Плавка бронзы Бр. О4Ц4С17 — Литейный цех
Ага. В общем понял следующее, поправьте, если что не так:
1. Отливка — половина цилиндра (разрез по вертикали), внешний диаметр 300 мм, внутренний 180 мм и высота 350 мм (толщина стенки 60 мм). Масса детали соответственно 70 килограмм.
2. Поры вскрылись на внутренней поверхности цилиндра после мех.обработки, на поверхности отливки пор нет.
3. Положение отливки во время заливки — вертикальное, заливка металла непосредственно в полость под отливку сверху.
Теперь что могу сказать:
1. Это не газовые поры, а усадочные дефекты. Данный сплав имеет широкий интервал кристаллизации и высокую ликвацию свинца в расплаве (поскольку при такой концентрации он там полностью не растворяется). Соответственно сначала кристаллизуется более тугоплавкая фаза и легкоплавкая. Из-за разницы объёмов жидкой и твердой фазы образуется распределенная усадка, а не концентрированная раковина. Соответственно нужно решать эту проблему, а не с газом мучится.
По моему (правда маленькому) опыту тут есть 2 варианта решения:
1) Установка прибылей — на такую деталь проблематично поставить. Отливка равностенная и протяженная. Сбоку прибыли не поставить, только сверху.
2) после заливки подпитывать отливку после заливки. Из опыта: был случай — отливали гайку из бронзы в кокиль, масса под 2 тонны. Заливку вели сверху. Во время заливки поверхность присыпали теплоизолирующим материалом, а после того как отлили детальку, но до того как она полностью кристаллизовалась делали доливку металла, причем не в одной точке а в 3-4 по периметру, если с одной стороны, то как говорили с одной стороны металл плотный, а с другой весь в порах.
2. По поводу плавки: уголь или графит сверху нужен для создания восстановительной атмосферы. Углерод окисляется и улетает унося с собой кислород, в том числе и из расплава. Соответственно при плавке под покровом углерода лучше накрывать печь или крышкой или тиглем. У нас печи маленькие используем тигли.
3) Хочу обратить внимание на химсостав отливки. Внизу и вверху отливки содержание свинца может различаться на несколько процентов. Недавно сами плавили высокосвинцовистую бронзу — для собственных нужд поэтому состав на глазок, но когда заливали последнюю отливку последний металл был явно с большим содержанием свинца, даже цвет был серый.
Бронзы Плавка — Энциклопедия по машиностроению XXL
При плавке на воздухе медь окисляется с образованием оксида меди. Для предохранения от окисления и поглощения водорода плавку ведут под слоем древесного угля. Нагретый до температуры 1200 °С расплав раскисляют фосфористой бронзой, затем вводятДля плавки меди и ее сплавов применяются шахтные, а при загрузке более 3 т-—барабанные печи и миксеры. Максимальная емкость их — примерно 35 т, удельный расход электроэнергии при плавке меди — около 300 кВт-ч/т, при плавке медных сплавов— около 200 кВт-ч/т. Коэффициент мощности при плавке меди составляет примерно 0,5 при плавке бронз и латуней— примерно 0,7 при плавке медноникелевых сплавов — примерно 0,8.
[c.275]
При выборе оловянных бронз конструктор должен максимально использовать возможности этого материала и стремиться к минимальному весу деталей. Свойства оловянных бронз, указанные в ГОСТах и технических условиях, являются минимальными особенно это касается литейных бронз, так как их свойства зависят не только от химического состава, но и от условий получения отливки (наличия и количеств примесей, качества плавки, свойств литейной формы, основных параметров заливки, толщины стенок отливки и многих других причин). Оловянные бронзы имеют хорошие литейные свойства, что позволяет получать из них отливки сложной конфигурации, с толщинами стенок от 3—5 мм и более.

При плавке магниевых и алюминиевых сплавов и бронз [c.11]
При плавке магниевых сплавов При плавке магниевых и алюминиевых сплавов и бронз и в качестве присадок при плавке кальциевых баббитов [c.11]
При изготовлении магниево-марганцовистых лигатур Для рафинировки алюминия и его сплавов, баббитов и оловя-нистых полуд При плавке магниевых и алюминиевых сплавов и бронз
Печь работает на мазуте. Удельный расход топлива — около 9%, а на первую плавку (включая разогрев печи) — около 12/о. Угар бронзы — около ЗО/о- [c.150]
Плавка бронз и латуней [c.193]
Для получения бронзы указанного состава составляют шихту из 65,5—64,0 /g u, 33,0 — 34,50/0 РЬ и 1,50/0 фосфористой меди МФ (12о/о) [8]. Плавку рекомендуется вести в продолжение 1,5—3 час. [c.158]
Данные о дуговых электропечах для плавки бронз и латуней приведены в табл. 10, о тигельных горновых печах— в табл. 11 и об электропечах для алюминиевых сплавов — в табл. 12.
[c.10]
Тигельные горно- Плавка бронзы и От 100 Мазут 10-14 От 100 5-8 [c.59]
Пламенные печи Плавка бронзы [c.59]
Электрические ду- Плавка бронзы и [c.59]
Электрические ин- Плавка бронзы и 600 — 300 400 1-2 [c.59]
Конец плавки можно определить по цвету наружной поверхности заливаемой заготовки. К концу заливки заготовка по всей длине приобретает ярко-желтый цвет. После этого питание дуги прекращают, а втулку продолжают вращать в течение нескольких минут до полного затвердевания бронзы (пока наружная поверхность втулки не станет темно-вишневого цвета). [c.357]
При заливке чугунных заготовок бронзой во избежание оплавления внутреннего слоя чугуна плавку нужно вести на пониженной силе тока и не допускать местных перегревов. Толщина стенок чугунных заготовок должна быть не менее 12—13 мм.
[c.357]
Наличие оловянной кислоты в бронзе является следствием того, что при плавке бронзы была допущена чрезмерно высокая температура в печи при наличии окислительной атмосферы. При этом выплавленный металл не был достаточно хорошо раскислен перед его разливкой по формам.
Плавка бронзы осуществляется электрической дугой в стальной или чугунной вращающейся втулке. [c.212]
Продолжительность плавки, мин оловянные бронзы .. 35—45 40—50 60 [c.26]
Расход электроэнергии на плавку, кВ оловянные бронзы ч/tj 300 — 360 250—320 230—290 [c.26]
Исходные материалы глинозем, кварцевый песок, магнезит, флюоритовый концентрат, фтористый натрий. Плавка в электропечи. Грануляция в воду. Применяется при наплавке и сварке бронзы электродными лентами. [c.101]
В условиях плавки цветных металлов и их сплавов (меди, бронзы, латуни) в индукционных печах наконечник из сплава Ti — 20 % Со, используемый совместно с платинородий-платиновой термопарой, имеет более высокую стойкость в расплаве, термо- и окалиностойкость при температурах 1100 °С по сравнению с наконечниками иэ молибдена и керамики [1].
Для предохранения от окислениям поглощения водорода плавку меди ведут под слоем древесного угля. Нагретый до температуры 1200 °С расплав раскисляют фосфористой бронзой, затем вводят лигатуры или чистые металлы для получения требуемого химического состава. При необходимости расплав вторично раскисляют фосфористой медью. [c.209]
В качестве генераторов высокой частоты для высокочастотной закалки применяются машинные генераторы с частотой 500—10 ООО гц при мощности 7,5—2000 /сет. При этом для поверхностной закалки наиболее универсальными, простыми и надежными в эксплуатации оказались генераторы с частотой 8000 гц. Машинные генераторы служат для поверхностной закалки на глубину 2—5 мм больших и малых валов, пальцев, шеек коленчатых валов, распределительных валов, шлицевых валов, всевозможных деталей автомобиля, гильз цилиндров, втулок и т. д., для плавки стали, бронзы и латуни, а также для кузнечного нагрева и пайки.
257]
По сравнению с оловянистыми бронзами алюминиевые обладают несколько худшими литейными качествами дают большую усадку, более склонны к образованию треш,ин при затрудненной усадке, при неблагоприятных условиях плавки и заливки больше насыщаются газами и окисляются. У алюминиевых бронз вследствие образования окислов алюминия труднее получить герметичные отливки сложной формы, наконец, они труднее поддаются пайке. [c.454]
Дуговые однофазные печи Д МК (табл. 12) косвенного нагрева применяют для плавки меди и ее сплавов (бронз, латуней). Расплавление и перегрев металла в печах проводят независимой дугой, питающейся однофазным трансформатором, переменным током от специального трансформатора. [c.293]
Медные сплавы плавят в пламенных, дуговых и индукционных печах. Плавка большинства медных сплавов на воздухе сопровождается окислением элементов шихты и растворением водорода. Окисление сплавов, содержащих алюминий, кремний, бериллий, происходит с образованием плотной оксидной пленки на поверхности расплава, которая оказывает влияние на механические свойства отливок. Медные сплавы при затвердевании склонны к образованию газовой пористости (за исключением латуни), особенно характерной для сплавов с широким температурным интервалом кристаллизации, в частности для оловянных бронз.
[c.306]
При переработке отходов меди ь ее сплавов чаще всего получают бронзы и латуни. Выплавку оловянных бронз осуществляют в отражательных печах латуней — в индукционных. Плавку ведут в переходящей ванне, объем которой составляет 35—45 % объема печи. При плавке латуни в первую очередь загружают стружку и флюс. Выход годного металла составляет 23—25 %, выход шлаков — 3—5 % массы шихты расход электроэнергии изменяется от 300 до 370 кВт-ч/т.
Магниевая бронза содержит 0,3—1% М и также при повышенных температурах представляет собой твердый раствор, из которого при понижении температуры выпадает соединение u2Mg. Магниевая бронза разработана как заменитель кадмиевой бронзы, плавка которой затруднена из-за выделения паров кадмия, опасных для здоровья человека. Кроме того, магний значительно дешевле и доступнее кадмия.
[c.222]
Особенностью алюминиевых бронз являете повышенная по сравнению с оловяинымн бронзами величина усадки, что вызывает необходимость применения особых предосторожностей при заливке для получения качественного. литья. Алюминиевые бронзы более склонны к трещииообразованию при затрудненной усадке, повышенному газонасыщению и окислению при неблагоприятных условиях плавки и заливки. Алюминиевые бронзы как материал обладают высокой гидроирочностью, однако получить из них герметичные отливки слол -1ЮЙ конфигурации часто труднее, чем из оловянных бронз из-за образующихся в сплаве окислов алюминия. Недостатком алюминиевых бронз является также трудность, с которой они поддаются пайке. [c.224]
В качестве примера таких испытаний можно привести работу П. Е. Дьяченко, А. И. Нисневича и В. Э. Вайнштейна [66], которые актировали образцы введением в плавку радиоактивного изотопа.

Научный и практический интерес представляет установление концентрационного интервала предельного легирования магнием бериллневых бронз. С этой целью исследовались сплавы одной плавки с содержанием магния от 0,13 до 0,4%, полученные в высокочастотной индукционной вакуумной печи (табл. 14). [c.60]
Бронза оловянно-цинковая — Плавка 6 — 193 Бронза оловянно-цинковая БрОЦ 4-3, BpOll [c.22]
Плавка чугуна нирезист производится в пламенных печах или в вагранках. По коррозио-стойкости и механическим свойствам (см. табл. 64 — 66) отливки близки к латуням и бронзам и превышают последние по износостойкости. Благодаря аустенито-графитной структуре в сплаве удачно сочетаются коррозиостойкость с жароупорностью и сохраняются прочность и плотность при длительных нагревах до высоких температур (при температуре 450° С предел прочности при растяжении падает всего на 3 кг мм , при 700° С — примерно на 50%).
[c.56]
Плавиковый шпат (ручного обогащения по ОСТ НКТП 7633-655). Плавиковый шпат, или флюорит, представляет собой минерал кристаллического строения, содержащий в основной своей массе СаРз. Удельный вес в твёрдом состоянии — 3,18, температура плавления 1378° С. Применяется в качестве флюса а) 2-й и 3-й сорта — при плавке чугуна и стали б) 1-й сорт—при илавке магниевых и алюминиевых сплавов, а также бронз. При плавке магниевых и алюминиевых сплавов может быть использован только в сухом состоянии, получаемом путём сушки и прокаливания. По содержанию составных частей плавиковый шиат ручного обогащения должен отвечать требованиям, приведённым в табл. 26. [c.7]
Пламенные Бронзы — в барабанных печах типа, Мечта», а также (в небольших литейных) в малых отражательных печах типа, Экономплав Бронзы и алюминий для крупных отливок — в больших отражательных печах Ковкий чугун в непоточном производстве — вращающиеся печи Бракельсберга, а также (для плавки на пылевидном топливе) отражательные печи, иногда серый чугун в малых пламенных печах Для тяжёлого литья (мартеновские печи)
[c. 145]
Печи с железным сердечником (типа ИЛН6) применяются для плавки латуней, мельхиора и бронз. Они представляют собой своеобразный тип трансформатора, у которого вторичной обмоткой служит расплавленный металл. Плазильное пространство печя (фиг. 309) состоит из двух частей шахты 1 и узкого плавильного канала 2, отформованного в специальном подовом камне 3. Канал, имеющий прямоугольное сечение и треугольную (или кольцевую) форму, охватывает сердечник 4 и первичную обмотку горизонтально расположенного трансформатора. [c.163]
Для того чтобы предотвратить насыщение металла газами, следует при плавке бронз избегать его перегрева и обязательно применять защитные покровы. Используются древесный уголь, сода, поташ, битое стекло, бура, кварцевый песок и т. д. Небольшие количества металла изготовляют в тиглях, большие — в пламенных печах (например типа Экономплав) или, лучше, в электрических печах типа Детройт. Последние дают меньший угар металла и обеспечивают его большую однородность благодаря перемешиванию при качании печи. Разливка бронз производится при температуре 1100—1150° С.
[c.193]
Ручная заливка баббитом или свинцовистой бронзой с предварительной сборкой формы для обычной (фиг. 30) или сифонной (фиг. 31) заливки Тигель для плавки сплава с газовым или электрическим подогревом Плита для сборки формы, стержень, черпак устройство для ускоренного охлаждения (обрызгиванием или обдувкой воздухом) Во избежание утечки сплава черея неплотности формы применяют обмазки Ь5°/о глины. 17о/о соли поваренной, 18°)о воды для баббита или 30°/о мела, 35° о графита и 350/о воды для свинцовистой бронзы [c.510]
Борткевича резцы 299 Бронзирование — Режимы 723 Бронзы — Сварка газовая 203 — Угар 56 — Усадка 22 — алюминиевые — Температура плавки и заливки 56 — оловяяистые — Температура плавки и заливки 56 Бруски для отделочного шлифования — Характеристика 423 — притирочно-шлифовальных головок— Размеры 420, 421 Бульдозеры 128, 129 Бутан—Характеристика 198
[c. 763]
Бериллиевые бронзы содержат 1,8,.,2,5% Be, применяются в промышленности после упрочнения путем закалки и отпуска. Структура этих бронз (например, БрБ2) после термической обработки содержит вьщеления СиВе, очень дисперсные и расположенные определенным образом внутри зерен твердого раствора. Образование высокодисперсных включений СиВе приводит к очень большому упрочнению бронз g= 1200… 1300 МПа, твердость 350…400 НВ при снижении пластичности до 1,2…2%. Кроме того, упрочненные бериллиевые бронзы характеризуются исключительно высокой упругостью и повышенной электропроводностью. Они хорошо обрабатьшаются резанием и свариваются. Недостаток бронзы БрБ2 — высокая токсичность паров бериллия, что требует соответствующей техники безопасности при плавке. [c.209]
S10, 41 47 МпО, 25—32 Na,0 10— 15 AlaOa 11—14 Покровные для оловянных бронз при плавке в печах с шамотной футеровкой [c.158]
Алюминиевые бронзы обладают повышенной по сравнению с оловянными бронзами усадкой при затвердевании, что требует особых технологических приемов при производстве фасонных отливок склонны к газонасы-щению и окислению при неблагоприятных условиях плавки и заливки более склонны к трещинообразованию при затрудненной усадке обладают высокой гигроскопичностью, что затрудняет получение фасонных отливок сложной конфигурации из-за образующихся в них окислов алюминия. Алюминиевые бронзы обладают более высокой жидкотекучестью, меньшей склонностью к дендритной ликвации.
[c.204]
Бронзы плавка — Справочник химика 21
Создание вакуума (давление ЫО Па) в печи позволяет осуществлять термотехнологические процессы, которые не могут протекать при других условиях (например, рафинирование алюминиевых сплавов, плавка хромистой бронзы и т. д.). Создание псевдоожижен- [c.117] Печи для плавки сплавов на основе меди. Канальные индукционные печи для плавки и подогрева меди и спла ВОВ на медной основе (латуни, бронзы, томпака, мель хиора и т. п.) изготавливаются как периодического, так и непрерывного действия (миксеры). Корпус печи кон струируется прямоугольной или цилиндрической формы В последнее время применяют печи барабанного типа со сменными индукционными единицами. На рис. 3.10 при ведена конструкция печи ИЛК-16, имеющей цилиндри ческую ванну и щесть индукционных отъемных единиц Футеровка выполняется из шамотной набивной массы Теплоизоляцией служит диатомитовый кирпич. При плавке латуней и бронз температура разлива составляет 1100—1200° С. Большой перегрев металла свыше указанного значения может вызвать так называемую цинковую пульсацию, которая возникает при парообразовании цинка, входящего в состав расплава (цинк кипит при 916° С, тогда как температура плавления меди 1083° С). Цинковая пульсация выражается в кратковременном прекращении тока в каналах печи и затем его восстановлении, так как парообразование при исчезновении тока прекращается. Это приводит к характерному качанию стрелок измерительных приборов. [c.124]
Обычно магнитопровод шихтуется из листов прямоугольной формы. Листы стягиваются шпильками, вдетыми в изолирующие втулки из текстолита или бакелита. Стяжные болты и шпильки изготовляются из немагнитной стали или бронзы. Для увеличения жесткости пакета наружные листы выполняются из немагнитной стали толщиной 5—10 мм. Поперечное сечеиие ярма и сердечника делаются прямоугольным или квадратным, и только в случае больших индукций сечение сердечника выполняется крестообразным или многоступенчатым.

Плавка хромистой бронзы в вакууме позволяет не только освободить металл от растворенных газов (водород, кислород, азот), но и снизить содержание вредных легкоплавких примесей висмута, свинца и сурьмы, оказывающих значительное влияние на снижение жаропрочности хромистой бронзы. [c.79]
Олово применяют для лужения жести, в производстве сплавов (бронз, баббитов), для пайки и припоя, для изготовления фольги. Мировое производство олова составляет сейчас около 250 тыс. т в год. В природе олово встречается в виде минерала касситерита ЗпОг. Оловянные руды, содержащие этот минерал, вначале обогащают (преимущественно гравитацией). Концентраты после предварительной обработки для удаления основного количества примесей (обжига, магнитной сепарации, спекания с содой и т. д.) подвергают восстановительной плавке в отражательных или электрических печах с получением чернового олова. [c.117]
Возникновение М. относится к глубокой древности, выплавка меди производилась уже в 7-б-м тыс. до н.э. (юго-зап. часть Малой Азии). Вначале человек познакомился с самородными металлами-золотом, серебром, медью и метеоритным железом, а затем научился производить металлы. Первые металлич. изделия изготовлялись в холодном состоянии. После открытия горячей обработки (ковки) металлич. изделия получают более широкое распространение. Первоначально выплавку Си производили из окисленных медных руд (литье, 5-4-е тыс. до н.э.), переработка сульфидных руд, их окисление и рафинирование Си относятся ко 2-му тыс. до н. э. (Ближний Восток и Центр. Европа). Во 2-м тыс. до н.э. медь стала вытесняться ее сплавом — бронзой (бронзовый век). В сер. 2-го тыс. до н.э. осваивается получение Ре из руд (сыродутный процесс). В дальнейшем успехи в произ-ве Ре (овладение процессами его науглероживания и закалки) привели к появлению литого металла и стали. Эти усовершенствования обеспечили главенствующее положение черным металлам среди материалов уже в 1-м тыс. до н.э. (железный век). На протяжении почти трех тысячелетий М. железа не претерпевала принципиальных изменений. В 18 в. в Европе открыт способ произ-ва литой стали (тигельная плавка), а в 19 в.-еще три новых процесса (бессемеровский, мартеновский и тома-совский). [c.52]
Особо чистое О. для полупроводниковой техники получают дополнит, очисткой-электролизом и зонной плавкой, восстановлением очищенных хлоридов. Вторичное О. извлекают из отходов белой жести и сплавов, напр, бронз. Для переработки бедных концентратов перспективно применение способов, основанных на высокой летучести хлоридов О. и их способности восстанавливаться А1, М Zn. [c.383]
Несколько иной является практика использования рафинировочных шлаков Московского медеэлектролитного завода. Их плавят в шахтной печи в составе шихт, содержащих шлаковый (15-20% Си) и латунный лом, агломерат, флюсы (все пр 15-25%) и 17% кокса. Продукт плавки — черновая бронза состава, % 82-85 Си 4,5-5,0 Sn 4,5-6,0 Ptr, [c.126]
В целом шахтная и конвертерная плавки обеспечивают достаточно высокое извлечение ряда металлов (медь, цинк, свинец, олово), однако неудовлетворительно извлекаются никель и кобальт. Последние на 70-80% переходят в черную, а затем черновую медь, из которой далее практически не извлекаются и, кроме того, отрицательно влияют на процесс получения катодной меди. Тем не менее восстановительная шахтная плавка и конвертирование остаются основными методами переработки медьсодержащего сырья на черновую медь и бронзу. В них заложены значительные резервы улучшения технико-экономических показателей производства, в частности шахтной плавки, за счет применения воздуха, обогащенного кислородом до 25%, и дутья, подогретого до 350°С (Худяков…-1985 г.). [c.129]
Недостатками дуговых печей являются некоторый угар металла вследствие местного перегрева в зоне электрической дуги, недостаточная стойкость футеровки, подвергающейся действию открытой дуги, а также значительный шум, создаваемый дугой. Поэтому дуговые печи косвенного нагрева имеют ограниченное применение, их используют для плавки медных и никелевых сплавов (латуни, бронзы и некоторых других). Угар металла, в основном цинка, при плавке латуни достигает 3—4%, удельный расход энергии находится в пределах 300—350 квт-ч1т для латуни, 350—400 квт-ч1т для меди и бронзы и 600— 850 квт-ч1т для медноникелевых сплавов. [c.269]
В печах со стальным сердечником достигается весьма малый угар металла (I—2%) и пониженный удельный расход электроэнергии по сравнению с печами дуговыми и сопротивления при плавке латуни 200—220 квт-ч т, бронзы — 300—350 квт-ч т, для алюминиевых сплавов — 450—500 квт-ч т. [c.275]
Индукционные печи с железным сердечником емкостью 0,3 0,6 1,2 и 2 т применяют в крупных литейных цехах для плавки меди, латуни, бронзы, никеля и других цветных металлов и сплавов. [c.234]
Отражательная печь для плавки бронзы и латуни (пыль, возгоны, в основном ZnO). ………….. 2,5-0,08 99—82 72—97 1,4 [c.110]
Зазор между кожухом и каркасом на участке, где нет огнеупорной кладки, заполняют теплоизоляционным материалом. Каркас из немагнитного металла для плавки бронзы и латуни набивают массой, состоящей из 96% мелкоизмельченного кварца, 2% буры, 1,5% дробленого стекла и 0,5% глины для плавки никелевых сплавов— 96,5% магнезита, 3% и 0,5% дробленого стекла. [c.252]
Факторы, влияющие на растворимость газов в жидкостях, учитываются в практической работе. Например, чтобы повысить содержание двуокиси углерода в готовом npo iyKTe, процесс получения газированных вод и шампанских вин ведут при повышенном давлении и сравнительно низкой температуре. Удаление растворенных газов из жидкостей, где их присутствие нежелательно, осуществляется длительным кипячением этих жидкостей. Так готовят дистиллированную воду, не содержащую двуокись углерода, для точных анализов. При получении высококачественных сталей, высокоэлектропроводной меди, бериллиевых бронз и изделий из них, не содержащих растворенных газов, применяют плавку и литье в вакууме. [c.253]
Плавка бронзы и латуни Камерная — 0,11—0,13 [c.187]
Термообработка стали нормализация закалка отпуск Плавка чугуна Плавка бронзы и латуни Обжиг цементного клинкера Обжиг шамотных огнеупоров Обжиг красного кирпича [c.133]
При плавке бронз и латуней……..0,60—0,80 [c.288]
Чистое железо не очень твердое. Однако в процессе плавки железо может вобрать в себя столько углерода из древесного угля, что в результате образуется поверхностный слой сплава железа и углерода, называемого сталью. Этот сплав тверже самой лучшей бронзы, и изготовленный из него наконечник после заточки долга остается острым. Получение стали явилось поворотным моментом в-нстории развития металлургии и в истории развития общества. Наступил железный век. [c.12]
При плавке алюминиевых сплавов и алюминиевых бронз содержащийся в сплаве алюминий химически взаимодействует с футеровкой, при этом он активно восстанавливает кремний из кремнезема П1 лукислой или алюмосиликатной футер. вки, Он также может реаги-рогать с оксидами железа и хрома, обычно в небольших количествах присутствующих в футеровочных материалах [c.88]
Большой проникающей способностью обладает свинец, оказывая пагубное действие на футеровку индукционных канальных печей при плавке свинцовых и оловосвинцовых бронз. Находясь в бронзах в элементарном состоянии, он хорошо смачивает футеровку и пропитывает почти всю толщу огнеупорной массы до слоев, где температура ниже температуры кристаллизации эвтектики (около 326 °С). Металлизация приводит к резкому возрастанию потерь теплоты кроме того, периферийные слои футеровки теряют пластичность, что обусловливает появление глубоких трещин и резкое сокращение срока службы футеровки. [c.110]
Основнуюмассу марганца выплавляют В виде ферромарганца (сплав 60—90% Мпи40—10% Ре). Марганец (в виде ферромарганца) обладая большим сродством к кислороду, используется как раскислитель при плавке стали.

Применение марганца и рения. Марганец в виде ферромарганца применяется для раскисления стали при ее плавке, т. е. для удаления из нее кислорода. Кроме того, он связывает серу, что также улучшает свойства сталей. Введение до 12% Мп в сталь, иногда в сочетании с другими легирующими металлами, сильно упрочняет сталь, делает ее твердой и сопротивляющейся износу и ударам. Такая сталь используется для изготовления шаровых мельниц, землеройных и камнедробильных машин и т. д. В зеркальный чугун вводится до 20% Мп. Сплав 83% Си, 13% Мп и 4% N1 (манганин) обладает высоким электросопротивлением, мало изменяющимся с изменением температуры. Поэтому его применяют для изготовления реостатов и пр. Марганец вводят в бронзы и латуни. Диоксид марганца используется как катализатор и наряду с другими соединениями (КМПО4 и т. п.) как окислитель. [c.343]
Окись бериллия, как и сам металл, находит применение в ядерной технике в качестве замедлителя и отражателя нейтронов и как конструкционный материал, особенно в высокотемпературных реакторах. В традиционных областях применения значение окиси бериллия не только сохранилось, но и увеличилось как огнеупорный материал ВеО в ряде случаев незаменима. Это касается, в частности, изготовления тиглей для плавки металлов (Ве, U, Th, Ti), где используется такое уникальное свойство ВеО, как необычайно высокая теплопроводность наряду с огнеупорностью. Широко используется при конструировании индукционных печей и вакуумных нагревательных приборов. Весьма перспективным огнеупорным материалом является пористая керамика из окиси бериллия, получаемая пенометодом [51] и выдерживающая температуру 1750°. В связи с высокой устойчивостью к тепловому удару ВеО находит применение в авиации для изготовления лопастей газовых турбин и деталей реактивных двигателей. Важная область применения окиси бериллия — получение медно-бериллиевой лигатуры, используемой в производстве бериллиевых бронз. Применяется ВеО и как катализатор в некоторых органических синтезах. [c.188]
Алюминиевые бронзы морозостойки, не магнитны и не дают искры при ударах. Отрицательным свойством этих сплавов по сравнению с оловянными бронзами является повышенная величина усадки при затвердевании, склонность к трещинообразованию, газонасыщению и окислению при неблагоприятньтх условиях плавки и заливки. Они трудно поддаются пайке мягкими и твердыми припоями. Поэтому применяются для литья деталей простых форм. [c.93]
ЛИГАТУРА (лат. ligatura — связка) — вспомогательный сплав, добавляемый в жидкие металлы или сплавы, чтобы изменить их хим. состав и улучшить свойства. Легирующий элемент усваивается из Л. лучше, чем при введении его в чистом виде. Л. получают сплавлением необходимых компонентов или восстановлением их из руд, концентратов или окислов. Наибольшее применение Л. находят в черной металлургии, гл. обр. для модифицирования и легирования сталей и чугунов. Использование в качестве модификаторов спец. Л. (преим. кремний — магний — железо и кремний — кальций — магний— церий — железо) дает возможность получать высокопрочный чугун с шаровидным графитом, значительно превосходящий по физико-мех. св-вам обычный серый чугун с пластинчатым графитом и не уступающий сталям некоторых марок. Л. добавляют непосредственно в плавильные агрегаты или в ковш. Большое значение имеют Л. в произ-ве алюминия сплавов, меди сплавов, цинка сплавов, магния сплавов, бронз, латуней и др. цветных сплавов, где служат промежуточными сплавами, вводимыми в осн. сплав в процессе плавки. Так, кремний, марганец, медь и др. элементы вводят в расплавленный алюминиевый (основной) сплав в виде предварительно сплавленных Л.
, напр. алюминий — кремний (20—25% Si), алюминий — марга- [c.700]
СУРЬМЯНИСТАЯ БРОНЗА — бронза, осн. легирующим элементом которой является сурьма. Относится к литейным бронзам. В СССР изготовляют С. б. четырех марок (табл. 1, 2). Структура С. б.— двухфазная. Альфа-фаза С. б., богатая медью, является твердым, раствором меди, сурьмы и никеля. Бета-фаза состоит из металлического соединения СизЗЬ, к-рое играет роль твердой составляющей. С. б. мало окисляется при литье. Отличается хорошими антифрикционными (из-за наличия двух фаз различной твердости) и мех. св-вами. Антифрикционные св-ва улучшает свинец. Добавки никеля, ципка и фосфора улучшают мех. св-ва и коррозионную стойкость. С. б. выплавляют в индукционных печах, в печах типа АЯКС, ДМК и др. Во избежание образования в отливке газовых раковин и трещин плавку ведут в слабоокислительной среде, используя предварительно прокаленные шихтовые материалы. С. б. ирименяют вместо оловянистой бронзы для изготов.тения подшипников, червяч- [c. 487]
Для экспрессного контроля содержания хрома в хромистой бронзе по ходу плавки нами был применен отечественный 36-канальный фотоэлектрический спектрометр ДФС-10. Пробами служили диски, отлитые в массивные чугунные изложницы открытого типа (рис. 1). Воздействию разряда подвергалось-плоское малое основание диска после удаления с него коркового слоя толщиной 1—2 мм [1]. Изучение макрошлифов показало, что эта форма пробы обеспечивает направленный рост мелкозернистых столбчатых кристаллов перпендикулярно обыскри-ваемой поверхности, спектральная проверка подтвердила однородность проб. [c.22]
Зазор между кожухом и каркасом на участке, где нет огнеупорной кладки, заполняют теплоизоляционным материалом. Каркас из немагнитного металла для плавки бронзы и латуни набивается массой, состоящей из 96% мелкоизмельченно-го. кварца, 2 /о буры, 1,5°/о дробленого стекла и 0,5 /о глины для плавки никелевых сплавов —96,5 /омагнезита 3 /о буры и 0,5% дробленого стекла. Сердечники (магнитопроводы) собирают из листов трансформаторной стали. Электрический ток напряжением 220 в подается к печи по гибкому медному кабелю. Производительность печи порядка 20 т в сутки при трехсменной работе. [c.235]
Полиалкилиден [(СНз)СН] , где п = 200—1000, представляет собой твердое, прозрачное, стеклообразное плавкое инертное вещество. Полимеры этого типа получают полимеризацией 1-ди-азоалкана с выделением Na катализатор — безводный uS04, u-бронза или Си-порошок. [c.194]
Применение. Важной областью применения Б. являются различные сплавы, в к-рые Б. вводится как легирующая добавка. Большое значение имеют сплавы Си—Ве, т. и. бериллиевые бронзы, содер-н ащие до 2,5% Ве с добавками Ni и Со (0,2—0,5%) приобретающие после закалки и отпуска (старения) высокую прочность и твердость, а также хорошую электропроводность, теплопроводность и коррозионную стойкость (см. Меди сплавы). Практич. применение нашли также сплавы Ni с 2—4% Б. Эти сплавы по сопротивлению коррозии, прочности п упругости сравнимы с высококачественнгдми нержавеющими сталями, но превосходят последние по твердости, способности к ковке и термич. обработке. К улучшению свойств приводит введение Б. и в железные сплавы. Ничтоншые добавки Б. к магниевым сплавам повышают их сопротивление коррозии, сильно уменьшают окисляемость сплавов во время плавки и разливки. Сплавы о Б. находят применение в самолетостроении, электротехнике и др. В конструкциях атомных реакторов Б. благодаря малому поперечному сечению захвата тепловых нейтронов используется как замедлитель и отражатель нейтронов. [c.212]
Пористые материалы. Регулированием зернистости исходных порошков и режимов прессования и спекания можно создать изделия с дисперсной и равномерно распределенной пористостью, что недостижимо методами плавки. К важнейшим изделиям из металлокерамич. пористых материалов относятся пористые подшипники, металлич. фильтры и др. Пористые подшипники производят из бронзы, железа, иногда на алюминиевой основе. Смесь исходных порошков и графита (2—3%) прессуют до заданной пористости (25—40%) и спекают в условиях, тормозящих усадку (см. ниже), после чего изделия калибруют в прессформе. Включения графита создают сухую смазку при эксплуатации подшипника. Поры подшипников пропитывают маслом или нек-рыми пластмассами. Такие самосмазывающиеся подшипники работают без внешней смазки, что важно в узлах машин, где затруднена подача смазки, или при опасности загрязнения продукции (в пищевой, текстильной пром-сти и др.). [c.135]
Другой способ удаления шабючов состоит в расплавлении их включением индуктора печи под напряжение при первой плавке. Для этого шаблоны должны изготовляться из металла нли сплава, желательно из того же, который будет выплавляться в печи, или близкого к нему по составу (например, шаблон печн для плавки латуни ]1ли бронзы может изготовляться из меди). Нагрев и расплавление литого шаблона во избежание растрескивания подового камня ведется по определенному графику и длится около суток. В некоторых случаях шаблоны изготовляются сварными из листовой стали (толщиной около 3 [c.309]
Особенности плавки медных сплавов » Все о металлургии
23.04.2015
Плавку меди ведут на воздухе, в среде защитных газов и в вакууме. При плавке на воздухе медь окисляется. Образующаяся закись (Cu2O) растворяется в жидкой меди Содержание кислорода в расплаве определяет выбор состава футеровки плавильных печей. Для плавки меди с повышенным содержанием кислорода используют футеровку из магнезита Применение футеровки из кремнезема SiO2 в этом случае недопустимо из-за возможного оплавления ее при взаимодействии с закисью меди с образованием легкоплавких силикатов: mCu2O+nSi02 → mCu2O*nSiO2.
Расплавленная медь взаимодействует с сернистым газом с образованием сульфида Cu2S и интенсивно растворяет водород (до 24 см3 на 100 г). Между содержанием кислорода и водорода в расплавленной меди устанавливается динамическое равновесие, характеризуемое диаграммой Аллена (рис.

Взаимодействие с газами идет тем интенсивнее, чем выше температура перегрева расплава. Для предохранения от окисления и поглощения водорода плавку меди ведут под покровом древесного угля, в восстановительной или защитной атмосфере. Необходимым условием применения древесного угля является тщательная сушка, а в ряде случаев прокалка его для удаления адсорбированной влаги и продуктов сухой перегонки. Однако и при соблюдении всех мер предосторожности окисление все же происходит; некоторое количество кислорода обнаруживается в меди после расплавления.
Содержание кислорода в расплавленной меди может быть определено по его активности. Этот метод основан на измерении электродвижущей силы высокотемпературного концентрационного (по кислороду) гальванического элемента, одним из электродов которого служит исследуемый расплав. Вторым электродом является электрод с известным постоянным окислительным потенциалом. Содержание кислорода в твердой меди определяют металлографическим путем по площади, занимаемой эвтектикой (Cu + Cu2O) или методом вакуум-плавления.
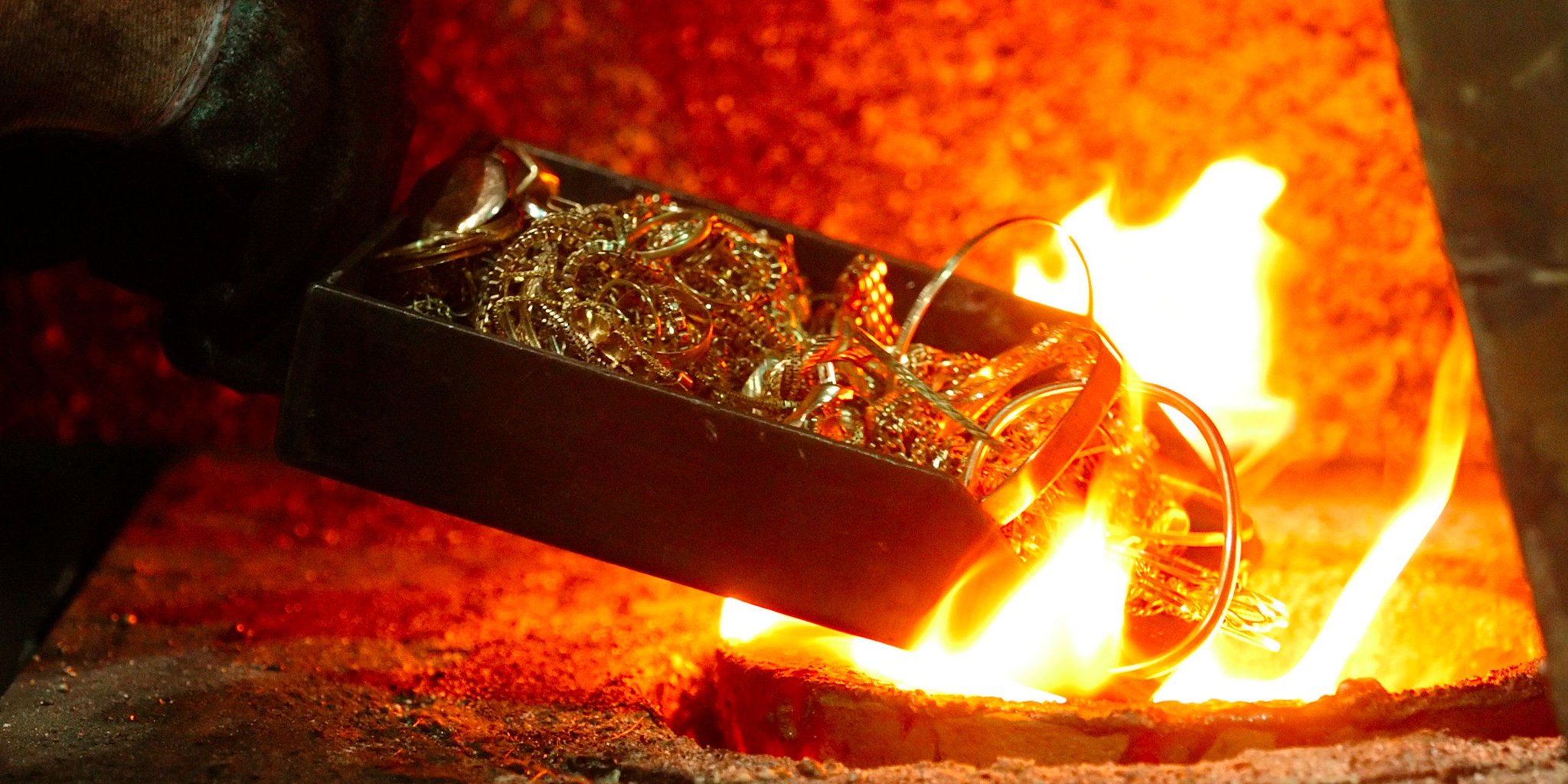
Для удаления кислорода медь раскисляют. Используют несколько способов очистки расплавленной меди от кислорода: «дразнение», вакуумную переплавку, раскисление нерастворимыми поверхностными и растворимыми раскислителями, фильтрование через слой раскаленного древесного угля
Удаление кислорода дразнением является обязательной операцией в процессе огневого рафинирования меди от металлических примесей как на заводах первичной металлургии, так и при переплавке скрапа и отходов. Дразнению подвергают медные расплавы, прошедшие огневое (окислительное) рафинирование и содержащие 3—7 % закиси меди. Для этого с поверхности расплава снимают шлак, засыпают На нее слой древесного угля и создают в печи восстановительную атмосферу. Дразнение осуществляют погружением в расплав сырой древесины. Водяной пар и продукты сухой перегонки, выделяющиеся при этом, интенсивно перемешивают и разбрызгивают расплавленную медь, выбрасывая капли расплава в восстановительную атмосферу.
Во время дразнения происходит восстановление окисленной меди по реакциям: 4Cu2О + Ch5 → CO2 + 2Н2О + 8Cu; Cu2O + CO → CO2 + 2Cu; 2Cu2О + С → CO2 + 4Cu; Cu2O + h3 → h3O + 2Cu, в результате чего содержание кислорода в меди постепенно снижается.
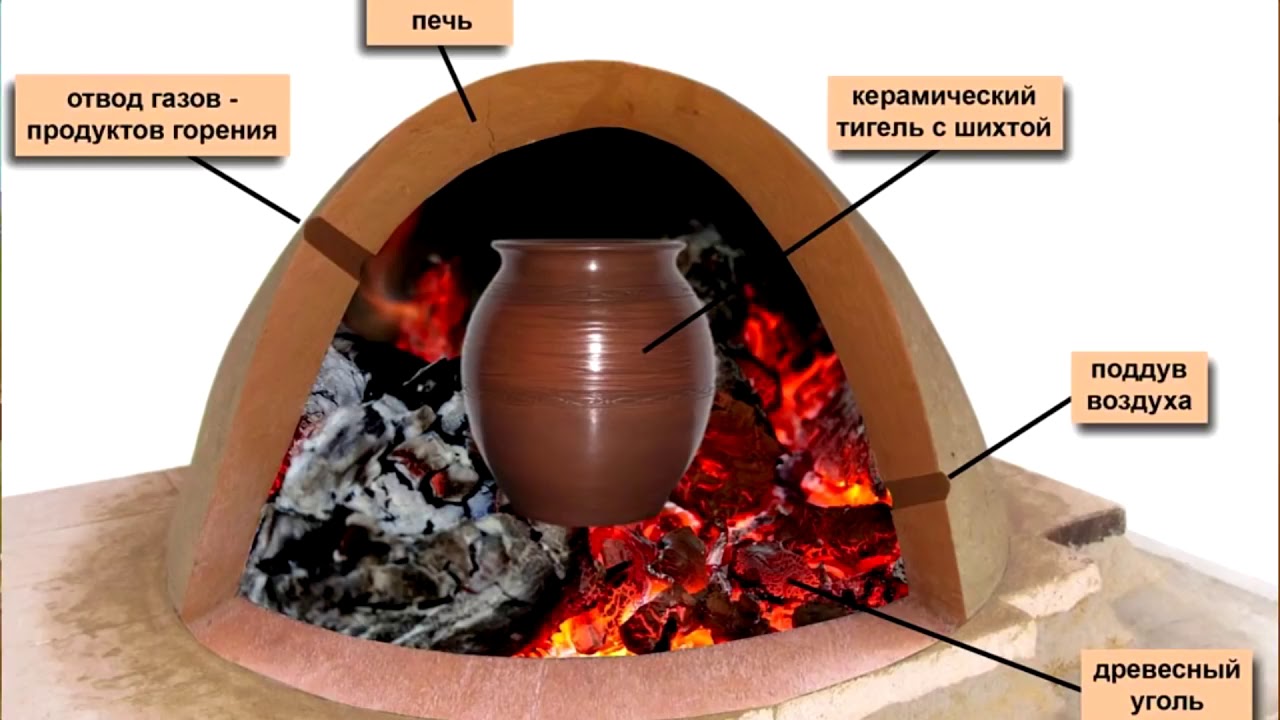
Окисленная медь имеет в изломе грубую структуру темнокрасного (кирпичного) цвета и кристаллизуется с образованием сосредоточенных (концентрированных) раковин; светло-розовый мелкокристаллический излом с большим количеством газовых раковин и выпучиванием металла при кристаллизации — показатели того, что металл «передразнен» (содержит много водорода). Оптимальному раскислению соответствует мелкокристаллический светло-розовый излом с ровной без вспучивания и раковин поверхностью пробы.
Плавка в вакууме, используемая для получения бескислородной меди, позволяет в результате диссоциации закиси меди снизить содержание кислорода до 0,001 %.
Удаление кислорода с помощью раскислителей широко применяется при плавке меди на воздухе Для этого в расплав вводят вещества, имеющие большее сродство к кислороду, чем медь. В качестве поверхностных раскислителей используют карбид кальция CaC2, борид магния Mg3B2, углерод и борный шлак (B2O3* MgO).

Из растворимых раскислителей чаще всего применяют фосфор, который вводят в виде лигатуры медь — фосфор (9—13 % Р). В зависимости от содержания кислорода в меди количество фосфора принимают в пределах 0,1—0,15 % от массы расплава. Восстановление меди может сопровождаться образованием пара P2O5 и одновременно CuPO3, находящейся при температурах рафинирования в жидком состоянии, т. е. образующиеся окисел и соль легко удаляются из расплава. Медь, используемую для электротехнических целей, раскисляют литием (0,1 %), так как избыток фосфора резко снижает ее электропроводность. Использование для раскисления меди угольных фильтров основано на взаимодействии Cu2O с углеродом по реакции, рассмотренной выше.
Плавку бескислородной меди ведут в индукционных печах с железным сердечником в среде сухого, обеспыленного генераторного газа под слоем древесного угля (100—150 мм) или в вакуумных высокочастотных печах.

Шихтой для выплавки бескислородной меди служат катодные листы марки MO (99,95 %) и отходы бескислородной меди (не более 15 % от массы шихты). Перед загрузкой в печь катодные листы разрезают, промывают от остатков электролита и просушивают. Разливку бескислородной меди ведут в атмосфере защитного газа пли в вакууме. Температура металла при литье 1170—1180 °С.
Плавку меди, содержащей металлические примеси, ведут в отражательных печах емкостью 20—50 т. Футеровку печей выше уровня металла выполняют из магнезита. Подина печи — кварцевая, набивная. Набивку подины производят сухим песком с добавкой небольшого количества меди или медной окалины. Шихтой для плавки служат всевозможные отходы (обрезь, отходы производства, промышленный и бытовой лом). Особенность плавки — окислительно-восстановительное рафинирование с целью удаления вредных примесей.

Шлаки медной плавки богаты закисью меди. Для уменьшения содержания меди в состав шлака вводят оксиды, у которых основность выше, чем у Cu2O, и которые могли бы вытеснять Cu2O из шлака в металл по реакции (Cu2O*SiO2) + (Ме’О) → (Мe’O*SiO2) + [Cu2O]. Такими оксидами являются CaO, MnO, FeO и др. В практике производства медных сплавов для этой цели чаще всего используют основной мартеновский шлак, содержащий 25— 40 % CaO, 10—15 % FeO, 10—15 % Al2O3, 8—12 % MnO и 25—30 % SiO2 в количестве 1,5—2 % от массы шихты.
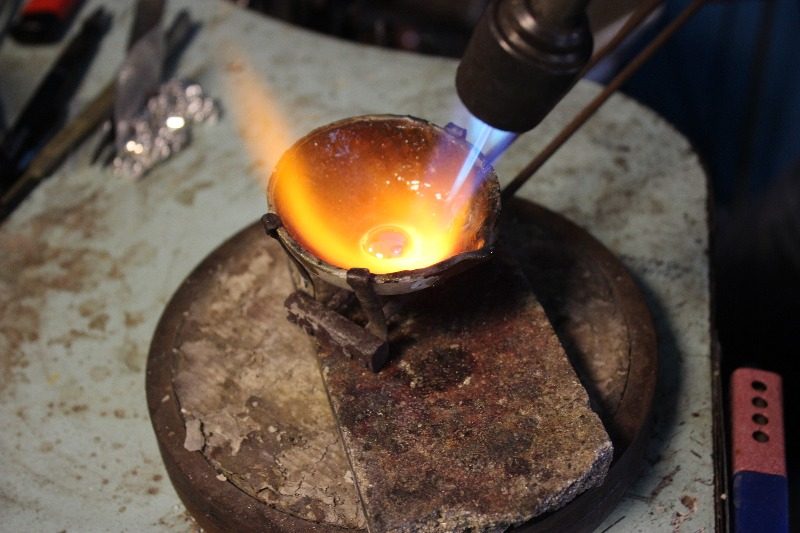
После удаления шлака медь раскисляют дразнением. Длительность операции (1—1,5 ч) определяется объемом металла. Поверхность расплава в этот период покрывают древесным углем, а в печи создают восстановительную атмосферу (коптящее пламя). Контроль процесса раскисления в производственных условиях осуществляют отбором проб на излом. Ввиду того что дразнением невозможно удалить кислород полностью, во время заливки производят дораскисление фосфористой медью (0,1—0,15 % от массы металла).
В ряде случаев для нейтрализации вредного влияния примесей висмута и свинца медь подвергают модифицированию. С этой целью в медные расплавы вводят 0,2—0,3 % (по массе) кальция, церия или циркония.

Плавка большинства медных сплавов на воздухе также сопровождается окислением и насыщением водородом. Окисляются преимущественно легирующие компоненты, поскольку в большинстве своем они имеют более высокий изобарный потенциал образования оксида, чем медь. По этой причине легирующие элементы (Al, Be, Sn и др.) раскисляют медь, образуя твердые, жидкие или газообразные оксиды. Окисление сплавов, содержащих алюминий, бериллий или титан, происходит с образованием тонкой, плотной окисной пленки на поверхности расплава. Наличие такой пленки тормозит окисление. Поскольку окисная пленка в процессе плавки неоднократно разрушается (перемешивание, рафинирование, модифицирование), обрывки ее могут замешиваться в расплав и попадать в отливку.
За исключением латуней и нейзильберов, растворению водорода в которых препятствует высокое давление паров цинка, все другие медные сплавы интенсивно поглощают водород и при кристаллизации склонны к газовой пористости.

Для защиты от окисления плавку сплавов ведут под покровом древесного угля или флюсов на основе фторидов, стекла, соды и других солей (табл. 35). Наиболее часто применяют древесный уголь. Степень загрязнения сплавов оксидами и водородом зависит от состава атмосферы печи. Восстановительная атмосфера способствует получению более газонасыщенных расплавов, чем окислительная.
Для предотвращения загрязнения расплавов твердыми, нерастворимыми оксидами легирующие компоненты вводят в медь после предварительного раскисления ее фосфором. Свое назначение фосфор выполняет лишь в том случае, когда его вводят в расплавленную медь в количестве 0,1—0,15 % перед введением других шихтовых материалов. Если же фосфор вводят перед разливкой, раскисляющего действия он не оказывает, так как оксиды цинка, алюминия, марганца и др.
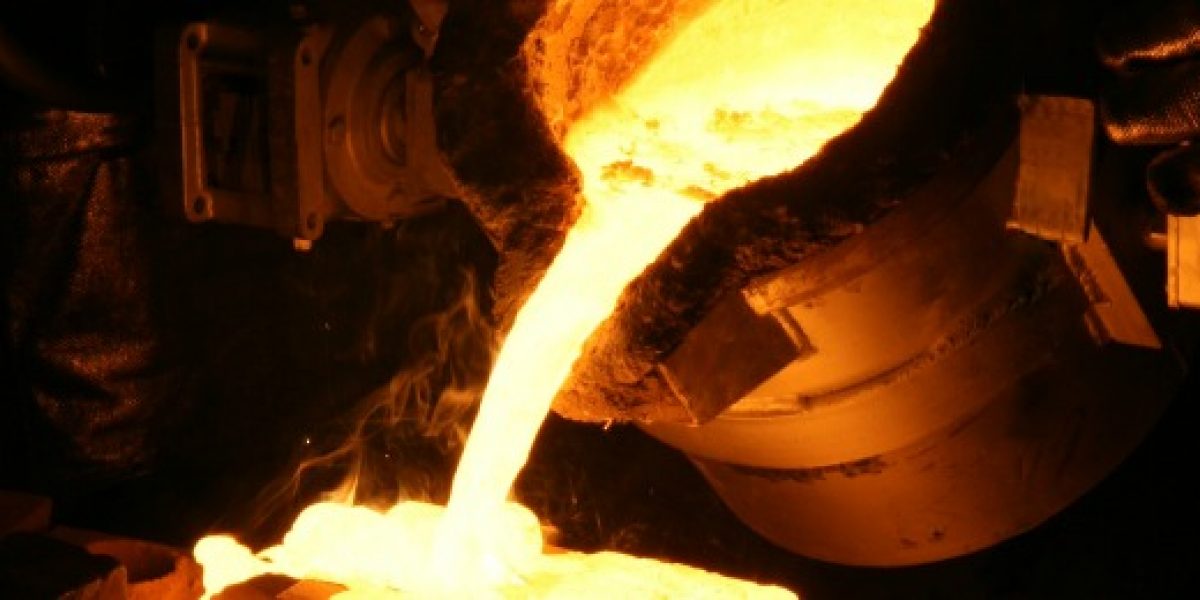
Многие сплавы чрезвычайно чувствительны к воздействию примесей. Так, например, тысячные доли процента алюминия резко снижают механические свойства и герметичность отливок из оловянных бронз и кремнистых латуней. На алюминиевые бронзы аналогичным образом влияет примесь олова. Поэтому при плавке медных сплавов особое внимание уделяют сортировке и подготовке отходов, используемых в шихту.
Рафинирование расплавов
Рафинирование инертными газами ведут при температурах расплава 1150—1200 °C. Расход газа 0,25—0,5 м3 на 1 т металла; длительность продувки при давлении газа 19,6—29,4 кПа составляет 5—10 мин.
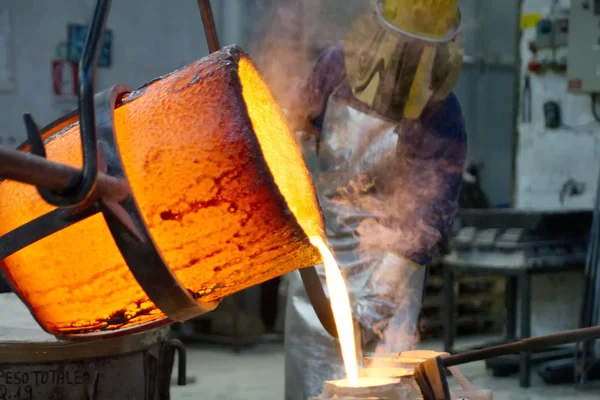
Вакуумирование применяют в тех случаях, когда сплав не содержит компонентов с высоким давлением пара. Применительно к медным сплавам этот процесс ведут при 1150—1300 °C и остаточном давлении 0,6—1,3 кПа. Длительность вакуумирования определяется массой металла, подвергающегося обработке; в большинстве случаев продолжительность обработки не превышает 20—25 мин.
Очистку оловянных бронз и латуней от примесей алюминия и кремния ведут в ряде случаев путем введения в расплав окислителей (MnO, медной окалины) или продувкой воздухом. Окислительное рафинирование проводят при 1180—1200 °С. Расход окислителей составляет 0,5—1,0 % от массы расплава. Для ускорения процесса очистки окислители замешивают в расплав.
Обработку расплавов флюсами применяют в основном для очистки от взвешенных неметаллических включений.

Оптимальным методом очистки от неметаллических включений сплавов, содержащих в своем составе такие легкоокисляющиеся элементы, как алюминий, титан, цирконий и бериллий, является фильтрование. Для этой цели используют зернистые фильтры. Для зернистых фильтров можно рекомендовать такие материалы, как магнезит, алунд, плавленые фториды кальция и магния.

Модифицирование сплавов
Измельчение первичного зерна в медных сплавах, содержащих алюминий (типа БрАЖМц, БрАЖ, ЛАЖ, ЛАЖМц и др.), достигается добавками тугоплавких элементов — Ti, V, Zr, В, W, Mo. Однако следует заметить, что модифицирующее действие присадок тугоплавких элементов во многом определяется наличием в сплаве железа.
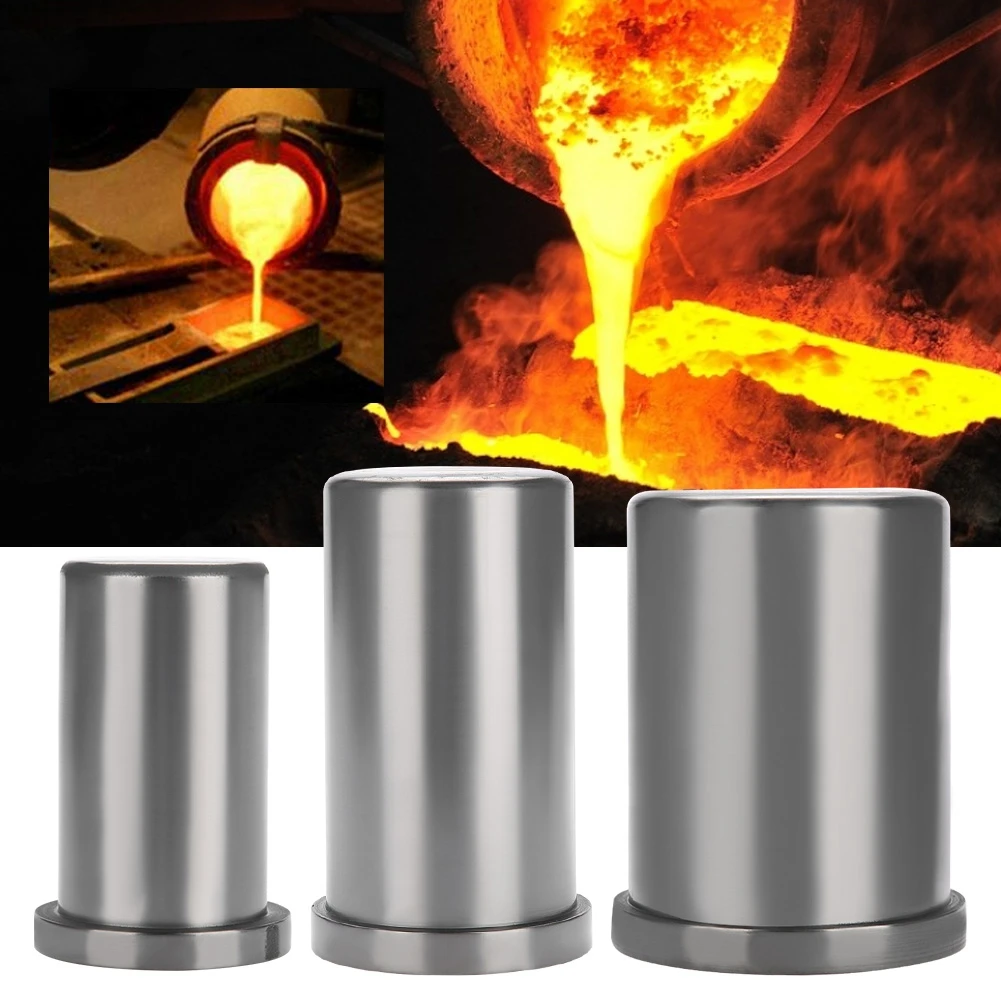
Измельчение зерна отливок из сплавов, не содержащих алюминия и железа (БрС30; БрОЗЦ6СЗ; латунь Л68), может быть достигнуто лишь при совместном введении 0,05 % указанных модификаторов с 0,02 % бора.
Введение тугоплавких модификаторов влечет за собой изменения и в микроструктуре сплавов. В некоторых случаях эти изменения особенно отчетливо выявляются после термической обработки.
Тугоплавкие модификаторы вводят в расплав с помощью лигатур алюминий — ванадий (до 50 %), медь — бор (3—4 % В), алюминий — титан, медь титан и др. в количестве 0,1—0,002 % от массы расплава при 1200—1250 °С. Перегрев модифицированного расплава перед заливкой выше 1180—1200 °С сопровождается огрублением зерна. Оптимальные концентрации модификаторов для некоторых медных сплавов приведены в табл. 36.
Для нейтрализации вредного влияния примесей висмута, свинца или мышьяка в расплавы вводят присадки кальция (0,2 %), церия (0,3 %), циркония (0,4 %) или лития (0,2 %).

Плавка латуней
Приготовление двойных латуней (Л68, Л62) ведут главным образом в индукционных печах, футерованных кварцем. Особенность плавки — высокая летучесть цинка, обусловленная низкой температурой его кипения (907 °С). По этой причине из-за сильного перегрева верхних слоев расплава нерациональна плавка в дуговых печах. В качестве защитного покрова используют древесный уголь, который загружают в печь вместе с первой порцией шихты. Добавка небольшого количества криолита — 0,1 % (по массе) делает шлак «сухим» и сыпучим, что способствует лучшему отделению корольков металла. Иногда вместо древесного угля применяют флюс, состоящий из 50 % стекла и 50 % плавикового шпата.
При выплавке латуней сначала расплавляют медь; в расплав вводят цинксодержащие отходы и вторичную латунь. Сплав нагревают до 1000—1050 °С и перед заливкой в него вводят цинк. Медь перед введением цинка или цинксодержащих отходов не раскисляют, так как цинк сам является хорошим раскислителем, а оксиды его не растворяются в расплаве и легко всплывают.
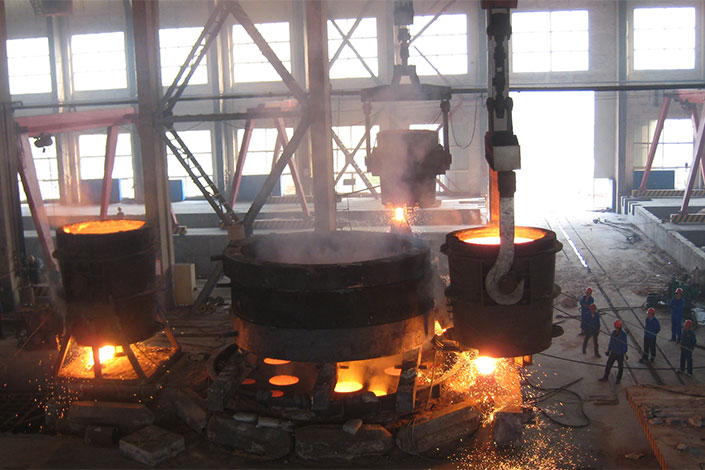
Кремнистые латуни отличаются большой склонностью к поглощению водорода, особенно в присутствии примесей алюминия. Они очень чувствительны к перегреву газонасыщенность расплава резко увеличивается при нагреве выше 1100 °С. В процессе кристаллизации растворенный газ выделяется, что приводит к «росту» отливки и появлению ликвационных выпотов на их поверхности. Плавку кремнистых латуней ведут в окислительной атмосфере под слоем флюса (30 % Na2CO3; 40 % CaF2; 30 % SiO2), не допуская перегрева расплава выше 1100 С. В целях предупреждения загрязнения расплава оксидами кремния медь перед введением отходов или кремния раскисляют фосфором. Кремний вводят лигатурой медь — кремний (15—20 % Si).

Плавка бронз
Особенность оловянных бронз — образование SnO2 при взаимодействии олова с Cu2O Наличие включений SnO2 заметно снижает механические и эксплуатационные свойства оловянных бронз. Поэтому перед введением олова или оловосодержащих отходов медь раскисляют фосфором. Плавку ведут в окислительной атмосфере под слоем древесного угля или флюса (сода + древесный уголь). Вначале под слоем угля расплавляют медь и нагревают ее до 1100—1150 °С. Введением фосфористой меди (9— 13 % Р) производят раскисление. Затем вводят цинк, олово или отходы сплава и в последнюю очередь свинец.

Плавка сложных оловянных бронз мало чем отличается от приведенной технологии. Плавку вторичных оловянных бронз ведут под слоем флюса в окислительной атмосфере.
Алюминиевые бронзы чувствительны к перегреву и больше оловянных склонны к поглощению газов, поэтому плавку их ведут в окислительной атмосфере под слоем флюса (см. табл. 35), не допуская перегрева расплава выше 1200 °С. Для предотвращения загрязнения расплава окисными пленками медь перед введением алюминия и других легирующих компонентов раскисляют фосфором. Большая разница в плотности меди и алюминия способствует расслоению их в процессе плавки. Поэтому необходимо очень тщательно перемешивать расплав перед заливкой.
Плавку алюминиевых бронз проводят в такой последовательности. Сначала под слоем флюса расплавляют медь и раскисляют ее фосфором (0,05—0,1 %). Если сплав содержит никель, то его загружают вместе с медью.

Плавка бериллиевой бронзы (БрБ2, БрБНТ) мало чем отличается от плавки оловянных бронз. Для этого используют индукционные печи с графитовыми тиглями. Плавку ведут под покровом древесного угля. Медь перед введением бериллия и титана раскисляют фосфором.
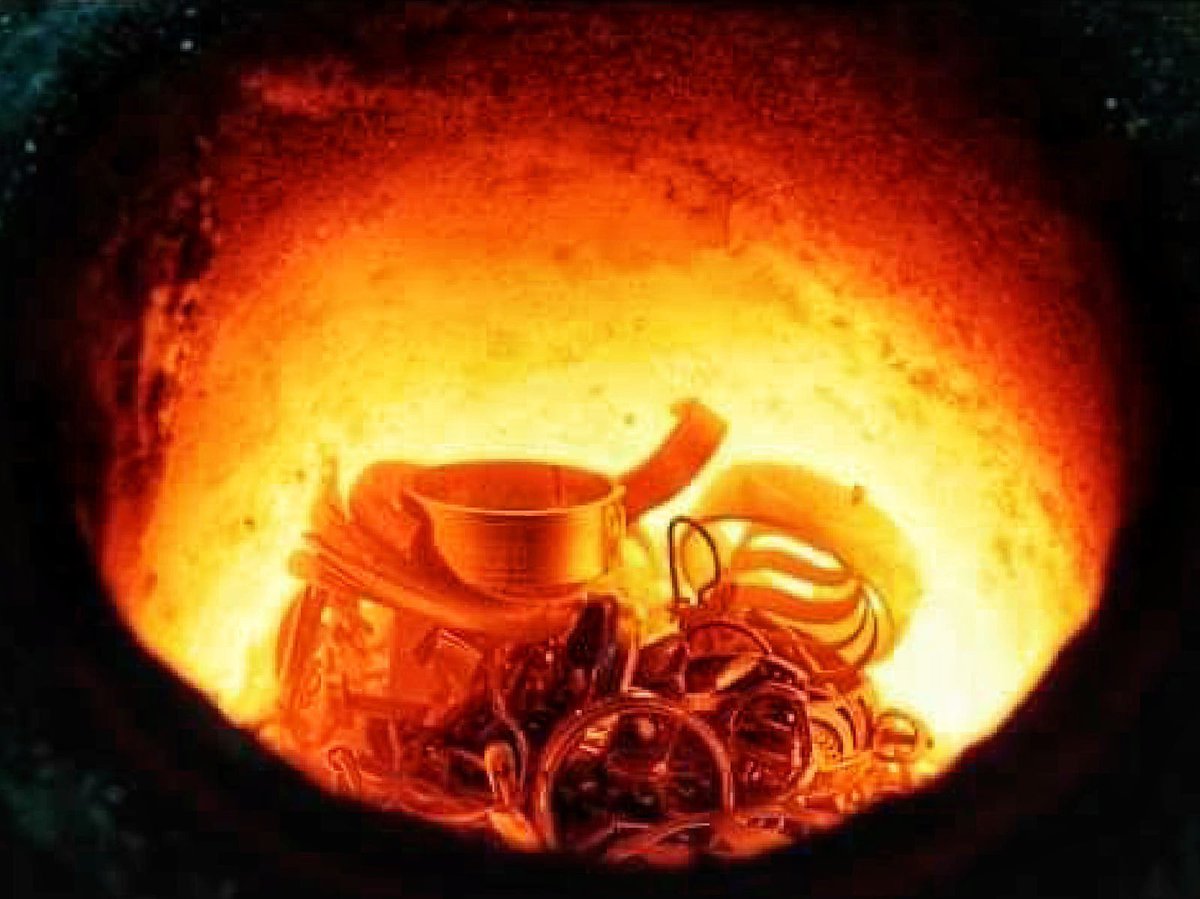
Кремнистые бронзы плавят в электрических индукционных печах под покровом древесного угля. Медь перед введением кремния или отходов раскисляют фосфором. Для получения расплавов с малым содержанием водорода недопустим перегрев выше 1250—1300 °С.
Особенность плавки свинцовых бронз (БрСЗО) — сильная ликвация по плотности. Наиболее однородные расплавы удается получать при плавке в индукционных печах, обеспечивающих интенсивное перемешивание. Для предупреждения ликвации в высокосвинцовистые бронзы рекомендуется вводить 2—2,5 % никеля, а охлаждение отливок вести с большими скоростями.
Плавка медноникелевых сплавов
Приготовление мельхиора, нейзильбера, куниалей, константана и манганина не представляет особых затруднений.
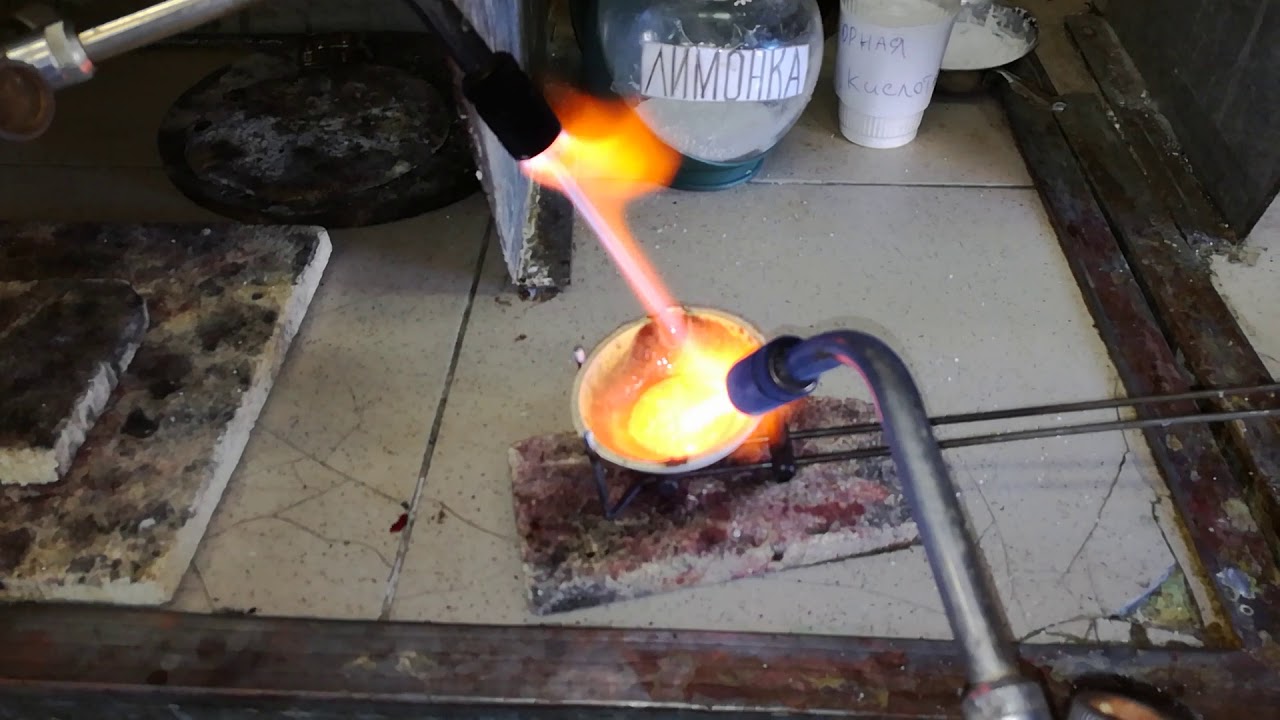
Приготовление этой группы сплавов, кроме куниалей, начинают с загрузки меди и никеля; по мере их расплавления загружают крупнокусковые отходы, а затем под зеркало металла — мелкие отходы. Цинк вводят в последнюю очередь. После полного расплавления шихты сплавы раскисляют марганцем и кремнием (для нейзильбера) или марганцем и магнием (для мельхиора и константана). Количество раскислителя определяется содержанием кислорода в расплаве. Обычно при сравнительно чистой шихте в расплав вводят 0,1—0,15 % Mn и до 0,1 % Mg. Магний вводят в виде лигатуры Ni—Mg (50 % Mg). После этого с поверхности расплава удаляют шлак и засыпают древесный уголь. Температуру расплава доводят до 1250—1300 °C и, если необходимо, рафинируют его хлористым марганцем.
В связи с тем что в состав куниалей входит алюминий, плавка их по описанной технологии связана с опасностью загрязнения расплава пленками Al2O3.

| Льячек для разлива меди и бронзы Льячек для разлива меди и бронзы использовался древними мастерами-литейщиками в процессе изготовления металлических изделий. На окраине поселка Соломенное известным московским археологом А.Я.Брюсовым в 1930-е гг. был раскопан уникальный памятник, имеющий большое значение для изучения древней металлургии Северной Европы – поселение и древняя мастерская Томица, относящаяся к эпохе бронзы. Здесь были открыты семь участков, где в древности происходила плавка бронзы, обнаружены льячки, обломки бронзовых предметов, камни для дробления руды, горны (печи) из камня, очаги, запасы глины, а также орудия из камня и обломки керамических сосудов. По находкам может быть восстановлен весь технологический цикл такого сложного производства, как плавка бронзы, требующего температуры до 1200 градусов. Такой температуры было невозможно достичь в обычном костре. Для плавки бронзы использовалась печь из вертикально поставленных камней, в которую мехами подавался воздух. Расплавленный в каменных печах металл разливался в формы с помощью небольших по объему льячек, что говорит о незначительном количестве выплавляемого металла. |
плавка в домашних условиях алюминиевой бронзы
Металлы и сплавыБронза – первый сплав, который научился изготавливать человек тысячи лет назад. С тех пор изделия из бронзы пользуются большой популярностью. В наши дни современные мастера пытаются адаптировать литейные технологии к домашним условиям, для этого необходимо знать химический состав и физические свойства бронзы, а также технические характеристики получаемых из нее сплавов, в том числе алюминиевой бронзы.
В этой статье рассказывается о таком важном показателе, как температура плавления, а также о том, как поэтапно осуществить процесс плавки и литья бронзы.
Температура плавления
Существует таблица температур плавления разных видов бронзы. Прежде чем приступить непосредственно к плавке, необходимо понять, от чего зависит температура, при которой тот или иной металл начинает плавиться или полностью переходит в жидкое состояние. Бронза на самом деле представляет собой целый ряд различных сплавов, в состав которых в качестве основного компонента входит медь, а в качестве дополнительных (легирующих) – другие элементы.
Такими легирующими веществами могут быть алюминий, бериллий, олово, кремний и так далее. Вот как раз от химического состава бронзы зависят все физические свойства металла, в том числе и температура плавления. Чтобы расплавить медный сплав, необходимо знать его химический состав, только так можно правильно определить температуру плавления в градусах Цельсия. Давайте ознакомимся с температурами плавления.
Чистого металла
Хотя чистую медь производить крайне невыгодно, поскольку ее технические свойства во многом уступают особым маркам, которые производят из этого металла в металлургической промышленности, тем не менее знать температуру плавления меди необходимо.
Почему? Дело в том, что те марки меди, которые используются в народном хозяйстве, имеют в своем составе ничтожно малое количество легирующих веществ, которые рассматривают как примеси. Таким образом, благодаря несущественности их количества, температура плавления марок меди близка к температуре плавления чистой меди и составляет примерно 1084,5 градуса Цельсия.
Как уже говорилось, температура плавления зависит от состава вещества, по этой причине температура плавления бронзы варьируется в пределах 900-1140 градусов Цельсия.
Смесей
Олово в составе бронзы снижает температуру плавления таких сплавов, она не превышает 900-950 градусов Цельсия.
Безоловянные, в том числе и алюминиевые бронзы обладают более широким диапазоном таких температур, которые зависят от химического состава медного сплава. Их температура плавления составляет 950-1080 градусов. Также необходимо учитывать, что бронза обладает большой вязкостью, поэтому ее перегревают после окончательного расплавления для обеспечения лучшей текучести расплава. Давайте рассмотрим процесс плавки и литья бронзы поэтапно.
Пошаговая инструкция
В кустарных условиях в основном изготавливают небольшие бронзовые изделия, например, элементы декора. Более сложные детали требуют высокоточного литья, технологию которого очень сложно осуществить без специально приспособленного для этих целей помещения, а также особого оборудования. В некоторых случаях приходится прибегать к доводке отливки до нужного состояния с помощью правки в домашних условиях, такой как удаление излишков расплавленного материала вручную, шлифовки и полировки изделия.
Прежде чем приступить к расплавлению металла, необходимо подготовить помещение и обзавестись необходимыми инструментами и оборудованием. Главным требованием, предъявляемым к помещению, является наличие хорошей вытяжной вентиляции, а также пол, выполненный из негорючих материалов, таких как бетон, цемент либо кирпич. При изготовлении небольших изделий эти требования соблюсти довольно просто, в противном случае придется воспользоваться гаражом.
Для того чтобы осуществить плавку бронзы в домашних условиях, необходимо приобрести специальную муфельную печь с возможностью регулирования температуры, но можно обойтись простым горном, топливом для которого послужит древесный уголь.
Подготовка инструментов
Начинающему литейщику следует приобрести либо самостоятельно изготовить следующие инструменты.
- Огнеупорный тигель из огнеупорного материала (такого как чугун или сталь) – специальный сосуд с носиком, куда кладутся куски расплавляемого металла.
- Приспособления для извлечения тигля из печи, которые сводят к минимуму риск обжечься – специальные крючки и щипцы.
- Форма для заливки расплавленного металла, которая изготавливается с помощью опоки и модели.
- Сама опока – два ящика, которые удерживают литейную форму с наполнителем из формовочной смеси.
- Костюм сварщика или просто очень плотный фартук и рукавицы, назначением которых является защита человека от летящих искр и брызг расплавленного металла.
После того как вы убедились в наличии всего вышеперечисленного, можно приступать непосредственно к плавлению бронзы.
- Разогревают печь, выставляя температуру с помощью регулятора.
Температура зависит от химического состава бронзы, о чем мы говорили выше. Например, для алюминиевой бронзы такая температура будет равняться 1040-1084 градусам Цельсия.
- Далее следует обязательно прогреть форму, это делается, чтобы расплавленный металл не застыл при попадании в холодную емкость. Форму помещают в печь, когда та прогреется до температуры 600 градусов, после чего выставляют терморегулятор в положение 900 градусов. Когда температура внутри печи поднимется до 900 градусов, оставляют форму прогреваться на 3-4 часа, после чего аккуратно ее извлекают с помощью специальных приспособлений и охлаждают до 500 градусов Цельсия.
- Помещают тигель с кусками бронзы, предназначенной для плавки, внутрь разогретой до нужной температуры плавления печи и доводят до полного расплавления металла. После этого оставляют тигель перегреваться еще на 5 минут, чтобы добиться лучшей текучести металла и лучшего качества отливки.
- Достают тигель из печи или горна с помощью крюков и щипцов и приступают к заливке в форму.
Давайте рассмотрим, как правильно изготовить форму для получения изделия высокого качества. В литейных мастерских такую форму изготавливают при помощи опоки, куда засыпают смесь, состоящую из глины, песка и каменноугольного порошка. Опока состоит из двух половин, каждая из которых представляет собой ящик, куда будет засыпаться формовочная смесь.
- Сначала берут первый ящик и начинают наполнять его смесью, насыпав ее до половины, помещают внутрь ящика модель.
- Далее продолжают насыпать сыпучий материал, пока не заполнят ящик до самого верха. Во время работы требуется постоянно разравнивать и утрамбовывать формовочную смесь.
- Устанавливают сверху второй ящик и продолжают насыпать смесь глины, песка и каменноугольного порошка.
- Во втором ящике необходимо предусмотреть литники – отверстия для заливки расплавленной бронзы внутрь формы.
- Когда оба ящика окажутся наполнены доверху, разделяют их с помощью острого предмета. Одна половина модели находится в одном ящике, другая – в другом.
- Достают аккуратно модель, вновь соединяют оба ящика – получившаяся внутри пустота и есть форма для заливки.
Заливка в литейную форму
Расплавленный металл тонкой струйкой переливают из тигля в литейную форму, следя, чтобы струйка текла непрерывно. Если отливаемая деталь отличается сложностью очертаний, нужно использовать специальную центрифугу, которая с помощью центробежной силы поможет расплаву правильно распределиться внутри формы, полностью заполнив ее.
Как повысить качество изделия?
На самом деле, по-настоящему качественную вещь невозможно получить в домашних условиях без доводки.
Также можно улучшить качество и внешний вид, изготовив форму с помощью легкоплавкого материала. Для этого предварительно делают гипсовый слепок с модели, по которой будет изготавливаться наша деталь, этот слепок должен состоять из двух частей, которые скрепляют друг с другом. В образовавшуюся полость заливают растопленный в кипящей воде парафин или воск, а после его застывания убирают гипсовую оболочку.
Далее помещают получившуюся легкоплавкую модель в специальную литейную массу, формируя отверстия для слива парафина и залива расплавленной бронзы. После этого литейную массу помещают в кипяток, парафин тает, и его легко выливают из формы.
Образовавшаяся литейная форма обладает большей гладкостью, из нее получаются более качественные изделия, чем из формы, изготовленной обычным способом.
В следующем видео представлен процесс плавки бронзы в домашних условиях.
Плавка и разливка медных сплавов
Плавка и разливка медных сплавов
Категория:
Литейное производство
Плавка и разливка медных сплавов
Медные сплавы, к которым относятся оловянные и безоловянные бронзы и латуни, выплавляют в основном в электрических дуговых и индукционных печах и реже в пламенных, работающих на жидком топливе. При небольших объемах производства иногда используются тигельные печи.
Так как почти все элементы, входящие в состав медных сплавов, легко окисляются, процесс плавки ведется форсированно, при этом принимаются меры к защите сплавов с поверхности (защитными или покровными флюсами), а отдельные легкоокисляемые элементы применяются в виде лигатур.
1. Шихтовые материалы
Шихтовыми материалами для медных сплавов могут быть свежие (чистые) металлы, вторичные сплавы, оборотный сплав, а также различные лигатуры, поставляемые промышленностью или собственного приготовления.
Для раскисления сплавов применяют фосфористую медь в виде плиток массой около 12 кг по ГОСТ 4515—78, которые перед употреблением разбивают на мелкие куски.
Лигатуры — это сплавы двух или нескольких элементов, которые присаживают к сплавам. Применение их обусловлено тем, что отдельные тугоплавкие компоненты сплава имеют более высокую температуру плавления, чем допускаемый перегрев сплава. Температуры плавления лигатур и металла, к которому их присаживают, должны быть близкими, и в то же время лигатуры должны иметь высокое содержание тугоплавкого элемента.
2. Расчёт шихты
Для получения сплава возможны различные сочетания шихтовых материалов. Шихта может состоять из одних свежих металлов, из свежих металлов или вторичных сплавов с добавлением лигатур, из оборотного сплава с добавлением свежих металлов и лигатур, из одного оборотного сплава или из одних вторичных сплавов. Обычно применяют шихту, состоящую из 50—60% свежих металлов, 25—35% оборотного сплава и 10—12% покупного лома, или плавку ведут на вторичных сплавах.
При расчете шихты учитывают угар различных элементов сплава, величина которого зависит от характера элементов, чистоты шихты и типа плавильной печи.
Рассмотрим пример расчета шихты для выплавки бронзы марки БрОЗЦ7С5Н1.
При изготовлении сплавов для менее ответственных отливок с целью экономии чистых металлов могут применяться только вторичные сплавы — паспортные бронзы марки БрОЗЦ8С4Н1.
3. Технология плавки медных сплавов
Плавка в тигельных печах. Для плавки медных сплавов используются самые разнообразные тигельные печи. При небольших объемах плавки они обеспечивают высокое качество сплава, так как в них отсутствует непосредственный контакт сплава с продуктами горения, а поверхность зеркала металла очень мала. Для плавки применяют графитовые или корундовые тигли.
Рис. 1. Электрическая печь типа ДМК: 1 — футеровка; 2 — стальной кожух; 3— зубчатые ободы; 4 — шланги для подвода воды; 5 — графитизированные электроды; 6 — шестерни; 7 — водоохлаждаемые уплотнители; 8 — дверцы; 9 — сливной носок; 10 — электродвигатель; 11 — приводной механизм.
Плавка в электрических печах. Электрические печи для плавки медных сплавов подразделяются на дуговые и индукционные.
Плавка в электродуговых печах. Для плавки применяют электродуговые печи с косвенным нагревом, т. е. такие, У которых электрическая дуга образуется между двумя горизон-альными графитовыми электродами.
Печь ДМК (рис. 1) имеет вид барабана с загрузочным кном, отверстиями для электродов и желобом для слива сплава.
Кожух печи футеруется динасовым или шамотным кирпичом. На торцы кожуха насажены зубчатые ободы, сцепленные с зубчатыми колесами, которые дают возможность покачивать печь в процессе плавки, благодаря чему обеспечивается получение однородного по составу и равномерно нагретого сплава.
Плавка начинается с подготовительных работ: тщательной очистки печи от остатков предыдущей плавки, проверки исправности механизмов и подачи воды к водоохлаждаемым уплотнителям. После этого футеровку прогревают до температуры 700—800 °С, выводят из печи электроды и на дно ее насыпают несколько лопат сухого прокаленного древесного угля, затем загружают предварительно подогретые до 150—200 °С шихтовые материалы: сначала мелочь, литники, скрап и сверху — крупные куски. Шихта должна располагаться не ближе чем в 50 мм от электродов и не должна мешать их свободному перемещению вдоль печи. После установки электродов закрывают загрузочное окно и возбуждают электрическую дугу, что осуществляется сближением электродов и быстрым удалением одного из них на небольшое расстояние с помощью ручного штурвала механизма их перемещения.
Процесс расплавления шихты ведется интенсивно. По истечении 20—30 мин включают реверсивный механизм покачивания печи вначале на 25—30°, потом постепенно доводят покачивание до 90°, а после расплавления всей шихты —до 160°. Это позволяет избежать местного перегрева сплава и способствует лучшему перемешиванию его. Сплав раскисляют, присаживают легкоплавкие добавки, рафинируют, подогревают до требуемой температуры и выпускают из печи.
Плавка в индукционных печах. Для плавки медных -сплавов применяют индукционные печи со стальным сердечником и без сердечника.
Индукционная печь со стальным сердечником, схематический разрез которой показан на рис. 2, представляет собой трансформатор, первичной обмоткой которого служит медная катушка, насаженная на сердечник из пластин электротехнической стали толщиной 0,35—0,5 мм. Вторичной обмоткой является кольцо Жидкого сплава, находящегося в плавильном канале. Переменный ток промышленной частоты, проходя через первичную обмотку, создает вокруг нее магнитный поток, замыкающийся через магнитны» стальной сердечник трансформатора, и индуктирует ток в сплаве, находящемся в кольцевых каналах. Заполняющий каналы сплав сообщается с ванной жидкого сплава и отдает ему тепло за чет циркуляции, создаваемой разностью температур сплава по высоте печи.
Рис. 2. Схема индукционной печи со стальным сердечником: 1 — камера; 2— футеровка; 3— тепловая изоляция; 4 — первичная обмотка; 5 — плавильный канал; 6 — магнитный сердечник.
Особенность плавки в индукционных печах заключается в том что жидкий сплав, заполняющий каналы, должен оставаться в печи и после выпуска плавки для образования замкнутой электрической цепи при последующей плавке. В связи с этим в индукционных печах затруднен переход к плавке нового сплава. В этом случае необходимо слить весь сплав из каналов и сделать одну-две промывные плавки сплава неответственного назначения.
После заполнения кольцевых каналов и «болота» (слой жидкого сплава толщиной 30—50 мм, находящийся над каналами) жидким сплавом и разогрева печи загружают предварительно подогретую шихту: сначала медь, а после ее расплавления — оборотный и вторичные сплавы. При расплавлении всей шихты производят раскисление, с поверхности удаляют шлак и вводят легко-окисляемые элементы. При сливе готового сплава необходимо оставить его в каналах и над ними слоем в 30—50 мм.
Плавка в индукционных тигельных печах. В последние годы для плавки сплавов на медной основе — бронз и латуней — стали применять индукционные тигельные печи типа ИЛТ. Угар металла в этих печах не превышает 0,5—1%.
4. Особенности плавки и разливки медных сплавов
При плавке медных сплавов в состав шихты обычно входит красная электролитическая медь, которую расплавляют и раскисляют фосфористой медью до загрузки в печь остальных составляющих шихты. Плавка меди должна происходить очень быстро под слоем хорошо просушенного и прокаленного древесного угля. Печь перед загрузкой меди надо хорошо разогреть. Качество раскисления можно проверить по технологической пробе: залитый и охлажденный брусок при загибе не должен давать трещин в месте изгиба.
Плавка оловянной бронзы.
В разогретую печь загружают часть вторичных и оборотного сплавов и покрывают слоем сухого древесного угля, который после расплавления шихты должен покрыть ровным слоем всю поверхность жидкого сплава. По мере расплавления первоначальной порции шихты в печь вводят частями или полностью остаток шихты, подогретой до температуры 150—200 °С. Из применяемых для под-шихтовки свежих металлов медь и никель загружают в печь одновременно с первой порцией шихты, а цинк, свинец и олово вводят непосредственно в ванну к концу плавки для уменьшения их угара.
После расплавления всей шихты и достижения требуемой температуры сплав раскисляют фосфористой медью в количестве 0,2% от массы шихты и покрывают хорошо просушенным флюсом, состоящим из 60% кальцинированной соды, 33% плавикового шпата и 7% буры. Расход флюса составляет 2—3% от массы шихты. Затем сплав нагревают до температуры 1250—1300 °С и 20—30 мин выдерживают под флюсом, периодически перемешивая его. После этого счищают образовавшийся шлак и выпускают сплав в ковш для разливки в формы.
Плавка латуней. Рассмотрим технологию плавки кремнистой латуни марки ЛКС80-3-3.
При плавке шихты из свежих металлов сначала расплавляют медь и раскисляют ее фосфористой медью, затем вводят меднокрем-нистую лигатуру, цинк и свинец.
Если шихта содержит оборотный сплав этой же марки, то его загружают вместе с медью в том случае, когда масса свежих металлов не превышает 30—40% от массы всей шихты. При большом количестве свежих металлов оборотный сплав загружают после расплавления меди и введения остальных элементов. Учитывая склонность этого сплава к поглощению газов, плавку необходимо форсировать, сохраняя нейтральную или слегка окисленную атмосферу в печи. В качестве флюса можно применять битое стекло и буру.
Для дегазации сплав нагревают до температуры 1150—1160 °С и выдерживают при этой температуре 10—15 мин. Выделяющиеся при выдержке пары цинка механически увлекают за собой растворенные газы и удаляют их из жидкого сплава. Для компенсации повышенного угара цинка при выдержке сплава перед его заливкой в печь вводят дополнительное количество цинка.
После окончания выдержки сплав охлаждают до температуры 1050—1100 °С и проверяют (путем взятия пробы) содержание в нем газов. При избыточном количестве газов в сплаве происходит «рост» пробы в стаканчике. В этом случае производят «замораживание» сплава путем охлаждения его до температуры затвердевания и затем быстро нагревают до температуры разливки.
В конце плавки берут пробу для химического анализа, а также технологическую пробу, которая позволяет определить по излому качество сплава и содержание в нем газов; пробу сравнивают с эталонами.
Для получения высококачественных медных сплавов необходим тщательный контроль за соблюдением правил подготовки исходных материалов и проведения процесса плавки. Особое внимание надо уделять контролю температуры жидкого сплава как в процессе самой плавки, так и при выпуске его из печи и разливке.
Обычно для измерения температуры сплава применяют термопары погружения с защитными чехлами из жароупорной стали. Термопары в сочетании с аппаратурой автоматического действия могут самостоятельно регулировать температурный режим в печах или же путем световой или звуковой сигнализации привлекать внимание рабочего к нарушению температурного режима.
Ввиду того что медные сплавы имеют склонность к поглощению газов и окислению, при заливке форм необходимо поддерживать небольшую высоту струи, не прерывать ее и не допускать разбрызгивания сплава. Разливку производят через носок ручных и крановых ковшей, подобных тем, которые применяют при разливке чугуна.
Реклама:
Читать далее:
Плавка и разливка алюминиевых сплавов
Статьи по теме:
Как плавить бронзу — Советы, как заботиться о своих деньгах каждый день
Что такое бронза
Творческое сочетание цинка и меди создает металл, наиболее известный своим декоративным оттенком: бронзу. Бронза, как и алюминий, имеет относительно низкую температуру плавления по сравнению с другими металлами, такими как сталь и золото. Однако из-за низкой температуры плавления его труднее плавить, чем золото, потому что, когда бронза достигает точки плавления, цинк и медь начинают разделяться. К счастью, бронзу можно безопасно плавить, если контролировать все переменные.
Купите или постройте печь для плавки металла. Вы можете приобрести небольшой в местном магазине украшений или поделок. На многих сайтах есть инструкции, как построить плавильную печь. Найдите сайт с хорошо задокументированными результатами, желательно от нескольких человек. Печь должна быть достаточно большой, чтобы в ней поместился тигель и материалы, которые будут выделять большое количество тепла.
Температура плавления бронзы
Температура плавления бронзы по Цельсию составляет 950 ° C .
Точка плавления бронзы по Фаренгейту составляет 1742 ° F .
Бронза обычно немагнитна, но некоторые сплавы, содержащие железо или никель, могут обладать магнитными свойствами.
Как плавить бронзу
Соберите и очистите бронзу. Чтобы расплавить любой металл безопасно, необходимо удалить все неметаллические детали. Выньте все куски стекла, пластика, ткани и всего остального. Вымойте и высушите бронзу, чтобы удалить все химические остатки. Любой материал или химический элемент, оставшийся в бронзе и помещенный в тигель, может вызвать случайный пожар.
Выберите тигель Если вы купили печь для украшений, тигель прилагается. В противном случае вам следует найти тигель, достаточно большой, чтобы вместить бронзу, но достаточно маленький, чтобы поместиться в духовке. Прочтите обертку, чтобы убедиться, что она способна выдерживать достаточно высокие температуры, чтобы бронза расплавилась. Также выбирайте металлические щипцы, подходящие к тиглю.
Нагревает духовку. Разместите его на открытом, хорошо вентилируемом месте, желательно на открытом воздухе. Очистите область вокруг духовки от всех легковоспламеняющихся материалов.Следуйте инструкциям, прилагаемым к духовке. С самодельной духовкой подумайте о том, чтобы попробовать ее пару раз, прежде чем пытаться расплавить бронзу. Имейте под рукой огнетушитель, но не ставьте его прямо перед пламенем.
Наденьте защитные сварочные перчатки, фартук и защитные очки. Поместите бронзу в тигель. С помощью щипцов поместите тигель в духовку в соответствии с инструкциями для пользователя. Вы можете попробовать огонь с небольшим количеством бронзы, чтобы попрактиковаться в точном и безопасном попадании в точку заклинания.Вылейте расплавленную бронзу в форму и дайте остыть.
ВЕК МЕТАЛЛА
ВЕК МЕТАЛЛАВЕК МЕТАЛЛА
Как только человек научился использовать камень, он, казалось, довольствовался этим.
единый способ изготовления инструмента на протяжении тысячелетий. Камня было много,
относительно легко работать и, казалось, удовлетворял его потребности.
Наконец, около 3500 г. до н. Э. человек отправился в эпоху металла. Первое металл, которым он научился работать, был медью.Этот металл очень мягкий, легко тает в простом костре и может превращаться в инструменты с относительными простота. Из меди делают инструменты низкого качества. Потому что медь мягкая (есть вы когда-нибудь пробовали гнуть медный электрический провод?) он не держит край (будьте внимательны) в течение любого времени. Медные ножи можно было сделать, но простое резание мяса животных мгновенно притупило лезвие, и оно быть реформированным. Медь использовалась для изготовления украшений, медные бусины могли легко. соединить вместе, чтобы получилось ожерелье.Вероятно, впервые была обнаружена медь как бусинки, просочившиеся из камней, которыми окружают костры. Если медь несущие камни использовались для вечернего костра, человек найдет на следующее утро расплавил «бусинки» меди в пепле. Медь превосходит большинство каменных орудий, но все же ненадежен.
Около 2500 г. до н. Э. человек перешел во вторую эпоху металла, бронзовую эпоху.
Бронза — это не элемент, а сплав, состоящий из меди и
банка. Оба металла относительно мягкие, используются по отдельности, но при смешивании друг с другом.
они образуют соединение, которое намного прочнее, чем любой другой.Бронза
превосходит медь, потому что дольше держит кромку и не сгибается.
Недостаток бронзы в том, что она очень хрупкая, ломается или трескается.
без труда. Таким образом, бронзовая головка копья убьет животное, если вы нанесете ему чистый удар.
и не задевать большие кости. Если ты ударишься о кость, ударишься о дерево или камень,
наконечник копья расколется или расколется, и его придется переделывать.
Наконец, около 1200 г. до н. Э. человек вступил в последний век металла, железного
Возраст. Из всех металлов железо намного превосходит любые другие.Железо не
гнуться, как медь, и не трескаться, как бронза. Он будет удерживать преимущество на неопределенный срок.
период времени (подумайте о кухонном ноже, который есть у вас дома, как долго
остается резким?). Единственный недостаток железа в том, что оно ржавеет и
что работать с ним крайне сложно. Любой из вас может работать с медью
и бронзу в простом огне, который можно развести дома. Это потому, что оба
металлы имеют низкую температуру плавления. Простой дровяной камин обеспечит все
тепло необходимо для плавления любого металла. Никакой дровяной огонь не горит достаточно горячим, чтобы расплавиться
железо.Таким образом, первобытному человеку нужно было разжечь огонь, который был более «горячим».
чем жарко. Это потребовало прогресса в технологиях. Мало того, что у человека было
чтобы знать, как отбирать горячие дрова, но ему пришлось изобрести способ
разогреть огонь. Эта задача решается добавлением «воздуха» в
Пожар. Вы когда-нибудь задували огонь и смотрели, как угли светятся ярче?
и горячее? Подаваемый вами воздух действительно разогрел огонь.
По такому же принципу работает железо. Нет, человек не собирался в круг
и подуть в огонь, вместо этого он изобрел мехи.Прокачивая сильфон
в огонь добавляли воздух, и можно было работать с железом.
Большинство ранних людей не знали, как работать с железом. Те, кто действительно имел непосредственное военное превосходство над всеми остальными. Бронзовое оружие, при ударе о железное оружие разрушалось при ударе. Таким образом, секрет Как работать с магическим блэк-металлом тщательно охраняли. Понять высокая ценность железа рассмотрим этот один пример. Один древний король торговался ему удалось купить шестидюймовый железный нож у торговца.Он хвастался своим соотечественникам, что он очень много наработал, и сорвал Купец, который так дешево продал нож. Что на самом деле заплатил этот король для шестидюймового железного ножа? Только ЕГО вес в золоте. Теперь ты понимаешь ценность железа для древнего человека?
Точки плавления металлов — Руководство по плавлению металлов
от CGM Findings от 3 октября 2012 г.
Для тех, кто интересуется плавкой металлов — теперь вы знаете. Разные температуры плавления для разных драгоценных металлов.
Есть над чем подумать при пайке, плавке, ковке горячего металла.
Мы не включали это. Спасибо кому-то из сети ювелирных художников, кто это сделал.
Это ценная информация, заслуживающая упоминания.
Посмотрите на разницу между алюминием и железом. Что-то думать о. Хотя у вас, возможно, даже не будет возможности поработать с ними, конечно, неплохо иметь приблизительное представление о том, с чем вы имеете дело.
Мы действительно удивлены, что латунь, серебро и золото на самом деле выше, чем мы могли подумать, глядя на цифры.
«Обратите внимание, что точки плавления варьируются от ресурса к ресурсу — эта диаграмма составлена с использованием многочисленных источников и перекрестных подтверждений».
Температура плавления металлов
Металл | Температура плавления по Цельсию | Температура плавления по Фаренгейту |
Алюминий | 659 | 1218 |
Латунь (85 Cu 15 Zn) | 900-940 | 1652-1724 |
Бронза (90 Cu 10 Sn) | 850–1000 | 1562-832 |
Чугун | 1260 | 2300 |
Медь | 1083 | 1981 |
Золото (24k) | 1063 | 1946 |
Утюг | 1530 | 2786 |
Свинец | 327 | 621 |
Никель | 1452 | 2646 |
Палладий | 1555 | 2831 |
Платина | 1770 | 3220 |
Красная латунь | 990–1025 | 1810–1880 |
Серебро (чистое) | 961 | 1762 |
Серебро (стерлингов) | 893 | 1640 |
Нержавеющая сталь | 1363 | 2550 |
Сталь с высоким содержанием углерода | 1353 | 2500 |
Средний углерод | 1427 | 2600 |
с низким содержанием углерода | 1464 | 2700 |
Олово | 232 | 450 |
Титан | 1795 | 3263 |
Желтая латунь | 905–932 | 1660–1710 |
цинк | 419 | 786 |
Эта информация взята из: Сеть художников-ювелирных художников [посмотрите и скажите им спасибо]
также у них есть версия в формате PDF, так что вы можете скачать эту таблицу!
http: // www. jewelryartistsnetwork.com/index/metals-melting-temperatures/
Ювелирных Художников — Что ЭТО?
«Сеть — это онлайн-сообщество художников, которые хотят делиться, учиться и расти.
Мы говорим о технике, дизайне, бизнесе и многом другом.
Здесь можно найти информационные статьи, учебные пособия, интервью с художниками, вдохновляющую галерею, видео, а также время от времени соревнования и раздачи подарков.
Цель — информировать, вдохновлять и поощрять рост ».
Бронза vs.Латунь — в чем разница?
Задолго до эры алюминия и стали был изобретен металлический сплав, то есть материал, созданный путем объединения двух синергетических металлов вместе. Таким образом, полученный сплав не только сохраняет некоторые свойства каждого элемента, но и может иметь новые свойства, которых нет ни у одного из них, что произвело революцию в нашем современном выборе материалов. Два сплава, которые положили начало этому сдвигу, — это бронза и латунь, которые представляют собой древние металлические сплавы, которые тысячелетиями использовались греками и другими бывшими империями. Эти металлы послужили отправной точкой для всех других сплавов, и в этой статье мы исследуем бронзу и латунь и их различия. Будут подробно описаны физические, химические и механические свойства бронзы и латуни, а также то, как они используются до сих пор. Эта статья призвана показать, как эти металлы, будучи более архаичными, чем большинство других инженерных материалов, по-прежнему являются необходимыми компонентами нашего успеха в современную эпоху.
бронза
Бронза — это результат добавления олова к меди, хотя часто бывает много дополнительных побочных элементов, потому что бронза была обнаружена примерно в 3500 году до нашей эры, до того, как были разработаны точные химические методы.В наше время бронза считается классом медных сплавов, который был определен на основе их рабочих свойств и конкретных легирующих элементов. Было обнаружено, что такие металлы, как свинец, марганец, сурьма, никель, цинк, кремний и другие, улучшают бронзу, поэтому теперь у дизайнеров есть широкий выбор марок бронзы. Чтобы узнать больше о различных типах бронзы, прочтите нашу статью о типах бронзы.
Типичная бронза красновато-коричневого / золотого цвета и хрупкая, но менее хрупкая, чем чугун.Он имеет относительную плотность около 8,8 г / см 3 и демонстрирует низкое трение при контакте с другими металлами. Он легко проводит тепло и электричество и имеет диапазон температур плавления 950-1050 ° C, в зависимости от количества присутствующего олова. Он окисляется на воздухе из-за высокого содержания меди, что придает бронзе отчетливую пятнистую патину. Это окисление предотвращает коррозию бронзы, особенно в морской среде; однако, если соединения хлора могут вступать в реакцию с бронзой, начинается процесс, известный как «болезнь бронзы», когда коррозия приводит к еще большей коррозии, медленно разрушая сплав с течением времени.Благодаря своей стойкости к соленой воде бронза может использоваться в фурнитуре лодок и подводных морских частях, а также в скульптурах, которые должны противостоять разложению во внешней среде. Он демонстрирует отличные литейные свойства и может быть легко отлит в виде подшипников, зажимов, электрических соединений, пружин и многого другого.
Если вы заинтересованы в покупке бронзы для своего проекта, не стесняйтесь просматривать нашу платформу покупки бронзы для поставщиков.
Латунь
Латунь была обнаружена около 500 г. до н.э. и представляет собой сплав меди и цинка, хотя она также содержит другие элементы, как и бронза.Поскольку латунь и бронза во многом пересекаются, латунь обычно обозначается большим процентным содержанием цинка и относительным отсутствием олова (хотя, что сбивает с толку, также существуют луженые латунные сплавы, что еще больше размывает линии). Свинец — обычная добавка к латуни, которая увеличивает ее обрабатываемость, а также к другим уникальным элементам, которые создали класс латунных сплавов.
Латунь — это цвет яркого золота, меди или даже серебра, в зависимости от соотношения цинка и меди. Она более пластична, чем бронза, и демонстрирует такое же низкое трение при контакте с другими металлами. Он имеет плотность около 8,73 г / см 3 и имеет низкую температуру плавления 900–1000 ° C, в зависимости от сплава. Латунь отлично проводит тепло и устойчива к коррозии, особенно к гальванической коррозии в морской воде. Он хорошо отливает, достаточно прочен и привлекателен и даже обладает некоторыми антимикробными свойствами благодаря высокому содержанию меди. Чаще всего латунь используется в музыкальных инструментах, декоративных накладках, винтах, радиаторах, гильзах для пуль и т. Д.
Если вы заинтересованы в покупке латуни для вашего проекта, не стесняйтесь просматривать нашу платформу закупок для поставщиков латуни.
Сравнение бронзы и латуни
Несмотря на то, что эти металлы связаны как по составу, так и по внешнему виду и даже по применению, латунь и бронза часто используются для разных целей. Будет полезно изучить, что отличает эти два медных сплава друг от друга, исследуя некоторые общие механические свойства, показанные ниже в таблице 1.
Таблица 1: Сравнение свойств материалов бронзы и латуни.

Свойства материала | бронза | Латунь | |||
Шт. | Метрическая система | Английский | Метрическая система | Английский | |
Теплопроводность (20 ° C) | 24 Вт / м-К | 15 БТЕ / (час фут ° F) | 120 Вт / м-К | 64. | |
Усталостная прочность | 90,0-352 МПа | 13100-51100 фунтов на кв. Дюйм | 22-360 МПа | 3190-52200 фунтов на кв. Дюйм | |
Температура плавления (средняя) | 1010 ° С | 917 ° С | |||
Твердость (по Бринеллю) | 40–420 | 55-73 | |||
Обрабатываемость (средняя) | 33. | 46,8% |
Теплопроводность — хороший способ узнать, будет ли металл использоваться в тепловых приложениях, потому что он показывает, сколько энергии может передаваться через материал и с какой скоростью. Теплопроводность латуни намного выше, чем у бронзы, что делает ее идеальным выбором для радиаторов отопления. Бронзу также можно использовать в тепловых приложениях, но латунь всегда будет иметь приоритет, если есть выбор между ними.
Усталостное напряжение — это напряжение, вызванное частой сменой небольших напряжений, которые могут вызывать микро- и даже макротрещины в материале в течение длительного периода времени. Это значение жизненно важно для понимания того, будет ли материал подвергаться постоянным нагрузкам, таким как частые изменения температуры или нагрузок, которые могут нарушить целостность сплава при достаточном количестве циклов. Усталостная прочность бронзы и латуни дана в виде диапазонов в таблице 1, поскольку существует множество сплавов каждого металла. Бронза обычно имеет более высокое сопротивление усталости, чем латунь, что можно увидеть, сравнив нижнюю границу их диапазонов усталостной прочности.Это качество делает бронзу более подходящей для морских частей и пружин, которые в процессе эксплуатации подвергаются постоянным нагрузкам.
Латунь имеет более низкую среднюю температуру плавления, чем бронза (917 против 1010 ° C), но обе они легко отливаются. При использовании любого из этих металлов для отливки форм учитывайте желаемые механические свойства; более устойчивый проект, скорее всего, выиграет от бронзы, в то время как более декоративный может использовать латунь для большего эффекта.
Твердость — это мера реакции материала на местные поверхностные напряжения и его реакции на царапины, вмятины и т. Д.Шкала твердости по Бринеллю — одна из многочисленных доступных шкал твердости, в которой используется собственный индентор для определения твердости для оценки реакции материала на стандартизованную силу. Для справки: типичное стекло получает 1500 баллов по шкале твердости Бринелля и свинец 5 баллов; Используя их в качестве ориентиров, таблица 1 ясно показывает, что бронза в среднем тверже латуни. Более твердый материал обычно более хрупкий, и бронза следует этому правилу, поскольку она гораздо более склонна к разрушению, чем латунь. Если обрабатываемость необходима, латунь, безусловно, лучший выбор, чем бронза.Однако, если важны прочность и износостойкость, бронза может быть лучшим вариантом.
Обрабатываемость — это сравнительная оценка, присваиваемая металлам, чтобы показать, как они реагируют на механические нагрузки, такие как токарная обработка, фрезерование, штамповка и другие процедуры. Важно понимать показатель обрабатываемости металла, поскольку он определяет, какие типы обработки могут быть выполнены, если таковые имеются. Процент обрабатываемости металла сравнивается с эталонным металлом, где этому металлу присваивается рейтинг 100% (легко обрабатывается).Металлу, который труднее обрабатывать, присваивается рейтинг ниже 100%, что относится как к бронзе, так и к латуни. Есть некоторые сплавы, разработанные специально для механической обработки (например, латунный сплав C360), но большинство медных сплавов слишком пластичны для обработки. Оба металла обладают отличными литейными характеристиками, поэтому перед обработкой этих металлов продумайте процедуру литья. Если его необходимо подвергнуть механической обработке, убедитесь, что выбранный вами сплав предназначен для механической обработки, иначе вы рискуете засорить вашу фрезу.
Бронза и латунь бывают разных форм, размеров и составов.Как всегда, запрашивайте у своего поставщика самую свежую информацию о том, что доступно и какой тип бронзы или латуни лучше всего подойдет для вашего применения.
Сводка
В этой статье представлено краткое сравнение свойств, прочности и областей применения бронзы и латуни. Для получения информации о других продуктах обратитесь к нашим дополнительным руководствам или посетите платформу Thomas Supplier Discovery Platform, чтобы найти потенциальные источники поставок или просмотреть подробную информацию о конкретных продуктах.
Источники:
- Руководство по металлургии
- О медных сплавах и латуни
- Обзор материалов для бронзы
- Обзор материалов для латуни
- Теплопроводность металлов, металлических элементов и сплавов
- Sequoia Brass & Copper: Справочник по картриджу из сплава 260, желтая латунь
- Sequoia Brass & Copper: Руководство по морской латуни
- Sequoia Brass & Copper: Справочник по латуни 272
Прочие изделия из бронзы
Больше от Metals & Metal Products
| |
| |
| |
| |
| |
| |
| |
| |
| |
| |
| |
| |
| |
| |
| |
| |
| |
|
Диаграмма — Точки плавления металлов
от Lexi, Content Development Group, эксклюзивно для Fire Mountain Gems and Beads®
При пайке твердым припоем важно знать температуру плавления металла, с которым вы работаете.

Тип металла | По Фаренгейту | Цельсия |
Оловянный | 440 | 226 |
Олово | 450 | 232 |
Цинк | 786 | 418 |
Алюминий | 1220 | 660 |
Золото 585 пробы | 1615 | 879 |
Стерлинговое Серебро | 1640 | 893 |
Латунь | 1652-1724 | 900-940 |
Золото 18 карат | 1700 | 926 |
Чистое серебро | 1760 | 960 |
Бронза | 1825 | 996 |
Золото (чистое) | 1948 | 1064 |
Медь | 1983 | 1084 |
Никель | 2030 | 1110 |
Высокоуглеродистая сталь | 2500 | 1371 |
Нержавеющая сталь | 2550 | 1398 |
Среднеуглеродистая сталь | 2600 | 1426 |
Низкоуглеродистая сталь | 2700 | 1482 |
Платина | 3221 | 1771 |
Как вам этот ресурс? Ваш отзыв помогает нам предоставлять ресурсы, которые наиболее важны для вас.
тиглей для плавления золота, серебра, меди, алюминия, платины, латуни, алюминия
Компания PMC Supplies предлагает большой выбор тиглей, изготовленных из керамики, графита, глины-графита и кварца для плавления драгоценных металлов. Наши тигли предназначены для работы с ведущими печами отрасли, в том числе: Kerr, Tabletop, MF Series, Vcella, RDO Induction, Procraft, Neycraft и другие.В дополнение к тиглям, разработанным специально для печей, PMC Supplies предлагает полную линейку литейных тиглей для пропановых и газовых кузн, керамических тиглей для малых масштабов и плавки горелок. Наши тигли идеально подходят для большинства металлов, включая золото, серебро, медь, латунь, алюминий, олово, платину и другие.
- Тигли серии MF Hardin
Сменные тигли для электропечей серии MF.Изготовлен из графита высокой плотности для обеспечения долговечности. Наши тигли имеют паз под ключ, что упрощает обращение с ними.
- Kerr Crucibles
Сменные тигли для электропечей серии KERR. Изготовлен из графита высокой плотности для обеспечения долговечности. - Графитовые чашки
Графитовые чашки тигля предназначены для плавки с использованием горелки.Идеально подходит для мелкомасштабных процессов плавления. Наши тигельные чашки из графита высокой плотности отлично подходят для плавления металлов. - Тигли печи R9
Тигли для электропечей Р9 и Р9Д.Доступны в размерах 4 и 10 унций, изготовлены из графита высокой плотности для обеспечения долговечности. Имеет носик для обеспечения точности при разливке металлов.
- Индукционные тигли
Просмотрите наш большой выбор тиглей для индукционных печей. Рабочие характеристики включают хорошее электрическое сопротивление, хорошую теплопроводность и высокую стойкость к химической коррозии. - Настольные тигли для печей
Сменные тигли для электропечей TableTop.Доступны в размерах 10, 30, 60, 100 и 120 унций. Изготовлен из графита высокой плотности для обеспечения долговечности. - Графитовые литейные тигли
Идеально подходит для работы с открытым пламенем; в основном используется в пропановых печах.* Это расходные материалы, особенно при работе с металлами при очень высоких температурах. Эффективно плавит золото, серебро, медь, латунь, алюминий и др.
- Тигли саламандры
Тигли Salamander Super Crucible изготовлены из высококачественного графита на керамической связке. Тигли Salamander обеспечивают стабильную работу в индукционных печах, работающих на топливе, а также в средне- и высокочастотных индукционных печах. - Пробирные тигли
Пробирные тигли в основном используются для плавки золотосодержащих рудных концентратов и черных песков с использованием флюса.Эти тигли представляют собой экономичное решение при рафинировании этих материалов. - Тигли для печей общего назначения
Графитовые тигли экономичного класса для бюджетной плавки.Работает с нашими плавильными печами серий MF и Hardin. Не рекомендуется для длительного использования.
- Керамические тигли
Ознакомьтесь с нашей керамической посудой и стаканами из плавленого кварца.Они являются отличным выбором для литья ювелирных изделий в горелках и печах, а также для плавления золота, серебра, меди и других металлов. - Центробежные тигли
Ознакомьтесь с нашими тиглями для центробежного литья и найдите лучшие в отрасли центробежные машины. - Платиновые тигли
Эти тигли предназначены для достижения высоких температур для плавления, разливки и литья платины.