Методы неразрушающего контроля сварных соединений труб и трубопроводов ГОСТ
Содержание
- Визуальный и измерительный контроль
- Ультразвуковой контроль
- Радиографический контроль
- Капиллярный контроль
- Магнитный контроль
- Тепловой контроль
- Вихретоковый контроль
Неразрушающим контролем (сокращенно — НК) называется проверка надежности как целого объекта, так и его составляющих. При НК используются особые методы, позволяющие провести работы без разборки или выведения из эксплуатации. Базой для методов и средств контроля, сохраняющих целостность объектов и их эксплуатационные характеристики, служит исследование физических принципов. Как классифицируются виды и методы НК? Эта информация содержится в ГОСТ 18353-79.
Визуальный и измерительный контроль
Базовый метод дефектоскопии, отличающийся информативностью, экономичностью и быстротой.
При внешнем осмотре специалисты проверяют, насколько качественно подготовлены заготовки для сварки и как выполнены сварочные швы, а также определяют качество металла. Визуальный контроль должен выявить, нет ли видимых дефектов — ржавчины, наплывов, вмятин и т.д.
Провести ВИК можно невооруженным глазом или при помощи оптических приборов (таких как зеркало, лупа или эндоскоп). Метод примечателен тем, что для него достаточно простых измерительных средств.
В настоящее время для ВИК применяются более мощные приборы, способные обнаружить даже незначительные дефекты. Визуальный и измерительный контроль нужен, чтобы оценить состояние материала и сварных соединений. Требования по выполнению процедуры перечислены в руководящих документах по оценке сооружений и технических устройств.
Ультразвуковой контроль
Один из главных методов неразрушающего контроля был предложен советским ученым С. Я. Соколовым в далеком 1928 году. Ультразвуковая дефектоскопия охватывает многие сферы, проверяя сварные соединения, трубопроводы, аппараты высокого давления и другую разнообразную продукцию. Существует множество изделий, от состояния которых зависит безопасность тысяч людей: рельсы для железнодорожного сообщения, элементы авиационных двигателей, трубопроводы атомных реакторов и др. При производстве и эксплуатации такой сложной продукции обязателен ультразвуковой контроль.
Необходимо сказать о преимуществах ультразвукового метода по сравнению с другими методами НК:
- Повышенная чувствительность, которая позволяет обнаружить опасные дефекты — трещины, непровары и пр.
- Экономичность.
- Безопасность для здоровья (в сравнении с рентгеновским методом).
- Возможность проводить процедуру без прерывания рабочего процесса.
- Сохранение целостности исследуемого объекта.
- Возможность исследовать материалы разного происхождения.
При всех преимуществах ультразвуковой метод обладает и своими недостатками. Во-первых, он не дает представления ни о реальном размере дефекта, ни о его характере. Во-вторых, при контроле металлов с крупнозернистой структурой возникают затруднения из-за рассеяния и затухания ультразвука и высоких требований к поверхности контроля.
Про проведении НК возникает множество задач, и необходимость их решения дала толчок к развитию ряда акустических методов контроля. Если обратиться к ГОСТ 23829-85, то такие методы делятся на активные и пассивные. Активные методы основаны на излучении и приеме акустических волн и колебаний, а пассивные — только на приеме.
Радиографический контроль
В основе радиографического контроля (РК) лежит зависимость интенсивности проходящего через исследуемый объект гамма-излучения от материала и толщины изделия. О наличии дефектов сигнализирует неравномерность поглощаемого излучения. Делать выводы о строении объекта контроля можно, регистрируя распределение излучения на выходе.
РК дает возможность выявить трещины, поры, превышение проплава, искажение корня шва, непровары, инородные включения в сварных соединениях.
Радиографический метод способен обнаружить дефекты минимальных размеров, но многое зависит от их формы и местонахождения. Проще всего выявить дефект, протяженность которого совпадает с пучком излучения. В таком случае удается получить четкое изображение на снимке границ (по сравнению с дефектами криволинейной формы).
Капиллярный контроль
Считается наиболее чувствительным методом неразрушающего контроля. Капиллярные методы основаны на том, что специальные жидкости проникают в поверхностные и сквозные дефекты. В процессе индикаторные жидкости оставляют следы — их регистрируют визуально или при помощи преобразователя. Капиллярные методы помогают определить, где расположен дефект, какова его протяженность и ориентация на поверхности. Для проведения капиллярного контроля создан ГОСТ 18442-80.
Если дефект настолько мал, что его невозможно обнаружить при ВИК, то применяется капиллярная дефектоскопия. К такому методу прибегают при работе с объектами всех размеров и форм. Что касается материалов, использованных для изготовления объектов, то к ним относятся металлы и сплавы (цветные и черные), а также неферромагнитные материалы (стекло, пластмасса и пр.). О контроле выполненных из ферромагнитных материалов объектов надо сказать отдельно. Капиллярная дефектоскопия помогает справиться с задачей, если по какой-либо причине использовать магнитопорошковый метод нельзя.
Список областей, где бывает задействован капиллярный контроль, очень широк: это авиа-, ракето-, автомобиле- и судостроение, металлургия, энергетика, химическая промышленность. Капиллярная дефектоскопия применяется для мониторинга важных объектов перед их вводом в эксплуатацию и в процессе работы.![]()
Магнитный контроль
Это совокупность методов НК, нужных для выявления дефектов в ферромагнитных металлах и сплавах. Магнитная дефектоскопия позволяет обнаружить включения неметаллического происхождения, трещины, волосовины, флокены. Найти дефекты можно при условии их нахождения на поверхности изделия или при залегании на небольшой глубине (2-3 мм).
Суть магнитных методов заключается в исследовании магнитных полей рассеяния возле прошедших намагничивание ферромагнитных материалов. На местоположение дефекта указывают перераспределенные магнитные потоки и сформированные магнитные поля рассеяния.
Тепловой контроль
В основе метода — фиксация и преобразование ИК-излучения в видимый спектр. Тепловой метод неразрушающего контроля используют во всех промышленных областях, в которых о состоянии объектов можно судить по неоднородности теплового поля.
Сегодня тепловой метод очень востребован в строительство, производстве и теплоэнергетике.
У теплового контроля масса плюсов — универсальность применения, оперативность, большая производительность. Кроме того, тепловой контроль можно осуществлять дистанционно. Есть несколько видов метода — контроль плотности тепловых потоков, контроль температуры, контроль теплопроводности и тепловизионный контроль.
Вихретоковый контроль
Основой для вихретокового метода НК служит взаимодействие электромагнитных полей — внешнего и поля вихревых токов, создаваемых в объекте контроля. Вихревые потоки заметил физик из Франции Араго в 1824 году. Ученый отметил, что находящийся под магнитной стрелкой медный диск вращается за счет вихревых токов.
Обычно источников электромагнитного поля становится вихретоковый преобразователь (ВТП) — индуктивная катушка.В катушках действует ток, который создает электромагнитное поле, возбуждающее вихревые токи. Их поле действует на ВТП, создавая в них ЭДС или преобразуя их сопротивление. Появившееся на катушках напряжение или сопротивление — ключ к информации о свойствах объекта.
С помощью вихретокового метода можно не только выявить дефекты и оценить свойства объектов контроля. Вихретоковый контроль широко применяется и при производстве деталей, и при их ремонте. Высокоточное современное оборудование — это возможность для обработки и хранения большого объема данных о результатах контроля. Системы сканирования автоматизированы, что увеличивает точность визуализации объекта контроля во много раз.
В каких областях используют вихретоковый контроль? Список широк:
- Вихретоковым методом исследуют сварные и резьбовые соединения, детали разнообразных форм и размеров для оборудования. Кроме того, это метод контроля корпусного оборудования, гибов трубопроводов, лопаток паровых турбин.
С помощью вихретокового метода также проверяют поверхность осевого канала роторов турбин.
- Вихретоковый контроль нужен, чтобы измерять толщину защитных покрытий, тонких труб и тонкого листового проката. Помимо этого, с помощью вихретокового метода ищут коррозионные повреждения.
- Вихретоковый метод позволяет оценить состояние металла тепломеханического оборудования (как исходное, так и текущее). Метод применим и для оценки качества термообработки; с его помощью проводят сортировку объектов и определяют состав контролируемого вещества.
Все методы и приборы неразрушающего контроля служат одной цели — выявить даже незначительные повреждения, в том числе грибок, коррозию, расслоение. Востребованность НК объясняется просто: его методы сочетают в себе множество достоинств и соответствуют строгим требованиям промышленной безопасности.
Магнитный метод неразрушающего контроля, контроль сварных швов и деталей
Неразрушающий контроль
Один из наиболее оптимальных на данный момент способов выявления дефектов в конструкциях из железа, кобальта, никеля и других ферромагнетиков — это магнитный контроль. Суть метода заключается в намагничивании исследуемых объектов и анализе образующихся магнитных полей. В местах повреждений формируются так называемые магнитные поля рассеяния. Но существует и ограничение: магнитный контроль позволяет обнаружить дефекты на поверхности либо же на глубине не больше двух-трех миллиметров.
Информационный вестник
популярные услуги
Станьте клиентом
Оставьте заявку и станьте клиентом прямо сейчас!
Стать клиентом
Александр Сергеевич Колесов
Основной целью метода магнитного контроля является изучение зависимости магнитного поля в местах повреждений от их формы и размера.Недостатком в этом случае является чувствительность к изменениям в толщине стенок объекта, очевидно, что это создает определенные трудности в изучении результатов исследования. Данный способ остается наиболее оптимальным благодаря высокой экономичности в технологических и временных затратах, несмотря на сложность в интерпретации коррозийных дефектов, трещин и повреждений в швах на разных направлениях по объему.
Магнитный контроль
Подробнее
абсолютное понимание и
опыт
Существует несколько государственных стандартов,определяющие магнитные и эл магнитные методы контроля трубопроводов неразрушающим способом:
· ГОСТ 24450-80 — терминология и определения метода.
· ГОСТ 21105-87 — магнитопорошковый метод неразрушающего контроля.
· ГОСТ 8.283-78 — использующиеся в методе дефектоскопы, их средства поверки.
· ГОСТ 26697-85 — технические требования к магнитным и вихретоковым дефектоскопам, использующимся в электромагнитном методе неразрушающего контроля.
Магнитные и электромагнитные методы неразрушающего контроля
Для изучения зависимостей магнитных полей в местах повреждений, выявления потоков рассеяния применяется следующие виды магнитного контроля. Они классифицируются соответственно государственному стандарту №24450-80 по способам получения данных.
Магнитопорошковый —в качестве индикатора дефектов используется магнитный порошок. Фиксируются повреждения и деформации на поверхности и на глубине до 2—3 мм. Является наиболее популярным методом магнитного контроля сварных швов и соединений в силу простоты технологии, высокой чувствительности и экономичности.
Магниторезисторный —основан на эффекте Гаусса. В данной разновидности метода магнитного контроля для регистрации полей рассеивания применяются полупроводниковые резисторы(магниторезистивные преобразователи).
Индукционный —в данном методе в качестве регистратора возмущений поля в местах повреждений применяются катушки индуктивности.
Магнитографический —для анализа зависимости магнитного поля объекта используется специальная запись состояний этого поля, которую можно просмотреть на цифровом устройстве.
Пондеромоторный —основывается на взаимодействии поля намагниченного исследуемого объекта с полем постоянного магнита, рамки, по которой течет электрический ток, либо же электромагнита.
Феррозондовый —в данном виде метода для исследования, например, сварочных швов на предмет повреждений, применяются феррозондовые преобразователи магнитного поля.Конструктивно феррозонд состоит из ферромагнитного сердечника и двух катушек индуктивности.
Метод эффекта Холла —основан на применении датчиков Холла, позволяющих определить местоположение дефектов по возмущению магнитного поля.
полное сопровождение и
профессиональные советы
В настоящее время метод магнитного контроля является наиболее популярным способом нахождения повреждений в ферромагнитных конструкциях, благодаря своей существенной простоте и эффективности. Он применяется в самых разных промышленных производствах и отраслях, таких как нефтедобывающая и нефтеперерабатывающая промышленность, тяжелая металлургия,машиностроение, кораблестроение, авиационная промышленность, при постройке электростанций различных типов, в строительстве инфраструктурных сооружений,железнодорожных путей и транспорта.
Виды магнитного неразрушающего контроля
Основой любых методов магнитного неразрушающего контроля является анализ взаимодействия магнитных полей намагниченных ферромагнетиков,что позволяет найти внутренние и внешние повреждения конструкций. Для этого объект, состоящий из ферромагнетика, намагничивают и по характеристикам его магнитного поля определяют местоположение дефекта, будь то коррозийное повреждение или же структурное повреждение в сварочных швах.
При намагничивании и перемагничивании объекта наблюдается явление петли гистерезиса, от которого и зависят многие параметры, такие как химический состав, структурные особенности и тому подобное.
Такие методы неразрушающего контроля, как магнитопорошковый,магнитных суспензий, индукционный и магнитографический, являются наиболее распространенными в настоящее время. Они применяются с целью определения толщины неферромагнитного слоя на самом ферромагнетике, обнаружения дефектов на поверхности объекта или на небольшой глубине, исследования электромагнитных свойств поля намагниченного объекта.
магнитные методы контроля сварных соединений и швов
Сварное соединение является одним из наиболее подверженных повреждениям участков металлических конструкций. При использовании магнитной дефектоскопии в местах повреждений на сварочных швах наблюдается возникновение полей рассеяния: при прохождении магнитного потока по сварному соединению он обходит участок дефекта, так как повреждение имеет значительно меньшую магнитную проницаемость, чем у ферромагнитного материала. Таким образом, часть магнитного потока оказывается вытесненной из структуры исследуемого объекта и образует локальный рассеянный магнитный поток.
Постоянный контакт &
Уверенность
нам доверяют
Клиенты
В своей работе мы опираемся исключительно на научные сведения и методы, зарекомендовавшие себя в мировой практике, а наша команда состоит из высококвалифицированных специалистов с огромным опытом работы в сфере стандартизации и сертификации. Таким образом, качество выполняемых процедур всегда остается на высоком уровне. Главными приоритетами в нашей деятельности были и остаются: ответственный подход, высококачественное планирование и оперативность. Серьезное отношение и внимание к каждому проекту является основой качественной работы в данной сфере. Именно это позволило нам заслужить доверие клиентов, всегда остающихся довольными выполненной задачей.
мы доказываем на практике
10-летний опыт
Одним из важнейших качеств любой команды является ее опыт, и это то, чем мы действительно можем похвастаться: более 10 лет работы в сфере стандартов качества позволяют нам снова и снова добиваться лучших результатов,высочайших стандартов качества и надежности. Наша экспертная группа беспрерывно занимается наращиванием информационной и нормативной базы, что позволяет нам идти в ногу со временем, не отставая от темпов развития законодательства.Решения компании Менделеев Тест в области стандартизации и сертификации основаны на обширных знаниях и более чем 10-летнем опыте работы в данной сфере,а довольные клиенты подтверждают наши слова, возвращаясь к нам снова и снова.
Руководитель отраслевой должности
Александр Сергеевич Колесов
Александр Сергеевич работает в сфере оценки соответствия более 8-ми лет. За это время он зарекомендовал себя, как компетентный специалист и грамотный руководитель. Уникальные знания, полученные в СПб ГУАП, а также значительный опыт позволили достичь высокого профессионального уровня. На его счету – десятки успешно выполненных проектов, связанных с проведением испытаний и оценкой соответствия технически сложного оборудования и средств связи. Александр Сергеевич осуществляет эффективное руководство специалистами нашей компании и пользуется заслуженным уважением среди коллег и партнеров.
1
Первый слайд презентации: Неразрушающие методы контроля: магнитный и акустический
Подготовил студент Гр. 08 ПГС – 2 Твердохлебова Т.В. Проверил: Лисов С.В.
Изображение слайда
2
Слайд 2: Содержание:
Магнитные методы неразрушающего контроля — Магнитопорошковый метод — Магнитный индукционный метод контроля Акустические методы неразрушающего контроля
Изображение слайда
3
Слайд 3: МАГНИТНЫЕ МЕТОДЫ КОНТРОЛЯ КАЧЕСТВА
Магнитный метод неразрушающего контроля — вид контроля, основанный на анализе взаимодействия магнитного поля с контролируемым объектом. Магнитный метод контроля применяют для контроля изделий из ферромагнитных материалов.
По способу получения первичной информации:
магнитопорошковый, магнитографический,
Феррозондовый, эффект Холла,
индукционный, пондеромоторный,
магниторезисторный.
Изображение слайда
4
Слайд 4: Магнитные методы контроля
При намагничивании объекта магнитный поток протекает по объекту контроля. В случае нахождения несплошности на пути магнитного потока, возникают поля рассеивания, форма и амплитуда которых несет информацию о размере, характере, и глубине залегания дефекта. Рис. 1. Схема осуществления магнитно-порошкового контроля: 1 — изделие; 2 — электромагнит; 3 — дефект; 4 — место скопления частиц порошка.
Изображение слайда
5
Слайд 5: Магнитопорошковый метод
Предназначен для выявления поверхностных и под поверхностных дефектов типа нарушения сплошности материала изделия: трещины, волосовины, расслоения, не проварка стыковых сварных соединений, закатов и т. д.
Этим методом можно контролировать изделия любых габаритных размеров и форм, если магнитные свойства материала изделия (относительная максимальная магнитная проницаемость не менее 40) позволяют намагничивать его до степени, достаточной для создания поля рассеяния дефекта, способного притянуть частицы ферромагнитного порошка.
Изображение слайда
6
Слайд 6: Виды магнитопорошкового контроля:
— «Сухой» и «мокрый» способы нанесения индикатора на контролируемый объект — Флуоресцентный или цветной индикатор для контроля при ультрафиолетовом УФ или дневном свете
Изображение слайда
7
Слайд 7: Этапы магнитопорошкового контроля
— Демонтажно-монтажные работы;
— Удаление загрязнений ;
— Удаление влаги;
— Предотвращение попадания влаги во внутренние полости деталей и изделий;
— Удаление лакокрасочного покрытия;
— Нанесение на поверхность детали белой краски
— Зачистка мест электрического контакта;
— Снятие электростатических зарядов с проверяемой детали. 1. Подготовительные работы:
Изображение слайда
8
Слайд 8: 2. Намагничивание детали
Рис. 1. Способы намагничивания при выявлении несплошностей : а — полюсный, б — циркулярный — Циркулярное намагничивание — Продольное (полюсное) намагничивание — Комбинированное намагничивание
Изображение слайда
9
Слайд 9: 3. Нанесение на поверхность детали магнитного индикатора
— окунании детали в бак, в котором суспензия хорошо перемешана, и в медленном удалении из него. — суспензию наносят с помощью аэрозоли, шланга или душа.
Изображение слайда
10
Слайд 10: 4.
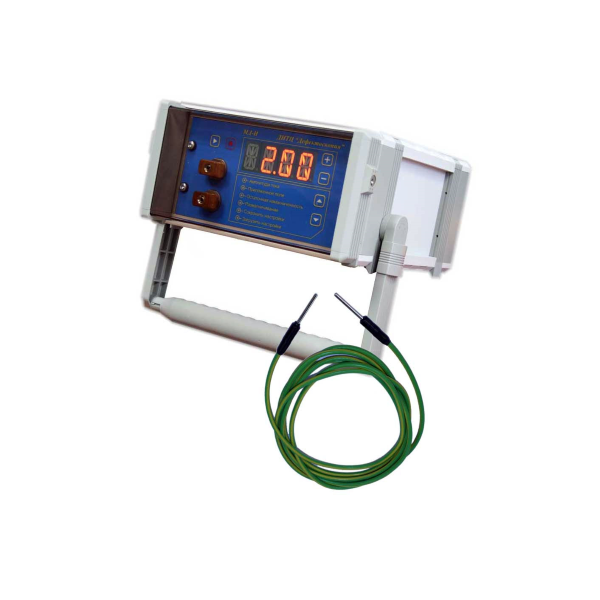
Дефектоскопист должен осмотреть деталь после стекания с нее основной массы суспензии, когда картина отложений порошка становится неизменной. Разбраковку деталей по результатам контроля должен производить опытный дефектоскопист. На рабочем месте дефектоскописта необходимо иметь фотографии дефектов или их дефектограммы, контрольные образцы с минимальными размерами недопустимых дефектов.
Изображение слайда
11
Слайд 11: 5. Размагничивание и контроль размагниченности
Применяют 3 основных способа размагничивания:
— Нагрев изделия до температуры точки Кюри.
— Прохождение детали через зону переменного или постоянного (с изменением направления) магнитного поля.
— Воздействием на деталь переменного или постоянного поля с уменьшающейся амплитудой тока.
Изображение слайда
12
Слайд 12: Материалы для магнитной дефектоскопии
Магнитный порошок MI-GLOW 850 Черная магнитная суспензия B103 Белая контрастная краска B104 А
Изображение слайда
13
Слайд 13: Приборы для магнитной дефектокоскопии
Намагничивающее устройство ДМП-60 Магнитометр ИМП-6 Дефектоскоп магнитно-порошковый переносной ПМД-70 Дефектоскоп магнитный ДМПУ-1
Изображение слайда
14
Слайд 14
Преимущества :
— относительно небольшая трудоемкость,
— высокой производительность,
— возможности обнаружения поверхностных и подповерхностных дефектов,
— выявляются не только полые несплошности, но и дефекты, заполненные инородным веществом,
— применяется не только при изготовлении деталей, но и в ходе их эксплуатации. Недостатки:
— сложность определения глубины распространения трещин в металле.
Изображение слайда
15
Слайд 15: Применяется в следующих отраслях промышленности:
— строительство (стальные конструкции, трубопроводы) — авиапромышленность — машиностроение — автомобильная промышленность — металлургия — транспорт (авиация, железнодорожный, автотранспорт) — судостроение
Изображение слайда
16
Слайд 16: Российские стандарты:
ГОСТ 24450-80 Контроль неразрушающий магнитный. Термины и определения;
ГОСТ 21105-87 Контроль неразрушающий. Магнитопорошковый метод;
ГОСТ 8.283-78 Дефектоскопы электромагнитные. Методы и средства поверки;
ГОСТ 26697-85 Контроль неразрушающий. Дефектоскопы магнитные и вихретоковые. Общие технические требования.
Изображение слайда
17
Слайд 17: Магнитный индукционный метод контроля
Магнитный индукционный метод контроля — магнитный метод неразрушающего контроля, основанный на регистрации магнитных полей дефектов индукционными преобразователями по величине или фазе индуцируемой эдс. Намагничивается изделие переменным током. Индукционным методом контролируют стыковые сварные соединения.
Изображение слайда
18
Слайд 18
Рис.. Схема проведения контроля индукционным методом: 1 — изделие; 2 — электромагнит; 3 — дефект; 4 —-искатель
Индукционный метод осуществляется с применением катушки индуктивности, перемещаемой относительно намагниченного объекта контроля. В катушке наводится электродвижущая сила соответственно характеристикам полей дефектов.
Используется для контроля сварных труб, перемещающихся относительно индукционной головки. Магнитные методы контроля широко применяются для ферромагнитных материалов, преимущественно для обнаружения поверхностных и подповерхностных дефектов в стыковых швах.
Изображение слайда
19
Слайд 19
Преимущества: — высокая производительность, — безвредность, — экономичность, — мобильность контроля, — возможность обнаружения глубинных дефектов. Недостатки: — усиление шва существенно снижает чувствительность магнитных методов контроля, — объемные включения выявляются хуже, чем плоские трещиноподобные.
Изображение слайда
20
Слайд 20: Преимуществами приборов
— отсутствие механического контакта между преобразователем и контролируемым изделием при проведении скоростной дефектоскопии изделий;
— получение однородного магнитного поля, глубоко проникающего в металл, для чего питание намагничивающей катушки осуществляют постоянным током, что дает возможность контролировать более глубокие, подповерхностные слои изделий;
— высокая помехоустойчивость при контроле ферромагнитных изделий и малая зависимость показаний регистратора от положения изделия внутри преобразователя;
— возможность проведения непрерывной записи и визуальных наблюдений за результатами контроля по диаграммной ленте самопишущего прибора.
Изображение слайда
21
Слайд 21: Применяется в следующих отраслях промышленности:
— строительство (стальные конструкции, трубопроводы) — авиапромышленность — машиностроение — автомобильная промышленность — металлургия — транспорт (авиация, железнодорожный, автотранспорт)
Изображение слайда
22
Слайд 22: АКУСТИЧЕСКИЕ МЕТОДЫ КОНТРОЛЯ КАЧЕСТВА
Акустический вид неразрушающего контроля основан на регистрации параметров упругих волн, возникающих или возбуждаемых в объекте. Чаще всего используют упругие волны ультразвукового диапазона (с частотой колебаний от 50 кГц до 50 МГц).
По характеру взаимодействия различают пассивный и активный методы.
Изображение слайда
23
Слайд 23: Активные методы контроля
— Методы прохождения; — Методы отражения; — Комбинированные методы. Пассивные методы контроля Вибрационно-диагностический метод; Шумо-диагностический метод.
Изображение слайда
24
Слайд 24: Метод прохождения:
а) амплитудный теневой метод; б) временной теневой метод; в) велосиметрический метод. На рисунке: 1 — генератор; 2 — излучатель; 3 — объект контроля; 4 — приемник; 5 — усилитель; 6 — измеритель амплитуды; 7 — измеритель времени пробега; 8 — измеритель фазы.ё
Изображение слайда
25
Слайд 25: Методы отражения:
а) эхо-метод;
б) эхо-зеркальный метод;
в) дельта-метод;
г) реверберационный;
На рисунке:
1 — генератор;
2 — излучатель;
3 — объект контроля;
4 — приемник;
5 — усилитель;
6 — синхронизатор;
7 — индикатор.
Изображение слайда
26
Слайд 26: Комбинированный метод:
а) зеркально-теневой метод; б) эхо-теневой метод; в) эхо-сквозной метод. На рисунке: 1 — излучатель; 2 — приемник; 3 — объект контроля
Изображение слайда
27
Слайд 27: Пассивные методы
а) импедансный ; б) резонансный; в) свободных колебаний; г) акустико-эмиссионный; На рисунке: 1 — генератор; 2 — излучатель; 3 — объект контроля; 4 — приемник, 5 — усилитель; 6 — индикатор; 7 – модулятор частоты ; 8 — регистратор резонанса; 9 — спектро-анализатор, 10 — вибратор.
Изображение слайда
28
Слайд 28
— строительство,
— котлонадзор,
— системы газоснабжения,
— подъемные сооружения,
— объекты горнорудной промышленности,
-объекты угольной промышленности,
— нефтяная и газовая промышленность,
— металлургическая промышленность,
— оборудование взрывопожароопасных и химически опасных производств,
— энергетики,
— объекты железнодорожного транспорта,
— объекты хранения и переработки зерна. Применяется в следующих областях:
Изображение слайда
29
Последний слайд презентации: Неразрушающие методы контроля: магнитный и акустический: Приботы для акустического метода контроля:
Прибор PARAS компании TestConsult Дефектоскоп АД-60К — SV 212
Изображение слайда
Магнитопорошковый метод неразрушающего контроля
В данной статье мы рассмотрим некоторые специальные методы неразрушающего контроля сварных соединений. Определение каждого метода контроля можно найти в ГОСТ 18353-79 «Контроль неразрушающий. Классификация видов и методов»
1. Визуально-измерительный метод неразрушающего контроля – первостепеннейший вид контроля. Сам метод можно условно разделить на две составляющих: визуальный метод неразрушающего контроля и измерительный метод. Визуальный метод или, как его еще называют, оптический метод неразрушающего контроля предполагает визуальный осмотр поверхности сварного соединения и проверку его на наличие или отсутствие дефектов. Измерительный метод следует за визуальным – мы замеряем размеры дефектов, если таковые обнаружены.
2. Магнитопорошковый метод неразрушающего контроля основан на обнаружении полей рассеивания, образующихся в местах расположения дефектов при намагничивании контролируемых сварных соединений. Поля рассеивания фиксируются на эластичной магнитной ленте, плотно прижатой к поверхности шва. Запись производят на дефектоскопе. Магнитный метод неразрушающего контроля можно применять только для проверки сварных соединений металлов и сплавов небольшой толщины, обладающих ферромагнитными свойствами.
Разновидностью данного метода является метод магнитной памяти металла, неразрушающий контроль в данном случае основан на измерении и анализе распределения собственных магнитных полей рассеяния металла изделий, отражающих их структурную и технологическую наследственность, включая сварные соединения. Подробнее о данном методе можно узнать из ГОСТ Р 52005-2003.
Еще одна разновидность магнитопорошкового метода — индукционный метод неразрушающего контроля. Данный метод основан на регистрации магнитных полей объекта контроля с помощью индукционных преобразователей
3. Акустический метод неразрушающего контроля основан на звуке, поэтому наиболее распространенным видом данного метода является ультразвуковой метод неразрушающего контроля. Данный метод основан на способности ультразвуковых колебаний отражаться от поверхности, разделяющей среды с разными акустическими свойствами.
Другой разновидностью акустического метода является акустико-эмиссионный метод неразрушающего контроля, который основан на излучении и регистрации волн напряжений при быстрой локальной перестройке структуры материала.
Импедансный метод неразрушающего контроля (от англ. impedance – сопротивление) также относится к акустическим методам неразрушающего контроля. Он широко применяется в аэрокосмической промышленности. Только этот метод позволяет достоверно оценить качество спайки сверхлегких сотовых панелей, применяемых в конструкциях элементов крыльев самолетов и корпусов спутников.
4. Вихретоковый метод неразрушающего контроля основан на законе электромагнитной индукции. Вихретоковый контроль позволяет обнаруживать как поверхностные, так и подповерхностные дефекты. Его применяют только для контроля объектов из электропроводящих материалов. Контроль вихревыми токами можно выполнять без непосредственного механического контакта преобразователей с объектом, что позволяет вести контроль при взаимном перемещении преобразователя и объекта с большой скоростью.
5. Тепловые методы неразрушающего контроля основаны на взаимодействии теплового поля объекта с термодинамическими чувствительными элементами, преобразовании параметров поля в электрический сигнал и передаче его на регистрирующий прибор. К тепловым методам относится контроль при помощи тепловизоров (тепловизионный метод неразрушающего контроля).
6. Вибродиагностический метод неразрушающего контроля основана на анализе параметров вибрации, которая создается или работающим оборудованием, или является вторичной вибрацией, обусловленной структурой исследуемого объекта.
7. К методам контроля проникающими веществами относится капиллярный метод неразрушающего контроля. Данный вид контроля основан на проникновении индикаторных жидкостей в полость несплошностей, которые должны быть выявлены у объекта: трещин, пор и т.д.
8. Радиографический метод контроля неразрушающего или рентген производят с целью выявления поверхностных и внутренних дефектов, к например, шлаковых включений, газовых пор, микротрещин, подрезов и шлаковых включений. Радиационный метод неразрушающего контроля основан на способности материалов к поглощению рентгеновских лучей.
9. Часто с радиографическим методом путают радиоволновой метод неразрушающего контроля. Радиоволновой метод применяется только для контроля объектов, изготовленных из диэлектрических или полупроводниковых материалов, или тонкостенных объектов. Данный метод основан на регистрации и анализе изменения параметров, которыми обладают взаимодействующие с объектом контроля электромагнитные волны радиодиапазона.
10. Электрический метод неразрушающего контроля основан на регистрации и последующем анализе параметров электрического поля, взаимодействующем с объектом контроля или возникающем в нём в результате воздействия извне.
Магнитные методы неразрушающего контроля Студент гр 4203 Шмаков
Магнитные методы неразрушающего контроля Студент гр. 4203 Шмаков Д. И.
Содержание 1. Основные понятия и средства МК 2. Типы приборов МК 3. Область применимости МК 4. Классификация методов МК 5. Обзор методов МК 6. Достоинства и недостатки МК
1. Основные понятия Магнитный неразрушающий контроль (МНК) — НК, основанный на регистрации магнитных полей рассеяния, возникающих над дефектами, или на определении магнитных свойств объекта контроля. Примечание. Дефект (по ГОСТ 15467 -80) – каждое отдельное несоответствие продукции установленным требованиям.
Магнитная дефектоскопия – выявление дефектов типа нарушения сплошности. материала объекта контроля методами МНК. Магнитная дефектометрия – измерение геометрических размеров дефектов и определение их местоположения в объекте контроля методами магнитного неразрушающего контроля. Чувствительность – способность метода НК к обнаружению несплошностей. Несплошность – нарушение сплошности, выраженное в виде естественных или искусственных разрывов физической структуры материала. Дефект – дефектность или несплошность, которая может быть обнаружена методами неразрушающего контроля и которая необязательно является недопустимой.
Магнитный порошок – порошок из ферромагнетика, используемый в качестве индикатора магнитного поля рассеяния. Магнитная паста – смесь, содержащая магнитный порошок, жидкую основу и, при необходимости, смачивающую антикоррозийную и другие добавки. Магнитная суспензия – взвесь магнитного порошка в дисперсионной среде, содержащей смачивающие, антикоррозийные и, при необходимости, антивспенивающие, антикоагулирующие и другие добавки.
2. Типы приборов МК Дефектоскоп – прибор, предназначенный для выявления дефектов типа нарушений сплошности материала объекта контроля и основанный на методе МНК; Толщиномер – прибор, предназначенный для измерения толщины объекта контроля или его покрытия и основанный на методе МНК; Структуроскоп – прибор, предназначенный для определения физикомеханических свойств или химического состава объекта контроля и основанный на методе МНК; Ферритометр – прибор для измерения процентного содержания ферритной фазы в структуре контролируемого объекта; Анализатор концентрации суспензии – прибор для определения концентрации магнитного порошка в магнитной суспензии. Намагничивающее устройство; Размагничивающее устройство;
3. Область применимости МК Магнитный вид контроля применяется для обнаружения нарушений сплошности (трещин, немагнитных включений и др. дефектов) в поверхностных слоях деталей из ферромагнитных материалов и выявления ферромагнитных включений в деталях из неферромагнитных материалов. Для обнаружения нарушений сплошности материала ферромагнитных (главным образом стальных) деталей. Магнитный метод применим для определения толщины немагнитных покрытий на ферромагнитной основе или в случае резкого различия магнитных свойств покрытия и основы. Магнитным методом могут быть определены толщины элементов конструкции из неферромагнитных материалов, если возможен одновременный доступ к соответствующим точкам поверхностей.
4. Классификация методов МК 1. По характеру взаимодействия физических полей с контролируемым объектом: — магнитный. 2. По первичному информативному параметру: — корцитивной силы; — намагниченности; — остаточной индукции; — магнитной проницаемости; — остаточной индукции; -эффекта Баркгаузена. 3. По способу получения первичной информации: — магнитопорошковый; — магнитографический; — феррозондовый; — индукционный; — эффекта Холла; — пондеромоторный; — магниторезисторный.
5. Обзор методов 1. 2. 3. 4. 5. 6. 7. 8. Магнитопорошковый метод Индукционный метод Феррозондовый метод Метод эффекта Холла Магнитографический метод Магниторезистивный метод Пондеромоторный метод Магнитополупроводниковый метод
Магнитопорошковый метод Метод магнитного неразрушающего контроля, основанный на использовании в качестве индикатора магнитного порошка
Индукционный метод Метод магнитного неразрушающего контроля, основанный на регистрации магнитных полей объекта контроля индукционными преобразователями
Феррозондовый метод Метод магнитного неразрушающего контроля, основанный на регистрации магнитных полей объекта контроля феррозондовыми преобразователями
Метод эффекта Холла Метод магнитного неразрушающего контроля, основанный на регистрации магнитных полей объекта контроля преобразователями Холла
Магнитографический метод Метод магнитного неразрушающего контроля, основанный на записи магнитных полей объекта контроля на магнитный носитель с последующим воспроизведением сигналограммы
Магниторезистивный метод Метод магнитного неразрушающего контроля, основанный на регистрации магнитного поля объекта контроля магниторезистивными преобразователями
Пондеромоторный метод Метод магнитного неразрушающего контроля, основанный на пондеромоторном взаимодействии регистрируемого магнитного поля объекта контроля и магнитного поля постоянного магнита, электромагнита или рамки с током
Магнитополупроводниковый метод Метод магнитного неразрушающего контроля, основанный на регистрации магнитного поля объекта контроля магнитополупроводниковыми приборами
5. Достоинства и недостатки Достоинства: 1. Наглядность 2. высокая чувствительность 3 высокая производительность 4. универсальность (примерно 80 % всех подлежащих контролю деталей из ферромагнитных материалов проверяется именно этим методом). Недостатки: 1. большая трудоемкость (для повышения надежности и достоверности контроля требуется зачистка поверхности сварного соединения или даже снятие усиления сварного шва; необходимо выполнить намагничивание и размагничивание конструкции).
Спасибо за внимание!
Книги | НИО-12 — ЗАО «НИИИН МНПО «СПЕКТР»
Шелихов Г.С.
Год издания: 1995. Объем: 220 стр.
В книге изложено описание всех технологических операций магнитопорошкового контроля. Приведены методики контроля конкретных деталей, расшифровки индикаторных рисунков, мнимых дефектов, размагничивания, определения режимов намагничивания.
Большое число рисунков, фотографий, схем позволило доходчиво изложить примеры контроля типовых деталей, выполнения расчетов режимов намагничивания и технологических операций.
Материал изложен с учетом интересов специалистов различного уровня подготовки.
Подробнее
0.00 RUBPrice:
В.В. Клюев, Ф.Р. Соснин, В.Н. Филинов и др.; Под ред. В.В. Клюева. – М.: Машиностроение, 1995. 488 с.: ил.
Подробно рассмотрены методы контроля: радиационные, магнитные, вихретоковые, электрические, оптические, вибрационные, акустические, комплексные системы качества продукции, методы и средства медицинской диагностики, промышленная рентгеновская вычислительная томография, системы технического зрения. Даны рекомендации по выбору и применению методов и средств НК и Д, технические характеристики отечественных и зарубежных приборов, технология эксплуатации приборов, передвижные средства контроля загрязнения окружающей среды.
Подробнее
0.00 RUBPrice:
Под общ. ред. В.В. Клюева. Т. 4: В. 3 кн. Кн. 1 В.А. Анисимов, Б.И. Каторгин, А.Н. Куценко и др. Акустическая тензометрия .Кн. 2:Г.С. Шелихов. Магнитопорошковый метод контроля. Кн. 3. М.В. Филинов. Капиллярный контроль. – М.: Машиностроение, 2004. 736 с.: ил.
В первой книге рассмотрен метод ультразвуковой диагностики затяжки разъемных соединений жидкостных ракетных двигателей космических аппаратов в процессе монтажа и испытаний. Изложены основы матричной теории акустоупругого эффекта, экспериментально проверены основные соотношения, описаны методы акустических измерений. Значительное внимание уделено метрологическим проблемам и конкретным методикам производственного контроля.
Приведенные методы внедрены в производство в ОАО НПО «Энергомаш» им. В.П. Глушко.
Во второй книге описаны технологические операции магнитопорошкового контроля. Приведены методики контроля конкретных деталей, расшифровки индикаторных рисунков дефектов, образуемых осаждением порошка над различными дефектами. Рассмотрены схемы и фотографии индикаторных рисунков мнимых дефектов и даны способы их расшифровки. Указаны области применения и технические характеристики дефектоскопов и приборов. Приведены примеры расчетов режимов намагничивания деталей, соответствующие требованиям стандарта по магнитопорошковой дефектоскопии.
Подробнее
0.00 RUBPrice:
Под общ. ред. В.В. Клюева. Т. 6: В. 3 кн. Кн. 1 В.В. Клюев, В.Ф. Мужицкий, Э.С. Горкунов, В.Е. Щербинин. Магнитные методы контроля .Кн. 2: В.Н. Филинов, А.А. Кеткович, М.В. Филинов. Оптический контроль. Кн. 3. В.И. Матвеев. Радиоволновой контроль. – М.: Машиностроение, 2004. 832 с.: ил.
В первой книге рассмотрены физические основы магнитного неразрушающего контроля, методы и средства магнитной дефектоскопии и структуроскопии, примеры взаимосвязи между магнитными параметрами и механическими характеристиками ферромагнитных металлов, применение для технической диагностики усталостных явлений и оценка остаточного ресурса. Обобщены результаты исследований закономерностей изменения магнитных, электрических и механических свойств сталей при вариации температуры отжига, закалки и отпуска. Проанализированы возможности использования магнитных характеристик для контроля качества закалки и отпуска, поверхностного упрочнения и оценки напряженного состояния изделий из сталей. Приведены результаты исследований контроля прочностных и пластических свойств сталей, а также приборы магнитного неразрушающего контроля.
Подробнее
0.00 RUBPrice:
Под общ. ред. В.В. Клюева. Т. 7: В. 2 кн. Кн. 1 В.И. Иванов, И.Э. Власов. Метод акустической эмиссии .Кн. 2: Ф.Я. Балицкий, А.В. Барков, Н.А. Баркова и др. Вибродиагностика. – М.: Машиностроение, 2005. 829 с.: ил.
В первой книге рассмотрены вопросы диагностирования промышленных объектов с использованием метода акустической эмиссии (АЭ). Изложены основные понятия, физические основы метода, показана связь параметров АЭ с параметрами процесса развития дефектов, что обеспечивает возможность оценки степени опасности дефектов для объекта диагностирования. Показаны области использования метода АЭ, подробно рассмотрены средства АЭ-контроля, сформулированы требования к средствам контроля и методы измерения их параметров.
Подробнее
0.00 RUBPrice:
Под общ. ред. В.В. Клюева. Т. 5: В. 2 кн. Кн. 1 В.П. Вавилов. Тепловой контроль .Кн. 2:К.В. Подмастерьев, Ф.Р. Соснин, С.Ф. Корндорф, Т.И. Ногачева, Е.В. Пахолкин, Л.А. Бондарева, В.Ф. Мужицкий. Электрический контроль. – М.: Машиностроение, 2004. 679 с.: ил. и цв. вкладка 24 с.
В первой книге рассмотрены физические модели теплового контроля (ТК), теплопередача в дефектных и бездефектных структурах, теплофизические свойства материалов, оптимизация процедур ТК, тепловая дефектометрия, обработка данных в ТК, системы активного и пассивного ТК, элементы статической оценки данных и принятия решений, области применения ТК, аттестация специалистов в области ТК, нормативные документы, типовая программа подготовки персонала по ТК и рекомендуемые вопросы общего экзамена по ТК.
Подробнее
0.00 RUBPrice:
Под общ. ред. В.В. Клюева. Т. 1: В. 2 кн. Кн. 1 Ф.Р. Соснин. Визуальный и измерительный контроль. Кн. 2. Ф.Р. Соснин. Радиационный контроль. – 2-е изд., испр. – М.: Машиностроение, 2008. 560 с.: ил.
В первой книге рассмотрены вопросы визуального и измерительного контроля: оптика, оптические свойства глаза, светотехника, оптические системы, металловедение и термическая обработка, основы линейных и угловых измерений, классификация дефектов, процедур визуального и измерительного контроля изделий металлургической промышленности, сварных соединений, отливок, паяных соединений, особенности визуального и измерительного контроля в некоторых отраслях промышленности.
Во второй книге кратко изложены основные понятия, физические и технические основы методов и средств радиационного контроля. Даны новые сведения по средствам и организации контроля на предприятиях, радиационной защите и технике безопасности. Рассмотрены отдельные вопросы применения метода при контроле качества материалов (выявление дефектов в слитках, литых изделиях, сварных и паяных соединениях и т.д.) и функционировании узлов и механизмов, а также в научных исследованиях (регистрация быстро протекающих процессов, физических явлений в непрозрачных средах и т.д.).
Подробнее
0.00 RUBPrice:
Под общ. ред. В.В. Клюева. Т. 2: В. 2 кн. Кн. 1 А.И. Евлампиев, Е.Д. Попов, С.Г. Сажин и др. Контроль герметичности /Кн. 2. Ю.К. Федосенко, В.Г. Герасимов, А.Д. Покровский, Ю.Я. Останин. Вихретоковый контроль. – 2-е изд., испр. – М.: Машиностроение, 2006. 688 с.: ил.
В первой книге рассмотрена технология контроля герметичности. Приведены физико-химические основы течеискания, характеристики сжатого воздуха, техника получения и измерения вакуума, практически все методы контроля герметичности, метрологическое обеспечение течеискания, контроль герметичности изделий массового производства, а также потенциально опасных объектов в процессе их эксплуатации, техника безопасности, примеры промышленного использования методов и средств контроля герметичности, требования к техническим знаниям персонала по рекомендациям ICNDT Wn 21-85.
Во второй книге изложены основы вихретокового контроля. Рассмотрены методы контроля: проходным преобразователем, накладным преобразователем, качества ферромагнитных изделий, вихретоковая дефектоскопия, структуроскопия немагнитных объектов. Приведены способы выделения информативных сигналов, вихретоковые приборы и средства контроля, их метрологическое обеспечение, аппаратура отечественных и зарубежных фирм (2002, 2003 гг. ), национальные и международные стандарты по сертификации специалистов, программы обучения и аттестации, перечня вопросов для сдачи квалификационных экзаменов.
Подробнее
0.00 RUBPrice:
Под общ. ред. В.В. Клюева. Т. 3: И.Н. Ермолов, Ю.В. Ланге. Ультразвуковой контроль. – 2-е изд., испр. – М.: Машиностроение, 2008. 864 с.: ил.
Ультразвуковой контроль – один из наиболее эффективных и универсальных видов неразрушающего контроля и диагностики отечественных изделий из различных металлических и неметаллических материалов, в т.ч. оценки их физико-механических характеристик – постоянных упругости, прочности, твердости и.т.п. Методы ультразвукового контроля очень многообразны. Они применяются для решения широкого круга задач во многих отраслях промышленности, а также в научных исследованиях.
В справочнике рассмотрены физические основы высокочастотных и низкочастотных акустических методов, их классификация, области применения, эксплуатационные возможности и особенности. Даны сведения об аппаратуре и методиках контроля типовых изделий. Приведены рекомендации по выбору метода для решения конкретных задач. Описаны не только широко известные, но и мало знакомые в России, но уже давно применяемые на Западе методы. Главное внимание уделено описанию физических явлений. Приведены требования к техническим знаниям персонала неразрушающего контроля Рекомендации ICNDT Wn 21-85 изм. 01 и Европейские стандарты по ультразвуковому контролю.
Подробнее
0.00 RUBPrice:
Под общ. ред. В.В. Клюева. Т. 8: В. 2 кн. Кн. 1 В.В. Клюев, А.А. Кеткович, В.Ф. Крапивин и др. Экологическая диагностика. Кн. 2: А.В. Ковалев. Антитеррористическая и криминалистическая диагностика. – М.: Машиностроение, 2005. 789 с.: ил.
В первой книге рассмотрены основные проблемы экодиагностики, объекты, методы, технологии и средства. Впервые представлен комплексный материал по диагностике землетрясений, радиационному мониторингу, химико-аналитическим методам диагностирования окружающей среды, оптическому контролю атмосферы, водной среды и поверхности земли, ультразвуковому, тепловому, радиоволновому и электромагнитному мониторингу, а также биологических методов диагностирования среды обитания. Изложена информация по компьютерным технологиям, организации мониторинга и метрологическому обеспечению экодиагностики.
Подробнее
0. 00 RUBPrice:
В.В. Клюев, Ф.Р. Соснин, С.В. Румянцев и др.; Под ред. В.В. Клюева. – 2-ое изд., испр. и доп. М.: Машиностроение, 2002. 632 с.: ил.
Термины и определения, история развития всех методов неразрушающего контроля, предприятия, организации, институты, аттестационные и учебные центры, ученые и ведущие специалисты в области неразрушающего контроля.
Подробнее
0.00 RUBPrice:
В.А. Комаров, В.Ф. Мужицкий. – Ижевск: НИЦ «Регулярная и хаотическая динамика», 2004. 536 с.
В монографии представлено описание двух электромагнитных методов, используемых при неразрушающей оценке физико-механических характеристик металлов: электромагнитного и электромагнитно-акустического. Оба метода связаны между собой, прежде всего одним типом излучателей и приемников вторичного поля – на основе катушек индуктивности, определяющих частотный (квазистационарный) диапазон их использования.
Подробнее
0.00 RUBPrice:
ISBN 5-217-01316-8
Год издания: 1992 г. Издание: 2-е. Объем: 1 том 480 стр. Формат: 60 х 90 1/16. Вес 1020 г.
Второе издание (1-е изд. 1980 г.) справочника является совместной работой советских и зарубежных специалистов в области рентгенотехники.
В первой книге изложены физические основы рентгеновских методов контроля, описаны дозиметрия рентгеновского излучения и защита от него, рентгеновские трубки и излучатели, преобразователи и усилители рентгеновских питающих устройств, штативы, вспомогательные устройства.
Подробнее
0.00 RUBPrice:
ISBN 5-217-01316-8
Год издания: 1992 г. Издание: 2-е. Объем: 2 том 368 стр. Формат: 60 х 90 1/16. Вес 1020 г.
Второе издание (1-е изд. 1980 г.) справочника является совместной работой советских и зарубежных специалистов в области рентгенотехники.
Во второй книге рассмотрены аппараты для промышленной дефектоскопии, методы рентгеноструктурного анализа и аппаратура для него, флуоресцентный рентгеноспектральный анализ, медицинские рентгеновские диагностические аппараты, средства и техника рентгенографии, установки рентгеновизуального контроля, рентгеновские пленки, нейтронная радиография.
Подробнее
0. 00 RUBPrice:
В.А. Комаров, В.Ф. Мужицкий, С.Ю. Гуревич – Челябинск-Ижевск: Изд-во ЮУрГУ, 1998. 304 с.
Монография, написанная в форме учебного пособия, посвящена основам теории акустики твердого тела. Значительное внимание уделяется аналитическому описанию закономерностей образования и распространения пространственно-неоднородных акустических колебаний вблизи границ раздела твердого тела с внешней средой (как правило, воздух), а также закономерностям образования упругого поля в пластинах и цилиндрах.
Все описание ведется на основе спектральной теории, позволяющей соединить характеристики акустического поля с параметрами излучателя.
Материал книги ориентирован на читателя, впервые знакомящегося с дисциплиной «Акустика».
Подробнее
0. 00 RUBPrice:
В.А. Комаров, В.Ф. Мужицкий, С.Ю. Гуревич – Челябинск-Ижевск: Изд-во ЮУрГУ, 2000. 627 с.
В монографии, написанной в форме учебного пособия, представлено аналитическое описание явления взаимной трансформации неоднородных упругих и электромагнитных волн в твердых телах (электромагнитно-акустическое преобразование _ ЭМАП), осуществляемое посредством индуктивных преобразователей.
Особое внимание уделяется рассмотрению магнитострикционного механизма генерации ультразвука и магнитоупругого механизма преобразования упругих колебаний в электромагнитное поле, поскольку в подобном варианте ЭМАР успешно используется как бесконтактный метод измерения и оценки физико-механических свойств материалов и изделий.
Ряд вычислений вторичного электромагнитного поля, дающий основную информацию о свойствах исследуемого объекта вблизи таких пространственно-ограниченных тел, как пластина и цилиндр, фактически доведен до возможности количественного сравнения с экспериментом.
Подробнее
0.00 RUBPrice:
В.А. Комаров, В.Ф. Мужицкий – Ижевск, 1997. 208 с.
В отличие от существующих учебников по теории электромагнитного поля, описание которого, как правило, дается в рамках модели плоских волн и, следовательно, годится для дальней зоны излучения в предлагаемом учебном пособии дано описание взаимодействия неоднородного электромагнитного поля пространственно-ограниченных индуктивных излучателей в квазистационарном режиме (поле ближней зоны излучения) с проводящей ферромагнитной средой, восприимчивость которой зависит от ориентации вектора магнитного поля (следствие его неоднородности).
Существенное внимание уделено учету спектрального состава поля ближней зоны.
Подробнее
0. 00 RUBPrice:
В.Г. Базулин, Е.Г. Вопилкин
Под ред. А.Х. Вопилкина
Год издания: 2008. Издание: 1-е. Объем: 368 стр. Формат: 70 х 100 1/16. Вес 980 г
ISBN 978-5-217-03436-9
Рассмотрены вопросы теории и практики ультразвуковой дефектометрии на основе алгоритмов цифровой акустической голографии применительно к эксплуатации объектов повышенной опасности. Приведены особенности различных алгоритмов получения когерентного изображения, в том числе проекции в спектральном пространстве, угловых спектров, эталонной голограммы и др.
Достаточно подробно описана разработанная аппаратура серии «Авгур» и ее модификации применительно к различным объектам контроля.
Подробнее
0.00 RUBPrice:
Неразрушающий контроль – Магнитопорошковая дефектоскопия (MPI)
Магнитопорошковая дефектоскопия (часто сокращенно MT или MPI) – это метод неразрушающего контроля, обеспечивающий обнаружение линейных дефектов, расположенных на поверхности ферромагнитных материалов или вблизи нее. Он рассматривается в первую очередь как метод исследования поверхности.
Магнитопорошковая дефектоскопия (MPI) — это очень эффективный метод обнаружения поверхностных разрывов и незначительных дефектов под поверхностью, таких как трещины, поры, холодный нахлест, несплавление боковых стенок в сварных швах и т. д. в магнитных материалах.
Существует множество различных техник. Наиболее универсальным методом является использование ручного электромагнитного магнита на 110 В переменного тока, белой удаляемой краски в качестве контрастного фона и магнитных «чернил», состоящих из частиц железного порошка в жидкой основе-носителе.
Участок намагничен ярмовым магнитом. В случае наличия поверхностного или слегка подповерхностного дефекта магнитные силовые линии будут деформироваться вокруг дефекта.
Наносится магнитная краска, и частицы железного порошка перекрывают зазор, вызванный дефектом, и дают видимую индикацию на белом контрастном фоне.
Магнитопорошковая дефектоскопия (MPI) обеспечивает очень хорошее разрешение дефектов и широко используется для. ..
Сварные изделия из магнитных материалов, отливки, локализация усталостных трещин в изделиях, подверженных циклическим нагрузкам
Схема линий потока, протекающих как через перпендикулярный, так и через параллельный дефект, и утечки потока, происходящей вокруг перпендикулярного дефекта
Магнитопорошковая дефектоскопия выполняется в четыре этапа.
- Создание магнитного поля в образце
- Нанесение магнитных частиц на поверхность образца
- Просмотр поверхности в поисках скоплений частиц, вызванных дефектами
- Размагнитить и очистить образец
Преимущества магнитопорошковой дефектоскопии
- Может обнаруживать как поверхностные, так и подповерхностные дефекты
- Некоторые форматы контроля чрезвычайно портативны и недороги
- Быстрая проверка с немедленными результатами
- Показания видны инспектору непосредственно на поверхности образца
- Может обнаруживать дефекты, замазанные
- Может проверять детали неправильной формы (внешние шлицы, коленчатые валы, шатуны и т.
д.)
Ограничения магнитопорошковой дефектоскопии
- Образец должен быть ферромагнитным (например, сталь, чугун)
- Краска толщиной более 0,005 дюйма должна быть удалена перед осмотром
- Часто требуется последующая очистка и последующее размагничивание
- Максимальная чувствительность к глубине обычно указывается как 0,100 дюйма (глубже в идеальных условиях)
- Важно согласование между магнитным потоком и дефектом
Стандарты Международной организации по стандартизации (ISO)
- ISO 3059, Неразрушающий контроль. Капиллярный контроль и магнитопорошковый контроль. Условия просмотра
- ISO 9934-1, Неразрушающий контроль. Магнитопорошковый контроль. Часть 1. Общие принципы
- ISO 9934-2, Неразрушающий контроль. Магнитопорошковый контроль. Часть 2. Среда обнаружения
- ISO 9934-3, Неразрушающий контроль. Магнитопорошковый контроль.
Часть 3. Оборудование
- ISO 17638, Неразрушающий контроль сварных швов. Магнитопорошковый контроль
- ISO 23279, Неразрушающий контроль сварных швов. Магнитопорошковый контроль сварных швов. Уровни приемлемости
Европейский комитет по стандартизации (CEN)
- EN 1290, испытание на поверхностные трещины
- EN 1330-7, Неразрушающий контроль. Терминология. Часть 7. Термины, используемые при магнитопорошковом контроле
- EN 1369, Основание. Магнитопорошковый контроль
- N 10228-1, Неразрушающий контроль стальных поковок. Часть 1. Магнитопорошковый контроль
- EN 10246-12, Неразрушающий контроль стальных труб. Часть 12. Магнитопорошковая дефектоскопия бесшовных и сварных труб из ферромагнитной стали для обнаружения дефектов поверхности
- EN 10246-18, Неразрушающий контроль стальных труб. Часть 18. Магнитопорошковая дефектоскопия концов бесшовных и сварных труб из ферромагнитной стали для обнаружения слоистых дефектов
Американское общество испытаний и материалов (ASTM)
- ASTM E1444-05
- ASTM A 275/A 275M Метод испытания магнитопорошкового исследования стальных поковок
- Спецификация ASTM A456 для магнитопорошковой дефектоскопии больших поковок коленчатого вала
- ASTM E543 Стандартные технические условия для оценки агентств, выполняющих неразрушающий контроль
- ASTM E 709 Руководство по испытаниям магнитопорошковым методом
- ASTM E 1316 Терминология неразрушающего контроля
- ASTM E 2297 Стандартное руководство по использованию источников и измерителей УФ-А и видимого света, используемых в пенетрантных и магнитопорошковых методах
NDT (неразрушающий контроль): полное руководство
NDT означает неразрушающий контроль. Он относится к набору методов проверки, которые позволяют инспекторам оценивать и собирать данные о материале, системе или компоненте без их постоянного изменения.
В полевых условиях неразрушающий контроль часто используется как общий термин для обозначения методов неразрушающего контроля, инструментов контроля или даже всей области неразрушающего контроля.
Для коммерческого применения цель неразрушающего контроля состоит в том, чтобы обеспечить надлежащее обслуживание критической инфраструктуры во избежание катастрофических аварий.
В то время как методы неразрушающего контроля, как правило, связаны с промышленными вариантами использования, такими как проверка слабых мест в котлах на нефтеперерабатывающем заводе, на самом деле их применение в медицине является одним из наиболее распространенных.
Например, беременная женщина, проходящая УЗИ для проверки здоровья своего ребенка, будет считаться вариантом использования неразрушающего контроля, как и рентген или МРТ, чтобы узнать больше о травме.
Но важно отметить, что неразрушающий контроль не обязательно требует использования специальных инструментов или вообще каких-либо инструментов.
Например, когда инспекторы в промышленных условиях осматривают корпус сосуда высокого давления невооруженным глазом, это подпадает под определение неразрушающего контроля, поскольку они собирают данные о состоянии котла, не повреждая его. С другой стороны, использование сложного инструмента, такого как ультразвуковой датчик, для поиска дефектов в определенном материале или объекте также называется неразрушающим контролем.
Вне зависимости от конкретного варианта использования, основной чертой всех этих примеров является сбор данных ненавязчивым образом.
Вот оглавление, которое поможет вам ориентироваться во всей информации, касающейся неразрушающего контроля, содержащейся в этой статье:
- Что такое неразрушающий контроль?
- В чем разница между разрушающим и неразрушающим контролем?
- 8 наиболее распространенных методов неразрушающего контроля
- Сварка НК
- Как дроны могут помочь с неразрушающим контролем
Что такое неразрушающий контроль?
Мы уже рассмотрели, что означает неразрушающий контроль и как эта фраза используется в полевых условиях. Теперь давайте погрузимся и более внимательно рассмотрим некоторые детали, которые управляют миром неразрушающего контроля.
Когда речь идет об обеспечении надлежащего обслуживания активов, невозможно переоценить важность неразрушающего контроля.
Вот основные причины, по которым неразрушающий контроль используется столь многими компаниями по всему миру:
- Сбережения . Наиболее очевидный ответ на этот вопрос заключается в том, что неразрушающий контроль более привлекателен, чем разрушающий контроль, поскольку он позволяет исследуемому материалу или объекту выдержать проверку целым и невредимым, тем самым экономя деньги и ресурсы.
- Безопасность . Неразрушающий контроль также привлекателен тем, что почти все методы неразрушающего контроля (кроме радиографического контроля) безвредны для людей.
- Эффективность . Методы неразрушающего контроля позволяют проводить тщательную и относительно быструю оценку активов, что может иметь решающее значение для обеспечения постоянной безопасности и производительности на рабочей площадке.
- Точность . Методы неразрушающего контроля доказали свою точность и предсказуемость — оба эти качества вам нужны, когда речь идет о процедурах технического обслуживания, предназначенных для обеспечения безопасности персонала и долговечности оборудования.
«Неразрушающий контроль — это кровь хорошо управляемого объекта, и любой обученный инспектор знает о высокой важности неразрушающего контроля. Методы неразрушающего контроля и воспроизводимые результаты зависят от высококвалифицированных техников, обладающих опытом и добросовестностью. Технический специалист должен не только должны быть сертифицированы по определенному методу неразрушающего контроля, но они также должны знать, как управлять оборудованием, используемым для сбора данных. Понимание возможностей и ограничений оборудования — это разница между принятием или отклонением решения».
— Джейсон Ачерби, генеральный менеджер MFE Inspection Solutions, «Ваш универсальный источник инспекции»
Где используется неразрушающий контроль?
В зависимости от того, насколько широко вы определяете неразрушающий контроль, вы можете сказать, что он используется почти во всех отраслях промышленности в мире, поскольку визуальные проверки (формальные или случайные) в той или иной форме проводятся почти на каждом рабочем месте.
При этом существуют определенные отрасли, которые требуют неразрушающего контроля и имеют формализованные процессы для его использования, кодифицированные перечисленными выше организациями, такими как API и ASME.
Эти отрасли включают:
- Нефть и газ
- Производство электроэнергии
- Химикаты
- Горнодобывающая промышленность
- Аэрокосмическая промышленность
- Автомобилестроение
- Морской
- Горнодобывающая промышленность
Во всех этих отраслях инспекторы используют три разных метода для получения доступа к труднодоступным местам или местам на высоте:
- Леса . Использование строительных лесов требует, чтобы инспекторы лично работали на высоте для сбора данных проверки.
- Веревочный доступ . Использование канатного доступа также требует от инспекторов работы на высоте для сбора данных проверки. Узнайте больше о веревочном доступе и о том, как его используют инспекторы, из этого руководства.
- Дроны . Инспекторы могут использовать дроны для удаленного сбора данных об инспекциях, что позволяет им безопасно оставаться за пределами замкнутых пространств или в безопасных местах на высоте. Прочтите следующий раздел, чтобы узнать больше о том, как можно использовать дроны для неразрушающего контроля.
Нормы и стандарты неразрушающего контроля
Методы неразрушающего контроля могут использоваться для всех видов контроля. Но некоторые из наиболее важных видов неразрушающего контроля относятся к активам, таким как котлы и сосуды под давлением, которые могут быть невероятно опасными, если их не обслуживать должным образом.
Поскольку надлежащее техническое обслуживание этих активов очень важно для безопасности тех, кто работает поблизости (или даже на расстоянии, когда речь идет об атомных электростанциях), в большинстве стран действуют законы, требующие от компаний соблюдения определенных правил и стандартов инспекции при проведении инспекции.
Эти стандарты и нормы обычно требуют периодического проведения проверок в соответствии с конкретными рекомендациями. Для большинства активов, представляющих наибольший риск, эти проверки должны проводиться сертифицированным инспектором и утверждаться сертифицированным свидетелем, работающим в официальном инспекционном органе.
Вот самые популярные организации в мире по созданию стандартов и норм неразрушающего контроля:
- API (Американский институт нефти)
- ASME (Американское общество инженеров-механиков)
- ASTM (Американское общество испытаний и материалов)
- ASNT (Американское общество неразрушающего контроля)
- COFREND (Французский комитет исследований в области неразрушающего контроля)
- CSA Group (Канадская ассоциация стандартов)
- CGSB (Канадский совет по общим стандартам)
В чем разница между разрушающим и неразрушающим контролем?
Неразрушающий контроль (НК) используется для сбора информации о материале таким образом, чтобы он не изменялся (т. е. не разрушался). Разрушающее тестирование (DT) используется для сбора информации о материале таким образом, чтобы изменить его (то есть разрушить).
По сути, разница между НК и DT заключается в том, что НК не требует от инспекторов повреждения материала, который они тестируют, в отличие от DT.
Например, при разрушающем контроле часть материала может быть соскоблена для анализа или иным образом изменена на месте.
Вот несколько примеров деструктивного тестирования:
- Макро-секционирование. Макросечение проверяет небольшой участок сварного материала путем его полировки и травления для проверки.
- Испытание на растяжение. Этот метод разрушающих испытаний, также называемый испытанием на растяжение, использует контролируемое натяжение, прикладываемое к материалу образца, чтобы увидеть, как он реагирует. Натяжение может применяться для проверки определенных нагрузок или условий или для проверки точки разрушения материала.
- Испытание на изгиб в 3 точках. Испытание на трехточечный изгиб проверяет прочность и гибкость (или пластичность) материала, беря его образец, называемый образцом, и сгибая его в трех точках под заданным углом.
Прочтите наше руководство по разрушающему тестированию, чтобы узнать больше.
NDT и NDE
Пока мы определяем термины, важно отметить, что есть несколько общих фраз, которые относятся к испытаниям материалов без их уничтожения.
NDT — наиболее распространенная фраза, но есть и другие:
- NDE (неразрушающий контроль или неразрушающая оценка)
- НДИ (неразрушающий контроль)
Полная форма неразрушающего контроля — неразрушающий контроль или неразрушающая оценка, а полная форма неразрушающего контроля — неразрушающий контроль.
8 наиболее распространенных методов неразрушающего контроля
Существует несколько методов, используемых в неразрушающем и неразрушающем контроле для сбора различных типов данных, каждый из которых требует своих инструментов, обучения и подготовки.
Некоторые из этих методов позволяют проводить полный объемный осмотр объекта, в то время как другие позволяют проводить только поверхностный осмотр. Аналогичным образом, некоторые методы неразрушающего контроля будут иметь различную степень успеха в зависимости от типа материала, на котором они используются, а некоторые методы, такие как, например, магнитно-порошковый неразрушающий контроль, будут работать только на определенных материалах (т. можно намагнитить).
Вот восемь наиболее часто используемых методов неразрушающего контроля:
- Визуальный неразрушающий контроль (ВТ)
- Ультразвуковой неразрушающий контроль (UT)
- Неразрушающий контроль рентгенографии (RT)
- Вихретоковый неразрушающий контроль (ET)
- Магнитопорошковый неразрушающий контроль (МТ)
- Неразрушающий контроль акустической эмиссии (AE)
- Неразрушающий контроль проникающей краской (PT)
- Проверка герметичности (LT)
1.

Определение : Визуальный неразрушающий контроль – это сбор визуальных данных о состоянии материала. Визуальное тестирование — это самый простой способ изучить материал или объект, не изменяя его каким-либо образом.
Как проводить визуальное тестирование
Визуальное тестирование может проводиться невооруженным глазом, когда инспекторы визуально осматривают материал или актив. При визуальном тестировании в помещении инспекторы используют фонарики, чтобы добавить глубину изучаемому объекту. Визуальное тестирование также может быть выполнено с помощью инструмента RVI (удаленный визуальный осмотр), такого как инспекционная камера. Чтобы установить камеру, инспекторы по НК могут использовать робота или беспилотник или просто повесить ее на веревке.
Прочтите наше руководство по визуальному тестированию.
2. Ультразвуковой контроль (UT)
Определение : Ультразвуковой неразрушающий контроль — это процесс проведения высокочастотных звуковых волн в материал для выявления изменений в свойствах материала.
Как проводить ультразвуковой контроль
Как правило, ультразвуковой контроль использует звуковые волны для обнаружения дефектов или дефектов на поверхности созданного материала.
Одним из наиболее распространенных методов ультразвукового контроля является эхо-импульс. С помощью этого метода инспекторы вводят звуки в материал и измеряют эхо (или звуковые отражения), создаваемые дефектами на поверхности материала, когда они возвращаются к приемнику.
Вот некоторые другие типы ультразвукового контроля:
- Ультразвуковой контроль с фазированной решеткой (PAUT)
- Автоматизированный ультразвуковой контроль (AUT)
- Времяпролетная дифракция (TOFD)
Прочтите наше руководство по ультразвуковому контролю.
3. Рентгенографический контроль (RT)
Определение : Рентгенографический неразрушающий контроль – это процесс использования гамма- или рентгеновского излучения на материалах для выявления дефектов.
Как проводить рентгенографический неразрушающий контроль
Радиографический контроль направляет излучение радиоактивного изотопа или генератора рентгеновского излучения через тестируемый материал на пленку или детектор другого типа. Показания детектора создают теневую диаграмму, которая раскрывает основные аспекты проверяемого материала.
Рентгенологическое исследование позволяет выявить аспекты материала, которые трудно обнаружить невооруженным глазом, например, изменения его плотности.
Прочтите наше руководство по промышленной рентгенографии.
4. Вихретоковый (электромагнитный) контроль (ET)
Определение : Вихретоковый неразрушающий контроль – это тип электромагнитного контроля, в котором используются измерения силы электрических токов (также называемых вихревыми токами) в магнитное поле, окружающее материал, чтобы сделать выводы о материале, которые могут включать в себя расположение дефектов.
Как проводить вихретоковые испытания
Для проведения вихретоковых испытаний инспекторы исследуют поток вихревых токов в магнитном поле, окружающем проводящий материал, для выявления прерываний, вызванных дефектами или несовершенствами материала.
Прочтите наше руководство по вихретоковому контролю.
5. Магнитопорошковый контроль (MPI)
Определение : Магнитопорошковый неразрушающий контроль – это процесс выявления дефектов в материале путем изучения нарушений в потоке магнитного поля внутри материала.
Как проводить магнитопорошковый контроль
Чтобы использовать магнитопорошковый контроль, инспекторы сначала индуцируют магнитное поле в материале, который очень чувствителен к намагничиванию. После создания магнитного поля поверхность материала затем покрывается частицами железа, которые обнаруживают нарушения в потоке магнитного поля. Эти нарушения создают визуальные индикаторы местоположения дефектов в материале.
Прочтите наше руководство по магнитопорошковому контролю.
6. Контроль акустической эмиссии (AE)
Определение : Неразрушающий контроль акустической эмиссии – это процесс использования акустической эмиссии для выявления возможных дефектов и несовершенств материала.
Как проводить испытания на акустическую эмиссию
Инспекторы, проводящие испытания на акустическую эмиссию, проверяют материалы на наличие всплесков акустической энергии, также называемых акустической эмиссией, которые вызваны дефектами материала. Интенсивность, местоположение и время прибытия могут быть проверены, чтобы выявить информацию о возможных дефектах в материале.
Прочтите наше руководство по испытаниям на акустическую эмиссию.
7. Контроль проникающей жидкости (PT)
Определение : Неразрушающий контроль проникающей способностью красителя (также называемый капиллярным контролем) относится к процессу использования жидкости для покрытия материала с последующим поиском разрывов. в жидкости для выявления дефектов в материале.
Как проводить испытания на пенетрантность
Инспекторы, проводящие испытания на пенетрантность, сначала покрывают испытуемый материал раствором, содержащим видимый или флуоресцентный краситель. Затем инспекторы удаляют лишний раствор с поверхности материала, оставляя раствор в дефектах, которые «ломают» поверхность материала.
После этого проверяющие с помощью проявителя выводят раствор из дефектов, затем с помощью ультрафиолетового света выявляют дефекты (для флуоресцентных красок). Для обычных красителей цвет проявляется в контрасте пенетранта и проявителя.
Прочтите наше руководство по тестированию проникающих красителей.
8. Испытание на герметичность (LT)
Определение : Неразрушающий контроль на герметичность относится к процессу изучения утечек в сосуде или конструкции с целью выявления в них дефектов.
Как проводить испытания на герметичность
Инспекторы могут обнаруживать утечки внутри сосуда, используя, среди прочего, измерения, сделанные с помощью манометра, испытаний с помощью мыльных пузырей или электронных подслушивающих устройств.
Прочтите наше руководство по тестированию на утечки.
Неразрушающий контроль сварки
Неразрушающий контроль сварки – это использование неразрушающего контроля для проверки сварного шва.
Сварные швы являются одной из наиболее частых частей промышленных объектов, которую проверяют инспекторы. Используя оборудование для неразрушающего контроля сварки, инспекторы могут определить, является ли сварной шов прочным или имеет потенциальные дефекты, которые могут поставить под угрозу его целостность.
Наиболее распространенные дефекты, обнаруживаемые при неразрушающем контроле сварных швов:
Плохое качество сварки из-за наличия шлака
Усталость, вызванная человеческим фактором
Дефекты, вызванные неправильной техникой или настройкой сварного шва
Повреждение сварного шва из-за окружающей среды (например, экстремальные температуры, присутствие влаги или использование несовместимых металлов)
Наиболее распространенные методы неразрушающего контроля сварки включают:
Ультразвуковой контроль НК
Магнитопорошковая дефектоскопия NDT
Акустическая эмиссия НК
Смачивающий краситель NDT
Рентгенография NDT
Вихретоковый неразрушающий контроль
Визуальный осмотр может использоваться для неразрушающего контроля сварных швов, чтобы помочь инспекторам сделать основные выводы о прочности сварного шва, хотя его результаты могут быть более ограниченными, чем описанные выше методы контроля сварки.
Сварочный неразрушающий контроль трещины методом магнитопорошковой дефектоскопии
Целью неразрушающего контроля при сварке является выявление дефектов на поверхности или внутри сварного шва, которые могут привести к его ухудшению или разрушению.
Если сварной шов выходит из строя, последствия могут быть очень серьезными, поскольку сварные швы часто имеют решающее значение для целостности крупных промышленных объектов, таких как котлы или сосуды под давлением.
Каков наилучший метод контроля сварки неразрушающим контролем?
Хотя для неразрушающего контроля сварки можно использовать все перечисленные выше методы, лучшим методом является ультразвуковой контроль с использованием подхода с фазированной решеткой.
Этот метод испытаний сварки может быть выполнен довольно быстро, без необходимости больших усилий по настройке или дополнительного оборудования для неразрушающего контроля, обеспечивая получение высококачественных данных за короткий период времени.
Разрушающий и неразрушающий контроль при сварке
Мы уже рассмотрели основные методы неразрушающего контроля сварки, которые используются инспекторами для проверки сварного шва, не вызывая его повреждения.
Но инспекторы также используют разрушающие испытания для проверки сварных швов.
Наиболее распространенными типами разрушающего контроля сварных швов являются:
Как дроны могут помочь в НК
В последние несколько лет дроны, оснащенные камерами, стали еще одним инструментом, обычно используемым в НК для сбора визуальных данных.
Из-за ограничений технологии в течение некоторого времени дроны могли предоставлять инспекторам только дополнительные визуальные данные, но не могли заменить инспекторов, физически собирающих визуальные данные.
Однако по мере совершенствования технологии дронов инспекторы все больше и больше могут использовать дроны в качестве инструментов RVI, в некоторых случаях полностью избавляя их от необходимости собирать визуальные данные вручную.
Вот два основных способа, которыми дроны сегодня помогают в неразрушающем контроле:
Безопасность
Избавляя инспекторов от необходимости входить в опасные замкнутые пространства для сбора визуальных данных, дроны помогают повысить безопасность на рабочем месте.
При наружной инспекции объектов, таких как линии электропередач или опоры, использование дрона для сбора визуальных данных сокращает время, необходимое человеку, чтобы физически находиться в воздухе на опоре или опоре.
Для внутреннего осмотра объектов, таких как сосуды под давлением или котлы, использование беспилотника, такого как Elios 3, для сбора визуальных данных означает, что инспектору не нужно входить в замкнутое пространство, чтобы сделать это, что также помогает значительно снизить подверженность риску.
Экономия
Дроны могут помочь компаниям повысить окупаемость инвестиций как внутри помещений, так и снаружи, но экономия особенно значительна при инспекциях внутри помещений.
Использование профессионального беспилотника для помещений вместо отправки инспектора для сбора визуальных данных вручную означает, что компании экономят на том, что им не нужно строить и сносить строительные леса, и могут сократить время простоя, связанное с этими требованиями, в некоторых случаях на 1–2 два дня.
Поскольку инспекционный дрон может быть установлен быстро, инспекции можно проводить чаще, что помогает выявлять проблемы раньше и увеличивает срок службы актива. Эти ранние открытия могут сэкономить компаниям сотни тысяч долларов за одну проверку.
Что дальше для дронов в неразрушающем контроле?
На сегодняшний день основным вариантом использования дронов в неразрушающем контроле был сбор визуальных данных.
Но в последние несколько лет, помимо камер, к дронам прикрепляют несколько типов датчиков, используемых в НТД, в том числе тепловые, ультразвуковые, магнитные и радиографические датчики.
Новые датчики, поддерживающие методы неразрушающего контроля, постоянно разрабатываются для использования с дронами, что позволяет инспекторам собирать еще более широкий спектр данных, даже не касаясь объекта.
Кроме того, программное обеспечение, разработанное для удовлетворения потребностей инспекторов, расширяется как с точки зрения рынка, так и с точки зрения возможностей. Программное обеспечение может напрямую работать со сбором данных дрона, например, Inspector 4.0, самая последняя версия программного обеспечения для проверки Flyability.
Используя Inspector 4.0, инспекторы могут быстро создать разреженную 3D-модель объекта, который они проверяют, после процесса сбора данных, который точно показывает, где в объекте находятся дефекты, успешно устраняя давнюю проблему инспекторов. Инспекторы могут увидеть дефект на изображениях, собранных дроном, а затем узнать, где он находился, используя информацию о местоположении модели, экономя часы работы.
Вручную просмотреть горы данных, предоставленных инспекционными дронами, было бы непосильно для человека. В результате программное обеспечение, предназначенное для того, чтобы помочь инспекторам разобраться в собранной информации, стало необходимостью, а не роскошью.
С помощью машинного обучения и искусственного интеллекта эти передовые программы могут обрабатывать и просматривать изображения активов и помечать проблемы для проверки человеком. WinCan, например, — это компания, которая производит программное обеспечение только для проверки канализации. Используя алгоритм на основе искусственного интеллекта, его программное обеспечение может получать необработанные визуальные данные из проверки канализации и выявлять все потенциальные дефекты, которые могут потребовать дополнительной проверки или ремонта.
Достижения в области технологий беспилотных летательных аппаратов, разнообразия полезной нагрузки и обработки данных открывают новую эру эффективности неразрушающего контроля и безопасности для инспекторов.
Узнайте о семи основных преимуществах беспилотных летательных аппаратов для неразрушающего контроля.
Мы проводим демонстрации по всему миру, чтобы продемонстрировать наш новый беспилотник для инспекции помещений.
Введение в неразрушающий контроль
Для посетителей, которые еще не знакомы с неразрушающим контролем, приведенная ниже общая информация предназначена для предоставления базового описания неразрушающего контроля и наиболее распространенных методов и приемов испытаний, используемых при выполнении неразрушающего контроля. Как таковой, он не является очень подробным или всеохватывающим, и для получения более полной информации читатели должны обратиться к публикациям ASNT, таким как Справочники ASNT по неразрушающему контролю или Серия учебных материалов ASNT для обучения персонала (PTP), все из которых доступны в книжном магазине ASNT. Кроме того, стандарты, охватывающие эти методы испытаний, перечислены на странице «Кодексы и органы стандартизации» на вкладке «Центр ресурсов по неразрушающему контролю». Для обеспечения согласованности методы, описанные для каждого метода испытаний, перечислены в Рекомендованной практике ASNT 2011 года № SNT-TC-1A.
Что такое неразрушающий контроль?
Неразрушающий контроль (НК) — это процесс осмотра, испытания или оценки материалов, компонентов или сборок на наличие неоднородностей или различий в характеристиках без нарушения работоспособности детали или системы. Другими словами, после завершения осмотра или испытаний деталь все еще можно использовать.
В отличие от неразрушающего контроля, другие виды испытаний носят разрушающий характер и поэтому проводятся на ограниченном количестве образцов («выборка партии»), а не на материалах, компонентах или узлах, фактически вводимых в эксплуатацию.
Эти разрушающие испытания часто используются для определения физических свойств материалов, таких как ударопрочность, пластичность, предел текучести и предел прочности при растяжении, вязкость разрушения и усталостная прочность, но неоднородности и различия в характеристиках материалов более эффективно обнаруживаются с помощью неразрушающего контроля.
Сегодня современные методы неразрушающего контроля используются при производстве, изготовлении и контроле в процессе эксплуатации для обеспечения целостности и надежности продукции, контроля производственных процессов, снижения производственных затрат и поддержания постоянного уровня качества. Во время строительства неразрушающий контроль используется для обеспечения качества материалов и процессов соединения на этапах изготовления и монтажа, а неразрушающий контроль в процессе эксплуатации используется для обеспечения того, чтобы используемые продукты сохраняли целостность, необходимую для обеспечения их полезности и безопасности. общественности.
Следует отметить, что хотя в области медицины используются многие из тех же процессов, термин «неразрушающий контроль» обычно не используется для описания медицинских применений.
Методы испытаний НК
Названия методов испытаний часто относятся к типу проникающей среды или оборудованию, используемому для проведения этого испытания. Текущие методы неразрушающего контроля: акустико-эмиссионный контроль (AE), электромагнитный контроль (ET), лазерные методы контроля (LM), контроль на герметичность (LT), утечка магнитного потока (MFL), контроль проникающей жидкости (PT), контроль магнитных частиц (MT). ), нейтронный радиографический контроль (NR), радиографический контроль (RT), тепловой/инфракрасный контроль (IR), ультразвуковой контроль (UT), вибрационный анализ (VA) и визуальный контроль (VT).
Шесть наиболее часто используемых методов испытаний: MT, PT, RT, UT, ET и VT. Здесь будет описан каждый из этих методов испытаний, за которым последуют другие, менее часто используемые методы испытаний.
В магнитопорошковом контроле используется одно или несколько магнитных полей для обнаружения поверхностных и приповерхностных несплошностей в ферромагнитных материалах. Магнитное поле может создаваться с помощью постоянного магнита или электромагнита. При использовании электромагнита поле присутствует только при подаче тока. Когда магнитное поле сталкивается с разрывом, поперечным направлению магнитного поля, силовые линии создают собственное поле рассеяния магнитного потока, как показано на рисунке 1. Поскольку магнитные силовые линии плохо перемещаются в воздухе, при очень тонком ферромагнитные частицы («магнитные частицы») наносятся на поверхность детали, частицы будут втягиваться в несплошность, уменьшая воздушный зазор и создавая видимую индикацию на поверхности детали. Магнитные частицы могут представлять собой сухой порошок или взвешенные в жидком растворе, они могут быть окрашены видимым красителем или флуоресцентным красителем, флуоресцирующим в ультрафиолетовом («черном») свете.
Методы МТ
Хомуты
Большинство проверок в полевых условиях выполняются с использованием Хомутов, как показано справа. Как показано на рис. 2(а), электрическая катушка наматывается вокруг центрального сердечника, и при подаче тока создается магнитное поле, которое распространяется от сердечника вниз через шарнирные ножки в деталь. Это известно как продольное намагничивание, потому что линии магнитного потока проходят от одного плеча к другому.
Когда ножки помещаются на ферромагнитную деталь и ярмо находится под напряжением, в деталь вводится магнитное поле, как показано на (b). Поскольку линии потока проходят от одного плеча к другому, могут быть обнаружены разрывы, ориентированные перпендикулярно линии, проведенной между плечами. Чтобы гарантировать отсутствие пропусков, хомут используется один раз в показанном положении, а затем снова используется с хомутом, повернутым на 90 o , чтобы не пропустить ни одного показания. Поскольку весь электрический ток проходит через ярмо, а через часть проходит только магнитное поле, этот тип применения известен как 9.0346 непрямой индукционный.
Продукты
В устройствах используется прямая индукция , при которой ток проходит через деталь, а вокруг ножек создается круговое магнитное поле, как показано на рис. 3. Поскольку магнитное поле между щупами распространяется перпендикулярно линии, проведенной между щупами, показания ориентированы параллельно линии, проведенной между стержнями. Как и в случае с коромыслом, делается два осмотра, второй с ориентацией стержней 90 o к первому приложению.
Катушки
Электрические катушки используются для создания продольного магнитного поля. Под напряжением ток создает магнитное поле вокруг проводов, составляющих катушку, так что результирующие линии потока ориентированы через катушку, как показано справа. Из-за продольного поля показания в деталях, помещенных в катушку, ориентированы поперек продольного поля.
Головки
Большинство горизонтальных машин с мокрой ванной («настольные устройства») имеют как катушку, так и набор головок, через которые может проходить электрический ток, создавая магнитное поле. Большинство из них используют флуоресцентные магнитные частицы в жидком растворе, отсюда и название «влажная ванна». Типичный настольный блок показан справа. При контроле детали между головками деталь помещается между головками, подвижная головка перемещается вверх так, чтобы проверяемая деталь плотно удерживалась между головками, деталь смачивается раствором ванны, содержащим магнитные частицы и ток применяется, когда частица течет по детали. Поскольку ток течет от головы к голове, а магнитное поле ориентировано 90 o к текущему, будут видны индикации, ориентированные параллельно линии между головками. Этот тип проверки обычно называют «выстрелом в голову».
Центральный проводник
При испытании полых деталей, таких как трубы, трубки и фитинги, между головками можно поместить токопроводящий круглый стержень, при этом деталь подвешивается на стержне («центральный проводник»), как показано на рис. 6. Затем деталь смачивается раствор в ванне, и подается ток, проходящий через центральный проводник, а не через деталь. Затем можно проверить внутренний и наружный диаметр детали. Как и при выстреле в голову, магнитное поле перпендикулярно потоку тока, оборачиваясь вокруг испытуемого образца, поэтому с помощью этого метода можно найти признаки, идущие в осевом направлении по длине детали.
Основной принцип капиллярной дефектоскопии заключается в том, что при нанесении на поверхность детали жидкости с очень низкой вязкостью (высокотекучей) (пенетранта) она проникает в трещины и пустоты, открытые на поверхности. Как только избыток пенетранта будет удален, пенетрант, попавший в эти пустоты, вытечет обратно, создавая индикацию. Капиллярный контроль можно проводить на магнитных и немагнитных материалах, но он плохо работает на пористых материалах. Пенетранты могут быть «видимыми», то есть их можно увидеть в окружающем свете, или флуоресцентными, требующими использования «черного» света. Процесс видимого проникающего красителя показан на рис. 7. При выполнении PT-контроля обязательно, чтобы проверяемая поверхность была чистой и не содержала каких-либо инородных материалов или жидкостей, которые могут препятствовать попаданию пенетранта в пустоты или трещины, открытые на поверхности. часть.
После нанесения пенетранта его выдерживают на поверхности в течение определенного периода времени («время пребывания пенетранта»), затем деталь тщательно очищают от излишков пенетранта с поверхности. При удалении пенетранта оператор должен следить за тем, чтобы пенетрант не попал в пустоты. Затем на поверхность наносится легкий слой проявителя и дается время («время выдержки проявителя»), чтобы пенетрант из любых пустот или трещин просочился в проявитель, создавая видимые признаки.
После предписанного времени выдержки проявителя деталь осматривают визуально с помощью черной лампы на наличие флуоресцентных пенетрантов. Большинство проявителей представляют собой мелкозернистые белые порошки, похожие на тальк, которые создают цветовой контраст с используемым пенетрантом.
Методы физической подготовки
Съемный растворитель
Съемный пенетрант с растворителем — это те пенетранты, для удаления излишков пенетранта которых требуется растворитель, отличный от воды. Эти пенетранты обычно видны в природе, обычно окрашены в ярко-красный цвет, который будет хорошо контрастировать с белым проявителем. Пенетрант обычно распыляют или наносят кистью на деталь, затем, по истечении времени выдержки пенетранта, деталь очищают тканью, смоченной пенетрантом, после чего наносят проявитель. По истечении времени выдержки проявителя деталь осматривают, чтобы обнаружить просачивание пенетранта через проявитель.
Смываемые водой
Смываемые водой пенетранты содержат эмульгатор, включенный в пенетрант, который позволяет удалять пенетрант с помощью распыления воды. Чаще всего они наносятся путем погружения детали в резервуар с пенетрантом, но пенетрант можно наносить на большие детали путем распыления или нанесения кистью. После того, как деталь полностью покрыта пенетрантом, ее помещают на дренажную доску на время выдержки пенетранта, затем доставляют на станцию ополаскивания, где ее промывают струей воды для удаления излишков пенетранта. После удаления избытка пенетранта деталь можно поместить в сушилку с теплым воздухом или перед несильным вентилятором до тех пор, пока не будет удалена вода. Затем деталь можно поместить в бак для сухого проявителя и покрыть проявителем или оставить на оставшееся время выдержки, а затем осмотреть.
Постэмульгируемые пенетранты
Постэмульгируемые пенетранты — это пенетранты, химический состав которых не включает эмульгатор, как водосмываемые пенетранты. Постэмульгируемые пенетранты наносят аналогичным образом, но перед этапом промывки водой на поверхность наносят эмульгатор на заданный период времени (выдержка эмульгатора) для удаления излишков пенетранта. По истечении времени выдержки эмульгатора деталь подвергают такой же промывке водой и процессу проявления, что и для водосмываемых пенетрантов. Эмульгаторы могут быть липофильными (на масляной основе) или гидрофильными (на водной основе).
Промышленная радиография включает в себя воздействие на исследуемый объект проникающего излучения таким образом, чтобы излучение проходило через обследуемый объект, а записывающий носитель располагался напротив противоположной стороны этого объекта. Для более тонких или менее плотных материалов, таких как алюминий, обычно используется электрически генерируемое рентгеновское излучение (рентгеновское излучение), а для более толстых или плотных материалов обычно используется гамма-излучение.
Гамма-излучение исходит от распада радиоактивных материалов, при этом двумя наиболее часто используемыми источниками гамма-излучения являются иридий-19. 2 (Ир-192) и Кобальт-60 (Со-60). IR-192 обычно используется для стали толщиной до 2-1/2-3 дюймов, в зависимости от силы Кюри источника, а Co-60 обычно используется для более толстых материалов из-за его большей проникающей способности.
Носителем записи может быть промышленная рентгеновская пленка или один из нескольких типов цифровых детекторов излучения. В обоих случаях излучение, проходящее через испытуемый объект, обнажает среду, вызывая конечный эффект наличия более темных областей, где через деталь прошло больше излучения, и более светлых областей, где проникло меньше излучения. Если в детали есть пустота или дефект, через нее проходит больше излучения, что приводит к более темному изображению на пленке или детекторе, как показано на рис. 8.9.0003
Методы РТ
Компьютерная рентгенография
Компьютерная рентгенография (КР) — это переходная технология между пленочной и прямой цифровой рентгенографией. В этом методе используется многоразовая гибкая пластина с фотостимулированным люминофором (PSP), которая загружается в кассету и экспонируется аналогично традиционной пленочной рентгенографии. Затем кассета помещается в лазерный считыватель, где она сканируется и преобразуется в цифровое изображение, что занимает от одной до пяти минут. Затем изображение можно загрузить на компьютер или другой электронный носитель для интерпретации и хранения.
Компьютерная томография
Компьютерная томография (КТ) использует компьютер для реконструкции изображения плоскости поперечного сечения объекта, в отличие от обычной рентгенограммы, как показано на рис. различные углы обзора, которые реконструируются с помощью компьютера. При традиционной рентгенографии положение внутренних несплошностей не может быть точно определено без экспозиций под разными углами для определения положения предмета с помощью триангуляции. При компьютерной томографии компьютер выполняет триангуляцию, используя каждую точку на плоскости, если смотреть с разных направлений.
Цифровая рентгенография
Цифровая рентгенография (ДР) оцифровывает излучение, проходящее через объект, непосредственно в изображение, которое можно отобразить на мониторе компьютера. Три основные технологии, используемые в прямом цифровом изображении, — это аморфный кремний, устройства с зарядовой связью (ПЗС) и комплементарные полупроводники на основе оксидов металлов (КМОП). Эти изображения доступны для просмотра и анализа за считанные секунды по сравнению со временем, необходимым для сканирования компьютерных рентгенографических изображений. Повышенная скорость обработки является результатом уникальной конструкции пикселей; расположение, которое также обеспечивает более высокое разрешение, чем в компьютерной радиографии и большинстве пленочных приложений.
Пленочная радиография
Пленочная радиография использует пленку, состоящую из тонкого прозрачного пластика, покрытого тонким слоем бромида серебра на одной или обеих сторонах пластика. Под воздействием радиации эти кристаллы вступают в реакцию, которая позволяет им при проявлении превращаться в черное металлическое серебро. Затем это серебро «фиксируется» на пластике в процессе проявления и после высыхания становится готовой рентгенографической пленкой.
Чтобы пленку можно было использовать, интересующая область (область сварки и т. д.) на пленке должна быть в пределах определенного диапазона плотности (темноты) и должна демонстрировать достаточный контраст и чувствительность, чтобы можно было увидеть интересующие разрывы. Эти параметры зависят от силы излучения, расстояния от источника до пленки и толщины проверяемой детали. Если какой-либо из этих параметров не соблюдается, необходимо сделать еще одну экспозицию («снимок») для этой области детали.
Ультразвуковой контроль использует тот же принцип, что и морской гидролокатор и эхолоты. Ультравысокочастотный звук проникает в проверяемую деталь, и если звук попадает на материал с другим акустическим импедансом (плотностью и акустической скоростью), часть звука отражается обратно к передающему устройству и может быть представлена на визуальном дисплее. . Зная скорость звука через деталь (акустическая скорость) и время, необходимое для возвращения звука к передатчику, можно определить расстояние до отражателя (индикатор с различным акустическим сопротивлением). Наиболее распространенные звуковые частоты, используемые в UT, находятся в диапазоне от 1,0 до 10,0 МГц, они слишком высоки, чтобы их можно было услышать, и не распространяются по воздуху. Низкие частоты имеют большую проникающую способность, но меньшую чувствительность (способность «видеть» небольшие признаки), в то время как более высокие частоты не проникают так глубоко, но могут обнаруживать более мелкие признаки.
Двумя наиболее часто используемыми типами звуковых волн, используемых в промышленных инспекциях, являются волна сжатия (продольная) и поперечная волна (поперечная), как показано на рисунке 10. Волны сжатия заставляют атомы в детали колебаться вперед и назад параллельно к направлению звука, а поперечные волны заставляют атомы вибрировать перпендикулярно (из стороны в сторону) направлению звука. Сдвиговые волны распространяются примерно вдвое медленнее продольных волн.
Звук подается в деталь с помощью ультразвукового преобразователя («зонда»), который преобразует электрические импульсы от УЗ-аппарата в звуковые волны, а затем преобразует возвращающийся звук обратно в электрические импульсы, которые могут отображаться в виде визуального представления на цифровом или ЖК-дисплее экран (на старых машинах ЭЛТ-экран). Если машина правильно откалибрована, оператор может определить расстояние от преобразователя до отражателя, и во многих случаях опытный оператор может определить тип несплошности (например, шлак, пористость или трещины в сварном шве), вызвавшей появление отражателя. Поскольку ультразвук не распространяется через воздух (атомы в молекулах воздуха слишком далеко друг от друга для передачи ультразвука), между лицевой стороной преобразователя и поверхностью детали используется жидкость или гель, называемый «контактной жидкостью», чтобы звук передается в часть.
УЗ-методы
Прямой луч
При контроле прямым лучом для исследования образца используются продольные волны, как показано справа. Если звук попадает на внутренний отражатель, звук от этого отражателя будет отражаться к преобразователю быстрее, чем звук, возвращающийся от задней стенки детали, из-за более короткого расстояния от преобразователя. В результате на экране появляется изображение, подобное показанному справа на Рисунке 11. Цифровые толщиномеры используют тот же процесс, но выходные данные отображаются в виде цифровых числовых значений, а не представления на экране.
Наклонный луч
При контроле наклонным лучом используется преобразователь того же типа, но он устанавливается на угловой клин (также называемый «зонд»), который предназначен для передачи звукового луча в деталь под известным углом. Наиболее часто используемые углы контроля: 45 o , 60 o и 70 o , при этом угол рассчитывается по линии, проведенной через толщину детали (а не через поверхность детали). Датчик 60 o показан на рисунке 12. Если частота и угол клина не указаны в руководящих нормах или спецификациях, оператор должен выбрать комбинацию, которая позволит адекватно проверить проверяемую деталь.
При контроле наклонным лучом комбинация преобразователя и клина (также называемая «щуп») перемещается вперед и назад по направлению к сварному шву, так что звуковой луч проходит через весь объем сварного шва. Как и при контроле прямым лучом, отражатели, расположенные более или менее перпендикулярно звуковому лучу, будут посылать звук обратно на преобразователь и отображать его на экране.
Испытание погружением
Испытание погружением — это метод, при котором деталь погружается в резервуар с водой, при этом вода используется в качестве связующей среды, позволяющей звуковому лучу проходить между преобразователем и деталью. Машина UT установлена на подвижной платформе («мосте») сбоку от резервуара, поэтому она может перемещаться по всей длине резервуара. Преобразователь крепится на шарнире на дне водонепроницаемой трубы, которую можно поднимать, опускать и перемещать по резервуару. Перемещение моста и трубки позволяет перемещать датчик по осям X, Y и Z. Все направления движения имеют зубчатый привод, поэтому преобразователь можно перемещать с точными приращениями во всех направлениях, а поворот позволяет ориентировать преобразователь таким образом, чтобы звуковой луч входил в деталь под требуемым углом. Круглые испытуемые детали часто устанавливаются на приводных роликах, чтобы деталь можно было вращать по мере движения датчика по ее длине, что позволяет тестировать всю окружность. Одновременно можно использовать несколько датчиков, что позволяет выполнять несколько сканирований.
Сквозная передача
Проверка сквозной передачи выполняется с использованием двух преобразователей, по одному с каждой стороны детали, как показано на рис. 13. Передающий преобразователь посылает звук через деталь, а принимающий преобразователь принимает звук. Отражатели в детали уменьшат количество звука, достигающего приемника, поэтому на экране будет отображаться сигнал с меньшей амплитудой (высотой экрана).
Фазированная решетка
Проверки с фазированной решеткой выполняются с помощью датчика с несколькими элементами, которые можно активировать по отдельности. Изменяя время активации каждого элемента, можно «направлять» результирующий звуковой луч, а полученные данные можно комбинировать для формирования визуального изображения, представляющего срез проверяемой детали.
Времяпролетная дифракция
Времяпролетная дифракция (TOFD) использует два датчика, расположенных на противоположных сторонах сварного шва, причем датчики устанавливаются на заданном расстоянии друг от друга. Один преобразователь излучает звуковые волны, а другой преобразователь действует как приемник. В отличие от других проверок под углом, датчики не перемещаются вперед и назад по направлению к сварному шву, а перемещаются по длине сварного шва, при этом датчики остаются на одном и том же расстоянии от сварного шва. Генерируются две звуковые волны, одна из которых проходит вдоль поверхности детали между преобразователями, а другая проходит вниз через сварной шов под углом, а затем обратно к приемнику. При обнаружении трещины часть звука дифрагирует от вершин трещины, создавая звуковую волну низкой мощности, которую может уловить приемное устройство. Усиливая и пропуская эти сигналы через компьютер, можно определить размер и местоположение дефекта с гораздо большей точностью, чем с помощью традиционных методов УЗК.
Электромагнитные испытания — это общая категория испытаний, которая включает в себя испытания на вихревые токи, измерения поля переменного тока (ACFM) и испытания в удаленном поле. Хотя магнитопорошковое испытание также является электромагнитным испытанием, из-за его широкого распространения оно считается самостоятельным методом испытаний, а не методом электромагнитных испытаний. Во всех этих методах используется индукция электрического тока или магнитного поля в проводящую деталь, затем регистрируются и оцениваются результирующие эффекты.
Техники ЭТ
Вихретоковые испытания
Вихретоковые испытания используется тот факт, что когда катушка переменного тока индуцирует электромагнитное поле в проводящем испытательном образце, вокруг поля магнитного потока создается небольшой ток, подобно тому, как создается магнитное поле. вокруг электрического тока. На схему течения этого вторичного тока, называемого «вихревым» током, будет влиять, когда он сталкивается с неоднородностью в образце для испытаний, и изменение плотности вихревого тока может быть обнаружено и использовано для характеристики несплошности, вызывающей это изменение. Упрощенная схема вихревых токов, создаваемых катушкой переменного тока («зондом»), показана на рис. 14-а. Варьируя тип катушки, этот метод испытаний можно применять к плоским поверхностям или трубчатым изделиям. Этот метод лучше всего работает на гладких поверхностях и имеет ограниченное проникновение, обычно менее ¼ дюйма 9. 0003
Опоясывающие катушки (рис. 14-b) используются для испытаний трубчатых и стержневых изделий. Трубку или стержень можно подавать через катушку с относительно высокой скоростью, что позволяет исследовать все поперечное сечение испытуемого объекта. Однако из-за направления линий магнитного потока с помощью этого приложения невозможно обнаружить ориентированные по окружности несплошности.
Измерение поля переменного тока
Измерение поля переменного тока (ACFM) использует специальный зонд, который подает переменный ток на поверхность испытуемого образца, создавая магнитное поле. В частях без несплошностей это поле будет однородным, но если на поверхности есть несплошность, магнитное поле будет течь вокруг и под неоднородностью, вызывая нарушение поля, которое может быть обнаружено датчиками внутри зонда. Полученная обратная связь затем может быть передана в программное обеспечение, которое может определить длину и глубину разрыва. ACFM обеспечивает лучшие результаты на шероховатых поверхностях, чем Eddy Current, и может использоваться со многими поверхностными покрытиями.
Дистанционные полевые испытания
Дистанционные полевые испытания (RFT) чаще всего используются для проверки ферромагнитных трубок из-за наличия в таких трубках сильного скин-эффекта. По сравнению со стандартными вихретоковыми методами дистанционный полевой контроль дает лучшие результаты по всей толщине трубы, имея примерно одинаковую чувствительность как на внутренней, так и на внешней поверхности трубы. Для неферромагнитных трубок вихревые токи обеспечивают большую чувствительность.
Визуальное тестирование является наиболее часто используемым методом тестирования в промышленности. Поскольку большинство методов испытаний требуют, чтобы оператор смотрел на поверхность проверяемой детали, визуальный осмотр присущ большинству других методов испытаний. Как следует из названия, ВТ предполагает визуальное наблюдение за поверхностью тестируемого объекта для оценки наличия неоднородностей поверхности. Проверки VT могут быть с помощью прямого просмотра, с использованием прямой видимости, или могут быть улучшены с использованием оптических инструментов, таких как увеличительные стекла, зеркала, бороскопы, устройства с зарядовой связью (ПЗС) и автоматизированные системы просмотра (удаленный просмотр). ). Коррозия, несоосность деталей, физические повреждения и трещины — это лишь некоторые из неоднородностей, которые могут быть обнаружены при визуальном осмотре.
Испытания на акустическую эмиссию выполняются путем приложения локальной внешней силы, такой как резкая механическая нагрузка или быстрое изменение температуры или давления, к испытуемой детали. Результирующие волны напряжения, в свою очередь, генерируют короткоживущие высокочастотные упругие волны в виде небольших смещений материала или пластической деформации на поверхности детали, которые обнаруживаются датчиками, прикрепленными к поверхности детали. При использовании нескольких датчиков результирующие данные могут быть оценены для обнаружения дефектов в детали.
Волноводные испытания трубопроводов используют управляемое возбуждение одной или нескольких ультразвуковых волн, которые распространяются по длине трубы, отражая изменения жесткости трубы или площади поперечного сечения. Кольцо преобразователя или сборка катушки возбудителя используется для подачи направленной волны в трубу и каждый преобразователь/возбудитель. Программное обеспечение для управления и анализа может быть установлено на портативный компьютер для управления кольцом преобразователя/возбудителем и для анализа результатов. Установка кольца преобразователя/возбудителя разработана специально для диаметра проверяемой трубы, и система имеет то преимущество, что позволяет контролировать объем стенки трубы на больших расстояниях без необходимости удаления покрытий или изоляции. Волноводное тестирование может обнаруживать разрывы как внутреннего, так и наружного диаметра, но не может различать их.
Лазерное тестирование включает в себя три метода: голографию, ширографию и профилометрию. Как следует из названия метода, все три метода используют лазеры для проведения проверок.
Методы ЛМ
Голографическое тестирование
Голографическое тестирование использует лазер для обнаружения изменений на поверхности детали по мере того, как она деформируется под действием индуцированного напряжения, которое может быть приложено в виде механического напряжения, тепла, давления или энергии вибрации. Лазерный луч сканирует поверхность детали и отражается обратно к датчикам, которые регистрируют различия в поверхности, создаваемые этим напряжением. Полученное изображение будет представлять собой топографическую карту, которая может отображать деформации поверхности в пределах от 0,05 до 0,005 микрон без повреждения детали. Сравнивая результаты испытаний с неповрежденным эталонным образцом, можно использовать голографические испытания для обнаружения и оценки трещин, расслоений, отслоений, пустот и остаточных напряжений.
Лазерная профилометрия
Лазерная профилометрия использует высокоскоростной вращающийся лазерный источник света, миниатюрную оптику и компьютер с программным обеспечением для высокоскоростной цифровой обработки сигналов. Идентификационная поверхность трубки сканируется в двух измерениях, и отраженный свет проходит через линзу, которая фокусирует этот свет на фотодетектор, генерируя сигнал, пропорциональный положению пятна в плоскости его изображения. По мере изменения расстояния от лазера до поверхности ИД положение фокального пятна на фотодетекторе изменяется из-за параллакса, создавая трехмерное изображение поверхности детали с высоким разрешением, которое представляет топографию поверхности детали. Этот метод можно использовать для обнаружения коррозии, точечной коррозии, эрозии и трещин в трубах и трубах.
Лазерная ширография
Лазерная ширография применяет лазерный луч к поверхности тестируемой детали, когда деталь находится в состоянии покоя (ненапряженной), а полученное изображение снимается устройством с зарядовой связью (ПЗС) и сохраняется на компьютер. Затем поверхность нагружается, и создается, записывается и сохраняется новое изображение. Затем компьютер накладывает два шаблона друг на друга, и если присутствуют дефекты, такие как пустоты или отслоения, дефект может быть обнаружен с помощью разработанных шаблонов. Таким образом могут быть обнаружены неоднородности размером всего в несколько микрометров.
Проверка на наличие утечек, как следует из названия, используется для обнаружения сквозных утечек с использованием одного из четырех основных методов низкотемпературного анализа: пузырьковый контроль, контроль изменения давления, галогенный диод и масс-спектрометрический контроль. Эти методы описаны ниже.
LT методы
Испытание на утечку пузырьками
Испытание на утечку пузырьками, как следует из названия, основано на визуальном обнаружении утечки газа (обычно воздуха) из системы под давлением. Небольшие детали могут находиться под давлением и погружаться в резервуар с жидкостью, а более крупные сосуды могут подвергаться давлению и проверяться путем распыления мыльного раствора, который создает мелкие пузырьки в проверяемой области. Для плоских поверхностей можно нанести на поверхность мыльный раствор и использовать вакуумную камеру (рис. 15) для создания отрицательного давления со стороны контроля. При наличии сквозных утечек образуются пузырьки, показывающие место утечки.
Испытание изменением давления
Испытание изменением давления можно проводить только в закрытых системах. Обнаружение утечки осуществляется путем создания давления в системе или создания вакуума с последующим контролем давления. Потеря давления или вакуума в течение заданного периода времени указывает на утечку в системе. Изменения температуры в системе могут вызвать изменения давления, поэтому, возможно, придется соответствующим образом скорректировать показания.
Проверка галогенных диодов
Проверка галогенных диодов выполняется путем подачи в систему смеси воздуха и индикаторного газа на основе галогенов. По истечении заданного периода времени для обнаружения утечек используется блок обнаружения галогенных диодов, или «детектор».
Масс-спектрометрические испытания
Масс-спектрометрические испытания можно проводить путем создания давления на испытуемую деталь гелием или смесью гелия/воздуха в испытательной камере с последующим исследованием поверхностей с помощью детектора, который отправляет пробу воздуха обратно в спектрометр. Другой метод создает вакуум в испытательной камере, так что газ в системе под давлением втягивается в камеру через любые утечки. Масс-спектрометр затем используется для отбора проб из вакуумной камеры, и любой присутствующий гелий будет ионизирован, что позволяет легко обнаруживать очень небольшие количества гелия.
Утечка магнитного потока обнаруживает аномалии в нормальных структурах потока, создаваемые неоднородностями в ферромагнитном материале, насыщенном магнитным полем. Этот метод можно использовать для осмотра трубопроводов и трубок, осмотра дна резервуара и других применений. В трубчатых применениях инспекционная головка состоит из приводной и сенсорной катушек, а также датчика положения, которые соединены кабелем обратно с источником питания и компьютером обработки сигналов. Эта головка помещается вокруг проверяемой трубы или трубки, и на приводную катушку подается напряжение, создавая магнитное поле в детали. Когда головка перемещается по длине детали, изменения толщины стенки из-за коррозии, эрозии, точечной коррозии и т. д. вызывают изменение плотности магнитного потока, которое может быть зафиксировано датчиком и отправлено обратно в компьютер. Местоположение этого сигнала передается датчиком положения, чтобы обнаруженная область могла быть отмечена для дальнейшей оценки. Этот метод можно использовать без снятия изоляции, что обеспечивает быстрый и экономичный способ проверки длинных участков труб или трубопроводов.
Инспекция дна резервуара использует тот же принцип, но использует ряд генераторов магнитного поля («мостов») и датчиков (как показано на рисунке 16), расположенных рядом друг с другом на передней части машины, похожей на вакуумную подметальную машину. Мосты создают магнитное поле, которое насыщает дно резервуара, и любое уменьшение толщины или потеря материала из-за точечной коррозии или коррозии приведет к «утечке» поля вверх из материала дна, где его могут уловить датчики. На самых простых машинах каждый датчик будет подключен к звуковому и/или визуальному дисплею, который позволяет оператору узнать о наличии индикации; более совершенные машины могут иметь как визуальные дисплеи, так и возможность записи, чтобы результаты можно было сохранять, анализировать и сравнивать с более ранними результатами для отслеживания роста разрывов.
Нейтронная радиография использует интенсивный пучок нейтронов низкой энергии в качестве проникающей среды, а не гамма- или рентгеновское излучение, используемое в обычной радиографии. Генерируемые линейными ускорителями, бетатронами и другими источниками нейтроны проникают в большинство металлических материалов, делая их прозрачными, но ослабляются большинством органических материалов (включая воду из-за высокого содержания водорода), что позволяет видеть эти материалы внутри проверяемого компонента. . При использовании с обычной рентгенографией можно увидеть как структурные, так и внутренние компоненты образца.
Тепловое/инфракрасное тестирование, или инфракрасная термография, используется для измерения или картирования температуры поверхности на основе инфракрасного излучения, испускаемого объектом при протекании тепла через этот объект, к нему или от него. Большая часть инфракрасного излучения имеет большую длину волны, чем видимый свет, но может быть обнаружена с помощью тепловизионных устройств, обычно называемых «инфракрасными камерами». Для точного ИК-тестирования исследуемая деталь (детали) должна находиться в прямой видимости с камерой, т. е. ее нельзя проводить с закрытыми крышками панелей, поскольку крышки рассеивают тепло и могут привести к ложным показаниям. При правильном использовании тепловидение можно использовать для обнаружения коррозионных повреждений, расслоений, отслоений, пустот, включений, а также многих других вредных условий.
Анализ вибрации относится к процессу наблюдения за вибрационными сигнатурами, относящимися к вращающемуся механизму, и анализу этой информации для определения состояния этого оборудования. Обычно используются три типа датчиков: датчики перемещения, датчики скорости и акселерометры.
Датчики смещения используют вихревые токи для обнаружения вертикального и/или горизонтального движения (в зависимости от того, используются ли один или два датчика) и хорошо подходят для обнаружения движения вала и изменений допусков зазора.
Базовые датчики скорости используют подпружиненный магнит, который перемещается по катушке провода, при этом внешний корпус датчика прикреплен к проверяемой детали. Катушка провода движется через магнитное поле, генерируя электрический сигнал, который отправляется обратно на приемник и записывается для анализа. Датчики вибрации более новой модели используют времяпролетную технологию и улучшенное программное обеспечение для анализа. Датчики скорости обычно используются в портативных датчиках.
В базовых акселерометрах используется пьезоэлектрический кристалл (преобразующий звуковые волны в электрические импульсы и обратно), прикрепленный к массе, которая вибрирует из-за движения части, к которой прикреплен корпус датчика. Когда масса и кристалл вибрируют, генерируется ток низкого напряжения, который проходит через предварительный усилитель и направляется на записывающее устройство. Акселерометры очень эффективны для обнаружения высоких частот, создаваемых лопатками высокоскоростных турбин, шестернями и шариковыми и роликовыми подшипниками, которые движутся со скоростью, намного превышающей скорость валов, к которым они прикреплены.
Карьерный центр ASNT был создан для всех специалистов по неразрушающему контролю на каждом этапе их карьеры. Откройте для себя и изучите общие пути развития карьеры в области неразрушающего контроля и получите доступ к программам, которые помогут вам продвинуться в своей профессии.
Учить больше
Ваш доступ к новейшим знаниям и ресурсам по неразрушающему контролю для поддержки и ускорения вашего профессионального развития.
Учить больше
Сертификация ASNT является наиболее признанным сертификатом для неразрушающего контроля. Получите сертификат, чтобы построить свою карьеру и продемонстрировать свой опыт в области неразрушающего контроля.
Учить больше
Сравнение методов неразрушающего контроля
Ниже вы найдете общее описание возможностей распространенных методов неразрушающего контроля (НК). Это задумано как краткое изложение возможностей каждой дисциплины.
Traditional NDT Technique Comparison
Excellent | Fair | Poor |
RAM Resonant Acoustic | ET Eddy Current | MT/PT Magnetic/ Penetrant | UT Ультразвук | RT Рентгенография | |
---|---|---|---|---|---|
Дефект/Проблема | |||||
Трещины/Сколы | |||||
Material Properties | |||||
Missed Operations | |||||
Structural Integrity | |||||
Вариант партии продукта | |||||
Defect Location | |||||
Surface (External) | |||||
Internal | |||||
Brazing/ Склеивание/сварка | |||||
Скорость/обучение/стоимость | |||||
Производительность | |||||
Training/Certification | |||||
Total Inspection Costs | |||||
Automation Capacity | |||||
Количественные результаты | |||||
Простота автоматизации | |||||
Cost of Automation |
Quick Links
Резонансная проверка (RI) | Ultrasonic Testing (UT) | raduography (RT) | (RT) | EDDY.![]() | Magnetic Particle (MT / MPI) | Infrared Thermography | Visual Inspection (VT) |
RESONANT INSPECTION (RI)
Resonant Inspection is a whole-body test method which detects resonant frequency shifts в результате изменения массы, жесткости или демпфирования детали. Резонанс может обнаруживать дефекты, такие как трещины, пустоты, сколы, проблемы с пайкой, узелковость, вариации в твердости, пропущенных производственных процессах, расслаивании и многом другом.
Области применения включают, помимо прочего, детали из порошкового металла, отливки, детали из ковкого чугуна, паяные сборки, поковки, штамповки и керамические детали.
Резонансно-акустический метод неразрушающего контроля (NDT-RAM) — это форма
резонансной инспекции, предлагаемой The Modal Shop. NDT-RAM доступен в автоматизированных, полуавтоматических, ручных системах и системах для испытаний на падение мелких деталей. Узнать больше о
какая система подходит именно вам.
Преимущества | Недостатки |
---|---|
|
УЛЬТРАЗВУКОВОЙ КОНТРОЛЬ (УЗИ)
Измеряет толщину, скорость или обнаруживает внутренние дефекты и изменения, такие как трещины, несплавление, расслоения и отсутствие связи.
Применения включают кованые металлы, сварку, паяные соединения, клеевые или клеевые соединения, неметаллические материалы, бывшие в употреблении детали.
Преимущества | Недостатки | |
---|---|---|
|
|
РАДИОГРАФИЯ (RT)
Измеряет или обнаруживает отсутствие, внутренние дефекты и изменения, геометрию, вариации, плотность, сплавление, коррозию, трещины, трещины неправильно собранные и несоосные детали.
Преимущества | Недостатки |
---|---|
|
|
ВИХРЕВОЙ ТОК (ET)
Измеряет или обнаруживает поверхностные и подповерхностные трещины и швы, содержание сплава, варианты термообработки, толщину стенки и покрытия, глубину трещин, проводимость и проницаемость.
Advantages | Disadvantages |
---|---|
|
|
LIQUID PENETRANT (LPI / PT)
Измеряет или обнаруживает дефекты, открытые на поверхности деталей, такие как трещины, пористость, швы, нахлесты и сквозные протечки.
Advantages | Disadvantages | ||||||||||||
---|---|---|---|---|---|---|---|---|---|---|---|---|---|
|
|