Магнитный метод (дефектоскопия) неразрушающего контроля
Магнитный контроль (МК) решает задачи, связанные с обнаружением дефектов внутри и на поверхности конструкций из ферромагнетиков (железо, кобальт, никель). Выявление флокенов, неметаллических включений, волосовин и прочих повреждений методами МК осуществимо, только когда они поверхностные или залегающие на глубине, не превышающей 2-3 мм.
В основе метода – регистрация и анализ магнитных полей рассеяния, образующихся вокруг ферромагнитных объектов после их намагничивания. О наличии дефектов свидетельствует перераспределение магнитных потоков, и формирование магнитных полей рассеяния над определенным местом.
Разновидности методов МК
Чтобы выявлять и фиксировать потоки рассеяния, указывающие на присутствие деформаций и повреждений, применяют несколько методов МК, различающихся в соответствии с ГОСТ 24450-80 по способам получения исходных данных:
- Магнитопорошковый – наиболее распространенный и востребованный метод. Отличающийся простотой применения, высокой сенсетивностью и универсальностью, он используется для обнаружения поверхностных и расположенных на глубине до 2 мм деформаций с помощью магнитного порошка в качестве индикатора
- Индукционный – основан на применении индукционных преобразователей (катушек), улавливающих локальные потоки возмущения поля, образующиеся над повреждениями намагниченного объекта контроля
- Магниторезисторный – использует магниторезистивные преобразователи для выявления и регистрации потоков рассеивания над деформациями намагниченного объекта контроля
- Магнитографический – использование записи магнитного поля исследуемого объекта на соответствующем носителе. Воспроизведение полученной сигналограммы анализируется для выявления дефектов
- Пондеромоторный – построен на пондеромоторном взаимодействии фиксируемого магнитного поля исследуемого объекта и магнитного поля постоянного магнита, электромагнита или рамки с током
- Феррозондовый – использование феррозондовых преобразователей для обнаружения и регистрации рассеяния магнитных полей сварочных швов и прочих исследуемых объектов
- Метод эффекта Холла – применение одноименных преобразователей для фиксации локальных возмущений полей над объектами контроля
Основой всех методов МК является обнаружение локальных возмущений поля, образуемых повреждениями намагниченного ферромагнетика. Магнитный поток перемещается по исследуемому объекту, создавая над обнаруженными дефектами поля рассеяния. Их форма и амплитуда отражают размер, параметры и глубину залегания разрушений
Выявляемые дефекты
Методы МК впервые были использованы в 19 веке. С их помощью оценивали прочность, а также структурное состояние ружейных затворов и оболочек разрывных снарядов. С тех пор успели сформироваться три основные сферы МК:
- Контроль сплошностей в ферромагнетиках
- Оценка прочности и структурного состояния ферромагнитных сталей и сплавов
- Определение фаз в конкретном сплаве
Контроль качества магнитными методами дает возможность выявлять повреждения, обладающие характеристиками:
- Брак с шириной раскрытия на поверхности обследуемого участка от 0,002 мм при глубине от 0,01 мм
- Крупные внутренние дефекты, залегающие на глубине от 2 мм
- Поверхностные повреждения глубиной до 2 мм
- Брак под немагнитным покрытием толщиною до 0,25 мм
Сегодня магнитный контроль востребован практически во всех промышленных отраслях:
- Нефтехимия
- Металлургия
- Машиностроение
- Энергетика (ТЕЦ, АЭС)
- НГК (трубопроводы, промышленные емкости)
- Авиа-, судо- и автомобилестроение
Грамотное применение методов МК позволяет на ранней стадии выявлять и устранять поверхностные и углубленные повреждения ферромагнетиков
Особенности технологии МК
Метод МК не требует специальной предварительной подготовки, поскольку является бесконтактным. Его суть заключается в анализе поля рассеяния, образующегося в местах скопления дефектов при намагничивании исследуемых объектов.
Проведение МК регулируется национальными и международными стандартами, включая, ГОСТ 21105-87, РД-13-05-2006 и EN 1290:1998.
- Магнитная проницаемость несплошности гораздо ниже, чем у остальной части исследуемого объекта. Ее наличие искривляет магнитные силовые линии. Некоторые из них выходят на поверхность пораженного участка, чтобы обойти повреждение и образуют локальный магнитный поток рассеяния
- Возникновение полей возмущения фиксируется магнитными преобразователями, среди которых наиболее распространены датчик Холла и его индукционные, феррозондовые, и магниторезистивные вариации
- Мероприятия контроля завершаются размагничиванием каждой используемой детали в поле солеонида, питаемого переменным током
Бесконтактный магнитный контроль чаще всего применяют в диагностике:
- Магистральных трубопроводов:
- Отдельных труб с любым диаметром
- Прокатных листов
- Арматуры
- Вертикальных стальных резервуаров
Проведение аттестации и обучение специалистов по неразрушающему контролю
Приборы и оборудование
Для намагничивания контролируемых объектов используют стационарные и портативные магнитные дефектоскопы. Первые позволяют с высокой точностью выявлять поверхностные и более глубокие повреждения любой направленности, вторые – контролировать объекты в полевых условиях.
Недостаток диагностических магнитных дефектоскопов заключается в узкой направленности и требовательности к температурному режиму. Для получения более корректных результатов эксперты рекомендуют использовать многоканальную модель с функцией ультразвукового анализа.
- Работа прибора начинается его калибровкой с проверкой по эталонам и очищением поверхности контролируемой детали
- Намагничивание детали в соответствии с типом намагничивания и параметрами чувствительности
- Нанесение индикаторного вещества
- Визуальный осмотр детали с возможностью фиксации индикаторного рисунка для дальнейшего анализа с помощью многофункционального дефектоскопа
На основании сравнения полученных рисунков с нормативными образцами делают заключение о возможности целевого применения исследуемого объекта.
Отправьте заявку на исследование магнитным методом контроля
Благодарственные письма наших клиентов
Среди наших клиентов
Магнитные методы контроля — Контроль работ по металлопокрытиям
Магнитные методы контроля
К
Контроль работ по металлопокрытиям
Магнитные методы контроля
Магнитные методы можно использовать только при контроле деталей из ферромагнитных материалов для выявления мест нарушения сплошности материала детали, расположенных на поверхности и в подповерхностных слоях, а в отдельных случаях — и внутри детали, т. е. трещин (усталостных, шлифовочных, закалочных, сварочных, ковочных, штамповочных), волосовин, закатов, расслоений (непараллельных поверхности), флокенов, надрывов, непроваров в сварных соединениях, неметаллических включений. Можно использовать эти методы для выявления ферритных включений в деталях из аустенитных сплавов.
Магнитными методами можно корректировать отдельные технологические процессы изготовления деталей (шлифование, термическую обработку, сварку, ковку, штамповку, протяжку и др.).
Благодаря высокой чувствительности, объективности, простоте и быстроте операций, четкости определения дефектов и надежности магнитные методы получили большое распространение в промышленности. Их преимуществом является также возможность контроля деталей сложной формы и любых размеров.
Магнитные методы контроля развивают в двух направлениях: с использованием в качестве индикаторов ферромагнитных порошков или электромагнитных и электронных систем. Рассмотрим магнитопорошковый, магнитоферрозондовый и магнитографический методы.
Магнитные методы контроля ферромагнитных деталей основаны на явлении возникновения магнитного поля рассеяния на поверхности намагниченной детали в местах расположения дефектов (нарушение сплошности материала или наличие включений с другой магнитной проницаемостью). Если на поверхности намагниченной детали создается магнитное поле рассеяния, значит в данном месте детали, вероятно, имеется дефект.
Для намагничивания изделий можно использовать переменный, постоянный, выпрямленный одно-, двухполуперйодный трехфазный ток, а также импульсный ток. Переменный ток наиболее эффективен для выявления поверхностных дефектов, так как действие магнитного поля ограничивается поверхностными слоями изделия. Переменный ток необходим и для размагничивания деталей. Для выявления подповерхностных дефектов предпочтительнее постоянный ток, так как создаваемое им магнитное поле проникает глубоко в изделие и более равномерно распределяется по всему сечению детали. Однополу-периодный выпрямленный ток эффективен для выявления подповерхностных и поверхностных дефектов при магнитопорош-ковом способе контроля. Выпрямленный двухполупериодный и трехфазный ток по характеру создаваемых магнитных полей близки к постоянному току.
Большое значение для выявления дефектов имеет правильный выбор- напряженности магнитного поля, которая зависит от формы и расположения предполагаемого дефекта, а также магнитных характеристик материала контролируемого изделия. Слишком высокая напряженность магнитного поля может вызвать осаждение ферромагнитного порошка по всей поверхности изделия и появление «ложных» дефектов, недостаточная напряженность приводит к уменьшению возможности выявления подповерхностных дефектов и снижению чувствительности метода при выявлении мелких поверхностных дефектов.
Магнитопорошковый метод — один из наиболее распространенных методов магнитного контроля. Его используют для обнаружения поверхностных нарушений сплошности шириной у поверхности 0,001 мм и более, глубиной 0,01 мм и более. Чувствительность метода повышается при использовании флуоресцирующего магнитного порошка (магнито-люминесцентный метод). В этом случае минимальная ширина у поверхности выявляемого дефекта 0,0005 мм, а протяженность его в глубь изделия 0,005 мм.
При контроле изделий магнитопорошковым методом магнитные поля рассеяния, возникающие на поверхности контролируемых изделий в местах нарушения сплошности, выявляют с использованием ферромагнитного порошка. Над местом нарушения сплошности материала изделия накапливаются ферромагнитные частицы. Площадь, занимаемая порошком, значительно больше площади дефекта, поэтому можно выявить очень незначительные по размеру дефекты, что имеет большое практическое значение.
Эффективность метода определяется способностью магнитных частиц перемещаться под действием магнитных полей рассеяния. В процессе нанесения на деталь ферромагнитные частицы находятся во взвешенном состоянии в воздухе («сухой» метод) или в таких жидкостях, как минеральное масло, керосин или вода, т. е. в виде суспензии («мокрый» метод). Для увеличения подвижности частиц сухого порошка его можно 164 распылять в виде облака, при этом изделие иногда встряхивают.
Преимущества магнитопорошкового метода: возможность контроля любого , изделия, изготовленного из ферромагнитного материала; выявление с достаточной степенью надежности всех нарушений сплошности материала изделия, расположенных на поверхности или вблизи нее; высокая чувствительность; простота методики контроля и высокая производительность; возможность использования портативного оборудования.
МагнитОпорошковый метод допускает контроль деталей, после оксидирования, окраски или нанесения гальванического покрытия (цинка, кадмия, хрома и др.) при условии, что толщина немагнитного покрытия не превышает 80 мкм. При более толстых покрытиях над дефектом создается очень слабое поле рассеяния.
Магнитопорошковым методом не рекомендуют контролировать сварные швы ферромагнитных изделий, полученные с использованием электродов из аустенитной стали, так как ферромагнитный порошок может осаждаться на границе аустенит-ного шва (мнимые дефекты).
Недостатки магнитопорошкового метода: возможность контроля только изделий из ферромагнитного материала; необходимость использования специального оборудования; невозможность выявления дефектов, расположенных на глубине более 2 мм от поверхности, а также дефектов под немагнитными покрытиями толщиной более 80 мкм при использовании магнитной суспензии. На вероятность обнаружения дефекта влияют многие факторы, в том числе его очертания, ориентация и глубина залегания.
Магнитноферрозондовый метод разработан при изыскании простых способов обнаружения ферромагнитных включений в неферромагнитных материалах. В результате были разработаны магниточувствительные датчики — феррозонды, позволяющие измерять однородные и неоднородные магнитные поля.
Метод контроля основан на обнаружении и измерении магнитных полей, в том числе и полей рассеяния, возникающих в зоне дефектов, с помощью феррозондов — магнитодинамиче-ских магнитометров. Магнитометр — это прибор, позволяющий обнаруживать и измерять, магнитные поля, а также определять степень намагниченности ферромагнитного тела по создаваемому им в пространстве магнитному полю.
Преимущество метода — возможность с помощью феррозондов, применяемых в дефектоскопии, выявлять и измерять очень слабые магнитные поля небольших размеров.
С использованием феррозондов можно:
— выявлять нарушения сплошности в ферромагнитных материалах и изделиях из них, причем не только поверхностные и подповерхностные, как при магнитопорошковом методе, но и удаленные на 10—15 мм от поверхности изделия, что является существенным преимуществом данного метода;
— контролировать и сортировать стальные детали (в том числе и автоматически) по твердости (после термической обработки) ;
— контролировать толщину цементованного, азотированного и поверхностно-закаленного слоя изделия;
— судить о прочности кристаллической решетки твердого раствора, дисперсионном твердении и т. п.;
— получать качественную и количественную характеристики магнитных свойств материала изделия, по которым можно судить о структуре и механических свойствах при магнитострук-турном анализе;
— измерять толщину стенок сложных отливок и листов большой площади из неферромагнитных материалов;
— определять наличие магнитной фазы в немагнитных сплавах, ферромагнитных примесей и характер их распределения в цветных сплавах или других немагнитных материалах, выявлять остаточный аустенит;
— определять степень размагниченности изделий, подвергаемых магнитному контролю или шлифованию на плоскошлифовальных станках с магнитными столами.
Магнитографический метод контроля предназначен для выявления мест нарушения сплошности материала в сварных швах трубопроводов, резервуаров и листовых конструкций из ферромагнитных материалов. В качестве индикаторов магнитных полей рассеяния применяют магнитную ленту. В зависимости от применяемого типа магнитографического дефектоскопа можно контролировать сварные швы с толщиной свариваемого материала до 16 мм. Этим методом хорошо выявляют поверхностные трещины. Внутренние дефекты (газовые и неметаллические включения, непровары и т. п.) обнаруживают в случае, если их размеры составляют приблизительно 8—10% толщины контролируемого шва.
Магнитографический контроль состоит в намагничивании зоны контролируемого сварного шва для создания над дефектом магнитного поля рассеяния, «записи» магнитного поля дефекта на магнитную ленту и воспроизведения «записи» на ленте. При воспроизведении «записанных» на ленте магнитных полей определяют расположение и размеры дефектов. Для намагничивания, как правило, применяют постоянный ток, так как необходимо выявлять в основном внутренние дефекты. Напряженность магнитного поля обычно выбирают экспериментально для четкого выявления характерных дефектов минимально допустимых размеров.
Реклама:
Читать далее:
Люминесцентный метод контроля
Статьи по теме:
МАГНИТНЫЙ КОНТРОЛЬ • Большая российская энциклопедия
-
-
-
В книжной версии
Том 18. Москва, 2011, стр. 381-382
-
Скопировать библиографическую ссылку:
Авторы: А. А. Воробьёв
МАГНИ́ТНЫЙ КОНТРО́ЛЬ (магнитная дефектоскопия), метод неразрушающего контроля, применяемый для выявления и регистрации дефектов изделий из ферромагнитных материалов, которые способны существенно изменять свои магнитные характеристики под воздействием внешнего (намагничивающего) магнитного поля. М. к. основан на исследовании искажений магнитного потока (поля рассеивания) в месте дефекта, имеющегося в изделии, и получении его магнитных характеристик, форма и амплитуда которых несёт информацию о размере, глубине залегания дефекта, его структуре, химич. составе, свойствах и др.
Выбор метода, способа и средств М. к. зависит от характера дефекта, причин его происхождения. При определении нарушений сплошности, выявлении наличия трещин, непроваров в поверхностных и подповерхностных слоях сварных швов применяют методы, основанные на намагничивании изделия путём пропускания через него тока с помощью воздействия электромагнитов, соленоидов и др. Индикатором может служить магнитный порошок на основе оксида железа (или его суспензия в масле с дисперсностью частиц 5–10 мкм), который наносят на поверхность изделия. При намагничивании изделия порошок оседает в местах расположения дефектов (магнитопорошковый метод). В качестве индикатора поля рассеяния и регистрации дефекта может служить магнитная лента, которую накладывают на исследуемый участок намагниченного изделия (магнитографич. метод). Для индикации дефекта может использоваться пассивный индукционный преобразователь, через который в процессе обработки продвигается изделие (напр., металлич. лента, ж.-д. рельс при прокатке). Глубинные дефекты протяжённостью до 10 мм определяют феррозондом – малогабаритным датчиком (активным преобразователем) с сердечником из магнитомягкого материала (пермаллоя) и катушкой возбуждения, поле которой взаимодействует с полем дефекта. При движении по изделию в месте дефекта датчик указывает на изменение импульса тока (феррозондовый метод). Для индикации поля дефекта применяют также преобразователи, работающие на основе эффекта Холла, и магниторезисторные, в которых используется эффект изменения электрич. сопротивления проводника под действием магнитного поля. М. к. также находит применение при исследовании структуры, режимов термич. обработки, механич. свойств материала (магнитная структурометрия), толщины (магнитная толщинометрия). Состояние и качество материала оценивают с помощью магнитных характеристик, для получения которых используют спец. приборы (напр., ферритометры, коэрцитиметры, магнитные анализаторы). При измерении толщины изделий и ферромагнитных покрытий (до сотен мкм с погрешностью, не превышающей 1–10 мкм) применяют приборы, основанные на пондеромоторном действии, заключающемся в измерении силы притяжения (отрыва) постоянного магнита или электромагнита к поверхности, к которой он прижат, либо на измерении (с помощью датчиков Холла, феррозондов) напряжённости магнитного поля в магнитопроводе, установленном на контролируемой поверхности. После окончания контроля изделия подвергают размагничиванию. Чувствительность методов М. к. зависит от магнитных характеристик материалов, применяемых индикаторов, режимов намагничивания изделий, чистоты контролируемой поверхности.
Магнитный метод неразрушающего контроля, контроль сварных швов и деталей
Существует несколько государственных стандартов,определяющие магнитные и эл магнитные методы контроля трубопроводов неразрушающим способом:
· ГОСТ 24450-80 — терминология и определения метода.
· ГОСТ 21105-87 — магнитопорошковый метод неразрушающего контроля.
· ГОСТ 8.283-78 — использующиеся в методе дефектоскопы, их средства поверки.
· ГОСТ 26697-85 — технические требования к магнитным и вихретоковым дефектоскопам, использующимся в электромагнитном методе неразрушающего контроля.
Магнитные и электромагнитные методы неразрушающего контроля
Для изучения зависимостей магнитных полей в местах повреждений, выявления потоков рассеяния применяется следующие виды магнитного контроля. Они классифицируются соответственно государственному стандарту №24450-80 по способам получения данных.
Магнитопорошковый —в качестве индикатора дефектов используется магнитный порошок. Фиксируются повреждения и деформации на поверхности и на глубине до 2—3 мм. Является наиболее популярным методом магнитного контроля сварных швов и соединений в силу простоты технологии, высокой чувствительности и экономичности.
Магниторезисторный —основан на эффекте Гаусса. В данной разновидности метода магнитного контроля для регистрации полей рассеивания применяются полупроводниковые резисторы(магниторезистивные преобразователи).
Индукционный —в данном методе в качестве регистратора возмущений поля в местах повреждений применяются катушки индуктивности.
Магнитографический —для анализа зависимости магнитного поля объекта используется специальная запись состояний этого поля, которую можно просмотреть на цифровом устройстве.
Пондеромоторный —основывается на взаимодействии поля намагниченного исследуемого объекта с полем постоянного магнита, рамки, по которой течет электрический ток, либо же электромагнита.
Феррозондовый —в данном виде метода для исследования, например, сварочных швов на предмет повреждений, применяются феррозондовые преобразователи магнитного поля.Конструктивно феррозонд состоит из ферромагнитного сердечника и двух катушек индуктивности.
Метод эффекта Холла —основан на применении датчиков Холла, позволяющих определить местоположение дефектов по возмущению магнитного поля.
Магнитопорошковый контроль (магнитный контроль, магнитопорошковая / магнитная дефектоскопия), дефектоскопические материалы
Материалы для магнитопорошковой дефектоскопии производства ЭЛИТЕСТ® Россия
Производство дефектоскопических материалов для магнитопорошкового контроля. Магнитный порошок, готовая магнитная суспензия и основа для её приготовления, грунтовочная краска — расходные материалы для магнитопорошковой дефектоскопии, выпускаемые в России под торговой маркой ЭЛИТЕСТ® можно приобрести у наших дилеров.
Индикаторные материалы для МПД
Чёрные и люминесцентные магнитные суспензии, концентраты
Средства для обработки контролируемой поверхности
Магнитопорошковый контроль (магнитный контроль, магнитопорошковая / магнитная дефектоскопия, МПД)
Магнитопорошковый неразрушающий контроль — один из способов обнаружения дефектов металла, залегающих непосредственно под поверхностью и выходящих на неё. Метод МПД основан на возникновении неоднородности магнитного поля в местах нарушений сплошности ферромагнитного материала (стали и сплавов на основе железа). На первом этапе проведения магнитопорошкового контроля в детали создают остаточное, либо приложенное магнитное поле. Затем поверхность контролируемого изделия обрабатывают специальными дефектоскопическими средствами, — магнитными порошками и суспензиями. Под действием электромагнитных сил частицы порошка или суспензии намагничиваются и сцепляются между собой в цепочки.
В качестве дефектоскопического материала может выступать магнитный порошок, с размером частиц от 1 микрона. Частицы порошка обладают ярко выраженными ферромагнитными свойствами и могут быть подкрашены активным пигментом — люминофором (люминесцентный магнитный порошок). Но чаще всего, в магнитопорошковом контроле используют готовую магнитную суспензию — взвесь магнитных частиц. В качестве основы для взвеси выбирают масло (например, Элитест МЛ1) или воду — в зависимости от условий контроля и типа оборудования. В результате действия магнитного поля над дефектами возникает искривление его направления. Магнитные частицы скапливаются в таких местах, образуя индикаторный рисунок, видимый при ультрафиолетовом освещении (люминесцентный контроль), либо при обычном освещении (в этом случае в качестве фона может использоваться грунтовочная краска).
Описанные явления составляют основу магнитопорошковой дефектоскопии.
Магнитопорошковая дефектоскопия
Обзор магнитного метода контроля на примере его применения в авиастроении.
Кроме диагностики отдельных элементов на стадиях производства и обслуживания, магнитопорошковый метод даёт возможность контролировать детали и узлы непосредственно в конструкции. Простота и эффективность метода обеспечили его широкое применение на авиаремонтных предприятиях и строевых частях военно-воздушных сил Российской Федерации.
В стальных деталях и узлах авиационной техники могут возникать трещины усталости, шлифовочные трещины, термические, волосовины и другие дефекты. При визуальном наблюдении эти дефекты не выявляются даже с помощью лупы. Магнитопорошковый метод позволяет эффективно обнаруживать невидимые глазу дефекты.
Для решения ряда задач магнитопорошковый контроль обладает преимуществами, выделяющими его среди других методов неразрушающего контроля. Так же как и капиллярный контроль, магнитная дефектоскопия позволяет выявлять поверхностные дефекты материалов, но чувствительность контроля при этом, будет значительно выше. При капиллярном контроле дефекты, расположенные близко к поверхности не выявляются. Для магнитопорошковой дефектоскопии подобного ограничения нет.
На чём основано обнаружение опасных трещин?
Метод основан на выявлении ферромагнитными частицами, взвешенными в жидкости или в воздухе магнитных полей рассеяния, возникающих над дефектами в стальных деталях. При контроле деталь намагничивают с применением специального оборудования — магнитных дефектоскопов. На крупных производствах, такие устройства представляют собой полуавтоматические линии для магнитопорошкового контроля, работающие по конвейерному принципу.
Физические основы метода магнитопорошкового неразрушающего контроля
При намагничивании объекта контроля возникает магнитное поле. Магнитный поток выходит из детали наружу только в местах трещин, образуя поле рассеяния. При этом, на краях трещин возникают магнитные полюсы. При намагничивании постоянным (выпрямленным) магнитным полем магнитный поток в детали и поле рассеяния остаются.
Ферромагнитные частицы, попадая в магнитное поле намагничиваются и под действием магнитных сил соединяются между собой в цепочки. На частицы также действуют силы:
- затягивающая;
- сила земного тяготения;
- сила выталкивающего действия жидкости;
- сила трения;
- электростатического отталкивания.
Под действием результирующей силы, частицы притягиваются к трещине и накапливаются над ней. Опустим деталь в суспензию и посмотрим на процесс осаждения порошка над трещиной:
Частицы соединённые в цепочки над трещиной образуют валик из магнитного порошка, по которому определяют наличие дефекта.
Подготовка деталей к контролю
Перед началом контроля с поверхности изделия удаляются продукты коррозии, окалины, масляные и прочие загрязнения. Краска уменьшает чувствительность метода, поэтому при подготовке деталей к контролю её удаляют. При толщине слоя краски более 0,1 мм поле рассеяния практически замыкается в слое краски и дефекты не выявляются.
Если в качестве дефектоскопического индикатора предполагается использовать чёрную магнитную суспензию, то для обеспечения необходимого контраста при наблюдении результатов, на контролируемую поверхность наносится белая грунтовочная краска.
Способы намагничивания
Ключевыми факторами для выбора условий намагничивания являются: размер и форма объекта, ориентация и характер ожидаемых дефектов, наличие лакокрасочных покрытий и магнитные свойства изделия, подлежащего магнитопорошковому контролю. При этом следует учитывать, что намагничивающее поле, расположенное перпендикулярно направлению предполагаемых дефектов является наилучшим условием для их выявления.
При магнитопорошковом контроле применяют следующие виды и способы намагничивания (О — объект контроля; Ф — магнитный поток;
I — электрический ток):
Циркулярное намагничивание
Кольцеобразные детали намагничивают пропусканием тока по тороидной обмотке. При этом обнаруживаются радиальные дефекты на торцовых, и продольные на внутренней и внешней поверхностях.
Намагничивание деталей пропусканием по ним тока эффективно для обнаружения дефектов, расположенных на внешней поверхности. Такое намагничивание позволяет выявлять волосовины, продольные трещины и другие дефекты.
Намагничивание пропусканием тока по участку детали эффективно при контроле сварных соединений. При этом обнаруживаются трещины, распространяющиеся вдоль линий, соединяющих точки установки электроконтактов. Циркулярное намагничивание несъёмных деталей, проводят с применением кабеля и передвижного дефектоскопа — мощной понижающей силовой установки, способной генерировать токи до 10000 Ампер. В этом случае выявляются трещины на деталях непосредственно в конструкции летательного аппарата.
Намагничивание по стержню эффективно для обнаружения дефектов, расположенных на внешней поверхности.
Продольное (полюсное намагничивание)
Для полюсного намагничивания применяют передвижные, приставные, стационарные и переносные соленоиды. А также электромагниты. При полюсном намагничивании имеются некоторые особенности при осаждении порошка. Ограничимся рассмотрением поля только в межполюсном пространстве электромагнита.
Магнитные силовые линии проходят вдоль детали. В этом случае над трещиной поле рассеяния состоит из двух областей.
Области 1, в которой плотность силовых линий увеличивается и области 2 в которой плотность силовых линий уменьшается по мере приближения к поверхности детали. При уменьшении тока магнитные силовые линии деформируются, полярность краёв трещины изменяется. Область 2 располагается теперь по другую сторону трещины.
Частицы в области 1 накапливаются а из области 2 они вытягиваются и осаждаются либо над трещиной, либо на участках вне области 2. В области 2 образуется зона не осаждения А. Эти зоны наиболее заметны при опылении деталей магнитным порошком в камере (способ опыления воздушной взвесью). В этом случае у трещин видны чёткие границы зон не осаждения.
Контактное намагничивание
Для намагничивания способом магнитного контакта, полюс магнита устанавливают на деталь обеспечивая хорошее прилегание полюсного наконечника и перемещают его по контролируемой поверхности. Этим способом обнаруживают трещины, расположенные перпендикулярно направлению перемещения магнита.
Размагничивание
Поля не размагниченных деталей могут вызывать погрешности в показаниях компаса, непредусмотренное срабатывания электромагнитных реле и элементов автоматики. Поэтому детали после контроля размагничивают. Намагниченная деталь может иметь максимальную остаточную индукцию. Размагничивание с применением катушки выполняют удалением из неё детали, или уменьшением силы тока.
Для размагничивания первым способом включают ток и в течение 10-15 секунд деталь перемещают вдоль оси катушки. При удалении индукция детали изменяя своё направление с частотой поля уменьшается до 0. На расстоянии более 70 см деталь оказывается размагниченной. Размагничивание уменьшением тока может осуществляться с помощью размагничивающего устройства с тоннелем.
При уменьшении тока до 0 деталь размагничивается. Контроль размагниченности деталей проводят с помощью магнитометра МФ-24ФМ. Прибор имеет датчик феррозондового типа. Перед контролем устанавливают ток питания, указанный на этикетке, затем переключают прибор в режим контроля. Датчиком проводят по детали и контролируют показания.
Магнитные индикаторы
В ремонтных предприятиях для обнаружения дефектов, намагниченные детали погружают в ванны, или поливают их суспензией. Для приготовления суспензии применяют пасту, порошки окислов железа и поверхностно-активные вещества (ПАВ). В качестве дисперсионной среды применяют керосин, минеральное масло (например, Элитест МЛ1) или их смесь. Размер основной массы частиц порошка составляет от 1 до 30 микрон. При воздействии магнитного поля частицы суспензии намагничиваются и соединяются между собой в цепочки. Если не применять ПАВ, то частицы суспензии под действием молекулярных сил слипаются в агрегаты. Находясь в жидкой среде они быстро выпадают в осадок. На поверхности детали слипшиеся частицы образуют фон, мешающий обнаружению дефектов.
Введём в состав суспензии ПАВ. Ранее частицы соединялись в агрегаты. При введении ПАВ на частицах порошка происходит абсорбция его молекул. Между частицами возникают электростатические силы отталкивания, которые предотвращают слипание частиц.
С помощью микро кино установки при большом увеличении можно наблюдать, что частицы теперь не соединяются. В такой суспензии дефекты выявляются чётко, а фон из частиц порошка отсутствует.
Мнимые дефекты
В ряде случаев порошок осаждается в местах, где нет дефектов, выявляя, так называемые, мнимые дефекты. Так, например, по карбидной полосчатости или клацанью в околошовных зонах, так называемых, зонах термического влияния, на границе раздела двух структур основного материала и наплавленного кольца, имеющих различные магнитные свойства.
Как отличить мнимый дефект от трещины? Над мнимым дефектом порошок накапливается в виде хорошо заметных длинных цепочек. А над трещиной образуются чёткий валик в котором цепочки не различимы. Отличить мнимый дефект от трещины можно только в процессе накопления порошка.
При контроле встречаются мнимые дефекты типа «магнитная запись». Они возникают в результате касания ферромагнитным предметом намагниченной детали. Вот пример. Магнитопорошковым методом выявлен дефект на штоке передней стойки. Для проверки повторно намагнитим шток. При повторном намагничивании и нанесении суспензии осаждения порошка не произошло, следовательно, дефект мнимый.
Опыт магнитопорошкового контроля показал его высокую эффективность при обнаружении невидимых дефектов. Грамотное применение этого метода является необходимым условием предотвращения разрушения стальных деталей авиационных конструкций и поддержания высокой надёжности летательных аппаратов.
Ограничения магнитопорошкового метода контроля
Магнитопорошковый метод не позволяет определять глубину и ширину дефектов расположенных на поверхности контролируемого материала, глубину залегания подповерхностных дефектов и их размеры. Изделия из неферромагнитных сталей, цветных металлов не могут быть проконтролированы с помощью магнитопорошковой дефектоскопии. Существенная магнитная неоднородность материала также является препятствием для данного метода. Объектом контроля не может выступать сварной шов выполненный немагнитным электродом.
Сущность магнитной дефектоскопии, её методы — Кафедра «Приборы»
Опубликовал admin
Магнитная дефектоскопия — один из методов неразрушающего контроля сварки. Сущность магнитных методов контроля сварных соединений заключается в выявлении рассеянных магнитных потоков, которые появляются в намагниченных изделиях в случае присутствия в них различных дефектов. Намагниченными материалами могут служить железо, никель, кобальт и некоторые сплавы на их основе.
Намагничивание изделия можно добиться, если, пропуская ток по нему, создать вокруг изделия магнитное или электромагнитное поле. Наиболее простым способом получения магнитного потока является пропускание тока плотностью 15-20 А/мм по виткам сварочной провода, намотанного витками на изделие. Количество витков обычно составляет 3-6. Для намагничивания соединения рекомендуется применять постоянный ток.
Принцип выявления дефекта в сварном шве состоит в следующем. Магнитный поток, проходя по сварному соединению и встречая на своём пути дефект, начинает обходить его из-за того, что магнитная проницаемость дефекта значительно ниже, чем магнитная проницаемость основного металла, а электрический ток, как известно, идёт по пути наименьшего сопротивления.
В результате этого, часть силовых линий магнитного потока вытесняется дефектом на поверхность, образуя местный рассеянный магнитный поток, см. рисунок:
Магнитные потоки рассеяния могут регистрироваться разными способами. По способу регистрации методы магнитного контроля разделяются на магнитопорошковый метод контроля (магнитопорошковая дефектоскопия), магнитографический метод контроля и индукционный метод контроля.
Магнитопорошковый метод контроля (магнитопорошковая дефектоскопия)
Как следует из названия, магнитопорошковая дефектоскопия проводится с помощью магнитного порошка. Существуют два метода магнитопорошкового контроля: сухой и мокрый.
В случае сухой магнитопорошковой дефектоскопии на поверхность сварного соединения наносится сухой магнитный порошок (железные опилки, окалина и др.). В случае мокрой магнитопорошковой дефектоскопии магнитный материал наносится в виде суспензий магнитного порошка с керосином, маслом, мыльным раствором.
Под действием электромагнитных полей рассеяния, частицы порошка равномерно перемещаются по поверхности сварного соединения. Над сварными дефектами магнитный порошок скапливается в виде валиков. По форме и размерам этих валиков можно судить о форме и размерах найденного дефекта.
Технология магнитопорошкового контроля
Метод магнитопорошковой дефектоскопии включает в себя следующие технологические операции:
1. Подготовка поверхности сварного соединения к проверке. Поверхности необходимо очистить от загрязнений, окалины, сварочных брызг, наплывов и шлака после сварки.
2. Подготовка суспензии, заключающаяся в динамичном перемешивании магнитного порошка с транспортируемой жидкостью
3. Намагничивание контролируемого изделия
4. Нанесение суспензии или магнитного порошка на контролируемую поверхность
5. Осмотр контролируемой поверхности сварного соединения и определение участков, на которых присутствуют отложения порошка
6. Размагничивание сварного соединения.
Эффективность магнитопорошковой дефектоскопии
Метод магнитопорошковой дефектоскопии обладает хорошей чувствительностью к тонким и мельчайшим сварным трещинам. Он прост в исполнении, даёт наглядные результаты, и не растянут по времени.
Чувствительность магнитопорошкового метода может различаться в каждом отдельном случае. Зависит это от следующих причин:
1. Величины частиц порошка и от метода его нанесения
2. Напряжения магнитного поля, воздействующего на сварное соединение
3. Рода применяемого тока (переменный или постоянный)
4. От формы и величины дефекта, от глубины его расположения, а также от того, как дефект ориентирован в пространстве.
5. От способа и направления намагничивания соединения
6. От качества и формы контролируемой поверхности
С помощью магнитных методов контроля лучше всего обнаруживаются плоскостные дефекты: сварочные трещины, несплавления и непровары, если наибольший их габарит ориентирован под прямым углом (или близким к прямому) относительно направления магнитного потока.
Дефекты округлой формы (поры, раковины, неметаллические включения) могут не создать достаточного рассеянного потока и при контроле обнаруживаются хуже всего.
Дефектоскопы для магнитопорошкового контроля
В состав дефектоскопов для такого метода контроля входят источники тока, устройства для подведения тока к контролируемой поверхности, приборы для намагничивания поверхности (соленоиды, электромагниты), устройства для нанесения магнитного порошка или суспензии на проверяемую поверхность, измерители величины тока (или напряжённости магнитного поля).
Магнитопорошковые дефектоскопы подразделяются на стационарные, передвижные и переносные. Стационарные дефектоскопы нашли широкое применение на заводах и других предприятиях с крупносерийным выпуском различной продукции. Среди них такие модели, как УМДЭ-2500, ХМД-10П, МД-5. Такое оборудование позволяет контролировать качество сварных соединений различной формы. Они способны обеспечить высокую производительность контроля — от нескольких десятков, до нескольких сотен изделий в час.
Распространённые, серийно выпускаемые модели переносных и передвижных дефектоскопов — это ПМД-70 и МД-50П. Переносной дефектоскоп для магнитного контроля ПМД-70 широко используется для контроля сварных соединений в полевых условиях. А передвижной дефектоскоп модели МД-50П чаще всего используется для контроля массивных крупногабаритных сварных соединений по участкам.
Видео: магнитопорошковая дефектоскопия с применением люминисцентных концентратов
Магнитографический метод контроля сварных соединений
Магнитографический контроль — один из двух методов магнитного контроля. Сущность данного метода состоит в намагничивании контролируемой поверхности сварного шва и зоны термического влияния, и одновременном записывании магнитного поля на магнитную ленту. Далее, записанную на ленту информацию считывают с помощью специальных устройств, входящих в состав магнитографического дефектоскопа.
Схема магнитографического контроля показана на рисунке слева. Позиции на рисунке:
1-сварной шов;
2-дефект в сварном шве;
3-магнитная плёнка;
4-намагничивающее устройство;
Технология магнитографического контроля
Метод магнитографического контроля сварного соединения включает в себя следующие технологические операции:
1. Очистка проверяемых поверхностей от шлака, сварочных брызг и других загрязнений
2. Наложение на сварной шов размагниченной магнитной ленты и прижатие её эластичной резиновой лентой
3. Намагничивание контролируемого соединения. Намагничивание производится при оптимальных режимах, которые зависят от типа намагничивающего прибора, толщины контролируемого металла, и его магнитных свойств.
4. Расшифровка результатов дефектоскопии. Для расшифровки результатов магнитную ленту, на которую записывалось магнитное поле, помещают в считывающее устройство дефектоскопа и по сигналам на его экранах обнаруживают дефекты.
Магнитографический метод контроля применяют, в большинстве случаем, для проверкистыковых сварных швов, выполненных сваркой плавлением. Чаще всего такой контроль применяют при дефектоскопии сварных соединений магистральных трубопроводов. Максимально возможная толщина металла, которую можно контролировать данным методом, составляет 20-25мм.
Эффективность магнитографического контроля
Эффективность по выявлению дефектов у магнитографического контроля примерно такая же, как и магнитнопорошкового. Факторами, влияющими на эффективность метода, являются величина и форма сварных дефектов, а также их пространственная ориентация и глубина расположения. Влияет также считывающая способность головки дефектоскопа и записывающая способность магнитной ленты.
Магнитографическим контролем хорошо обнаруживаются плоскостные сварные дефекты (это различные трещины в металле, непровары и несплавления), а также различные цепочки неметаллических включений и шлака. Лучше всего выявляются дефекты, расположенные перпендикулярно движению магнитного потока, а хуже всего обнаруживаются те, которые имеют сферическую форму — поры, раковины и др.
Опытным путём было выяснено, что магнитографический метод контроля с очень высокой долей вероятности позволяет выявить плоскостные дефекты в том случае, если их вертикальный размер равен 8% и более от толщины сварного соединения.
На эффективность этого метода контроля существенное влияние оказывает высота сварного шва, его форма и качество поверхности. Если усиление шва удалить, то чувствительность магнитографии к вышеназванным дефектам достигает 5%. Дефекты сферической формы выявить значительно сложнее. Они выявляются в том случае, если их высота составляет 20% или более от толщины соединения.
Высокая производительность магнитографического контроля является главным его преимуществом перед магнитопорошковой дефектоскопией. Запись на магнитную ленту происходит без какой-либо подготовки, а время её считывания и воспроизведения незначительно.
Магнитографический дефектоскоп и магнитная лента
Регистратором магнитных полей при магнитографическом контроле служит специальная магнитная лента. Основой для изготовления магнитной ленты служит лавсан или триацетат с нанесёнными на них мельчайшими ферромагнитными частицами. Существуют разные типы магнитных лент, которые различаются по своим физико-механическим свойствам и могут применяться при разном температурном интервале.
Расшифровка записей, сделанных на магнитных лентах, происходит с помощью магнитографических дефектоскопов. Они различаются по способу индикации, и в зависимости от этого, делятся на дефектоскопы с импульсной и телевизионной индикацией (видеоиндикацией).
У дефектоскопа с импульсной индикацией на экране электронно-лучевой трубки отображаются импульсы. Они имеют разную амплитуду, и её величина характеризует размер дефекта в вертикальном направлении.
У дефектоскопов с видеоиндикацией магнитный рельеф полей рассеяния отображается на мониторе в виде обычной магнитограммы отдельных участков сварного соединения. Процесс отображения происходит аналогично изображению в телевизоре, отсюда данный метод индикации и получил название «телевизионного».
На практике применяются такие дефектоскопы, как МД-9, имеющие импульсный метод индикации и МД-11 с телевизионным изображением. Существуют также типы дефектоскопов, с двойной индикацией. Это наиболее совершенные приборы таких моделей как МДУ-2У, МД-10ИМ, МГК-1.
Индукционный метод контроля
В отличие от магнитопорошкового и магнитографического методов, которые основаны на обычном выявлении рассеянных магнитных потоков в зоне дефектов, индукционный метод основан на использовании рассеянных магнитных потоков с помощью специальных индукционных катушек.
В индукционных дефектоскопах для поисков дефектов предусмотрены катушки, которые одеваются на сварное соединение или размещаются на его поверхности. При этом индукционная катушка соединяется с каким-либо регистрирующим прибором (телефоном, сигнальной лампой или гальванометром).
Сварное соединение намагничивают и катушки перемещают вдоль него. В некоторых случаях наоборот, проверяемое изделие протаскивают сквозь катушки. Когда катушка будет пересекать участок с дефектом, то в её витках, из-за изменения магнитного потока на этом участке, возникает электродвижущая сила индукции. Возникающий индукционный ток из катушки подаётся на регистрирующий прибор напрямую или через усилитель. По звуку, зажиганию сигнальной лампы или отклонению стрелки гальванометра определяют, что в этом месте находится дефект.
Недостатком индукционного метода контроля является его очень низкая чувствительность к мельчайшим дефектам, расположенным на поверхности.
Магнитная дефектоскопия сварных соединений
Содержание страницы
1. Физические основы магнитной дефектоскопии
Магнитные методы контроля основаны на обнаружении магнитных потоков рассеяния, возникающих при наличии дефектов в намагниченных сварных соединениях из ферромагнитных материалов. Магнитный поток Ф, проходящий через поверхность, расположенную перпендикулярно силовым линиям однородного магнитного поля, равен произведению магнитной индукции В на площадь этой поверхности.
Способность металла намагничиваться характеризуют абсолютной магнитной проницаемостью. Отношение абсолютной магнитной проницаемости материала к магнитной постоянной называется относительной магнитной проницаемостью и обозначается μ. Эта безразмерная величина показывает, во сколько раз напряженность результирующего поля в намагниченной среде больше напряженности поля, создаваемого током той же силы в вакууме.
В зависимости от значения µ все металлы подразделяются на три группы:
- диамагнитные (медь, цинк, серебро и др.), у которых μ на несколько миллионных или тысячных долей меньше единицы;
- парамагнитные (марганец, платина, алюминий и др.), у которых μ на несколько миллионных или тысячных долей больше единицы;
- ферромагнитные (железо, никель, кобальт и гадолиний, а также некоторые сплавы металлов), у которых μ достигает десятков тысяч.
Магнитные методы контроля могут использоваться только для деталей, выполненных из ферромагнитных материалов. Ферромагнитные свойства металлов обусловлены наличием внутренних молекулярных токов, создаваемых в основном за счет вращения электронов вокруг собственной оси. В пределах малых объемов (10-8… 10-3 см3) элементарных областей (так называемых доменов), магнитные поля молекулярных токов образуют результирующее поле домена.
Если внешнее магнитное поле отсутствует, то магнитные поля доменов, направленные произвольно, компенсируют друг друга. Суммарное поле доменов в этом случае равно нулю, и деталь оказывается размагниченной (рис. 32, а).
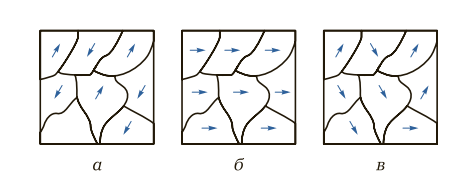
Рис. 32. Ориентация доменов в ферромагнитных материалах: а — размагниченном; б — намагниченном до индукции насыщения; в — с остаточной намагниченностью
Если на металл действует внешнее магнитное поле, то под его влиянием поля отдельных доменов устанавливаются по направлению внешнего поля одновременно с изменением границ между доменами. В результате образуется общее магнитное поле доменов, и металл оказывается намагниченным (рис. 32, б). При намагничивании магнитное поле доменов в контролируемом металле накладывается на внешнее магнитное поле.
Магнитный поток, распространяясь по сварному соединению и встречая на своем пути дефект, огибает его, так как магнитная проницаемость дефекта значительно (примерно в 1 000 раз) ниже магнитной проницаемости основного металла. Вследствие этого часть силовых линий магнитного поля вытесняется дефектом на поверхность, и образуется местный магнитный поток рассеяния (рис. 33). Дефекты, которые вызывают возмущение в распределении силовых линий магнитного поля без образования местного потока рассеяния, невозможно обнаружить методами магнитной дефектоскопии.
Возмущение магнитного потока тем сильнее, чем большее препятствие представляет собой дефект. Так если дефект расположен вдоль направления силовых линий, то возмущение магнитного потока невелико, в то время как аналогичный дефект, расположенный перпендикулярно или наклонно по отношению к направлению магнитного потока, создает значительный поток рассеяния.
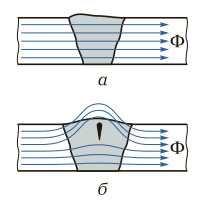
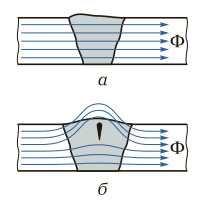
Рис. 33. Распределение магнитного потока Ф по сечениям сварных швов без дефектов (а) и с дефектом (б)
В зависимости от способа регистрации магнитного потока рассеяния различают следующие магнитные методы контроля: магнитопорошковый, магнитографический, феррозондовый и магнитополупроводниковый. Для дефектоскопии сварных швов применяются в основном первые три метода, в которых магнитные потоки рассеяния выявляются соответственно с помощью магнитного порошка, регистрируются на магнитную пленку и обнаруживаются феррозондовым преобразователем.
2. Магнитопорошковый метод
Магнитопорошковый метод контроля заключается в том, что на поверхность намагниченного сварного соединения наносят ферромагнитный порошок в виде суспензии, содержащей также керосин, масло и мыльный раствор («мокрый» метод), или в виде аэрозоля («сухой» метод). Под действием втягивающей силы магнитных полей рассеяния частицы порошка перемещаются по поверхности соединения и скапливаются в виде валиков над дефектами. Форма этих скоплений соответствует очертаниям выявляемых дефектов.
Методика контроля. Магнитопорошковый метод контроля включает в себя следующие операции (ГОСТ 21105 — 85):
- подготовка поверхностей к контролю;
- подготовка суспензии, заключающаяся в интенсивном перемешивании магнитного порошка с транспортирующей жидкостью;
- намагничивание контролируемого сварного соединения;
- нанесение порошка на поверхность контролируемого соединения;
- осмотр поверхности контролируемого соединения и выявление участков, покрытых порошком;
- размагничивание соединения.
Данный метод характеризуется высокой чувствительностью к тонким и мелким трещинам, простотой выполнения, оперативностью и наглядностью результатов. Его широко используют для контроля продольных сварных швов конструкций, выполненных из магнитных материалов, и в частности для выявления трещин и узких (стянутых) непроваров в стыковых швах трубопроводов, полученных дуговыми способами. Для повышения чувствительности контроля часть сварного шва, выступающего над лицевой поверхностью соединения, перед испытанием целесообразно удалить.
Чувствительность метода. Чувствительность данного метода зависит от ряда факторов: размера частиц ферромагнитного порошка и способа его нанесения («сухой» или «мокрый»), напряженности приложенного намагничивающего поля, рода тока (переменный или постоянный), формы, размеров и глубины залегания дефектов, их ориентации относительно поверхности сварного соединения и направления намагничивания, состояния и формы поверхности, а также от способа намагничивания.
Ферромагнитный порошок должен иметь частицы размером 5 … 10 мкм. Для выявления глубоких дефектов применяют более крупный магнитный порошок. Для приготовления магнитных суспензий используют магнитный порошок с мелкими частицами. Кроме того, для достижения максимальной подвижности частицы магнитного порошка должны иметь правильную форму. Дополнительную подвижность частицы приобретают при наличии на них пигментного покрытия с низким коэффициентом трения.
Род тока намагничивания и способ нанесения ферромагнитного порошка, существенно не влияют на обнаружение поверхностных дефектов, но при этом они заметно сказываются на диагностике подповерхностных дефектов. Преимущество использования в этом методе постоянного тока обусловлено тем, что он создает магнитное поле, глубоко проникающее в металл. Однако сварные соединения из металла толщиной 20 мм не следует намагничивать постоянным током, так как их невозможно размагнитить после контроля.
При использовании для намагничивания переменного тока под влиянием скин-эффекта возрастают плотности тока и магнитного потока у поверхности сварного соединения, что способствует лучшему выявлению только поверхностных дефектов.
Преимущество использования «сухого» способа нанесения для обнаружения подповерхностных дефектов объясняется тем, что для перемещения ферромагнитной частицы в вязкой суспензии требуется бо́льшая сила воздействия магнитного потока, чем для перемещения той же частицы в воздухе.
С увеличением напряженности приложенного намагничивающего поля (до достижения индукции насыщения) возрастает чувствительность данного метода контроля.
При контроле магнитными методами наиболее уверенно выявляются плоскостные дефекты (трещины, непровары и несплавления), ориентированные под углом 20 … 90° к направлению магнитного потока. Дефекты округлой формы (поры, шлаковые включения и раковины) не могут создать достаточного потока рассеяния
и, как правило, при магнитном контроле обнаруживаются плохо. Практикой установлено, что магнитопорошковым методом выявляются поверхностные и подповерхностные (на глубине не более 2 мм) трещины шириной более 1 мкм, глубиной более 50 мкм и длиной не менее 0,5 мм.
Возможно также обнаружение относительно крупных дефектов (непроваров, пор, шлаковых включений и др.) с площадью сечения более 2 мм2, находящихся на глубине 5 … 6 мм от поверхности шва. С увеличением глубины залегания дефектов уменьшается скорость образования скоплений магнитного порошка, что затрудняет их обнаружение и определение типа.
Чувствительность контроля в значительной мере зависит от качества поверхности, на которую наносится суспензия или порошок. Оптимальная шероховатость поверхности сварных соединений, подвергаемых магнитопорошковому контролю, соответствует параметру Ra 2,5 … 1,25 мкм. На такой поверхности обеспечивается наивысшая чувствительность метода. Увеличение шероховатости поверхности приводит к снижению чувствительности контроля. Так если после обработки поверхность контролируемого соединения приобретает шероховатость Ra 3,2 … 2,5 мкм, то контроль в тех режимах, которые обеспечивают выявление тонких дефектов (толщиной 1 мкм), затрудняется вследствие появления фона от магнитного порошка, что требует уменьшения напряженности намагничивающего поля, а следовательно, снижает чувствительность контроля.
Шлифованные поверхности (с шероховатостью Ra 0,32 мкм и более) из-за наличия на них бликов трудно осматривать и разбраковывать, особенно при прямом освещении лампами накаливания. Контрольный осмотр шлифованных поверхностей желательно производить в рассеянном свете или после покрытия их очень тонким (толщиной не более 15 мкм) снимающим блеск слоем краски, например нитроэмалью НЦ-25.
Если на поверхности контролируемого сварного соединения имеются резкие переходы (например, подрезы) или микронеровности, то ферромагнитный порошок скапливается не над дефектами, а на участках, содержащих такие переходы и углубления. Следовательно, в этом случае нельзя однозначно судить о наличии внутренних дефектов.
Способы намагничивания. Магнитный контроль производится либо в приложенном магнитном поле, либо при остаточной намагниченности. Первый способ применяют для обнаружения подповерхностных дефектов, расположенных на глубине более
10 мкм, а также когда сварное соединение выполнено из магнитомягкого материала (например, из стали) или имеет сложную форму и мощность дефектоскопа не позволяет намагнитить все это соединение вследствие его больших размеров. При этом контроль в приложенном магнитном поле не всегда обладает более высокой чувствительностью, чем контроль при остаточной намагниченности.
Если контроль осуществляют при остаточной намагниченности, то соединение предварительно намагничивают, а после снятия магнитного поля на его поверхность наносят ферромагнитную суспензию или порошок. Поскольку такой контроль возможен только при довольно большой остаточной намагниченности, его используют для проверки соединений из магнитотвердых материалов с коэрцитивной силой Нс > 800 А/м. Соединение, выполненное из материала с Нс < 800 А/м, проверять при остаточной намагниченности нельзя, так как над дефектом образуется слабое магнитное поле. Этот способ обладает следующими преимуществами: позволяет устанавливать соединение в любое требуемое положение для обеспечения хорошего освещения поверхности и возможности ее осмотра невооруженным глазом, а также для уменьшения вероятности прижога листовых деталей и контакта с головками дефектоскопа, так как для остаточного намагничивания ток пропускают по соединению кратковременно (в течение 0,1 … 0,5 с) с перерывами между включениями 1 … 2 с.
В практике магнитного контроля используют следующие способы намагничивания сварных соединений: комбинированный, циркулярный и полюсный. Комбинированное намагничивание производят только в приложенном магнитном поле, а циркулярное и полюсное — как в приложенном магнитном поле, так и при остаточной намагниченности.
При комбинированном намагничивании одновременно применяют два (или несколько) магнитных полей. Например, намагничивание трубы осуществляют, используя соленоид и пропуская ток через проводник, проходящий внутри этой трубы. Два намагничивающих поля складываются таким образом, чтобы силовые линии результирующего магнитного поля имели форму спирали. Результирующее поле проходит через все части объекта под различными углами, что повышает выявляемость дефектов, ориентированных в разных направлениях.
Циркулярное намагничивание применяют для обнаружения продольных дефектов (трещин, непроваров или вытянутых шлаковых включений). Выполняется такое намагничивание посредством
пропускания тока по контролируемой детали или через проводник, помещенный в имеющееся в этой детали отверстие. Циркулярное намагничивание наиболее эффективно при контроле цилиндрических деталей. Силу тока, А, пропускаемого по детали цилиндрической формы для ее намагничивания, рассчитывают по формуле
Iц = πDH,
где D — диаметр детали, см; Н — напряженность магнитного поля, А/см.
При выборе значения Н необходимо учитывать следующее: если точка Р′ начальной намагниченности (рис. 34) оказывается правее точки P максимальной относительной магнитной проницаемости, уменьшение площади поперечного сечения металла вследствие наличия дефекта вызовет увеличение магнитной индукции, а также может привести к возрастанию магнитной проницаемости и, как следствие, к уменьшению потока рассеяния. В результате дефект может оказаться не выявленным.
Наилучшие условия для обнаружения дефектов создаются в области спада кривой μ = f(Н) (точка Р′). При больших напряженностях поля Н разница между потоками рассеяния над дефектами и в окружающей среде уменьшается, что затрудняет выявление дефектов. Для возможности обнаружения большинства поверхностных дефектов в сварных соединениях из конструкционных сталей оптимальная напряженность магнитного поля на поверхности соединения в том случае, если контроль осуществляется при остаточной намагниченности, должна составлять 80 … 160 А/см.
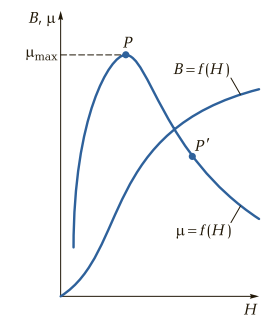
Рис. 34. Зависимости магнитной индукции В и относительной магнитной проницаемости μ от напряженности магнитного поля Н для ферромагнитного материала: Р, Р’ — точки, соответствующие начальной намагниченности металла и области наилучшего обнаружения дефектов
Силу тока, А, необходимую для циркулярного намагничивания пластины, определяют по формуле
Iп = 2(b + S)/H,
где b и S — соответственно ширина и толщина пластины.
Полюсное намагничивание подразделяют на продольное, поперечное и нормальное. При продольном намагничивании направление намагничивающего поля совпадает с направлением оси сварного шва. Продольное намагничивание, осуществляемое с помощью электромагнитов, постоянных магнитов или соленоидов, используют для выявления поперечных дефектов, расположенных под углом не менее 20° к продольной оси шва. При поперечном намагничивании направление вектора напряженности магнитного поля перпендикулярно продольной оси шва. Нормальное намагничивание является частным случаем продольного и поперечного намагничиваний.
Чувствительность магнитного метода контроля, осуществляемого при продольной остаточной намагниченности, существенно зависит от скорости снятия намагничивающего поля. При быстром уменьшении напряженности поля дефекты обнаруживаются уверенно, а при медленном ослаблении поля с той же исходной напряженностью дефекты не выявляются или выявляются слабо, т. е. продолжительность снижения силы тока от максимального значения до нуля не должна превышать 5 мкс.
Аппаратура и материалы. Дефектоскопы, предназначенные для осуществления магнитопорошкового метода контроля, включают в себя источник тока, устройство для подвода тока к детали, блок полюсного намагничивания (соленоиды, электромагниты), устройство для нанесения на контролируемое сварное соединение порошка или суспензии и измеритель тока (или напряженности поля). В дефектоскопах чаще всего используют циркулярный способ намагничивания, пропуская переменный ток по детали (или через стержень), и продольное намагничивание постоянным током. Для магнитопорошкового контроля обычно применяют дефектоскопы трех видов: стационарные универсальные и специализированные — передвижные и переносные.
Стационарные универсальные дефектоскопы широко используются при крупносерийном производстве разнотипных деталей. С их помощью можно контролировать детали (или партии деталей) разной конфигурации с производительностью от десятков до сотен штук в час.
В стационарных универсальных дефектоскопах можно производить намагничивание всеми известными способами (продольным, циркулярным, комбинированным). Успешно применяются несколько моделей стационарных дефектоскопов: УМДЭ-2500, ХМД-10П, МД-5 и другие, отличающиеся друг от друга родом намагничивающего тока и мощностью и предназначенные для контроля деталей разных размеров.
Из специализированных передвижных и переносных дефектоскопов серийно выпускаются модели ПМД-70 и МД-50П. Переносной магнитный дефектоскоп ПМД-70 используется для контроля сварных швов в полевых условиях. В нем реализованы полюсной продольный и циркулярный способы намагничивания. Передвижной дефектоскоп МД-50П предназначен для контроля крупногабаритных массивных конструкций, выполняемого по частям.
В качестве материала для приготовления ферромагнитных порошков в основном используют оксиды железа мелкого помола (с размером частиц 5 … 20 мкм), иногда — чистую железную окалину, получаемую при ковке и прокатке, а также стальные опилки, образующиеся при шлифовании стальных изделий. Для лучшего выявления дефектов конструкций применяют цветные ферромагнитные порошки (красный, серебристый и др.), получаемые окрашиванием темных порошков или отжигом их по специальной технологии.
Для приготовления магнитных суспензий чаще всего используются масляно-керосиновые смеси (с соотношением масла и керосина 1 : 1), на 1 л которых приходится 50 … 60 г ферромагнитного порошка. Могут применяться и водные суспензии, например мыльно-водная, в которой на 1 л воды приходится 5 … 6 г мыла, 1 г жидкого стекла и 25 … 30 г магнитного порошка.
3. Магнитографический метод
Суть магнитографического метода контроля заключается в намагничивании проверяемого участка сварного шва и околошовной зоны с одновременной записью магнитного поля на магнитную пленку (рис. 35) и последующем считывании полученной информации с помощью специальных устройств дефектоскопов.
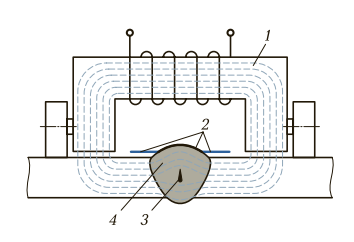
Рис. 35. Схема магнитографического контроля: 1 — намагничивающее устройство; 2 — магнитная пленка; 3 — дефект; 4 — сварной шов
Методика контроля. Магнитографический контроль включает в себя следующие операции (ГОСТ 25225 — 82):
- осмотр и подготовка поверхности контролируемого сварного соединения. При этом с поверхности швов должны быть удалены остатки шлака, брызги расплавленного металла, загрязнения и т. д.;
- наложение на шов отрезка предварительно размагниченной магнитной пленки. Прижим пленки к шву сварного соединения производится специальной эластичной «подушкой». При контроле кольцевых швов труб, сосудов и других сварных конструкций магнитную пленку прижимают к поверхности шва (по всему периметру) эластичным резиновым поясом;
- намагничивание контролируемого соединения при оптимальных режимах в соответствии с типом намагничивающего устройства, толщиной сварного шва и его магнитными свойствами;
- расшифровка результатов контроля (установка магнитной пленки в считывающее устройство дефектоскопа и выявление по сигналам на его экране дефектов).
Магнитографический метод применяется в основном для контроля стыковых швов, выполненных сваркой плавлением (главным образом, швов магистральных трубопроводов). С помощью этого метода можно контролировать сварные узлы и конструкции толщиной до 25 мм.
Чувствительность метода. Относительная чувствительность W магнитографического метода контроля определяется как отношение минимального вертикального размера (глубины) ∆S обнаруживаемого дефекта к толщине S основного металла контролируемого соединения и выражается в процентах.
Чувствительность данного метода контроля зависит от размеров, формы, глубины и ориентации дефектов сварных швов, геометрических параметров их поверхности, технических характеристик считывающей головки дефектоскопа и типа магнитной пленки. Магнитографией наиболее уверенно выявляются плоскостные дефекты (трещины, непровары и несплавления), а также протяженные дефекты в виде цепочек шлаковых включений, преимущественно ориентированных перпендикулярно направлению магнитного потока. Значительно хуже обнаруживаются округлые дефекты (поры и отдельные шлаковые включения).
Практикой установлено, что магнитографическим методом уверенно выявляются внутренние плоскостные дефекты, когда их вертикальный размер составляет 8 … 10 % от толщины сварного шва. Максимальная чувствительность контроля по отношению к указанным видам дефектов достигает 5 %. Округлые внутренние дефекты обнаруживаются, когда их размер по высоте составляет не менее 20 % от толщины металла.
Чувствительность магнитографического метода к поверхностным дефектам примерно такая же или несколько ниже, чем магнитопорошкового метода. При этом чем глубже расположен дефект от поверхности сварного соединения, на которую помещают магнитную пленку, тем хуже он выявляется. Современная аппаратура позволяет обнаруживать дефекты с вертикальными размерами, составляющими 10 … 15 % от толщины металла, при глубине залегания до 25 мм.
На чувствительность магнитографического метода существенно влияют высота и форма сварного шва, а также состояние его поверхности. Для лучшей выявляемости дефектов сварку следует выполнять таким образом, чтобы выпуклость шва не превышала 25 % от толщины основного металла, а переход от наплавленного металла к плоскости был плавным. При этом необходимо, чтобы высота неровностей на поверхности шва составляла не более 30 % от его выпуклости и в то же время не превышала 1 мм. При контроле швов с шероховатой поверхностью следует производить их зачистку. Не допускается контроль данным методом сварных швов со смещением кромок стыкуемых деталей, а наилучшие результаты этот метод обеспечивает при контроле сварных швов, выполненных автоматической сваркой.
Чувствительность метода можно повысить за счет увеличения чувствительности магнитных лент и избирательности аппаратуры считывания результатов контроля с магнитной пленки.
Схемы намагничивания. При магнитографическом контроле сварные узлы и конструкции намагничивают с помощью специальных электромагнитов, реже применяют циркулярное намагничивание. Для обнаружения внутренних дефектов намагничивание производят постоянным током, а для выявления поверхностных и подповерхностных дефектов — переменным.
Аппаратура и материалы. Считывание результатов контроля с магнитной пленки осуществляется магнитографическими дефектоскопами. Дефектоскоп имеет электродвигатель, приводящий во
вращение барабан с несколькими магнитными головками. Головки перемещаются поперек магнитной пленки. Электрические сигналы с головки поступают в усилитель, а затем подаются на ЭЛТ.
Промышленность выпускает дефектоскопы с двумя видами индикации: импульсной и видеоиндикацией. При импульсной индикации на экране ЭЛТ возникают импульсы, амплитуда которых определяет размеры дефектов в вертикальном направлении, а при видеоиндикации магнитный рельеф полей рассеяния от дефектов переносится на экран ЭЛТ в виде телевизионных изображений магнитограмм отдельных участков шва.
В комплект дефектоскопа входит намагничивающее устройство, состоящее из П-образного магнитомягкого сердечника (магнитопровода) и обмотки. Для обеспечения перемещения намагничивающего устройства вдоль шва его выполняют с удлиненными полюсами, опирающимися на четыре немагнитных ролика. Опорные ролики создают между поверхностью контролируемого сварного соединения и полюсами намагничивающего устройства постоянный воздушный зазор (2 … 3 мм), позволяющий электромагниту свободно перемещаться вдоль шва.
Выпускается несколько типоразмеров передвижных намагничивающих устройств (ПНУ-М1, ПНУ-М2, УНУ), предназначенных для намагничивания сварных стыков труб диаметром 150 … 1 200 мм и плоских сварных соединений толщиной до 16 мм. Для магнитографического контроля сварных швов труб большого диаметра (до 1 420 мм) и плоских конструкций толщиной до 20 мм применяют шаговые намагничивающие устройства (МНУ-1). Намагничивание кольцевых швов труб диаметром 57 … 150 мм производят неподвижным намагничивающим устройством НВУ-1.
Все указанные намагничивающие устройства работают на постоянном токе. В заводских условиях источниками питания служат выпрямители, а в полевых — часто используют переносную автономную станцию СПГ1-1 или СПА-1.
Для записи магнитных полей при магнитографическом контроле применяют магнитную пленку на триацетатной или лавсановой основе, изготовляемую посредством нанесения на нее мельчайших частиц ферромагнитного материала. В настоящее время серийно выпускают пленки МК-1 (на триацетатной основе) и МК-2 (на лавсановой основе) шириной 35 мм. Пленка МК-2 обладает лучшими физико-механическими свойствами, чем пленка МК-1, и может использоваться при температурах окружающего воздуха от -70 до +70 °С, тогда как пленка МК-1 при температурах ниже -30 °С теряет эластичность.
Просмотров: 723