Наши услуги ИНФОРМАЦИЯ:МЫ БЫЛИ ВЫБРАНЫ В 2019 г. АДМИНИСТРАЦИЕЙ НИЖНЕУДИНСКОГО МУНИЦИПАЛЬНОГО ОБРАЗОВАНИЯ ДЛЯ ПРОВЕДЕНИЯ ОБСЛЕДОВАНИЯ ЗДАНИЙ ПОСЛЕ ЗАТОПЛЕНИЯ В ИРКУТСКОЙ ОБЛАСТИ НАС ВЫБИРАЮТ АРБИТРАЖНЫЕ СУДЫ ПОЧЕМУ СУДЫ ОТКЛОНЯЮТ ЗАКЛЮЧЕНИЯ Читать статью! ******* МЫ РАБОТАЕМ с 8-00 до 22-00 Ждем Ваших звонков не только в будние дни, а также в субботу и в воскресенье. Наши эксперты выезжают на экспертизу и обследование ежедневно и без выходных. ******* СТРОИТЕЛЬНЫЙ АДВОКАТ Бесплатная консультация нашего строительного юриста. Анализ перспектив Вашего спора в суде или в досудебном порядке. Юридические услуги оказывают юристы в области строительного права. ******* ДОСТАВКА курьером строительного заключения, актов приемки-сдачи, счетов-фактур. ******* ОСТОРОЖНО! В последнее время появилось большое количество мошенников и непрофессионалов. Читать Проверка экспертной организации. ******* ДОСТИЖЕНИЯ МНСЭ 352 проведенных строительных экспертиз; 126 проведенных обследований; 12 проведенных энергоаудита; 389 разработанных проектов. ******* МНСЭ — участник и докладчик ******* ПЛАГИАТ Увидели у конкурентов похожий на наш сайт по структуре или по содержанию. НАШИ КЛИЕНТЫ: Арбитражный суд г. Москвы Арбитражный суд МО Арбитражный суд Санкт-Петербурга и Ленинградской области ОАО «Мосметрострой» ОАО «Одинцовский лакокрасочный завод» ГУ РАН «Московский дом-пансионат» ОАО «Балтинвестбанк» ЗАО «Останкинский завод бараночных изделий» ОАО «ЭХО» ЗАО «КСПЗ» ОАО «Пятовское карьероуправление» ОАО «Фабрика-химчистка № 21» ЗАО «ЦТК» ЗАО «НТ СМУ-333» ЗАО «КАСКАД-МЕБЕЛЬ» ООО СМУ Варшавское» ЗАО «Строймеханика» УК «Регионгазфинанс» ОАО «Московский станкостроительный завод имени Серго Орджоникидзе» ЗАО «БРПИ» ОАО «Стройтрансгаз» ЗАО ЦНТУ «Механика» ОАО «Ростелеком» ОАО «Икшинское опытно-производственное предприятие» | Существует несколько видов неразрушающих методов контроля сварных соединений. Внешний осмотр не требует материальных затрат, поэтому самый доступный и распространенный метод. Его применяют обязательно в начале исследования сварных соединений вне зависимости от использования в дальнейшем других методов. Он позволяет выявить все виды наружных дефектов: непровары, наплывы, подрезы и другие дефекты. Внешний осмотр подразумевает также и обмер сварных соединений и швов, замер подготовленных коромок. Сварные соединения измеряют стандартными мерительными шаблонами. Для определения непроницаемости емкостей и сосудов, работающих под давлением, используют гидравлические и пневматические испытания. Сосуд заполняют водой, после этого осматривают. Влажные швы будут свидетельствовать о плохой герметичности. Громоздкие изделия испытывают поливом под давлением. Гидравлическое испытание проводят также с повышенным давлением. Герметичность проверяют по наличию влаги на швах и величине снижения давления. В тех случаях, когда гидравлическое испытание невозможно, проводят пневматические испытания. Сосуд заполняют сжатым воздухом, швы смачивают мыльным раствором или погружают изделие в воду. Если пузырей нет — сосуд герметичен. Есть вариант проверки сосуда гелием, который отличается исключительной проницаемостью. Внутри сосуда создают вакуум, а снаружи обдувают смесью воздуха с гелием. Герметичность швов проверяют также керосином. Он имеет высокую проникающую способность, поэтому, если швы неплотные, обратная сторона темнеет или появляются пятна. Существует также и химический метод, основанный на использовании взаимодействия аммиака с контрольным веществом. Магнитный контроль. Дефекты швов обнаруживают при рассеивании магнитного поля. На поверхность намагниченного соединения наносят железные опилки, окалину и т.п., которые реагируют на магнитное поле. Радиационный контроль дает возможность обнаружить дефекты шва, не видимые при наружном осмотре. Сварной шов просвечивают рентгеновским или гамма-излучением, проникающим через металл. Рентгеновский метод требует громоздкой аппаратуры, поэтому чаще используется гамма-метод контроля сварных соединений. Однако у радиографического контроля есть недостатки: просвечивание не позволяет выявить трещины, которые находятся не по направлению основного луча. Кроме радиационных методов контроля используют рентгеноскопию, когда сигнал о дефектах появляется на экране прибора. Этот метод более производителен и точностью практически не уступает радиационным методам. Ультразвуковой метод, относящийся к акустическим, позволяет обнаружить дефекты с малым раскрытием: трещины, газовые поры и шлаковые включения, даже те, которые не удается определить радиационной дефектоскопией.
Вместе с этой страничкой посетители нашего сайта просматривают: |
Методы неразрушающего контроля сварных соединений
Для выявления внутренних дефектов сварных соединений в Правилах регламентируются следующие методы неразрушающего контроля сварных соединений радиографический и ультразвуковой, капиллярный и магнитопорошковый кон 1 роль стилоскопированием и измерением твердости. [c.49]Выбор методов неразрушающего контроля сварных соединений [c.573]
Выбор методов неразрушающего контроля сварных соединений сосудов и аппаратов, изготавливаемых по ОСТ 26-291—79, регламентирован ОСТ 26-2079—80. Этот стандарт предусматривает применение следующих методов неразрушающего контроля
[c.574]
Методы неразрушающего контроля сварных соединений выбирают в зависимости от материала и толщины свариваемых элементов сосудов в соответствии с рекомендациями (см. табл. 5.20). При этом в зависимости от чувствительности и разрешающей способности метода предусматривают три ступени эффективности А, Б и В. Контроль качества сварных соединений выполняют одним из методов, указанных в -рафе требуемой эффективности, или вариантов сочетания этих методов. При регламентированном 100%-ном объеме контроля сварных соединений необходимо обеспечивать эффективность контроля, соответствующую ступени А. Во всех остальных случаях эффективность контроля должна быть не ниже ступени Б. Если конструктивные особенности сосудов и аппаратов не позволяют применять методы, соответствующие ступеням эффективности А и Б, то контроль проводят в исключительных случаях методами, предусмотренными для ступени эффективности В.
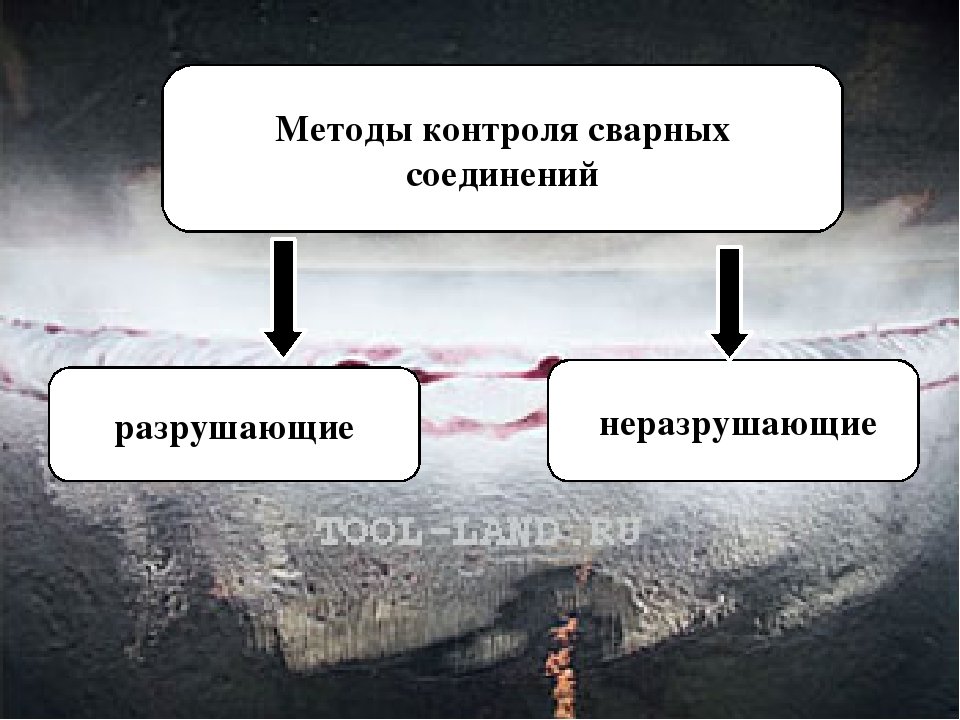
Занимается разработкой и внедрением новых методов неразрушающего контроля сварных соединений и элементов многослойных рулонированных сосудов высокого давления. С его участием разработаны и внедрены методики радиографического контроля сварных соединений. [c.447]
Такая подготовка ведется в МВТУ м. Баумана на курсах повышения квалификации ИТР по современным методам неразрушающего контроля сварных соединений по следующей программе [c.150]
Трудности при УЗ-контроле. Ультразвуковая дефектоскопия в ряде отраслей промышленности (железнодорожный транспорт, судостроение, энергетическое и химическое машиностроение) является основным методом неразрушающего контроля сварных соединений из низкоуглеродистых и низколегированных сталей. Это обусловлено прежде всего высокой достоверностью (90—95%) обнаружения плоскостных дефектов, низкой стоимостью и высокой оперативностью.
[c. 275]
Правилами котлонадзора [8] предусмотрено использование разных методов неразрушающего контроля сварных соединений и исследования их качества и свойств на образцах контрольных проб. [c.212]
Методы неразрушающего контроля сварных соединений группируют по видам исходя главным образом из общности физических явлений, используемых для обнаружения дефектов и других отклонений в контролируемых объектах, недопустимых по техническим условиям на их изготовление и эксплуатацию. [c.9]
Рассмотрены основные виды сварки, различные сварные соединения и швы, а также оборудование, применяемое при сварке и резке. Приведены сведения о сварочных материалах, условиях их хранения и транспортировки, а также об особенностях сварки различных металлов и сплавов. Изложены методы неразрушающего контроля сварных соединений.
Неразрушающий контроль сварных соединений и ПОУ методами ультразвуковой дефектоскопии осуществляют в соответствии с [102, 103, 113-115].

Методы ультразвукового контроля сварных соединений установлены ГОСТ 14782—76 Контроль неразрушающий. Швы сварные. Методы ультразвуковые . [c.507]
ЗАКЛЮЧИТЕЛЬНЫЙ КОНТРОЛЬ И МЕТОДЫ НЕРАЗРУШАЮЩИХ ИСПЫТАНИЙ СВАРНЫХ СОЕДИНЕНИЙ [c.245]
Методы контроля сварных соединений разделяют на две основные группы неразрушающего контроля (IIK) и разрушающего контроля (РК). [c.113]
Контроль всех сварных соединений производится в корпусах судов, на авиационных объектах. Однако многие конструкции, особенно в области строительной техники, парк которых очень велик, контролируются методами неразрушающего контроля выборочно. В первую очередь контролируют стыковые соединения. [c.151]
ОСТ 26-2079-80. Швы стыковых и угловых сварных соединений сосудов и аппаратов, работающих под давлением. Выбор метода неразрушающего контроля. [c.266]
ОСТ 26-5-88. Контроль неразрушающий. Цветной метод контроля сварных соединений, наплавленного и основного металла.
[c.267]
Механические свойства основного металла и металла сварных соединений трубопроводов определяют путем испытаний на растяжение по ГОСТ 1497-84 и ГОСТ 6996-66 соответственно, а также на ударный изгиб на образцах Шарпи — по ГОСТ 9454-78 и ГОСТ 6996-66 соответственно. Предел текучести и временное сопротивление металла определяют также неразрушающим методом в зонах контроля сварных соединений с помощью переносных твердомеров по ГОСТ 22761-77 и ГОСТ 22762-77. Выполняют не менее пяти замеров и за искомую твердость принимают их среднее арифметическое значение [74]. [c.164]
В таблицу сведений по сварке включают номер стыка, сведения о способе сварки, присадочных материалах и сварщиках, результаты контроля сварных соединений неразрушающими методами и внешним осмотром. Ремонтный формуляр оформляют на стандартном формате (ГОСТ 2.301—68) со штампом установленного образца Рекомендуемая форма ремонтного формуляра
[c. 452]
В соответствии с ГОСТ 7512—82, регламентирующим радиографический метод неразрушающего контроля, при радиографии в сварных соединениях выявляются внутренние дефекты трещины, непровары, усадочные раковины, поры, шлаковые, вольфрамовые, оксидные и другие включения, а также недоступные для внешнего осмотра наружные дефекты, утяжины, прожоги, подрезы, превышение проплава. [c.530]
В зависимости от конструкции сварных изделий расположение сварных стыковых продольных и кольцевых швов в обечайках, трубах, корпусах, а также швов приварки штуцеров, лазов, люков и т. п. принимают при конструировании и изготовлении изделия таким, чтобы можно было проводить контроль их качества всеми методами неразрушающего контроля, предусмотренными Правилами устройства и безопасной эксплуатации сосудов, работающих под давлением и техническими условиями. Особое внимание при этом обращают на доступность соединения для конт- [c.575]
Если при металлографическом исследовании в контрольном сварном соединении, проверенном ультразвуком или просвечиванием и признанном годным, будут обнаружены недопустимые дефекты, которые должны и могли быть выявлены данным методом неразрушающего контроля, то все производственные сварные соединения, представленные дефектным контрольным соединением, подлежат новой 100 %-ной проверке тем же методом дефектоскопии вне зависимости от предусмотренного и выполненного объема контроля. Новую проверку качества всех производственных стыков должен осуществлять наиболее опытный и квалифицированный дефектоскопист.
[c.599]
Ультразвуковая дефектоскопия и просвечивание сварных соединений по согласованию с Госгортехнадзором СССР могут быть заменены другим эффективным методом неразрушающего контроля. [c.600]
Если при металлографическом исследовании в контрольном сварном соединении, проверенном ультразвуком или просвечиванием по ст. 4-7-41 и признанном годным, будут обнаружены недопустимые внутренние дефекты, которые должны и могли быть выявлены данным методом неразрушающего контроля, все производственные сварные соединения, контролируемые дефектным контрольным соединением, подлежат новой 100%-ной проверке тем же методом дефектоскопии вне зависимости от предусмотренного и выполненного объема неразрушающего контроля. При этом новая проверка качества всех производственных стыков должна осуществляться наиболее опытным и квалифицированным дефектоскопистом. Выполнение указанного контроля дефектоскопистом, производившим проверку контрольного соединения, не допускается,
[c.37]
ВИИ с п,. 1.3.9, будут обнаружены пропущенные недопустимые дефекты, выявляемые данным методом неразрушающего контроля, то все производственные сварные соединения, контролируемые дефектным контрольным соединением, подлежат новой 100%-ной проверке тем же методом дефектоскопии вне зависимости от предусмотренного и выполненного объема неразрушающего контроля. При этом качество всех производственных сварных соединений должно проверяться наиболее опытным и квалифицированным дефектоскопистом (оператором). Выполнять указанный контроль дефектоскопистом, производившим проверку контрольного соединения, не разрешается. [c.563]
Если при металлографическом исследовании контрольного сварного соединения, прошедшего проверку ультразвуком или просвечиванием в соответствии с п. 1.3.9, будут обнаружены недопустимые внутренние дефекты, не выявляемые данными методами неразрушающего контроля, а также при обнаружении любых недопустимых внутренних дефектов при металлографическом исследовании контрольных сварных соединений, не подвергаемых проверке ультразвуком и просвечиванием, должно быть выполнено металлографическое исследование сварных соединений, вырезаемых из изделия (в удвоенном количестве по сравнению с установленным объемом выполнения контрольных сварных соединений). При этом вырезке подлежат производственные сварные соединения из числа контролируемых дефектным контрольным соединением (и выполненных тем же сварщиком), а количество образцов (шлифов), вырезаемых из каждого соединения, удваивается.
[c.563]
Какие методы неразрушающего контроля применяют для выявления внутренних дефектов в сварных соединениях и их сущность [c.287]
В области контроля качества сварных соединений получит широкое использование аппаратура автоматического и дистанционного рентгенозского-просвечивания с применением электронно-оптических преобразователей и телевизионной техники. Будут разработаны методы неразрушающего контроля сварных соединений с одновременным воздействием непосредственно на процесс сварки (активный контроль).
[c.143]
Сварные соединения сосудов подвергают неразрушающему контролю в объемах, предусмотренных правилами [24] и приведенных в табл. 5.19. Выбор методов неразрушающего контроля сварных соединений сосудов регламентирован ОСТ 26-291—79 и Руководящими техническими материалами РТМ 26-290—75 и РТМ 26-230—75. Эти руководящие материалы предусматривают осуществление контроля при сварке малоуглеродистых и низколегированных сталей, высоколегироваиных коррозионно-стойких [c.192]
В настоящее время ультразвуковая сварка является одним из наиболее прогрессивных и производительных методов соединения полимерных материалов. В связи с массовым пронз-водством и отсутствием надежных методов неразрушающего контроля сварных соединений из полимеров для ультразвуковой сварки пластмасс особое значение приобретают надежность и стабильность технологического процесса сварки. Требования к такому стабильному и надежному процессу состоят в следующем 1) высокое качество единичного сварного соединения 2) повторяемость и стабильность свойств сварных соединений.
[c.222]
Основным методом неразрушающего контроля сварных соединений узлов самолета Ил-86 является радиографический метод (просвечивание их излучением промышленных рентгеновских аппаратов на рентгеновскую пленку). Контролю подлежат сварные соединения пз сплавов на основе тптана толщиной 0,8—80 мм, сплавов на основе алюминия (0,8—25 мм) и сталей (0,8—39 мм). [c.256]
Неразрушающий контроль сварных соединений следует про-извооить приборами и аппаратами, представленными в РД 22-322 методами, изложенными в прилагаемых к приборам и аппаратам инструкциях, а также в стандартах ГОСТ 7512, ГОСТ 14782, ГОСТ 18442, ГОСТ 21105. [c.205]
Усугубляющим снижение надежности при сварке однородными электродами является то, что возникшие холодные трещины имеют микроскопическое раскрытие (слипшиеся трещины), поэтому они не всегда могут быть обнаружены методами неразрушающего контроля и могут явиться ( лелс г вием развития трещин при термической обработке изделия Процесс эксплуатации таких сварных соединений опасен. В особенности опасны околошовные зоны перегрева по линии сплавления, имеющие наиболее крупнозернистое строение.
[c.78]
Дефекты основного металла и сварных соединений приводят к образованию некогерентных границ зерен, коррозионно нестойких пленок, создают концентрацию макро- и микронапряжений, повышают термодинамическую неустойчивость дефектных участков поверхности и интенсифицируют их наво-дороживание и электрохимическое растворение. Поэтому для повышения надежности оборудования и коммуникаций, контактирующих с сероводородсодержащими средами, наряду с тщательным входным контролем соответствия материалов конструкций техническим условиям на их поставку и неразрушающим контролем монтажных сварных соединений, эффективными являются предпусковые гидроиспытания металлоконструкций давлением, создающим напряжения до 95% от минимального нормативного значения предела текучести металла [33, 34]. В ходе этих испытаний разрушаются участки основного металла и сварных соединений, содержащие потенциально опасные дефекты. Вокруг оставшихся неопасных дефектов образуются зоны остаточного сжатия, повышаюшего коррозионную стойкость сварных соединений. Кроме того, после гидравлических испытаний в 2-3 раза снижаются максимальные остаточные напряжения в зоне сварных соединений труб за счет пластического удлинения растянутых областей металла. Одновременно снижаются наиболее высокие монтажные напряжения в трубопроводах. Там, где по техническим причинам проведение гидроиспытаний не представляется возможным, для выявления недопустимых дефектов необходимо применять 100%-ный радиографический контроль сварных соединений и его 100%-ное дублирование ультразвуковым методом [25, 35].
[c.67]
В книге рассмотрены дефекты сварных соединений, причины их возникновения и их классификация. Изложены методики расчета прочности сварных соединений с дефектами с учетом их механической неоднородности. Даны подходы к нормированию дефектов сварки.

Контроль сварных соединений по методам его проведения подразделяется на неразрушающий и разрушающий. В настоящем разделе остановимся на физических приш и-пах, аппаратуре, технических возможностях и технологии основных методов неразрушающего контроля. К ним относят [c.138]
Контроль сварных соединений многослойных труб осуществляется следующими неразрушающими методами наружных и внутренних соединений — внешним осмотром и измерением внутренних нахлесточных соединений обечаек — течеисканием и ультразвуковым кольцевых стыковых соединений — течеисканием (с внутренней стороны трубы) и рентгентелевизионным концы монолитных торцевых обечаек — ультразвуковым.
[c.242]
Неразрушающий контроль сварных соединений трубопроводов
- Методы неразрушающих исследований
Проведение неразрушающего контроля (НК) является одним из основных методов диагностики технологического оборудования. Оно обеспечивает эффективное выявление дефектов техники и других объектов, препятствующих их нормальной эксплуатации, и достоверное определение остаточного ресурса службы. При этом не нарушается работоспособное состояние приборов и конструкций, поэтому сразу же после завершения обследования их можно снова использовать на производстве. Поэтому объемы контроля неразрушающими методами сварных соединений трубопроводов и других объектов постоянно увеличиваются.
Методы неразрушающих исследований
Общий порядок реализации НК для всех типов объектов определен положениями приказа Ростехнадзора от 21 ноября 2016 года N 490. Он устанавливает основные принципы выполнения работ в этой области, а также последовательность их реализации и требования к исполнителям. Для проверки различных типов объектов методами НК применяются специальные нормативные документы. Они определяют правила проведения контроля с учетом их производственной специфики.
Полный перечень методов НК зафиксирован в национальном стандарте ГОСТ 18353-79. Он включает в себя следующие позиции:
- электрический и магнитный контроль;
- вихретоковое обследование;
- исследование объектов при помощи звуковых и радиоволн;
- анализ объектов при помощи тепловых и радиационных излучений;
- применение оптических методов;
- проверка объекта с применением различных типов проникающих веществ.
Методы неразрушающего контроля сварных соединений трубопроводов
Практика показала, что некоторые из этих методов имеют наибольшую эффективность при проведении проверки качества сварных соединений трубопроводов. Для этих методов были разработаны специальные нормативные документы, устанавливающие четкий порядок выполнения работ. Он обеспечивает достижение максимально достоверного результата исследований и упрощает процедуру его проведения. Например, среди таких документов можно назвать ГОСТ на неразрушающий контроль сварных соединений трубопроводов магнитографическим способом (ГОСТ 25225-82). Также применяются отраслевые стандарты исследований — например, ОСТ 36-75-83 для проведения исследований трубопроводов с применением ультразвука.
Методы неразрушающего контроля сварных соединений грузоподъемных устройств
Грузоподъемные механизмы попадают в категорию наиболее ответственных сооружений машиностроительной промышленности. Надежность эксплуатации этих ответственных устройств во многом зависит от качества сварных соединений. Не зря на законодательном уровне закреплено требование осуществления постоянного мониторинга состояния сварных швов методами неразрушающего контроля на протяжении всего периода эксплуатации грузоподъемных механизмов. Принятие соответствующих мер по обеспечению промышленной безопасности зависит от правильно выбранного метода контроля, а также его периодичности и глубины.
Основными критериями, влияющими на выбор метода неразрушающего контроля, являются:
- характер вероятных дефектов и их местоположение;
- функциональные особенности методов;
- особенности элементов и конструкций, на которых расположены контролируемые швы;
- фактическое состояние контролируемых элементов и другое.
Согласно классификации, все дефекты сварных швов различаются в зависимости от размеров, формы, местоположения, а также среды, которая в них присутствует. Различают поверхностные и внутренние дефекты. К первым относят подрезы, наплывы, кратеры, прожоги, свищи, а ко вторым – непровары и шлаковые включения. Трещины, поры и раковины, в свою очередь, могут наблюдаться, как внутри шва, так и на его поверхности. Плоскостные дефекты, к которым относятся непровары, трещины и подрезы, характеризуются протяженными очертаниями с различной степенью глубины и раскрытия. Внутри дефектных швов могут присутствовать оксиды, нагар и другие загрязнения. К объемным дефектам, обладающим округлой формой, относятся поры и раковины, и чуть реже – шлаковые включения.
В настоящее время в качестве металла для сооружения грузоподъемных кранов применяют высокопрочные низколегированные марки стали (14Х2ГМ, 14Х2ГМР, 14ХГНМ, 12ГН2М). Особенности сварочных работ с данными сталями проявляются в виде увеличения вероятности образования таких дефектов, как трещины в сварных швах и в их околошовной зоне. Назначение неразрушающего контроля связано с определением наличия трещин, образовавшихся во время эксплуатации.
Основным критерием выбора метода неразрушающего контроля является обеспечение наибольшей степени определения наличия дефектного шва. В качестве обязательных методов контроля применяют визуальный и измерительный методы. С их помощью можно определить наличие поверхностных дефектов.
Для выявления сварочных дефектов объемного типа более всего подходит радиационный метод контроля, который целесообразнее всего применять на стадии производства металлических конструкций грузоподъемных сооружений.
К универсальным способам контроля относят ультразвуковой метод, который позволяет определять наличие непроваров и трещин, как на стадии производства, так и в процессе эксплуатации.
Для выявления поверхностных дефектов, которые невозможно определить с помощью визуального контроля, оптимальным способом является применение магнитопорошкового контроля. Его допускается использовать для контроля не только сварных соединений, но и для проверки качества основного металла. При контроле сварных соединений данным методом не требуется снимать усиление шва или обеспечивать плавность перехода к основному металлу. Благодаря этому магнитопорошковый метод контроля целесообразно использовать на стадиях ремонта, изготовления и диагностики металлических конструкций, выполненных из высокопрочных низколегированных сталей. Следует отметить, что для осуществления технологии магнитопорошкового метода требуется наличие зоны намагничивания, поэтому говорить о его универсальности не приходится. В этом случае необходимо использовать капиллярный или вихретоковый методы. В первом случае потребуется обеспечение плавности перехода от шва к основному металлу, а во втором случае – устранить усиление швов.
Наибольшую эффективность для диагностики соединений сварных швов в процессе эксплуатации получил акустико-эмиссионный метод. С его помощью можно обнаружить дефекты на стадии их развития, что обеспечит получение информации о степени их опасности. Однако массовое применение данного метода ограничивается особенностями его технологии, дорогостоящим оборудованием, а также потребностью в высококвалифицированном персонале.
Несмотря на многообразие существующих методов контроля сварных швов, основным подготовительным мероприятием в данном направлении должно быть определение оптимального способа контроля, который позволит достичь наибольшего эффекта. С этой целью следует обратить внимание на такие параметры, как состав контролируемого материала, стадия контроля и объект контроля.
Если вы нашли ошибку, пожалуйста, выделите фрагмент текста и нажмите Ctrl+Enter.
Услуги по неразрушающему контролю (НК) и инспекции
Мы специализируемся на исследованиях и разработках новых технологий и приложений, таких как:
- Система ФАР «Политест» для выездного контроля стыков полиэтиленовых трубопроводов
- Система Railect для ультразвукового контроля алюминотермических сварных соединений рельсов
- PAUT проверка алюмингов ветряных турбин
- Программа Intacom по разработке роботизированных систем контроля под руководством Центра передовых неразрушающих испытаний TWI в Порт-Талботе, Южный Уэльс.
Инновационные решения для контроля
Нас часто просят разработать инновационные решения конкретных проблем. Эти решения обычно включают:
- Разработка техники (включая моделирование)
- Подготовка к процедуре
- Подтверждение инспекцией/техническое обоснование
- Развертывание сайта
- Обучение и внедрение
Услуги по неразрушающему контролю (НК)
Услуги по неразрушающему контролю TWI включают:
В наших услугах по неразрушающему контролю используются все доступные технологии неразрушающего контроля, и наша команда имеет большой опыт в определении оптимального решения для любого практического промышленного применения.
Проверка третьей стороной
TWI может предоставить высококвалифицированный и опытный персонал для осуществления надзора третьей стороны во всех областях контроля неразрушающего контроля. Глубокий опыт нашей команды включает в себя экспертов из разведки нефти и газа и аэрокосмической отрасли, с квалификацией до ISO 9712 NDT Level 3 и ASNT NDT Level III по всему спектру методов.
Квалификация и валидация неразрушающего контроля
Квалификация инспекции— это формальный процесс для получения уверенности в том, что ваши процедуры инспекции неразрушающего контроля могут соответствовать их целям и обнаруживать дефекты, которые вам действительно нужно найти, демонстрируя вашему руководству и регулирующим органам, что компонент или сварной шов подходят для своей цели.
Квалификационная оценка охватывает весь процесс неразрушающего контроля путем проверки как по отдельности, так и в сочетании элементов оборудования, процедур и персонала. TWI может предоставить консультации и информацию обо всем процессе квалификации, начиная с наиболее подходящих кодексов и стандартов для применения, подготовки технического обоснования, производства образцов для квалификационных испытаний и предоставления квалифицированного персонала для органа по сертификации.
Полный контроль качества
Полный контроль качества (TQI) представляет собой целостный подход к совершенствованию эксплуатационного контроля критически важных конструкций и технологических установок. Полный контроль качества является частью инициативы TWI, продвигаемой промышленными членами, по повышению эффективности неразрушающего контроля, особенно в нефтяной, газовой и нефтехимической промышленности, где наблюдается отставание от показателей, достигнутых в аэрокосмической и ядерной промышленности.
Для получения дополнительной информации, пожалуйста, напишите по адресу [email protected].
Радиографический контроль — неразрушающий контроль
Радиографический контроль (РТ) — это метод неразрушающего контроля (НК), в котором используются рентгеновские или гамма-лучи для исследования внутренней структуры изготовленных компонентов с целью выявления любых изъянов или дефектов.
При радиографическом контроле тестовая деталь помещается между источником излучения и пленкой (или детектором). Различия в плотности и толщине материала испытуемой части будут ослаблять (т. е. уменьшать) проникающее излучение за счет процессов взаимодействия, включающих рассеяние и/или поглощение. Различия в поглощении затем регистрируются на пленке (пленках) или с помощью электронных средств. В промышленной рентгенографии доступно несколько методов визуализации, методов отображения окончательного изображения, т.е.е. Пленочная рентгенография, рентгенография в реальном времени (RTR), компьютерная томография (CT), цифровая рентгенография (DR) и компьютерная рентгенография (CR).
Для промышленного использования доступны два различных радиоактивных источника; Рентгеновское и гамма-излучение. Эти источники излучения используют более высокий уровень энергии, т.е. более короткую длину волны, версии электромагнитных волн. Из-за радиоактивности, связанной с рентгенографическими испытаниями, крайне важно обеспечить строгое соблюдение Местных правил во время работы.
Компьютерная томография (КТ) — это один из передовых лабораторных методов неразрушающего контроля, который TWI предлагает промышленным предприятиям. КТ — это метод, основанный на рентгенографии, который позволяет получить как поперечное, так и трехмерное объемное изображение исследуемого объекта. Эти изображения позволяют проверять внутреннюю структуру тестируемого объекта без присущего 2D-радиографии наложения. Эта функция позволяет проводить детальный анализ внутренней структуры широкого спектра компонентов.
Ресурсы TWI
TWI имеет следующее цифровое рентгенографическое оборудование с возможностью компьютерной томографии для удовлетворения промышленных потребностей.
- Микрофокусная компьютерная томографическая система Nikon 450 кВ
- Промышленная широкофокусная система X-Tek 450 кВ
- Микрофокусная система X-Tek 225 кВ
Преимущества
- Может проверять собранные компоненты
- Требуется минимальная подготовка поверхности
- Обнаруживает как поверхностные, так и подповерхностные дефекты
- Обеспечивает постоянную запись осмотра
- Проверка внутренних дефектов сложных конструкций
- Изолировать и проверить внутренние компоненты
- Автоматическое обнаружение и измерение внутренних дефектов
- Измерение размеров и углов в образце без разреза
- Чувствителен к изменениям толщины, коррозии, дефектам и изменениям плотности материала
Приложения
Радиографический контрольшироко используется в;
TWI также предлагает обучение рентгенографическим исследованиям.
Для получения дополнительной информации об услугах TWI по рентгенографическому тестированию, пожалуйста, напишите по адресу [email protected].
Что такое акустико-эмиссионное тестирование? Полное руководство
Испытания на акустическую эмиссию (AE) — это метод неразрушающего контроля (NDT), который обнаруживает и контролирует выброс ультразвуковых волн напряжения от локализованных источников, когда материал деформируется под нагрузкой.
Содержимое
Щелкните здесь , чтобы посмотреть наши последние технические подкасты на YouTube .
Испытания на акустическую эмиссию проводятся путем установки небольших датчиков на испытуемый компонент. Датчики преобразуют волны напряжения в электрические сигналы, которые передаются на компьютер для сбора данных для обработки. Волны фиксируются, когда компонент подвергается внешнему воздействию, например, высокому давлению, нагрузке или температуре. По мере роста повреждения в компоненте происходит большее выделение энергии. Частоты обнаружения акустической эмиссии, активность и интенсивность акустической эмиссии, громкость контролируются и используются для оценки структурной целостности и контроля состояния компонентов.
Акустическая эмиссия может рассматриваться как крошечные землетрясения, происходящие в материале. Этот метод обеспечивает глобальный мониторинг компонента на наличие дефектов, позволяя контролировать большие конструкции и машины во время работы с минимальными нарушениями, в отличие от разрушающих испытаний. Используя несколько датчиков, можно локализовать источники акустического излучения (и, следовательно, повреждения). С помощью анализа сигналов также можно определить наличие различных механизмов источника.
Существует два метода тестирования АЭ: переходный и непрерывный.Метод переходных процессов фиксирует всплески АЭ, которые превышают пороговое значение (уровень громкости), и извлекает такие характеристики, как пиковая амплитуда, энергия сигнала и продолжительность всплеска. Затем эти функции используются для оценки состояния тестируемого компонента. Этот метод хорошо подходит для проверки конструкций на наличие таких дефектов, как трещины.
Непрерывный метод фиксирует все АЭ в течение заданного периода времени, например, 1/10 секунды. Затем извлекаются такие характеристики, как средний уровень сигнала и среднеквадратичное значение (RMS).Этот метод хорошо подходит для приложений, где много фоновой АЭ или амплитуда АЭ мала, например, при тестировании редукторов или обнаружении утечек.
Испытания на акустическую эмиссию можно проводить как в лаборатории, так и в полевых условиях как в течение относительно короткого периода времени, например нескольких часов, так и в течение более длительного времени, например нескольких месяцев. Методы беспроводной передачи данных позволяют анализировать данные удаленно.
Акустическая эмиссия имеет много преимуществ перед другими методами.К ним относятся:
- Способность обнаруживать ряд механизмов повреждения, включая, помимо прочего, разрывы волокна, трение, удары, растрескивание, расслоение и коррозию на ранних стадиях, прежде чем они станут серьезными проблемами
- Может проводиться в процессе эксплуатации, при квалификационных (контрольных) испытаниях или опытно-конструкторских испытаниях
- Может обнаруживать источники повреждений и различать их на основе акустических сигнатур
- Глобальный мониторинг конструкции
- Оценка конструкции или машины в реальных условиях эксплуатации
- Неинвазивный метод
- Эксплуатация в опасных средах, включая высокие температуры, высокое давление, коррозионные и ядерные среды
- Можно проводить дистанционно
- Может обнаруживать повреждения в дефектах, к которым трудно получить доступ с помощью обычных методов неразрушающего контроля
Однако этот метод имеет некоторые ограничения:
- Ограничено оценкой структурной целостности или работоспособности машины путем выявления проблем, для полной диагностики проблем обычно требуется дальнейшая проверка
- Не удается обнаружить дефекты, которые могут присутствовать, но не перемещаются и не увеличиваются
- Может быть медленнее, чем другие методы неразрушающего контроля
Акустическая эмиссия может быть применена к целому ряду приложений и материалов. К ним относятся:
Конструкции
- Бетонные конструкции, такие как мосты и здания
- Металлические конструкции, такие как сосуды под давлением, трубопроводы, резервуары для хранения, конструкции самолетов и стальные тросы
- Композитные конструкции, такие как конструкции самолетов, конструкции для автоспорта и композитные балки
Машины
- Вращающееся оборудование, такое как обнаружение преждевременного износа подшипников и редукторов
- Электрические машины, такие как обнаружение частичных разрядов в трансформаторах и изоляторах
Процессы
- Аддитивное производство для оценки качества сборки во время сборки
- Обнаружение утечек в трубопроводах и напорных системах
- Удары частиц
- Процессы трения
Обзор и экспериментальное исследование
и сварка лазерным лучом (LBW) выполнены на низкоуглеродистой стали
(стальной лист Corten ASTM A588). В процессе сварки шва
возникают дефекты, которые выявляются методом неразрушающего контроля
. Визуальный осмотр, испытание на проникновение жидкости, рентгенографию
, магнитопорошковый контроль и ультразвуковой контроль — это пять
методов неразрушающего контроля, которые используются в данной исследовательской работе для выявления
различных дефектов в сварных листах.
При визуальном осмотре пластин, сваренных методом GTAW, наблюдаются дефекты от 0 до
5 мм визуальная трещина, от 130 до 150 мм одиночная пора и от 4 до
10 мм на корневом участке избыточное проплавление.В сварных листах GMAW
, дефекты от 0 до 10 мм, одиночные поры, от 15 до 35 мм
абсорбированы излишки валиков, 100 мм одинарные разбрызганные поры абсорбированы.
Но в листе, сваренном лазером LBW, дефектов не наблюдается, что делает лист, сваренный лазером LBW приемлемым.
При использовании теста на проникновение жидкости при сварке в среде защитного газа, дефекты от 0
до 5 мм визуальная трещина, от 130 до 150 мм одиночная пора, от 4 до 10 мм
на избыточном проплавлении корневого участка. При сварке GMAW
дефекты на уровне 0–10 мм, одинарная пора, 15–35 мм избыточные валики
поглощаются, 100 мм поглощаются одиночные распыленные поры.Но при лазерной сварке LBW
дефектов не наблюдалось, что делает лист
LBW, сваренный лазерным лучом, приемлемым для жидкостного контроля.
При радиографическом контроле низкоуглеродистой стали, сваренной методом GTAW (стальной лист Cor-
ten ASTM A588) в месте AB, обнаружены дефекты.
Следовательно, плита, сваренная методом GTAW, неприемлема. Аналогично, сварная пластина
GMAW в месте AB; обнаружены дефекты, из-за которых
лист, сваренный методом GTAW, неприемлем.Но при лазерной сварке LBW
дефектов не наблюдается, что делает допустимой лазерную сварку LBW
.
При проведении магнитопорошковых испытаний на сварных листах, сваренных методом GTAW, GMAW и
LBW, в сварном соединении GMAW было обнаружено три дефекта
, в процессе сварки GTAW было обнаружено четыре дефекта
, Но в листах, сваренных лазерным лучом LBW, a 100 % наблюдается непровар
по всей оси шва. Если сравнивать
с другими методами сварки, сварка GMAW имеет минимальное количество дефектов
.Но наблюдения за магнитопорошковым
испытанием низкоуглеродистых (сталь CortenA588) сварных листов в процессе сварки
GTAW имеют сравнительно большее количество
дефектов и дефектов серьезности.
При использовании метода ультразвукового контроля в сварном соединении GMAW были обнаружены три дефекта
(непровар). В процессе сварки GTAW
наблюдалось отсутствие дефектов проплавления.
Аналогично, в пластинах, сваренных методом LBW лазерной сварки, непровар наблюдается на оси шва.
Из этой исследовательской работы мы можем сделать вывод, что среди листов, сваренных методом GTAW,
GMAW и LBW, лист LBW для лазерной сварки
является весьма приемлемым, поскольку сварной лист LBW приемлем для
трех методов неразрушающего контроля. Среди различных методов неразрушающего контроля, таких как
Радиографический, ультразвуковой, магнитно-порошковый, проникновение жидкости
и визуальный контроль, которые используются для проверки сварных плит GTAW,
GMAW и LBW, радиографический контроль остается хорошим.
Это происходит благодаря легкому обнаружению внутренних дефектов и пор на
внутренней поверхности свариваемых листов.
Заявление об авторском вкладе CRediT
Дж. Р. Дипак: Концептуализация, методология, надзор,
Письмо — первоначальный проект. В.К. Бупеш Раджа: Расследование. D. Sri-
kanth: Письмо — первоначальный черновик. Х. Сурендран: Письмо — оригинальный черновик
. М.М. Николай: .
Декларация о конкурирующих интересах
Авторы заявляют, что у них нет известных конкурирующих
финансовых интересов или личных отношений, которые могли бы
повлиять на работу, представленную в этой статье.
Ссылки
[1] L.S. Росадо, Т.Г. Сантос, М. Пьедаде, П.М. Рамос, П. Виласа, Усовершенствованная методика
для неразрушающего контроля сварки металлов трением с перемешиванием, Измерение 43
(8) (2010) 1021–1030, https://doi.org/10.1016/j.measurement. 2010.02.006.
[2] К. Ашок Редди, Неразрушающий контроль, оценка материалов из нержавеющей стали
, Матер. Сегодня проц. 4 (8) (2017) 7302–7312, https://doi.org/
10.1016/j.matpr.2017.07.060.
[3] А. Али, А. Кумар, К. Кумар, YRC Murthy, Б. Равиндер, К. Капур, К.П. Babu,
Ультразвуковой контроль в качестве альтернативы рентгенографии для оценки покрытия PFBR
целостность сварного шва штифтовой пробки, Procedia Struct. Целостность 14 (2019) 273–281,
https://doi.org/10.1016/j.prostr.2019.05.035.
[4] Н. Амири, Г.Х. Фаррахи, К. Реза Кашизаде, М. Чизари, Применение методов ультразвукового контроля
и машинного обучения для прогнозирования статического и
усталостного поведения точечных сварных соединений, 2020.
[5] Дж. Р. Дипак, В.К.Б. Раджа, Дж.Дж. Арпутабалан, Г.Р.Ю. Кумар, С.К. Thomas,
Экспериментальное исследование присадочной проволоки Corten A588 для сварки атмосферостойких материалов
Steel, Mater. Сегодня проц. 16 (2019) 1233–1238, https://doi.org/10.1016/
j.matpr.2019.05.219.
[6] Б. Шассиноль, Р. Эль Герджума, М.-А. Ploix, T. Fouquet, Ultrasonic and
структурная характеристика сварных швов из анизотропной аустенитной нержавеющей стали:
На пути к повышению надежности ультразвукового неразрушающего контроля, NDT E Int.43
(4) (2010) 273–282, https://doi.org/10.1016/j.ndteint.2009.12.005.
[7] T. Warren Liao, Jiawei Ni, Автоматизированная радиографическая система неразрушающего контроля сварных швов
. Часть I. Извлечение сварных швов, 1995. Maz
ˇeika, V. Samaitis, V. Cice
˙nas, D. Mattsson, Ультразвуковой неразрушающий контроль сложных соединений титан/углеродное волокно,
Ultrasonics 95 (2019) 13–21, https: //дои.org/10.1016/j.ultras.2019.02.009.
[9] B. Ehrhart, B. Valeske Неразрушающая оценка (NDE) аэрокосмических композитов
: методы испытаний клеевых композитов, 2013.
[10] Nivin Joy et al., Экспериментальное исследование и анализ сверление в Grade 5
Титановый сплав (Ti-6Al-4V), матер. Сегодня проц. 21 (2020) 335–339.
[11] Nivin Joy et al 2020 IOP Conf. Сер.: Матер. науч. англ. 923 012032.
[12] Сандип Кумар Двиведи, Маниш Вишвакарма, Ахилеш Сони, Advances and
Исследования в области неразрушающего контроля: обзор, 2017.
[13] Дж. Р. Дипак, В.К. Бупеш Раджа, Гоби Сараванан Калиарадж, Механическое и
коррозионное поведение гальванопокрытий Cu, Cr, Ni и Zn на стали Corten A588
для улучшения условий применения в строительстве, 2019.
Таблица 11
Дефекты сварки, обнаруженные ультразвуком контрольная работа.
Пластина Расположение Траектория луча Глубина поверхности Глубина Толщина Дефект
GMAW 0–38 мм 35 мм 18,17 6,8 мм 2 мм Непровар
GTAW 0–150 мм 21 мм 19.7 7,1 мм 2 мм Непровар
LBW 0–20 мм 20 мм 12,7 1,5 мм 2 мм Непровар
J.R. Deepak, V.K. Бупеш Раджа, Д. Срикант и др. Materials Today: Proceedings xxx (xxxx) xxx
6
Применение нескольких методов неразрушающего контроля для оценки сварных соединений стального моста ASTM-A-588
[1]
Р. Оспина Л., К. Эрнандо Т., Х. Парра Л., в: Применение и выбор неразрушающего контроля для оценки сварных соединений, Scientia et Technical Year XVI, vol. 48, Технический университет Перейры, стр. 196–201, август (2011 г.).
[2] Луис С.Росадо, Тельмо Г. Сантос, Моисес Пьедаде, Педро М. Рамос, П. Вильяка., В: Передовой метод неразрушающего контроля сварки металлов трением с перемешиванием, Измерение, том. 43, стр. 1021-1030, февраль (2010 г.).
DOI: 10. 1016/j.measurement.2010.02.006
[3] A Sifa et al 2017 IOP Conf.Сер.: Матер. науч. англ. 180 012101.
[4]
М. Табатабаипор, Дж.Hettler, S. Dulcre and K. Van Den Abeele, Неразрушающий ультразвуковой контроль корневых дефектов в стыковых соединениях, сваренных трением с перемешиванием, NDT and E International, vol. 80, стр. 23-34, февраль (2016).
DOI: 10.1016/j.ndteint.2016.02.007
[5] Сараванан Т., Лахири Б.Б., Арунмуту К., Багаватиаппан С., Сехар А.С., Pillai VPM, et al. Неразрушающая оценка соединений, сваренных трением с перемешиванием, с помощью рентгеновской радиографии и инфракрасной термографии, Procedia Engineering, том 86, стр. 469-475, (2014).
DOI: 10. 1016/j.proeng.2014.11.060
[6] С.Мандаш, Д. Левек, Л. Дюбур и П. Гужон., Неразрушающий контроль дефектов непровара в сварных швах трением с перемешиванием, Наука и технология сварки и соединения, Канада, том 17, стр. 295-303, январь ( 2012).
DOI: 10.1179/1362171812y.0000000007
[7]
Т. Эндрамаван и А. Сифа, Конференция IOP, 2018 г.Сер.: Матер. науч. англ. 306 012122.
[8] A Sifa et al 2018 IOP Conf.Сер.: Матер. науч. англ. 306 012009.
[9]
Т. Паван Кумар и П.Прабхакар Редди 2017 IOP Conf. Сер.: Матер. науч. англ. 225 012060.
DOI: 10.1088/1757-899x/225/1/012060
5 основных методов неразрушающего контроля
Все мы, наверное, слышали о разрушающем контроле при сварке.В конце концов, те из нас, кто является сертифицированным сварщиком или работает в месте, где требуется сертификация сварочных процедур, в тот или иной момент слышали об испытании на изгиб или испытании по Шарпи с V-образным надрезом. Однако существует несколько видов неразрушающего контроля. Как вы понимаете, деструктивное тестирование готовой продукции плохо влияет на конечный результат. Иногда даже выборка всего нескольких готовых продуктов представляла собой огромные расходы. К счастью, есть несколько методов неразрушающего контроля. Некоторые из этих тестов требуют оборудования, а некоторые требуют от инспектора высокой степени специализации. Ниже приведены основные методы неразрушающего контроля.
ВИЗУАЛЬНЫЙ: Ищет поверхностные дефекты, такие как пористость, трещины, кратеры и шлаковые включения. Визуальный осмотр также позволяет выявить другие проблемы, которые не обязательно могут повлиять на целостность сварного шва, но могут стоить компании денег или могут привести к дефекту сварного шва. Это недоварка, переварка, коробление деталей (вынос их за пределы допуска), подрезка и неправильная подгонка.Визуальный контроль является наиболее широко используемым видом неразрушающего контроля из-за его низкой стоимости и может проводиться во время и после сварки. Недостаток использования визуального как единственного метода контроля заключается в том, что мы можем обнаружить только поверхностные дефекты. Такие элементы, как внутренняя пористость, внутренние трещины или несплавление, не могут быть обнаружены.
РЕНТГЕНОГРАФИЧЕСКИЙ: Этот метод позволяет обнаружить микроскопические внутренние дефекты, такие как трещины, пористость, пузыри, неметаллические включения, неполное проникновение корня и подрезку.Когда создается рентгеновская пленка, клиенты имеют постоянную запись испытаний, которую можно использовать для отслеживания. Испытательное оборудование может стоить несколько тысяч долларов. Тем не менее, для компаний, нуждающихся в тестировании всех готовых узлов, а не только образцов для квалификационных испытаний, это относительно недорогой метод. Этот метод требует от инспектора навыков определения правильных углов для съемки рентгеновского снимка, а также интерпретации пленки.
Радиографический контроль
МАГНИТНАЯ ЧАСТИЦА: Очень хорошо обнаруживает дефекты поверхности, такие как трещины.Этот метод использует специализированное оборудование и расходные материалы, такие как магнитные порошки. Его проще использовать, чем радиографический контроль, и он дешевле, но, как и визуальный, он обнаруживает только дефекты поверхности. Однако он обнаружит трещины, которые иногда невозможно увидеть невооруженным глазом. Это также требует высокой квалификации инспектора.
Испытание магнитными частицами
ПРОНИКАЮЩАЯ ЖИДКОСТЬ: Этот метод требует использования флуоресцентных или красящих пенетрантов и проявителей.Он обнаруживает поверхностные трещины, которые не видны невооруженным глазом. Этот метод используется для обнаружения утечек, и он особенно выгоден, когда экономически нецелесообразно заполнять и собирать воду или газ для проверки на наличие утечек. Преимущество по сравнению с магнитными частицами заключается в том, что их можно использовать на немагнитных материалах, таких как алюминий. Этот процесс тестирования недорог и прост в выполнении.
Испытание на проникновение жидких красителей
УЛЬТРАЗВУКОВОЙ: Требуется специальное оборудование.Этот метод обнаруживает как поверхностные, так и подповерхностные дефекты, которые не обнаруживаются другими методами. УЗ-тестирование очень полезно при тестировании сборок, которые не подходят для рентгеновского оборудования. Это требует очень высокого уровня навыков для интерпретации показаний, и это не создает постоянную запись, как при рентгенографии.
Ультразвуковой контроль
Источник: Руководство по дуговой сварке, 14-е издание
Неразрушающий контроль сварных соединений | Лучшие методы неразрушающего контроля
Сварное соединение NDT
Стыковые сварные швы требуют специального набора процедур неразрушающего контроля, чтобы обеспечить полную оценку дефектов.Эти виды сварных швов подвержены деформации, растрескиванию, коррозии, которые могут ухудшить общую целостность активов. В мире неразрушающего контроля наиболее предпочтительные методы часто включают радиографический контроль (RT), ультразвуковой контроль с фазированной решеткой (PAUT) и (вихретоковую решетку) ECA. Но возникает вопрос, какой метод лучше всего использовать для стыковых сварных соединений.
Лучший метод неразрушающего контроля стыковых сварных швов
Не существует одного наилучшего метода неразрушающего контроля для проверки стыковых сварных швов.Определенные методы работают лучше всего в определенных ситуациях.
Радиографический контроль стыковых сварных швов
Радиографический контроль использует трубку для получения источника рентгеновского или гамма-излучения. Эти лучи указываются на свариваемых материалах для захвата изображения объекта на фотопленке. При растрескивании сварного соединения обуви на рентгенографической пленке появляется темный контур. С помощью радиографического контроля лаборант может выявить различные дефекты стыкового шва, такие как трещины, пористость, пустоты, нахлест и т. д.Однако важно отметить, что RT имеет существенные недостатки, в том числе:
- Опасность для здоровья в результате радиационного облучения, особенно в течение длительного периода времени.
- Снижение эффективности, поскольку требуемое время тестирования значительно больше, чем при использовании других методов
- Сложность определения глубины дефекта до проведения испытания под разными углами
ПАУТ стыковых сварных швов
Ультразвуковой контрольпредлагает высокую адаптируемость и точность и идеально подходит в тех случаях, когда глубина и проникновение являются первоочередными задачами.Стандартный УЗК эффективен при сканировании сварных соединений, но он не обеспечивает такого высокого уровня настройки, который может предложить УЗК.
PAUT идеально подходит для комплексной проверки сложных сварных швов, таких как нержавеющая сталь и аустенитные сварные швы. Поскольку аустенитный сварной шов содержит большое количество отражений зерен, которые искажают данные, аналитикам требуется датчик PAUT, который может проникать в сварные швы без неполного отражения. PAUT также может предоставлять низкочастотные параметры, которые помогают аналитикам противостоять проблемам распространения, вызванным высоким затуханием.
ЭКА стыковых сварных швов
Как было показано ранее, PAUT может быть более подходящим для обнаружения несплошностей на объемном уровне, чем другие методы неразрушающего контроля, лишь немногие подходы приближаются к ECT (вихретоковому контролю) в обнаружении поверхностных дефектов в сварных соединениях. ECT хорошо подходит для обнаружения более тонких сварных швов, которые труднее обнаружить с помощью методов UT или PAUT.
Специализированная технология ECA может предложить большое преимущество, например:
- Повышенная точность и охват
- Маршрутизируемые сканеры могут определять местоположение дефекта и характеризовать размер дефекта
- обеспечивает большую стабильность во время тестирования
ECA имеет несколько ограничений, одно из которых заключается в том, что когда оператор перемещает датчик по материалу, катушка возбуждения должна находиться близко к поверхности материала для точного обнаружения и качества сигнала. Это может быть довольно сложно при работе со сложной геометрией, различными формами сварных швов и материалами, а также с шероховатыми поверхностями, поскольку зоны контроля труднодоступны.
ECA более совершенен и предназначен для контроля стыковых швов. датчики, способные контролировать сварные швы сложной геометрии с использованием нескольких катушек, могут иметь большое значение. Катушки массива позволяют пользователям покрывать большую площадь поверхности и считывать зоны теплового воздействия. Ищете конструкцию зонда, которая удерживает катушки или другие датчики точно и точно на одной линии с поверхностью материала, когда оператор скользит по ней.
для достижения наилучших результатов, аналитикам необходимо портативное устройство с лучшим в отрасли качеством сигнала. в сочетании с возможностями массива поверхностей пользователи могут добиться визуализации обнаружения сварных швов и значительно сократить время контроля.
Улучшение контроля стыковых сварных швов
Как было показано ранее, если сварку необходимо контролировать на объемном уровне, идеально подходит ультразвуковой контроль. Рентгенографический контроль предназначен для проверки поверхностных и внутренних аберраций. Но для контроля поверхностных и подповерхностных дефектов вихретоковый контроль является идеальным решением как наиболее эффективным.
При выборе правильного подхода жизненно важно провести эффективную и действенную проверку. Независимо от используемых методов проверки жизненно важно обеспечить высочайший уровень достоверности проверки и качества данных.
.