Последовательное соединение средней частоты Индукционная индукционная латунная плавильная печь для меди / латуни / бронзы алюминия разработана специально для плавки металла с низкой плотностью, с использованием точно подходящих температур и равномерного распределения тепла. Это необходимо для плавки таких металлов, как латунь, медь, бронза, если вы хотите сохранить ожидаемый срок службы латуни, меди и ее качество. Идеальная плавильная печь для латуни / меди обеспечит точный контроль температуры для достижения этой цели.
AПреимущества электромагнитной индукционной печи медной / бронзовой / латунной плавильной печи средней частоты:
1, экономьте энергию и снижайте температуру окружающей среды
Оригинальная дизельная печь мастерской по загрязнению, а также вспомогательным выхлопным трубам, внутри и снаружи печи тепло имеет большое количество распределения в мастерской, в результате чего высокотемпературная мастерская.
2, быстрый нагрев, точный контроль температуры в реальном времени
Электромагнитный индукционный метод нагревания через магнитные силовые линии делают нагревание быстрым нагревом, быстрым плавлением алюминиевого сплава. Контроль температуры в режиме реального времени и точный, что улучшает качество продукта и повышает эффективность производства!
3 и длительный срок службы, простота обслуживания
Традиционный метод нагрева электропечи заключается в использовании резистивного нагрева проволоки, сопротивление проволоки в высокотемпературной среде в течение длительного времени при использовании окисления приведет к сокращению срока ее службы, высоким затратам на техническое обслуживание. Электромагнитная нагревательная катушка изготовлена из изоляционного материала и высокотемпературного провода, поэтому срок службы большой и не требует технического обслуживания.
4, мощность
Электромагнитный индукционный нагрев с развитием и зрелостью технологии, процесса производства и технологии компонентов, программного обеспечения, таких как надежная защита текущей мощности может быть 2-200KW.
5, безопасный
Полезная модель использует электромагнитный индукционный нагрев, который может снизить температуру поверхности машины, и можно безопасно прикоснуться к человеческому телу, чтобы избежать ожогов и ожогов, вызванных традиционным режимом нагрева, и защитить производственную безопасность. сотрудников.
Особенности
1 энергосбережение и защита окружающей среды, силовые устройства IGBT Германии, высокая надежность, стабильная работа и низкие затраты на техническое обслуживание.
2) частота цифровой фазовой автоподстройки, автоматическое согласование импеданса нагрузки.
Управление замкнутым контуром питания 3, чтобы избежать изменения температуры, вызванного отключением питания.
4) перенапряжение, пониженное напряжение, отсутствие фазы, перегрузка по току, защита от перегрева, отображение параметров в режиме реального времени, диагностика неисправностей и аварийный сигнал; автоматическая сигнализация утечки, отключение электропитания и отображение рабочего состояния в режиме реального времени.
5) Система ПИД-регулирования нагрева, равномерная температура нагрева, предотвращение температурного дрейфа расплавленного алюминия, меньшее сжигание, однородные металлические компоненты для повышения квалификации продукта.
Цифровой терморегулятор 6 (LED), измеряющий и контролирующий погрешность температуры до 3 градусов Цельсия, качество алюминиевого супа хорошее, температура плавления быстро повышается, температуру в печи легко контролировать, эффективность производства высокая;
7) интегральная структура поликристаллических муллитовых волокон печи, небольшой объем, хорошие изоляционные свойства, низкое энергопотребление, высокая эффективность, температура выше градусов 1200, длительный срок службы;
8.
9 (100%) продолжительность нагрузки, максимальная мощность, чтобы обеспечить работу часов 24.
Плавильная мощность серии SMJD Connection Mid Индукционная печь для выплавки меди, меди / латуни:
Тип | Входная мощность | Плавящая способность | Максимальная температура | ||
сталь, нержавеющая сталь | медь, золото, серебро (лом, шлак) | алюминий, алюминиевый сплав, Алюминиевый лом, Алюминиевый шлак, поп-банка | 1800 ℃ | ||
SMJD-463 | 60 кВт | 200 KG | 500 KG | 200 KG | |
SMJD-480 | 60 кВт | 150 KG | 500 KG | 150 KG | |
SMJD-580 | 80 кВт | 200 KG | 600 KG | 200 KG | |
SMJD-600 | 60 кВт | 230 KG | 560 KG | 230 KG | |
SMJD-900 | 120 кВт | 300 KG | 900 KG | 300 KG | |
SMJD-905 | 80 кВт | 300 KG | 900 KG | 300 KG | |
SMJD-1250 | 80 кВт | 400 KG | 1200 KG | 400 KG | |
SMJD-1250 | 120 кВт | 450 KG | 1350 KG | 450 KG | |
SMJD-1500 | 120 кВт | 500 KG | 1500 KG | 500 KG | |
SMJD-1550 | 120 кВт | 520 KG | 1560 KG | 520 KG | |
SMJD-1700 | 160KW | 600 KG | 1700 KG | 600 KG | |
SMJD-2300 | 160KW | 800 KG | 2000 KG | 800 KG | |
SMJD-3100 | 200KW | 1200 KG | 3000 KG | 1200 KG |
Алюминиевые отходы, перерабатывающие процесс плавления
Параметр индукционной плавильной печи SMJD
Руководство по эксплуатации индукционной плавильной печи из алюминия, меди и железа
[pdf-embedder url = ”https://dw-inductionheater. com/wp-content/uploads/2018/12/AluminiumCopperIron-Induction-Melting-Furnace-manual.pdf” title = ”Индукционная плавильная печь для алюминия, меди, чугуна руководство по эксплуатации»]
Особенности плавки медных сплавов » Все о металлургии
23.04.2015
Плавку меди ведут на воздухе, в среде защитных газов и в вакууме. При плавке на воздухе медь окисляется. Образующаяся закись (Cu2O) растворяется в жидкой меди Содержание кислорода в расплаве определяет выбор состава футеровки плавильных печей. Для плавки меди с повышенным содержанием кислорода используют футеровку из магнезита Применение футеровки из кремнезема SiO2 в этом случае недопустимо из-за возможного оплавления ее при взаимодействии с закисью меди с образованием легкоплавких силикатов: mCu2O+nSi02 → mCu2O*nSiO2.

Взаимодействие с газами идет тем интенсивнее, чем выше температура перегрева расплава. Для предохранения от окисления и поглощения водорода плавку меди ведут под покровом древесного угля, в восстановительной или защитной атмосфере. Необходимым условием применения древесного угля является тщательная сушка, а в ряде случаев прокалка его для удаления адсорбированной влаги и продуктов сухой перегонки. Однако и при соблюдении всех мер предосторожности окисление все же происходит; некоторое количество кислорода обнаруживается в меди после расплавления.

Для удаления кислорода медь раскисляют. Используют несколько способов очистки расплавленной меди от кислорода: «дразнение», вакуумную переплавку, раскисление нерастворимыми поверхностными и растворимыми раскислителями, фильтрование через слой раскаленного древесного угля
Удаление кислорода дразнением является обязательной операцией в процессе огневого рафинирования меди от металлических примесей как на заводах первичной металлургии, так и при переплавке скрапа и отходов. Дразнению подвергают медные расплавы, прошедшие огневое (окислительное) рафинирование и содержащие 3—7 % закиси меди. Для этого с поверхности расплава снимают шлак, засыпают На нее слой древесного угля и создают в печи восстановительную атмосферу. Дразнение осуществляют погружением в расплав сырой древесины. Водяной пар и продукты сухой перегонки, выделяющиеся при этом, интенсивно перемешивают и разбрызгивают расплавленную медь, выбрасывая капли расплава в восстановительную атмосферу.
Во время дразнения происходит восстановление окисленной меди по реакциям: 4Cu2О + Ch5 → CO2 + 2Н2О + 8Cu; Cu2O + CO → CO2 + 2Cu; 2Cu2О + С → CO2 + 4Cu; Cu2O + h3 → h3O + 2Cu, в результате чего содержание кислорода в меди постепенно снижается.

Окисленная медь имеет в изломе грубую структуру темнокрасного (кирпичного) цвета и кристаллизуется с образованием сосредоточенных (концентрированных) раковин; светло-розовый мелкокристаллический излом с большим количеством газовых раковин и выпучиванием металла при кристаллизации — показатели того, что металл «передразнен» (содержит много водорода). Оптимальному раскислению соответствует мелкокристаллический светло-розовый излом с ровной без вспучивания и раковин поверхностью пробы.
Плавка в вакууме, используемая для получения бескислородной меди, позволяет в результате диссоциации закиси меди снизить содержание кислорода до 0,001 %.
Удаление кислорода с помощью раскислителей широко применяется при плавке меди на воздухе Для этого в расплав вводят вещества, имеющие большее сродство к кислороду, чем медь. В качестве поверхностных раскислителей используют карбид кальция CaC2, борид магния Mg3B2, углерод и борный шлак (B2O3* MgO).

Из растворимых раскислителей чаще всего применяют фосфор, который вводят в виде лигатуры медь — фосфор (9—13 % Р). В зависимости от содержания кислорода в меди количество фосфора принимают в пределах 0,1—0,15 % от массы расплава. Восстановление меди может сопровождаться образованием пара P2O5 и одновременно CuPO3, находящейся при температурах рафинирования в жидком состоянии, т. е. образующиеся окисел и соль легко удаляются из расплава. Медь, используемую для электротехнических целей, раскисляют литием (0,1 %), так как избыток фосфора резко снижает ее электропроводность. Использование для раскисления меди угольных фильтров основано на взаимодействии Cu2O с углеродом по реакции, рассмотренной выше.
Плавку бескислородной меди ведут в индукционных печах с железным сердечником в среде сухого, обеспыленного генераторного газа под слоем древесного угля (100—150 мм) или в вакуумных высокочастотных печах.

Шихтой для выплавки бескислородной меди служат катодные листы марки MO (99,95 %) и отходы бескислородной меди (не более 15 % от массы шихты). Перед загрузкой в печь катодные листы разрезают, промывают от остатков электролита и просушивают. Разливку бескислородной меди ведут в атмосфере защитного газа пли в вакууме. Температура металла при литье 1170—1180 °С.
Плавку меди, содержащей металлические примеси, ведут в отражательных печах емкостью 20—50 т. Футеровку печей выше уровня металла выполняют из магнезита. Подина печи — кварцевая, набивная. Набивку подины производят сухим песком с добавкой небольшого количества меди или медной окалины. Шихтой для плавки служат всевозможные отходы (обрезь, отходы производства, промышленный и бытовой лом). Особенность плавки — окислительно-восстановительное рафинирование с целью удаления вредных примесей.
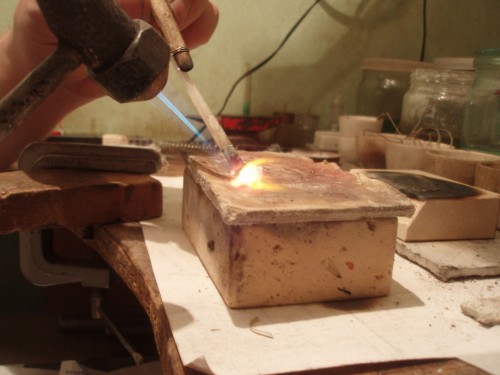
Шлаки медной плавки богаты закисью меди. Для уменьшения содержания меди в состав шлака вводят оксиды, у которых основность выше, чем у Cu2O, и которые могли бы вытеснять Cu2O из шлака в металл по реакции (Cu2O*SiO2) + (Ме’О) → (Мe’O*SiO2) + [Cu2O]. Такими оксидами являются CaO, MnO, FeO и др. В практике производства медных сплавов для этой цели чаще всего используют основной мартеновский шлак, содержащий 25— 40 % CaO, 10—15 % FeO, 10—15 % Al2O3, 8—12 % MnO и 25—30 % SiO2 в количестве 1,5—2 % от массы шихты.

После удаления шлака медь раскисляют дразнением. Длительность операции (1—1,5 ч) определяется объемом металла. Поверхность расплава в этот период покрывают древесным углем, а в печи создают восстановительную атмосферу (коптящее пламя). Контроль процесса раскисления в производственных условиях осуществляют отбором проб на излом. Ввиду того что дразнением невозможно удалить кислород полностью, во время заливки производят дораскисление фосфористой медью (0,1—0,15 % от массы металла).
В ряде случаев для нейтрализации вредного влияния примесей висмута и свинца медь подвергают модифицированию. С этой целью в медные расплавы вводят 0,2—0,3 % (по массе) кальция, церия или циркония.
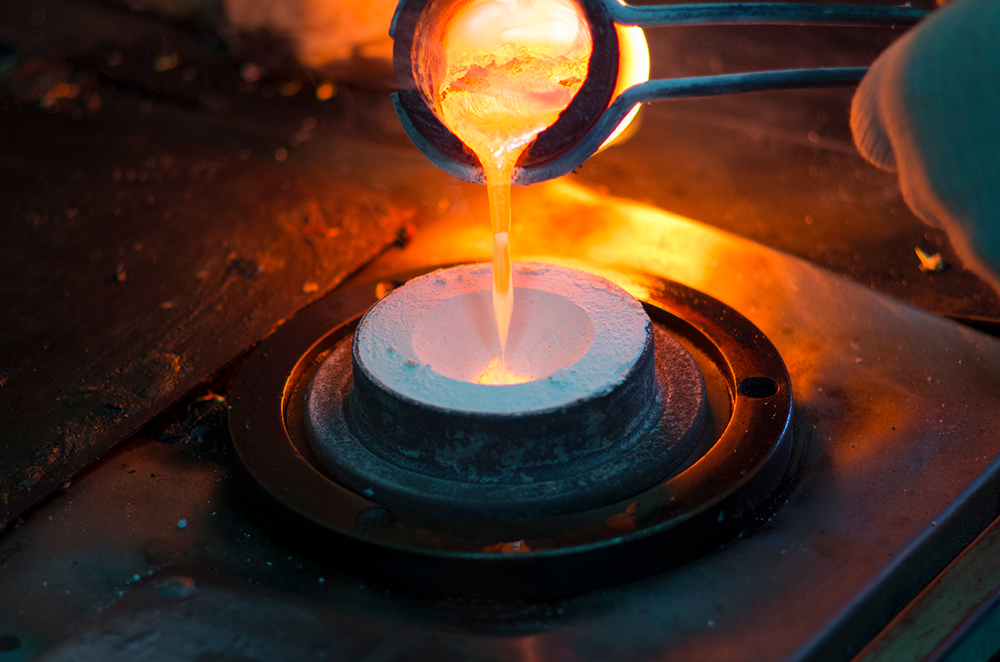
Плавка большинства медных сплавов на воздухе также сопровождается окислением и насыщением водородом. Окисляются преимущественно легирующие компоненты, поскольку в большинстве своем они имеют более высокий изобарный потенциал образования оксида, чем медь. По этой причине легирующие элементы (Al, Be, Sn и др.) раскисляют медь, образуя твердые, жидкие или газообразные оксиды. Окисление сплавов, содержащих алюминий, бериллий или титан, происходит с образованием тонкой, плотной окисной пленки на поверхности расплава. Наличие такой пленки тормозит окисление. Поскольку окисная пленка в процессе плавки неоднократно разрушается (перемешивание, рафинирование, модифицирование), обрывки ее могут замешиваться в расплав и попадать в отливку.
За исключением латуней и нейзильберов, растворению водорода в которых препятствует высокое давление паров цинка, все другие медные сплавы интенсивно поглощают водород и при кристаллизации склонны к газовой пористости.
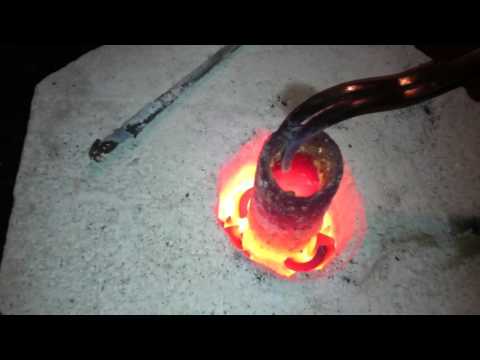
Для защиты от окисления плавку сплавов ведут под покровом древесного угля или флюсов на основе фторидов, стекла, соды и других солей (табл. 35). Наиболее часто применяют древесный уголь. Степень загрязнения сплавов оксидами и водородом зависит от состава атмосферы печи. Восстановительная атмосфера способствует получению более газонасыщенных расплавов, чем окислительная.
Для предотвращения загрязнения расплавов твердыми, нерастворимыми оксидами легирующие компоненты вводят в медь после предварительного раскисления ее фосфором. Свое назначение фосфор выполняет лишь в том случае, когда его вводят в расплавленную медь в количестве 0,1—0,15 % перед введением других шихтовых материалов. Если же фосфор вводят перед разливкой, раскисляющего действия он не оказывает, так как оксиды цинка, алюминия, марганца и др. имеют более низкую упругость диссоциации, чем P2O5, и по этой причине не восстанавливаются им. Однако введение фосфора перед заливкой оказывает благоприятное влияние на отделение неметаллических включений, так как он способствует снижению поверхностного натяжения и повышению жидкотекучести расплава. Для раскисления используют также кальций, натрий и магний в количестве 0,02—0,04 °6 (по массе).
Многие сплавы чрезвычайно чувствительны к воздействию примесей. Так, например, тысячные доли процента алюминия резко снижают механические свойства и герметичность отливок из оловянных бронз и кремнистых латуней. На алюминиевые бронзы аналогичным образом влияет примесь олова. Поэтому при плавке медных сплавов особое внимание уделяют сортировке и подготовке отходов, используемых в шихту.
Рафинирование расплавов
Рафинирование инертными газами ведут при температурах расплава 1150—1200 °C. Расход газа 0,25—0,5 м3 на 1 т металла; длительность продувки при давлении газа 19,6—29,4 кПа составляет 5—10 мин. Хлористый марганец вводят в количестве 0,1— 0,2 % от массы расплава при 1150—1200 °С с помощью колокольчика. Перед разливкой рафинированный сплав выдерживают в течение 10—15 мин для отделения пузырьков рафинирующего газа .
Вакуумирование применяют в тех случаях, когда сплав не содержит компонентов с высоким давлением пара. Применительно к медным сплавам этот процесс ведут при 1150—1300 °C и остаточном давлении 0,6—1,3 кПа. Длительность вакуумирования определяется массой металла, подвергающегося обработке; в большинстве случаев продолжительность обработки не превышает 20—25 мин.
Очистку оловянных бронз и латуней от примесей алюминия и кремния ведут в ряде случаев путем введения в расплав окислителей (MnO, медной окалины) или продувкой воздухом. Окислительное рафинирование проводят при 1180—1200 °С. Расход окислителей составляет 0,5—1,0 % от массы расплава. Для ускорения процесса очистки окислители замешивают в расплав.
Обработку расплавов флюсами применяют в основном для очистки от взвешенных неметаллических включений. Наиболее высокими рафинирующими свойствами обладают фторидные флюсы, в частности смесь фторидов кальция и магния. Перед рафинированием расплав нагревают до 1150—1250 °С, снимают шлак и на зеркало металла засыпают порошок переплавленного и измельченного флюса в количестве 1,5—2,0 % от массы металла. В течение 8—15 мин флюс перемешивают с металлом, что обеспечивает лучшее отделение взвесей. Перед заливкой для более полного всплывания капель флюса расплав выдерживают в течение 10—15 мин при температуре заливки. Обработку флюсами применяют также для удаления вредных примесей из оловянных и алюминиевых бронз. Например, флюс, состоящий из 33 % Cu2O, 34 % SiO2 и 33 % Na2B4O7, используют для очистки оловянных бронз от алюминия и кремния.
Оптимальным методом очистки от неметаллических включений сплавов, содержащих в своем составе такие легкоокисляющиеся элементы, как алюминий, титан, цирконий и бериллий, является фильтрование. Для этой цели используют зернистые фильтры. Для зернистых фильтров можно рекомендовать такие материалы, как магнезит, алунд, плавленые фториды кальция и магния. Из солевых расплавов для целей рафинирования наиболее пригодны чистые фториды или их смеси. Толщину фильтрующего слоя принимают равной 60—150 мм, а размер зерна фильтра 5—10 мм в поперечнике. Зернистые фильтры перед фильтрованием нагревают до 700—800 °C. Установлено, что фильтр из фторида кальция с размером зерен 5—10 мм в поперечнике и толщиной 70—100 мм позволяет в 1,5—3 раза снизить содержание неметаллических включений в расплаве БрБНТ2 по сравнению с плавкой без фильтрации. Так же как и в случае алюминиевых сплавов, фильтрование расплава бронзы через зернистые фильтры сопровождается укрупнением макрозерна, повышением пластических и усталостных характеристик, некоторым снижением газосодержания.
Модифицирование сплавов
Измельчение первичного зерна в медных сплавах, содержащих алюминий (типа БрАЖМц, БрАЖ, ЛАЖ, ЛАЖМц и др.), достигается добавками тугоплавких элементов — Ti, V, Zr, В, W, Mo. Однако следует заметить, что модифицирующее действие присадок тугоплавких элементов во многом определяется наличием в сплаве железа. В сплавах, не содержащих железа, модифицирующее действие титана, бора и вольфрама не проявляется.
Измельчение зерна отливок из сплавов, не содержащих алюминия и железа (БрС30; БрОЗЦ6СЗ; латунь Л68), может быть достигнуто лишь при совместном введении 0,05 % указанных модификаторов с 0,02 % бора.
Введение тугоплавких модификаторов влечет за собой изменения и в микроструктуре сплавов. В некоторых случаях эти изменения особенно отчетливо выявляются после термической обработки.
Тугоплавкие модификаторы вводят в расплав с помощью лигатур алюминий — ванадий (до 50 %), медь — бор (3—4 % В), алюминий — титан, медь титан и др. в количестве 0,1—0,002 % от массы расплава при 1200—1250 °С. Перегрев модифицированного расплава перед заливкой выше 1180—1200 °С сопровождается огрублением зерна. Оптимальные концентрации модификаторов для некоторых медных сплавов приведены в табл. 36.
Для нейтрализации вредного влияния примесей висмута, свинца или мышьяка в расплавы вводят присадки кальция (0,2 %), церия (0,3 %), циркония (0,4 %) или лития (0,2 %).
Плавка латуней
Приготовление двойных латуней (Л68, Л62) ведут главным образом в индукционных печах, футерованных кварцем. Особенность плавки — высокая летучесть цинка, обусловленная низкой температурой его кипения (907 °С). По этой причине из-за сильного перегрева верхних слоев расплава нерациональна плавка в дуговых печах. В качестве защитного покрова используют древесный уголь, который загружают в печь вместе с первой порцией шихты. Добавка небольшого количества криолита — 0,1 % (по массе) делает шлак «сухим» и сыпучим, что способствует лучшему отделению корольков металла. Иногда вместо древесного угля применяют флюс, состоящий из 50 % стекла и 50 % плавикового шпата.
При выплавке латуней сначала расплавляют медь; в расплав вводят цинксодержащие отходы и вторичную латунь. Сплав нагревают до 1000—1050 °С и перед заливкой в него вводят цинк. Медь перед введением цинка или цинксодержащих отходов не раскисляют, так как цинк сам является хорошим раскислителем, а оксиды его не растворяются в расплаве и легко всплывают. Сложные латуни (ЛМц, ЛН, ЛАЖМц) плавят так же, как двойные. Различие состоит лишь в том, что перед введением отходов и легирующих компонентов, особенно алюминия, медь раскисляют фосфором. Для удаления неметаллических включений сложные латуни подвергают рафинированию хлористым марганцем или фильтрацией через зернистые фильтры.
Кремнистые латуни отличаются большой склонностью к поглощению водорода, особенно в присутствии примесей алюминия. Они очень чувствительны к перегреву газонасыщенность расплава резко увеличивается при нагреве выше 1100 °С. В процессе кристаллизации растворенный газ выделяется, что приводит к «росту» отливки и появлению ликвационных выпотов на их поверхности. Плавку кремнистых латуней ведут в окислительной атмосфере под слоем флюса (30 % Na2CO3; 40 % CaF2; 30 % SiO2), не допуская перегрева расплава выше 1100 С. В целях предупреждения загрязнения расплава оксидами кремния медь перед введением отходов или кремния раскисляют фосфором. Кремний вводят лигатурой медь — кремний (15—20 % Si). После введения лигатуры расплав перемешивают графитовой мешалкой для полного растворения присадки, затем вводят цинк и последним — свинец. Готовность сплава оценивают пробами на излом и газонасыщенность. Если излом мелкозернистый, а на поверхности пробы отсутствуют ликвационные наплывы, сплав разливают в формы. В том случае, когда на поверхности пробы образуются выпоты, расплав дегазируют перегревом или продувкой азотом. Разливку ведут при 950—980 °С.
Плавка бронз
Особенность оловянных бронз — образование SnO2 при взаимодействии олова с Cu2O Наличие включений SnO2 заметно снижает механические и эксплуатационные свойства оловянных бронз. Поэтому перед введением олова или оловосодержащих отходов медь раскисляют фосфором. Плавку ведут в окислительной атмосфере под слоем древесного угля или флюса (сода + древесный уголь). Вначале под слоем угля расплавляют медь и нагревают ее до 1100—1150 °С. Введением фосфористой меди (9— 13 % Р) производят раскисление. Затем вводят цинк, олово или отходы сплава и в последнюю очередь свинец. Сплавы нагревают до 1100—1200 С, рафинируют хлористым марганцем или азотом, модифицируют и разливают в формы при 1150—1300 С.
Плавка сложных оловянных бронз мало чем отличается от приведенной технологии. Плавку вторичных оловянных бронз ведут под слоем флюса в окислительной атмосфере.
Алюминиевые бронзы чувствительны к перегреву и больше оловянных склонны к поглощению газов, поэтому плавку их ведут в окислительной атмосфере под слоем флюса (см. табл. 35), не допуская перегрева расплава выше 1200 °С. Для предотвращения загрязнения расплава окисными пленками медь перед введением алюминия и других легирующих компонентов раскисляют фосфором. Большая разница в плотности меди и алюминия способствует расслоению их в процессе плавки. Поэтому необходимо очень тщательно перемешивать расплав перед заливкой.
Плавку алюминиевых бронз проводят в такой последовательности. Сначала под слоем флюса расплавляют медь и раскисляют ее фосфором (0,05—0,1 %). Если сплав содержит никель, то его загружают вместе с медью. После этого в расплав вводят железо и марганец в виде соответствующих лигатур с медью. После растворения лигатур расплав вторично раскисляют фосфором (0,05 %) и вводят алюминий или лигатуру медь — алюминий. По окончании растворения алюминия поверхность расплава засыпают флюсом. Недопустимо вводить алюминий перед марганцем и железом. Образующиеся при этом пленки делают расплав непригодным к заливке. Перед заливкой при 1100—1200 °С расплав рафинируют хлористым марганцем или криолитом, количество которых берут в пределах 0,1—0,3 от массы расплава. Алюминиевые бронзы очень часто модифицируют ванадием, вольфрамом, бором, цирконием или титаном. Эти присадки в виде лигатур с алюминием и медью вводят в расплав в количестве 0,05—0,15 % при 1200—1250 °С.
Плавка бериллиевой бронзы (БрБ2, БрБНТ) мало чем отличается от плавки оловянных бронз. Для этого используют индукционные печи с графитовыми тиглями. Плавку ведут под покровом древесного угля. Медь перед введением бериллия и титана раскисляют фосфором. Угар бериллия составляет 5—10%- Ввиду токсичности паров и пыли бериллия плавку бериллиевых бронз ведут в изолированных помещениях, оборудованных хорошей приточно-вытяжной вентиляцией. Для отделения неметаллических включений при разливке бериллиевых бронз используют различные фильтры.
Кремнистые бронзы плавят в электрических индукционных печах под покровом древесного угля. Медь перед введением кремния или отходов раскисляют фосфором. Для получения расплавов с малым содержанием водорода недопустим перегрев выше 1250—1300 °С.
Особенность плавки свинцовых бронз (БрСЗО) — сильная ликвация по плотности. Наиболее однородные расплавы удается получать при плавке в индукционных печах, обеспечивающих интенсивное перемешивание. Для предупреждения ликвации в высокосвинцовистые бронзы рекомендуется вводить 2—2,5 % никеля, а охлаждение отливок вести с большими скоростями.
Плавка медноникелевых сплавов
Приготовление мельхиора, нейзильбера, куниалей, константана и манганина не представляет особых затруднений. Эти сплавы плавят в индукционных печах с кварцевой футеровкой под слоем прокаленного древесного угля. В шихту допускается вводить до 80 % отходов.
Приготовление этой группы сплавов, кроме куниалей, начинают с загрузки меди и никеля; по мере их расплавления загружают крупнокусковые отходы, а затем под зеркало металла — мелкие отходы. Цинк вводят в последнюю очередь. После полного расплавления шихты сплавы раскисляют марганцем и кремнием (для нейзильбера) или марганцем и магнием (для мельхиора и константана). Количество раскислителя определяется содержанием кислорода в расплаве. Обычно при сравнительно чистой шихте в расплав вводят 0,1—0,15 % Mn и до 0,1 % Mg. Магний вводят в виде лигатуры Ni—Mg (50 % Mg). После этого с поверхности расплава удаляют шлак и засыпают древесный уголь. Температуру расплава доводят до 1250—1300 °C и, если необходимо, рафинируют его хлористым марганцем.
В связи с тем что в состав куниалей входит алюминий, плавка их по описанной технологии связана с опасностью загрязнения расплава пленками Al2O3. Поэтому перед введением алюминия или отходов куниали медноникелевый расплав раскисляют 0,1—0,15 % марганца. В остальном технология плавки куниалей аналогична плавке алюминиевых бронз.
- Печи для плавки медных сплавов
- Состав и свойства меди и ее сплавов
- Особенности технологии производства фасонных отливок из титановых сплавов
- Особенности плавки титановых сплавов
- Печи для плавки титановых сплавов
- Состав и свойства титановых сплавов
- Особенности технологии производства фасонных отливок из магниевых сплавов
- Особенности плавки магниевых сплавов
- Печи для плавки магниевых сплавов
- Состав и свойства магниевых сплавов
Плавка и разливка медных сплавов Категория: Литейное производство Плавка и разливка медных сплавов Медные сплавы, к которым относятся оловянные и безоловянные бронзы и латуни, выплавляют в основном в электрических дуговых и индукционных печах и реже в пламенных, работающих на жидком топливе. Так как почти все элементы, входящие в состав медных сплавов, легко окисляются, процесс плавки ведется форсированно, при этом принимаются меры к защите сплавов с поверхности (защитными или покровными флюсами), а отдельные легкоокисляемые элементы применяются в виде лигатур. 1. Шихтовые материалы Шихтовыми материалами для медных сплавов могут быть свежие (чистые) металлы, вторичные сплавы, оборотный сплав, а также различные лигатуры, поставляемые промышленностью или собственного приготовления. Для раскисления сплавов применяют фосфористую медь в виде плиток массой около 12 кг по ГОСТ 4515—78, которые перед употреблением разбивают на мелкие куски. Лигатуры — это сплавы двух или нескольких элементов, которые присаживают к сплавам. Применение их обусловлено тем, что отдельные тугоплавкие компоненты сплава имеют более высокую температуру плавления, чем допускаемый перегрев сплава. Температуры плавления лигатур и металла, к которому их присаживают, должны быть близкими, и в то же время лигатуры должны иметь высокое содержание тугоплавкого элемента. 2. Расчёт шихты Для получения сплава возможны различные сочетания шихтовых материалов. Шихта может состоять из одних свежих металлов, из свежих металлов или вторичных сплавов с добавлением лигатур, из оборотного сплава с добавлением свежих металлов и лигатур, из одного оборотного сплава или из одних вторичных сплавов. Обычно применяют шихту, состоящую из 50—60% свежих металлов, 25—35% оборотного сплава и 10—12% покупного лома, или плавку ведут на вторичных сплавах. При расчете шихты учитывают угар различных элементов сплава, величина которого зависит от характера элементов, чистоты шихты и типа плавильной печи. Рассмотрим пример расчета шихты для выплавки бронзы марки БрОЗЦ7С5Н1. При изготовлении сплавов для менее ответственных отливок с целью экономии чистых металлов могут применяться только вторичные сплавы — паспортные бронзы марки БрОЗЦ8С4Н1. 3. Технология плавки медных сплавов Плавка в тигельных печах. Для плавки медных сплавов используются самые разнообразные тигельные печи. Рис. 1. Электрическая печь типа ДМК: 1 — футеровка; 2 — стальной кожух; 3— зубчатые ободы; 4 — шланги для подвода воды; 5 — графитизированные электроды; 6 — шестерни; 7 — водоохлаждаемые уплотнители; 8 — дверцы; 9 — сливной носок; 10 — электродвигатель; 11 — приводной механизм. Плавка в электрических печах. Электрические печи для плавки медных сплавов подразделяются на дуговые и индукционные. Плавка в электродуговых печах. Для плавки применяют электродуговые печи с косвенным нагревом, т. е. такие, У которых электрическая дуга образуется между двумя горизон-альными графитовыми электродами. Печь ДМК (рис. 1) имеет вид барабана с загрузочным кном, отверстиями для электродов и желобом для слива сплава. Кожух печи футеруется динасовым или шамотным кирпичом. Плавка начинается с подготовительных работ: тщательной очистки печи от остатков предыдущей плавки, проверки исправности механизмов и подачи воды к водоохлаждаемым уплотнителям. После этого футеровку прогревают до температуры 700—800 °С, выводят из печи электроды и на дно ее насыпают несколько лопат сухого прокаленного древесного угля, затем загружают предварительно подогретые до 150—200 °С шихтовые материалы: сначала мелочь, литники, скрап и сверху — крупные куски. Шихта должна располагаться не ближе чем в 50 мм от электродов и не должна мешать их свободному перемещению вдоль печи. После установки электродов закрывают загрузочное окно и возбуждают электрическую дугу, что осуществляется сближением электродов и быстрым удалением одного из них на небольшое расстояние с помощью ручного штурвала механизма их перемещения. Процесс расплавления шихты ведется интенсивно. По истечении 20—30 мин включают реверсивный механизм покачивания печи вначале на 25—30°, потом постепенно доводят покачивание до 90°, а после расплавления всей шихты —до 160°. Это позволяет избежать местного перегрева сплава и способствует лучшему перемешиванию его. Сплав раскисляют, присаживают легкоплавкие добавки, рафинируют, подогревают до требуемой температуры и выпускают из печи. Плавка в индукционных печах. Для плавки медных -сплавов применяют индукционные печи со стальным сердечником и без сердечника. Индукционная печь со стальным сердечником, схематический разрез которой показан на рис. 2, представляет собой трансформатор, первичной обмоткой которого служит медная катушка, насаженная на сердечник из пластин электротехнической стали толщиной 0,35—0,5 мм. Вторичной обмоткой является кольцо Жидкого сплава, находящегося в плавильном канале. Переменный ток промышленной частоты, проходя через первичную обмотку, создает вокруг нее магнитный поток, замыкающийся через магнитны» стальной сердечник трансформатора, и индуктирует ток в сплаве, находящемся в кольцевых каналах. Рис. 2. Схема индукционной печи со стальным сердечником: 1 — камера; 2— футеровка; 3— тепловая изоляция; 4 — первичная обмотка; 5 — плавильный канал; 6 — магнитный сердечник. Особенность плавки в индукционных печах заключается в том что жидкий сплав, заполняющий каналы, должен оставаться в печи и после выпуска плавки для образования замкнутой электрической цепи при последующей плавке. В связи с этим в индукционных печах затруднен переход к плавке нового сплава. В этом случае необходимо слить весь сплав из каналов и сделать одну-две промывные плавки сплава неответственного назначения. После заполнения кольцевых каналов и «болота» (слой жидкого сплава толщиной 30—50 мм, находящийся над каналами) жидким сплавом и разогрева печи загружают предварительно подогретую шихту: сначала медь, а после ее расплавления — оборотный и вторичные сплавы. Плавка в индукционных тигельных печах. В последние годы для плавки сплавов на медной основе — бронз и латуней — стали применять индукционные тигельные печи типа ИЛТ. Угар металла в этих печах не превышает 0,5—1%. 4. Особенности плавки и разливки медных сплавов При плавке медных сплавов в состав шихты обычно входит красная электролитическая медь, которую расплавляют и раскисляют фосфористой медью до загрузки в печь остальных составляющих шихты. Плавка меди должна происходить очень быстро под слоем хорошо просушенного и прокаленного древесного угля. Печь перед загрузкой меди надо хорошо разогреть. Качество раскисления можно проверить по технологической пробе: залитый и охлажденный брусок при загибе не должен давать трещин в месте изгиба. Плавка оловянной бронзы. В разогретую печь загружают часть вторичных и оборотного сплавов и покрывают слоем сухого древесного угля, который после расплавления шихты должен покрыть ровным слоем всю поверхность жидкого сплава. По мере расплавления первоначальной порции шихты в печь вводят частями или полностью остаток шихты, подогретой до температуры 150—200 °С. Из применяемых для под-шихтовки свежих металлов медь и никель загружают в печь одновременно с первой порцией шихты, а цинк, свинец и олово вводят непосредственно в ванну к концу плавки для уменьшения их угара. После расплавления всей шихты и достижения требуемой температуры сплав раскисляют фосфористой медью в количестве 0,2% от массы шихты и покрывают хорошо просушенным флюсом, состоящим из 60% кальцинированной соды, 33% плавикового шпата и 7% буры. Расход флюса составляет 2—3% от массы шихты. Затем сплав нагревают до температуры 1250—1300 °С и 20—30 мин выдерживают под флюсом, периодически перемешивая его. После этого счищают образовавшийся шлак и выпускают сплав в ковш для разливки в формы. Плавка латуней. Рассмотрим технологию плавки кремнистой латуни марки ЛКС80-3-3. При плавке шихты из свежих металлов сначала расплавляют медь и раскисляют ее фосфористой медью, затем вводят меднокрем-нистую лигатуру, цинк и свинец. Если шихта содержит оборотный сплав этой же марки, то его загружают вместе с медью в том случае, когда масса свежих металлов не превышает 30—40% от массы всей шихты. При большом количестве свежих металлов оборотный сплав загружают после расплавления меди и введения остальных элементов. Учитывая склонность этого сплава к поглощению газов, плавку необходимо форсировать, сохраняя нейтральную или слегка окисленную атмосферу в печи. В качестве флюса можно применять битое стекло и буру. Для дегазации сплав нагревают до температуры 1150—1160 °С и выдерживают при этой температуре 10—15 мин. Выделяющиеся при выдержке пары цинка механически увлекают за собой растворенные газы и удаляют их из жидкого сплава. Для компенсации повышенного угара цинка при выдержке сплава перед его заливкой в печь вводят дополнительное количество цинка. После окончания выдержки сплав охлаждают до температуры 1050—1100 °С и проверяют (путем взятия пробы) содержание в нем газов. При избыточном количестве газов в сплаве происходит «рост» пробы в стаканчике. В этом случае производят «замораживание» сплава путем охлаждения его до температуры затвердевания и затем быстро нагревают до температуры разливки. В конце плавки берут пробу для химического анализа, а также технологическую пробу, которая позволяет определить по излому качество сплава и содержание в нем газов; пробу сравнивают с эталонами. Для получения высококачественных медных сплавов необходим тщательный контроль за соблюдением правил подготовки исходных материалов и проведения процесса плавки. Особое внимание надо уделять контролю температуры жидкого сплава как в процессе самой плавки, так и при выпуске его из печи и разливке. Обычно для измерения температуры сплава применяют термопары погружения с защитными чехлами из жароупорной стали. Термопары в сочетании с аппаратурой автоматического действия могут самостоятельно регулировать температурный режим в печах или же путем световой или звуковой сигнализации привлекать внимание рабочего к нарушению температурного режима. Ввиду того что медные сплавы имеют склонность к поглощению газов и окислению, при заливке форм необходимо поддерживать небольшую высоту струи, не прерывать ее и не допускать разбрызгивания сплава. Разливку производят через носок ручных и крановых ковшей, подобных тем, которые применяют при разливке чугуна. Реклама:Читать далее:Плавка и разливка алюминиевых сплавов
Статьи по теме:
Главная → Справочник → Статьи → Блог → Форум |
Помощь в плавке латуни — Обсуждение ювелирных изделий
daniellefiroozi
#1
Нуб здесь. Пытаюсь расплавить небольшое количество латуни, нужна помощь!
-Глиняный тигель диаметром 6 см на стопке керамической плитки
-bernzomatic ts8000 и портативный резервуар для карт.
— нагревал тигель в течение 30 секунд или минуты (не очень долго)
— пытался расплавить 1/2 чайной ложки латунных гранул в течение примерно 5 полных минут при максимальном нагреве с bernzomatic
Гранулы раскалились докрасна, а затем обесцветились. Я включил изображение моей установки ниже.
Будем признательны за любую помощь. Опять же — полный нуб.
Рмейкснер
#2
Вы не говорите, что будете делать с расплавленной латунью. Что бы вы ни собирались делать, у вас должна быть готовая форма (угольная, закрытая сталь, открытая сталь, дельфтская глина или что-то еще) для приема расплавленного металла. Я никогда не использовал берзоматическую горелку или газ MAP, но отсутствие достаточного количества тепла похоже на вашу проблему. Вы можете построить небольшую палатку вокруг своего тигля, чтобы удерживать тепло, которое у вас есть, используя некоторые материалы, которые у вас есть под рукой. Я использую небольшие кусочки подложки для плитки. Вы можете купить его в большом магазине коробок и вырезать любую форму, которую вы хотите. Вы также можете использовать огнеупорный кирпич. Имейте в виду, что все эти материалы будут поглощать некоторое количество тепла. Я не могу сказать по вашей картинке, из чего сделан ваш тигель. Я когда-либо использовал только белый высокотемпературный тигель, покрытый бурой. Это важно для драгоценного металла. Насчет латуни не уверен. Опять же, я думаю, что вам нужно больше тепла. Подумайте о пропане и O2 или ацетилене.
Я использую Meco, Little Torch и EZ Torch. Я знаю, что Меко и Маленький Факел расплавят медь, потому что я это сделал. Я не уверен насчет EZ Torch, но попробую позже в тот же день. Удачи… Роб
1 Нравится
3 июня 2020 г., 14:16
#3
Большое спасибо за ответ, Роб.
Какие-нибудь советы по безопасности дыма с палаткой? У меня есть респиратор, и мое помещение хорошо проветривается, по сути, я работаю рядом с открытой дверью гаража.
Розовая бетонная плита справа имеет много отверстий от заполнителя (который на самом деле является мыльной пеной). Я планирую заполнить отверстия латунью (для скульптуры, которую я делаю). Бетон огнестойкий, полностью затвердевший и сухой — таков план!
Еще раз спасибо
рмейкснер
#4
Звучит как классный проект. Вы должны быть осторожны в первый раз, когда вы заливаете. Каким бы сухим ни казался бетон, в нем может быть достаточно влаги, чтобы вызвать проблемы при заливке (шипение, разбрызгивание, растрескивание бетона). Это одна из причин, по которой закрытые стальные формы нагревают перед заливкой. Вы не думали о заливке смолы в пустоты. Я говорю это только потому, что иногда использую смолу вместо гранита, и с ней очень весело работать.
1 Нравится
3 июня 2020 г., 15:18
#5
Спасибо, Роб! Я забыл ответить на один из ваших других вопросов — это глиняный тигель.
На самом деле я планировал попробовать смолу, если чувствовал, что расплавленная латунь не выглядит эстетично. Услышал вас относительно уверенности в том, что бетон не содержит влаги — плита довольно старая, а я живу в сухом климате, и это тест, так что, надеюсь, он будет информативным и многообещающим!
Рмейкснер
#6
Мне не удалось расплавить небольшой кусочек латуни с помощью моей горелки EZ. Meco и Little Torch работают нормально… Роб
daniellefiroozi
#7
Спасибо, Роб!
ройджон
#8
Привет Даниэль,
У меня есть несколько комментариев по этому поводу. Во-первых, ваша проблема может заключаться в том, что вы держите резак слишком близко к металлу. Самая горячая часть пламени будет сразу за синим конусом, и это также будет восстановительная часть пламени, которая, вероятно, будет лучше плавить этот медный сплав.
Поскольку температура плавления латуни составляет от 1650 до 1720 F, а пламя пропана/воздуха составляет не менее 1900 F и газ MAPP горячее, чем пропан, ваша установка может работать с пропаном. Я вижу по Google, что для газа MAPP требуется головка «Turbotorch», так что может случиться так, что смесь топлива и кислорода просто неверна для вашей пропановой головки. Если отступление от другой части пламени не работает, вы можете попробовать использовать канистру с пропаном (около 5 долларов) и посмотреть, работает ли эта головка горелки с топливом, для которого она предназначена. Использование какой-либо бухты вокруг тигля, как описывает Роб, может помочь. Вы также можете найти газовую головку MAPP и использовать ее с имеющейся у вас канистрой MAPP. Я вижу несколько голов в очереди примерно за 15 долларов.
Я видел видео, где кто-то плавил латунь, чтобы отлить кусок размером с полдоллара, примерно в два раза толще полдоллара… он использовал пропановую горелку с головкой немного больше вашей, чтобы расплавить в тигле, и это заняло 6 минут, 30 секунд. Так что, возможно, вам придется проявить настойчивость. Я удивлен, что горелка Роба не плавит латунь, но, может быть, это займет некоторое время. Конечно, пропан / кислород подойдет, но приобретение новой горелки и двух регуляторов в дополнение к кислородному баллону потребует гораздо больше денег и IDK, если у вас есть другие предполагаемые варианты использования позже, которые сделают эту покупку хорошей. -Ройджон
1 Нравится
рмейкснер
#9
royjohn… Я подозреваю, что со временем Факел EZ расплавил бы медь. В конце концов он плавит серебро. У меня просто не хватает терпения ждать, пока это произойдет, когда у меня есть другие варианты. Я думаю, что это нечто большее, чем температура плавления металла и температура, при которой горит газ. В зависимости от состояния горелки, количества фактического тепла, которое горелка может произвести при этой температуре, условий, окружающих тигель, и необходимости нагревания непосредственной области, металл может фактически не достичь точки плавления. Затем вам нужно поддерживать плавление расплава, пока вы переходите к заливке в форму, которую вам, возможно, также пришлось нагреть, и я бы предпочел иметь пропановую и кислородную горелку. Я знаю, что есть газовые и воздушные горелки с плавильными наконечниками, но, за исключением старого Prest-O-Lite, я никогда не использовал их для плавки серебра или латуни, поэтому я не могу их комментировать, но они могут быть способ избежать нескольких регуляторов и источника O2 (я использую медицинский генератор O2). В конце концов, вам нужен газ, который горит при достаточно высокой температуре и достаточном количестве тепла, чтобы поддерживать эту температуру достаточно долго, чтобы металл расплавился. Спасибо… Роб
1 Нравится
3 июня 2020 г. , 19:32
#10
Надеюсь, вы не собираетесь заливать расплавленной латунью трещины в бетоне. Каким бы старым или кажущимся сухим он ни казался, бетон содержит химически связанную воду, которая может внезапно высвобождаться при контакте с горячим металлом. Образовавшийся паровой взрыв разнесет повсюду раскаленный металл — вам не захочется находиться поблизости. Это известная проблема литейного производства; следует избегать использования бетона в качестве материала для пола, если существует опасность разлива металла.
Если вы хотите сделать трещину заполненной металлом, я бы посоветовал вместо этого использовать цинк или олово; у него меньше шансов взорваться, и у него не будет проблем с плавлением вашей пропановой / воздушной горелки.
1 Нравится
3 июня 2020 г., 23:46
#12
Спасибо, Рой Джон. Очень ценю это понимание. Учитывая опасность заливки расплавленного металла в бетон, о которой упоминал @awerby, я собираюсь перейти на цинк или олово. Береженого Бог бережет. Я вернусь к латуни для другого проекта в будущем.
Даниэльфирузи
№13
Спасибо всем за вдумчивую и подробную помощь. Рад, что присоединился к ганоксин!
Даниэльфирузи
№14
Я точно был. Я думаю, что переход на цинк или олово — это решение. С моей установкой легче плавиться и, что самое главное, намного безопаснее.
Спасибо за обращение.
кваттрокки
№15
Думаю, для плавки латуни и заливки щелей вам понадобится горелка погорячее. Олово или олово будет легче расплавить. Тем не менее, я бы посоветовал вам использовать смолу и смешать ее с латунными опилками или посыпать ею сверху, когда вы только что ее залили. Немного подпилите поверхность, чтобы обнажить латунь.
Смолы сегодня менее токсичны, чем раньше.
Ура, Брайан в Новой Зеландии
1 Нравится
4 июня 2020 г., 1:41
№16
Интересно. Мне нравится, где ваши головы.
КейДэвис
# 17
Uhhh вы можете пересмотреть Цинк…. Погуглите «цинковая лихорадка», а потом решите…
аверби
# 18
Цинковая лихорадка — это плохо, но она возникает из-за сжигания, а не просто плавления. Если вы пытаетесь сварить оцинкованную сталь, это проблема, но плавление цинка для литья не дает большого дыма. Конечно, обеспечение адекватной вентиляции важно всякий раз, когда вы нагреваете металл.
КейДэвис
# 19
Эндрю, я согласен, однако нагрейте его слишком сильно, и у вас будут пары, и да, вентиляция важнее всего, но я хочу сказать, что есть другие металлы, которые более дружелюбны для тех, кто плохо знаком с работой с расплавленным металлом. с.
Кей
vera_m
#20
Относительно потенциальной проблемы заливки латуни в «сухой» бетон: если вы возьмете камень из «сухого» гравия, который вы найдете где-то снаружи, и ударите по нему фонариком, он может взорваться, а может и не взорваться. Камни могут содержать карманы воды, даже если они кажутся сухими. Так что просто надевайте соответствующие средства защиты при заливке бетона (очки или, лучше, защитную маску, длинные рукава, магазинный фартук, огнетушитель поблизости). Безопасность стоит проблем.
Плавка латуни
Этот раздел взят из книги Эрнеста Спона «Издание Американской библиотеки о квитанциях о семинарах». Также доступно на Amazon: American Library Edition Of Workshop Receipts.
Наилучший план плавки латуни состоит в том, чтобы сначала расплавить медь в тигле из черного свинца, максимально высушить цинк и погрузить весь цинк в медь, когда последняя не горячее, чем едва поддерживать текучесть . Бросьте в кастрюлю кусочек буры размером с грецкий орех. Когда поверхность раскаленного металла покрыта мелким древесным углем или бурой, он не горит и сохраняется наименьшая потеря цинка.
Плавка олова и меди менее трудна, чем цинка и меди, потому что олово не так склонно к испарению, как цинк, и теряется мало металла. Внешний вид сплава можно улучшить, покрыв расплавленный металл примерно одним процентом высушенного поташа; или, еще лучше, смесь поташа и соды. Этот флюс оказывает заметное влияние на цвет и особенно на прочность сплава. Первые становятся более красными, а вторые сильнее. Накипь, образующаяся на поверхности при этой добавке, должна быть удалена до отливки металла. Олово и медь склонны к разделению при охлаждении: этого можно предотвратить, по крайней мере частично, если перевернуть форму, содержащую жидкий металл, и оставить ее в движении, пока она не остынет.
Медь и свинец объединяются лишь до определенной степени: 3 свинец и 8 медь — это обычный горшечный металл. Весь свинец может остаться в этом сплаве, если отливаемый объект не слишком толстый. Когда отливка тяжелая или используется много свинца, она выдавливается медью при охлаждении. 1 свинец, 2 медь, при охлаждении свинец отделяет — он вытекает из пор металла: 8 медь и 1 свинец пластичен; больше свинца делает медь хрупкой. Между 8 к 1 и 2 к 1 является пределом для медных и свинцовых сплавов. Все эти сплавы хрупки в горячем или просто теплом состоянии.
Равные части меди и серебра и 2 проц. мышьяк образует сплав, похожий на серебро, но немного более твердый, но почти такой же прочности и ковкости. Сурьма придает меди своеобразный красивый красный цвет, меняющийся от розово-красного в небольшом количестве меди и большом количестве сурьмы до малинового или фиолетового, когда равные части этих металлов сплавляются вместе.
Обычная латунь для отливок: 20 медь, 2 1/2 олово, 1 1/4 цинк.
Твердая латунь для отливок: 25 меди, 4 1/2 олова, 2 цинка.
Красная латунь для тонкого литья: 24 меди, 5 цинков, 1 висмута; добавьте висмут в последнюю очередь перед сливом.
Красная латунь для токарной обработки: (a) 24 меди, 5 цинков, 1/2 свинца; добавьте свинец в последнюю очередь перед тем, как слить. (6) 32 меди, 10 цинка, 1 свинец, (c) 160 фунтов меди, 50 фунтов цинка, 10 фунтов свинца, 44 унции. сурьма.
Латунный прокат: 32 меди, 10 цинка, 1 1/2 олова.
Желтая латунь: (a) 70 медь, 30 z;nc. (6) 20 фунтов меди, 10 фунтов цинка, от 1 до 5 унций. свинец добавляется непосредственно перед заливкой.
Осветляемое и окрашенное изделие сначала отжигают в раскаленном муфеле или над открытым огнем, выдерживая охлаждение в течение часа; целью нагрева является удаление жира или грязи, которые могли накопиться в процессе установки. Мягкие спаянные изделия, однако, должны быть отожжены перед сборкой, а затем прокипячены в поташном щелоке; это также делается с работой, имеющей декоративные поверхности. Затем его погружают в ванну с разбавленным маслом купороса или аквафортиса, которую можно приготовить из двух или трех частей воды и одной части кислоты; но часто предпочитают старую кислоту, содержащую небольшое количество меди в растворе. Работа остается в этой жидкости на один или два часа, в зависимости от силы кислоты; затем его хорошо промывают в воде, очищают песком, наносимым обычной щеткой, и промывают. Травильная ванна готовится путем растворения одной части цинка в трех частях азотной кислоты 36° B в фарфоровом сосуде и добавления смеси восьми частей азотной кислоты и восьми частей купороса.
Затем применяется тепло, и я, когда жидкость закипает, погружается в нее на полминуты или до тех пор, пока бурное выделение азотистых паров не прекратится и поверхность не станет однородной. Затем его погружают в чистую воду и хорошо промывают, чтобы удалить кислоту. Обычный темный серовато-желтый оттенок, который при этом очень часто получается, удаляется при повторном погружении работы в аквафортис на очень короткое время. Затем его погружают в чистую или слабощелочную воду, хорошо промывают от кислоты, погружают в теплые сухие опилки бука или самшита и натирают до полного высыхания. Для предотвращения воздействия атмосферы он покрыт лаком; если необходимо получить зеленый оттенок, лак окрашивают куркумой.