Официальный интернет-портал Администрации Томской области — Ошибка
array
(
'code' => 404
'type' => 'CHttpException'
'errorCode' => 0
'message' => 'Невозможно обработать запрос \"uploads/ckfinder/298/userfiles/files/%d0%9f%d0%9e%d0%a2%20%d0%a0%d0%9c-027-2003%20%d0%9d%d0%90%20%d0%90%d0%92%d0%a2%d0%9e%d0%9c%d0%9e%d0%91%d0%98%d0%9b%d0%ac%d0%9d%d0%9e%d0%9c%20%d0%a2%d0%a0%d0%90%d0%9d%d0%a1%d0%9f%d0%9e%d0%a0%d0%a2%d0%95.docx\".'
'file' => '/var/www/production/yii/framework/yiilite.php'
'line' => 1803
'trace' => '#0 /var/www/production/yii/framework/yiilite.php(1719): CWebApplication->runController(\'uploads/ckfinde...\')
#1 /var/www/production/yii/framework/yiilite.php(1236): CWebApplication->processRequest()
#2 /var/www/production/public/index.php(72): CApplication->run()
#3 {main}'
'traces' => array
(
0 => array
(
'file' => '/var/www/production/yii/framework/yiilite.
php'
'line' => 1719
'function' => 'runController'
'class' => 'CWebApplication'
'type' => '->'
'args' => array
(
0 => 'uploads/ckfinder/298/userfiles/files/%d0%9f%d0%9e%d0%a2%20%d0%a0%d0%9c-027-2003%20%d0%9d%d0%90%20%d0%90%d0%92%d0%a2%d0%9e%d0%9c%d0%9e%d0%91%d0%98%d0%9b%d0%ac%d0%9d%d0%9e%d0%9c%20%d0%a2%d0%a0%d0%90%d0%9d%d0%a1%d0%9f%d0%9e%d0%a0%d0%a2%d0%95.docx'
)
)
1 => array
(
'file' => '/var/www/production/yii/framework/yiilite.php'
'line' => 1236
'function' => 'processRequest'
'class' => 'CWebApplication'
'type' => '->'
'args' => array()
)
2 => array
(
'file' => '/var/www/production/public/index.php'
'line' => 72
'function' => 'run'
'class' => 'CApplication'
'type' => '->'
'args' => array()
)
)
)
Официальный интернет-портал Администрации Томской области — Ошибка | Департамент по социально-экономическому развитию села Томской области404
Просим прощения, ведутся технические работы
/var/www/production/yii/framework/yiilite.
#0 /var/www/production/yii/framework/yiilite.php(1719): CWebApplication->runController('uploads/ckfinde...') #1 /var/www/production/yii/framework/yiilite.php(1236): CWebApplication->processRequest() #2 /var/www/production/public/index.php(72): CApplication->run() #3 {main}
Сварка металла: разновидности и технология
Технологический процесс создания неразъемного соединения однородных материалов за счет образования атомных связей называется сваркой. При этом в месте контакта происходит плотное сплавление двух материалов в один. Несмотря на то что такое соединение используется уже длительное время, современная сварка металлов, виды и технология ее выполнения совершенствуются постоянно, что позволяет производить стыковку различных изделий с повышенной надежностью и качеством.
Особенности сваривания поверхностей
Весь процесс сварки металлов протекает в две стадии. Сначала поверхности материалов необходимо приблизить друг к другу на расстояние сил межатомного сцепления. При комнатной температуре стандартные металлы не способны соединиться даже при сжатии со значительным усилием. Виной этому служит их физическая твердость, поэтому контакт при сближении таких материалов происходит лишь в некоторых точках, независимо от качества обработки поверхностей. Именно загрязнение поверхности существенно влияет на возможность сцепления материалов, ведь пленки, окислы, а также слои примесных атомов всегда присутствуют в естественных условиях.
Поэтому создание контакта между кромками деталей может достигаться либо за счет пластических деформаций, которые возникают в результате приложенного давления, либо в случае расплавления материала.
На следующей стадии сварки металла осуществляется электронная диффузия между атомами соединяемых поверхностей. Поэтому поверхность раздела между кромками исчезает и получается или металлическая атомная связь, или ионная и ковалентная связи (в случае полупроводников или диэлектриков).
Классификация видов сварки
Технология проведения сварочных работ постоянно совершенствуется и становится разнообразнее. На сегодняшний день существует около 20 видов сварки металла, которые классифицируются на три группы:
- Сварка давлением осуществляется приложением механической энергии, когда связи между кристаллами получаются методом пластической деформации материала. В результате металл начинает течь, перемещаясь вдоль линии стыковки деталей, унося с собой слой загрязненных примесей. Процесс деформирования и соединения поверхностей без предварительного подогрева называется холодной сваркой для металла. В этом случае образуются межатомные связи, что приводит к плотной стыковке деталей.
- Сварка плавлением осуществляется путем соединения изделий без применения давления. Источниками тепла при такой сварке металла являются газовое пламя, электрическая дуга, энергия лучевого типа. При сваривании поверхности нагреваются и расплавляются, образуя межатомные связи между двумя металлами и электродом, объединяясь в общую сварочную ванну. После охлаждения и затвердевания состава образуется сплошной литой шов.
- Термомеханическая сварка металла осуществляется с использованием нагрева и давления. Место стыковки материала сначала разогревается, а затем прессуется. Подогрев детали придает ей необходимую пластичность, а механическое воздействие объединяет части изделия в монолитное соединение.
Сварка плавлением
Этот вид сварочных работ находит широкое применение, как в промышленных условиях, так и в быту. К соединению металлов плавлением относятся:
- Электродуговая сварка. Производится созданием между металлом и электродом высокотемпературной электрической дуги.
- При плазменном соединении источником тепла служит ионизированный газ, который проходит с высокой скоростью через электрическую дугу.
- Шлаковая сварка осуществляется благодаря нагреву расплавленного флюса (шлака) электрическим током.
- Лазерное соединение происходит благодаря обработке металлической поверхности лазерным лучом.
- При электронно-лучевой сварке нагревание места стыка осуществляется за счет кинетической энергии движущихся электронов в вакууме под воздействием электрического поля.
- Газовая сварка металлов основана на нагревании точки соединения потоком огня, который образуется при сгорании кислорода и газа.
Электродуговое сварочное соединение
Дуговая сварка предполагает использование источника тока с большим номинальным значением, при этом аппарат имеет небольшое напряжение. Подключение трансформатора происходит одновременно на металлическую заготовку и сварочный электрод.
В результате сварки металла электродом образуется электрическая дуга, за счет которой происходит расплавление кромок соединяемых заготовок. В зоне действия дуги создается температура около пяти тысяч градусов. Такого нагрева вполне достаточно для расплавления любых металлов.
Во время плавления металла соединяемых деталей и электрода формируется сварочная ванна, в которой и происходят все процессы сцепления. Шлак поднимается на поверхность расплавленного состава и формирует специальную защитную пленку. В процессе дуговой сварки металла применяются электроды двух типов:
- неплавящиеся;
- плавящиеся.
При использовании неплавящегося электрода необходимо в зону действия электрической дуги вводить специальную проволоку. Плавящиеся электроды сварной шов формируют самостоятельно. В состав таких электродов добавляются специальные присадки, которые не позволяют дуге гаснуть и увеличивают ее устойчивость. Это могут быть элементы с высокой степенью ионизации (калий, натрий).
Способы соединения дугой
Электродуговая сварка осуществляется тремя способами:
- Ручным методом. В этом случае все этапы соединения выполняются вручную, с применением простой электродуговой сварки.
- Более производительной является сварка металла полуавтоматом. При таком способе сварной шов делается вручную, а присадочная проволока подается в автоматическом режиме.
- Автоматическая сварка производится под наблюдением оператора, а вся работа делается сварочным станком.
Технология газосварки
Этот вид сварочных работ позволяет соединять различные металлические конструкции не только на промышленных предприятиях, но и в бытовых условиях. Технология сварки металла не очень сложная, газовая смесь при горении расплавляет кромки поверхности, которые заполняются присадочной проволокой. При остывании шов кристаллизуется и создает прочное и надежное соединение материалов.
Газовая сварка имеет много положительных аспектов:
- Возможность соединять различные детали в автономном режиме. Причем для этой работы не требуется мощный источник энергии.
- Простое и надежное оборудование газосварки легко поддается транспортировке.
- Возможность осуществлять регулируемый процесс сварки, так как легко вручную изменять угол наклона огня и скорость нагрева поверхности.
Но есть и недостатки применения такого оборудования:
- Место нагрева имеет большую площадь, что отрицательно сказывается на соседних элементах детали.
- Отсутствие возможности автоматизировать процесс сварки.
- Необходимость строго соблюдать меры безопасности. Работа с газовой смесью имеет высокую степень взрывоопасности.
- Толщина металла для качественного соединения должна быть не более 5 мм.
Шлаковая сварка
Такой вид соединения считается принципиально новым способом получения сварного шва. Поверхности свариваемых деталей покрываются шлаком, который нагревается до температуры, превышающей плавление проволоки и основного металла.
На начальной стадии сварка аналогична дуговому соединению под флюсом. Затем, после образования сварочной ванны из жидкого шлака, дуга прекращает свое горение. Дальнейшее расплавление кромок детали осуществляется за счет тепла, которое выделяется при протекании тока. Особенностью этого вида сварки металла является высокая производительность процесса и качество сварочного шва.
Сварочное соединение давлением
Соединение металлических поверхностей посредством механического деформирования чаще всего производится в условиях промышленного производства, так как для выполнения такой технологии требуется дорогостоящее оборудование.
К сварке давлением относятся:
- Ультразвуковая стыковка частей металла.
Выполняется благодаря колебаниям ультразвуковой частоты.
- Холодная сварка. Осуществляется на основе межатомного соединения двух деталей путем создания большого давления.
- Кузнечно-горновой метод. Известен с давних времен. Материал нагревается в горне, а затем сваривается механической или ручной проковкой.
- Газовая с прессовкой сварка. Очень похожа на кузнечный метод, только для нагрева применяется газовое оборудование.
- Контактное электрическое соединение. Считается одним из самых популярных видов. При такой сварке нагрев металла осуществляется прохождением по нему электрического тока.
- При диффузионной сварке сила давления на металл невысокая, но зато необходима большая температура нагрева места соединения.
Точечная контактная сварка
Соединяемые поверхности при такой сварке находятся между двумя электродами. Под действием пресса электроды сжимают детали, после чего подается напряжение. Нагрев места сварки происходит за счет прохождения тока. От размера контактной площадки электрода полностью зависит диаметр места сварки.
От того, как расположены электроды по отношению к соединяемым деталям, контактная сварка может быть односторонней или двусторонней.
Существует много видов контактной сварки, работающих по аналогичному принципу. К ним можно отнести: стыковую сварку, шовную, конденсаторную.
Техника безопасности
Работа со сварочным оборудованием сопряжена со многими опасными для здоровья оператора факторами. Высокая температура, взрывоопасная среда и вредные химические испарения требуют от человека строгого соблюдения мер безопасности:
- Все электрические агрегаты и устройства должны быть надежно заземлены и заизолированы.
- Работать необходимо в сухой спецодежде и рукавицах. Для защиты кожи лица и глаз обязательно нужно применять маску с темным стеклом.
- Обязательно должна находиться на рабочем месте сварщика аптечка и огнетушитель.
- Помещение, где проводятся сварочные работы, должно иметь хорошую вентиляцию.
- Работы запрещено проводить в непосредственной близости к легковоспламеняющимся предметам.
- Запрещено оставлять газовые баллоны без присмотра.
Существует большое количество видов сварки металла, какой из них выбрать решает сам сварщик, исходя из наличия оборудования и способности достичь требуемого результата работы. Сварщик должен знать устройство и принципы работы на определенном оборудовании.
Допуски и посадки. Основные сведения.
Сопрягаемые детали. Рассматривая соединения деталей машин, мы замечаем, что они в различных парах очень разнообразны по своему характеру. В некоторых случаях одна из деталей какой-либо пары во время работы машины остается неподвижной по отношению к другой детали этой же пары; в других случаях — совершает то или иное движение (например, вращательное, поступательное и т. д.) относительно другой детали.
Две детали, составляющие пару, подобную одной из только что рассмотренных, называются сопряженными.
Охватывающие и охватываемые детали. При сопряжении двух деталей одна из них как бы охватывает другую, поэтому первая из этих деталей (по отношению к другой) называется охватывающей, а вторая — охватываемой.
Формы сопрягаемых деталей весьма разнообразны и наименования их, точно соответствующие действительности, во многих случаях громоздки и неудобны для произношения и для записей. Поэтому условились во всех случаях охватывающую деталь(поверхность этой детали, участвующую в данном сопряжении) называть отверстием, а охватываемую деталь (поверхность, участвующую в данном сопряжении) — валом.
Понятие о посадке. Если бы при обработке сопряженных деталей (обеих или одной из них) либо при сборке машины не был учтентребуемый характер их сопряжения, то очевидно, что машина, собранная из таких деталей, оказалась бы негодной для работы
Другими словами, непременными условиями удовлетворительной работы всякой машины являются правильный выбор и осуществление характера сопряжений ее деталей, или, как говорят, посадок.
Посадкойназывается характер сопряжения двух деталей, определяющий большую или меньшую свободу их относительного перемещения, или степень сопротивления их взаимному смещению.
Посадки неподвижные и подвижные. Посадки, при которых должна быть обеспечена прочность соединения сопряженных деталей, называются неподвижными.
Соединения такого характера получаются в том случае, если до сборки сопряженных деталей диаметр вала несколько больше диаметра отверстия, в связи с чем после сборки деталей между ними возникает напряженное состояние.
Посадками для свободного движения, или (кратко) подвижными, называются такие, при которых предусматривается постоянное относительное движение сопряженных деталей во время ихработы. Возможность относительного движения этих деталей получается в том случае, если диаметр отверстия несколько больше диаметра вала.
Посадки, принятые в машиностроении. В нашем машиностроении установлен и применяется ряд посадок: от посадки, при которой вал вставляется в отверстие с большим напряжением, чем достигается высшая прочность соединения деталей, до посадки, при которой вал вращается в отверстии совершенно свободно:
Неподвижные посадки Подвижные посадка
- Прессовая 3-я (ПрЗ)1.
Скользящая (С)
- Прессовая 2-я (Пр2)2. Движения (Д)
- Прессовая 1-я (Пр1)3. Ходовая (X)
- Горячая (Гр)4. Легкоходовая (Л)
- Прессовая (Пр)5. Широкоходовая (Ш)
- Легкопрессовая (Пл)6. Тепловая ходовая (ТХ)
- Глухая (Г)
- Тугая (Г)
- Напряженная (Н)
- Плотная (Я)
В скобках указаны принятые сокращенные условные обозначения посадок.
В приведенном перечне посадки указаны в известной последовательности: от наиболее прочной, обеспечивающей неподвижность соединения деталей (посадки ПрЗ и Гр)
ПосадкиГ, Т, Н и П точнее называются переходными, так как при некоторых действительных размерах сопрягаемых деталей соединение их получается неподвижным, а при других размерах — подвижным.
Номинальные и действительные размеры.Размеры деталеймашин устанавливаются конструктором, проектирующим данную машину (или деталь), который исходит из самых разнообразных требований. Эти размеры (общие для вала и отверстия, если они являются сопряженными) указываются на чертеже детали и называютсяноминальными.
Выше мы видели, что по ряду причин невозможно обработать какую-либо деталь так, чтобы размеры ее, получившиеся после обработки, точно совпали с номинальными.
Размеры, полученные после обработки, условились называть действительными.Таким образом, действительный размер детали есть тот размер, который установлен путем измерения.
Алгебраическая разность между действительным и номинальным размерами называется действительным отклонением размера. Действительные отклонения могут быть положительными и отрицательными.
Предельные размеры.Действительные размеры одинаковых деталей, даже при одном и том же способе их обработки, не получаютсяравными между собой, а колеблются в некоторых пределах.
Предельныминазываются те размеры, между которыми может колебаться действительный размер. Один из них называется наибольшим, другой — наименьшим предельным размером.
Требуемый характер сопряжения двух деталей создается, очевидно, лишь в том случае, если допустимые предельные размеры деталей установлены заранее опытным или расчетным путем и действительные размеры лежат между предельными.
В зависимости от характера посадки наибольший и наименьшийпредельные размеры вала могут быть больше (рис. 69, а) или меньше(рис. 69, б) его номинального размера. Точно так же наибольший инаименьший предельные размеры отверстия могут быть больше (рис. 70, а) или меньше (рис. 70, б) его номинального размера. Возможно также расположение предельных размеров отверстия иливала по разные стороны от номинального.
На рис. 69 и 70 цифрами 00 обозначена так называемая нулевая линия. Она соответствует номинальному диаметру вала или отверстия и служит началом отсчета отклонений от номинального размера.
Предельные отклонения. Алгебраическую разность между наибольшим предельным и номинальным размерами называют верхним предельным отклонением.
Алгебраическую разность между наименьшим предельным и номинальным размерами называют нижним предельным отклонением.
Верхние и нижние предельные отклонения могут быть положительными, отрицательными и равными нулю, как и действительные.
Чтобы не смешивать положительные и отрицательные отклонения, принято перед их числовой величиной ставить знак плюс (+), если отклонение положительное, и знак минус (—), если отклонение отрицательное.
Допуск. Остановимся теперь на определении, отчетливое понимание которого необходимо для усвоения всего вопроса о допусках и посадках.
Допуском, точнее — допуском на неточность обработки называется разность между наибольшим и наименьшим предельными размерами.
Так, например, если наибольший предельный размер вала 65, 040 мм, а наименьший — 65, 020 мм, то допуск в данном случае равен 65, 040 — 65, 020 = 0, 020 мм.
На рис. 69 и 70 допуски (на графиках они называются полями допусков) показаны жирными линиями. Толщина этих линий берется на графиках всегда в увеличенном масштабе (в сравнении с номинальными размерами) для лучшего усвоения. Допуск на обработку колеблется, как правило, в пределах от нескольких десятых до нескольких тысячных долей миллиметра, что требует обязательного увеличения масштаба.
Величины отклонений и допусков в разных таблицах допускови посадок выражаются не в долях миллиметров, как это сделано в приведенном выше примере, а в микрометрах (микронах). Микрометр равен 0, 001 мм и обозначается сокращенно мкм.
Обозначения допусков на чертежах числовыми величинами отклонений. Допустимые предельные отклонения размеров детали от номинальных могут указываться на чертежах числовыми отклонениями, которые проставляются с соответствующими знаками: положительные со знаком (+), отрицательные со знаком (—) вслед за данным размером. Отклонение, равное нулю, на чертеже не указывается. Верхнее и нижнее отклонения записываются одно под другим: верхнее — выше, нижнее — ниже, в долях мм. Примеры простановки отклонений на чертежах показаны на рис. 71, а—е.
Натяги и зазоры. Выше мы установили, что характер посадки зависит от соотношения действительных размеров сопрягаемых деталей или, как говорят, от наличия натяга (рис. 72, а) илизазора (рис. 72, б)между данными деталями.
Натягом называется положительная разность между диаметрами вала и отверстия до сборки деталей (размер вала больше размера отверстия).
При различных соотношениях предельных размеров вала и отверстия натяг называется наибольшим или наименьшим (рис. 72, а).
Зазором называется положительная разность между диаметрами отверстия и вала (размер отверстия больше размера вала).
В зависимости от соотношения предельных размеров отверстияи вала определяются наибольший и наименьший зазоры (рис. 72, б).
Система отверстия и система вала. Стандартами допусков и посадок в нашей промышленности установлены две возможные к применению совокупности посадок — система отверстия и система вала.
Системойотверстия называется совокупность посадок, в которых предельные отклонения отверстий одинаковы (при одном и том же классе точности и одном и том же номинальном размере), а различные посадки достигаются путем изменения предельных отклонений валов (рис. 73, а). Во всех посадках системы отверстия нижнее предельное отклонение отверстия всегда равно нулю.
Такое отверстие называется основным отверстием. Из рисункавидно, что при одном и том же номинальном размере (диаметре) и постоянном допуске основного отверстия могут быть получены разные посадки за счет изменения предельных размеров вала. В самом деле, вал 1 даже наибольшего предельного диаметра свободно войдет в наименьшее отверстие. Соединив вал 2 при наибольшем предельном его размере с наименьшим отверстием, мы получим зазор, равный нулю, но при других соотношениях диаметров отверстия и вала в этом сопряжении получается подвижная посадка. Посадки Балов 3 и 4 относятся к группе переходных, так как при одних значениях действительных размеров отверстий и валов 3 и 4 будет иметь место зазор, а при других натяг. Вал 5 при всех условиях войдет в отверстие с натягом, что всегда обеспечит неподвижную посадку.
Основное отверстие в системе отверстия обозначается сокращенно буквой А в отличие от обозначения второй (не основной) детали, входящей в сопряжение, которая обозначается буквами соответствующей посадки.
Системой вала называется совокупность посадок, в которых преельные отклонения валов одинаковы (при одном и том же классе точности и одном и том же номинальном размере), а различные посадки достигаются путем изменения предельных отклонений отверстий. Во всех посадках системы вала верхнее предельное отклонение вала всегда равно нулю. Такой вал называется основным валом.
Схематическое изображение системы вала дано на рис. 73, б, из которого видно, что при одном и том же номинальном размере(диаметре) и постоянном допуске основного вала могут быть получены различные посадки за счет изменения предельных размеров отверстия. Действительно, соединяя с данным валом отверстие 1, мы при всех условиях будем получать подвижную посадку. Подобную же посадку, но с возможным получением зазора, равного нулю, мы получим при сопряжении с данным валом отверстия 2. Соединения вала с отверстиями 3 и 4 относятся к группе переходных посадок, а с отверстием 5 — к неподвижной посадке.
Основной вал в системе вала обозначается сокращенно буквой В.
Сопоставление системы отверстия и системы вала. Области применения этих систем. Каждой из этих систем свойственны достоинства и недостатки, определяющие области их применения.
Существенным преимуществом системы отверстия в сравнениис системой вала является то, что обработка валов одного номинального размера, но с разными предельными диаметрами может бытьвыполнена одним режущим инструментом (резцом или шлифовальным кругом), в то время как в тех же условиях для обработки точных отверстий требуется столько режущих инструментов (если обработка ведется одномерным инструментом, например разверткой), сколько имеется отверстий. Таким образом, для обработки отверстий и валов при наличии 12 посадок в системе отверстия для каждого номинального диаметра необходимо иметь одну развертку и резец или шлифовальный круг, а для обработки тех же деталей в системе вала требуется резец или шлифовальный круг и 12 разверток.
Система отверстия имеет и другие преимущества по сравнению с системой вала, но тем не менее последняя все же применяется в ряде областей машиностроения, хотя значительно реже, чем система отверстия.
Например, система вала применяется при изготовлении некоторых текстильных машин. Одной из основных деталей текстильных машин является обычно длинный гладкий вал одного номинального размера по всей длине, на который насаживаются с разными посадками различные шкивы, муфты, шестерни и т. д. При применении системы отверстия эти валы должны быть ступенчатыми, что усложняет их изготовление.
Классы точности. В нашем машиностроении для диаметров от 1 до 500 мм применяются следующие классы точности: 1-й, 2, 2а, 3, За, 4, 5, 7, 8, 9-й; 6-й класс отсутствует.
- 1-й класс является самым точным из поименованных. Он применяется сравнительно редко, так как обработка деталей по этому классу стоит очень дорого. Им пользуются в точном машиностроении, когда требуется очень строгая определенность посадок, например при изготовлении деталей шарикоподшипников.
- 2-й класс имеет значительно большее распространение и применяется главным образом в точном машиностроении и приборостроении, в станкостроении и моторостроении, частично при изготовлении текстильных машин и т. п. Этот класс является в нашем машиностроении основным.
- 3-й класс точности применяется в тех случаях, когда требования, предъявляемые к определенности посадок, не так велики, как во 2-м классе, но должен быть сохранен требуемый характер каждой посадки.
- 4-й класс точности применяется для деталей, между которыми допустимы сравнительно большие зазоры или натяги и которые могут обрабатываться с большими допусками.
- 5-й класс точности предназначается для подвижных посадок, к которым не предъявляются высокие требования определенности характера сопряжений.
Кроме того, этот класс предусматривается для свободных размеров, т. е. относящихся к несопрягаемым поверхностям деталей машин, и для точных заготовок.
- 7, 8 и 9-й классы применяются главным образом для свободных размеров, а также для заготовок, изготовляемых горячей штамповкой, литьем и т. п.
В отдельных случаях применяются классы 2а — промежуточный между 2 и 3-м классами, а также За — промежуточный между 3 и 4-м. Они введены в систему допусков позднее и поэтому имеют такие обозначения.
Классы точности, применяющиеся в машиностроении, обозначаются так:
Эти обозначения приписываются справа, несколько ниже обозначения основной детали системы или посадки.
Таким образом, А5 обозначает основное отверстие 5-го класса, В1 — основной вал 4-го класса, С3 — скользящую посадку 3-го класса, Гг — глухую посадку 1-го класса и т. д.
Посадки и основные детали систем 2-го класса точности как основного обозначаются без цифрового индекса, указывающего класс точности. Таким образом, буквы А и В обозначают основное отверстие и основной вал 2-го класса, буква Ш обозначает широкоходовую посадку 2-го класса, буква С — скользящую посадку этого же класса и т. д.
Обозначения посадок и классов точности на чертежах проставляются сразу же за цифрой, указывающей размер, к которому относится данное обозначение.
Посадки в разных классах точности. 2-й класс является основным, и в нем применяются все посадки, перечисленные на стр. 94, за исключением прессовой третьей(ПрЗ), прессовой второй (Пр2) и прессовой первой (Пр1).Обозначения этих посадок указаны там же.
Число применяемых посадок в 1, 3-м и в других классах точности значительно меньше, чем во 2-м, и различно в системе отверстия и системе вала.
В системе отверстия в 1-м классе применяются девять посадок, а именно: прессовая вторая (Пp21), прессовая первая (Пр11), глухая (Г1), тугая (Т1), напряженная (Н1), плотная (П1), скользящая (Cj), движения (Д1 )и ходовая (Xj).
В 3-м классе установлено шесть посадок: прессовая третья (Пр33), прессовая вторая (Ilp2s), прессовая первая (Пр13), скользящая (С, ), ходовая (Х3) и широкоходовая (Ш3).
4-й класс содержит четыре посадки: скользящую (С4), ходовую (Х4), легкоходовую(Л4) и широкоходовую, (Ш4).
В 5-м классе имеются всего только две посадки — скользящая (С5) и ходовая (Х5).
7, 8 и 9-й классы точности посадок не имеют ни в системе отверстия, ни а системе вала. Любое отверстие в этих классах обозначается соответственноА7, А8 или А9, а любой вал — В7, В8 или В9.
Пример чертежа вала с указанием посадок для некоторых его поверхностей приведен на рис, 74.
Практическое значение обработки деталей с обусловленными заранее предельными размерами. Изготовление деталей в таких условиях обеспечивает возможность их взаимозаменяемости.
Взаимозаменяемостью деталей называется такое их свойство, при наличии которого сборка станка, машины и пр. происходит без какой-либо подгонки или подбора деталей, причем посадка, требующаяся в каждом отдельном сопряжении, получается именнотакой, какой она должна быть в данном сопряжении.
Необходимость пригонки отпадает благодаря тому, что действительные размеры деталей, поступающих в сборочный цех, находятся в пределах допуска, и детали не требуют дополнительной обработки. Выполнение характера посадки обеспечивается тем, что отклонения действительных размеров сопрягаемых деталей от номинальных, создающие характер посадки, обеспечиваются рабочим (или рабочими), обрабатывающим данные детали, а назначаются и указываются на чертеже детали конструктором, проектирующим машину, в состав которой входят эти детали.
Достоинства взаимозаменяемости деталей мы наблюдаем постоянно. Всем известно, что любая деталь велосипеда заменяется новой без какой-либо пригонки, каждая электрическая лампочка ввертывается в любой патрон и т. д. Все сельскохозяйственные машины, начиная с плугов и кончая тракторами и комбайнами, состоят из взаимозаменяемых деталей, так как только при этомусловии возможна быстрая замена сломанных или износившихся деталей машин без пригонки даже в полевой обстановке.
В настоящее время почти вся продукция отечественного машиностроения, за исключением опытных образцов и отдельных сопряжений изделий серийного производства, изготавливается с обеспечением взаимозаменяемости деталей и сборочных единиц (узлов).
РКЦ WSR
РЕГИОНАЛЬНЫЙ КООРДИНАЦИОННЫЙ ЦЕНТР WORLDSKILLS RUSSIA СВЕРДЛОВСКОЙ ОБЛАСТИ
VI Финал Национального чемпионата «Молодые профессионалы (ВОРЛДСКИЛЛС РОССИЯ)»
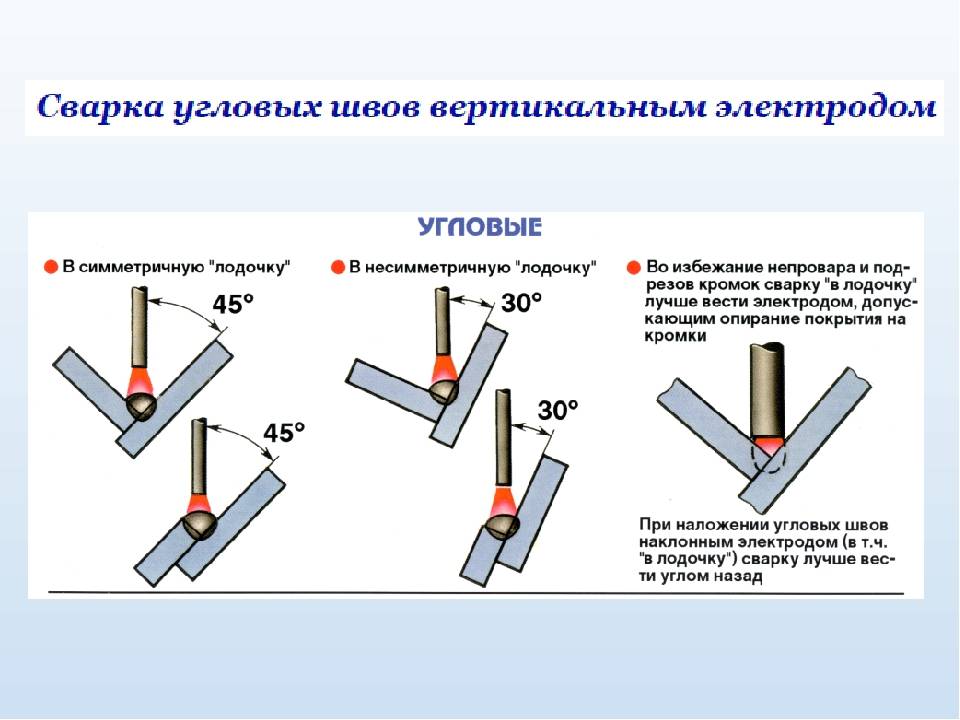
Результаты распределения квот в рамках Отборочных Соревнований на право участия в VI Финале Национального чемпионата «Молодые профессионалы (ВОРЛДСКИЛЛС РОССИЯ)»
Программы повышения квалификации Академии Ворлдскиллс
Инфраструктурные листы по компетенциям Финала WSR 2018
Отборочные соревнования на право участия в Финале Национального чемпионата «Молодые профессионалы» (WorldSkills Russia) — 2018
Конкурсная документация по отборочным соревнованиям в рамках Финала Национального чемпионата WorldSkills Russia в 2018 году
Демонстрационный экзамен 2018
Результаты проведения Регионального чемпионата по стандартам WorldSkills в Свердловской области в 2018 году
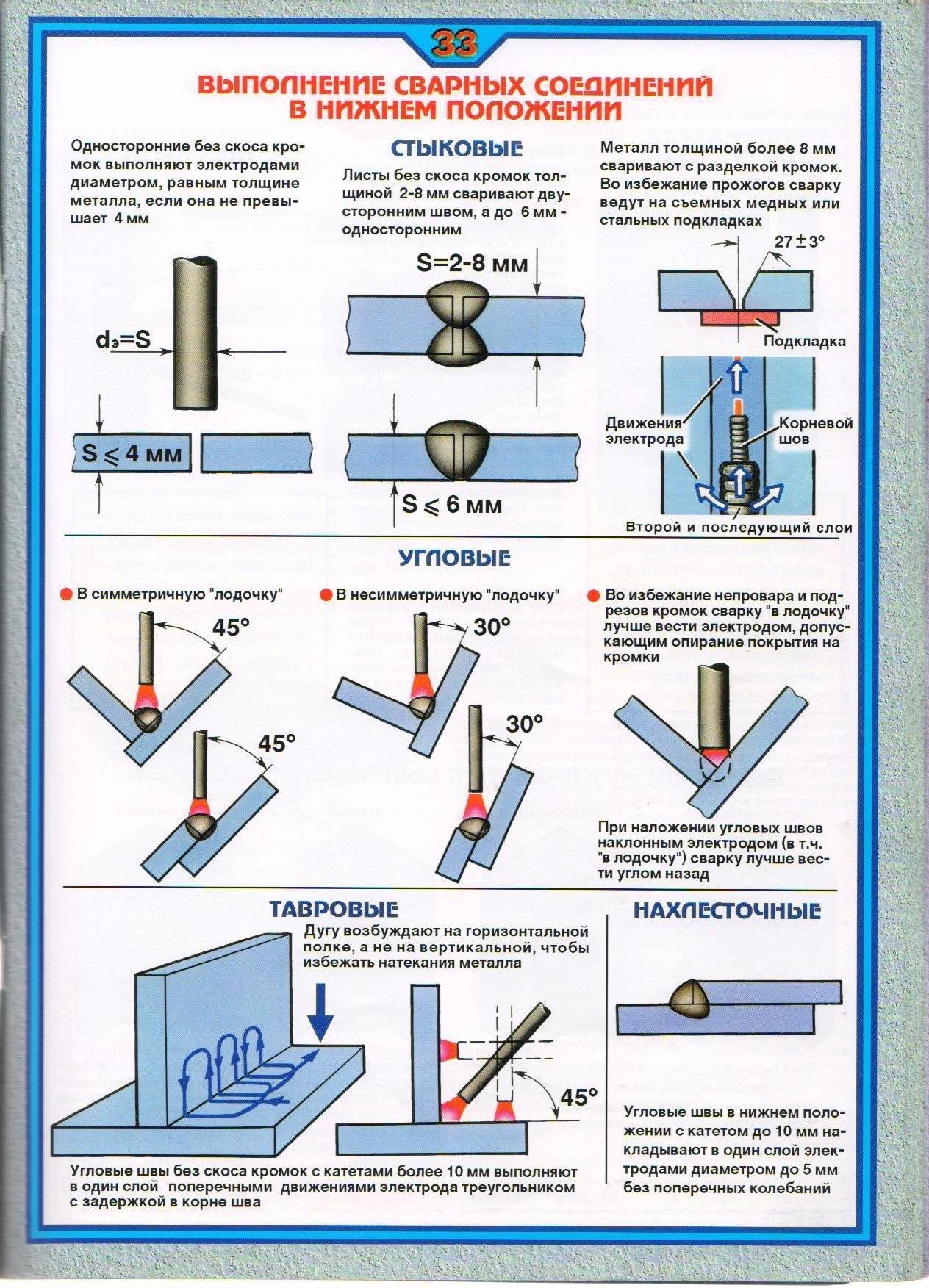
Итоги VI открытого Регионального чемпионата «Молодые профессионалы» (WorldSkills Russia) Свердловской области
СМИ о региональном чемпионате WorldSkills 2018
Контактная сварка металла за 500 руб.
Контактная сварка металла – это технология соединения деталей, конструкций, при которой происходит их нагрев посредством проходящего сквозь электрического тока и сдавливание в местах соединения. Контактная сварка создает до 600 соединений в минуту.
Виды контактной сварки
Различают такие разновидности контактной сварки, как:
- Точечная. Самым популярным видом стала точечная сварка, которая в технологическом плане самая простая и экономичная. Соединение деталей происходит в нескольких точках с экономией электроэнергии.
- Рельефный вид позволяет создавать соединение в зависимости от рельефа заготовок.
- Стыковый вид – при нем происходит оплавление всех точек соприкосновения плоских поверхностей.
- Шовная формирует равномерный сплошной шов, плотное прилегание всех участков.
- Контактно импульсная сварка используется в тех случаях, когда заготовки имеют значительную толщину. Выполняется с минимальной вероятностью появления дефектов.
Сжимающее усилие может быть выполнено такими способами:
- механический – за счёт ручных, автоматических рычагов;
- пневматический – под напором сжатого воздуха;
- гидравлический – под давлением сжимаемой жидкости.
Достоинства услуги
Контактная сварка металла на заказ – это доступная по цене услуга, которая имеет много достоинств:
- быстродействие и высокая скорость выполнения работ;
- высокое качество соединения;
- небольшое энергопотребление;
- в процессе не выделяются вредные и опасные вещества для здоровья;
- шов формируется внутри металла, поэтому сваренная поверхность остается чистой.
Чтобы заказать услугу контактного сваривания в Ростове Великом Ярославской области, клиенту нужно обратиться в «Металлпроект+». Специалисты выполняют для заказчика сварочные работы любой сложности, есть все необходимое оборудование и инструменты для этого
Сокращение переделок в производстве: 5 советов по улучшению сварки листового металла MIG
Наконечники для сварки листового металла
Листовой алюминий легкий, легко формуется и не ржавеет, что дает производителям возможность пропустить этап окраски при производстве деталей из этого материала. Эти преимущества делают листовой алюминий популярным в различных областях применения, от ящиков для инструментов и лодок до вывесок и навесов.Но сварка этого тонкого материала сопряжена с некоторыми трудностями.
Узнайте о пяти советах, которые помогут контролировать тепловложение и улучшить технику для оптимизации результатов и сокращения переделок при сварке MIG-сваркой алюминиевого листа на производстве.
Что такое листовой металл?
Во-первых, важно понять, что подразумевается под термином «листовой металл». При обсуждении листового металла люди часто имеют в виду материал толщиной 1/8 дюйма (0,125) или меньше. Листовой металл бывает разной толщины, и у людей могут быть разные определения того, что они считают листовым металлом, в зависимости от их применения.Для целей данной статьи термин «листовой металл» относится к материалу толщиной 1/8 дюйма или меньше.
Совет 1. Используйте импульсную сварку MIG
Правильный процесс сварки может помочь улучшить результаты сварки листового алюминия. Импульсная сварка MIG снижает тепловложение, облегчает сварку тонких материалов и сводит к минимуму прожоги.
Импульсная сварка MIG чередует высокий пиковый ток и низкий фоновый ток, что снижает общую силу тока. Импульс пикового тока продвигает расплавленную каплю через дугу и обеспечивает энергию для хорошего плавления, связанного с переносом струи, в то время как низкий фоновый ток позволяет охлаждать сварочную ванну.
В чем преимущества импульсной сварки MIG?
- Операторы могут прокладывать провода большего диаметра при более низких токах, чем те, которые требуются для запуска неимпульсного процесса, такого как CV MIG.
- Этот процесс обеспечивает лучший контроль профиля борта. Набор более широкого конуса дуги помогает врезке с обеих сторон соединения или на внешнем углу. Узкий конус дуги помогает сфокусировать дугу и обеспечить хороший сплав в корне сустава.
- Регулировка длины дуги (напряжения) и скорости подачи проволоки для достижения оптимальной производительности помогает исключить избыточное тепловложение, пересварку и шлифовку после сварки.
Совет 2: Выбирайте наилучший сплав присадочного металла из возможных
Существует множество факторов, которые следует учитывать при выборе наилучшего присадочного металла для сварки листового алюминия. К ним относятся сплав основного металла, рабочая температура и окружающая среда, формуемость и многое другое.
Двумя наиболее распространенными алюминиевыми присадочными металлами являются 4043 и 5356, и они дают очень разные результаты при сварке листового металла. Характеристики присадочного металла 4043 включают:
- Более низкая температура плавления и улучшенная текучесть благодаря кремнию в качестве основного легирующего элемента.
- Смачивается лучше, чем присадочный металл 5356.
- Меньше сжимается по мере остывания сварного шва благодаря высокому содержанию кремния, так как кремний расширяется по мере затвердевания.
- Совместим с основными металлами 3003, 3004, 6061, 6063, 5005, 5050 и 5052.
- Присадочный металл 4047 имеет немного более низкую температуру плавления и содержит примерно в два раза больше кремния, чем 4043, поэтому сварные швы сжимаются/деформируются еще меньше.
При импульсной сварке MIG материала толщиной от 1/8 дюйма до 16 калибра можно использовать присадочный металл толщиной 3/64 дюйма при условии плотной посадки. Для еще более тонких материалов попробуйте присадочный металл толщиной 0,035 дюйма. Для сварки CV MIG на листовом металле рекомендуется использовать проволоку диаметром 0,035 дюйма.
Защитный газ, состоящий из 100 % аргона, наиболее часто используется при сварке алюминиевых листов MIG.
Совет 3: уделите время правильной подгонке
Правильная и плотная посадка деталей особенно важна при сварке тонких материалов. Зазоры между свариваемыми деталями могут способствовать короблению.Даже небольшой зазор может превратиться в больший зазор, если деталь деформируется, что вынуждает оператора снижать скорость, чтобы заполнить больший зазор и добавить нежелательного тепла в сварной шов.Это может привести к узким местам в вашей линии.
Убедитесь в отсутствии зазоров в подгонке детали. Также рекомендуется, чтобы края кусочков слегка перекрывались. Используйте подгонку угловой части внахлест, а не подгонку внешнего угла, чтобы уменьшить вероятность прожога.
Другим вариантом борьбы с прожогами является использование медной подложки при сварке листового металла MIG. Поместите или закрепите медный стержень на задней стороне зоны сварки, что помогает рассеивать тепло быстрее, чем просто атмосферное охлаждение.
Услуги по сварке и металлообработке
Делать все правильно в первую очередь, каждый раз — наша цель в каждом проекте. Это уровень самоотверженности, на котором был построен бизнес и который обеспечивает устойчивый рост с 1989 года. То, что мы делаем и как мы это делаем, продолжает совершенствоваться благодаря знаниям и навыкам, которые мы развили. Проще говоря, наши возможности и качество изготовления должны соответствовать требованиям заказчика, будь то изготовление базовой детали или изготовление сложной сварки в соответствии со спецификациями AWS или Military, а также с высокой точностью и качеством.Мы не только стремимся сделать работу правильно с первого раза, но и доставляем вовремя и по конкурентоспособной цене.
Сварочные услуги
Более 30 лет производства прецизионных деталей и изделий позволили создать высококвалифицированную рабочую силу в области сварки. Опыт, обучение и инвестиции, сделанные для выполнения сварки в соответствии с американскими стандартами сварки и военными стандартами, обеспечивают знания и навыки для удовлетворения требований наших клиентов. Опыт работы со сталью, нержавеющей сталью и алюминием потребовал разработки сотен процедур сварки, которые были рассмотрены и одобрены нашими клиентами и одобрены ими на следующем уровне, включая NAVSEA, Американское бюро судостроения (ABS) или клиентов следующего уровня, таких как Raytheon. , Newport News Shipyard, Ingalls
Щелкните здесь, чтобы узнать больше о сварочных возможностях FVMT
Прецизионные детали и изделия
Fox Valley Metal Tech взяла на вооружение передовые методы производства и разработала процессы и методы документирования, которые позволяют производить точные детали и изделия, отвечающие требованиям наших клиентов.Многие из изделий, которые мы производим, требуют точного изготовления для их применения, например, в упаковочной или полиграфической промышленности. Эти детали и изделия должны быть взаимозаменяемы с оригинальными деталями, поставляемыми для нестандартного оборудования, поэтому наша документация и используемый производственный процесс должны производить точно такие же детали, как и исходно поставленные детали или изделия. Кроме того, мы производим множество изделий для оборонной промышленности, которые требуют сопряжения с высокоточными деталями или электроникой и должны иметь очень жесткие допуски на сварку.Способность FVMT предоставлять эти услуги является результатом инвестиций в разработку и производство нестандартных приспособлений и приспособлений, подробных рабочих инструкций, больших обрабатывающих центров, разработки руководств по усадке при сварке и других уникальных производственных технологий.
Щелкните здесь, чтобы узнать больше о прецизионных деталях и возможностях изготовления FVMT
Услуги по покраске
В 2013 году Fox Valley Metal Tech добавила покраску в качестве внутреннего процесса. Это обеспечило больший контроль над производимой нами продукцией, улучшило качество и своевременную доставку. Многие товары, производимые для наших клиентов, требуют тщательной маскировки и специальной обработки, чтобы обеспечить продукт, отвечающий их требованиям. FVMT может обеспечить покраску в соответствии с военными спецификациями, включая CARC. Raytheon и Lockheed Martin провели аудит систем окраски, процессов и документации и предоставили FVMT разрешения или сертификаты на выполнение окраски для них.
Нажмите здесь, чтобы узнать больше о возможностях рисования FVMT
Услуги по обеспечению качества
Компания Fox Valley Metal Tech сертифицирована по стандарту ISO 9001 с 2005 г. и соответствует стандартам ISO.Имеющиеся процессы и оборудование позволяют полностью удовлетворить требования наших клиентов к качеству. Наших сотрудников обучают методам «Качество у источника», начиная с ориентации на новых сотрудников и заканчивая ежедневным контролем со стороны руководителей, аудиторских групп и руководства наших самых опытных сотрудников. FVMT может предоставить сертификаты материалов и прослеживаемость материалов, инспекции первого изделия, картирование сварных швов, сертификат соответствия и другие документы пакета данных о качестве. Инспекционная группа имеет сертификаты для визуального контроля уровня II и имеет в штате несколько сертифицированных инспекторов по сварке.(Сертификат ISO)
Нажмите здесь, чтобы узнать больше о возможностях FVMT Quality Services
Услуги по сборке
Fox Valley Metal Tech — хорошо зарекомендовавший себя производитель металлоконструкций на заказ, наладивший тесные партнерские отношения со многими нашими клиентами. Мы упорно трудились, чтобы установить эти тесные отношения с ключевой целью сделать наших клиентов успешными. Мы спросили, что еще мы можем сделать, чтобы помочь им добиться успеха. Это привело к множеству возможностей предоставления услуг по сборке наряду с производством металлических деталей и изделий.FVMT собрала сушильное оборудование для полиграфической промышленности, конвейеры и машины для упаковочной промышленности, полностью оборудованные лоцманские рубки для кораблей береговой охраны, мясорубки и плавильные машины для пищевых продуктов, установила автоматические выключатели и шинопроводы, а также водонепроницаемые двери с гидравлическим приводом. назвать несколько примеров. Позвольте нам помочь вам добиться успеха.
Нажмите здесь, чтобы узнать больше о возможностях сборки FVMT
Управление программами
Fox Valley Metal Tech обладает возможностями для выполнения проектов всех типов и размеров.Клиенты могут заказывать сотни позиций, которые можно отслеживать, и при необходимости предоставлять отчеты о состоянии. Открывайте отчеты о заказах, которые предоставляют историю действий и сообщений по дате для каждого элемента в заказе. Проекты, которые имеют сложные планы сборки и требования к специальным материалам, могут быть настроены с помощью менеджера программы и команды, которые проводят еженедельные совещания по статусу вместе с интегрированными основными расписаниями, отслеживанием процента выполнения, отслеживанием действий, ключевых дат и вех. Команды могут включать инженера по качеству, менеджера по работе с ключевыми клиентами, руководителя проекта, координатора проекта, специалиста по планированию производства и бухгалтера или других специалистов по мере необходимости.
Нажмите здесь, чтобы узнать больше о возможностях управления программой FVMT
Когда нужно быть герметичным: сварка трением с перемешиванием!
Алюминий набирает обороты Во время сварки трением с перемешиванием, сварки в твердой фазе, не происходит расплавления, пор или горячих трещин, которые часто могут вызывать утечки при обычной сварке плавлением. Этот эффект усиливается при использовании литого алюминия, который стал стандартом для многих конструкций и компонентов систем с жидкостным охлаждением в таких отраслях, как автомобилестроение, силовая электроника, производство аккумуляторов, строительство рельсовых транспортных средств, аэрокосмическая техника и бытовая электроника.Особенно в случае соединения алюминия и алюминиевых сплавов, таких как металлический лист и литой материал, методы сварки трением с перемешиванием демонстрируют свои преимущества и обеспечивают высококачественные соединения с превосходным качеством поверхности; трудоемкие доработки, такие как удаление заусенцев со сварных швов, устарели.
Во время сварки трением с перемешиванием вращающийся износостойкий фрикционный штифт создает тепло рядом с соединением.Материал пластически деформируется и перемешивается по стыку фрикционным штифтом, не достигая температуры плавления материала. Пластифицированный материал уплотняется над уступом инструмента, и между заготовками создается прочное, плотное и герметичное соединение.
По сравнению с обычными методами сварки плавлением, такими как дуговая сварка, сварка трением с перемешиванием не требует сварочной проволоки, защитного газа или сложных вентиляционных систем. Кроме того, этот метод сварки не создает заметных вибраций, шума, эмиссии или оптического излучения.
Блестящая отделка Сварка часто является последним шагом в технологической цепочке. Если по пути происходят какие-либо утечки, весь продукт теряется. Те, кто инвестирует в технологию FSW, также инвестируют в безопасное завершение технологической цепочки. Легкое завершение процесса и герметичность, которые могут быть достигнуты легко и с высокой воспроизводимостью; это делает инвестиции в оборудование в секторе ЖКТ столь перспективными.
Более высокие объемы производства во многих отраслях промышленности могут быть обеспечены за счет сокращения времени цикла технологии СТП.Кроме того, все время вторичной обработки должно быть сведено к минимуму, чтобы сэкономить полезное время цикла. Для этого перестановка компонентов, а также загрузка и разгрузка оборудования осуществляется полностью автоматически. Новое поколение машин FSW DSM1400 и DSM2400 производства Grenzebach было впервые представлено на выставке Schweißen & Schneiden 2017 в Дюссельдорфе. Он имеет модульную конструкцию и может быть расширен для различных систем питания компонентов. Благодаря двум мобильным узлам предварительного напряжения второй узел можно загружать и разгружать одновременно со сварочными работами. Оборудование может продолжать выполнять сварочные работы; холостой ход сведен к минимуму.
Как системный интегратор и поставщик сварки трением с перемешиванием с многолетним опытом, Grenzebach поставляет комплексные технологические решения FSW для промышленного серийного производства. Комплексный подход Grenzebach включает в себя, помимо сварочного оборудования и поставки сварочных аппаратов, разработку процесса для соответствующего применения клиента, а также поставку адаптированных инструментов фрикционного перемешивания.
Сварочные процессы — производство SAMS
Сварка возникает, когда сходные куски металла соединяются, вызывая плавление и смешивание поверхности раздела до затвердевания в виде однородного металлического соединения. Процесс может быть вызван теплом, давлением или их комбинацией. Когда используется только тепло, процесс называется сваркой плавлением.
Сварка давлением обычно включает нагрев поверхностей до ковкого состояния и последующее скрепление металла. Способ нагрева может быть электрическим током или трением, возникающим в результате перемещения одной поверхности относительно другой.
Оборудование, используемое для сварки металлов, также связано с резкой металла. Есть много родственных сварочных процессов.
Ниже приведены краткие сведения о некоторых процессах сварки.
Пайка
Пайка подходит для легкого соединения листов, труб, электрических и электрических соединений. Это заниженный, но широко используемый процесс в промышленности листового металла, который чаще всего используется для соединения латуни и меди, а также легких изделий, где сварка требует слишком много тепла.Припой представляет собой сплав свинец-олово, плавящийся при температуре 180 — 280° в зависимости от состава. Поверхности, подлежащие пайке, тщательно очищают и обрабатывают флюсом. Соединяемый материал предварительно нагревается, и припой при нанесении смачивает металл через тесное соединение и образует интерметаллическую связь. Наиболее благоприятным методом является обеспечение того, чтобы зазор, подлежащий заполнению, контролировался примерно до 0,1 мм, а затем припой втягивался в соединение под действием капиллярного эффекта для получения равномерно заполненного соединения.Стык прогревается паяльником или газовым пламенем. Важно, чтобы поверхности располагались надлежащим образом при выполнении соединения и чтобы не было разделяющих усилий.
Сопротивление сдвигу паяного соединения в зависимости от состава припоя и материалов находится в пределах от 30 до 45 Н/мм2.
Флюс необходим для удаления любого окисления на металле и для защиты поверхностей от загрязнения, а также для уменьшения поверхностного натяжения наполнителя, чтобы облегчить проникновение.Для мягкой пайки флюсом обычно является хлорид цинка или смола на основе флюса.
Пайка
Пайка – это процесс соединения, аналогичный пайке, но с использованием присадочного материала со значительно более высокой температурой плавления (от 450 до 800°С). Медь, никель, серебро являются наиболее часто используемыми основными металлами для припоев. Этот процесс широко используется для соединения и герметизации изделий с более высокими эксплуатационными характеристиками, таких как сплавы на основе меди, т.е. трубные изделия, теплообменники и сосуды.Он также используется для соединения латуни, когда пайка и сварка TIG не подходят.
Паяные соединения прочнее пайки. Более высокие температуры, необходимые для пайки, могут привести к таким проблемам, как деформация изделия. Можно использовать различные методы нагрева, включая наиболее распространенные газовую горелку, печь, индукционный нагрев, резистивный нагрев и ванну с расплавленным флюсом, которые менее распространены в секторах листового металла и общего производства.
Прочность паяного соединения на сдвиг зависит от подготовки соединения, но обычно находится в диапазоне 250-310 Н/мм2.
Как при пайке, так и при пайке соединяемые детали из основного металла не сплавляются, в отличие от всех других процессов соединения, рассматриваемых на этой странице.
Газовая сварка и газовая резка
В процессе газовой сварки используется тепло для получения сплава основного металла и присадочного стержня, что достигается путем сжигания подходящего газа в кислороде или воздухе. Ацетилен является наиболее популярным используемым газом, так как он сгорает в кислороде и дает высокую температуру пламени 3100° — 3200°. C. Кислород и ацетилен хранятся под давлением в металлических баллонах.Газы проходят через гибкие трубки к горелке. Пропорции кислорода или ацетилена можно регулировать таким образом, чтобы пламя было нейтральным или имело восстановительные или окислительные свойства. Для большинства материалов используется нейтральное пламя, за исключением сварки высокоуглеродистой стали, алюминия и связанных с ними сплавов, где используется окислительное пламя.
Капитальные затраты на газосварочное оборудование, кислородно-ацетиленовая сварка ниже, чем на дуговую сварку. Оборудование также легко переносится, и процесс очень универсален. Тем не менее, это сравнительно медленно по сравнению с дуговой сваркой, если необходимо выполнить значительный объем сварки.
требуется следующее оборудование.
1) Баллон с кислородом (полное давление около 15 МПа)
2) Баллон с ацетиленом (полное давление около 1,7)
3) Клапаны регулятора давления на каждый баллон
4) Шланги для передачи потока газа на горелку.
5) Сварочная горелка с наконечниками различных размеров
Давление газа на горелке должно составлять от 7 до 70 кПа каждое и может регулироваться для получения желаемого пламени.
Пламенная резка
Пламенная резка с использованием кислородно-ацетиленового пламени является хорошо известным инженерным и производственным методом. Резаком можно управлять вручную, если допустима низкая точность, или, если требуется более высокая точность, резак механически крепится к гусеничной системе или шарнирному рычагу и управляется числовым способом или с помощью системы магнитного трассирования. Внешнее кислородно-ацетиленовое пламя используется для предварительного нагрева металла примерно до 1000°C.Затем быстро инициируется внутренняя струя кислорода, которая окисляет раскаленный докрасна металл, позволяя резать толстые материалы. Затем процесс резки продолжается с использованием обеих форсунок на
.
Процесс ручной дуговой сварки металлическим электродом
Электродуговая сварка представляет собой электрическую цепь, состоящую из источника электрического тока, пути подачи и возврата, электрода и обрабатываемого изделия. Процесс дуговой сварки включает в себя создание подходящего небольшого зазора между электродом и заготовкой.При замыкании цепи протекает большой ток и между электродом и заготовкой образуется дуга. В результате этого процесса возникают высокие температуры, вызывающие плавление заготовки и электрода. Электрод является расходуемым. Он состоит из металла для сварки, покрытия, которое выгорает с образованием защитных газов, защищающих сварной шов от воздуха, и флюса, который соединяется с нитридами и оксидами, образующимися в точке сварки. Когда сварной шов затвердевает, образуется корка из примесей, образовавшихся в процессе сварки, которые также известны как шлак.Шлак легко удаляется отбойным молотком.
Сварка TIG и MIG
Эти два метода являются наиболее часто используемыми процессами сварки в листовой металлургии и производстве общего назначения.
В системе с вольфрамовым инертным газом (TIG) используется электрод из вольфрама и защитный экран из инертного газа из аргона или гелия.
Первоначально процесс TIG был разработан для сварки магния, и в настоящее время он широко используется для сварки алюминия, меди, низкоуглеродистой стали, нержавеющей стали и широкого спектра других трудносвариваемых металлов, таких как латунь.Сварка TIG также может использоваться для сварки отливок из сплавов, таких как крышки коробок передач и других различных деталей автомобильных двигателей и трансмиссий. Расходуемые стержни, также называемые присадочной проволокой, могут использоваться в зависимости от типа сварного шва и его толщины.
В процессе металлического инертного газа (MIG) используется расходуемый электрод в форме проволоки, обычно в змеевике, и защитный слой из инертного газа из двуокиси углерода при сварке углеродистой стали, чаще всего называемой смесью аргона с Co2. Спиральная электродная проволока обеспечивает непрерывную подачу присадочного металла, что позволяет сваривать швы любой длины без остановки.Защита от инертного газа предотвращает разбрызгивание шлака и обеспечивает более чистый и прочный сварной шов. Этот процесс широко используется для изготовления изделий общего назначения, где эстетика сварного шва менее важна. Как правило, сварка MIG является более быстрым процессом, чем сварка TIG.
Дуговая сварка под флюсом
Этот процесс обычно не используется в производстве листового металла. Процесс включает в себя сварочную дугу, постоянно погруженную под насыпь гранулированного флюса. Сырой металл подается автоматически и регулируется, что поддерживает сварочную дугу.
Так как дуга и расплавленный металл покрыты горой флюса, нет ни брызг, ни искр, ни дыма. Полученный сварной шов является однородным с хорошими физическими и химическими свойствами.
Сварка сопротивлением и точечная сварка
Точечная сварка использует сильный ток при низком напряжении, который проходит через точку на двух кусках металла, обычно листового металла, в течение короткого периода времени, расплавляя соединенные внахлест материалы. Этот процесс выполняется с помощью точечной сварки.Сопротивление потоку тока приводит к локализованному выделению тепла, которое расплавляет металл между медными электродами. Электроды или сварочные щипцы оказывают умеренное давление, сжимая две металлические детали на месте. Место сварки образуется на границе раздела.
Фактическая операция точечной сварки включает в себя следующие
ВРЕМЯ СЖИМА — время между приложением давления и сваркой.
ВРЕМЯ НАГРЕВА ИЛИ СВАРКИ — Время сварки.
ВРЕМЯ ВЫДЕРЖКИ — время, в течение которого сохраняется давление после выполнения сварки.
ВРЕМЯ ВЫКЛЮЧЕНИЯ — электроды выключены, чтобы разрешить разделение и перемещение компонента в следующую позицию
Время сварки может варьироваться от 1 до 120 Гц. Предполагая, что питание 50 Гц в Великобритании, например. 25 Гц = 0,5 секунды
Диаметр наконечника может варьироваться от 2,5 мм до 15 мм, расчет основан на совокупной толщине свариваемого листа.
Грубая формула для листа из мягкой стали = Диаметр кончика (мм) = 2,5 мм + 2. Толщина листа (мм)
Типовой диапазон спецификаций
Длина руки — от 300 до 450 мм
Номинальная мощность — 1.5 кВА — 20 кВА
Номинальная мощность — 3600A — 2500A
Комбинированная толщина металла – от 2 мм до 6 мм
Выступающая сварка
Выступающая сварка аналогична точечной сварке, за исключением того, что одна из поверхностей, контактирующих с электродами, имеет локальный выступ. Проекция определяет площадь сварного шва, а не размер электродов. Выступ обычно находится на более толстом компоненте или на компоненте с наибольшим сопротивлением. Этот процесс обычно приводит к разрушению выступа при формировании сварного шва.
Шовная сварка
Сварка швом аналогична процессу точечной сварки, при котором ток непрерывно или периодически подается на два круговых электрода из медного сплава, которые заменяют стержневые электроды, используемые для точечной сварки. Этот процесс идеально подходит для изготовления герметичных соединений в банках. Заготовки из листового металла, которые накладываются внахлест, пропускаются через медные ролики и свариваются швом. Шов непрерывный и равномерный.
Сварка твердого тела
Сварка в твердом состоянии — это процесс сварки, при котором происходит соединение металлов при температурах ниже точки плавления основного материала без необходимости использования присадочного металла.Давление обычно требуется, но не обязательно. Эти процессы сварки включают холодную сварку давлением, диффузионную сварку, сварку взрывом, такую как приварка шпилек, кузнечная сварка, горячая сварка давлением, сварка трением, сварка роликами и ультразвуковая сварка.
Электронно-лучевая сварка
Это специальный процесс сварки. В этом процессе состоит из концентрированного луча электронов, которые бомбардируют основной металл, заставляя его плавиться и сплавляться. Процесс наиболее эффективен, когда он проводится в вакууме.Размер вакуумной камеры ограничивает размер свариваемых деталей. Преимущества электронно-лучевой сварки включают в себя возможность получения сварных швов чрезвычайно высокой чистоты, способность плавить любой известный материал, возможность сваривать разнородные металлы и возможность сваривать швы на глубину до 150 мм.
Электронно-лучевая сварка чрезвычайно дорога по двум основным причинам;
1) дороговизна оборудования
2) потери времени на откачку вакуумной камеры между сварными швами.
Когда сварка не выполняется в вакууме, многие преимущества процесса снижаются.
Лазерная сварка
(Усиление света за счет стимулированного излучения).
Лазерный луч представляет собой высококонцентрированный луч света с достаточной энергией для генерации локализованного тепла на поверхности металла, вызывающего плавление металла. Используются два типа лазеров;
1) Газовые лазеры
2) Твердотельные лазеры.
Газовые лазеры генерируют непрерывный лазерный луч, который лучше всего подходит для непрерывной сварки и резки. Твердые лазеры выделяют свою энергию импульсами или короткими всплесками со скоростью от 6 до 10 в минуту.Каждый импульс длится всего несколько миллионных долей секунды, в результате чего основной металл остается жидким только на несколько мгновений, а время для химических реакций ограничено. Поэтому для получения качественных сварных швов не требуется защита типа флюса.
Лазерные системы точно управляются с помощью современных компьютерных технологий и обладают достаточной мощностью для сварки и даже испарения любых известных металлов. Другие преимущества включают возможность сварки через прозрачные покрытия и расположение сварных швов в местах, недоступных для обычного сварочного оборудования.Однако ограниченная глубина проплавления ограничивает использование лазерной сварки относительно тонкими материалами.
Обозначения сварочных процессов
Приведенные ниже обозначения процессов сварки основаны на стандарте BS EN ISO 4063 и используются при идентификации сварных швов в соответствии со стандартом BS EN 22553
. 1 Дуговая сварка
11 Дуговая сварка металлом без газовой защиты.
111 Дуговая сварка покрытым электродом.
112 Дуговая сварка покрытым электродом.
113 Дуговая сварка неизолированной проволокой.
114 Дуговая сварка металлическим электродом с порошковой проволокой.
115 Дуговая сварка металлическим электродом с покрытием.
118 Петардная сварка.
13 Дуговая сварка металлическим электродом в среде защитных газов
131 Сварка МИГ: дуговая сварка металлическим электродом в среде инертного газа
135 Сварка МАГ: дуговая сварка металлическим электродом в среде активного газа
136 Дуговая сварка металлическим электродом с порошковой проволокой в среде активного газа
14 В среде защитных газов сварка неплавящимся электродом
141 Сварка ВИГ: дуговая сварка вольфрамовым электродом в среде инертного газа
149 Атомно-водородная сварка
15 Плазменная дуговая сварка
18 Прочие процессы дуговой сварки
181 Дуговая сварка углеродом
185 Сварка вращающейся дугой
2 Сварка сопротивлением
21 Точечная сварка
22 Шовная сварка
221 Сварка внахлестку
225 Шовная сварка с полосой.
23 Выступающая сварка
24 Сварка оплавлением
25 Стыковая сварка сопротивлением
29 Другие процессы контактной сварки
291 ВЧ (высокочастотная) контактная сварка
31 Газокислородная сварка
311 Кислородно-ацетиленовая сварка
312 Кислородно-пропановая сварка
313 Кислородно-водородная сварка
4 Сварка давлением
41 Ультразвуковая сварка
42 Сварка трением
43 Кузнечная сварка
44 Сварка большой механической энергией
441 Сварка взрывом
45 Диффузионная сварка
47 Сварка газовым давлением
48 Сварка холодным давлением.
Другие процессы сварки
71 Термитная сварка
72 Электрошлаковая сварка
73 Электрогазовая сварка
74 Индукционная сварка
75 Сварка световым излучением
751 Лазерная сварка
752 Дуговая сварка
753 Инфракрасная сварка
76 Электронно-лучевая сварка
76 Ударная сварка
78 Приварка шпилек
781 Дуговая сварка шпилек
782 Сварка шпилек сопротивлением
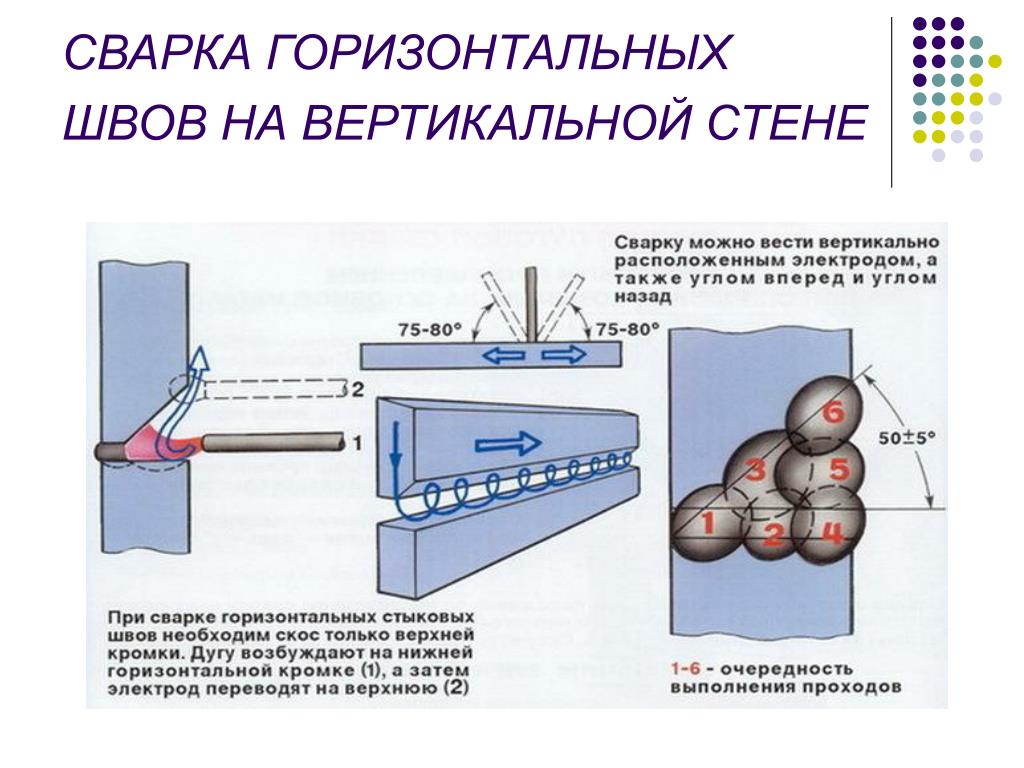