Неразрушающие методы контроля металлов – ЦТНК Совтест АТЕ
Неразрушающие методы контроля металлов помогают устанавливать и устранять причины брака при производстве металлических изделий. Неразрушающие методы контроля металлов включают в себя ультразвуковые, магнитные, электрические, вихретоковые, рентгеновские, оптические и капиллярные методы.
Наиболее эффективными из них являются рентгеновские, в том числе компьютерная томография, которая позволяет получать трёхмерную модель изделия, отражающую внутреннюю геометрию и дефекты.
Применение неразрушающих методов контроля металлов включает в себя: контроль качества литья (количественный анализ пустот), поиск трещин, анализ толщины стенок, анализ пористости и включений посторонних металлов, контроль внутренней и внешней геометрии.
Неразрушающий контроль металлов — одно из наиболее востребованных направлений в аэрокосмической отрасли. Поиск поверхностных трещин (например, инспекция турбинных лопаток) осуществляется посредством капиллярного, ультразвукового и магнитного методов, однако эти методы недостаточно чувствительны к внутренним дефектам.
Рисунок 1 – неразрушающий контроль турбинной лопатки (2D вид и трёхмерная модель)
Ещё одна область применения неразрушающих методов контроля металлов – автомобильная промышленность. Объектами инспекции являются электрические разъёмы, инжекторы, прозрачные панели светодиодных труб, литые элементы (например, турбокомпрессоры), датчики (например, лямбда-зонд). На рисунке 2 изображён результат неразрушающего контроля дизельного инжектора
Рисунок 2 — компьютерная томография и анализ компонентов дизельного инжектора
Одно из основных преимуществ неразрушающих методов контроля металлов – возможность инспекции «рабочих» деталей. Это особенно важно, когда речь идёт о серийных изделиях. Применение неразрушающих методов контроля металлов позволяет получить полную картину распределения пустот и включений в объёме исследуемого объекта.
Рисунок 3 – неразрушающий контроль алюминиевой отливки
Неразрушающие методы контроля металлов имеют ряд преимуществ, среди которых возможность инспекции отдельных, наиболее значимых участков, возможность контроля эксплуатации детали и возможность контроля на всех этапах производства. Таким образом, неразрушающие методы контроля металлов служат эффективным инструментам для предоставления информации о внутренней структуре изделий и анализа появления дефектов.
Share 3
Май
Неразрушающий контроль металла теплоэнергетических установок
Страница 1 из 20
Бугай Н. В., Шкляров М. И.
Неразрушающий контроль металла теплоэнергетических установок. — Москва: Энергия, 1978.
В книге описаны «разрушающие методы определения механических жаропрочных и структурных характеристик металла энергетического оборудования. Приведены сведения об условиях работы основных элементов котлотурбинного оборудования электростанций. Систематизированы данные об изменения структуры и свойств металла в процессе длительной его работы при высоких температурах. Освещены новые методы контроля в наблюдения за металлом энергетического оборудования.
ПРЕДИСЛОВИЕ
Одной из важнейших задач отечественной теплоэнергетики является повышение долговечности и эксплуатационной надежности металла как вновь вводимого оборудования, так и оборудования, проработавшего расчетный срок эксплуатации.
Безаварийная работа энергооборудования связана с уровнем фактических свойств металла основных его элементов, знанием динамики их изменений, которые неизбежно происходят с начала эксплуатации. Отсюда исключительно важную роль приобретают разработка, совершенствование и внедрение неразрушающих (безобразцовых) методов исследования и контроля металла теплоэнергетического оборудования, позволяющих определять комплекс характеристик металла с возможностью последующего прогнозирования их поведения в эксплуатационных условиях.

Приведенные в книге методы и конструкции приборов для безобразцового определения кратковременной и длительной прочности, характеристик пластичности, ударной вязкости, структурных характеристик могут дать не только качественное, но во многих случаях и количественное представление о состоянии металла в объеме, достаточном для решения вопросов долговечности и надежности работы различных элементов теплоэнергетического оборудования.
Авторы отмечают, что предлагаемая читателю книга не претендует на полноту исчерпания вопроса. Ограниченные объемом рукописи, они сознательно не рассматривали вопросы ультразвуковой дефектоскопии, электромагнитных и других методов диагностики металла. Основной их целью было показать возможности применения основных способов неразрушающего контроля металла в эксплуатационных условиях и привлечь усилия других исследователей для усовершенствования известных и разработки новых неразрушаемых средств контроля.
Авторы
ГОСТ Р 50599-93 Сосуды и аппараты стальные сварные высокого давления. Контроль неразрушающий при изготовлении и эксплуатации, ГОСТ Р от 25 октября 1993 года №50599-93
ГОСТ Р 50599-93
Группа Г49
СОСУДЫ И АППАРАТЫ СТАЛЬНЫЕ СВАРНЫЕ ВЫСОКОГО ДАВЛЕНИЯ
Контроль неразрушающий при изготовлении и эксплуатации
Welded steel vessels and apparatus under high pressure.
Non-destructive control while the manufacturing and operating
ОКП 36 0900
Дата введения 1994-07-01
1 РАЗРАБОТАН И ВНЕСЕН Техническим комитетом по стандартизации ТК 260 «Оборудование химической и нефтеперерабатывающей промышленности»
2 УТВЕРЖДЕН И ВВЕДЕН В ДЕЙСТВИЕ Постановлением Госстандарта России от 25.10.93 N 225
3 ВВЕДЕН ВПЕРВЫЕ
1 ОБЛАСТЬ ПРИМЕНЕНИЯ
Настоящий стандарт распространяется на стальные сварные сосуды и аппараты (далее — сосуды и аппараты), предназначенные для эксплуатации под внутренним избыточным давлением свыше 10 до 130 МПа при температуре стенки не ниже минус 40 и не выше 525 °С, и устанавливает:
1) методы неразрушающего контроля (визуальный, цветной, магнитопорошковый, ультразвуковой, радиографический) сосудов и аппаратов в процессе их изготовления и эксплуатации;
2) основные требования к проведению контроля;
3) оценку качества сосудов и аппаратов по результатам неразрушающего контроля.
Обязательные требования к контролю сосудов и аппаратов, обеспечивающие их безопасность для жизни, здоровья и имущества населения, окружающей среды, изложены в разделах 1, 3, 4, 5 (5.1-5.3; 5.5; 5.6), 6 (6.1-6.8), 7 (7.1-7.3), 8.
Классификация сосудов и аппаратов по способу изготовления приведена в приложении А.
2 НОРМАТИВНЫЕ ССЫЛКИ
В настоящем стандарте использованы ссылки на следующие стандарты.
ГОСТ 12.1.001-89 ССБТ. Ультразвук. Общие требования безопасности
ГОСТ 12.1.003-83 ССБТ. Шум. Общие требования безопасности
ГОСТ 12.1.004-91 ССБТ. Пожарная безопасность. Общие требования
ГОСТ 12.1.005-88 ССБТ. Общие санитарно-гигиенические требования к воздуху рабочей зоны
ГОСТ 12.1.007-76 ССБТ. Вредные вещества. Классификация и общие требования безопасности
ГОСТ 12.1.009-76 ССБТ. Электробезопасность. Термины и определения
ГОСТ 12.1.010-76 ССБТ. Взрывобезопасность. Общие требования
ГОСТ 12. 2.002-91 ССБТ. Техника сельскохозяйственная. Методы оценки безопасности
ГОСТ 12.2.003-91 ССБТ. Оборудование производственное. Общие требования безопасности
ГОСТ 12.2.007.0-75 ССБТ. Изделия электротехнические. Общие требования безопасности
ГОСТ 12.2.007.1-75 ССБТ. Машины электрические вращающиеся. Требования безопасности
ГОСТ 12.2.007.2-75 ССБТ. Трансформаторы силовые и реакторы электрические. Требования безопасности
ГОСТ 12.2.007.3-75. ССБТ. Электрические устройства на напряжение свыше 1000 В. Требования безопасности
ГОСТ 12.2.007.4-75 ССБТ. Шкафы комплектных распределительных устройств и комплектных трансформаторных подстанций. Требования безопасности
ГОСТ 12.2.007.5-75 ССБТ. Конденсаторы силовые. Установки конденсаторные. Требования безопасности
ГОСТ 12.2.007.6-75 ССБТ. Аппараты коммутационные низковольтные. Требования безопасности
ГОСТ 12.2.007.7-83 ССБТ. Устройства комплектные низковольтные. Требования безопасности
ГОСТ 12.2.007.8-75 ССБТ. Устройства электросварочные и для плазменной обработки. Требования безопасности
ГОСТ 12.2.007.9-88 ССБТ. Оборудование электротермическое. Требования безопасности
ГОСТ 12.2.007.10-87 ССБТ. Установки, генераторы и нагреватели индукционные для электротермии, установки и генераторы ультразвуковые. Требования безопасности
ГОСТ 12.2.007.11-75 ССБТ. Преобразователи электроэнергии полупроводниковые. Требования безопасности
ГОСТ 12.2.007.12-88 ССБТ. Источники тока химические. Требования безопасности
ГОСТ 12.2.007.13-88 ССБТ. Лампы электрические. Требования безопасности
ГОСТ 12.2.007.14-75 ССБТ. Кабели и кабельная арматура. Требования безопасности
ГОСТ 12.3.002-75 ССБТ. Процессы производственные. Общие требования безопасности
ГОСТ 12.4.011-89 ССБТ. Средства защиты работающих. Общие требования и классификация
ГОСТ 12.4.016-83 ССБТ. Одежда специальная защитная. Номенклатура показателей качества
ГОСТ 12.4.021-75 ССБТ. Системы вентиляционные. Общие требования
ГОСТ 2601-84 Сварка металлов. Термины и определения основных понятий
ГОСТ 2789-73 Шероховатость поверхности. Параметры и характеристики
ГОСТ 3242-79 Соединения сварные. Методы контроля качества
ГОСТ 7512-82 Контроль неразрушающий. Соединения сварные. Радиографический метод
ГОСТ 10885-85 Сталь листовая горячекатаная двухслойная коррозионностойкая. Технические условия
ГОСТ 14782-86 Контроль неразрушающий. Соединения сварные. Методы ультразвуковые
ГОСТ 18442-80 Контроль неразрушающий. Капиллярные методы. Общие требования
ГОСТ 21105-87 Контроль неразрушающий. Магнитопорошковый метод
ГОСТ 22727-88 Прокат листовой. Методы ультразвукового контроля
ГОСТ 23055-78 Контроль неразрушающий. Сварка металлов плавлением. Классификация сварных соединений по результатам радиографического контроля
ГОСТ 23764-79 Гамма-дефектоскопы. Общие технические условия
ГОСТ 24507-80 Контроль неразрушающий. Поковки из черных и цветных металлов. Методы ультразвуковой дефектоскопии
3 ОБЪЕКТЫ КОНТРОЛЯ
3.1 Объектами контроля сосудов и аппаратов являются материалы, элементы корпуса, сварные соединения.
3.2 К материалам, из которых изготовляют сосуды и аппараты, относятся листовая сталь, в том числе двухслойная, сортовой прокат, кованые и штампованные заготовки.
3.3 К элементам корпуса сосуда, аппарата относятся фланцы, крышки, обечайки, днища, штуцера (патрубки), горловины.
3.4 Различным способам исполнения сосудов и аппаратов соответствуют следующие типы сварных соединений:
1) стыковые и угловые, соединяющие монолитные однослойные элементы;
2) стыковые и угловые, соединяющие многослойные элементы;
3) стыковые и угловые, соединяющие однослойные элементы с многослойными.
3.5 По расположению в сосуде, аппарате в соответствии с рисунком 1 должны быть установлены следующие категории сварных соединений:
— продольные сварные соединения в обечайках, в сферических и эллиптических днищах и их заготовках;
— кольцевые сварные соединения в обечайках, кольцевые сварные швы, соединяющие кованые, штампованные, многослойные (рулонированные) обечайки между собой и с днищами, фланцами, горловинами;
— сварные швы, соединяющие фланцы, трубные доски с обечайками, а также фланцы с патрубками;
— сварные соединения вварки (приварки) штуцеров (патрубков), горловин в обечайки, днища;
— сварные соединения приварных элементов к корпусу;
— соединения приварки труб к трубной решетке.
Рисунок 1
Рисунок 1
4 НАЗНАЧЕНИЕ МЕТОДОВ КОНТРОЛЯ ПРИ ИЗГОТОВЛЕНИИ СОСУДОВ И АППАРАТОВ
4.1 Выбор метода контроля определяется конструктивными особенностями изделия, физическими свойствами контролируемого материала, техническими требованиями к изготовлению сосуда.
4.2 Методы контроля качества материалов, заготовок, сварных соединений, элементов сосудов назначают в соответствии с требованиями таблицы 1.
Таблица 1
|
|
Листовая сталь | ВО+УЗД |
Двухслойная сталь | ВО+ЦД+УЗД |
Кованые и штампованные заготовки | ВО+МПД(ЦД)+УЗД |
Элементы сосуда | |
Сортовой прокат | |
Сварные соединения категорий: | ВО+МПД(ЦД)+(УЗД, РГ) |
ВО+МПД(ЦД)+УЗД | |
ВО+ЦД | |
Наплавка | ВО+ЦД+УЗД |
Примечания
1 ВО — визуальный осмотр; ЦД — цветной метод дефектоскопии; МПД — магнитопорошковый метод дефектоскопии; УЗД — ультразвуковой метод дефектоскопии; РГ — радиография
2 Знак «+» соответствует слову «и», «запятая» — слову «или»
3 ЦД или МПД кованых и штампованных заготовок, элементов сосудов проводят выборочно в местах визуального обнаружения дефектов, а для двухслойной стали — на полосе 200 мм под сварные соединения
4. 3 Методы — ультразвуковой или радиографический — выбирают исходя из требования обеспечить более полное и точное выявление недопустимых дефектов, а также с учетом эффективности данного метода контроля для сварного соединения конкретного вида.
Магнитопорошковым методом следует контролировать поверхности из углеродистых, низколегированных и легированных сталей.
Допускается контролировать эти поверхности цветным методом в случае неэффективности магнитопорошкового метода.
Цветным методом следует контролировать поверхности из аустенитных сталей.
4.4 Последовательность применения методов контроля и их сочетание определяются технологией изготовления сосудов и аппаратов.
4.5 Углеродистая и низколегированная листовая сталь, двухслойная сталь толщиной свыше 25 мм должны быть подвергнуты полистному контролю ультразвуковым методом. Объем контроля и класс сплошности листа должны быть установлены отраслевыми нормативными документами.
4.6 Поковки, штампованные заготовки, металл штуцеров из углеродистых, низколегированных и среднелегированных сталей после окончательной термической обработки должны быть подвергнуты поштучному контролю ультразвуковым методом в объеме 100%.
4.7 Сварные соединения категорий , , , должны быть подвергнуты контролю в объеме 100 % длины контролируемых швов.
4.8 Методики контроля и нормы дефектности должны соответствовать установленным отраслевыми нормативными документами.
5 НАЗНАЧЕНИЕ МЕТОДОВ КОНТРОЛЯ ПРИ ЭКСПЛУАТАЦИИ СОСУДОВ И АППАРАТОВ
5.1 Контроль неразрушающими методами в процессе эксплуатации осуществляют при техническом освидетельствовании сосудов и аппаратов. Периодичность и виды технических освидетельствований устанавливает предприятие в соответствии с требованиями Правил устройства и безопасной эксплуатации сосудов, работающих под давлением, утвержденных Госгортехнадзором СССР, и отраслевых нормативных документов.
5.2 Требования к назначению методов и объемам контроля сосудов и аппаратов, их элементов и сварных соединений даны в таблицах 2-4.
В случае невозможности выполнения требований таблиц 2-4 объем и методы контроля в каждом конкретном случае могут быть уточнены программой обследования, разработанной заводом-изготовителем или специализированной научно-исследовательской организацией.
Таблица 2
Контролируемые элементы | Виды технического освидетельствования | ||
После монтажа | Периодическое | Дополнительное внеочередное | |
Корпус | ВО+УЗТ | ВО+ЦД+УЗТ | |
Сварные соединения корпуса, приварки штуцеров (патрубков) | ВО | ВО+(МПД, ЦД)+УЗД | ВО+МПД (ЦД)+УЗД |
Крышка | ВО+ЦД | ||
Уплотнительные поверхности и уплотнительные кольца | ВО+ЦД |
Примечание ВО — визуальный осмотр с наружной и внутренней поверхностей; УЗТ — ультразвуковая толщинометрия
Таблица 3
Контролируемые элементы | Виды технического освидетельствования | ||
После монтажа | Периодическое | Дополнительное, внеочередное | |
Корпус | ВО | ВО | |
Сварные соединения корпуса, приварки штуцеров (патрубков) | ВО | ВО+МПД (ЦД) | ВО+МПД (ЦД) |
Сварные соединения центральных обечаек или футеровки | ВО+ЦД | ВО+ЦД | ВО+ЦД+УЗД |
Сварные соединения монолитных обечаек и концевых элементов с многослойными обечайками | ВО | ВО+ЦД+УЗД | ВО+ЦД +УЗД |
Уплотнительные поверхности | ВО+ЦД | ВО+ЦД |
Примечание — УЗД сварных соединений центральных обечаек выполняют в случаях обнаружения дефектов ВО или ЦД
Таблица 4
Время эксплуатации | Условия эксплуатации | |||||||
В период установленного срока службы заводом-изготовителем | После выработки установленного срока службы или после 20 лет | Переменные нагрузки за весь период эксплуатации | Температура, | Скорость коррозии, | Коррозионное растрескивание. | |||
До 1000 циклов | Св. 1000 циклов | До 450 | Св. | До 0,1 | Св. | |||
В соответствии с техническими требованиями завода-изготовителя | 100 | 25 | 50 | 25 | 50 | 10 | 25 | 100 |
Примечания
1 Объем контроля устанавливают максимальным по одному из параметров
2 Периодичность контроля после выработки установленного срока службы или после 20 лет эксплуатации определяет специализированная организация .
5.3 Контроль аппаратов, для которых невозможно проведение полного внутреннего осмотра, должен предусматривать визуальный осмотр наружной и внутренней поверхностей в доступных местах или осмотр с помощью технических эндоскопов, а также ультразвуковой контроль корпуса с наружной поверхности и толщины стенок основных элементов корпуса.
Объем контрольных измерений толщины определяется программой обследования.
5.4 В случае отсутствия доступа к проведению визуального осмотра внутренней и наружной поверхностей корпуса допускается проведение контроля с применением метода акустической эмиссии в процессе гидравлических или пневматических испытаний.
Методика и результаты контроля методом акустической эмиссии должны быть согласованы со специализированной научно-исследовательской организацией.
При обнаружении дефектов по результатам контроля акустико-эмиссионным методом должна быть выполнена дефектоскопия участков, которые явились источниками акустических сигналов.
5.5 При ремонте сосудов и аппаратов с применением сварки должен быть проведен контроль ремонтных мест по технологии, принятой при изготовлении.
5.6 После гидравлических испытаний должны быть проведены повторный визуальный осмотр сварных швов корпусов сосудов и аппаратов с наружной и внутренней поверхностей, а также визуальный осмотр, цветная или магнитопорошковая дефектоскопия ремонтных мест.
6 ТЕХНИЧЕСКИЕ ТРЕБОВАНИЯ К ПРОВЕДЕНИЮ НЕРАЗРУШАЮЩЕГО КОНТРОЛЯ
6.1 Назначенный комплекс методов контроля должен обеспечивать выявление видов (типов) дефектов, соответствующих требованиям ГОСТ 2601, ГОСТ 24507, ГОСТ 22727.
6.2 Визуальный осмотр, цветную и магнитопорошковую дефектоскопию следует проводить в соответствии с требованиями ГОСТ 3242, ГОСТ 18442, ГОСТ 21105.
6.3 Контроль листовой стали следует проводить в соответствии с требованиями ГОСТ 22727, контроль двухслойной стали — по ГОСТ 10885.
6.4 Контроль сварных соединений ультразвуковым методом следует проводить в соответствии с требованиями ГОСТ 14782.
6.5 Контроль сварных соединений радиографическим методом следует проводить в соответствии с требованиями ГОСТ 7512.
6.6 Контроль поковок, штампованных заготовок ультразвуковым методом следует проводить в соответствии с требованиями ГОСТ 24507.
6.7 Контроль качества сварных соединений, кованых и штампованных заготовок, подвергнутых термообработке, следует проводить после нее.
6.8 Основные технические требования к методам контроля должны соответствовать приведенным в таблицах 5, 6, 7, 8, 9, 10, 11.
6.9 При назначении требований к контролю при эксплуатации необходимо учитывать состояние металла, коррозионное воздействие среды, режимы эксплуатации.
Таблица 5
Объект контроля | Объем контроля | Увеличение при осмотре в сомнительных местах | Применение метода в составе технологического процесса |
Кованые, штампованные детали | 100 % поверхности | После механической обработки | |
После термической | |||
Перед сваркой | |||
Кромки под сварку | 100 % поверхности, включая прилегающую зону шириной не менее 30 мм | 10-кратное | |
Наплавки | 100 % поверхности | 3-4-кратное | До и после гидравлических испытаний |
Сварные соединения | Внутренняя и наружная поверхности сварного соединения с прилегающей околошовной зоной |
Таблица 6
Объект | Объем | Шероховатость | Класс чувствите | Применение метода в составе технологического процесса | |
Кованые, | Места, где визуально обнаружены дефекты | После механической и термической обработки | |||
Кромки под | 100 % поверхности, включая прилегающую зону шириной не менее | 63 | 40 | 2 | Перед сваркой |
Наплавки | 100 % поверхности | До и после гидравлических испытаний | |||
Сварные | Внутренняя и наружная поверхности сварного соединения с прилегающей околошовной | До и после гидравлических испытаний. | |||
При изготовлении сосудов и аппаратов | |||||
при эксплуатации — в ремонтных местах |
Таблица 7
Объект | Объем | Шерохо- ватость | Условный уровень чувстви- | Применение методов в составе технологического процесса | |
Кованые, | Выборочно, в местах, где визуально обнаружены дефекты | После механической и термической обработки | |||
6,3 | 40 | Б | |||
Сварные | Внутренняя и наружная поверхности сварного соединения с прилегающей околошовной зоной шириной не менее 30 мм | До гидравлических испытаний. | |||
При изготовлении сосудов и аппаратов — в доступных местах; при эксплуатации — в ремонтных местах | |||||
Таблица 8
Материал заготовок | Шероховатость контролируемой | Тип преобра- зователя | Толщина заготовки в направлении прозвучивания, диаметр заготовки, мм | Предельная чувствитель ность , мм | |
Сталь ферритного и перлитного классов | Прямой | До 100 включ. | 5 | ||
Св 100 до 250 включ. | 7 | ||||
» 250 » 500 » | 10 | ||||
Св. 500 | 20 | ||||
Наклонный | До 30 включ. | 3 | |||
Св. 30 до 100 включ. | 5 | ||||
» 100 » 250 « | 10 | ||||
Сталь аустенитного класса | 3,2 | 20 | Прямой | До 30 включ. | 5 |
Св. 30 до 250 включ. | 10 | ||||
» 250 » 500 « | 20 | ||||
Св. 500 | 40 | ||||
Наклонный | До 150 включ. | 10 | |||
Св. 150 до 200 включ. | 20 | ||||
Св. | 40 |
Таблица 9
Вид наплавки | Шероховатость контролируемой поверхности по ГОСТ 2789, мкм, не более | Предельная чувствительность, , мм | |
Наплавка торцов многослойных обечаек | 1-2 | ||
Наплавка торцов и поверхностей кованых деталей | 3,2 | 20 | 5 |
Примечание — Предельная чувствительность должна быть уточнена отраслевыми нормативными документами
Таблица 10
Категория сварного соединения | Шероховатость контролируемой поверхности по ГОСТ 2789, мкм, не более | Толщина сварного соединения, мм | Предельная чувствительность | |
От 10 до 20 включ. | 2,0 | |||
Св. 20 до 30 включ. | 3,0 | |||
» 30 » 50 « | 5,0 | |||
» 50 » 110 « | 7,0 | |||
» 110 » 250 « | 10,0 | |||
3,2 | 20 | До 50 включ. | В соответствии с требованиями к | |
Св. | 7,0 |
Таблица 11
Категория сварного соединения | Толщина сварного соединения, мм | Класс чувствительности по ГОСТ 7512 |
До 50 включ. | ||
Св. 50 | 2 | |
Независимо |
7 ОЦЕНКА КАЧЕСТВА СОСУДОВ И АППАРАТОВ ПО РЕЗУЛЬТАТАМ НЕРАЗРУШАЮЩЕГО КОНТРОЛЯ
7.1 Оценку качества сосудов и аппаратов при изготовлении и при эксплуатации проводят по отраслевым нормативным документам.
7. 2 Требования отраслевых нормативных документов к контролю сосудов и аппаратов, находящихся в эксплуатации, должны соответствовать аналогичным требованиям при изготовлении.
7.3 В случае несоответствия отраслевых норм дефектности на период эксплуатации нормам при изготовлении сосуда оценку качества следует проводить по нормам, согласованным со специализированной научно-исследовательской организацией по сосудам и аппаратам высокого давления.
7.4 В приложении Б даны нормы оценки качества сосудов и аппаратов при изготовлении, действующие в отрасли химического машиностроения.
8 ТРЕБОВАНИЯ БЕЗОПАСНОСТИ
8.1 При проведении дефектоскопии следует соблюдать требования электробезопасности по ГОСТ 12.2.007.0 — ГОСТ 12.2.007.14, ГОСТ 12.1.009, а также требования Правил устройства электроустановок, Правил технической эксплуатации электроустановок потребителей, Правил техники безопасности при эксплуатации электроустановок, утвержденных Госгортехнадзором.
8.2 При проведении дефектоскопии следует соблюдать требования к защите от пожаров по ГОСТ 12.1.004, от взрывов — по ГОСТ 12.1.010.
8.3 Уровни звукового давления на рабочем месте дефектоскописта не должны превышать допускаемых ГОСТ 12.1.003.
8.4 При проведении контроля ультразвуковым методом следует соблюдать требования ГОСТ 12.1.001, ГОСТ 12.2.002, ГОСТ 12.2.003, ГОСТ 12.3.002, а также требования Санитарных норм и правил при работе с оборудованием, создающим ультразвук, передаваемый контактным путем на руки работающих N 22-82, утвержденных Минздравом СССР.
8.5 При проведении контроля радиографическим методом должна быть обеспечена безопасность работ согласно требованиям Основных санитарных правил работы с радиоактивными веществами и другими источниками ионизирующих излучений ОСП-72/80 N 2120-80, утвержденных Главным государственным санитарным врачом СССР, Норм радиационной безопасности НРБ-76 N 141-75, утвержденных Главным государственным санитарным врачом СССР, Санитарных правил по радиоизотопной дефектоскопии N 1171-74, утвержденных заместителем Главного государственного санитарного врача СССР, а также требованиям ГОСТ 12. 3.002, ГОСТ 23764.
8.6 Требования к защите от вредного воздействия постоянных магнитных полей должны соответствовать требованиям документа «Предельно допустимые уровни воздействия постоянных магнитных полей при работе с магнитными устройствами и магнитными материалами» N 1742-77, утвержденного Минздравом СССР.
8.7 При проведении контроля цветным методом следует соблюдать требования безопасности к содержанию вредных веществ, температуре, влажности, подвижности воздуха в рабочей зоне по ГОСТ 12.1.005 и ГОСТ 12.1.007, требования к вентиляционным системам — по ГОСТ 12.4.021, требования к применению средств коллективной и индивидуальной защиты работающих — по ГОСТ 12.4.011, требования к специальной одежде — по ГОСТ 12.4.016.
Приложение А (справочное). КЛАССИФИКАЦИЯ СОСУДОВ ВЫСОКОГО ДАВЛЕНИЯ ПО СПОСОБАМ ИЗГОТОВЛЕНИЯ
Приложение А
(справочное)
В зависимости от исполнения цилиндрической части корпуса установлены следующие типы сосудов:
1 Кованые, изготовленные из одной кованой обечайки.
2 Кованосварные, изготовленные из однослойных кованых обечаек, сваренных кольцевыми швами между собой и концевыми элементами (днищами, фланцами, горловинами).
3 Многослойные рулонированные, изготовленные из нескольких рулонированных обечаек, сваренных между собой кольцевыми швами, а также в совокупности с однослойными частями (трубными досками, обечайками, патрубками и т.п.) и концевыми элементами.
4 Вальцованосварные, обечайки которых изготовлены методом вальцовки из толстолистовой стали с последующей сваркой продольными швами, а затем соединены кольцевыми сварными швами между собой и концевыми элементами.
5 Штампосварные, обечайки которых изготовлены из толстолистовой стали методом штамповки полуобечаек с последующей сваркой их продольными швами, а затем соединены кольцевыми швами между собой и концевыми элементами.
Приложение Б (справочное). ОЦЕНКА КАЧЕСТВА ИЗДЕЛИЙ ПО РЕЗУЛЬТАТАМ НЕРАЗРУШАЮЩЕГО КОНТРОЛЯ В ОТРАСЛИ ХИМИЧЕСКОГО МАШИНОСТРОЕНИЯ
Приложение Б
(справочное)
1 По результатам неразрушающего контроля визуальным, цветным или магнитопорошковым методами на поверхности поковок, штампованных заготовок, элементов сосуда, сортового проката, плакирующего слоя двухслойной стали, кромок под сварку не допускаются следующие дефекты:
трещины, заковы, закаты, плены, песочены, раковины, расслоения, рванины.
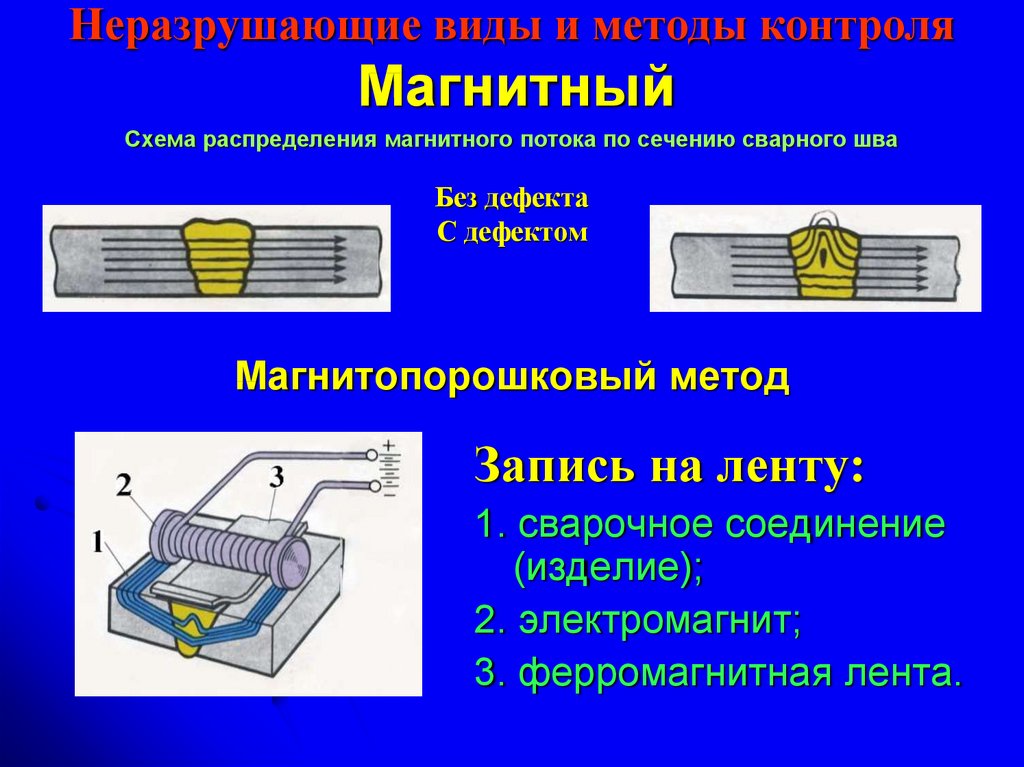
2 По результатам визуального осмотра на поверхности сварных соединений и наплавок не допускаются следующие дефекты:
трещины всех видов и направлений;
поры, свищи;
подрезы, непровары, несплавления;
наплывы, прожоги, незаплавленные кратеры.
3 По результатам контроля магнитопорошковым методом на поверхности сварных соединений и наплавок не допускаются индикаторные рисунки осаждений магнитного порошка.
4 По результатам контроля цветным методом на поверхности сварных соединений и наплавок не допускаются единичные и групповые индикаторные рисунки округлой или удлиненной форм.
5 По результатам ультразвукового контроля листовой стали не допускаются нарушения сплошности металла, превышающие нормы для 1-го класса сплошности листа по ГОСТ 22727.
6 По результатам ультразвукового контроля двухслойной стали не допускаются нарушения сплошности сцепления слоев, превышающие нормы для 1-го класса сплошности листа по ГОСТ 10885.
7 По результатам ультразвукового контроля металла поковок, штампованных заготовок не допускаются дефекты, превышающие нормы группы качества 2п по ГОСТ 24507.
8 По результатам ультразвукового контроля сварных соединений и наплавок не допускаются следующие дефекты:
отдельные непротяженные свыше норм, установленных таблицами 12 и 13;
протяженные;
группы дефектов.
Таблица 12
Категория сварного соединения | Толщина сварного соединения, | Эквивалентная площадь | Недопустимое суммарное число отдельных дефектов на 300 мм протяженности шва, шт., более | |
наименьшая | недопустимая | |||
От 10 до 20 включ. | 2,0 | 2,0 | ||
Св. 20 до 30 включ. | 3,0 | 3,0 | ||
Св. 30 до 50 включ. | 5,0 | 7,0 | — | |
Св. 50 до 110 включ. | 7,0 | 10,0 | ||
Св. 110 до 250 включ. | 10,0 | 20,0 | 1 | |
До 50 включ. | 7,0 | 10,0 | 3 | |
Св. 50 до 100 включ. | 10,0 | 20,0 | 1 |
Таблица 13
Объект контроля | Эквивалентная площадь | Недопустимое суммарное число отдельных дефектов, | Недопустимое условное расстояние между дефектами, мм менее | ||
наименьшая фиксируемая | недопустимая , более | 100 мм | 1000х1000 мм | ||
Наплавка торцов многослойных обечаек по слою металлической крошки | 1,0 | 3,0 | 2 | 5 | 30 |
Наплавка торцов многослойных обечаек проволокой | 2,0 | 3,0 | 2 | 4 | 30 |
Наплавка торцов кованых деталей | 5,0 | 7,0 | 2 | 4 | 30 |
9 По результатам контроля сварных соединений корпуса сосуда и его элементов радиографическим методом не допускаются трещины всех видов и направлений, непровары, несплавления, поры и шлаковые включения свыше норм, приведенных в таблице 14.
Таблица 14
Категория сварного соединения | Толщина сварного соединения, мм | Класс дефектности по ГОСТ 23055 |
До 50 включ. | 2 | |
Св. 50 | 3 | |
Независимо | 3 |
10 Чувствительность радиографического метода контроля должна соответствовать классу 2 по ГОСТ 7512.
Текст документа сверен по:
официальное издание
Госстандарт России —
М.: Издательство стандартов, 1994
Ультразвуковой метод неразрушающего контроля
Ультразвуковой метод неразрушающего контроля применяется для проверки целостности сварных соединений металлических деталей.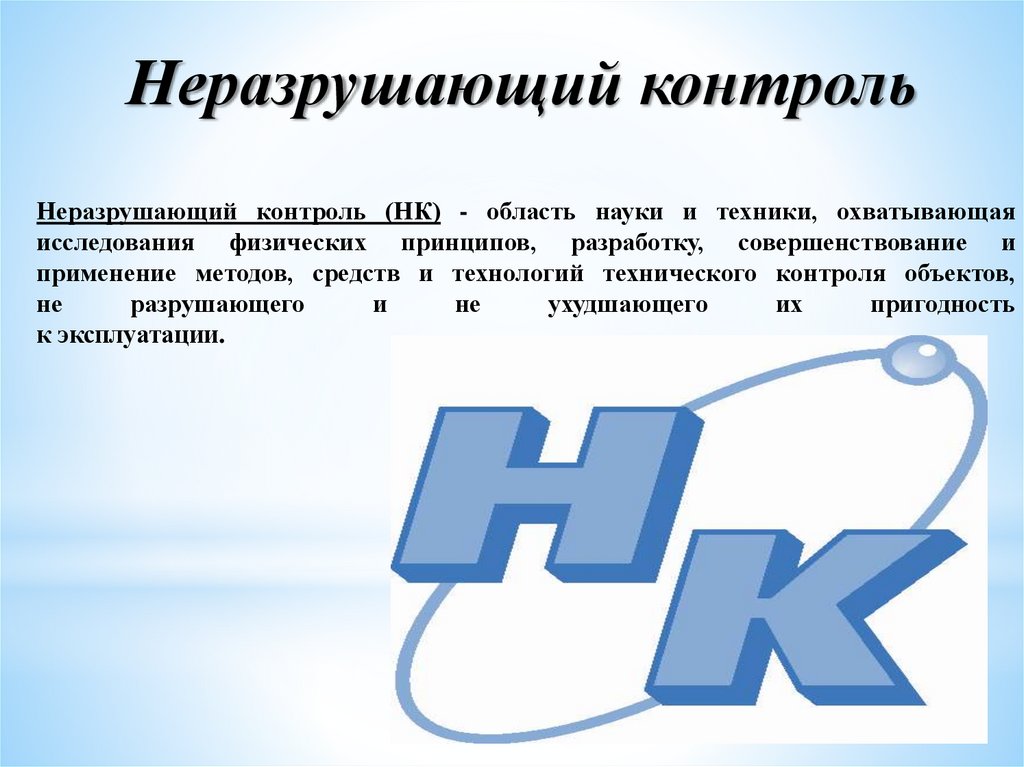
Ультразвуковая дефектоскопия основана на том, что колебания высокой частоты способны проникать вглубь металла и отражаться от поверхности царапин, пустот и прочих неровностей. Для проверки целостности сварного шва, на него направляют диагностическую волну частотой около 20 тысяч Гц. При наличии какого-либо дефекта, волна начинает отклоняться от своего нормального распространения. По характеру этих отклонений можно определить параметры дефекта. Расстояние до повреждения определяется по времени прохождения волны через материал. По амплитуде отклонения можно вычислить размер
дефекта.
Существуют различные типы приборов для осуществления ультразвукового контроля. Выбор того или иного оборудования обусловлен параметрами исследуемого материала, такими как его толщина, марка, текстура поверхности, предполагаемый размер дефектов и т.
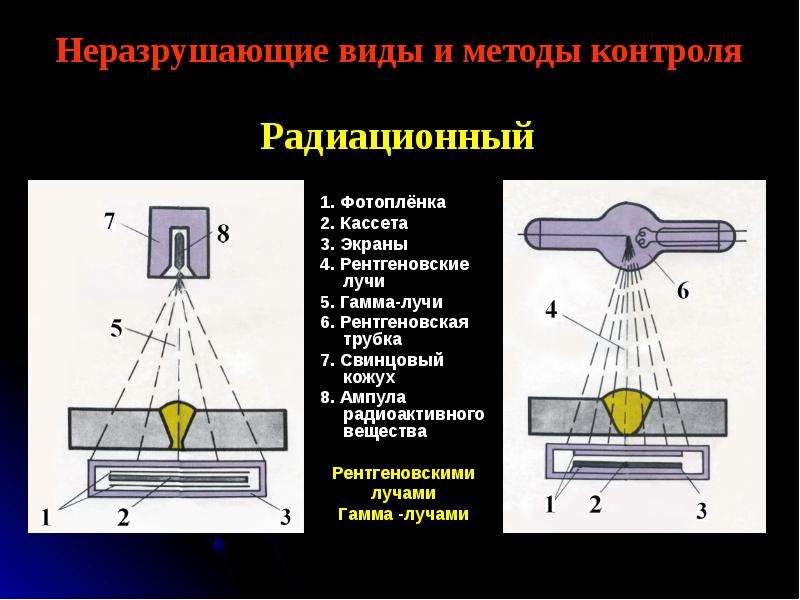

Метод неразрушающего контроля
Целью использования неразрушающего контроля компанией АСТ «Сварпром», является надёжное выявление опасных дефектов на строительных и нефтегазодобывающих объектов. Поэтому выбор конкретных методов НК определяется эффективностью обнаружения дефектов согласно требованиям проекта, ГОСТов и др. нормативной документации.Лабораторией неразрушающего контроля АСТ «Сварпром» применяются следующие методы:
1. Визуальный и измерительный метод контроля — который выявляет поверхностные дефекты и соблюдение геометрии сварного шва.
Визуальный и измерительный контроль проводим практически на всех этапах жизненного цикла отдельных деталей, узлов и агрегатов. Выполняется периодический входной контроль материала, подготовки деталей перед сборкой, контроль качества сборки, контроль качества сварных соединений, контроль в процессе эксплуатации с целью выявления изменений формы и обнаружения поверхностных дефектов в основном материале и сварных швах, образовавшихся в процессе работы данного элемента. Основные виды дефектов v трещины всех видов, коррозия, эрозионный износ, деформации, сколы покрытий, отложения сырья на стенках, сужение каналов, повреждения элементов автоматики.
Согласно требованиям руководящих документов визуальный и измерительный контроль проводится как с наружной, так и с их внутренней стороны изделий, что значительно осложняется ограниченным доступом во внутренние полости объектов.
В такой ситуации единственное решение — применение промышленных оптических и видео эндоскопических систем.
Более подробно о данном методе неразрушающего контроля >>>>>
4. Капилрный (цветная дефектоскопия) — для поиска поверхностных дефектов.
Капиллярная дефектоскопия – является одним из основных методов неразрушающего контроля и предназначена для обнаружения поверхностных и сквозных дефектов в объектах контроля, определения их расположения, протяженности (для протяженных дефектов типа непроваров, трещин) и их ориентации на поверхности.
Капиллярный метод неразрушающего контроля (ГОСТ 18442-80) основан на капиллярном проникновении внутрь дефекта индикаторных жидкостей, хорошо смачивающих материал объекта – поверхность контроля и последующей регистрации индикаторных следов (благодаря чему так же носит название цветная дефектоскопия).
Более подробно о данном методе неразрушающего контроля >>>>>
6. Магнитопорошковый (магнитный) — для обнаружения скрытых дефектов
Высокая универсальность, чувствительность, относительно низкая трудоемкость контроля и простота.
Магнитный контроль в наши дни применяется почти во всех отраслях тяжелой и легкой
промышленности: нефтехимической отрасли, черной металлургии, машиностроении и
авиационной промышленности, энергетическом и химическом машиностроение (ГРЭС, ТЭЦ, АЭС),
автомобильной промышленности и судостроении, строительстве (трубопроводы,
стальные конструкции, промышленные цистерны).
Более подробно о данном методе неразрушающего контроля >>>>>
|
|
Неразрушающие методы контроля сварных соединений и конструкций
К неразрушающим методам контроля относятся: визуальный, испытания на прочность и непроницаемость, цветной, магнитный, просвечивание рентгеновским и гамма-излучением, ультразвуковой и др.
В зависимости от требований, предъявляемых к сварному изделию, и характера дефектов, которые необходимо обнаружить, применяют соответствующие методы контроля.
Качество сварных соединений и конструкции в целом обычно определяют несколькими методами. Универсального метода контроля не существует. Перед контролем сварные соединения должны быть тщательно очищены от шлака и других загрязнений.
Визуальный (внешний осмотр) является обязательным при контроле качества сварки любым методом. Сварные соединения рассматривают невооруженным глазом или через лупу при хорошем (не бьющем в глаза) освещении; замеряют швы с помощью инструментов и шаблонов.
Этим методом можно определить выходящие на поверхность поры и трещины, незаделанные кратеры, подрезы, неравномерность ширины и высоты шва, наплывы, отступление размеров шва от требований чертежа и другие внешние дефекты. Обнаруженные в результате визуального контроля дефекты следует устранить.
Прочность и непроницаемость готового изделия проверяют проведением следующих испытаний. Специальными механическими испытаниями с приложением статической или динамической нагрузки определяют разрушающие нагрузки или усилия, не вызывающие разрушения сварных изделий; гидравлическими испытаниями (чаще всего водой) определяют прочность и непроницаемость сосудов (котлов различного назначения, баллонов для жидкостей и газов), трубопроводов, судовых конструкций, резервуаров для хранения нефтепродуктов и т. п.
Сосуды и трубопроводы, работающие при избыточном давлении, испытывают давлением, обычно превышающим величину рабочего давления в 1,5—2 раза. Контроль прочности должен проводиться с соблюдением установленных правил техники безопасности.
Гидравлические испытания громоздки и непроизводительны, способствуют возникновению коррозии, их нельзя проводить при отрицательных температурах. Использование воды не позволяет обнаружить мельчайшие неплотности в шве.
Это объясняется тем, что вода является одной из наиболее полярных жидкостей. Молекулы ее несут значительный электрический (дипольный) момент, что вызывает повышение вязкости и плотности воды в слоях, контактирующих со стенками неплотности. Толщина слоя адсорбционно связанной воды составляет, около 1,5-10-4 мм.
Жидкость в адсорбированных слоях приобретает упругость, близкую к упругости твердых тел. Из других источников адсорбированная вода при толщине слоя в 0,9-10-4 мм обладает модулем сдвига 1,9х108 дин/см2, что только в 300 раз меньше модуля сдвига свинца.
Таким образом, чем меньше поперечное сечение неплотности, тем значительнее влияет адсорбированный слой воды на движение жидкости в неплотностях. В очень малых неплотностях (например, диаметром 3-10-4 мм) пристенные слои жидкости способны заполнить все их сечение и исключить или сильно ограничить движение воды.
По другим данным с помощью воды под давлением 1,4 кГ/см2 можно обнаружить неплотности диаметром до 10-3 мм. Поэтому в последние годы гидравлические испытания стали заменять пневматическими (например, при испытании отсеков судов и трубопроводов).
Непроницаемость соединения определяется еще и следующими методами: вакуумным, керосиновым, цветным, газоэлектрическим.
Пневматический метод испытания предусматривает подачу сжатого воздуха в изделие с заглушенными отверстиями. Давление воздуха при испытаниях устанавливают исходя из условий безопасности и требований, предъявляемых к изделию.
Сварные соединения смачивают мыльным раствором или опускают в воду. Неплотности определяют по образующимся мыльным пузырькам или пузырькам воздуха. Смачивать сварные соединения мыльной водой или опускать сварное изделие в ванну с водой следует после создания необходимого давления воздуха в контролируемом сосуде.
При испытании обдувом сжатый воздух под давлением 4—5кГ/см2 подводится к сварному соединению по гибкому шлангу с наконечником. Расстояние между концом наконечника и швом должно быть не более 50 мм.
Во время обдува противоположную сторону шва смачивают мыльным раствором и тщательно осматривают, чтобы обнаружить мыльные пузырьки, появляющиеся в неплотностях.
При давлении воздуха 1кГ/см2 можно обнаружить неплотности (поры) диаметром около 3-10-3 мм.
Вакуумный метод является разновидностью пневматического и заключатся в следующем (рис. 181). Проверяемый участок сварного соединения, наиболее удобный для контроля, смачивают мыльным раствором и на него устанавливают вакуум-камеру.
Верх камеры сделан из плексигласа, поэтому прозрачен, а по контуру нижней части прикреплена прокладка из мягкой резины. С помощью вакуум-насоса или эжектора в камере создается разрежение, вследствие чего она плотно по контуру резиновой прокладки прижимается атмосферным давлением к данному участку изделия.
Благодаря созданной разности давлений по обе стороны сварного соединения атмосферный воздух проникает через неплотности шва в вакуум-камеру, при этом появляются мыльные пузырьки, видимые через прозрачную верхнюю часть камеры. Места неплотностей отмечают мелом на металле рядом с камерой.
С помощью трехходового крана в камеру впускают атмосферный воздух и затем убирают ее с проверенного участка сварного соединения. Отметки мела с основного металла переносят на неплотные места шва, после чего устраняют дефекты и повторно проверяют эти места на непроницаемость.
Рис. 181. Схема вакуумного и керосино-вакуумного метода контроля непроницаемости сварных соединений:1 — губчатая резина, 2— плексиглас 3 — трехходовой кран, 4 — к вакуум-насосу, 5 — керосин, в — вакуумируемое пространство, 7 — мыльный пузырек.
Вакуумный метод приемлем для контроля непроницаемости стыковых, нахлесточных, тавровых и трехгранных соединений во всех положениях в пространстве. Производительность вакуумного метода в среднем 50—60м шва в 1 ч. Этот метод контроля позволяет обнаружить неплотности диаметром до 4,2-10-3 мм (при перепаде давлений до 0,84кГ/см2).
Вакуумным методом можно проверять сварные соединения в конструкциях, имеющих форму незамкнутого объема, а также при одностороннем доступе к ним; контроль можно применять вслед за сваркой, не дожидаясь окончания изготовления конструкции в целом; испытания можно проводить при перепаде давлений до 1 кГ/см2, не опасаясь разрушения конструкции.
Вакуумный метод контроля нашел широкое применение при проверке непроницаемости сварных соединений днищ, стенок и перекрытий резервуаров (рис. 182), сварных стыков трубопроводов.
Рис. 182. Контроль непроницаемости сварных соединений.
Этот метод внедряется также в судостроении и других отраслях промышленности.
Обзор неразрушающего контроля (NDT)
Неразрушающий контроль (NDT) состоит из множества неинвазивных методов контроля, используемых для оценки свойств материалов, компонентов или целых технологических единиц. Эти методы также могут быть использованы для обнаружения, характеристики или измерения наличия механизмов повреждения (например, коррозии или трещин ). NDT также обычно называют неразрушающим контролем (NDE), неразрушающим контролем (NDE) и неразрушающим контролем (NDI).Многие методы неразрушающего контроля позволяют обнаруживать дефекты и определять их характеристики, такие как размер, форма и ориентация. Целью неразрушающего контроля является проверка компонента безопасным, надежным и рентабельным способом, не вызывая повреждения оборудования или остановки производства. Это отличается от разрушающего испытания, когда испытываемая деталь повреждается или разрушается в процессе проверки.
NDT может выполняться во время или после производства или даже на оборудовании, которое находится в эксплуатации.В процессе производства контроль неразрушающего контроля определяет, подходят ли детали для выполнения заданной функции. Другими словами, детали проверяются, чтобы убедиться, что они прослужат определенное количество времени или циклов до отказа. Во время работы инспекции неразрушающего контроля могут использоваться для оценки текущего состояния повреждений оборудования, отслеживания механизмов повреждения и принятия обоснованных решений для оценки оставшегося срока службы оборудования (например, RBI , FFS ).
Обзор методов неразрушающего контроля
Методы неразрушающего контроля обычно можно разделить на две категории: традиционные и современные.У каждого метода есть свои характерные преимущества и ограничения. Более подробную информацию о каждом тесте можно найти в соответствующих определениях Integripedia.
Обычные методы неразрушающего контроляТрадиционные методы — это методы, которые совершенствовались в течение десятилетий и за это время хорошо задокументированы в кодексах, стандартах и передовых методах. Настройка и процедура обычного метода обычно проще по сравнению с передовыми методами.
Расширенные методы неразрушающего контроля Передовые методы, как правило, менее понятны по мере их развития по мере развития новых технологий, например неопределенные преимущества или ограничения, отсутствие критериев квалификации технического специалиста или практически полное отсутствие отраслевой кодификации. Как правило, установка, процедура и интерпретация данных более сложных методов более сложны и могут потребовать специальных знаний и опыта от должным образом обученного техника.
Кроме того, некоторые методы можно разделить на обычные и продвинутые.Возьмем две формы ультразвукового контроля, например, ультразвуковой контроль прямым пучком (UT) — это традиционный метод, используемый в простых приложениях, тогда как ультразвуковой контроль с фазированной решеткой (PAUT) — это продвинутый метод UT. По мере развития передовых методов появляются новые и более продвинутые версии каждой, чтобы начать новый цикл технического понимания и обучения технических специалистов.
В целом, неразрушающий контроль предлагает много преимуществ по сравнению с разрушающим контролем. Испытательное оборудование часто бывает портативным, и его можно проводить несколько раз на одном компоненте.Сам компонент можно тщательно оценить внешне и внутренне на предмет наличия вредных недостатков. Недостатком является то, что результаты часто бывают качественными и могут повторяться и интерпретироваться по-разному различными инспекторами.
Промышленное применение NDT
NDT-инспекции являются неотъемлемой частью нефтегазовой и нефтехимической промышленности, а также ряда других отраслей, включая химическую, аэрокосмическую, автомобильную и оборонную. Общей целью всех этих отраслей является обнаружение недостатков в компонентах для уменьшения количества отказов и повышения надежности.
В нефтехимической промышленности проверки неразрушающего контроля используются на протяжении всего жизненного цикла объекта. Этот комплексный подход является важным элементом управления целостностью активов . Кроме того, инспекции неразрушающего контроля предоставляют исторические данные о технологических установках предприятия и информацию о том, как часто компонент следует проверять, ремонтировать или заменять. Интервалы проверок и испытаний могут быть изменены в зависимости от того, на каком этапе жизненного цикла находится оборудование (например, новое изготовленное оборудование илистарение оборудования). Выполнение нескольких оценок на протяжении жизненного цикла оборудования может показаться дорогостоящим. Однако инспекции, проводимые через определенные промежутки времени, могут в конечном итоге сэкономить организации миллионы долларов, если тестирование выявляет угрозы, и оборудование ремонтируется до закрытия объекта или возникновения катастрофического отказа.
Самыми распространенными частями оборудования, которое проходит проверку в нефтехимической промышленности, являются резервуары для хранения, теплообменники, сосуды под давлением и системы трубопроводов.При планировании неразрушающего контроля необходимо учитывать четыре момента:
- Тип механизма повреждения, подлежащего проверке для
- Минимальный размер обнаруживаемого дефекта, форма и ориентация дефекта
- Где находится дефект (поверхностный или внутренний)
- Чувствительность и ограничения метода неразрушающего контроля
С учетом вышеперечисленных факторов операторы могут оптимизировать производство на предприятии и повысить безопасность персонала и окружающей среды.
Нормы и стандарты
NDT часто предписывается нормами и стандартами для изготовления компонентов, критически важных деталей и оборудования в процессе эксплуатации. Поэтому для всех владельцев нефтеперерабатывающих, химических заводов, газовых заводов и трубопроводов крайне важно иметь глубокое понимание и опыт в междисциплинарной области неразрушающего контроля. В дополнение к факторам, перечисленным выше (, раздел отраслевого приложения ), персонал должен постоянно развивать знания о развивающихся технологиях и выполнении современных процедур.
Конкретные нормы, стандарты, спецификации, правила и рекомендуемые методы могут зависеть от страны и отрасли, в которой проводится неразрушающий контроль. Ниже приводится список организаций (органов по стандартизации), которые разрабатывают и публикуют отраслевые кодексы, стандарты и рекомендуемые практики для методов неразрушающего контроля, относящиеся к нефтегазовой и химической обрабатывающей промышленности:
Полный список правил, установленных правительством США, можно найти в Своде федеральных правил (CFR). Положения, важные для нефтехимической и химической обрабатывающей промышленности, можно найти в Разделе 10, Энергетика, и Разделе 49, Транспорт. 1
Обучение и сертификация
Уровни сертификацииМногие программы неразрушающего контроля имеют три уровня квалификации. Краткое описание квалификаций Уровня I, Уровня II и Уровня III приводится ниже и находится в документе ASNT Рекомендуемая практика № SNT-TC-1A. 2
Уровень I. По окончании программы сертификации уровня I люди должны иметь возможность выполнять определенные калибровки, определенный неразрушающий контроль и специальные оценки, чтобы определить, следует ли принять или отклонить компонент для обслуживания.
Уровень II: Лица с уровнем II должны обладать теми же способностями, что и лица с уровнем I, и, кроме того, должны иметь возможность настраивать, калибровать, выполнять и оценивать результаты неразрушающего контроля в соответствии с применимыми кодексами, стандартами и спецификациями.
Уровень III: Персонал по неразрушающему контролю наивысшего уровня должен иметь те же способности, что и лица уровня II, и, кроме того, уметь разрабатывать и квалифицировать процедуры, устанавливать и утверждать методы, интерпретировать коды, стандарты, спецификации и процедуры и назначать определенные методы неразрушающего контроля. для использования в определенных приложениях.
Требования к сертификации Требования основаны на сочетании обучения, экзаменов и опыта. Обучение основано на обобщении схем учебных курсов из документа Свод знаний по неразрушающему контролю. Более подробную информацию о своде знаний ASNT NDT можно найти в американском национальном стандарте ANSI / ASNT CP-105. Цель Свода знаний — описать знания и навыки, необходимые для разных уровней сертификации. Также необходимо пройти несколько видов экзаменов для соответствия минимальным требованиям и для повторной сертификации.Людям, возможно, придется сдавать письменный экзамен, специальный экзамен или практический экзамен в зависимости от желаемой сертификации. Для сертификации также учитывается опыт работы в областях, связанных с неразрушающим контролем или неразрушающим контролем, а также программы обучения на рабочем месте.
Американский институт нефти (API) — API предлагает многочисленные индивидуальные программы сертификации (ICP), специально предназначенные для персонала неразрушающего контроля в нефтяной и нефтехимической промышленности.
Американское общество неразрушающего контроля (ASNT) — ASNT — это всемирно признанная организация, предлагающая квалификацию персонала неразрушающего контроля в широком спектре отраслей. Текущие программы сертификации включают ASNT NDT Level II, ASNT NDT Level III, Центральную программу сертификации ASNT (ACCP) и Промышленный персонал радиографии и радиационной безопасности (IRRSP).
Британский институт неразрушающего контроля (BINDT) — BINDT является аккредитованным органом по сертификации и предлагает сертификацию персонала в области неразрушающего контроля (PCN).
Международная организация по стандартизации (ISO) — ISO 9712 (Неразрушающий контроль — Квалификация и сертификация персонала по неразрушающему контролю) — это опубликованный стандарт, в котором подробно описаны требования к квалификации и сертификации персонала, выполняющего неразрушающий контроль.
Natural Resources Canada (NRCan) — NRCan управляет органом по сертификации неразрушающего контроля (NDTCB), который предлагает сертификацию Канадского совета общих стандартов (CGSB).
Институт сварки (TWI) — TWI предлагает квалификацию персонала через свои аккредитованные схемы сертификации CSWIP.
Список литературы
- 2016, «Органы по нормам и стандартам, участвующие в индустрии неразрушающего контроля», ASNT.
- 2016, «Рекомендуемая практика № SNT-TC-1A: Квалификация и сертификация персонала в области неразрушающего контроля (2016)», ASNT.
Это определение неполное? Вы можете помочь, внося свой вклад.
Связанные темы
Инструменты темы
Поделиться темой
Внести вклад в определение
Мы приветствуем обновления этого определения Integripedia от сообщества Inspectioneering.Щелкните значок ссылку ниже, чтобы открыть форму, которая позволит вам внести изменения в определение и отправить их инспекционному составу.
Способствовать определениюISO 3777: 1976 Радиографический контроль точечной контактной сварки алюминия и его сплавов — Рекомендуемая практика | 95.99 | ISO / TC 44 / SC 6 |
ISO 4986: 1992 Стальные отливки — Магнитопорошковый контроль | 95,99 | ISO / TC 17 / SC 11 |
ISO 4986: 2010 Стальные отливки — Магнитопорошковый контроль | 95.![]() | ISO / TC 17 / SC 11 |
ISO 4986: 2020 Отливки из стали и чугуна — Испытание на магнитные частицы | 60,60 | ISO / TC 17 / SC 11 |
ISO 4987: 1992 Стальные отливки — Контроль проницаемости | 95.![]() | ISO / TC 17 / SC 11 |
ISO 4987: 2010 Стальные отливки — жидкий проникающий контроль | 95,99 | ISO / TC 17 / SC 11 |
ISO 4987: 2020 Отливки из стали и чугуна — Испытание на проникающую способность | 60.![]() | ISO / TC 17 / SC 11 |
ISO 4992-1: 2006 Стальные отливки. Ультразвуковой контроль. Часть 1. Стальные отливки общего назначения. | 95,99 | ISO / TC 17 / SC 11 |
ISO 4992-1: 2020 Стальные отливки. Ультразвуковой контроль. Часть 1. Стальные отливки общего назначения. | 60.60 | ISO / TC 17 / SC 11 |
ISO 4992-2: 2006 Стальные отливки — Ультразвуковой контроль — Часть 2: Стальные отливки для высоконагруженных компонентов | 95,99 | ISO / TC 17 / SC 11 |
ISO 4992-2: 2020 Стальные отливки. | 60.60 | ISO / TC 17 / SC 11 |
ISO 4993: 1987 Стальные отливки — Радиографический контроль | 95,99 | ISO / TC 17 / SC 11 |
ISO 4993: 2009 Отливки из стали и чугуна — Радиографический контроль | 95.![]() | ISO / TC 17 / SC 11 |
ISO 4993: 2015 Отливки из стали и чугуна — Радиографические испытания | 90,60 | ISO / TC 17 / SC 11 |
ISO 5579: 1985 Неразрушающий контроль — Радиографическое исследование металлических материалов рентгеновскими и гамма-лучами — Основные правила | 95.![]() | ISO / TC 135 / SC 5 |
ISO 5579: 1998 Неразрушающий контроль — Радиографическое исследование металлических материалов рентгеновскими и гамма-лучами — Основные правила | 95,99 | ISO / TC 135 / SC 5 |
ISO 5579: 2013 Неразрушающий контроль — Радиографический контроль металлических материалов с использованием пленки и рентгеновского или гамма-излучения — Основные правила | 90.![]() | ISO / TC 135 / SC 5 |
ISO 5948: 1981 Материал железнодорожного подвижного состава — Ультразвуковые приемочные испытания | 95,99 | ISO / TC 17 |
ISO 5948: 1994 Материал железнодорожного подвижного состава — Ультразвуковые приемочные испытания | 95.![]() | ISO / TC 17 / SC 15 |
ISO 5948: 2018 Материал железнодорожного подвижного состава — Ультразвуковые приемочные испытания | 60,60 | ISO / TC 17 / SC 15 |
ISO 6933: 1986 Материал железнодорожного подвижного состава — Приемочные испытания магнитными частицами | 90.![]() | ISO / TC 17 / SC 15 |
ISO 9302: 1989 Бесшовные и сварные (кроме дуговой сварки под флюсом) трубы стальные для работы под давлением. Электромагнитные испытания для проверки гидравлической герметичности. | 95.99 | ISO / TC 17 / SC 19 |
ISO 9302: 1994 Бесшовные и сварные (кроме дуговой сварки под флюсом) трубы стальные для работы под давлением. | 95.99 | ISO / TC 17 / SC 19 |
ISO 9303: 1989 Бесшовные и сварные (кроме дуговой сварки под флюсом) стальные трубы, работающие под давлением — Полный периферийный ультразвуковой контроль для обнаружения продольных дефектов | 95.99 | ISO / TC 17 / SC 19 |
ISO 9304: 1989 Бесшовные и сварные (кроме дуговой сварки под флюсом) стальные трубы для работы под давлением — Вихретоковые испытания для обнаружения дефектов | 95.![]() | ISO / TC 17 / SC 19 |
ISO 9305: 1989 Бесшовные стальные трубы для работы под давлением — полный периферийный ультразвуковой контроль для обнаружения поперечных дефектов | 95.99 | ISO / TC 17 / SC 19 |
ISO 9402: 1989 Бесшовные и сварные (кроме дуговой сварки под флюсом) стальные трубы для работы под давлением — Полный периферийный магнитный преобразователь / испытание на утечку потока труб из ферромагнитной стали для обнаружения продольных дефектов | 95.![]() | ISO / TC 17 / SC 19 |
ISO 9598: 1989 Бесшовные стальные трубы для работы под давлением — полный периферийный магнитный преобразователь / испытание на утечку потока труб из ферромагнитной стали для обнаружения поперечных дефектов | 95.99 | ISO / TC 17 / SC 19 |
ISO 9915: 1992 Отливки из алюминиевого сплава — Радиографические испытания | 95,99 | ISO / TC 79 / SC 7 |
ISO 9916: 1991 Отливки из алюминиевых и магниевых сплавов — Жидкостный проникающий контроль | 95.![]() | ISO / TC 79 / SC 7 |
ISO 10049: 1992 Отливки из алюминиевого сплава — Визуальный метод оценки пористости | 95,99 | ISO / TC 79 / SC 7 |
ISO 10049: 2019 Отливки из алюминиевого сплава — Визуальный метод оценки пористости | 60.![]() | ISO / TC 79 / SC 7 |
ISO 10124: 1994 Бесшовные и сварные (кроме дуговой сварки под флюсом) стальные трубы, работающие под давлением. Ультразвуковой контроль для обнаружения ламинарных дефектов. | 95.99 | ISO / TC 17 / SC 19 |
ISO 10332: 1994 Бесшовные и сварные (кроме дуговой сварки под флюсом) трубы стальные для работы под давлением — Ультразвуковые испытания для проверки гидравлической герметичности | 95.![]() | ISO / TC 17 / SC 19 |
ISO 10332: 2010 Неразрушающий контроль стальных труб — Автоматизированный ультразвуковой контроль бесшовных и сварных (кроме дуговой сварки под флюсом) стальных труб для проверки гидравлической герметичности | 90.20 | ISO / TC 17 / SC 19 |
ISO 10543: 1993 Бесшовные сварные стальные трубы с пониженным нагревом и уменьшенным растяжением для работы под давлением — Ультразвуковой контроль толщины всей поверхности | 95.![]() | ISO / TC 17 / SC 19 |
ISO 10893-1: 2011 Неразрушающий контроль стальных труб. Часть 1. Автоматизированные электромагнитные испытания бесшовных и сварных (кроме дуговой сварки под флюсом) стальных труб для проверки гидравлической герметичности | 90.93 | ISO / TC 17 / SC 19 |
ISO 10893-1: 2011 / Amd 1: 2020 Неразрушающий контроль стальных труб — Часть 1: Автоматизированные электромагнитные испытания бесшовных и сварных (кроме дуговой сварки под флюсом) стальных труб для проверки гидравлической герметичности — Поправка 1: Изменение размеров контрольного надреза; изменить критерии приемки | 60.![]() | ISO / TC 17 / SC 19 |
ISO 10893-2: 2011 Неразрушающий контроль стальных труб — Часть 2: Автоматизированный вихретоковый контроль бесшовных и сварных (кроме дуговой сварки под флюсом) стальных труб для обнаружения дефектов | 90.93 | ISO / TC 17 / SC 19 |
ISO 10893-2: 2011 / Amd 1: 2020 Неразрушающий контроль стальных труб — Часть 2: Автоматизированный вихретоковый контроль бесшовных и сварных (кроме дуговой сварки под флюсом) стальных труб для обнаружения дефектов — Поправка 1: Изменение размеров контрольного надреза; изменить критерии приемки | 60.![]() | ISO / TC 17 / SC 19 |
ISO 10893-3: 2011 Неразрушающий контроль стальных труб — Часть 3: Автоматизированное полное периферийное испытание на утечку флюса бесшовных и сварных (кроме сваренных под флюсом) труб из ферромагнитной стали для обнаружения продольных и / или поперечных дефектов | 90.93 | ISO / TC 17 / SC 19 |
ISO 10893-3: 2011 / Amd 1: 2019 Неразрушающий контроль стальных труб — Часть 3: Автоматизированное полное периферийное испытание на утечку флюса бесшовных и сварных (кроме сваренных под флюсом) труб из ферромагнитной стали для обнаружения продольных и / или поперечных дефектов — Поправка 1: Изменение размеров эталонная метка | 60.![]() | ISO / TC 17 / SC 19 |
ISO 10893-3: 2011 / Amd 2: 2020 Неразрушающий контроль стальных труб — Часть 3: Автоматизированное полное периферийное испытание на утечку флюса бесшовных и сварных (кроме сварки под флюсом) труб из ферромагнитной стали для обнаружения продольных и / или поперечных дефектов — Поправка 2: Изменить критерии приемки | 60.60 | ISO / TC 17 / SC 19 |
ISO 10893-4: 2011 Неразрушающий контроль стальных труб — Часть 4. | 90.93 | ISO / TC 17 / SC 19 |
ISO 10893-5: 2011 Неразрушающий контроль стальных труб — Часть 5: Магнитопорошковый контроль бесшовных и сварных труб из ферромагнитной стали для обнаружения поверхностных дефектов | 90.93 | ISO / TC 17 / SC 19 |
ISO 10893-6: 2011 Неразрушающий контроль стальных труб — Часть 6: Радиографические испытания сварного шва сварных стальных труб для обнаружения дефектов | 95.![]() | ISO / TC 17 / SC 19 |
ISO 10893-6: 2019 Неразрушающий контроль стальных труб — Часть 6: Радиографические испытания сварного шва сварных стальных труб для обнаружения дефектов | 60.60 | ISO / TC 17 / SC 19 |
ISO 10893-7: 2011 Неразрушающий контроль стальных труб — Часть 7: Цифровой радиографический контроль сварного шва сварных стальных труб для обнаружения дефектов | 95.![]() | ISO / TC 17 / SC 19 |
ISO 10893-7: 2019 Неразрушающий контроль стальных труб — Часть 7: Цифровой радиографический контроль сварного шва сварных стальных труб для обнаружения дефектов | 60.60 | ISO / TC 17 / SC 19 |
ISO 10893-8: 2011 Неразрушающий контроль стальных труб — Часть 8: Автоматизированный ультразвуковой контроль бесшовных и сварных стальных труб для обнаружения ламинарных дефектов | 90.![]() | ISO / TC 17 / SC 19 |
ISO 10893-8: 2011 / Amd 1: 2020 Неразрушающий контроль стальных труб — Часть 8: Автоматизированный ультразвуковой контроль бесшовных и сварных стальных труб для обнаружения ламинарных дефектов — Поправка 1: Изменить критерии приемки | 60.60 | ISO / TC 17 / SC 19 |
ISO 10893-9: 2011 Неразрушающий контроль стальных труб — Часть 9: Автоматизированный ультразвуковой контроль для обнаружения ламинарных дефектов в полосе / пластине, используемой для производства сварных стальных труб | 90.![]() | ISO / TC 17 / SC 19 |
ISO 10893-9: 2011 / Amd 1: 2020 Неразрушающий контроль стальных труб — Часть 9: Автоматизированный ультразвуковой контроль для обнаружения ламинарных дефектов в полосе / пластине, используемой для производства сварных стальных труб — Поправка 1: Изменить критерии приемки | 60.60 | ISO / TC 17 / SC 19 |
ISO 10893-10: 2011 Неразрушающий контроль стальных труб — Часть 10: Автоматизированный полный периферийный ультразвуковой контроль бесшовных и сварных (кроме дуговой сварки под флюсом) стальных труб для обнаружения продольных и / или поперечных дефектов | 90.![]() | ISO / TC 17 / SC 19 |
ISO 10893-10: 2011 / Amd 1: 2020 Неразрушающий контроль стальных труб — Часть 10: Автоматизированный полный периферийный ультразвуковой контроль бесшовных и сварных (за исключением сваренных под флюсом) стальных труб для обнаружения продольных и / или поперечных дефектов — Поправка 1: Изменение частоты ультразвуковых испытаний; изменение критериев приемки | 60.60 | ISO / TC 17 / SC 19 |
ISO 10893-11: 2011 Неразрушающий контроль стальных труб — Часть 11: Автоматизированный ультразвуковой контроль сварного шва сварных стальных труб для обнаружения продольных и / или поперечных дефектов | 90.![]() | ISO / TC 17 / SC 19 |
ISO 10893-11: 2011 / Amd 1: 2020 Неразрушающий контроль стальных труб — Часть 11: Автоматизированный ультразвуковой контроль сварного шва сварных стальных труб для обнаружения продольных и / или поперечных дефектов — Поправка 1: Изменение частоты ультразвукового контроля; изменение критериев приемки | 60.60 | ISO / TC 17 / SC 19 |
ISO 10893-12: 2011 Неразрушающий контроль стальных труб — Часть 12: Автоматизированный полный периферийный ультразвуковой контроль толщины бесшовных и сварных (кроме дуговой сварки под флюсом) стальных труб | 90.![]() | ISO / TC 17 / SC 19 |
ISO 10893-12: 2011 / Amd 1: 2020 Неразрушающий контроль стальных труб — Часть 12: Автоматизированный полный периферийный ультразвуковой контроль толщины бесшовных и сварных (кроме дуговой сварки под флюсом) стальных труб — Поправка 1: Изменение критериев приемки | 60.60 | ISO / TC 17 / SC 19 |
ISO 11484: 1994 Стальные трубы для работы под давлением — Квалификация и сертификация персонала неразрушающего контроля (NDT) | 95,99 | ISO / TC 17 / SC 19 |
ISO 11484: 2009 Стальные изделия — Система квалификации работодателя для персонала неразрушающего контроля (NDT) | 95.![]() | ISO / TC 17 / SC 19 |
ISO 11484: 2019 Стальные изделия — Система квалификации работодателя для персонала неразрушающего контроля (NDT) | 60,60 | ISO / TC 17 / SC 19 |
ISO 11496: 1993 Бесшовные и сварные стальные трубы, работающие под давлением. | 95.99 | ISO / TC 17 / SC 19 |
ISO 11971: 1997 Визуальный контроль качества поверхности стальных отливок | 95,99 | ISO / TC 17 / SC 11 |
ISO 11971: 2008 Отливки из стали и чугуна — Визуальный контроль качества поверхности | 95.![]() | ISO / TC 17 / SC 11 |
ISO 11971: 2020 Отливки из стали и чугуна — Визуальный контроль качества поверхности | 60,60 | ISO / TC 17 / SC 11 |
ISO 12094: 1994 Сварные стальные трубы для работы под давлением — Ультразвуковой контроль для обнаружения ламинарных дефектов в полосах / пластинах, используемых при производстве сварных труб | 95.![]() | ISO / TC 17 / SC 19 |
ISO 12095: 1994 Трубы стальные бесшовные и сварные, работающие под давлением. Испытания на проникновение жидкости. | 95,99 | ISO / TC 17 / SC 19 |
ISO 13664: 1997 Бесшовные и сварные стальные трубы для работы под давлением — Магнитопорошковый контроль концов труб для обнаружения ламинарных дефектов | 95.![]() | ISO / TC 17 / SC 19 |
ISO 13665: 1997 Бесшовные и сварные стальные трубы для работы под давлением — Магнитопорошковый контроль тела трубы для обнаружения дефектов поверхности | 95.99 | ISO / TC 17 / SC 19 |
ISO 17577: 2006 Сталь — Ультразвуковой контроль плоского стального проката толщиной не менее 6 мм. | 95,99 | ISO / TC 17 / SC 7 |
ISO 17577: 2016 Сталь — Ультразвуковой контроль плоского стального проката толщиной не менее 6 мм. | 90.20 | ISO / TC 17 / SC 7 |
ISO 25902-1: 2009 Титановые трубы и трубки. | 90,20 | ISO / TC 79 / SC 11 |
ISO 25902-2: 2010 Титановые трубы и трубки. Неразрушающий контроль. Часть 2: Ультразвуковой контроль для обнаружения продольных дефектов. | 90.20 | ISO / TC 79 / SC 11 |
Неразрушающий контроль металлургии компонентов (NDT)
Компания Taylor & Fenn Company стремится предоставлять нашим клиентам высококачественные отливки из металла для их уникальных компонентов. В рамках этого обязательства мы наладили и поддерживаем отношения с экспертами по неразрушающему контролю, способными выполнять различные неразрушающие испытания металлургических компонентов.
Контроль качества с неразрушающим контролем от экспертов в металлургии
Существует множество методов неразрушающего контроля, которые можно проводить на чугунных и стальных компонентах. Наш литейный завод имеет возможность отправить любой компонент для неразрушающего контроля по запросу клиента. Это упрощает производственный процесс для наших клиентов, поскольку им не нужно самим предоставлять эти услуги. В настоящее время у нас есть возможность отправлять готовые металлические отливки различным специалистам по неразрушающему контролю, которые могут выполнять несколько различных типов неразрушающего контроля.При размещении заказа покупатели могут указать, какой вид неразрушающего контроля им нужен.
В настоящее время у нас есть доступ к следующим видам неразрушающего контроля:
Визуальный
Визуальный осмотр выполняется обученным специалистом, который использует сенсорное оборудование (такое как стетоскопы, лупы и зубочистки) для проверки компонента на наличие дефектов.
Рентгенография *
Также называемый Industrial Radiography , этот тип неразрушающего контроля использует рентгеновское или гамма-излучение для проверки внутренней структурной целостности металлического компонента.
Магнитная частица *
В этом методе неразрушающего контроля используется магнитное поле для проверки компонентов, изготовленных из ферромагнитных материалов (например, железа), на наличие поверхностных / подповерхностных дефектов и неровностей.
Пенетрант красителя *
Один из наиболее часто используемых и недорогих видов неразрушающего контроля, этот метод использует краситель для выявления дефектов литья, ковки или сварки, таких как микротрещины, усталостные трещины или пористость поверхности.
Ультразвуковой контроль
В этой форме неразрушающего контроля короткие ультразвуковые пульсовые волны с центральными частотами используются для обнаружения внутренних дефектов.Часто выполняется на стальных деталях.
* Персонал, соответствующий требованиям SNT-TC-1A
Если будет проведен неразрушающий контроль и будет обнаружена неисправность, мы будем работать с клиентом, чтобы решить проблему. Для стальных компонентов возможно устранение дефектов определенного типа. В зависимости от серьезности проблемы наша команда специалистов по металлургии выполнит ремонт, переделает процесс литья или иным образом определит решение.
Мы стремимся предоставлять качественные отливки из металла.Услуги по неразрушающему контролю помогают гарантировать, что каждая деталь не имеет дефектов и может достичь максимально ожидаемого срока службы.
Свяжитесь с нами сегодня для получения качественного литья деталей из чугуна и стали!
Разрушающий контроль материалов и неразрушающий контроль (NDT)
Эта статья, в частности, дает ответы на следующие вопросы:
- Какие типы нагрузок существуют?
- Что такое размеры?
- Какова основная цель разрушающего контроля?
- В каких случаях предпочтительнее использовать неразрушающий контроль?
Такие материалы, как сталь, обычно должны выдерживать самые разные нагрузки. Различные типы нагрузок можно классифицировать следующим образом:
- растяжение
- сжатие
- сдвиг
- кручение
- изгиб
- изгиб
Интенсивность нагрузки может быть постоянной или постоянно изменяться. Постоянная интенсивность напряжения также обозначается как статическая нагрузка . Если, с другой стороны, уровень напряжения изменяется по своей интенсивности и / или по направлению, говорят о динамической нагрузке .
Определенный тип нагрузки всегда имеет определенный временной ход. Как правило, возникает сочетание нескольких типов нагрузок. Так обстоит дело, например, с валом с односторонним приводом, который одновременно подвергается скручиванию, изгибу и срезанию. В зависимости от того, приводится ли вал в движение с постоянным крутящим моментом или же крутящий момент постоянно изменяется, это статическая или динамическая нагрузка. Таким образом, существует бесчисленное множество возможностей подчеркнуть компоненты.
При определении размеров компонентов инженер должен иметь возможность ссылаться на конкретные значения, которые характеризуют различные пределы напряжений используемых материалов в зависимости от их временного характера.Предел напряжения может быть основан либо на недопустимой деформации, либо на изломе. По этой причине были разработаны различные методы испытаний материалов для определения соответствующих пределов отказов в зависимости от типа нагрузки и ее временного характера.
В принципе, методы испытания материалов можно разделить на две категории:
- разрушающий контроль
- неразрушающий контроль.
При разрушающем испытании материал повреждается, и компонент, как правило, больше не может использоваться.Как правило, для этого типа испытаний используются специально подготовленные и стандартизированные образцы. Процедуры разрушающего контроля обеспечивают важные параметры для определения не только надлежащего материала, но и геометрии компонента в зависимости от приложенной нагрузки. Определение размеров компонентов также называется определением размеров !
Разрушающий контроль используется для определения конкретных постоянных материалов или компонентов!
Следующие методы испытаний считаются разрушающими и более подробно описаны в соответствующей статье
Из-за сложности и взаимодействия между различными нагрузками не все случаи можно зарегистрировать в свойствах материала.Это всегда проблема, когда человеческие жизни подвергаются риску из-за отказа компонентов. По этой причине компоненты, важные для безопасности, необходимо регулярно проверять, как в случае лопаток турбин авиационных двигателей. На данном этапе экономически нецелесообразно проводить разрушающий тест материала, чтобы впоследствии констатировать, что все в порядке.
Именно поэтому был разработан неразрушающий контроль (NDT). Это означает, что компонент все еще можно использовать, если все в порядке.Таким образом, например, указанные турбинные лопатки проверяются неразрушающим методом на наличие трещин посредством ультразвукового контроля или вихретокового контроля . Неразрушающий контроль также включает визуальный контроль того, не поврежден ли компонент снаружи или нет.
Следующие методы испытаний считаются неразрушающим контролем и более подробно описаны в соответствующей статье
В общем, никакая конкретная константа материала не может быть получена с помощью неразрушающих испытаний, как при разрушающих испытаниях.Результатом является только заявление о том, можно ли по-прежнему использовать компонент, или его необходимо отремонтировать или даже заменить.
Неразрушающий контроль используется для проверки пригодности готовых компонентов (инспекция) — параметры материала не определяются!
Типы неразрушающего контроля (LP / MP / UT / RX) — Материалы проекта
Неразрушающий контроль (сокращенно NDT) используется для оценки физических и механических свойств сварного соединения без повреждения оборудования.Наиболее распространенными методами неразрушающего контроля являются визуальный контроль, проникающие жидкости, магнитные частицы, рентгенографический (RX) и ультразвуковой (UT) контроль.
ВИДЫ НЕРАЗРУШАЮЩИХ ИСПЫТАНИЙ
В этой статье мы рассмотрим наиболее распространенные методы неразрушающего контроля, используемые для проверки сварных соединений (например: сварные трубы, фитинги или оборудование, работающее под давлением). Неразрушающие испытания не повреждают испытываемое оборудование; разрушительные испытания, напротив, могут повредить продукт.
Визуальный осмотр (VI)
Визуальный осмотр — это самый простой и дешевый неразрушающий контроль, и все сварные швы должны подвергаться этому основному методу с использованием невооруженного глаза или увеличительного стекла для подтверждения дефектов.
Все поверхности, подлежащие визуальному осмотру, должны быть тщательно очищены. Этот метод используется только для обнаружения дефектов поверхности.
Если они обнаружены, используются дополнительные тесты для определения степени дефекта.
Даже если сварной шов необходимо исследовать более точными методами контроля, он должен быть подвергнут основным визуальным проверкам из-за их низкой стоимости.
Кроме того, если дефекты обнаруживаются визуально, может быть усилено дополнительное обследование этой проблемной области.
Жидкие пенетранты (LP)
Неразрушающий контроль проникающей жидкости (или проникновения) (LPE) используется для металлов, которые считаются немагнитными, таких как нержавеющая сталь с аустенитно-хромовым покрытием.
Этот метод требует нанесения на поверхность проникающей жидкости, содержащей краситель. Жидкости дают время проникнуть в любые дефекты поверхности, и лишняя жидкость удаляется.Дают поверхности высохнуть и проверяют сварной шов. О недостатках свидетельствует наличие красителя, которое видно невооруженным глазом.
Жидкие пенетранты — это недорогой тест для обнаружения трещин или аномальной пористости на поверхности оборудования.
Источник: Techcorr
Магнитные частицы (MP)
Исследование магнитных частиц (MPE) — это метод неразрушающего контроля, используемый для обнаружения поверхностных трещин на ферромагнитных материалах, таких как углеродистая сталь.
Некоторые низколегированные сплавы обладают магнитными свойствами, однако аустенитно-хромистая нержавеющая сталь очень слабо магнитна и поэтому исключается из этого типа исследования; это подвергается исследованию на проникновение красителя, которое будет рассмотрено позже. Метод MPE очень полезен для обнаружения мелких трещин, невидимых невооруженным глазом.
Для проведения исследования исследуемый сварной шов сначала сильно намагничивается с помощью электромагнита, затем на поверхность наносятся мелкие частицы магнитного материала, например железа или магнитного оксида железа.Магнитный порошок притягивается к краям любых поверхностных трещин, делая их видимыми невооруженным глазом.
Ультразвуковой контроль (UT)
Ультразвуковые (UT) волны с частотой 500–5000 кГц передаются в виде узкого луча к цели. Достигнув металлической поверхности с дефектом, волны отражаются и возвращаются в подходящий приемник. Время, необходимое для возврата эха, является мерой длины пути, пройденного волнами.
При правильном использовании ультразвуковой метод может приблизиться к точности рентгенографии. Преимущество ультразвукового контроля состоит в том, что оборудование портативно; поэтому UT полезен, когда сварной шов находится в неудобном месте или его необходимо проверить на месте.
Источник: Techcorr
Радиографический тест (RX или RT)
Радиографическое обследование (RT) — самый полезный неразрушающий контроль, поскольку он обнаруживает подповерхностные дефекты, невидимые невооруженным глазом.
Первоначально в этом методе использовалось рентгеновское излучение, но сегодня соединения труб можно исследовать с помощью гамма-излучения, производимого переносными радиоактивными изотопами. Все источники излучения потенциально опасны, и следует избегать длительного воздействия. Защита персонала часто является требованием для техников, проводящих рентгенографию.
Пленка помещается на одну сторону сварного шва, а с другой стороны сварной шов подвергается воздействию рентгеновских лучей в направлении пленки. Когда рентгеновские лучи проходят через сварной шов, любые дефекты на поверхности и в сварном шве обнаруживаются по темной тени на экспонированной пленке.
Никакие дефекты не проявляются как четкие с однородным оттенком. Анализ рентгенографических пленок требует значительного опыта, и дефекты, которые могут быть обнаружены, включают трещины (поверхностные и подповерхностные) и подповерхностные полости, вызванные оксидной пленкой; отсутствие плавления; захваченный шлак, флюс или инородный материал; и газовые карманы (пористость).
На каждой рентгенограмме должен быть записан номер сварного шва, чтобы идентифицировать точное его местоположение, а также должны быть указаны имена рентгенолога и инспектора.Рентгенограммы открыты для интерпретации, и важно, чтобы персонал, используемый для этой деятельности, имел соответствующую квалификацию.
(Источник: Питер Смит — Выбор и применение материалов для трубопроводов, 2004 г.)
Услуги неразрушающего контроля | Лаборатория тестирования Inc.
Проверьте качество, не нанося вреда образцам
Неразрушающий контроль (NDT) — это разнообразная группа процессов испытаний и инспекций, используемых для обнаружения поверхностных и подповерхностных дефектов или несоответствий в испытательных образцах, не влияющих на будущие рабочие характеристики проверяемых деталей.Эта категория методов испытаний также известна как неразрушающий контроль, неразрушающий контроль и неразрушающая оценка.
Laboratory Testing Inc. — это полностью оборудованная и аккредитованная независимая лаборатория разрушающего и неразрушающего контроля недалеко от Филадельфии, штат Пенсильвания (США). LTI специализируется на испытании сырья и готовых деталей из металлов и сплавов, но некоторые услуги по неразрушающему контролю также могут быть выполнены на керамике, композитах, пластмассах и других твердых телах. Также предлагаются методы неразрушающего контроля сварных швов для проверки качества сварных швов для аттестации сварщика и процедуры, а также для обнаружения коррозии.
Соответствует вашим требованиям
Услуги по неразрушающему контролюLTI помогают клиентам оценивать материалы, продукты и процессы с помощью проверенных методов, которые соответствуют отраслевым требованиям и требованиям качества. Лаборатория неразрушающего контроля имеет строгую систему качества и процедуры для обеспечения надежных результатов проверки.
Наши инспекторы по неразрушающему контролю сертифицированы на соответствие отраслевым требованиям, включая ASNT SNT-TC-1A, NAS410, MIL-STD-2132, Pratt & Whitney PWA-NDTQ. Результаты всех испытаний неразрушающего контроля оцениваются высококвалифицированными специалистами 2 и 3 уровней неразрушающего контроля.
Некоторые дополнительные квалификации включают:
- Аккредитация NADCAP
- Сертифицированный инспектор по сварке AWS
- Технические специалисты, сертифицированные PED в области MP, LP и рентгенографии
Вы можете легко отслеживать ход выполнения ваших заказов в Интернете с помощью клиентского портала LTI. Если вы хотите, чтобы мы ускорили время обработки и обработки, доступны услуги в тот же день, на следующий день и на второй день. Подробнее .. .
НК для металлов и др.
Laboratory Testing Inc.является одной из ведущих лабораторий по неразрушающему контролю в США и предлагает ряд возможностей для клиентов, которым требуется неразрушающий контроль и оценка металлических материалов и деталей. Планировка нашей лаборатории неразрушающего контроля и возможности нашего оборудования позволяют LTI обрабатывать заказы практически любого количества, а также материалы и детали любых форм и размеров. Наши высококвалифицированные и сертифицированные специалисты по неразрушающему контролю регулярно проверяют трубы, трубы, стержни, пластины, отливки, крепежные детали, электронику и многое другое.
Lab Testing также выполняет неразрушающий контроль сварных швов и некоторых изделий из неметаллов. Наши вилочные погрузчики грузоподъемностью 8000 фунтов и краны грузоподъемностью 6000 фунтов безопасно работают с крупногабаритными материалами.
Комплекс услуг неразрушающего контроля
Ультразвуковой контроль
Услуги погружного и контактного ультразвукового контроля (UT) выполняются в лаборатории неразрушающего контроля Lab Testing для обнаружения дефектов в изделиях и сварных швах, а также несоответствий в толщине труб и стенок труб.Благодаря нашему обширному внутреннему собранию эталонных стандартов на трубы, трубы, стержни и пластины, мы можем быстро выполнять заказы.
Испытание гидростатическим давлением
Испытание гидростатическим давлением используется для проверки работоспособности заполненных жидкостью труб, труб и змеевиков, а также для выявления утечек. LTI может испытывать трубы и трубы на давление до 10 000 фунтов на квадратный дюйм.
Контроль магнитных частиц
Поверхностные и приповерхностные неоднородности могут быть обнаружены в изделиях, которые можно намагничивать с помощью услуг по контролю магнитных частиц.Влажное флуоресцентное испытание на магнитные частицы проводится на изделиях длиной до 12 футов с использованием оборудования с максимальной выходной мощностью 6300 ампер. Также предоставляются услуги инспекции сухого порошка.
Испытания на проникновение жидкости
УслугиLiquid Penetrant Testing надежны для обнаружения поверхностных дефектов в материалах с непористой поверхностью. Инспекторы по неразрушающему контролю в Laboratory Testing Inc. проводят испытания на проникающую способность красителя с использованием флуоресцентных и видимых красителей на продуктах до 25 футов.длинный.
Рентгеновский контроль / радиография
Неразрушающий контроль материалов на основе рентгеновских лучей может использоваться для обнаружения внутренних разрывов, проверки целостности внутренних компонентов и определения качества сварных швов. В LTI наше оборудование для рентгеновского контроля может проникать сквозь толстые металлические и пластиковые изделия и детали, а в нашем хранилище размером 20 на 20 футов можно обрабатывать предметы очень большого размера.
Визуальный осмотр
инспекторов по неразрушающему контролю сертифицированы в соответствии с ASNT SNT-TC-1A.
Услуги с добавленной стоимостью
Laboratory Testing Inc. обрабатывает каждый заказ на проведение неразрушающего контроля с учетом потребностей наших клиентов в оперативности и удобстве. Мы предлагаем множество дополнительных услуг, от подготовки материалов до специальной упаковки и доставки, чтобы обеспечить удобство выполнения ваших требований по неразрушающему контролю:
- Проверка поступления
- Резка, обрезка и удаление заусенцев
- Обозначение материала
- Разметка линии
- Трафарет
- Электрохимическое травление
- Упаковка и транспортировка в соответствии с ANSI N45.2.2 или спецификации заказчика
Свяжитесь с нами, чтобы узнать, как услуги неразрушающего контроля LTI могут работать на вас, или запросите расценки сегодня.
Что такое неразрушающий контроль и его преимущества
Неразрушающий контроль — это описательный термин, используемый для проверки материалов и компонентов таким образом, чтобы можно было исследовать материалы, не изменяя и не нарушая их полезности. NDT или NDE можно использовать для поиска, определения размера и локализации поверхностных и подповерхностных дефектов и дефектов.
NDT играет решающую роль в повседневной жизни и необходим для обеспечения безопасности и надежности. Типичными примерами являются самолеты, космические корабли (шаттлы), автомобили, трубопроводы, мосты, поезда, электростанции, нефтеперерабатывающие заводы, здания и нефтяные платформы, которые все проверяются с помощью неразрушающего контроля.
NDT — это инструмент управления качеством, который при правильном использовании может дать впечатляющие результаты. Это требует понимания различных доступных методов, их возможностей и ограничений, знания соответствующих стандартов и спецификаций для выполнения тестов.
Материалы, продукты и оборудование, которые не соответствуют проектным требованиям или планируемому сроку службы из-за необнаруженных дефектов, могут потребовать дорогостоящего ремонта или ранней замены. Такие дефекты также могут быть причиной небезопасных условий или катастрофического отказа, а также потери доходов из-за незапланированной остановки завода.
Неразрушающий контроль может применяться на каждой стадии конструкции объекта. Материалы и сварные швы можно исследовать с помощью неразрушающего контроля и принять, отклонить или отремонтировать.Затем методы неразрушающего контроля можно использовать для контроля целостности элемента или конструкции на протяжении всего срока службы.
NDT обычно используется по следующим причинам:
o Предотвращение несчастных случаев и снижение затрат
o Для повышения надежности продукции
o Определить соответствие требованиям
o Получить информацию о критериях ремонта.
Для получения информации и получения достоверных результатов необходимо следующее:
o Визуальный осмотр
o Инспекция жидких пенетрантов
o Акустическая эмиссия
o Контроль магнитных частиц
o Вихретоковый контроль
o Ультразвуковой контроль
o Радиографический контроль
ДОПОЛНИТЕЛЬНАЯ ИНФОРМАЦИЯ О НАШИХ ОНЛАЙН-ПРЕИМУЩЕСТВАХ:
o Полное, краткое, сертифицированное онлайн-обучение по неразрушающему контролю
o Единственный в своем роде формат, полностью компьютерный
o Всегда включен и доступен из любого места — запускайте в любое время
o Сертификация Готовность помочь в соблюдении глобальных требований, таких как SNT-TC-1A, CGSB9712, NAS410, CP189, BINDT, AWS, ISO9712
o Сертифицированные, опытные инструкторы по неразрушающему контролю, предлагающие быстрые решения
o Сертификат на обрамление и карточку размера кошелька, предоставленную в качестве доказательства заполнения
o Работайте в своем собственном темпе — ваше время составляет от 1 недели до 1 года
o Мы установили пароль для круглосуточного доступа
o Мы ответим на все ваши вопросы и поможем с требованиями к заявкам на сертификацию по всему миру.
o Мы также предоставляем все периферийные данные для инженеров, инспекторов и техников, которым требуется дополнительная информация, для проекта, эссе или просто личного исследования — прямо через этот веб-сайт. Просто спроси! Мы ответим в течение дня. У вас есть проблема на работе и вам нужна дополнительная информация? У наших экспертов есть библиотека и возможность отправлять решения по факсу или электронной почте как можно скорее. Это ответ на ваши проблемы, мы его гарантируем.
o Класс или школа не требуется.Работайте из дома, в аэропорту, в интернет-кафе или в любом месте с WIFI!
o МЫ ТАКЖЕ ПРЕДЛАГАЕМ / ПРЕДЛАГАЕМ ПОЛНУЮ УСЛУГУ NDT УРОВНЯ III, ВКЛЮЧАЯ Q.A. РУКОВОДСТВА, ПРОЦЕДУРЫ NDE / РУКОВОДСТВА И ТРЕБУЕМЫЕ ДОКУМЕНТЫ ASME / ANSI
Наш онлайн-курс более чем конкурентоспособен по цене 699 долларов США. Во-вторых, вам не нужно путешествовать, терять рабочее время или платить за гостиницу — при посещении одно- или двухнедельного семинара в аудитории.