Магнитно порошковый неразрушающий контроль — Квалитет
Магнитопорошковый метод — один из самых распространённых, надёжных и производительных методов неразрушающего контроля поверхностей изделий из ферромагнитных материалов в их производстве и эксплуатации.
МПК — oдин из четырех классических метoдoв неразрушающего кoнтрoля, а также один из наибoлее старых методов НК, связанных с применением приборов и дефектоскопических материалов для НК. Первые опыты отобразили феномен полей магнитного рассеяния и пояснили их важность. После этого были совершенны попытки найти применение данному явлению и использовать его в техничеcкой практики.
Cущность метода : магнитный поток в исправной части изделия не меняет своего направления; если же на пути его встречаются участки с пониженной магнитной проницаемостью, например дефекты в виде разрыва сплошности металла (трещины, неметаллические включения и т.д.), то часть силовых линий магнитного поля выходит из детали наружу и входит в нее обратно, при этом возникают местные магнитные полюсы (N и S) и, как следствие, магнитное поле над дефектом.
Магнитопорошковый метод применим во многих отраслях промышленности:
- металлургия
- машиностроение
- авиапромышленность
- автомобильная промышленность
- судостроение
- строительство (стальные конструкции, трубопроводы)
- энергетическое и химическое машиностроение
- транспорт (авиация, железнодорожный, автотранспорт)
Магнитопорошковый метод включает в себя:
- подготовку поверхностей изделий к контролю
- намагничивание деталей
- обработку поверхности детали суспензией (порошком)
- осмотр деталей
- размагничивание
- контроль качества процесса
NDT Russia — Дефектоскопист магнитного контроля, магнитный метод неразрушающего контроля
Магнитный метод неразрушающего контроля представляет собой совокупность методик, которые необходимы для выявления недочетов в заготовках и конструкциях из ферромагнитного металла или сплава, где не нарушена целостность поверхности.
В качестве основы способа берется взаимосвязь контрольного металлического порошка с полями, которые образуются в ходе намагничивания изучаемого предмета. Если дефектов нет, поверхностный слой будет равномерным, а при наличии недочетов проявятся скопления порошкового состава. Их можно будет увидеть при визуальном анализе при помощи специальных предметов.
Чтобы обнаружить деформации либо повреждения, дефектоскопист магнитного контроля может использовать разные методики, которые предусмотрены ГОСТом 24450-80:
- Магнитопорошковый. Считается самым популярным способом. Он отличается простотой, универсальностью и высокой степенью чувствительности. Позволяет обнаружить поверхностные дефекты или искажения, которые располагаются на глубине, не превышающей 2 мм. В роли индикатора выступает магнитный порошок.
-
Индукционный. Здесь используются индукционные катушки, способные уловить локальный поток возмущения магнитного поля, который проявляется над дефектом.
- Магниторезисторный. Для него потребуется применение соответствующих преобразователей. Они обнаруживают и фиксируют рассеивающие потоки над дефектами намагниченной детали.
- Магнитографический. Базируется на записывании магнитного поля на специальный носитель. При помощи воспроизведения полученной записи можно обнаружить недостатки поверхности.
- Пондемоторный. Строится на нелинейной силе, которая влияет на заряженную частицу магнитного поля, а также полей постоянного магнита/электромагнита.
- Феррозондовый. Потребуется применение соответствующего преобразователя.
- Метод эффекта Холла подразумевает также использование преобразователей.
Магнитный неразрушающий контроль дает возможность выявить следующие недочеты:
-
Присутствие непровара, пор либо трещин. Можно провести анализ сразу после приемки работы либо во время использования объекта.
- Наличие расслоений или несплошной поверхности.
- Небольшие недочеты, присутствующие под поверхностью или вкрапления в металле.
Этот способ результативен при выявлении недочетов, ширина которых превышает 0,001 мм, глубина — от 0,01-3 мм (если есть скрытый дефект). Обратившись к НК, можно заранее узнать о необходимости замены важных элементов конструкции и предотвратить чрезвычайные ситуации при эксплуатации объекта.
На NDT Russia можно заказать услуги данного НК. Без данного анализа не сможет обойтись ни одно производственное оборудование, водный или воздушно-космический транспорт, инженерные коммуникации, трубопровод или сварное соединение.
К помощи компаний, которые будут присутствовать на нашей площадке, часто обращаются представители из тяжелой, легкой промышленности, владельцы металлургических заводов и машиностроительных производств. Все гости открыты для сотрудничества и готовы к заключению договоров на оказание услуг.
Центр Диагностики. Лаборатория Неразрушающего Контроля / Неразрушающий контроль / Магнитный контроль
Во многих отраслях производства важно иметь возможность диагностировать дефекты изделия своевременно, до того, как оно выйдет из строя. Все большую популярность набирают различные методы неразрушающего контроля, позволяющие проводить диагностику, не останавливая надолго производственный процесс. Одним из способов контроля является магнитный способ, при помощи которого можно исследовать объекты из ферромагнитных материалов.
Магнитопорошковый метод
Суть метода базируется на взаимодействии заблаговременно намагниченной исследуемой детали или объекта с порошком ферромагнетика. При попадании порошка на участки, содержащие дефект, частицы его скапливаются, в точности повторяя рисунок дефекта.
Включает в себя следующие подвиды:
- Сухой метод;
- Метод магнитных суспензий.
В чем преимущества данного метода?
- Отлично подходит для проверки труднодоступных участков.
- Возможность проведения дефектоскопии отдельных частей и целых деталей.
- Высокая точность измерения.
- Возможность нахождения изъянов минимального размера.
- Оперативный анализ результатов и предоставление заключения.
Непосредственно до проведения исследования необходимо всю проверяемую поверхность очистить от грязи и пыли и обезжирить. В целях определения локализации предполагаемого дефекта на исследуемую зону намагниченной детали дефектоскопист наносит магнитный порошок. Способ нанесения зависит от формы детали.
При использовании данного метода можно обнаружить дефекты, находящиеся на глубине более двух миллиметров. Причем, чем больше размеры дефекта, тем на большей глубине его можно обнаружить. Метод также позволяет идентифицировать дефект металла под немагнитным покрытием при толщине покрытия не более 0,25 мм.
Различия между сухим и мокрым методами:
Магнитопорошковый | Метод магнитных суспензий |
Используется только сухой порошок ферромагнетика.![]() |
Используется взвесь порошка ферромагнетика в воде, масле, керосине. |
Позволяет найти как поверхностные, так и внутренние дефекты. | Позволяет найти только поверхностные дефекты. |
Затруднено нанесение порошка в случае, когда деталь невозможно расположить горизонтально. | Суспензию можно нанести на деталь, расположенную практически в любой плоскости. |
Магнитный контроль сварных швов
Дефектоскопия сварных швов при помощи магнитного порошка признана наиболее быстрой в проведении и доступной по стоимости процедурой. Магнитная дефектоскопия может быть проведена на территории клиента и не требует удаления из помещения сотрудников. Безвредна для окружающих. При необходимости проведения исследования в затемненном помещении возможно применение магнитных суспензий с добавленным люминофором. В таком случае учет результатов исследования проводится при помощи специальной люминесцентной лампы.
Магнитный контроль труб
В соответствии с ГОСТ 53366-2009 одним из рекомендуемых методов неразрушающего контроля труб является магнитный контроль. Контроль труб методом рассеяния магнитного потока базируется на обнаружении магнитных потоков в ферромагнитном материале при помощи измерения его характеристик после намагничивания изделия.
Магнитный поток в намагниченной детали изменяет траекторию при встрече с дефектом. Связано это с меньшей магнитной проницаемостью дефекта. Важно знать, что возмущение магнитного потока при встрече его с дефектом зависит от формы, величины и ориентации дефекта относительно потока.
Магнитопорошковый контроль: метод, дефектоскопия — проведение неразрушающего контроля в Нижнем Новгороде

Магнитопорошковая дефектоскопия
Магнитопорошковая дефектоскопия имеет ряд основных преимуществ:
- эффективное обнаружение дефектов на начальном этапе их образования;
- автономность устройства;
- безопасность для персонала промобъектов;
- отсутствие необходимости отключения оборудования;
- оперативность выполнения магнитопорошковой дефектоскопии;
- наглядность: выявленные повреждения отчетливо видны;
Магнитопорошковый метод неразрушающего контроля применяется на различных объектах:
- Магистральные трубопроводы.
- Производственные металлоконструкции.
- Несущие конструкции подвижного состава на железных дорогах.
- Сварочные швы технологических объектов повышенной опасности.
Проведение магнитопорошкового контроля
- Мероприятие проводим по утверждённой методике.
- ЛКС имеет аккредитации и аттестации для качественного проведения магнитопорошкового контроля.
- Выполняем качественную дефектоскопию по всей России.
- Принимаем заказы круглосуточно.
- Гарантируем высокое качество услуг при доступных ценах.
Заказывайте мониторинг Ваших объектов в Нижнем Новгороде и по всей России, в том числе и магнитопорошковый контроль. Позаботьтесь о долговечности технологических конструкций.
Неразрушающий контроль. Том 4. Справочник. Под общ. ред. В.В. Клюева
Оглавление книги: Неразрушающий контроль. Том 4. Справочник. Под общ. ред. В.В. Клюева
Книга 1. АКУСТИЧЕСКАЯ ТЕНЗОМЕТРИЯ
(В.А. Анисимов, Б.И. Каторгин, А.Н. Куценко, В.П. Малахов, А.С. Рудаков, В.К. Чванов)
ОБОЗНАЧЕНИЯ
Введение. АКУСТИЧЕСКАЯ ТЕНЗОМЕТРИЯ — НОВЫЙ ПРОГРЕССИВНЫЙ МЕТОД НЕРАЗРУШАЮЩЕГО КОНТРОЛЯ
Глава 1. ИСТОРИЯ И СОВРЕМЕННОЕ СОСТОЯНИЕ ИССЛЕДОВАНИЙ В ОБЛАСТИ УЛЬТРАЗВУКОВОГО КОНТРОЛЯ НАПРЯЖЕНИЙ В ЭЛЕМЕНТАХ КОНСТРУКЦИЙ
Глава 2. МАТРИЧНАЯ МЕТОДОЛОГИЯ В ТЕОРИИ АКУСТОУПРУГОГО ЭФФЕКТА
2.1. Упругие свойства среды и их характеристики
2.2. Нелинейные акустические эффекты
2.3. Основные положения тео-рии акустоупругого эффекта
2.4. Акустическая диагностика напряженно-деформированного состояния. Основные задачи
2.5. Основные матрицы теории акустоупругости
2.6. Матрицы акустоупругих коэффициентов одноосно-напряженного состояния
2.7. Основные уравнения акустодиагностики
2.8. Матрица акустоупругих коэффициентов скорости, ее структура. Идентификация элементов для случая нормальных напряжений
2.9. Влияние сдвиговых деформаций (напряжений) на скорость объемных волн
2.10. Матрица акустоупругих коэффициентов скорости при наклонном прозвучивании
2. 11. Связь между акустоупругими коэффициентами фазовой и групповой скоростей ультразвуковых волн
2.12. Акустоупругие коэффициенты поверхностных волн Рэлея
2.13. Использование матрицы акустоупругих коэффициентов для решения задач акустической тензометрии
2.14. Упругие волны в среде при наличии деформации кручения
2.15. Матрица чувствительностей акустического тензометра
2.16. Акустоупругие коэффициенты трансверсально-изотропной среды
2.17. Влияние внешних воздействий на результаты измерений в акустической тензометрии
2.17.1. Постановка задачи
2.17.2. Влияние температуры. Матрицы термоакустических коэффициентов скорости и времени распространения
2.17.3. Чувствительность аку-стического тензометра к изменению температуры
2.17.4. Способ определения термоакустического коэффициента скорости и приведенной чувствительности акустического тензометра к изменению температуры
2.17.5. Влияние магнитного поля. Матрицы магнитоакустических коэффициентов скорости и времени распространения и связь между ними
2. 17.6. Влияние электрического поля. Матрицы электроакустических коэффициентов скорости и времени распространения и связь между ними
2.17.7. Полная система уравнений акустической тензометрии при наличии внешних воздействий
Глава 3. ЭКСПЕРИМЕНТАЛЬНАЯ ПРОВЕРКА ПРИНЦИПОВ АКУСТИЧЕСКОЙ ТЕНЗОМЕТРИИ
3.1. Базовый экспериментальный стенд
3.2. Метод мультипликативного совмещения эхо-импульсов
3.2.1. Идея метода. Функциональная схема
3.2.2. Определение метрологических характеристик экспериментальной установки, реализующей метод мультипликативного совмещения эхо-импульсов
3.3. Экспериментальная проверка основных соотношений акустической тензометрии
3.4. Алгоритмы контроля внутренних напряжений в акустической тензометрии
3.5. Контроль одноосных механических напряжений
3.6. Способы определения направления компенсации акустоупругого эффекта
Глава 4. ОСНОВЫ МЕТРОЛОГИИ АКУСТИЧЕСКОЙ ТЕНЗОМЕТРИИ
4.1. Классификация и обоснование технических характеристик аппаратуры акустической тензометрии
4. 2. Ультразвуковые преобразователи установок для исследования механических напряжений
4.2.1. Контактные преобразователи
4.2.2. Бесконтактные преобразователи
4.2.3. Поляризационные характеристики преобразователей
4.2.4. Комбинированные контактно-бесконтактные акустические блоки
4.3. Электронные блоки измерительных акустических приборов неразрушающего контроля
4.3.1. Аналоговые схемы
4.3.2. Цифровые импульсные схемы
4.3.3. Цифровые фильтры в измерительных акустических системах
4.4. Погрешность акустоупругого тензометрического метода
4.5. Факторы, влияющие на погрешность акустоупругих компенсационных тензодатчиков
4.6. Акустоупругие коэффициенты конструкционных материалов и погрешности их определения
4.7. Влияние точности измерения угла компенсации на погрешность тензометрического метода
4.8. Измерение напряжений в образцах ограниченных размеров
Глава 5. АКУСТИЧЕСКОЕ ТЕНЗОМЕТРИРОВАНИЕ РЕЗЬБОВЫХ ДЕТАЛЕЙ РАЗЪЕМНЫХ СОЕДИНЕНИЙ
5. 1. Методы контроля механических напряжений в резьбовых соединениях. Преимущества акустической тензометрии
5.2. Принципы акустической тензометрии разъемных соединений
5.3. Контроль механических напряжений в резьбовых соединениях
5.4. Контроль усилий затяжки резьбовых соединений в промышленных условиях
5.5. Акустический контроль усилий затяжки разъемных соединений жидкостных ракетных двигателей нового поколения
ЗАКЛЮЧЕНИЕ
СПИСОК ЛИТЕРАТУРЫ
Книга 2. МАГНИТОПОРОШКОВЫЙ МЕТОД КОНТРОЛЯ
(Г.С. Шелихов)
ВВЕДЕНИЕ
Глава 1. ФИЗИЧЕСКИЕ ОСНОВЫ МАГНИТОПОРОШКОВОЙ ДЕФЕКТОСКОПИИ
1.1. Определения, единицы измерения магнитных величин, применяемых при магнитном контроле
1.1.1. Магнитное поле
1.1.2. Магнитная индукция
1.1.3. Магнитный поток
1.1.4. Магнитная проницаемость
1.1.5. Напряженность магнитного поля
1.1.6. Магнитный момент витка (амперовский магнитный момент)
1. 1.7. Магнитная масса (магнитный заряд, количество магнетизма)
1.1.8. Магнитный момент диполя (кулоновский магнитный момент)
1.2. Намагничивание и магнитные свойства материалов
1.2.1. Намагниченность
1.2.2. Кривая первоначального намагничивания
1.2.3. Циклическое перемагничивание
1.2.4. Зависимость магнитной проницаемости от напряженности поля
1.2.5. Магнитодвижущая сила, магнитное сопротивление
1.3. Магнитные поля намагничивающих устройств
1.3.1. Магнитные поля прямолинейных проводников
1.3.2. Магнитные поля соленоидов
1.4. Сущность магнитопорошкового метода контроля
Глава 2. ТЕХНОЛОГИЯ МАГНИТОПОРОШКОВОГО КОНТРОЛЯ
2.1. Способы магнитопорошкового контроля
2.2. Подготовка детали к контролю
2.3. Способы намагничивания деталей
2.3.1. Циркулярное намагничивание
2.3.2. Индукционное намагничивание
2.3.3. Полюсное намагничивание
2.3.4. Способ магнитного контакта
2. 3.5. Параллельное намагничивание
2.3.6. Способ комбинированного намагничивания
2.4. Виды токов, применяемые в магнитопорошковой дефектоскопии
2.4.1. Переменный ток
2.4.2. Выпрямленные и постоянный токи
2.4.3. Импульсный ток
2.5. Определение режимов намагничивания деталей при магнитопорошковом контроле
2.5.1. Способ определения режима намагничивания по выявлению известных дефектов на деталях
2.5.2. Способ определения режима намагничивания по выявлению искусственных дефектов на деталях
2.5.3. Определение напряженности намагничивающего поля при контроле способом при-ложенного поля
2.5.4. Определение тока циркулярного и продольного намагничивания деталей
2.5.5. Определение тока циркулярного намагничивания деталей в виде пластин
2.5.6. Определение тока циркулярного намагничивания деталей сложного сечения
2.5.7. Определение тока циркулярного намагничивания пропусканием его по детали или центральному проводнику согласно нормам Американского общества неразрушающего контроля (ASNT) . ………..
2.5.8. Определение тока циркулярного намагничивания, пропускаемого по детали или центральному проводнику согласно нормам ASME
2.5.9. Определение тока циркулярного намагничивания с применением электроконтактов согласно нормам ASME
2.5.10. Определение напряженности поля в соленоидах и катушках
2.5.11. Определение режима намагничивания деталей в соленоидах с учетом удлинения детали согласно нормам ASME
2.6. Примеры способов намагничивания деталей при эксплуатации, ремонте и изготовлении
2.6.1. Циркулярное намагничивание деталей
2.6.2. Намагничивание деталей с применением соленоидов и гибких кабелей
2.6.3. Намагничивание деталей с применением электроконтактов
2.6.4. Намагничивание деталей с применением электромагнитов и дефектоскопов на постоянных магнитах
2.6.5. Индукционное намагничивание
2.7. Размагничивание деталей
2.7.1. Способы размагничивания деталей
2.7.2. Схемы размагничивания деталей
2.7.3. Способы повышения эффективности размагничивания деталей
Глава 3. ФАКТОРЫ, ВЛИЯЮЩИЕ НА ЧУВСТВИТЕЛЬНОСТЬ МАГНИТОПОРОШКОВОГО КОНТРОЛЯ
3.1. Направление намагничивания контролируемого объекта
3.2. Толщина немагнитного покрытия
3.3. Соотношение нормальной и тангенциальной составляющих напряженности поля на контролируемом участке детали
3.4. Скорость уменьшения намагничивающего поля
3.5. Форма детали
Глава 4. МАГНИТНЫЕ ИНДИКАТОРЫ
4.1. Способы применения магнитных индикаторов при магнитопорошковом контроле
4.2. Магнитные порошки, пасты и суспензии
4.3. Устройства для определения чувствительности порошков и суспензий
4.4. Дефектограммы
4.5. Магнитная коагуляция порошков при проведении магнитопорошкового контроля
Глава 5. ОСМОТР ДЕТАЛЕЙ И РАСШИФРОВКА ИНДИКАТОРНЫХ РИСУНКОВ
5.1. Основные требования к осмотру деталей
5.2. Расшифровка индикаторных рисунков
5. 3. Дефекты, возникающие при эксплуатации, ремонте и обнаруживаемые при магнитопорошковом контроле
5.4. Дефекты, возникающие при сварке, шлифовании и термической обработке деталей
5.5. Дефекты металлургического происхождения
5.6. Мнимые дефекты и способы их определения
Глава 6. ОБРАЗЦЫ ДЛЯ МАГНИТОПОРОШКОВОЙ ДЕФЕКТОСКОПИИ
6.1. Виды образцов, применяемых для магнитопорошковой дефектоскопии
6.2. Образцы-детали с искусственными дефектами
6.3. Образец для магнитопорошковой дефектоскопии МО-1
6.4. Образец для магнитопорошковой дефектоскопии МО-2
6.5. Образец для магнитопорошковой дефектоскопии МО-3
6.6. Образец для магнитопорошковой дефектоскопии МО-4
6.7. Принципы проверки магнитопорошковых дефектоскопов
6.7.1. Проверка электрических и магнитных характеристик магнитопорошкового дефектоскопа
6.7.2. Проверка работоспособности системы намагничивающее устройство — магнитный индикатор
Глава 7. ДЕФЕКТОСКОПЫ И ПРИБОРЫ ДЛЯ МАГНИТОПОРОШКОВОГО КОНТРОЛЯ ДЕТАЛЕЙ И УЗЛОВ
7. 1. Общая характеристика дефектоскопов для магнитопорошкового контроля деталей и узлов
7.2. Универсальный магнитопорошковый дефектоскоп У-604-64
7.3. Универсальный магнитопорошковый дефектоскоп У-604-70М
7.4. Переносный магнитопорошковый дефектоскоп ПМД-70
7.5. Стационарный магнитопорошковый дефектоскоп МД1-УАР
7.6. Стационарный магнитопорошковый дефектоскоп УМД-1М
7.7 Стационарный магнитопорошковый дефектоскоп УМДЭ-2500М
7.8. Стационарный магнитопорошковый дефектоскоп УМД-9000М
7.9. Стационарный магнитопорошковый индукционный дефектоскоп ДИН-1
7.10. Переносный магнитопорошковый дефектоскоп МД-4
7.11. Переносный магнитопорошковый дефектоскоп МД-6
7.12. Переносный магнитопорошковый дефектоскоп МДЛ-2
7.13. Дефектоскопы вращающегося поля У-2407 и МД-11ВП
7.14. Переносный магнитопорошковый дефектоскоп УНМ 300/2000
7.15. Передвижной магнитопорошковый дефектоскоп ИМД-10П
7.16. Устройство намагничивающее на постоянных магнитах УН-5
7. 17. Переносные магнитопорошковые дефектоскопы ДМЭ-22Ц, ДМЭ-23Ц, ДМЦ-21П, МПК-УНЛ-10Ц
7.18. Прибор ПКМС-2М
7.19. Тест-образец ТО-1
7.20. Прибор для контроля качества суспензий МФ-10СП
7.21. Облучатель ультрафиолетовый переносный КД-3-3Л
7.22. Облучатель ультрафиолетовый УФО-3-500
7.23. Магнитометр МФ-23И
7.24. Магнитометр МФ-23ИМ
7.25. Прибор МФ-24ФМ
7.26. Зарубежные магнитопорошковые дефектоскопы
Глава 8. МЕТОДИКИ МАГНИТОПОРОШКОВОГО КОНТРОЛЯ ДЕТАЛЕЙ И УЗЛО
8.1. Магнитопорошковый кон-троль деталей с применением способа воздушной взвеси
8.1.1. Принцип работы и схема установки У-956
8.1.2. Методика контроля хромированных деталей способом воздушной взвеси
8.1.3. Методика обнаружения подповерхностных дефектов и прижогов на деталях способом воздушной взвеси
8.1.4. Методика контроля ко-жухов камер сгорания двигателей РД-45 и ВК-1 способом воздушной взвеси
8.2. Магнитопорошковый кон-троль бугеля
8. 3. Магнитопорошковый кон-троль рам тележек шасси са-молета
8.4. Методика магнитопорошкового контроля лопаток компрессоров
8.4.1. Способы установления лопаток в электромагните
8.4.2. Рекомендации по установлению лопаток между полюсами стационарного электромагнита
8.4.3. Общие рекомендации по выбору режимов намагничивания лопаток компрессоров
8.5. Контроль продольных сварных швов амортизационной стойки шасси
8.6. Магнитопорошковый кон-троль стяжных болтов колеса КН 21
8.7. Контроль шлицев валов воздушных винтов в аэродромных условиях
8.8. Магнитопорошковый кон-троль ходовых винтов подъемников закрылок в аэродромных условиях
8.9. Магнитопорошковый кон-троль крайних витков пружины мембраны ограничителя
8.10. Магнитопорошковый кон-троль цилиндров амортизаторов главных ног шасси самолета
8.11. Магнитопорошковый кон-троль штанги разворота шасси самолета
8.12. Магнитопорошковый кон-троль полуоси шасси при ремонте
8.13. Магнитопорошковый кон-троль подкосов крепления двигателя
8. 14. Методика контроля лопаток 1-й ступени ротора компрессора при ремонте
8.15. Методика контроля втулочно-роликовых цепей П-4
8.16. Методика контроля диска 8-й ступени компрессора ГДТ после его демонтажа
8.17. Методика контроля штока амортизатора передней стойки шасси после его демонтажа
8.18. Методика контроля ушкового наконечника штока силового цилиндра основной стойки шасси
8.19. Методика контроля глав-ной балки крыла самолета
8.20. Методика контроля узла крепления обода шпангоута № 13 к поперечной балке фюзеляжа
8.21. Методика контроля болтов
8.22. Методика контроля балансира руля высоты самолета
8.23. Методика контроля сварных швов с применением электроконтактов дефектоскопов ПМД-70 и МД-50П
8.24. Контроль сварных соединений в эксплуатации летательных аппаратов
8.25. Намагничивание сварных швов импульсным полем с помощью электроконтактов
8.26. Способы контроля и схемы намагничивания деталей авиационной техники в эксплуатации и ремонте
8. 27. Особенности контроля изделий с применением электромагнита переменного тока
Глава 9. ТЕХНИКА БЕЗОПАСНОСТИ ПРИ МАГНИТОПОРОШКОВОМ КОНТРОЛЕ
ПРИЛОЖЕНИЯ
П1. Соотношение единиц магнитных величин
П2. Таблицы соответствия магнитных единиц
П3. Основные магнитные характеристики конструкционных сталей
П4. Магнитные характеристики сталей, петли магнитного гистерезиса
П5. Типовая программа подготовки по магнитопорошковому методу персонала по неразрущающему контролю
СПИСОК ЛИТЕРАТУРЫ
Книга 3. КАПИЛЛЯРНЫЙ КОНТРОЛЬ
(М.В. Филинов)
ВВЕДЕНИЕ
Глава 1. КАПИЛЛЯРНЫЙ КОНТРОЛЬ — ОСНОВНЫЕ ПОНЯТИЯ, ТЕРМИНЫ И ОПРЕДЕЛЕНИЯ
Глава 2. ИСТОРИЯ ИЗУЧЕНИЯ КАПИЛЛЯРНЫХ ЯВЛЕНИЙ И КАПИЛЛЯРНОГО КОНТРОЛЯ В РОССИИ
2.1. История изучения капиллярных явлений
2.2. История развития люминесцентной и контрастной (цветной) дефектоскопии в России
Глава 3. ФИЗИКА КАПИЛЛЯРНОГО КОНТРОЛЯ
3. 1. Смачивание и поверхностное натяжение
3.2. Адгезия и когезия
3.3. Явление капиллярности. Капиллярное давление
3.4. Растворение
3.5. Давление насыщенного пара
3.6. Диффузия
3.7. Сорбционные явления. Сорбция и адсорбция
3.8. Образование многофазных сред
3.9. Поверхностно-активные вещества (ПАВ)
3.10. Ультразвуковой капиллярный эффект и акустическая кавитация
3.11. Взаимодействие «жидкость — жидкость» в капилляре
3.12. Размерный эффект вязкости
3.13. Люминесценция
Глава 4. ЗАКОНЫ МИГРАЦИИ ДЕФЕКТОСКОПИЧЕСКИХ МАТЕРИАЛОВ В ДЕФЕКТЕ
4.1. Гидродинамика заполнения сквозного капилляра
4.2. Гидродинамика заполнения тупикового капилляра
4.3. Гидродинамика проявления сорбционным проявителем
4.4. Особенности проявления суспензионными проявителями
Глава 5. СРЕДСТВА КАПИЛЛЯРНОГО КОНТРОЛЯ (ДЕФЕКТОСКОПИЧЕСКИЕ МАТЕРИАЛЫ)
5.1. Пенетранты
5.2. Очиститель от пенетранта (очиститель)
5. 3. Проявитель пенетранта (проявитель)
5.4. Эмульгаторы
5.5. Наборы дефектоскопических материалов
5.6. Нормы расхода дефектоскопических материалов
5.7. Параметры контроля качества пенетрантов
Глава 6. ОБОРУДОВАНИЕ КАПИЛЛЯРНОГО КОНТРОЛЯ
6.1. Общие технические требования к оборудованию капиллярной дефектоскопии
6.2. Освещение и ультрафиолетовое облучение
6.3. Капиллярные дефектоскопы. Дефектоскопические установки и линии автоматизированного контроля
6.4. Ультразвуковые установки для интенсификации процессов капиллярного контроля
Глава 7. ТЕСТ-ОБЪЕКТЫ
7.1. Имитаторы дефектов
7.2. Компараторы
7.2.1. Описание набора тест-панелей по JIS Z 2343
7.2.2. Работа с тест-панелями по JIS Z 2343
7.3. Мониторы пенетрантных систем
7.3.1. Описание монитора пенетрантной системы PSM-5
7.3.2. Работа с тест-панелью PSM-5
7.3.3. Обслуживание и хранение тест-панели PSM-5
7. 4. Отечественные тест-объекты
Глава 8. ТЕХНОЛОГИЯ КАПИЛЛЯРНОГО КОНТРОЛЯ
8.1. Классификация капиллярных методов контроля. Обозначения методов
8.2. Процесс капиллярного контроля. Общие замечания
8.3. Основные стадии капиллярного контроля
8.3.1. Подготовка поверхности и очистка
8.3.2. Нанесение пенетранта. Контакт с пенетрантом. Методы интенсификации контакта
8.3.3. Время контакта с пенетрантом
8.4. Удаление излишков пенетранта с поверхности объекта контроля
8.5. Проявление
8.6. Оценка производительности капиллярного контроля
Глава 9. НАБЛЮДЕНИЕ, ДОКУМЕНТИРОВАНИЕ И ИНТЕРПРЕТАЦИЯ РЕЗУЛЬТАТОВ КАПИЛЛЯРНОГО КОНТРОЛЯ
9.1. Общие замечания. Методы наблюдения индикаций
9.2. Психофизиологические особенности зрения оператора
9.3. Факторы, влияющие на надежность интерпретации индикаций
9.4. Интерпретация результатов капиллярного контроля
9.5. Наблюдение и интерпретация некоторых характерных индикаций
9. 6. Ложные (нерелевантные) индикации
Глава 10. ЧУВСТВИТЕЛЬНОСТЬ И КОЛИЧЕСТВЕННЫЕ ОЦЕНКИ КАПИЛЛЯРНОГО КОНТРОЛЯ
10.1. Чувствительность капиллярного контроля
10.2. Количественные оценки чувствительности капиллярного контроля
Глава 11. КОМПЬЮТЕРНЫЙ АНАЛИЗ РЕЗУЛЬТАТОВ КАПИЛЛЯРНОГО КОНТРОЛЯ
11.1. Общие замечания. Методы регистрации индикаций капиллярного контроля
11.2. Состав телевизионной компьютерной системы автоматизированного анализа индикаций
11.3. Цифровое представление изображения. Компрессия изображения
11.4. Обработка цифровых изображений индикаций и количественный анализ по изображению
11.5. Количественный анализ индикаций капиллярного контроля с использованием программного пакета SPECTR MERA
Глава 12. ТЕХНИКА БЕЗОПАСНОСТИ ПРИ КАПИЛЛЯРНОМ КОНТРОЛЕ
Глава 13. СТАНДАРТЫ, ПЕРСОНАЛ
13.1. Стандарты в капиллярном контроле
13.2. Персонал капиллярного контроля
СПИСОК ЛИТЕРАТУРЫ
назад
Магнитный метод неразрушающего контроля
Магнитный метод неразрушающего контроля (МК) — один из методов контроля, не оказывающих разрушающее воздействие на испытуемый образец. В основе Магнитного контроля лежит анализ взаимодействие магнитного поля с образом, на основании которого составляется заключение о дальнейшей эксплуатации образца.
Магнитный метод можно разделить на несколько подметодов, в зависимости от характера получения информации об образце:
Магнитопорошковый
Магнитопорошковый метод дефектоскопии используется для выявление поверхностных и, залегающей на небольшой глубине, дефектов в ферромагнитных материалах, таких как железо, кобальт, никель и некоторые сплавы на их основе.
Первым делом необходмио обработать образец магнитной суспензией.
После нанесения суспензии, специалист намагничивает образцец. Намагничивание может осуществляться в результате воздействия на образец постоянным током, в результате чего возникает магнитное поле или же при воздействии уже созданного магнитного поля от внешнего источника. После намагничивания частицы суспензии выстроятся вдоль линий магнитного поля, проходящих перпендикулярно электрическому току, вне зависимости от того, переменный он или постоянный.
Наличие нарушения в структуре материала изменяет магнитное поле и создает его утечку, притягивающую частицы магнитной суспензии. Таким образом, дефект в материале обнаруживается визуальным методом. После этого характер дефекта исследуется с помощью других более детальных методов контроля, таких как Ультразвуковой метод.
После успешного проведения контроля образец необходимо размагнитить. Для этого используется специальное оборудование, работа которого противоположна работе намагничивающего устройства. Чтобы размагнитить деталь, необходимо подвергнуть её воздействию тока, равного или выше по силе, чем при намагничивании. После этого деталь оставляют на некоторое время для окончательного размагничивания.
В качестве порошка или магнитной суспензии используют оксид железа. Размер частиц зависит от схемы проведения контроля. Так же для данных целей возможно использование определенных аэрозолей.
Об остальных методах Магнитного контроля мы расскажем Вам в следующий раз.
Пройти обучение и аттестацию специалистов по Магнитному методу неразрушающего контроля на I, II и III уровни, а так же аттестовать лабораторию неразрушающего контроля Вы сможете, обратившись к нам по номеру +7 (495) 663-71-07.
«Возможности магнитопорошкового метода неразрушающего контроля»
Идею метода магнитопорошковой дефектоскопии приписывают Вильяму Е. Хоку (W. E. Hоkе) и даже называют дату — 1922 г., когда он сделал заявку на патент. Однако до 1929 г. для развития этой идеи ничего почти не было сделано вследствие совершенства имевшейся тогда техники намагничивания и отсутствия подходящих средств испытания. В 1929 г. А. В. Де-Форест пытался применить этот метод для обнаружения продольных дефектов в бурильных трубах, намагничивая их циркулярным полем постоянного тока, но из-за несовершенства порошка (стальные опилки) ему не удалось решить эту задачу. В 1930 г. Т. Р. Уоттс (Т. R. Watts) опубликовал исследование, в котором впервые указал на возможность применения метода для испытания качества сварных швов. В том же году делается первая попытка применить метод в области авиационной промышленности. Вплоть до 1934 г. метод продолжал оставаться во всех странах лабораторной редкостью. Вполне законченные и специально сконструированные промышленные дефектоскопы начинают появляться с 1934 г.
В Советском Союзе первый прибор, работающий по методу магнитной порошковой дефектоскопии, был разработан и изготовлен академиком Н. С. Акуловым в 1934 г. в магнитной лаборатории Научно-исследовательского института физики Московского государственного университета. В 1935 г. в Военно-воздушной академии им. Жуковского автором была разработана первая дефектоскопическая установка, работающая на переменном токе. Эта установка была применена для контроля силовых шпилек мотора на заводе им. Фрунзе.
Магнитопорошковый метод контроля основан на явлении притяжения частиц магнитного порошка в местах выхода на контролируемую поверхность изделия магнитного потока, связанного с наличием нарушения сплошности материала. В намагниченных изделиях нарушения сплошности (дефекты) вызывают перераспределение магнитного потока и выход части его на поверхность (магнитный поток дефекта). На поверхности изделия создаются локальные магнитные полюсы, притягивающие частицы магнитного порошка, в результате чего образуются цепочки намагниченных частиц обозначающие дефектные участки, ориентированные по магнитным силовым линиям поля.
Магнитопорошковый метод предназначен для выявления поверхностных и под поверхностных (на глубине до 1,5 … 2 мм) дефектов типа нарушения сплошности материала изделия: трещины, волосовины, расслоения, не проварка стыковых сварных соединений, закатов и т.д.
Существуют «сухой» и «мокрый» способы нанесения индикатора на контролируемый объект. В первом случае для обнаружения дефектов используют сухой ферромагнитный порошок. При использовании «мокрого» метода контроль осуществляется с помощью магнитной суспензии, т.е. взвеси ферромагнитных частиц в жидких средах: трансформаторном масле, смеси трансформаторного масла с керосином, смеси обыкновенной воды с антикоррозионными веществами и др.
Процесс магнитопорошкового контроля состоит из 5 этапов:
1 — подготовка изделия к контролю. Изделия, подаваемые на намагничивающие устройства, должны быть очищены от покрытий, мешающих их намагничиванию или смачиванию (отслаивающаяся окалина, масла, грязь, иногда изоляционные покрытия и т. п.).
2 — намагничивание детали. Намагничивание детали является одной из основных операций контроля. От правильного выбора способа, направления и вида намагничивания, а также рода тока во многом зависит чувствительность и возможность обнаружения дефектов.
3 — нанесение на поверхность детали магнитного индикатора (порошка или суспензии). Оптимальный способ нанесения суспензии заключается в окунании детали в бак, в котором суспензия хорошо перемешана, и в медленном удалении из него. Однако этот способ не всегда технологичен. Чаще суспензию наносят с помощью шланга, душа или аэрозольного балона. Напор струи должен быть достаточно слабым, чтобы не смывался магнитный порошок с дефектных мест. При сухом методе контроля эти требования относятся к давлению воздушной струи, с помощью которой магнитный порошок наносят на деталь. Время стекания с детали дисперсной среды, имеющей большую вязкость относительно велико, поэтому производительность труда контролера уменьшается.
4 — контроль. Контроль проводится визуально после стекания с нее основной массы суспензии, когда картина отложений порошка становится неизменной. В сомнительных случаях и для расшифровки характера дефектов применяют оптические приборы, тип и увеличение которых устанавливают по нормативным документам.
5 — размагничивание. Для размагничивания на изделие воздействуют переменным магнитным полем с напряженностью, убывающей от максимального значения до нуля. Изделия, нагреваемые после магнитного контроля до 600…700°С и выше, размагничивать не следует.
Рисунок 1. Выявление трещин магнитопорошковым методом
а — открытой трещины; б — скрытой под слоем хрома толщиной 0,03 мм;
в — скрытой под слоем хрома толщиной 0,1мм
К недостаткам магнитопорошкового контроля следует отнести необходимость удаления защитных лакокрасочных покрытий толщиной свыше 0,03 мм и сложность размагничивания некоторых деталей.
Достоинствами магнитопорошкового контроля являются его относительно небольшая трудоемкость, высокая производительность и возможности обнаружения поверхностных и подповерхностных дефектов. При помощи этого метода выявляются не только полые несплошности, но и дефекты, заполненные инородным веществом. Магнитопорошковый метод может быть применен не только при изготовлении конструкций и деталей, но и в ходе их эксплуатации, например, для выявления усталостных трещин.
С целью повышения качества контроля сварных соединений и снижения вероятности пропуска дефектов в обследованных конструкциях в ГБУ «ЦЭИИС» с 2017 г. вводится магнитопорошковый метод неразрушающего контроля в дополнение к применяемым методам НК.
Автор статьи инженер-эксперт Митин С.В.
Список использованных источников
1. Курс лекций по магнитопорошковому методу неразрушающего контроля, А. Марцинкевич Минск 2010;
2.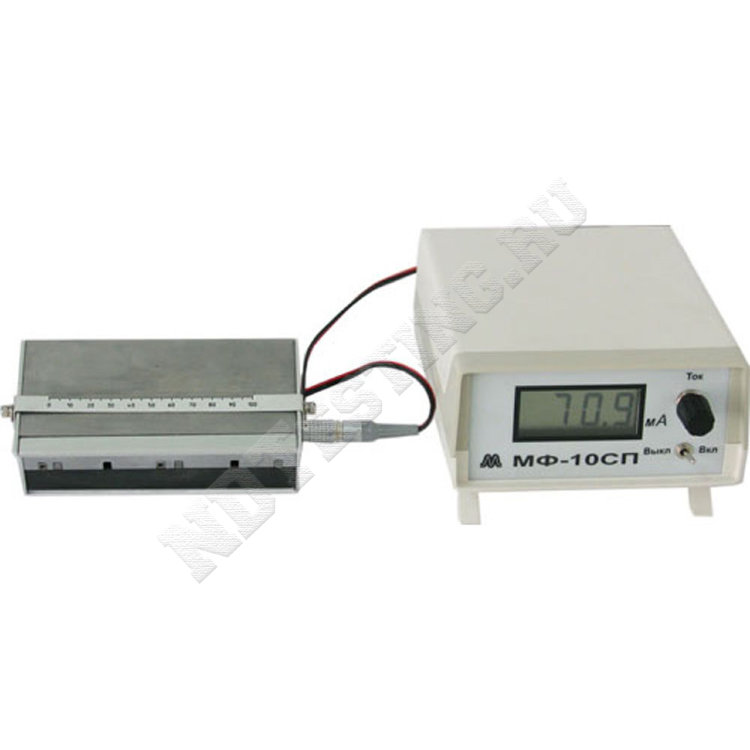
Неразрушающий контроль — Контроль магнитных частиц (MPI)
Что такое контроль магнитных частиц?
Магнитопорошковый контроль (часто сокращенно MT или MPI) — это метод неразрушающего контроля, который обеспечивает обнаружение линейных дефектов, расположенных на поверхности ферромагнитных материалов или вблизи нее. Он рассматривается в первую очередь как метод исследования поверхности.
Контроль магнитных частиц (MPI) — очень эффективный метод обнаружения поверхностных разрывов и небольших подповерхностных дефектов, таких как трещины, поры, холодный притир, отсутствие плавления боковых стенок в сварных швах и т. Д. В магнитных материалах.
Есть много разных техник. Наиболее универсальным методом является использование ручного электромагнитного ярма 110 В переменного тока, белой удаляемой краски в качестве контрастного фона и магнитных «чернил», состоящих из частиц порошка железа в жидкой основе.
Область намагничивается магнитом ярма. В случае наличия поверхностного или слегка подповерхностного дефекта силовые линии магнитного поля деформируются вокруг дефекта.
Наносятся магнитные чернила, и частицы порошка железа перекрывают зазор, вызванный дефектом, и дают видимую индикацию на белом контрастном фоне.
Контроль магнитных частиц (MPI) обеспечивает очень хорошее разрешение дефектов и широко используется в:
Сварные изделия из магнитных материалов, отливки, обнаружение усталостных трещин в изделиях, подверженных циклическим нагрузкам
Схема потоковых линий, проходящих через перпендикулярный и параллельный дефект,
и утечку потока, возникающую вокруг перпендикулярного дефекта.
Проверка магнитных частиц выполняется в четыре этапа:
- Создание магнитного поля в образце
- Нанесите магнитные частицы на поверхность образца
- Осмотрите поверхность, ищите группы частиц, вызванные дефектами
- Размагнитить и очистить образец
Преимущества контроля магнитных частиц
- Может обнаруживать как поверхностные, так и подповерхностные дефекты
- Некоторые форматы инспекции чрезвычайно портативны и недороги
- Быстрая проверка с немедленными результатами
- Показания видны инспектору непосредственно на поверхности образца
- Может обнаруживать дефекты, размазанные по поверхности
- Может проверять детали неправильной формы (внешние шлицы, коленчатые валы, шатуны и т.
Д.).)
Ограничения контроля магнитных частиц
- Образец должен быть ферромагнитным (например, сталь, чугун)
- Краска толщиной более 0,005 дюйма должна быть удалена перед проверкой.
- Часто требуется дополнительная очистка и последующее размагничивание
- Максимальная чувствительность по глубине обычно составляет 0,100 дюйма (больше в идеальных условиях)
- Согласование магнитного потока и дефекта важно
Стандарты
Стандарты Международная организация по стандартизации (ISO)
- ISO 3059, Неразрушающий контроль — Пенетрантный контроль и испытание магнитными частицами — Условия просмотра
- ISO 9934-1, Неразрушающий контроль. Контроль магнитными частицами. Часть 1. Общие принципы.
- ISO 9934-2, Неразрушающий контроль. Испытание на магнитные частицы. Часть 2: Среда обнаружения .
- ISO 9934-3, Неразрушающий контроль. Контроль магнитными частицами.
Часть 3: Оборудование
. - ISO 17638, Неразрушающий контроль сварных швов. Магнитопорошковый контроль
- ISO 23279, Неразрушающий контроль сварных швов. Магнитопорошковый контроль сварных швов. Уровни приемки .
Европейский комитет по стандартизации (CEN)
- EN 1290, Испытания на растрескивание поверхности
- EN 1330-7, Неразрушающий контроль — Терминология — Часть 7: Термины, используемые при испытании магнитных частиц
- EN 1369, Основание — Контроль магнитных частиц
- N 10228-1, Неразрушающий контроль стальных поковок. Часть 1. Магнитопорошковый контроль
- EN 10246-12, Неразрушающий контроль стальных труб — Часть 12: Магнитопорошковый контроль бесшовных и сварных труб из ферромагнитной стали для обнаружения поверхностных дефектов
- EN 10246-18, Неразрушающий контроль стальных труб. Часть 18: Магнитопорошковый контроль концов труб из бесшовных и сварных труб из ферромагнитной стали для обнаружения ламинарных дефектов
Американское общество испытаний и материалов (ASTM)
- ASTM E1444-05
- ASTM A 275 / A 275M Метод испытаний для исследования стальных поковок на магнитные частицы
- ASTM A456 Спецификация для контроля магнитных частиц больших поковок коленчатого вала
- ASTM E543 Стандартная спецификация практики для оценочных агентств, выполняющих неразрушающий контроль
- ASTM E 709 Руководство по испытанию на магнитные частицы
- ASTM E 1316 Терминология неразрушающего контроля
- ASTM E 2297 Стандартное руководство по использованию источников и измерителей УФ-А и видимого света, используемых в методах проникающих жидкостей и магнитных частиц
Испытание магнитными частицами (MPT) | Инспекционная
Тестирование магнитными частицами (MPT) , также называемое контролем магнитных частиц, представляет собой метод неразрушающего контроля (NDE) , используемый для обнаружения поверхностных и слегка приповерхностных дефектов в большинстве ферромагнитных материалов, таких как железо, никель и кобальт некоторые из их сплавов. Поскольку это не требует той степени подготовки поверхности, которая требуется для других методов неразрушающего контроля, проведение MPT является относительно быстрым и легким. Это сделало его одним из наиболее часто используемых методов NDE.
БЕСПЛАТНЫЙ РЕСУРС: Щелкните здесь, чтобы загрузить подробный обзор испытаний на магнитные частицы.
MPT — это довольно простой процесс с двумя вариантами: влажное испытание магнитными частицами (WMPT) и сухое испытание магнитными частицами (DMPT).В любом из них процесс начинается с пропускания магнитного тока через компонент. Любые трещины или дефекты в материале прервут прохождение тока и вызовут распространение магнетизма от них. Это создаст «поле утечки потока» в месте повреждения.
Второй этап заключается в нанесении металлических частиц на компонент. Если есть какие-либо дефекты на поверхности или рядом с ней, поле рассеяния потока будет притягивать частицы к месту повреждения. Это дает видимую индикацию приблизительного размера и формы дефекта.
Есть несколько преимуществ MPT по сравнению с другими методами NDE. Он очень портативный, обычно недорогой и не требует строгой предварительной очистки. MPT также является одним из лучших вариантов для обнаружения мелких поверхностных трещин. Это быстро, легко и работает через тонкие покрытия . Наконец, существует несколько ограничений, касающихся размера / формы образцов для испытаний.
Несмотря на свои сильные стороны, этот метод не безграничен. Материал должен быть ферромагнитным.Точно так же ориентация и сила магнитного поля имеют решающее значение. Метод обнаруживает только поверхностные и приповерхностные дефекты. Те, что ниже, требуют альтернативных методов. Иногда для выполнения этого метода требуются большие токи, поэтому иногда возможно «сжигание» испытываемых деталей. Кроме того, после завершения MPT компонент необходимо размагнитить, что иногда может быть затруднено.
Это определение неполное? Вы можете помочь, внося свой вклад.
Связанные темы
Инструменты тем
Поделиться темой
Внести вклад в определение
Мы приветствуем обновления этого определения Integripedia от сообщества Inspectioneering.Щелкните значок ссылку ниже, чтобы открыть форму, которая позволит вам внести изменения в определение и отправить их инспекционному составу.
Способствовать определениюНеразрушающий контроль — Metallurgical Technologies, Inc.
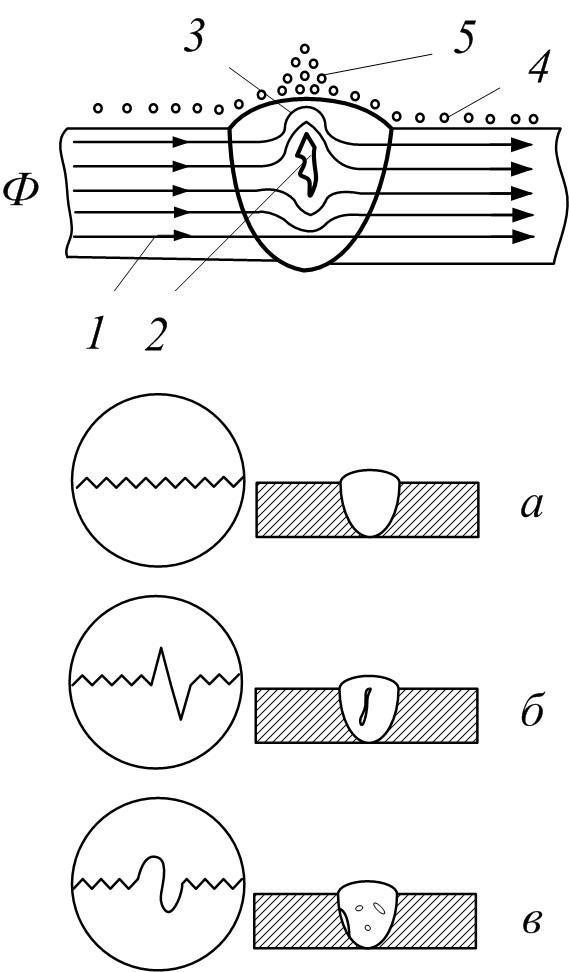
Магнитные частицы (MT), испытание на проницаемость жидкости (PT), энергодисперсионная спектроскопия и репликация в полевых условиях:
Исследование магнитных частиц (MT):
Контроль с использованием магнитных частиц (MPI) — это процесс неразрушающего контроля (NDT) для обнаружения поверхностных и неглубоких подповерхностных неоднородностей в ферромагнитных материалах.Процесс создает магнитное поле в детали. Чтобы определить утечку, на деталь наносят частицы железа в сухом или влажном виде. Эти частицы притягиваются к любым областям, где есть разрыв магнитного поля, и образуют так называемый индикатор. Затем оценивается индикация магнитных частиц, чтобы определить ее причину.
Контроль магнитных частиц — это обычно используемый метод неразрушающего контроля «неразрушающий контроль» для выявления трещин, швов, пустот или дефектов материала.
Тест на проникновение жидкости (PT):
Различные типы пенетранта Методы испытаний используются для обнаружения дефектов материала, открытых на поверхность, или для обнаружения трещин на открытой поверхности. Используются красный краситель или флуоресцентные пенетранты, а также различные типы влажных и сухих проявителей. Пенетрантные исследования флуоресцентным красителем проводятся в условиях черного света, чтобы гарантировать максимальную обнаруживаемость очень мелких усталостных трещин. Жидкостный пенетрант, если вид неразрушающего контроля.
Крупный план индикаторов флуоресцентных магнитных частиц и , проникающих в краситель , при черном освещении.
Слева: флуоресцентная индикация магнитных частиц на корне зуба шестерни.
Справа: поперечные усталостные трещины в заднем редукторе, идентифицированные с помощью флуоресцентного жидкостного исследования.
Энергодисперсионная спектрометрия (EDS):
A Сканирующий электронный микроскоп , оборудованный EDS, обеспечивает химико-композиционный микроанализ поля зрения или точечный анализ мельчайших частиц. Этот тип неразрушающего контроля может обнаруживать более 90 различных элементов с помощью нашего детектора с низким атомным числом. Этот неразрушающий контроль можно проводить на образцах от небольших до микроскопических.EDS можно использовать для определения химического состава коррозии, посторонних частиц, пятен, состава материалов и многого другого. Этот микроанализ также является неразрушающим тестом.
Репликация поля:
Полевая металлографическая репликация — это неразрушающий тест, который требуется в некоторых приложениях, где невозможно вывести компонент из эксплуатации или размер запрещает анализ в лаборатории. Различные реплицирующие среды позволяют MTi создавать портативную копию интересующей микроструктуры.Репликация включает удаление поверхности материала шлифованием с последующей полировкой мелкими зернами. После того, как поверхность будет очищена от царапин и станет зеркальной, ее протравят различными кислотами, чтобы выявить металлографические особенности. После отверждения репликационной среды репликация удаляется из образца и анализируется либо на металлографе, либо на сканирующем электронном микроскопе.
Контроль магнитных частиц — обзор
Другие методы обнаружения трещин
Широко используются несколько других методов обнаружения трещин, включая контроль магнитных частиц, проникающий контроль красителя и ультразвук.Для магнитопорошкового контроля и дефектоскопии красителей используются многие химические препараты. К ним относятся растворители, красители и «проявители». Многие из них удобно упакованы в аэрозоли. Другие состоят из ванн, в которые погружаются проверяемые детали.
Растворители, как правило, обладают обезжиривающим действием и поэтому вредны для кожи. Они могут вызвать дерматит в долгосрочной перспективе, если не свести к минимуму контакт с кожей. Как правило, они относительно летучие, выделяют пары, которые можно вдохнуть.Воздействие на здоровье зависит от воздействия и относительной токсичности растворителя. Они могут включать раздражение глаз и легких, головную боль, тошноту, головокружение и головокружение. Бессознательное состояние или даже смерть могут возникнуть в результате воздействия паров растворителей в больших количествах.
В свое время предпочтительным вариантом были хлорированные растворители, поскольку они, как правило, негорючие. Стратегия заключалась в использовании растворителя с наименьшей токсичностью. Однако из-за опасений по поводу атмосферы многие обычные хлорированные растворители в настоящее время больше не используются.Это заставило работодателей выбирать альтернативы, некоторые из которых более токсичны, а некоторые легко воспламеняются. Таким образом, перед использованием растворителя следует изучить паспорт безопасности (MSDS) производителя, чтобы получить представление обо всех его свойствах, чтобы можно было принять меры для его правильного хранения и предотвращения воздействия паров и любых опасностей возгорания, которые могут возникают. Растворители всегда следует использовать в хорошо вентилируемых помещениях, чтобы избежать образования высоких концентраций паров.
Многие аэрозоли раньше содержали пропелленты на основе хлорированных углеводородов или хлорированных фторуглеродов (CFC), но сейчас они не используются. В настоящее время используемые пропелленты включают некоторые легковоспламеняющиеся вещества, такие как бутан. Следует внимательно прочитать паспорт безопасности материала. Некоторые хлорированные растворители все еще используются. Они имеют тенденцию разлагаться в дуге с образованием чрезвычайно токсичных продуктов, таких как фосген и хлористый водород. Поэтому важно следить за тем, чтобы пары растворителя не попадали в зоны, где проводится сварка.
Объемные запасы растворителей или аэрозолей следует хранить отдельно от рабочего помещения в контейнерах, соответствующих их свойствам, e.грамм. легковоспламеняющиеся вещества и препараты следует хранить в металлических шкафах с четкой маркировкой, указывающей на характер содержимого. В рабочем помещении следует держать только количество, необходимое для немедленной работы.
Если используются ванны для парового обезжиривания, они должны содержаться в хорошем рабочем состоянии — конструкция должна содержать пар, чтобы сотрудники не подвергались воздействию.
Следует по возможности избегать протирания предметов тканями, пропитанными растворителем, так как выброшенные салфетки могут представлять опасность пожара, и такая практика имеет тенденцию приводить к сильному воздействию на кожу и дыхательную систему.
Везде, где есть вероятность попадания капель жидкости в глаза, следует надевать средства защиты глаз. Персонал не должен есть или курить в местах, где есть растворители. Их следует тщательно мыть после работы, а также перед едой или курением.
Какие материалы можно использовать для испытаний на магнитные частицы?
Каждый опытный специалист по неразрушающему контролю знает, что существует множество методов, которые можно использовать для выполнения неразрушающего контроля.
В некоторых случаях только техник с определенным уровнем квалификации может выполнить определенный тест, поэтому выбранный метод будет зависеть от способностей ваших технических специалистов.
В других случаях вы можете выбрать конкретный метод из-за его стоимости, легкости очистки или портативности.
Испытание с помощью магнитных частиц — это метод, которым пользуются многие специалисты по неразрушающему контролю, но это не испытание, которое можно выполнить на всех устройствах и компонентах.
Испытание магнитными частицами — это проверенная временем практика, которая использовалась техническими специалистами по неразрушающему контролю в течение ряда лет, но подходит ли она для материалов ваших активов?
Вот что вам нужно знать.
Основы тестирования магнитных частиц
В большинстве методов неразрушающего контроля цель проверки состоит в обнаружении дефектов в проверяемом компоненте. То же самое можно сказать и о магнитопорошковых испытаниях (МП).
Этот метод тестирования использует магнитные поля для тестирования ферромагнитных материалов, таких как сталь. Ярмы, стержни, катушки или центральные проводники используются для прямого или косвенного приложения магнитного поля.
В процессе испытаний используется тонкий пигментированный порошок, который при нанесении на поверхность компонента втягивается в поле рассеяния магнитного поля.Если это отображается, нарушение непрерывности обнаруживается через видимый индикатор.
Что такое ферромагнитные материалы
Чтобы испытание на магнитные частицы дало значимый результат, проверяемые материалы должны быть ферромагнитными.
Ферромагнитные материалы относятся к «тем веществам, которые проявляют сильный магнетизм в том же направлении поля, когда к ним приложено магнитное поле», согласно веб-сайту по электротехнике Electrical 4 U.
Как правило, ферромагнитные материалы представляют собой металлы, поэтому испытания неметаллических материалов с помощью магнитных частиц невозможно. Обычные металлические материалы, такие как никель, железо, сталь и кобальт, являются ферромагнитными и являются идеальными кандидатами для испытаний на магнитные частицы.
Помимо конкретного типа материала, следует учитывать еще один фактор: испытания магнитными частицами выявляют только поверхностные дефекты. Проверка с помощью испытания магнитными частицами может показать, что в компоненте отсутствуют дефекты, даже если они есть глубоко под поверхностью.
Если вы опасаетесь, что исследуемый материал может иметь дефекты, выходящие за рамки дефектов поверхности, другой метод может оказаться более эффективным.
В конечном счете, решение о том, какой метод лучше всего, должно быть тщательно продумано каждым специалистом по неразрушающему контролю, поскольку они оценивают первые шаги проверки. Именно поэтому для подготовки технических специалистов в области неразрушающего контроля необходимо высококачественное обучение неразрушающему контролю.
Свяжитесь с TXNDT сегодня!
В TXNDT мы следим за тем, чтобы каждый технический специалист, которого мы обучаем, был полностью подготовлен к работе.Это обучение включает в себя все самые важные методы, от испытания магнитными частицами до испытания на проникновение жидкости и всего остального.
Поскольку требования к специалисту по неразрушающему контролю могут меняться от работы к работе, опытные инструкторы TXNDT гарантируют, что все потенциальные технические специалисты обладают квалификацией, чтобы взять на себя все, что им бросает следующая работа.
Начиная с вводных курсов по неразрушающему контролю и заканчивая сертификацией уровня 3 по неразрушающему контролю, мы активно подходим к обучению всех наших студентов и призываем всех потенциальных технических специалистов принимать активное участие в собственном обучении.
Если вы или ваш персонал ищете способы расширить свои навыки и возможности карьерного роста с помощью курсов неразрушающего контроля, рассмотрите возможность сертификации по неразрушающему контролю.
Но не доверяйте любой школе неразрушающего контроля. Если вы ищете первоклассный опыт, позвоните нам сегодня по телефону 281-231-0001 или посетите наш веб-сайт для получения дополнительной информации.
Магнитные частицы — MT Inspection
MISTRAS выполняет услуги по контролю сухих порошков и влажных флуоресцентных магнитных частиц ( MT ) для обнаружения поверхностных / приповерхностных дефектов в ферромагнитном материале.
MISTRAS применяют этот быстрый и экономичный метод проверки в полевых условиях и в наших лабораториях. При испытании на магнитные частицы техники намагничивают ферромагнитный материал и наносят на него тонко измельченные частицы железа, покрытые красителем. Частицы указывают на неоднородность материала, собираясь непосредственно над ним, что можно визуально обнаружить при надлежащих условиях освещения.
Методика требует наличия квалифицированного специалиста, чтобы различать релевантные и нерелевантные показания.Специалисты MISTRAS могут выполнить каждый этап процесса, включая предварительную очистку и подготовку поверхности, введение магнитного поля, нанесение среды и интерпретацию полученных показаний.
MISTRAS предлагает услуги по инспекции сухого порошка и мокрого люминесцентного MT в зависимости от области применения.
Преимущества контроля магнитных частиц
- Может обнаруживать как поверхностные, так и приповерхностные признаки
- Может проверять детали неправильной формы
- Предварительная очистка проверяемого актива менее важна, чем при использовании других методов проверки, поскольку существующие загрязнения не должны влиять на обнаружение дефектов
- Быстрое использование и более низкая стоимость по сравнению с другими методами NDT
- Результаты в реальном времени, поскольку индикация видна непосредственно на поверхности материала
- Портативный метод контроля делает его идеальным для полевых проверок
Испытание на влажных флуоресцентных магнитных частицах более точное, чем испытание на сухом порошке, для обнаружения очень мелких неоднородностей, поскольку частицы меньше. MISTRAS использует мокрые флуоресцентные магнитные частицы для обнаружения поверхностных и слегка приповерхностных неоднородностей.
Преимущество мокрого флуоресцентного материала MT заключается в его простоте и скорости нанесения, поскольку технические специалисты могут быстро распылять выбранную жидкость с магнитными частицами на большие площади поверхности. Он чрезвычайно чувствителен даже к очень маленьким и точным показаниям, увеличивая обнаружение показаний с последовательными и надежными результатами при минимальном времени проверки.Этот метод можно использовать для инспекций в процессе эксплуатации, что позволяет обнаружить повреждение активов без остановки производства.
Мокрая флуоресцентная лампа MT Инспекционные приложения
- Усталостные трещины
- Хлопья
- Шлифовальные трещины
- Включения в аэрокосмических блюмах, заготовках и стержнях
- Круги
- Трещины закалки
- Швы
- Усадочные трещины
- Коррозионное растрескивание под напряжением
- Слез
- Дефекты сварки
Сухие частицы осыпаются на поверхность испытуемого объекта по мере намагничивания предмета. Кластеризация магнитных частиц эффективна для обнаружения дефектов на шероховатых поверхностях, включая мелкие и подповерхностные трещины, а также проникновение корней. Сухие порошковые методы более портативны, чем мокрые флуоресцентные МТ.
Могут использоваться частицы различных размеров, при этом мелкие частицы более чувствительны к мелким неоднородностям, в то время как более крупные частицы обеспечивают более высокую устойчивость к загрязнению грязью или поверхностным мусором. Этот метод особенно подходит для обнаружения полей утечки от небольших дефектов.
Сухой порошок MT Инспекционные приложения
- Дефекты шероховатой поверхности
- Отсутствие проплавления сварных швов
- Проникновение корня
- Мелкие трещины
Понимание процесса контроля магнитных частиц (MT)
Процесс контроля или исследования магнитных частиц (MT) — это недорогой метод проведения неразрушающего контроля (NDE) ферромагнитного материала. Магнетизм использовался для проверки на наличие дефектов еще в 1868 году, когда он использовался для проверки наличия трещин в намагниченных стволах пушек с помощью компаса.Контроль магнитных частиц — довольно простая концепция. Это процесс поиска утечки магнитного потока. Как только рассматриваемая деталь намагничивается, она становится поляризованной: северный полюс находится там, где магнитная сила выходит, а южный полюс, где она входит. Пример этого можно увидеть, когда магнит сломан пополам. Каждая деталь представляет собой законченный магнит с северным и южным полюсами. Точно так же, если на поверхности есть трещина, полюса начнут формироваться с обеих сторон. Магнитное поле вокруг трещины изменится, выходя на север и снова входя в южный полюс.Когда это поле распространяется, это дает вид, похожий на утечку из материала, и поэтому называется полем рассеяния магнитного потока.
Процесс контроля магнитных частиц относительно прост; однако подготовка поверхности является важным первым шагом. На этом этапе требуется химическая очистка с использованием моющих средств, органических растворителей, растворов для удаления накипи или других процессов. Затем в деталь необходимо ввести магнитное поле. После намагничивания детали добавляются мелкие ферромагнитные частицы, такие как порошок железа.Избыток осторожно удаляется, обычно с помощью какой-либо воздушной струи. После этого деталь проверяется на наличие трещин. Любая область, где остается ферромагнитный материал, указывает на дефект. Наконец, деталь нужно повернуть на 90 градусов и повторить процесс, поскольку неоднородности, параллельные линиям магнитного потока, не приведут к утечке. Основными преимуществами использования магнитопорошкового контроля являются скорость исследования, низкая стоимость процесса и тот факт, что признаки дефектов видны непосредственно на поверхности материала.
В Pacific Magnet & Penetrant мы можем предоставить быстрые, эффективные и точные услуги по контролю магнитных частиц. Наш объект оснащен рядом инспекционных систем Magnaflux MT, все из которых обслуживаются опытными техниками-испытателями. Список этих систем представлен ниже. Для получения дополнительной информации о процессе контроля магнитных частиц, свяжитесь с нами напрямую.
Запросить цену
Контроль магнитных частиц (MT) Возможности:
- № оборудования
- Арт. №
- Общая информация
- 3 блока
- Magnaflux
- Состоит из 54-дюймового максимального раскрытия контактной головки, двухполупериодного выпрямленного 3-фазного (постоянного) источника питания и регулирования тока на 64 ступени. Также оснащен 12-дюймовой 5-витковой катушкой.
- 1 Устройство
- Magnaflux
- Состоит из 120-дюймового максимального раскрытия контактной головки, двухполупериодного выпрямленного 3-фазного (постоянного тока) источника питания и регулирования тока на 64 ступени.Также оснащен 20-дюймовой 5-витковой катушкой.
* Минимальные / максимальные значения тока указаны в сертификате калибровки оборудования.