Оборудование Алюмлит для литья алюминия, бронзы
Компания Алюмлит использует современное оборудование на всех этапах работы. Мы отдаем предпочтение функциональному оборудованию, обладающему высокой надежностью и полностью соответствующему технологическим потребностям производства.
Плавка алюминиевых сплавов
Плавка алюминия для больших объемов заливки и для отливок массой более 120 кг осуществляется в плавильной тигельной поворотной печи ПП2000М
Максимальная загрузка: 490 кг по алюминию
Макс. температура расплава: 1100°С
Мощность: 92 кВт
Плавка алюминия для средних объемов заливки и литья единичных отливок массой 15 — 110 кг осуществляется в плавильной тигельной поворотной печи ПП450М
Максимальная загрузка: 200 кг
Макс. температура расплава: 1100°С
Мощность: 40 кВт
Плавка алюминия для средних объемов заливки и литья единичных отливок массой 15 — 100 кг осуществляется в индукционной плавильной печи ИПУ-150А-8ФТ
Макс.

Мощность: 84 кВт
Плавка алюминия для опытных партий и подогрев тиглей осуществляется в плавильной шахтной печи ППШ-60
Максимальная загрузка: 15 кг по алюминию
Макс. температура расплава: 950°С
Мощность: 21 кВт
Плавка медных сплавов
Плавка медных сплавов (бронзы, латуни) осуществляется в индукционной плавильной печи ИПУ-250М/160НГ
Максимальная загрузка: 300 кг по меди
Макс. температура расплава: 1400С
Мощность: 160 кВт
Приготовление холодно-твердеющей смеси (ХТС)
Приготовление смеси ХТС осуществляется в смесителе постоянного действия С-110
Производительность: 10 тонн смеси в час
Непрерывная подача смеси в форму
2 режима затвердевания форм
Уплотнение формовочной смеси осуществляется на вибростоле ВС-11-50
Размеры:2100*1250 мм
Регулируемая амплитуда вибрации
Термическая обработка алюминиевых сплавов
Закалка и старение отливок производятся в печи СНО 700/12-ВП
Размеры рабочего пространства: 1000х1200х640 мм
Макс. температура в рабочем пространстве: 1250°С
Мощность: 52 кВт
Старение отливок производится в печи НК 7.7.7/3,5 ИЗ
Размер рабочей камеры: 700х700х700 мм
Максимальная температура в рабочем пространстве: 350°С
Мощность: 6 кВт
Модельное производство
Изготовление оснастки небольших габаритов осуществляется на станке PureLogic PLRA1
Размер рабочей области: 930*630*180мм
Точность позиционирования: 0,01мм
Печать 3D макета для литья по выжигаемым и выплавляемым моделям и модельного комплекта осуществляется на 3D-принтере Designer XL PRO.
Область печати: 360х360х610 мм
Максимальная потребляемая мощность: 1300 Вт
Скорость печати: до 100 см3/ч
Механическая обработка
Токарная обработка осуществляется на универсальном станке 16к20
Максимальное сечение детали: 310 мм
Макс. вес детали: 1300 кг
Фрезерная обработка, сверление, расточные работы осуществляются на станке 6Р11
Рабочая поверхность стола: 1000х250 мм
Прямая и фигурная резка металла осуществляется на ленточной пиле
Возможность резки под углом
Максимальный диаметр обрабатываемой заготовки: 500 мм
Лаборатория
Измерение твердости производится твердомером ТБ 5015 Tochline
Измерение по шкале Бринелля 3-450 HB
Проводится контроль твердости на отдельно отлитых образцах и на отливках.
Для количественного спектрального анализа сплавов используется спектрометр ПАПУАС-4ДИ.
Рабочий спектральный диапазон: 185-410 нм
Контроль проводится на образцах-свидетелях.
Определение предела прочности формовочной смеси производится на специализированной разрывной машине.
Контроль производится на отдельных образцах смеси ХТС по утвержденной методике.
В технологическом процессе задействован ряд единиц вспомогательного оборудования, в том числе:
- грузоподъемное оборудование
- компрессоры
- муфельные печи
- оборудование для обрезки и зачистки
Все оборудование исправно работает и проходит все плановые мероприятия по техническому обслуживанию и ремонту.
По запросу возможен визит для ознакомления с возможностями производства.
Чтобы узнать больше, звоните +7 (495) 789-01-90
Высокоэффективная плавка алюминия с помощью STRIKOMELTER
High-Performance Melting of Aluminium with the Help of StrikoMelter®
StrikoMelter® metal foundry equipment has high efficiency due to introduction of differentiated heat energy consumption control system, reusability of such energy and the new conception of melting process with patented specially for StrikoMelter ® ETAmax® technology. There were also experiments and observation of StrikoMelter® equipment by StrikoWestofen GmbH specialists. All the results are presented in the article.
Оборудование типа StrikoMelter®, работающее по запантентованной технологии ETAmax® немецкой фирмы StrikoWestofen GmbH, представляет собой литейный агрегат, отвечающий всем требованиям современного плавильного производства. Подтверждением эффективности и высокой рентабельности StrikoMelter® служат характеристики литейных производств, где находятся в эксплуатации подобные установки.
Томас Платцер, дипломированный инженер, StrikoWestofen GmbH,
Вальдемар Хеннинг, доктор-инженер, Friedrich Giessereitechnik (Германия)
Высокие требования рынка и постоянно растущие цены на сырье и энергию все острее ставят перед предприятиями, выпускающими алюминиевое литье, вопрос достижения более эффективного выхода металла с помощью внедрения более совершенных технологий. Кроме того, важно достижение таких характеристик процесса, как высокая мощность плавки при низком расходе электроэнергии, действующие и перспективные требования по защите окружающей среды и охране труда, высокая эффективность, низкие расходы на техобслуживание и уход за оборудованием, а также длительный срок службы огнеупорной обшивки печи.
Установка для литья алюминия StrikoMelter® (рис. 1, 2) отвечает всем этим требованиям за счет внедрения дифференцированного управления расходом тепловой энергии горелки, возможности многократного использования этой энергии и инновационной концепции самой технологии плавки. Базовый принцип устройства работы оборудования — разделение пространства печи на три зоны: предварительного нагрева, плавки и выдержки, а также специально разработанная и запатентованная для StrikoMelter ® технология ETAmax®.
Горячий воздух от горелки, находящейся в зоне выдержки, способен использоваться несколько раз за счет того, что направляется сначала в зону плавки, а затем — в верхнюю зону предварительного подогрева. Кроме того, горячий газ, образующийся при плавке, выводится через зону подачи материала на плавку. Такая технология позволяет вести предварительную просушку и подогрев шихты перед ее поступлением в печь.
Данная концепция, в отличие от используемых в других печах, обеспечивает как значительную экономию потребляемого топлива, так и снижение потерь сырья.
Как правило, алюминий, поступающий на плавку, имеет очень хорошее металлургическое качество. Проблемой плавильного производства является сохранение этого качества и предохранение металла от загрязнения. Значительную опасность представляет влага, оксидирование кислородом воздуха, а также загрязние твердыми составляющими, например, изгарью.
Воздействие влаги, например, при хранении возвратного материала или чушек под открытым небом, значительно снижает качество сплава. Отрицательное влияние оказывает также повышение содержания водорода в сплаве. В StrikoMelter® эта проблема решается за счет испарения воды или влаги в зоне предварительного подогрева, в результате чего в зону плавки поступает безупречно просушенный материал. Кроме того, в StrikoMelter ® дополнительно снижается контакт расплавляемого металла с кислородом воздуха. Горелка в зоне плавки размещена таким образом, чтобы исключить непосредственный контакт «пламя — металл» и тем самым снизить образование оксидов. Алюминий плавится в самой нижней зоне плавильной шахты и затем самым коротким путем ламинарно стекает в ванну для выдержки. Изгарь и твердые осадки остаются в зоне плавки и затем удаляются из нее.
Дополнительным преимуществом двухкамерной концепции, предусматривающей отделение зон плавки и выдержки, является постоянная температура сплава в зоне выдержки (диапазон отклонения ± 5 °C). Данная конструкция гарантирует непрерывность плавки даже во время отбора жидкого металла.
Все описанное выше, а также применение автоматизированной системы загрузки позволяет практически достичь выхода металла на уровне более чем 98 %.
Опыт применения установки
Осенью 2005 г. специалистами компании StrikoWestofen GmbH проводились замеры параметров работы установки, работающей в цехе литья под давлением компании «В. Хессе & Ваукхаге» в г. Люденшайд (Германия). На этом производстве с 2001 г. используются две установки StrikoMelter® MH II-N 2000/1000 G-eg (рис. 3).
Основой замеров послужили следующие условия эксплуатации:
используемые сплавы: 231D, AlSi12Cu1(Fe) EN-AC 47100-239, EN-AC-43000;
заказчик — StrikoWestofen GmbH.
Материал: 50 % алюминиевых чушек весом по 5–7 кг, 50 % — сухой возвратный материал с незначительной частью вкраплений.
Примечание: в процессе использовалась специальная соль на плавильном мостике и на поверхности сплава.
Контролировался выход металла брутто и нетто. Выход металла брутто (соотношение загруженного металла к весу выпускаемой плавки) при плавке только чушек составил 99,75 %. При использовании 50 % чушек и 50 % возвратного материала эта величина составила 99,40 %.
Выход металла нетто зависит от остатка металла в ковше, который можно получить после дополнительной обработки изгари. Для этого ковш весом 300 кг взвешивался на прецизионных весах сначала с изгарью, а затем после удаления изгари.
В табл. 1 приведены результаты замера по выходу металла нетто, а также для сравнения — ранее проводимые замеры. Из этой таблицы видно, что во всех случаях потери металла составляют менее 1 %.
Таким образом, результаты замеров не только подтверждают низкие потери металла, но даже значительно превышают данные, приведенные в проспектах фирмы-изготовителя.
На базе замеров можно сделать расчет, результаты которого демонстрируют значительное преимущество установки типа StrikoMelter® (табл. 2).
Как видно из таблицы, увеличение выхода металла даже на 1 % дает годовую экономию в 158000 евро. А если учитывать, что по сравнению с печами старых конструкций StrikoMelter® обеспечивает экономию до 8 %, их внедрение позволит литейным производствам достичь значительно более высокой эффективности. Как показывает опыт, инвестирование в современные установки StrikoMelter® окупаются за 6–12 месяцев. Кроме того, технология ETAMAX® гарантирует существенную экономию за счет снижения расходов на элекроэнергию, а также процента брака отливок, что обусловлено высоким качеством сплава.
StrikoWestofen GmbH Fritz — Kotz –Str. 2-4 D — 51674 Wiehl
Tel + 49 / 2261 / 70 91-0 Fax + 49 / 2261 / 70 91- 107
sales@strikowestofen. com www. strikowestofen.com
FRIEDRICH Giessereitechnik Hauptstrasse 8 D- 73650 Winterbach
Tel: + 49 (0) 7181/6 06 96-0 Fax: + 49 (0) 7187/6 06 96-20
[email protected] www.globalactivities-fgt.de
Контакт на русском языке
Тел.: +49 (0) 7181/9 92 16-1 Факс: +49 (0) 7181/9 92 16-2
waldemar.henning@friedrich-fgt. de
Переплавка отходов литейных сплавов :: Технология металлов
В литейном производстве используют отходы собственного производства (оборотные ресурсы) и отходы, поступающие извне (товарные ресурсы). При подготовке отходов выполняют следующие операции: сортировку, сепарацию, разделку, пакетирование, обезвоживание, обезжиривание, сушку и брикетирование. Для переплава отходов используют индукционные печи. Технология переплава зависит от характеристик отходов — марки сплава, крупности кусков и т. д. Особое внимание необходимо уделять переплавке стружки.
АЛЮМИНИЕВЫЕ И МАГНИЕВЫЕ СПЛАВЫ.
Самую большую группу алюминиевых отходов составляет стружка. Ее массовая доля в общем количестве отходов достигает 40%. К первой группе отходов алюминия относят лом и отходы нелегированного алюминия;
во вторую группу — лом и отходы деформируемых сплавов с низким содержанием магния [до 0,8% (маc. доля)];
в третью — лом и отходы деформируемых сплавов с повышенным (до 1,8%) содержанием магния;
в четвертую — отходы литейных сплавов с низким (до 1,5%) содержанием меди;
в пятую — литейные сплавы с высоким содержанием меди;
в шестую — деформируемые сплавы с содержанием магния до 6,8 %;
в седьмую — с содержанием магния до 13%;
в восьмую — деформируемые сплавы с содержанием цинка до 7,0%;
в девятую — литейные сплавы с содержанием цинка до 12 %;
в десятую — остальные сплавы.
Для переплавки крупных кусковых отходов используют индукционные тигельные и канальные электропечи.
Размеры кусков шихты при плавке в индукционных тигельных печах не должны быть менее 8—10 см, так как именно при этих размерах кусков шихты происходит максимальное выделение мощности, обусловленное глубиной проникновения тока. Поэтому не рекомендуется проводить плавку в таких печах с использованием мелкой шихты и стружки, особенно при плавке с твердой завалкой. Крупные отходы собственного производства имеют обычно повышенное электросопротивление по сравнению с исходными первичными металлами, что определяет порядок загрузки шихты и последовательность введения компонентов в процессе плавки. Сначала загружают крупные кусковые отходы собственного производства, а затем (по мере появления жидкой ванны) — остальные компоненты. При работе с ограниченной номенклатурой сплавов наиболее экономична и производительна плавка с переходящей жидкой ванной — в этом случае возможно использование мелкой шихты и стружки.
В индукционных канальных печах переплавляют отходы первого сорта — бракованные детали, слитки, крупные полуфабрикаты. Отходы второго сорта (стружку, сплесы) предварительно переплавляют в индукционных тигельных или топливных печах с разливкой в чушки. Эти операции выполняют в целях предотвращения интенсивного зарастания каналов оксидами и ухудшения работы печи. Особенно отрицательно сказывается на зарастании каналов повышенное содержание в отходах кремния, магния и железа. Расход электроэнергии при плавке плотного лома и отходов составляет 600—650 кВт-ч/т.
Стружку алюминиевых сплавов либо переплавляют с последующей разливкой в чушки, либо добавляют непосредственно в шихту при приготовлении рабочего сплава.
При подшихтовке базового сплава стружку вводят в расплав либо брикетами, либо россыпью. Брикетирование повышает выход металла на 1,0%, однако более экономично введение стружки россыпью. Введение стружки в сплав более 5,0 % нецелесообразно.
Переплав стружки с разливкой в чушки осуществляют в индукционных печах с «болотом» при минимальном перегреве сплава выше температуры ликвидуса на 30—40 °С. В течение всего процесса плавки в ванну малыми порциями подают флюс, чаще всего следующего химического состава, % (масс. доля): КСl -47, NaCl-30, NO3AlF6 -23. Расход флюса составляет 2,0—2,5 % массы шихты. При плавке окисленной стружки образуется большое количество сухих шлаков, происходит зарастание тигля и снижается выделяемая активная мощность. Нарастание шлака толщиной 2,0—3,0 см приводит к снижению активной мощности на 10,0—15,0 %, Количество используемой в шихте предварительно переплавляемой стружки может быть более высоким, чем при непосредственном добавлении стружки в сплав.
ТУГОПЛАВКИЕ СПЛАВЫ.
Для переплавки отходов тугоплавких сплавов чаще всего используют электроннолучевые и дуговые печи мощностью до 600 кВт. Наиболее производительна технология непрерывного переплава с переливом, когда плавка и рафинирование отделены от кристаллизации сплава, а печь содержит четыре-пять электронных пушек различной мощности, распределенных по водоохлаждаемому поду, изложнице и кристаллизатору. При переплаве титана жидкая ванна перегревается на 150— 200 °С выше температуры ликвидус; сливной носок изложницы обогревается; форма может быть неподвижной или вращающейся вокруг своей оси с частотой до 500 об/мин. Плавка происходит при остаточном давлении 1,3-10~2 Па. Процесс плавки начинают с наплавления гарнисажа, после чего вводят лом и расходуемый электрод.
При плавке в дуговых печах используют электроды двух типов: нерасходуемые и расходуемые. При использовании нерасходуемого электрода шихту Загружают в тигель, чаще всего медный водоохлаждаемый или графитовый; в качестве электрода используют графит, вольфрам или другие тугоплавкие металлы.
При заданной мощности плавка различных металлов отличается скоростью плавления и рабочим вакуумом. Плавка делится на два периода — нагрев электрода с тиглем и собственно плавление. Масса сливаемого металла на 15—20 % меньше массы загруженного в связи с образованием гарнисажа. Угар основных компонентов составляет 4,0—6,0 % (мае. доля).
НИКЕЛЕВЫЕ, МЕДНЫЕ И МЕДНО-НИКЕЛЕВЫЕ СПЛАВЫ.
Для получения ферроникеля переплав вторичного сырья никелевых сплавов осуществляют в дуговых электропечах. В качестве флюса используют кварц в количестве 5— 6 % массы шихты. По мере расплавления шихта оседает, поэтому необходимо проводить догрузку печи, иногда до 10 раз. Образующиеся шлаки имеют повышенное содержание никеля и других ценных металлов (вольфрама или молибдена). В дальнейшем эти шлаки перерабатывают вместе с окисленной никелевой рудой. Выход ферроникеля составляет около 60 % массы твердой шихты.
Для переработки металлоотходов жаропрочных сплавов проводят окислительно-сульфидирующую плавку или экстрагирующую плавку в магнии. В последнем случае магний экстрагирует никель, практически не извлекая вольфрам, железо и молибден.
При переработке отходов меди и ее сплавов чаще всего получают бронзы и латуни. Выплавку оловянных бронз осуществляют в отражательных печах; латуней -— в индукционных. Плавку ведут в переходящей ванне, объем которой составляет 35—45 % объема печи. При плавке латуни в первую очередь загружают стружку и флюс. Выход годного металла составляет 23—25 %, выход шлаков — 3—5 % массы шихты; расход электроэнергии изменяется от 300 до 370 кВт-ч/т.
При выплавке оловянной бронзы в первую очередь загружают также мелкую шихту — стружку, выштамповки, сетки; в последнюю очередь — крупногабаритный лом и кусковые отходы. Температура металла перед разливкой 1100—1150 °С. Извлечение металла в готовую продукцию составляет 93—94,5%.
Безоловянные бронзы переплавляют в поворотных отражательных или индукционных печах. Для предохранения от окисления используют древесный уголь или криолит, плавиковый шпат и кальцинированную соду. Расход флюса составляет 2—4% массы шихты.
В первую очередь в печь загружают флюс и легирующие компоненты; в последнюю очередь — отходы бронзы и меди.
Большинство вредных примесей в медных сплавах удаляют продувкой ванны воздухом, паром или введением медной окалины. В качестве раскисли-теля используют фосфор и литий. Раскисление фосфором латуней не применяют из-за высокого сродства цинка к кислороду. Дегазация медных сплавов сводится к удалению из расплава водорода; осуществляется продувкой инертными газами.
Для плавки медноникелевых сплавов используют индукционные канальные печи с кислой футеровкой. Стружку и другие мелкие отходы добавлять в шихту без предварительного переплава не рекомендуется. Склонность этих сплавов к науглероживанию исключает использование древесного угля и других углесодержащих материалов.
ЦИНКОВЫЕ И ЛЕГКОПЛАВКИЕ СПЛАВЫ.
Переплавку отходов цинковых сплавов (литников, стружки, сплесов) проводят в отражательных печах. Сплавы от неметаллических примесей очищают рафинированием хлоридами, продувкой инертными газами и фильтрованием. При рафинировании хлоридами в расплав с помощью колокольчика при 450—470 °С вводят 0,1—0,2% (мае. доля) хлористого аммония или 0,3—0,4 % (мае. доля) гексахлорэтана; в этом же случае рафинирование можно выполнить перемешиванием расплава до прекращения выделения продуктов реакции. Затем производят более глубокую очистку расплава фильтрованием через мелкозернистые фильтры из магнезита, сплава фторидов магния и кальция, хлорида натрия. Температура фильтрующего слоя 500 °С, его высота 70—100 мм, размер зерен 2—3 мм.
Переплав отходов оловянных и свинцовых сплавов ведут под слоем древесного угля в чугунных тиглях печей с любым нагревом. Полученный металл рафинируют от неметаллических примесей хлористым аммонием (добавляют 0,1—0,5%) и фильтруют его через зернистые фильтры.
Переплав отходов кадмия осуществляют в чугунных или графито-шамотных тиглях под слоем древесного угля. Для уменьшения, окисляемости и потерь кадмия вводят магний [0,05 % (мае. доля)]. Слой древесного угля меняют несколько раз.
Необходимо соблюдать те же меры безопасности, что и при плавке сплавов кадмия.
Плавка алюминиевых сплавов
При плавке и разливке на воздухе алюминиевые сплавы легко окисляются и насыщаются водородом, причем вредное влияние растворенных газов на качество отливок заметно уже при небольших количествах их в расплаве. Практикой установлено, что предельно допустимое количество водорода в алюминиевых сплавах, позволяющее получать качественное литье, оценивается 0,1—0,20 см3/100 г металла. Поэтому основное внимание при плавке уделяют предупреждению излишнего окисления и газонасыщения сплава. Учитывая вредное влияние примесей в алюминиевых сплавах, стремятся также получить сплав с минимальными количествами этих примесей, особенно железа.
Способы плавки алюминиевых сплавов зависят от применяемого типа печей и шихтовых материалов. Тип плавильных печей выбирают в зависимости от характера производства и назначения сплава.
Плавку алюминиевых сплавов производят в тигельных печах с нефтяным, газовым и электрическим обогревом, в пламенных отражательных печах, подовых электропечах сопротивления и индукционных печах. По назначению различают печи плавильные, раздаточные и плавильно-раздаточные.
Наиболее качественный металл получается при плавке в индукционных печах. В этих печах плавка идет быстро, металл получается хорошо перемешанным и менее газонасыщенным. Отражательные печи, отапливаемые газом, применяют для плавки алюминиевых сплавов в цехах заготовительного литья, а также для переплавки отходов и стружки. В фасоннолитейных цехах распространены отражательные электропечи сопротивления.
Тигельные печи с различными способами нагрева применяют для плавки сравнительно небольших количеств металла (особенно они удобны как раздаточные печи).
Для плавки алюминиевых сплавов применяют преимущественно металлические сварные, литые, реже кованые тигли.
При плавке в металлических тиглях имеется опасность взаимодействия сплава с тиглем и загрязнение его примесями железа. Наиболее агрессивны по отношению к чугунным тиглям алюминиевые сплавы с кремнием, затем с магнием и менее с медью и цинком. Поэтому стенки тиглей перед плавкой покрывают специальными защитными красками, кроме того, подбирают составы чугуна или стали, более стойкие по отношению к алюминию. Например, серые чугуны более стойки, если в них больше графита и он находится в сильно разветвленной форме. Кремний в чугуне (как и кремний в расплаве) способствует взаимодействию металла с материалом тигля поэтому стремятся снижать содержание его в чугуне до нижнего предела, а в качестве графитизирующего элемента при выплавке используют алюминий (1,2—3,0%). Алюминий, кроме того, снижает окисляемость тигля и с наружной стороны. Содержание марганца должно быть минимальным. Высокую стойкость имеют тигли из чугуна с содержанием алюминия до 8% и с присадками хрома (0,4—1,0%), а также никеля и молибдена.
Рекомендуются следующие общие правила приготовления алюминиевых сплавов:
- При плавке на свежих шихтовых материалах и лигатурах в первую очередь загружают (целиком или по частям) алюминий, а затем растворяют лигатуры.
- Если плавка ведется на предварительном чушковом сплаве или на чушковом силумине, в первую очередь загружают и расплавляют чушковые сплавы, а затем подшихтовывают сплав необходимым количеством алюминия и лигатур.
- Сильно склонные к угару металлы, например цинк, магний, вводят в сплав в последнюю очередь, желательно под слой флюса.
- Если шихта состоит из отходов и чушковых металлов, очередность загрузки определяется количеством составных частей шихты: в первую очередь загружают в печь и расплавляют наибольшую часть шихты. Если, однако, отходы сильно загрязнены, то лучше их вначале расплавить, дегазировать и затем загружать чушковый металл.
- Если емкость печи и габариты шихты позволяют загружать различные ее составляющие одновременно, то вместе загружают то, что имеет близкую температуру плавления, например силумин, отходы, чушковый алюминий. Шихту подбирают с наименьшим количеством примесей для данного сплава. Укладку шихты в печь надо производить компактно, расплавление вести быстро. При загрузке в жидкую ванну твердую шихту необходимо предварительно подогревать.
Шихтовые материалы и возвраты необходимо хранить в сухих и теплых помещениях. Хранение их в сырых помещениях или же на открытом воздухе приводит к адсорбции влаги и усиленному окислению.
Шихту обычно составляют из отходов и 20—60% свежих материалов, тщательно взвешивают в соответствии с расчетными данными. Расчет шихты литейных алюминиевых сплавов проводят по данным ГОСТа (по среднему или оптимальному составу). В зависимости от особенностей сплавов и требований к свойствам отливки состав одних компонентов рассчитывают по минимальному количеству, других — по максимальному, а третьи компоненты рассчитывают по среднему количеству.
Например, при расчете шихты для приготовления слитков из алюминиевых сплавов АК4, АК5, АК6 и Д16 содержание меди в сплавах берут по верхнему пределу, что способствует снижению склонности сплавов к трещинообразованию, а содержание железа, магния и кремния принимают, наоборот, по нижнему пределу, для уменьшения ликвации.
Сплав АЛ4 имеет следующие пределы химического состава по ГОСТу: 8—10,5% Si, 0,25—0,5% Mn, 0,17—0,3% Mg, остальное Al. Обычно расчет ведут на содержание кремния 8,25—9,25%. Пониженное по сравнению со средним (9,25%) содержание кремния берут потому, что это способствует повышению прочности, уменьшению концентрированной усадки и ликвации сплава. Но чрезмерное понижение кремния вызывает уменьшение жидкотекучести и механических свойств, что особенно важно при литье тонкостенных деталей. Поэтому в таких случаях расчет ведут на содержание кремния 9,25%. Марганец вводят в сплав АЛ4 главным образом для устранения вредного влияния железа, но повышенное содержание марганца может вызвать сильную ликвацию. Поэтому если шихта сравнительно чистая по железу, то расчет ведут на среднее содержание марганца (0,37%), а если шихта сильно загрязненная, то количество марганца доводят до 0,45%, т. е. ближе к верхнему пределу. Особенно важно при составлении шихты сплава АЛ4 учитывать влияние магния на механические свойства этого сплава. При содержании магния на нижнем пределе сплав будет иметь пониженную прочность и твердость, но высокую пластичность.
Часто при выборе оптимального состава сплава приходится учитывать одновременно влияние на свойства сплава нескольких компонентов и затем выбирать наиболее удобные их сочетания. Например, сплав Д19 (3,8—4,3% Cu; 1,8—2,3% Mg) высокие жаропрочные свойства имеет в том случае, если суммарное количество меди и магния в сплаве будет равным 6,1%, что необходимо учитывать при расчете шихты. При плавке сплава АЛ19 (4,5—5,3% Cu, 0,6—1,0% Mn, 0,25—0,35% Ti, <0,3% Fe, <0,3% Si, 0,05% Mg, остальное Al) высокие прочностные и пластические свойства получаются в том случае, когда содержание меди и марганца находятся на среднем уровне марочного состава сплава (5% Cu, 0,8% Mn,0 3% Ti, остальное Al). Любые отклонения от среднего содержания этих металлов неблагоприятно сказываются на механических свойствах.
Поэтому при плавке некоторых алюминиевых сплавов (особенно многокомпонентных) приходится иногда вначале готовить из чистых металлов подготовительный сплав определенного химического состава, разливать его в чушки, анализировать состав и потом уже при условии соответствия заданному составу использовать его в качестве исходной шихты для приготовления рабочего сплава, непосредственно идущего для заливки литейных форм.
Стандартные сплавы, технология плавки которых достаточно хорошо отработана, обычно готовят однократно из шихтовых материалов и сразу же заливают металл в формы.
Расплавление шихты ведут форсировано, но не рекомендуется чрезмерно перегревать расплав. Если шихта мелкогабаритная, та для предохранения от чрезмерного окисления плавку осуществляют с применением покровных флюсов из смеси хлористых солей, которые загружают вместе с металлической шихтой в количестве 2—3% от массы металла. По достижении необходимого перегрева металл контролируют по технологическим пробам на газонасыщенность и загрязненность окисными включениями и в случае необходимости приступают к рафинированию и дегазации сплава. На всем протяжении плавки, начиная с подготовки шихтовых материалов, необходимо не допускать излишнего окисления и газонасыщения расплава. Для этого надо тщательно готовить к плавке шихту и очищать ее от посторонних примесей, а также держать чистыми печь и весь инструмент. Чем больше внимания и времени уделяется подготовке шихты и печи, тем меньше окислов и газов окажется в расплаве и тем легче отрафинировать расплав перед разливкой. Небрежная плавка, в том случае, когда используют загрязненную, влажную шихту, не просушивают футеровку печи (в расчете на последующую очистку расплава в результате рафинирования и дегазации в конце плавки), не дает хороших результатов, так как зачастую легче предотвратить попадание в расплав окислов и газов, чем затем освободиться от них.
Практика плавки алюминиевых сплавов показывает, что существует прямая связь между количеством окисных пленок в расплаве и его газонасыщенностью. Чем больше в сплаве окисных пленок, тем выше газонасыщенность. Поэтому излишнего перемешивания расплава следует избегать, особенно если плавку ведут без покровных флюсов.
Переплавка и рафинирование алюминия — Справочник химика 21
Переплавка и рафинирование алюминия [c.283]Переплавка и рафинирование алюминия……. . 663 [c.7]
Переплавка и рафинирование алюминия [2, 8] [c.252]
Металл, извлеченный из электролизеров, содержит 98,5—99,8 % алюминия, механические примеси (электролит, окись алюминия, уголь, иногда карбид алюминия) и сплавы с элементами, которые встречаются в алюминиевых рудах (Fe, Si, Ti, u). Механические примеси и адсорбированные газы можно удалить переплавкой сырого алюминия, а /келезо, кремний, титап и медь удаляют электролитическим рафинированием. [c.284]
Извлечение алюминия из ванны производится один раз в 3—4 суток двумя путями слив алюминия через чугунный сифон в ковш, расположенный вне ванны ниже уровня металла, или отсасывание алюминия в ковш,, находящийся под вакуумом. Алюминий подвергается затем переплавке в слитки. Лучшие сорта алюминия содержат 99,8% А1, остальное — железо и кремний. Для получения металла, содержащего 99,99% А1, технический алюминий подвергают рафинированию. [c.341]
Очистка алюминия от железа и кремния представляет большие трудности ее осуществляют электролитическим рафинированием. Механические же примеси и газы удаляют простой переплавкой алюминия. [c.663]
Обычно при получении технического металла последней операцией является переплавка брикетированной губки под слоем щелочи с целью получения компактного таллия. При этом заметно снижается содержание ряда примесей, например цинка. Если к щелочи добавляется окислитель (нитрат калия или натрия), щелочное рафинирование становится гораздо эффективнее. Расход нитратов составляет 1—2% от массы брикетов, расход щелочи 50%. Температура рафинирования 350—400° С, продолжительность (при эффективном перемешивании расплава) 1—2 ч. Перемешивание расплава можно проводить как механическим путем, так и, скажем, продувкой воздуха. При проведении однократного рафинирования в этих условиях содержание примесей, в особенности цинка, свинца, олова и алюминия, резко снижается, и из металла с содержанием суммы примесей 3—5 10 % можно получить металл с содержанием примесей 1 -10 % и даже меньше. 2—3-кратным щелочным рафинированием получают металл, в котором содержание свинца, меди, кадмия, индия, олова, железа и других примесей не превышает 1 х X 10 % каждого элемента [184]. [c.231]
Во время электролиза образующийся металл перио. дически удаляется со дна электролизера, он содержит обычно 98,5—99,8% алюминия, механические примеси (электролит, окись алюминия, уголь, адсорбированные газы) и сплавы с элементами, которые встречаются в алюминиевых рудах (З), Ре). Механические примеси и адсорбированные газы обычно удаляют переплавкой алюминия-сырца, а железо, кремний удаляют последующим электролитическим рафинированием. После электролитического рафинирования получают алюминий [c.333]
Естественно, что катоды для осаждения цинка следовало бы депать из тонких листов цинка (как при электролитическом рафинировании меди, см. 42) и на них наращивать новую толщину металла полученные после этого толстые цинковые катоды можно было бы без переплавки отправлять потребителю. Однако попытки применения цинковых катодов оказались неудачными потому, что тонкие листы цинка легко разрушались кислотой на границе с воздухом поэтому перешли к применению катодных листов из алюминия. При таком устройстве цинк при электролизе растет на алюминии, покрытом пленкой окиси, и после достижения известной толщины должен быть снят или содран , как говорят в производстве. [c.284]
Извлеченный из ванны алюминий загрязнен железом, кремнием, титаном и другими элементами, сильно ухудшающими его качество. Алюминий от загрязнений освобождается рафинированием. Неметаллические и газообразные примеси, а также натрий удаляются переплавкой и продуванием металла хлором. Другие металлические примеси удаляются электролитическим рафинипо-ванием. Хлорирование алк>миния производится при 750—770°С. Ковш емкостью 1200—1300 кг хлорируется продуванием хлопа в течение Ю—15 мин. Расход хлора равен 0,1% от веса алюминия, потери последнего около 1%. [c.201]
на БоАЗе получена миллионная тонна алюминия
Миллионная тонна товарного металла произведена на линии литейного комплекса № 5, где в 2015 в миксер был залит первый металл БоАЗ.
Почетным гостем юбилейной плавки стал губернатор Красноярского края Александр Усс, поздравивший заводчан с таким значимым для завода и всей металлургической отрасли края событием.«Богучанский завод действительно флагман российской металлургии, это гордость не только Красноярского края, но и всей России. Предприятий такого уровня, с такими технологиями, которые в последние годы строились с нуля, в России не так уж и много. Очень важно, что здесь за эти годы сформировался молодой и сплоченный коллектив. Это предопределило тот факт, что сегодня у нас большое, серьезное событие, достигнут важный рубеж — миллион тонн алюминия», — сказал Александр Усс.
Сошедшая с линии литья миллионная тонна была упакована, на ней прикрепили памятную табличку, с указанием даты выпуска. Юбилейные слитки станут экспонатами будущего музея БоАЗ.
И.о. генерального директора БоАЗ Алексей Чижов вручил почетному гостю памятный сувенир в виде алюминиевого слитка, как участнику юбилейной плавки. И в свою очередь также поздравил коллектив с отличным результатом, которого достигли в год пятилетия со дня пуска завода и получения первого металла, что символично. Он выразил уверенность, что взятый темп и качество продукции БоАЗ останутся на высоте и в будущем.
Алексей Чижов, и.о. генерального директора БоАЗ: «За эти пять лет со дня пуска завода пройден очень большой путь. Посреди тайги мы запустили самое современное алюминиевое производство, получили первый металл, поселок Таежный с запуском завода стал наполняться новой жизнь и кардинально преобразился. И вот теперь мы произвели наш первый миллион. Это отличный результат, которым можно гордиться! В каждой из этих тонн – ваш самоотверженный добросовестный труд, частичка вашей души. И я хочу поблагодарить всех за хорошую работу».
В завершении праздника прошла церемония награждения лучших сотрудников и ветеранов завода. Они были отмечены благодарственными письмами и почетными грамотами.
Почетными грамотами также наградили победителей конкурса Профессионального мастерства.
Плавка и разливка алюминиевых сплавов
Плавка и разливка алюминиевых сплавов
Категория:
Литейное производство
Плавка и разливка алюминиевых сплавов
Для плавки алюминиевых сплавов используют тигельные печи, обогреваемые различными видами топлива, стационарные пламенные и электрические — сопротивления и индукционные.
1. Шихтовые материалы
В качестве исходных шихтовых материалов применяют первичные и вторичные металлы и сплавы, оборотные сплавы и лигатуры.
Первичный алюминий поставляется по ГОСТ 11069—74 в виде чушек массой 5, 15 и 1000 кг. Для производства алюминиевых сплавов обычно используют алюминий марок А5, А6 и АО, а для изготовления отливок высокоответственного назначения — алюминий особой и высокой чистоты.
Вторичные алюминиевые сплавы получают переплавкой и рафинированием лома и отходов. Они поставляются в виде чушек различных марок по ГОСТ 1583—73.
Свежие металлы. В состав алюминиевых сплавов входят цинк, магний, кремний, марганец, медь, бериллий, никель, железо, титан и другие элементы. Для алюминиевых сплавов обычно применяют цинк марок Ц1 и Ц2. Магний поставляется по ГОСТ 804—72 в чушках массой 8,0±1 кг. Ввиду большой склонности его к коррозии поверхность чушек подвергается антикоррозионной обработке. Кремний вводят в алюминиевые сплавы в виде чушкового силумина (сплав кремния с алюминием), поставляемого по ГОСТ 1521—76, а марганец —в виде лигатуры алюминий — марганец, содержащей около 10% марганца. Для приготовления лигатур используют марганец марок Mp1, Мр2 и Мр3.
Качество отливок в большой степени зависит от тщательности подготовки шихтовых материалов к плавке и способов их хранения. Они должны храниться в сухих крытых помещениях раздельно по маркам сплавов. Оборотный сплав должен очищаться от песка в очистных барабанах.
Лигатуры. При плавке алюминиевых сплавов, как правило, применяют двойные лигатуры — сплавы из двух компонентов. Введение лигатур обеспечивает получение сплава с точным содержанием элементов, что особенно важно для сплавов, содержащих магний, так как даже малые добавки его сказываются на свойствах сплавов.
2. Расчет шихты
Шихта для приготовления алюминиевых сплавов может состоять из чушкового алюминия, силумина, оборотного металла, лигатур и чистых металлов.
Рассмотрим пример расчета шихты для сплава АЛ5 при плавке в тигельной печи. Средний химический состав этого сплава: 5% кремния, 0,4% магния, 1,25% меди, остальное — алюминий. Допустимое содержание железа при заливке в металлические формы не должно превышать 1%. Расчет ведем на 100 кг сплава. Угар принимаем в следующих размерах, в %: кремния—1, магния — 3, меди — 1, алюминия — 1.
Для доведения до необходимого количества содержания кремния применяем чушковый силумин (с Si=13%), а магния и меди— алюминиево-магнневую и алюминиево-медную лигатуры.
3. Флюсы, рафинирующие и модифицирующие материалы
Для получения высококачественных сплавов осуществляют плавку под флюсом, рафинирование сплава для удаления неметаллических включений, а также модифицирование для получения мелкой структуры и повышения механических свойств.
Для рафинирования и модифицирования алюминиевых сплавов часто применяют универсальные флюсы, состоящие из смеси солей и криолита. Универсальные флюсы используются как в жидком, так и в порошкообразном состоянии.
4. Плавка в тигельных печах
Плавку алюминиевых сплавов в небольших объемах осуществляют в тигельных печах, работающих на нефти и газе. .
Печь состоит из стального кожуха с футеровкой и вставленного в него сверху чугунного тигля. Последний своим широким фланцем крепится к стальному кольцу, перекрывающему шахту сверху, что обеспечивает полную изоляцию расплавленного металла от печных газов. Печь установлена на сварной или литой раме. Поворот ее осуществляется штурвалом. Для увеличения срока службы тиглей и уменьшения насыщения сплавов железом внутреннюю поверхность их рекомендуется окрашивать краской, состоящей из 60% кварцевого песка, 30% огнеупорной глины и 10% жидкого стекла.
Рис. 1. Поворотная тигельная печь.
5. Плавка в электрических печах
Плавку алюминиевых сплавов производят в электрических печах сопротивления, тигельных и отражательных печах, а также в индукционных.
Плавка в электрических отражательных печах. На предприятиях, где алюминиевые сплавы выплавляются в больших объемах, применяют электрические печи САН (печи сопротивления для алюминиевых сплавов, наклоняющиеся) и камерные стационарные.
Печь САН (рис. 2) имеет удлиненный металлический корпус, установленный на катках и укрепленный на фундаменте. Корпус изнутри выложен кирпичом. В торцах печи расположены две форкамеры, а в середине — центральная ванна. Свод печи выложен фасонными огнеупорными кирпичами, в гнездах которых уложены нагревательные спирали. Такие же спирали имеются и в форкамерах.
Шихту загружают через окна. Она плавится в форкамерах за счет тепла, отраженного от свода и стенок печи, и по наклонным плоскостям стекает в центральную ванну. Слив готового металла из печи осуществляется через лётку при повороте печи на опорных катках с помощью штурвала или электропривода.
Плавка в тигельных электрических печах сопротивления. При сравнительно небольших масштабах производства для плавки алюминиевых и магниевых сплавов применяют однотигельные печи сопротивления САТ-0,15 и САТ-0,25, а также двухтигельные печи СЖ.Б-230 и ОКБ-75.
Рис. 2. Электрическая печь типа САН.
Печи CAT выполнены в виде сварного цилиндрического кожуха, футерованного фасонным легковесношамотным кирпичом, и имеют теплоизоляцию. Нагрев чугунного тигля, установленного на литом чугунном кольце, производится нихромовыми нагревателями, которые уложены на полочках фасонных шамотных кирпичей и укреплены металлическими крючками. В нижней части печи имеется аварийное отверстие для выпуска сплава на случай прогорания тигля. Температура автоматически регулируется самопишущим потенциометром с помощью хромель-алюмелевой термопары.
Плавка в индукционных электрических печах. Различают индукционные печи со стальным сердечником и индукционные тигельные печи ИАТ. Печи со стальным сердечником широко применяются для плавки как алюминиевых, так и медных сплавов. Они имеют ряд преимуществ по сравнению с печами сопротивления: более высокую производительность, меньший удельный расход электроэнергии, возможность рафинирования металла в печи, обеспечивают высокое качество сплава с минимальным содержанием газов. В этих печах интенсивное движение металла происходит в устьях каналов, а поверхность жидкого сплава в самой печи находится в спокойном состоянии, что обеспечивает сплошность окисной пленки и предохраняет сплав от дальнейшего окисления.
Рис. 3. Тигельная электропечь.
В последнее время получили распространение бессердечниковые тигельные индукционные печи ИАТ емкостью 0,4—0,6 т и производительностью 0,235—2,0 т/ч.
6. Особенности технологии плавки и разливки алюминиевых сплавов
Для большинства алюминиевых сплавов принята одна технология плавки вне зависимости от конструкции печи.
Шихтовые материалы перед загрузкой тщательно очищают от загрязнений и подогревают до 100—150 °С для удаления с их поверхности влаги.
Плавка алюминиево-кремнистых сплавов. Как уже указывалось, лучше всего вести плавку в индукционных печах высокой или промышленной частоты и в электрических печах сопротивления. В качестве шихтовых материалов применяют чушковые силумины, первичный алюминий и оборотный металл (до 50% от массы шихты).
Плавку осуществляют в следующей последовательности. Печь или тигель нагревают до температуры 600—700 °С, загружают в них подогретые чушки силумина и предварительно очищенный в барабане оборотный сплав. После расплавления металл перегревают до 720—730 °С, рафинируют хлористым цинком (0,1% от массы шихты) и производят его модифицирование.
Рафинирование осуществляют путем погружения навески хлористого цинка на дно тигля с помощью «колокольчика», который медленно водят по дну тигля до полного прекращения выделения пузырьков газа.
Модифицирование смесью хлористых и фтористых солей калия и натрия производят путем покрытия ими очищенной от шлака поверхности сплава и выдержки в течение 12—14 мин. Затем соли рубят и замешивают в сплав в течение 2 мин, после чего модификатор снимают с поверхности сплава.
При использовании универсальных флюсов операции рафинирования и модифицирования совмещают.
Плавка алюминиевых сплавов, содержащих магний. Во избежание насыщения сплава вредными примесями — железом и кремнием — плавка ведется только в графитовых тиглях. Вспомогательный инструмент — счищалка, колокольчики и др. — также изготовляется из графита или титана.
В качестве шихтовых материалов применяют первичный алюминий высокой чистоты, магний и лигатуры алюминиево-бериллие-вую, алюминиево-титановую, алюминиево-циркониевую и оборотный сплав соответствующей марки (до 50—60% от массы всей шихты).
После нагрева тигля до температуры 600 °С. загружают чушки первичного алюминия и алюминиево-бериллиевую лигатуру. При температуре сплава 670—700 °С вводят лигатуры алюминий — титан и алюминий — цирконий и после полного растворения всех лигатур с помощью графитового колокольчика вводят магний. При этом необходимо следить, чтобы магний все время был погружен в сплав. После ввода магния сплав рафинируют. Затем с поверхности ванны снимают шлак, сплав тщательно перемешивают и опять снимают шлак, после чего производят разливку. На протяжении всей плавки не допускается перегрев сплава свыше 750 °С.
Для разливки применяют разливочные тигли и футерованные ковши емкостью до 1000 кг. Длина струи сплава должна быть минимальной. Тигли, ковши и разливочный инструмент обязательно прокаливают и покрывают специальными красками.
Реклама:
Читать далее:
Плавка и разливка магниевых сплавов
Статьи по теме:
Как расплавить алюминиевые банки и фольгу в домашних условиях
Вы можете расплавить алюминий дома, чтобы использовать его в научных или художественных проектах.
Алюминиевые банки и фольгу легко расплавить, чтобы переработать чистый металл. Алюминий полезен, потому что он легкий, безопасный для еды и кожи, податливый и устойчивый к коррозии. Вылейте расплавленный алюминий в формы, чтобы сделать посуду, украшения, скульптуры или украшения.
Точка плавления алюминия
Переработка банок и фольги — это просто, но это проект только для взрослых, потому что вам нужна высокая температура.Температура плавления алюминия составляет 660,32 ° C или 1220,58 ° F. Это намного выше, чем тепло, выделяемое духовкой или грилем (поэтому алюминий отлично подходит для посуды), но ниже, чем температура плавления железа (1535 ° C или 2795 ° F) или нержавеющей стали (около 1500 ° C или 2750 ° F). Чтобы достичь точки плавления алюминия, вам понадобится горелка для бутана (1430 ° C или 2610 ° F), пропановая горелка (1995 ° C или 3623 ° F) или печь для обжига.
Материалы для плавки алюминия
- Алюминиевые банки или фольга
- Горелка для бутана или пропана или электрическая печь
- Чугунная сковорода или стальная чаша
- Термостойкие перчатки
- Металлические щипцы
- Формы для расплавленного алюминия
Банки не нужно чистить перед плавлением, если они не покрыты грязью или песком. Органические материалы, такие как остатки соды или пластиковое покрытие, сгорают в процессе плавления.
Как плавить алюминий
- Раздавите банки и смять фольгу, чтобы как можно больше в чашу или сковороду. Ожидайте, что на каждые 40 банок будет приходиться около одного фунта алюминия.
- Безопасность прежде всего! Наденьте защитные очки и термостойкие перчатки. Соберите длинные волосы назад и носите длинные брюки и обувь с закрытыми носками.
- Если вы используете печь, нагрейте ее до 1220 ° F или немного выше (стараясь оставаться ниже точки плавления стали или железа, в зависимости от того, что вы используете).Поместите алюминиевый контейнер в печь. Он плавится почти сразу после достижения точки плавления, но подождите не менее 30 секунд, чтобы расплавился весь алюминий. В теплозащитных перчатках осторожно извлеките емкость из печи щипцами.
- Если вы используете фонарик, поместите алюминиевый контейнер на жаропрочную поверхность. Нагрейте алюминий, стараясь не повредить емкость.
Это особенно важно, если вы используете пропановую горелку, потому что пропан может гореть при температуре, достаточной для плавления железа и стали!
- После того, как у вас будет расплавленный алюминий, вылейте его в форму (творческие идеи можно найти на YouTube).Вы можете поместить форму, полную алюминия, в ведро с холодной водой, но будьте осторожны, потому что при нагревании образуется много пара. В противном случае дайте форме остыть и затвердеть самостоятельно. Для затвердевания металла потребуется около 15 минут.
- Возможно, у вас в контейнере остались остатки алюминия. Вы можете выбить его из контейнера, постучав им о твердую поверхность. Другой вариант — освободить его, изменив температуру контейнера (нагревая или охлаждая). Это работает, потому что алюминий и контейнер имеют разные значения коэффициента расширения.
Переработка алюминия
Около 36% алюминия в США производится из переработанного металла, в то время как Бразилия лидирует в мире по переработке алюминия, повторно используя 98,2% металла. Переработка требует 5% энергии, необходимой для очистки элемента от его руды.
Ссылки
- Greenwood, Norman N .; Эрншоу, Алан (1997). Химия элементов (2-е изд.). Баттерворт-Хайнеманн. ISBN 978-0-08-037941-8.
- Моррис, Дж. (2005). «Сравнительные LCA для рециркуляции обочины по сравнению с захоронением или сжиганием с рекуперацией энергии». Международный журнал оценки жизненного цикла , 10 (4), 273–284.
- Оскамп С. (1995). «Сохранение и переработка ресурсов: поведение и политика». Журнал социальных проблем . 51 (4): 157–177. DOI: 10.1111 / j.1540-4560.1995.tb01353.x
- Шлезингер, Марк (2006). Переработка алюминия . CRC Press. ISBN 978-0-8493-9662-5.
Быстрая и дешевая установка плавильной печи для алюминия: 4 этапа
Это руководство показывает быструю и дешевую установку для плавления нескольких партий алюминия для литья до того, как тонкое металлическое оборудование начнет ломаться.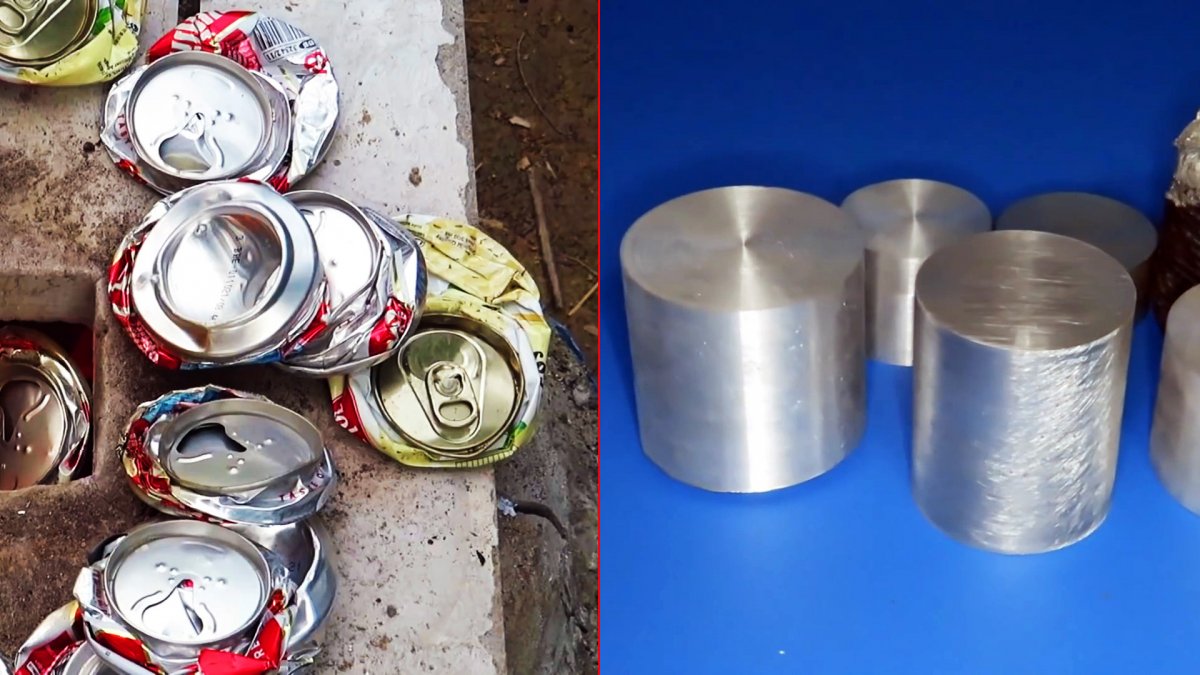
Для печи использовались два металлических ведра по пять галлонов (с крышками), кусок 3-дюймовой печной трубы, фен и, конечно же, изолента.
Для тигля (маленького ведерка, в котором находится расплавленный металл) использовался баллон с пропаном на 16 унций; верх был отрезан и добавлены болты для захвата тигля щипцами.
Некоторые основные инструменты я сделал из стального лома из старой пружинной коробки. Вам понадобятся щипцы для тигля, какой-то крючок для овец, чтобы опрокинуть тигель при заливке, и простой стержень с небольшим изгибом на конце, чтобы протыкать предметы и снимать шлак (примеси в алюминии).
Использование показанного оборудования опасно из-за очень высоких температур расплавленного металла, дыма и дыма и т. Д. Соблюдайте осторожность и будьте осторожны, надевая кожаные перчатки, средства защиты лица и другую защитную одежду. Делайте это на открытом воздухе и используйте его, когда немного ветрено, чтобы дым и пары быстро рассеивались, также используйте это в сухих условиях, потому что капание расплавленного металла на влажные поверхности может вызвать небольшие взрывы горячего металла (например, вода или горячее масло на кухне). Я не несу ответственности за любые травмы, которые вы можете получить при использовании оборудования и техники, показанных здесь.
Прочтите, прочтите, прочтите много материалов по литью металла перед началом работы.
Литье алюминия на submarineboat.com
Home Foundry
BackyardMetalcasting.com … Самостоятельная плавка и литье металла
Вот немое кино о работе литейного цеха.
youtube.com/embed/FyIjnM0rvpA»/>
Печи для плавки и сплавов | Плавка и литье алюминия
Inductotherm — лидер отрасли в разработке и производстве технологически передовых систем практически для всех металлов и материалов, включая алюминий.От начала до конца алюминиевая технология Inductotherm работает. Преобразование глинозема в чистый алюминий и, в конечном итоге, в полезные алюминиевые сплавы — это энергоемкий процесс, поэтому энергоэффективные печи, производимые Inductotherm, доказали свою ценность на алюминиевых заводах по всему миру. Технологии индукционных печей Inductotherm могут конкурировать с более традиционными методами, такими как печи на ископаемом топливе и печи сопротивления. Индукция практична для всех применений при плавке алюминия и имеет много преимуществ по сравнению с обычными печами для плавки алюминия.
Какие области применения алюминия могут успешно получить выгоду от индукции?
- Литейное производство / литье
- Ролики для алюминиевых заготовок
- Переработка / переплавка
- Литье под давлением
- Плавка стружки
- Литье по выплавляемым моделям
- Первичный алюминий
- Вторичный алюминий
Плавка алюминиевой стружки
Алюминиевая стружка сложно плавить из-за ее тенденции всплывать на поверхности расплавленного алюминия при добавлении в большинство печей.
Система плавления алюминиевой стружки, использующая традиционную индукционную печь без сердечника, может помочь преодолеть это за счет присущего ей перемешивания. Перемешивание помогает погрузить в воду и разбить комки алюминиевой стружки, позволяя плавить их более эффективно, чем в печи с небольшим перемешиванием или без него.
Преимущества использования технологии индукционной плавки для плавки и литья алюминия:
- Эксплуатационная гибкость
- Системы индукционных печей меньше по размеру и занимают более удобную площадь.
- Легко заменять сплавы
- Можно немедленно отключить, если это необходимо, без дорогостоящих последствий. источником является сам металл
- Газовые печи имеют КПД около 20%, тогда как наша система Acutrak ® DEH имеет КПД до 92%, а большинство индукционных печей обычно имеют КПД 60%
- Лучшее / более чистое качество металла
- Индукционные плавильные печи не выделяют газы
- Газовые печи и печи сжигания подвергают металл воздействию газов и кислорода, которые добавляют к металлу примеси
- Лучшая рабочая среда / удобство для персонала
- Индукционная плавка мало остаточного тепла и минимальный шум
- Газовые печи д.
е выключается много тепла, и топочные печи очень шумные
Впервые на индукционной? Вот что вам нужно знать о том, как работает индукция
Когда ток течет через индукционную катушку, создается магнитное поле.Подача переменного тока через эту катушку приведет к изменению направления магнитного поля с той же скоростью, что и частота переменного тока. Когда добавляется алюминиевый шихтовый материал, действует закон Фарадея. Индуцированное напряжение приведет к протеканию тока через материал в магнитном поле. Поскольку ток течет через материал, движение электронов сопротивляется. Материалы, которые более устойчивы к потоку электронов, будут выделять больше тепла, когда через них протекает ток.Индукционное тепло генерируется в материале продукта за счет протекания тока. Затем тепло от поверхности продукта передается через материал с теплопроводностью.
Когда металл расплавляется, магнитное поле также заставляет ванну двигаться. Это называется индуктивным перемешиванием, при котором происходит перемешивание ванны для получения более однородной смеси, что способствует легированию. Системы водяного охлаждения обычно обеспечивают охлаждение змеевиков, однако, поскольку алюминий является низкотемпературным металлом, наша система прямого электрического нагрева Acutrak ® может иметь воздушное охлаждение, что делает ее отличным вариантом для плавления алюминия.
Лучшие индукционные печи и системы для алюминия
В зависимости от вашего применения, Inductotherm предлагает множество передовых печных систем для плавки алюминия.
Прямое электрическое нагревание (DEH)
- Точно регулируемая индукционная плавка
- Более быстрое, чистое и эффективное плавление
- Автономный источник питания и компактная печь для сокращения времени, усилий и затрат на установку
- Идеально подходит для литья под давлением, постоянных форм и литья алюминия
- Система Acutrak ® DEH хорошо подходит для операций литья под давлением, непрерывного литья в формы и для литейных цехов.
Печи Hybrid ™
- Проверенная технология индукционных печей без сердечника
- Дополнительные преимущества верхнего кожуха канальной печи
- Повышенная гибкость сплава и стойкость огнеупора
- Обеспечение защиты от инертного газа, удаления окалины и быстрой замены сплава
- Идеально подходит для литья слябов и заготовок в аэрокосмической и коммерческой сферах.
- Разливщики алюминиевых заготовок могут обнаружить, что наша уникальная печь Hybrid ™ станет для них отличным выбором.
Традиционные печи без сердечника Inductotherm
- Индукционные печи без сердечника обеспечивают превосходную производительность и исключительную долговечность для всех нужд плавильного цеха, независимо от размера вашего литейного цеха.
- Отвечает высоким требованиям литейщиков, специальных литейных цехов и алюминиевой промышленности.
- Dura-Line ® Печи разработаны, чтобы предоставить литейным предприятиям еще один выбор для малых и средних предприятий, в то время как наши печи с тяжелым стальным кожухом созданы для самых крупных литейных производств.
Съемные тигельные печи
- Широко используется в плавильных цехах алюминия
- Убедитесь, что расплавленный алюминий всегда доступен из одного или другого тигля.
- Обеспечивает большую гибкость сплава
- Выберите дизайн и конфигурацию в соответствии с вашим пространством и требованиями к эксплуатации
- Наши съемные тигельные печи Выдвижная печь или подъемно-поворотная печь могут помочь гарантировать, что расплавленный алюминий всегда доступен из одного тигля или из другого.
Алюминий скапливается вместо плавления: Metalfoundry
Оксид алюминия не плавится, как металлический алюминий.Вместо этого он образует шлак, который можно вычерпать шумовкой и выбросить. Невозможно превратить оксид алюминия обратно в алюминий.
Алюминий естественным образом образует поверхностный слой оксида, вступая в реакцию с атмосферой. В отличие от оксида железа / ржавчины, окисление не продолжается за пределами поверхности. Это окисление алюминия ускоряется / облегчается за счет нагрева металла. Чем больше площадь поверхности, подверженной воздействию воздуха для данного объема алюминия, тем выше отношение оксида алюминия к металлическому алюминию, которое вы получите.Из-за этого алюминиевую стружку из механического цеха использовать для литья металлов нереально. Если вы не выполняете очень глубокие пропилы, полученная стружка будет иметь высокое отношение площади поверхности к объему. И если вы не используете смазочно-охлаждающую жидкость, они выходят из машины довольно горячими; окисляя поверхность практически сразу.
Другая проблема заключается в том, что сплавы, которые лучше всего подходят для механической обработки, часто не подходят для литья металлов. На этом мои познания в химии заканчиваются, но в результате сплав сопротивляется превращению в свободно текущую жидкость.
Лучшее, что вы можете сделать, это начать с плавления литых алюминиевых слитков или больших кусков литого алюминиевого лома. Как только он растает. Когда он станет жидким, вылейте стружку и погрузите ее ковшом или ложкой с длинной ручкой. Убедитесь, что на стружках нет воды или даже конденсата, иначе жидкий алюминий будет стрелять повсюду. Если чипсы маслянистые, вы можете получить огонь, но ничего страшного. Этот метод позволит вашей микросхеме плавиться очень быстро и вдали от кислорода, который в противном случае может постоянно повторно окислять любой металлический алюминий, который обнажается, когда жидкие центры чипа становятся обнаженными.
Бура и легкая соль могут немного помочь в сборе оксида алюминия; но не ожидайте, что этот аспект принесет такую же пользу.
Алюминий безопасности | Алюминиевая ассоциация
Данные о травмах и заболеваниях, собранные Алюминиевой ассоциацией, показывают, что алюминиевые заводы являются относительно безопасным местом для работы. Ежедневно миллионы фунтов алюминия плавятся и отливаются безопасно в литейных цехах, литейных цехах, на предприятиях по переработке и утилизации по всему миру. Однако, как и любой производственный процесс, производство и изготовление нашего металла сопряжено с неотъемлемыми рисками и опасностями.
Алюминиевая ассоциация считает, что эти опасности можно свести к минимуму или полностью исключить, если уделить особое внимание методам безопасного обращения и обмену передовым опытом. С этой целью программы безопасности Ассоциации включают:
- Разработка и распространение публикаций по безопасному производству алюминия и обращению с ним
- Ежегодные семинары по технике безопасности в литейных цехах для обучения рабочих и руководителей предприятий технике безопасности на рабочем месте
- Выпуск ежегодного отчета об инцидентах с расплавленным металлом для обмена информацией о взрывах и связанных с ними событиях на предприятиях по плавке алюминия
- Текущие испытания и отчетность с компаниями-членами для постоянного улучшения безопасности
Ниже приводится общая информация о безопасности в алюминиевой промышленности, а также соответствующие технические материалы. Пожалуйста, свяжитесь со старшим директором Ассоциации по регуляторным вопросам Куртом Уэллсом с любыми конкретными вопросами.
Перейти к
Расплавленный алюминий
Несоблюдение надлежащих процедур плавления и литья алюминия может быть опасным. Расплавленный алюминий обычно обрабатывают при температуре 1300–1450 градусов по Фаренгейту, чтобы избежать преждевременного затвердевания. Контакт с расплавленным алюминием может вызвать серьезные ожоги и создать серьезную опасность пожара. Смешивание воды или других загрязняющих веществ с расплавленным алюминием может вызвать взрыв.Взрывы также могут происходить в процессе переплавки алюминиевого лома из-за влажности и загрязнения лома.
Эти взрывы различаются по степени насилия и могут привести к травмам или смерти, а также к разрушению оборудования и производственных мощностей. Там, где есть вероятность попадания брызг или другого прямого воздействия, персонал, работающий с расплавленным алюминием, должен носить средства защиты глаз и лица, а также защитную одежду.
Алюминиевая ассоциация выпускает ежегодный отчет об инцидентах с расплавленным металлом, в котором содержится информация об опасных событиях, которые происходят на предприятиях по плавке алюминия.Отчет является продуктом добровольной программы, начатой в 1985 году с целью обмена информацией о безопасности между предприятиями. Хотя отчет не предназначен для статистической репрезентативности всей отрасли, он предоставляет полезную информацию, которая поможет направить усилия по обеспечению безопасности в среде расплавленного алюминия. Последний отчет об инциденте с расплавленным металлом находится ниже.
Основы безопасности литейных домов
Ассоциация теперь предлагает 40-минутный онлайн-учебный модуль под названием Основы безопасности литейных домов , который был разработан на основе презентации, первоначально сделанной на выставке AluminiumUSA в 2017 году.Этот модуль предназначен для ознакомления с принципами безопасности литья алюминия для лиц, не участвующих непосредственно в процессе литья, и / или для обеспечения доступного освежения информации в промежутке между очными занятиями по технике безопасности в литейном цехе. К нему прилагается сопроводительный рабочий лист, который можно использовать для проверки понимания представленного материала. Если у вас есть какие-либо вопросы по поводу этой информации, свяжитесь со старшим директором Ассоциации по регуляторным вопросам Куртом Уэллсом по адресу cwells @ aluminium.орг.
Безопасность при переработке металлолома
Переработка алюминия — получение, подготовка и плавление алюминиевого лома для использования в производстве новых алюминиевых продуктов — играет жизненно важную роль в экономических и экологических характеристиках алюминия. Ключевой частью устойчивости переработки алюминия является обеспечение безопасности рабочих на протяжении всего процесса, и Алюминиевая ассоциация публикует различные инструкции по безопасности, которые дополняются рекомендациями по безопасности от других. В США Управление по охране труда и технике безопасности (OSHA) опубликовало «Руководство по выявлению и контролю рисков для безопасности и здоровья при переработке металлического лома» (доступно здесь для бесплатной загрузки), которое является еще одним ресурсом, помогающим повысить безопасность в отрасли переработки. .
Алюминий Разливка и загрузка свиноматок
Алюминий в больших объемах, предназначенный для переплавки, часто отливают в форме больших форм весом от 700 до 2000 фунтов, широко известных как свиноматки. Процесс литья свиноматок обычно приводит к неизбежным внутренним полостям усадки, которые могут стать резервуарами для сбора большого количества воды. Свиноматки также подвержены воздействию поверхностной влаги и других загрязнителей. Это загрязнение может привести к опасным взрывам в процессе переплавки.Поэтому операторы должны прилагать все усилия, чтобы не загружать свиноматок, содержащих влагу, захваченную или на поверхности, в расплавленный алюминий.
Алюминиевая ассоциация не рекомендует сушить свиноматок, помещая их на подоконники печи, содержащие расплавленный алюминий. Взрывы могут произойти из-за того, что свиноматки поскользнутся в ванне с расплавом до полного высыхания, или из-за конденсации воды между штабелями свиноматок.
Защитные покрытия для литейных ям и оборудования
Несколько типов защитных покрытий были испытаны на сегодняшний день и признаны эффективными в предотвращении взрывов расплавленного металла и воды, когда расплавленный металл контактирует со сталью или бетоном после вытекания и разливов во время Кастинг постоянного тока. Подробные сведения об этом испытании и дальнейших испытаниях для изучения влияния времени отверждения покрытия на адгезию и предотвращение взрыва можно найти в двух отчетах ниже.
Исследование покрытий, предотвращающих взрыв расплавленного алюминия / воды
Влияние времени отверждения покрытия на предотвращение адгезии и взрыва, конкретные объемные испытания и демонстрация предотвращения взрыва с проникновением неконденсируемого газа
Алюминиевая мелочь и порошок
При выполнении операций, включая шлифовку, полировку, пиление, резку, шлифование и чистку алюминия щеткой, образуются мелкие частицы алюминия, некоторые из которых потенциально взрывоопасны.Эти частицы известны как «мелочь», «пыль» или «порошок».
В случае алюминия взрыв может произойти, если возгорание происходит, когда частицы взвешиваются в воздухе в виде облака пыли, поскольку горение распространяется от одной частицы к другой с экстремальной скоростью. Возможные источники возгорания включают открытое пламя, сварочное оборудование, резаки, спички, сигареты, неисправное электрическое оборудование и статические электрические заряды.
Квалифицированный персонал может определить степень опасности любой операции путем лабораторных испытаний.Системы улавливания пыли, сухого или влажного типа, надежно улавливают потенциально взрывоопасные частицы алюминия. Кожухи или вытяжные колпаки обеспечивают эффективный сбор мелких частиц с машины или оборудования.
Ниже приведены несколько источников по безопасному обращению с алюминиевой мелкозернистой пылью и порошком.
Горючесть сплава
Для получения информации о горючести и воспламеняемости алюминиевых сплавов Алюминиевая ассоциация заказала испытания в соответствии со стандартом ASTME 136-11 «Стандартный метод испытаний для определения поведения материалов в вертикальной трубчатой печи при 750 ° C». на обычных сплавах 3003, 5052, 5083 и 6061.Испытания показали, что все четыре сплава соответствуют критериям эффективности, представленным в ASTM E 136-11. В 2020 году сплавы, обычно используемые в строительстве, были испытаны в соответствии с обновленным стандартом ASTM E 136-19. Сплавы 5005, 6005/6105, 6005A, 6061, 6063 и 6351, а также алюминий товарной чистоты P1020A прошли испытания и прошли испытания. Ссылки на отдельные отчеты об испытаниях приведены ниже.
Советы по плавке алюминия в литейном производстве
При плавлении алюминия наилучшие результаты достигаются при быстром плавлении.Сохранение расплавленной пятки алюминия в тигле ускоряет процесс плавления. Если необходимо нагреть несколько зарядов, рекомендуется оставить 1/3 тигля заполненным расплавленным алюминием, чтобы уменьшить тепловой удар тигля и ускорить плавление новой загрузки. Все инструменты, флюсы, емкости и все, что соприкасается с расплавленным металлом, необходимо предварительно нагреть, чтобы минимизировать количество воды, присутствующей на их поверхностях или во флюсе. Поддерживайте температуру алюминия как можно ниже, но настолько высокую, насколько это необходимо для правильной заливки.Не держите металл при высоких температурах в течение длительного времени. Быстро растопить и разлить.
Проблемы, возникающие при плавлении:
Две основные проблемы, возникающие при плавлении алюминия, — это образование шлака и пористость газа. И металлическая шихта, и печь при плавке должны быть чистыми. Тигель и инструменты следует очищать от налипшего шлака и металла соскабливанием после каждой плавки. Если этот материал не удалить, он может расплавиться и смешаться с алюминием.Зарядные материалы должны быть чистыми и не содержать оксидов, воды или масел. Оксиды поглощают влагу, что может привести к пористости отливок. Лучший способ избавиться от влаги и масел — это предварительно нагреть загружаемые материалы.
Образование окалины:
Металлический алюминий обычно покрыт тонкой пленкой оксида, потому что металл легко окисляется на воздухе при комнатной температуре. Эта оксидная пленка образует защитный барьер от дальнейшего окисления. При плавлении алюминия открытая поверхность расплавленного металла окисляется с образованием шлака. Этот шлак может плавать наверху, опускаться на дно или смешиваться с расплавом. Если окалина не «смачивается» алюминием, она будет плавать. Однако, если он намокнет, он может смешаться с расплавом или опуститься на дно. Удельный вес (вес относительно равного объема воды) некоторых материалов, содержащихся в окалине, указан ниже.
Удельный вес компонентов окалины
мг | 1,74 | ||
Si | 2.40 | ||
SiO 2 | 2,40 | ||
Al 2 O 3 3H 2 O | 2,42 | ||
Al | 2,70 | ||
MgO | 3,65 | ||
Al 2 O 3 | 3.99 | ||
CuO | 6,40 |
Другие факторы, увеличивающие количество окалины, включают использование магнийсодержащих сплавов в загружаемом материале, использование тонкого, тонкого или корродированного лома и высокую температуру газа на поверхности расплава. Быстрое плавление снижает количество образования шлака за счет ограничения времени выдержки расплава в атмосфере. Потери при плавлении также выше при «замачивании» или выдержке металла при высокой температуре в течение длительного времени, а также при сжигании топлива с большим избытком воздуха.Неповрежденная пленка оксида обеспечивает защиту расплава, предотвращая дальнейшее окисление и поглощение водорода. Однако, если пленка разорвана, окисление начинается снова при разрыве.
Пористость по газу:
Обычно жидкости растворяют меньше газа при более высоких температурах, однако металлы растворяют больше газа при более высоких температурах. Водород легко растворяется в расплавленном алюминии выше температуры плавления. На 1220 град. F наблюдается значительное увеличение количества газа, который может быть растворен в расплаве, и с повышением температуры увеличивается и способность.Газ в стояке
из алюминия для растворения большего количества газа. По мере охлаждения отливки способность алюминия удерживать газ в растворе уменьшается, и газ образует пузырьки. Они выглядят как точечные отверстия в готовых отливках. Газообразный металл часто образует головку «цветной капусты» наверху стояков. Водород в расплаве алюминия поступает в основном из водяного пара. Выделение алюминия из-за водяного пара вызвано реакцией:
2Al + 3H 2 O -> AlO 3 (дросс) + 6H, растворенный в алюминии.
Количество водяного пара, необходимое для воздействия на алюминий, настолько мало, что количество пара в одном кубическом дюйме воздуха может испортить более 1 фунта металла.
Водяной пар может исходить от поверхности загружаемых материалов, оксидов на загружаемых материалах, влажного флюса, грязных инструментов и скиммеров или от продуктов сгорания. Водород также может поступать из масляного лома. К счастью, большую часть водяного пара и масел можно удалить путем предварительного нагрева и поддержания всего, что соприкасается с металлом, в ГОРЯЧИМ состоянии.Водород также может попасть в поверхностный шлак. При перемешивании расплав может образоваться газ.
Алюминий восстанавливает многие оксиды. Если присутствует оксид железа (ржавчина), то происходит следующая реакция.
Fe 2 O 3 + 2Al -> Al 2 O 3 + 2Fe
При контакте с кремнеземистыми материалами происходит следующая реакция:
4Al + 3SiO 2 -> 3Si + 2Al 2 O 3
Кремний переходит в раствор и образуется дросс.
Алюминий растворяет железо. Сталь более растворима, чем чугун. Однако хромистые стали наиболее устойчивы к коррозионному воздействию жидкого алюминия. Тип расплавленного сплава также влияет на воздействие расплавленного алюминия на сталь, причем цинкосодержащие сплавы являются наиболее агрессивными. Промывки используются для стальных инструментов и тиглей, чтобы предотвратить налипание железа. Доступно несколько коммерческих промывок, однако также используется множество домашних напитков, содержащих слюду, тальк или известняк и силикат натрия.Одна такая промывка состоит из семи фунтов порошкообразного известняка (CaCO 3 ) и 4 унций силиката натрия, смешанных с галлоном воды. Теплый ковш (от 200 до 400 градусов F) окрашивают так, чтобы материал быстро схватывался, а затем сушат на красном огне. Небольшой литейщик легко может использовать для мойки ковша Alum-a Kote, продаваемого Mifco. Покрытия для промывки ковша необходимо будет обновить, так как они трескаются при охлаждении ковша.
Чистота литейного производства предотвращает большинство проблем с выделением газа, однако существуют методы дегазации.Алюминий можно дегазировать путем барботирования сухого азота, аргона или смеси азота и фреона, или азота и хлора, или азота и фтора. Хлор работает хорошо, потому что он снижает поверхностное натяжение металла и позволяет оксидам подниматься вверх. Лучшие дегазаторы создают очень мелкие пузырьки, которые хорошо растворяются в расплаве. Эти более мелкие пузырьки не вызывают сильной турбулентности на поверхности металла, поэтому менее вероятно, что загрязняющие вещества вернутся в расплав. Это достигается с помощью копья с мелкими отверстиями или порами.Наконечники из пористого карбона часто используются на фурмах. Таблетки для дегазации хлора используются, прижимая их ко дну ковша с помощью стержня и чашки. Некоторые домашние мастера-литейщики используют половину чайной ложки «pool Shock », завернутую в кусок алюминиевой фольги, чтобы дегазировать расплав (сохранить его сухим). Я не пробовал использовать хлор для бассейнов и не могу прокомментировать его эффективность. EPA сократило использование прямого хлора.
Часто, если флюсы не высушены и не используются должным образом, они создают больше проблем, чем устраняют для домашнего литейщика.Дегазация не должна использоваться для исправления плохой практики плавления. Проблемы минимальны с «практикой чистой плавки».
Температура заливки алюминия составляет примерно 1380 град. F. Температура заливки определяется текучестью конкретного сплава и типом отливки. Для длинных тонких отливок требуются более высокие температуры, чем для толстых массивных отливок. Некоторые литейщики утверждают, что имеют хорошие результаты при температурах до 1250 градусов. до 1275 град. Ф.
Проверка температуры алюминия
с помощью цифрового термометра
Другие виды:
Автор: Стив Честейн — стивенчастейн.com
Снижение окислительных потерь в расплаве алюминия и его сплавов (Технический отчет)
Дас, Субодх К. и Нингилери, Шридас. Снижение окислительных потерь в расплаве алюминия и его сплавов . США: Н. П., 2006.
Интернет. DOI: 10,2172 / 877410.
Дас, Субодх К. и Нингилери, Шридас. Снижение окислительных потерь в расплаве алюминия и его сплавов .
Соединенные Штаты. https://doi.org/10.2172/877410
Дас, Субодх К. и Нингилери, Шридас. Пт.
«Снижение окислительных потерь в расплаве алюминия и его сплавов». Соединенные Штаты. https://doi.org/10.2172/877410. https://www.osti.gov/servlets/purl/877410.
@article {osti_877410,
title = {Снижение окислительных потерь в расплаве алюминия и его сплавов},
author = {Дас, Субодх К. и Нингилери, Шридас},
abstractNote = {Этот проект привел к лучшему пониманию механизмов образования шлака.Определена эволюция микроструктуры в образцах промышленного шлака. Результаты показали, что окалина формируется слоями, структура и состав которых определяются только локальной концентрацией магния. Этот вывод подтверждается фундаментальными исследованиями поверхностей расплавленного металла. Данные рентгеновской фотоэлектронной спектроскопии показали, что только магний выделяется на поверхности расплавленного алюминиевого сплава и реагирует с образованием растущего оксидного слоя. Методы дифракции рентгеновских лучей, которые использовались для исследования поверхности окисляющегося расплавленного алюминиевого сплава, впервые подтвердили, что оксид магния является исходной кристаллической фазой, которая образуется во время окисления металла.Аналитические методы, разработанные в этом проекте, теперь доступны для исследования других поверхностей расплавленного металла. На основе улучшенного понимания зарождения, образования и роста дросса была разработана технология, позволяющая минимизировать потери расплава. Эта концепция основана на покрытии поверхности расплавленного металла физическим барьером многоразового использования. Испытания в лабораторной отражательной печи подтвердили результаты стендовых испытаний. Основные моменты проделанной работы включают: Получено четкое понимание кинетики образования дросса и влияния различных легирующих элементов на образование дросса.
Было определено, что шлак эволюционирует аналогичным образом независимо от плавящегося алюминиевого сплава, и результаты показали, что сначала образуется аморфный нитрид алюминия, а затем аморфный оксид магния и кристаллический оксид магния во всех сплавах, содержащих магний. Оценка поверхности расплавленного алюминиевого сплава во время плавления и выдержки показала, что оксид магния является первой кристаллической фазой, которая образуется во время окисления чистой поверхности алюминиевого сплава. На основании оценки окалины и испытаний на плавление стало ясно, что основной фактор, способствующий образованию окалины алюминиевых сплавов, - это сплавы с содержанием Mg.Mg был определен как основной фактор, ускоряющий образование шлака, особенно при переходе от двухфазного к трехфазному росту. Таким образом, ограничение окисления магния на поверхности расплавленного алюминия становится ключом к минимизации потерь расплава, и была разработана технология, предотвращающая окисление магния на поверхности алюминия.
Это привело к тому, что большая часть работы была сосредоточена на контроле окисления Mg. Были идентифицированы два потенциальных покрывающих агента из расплавленного металла, которые могут препятствовать образованию шлака во время плавления и выдержки, состоящие из борной кислоты и нитрида бора.Последнее было отвергнуто промышленностью, так как оно привело к улавливанию бора расплавом сверх того, что допускается спецификациями во время заводских испытаний. Понимание кинетики образования дросса отраслевыми партнерами помогло им понять, как температура, химический состав сплава и атмосфера в печи (регуляторы горения - например, избыток воздуха) влияют на образование дросса. Это позволяет им вносить изменения в производственный процесс, которые сокращают ненужную выдержку при высоких температурах, управлять конфигурациями горелок, уменьшать количество дверных проемов, чтобы избежать попадания воздуха, и оптимизировать загрузочные смеси для обеспечения быстрого плавления и предотвращения избыточного окисления.