несплошность — это… Что такое несплошность?
несплошность — Нарушение однородности материала, вызывающее скачкообразное изменение его акустических характеристик плотности, скорости звука, волнового сопротивления. Примеры несплошностей: трещины, шлаковые включения, непровары, раковины и т.п Примечания: 1.… … Справочник технического переводчика
Несплошность — ДЕФЕКТЫ СВАРНЫХ СОЕДИНЕНИИ ПРИ ВИЗУАЛЬНОМ И ИЗМЕРИТЕЛЬНОМ КОНТРОЛЕ Несплошность Обобщенное наименование трещин, отслоений, прожогов, свищей, пор, непроваров и включений. Источник: РД 03 606 03: Инструкция по визуальному и измерительному контролю… … Словарь-справочник терминов нормативно-технической документации
Несплошность сварного соединения — обобщенное наименование всех нарушений сплошности и формы сварного соединения (трещины, непровары, несплавления, включения)… Источник: Методические рекомендации по определению технического состояния систем теплоснабжения, горячего водоснабжения … Официальная терминология
несплошность плоскостного типа сварного шва — Обобщенное наименование трещин, отслоений, прожогов, свищей, пор, непроваров и включений. [РД 01.120.00 КТН 228 06] Тематики магистральный нефтепроводный транспорт … Справочник технического переводчика
Несплошность сварного соединения — Обобщенное наименование всех нарушений сплошности и формы сварного соединения (трещина, непровар, несплавление, включение и др.) Источник: РД 34.10.130 96: Инструкция по визуальному и измерительному контролю … Словарь-справочник терминов нормативно-технической документации
искусственная несплошность — Несплошность известных размеров, формы и расположения, выполненная в образце и служащая для получения акустических сигналов. [Система неразрушающего контроля. Виды (методы) и технология неразрушающего контроля. Термины и определения (справочное… … Справочник технического переводчика
сквозная несплошность — Поверхностная несплошность с выходом на противоположную поверхность контролируемого объекта. Примечание Если поверхностная и сквозная несплошности являются дефектами, то допускается вместо них применять термины «поверхностный дефект»… … Справочник технического переводчика
поверхностная несплошность — Наличие разрыва поверхности контролируемого объекта без выхода его на противоположную поверхность. [Система неразрушающего контроля. Виды (методы) и технология неразрушающего контроля. Термины и определения (справочное пособие). Москва 2003 г.]… … Справочник технического переводчика
дефект — 02.02.22 дефект (изображение) [defect]: Отсутствие или недостаточность характеристики, необходимой для удовлетворения требованиям по применению, что может отрицательно влиять на способность функциональной единицы к выполнению требуемой функции.… … Словарь-справочник терминов нормативно-технической документации
несовершенство — 4.18 несовершенство (imperfection): Несплошность или неоднородность в стенке изделия или на его поверхности, выявляемая методами контроля, указанными в настоящем стандарте. Источник: ГОСТ Р ИСО 3183 2009: Трубы стальные для трубопроводов нефтяной … Словарь-справочник терминов нормативно-технической документации
прозрачность несплошности — Способность упругой волны проходить через несплошность, выраженная в виде отношения амплитуды волны, прошедшей через несплошность, измеренной на определенном расстоянии от нее, к амплитуде волны, измеренной в той же точке при отсутствии… … Справочник технического переводчика
Несплошность сварного соединения — это… Что такое Несплошность сварного соединения?
- Несплошность сварного соединения
«…несплошность сварного соединения — обобщенное наименование всех нарушений сплошности и формы сварного соединения (трещины, непровары, несплавления, включения)…»
Источник:
» Методические рекомендации по определению технического состояния систем теплоснабжения, горячего водоснабжения, холодного водоснабжения и водоотведения»
(утв. Минрегионом России 25.04.2012)
Официальная терминология. Академик.ру. 2012.
- Неспециализированный кастодиальный депозитарий
- Несправедливость приговора в уголовном процессе
Смотреть что такое «Несплошность сварного соединения» в других словарях:
Несплошность сварного соединения — Обобщенное наименование всех нарушений сплошности и формы сварного соединения (трещина, непровар, несплавление, включение и др.) Источник: РД 34.10.130 96: Инструкция по визуальному и измерительному контролю … Словарь-справочник терминов нормативно-технической документации
Дефект сварного соединения — 1.4.16 Дефект сварного соединения несплошность в сварном шве, околошовной зоне, между швом и основным металлом свариваемых элементов, или отклонение геометрических параметров сварного соединения от номинальных значений, определяемых требованиями… … Словарь-справочник терминов нормативно-технической документации
Несплошность — ДЕФЕКТЫ СВАРНЫХ СОЕДИНЕНИИ ПРИ ВИЗУАЛЬНОМ И ИЗМЕРИТЕЛЬНОМ КОНТРОЛЕ Несплошность Обобщенное наименование трещин, отслоений, прожогов, свищей, пор, непроваров и включений. Источник: РД 03 606 03: Инструкция по визуальному и измерительному контролю… … Словарь-справочник терминов нормативно-технической документации
дефект соединения сварного — Несплошность сварного шва или несплошность по линии сплавления между слоями шва, швом и основным металлом свариваемых элементов, или отклонение геометрических параметров сварного соединения от номинальных значений, определяемых требованиями… … Справочник технического переводчика
РД 34.10.130-96: Инструкция по визуальному и измерительному контролю — Терминология РД 34.10.130 96: Инструкция по визуальному и измерительному контролю: Асимметрия углового шва (512) Несоответствие фактического значения катета шва проектному значению, рис. ПА 51 Определения термина из разных документов: Асимметрия… … Словарь-справочник терминов нормативно-технической документации
дефект — 02.02.22 дефект (изображение) [defect]: Отсутствие или недостаточность характеристики, необходимой для удовлетворения требованиям по применению, что может отрицательно влиять на способность функциональной единицы к выполнению требуемой функции.… … Словарь-справочник терминов нормативно-технической документации
РД 08.00-60.30.00-КТН-046-1-05: Неразрушающий контроль сварных соединений при строительстве и ремонте магистральных нефтепроводов
— Терминология РД 08.00 60.30.00 КТН 046 1 05: Неразрушающий контроль сварных соединений при строительстве и ремонте магистральных нефтепроводов: 1.4.15 Бригада сварщиков группа аттестованных в установленном порядке сварщиков, назначенных… … Словарь-справочник терминов нормативно-технической документацииРД 03-606-03: Инструкция по визуальному и измерительному контролю — Терминология РД 03 606 03: Инструкция по визуальному и измерительному контролю: Асимметрия углового шва Несоответствие фактического значения катета шва проектному значению, рис. А.48 Определения термина из разных документов: Асимметрия углового… … Словарь-справочник терминов нормативно-технической документации
РД 19.100.00-КТН-545-06: Ультразвуковой контроль стенки и сварных соединений при эксплуатации и ремонте вертикальных стальных резервуаров — Терминология РД 19.100.00 КТН 545 06: Ультразвуковой контроль стенки и сварных соединений при эксплуатации и ремонте вертикальных стальных резервуаров: Дефект : здесь: несплошность в металле стенки резервуара, в сварном соединении, отклонение… … Словарь-справочник терминов нормативно-технической документации
ГОСТ Р 54383-2011: Трубы стальные бурильные для нефтяной и газовой промышленности. Технические условия — Терминология ГОСТ Р 54383 2011: Трубы стальные бурильные для нефтяной и газовой промышленности. Технические условия оригинал документа: 3.43 «слоновая кожа» (elephant hide): Несплошности наружной поверхности тела бурильной трубы, образующиеся в… … Словарь-справочник терминов нормативно-технической документации
НЕСПЛОШНОСТИ В ТЕЛЕ ОТЛИВКИ — это… Что такое НЕСПЛОШНОСТИ В ТЕЛЕ ОТЛИВКИ?
- НЕСПЛОШНОСТИ В ТЕЛЕ ОТЛИВКИ
- — классификационная характеристика следующих дефектов отливок: горячая трещина, ГОСТ 19200-80.
- НЕСПАЙ
- НЕСТАРЕЮЩАЯ СТАЛЬ
Смотреть что такое «НЕСПЛОШНОСТИ В ТЕЛЕ ОТЛИВКИ» в других словарях:
ГОСТ 19200-80: Отливки из чугуна и стали. Термины и определения дефектов — Терминология ГОСТ 19200 80: Отливки из чугуна и стали. Термины и определения дефектов оригинал документа: 42 . Вскип Ндп. Кип Дефект в виде скопления раковин и наростов, образовавшихся вследствие парообразования в местах переувлажнения литейной… … Словарь-справочник терминов нормативно-технической документации
НЕПРОВАР ЖЕРЕБЕЕК (ХОЛОДИЛЬНИКОВ) — дефект в виде несплошности соединения металла отливки с поверхностью жеребеек (холодильников) вследствие их загрязнения, несоответствия масс, пониженной температуры заливаемого металла (рис. Н 5). ГОСТ 19200 80. Рис. Н 5. Схема образования… … Металлургический словарь
ГОРЯЧАЯ ТРЕЩИНА — дефект в виде разрыва или надрыва усадочного происхождения, возникшего в теле отливки в интервале температур затвердевания. Горячая трещина располагается по границам кристаллов, имеет неровную окисленную поверхность, на которой иногда видны… … Металлургический словарь
непровар жеребеек (холодильников) — Дефект в ряде несплошности соединения металла отливки с поверхностью жеребеек (холодильников) вследствие их загрязнения, несоответствия масс, пониженной температуры заливаемого металла. [ГОСТ 19200 80] Тематики отливки из чугуна и стали… … Справочник технического переводчика
МЕЖКРИСТАЛЛИЧЕСКАЯ ТРЕЩИНА — дефект в виде разрыва тела отливки при ее охлаждении в форме, образующийся на границах первичных зерен аустенита в температурном интервале распада. Межкристаллическая трещина в изломе термически обработанной пробы (отливки) имеет вид сглаженных… … Металлургический словарь
СИТОВИДНАЯ РАКОВИНА
УСАДОЧНАЯ ПОРИСТОСТЬ — дефект в виде мелких пор, образовавшихся вследствие усадки металла во время его затвердевания при недостаточном питании отливки (рис. У 12). пористость WIDTH=547 HEIGHT=514 BORDER=0> Рис. У 12. Усадочная пористость: а серого чугуна при… … Металлургический словарь
УСАДОЧНАЯ РАКОВИНА — дефект в виде скрытой или открытой полости (рис. У 13) с грубой шероховатостью, иногда окисленной поверхностью, образовавшейся вследствие усадки при затвердевании металла. ГОСТ 19200 80. Сечение отливки с усадочными раковинами WIDTH=312… … Металлургический словарь
ХОЛОДНАЯ ТРЕЩИНА — дефект в виде разрыва тела затвердевшей отливки вследствие внутренних напряжений или механических воздействий. Холодная трещина обычно имеет чистую светлую или с цветами побежалости зернистую поверхность. * * * Холодная трещина это дефект отливки … Металлургический словарь
межкристаллическая трещина — Дефект в виде разрыва тела отливки при охлаждении отливки в форме на границах первичных зерен аустенита в температурном интервале распада. Примечание Межкристаллическая трещина в изломе термически обработанной пробы (отливки) имеет вид сглаженных … Справочник технического переводчика
Выявление нарушения сплошности металла — Студопедия
Для выявления нарушения сплошности металлов применяются следующие методы дефектоскопии: магнитные, капиллярные, ультразвуковые, просвечивание.
Магнитные порошковые методы дефектоскопии являются неразрушающими и основаны на изменении распределения магнитных силовых линий в намагниченной детали при наличии в ней полости – дефекта с иными, чем у основной детали, ферромагнитными свойствами. Силовые линии огибают полость, при этом на её краях образуются полюса магнита. Если дефектный район детали посыпать ферромагнитным порошком , то частицы следуя за магнитными силовыми линиями, покажут очертания полости дефекта.
Капиллярный метод дефектоскопии основан на высокой смачивающей способности некоторых жидкостей. Такие жидкости, нанесённые на поверхность детали, проникают в имеющиеся на поверхности полости и выявляются во время последующей обработки поверхности детали.
Ультразвуковые методы дефектоскопии позволяют обнаруживать объёмные пороки, расположенные внутри детали. Эти методы основаны на явлениях прямого и обратного пьезоэлектрических эффектов. На противоположные поверхности детали устанавливаются пьезоэлементы, один из которых является генератором упругих колебаний материала детали, другой играет роль приёмника.
— 24 —
Методы дефектоскопии просвечиванием основаны на способности рентгеновских лучей проникать в глубь материалов. Поглощаемость лучей зависит от плотности материала
: чем больше плотность и толщина, тем интенсивнее поглащение.
Занятие № 19 – 2 часа.
Практическая работа № 12: «Контрольно-измерительные приборы в машиностроении».
Занятие № 20. Лекция – 2 часа.
Тема: «Проверка плотности соединений. Восстановление деталей сваркой».
Плотность соединений проверяют путём воздушных или гидравлических испытаний или с помощью течеискателей. В первом случае во внутренних полостях контролируемой детали создают повышенное давление жидкости (обычно воды) или воздуха. Место течи определяют визуальным осмотром или с помощью манометра. Величина давления зависит от температурных условий работы и механических свойств материалов узла, степенности агрессивности рабочей среды, величины рабочего давления при эксплуатации.
Плотность сварных соединений контролируется вакуумным методом. Наиболее доступную для контроля сторону детали покрывают мыльным раствором, после чего на контролируемое место устанавливают вакуумную камеру, представляющую собой П-образную рамку с уплотнениями из губчатой резины, с прозрачной крышкой и краном. Сварной шов изделия с трещиной, на которой мыльная пена пузырится, хорошо виден через прозрачную крышку камеры. Разряжение внутри камеры определяется вакуумометром.
При контроле судовых цистерн на плотности соединений путём гидропневматических испытаний из соображения безопасности давление не повышают более чем на 0.15-0.70 кгс/см2.Чувчствительность течеискателей значительно выше той, которую могут обеспечить гидравлические испытания. Основными типами течеискателей являются галоидные, гелевые и ультрозвуковые.
Галоидный течеискатель отыскивает неплотности в узлах, внутри которых имеется или создаётся избыточное давление рабочей среды, содержащей галоиды (фтор, хлор, йод и т.п.).
Работа ультрозвукового течеискателя основана на измерении звукового давления, создоваемого вытекающим через неплотность газом, и преобразовании ультозвуковых колебаний струи газа в звуковые колебания. Современные ультрозвуковые течеискатели обнаруживают утечку воздуха через отверстие диаметром 0,15 мм на расстоянии до 15 метров.
Контроль сплошности металла — Энциклопедия по машиностроению XXL
Предусмотрены следующие виды контроля отливок визуальный с измерениями основных размеров определение химического состава (поплавочно) определение механических свойств (включая твердость) гидравлическое испытание по ГОСТ 356—80 неразрушающий контроль сплошности металла отливок магнитопорошковая дефектоскопия радиусных переходов и просвечивание рентгеновскими лучами или гаммаграфия концов присоединительных патрубков). [c.193]КОНТРОЛЬ сплошности МЕТАЛЛА [c.71]
Совершенствование качества изготовления, монтажа, ремонта и эксплуатации должно приводить к полному исключению дефектов, нарушающих сплошность металла. Дефекты, являющиеся нарушениями сплошности металла, можно подразделить на критические, значительные (недопустимые), малозначительные (допустимые), исправляемые и неисправляемые. К критическим недопустимым дефектам сплошности относятся дефекты, при наличии которых эксплуатация деталей или узлов не удовлетворяет требованиям безопасности и надежности и не допускается. Малозначительные (допустимые) дефекты не оказывают существенного влияния на безопасность. Исправимый дефект — это дефект, устранение которого технически возможно и целесообразно. К неисправимым дефектам относятся дефекты, устранение которых технически невозможно и нецелесообразно детали с такими дефектами к эксплуатации не допускаются. Основная задача по обеспечению надежной и безопасной эксплуатации может быть решена только при надежном контроле сплошности металла наиболее ответственных деталей (ГОСТ 18353—79). В зависимости от принципа работы контрольных средств [c.71]
АКУСТИЧЕСКИЕ МЕТОДЫ КОНТРОЛЯ СПЛОШНОСТИ МЕТАЛЛА [c.115]
Отливки должны подвергаться следующим видам контроля визуально с измерениями основных размеров контролю химического состава (поплавочно) контролю механических свойств (включая твердость) гидравлическому испытанию неразрушающему контролю сплошности металла отливок (МПД радиусных переходов и рентгенопросвечивание или гаммаграфия концов присоединительных патрубков). [c.116]
Кроме того, отливки должны проходить следующие виды контроля визуальный с измерениями основных размеров химического состава (по плавкам) механических свойств (включая твердость) гидравлические испытания неразрушающий контроль сплошности металла отливок (МПД радиусных переходов и рентгенопросвечивание или гаммаграфия концов присоединительных патрубков). [c.136]
Контроль сплошности металла. Размеры выявляемых дефектов длина 5 мм, ширина 0,01—0,2 мм, глубина свыше 0,1 мм, глубина залегания до 7 мм, расстояние между преобразователем и объектом до 3 мм. [c.71]
Термическая обработка перед нанесением покрытия, после которой производится контроль сплошности металла и макроструктуры, механических свойств и длительной прочности. [c.354]
Средства контроля сплошности металла [c.48]
Контроль сплошности основного металла (в объеме от 15 до 30%) сосудов и трубопроводов ультразвуковым методом в соответствии с [100, 103, 114-116] и специальными методиками, учитывающими специфику развития водородного расслоения, проводят в зонах шириной 200 мм по обе стороны от контролируемых сварных швов и ПОУ. Остальные зоны обследуют согласно карте контроля. УЗК основного металла конструкции осуществляют с помощью прямого раздельно-совмещенного преобразователя (частота 4-5 МГц, рабочий диаметр не более 18 мм) путем многократного дискретного линейного сканирования дефектного участка конструкции в продольном направлении с шагом не более 20 мм. В области контура дефекта и в примыкающей к ней зоне шириной 100 мм шаг сканирования не должен превышать 10 мм. При малых размерах дефектов в плане (менее 50 мм) и их условной высоте более 20% толщины стенки конструкции проводят сплошное сканирование. Условные линейные размеры протяженных (более 50 мм) дефектов определяют с точностью не менее одного шага сканирования, а глубину их залегания — не менее 0,3 мм. [c.162]
В ряде случаев с целью выявления сплошности металла сварного шва применяются также другие методы контроля качества сварных соединений. [c.293]
Визуальный и измерительный контроль проводят невооруженным глазом или с помощью лупы 4…7-кратного увеличения с обязательным применением источника света и шаблонов или мерительного инструмента. Перед визуальным контролем сварные швы и прилегающие к ним с двух сторон поверхности основного металла шириной не менее 20 мм должны быть очищены от шлака, брызг расплавленного металла, окалины и других загрязнений. При проведении контроля определяют соответствие геометрических параметров сварного соединения стандартам на тот или иной вид сварки и размеры поверхностных нарушений сплошности металла. После этого их сравнивают с нормативными значениями. Если превышения нет, то сварное соединение считается прошедшим данный вид контроля. [c.374]
ДЕФЕКТЫ СПЛОШНОСТИ МЕТАЛЛА И ВЫБОР МЕТОДА КОНТРОЛЯ [c.71]
В связи с изложенными факторами проводят эксплуатационный контроль температурного режима, термических перемещений и со стояния металла. Эксплуатационный контроль металла включает наблюдение за ростом остаточной деформации, изменениями структуры и механических свойств, состоянием сварных соединений и сохранением сплошности металла в местах конструктивных и эксплуатационных концентраций напряжения. Возможности эксплуатационного контроля металла должны быть предусмотрены при проектировании, монтаже, ремонтах и эксплуатации теплосилового оборудования. При длительной эксплуатации при высоких температурах я давлении свойства металла паропроводов и котлов изменяются, что проявляется в развитии процесса ползучести, окалинообразования, усталости, коррозии, эрозионного износа, а также в снижении работоспособности. Эксплуатационный контроль металла котлов и трубопроводов проводят в соответствии с требованиями Инструкции по контролю за металлом котлов, турбин и трубопроводов И 34-70-013—84 Минэнерго. [c.210]
Повреждения шпилек при эксплуатации представляют собой поперечные трещины и обрывы по впадине 1—3 витка резьбы (рис. 7.11). Эти повреждения связаны либо с несоответствием металла температурным условиям работы, либо с некачественной термообработкой, либо с повышенными эксплуатационными напряжениями, обусловленными неправильным затягом шпилек при монтаже. Поэтому основные этапы контроля шпилек фланцевых соединений следующие стилоскопирование внешний осмотр контроль уровня начальных напряжений затяжки ультразвуковой контроль сплошности контроль твердости неразрушающим способом оценка механических свойств. [c.230]
Окончательную оценку сплошности металла гиба проводят после удаления наружных дефектов и повторной ультразвуковой дефектоскопии. Гибы годны , если в процессе контроля не обнаружены дефекты с браковочными признаками. [c.257]
Иногда поврежденный участок металла не вырезают. Его выбирают и подваривают. Но при этом требуется исследовать механические свойства металла, химический состав и микроструктуру. Аналогичная ситуация иногда возникает при обследовании барабанов долго работавших котлов. В этом случае из обечайки сосуда или барабана вдали от сварных швов, полей отверстий под трубы или других концентраторов напряжений вырезают механическим способом диск диаметром около 100 мм так, чтобы затем на его место можно было бы установить заглушенный штуцер с внутренним диаметром менее 100 мм. В этом случае согласно Правилам по котлам [1] рентгенографический или ультразвуковой контроль сплошности шва не требуется. Диск обычно высверливают по контуру или вырезают специальной корончатой фрезой. Из него изготавливают образцы.. [c.303]
Изучение сплошности металла шва физическими методами контроля [c.700]
Механические испытания, металлографические исследования и проверка сплошности металла шва и сварных соединений физическими методами контроля [c.701]
Испытания на свариваемость с определением технологических свойств материалов механические испытания металлографические исследования макро- и микроструктуры сварного соединения проверка стойкости металла шва против межкристаллитной коррозии определение сплошности металла шва физическими методами контроля [c.689]
Прибор позволяет обнаруживать дефекты, являющиеся нарушением сплошности материала (трещины, раковины, поры, неметаллические включения, расслоения и т. д.), на глубину до 1,5м, а также измерять с высокой точностью толщину изделий при доступе с одной стороны. Прибор осуществляет контроль структуры. металлов относительным методом [1—3]. [c.253]
Однако в последнее время в связи с разработкой новых материалов, неоднородных по своему строению, крупнозернистых, обладающих большим коэффициентом затухания и высоким уровнем структурной реверберации, например жаропрочных сплавов, сплавов на основе титана, специальных чугунов, появилась необходимость контроля изделий из них. Контроль должен производиться на пониженных частотах и, следовательно, при меньшей чувствительности. При этом представляет интерес не только обнаружение нарушений сплошности металла, но также и обнаружение зон, отличающихся по величине зерна, т. е. контроль структуры металла. Это может быть осуществлено на основе оценки затухания УЗК различной частоты лри распространении их в металле, обладающем различной величиной зерна. [c.125]
Неразрушающий контроль основного металла изделий на сплошность и УЗ-толщинометрия основного металла и штуцеров диаметром более 50 мм в соответствии с ГОСТ 28702-90, ГОСТ 22727-88, ГОСТ 17410-78, ГОСТ 24507-80, ГОСТ 18442-80, ГОСТ 18442-80, ОСТ 3675-83, ОСТ 26-291-94, [c.226]
Дефектоскоп состоит из приводного механизма сменных измерительных блоков и внешнего записывающего устройства. Приводной механизм включает электропривод, ведущую и стабилизирующую головки. Ведущая головка является преобразователем вращательного движения в поступательное. Стабилизирующая головка отличается от ведущей только продольным расположением роликов. Приводной механизм обеспечивает обратное движение при подходе к краю трубы. Блок контроля сплошности диэлектрических покрытий содержит преобразователь напряжения, высоковольтный трансформатор, умножитель напряжения и скользящий контакт в виде кольцевой проволочной оболочки, надетой на корпус блока. Наличие трещин обнаруживается по искровому разряду между скользящим контактом и металлом трубы, записываемому самописцем. [c.589]
Во время контроля сплошности металла барабана состав тяют формуляр развертки барабана, на котором пронумеровывают ьсе тр бные отверстия отмечают отверстия с Т1 ещ111 ами, коррозионными 5 звами па ич поверхности и в зонах, прилегающих к тр бным отверстиям наносят выявленные визуально и с помощью МПД и УЗД дефекты сплошности металла и сварных швов (трещины, раковины и т. п.) с указанием их размеров, а также наибольшей глубины и контуров вышлифовки каждого дефекта. [c.44]
Контроль поверхности барабана, трубных отверстий, штуцеров и сварных соединений при обследовании металла и выборке дефектов проводят внешним осмотром и при помощи магнитно-порошковой дефектоскопии. Поверхность металла барабана и его сварные швы проверяют ультразвуковым дефектоскопом. Если при выборочном контроле поверхностей барабана обнаружены дефекты, проверяют магнитно-порошковой дефектоскопией поверхности всех гнезд. В случае обнаружения при выборочном ультразвуковом контроле швов дефектов, по размерам больше допустимых нормами Госгортехнадзора СССР для котельных барабанов, такие швы подвергают 100 %-ному контролю. На кромках отверстий диаметром более 70 мм с внутренней стороны барабана снимают фаску с катетом 7.. . 10 мм (допускается округление радиусо.м 7.. . 10 мм). Во время контроля сплошности металла барабана составляют формуляр развертки барабана, на котором пронумеровывают трубные отверстия, отмечают отверстия с трещинами, коррозийными язвами на их поверхности и в зонах, прилегающих к трубным отверстиям, наносят выявленные визуально и с помощью указанных методов контроля дефекты сплошности металла и сварных швов (расслоения, трещины, раковины, [c.280]
Ультразвуковой контроль сплошности металла УД2-12 (Кишинев) USK-7D ф. Krautkramer (Германия) [c.48]
Основные технические характеристики установки МД-90И следующие. Объект контроля — холоднокатаные полосы из низкоуглеродистых сталей толщиной 0,5—2,5 мм по ГОСТ 1050—74 , выявляемые дефекты — сварной шов, рваная кромка, дыра, плена, раковина, вдавлина, царапина, вкатанная окалина и другие нарушения сплошности металла глубиной более 5 % от толщины полосы. Рабочий зазор между индукционными преобразователями и полосой,3—5 мм. Число вращающихся преобразователей 96, неподвижных — 12. Число вращающихся блоков обработки сигналов преобразователей 48, неподвижных — 12. [c.53]
При контроле качества сплошности металла труб применяют эхоимпульсный, эхо-теневой, теневой или зеркально-теневой методы. Трубы малых и средних диаметров с небольшой толщиной стенки контролируют продольными волнами, а толстостенные — поперечными по окружности или вдоль образующей. При контактном способе контроля рабочую поверхность преобразователя притирают по поверхности трубы или используют насадки и опоры на преобразователь. В качестве испытательного образца используют бездефектный отрезок трубы. [c.56]
HO сосуда и возможность его эксплуатации на момент испытания и не дают представления об остаточной надежности сосуда, достаточности ее для обесиечения безопасной эксплуатации на период до следующего технического освидетельствования. Количественную оценку надежности (в том числе и остаточной) позволяют дать замеры скорости коррозии и величины износа, определение характеристик механических свойств металла, микроструктурный анализ, а также контроль сплошности сварных соединений. [c.374]
Визуальный послойный контроль проводят для определения качества шва и исключения нарушений технических требований при его выполнении по глубине проплавленпя свариваемых кромок и сплошности металла. Визуальный послойный контроль позволяет выявить в каждом слое после зачистки следующие наружные дефекты трещины, непро-вары (несплавления), свищи, поры, шлаковые включения, подрезы, наплывы, прожоги, незаплавленные кратеры, смещение и увод свариваемых кромок. Глубину проплавления оценивают косвеино при осмотре первого (корневого) валика шва по его размерам и характеру формирования в соответствии с требованиями технологического процесса. [c.580]
На эксплуатационную надежность деталей и механизмов существенное влияние оказывают нарушения сплошности металла (раковины, непровары, расслоения, пористость, флоке-ны, трещины, волосовина и другие дефекты), которые могут возникать в процессе изготовления и эксплуатацпи изделий. Обнаружение дефектов и отбраковка заготовок и деталей в процессе производства является одним из решающих факторов повышения надежности и долговечности. Большое значение при этом имеют физические методы неразрушающего контроля, среди которых ультразвуковой метод наиболее универсальный и приемлемый. [c.249]
Для контроля качества сварных швов и ответственных отливок широко применяется просвечивание рентгеновскими лучами или гамма-лучами (радиопросвечивание). Просвечивание сварных швов или отливок рентгеновскими или гамма-лучами имеет своей целью определение сплошности металла, т. е. выявление наличия дефектов в виде непроваров, шлаковых включений, пор и трещин. [c.274]
Непрерывный технический прогресс в развитии народного хозяйства нашей страны на современном этапе ставит задачу большой государственной важности — повышение надежности и безопасности работы применяемых в промышленности паровых и водогрейных котлов, трубопроводов пара и горячей воды и сосудов, работающих под давлением. Обеспечение выполнения этой задачи требует совершенствования производства на всех стадиях — от научно-технических разработок и проектирования до изготовления, монтажа, эксплуатации и ремонта. Одним из путей повышения надежности и безопасности является контроль качества основного металла и сварных соединений. При этом большое значение приобретает знание возможностей современных иеразрушающих методов контроля свойств и сплошности металла. [c.3]
Изделия, подлежащие контролю, погружают в подготовленную жидкость, которая проникает в дефектные места. Излищки жидкости удаляют, а поверхность посыпают порошком, обладающим высокой поглощающей способностью (окись магния, тальк и др.). Порошок извлекает жидкость из полости дефекта. Нарушение сплошности металла устанавливают по сечению смоченного жидкостью порошка при облучении ультрафиолетовыми лучами в темном помещении. [c.33]
Метод магнитной дефектоскопии применяется для выявления дефектов, нарушающих сплошность металла в ферромагнитных металлах и главным образом в стали,— мелких поверхностных или внутренних трещин, плен, волосовин, раковин и т. п., а также для контроля качества термической обработки. Преимуществом метода магнитной дефектоскопии по сравнению с металлографическим методом являются возможность производить выявление дефектой без разрушения деталей и быстрота данного метода, что позволяет при необходимости контролировать 100% деталей. [c.136]
Основные технические характеристики установки следующие. Объект контроля — холоднокатаные полосы из низкоуглеродистых сталей толщиной 0,5. .. 2,5 мм, выявляемые дефекты — сварной шов, рваная кромка, дыра, плена, раковина, вдавлина, царапина, вкатанная окалина и другие нарушения сплошности металла глубиной более 5 % от толщины полосы. Рабочий зазор между индукционными преобразователями и полосой 3. .. 5 мм. [c.357]
Осаждение магнитного порошка не всегда указывает на наличие дефекта. Иногда магнитный порошок скапливается над магнитонеоднородными местами изделия с местным наклепом, структурной неоднородностью и резким изменением площади поперечного сечения. Это явление относят к ложным, или мнимым, дефектам. Осаждение порошка на ложных дефектах, не связанное с нарушением сплошности металла изделия, не является основанием для браковки изделия при магнитном контроле. Чтобы отличить дефекты, выходящие на поверхность, от ложных, можно применять в качестве контрольных капиллярные методы дефектоскопии. [c.337]
Контроль сплошности металла
Для приближенного определения твердости пользуются тарированными напильниками плоской, квадратной или треугольной формы, предварительно термически обработанными на различную твердость насечки с интервалом 3-5 единиц по Роквеллу. Тарирование напильников проводят по специальным эталонным плитам, твердость которых точно определена прибором. Твердость насечки напильника обозначают на его нерабочей части (например, 56 НЯС, 60 НЯС и т. п.). При контроле твердости детали подбирают такую пару напильников с минимальным интервалом по твердости, чтобы напильник с меньшей твердостью скользил по поверяемой поверхности, а напильник с большей твердостью слегка ее царапал. Следовательно, твердость исследуемой поверхности будет находиться в пределах твердости напильников.
Контроль сплошности металла с помощью дефектоскопа. Исследуемую деталь намагничивают на специальных установках — магнитных дефектоскопах. Поверхность ее смачивают суспензией, состоящей из 0,5 кг порошка оксида железа и 1 л трансформаторного масла. В местах несплошности металла осаждаются частицы оксида железа, в результате чего рельефно выделяется дефект. После контроля деталь размагничивают в соленоиде.
При люминесцентном методе контроля поверхностных дефектов немагнитных металлов элементы контролируемой детали погружают в специальную жидкость, содержащую флюороль - вещество, которое светится под действием ультрафиолетовых лучей. Затем деталь промывают водой, при этом жидкость удаляется только с гладкой поверхности, а в дефектных местах она остается. После этого на поверхность насыпают мелкий порошок, обычно силикагель. Порошок впитывает жидкость из полостей и остается по краям дефекта при последующей обдувке поверхности. Если такую деталь осветить в темном помещении ультрафиолетовыми лучами, места дефектов будут светиться
сине-голубым светом.
РАССЛОЕНИЕ МЕТАЛЛА — это… Что такое РАССЛОЕНИЕ МЕТАЛЛА?
- РАССЛОЕНИЕ МЕТАЛЛА
- РАССЛОЕНИЕ МЕТАЛЛА
порок металла, вызываемый дефектами его изготовления, чаще всего недостаточной обрезкой перед прокатом слитка или блюмса, неправильным режимом прокатки и т. д. Р. м. проявляется в виде плен на поверхности металла или трещин, простирающихся по кромке листа или уголка вдоль проката. В ответственных деталях Р. м. не допускается; в случае обнаружения такого недостатка соответственные части бракуются и заменяются исправными.
Технический железнодорожный словарь. — М.: Государственное транспортное железнодорожное издательство. Н. Н. Васильев, О. Н. Исаакян, Н. О. Рогинский, Я. Б. Смолянский, В. А. Сокович, Т. С. Хачатуров. 1941.
.
- РАССЕИВАЮЩЕЕ СТЕКЛО
- РАССТАНОВКА ЖЕЛЕЗНОДОРОЖНЫХ СИГНАЛОВ
Смотреть что такое «РАССЛОЕНИЕ МЕТАЛЛА» в других словарях:
расслоение — Дефект сплошности металла в виде трещин, параллельных поверхности проката, образовавшихся от повышенной загрязненности металла неметаллическими включениями. [РД 01.120.00 КТН 228 06] расслоение Дефект поверхности в виде трещин на кромках и торцах … Справочник технического переводчика
Расслоение — – раств. свойство растворной смеси, характеризующее связность ее составляющих при вибрационных воздействиях. [ГОСТ 4.233 86] Расслоение – керам. слоистая структура черепка керамической плитки. [СТ СЭВ 3979 83] Расслоение –… … Энциклопедия терминов, определений и пояснений строительных материалов
расслоение (дефект проката черных металлов) — расслоение Дефект поверхности в виде трещин на кромках и торцах листов и других видов проката, образовавшихся при наличии в металле усадочных дефектов, внутренних разрывов, повышенной загрязненности неметаллическими включениями и при пережоге.… … Справочник технического переводчика
расслоение — 3.9 расслоение: Нарушение сплошности металла, ориентированное вдоль направления деформации. Источник: ГОСТ Р 52597 2006: Прутки латунные для обработки резанием на автоматах. Технические условия … Словарь-справочник терминов нормативно-технической документации
РАССЛОЕНИЕ — [exfoliation of tube] дефект, видимый на торце трубы, представляющий собой нарушение сплошности металла, не выходящее на поверхность и образующееся из за несвариваемости металла при наличии в нем грубой рыхлости, шлаковых включений, затонувших… … Металлургический словарь
расслоение — ГОСТ 21014 88 Расслоение Deutsch: Dopplung English: Delamination Français: Exfoliation Ндп. Раздвоение, Расслой, Расщепление, Следы усадочной рыхлости, Торцевой вырыв, Язык Дефект поверхности в виде трещин на кромках и торцах листов и других… … Металлургия. Терминология ГОСТ
Расслоение — Exfoliation Расслоение. Коррозия, которая распространяется параллельно к поверхности, обычно по границам зерен. Образующиеся продукты коррозии способствуют отделению слоев металла от основного материала, вызывая расслоение. Наиболее часто имеет… … Словарь металлургических терминов
Расслоение — Fibering Расслоение. Удлинение и выравнивание внутренних границ, вторичных фаз и включений в определенных направлениях, соответствующих направлению потока металла во время деформации. (Источник: «Металлы и сплавы. Справочник.» Под редакцией Ю.П.… … Словарь металлургических терминов
Расслоение — Lamination Расслоение. (1) Тип разрыва или неоднородности с разделением или ослаблением, обычно направленным параллельно рабочей поверхности металла. Может быть результатом усадки, швов, окалины, включений или сегрегации, вытянутых и направленно… … Словарь металлургических терминов
Расслоение — [lamination] 1. В твердых растворах не полное статистическое распределение атомов компонентов в узлах кристаллической решетки; выражается в преимущественно окружении атома атомами того же компонента. 2. Дефект проката в виде трещин на кромках и… … Энциклопедический словарь по металлургии
10 Дефекты сварки и нарушения непрерывности Причины и способы устранения
Дефекты сварки — Знаете ли вы, что как бы вы ни старались поддерживать порядок, в конце концов, ошибка все равно произойдет? Например, когда вы случайно едете в свой университетский городок или на работу, независимо от того, как часто вы проверяете состояние своего автомобиля, в один из этих дней он выйдет из строя.
Либо у вас лопнуло колесо, либо неисправна трансмиссия, либо даже внешние помехи, такие как аварии и получение штрафа от патрульного полицейского.Кажется, что есть сила природы, которая вмешивается, чтобы превратить вещи в беспорядок или хаос. Если вы так думаете, знайте, что вы не ошиблись.
Такое поведение природы называется энтропией — поведением, которое требует от нас дополнительных усилий, чтобы свести на нет тенденцию вещей к беспорядку и поддерживать ее в порядке. Вот почему вам нужно регулярно проверять свою машину и брать с собой дополнительные шины, куда бы вы ни пошли.
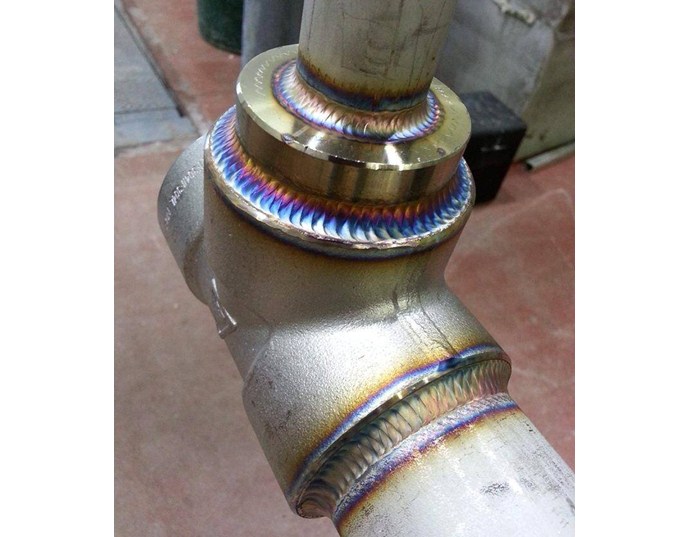
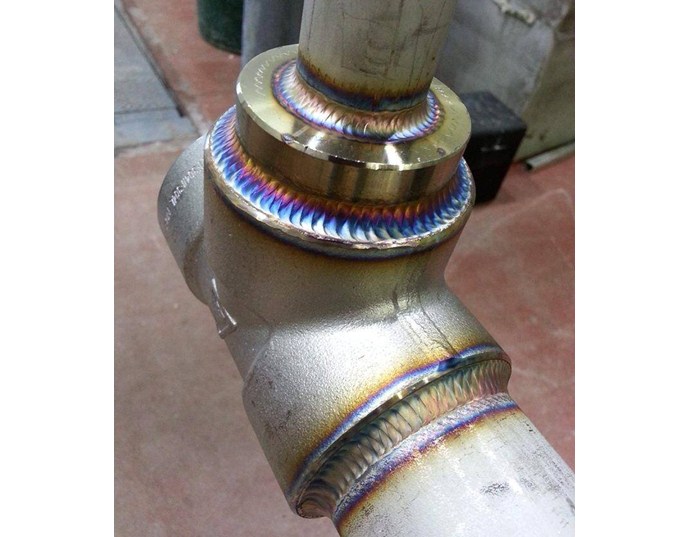
Та же сила природы распространяется и на сварной шов.Как сварщик, вы действительно хотите сварить прочный шов. Качественный сварной шов означает однородность (с очень небольшим допуском отклонений) везде, которую вы видите, будь то поверхность шва или подповерхность.
Надежный сварной шов — это лучшая форма сварного шва, он будет способен выдерживать расчетное напряжение, а это означает, что качество плавления металла шва и основного металла на высшем уровне. Однако энтропия также играет свою роль в распространении хаоса при сварке. Если сварщик ничего не знает и каким-то образом ошибается, это приведет к неравномерному сварному металлу.
Это неоднородное явление мы называем разрывом. Так что же такое несплошность и как предотвратить образование несплошностей при сварке? Эта статья даст вам четкое определение самой прерывности, что наверняка поможет вам как сварщику.
Что такое дефекты сварки?
Теперь мы знаем, что наличие несплошности означает, что сварная деталь не является прочной. По сути, существует две основные категории неоднородности, основанные на нанесенном им повреждении материала.
- Устранение дефектов.
Как следует из названия, нарушение сплошности в этой категории считается безопасным для материала, и простое действие по ремонту могло бы решить проблему. Большинство механических повреждений, таких как; царапины, вмятины и даже поверхностная коррозия подпадают под эту категорию, за исключением огромной вмятины, потому что вы каким-то образом находите способ уронить на нее огромный бетонный блок. Во время сварки несплошностей, таких как; пористость, включение шлака и поднутрение можно назвать несплошностью или дефектом.
Даже тогда, когда этот тип прерывистости весьма допустим. Для вас мудро всегда избегать этого, чтобы тренировать свой ум, чтобы делать что-то изо всех сил. Так что, когда вам придет время заняться работой с более строгими требованиями о прерываниях, вы будете готовы. - Непоправимый разрыв.
В некоторых случаях нарушение сплошности может сильно повлиять на качество сварки. Разрывы, такие как отсутствие плавления, ламинарный разрыв и большинство форм трещин, являются одними из них.Как бы вы ни старались отремонтировать его, вы только потратите впустую свое время и ресурсы, и это не стоит суеты. Поэтому лучше всего сразу же избежать этого, соблюдая правильную процедуру сварки.
Как бороться с дефектами?
Поскольку существует так много форм нарушения непрерывности, существует также множество способов их устранения. Чтобы упростить задачу, давайте поговорим об этом по порядку.
Дефекты сварки:
Здесь объясняются типы дефектов сварки, их изображения, причины и способы устранения.
1. Пористость.
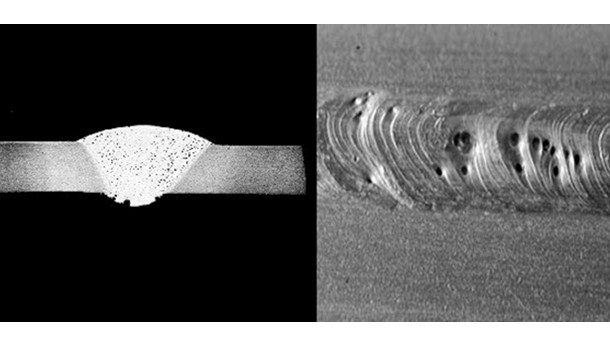
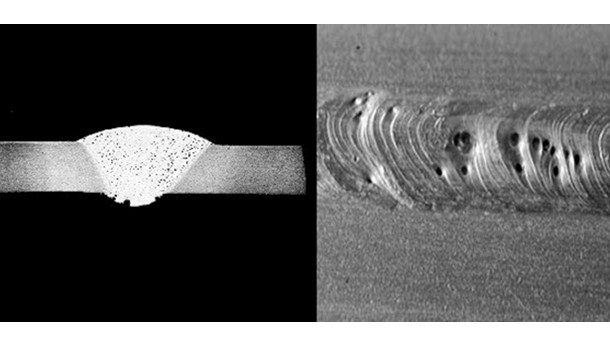
Пористость — одна из классических неоднородностей, возникающих при сварке. Это случается, когда во время сварки внутри оказывается слишком много молекул газа. Эти газы могут исходить от влажного электрода, потому что молекулы воды на электроде будут растворяться из-за высокой температуры сварки, что приведет к образованию захваченного кислорода, который никогда не выходит наружу, пока сварочная ванна не станет твердой.
Ветерок также может способствовать образованию пористости, поскольку ветер нарушает защитную среду вокруг сварочной дуги и позволяет газам проникать в расплавленный металл.Этой пористости можно легко избежать, избегая контакта с влажной средой во время сварки и убедившись, что сварочная ванна должным образом защищена либо флюсом, либо газовой защитой, либо обоими. Несколько методов исследования могут обнаружить пористость, например: визуальный осмотр, жидкий пенетрант, рентгенографическое исследование и т. д.
Причины:
- Воздух в защитном газе.
- Флюс в электроде влажный.
- Слишком большое расстояние для дуговой сварки.
- В процессе сварки, в котором используется защитный газ, скорость потока слишком высока, поэтому может возникнуть турбулентность.
Профилактика:
- Используйте электрод в хорошем состоянии (сухой), иначе корпус электрода не сломан.
- Очистить поверхность материала от масла и других загрязнений.
- Необходимо уменьшить длину дуги в соответствии с процедурой сварки.
- Используйте расход газа, соответствующий спецификации процедуры сварки.
2. Шлаковые включения.


Вкрапления шлака также являются одним из классических нарушений сплошности, возникающих при сварке.Это ситуация, когда шлак — защитный слой, который должен восстанавливать поверхность и защищать расплавленную сварочную ванну — задерживается под геометрией самого сварного шва.
Захваченный шлак заменяет предполагаемый металл сварочного шва куском оксида марганца (может отличаться), который, когда вы его откалываете, оставляет отверстие незащищенным, что делает его бесполезным. Различные факторы могут вызвать включение шлака, грязную поверхность сварного шва, и предполагается, что использование относительно низкого параметра сварки является основной причиной.Обнаруживается визуально, но наличие подповерхностных включений шлака может быть обнаружено только при рентгенографическом или ультразвуковом исследовании.
Причины:
- При очистке шлак в промежуточном проходе не очищается.
- Сварочный шлак сначала плавится перед сварочной дугой.
- Сварочный шлак в сварочной ванне.
Способы устранения:
- Убедитесь, что все проходы чистые.
- Чтобы предотвратить включение шлака, убедитесь, что угол электрода правильный.
3. Дефект сварки с подрезкой.
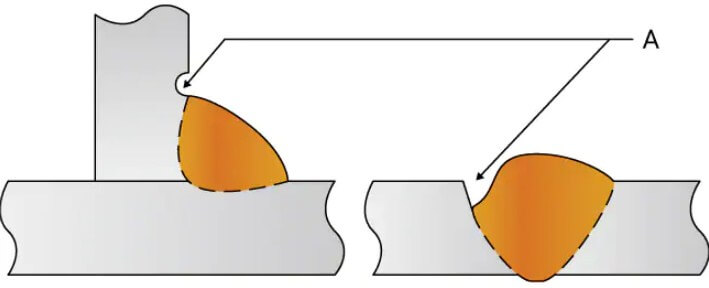
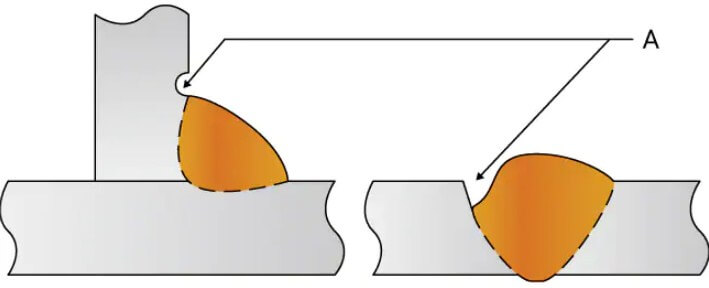
Поднутрение — одна из классических вещей, наряду с включениями шлака и пористостью, которые чаще всего встречаются при сварке. В первую очередь это происходит из-за того, что сварщик совершил плохой маневр, когда дуга расплавляет край ванны, не заполняя ее должным образом.
Хотя это выглядит крошечным, поднутрение может быть одним из источников первоначальной трещины, которая в дальнейшем будет распространяться и разрушать материал. Чтобы избежать этого, старайтесь избегать использования слишком высоких параметров сварки при равномерном перемещении вдоль сварного шва, чтобы избежать слишком быстрого перемещения.Поднутрения обычно представляют собой дефекты поверхности, поэтому их легко обнаружить визуально. Пенетрантная жидкость и исследование магнитных частиц также могут помочь обнаружить его.
Причины Дефект сварки с подрезом:
- Сварщик некомпетентен при плетении электрода.
- Угол электрода неправильный.
- Слишком высокий сварочный ток.
- Неправильный выбор защитного газа при использовании процесса MAG.
Предотвращение:
- Необходимо уменьшить сварочный ток.
- Используйте многопроходную сварку в горизонтальном положении.
- Уменьшите ширину плетения или перейдите на сварку в несколько проходов.
- При использовании процесса сварки MAG можно смешивать состав газа в соответствии с толщиной материала.
4. Трещины.
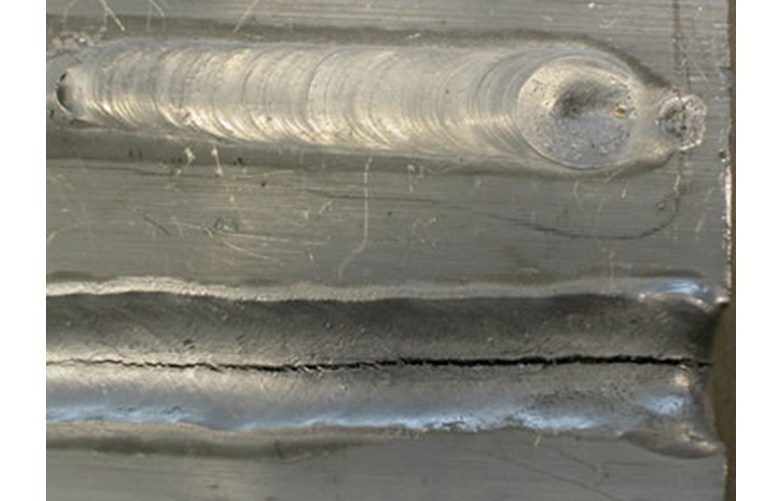
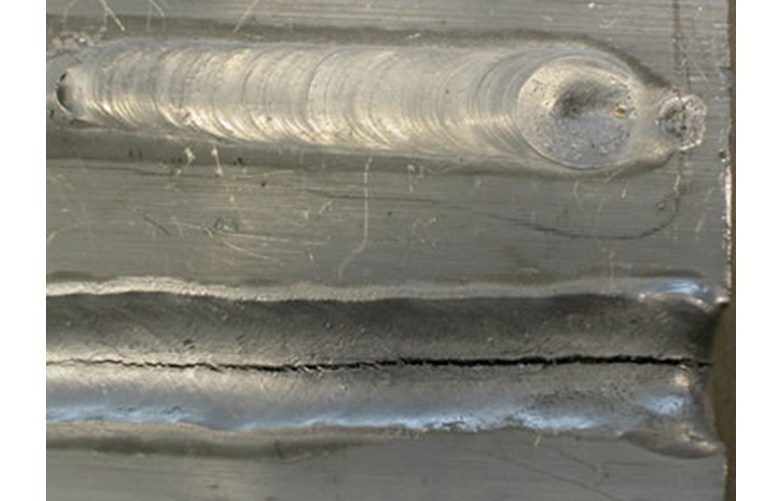
Хотя существует множество причин, по которым может возникнуть трещина, трещина также может возникнуть во время сварки, поэтому стоит упомянуть об этом. Трещина очень опасна, потому что она значительно снижает прочность материала и будет распространяться по пути при нагрузке на материал.
Поэтому полную процедуру ремонта следует проводить сразу же после обнаружения трещины любым методом исследования (рентгенография, проникающая жидкость и магнитные частицы). Некоторые трещины могут возникнуть во время несварочного процесса, например, разрыв пластин. А трещины, такие как горячие и холодные, возникают в основном из-за сварки.
В горячих трещинах трещины возникают из-за присутствующих ранее загрязнителей, таких как; сера и фосфор внутри основного металла. Эти загрязнения образуют карбид, который имеет более низкую температуру плавления, чем сам основной металл.Когда тепло от сварки сильно увеличивает температуру, эти карбиды плавятся и снижают прочность материала.
В сочетании с нагрузкой на материал он ломается и быстро распространяется, даже не дожидаясь, пока материал остынет. Отсюда и название «горячая трещина». Заказ обработанного материала может значительно снизить вероятность возникновения горячих трещин, или простое регулирование температуры между проходами также может работать.
Другое дело происходит с холодной трещиной, основная причина — высокая концентрация водорода вокруг металла шва.Когда металл сварного шва горячий, водород из окружающей среды может попасть в металл посредством диффузии. Этот атом водорода будет в основном находиться в ЗТВ (зоне теплового воздействия), где кристаллы наиболее восприимчивы из-за своей крупности.
Наличие водорода превращает материал в хрупкое состояние, которое постоянно создает внутреннее напряжение вплоть до точки разрушения. Этот процесс занимает столько времени, что его критический момент наступит даже тогда, когда все уже остынет.Отсюда и название холодная трещина. Чтобы избежать этого, очень поможет использование электрода с низким содержанием водорода, а также выполнение PWHT (послесварочная термообработка) может снизить остаточное напряжение, а также позволит уйти водороду.
5. Включения вольфрама.
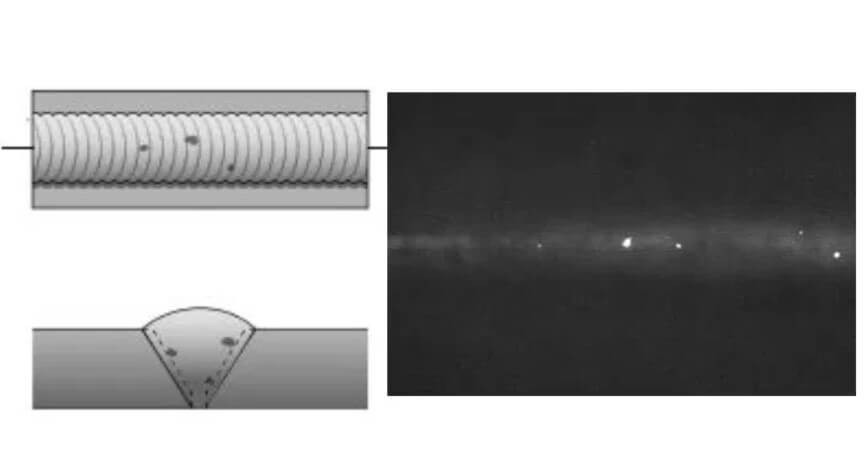
Причины включения вольфрама:
- Вольфрамовый электрод находится в контакте со сварочной ванной во время процесса сварки.
- Горячий вольфрамовый электрод контактирует с присадочным металлом.
- Возникла трещина в вольфрамовом электроде.
- Использование сварочного тока превышает максимально допустимую температуру вольфрамовых электродов.
Способы устранения:
- Держите конец электрода на расстоянии от сварочной ванны.
- Убедитесь, что состояние электрода хорошее для использования или на нем нет трещин.
- Используйте сварочный ток в соответствии с максимальной температурой электрода.
- Не допускайте контакта горячего электрода с присадочным металлом
6.Неполное проникновение.
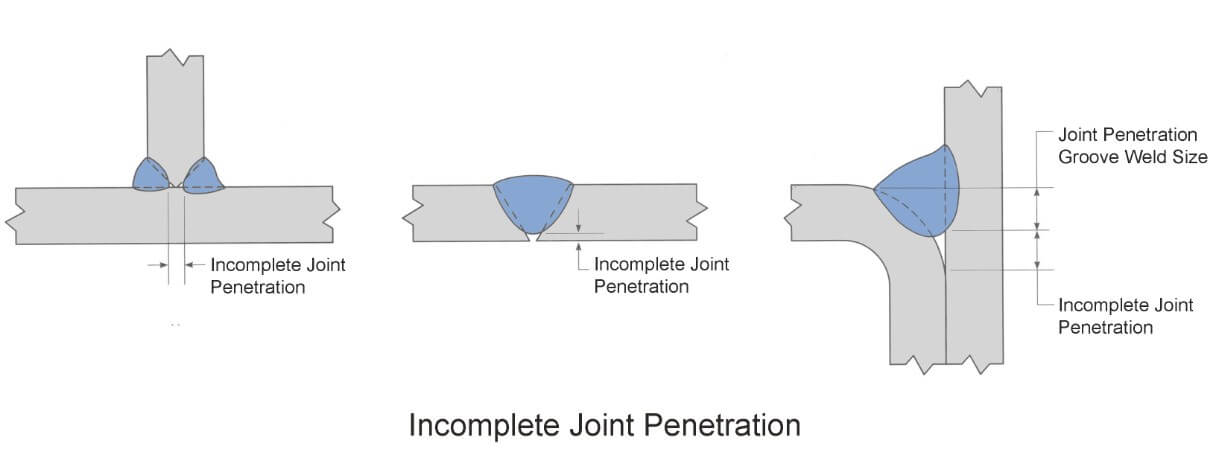
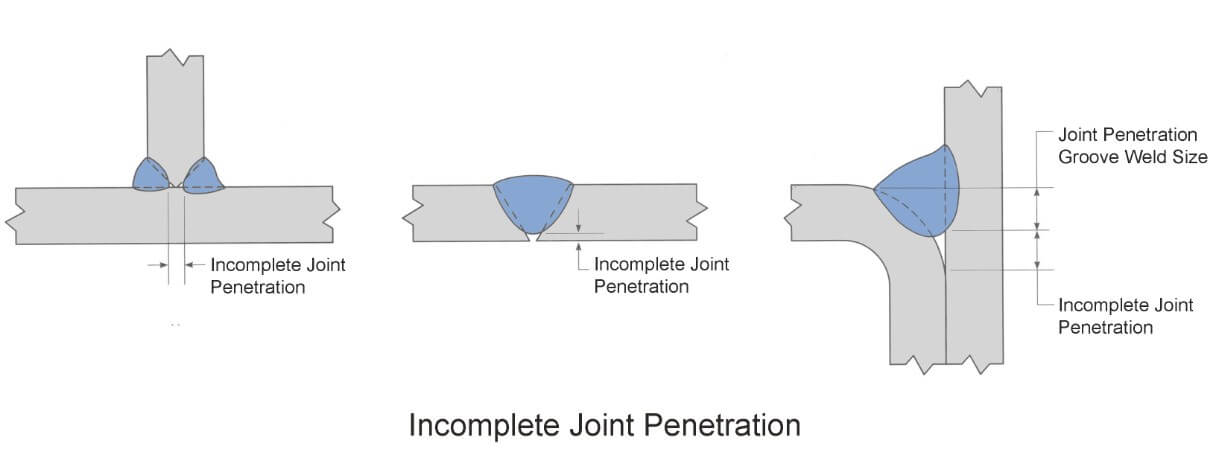
Сварочные дефекты возникают в корневой зоне сварного шва.
Причины:
- Меньший сварочный ток.
- Неправильное положение электрода.
- Слишком быстрое движение электрода, а также слишком большой диаметр электрода.
Профилактические:
- Вы должны увеличить сварочный ток, соответствующий сварочной процедуре.
- Используйте электрод правильного диаметра, соответствующий толщине материала.
7. Чрезмерные брызги.


Брызги можно удалить путем измельчения или удара молотком. Причина этого дефекта в том, что слишком большой ток и слишком сильная сварочная дуга.
Причины:
- Сварочный ток слишком велик.
- Слишком большое расстояние дуги между электродом и деталью.
- Электрод из влажного флюса.
- Газовая защита в процессе GMAW 100 CO2.
Профилактические:
- Используйте правильный сварочный ток (см. WPS).
- Необходимо уменьшить длину дуги.
- Перед использованием электрод необходимо просушить в духовке.
- Смешивание защитного газа CO2 с Ar.
8. Искажения.


Деформация, вызванная чрезмерным подводом тепла, из-за которой материал претерпевает изменение угла.
Причины Деформация:
- Неправильная подготовка к сварке, начало с неправильного прихваточного шва.
- Неправильная последовательность сварки.
Способы устранения Деформация:
- Перед сваркой убедитесь, что соединяемый материал прямой, а прихваточный шов прочный.
- У вас должна быть квалифицированная последовательность сварки.
9. Удар дуги.


Дуговой разряд — это тип сварочных дефектов, возникающих в материале и прилегающих к металлу шва. Потому что сварщики случайно коснутся электродом области заготовки, что приведет к возникновению дуги.
Причины дефектов дуговой сварки:
- Доступ к сварочной канавке затруднен.
- Отслаивается покрытие электрододержателя.
- Неправильная установка держателя электрода.
- Зажим на основном металле плохой.
Предотвращение:
- Доступ к сварке должен быть проще.
- Периодически проверяйте электрододержатель.
- Обеспечивает место для установки электрододержателя.
10. Прогорание.
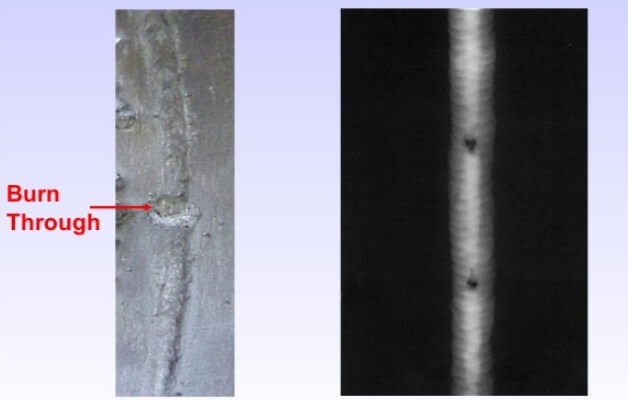
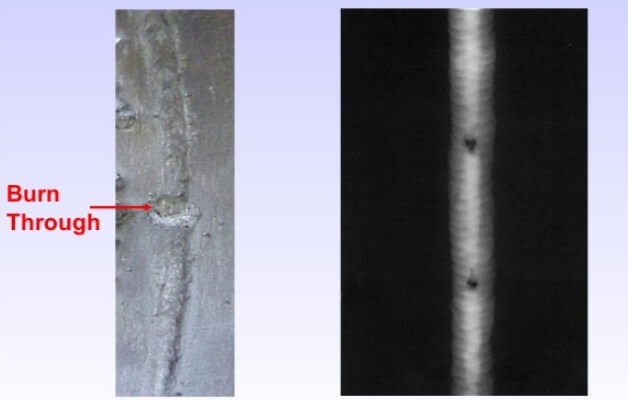
Это происходит в корне сварного шва, такой формой сварочного дефекта является отверстие.
Причины перегорания:
- Слишком большой сварочный ток.
- Корневая поверхность и корневой зазор слишком большие.
- Сварщик некомпетентный.
Способы устранения:
- Чтобы установить правильный сварочный ток, обратитесь к разделу «Процедура сварки».
- Необходимо увеличить скорость сварочного хода.
- Подготовка к сварке должна быть правильной, вы можете посмотреть процедуру сварки, чтобы установить правильный размер корневого зазора и поверхности корня.
- Сварщики должны быть обучены.
См .: Определение сварки и история
Заключение
После того, как мы узнаем, что существует слишком много переменных, которые могут вызвать прерывание.Просто невозможно избежать каждого из них, поэтому время от времени совершать ошибки вполне нормально, если мы знаем, как с ними бороться.
Однако это не означает, что мы должны принимать вещи как должное. Мы, несомненно, можем сделать все возможное, чтобы избежать столь частых ошибок, если будем стремиться. Вот что мы должны делать, чтобы бороться с энтропийной силой природы, стремясь к совершенству.
.Типы разрывов — Учебные материалы для IIT JEE
Мы уже обсуждали концепцию ограничений и непрерывности в предыдущих разделах.Пределы, непрерывность и дифференцируемость являются строительными блоками дифференциального исчисления. Они закладывают основу для всех остальных тем.
Функция f (x) называется непрерывной при x = a, если
lim x → a — f (x) = lim x → a + f (x) = f (a).
Таким образом, в отличие от пределов, для непрерывности важно, чтобы функция определялась в этой конкретной точке, а предельное значение функции должно быть равно f (a).
Функция f (x) будет разрывной при x = a в любой из следующих ситуаций:
1.lim x → a — f (x) и lim x → a + f (x) существуют, но не равны.
2. lim x → a — f (x) и lim x → a + f (x) существуют и равны, но не равны f (a).
3. f (a) не определен.
4. По крайней мере, один из ограничений не существует.
Важные моменты
|
Могут быть разные типы несплошностей. В приведенной ниже таблице показаны основные типы несплошностей:
Теперь мы подробно обсудим каждый из этих разрывов один за другим вместе с различными примерами:
Съемный разрыв
В случае устранимой несплошности предел функции i.е. lim x → a f (x) обязательно существует, но проблема в том, что оно либо не равно значению функции в «a», то есть f (a) или f (a) не определено. Однако, следовательно, можно переопределить функцию таким образом, чтобы предел равнялся значению функции в этой конкретной точке, то есть lim x → a f (x) = f (a).
Теперь устраняемый разрыв можно разделить на разрыв с отсутствующей точкой и разрыв с изолированной точкой.
Иллюстрация:
Переопределите функцию f (x) = [x] + [-x] так, чтобы она стала непрерывной для x ∈ (0, 2).
Решение:
Здесь lim x → 1 f (x) = -1, но f (a) = 0
Следовательно, f (x) имеет устранимый разрыв при x = 1.
Чтобы удалить это, мы определяем f (x) следующим образом
f (x) = [x] + [-x], x ∈ (0, 1) U (1, 2)
= -1, х = 1.
Теперь f (x) непрерывна при x ∈ (0, 2).
Недостающая точка Обрыв
Разрыв называется типом отсутствующей точки, если предел функции существует в точке «a», но функция не определена в этой точке, т.е.е. lim x → a f (x) существует, но f (a) не определено.
Рассмотрим функцию f (x) = (x 2 — 4) / (x — 2), где x ≠ 2.
Из графика, а также из определения функции видно, что f (2) не определена и, следовательно, f (x) имеет недостающую точку разрыва при x = 2.
Разрыв изолированной точки
При этом типе разрыва не только предел функции существует в конкретной точке, но функция также определена в этой точке, но оба они не равны, т.е.е. lim x → a f (x) существует, но lim x → a f (x) ≠ f (a).
Пример: рассмотрим функцию
f (x) = sgn (cos 2x — 2sin x + 3) = sgn (2 (2 + sin x) (1 — sin x)) = 0, если x = 2nπ + π / 2
= +1, если x ≠ 2nπ + π / 2
имеет изолированную точку на разрыве x = 0 как x = 2nπ + π / 2.
Просмотрите следующее видео о типах несплошностей:
Несъемный разрыв
Говорят, что функция обладает неустранимым разрывом, если предел функции не существует.Таким образом, поскольку lim x → a f (x) не существует, невозможно каким-либо образом переопределить функцию, чтобы сделать ее непрерывной. Несъемные несплошности можно разделить на три группы:
(a) Конечный тип :
В несплошности этого типа существуют и левая, и правая границы, но они не равны. Рассмотрим некоторые примеры в этом контексте:
(1) lim x → 0 tan -1 (1 / x), теперь рассмотрим пределы
f (0 + ) = π / 2
f (0 — ) = — π / 2
Следовательно, скачок в этом случае равен π.
(2) lim x → 0 | sin x | / x
f (0 + ) = 1
f (0 — ) = — 1
Следовательно, скачок в данном случае равен 2.
Неотрицательная разница между двумя пределами называется скачком разрыва .
Иллюстрация :
Рассмотрим f (x) = [x], где [x] наибольшее целое число Решение: Рассмотрим x = 1.Где I — какое-то целое число RHL = lim x → 1 + f (x) = 1 и LHL = lim x → a — f (x) = 1-1 Следовательно, и RHL, и LHL — конечные действительные числа, но они не равны. ______________________________________________________________ Функция, имеющая конечное число скачков на заданном конечном интервале, называется кусочно-непрерывной функцией. (b) In конечный тип : Разрыв считается бесконечным, если хотя бы один из двух пределов бесконечен.Проиллюстрируем эту концепцию на следующих примерах: (1) f (x) = x / (x — 1) при x = 1 f (1 + ) = — ∞ f (1 — ) = + ∞ (2) f (x) = x / (x — 1) при x = 0 f (0 + ) = ∞ f (0 — ) = ∞ (c) Колебательный : Разрыв называется колебательным, когда пределы колеблются между двумя конечными величинами. В случае тригонометрических функций, скажем, f (x) = cos 1 / x или sin 1 / x, при x = 0 предел колеблется между -1 и 1. Теперь обсудим некоторые иллюстрации, основанные на обсуждаемых концепциях: Функция f (x) = [журнал (1 + ax) — журнал (1 — bx)] / x не определен при x = 0. Значение, которое должно быть присвоено f при x = 0, чтобы оно было непрерывным при 0, равно…? (IIT JEE 1983) (а) а-б (б) а + б (c) log a + log b (d) Ни один из этих Мы знаем, что для непрерывности функции f необходимо иметь f (0) = lim x → 0 f (x) = lim x → 0 [log (1 + ax) — log (1 — bx)] / x = lim x → 0 a [log (1 + ax) / ax + b log (1 — bx)] / -bx = а.1 + b.1 = a + b (поскольку f (0) = a + b). _____________________________________________________________________ Функция f (x) = [x] 2 — [x 2 ] не является непрерывной в (IIT JEE 1999) (a) все целые числа (б) все целые числа, кроме 0 и 1 (c) все целые числа, кроме 0 (d) все целые числа, кроме 1 Этот вопрос основан на наибольшей целочисленной функции.Мы знаем, что все целые числа являются критическими точками для наибольшей целочисленной функции. Случай 1: Когда x ∈ I f (x) = [x] 2 — [x 2 ] = x 2 –x 2 = 0 Случай 2: Когда x не принадлежит I Если 0 И 0 Далее, если 1 ≤ x 2 <2 Тогда 1 ≤ x <√2 Итак, [x] = 1 и [x 2 ] = 1 Следовательно, f (x) = [x] 2 — [x 2 ] = 0, если 1 ≤ x <√2 Следовательно, f (x) = 0, если 0 ≤ x <√2 Это показывает, что f (x) непрерывна при x = 1. Следовательно, f (x) разрывна в (-∞, 0) ∪ [√2, ∞) во многих других точках. 1 кв. Что из следующего неверно в случае прерывистой функции? (a) lim x → a — f (x) и lim x → a + f (x) существуют, но не равны. (b) lim x → a — f (x) и lim x → a + f (x) существуют и равны, но не равны f (a). (c) f (a) не определен. (d) ни один из этих 2 кв. Какие из следующих функций являются непрерывными в своей области? (а) полиномиальные, экспоненциальные и логарифмические функции (b) сигнум-функция (c) сигнум и полиномиальные функции (d) ни один из этих 3 кв. Произведение непрерывной и прерывистой функции: (а) обязательно непрерывный (b) может быть или не быть прерывистым (в) обязательно прерывистая (d) ни один из этих 4 кв.Удаляемый разрыв может быть дополнительно классифицирован как (а) отсутствующая точка и колебательный разрыв (б) изолированная точка и смешанный разрыв (c) отсутствие точки и разрыв изолированной точки (d) неоднородность смешанного типа и неоднородность отсутствующей точки Q5. Какие из следующих утверждений верно? (а) прерывность подразумевает невозможность вывода (b) непрерывность подразумевает выводимость (c) невозможность вывода подразумевает разрыв (d) ни один из этих 1 кв. 2 кв. 3 кв. 4 кв. Q5. (г) (а) б) (в) (а) Чтобы узнать больше, купите учебные материалы по номеру Limtis and Continuity , включая примечания к исследованию, примечания к пересмотру, видеолекции, решенные вопросы за предыдущий год и т. Д.Также просмотрите дополнительные учебные материалы по математике здесь . Не все дефекты сварного шва являются дефектами сварного шва, но все дефекты сварного шва являются несплошностями. Понимание разницы позволит вам узнать, нужно ли выбросить деталь, отремонтировать ее или просто добавить сварной шов. Есть много кодов в зависимости от того, на каком типе продукта вы свариваете. Коды используются производителями в качестве руководства для написания собственных спецификаций. Только потому, что определенный Кодекс допускает определенную пористость, производитель может не допускать ее наличия у своих поставщиков. Рентгеновский снимок испытания алюминиевого шва с разделкой кромок. Поверхность не показала пористости. Темные пятна представляют собой пустоты (пористость) и кажутся темными из-за областей с меньшей плотностью. Пористость не всегда присутствует на поверхности сварного шва. Чтобы избежать пористости, необходимы соответствующая газовая защита, чистый основной металл и надлежащая процедура сварки. Большинство дефектов в списке ниже можно обнаружить визуально. Визуальный осмотр — самый простой и наименее затратный из всех методов неразрушающего контроля.Инструменты, необходимые для визуального осмотра, немногочисленны и недороги. Такие инструменты, как линейки, сварочные щупы и увеличительное стекло — это почти все, что вам нужно. Очень важно, чтобы контроль сварных швов проводился до, во время и после сварки. Несплошность сварного шва — это дефект в сварном шве. Как указано выше, несплошности не обязательно являются дефектами сварного шва. Они становятся дефектами сварного шва, когда превышают указанные максимальные значения кодекса или требований заказчика. Это означает, что у вас могут быть несплошности сварного шва, но при этом он останется приемлемым.Однако мы всегда хотим, чтобы сварные швы были без разрывов, когда это возможно. Ниже приведены 10 наиболее распространенных типов несплошностей сварных швов. Это не полный список всех возможных неисправностей. 1. Пористость — Полости в сварном шве, вызванные захваченным газом во время затвердевания металла шва. Распространенными причинами являются отсутствие защитного газа, чрезмерная длина дуги или грязный основной материал. Другой не столь распространенной причиной может быть дуга, когда магнитные поля вызывают неустойчивую дугу.По нормам или спецификациям производителя может присутствовать пористость, но каждое отдельное отверстие не должно превышать определенной длины, а общая длина всех отверстий не может превышать определенного значения на дюйм сварного шва. Пористость может быть вызвана многими причинами, начиная от недостатка защитного газа и заканчивая загрязнением цветными металлами. 2. Отсутствие Fusion — также называется непровар или холодный притир. Отсутствие сплавления относится к основному материалу, который не сплавлен должным образом с другой деталью или самим металлом сварного шва.Это вызвано слишком низкими параметрами сварки. Хотя это не может быть обнаружено после сварки, по крайней мере, непросто, сварщик сам может увидеть это во время сварки. Обученный сварщик сможет определить, правильно ли дуга проникает в основной материал. Отсутствие сплавления визуально не обнаруживается. На изображении выше показан макротекст углового сварного шва, демонстрирующий отсутствие проплавления корня. 3. Поднутрение — Это бороздка, которая появляется на одном из обоих пальцев сварного шва.Это вызвано отсутствием заполнения. Отсутствие наполнения может быть связано с чрезмерным напряжением или слишком низкой скоростью подачи проволоки. Также может быть вызвано неправильной техникой сварки. Как и в случае с пористостью, может быть приемлемо некоторое поднутрение. Выточка создает механическую выемку, которая действует как концентратор напряжения. Это также уменьшает полезную площадь основного металла. На изображении выше также показано перекрытие (нижняя кромка сварного шва). 4. Неправильное размещение валика — Как видно из названия, эта неоднородность возникает, когда сварной шов находится не в правильном месте.Это может означать полное отсутствие стыка или отсутствие равных участков углового шва. Неправильное размещение валика может быть дефектом сварного шва, если корень отсутствует или если наименьший размер ножки не соответствует минимуму спецификации. 5. Брызги — Это маленькие капли сварочного металла, которые покидают дугу и падают на прилегающий основной материал, сплавляясь с ним. Брызги не являются дефектом сварного шва, но, опять же, максимально допустимые значения указаны в спецификации заказчика. Брызги возникают из-за неправильных процедур сварки, включая силу тока, вольт, скорость сварки, ход и рабочие углы и даже использование защитного газа. Подробнее о брызгах читайте: 7 причин появления брызг при сварке и способы их устранения Брызги не влияют на структурную целостность сварного шва в большинстве случаев, но почти всегда их необходимо удалять, увеличивая общую стоимость. 6. Неверный размер сварного шва — Это может быть слишком большой или слишком маленький сварной шов. Хотя большие сварные швы предпочтительнее небольших сварных швов, иногда все же иметь большой сварной шов вредно из-за чрезмерного тепловложения, сварочных напряжений и деформации.На размер сварного шва влияют скорость перемещения и процедуры сварки, особенно скорость подачи проволоки. Его легко измерить с помощью сварочных манометров. 7. Включения шлака — Это шлак, застрявший между проходами. Это невозможно обнаружить с помощью проверки сварного шва после завершения сварки и очень трудно обнаружить во время сварки. Причины — недостаточная очистка поверхности шва между проходами. Это также может происходить в однопроходных сварных швах, когда шлак попадает в корень и концы сварного шва. Сварочные процессы, такие как SMAW и FCAW, подвержены образованию шлаковых включений. Включения шлака препятствуют правильному плавлению и могут иметь острые концы, что создает трещиноподобное поведение. 8. Чрезмерное усиление — Это сварной шов, который слишком большой или имеет слишком большую выпуклость (слишком много наростов). Обычно вызвано низкой скоростью движения или неправильными процедурами. Чрезмерное армирование создает высокие уровни концентрации напряжений на носках сварного шва. 9. Насквозь — Это происходит, когда сварочные процедуры и / или техника обеспечивают слишком большой проплавление и металл выходит из задней части соединения. Растекание прихваточного шва на тонком материале. Это не просто тепловая отметка, это металл, выступающий из поверхности основного металла. 10. Трещины — Трещины являются наиболее разрушительным нарушением целостности сварного соединения. Трещины в любом количестве будут считаться дефектом за очень немногими исключениями.Одно из этих исключений — трещины из-за снятия напряжений в наплавленных швах. Трещины имеют острые концы, что позволяет им разрастаться, в некоторых случаях очень быстро. Для дальнейшего объяснения вы можете прочитать «Понимание причин появления трещин при сварке швов». Трещины могут привести к катастрофическому отказу за относительно короткий промежуток времени. Допустимое количество описанных выше дефектов, если таковые имеются, будут определять нормы, стандарты и спецификации сварки. Нормы касаются структурной целостности сварных швов, а не столько эстетики.Таким образом, некоторые производители будут иметь внутренние стандарты качества, которые не допускают разбрызгивания или уменьшают допустимое количество других дефектов. Критерии приемки сварочных норм должны использоваться как минимум. Артикул: Руководство для производителей и монтажников стальных сварных конструкций Сварка, металлургия и свариваемость, Джон К. Липпольд The Moho: Изображение внутренней структуры Земли, сделанное Геологической службой США — разрыв Мохоровича (красная линия) добавлено Geology.com. Разрыв Мохоровича или «Мохо» — это граница между корой и мантией. Красная линия на схеме показывает его расположение. В геологии слово «разрыв» используется для обозначения поверхности, на которой сейсмические волны меняют скорость.Одна из этих поверхностей существует на средней глубине 8 километров под океаническим бассейном и на средней глубине около 32 километров под континентами. На этом разрыве сейсмические волны ускоряются. Эта поверхность известна как разрыв Мохоровича или ее часто называют просто «Мохо». Разрыв Мохоровичич был открыт в 1909 году хорватским сейсмологом Андрией Мохоровичичем.Мохоровичич понял, что скорость сейсмической волны связана с плотностью материала, через который она движется. Он интерпретировал ускорение сейсмических волн, наблюдаемых внутри внешней оболочки Земли, как изменение состава внутри Земли. Ускорение должно быть вызвано наличием на глубине материала с более высокой плотностью. Материал с более низкой плотностью, находящийся непосредственно под поверхностью, теперь обычно называют «земной корой». Материал с более высокой плотностью под корой стал известен как «мантия Земли».«Путем тщательных расчетов плотности Мохоровичич определил, что базальтовая океаническая кора и гранитная континентальная кора подстилаются материалом, который имеет плотность, аналогичную плотности богатой оливином породы, такой как перидотит. Карта толщины земной коры: Толщина земной коры, составленная Геологической службой США — поскольку Мохо находится в основании коры, на этой карте также показана глубина до Мохо. Разрыв Мохоровичича отмечает нижнюю границу земной коры.Как указано выше, это происходит на глубине , средней , примерно в 8 км под океанскими бассейнами и в 32 км под поверхностью континентов. Мохоровичич смог использовать свое открытие для изучения изменений толщины коры. Он обнаружил, что океаническая кора имеет относительно однородную толщину, в то время как континентальная кора наиболее толстая под горными хребтами и тоньше под равнинами. Карта на этой странице показывает толщину земной коры.Обратите внимание, как самые толстые области (красные и темно-коричневые) находятся под некоторыми важными горными цепями Земли, такими как Анды (западная сторона Южной Америки), Скалистые горы (западная часть Северной Америки), Гималаи (север Индии в южной и центральной Азии), и Урал (тренд с севера на юг между Европой и Азией). Мантийная порода на поверхности: Ордовикский офиолит в национальном парке Грос Морн, Ньюфаундленд, Канада. Древняя мантийная порода обнажена на поверхности. (Образ лицензии свободной документации GNU). Никто никогда не был достаточно глубоко под землей, чтобы увидеть Мохо, и никогда не было пробурено достаточно глубоких скважин, чтобы проникнуть в него. Бурение скважин на такую глубину очень дорого и очень сложно из-за экстремальных условий температуры и давления. Самая глубокая скважина, пробуренная на сегодняшний день, находится на Кольском полуострове Советского Союза. Его пробурили на глубину около 12 километров. Бурение до Мохо через океаническую кору также не увенчалось успехом. Есть несколько редких мест, где материал мантии был вынесен на поверхность тектоническими силами. В этих местах порода, которая раньше находилась в коре / мантии
граница присутствует. Фотография камня с одного из этих мест показана на этой странице. Рисунок 1:
Раствор:
Рисунок 2:
Раствор:
Связанные ресурсы Особенности курса
. Объяснение 10 типов неоднородностей при сварке
Mohorovicic Discontinuity — Мохо
Что такое разрыв Мохоровича?
Как был обнаружен Мохо?
Насколько глубокий Мохо?
Кто-нибудь когда-нибудь видел Мохо?
Найдите другие темы на Geology.com:
. Породы: Галереи фотографий вулканических, осадочных и метаморфических пород с описаниями. Минералы: Информация о рудных минералах, драгоценных камнях и породообразующих минералах. Вулканы: Статьи о вулканах, вулканических опасностях и извержениях прошлого и настоящего. Драгоценные камни: Цветные изображения и статьи об алмазах и цветных камнях. Общая геология: Статьи о гейзерах, маарах, дельтах, перекатах, соляных куполах, воде и многом другом! Geology Store: Молотки, полевые сумки, ручные линзы, карты, книги, кирки твердости, золотые кастрюли. Бриллианты: Узнайте о свойствах алмаза, его многочисленных применениях и открытиях.