Деформации и напряжения при сварке. Сварочные работы. Практический справочник
Деформации и напряжения при сварке
Процесс, при котором в результате воздействия силы форма и размер твердого тела изменяют свою форму, называется деформацией. Различаются следующие ее виды:
– упругая, при которой тело восстанавливает исходную форму, как только действие силы прекращается. Такая деформация, как правило, бывает незначительной, например для низкоуглеродистых сталей она составляет не более 0,2 %.
– остаточная (пластическая), возникающая в том случае, если тело после устранения воздействия не возвращается в первоначальное состояние. Этот вид деформации характерен для пластичных тел, а также отмечается при приложении к телу очень значительной силы. Для пластической деформации нагретого металла, в отличие от холодного, требуется меньше нагрузки.
Степень деформации зависит от величины приложенной силы, т. е. между ними прослеживается прямо пропорциональная зависимость: чем больше сила, тем сильнее деформация.
Силы, которые действуют на изделие, делятся на:
– внешние, к которым относятся собственно вес изделия, давление газа на стенки сосуда и пр. Такие нагрузки могут быть статическими (не изменяющимися по величине и направлению), динамическими (переменными) или ударными;
– внутренние, возникающие в результате изменения структуры металла, которое возможно под воздействием внешней нагрузки или, например, сварки и др. Рассчитывая прочность изделия, внутреннюю силу обычно называют усилием.
Величину усилия характеризует и напряжение, которое возникает в теле в результате этого усилия. Таким образом, между напряжением и деформацией имеется тесная связь.
Относительно сечения металла действующие на него силы могут иметь разное направление. В соответствии с этим возникает напряжение растяжения, сжатия, кручения, среза или изгиба (рис. 3).
Рис. 3. Виды напряжения, изменяющие форму металла и сплава (стрелки указывают направление уравновешивающих сил): а – растяжение; б – сжатие; в – кручение; г – срез; д – изгиб
Появление деформации в сварных конструкциях объясняется возникновением внутренних напряжений, причины которых могут быть разными и подразделяются на две группы.
К первой относятся неизбежные причины, которые обязательно возникают в ходе обработки изделия. При сварке это:
1. Кристаллизационная усадка наплавленного металла. Когда он переходит из жидкого состояния в твердое, его плотность возрастает, поэтому изменяется и его объем (это и называется усадкой), например уменьшение объема олова в таком случае может достигать 26 %. Данный процесс сопровождается растягивающими напряжениями, которые развиваются в соседних участках и влекут за собой соответствующие им напряжения и деформации. Усадка измеряется в процентах от первоначального линейного размера, а каждый металл или сплав имеет собственные показатели (табл. 1).
Напряжения, причиной которых является усадка, увеличиваются до тех пор, пока не наступает момент перехода упругих деформаций в пластические. При низкой пластичности металла на наиболее слабом участке может образоваться трещина. Чаще всего таким местом бывает околошовная зона.
При сварке наблюдаются два вида усадки, которые вызывают соответствующие деформации:
а) продольная (рис. 4), которая приводит к уменьшению длины листов при выполнении продольных швов. При несовпадении центров тяжести поперечного сечения шва и сечения свариваемой детали усадка вызывает ее коробление;
Рис. 4. Продольная усадка и деформации при различном расположении шва по отношению к центру тяжести сечения элемента: а – при симметричном; б, в – при несимметричном; 1 – график напряжений; 2 – шов; ?L – деформация; b – ширина зоны нагрева; напряжение сжатия; + – напряжение растяжения; г – при несимметричном; 2 – шовб) поперечная (рис. 5), следствием которой всегда является коробление листов в сторону более значительного объема наплавленного металла, т. е. листы коробятся вверх, в направлении утолщения шва. Фиксация детали воспрепятствует деформации от усадки, но станет причиной возникновения напряжений в закрепленных участках.
Рис. 5. Поперечная усадка и деформации: а – деформации до и после сварки; б – график распределения напряжения (О – центр тяжести поперечного сечения шва; напряжение сжатия; + – напряжение растяжения)Величина деформаций при сварке зависит, во-первых, от размера зоны нагрева: чем больший объем металла подвергается нагреванию, тем значительнее деформации. Следует отметить, что для различных видов сварки характерны разные по размеру зоны нагрева и деформации, в частности при газовой сварке кислородно-ацетиленовым пламенем она больше, чем при дуговой сварке.
Во-вторых, имеют значение размер и положение сварного шва. Величина деформации тем существеннее, чем длиннее шов и больше его сечение, определенную роль играют также несимметричность шва и главной оси сечения свариваемого изделия.
В-третьих, если деталь сложна по своей форме, то швов на ней бывает больше, поэтому можно предположить, что напряжения и деформация обязательно проявятся.
2. Неравномерный нагрев свариваемых частей или деталей. Как известно, при нагревании тела расширяются, а при охлаждении – сужаются. При сварке используется сосредоточенный источник тепла, например сварочная дуга или сварочное пламя, который с определенной скоростью перемещается вдоль шва и поэтому неравномерно нагревает его. Если свободному расширению или сокращению мешают какие-либо препятствия, то в изделии развиваются внутренние напряжения. Более холодные соседние участки и становятся такой помехой, поскольку их расширение выражено в меньшей степени, чем у нагретых участков. Поскольку термические напряжения, ставшие следствием неравномерного нагревания, развиваются без внешнего воздействия, то они называются внутренними, или собственными. Наиболее важными являются те из них, которые возникают при охлаждении изделия, причем напряжения, действующие вдоль шва, менее опасны, поскольку не меняют прочности сварного соединения, в отличие от напряжений, перпендикулярных шву, которые приводят к образованию трещин в околошовной зоне;
3. Структурные трансформации, которые развиваются в околошовной зоне или металле шва. В процессе нагревания и охлаждения металла размер и расположение зерен относительно друг друга изменяются, что отражается на объеме металла и становится причиной возникновения внутренних напряжений со всеми вытекающими последствиями, представленными в первом пункте. В наибольшей степени этому подвержены легированные и высокоуглеродистые стали, предрасположенные к закалке; низкоуглеродистые – в меньшей. В последнем случае при изготовлении сварных конструкций это явление может не приниматься в расчет.
Вторую группу составляют сопутствующие причины, которые можно предупредить или устранить. К ним относятся:
– ошибочные конструктивные решения сварных швов, например небольшое расстояние между соседними швами, слишком частое пересечение сварных швов, ошибки в выборе типа соединения и др.;
– несоблюдение техники и технологии сварки, в частности плохая подготовка кромок металла, нарушение режима сварки, использование несоответствующего электрода и др.;
– низкая квалификация исполнителя.
Величина деформаций при сварке во многом определяется теплопроводностью металла. Между ними существует прямо пропорциональная зависимость: чем выше теплопроводность, тем более равномерно распространяется поток тепла по сечению металла, тем менее значительными будут деформации. Например, при сварке нержавеющей стали как менее теплопроводной возникают большие деформации, чем при сварке низкоуглеродистых сталей.
Напряжения и деформации, которые имеют место исключительно в ходе сварки, а по ее окончании исчезают, называются временными; а если они сохраняются после охлаждения шва – остаточными. Практическое значение последних особенно велико, поскольку они могут сказываться на работе детали, изделия, всей конструкции. Если деформации носят локальный характер (например, на отдельных участках появляются выпучины, волнистость и др.), то они называются местными; если в результате деформации терпят изменения геометрические оси и размеры изделия или конструкции в целом – общими.
Кроме того, деформации могут возникать как в плоскости изделия, так и вне ее (рис. 6).
Рис. 6. Некоторые виды деформации: а – в плоскости сварного соединения; б – вне плоскости сварного соединения; 1 – форма изделия до сварки; 2 – форма изделия после сваркиДля уменьшения деформаций и напряжений при сварке придерживаются следующих конструктивных и технологических рекомендаций:
1. При подборе материала для сварных конструкций руководствуются правилом: использовать такие марки основного металла и электродов, которые либо не имеют склонности к закалке, либо подвержены ей в наименьшей степени и способны давать пластичный металл шва.
2. Избегают закладывать в конструкциях (особенно в ответственных), тем более рассчитанных на работу при ударах или вибрации, многочисленные сварные швы и их пересечения, а также использовать короткие швы замкнутого контура, поскольку в этих зонах, как правило, концентрируются собственные напряжения. Чтобы снизить тепловложения в изделие или конструкцию, оптимальная длина катетов швов должна быть не более 16 мм.
3. Стараются симметрично располагать ребра жесткости в конструкциях и сводят их количество к минимуму. Симметричность необходима и при расположении сварных швов, так как это уравновешивает возникающие деформации (рис. 7), т. е. последующий слой должен вызывать деформации, противоположные тем, которые развились в предыдущем слое.
Рис. 7. Последовательность наложения сварных швов для уравновешивания деформацийЭффективен и способ обратных деформаций (рис. 8). Перед сваркой в конструкции (как правило, швы в ней должны располагаться с одной стороны относительно оси либо на различных расстояниях от нее) вызывают деформацию, обратную той, что возникнет в ней при сварке.
Рис. 8. Сваривание гнутых профилей как пример применения обратной деформации4. Ограничивают применение таких способов соединения, как косынки, накладки и др.
5. По возможности отдают предпочтение стыковым швам, для которых концентрация напряжений не столь характерна.
6. Предполагают минимальные зазоры на разных участках сварки.
7. В сопряжениях деталей предусматривают возможность свободной усадки металла шва при охлаждении в отсутствие жестких заделок.
8. Практикуют изготовление конструкций по секциям, чтобы потом сваривать готовые узлы. Если последние имеют сложную конфигурацию, то заготавливают литые и штампованные детали, чтобы снизить неблагоприятное воздействие жестких связей, которые дают сварные швы.
9. Выбирают технологически обоснованную последовательность (рис. 9) выполнения сварных швов, при которой допускается свободная деформация свариваемых деталей. Если, например, требуется соединить листы, то в первую очередь выполняют поперечные швы, в результате чего получают полосы, которые потом сваривают продольными швами. Такая очередность исключает жесткую фиксацию соединяемых частей листов и позволяет им свободно деформироваться при сварке.
Направление ведения сварного шва также имеет значение. Если вести его на проход либо от центра к концам, то в середине шва разовьются поперечные напряжения сжатия; если двигаться от краев к центру, то в середине шва не избежать появления поперечных напряжений растяжения, следствием которых будут трещины в околошовной зоне или самом шве (рис. 10).
Рис. 10. Напряжение в продольном сечении шва при сварке (– – напряжение сжатия; + – напряжение растяжения): а – на проход; б – от концов к центру10. При соединении частей из металла значительной толщины (более 20–25 мм) применяют многослойную дуговую сварку, выполняя швы горкой или каскадом (рис. 11). Шов горкой накладывается следующим образом: первый слой имеет длину примерно 200–300 мм, второй длиннее первого в 2 раза, третий длиннее второго на 200–300 мм и т. д. Достигнув «горки», сварку продолжают в обе стороны от нее короткими валиками. Такой способ способствует поддержанию участка сварки в нагретом состоянии. В результате тепло распространяется по металлу более равномерно, что снижает напряжения.
Рис. 11. Очередность наложения швов при многослойной дуговой сварке (размеры указаны в миллиметрах): а – горкой; 1 – ось «горки»; 2 – толщина металла; б – каскадом11. Помогает снизить коробление швов соединяемых конструкций и деталей выполнение швов в обратноступенчатом порядке (рис. 12). Для этого протяженные швы делят на части длиной 150–200 мм и сваривают их, ведя каждый последующий слой в направлении, обратном предыдущему слою, причем стыки следует размещать вразбежку. Причина таких действий заключается в том, что деформации в соседних участках будут противоположно направленными по отношению друг к другу и равномерными, поскольку металл будет прогреваться равномерно.
Рис. 12. Последовательность наложения обратнопоступательного шва12. Рассчитывают адекватный тепловой режим сварки. Если при работе есть возможность перемещать изделие (деталь) или если основной металл предрасположен к закалке, тогда используют более сильный тепловой режим, благодаря чему объем разогреваемого материала возрастает, а сам он остывает медленнее. В определенных ситуациях (если сварка проводится при пониженной температуре воздуха, металл имеет большую толщину или является сталью, склонной к закалке, и др.) помогают предварительный или сопровождающий подогрев либо околошовной зоны, либо всего изделия. Температура, до которой следует довести металл, зависит от его свойств и составляет 300–400 °C для бронзы, 250-270 °C для алюминия, 500–600 °C для стали, 700–800 °C для чугуна и т. д.
Если сваривают жестко зафиксированные детали или конструкции, тогда применяют менее интенсивный тепловой режим и варят электродами, способными давать пластичный металл шва.
13. Осуществляют отжиг и нормализацию изделия или конструкции после окончания сварки (последнее полностью ликвидирует напряжения). При отжиге температуру стального изделия доводят до 820–930 °C, выдерживают (общее время составляет примерно 30 минут, длительная выдержка нежелательна, поскольку приводит к росту зерен) и постепенно охлаждают (на 50–75 °C в час), доводя температуру до 300 °C. Это дает ряд преимуществ: во-первых, шов приобретает мелкозернистую структуру с улучшенным сцеплением зерен, благодаря которой металл шва и околошовной зоны становится более пластичным, во-вторых, металл шва получается менее твердым, что имеет большое значение для последующей обработки резанием или давлением; в-третьих, это полностью снимает внутренние напряжения в изделии.
Основные отличия нормализации от полного отжига – более высокая скорость охлаждения, для чего температура, до которой нагревают изделие, на 20–30 °C превышает критическую, и то, что выдержка и охлаждение проводятся на воздухе.
14. Избегают планировать в изделиях и конструкциях сварные швы, неудобные для выполнения, например вертикальные, потолочные.
15. Обеспечивают минимальную погонную энергию, достижимую при высокой скорости сварки в сочетании с наименьшими поперечными сечениями швов.
16. Уменьшают число прихваток и их сечения.
17. Проковывают швы в холодном или горячем состоянии, что уменьшает внутренние напряжения и увеличивает прочность конструкции. Данный текст является ознакомительным фрагментом.Читать книгу целиком
Поделитесь на страничкеих разновидности и причины возникновения
Сварка обеспечивает самое прочное и надежное соединение, если проведена правильно. Однако при нарушении технологии в конструкции возникают напряжения и деформации, вызванные сварочным процессом. Искажается форма и размеры изделия, в результате чего оно не может выполнять свои функции.
Что такое напряжение
Сварочное напряжение определяют как силу, действующую на единицу площади изделия. Оно может быть вызвано растягивающим, изгибающим, крутящим, сжимающим или срезающим усилием.
Эти силы достигают таких величин, что в процессе эксплуатации напряжения и деформации в отдельных деталях приводят к разрушению всей конструкции. Кроме этого происходит снижение антикоррозионных свойств, меняются геометрические размеры и жесткость конструкции.
Напряжения и деформации бывают временными и остаточными. Какие сварочные деформации называют временными, а какие остаточными определяется просто. Временные появляются во время сваривания деталей, вторые появляются и остаются после окончания сварки и охлаждения конструкции.
Причины появления
Главные причины возникновения напряжений и сварочных деформаций такие:
- неоднородный нагрев металлических заготовок;
- усадочные изменения сплава в сварном шве;
- фазовые изменения, возникающие при переходе расплавленного металла из одного состояния в другое.
Одним из свойств металлов является их способность расширяться при повышении температуры и сжиматься при охлаждении. При плавлении в области сварочного соединения появляется неоднородная термозона.
Она вызывает напряжения сжимающего или растягивающего свойства. Если эти напряжения превышают предел текучести металла, то происходит изменение формы изделия, возникают остаточные деформации.
Разновидности деформаций зависят от того, в каких объемах они проявляются. Выделяют три рода. Деформации первого рода действуют в макрообъемах, деформации второго рода происходят в пределах кристаллических зерен, а третьего рода происходят в кристаллической решетке металла.
Деформации и напряжения при сварке возникают и при кристаллизации сварного шва, когда происходит усадка жидкого металла. Объем остывающего жидкого металла уменьшается, это вызывает напряжения внутри металла. Параллельно и перпендикулярно оси сварочного шва формируются напряжения, которые вызывают изменение формы изделия. Продольные силы вызывают изменения длины сварного шва, а поперечные приводят к угловым деформациям.
При превышении определенных предельных температур при сваривании углеродистых и легированных сталей происходит их структурное превращение. У них появляется другой удельный объем и изменяется коэффициент линейного расширения, что приводит к огромным сварочным напряжениям.
Самые большие из них возникают в легированных сталях. В них образуются закалочные структуры, которые при охлаждении не возвращаются к прежней структуре металла, как в большинстве случаев, а сохраняют колоссальные напряжения могущие привести к разрушению сварного шва.
Для этих сплавов разрабатываются специальные технологические процессы, снижающие остаточные напряжения и деформации.
Как предотвратить
Для предупреждения вредных воздействий сварочных деформаций необходимо соблюдать следующие правила и провести несколько мероприятий:
- сварных швов должно быть минимум, и они должны быть как можно короче;
- количество пересекающихся и разнотолщинных швов так же сводят к минимуму;
- сварочные соединения делают с плавным переходом толщин;
- металл наплавляют в минимальном количестве;
- в самых напряженных местах конструкции швы вовсе не делают;
- оставляют припуск на усадку.
Необходимо правильно выбирать способ сварки, который зависит от свариваемости материалов, энергии и режима. Чтобы уменьшить зону прогрева, нужно увеличить скорость сваривания. Для увеличения глубины сварки (прогрев в толщину) необходимо увеличить силу тока.
Для уменьшения вредных воздействий нагрева в зоне сваривания сварщику необходимо по возможности избегать прихваток.
Положительный результат дает использование зажимов и других сварочных приспособлений. Они позволяют сохранить подвижность деталей при сварке в продольном направлении и препятствовать угловому перемещению.
Заготовки располагают таким образом, чтобы возникающие при остывании сварочные деформации были противоположны напряжениям.
Для уменьшения остаточных напряжений и деформаций надо использовать предварительный нагрев. Кроме этого нужно правильно выбрать технологию сварки.
Последовательность наложения швов должна уравновешивать возникающие напряжения. Накладывать швы надо так, чтобы свариваемые детали имели наибольшую подвижность.
В процессе сварки проводят проковку сварного шва, что деформирует остывающее сварное соединение и уменьшает воздействие усадки.
Способы устранения напряжений
Напряжения устраняют отжигом или механическими методами. Отжиг является самым эффективным методом снятия напряжений. Его применяют, когда к изделию предъявляются повышенные требования к точности геометрических размеров.
Он может быть общим или местным. Чаще всего отжиг производят при 550-680 °C. Выделяют три его стадии: нагрев, выдержка, остывание.
Из механических способов устранения напряжений применяют проковку, прокатку, вибрацию, обработку взрывом, приводящие к пластической деформации обратного знака.
Проковку делают пневмомолотком, а виброобработку специальным устройством вызывающим вибрацию изделия с резонансной частотой в пределах 10-120 Гц в течение нескольких минут.
Способы устранения деформаций
Сварочные деформации могут проходить в плоскости и с выведением из плоскости. О деформациях в плоскости говорят, когда изменяются геометрические размеры конструкции. Деформация из плоскости соответствует угловым изменениям детали, искривлению листовой поверхности.
Для устранения таких явлений применяют термическую правку с местным или общим нагревом, холодную механическую и термомеханическую.
Термический способ с местным нагревом основывается на том, что при охлаждении металл сжимается. Для устранения сварочных деформаций растянутую часть изделия сначала нагревают (горелкой или дугой), при этом окружающий сплав остается холодным и не дает горячему участку сильно расшириться.
При остывании изделие выпрямляется. Так правят балки, листовые полосы и некоторые другие детали.
Если происходит полный отжиг, то конструкцию закрепляют в устройстве, создающем давление на требуемые зоны, и помещают в печь для нагрева.
Холодную правку делают, используя постоянные нагрузки. Для этого применяют различные прессы или валки для прокатки длинномерных изделий типа труб или двутавровых балок, в необходимых местах они деформируются.
Термомеханическую правку производят с применением силовой нагрузки при местном нагреве изделия. Такой способ применяют к сильно растянутым деталям. Вначале собирают излишек металла в так называемые купола, а затем прогревают эти участки.
Технологию правки выбирают в зависимости от особенностей сварочной деформации и типа металлического изделия, его размеров, конфигурации. Обращают внимание также и на трудозатраты, останавливаясь на самом эффективном методе.
ДЕФОРМАЦИИ И НАПРЯЖЕНИЯ ПРИ СВАРКЕ [виды и решения]
Прочность конструкции и качество сварочного шва находятся в прямой связи. Любая [сварка] связана с нагреванием и остыванием металла, а это означает, что материал будет подвергаться структурным и объемным изменениям с вероятными остаточными напряжениями.
Отчего возникают сварочные деформации напряжения
Причина напряжения в металле при сварке — это прежде всего вызванные нагревом изменения. По мере нарастания температуры происходит размягчение и плавление, а в момент достижения предела температуры текучести нарастают структурные факторы. Особенно ярко проявляются деформирующие эффекты при сваривании сталей разного сорта. Это объясняется:
различиями в температуре плавления;
разницей в крупности кристаллического зерна, особенностях структурных связей;
наличием в стали углерода — эти сорта имеют крайне низкие способности к свариванию;
перестройкой структуры металла по мере нагрева и остывания.
Специалистам известно, что наилучшие показатели сваривания присущи нелегированным сортам стали с низким и средним содержанием углерода. В процессе сварки в них формируются новые структуры, со своими особенностями взаимодействия и разной подвижностью. Именно эти особенности и приводят к временному и остаточному напряжению в сварочном шве.
Элементы структуры стали и внутренние напряжения
Под воздействием высокой температуры в стали происходят структурные изменения. Взаимодействующие компоненты состава металла образуют свои кристаллические формации.
Аустенит — растворенный в железе твердый углерод, который начинает возникать при температуре от 723 С. В зависимости от концентрации, аустенит может сохраняться в металле до температур от 1100 до 1350 С, поддерживая высокую подвижность металлического зерна. Такая сталь при постепенном охлаждении сохраняет пластичность, потому напряжения в ней оказываются незначительными. Часть аустенита остается в металле после остывания.
Цементит, он же карбид железа обладает высокой твердостью поверхности, потому ограничивает подвижность зерна в ромбовидной решетке.
Феррит формируется при сварке в присутствии флюса и обеспечивает хорошую пластичность металла за счет округлости зерен. Образуется при остывании стали и поддерживает ее пластичность.
При смешивании феррита и цементита образуется пластинчатый или зернистый перлит с вытянутыми или округлыми зернами. Быстрое охлаждение металла приводит к замене перлита трооститом.
Зерна мартенсита относятся к неравновесным структурным элементам стали, существующим только в определенном температурном диапазоне (от 750 до 900 С). Закалка стали с быстрым охлаждением приводит к фиксации мартенсита в структуре, что придает металлу повышенную прочность, но ограничивает пластичность.
Если речь идет о легированной стали, то при изменении температур в ее структуре появляются нитридные и карбидные элементы перечисленных структурных компонентов. Разные размеры, время и условия существования кристаллических зерен и определяют возникновение напряжений.
Диагностика сварочного напряжения
[Методы выявления сварочного брака] рассчитаны обнаружение [дефектов сварных швов], часть из которых связана с возникшими в процессе напряжениями. Их принято классифицировать как остаточные (внутренние) и поверхностные. Условия для первых формируются при остывании стали.
Внутренние деформирующие напряжения
Усадка металла после сварки, угловая деформация, внутренний разрыв возникают при внутреннем напряжении, которое может быть не выявлено методами визуального осмотра. Серьезные проблемы возникают, если напряжение нарастает по мере использовании сварной детали. Сокращается срок эксплуатации конструкции, растет риск разрушения шва, потери прочности и разрушения.
Поверхностные дефекты
Поверхностные напряжения выявляются по видимому короблению деталей, расхождению швов, появлению трещин при превышении предела прочности металла. В отдельных случаях, в зависимости от степени ответственности детали, допускается переваривание шва, закрытие трещин.
Объемное напряжение
Наиболее опасно с точки зрения целостности и предсказуемости детали объемное напряжение с признаками внутренней и внешней деформации. Практически невозможно определить силу, направление и развитие деформации, если напряжение связано с разницей в структурной сетке металла с разнонаправленными внутренними линиями растяжения и сжатия.
Последствия напряжения сварного шва
Последствия напряжения различают и по характеру деформации — упругая поверхностная может быть устранена или постепенно сойдет сама в процессе остывания. Пластическая деформация шва необратима, устранить ее без переваривания практически невозможно, при этом изменяется структура металла и его прочностные свойства.
Равномерность распределения
При оценке деформации используется коэффициент неравномерности, который позволяет учесть направление сил напряжения и заранее принять профилактические меры. Например, неравномерность будет выраженной, если часть заготовки контактирует с массивными холодными тисками, фиксируется ими, а при остывании именно в этой зоне формируется зона наибольшего напряжения. Имеет значение и разница в габаритах деталей — больший размер связан с изменением динамики нагрева и остывания, при соединении с фрагментом меньшего размера возникает неравномерно распределенное усилие.
Профилактика и снятие напряжений металла при сварке
Основным способом предотвращения напряжений в сварочном шве можно назвать правильный выбор стали для соединения. Чем ближе по составу и структуре соединяемые фрагменты, тем меньше вероятность напряжения и последующей деформации. Особое внимание уделяют качеству и [технике сварки тонких металлов инвертором], так как небольшая толщина металла — это условие для разрыва и активного коробления.
Способы уменьшения сварочной деформации
Помогает избежать коробления и внутренних напряжений использование коротких швов, не пересекающихся соединений. Тщательная зачистка кромок позволяет плотно смыкать детали при стыковой сварке.
Опытный сварщик уравновешивает напряжения, используя подготовку кромок в виде параболических треугольников с взаимно совпадающей встречной кривизной — поверхности с изгибом распределяют нагрузку при деформации навстречу, компенсируя ее. Применяется методика сварки по оси симметрии деталей разной толщины, чтобы уравновесить деформирующие силу при остывании.
Для компенсации используются вставки из мягких и плавких металлов, тиски с подогревом и охлаждением губок. В практике сварки больших по размеру конструкций предусмотрено использование механических зажимов. При неизбежности нарастания напряжения может использован последующий отжиг металла. Методы борьбы с угловыми деформациями построены на предварительном напряжении зоны шва и отклонении заготовок.
Напряжения и деформации при сварке и меры борьбы с ними
Содержание страницы
Причины возникновения сварочных напряжений и деформаций
Сварка, как и другие процессы обработки металлов (литье, термообработка, штамповка и др.), вызывает возникновение в деталях собственных (внутренних) напряжений. Во многих случаях собственные напряжения бывают настолько высокими, что вызывают значительные деформации детали и снижение ее работоспособности.
Основные причины возникновения напряжений и деформаций следующие:
- неравномерный нагрев металла. Местный нагрев металла в зоне сварки от температуры окружающей среды до температуры плавления и затем быстрое охлаждение приводят к образованию тепловых напряжений;
- линейная усадка наплавленного металла. Затвердевший металл уменьшается в объеме, а так как он жестко связан с основным металлом детали, то в переходной зоне возникают внутренние напряжения растяжения;
- структурные изменения возникают в металлах при быстром охлаждении, когда перлитно-ферритная или аустенитная структура околошовной зоны переходит в мартенситную, объем которой больше объема исходной структуры.
Широкий диапазон изменения температуры в месте сварки приводит к изменению физических и механических характеристик металла в околошовной зоне. Из графика (рис. 1) видно, что относительное удлинение δт в интервале температур от 100 до 350 °C снижается, а предел прочности стали σв повышается. Максимальное возрастание прочности в интервале 200—350 °C при понижении пластичности часто бывает причиной образования в металле трещин. Коэффициент
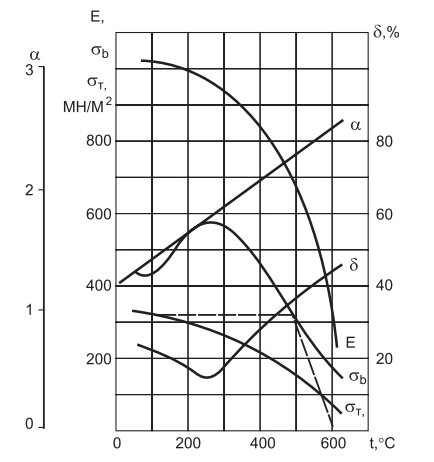
Рис. 1. Изменение свойств низкоуглеродистой стали в зависимости от температуры.
линейного расширения α с повышением температуры возрастает, а модуль упругости Е резко падает и при температуре около 650 °C практически равен нулю, т. е. сталь утрачивает свои упругие свойства. Предел текучести σ, с повышением температуры снижается. Изменение предела текучести в зависимости от температуры аппроксимируют ломаной прямой линией и принимают таким, как показано на графике штриховой линией.
Структурные изменения, происходящие в металле при нагреве и охлаждении, сопровождаются объемными изменениями, которые и становятся причиной возникновения структурных напряжений. На рис. 2 показана зависимость объемных изменений в стали при нагреве и охлаждении.
Границы нагрева АС1 и АС3 показывают начало и конец образования аустенита, а кривая 1 — изменение объема сталей всех марок при нагреве. В интервале температур АС1 — АС3 α-железо переходит в γ-железо, плотность которого выше, т. е. наблюдается уменьшение объема при нагревании. При охлаждении изменение объема идет по кривой 2. В низкоуглеродистых сталях распад аустенита происходит в интервале температур 900—700 °C, когда сталь пластична, поэтому объемные изменения не вызывают заметного образования структурных напряжений. У закаливающихся и особенно у легированных сталей из-за податливости к переохлаждению распад аустенита происходит при более низких температурах.
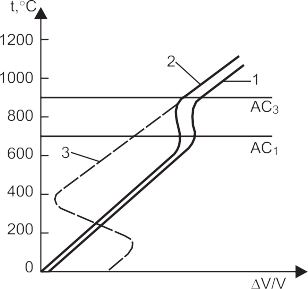
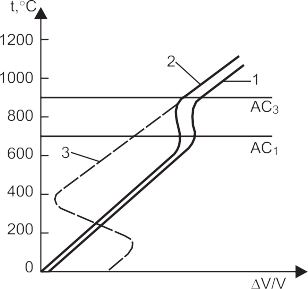
Рис. 2. Объемные изменения в стали при нагреве и охлаждении
Так, при полной закалке аустенит переохлаждается до температуры 200—350 °C и затем сразу переходит в мартенсит с резким увеличением объема (кривая 3 на рис. 2). В интервале температур 200—350 °C сталь имеет высокую прочность и упругость, поэтому объемные изменения сопровождаются образованием структурных напряжений. В объемах с мартенситной структурой возникают остаточные напряжения сжатия, а по границам — продольные напряжения растяжения. В более пластичных сталях растягивающие напряжения вызывают пластические деформации, а в более хрупких — трещины и даже отколы.
Влияние пористости швов на характеристики сварных соединений
Поры в сварном шве влияют на плотность и механические характеристики сварного соединения. Присутствие пор в шве приводит к уменьшению фактического поперечного сечения шва и, как следствие, к ухудшению механических характеристик сварного соединения в целом. При уменьшении сечения шва до 5% предел текучести, относительное удлинение и угол загиба существенно не изменяются. Более высокая пористость приводит к резкому снижению упомянутых характеристик. Механические свойства сварных соединений высокопрочной стали более подвержены влиянию пористости, чем низкоуглеродистой. Пористость больше сказывается на свойствах угловых швов и меньше — стыковых. При испытании на статический изгиб даже мелкие поры вызывают надрывы, если они расположены близко к поверхности шва. Влияние пор на сопротивление усталости сварных соединений при переменных нагрузках значительнее, чем при статических испытаниях. Установлено, если поры уменьшают площадь поперечного сечения шва всего на 0,8%, то сопротивление усталости сварного соединения снижается на 20%. При более значительном уменьшении сечения сопротивление усталости сварного соединения снижается почти в три раза. Наличие пор в продольных швах менее опасно, чем в поперечных, особенно при низких рабочих напряжениях. Поры, выходящие на поверхность шва (свищи), уменьшают коррозионную стойкость сварного соединения. Требования к качеству сварных швов устанавливаются стандартами, техническими условиями и правилами по контролю и приемке сварных соединений. Допустимость по количеству, размерам и распределению пор решается в зависимости от условий эксплуатации сварных конструкций. Пористость швов не допускается в сварных сосудах, работающих под давлением или вакуумом, а также предназначенных для хранения и перевозки жидких и газообразных продуктов.
Если количество, размер и распределение пор в швах не превышают требований допустимых норм, это не приводит к потере несущей способности сварной конструкции. Для обнаружения пор в швах применяются следующие методы:
- внешний осмотр;
- осмотр изломов швов, полученных при сварке технологических проб;
- осмотр микрошлифов;
- ультразвуковой контроль;
- радиографический контроль.
Меры борьбы со сварочными напряжениями и деформациями
Наиболее эффективное средство снижения собственных напряжений — подогрев детали перед сваркой и медленное охлаждение после нее. Предварительный подогрев в значительной степени снижает тепловые и усадочные напряжения, а медленное охлаждение предотвращает структурные превращения, особенно в околошовной зоне.
Стали, податливые закалке, с содержанием углерода 0,35% и более подогревают до температуры 150—280 °C. Для получения наплавленного слоя высокого качества высокоуглеродистые (более 0,35% углерода) и легированные стали после сварки или наплавки подвергают термической обработке, которая не только улучшает качество шва, но и снимает собственные напряжения. В некоторых случаях применяют высокотемпературный отпуск стали после наплавки, т. е. нагрев до температуры 600—650 °C, выдержка при этой температуре из расчета 2—3 мин на 1 мм толщины металла и медленное охлаждение вместе с печью.
Для подогрева деталей используют индукторы, многопламенные и однопламенные газовые горелки, специальные печи и т. п. Применение предварительного нагрева, отпуска и термообработки всегда связано со значительным усложнением процесса и снижением производительности. Поэтому для уменьшения собственных напряжений и деформаций разработаны и успешно применяются менее трудоемкие способы.
При сварке и наплавке симметричных деталей сварочные швы накладывают в определенной последовательности, вызывающей уравновешивающие деформации (рис. 3). Иногда при подготовке деталей к сварке создают деформации, обратные деформациям, ожидаемым после сварки (рис. 4). При многослойной наплавке деталей рекомендуется послойная проковка швов пневматическим зубилом с закругленным лезвием. Чтобы не вызвать трещин и надрывов, первый и последний швы не проковывают. Не рекомендуется проковывать хрупкие и закаленные швы.
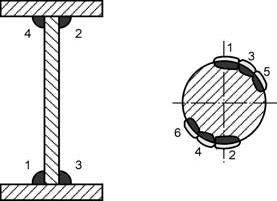
Рис. 3. Последовательность наложения швов на симметричные детали
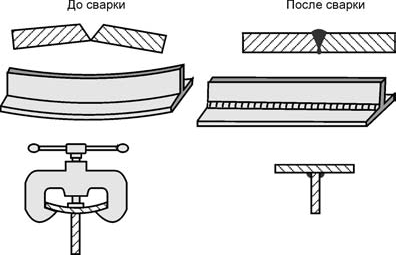
Рис. 4. Создание обратных деформаций при сварке
Деформации, возникающие в деталях после наплавки, устраняются механической или термической правкой.
Для механической правки применяют молоты, различные правильные (рихтующие) вальцы и прессы.
При термической правке выпуклую сторону деформированной детали быстро нагревают до температуры 700—800 °C и свободно охлаждают. Уравновешивающие деформации, возникающие при этом, выравнивают деталь.
Часто для термической правки в качестве источника тепла используют газовые горелки.
При сварке двутавровых балок для предотвращения грибовидности поясов целесообразно применять предварительный обратный изгиб заготовок поясов. Величину изгиба определяют опытным путем. Устранение образовавшейся грибовидности поясов обеспечивается при местном концентрированном нагреве деформированного участка газовым пламенем и быстром его охлаждении. В результате в исправляемом элементе конструкции возникают усилия, достаточные для уменьшения или исправления местного дефекта. Для устранения значительных деформаций одновременно с нагревом применяют механизированные средства — струбцины, домкраты, тиски и т. п. Нагрев ведут, как правило, со стороны выпуклой части деформированной поверхности (рис. 5). Детали охлаждают естественным путем на воздухе, но возможно водяное охлаждение для сталей, не склонных к закалке. Нагрев производят универсальными горелками типа ГЗ-3, работающими на ацетилене или газозаменителях.
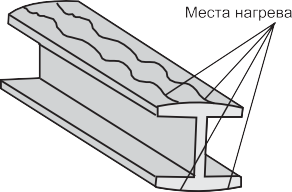
Рис. 5. Места нагрева деформированного участка
Техника правки состоит в следующем. Сначала выбирают участок нагрева и определяют ширину зоны нагрева. Эта зона должна составлять 0,5—2 толщины листа. Нагревают выбранную зону пламенем горелки до температуры 250—650 °C в зависимости от величины прогиба. Следует учитывать, что температура нагрева не должна превышать температуру начала структурных превращений исправляемого металла.
Просмотров: 488
Деформации и напряжения при сварке. Сварочные работы. Практический справочник
Деформации и напряжения при сварке
Процесс, при котором в результате воздействия силы форма и размер твердого тела изменяют свою форму, называется деформацией.
Различаются следующие ее виды:
? упругая, при которой тело восстанавливает исходную форму, как только действие силы прекращается. Такая деформация, как правило, бывает незначительной, например для низкоуглеродистых сталей она составляет не более 0,2 %.
? остаточная (пластическая), возникающая в том случае, если тело после устранения воздействия не возвращается в первоначальное состояние. Этот вид деформации характерен для пластичных тел, а также отмечается при приложении к телу очень значительной силы. Для пластической деформации нагретого металла, в отличие от холодного, требуется меньше нагрузки.
Степень деформации зависит от величины приложенной силы, т. е. между ними прослеживается прямо пропорциональная зависимость: чем больше сила, тем сильнее деформация.
Силы, которые действуют на изделие, делятся на:
? внешние, к которым относятся собственно вес изделия, давление
газа на стенки сосуда и проч. Такие нагрузки могут быть статическими (не изменяющимися по величине и направлению), динамическими (переменными) или ударными;
? внутренние, возникающие в результате изменения структуры металла, которое возможно под воздействием внешней нагрузки или, например, сварки и др. Рассчитывая прочность изделия, внутреннюю силу обычно называют усилием.
Величину усилия характеризует и напряжение, которое возникает в теле в результате этого усилия. Таким образом, между напряжением и деформацией имеется тесная связь.
Относительно сечения металла действующие на него силы могут иметь разное направление. В соответствии с этим возникает напряжение растяжения, сжатия, кручения, среза или изгиба (рис. 3).
Появление деформации в сварных конструкциях объясняется возникновением внутренних напряжений, причины которых могут быть разными и подразделяются на две группы.

Рис. 3. Виды напряжения, изменяющие форму металла и сплава (стрелки указывают направление уравновешивающих сил): а – растяжение; б – сжатие; в – кручение; г – срез; д – изгиб
К первой относятся неизбежные причины, которые обязательно возникают в ходе обработки изделия. При сварке это:
1. Кристаллизационная усадка наплавленного металла. Когда он переходит из жидкого состояния в твердое, его плотность возрастает, поэтому изменяется и его объем (это и называется усадкой), например уменьшение объема олова в таком случае может достигать 26 %. Данный процесс сопровождается растягивающими напряжениями, которые развиваются в соседних участках и влекут за собой соответствующие им напряжения и деформации. Усадка измеряется в процентах от первоначального линейного размера, а каждый металл или сплав имеет собственные показатели (табл. 1).
Таблица 1
Линейная усадка некоторых металлов и сплавов

Напряжения, причиной которых является усадка, увеличиваются до тех пор, пока не наступает момент перехода упругих деформаций в пластические. При низкой пластичности металла на наиболее слабом участке может образоваться трещина. Чаще всего таким местом бывает околошовная зона.
При сварке наблюдаются два вида усадки, которые вызывают соответствующие деформации:
а) продольная (рис. 4), которая приводит к уменьшению длины листов при выполнении продольных швов. При несовпадении центров тяжести поперечного сечения шва и сечения свариваемой детали усадка вызывает ее коробление;
б) поперечная (рис. 5), следствием которой всегда является коробление листов в сторону более значительного объема наплавленного металла, т. е. листы коробятся вверх, в направлении утолщения шва. Фиксация детали воспрепятствует деформации от усадки, но станет причиной возникновения напряжений в закрепленных участках.
Рис. 4. Продольная усадка и деформации при различном расположении шва по отношению к центру тяжести сечения элемента: а – при симметричном; б, в – при несимметричном; 1 – график напряжений; 2 – шов; ?L – деформация; b – ширина зоны нагрева; – напряжение сжатия; + – напряжение растяжения; г – при несимметричном; 2 – шов
Величина деформаций при сварке зависит, во-первых, от размера зоны нагрева: чем больший объем металла подвергается нагреванию, тем значительнее деформации. Следует отметить, что для различных видов сварки характерны разные по размеру зоны нагрева и деформации, в частности при газовой сварке кислородно-ацетиленовым пламенем она больше, чем при дуговой сварке.

Рис. 5. Поперечная усадка и деформации: а – деформации до и после сварки; б – график распределения напряжения (О – центр тяжести поперечного сечения шва; – напряжение сжатия; + – напряжение растяжения)
Во-вторых, имеют значение размер и положение сварного шва. Величина деформации тем существеннее, чем длиннее шов и больше его сечение, определенную роль играют также несимметричность шва и главной оси сечения свариваемого изделия.
В-третьих, если деталь сложна по своей форме, то швов на ней бывает больше, поэтому можно предположить, что напряжения и деформация обязательно проявятся.
2. Неравномерный нагрев свариваемых частей или деталей. Как известно, при нагревании тела расширяются, а при охлаждении – сужаются. При сварке используется сосредоточенный источник тепла, например сварочная дуга или сварочное пламя, который с определенной скоростью перемещается вдоль шва и поэтому неравномерно нагревает его. Если свободному расширению или сокращению мешают какие-либо препятствия, то в изделии развиваются внутренние напряжения. Более холодные соседние участки и становятся такой помехой, поскольку их расширение выражено в меньшей степени, чем у нагретых участков. Поскольку термические напряжения, ставшие следствием неравномерного нагревания, развиваются без внешнего воздействия, то они называются внутренними, или собственными. Наиболее важными являются те из них, которые возникают при охлаждении изделия, причем напряжения, действующие вдоль шва, менее опасны, поскольку не меняют прочности сварного соединения, в отличие от напряжений, перпендикулярных шву, которые приводят к образованию трещин в околошовной зоне;
3. Структурные трансформации, которые развиваются в околошовной зоне или металле шва. В процессе нагревания и охлаждения металла размер и расположение зерен относительно друг друга изменяются, что отражается на объеме металла и становится причиной возникновения внутренних напряжений со всеми вытекающими последствиями, представленными в первом пункте. В наибольшей степени этому подвержены легированные и высокоуглеродистые стали, предрасположенные к закалке; низкоуглеродистые – в меньшей. В последнем случае при изготовлении сварных конструкций это явление может не приниматься в расчет.
Вторую группу составляют сопутствующие причины, которые можно предупредить или устранить. К ним относятся:
? ошибочные конструктивные решения сварных швов, например небольшое расстояние между соседними швами, слишком частое пересечение сварных швов, ошибки в выборе типа соединения и др.;
? несоблюдение техники и технологии сварки, в частности плохая подготовка кромок металла, нарушение режима сварки, использование несоответствующего электрода и др.;
? низкая квалификация исполнителя.
Величина деформаций при сварке во многом определяется теплопроводностью металла. Между ними существует прямо пропорциональная зависимость: чем выше теплопроводность, тем более равномерно распространяется поток тепла по сечению металла, тем менее значительными будут деформации. Например, при сварке нержавеющей стали как менее теплопроводной возникают большие деформации, чем при сварке низкоуглеродистых сталей.
Напряжения и деформации, которые имеют место исключительно в ходе сварки, а по ее окончании исчезают, называются временными; а если они сохраняются после охлаждения шва – остаточными. Практическое значение последних особенно велико, поскольку они могут сказываться на работе детали, изделия, всей конструкции. Если деформации носят локальный характер (например, на отдельных участках появляются выпучины, волнистость и др.), то они называются местными; если в результате деформации терпят изменения геометрические оси и размеры изделия или конструкции в целом – общими.
Кроме того, деформации могут возникать как в плоскости изделия, так и вне ее (рис. 6).

Рис. 6. Некоторые виды деформации: а – в плоскости сварного соединения; б – вне плоскости сварного соединения; 1 – форма изделия до сварки; 2 – форма изделия после сварки
Для уменьшения деформаций и напряжений при сварке придерживаются следующих конструктивных и технологических рекомендаций:
1. При подборе материала для сварных конструкций руководствуются правилом: использовать такие марки основного металла и электродов, которые либо не имеют склонности к закалке, либо подвержены ей в наименьшей степени и способны давать пластичный металл шва.
2. Избегают закладывать в конструкциях (особенно в ответственных), тем более рассчитанных на работу при ударах или вибрации, многочисленные сварные швы и их пересечения, а также использовать короткие швы замкнутого контура, поскольку в этих зонах, как правило, концентрируются собственные напряжения. Чтобы снизить тепловложения в изделие или конструкцию, оптимальная длина катетов швов должна быть не более 16 мм.
3. Стараются симметрично располагать ребра жесткости в конструкциях и сводят их количество к минимуму. Симметричность необходима и при расположении сварных швов, так как это уравновешивает возникающие деформации (рис. 7), т. е. последующий слой должен вызывать деформации, противоположные тем, которые развились в предыдущем слое.
Рис. 7. Последовательность наложения сварных швов для уравновешивания деформаций
Эффективен и способ обратных деформаций (рис. 8). Перед сваркой в конструкции (как правило, швы в ней должны располагаться с одной стороны относительно оси либо на различных расстояниях от нее) вызывают деформацию, обратную той, что возникнет в ней при сварке.
4. Ограничивают применение таких способов соединения, как косынки, накладки и др.
5. По возможности отдают предпочтение стыковым швам, для которых концентрация напряжений не столь характерна.
6. Предполагают минимальные зазоры на разных участках сварки.
Рис. 8. Сваривание гнутых профилей как пример применения обратной деформации
7. В сопряжениях деталей предусматривают возможность свободной усадки металла шва при охлаждении в отсутствие жестких заделок.
8. Практикуют изготовление конструкций по секциям, чтобы потом сваривать готовые узлы. Если последние имеют сложную конфигурацию, то заготавливают литые и штампованные детали, чтобы снизить неблагоприятное воздействие жестких связей, которые дают сварные швы.
9. Выбирают технологически обоснованную последовательность (рис. 9) выполнения сварных швов, при которой допускается свободная деформация свариваемых деталей. Если, например, требуется соединить листы, то в первую очередь выполняют поперечные швы, в результате чего получают полосы, которые потом сваривают продольными швами. Такая очередность исключает жесткую фиксацию соединяемых частей листов и позволяет им свободно деформироваться при сварке.
Рис. 9. Оптимальная последовательность выполнения сварных швов при сварке листов: а – настила; б – двутавровой балки
Направление ведения сварного шва также имеет значение. Если вести его на проход либо от центра к концам, то в середине шва разовьются поперечные напряжения сжатия; если двигаться от краев к центру, то в середине шва не избежать появления поперечных напряжений растяжения, следствием которых будут трещины в околошовной зоне или самом шве (рис. 10).
10. При соединении частей из металла значительной толщины (более 20–25 мм) применяют многослойную дуговую сварку, выполняя швы горкой или каскадом (рис. 11). Шов горкой накладывается следующим образом: первый слой имеет длину примерно 200–300 мм, второй длиннее первого в 2 раза, третий длиннее второго на 200–300 мм и т. д. Достигнув «горки», сварку продолжают в обе стороны от нее короткими валиками. Такой способ способствует поддержанию участка сварки в нагретом состоянии. В результате тепло распространяется по металлу более равномерно, что снижает напряжения.

Рис. 10. Напряжение в продольном сечении шва при сварке (– напряжение сжатия; + – напряжение растяжения): а – на проход; б – от концов к центру
11. Помогает снизить коробление швов соединяемых конструкций и деталей выполнение швов в обратно-ступенчатом порядке (рис. 12). Для этого протяженные швы делят на части длиной 150–200 мм и сваривают их, ведя каждый последующий слой в направлении, обратном предыдущему слою, причем стыки следует размещать вразбежку. Причина таких действий заключается в том, что деформации в соседних участках будут противоположно направленными по отношению друг к другу и равномерными, поскольку металл будет прогреваться равномерно.
Рис. 11. Очередность наложения швов при многослойной дуговой сварке (размеры указаны в миллиметрах): а – горкой; 1 – ось «горки»; 2 – толщина металла; б – каскадом

Рис. 12. Последовательность наложения обратнопоступательного шва
12. Рассчитывают адекватный тепловой режим сварки. Если при работе есть возможность перемещать изделие (деталь) или если основной металл предрасположен к закалке, тогда используют более сильный тепловой режим, благодаря чему объем разогреваемого материала возрастает, а сам он остывает медленнее. В определенных ситуациях (если сварка проводится при пониженной температуре воздуха, металл имеет большую толщину или является сталью, склонной к закалке, и др.) помогают предварительный или сопровождающий подогрев либо околошовной зоны, либо всего изделия. Температура, до которой следует довести металл, зависит от его свойств и составляет 300–400 °C для бронзы, 250–270 °C для алюминия, 500–600 °C для стали, 700–800 °C для чугуна и т. д.
Если сваривают жестко зафиксированные детали или конструкции, тогда применяют менее интенсивный тепловой режим и варят электродами, способными давать пластичный металл шва.
13. Осуществляют отжиг и нормализацию изделия или конструкции после окончания сварки (последнее полностью ликвидирует напряжения). При отжиге температуру стального изделия доводят до 820–930 °C, выдерживают (общее время составляет примерно 30 минут, длительная выдержка нежелательна, поскольку приводит к росту зерен) и постепенно охлаждают (на 50–75 °C в час), доводя температуру до 300 °C. Это дает ряд преимуществ: во-первых, шов приобретает мелкозернистую структуру с улучшенным сцеплением зерен, благодаря которой металл шва и околошовной зоны становится более пластичным, во-вторых, металл шва получается менее твердым, что имеет большое значение для последующей обработки резанием или давлением; в-третьих, это полностью снимает внутренние напряжения в изделии.
Основные отличия нормализации от полного отжига – более высокая скорость охлаждения, для чего температура, до которой нагревают изделие, на 20–30 °C превышает критическую, и то, что выдержка и охлаждение проводятся на воздухе.
14. Избегают планировать в изделиях и конструкциях сварные швы, неудобные для выполнения, например вертикальные, потолочные.
15. Обеспечивают минимальную погонную энергию, достижимую при высокой скорости сварки в сочетании с наименьшими поперечными сечениями швов.
16. Уменьшают число прихваток и их сечения.
17. Проковывают швы в холодном или горячем состоянии, что уменьшает внутренние напряжения и увеличивает прочность конструкции.
Данный текст является ознакомительным фрагментом.Читать книгу целиком
Поделитесь на страничкеСледующая глава >
Свариваемость металлов, напряжения и деформации при сварке
Понятия о напряжениях и деформациях
Любое силовое воздействие на тело сопровождается возникновением в нем напряжений и развитием деформаций.
Напряжением называют силу, отнесенную к единице площади сечения тела: о = P/F, где о — напряжение, МПа; Р — действующее усилие, Н; F — площадь поперечного сечения детали, м2.
В зависимости от характера приложенных сил различают напряжения растяжения, сжатия, изгиба, кручения и среза.
Деформацией называют изменение размеров или формы тела под действием приложенных к нему сил. Деформации могут быть упругими и пластическими. Если размеры и форма тела восстанавливаются после прекращения силового воздействия, то такая деформация является упругой. Деформацию, остающуюся после снятия нагрузки, называют пластической или остаточной.
Помимо напряжений и деформаций, возникающих в деталях под действием приложенных нагрузок, в них могут быть так называемые собственные напряжения и деформации и существующие в телах при отсутствии внешних сил. К ним относятся и сварочные напряжения и деформации, наблюдаемые в свариваемых деталях. В зависимости от продолжительности существования их разделяют на временные, существующие в период выполнения сварки, и на остаточные, устойчиво сохраняющиеся в течение длительного времени после сварки. В зависимости от характера и объемов распределения напряжения различают одноосные (линейные), двуосные (плоскостные) и трехосные (объемные), а также напряжения I рода (в макрообъемах тела), II рода (в пределах кристаллических зерен металла) и III рода (в пределах кристаллической решетки).
Сварочные деформации обычно характеризуют прогибами элементов, углами поворота, укорочениями, величинами выхода точек тела из плоскости равновесия и др. (рис. 1).
Деформации, приводящие к изменению размеров всего изделия, искривлению его геометрических осей, называют общими. А деформации, относящиеся к отдельным участкам его, называют местными.
Причины возникновения напряжений и деформаций при сварке
Основными причинами возникновения собственных напряжений и деформаций в сварных соединениях и конструкциях являются неравномерное нагревание металла при сварке, литейная усадка, структурные и фазовые превращения в затвердевающем металле при охлаждении.
Неравномерное нагревание металла. Все металлы при нагревании расширяются, а при охлаждении сжимаются. Процессы сварки плавлением характеризуются местным нагревом металла с образованием неравномерного температурного поля в сварном соединении. При наличии непрерывной связи между нагретыми и холодными участками металла свариваемой детали в нем возникают сжимающие и растягивающие внутренние напряжения. Механизм образования их рассмотрим на примерах. Представим себе металлический стержень, свободно лежащий на сварочном столе. При местном нагреве в центральной части его длина L увеличится на дельта L (рис. 2, а).
Это будет зависеть от коэффициента линейного расширения данного металла, длины нагретой зоны и температуры ее нагрева. В процессе охлаждения удлинение будет уменьшаться и при достижении начальной температуры станет равным нулю. После полного охлаждения стержень восстанавливает первоначальные размеры и в нем не будет ни внутренних напряжений, ни остаточных деформаций.
При местном нагреве того же стержня, жестко закрепленного с обоих концов (рис. 2, б), возможность свободного удлинения его исключается. Поэтому в нем возникают сжимающие внутренние напряжения, при опре
Деформации и напряжения при сварке
Деформации и напряжения металлов при сварке способны возникать из-за множества различных причин. Они отрицательно влияют на механическую прочность свариваемых конструкций. Наиболее распространенные причины проявления деформаций, напряжений — это неравномерно осуществляемое нагревание, охлаждение соединяемых деталей, структурные модификации металла шовного соединения, литейная усадка наплавляемого металла.
Причины проявления деформаций, напряжений материалов
При сварных работах соединяемые образцы подвергаются воздействию достаточно высоких температур. Напряжения, деформации могут образовываться в следующих ситуациях:
- литейная усадка;
- нагревание материала на соединяемом участке осуществляется неравномерно;
- изменения структуры металла при охлаждении после нагревания. Сначала происходит деформация кристаллических зерен, после — всей металлической конструкции.
Литейная усадка
Данный процесс происходит из-за образования в поверхностных слоях металла, которые непосредственно касаются сварного шва, остаточных напряжений. Основная причина этого — уменьшение объема охлаждаемой сварной ванны. Происходит растягивание ближайших слоев металла изделий. При минимальном объеме ванны деформации, напряжения, формирующиеся в процессе ее затвердевания, тоже минимальны.
Нагревание/охлаждение производится неравномерно
В результате неравномерного увеличения температуры металла, в нем формируются напряжения тепловые, осуществляется изменение пластичности, прочностных характеристик. Если температура нагревания высокая, показатель теплопроводности материала минимальный, тогда напряжения тепловые будут повышенными.
Деформации и напряжения при сварке формируются под воздействием тепловой энергии электротока. Основными причинами их возникновения является неравномерный разогрев материала, неправильное охлаждение, усадка жидкого материала ванны, изменения структуры металла на участке термического воздействия, в соединительном шве.
Изменения структуры материала
Причинами данного процесса являются образования растягивающих/стягивающих напряжений. Подобные преобразования иногда способствуют изменению объема соединяемого металла. В процессе сварки образцов из сталей низкоуглеродистой группы, напряжения незначительны, существенно не влияют на качество сваривания. Достаточно большие деформации возникают в период сваривания образцов из сталей легированной группы с наличием углерода больше 0,35 процентов. В данном случае не исключено образование в сварочных швах горячих трещин.
Процедуру деформации металла можно охарактеризовать:
- углом поворота;
- укорочениями, прогибами образцов;
- величинами точек шва;
- параметрами выхода из плоскости, образующей равновесие.
Мероприятия, способствующие снижению деформаций
Достичь сокращения сварочных напряжений и уменьшения деформации при соединении металлических образцов достаточно сложно. Для этого нужно предпринимать следующие меры:
- Предварительно до начала сварных работ, еще в процессе проектирования металлоконструкции, анализируются последствия взаимодействия металлов при выполнении сварочных работ. Если подобранные материалы не сочетаются друг с другом, для выполнения соединения необходимо приложить большие усилия, сварочная процедура требует дополнительных материальных вложений, можно подобрать другой металл, уменьшить скорость выполнения шва, поменять конструкцию, сделать в ней минимальное число сварных швов.
- При непосредственном проведении сварных работ нужно правильно организовать последовательность выполнения соединения деталей. Замыкающие швы конструкции должны производиться в самую последнюю очередь. При выполнении сварки вручную, когда сварные швы достаточно длинные, соединение необходимо выполнять в ступенчатом порядке, и максимально жестко скреплять между собой узлы.
- Кроме этих мероприятий, непосредственно перед началом выполнения соединения изделий, можно незначительно повредить их кромки в направлении, обратном направлению предполагаемой деформации.
- Если предварительно соединяемые металлические детали незначительно подогреть, сварочные деформации металла шва будут минимальными. Сварочное напряжение, на которое не обратили внимания в период проведения сварочных работ, способно отрицательно повлиять на жесткость, прочность соединяемой конструкции.
По окончании сварки обязательно производится термический отпуск. Подобная процедура обеспечивает уменьшение остаточных напряжений, повышает пластические свойства сварочного соединения.