Сварка и пайка алюминия. Припои и флюсы.
Пайка различных металлов и сплавов
Изделия, очищенные и подготовленные для пайки, не должны храниться продолжительное время во избежание окисления. Их следует возможно скорее загружать в печь или контейнер с обеспечением защитной среды. Особенное внимание должно быть уделено удалению воздуха при пайке высоколегированных сталей и сплавов, содержащих легкоокисляемые элементы. Удаление воздуха может достигаться вакуумированием или продуванием защитного газа — аргона. При продувании температура должна повышаться постепенно, начиная от комнатной до 800—900 С (1073— 1173 К). Этот процесс требует значительного расход аргона. Вакуумирование более рационально, так как при этом значительно снижается расход аргона. Большое значение при пайке имеет контроль температуры нагрева изделия; перегрев может оказать вредное влияние.
Общее время пребывания припоя в расплавленном состоянии состоит из времени:
t = t1 + t2 + t3
где t1 — время нагрева от температуры плавления припоя до температуры пайки; t2 — время выдержки при пайке; t3 — время охлаждения от температуры пайки до температуры кристаллизации припоя.
В случае взаимодействия припоя с основным металлом t1 и следует, возможно, сокращать. После окончания процесса панки необходимо удалить флюс, очистить окисленные поверхности, устранить наплывы и участки растекания припоя, в особенности в тех местах, которые подлежат последующей обработке. Требование удаления флюса вызвано возможным отрицательным влияние его, например появлением коррозии (в алюминиевых сплавах).
Флюсы (для пайки алюминиевого сплава) удаляют промывкой горячей и холодной водой при условии последующей обработки в растворе хромового ангидрида. Флюсы на основе буры образуют на поверхности твердую корку. Их удаляют механическим путем или погружением деталей в горячую воду. Паяные швы на алюминиевых сплавах обрабатывают металлической щеткой и вторично промывают от флюсов, могущих остаться в порах швов. Растекающийся припой удаляют механическим, химическим или электромеханическим способами.
Для контроля качества паяных соединений применяют разные методы. Существенное значение имеет внешний осмотр швов. Швы проверяются на прочность, плотность, электропроводность. Паяные швы можно контролировать физическими методами: рентгеновским просвечиванием, применением радиоактивных изотопов, прозвучиванием.
Кроме испытания паяных образцов без их разрушения, нередко применяют испытания с доведением их до разрушения. Результаты, полученные при испытаниях до разрушения нескольких образцов, позволяют установить механические свойства серии аналогичных изделий.
К углеродистым и низколегированным сталям относится стали, имеющие температуру плавления 1450—1520 С (1723—1793 К). При низкотемпературной пайке сталей применяются главным образом оловянно-свинцовые припои с активными флюсами. Перед пайкой рекомендуется детали облуживать. Это ускоряет процесс пайки и позволяет обеспечивать высокие механические свойства соединений.
Более часто для пайки сталей применяют высокотемпературные медно-цинковые припои с добавкой серебра (температура плавления 940—700 С (1213—973 К). Однако вследствие легкого испарения цинка эти припои не применяют для вакуумной панки. Их целесообразно использовать при пайке в среде с низкими окислительными свойствами, например продуктов неполного сгорания азотно-водородной смеси с флюсом в виде буры, борного ангидрида и т. д. Для пайки углеродистых сталей в качестве припоя применяют также чистую медь, в особенности при пайке в печах в среде водорода. Медь хорошо растекается, заполняет малые зазоры. При этом прочность соединений превосходит прочность самой меди.
К высоколегированным сплавам относятся коррозионно-стойкие аустенитные стали 0Х18Н9, 12Х18Н9 со стабилизирующими добавками — титаном, ванадием, ниобием и т. д., кислотоупорные хромистые стали Х17, Х25 и другие ферритного класса, жароустойчивые никелевые сплавы, например, имеющие около 80% Ni и др.
Указанные сплавы могут паяться легкоплавкими припоями с применением активных флюсов. Однако пайка легкоплавкими припоями указанной группы сплавов технически нецелесообразна. Рациональнее применять для их соединений высокотемпературные припои (табл. 1).
В соответствии с маркой припоя применяются флюсы с различными составляющими. Некоторые припои при быстром нагреве т. в. ч. теряют свои составляющие.
Высоколегированные сплавы и стали можно паять в среде аргона, водорода, в вакуумных печах, Недостаток пайки в аргоне — не вполне удовлетворительная растекаемость припоя. Для улучшения растекаемости во флюсы вводят добавки, например литий. Пайка в атмосфере водорода требует высокой его чистоты; использование водорода всегда сопряжено с некоторой опасностью взрыва.
Пайка в вакууме дает хорошие результаты при применении припоев, не содержащих легко испаряющихся элементов (цинка и др.). При пайке указанных выше материалов могут возникать поры вследствие испарения некоторых составляющих припоя, например, цинка: непровары в результате неудовлетворительного смачивания расплавленным припоем соединяемых частей или недостаточной очистки поверхностей; трещины при проникновении жидкого припоя между границами зерен основного металла. Особенно часто образуются трещины при пайке медно-цинковыми и медно-серебряными припоями. Применением более высокотемпературных припоев можно избежать растрескивания паяных соединений.
Таблица 1. Состав припоев, %
Применение никелевых припоев иногда сопровождается образованием подрезов основного металла в местах перехода к швам. Это происходит вследствие того, что припой этого рода имеет способность растворять основной металл. Чтобы избежать этого явления, следует вести технологический процесс пайки при возможно более низкой температуре.При помощи пайки хорошо соединяются изделия из чистой меди и медных сплавов. Чистая медь хорошо паяется при нагреве в вакуумных печах, а также в атмосфере хорошо очищенного водорода без каких-либо примесей кислорода. Медно-цинковые сплавы, содержащие 4—38% Zn, при длительном нагреве теряют его (цинк испаряется), поэтому латунные детали перед пайкой целесообразно покрывать медью.
Пайка широко применяется для соединений различных бронз; алюминиевых, содержащих 5—10% Аl; бериллиевых, применяемых в приборостроении и имеющих в своем составе 2—2,5% Be; хромовых, содержащих около 0,5% Сr; оловянных, применяемых при обработке давлением, содержащих олово, а также фосфор и др.
Медь и ее сплавы легко паяются при применении низкотемпературных припоев с использованием канифольных флюсов, не вызывающих коррозии. Нередко перед пайкой поверхности деталей облуживают чистым оловом слоем толщиной 0,005 мм на стали и 0,0075 мм на меди. Низкотемпературные припои не обеспечивают высокой прочности паяных соединений, поэтому рекомендуется пайка в печах высокотемпературными твердыми припоями. Целесообразно применение медно-фосфорных и серебряных припоев и флюсов на основе буры с добавлением фтористых соединений. Алюминиевые бронзы хорошо паяются серебряными припоями с никелем, который препятствует проникновению в припой алюминия и повышает производительность технологического процесса.
Титан и его сплавы паяют в электрических печах, т. в. ч., газопламенным горелками. Наилучшие механические свойства спая достигаются при пайке ТВЧ. Это объясняется тем, что в результате сокращения термического цикла при этом способе пайки отсутствует рост зерна, приводящий к охрупчиванию соединений.
Очень важная задача производства — соединение пайкой различного рода керамических материалов и окислов друг с другом и с металлами. Возможны разные случаи: металлы более тугоплавки, нежели керамика, при этом соединение обеих деталей происходит в твердом состоянии, контакт обеспечивается необходимым давлением, применением покрытий. В последнем случае соединение достигается при температурах ниже температуры плавления каждой из соединяемых деталей.
Особенно благоприятные условия для соединения, когда металлы имеют температуру плавления ниже температуры плавления керамики и в результате своих специфических химических свойств склонны к образованию связи с последней. Гак, например, титан и цирконий имеют большое сродство к кислороду и образуют твердые растворы со многими металлами и окислами. Окислы титана и циркония весьма тугоплавки. При некоторых условиях эти металлы восстанавливают окислы металлов, образующих керамику, и присоединяют к себе освобожденный кислород. Такое восстановление, необходимое для прессовой пайки, следует проводить в условиях вакуума или в среде аргона.
Серьезные затруднение пайки керамик с металлами — существенная разница в их температурных коэффициентах расширения, в результате чего в соединениях образуются остаточные напряжения значительной величины. В неблагоприятных случаях, при недостаточной пластичности материалов в них возникают трещины. Для устранения этого явления иногда между соединяемым металлом и керамикой прокладывают пластины из пластичного металла, например молибдена. При пластических деформациях последнего опасность возникновения трещин в керамике значительно уменьшается.
С помощью специальных присадочных металлов можно получать качественные соединения не только однородных элементов, например Al2O3 + Al2O3, но и разнородных. Сплавы, содержащие сильные карбидообразующие элементы — молибден, тантал, титан, цирконий и др., — хорошо смачивают графит.
Припои и флюсы для пайки
Большинство способов пайки осуществляют с применением различных припоев и лишь в тех случаях, когда в процессе пайки между металлами могут образоваться легкоплавкие эвтектики, пайка возможна без специального припоя.
К припоям предъявляют ряд требований общего характера. Припой должен хорошо растекаться по поверхности основного металла, смачивать и растворять его, легко заполнять зазоры между деталями, обеспечивать необходимую прочность соединения и т. п.
Широкое применение в качестве припоев получили высокотемпературные припои — сплавы на основе серебра, алюминия, меди и др., обладающие, как правило, температурой плавления выше 450—500 С (723—773 К). Медно-цинковые припои ПМЦ 36, ПМЦ 48, ПМЦ 54 имеют предел прочности σв = 21-35 кгс/мм2 (206,0—343,2 МН/м3), относительное удлинение до 26%, рекомендуются для пайки изделий из меди, томпака, латуни, бронзы. Серебряные припои имеют температуру плавления 740—830 С (413—1103 К). Согласно ГОСТ 8190-56 марки припоев разделяют в зависимости от содержания в сплавах серебра, которое изменяется в пределах от 10 (ПСр 10) до 72% (ПСр 72). В них также содержатся цинк, медь и в небольшом количестве свинец. Эти припои применяют для пайки тонких деталей, соединения медных проводов и в случаях, когда место спая не должно резко уменьшать электропроводность стыковых соединений.
Низкотемпературные припои имеют температуру плавления ниже 450—400 С (723—673 К). Они обладают небольшой прочностью. Их применяют для пайки почти всех металлов и сплавов в разных их сочетаниях. В большинстве случаев низкотемпературные припои содержат значительный процент олова.
Низкотемпературные оловянно-свинцовые припои (ГОСТ 1499—70) имеют верхнюю критическую точку плавления 209—327° С (482—600 К). Олово имеет точку плавления 232 С (505 К). Его предел прочности при растяжении 1,9 кгс/мм2 (18,6 МН/м2), относительное удлинение 49%, НВ 6.2 кгс/мм2 (60,8 МН/м2). Оловянно-свинцовые припои ПОС-90, ПОС-61, ПОС-40 и др. применяют при пайке медных аппаратов, авиационных радиаторов, изделий из латуни и железа, медных проводов и т. д.
Образование качественного паяного соединения в значительной степени зависит от возможности наиболее полного удаления с поверхности металла окисных, адсорбированных газовых и жидких пленок. В практике пайки для удаления поверхностных пленок применяют различного рода флюсы, восстановительную атмосферу или вакуум. В последнее время для этой цели успешно используют механическое разрушение пленок с помощью ультразвуковых упругих колебаний.
Флюсы при пайке имеют несколько назначений. Они защищают основной металл и припои от окисления, растворяют или восстанавливают образовавшиеся окислы, улучшают смачивание поверхностей, способствуют растеканию припоев. Флюсы можно применять в твердом, жидком и газообразном виде (в виде порошков, паст, растворов газов). Роль флюса выполняют некоторые специальные газовые атмосферы и вакуум, которые также могут способствовать восстановлению окислов и улучшению условий смачивания. Флюсующее действие оказывают в некоторых случаях отдельные составляющие, входящие в состав припоев. Например, фосфористые припои не требуют флюсов при пайке медных сплавов.
Флюсы сварочные
Флюсами называют специально приготовленные неметаллические гранулированные порошки с определенным размером зерен.
Назначение флюсов – расплавляясь, они создают шлаковый купол над зоной дуги, а после химико-металлургического воздействия образуют шлаковую корку на поверхности, в ней остаются окислы, вредные примеси и газы.
Флюсы делят на неплавящиеся, керамические и плавильные.
Керамические флюсы.
Изготавливают так же, как и электродное покрытие.
Сухие компоненты шихты замешиваются в жидком стекле. Полученную массу измельчают путем продавливания. Потом прокаливают, просеивают для получения частиц определенного размера.
Частицы сухой смеси могут быть скреплены за счет спекания. Происходит это при повышенных температурах без расплавления. Затем гранулируют до необходимого размера.
Не плавильные флюсы приготавливаются в виде механической смеси. Наиболее распространенны керамические флюсы. По составу близки к составу основного покрытия.
Легирование металла флюсом достигается путем введения в их состав ферросплавов.
Сочетание легирующих элементов может быть различно, а это позволяет получать практически любой состав металла шва.
Это наиболее характерная особенность керамических флюсов.
Химический состав шва также зависит от параметров сварки.
Чтобы определить, как изменились свойства шва, надо замерить твердость в различных местах.
Наиболее критичная зона – зона сплавления и околошовная зона. Керамические флюсы имеют и свои недостатки: малая прочность, вследствие чего в процессе транспортировки или эксплуатации меняют свою грануляцию.
Часто применяют для сварки высоколегированных и специальных сталей, а также для наплавочных работ.
Плавильные флюсы.
Сплавы оксидов и солей металлов. Процесс их изготовления включает следующие стадии:
1. Расчет и подготовка шихты.
2. Выплавка флюса.
3. Грануляция.
4. Сушка, если использовалась мокрая грануляция.
5. Просеивание.
Предварительно измельченные части флюса загружают в дуговые или плавильные печи. После расплавления и выдержки до окончания реакции при температуре 1400 C флюс выпускают из печи.
При сухой грануляции флюс выливается в металлические формы. После остывания отливка дробится, при этом используются валки. Размер частиц 0,1-3 мм. Затем флюсы просеивают.
Сухая грануляция применяется для гигроскопических флюсов, содержащих большое количество фтористых и хромистых солей.
Преимущество этих флюсов в том, что они могут быть использованы несколько раз.
Используют для сварки алюминиевых и титановых сплавов.
Мокрый способ грануляции: расплавленный флюс выпускается из печи достаточно тонкой струей и попадает в емкость с проточной водой. В ряде случаев используют дополнительную струю воды.
Далее идет просеивание.
Получают различную грануляцию. Флюс сушат при температуре 250-300 C, а после дробят, если возникает необходимость. После этого просеивают.
Флюс представляет из себя неровные зерна светло-серого, красно-бурого и коричневого цвета.
Транспортируют в герметичной таре, полиэтиленовых мешках, бочках.
Плавильный флюс не может содержать легирующих элементов в чистом виде, так как они окисляются в процессе изготовления. Поэтому легирование происходит путем восстановления окислов флюсов.
В основу классификации флюсов по химическому составу положено содержание в нем оксидов и солей.
Различают окислительные флюсы, имеющие оксид марганца и кремния в составе.
Для получения определенных свойств флюса, в его состав вводят другие компоненты – плавиковый шпат, более прочные оксиды.
Чем больше во флюсе оксида марганца и кремния, тем сильнее он может легировать металл данными элементами, но тем больше он будет окислять этот металл.
Плавильные флюсы применяются для сварки углеродистых и низколегированных сталей.
Безокислительные флюсы практически не содержат оксидов марганца и кремния, в их состав входят фториды, используются для сварки высоколегированных сталей.
Также безокислительные флюсы могут состоять из фтористых и хлоридных солей и элементов, не содержащих кислород.
Используют для сварки высокоактивных металлов – алюминия и титана.
В связи с широким применением флюсов, есть ГОСТ на основные марки: ГОСТ 9087-81 «Флюсы сварочные плавильные».
Регламентирует химический состав.
Различают стекловидный и пемзовидный характер зерна.
Строение зерна зависит от состава расплава флюса, степени его перегрева.
В зависимости от этого, флюс может получаться плотным, прозрачным, пористым, рыхлым.
Следует учитывать, что пемзовидный флюс при том же химическом составе, имеет в полтора-два раза меньший вес, чем стекловидный.
Данные флюсы хуже защищают металл от воздействия воздуха, но обеспечивают хорошее формирование шва при больших плотностях тока и скоростях сварки.
Буквы в обозначениях флюсов:
- М – мелкий
- С – стекловидный
- П – пемзовидный
- СП – смешанный
Сварка под флюсом
На первый взгляд может показаться, что одно из основных преимуществ сварки под флюсом — возможность получения большой глубины проплавления свариваемого металла — противоречит условиям сварки тонколистовой стали. Однако при определенных условиях сварка под флюсом допускает регулирование глубины проплавления металла, начиная от долей миллиметра, и поэтому хорошо известные ее достоинства могут быть использованы для сварки тонколистовой стали.
Успешное внедрение в производство сварки под флюсом изделий из тонколистовой стали стало возможным, главным образом, благодаря применению тонкой сварочной проволоки. Известны примеры сварки тонколистовой стали и обычной электродной проволокой диаметром, например, 4 мм. Однако в этом случае удавалось сваривать сталь толщиной не менее 3—4 мм при условии весьма тщательной сборки изделия.
Для сварки тонколистовой стали большое значение имеет применение приспособлений, облегчающих точную сборку изделия и обеспечивающих надежное поджатие к свариваемому стыку медной или флюсомедной подкладки, флюсовой подушки и т. п. Опыт показывает, что производительность автоматической сварки изделий из тонколистовой стали со сравнительно короткими швами зависит не столько от машинной скорости сварки, сколько от затрат времени на подготовительные и вспомогательные операции. Поэтому важной задачей является разработка эффективно действующих сборочных и сборочно-сварочных приспособлений.
Чем меньше величина тепловой энергии, передающейся от дуги основному металлу в процессе сварки, тем меньше глубина его проплавления и, следовательно, тем более тонкий металл можно сваривать без прожогов. Тепловая энергия, передаваемая основному металлу, может быть уменьшена за счет уменьшения мощности дуги или увеличения скорости ее перемещения по свариваемому соединению.
Для сварки тонколистовой стали в основном применяют уменьшение мощности дуги, а не увеличение скорости сварки. Это в значительной мере объясняется тем, что применение больших скоростей сварки (более 150—200 м/час) связано с жесткими требованиями к точности поддержания режима сварки, необходимостью тщательной очистки свариваемых кромок, с очень точной сборкой стыков, в ряде случаев со специальным наклоном изделия и электрода и т. п. При указанных скоростях сварки металл шва может быть поражен порами, поперечными трещинами и другими дефектами. Если при этом учесть, что производительность сварки тонколистовой стали, как указывалось выше, главным образом, зависит от затрат времени на установочные и подготовительные операции, то станет ясным, почему увеличение скорости не стало основным способом уменьшения погонной тепловой энергии.
Устойчивость процесса сварки
При сварке тонколистовой стали равномерность глубины проплавления имеет особенно важное значение. Если сваривая сталь толщиной более 4—5 мм, можно допустить колебание глубины проплавления в пределах ± 1 мм, не опасаясь возникновения прожогов, то в случае сварки тонких листов стали такое же колебание совершенно недопустимо.
Равномерность глубины проплавления зависит от устойчивости режима сварки, главным образом, от колебаний сварочного тока. Колебания скорости сварки, а также напряжения дуги сказываются в меньшей степени. Исходя из этого, для сварки тонколистовой стали следует рекомендовать сварочные автоматы с постоянной скоростью подачи электродной проволоки, так как они обеспечивают практически почти постоянные значения тока при колебании напряжения в сети или случайных изменениях длины дуги в процессе сварки. При этом сохраняются почти постоянной глубина проплавления, а также количество наплавляемого металла. Сварочные головки с регулируемой скоростью подачи электродной проволоки в тех же условиях не обеспечивают постоянство тока и поэтому применять их не рекомендуется.
Понижение мощности дуги, требующееся для сварки тонколистовой стали, может быть осуществлено только до определенного предела, зависящего от диаметра электродной проволоки. Дальнейшее снижение мощности резко ухудшает устойчивость процесса сварки и приводит к неудовлетворительному формированию шва. В случае сварки переменным током этот предел достигается при значительно большей мощности дуги, чем в случае сварки постоянным током обратной полярности. Поэтому сварку тонколистовой стали рекомендуется осуществлять постоянным током обратной полярности (положительный полюс присоединен к электроду). В табл. 1 приведены полученные опытным путем значения минимально-допустимых сварочных токов для электродной проволоки различных диаметров при сварке под флюсом АН-348 постоянным током обратной полярности.
Как следует из табл. 1, для обеспечения устойчивого горения дуги при понижении ее мощности необходимо увеличивать плотность тока в электроде, что практически достигается путем уменьшения диаметра электродной проволоки. Эту таблицу можно использовать для выбора диаметра электродной проволоки при сварке на заданном режиме.
При рассмотрении условий устойчивого горения электрической дуги пользуются ее статическими вольтамперными характеристиками. Вольтамперной характеристикой называется зависимость между током и напряжением дуги при постоянной ее длине. На фиг. 1 приведены такие характеристики для дуг различной длины. Каждая вольт- амперная характеристика дуги состоит из нескольких участков: падающего (с ростом тока напряжение падает), почти горизонтального (жесткий участок) и растущего (с ростом тока напряжение увеличивается). В зависимости от условии сварки, дуге соответствует тот или иной участок характеристики. Так, например, при сварке неплавящимся угольным или вольфрамовым электродом, при ручной сварке качественными электродами, при автоматической сварке под флюсом со сравнительно небольшой плотностью тока и в некоторых других случаях характеристика сварочной дуги является падающей с переходом к жесткой. При сварке под флюсом или в защитной газовой среде с повышенной плотностью тока в плавящейся электродной проволоке характеристика дуги становится растущей.
Если дуга имеет падающую вольтамперную характеристику, то устойчивое ее горение возможно только при том условии, что внешняя характеристика сварочного генератора также будет падающей, т. е. напряжение холостого хода генератора значительно превышает напряжение дуги при сварке.
С ростом плотности тока в плавящемся электроде изменяются свойства сварочной дуги. Эти изменения настолько существенны, что позволяют предъявить совершенно другие требования к характеристикам источников питания постоянного тока.
Еще в 1950 г. в Институте электросварки им. Е. О. Па- тона было доказано, что при повышении плотности тока в плавящемся электроде может быть получен устойчивый процесс сварки при использовании в качестве источника питания генератора постоянного тока с жесткой внешней характеристикой (напряжение холостого хода генератора практически равно напряжению дуги при сварке). В отечественной и зарубежной практике в последние годы такие генераторы нашли широкое применение.
Генераторы с жесткими внешними характеристиками значительно более экономичны, чем обычные сварочные генераторы с крутопадающими характеристиками и высоким напряжением холостого хода, так как пропорционально снижению напряжения холостого хода генератора снижаются затраты на активные материалы, уменьшается вес генератора и его стоимость.
Чем больше скорость подачи электродной проволоки п меньше сварочный ток, тем труднее возбудить дугу путем непосредственной подачи электродной проволоки к изделию. Опыт показывает, что при использовании обычных сварочных генераторов с крутопадающей внешней характеристикой в ряде случаев этот способ возбуждения дуги практически оказывается неосуществимым. Совершенно иное наблюдается в случае применения генераторов с жесткими внешними характеристиками. Резкое нарастание тока при закорачивании электрода на изделие обеспечивает безотказное возбуждение дуги. Короткое замыкание не наносит ущерба генератору, так как тонкая электродная проволока выполняет роль плавкой вставки в цепи, ограничивая время протекания и величину тока короткого замыкания.
В тех случаях, когда генераторы с жесткими внешними характеристиками по какой-либо причине не могут быть применены для сварки тонкого металла, следует применять генераторы с весьма пологопадающими характеристиками, т. е. с большой величиной тока короткого замыкания.
Чем резче изменяется ток в цепи при случайных изменениях длины дуги, тем интенсивнее протекают процессы саморегулирования и тем быстрее восстанавливается заданный режим сварки. Генераторы с крутопадающими внешними характеристиками дают значительно меньшие изменения тока при случайных колебаниях длины дуги, чем генераторы с пологопадающими, жесткими или растущими характеристиками, благодаря чему обеспечивают большую устойчивость процесса сварки тонкой электродной проволокой.
Весьма характерно влияние внешних характеристик генераторов на процесс сварки и формирование шва при изменении величины зазора в соединении. Опыт показывает, что в случае питания дуги от генераторов с жесткой или пологопадающей внешней характеристикой можно допустить большие по величине зазоры в стыке, не нарушая нормального формирования шва. Такое же явление наблюдается при увеличении плотности тока в электроде.
В табл. 2 приведены режимы сварки стыковых соединений стали толщиной 3 мм, собранных с постепенно возрастающим зазором от 0 до 5 мм при длине образцов 500 мм. Образцы сваривались электродной проволокой диаметром 3 мм при питании от генератора с крутопадающей внешней характеристикой и генератора с пологопадающей характеристикой. Один из образцов был сварен электродной проволокой диаметром 1,6 мм при питании от генератора с крутопадающей характеристикой. Как следует из табл. 2 и фиг. 2, где изображены образцы сварных соединений, в случае внешней характеристики генератора, приближающейся к жесткой (пологопадающей), а также в случае большей плотности тока в электроде (меньший диаметр электрода), максимальный зазор, при котором еще происходит правильное формирование шва, значительно больше.
Не следует считать, что приведенные в таблице максимальные зазоры могут быть рекомендованы как допустимые при сборке стыков. В данном случае имеет место плавное возрастание зазора, что не равноценно резким изменениям зазоров, которые могут наблюдаться в практике.
Влияние формы внешней характеристики, а также плотности тока на формирование швов при сварке с зазорами в стыке связано, по-видимому, с изменением интенсивности процессов саморегулирования.
При автоматической сварке стыкового соединения одно из активных пятен дуги расположено на расплавленном металле ванны, заполняющей разделку. В отдельные моменты времени скорость перемещения ванны расплавленного металла может отличаться от скорости движения электрода вдоль стыка. Одной из причин этого бывает изменение величины зазора между свариваемыми кромками или изменение зазора между подкладкой и свариваемыми листами.
При увеличении зазора в стыковом соединении или возникновении большего зазора между подкладкой и свариваемыми листами скорость перемещения ванны расплавленного металла уменьшается. Так как скорость движения электрода при этом остается прежней, имеет место рост дугового промежутка. Резкое увеличение дугового промежутка вызывает обрыв дуги и нарушение процесса сварки. При плавном удлинении дуги процесс может не нарушиться, активное пятно успеет занять новое положение, обеспечивая восстановление прежней длины дуги.
Если питание дуги осуществляется от генератора с крутопадающей внешней характеристикой, то при удлинении дуги, как показали исследования, наблюдается рост ее мощности, что ведет к дополнительному оплавлению кромок в месте повышенного зазора, где начала удлиняться дута. При этом электродного металла окажется недостаточно для заполнения зазора между оплавленными кромками, в результате чего образуется не заполненный металлом участок — прожог.
Увеличение интенсивности саморегулирования дуги, имеющее место в случае применения генераторов с жесткими внешними характеристиками или при повышенной плотности тока в электроде, в известных пределах может предотвратить возникновение прожогов. Благодаря интенсивному саморегулированию значительное удлинение или обрывы дуги не будут наблюдаться при отставании ванны жидкого металла в месте увеличившегося зазора. При этом длина дуги будет поддерживаться постоянной и опасный участок с увеличенным зазором может быть пройден без нарушения процесса сварки (без обрывов дуги, прожогов и пр.). Этот участок от остальной части шва будет отличаться только меньшим усилением шва или даже полным отсутствием усиления.
Как известно из практики автоматической сварки под флюсом, с увеличением плотности тока в электроде глубина проплавления заметно возрастает. Например, при сварке на токе 500 а увеличение плотности тока приблизительно в 3 раза, за счет уменьшения диаметра электродной проволоки от 5 до 3 мм, вызывает увеличение глубины проплавления на 25%. Так как переход к сварке тонкой электродной проволокой связан с еще большим увеличением плотности тока в электроде, то возникает опасение, не может ли интенсивный рост глубины проплавления в этом случае стать препятствием на пути применения тонкой электродной проволоки и повышенной плотности тока для сварки тонколистовой стали. Проведенные опыты показали, что это опасение несостоятельно.
На фиг. 3 приведен график зависимости глубины проплавления от диаметра электродной проволоки. Как видно из графика, рост глубины проплавления с увеличением плотности тока (уменьшением диаметра электрода) наблюдается только при сварке на токах, превосходящих 300—350 а. Что же касается интересующего пас диапазона токов, применяемых для сварки тонкой стали (до 300—350 а), то в нем увеличение плотности тока не вызывает изменения глубины проплавления. Это объясняется некоторыми особенностями, отличающими маломощные электрические дуги от дуг большей мощности.
Материал с сайта: http://ruswelding.com
Сварка алюминия – процесс, требующий профессионального подхода
Соединять алюминиевые конструкции можно с помощью пайки или сварки отдельных деталей из алюминия.
Пайка алюминия
Пайка алюминия – довольно кропотливый процесс. Она проводится в небольших объёмах. Для пайки используется оловянно-свинцовый припой (ПОС50, ПОС61, ПОС90), который содержит более 50% олова. Оптимальное соотношение – 80% олова и 20% свинца. В качестве флюса лучше всего использовать щелочное минеральное масло, которое применяется для чистки оружия. Допустимо использование минерального масла для швейных машин и точных приборов. После нанесения флюса с помощью скребка удаляется оксидная плёнка. Для пайки алюминия толщиной менее 1 мм необходим паяльник мощностью 50 Вт, более 1 мм – 90 Вт. Алюминий толщиной более 2 мм прогревается паяльником в месте пайки, прежде чем на него наносится флюс.
Для пайки алюминия может использоваться припой П250А, который содержит 80% олова и 20% цинка. Однако паяльные швы при данном методе пайки более подвержены коррозии, чем при пайке свинцово-оловянными припоями.
Сварка алюминия аргоном
Химические особенности алюминия таковы, что при нагреве металла и соприкосновении с кислородом воздуха на поверхности материала мгновенно образуется оксидная плёнка. Она обладает высокой температурой плавления (2050 0С), не расплавляется при сварке и покрывает металл плотной оболочкой. Адсорбируя газы и водяные пары, плёнка способствует растворению газов в металле и образованию в нём пустот. Отдельные части плёнки, попадая в соединительные швы, делают их непрочными и снижают работоспособность соединений. Становится невозможным обрабатывать алюминий с помощью обычной электродуговой сварки.
Чтобы разрушить и удалить оксидную плёнку и защитить металл от повторного окисления, используются сварочные флюсы для растворения и смывания диспергированной окисной пленки.
Чтобы предотвратить взаимодействие с кислородом, при сварке конструкций из алюминия применяется инертный защитный газ, чаще всего аргон чистотой не менее 99,9% (ГОСТ 10157—73, сорта: высший, первый и второй) или смеси аргона с гелием. Инертный газ не позволяет возникнуть оксидной плёнке на поверхности детали. Поэтому соединение алюминия называется аргонной сваркой, аргонно-дуговым соединением или сваркой аргоном. Её преимуществом является высокая устойчивость горения дуги, что даёт возможность соединять тонкие листы алюминия.
Наша компания имеет все необходимые условия и компоненты для проведения качественной сварки алюминия:
- аргон;
- нужные расходные материалы;
- качественное современное оборудование;
- специалистов высокой квалификации.
Сварку алюминия мы производим на основе передовых современных технологий, позволяющих добиться максимального эффекта сварочных работ. При их проведении мы учитываем то, что качественное соединение конструкций из алюминия можно произвести только при одном условии. А именно – если соединительная проволока по своему химическому составу будет точно соответствовать металлу алюминиевой конструкции, которая подлежит восстановлению.
Сварку алюминия проводят с применением тугоплавких вольфрамовых электродов. Через керамическое сопло, которым окружён электрод, к месту сварки под высоким давлением нагнетается аргон. Этот инертный газ создаёт в месте соединения среду с очень низким содержанием кислорода, предотвращая образование оксидной плёнки, поскольку он на 38% тяжелее воздуха. Сварочная ванна изолируется от контакта с атмосферой. За счёт этого создаются условия для удерживания электрической дуги между свариваемой деталью и концом тугоплавкого электрода. При этом происходит плавка детали и присадочного прутка. В зависимости от вида соединяемого металла в качестве присадки используется присадочная проволока различного состава. Сварка алюминия может выполняться на постоянном (DC) и переменном (АС) токе.
Аргонная сварка – наиболее приемлемый метод ремонта при механическом повреждении алюминиевых элементов, которые используются во всех областях современной техники. Стоимость сварочных работ значительно ниже, чем замена всего узла или даже его детали.
Аргонно-дуговая сварка широко применяется при ремонте различных агрегатов автомобиля:
- блока двигателя;
- кондиционерных трубок;
- радиатора;
- поддона картера;
- силуминовых кронштейнов и т. д.
У Вас возникли вопросы? Хотите получить консультацию нашего специалиста? Мы с радостью ответим на все Ваши вопросы, звоните нам по телефону 8 (499) 391-45-36 или пишите нам на адрес электронной почты [email protected] Приезжайте к нам по адресу г. ![]() |
Сварочная проволока
При аргонно-дуговой сварке используется алюминиевый соединительный пруток ER 5356 (аналог СВ-АМг5). Он подходит для соединения металлоконструкций из алюминиево-магниевых сплавов, содержащих более 3% магния (AlMg3, AlMg4, AlMg5, AlMg6). Также для этого типа соединения хороша алюминиевая сварочная проволока OK Autrod 4043 (ОК Autrod 18.04). Сварочные работы можно проводить на переменном токе AC, применяя в качестве защитного газа аргон.
Соединительная проволока ER 4043 (аналог изделий, маркированных как СВ-АК5) закупается для аргонно-дуговой TIG и полуавтоматической сварки металлоконструкций из алюминиево-кремниевых и алюминиево-магниевых сплавов типа АД35, АД33, АД31. Сварку производят на переменном токе AC, используя аргон. Для этого типа работ можно использовать также алюминиевую соединительную проволоку OK Autrod 4043 (ОК Autrod 18.04) с пределом текучести 55 МПа, пределом прочности 165 МПа и удлинением 18%.
Для сварки чистого алюминия, а также пластичных алюминиевых сплавов применяется соединительная проволока OK Autrod 1070 (OK Autrod 18.01). Она стойка к химическому и атмосферному воздействию, обладает хорошими сварочными характеристиками.
Для получения высококачественного шва используют алюминиевую сварочную проволоку, стойкую к неблагоприятным воздействиям среды, – OK Autrod 1450 (OK Autrod 18.11). За счёт незначительной добавки титана достигается мелкозернистость шва. Проволока применяется для сварки чистого алюминия и его сплавов в пищевой промышленности и авиастроении.
В пивоваренной и молочной промышленности для сварки алюминиево-магниевых сплавов, содержащих до 5% магния, и алюминиево-марганцевых сплавов подходит сварочная проволока OK Autrod 5183 (OK Autrod 18.16). Она также применяется в судостроении для соединения деталей, которые подвергаются воздействию морской воды.
Для обеспечения высокой прочности сварного соединения при обработке алюминиево-магниевых сплавов, содержащих до 6% магния (AlMg4,5Mn, AlMg5Cr, а также AlMg5Mn) используется алюминиевая соединительная проволока OK Autrod 18. 22 в композиции AlMg6Mn Zr. Она применяется в судостроении для сварки высокопрочных конструкций.
Цены
Ценовая политика нашей компании отличается демократичностью, поскольку мы работаем напрямую с производителями. Наши постоянные клиенты пользуются гибкой системой скидок. Мы выполняем все работы и поставки в сроки, предусмотренные договором.
Для уточнения стоимости работ и сроков звоните нам по телефону 8 (499) 391-45-36 или пишите на адрес электронной почты [email protected] |
припой : Припой для пайки алюминия HTS-2000
HTS-2000 — это припой в форме стержней, применяемый для низкотемпературной пайки и сварки алюминия, алюминиевых сплавов и цветных металлов без флюса. Для работы достаточно газовой горелки, например, пропановой, ацетиленовой или MAФ.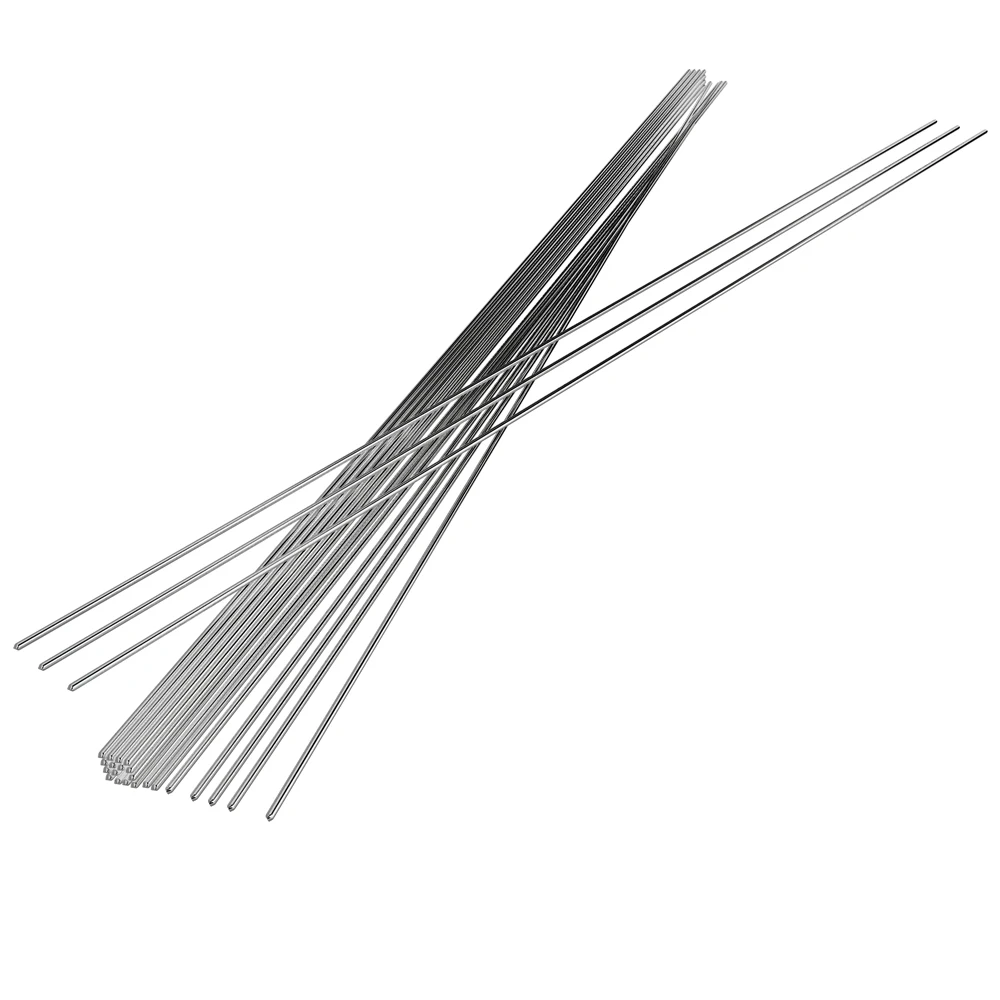
Припой HTS-2000 — это продукт последних достижений в области металлургии, представляющий собой сплав нового поколения, надежность и прочность которого превосходят предыдущие аналоги. Доступность и простота в использовании делают HTS-2000 лидером среди всех известных припоев.
HTS 2000 — это уникальный сплав, состоящий из девяти компонентов. Припой HTS-2000 имеет вязкость и тянется на 10% (в то время как сплавы первого поколения растягиваются на 3% при удлинении 50мм), что делает его в 3 раза пластичней и прочней аналогов. Кроме этого, плохо подготовленная поверхность металла и оксидная пленка не влияет на прочность шва. При нагреве расплавленный припой HTS 2000 проникает через пленку оксида алюминия (на поверхности детали) и создает прочные молекулярные связи. Коррозия для такого соединения не страшна, т.к. электрохимический потенциал между материалом припоя и алюминия невелик. Такое соединение прослужит не меньше десяти лет при эксплуатации в агрессивных средах.

Область применения припоя для алюминия HTS 2000.
— Ремонт и восстановление головок блока цилиндров (трещины, сколы, прогары и др.)
— Ремонт топливных баков из алюминия
— Пайка алюминиевых и медных трубок в различных сочетаниях
— Ремонт трубок насосов, компрессоров , кондиционеров
— Ремонт днищ лодок, выполненных из алюминиевых сплавов
— Ремонт картеров автомобилей
— Восстановление деталей после износа, поломки, скола
— Ремонт алюминиевых корпусов, ремонт радиаторных трубок
— Восстановление резьбовых отверстий
Достоинства.
— Не требует флюсов и полученное соединение 100% металлическое
— Прочней чем обычные сплавы — до 45900 PSI
— Низкая температура плавления. Рабочая температура 337 — 357 С
— Температура плавления на 300 градусов ниже, чем у алюминия
— Для работы достаточно газовой горелки.
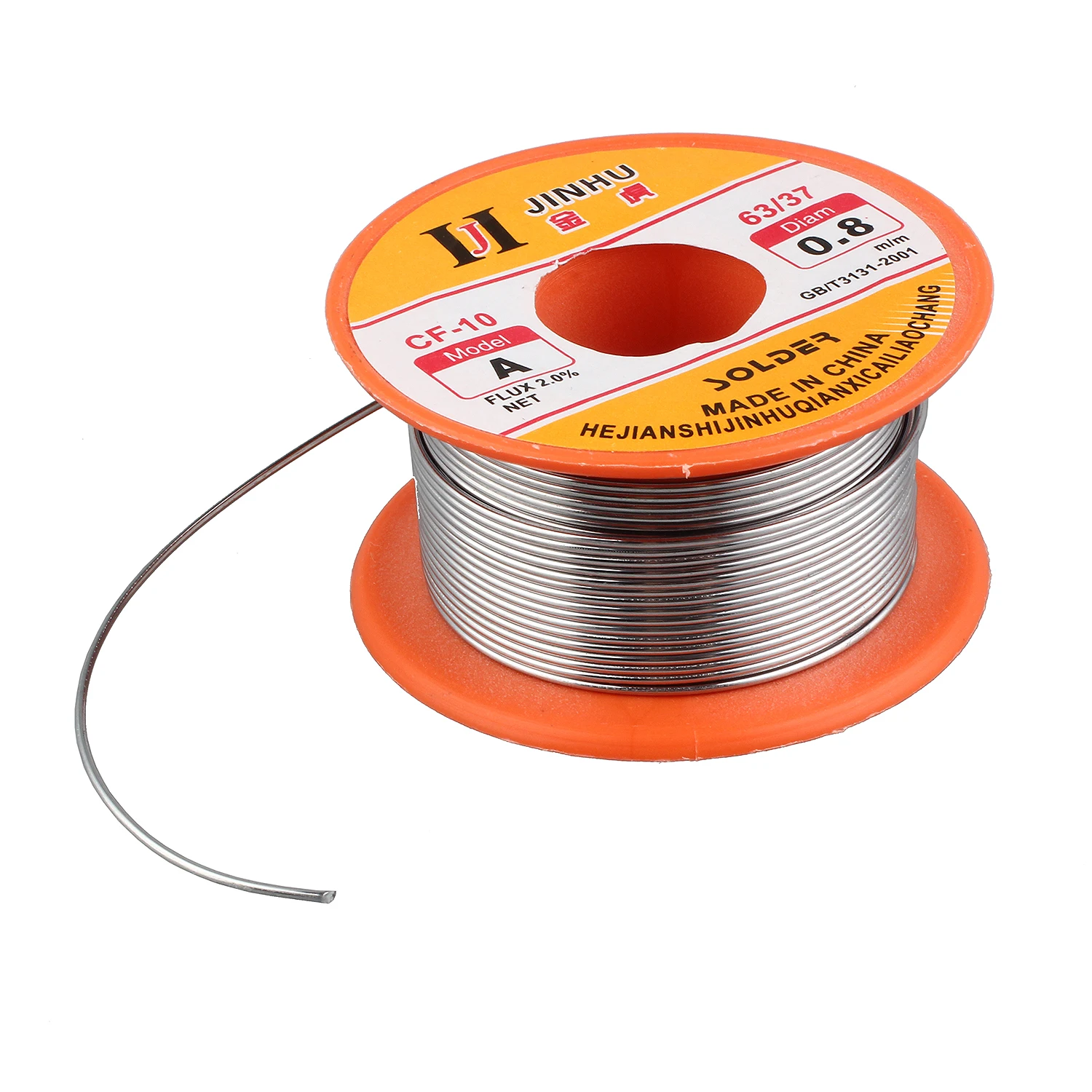
Температура плавления алюминия около 660ºС, при этом тонкостенные алюминиевые детали начинают деформироваться. Припой HTS-2000 плавится при температуре 390 градусов, что значительно упрощает пайку тонкостенных деталей.
После подогрева алюминиевой детали и HTS 2000, припой проникает под оксидную пленку и создает молекулярную связь, которая прочней чем связь молекул в образце. Важным свойством HTS 2000 является устойчивость к электрической коррозии.
HTS 2000 подходит для работы со всеми сплавами цветных металлов, включая все алюминиевые сплавы, сплавы магния и алюминия, цинка, меди, бронзы, никеля, титана и оцинкованных частей.
Физические свойства.
Растяжение: 45900 PSI Therm. Опыт:. 15,2 х 10 — 6in./in./F °
Удлинение: 10% в 2 дюйма Elec. Cond: 26 (% меди станд.)
Воздействие: 43 Ft. фунтов (Шарпи) С. П. Grav. 6,6
Сдвиг: 31000 PSI
Вес: 0,24 кг / куб.

Точка плавления: 390 С
Диаметр: 2.5 — 3 мм
Длина: 460 мм
Инструкция по применению HTS-2000
Шаг 1:
Область соединения должна быть зачищена щеткой, наждачной шкуркой или надфилем (для удаления оксидной пленки).
Шаг 2:
Нагрейте рабочую поверхность (НЕ ПРИПОЙ) до 200 С и, для лучшего сцепления, нагретую поверхность зачистите ещё раз (при нагревании на алюминии появляется оксидная пленка), после чего доведите температуру детали до температуры плавления припоя (390 С). НЕ ПОМЕЩАЙТЕ СТЕРЖЕНЬ В СТРУЮ ПЛАМЕНИ ГОРЕЛКИ! Вы должны довести температуру свариваемого металла до температуры плавления припоя HTS-2000. Тепло должно переходить с открытой поверхности на стержень припоя.
Шаг 3:
После достижения рабочей температуры, проведите прутком припоя HTS-2000 по поверхности алюминия для удаления царапин.
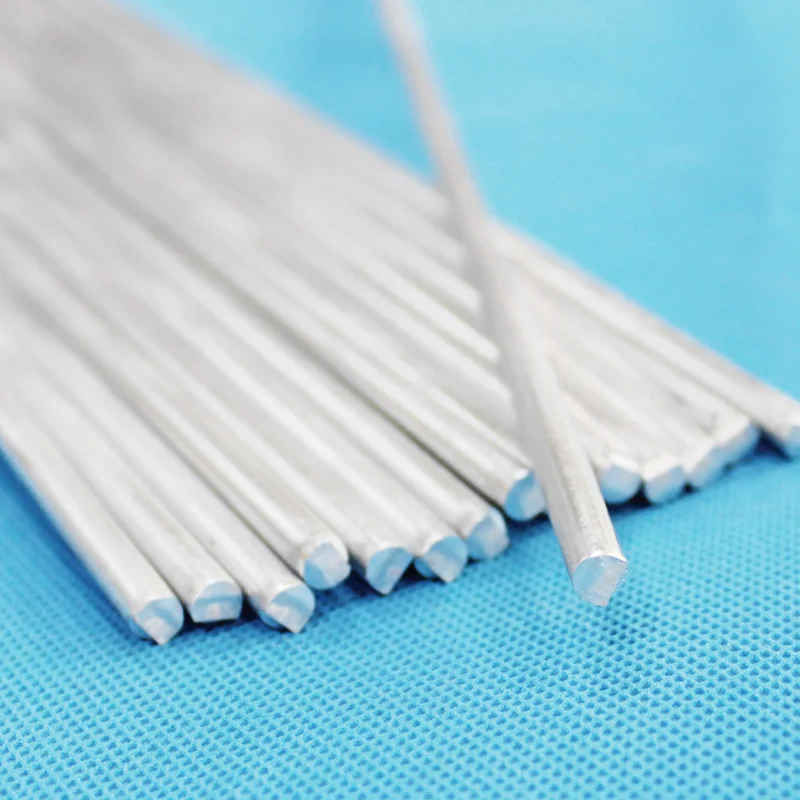
В остальных случаях используйте лудильную щетку из нержавеющей стали для лужения поверхности с помощью сплава HTS 2000. Соблюдение этих рекомендаций приведет к отличным результатам.
Шаг 4:
После завершения работы всегда давайте детали остывать естественным путём. Пропан лучше подходит для работы с изделиями до 10мм, для изделий толще 10мм можно использовать MAPP-газ (он продается в желтых болонах), его температура выше на 200 градусов.
При более сложной работе или в целях экономии времени, используйте кислородно-ацетиленовую горелку либо предварительно прогревайте деталь дополнительным источником тепла (например, паяльной лампой или электрической плиткой). Чем толще материал, тем больше требуется времени для его нагрева.
При работе с кислородно-ацетиленовой смесью всегда используйте рассеивающий наконечник либо осуществляйте нагрев нейтральным пламенем. Не помещайте стержень припоя HTS-2000 в струю пламени.
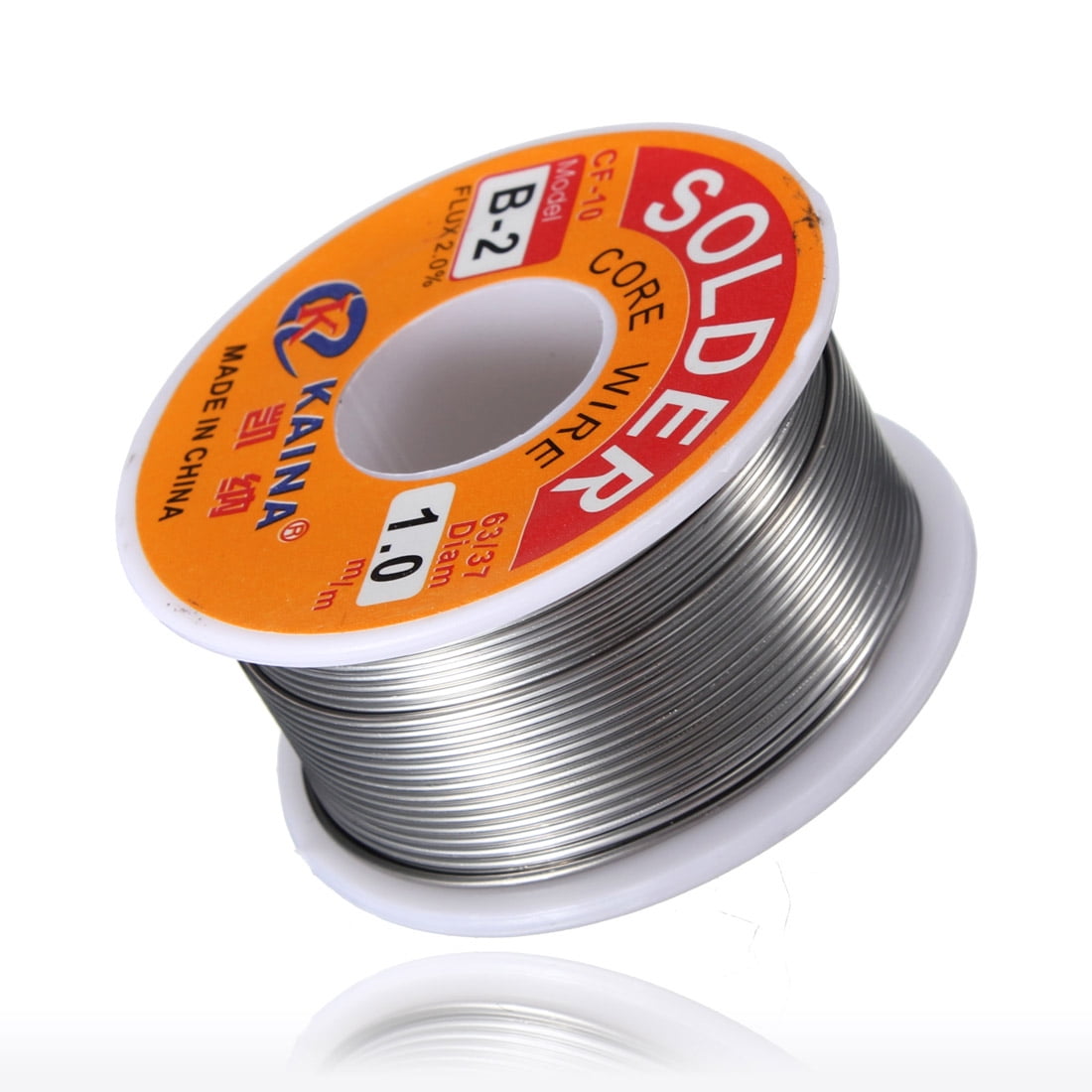
Описание работы с HTS 2000.
Пайка алюминия.
Предварительно нагрейте места пайки до 260 С, до температуры выгорания углерода. При первоначальном применении ацетилена для нагрева место пайки почернеет. Далее нагревайте почерневшую поверхность нейтральным пламенем до тех пор, пока углерод не исчезнет. Нагрев продолжайте до достижения температуры чуть более 400 С – это нужно для расплавления припоя во время лужения поверхности заготовки. Во время нагрева пруток держите в стороне от открытого пламени. После лужения нарастите поверхность с помощью пламени и прутка. Постепенно остудите обработанную деталь. Использовать воду для охлаждения не рекомендуется.
Пайка «ушек» из алюминия.
Тщательно покройте место разлома припоем. Возможно использование стальной формы в виде старого ушка. Форму заполните припоем.
Если оказалось, что часть ушка после зачистки отсутствует, то можно использовать болт и шайбу требуемого размера.
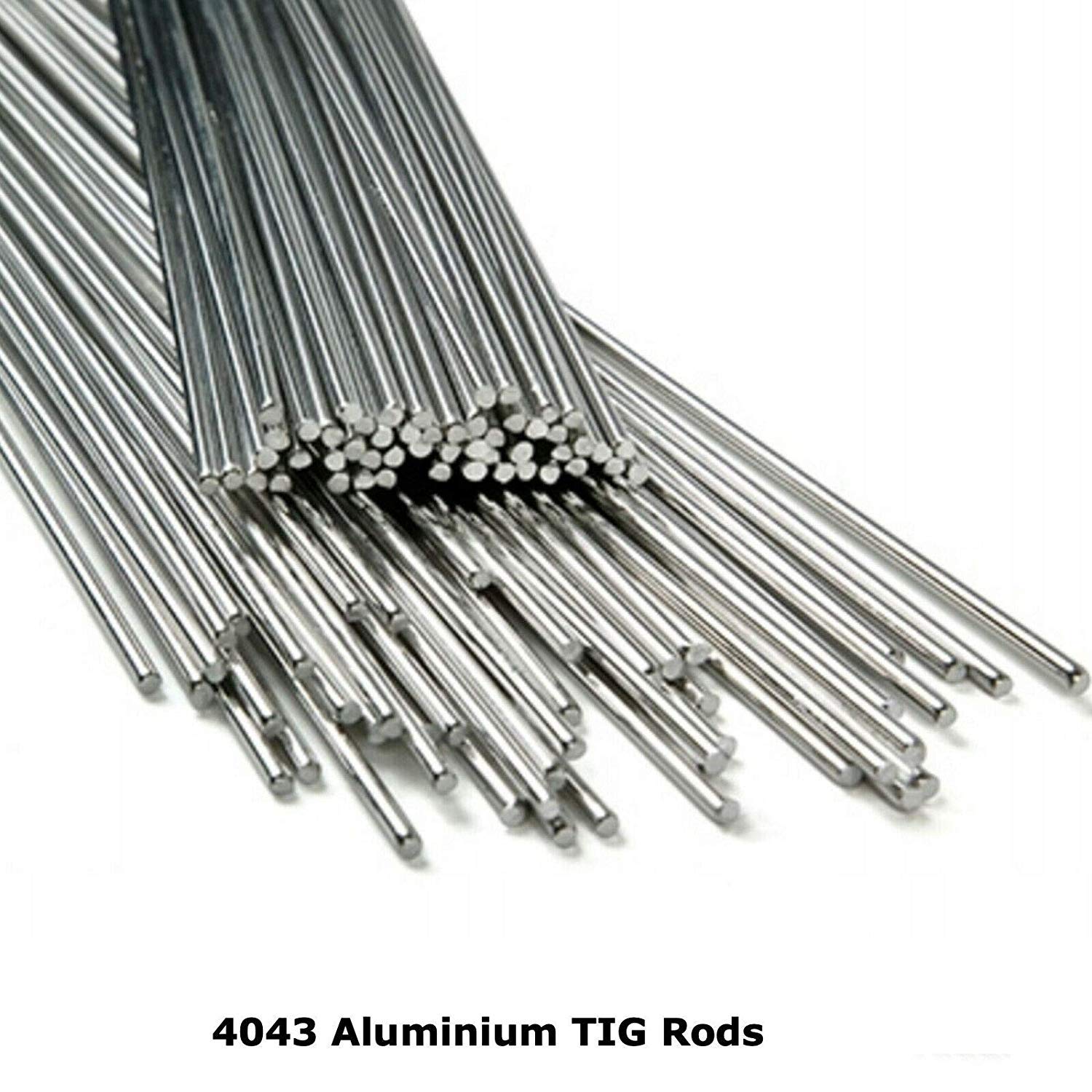
Трудно нагреть две сплавляемые части одновременно – в этом случае, можно напаять припой на каждую часть по отдельности, затем совместить обе части и нагреть до точки плавления припоя.
При соединении внахлест нужно предварительно напаять припой HTS-2000 на поверхность обеих заготовок, и соединить — пока он расплавлен. С помощью припоя можно округлить края, соединенные внахлест. Пайка алюминия таким способом очень эффективна.
Восстановление сорванной резьбы.
Способ а). Высверлить старую резьбу сверлом большего размера, примерно на 3 мм. Если резьба сквозная, нужно плотно закрыть одно отверстие с помощью стальной пластины. Энергично натирая внутреннюю поверхность отверстия, затолкните припой и дайте ему возможность полностью расплавиться.
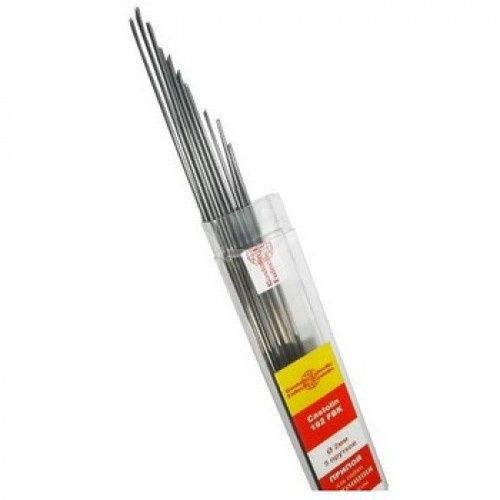
Способ б). При ремонте болтов, вначале нагрейте его и материал основы до температуры плавления припоя. Залейте припой HTS 2000 вокруг болта до незначительного переполнения. После охлаждения выкрутите болт. Такой способ не годится для ремонта мелких болтов, так как усилие при выкручивании болта может его деформировать.
Работа с медью.
Для открытия структурных пор медь требует большего прогрева. Очистить и нагреть рабочую поверхность до тех пор, пока прут не будет оставлять хорошо видимый след при ударных движениях. После появления заметной линии нужно увеличить нагрев. Когда тестовая линия начнет впитываться в поверхность, продолжайте нагрев до полного открытия пор и проникновения сплава в медь.
Заполнение больших отверстий.
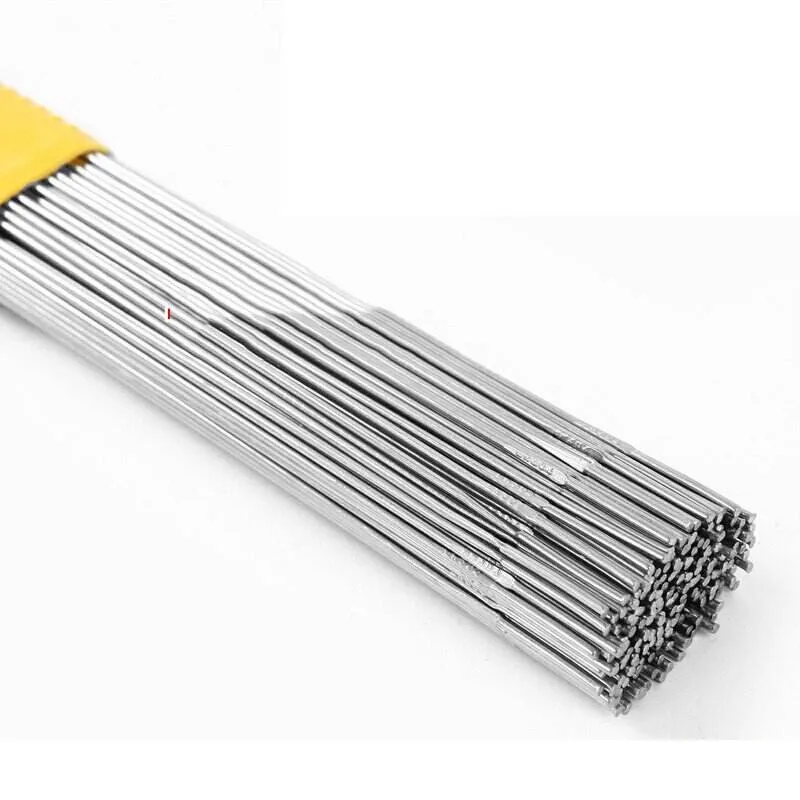
1. Очистить обрабатываемую поверхность. Покрыть внутреннюю полость отверстия тонким слоем припоя HTS-2000. Закрыть вторую сторону отверстия стальной пластиной и зафиксировать ее. Обработанное отверстие заполняем расплавленным припоем непрерывно — пруток за прутком.
2. Большое отверстие можно заделать с помощью заплаты. Заплату из любого вида алюминиевой пластины или фольги и края отверстия залудить, удерживая заплату, после чего нагреть.
Медно-свинцовые сплавы, гальванизированные и баббит металлы.
С такими материалами производить пайку можно без предварительного нагрева рабочей поверхности. Температура плавления металла и припоя примерно одинаковая. Для стабилизации температуры, при восстановлении медно-свинцовых сплавов, применяют иногда контейнер с сырым песком.
УЗНАТЬ СТОИМОСТЬ: под ценой и надписью «Доступные варианты» находится окошко с количеством в штуках (в данный момент от 20 шт. по цене 120,00 грн. за 1 шт).
Нажимаете курсором мышки на это окошко и выбираете «кликом» необходимое Вам. Сверху автоматически появится цена.
Благодарим за покупку !
Видео работы с припоем HTS-2000.
Купить припой для алюминия HTS 2000 Вы можете в сети магазинов «ЗВАРЮВАННЯ».
Припой для пайки алюминия HTS-2000 купить в г. Кривой Рог Вы можете в сети магазинов «ЗВАРЮВАННЯ»:
• магазин ЗВАРЮВАННЯ — ул. В. Матусевича (22-го партсъезда), д. 55, р-он ГосЦирка;
Тел.: (067) 379-07-77, (067) 569-35-66, (099) 047-64-46, (093) 610-90-26. Низкие цены. Гарантия от ведущих производителей. Доставка во все регионы Украины.
Покупка у официального дилера – гарантированный способ получить высокое качество и конкурентоспособные цены на сварочные материалы.
Припой для алюминия HTS-2000 купить. Припой HTS-2000 купить. HTS 2000 купить. Припой для алюминия HTS купить. Припой для алюминия HTS-2000 цена. Припой для алюминия HTS-2000 Кривой Рог.Припой для пайки алюминия Castolin 1827 д.2,0 мм (пруток)
Припой Castolin 1827 — мягкий припой содержащий серебро на кадмий-цинковой основе.
Хорошие смачивающие и текучие свойства.
Плотные, чистые швы. Для пайки алюминия, алюминиевых сплавов, меди и медных сплавов (латунь), нелегированных, низколегированных и нержавеющих сталей и соединений алюминия с медью, медными сплавами и сталями.
Для получения качественного паяного соединения необходимо использовать в сочетании с флюсом Castolin AluTin 51L.
Диапазон плавления — от +270º С до +280º С
Предел прочности Rm — 150-180 МПа
Хладостойкость — до -200º С
Химический состав:
Серебро Ag — 1. 6 %
Кадмий Cd — 82.1 %
Цинк Zn — 16.3 %
Диаметр — 2 мм
Длина — 500 мм
Упаковка — 5 прутков
Важно! Припой содержит кадмий — производите пайку в хорошо проветриваемом помещении и не используйте данный припой если изделие контактирует с пищевыми продуктами.
Припой Castolin 1827:
- хорошая текучесть
- соединение разнородных металлов
- отличное механическое сопротивление
- хорошие механические и электрические характеристики
Область применения:
- Элементы электрических коммуникаций, кабели, патроны ламп, холодильные установки
- Благодаря хорошим низкому электро сопротивлению и высокой температуре распая, идеально подойдет для пайки электрических шин
Источники нагрева:
- комплект газосварочный Castolin 2000 Flex, Castolin 3000 Flex, Castolin 4000 Flex Pro или аналоги
- горелка газовая Castolin CT27 пьезо, Castolin СТ26 (BernzOmatic T757) пьезо, Castolin 500, Castolin 600 пьезо, Castolin 1350 пьезо или аналоги
Припой Castolin 1827 изготовлен в Европе.
Компания Castolin основана в 1906 году в Лозанне, Швейцария и, с тех пор, находится на переднем крае технологий защиты от износа и специальных соединений материалов.
Изделие имеет все необходимые сертификаты и разрешения, для использования на территории РФ.
Припой для пайки алюминия Castolin 192FBK — пыль в глаза или страшный кошмар аргонщиков?
Ни для кого не секрет, что любые проблемы, связанные с ремонтом изделий и деталей из алюминия и его сплавов, скрывают за собой множество проблем. Сам алюминий и его сплавы имеют сравнительно небольшой вес, высокую электропроводность и теплопроводность и при этом устойчивость к мех. воздействию. Сварка алюминия затрудняется как минимум его характеристиками. И самое главное — это затратное дело.
Самая популярная сварка алюминия ( ни для кого не секрет) — сварка TIG в среде аргона. Используемые для этого присадки легко справляются с разными алюминиевыми сплавами. Но далеко не у всех в гараже завалялся TIG аппарат с режимом PULSE AC/DC с заправленным аргоновым баллоном. Если отдавать в ремонт, то он зачастую выходит очень дорого и неоправдано.
Также есть возможность сварки алюминия полуавтоматической MIG/MAG проволокой. Но для этого нужны дополнительные вложения и изменение конструкции рукава и подающих роликов, что тоже не является дешевым вариантом.
И наконец есть даже электроды для ММА сварки по алюминию Но здесь тоже есть подводные камни. На открытом воздухе алюминий забирает всю имеющуюся в воздухе влагу, окисляется и обмазка довольно быстро осыпается. Поэтому большинство пачек с такими электродами запакованы либо в вакуумный тубус, либо плотно запечатаны в картонную пачку. Конечно же при этом умение сваривать алюминий и знать тонкости РДС с алюминием является одним из самых главных условий.
У каждого здравомыслящего человека возникает вопрос — неужели нет относительно дешевого способа восстановить поврежденную алюминиевую деталь или спаять две алюминиевые трубки?
Способ есть , но связан он не со сваркой, а с пайкой!
Castolin 192 FBK — это припой с флюсом для пайки алюминия, его сплавов, алюминия с медью, алюминия с нержавейкой и с гальванизированными сталями. Флюс, содержащийся в этом припое не ржавеет, тем самым его необязательно удалять и переживать за дальнейшую коррозию. Дополнительных материалов для пайки не требуется!
Самый главный плюс — это температура пайки 380°C. То есть осуществлять пайку достаточно с помощью обычной горелки с баллончиком пропан-бутан!
Состав припоя:
- Алюминий 2%
- Цинк 98%
Получил широкое применение в пайке и ремонте холодильной техники, бытовых и автомобильных систем кондиционировании, посуды.
При сравнительно небольшой стоимости впечатляет качеством пайки и таким образом оставляет без работы всех «аргонщиков»! К тому же пайка не требует особых умений при работе с алюминием и сплавами, что несомненно является большим преимуществом перед вышеперечисленными методами сварки.
Вывод:
При работе с алюминием и алюминиевыми сплавами требуются знания. Способов сварки и пайки алюминия огромное количество, но самым дешевым и неприхотливым является именно низкотемпературная пайка вместе с Castolin 192 FBK.
Припой для пайки алюминия HTS-2000
Припой hts 2000 предназначен для пайки и ремонта деталей из алюминиевых сплавов. Со слов продавцов можно подумать, что он универсальный. В теории. Но это, конечно, совсем не так.
А что в реальной жизни, когда берешь пруток в руку и паяешь?
Hts 2000 хорош для бытовой пайки. Не требует флюса, так как представляет собой металлическую оболочку внутри которой находится флюсующий порошок. Если провести небольшую опытную работу, взять дюралюминий, завалявшийся в гараже и спаять пару его листов внахлест, а потом «испытать» на отрыв, то все будет хорошо. Ничего не отвалится при попытке согнуть-разогнуть образцы. Прочность паяных швов по заявлению производителя до 45900 PSI, что выше, чем прочность некоторых алюминиевых сплавов, например, таких как АМг, АМц, которые термической обработкой не упрочняются и представляют собой очень «мягкие» по твердости сплавы, если сравнивать их с термообработанными Д16 или АК6 и другими.
Но достаточно ли этой прочности для пайки более- менее нагруженных узлов? Однозначный ответ, нет.
Так же припой используется по заверениям продавцов для пайки холодильной техники. Но тут сразу же нужно оговориться. Если у вас коррозия съела металл до дыр в морозильной камере, запаивать их нельзя. Припой содержит цинка 97.3% (остальное медь) и при большом перепаде температур разница в коэффициентах линейного расширения металлов настолько велика, что припой отвалится буквально через пару заморозок и оттаиваний. Так же нельзя ремонтировать рамы. В былые времена был популярен советский припой 34А и флюс 34 – держал прочно, так как основа у него алюминий, но и паять им было трудно.
Смачивает не все алюминиевые сплавы. Сплавы с большим содержанием магния не спаять.
В рекламных описаниях утверждается, что припой может проникать даже через оксидную пленку, достаточно только убрать грязь с поверхности металла. На практике его нужно слегка втирать в не очищенную поверхность металлическим прутком (например, гвоздь. )
Зато профессиональные сварщики hts хвалят, наверное, из-за того, что после провальных попыток спасти деталь пайкой, цена сварки увеличивается в несколько раз!
Где основательно прижился припой, это в ремонте алюминиевых авторадиаторов (хотя лучше менять целиком) в ремонте лодок и деле восстановления резьб. Но для этих целей можно купить аналог HARRIS 52, который стоит дешевле.
Припой HTS-2000 для алюминия
Припой HTS-2000 cамый сильный , самый быстрый и самый легкий способ для ремонта и восстановления алюминиевых деталей.
Припой HTS-528 подходит для пайки черных металов и их сплавов (чугун, сталь), цветных металов и сплавов (медь, латунь, никель и др. с высокой температуров плавления) .Припой HTS-2000 это высокопрочный пруток для пайки позволяет восстановить или изготовить алюминиевые детали прочнее, чем при использовании сварочного аппарата. Сварка алюминия не нужна! Все, что Вам нужно для ремонта и восстановления деталей – это газовая горелка ( пропановая, ацителеновая или на МАПП газе) и пруток припоя HTS-2000. Эта новая технология отлично подходит для пайки алюминия, алюминиевых сплавов, меди, магния, цинка, латуни, титана.
Вы можете легко исправить поломки в пропитанных маслом областях, ремонт которых сварочным аппаратом с алюминиевыми электродами практически невозможен.
Всего лишь несколько из множества деталей, которые могут быть легко восстановлены припоем HTS2000 и HTS528 | ||
|
|
|
Закажите сейчас он-лайн , убедитесь в том как этот доступный и удивительный припой может быть Вам полезен в ремонте!
Если у Вас есть вопросы по пайке нашим припоем , нажмите здесь.

0%
5 900 руб 5 900 руб
0%
11 200 руб 11 200 руб
0%
11 900 руб 11 900 руб
0%
6 550 руб 6 550 руб
0%
360 руб 360 руб
-11%
3 800 руб 3 400 руб
-14%
2 200 руб 1 900 руб
0%
1 400 руб 1 400 руб
Продукты для сварки, пайки и пайки алюминия
77 Продукты для сварки, пайки и пайки алюминия
Muggy Weld предлагает 2 решения для ремонта алюминия: низкотемпературный припой Super Alloy 1 и ремонтный стержень для алюминия Super Alloy 5 и комплект флюса.
Super Alloy 1 — это алюминиевый припой, который течет при такой низкой температуре, что его можно даже использовать с тепловым пистолетом на небольших алюминиевых деталях для сварки, пайки и пайки алюминия. Для этого продукта рекомендуется косвенный нагрев, так как он имеет рабочую температуру 350 ° F.Super Alloy 1 идеально подходит для деликатных, чувствительных к температуре деталей.
Помимо алюминия, пруток и флюс из Super Alloy 1 связываются со многими другими металлами без искажения с основным металлом: металлический горшок, медь, оцинковка, латунь и другие. Super Alloy 1 даже соединяет разнородные металлы, такие как латунь, с алюминием — результирующая связь составляет 20 000 фунтов на квадратный дюйм. (Super Alloy 1 нельзя наносить на алюминиевые лодки, литой алюминий или большой / толстый алюминий. Для этих целей используйте Super Alloy 5)
Super Alloy 5 — это пруток для пайки при температуре 600 ° F, который восстанавливает алюминий до прочности сварного шва с помощью любой горелки: пропана, оксиацетилена, газа MAPP, окси-MAP или природного газа. Его даже можно использовать как стержень для сварки TIG.
Super Alloy 5 не требует предварительной очистки благодаря порошковому флюсу. Этот уникальный флюс удаляет загрязнения во время работы и действует как абсолютный ориентир температуры — он превращается из порошка в жидкость, когда основной металл достигает надлежащей рабочей температуры. Это точный индикатор того, когда пора применять наполнитель.
Super Alloy 5 хорошо работает как с тонким алюминием, так и с более толстыми отливками. (Для более тяжелого алюминия и литого алюминия следует использовать кислородно-ацетиленовую горелку), и ее результирующее сцепление составляет 30 000 фунтов на квадратный дюйм.
У нас есть универсальные продукты для сварки, пайки и пайки алюминия Super Alloy 1 и Super Alloy 5, которые устранят необходимость в полном ремонте.
Примечание : При использовании продуктов Muggy Weld соблюдайте все рекомендации AWS по безопасности и охране здоровья.
Как паять алюминий — Обсуждение ювелирных изделий
Что делает алюминий в продаже? Работает нормально? Уилл Сильвер Припой работать?
Лаура,
Алюминий — это металл, сильно отличающийся от серебра.Одно из ключевых отличий
заключается в том, что он обладает исключительным сродством к кислороду. Любая открытая поверхность алюминия
образует мгновенный непроницаемый оксидный слой, который затем предотвращает попадание кислорода
на поверхность, и поэтому металл
сохраняет свою металлическую природу. Но этот оксидный слой препятствует нормальной пайке
. Серебряные или золотые припои вообще не подойдут. Фактически,
многие из них плавятся при более высокой температуре, чем сам алюминий, что не принесет вам особой пользы от
.
, однако, есть припои, предназначенные для алюминия.Обычно это
комбинация довольно твердого припоя и специально разработанного флюса
. При использовании вы «протираете» припой на стыке
, который механически помогает флюсу вытеснить этот очень прочный оксидный слой
, чтобы припой прилип. Припои гораздо больше похожи на припои на основе олова
, которые ювелиры называют «мягкими» или «свинцовыми» припоями. Но они
работают. Тем не менее, эти вещи обычно предназначены для ремонта перил крыльца
, а не для изготовления ювелирных изделий.Если вы думаете о
о том, чтобы аккуратно поместить маленькие пайетки из алюминиевого припоя вокруг алюминиевой рамки
, пока вы припаяете ее к алюминиевому кольцу,
вам не повезло. Вы, вероятно, не добьетесь того, чтобы это работало … Обратите внимание, что
, как правило, эти припои предназначены для соединения алюминия с алюминием.
Не алюминий по отношению к другим металлам.
Алюминий обычно крепится с использованием так называемого «холодного склеивания»
, такого как ривиты, винты, механические соединения и т.п.Одним из методов плавления металлов является сварка плавлением
, для которой требуется специальный аппарат. Обычно это используется для
вещей, таких как серьги или аналогичные находки, прикрепляемые к алюминию
. Они сделаны специально для этого использования, с крошечным «наконечником» металла
, выступающим вниз из области, предназначенной для приклеивания к алюминию
. Машина помещает электрический заряд между находкой
и деталью, к которой нужно прикрепить, и хлопает их вместе. Когда этот маленький наконечник
просто касается другого куска металла, он вызывает искру.
Искра обращается с этим маленьким наконечником, как с предохранителем, пережигая его. По сути,
делает то же самое, что и отвертка, которой вы случайно случайно коснулись
провода под напряжением. Помнить? испарил половину наконечника отвертки
, когда он образовал дугу? Будет, это контролируется, но это
маленькое «перо» металла испаряется, когда две большие поверхности
соединяются вместе. Это создает очень горячую плазму на мгновение
между металлами, которая не только вытесняет весь атмосферный газ,
включая кислород, но также расплавляет поверхности достаточно, чтобы они могли смешиваться
и связываться друг с другом.
Сварка плавлением, как я уже отмечал, обычно используется для установки штифтов сережек и
других деталей. но его можно использовать как более универсальную технику склеивания
, если учесть, что хорошо приклеенный штырь серьги
также можно рассматривать как заклепку, готовую для вставки через отверстие в другом куске металла
и зачищенной поверх … идеи?
Машины, начиная с маленьких «игристых» сварочных аппаратов, проданных за
около 400 баксов…
И если у вас есть доступ к обычному оборудованию для электродуговой сварки,
есть также методы сварки, предназначенные для алюминия.Обычно они
требуют какой-то газовой защиты зоны сварки, например, при сварке TIG
или MIG. Опять же, это обычно не ювелирная шкала, но кто знает
…
Надеюсь, это поможет.
Питер Роу
В чем разница между пайкой, пайкой и сваркой?
Кратко:
- Микро-литье под давлением ориентировано на производство небольших высокоточных деталей и компонентов с микронными допусками.
- Дизайнеры, которые строго придерживаются набора правил, ограничивают свои собственные возможности и творческий потенциал.
- Понимание свойств материала и опыт подбора материала с соответствующей геометрией могут иметь решающее значение.
Скорость расширения миниатюрных высокоточных инженерных компонентов опровергает утверждение о том, что микролитье — это ниша. Спрос на носимые интеллектуальные устройства и имплантируемые датчики с небольшими компонентами с жесткими допусками не ослабевает.
Нигде это не проявляется более очевидно, чем в индустрии медицинского оборудования, где усилия по оптимизации форм-факторов — меньших, более быстрых, дешевых — ограничиваются только способностью к инновациям.Системы доставки лекарств, системы доставки медикаментов, микрофлюидика и электронные компоненты — это лишь малая часть примеров.
В то время как литье под давлением — это процесс производства деталей путем впрыскивания расплавленного материала в форму, микролитьевое формование фокусируется на производстве небольших высокоточных деталей и компонентов с микронными допусками. В обоих случаях процесс включает нагнетание расплавленного пластика в полости стальной формы. После охлаждения детали выталкиваются.
Аарон Джонсон, вице-президент по маркетингу и стратегии работы с клиентами в Accumold, излагает критерии успешных приложений для микролитья.Accumold
Микро-литье под давлением также обеспечивает высокий уровень настройки и сложности, что делает его подходящим для специализированных и миниатюрных приложений в медицинских устройствах и автомобильной промышленности, где производители должны производить миллионы деталей с постоянным уровнем качества, точности и надежности .
В основе успешного проектирования микролитых компонентов и деталей лежит четкое понимание заявленных и неустановленных потребностей конечного пользователя. Это связано с тем, что производство компонентов и устройств на основе проектных параметров для небольших или микродеталей сопряжено с уникальным набором проблем и возможностей, которые обычно не связаны с традиционными методами литья под давлением, утверждает Аарон Джонсон, вице-президент по маркетингу и стратегии работы с клиентами в Accumold. во время ноябрь.Презентация 30 Virtual Engineering Week.
Его работодатель, Accumold, предлагает оснастку, формование, упаковку и метрологию. Компания работает на территории кампуса площадью 15 акров недалеко от Де-Мойна, штат Айова, где на ее территории с климат-контролем находится пять чистых комнат. Производимые здесь детали и компоненты обычно измеряются в микронах; они варьируются от микрооптических формованных линз и небольших расширителей зрачков формы до шестерен микротора и микролитых шестерен, а также некоторых с микрочастицами, которые могут быть отформованы внутри и вокруг существующих компонентов.
Микро-литье под давлением подходит для деталей, которые спроектированы с массой менее миллиграмма и размером менее 1 мм. Accumold
По мнению Джонсона, компонент или производственная деталь, которая весит менее грамма, считается кандидатом для микролитья и может быть дополнительно определен по трем критериям:
- Размер: «Работа с деталями, размер которых во многих случаях меньше сантиметра».
- Микро-характеристики: «Это относится к немного более крупным деталям с микрочипами.Иногда мы производим большую деталь, которая может достигать трех, четырех или пяти сантиметров, но в ней есть микрофлюидные каналы длиной 100 микрон, глубиной или шириной ».
- Допуск: «Это когда позиционные или геометрические допуски должны быть относительно идеальными; мы говорим о микрометрах ».
Посредством серии тематических исследований его презентация показала, как знания материалов, знания в области обработки, допуски на размеры, тонкие стенки, скорость впрыска и сборка повлияли на процесс микропроизводства (DfMM) до того, как можно будет производить компоненты.
Джонсон отметил, что инженеры-конструкторы часто могут проектировать инновационные продукты на экране, но это не обязательно переводится в процесс формования. «Дизайн в микромасштабе требует особого внимания к тому, что в противном случае могло бы не иметь большого значения для более крупных деталей», — сказал он. «Вы можете проектировать в САПР вещи, которые нельзя слепить».
Его коллеги могут согласиться. «Некоторые законы физики, такие как электростатическая индукция, трибоэлектрический эффект и закон Ленца, могут заставить очень небольшую часть не идти туда, куда нам нужно, в частности, вниз на землю под действием силы тяжести», — писал его коллега Рон Байотто в блог компании.
Маленькие компоненты слухового аппарата.Accumold
Выбросьте традиционные правила
Часто задаваемый вопрос о микролитье заключается в том, есть ли у него какие-либо рекомендации по микролитью. Общие рекомендации могут включать следующие правила:
- Тонкие стенки должны быть толщиной 0,004 дюйма (0,1 мм) или больше, и особое внимание следует уделять переходам от толстой к тонкой стенке, а также к толщине стенки. единообразие.
- Соотношение сторон примерно 6: 1 (хотя это сильно зависит от материала).
- Ворота могут иметь размер от 0,1 мм, а выталкивающие штифты — от 0,25 мм.
- Также важно понимать, как степень усадки повлияет на деталь, и знать о несовпадении линий разъема.
Но Джонсон отметил, что предоставление набора правил может быть ограничивающим, особенно когда правила основаны на принципах, предназначенных для традиционного литья под давлением. «Руководящие принципы нарушаются, когда вы начинаете раздвигать границы», — сказал он. «Я спросил одного из наших менеджеров по технологиям, который работает здесь почти 35 лет:« Каковы ваши рекомендации по поводу соотношения сторон изображения? »Первоначально он сказал мне шесть к одному.Тогда вы могли бы подтолкнуть его, и он мог сказать 10 к одному или восемь к одному — где-то в этом мире ».
В результате, по словам Джонсона, проектирование микроформованных компонентов носит ситуационный характер, и дизайнеры, которые строго связаны набором правил, ограничивают свои собственные возможности и творческий потенциал, что ограничивает результаты. По его словам, стоит отметить одно правило дизайна микролитья: «Начните со своего идеала… на самом деле все сводится к тому, чего вы в конечном итоге пытаетесь достичь».
Невероятно точное микролитье позволяет изготовить эту деталь, микролитую шестерню ротора с 18 зубьями вокруг.Диаметр 092 дюйма (2,3 мм) и отклонение от концентричности из 0,0005 (13 мкм). Accumold
Переменные и компромиссы
По словам Джонсона, компания OEMS, заинтересованная в приобретении микромформованных компонентов, обычно испытывает боль точки, которые вращаются вокруг двух аспектов: геометрии и масштаба.
С точки зрения геометрии, проектировщики должны задать основные вопросы о механических потребностях: является ли конструкция формуемой? Может ли конструкция соответствовать допускам? Есть ли способ открыть и закрыть или извлечь компонент из формы? «Иногда возникает мнение, что из-за того, что он маленький, ему не нужны некоторые из этих [параметров], и тем не менее традиционные правила литья под давлением все еще применяются», — сказал Джонсон.
Материалу присущи некоторые механические свойства, которые обычно являются отправной точкой для проектирования, сказал Джонсон. При выборе материала важными факторами являются такие критерии, как биосовместимость, отклонение тепла, характер износа или гибкость. Accumold работает с обычными термопластическими материалами, включая PEEK, Ultem, нейлон со стеклонаполненным покрытием и другие материалы медицинского назначения и ослабленные материалы.
Когда клиент указывает конкретный материал, чтобы соответствовать условиям окружающей среды, геометрия должна быть адаптирована к этому выбору.По словам Джонсона, в некоторых случаях технологические свойства материала могут повлиять на успех проекта.
Рассмотрим в качестве примера PEEK (полиэфирэфиркетон). Этот материал, обычно используемый в имплантируемых устройствах, на 30% армирован стекловолокном и гранулирован для литья под давлением. Обратной стороной его использования является то, что он не может заполнять ультратонкие области. То же самое относится и к Ultem, еще одному прочному термопласту, используемому в микрооптике, а также в аэрокосмической и автомобильной промышленности.
Производство детали самого высокого качества требует понимания потенциальных недостатков, которые могут повлиять на ее применение, сказал Джонсон. Эти детали должны быть частью процесса проектирования микролитья (DfMM) в начале каждого проекта. По сути, в Accumold процесс DfMM включает в себя соединение клиента с инженером проекта, проектировщиком пресс-форм и инженером по качеству, которые проводят клиентов по этапам процесса. По его словам, значительное количество времени уходит на предварительную обработку проектов, чтобы полностью понять потребности и требования клиентов.
Accumold также связывает клиентов и поставщиков смол, чтобы они могли исследовать различные материалы, которые могут соответствовать требованиям уникального компонента. «Наша цель — предоставить клиентам компоненты, готовые к изготовлению», — сказал он.
И вместо того, чтобы отказываться от идеи, которая кажется слишком сложной, Джонсон советует обсудить ее с опытным специалистом по формованию микропластов. По его словам, понимание свойств материала и опыт подбора материала с соответствующей геометрией могут иметь решающее значение.
Алюминиевый ремонтный стержень | Капп Сплав
- Более низкая температура плавления облегчает деликатный ремонт алюминиевых радиаторов.
- Matching Kapp Golden Flux ™ действует как ориентир температуры, обеспечивая простое нанесение и успешное склеивание.
- Используйте любой источник тепла — кислородно-ацетиленовую, газовую или пропановую горелку, тепловую пушку или паяльник.
- Превосходный многоцелевой припой, может использоваться для алюминия, нержавеющей стали, белого металла, олова, меди, латуни и гальваники.
- В большинстве случаев ремонт прочнее оригинального металла.
- Может быть покрыт хромом, никелем или медью.
Физические свойства:
Состав: 40 олово — 27 цинк — 33 кадмий
Диапазон плавления: 350 — 500 ° F / 176 — 260 ° C
Электропроводность: 23 (% IACS при 68 o F)
Прочность на растяжение: 20 000 фунтов на кв. Дюйм
Прочность на сдвиг: 11000 фунтов на кв. Дюйм
Успешная пайка с помощью KappRad ™
Шаг 1 — Предварительно очистите основной металл или соединяемые металлы.Используйте ткань emory, проволочную щетку, пескоструйную очистку и т. Д. Подготовьте алюминиевые поверхности чистой проволочной щеткой из нержавеющей стали .
Шаг 2 — Нанесите неагрессивную жидкость Golden Flux ™ компании Kapp на место ремонта. Вы можете использовать стержень для распределения флюса.
Шаг 3 — С помощью мягкого пламени, теплового пистолета или паяльника нагрейте основной металл, прилегающий к зоне ремонта. Прямое пламя на участке ремонта может привести к перегреву припоя и флюса.
Шаг 4 — Удерживайте наконечник резака на расстоянии 4–6 дюймов от основного металла. Если необходимо подать пламя напрямую
к стержню или флюсу, оттяните наконечник резака еще дальше от рабочей поверхности и продолжайте движение.
Шаг 5 — Флюс начнет пузыриться и станет светло-коричневым. Это подготовит основной металл к припою и укажет на правильную рабочую температуру. (Если флюс становится черным, значит он перегрет.Дайте области остыть, очистите ее и начните заново с шага 1.) Проведите стержнем припоя по области, которую нужно припаять, пока он не начнет течь. ПРЕКРАТИТЕ НАГРЕВ! При необходимости нанесите дополнительные слои.
Шаг 6 — Иногда необходимо слегка нагреть кончик стержня пламенем, чтобы припой легче стекал на место ремонта. НЕ НАГРЕВАЙТЕ ПРУТ ДО ТОЧКИ ПЛАВЛЕНИЯ!
Шаг 7 — Наблюдайте за отложением припоя.Припой должен плавно приклеиваться. НЕ ПЕРЕГРЕВАЙТЕ! Стержень плавится при перегреве, но не соединяется должным образом.
Шаг 8 — Если вы прекратили пайку и хотите нанести больше припоя или выпустить существующий слой, дайте ему остыть, добавьте еще флюса и повторно нагрейте. Флюс поможет процессу склеивания, будь то добавление стержня или просто вытекание предыдущего осадка.
Шаг 9 — Удалите излишки флюса теплой водой и тканью или металлической щеткой.
Ремонт алюминия с помощью низкотемпературного алюминиевого припоя KappAloy ™
Перед
Разрушение оксидного покрытия перемешиванием и флюсованием — один из ключей к успешной пайке, особенно для алюминиевых деталей. Важно выполнять эти шаги в своевременной непрерывной последовательности 1-2-3…. В противном случае прочное оксидное покрытие может образоваться и затруднить соединение припоя. Итак, перед тем, как начать, убедитесь, что у вас есть все инструменты и расходные материалы, готовые к работе.
Предварительное лужение
Для некоторых трудно поддающихся пайке соединений с большой площадью поверхности может быть очень полезно предварительно залудить область соединения на каждой части припоем перед тем, как соединить детали. Просто выполните следующие действия, чтобы покрыть область стыка каждой детали ровным слоем припоя. Затем, когда детали остынут, повторите шаги еще раз, чтобы соединить детали.
Здесь также применяется правило 1-2-3. Не стоит сегодня оловить заранее, а на следующий день паять.Свежая поверхность без окислов важна для успешной пайки. Предварительное лужение деталей с помощью правильного припоя может значительно улучшить соединения на трудно паяемых металлах и деталях с большой площадью поверхности.
Шаг 1
Предварительно очистите основной металл или соединяемые металлы. Сделайте фаску на краях деталей в месте соединения, чтобы припой мог заполнить и приклеиться к деталям. Подготовьте алюминиевые поверхности проволочной щеткой из нержавеющей стали. Разрушение прочного оксидного покрытия на алюминиевых деталях является секретом прочных и надежных паяных соединений.Эти барьеры быстро восстанавливаются, поэтому следует быстро перемешивать, флюсовать и паять.
Шаг 2
Нанесите Kapp Golden ™ Flux, чтобы разрушить оксидный барьер и втянуть припой в зону соединения / ремонта. Не забудьте оставить достаточный зазор, чтобы флюс и припой могли течь между деталями. Активный диапазон Kapp Golden Flux составляет 350-550 ° F. Вы можете легко использовать припой для распределения флюса.
Шаг 3
С помощью мягкого пламени, теплового пистолета или паяльника нагрейте основной металл, прилегающий к зоне ремонта.Прямое пламя на участке ремонта может привести к перегреву припоя и флюса.
ЗАПРЕЩАЕТСЯ НАГРЕВАТЬ ПАЯЛЬНУЮ СТАНКУ или ПОТОК!
Шаг 4
При использовании резака держите наконечник резака на расстоянии 4–6 дюймов от основного металла. Если необходимо подать пламя непосредственно на стержень или флюс, оттяните наконечник резака еще дальше от рабочей поверхности и продолжайте движение.
Шаг 5
Флюс начнет пузыриться и станет светло-коричневым. Помимо подготовки основного металла к припою, эти изменения указывают на правильную рабочую температуру флюса. Если флюс станет черным, дайте области остыть, очистите ее и начните заново.
Шаг 6
Когда флюс пузырится и становится коричневым, пора применить стержень. Перетащите стержень по области, которую нужно припаять, пока он не начнет течь. ПОСЛЕ ПОТОКА СТЕРЖНИ ПРЕКРАТИТЕ ПОДАЧУ ТЕПЛА!
Если необходимы дополнительные слои, продолжайте перетаскивать стержень по области.В некоторых случаях, например, при использовании очень тонких проводов, перед пайкой деталей может оказаться полезным залудить алюминиевую поверхность стержнем. В этом случае выполните шаги 1-6, чтобы нанести ровный слой припоя на алюминиевые детали. Дайте этим деталям остыть, а затем снова выполните шаги 1-6, спаяв детали вместе. Это часто приводит к более плотному пайке мелких деталей.
Шаг 7
Иногда необходимо нагреть кончик стержня пламенем, чтобы припой легче стекал на место ремонта. НЕ НАГРЕВАЙТЕ ПРУТ ДО ТОЧКИ ПЛАВЛЕНИЯ!
Шаг 8
Обратите внимание на отложение припоя. Припой должен плавно приклеиваться. НЕ ПЕРЕГРЕВАЙТЕ! Стержень плавится при перегреве, но не соединяется должным образом.
Шаг 9
Если вы прекратили пайку и хотите нанести больше припоя или вылить осадок, дайте ему немного остыть, добавьте еще флюса и повторно нагрейте.Флюс поможет процессу соединения, будь то добавление припоя или просто вытекание предыдущего слоя.
Шаг 10
Удалите излишки флюса теплой водой и металлической щеткой.
Ремонт литого алюминия, литья под давлением и горшечного металла с помощью алюмита
До
Разрушение оксидного покрытия путем перемешивания и флюсования является одним из ключей к успешной пайке, особенно для деталей из алюминия, нержавеющей стали и никелированных деталей.Важно выполнять эти шаги в своевременной непрерывной последовательности 1-2-3…. В противном случае прочное оксидное покрытие может образоваться и затруднить соединение припоя. Итак, перед тем, как начать, убедитесь, что у вас есть все инструменты и расходные материалы, готовые к работе.
Предварительное лужение
Для некоторых трудно поддающихся пайке соединений с большой площадью поверхности может быть очень полезно предварительно залудить область соединения на каждой части припоем перед тем, как соединить детали.Просто выполните следующие действия, чтобы покрыть область стыка каждой детали ровным слоем припоя. Затем, когда детали остынут, повторите шаги еще раз, чтобы соединить детали.
Здесь также действует правило 1-2-3. Не стоит сегодня оловить заранее, а на следующий день паять. Свежая поверхность без окислов важна для успешной пайки. Предварительное лужение деталей с помощью правильного припоя может значительно улучшить соединения на трудно паяемых металлах и деталях с большой площадью поверхности.
Пайка алюмитом и лунным флюсом Каппа
При пайке алюминия невидимая оксидная пленка должна быть разрушена припоем для обеспечения контакта металла с металлом. ЕСЛИ вся поверхность соединения доступна для взбалтывания щеткой и припоем, оксид можно просто и эффективно разрушить без химического флюса с помощью АЛЮМИТА. Однако для стыковых и других труднодоступных стыков поверхность стыка должна быть хорошо залужена АЛЮМИТОМ, в противном случае потребуется флюс Kapp LUNAR.
НЕОБХОДИМО НАГРЕВАТЬ ЧАСТИ ДО ТЕМПЕРАТУРЫ, КОТОРАЯ РАСПЛАВАЕТ КОНЦЫ ПРИГОТОВЛЕНИЯ ПРИГОТОВЛЕНИЯ НА ПОВЕРХНОСТИ НАГРЕВАЕМЫХ ЧАСТЕЙ.
Твердый конец алюмитового стержня сначала прокалывает и разрыхляет оксидный слой, позволяя припою течь под ним. Это известно как «лужение поверхности».
С использованием этой безфлюсовой техники возможно множество видов ремонта и строительства; однако алюминиевая поверхность должна быть доступна для поглаживания стержнем припоя из алюминия. Припой не потечет сам по себе в узкий стык. Чтобы втянуть припой в узкий стык, требуется дополнительный флюс — Lunar Flux.
ВСЕГДА ИСПОЛЬЗУЙТЕ НЕЙТРАЛЬНОЕ ПЛАМЯ! ВСЕГДА ПОДДЕРЖИВАЙТЕ ОГОНЬ В ДВИЖЕНИИ! ВСЕГДА МЕДЛЕННО ОХЛАЖДАЕТСЯ! НИКОГДА НЕ ОГОНЯЙТЕ НАГРЕВАЕМЫЕ ЧАСТИ В ВОДУ!
Т — шарниры
Для максимальной прочности залудите оба элемента, как описано выше, и соедините вместе. Нагрейте детали и нанесите на место пересечения полоску припоя. Скругления изготавливаются путем пропускания припоя вдоль установочных элементов, где требуется контакт.Позвольте теплу от элементов, а НЕ ПЛАМЕНИ расплавить припой. Пропустите твердый конец припоя через расплавленную кромку, чтобы удалить застрявший оксид. Во многих случаях достаточную прочность можно получить без предварительного лужения. Однако, когда элементы не были предварительно лужены, скругления сами по себе поддерживают нагрузку на соединение, поскольку элементы не соединяются друг с другом, а только с галтелями.
Стыковые соединения
Наиболее эффективно обработать стыковые поверхности алюминиевым стержнем перед сборкой деталей для окончательной сборки.Нанесите Kapp Lunar Flux на стыковые поверхности. Концы скошены и сведены. Следуйте процедуре лужения, нанося АЛЮМИТ на обе скошенные поверхности стыка.
Круглые соединения
Детали можно лужить и сдвигать вместе, пока припой еще расплавлен. В качестве альтернативы, можно нанести обильную кромку припоя на края стыка внахлест, чтобы обеспечить лужение, пропустив стержень через расплавленный припой.
Соединения под углом в окнах, дверях, экранах, рамах
Члены должны быть надежно привязаны.над областью стыка зажигают нейтральное пламя, пока АЛЮМИТ не расплавится при прохождении через стык. Убедитесь в наличии лужения, протянув твердый конец припоя через слой расплавленного припоя. После лужения шов можно наращивать и обрабатывать по желанию. Эти соединения устойчивы к высокой влажности и остаются в идеальном состоянии после многих лет выдержки.
Ремонт и изменение конструкции алюминиевых матриц и штампов
Обрабатываемая секция очищается опиливанием или шлифовкой, затем лужится путем нагрева алюминия до температуры, при которой припой плавится, трясь о поверхность.ПРИ ЛУДОВАНИИ АЛЮМИТОВАЯ ПАЛКА ВСЕГДА НЕ ДОПУСКАЕТСЯ БЕЗ ПЛАМЕНИ. Воспламените материал мягким пламенем. Предварительный нагрев всей матчевой пластины матрицы примерно до 600 ° F облегчает эту процедуру.
Сварка отливок на основе цинка с АЛЮМИТОМ
Удалите покрытие, естественный оксид или посторонние предметы с соединяемых поверхностей. «V» из трещины и надежно настроить работу. Используйте наконечник №1 или №2, чтобы предварительно нагреть область вокруг перелома.Затем выполняется сварка путем нагревания трещины непосредственно нейтральным пламенем до тех пор, пока ПОВЕРХНОСТЬ основного металла не может быть разрушена путем прикосновения к ней АЛЮМИТОВЫМ стержнем. ПРИ ЗАПУСКЕ СВАРОЧНОЙ СВАРКИ НЕ ДОПУСКАЙТЕ ПРУТКА ОТ ПЛАМЕНИ. Продолжайте приваривать трещину, нанося припой на основной металл. НИКОГДА НЕ ОГНАТЬСЯ В ВОДУ ДЛЯ ОХЛАЖДЕНИЯ. Готово по желанию.
Сварка белого металла с АЛЮМИТОМ
Очистить покрытие и окалину с свариваемой поверхности.»V» из трещины и надежно настроить работу. Обычно предварительно нагревают нейтральным или ацетиленовым пламенем. Нагрейте до тех пор, пока основной металл не начнет плавиться, затем окуните стержень припоя в расплавленную лужу и вытащите из нее до желаемого нароста.
НИКОГДА НЕ ОГНАТЬСЯ В ВОДУ ДЛЯ ОХЛАЖДЕНИЯ . Готово по желанию.
Ремонт снятой резьбы с помощью АЛЮМИТА
Просверлите старую резьбу на больший размер, чтобы при добавлении нового галтеля все сверление и нарезание резьбы выполнялись из АЛЮМИТА.Это облегчит работу и увеличит силу. После сверления нагрейте основной металл снизу вверх. Прижмите стержень к стенке отверстия, начиная снизу и двигаясь вверх. Заполните отверстие, остудите, просверлите и постучите по нему по мере необходимости.
Физические свойства и технические данные Alumite ™ | |
Диапазон плавления | 715 ° F — 735 ° F / 379 ° C — 391 ° C |
Предел прочности на разрыв | 39000 фунтов на кв. Дюйм |
Прочность на сжатие | от 60 000 до 75 000 фунтов на кв. Дюйм |
Прочность на сдвиг | 34,000 фунтов на кв. Дюйм |
Ударная вязкость (по Шарпи) | 4 фут. |
Твердость (нагрузка по Бринеллю-500 кг.) | 100 |
Пластичность | Хорошо |
Плотность | 0,25 фунта / куб. дюйм |
Удлинение | 3% в 2 дюймах |
Коэффициент линейного расширения | 15.4 x 106 / ° F |
Электропроводность | 24,9 (% IACS) |
Теплопроводность | ,24 кал / см 3 / ° C |
Проникновение коррозии | 300 x 106 дюймов 1 1 / R |
Флюс | Отсутствуют на доступных соединениях |
MIL Технические характеристики | Отвечает MIL-R4208 |
* Примечание: Прочность на сдвиг для соединений внахлест, прочность на разрыв зависит от основного металла, методов пайки и типа соединения. |
Алюминиевый пруток для сварки припоя Алюминиевый припой Сварочная проволока Паяльный стержень с флюсом — купить по низким ценам в интернет-магазине Joom
Спецификация продукта Количество: 20/10/30/50 шт. Материал: алюминий. Цвет: серебристый Рабочая температура: 420 ℃ Диаметр: 2 мм / 0,08 дюйма, 1,6 мм / 0,06 дюйма Длина: 500 мм / 19,7 «
Комплектация: 20 * алюминиевая сварочная проволока 10 * алюминиевая сварочная проволока 30 * алюминиевая сварочная проволока 50 * алюминиевая сварочная проволока
Характеристики:
1.Широкое применение — подходит для сварки или наплавки сварочного сплава с высокой прочностью, хорошей ковкостью и хорошей коррозионной стойкостью.
2. Материал хорошего качества — изготовлен из алюминиевого материала, нетоксичного, без запаха и прочного материала.
3. Не требуется порошок припоя — нет необходимости использовать другой порошок флюса с алюминиевым сплавом в качестве сварочного сердечника и покрытием в качестве солевой основы. 4. Применение — включает сварочную присадочную проволоку, а также проволоку для распыления и газовой металлизации. Он также используется для аргонно-дуговой сварки и наполнения чистого алюминия, соединения с алюминиевой шиной и направляющего стержня электролитического алюминиевого завода, а также для электроэнергетики, химии, продуктов питания и так далее.5. Идеальный сварочный эффект — разработан с полным и плавным сварочным эффектом, потому что изделие имеет внутренний порошок, отличную свариваемость и коррозионную стойкость, высокую теплопроводность, высокую электрическую проводимость и отличные характеристики обработки.
Использование:
1. Очистите и отполируйте физическую поверхность.
2. Нагрейте поверхность металлического материала, пока температура проволоки не достигнет рабочей температуры 420 ℃.
3. Основной алюминий нагревается до соответствующей рабочей температуры при ремонте тонкого алюминия, а затем с помощью трения проволоки и плавления формируется сварной шов.4. Используйте пропан для сварки небольших предметов и используйте промышленный газ или индукционное нагревательное устройство для нагрева и сваривания большого объекта. После сварки вы должны охладить его естественным образом.
Внимание:
1. Чем толще кусок, тем труднее его нагреть, поэтому важно использовать разумный источник тепла.
2. Пока температура поверхности основного металла достигает рабочей температуры сварочной проволоки, можно начинать сварку.
3. При использовании кислородно-ацетиленовой сварки следует использовать сварку в нейтральном пламени, но, пожалуйста, не сжигайте проволоку напрямую.4. Применимый источник тепла: например, пропан, оксиацетилен и так далее.
5. Хранение: хранить в сухом и вентилируемом месте.
Примечание:
1. Поверхность основного металла должна быть чистой.
2. Температура основного металла должна достигать 420 градусов, включая процесс сварки, температура основного металла должна поддерживаться на уровне 420 ℃, а температура может быть высокой или низкой. Диаметр: 2 мм / 1,6 мм.
Длина: 500 мм
Тип продукта: Сварочные принадлежности
Какой сварщик мне нужен для сварки алюминия?
Алюминиевые сплавы представляют собой большую проблему для сварщиков, чем стальные сплавы. Алюминий имеет более низкую температуру плавления и более высокую проводимость, чем сталь, что может привести к прожогу, особенно в более тонких алюминиевых листах. Алюминиевая проволока для подачи мягче, чем ее стальная проволока, и может запутаться в устройстве подачи. Выбор метода сварки алюминия зависит от потребностей конкретного применения и навыков сварщика, который будет выполнять изготовление.
Сварка TIG
Сварка вольфрамовым электродом в среде инертного газа (TIG) является основным методом сварки алюминия.Поскольку алюминиевой заготовке требуется много тепла, чтобы нагреться до температуры, но она может удерживать это тепло в течение длительного времени, сварочный аппарат с регулированием тока полезен для предотвращения перегрева алюминиевой заготовки, вызывающего прогорания. Сварка TIG может применяться как к тонкому алюминиевому листу, так и к более толстому алюминиевому листу. Поскольку для сварки TIG требуется отдельный присадочный пруток, сварщик должен выбирать сварочный пруток со сплавом, максимально близким к сплаву деталей.
Сварка МИГ
Сварка металла в среде инертного газа (МИГ) может успешно использоваться для сварки алюминия.При выборе сварщика необходимо решить, какой метод сварки будет использоваться — дуговая сварка или импульсная сварка. Для импульсной сварки требуется инверторный источник питания, в то время как аппараты постоянного тока и постоянного напряжения могут использоваться для дуговой сварки со струйным переносом. Сварка MIG лучше всего подходит для алюминиевых листов меньшей толщины из-за необходимого количества тепла. При выборе защитного газа для сварки алюминия методом MIG лучше всего использовать 100% аргон. Сварщик должен выбрать сварочную проволоку или пруток из сплава, максимально близкого к сплаву деталей, чтобы получить качественный сварной шов.
Сварка горелкой
Алюминий можно сваривать с помощью газовой горелки, но этот метод сложнее, чем сварка MIG и TIG. Сложнее контролировать тепло, прикладываемое к заготовке с помощью резака, и вероятность прожога более высока при использовании резака. Для сварки алюминия горелкой требуется ловкий сварщик, который может надлежащим образом управлять горелкой и присадочным стержнем.
Очистка алюминиевых деталей
Независимо от того, какой сварочный аппарат используется для изготовления алюминиевых сварных деталей, детали должны быть очень чистыми перед началом сварки.Оксид алюминия имеет гораздо более высокую температуру плавления, чем основной алюминий, поэтому любые оксиды, которые остаются на поверхности обрабатываемой детали, могут привести к оксидным включениям в сварном шве, снижая общую прочность и внешний вид сварного шва. Заготовки можно очистить с помощью процесса химического травления или очистить механически с помощью металлической щетки.
Лучшая цена на проволоку для припоя алюминия — Выгодные предложения на проволоку для припоя алюминия от мировых продавцов проволоки для припоя алюминия
Отличные новости !!! Вы попали в нужное место для алюминиевого припоя. К настоящему времени вы уже знаете, что что бы вы ни искали, вы обязательно найдете это на AliExpress. У нас буквально тысячи отличных продуктов во всех товарных категориях. Ищете ли вы товары высокого класса или дешевые и недорогие оптовые закупки, мы гарантируем, что он есть на AliExpress.
Вы найдете официальные магазины торговых марок наряду с небольшими независимыми продавцами со скидками, каждый из которых предлагает быструю доставку и надежные, а также удобные и безопасные способы оплаты, независимо от того, сколько вы решите потратить.
AliExpress никогда не уступит по выбору, качеству и цене. Каждый день вы будете находить новые онлайн-предложения, скидки в магазинах и возможность сэкономить еще больше, собирая купоны. Но вам, возможно, придется действовать быстро, так как этот верхний алюминиевый припой в кратчайшие сроки станет одним из самых востребованных бестселлеров. Подумайте, как вам будут завидовать друзья, когда вы скажете им, что купили алюминиевый припой на AliExpress.Благодаря самым низким ценам в Интернете, дешевым тарифам на доставку и возможности получения на месте вы можете еще больше сэкономить.
Если вы все еще не уверены в правильности выбора алюминиевого припоя и думаете о выборе аналогичного товара, AliExpress — отличное место для сравнения цен и продавцов. Мы поможем вам разобраться, стоит ли доплачивать за высококачественную версию или вы получаете столь же выгодную сделку, приобретая более дешевую вещь.А если вы просто хотите побаловать себя и потратиться на самую дорогую версию, AliExpress всегда позаботится о том, чтобы вы могли получить лучшую цену за свои деньги, даже сообщая вам, когда вам будет лучше дождаться начала рекламной акции. и ожидаемая экономия.AliExpress гордится тем, что у вас всегда есть осознанный выбор при покупке в одном из сотен магазинов и продавцов на нашей платформе. Реальные покупатели оценивают качество обслуживания, цену и качество каждого магазина и продавца.Кроме того, вы можете узнать рейтинги магазина или отдельных продавцов, а также сравнить цены, доставку и скидки на один и тот же продукт, прочитав комментарии и отзывы, оставленные пользователями. Каждая покупка имеет звездный рейтинг и часто имеет комментарии, оставленные предыдущими клиентами, описывающими их опыт транзакций, поэтому вы можете покупать с уверенностью каждый раз. Короче говоря, вам не нужно верить нам на слово — просто слушайте миллионы наших довольных клиентов.
А если вы новичок на AliExpress, мы откроем вам секрет.Непосредственно перед тем, как вы нажмете «купить сейчас» в процессе транзакции, найдите время, чтобы проверить купоны — и вы сэкономите еще больше. Вы можете найти купоны магазина, купоны AliExpress или собирать купоны каждый день, играя в игры в приложении AliExpress. Вместе с бесплатной доставкой, которую предлагают большинство продавцов на нашем сайте, вы сможете приобрести aluminium solder wire по самой выгодной цене.
У нас всегда есть новейшие технологии, новейшие тенденции и самые обсуждаемые лейблы.На AliExpress отличное качество, цена и сервис всегда в стандартной комплектации. Начните самый лучший шоппинг прямо здесь.
.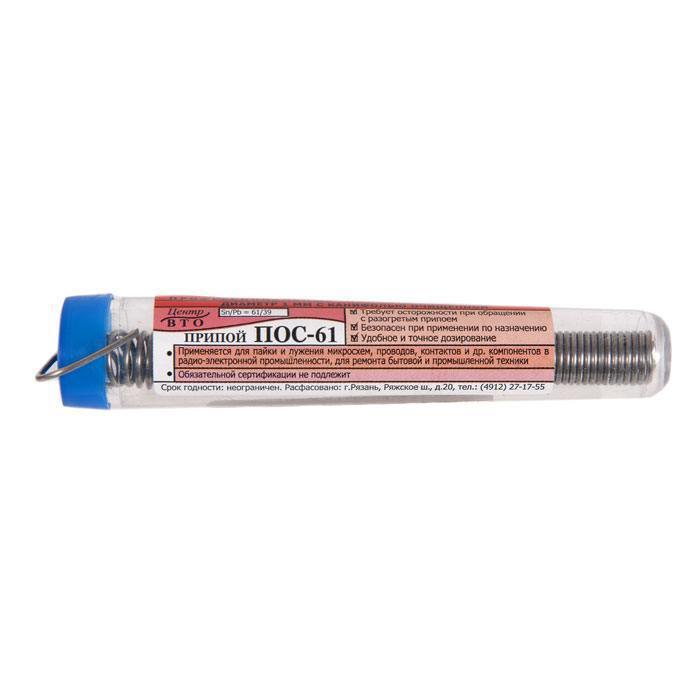