процесс начинается с грубого точильного бруска с крупным зерном. Профессионалы советуют использовать алмазные камни для заточки ножей.
Движения осуществляются вдоль бруска до появления заусенца. Переходим к камню с зерном чуть меньше, двигая клинок поступательно. Процесс не требует быстрых и резких движений. Проводя заточку необходимо держать постоянный угол. Зависит он от будущего применения ножа. Оптимальным углом называют вариант в 20-25 град.
Для снятия заусенца необходимо работать на самом мелком зерне. Не забываем смачивать водой брусок. Заточка ножа потребует немалых усилий. Рессорно-пружинная сталь, после закалки, очень твёрдая.
Учитывая условия эксплуатации, наточив лезвие единожды – клинок затупится нескоро. Правильно заточенное изделие, способно резать жестяные листы без потери своих качеств.
Как сделать нож из рессоры. Изготовление ножа из автомобильной рессоры
quote: Originally posted by Golovorub:
Господа ножеманы, что вы думаете об изготовлении ножа из рессоры,
Мы об этом стараемся не думать.
Сейчас без труда можно достать более удобные для ножа железки, начиная от 95х18 или Х12МФ и выше, вплоть до дорогих порошков.
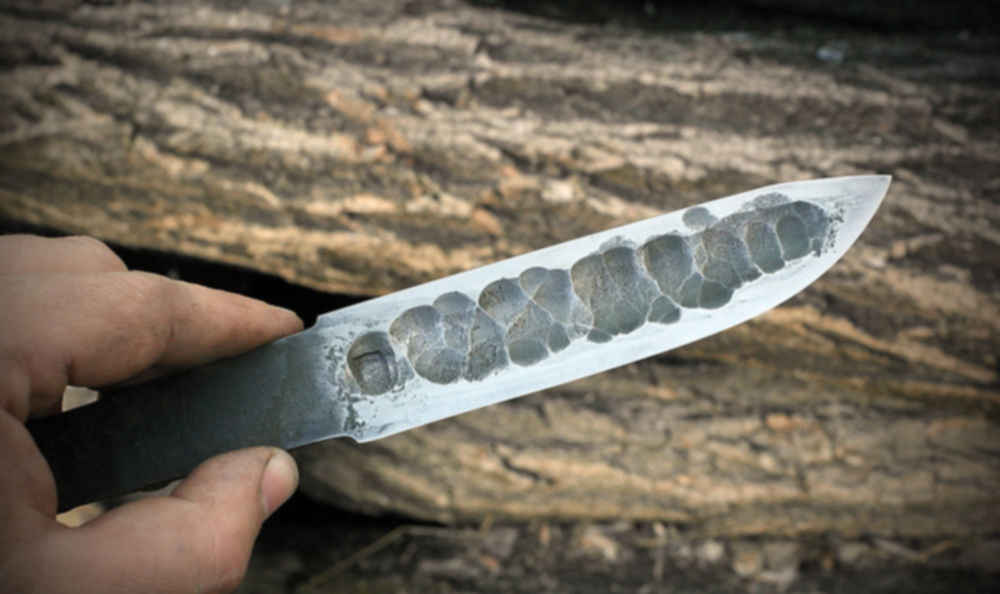
TriVX | posted 25-6-2010 09:24
Еще момент – рессоры на большую твердость не калят, если хочется хорошую железку – готовтесь перековать и закалить. Иначе заморачиваться не стоит – проще строгальный нож переточить. |
Пан | posted 25-6-2010 10:12
ИМХО конечно но рессорная сталь 50ХГА что-то близко к 420-й стали. А 420-я используется довольно активно. Сейчас у меня лежит несколько заготовок из рессоры. Сделаю, скажу как будет в работе. |
семен | posted 25-6-2010 10:22 Есть у меня ножик из рессоры винтажного Студебеккера, изготовлен американским мастером, рессора прокованна, не уступает Рэндаллам с их О-1 сталью.![]() |
TriVX | posted 25-6-2010 10:26 Тут уж от кузнеца много зависит. Это больше ему зачет! Пружинные стали вполне подходят для режиков, прочны, надежны, неплохо резучи, РК держат средненько но зато отлично точатся. Ржавеют сцуки обычно сильно, неважно работают по “абразивным” материалам (ну, с жесткими включениями). Хороший кованый нож из такой легированной “среднеуглоеродистой” стали – моя тайная страсть – очень я люблю такое дело. |
EAK | posted 25-6-2010 16:05
Да ну, близка. В 420й еще 13% хрома, ну и углерода поменьше. |
Bad_Alastor | posted 25-6-2010 17:58 У меня тоже есть заготовочка из 65Г, точнее ее щас на закалку унесли, вот на днях принесут, скажу что и как.![]() |
Golovorub | posted 25-6-2010 18:18
В том то и дело, что у нас нельзя! |
orm2006 | posted 25-6-2010 19:26
а подшипники и напильники у вас кончились? |
mara20s | posted 25-6-2010 20:33 Есть некоторое количество ножей из 65Г, мастер принципиально не калит более 57-58 ед.![]() |
mara20s | posted 25-6-2010 20:37 Плюсы – сырья хоть анусом кушай и технология у местных мастеров освоена за несколько десятилетий. Резучесть (у старых мастеров) может посоперничать с порошками типа S30V |
Golovorub | posted 25-6-2010 22:56 Старая рессора ничего не стоит и клинок из нее сделать проще. Ковать я не умею да и негде. |
slalomandro | posted 25-6-2010 23:35 кукри делаются из рессор, но там еще зонная закалка используется. если термисты знакомые есть, то можете пробовать. |
Меч из рессоры своими руками
Как сделать нож из рессоры
Чтобы получить нож из рессоры в домашних условиях, подготовим список таких материалов и инструментов:
• рессора автомобиля;
• кусок древесины для отделки рукояти;
• эпоксидный клей;
• болгарка;
• дрель или сверлильный станок;
• наждачная бумага с разной зернистостью;
• печь для закалки металла, масло;
• лобзик или другие инструменты для резки дерева;
• струбцины.
Ковка ножа из рессоры проходит в несколько этапов
Этап 1.
В первую очередь нужно собрать все материалы для работы, чтобы они были наготове. У автора исходным материалом послужил лист рессоры от старой машины.
Поскольку рессора выполнена в изогнутой форме, то ее необходимо выгнуть. Это делается так: металл нагревается, после чего постепенно остывает. Для нагрева подойдет горелка, также можно просто положить лист рессоры в хорошо разожженный костер.
После того, как заготовка остынет, нужно взять молоток и наковальню, и обработать рессору так, чтобы она стала прямой пластиной. После отпуска металл стал более мягок, он будет легко поддаваться резке, сверлению, и т. д.
Этап 2.
Сначала нужно изготовить шаблон ножа. Автор использовал готовый шаблон из интернета. Если есть желание – его можно улучшить. После распечатки шаблона бумагу нужно наклеить на картон и ножницами вырезать шаблон. Подержав его в руках, мы можем прикинуть, как будет выглядеть нож из рессоры.
После этого нужно приложить шаблон к металлу и обвести маркером.
Этап 3.
Сейчас мы приступаем к самому тяжелому этапу работы – нам нужно вырезать профиль ножа. Это делается с помощью болгарки – орудуя этим инструментом, не рекомендуется перегревать металл. Если в месте резки сталь начинает менять цвет – это значит, что он перегревается. В таком случае металл нужно полить водой. В тех местах, где нельзя вырезать, металл можно просверлить рядом отверстий и потом эту часть обломать.
Этап 4.
Это заключительный этап формировки основного профиля лезвия. Для такой работы очень удобен и прост ленточный шлифовальный станок. Умельцы с большим опытом могут использовать болгарку. Наружную плоскость ножа следует отшлифовать, чтобы она блестела. Для прижатия заготовки к шлифовальной ленте автор воспользовался бруском. Здесь также нужно следить, чтобы металл не перегревался.
Другой ответственный момент шлифовки заключается в изготовлении на ноже скосов.
Этап 5.
Чтобы надежно закрепить накладки на рукоятке, в данном ноже используется 4 штифта. Для них нужно просверлить отверстия. Для подбора диаметра ориентируемся на имеющиеся штифты, которыми традиционно служат стержни из латуни. Для этого случая подойдут и обычный стальные гвозди.
Этап 6.
После закалки клинок приобретает твердость и долго не тупится. Чтобы закалить лезвие, нужно взять масло – подойдет моторное или растительное, печка или хороший костер. Металл необходимо нагреть до такого состояния, при котором к нему не будет притягиваться постоянный магнит. Как отмечает автор, во время нагрева металл отличается тусклым красным цветом. После этого нужно опустить заготовку в масло. Следует быть осторожными, поскольку масло часто воспламеняется с дымом и брызгами, летящими в разные стороны. Емкость для закалки нужно брать металлическую.
Случается, что во время закалки металл начинает деформироваться. Такую ситуацию можно исправить. Для решения проблемы нужно нагреть заготовку, выровнять, и затем опять попробовать закалить.
Этап 7.
Для изготовления накладок на рукоятку, берем две дощечки небольшой толщины. Вырезаем их до требуемого размера и сверлим в них отверстия для штифтов.
Теперь склеиваем заготовки при помощи эпоксидного клея, нанеся по хорошему слою на обе накладки. Затем нужно вставить штифты и хорошо зажать ручку струбциной. Оставляем в таком виде на 24 часа, чтобы клей полностью высох. Сразу для удаления остатков клея берем тряпочку или туалетную бумагу.
После того, как клей высохнет, нож нужно достать и окончательно сформировать форму рукояти. Для этих работ используем ленточный шлифовальный станок.
На завершающем этапе нож полируем, если нужно – делаем поверхность клинка зеркальной. Можно отполировать и рукоятку, так она станет гладкой.
Деревянные накладки в обязательном порядке пропитываем льняным маслом или другими пропитками. Иногда для этого нагревают пчелиный воск и смешивают его со льняным маслом.
В конце работы наш нож нож из рессоры своими руками следует хорошо наточить. Самым доступным вариантом является мелкозернистая наждачная бумага.
Главной движущей силой в развитии металлообработки и металлургии было изготовление оружия. Любой металл, открытый человеком, тут же приспосабливали под производство этих орудий, открывая и разрабатывая новые технологии. Эти изыскания привели к открытию железа, а позже и стали, причем качество последней постоянно старались улучшить.
Ковка меча и сегодня довольно непростой технологический процесс. Как его можно изготовить в своей мастерской и из каких материалов? А также что нужно знать об изготовлении мечей?
Из чего ковать меч
Первые мечи пытались ковать из бронзы, однако качество их было, мягко говоря, не очень, слишком мягкий материал использовался. Первые железные и стальные образцы так же были плохого качества, их приходилось выравнивать после нескольких ударов. Именно поэтому на первых порах главным оружием было копье с топором.
Все изменилось с изобретением нескольких новых технологий, например, послойной сварки и проковки, что давало прочную и, главное, пластичную полосу стали (харлужная сталь), из которой ковали мечи. Позже появились фосфоритные сорта металла, производство этого вида оружия стало дешеветь, а приемы их изготовления упрощаться.
С чего можно выковать меч сегодня? Многие специалисты рекомендуют использовать марку стали 65Г. Это рессорно-пружинный сорт металла, использующийся при производстве рессор, пружин амортизаторов, корпусов подшипников. Марка имеет в составе низкий процент углерода и дополнена такими легирующими элементами, как никель, хром, фосфор. Такая сталь имеет прекрасные показатели прочности, а, главное, она пружинистая, что не даст мечу изгибаться при нагрузке.
Выбирая материал для изготовления меча, изначально надо решить, как он будет использоваться. Если просто как декоративное украшение интерьера, то качество металла не столь важно. Для реконструкторских боев потребуется хорошая сталь, которую нужно будет дополнительно закалить.
Также можно поискать элементы рессор от автомобилей или тракторов, которые производят из марок стали 55ХГР, 55С2ГФ и других подобных аналогов.
Для декоративных мечей можно просто приобрести прокат в виде прутка или полосы на ближайшей металлобазе. Однако, подбирая материал, стоит учесть, что при ковке будет утрачена часть объема, а, значит, размеры заготовки должны быть больше.
После приобретения стали нужно озаботиться наличием оборудования для ее обработки.
Что нужно для ковки меча
Основная проблема обработки заготовки при ковке меча — наличие соответствующего размерам оборудования. Образцы такого оружия имеют длину 1000-1200 миллиметров. Следовательно, нужно иметь горн, который позволит разогревать металл полностью на всю протяженность.
Кузнечный горн с нужными параметрами можно сложить своими руками, используя огнеупорный кирпич. Для этого выкладывают печь, например, с открытым верхом и длинной очага 1,2-1,4 метра.
Также потребуется стандартный кузнецкий набор: наковальня, клещи, подбойник. Обязательно потребуется молот ручник, которым делают все кузнечные работы. Резку металла и его шлифовку можно осуществлять с помощью болгарки.
Значительно упрощает и ускоряет ковку наличие механического кузнечного молота.
Еще один немаловажный момент — это закалка меча. Особенно, если нужно получить прочное изделие. Для этого придется поискать какую-то посуду по длине клинка, залив в нее машинное масло или воду.
Когда собрано все необходимое оборудование, потребуется изготовить хотя бы простейший чертеж, по которому будет осуществляться дальнейшая ковка и сборка меча.
Когда все готово, приступают непосредственно к ковке.
Как ковать меч
Независимо от того, что послужит исходной заготовкой для будущего меча (пруток или полоса с рессоры), ее нужно нагреть. Главное — соблюдать температурные рамки разогрева стали.
Нижняя граница ковкости низкоуглеродистых сталей составляет показатель 800-850 градусов. Без приборов определить прогрев материала можно двумя способами.
- Первый — при определенной температуре накала сталь приобретает соответствующий окрас. При 800-830 градусах — светло-красные и светло-вишневые тона.
- Второй — магнитные свойства материала. Их проверяют обычным магнитом. Когда сталь нагревается до показателя 768 градусов и более, она теряет свои магнитные свойства. После остывания они восстанавливаются.
Итак, заготовка разогрета, как ее формировать ковкой?
- Если это пруток, то его нужно проковать вдоль протяженности, сделав из него полосу нужного сечения.
Во время поковки на поверхности металла будет образовываться слой окалины. Часть ее сама отвалиться, но всю поверхность нужно периодически зачищать, пользуясь щеткой по металлу.
- Спуски будущего меча можно сформировать после ковки, используя наждачный круг, либо проковать их, сформировав приблизительные формы клинка.
- На конце полосы, где будет собрана рукоять, нужно сделать хвостовик. Для этого часть полосы проковывают с торцов и плоскостей, образовывая конус.
- В месте, где хвостовик соединяется с клинком, ковкой формируют плечи меча.
- Вдоль плоскостей лезвия нужно проковать долы. Их формируют, используя подбойники или шаблоны.
- Гарда обычно изготавливается отдельно и ее не куют вместе с клинком меча.
- После окончания работы изделие очищают от окалины и стабилизируют (отпускают). Для этого в горне клинок разогревают до красного цвета и оставляют остывать вместе с очагом.
- Закалку делают после остывания при стабилизации металла. Меч нужно прогревать равномерно по всей длине, следя, чтобы подаваемый воздух не попадал на клинок. Когда металл станет едва красным, его быстро опускают в воду полностью. После чего нужно снова отпустить материал. Для этого его предварительно зачищают и греют до золотистого цвета. Остывание проводят уже на открытом воздухе.
Это самая простая технология того, как выковать меч в домашних условиях. Потренировавшись, можно будет изготовить отличный клинок.
Важно соблюдать температуры нагревания, а также правильно провести закалку клинка.
Перекалив металл, получиться очень хрупкое изделие, а плохо закаленный материал будет слишком мягким.
Закончив ковочные процессы, изготавливают граду, рукоять и навершие.
Конечно, можно изготовлять мечи и без кузнечных технологий, используя слесарные приемы. Однако, именно кованое изделие будет прочным и натуральным.
В примитивных условиях очень трудно соблюдать правильную технологию изготовления кованного меча хорошего качества. Особенно без опыта кузнечных работ. Лучше всего изначально потренироваться, куя, например, коротки ножи или другие подобные изделия.
Огромное преимущество дает наличие механизированного оборудования. Как пример изготовления меча кузнечным способом с использованием механического молота можно посмотреть на предоставленном видео:
А есть ли у Вас опыт изготовления длинномерных предметов и, в особенности, мечей? Поделитесь способами и приемами обработки металла, примите участие в обсуждении в блоке комментариев.
Нож – это отличная вещь, которая может быть полезна не только в качестве прекрасного инструмента, но и в виде замечательного сувенира. Каждый мальчишка будет рад такому подарку. Если нож изготовлен вручную, то он сразу становится уникальной ценностью в глазах владельца.
Взрослые тоже не всегда используют ножи исключительно в бытовых целях – многие люди их коллекционируют. Критерии выбора у всех разные, но каждый знает, что качественная сталь – это обязательное условие для хорошего ножа. Но и красиво выполненная ручка может произвести не меньшее впечатление, чем прочное лезвие, способное долго держать заточку.
В чем же особенность ножа из рессоры?
Причина популярности такого изделия, как нож из рессоры, заключается в свойствах металла. Высокая износостойкость и прочность в сочетании с высокой пластичностью позволили многим поколениям мастеров пользоваться рессорами как главным источником сырья.
Характеристики рессорно-пружинной стали
Рессоры изготавливают из рессорно-пружинной стали 65Г, но могут быть применены другие марки: 50ХГСА, 50ХГА, 50ХФА. Это тоже рессорно-пружинные стали – определить какая из них взята в качестве материала для клинка можно только с помощью химического анализа. Либо по нюансам поведения металла при обработке, но с этим справятся только опытные мастера. Для начинающего изготовителя разница между перечисленными материалами будет практически незаметна.
Применение рессорной стали
65Г считается одной из самых дешевых пружинных сталей. При этом она обладает рядом уникальных свойств, делающих ее незаменимой для создания пружин. Рессорная сталь для ножа содержит хром, никель, марганец, кремний. Эти элементы придают свойства, за которые изготовителями выбирается именно этот материал:
- хорошая гибкость;
- высокая ударная вязкость;
- твёрдость;
- износостойкость;
Термообработка играет большую роль в улучшении качеств материала. Сталь становится прочнее, повышается ее твердость. К сожалению, она недостаточно устойчива к коррозии – имеет обыкновение ржаветь. Но достоинства перевешивают недостатки и ее часто используют как материал для клинка.
Такие ножи применяют в самых разных сферах. В первую очередь в качестве кухонных – крепкие, прочные, долговечные – что ещё нужно для ежедневной работы на кухне и, например, для разделки мяса? Те же соображения заставляли охотников, рыбаков и туристов стараться заполучить в свой арсенал эту качественную «самоделку». Поэтому многие мастера делали на продажу туристические и охотничьи ножи.
Благодаря хорошим характеристикам стали, эти ножи были популярны среди военных. Солдаты срочной службы, имевшие доступ к инструментам для металлообработки, в кустарных условиях изготавливали армейские ножи.Со временем, изготовители начали замахиваться на более серьёзные изделия: топоры, мечи, мачете, катаны. Из-за хорошей ударной вязкости рессорные стали прекрасно подходят для ковки. Ковкой можно изготовить клинок любой формы, даже самой причудливой.
Как сделать нож из рессоры
Изготовление ножа из рессоры может отнять много времени и сил, особенно, если человек делает это в первый раз. Но рессорно-пружинная сталь хорошо поддаётся обработке и «стерпит» ошибки новичка, поэтому именно из неё лучше всего создавать свой первый нож.
Обычно, материал находят на открытом воздухе: на улице, на автобазах, рядом с гаражами, на автомобильных свалках и других аналогичных местах. Поэтому рессора может быть покрыта грязью и ржавчиной и перед работой ее надо тщательно отчистить. Если необходимо выпрямить выгнутую рессору, то её нагревают до красна, а затем дают остыть в нормальных условиях – при комнатной температуре.
Как сделать нож из рессоры с помощью ковки
Все рессорно-пружинные стали, в том числе 65Г, объединяет одно качество: они прекрасно поддаются ковке. Ножи из рессорной стали, изготовленные ковкой, будут более надёжными и долговечными, потому что в процессе обработки происходит упрочнение металла за счёт пластической деформации и изменения макроструктуры.
youtube.com/embed/bSWgECVp0xU?feature=oembed»/>
Прежде чем проковать рессору, необходимо вырезать из неё профиль будущего клинка. Затем заготовку надёжно крепят, и нагревают до красна. Ковкой создаётся остриё и лезвие. Этим способом легко придать клинку требуемую форму, а также задать его ширину. Ковкой из рессоры хорошо удается изготавливать топоры и различные экзотические вещи, такие как мачете или меч.
Лезвию дают остыть до температуры окружающей среды после того как работа закончена.
Как выточить нож из рессоры своими руками
Необходимо, в первую очередь, определиться с внешним видом будущего изделия. Форма зависит от назначения ножа: кухонный, охотничий, сувенирный или какой-либо другой. В итоге клинок может быть любой – на это влияют только фантазия и возможности изготовителя. Если выбор сделан, то нужно взять готовый шаблон или выполнить его самостоятельно из картона или плотной бумаги.
com/embed/S8myBkMWbaw?feature=oembed»/>
Далее, чтобы изготовить нож из рессоры своими руками, надо быть готовым начать работу с металлом. Сначала шаблон необходимо приложить к металлической заготовке и обвести маркером, карандашом, чертилкой (ГОСТ 24473-80) или другим разметочным инструментом. По контуру, полученному посредством шаблона, требуется вырезать профиль изделия. Подойдут следующие инструменты:
- ленточная пила;
- угловая шлифмашинка, она же «болгарка» – важно не перегреть заготовку при отрезании;
- сверлильный станок или дрель – в этом случае вдоль контура сверлят отверстия, затем перегородки между ними ломают или выпиливают;
- можно использовать ручной инструмент;
Сам процесс обработки достаточно прост, хотя и требует определённой концентрации, чтобы вырезать заготовку в соответствии с разметкой. Когда обработка успешно завершена и заготовка стала соответствовать шаблону, то можно приступать к формированию клинка. Основная задача – сделать скосы. Лезвие снова размечают, определяя размеры скосов. При дальнейшей обработке следует строго придерживаться разметки.
Для работы лучше всего использовать электрическое точило. Также подойдут и ленточная шлифмашинка, и «болгарка», но, в случае последней, требуется хорошее владение инструментом. Можно выточить скосы вручную – напильником. На этом работы по металлу должны быть закончены, потому что далее клинок пройдёт термическую обработку, после которой сделать с заготовкой что-либо ещё будет очень сложно.
Закалка лезвия
Основной вид термической обработки – это закалка. Она нужна, чтобы лезвие было прочным, и могло оставаться острым долгое время после заточки. Существуют разные приёмы:
— закалка, с нагревом только режущей кромки;
— закалка режущей кромки нагревом изделия целиком;
— закалка с отпуском;
В первом случае только крайняя часть лезвия нагревается до немагнитного состояния, после чего его помещают в масло и выдерживают, пока масло не перестанет пузыриться. Второй способ сложнее: нагревается нож целиком, но погружать его в масло требуется только на треть – чтобы режущий край был покрыт жидкостью.
Закалка с отпуском – это метод, при котором остывание заготовки проводится в два этапа: сначала в при повышенной температуре, но ниже температуры закалки, затем при комнатной температуре.
Самый простой способ закалки – это полная закалка клинка, но при этом способе есть вероятность, что лезвие поведёт. Тогда надо провести рихтовку испорченной заготовки. Это можно сделать как предварительно разогрев лезвие, так и в холодном состоянии.
Изготовление рукоятки
Ручку можно изготовить практически из любого сырья, но особой популярностью пользуются дерево, пластик, кожа, кость. Красиво выглядят наборные ручки с чередующимися слоями, например, кожи и бересты.
Кость – это традиционный материал, для изготовления разнообразных безделушек и предметов быта. Обладая навыком резьбы по кости можно сделать уникальную, красивую ручку. Но проще всего взять две деревянные или пластиковые накладки, поместить их по обе стороны от хвостовика и закрепить между собой заклепками, а для большей прочности ещё и эпоксидным клеем. Иногда для крепления используют винты и гайки, но если важен внешний вид, то лучше их не применять.
Рукоять должна быть удобной, поэтому требуется уделить большое внимание ее обработке. Для этого используются сначала напильники, а затем наждачная бумага. Если накладки деревянные, то их обязательно надо пропитать маслом, чтобы обеспечить долговечность древесины. Пропитка подчеркивает структуру дерева и придает изделию привлекательный внешний облик. После закрепления рукоятки проводят ее окончательную шлифовку.
Заточка ножа
Работа над ножом из рессоры практически завершена, осталось только заточить его. Для этого используют:
- бруски;
- мусаты;
- точильные станки;
- механические точилки;
- электрические точилки;
Действительно хорошие результаты получают применяя брусок или электрическую точилку. Чтобы хорошо заточить нож с помощью бруска или точильного камня понадобится не мало времени. Если на обычный кухонный нож достаточно потратить около получаса, то выравнивание и заточка длинного кованого ножа может занять несколько дней.
Для лучшего контроля процесса заточки точильный камень помещают на устойчивую горизонтальную поверхность. Оптимальный его размер – примерно в полтора раза длиннее лезвия. Начинать заточку требуется грубым точильным камнем, с крупным зерном. Продолжать надо до тех пор, пока не появится заусенец. После этого берётся мелкозернистый камень, далее процесс продолжается с его помощью. Чтобы самодельный нож из рессоры стал острым, а заточка держалась долго, надо соблюдать следующие правила:
- движение осуществляется путём поступательных перемещений ножа вдоль бруска – режущей частью вперёд;
- конец бруска и конец лезвия должны «встретиться». Нужно синхронизировать смещение ножа поперёк бруска (от ручки к лезвию) и перемещение ножа вдоль бруска;
- плоскость клинка и поверхность бруска должны составлять угол от 20 до 25 градусов – это универсальный угол заточки.
В зависимости от назначения ножа, угол может меняться, но важно, чтобы он удерживался постоянным всё время пока происходит затачивание ножа;
В конце необходимо провести шлифовку лезвия, чтобы надолго сохранить нож острым. Для этого берётся точильный камень с самым мелким зерном. Затем аккуратно, чтобы не испортить уже сделанное, снимается заусенец.
Заточка — процесс требующий терпения и внимательности. Навык приходит только с опытом, поэтому все, кто не хочет ждать, могут воспользоваться электрической точилкой. Это сэкономит время, а также позволит сохранить ножи в превосходном состоянии.
Изготовление ножа — это процесс сложный, требующий внимания, концентрации, тщательности, навыков работы с металлом. Но труд не будет напрасным, ведь в итоге получится прекрасное изделие, созданное своими руками. Чем с большей любовью и старанием мастер подходил к делу, тем лучше будет изделие. Даже новичок, если окажется терпелив и настойчив, сможет овладеть навыками и тоже станет гордиться результатами своей работы.
Если вы нашли ошибку, пожалуйста, выделите фрагмент текста и нажмите Ctrl+Enter.
Ковка ножа кукри из рессоры
Здравствуйте все. Как всегда, гулял в сети и случайно наткнулся на статью, где автор рассказывал про ковку интересного на вид ножа под названием кукри. Не стал особенно искать историю такого вида ножа так поверхностно почитал и ничего особенно не понял про происхождение ножа кукри. В основном этот нож используется для хозяйственных нужд для рубки кустов небольших деревцев типов нож для выживания. На видео обзорах вроде бы интересный нож его используют как заменитель мачете кстати в нашей стране не является холодным оружием даже при длине 40 см длиной, так как им почти не реально произвести калящий удар.Мне стало интересно как реально работает, как им пользоваться и я решил ковать себе нож кукри. В этой статье об этом и пойдет речь кому не интересно просто пролистайте фото в статье все не особо профессиональные выводы и действия.
Понадобится инструмент
- Дрель
- Болгарка
- Грин дер с набором лент
- Кузнечный горн
- Молот разного веса для ковки
Понадобится материалы
- Кусок рессоры от грузового авто
- Дерево для рукояти сухое
- Клей
- Наждачная бумага разная
- Диски на болгарку отрезной и шлифовочный
- Масло для пропитки рукояти
Ковка клинка
1. Для дальнейшей ковки нагреваю до желтого цвета рессору и даю ей остыть процедуру повторил два раза второй раз нагревал сильнее чем первый. Так произошел отпуск металл теперь ковать будет проще. Нагреваю полосу до желтого цвета, и наношу удары бойком молотка вытягивая немного по длине. При достижении необходимой длинны и толщены начинаю формировать острие. От кончика начинаю ковать спуски одновременно формируя примерный вид лезвия. Отковав 15 см от кончика ставлю на край наковальни обух и произвожу изгиб лезвия характерный для ножа кукри. При сгибании клинка в месте сгибания проковал лезвие чтобы не было утолщения. От места изгиба продолжаю проковать лезвие, но уже стараясь сделать уже чем кончик клинка. Спуски отковал приступать к хвостовику сильно не мучился все равно болгаркой отрезать лишнее придется. Толщина на обухе 4 мм спуску до 1.5 мм чтобы при закалке не сжечь режущею кромку. Вот и все с ковкой выключаю горн он еще с углями ложу клинок на угли, и оставляю до полного остывания вместе с горном иначе нож будет твердым при шлифовке так как структура металла очень мелкая напряжена и клинок может даже лопнуть при ударе или при закалках, а это обидно после пару часов труда случайно сломать клинок было у меня такое и не раз.
Шлифовка клинка и нарезка дола
2. После обрезки всего лишнего зажимаю хвостовик в тески обдирочным диском шлифую поверхность в черновую до толщены 1.2 мм. С обеих сторон отшлифовав спуски делаю разметку дола он там необязателен, но все делают, и я сделал так нож брутальный смотрится. Дол прорезал тонким отрезным диском потом шоркал про наждачной бумагой. Напильником сделал шип у рукояти не помню как его называют и не знаю зачем он там как я понял этот шип как печать или знак мастера кузнеца, а люди раздули типа увеличивает прочность клинка по моему это бред. После всего этого на Гриндере шлифую разной наждачной бумагой, но не в блеск самая мелкая бумага 120. Металл хоть и не калил еще, но бумага ест его бедно. Спустя два часа наконец то закончил мучиться на Грин дере попив кофе приступил к розжигу горна для закалки клинка горн буду топить древесным углем не знаю почему, но на древесном угле закалка происходит лучше, чем на каменном угле.
После полного прогрева углей нагреваю клинок до состояния когда клинок не прилипает к магниту держу еще секунд 30ть. Окунаю в подогретое заранее масло до шестидесяти градусов вот и все. Сталь 65г не закалится до 60 единиц, но 40-45 единиц получить можно. После закалки произвожу отпуск по-простому просто нагреваю клинок до цвета побежалости почти темно золотого цвета, и как побежалость меняет цвет на синий со стороны обуха перестаю нагревать и даю остынуть зажав хвостовик в тесках. Стаю смотрю на клинок и думаю может оставить клинок таким цветным все равно его хотел травить. В общем так и оставил красивый хамелеон. По качеству закалки клинок прочный упругий точится так себе кромка не крошиться в общем закалка произошла успешно.
Рукоять
Для рукояти взял кусок сухой древесины не знаю что за дерево валялся среди кучи кусков выбрал подходящей формы и без трещин сучков. Дата закладки на сушку 17 год октябрь есть и еще старше не стал брать оставлю для лучших времен. Стругаю немного дерева ножом формируя примерную форму чтобы на Гриндере не трудится долго. Делаю разметку для хвостовика просверливаю отверстие в дереве, и делаю насечки на хвостовике для более хорошего удержание рукояти. Приклеиваю все на двух составной клей и оставляю сохнуть на пару часов. После высыхания приступаю к шлифовке ручки на Гриндере сначала грубой лентой, а потом и мелкой. Форму формировал на глаз просто примерял к руке и шлифовал что мешало в общем подогнал под свою руку и шлифовал мелкой наждачной вручную. Для декора пропитал на паровой бане натуральным воском в течение двух часов пока пузырись не перестала ручка чтобы не портилась ручка от влаги, и для декора обжог немного газовой горелкой и шлифовал немного на войлочном диске чтобы не марало руки, а также для блеска да и эстетичней выглядеть стала.
Вот и все ковка ножа кукри из стали 65г завершена. Нож решил проверить на зимней рыбалке немного порыбачил, подмерз, взял свой кукри и пошел в лес с первого удара нож мне понравился рубить хорошо щепу колит на ура классный нож для приготовления дровишек для костра, а так мне кажется бесполезная игрушка.
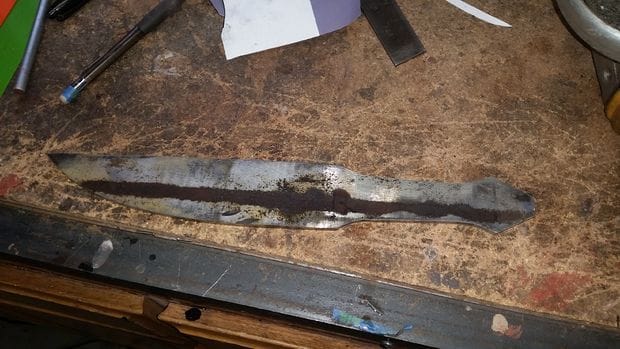
Становитесь автором сайта, публикуйте собственные статьи, описания самоделок с оплатой за текст. Подробнее здесь.
Ковка ножей в домашних условиях своими руками, технология ковки
На чтение 10 мин. Просмотров 10.2k. Опубликовано Обновлено
Хороший нож – вещь крутая, нужная и красивая. Хороший нож своими руками – уже не вещь, а символ человека, который его сделал. Это непросто, но если задаться целью, то добиться успеха в ковке ножей собственного дизайна реально.
Несмотря на то, что речь идет о технологии горячей ковки с использованием качественной легированной стали, подготовка работ и изготовление ножа – процессы вполне доступные для каждого человека. Главное – принять решение.
Что такое хороший нож
Для начала договоримся о функциональном назначении ножа, который вы собираетесь делать своими руками. Скорее всего, самым оптимальным выбором будет ориентация на изготовление качественного охотничьего ножа. С охотничьими ножами тоже нужна ясность: какой именно является самым универсальным?
[box type=”fact”]Опытные охотники могут иметь солидные коллекции охотничьих ножей самого разного размера и качества, но на охоту они ходят только с одним.[/box] Ковка ножа из троса.Он будет самым подходящим. После анализа и опросов в охотничьих источниках появилось описание усредненного ножа охотников, который может считаться самым универсальным.
Для российских условий охоты таким будет нож, средний по размерам со следующими габаритами:
- Клинок может быть длиной от 12 до 14 сантиметров, шириной – не более 3-х см.
- Толщина лезвия – примерно 3 – 4 мм.
- Общая длина ножа насчитывает от 23 до 27 сантиметров.
Сталь и только сталь
Выбор металла небогатый, если точнее – выбора у вас нет вообще. Только сталь для ковки ножей, без вариантов. Разберемся, что такое сталь в принципе: это сплав железа с углеродом. Обычный углеродный диапазон содержания в стали – от 0,1% до 2,5%. Чем выше уровень его содержания, тем сталь прочнее и устойчивее к внешним воздействиям, но она сразу же теряет пластичность и вязкость.
Свойства стали, которые оказывают самое прямое влияние на хорошее качество изделия:
- Высокая устойчивость к износу зависит от твердости стали, которая, в свою очередь, зависит от содержания в сплаве углерода.
- Высокая прочность – сохранение целостности изделия под действием внешних сил.
- Твердость – ее сопротивление деформации.
- Высокая пластичность – способность стального изделия гнуться под влиянием внешних сил, а затем восстанавливать форму.
- Красностойкость – это устойчивость металла к высоким температурам. Твердые марки стали – самые красностойкие.
Немаловажно то, что все пять показателей тесно взаимосвязаны. Чем, например, пластичнее марка стали, тем ниже ее твердость. Свойствами сплавов можно управлять с помощью добавок и легирующих элементов.
Теперь о легировании. Это целенаправленное добавление в металл добавок для изменения различных свойств в лучшую сторону. Чем только сталь не легируют: никелем, молибденом, кобальтом и др. Нас интересует легированная инструментальная сталь, обладающая вышеописанным свойствами. Марок высококачественных металлов много, их характеристики можно найти в многочисленных справочниках и руководствах.
Нам же достаточно понимать общие принципы, чтобы найти подходящую сталь для нашего ножа. Далеко за ней ходить не нужно, ножа производится из подшипников, напильников, рессор, сверл и даже металлических тросов. В каждом случае есть технические нюансы, но общие правила ковки ножей дома одинаковые и строгие.
Дизайн клинка, нож и закон
Ковка ножа из цепи.Речь не о красоте, а о форме клинка, которую необходимо выбрать и сделать эскиз на старте подготовительных работ. Основных форм профилей клинков немного: кинжал, прямой обух, профили с повышенной или пониженной линей обуха, финка или «боуи, козья ножка, «танто».
Сразу заметим, что, например, «танто» или финка и «боуи» относятся к холодным видам оружия.
[box type=”info”]Внимание! Перед выбором формы клинка нужно внимательно прочитать о характеристиках холодного оружия, чтобы не попасть с выбранной формой под уголовную статью. Если ношение холодного оружия штрафуется небольшой денежной суммой, то за изготовление и сбыт холодного оружия можно получить два года лишения свободы.[/box]youtube.com/embed/7IwLYDIHcS4?feature=oembed»>
Инструменты для ковки ножей
Какие инструменты потребуются для ковки:
- большой молот до 4 кг и маленький молоток до 1 кг;
- ;
- и болгарка;
- точильный станок;
- печь;
- щипцы и разводной ключ.
youtube.com/embed/dxvVLqhEURg?feature=oembed»>
Нож из сверла, этапы работы
Как правильно сделать нож из сверла:
Кузнец создает заготовку ножа.- Разбираемся со сверлами и сталью. – один из самых популярных источников стали для самодеятельных кузнецов. В самом деле, у легированной вольфрамом и молибденом стали Р6М5 великолепные характеристики для будущего классного ножа: она чрезвычайно прочная, обладает высокой устойчивостью к износу и к тому же легко затачивается, а это особенно важно для ножей. Аналогичная сталь на импортных, исключая китайские, сверлах обозначается как HHS – High Speed Steel, сталь для работы на больших скоростях. Самым лучшим вариантом будет сверло из стали, в которую кроме вольфрама и молибдена добавлен кобальт, она еще устойчивее и называется Р6М5К5.
Ну а импортные сверла станут в этом случае HHS-Co. Итак, запоминаем: ищем отечественные сверла из Р5М5 с добавлением кобальта, или импортные, исключая китайские) HHS тоже с добавкой Co.
Если у вас в руках большое сверло, рассмотрите его внимательно. Обычно они состоят из двух частей: хвостовика из самой обычной стали и рабочей спирали из нужной нам стали Р6М5. Границу можно определить по искрам при проточке сверла вдоль его длины. Сноп искр на участке легированной стали будет красноватый и редким. На участке обычной стали искры выйдут желтыми, сноп будет большим. - Обжиг стали. Это простой и «спокойный» этап работы. Печь нужно разжечь и нагреть в ней заготовку примерно до 600° – 700°, выдержать такой режим около четырех часов, затем дать остыть печке вместе с заготовкой.
Внимание! Этот этап во многих источниках и руководствах не описан. Зачем это делать? Дело в том, что большинство кустарных мастеров делают ножи из уже готовых и закаленных инструментов.Их обжиг нужен именно в таких случаях, иначе при дальнейшей ковке в структуре металла может возникнуть ненужное напряжение. Для справки: температуру в 700° легко проверить с помощью соли – при этой температуре она начинает плавиться.
- Разогрев сверла. Затапливаем печь с подачей воздуха, после разогрева углей размещаем сверло в печке с помощью клещей. Если ковка ножа выполняется вами впервые, вы можете сделать ошибку с определением температуры нагрева – или перегреть, или нагреть недостаточно. В любом случае температура нагрева должна быть выше 1000° с оранжевым цветом заготовки. Сразу же сверло вынимается из печки и хвостовиком зажимается в тисках. Самое первое и срочное дело – расправить спираль сверла, зажав верхушку разводным ключом. Если вы не успеете раскрутить спираль, сверло может сломаться. Если за один раз спираль не раскрутилась, можно нагреть сверло повторно. В итоге вам нужно получить ровную стальную полоску.
- Ковка и раскатка.
Снова раскаливаем стальную полоску и начинаем выравнивать ее ударами тяжелого молота. В итоге полоска должна стать шире и тоньше: от 4-х до 5-ти мм. Ковка ножа – это постоянный контроль цвета стальной полоски. Если она начинает тускнеть и появляются вишневые оттенки, сразу же отправляем ее в печку снова нагреться.
- Внимание! Главное правило печки: лучше лишний раз нагреть и даже перегреть, чем сломать остывшее изделие ударами молота. В помощь кузнецам существует специальная шкала температур и окраски стали. Если при низких температурах уровня 500° – 600° сталь будет темно-коричневого цвета, то при 1000° сталь станет оранжевой. Ну а при самом высоком разогреве до 1300° она станет ослепительно белой.
- Ковка острия лезвия. Один из самых сложных этапов, это и есть та самая ковка ножа по сути. Лезвию нужно придать нужную форму, не изменяя при этом толщину – вы уже добились нужной толщины в 4 – 5 мм на предыдущих этапах. Здесь нужна кое-какая практика: острие нужно постепенно закруглять, а лезвие одновременно оттягивать в длину.
Эта работа может не получиться с первого раза, будьте готовы к такой ситуации. Вы ведь обладаете личным качеством под названием «терпение»?
- Ковка режущей кромки. Тоже непростой и важный этап. Он выполняется малым молотком: аккуратными ударами режущая кромка делается как можно тоньше, начиная с середины лезвия. Лезвие при этом должно оставаться ровным. На этом этапе также чрезвычайно важен нагрев заготовки: следить за цветом и при необходимости подогревать его в печке.
- Проковка хвостовика. Здесь все намного проще. Раскаливаем хвостовик в печке и раскатываем его большим молотом. Форма будет зависеть от вашего выбора дизайна ручки, что в данном обзоре не рассматривается.
- Шлифовка. Благодарная и приятная работа: снять лишние слои и неровности, выровнять поверхность до блестящего состояния – одно удовольствие. Следует помнить, что при шлифовке толщина уменьшится, может потеряться до 2-х мм. В итоге нож станет легче и тоньше.
Заточка также делается на этом этапе.
- Закалка ножа. Ни в коем случае не пренебрегать этим этапом, несмотря на то, что ваш нож великолепно выглядит и кажется полностью готовым к употреблению. От закалки будут зависеть главные рабочие свойства ножа. После шлифовки и полного остывания нож подогревают в печке до оранжевого или светло-красного цвета, температура примерно 500° – 700°. Затем его быстро опускают в подсоленную воду или масло. В воде сталь начинает «дрожать» – это и есть процесс закалки. Некоторые производят еще одну операцию «на дорожку»: отпускают клинок. Отпуск заключается в небольшом финишном нагреве до появления тонкой оранжевой пленки: тут же убираем нож из печки и даем ему самостоятельно остыть.
Ножи из напильника, рессоры, троса, подшипника
Особенности обработки заготовок:
Создание заготовки в кузнечной мастерской.- Нюансы с подшипником. Очень популярный материал. Обычно используется внутренний обод подшипника. Работа практически такая же, как со сверлом. Разница лишь в неудобстве на первых этапах: заготовку из обода очень неудобно держать, поэтому ее лучше приварить к пруту арматуры. Стальную полоску выковывать легче, чем из сверла – здесь ее достаточно выровнять.
- Автомобильная рессора. Великолепный материал с высокой упругостью и стойкостью к износу. Заготовку отрезаем болгаркой, привариваем ее к пруту арматуры так же, как обод подшипника – в этом случае работать намного комфортнее.
- Напильник – второй по популярности вид подручного материала для высококлассных ножей.
Особенности стали в напильниках – редкая долговечность и отличная режущая кромка. Нюансы работы с напильником заключаются в обязательной очистке поверхности напильника от насечек с помощью болгарки.
- Ножи из металлического троса. Вариант довольно редкий. Сталь в тросах отвечает далеко не всем требованиям для хорошего ножа. Чаще всего такие ножи делают из-за остающегося рисунка на клинке, который напоминает дамасскую сталь. Такого рода производством нередко занимаются жулики, чтобы продать дилетантам ножи невысокого качества, похожие на знаменитые дамасские. Ковка ножа из троса – сложный процесс, который вряд ли подойдет в качестве дебюта для новичков.
Ковка ножа своими руками – интереснейшее занятие, которое принесет вам серьезную практическую пользу, эстетическое удовольствие и повышение самооценки. Скорее всего, вы не остановитесь на одном ноже. Нигде нет пределов совершенству, а уж в кузнечном мастерстве тем более. Желаем хорошего металла, горячей печки и добрых друзей!
Нож из рессоры, ключевые характеристики, плюсы и минусы металла
На нашем сайте Выживание мы уже писали про то как сделать нож. Есть инструкция изготовление ножа из сверла, так же рассмотрено как отковать нож, сегодня поговорит про изготовление ножа из рессоры. Рессорная сталь хорошо поддается термообработке – закалке и отпуску, она не ржавеет и из нее получаются просто отличные ножи!
Раньше старые рессоры можно было найти на свалках около автобусных предприятий – там оставляли их на ночь, чинили и тд. Оставшееся после ремонта вытаскивали за забор и раз в пару месяцев увозили. Сегодня вы можете купить кусок рессорной стали 5160 в магазине или воспользоваться услугами авторазборов.
Для изготовления своего первого самодельного ножа выберете дизайн попроще. Прямой клинок гораздо легче обрабатывать – напильником удобнее работать по прямой плоскости.
Дизайн ручки для ножа тоже стоит делать не сложный, помните, в первый раз вы отрабатываете технологию, а после получения навыков можно будет сделать любой нож, даже культовый Нож Рембо.
Для начала разметим форму ножа с помощью маркера и насверлим вокруг контура дырок с помощью электродрели. Это позволит уменьшить количество усилий для вырезания формы с помощью ножовки.
Проще всего пилить прикрутив заготовку к чему либо, ну или зажав в тиски (если они есть).
Для начала выпиливается рукоять, как только ручка ножа приобретет свою форму, закрепляем заготовку с помощью шурупов сквозь отверстия в рукояти и продолжаем работать, теперь уже над клинковой частью.
После того, как с выпиливанием будет закончено, придет время использовать напильник. Напилингом над самодельным ножом придется заниматься долго. Конечно, если у вас есть мотор с абразивными кругами, то такая работа пойдет на порядок быстрее, но и с помощью напильника можно сделать нож своими руками!
Итак, часть работ позади! Самодельный нож из рессоры начал принимать свою форму.
Сгон лезвия к острию можно сделать в два захода с разным углом. Режущая кромка будет иметь более острый угол, а верхняя часть меньший.
Или равномерный угол
Обрабатывать самодельный нож проще всего прикрутив его шурупами за рукоять или зажав заготовку в тиски.
В работе очень помогает закрашивание лезвия маркером – главное не заваливать напильник и обтачивать поверхность ровно, по маркерному следу сразу видно где происходит завал напильника.
После того, как грубая обработка напильником закончена, приходит время наждачной бумаги, наклеиваем ее на деревянный брусок и начинаем шлифовку лезвия. Шлифуем меняя от грубой наждачки к более мелкой, самый низ для обработки 120 номер. Необходимо свести все царапины оставленные напильником и выровнять плоскость клинка.
Необходимо максимально остро заточить клинок, после закалки точить будет гораздо сложнее!
Лучше всего пользоваться водостойкой наждачкой, тогда можно использовать воду и мыло для того, что бы убирать опилки металла и очищать наждачную бумагу. Расход наждачки в таком случае будет меньше.
Когда самодельный нож будет готов, можно приступать закалке.
Для этого потребуется развести огонь, можно воспользоваться ветками, но лучше всего использовать древесный уголь и поддув, как это сделать – смотрите в ссылках на изготовление ножа из сверла и ковку в начале статьи.
Для контроля температуры вполне пригодятся дедовские методы – обычный магнит. Дело в том, что раскаленный до точки Кюри (около 770 градусов Цельсия) теряет свои магнитные свойства. Именно это и позволит нам легко проконтролировать нужную температуру.
Еще понадобится держатель, проще всего его сделать из старых плоскогубцев, надеваем металлические трубки на концы рукояток, плющим трубки получаем отличные клещи для горна!
Берем клещами клинок и кладем его в угли на 10 минут, затем начинаем доставать его каждую пару минут и проверять режущий край магнитом. Само лезвие перегревать не стоит, как только режущий край перестанет магнититься, пора закалять.
В качестве масла прекрасно походит отработка из двигателя авто. Впрочем, можно использовать и новое, просто отработка – это полная халява, ее все равно выбрасывают.
Закалка самодельного ножа производится опусканием лезвия по диагонали на 2/3 со стороны режущей кромки, после того как погаснет пламя горящего масла можно медленно опустить нож полностью и удерживать там до тех пор, пока не перестанет идти дым.
Еще одна хитрость – для закалки надо использовать ведро с маслом! Не банку, а именно ведро! Мало то тоже нагревается! Теперь вы понимаете почему я говорил про отработку :).
После того как закаленный нож достается из масла – он все еще горячий, кладем его в ведро с водой и даем полностью остыть. Остатки масла удаляем с помощью щетки и мыла, вытираем нож насухо.
Проверка на закалку осуществляется следующим образом, прикладываем к кромке лезвия напильник или надфиль под углом 30 градусов и прижимая ведем вдоль кромки. Напильник должен скользить пытаясь зацепиться за металл. Если напильник цепляется и царапает металл, то это значит – закалку надо повторить.
После того, как самодельный нож закален, его необходимо отпустить, иначе режущая кромка будет выкрашиваться, а при броске нож может сломаться.
Отпуск делается в обычной духовке, разогреваем ее до 350-400 градусов и прогреваем нож в течении 45 минут, затем достаем и даем остыть на воздухе до комнатной температуры, затем повторяем процедуру.
Итак, клинок самодельного ножа готов. Можно приступить к изготовлению рукояти.
На клепки используется медная или алюминиевая проволока, медная красивее.
Сверлим отверстия в заготовках рукояти и примеряем проволоку.
В качестве материала для рукояти очень хорошо подходят дубовые плашки.
Сначала делаем одну сторону, потом вторую, соединяем их и обрабатываем до зеркальной одинаковости.
Затем ставим накладки на нож и проверяем, что бы они ровно прилегали к металлу.
Когда внешний вид накладок, их удобство в удержании ножа будет для вас наилучшим, можно приступать к фиксации.
Для начала подгоняем прутки проволоки под размер, необходимо что бы они были заподлицо с рукоятью.
Зачищаем рукоять мелкой шкуркой и обезжириваем ацетоном или спиртом, то же самое делаем и с внутренней поверхностью накладок.
Теперь разводим эпоксидную смолу, смазываем внутренние части деревянных накладок, рукоять ножа и протки проволоки тонким слоем смолы, а затем соединяем, сжимаем, аккуратно удаляем излишки смолы (смотрите что бы не попало на внешнюю сторону рукояти) и зажимаем.
Самый простой способ зажать – сунуть рукоять в полиэтиленовый пакет и обмотать резиновым бинтом или уложить сверху груз. Пакет нужен для того, что бы небольшие оставшиеся излишки эпоксидки не приклеились к грузу или резине.
Все, самодельный нож готов!
Рекомендую посмотреть Как правильно затачивать нож, любой нож нуждается в периодической правке режущей кромки и заточке.
Так же рекомендую сделать ножны и пропитать рукоять ножа воском, технология описана тут, пропитка сделает древесину невосприимчивой к влаге и грязи.
Итак, если вы следовали инструкции, то у вас получился отличный самодельный нож сделанный своими руками!
Школа выживания
Метки: «нож», «изготовление оружия»
Gator комментирует:
Технология изготовления ножа — так себе. Внушает уважение минимум использовавшихся инструментов и проверка правильности разогрева с помощью магнита. О последнем я слышал краем уха, но толком не знал как именно это сделать.
22.10.2013
Особенности ножа из рессоры
Характерной чертой рессорных марок стали, является свойство изделия принимать первоначальную форму после деформирования – скручивания или изгиба. Детали, принимающие участие в механизмах со специфическими нагрузками, обязаны иметь непростые свойства.
Сплав активно использующийся профессиональными ножеделами, позволяет получить клинок с уникальными свойствами. Высочайшая прочность плюс пластичность и износостойкость материала, позволяет мастерам изготавливать достойные внимания клинки.
Рессорно-пружинная сталь – недорогой вариант углеродистой стали. Химсостав придаёт ей упругость и ударную вязкость. Закалка сплава придаёт твёрдость 60-62 единицы по Роквеллу. Современные мастера берутся изготавливать изделия из стали 65Г, считая её самой подходящей.
Свойства рессорной стали
Существует множество мнений о рессорах автомобилей родом из СССР. Якобы они являются реально хорошим материалом для клинка. Спорить бесполезно, проще узнать из какой марки стали состоит изделие. Бывалые металлурги утверждают, что рессорно-пружинная сталь включает в себя немало марок:
- пружины для железнодорожных вагонов и рессоры для автомобилей производят из: 50ХГ и 50ХГА, 50ХГФА;
- машиностроение, тракторостроение использует 55С2;
- сверхпрочные пружинные механизмы и рессоры изготавливают из55С2ГФ;
- детали наименее подверженные ударным нагрузкам используют 65Г.
Список довольно продолжительный и освящать весь нет смысла. Но отметить приблизительную сходность данных марок стали и по химсоставу, и по физическим свойствам, стоит.
Главным ориентиром создания таких изделий, является способность восстановления первоначальной формы, после различных нагрузок, т.е. – пружинить. Недопустима малейшая деструкция во время работы изделия. В соответствии с ГОСТом к подобным сплавам предъявляются завышенные требования.
Применение рессорной стали для изготовления ножа
Пружинный материал 65Г применяют для изготовления ножей ножеделы любители. Благодаря уникальным характеристикам металл находит своё применение в различных сферах.
Рессорная сталь.
Клинки для кухни, охоты, туризма – все показывают отличные режущие качества. При особой надобности, реально выковать меч либо топор. После закалки сталь приобретает хорошую жёсткость, что позволяет изделием рубить. Примеры использования рессорной стали:
- Кухонный нож. В не лучшие времена для страны, после распада СССР, не все люди могли позволить себе хороший кухонный набор ножей. Приходилось выкручиваться. Рессоры и пластины из стали 65Г были легкодоступны.
На кухнях постсоветского пространства часто встречались самодельные изделия. Рукоять изготавливали из подручного материала: дерево, простая эпоксидка, и изолента – не мешали ножам оставаться на высоте.
- Туристический нож. Минус пружинного металла – он подвержен коррозии, требует постоянного ухода после использования. Нож подойдёт для применения в походных условиях. Важным моментом является закалка. При слабой – лезвие быстро затупится о консервную банку. Следует знать твёрдость ножа.
- Армейский. Тактические или в нынешнее время – армейские ножи, отлично справляются со своими обязанностями. Серрейторная заточка увеличит сферы применения клинка. Колющие удары выдерживает без проблем. В бытовых условиях бойцу или «выживальщику» станет ценным помощником.
- Топор, мачете или меч. Сплав 65Г и аналоги, позволяет изготовить действительно грозное оружие. Непременно толщина изделия играет немалую роль. Производя такой шедевр, необходимо запастись рессорой от грузовика, или раздобыть длинную пластину.
При правильной обработке металла мы гарантировано получим отличный клинок. Мало опыта с изготовлением изделий из стали, ерунда. Далее, в статье предоставим подробное описание изготовления ножей из рессоры, различными способами.
Подводим итоги
Конечно, это очень упрощённый процесс закаливания ножа, но всё же несколько выводов можно сделать:
- обязательно подготовьте хорошую камеру, в которой будет просто закаливать нож;
- не нагревайте слишком быстро, равно как слишком быстро не охлаждайте;
- ориентируйтесь на цвета, которые приобретает лезвие в процессе накаливания, так проще понять, когда нужно остановиться;
- придерживайтесь мер безопасности и будьте предельно осторожны, работая с высокими температурами.
При использовании материалов thebestvideo.ru необходима ссылка на источник.
Как сделать нож из рессоры с помощью ковки
Работа с металлом – дело тонкое. Ковка изделия требует определённых навыков. Нет ничего зазорного, испортить одну заготовку. Полученный опыт пригодится при очередной попытке. Работать будем с рессорой, ориентировочно марки стали 65Г, выяснить точно сплав поможет цвет заготовки при накаливании.
Профессионалы считают ковочный метод более практичным. При многократном нагревании и охлаждении металла происходят процессы на молекулярном уровне. Уплотнение металла и изменение структуры, скажутся на качестве изделия.
Кованый нож из рессоры.
Инструменты и материалы
Работы следует проводить на свежем воздухе или в просторном гараже с вытяжкой. Стоит позаботиться о своём здоровье, найти маску и жаропрочные перчатки. Набор для ковки выглядит так:
- стальная заготовка из рессоры;
- горн или печь;
- молот большой 4-5 кг, молот маленький 1-1,5 кг;
- наковальня, щипцы;
- шлифовальный станок;
- сварочный аппарат, УШМ.
В качестве нагревательного элемента вполне подойдёт простой костёр с подачей воздуха. Закинуть каменного угля и трудностей с нагревом не возникнет.
Ковка клинка
Все пружинные изделия проходят закалку на предприятии. Сталь необходимо отжечь. Процесс производят постепенным нагреванием заготовки до температуры до 800-900 °С и оставляют остывать на воздухе. Деталь готова к работе:
- После отжига металл становится более податливым к любым манипуляциям. Проще приварить пруток, для удобства в дальнейшей работе, щипцы не понадобятся.
- Если заготовка имеет изогнутую форму, стоит её нагреть докрасна и малым молотом выпрямить. Следить за температурой обязательно. Не работать с остывшим металлом.
- Ковочная температура 1000-1100 °С, не имея термометра, определять её стоит на глаз (темно-жёлтый), либо магнитом – заготовка перестанет прилипать к нему. Цвет и термометр подсказывают, что сталь реально марки 65Г.
- Крупным молотом проковываем изделие и вытягиваем в длину. Рессоры в основном имею толщину в 5-6 мм, вытягивание следует продолжать до толщины в 3-4 мм.
- Лучше выковать спуски и носик к острию клинка сразу, в будущем меньше мороки на шлифовальном станке.
Приобретя вид клинка, изделие следует остудить на воздухе, срезать болгаркой пруток. Разметив конкретнее спуски и хвостовик, продолжить обработку на шлифовальном станке. Процессы изготовления рукояти и закалки клинка, обязательно опишем ниже.
Закалка лезвия
Основной вид термической обработки – это закалка. Она нужна, чтобы лезвие было прочным, и могло оставаться острым долгое время после заточки. Существуют разные приёмы:
— закалка, с нагревом только режущей кромки;
— закалка режущей кромки нагревом изделия целиком;
— закалка с отпуском;
В первом случае только крайняя часть лезвия нагревается до немагнитного состояния, после чего его помещают в масло и выдерживают, пока масло не перестанет пузыриться. Второй способ сложнее: нагревается нож целиком, но погружать его в масло требуется только на треть – чтобы режущий край был покрыт жидкостью.
Закалка с отпуском – это метод, при котором остывание заготовки проводится в два этапа: сначала в при повышенной температуре, но ниже температуры закалки, затем при комнатной температуре.
Самый простой способ закалки – это полная закалка клинка, но при этом способе есть вероятность, что лезвие поведёт. Тогда надо провести рихтовку испорченной заготовки. Это можно сделать как предварительно разогрев лезвие, так и в холодном состоянии.
Как выточить нож из рессоры своими руками
Резать или ковать – персональный выбор ножедела. Чтобы выгнуть заготовку нужна печь. Рессору лучше взять потоньше, иначе будет много возни с толщиной заготовки: устанешь её убирать и сотрёшь несколько кругов. Требуемый инструмент немного отличается от ковочного варианта
- УШМ, шлифовальный станок, круги к ним с разным зерном;
- печь и заготовка рессоры;
- напильники, молоток, наковальня;
- маркер, бумага;
- наждачка с разным зерном.
Выточенный нож из рессоры.
Молотом работать не придётся, больше мороки с болгаркой и шлифстанком. Приступая к работе, защитите глаза и руки.
Процесс изготовления ножа из рессоры
Следуя инструкции, клинок выйдет не хуже кованного. Важно, не перегреть заготовку и точно провести закалку:
- Произведя процесс отжига, и выпрямив заготовку, необходимо изготовить шаблон будущего клинка. Фантазия ножедела и интернет позволят создать уникальный шаблон клинка.
- Эскиз выполнить необходимо с запасом в пару миллиметров, на случай перегрева металла. Обвести его маркером на заготовке и приступить к трудоёмкому процессу – вырезанию.
- Толстую рессору придётся снять до 3-4 мм, сделать это поможет УШМ или шлифстанок. Снарядив болгарку отрезным кругом, и закрепив заготовку в тиски, вырезаем по контуру будущий клинок. Следите за цветом металла, не допускайте его изменения. Меняет цвет – перегрев. Поливайте больше водой.
- По заключению процесса вырезания снять заусенцы помогут напильники.
Разметьте симметрично спуски и на шлифмашине снимите их.
Получив изделие близкое к клинку, затачивать сразу не следует. Не забывайте обработать хвостовик. Нож почти готов, осталось несколько нюансов.
Закалка лезвия
Вариантов закалки достаточно. Работая со сталью 65Г и аналогами, профессионалы рекомендуют, производить её в масле. Но присутствует мнение, что предпочтительнее процесс провести на воздухе. Остановимся на масляном методе.
Разогрев печь до 900 °С, ниже отметки ковки, аккуратно помещаем клинок и следим за нагревом. Достигнув оранжевого цвета детали, вынимаем клещами и на 3-и сек опускаем в масло. Вытаскиваем, ждём полного остывания. Опять помещаем в печь, нагреваем и в масло. Время выдержки увеличиваем на 1-у сек.
Сделать процедуру необходимо 3-и раза с постепенным увеличением времени окунания на 1-у сек. Клинок приобретёт высокую твёрдость и не потеряет пластичных качеств. Наш ресурс содержит более подробную процедуру закалки ножей в домашних условиях.
Важный момент – отпуск клинка. Производят отпуск при температуре от 200 до 300 °С. Процесс произвести реально в духовом шкафу газовой плиты. Нагрев заготовку до необходимой отметки, следует оставить её на 2-3 часа, не уменьшая показатели термометра.
Изготовление рукоятки
Существует 2-а типа рукояти: накладная и всадная. Для клинков с высокой твёрдостью применяют 1-ый вариант.
Чертеж элементов рукоятки ножа.
Способ несложный, потребуется:
- брусок древесины;
- дрель, свёрла;
- эпоксидный клей, штифты;
- наждачку;
- шлифовальный станок.
Древесину дозволительно заменить на: пластик, оргстекло и т.д. Материал подойдёт для применения различный. Вырезав подходящие по размеру накладки, насверливаем отверстия в хвостовике. В заготовках рукояти аналогично.
Доведя накладки наждачной бумагой до идеальной плоскости, приклеиваем их к хвостовику и вставляем штифты – их можно заклепать. Струбцинами закрепляем конструкцию, оставляем на 24 часа высыхать. На шлифовальном станке доводим рукоять до необходимых размеров.
Дерево обязательно требуется пропитать маслами или средствами против старения древесины. На нашем ресурсе имеется подробная статья о монтаже рукояти.
Заточка ножа
Твёрдость получившегося ножа составит 60-62 единицы по шкале Роквелла. Убедившись в симметричности спусков, можно приниматься за заточку. Процесс начинается с грубого точильного бруска с крупным зерном. Профессионалы советуют использовать алмазные камни для заточки ножей.
Заточка ножа бруском.
Движения осуществляются вдоль бруска до появления заусенца. Переходим к камню с зерном чуть меньше, двигая клинок поступательно. Процесс не требует быстрых и резких движений. Проводя заточку необходимо держать постоянный угол. Зависит он от будущего применения ножа. Оптимальным углом называют вариант в 20-25 град.
Для снятия заусенца необходимо работать на самом мелком зерне. Не забываем смачивать водой брусок. Заточка ножа потребует немалых усилий.
Рессорно-пружинная сталь, после закалки, очень твёрдая.
Учитывая условия эксплуатации, наточив лезвие единожды – клинок затупится нескоро. Правильно заточенное изделие, способно резать жестяные листы без потери своих качеств.
Определяемся с температурой
Не забывайте обязательно учитывать, как нагревать нож и до какой температуры. Главное правило в том, что быстрый нагрев приведёт к повышенной хрупкости металла, потому это делать не нужно. Что касается максимума, то тут всё зависит от состава.
Например, высокоуглеродистый сплав может выдержать до 850 градусов, низкоуглеродистые могут перенести до 950 градусов, ну а у легированных сплавов нагрев может доходить до 1150 градусов. Также важно помнить про равномерность прогрева, иначе могут образоваться совершенно нежелательные поперечные трещины.
Изготовление ножа из танковой рессоры. Правильно куем нож сами
В современном мире на рынке предоставлены ножи разного вида назначения, а также функциональных возможностей, но ковка ножа своими руками до сих пор пользуется успехом.
Такие изделия приятно дарить на праздники или хранить, как талисман. Такое солидное орудие будет служить длительное время своему хозяину.
Основные требования к эффективному процессу
Чтобы сделать хороший резак, нужно соблюдать некоторые правила и инструкции именитых мастеров:
- Для ковки ножа, прежде всего, требуется качественная сталь. Это может быть и вторичное сырье. Необходимо чтобы оно соответствовало всем пунктам по надежности, пластичности и прочности. В противном случае не получится острый и крепкий резак.
- Необходимо иметь для ковки все необходимые инструменты: молот большой, молоток до 1 килограмма, наковальня, тиски, болгарка, инструмент для шлифовки, плоскогубцы, точило. А также необходима печь или приспособление, на котором будет происходить нагревание.
- Прежде чем изготавливать кованый нож, нужно начертить схему работ. В ней будет представлена форма острия и ручки. Для неопытных мастеров лучше заготовить макет, который поможет сформировать представление о будущем клинке.
Схема ковки ножа из сверла
Накаливание в печи необходимо производить очень осторожно, иначе изделие сильно расплавится. Чтобы определить момент, когда необходимо его вынимать из печки, мастера рекомендуют поднять сталь на свет: она обычно темнеет или краснеет.
Изготовление кованного железным молотом изделия лучше выполнять на улице или в гараже. С одного раза ковки ножи могут не получиться, но набравшись опыта, каждый сможет это виртуозно делать в домашних условиях. Не стоит забывать надевать защитные перчатки и маску.
Описание ковки из различных материалов
Для ковки таких изделий применяются материалы из разного сырья:
- сверла;
- подшипника;
- троса;
- рессоры;
- цепи;
- напильников.
Ковка ножа из сверла своими руками
Как выполняются эти ковки
Ковка ножа из сверла, которое изготовлено из качественной инструментальной стали принесет хорошие плоды, если оно ранее предназначалось для металла. Такие сверла не требуют высокого нагревания во время переделок, а также относятся к быстро режущимся материалам.
Методика ковки несложная:
- сверло помещают в печь для накаливания, оно обязано покраснеть;
- его вынимают и зажимают тисками хвост для процедуры выравнивания;
- уже приступают к изготовлению формы резца и ручки;
- заточка производится с помощью молота или шлифовальной машины. Болгаркой быстрее всего работать;
- ковка ножа из сверла делается в несколько этапов для того, чтобы не изделие не потрескалось и не сломалось.
Ковка ножа из рессоры – процесс тонкий, требующий внимания. Главное, не перегреть сталь, иначе изделие станет некрепким и испорченным.
Если ковка ножа из рессоры произведена из высококачественного советского сырья изделие получится прочным и долговечным. Использование рессорного материала сделает изделие долговечным и крепким.
Последующая обработка
Для начала необходимо отшлифовать и выровнять стальную поверхность. Затем происходит процесс накаливания, ведь изделие плавится довольно легко. После этого выполняется ковка ножа из рессоры, то есть имеющимися инструментами придается форма, ширина, толщина и дизайн острого конца, а также ручки.
Когда нож остынет, необходимо произвести финишную шлифовку поверхности, а потом заточить острие.
Технология точения ножей
Теперь нож можно использовать на кухне, в походе или хранить, как коллекцию.
Наиболее простой вариант переделки напильника, он часто используется профессионалами:
- для начала стоит очистить крайнюю часть от насечек и ржавого налета. Эту процедуру выполняют шлифовальным диском с помощью машины;
- накаливают до нужной температуры;
- вырезают форму ручки и клинка, такую же, как на макете;
- толщину тоже лучше регулировать пока материал нагретый.
К такому ножу лучше приобрести съемную ручку, ведь у напильников они стальные.
Для ковки ножа из стального троса используют сварочный инструмент. Он нужен для того, чтобы сплавить между собой все тонкие нити стали. Это процесс трудоемкий, поэтому требует терпения.
Изготовление ножей в домашних условиях – процесс нелегкий, но он стоит тех прилагаемых усилий и времени, потому что в результате получиться полезный и уникальный предмет.
Видео: Ковка ножа из рессоры своими руками
Наглядное видео:
Очень прочные и надежные ножи получаются из автомобильных рессор – это вам подтвердит любой кузнец. Главное правильно обработать этот качественный стальной материал. Рессора в качестве материала для ножа была выбрана неслучайно, т.к. :
1) её куски можно легко найти
2) обрабатывается она значительно легче, чем полоса «быстрореза»
3) стоимость ножа сравнительно мала
И так, начнём с того, что автомобильная подвеска бывает рессорной и пружинной. Нас будет интересовать рессорная.
Благо в России две беды: дураки и дороги. В результате сочетания первого и второго, мы имеем множество пригодных (для изготовления ножа) кусков рессоры прямо на догоге. Бесплатно и вне очереди.
Более подробные сведения об изготовлении самодельных ножей с наглядными фото смотрите по прямым ссылкам, расположенным справа >>>>>>>>
Рессора изготавливается из горячекатного стального проката, для которого есть ГОСТ. А теперь несколько слов о самой красавице: Рессора — упругий элемент в подвеске автомобилей, троллейбусов, автобусов. Соединяют кузов с мостами.Воспринимают тяговые и тормозные усилия при движении.
Рессора намного старше автомобиля. К примеру, гоголевские персонажи, обсуждавшие «доедет ли колесо…» глядели, скорее всего, на рессорную коляску. Естественно, унаследовали ее и самобеглые экипажи. В разное время ее очень широко, порою почти тотально использовали в подвесках автомобилей. И сегодня на старой технике можно встретить множество просто потрясающих конструкций. Но разбирать их здесь мы не будем, поскольку и практическая ценность этой информации небольшая, да и места для приличного обзора потребуется намного больше, чем есть во всем журнале.
А потому поговорим о том, что выкристаллизовалось в процессе развития к сегодняшнему дню.
Конструкция:
Рессоры бывают много-, мало- и однолистовыми. До недавнего времени во всем мире были, а в нашей стране еще и сегодня наиболее распространены многолистовые рессоры. Поскольку график изменения изгибающего рессору момента имеет форму треугольника с вершиной в точке нагружения (мост), то этот треугольник и «заполняют листами», чтобы получить более равномерные напряжения в каждом из них. В результате удается убить не одного, не двух, а целое стадо зайцев.
Изготовление:
Для изготовления листов обычно используют горячекатаную полосу из углеродистой пружинной стали. Нужный выгиб придается рихтовкой, а в заводских условиях – в штампах. После этого делается термообработка. Нередко поверхность упрочняется дробеструйной обработкой.
Виды сечения рессоры:
Сечение листа до некоторого времени было прямоугольным со скругленными кромками. Но поскольку усталостное разрушение листов почти всегда начинается сверху, нижнюю поверхность сократили скосами или выемками. В результате в сечении листы большинства современных рессор имеют или трапецию, или своеобразное «Т» с очень толстой ножкой.
Какую рессору взять:
Многие ножеделы сходятся во мнении, что лучше брать рессору, сделанную в глубокие совковые времена. Поскольку там сталь 65Г была значительно лучше, чем сейчас.
Само качество металла зависит не только от соотношения добавок, но и от технологии термообработки. Возможно в советские времена «термитчики» были более квалифицированы. Упорно прививается, что многие «секреты стали» утеряны в далёких-далёких временах. И что современные ножи — не ножи вовсе… Думаю, сталь, она как была так и осталась. Просто когда работаешь с куском «советской рессоры», ты создаёшь нож с «историей».
Не стоит забывать, что многие качества ножа из любого металла задаются технологией его производства. Например, можно перекалить полотно «быстрореза» при работе на наждаке и потом всем рассказывать, какие хрупкие ножи из Р6М5.
Для первого ножа, пойдёт любой кусок. Первой особенностью для вас тогда станет вопрос о распрямлении рессоры. Для этого вам нужно будет осилить:
2. и само Выпрямление — наковальня+молот
Отжиг:
Разведите костёр нагрейте рессору до «красна» и очень медленно охлаждайте. Можно оставить прямо в углях.
После отжига на рессоре может появиться желтый, коричневый или голубой «налёт», легко снимаемый наждачкой.
Выпрямление:
Это дело бесхитростное. Нужна наковальня (можно использовать кусок рельс) и молот, что потяжелее.
Самый лучший вариант — расковывать железо пока горячо.
Можно и на «холодную», но велик шанс расколоть.
Материалы:
Единицы измерения в тексте: 1 дюйм — 2,54 см; 1 фут — 30,5 см; 1 фунт — 0,454 кг. (Прим: для вашего удобства я пересчитал импортные величины в привычные)
Если вы горите желанием сделать нож своими руками, и у вас нет дорогого оборудования, то вот небольшой список материалов, которые могут пригодиться. Я понимаю, что это не самые лучшие материалы, но это работает, хотя может вызвать улыбку.
Кусок рессорной стали 5160 из магазина, примерно 800 гр весом, или около этого. Отмерьте 18-20 см длины от куска, или сколько решите, и берите новую пластину, а не старую автомобильную рессору.
Теперь отправляйтесь в магазин для столяров, и купите:
за 4 доллара дубовый брусок размером 3,5 х 5 х 7,5 см (Прим: собсно, это будет рукоять)
в сварочном отделе купите медный пруток толщиной 3 мм за 1.50 доллара
2 сверла 3 мм за 2 доллара и ещё одно 6 мм сверло
2 напильника, один плоский, и один полукруглый — 7.50 доллара
2 куска водостойкой наждачной бумаги номер 120 за 1 доллар
2 куска водостойкой наждачной бумаги номер 240 за 1 доллар
дешевое зубило
достаточно большая струбцина, которой вы будете прижимать нож к столу или скамье (но можно обойтись и без неё)
Когда будете подбирать стальную полосу в магазине, посмотрите, можно ли купить самую тонкую пластину из того, что у них есть. Мой магазин располагает материалом 0,5 см толщиной и 4 см шириной. Это довольно толстовато для маленького клинка, но все равно годится. (Прим: в нашем случае с напильником придётся повозиться — толщина ресооры будет больше. Но, после уроков труда в далёком дестве, это — не проблема)
Еще вам нужна будет ручная электродрель. Возьмите ее у кого-нибудь на время, т.к. с ней ничего не случится — вы только просверлите несколько отверстий. Далее я буду использовать картинки, чтобы объяснять свои действия.
Для своего первого ножа выбирайте дизайн попроще. 7.5 — 9 см будет подходящей длиной для клинка, потому что вам придется использовать напильники при обработке лезвия. Прямой клинок без выкрутасов легче обрабатывать, да и напильником проще работать по прямой плоскости.
Ручку для ножа тоже выбирайте несложную, без большого количества причудливых углублений под пальцы, и без гарды.Силуэт ножа нарисован маркером, затем я сверлом 6 мм насверлил вокруг рисунка кучу дырок. Придется много поработать ножовкой по металлу вокруг всего этого.
Прикрутите нож к скамье, пню, или что у вас там есть, и с помощью ножовки удалите часть металла вокруг ручки. Делайте это так, чтобы потом напильником можно было рукоятке придать нужную форму. Это должно быть выполнено в первую очередь, потому что если удалите металл вокруг клинка, то потом не сможете его прикрепить к скамье. Рукоять обрабатывается в первую очередь! Как только она приобретет форму, удалите ненужный материал, прикрепите нож сквозь отверстия в рукояти, и принимайтесь за клинок.
Итак, я обсверлил весь силуэт ножа — это здорово облегчит работу ножовочному полотну при его опиливании. Затем я открутил заготовку от скамьи, и заново прикрепил ее так, чтобы удалить лишний металл с рукояти. Сверлом 3 мм были сделаны отверстия в рукояти под медные прутки, а сверлом 6 мм — чтобы ее можно было крепить к скамье, когда обрабатывается какая-то часть лезвия.
Потом я опилил ручку, и добавил пару углублений под пальцы, чтобы она крепче держалась в руке. После этого я обработал напильником остальную часть силуэта, и опилил скос — будьте терпеливы, т.к. работа напильником требует времени. Хорошо, теперь у меня есть заготовка ножа, опиленная ножовкой по металлу, и обработанная напильником. Это начинает приобретать форму.
Я отметил режущий край с помощью моего 6 мм сверла. Зачернил клинок маркером, а потом начал передвигать конец сверла по режущей кромке так, что появилась тонкая линия. Переверните нож, и повторите то же самое на другой стороне, получив две линии, на расстоянии примерно 0,6 мм — 0,8 мм друг от друга. Если эти две линии получились слишком близко друг к другу, то снова отметьте нужное место маркером, возьмите сверло, и передвиньте его вверх или соответственно вниз, повторив все заново. Линии будут отстоять друг от друга примерно на 1/2 толщины пенсовой монеты.
Затем, с помощью подходящих шурупов для дерева, прикрутите нож к верху скамьи. Начинайте обрабатывать напильником плоскость клинка. Цель в том, чтобы соединить процарапанные линии и вершину режущей кромки ножа в одно и то же время. Это потребует много тяжелой упорной работы и терпения.
И, может быть, несколько перерывов по дороге. Чтобы помочь себе в обработке плоскости, я использовал маркер, и обтачивал очень медленно, пытаясь удержать напильник плоско. Маркер покажет вам неровности, которые надо сточить.
Попробуйте закрепить полоску наждачной бумаги на какой-нибудь недорогой основе, например, на шпателе для нанесения краски. Вначале я зачищал наждаком область, которую мы назвали углубление, с помощью плоской дощечки и бумаги номер 120. Потом я стал обрабатывать плоскость продольными движениями к концу клинка, пока все грубые царапины от напильника не исчезли. Это так же выравнивает плоскость.
Используйте немного мыла и воды, чтобы уберечь наждачную бумагу от загрязнения, а когда закончите работу, убедитесь, что вытерли нож насухо, иначе до завтра он поржавеет. Начните обрабатывать наждачкой плоскость клинка и рукоять. Не удаляйте все огрехи, а только излишки, пока не получите немного голого металла — такая «суровость» придаст характер уже готовому ножу.
ОК, огонь зажжен. Я занялся этим на заднем дворе, в специально огороженном месте. Огонь пылает за оградой, и дует несильный ветерок, который помогает нашей работе. Нужно будет еще несколько вещей, чтобы работать с ножом дальше. Магнит я достал из игрушечной коробки моих мальчишек, а после борьбы с проблемой надежно/дешево пришел к следующему.
Взяв два куска 12 мм квадратной трубы 90 см длиной, я вставил в них концы рукояток старых плоскогубцев и сплющил металл по краю, чтобы закрепить соединение. И еще одна важная, необычайно секретная вещь, на которую я вам намекну: старые масляные фильтры, остающиеся после замены масла в автомобилях.
Суньте клинок в горячие угли. Ножу следует находиться там примерно 10 — 15 мин, в зависимости от того, как сильно разгорелись угли. Это ваш первый раз, поэтому вытаскивайте нож из огня на пару секунд каждые 2 — 3 минуты, смотрите на его цвет, и проверяйте режущий край магнитом.
Если сталь притягивается, значит нож еще не готов, суйте его обратно в огонь и грейте до вишнево-красного цвета. Постарайтесь не перегревать нож дольше, чем необходимо, поэтому проверяйте клинок каждую минуту — две, когда решите, что момент готовности уже близок.
Пришло время опустить нож в секретное масло. Магнит не притягивается, цвет стали хорош, и слюни текут от предвкушения. Я закалял сталь, опуская в масло только 2/3 ножа. 2/3 клинка со стороны режущей кромки я держал в масле, пока не погасло пламя — около минуты — а потом медленно погрузил остальную часть ножа, пока он не погрузился полностью, и не перестал идти дым. Когда мы вытаскиваем нож, он выглядит черным и противным. Я опустил его в сосуд с водой, пока он не остыл настолько, чтобы можно было взять его в руки. Теперь вы спросите — этот нож действительно твердый? Ну что ж, давайте проверим. Возьмите напильник, и пройдитесь им по клинку, прикладывая под углом 30 градусов и прижимая деликатно, а не жестко. Напильник будет скользить по режущей кромке, пытаясь за нее зацепиться. Если клинок слишком скользкий, вытрите его тряпкой, удаляя масло. Чтобы лучше очистить металл, можно использовать так же мыло и воду.
Если напильник цепляется за нож, значит закалка не удалась, возвращайтесь к огню, и повторяйте все сначала. Предположим, что клинок прошел пробу напильником, и закалился как следует. Теперь надо его отпустить, так как мы не хотим, чтобы лезвие или его кончик крошились. Напильники очень хрупкие, и наш нож сейчас тоже очень твердый и ломкий. Разогрейте кухонную духовку до температуры 375 — 400 градусов. «Пеките» нож в духовке 45 минут, позвольте ему остыть до комнатной температуры, и снова суньте в духовку на 45 минут при той же температуре. Кстати, не забудьте смыть предварительно с ножа все масло, если не хотите закоптить весь дом. После отпуска стали можно очистить клинок. Беритесь снова за наждачную бумагу, и готовьтесь накладывать деревянные рукоятки на этого малыша.
Я поместил нож в тиски, и обрезал два куска для накладок на будущую рукоять. Положите нож ближе к верхнему краю бруска, тогда будет проще «привязаться» хотя бы к одному его краю. У меня есть медные прутки, и я готов сделать следующий шаг. Просверлите для них отверстия в рукояти.
Я вставил все три стержня, и очертил контур ножа на дубовой плашке, определившись, где будет «лицо» бруска, когда я прикреплю эпоксидкой и медными прутьями дерево к стали. Это фото не очень хорошее, но, думаю, вы сможете увидеть нужный вид с черной полосой на ноже. Я отметил на древесине начало и конец этой линии, а потом соединил их дугой.
Левая щечка рукояти будет обработана и прикреплена, когда мы не сможем нарушить форму после того, как дерево приклеится к ножу. Теперь карандашом надо сформировать левую часть рукояти, в основном ее перед.
Проверьте, достаточно ли хорошо подготовлена накладка, как она прилегает к металлу, и если надо, выгладите ее на наждачной бумаге, чтобы плоскость была совершенной.Соедините оба куска медными прутками, опилите их и обработайте наждачной бумагой, пока накладки не станут зеркально подобными. Еще раз напоминаю о переднем крае! Потом проверьте их на ноже.
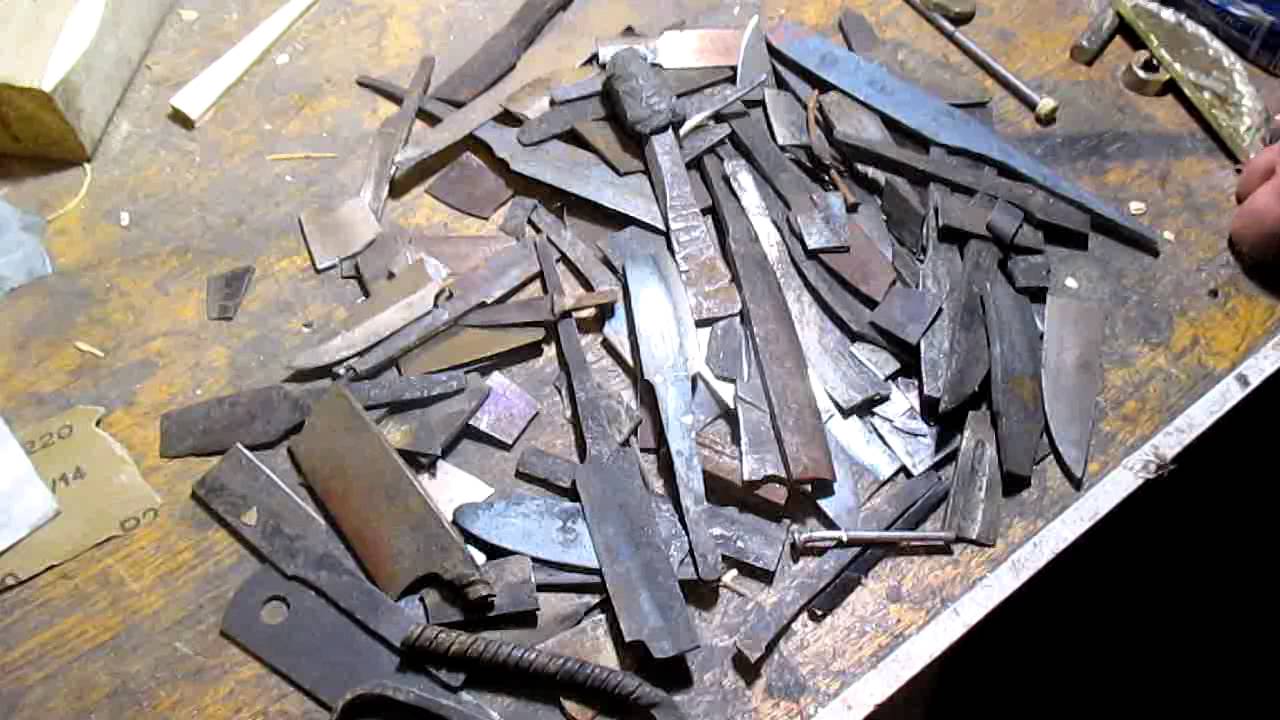
Теперь, если обе накладки достаточно хороши, и нет пустоты между ними и ножом, можно обрезать лишнюю длину прутьев, так, чтобы они были заподлицо с деревом. Тщательно очистите нож — там, где будет прилегать дерево. Мыло, горячая вода и старая зубная щетка, потом тщательно ополосните его и вытрите досуха. Если хотите, чтобы он был совершенно сухим, воспользуйтесь сушилкой для волос.
Я обрезал прутки, и зачистил наждачкой грани, чтобы потом не откалывались щепки. Потом эпоксидной смолой смазал внутренние части деревянных накладок, рукоять ножа и стержни, и соединил все вместе.
Обернув все это четырьмя жирными резиновыми полосами (жирными — чтобы не прилипли), я оставил нож до высыхания, а потом удалил излишки выступившей смолы, и получил готовый нож.
Нож – это отличная вещь, которая может быть полезна не только в качестве прекрасного инструмента, но и в виде замечательного сувенира. Каждый мальчишка будет рад такому подарку. Если нож изготовлен вручную, то он сразу становится уникальной ценностью в глазах владельца.
Взрослые тоже не всегда используют ножи исключительно в бытовых целях – многие люди их коллекционируют. Критерии выбора у всех разные, но каждый знает, что качественная сталь – это обязательное условие для хорошего ножа. Но и красиво выполненная ручка может произвести не меньшее впечатление, чем прочное лезвие, способное долго держать заточку.
В чем же особенность ножа из рессоры?
Причина популярности такого изделия, как нож из рессоры, заключается в свойствах металла. Высокая износостойкость и прочность в сочетании с высокой пластичностью позволили многим поколениям мастеров пользоваться рессорами как главным источником сырья.
Рессоры изготавливают из рессорно-пружинной стали 65Г, но могут быть применены другие марки: 50ХГСА, 50ХГА, 50ХФА. Это тоже рессорно-пружинные стали – определить какая из них взята в качестве материала для клинка можно только с помощью химического анализа. Либо по нюансам поведения металла при обработке, но с этим справятся только опытные мастера. Для начинающего изготовителя разница между перечисленными материалами будет практически незаметна.
Применение рессорной стали
65Г считается одной из самых дешевых пружинных сталей. При этом она обладает рядом уникальных свойств, делающих ее незаменимой для создания пружин. Рессорная сталь для ножа содержит хром, никель, марганец, кремний. Эти элементы придают свойства, за которые изготовителями выбирается именно этот материал:
- хорошая гибкость;
- высокая ударная вязкость;
- твёрдость;
- износостойкость;
Термообработка играет большую роль в улучшении качеств материала. Сталь становится прочнее, повышается ее твердость. К сожалению, она недостаточно устойчива к коррозии – имеет обыкновение ржаветь. Но достоинства перевешивают недостатки и ее часто используют как материал для клинка.
Такие ножи применяют в самых разных сферах. В первую очередь в качестве кухонных – крепкие, прочные, долговечные – что ещё нужно для ежедневной работы на кухне и, например, для разделки мяса? Те же соображения заставляли охотников, рыбаков и туристов стараться заполучить в свой арсенал эту качественную «самоделку». Поэтому многие мастера делали на продажу туристические и охотничьи ножи.
Благодаря хорошим характеристикам стали, эти ножи были популярны среди военных. Солдаты срочной службы, имевшие доступ к инструментам для металлообработки, в кустарных условиях изготавливали армейские ножи.Со временем, изготовители начали замахиваться на более серьёзные изделия: топоры, мечи, мачете, катаны. Из-за хорошей ударной вязкости рессорные стали прекрасно подходят для ковки. Ковкой можно изготовить клинок любой формы, даже самой причудливой.
Как сделать нож из рессоры
Изготовление ножа из рессоры может отнять много времени и сил, особенно, если человек делает это в первый раз. Но рессорно-пружинная сталь хорошо поддаётся обработке и «стерпит» ошибки новичка, поэтому именно из неё лучше всего создавать свой первый нож.
Обычно, материал находят на открытом воздухе: на улице, на автобазах, рядом с гаражами, на автомобильных свалках и других аналогичных местах. Поэтому рессора может быть покрыта грязью и ржавчиной и перед работой ее надо тщательно отчистить. Если необходимо выпрямить выгнутую рессору, то её нагревают до красна, а затем дают остыть в нормальных условиях – при комнатной температуре.
Как сделать нож из рессоры с помощью ковки
Все рессорно-пружинные стали, в том числе 65Г, объединяет одно качество: они прекрасно поддаются ковке. Ножи из рессорной стали, изготовленные ковкой, будут более надёжными и долговечными, потому что в процессе обработки происходит упрочнение металла за счёт пластической деформации и изменения макроструктуры.
Прежде чем проковать рессору, необходимо вырезать из неё профиль будущего клинка. Затем заготовку надёжно крепят, и нагревают до красна. Ковкой создаётся остриё и лезвие. Этим способом легко придать клинку требуемую форму, а также задать его ширину. Ковкой из рессоры хорошо удается изготавливать топоры и различные экзотические вещи, такие как мачете или меч.
Лезвию дают остыть до температуры окружающей среды после того как работа закончена.
Как выточить нож из рессоры своими руками
Необходимо, в первую очередь, определиться с внешним видом будущего изделия. Форма зависит от назначения ножа: кухонный, охотничий, сувенирный или какой-либо другой. В итоге клинок может быть любой – на это влияют только фантазия и возможности изготовителя. Если выбор сделан, то нужно взять готовый шаблон или выполнить его самостоятельно из картона или плотной бумаги.
Далее, чтобы изготовить нож из рессоры своими руками, надо быть готовым начать работу с металлом. Сначала шаблон необходимо приложить к металлической заготовке и обвести маркером, карандашом, чертилкой (ГОСТ 24473-80) или другим разметочным инструментом. По контуру, полученному посредством шаблона, требуется вырезать профиль изделия. Подойдут следующие инструменты:
- ленточная пила;
- угловая шлифмашинка, она же «болгарка» – важно не перегреть заготовку при отрезании;
- сверлильный станок или дрель – в этом случае вдоль контура сверлят отверстия, затем перегородки между ними ломают или выпиливают;
- можно использовать ручной инструмент;
Сам процесс обработки достаточно прост, хотя и требует определённой концентрации, чтобы вырезать заготовку в соответствии с разметкой. Когда обработка успешно завершена и заготовка стала соответствовать шаблону, то можно приступать к формированию клинка. Основная задача – сделать скосы. Лезвие снова размечают, определяя размеры скосов. При дальнейшей обработке следует строго придерживаться разметки.
Для работы лучше всего использовать электрическое точило. Также подойдут и ленточная шлифмашинка, и «болгарка», но, в случае последней, требуется хорошее владение инструментом. Можно выточить скосы вручную – напильником. На этом работы по металлу должны быть закончены, потому что далее клинок пройдёт термическую обработку, после которой сделать с заготовкой что-либо ещё будет очень сложно.
Закалка лезвия
Основной вид термической обработки – это закалка. Она нужна, чтобы лезвие было прочным, и могло оставаться острым долгое время после заточки. Существуют разные приёмы:
— закалка, с нагревом только режущей кромки;
— закалка режущей кромки нагревом изделия целиком;
— закалка с отпуском;
— полная закалка;
В первом случае только крайняя часть лезвия нагревается до немагнитного состояния, после чего его помещают в масло и выдерживают, пока масло не перестанет пузыриться. Второй способ сложнее: нагревается нож целиком, но погружать его в масло требуется только на треть – чтобы режущий край был покрыт жидкостью.
Закалка с отпуском – это метод, при котором остывание заготовки проводится в два этапа: сначала в при повышенной температуре, но ниже температуры закалки, затем при комнатной температуре.
Самый простой способ закалки – это полная закалка клинка, но при этом способе есть вероятность, что лезвие поведёт. Тогда надо провести рихтовку испорченной заготовки. Это можно сделать как предварительно разогрев лезвие, так и в холодном состоянии.
Изготовление рукоятки
Ручку можно изготовить практически из любого сырья, но особой популярностью пользуются дерево, пластик, кожа, кость. Красиво выглядят наборные ручки с чередующимися слоями, например, кожи и бересты.
Кость – это традиционный материал, для изготовления разнообразных безделушек и предметов быта. Обладая навыком резьбы по кости можно сделать уникальную, красивую ручку. Но проще всего взять две деревянные или пластиковые накладки, поместить их по обе стороны от хвостовика и закрепить между собой заклепками, а для большей прочности ещё и эпоксидным клеем. Иногда для крепления используют винты и гайки, но если важен внешний вид, то лучше их не применять.
Рукоять должна быть удобной, поэтому требуется уделить большое внимание ее обработке. Для этого используются сначала напильники, а затем наждачная бумага. Если накладки деревянные, то их обязательно надо пропитать маслом, чтобы обеспечить долговечность древесины. Пропитка подчеркивает структуру дерева и придает изделию привлекательный внешний облик. После закрепления рукоятки проводят ее окончательную шлифовку.
Работа над ножом из рессоры практически завершена, осталось только заточить его. Для этого используют:
- бруски;
- мусаты;
- точильные станки;
- механические точилки;
- электрические точилки;
Действительно хорошие результаты получают применяя брусок или электрическую точилку. Чтобы хорошо заточить нож с помощью бруска или точильного камня понадобится не мало времени. Если на обычный кухонный нож достаточно потратить около получаса, то выравнивание и заточка длинного кованого ножа может занять несколько дней.
Для лучшего контроля процесса заточки точильный камень помещают на устойчивую горизонтальную поверхность. Оптимальный его размер – примерно в полтора раза длиннее лезвия. Начинать заточку требуется грубым точильным камнем, с крупным зерном. Продолжать надо до тех пор, пока не появится заусенец. После этого берётся мелкозернистый камень, далее процесс продолжается с его помощью. Чтобы самодельный нож из рессоры стал острым, а заточка держалась долго, надо соблюдать следующие правила:
- движение осуществляется путём поступательных перемещений ножа вдоль бруска – режущей частью вперёд;
- конец бруска и конец лезвия должны «встретиться». Нужно синхронизировать смещение ножа поперёк бруска (от ручки к лезвию) и перемещение ножа вдоль бруска;
- плоскость клинка и поверхность бруска должны составлять угол от 20 до 25 градусов – это универсальный угол заточки.
В зависимости от назначения ножа, угол может меняться, но важно, чтобы он удерживался постоянным всё время пока происходит затачивание ножа;
В конце необходимо провести шлифовку лезвия, чтобы надолго сохранить нож острым. Для этого берётся точильный камень с самым мелким зерном. Затем аккуратно, чтобы не испортить уже сделанное, снимается заусенец.
Заточка — процесс требующий терпения и внимательности. Навык приходит только с опытом, поэтому все, кто не хочет ждать, могут воспользоваться электрической точилкой. Это сэкономит время, а также позволит сохранить ножи в превосходном состоянии.
Изготовление ножа — это процесс сложный, требующий внимания, концентрации, тщательности, навыков работы с металлом. Но труд не будет напрасным, ведь в итоге получится прекрасное изделие, созданное своими руками. Чем с большей любовью и старанием мастер подходил к делу, тем лучше будет изделие. Даже новичок, если окажется терпелив и настойчив, сможет овладеть навыками и тоже станет гордиться результатами своей работы.
Если есть немного свободного времени и ненужная рессора от грузовика или другого автомобиля, то можно своими руками сделать достаточно красивый и уникальный нож. Возможно, с первого раза он не будет совсем идеальным, но главное – сделан своими руками. Главной прелестью этой самоделки является то, что нож может быть практически любой формы, необходимо просто включить немного фантазии.
Материалы и инструменты для самоделки:
болгарка;
рессора от грузовика;
надфиль;
эпоксидная смола;
льняное масло.
Процесс изготовления ножа
Материал для клинка можно достать на любом авторынке, иногда автомобили могут потерять рессору прямо посреди дороги. В данном случае используется рессора от Камаза. Можно взять и от другого автомобиля, в таком случае толщина клинка будет меньше, и ее ненужно будет уменьшать вручную.
Шаг 1. Подготовка материала
При помощи болгарки автор разрезал ее на три части, так как деталь имеет разную толщину и закругленную форму, необходимо выбрать оптимальную часть для данного типа ножа. Та часть рессоры, которая идеально подошла для клинка распиливается еще пополам, в итоге имеется две одинаковых заготовки.
Шаг 2. Форма ножа
Нужно взять заготовку и примерно разделить ее на две части пополам, из одной половины будет изготовлено само лезвие ножа, вторая половина будет входить внутрь ручки. Ту часть, которая будет находиться в ручке, необходимо немного обрезать с двух сторон, чтобы она стала меньше и могла поместиться в рукоятке.
Так как рессора имеет толщину примерно в 8 мм, а таких ножей практически не бывает, то нужно наждаком длительное время убирать толщину до желаемой. Затем на станке нужно придать форму лезвия, желательно, чтобы был мелкозернистый камень, в противном случае, нож будет выглядеть шероховатым и немного не аккуратным.
Шаг 3. Создание рукояти
Необходимо взять небольшой деревянный брусок (уделите особое внимание выбору дерева для рукояти) и выточить рукоять нужной формы, в данном случае нужно воспользоваться фантазией и представить, каким вы хотите видеть свой будущий нож.
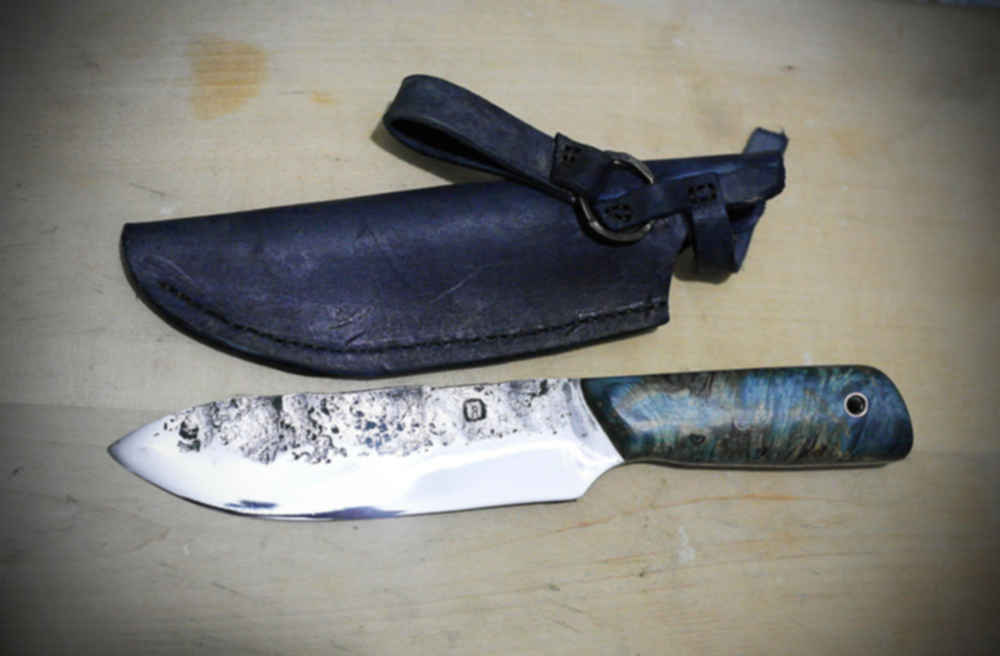
Автор решил сделать ручку комбинированную, используя резину, бересту и березовый кап.
Отрезаем лишнее и шлифуем…
После проведения всех процедур нужно обработать ручку. Понадобится льняное масло, подогретое на водяной бане до температуры 70-75 градусов. Нож при этом предварительно нужно спрятать в морозильную камеру на 30 – 40 минут. При соединении холодного ножа и теплого масла, по рукояти начинают бежать пузырьки, таким образом, воздух из дерева выходит, а это место заполняется льняным маслом. Такую процедуру нужно проделать несколько раз. После этого ручка ножа помещается в масло минимум на сутки.
Шаг 4. Изготовление ножен
Потребуется небольшой кусок кожи, по форме ножа нужно сделать выкройку.
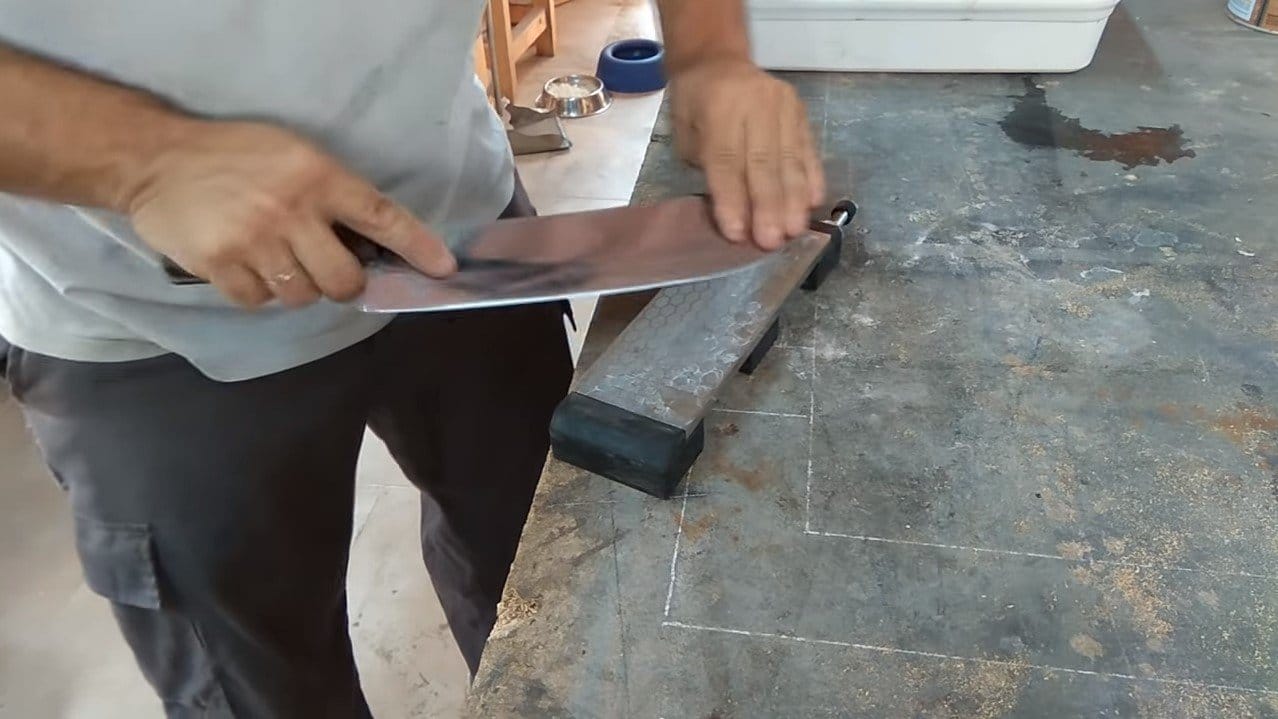
Сегодня, даже при таком большом ассортименте различных ножей прекрасного качества от известных производителей, ножи ручной ковки по-прежнему пользуются особой популярностью. Это и неудивительно, так как такие ножи обладают особой энергетикой и привлекательностью. А если сам клинок сделан из легированной стали и со знанием дела, то такой нож бесценен. Из различных способов собственноручного изготовления ножа наиболее трудоемким является ковка ножа своими руками. Следует отметить тот факт, что ковка ножа позволяет создать наиболее прочный и качественный клинок, который прослужит не один десяток лет и при этом сохранит свои качества. Ковка ножа своими руками — дело, требующее от мастера высокого уровня навыков владения инструментом, знания металлов и их свойств. Для тех, кто решил выковать нож впервые, описанные ниже рекомендации помогут сделать свой первый клинок.
Как выбрать сталь для ножа
Качественный самодельный нож отличает правильный подбор стали для него, от этого будут зависеть режущие и прочностные характеристики самого ножа. Чтобы правильно подобрать сталь, необходимо знать и понимать, какими свойствами обладает сама сталь. Для ковки ножа своими руками нужно ориентироваться на пять основных свойств стали — устойчивость к износу, твердость, прочность, вязкость, красностойкость.
Твердость — это свойство стали, указывающее на её способность сопротивляться проникновению в неё другого более твердого материала. Говоря проще, твердая сталь лучше сопротивляется деформации. Сам показатель твердости измеряется по шкале Роквела и имеет показатель от 20 до 67 HRC.
Устойчивость к износу — сопротивление материала изнашиванию в процессе эксплуатации. Это свойство напрямую зависит от твердости самой стали.
Прочность указывает на способность сохранять целостность под воздействием различных внешних сил. Проверить прочность можно на изгиб или при сильном ударе.
Пластичность — способность стали поглощать и рассеивать кинетическую энергию во время удара и деформации.
Красностойкость — это показатель, отвечающий за устойчивость стали к температурам и сохранению её изначальных качеств при нагреве. От того насколько сталь устойчива к термообработке, зависит минимальный показатель температуры, при котором её можно ковать. Самыми красностойкими сталями являются твердые марки, рабочая температура ковки для которых более 900 °C. При этом необходимо отметить, что температура плавления стали составляет 1450 — 1520 °C.
Все эти свойства связаны между собой и преобладание одного из них ведет к ухудшению другого. При этом то или иное свойство стали зависит от содержания в ней различных легирующих элементов и добавок, таких как кремний, углерод, хром, ванадий, вольфрам, кобальт, никель, молибден.
Наличие тех или иных легирующих элементов и их пропорциональное использование при изготовлении стали, знание свойств, которые придают легирующие элементы и добавки, позволило создавать сталь для определенных целей и нужд. Такие стали имеют каждая свою маркировку. При этом отечественные и зарубежные марки стали обозначаются по-разному. Для удобства в марке стали указан основной состав одного или нескольких легирующих элементов. Например, сталь марки У9 говорит о содержании в ней углерода в десятых долях процента. Аналогом стали марки «У» являются стали 10хх, где «хх» — это содержание углерода. И чем меньше значение, тем меньше его содержание. Или такая сталь как Х12МФ указывает на высокое содержание хрома и молибдена, что говорит о нержавеющих и высокопрочностных свойствах стали.
К отечественным маркам, которые часто используются при ковке ножей в домашних условиях, относятся все стали с маркировкой от У7 до У16 , ШХ15 , 65Г , Р6М5 , Х12МФ . Из зарубежных аналогов можно выделить сталь O-1 , 1095 , 52100 , M-2 , A-2 , 440C , AUS , ATS-34 , D-2 . Каждая их вышеприведенных марок используется в изготовлении ножей, различного инструмента и запчастей. Например, марки стали Р6М5, У7-У13, 65Г применяют для производства сверел, буров, тросов, рессор, подшипников, напильников. Поэтому именно из этих предметов народные умельцы делают ножи ручной ковки.
Конечно, можно найти и другие изделия из той или иной стали. Для этого достаточно будет прочитать полное описание марки стали и её применение в Марочнике Стали и Сплавов, а потом использовать изделие из неё для ковки ножа.
Для ковки ножа потребуется определенный инструмент кузнеца, который можно приобрести в магазине. Но можно использовать и непрофессиональный инструмент:
- молот на 3 — 4 кг и молоток меньшего веса до 1 кг;
- кузнеческие щипцы или обычные пассатижи, но без изоляции на ручках, а также разводной ключ;
- тиски;
- наковальня или её самодельный аналог из двутавра;
- болгарка и сварочный аппарат;
- точильный станок;
- печь.
Если с обычным инструментом все более-менее понятно, то по поводу печи необходимо сделать некоторые пояснения. Все дело в том, что в обычном очаге сложно получить температуру более 900 °С. Да и греться заготовка там будет целую вечность. Поэтому необходимо немного усовершенствовать очаг. Если ранее Вы не занимались хотя бы закалкой металла, то придется сделать с нуля небольшую печь из толстостенного металла. Затем присоединить к ней трубу, по которой будет поступать воздух при помощи вентилятора или старого пылесоса. Таким нехитрым образом можно получить достаточно надежное горнило для доведения заготовок до температуры 900 — 1200 °С. В качестве топлива используется обычный древесный уголь, желательно такой, который дает как можно больше жару и горит подольше.
Прежде чем приступить к самим работам, необходимо сделать эскиз самого ножа.
По сути, нож довольно простой предмет, состоящий из клинка и рукоятки. Но вот каждый из этих элементов имеет целый набор составляющих. На демонстрирующем конструкцию ножа фото можно увидеть все элементы ножа и как они называются.
Также необходимо знать и о некоторых основных профилях клинков, чтобы сделать наиболее подходящий эскиз. На фото ниже приведены профили ножей.
Выбрав наиболее подходящий для Вас профиль, можно смело приниматься за создание эскиза. Конечно, опытные мастера обходятся без зарисовки, но для новичка все же важно сделать эскиз и держать его перед глазами в процессе ковки.
Ковка ножа из сверла
Сверла получили большую популярность при ковке ножей благодаря используемой в них легированной стали Р6М5, которая отличается прочностью, легкостью заточки и износоустойчивостью.
При выборе сверла для ковки следует отметить один важный момент. Большие сверла состоят из рабочей спиралевидной части из Р6М5 и хвостовика из обычной стали. Маленькие сверла обычно полностью из Р6М5. При ковке ножа из большого сверла необходимо сразу определить, где какая сталь и где между ними граница. Сделать это можно достаточно просто, всего лишь немного проточив сверло по всей длине. Там, где обычная сталь, сноп искр будет большой и желто-оранжевого оттенка. А вот там, где легированная сталь, сноп будет реденьким и ближе к красноватому оттенку. Описанная выше процедура необходима для того, чтобы определить, где у ножа будет начинаться клинок, а где хвостовик. Закончив с этим, переходим к самой ковке.
Вначале разводим огонь в печи , подключаем поддув и ждем, когда угли разгорятся достаточно сильно, после чего помещаем сверло в горнило . Но делаем это с помощью клещей и так, чтобы хвостовик большей частью оставался вне огня.
Важно! Выполняя ковку ножа впервые, можно не сразу определить, когда металл нагрелся до необходимой температуры. Вследствие чего можно испортить не одно сверло. Поэтому прежде чем браться за ковку сверла, можно немного потренироваться с нагревом и ковкой металла на обычной арматуре. При этом необходимо запоминать, какого цвета был металл и когда он ковался наиболее мягко. Также стоит помнить о том, что на солнечном свете даже нагретый до 1100 °С металл будет выглядеть темным.
Как только сверло нагреется до необходимой температуры, а это более 1000 °С , его сразу же необходимо вынуть из горнила , и зажать низ хвостовика в тисках. После чего взять разводной ключ, зажать им верхушку сверла и сделать круговое движение, расправляя спираль. Делать все необходимо быстро, чтобы металл не успел остыть, иначе рискуете сломать сверло. Если не получилось сделать это за один раз, ничего страшного. Просто повторно раскалите сверло и повторите процедуру. В результате должна получиться относительно ровная полоска металла.
Следующим шагом будет ковка сверла и раскатка металла до приемлемой толщины . Тут все довольно просто. Раскалив металл до необходимой температуры, берем тяжелый молот и начинаем сильными, но равномерными ударами ровнять металл и придавать ему ровную форму. В результате должна получиться полоска металла толщиной около 4 — 5 мм.
Важно! При ковке металла необходимо постоянно следить за цветом заготовки. Как только она начала тускнеть, приобретая вишневый цвет, её сразу же возвращаем в горн. Лучше лишний раз накалить металл, чем сломать его под ударом молота.
Далее выковывается острие ножа . Тут все несколько сложнее. Дело в том, что необходимо придать заокругленную форму и при этом сохранить необходимую толщину лезвия. Вся работа практически ювелирная и потребует определенной ловкости. Ковка выполняется таким образом, чтобы постепенно заокругливая острие, понемногу оттягивалось лезвие в длину. Удары должны быть сильные, но аккуратные. У новичка может не получиться с первого раза, но немного практики все исправит.
Следующим шагом будет проковка режущей кромки ножа . Это довольно важный и сложный этап. Для этого потребуется более легкий молот и желательно с заокругленным бойком. Начиная с середины лезвия, постепенно сдвигаем металл вниз к режущей кромке. Стараемся сделать режущую кромку как можно тоньше. При этом следим, чтобы само лезвие оставалось прямым и ровным. Удары наносим очень аккуратно и стараемся прилагать лишь столько усилий, сколько требуется для небольшой деформации раскаленного металла. Помним о цвете заготовки и при необходимости отправляем её обратно в горнило.
После того как удалось выковать лезвие и острие, переходим к проковке хвостовика . Сами работы будут намного проще, чем при выковке лезвия. Вначале накаливаем круглый хвостовик сверла и затем раскатываем его сильными ударами молота. В зависимости от эскиза хвостовик может быть как узким, так и широким. Тут уже кому как нравится делать ручку ножа. Кто-то делает простые накладки, а кто-то делает наборную рукоятку.
По завершению ковки даем металлу постепенно остыть и затем переходим к шлифовке . На шлифовальном станке снимаем лишние слои металла и неровности, делая нож идеально ровным и блестящим. При шлифовке может уйти до 2 мм толщины, и нож станет намного легче и тоньше. Также на этом этапе можно выполнить заточку ножа. Напоследок выполняем закалку ножа. О том, как это делается, будет написано ниже.
Ковка ножа из сверла видео-обзор :
Еще одним популярным материалом для ковки ножей является подшипник, а именно его внутренний или внешний обод. Причем внутренний даже предпочтительней. Все работы по ковке ножа из подшипника практически идентичны ковке из сверла. За некоторым исключением.
Во-первых, заготовку из ободка подшипника вырезаем при помощи болгарки. Длину стараемся взять с запасом, так чтобы и на нож хватило и еще 1 — 2 см осталось. Во-вторых, на начальной стадии ковки вырезанную заготовку следует приварить к прутку арматуры. И в таком виде накалять и ковать. В-третьих, если в случае со сверлом заготовку раскатывали из круглой в плоскую, то для обоймы подшипника её необходимо просто выровнять. А дальнейшие действия по ковке самого клинка и хвостовика полностью аналогичны. Единственное, что стоит отметить, — из подшипника все же удобнее делать нож с накладными рукоятками.
Ковка ножа из подшипника видео-обзор :
В поисках подходящей стали для качественного ножа многие используют рессору. Металл этой автомобильной запчасти отличается высокой упругостью и долговечностью, что делает его прекрасным образцом для ножей ручной ковки. Справедливости ради, необходимо отметить, что нож из рессоры можно изготовить и обычным вырезанием профиля ножа с дальнейшей заточкой и закалкой. Но все же, чтобы нож был действительно надежным, его лучше проковать, тем более что толщина рессоры достаточно велика, а для хорошего ножа её следует уменьшить.
Ковку ножа из рессоры начинаем с зачистки болгаркой от ржавчины и разметки пластины. Потребуется лишь небольшая часть рессоры, поэтому отметив её, отрезаем при помощи болгарки. Далее привариваем заготовку к арматуре и накаляем её. После чего постепенно проковываем, доводя до необходимой толщины. Выковываем острие и режущую кромку, как это делать, описано выше на примере ковки ножа из сверла. Добившись желаемого, оставляем нож постепенно остывать и затем шлифуем и затачиваем его.
Ковка ножа из рессоры видео-обзор :
Ковка ножа из напильника
Износостойкую и прочную сталь можно найти в различном слесарном инструменте и напильник тому яркий пример. Изготовление ножей из напильника достаточно популярное занятие. Тем более что клинки получаются на редкость долговечными с прекрасной режущей кромкой. Но ковка ножа из напильника имеет свои особенности.
Прежде всего, потребуется очистить напильник от насечек и возможной ржавчины. Сделать это можно с помощью болгарки. Далее при необходимости отрезаем от напильника заготовку необходимой длины. После чего привариваем её к куску арматуры и засовываем в горнило. Накалив заготовку до нужной температуры, приступаем к раскатке заготовки до необходимой нам толщины. Затем делаем острие и режущую кромку. Хвостовик ножа из напильника лучше всего сделать под накладную ручку.
Ковка ножа из напильника видео-обзор :
Ковка ножа из троса
Изготовление ножа из стального троса довольно редкое явление. Так как в отличие от всех описанных выше заготовок, трос представляет собой разрозненные волокна проволоки, и ковать их довольно сложно. К тому же сталь троса не обладает такими высокими характеристиками, как сталь сверла или напильника. В большинстве своем ножи из троса куют из-за их необычного рисунка на клине, отдаленно напоминающего дамасскую сталь. Для того чтобы сделать такой нож, необходимо приложить несколько больше усилий, чем при ковке из обычного бруска стали.
Ковка ножа из троса начинается, как и обычная ковка. Вот только есть несколько маленьких секретов. Во-первых, это касается хвостовика. Многие мастера делают хвостовик ножа из троса в виде готовой рукоятки. Смотрится это весьма необычно и красиво. И тут есть два подхода в изготовлении рукоятки. Взять толстый трос и затем сварить его конец, сделав монолитным куском. Или сделать рукоятку в форме петли, а из концов выковать клинок. Во-вторых, ковка троса — дело сложное из-за разрозненных проволок, из которых состоит трос. Чтобы сделать нож, потребуется их сварить между собой. А это целое искусство и рассчитывать, что нож из троса получится с первого раза, не стоит. Сварку можно выполнить двумя путями. Первый — проварить электросваркой вдоль больших канавок. Второй — выполнить кузнеческую сварку. Второй вариант сложнее и в то же время предпочтительней.
Итак, выбрав способ создания рукоятки, приступаем к ковке ножа. Для этого раскаливаем трос до ярко-красного цвета. Затем вынимаем его и посыпаем бурой. После чего вновь отправляем в горнило. Таким нехитрым образом выполняется подготовка к кузнеческой сварке. представляет собой соль тетраборной кислоты и применяется мастерами для сварки отдельных слоев стали. По сути это флюс, который облегчает процесс плавки и предохраняет расплавленный металл от попадания кислорода и устраняет оксиды металла. Буру можно найти в свободном доступе без особых проблем.
После того как трос обработали бурой со всех сторон и он раскалился от 900 до 1200°С и более, вынимаем его из горнила и начинаем проковывать. Удары наносим тяжелым молотом, но при этом стараемся сохранить волокна троса вместе. Сложность ковки троса именно в этом. Но потренировавшись можно добиться приемлемых результатов. В конце концов, трос можно накалять и проковывать сколько угодно раз. Но при этом каждый раз, нагревая его в горне, посыпать трос бурой. В результате получится монолитный кусок стали, состоящий из множества слоев, почти как у дамасской стали. После чего остается лишь выковать клинок необходимой формы. На демонстрирующих ковку ножей видео уже не раз было показано, как именно делается раскатка клинка, создание режущей кромки и острия.
Закалка и отпуск клинка
Как уже отмечалось ранее, закалка ножа — это один из самых важных этапов его изготовления. Ведь именно от того насколько правильно была она выполнена, зависят рабочие характеристики ножа. Сам процесс закалки выполняется уже после того, как нож остыл и был отшлифован на точильном станке.
Начинается с его нагрева от светло-красного до оранжевого цвета. После чего нож опускается в воду или масло. При этом в воду добавляется 2 — 3 ложки поваренной соли на 1 л, а температура воды должна быть 18 — 25 °С, масла 25 — 30 °С. Закалка выполняется довольно быстро и чтобы все прошло удачно после закалки клинок необходимо отпустить. Сама закалка стали происходит в диапазоне температур от 750 до 550 °С. Момент закалки можно даже прочувствовать, когда сталь начинает «дрожать и стонать» в жидкости. Как только процесс заканчивается, клинок необходимо достать и дать ему остыть естественный образом.
Отпуск клинка выполняется уже после закалки. Сам процесс подразумевает ослабление внутреннего напряжения стали, что делает его более гибким и устойчивым к различного рода нагрузкам. Перед тем как сделать отпуск, клинок следует очистить от возможной окалины и затем вновь нагреть. Но температура при отпуске значительно меньше. Сам нож нужно уже держать над пламенем и наблюдать за ним. Как только вся поверхность покроется желто-оранжевой пленкой, убираем нож от огня и даем ему остыть естественным образом.
Иногда закалка и отпуск производятся при помощи масла или воды, а иногда через масло в воду. Такая закалка выполняется очень быстро. Сначала клинок опускается в масло на 2 — 3 секунды, а затем в воду. При таком подходе риск сделать закалку неправильно минимален.
Ковка ножа своими руками лишь кажется простой задачей. Кроме того что придется довольно много помахать кузнечным молотом, так еще и без опыта в вопросе ковки металла с первого раза может не получиться выковать нож. Поэтому сначала необходимо набить руку и немного потренироваться, а затем уже приступать к ковке ножа.
Рекомендуем также
Нож из автомобильной рессоры: 13 шагов (с изображениями)
Введение: нож из автомобильной рессоры
Это мое первое руководство, поэтому я надеюсь, что оно имеет смысл. Я покажу основные этапы изготовления ножа из листовой пружины с грузовика. Каждый нож будет отличаться, поэтому я просто объясню основные шаги и альтернативные способы его изготовления, если у вас нет таких инструментов, как у меня.
Добавьте TipAsk QuestionDownload
Шаг 1: Необходимые материалы
Ленточная пила (или ножовка)
Листовая рессора
Ленточная шлифовальная машина
Файлы
Наждачная бумага
Сверлильный пресс (или ручная дрель)
Кузница (или самодельная кузница)
Духовка
1/4 «x4» x 12 «дерево. Мой был дубовый.
Болты
Добавить TipAsk QuestionDownload
Шаг 2: Создайте свой нож
Нарисуйте на листе бумаги то, как вы хотите, чтобы ваш нож выглядел. Нарисуйте его в нужном масштабе в соответствии с размером вашего ножа. Примите во внимание диаметр и длину стали, с которой вам нужно работать.
Добавить TipAsk QuestionDownload
Шаг 3: Нагрейте вашу сталь и сплющите ее
Большинство пружинных сталей от транспортных средств имеют дугу, поэтому вам понадобится
чтобы нагреть его, и разбейте его большим молотком.Для этого также потребуется гладкая ровная поверхность.
Кроме того, если у вас нет кузницы, вы можете сделать ее, выкопав яму и выложив ее огнеупорным кирпичом, и просто используйте воздуходувку с прикрепленным к ней воздуховодом, ведущим в яму. Заполните яму древесным углем и отправляйтесь в гонки. Вы также можете использовать кислородно-ацетиленовую горелку. И у меня даже есть друг, который использовал очень горячий костер Бон, однако нагрев трудно контролировать и поддерживать даже в таком режиме.
Добавить TipAsk QuestionDownload
Шаг 4: Вырежьте свой дизайн
Вырежьте бумажный шаблон, который вы нарисовали, и приклейте его к стали.Затем нарисуйте его на стали и вырежьте ленточной пилой или ножовкой
Добавьте TipAsk QuestionDownload
Шаг 5: Заточите кромку
Используйте ленточную шлифовальную машину и напильники, чтобы сделать фаску и отшлифовать кромку. Чем плавнее будет конус стали и чем больше острый угол, тем лучше будет резать ваш нож.
Примечание …. Я очистил весь нож, чтобы он стал блестящим и красивым на этом этапе, что оказалось бессмысленным, потому что мне нужно было повторно нагреть его позже, и вы тоже.
Добавить TipAsk QuestionDownload
Шаг 6: Просверлите отверстия
На предыдущем рисунке показаны отверстия, которые уже просверлены. На самом деле это не имеет значения, когда вы их просверливаете, но их просто нужно просверлить, прежде чем закалять нож.
Добавить TipAsk QuestionDownload
Шаг 7: термообработка лезвия
Вот несколько быстрых металлургических операций для вас. Надеюсь, это имеет смысл. Когда вы изначально нагревали лезвие, чтобы устранить изгиб, он, скорее всего, был очень равномерным, я знаю, что мой — нет, и вы даете ему постепенно остыть до естественной температуры с течением времени.Это сделает нож мягким, и он погнется под нагрузкой. Теперь вам нужно равномерно нагреть все лезвие, пока оно не достигнет вишнево-красного цвета, не яркого, а от среднего до темно-красного. Еще один способ узнать, что это правильная температура, — это сделать ее немагнитной. Это можно сделать, если взять магнит и приклеить его к горячему металлу. Когда он достигнет нужной температуры, он больше не будет прилипать. Когда он станет немагнитным, вы окунете все лезвие в емкость с маслом или водой.Это называется закалкой. Извините, у меня нет фотографий этого процесса. Все происходит очень быстро, и на это нужно обращать внимание. Я использовал оливковое масло и вылил его в одноразовый противень. Можно использовать воду, но масло сделает лезвие более гибким. Многие люди говорят, что нужно просто использовать старое моторное масло, но я читал много форумов об ужасных историях из-за примесей в нем, поэтому я держался подальше.
Добавьте TipAsk QuestionDownload
Step 8: Pretty Knife Ruined
Вот почему бессмысленно делать ваш нож красивым, прежде чем вы его закалите lol
Добавить TipAsk QuestionDownload
Шаг 9: Закалите лезвие
Теперь, когда вы закалили свое лезвие, вы захотите закалить его.В основном теперь, когда вы его замочили. Он достиг затвердевшего состояния. Но молекулы находятся под напряжением из-за быстрого удара закалки, поэтому вы берете лезвие и кладете его в духовку с температурой около 450-500 • на час или около того. Затем выключите духовку и дайте лезвию постепенно остыть, как в духовке. Некоторые делают это два или три раза. Я сделал это только один раз и никаких проблем не было. Это заставляет молекулы расслабляться, а нож становится более гибким и менее подверженным щелчкам.
Примечание… Одно из моих первых лезвий, которое я сделал, я нагрел до горячего … закалил в воде и не закалял. Я один раз швырнул его в пень, и он разлетелся на 7 частей. Так что эти шаги важны.
Добавьте TipAsk QuestionDownload
Шаг 10: Сделайте ручку
Обведите ручку и вырежьте ее ленточной пилой или ножовкой
Добавьте TipAsk QuestionDownload
Шаг 11: Просверлите отверстия в ручке
Прикрепите одну сторону рукоятью к ножу, затем просверлите стальные отверстия и древесину.Затем снимите его и повторите шаг для плиты ручки с другой стороны.
Добавить TipAsk QuestionDownload
Шаг 12: Завершите свои ручки
Присоедините ручки к ножу и отшлифуйте их до тех пор, пока они не будут удобно держать в руке. Затем удалите их и добавьте либо несколько слоев масла, либо то, что я сделал, это просто прозрачный внешний слой варатана.
Добавить TipAsk QuestionDownload
Шаг 13: прикрепите ручки и готово !!
Прошу прощения, но я не могу вспомнить, как называются эти болты, которыми я прикрепил ручку.Они ввинчиваются посередине, и на одной стороне есть наружная резьба, а на другой стороне — внутренняя резьба, а на одном конце есть насадка с шлицевой головкой для затяжки. Я уверен, что есть много разных стилей, но я их использовал.
В любом случае это реализованный проект. Надеюсь, вы нашли это информативным. Я также сделал кожаные ножны для этого ножа и скоро сделаю инструкции, как их сделать.
Ура
Добавить вопрос Задать вопросСкачать
1 человек сделал этот проект!
Вы сделали этот проект? Поделитесь с нами!
Я сделал это!Рекомендации
Пружинный лист от машины, пригодный для изготовления ножей.Если это то, что делает его таким хорошим: кузнечное дело
Плюсы листовых рессор: высокое содержание углерода, высокая прочность, довольно легко поддается термообработке в домашней кузнице, дешево, как грязь
Минусы листовых рессор: зависит от возраста, старые листовые рессоры из легковых и грузовых автомобилей 60-х годов обычно 5160, более новые листовые рессоры могут быть из разных сплавов, которые могут сбить вас с толку при термической обработке. Кроме того, любая листовая рессора, которая была выброшена, может пройти сотни тысяч миль, что может привести к микротрещинам в стали.Кроме того, ее намного труднее перемещать с молотка, чем большинство других простых высокоуглеродистых сталей.
Нет ничего более неприятного, чем потратить десятки часов работы на нож только для того, чтобы найти трещины в стали на последних этапах шлифования. На большинстве форумов кузнецов самый частый совет, который вы найдете для новичков, — это просто купить известную сталь у хорошего поставщика стали. Таким образом, вы можете провести свое исследование и точно знать, как его обрабатывать, что, возможно, является наиболее важным шагом в создании ножа по сравнению с объектом в форме ножа.Сталь 1084 является наиболее рекомендуемой для новичков, так как она имеет очень простительные свойства термообработки в домашней кузнице и хорошо перемещается с молотка. Это также не так дорого.
При этом я люблю перерабатывать старые материалы, чтобы использовать их для изготовления ножей. Листовые пружины, спиральные пружины, зубья рототиллера, напильники, рашпили и т. Д. Практически все, что когда-то было инструментом, можно использовать для изготовления нового. Просто имейте в виду, что вы рискуете потратить время на то, что с самого начала имеет фатальные недостатки.Обязательно вырежьте кучу пробных образцов одинакового размера, чтобы вы могли попробовать разные закалочные среды, чтобы найти то, что лучше всего подходит для неизвестного материала, прежде чем пытаться провести термообработку чем-то, на что вы потратили время.
Я говорю молотком по всему, что найдешь, чтобы практиковать свои навыки. Даже если это не удастся, вы кое-чему научились. Когда вы сделали несколько штук, которые соответствуют вашим стандартам, и вы довольны своими навыками, купите 1084 и сделайте то, во что вы можете положиться. Вы будете удивлены, насколько легко 1084 может двигаться под молотом, если вы тренировались на старых листовых рессорах.Удачи вам.
Как выковать нож для начинающих
В изготовлении собственных инструментов есть что-то особенное, и ножи не исключение. Планируете ли вы изготовить кинжалы, чтобы бросать их для развлечения, сделать нож для улицы для своей мастерской или хотите сделать индивидуальное дополнение к своему набору столовых приборов, ковка ножа позволит вам сделать все это — и многое другое.
Это руководство предназначено для очень высокого уровня обзора различных частей процесса. Я буду ссылаться на подробные руководства по пути, где вы сможете глубже изучить любую конкретную часть процесса, например, закалку или заточку.Но это руководство даст вам все, что вам нужно знать, чтобы выбраться и выбить свой первый нож.
Но почему вы должны делать нож самостоятельно, вместо того, чтобы покупать один из миллионов вариантов, имеющихся на рынке? Для начала, во многих случаях дешевле изготовить собственный нож, потому что лом можно расплавить и превратить в нож, что существенно снижает затраты до вашего времени.
Кроме того, если вы не планируете платить тонну за нестандартный нож от производителя ножей, у вас не будет такого же уровня настройки или истории за лезвием, которое является одной из самых крутых частей ковки лезвия.
Если вы чувствуете, что теперь вам нужен собственный нож (или ножи), вы находитесь в нужном месте. Следующее руководство проведет вас через вашу первую ковку ножа, помогая соответствующим образом подготовиться и выковать лучший нож от начала до конца.
Выбор металла
Первое и, вероятно, самое важное решение, которое вам придется принять перед ковкой, — это выбор металла. Существует множество различных видов металлов, однако сочетание твердости, прочности и способности удерживать кромку стали делает ее идеальным выбором.Однако тип стали также может быть разным.
Если вы чувствуете себя бережливым (или живете рядом со свалкой), вы можете повторно использовать другие куски стали, сломав или отрезав кусок и выковав из него нож. Некоторые распространенные отходы, которые вы можете найти, включают железнодорожные шипы, винтовые пружины или листовую рессорную сталь, такую как подвеска автомобиля. Они являются хорошими вариантами, потому что сделаны из качественной стали (в первую очередь из-за регулярного износа), которая в размотанном или кованном виде хорошо держит лезвие для ножа и хорошо затвердевает.
Если вы ищете что-то более точное с научной точки зрения или более высокое качество, вы можете купить металлические прутья для изготовления ножа. Они бывают нескольких типов, у каждого из которых есть свои плюсы и минусы, а также отдельные сорта, объясняющие химический состав металла, поэтому вы можете точно знать, как его использовать.
Углеродистая сталь
Углеродистая сталь — это именно то, что вы ожидаете — сталь, пропитанная углеродом для повышения прочности и твердости, при этом теряя некоторую коррозионную стойкость.Лучше всего для ножей, которые будут подвергаться ударам, а не полагаться на остроту, потому что она может потерять остроту в пользу твердости. C1045 является примером твердой углеродистой стали, которая обычно используется для ковки ножом, но есть из чего выбрать.
Инструментальная сталь
Инструментальная сталь очень похожа на углеродистую сталь, но содержит дополнительные сплавы, которые делают ее более устойчивой к коррозии, поэтому ее можно использовать в большем количестве ситуаций (например, для многих наружных инструментов). Инструментальная сталь прочна, устойчива к коррозии и хорошо держит кромку.Однако, в зависимости от марки металла, некоторые аспекты ковки будут лучше. Например, инструментальная сталь A2 является жесткой, но более склонной к ржавчине, в то время как D2 обеспечивает лучшую коррозионную стойкость и более острую кромку, но теряет некоторую ударную вязкость, поэтому лучше всего подходит для малой ударной нагрузки.
Нержавеющая сталь
Нержавеющая сталь, в основном используемая в кухонных приборах и изделиях из серебра, также может использоваться для ковки ножами. В него добавлен хром и другие сплавы, которые обеспечивают повышение коррозионной стойкости, но они страдают, когда дело доходит до твердости и остроты кромок.Тем не менее, некоторые марки с более высоким содержанием углерода, такие как 440, можно использовать для изготовления ножей, при этом они все еще соответствуют своим обязанностям.
Выбор топлива
После выбора кузнечной стали следующим решением будет источник топлива для кузницы. В зависимости от конкретной настройки ковки, наличия топлива и местоположения, вероятно, для вас будет идеальный выбор — пропан, уголь или древесный уголь.
Пропан
Чистый, легко доступный и невероятно горячий.С помощью простой пропановой горелки, которую вы можете построить за полдня, вы можете напрямую нагреть металл до такой степени, чтобы он стал работоспособным. Конечно, это неэффективно для ковки более крупных деталей, но та же идея применима и к вашей кузнице. Вы также можете купить кузницу со встроенным источником тепла на пропане, чтобы новичку было еще проще настроить.
Уголь
Очень горячий источник топлива, который легко помещается во многие кузницы, но может вывести вас из мастерской без надлежащей вентиляции.Хотя дым является эффективным источником топлива, он густой, что может предупредить местные власти о потенциальном пожаре и принести вам крупный штраф. По этой причине (и в целом загрязнение окружающей среды) уголь может быть незаконным для вас, поэтому проверьте местные законы, прежде чем вы решите курить.
Древесный уголь
Один из наиболее доступных источников топлива, который вы можете использовать, но не для всех. Древесный уголь можно сделать самостоятельно, сжигая дрова, поэтому его очень легко достать. Однако даже невероятно эффективные кузницы могут с трудом достичь и поддерживать температуру, необходимую для ковки стали.Если ваш единственный вариант — уголь, не помешает попробовать вначале, но имейте в виду, что у вас может быть не лучший опыт.
Какие инструменты вам понадобятся
После того, как вы определились с выбором топлива и металла, вам понадобится кузница, работающая на выбранном вами топливе. Если вы выберете пропан, вы можете найти несколько готовых кузниц, которые просто нужно заправлять из баллона с пропаном.
В качестве альтернативы, если вы хотите сделать это самостоятельно, кузницу можно построить с любым из трех видов топлива, которые отлично работают.Вам просто нужен поток воздуха, чтобы поддерживать тепло, достаточно места, чтобы нагреть нож, и все.
После кузницы вам понадобится кузнечный молот и кузнечный стол или наковальня, с помощью которых вы сможете отбить металл. Он должен быть жаропрочным, чтобы чрезвычайно горячие металлы не прожгли дыру и не подожгли ее, а молоток должен быть достаточно тяжелым и прочным, чтобы выдержать удар по стали.
Наконец, необходима печь или кирпичный ящик для закалки стали после ее ковки и формовки.
У меня есть руководство по снаряжению, которое вам понадобится для начала, если вам нужно больше деталей, посмотрите его здесь.
Процесс ковки
Для начала вам необходимо нагреть сталь до температуры, чтобы ее можно было обрабатывать. Если у вас есть кузница с термостатом для нагрева, вам нужно установить температуру около 2200 ° F или использовать цветовую шкалу для определения температуры стали.
После того, как сталь станет пластичной, перенесите ее в «зону ударов», чтобы ее можно было отбить молотком и начать формирование лезвия.Когда вы ударяете по одной стороне, чтобы получить лезвие, не забудьте оставить несколько дюймов для хвостовика, чтобы с ним было легче обращаться, и переверните лезвие, чтобы оно не перекосилось в одну сторону.
После того, как вы сформировали базовую форму ножа, ее нужно будет отжечь, прежде чем вы сможете продолжить ее совершенствование. Отжиг смягчает металл, что упрощает формование, и вы можете получить более естественный вид ножа. Вы можете сделать это, нагревая лезвие до красного цвета и давая ему остыть на воздухе 2-3 раза.
После отжига вы можете подпилить его, чтобы он начал выглядеть отполированным, прежде чем отправить его обратно в кузницу для начала закалки.Закалка включает нагрев металла до докрасна температуры, а затем быстрое охлаждение, погружая его в воду, масло или другие вещества, которые быстро снизят температуру и позволят ему затвердеть, зафиксировав молекулы на месте. После погружения в воду кончиком вперед перемешайте лезвие, чтобы оно могло равномерно остыть в окружении другой воды или масла, которое еще не нагрето.
Если у вас есть твердое лезвие, пора его закалить, чтобы лезвие не было слишком хрупким для использования. Это небольшое размягчение стали приведет к тому, что она будет двигаться от всего пути к твердому, ближе к середине, где она наиболее эффективна в качестве ножа.Вы можете сделать это, нагрея его в духовке до 300 ° F в течение 2 часов, а затем охладив водой. Теперь у вас есть нож!
Последние штрихи
После того, как вы выковали, отожгли и отпустили лезвие, пора нанести последние штрихи, чтобы им можно было пользоваться и прорезать все, с чем вы сталкиваетесь.
Для лезвия нужна рукоятка вместо хвостовика, который вы оставили при ковке. У вас есть множество вариантов того, как обращаться с ножом, но обычно просверливают отверстия и прикрепляют к хвостовику деревянные или резиновые ручки.Если у вас нет доступа к дрели, вы можете обработать ее веревкой, резиной, деревом или чем-нибудь еще, что обеспечит надежный захват ножа. Просто оберните его вокруг хвостовика и зафиксируйте для захвата.
Вам также нужно заточить лезвие на напильнике, а затем на точильном камне, чтобы улучшить его режущую способность. Это особенно важно для лезвий с меньшим удержанием лезвия, потому что они могут легко затупиться и стать менее полезными.
Заключение
Если вы когда-нибудь испытывали желание выковать собственный нож, но не знали, с чего начать, вы, надеюсь, выучили достаточно из этой статьи, чтобы попробовать.Помните, что работать с таким горячим предметом может быть опасно, поэтому важно знать, что вы делаете, прежде чем приступить к этому. Однако, как только вы освоитесь, ковка ножей может стать веселым и расслабляющим способом скоротать время или сделать что-то особенное. Только не расстраивайтесь, если сломаете лезвие или 2. Это случается со всеми.
— ОСТАВАЙСЯ ДОМА, ПАПА
СТАЛИ, ИСПОЛЬЗУЕМЫЕ НОЖНИЦАМИ
СТАЛЬ, ИСПОЛЬЗУЕМЫМ НОЖИИнформация и оборудование для заточки ножей
| Главная | | Школы заточки | | Заточка Книга Made Easy | | Буклеты / DVD / Учебники | | Оборудование | | Больше информации |
См. также https: // www.osograndeknives.com/catalog/blade-steels.html
СТАЛИ, ИСПОЛЬЗУЕМЫЕ НОЖОМ MAKERS
Боб Энгнант
0-1, пожалуй, самая щадящая сталь из всех ножевых качеств, кроме очень простые типы сплавов, и производит лезвие отличного качества для наиболее нормальное использование. Он очень легко поддается термической обработке. Дополнительные ссылки? Что ж, старый хозяин, Купер, использовал его много лет, и люди его любят его лезвия, потому что они крепкие. Некоторое время назад один из лучших кузнецы клинков сказали, что при хорошем обращении 0: 1 превзойдет любой дамаск, и нет один спорил с ним.Удержание края исключительное. 0-1 — точная шлифовка если только вам не повезет наткнуться на какой-нибудь мельничный стержень. Лох вверх термообработка и 0-1 позволит вам пробовать снова так часто, как вы хотите, пока вы не перегреваете металл. Жесткие шлифовальные ленты.
0-6 — это следующий шаг по сравнению с 0-1 легкой термической обработкой, но чистым измельчением. Он значительно прочнее, с более мелкой кристаллической структурой и твердым графитовые частицы, устойчивые к износу. Поставка горячекатаная и точная шлифовка.Цены на горячекатаный прокат приемлемые. Очень сложно шлифовать. Края невероятны, служат даже дольше, чем лучший дамаск и даже 0-1. Имеет странную оранжевую искру.
СталиW-1, W-2 и серия 10— с 1045 по 1095 являются максимальная простота и очень мелкое затвердевание, поэтому их можно использовать для сделайте выборочно закаленное лезвие, как на старых японских мечах. Превосходная прочность, эти сплавы используются для изготовления лезвий грейдеров. кромки, грузовые пружины и напильники.Использует шлифовальные ленты довольно быстро. ставка. Края приемлемы для 1045, хороши для 1060, хороши для 1084 и отлично с 1095, W-1 или W-2. Последние два часто упоминаются как О-Ф, старый файл. Получить более высокий углеродный конец этой серии очень легко. слишком сложно сделать хороший нож.
5160 — обычная пружинная сталь, в основном 1060 с одним процентом хром добавлен для его глубокого затвердевания. (Это может быть выборочно при желании нарисовать более мягкую спинку.) Отличная сталь для мечей, или любой другой клинок, которому придется немного побить. Выбор Джима Хрисулас, который делает одни из лучших рабочих мечей в своем деле. Длинные лезвия лучше всего подходят примерно к середине 50-х годов по шкале Роквелла, в то время как небольшие рабочие лезвия могут быть введены в эксплуатацию при полном 60 RC. Кованые лезвия с хорошо утрамбованной кромкой режут вечно! Черновая шлифовка ремни. В шутку называется O-C-S, Old Chevy Spring.
52100 — это сталь для шарикоподшипников, которая обычно не используется при шлифовании. размеры, но потрясающие по удержанию кромки и прочности.52100 — это 5160 с отношение, больше сплава и больше углерода, что делает его тяжелее и жестче. Подобно 5160, бросает блестящую желтую искру. Эд Фаулер разработал превосходная технология термической обработки этой стали.
L-6 — это сталь для ленточных или дисковых пил, используемых на большинстве лесопильных и совершенно сложно найти в любой другой форме. Затвердевает в масле до RC 57. и берет острую кромку для большей части резки, особенно там, где кромка может вернуться в форму.Отлично там, где требуется гибкость но легко ржавеет, как практически все простые углеродистые стали. L-7 это то же самое с чуть большим количеством углерода.
A-2 — это сталь исключительного качества с прекрасными износостойкими качествами и отличная устойчивость к отжигу и короблению. Шлифовка заметно сложнее, чем 0-1, но не очень сложно. Пиление сложнее и связывает до пяти процентов хрома в химическом составе этих сталей. Действительно мило закончить шлифовальной машиной, и при полировке появляется очень мало зерна.Отличная гибкость. Фил Хартсфилд получил невероятные режущие способности из этой стали. Несколько других из серии A также сделают прекрасные лезвия.
D-2 предлагает другую инструментальную сталь для закалки на воздухе, но с 12% хрома и отличная, если не превосходная, износостойкость. Сопротивление также верно как при распиловке, так и при шлифовании, даже когда сталь полностью отожжена. Пока использовать ремни быстрее, чем в среднем, D-2 не особенно трудно шлифовать свежими ремнями.Использование старых ремней вызывает достаточно нагрейте до упрочнения стали. D-2 отжигает при несколько более высокой температуре чем А-2 и не возьму истинную, зеркальную полировку. Определенно сталь для передовой мастер. Главный недостаток — апельсиновая корка. внешний вид поверхности после доведения до блеска. Один производитель ножей часто цитируют, говоря, что D-2 берет паршивое преимущество и держит его навсегда. Часто встречается как излишки деревянных лезвий. D-4 и D-7 также хорошие сплавы для столовых приборов, но их трудно найти в подходящих размерах.Воздуха закаленные стали могут затвердеть во время шлифования, если вы получите сток слишком горячий. На кофемолке это мало что значит, но когда вы пытаетесь сделайте защитную выемку, файл просто скользит.
М-2 — жаропрочная сталь для токарного режущего инструмента, имеющая чертовски мало общего с ножами, но позволяет действительно приготовить лезвие в отделка после термообработки без отжига. М-2 возможно немного лучше держит ребро, чем D-2.Также он довольно хрупкий и не рекомендуется для больших ножей.
440C был первым общепринятым производителем ножей из нержавеющей стали и остается довольно популярны, особенно потому, что процесс отрицательной температуры был разработан для добавить жесткости. На кофемолке он липкий и быстро нагревается, но режет намного быстрее и проще, чем любая углеродистая сталь. Ваши ремни будут сократить примерно в 2–3 раза больше 440-C, чем 0-1. Используя ручные ножовки по нему в спешке изнашивает множество лезвий.Но при должном уходе хорошо термообработка и отделка, 440C производит отличные, удобные и прочный нож, даже для нового производителя ножей. Отжигает при очень низкой температура. Обратите внимание, что 440A и 440B — похожие сплавы, часто перепутал с 440C, но не стоит использовать нож. Коммерческий производители ножей часто маркируют лезвия 440, когда они желательные версии, дающие плохую репутацию реальным материалам. 440C также доступны в большем количестве размеров и в большем количестве мест, чем любая нержавеющая сталь сплав, подходящий для ножей.Также важно помнить, что коллекционеры ненавидят, когда один из их призов становится коричневым в ножнах, и 440C очень хорошо справляется с коррозионной стойкостью. Пока вариация, 440-V кажется не таким сложным, но держит преимущество намного дольше и шлифовать его гораздо труднее.
154 CM многие считали суперсталью, если вы сможете найти старый производственный инвентарь. Новые партии не производятся в стандарты, которые мы привыкли ожидать от ножевой стали.Хотя отлично в 154 CM съедает лучшие полотна ножовочной пилы за один поперечный разрез 1-1 / 2 «. Его обрабатывающие и шлифовальные качества аналогичны 440C и не получит никаких наград за легкость в работе. Однако при использовании этот сплав имеет Несомненное преимущество как в твердости, так и в прочности выше 440 ° C. 154 CM не является общепринятым стандартным обозначением степени, а скорее торговое наименование производителя.
АТС-34 японского производства нержавейка считается равной 154 см.импорт ограничения были несколько ослаблены, хотя были вынуждены поднять цена на 50%. Чище, чем 154 CM. (154 CM больше не используется в приложениях, определенных правительством, и не является продуктом вакуумной плавки что мы когда-то ценили.) ATS-34 — практически тот же сплав, что и 154 CM, минус 0,04% одного из менее важных элементов. АТС-34 двухместный вакуум расплавленный и очень чистый. Он также имеет твердую черную кожу, которая придаст блеск вашей шлифовальной ленте раньше, чем вы это заметите.Мы рекомендуем сбивание кожи старыми ремнями перед сужением хвостовика или Vee шлифование. Один парень попытался снять шкуру промышленным мотором ведомое колесо проволочной щетки. Все, что он сделал, это отполировал. Теперь у нас есть пояс специально разработан для удаления этого накипи. ATS-34 — торговое наименование. В три, 154 CM, ATS-34 и 440-C, у всех есть небольшая красноватая искра, отчетливая, но трудно различимая карбоновая вилка. ATS-34 также является торговое наименование. Эта сверхтвердая черная кожа на некоторых из этих сталей, а также окалину ковки, можно «протравить», чтобы удалить.Купите галлон недорого белый уксус и оставьте в нем сталь на ночь. Работает как по волшебству. Если это не работает, или от магазина пахнет салатом, вините Дуга Брэка, кто дал мне этот намек.
AEBL кажется примерно 440B. Чрезвычайно легко измельчить, на самом деле, я думаю, что возможно, установил мировой рекорд несколько лет назад, более ста лезвия из пруткового материала до зернистости 220 в течение восьми часов. Термическая обработка как 440С. Удержание кромки лучше всего, когда термическая обработка включает цикл замораживания.Очень легко полировать и полировать. Очень хороший выбор для миниатюры, кухни. ножи и т. д. У AEBL есть несколько причудливых привычек в заточке, которые делают его трудно использовать с более толстыми или большими ножами. Делает хорошие кухонные ножи. «Хосс» использует это в своем прекрасном нержавеющем Дамаске и сообщает, что это держится очень хорошо.
420 модифицированная нержавеющая сталь, успешно использовалась в некоторых коммерческих производители ножей, но наличие ножей для хобби непрактично производитель, поскольку, черт возьми, немногие из нас заказывают сталь в прокатных валках.
VASCO WEAR довольно дорогая, но очень и очень хорошо держит кромку. Также очень хорошо сопротивляется шлифованию! Вы поклянетесь, что ваши ремни потускнели когда попробуешь. Сделайте все необходимое перед термообработкой, потому что вы конечно, потом ничего не получится. По цене как омар хвосты, когда вы можете их найти. Попробуйте Vasco-Pacific в районе Лос-Анджелеса. Vasco — Pacific использует свои собственные названия для своих сплавов.
СтальDAMASCUS настолько широко производится, что ее невозможно делать слишком много общих заявлений об этом, кроме того, что кажется коллекционеры лучше любого другого типа.Каждый кузнец делает свое по-разному, начиная с того, кто выдерживает это, начиная с трех слоев, парню, который сваривает 300-слойный сэндвич из прокладки в заготовка с одного удара на 40-тонном прессе. Они все красивые. Риз Вейланд предполагает, что последнее травление дамасского клинка должно быть выполнено фосфорным кислота, которая как бы припаркует металл и поможет защитить его. Он сказал что вам нужно поиграть с концентрацией кислоты и время погружения немного, в зависимости от используемой стали.Это также работают на большинстве лезвий из углеродистой стали. Если дамасский клинок закален с более мягким разделом на позвоночнике или защитном кожухе вы получите гораздо лучшее если вы сначала используете соляную кислоту, чтобы получить желаемую глубину, а затем хлорид железа для добавления цвета.
STELLITE 6-K относится к той же категории, что и одежда Vasco Wear. область сопротивления, но не требует термической обработки, так как в ней нет железа это вообще. Хитрость заключается в том, что исключительно твердые частицы помещены в довольно мягкий сплав.Очень гибкий и легко сгибаемый. Практически невозможно довести до зеркальная отделка. Лезвия из стеллита очень востребованы некоторыми коллекционеры. Сплав, который лучше всего подходит для ножей, теперь необходимо заказывать в Канада и стоит около ста баксов за фунт. Часть стеллита Прочность зависит от процесса прокатки, используемого для формирования прутков. Бросать Стеллит не такой прочный.
ТИТАН — металл для лезвия ножа только в минимальной степени. Это не может быть более твердым после середины 40-х по шкале С Роквелла, и это весна, или территория метательного ножа.Помимо этого, я уверен, что скоро коллекционные титановые ножи появятся у многих изготовителей на заказ столы, предназначенные для ловли коллекторов, а не для разделки.
Авторское право 1997 г., Blades ‘N’ Stuff — ВСЕ ПРАВА ЗАЩИЩЕНЫ
Мы ожидаем, что люди будут копировать и распространять эту информацию без
ограничение, пока мы указаны в качестве источника.
| Главная | | Контакты | | О нас | | ССЫЛКИ | | Поставщики | | Фотографии | | Школы заточки |
Авторские права 1996-2021, Стив Ботторфф
Ковка кинжала — Кузница Дыхания Дракона — Кузнец на заказ
Мэтью Паркинсон
Скачать учебникШаги по изготовлению кинжала с самообслуживанием
1) нарисуйте конус
2) профильное полотно
3) поковка со скосом
4) отрезать
5) форма рукоятки
6) шлифовать, полировать и термообработать.
Этапы изготовления кинжала с рукоятью
1) нарисуйте точку на баре
2) профиль профиля лезвия
3) фаска
4) в хвостовике
5) выковной хвостовик
6) шлифовка / полировка и термообработка.
7) изготовить и собрать ручку
(шаги третий и четвертый можно поменять местами.)
Методы конструкции ручки
Полный тан
Нож этого типа имеет хвостовик, равный полной ширине и длине рукоятки.Болстеры обычны, но гвардии и навершие — нет. Рукоятка состоит из двух пластин, приклеенных к хвостовику. К этой категории также относятся ножи с ручным управлением. Это прочная ручка, но она подвержена повреждениям от влаги.
Частичный тан
Этот тип ножа имеет хвостовик, который частично проходит через рукоять и прикрепляется булавками или приклеивается на место. Гвардии и валики обычны, но навершие — нет. Этот стиль почти всегда используется с рогами для коронок. Это надежный и стабильный метод, но в некоторых конструкциях нож может быть плохо сбалансирован.
через отбортовку
В этом стиле используется хвостовик, проходящий по всей длине рукоятки. Гвардейские валики и навершия обычны. Конец хвостовика прикрепляется к этому стилю путем зачистки, ввинчивания в навершие, декоративной гайки или, в некоторых случаях, с помощью булавки. При правильном проектировании это очень сильный метод строительства. Даже большинство западных мечей используют этот стиль конструкции.
Работа со средне- и высокоуглеродистыми сталями
При изготовлении ножа необходима высокоуглеродистая или среднеуглеродистая сталь.Этот вид сплава также называют «пружинной сталью» или «инструментальной сталью». При работе с этими сталями, чем выше содержание углерода и чем выше содержание легирующих элементов, тем более чувствительной будет сталь к правильным диапазонам температур. Некоторые из этих сплавов могут быть красными твердыми (температурный диапазон, в котором сталь слишком тяжелая для обработки) или красными короткими (температурный диапазон, в котором сталь склонна к растрескиванию или крошению). Как правило, эти проблемы чаще встречаются в высоколегированных сталях. Простые высокоуглеродистые стали, как правило, меньше сталкиваются с этими проблемами, но при выдержке при высокой температуре развиваются большие размеры зерна.Большой размер зерна ослабляет сталь и ухудшает режущую способность готового ножа.
Чтобы избежать повреждения стали, с которой вы работаете, нужно знать, какой сплав вы используете. Посмотрите этот сплав в Интернете или в одном из многочисленных справочников. Узнайте, к чему этот сплав склонен (красный короткий или красный твердый), и каковы диапазоны закалки и отпуска (эта информация вам понадобится позже). С любым из этих сплавов следует сделать несколько вещей. Во-первых, не замачивайте сталь в кузнице.Во-вторых, не нагревайте сталь до более высокой температуры, чем это необходимо для обработки. И в-третьих, по мере приближения к готовой форме работайте при все более низких температурах. Наконец, нормализуйте сталь перед чистовой обработкой ножа (шлифовка опилок и т. Д.). Для нормализации нагрейте сталь до критической температуры. Эту температуру можно найти, используя магнит, чтобы найти точку Кюри (точка, при которой нагретая сталь становится немагнитной). Критическая температура на несколько сотен градусов выше точки Кюри. Нагрейте до критической температуры и дайте остыть на неподвижном воздухе примерно до 400 градусов F.Сделайте это три раза или циклически. Это уменьшит размер зерна, разрушит любые карбиды, которые могли образоваться, и смягчит сталь, что облегчит шлифование / опиливание.
В США стальные сплавы классифицируются по двум основным системам. Первая — это числовая система (SAE, AISI). В этой системе есть 4 или 5 цифр, которые определяют сплав. Первые два определяют содержание сплава, а последние два или три — содержание углерода. Это так называемые точки. 100 баллов равняются 1 мас.% Углерода.Сталь 1050 будет простой углеродистой сталью (10 = простая углеродистая сталь) с содержанием углерода 0,50%. Минимальное содержание углерода для изготовления хорошего ножа составляет около 40 баллов (0,40%), а максимальное — около 1%.
Вторая система классификации — это буквенная система номеров инструментальных сталей. Это специальные сплавы, которые были разработаны с определенной целью. В одном наборе сталей (например, серии О) может происходить полное изменение сплавов с аналогичными выловленными свойствами. Некоторые из наиболее распространенных сталей в этой системе — это O1, W1, W2, L6, S7 и D2.Из большинства этих сталей можно делать очень хорошие ножи, но с некоторыми очень сложно работать.
Основная металлургия
Понимание того, что происходит со сталью во время термообработки, позволяет мастеру по лезвиям знать, когда безопасно «что-то сойти с рук», а когда нет. Это также позволяет мастеру по лезвиям находить решения проблем, которые время от времени возникают при работе с новой сталью. Сталь определяется как железо, легированное углеродом. Все современные стали имеют сплавы, кроме углерода, но все стали должны содержать углерод, чтобы быть сталью.
Определение терминов:
- Твердость — это мера сопротивления материала деформации. Для сталей это измеряется по шкале Роквелла С.
- Прокаливаемость — это способность стали достигать твердости. Абсолютная твердость (на поверхности) и по глубине затвердевания (твердость в центре).
- Вязкость — это мера способности стали выдерживать напряжение (сопротивление удару, гибкость, деформация и т. Д.).
Каждый разный легирующий металл изменяет свойства стали.На что способен каждый сплав и на то, что разные сплавы вместе, — это целая жизнь изучения. Поэтому я не буду вдаваться в подробности, кроме как сказать, что большинство сплавов используются для изменения качества стали (т.е. более мелкое зерно, более высокая прокаливаемость и т. Д.).
Сталь — это кристаллический материал, который может образовывать несколько различных структур внутри кристаллической матрицы. Первая структура — это феррит, который представляет собой чистые кристаллы железа в стали с цементитом (карбидом железа), связывающим подавляющее большинство углерода.Феррит представляет собой объемно-центрированный куб из 9 атомов (8 атомов железа по углам и один атом железа в центре), в котором металлические сплавы, такие как никель, могут заменять один или несколько атомов железа. Когда сталь нагревается выше ее «критической» температуры, образуется структура, называемая аустенитом. Это гранецентрированный куб из 14 атомов железа (опять же, металлические сплавы могут заменять атомы железа в структуре), который может содержать до 2% углерода по весу между атомами железа. По большей части аустенит присутствует только при температурах выше температуры аустенизации (начиная с 1375 ° F).После закалки аустенит становится мартенситом, который представляет собой закаленную сталь. Мартенсит образуется, когда аустенит «замораживается» при закалке, и имеет структуру объемноцентрированного тетрагонального.
Целью термической обработки для кузнецов является освобождение углерода от карбидов и доведение его до раствора с железом (аустенитом), а затем закалка для превращения углерода в раствор. На практике это 3 основных этапа: нормализация, закалка и отпуск. Целью нормализации является измельчение карбидов, уменьшение размера зерна и возможность быстрого образования аустенита.Это позволит сократить время выдержки при температуре во время закалки и более мелкозернистый мартенсит после закалки. Нормализация определяется как нагрев до верхней точки превращения (около 1400-1500 ° F) и медленное охлаждение до нижней точки превращения (около 900 ° F). Несколько циклов нормализации могут иметь большие преимущества (это также называется термоциклированием).
Этап закалки состоит из нагрева до температуры выше верхней точки превращения и охлаждения в течение заданного времени (закалка).Время между нагревом и охлаждением определяется сплавом (скоростью закалки). Эту скорость можно найти на диаграмме TTT (преобразование времени-температуры). На графике ТТТ кривая упрочнения будет выглядеть как нос. Пока сталь остынет ниже кончика носа в течение отведенного времени, она затвердеет. На диаграмме TTT также показаны точные верхняя и нижняя точки трансформации, а также точки аустенизации и точка Кюри (точка, в которой сталь становится немагнитной).После закалки сталь в основном будет мартенситной с остаточными карбидами, а в случае высоколегированных сталей часто также присутствует остаточный аустенит. После закалки сталь находится в сильно напряженном состоянии. Он очень твердый, но при этом очень хрупкий. За счет отпуска (нагрев между 250-1100˚F) большая часть напряжения снимается. Часть любого остаточного аустенита превращается в мартенсит, и общая твердость снижается. По мере уменьшения твердости уменьшается хрупкость и увеличивается ударная вязкость.Второй цикл закаляет как исходный, так и вновь образованный мартенсит и преобразует большую часть остаточного аустенита в мартенсит. Если цикл отпуска повторяется 3 раза, 90% или более остаточного аустенита превратятся в отпущенный мартенсит. Для обычной ножевой стали в этом нет необходимости, поскольку в низколегированных сталях остаточный аустенит после закалки практически отсутствует. Для лезвий из высоколегированных сталей это может стоить дополнительных усилий, а в некоторых случаях действительно необходимо.
Мой метод — начать отпуск на 50 градусов ниже чистового (т.е. температура 375˚F будет запущена при температуре 325˚F). Выдержите при более низкой температуре 1 час, снимите и дайте остыть. Затем снова поставьте духовку на 25 градусов выше, темперируйте 1 час, снимите и дайте остыть. Затем завершите окончательную закалку на 25 градусов выше, закажите 1 час, снимите лезвие и дайте остыть.
Стали делятся на три класса: доэвтектоидные (меньше углерода, чем эвтектоидные), эвтектоидные и гиперэвтектоидные (больше углерода, чем эвтектоидные). Точка эвтектоида (примерно 0,75% углерода по весу) в стали — это точка, в которой количество присутствующего углерода «насыщает» низкотемпературный материал, но еще не является достаточным для образования «свободных» карбидов.В незакаленных сталях весь материал должен быть перлитом, который представляет собой смесь феррита (чистого железа) и цементита (карбида железа). Ниже эвтектоидной точки материал будет представлять собой смесь феррита и перлита, а выше эвтектоидной точки материал будет представлять собой смесь перлита и свободных карбидов.
Гипоэвтектоидные стали содержат от 0,01% до 0,75% углерода по весу. Стали с содержанием углерода более 0,4% будут затвердевать и будут довольно прочными, хотя и не особенно твердыми. Добавление других сплавов может улучшить твердость и прокаливаемость.Обычно гипоэвтектоидные стали легко поддаются ковке, шлифовке и термообработке.
Эвтектоидная сталь имеет содержание углерода около 0,75% по весу. Эти стали хорошо затвердевают и, как правило, не требуют больших усилий при работе с ними, но не обладают такой повышенной ударной вязкостью, как доэвтектоидные стали без добавленных сплавов. Это лучшие стали для начинающих кузнецов из-за их щадящего характера и относительно высоких характеристик.
Гиперэвтектоидная сталь содержит от 0,75% до 1,25% углерода по весу.Эти стали могут давать самые высокие характеристики, поскольку избыток углерода может образовывать различные карбиды. Они почти всегда содержат большое количество сплавов, особенно таких карбидообразователей, как хром, ванадий и вольфрам. При правильном обращении эти стали обладают лучшими характеристиками удержания кромок и износостойкости, но с ними трудно работать, поскольку они плохо реагируют на перегрев. Хорошие знания в области металлургии и надлежащий контроль температуры ковки и термообработки являются обязательными, прежде чем углубляться в эту группу.
Ковка профиля лезвия по форме
Начните с создания точки на конце стержня. Сделайте конус примерно на 1/3 короче желаемой конечной длины лезвия. Если вы начинаете с круглой или квадратной ложи, сначала выковайте 4-сторонний конус, а затем расплющите. Помните, что форма и длина конуса будут отражаться на форме и острие готового лезвия, но готовое лезвие будет длиннее и шире после снятия фаски. После того, как профиль будет придан нужной формы, хвостовик можно закрепить с помощью пружинного долота.Чтобы лучше контролировать длину готового лезвия, после ковки скосов можно установить хвостовик. На этом этапе хвостовик должен оставаться от ½ до 2/3 ширины лезвия. При изготовлении лезвия с ручным управлением сделайте ковку в переходе к рукоятке и срежьте лишний материал. При изготовлении клинка с рукояткой, после ковки в переходе отрежьте, оставив 1-2 дюйма ложа после ступеньки, вкованной из пружинного долота. Затем выковать запах.
Наконечники
- Оставьте точку конуса не менее 3/16 квадрата для облегчения снятия фаски.
- Используйте конец каждого нагрева, чтобы расплющить лезвие перед повторным нагревом.
- Обрабатывайте сталь только до ярко-красного огня. ЗАПРЕЩАЕТСЯ замачивать сталь в кузнице при высокой температуре.
Ковка на фаске
Начните ковку скосов на выступе. Для этого наклоните режущую кромку лезвия к наковальне и ударьте под тем же углом. Ударьте как можно ближе к краю, и как только скос станет неглубоким, уменьшите углы и начните работать на лезвии выше, чтобы сместить скос вверх по стороне лезвия, пока он не достигнет позвоночника.
Поскольку кромка расширяется по мере того, как она становится более тонкой, лезвие изгибается в сторону от кромки. Исправьте это в конце каждого плавания, когда лезвие все еще находится в красном цвете, установив острие ножа на наковальню и сильно ударив лезвие обратно в прямое положение. Поскольку скосы являются коваными, убедитесь, что обе стороны обработаны равномерно. Переверните лезвие и обработайте другую сторону, сохраняя тот же угол, что и на первой. Лучше всего работать с обеими сторонами на одном и том же огне, но если это окажется трудным, работоспособным вариантом будет чередование стороны в сторону от одного плавления к другому.Поскольку фаски кованы с упором на то, чтобы кромка оставалась по центру, фаски были ровными и одинаковой толщины. Сделайте скосы толщиной примерно в десять центов по краю.
Лезвия для снятия фаски с двух сторон
Обработка скосов на лезвии с обоюдоострым краем во многом такая же, как и на лезвии с одной кромкой, только что выполняется с обеих сторон. Все четыре грани алмаза необходимо обработать равномерно. Вы можете работать от хвостовика к точке или от точки к хвостовику. Используйте одинаковый угол на всех 4 гранях.Лезвие не будет выгибаться, если скосы кованы равномерно при каждой плавке. Это хороший показатель того, что ковка идет равномерно. Убедитесь, что угол наклона молотка соответствует углу, при котором стержень удерживается на наковальне на ВСЕХ ЧЕТЫРЕХ гранях. Осторожно выковайте скосы до рикассо (если он есть) или до хвостовика, если рикассо отсутствует. Обработайте край до 1/16 дюйма или около того и выковывайте скосы до тех пор, пока корешок к краю не станет одной плоскостью сплющенного алмаза.
Насадки для снятия фаски
- Выпрямляйте и выпрямляйте в конце каждого плавания.Выпрямляйте только плоские поверхности скосов.
- Пробковый винт вызывается изменением углов от грани к грани. Для исправления установите высоту скрутки вниз и вверх по углам скоса. Обработайте обе противоположные грани.
Шлифовальный
Используя изношенную ленту с крупными зернами, отшлифуйте кромку плоской плиты или контактного колеса шлифовального станка. Очистите профиль лезвия, при необходимости изменив форму кончика, пока лезвие не станет ровным и центрированным. Затем проведите кромкой лезвия вертикально по шлифовальной машине так, чтобы все следы шлифования проходили по кромке вертикально.Затем используйте маленькую насадку на шлифовальном станке, чтобы выровнять место стыка хвостовика или область захвата ножа. Если небольшое крепление для колеса недоступно, используйте файлы для уточнения формы хвостовика или рукоятки. Зона соединения между хвостовиком и лезвием должна быть не менее 1/8 радиуса (1/4 дюйма окружности), в идеале без следов инструмента, пересекающих край. Это предотвратит образование повышенных напряжений и сделает лезвие более прочным.
После завершения профилирования начните шлифование скосов, используя изношенную ленту с крупными зернами на плоской плите.После удаления окалины используйте свежую шлифовальную ленту для шлифования скосов краем вверх. При измельчении у каждого есть слабая сторона и сильная сторона. Начните шлифовать со своей слабой стороны и сопоставьте с ней свою более сильную, так как это дает больший контроль. Отшлифуйте скосы до тех пор, пока корешок не станет ровным и центрированным, а край не станет равной толщины и толщиной с десять центов. Если конструкция не имеет резких врезаний, перейдите к 8-дюймовому контактному диску с лентой с зернистостью 120 и отшлифуйте скосы вертикально, пока не будут удалены все грубые следы зерен.Если конструкция требует резкого погружения, переточите плоскую плиту. Сначала измельчите зернистостью 120, а затем измельчите зерном 220. На этом этапе лезвие готово к термообработке.
Фитинг защитного кожуха или валика
Начните с разметки центральной линии на ограждении с помощью писца. Далее штангенциркулем измерьте ширину и толщину хвостовика. Отметьте ширину на кожухе по центру, где будет проходить язычок. Затем найдите центр и начертите там линию. Разложите прорезь за отметкой центральной линии.Используйте сверло на один размер меньше толщины хвостовика. Отметьте и пробейте внешние отверстия ½ толщины сверла от внешних линий. Отцентрируйте кернер и отметьте ширину сверла от последней отметки керна. Просверлите центральные метки. С помощью надфиля срежьте полотно материала между отверстиями. Теперь отредактируйте прорезь по размеру, используя размеченные линии в качестве ориентира. Как только хвостовик пройдет через прорезь, подпилите радиус, чтобы плечо выступа полностью вошло в седло.Вращающийся инструмент или резак можно использовать, чтобы прорезать карман, в который вставляется лезвие, для более чистого перехода. Отметьте это после того, как лезвие встанет на место, проследив лезвие на щитке разметкой. Затем вырежьте внутри линий. Часто проверяйте посадку и удаляйте только достаточно материала, чтобы лезвие точно прилегало. После установки защитному кожуху можно придать желаемую форму.
Установка ручки
Нарисуйте выступ на материале ручки. Отметьте осевую линию на стороне 90 градусов. из этого. Используйте квадрат, чтобы продолжить эти линии до верха материала.Используя эти линии в качестве направляющих, зажмите материал в сверлильном станке и, используя сверло немного меньшего размера, просверлите паз для хвостовика. Зажмите рукоятку тисками и осторожно нагрейте хвостовик ножа примерно до 900 градусов F. Затем используйте наконечник, чтобы прожечь прорезь для идеальной посадки. Если лезвие подвергалось термообработке, убедитесь, что хвостовик не проходит мимо места соединения с ограждением, так как это приведет к необходимости повторной термической обработки лезвия. Если это вызывает беспокойство, стальной пруток может иметь форму, соответствующую хвостовику, и использоваться для выжигания материала ручки.Как только хвостовик будет подходящим, нарисуйте профиль на отмеченной стороне ручки. С помощью ленточной пилы или ленточно-шлифовального станка сделайте шероховатую форму до этих отметок (на этом этапе, если штифт включен в дизайн, подходит, то продолжайте). Повторите то же самое для двух других граней. Затем округлите и придайте форму рукоятке по своему желанию. Проверьте соответствие между кожухом и ручкой. При необходимости отрегулируйте. Отшлифуйте ручку / рукоятку до зернистости примерно 400 для достижения наилучшего результата.
- При ручном шлифовании дерева всегда шлифуйте по зерну.
- Слегка намочите древесину между зернами, чтобы увеличить шероховатость и добиться более тонкой отделки
Добавление штифтов к ручке
С ручкой, профилированной по форме и подходящей к ограждению, отметьте, где будут размещены штифты.Используя сверло подходящего размера, просверлите отверстия под штифт в рукоятке (отверстия под штифт следует просверлить на штифте размером IE 1/16 дюйма, используйте сверло 1/16 дюйма). Теперь соберите нож и удерживайте его длинным зажимом. Используйте отверстия в ручке в качестве ориентира, чтобы сверлить отверстия в хвостовике. Отрежьте кусок булавки на 1 дюйм длиннее, чем ширина ручки. Оберните штифт грубой бумагой и заострите один конец. Согните последнюю ¼-1/2 несконусного конца более чем на 90 градусов. Вставьте штифт в отверстие и проверьте посадку сборки.
Если подгонка нарушена, аккуратно удалите излишки материала или воспользуйтесь прокладкой для восстановления посадки. Кожа работает хорошо, так как она сжимается и воспринимает любые нестабильности, когда булавка вбивается. После приклеивания кожа будет устойчивой и защищенной от влаги.
Основная термообработка
Основная термическая обработка ножей состоит из трех этапов. Именно термическая обработка является наиболее важной частью изготовления ножа. Именно термическая обработка превращает предмет в форме ножа в нож.Первый этап — нормализация, второй этап — закалка, третий — отпуск.
Шаг первый: нормализация. Нагрейте лезвие до оранжевого огня и дайте остыть на неподвижном воздухе до черного огня. Сделайте это трижды. Это устранит любые напряжения, возникающие при шлифовании, уменьшит размер зерна и оставит сталь в наилучшем состоянии для закалки.
Шаг второй: закалка. Нагрейте лезвие до критической температуры (температура, при которой весь углерод находится в растворе железа) и закалите его (в большинстве случаев в масле).Это приведет к тому, что сталь станет самой твердой. Критическая температура варьируется от сплава к сплаву (обычно между 1450-1550 ° F). Чтобы определить критическую температуру, нагрейте сталь и проверьте ее магнитом. Температура, при которой он теряет магнетизм, называется точкой Кюри. Примерно на 100 градусов выше этой точки критично. На практике закалка с точки зрения потери магнетизма стали достаточно близка. На оценку температуры по цвету влияет окружающий свет. При использовании стали, с которой вы знакомы, рекомендуется проверить температуру с помощью магнита.Нагрейте лезвие до этой точки и охладите лезвие в масле. Погрузите лезвие лезвия в масло или сначала острием. Не наклоняйте лезвие при входе в закалку, иначе лезвие покоробится. Для большинства сталей подходят растительные или арахисовые масла, которые не токсичны. Также можно использовать моторное масло (свежее не использованное) и трансмиссионную жидкость. Для более последовательной закалки и при работе со сталями с быстрой закалкой следует использовать промышленные закалочные присадки, такие как Parks-50. Погасите лезвие, пока весь цвет не исчезнет с лезвия, затем дайте ему остыть до комнатной температуры.Проверьте край с помощью напильника, чтобы убедиться, что лезвие затвердело. Если напильник «катится», то приступайте к закалке. Если напильник «прикусил», значит, лезвие не затвердело. Разогрейте до немного более высокой температуры и снова охладите, затем проверьте еще раз. Если лезвие все еще не затвердевает, возможно, лезвие обезуглерожилось. Слегка заточите лезвие и проверьте еще раз. Если она все еще не твердая, в используемой стали может не хватать углерода для затвердевания.
Шаг третий: темперирование. При отпуске сталь нагревается до 150-1000 градусов F.Это снизит хрупкость и некоторую твердость стали. Температуры отпуска будут варьироваться в зависимости от используемого сплава, а также размера и типа изготавливаемого ножа. По большей части обычным явлением является температура 300-450 градусов по Фаренгейту в течение часа. Твердость стали измеряется по шкале Роквелла С (RC). Эта шкала варьируется от RC30 (незакаленная сталь) до примерно RC70. Для ножа среднего размера (лезвие 6-8 дюймов) твердость около RC58-60 примерно соответствует уровню. Нож меньшего размера может быть тверже (RC58-62), а нож большего размера должен быть немного мягче (RC52-58).
Диапазоны отпуска для некоторых распространенных сталей для лезвий
Сталь AS Hard 300 Deg 400Deg 500deg
1050 RC59 RC55 RC52 RC48
1075 RC64 RC62 RC59 RC58
5160 RC62 RC59 RC56 RC54
О1 RC64 RC62 RC60 RC58
W1 Rc65 RC63 Rc61 RC59
(диапазоны темпов можно найти в Интернете на сайтах различных производителей)
Повторная полировка
После термообработки слегка переточите лезвие с помощью ленты с зернистостью 120 (не забывайте держать лезвие в холодном состоянии).Затем перейдите к ленте с зернистостью 220, а затем к зернистости 400 (или начните шлифование вручную в любой момент).
Начните ручное шлифование, начиная с зернистости на один меньше последнего, использованного на шлифовальном станке. Шлифуйте под углом к последней зернистости, пока не получите ровную поверхность без каких-либо линий от последней песчинки. Затем переходите к следующей зернистости. Опять же, под углом к последней зернистости, отшлифуйте до тех пор, пока не будут удалены все следы последней песчинки. Первая использованная зернистость должна проходить по длине лезвия для наилучшей обработки.
Для получения более яркого покрытия лезвие можно отполировать с помощью полировального круга.Зарядить круг наждаком и отполировать лезвие. Очистите наждак ацетоном и отполируйте зеленым хромом.
Небольшое предупреждение: буфер — очень опасный инструмент. Не подвергайте колесо острие, иначе оно зацепится за колесо и его бросит. Производители ножей получили серьезные травмы, когда лезвие, которое они полировали, было поймано и брошено в них.
Окончательная сборка
После повторной полировки соберите нож и еще раз проверьте все соединения. Разберите нож и разложите все детали по порядку и в правильной ориентации.Закройте лезвие лентой (убедитесь, что лезвие правильно ориентировано) и установите защитный кожух обратно на выступ. Смешайте эпоксидную смолу и нанесите покрытие на хвостовик. Переместите ограждение и залейте под него эпоксидную смолу. Затем нанесите покрытие на внутреннюю часть рукоятки и в любом месте, где рукоятка будет касаться ограждения. Вместе с проставками, если таковые используются, вставьте язычок в рукоятку. Смажьте все штифты и вставьте их в отверстия для штифтов. Удалите излишки эпоксидной смолы и дайте настояться. Как только эпоксидная смола застынет, используйте кусачки или болторезные инструменты, чтобы удалить излишки штифта.Штифты напильника прижмите к рукоятке и зашлифуйте. Повторно отполируйте рукоятку и уплотнение. Снимите ленту с лезвия и очистите ее WD-40, ацетоном или денатурированным спиртом. Лезвие, ограждение и рукоятку теперь можно покрыть воском или маслом.
Наконечники
- Латунное долото можно использовать для удаления излишков эпоксидной смолы, затвердевшей на лезвии, без царапин.
- Нанесите WD-40 на тряпку, чтобы удалить излишки эпоксидной смолы.
- Слой воска на участках, на которых не должно быть эпоксидной смолы, поможет очистить его.
Заточка
Первая кромка только что обработанного ножа должна быть прорезана шлифовальной машиной, чтобы получился второй скос.Как только это будет сделано, лезвие можно снова заточить или обработать камнями.
На всех ножах со вторичной фаской (в основном все, кроме бритв и бритв в японском стиле) есть три типа лезвия: плоская, выпуклая и вогнутая (полая шлифованная кромка). Большинство производственных ножей имеют плоскую заточенную кромку от 15o до 25o. Плоский отшлифованный край можно легко повторно затачивать и хорошо режет. Большинство изготовителей нестандартных ножей используют выпуклый край с тем же основным углом 15-25. Этот тип лезвия такой же острый, как и плоский край, но он прочнее и может дольше удерживать лезвие.Однако ручными камнями повторная заточка немного сложнее. Вогнутая кромка — это стиль, который хорошо подходит для некоторых ножей, таких как ножи для разделки мяса, для заточки которых будет использоваться сталь, но имеет ограниченную полезность для повседневного ножа, поскольку это относительно слабое лезвие, быстро затупится и его невозможно переточить ручными камнями.
Как уже было сказано, большинство изготовителей нестандартных ножей используют выпуклую кромку. Для установки этого типа лезвия лезвие притирается к провисшему ремню шлифовального станка. Обычно я обрезаю край лентой с зернистостью 120, чтобы край часто остывал.Удерживайте лезвие ножа под углом 10o (измеряется от центральной линии лезвия до шлифовальной машины). Начиная с основания лезвия, слегка вдавите его и сделайте один непрерывный проход по всей кромке. Остудите лезвие и повторите эти шаги с противоположной стороны. Продолжайте этот процесс, чередуя стороны, пока не образуется заусенец (край проволоки) по всему краю.
На этом этапе перейдите к более тонкой ленте (зернистость 220) и продолжайте чередовать стороны. Затем воспользуйтесь лентой с зернистостью 400 для повторной полировки кромки.Затем натяните край буфера, чтобы удалить бор. Нож должен быть острым. Если после полировки кромка не острая, вы снова обрежьте ее под немного более крутым углом и повторите шаги снова.
Двухколесные и трехколесные шлифовальные машины
Рекомендовать к прочтению:
Уэйн Годдард
- $ 50 Магазин ножей
- Чудо изготовления ножей
Джим Хрисулас
- Мастер клинка
- Полный мастер по изготовлению клинков
Ссылки:
Справочник по машинному оборудованию
Нож ручной ковки: Введение в изготовление лезвий
РЕГИСТРАЦИЯ ПО КРЕДИТНОЙ КАРТЕ РЕГИСТРАЦИЯ В PAYPAL
Этот класс ограничен только 8 учениками в порядке очереди.
Это вводный курс, который научит студентов, как сделать нож за два дня и как использовать вторичные материалы из листовых рессор, роликовых подшипников и других квалифицированных стальных деталей для изготовления лезвий.
О классе:
Этот 2-дневный курс разработан, чтобы служить базовым практическим введением в ремесло изготовления лезвий. Инструкция будет включать информацию об инструментах и оборудовании, выборе материала, механике корпуса, конструктивных соображениях, методах ковки, основных принципах термообработки и методах отделки.Это будет довольно активный класс с большим упором на участие учеников, и в нем будет много тепла, шума, пота и физических нагрузок. Каждый ученик начнет с сегмента 1/4 ″ x3 / 4 ″ x6 ″ из высокоуглеродистой пружинной стали и, выполнив ковку, профилирование, снятие фаски, термообработку и отделку, создаст собственное собственное лезвие ручной ковки.
Этот класс в первую очередь будет посвящен ознакомлению с основами кузнечного дела. Это не просто урок изготовления ножей. Вы не просто шлифуете узор, а затем подвергаете его термообработке.Не то чтобы в таком способе изготовления ножей что-то не так, но изучение кузнечного дела дает вам совершенно другой набор навыков и огромный диапазон возможностей в работе с металлоломом (как в пост-катастрофической или постапокалиптической ситуации). вы не можете достичь, просто отшлифуя узор лезвия.
Ножи будут кузнечно-обработанными, и, если у вас все будет хорошо, вы пойдете домой с готовым ножом с ручкой из паракорда. Кроме того, вы получите пару защитных очков, беруши, файл и карточку для файлов, которые вы сможете использовать в классе и взять с собой.
Вы фактически научитесь нагревать, толкать и формировать из пружинной стали лезвие. Будьте готовы к большому количеству молотков.
Студенты познакомятся с металлами, нагревом, ковкой, ковкой, ковкой, правкой, шлифованием, формованием, изготовлением ножей и ручек.
Не возлагайте больших надежд на качество вашего первого лезвия. 🙂 Сделать приличное лезвие в самый первый раз, когда вы когда-либо взмахнете молотком, довольно амбициозно, но вы сделаете его и узнаете достаточно, чтобы сделать это самостоятельно, или, конечно, сделаете это снова в более продвинутом классе с больше информации и техники в следующий раз.
==================
Расписание занятий и подробности
Даты занятий: 22 — 23 октября, 9.00 — 16.00 ежедневно
Обед будет предоставлен.
Стоимость обучения в классе: 220 долларов. Для RSVP для этого класса требуется депозит в размере 110 долларов США.
Обучение должно быть оплачено до того, как класс займет ваше место. Приоритет отдается студентам, полностью оплатившим обучение.
===================
КАК РЕГИСТРАЦИЯ
Чтобы зарегистрироваться с помощью кредитной карты , посетите наш магазин Square
Чтобы зарегистрироваться в Paypal , посетите нашу страницу встречи
Чтобы зарегистрироваться с помощью наличных денег, денежного перевода или чека, отправьте нам электронное письмо по адресу:
Is 5160 Steel Good for Knives: Полное руководство
RogueSurvival.co является участником программы Amazon Associates. Этот пост также содержит партнерские ссылки. Это означает, что если вы что-то купите по нашей ссылке, мы получим небольшую комиссию. Прочтите отказ от ответственности.
Если вы исследовали ножи в какой-либо степени, вы, вероятно, поняли, что существует множество различных сталей, которые используются в производстве ножей. Различные виды сталей варьируются от более мягкой стали, которую очень легко затачивать, но с трудом удерживают лезвие, до твердой стали, которая прекрасно держит лезвие, но ее труднее затачивать.
Важно выбрать подходящую сталь. Подходит ли сталь 5160 для ножей? Хотя сталь 5160 сама по себе хорошо подходит для ножей, вы не найдете ее во многих. Сталь 5160 в основном используется в мечах и больших ножах, таких как ножи для выживания. Одна из причин этого заключается в том, что 5160 — это очень прочная сталь, которая также очень гибкая, что очень важно для длинных лезвий.
Хотя сталь 5160 в основном используется в более длинных лезвиях, таких как мечи, представляет собой пример ножа, в котором используется сталь 5160.
Если вы хотите создать свой собственный нож из стали 5160, обратите внимание на эту плиту из стали 5160 на Amazon .
Что такое 5160 Сталь
Легированная стальЗнаете ли вы, что 5160 фактически относится к категории пружинной стали?5160, также продаваемая как AISI 5160, представляет собой высокоуглеродистую и хромистую пружинную сталь. Он предлагает пользователям выдающуюся прочность, высокий уровень пластичности и отличную устойчивость к усталости. Легированная сталь 5160 также используется в автомобилестроении в ряде различных применений тяжелых пружин, особенно для листовых рессор.Важно отметить, что легированная сталь 5160 может быть трудной для сварки и обработки и может потребовать специальных процедур.
continentalsteel.com
Пружинная сталь — это название, данное широкому спектру сталей, используемых при производстве пружин, особенно в автомобильных и промышленных подвесках. Эти стали обычно представляют собой низколегированные марганцевые, среднеуглеродистые или высокоуглеродистые стали с очень высоким пределом текучести.Это позволяет объектам из пружинной стали возвращаться к своей первоначальной форме, несмотря на значительное отклонение или скручивание.
wikipedia.com
Термическая обработка
Легированная стальAISI 5160 обычно закаливается в масле. По этой же причине на крупных ножевых производствах эта сталь не используется. Сталь закаливают при температуре 1525 ° F и отпускают при температурах от 800 до 1300 ° F .
Ковка
Ковка легированной стали 5160 выполняется при температурах от 1149 до 1204 ° C (от 2100 до 2200 ° F).
Приложения
Легированная стальAISI 5160 подходит для изготовления листовых рессор, используемых в автомобильной сфере.
Насколько долговечна сталь 5160
Сталь5160 представляет собой сплав с высоким содержанием углерода и хрома (содержание углерода 0,6%, содержание хрома 0,9% и содержание марганца 1%).
Кроме того, сталь 5160 широко используется производителями мечей благодаря своим уникальным свойствам. Он особенно хорошо подходит для инструментов, требующих высокой степени ударопрочности и способных удерживать лезвие при длительном использовании, например, мечи и большие ножи.
Насколько популярна 5160 Сталь
Углеродистая сталь5160 более популярна среди кузнецов, чем кто-либо другой. На самом деле это простая пружинная сталь с добавлением хрома для повышения твердости. Сталь 5160 хорошо держит кромку, оставаясь при этом прочной и гибкой. 5160 в основном используется в мечах, но может быть найден в некоторых ножах и томагавках.
5160 Сталь и 1095 Сталь
Сталь 1095 — очень популярная сталь, особенно для боевых ножей. Фактически, сталь 1095 используется во многих боевых ножах США.95 из 1095 означает содержание углерода в стали 0,95%.
Как указано выше, сталь 5160 — это пружинная сталь. Из-за этого он очень популярен в производстве мечей и некоторых ножей для выживания благодаря своей гибкости. Однако, поскольку это пружинная сталь, она не имеет некоторого удержания кромок по сравнению со сталью 1095.
В зависимости от того, какой нож вы ищете, меньшее удержание лезвия лучше. Если вы ищете нож для выживания, вам нужен нож с меньшим удержанием лезвия.Причина этого в том, что если вы попали в настоящую ситуацию выживания, вам нужен нож, который можно легко заточить, используя что-то вроде камня, потому что у вас может не быть точилки для ножей. Нож с более прочным удержанием лезвия означает, что его будет труднее точить.
СВЯЗАННЫЙ: Что делает хороший нож для выживания: как выбрать правильный
Уход за сталью 5160
Несмотря на добавление хрома, сталь 5160 подвержена коррозии так же, как и другие углеродистые стали.Следует проявлять осторожность, чтобы предотвратить окисление лезвия, но для этого нужно всего несколько минут каждую неделю.
После каждого использования тщательно протирайте лезвие от мусора, отпечатков пальцев или жидкости.
Уделите несколько минут каждые пару недель, чтобы нанести тонкий слой минерального масла. Если вам необходимо хранить лезвие в течение какого-то времени, нанесите на лезвие покрытие из вазелина или ренессанса, чтобы создать физический барьер между элементами и лезвием.
Заключение
В заключение, сталь 5160 в основном используется в мечах. Частично причина того, что 5160 вы не найдете в маленьких ножах, связана с производственным процессом. Производителям дороже изготавливать ножи из стали 5160 из-за производственного процесса, чем из других сталей, таких как 1095.
Вот краткий обзор стали 5160:
- Гибкость.
- Он прочный.
- У нее меньшее удержание кромки по сравнению со сталью 1095.
- Это пружинная сталь .
- В основном встречается в мечах или больших ножах.
Если вам понравилась эта статья, обязательно поделитесь ею!
.